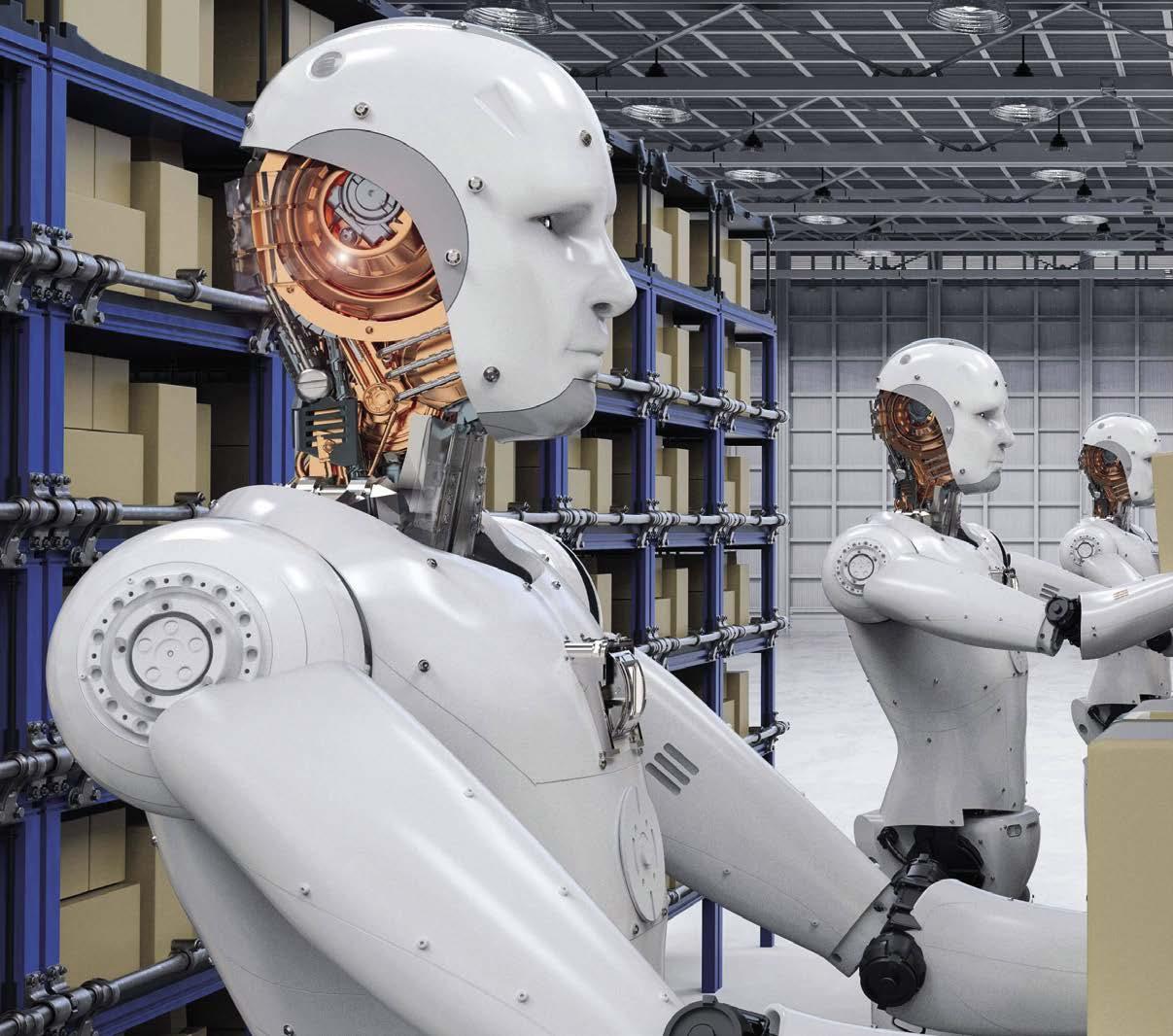
8 minute read
Robotica e Meccatronica per la fabbrica di domani
Non si arresta l’avanzata dei robot nel mondo della produzione. Macchine sempre più integrate, intelligenti, autonome e collaborative. Sistemi mobili, interconnessi e versatili superano la separazione tra plant produttivo e logistica. Mentre si diffondono i sistemi di trasporto a levitazione magnetica.
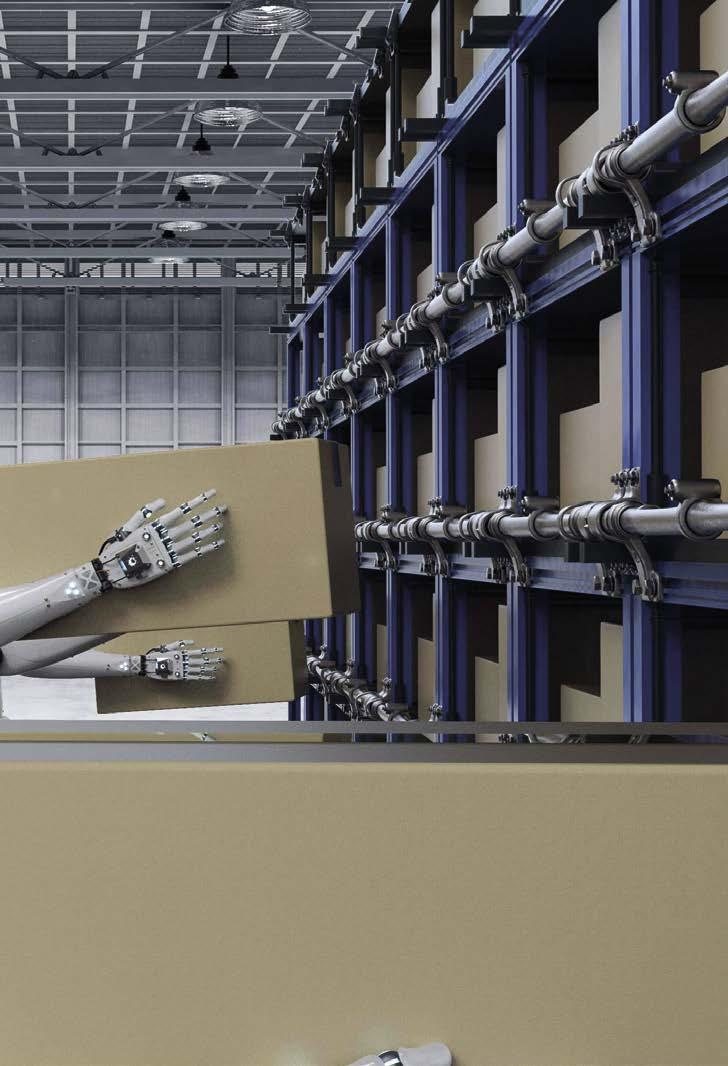
L’obiettivo di una produzione realmente flessibile e personalizzata è L’ sempre più vicino e sono molte le realtà industriali che se ne stanno accorgendo e che stanno applicando a tale scopo, con significativi risultati, le nuove tecnologie emergenti in particolare nel campo della robotica e della meccatronica. Ne hanno parlato, offrendo eloquenti esemplificazioni, esponenti di alcune aziende che hanno partecipato a una sessione dedicata proprio a questa tematica nel corso dei recenti Digital Days organizzati da SPS Italia sulla piattaforma Contact Place. L’avanzata della robotica a livello mondiale è impressionante: negli ultimi 20 anni l’utilizzo dei robot è più che raddoppiato e ha modificato sensibilmente il panorama delle fabbriche. Limitandoci alla situazione degli Usa, se nel 1995 c’era una quota di robot pari a 0,49 ogni mille lavoratori, nel 2017 tale quota è salita a 1,79. D’altra parte dal mondo della produzione emergono una serie di richiesta quali: una capacità di gestione di applicazioni sempre più complesse, una maggior integrazione tra meccanica e software, una maggior sicurezza nel rapporto uomo-macchina, la possibilità di rapidi cambi di produzione e di rimodulazione degli impianti, la riduzione dei tempi di commissioning e startup, una ricerca guasti più veloce, una raccolta dati semplificata.
Robotica sempre più integrata
Sono tutte esigenze che portano ad affermare l’importanza – come ha sottolineato Michele Scarpulla di Rockwell Automation – di una maggiore integrazione della robotica nel mondo PLC. Il robot non è più una cella a se stante ma sta diventando una componente intelligente dell’impianto che quindi va ad integrarsi nel sistema di controllo generale. È necessario perciò trovare per ogni applicazione il giusto PLC, il giusto software, i tool giusti che riescano a assolvere a un insieme di funzioni. Integrazione del robot nel PLC significa che non c’è più un controller specifico per il robot che diventa una componente funzionale del PLC il quale a sua volta controllerà tutto del robot. Il vantaggio è evidente: in un solo tool di sviluppo, acquisizione dati, debugging, scambio dati veloce si possono integrare in modo semplice tutti i componenti di un impianto. Il crescente ruolo dei robot nell’industria aumenta l’esigenza di prestazioni elevate e di una grande affidabilità dei sistemi messi in campo. In proposito, uno degli aspetti importanti, messo in evidenza da Paolo Guglielmone Pasquini di Murrplastik Italia è quello dell’allestimento: “avere un buon allestimento significa evitare problemi fino al fermo macchina. Le esigenze di un buon allestimento robotico sono tali che la configurazione dei robot viene affidata ad aziende specializzate nel creare ad hoc soluzioni industriali robotizzate”. Non basta quindi collocare i robot sulle linee di produzione: il robot deve essere “vestito” per lo specifico lavoro che deve svolgere e perciò ci vuole un “sarto” che gli confezioni l’abito adatto, con i materiali e i supporti idonei per potersi muovere in piena libertà, senza costrizioni e rischi di rottura. I prodotti destinati ai robot presentano sfide in termini di proprietà meccaniche, chimiche e termiche: devono infatti resistere ad accelerazioni e decelerazioni molto rapide, a trazioni, compressione e torsione oltre che e ai milioni di cicli di flessione; inoltre
può essere necessaria la resistenza alle alte temperature, all’olio e a vari altri prodotti chimici. Una priorità assoluta deve essere data alla salvaguardia della sicurezza, insieme all’affidabilità delle soluzioni di sistema. Tutto ciò assume una rilevanza ancora maggiore nel caso dei robot collaborativi, i Cobot, che sono sempre più utilizzati da un’ampia tipologia di aziende. Gli equipaggiamenti per i Cobot sono studiati per semplificare la progettazione della configurazione ottimale e per garantire un montaggio semplice e veloce oltre a un’ergonomia sicura per le applicazioni vicine all’uomo. La proposta di Murrplastik prevede dress-pack personalizzati per Cobot di qualsiasi forma, dotati di supporti con strutture variabili a strappo in materiale antiscivolo.
Le sfide della mobilità
Così impostati e così equipaggiati, i robot possono m dare un valido contributo per l’affronto di alcune sfide presenti in un plant produttivo moderno. Una di queste è la sfida dell’intralogistica. Attualmente – osserva Marco Mina di Omron Electronics - una grande quantità di materiali viene spostata manualmente; inoltre il personale sposta carrelli, manovra transpallet e guida muletti. “Questo tipo di trasporti non è flessibile, è difficile da tracciare, non sicuro e, soprattutto, non rispondente alle esigenze produttive odierne”. Le aziende, per completare il processo intralogistico, devono spostare merci e componenti nei loro plant, da piccoli particolari a grandi pesi, inclusi pallet. Tutte queste problematiche possono essere adeguatamente affrontate con l’impiego di robot mobili, quelli che attualmente vengono denominati AMR (Autonomous Mobile Robot): la loro caratteristica principale è di non aver bisogno di riferimenti fissi per navigare grazie all’utilizzo di una mappa che hanno memorizzato e imparato a leggere; sono così in grado di evitare ostacoli e di ricalcolare i percorsi se diventano impraticabili. La flotta di robot mobili viene governata dal Fleet Manager, che raggiunge i singoli robot tramite connessione wi-fi e si connette allo shop floor e ai PLC tramite SQL; il collegamento con le parti superiori del sistema aziendale, MES, WMS o ERP, è assicurato da opportune applicazioni software. Il Fleet Manager ottimizza l’efficienza, assegnando intelligentemente i compiti e gestendo i movimenti e il traffico; massimizza la produttività fornendo aggiornamenti automatici a tutti i componenti e gestendo le ricariche; infine aumenta la flessibilità favorendo la facile integrazione con i sistemi IT e gestendo anche flotte miste. Anche Sew Eurodrive Italia parla di robot mobili e inquadra la loro presenza nel contesto della fabbrica automatizzata. Franco Zannella mostra un’infrastruttura hardware e software per AGV. La piattaforma di automazione, con la combinazione di moduli e prodotti, riesce a dare una risposta anche alle problematiche di queste flotte di sistemi mobili, in termini di: controllo della navigazione dei veicoli, controllo della flotta, controllo della potenza locale, gestione intelligente dell’energia, gestione e trasporto dei carichi, comunicazione verticale e machineto-machine, sicurezza funzionale. Saranno i system integrator poi a integrare tutta la specifica componentistica meccanica ed elettronica per mettere a punto i singoli veicoli come pure a connettere tutti i componenti necessari per automatizzare gli AVG: dai servoazionamenti, ai PLC di sicurezza, ai motion controller fino ai pannelli operatore. Il tutto in un’unica piattaforma, come viene sempre più richiesto dalle aziende, sia dai costruttori di macchine che dagli utenti finali. Sempre in tema di mobilità e nella prospettiva di una produzione adattiva e flessibile, è interessante considerare una nuova tecnologia come quella dei sistemi di trasporto basati sulla levitazione magnetica che aprono la strada alla swarm production, la produzione a sciami.
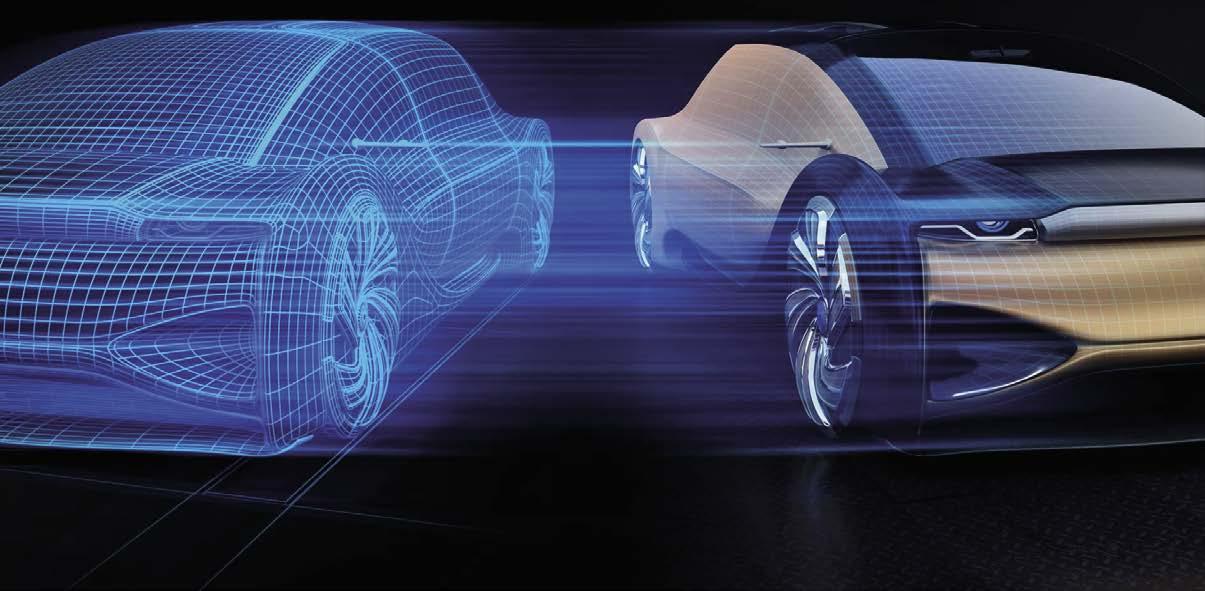
L’hanno raccontata Davide Poli di B&R Automazione IndustrialeB&R e Sergio Beretta di Beckhoff Automation, mostrandone le grandi potenzialità. Si tratta di sistemi formati da alcuni shuttle sui quali sono presenti dei magneti permanenti che li mettono in condizioni di poter fluttuare su una superficie piana, come moderni “tappeti volanti” tecnologici. Poli ha descritto un sistema che mette a disposizione dell’utente sei gradi di libertà: due riguardano il movimento bidimensionale, che facilita la condivisione dello spazio di lavoro e delle stazioni di processo e favorisce una riduzione dell’ingombro di macchine e linee; una riguarda la levitazione, cioè il movimento senza contatto; altre due riguardano il rollio e beccheggio, e consentono la funzionalità “antisloshing” avanzata; c’è poi l’imbardata, che segue l’orientamento dei prodotti e semplifica molti processi; infine le funzioni convoglio, per la quale uno shuttle virtuale controlla diversi shuttle reali, e il collegamento meccanico che permette l’incrocio di traiettorie e lo svolgimento di processi paralleli, ottimizzando lo spazio di lavoro. Beretta ha descritto sistemi di flying motion adatti per trasportare vari tipi di carichi, con diversi pesi e dimensioni. La macchina volante si integra in un sistema a carrelli indipendenti, con percorsi flessibili e configurabili via software; sempre il software gestisce alcune funzionalità, come ad esempio la rotazione o l’orientamento prodotti. La tecnologia sottostante è molto avanzata: ad esempio per la gestione del feedback, cioè della posizione degli elementi mobili, che è un problema matematicamente molto complesso, si ricorre ad algoritmi di Machine Learning che generano modelli sulla base dei dati raccolti dai sensori. Tra i vantaggi di queste applicazioni a levitazione ci sono senz’altro, oltre alla flessibilità, l’assenza di usura meccanica e una notevole condizione di pulizia e ordine durante i processi lavorativi. Le applicazioni sono numerose ma risultano particolarmente efficaci nei settori alimentare, farmaceutico, microelettronico.
Prospettive dell’Advanced Manufacturing
Tutte le soluzioni e applicazioni mostrare fin qui trovano una loro collocazione e possono essere meglio apprezzate all’interno di una più organica visione dell’Advanced Manufacturing che è emersa un po’ da tutti i contributi proposti al convegni di SPS ma che è stata sinteticamente illustrata da Olgu Can Yilmaz di Bosch Rexroth. Considerata la crescente complessità dei sistemi produttivi attuali è evidente la necessità delle aziende di incrementare efficienza e semplicità in specifiche aree produttive quali: la logistica interna ed esterna, le macchine automatiche di produzione, la raccolta dati relativi ai processi produttivi e all’ambiente. L’aumento di efficienza si può ottenere agendo su tutti i fattori produttivi ma non singolarmente bensì visti come un ecosistema digitale interconnesso; è possibile quindi agire su un backbone, basato sui dati, che connette unitariamente il mondo dell’automazione e l’IT. Si opera così in un ambiente monitorato in real time, con un flusso della logistica ottimizzato e la movimentazione dei materiali sicura ed efficiente. Anche le performance produttive vengono monitorate in tempo reale, grazie alle piattaforme IoT che analizzano il comportamento di ogni macchina e raccolgono dati per tracciare la qualità dei vari processi o lo stato di salute delle macchine per fare quindi manutenzione predittiva, per ridurre gli scarti, per garantire la sicurezza e per aumentare l’efficienza energetica. Il superamento della separazione tra mondo della produzione, mondo della logistica e maintenance è uno dei punti di forza del nuovo approccio ecosistemico, con un insieme di vantaggi strutturali sintetizzati così da Ylmaz: riduzione della complessità, aumento della produttività, possibilità di un reale Just-In-Time, riduzione dei tempi di engineering e di setup, stabilità e continuità dell’intero sistema.
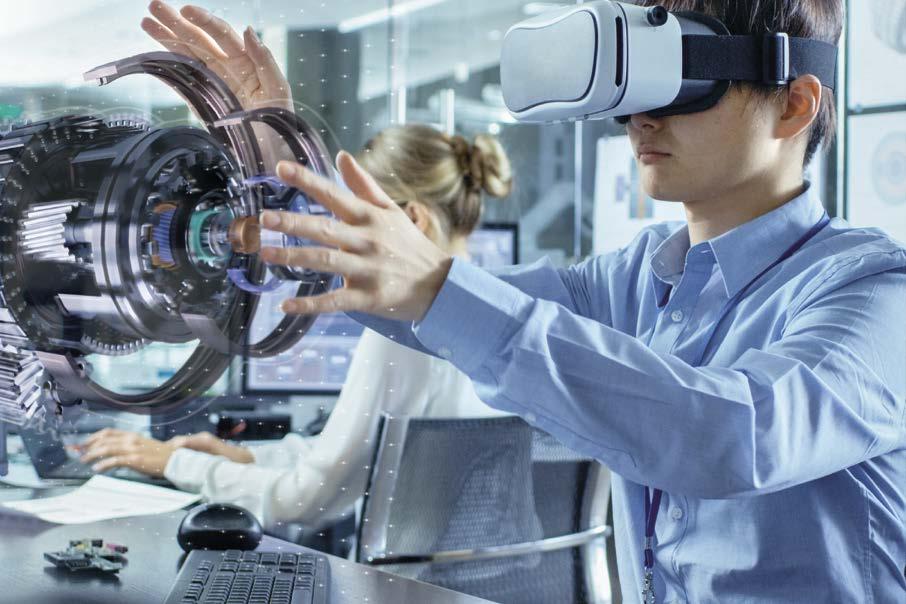