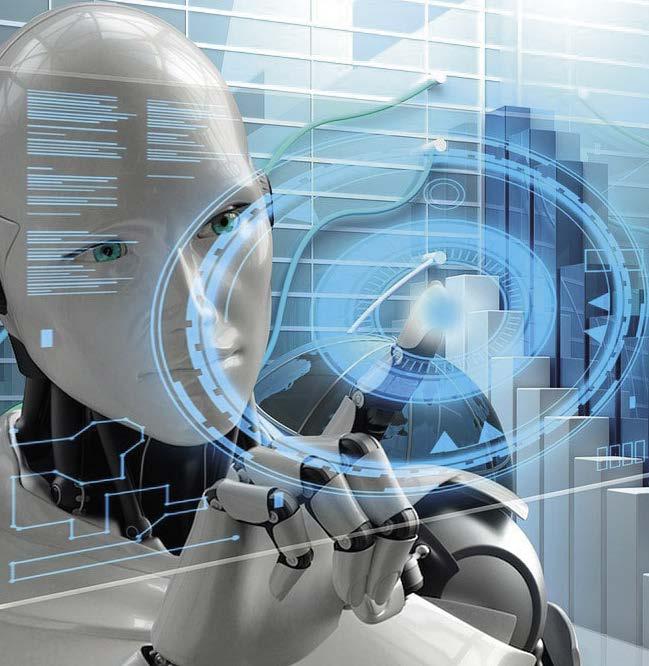
9 minute read
Automazione avanzata per l’industria intelligente
di Mario GargantiniDigital trasformation
AUTOMAZIONE AVANZATA PER L’INDUSTRIA INTELLIGENTE
Un modello reticolare indirizza lo sviluppo dei sistemi produttivi, dove le nuove tecnologie consentono di collegare il mondo fisico e quello digitale. Software di Intelligenza Artificiale trasformano i dati in informazioni mentre la costruzione di prototipi virtuali di processi e prodotti permette di ottimizzare tutte le fasi del manufacturing, dalla progettazione alla manutenzione. Con una particolare attenzione al tema della sostenibilità ambientale.
S
Si iniziano a delineare gli scenari dell’industria del futuro: la digital transformation sta entrando prepotentemente nel manufacturing e i cambiamenti non coinvolgono soltanto le grandi organizzazioni ma arrivano a toccare anche le realtà medio piccole e in generale tutto quello che ormai sempre più viene denominato “ecosistema digitale”. Un’idea già di come può cambiare e sta cambiando l’industria è emersa chiaramente nel corso del convegno “Le nuove frontiere dell’automazione”, svoltosi a fine maggio nell’ambito dei Digital Days di SPS Italia. Che la tradizionale piramide dell’automazione non rappresentasse più la struttura organizzativa e funzionale dell’industria era già abbastanza evidente da tempo, pur con i significativi aggiornamenti del modello nella sua parte alta dove, sopra il livello del controllo, erano collocati i sistemi MES, PLM e ERP. Nella nuova visione presentata da Cristian Sartori di Siemens, la piramide lascia il posto a una struttura reticolare dove sopra il livello del campo, con le sue macchine sempre più accessoriate con sensori e interfacce, si colloca uno strato popolato di sistemi di controllo e di edge computing tra loro interconnessi e collegati al Cloud; sopra ci sono ancora MES, PLM e ERP ma non stratificati bensì collegati a tutto il sistema di Industrial Internet of Things (IIoT) e alle applicazioni di Intelligenza Artificiale che utilizzano i Big Data e consentono di gestire in modo completamente innovativo aspetti come la manutenzione e la sicurezza.a Questo modello è quello più adeguato per indirizzare l’evoluzione del manufacturing che sta avvenendo a grande velocità. I sistemi produttivi hanno visto e vedono un’esplosione di complessità e si trovano sottoposti a una pressione competitiva senza precedenti; d’altra parte l’integrazione presenta qualche difficoltà e lo sviluppo tradizionale del software non riesce a tenere il passo. È necessaria una nuova gestione per collegare il mondo fisico e quello digitale. Il modello illustrato da Sartori vede l’organizzazione concettuale sviluppata su quattro livelli dove il primo è quello del campo e del controllo, con sensori, attuatori e controllori, il terzo è quello del Cloud dove sono sempre più evidenti i benefici derivanti dalla possibilità di portare i dati appunto sul cloud. In mezzo c’è lo strato relativo all’industrial edge computing e al di sopra c’è la piattaforma di sviluppo di applicazioni di tipo low-code. Il primo consente la raccolta dati e l’analisi locale aperta, veloce e scalabile; rende inoltre possibile portare sul campo tutte queste nuove tecnologia grazie alla gestione centralizzata delle applicazioni e relativo upgrade; infine porta a una riduzione dei costi organizzando efficacemente lo storage dei dati. L’altro strato è quello che consente lo sviluppo di applicazioni con metodologia low-coding, con un approccio visuale semplice, accessibile e aperto; consente la loro pubblicazione, su edge o su cloud, e garantisce il loro mantenimento. Questa struttura è quella che meglio sviluppa e sfrutta le novità introdotte nelle fabbriche dalla digitalizzazione.
Le persone al centro dell’ecosistema digitale
I contributi di Carlo Di Nicola di Ifm e di Marino Crippa di Keb hanno permesso di farsi un’idea del nuovo contesto in cui agiscono i sistemi produttivi: l’insieme dei reparti, degli impianti, delle macchine è sempre più intrecciato e avvolto nel già citato ecosistema digitale che determina e trasforma tutte le funzioni e le operation sulla base dei dati e della loro elaborazione. Il processo più frequente e decisivo che si svolge ininterrottamente nelle fabbriche che seguono il modello Industry 4.0 è il passaggio dal dato all’informazione che avviene attraverso una sequenza di passaggi che vedono in campo le principali tecnologie abilitanti. Possiamo quindi descrivere lo schema - tipo di questo processo partendo dalla singola macchina dove vengono individuati i punti qualificanti nei quali applicare una varietà di sensori – forza, vibrazione, temperatura ecc. – e di strumenti di misura smart; da qui un’enorme mole di dati grezzi viene convogliata verso sistemi di controllo
Digital trasformation
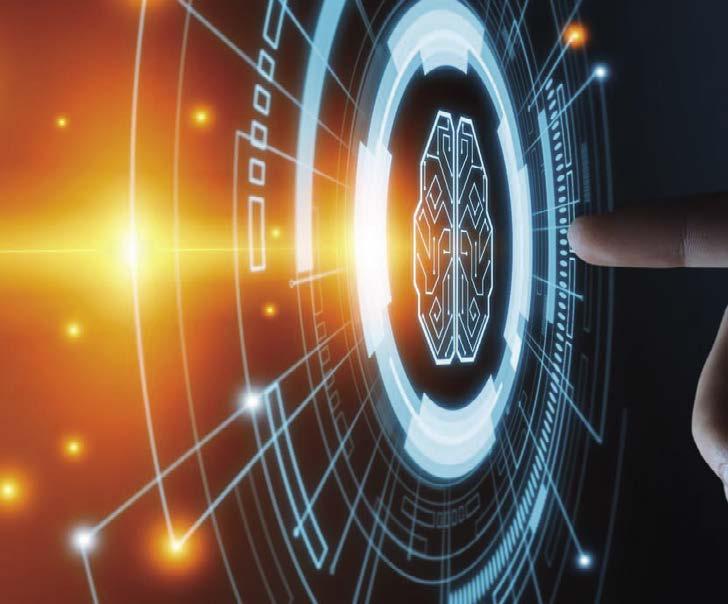
e di elaborazione che iniziano ad aggregarli per poi sottoporli a sofisticati e specifici algoritmi; infine, l’applicazione di software di Intelligenza Artificiale, di Machine Learning e Deep Learning consente di trasformare il dato in informazione e di passare le informazioni ai sistemi di livello più alto. Non è difficile intravvedere i vantaggi della digitalizzazione diffusa come pure non si possono ignorare le criticità. Tra i vantaggi va citato il risparmio di risorse informatiche, la semplificazione delle interfacce che non richiede la presenza di esperti informatici, la possibilità di trasformare i dati in informazioni e quindi poter intervenire efficacemente in caso di problema e malfunzionamenti. I dati ormai si possono considerare come una commodity ma – come ha sottolineato Crippa - non è ovvio quali utilizzare e quali portare nel cloud e quali lasciare in fabbrica; come pure è importante lavorare sui processi, migliorarli perché possano meglio sfruttare le nuove risorse informatiche disponibili; ed è importante operare sulle architetture abilitanti, sempre seguendo un approccio open per poter connettere e organizzare in modo semplice e scalabile tutti i dati con la loro disomogeneità. È essenziale quindi l’orchestrazione di dati, processi e conoscenze delle persone che li governano; le persone restano al centro di tutto l’ecosistema digitale e le loro azione diventano ancor più importanti ed efficaci perché supportate dai dati e dalle informazioni che l’Intelligenza Artificiale ne ha tratto. Tra le criticità è doveroso segnalare – come ha fatto Di Nicola – la carenza di competenze tecniche adeguate all’ecosistema digitale da parte degli user, dei conduttori dei nuovi sistemi che vengono installati. Poi si nota ancora la permanenza dello scoglio del “primo investimento”, spesso manca il coraggio di fare il primo passo verso il digitale soprattutto per l’incertezza sui tempi di ritorno; questa criticità può essere superata facendo progetti semplici, pragmatici e con benefici a brevissimo termine. Infine c’è da registrare la debolezza delle infrastrutture informatiche di molte PMI: per questo una soluzione è sicuramente l’utilizzo del cloud, insieme a una attenta ottimizzazione di tutte le risorse impegnate nel digital.
Innovazioni in fabbrica
Il nuovo scenario della fabbrica intelligente trova già diverse interessanti esemplificazioni, alcune delle quali hanno trovato posto nel convegno di SPS. Un esempio è stato offerto da Rittal e illustrato da Alberto Gironi che ha mostrato il valore dell’innovazione nella produzione dei quadri elettrici. L’iter innovativo è partito da un’analisi degli attuali processi produttivi che si sviluppano secondo questa sequenza: disegno e progetto, scelta e quotazione, ordine e consegna, lavorazioni, assemblaggio e cablaggio, installazione e service. L’analisi ha rilevato alcuni aspetti che richiedono un intervento innovativo e migliorativo: troppo spesso la qualità non costante; i tempi di produzione sono in genere troppo lunghi; c’è una ridondanza delle lavorazioni, molte fatte a mano; le offerte non vengono supportate da dati coerenti; la documentazione as built è molte volte imprecisa. A fronte di questo sono stati fissati alcuni obiettivi di cambiamento, relativamente a: miglioramento della qualità dei prodotti, riduzione dei tempi di produzione, sostenibilità delle offerte, ripetibilità della produzione. Le tecnologie abilitanti per conseguire tali obiettivi non mancano e permettono una progettazione che porta alla realizzazione di un gemello digitale del prodotto, in 3D; da questo si possono estrarre dei file da inviare alle macchine di produzione che eseguono le varie operazioni, dalle forature, all’assemblaggio meccanico, ai cablaggi. Si può quindi ripercorrere la sequenza indicata prima e riformulare tutti i passaggi “in digitale”. Si possono poi individuare le principali aree di criticità e quantificare gli ambiti di miglioramento: dalla predisposizione dei componenti, alla fabbricazione dei fili, all’etichettatura dei dispositivi, all’assemblaggio delle morsettiere, all’in-
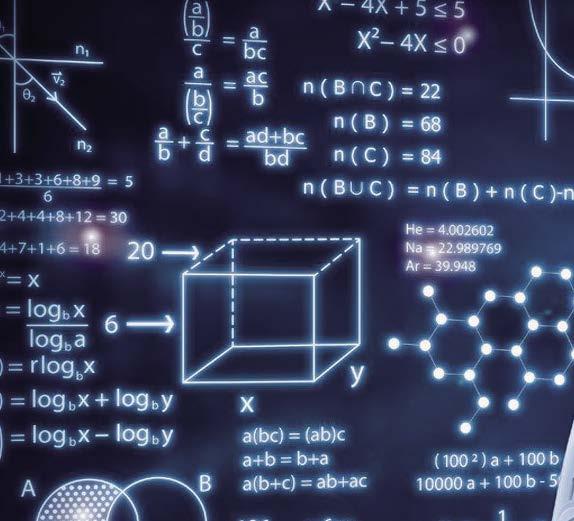
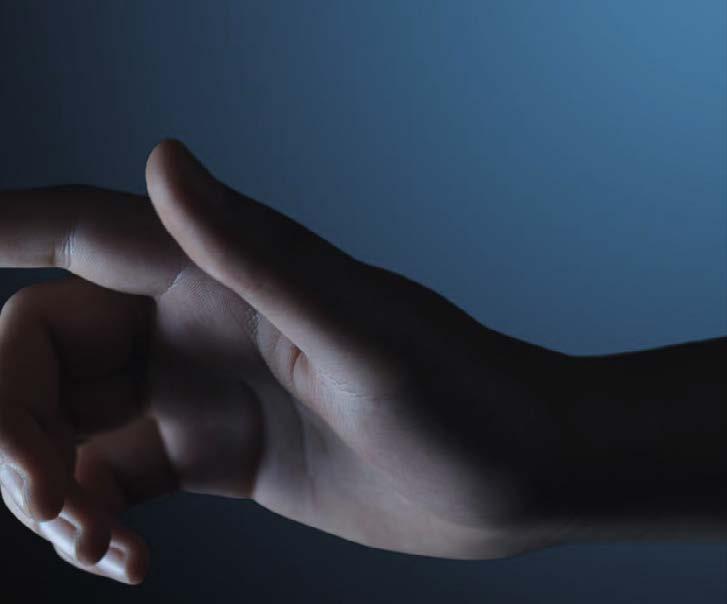
stallazione meccanica; per ciascuna si possono bilanciare tempi di esecuzione e costi e arrivare a un miglioramento complessivo sensibile che giustifichi l’investimento fatto e preveda un ritorno in tempi accettabili. “Un sistema così integrato – osserva Gironi - evita ridondanze, ri-lavorazione e scarti di produzione. Il dato dal progetto alla produzione e alla manutenzione ci guida fino al completamento delle operazioni, in pura logica 4.0. Tempi di produzione ridotti garantiscono il rispetto delle consegne e l’aumento dell’efficacia produttiva dell’azienda”. Il secondo esempio, presentato da Marco Lombardi e da Filippo Marabelli di Lenze Italia, riguarda la manutenzione avanzata e il virtual commissioning applicato ai magazzini automatici, che sono ormai parte vitale di molti processi produttivi. Le nuove sfide che i magazzini automatici devono affrontare oggi sono legate alle performance, ai tempi di progetto e ai costi. Sempre più processi produttivi dipendono dalla disponibilità continua di un magazzino di stoccaggio, con prodotti disponibili h24 per consegne in tempi brevissimi; i tempi di fermata del magazzino ha costi importanti per la produzione, spesso non recuperabili; al magazzino si richiede quindi la massima performance senza che questo incida sulla disponibilità. Inoltre tempi di progetto sono sempre più limitati e il numero di risorse non aumenta al pari del numero di progetti mentre c’è da notare che i tempi di commissioning rappresentano un buon 25% del progetto. A queste esigenze viene incontro l’impostazione architetturale che si sta sempre più affermando: è quella basata sull’approccio controller based, nel quale l’intelligenza è spostata dal drive a un controllore che gestisce tutte le funzionalità della macchina e ne aggiunge di nuove e prima impensabili, come ad esempio il controllo delle oscillazioni della colonna o la gestione dell’efficienza energetica. Insomma, il trasloelevatore diventa intelligente e interconnesso e ciò consente operazioni come il Condition monitoring, cioè il monitoraggio continuo dei dati macchina per identificare i cambiamenti che indicano danni o usura; o come la Diagnostica predittiva, cioè la previsione di eventi dannosi o il calcolo della probabilità che essi accadano. Se poi applichiamo le tecnologie di virtual commissioning, anche sul fronte dei tempi otteniamo sensibili vantaggi. Questo perché i processi di engineering (meccanico, elettronico, software) vengono gestiti in parallelo e non in modo sequenziale e ciò riduce la complessità ed evita la ridondanza dei dati; il risultato finale infatti è la costruzione di un modello che può essere implementato su una virtual machine che simula e anticipa il commissioning vero e proprio, testando tutta la parte di logica e controllo del sistema-macchina. La disponibilità della virtual machine inoltre facilita il training degli operatori, che non deve aspettare che la macchina sia completamente assemblata; e offre vantaggi anche after sale, consentendo di sviluppare nuove funzionalità senza dover interrompere il ciclo produttivo della macchina.
Trasformazione digitale e sostenibilità
Un tema trasversale, che ormai non può essere disatteso da chiunque si occupi di innovazione e di trasformazione dell’industria, è quello della sostenibilità ambientale e, nel suo ambito, quello della gestione dell’energia. La trasformazione digitale delle aziende viene incontro anche a questo tipo di esigenze, come hanno documentato i partecipanti al convegno SPS. Sono molti i sistemi nei quali l’attività delle macchine viene analizzata in tempo reale, prelevando i dati direttamente a livello macchina per poi, tramite opportuni algoritmi di Intelligenza Artificiale, accertare la correttezza dell’utilizzo di corrente e arrivare a una valutazione energetica; altri implementano specifici moduli per monitorare l’efficienza energetica. In ogni caso, sono sempre le tecnologie digitali che si pongono come fattore di innovazione, e anche in campo ambientale si pongono come elemento decisivo e uniformante di trasformazione dei processi e dell’intero assetto aziendale.
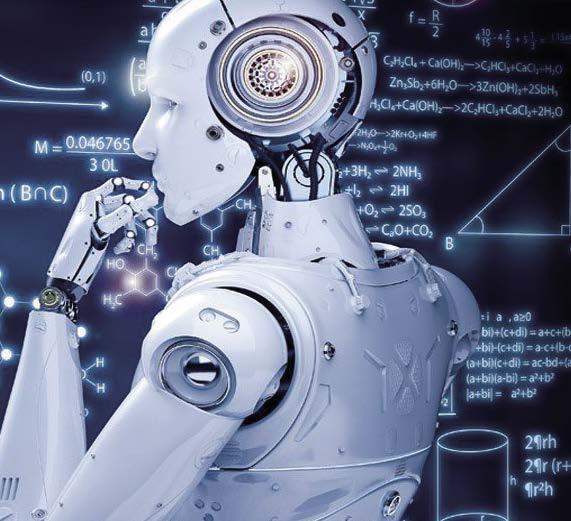