Register for 2023’s best ever digital manufacturing event.
Revolutionizing converter steelmaking.
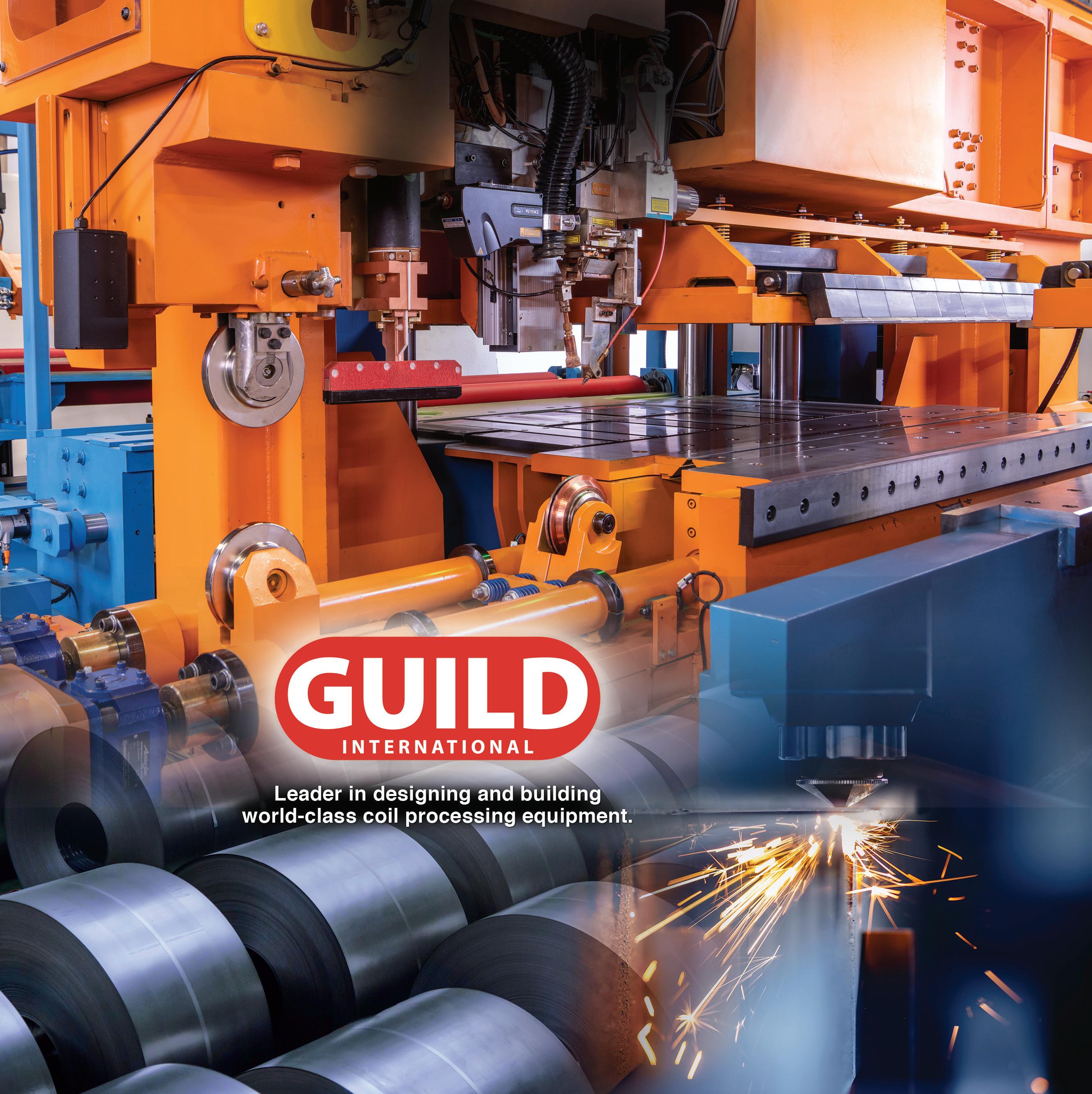
#itsmorethanjustamachine
Register for 2023’s best ever digital manufacturing event.
Revolutionizing converter steelmaking.
#itsmorethanjustamachine
3-ROLL TECHNOLOGY FOR SBQ SIZING. A Reducing & Sizing Block for long products keeping its promises. Achieve your goals with KOCKS RSB®
up to 160mm
finishing size in round or hexagonal dimensions
up to 20%
increase in production
up to 10% energy savings in the mill line
EDITORIAL
Editor Matthew Moggridge
Tel: +44 (0) 1737 855151
matthewmoggridge@quartzltd.com
Assistant Editor
Catherine Hill
Tel:+44 (0) 1737855021
Consultant Editor
Dr. Tim Smith PhD, CEng, MIM
Production Editor
Annie Baker
Advertisement Production
Martin Lawrence
SALES
International Sales Manager
Paul Rossage paulrossage@quartzltd.com
Tel: +44 (0) 1737 855116
Sales Director
Ken Clark kenclark@quartzltd.com
Tel: +44 (0) 1737 855117
Managing Director
Tony Crinion tonycrinion@quartzltd.com
Tel: +44 (0) 1737 855164
Chief Executive Officer
Steve Diprose
SUBSCRIPTION
Jack Homewood
Tel +44 (0) 1737 855028
Fax +44 (0) 1737 855034
Email subscriptions@quartzltd.com Steel
Cover courtesy of Guild International Guild International is a world leader in engineering and building coil processing and end-welding machines for steel processing lines. The company’s products include laser welders, arc welders and resistance welders and are regarded as the most technically advanced welding machines on the market. Guild International also produces a full line of tube mill entry equipment including uncoilers, speed funnels, flatteners and accumulators. Each one of these machines is designed and manufactured to improve the productivity of any strip processing line requiring coil handling and coil end joining and welding. For more information, please visit Guild’s website at www.guildint.com
36 Processing Keeping order.
39 Lubrication Raising the game.
42 Oxygen steelmaking Revolutionizing converter steelmaking.
46
Perspectives Q&A: Quantolux Optimizing production.
48
History
Meldon viaduct – UK’s wrought iron trellis viaduct on Dartmoor.
England.
Tel: +44 (0)1737 855000 Fax: +44 (0)1737 855034 www.steeltimesint.com
Steel Times International (USPS No: 020-958) is published monthly except Feb, May, July, Dec by Quartz Business Media Ltd and distributed in the US by DSW, 75 Aberdeen Road, Emigsville, PA 17318-0437. Periodicals postage paid at Emigsville, PA. POSTMASTER send address changes to Steel Times International c/o PO Box 437, Emigsville, PA 17318-0437.
ISSN0143-7798
matthewmoggridge@quartzltd.com
I would rather not be viewed as somebody who supports Shell – the multinational conglomerate still buying Russian oil – but when I read recently that Wael Sawan, the oil giant’s head honcho, believes that cutting oil and gas production would be ‘dangerous and irresponsible’ – bearing in mind that alternative energy sources are not being developed fast enough – I did stop and wonder. Was he being truthful or simply mindful of protecting his and his shareholders’ profits as the climate lobby cranks up the pressure? I guess the answer depends on your perspective. On both sides of the argument, viewpoints are entrenched in long-held beliefs about the climate emergency, so we’ll never get to the heart of the matter unless something actually happens (or doesn’t happen) and those on one side of the argument either apologise or smugly announce ‘I told you so’. Sawan says ‘if we’re going to have a transition it needs to be a just transition.’ Who am I to disagree with that? It’s all very well Western countries dictating that the whole world should transition yesterday, but that’s because the West has had its industrial revolution, thank you very much. Other nations (notably India
and China) are still in the midst of theirs.
Where steel manufacturing is concerned, development by Global Energy Monitor of a Global Blast Furnace Tracker is a good idea and a helpful resource, but it shouldn’t be used to name and shame developing nations still actively building blast furnaces in order to develop their economies. While it is clear that – environmentally – the BF is the steel industry’s climate ‘villain’, they’re not going anywhere, and some say they will never leave the building because there are specific types of steel that can only be produced using traditional processes.
Personally, I am hopeful that some of the many technologies under development will mitigate the effect blast furnaces are having on the planet, even if CCUS – something I have always regarded as a ‘go to’ solution for greener BF steelmaking – will not play a major role in the decarbonization of steelmaking going forward, or so says the Institute for Energy Economics and Financial Analysis (IEEFA).
Having recently chaired a debate on the use of CCUS in the global steel industry, I find it hard to believe that it can be written off so decisively when so many companies are actively engaged in its development.
Combilift is the perfect fit for the steel industry. Our multidirectional forklifts, straddle carriers and mobile gantry cranes are perfect for handling long product, allowing you to maximise your storage, efficiency and safety.
• Safer product handling
• Optimised production space
• Improved storage capacity
• Increased productivity & output
• Enhanced profits
Automatic Yard means no human on the floor, nor on the cranes. Q3-DYMS represents a breakthrough technology to automate semifinished and finished product logistic operations, simplifying the complex management of a yard during production in fully automatic mode. Its features make it part of a plant digitalization strategy.
Tata Steel celebrated World Environment Day on 5 June with several plantation drives, and events organised across Jamshedpur, India. A plantation drive was organised at CRM Bara Transport Park in the morning followed by a plantation drive at New Bara Flats, Agrico Colony where Mamta Priyadarshi, divisional forest officer, Jamshedpur forest division and Chanakya Chaudhary, vice president, corporate services, were both present. Several plantation drives were organised inside Tata Steel’s Jamshedpur works, with over 5,000 saplings being planted across multiple locations in a day.
Source: The Avenue Mail, 5 June 2023.
South Korean steelmaker POSCO has launched Greenate: a ‘groundbreaking low-carbon steel product’, as part of the company's ambitious mission to achieve carbon neutrality by 2050. This eco-friendly steel has already gained its first customer, with LG Electronics becoming the inaugural client to purchase the lowemission steel for its home appliances production, as per a report from Korea Herald. In addition, Samsung Electronics is currently considering the procurement of Greenate certified steel for its premium ovens.
Source: Steel Guru, 5 June 2023.
Attacks by the Russian army on a hydroelectric power plant in Nova Kakhovka in southern Ukraine on 6 June has affected steelmaking operations at Kryvyi Rih, where ArcelorMittal’s Ukrainian steel mill and Metinvest’s mining and processing plants are located, Fastmarkets reported. “70% of the water supply to Kryvyi Rih comes from the Kakhovka Reservoir, so the situation with the city’s water supply is complicated, but it is under control,” Oleksandr Vilkul, head of the Kryvyi Rih Defence Council, said in a social media message.
Source: Fastmarkets, 6 June 2023.
British Steel has secured a major contract win with Belgian railway infrastructure manager Infrabel. The fouryear agreement will see British Steel supply 40kt of high-quality rail in various profiles for the maintenance and renewal of track across Belgium’s rail network. It is the second successive contract, having penned a deal in late 2018 that saw the Brussels team return to British Steel after a ‘short break’, with quality, security of supply and reliability all being raised as areas of priority for Infrabel.
Source: Business Live, 7 June 2023.
Turkish steel profile manufacturer Kocaer Celik has announced plans to conduct a feasibility study for a 24-MW geothermal power plant investment in Kuyucak District, Turkey. Through this investment, the company aims to diversify its clean energy production resources with geothermal energy production, following the success of its roof-type solar power plants. An operating license and a total area of 10,844.18 hectares have been acquired by Kocaer Celik for the plant’s construction.
Source: Think Geo Energy, 7 June 2023.
Danish clean energy giants Ørsted and Vestas have entered a commercial sustainability alliance to use low-carbon steel in their jointly developed offshore wind projects. The partnership will see Vestas, a wind turbine manufacturer, supplying green energy solution provider Ørsted with low-carbon steel towers and blades made from recycled materials. Both companies have highlighted the need to limit carbon in the manufacture of materials and components used in wind farms and to put in place cost-efficient solutions to resolve decarbonization challenges and circularity issues in the wind sector. Source: Power Technology, 8 June 2023.
Tata Power Renewable Energy, through its subsidiary TP Vardhaman Surya, has received a contract to set up a 966MW round-the-clock hybrid renewable power project for Tata Steel. The project has the hybrid renewable capacity of 379MW solar and 587MW wind power, a company statement said. Praveer Sinha, CEO and managing director, Tata Power, said in the statement: "The 966MW round-the-clock hybrid renewable power project marks a significant step towards our combined efforts to accelerate the adoption of clean and green energy to meet the net zero target." Source: The Economic Times, 8 June 2023.
Trinidad and Tobago's TT Iron Steel Company (TTIS) has agreed to purchase an idled iron and steel plant, originally owned by ArcelorMittal, the company has announced. The purchase agreement comes seven years after ArcelorMittal closed operations in Trinidad following layoffs amid low global steel prices, which have since rebounded. The plant, built in 1980, will be subject to initial refurbishment expected to cost between $150 million and $200 million. Source: Reuters, 8 June 2023.
The chairman of Tata Steel UK has called for a ‘level playing field’ as it seeks UK government subsidies to decarbonize its Port Talbot steelworks. Henrik Adam, CEO, Tata Steel Europe, said European competitors were receiving ‘billions of pounds’ from governments to transition to greener operations. The UK government department for business and trade said: "The business secretary knows how critical the steel industry is to Wales, and made her commitment to securing a
decarbonized, competitive future for the sector clear when she visited Port Talbot earlier this year…we cannot comment on commercially sensitive negotiations."
Source: BBC, 13 June 2023.
Gerdau North America has commissioned UK-based plant supplier Primetals Technologies to supply a new static synchronous compensator (Statcom) for the company's steel mill located in Petersburg, Virginia, USA. Primetals Technology plans to build the largest Statcom that has ever been implemented in North American steelmaking operations in order to supply power for the facility's 69-kilovolt alternating current electric arc furnace. Source: Kallanish, 8 June 2023.
Mining company Rio Tinto and China’s Baowu Steel Group have signed a memorandum of understanding (MOU) to explore several initiatives including setting up green steel facilities in China and Western Australia, Rio Tinto said in a statement. “This MOU aims to address one of the biggest challenges faced by the industry – developing a low-carbon pathway for low-tomedium grade iron ores, which account for the vast majority of global iron ore supply,” Rio Tinto’s chief commercial officer Alf Barrios said in a statement. Source: SCMP, 12 June 2023.
Mining giant Glencore has made a proposal to buy Teck Resources’ steelmaking coal business as part of an ongoing takeover deal. Glencore first made an unsolicited takeover bid for the entirety of Teck’s operations in April. Teck rejected the $23bn offer, calling it ‘unsolicited and opportunistic’.
Under Glencore’s latest proposal it would buy the coal and steelmaking element of Teck’s business, joining the unit with its own demerged energy coal assets two years after the deal closes. Source: Mining Technology, 12 June 2023.
United States Steel Corporation has issued its 2022 Environmental, Social and Governance (ESG) report entitled, ‘Essential for our Future,’ which the company has stated reaffirms its commitment to sustainable steelmaking and a greener
economy. "Every single employee is playing a role in creating a more sustainable future," said David B. Burritt, US Steel president and chief executive officer. "Steel's importance to our society is undeniable, both in the past and into the future as we collectively tackle climate change. It’s of particular significance that we were the first American steel company to set a goal of achieving net-zero greenhouse gas emissions by 2050.”
Source: Business Wire, 13 June 2023.
Tata Steel has said that 18 people were injured, with two in intensive care, following a steam leak at its Odisha power plant. The company reported that the accident occurred at its Meramandali BFPP2 power plant in Dhenkanal, Odisha, during an inspection, leaving a few people injured, and has started an internal investigation into the cause of the accident. The injured persons were immediately shifted to the Occupational Health Centre inside the plant premises and then to a hospital in Cuttack for further treatment. Source: Reuters, 14 June 2023.
Tata Steel has signed a MOU with Germany plant supplier SMS group to collaborate on technology to reduce carbon emissions from the steelmaking process. Under the MOU, the two companies will hold technical discussions and demonstrate SMSdeveloped decarbonization technology at a blast furnace in Tata’s Jamshedpur plant in Jharkhand, India. The technology aims to reduce more than 50% of CO2 emissions from the blast furnace’s baseline operation.
Source: Mining Technology, 15 June 2023.
Singapore based steelmaker Meranti Steel has announced that it has signed a MOU with Thailand-based energy company Global Power Synergy to establish renewable solutions for its new green steel plant to be built in Thailand. Meranti Steel aims to use renewable solutions such as solar and wind energy and create a future green hydrogen supply chain for its new plant. The plant, which will have a capacity of 2Mt/yr of hot rolled coil, is planned to start production in late 2027.
Source: Steel Orbis, 15 June 2023.
Brazilian steelmaker Gerdau has said that it will invest $666.64 million by 2026 in a new sustainable mining platform in the Minas Gerais state, in a bid to boost its iron ore output while reducing emissions. The new platform will raise the production capacity of Gerdau's Miguel Burnier mine to 5.5Mt/yr of iron ore and is scheduled to start operating at the end of 2025, according to the company. The project will rely on the dry stacking method for disposal of 100% of the mining tailings, eliminating the need to use a dam, Gerdau said. Source: Reuters, 15 June 2023.
A steel frame measuring more than twice the size of Wembley football pitch is nearing completion at a new facility to support the British Army’s vehicle and equipment fleet. The Vehicle Storage and Support Programme at the Ministry of Defence site in Ashchurch aims to enhance the British Army’s operational readiness and future capability, through the delivery of modern sustainable storage and maintenance solutions for its vehicle and equipment fleet.
Source: Gov.uk, 16 June 2023.
ArcelorMittal has announced that it has partnered with Japan-based Sekisui Chemicals on a project called NEDO to
capture and reuse carbon from steelmaking. The companies have achieved a carbon conversion rate of 90%, and a hydrogen conversation rate of 75% using blast furnace gas at ArcelorMittal’s Asturias plant in Spain, higher than the projected target of 85% for carbon conversion and 60% for hydrogen conversion.
Source: Steel Orbis, 20 June 2023.
Liberty Steel Georgetown in South Carolina, USA, has announced the commencement of a new apprenticeship programme, which will allow workers
One person was killed and three others were injured in an explosion at a steel factory in Palakkad district, southwestern India, on 20 June. The incident took place at 0500hrs with a loud explosion, according to local people. According to preliminary investigations, the explosion started in the furnace. There have since been allegations about security lapses in the factory. A district collector has said that action will be taken against the factory if this is the case, adding that the police and the pollution control board are investigating the accident.
Source: The Hindu, 20 June 2023
at the company’s South Fraser Street mill to train at Horry-Georgetown Technical College. Starting later this year, the programme will focus on improving the technical skills of present employees on campus and on the job. New hires will also receive training, and Liberty Steel hopes the programme will expand to serve as a pipeline for future workers.
Source: Georgetown Times, 20 June 2023.
Ternium Mexico, a subsidiary of Ternium, has stated that its new slab mill will be built in Pesqueria. The mill will be located next to the existing hot rolling mill, which has a capacity of 4.4Mt/yr. The company will invest $3.2 billion in the new electric
arc furnace steel mill which will create more than 1,800 jobs. Construction of the mill is expected to begin in December this year, while it is anticipated to commence operations in early 2026.
Source: Steel Orbis, 21 June 2023.
Engineers at Swansea University, UK, have developed a heat storage material made from seaweed that they plan to test at Tata Steel’s Port Talbot-based steel plant to see how well it can capture waste heat from industrial operations. The new thermochemical material is made using alginate, a polymer produced by seaweed. The team has created beads using the material which capture heat and can be made to release it using humid air.
Source: The Chemical Engineer, 3 July 2023.
Tata Power has emerged as India’s most ‘attractive employer brand’, followed by e-commerce giant Amazon and Tata Steel, a research report has revealed. HR services provider Randstad India’s annual report ‘Randstad Employer Brand Research (REBR) 2023’ revealed that Tata Power scored highly on financial health, good reputation, and career progression opportunities. IT company Tata Consultancy Services secured 4th position in the top 10 most ‘attractive employer brand’, followed by Microsoft, Samsung India, Infosys, Tata Motors, IBM and Reliance Industries.
Source: The Indian Express, 21 June 2023.
A new report has found that carbon capture, usage and storage (CCUS) for coalconsuming blast furnaces will not play a major role in global steel decarbonization, and that a phase-out of coal in the steel sector is technically feasible by the early 2040s. Research undertaken by IEEFA has highlighted that CCUS has a long history of significant under-performance and failure in other sectors, and ‘even projects that the fossil fuel industry likes to cite as successes raise major questions about project risk and the feasibility of rolling out such projects globally.’
Source: IEEFA, 3 July 2023.
Out of three offers to buy the assets of two Liberty Steel plants in Liége, Belgiium, one has finally been accepted by the Liége Court of Appeal.
Liberty Steel Galati, the Romanian subsidiary of UK steelmaker Liberty Steel, has beaten ArcelorMittal and a NLMK/Marcegaglia consortium for the two plants, which employ a total of 582 workers. The Liberty Galati offer took preference over the others, according to a report by The Brussels Times, because it included the acquisition of all activities and workers. However, while the workers are confident they will be able to return to work soon, no deadline has been given.
Source: The Brussels Times, 21 June 2023
The European Commission has said that it has approved $308 million in state aid granted by Belgium to steel maker ArcelorMittal to help it decarbonize its steel production. The aid will support the construction of a direct reduction iron
plant, which together with a new electric arc furnace will replace one of two existing blast furnaces. The plant, which is expected to be operational by 2026, will ultimately be operated using renewable hydrogen.
Source: Reuters, 22 June 2023
Plant supplier ABB will provide electrification and automation systems for ArcelorMittal Nippon Steel India’s advanced steel cold rolling mill (CRM) in Gujarat, India. ArcelorMittal Nippon Steel India (AM/NS India), a joint venture between steel companies ArcelorMittal and Nippon Steel, is setting up the new CRM as part of its downstream expansion and sustainability plans. The steel manufacturer has a crude steel capacity of 9Mt/yr. It produces a range of flat steel products and has a pellet capacity of 20Mt.
Source: Power Engineering International, 4 July 2023.
cunova, a market leader for customised products and solutions made of copper and copper alloys, is adding a fourth supporting pillar to its business units. In addition to melting and casting technologies, industrial applications, and maritime applications, the service division will be integrated into the company’s organisational structure with immediate effect, according to CEO Werner Stegmüller.
The new unit will be headed by Jack A. Roser, CEO of the US company Roser Technologies Inc (RTI), which was acquired by cunova last year. For more than 20 years, RTI has set the standards in service offerings in the field of melting and casting technology, and has ‘remarkable expertise’, according to industry sources. With the integra-
tion of RTI into the cunova group of companies, successfully tried and tested processes and structures can now be applied to all cunova service centres worldwide.
“We are convinced that we can leverage significant potential in the service sector by improving our organisational structure,” emphasised Stegmüller. “With the decision to establish a fourth business unit for Service Division, we underline our high demand for the best possible customer and service orientation. We are convinced that this decision will enable us to achieve our ambitious growth targets even better.”
For further information, log on to www.cunova.com
which mostly include grades traditionally produced via the integral cycle only, such as interstitial-free grades for the automotive industries and the much-coveted electric steel grades required, for instance, by all providers of electrical mobility and green power generation solutions.
EAF safety and user-friendliness some BOF users might still harbour.
Tenova, a leading developer and provider of sustainable solutions for the green transition of the metals industry, will supply an electric arc furnace (EAF) equipped with Consteel® and Electromagnetic Stirrer Consteerrer® to POSCO for its Gwangyang plant in South Korea.
The South Korean steelmaker, the sixth largest worldwide with about 43Mt of steel produced in 2022, has a track record of pursuing the decarbonization of its high-quality steel products,
A key part of this transformation towards sustainability consists in the gradual conversion from the BF-BOF route towards electric steelmaking based on EAF. After a two-year process of co-engineering and competitive comparison, POSCO has selected Tenova’s equipment: a full-platform EAF capable of tapping 280t of liquid steel, equipped with the continuous scrap charging system Consteel® and the electromagnetic stirring system Consterrer® - jointly patented by Tenova and ABB.
The new EAF will be uniquely designed to match the needs of quality, productivity, and efficiency that such an experienced steelmaker demands, and will be equipped with a full set of robotic applications and enhanced safety solutions such as the Safe+ EAF water leakage detection system to dispel any concerns about
“Besides requiring a radical re-thinking of the production process, an EAF of this size and power is an entirely new machine for most integral steelmakers and may understandably scare away engineers who are accustomed to the relative quietness of most BOF Converters halls,” said Paolo Stagnoli, sales director for EAF and LF, Tenova. “As a member of Tenova, I find profoundly gratifying that such a top-class steelmaker recognized our unique experience in large EAFs and understood the value of our patented technology. We are committed to become a long-standing partner of POSCO as we build together a new environmentally friendly and record-breaking furnace.”
The new EAF will be installed in a dedicated new section of the Gwangyang plant and is scheduled to enter production by the end of 2025.
For further information, log on to www.tenova.com
A growing demand for electrification within several industries like steel, solar and semiconductors has provoked Kanthal to expand its production site in Walldorf, Germany. The aim of the investment is to capture the growth within electric industrial heating and drive operational improvements through increased automation.
At the Walldorf site, Kanthal manufactures
products such as Fibrothal® heating modules, flow heaters, metallic heating elements, and diffusion cassettes. All these products, says Kanthal, enable industries to make the green technology shift.
The investment includes expanding the current premises with ~2500 m² manufacturing area through a lease agreement of a nearby facility, as
well as new equipment and automation improvements. The number of employees is expected to increase by approximately 10 people.
“The investment ensures that we can capture the growth in electrification of industrial heating, which will require a ramp-up of our operations globally. We expect a rapidly growing demand for our traditional heating solutions, but also for our
Austrian solutions provider ELIN Motoren and global technology company Voith have launched the first electric motor with integrated safety coupling for the main drive of tunnel boring machines. Water-cooled asynchronous motors from ELIN Motoren contain either the Voith SafeSet to safeguard the entire drive train or the Voith SmartSet for continuous operation, even with frequent torque peaks. According to Voith, torque limitation increases the productivity of the TBM, protects the machine components, and avoids costly downtimes.
Depending on size and geology, the cutting head of a TBM is powered by between four and 24 drive units. These drive trains consist of a pinion, planetary gear unit, torsion shaft, safety coupling, and electric motor and represent the heart of a TBM that should be protected. Clogging in the cutting head causes a sudden torque much higher than the maximum permissible torque with which the drive train is rated. As it is activated at a predefined torque, the integrated safety coupling in the new MKH-SafeSet and MKH-SmartSet electric motors from ELIN Motoren protects all the drive train components of tunnel boring machines. A triggered coupling can be re-activated within a few minutes. If only a few couplings are released, the TBM can continue to tunnel until the next maintenance shift.
The weight of the new Voith SafeSet has been reduced by more than 80% and is only around 15% of that of conventional safety couplings. A lower mass minimizes rotor inertia and the bearing loads of the drive train, which improves efficiency and achieves lower temperatures, thus extending the service life of the drive train.
The MKH-SmartSet is an optional add-on to the MKH-SafeSet and allows continuous tunnelling despite any torque peaks that are non-critical for the drive train. Adding a SmartSet results in an automatic reset if the TBM slows down or comes to a stop which allows continuous operation, even if the frequency of high torque load peaks increases, which positively affects the productivity of the TBM.
“Partnering with ELIN Motoren, we have a powerful new to-the-market technical solution that will transform the tunnelling boring market segment,” stated Per-Olof Berg, product management torque limiting and connection couplings
at Voith. Berg added: “The new MKH-SafeSet and MKH-SmartSet is a further development of the well-known SafeSet portfolio which is in operation on thousands of ELIN Motoren cutter head motors. The new MKH-SmartSet instantly shaves the torque peak and protects the drive without releasing. Furthermore, MKH-SafeSet, with the coupling integrated into the cutter head motors from ELIN Motoren, is the perfect lightweight and compact solution for tunnel boring machines that do not need peak shaving and automatic resetting.”
“The pooling of the expertise of ELIN Motoren and Voith offers manufacturers of tunnel boring machines a powerful yet safe technical solution from a single source,” said Markus Frickh, key account manager at ELIN Motoren. “As a manufacturer of customized electric motors, we aim to offer products that meet the stringent individual requirements in the mechanized tunnelling segment.”
For further information, log on to www.voith.com
newly developed high temperature process gas heaters that are currently being tested in a number of pilot projects,” said Aaron Roy, president of business unit heating systems at Kanthal.
“This will benefit customers with better availability and faster delivery of products that will be key in achieving their sustainability goals. In addition, the expansion shows the local community
that we are investing in Walldorf and offering new and attractive jobs.”
The initiative started in May and is expected to be fully implemented in early 2024.
For further information, log on to www.kanthal.com
IIoT service provider thyssenkrupp Materials IoT is automating the calculation and assembly of knives in steel service centres with the help of its new toii®.Cut software. The software solution digitalizes all preparatory and execution steps on slitting lines: from software-based knife calculation and the automated creation of knife assembly plans to digital tool management. It is a further module of toii®, the IIoT platform that digitizes and automates production in the steel and metalworking industry.
The high degree of automation on the shop floor leads to more efficient work, the company says, and helps to sustainably save costs and reduce throughput times. In addition, the use of the solution means that users are able to focus on infrequently occurring cases, such as calculated knives with warnings or error messages.
The toii®.Cut software was developed in a
two-year cooperation with the processing specialist thyssenkrupp Materials Processing Europe. The aim was to find a solution that could be seamlessly integrated into thyssenkrupp Materials Processing Europe’s existing IT system – including its own ERP system – in the ongoing digitalization of steel service centres.
With the help of the solution, the processing specialist is now able to meet increasing requirements such as on-time delivery, even for orders with small batch sizes or a large quantity of knives to be built. Handwritten work and paper-based processes are also to be replaced.
“From an operational excellence point of view, with toii®.Cut we have another building block to increase efficiency, process stability and quality at all our sites through digitalization,” said Michael Panzer, head of operational excellence at thyssenkrupp Materials Processing Europe.
The web-based software solution promises its users a cross-site application with numerous functions and features as well as an intuitive user interface. With the aid of integrated tool management, the use of tools can be optimized and longer knife service lives achieved.
“We are in contact with our customers in steel service centres from all over Europe beyond the initial development process and have gained a very good understanding of their requirements. This allows us to ensure that our software remains up-to-date and also meets the individual needs of users,” explained Sebastian Lang, managing director of thyssenkrupp Materials IoT.
For further information, log on to www.thyssenkrupp-materials-services.com
ABB will purchase low-carbon copper winding wire from global provider Dahrén for use in the manufacturing of its electromagnetic stirring (EMS) equipment. The commitment builds on similar supply chain connections for ABB stirrers used in the production of metals.
The supplier, which operates primarily in Sweden, Germany and Poland, will receive raw copper mined by Swedish mining and smelting company Boliden using fossil-free energy, then processed into wire. Copper is a vital material for manufacturing industrial electrical equipment, but its production is energy intensive. The carbon footprint of the Boliden product used by Dahrén is known to be 65% lower than the industry average, says ABB.
“We believe we are in a breakthrough year for low-carbon and recycled copper,” said Håkan Svensson, CEO of Dahrén. “Thanks to the longterm partnerships in our supply chain, we are able to secure a significant supply of this raw material and offer our customers the possibility to reduce their own carbon footprint, while retaining the high quality and performance of
their products.”
“Through close collaboration with Dahrén and Boliden, ABB is helping to build a supply chain ecosystem with a low-carbon and ultimately a zero-carbon approach at its centre,” said Ola Norén, head of metallurgy products, process industries, ABB. “We are increasing our use of low-carbon and recycled copper winding wire in our EMS technologies all the time.”
ABB’s Metallurgy Products team has now ordered a stock of copper wire from Dahrén for use in the air-cooled EMS for aluminium applications, and the intention is to grow this to higher volumes in the future. The largest model has
2,200kg of copper wire per unit and the smallest 500kg of copper wire per unit.
Separately, ABB has a relationship with Finnish metals manufacturing specialist Luvata for hollow conductor wire made from Boliden’s certified recycled copper. The models of stirrers constructed using this stock of copper each have up to 2,700 kg of copper, saving up to 6,700 kg of CO2 per stirrer, based on verified industry-standard calculations.
For further information, go to go.abb/processautomation
The most technically advanced coil joining equipment available. Period.
Guild International can design and build the welding machinery you need to keep your coil processing lines up and running smoothly and profitably. We are the world leader in supplying highly-engineered coil processing equipment known for reliability and performance. Contact us today to begin designing the perfect coil joining equipment for your processing lines.
For more information, visit our website at www.guildint.com or call +1.440.232.5887
World Leader in Coil Processing Equipment for the Steel Processing, Tube Producing and Stamping Industries Since 1958
WHEN inflation began raising its ugly head some time ago, the industry’s Cassandras were quick to chorus the sentiment that the US economy was in the throes of a deep recession which would leave its scars on everyone connected with steelmaking – suppliers, sub-contractors, the industries which relied on steel, workers’ jobs and what have you.
Fortunately, that has not come to pass, or at least not on the scale feared. It was a high-inflation situation with no job losses – a soft landing then? The politicians who support the steel industry, and also expect to be supported by the latter, heaved a sigh of relief that it was not a stagflation, the horror situation that we had experienced in the past. The job market right now is pretty much strong and many industries, including steel, are willing to pay a premium to get good and able workers.
Of interest in this regard is the recently released 2022 Annual Statistical Report by the American Iron and Steel Institute, which is touted as the steel industry’s ‘voice’. The report contains comprehensive data on the US and North American steel industry.
According to the AISI report, US steel shipments in 2022 amounted to 89.5Mt (net tons), down 5.5% from the previous
year. The nation’s crude steel production in 2022 declined by 6.2% to 94.7Mt (net tons). Total domestic steel imports into the US declined 2.0% in 2022 over the previous year, while finished steel imports rose 11%, accounting for a 24% share of apparent steel consumption. The construction and automotive industries remained the primary end-use markets for US steel products.
Describing the steel industry as ‘constantly evolving’, AISI president and CEO, Kevin Dempsey, said that the annual statistical report (ASR) provided the industry standard for reporting on the steel industry in the US.
Steel mills remained below 80% capacity as of the third week of June but, as Dempsey puts it, have been ‘inching back toward that key threshold for financial success for the steel sector’.
After years of record profitability, the industry saw imports account for 24%
of market share last year as prices started to tumble once again from all-time highs. Steel prices have since been on the mend as automotive orders have picked up and automotive production has risen while appliance manufacturing has remained stable.
Moving on to that hotlydebated subject of tariffs under Section 232, some countries have been quietly trying to get exemption on their exports from steel and aluminium tariffs.
India is a case in point. It had already asked the Biden administration for exemption off tariffs, offering to exempt US agricultural exports from tariffs; however, Washington remained unmoved. The exemption gesture would have been portrayed as an ‘achievement’ during the high-profiled state visit of Indian Prime Minister Narendra Modi to Washington in the third week of June.
Section 232 tariffs were imposed by former President
There’s never a dull moment in the US steel industry what with rising inflation possibly leading to a recession but not quite, Section 232 tariffs still in place and some nations, like India, trying to be exempted from them, and, of course, China still producing far too much steel than is needed. Throw decarbonization into the mix and it starts to get even more exciting. Manik Mehta* reports.
Amid the ongoing emphasis on decarbonization and producing ‘green steel’ by the industry – which is said to be responsible for generating some 7% to 9% of the world’s CO2 emissions – attention has turned to Boston Metal which reportedly worked for some 10 years to develop, refine and scale technologies aimed at reducing carbon emissions and combatting climate change; the company is trying to reinvent a process, originally developed by the Massachusetts Institute of Technology (MIT), to reduce CO2 emissions.
Boston Metal was formed in 2013 and has since raised a total of $250 million to develop a ‘green path’ to steel production which is the backbone of modern infrastructure construction.
Though Boston Metal has yet to generate revenue and is still working on the final technology to be applied on scale for clean steel production, the company has, nevertheless, signed a $20 million funding arrangement with the International Finance Corp (IFC)., the private sector investment organization of the World Bank.
IFC’s director William Sonneborn has been telling the media that this is the first-ever investment made by the IFC in a pre-revenue start-up, thus underscoring the importance which the World Bank attaches to helping low-income nations produce steel without the CO2 emissions.
Sonneborn, who was recently in Africa, has been pointing out that there are hundreds of millions of people who do not have a proper house and that, at some
stage, they will need steel for properlyconstructed houses. Thus, the incremental steel production of the world will not be in the US, even though the technology may have been developed at the MIT. Indeed, the bulk of crude steel, estimated at 59%, was produced in developing countries in 2021, the IFC claims. Boston Metal’s process will be particularly attractive in developing nations that also have access to clean electricity such as Chile, Ethiopia, Malawi, Uruguay and Zambia, according to the IFC.
Meanwhile, Boston Metal, based in Woburn, Massachusetts, has attracted investments from ArcelorMittal, Microsoft’s Climate Fund, and Bill Gates’ Breakthrough Energy Ventures besides the World Bank. It is not surprising that many steel executives are closely monitoring Boston Metal’s activities. American steelworkers have voiced concern over unfair trade which threatened their jobs. At a recent hearing of the Congressional Steel Caucus (CSC), labour and business representatives urged
Congress ‘not to let down its guard’ against unfair trade practices.
The nation’s steel industry, after years of job losses and plant closures resulting from surging imports of – particularly subsidized – steel, has been on a growth trajectory since the start of this decade
Section 232 tariffs imposed during the Trump administration – and retained by the successor Biden administration – have helped stabilize the industry and created thousands of new jobs in the steel industry nationwide, attracting investments in and upgrading of existing steelmaking facilities. The industry is also engaged in reducing CO2 emissions and producing clean steel, with Cleveland Cliffs investing $1 billion
to build a direct reduction plant that has helped the company reduce greenhouse gas emissions by some 32%, the company’s CEO and president Lourenco Goncalves recently said.
US Steel has also announced a goal of net zero carbon emissions by the year 2030. However, the problem of excess steel capacity worldwide remains. China continues to be the worst offender of excessive steel production. According to a 2021 report of the Economic Policy Institute, China ‘used subsidies and other forms of distortionary government support to expand steel capacity by 418% (about 930 million metric tonnes) since 2000; it controlled just shy of half of global steel capacity’.
The problem seems to have taken a turn for the worse; China is now investing in steel production in a number of third countries. The United Steelworkers’ legislative director Roy Houseman testified that China will add ‘nearly 100 million tons of steel capacity in Southeast Asia alone, if all planned investments in the region go forward. �
While an estimated 72% of Columbian steel demand is related to construction, recent years have been challenging for indigenous steel companies active in the field of long products fabrication. According to one of them – Acerías Paz del Río, part of Andi Acero (the Columbian Committee of Steel Producers) – a better performance from the construction market is anticipated this year. By Germano Mendes de Paula*
THE Colombian Committee of Steel Producers (Andi Acero) represents the five steel companies dedicated to the fabrication of long steel products in Colombia. Those five companies are: Acerías Paz del Río (ADP), Gerdau Diaco, Siderúrgica Nacional (Sidenal), Siderúrgica Del Occidente (Sidoc), and Ternium. According to Andi Acero, the apparent consumption of long steel products in Colombia expanded slightly from 2.2Mt in 2018 to 2.3Mt in 2019. However, because of COVID-19, it temporarily retracted to 1.8Mt in 2020, followed by a quick and substantial recovery to 2.4Mt in 2021 (Fig 1).
The share of rebar in Colombian long steel demand has been relatively stable at
around the 66% plateau along the referred period. The same trajectory was observed for wire rod (20%) and other products (14%).
Due to its prominence, rebar is an important segment of the market and, therefore, needs attention. A webinar promoted by Andi Acero examined the different perspectives of the Colombian steel market earlier in the year. ADP, a participant in the webinar, delivered an interesting presentation. The following information is based on ADP’s lecture.
Fig 2 shows the evolution of rebar steel consumption over the period 2018 to 2022, highlighting that the latest year has
preliminary figures.
The market recovery of 2021 was not sustainable, as rebar demand retracted to 1.4Mt in 2022, which was the same amount registered in 2018. Nonetheless, it is important to highlight that the market share of imported products diminished from 32% in 2018 to 17% in 2022. This outcome derived from the expansion of domestic installed capacity. In particular, Ternium commissioned a new 520kt/yr rebar rolling mill in Palmar de Varela in November 2020. It was added to a previous 220kt/yr nominal capacity. Not surprisingly, the main motivation of this $76M investment was to replace imports.
Regarding the origin of the imports, Fig 3 shows that Mexico was a key
* Professor in Economics, Federal University of Uberlândia, Brazil. E-mail: germano@ufu.br
supplier with a share of 62% in 2022. It maintained its participation around the 60% level during the analysed period. However, Peru gained considerable traction, by enlarging its share from 1% in 2018 to 16% in 2022. Turkey, the world’s largest exporter of rebar, diminished its relative importance from 21% to 16%, respectively. Brazil, after improving its participation from 17% in 2018 to 25% in 2020, had a disappointing performance, ending with a 5% share.
Roughly 83% of the imported rebar came from countries that have free trade agreements (FTAs) with Colombia. The country has signed FTAs with several nations or trade blocs aimed at liberalising trade between them. Currently, it is negotiating with Japan and Turkey. Imports from countries without FTAs are subject to tariffs of between 5% and 10%.
Domestic rebar production was boosted from 790kt in 2019 to 922kt in 2022 (Fig 4). Meanwhile, the respective numbers for wire rod were 154kt and 213kt. Other long steel products registered a slight decrease from 392kt to 350kt. As a whole, the aggregate production of long steel products in Colombia amplified from 1.34Mt in 2019 to 1.49Mt in 2022.
It is estimated that approximately 72% of Colombian steel demand is related to
the construction sector. Obviously, this is of great importance to the long steel segment. In 2022, higher interest rates and inflation combined with political uncertainty (due to the Presidential elections) led to an unsatisfactory performance of the construction industry. ADP data ratifies the weak conditions of the country’s construction market in 2022 year-on-year by showing that: a) real estate launches plummeted 17.2%; b) construction starts declined 0.5%; c) sales decreased by 11.2%;
rates are estimated to be transitory, returning to historical averages as of Q3 and Q4; b) continuity of housing policy instruments: subsidies to the “Mi Casa Ya” programme will achieve the historical maximum; c) construction risk indicators at favourable levels: builders do not expect project interruption, and the drop-out ratio is within typical parameters; d) acceleration in the execution of large infrastructure projects, such as the improvement of roads, the expansion of Bogotá and Cartagena airports, and the investments related to 4G and 5G networks.
Bearing all this in mind, ADP forecasts that the construction industry’s demand for long steel products will reach 1.9Mt in 2023, equivalent to an increase of 5% year-on-year, recovering to the level verified in 2021 (Fig 5). In 2023, the informal segment (which means building without appropriate licenses and permits) will be equivalent to 33%, followed by residential (31%), infrastructure (23%), wire rod (9%), and others (3%).
and d) supply dropped 7.1%.
ADP, however, expects a better performance from the construction market in 2023, because of: a) increased interest
In conclusion, the ‘hangover’ that characterised the Colombian long steel market in 2022 is over. It is highly likely that the import ratio will continue to decline as a consequence of the Ternium Palmar de Varela’s ramp-up. It is not clear, however, if and when the industry will start facing a less unstable demand trajectory. �
A boost in India’s infrastructure spending has supported a rapid rise in steel consumption – with the country expected to become one of the largest economies in the world. By Dilip Kumar Jha*
AFTER witnessing double-digit growth in the past two years, India’s steel consumption is likely to increase by 7-8% in the current financial year (FY) 2023-24 (April-March) due to the government’s massive capital expenditure on the construction of new infrastructure and the upgrade of existing ones, along with the rapidly expanding road and rail network. With economists forecasting India’s economic growth at 6.5-6.8% in FY 202324, after recording the world’s fastest 7.2% growth in the previous financial year, the government is confident about increasing capex on infrastructure. This increase is expected to support the rise in India’s steel consumption this year.
The Union Ministry of Steel has reported that India’s steel consumption reached an all-time high record at 119.17Mt in the financial year 2022-23, compared to 105.75Mt in the previous year. The growth in steel consumption for FY 2022-23 represents more than a quarter of 94.89Mt recorded in the pandemic years FY 2020-21. India’s crude steel production, according to the Ministry of Steel, stood at 125.32Mt in FY2022-23 as against 120.29Mt reported in the previous year. Similarly, finished steel production in the country was reported at 121.29Mt in FY 2022-23 versus 113.60Mt in FY 2021-22. India recorded a record production of crude and finished steel
production in the recently ended FY 202223.
Jayanta Roy, senior vice-president and group head of the Indian Credit Rating Agency (otherwise known as Icra) stated that the steel sector in India is expected to witness two significant milestones in FY 2022-23. “Firstly, the central government’s current year capex is expected to reach the average annual run-rate envisaged in the National Infrastructure Pipeline for the first time. Secondly, the sector will experience phenomenal consumption growth following two consecutive years of doubledigit booster, after more than a decade.”
According to the Ministry of Steel, India’s crude steel production stood at 125.32Mt in FY 2022-23, compared to 120.29Mt in the previous year. Similarly, finished steel production in the country was reported at 121.29Mt in FY 2022-23, compared to 113.60Mt in FY 2021-22. India achieved a record production of crude and finished steel in the recently ended FY 2022-23.
Roy further added that the first time
this feat was achieved was in FY 2009-10 and FY 2010-11. Although private sector investments have been relatively subdued, the government’s capex drive has helped maintain the industry’s capacity utilization rate at an estimated 79% in FY 202223. With steel consumption expected to grow in the high single-digit next year, it is anticipated that the industry’s capacity utilization rate will improve to around 80% in FY 2023-24, despite the commissioning of more new expansion projects.
T V Narendran, managing director of Tata Steel, stated that India’s steel demand will continue to remain strong this year. Urban demand has recovered to some extent, particularly in the automotive sector, which has returned to pre-Covid levels.
Commercial vehicles, the steel-intensive segment of the automotive demand, are back on track. However, motorcycle demand, which reflects rural consumption trends, appears to be more fragile. Nevertheless, there is a reasonable demand for construction steel.
Dave Stickler is no stranger to success in the sphere of developing hi-tech and green steel mills. The chief architect behind Big River Steel in Osceola, Arkansas – now part of US Steel – is now pushing ahead with Hybar LLC, another ambitious project that represents the zeitgeist of 21st Century steel making.
By Richard McDonough*MISSISSIPPI County, Arkansas, is on its way to likely being proclaimed as the county with the largest amount of steel production in the United States of America (US). Currently, it is likely ranked as the second largest such county. Its growth has come, for the most part, in just the past 35 plus years.
This county is located along the river of the same name between Memphis and St. Louis.
To provide some perspective on this growth, consider a statement from the Great River Economic Development
Foundation: “Between 1932 and 1960, Mississippi County held the title of largest cotton-producing county in America… Today, the county stands as the #2 steel producing county in the US...”
Part of that anticipated growth will be coming from a new rebar mini mill planned by Hybar LLC in the Osceola area of Mississippi County.
On 1 November 2022, Hybar LLC (then using the name of “Highbar LLC”) announced in a news statement that it would be investing approximately (US) $500 million to build a new rebar mini mill
on a site of more than 600 acres in this community in the central US.
According to that news statement, “Hybar LLC [will be] focused on sustainable scrap metal recycling and steel production.”
Preliminary geotech work has been underway during the subsequent months.
Ground breaking is scheduled for late July/early August of 2023, with construction anticipated to take about 22 months after the first shovel of dirt is moved at the ceremony. “Peak construction employment is expected to exceed 600 jobs,” according to a press announcement from the
company. Commercial steel operations are projected to begin in the Spring of 2025.
Annual production is anticipated to be 630kt of steel.
“We’ll be the steel company with the lowest carbon footprint and the lowest water usage,” said Dave Stickler, senior managing partner of Global Principal Partners LLC (GPP) and chief executive officer of Hybar LLC (Hybar). “We aim to be the most environmentally-sensitive steel plant.”
GPP is 20% owner of Hybar.
“The other 80% ownership is composed of high-profile equity investors that have invested alongside GPP in previous projects,” stated Mr. Stickler. “GPP will manage and oversee the construction and operations of Hybar.”
Local and state officials have welcomed
the new investment in Mississippi County.
“The addition of [Hybar’s] first rebar mill in Arkansas will not only support the growing steel industry in northeast Arkansas, but it will further diversify our economy and provide hundreds of highwage jobs to deserving families,” [then] Governor Asa Hutchinson said in a news statement dated 1 November 2022.
“I’m excited about the opportunities this
significant investment will bring to the region.”
“We’re excited for Osceola and Mississippi County to have another steel company locate here,” stated Megan Owens, executive director of the Osceola/ South Mississippi County Chamber of Commerce. “The new jobs created here will be life changing for our residents. We look forward to working with Hybar.”
Approximately 200 high-paying, permanent jobs – both direct and indirect – will come from this development.
“We will directly have 140 workers, with average annual incomes of no less than (US) $125,000,” noted Mr. Stickler. “In addition, we will be paying weekly bonuses to workers.”
Beyond the direct employees, Mr. Stickler indicated that because of Hybar, “there will also be about 60 indirect workers, including people working at the port and in slag handling, for example. These workers will be earning (US) $75,000 in annual income, on average.”
Part of the labour structure planned by Hybar involves few layers of management.
“We tend to be the employer of choice,” said Mr. Stickler. “We’re able to take a clean piece of paper to develop work rules from scratch.”
Hybar will stay focused on rebar manufacturing and only rebar
manufacturing, according to Mr. Stickler.
“We’re not going to get into the fabrication business,” he stated. “There are two big rebar steel companies – Nucor and Commercial Metals Company. Both also do fabrication.”
“We’re going to convert scrap into highquality steel,” Mr. Stickler continued. “Our customers can then fabricate our rebar steel.”
He sees demand increasing for ‘green’ rebar steel at competitive pricing.
A substantial amount of the planned annual production of rebar steel has already been sold by Hybar.
“We have sold 23% of our annual projected output to LMS Reinforcing Steel Group (LMS),” detailed Mr. Stickler. “This company is based in British Columbia in Canada. The firm has agreed to purchase 150,000 tonnes of our rebar steel each year for the next 10 years.”
According to a statement from LMS, the firm describes itself as “…a leading independent fabricator and installer of reinforcing steel.” (Pic 1, Pic 2 and Pic 3)
Sustainability is being built into the operations of Hybar even before its rebar mini mill opens.
“We will have a closed water system,” explained Mr. Stickler. “The only water loss will be through evaporation. There will be 0% discharge into the environment.”
“We’re also having our own solar energy system directly connected to the plant,” continued Mr. Stickler. “This will produce 100% renewable energy for our operations.”
In addition, he stated that “we’ll be using DC [Direct Current] in our operations. We’ll have an electric arc furnace, single-strand caster and a 14-housingless-stand rolling mill with an eight-pass, high-speed finishing block. Most rebar mills use AC [Alternating Current]. DC improves energy efficiency, allows better energy controls, and allows for a larger hot heel.”
The rebar mini mill is designed to utilise less energy on a day-to-day basis.
“The design of the furnace is specifically targeted to reduce the amount of energy needed to produce a tonne of steel,” said Mr. Stickler. “The evacuation system – the bag house – is designed to capture a higher percentage of emissions. This improves
plant operations and overall, creates an environmentally-sustainable footprint.”
The rebar mini mill will be built by SMS group Inc. The company has its headquarters in Pittsburgh, Pennsylvania. It is part of SMS group GmbH headquartered in Düsseldorf, Germany.
“SMS has been and continues to be at the forefront of advancing the world’s steel industry in terms of operating efficiency, ever-increasing quality capabilities, and environmental sustainability,” stated Mr. Stickler. “I fully expect the SMS-supplied rebar mini mill to build on the tremendous success my partners and I have had
developing many of the finest scrap metal recycling and steel production facilities in the world whilst using SMS technology.”
According to a news statement issued by SMS on 6 February 2023, “SMS group’s relationship with the founders of Hybar stretches back almost three decades with a high number of successful projects being completed between the two partners.”
“SMS group appreciates the continued trust of Hybar in our innovations,” said Jens Oliver Haupt, chief sales officer for SMS group Inc. “Jointly, we stand for bringing the most profitable combination of technology and talent to create cutting edge solutions for the industry.” (Pic 4)
There were several strategic reasons why this specific location – Mississippi County, Arkansas – was chosen to be the site for this rebar mini mill by Hybar.
“The Mississippi River is important,” Mr. Stickler stated. “It’s key to transportation. We can bring in scrap steel to the plant, and we can ship out finished goods.”
Mr. Stickler also said that this community has a better logistics network when compared to other locales. In particular, he noted that in addition to transport options available because of the Mississippi River, there is transit access through a Class 1 railroad as well as nearby interstate highways.
He stated that while there are other states along the Mississippi River with interstate highways and railroads, this area has the labour pool of skilled workers needed for steel operations.
The power contract was significant – both in terms of expenses and sources of energy.
“The area has a highly competitive electricity rate,” he continued. “Even more so, a high percentage of the electricity produced is based on low-carbon sources like nuclear energy and solar energy. And those levels are growing.”
He indicated that Hybar will be using minimal amounts of natural gas in its operations.
Changes in energy use are possible in future years.
“Initially, we’re not using hydrogen to power the plant,” detailed Mr. Stickler. “The technology is not there yet. The design of the equipment being built for this plant will allow us the flexibility to convert portions of
operations to hydrogen in the future.”
“We are also considering battery storage, but no final decision has been made,” he said. Governmental support was an important aspect of the decision to locate the first Hybar rebar mini mill in Arkansas.
“There has been a true embrace of operational technologies and steel production here,” Mr. Stickler continued. “Arkansas has been a favourable place to conduct business through the years. The support for investments in the steel industry has been seamless between Republican and Democrat administrations.”
Mr. Stickler explained that Hybar is receiving some tax credits – “available to any other business” – in the area of recycling as well as credit rebates to assist with payroll during training of workers.
“All of these tax credits only come to us after we make the specific investments in the plant and after we have hired and paid our workers,” stated Mr. Stickler.
Hybar publicly committed in March of this year that, upon the rebar mini
36Mt new capacity in three years
Fresh steel capacities totalling around 36Mt/yr are scheduled for commissioning by FY 2025-26. Despite these upcoming capacities, the government’s capex drive and the resulting push towards domestic steel consumption are expected to maintain the industry’s capacity utilization rate at around 80% in FY 2023-24. However, as the industry’s earnings moderate from the high levels of FY2021-22, there is likely to be an increased reliance on external financing to meet expansion plans. Early signs of this can be seen in the 22% increase in the steel industry’s bank borrowings during FY 2022-23.
As a result, the industry’s leverage (total debt to operating profits) is expected to deteriorate to an estimated 2.5-3.0 times in FY 2022-23 and FY 2023-24, compared to 1.1 times in FY 2021-22. However, this is still lower than the industry’s leverage level of 2.9 times recorded during the previous upcycle of FY 2018-19. The industry’s average EBITDA (earnings before interest, taxes, depreciation, and amortization) per metric tonne is expected to be around $110-115 per tonne in FY 2023-2024.
mill beginning operations, the firm will be providing Osceola (US) $1.5 million annually for the next 30 years.
“This annual contribution will be in addition to our taxes that we will be paying,” said Mr. Stickler. “The funds we will be contributing will be part of our corporate contributions to the local community. Funds will be used in the local schools as well as for fire, police, and ambulance services in the community.”
While Hybar was newly-formed, it was founded by individuals with a long history in steel production.
Mr. Stickler has been active in steel and finance for decades, leading and structuring “…a number of transactions involving scrap metal recycling companies and scrap substitute facilities,” his biography stated.
“Dave and his wife, Rebecca Li, formed GPP in 2003 to provide capital raising and hands-on management services to metals industry participants in North America and China,” noted his biography. “Based on GPP’s early success in working with both
mini mill and integrated steel producers, GPP expanded its business to include direct investment.”
GPP has made past investments in such companies as Big River Steel, now part of US Steel; Mississippi Silicon; and SeverCorr, now part of Steel Dynamics, Inc.
GPP and Hybar has ambitious plans for its latest venture in the steel industry.
Mississippi County is anticipated to be just the start of Hybar operations.
Two additional rebar mini mills are planned by the firm, each projected to have a capacity of approximately 600kt/yr (short tonnes) of steel.
Locations for the second and third mini mills have not yet been disclosed, but those sites are likely to be in other parts of North America.
“Arkansas is a great place for us to locate our first plant,” Mr. Stickler explained. “But geographic diversity is important.”
Details of new locations chosen by Hybar will be published in an upcoming edition of Steel Times International. �
Indian steel mills are expected to be more resilient in facing any deterioration in the macroeconomic environment in fiscal years 2023-24.
A strong infrastructure is the cornerstone of any developed economy, yielding a multiplier effect with manifold growth across various sectors. India is now taking measures to achieve the target of becoming a $5 trillion economy (up from the current $3.5 trillion) earlier than forecasted by the International Monetary Fund (IMF) by 2025-26.
There has been a significant increase in budgetary allocations for infrastructure development, with the government believing it will pave the way for India to become a developed economy. Consequently, the government has been consistently expanding existing infrastructure projects and planning new ones to accelerate economic growth. This growth in the infrastructure sector will also provide impetus to other critical areas such as education and skill development, urban development, the green economy, job
creation, and global competitiveness.
The infrastructure sector in India has witnessed a paradigm shift in recent years, with increased government allocations and incentives for private players to boost capital expenditure in the steel industry. The government’s focus is on infrastructure development through increased budget allocations. India has allocated INR 100 trillion ($122 billion) for FY 2023-24 for infrastructure, representing a 33% increase from the previous year and equivalent to 3.3% of India’s GDP.
According to a report by the Confederation of the Indian Economy, India is expected to become one of the largest economies in the world, with a gross domestic product of approximately $35-40 trillion by 2047, compared to around $3.5 trillion in 2022. India has implemented the National Infrastructure Pipeline, which has facilitated projects worth INR 108 trillion ($1.3 trillion). These projects are at various stages of completion. �
AIST executive director Ron Ashburn opened the 2023 President’s Breakfast at the AISTech convention and exposition with some rousing, senatorial comments. “We’re going to make this industry as green as it can be,” he told the assembled masses as they tucked into their bacon and eggs. It was a theme picked up by AIST president Keith Howe, ArcelorMittal North America’s CEO John Brett, Nucor Corporation’s chairman, president and CEO Leon Topalian and SSAB’s executive vice president and chief technology officer, Martin Pei. Matthew Moggridge* was there.
WANDERING the mean streets of Windsor, Ontario, on the opposite side of the Detroit River in Canada, I found a record store and dived in to see if I could find an album that has eluded me ever since I ditched vinyl for CDs back in nineties. At the time I thought it was progress, but for some time now I’ve bemoaned the loss of vinyl in my life and the fact that I only possess three ‘long players,’ which are stored away in my loft.
The album in question was Future Games – a Kahauna Dream by Spirit, and when I later inserted it into the CD player of my decidedly uncool car I was transported back to some weird times. One track on the album was entitled Detroit City and, true to the lyric, ‘I walked into Detroit City with a suitcase in my hand,’ although I had no intention of playing ‘with a group called Angels to prove I was a man’. I did manage to talk to the people and walk among the crowd, and if I’m honest, I would have to say out loud, that it was a ‘good, good feeling’ and that’s about as far as I can take this musical allusion.
That said, while I did walk into Detroit City with a suitcase, it wasn’t so much in my hand, it was on plastic casters, and I pulled it noisily behind me as I walked towards a taxi that would ferry me across the river to where I was staying in the Doubletree by Hilton on the riverside. Room 526 offered panoramic views of the Detroit skyline. I could even see the Huntingdon Convention Centre where I would be spending the next three or four days at an event I’ve praised for many years, AISTech. Every day I took the bus across the river, showed my passport, answered a few border control questions, such as ‘am I carrying any firearms?’ and then repeated the process on the Canadian side of the border later in the day.
Ron Ashburn, executive director of the AIST, always looks the same – which is a good thing – he doesn’t age, and it was good to see his familiar face on stage at the start of the President’s Breakfast. “We’re going to make this industry as green as it can be,” he said, senatorially, adding
*Editor, Steel Times International
that the ‘steel industry has helped build the modern world’ and that ‘clean energy needs steel and vice versa’. Ron insisted that ‘what we do is really good for the world’, sounding like he was campaigning in the primaries, but he was preaching to the converted, all 1,300 of us who were sitting there eating our bacon and eggs and Danish pastries. I was thanking my lucky stars that the need to take an early bus through the Windsor-Detroit tunnel stopped me enjoying a hotel breakfast. Normally, I manage to eat both, but not on this occasion.
Ron continued, stating that we’d have ‘net zero in three decades’ and then provided a few facts about the event that was soon to unfold upon the great and the good of the American steel industry. In truth, it wasn’t just American steelmakers present in Detroit. Representatives of the global industry were in the Motor City contributing to the 445 technical presentations and being a part of the 588 exhibitor companies.
When AIST president Keith Howe took to the podium he described decarbonization as ‘the moon shot of our time’. The race to decarbonize society was on, he said, and it was a great opportunity, a global problem that needed a global solution, but, he asked, can it be achieved? “Some say the answer is elusive, but it’s not impossible,” he added. “It is achievable, we have the talent and the will,” he continued, acknowledging that words and phrases like ‘green steel’ and ‘decarbonization’ were now commonplace and that society is demanding decarbonization. “It won’t be easy or inexpensive,” he concluded, stating that there was no single road to reach carbon neutrality.
Howe reminded the attentive audience that the AIST now has 16,643 members and that female membership was up 23.4%.
Martin Pei, executive vice president and chief technology officer at Swedish steelmaker SSAB was in town to pick up the Tadeusz Sendzimir Medal and was keen to point out that steel was a fantastic material, infinitely recyclable, and that demand
will increase in future. He pointed out, however, that steelmaking with iron ore was associated with massive greenhouse
‘the climate frontline’. “What we’ve done so far is not enough,” he said, which was an odd thing to say when you consider that SSAB is, arguably, streets ahead of any other steel company in the sphere of developing green steel technology, but I think he was referring to the global steel industry. Pei said that in 2015 the time felt right to launch a new process involving the use of hydrogen gas instead of coal as a reducing agent for ironmaking. The company has since proved that it’s possible to produce steel using hydrogen-reduced iron, but Pei admitted that the industry was still at the beginning of its journey towards fossil-free steel.
Leo Topalian, chair, president and chief executive officer of Nucor Corporation described winning the 2023 Steelmaker of the Year award as an ‘incredibly humbling honour’. Speaking of the AIST’s first ever winner of the award, Ken Iverson, Topalian said, “We stand on the shoulders of giants”. He said that Nucor’s goal was to become the world’s safest steel company and said there were several exciting greenfield projects coming through. “We’ve just come off two phenomenal years across a range of use markets,” he said, adding that the industry ‘must remain vigilant on trade laws’. He said that American manufacturing was experiencing a renaissance, that the North American steel industry has an ‘enormous competitive advantage’ and that ‘sustainability transcends competition’.
John Brett, CEO of ArcelorMittal North America, talked about decarbonization as a path forward, brazenly promoting the business and boasting steel manufacturing in 16 countries, customers in 155 countries, steel production of 59Mmt, 8.2Mt in North America alone. He spoke of an EBITDA of $14.2 million, 158,000 employees globally, 16,000 in the USA, free cashflow of $6.4 billion in the USA and record low net debt of $2.2bn.
Brett said that ArcelorMittal North America was gunning for net zero carbon emissions by 2050 and that company has more than 150 research and development programmes on the go.
gas emissions, ‘a problem that needs to be solved’. Pei said that SSAB had been working for a long time on what he called
He said that health and safety had been a top priority since the company was formed in 2006 and that the plan was to double the number of women in management positions. In short, he was throwing out a lot of positive facts about the business, including that 41 new
“We’re going to make this industry as green as it can be.”
RON ASHBURN, EXECUTIVE DIRECTOR OF THE AIST
products and solutions were launched in 2022 and that 79 new inventions had been protected last year.
On decarbonization, Brett was a little more cautious. He said that while 70% of the global economy has established a net zero target, concrete plans to deliver on those commitments were in their infancy for two reasons: staggering costs and technical readiness. “Sure, increasing scrap will reduce our CO2 emissions, but sufficient quantities of scrap will not be available for decades. Primary steelmaking will be around for years so how do we decarbonize the steel industry? There are multiple ways to make steel so multiple paths to decarbonize, that’s the approach we’re taking at ArcelorMittal.”
Brett said that the first pathway to decarbonize was ‘smart carbon’ – meaning increased use of clean fuels. He highlighted a number of pilot programmes in progress around the world including one at Torero where waste wood and end-of-life plastics were being converted into bio-coal, and a joint development with Lanzatech involving gas fermentation transforming waste gas into bio-ethanol. He also discussed the IGAR project at the company’s Dunkirk facility where the name of the game is reforming carbon to reduce iron ore.
The idea is to capture waste CO2 from the blast furnace and convert it into a synthetic gas (syngas) that can be reinjected into the blast furnace in place of fossil fuels. “Since the amount of coal and coke needed in steelmaking is reduced, this process helps to reduce CO2 emissions,” claims ArcelorMittal.
The syngas is made up of carbon monoxide (CO) and hydrogen (H2) and is formed by heating waste CO2 with natural gas to high temperatures using a ‘plasma torch’ in a process known as dry reforming. ArcelorMittal’s plan is to use bio-gas or waste plastics instead of natural gas, furthering the use of circular carbon. With the plasma torch running on clean power, the entire process enables substantial emissions reductions, it is claimed. The IGAR project has been through a number of phases, says ArcelorMittal. “Last year, to overcome the corrosive effects of the high-temperature syngas involved, our R&D labs in Maizières, France, developed both the specialist metals and refractories needed,” the company says on its website, adding that, “Today in Dunkirk, France, ArcelorMittal is running a €20 million project, supported by the French ADEME,
to construct a plasma torch. To test-use the hot syngas created by the plasma torch, a pilot project is also running at the same plant.”
Brett said that the scale of ArcelorMittal globally means there are pilot programmes underway around the world. He said that the company was investing $500 million in tech companies supporting decarbonization – referencing Boston Metal, Heliogen and Lanzatech – and claimed that half of that money had already been committed: Projects like a state-of-the-art 5.3Mt finishing facility with a 1.5Mt EAF and an option to double capacity intensity at ArcelorMittal/NipponSteel’s Calvert facility; ArcelorMittal Mines Canada converting 10Mt of annual pellet production to DRI pellets by the end of 2025 to supply feedstock to ArcelorMittal’s North America operations; and ArcelorMittal Mexico’s 4.5Mt DRI capacity, four 3.8Mt EAFs and new hot strip mill that produced its first coil in December 2021.
“Incentives contained in the USA’s Inflation Reduction Act IRA provide economically viable paths to address the vast majority of remaining CO2 emissions,” said Brett, who then name-checked the recently acquired ArcelorMittal HBI Texas, a 2Mt capacity facility with its own deep water port.
Brett said he was ‘very very excited’ about the future for ArcelorMittal North America. It was, he said, very fortunate that the US and Canadian governments provided assistance to support what he called ‘the tremendous cost of decarbonization’.
On the question of standards, Brett said that the industry should be ‘proactively engaged’ and provide guidance to define grades of low carbon steel. Primary steelmaking, Brett believes, will be around for decades and standards should clearly define boundaries as to how CO2 is going to be counted.
“We have to play a primary role in decarbonizing the industry, but we need co-operation,” said Brett.
“Net zero, let’s not just talk about it, let’s make it happen,” he concluded.
As the crowds filed out of the auditorium and the breakfast plates were being cleared away, I hot-footed it to a small press conference elsewhere in the convention centre where Philip K Bell, head of the Steel Manufacturers Association, told me there will always be a place in steelmaking for the blast furnace.�
IF ever AISTech’s Town Hall Forum finds its way on to a pub quiz, one question would have to be who came up with the idea? The answer would be George Konig, currently a steel sector consultant working for Hatch Associates Consultants and formerly of Berry Metals.
George informed the audience in Detroit that the Forum was now 21 years old. It was formed, he said, when the industry was going through a difficult time.
The format is simple: a handful of industry leaders chatting informally on a raised stage; it’s a friendly, unscripted interaction and the whole thing, as always, is moderated by Jon Delano, money and politics editor for KDKA-TV, part of the CBS network. This year’s Forum was Jon’s 14th as host.
Ron Ashburn told the audience that the Forum’s mission was, as always, to tackle the key issues and disseminate ideas. He said that the steel industry should insist on continuous improvement, reduce energy consumption, build reliable supply chains and do the right things all the time. “We need to be accountable to all in the value chain,” he said, adding that ‘it takes great people to build great companies that go on
to do great things’.
This year’s Town Hall panel consisted of Traci L Forrester, executive vice president, environmental and sustainability at Cleveland Cliffs Inc; Richard L Fruehauf, senior vice president – chief strategy and sustainability officer, US Steel; Barry T Schneider, president and chief operating officer, Steel Dynamics Inc; Sushma Walker, president, Nucor Business Technology, Nucor Corporation; and Michael Williams, president and chief executive officer of TimkenSteel Corporation.
The Town Hall Forum always starts the same way…or certainly since Jon Delano took over.
“Good morning everybody!” exclaims Jon, and there are murmurs from the floor.
“You can do better, Good morning, everybody!” There’s a louder good morning and proceedings then begin. “Good morning, good morning, welcome to Detroit! Twenty one years old! This brainchild of George Konig has now come of age!”
Get your motor
Do Town Hall Forums have themes, I wondered? Clearly they do as this year it was entitled STEEL 23 – Get Your Motor Running, the latter part being a reference to
Steppenwolf’s hit Born to be Wild from the movie Easy Rider and, of course, the fact that we were in Detroit, the Motor City.
Delano then acknowledged the fact that this year there were two women on the panel. “It’s about time!” he exclaimed and then added, “This is not your grandfather’s steel industry,” taking me back to last year’s Town Hall when US Steel’s head honcho David Burritt said virtually the same thing, something like ‘This ain’t your grand pappy’s steel industry’– spawning, if I say so myself, a great headline in last year’s July/ August edition of Steel Times International.
Another staple of Town Hall Forums is asking the panelists for just one word to describe the state of the steel industry today. Delano didn’t disappoint. Barry Schneider said ‘courageous’, Traci Forrester went with ‘misunderstood’, Michael Williams offered ‘futuristic’, Sushma Walker suggested ‘evolving’, and Richard Fruehauf said ‘changing’. But Delano wasn’t going to leave it at that, oh no, he wanted to know why they chose those words.
Barry Schneider qualified his remark –‘courageous’ – by saying it’s all about doing the hard things, it’s all about safety too and being confident that the team is safe, ‘all the way up to making good business decisions’.
AISTech’s Town Hall Forum has proved itself time and time again over the years to be a top-notch debate on issues of importance to the US and global steel industry. The 2023 event was no exception. With five top steel industry executives on stage, including two women – from Nucor Corporation and Cleveland Cliffs – the stage was set for another scintillating discussion. Matthew Moggridge* was there.
with electric steelmaking. Steel is part of the solution, and we must start communicating how steel is part of the future.”
Sushma talked of global overcapacity and the need to be much more sustainable. “We can only control what’s happening here in the USA,” she said. Barry argued that ‘we must be diligent with our trade laws’, adding that the US leads the world with incredible technology and shouldn’t let bad things into the country. “We can’t be a target,” he said. Michael said he agreed with the other panelists but added that global instability keeps him awake at night. “There’s a lot going on, stuff we don’t know about, and we must communicate how cool steel is and go out there [meaning to the exhibition hall] and see the 600 vendors to check out the technology on offer.”
Traci Forrester felt she had to qualify her word – ‘misunderstood’ – by saying “I don’t mean the folks here [at the Town Hall] are misunderstood.” She didn’t want the audience to misunderstand her! She didn’t want to escape through a trap door as a baying mob of steelmakers invaded the stage. No, she meant that when she discusses the great strides the steel industry has taken to be ‘clean’ she feels that the wider world appears to ‘misunderstand’ her as the general view, perhaps, has always been that steelmaking is a dirty and dangerous business full of polluting and billowing smokestacks.
As for Michael Williams, his word –‘futuristic’ – related to the steel industry’s use of high tech for its various processes. “This industry has innovative tech for processes, but if you look at the challenges facing us, there needs to be rapid innovation to establish goals. The future is bright and technology will lead the way for us,” he said.
Sushma Walker’s word – ‘evolving’ –related to how the steel industry has always evolved, she said. “We need to make sure that our teams are ready for how we’ll make steel in the future.” She said that the steel industry needs to be a solutions provider. “Steel is the foundation of everything we’re doing,” she added.
For Richard Fruehauf, ‘changing’ related
to the pace of change within the steel industry. “I’m not a lifer in steel, I’ve been here almost nine years, and the changes are rapid and accelerating and huge,” he said.
Barry said that the word ‘changing’ is interesting, adding that SDI’s sustainable footprint is so low that ‘we have automotive people reaching out to us for solutions’.
Michael Williams said that the steel industry needs to figure out how to make itself cool again and stressed a need to recruit and retain talent.
Jon Delano asked the panel what keeps them up at night, prompting Cleveland Cliffs’ Traci Forrester to comment: “I don’t think there is one existential threat to the steel industry. It’s a material of choice, steel is needed and we’re in a good place.” Presumably, then, she sleeps like a log.
US Steel’s Richard Fruehauf said that the existential threat was climate change and that the steel industry remains a major creator of greenhouse gas emissions, a problem which is much reduced if EAFs are used in place of blast furnaces. “It’s all about public perception,” he argued. “We hear it when we talk to investors. We don’t see more recruitment, we’re old and dirty. We need to admit that, yes, BOF steelmaking leads to high emissions, less so
Jon Delano asked whether the industry had fully recovered from COVID. Michael Williams said the industry was still in recovery and that there were still sporadic fluctuations in the supply chains and the re-sourcing of micro alloys because of the Russian situation.
Richard Fruehauf said that COVID supply chains were largely resolved. While there was still a problem with the Ukraine/Russia pig iron supply situation, it was boom time for the North American market. He argued that the period 2022 to 2030 will be ‘the steel market of a lifetime’ for the United States and said that the emphasis with customers was on supply chain security. He spoke of the decoupling of the global trading system and new USMCA rules which, he said, would have a huge impact on the automotive sector.
Traci Forrester said that Cleveland Cliffs was vertically integrated and that through COVID the company became a steel company. “I do see a future where we’re reshoring manufacturing, bringing it back to the forefront of conversations, filling the talent void and generating more prime scrap in this country,” she said.
Barry Schneider said that Mexico presented a great growth opportunity. “It’s important for us to be with our customers in Mexico,” he said, adding that with high tech manufacturing these were exciting times.
Sushma praised the flexibility of the steel industry and its ability to adapt. “I love the current optimism,” she said.
Jon Delano liked the optimism and threw in a curve ball: global instability. He said that an increase in steel demand was driven by the situation in Ukraine and added that, at some stage, Ukraine will have to rebuild. Barry Schneider said that the pig iron situation was a problem and that SDI quickly sourced a lot of materials. “I don’t want to be cold to the human lives lost in Ukraine, but the world market has been a little uneasy,” he said.
Richard Fruehauf said that US Steel has a steel mill in Eastern Slovakia, 60 miles from the Ukrainian border. While Russia’s unprovoked invasion of a sovereign nation affected the mill, things have since stabilised. “We have lower-priced electricity than elsewhere in the world,” he said, adding that the company’s facility in Gary, Indiana, has been making 500kt of pig iron. He added that independence of supply would be a future benefit.
Asked whether China still presented a problem, SDI’s Barry Schneider said ‘absolutely’. “I’m not sure about the latest estimates, but [Chinese production] is around one billion tonnes/year. He stressed the importance of educating consumers about the perils of cheap steel.
Traci said that Cleveland Cliffs was big on electric steels, which are a very profitable part of the business, so why let it continue overseas? “We need to produce the electrical steels here [in the USA] and we’re doing that, we’re taking action now,” she said.
Jon Delano said that President Joe Biden maintained tariffs on imported steel and asked the panel what it thought of the current administration. Richard Fruehauf said the move was positive and that Biden
deserved a round of applause. “I think I’m optimistic,” he said, citing the bi-partisan agreement and his own assertion that a boom time lay ahead. Barry Schneider was glad that Section 232 was kept in place. Cleveland Cliffs’ Traci Forrester said the current administration had been good. “They want to support steel,” she said. Nucor’s Sushma said that trade laws must evolve, and that the industry needs to pay attention to what those laws are.
AMC 65. But who had the coolest wheels? I guess we’ll never know.
There was a brief chat about electric vehicles. S&P predicts that 40% of all car sales by 2030 will be for EVs and what’s more, the aforementioned Infrastructure Bill is pumping billions into charging stations.
As the largest producer of flat-rolled steel in USA, Cleveland Cliffs counts the automotive industry as a big customer. Traci Forrester said, “Our steel is poised to serve, we’re working on developing high quality steels and anticipate growing demand whilst meeting current demand.”
Things went a little off piste when Delano asked the panelists about their first car.
Richard Fruehauf mentioned his old 1978 Ford Bronco. “It was pretty beat up, that’s why I was allowed to drive it,” he said. Sushma recalled her Chevrolet Malibu but said nothing about it, while Barry Schneider talked lovingly of his 1966 Buick Skylark. “I spent more time under it,” he said. As for Traci Forrester, she couldn’t remember the make, but said she had a wood-panelled station wagon. Mike Williams drove an S10 pick-up. As for Jon Delano, he had an
Richard Fruehauf said that US Steel was bullish on automotive, but the whole issue of charging stations might slow things down a little. SDI’s Barry Schneider commented: “We’re spending a lot of time on the automotive industry, we do a lot of recycling and getting metal out of the batteries is hard.” Michael Williams said that Timken was heavily invested in the engines of yesterday but also pursuing the EV platform through its machine components division. “From our perspective, we’re happy, very positive, but we don’t believe it will go as fast as predicted and that hybrids will be more prominent,” he said.
“We spend a lot of time talking about decarbonization,” said Jon Delano. “Sustainability is an important topic, but how is your company leveraging renewables and how is it a growth market for you company?”
Traci Forrester said that Cleveland Cliffs was proud of its groundbreaking project at the company’s Middletown works in Ohio. The company recently completed
a hydrogen injection trial at the plant, which it described online as ‘a significant step toward the future decarbonization of blast furnaces, which are necessary for the continued service of the most qualityintensive steel applications, particularly for the automotive industry.’ She said it would be impossible to eradicate the use of coke, but the company is trying to reduce it. “You can’t run a steel mill on renewables,” she said.
Barry Schneider said he was big fan of nuclear power, and that SDI has a strong nuclear portfolio and was taking it to the next level. Nucor’s Sushma Walker said that Nucor had invested $15 million in NuScale Power, a developer of small modular (SMR) nuclear plants, reinforcing a message released by the steelmaker around a month earlier when the company stated that the North American steel giant had entered into an agreement to fund NuScale via a private placement in the Special Purpose Acquisition Company, Spring Valley Acquisition Corporation, that intends to merge with NuScale. At that time, Nucor president and CEO Leo Topalian commented: “Sustainability is driving the business decisions of leading companies around the world. As America’s largest steel producer and a significant energy consumer, we are looking for safe and reliable sources of power generation that are consistent with our sustainability goals.” Sushma Walker said: “We believe it’ll be a game changer and are committed to it globally.”
US Steel’s Richard Freuhauf said that investors want further decarbonization of the industry and added that US Steel was ‘extremely pro-nuclear’. He said that the company was seeing increased demand from solar and wind customers and that it was impossible to downplay the importance of nuclear power and renewables generally.
TimkenSteel Corp’s Michael Williams commented: “We’re located in northeast Ohio and on that grid only 5% is renewable. We’re not scared of nuclear, it should be part of the energy portfolio”.
Cleveland Cliffs’ Traci L Forrester said the company was a strong believer in nuclear power and where renewable energy was concerned has set itself a target to purchase 2MWh of renewable energy annually that is newly developed or additional to the grid. According to the company’s website, ‘Cleveland Cliffs has recently executed a 15year power purchase agreement with EDP
Renewables SA for 180MW of the 200MW Headwaters lll Wind Farm in Randolph County, Indiana.’ The wind farm will be operational in 2025 and has the capability to power the equivalent of more than 54,000 homes.
Do we need CBAMs?
“As American steel becomes cleaner and greener,” said Jon Delano, “the question is how do we reward those companies that have reduced their carbon footprint?” With a Carbon Border Adjustment Mechanism (CBAM) introduced last year, Delano wanted to know whether it was necessary.
Richard Freuhauf of US Steel commented: “We have a facility in Europe so we’re familiar with CBAM,” explaining how it was a carbon tax and that US Steel is taxed on its emissions. Nucor’s Sushma Walker said that CBAM is needed. “If there is regulation, we need border adjustment in place,” she said.
Steel Dynamics Inc’s Barry Schneider said the process itself should be straightforward. “I do believe we have to watch our borders and make sure products don’t sneak in. We need some kind of security.” Cleveland Cliffs’ Traci Forrester said that her company doesn’t need a marketing label for its steel. “All our steels are driving emissions down and we will continue on that journey,” she said.
TimkenSteel’s Michael Williams said that CBAM was a complex issue and that it can’t just relate to steel, but anything with steel content. “Let us compete in the green steel space,” he said.
Safety is one of the old chestnuts at the
AISTech Town Hall Forum and it goes without saying that all those steel company representatives on stage were keen to stress that they were on top of their game when it came to safety issues. As Nucor’s Sushma Walker pointed out, the key is culture. Safety, she said, must be a core value. “We show up daily and do it,” she said. “It’s living the culture, not just words. The team shows up daily to take care of themselves and others.”
At US Steel it was a similar story. Richard Fruehauf also used the word ‘culture’ stating that industry leaders must make it a top priority. “We coined the phrase ‘safety first’ in 1908,” he said, adding that the company has weekly chats on safety performance and regular campaigns to keep it top-of-mind.
SDI’s Barry Schneider also came down on the side of ‘culture’, saying that he asked supervisors to step back from production and take control of safety as it was all about teaching and educating all the time. On the use of technology he said that lots of tools were available, adding that the industry has to be aware of the technology available but acknowledge that it’s not going to be perfect all the time. The question is ‘how do we ensure these things are safe?’
Michael Williams was upfront and acknowledged that TimkenSteel suffered a fatality last year and was in the process of modernizing its safety programme as a result, with a heavy emphasis on training and reducing the man/machine interface. The company has engaged in AI projects and used camera technology as well as monitoring processes collecting hundreds of thousands of data points. In other words, action is being taken. He said that the
company was investing 20% of its capex budget on safety with the aim of driving a safer working environment.
Traci Forrester said that Cleveland Cliffs had gone back to basics and capped shifts at 12 hours and has added 7,000 employees. She also said that artificial intelligence was a good tool to assess ergonomics, but added that the human brain was good too. In addition to AI, she explained how employees have wearable devices that prevent heat exhaustion, and the company uses ‘a lot more robots’. All Cleveland Cliffs control rooms are digital and all-round things are ‘smarter’.
Another big subject for the AISTech Town Hall Forum is the workplace and with that in mind, Jon Delano kicked off with the subject of women in steel, briefly mentioning (again) that there were two women sitting on the panel. “This is a changing industry,” he said. “It’s no longer a place for older males,” he added, which I’d imagine caused a large percentage of the audience to bristle and shift uncomfortably in their seats. “Making steel today requires different skills, and companies like Microsoft and Google are laying off high tech workers – there is a place for them in the steel industry,” he said, prompting Nucor’s Sushma Walker to express her excitement about the workforce topic. “We’ve got so much going on,” she said, and went on to discuss – or at least mention – the words ‘sustainability’ and ‘tech’, adding AI and machine learning. She referenced the 400-plus papers being presented at AISTech 2023 and said that ‘we have to keep evolving’. “It’s a great time to be a part of the steel industry and it’s a place for women,” she added, explaining that she had an IT background. “Come and join us, it’s some of the coolest work you’re going to do,” she concluded.
Cleveland Cliffs’ Traci Forrester told the audience how the company partners with the unions and how there’s plenty of room for college-educated engineers. The total median income across the company, said Forrester, was around $132,000 per annum. “We should be able to give the brightest and the best challenging and meaningful work,” she said.
US Steel’s Richard Fruehauf spoke of the need to increase inclusivity and spoke of ‘infinity groups’ looking at what’s working and what isn’t. “Younger employees are
looking for purpose in their work,” he said, adding that it’s also important to have a pay cheque, although why he said that and in what context I can’t recall. Either way, he’s right, who works for nothing?
Delano said that mentorship was always important and Steel Dynamics’ Barry Schneider agreed stating that it goes on today, ‘engineers interacting on the floor with our people is very important’. He said that mentorships involved being exposed to leadership, adding that the industry needs leaders to come in and challenge the status quo. “That’s a hard thing to do remotely,” he added. “Teamwork is essential, engaging each other, it’s important in every aspect of our lives.”
The Town Hall was nearing an end, and it was a strange moment. Or at least it was for me; having been in Detroit for the best part of a week, wandering the exhibition hall, talking to representatives of the US steel industry, having lunch at Frank’s Deli – the gem of the trip – wandering around later in the day on the Canadian side of the Detroit River. I grew accustomed to it all and didn’t really want it to end, mainly because there was a long flight back to the dreary United Kingdom. But there was still one topic obscuring the view of the final straight and that was what the steel industry might look like in 25 years’ time. “Share with us: what will the industry look like in 2050,” asked Delano.
Steel Dynamics’ Barry Schneider said ‘small plants taking advantage of local resources and mills going where the power is’. US Steel’s Richard Fruehauf added, “We’ll be net zero, cleaner and greener, there will be more technology, the opportunities for automation will be incredible and computer scientists (like Michael Williams) will be running the mills. Cleveland Cliffs’ Traci Forrester said that the company will still be going strong. “You’ll no longer hear about smokestacks, there will be recycling partnerships and we will be a clean steel manufacturer,” she said. Michael Williams was short and to the point: “Steelmaking will be really cool,” he said, and let’s face it, he has a point.
TimkenSteel Corp’s Michael Williams added: “You have to have a competitive benefit, we show them the technology at our facilities, it’s not just sledgehammers and shovels, there’s lots of technology. We show them we’re an engineer-oriented business operating based on science,” he continued, explaining how the company recently changed its approach and its internship programme. “We got 40 interns coming in this week, we’re going to the high schools, we’ve reimplemented our apprentice programme as we can’t find people off the street anymore. “Our board is made up of 27% women,” said Williams, adding that 37% of the company’s salaried workforce are women. “So, we have a focus on a very diverse work environment and value everybody’s opinion. Williams has a background as a computer scientist, proving that it takes all sorts.
And that was it, time to file out of the hall, find somewhere to have lunch and appraise the week gone by, time to revisit the exhibition hall for the last time, check out the free chocolates and other freebies –tee-shirts, baseball caps, pens, torches, and socks – socks? Yes, socks, two pairs! Unbeknown to AIST exhibitors who were giving stuff away, I will be carrying the flame for them as I ride my pushbike through the summer months, providing them with free advertising in the UK.
It was a good event, it always is. There were people I look forward to meeting, like AIST’s Sam Kusic and Ron Ashburn, and Philip Bell of the SMA to name but three.
It’s good to see that the American steel industry is flying high on a swelling tide of optimism as it faces the future head on and deals with the challenges of decarbonization and digitalization, not to mention threats posed by current geopolitical strife.
Next year, AISTech 2024 will be in Columbus, Ohio. Hope to see you there. �
Amid a rampant increase in the use of the term ‘green steel’, issues are arising from its lacking critical definition, widening application in global contexts, and amplified impacts upon an industry under pressure to decarbonize.
WHAT makes steel ‘green’? The term is still in its infancy, in the context of climate change and heavy industry. Global warming didn’t reach wider public discussion until the late 1980s, with the hottest summer on record, beating out the drought of 1955. ‘’At least we accomplished something,’’ said Geoff O’Toole, a meteorologist with the Central Weather Service in a 1988 issue of the Chicago Tribune. We’ve not known for long that the Earth has been exhausted from decades of unconscious, and now conscious abuse – but with roughly 7% of carbon emissions today generated from steel production, it’s a fact that has required rapid adjustment to prevent disaster. Companies are now obliged to provide their shareholders with ‘green stories’, says Alexander Fleischanderl, head of green steel at Primetals Technologies, adding that ‘the whole ESG topic is driving the direction toward net zero’. What has yet to be addressed, however, is the linguistic gaps that are left in the nascent use of such terms, that has come prior to their explicit definition. If there is no specific criteria for ‘green steel’, then companies
are left with anarchic sub-spaces of marketing, in which grey can appear green, community and workforce complaints can be glossed over with vague sustainability claims, and decarbonization evolves into what Annie Heaton, CEO of certification company ResponsibleSteel refers to as a ‘commercial and competitive landscape’. ‘‘I think the green transformation is going to be hugely important’’, said Kemel Sarac, general manager of Turkish steelmaker Yucel Boru, at the 2022 Steel Orbis conference, ‘’and I’m not just talking about green of the trees, I’m talking about green of the dollars.’’ The financial incentive driven by the need to provide ‘green stories’ has created a hastiness in applying such terms, before their meaning has been fully assessed –making what should be critical evidence of action, ambiguous, and opaque. Via the emergence, and now ubiquitous quality of sustainability terminology, the opportunity has arisen for manipulation, profit, and even scapegoating – with all its speakers standing to benefit, without much, if any substantiation.
In 2021, a report by public health agency RIVM found that dust emissions from the steel industry in North Holland’s IJMond region contained a ‘damaging amount of substances and metals that can cause cancer’, with samples taken closest to a steel plant owned by Tata Steel showing the highest concentrations. According to Dutch emission authorities, Tata’s steelworks is one of the largest CO2 emitters in the Netherlands. On the company’s website today reads the following marketing slogan; ‘We are passionate about preserving our planet and taking care of our communities…. we do everything we can to be a steel producer that is responsible in all respects.’ In 2022, the Securities and Exchange Commission charged Brazilian mining company and one of the world’s largest iron ore producers, Vale S.A., with making false and misleading claims about the safety of its dams prior to the January 2019 collapse of its Brumadinho dam. The collapse killed 270 people, caused ‘immeasurable environmental and social harm’, and according to the SEC’s complaint, was a result of the company
manipulating multiple dam safety audits, obtaining numerous fraudulent stability certificates, and regularly misleading local governments, communities, and investors about the dam’s safety. In 2020, mining company Rio Tinto blew up ancient aboriginal caves at Juukan Gorge, in Western Australia, later telling a senate inquiry that it proceeded with detonation despite knowing one of the shelters was of ‘the highest archaeological significance in Australia’, in order to access lucrative volumes of high-grade ore. These crises, bred from the production of steel, offer commentary on the tension between sustainable language, and responsible actions; real accounts of how language can be manipulated to detract from, or even rewrite the truth. Professional services brand PriceWaterhouseCoopers recently surveyed 729 companies within sectors such as transport, mining, and industrial products, regarding sustainable development goals (SDGs), a collection of 17 interlinked objectives designed by the UN to serve as a ‘shared blueprint for peace and prosperity for people and the planet, now and into the future’. The survey demonstrated that although half of the companies acknowledged, or had identified priority SDGs, only about
one-quarter disclosed meaningful targets and key performance indicators (KPIs) or mentioned SDGs as part of their business strategy. Additionally, authors of the report found that ‘reporting could be used to camouflage business-as-usual by applying SDG-related sustainability rhetoric’– making corporate involvement in SGDs largely ‘symbolic’, rather than substantive. With many of the companies surveyed relating to steel production, a nefarious connection is established – between the use of language to distort and imply a reality that has yet to exist. The European steel association (EUROFER) listed one of the most pressing issues within the industry as the lack of a ‘consistent approach to assessing recycling performance…too often products claim to be ‘fully recyclable whereas the reality of end-of-life is completely different’. In reality, however, substantiating claims of sustainability are more complex than exposing figures – according to Fleischanderl. When companies calculate and publish their carbon footprint, the exclusion of Scope 3 emissions, which can be interpreted as misrepresentation, is not ‘necessarily due to a lack of transparency… but the fact that Scope 3 is really difficult for some companies to calculate, especially in terms of stainless steel where the
ferro-alloys contribute significantly to Scope 3; therefore it’s relevant where this is purchased from’. However, this doesn’t account for the continued use of terminology that remains to be evidenced – if the figures are incomplete, how can a company reliably quantify its sustainability?
In an effort to acknowledge this conflict between implication and actuality, producers are now engaging in what John Brett, CEO of ArcelorMitttal North America refers to as a ‘standards race’; with organizations and standards such as ResponsibleSteel, First Mover’s Coalition, and the Steel Climate Standard touting protocols of labelling and certifying ‘green’ steel. However, far from reaching an aligned vision of a decarbonized future, the standards have raised questions over what types of production the labelling should include; with Leon Topalian, CEO of Nucor, stating that the sliding scale approach offered by organizations including ResponsibleSteel, which features one standard for steel made from traditional production processes and another for steel made from circular processes such as using electric-arc furnaces, seeks to ‘dump problems on [American] shores by promoting a dirty standard’, and Philip K. Bell, president of the Steel Manufacturers Association referring to the approach as a form of ‘greenwashing’. The debate in standardization makes murky what is already a deeply complex topic; in the attempt to reconcile language, hierarchies are formed, with steel companies often investing in whichever standard offers them the most significant advantage. Heaton offers a single statement to the critics of ResponsibleSteel; that ‘greening steel is a more helpful concept than green steel’. ‘’It provokes a level of maturity in the conversation,’’ Heaton adds, saying that standards need to reward ‘shades of green’, in order to incentivize progress. ‘’Language is a critical part of this, it is perilous, and can be misused. Rather than go into battle, we call on all stakeholders to collaborate on how we can align’’. Brett, as a member of ResponsibleSteel, echoes Heaton’s statements; ‘we believe that standards should incentivize all forms of steelmaking through technology shifts’. However, ArcelorMittal’s involvement in both low emissions projects, and ‘some of the most emissions-intensive, coal-based steelmaking plants’ raises questions over its intentions, says Caitlin Swalec, programme director at
Global Energy Monitor, stating; ‘‘we have to question whether these companies are seriously pursuing a 1.5 degree future or simply hedging their bets on industrial decarbonization and our climate future.’’ There is a divide between belief in capacity – how much should companies be held to account for their current actions, and how do we then accommodate, and reward their progress? This is not a question that can be answered by the existence of multiple diversified standards – alignment is crucial and demands a wide-reaching debate.
It’s not just about the fight over ‘green’, however – impacts of language draw on wider contexts of race, and victimhood; perpetuated phrases of China being a ‘dirty villain’ of the industry are often offered as a way to bolster the outward success of other regions’ decarbonization efforts. Relying on the mutable definition of ‘green’ production, concretized statements are made, which reduce to an ‘us versus them’ mentality centred around ownership of terminology which is as volatile as the market in which it attempts to function. The reality is that Chinese citizens produce less than half the CO2 per person than people in the US, Australia, or Canada, with Maureen A. Huebel, an Australian academic, commenting that: “On a per capita basis, Australia’s carbon footprint, including exports, is nine times higher than China’s”. There’s no denying that China’s carbon footprint is substantial, with the coal industry representing around threequarters of emissions, but the significance of other countries’ reliance on China for manufacturing is an often-overlooked factor, with half the world’s supply of steel being manufactured in China. The ongoing narrative of China as the sinner of the industry is tied into sinophobic discourses, evolved from
Brendan O’Neill described as a ‘western fear of the supposed limitless hordes of Chinese overrunning white countries’. Mass industrialization in China took place decades after its Western counterparts, meaning that its decarbonization timeline can bear little comparison to western efforts. That is not to say China does not hold the onus to enforce stringent agendas to lower emissions – but the oversimplification of its identity as an instinctual environmental offender merely reinforces patterns of western reaction to crisis; as stated by O’Neill; “[P]eriodic transformations in dominant Western
images [the East], from positive to negative and back again, indicate the tremendous malleability of perceptions of the ‘other’ in response to specific historical circumstances, and especially in response to circumstances in Western nations themselves.” In a time of crisis, it is all too familiar to turn to a tangible source of blame. Environmental responsibility, however, carries beyond regional boundaries, and will not be distracted by linguistic margins of ‘clean’, and ‘dirty’; ‘green’, or ‘grey’, but by a globalized transformation, enforced by aligned agendas.
It is unlikely that the term ‘green steel’ will lose any traction in the next few decades; it is an easily marketable, and commodified recolouring of an industry that faces significant attention in its decarbonization targets. However, with ‘increasing numbers of steelmakers committing to reaching net zero by 2050, details on how these targets are to be
achieved [remain] vague, and often rely on unproven technology’, says Simon Nicholas, energy finance analyst at IEFA – indeed, if the industry is supposedly ‘green’ by 2050, what meaning will this hold? Standardization of green steel is inevitably due to become a defining force, creating further debate in terms of what is included, and what is left behind. Market priorities are undergoing a huge shift, as companies must justify production in terms of its sustainability; it’s no longer a fight for quantity, but for quality – as new levels of environmental grading will prevent the justification of unnecessary impacts. What remains to be seen is what middle ground will be reached – with inevitable compromise due to take place.
‘Green steel’ initially offers a simple, compound future – but the complexity of industrial decarbonization asserts a critical gap; there are, in fact, many shades of green. �
2023
The Future Steel Forum, now in its SEVENTH successful year, is heading for Vienna this September to examine the important relationship between digital manufacturing and the decarbonization of the steelmaking process. Come and listen to experts from the two most important areas of global steelmaking at present. This is a must-attend conference
SPEAKERS FOR FUTURE STEEL FORUM IN VIENNA INCLUDE:
BUSINESS is seen as being very robust for US companies that provide steel-related processing and first stage fabrication services for various end-use markets, even as they face certain challenges.
However, fear of an economic downturn – even a recession – is adding a measure of uncertainty, with a tight labour market and long lead times for new equipment affecting what both service centres and independent toll processors are able to accomplish. Also, companies are being impacted by regional shifts of steel demand.
Overall, steel processing dynamics haven’t been changing all that much, Eduardo Gonzalez, president and chief executive officer of Ferragon Corp., said, explaining the processors continue to fulfil a need when their customers can’t justify having processing equipment in-house, which involves not only buying and installing equipment, but having enough trained people to operate it efficiently.
That said, over the past few years certain
factors have impacted both purchases of steel processing equipment and companies involved in processing steel. Dean Linders, vice president of marketing and sales for coil processing equipment maker Red Bud Industries, observed that for a period of time at the height of the Covid pandemic, companies that were unsure what the future would hold held back from buying processing equipment. However, within six months or so, that changed.
Linders said that even with the talk of a potential recession, toll processors, steel service centres and even some mills and large OEMs, have been placing orders for processing equipment at a record pace and continue to do so. As result, Linders stated that the past two years have been
Red Bud’s best years ever – as much as 50% better than its previous record year – and that US processing equipment lead times are quite extended, generally out 18 months or longer.
Similarly, the processing industry has been very strong – or at least above average – since it came out of Covid. In fact, Tim Bilkey, president of Voss Steel, said that it is getting an additional push due to an easing of the semiconductor chip shortage and certain other supply chain issues, enabling North American auto production to pick up again, although it has yet to return to full forecasted values.
“For the most part, that has kept the US processing community busy, although we could be busier,” Bilkey said, noting that they are as busy as they are capable of being right now with its current staffing levels. “It is a fine line,” he explained. “While we would like to take on more volumes of work, we want to make sure it is a reasonable working environment.”
It is somewhat cloudy as far as how
much of US steel processing demand is being met by independent toll processors and how much is being met by US steel service centres, who buy and distribute steel as well as offering various value-added services, and how much the ratio has been changing, said Josh Spoores, principal steel analyst for CRU.
He explained that while more service centres are going downstream, or further downstream than they had been in the past, not all service centres are doing so. Many of those that are doing so are companies that had already been going downstream, providing more valueadded services to be more profitable and competitive, seeing it as an opportunity to grow and to lock in certain customers looking for such services.
Overall, US steel service centres are doing well this year, helped by the recently elevated prices, Michael Barnett, president of Grand Steel and chairman of the Association of Metals Processors & Distributors (AMPD) said, although with concerns of a potential recession, steel pricing arrows seem to be pointing slightly
lower for later this year. That, he said, is translating into a slight decline in service centre activity. “But it isn’t that demand is falling off of a cliff,” he noted. “While things have slowed down a little, there is still good activity going through the system. In fact, Philip Gibbs, a senior metals equity analyst for KeyBanc Capital Markets, said that the latest data from the Metals Service Centre Institute (MSCI) indicates that service centre steel shipments were up 5% yearover-year during the first quarter of this year, although it could be dicier as the year goes on given the amount of demand that got pulled forward early this year.
But that doesn’t necessarily translate into the value-added services that service centres offer given that, as Bob Weidner, MSCI’s president, points out, US steel service centre business fits into three basic buckets – pure steel distribution (buying, stocking and shipping steel); simple processing (such as slitting, cut-to-length, etc.); and adding three or more sophisticated value-added processes.
“Every service centre has their own niche as to what they want to do,” Weidner said, noting that while it has been, and continues to be, a conscious business strategy for certain service centres to move up the value-added chain and to make investments in technology, equipment, and people to do so, that isn’t the case for all service centres.
It is generally perceived that some of the larger, publicly owned service centres have been the most aggressive moving in this direction. For example, Gibbs stated that over 50% of Reliance Steel & Aluminum Co. (RSAC) shipments include some type of value-added processing, and that the percentage increases every year. In fact, during its first quarter earnings conference call, Karla Lewis, its president and chief executive officer, noted that the capital expenditures that RSAC will be making
this year will largely be for cutting-edge equipment to expand the company’s valueadded processing capabilities.
Some small-to-medium-sized service centres are doing this as well, CRU’s Spoores said, explaining, “It is a way for smaller companies to be more competitive. They can’t buy steel as cheap as larger companies, but offering value added services gives them more of a competitive advantage.”
This is a continuation, and possibly an acceleration, of a long-term trend for certain services to get involved with value added services, even some fabrication services, Mike Lerman, president of Steel Warehouse, said. Lerman added this is partly due to the fear of being seen as competing with their customers being less of an issue than it was in the past, especially if the customer and the service centre have a trusting, long-term relationship.
It isn’t, however, that there is a big slope in the curve in steel distributors going further downstream, one service centre executive, said, maintaining that it has been generally moving at somewhat of a measured pace, particularly for small-and medium-sized regional service centres. In fact, Ferragon’s Gonzalez said he doesn’t believe that there has been much change in how much steel processing is being done by service centres versus independent toll processors. Voss’ Bilkey declared that toll processors don’t have to lose as much sleep over changes in steel processing, especially when it comes to its mill direct business.
But in general – whether by service centres or toll processors – investments in processing and fabrication equipment aren’t being adversely affected by the potential economic downturn, Barnett said, given that companies are not so much making investments based upon current economic conditions but to set themselves
While it may not be a record year, US service centres and independent toll processors are continuing to invest in new technology and equipment, while demand remains strong.
By Myra Pinkham*
up for future opportunities. This, he said, is especially the case given that many of these processing upgrade projects have at least a two-year lead time.
One big reason for investments, whether by toll processors or service centres, is due to pent-up demand for equipment, Red Bud’s Linders said, as some projects that were halted during the pandemic are now starting to come back to life. As a result, companies believe that the time is now right to invest in new processing technology.
The willingness to make such investments, however, varies company by company, depending upon the appetite the company has for risk, Marc Lerman, Steel Warehouse’s chief commercial officer, pointed out. However, more companies see an advantage, especially as equipment technology advances. “We are always looking for ways to do things better and there is no question that new equipment has more capabilities than older equipment.”
The regional shift of the steel industry from the Midwest to the South has also had an impact upon the need for investment, Barnett said, noting that in the South there is high demand for heavier gauge processing for oil country tubular goods, as well as to have the ability to process high strength steels for the automotive market.
In fact, Gonzalez said that one big evolutionary change behind this push for investment are the challenges related to the development of new advanced high strength (AHSS) and ultra-high strength
(UHSS) steels. These, he said, have prompted companies to add heat treating lines. In fact, he said, the heat-treating line that Ferragon recently added to its HyCAL operation in Gibraltar, Mich. is not just the company’s largest investment ever, but is the largest heat treat line in the US and the only one that quenches with hydrogen. But the push toward more AHSS has even more implications for process equipment investment than just heattreating lines. Bilkey pointed out that AHSS itself has certain mechanical properties that makes it hard, if not impossible, to be processed using some older processing equipment.
Another big change is a move toward more automation. Linders said that in the past there hadn’t been as much of a push for automated equipment in North America, partly because of the cost. But, largely out of necessity, that has changed. Not only do
companies now have the money to invest, but they need to do so due to the tight labour market. “The new machines on the market have cutting edge technologies designed to reduce personnel requirements while maintaining or increasing the level of throughput that companies are accustomed to,” he explained. Some companies are also investing in some robotics in light of their labour issues, Spoores noted, both to do certain types of processing and to aid in logistics.
But perhaps the biggest challenge that processors are facing is geographical changes in the markets that processors serve, Gonzalez said. “If you have bricks and mortar operations and your market or your steel suppliers move, it is difficult to keep up with what will be happening next,” he explained. “Having to rationalize moving your assets or starting up new ones is a tough challenge.”
While it might not be another record year, Linders said that this year, both service centres and independent toll processors will be continuing to invest in processing equipment, with their customers continuing to look for them to provide various valueadded services. Gibbs agreed that that is the case even with the talk of a potential economic downturn. “They are making investments with one eye on the future, trying to grow their business and managing the needs of their customers with the things they need to be more efficient and competitive,” he said, adding that they currently have enough cash on hand to do so. �
IF rotating equipment had a choice of where to work, it would surely never choose the steel industry. Here, the heat and the humidity alone are enough to give maintenance engineers nightmares – as they wonder just how long the bearings in their machines are going to last.
Water may be vital to life, and to many industrial processes, but it can play havoc with bearings. In steelmaking, where cooling water turns instantly to steam, moisture works its way into bearing housings to cause premature failure and potential line shutdowns. The lifespan of a bearing in steelmaking can be a short one.
There are ways to offset this, such as by using more robust bearings, housings and seals, though no single technique can overcome the challenges of such a harsh environment. However, when applied properly, lubrication – and lubrication management – can help to address the demands of such a harsh production environment. It can be a key tool to help steelmakers address many of their pain points around rotating equipment.
Lubrication management goes beyond simply choosing the most appropriate lubricant. It also includes factors such as storage, logistics, sustainability and delivery – typically through an automated lubrication system.
Lubrication is a vital, though often invisible, factor in engineering. Poor lubrication plays a huge role in machine downtime – and is the main cause of premature bearing failure. So, it stands to reason that better lubrication management can help to raise manufacturing efficiency.
The steel industry has similar performance goals as other manufacturing sectors: reducing the cost of production; maintaining or raising safety; improving sustainability; and raising product quality. Correct lubrication management can
contribute to all these goals.
A good place to start is with water. It is vital to steelmaking – but can also cause problems. The most pernicious of these is lubricant emulsification. Here, water that makes its way into bearings, via an oil circulation system, mixes with the lubricant and degrades it. Once lubricant loses viscosity, it needs to be replaced. The challenge is to keep the oil circulating and maintain its quality – so that it still acts as a lubricant.
– on the principle that oil and water do not mix. The trick is to do this quickly enough and recirculate only ‘clean’ lubricant.
In a modern automated lubrication system – such as SKF Flowline – this is done by storing circulating lubricant in a tank, where the two components (lubricant and water) quickly separate out. The water is drained off from the bottom of the tank – and the lubricant recirculates. The latest tank designs are around one-third the size of older versions, so offer separation in a much smaller footprint.
Different applications within the steel industry – from continuous casting to sheet-making – may require different types of lubricant, or different ways of applying it. Sometimes, circulating oil is more appropriate; in others, grease is the way to go.
In each case, the recommendation comes from the original equipment manufacturer (OEM), though often the original advice may now be out of date. Machinery is typically driven harder and faster than it was in the past – and this cannot be done using an outdated lubrication management regime.
A modern lubrication circulation system can help. It is designed to carry out two vital tasks: cooling and cleaning. Firstly, heat exchangers help to cool the oil – and ensure that bearings do not run ‘hot’. This all happens against a background of having to circulate the oil quickly, in order to run machinery faster. Newer systems are better able to achieve this.
In addition, it removes contaminants in a number of different ways. Solid particles are removed by filtration, for instance. Water can be more complicated. As long as an emulsion has not been created, any water in the lubricant will naturally separate out
It’s a delicate task to balance performance with longevity. For instance, lubricant can be pumped into bearings using an ‘oil/air’ system. Here, compressed air both cools the oil and improves its circulation. However, it is vital that the system has a good filter, otherwise there is a danger of introducing contaminants –including both air and water.
Another avenue is to use solid grease, rather than liquid lubricant. This has two main benefits: it excludes water from the bearing (by filling the space); and, it can withstand higher temperatures. However, it can cause an environmental issue – as at some point the grease will be ejected as waste. It’s true to say that there is no single
‘right’ answer. This is where the advice of a lubrication expert is critical.
In a busy manufacturing environment, automated systems – which deliver lubricant to a set of lubrication points via a tubing system – offer many advantages. Firstly, they dispense the correct amount of lubricant to the right places when it is needed. This is vital for the smooth running of rotating equipment.
In a harsh environment like steelmaking, it also has a huge safety advantage. Some areas are so hazardous that manual lubrication is either dangerous or impossible. Here, an automated system helps to ensure worker safety and efficient relubrication.
There is also a balancing act in play here. For instance, the system cannot be located too close to a continuous casting line, due to the excessive heat. However, it must be close enough to deliver lubricant quickly. The line that delivers the lubricant must work at elevated temperatures – which typically means using stainless steel.
Storage is an often-overlooked factor in lubrication management. Where should lubricant be kept until it is needed?
SKF routinely carries out lubrication management audits, and we see it stored in the most inappropriate ways. Outdoors, in the sun and rain, is a favourite; we’ve also seen barrels of lubricant in rooms that have water dripping from the ceiling. These customers might have the bestquality bearings and systems in place but their lubricant is highly likely to introduce contaminants into their sophisticated machinery.
management. It consists of 40 questions in four sections, including one on ‘strategy’. One question asks customers what their strategy is on lubrication management –but many leave this blank. We also find that many have no storage room. When we go through the answers with them, they see that lubrication management is much more than delivering barrels and putting them in a corner until they are needed.
The ‘40 questions’ usually leads to a full audit of their lubrication management programme. This will take two or three days, as our engineers delve into factors such as lubrication systems, lubrication points and training needs.
The first move was to install an oil circulation system. One key issue that we solved was under-lubrication in a set of gearbox bearings. A root cause analysis showed contaminant ingress, and little – if any – lubrication. Part of the reason for this was that lubricant was not leaving the gearbox sump quickly enough.
Changing the flow rate of the lubricant – and opening up a larger outlet at the bottom of the sump – helped to solve the oil return issue. At the end of the year, there had been no line shutdowns.
SKF has also initiated a pilot project to help a steel mill in the UK improve one of its automated grease lubrication systems – by pairing it with condition monitoring (CM). Here, if the CM system detects an issue with a bearing, it triggers a dose of grease in the problem area. SKF calls this condition-assisted lubrication, or CAL. It is not the same as ‘lubrication on demand’ –which automatically ‘tops up’ lubrication points. The pilot system lubricates in direct response to a ‘trigger’. It also offers targeted lubrication – to a single bearing. This is in contrast to existing automated systems – including those from SKF – which will lubricate all bearings at the same time.
One steel industry customer was having constant bearing issues on a casting line. Here, SKF signed a performance contract, where we took responsibility for the line – promising no more than one bearingrelated shutdown in one year.
This has involved redesigning our dosers and valves, allowing them to dispense at an individual level. Another challenge was to introduce ‘logic’ to the process – something automated lubrication systems do not possess. We did this by using an industrial PLC to control the pump. The PLC effectively acted as the ‘connection’ with the CM system.
Condition-assisted lubrication cannot be deployed across an entire continuous casting operation in a steelmaking mill. Instead, it targets critical equipment that uses up to eight bearings. This limitation is based on the CM system – which can only have eight vibration channels linked to eight lubrication points – though this may change in future.
proper storage facility is not just a place to
Manufacturers, including steelmakers, work under constant challenge – including thinly stretched resources. One issue is the deceptively simple one of running a store room – or not, as is more likely the case. A proper storage facility is not just a place to keep things until it is needed. It should be properly managed and controlled – with dedicated, qualified members of staff. When resources are tight, it is common to assign staff to the production line –contributing to profits – rather than sit them in a storage room, eating up cost.
This is where an audit can help – and these come in several forms. One is called a client-need analysis of lubricant
The customer has been so impressed with the system that it now wants to order 10 more – and make it a company-wide standard.
Steelmaking is undoubtedly one of the more punishing industrial environments – where early bearing failure seems inevitable. However, paying close attention to lubrication management – from selection and storage, to the intelligent use of automated systems – can help to extend bearing life and avoid costly shutdowns. �
Steel Times International is the key publication for the steel market, reporting on iron and steel making issues from all corners of the globe.
The Steel Times International Directory is the essential guide to steel manufacturers, producers, suppliers of plant equipment and services to the steel industry. Order your print or digital copy priced from £105 or subscribers.
Packed with information on the steel industry and continually updated with news for steel professionals, www.steeltimesint.com features special articles and interviews with leading industry gures.
A round-up of the top news stories is sent to more than 7,000 industry professionals each week. You can register online to receive the weekly newsletter and keep up-to-date with the latest news from across the steel manufacturing industry. www.steeltimesint.com/e-newsletter
The continuous improvement and optimization of BOF process automation is essential to cope with operator demands such as high process accuracy, stability, flexibility, short ramp-up time, and low consumption figures. Primetals Technologies is constantly extending its principle equation-based process models and, in parallel, introducing data and rule-based functions, leading to hybrid simulation tools for process control and optimization.
THERE are various reasons why process optimization systems are applied for monitoring, control, and optimization of the converter process in steel plants: To meet the demand and maintain competitiveness, the highest flexibility, productivity, and metallic yield must be achieved. Optimization of consumption figures resulting in decreased consumption enables the reduction of costs. At the same time, the focus is on consistent quality. Different systems for monitoring and adjusting the process are applied, which support meeting these targets. Furthermore, the generation of know-how and the provision of it is essential. Tools for supervision of the process are developed, enabling data recording, evaluation, visualization, and reporting, increasing the transparency of the process.
Optimization systems must be continuously improved and adapted with new features to meet market demands. One approach is the expansion of the well-proven first principle process models with data-driven and rule-based functions, leading to hybrid process models.
The strengths of different models
By Anna Mayrhofer*are used to improve the accuracy of the predictions and obtain a more comprehensive understanding of the process. Hybrid process models enable process control optimization by identifying the optimal process condition, resulting in improved product quality and reduced costs.
These hybrid process models are additionally used to form a Digital Twin –i.e., a virtual representation of a physical system, such as a machine, process, or entire manufacturing facility. They contribute to improving quality by detecting and removing quality-related problems and increase safety by allowing for a better understanding of the behaviour of the physical system. With a Digital Twin, it is possible to simulate and test different scenarios before implementing them in the real world.
Three types of Digital Twins are applied in Primetals Technologies’ automation and digitalization systems:
• Digital Twin Automation: Digital Twins are used as training simulators for operators and engineers. Simulations can help improve the workforce’s skills and
reduce the risk of human errors during hot commissioning and actual production.
• Digital Twin Process: Digital Twins simulate the steelmaking process and test different configurations with defined parameters to find the optimal settings. In this way, it enables efficient offline development of steel grades.
• Digital Twin Product: Historical view of all heats produced with detailed analysis options for properties.
In the Process Pre-Calculation figure, the different models of the BOF Optimizer are explained based on the occurrence during the heat from scrap and hot metal preparation until the end of tapping.
As an integral part of the Digital Twin Process, it simulates the whole process covering all production steps from charging to tapping.
• Calculation and distribution of gas volumes, heating and cooling agents, alloys, and fluxes to reach the target steel temperature, the target steel weight and analysis, and the target slag basicity
• Calculation of ongoing reactions to predict the weight and analysis of steel, slag, and off-gas, as well as the steel bath temperature after each process step
• Information and warnings for the operator if target values for a process phase are not reached.
The Process Pre-Calculation can be restarted anytime during the heat with the latest data or before production starts. Process Pre-Calculation enables an adaptation of the process treatment even if the heat is already ongoing. Additionally, it can be used for production planning, simulation, and the development of new steel grades. Fig 1
(First Charge Calculation FCC) (Fig b)
If the situation in the steel plant allows it, especially if a flexible provision of hot metal (HM) and scrap is possible, an optimization of the amount of HM or scrap, or both,
can be done. In this way, the addition of heating and cooling agents is largely reduced, or in the best case, not even necessary. The Hot Metal and Scrap Order Calculation is part of the Process PreCalculation and determines the amount of HM and scrap before the treatment starts. A preparation of HM and scrap can be done accordingly.
The latest developments focus on the individual specification and selection of different HM-to-scrap strategies for controlling the input ratios of HM and different types of scrap. In this way, it is possible to optimize the mixing ratio depending on the current production philosophy and availability and the costs of HM and scrap. Fig 2
Standard Melting Practice and Automatic SMP Selection (Fig c)
Standard Melting Practices (SMP) define process setpoints covering various input settings to reach target figures.
SMPs represent the technological and metallurgical know-how, forming a standardized basis for targeted control to changing initial situations. The main setpoints for the BOF are lance position and oxygen flow rate, bottom stirring, and material addition pattern. With customizable rules, the selection of SMPs is made automatically depending on HM and scrap properties, tapping target values and considering the used lance tip. Fig 3
Second Charge Calculation (Fig d)
Once data from charged HM and scrap is available, the Hot Metal and Scrap Order Calculation is updated by the Second Charge Calculation (SCC). Slag formers, heating and cooling materials with timing and portioning, oxygen amount, blowing and stirring pattern, and the resulting steel bath level are determined. The basis for calculation is the target steel analysis and temperature, actual data of charged hot metal and scrap, the selected SMP, and the
material availability.
Online Supervision (Fig e)
First-principle models like mass and heat balance are used for Online Supervision. Ongoing reactions, including melting and scrap dissolution, addition, oxidation, and reduction, are cyclically calculated. In this way, the current steel and slag analysis, weight, and temperature are provided. Supervision during the whole blowing period is also possible. Visualizing essential process parameters enables process diagnostics at a glance and gives the operator a good overview of the current status of the heat. Fig 4
Blow end control (Fig f)
The target window for steel temperature and analysis must be achieved at the end of blowing. The final correction of setpoints for remaining oxygen volume and automatic triggering of blow end based on actual parameters is done via pre-defined strategies. Additional measurements are required to get the current condition of the heat.
In the case of an inblow measurement system, the amount of cooling or heating agents, fluxes, and remaining oxygen to be blown is determined based on the latest results from this measurement (T, express C). Corrective measures due to influences from the blowing lance hot spot are considered. Alternatively, data from
an off-gas analysis system – e.g., Primetals Technologies’ LOMAS (Low Maintenance Gas Analyzing System) – is used. The gas components – like CO, CO2, and O2 – are measured, and actual carbon content, decarburization rate, temperature, and slag FeO content are cyclically determined. These measurements are the basis for determining the remaining necessary amount of oxygen, triggering blow stop, and enabling dynamic process control. In the best case scenario, both systems are installed. Fig 5
Reblow Control (Fig g)
Suppose steel analysis or temperature are not within the specified target limits by the end of blowing. In that case, a pre-defined countermeasures strategy is selected depending on which values are not within the valid range. Actual steel analysis from
sample and temperature measurements are used to determine the amounts of cooling or heating agents, fluxes, and oxygen to be blown. The analysis ensures targeted reaction, prompt execution, and standardized selection of correction measures.
Alloy control (Fig h)
The necessary types, weights, and timing of deoxidants and alloying materials during tapping are determined to reach the target steel analysis. At the same time, the costs of the used materials are considered. Steel and slag analysis in the converter before tapping, target steel analysis after tapping, material properties and constraints, and, if available, the thermal condition of the teeming ladle are also considered.
The tuning of process models is essential to achieve the required accuracy. Current developments focus on Feedback Calculation, a tool that uses the measured and calculated data from the heats produced to improve the tuning parameters used for calculation. Completed heats can be recalculated with modified tuning parameters. There are two different methods to select new tuning parameters:
• Sandbox Mode: manual selection and adaption of tuning parameters
• Optimize Mode: an optimal set of tuning parameters is calculated
The results for a set of completed heats are calculated by the optimization system with the selected tuning parameters and compared to the temperature and steel analysis measurements of the heats. In this way, it is possible to gradually improve calculation accuracy by selecting more suitable tuning parameters, resulting in reduced deviations between calculated and measured values. Fig 6
Automatically selected tuning parameters from Optimize Mode show an overall
better match between measured data (y axis) and calculated values (x axis) for both temperature and carbon. One can see that the calculated values with the optimized parameters (green) are overall closer to the ideal line (blue, measured = calculated) compared to the calculated values with the previous tuning parameters (red).
An optimal database must be available for the Optimize Mode of Feedback Calculation to function properly. An evaluation of data of the heats produced ensures this. With Heat Data Evaluation an index is calculated, which gives feedback on the quality of process operation, data, and calculation accuracy. The following information is considered:
• Quality of input data, e.g., hot metal weight, chemical analysis
• Deviation from a standard operation, e.g., material additions shortly before measurements
• Availability of measurements and sample results for metal and slag, e.g., complete inblow and endblow measurement
• Matching of model results and measurements
• Occurrence of abnormal events, e.g., blowing interruptions, slopping
Furthermore, the Heat Data Evaluation supports process metallurgists and engineers in evaluating the heats by providing a fast overview of the right KPIs.
Conclusion
Dynamic and accurate process control is enabled by combining first principle models applied over decades with the latest developments containing data-driven and rule-based functions. This results in hybrid process models with the highest hitting rates for carbon and temperature and leads to low reblow rates, ensuring efficient and flexible high-quality carbon steel production. A targeted selection of hot metal, scrap, and materials that are added during the process reduces production costs.
Tools are developed focusing on improving the calculation accuracy by selecting more suitable tuning parameters and enabling an even better prediction of the whole process. These tools significantly impact the Digital Twin, perfectly reflecting reality. �
Alexander Schlemminger* discusses the ‘expanding global presence’ of QuantoLux, which looks to revolutionize EAF, BOF, and LF operations through the use of its rapid slag analysis.
1. How are things going at QuantoLux? Is the steel industry keeping you busy?
The steelmaking industry is experiencing a growing demand for change, resulting in an influx of requests. We are actively working on converting this demand into a feasible plan to serve our customers promptly. Our efforts include attracting top talent, securing reliable suppliers, and scheduling the construction of our company building in Kleve. In summary, we are fully occupied with these tasks.
2. What is your view on the current state of the global steel industry?
The steelmaking industry has played a crucial role in industrialization for centuries, with significant strategic and political implications. It is now at a crossroads, with a need for a complete transformation in a relatively short period – even less than half the average lifetime of its primary equipment, the blast furnace. This transformation will have far-reaching consequences, rendering former knowhow irrelevant, much like the shift from combustion to electric engines in the automotive industry. It is imperative for the steelmaking industry to adapt and evolve quickly to meet the demands of the future.
3. In which sector of the steel industry does QuantoLux mostly conduct its business?
Our rapid slag analysis technology is revolutionizing EAF, BOF, and LF operations by revealing previously concealed information. Steel mills can now adapt to in-situ deviations in real-time, enhancing yield, product quality, and process efficiency.
4. Where in the world are you busiest at present?
Over the past year, the development and market implementation of our latest
product, the QLX9 rapid slag analyzer, has been a top priority, starting with Germany and followed by other European countries. We’re excited to announce that due to high demand from our global partners, we’ll be taking the QLX9 beyond Europe in 2023, with Turkey and the USA being our next destinations. In 2024, we plan to introduce the QLX9 to the first Asian countries. Stay tuned for more updates on our expanding global presence!
the aluminium and steel industries. While both materials have their advantages, one key advantage of steel is the presence of real recycling processes already in place. In the aluminium making, we mostly rely on down-cycling and refer to it as recycling. For instance, a car door made of aluminium cannot be turned into another car door. On the other hand, with precise pyrometallurgical treatment in steelmaking, a rebar steel can be transformed into a car body part in its next life and back. This is a significant advantage, however, as technologies for high-purity aluminium sorting continue to develop, the gap between the recycling capabilities of aluminium and steel is gradually narrowing.
7. What are your views on Industry 4.0 and steelmaking and how, if at all, is QuantoLux using it?
5. Can you discuss any major steel contracts you are currently working on?
We work with five existing clients, all of which are either integrated or electric steel mills that prioritize energy and resource efficiency. As our customers seek to use more secondary resources, our rapid slag analysis technology becomes essential in managing process variations safely, without compromising quality or efficiency.
6. Where does QuantoLux stand on the aluminium versus steel argument? At QuantoLux, we are present in both
The steel industry must embrace ‘Industry 4.0’ swiftly for efficient use of equipment and advanced decision-making tools, as outdated steelmaking methods won’t suffice in the future. Our QLX9 provides valuable data for simulations and decisionmaking, meeting Industry 4.0 standards. By establishing digital homogenization of data instead of physical homogenization of samples within our product, we enable a quantum leap in improvement. At our company, we prioritize software development that aligns with Industry 4.0 standards, including a unified architecture that enables seamless integration of our products into modern manufacturing processes. We recognize the importance of interoperability and communication across different operating systems and strive to provide added value for our users by ensuring compatibility with various platforms.
8. Hydrogen steelmaking appears to be the next big thing. What’s your view?
Hydrogen is being touted as a versatile solution for a wide range of problems, including steelmaking and vehicle power. However, it is important to avoid viewing it as a universal solution that simply shifts the problem of limited energy supply from one source to another. Steelmakers should also be aware that the use of hydrogen represents a major change in existing processes, rendering previously developed strategies obsolete. The use of DRI/HBI, for example, significantly increases treatment times in the EAF. To address these challenges, new ways of adjusting processes are needed. This is where rapid slag analysis can be helpful, as in-situ analysis values enable highly volatile processes to be operated with little experience and optimized for the best possible results.
9. In your dealings with steel producers, are you finding that they are looking to companies like QuantoLux to offer them solutions in terms of energy efficiency and sustainability? If so, what can you offer them?
Steel producers seek practical solutions to enhance their processes, yet the conservative and demanding nature of the industry poses a challenge. To gain their trust, we’ve comprehensively understood their requirements and customized our Rapidslag analyzer to meet their demands for practicality. Additionally, we provide tools like the slag knock-off funnel, which streamlines and expedites sampling to further enhance the overall process.
10. How quickly has the steel industry responded to ‘green politics’ in terms of making the production process more environmentally friendly and are they succeeding or fighting a losing battle?
I think the turn to ‘green politics’ has been rather fast. And I think that is reasonable, since green steel will be a valuable business case in the long term as well.
11. Where does QuantoLux lead the field in terms of steel production technology?
Our QLX9 analyzer provides the fastest, reliable slag composition analysis on the market. In the past, analysis took over 10 minutes, but our analyzer can provide accurate results in just six seconds, which surpasses previous approaches by a factor
of 10. This is crucial because the slag holds important information about the steelmaking process, allowing for a more precise choice of process windows and immediate adaptation to deviations. By optimizing slag composition, energy consumption, iron yield, and other factors in EAF, BOF, and LF can be significantly improved.
12. How do you view QuantoLux’s development over the short-tomedium term in relation to the global steel industry?
Our latest product is in high demand due to its revolutionary character and the need for improvements in the steel industry. We are prioritizing the markets we target and will accelerate the global roll-out as demand fluctuates. This strategy will ensure sustainable growth over the next three to five years, independent of the global steel economy.
13. Where do you see most innovation in terms of production technologies – primary, secondary or more downstream?
While I personally observe significant advancements and progress in primary and secondary steelmaking, I acknowledge that my perspective may be biased as our solution is centred around that domain, and therefore, may not be universally applicable.
14. How optimistic are you for the global steel industry going forward and what challenges face global producers in the short-to-medium term?
History has taught that turbulent and
uncertain times can offer significant opportunities for innovative and adaptable individuals and organizations. Similarly, in the steel industry today, companies that invest in cutting-edge technologies rather than remaining complacent have tremendous potential for success.
15. QuantoLux is headquartered in Germany; what’s happening steel-wise in the country?
While energy costs remain a concern for steel producers, they have decreased by approximately 50-70% since reaching an all-time high at the end of 2022. While this has eased the existential fear for many producers, there remains a necessity for optimization within the industry. To this end, there are a wide range of activities underway to drive improvements and efficiencies across the sector.
16. Apart from strong coffee, what keeps you awake at night?
Thanks to our resilient supply chain and strong customer demand, I can easily break from my daily routine. However, my lack of sleep is typically caused by our two young children who tend to stay up during the early morning hours and resist going to sleep.
17. If you possessed a superpower, how would you use it to improve the global steel industry?
I would look into the future and find out which green-steel approach turned out to be the perfect fit. Based on that knowledge, I would work on the steel industry taking the right path to the future. �
In 1874, the London and South Western Railway opened a new route from London to Plymouth as a rival to Brunel’s Great Western Railway. An iron trestle construction was employed to reduce windage on the structure, which was built close to Dartmoor’s highest elevation of 621m.
WHEN the London and South Western Railway opened a new route from London to Plymouth in 1874 to rival Brunel’s Great Western Railway, they chose a route crossing the northern edge of the granite outcrop of Dartmoor. This contrasted with Brunel’s coastal route to the south of this high ground. One of the obstacles was the steep valley of the West Okement river. To cross this, LSWR’s engineer, William Robert Galbraith, designed a trestle viaduct
spanning 163m with a maximum height of 43m.
The choice of an iron trestle construction for the piers rather than the usual arched stone construction was said to be to reduce windage on the structure built close to Dartmoor’s highest elevation of 621m. The viaduct initially carried a single track. Photographs show this to be an alarmingly spindly structure. Just four years later, a second line was added requiring the building of a second viaduct alongside the first, the two being braced together to improve stability. Both structures were of wrought iron with cast iron trusses forming triangles in a single plane, but the first was of a riveted construction and the latter a welded structure.
The viaduct carried through trains until 1968 when the line was closed. However, it was still in use as a ‘head shunt’ for the nearby Meldon quarry which had opened in 1894 to supply stone for track ballast throughout Southern Railway’s network, which took over LSWR in 1923. Threequarters of all Southern’s ballast came from
the quarry amounting to 100kt/yr. The stone was the form of very hard ‘hornfels’ arising by the heating of sedimentary rock by volcanic action which metamorphosized it some 290 million years ago in the late Carboniferous period.
In 1996, the viaduct became part of the ‘Granite Way’ an 11-mile walking and cycle path between the towns of Okehampton and Lydford. A year later, the viaduct, Okehampton station and two miles of track between the two were sold to Devon County Council for a nominal £1 and a trust set up to maintain these structures. In 1970, the down line was replaced with a concrete platform for lorries to carry construction materials for the building of Meldon Dam, to create a reservoir.
The quarry closed in 2012 but the track
from Exeter to the viaduct remained with occasional excursion trains between Exeter and Okehampton station. A heritage railway operated between Okehampton station as far as, but not onto, the viaduct, but this sadly closed in 2019.
In 2021, the line was surveyed for reinstatement for passenger traffic from Exeter to Okehampton station by Network Rail. 11 miles of single track were relaid laying 24,000 concrete sleepers and nearly 29,000 tonnes of stone ballast. An innovative track laying machine was used which simultaneously dropped the sleepers into position, laid the rails and clamped them to the sleepers. The line opened just a year later and, taking the name of the previous heritage railway, ‘The Dartmoor Line’ now offers an hourly service between
Exeter and Okehampton. The line is run by the revived Great Western Railway company, an ironic twist since it was originally built to compete with the original GWR for traffic from London to Plymouth and on into Cornwall.
Some 150 years after first opening the line, once again it is serving the local community. When the line reached Okehampton in 1874, it replaced an arduous journey of two days by stagecoach from London. First small industries appeared, an artificial ‘manure’ works, a boot and shoe factory, a cabinet-making firm and a draper. In 1894, the quarry opened employing a workforce of some 3000. Agricultural produce could be sent to London in a journey time of around six hours and tourists were attracted to walk the tors of Dartmoor.
When the line closed in 1968, the town of Okehampton and surrounding countryside had to rely on road transport to Exeter to the nearest railway. With the line re-opening, not only does the line once again offer excellent access to the northern edge of the moors, but is also a valuable commuter link to Exeter and further afield.�
Other developments & technologies aiming at decarbonizing the steel industry:
VolteronTM: CO2-free Steel
Production Process
Furnace Electrification
Carbon Capture
Heat Recovery
The JVD line introduces a technological breakthrough in the steel coating of advanced high resistant steel grades difficult to galvanize by hot dipping. This genuine alternative to Electro-Galvanizing and Hot-Dip-Galvanizing considerably reduces the cost of galvanized steel and provides multiple advantages when it comes to quality, speed and OPEX. Developed for ArcelorMittal with the help of our experts, John Cockerill is in charge of commercializing this unique technology worldwide.
Our E-SiTM equipment and processing lines are designed for the production of strong, ultrathin, lightweight, and highquality Non-Grain Oriented (NGO) steel grades essential for the future of e-mobility.
High-performance Acid Regeneration supporting responsible steel making and the circular economy
John Cockerill Industry’s ARPs come with smart plant control systems, provide waste energy recovery and drastically reduce pickling process plants’ fresh acid demands and waste streams in general. What is more, they are providing the lowest emissions in the market.