Utilizing live data to refine scrap.
How upcycling scrap unlocks routes to decarbonization.
Ambitious steps forward in understanding steel scrap.
Uncovering lost dates: Darby’s Coalbrookdale furnace.
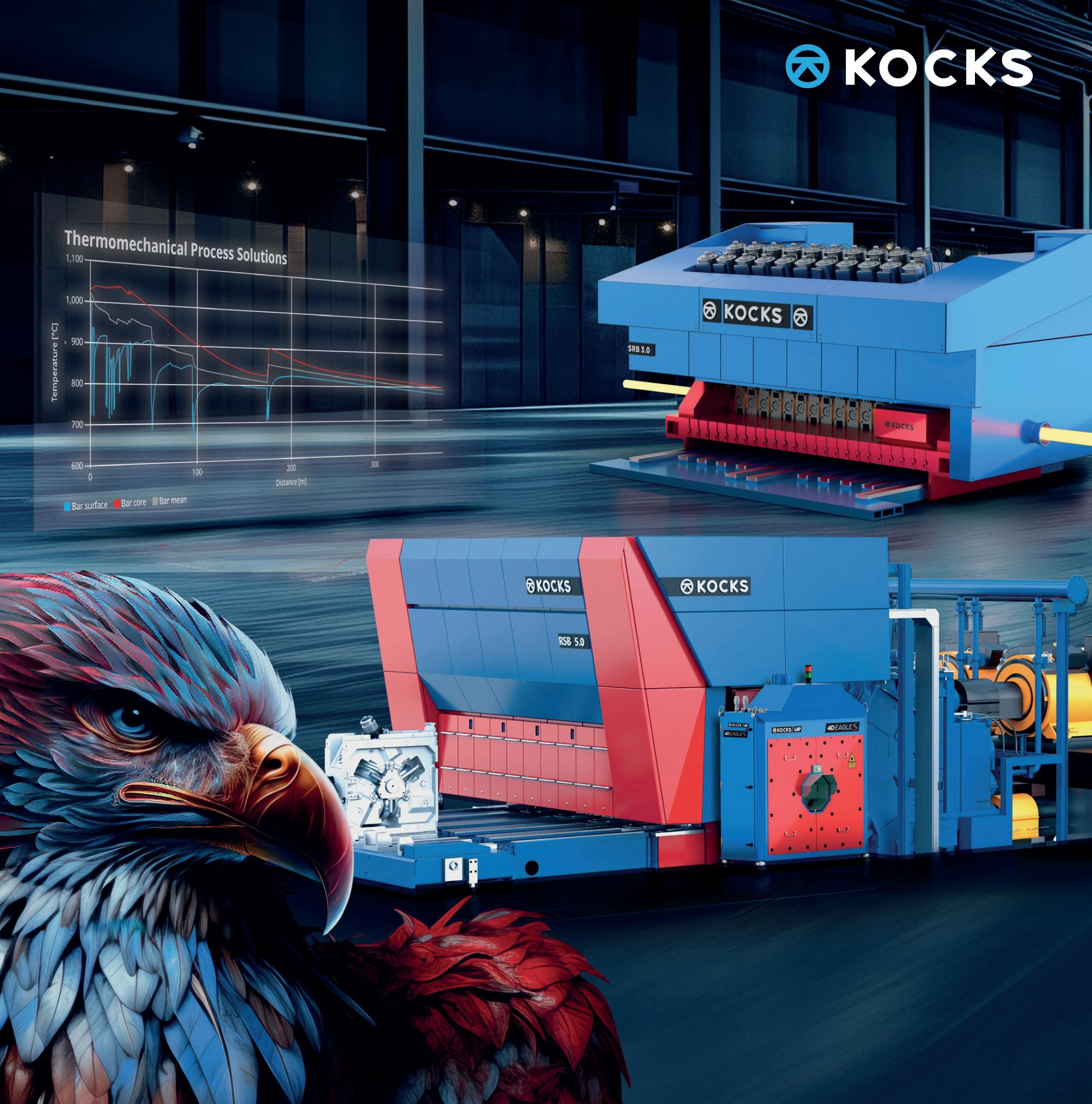
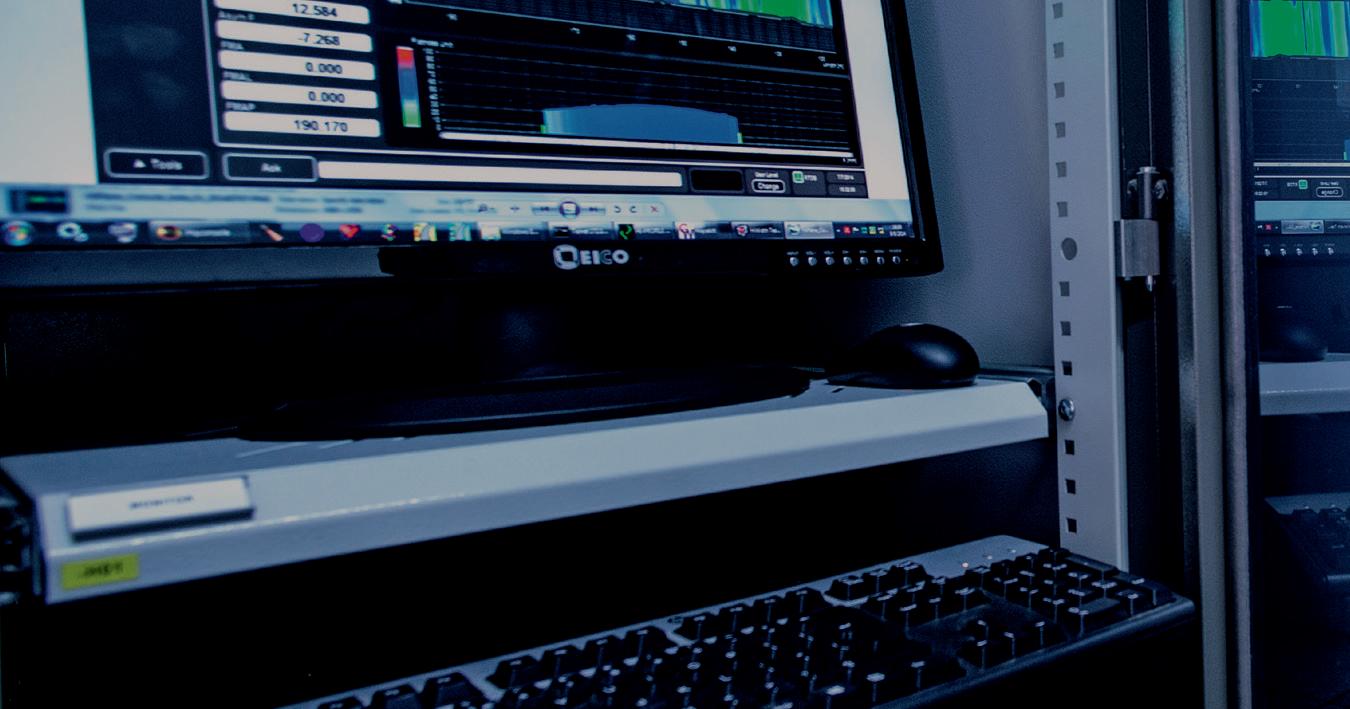
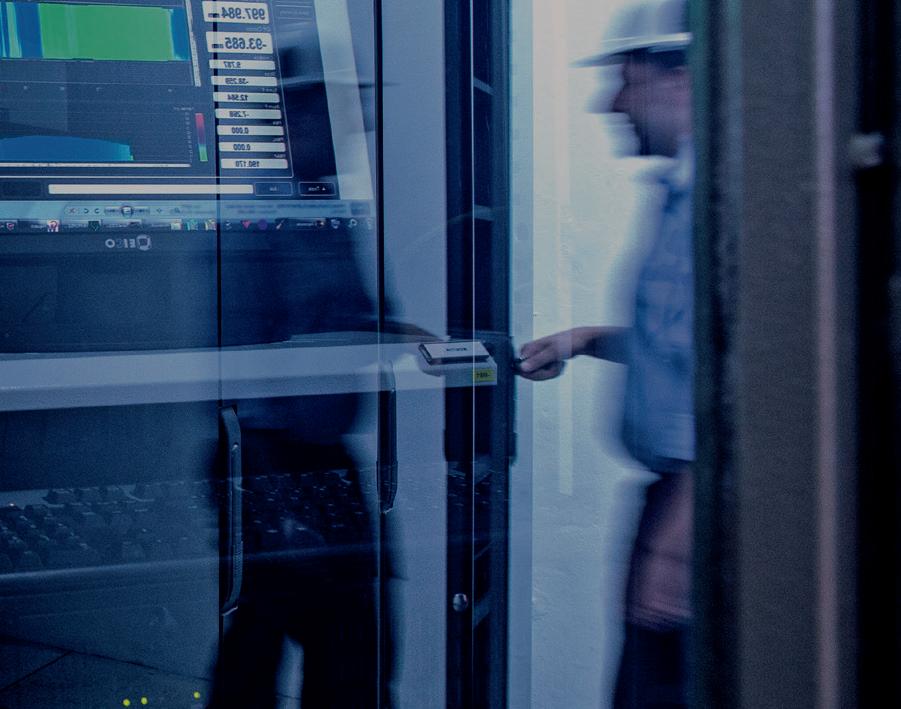
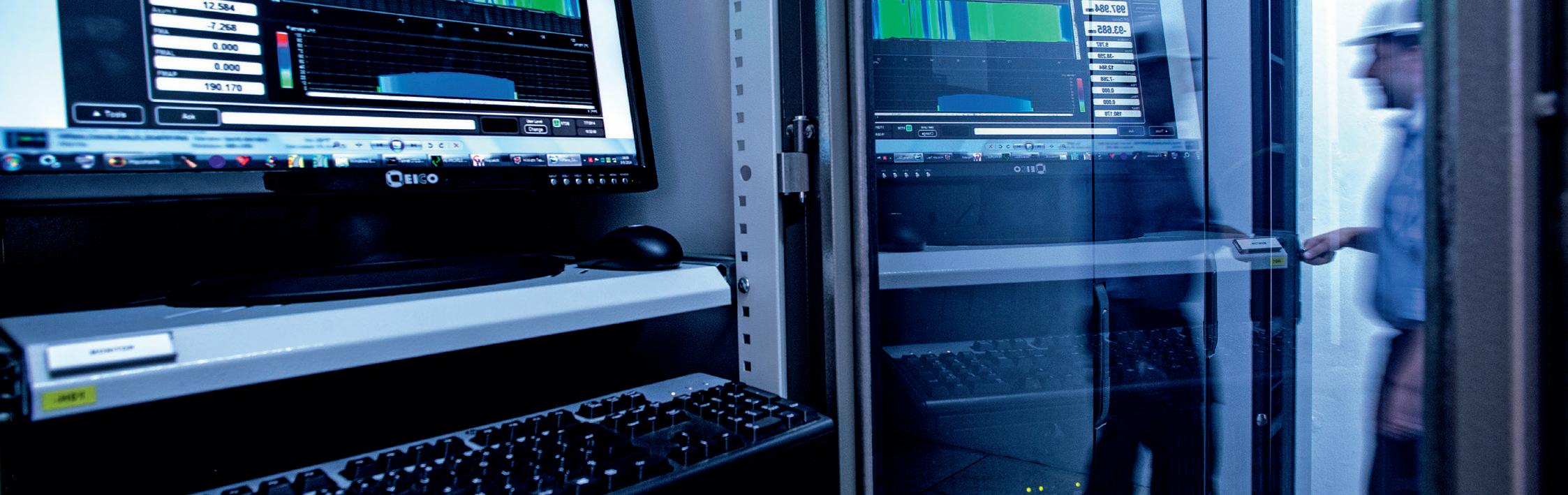
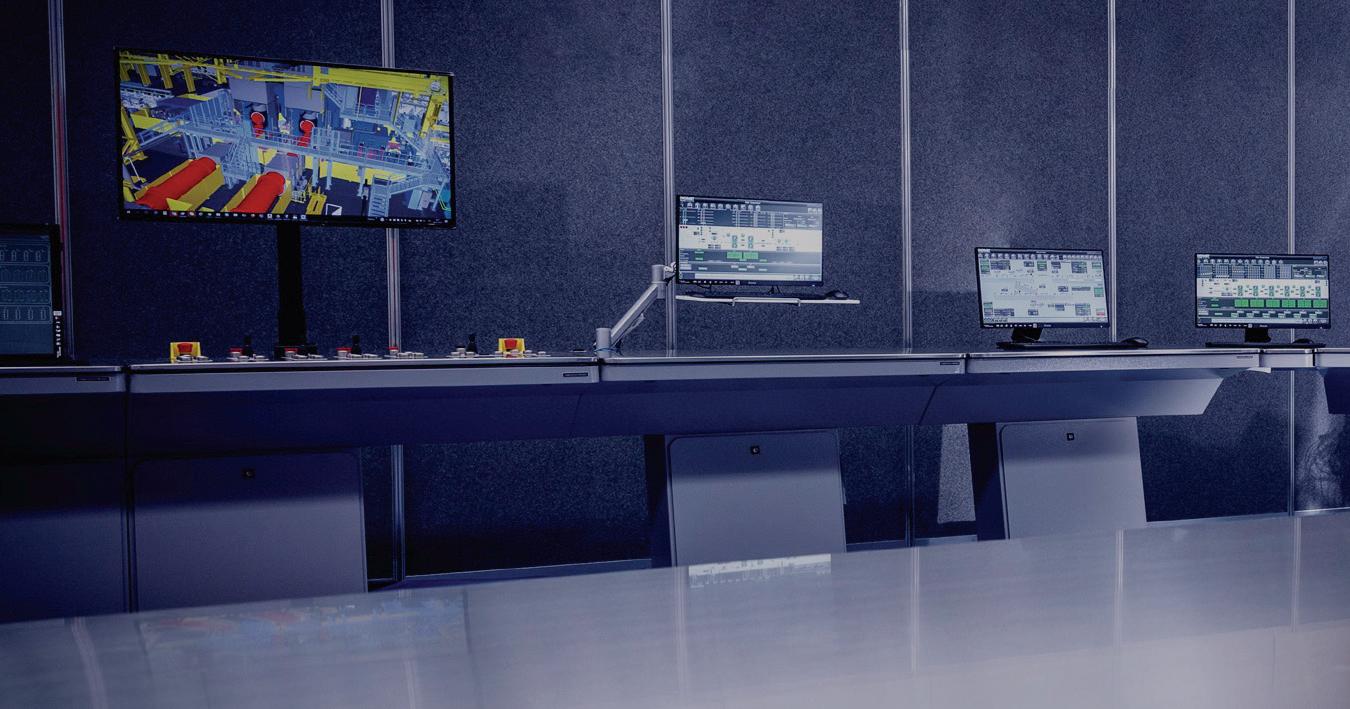
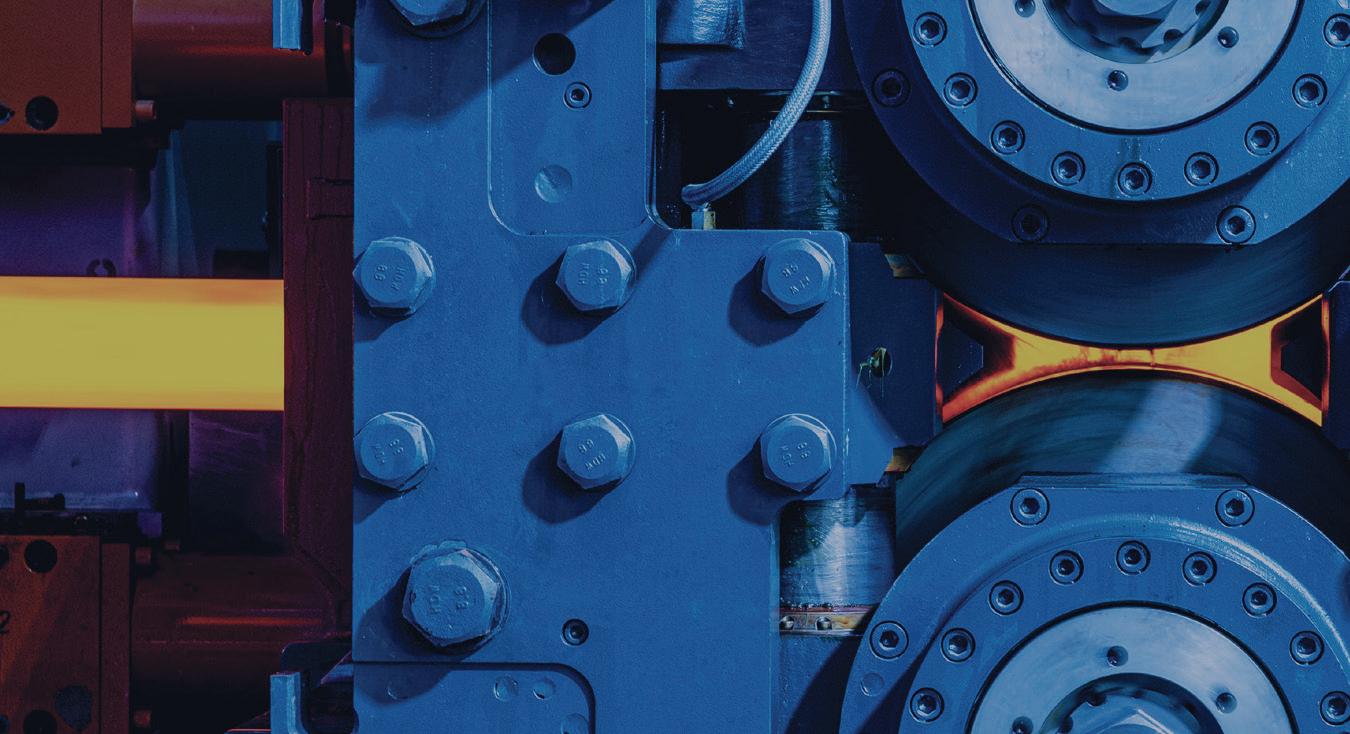
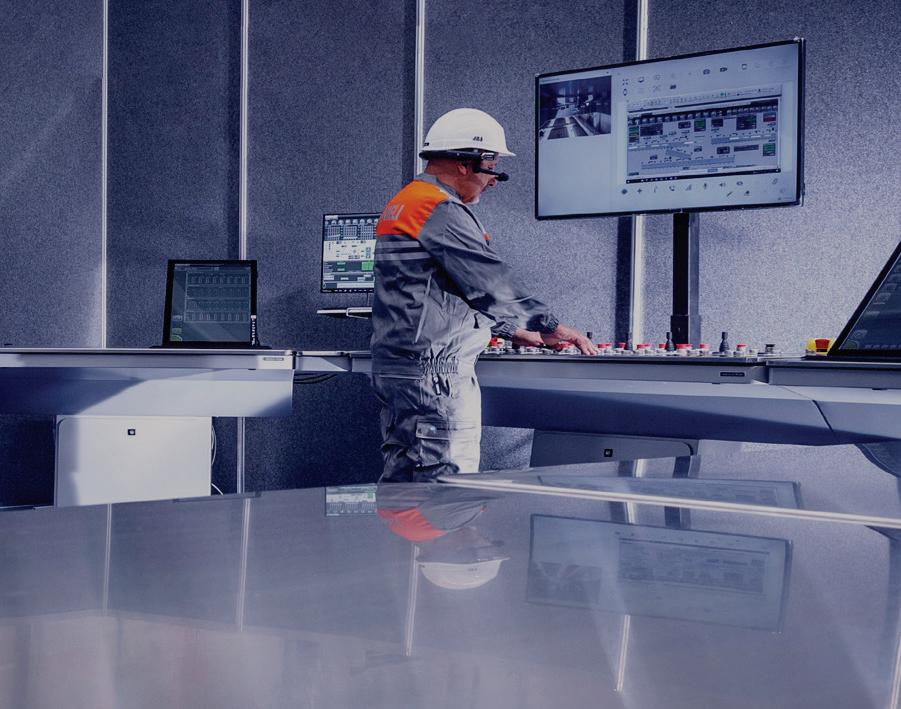

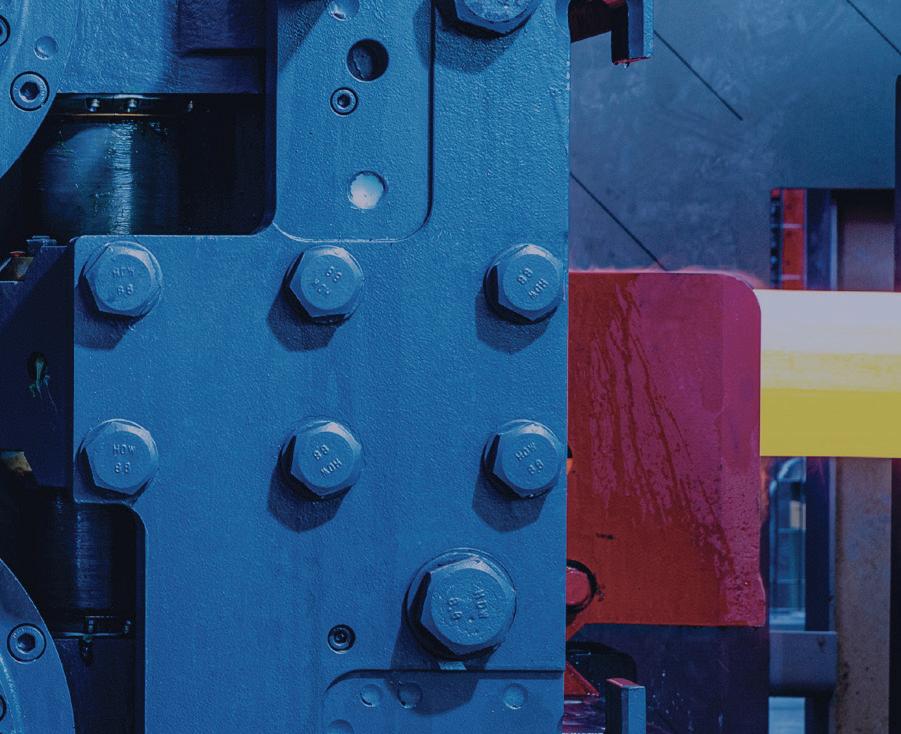
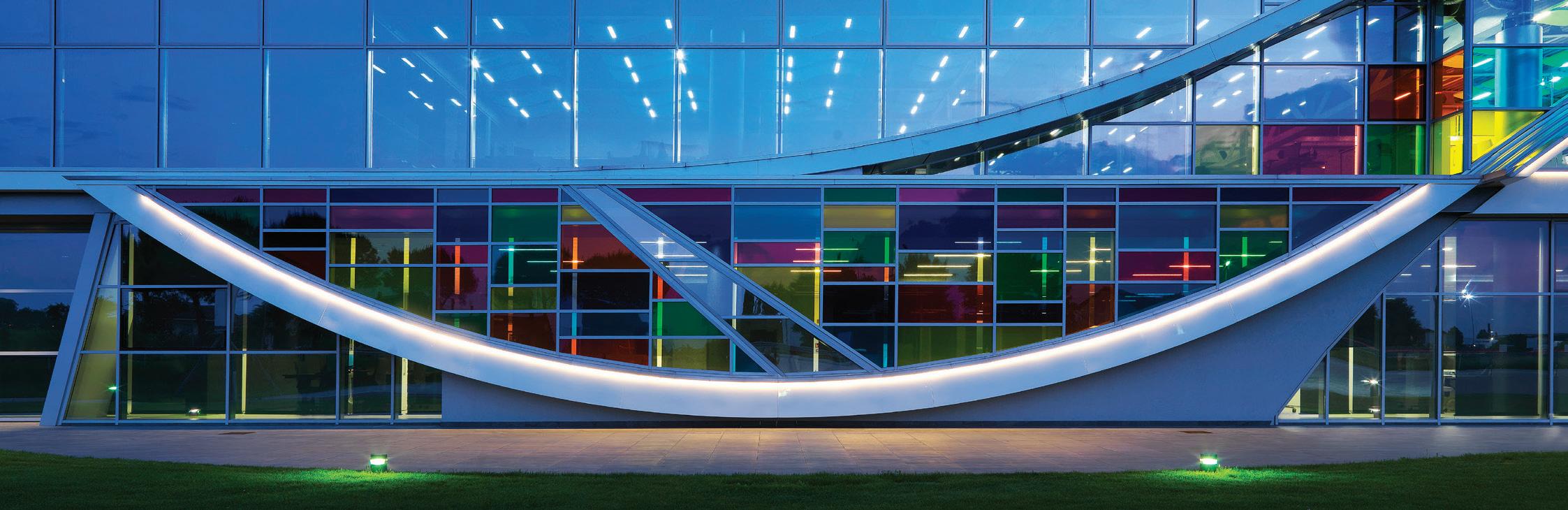

Utilizing live data to refine scrap.
How upcycling scrap unlocks routes to decarbonization.
Ambitious steps forward in understanding steel scrap.
Uncovering lost dates: Darby’s Coalbrookdale furnace.
EDITORIAL
Editor
Matthew Moggridge
Tel: +44 (0) 1737 855151
matthewmoggridge@quartzltd.com
Assistant Editor
Catherine Hill
Tel:+44 (0) 1737855021
Consultant Editor
Dr. Tim Smith PhD, CEng, MIM
Production Editor Annie Baker
Advertisement
SALES
International Sales Manager
Paul Rossage
paulrossage@quartzltd.com
Tel: +44 (0) 1737 855116
Sales Director
Ken Clark
kenclark@quartzltd.com
Tel: +44 (0) 1737 855117
Managing Director
Tony Crinion
tonycrinion@quartzltd.com
Tel: +44 (0) 1737 855164
Chief Executive Officer
Steve Diprose
SUBSCRIPTION
Jack Homewood
Tel +44 (0) 1737 855028
Fax +44 (0) 1737 855034
Catherine Hill Assistant editor catherinehill@quartzltd.com
America has elected Donald Trump as its 47th president, beckoning a new era of domestic and international politics, with reverberations across the intersectional fabric of American society. Policies proposed in Agenda 47 and Project 25 outline a significant shift in the American body politic, including expansions of presidential power, the execution of the US military for the largest mass deportation of illegal immigrants in history, and withdrawal from the Paris Climate Agreement. Implications for the steel industry are manifold; Trump’s campaign promised to prioritise American interests by implementing a general tariff of up to 20% on all imported goods, in a bid to reduce over-reliance on foreign products, with critics citing increased input costs, and retaliatory tariffs from other countries outweighing the short-term gain. Trump’s appointment of ‘fracking pioneer’ Chris Wright as energy secretary also signals a hard fracturing from Biden’s engagement with climate issues, with the president elect having previously referred to global warming as an ‘expensive hoax’. With an almost five million lead in the popular
vote, American voters have expressed an unmistakable appetite for an alternative set of values, ranging from the sociological, to the economic. There will be echoes of these changing sentiments across the globe, in patterns that are continuing to emerge, but visible in the increasing self-assurance of right-wing supporters, emboldened by a dichotomous rhetoric that offers uncomplicated solutions to categorical issues. The American steel industry has long prided itself on its high proportion of EAF-based production which symbolises both an intent to decarbonize and a basic recognition of the environmental backdrop in which developments take place. Under Trump’s leadership, governmental spending on nascent ‘green’ technologies are unlikely to retain the same impetus. Can two such opposing approaches comfortably exist? In the eyes of over 76 million voters, it is certainly possible. On January 20th, Donald Trump will take the oath of office at the US Capitol, arguably the most recognised symbol of democratic government in the world. Change, undeniably, now rests in his empowered hands.
Process improvement is like sailing.
With an experienced partner, you can achieve more.
Optimizing processes and maximizing efficiency is important to remain competitive. We are the partner that helps you master yield, quality and compliance. With real-time inline insights and close monitoring of cricial parameters, we support manufacturers to optimize processes, reduce waste and increase yield.
Do you want to learn more? www.endress.com
Metals offers the entire steel value chain an exceptional opportunity for curbing their CO2 emissions.
The unique combination of its historic and recently developed product portfolio, make John Cockerill one of the industry’s most relevant suppliers of equipment for both the hot and cold phase of the steelmaking and processing industry.
Our three distinct business segments are addressing todays and tomorrow’s challenges supporting sustainable and green steel production:
Our new upstream offering related to DRI (Direct Reduced Iron), EAF (Electric Arc Furnaces) technologies and the use of hydrogen in steelmaking. Next to offering indirect electrification (DRI-EAF&H2-DRI-EAF),John Cockerill is also working on Volteron®: A first-of-a-kind iron reduction and steel processing route via direct cold electrolysis. This CO2 free steelmaking process, has been co-developed with the world’s leading steelmaker ArcelorMittal.
Regrouping our historical downstream product portfolio, this segment also includes:
¡ the Jet Vapor Deposition (JVD®) technology set to replace today’s hot-dip or electro galvanizing processes. This novel high-productivity vacuum coating technology provides previously unknown coating flexibility and possibilities, all while offering lower CAPEX and OPEX.
¡ our E-Si® equipment & processing lines specifically designed to produce high-quality Non-Grain Oriented (NGO) steel in response to the need for electrical steel meeting precise metallurgical properties, essential to support the shift towards green mobility.
This segment not only embraces all services and after-sales activities but will be strongly focusing on downstream furnace electrification (reheating and processing line furnaces), as well as hydrogen combustion, and the optimization of plant operations, including energy audits and the modernization of steel production equipment and installations.
LanzaTech, a carbon recycling company transforming above-ground carbon into sustainable fuels, chemicals, materials, and proteins, has announced plans to develop a commercial-scale Carbon Capture and Utilization (CCU) facility at Herøya Industrial Park in Porsgrunn, Norway. The plant will produce ethanol and is expected to begin operations in 2028.
Source: Azo Cleantech, 1 November 2024.
South Korean steel giant POSCO Holdings is seeking to sell its entire stake in a Chinese stainless steel joint venture as it faces growing competition with Chinese steelmakers amid a supply glut. Industry sources have said that POSCO Holdings,
Cleveland-Cliffs has successfully completed its acquisition of Canadian steel company Stelco. The addition of Stelco enhances Cliffs’ position as the largest flatrolled steel producer in North America, diversifies Cliffs’ end-markets and expands its geographical presence in Canada, the North American steelmaker has said. Stelco will continue operations as a wholly-owned subsidiary of Cliffs, preserving the name and legacy of the business.
Source: Business Wire, 1 November 2024.
the parent of Korea’s top steelmaker POSCO, plans to sell its stake in POSCO
Zhangjiagang Stainless Steel Co. (PZSS), a JV with Shagang Group, China’s second-largest steel producer, also known as Shasteel.
Source: The Korea Economic Daily, 8 November 2024.
AM/NS India, a joint venture between ArcelorMittal and Japan’s Nippon Steel, is set to establish an integrated steel plant with 17.8Mt capacity, in the Anakapalli district of Andhra Pradesh. This would be one of the largest greenfield projects in recent times, the company has said. In the first phase of the project, ArcelorMittal Nippon Steel will establish a 7.3Mt/yr capacity blast furnace steel plant with an initial investment of Rs 80,000 crore. Source: The Economic Times, 3 November 2024.
Progress is being made on one of the world’s largest offshore wind plants being built on Teesside, supplied with steel produced by British Steel. SeAH Wind’s £900 million monopile manufacturing facility on the south bank of the River Tees at Teesworks is currently 90% complete. Once finished, the 800-metre-long building will be the world’s biggest monopile facility and the only one of its kind in the UK. Each week, the 40-metre-high building will annually produce two to four monopiles – the structures which form the foundations of offshore wind turbines. Source: British Steel, 4 November 2024.
A number of procurement agreements were signed between China Baowu Steel Group Corp and its global partners during the 7th China International Import Expo. A total of 10 global corporations reached deals with the Shanghai-based steelmaker, including the purchase of coking coal, manganese ore, chrome ore, and ferroniobium.
Source: China Daily, 11 November 2024.
Swiss Steel Group has introduced its lead-free machinable steel, 11SMn30+BX, a sustainable alternative to traditional leaded machinable steel, the company claims. Using boron instead of lead as an alloying element, the material aims to maintain workability while aligning with future regulatory standards. The addition of boron to free-cutting steel improves machinability if the metallurgical processes in the steelworks are properly controlled, Swiss Steel Group added.
Source: Green Car Congress, 10 November 2024.
A year on from the announcement of a £1.25 billion green transition for British Steel, it is claimed dozens of workers are quitting its Scunthorpe site every month. According to a report by the BBC, despite ongoing discussions, there is no announcement of a firm deal on the table regarding the future of the plant, leading workers to leave due to the job uncertainty.
Source: BBC, 11 November 2024.
Cleveland-Cliffs’ Middletown, Ohio steel mill is planning to switch to a greener production process. The Middletown plant will get up to $575 million from the Inflation Reduction Act to retire its old blast furnace and install two electric furnaces. Advocacy group Industrious Labs recently released a report, detailing the health impacts of steel mills across the nation including in Ohio. The report focused on the health effects of steel production. Hilary Lewis, steel director at Industrious Labs, said Cleveland-Cliffs action is an encouraging move in Ohio’s steel production.
Source: WYSO, 13 November 2024.
Petroleum company Petrobras and Brazilian steelmaker Gerdau have signed contracts for the supply of natural gas on the free market, serving the latter’s special steel production unit located in Rio Grande do Sul. “The expansion of the alliance between Petrobras and Gerdau in the free gas market demonstrates that Petrobras’ natural gas sales portfolio is increasingly competitive and attractive. We are investing more than $7 billion in new natural gas supply infrastructure, in addition to offering several flexible contracting options,’’ said the director of energy transition and sustainability at Petrobras, Maurício Tolmasquim.
Source: Alfajr News, 12 November 2024.
ArcelorMittal and Hewlett Packard (HP) have announced a strategic collaboration to advance the use of steel in Additive Manufacturing. Together, the partners will work to bring new steel solutions to a sufficient Technology Readiness Level (TRL), then leverage the ArcelorMittal Research Centre as an incubator for new applications developed in collaboration with customers. The move is intended to save customers the initial investment needed to evaluate and qualify the technology, up until the process can be transferred to a contract manufacturer for final industrialisation and production. Source: Metal AM, 12 November 2024.
Global trade unions are concerned about the cumulative loss of tens of thousands of jobs in the steel sector and related industries around the world, according to a report by global union federation IndustriALL. Representatives of the Trade Union Advisory Committee to the OECD (TUAC), IndustriALL and IndustriAll Europe, who took part in a meeting of the OECD Steel Committee, warned of the risk of deindustrialization in the countries of the organization and other countries.
Source: GMK Center, 14 November 2024.
ArcelorMittal has initiated the expansion of its Vega facility in São Francisco do Sul, Santa Catarina, Brazil. The new unit will produce Magnelis, a corrosion-resistant material developed by the company, marking the first time this product will be manufactured outside of Europe. The new continuous galvanizing and annealing line has increased the plant’s annual production capacity from 1.6Mt to 2.2Mt. Jorge Adelino, vice president of operations for ArcelorMittal flat steel in Latin America, noted that this is the largest private sector investment in Santa Catarina. Source: International Valor, 14 November. 2024.
European steel association EUROFER has continued to lobby the European Commission to curb scrap exports as the industry looks to decarbonize. On 12 November, EUROFER reiterated its view that the commission should ‘recognise steel scrap as a strategic secondary raw material under the critical Raw Material Act, ensure the robust implementation and effective enforcement of the revised EU Waste Shipment Regulation to ensure compliance with the EU environmental standards in third countries and avoid circumvention.’
Source: Argus Media, 12 November 2024.
A winding up petition has been lodged against a South Yorkshire steel firm amid major restructuring plans. A hearing at London's Business and Property Courts in November considered Harsco Metal Group Limited's claim that Speciality Steel UK Limited, a division of Liberty Steel, owes money and should be closed by the courts if it cannot pay creditors. Speciality Steel UK Limited, which has sites in Stocksbridge and Rotherham, previously shared restructuring plans which aimed to ‘significantly’ reduce its debts.
Source: BBC, 15 November 2024.
Steelmaker ArcelorMittal is considering closing two service centres in France as part of the restructuring of its Centres de Services business, the Journal de l’Economie has reported. This decision may affect 130 jobs and has provoked outcry from trade unions. In a statement in November, ArcelorMittal presented a project to reorganize its subsidiary
Officials from the US and Ukraine said the countries will partner on building small modular reactors (SMRs) to replace the latter's coalfired power generation, with the SMRs used to help Ukraine decarbonize its steel industry. A statement from the US State Department, released at the UN Climate Change Conference in Baku, Azerbaijan, on 16 November, said the countries will develop a roadmap to ‘rebuild, modernize, and decarbonize Ukraine's steel industry with SMRs.’
Source: yahoo!finance, 16 November 2024.
Acerinox, a manufacturer and distributor of stainless steel, has completed the acquisition of Haynes International, a US manufacturer and marketer of alloys. “We are thrilled to officially welcome Haynes”, Bernardo Velázquez Herreros, chief executive officer of
Telecommunications company China Telecom and joint iron and steel enterprise Meishan Iron and Steel have announced plans to partner on the development of a ‘5G smart factory’, which the companies claim will ‘open a new chapter of developing green and ecological steel culture, promoting the change of the steel industry from ‘labour-intensive’ to ‘technology-intensive”.
Source: Mobile World Live, 18 November 2024.
Acerinox, said. “Haynes has built a leading highperformance alloys business. Their addition to Acerinox
Austrian steelmaker voestalpine has said that its natural gas supply is secure even if Russian gas giant Gazprom stops deliveries to Austria altogether. Gazprom halted supplies to Austrian energy company OMV in midNovember after OMV won an arbitration case against Gazprom awarding it more than €230 million in damages and said it would recover that money by not paying Gazprom's invoices.
Source: Reuters, 18 November 2024.
strengthens our global position in this segment, creating opportunities for growth in the aerospace sector and in the attractive US market. This transaction will enable us to broaden the range of products that we offer.”
Source: Acerinox, 21 November 2024.
ArcelorMittal Service Centres, which specializes in the wholesale of metals and minerals. The company explained that it has faced a decline in activity among its industrial customers, especially in the automotive sector, and this trend has intensified in recent months.
Source: GMK Center, 21 November 2024.
The Italian Ministry of Business and Ukrainian steel and mining group Metinvest have signed a declaration agreeing to the construction of a steel plant in Piombino. The new plant, worth €2.5
billion, will contribute to the decarbonization of steel production and the strengthening of economic co-operation, the project participants have said. The plant is to be built on an area of 260 hectares, with a planned capacity of 2.7Mt of hot-rolled coils per year. Using Ukrainian raw materials, the production will help reduce Italy’s dependence on steel imports from outside the EU.
Source: GMK Center, 21 November 2024.
Bioengineering firm ByoMax has signed a non-binding Letter of Intent (LOI) with Green Steel WA to supply ‘ByoCoke’, a product made from waste biomass as a sustainable replacement for coal and coke, at the company’s Collie, Western Australia green steel plant. Green Steel WA is developing an electric arc furnace to recycle scrap and the state’s first green hydrogen directreduced iron (DRI) plant at the former coal mining town.
Source: AU Manufacturing, 25 November 2024
President-elect Trump has vowed to block Japanese steel firm Nippon Steel’s acquisition of US Steel. “I am totally against the once great and powerful US Steel being bought by a foreign company, in this case Nippon Steel of Japan,” Trump wrote in a social media post. He made the same promise on the campaign trail earlier this year.
Source: The Hill, 3 December 2024.
The Steel Authority of India Limited (SAIL), India’s largest public sector steel producer and a Maharatna company, has entered into a strategic collaboration with John Cockerill India Limited (JCIL), a subsidiary of the global John Cockerill Group. The two companies signed a Memorandum of Understanding (MoU) in Mumbai, aiming to leverage their collective expertise in innovation and sustainability within the steel industry.
Source: ET Energy World, 29 November 2024.
Singapore’s Meranti Green Steel plans to build a green steel plant in Thailand, said Sebastian Langendorff, the company’s chief executive officer, in an interview with S&P Global. The new facility, which will be located in the IRPC Eco-Industrial Zone in Rayong province, will have
South Korean steel conglomerate POSCO Group has announced plans to invest in Neuromeka, a domestic robotics company, to boost its steel business through factory automation. Neuromeka produces collaborative robots, which can work with humans in the same space without the need for safety fences, and industrial robots, which can move on three or more axes and are used in manufacturing with programmable and automated systems.
Source: SEAISI, 2 December 2024.
The European Commission (EC) is considering extending measures to restrict steel imports as part of an overall plan to protect the sector during its decarbonization process, a comment stated by the executive vice president of the European Commission Stéfan Séjourné. During a visit to ArcelorMittal’s plant in Ghent, Belgium, Séjourné,
a capacity of up to 2.5Mt of low-carbon hot-rolled coils per year. Construction is expected to begin in 2026, with investment approvals slated for completion in 2025, and the plant is scheduled to start-up in mid-2028.
Source: GMK Center, 4 December 2024.
Australian energy firm APA Group has opened a solar farm and battery storage facility at Western Australia's Port Hedland in a move designed to support mining giant BHP's emissions-reduction goals. APA's plant will power most of BHP's Port Hedland operations from January 2025, under the terms of a power purchase agreement signed between the two firms. Work on the project began last year, supported by a A$1.5m ($970,000) grant from Western Australia's Clean Energy Future Fund.
Source: Argus Media, 3 December 2024.
who is responsible for EU industrial policy, said that at the beginning of his term of office, the priority will be reducing high energy costs and fending off Chinese overcapacity at a time when European steelmakers are cutting carbon emissions.
Source: GMK Center, 4 December 2024.
DYSENCASTER®
HYDROGEN-READY AND ELECTRIC TUNNEL FURNACES
Performances, operational reliability and quick startups are the result of 30 years of continuous R&D activities, carried out at the Danieli research center and onsite together with partnering customers.
QSP-DUE can make use of more than 20 Danieli patents covering technological layouts, production equipment and Danieli Automation solutions, such as power, instrumentation and intelligent digital controls.
— The most efficient, digitally controlled electric steelmaking with no impact on the power grid.
— 6 m/min casting speed, allowing up to 4.5-Mtpy productivity on a single strand, with dynamic adjustment of slab thickness and width at any speed. In-mould fluidodynamic control with MultiMode Electromagnetic Mould Brake (MM-EMB) for no quality limitation.
— Hydro-MAB burners ready for 100% hydrogen operations and electric tunnel furnaces for carbon-free slab reheating.
— Split mill layout, intensive cooling and dynamic transfer bar reheating for true thermomechanical rolling and endless operation of ultra-thin gauges.
— Danieli Automation robotics and artificial intelligence for zero-men on the floor.
— Least power-consuming process with the lowest carbon footprint.
— The most competitive plant in terms of CapEx and OpEx.
— The highest production flexibility due to three rolling modes available in a single line.
QSP-DUE® ENDLESS CASTING-ROLLING PLANTS
SGJT and Yukun are enjoing their QSP-DUE plants operating in coil-to-coil, semi-endless and endless mode, based on HRC market requests. The Nucor Steel QSP-DUE plant is under construction.
15 QSP PLANTS
Carbon Clean, a supplier of carbon capture solutions, has announced the launch of its CycloneCC C1 series, marking the penultimate stage in the technology’s commercialisation. The CycloneCC C1 series is available in concentrations ranging from 3% to 20%, capturing up to 100kt of CO2 per year. The CycloneCC C1 unit is fully modular and columnless, and, according to Carbon Clean, achieves a height reduction of 70% compared to conventional solutions. Rotating Packed Bed (RPB) technology replaces every column used in a conventional plant, which reduces the steel required by 35% and lowers the unit’s carbon footprint, says Carbon Clean.
The unit footprint is up to 50% smaller than conventional carbon capture plants, claims the company, with its largest equipment sizes reduced by a factor of 10. Each unit is prefabricated, skid-mounted and delivered on road
truckable modules, with an aim to cut the costs associated with transport, logistics, site preparation and installation. CycloneCC C1 uses firstof-a-kind (FOAK) technology to reduce the total installed cost of carbon capture by up to 50% compared to conventional solutions.
Prateek Bumb, co-founder and chief technology officer of Carbon Clean, said: “The launch of the CycloneCC C1 series is a major milestone in the technology’s commercialisation. Repeatability is key to mass adoption, as demonstrated with solar panels and EV batteries. Carbon Clean is leading a similar transformation through eliminating the columns used in conventional carbon capture solutions. Delivering fully modular, columnless, replicable units with a substantially smaller footprint is a technological breakthrough. CycloneCC’s ‘Lego-block’, ‘plug and play’ design makes it simple and cost-effective to install, mak-
ing carbon capture financially and logistically viable to be deployed at scale. First-mover customers and early adopters will have the advantage of tangible decarbonization results while benefiting from a staggered approach to capital investment due to CycloneCC C1’s modular design.”
At the heart of CycloneCC C1 is the combination of two process intensification technologies: rotating packed beds (RPBs) and Carbon Clean’s proprietary APBS-CDRMax solvent. According to Carbon Clean, using RPBs to replace the columns used in conventional carbon capture solutions both reduces the size of the plant and accelerates the mass transfer process, increasing CO2 absorption.
For further information, log on to www.carbonclean.com
Global manufacturer of non-contact measuring technologies, ZUMBACH Electronic, has developed the PROFILEMASTER® SPS product family with high-speed versions, in answer to the growing demand for surface fault detection. This enhancement adds to the continued success of the PROFILEMASTER® SPS, says the company, by equipping it with the latest generation of highspeed cameras that enable the acquisition of full product contours, at a rate of 2000Hz. This new specification produces six times more contours within a specified length, enabling classification
of defects in addition to their detection.
New features are cited to include:
� Higher sampling rate up to 2000/second
� Higher resolution with full area of interest
� Improved optical path
� Improved stability in data acquisition
� Improved defect detection/analysis
� Better overall dimension control
� Improved defect visualization/
3D modelling
The new design enhancement aims to improve
the performance of the optical path of the cameras, optics and lasers and boosts the sampling rate from previously 500 per second, to up to 2000 per second, providing far greater resolution and surface detail. The new high-speed set-up enables the PROFILEMASTER® SPS product family to work under harsh light absorbing surface conditions of hot steel products.
For further information, log on to www.zumbach.com
Tenova, a developer and provider of sustainable solutions for the green transition of the metals industry, has announced a significant milestone for Nucor Steel Louisiana, USA. In August 2024, the ENERGIRON direct reduction (DR) plant of the steelmaker achieved what the company claims is a world production record of 330.3 tons per hour (tph) of cold direct reduced iron (CDRI), yielding 7,928 tons per day (tpd).
The 2.5Mt/yr DR plant, based on ENERGIRON technology, jointly developed by Tenova and Danieli, demonstrates increased production levels and improved operational reliability, says Tenova. It achieved over 98% operational reliability and
97.50% availability in 2024, underscoring the collaborative efforts between Tenova and Nucor.
“The most important factor that helped Nucor Steel Louisiana reach a world record production rate is our team and our culture. Each member of our team has played a crucial role in this achievement. It is their commitment and passion that has made achieving this record possible. When you can be inclusive and harness the collective efforts of individuals, there are no challenges that we cannot overcome. Here’s to our team and this remarkable achievement and to many more milestones ahead!” commented Calvin Hart, vice president and general manager of Nucor Steel
Louisiana.
“We are thrilled to recognize this remarkable achievement in our ENERGIRON Direct Reduction Plant,” said Stefano Maggiolino, Tenova HYL president and CEO. “This record is a testament to the continuous pursuit of operational excellence and our innovation in cutting-edge technology that enhances our direct reduction plants’ production capabilities while reducing the environmental footprint.”
For further information, log on to www.tenova.com
Maxcess, a supplier of products and services for automated web handling applications, has launched the new Tidland SmartSlit automated slitting system. Tidland SmartSlit ensures automatic and precise placement of slitting blades, says the company, eliminating the need for manual adjustments, and reducing set-up time.
“SmartSlit is ideal for tag and label producers and narrow web converters looking to
automate manual finishing operations or add finishing operations to their current lines. It is a safe, versatile, user-friendly solution to slitting operations, significantly enhancing productivity, and reducing operational costs,” said Richard Provencher, global product manager for Tidland slitting and winding. “Our automatic machinery movement minimizes manual hand adjustment and reduces safety concerns and operator errors.
Users get improved ergonomics and greater accuracy versus manual position alternatives. You can also store repeat jobs for reuse later. The best part is Tidland SmartSlit usually pays for itself in less than two years compared to manual systems on the market,” Provencher concluded.
For further information, log on to www.maxcessintl.com
Kyocera Unimerco, a specialist in cutting tool solutions, has introduced two new hydraulic chucks, the Hydro Chuck Uni and the Hydro Chuck HD, developed for precision drilling, milling, threading, and other machining operations.
Hydraulic chucks use a hydraulic mechanism to securely clamp tools such as drills, milling cutters, or thread cutters and other cutting tools. Pressurised oil ensures the tool is firmly held in place while simultaneously minimising disruptive vibrations, enabling stable and precise operation.
Kyocera Unimerco presents two hydraulic chucks, each for different applications:
� Hydro Chuck Uni aims to provide high precision across a wide range of machining tasks
� Hydro Chuck HD (Heavy Duty), has been specifically engineered for cutting (HPC) applications, and is capable of withstanding extreme torque
Both chucks are suitable for tools with various
shank types and diameters ranging from 6-32 mm, without the need for special sleeves or adapters. During operation, the hydraulic mechanism provides vibration damping and ensures a run-out accuracy of less than 0.003 mm, says the company. An adjusting screw allows for axial length adjustment.
Both chucks offer a balance grade of G2.5 at 25,000rpm/Umax < 1 gmm, and the tool shanks meet h6 quality standards.
For further information, log on to www.kyocera-unimerco. com
Seals are crucial for ensuring the efficiency and reliability of steelmaking operations. Contaminants and process fluid within the lubricant are detrimental to bearings, a well-known issue among operators and maintenance engineers. When examining a mill chock, it’s common to
see significant water spillage from the bearing, as they are often exposed to water during operations. Proper seals, sealing systems, and regular maintenance can significantly reduce or eliminate this problem. SKF sealing solutions are designed to endure these conditions, offering a way to
extend the lifespan of essential equipment and lower unplanned downtime and maintenance costs.
With the acquisition of Tenute SRL, SKF hopes to offer even more advanced solutions. Tenute’s proprietary skills and designs aim to enhance the
durability and performance of seals, ensuring they can endure extreme temperatures, high speeds, and heavily contaminated environments.
SKF sealing solutions offering includes heavy industrial shaft seals, hydraulic seals for heavy-duty cylinders, and a range of engineered solutions
for specific applications. By combining SKF’s knowledge with Tenute’s technology, customers can expect improved reliability, reduced maintenance costs, and enhanced OEE, says SKF.
Commenting on the acquisition, industry expert Robert Blachfellner stated, “The integra-
tion of Tenute SRL’s advanced sealing technology with SKF’s extensive industry experience is a game-changer for the steel sector.”
For further information, log on to www.skf.com
Are you searching for ways to enhance process reliability while minimizing maintenance expenses?
Look no further than SKF Seals. Our commitment to manufacturing excellence and improved Overall
Discover
Equipment Effectiveness (OEE) makes us the go-to solution for cost-effective and dependable machine operation.
At SKF Seals, we understand the importance of reliable processes in achieving operational efficiency.
Cleveland, Ohio-based Cleveland-Cliffs announced in early November that it had successfully completed the Stelco Holdings acquisition process after the former received the regulatory programme approvals for its Stelco acquisition under the Investment Canada Act and Strategic Innovation Fund.
By Manik Mehta*
CLEVELAND-CLIFFS, a leading North American steel producer, with focus on value-added sheet products, particularly for the automotive industry, is vertically integrated, including the mining of iron ore, production of pellets and direct reduced iron (DRI), and processing of ferrous scrap through primary steelmaking and downstream finishing, stamping, tooling and tubing.
Cleveland-Cliffs maintained that the Stelco addition had further strengthened its position as North America’s largest flat-rolled steel producer, and would diversify Cliffs’ end-markets and expand its geographical presence in Canada. Stelco, Cliffs added, would continue operations as a wholly-owned subsidiary of Cliffs, ‘preserving the name and iconic Canadian legacy of the business’.
Lourenco Goncalves, chairman, president and CEO of Cliffs, called the acquisition a ‘transformative step forward for ClevelandCliffs’. “By bringing Stelco into the Cliffs family, we are building on our commitment
to integrated steelmaking and good paying union jobs in North America. This acquisition allows us to further diversify our customer base and lower our cost structure,’’ he said.
In keeping with Federal Securities Laws, Cliffs also cautioned that any forwardlooking statements would be subject to risks and uncertainties. The company
*US correspondent, Steel Times International
listed some risks including the continued volatility of steel, iron ore and scrap-metal market prices, disruptions of operations, and reduced demand for the company’s products.
Tariffs are worrisome, particularly, to USbased steel-consuming SMEs which have been affected by tariffs and, in effect, by higher import prices. The nation’s established steel producers, with trade unions also pitching in for higher steel tariffs to protect jobs, have worked closely with politicians, amid the feverish election campaigning, courting both producers and workers, and pledging to restrict the heavily-subsidized and polluted steel shipped by certain countries, including China.
Tariffs weigh heavily on steel-consuming industries, particularly the nation’s SMEs, which depend on imports. Their production costs have risen sharply following rising prices of imported metals and other raw
materials, as some participants attending the three-day World Trade Centre Association (WTCA) Forum 2024, held in New York at the end of October, told Steel Times International
John Drew, the chairman of the WTCA acknowledged in an interview that some SMEs had expressed concern about tariffs and, in effect, higher prices. “We were told that some SME members of the WTCA are worried over higher prices resulting from tariffs that have raised the overall costs of foreign supplies,” he said.
Indeed, some small companies told this correspondent that they faced issues with price-conscious consumers that seek relief from the high inflation that affected basic necessities. They argued that when the US government imposed a tariff on, say, foreign-made steel, it meant that US steel-importing companies had to pay an extra fee to import the commodity into the country.
The added tariff cost is then passed on to US manufacturers, who pass it to consumers through higher prices of products that contain steel, such as cars, washing machines and outdoor grills, etc.
After the US imposed a 25% tariff on steel imports in 2018, US-built cars cost more by about $400 per vehicle, cost of an average single-family home construction rose by about $7,000, and kitchen appliances by up to 7%.
Cheaper domestic steel? Not neccessarily
SME representatives also reject the argument that the added cost of tariffs make domestically-produced steel and products using steel cheaper by comparison. “That’s a simplistic view…a tariff raises the price of imported goods. However, domestic producers would raise their prices without fear of being undercut
by foreign competition. This means higher prices across the board, whether you’re buying imported or US-made products,” explained Richard West, a New York-based analyst.
Following the 25% tariff imposed by the US in 2018, according to a price analysis, prices of many items surged. Within a few months, prices of washing machines, both domestic and imported, rose 12%, with the extra cost being paid by US consumers.
But, as some argue, tariffs also deter US buyers from engaging in any large-scale imports of heavily-subsidized and polluted steel from China.
China’s exports face tariffs in other markets
China, as the world’s biggest steel producer, is also the biggest exporter of the metal. After its exports touched the level of 10Mt a month in 2016, exports started to decline following the imposition of tariffs, a slow-down in China’s manufacturing activities and the slump in China real estate development, which is a major source of steel consumption. While exports, meanwhile, have surged again this year and are expected to cross the 100Mt mark, touching almost the 2016 level, some analysts, for example, at the Macquarie Group, predict that the country’s steel exports would decline to about 96Mt next year.
China’s massive surplus of steel produced is dependent on demand in foreign markets, with the US being an important buyer until the onset of the tariffs.
But US steel tariffs are also encouraging other markets to follow the US example and stem the Chinese steel import tide. Thailand, for instance, imposed antidumping duties of 31% on hot-rolled coil and high-strength steel, the latter being used for critical infrastructure construction.
Even Mexico, which Chinese steel companies use to take advantage of the USMCA trade pact to penetrate into the US market, imposed a tariff on some Chinese steel exports late last year. Canada, Brazil and others have followed suit.
Chinese steel producers have, traditionally, turned their attention to another country when one country imposed trade restrictions. China is also eyeing the Indian market with its ambitious infrastructure plans that will generate huge steel demand. India, itself a major steel producer, may have to eventually buy some foreign steel if its insatiable demand for steel cannot be met from domestic production. Indeed, the Indian government also recently imposed tariffs ranging from 12% to 30% on some steel products from China and Vietnam.
While President Joe Biden’s administration has staunchly supported Ukraine and tried to mitigate the hardships of the Ukrainian people with humanitarian, economic and military aid, with an estimated overall $100 billion following Russia’s invasion, a muchanticipated event for the US industry is the Ukraine Reconstruction Conference 2025 to be held next July; Western companies, including American, hope that details of Ukraine’s reconstruction programme will then be revealed. Much of the country’s infrastructure has been damaged or affected by the ongoing war. Infrastructure projects are expected to generate strong demand for steel.
The Ukraine reconstruction plan will open up projects for Western and US companies to participate in the reconstruction of the war-ravaged country’s infrastructure, inherent with potential for steel and steelbased products. �
Tebulo Robotics specializes in the design and supply of innovative robotic solutions that operates under extreme conditions. With our many years of experience, knowledge in technology and driving forward advancements in engineering and robotics, we are able to offer a wide range of superior solutions that accelerate industrial processes.
Tebulo Robotics creates high quality robot applications that are the solution for making industrial processes faster, better, safer, cleaner and more productive.
Key features include:
• Coil dimensional control system,
• Weighing system
• Spray-paint marking system for visual product identification
• Automatic traceability system for the welded joint,
• Laser marking for the binding wire
• Exhausted coil recognition system
The New Horizontal Compactor Machine HCM400-4W is a fully automated horizontal compactor designed for tying multicoils.
The machine handles coils that weight between 1 and 5 tons and measure between 1200 mm and 1600 mm in diameter
The system achieves a complete loading and unloading cycle in just 2.5 minutes. The compactor can also be installed in wire rod mills ensuring a compacting cycle time of 33 seconds.
Combilift’s range of multidirectional forklifts, pedestrian reach trucks, straddle carriers and container loaders will allow you to maximize the capacity, improve efficiency and enhance the safety of your facility.
Contact Us Today
To find out how Combilift can help you unlock every inch of your storage space.
Mining companies Vale and BHP have reached a settlement with Brazilian authorities following the 2015 Mariana disaster. By Germano Mendes de Paula*
VALE and BHP, each owning 50% of the iron ore pelletizing company Samarco, finalised a definitive settlement of R$170 billion (approximately $30 billion) with Brazilian authorities in late October 2024, in regard to the Mariana disaster. The tragedy, which took place in November 2015, involved the rupture of a structure containing mining waste, resulting in the loss of 19 lives and a subsequent inundation of mud and mining byproducts that devastated large areas, sweeping away homes and contaminating rivers while impacting local ecosystems and communities. The pollution even reached the Atlantic Ocean’s coast in the state of Espírito Santo. Four years post-disaster, another tailings dam managed by Vale failed in Brumadinho, resulting in 270 fatalities. These tragedies prompted Brazilian authorities to legislate the gradual elimination of upstream tailings dams, which, while cheaper, are deemed more hazardous than downstream options. Both Mariana and Brumadinho are located in the
state of Minas Gerais, where Vale conducts extensive iron ore mining activities.
The agreement
Vale has not only confirmed the definitive settlement related to the Mariana disaster, but has also outlined expected cash disbursements for the next two decades.
This settlement encompasses both past and future obligations intended to support the people, communities, and environment affected by the dam failure. The obligations are categorised into three main areas: a) R$100 billion dedicated to instalment payments over 20 years to the federal government, the states of Minas Gerais and Espírito Santo, and municipalities for funding compensatory programmes and related public policies, adjusted for Brazilian inflation; b) R$38 billion linked to amounts already spent on remediation and compensation; and c) R$32 billion related to performance obligations by Samarco, covering individual indemnification, resettlement, and environmental recovery
initiatives.
Disbursements for Vale, BHP, and Samarco are expected to peak at R$22.8 billion in 2025, with a substantial R$12 billion disbursement in 2026, which will then decrease to an average of R$5.9 billion from 2027 to 2030 and further to R$5.1 billion during the years 2031 to 2043 (see Table 1). Samarco will be responsible for the net disbursement difference between the total agreement and contributions from Vale and BHP, starting its payments in 2025 and increasing from R$1.5 billion in 2028 to R$1.9 billion in 2029, reaching R$2.9 billion in 2030, and maintaining an average of R$5.1 billion from 2031 to 2043. This means that of the remaining R$132 billion to be disbursed, approximately R$73 billion (or 55%) will be funded by Samarco itself. Financial analysts have reacted positively to the implications for Vale. JP Morgan noted: “Minimum dividends are not at risk, but extraordinary dividends might be. After adjusting our models to incorporate Q3 results and new cash disbursements,
* Professor in Economics, Federal University of Uberlândia, Brazil. E-mail: germano@ufu.br
The Thermo Scientific™ ARL iSpark™ Plus Series OES Metal Analyzer uses single-spark acquisition to provide rapid elemental analysis—up to 15% faster than previous models. The increased speed and reliability minimize tap to tap times, save energy, reduce carbon footprints, and realize a faster return on investment.
Capable of providing ultra-fast, on-line analysis of nonmetallic inclusions, the ARL iSpark Plus adds to the versatility, dependability, and productivity of metal processing operations.
we expect Vale’s ability to pay minimum dividends to remain unchanged. From a credit perspective, Vale’s balance can remain conservative despite the increased settlement amount”. Itaú BBA Bank remarked: “This is a win for the government and society, as well as for Vale. If an agreement is indeed reached, it will be one of the largest settlements in Brazil’s history. We also welcome the potential end of one of the most significant overhangs on the stock in recent years. This will allow the incoming management to fully focus on the company’s short and long-term operating strategies”.
UBS added: “We see this as a positive for Vale (albeit widely expected) as it lifts a significant overhang and suggests relations with the Brazilian government and society more broadly may be starting to normalise. Vale’s view is that the closing of the settlement is an important indication that Brazil is the right jurisdiction for this case. The company believes the Brazilian settlement undermines the case in the UK, since the key argument was that the case needed to be moved to London because there was no solution being provided in Brazil”. Notably, the settlement announcement coincides with the beginning of hearings in the High Court in London for a separate multi-billion-pound lawsuit against Vale and BHP, representing approximately 620,000 alleged victims.
Samarco’s production
Financial analysts have primarily focused on Vale’s cash flow as it is a crucial determinant of the company’s valuation. However, for the steel industry, the outlook for Samarco’s production is more
interesting. Its production capacity is 30Mt/yr, and prior to the dam rupture, it produced about 27Mt/yr. Operations in the states of Minas Gerais and Espírito Santo were suspended until 2020, when the first recovery phase commenced, limited to 9Mt of annual production with some equipment operational. The second phase aims to escalate production to 15Mt/ yr, originally planned for Q1 2025, but is now set to start ramping up in December 2024. This increase required an investment of R$1.6 billion and the creation of 3000 jobs, all of which have been filled along 2024. Currently, the company generates approximately 15,000 jobs, both directly and indirectly. The third phase is expected to commence in 2028, with the goal of returning to pre-2015 production levels. Notably, the company has eliminated the use of tailings lagoons in its processes; instead, waste is now filtered and stacked dry in a designated area in Mariana, with a
smaller fraction being disposed of in a pit.
Samarco’s financial situation
By accelerating its production plan from the current 9Mt/yr to 15Mt/yr of pellets, Samarco anticipates a corresponding increase in revenue. In August 2024, the company projected that it would close the year with approximately $1.2 billion in revenue, and that the planned production increase could elevate sales to between $1.8 billion and $2.0 billion, assuming prices remain similar to current levels. Since resuming operations in 2020, Samarco has reportedly experienced cash surpluses that enabled it to allocate $2.2 billion for repair efforts following the catastrophe. The financing for the current expansion has also come from these cash reserves, offsetting the need for debt or additional shareholder contributions. Samarco claims to have been fully operationally independent since 2020. Nonetheless, although it has paid its debts to employees and suppliers, it is still under a reorganization plan. Indeed, it still faces substantial debt obligations with bondholders from notes issued prior to the 2015 disaster. In December 2023, as part of its recovery plan, Samarco issued new bonds worth $3.98 billion, scheduled to mature in 2031.
It took nine years to reach an agreement between Samarco (and its shareholders) and the Brazilian authorities regarding the Mariana tragedy. For the steel industry, this resulted in the suspension of Samarco’s operations until 2020. The company is now recovering to half of its installed capacity; it will only return to pre-accident levels in 2028. �
AMID a global economic slowdown, major importing countries have imposed trade restrictions such as safeguard duties, import taxes, and quotas to reduce dependency on imports and fulfil domestic demand with local products.
According to the Joint Plant Committee (JPC), a division of India’s Union Ministry of Steel, finished steel exports from India dropped to 2.31Mt in April-September 2024, a 36% decline from 3.6Mt in the corresponding period the previous year. Following a peak of 13.49Mt in the financial year (FY) 2021-22 (April-March), India’s finished steel exports declined steadily to 7.49Mt in FY 2023-24. If the current trend persists, steel exports are projected to fall to 4.62Mt for FY 2024-25, a decrease of 39% year-on-year.
In contrast, steel imports have continued to rise. During April-September 2024, India’s steel imports surged by 41% to 4.7Mt compared to 3.33Mt in the same
Source: Joint Plant Committee (JPC), Ministry of Steel, Indian government; Period from April to March; *April-September 2024
Source: Joint Plant Committee (JPC), Ministry of Steel, Indian government
period last year, resulting in a net import balance of 2.39Mt. This shift reverses the government’s goal of boosting exports and reducing imports, with imports now exceeding exports by a substantial margin. In response, the domestic steel industry
has called for protections against low-cost imports from China and intermediaries like Vietnam, seeking measures similar to the anti-dumping and safeguard duties imposed by the United States, European Union, Canada and other nations.
India’s steel exports fell sharply by nearly 36% in the AprilSeptember 2024 period as several countries heightened protectionist measures to curb cheap imports and protect local industries.
By Dilip Kumar Jha*
years. Italy emerged as the largest importer of Indian steel, with total volume rising to 1.04Mt in FY 2023-24, followed by Vietnam at 0.87Mt and United Arab Emirates (UAE) at 0.7Mt. Additionally, several Middle Eastern countries have increased their imports of Indian steel. In FY 2018-19, Vietnam was India’s biggest importer of steel at 2.4Mt, followed by Nepal at 1.9Mt, Italy at 1.3Mt, and UAE at 0.9Mt.
Meanwhile, India’s steel industry is already grappling with cheap imports from China and faces further challenges in meeting the European Union’s Carbon Border Adjustment Mechanism (CBAM)
The decline in India’s steel exports is primarily driven by two key factors: a contraction in global demand and the implementation of protective trade measures by multiple countries. According to the World Steel Association, global steel demand fell by 1.1% to 1,763Mt in 2023 during the January-August 2024 period, with production dropping by 1.5%. Amid a global economic slowdown, major steelimporting nations have increased trade barriers.
India’s steel sector now faces a challenging environment as numerous countries have introduced protective tariffs against low-cost imports and alleged unfair trade practices. The European Union, for example, has imposed anti-dumping duties of up to 25.3% on cold and hotrolled stainless steel, along with a 25% safeguard tariff on steel imports exceeding specified quotas. Similarly, Brazil, Mexico, and the United States have adopted similar measures, with the United States levying
anti-dumping and countervailing duties as high as 190.71% on stainless steel sheets and coils.
Several Asian countries, including Vietnam, Thailand, and Malaysia, have also introduced trade measures aimed at imports of hot-rolled coil and tinplate from India, China, and other sources. This global shift underscores a broad push to protect domestic steel industries from international competition and concerns about excess capacity. India remains susceptible to trade diversions due to a lack of comparable protective measures. The United States and Canada imposed 25% safeguard duties, while the European Union has enforced a 25% duty on imports beyond set quotas. Recently, countries such as Turkey, Indonesia, Malaysia, Vietnam, and Japan have taken swift actions to shield their markets.
There has been a substantial shift in shipment destinations over the past four
requirements, set to take effect in January 2026. The European Union’s safeguard measures, in place since 2018, have significantly reduced India’s export volumes to the EU, leading to considerable financial losses. Despite rising inventory levels over the past two years, India’s steel imports have continued to grow. “This is a matter of concern and points to the fact that imported steel is crowding out domesticallyproduced material to a large extent and, therefore, needs to be curbed with a high import duty”, said T V Narendran, managing director of Tata Steel.
Steel prices in the domestic market have been steadily declining, driven by falling international prices and low-priced steel dumping by China. The Indian Steel industry has been urging an increase in basic customs duty on steel imports to curb steel shipments from China, both direct and indirect. Meanwhile, the Ministries of Commerce and Finance are evaluating the situation to consider potential safeguard measures. �
Upcycling steel scrap is a key step to achieve the sustainability of the steel sector. The University of Warwick’s Advanced Steel Research Centre, has been extensively researching technologies to enable steel scrap upcycling in the whole steel value chain to improve scrap quality for producing high-quality steels via scrap-based EAF steelmaking, and to understand the effects of residual elements on the downstream manufacturing process.
By Zushu Li and Claire Davis*
GLOBAL steel scrap supply, as estimated by the World Steel Association, stood at 400Mt in 2019, and will increase to 600Mt in 2030 and 900Mt in 2050.1) The scrap supply varies according to different territories, with developed countries/regions such as the USA, Europe and the UK being net scrap exporters. The UK exports 80% of the domestically generated 11Mt steel scrap per year. 2) In developing countries, the scrap supply increases alongside their economic development. Using China as an example, after experiencing a period of unprecedented economic growth, the scrap supply is estimated to significantly increase from 260Mt in 2022 to 600Mt in 2050, while crude steel production is estimated to decrease from 1,035Mt to 690Mt in the same period.3) Recycling 1t of steel scrap saves 1.4~1.5t of iron ore, 0.5~0.6t of coal, and up to 75% of the energy required for primary steel production. Because of its critical role in decarbonizing the steel sector, EUROFER (the European Steel Association) called on the European Union
to include scrap metal in the list of critical raw materials.4)
Steel is considered 100% recyclable, and scrap quality is not considered a big issue while steel manufacturing is dominated by the iron ore/fossil fuel-based integrated process. However, under the scenario of increased scrap supply and the transition to scrap-based EAF steelmaking resulting from the urgent decarbonization agenda, the residual elements in the scrap due to repeated recycling will gradually increase to a level that the steel scrap cannot be used to make higher or even equivalent quality new steels.4,5) For example, the current handling practice for end-of-life vehicles is to shred the whole vehicle in mass production and generate shredded scraps containing 0.20~0.35% Cu, which cannot be used to make high-quality automotive steels (such as exposed sheet steels requiring <0.08% Cu via the scrap-based EAF steelmaking route) unless significant dilution is made with ore-based metallics (OBMs).
Different countries/regions have their own scrap specifications or standards, classifying scrap into tens of types. All these classifications are primarily based on the scrap sources (e.g. old scrap, heavy scrap, rails, construction), processing methods (shredded materials, bales), dimensions, bulk density, and health and safety implications. Only the EU scrap specification lists the maximum value of residual elements for some types of steel scrap, other than that, no other scrap specifications/standards list the maximum residual element content let alone the full chemistry of the scraps. No international standard is available for steel scrap, which is probably because the scrap quality (e.g. residual element level) varies significantly with countries/regions. The scrap (e.g. rail scrap) in the countries/regions with the BFBOF integrated route being the dominant steelmaking process most likely have much lower levels of residual elements than those in the countries/regions with the EAF route being dominant.
*Professors Zushu Li and Claire Davis are both with the Advanced Steel Research Centre (ASRC) within the academic department WMG, at the University of Warwick, UK (z.li.19@warwick.ac.uk)
One of the key tasks for steelmakers is to make the right steel chemistry in the heavy end of the manufacturing process, which will be extremely challenging to achieve without knowing the chemistry of the scrap, the main metallic charge in scrap-based EAF steelmaking. To upcycle steel scrap, steel scrap specifications/ standards should have at least the residual elements and alloy element contents. However, considerable efforts have been made by the steel community, but it is still not successful in developing technologies to measure the chemistry of either bulk or loose scraps. Alloy elements in steel scrap are unknown and will distribute slag and dust (off gas) during steelmaking, which potentially causes issues with specifications and the recycling of slag and dust, with chromium and vanadium being exemplary elements. The waste of alloy elements also reduces the material’s efficiency as ferrous alloys are expensive and produce more CO2 emissions than the steel itself. This is the area requiring careful consideration.
While the residual elements in steel scrap are fundamentally causing the downcycling issues, removal of the residual
elements in the solid state and/or in the liquid steel has always been attractive. In the solid state, various methods have been developed to remove the residuals in the ‘free’ state, either in coating or as free objects intertwined with scrap. Because of the increase in the residual element levels in the steel itself, removal of residual elements in liquid steel, if successful, will be beneficial. Measures such as using chlorine, sulphide, solvent extraction and vacuum evaporation have been developed successfully in laboratories with some – like the sulphide method – being trialled at pilot scale, however, none of them have been industrialised for various reasons. In the future it might be possible that a method to remove residual elements can be implemented in the industry with technology advancements.
While the removal of residual elements in a solid state and/or in liquid steel is not practical now, attention has been shifted to improve the scrap quality from the beginning, that is in the stage of scrap sorting. Significant changes are required to improve the current scrap sorting processes, including clear control of the
scrap sources, and intensified scrap sorting. In the long-term, designs for disassembly, materials passport, selective disassembly, and, for certain steel grades, closed-loop recycling, are potential routes to follow to significantly improve scrap quality.
The residual element level is only one side of the scrap quality issue. Other important factors include the consistency of the scrap quality, compatibility with steel chemistry and sterile content. The sterility in the scrap increases energy consumption, flux consumption, yield loss, and cost. Steelmakers should place more attention on scrap value rather than scrap price in the scrap-based EAF route. Artificial intelligence has started to find its application in scrap sorting and quality control in combination with advanced analytics. Our research mainly focuses on the computer visionbased algorithm development for object detection for scrap recyclers to selectively remove non-steel items on the conveyor belt such as ‘copper meatballs’, and another application is to provide a tool for scrap quality estimation when scrap comes into the steelmakers’ scrap yard (weighing bridge) and during scrap charging. This
In-Line Profile Measurement Systems for Hot / Cold Steel Applications with increased sampling rate up to 2 kHz.
10+ Years
Over 10 years of
Benefits:
Best measuring accuracy thanks to temperature-stabilized measuring systems
New algorithms for surface inspection and defect detection
Defect detection based on multiple maps and surface properties (reflectivity and intensity)
Detects process problems at an early stage
Quick maintenance and easy cleaning
Profile measuring solutions with global references
area requires significant efforts as currently there are no effective tools to measure scrap quality either in loose materials or in bulk materials.
Scrap melting has long been studied, however, in scrap-based EAF steelmaking, this topic will become more challenging due to current decarbonization targets. In BOF steelmaking, the carbon content of hot metal will help melt steel scrap. In scrap-based EAF steelmaking with the addition of hydrogen direct reduced iron (HDRI), the lack of carbon will extend the melting of scrap and HDRI, and at a higher temperature, a focus area of our study.
Increasing the residual element content in steel can affect every stage of its downstream production and use. During and after the solidification of steels with residual elements, in the higher temperature region (>1200 °C), interdendritic segregation of P, S, Si and Mn can cause a hot-tearing problem, while for the lower temperature region (<1200°C), inter-granular fracture can occur due to embrittling precipitates (fine (Fe,Mn)S or Nb(C/N) or copper-oxy-sulphide/coppersulphide particles), surface hot-shortness due to Cu, and hot cracking due to solidstate segregation of Sn. By optimising the cooling rate, the deformation temperature (for strand straightening operations during continuous casting), strain rate, chemical composition and the above-mentioned hotductility problems, can be minimised.6)
During the steel reheating phase (~1200 °C), the preferential oxidation of iron will leave the noble element Cu in the liquid metallic state at the oxide-steel interface and along the austenite grain boundary. This is intensified by the presence of Sn
and Sb through reducing the solubility of Cu in the austenite phase and forming a low-melting point liquid phase. Upon deformation (hot rolling), the steel cracks in the form of surface hot shortness.7)
Residual elements such as Cu, Sn, Ni may significantly slow recrystallisation, which can increase the deformation resistance and rolling loads during hot rolling. In a recrystallisation kinetic study of low carbon steel (0.17%C) using dilatometry, the addition of residual elements (0.58 wt% Cu, 0.30 wt% Ni, 0.06 wt% Sn) greatly reduces the start and finish temperatures of recrystallisation at varying cooling rates from 0.05 to 50 °C/S and increases hardenability due to the residual elements.8)
Microstructure examination under varying cooling rates revealed that the residual elements can distribute in the steel matrix (e.g. ferrite phase) in the form of atomic or precipitates, along the grain boundaries, and concentrating on specific phases such as the cementite phase, which reveals the mechanisms of residual elements affecting the strength and formability of steels.8,9)
Extensive research facilitates the development of effective strategies for minimising the detrimental impacts of these residual elements, through improved scrap sorting, advanced alloy design, and optimized thermomechanical processing techniques. One important strategy is to utilise the presence of residual elements in a positive way to reduce the need for deliberate alloying additions, for example, if the effects of residual elements on strengthening and recrystallisation control are well understood, it could lead to a reduction in the amount of Nb required for those specific effects.
In summary, upcycling steel scrap will play a key role in achieving steel sustainability. Significant efforts are needed to ensure that scrap quality is compatible with steel chemistry, and understanding the impact of residuals on processability and steel properties can help adjust process parameters and develop new alloys with higher residual element levels. �
References
1. 2021 fact sheet – scrap use in the steel industry. https://worldsteel.org/wp-content/ uploads/Fact-sheet-on-scrap_2021.pdf.
2. R. Hall, W. Zhang and Z. Li (2021). Domestic scrap steel recycling – economic, environmental and social opportunities (EV0490). University of Warwick.
3. G. Wang et al. SSCAE. Vol26(3) 2024. DOI 10.15302/J-SSCAE-2024.03.004.
4. https://www.eurofer.eu/press-releases/ ensuring-access-to-critical-materials-for-steeland-wind-sectors-essential-for-eu-clean-techeconomy
4. S. Spooner, C. Davis and Z. Li: Ironmaking & Steelmaking 2020, pp.1100-1113.
5. K. E. Daehn, A. C. Serrenho, J. M. Allwood: Environmental Science & Technology. 2017 (51), 6599-6606.
6. I. Kapoor, C. Davis and Z. Li: Ironmaking & steelmaking, 2021, VOL. 48, NO. 6, 712–727.
7. I. Kapoor, C. Davis and Z. Li: Steel Research International. 2024. DOI:10.1002/ srin.202400116
8. J. Duan, D. Farrugia, J. Poplawsky, C. Davis and Z. Li: Materialia 2024. https://doi. org/10.1016/j.mtla.2024.102141
9. J. Duan, D. Farrugia, C. Davis and Z. Li: Ironmaking & Steelmaking. Vol 49(2022). Pp.140-146
Steel scrap has the potential to become the raw material to meet close to half of global steel demand. However, to unlock its full capability, steelmakers must invest in a combination of innovative sorting processes, and inline analytics. By Heiner Guschall*
ECONOMISTS are predicting that available steel scrap will increase until 2050. This prediction is based upon the mean lifecycles for steel-based products and their cyclic entry into the scrap market. Most available scrap is situated in the northern hemisphere. Europe and the USA have enough domestically available steel scrap to support over 90% recycled steel. In contrast the southern hemisphere has the iron ore deposits and low-cost energy resources to support a hydrogen reduction process to meet their steel product demand. One quarter of the sector’s CO2 emissions arise from transporting raw materials across the globe. If steelmaking is to have a lowcarbon future, then we should accept and work with consuming raw materials that are domestically available.
scrap
Steel scrap has a history of being downcycled from high-quality end-of-life products, which are melted into longproducts with lower chemical requirements. If Europe is to transition steel into a lowcarbon emissions product, the downcycling must be reversed.
This goal is not only feasible but also economically advantageous. Efficient decontamination is an established process, but not universally used. If this step is supported with an integrated online analysis, steelmakers will have a raw material with high Fe levels (up to 98%) that can be consumed effectively and charged into a furnace with an accurately established chemical makeup in its ‘cold’ condition. The control of scrap quality is managed by commercial enterprises with
business models driven by throughput and profit. Unless consumers of this scrap demand better quality, quantity will continue to determine value. The result of this focus on quantity over quality has seen an observable decline in density (in the case of shredded scrap), increased contamination, and a reduced Fe content over the past years. The demand for improved consumer products has seen a growth in the use of non-ferrous metals to enhance product automation. This increased consumption of non-ferrous materials has added a layer of complexity to the decontamination of these enhanced end-of life products.
Over the last 20 years, the mean Fe content of steel scrap has frequently reduced to less than 90% and the mean melt Cu has increased to 0.37% for
*Founder, co-partner, and managing director of SICON GmbH, a company that has specialized in the processing of ferrous and non-ferrous metals for over 25 years.
shredded scrap. If nothing changes, melt Cu will reach 1% by 2050 (Cambridge University). As Cu and other elements are alloyed in the steelmaking process they cannot be successfully removed from steel once it has been melted. This contamination presents a cumulative issue upon each cycle of the recycling process, making it increasingly difficult to blend or dilute.
Decontaminating steel scrap by innovative refining techniques
The quality and chemistry of steel scrap is critical to efficient production. According to EU scrap grade specifications, the copper content in grade E40 should be a maximum of 0.25%, yet it currently stands at 0.37%. Since copper and other critical elements cannot be efficiently removed from liquid steel, blending in high-cost raw materials, such as scrap grade E8 or DRI/HBI, becomes necessary. Innovative techniques in scrap
processing and advanced online analytics offer the key to escaping this cycle of quality degradation and will sate the demand appetite for higher scrap input rates. These easily implementable tools are essential for the quality control of raw materials while delivering economic opportunities.
SICON GmbH, offers a range of modular tools referred to as ‘Refining’ and focuses on grades E40, E46 and E1 (HMS 1/2). The range includes ScrapTuning®, EcoScan® Online, and HMS Cleaning Advanced.
The necessity for implementing such procedures in raw material preparation varies depending on the plant, location, and production programme. In general, the scrap mix is based upon subjective specifications and not objective, measured properties. AI-based predictive models for scrap quality work well if the steel scrap has no attached materials, copper wires, aluminium castings or weight-reducing plastics. AI solutions can be used to support
analyses coupled to a steel scrap blending facility.
The ScrapTuning® and HMS Cleaning Advanced tools pursue three main objectives:
a) Concentrating the metallic Fe
b) Complete decontamination from inert materials, non-ferrous metals, non-metallic components, and composite materials
c) Isolation and separation of steel scrap particles with high inherent residual content (Cu, Ni and Cr)
Sicon HMS Cleaning Advanced has proven effective in numerous steel plants to decontaminate sheared scrap. In its standard configuration, HMS Cleaning Advanced includes uniform dosing, screening, and iron separation. The cascading screening ensures that the shearing scrap is tumbled, enhancing decontamination. The isolated contaminants contain high-value nonferrous metals, easily sold to recover operating costs.
Current magnetic separation facilities are inefficient and require stronger magnetic fields with enough space to support effective separation of the magnetic from non-magnetic materials. This approach increases efficiency to 99%.
The scrap sector often uses pressing operations to compact loose light gauge scrap into dense bundles. This increase in density reduces transport costs for the supplier and improves basket density for the steelmaker. The downside is that contaminants cannot be removed, and the bundle’s chemistry is unmeasurable. To resolve this issue, a newer configuration of HMS Cleaning Advanced includes a slowrunning pre-shredder. The EcoRip® Neo, is part of the Sicon portfolio and specifically designed to address the challenges of scrap bundles via delivering steel scrap at the desired densities, offering complete decontamination and the ability to analyse 100% of the raw material.
Pre-treatment with the EcoRip® Neo homogenizes shearing scrap and further improves cleaning efficiency. This process sequence increases the liquid steel yield in steel plants. An additional step is available for flat-steel producers, which is based upon an AI-based optical inspection, automatically sorting undesirable components. The AI and sorting algorithm are trained and optimized depending on production needs.
• Efficient cleaning of HMS 1/2 at throughputs of up to 300 tph
• Separation efficiency > 99%
• Integration of AI-based quality improvement and online analysis (EcoScan® Online)
• Realization with all necessary conveying equipment up to the meltshop
• Refining of Shredded Scrap to remove all unwanted impurities
• Generation of a Crafted Scrap based on meltshop requirements
SICON GERMANY
Vordere Insbach 26 | 57271 Hilchenbach
Tel.: +49 (2733) 811 76-0 | info@sicon.eu
www.sicon.e u
An essential and integral part of HMS Cleaning Advanced is the continuous massbalancing of material flow. This enables rapid supplier assessment, and a measurable control of quality. Precise data is preferable to visual inspection during the unloading stage. Steel plants importing by sea can accurately process and measure scrap quality at a rate of 300 tph, allowing for complete deliveries to be cleaned and assessed during vessel discharge. As previously noted, the copper content in scrap presents an increasing problem. ScrapTuning® for Shredded Scrap is designed to turn fluctuating supplier quality into a quality-controlled raw material without the need for an in-house shredder. Shredded scrap is cleaned in multiple stages. Only the magnetic separation stage, using polishing magnets, is generally insufficient. Sicon has designed a magnetic cascade with innovative underflow separation, requiring an advanced magnetic design (MagSpin). This process is supported by an additional air separation stage, to isolate and recover the final non-magnetic contaminants, resulting in a melt Cu content of 0.16 to 0.20%.
An additional cleaning stage is also available to reduce melt copper to a maximum of approximately 0.12%. The Sicon EcoFlip™ is a combination of AIbased optical recognition and integrated XRF analysis. The Sicon EcoFlip™ separates alloyed scrap parts above the residual threshold.
Optimized processing and sorting technology alone is not sufficient. Inline
analysis should follow the refining process. Comprehensive and continuous analysis of the scrap composition is crucial. While the approach of inline analytics is not new, techniques and process integration have improved, significantly enhancing performance criteria. Previous negative experiences and high maintenance costs have tarnished the reputation of inline analytics. The modern approach is XRFbased analysis, replacing radioactive neutron sources. This method ensures high precision through a higher count rate for surface elements, even at low concentrations. Simple and fast calibration enhances operational security and measurement stability, keeping costs per ton under €0.50. Online analytics is no longer a luxury but an absolute necessity. By combining sorting with final analysis, scrap quality can meet the limits set by the melting plant based on production planning, identified as ‘crafted scrap.’ Flexible adjustments to target quality are possible. This process overturns traditional thinking and creates the opportunity for the steelmaker to measure chemistry, density and Fe content in the charging basket.
In EAF steelmaking, steel scrap accounts for over 75% of operational costs and its inconsistent chemistry is responsible for it being limited mainly to long products with wider chemical specifications. Moving steel scrap from a subjective physical inspection to a measured objective specification allows steel plants to assess the true value of the raw materials they are consuming. The XRF-based solution, with EcoScan® Online, has proven to be a very precise and reliable solution in numerous facilities.
The combination of refining and innovative online analytics will increase scrap utilisation to the maximum. This is not only a step toward more sustainable steel production, but also an example of the industry’s innovation potential in the decarbonization process.
The steel sector should consider their answers to the following questions:
1. Can steel scrap be engineered to remove the contaminants?
2. Is the technology to achieve this proven?
3. Is the investment to develop a ‘crafted scrap’ lower than developing a (green) hydrogen-based reductant?
One crucial aspect to consider is the substantial CO2 reduction. By using optimally cleaned and refined sheared scrap instead of the commonly utilized HMS 1/2 grades, CO2 emissions can be reduced by approximately 170 kg per ton of crude steel. This calculation assumes a reduction of foreign substances by about 10%, with additional potential savings in transport and other areas not yet factored in.
George Bond, a veteran of the UK steel industry summarized: “Years of successful steelmaking is based upon blending variable iron-ore chemistries into a planned chemistry furnace charge. If steel scrap is to succeed in replacing iron-ore, it must become a fully measured and specified raw material that can be blended into a planned cold charge.” �
A Reducing & Sizing Block for long products keeping its promises. Achieve your goals with KOCKS RSB®
finishing size in round or hexagonal dimensions up to 160mm
increase in production up to 20%
up to 10% energy savings in the mill line
The EU-funded PURESCRAP project, a consortium comprised of 12 industry partners, has taken an ambitious step forward in the area of scrap analysis. By Johannes Rieger1*, Melanie Leitner1, Valentina Colla2, Alice Petrucciani2, Lars Sandberg3, and Jonas Petersson3
FORECASTS reveal that crude steel demand will be 30% higher in 2050 than it is today. Furthermore, increasing scrap availability means that the contribution of scrap in the total steel charge will likely grow to 40% in 2050 from the present level of 30% (see Fig 1).
Limits to the quantity and quality of available scrap also mean that decarbonizing primary (ore-based metallics, OBM) production remains critical to a net-zero future, which includes efforts to enhance the recycling of all available scrap qualities including low-quality post-consumer scrap. An increasing share of post-consumer scrap has also been predicted (see Fig 2 [2]), which will not
allow for the complete recycling of all highquality steel grades.
For some steel grades, tramp elements, such as copper, tin, chromium, nickel or molybdenum, prevent the reuse of large shares of post-consumer scrap. This surplus in low-quality scrap within the EU generates enormous scrap exports. In 2022, these amounted to ~18Mt [3]. On the contrary, higher quality scrap is imported to the EU to fulfill the scrap demand for steel production.
Spectroscopic sensor-based scrap material identification can be done by applying X-rays, spectroscopy with and without the
formation of plasma, or neutron activation [4]. X-ray-based sensors mainly include X-ray transmission (XRT) and X-ray fluorescence (XRF). Plasma-based systems cover Optical Emission Spectroscopy (OES [5]) including Laser-Induced Breakdown Spectroscopy (LIBS [4, 5]). Further spectroscopic systems encompass Infrared (IR) and Near-Infrared (NIR) spectroscopy. Finally, neutron-based systems include Prompt Gamma Neutron Activation Analysis (PGNAA) or Pulsed Fast Thermal Neutron Activation (PFTNA). XRT sensors are used on an industrial scale by metal recyclers in belt-type particle sorters to separate light metal particles (Al, Mg) from dense non-ferrous metals (zinc, copper, brass). XRT is also applied
T1 K1-MET GmbH, Austria; *corresponding author (johannes.rieger@k1-met.com)
2 Sant’Anna School of Advanced Studies - Pisa, Italy 3 Swerim AB, Sweden
to sort out the non-metallics, e.g., from automotive shredder residue [4]. Handheld XRF systems gain importance in manually identifying alloys in the scrap yard by random analysis. XRF penetrates a few µm of the scrap surface, though it faces limitations in detecting light elements. LIBS is a point measurement technology which, in each laser-pulse, analyses surface composition. Although many LIBS systems are being installed at industrial sites, no full-scale LIBS analyzer system with complete area coverage (e.g., installed over a conveyor belt) for steel scrap is available yet [4-8]. IR and NIR are also not yet used for steel scrap (industrial systems exist for the sorting of e.g., glass or plastics [4]). PGNAA and PFTNA are well established in the mining industry to handle large volume flows. Research work was done to apply PGNAA for steel scrap (with no commercial solution available yet). One main challenge for PGNAA/PTFNA is to ensure safe operations due to radioactive materials used (e.g., Californium as a neutron source).
In recent years, digital technologies,
including Artificial Intelligence (AI), have been applied in the steel industry to improve plant efficiency, support maintenance, and optimize resource and energy utilization. Machine Learning (ML) and computer vision were used for scrap recognition and classification [9] by utilizing images from cameras. The model architectures are generally based on Convolutional Neural Networks (CNN), such as the material segmentation and classification model of scrap (3D-2D CNN hybrid architecture) [10]. In addition, several studies were conducted to combine LIBS via ML, including by combining LIBS, ML, and deep learning (DL) and testing different ML algorithms to classify aluminium scrap [11]. Although several ML-based models for image-based automatic scrap detection systems have recently been developed, improvements are still needed to apply them at an industrial level.
Regarding scrap characterization at industrial level, optical scrap inspection is state-of-the-art (SoA). Especially at the scrap yard entrance (for both, the scrap
supplier and the steelmaker) cameras record the incoming scrap on a truck or a wagon. Furthermore, 3D radars (mounted on crane grabbers) are used together with integrated weighing systems to create a 3D profile of the scrap yard and ensure a certain sorting of the different scrap qualities. However, scrap characterization and quality monitoring are often done manually. This subjective assessment, depending on the experience of the operators, provides a suboptimal way for a proper scrap classification.
Compared to the above example, the PURESCRAP project, with a three-and-ahalf-year duration (running since January 2023) and funded within the Clean Steel Partnership of the Horizon Europe Framework Program of the European Union (EU), takes an ambitious, major step forward. In concrete terms, the focus lies on the precise characterization of postconsumer scrap prior to melting the scrap
by applying highly efficient sensor stations (see Fig 3). The PURESCRAP approach goes beyond optimal scrap inspection by combining multiple sensors for a more complete analysis. Each sensor has its own unique advantages and limitations. This exceeds other previous studies, which used individual sensors using optical sensors to guide a LIBS sensor [12, 13]. For implementation in an industrial scrap-processing plant, sensor fusion is a completely novel concept.
The overall project goals are as follows:
• Concepts of a combined spectroscopic and vision system to characterize and analyze heavy and shredded scrap installed at a scrap supplier site
• Improving scrap characterization through image detection and processing models using Deep Learning solutions
• Use of sorted scrap to demonstrate its ability to produce standard steel grades at least in semi-industrial scale
The consortium comprises of 12 partners with a well-balanced mix of industry players (plant builder, scrap processor, steelmaker), academic institutions, research technology organizations (RTOs) as well as the European Steel Technology Platform (ESTEP) as an important link between all stakeholders along the steel value chain. The consortium includes (in alphabetical order) Danieli Automation SpA (ITA), ESTEP
ASBL (BEL), K1-MET GmbH (AUT), Luleå University of Technology (SWE), REDWAVE Competence Centre of BT-Systems GmbH (AUT), Sant’Anna School of Advanced Studies – Pisa (ITA), Spectral Industries BV (NED), SSAB AB (SWE), Stena Recycling AB (SWE), Swerim AB (SWE, Project Co-ordinator), TU Dortmund (GER), and voestalpine Stahl Donawitz GmbH (AUT).
To reach the objectives set, smart combinations of optic and spectroscopic sensors were defined. This was done both to enhance scrap processing (i.e., sorting) efficiency, and improve analysis of scrap batches. The approach of batchwise scrap analysis enables a more reliable planning of scrap charging for crude steel production. Fig 4 shows a test line to train the sensor concept for shredded scrap. The sensor chain comprises of a camera, LiDAR (Laser imaging, detection, and ranging) and depth camera to generate a highresolution 3D map of the analyzed scrap, LIBS, and XRF. The sensors are coupled with a comprehensive information and communication technology (ICT) network and a hybrid ML approach to jointly exploit images and spectroscopic data. The sensor station will be installed on a real shredder line of a scrap processor.
Fig 5 shows the sensor station arrangement of the heavy scrap sensor station. The sensor module (grey part) will be installed at the output of the shear at the site of a scrap processor. Heavy scrap is less complex, but instead provides more demanding surface conditions compared to shredded scrap. The sensor station for
project consortium, planned sensor stations not
heavy scrap has no XRF and the LIBS sensor is mounted on a robot unit. Sensors are again coupled with an ICT network. As one of the main Key Performance Indicators (KPIs), purity levels (limits for non-ferrous tramp elements) were specified for the sorted scrap product (outputs). Among others, limits for copper (ranges 0.05/0.10/0.15/0.20/0.25, all values in wt.%), nickel (ranges 0.05/0.15/0.25) or molybdenum (ranges 0.05/0.25/0.45) were defined (other metals, such as tin were also considered). These KPI values are important to validate the efficiency of the PURESCRAP sensor stations. It is crucial that the qualities of the sorted scrap products are fully in-line with the expectations of the steel producing consortium partners. The long-term goal focuses on the enhanced use of sorted postconsumer scrap to produce standard steel grades without a loss on quality or material properties relevant for final applications. To finally prove that sorted scrap is of sufficient quality to produce standard pre-defined steel grades, sorted scrap batches will be used for steelmaking sequences, at least on a semi-industrial scale. During this, the whole steelmaking and refining chain will be covered starting with scrap melting in a batchwise operated 5-ton induction furnace
to simulate the operation of an electric arc furnace (EAF) for crude steelmaking. This will be followed by secondary metallurgical treatment in a vacuum degassing furnace
and vertical continuous casting into round casted material (Ø 230 mm) or ingots (270x360 mm). Comprehensive material analyses will follow to ensure that typical
properties, such as material strength, are inline with standard steel grade specifications. Furthermore, it is also envisaged to use sorted scrap batches in an industrial-scale Basic Oxygen Furnace (BOF) process.
Environmental impact assessment
As accompanying parts of the PURESCRAP project, Material Flow Analysis (MFA), Life Cycle Assessment (LCA) and Life Cycle Costing (LCC) have been executed in an aim to derive a comprehensive environmental
and economic impact assessment for the reuse of post-consumer scrap. This also provides the basis for a business model development planned within the last period of the project. A cradle-to-gate approach is used for the LCA (life phase of a product, until it leaves the steelmaking production site). Since scrap processors plan to implement comprehensive sensor stations at their sites (possibly also steelmakers), workers at industrial sites need to be prepared since working practices will
obviously change (other handling strategies of scrap, additional effort of maintenance work etc.). This topic will also be covered as part of the project via a social impact assessment. �
Funding information
This project receives funding by the European Union’s Horizon Europe Framework Program (Clean Steel Partnership, Grant Agreement no. 101092168).
References
[1] Mission Possible Partnership, Net-Zero Steel - Sector transition strategy, 2021
[2] Worldsteel Association, Scrap use in the steel industry, fact sheet, 2021
[3] Bureau of International Recycling, World steel recycling in figures, 14th edition, 2023
[4] Brooks, L., Gaustad, G., Gesing, A., Mortvedt, T., Freire, F., Waste Management, Vol. 85, pp. 519-528, 2019
[5] Bengtson, A., Spectrochimica Acta Part B, Vol. 134, pp. 123-132, 2017
[6] Noll, R., Fricke-Begemann, C., Connemann, S., Meinhardt, C., Sturm, V., Journal of Analytical Atomic Spectrometry, Vol. 33, pp 945–956, 2018
[7] Legnaioli, S., Campanella, Poggialini, B., Pagnotta, S., Harith, M. A., Abdel-Salam, Z. A., Palleschi, V., Analytical Methods, Vol. 12, pp 1014-1029, 2020
[8] Pedarnig, J.D., Trautner, S., Grünberger, S., Giannakaris, N., EschlböckFuchs, S. Hofstadler, Jorunal of Applied Sciences, Vol. 11, pp 9274-9319, 2021
[9] Colla, V., Pietrosanti, C., Malfa, E., Peters, K., Environment 4.0: How digitalization and machine learning can improve the environmental footprint of the steel production processes, (2020) Materiaux et Techniques, 108 (5-6), art. no. 2021007, https://doi.org/10.1051/ mattech/2021007
[10] De la Peña, B., Iriondo, A., Gutierrez,
A., Rodriguez, J., Lluvia, I., Vicente A., Steel Research International, Vol. 94 , no. 11, paper no. 2200943, 2023
[ 11] Díaz-Romero, D. J., Van den Eynde, S., Sterkens, W., Eckert, A., Zaplana, I., Goedemé, T., Peeters, J., Spectrochimica
Acta Part B: Atomic Spectroscopy, Vol. 196, paper no. 106519, 2022
[12] SHREDDERSORT Project (EU-funded), Grant agreement ID: 603676
[13] Venturo, A., Pierre, R., Ansseau, O. et al.: Optimization of scrap charge management and related process adaptation for performances improvement and cost reduction (OPTISCRAPMANAGE), RFSR-CT-2014-00007, final project report, 2019
DNV’s recent report, Shaping the future of sustainable steel: Lessons from Europe’s steel industry, spotlighted a number of ongoing challenges within the European sector, with steelmakers continuing to grapple with the complex and changeable obstacles of the global economic landscape. Catherine Hill* interviews Christopher Lilholm**.
COP29, held last month in Baku, Azerbaijan, raised existential concerns not only surrounding the growing divide between wealthier nations and emerging economies, but the efficacy of the conference itself – with climate experts claiming that the talks were ‘no longer fit for purpose’, and required an ‘urgent overhaul’. Amid a bubbling atmosphere of confrontation between environmental campaigners and political representatives, Azerbaijani president Ilham Aliyev informed participants that oil and gas were a ‘gift from God’, adding that his role in their market presence should be without criticism. Cultural and political fault lines have sunk deeper, and gaped wider –with momentum continuing to gather in the approach to 2025. As part of this rapidly shifting global and environmental context, DNV, an independent assurance and risk management provider, published a new report outlining the challenges and opportunities for the global industry in transitioning to low-emissions steel; Shaping the future of sustainable steel: Lessons from Europe’s steel industry, was written following research and interviews undertaken in the preceding climate conference, COP28, held in Dubai.
presence in this area, let’s zoom in from ‘Lean and green’, and make the report more sector specific’’, Lilholm said.
The new report consists of the impressions of 100 professionals, with a specific focus on the European industrial landscape. Researchers interviewed a number of steelmakers, downstream players, and sustainability experts – all with a purpose to gain insights into the complex dynamics of European steelmaking.
The word ‘green’ appears a number of times in the document, referred to as a ‘catch-all term’. What lies ahead for this most context-defiant of colours? ‘‘There is no global defector on what green steel is,’’ said Lilholm. ‘‘I think steelmakers are navigating this, and they are testing the boundaries.’’ The two key areas for an effective definition of green steel, Lilholm felt, are ‘credibility and transparency’; extending to how the steel is produced, and then travels downstream. ‘‘It needs to be clear for the general public, for example, when they are buying a car that claims to be made with ‘low-carbon steel’, as to what this actually entails’’.
Christopher Lilholm, who was part of the launch of the sustainable steel report, noted that the initial basis was a larger report launched during COP28, named Lean and green: building sustainable and costefficient supply chains. This was structured around a set of 525 respondents from operations, the supply chain, procurement, IT, and sustainability, with DNV gathering data quantitively based on their priorities and readiness in terms of efficiency and sustainability. ‘‘We saw promising evidence that some companies were able to do both, without one effort being compromised, and then we thought, since DNV has a big
MCB Group, stated in the report that ‘70% of the material we ship and 30% is scrap.’ ‘‘Meanwhile,’’ he added, ‘‘manufacturers are desperately looking for scrap material. So, we are looking into our whole supply chain to find ways to do this”. Other constraints, according to Lilholm, include a broader ‘access to finance the transition’, as well as the willingness to decarbonize in certain markets ‘where they are not able to immediately benefit from the green premium’.
Further to the issue of regulatory definitions, lies the proverbial concern of scrap, more specifically, its impending scarcity. ‘‘There is a kind of consensus that there is not enough scrap steel available to be recycled, in order to meet global steel demand. The world needs to continue urbanising, and it’s beyond what is available with current amounts of scrap, so decarbonization technologies must be developed in the primary route”. It’s not only about working around the issue, however, but the report also asserts that the mechanisms in which scrap is utilized across the supply chain could benefit from improved connectivity, and crosssectoral dialogue. Serge Timmermans, chief commercial officer at metal wholesaler
A somewhat more hackle-raising point of conversation for a number of steel industry players is the looming introduction of the Carbon Border Adjustment Mechanism (CBAM), which will apply in its definitive regime from 2026, while the current transitional phase was launched last year, and will continue until the end of 2025. When the CBAM is fully implemented, steel importers will be required to pay the same carbon price as EU producers for each metric ton of embedded CO2 they sell in the EU market. Over time, this tariff will eliminate the free ETS allowances that the steel industry has benefitted from for most of its production volumes. These free allocations would decline by 10% from 2026 onward before being completely removed in 2035. ‘‘Steelmakers may have mixed perceptions [of the CBAM]’’, Lilholm said, ‘‘but the ultimate goal is to mirror what has been the EU Emissions Trading Scheme, and create a level playing field for those outside of the EU’’. Lilholm maintained that he had personally met some of the CBAM regulators, and noted that their position was that the mechanism was ‘an instrument for decarbonization, rather than a purpose to gain capital from tax and tariffs’. ‘‘They would actually say that there is an element of reciprocity’, he concluded, referring to the ongoing global effort to lower emissions, and the
*Assistant editor, Steel Times International **Global head of sustainability and ESG services, DNV Supply Chain and Product Assurance
significant investments that this inevitably requires. ‘‘It’s considered a transitional phase for CBAM, so this is a moment for steelmakers and players in Europe to voice their concerns, because once it becomes fully effective, this will be much harder. What we witnessed in our steel report is a low number of steelmakers showing readiness or being compliant with CBAM –less than half – so there is still a lot of work to be done.’’
A significant area of the report is focused on the increasing interrelation between digitalization and industrial processes, with the research claiming that a high proportion of metals and mining companies view digital transformation as their top supply chain priority both today and in the near future. ‘‘Once you have granular data, you can make choices where you know the impacts, and by doing that, you can reduce negative effects,’’ Lilhom summarised. An important area of development, Lilholm noted, was a forthcoming regulatory technology referred to as a digital product passport, or DPP. The DPP serves as a data carrier that can collect environmental data of products across the value chain, and would, said Lilholm, enable the aggregation of material footprints, which would be pivotal in creating a verified information bank of scrap availability, and thus drive a more ‘circular approach’. The benefit of using a DPP, said Lilholm, would echo across the entire value chain. Knowledge gaps still exist in the realm of the digital, however, with Lilholm drawing particular
attention to Life Cycle Assessment (LCA) methodology, a tool that report contributor and senior sustainability consultant at DNV, Timothy Bankroff, refers to as ‘an important tool that many organizations consider to be a fundamental way to understand product impacts.’ ‘‘Without an LCA,’’ Bankroff summarised, ‘‘you simply do not understand the whole picture’’. The lack of industrial understanding with regard to LCAs was highlighted as the most substantial barrier to implementing supply chain sustainability within the report, and Lilholm believes that this specific epistemological shortfall can be attributed to the idea that those working on the topic are possibly sileod within a single department, with only a small number able to produce strategically relevant LCA content that embeds a life cycle thinking approach into their sustainability strategy and overall business strategy. He added that LCAs are not only a tool for buyers to verify data toward a product, but a method to explore alternative production technologies, and model their applicability. However, Lilholm emphasised that the conversation surrounding such areas required nuance, referring to the concept of a ‘carbon tunnel’. ‘‘We want to avoid achieving decarbonization at the cost of other topics’’, he said, highlighting the symbiotic relations that exist within the industry, with all facets benefitting from a shared level of public and corporate attention.
Despite the detailed findings unearthed in the report, burning questions, for Lilholm, remain. With the MENA region being able to produce steel with renewable energy at a lower cost basis due to its logistically favourable position, Europe is then left at a fork in the road; either to import cheaper energy from alternative areas, or import the final steel product. And, said Lilholm, it is important to recognise that even if Europe is setting a clear pathway for sustainable steel, ‘half of the world’s steel comes from China, so if we are to move the needle on a global scale, we need to see more movement there’. Lilholm added that a notable area of tension is the seeming failure of communication between steel producers and traders; ‘‘There are steelmakers saying that they are expected to decarbonize as part of a commitment to sustainability, but cannot find a client that’s willing to pay more for the steel, and there are also steel importers saying that they cannot find enough sustainable steel.
GLAMA Maschinenbau GmbH
Hornstr. 19, 45964 Gladbeck, Germany fon: +49 2043 9738 0 fax: +49 2043 9738 50
GLAMA Maschinenbau GmbH
email: info@glama.de
Hornstr. 19, 45964 Gladbeck, Germany
GLAMA USA Inc.
fon: +49 2043 9738 0 fax: +49 2043 9738 50 email: info@glama.de
60 Helwig St., Berea, Ohio 44017 fon: +1 877 452 62 66 email: sales@glama-us.com
Clearly there needs to be a better sense of connectivity.’’ As the report emphasises, pressure is mounting from all angles to propel the industry toward a greener future. Yet, there remains a disconnect apparent in components as essential as language; in dialogue that drifts to nowhere, in words that mislead, and in the vast echo chamber of economic rhetoric, that often accentuates the compelling point of issue, over a potential solution. The report concludes by foregrounding the requirement of ‘continued collaboration’, and the concept of collective action in the face of environmental adversity.
With an increasingly binary political dynamic that continues to fracture throughout Europe, much as in the wider world, ambitions for widespread co-operation appear more a vision of a utopic ideal, rather than a plausible near-future scenario. There is hope to be found in the multi-faceted incentives of ‘going green’, primarily in the profit margins created by legislative obligations, increased environmental consciousness,
and the maintenance of externally visible ESG frameworks. Whatever values these are bred from, the results are largely the same. Steel production, after all, can only be as sustainable as the business that directs it.
A link to DNV’s report can be found by following this link: https://www.dnv.com/ about/supplychain/shaping-the-future-ofsustainable-steel/ �
To ensure continuously high levels of productivity, lift truck specifications often need to go beyond standard. The high-quality Konecranes lift trucks, available in both diesel and fully electric variants, with extra options or custom-made adaptations make it ready to handle any of the demands of a steel manufacturing plant. But it isn’t only the lift trucks that matter - protecting your people and providing a safe work environment are just as important.
These are a Konecranes specialty!
Discover more at www.kclifttrucks.com
The recent collaboration between Equinor, Fieldmade, and f3nice demonstrated the potential to improve material circularity, and utilize the unique features of metal AM technologies. By Sepideh Gholamzadeh1, Mattia Cabrioli1, Matteo Vanazzi1, Philip Hansteen1, Svein Hjelmtveit2, and Brede Lærum3
METAL Additive Manufacturing (AM) –commonly referred to as metal 3D printing – is a transformative technology that enables the production of complex metal parts through various innovative processes. Metal AM is utilized in various sectors including aerospace, automotive, medical
devices, and tooling, due to the recurring need in terms of low-volume custom applications.
Along with other energy majors, Equinor ASA – a company headquartered in Stavanger, Norway – has already started to utilize the adoption of metal AM to
boost its digital transition, aiming to digitalize 50% of its estimated €3 billion inventory by 2032. Based on current data, around 80% of these parts are rarely utilized. Therefore, by shifting towards a digital inventory model, Equinor expects to significantly reduce physical stock and
1 f3nice AS, Filipstad Brygge 1, 0252, Oslo, Norway. 2 Fieldmade AS, Ole Deviks 14B, 0666, Oslo, Norway.
3 Sandslivegen 90, 5254 Sandsli, Norway.
associated storage costs[1]. To promote this process, Equinor has collaborated with key players in the metal AM business, including Fieldmade AS, a Norwegian company focusing on creating mobile micro-factories capable of manufacturing spare parts on site, and f3nice AS, an international start-up founded in 2020 specializing in producing high-quality metal powder for additive manufacturing, utilizing 100% recycled metal scrap.
The impacts of this revolutionary approach have been recently demonstrated in the commissioning of the Johan Castberg vessel in Stord, Norway. The Johan Castberg, a Floating Production, Storage and Offloading (FPSO) vessel, has been designed to produce around
200,000 barrels of oil per day, reserving between 450 and 650 million barrels of oil throughout a 30-year lifetime. The commissioning of the Johan Castberg project – of which the costs have been estimated to hit around €7.5 billion – is now under completion, with production slated to start by the end of Q4 2024[2] Equinor has decided to involve Fieldmade and f3nice in the final commissioning phase, to support on-site activities by deploying a mobile micro-factory for the printing of components, by using powder obtained from the recycling of scrap material and obsolete spare parts from Equinor’s own assets in Norway.
From scrap, to powder, to metal parts Decommissioned or obsolete parts, which were retrieved from Equinor inventories, were allocated for upcycling and transformation into metal powder. Sustainable metal powder produced by f3nice was used to manufacture parts on demand for the Johan Castberg vessel.
To kick off the operations, f3nice sorted scrap metals and selected high value alloys for further processing. The material was firstly gathered at f3nice premises, then screened by means of handheld X-Ray Fluorescence (XRF) spectrometers, to segregate the different alloys by type. Through this powerful on-site analytical technique, it was possible to reliably assess the alloy type of various scrap parts before undergoing any further process. This way, the following high value alloys were identified: austenitic stainless steels (e.g., 316L SS), super duplex stainless steels,
nickel-based superalloys such as Inconel® materials, and copper. An overview of the secondary-sourced metal is represented in Fig 1[3]
After the sorting phase, additional pre-processing steps were carried out to downsize the metal scrap to easy-to-handle dimensions and to clean the scrap from contamination by oil, grease and lubricants. Eventually, the material was ready to become metal powder. The atomization process called Vacuum induction melting Inert Gas Atomization (VIGA) was selected by f3nice for this step. VIGA is a sophisticated multi-phase process used to produce high-quality metal powders, primarily for applications in AM and other advanced manufacturing technologies. In the first phase, the material is heated up by electromagnetic induction and melted in a vacuum or inert gas atmosphere, to preserve the purity of the processed alloys and reduce the risk of contamination. Subsequently, the liquid metal is poured through a nozzle in a sealed chamber, where the molten metal is subjected to gas jets at high temperature and pressure, to be rapidly cooled down and create spherical metal powder particles. An example of powder obtained by f3nice is included in Fig 2
For this project, two different alloys were recycled by f3nice, namely 316L SS and Inconel® 625. The powder, after undergoing the standard quality controls to assess its compliance with quality requirements and industry regulations, was used to manufacture parts by means of Powder Bed Fusion – Laser Beam (PBF-LB)
technology. In this AM process, the material is initially disposed in a powder bed, then consolidated by a laser with high power, to melt down the powder particles at precisely designed locations and build a new metal component, layer by layer. This technology was chosen by Fieldmade to be installed at its micro-factory and then operated locally to produce metal components for the Johan Castberg vessel.
Some of the most relevant use cases printed with f3nice powder are reported in Fig 3[4]
When the collaboration started in late 2022, the initial goal of the micro-factory was set at 100 cases (i.e., parts design) in one year. However, the project turned out to be more successful than expected: in the first year of operation at Stord, Fieldmade and Equinor teams were able to identify about 350 use cases and print around 3,000 parts (including both metallic and polymeric parts). Due to this success, the collaboration was extended, to continue in 2024. According to the latest information (i.e., March 2024) it was possible to produce more than 600 use cases as well as more than 10,000 printed parts, in a
total period of one and a half years[3]. In the end, around 1.5 tons of metal powder by
f3nice were used at Stord, showcasing the feasibility of the circular economy approach promoted by the three companies.
Life Cycle Assessment (LCA) analysis on metal parts
To thoroughly validate the sustainability of the circular approach here presented, a comprehensive Life Cycle Assessment (LCA) was carried out. This iterative approach analyses all stages of the life cycle – ranging from raw material extraction to production, usage, and end-of-life phase – based on a pre-defined functional unit[5]
Before initiating this analysis, f3nice conducted an independent LCA on the metal powder, to evaluate its environmental performance. This cradle-to-gate LCA has demonstrated the significant environmental benefits of f3nice metal powders compared to conventional production methods. By utilizing 100% recycled scrap metal, the f3nice process achieves an approximate 80% reduction in global warming potential, a 98% decrease in abiotic resource depletion (elements), more than a 90% reduction in fossil fuel consumption, and a 78% reduction in water scarcity impacts. These results represent the average performance of f3nice powders and highlight their remarkable efficiency. By conserving resources, minimizing emissions, and reducing water usage, the
– thus there are no percentages for
f3nice process sets new benchmarks for sustainability in metal powder production[3] For the present work, a use case among the ones printed by Fieldmade was identified. The study focused on a strainer, a component used across various industrial applications such as mud/fuel tanks, power/ pump stations, and shaker units (Fig 4). The LCA analysis was conducted using the SimaPro software, with environmental impacts evaluated according to EPD 2018. The LCA analysis compared two production scenarios: the conventionally manufactured strainer and the additively manufactured one, produced using f3nice powder. In both cases, the functional unit was defined as the finished, printed strainer, with mass as the key measurement for
comparison.
In the conventional manufacturing process, production begins with the mining and creation of Inconel® 625, which is then processed to obtain the finished strainer. In this process, the strainer includes different sub-components such as a base ring with a handle, an inner ring to stabilize the walls, two wall layers with different hole sizes, and two top layers, also with varying hole sizes. All components are then welded together to form the final strainer (Fig 5).
In contrast, the AM-manufactured strainer using f3nice powder is made from 100% recycled scrap metal. This powder is used in the Additive Manufacturing process, which includes the Powder Bed Fusion
Laser Beam (PBF-LB) process followed by machining to complete the strainer (Fig 6). The comparison of results for the two scenarios, evaluated with EPD 2018 method, are shown in Fig 7
The AM-manufactured strainer using f3nice powder demonstrates significantly improved results in several environmental categories compared to the conventionally manufactured strainer. Notably, there is a 94% reduction in abiotic depletion (elements) and a 54% reduction in water scarcity. Additionally, the f3nice powder performs much better in terms of acidification and photochemical oxidation. These results can be largely attributed to the fact that the f3nice powder used in the AM-manufactured
strainer is produced from 100% recycled scrap metal. The conventional process, on the other hand, relies on virgin materials, which contribute significantly to its environmental impact, especially in the powder production stage. As a result, the AM-manufactured strainer shows a lower overall environmental burden, highlighting the importance of using recycled materials in the manufacturing process. In contrast, the results for eutrophication, abiotic depletion (fossil fuels), and global warming are nearly identical, with the conventionally manufactured strainer demonstrating only a slightly better performance. Notably, the conventionally manufactured strainer achieves a significant 77% improvement in ozone layer depletion compared to its AMmanufactured counterpart.
While it is true that the PBF-LB process is largely energy-intensive – and the use of inert gases like argon in several AM steps contributes to the increase of environmental impact – it is also important to consider other factors that might influence the LCA results. For instance, the final mass of the strainers is a crucial aspect. Although both the AM-manufactured and conventionally manufactured strainers were modelled with nearly identical masses, the AM strainer should ideally be lighter due to the superior design opportunities by AM. However, in this case, design limitations and production constraints led to an almost identical mass in this instance, which could significantly
affect the LCA outcomes. This discrepancy highlights the importance of considering all factors when interpreting the findings, as variations in mass could alter the environmental impact analysis.
In conclusion, the collaboration between Equinor, Fieldmade, and f3nice was highly effective during the commissioning of the Johan Castberg FPSO, enabling a circular economy approach to be promoted by the three companies. �
References
[1] Equinor’s Digital Inventory: shapes of things to come [Internet]. [cited 2022 Aug 9]. Available from: https://valve-world.net/equinorsdigital-inventory-shapes-of-things-to-come.
[2] Johan Castberg project update [Internet]. 2023 [cited 2024 Jun 12]. Available from: https://www.equinor.com/news/20230919-johancastberg-projectupdate.
[3] f3nice & Equinor. (2024, July 5). Circular Economy Model to Produce Sustainable Metal Powder: PHOENIX Project.
[4] Matre E. Experiences using a micro factory for on-site manufacturing. 2024.
[5] International Organization for Standardization. (2020). ISO 14040 and 14044:2006/Amd.1:2020 - Environmental Management Life cycle assessment — Principles and framework. Geneva: ISO.
BIGGER.
Superior Machine has joined the Woodings’ group creating the most capable hot metal equipment supplier group in North America. Offering the combined knowledge, engineering, manufacturing, and construction expertise for all your equipment needs.
Wherever hot metal is produced, you will find equipment from Woodings, Superior Machine, and
Munroe operating at the highest level in the most demanding conditions. Our products and professional installation services reduce downtime and extend campaign cycles.
We are better together. Let us show you. woodings.com
We can provide you with more value than ever before from concept to installation, service to replacement, our size, scope, and experience gives us a unique ability to help you increase productivity and solve problems.
Following several years of market stasis, the North American scrap market can look forward to brighter skies on the horizon.
By Myra Pinkham*
THE US ferrous scrap market has been somewhat lacklustre and challenging for much of this year and – at least over the near term – it is expected to continue to be so, even with the new domestic electric arc furnace (EAF) steelmaking capacity gradually coming online.
“In part this is because we continue to see sluggish growth in US manufacturing activity,” Joseph Pickard, chief economist for the Recycled Materials Association (ReMA) said, noting that manufacturing is a big driver of the ferrous scrap market, including being a large generator of prime scrap.
This view is supported by several forward-looking indicators, including the Institute for Supply Management’s US manufacturing purchasing managers index, which as of October had been below 50%, therefore indicating contractionary manufacturing activity, for 23 of the past 24 months. At the same time, Pickard pointed out that in the year to date through to mid-October, US crude steel production was down 1.7% from the same period in 2023, with domestic mills operating at a lower than desired capacity utilization rate, which, according to the American Iron and Steel Institute (AISI) was only 73.3% as of the beginning of November. This, Pickard said, isn’t great for overall US ferrous scrap demand, and correlates with a 1.8% year-on-year decline in domestic scrap consumption in the first half of this year.
Still, Kevin Dempsey, AISI’s president and chief executive officer, pointed out that given significant efforts over the last few decades to increase the collection and recycling of end-of-life products, the US has much higher rates of scrap usage by both EAF and blast furnace steelmaking operations than is the case in most other regions of the world.
Alexandra Anderson, a senior steel analyst at CRU, noted that one thing that hasn’t been helpful to steel and, therefore, scrap,
demand, has been how much uncertainty there has been about the US economy throughout the year.
But while the auto market (which is the main prime scrap generator) has been somewhat of a bright spot with auto production remaining relatively consistent year-over-year, Philip Gibbs, a senior equity research analyst for KeyBanc Capital Markets, said that some industrial markets, such as heavy equipment and energy applications, are weaker than expected. The same is the case for certain non-residential construction sectors. That, Anderson noted, has affected demand for some types of steel products, therefore hindering interest in mills purchasing scrap – particularly obsolete grades.
Still, AISI’s Dempsey points out that high-quality steel scrap is an important raw material that can help American steel producers reduce greenhouse gas emissions and support their broader decarbonization efforts.
Also, it remains to be seen what the impact will be now that the US presidential election, which had added to the other uncertainties affecting the market, is over. Greg Dixon, chief executive officer of Smart Recycling Management, said that the angst over the election, given that it had been expected to be very close, had added to the sluggishness of the US scrap market with people holding back starting some big projects, and mills somewhat lowering their production rates and, therefore, scrap usage, until they got more clarity.
But some early speculation is that the second Trump presidency could make companies more optimistic about both the US steel and scrap markets and could result in a higher pricing environment.
Alexander Kershaw, a senior steel analyst at Fastmarkets, observed that, at least in September and October, another issue was that there had been several temporary
steel mill production outages – largely maintenance outages, although that impact is expected to be short-lived.
“Meanwhile, demand from overseas markets has been a little tricky,” Pickard said. While overall, US exports of recycled iron and steel (excluding stainless and alloy steel scrap) were down 1.31% year-to-date through August, there has been a lot of variation by market.
This, said Ashima Tyagi, an associate director of S&P Global Market Intelligence’s pricing and purchasing service, comes as the US continues to be the largest exporter of ferrous scrap, followed by Germany, the United Kingdom, the Netherlands and Japan.
Pickard noted that while countries such as Turkey, Bangladesh, Peru, Pakistan and Egypt, had been consistently placing scrap orders, many other countries have been buying less scrap this year. He said some of that demand could be attributed to a pickup in Chinese steel shipments to Southeast Asia.
Traditionally Turkey has been the largest buyer of ferrous scrap, KeyBanc’s Gibbs said, given that the vast amount of its steel is produced via EAFs and doesn’t have a large enough domestic reservoir to support
*North America correspondent, Steel Times International
its scrap requirements.
Given that the US is its largest supplier, Pickard said that it isn’t surprising that the 17% year-to-date increase in US ferrous scrap exports is in line with reports by the World Steel Association that Turkey’s steel production increased 15% year-to-date through August.
Pickard said that Bangladesh, while still a relatively small steel-producing nation, is another good news story, buying 40.7% more ferrous scrap this year. He noted that on the back of its economic growth, Bangladesh’s steelmaking capacity, which is all EAF or induction furnace-based, has increased from 5.5Mt in 2018 to about 9Mt in 2023 and the mills there are continuing to invest in new capacity.
On the other hand, given transportation bottlenecks at the Panama Canal and in the Red Sea, Pickard said that US ferrous scrap exports to India were down about 7% yearto-date through August even with its strong economic growth and its steel production rising 6.5% year-to-date.
Fastmarket’s Kershaw said that in general, Southeast Asia will increasingly be a bright spot for steel production and, therefore, scrap demand due to governmental incentives, although he pointed out that not all of the scrap will be coming from the US, but also Europe, the Middle East
and Africa. He said there have also been larger US export declines this year in certain other countries, including Mexico, where they were down 21% year-to-date, and Vietnam, where there was a 57% decline, with Chinese steel shipments being seen as one of the causes with lower manufacturing activity in those countries also a factor.
While there is currently an ample supply of scrap in the US to meet the demand, CRU’s Anderson pointed out that one big topic of conversation recently has been whether there will continue to be enough
scrap available once all the new planned EAF steelmaking capacity comes online over the next several years, and whether there will be a need to put certain incentives in place to increase scrap flows to ensure that availability.
Smart Recycling’s Dixon said that he doesn’t believe it will be an issue, explaining, “I believe that steel mills are very savvy to be sure that they have enough scrap or other raw materials such as pig iron, direct reduced iron (DRI), and hot briquetted iron (HBI).” He added that while the mills have been using more alternative iron products in their mix than they had in the past, their preference continues to be to utilize scrap the best they can, given that it is cheaper.
One of the biggest areas of concern, Fastmarkets’ Kershaw said, will be prime scrap availability, although he said that this can be solved by combining prime with shredded and alternative iron units. “But the only question will be at what price, as with a tighter supply, scrap prices, which have only recently started to bottom out, could begin to move up.”
S&P Global’s Tyagi pointed out that following a decline earlier in the year and a period of stable pricing in August and September, US ferrous scrap prices settled moderately higher in October and could increase over the winter before staying rangebound for much of next year.
Even though, in many segments of the industry, scrap remains the predominant raw material input, AISI’s Dempsey said that given the presence of tramp elements like copper in many forms of obsolete scrap, the steel industry still must use significant
•
•
•
•
•
•
•
FURNACES DECEMBER ISSUE:
Glassman Asia 12-13 Feb
FURNACES MARCH ISSUE:
AISTech 5-8 May
2025 China (Guangzhou) International Metal and Metallurgy Exhibition 10-12 May
Glassman Europe 14-15 May
ALUMINUM USA 28-29 May
FURNACES JUNE ISSUE:
Future Steel Forum June 25
Furnace Solutions June 25
ALUMINIUM China 9-11 July
UK Metals Expo 10-11 Sept FURNACES SEPTEMBER ISSUE:
volumes of hot metal, pig iron and DRI to dilute those impurities – particularly when producing flat-rolled steel products.
Anderson said that one thing that domestic steelmakers have been doing in recent years to ensure that they have adequate captive supply of the feedstock they need is to acquire more recycling assets. She pointed out that from 201924, mills have made 13 such acquisitions, including four over the past two years by Nucor’s River Metals Recycling unit, Commercial Metals Company, Charter Manufacturing and Gerdau.
However, KeyBanc’s Gibbs pointed out that the pace of such acquisition activity has been lower and much more regional and strategic in nature than what had occurred at its height in 2006-10.
Moves towards consolidation
There have recently been more moves to consolidate, with larger independent recyclers buying smaller companies. For example, in August, Alter Trading Corp., which had already made several acquisitions, purchased all the operating assets of Andersen’s Sales and Salvage Inc.
Also, another major recycling company – SA Recycling – is reportedly nearing completion of a deal to buy four or five more scrapyards in Georgia.
Gibbs said that while 2024 has been a challenging year for US ferrous scrap recyclers, he is hopeful that there will be better times ahead. Kershaw agreed, stating that while developments are coming somewhat slower than was originally expected, the market should see both a pick-up in ferrous scrap demand and pricing next year and most likely over the next few years as well. �
Gustavo Sanchez* describes the challenging yet rewarding future ahead for the steel industry, with digital solutions, such as those supplied by PSI, building momentum within an increasingly automated sector.
1. What is your view on the current state of the global steel industry?
The steel industry is a market that forces us to constantly give our best in order to remain a global leader of innovative production management solutions while creating value for our clients. In 2024, we saw the steel market demand decline and there is a projected recovery in 2025. There are reasons to believe that by the end of this decade, there will be increased demand in major economies. In summary, there is a lot of dynamism, opportunities, challenges and certainly long-term progression on global demand.
2. In which sector of the steel industry does PSI mostly conduct its business?
Our customers include steel producers in primary and secondary steelmaking and refining, casting and solidification, rolling and forming, finishing and coating, fabrication and manufacturing, and recycling. We offer Manufacturing Execution Systems (MES), Enterprise Resource Planning (ERP) and end-to-end Supply Chain Management (SCM) solutions to support steel producers in various sectors.
3. Where in the world are you busiest at present?
From a growth perspective, I have to highlight the North American market. Within 10 years, we could establish a strong market presence there, becoming a valued partner in many ongoing digitalization programmes. In Europe, the focus is mostly on decarbonization and we are proud to be the selected partner for several lighthouse projects. Besides these two examples, I would say that we are ‘globally busy’.
4. Can you discuss any major steel contracts you are currently working on?
We have contracts with big and small global steel producers. At PSI, instead of focusing on contracts, we strive to deliver successful projects for our customers that result in long-term collaborations and partnerships.
5. Where does PSI stand on the aluminium versus steel argument?
We care for steel, aluminium, and copper producers. Our experts dedicate themselves to delivering excellent services and consultation for the metals industries. Our mission is to support metals producers holistically – addressing their specific needs by implementing tailored functions into our product and leveraging experienced professionals across all domains. So for PSI there is no ‘versus.’ but an ‘and’.
6. What are your views on Industry 4.0 and steelmaking?
We see a tremendous opportunity to harness the advancements in big data, Internet of Things and AI. By leveraging these technologies, we aim to create a competitive advantage and transform
production, scheduling, logistics, demand planning and sales planning processes to make the industry more efficient, with lower costs and better customer service.
Imagine a future where the entire steel supply chain is fully transparent to enable the detection of major disruptions in order to act in real time. This will improve the short-term response and minimize any negative impact or proactively maximize benefits. One important detail: this isn’t merely a vision but a reality in progress –one that we are actively paving the way to make feasible and achievable.
7. In your dealings with steel producers, are you finding that they are looking to companies like PSI to offer them solutions in terms of energy efficiency and sustainability? Yes, many steel producers are increasingly seeking solutions for energy efficiency and sustainability as they face mounting pressures to reduce their carbon footprint and improve operational efficiency. PSI is well-positioned to help by offering a range of solutions, including: energy and process optimization solutions, product carbon footprint tracking, efficient resource management, quality management, sales and operations planning etc.
8. How quickly has the steel industry responded to ‘green politics’ in terms of making the production process more environmentally friendly and are they succeeding or fighting a losing battle?
The steel industry is moving towards more sustainable production, but it is far from having solved all the problems related to carbon emissions. While some flagship projects, like SSAB building the world’s first fossil-free steel mill (which when completed will remove 17% of the national CO2 emissions in Sweden and Finland combined) may represent a promising avenue, most
*Senior business consultant, PSI Metals Belgium (https://www.psi.de/en/solutions/products/psimetals).
companies are still in the early stages of adopting clean technologies. Although the response to green policies is becoming more rapid and proactive in some cases, the industry is still struggling with the transition to full carbon-free production methods. However, the overall direction is positive, and investment in research and development continues to grow, suggesting substantial progress could be made over time.
9. Where does PSI lead the field in terms of steel production technology?
PSI leads the field in steel production technology through its innovative solutions designed to enhance efficiency, sustainability, and automation in steel manufacturing. Our production management solutions enable steel producers to manage their energy consumption, track their carbon emissions on a piece and product level, manage product quality to reduce downgrade and rework, optimize their scrap material and overall production to react quickly to customer orders. We offer planning solutions that manage demand planning, sales planning, due date quoting and sales and operations planning.
10. How do you view PSI’s development over the short-tomedium term in relation to the global steel industry?
PSI’s short-to-medium term development is well-positioned as we are committed to bringing simplicity to very complex problems faced by the global steel industry. Managing energy consumption particularly in the hybrid steel plant which operates both BOF and EAF simultaneously is a wellknown challenge. We offer solutions that enable these plants to optimize their energy use for intraday markets, provide insights into weekly and monthly energy purchase data, helping them effectively address their energy management needs.
We provide demand planning and sales and operations planning to help them manage the complexity of their supply chain planning. Furthermore, all our solutions enable third party integration on our Service Platform.
11. Where do you see most innovation in terms of production technologies – primary, secondary or more downstream?
Most innovation is happening in primary and secondary production technologies. In primary production, hydrogenbased reduction and electrification are revolutionizing steelmaking, aiming to reduce CO2 emissions. Secondary production is improving with more efficient electric arc furnaces and automation, making recycling processes greener and more cost-effective. While downstream innovations, like product customization and digitalization, are advancing, they don’t match the transformative impact seen in primary and secondary sectors.
12. How optimistic are you for the global steel industry going forward?
In the short-to-medium term, there are several aspects to consider. The high cost and scalability of new technologies, particularly in primary production are hurdles. Additionally, fluctuations in steel demand could create volatility in the market. The industry also faces rising raw material costs and pressure to meet increasingly stringent environmental regulations, which could strain profit margins. The transition to sustainable practices has its benefits, but before we achieve them, substantial investment and time to implement at scale will be needed.
13. How does PSI address sustainability challenges in the supply chain?
When considering supply chain and sustainability in the steel industry, it is essential to focus on the natural resources consumed. Access to resources such as fossil-free energy, scrap, alloys, and zinc is often constrained, either in terms of
availability or lead times for delivery. These inventories must be closely monitored to effectively manage the capacity balancing process.
However, we recognize that stakeholders often have conflicting objectives and do not always communicate effectively during production planning. To address this, PSImetals Sales & Operations Planning (S&OP) solution facilitates cross-functional collaboration. By integrating procurement, production, logistics, and sustainability teams, it ensures that all aspects of resource availability are considered, creating a more sustainable and efficient planning process.
14. What exhibitions and conferences will PSI be attending over the next six months?
We look forward to an exciting year packed with events, conferences and opportunities. In, February, we will participate in the 2nd Global Steel Sustainability Europe 2025, AISTech and Aluminum US – both in May and both in Nashville, USA. Again in May, together with our partner Regesta, we will attend the Made In Steel event in Milan, Italy. To conclude the first half of the year, we will attend the Future Steel Forum in June in Spain.
15. If you possessed a superpower, how would you use it to improve the global steel industry?
If I had a superpower, I would use it to instantly get thousands of young openminded talents to the steel industry. This way, we would accelerate digital transformation, sustainability, and use of AI in the sector. Even a global collaborative platform could be created for real-time sharing of best practices. The final goal would be to minimize environmental impact without sacrificing pricing, competitiveness, or efficiency.
16. Apart from strong coffee, what keeps you awake at night?
The strong coffee that you just took off the list! But in all seriousness, innovating steel production is quite challenging. Whether it’s AI-driven systems or revolutionary production techniques, I can’t stop thinking about the future we’re building. The thrill of creating what once seemed unimaginable is enough to keep me awake long after the coffee is gone. �
Since 1866
Steel Times International is a leading publication serving the global steel industry and offering its readers a strong focus on all aspects of the production process embracing both basic oxygen and electric steelmaking.
Choose your subscription package...
PRINT + DIGITAL SUBSCRIPTION
8 print copies and a printed copy of the Steel Times International Directory
Digital copy of the magazine delivered to your inbox every month
Access to our digital archive of past issues and webinars
Weekly Steel Times International newsletter
PLUS access to all digital issues of Furnaces International
DIGITAL ONLY SUBSCRIPTION
With a digital subscription you will receive all the benefits of the Print + Digital option, excluding print copies!
Discrepancies over lettering and historical records suggest the humble origins of Abraham Darby I’s Coalbrookdale furnace may not be quite as long ago as initially speculated. By Tim Smith*
A 19th century photograph of the casting arch of Upper (Old) furnace showing the date 1658. Paint has been used to trace the date and monographs cast into the lower lintel, no doubt to enhance the picture. The monographs are a superimposed B, L, E (or possibly F) and W. The upper two lintels show the date 1777 when the furnace was enlarged by Abraham Darby III to make castings for the Iron Bridge (Copyright Ironbridge Gorge Museum Trust)
ABRAHAM Darby I is famed for being the first person to successfully smelt iron using coke in the blast furnace as the reductant and fuel. However, Darby was not the first to try replacing the established method using charcoal as fuel and reductant with the cheaper alternative derived from coal, since Dud Dudley is credited with smelting
iron with ‘pitcoal’ some 80 years earlier in the 1620s, a process patented by him in 1638. (See Steel Times International’s November 2024 History page). However, a family feud resulted in Dud’s furnace being vandalised in 1631, bringing an end to his achievements.
Nevertheless, evidence shows that
*Consulting editor, Steel Times International
Abraham Darby I, a Quaker, came to Coalbrookdale, in the English West Midlands, to cast pots in iron as a means of enabling the ‘poor’ to buy this essential utility, previously cast in brass. Darby had completed an apprenticeship as a malt miller in Birmingham, but after marrying, moved to Bristol to manage a brass foundry
casting cooking pots.
Arriving in Coalbrookdale in 1708, Darby leased a dilapidated blast furnace, known as Upper or ‘Old’ Furnace, renovated it and successfully smelted local Shropshire ore the following year using local coal converted to coke by burning it in piles covered with earth and wet coal dust and ash in a process reminiscent of charcoal making. The use of coke as a ‘cleaner’ fuel would be known to Darby from his years as a malt miller where coke was used to heat the sprouted barley grain to halt further germination, the roasted sprouts being the ‘malt’ of the process. The Shropshire clod coal was ideal for this, being low in sulphur. Also, by this time, coke was being used in brass foundries to melt the brass in reverberatory furnaces, a method he would know from his time in Bristol.
The iron Darby produced was ideal for thin-walled castings, such as pots, as it ran fluid from the furnace because the ore was rich in phosphorus and the coke was low in sulphur. Although the iron was of little use to the forges refining charcoal blast furnace iron to malleable bar iron, Darby’s iron was ideal for his needs.
Swedish engineer Reinhold Angerstein visited Coalbrookdale in 1754, and described a furnace in which a ‘Mr Darby’, and others, owned shares. This was Darby’s son, who by then was managing the works, since Darby I had died in 1717. Angerstein
describes the furnace as being charged 12 times per 24 hours, first with nine baskets of ‘coal’ (evidently coke as Angerstein uses the word ‘coal’ on a previous visit to Clifton blast furnace, Whitehaven, and then goes on to describe how it is coked in piles prior to charging) with each basket measuring 1.5’ x 2.75’ deep, on top of which 45 bushels of ore, each holding 50lb
(22.6kg), are placed in the centre of the furnace throat, followed by two bushels of limestone. He reports less ore is charged at the start and end of a furnace campaign. 12 to 13 tons of iron are produced a week using coke, but 18 to 19 tons, if charcoal is used. He comments that the iron made with coke is best for castings, but not fit for making bar iron. It sells for £7 as sows (presumably per ton).
Darby’s furnace was enlarged by his grandson Abraham Darby III in 1777 to cast components for the first iron bridge over the River Severn, a monument that remains today as the World Heritage site ‘Ironbridge’ a mile or so below the furnace, and gives its name to the present day ‘Ironbridge Gorge’ with its museums reflecting the industries of the region, not only ironmaking, but tilemaking, coal mining, tar extraction, water use and transport.
Darby’s furnace was in use until the 1820s, by which time the surrounding area had been built on, including the construction of a second furnace (that went unused), and other industrial complexes. Although the historic importance of the furnace was recognised in the 1800s, it was not until demolition of many of the surrounding structures started in the 1930s and later in the 1950s that a group from Birmingham visited the site at the request of the Shropshire Archaeology Society to
assess if it was worth preserving. Despite some misgivings as to whether this was feasible, it was agreed to go ahead and consolidate the structure. In 1959, a small museum was opened which was later to grow into the present Ironbridge Gorge Museum. With the building of the nearby New Town of Telford starting in 1963, the Ironbridge Gorge Museum Trust was established in 1967 with a remit to preserve, restore, improve and enhance features and objects of historical and industrial interest in East Shropshire. This wider remit was not generally met in the development of Telford New Town, but was more successful in preserving sites in Coalbrookdale and adjacent Ironbridge Gorge.
In 1982, a building was erected over the Darby furnace to protect it from the elements. Early 19th century photographs of the lintels supporting the casting arch indicated that dates and monograms had been cast on these. Such dates were commonly cast into the lintels on first construction and more if any later enlargement of the furnace took place. These features had been outlined in paint, no doubt to enhance the picture. There is a discrepancy in the date of the furnace,
as early pictures clearly show the date as 1658, whereas the lintel today bears the date 1638. No evidence has been found for the building of the furnace, and over the many years that it was exposed to the elements the features on the lintels have corroded badly. Attempts to decipher these using infrared imaging and laser scanning have failed to confirm a date, but it seems reasonable to assume that the early 19th century photography, prior to the restoration of the furnace in the 1950s, is more likely to be correct since the lintels would be less corroded at that time.
In addition to the dates, monograms in the early pictures show a superimposed B, L, E, and a W. Today, the W appears as a crown giving rise to the suggestion that Sir Basil Brooke, who owned the land and was a Royalist, built the original furnace. The L and B have been interpreted as an emblem for the Brooke family and the E for his wife, Etheldreda. However, although Brooke was active in Coalbrookdale, his activities revolved around coal mining and steelmaking using cementation furnaces, for which he brought pig iron made from hematite ore from the Forest of Dean, with this first being refined to bar, as the high phosphorus content of iron made
from Shropshire ore was unsuitable for steelmaking.
It seems more creditable that the B and L stand for the partnership of Silvanus Boycott and James Lacton who ran the furnace for a time, and the W for Francis Woolfe who managed the industrial aspects of the Estate, but post 1638. The E is unlikely to represent Brooke’s wife, Etheldreda as she had died prior to 1638, and the evidence of a shorter bottom horizontal on the ‘E’ in early photographs suggest it may represent an early ‘F’ standing then for Francis Wolf.
The evidence thus seems to place the building of the furnace at the later date of 1658 rather than the presently shown date of 1638, a warning to overvigorous conservationists that speculative interpretations should always seek alternative evidence. �
The author acknowledges the use of the PhD thesis of Dr Paul Belford, ‘Industrialisation and Identity in Shropshire: the Brookes of Madeley, 1544-1646’ University of York Archaeology September 2015.
Stay ahead with Steel Times International, delivering 12 issues annually. With 8 printed and 4 digital editions, our magazine provides expert insights, the latest developments, and key innovations in steel manufacturing.
Stay in the loop with our Weekly Newsletter—bringing you up-to-the-minute news straight to your inbox, featuring the most crucial updates impacting the global steel industry.
Join us for exclusive webinars each year! Focused on critical topics shaping the ture of steel manufacturing, our webinars o er expert panels, industry discussions, and real-time insights.
The ultimate Steel Industry Directory—your go-to resource for steel manufacturers, producers, and suppliers of plant equipment and services. Whether you're looking for the best in steel production or the latest technology, nd what you need at your ngertips.
Explore steeltimesint.com - a hub for breaking steel industry news, industry trends, and upcoming events. Bookmark the latest key dates and never miss an opportunity to engage with the steel community.
Meet the brightest minds in the industry at the annual Future Steel Forum. A premier event where thought leaders discuss cutting-edge technologies and innovations shaping the ture of steel manufacturing.