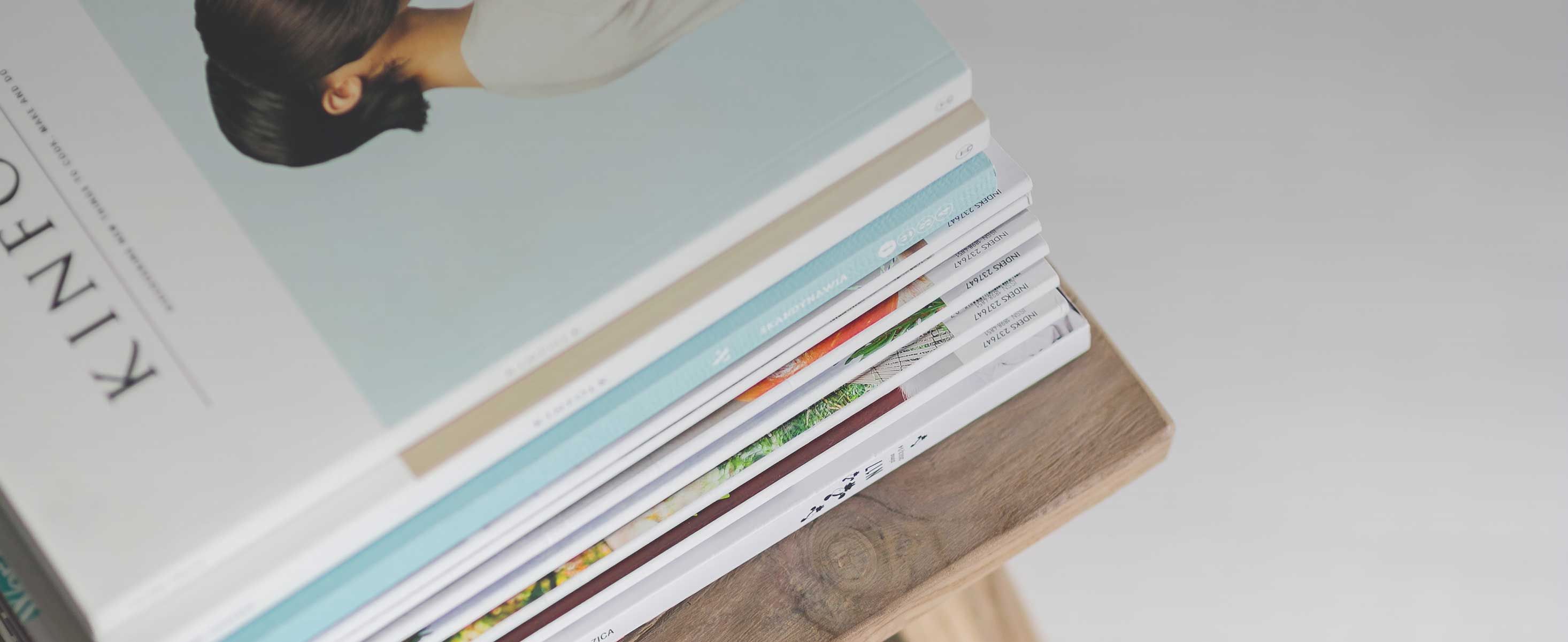
2 minute read
Food&Beverage / GARGANTINI
da essere certi di escludere qualsiasi possibilità di errore e/o perdita di informazioni. La soluzione adottata prevede l’identificazione dei prodotti con tag Rfid Omron resistenti ad alte temperature, la lettura/scrittura dei dati con antenne e controllori specifici e la realizzazione della tracciabilità tramite l’integrazione con un software di supervisione, specificatamente studiato per Conserve Italia. La soluzione Rfid messa a punto da Schneider Electric riguarda il controllo mescole per lo stampo di vaschette alimentari di diversi colori, spessore e consistenza. La produzione di tali vaschette, prevede prima dello stampo l’utilizzo di materie prime diverse che, mescolate tra loro, generano il foglio da usare per la termoformazione della vaschetta. Per garantire e automatizzare la scelta del composto corretto da fornire ai bocchettoni dei miscelatori, sono state installate antenne Rfid a 13,56 MHz sulla console centrale, mentre su ogni ghiera di aggancio del bocchettone è stata montata una Tag di capacità 256 byte; ogni antenna è stata collegata in comunicazione diretta una con l’altra in Modbus TCP/IP e connessa a un PLC e HMI della gamma Next Generation Machine Solution. Nel caso di Siemens, la tecnologia Rfid UHF ha permesso di ottimizzare i processi di Supply Chain per l’approvvigionamento di oltre 700 negozi in tutta Europa di una rinomata catena di negozi di alimentari e drogherie. Nei vari magazzini, l’identificazione e la verifica della correttezza nella movimentazione di tutti i carrelli durante il caricamento dei camion (140 camion al giorno) hanno permesso di minimizzare i tempi di consegna; anche in altri punti della rete di magazzini, l’utilizzo della tecnologia Rfid ha reso i processi logistici più efficienti e trasparenti. L’intero processo rappresenta una sfida logistica molto impegnativa, poiché fino a 25.000 carrelli devono essere ordinati e riempiti ogni giorno su due turni, evitando disservizi verso l’esterno e rallentamenti nei processi intra-logistici.
Digital Twin
Le potenzialità dei sistemi di simulazione si stanno manifestando in tutti gli ambiti del mondo della produzione e anche tutta la filiera dell’agroalimentare ne sta sperimentando i vantaggi e la vasta applicabilità. In tutte le fasi del processo produttivo, dalla coltivazione dei prodotti della terra, alla trasformazione industriale, al confezionamento e alla distribuzione, poter simulare nel mondo virtuale i processi consente di descrivere e osservare le loro interazioni reciproche e quelle con l’ambiente per poi trasferirle nel mondo reale col risultato di ottimizzare i processi e, nel caso del settore alimentare, assicurare più facilmente una corretta alimentazione a tutta la popolazione mondiale, in costante crescita, utilizzando una minor quantità di risorse.
È il grande vantaggio del Digital Twin, il gemello digitale, che sviluppa ed estende le performance dei sistemi di progettazione assistita da computer (CAD) degli inizi dell’era informatica, passati poi al rendering 3D di modelli di asset e successivamente alla simulazioni di processo. Oggi il concetto di gemello digitale si è affermato e le possibilità di simulazione sono aumentate a dismisura, facendo tesoro anche delle risorse offerte dai Big Data e dall’Intelligenza Artificiale. Il Digital Twin è in pratica una replica virtuale di un determinato processo reale, collegata al mondo reale tramite sensori che raccolgono dati continuamente elaborati con avanzati strumenti di analisi.

Nel caso della catena di produzione alimentare, da tempo si stanno sviluppando modelli matematici dei processi; la modellazione può essere basata, a seconda della complessità del processo, sull’osservazione diretta oppure può essere completamente basati sulla fisica-chimica: in anni recenti ci sono stati notevoli avanzamenti nella comprensione di fenomeni che si verificano durante la lavorazione degli alimenti, come il flusso dei fluidi, il trasferimento di calore e massa e la deformazione meccanica, e queste conoscenze sono state utilizzate per progettare nuovi processi alimentari o per ottimizzare quelli esistenti. La modellazione è maturata con lo sviluppo di approcci multiscala, multifase e multifisici; nel contesto della digitalizzazione dell’industria e con l’avvento dell’Internet of Things, sono emersi strumenti numerici e piattaforme software sempre più complete che consentono di migliorare le conoscenze e ottimizzare progetti e processi.
La diffusione dell’approccio Digital Twin nell’agroalimentare è appena iniziata e molte verifiche restano da fare per valutarne pienamente l’estendibilità e la convenienza. Tra i vantaggi attesi possiamo indicare senz’altro: la ridotta variabilità interprodotto, una migliore qualità e durata di conservazione, la minimizzazione delle perdite, la riduzione dell’utilizzo delle risorse, una migliore manutenzione, una miglior logistica, l’ottimizzazione della produzione, il risparmio energetico e, naturalmente, una riduzione dei costi.

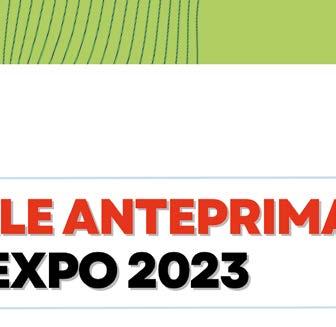
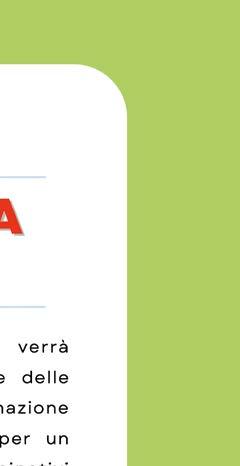
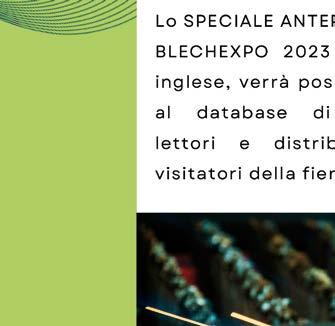
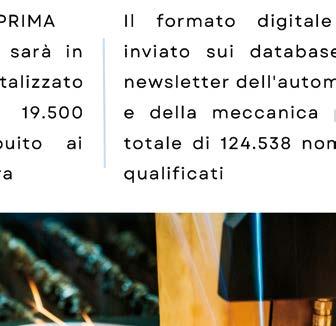
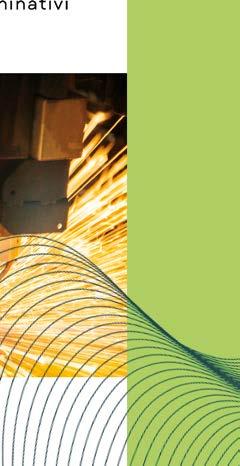
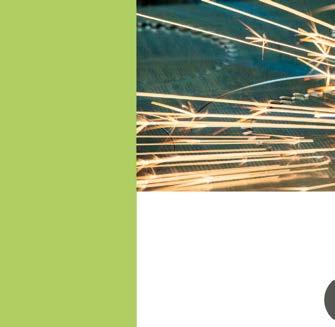
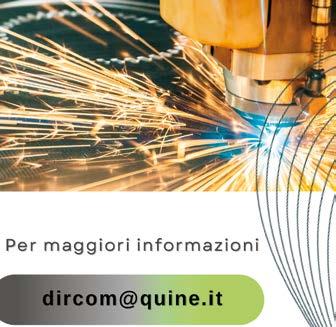