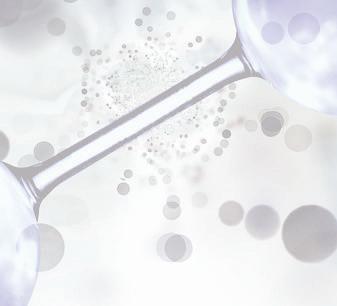
7 minute read
Carbon neutrality: the industry’s goal
HYDROGEN STEELMAKING
POSCO lays out its roadmap for decarbonization, featuring its hydrogen reduction ironmaking process (HyREX), in an aim to achieve carbon neutrality by 2050. By Kisoo Kim*
GLOBAL CO2 emissions amounted to about 40 Mt, and South Korea accounts for 2% of the total.1) To play an active role in the global climate crisis, South Korea declared in 2020 that the country would aim to reach carbon neutrality by 2050. As a manufacturing-intensive country, it is predicted that a signifi cant industrial transition is required for the economy to achieve its net-zero goals, which will include introducing green infrastructure. The steel sector, which is responsible for 14% of the country’s total CO2 emissions, is one of the main industries working to transform its traditional production process, that is, coal-based blast furnace ironmaking.
POSCO, the key material supplier to shipbuilding, automotive and construction industries in South Korea, has also pledged to become carbon neutral by 2050 with a plan to reduce CO2 emissions by 20% in the short-term by 2030 (10% in Scope 1 and 10% in Scope 2&3). This target can be achieved by increasing energy effi ciency, replacing coal as a reducing agent and fuel with coke oven gas (COG) and natural gas (NG) in the existing integrated route of steel manufacturing. Green energy steel production from steel scrap will be increased by using electric arc furnaces (EAFs) in the mid-term.
To achieve carbon neutral steelmaking, POSCO will further develop hydrogen

Carbon neutrality: the industry’s goal
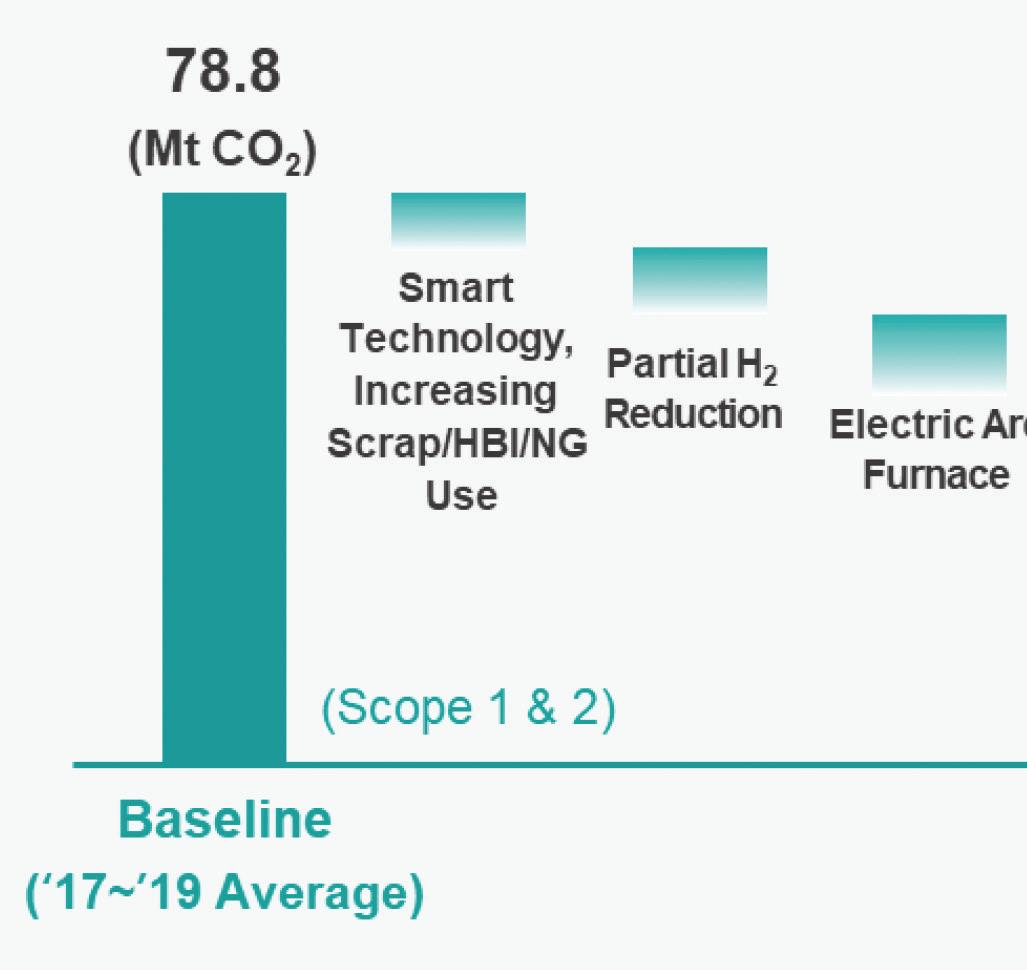
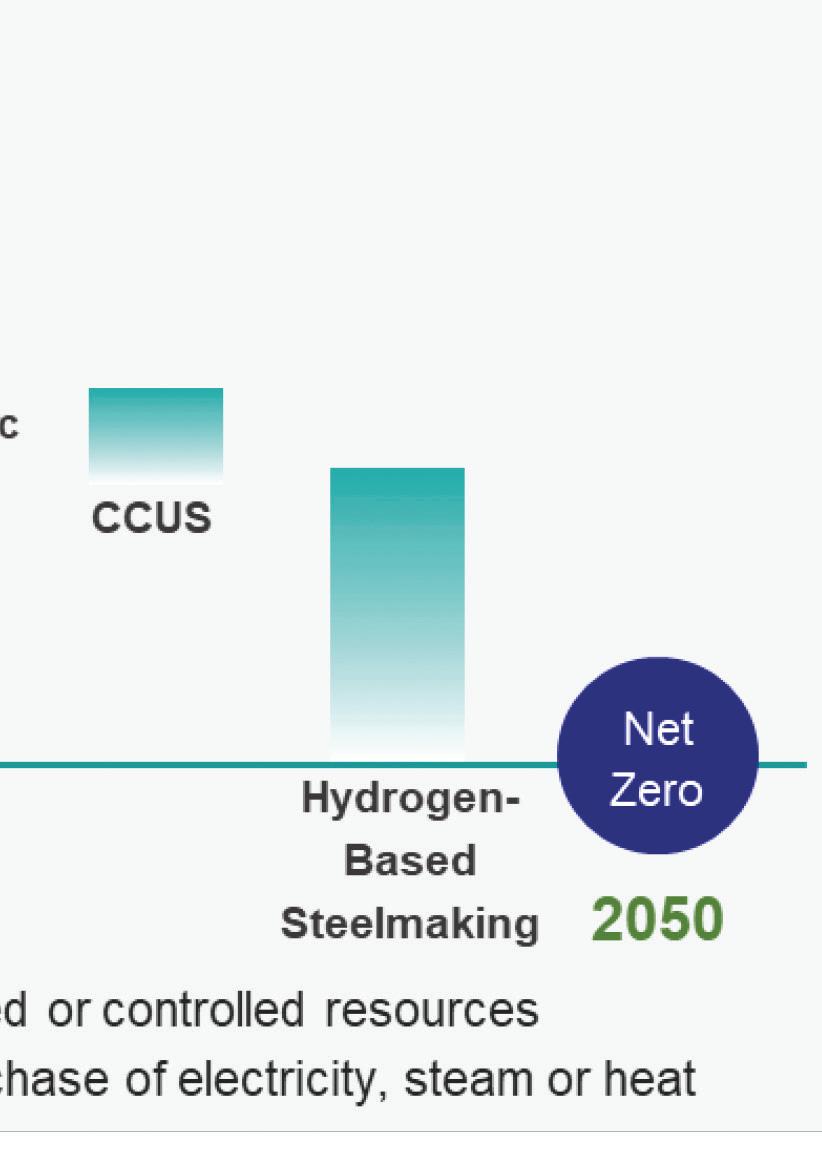

Fig 1. POSCO’s roadmap to carbon neutrality
ironmaking, and a DRI/HBI reduction technology named HyREX. Benefi ting from 30 years of R&D, and a commercialization experience of 250Mt FINEX (Fine Iron Ore Reduction) included in its process, HyREX is expected to be a powerful addition to innovative hydrogen ironmaking technologies. (Fig 1)
Low-carbon technology based on the existing FINEX process
POSCO owns the expertise and know-how through the long-term development and operation of FINEX, the environmentallyfriendly process of eliminating coking and sintering. In the FINEX process, reduction and melting are progressed in separated reactors. FINEX fl uidized bed reactors produce DRI with a reduction degree of approximately 65%, which is then charged into a meltergasifi er to produce hot metal. The fi ne ores are charged into the top fl uidized bed reactor, and the reaction gas is supplied from the bottom reactor. The fi ne ore particles are perfectly mixed by the gas and form the fl uidized bed. In current FINEX fl uidized beds, the fi nes ores are reduced by coal gas generated from the melter-gasifi er and the reducing gas contains 25% hydrogen. Also, it is easy to separate CO2 and recycle H2 and CO using a CO2 removal system, since pure oxygen is used instead of air in the meltergasifi er (Fig 2).
HyREX process rechnology sevelopment and commercialization
POSCO is willing to develop the HyREX process using hydrogen as a reducing gas based on FINEX fl uidized bed technology. In the HyREX process, the fl uidized bed reactors will produce DRI with a reduction degree of 95% using green hydrogen.
The biggest potential competitiveness of HyREX is the direct use of fi ne iron ores. At present, the fi ne iron ore occupies 71% of total seaborne iron ores, while pellet and pellet feed occupy only 13%. While shaft type hydrogen reduction technology requires high quality pellets, HyREX can use fi ne iron ores directly.
Also, hydrogen shows better diffusion behaviour compared with coal gas because the molecule size and viscosity of hydrogen are lower when compared with carbon monoxide.2) The fl uidization behaviour was also investigated with hydrogen in the POSCO laboratory, and it was confi rmed that the fi ne iron ore and hydrogen gas form a fl uidized bed and that a uniform reduction can be obtained.
The HyREX process is composed of multi-stage fl uidized bed reactors which are connected in series. An advantage of multi-stage fl uidized bed reactors is an easier supply of heat between reactors to compensate the heat defi ciency caused by the strong endothermic reaction of hydrogen reduction (Fig 3).
HYDROGEN STEELMAKING

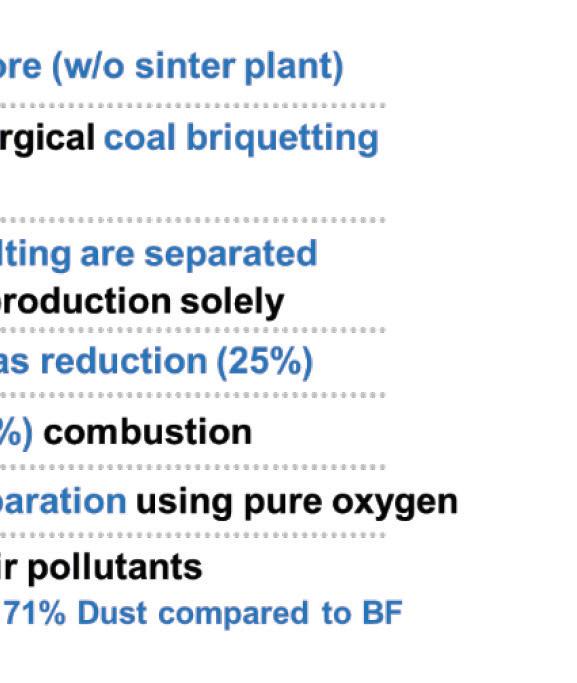
Fig 2. Seven features of the FINEX process
Two options
Two types of downstream processes are considered following hydrogen fl uidized bed reactors. The fi rst type of downstream process is to melt DRI with scrap in an EAF, and then proceed to the next steps of secondary refi ning and continuous casting. Thus, it is expected that mid-quality steel products such as hot-rolled steels and heavy plates can be manufactured. The other type of downstream process is to produce all the steel grades including high-quality steels such as automotive steels and high-grade silicon (Si) steels. Hydrogen reduced DRI is smelted with carbon loaded in an electric smelting furnace (ESF) to produce the hot metal. Subsequently, the hot metal is processed similarly to the conventional process of BOF, secondary refi ning and continuous casting. The latter process is expected to be better in controlling impurity contamination including nitrogen. The production of hot metal by ESF has some disadvantage in terms of CO2 emissions compared to that of molten steel by EAF, but CCUS (Carbon Capture, Utilization and Storage) will be a part of a carbon neutral solution instead.
SNNC (Société de Nickel de Nouvelle Calédonie et Corée), a member of POSCO Group, has been operating the world’s largest ESF since 2008 to produce FeNi(ferro nickel).
Through this, experience and knowledge concerning a large ESF has been accumulated and will serve as a foundation for the development of ESF for hydrogen reduced DRI smelting.
HyIS
The HyIS (Hydrogen Iron & Steelmaking) Forum in October 2021 has been hosted by POSCO for technical exchange and information sharing. The collaboration on innovative hydrogen reduction technologies has also been discussed, among global steel manufacturers, engineering and mining companies. A total of 2,028 people participated on and off-line, from 348 institutes in 48 countries including government organizations, academia, and car companies. The participants discussed policies, technologies, and energy supplies needed to achieve carbon neutrality in the steel industry. The common consensus was that not only the technological development, but the cross-functional co-operation of governments, societies, and related industries is crucial for carbon neutrality.
The HyIS 2022 Forum will be held in Stockholm, Sweden, in October, which is co-hosted by SSAB, IVA, NAEK and POSCO, focusing on green steel products, hydrogen for steel works and carbon neutral iron and steelmaking (Fig 4).
Stable sourcing of raw materials, green hydrogen and power
Stable sourcing of raw materials, green hydrogen, and green power are essential for the conversion to carbon neutral steelmaking. It is necessary to foster domestic and foreign bases of scrap, have long-term supply contracts to produce DRI suitable for the process considering economic feasibility, and import green hydrogen from overseas or establish a domestic production system.3)
For these reasons, the government’s active support and close co-operation system between steel companies and domestic energy suppliers are very important for carbon neutrality.
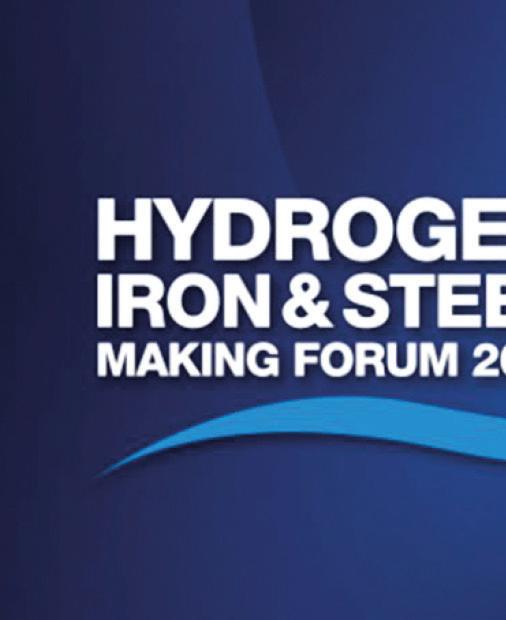
HYDROGEN STEELMAKING
Fig 3. HyREX, POSCO Hydrogen Ironmaking Process


POSCO has committed to carbon neutrality by 2050 and is developing HyREX – a hydrogen ironmaking process based on multistage fl uidized bed reactors, which is directly connected to the electric furnace. Carbon neutrality is the global steel industry’s goal, not a company’s goal. POSCO, therefore, is willing to develop the carbon neutral steelmaking process in co-operation with global steel companies, hydrogen suppliers and engineering companies.
POSCO hopes that global steelmakers and experts will join the 2022 forum in October and hold various discussions on the common goal of achieving carbon neutrality in the steel industry. �
References
1) Mckinsey Global Institute, ‘The net-zero transition: What it would cost, what it could bring’, McKinsey & Company, January 2022 2) D. Spreitzer and J. Schenk, ‘Reduction of Iron Oxides with Hydrogen – A Review’, Steel Research International, 2019, 90, 1900108 3) A. Doyle and T. Voet, ‘The DRI dilemma: Could raw material shortages hinder the steel industry’s green transition?’, McKinsey & Company, July 2021
Fig 4. World’s First International Hydrogen Iron & Steelmaking Forum (HyIS 2021)
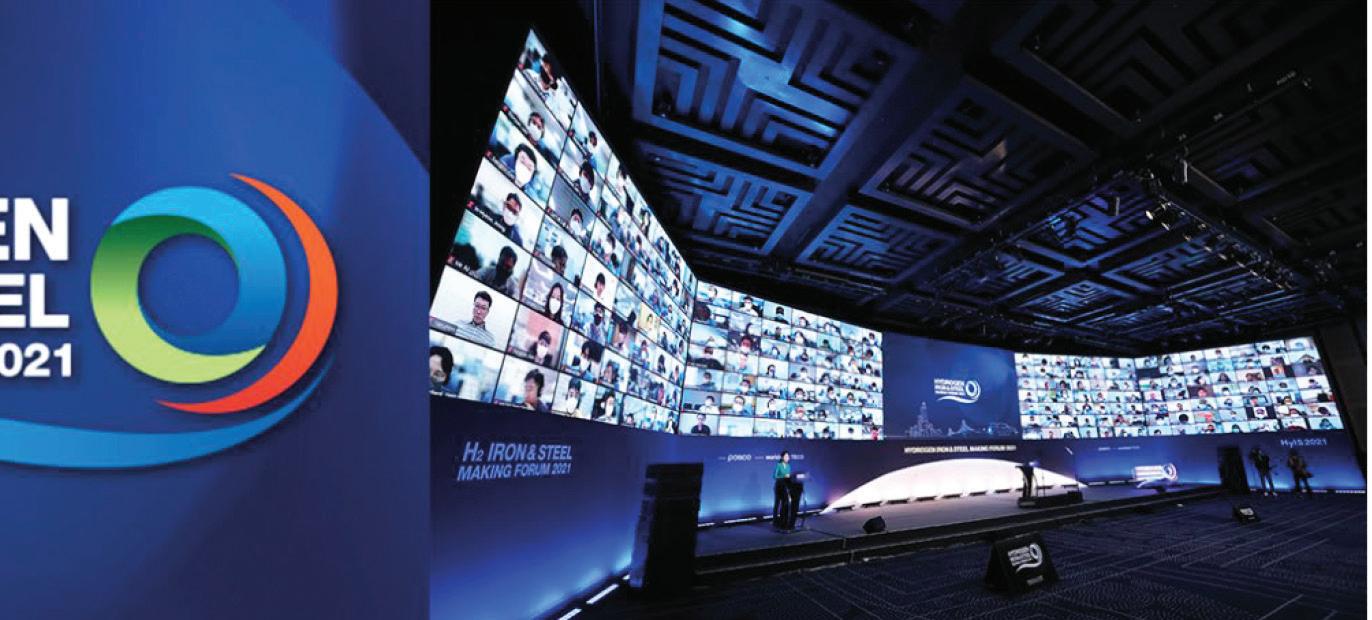