
7 minute read
From waste gases into dollars
WASTE GASES
From waste gases into dollars
WASTE GASES

Microbes have the potential to transform the current climate crisis; turning pollution into chemicals, and reducing fossil oil across the value chain. With LanzaTech, this technology can be utilized to both decarbonize the industry, and create valuable products for the economy. By Tom Dower1, Greg Archer2 , and Sanjeev
Manocha3
THE climate emergency, evolving customer demands, and the increasing costs of carbon emissions are now driving the transition to green steel. With 70% of global blast furnaces scheduled to be relined by 2030, the transition is rapid, and both risks and opportunities to steel producers are huge. There is no silver bullet solution to decarbonize the sector. Rather, eliminating carbon emissions will be achieved through the integration of multiple technologies to deliver bespoke solutions suited to the local market and circumstances. Among the options is an innovative carbon capture and use technology developed by LanzaTech. This uses the power of biology to feed the carbon-rich waste gases to micro-organisms which transform the pollution into ethanol and a range of other chemicals. These valuable products are the feedstock for essential materials as diverse as textiles, plastics and jet fuel. The technology creates value from a polluting liability and in doing so reduces fossil oil and gas extraction across the value chain, creating a more secure energy paradigm and a circular carbon economy.
1. Vice president, public policy. 2. European policy director. 3. Director of business development at Lanzatech
WASTE GASES
Climate emergency
The Earth has already warmed by more than 1˚C and could exceed the critical 1.5˚C threshold by the end of this decade unless global emissions are cut by 45% (from 2010 levels) and net-zero emissions achieved by 2050. In response, countries globally are accelerating efforts to reduce dependence on fossil fuels, pricing emissions and regulating polluters. Energy price spikes exacerbated by the Russian invasion of Ukraine are in turn driving global inflation and an increased focus on energy and food security.
Steel accounts for seven to nine per cent of global CO2 emissions and demand for green or lower carbon steels from customers, like the automotive industry, is creating an increased urgency to cut, and eventually eliminate, carbon emissions. Notably, emission trading schemes, which set a cap on emissions and require emitters to purchase credits to cover greenhouse gases released, are expanding beyond Europe. In North America, emissions trading operates in California and 12 north-eastern US states plus two in Canada with a trial scheme in Mexico. However, the price of carbon in North America is typically an order of magnitude lower than in the EU where prices have remained around €80 per ton of CO2 throughout 2022. In Asia, South Korea operates a successful emissions trading scheme and China has a two-tier approach with controls at both a national level and in major cities. Japan also operates two city level schemes. As pressure grows on countries to deliver promised emissions reductions, the geographical coverage of schemes is expected to expand as the available carbon budgets shrink causing the cost of emissions to rise.
Around the world, steelworks are ageing with 40% of blast furnaces globally due for relining by 2025, and 30% by 2030. With each relining costing around €100m, this presents a critical decision-making moment for the industry. A business-as-usual approach is likely to result in increasing the unsustainable costs of carbon emissions. The average steelworks today emits two tons of CO2 per ton of steel and with the rising price of carbon, emissions will increasingly squeeze margins and erode the commercial viability of unabated production. Selecting and integrating the right suite of technologies is crucial – but the best combination is highly dependent upon local circumstances and will evolve over time; there are no silver bullets. The majority of steel producers are already working to optimize and improve energy and resource efficiency to remain competitive. In addition, some are cutting emissions by progressively replacing solid fossil fuels with sustainable biomass or biochar which is most likely to be an option in areas with substantial biomass resources, such as Australia or Brazil. However, considerable care will be needed in identifying sustainable biomass supplies to ensure that the growing of energy crops or harvesting of biomass for use in steel production does not drive land use change or impact biodiversity.
Alternatively, where gas supplies are readily available, solid fossil fuels can be substituted by natural gas in a direct reduced iron furnace that reduces emissions from about two tonnes of CO2 per tonne of steel to 1.2 tons or less using natural gas, or potentially biomethane, which can also be used in combination with carbon capture. However, switching from solid fuels to gas comes with significant capex and energy costs.
Going further and displacing the natural gas with low-carbon hydrogen will progressively reduce, and could ultimately eliminate, most of the carbon emissions. But using only hydrogen to reduce the iron oxide presents major challenges with storage and melting of direct reduced iron. Producing the huge quantities of hydrogen required also represents a major challenge. Green hydrogen, made through electrolysis of water using renewable electricity, requires both large amounts of water and massive generation of renewable electricity. There are already multiple demands on the small quantities of green hydrogen that are starting to become available and the competing demands for renewable electricity, notably to decarbonise electricity grids and electrify the transport and domestic heat sectors, are considerable. Only small amounts of green hydrogen are likely to be available for steel production in the foreseeable future.
Steel recycling
Maximising steel recycling is always beneficial and a scrap-based electric arc furnace emits less than 0.5 tons of CO2 and is comparatively low capex. But scrap availability is limited, and it is a significant challenge to produce higher quality steels due to tramp elements such as other metals present in many scrap supplies.
To complement fuel switching and recycling, carbon capture and storage (CCS) of the CO2 may be viable in some locations such as the UAE, Norway, the Netherlands and the USA where there are natural storage sites and some existing pipeline networks. But in other locations the costly infrastructure to transport and store CO2 will be prohibitive. In contrast, carbon capture and utilization (CCU), generates a new value stream with little to no changes in the existing steel making technologies or new infrastructure needs. This can replace heat and electricity generation through combustion of the flue-gases or in less advanced production sites’ flaring of waste gases.
With LanzaTech, carbon recycling technologies transform waste gases (offgases) containing carbon monoxide (CO), hydrogen (H2), and CO2 into ethanol and other products. This provides steel producers with an economical, sustainable, and flexible means of creating value from waste off-gas through conversion into sustainable products. The technology has been successfully deployed in two commercial operating facilities at a steel
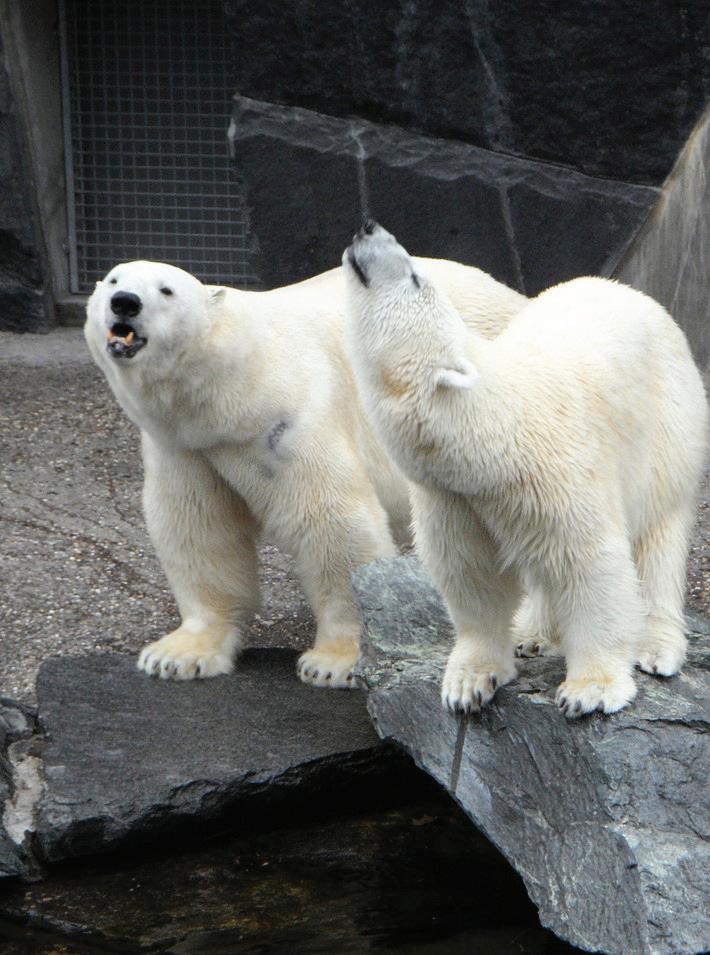
WASTE GASES
and ferro alloy mill, with seven additional commercial plants in construction and several more in the engineering phase. Depending on the feedstock and geography, this gas fermentation technology can reduce emissions by up to 90% and in the process make intermediates for producing the chemicals, fuels and materials on which society relies. This is the circular economy in action.
Low carbon chemicals produced through the LanzaTech process have been used in surfactants for detergents by Unilever. L’Oréal has used the ethanol as a building block to make polyethylene for packaging; and fashion brand Zara produced a boutique range of dresses made with polyester fi bres, all made with industrial carbon emissions directly captured and repurposed through LanzaTech technology. CarbonSmartTM products can either mechanically recycled or chemically recycled using LanzaTech’s process, which couples gasifi cation with gas fermentation. Through this chemical recycling process, end of life solid wastes are transformed to a synthesis gas that is converted by the microbes in the same way as industrial emissions. This enables the carbon to be infi nitely recycled, locking it into the circular economy.
Using biology enables multiple chemical products to be produced from recycled carbon using a wide range of waste gases. Steel mills can also switch production between valuable products as desired without changing the equipment and feedstock and while using a simple biological process. Traditional oil refi neries and petrochemical facilities require numerous complex reactor steps and large-scale complexes to achieve product fl exibility. LanzaTech technology is also future-proof as it can utilize a variety of gas streams without any noticeable alterations to equipment or technology. So, if the steel plant decided to move on from blast furnace to DRI, the technology will still integrate with new gas streams.
In response to the climate emergency the steel industry is reducing its emissions and will ultimately become carbon neutral and move towards producing green steel by 2050. But as the industry transitions there is no single pathway but a range of solutions that will both compete and integrate to lower emissions.
LanzaTech has the potential to transform carbon liabilities into valuable products for industries with carbon rich waste streams and create a circular carbon economy. �
