
10 minute read
Raising the (re)bar high!
Dave Stickler is no stranger to success in the sphere of developing hi-tech and green steel mills. The chief architect behind Big River Steel in Osceola, Arkansas – now part of US Steel – is now pushing ahead with Hybar LLC, another ambitious project that represents the zeitgeist of 21st Century steel making.
By Richard McDonough*
MISSISSIPPI County, Arkansas, is on its way to likely being proclaimed as the county with the largest amount of steel production in the United States of America (US). Currently, it is likely ranked as the second largest such county. Its growth has come, for the most part, in just the past 35 plus years.
This county is located along the river of the same name between Memphis and St. Louis.
To provide some perspective on this growth, consider a statement from the Great River Economic Development
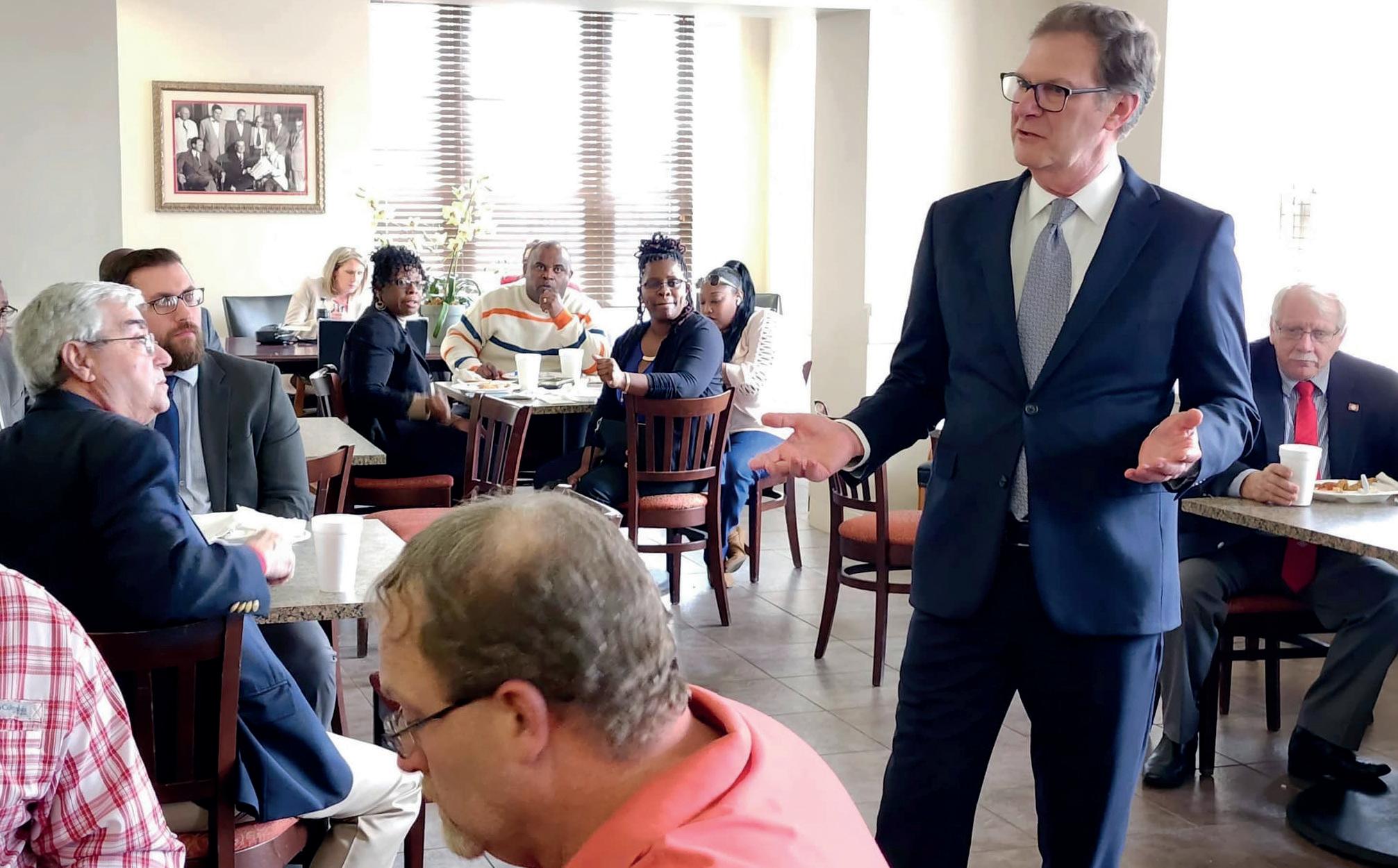
Foundation: “Between 1932 and 1960, Mississippi County held the title of largest cotton-producing county in America… Today, the county stands as the #2 steel producing county in the US...”
Part of that anticipated growth will be coming from a new rebar mini mill planned by Hybar LLC in the Osceola area of Mississippi County.
On 1 November 2022, Hybar LLC (then using the name of “Highbar LLC”) announced in a news statement that it would be investing approximately (US) $500 million to build a new rebar mini mill on a site of more than 600 acres in this community in the central US.
According to that news statement, “Hybar LLC [will be] focused on sustainable scrap metal recycling and steel production.”
Preliminary geotech work has been underway during the subsequent months.
Ground breaking is scheduled for late July/early August of 2023, with construction anticipated to take about 22 months after the first shovel of dirt is moved at the ceremony. “Peak construction employment is expected to exceed 600 jobs,” according to a press announcement from the company. Commercial steel operations are projected to begin in the Spring of 2025.
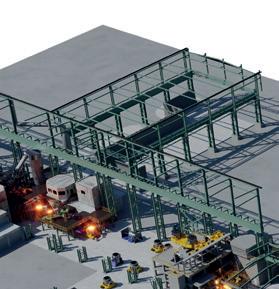
Annual production is anticipated to be 630kt of steel.
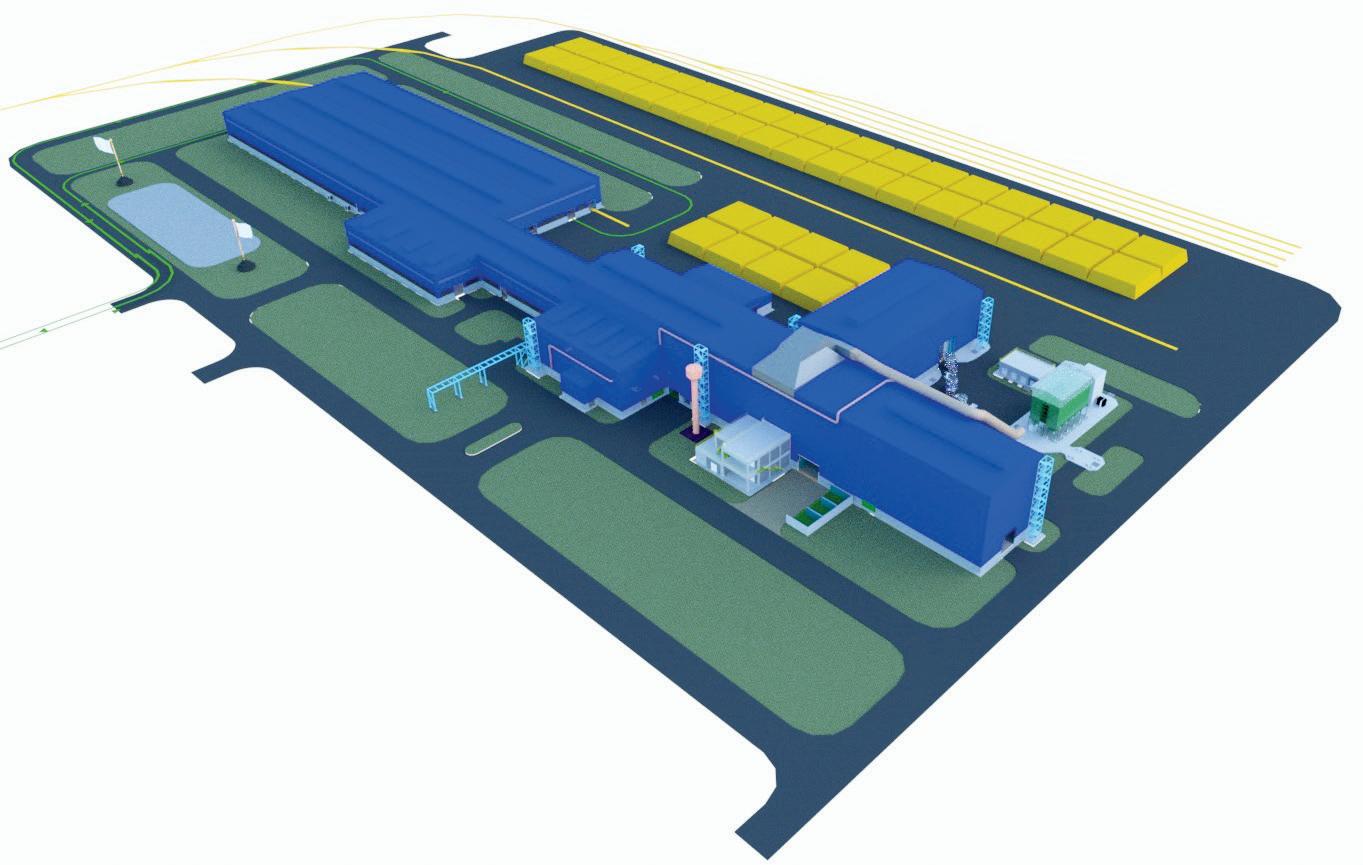
“We’ll be the steel company with the lowest carbon footprint and the lowest water usage,” said Dave Stickler, senior managing partner of Global Principal Partners LLC (GPP) and chief executive officer of Hybar LLC (Hybar). “We aim to be the most environmentally-sensitive steel plant.”
GPP is 20% owner of Hybar.
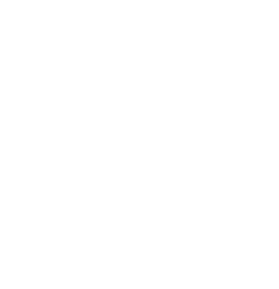
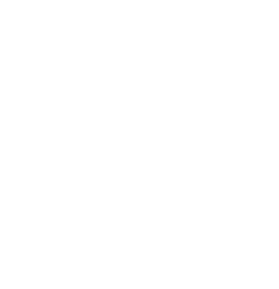
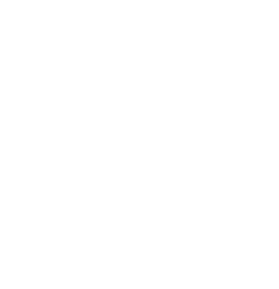
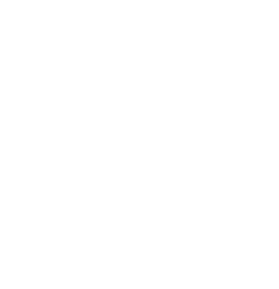
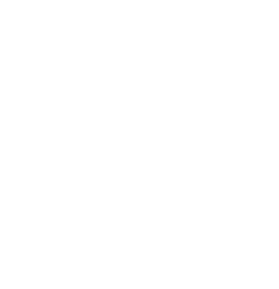
“The other 80% ownership is composed of high-profile equity investors that have invested alongside GPP in previous projects,” stated Mr. Stickler. “GPP will manage and oversee the construction and operations of Hybar.”
Local and state officials have welcomed the new investment in Mississippi County.
“The addition of [Hybar’s] first rebar mill in Arkansas will not only support the growing steel industry in northeast Arkansas, but it will further diversify our economy and provide hundreds of highwage jobs to deserving families,” [then] Governor Asa Hutchinson said in a news statement dated 1 November 2022.
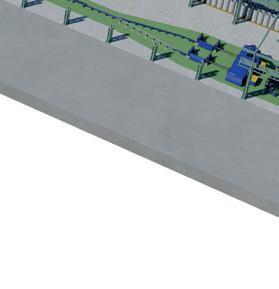
“I’m excited about the opportunities this significant investment will bring to the region.”
“We’re excited for Osceola and Mississippi County to have another steel company locate here,” stated Megan Owens, executive director of the Osceola/ South Mississippi County Chamber of Commerce. “The new jobs created here will be life changing for our residents. We look forward to working with Hybar.”
Background of Hybar
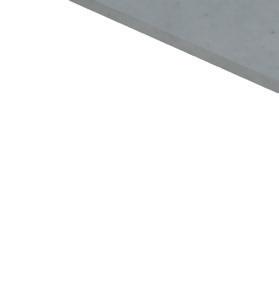
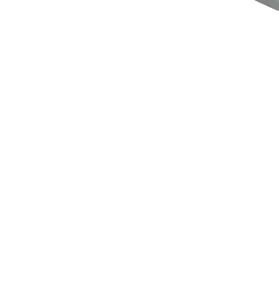
Approximately 200 high-paying, permanent jobs – both direct and indirect – will come from this development.
“We will directly have 140 workers, with average annual incomes of no less than (US) $125,000,” noted Mr. Stickler. “In addition, we will be paying weekly bonuses to workers.”
Beyond the direct employees, Mr. Stickler indicated that because of Hybar, “there will also be about 60 indirect workers, including people working at the port and in slag handling, for example. These workers will be earning (US) $75,000 in annual income, on average.”
Part of the labour structure planned by Hybar involves few layers of management.
“We tend to be the employer of choice,” said Mr. Stickler. “We’re able to take a clean piece of paper to develop work rules from scratch.”
Hybar will stay focused on rebar manufacturing and only rebar manufacturing, according to Mr. Stickler.


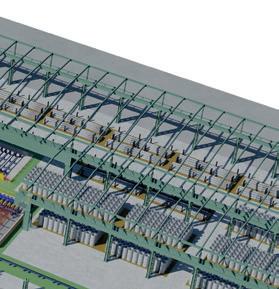

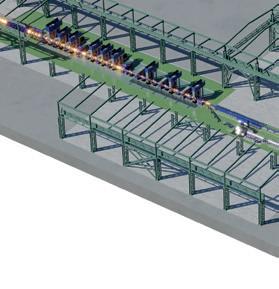
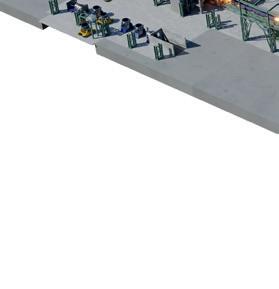
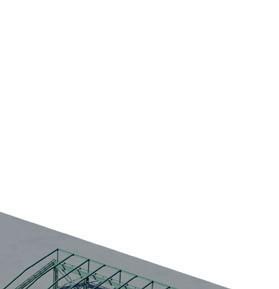
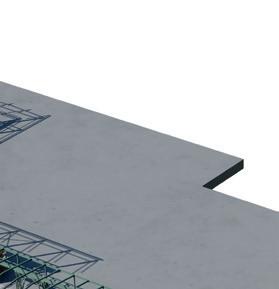

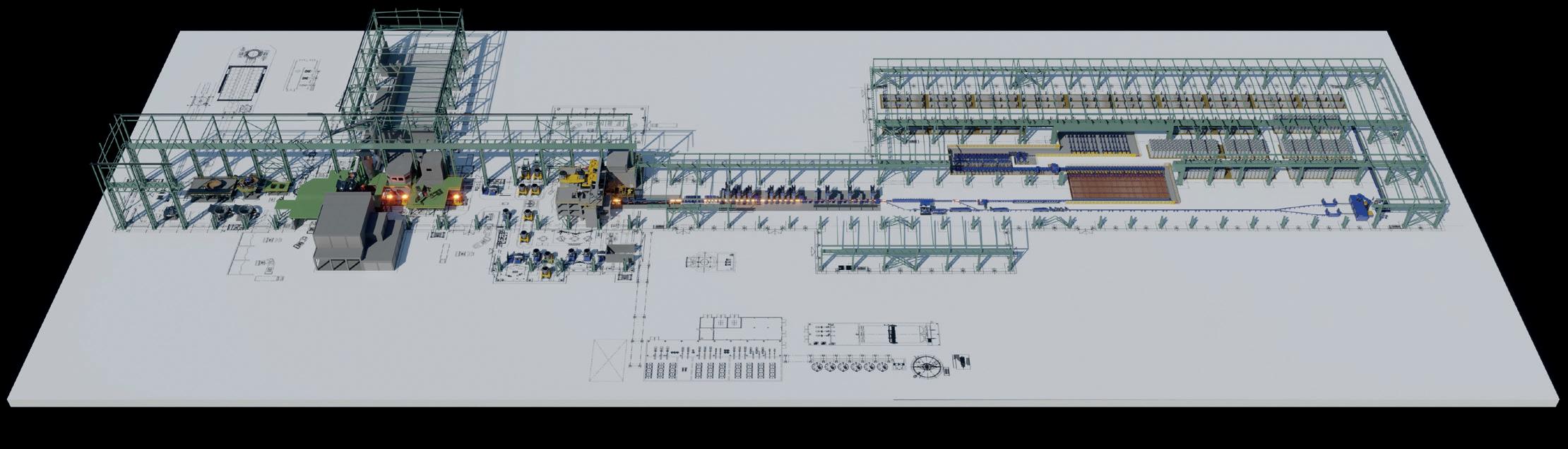
“We’re not going to get into the fabrication business,” he stated. “There are two big rebar steel companies – Nucor and Commercial Metals Company. Both also do fabrication.”
“We’re going to convert scrap into highquality steel,” Mr. Stickler continued. “Our customers can then fabricate our rebar steel.”
He sees demand increasing for ‘green’ rebar steel at competitive pricing.
A substantial amount of the planned annual production of rebar steel has already been sold by Hybar.
“We have sold 23% of our annual projected output to LMS Reinforcing Steel Group (LMS),” detailed Mr. Stickler. “This company is based in British Columbia in Canada. The firm has agreed to purchase 150,000 tonnes of our rebar steel each year for the next 10 years.”
According to a statement from LMS, the firm describes itself as “…a leading independent fabricator and installer of reinforcing steel.” (Pic 1, Pic 2 and Pic 3)
Sustainability
Sustainability is being built into the operations of Hybar even before its rebar mini mill opens.
“We will have a closed water system,” explained Mr. Stickler. “The only water loss will be through evaporation. There will be 0% discharge into the environment.”
“We’re also having our own solar energy system directly connected to the plant,” continued Mr. Stickler. “This will produce 100% renewable energy for our operations.”
In addition, he stated that “we’ll be using DC [Direct Current] in our operations. We’ll have an electric arc furnace, single-strand caster and a 14-housingless-stand rolling mill with an eight-pass, high-speed finishing block. Most rebar mills use AC [Alternating Current]. DC improves energy efficiency, allows better energy controls, and allows for a larger hot heel.”
Reduced energy
The rebar mini mill is designed to utilise less energy on a day-to-day basis.
“The design of the furnace is specifically targeted to reduce the amount of energy needed to produce a tonne of steel,” said Mr. Stickler. “The evacuation system – the bag house – is designed to capture a higher percentage of emissions. This improves plant operations and overall, creates an environmentally-sustainable footprint.”
The rebar mini mill will be built by SMS group Inc. The company has its headquarters in Pittsburgh, Pennsylvania. It is part of SMS group GmbH headquartered in Düsseldorf, Germany.
“SMS has been and continues to be at the forefront of advancing the world’s steel industry in terms of operating efficiency, ever-increasing quality capabilities, and environmental sustainability,” stated Mr. Stickler. “I fully expect the SMS-supplied rebar mini mill to build on the tremendous success my partners and I have had developing many of the finest scrap metal recycling and steel production facilities in the world whilst using SMS technology.”
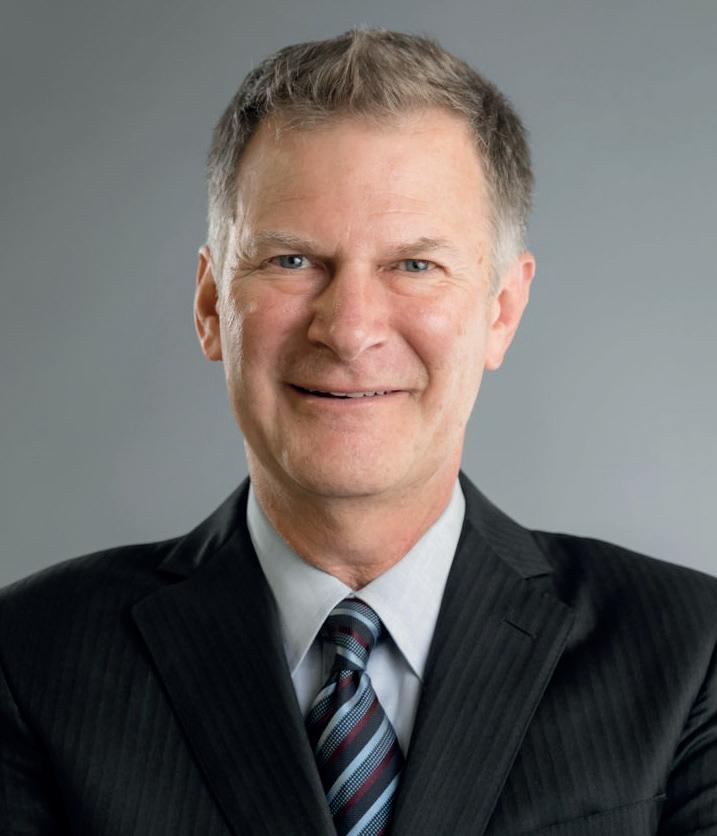
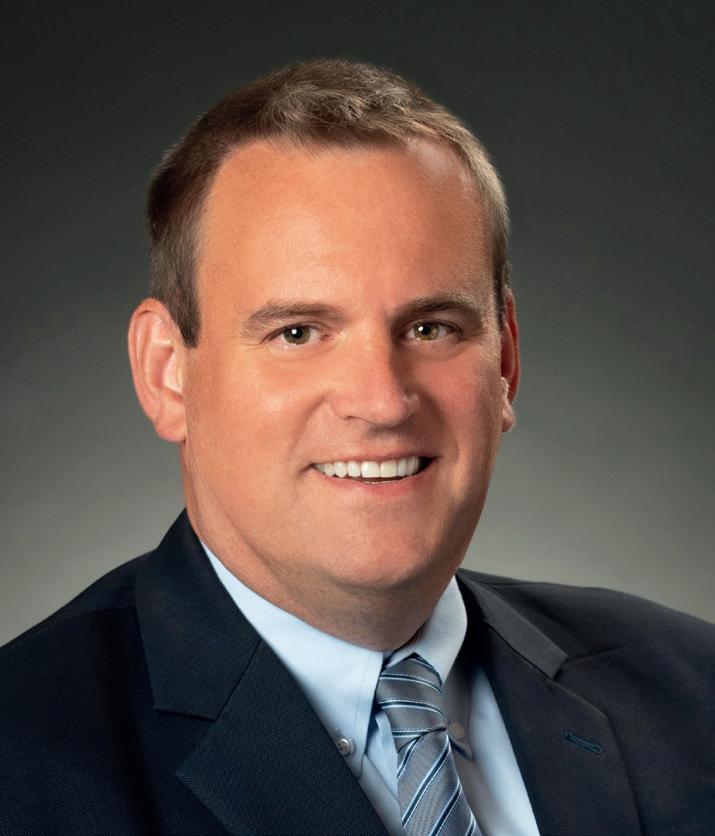
According to a news statement issued by SMS on 6 February 2023, “SMS group’s relationship with the founders of Hybar stretches back almost three decades with a high number of successful projects being completed between the two partners.”
“SMS group appreciates the continued trust of Hybar in our innovations,” said Jens Oliver Haupt, chief sales officer for SMS group Inc. “Jointly, we stand for bringing the most profitable combination of technology and talent to create cutting edge solutions for the industry.” (Pic 4)
Site selection
There were several strategic reasons why this specific location – Mississippi County, Arkansas – was chosen to be the site for this rebar mini mill by Hybar.
“The Mississippi River is important,” Mr. Stickler stated. “It’s key to transportation. We can bring in scrap steel to the plant, and we can ship out finished goods.”
Mr. Stickler also said that this community has a better logistics network when compared to other locales. In particular, he noted that in addition to transport options available because of the Mississippi River, there is transit access through a Class 1 railroad as well as nearby interstate highways.
He stated that while there are other states along the Mississippi River with interstate highways and railroads, this area has the labour pool of skilled workers needed for steel operations.
Low carbon energy sources
The power contract was significant – both in terms of expenses and sources of energy.
“The area has a highly competitive electricity rate,” he continued. “Even more so, a high percentage of the electricity produced is based on low-carbon sources like nuclear energy and solar energy. And those levels are growing.”
He indicated that Hybar will be using minimal amounts of natural gas in its operations.
Changes in energy use are possible in future years.
“Initially, we’re not using hydrogen to power the plant,” detailed Mr. Stickler. “The technology is not there yet. The design of the equipment being built for this plant will allow us the flexibility to convert portions of operations to hydrogen in the future.”
“We are also considering battery storage, but no final decision has been made,” he said. Governmental support was an important aspect of the decision to locate the first Hybar rebar mini mill in Arkansas.
“There has been a true embrace of operational technologies and steel production here,” Mr. Stickler continued. “Arkansas has been a favourable place to conduct business through the years. The support for investments in the steel industry has been seamless between Republican and Democrat administrations.”
Tax credits
Mr. Stickler explained that Hybar is receiving some tax credits – “available to any other business” – in the area of recycling as well as credit rebates to assist with payroll during training of workers.
“All of these tax credits only come to us after we make the specific investments in the plant and after we have hired and paid our workers,” stated Mr. Stickler.
Hybar publicly committed in March of this year that, upon the rebar mini
� 17 - India Update
36Mt new capacity in three years mill beginning operations, the firm will be providing Osceola (US) $1.5 million annually for the next 30 years.
Fresh steel capacities totalling around 36Mt/yr are scheduled for commissioning by FY 2025-26. Despite these upcoming capacities, the government’s capex drive and the resulting push towards domestic steel consumption are expected to maintain the industry’s capacity utilization rate at around 80% in FY 2023-24. However, as the industry’s earnings moderate from the high levels of FY2021-22, there is likely to be an increased reliance on external financing to meet expansion plans. Early signs of this can be seen in the 22% increase in the steel industry’s bank borrowings during FY 2022-23.
As a result, the industry’s leverage (total debt to operating profits) is expected to deteriorate to an estimated 2.5-3.0 times in FY 2022-23 and FY 2023-24, compared to 1.1 times in FY 2021-22. However, this is still lower than the industry’s leverage level of 2.9 times recorded during the previous upcycle of FY 2018-19. The industry’s average EBITDA (earnings before interest, taxes, depreciation, and amortization) per metric tonne is expected to be around $110-115 per tonne in FY 2023-2024.
“This annual contribution will be in addition to our taxes that we will be paying,” said Mr. Stickler. “The funds we will be contributing will be part of our corporate contributions to the local community. Funds will be used in the local schools as well as for fire, police, and ambulance services in the community.”
Background in steel production
While Hybar was newly-formed, it was founded by individuals with a long history in steel production.
Mr. Stickler has been active in steel and finance for decades, leading and structuring “…a number of transactions involving scrap metal recycling companies and scrap substitute facilities,” his biography stated.
“Dave and his wife, Rebecca Li, formed GPP in 2003 to provide capital raising and hands-on management services to metals industry participants in North America and China,” noted his biography. “Based on GPP’s early success in working with both mini mill and integrated steel producers, GPP expanded its business to include direct investment.”
GPP has made past investments in such companies as Big River Steel, now part of US Steel; Mississippi Silicon; and SeverCorr, now part of Steel Dynamics, Inc.
Future growth
GPP and Hybar has ambitious plans for its latest venture in the steel industry.
Mississippi County is anticipated to be just the start of Hybar operations.
Two additional rebar mini mills are planned by the firm, each projected to have a capacity of approximately 600kt/yr (short tonnes) of steel.
Locations for the second and third mini mills have not yet been disclosed, but those sites are likely to be in other parts of North America.
“Arkansas is a great place for us to locate our first plant,” Mr. Stickler explained. “But geographic diversity is important.”
Details of new locations chosen by Hybar will be published in an upcoming edition of Steel Times International. �
Indian steel mills are expected to be more resilient in facing any deterioration in the macroeconomic environment in fiscal years 2023-24.
Infrastructure boost
A strong infrastructure is the cornerstone of any developed economy, yielding a multiplier effect with manifold growth across various sectors. India is now taking measures to achieve the target of becoming a $5 trillion economy (up from the current $3.5 trillion) earlier than forecasted by the International Monetary Fund (IMF) by 2025-26.
There has been a significant increase in budgetary allocations for infrastructure development, with the government believing it will pave the way for India to become a developed economy. Consequently, the government has been consistently expanding existing infrastructure projects and planning new ones to accelerate economic growth. This growth in the infrastructure sector will also provide impetus to other critical areas such as education and skill development, urban development, the green economy, job creation, and global competitiveness.
Conclusion
The infrastructure sector in India has witnessed a paradigm shift in recent years, with increased government allocations and incentives for private players to boost capital expenditure in the steel industry. The government’s focus is on infrastructure development through increased budget allocations. India has allocated INR 100 trillion ($122 billion) for FY 2023-24 for infrastructure, representing a 33% increase from the previous year and equivalent to 3.3% of India’s GDP.
According to a report by the Confederation of the Indian Economy, India is expected to become one of the largest economies in the world, with a gross domestic product of approximately $35-40 trillion by 2047, compared to around $3.5 trillion in 2022. India has implemented the National Infrastructure Pipeline, which has facilitated projects worth INR 108 trillion ($1.3 trillion). These projects are at various stages of completion. �