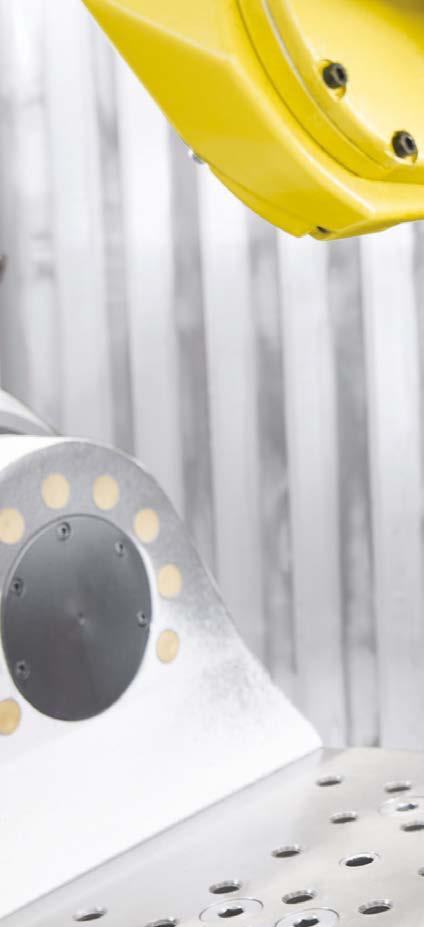
13 minute read
serraggio e fissaggio
ALTA RIPETIBILITÀ, RAPIDITÀ D’USO, SEMPLICITÀ, GRANDE VERSATILITÀ E FLESSIBILITÀ, MODULARITÀ E POSSIBILMENTE BASSI COSTI: QUESTE LE
CARATTERISTICHE DI UN BLOCCAGGIO E FISSAGGIO OTTIMALI DEL PEZZO PER RIDURRE TEMPI DI ATTREZZAGGIO E
SSolo grazie ad una elevata capacità di innovazione e di ottimizzazione dei processi produttivi è possibile competere in un mercato globale sempre più esigente, che richiede pezzi sempre più complessi e precisi, lavorati nel modo migliore e nel minor tempo possibile. È quindi grazie a tecnologie innovative e sempre più performanti che i moderni centri di lavoro e le nuove macchine multi-tasking riescono ad eseguire lavorazioni sempre più precise. Tuttavia, la macchina utensile, anche se di ultima generazione, da sola non basta ad eseguire una lavorazione per asportazione di truciolo di successo! A questo risultato concorrono, infatti, sinergicamente una serie di fattori che sono imputabili tanto alla macchina quanto all’utensile, alle attrezzature, al corretto posizionamento del pezzo sulla macchina e al suo bloccaggio, dove con “posizionamento” si intende la relazione tra la posizione dell’utensile e quella del pezzo, mentre con “bloccaggio” ci si riferisce al sistema che consente di mantenere il pezzo in una determinata posizione, pur sotto l’effetto delle sollecitazioni della lavorazione.
Questi due aspetti vengono solitamente identificati con i concetti di “serraggio e fissaggio”, con i quali si fa riferimento all’ottimale posizionamento del pezzo, in maniera che esso sia solidale con il sistema a cui è collegato e così sia impossibilitato nel movimento, evitando il più possibile vibrazioni e deformazioni. Per soddisfare l’esigenza di lavorazioni sempre più performanti ed efficienti, occorre che tutto il sistema produttivo sia collaborativo, che tutti gli elementi del processo lavorino, appunto, in maniera collaborativa e sinergica: il serraggio, in tal senso, svolge un ruolo chiave.
Di fatto un pezzo non perfettamente fissato, un sistema di bloccaggio che lascia tracce indesiderate, che richiede tempi lunghi di attrezzaggio macchina, possono rendere inutile qualsiasi successiva operazione volta a rendere il processo high performance. Per essere competitivi sui mercati, servono serraggi efficienti e precisi che riducano notevolmente i tempi di allestimento e sostituzione, perchè la gestione rapida e semplice dei pezzi è un fattore decisivo per ridurre al minimo i tempi non produttivi.
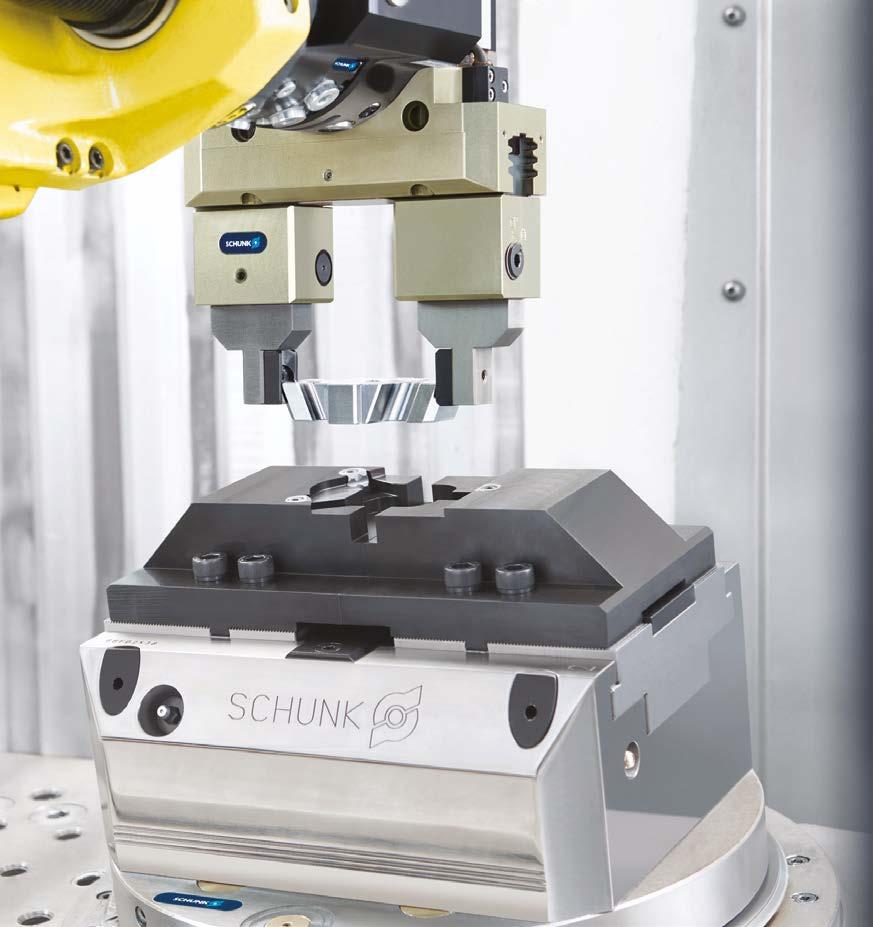
Negli anni, l’importanza del serraggio è divenuta sempre più centrale, tanto da essere oggetto di sperimentazioni e studi che hanno portato ad individuare un’ampia varietà di soluzioni tecnologiche, in grado di rispondere adeguatamente alle esigenze delle moderne realtà produttive. Dagli ingombri al passaggio utensile, dal mandrino a tutti gli eventuali accessori presenti, lo studio dell’attrezzatura di staffaggio può richiedere tempi di progettazione e costruzione anche lunghi, ma, evidentemente tutti i fattori sono determinanti. In questo gioco di squadra, le attrezzature di serraggio devono essere costantemente manutenute e verificate, in modo da garantire un bloccaggio sicuro e riproducibile.
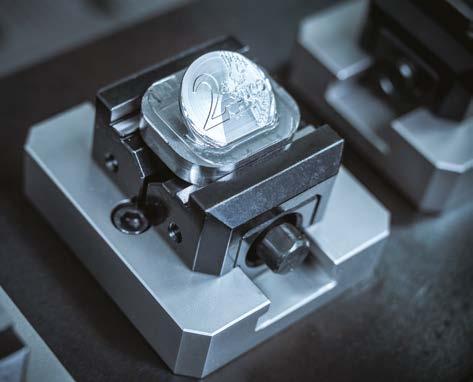
Soluzioni sempre più innovative vengono richieste anche nel settore dei sistemi di fissaggio, per i quali vengono proposte soluzioni specifiche ed elementi di collegamento in grado di soddisfare tutte le esigenze di applicazioni che necessitino, in particolare, di elevata resistenza alla trazione e allo strappo. Molti di questi elementi di collegamento offrono soluzioni universali e intelligenti, che trovano il loro utilizzo nei settori automobilistico, navale, produzione di mobili, costruzione di macchine e in molti altri campi. Che si tratti di auto-aggancianti, inserti filettati, rivetti, bulloni a strappo o altri elementi di fissaggio rapidi utilizzati negli assemblaggi, i moderni sistemi di fissaggio richiedono una forte tenuta alla resistenza meccanica in parti soggette ad alte vibrazioni e sono in grado di fornire la corretta soluzione per ogni settore o applicazione industriale.
Il serraggio del pezzo
Riuscire ad anticipare le richieste del mercato è l’unico modo per rimanere competitivi e per avere un vantaggio sulla concorrenza. Nelle lavorazioni meccaniche, questo è possibile dedicando un forte impegno nella ricerca e nello sviluppo di attrezzature di presa pezzo innovative, che perseguano l’obiettivo di massimizzare performance e flessibilità. L’esatta conoscenza di posizione e orientamento del sistema di riferimento del pezzo rispetto a quello della macchina, il mantenimento della posizione durante la lavorazione e la compensazione delle sollecitazioni dovute alle forze in gioco, sono i tre principi da perseguire per raggiungere gli obiettivi richiesti ad un moderno sistema di serraggio, indipendentemente dal tipo di lavorazione.
La definizione del riferimento rispetto allo spazio di lavoro, un bloccaggio stabile che non induca a deformazioni, la considerazione delle possibili variabili legate alle tecnologie del processo, sono elementi che garantiscono di ottenere complessivamente il miglior risultato possibile, coerentemente con il tipo di applicazione. Tutti concorrono alla definizione di un sistema ottimale per ogni impiego, per ogni utensile e ogni lavorazione, sempre nel rispetto del fattore costo.
Per quanto riguarda il dimensionamento dell’attrezzatura, il riferimento è al posizionamento isostatico del pezzo nello spazio, che a partire dai 6 gradi di libertà richiesti, comporta la loro progressiva eliminazione fino ad arrivare al numero minimo di punti di contatto tra pezzo e attrezzatura. Oggi, anche grazie al diffondersi di soluzioni standardizzate, il setup è virtuale, effettuato con software dedicati che consentono una pianificazione della produzione estremamente realistica, con conseguente ottimizzazione del carico di lavoro delle macchine.
I sistemi di serraggio più diffusi sono di tipo modulare; grazie ad essi la produzione riesce ad adattarsi celermente alle crescenti richieste di flessibilità, con tempi di sostituzione e approntamento ridotti al minimo. Questi sistemi possono essere visti come un kit di elementi combinabili, in funzione della forma, anche molto complessa, del manufatto da lavorare. I limiti dei primi sistemi modulari, ovvero il raggiungimento della flessibilità a scapito di rigidezza, forza di bloccaggio e compattezza dell’insieme – le grandezze tipiche di un sistema di serraggio – oggi sono pienamente superati da uno studio e un’ottimizzazione virtuale, possibile grazie alla definizione della “composizione” ottimale mediante le numerose librerie elettroniche fornite dai vari costruttori. Da ultimo, l’introduzione dei sistemi a punto zero permette di annullare i possibili errori dell’operatore nel posizionamento dell’attrezzatura.
Sistemi di serraggio e automazione
Anche la tendenza del mercato verso una maggiore automazione dei carichi macchina incide sulla tecnologia di serraggio: i dispositivi di serraggio vengono infatti progettati per rispondere più velocemente ai requisiti dei processi automatizzati. Fattori come l’accessibilità, la flessibilità e l’efficienza energetica della durata dei cicli, oltre all’affidabilità dei processi, diventano sempre più cruciali.
Inoltre, la crescente domanda di lavorazioni di piccoli componenti, legata a comparti come l’elettronica e la tecnologia medica, che acquisiscono sempre maggiori quote di mercato, comporta il superamento di diversi ostacoli e sfide, con particolare attenzione alla presa del pezzo da lavorare. Ma soprattutto, richiedono quella flessibilità nella lavorazione dei pezzi necessaria per adattarsi alla domanda, risolta anche con il ricorso alla costruzione modulare dei sistemi di serraggio, per i quali, ancora una volta, tempi di sostituzione e approntamento devono essere ridotti al minimo.
Così facendo, infatti, grazie all’ottimizzazione dell’uso della macchina, è possibile incrementare la produttività e ottenere un importante risparmio sui costi di eventuali altri acquisti.
Oltre alla facilità di montaggio, l’elevata flessibilità, la grande versatilità, il risparmio di tempo e risorse, i moderni sistemi di fissaggio e serraggio richiedono anche la precisione nella ripetizione della lavorazione. Per poter ottenere una corretta lavorazione, inoltre, è molto importante la fase di montaggio del pezzo sulla macchina; gli obiettivi da raggiungere sono la conoscenza della posizione e dell’orientamento del sistema di riferimento del pezzo rispetto a quello della macchina; il mantenimento della posizione durante la lavorazione e la compensazione delle sollecitazioni che nascono durante la lavorazione. I principali sistemi di bloccaggio per centri di lavoro possono essere, quindi, suddivisi in due grandi sotto insiemi: convenzionali e flessibili. Per effettuare la scelta del sistema più idoneo per una specifica applicazione è necessario analizzare tutte le condizioni di utilizzo e definire le caratteristiche del pezzo da realizzare necessarie al sistema di bloccaggio, il quale deve collocare il pezzo nello spazio di lavoro della macchina e bloccarlo in posizione stabile e senza deformazioni. La scelta dell’attrezzatura idonea deve essere tale da soddisfare le esigenze esplicitate dall’analisi delle superfici del pezzo, delle lavorazioni da effettuare in ogni fase e sotto-fase del processo, della precisione dimensionale e della tolleranza di lavorazione richiesta.
Il serraggio dell’utensile
Il serraggio dell’utensile incide in maniera significativa anche sulla durata dell’utensile e sullo stato di sollecitazione. Si tratta di un aspetto molto delicato, che deve tenere conto di numerosi fattori quali, ad esempio, la truciolatura, la precisione dimensionale, la qualità superficiale, nonché i tempi di lavorazione e l’usura dell’utensile; fattori che incidono sui costi globali di processo.
Quando non vengono richieste particolari prestazioni, il tipo di serraggio utensile più semplice da utilizzare è quello con il mandrino a pinza. Il compito del mandrino è quello di garantire il serraggio e la centratura dell’utensile montato, in modo da rendere la lavorazione precisa. Questo tipo di serraggio utensile può presentare dei limiti al crescere del livello di prestazioni e della precisione di lavorazione. In questi casi, la tendenza è quella di optare per mandrini che permettano una lavorazione più stabile e sicura, con una precisione anche elevata di run out (oscillazione) e conseguente migliore qualità superficiale, drastica riduzione delle vibrazioni e un aumento della durata del tagliente.
Il ruolo del mandrino
Il ruolo del mandrino è quello di garantire il serraggio e la centratura dell’utensile montato, in modo da rendere la lavorazione precisa, anche a velocità elevate. Questo presuppone una progettazione che assicuri una forza di serraggio tale da rispondere alle esigenze delle varie tipologie di lavorazione, anche in condizioni estreme, di forti sollecitazioni, su qualsiasi moderna macchina utensile CNC, anche di grandi dimensioni.
I mandrini autocentranti, composti da un corpo cilindrico portante, normalmente cavo, a tre o quattro griffe a gradini, regolabili, vengono solitamente impiegati nelle lavorazioni assiali simmetriche, quando la lunghezza del pezzo, rispetto al suo diametro, non è eccessivamente elevata. Le griffe, per interni o per esterni, vengono numerate, in modo che ciascuna griffe corrisponda a una determinata guida. Se il pezzo presenta una lunghezza elevata, potrebbe incorrere in deformazioni durante la lavorazione, quindi l’estremità libera viene fissata con una contropunta, che va a impegnarsi sul pezzo, precedentemente forato con un foro conico. Per il bloccaggio di pezzi snelli, nell’operazione di tornitura, per esempio, si possono utilizzare degli elementi detti lunette, che vengono impiegati per contrastare le forze di inflessione sull’albero. Da tempo, nelle lavorazioni di alesatura e fresatura di precisione, giocano un ruolo di primo piano i mandrini idraulici, in virtù della stabilità della concentricità, della precisione e dell’affidabilità dimostrata. Negli anni, la funzione dei mandrini si è evoluta e ampliata con la diffusione dei centri di lavoro a 5 assi, delle macchine multitasking e ad alta velocità, tanto da essere impiegati per eseguire le operazioni più diverse. A causa delle numerose applicazioni, gli attacchi idraulici sono oggi sviluppati ponendo particolare attenzione ai requisiti di precisione, miniaturizzazione, maggiore velocità e multifunzionalità, così come all’accessibilità del pezzo.
Il giusto dispositivo per ogni lavorazione
Il tipo di lavorazione determina la selezione del dispositivo di serraggio più idoneo. Nella tornitura, ad esempio, valgono dei criteri particolari, in quanto durante la rotazione dei componenti di tornitura, soprattutto nel caso di regimi elevati, si generano forze centrifughe che richiedono un bloccaggio particolarmente sicuro del pezzo.
Mandrini per il serraggio esterno o mandrini a espansione per il serraggio interno, con le griffe che spingono dall’interno e che, grazie al loro design e funzionamento, garantiscono un serraggio affidabile e precisioni di concentricità massime, per realizzare accoppiamenti precisi e ripetibili, sono quelli più idonei nelle lavorazioni di tornitura.
Nelle lavorazioni di finitura, tornitura, rettifica, dentatura e controllo, invece, hanno un ruolo primario i mandrini a espansione.
In generale, nelle lavorazioni in cui si sviluppano forze elevate, per la prevenzione delle vibrazioni, sono richiesti requisiti qualitativi altissimi per i sistemi di serraggio; è il caso, ad esempio, delle lavorazioni di fresatura su più assi, dove è necessaria anche un’elevata accessibilità del pezzo, per cui la soluzione di serraggio deve essere la più compatta possibile.
La moderna produzione nell’ambito della rettifica richiede invece sistemi di bloccaggio flessibili e con particolare precisione di ripetibilità.
Le scanalature presenti nel corpo dei mandrini assicurano una deformazione omogenea degli stessi, garantendo così una forza di serraggio uniforme e forte. Il vantaggio principale di queste soluzioni è che la manipolazione diventa molto più semplice, in quanto i trucioli non restano bloccati all’interno del mandrino. Grazie alla geometria e alla sigillatura delle cave interne, quest’ultime infatti non sono mai a rischio di infiltrazione di trucioli. Impedire la penetrazione dello sporco prodotto nel dispositivo, come ad esempio il pulviscolo, è determinate ai fini della precisione richiesta.
Inoltre questo li rende più facili da pulire, per esempio, quando si cambiano i diametri. Data la minore probabilità di tralasciare residui di lavorazione, l’affidabilità del processo di serraggio viene garantita con un maggior grado di sicurezza.
Il portautensile come parte di un sistema collaborativo
Come già accennato, la crescente diffusione dei centri di lavoro a 5 assi, delle macchine multitasking e ad alta velocità, ha portato i mandrini ad assumere un ruolo più ampio, tanto da essere utilizzati per eseguire le più diverse operazioni.
Per loro natura, i mandrini idraulici hanno un eccellente grado di precisione nell’oscillazione radiale ed assiale e sono in grado di trasmettere coppie di bloccaggio elevate. In tal senso vengono considerati portautensili ideali per i processi di lavorazione che richiedono un’elevata precisione, come foratura, alesatura, fresatura di precisione, grazie alla stabilità della concentricità, alla precisione e all’affidabilità dimostrata.
La scelta del giusto portautensile, nei più moderni centri di lavoro, influenza la buona riuscita della lavorazione. Data l’ampia gamma delle tecnologie di serraggio e la sempre maggiore importanza che stanno acquisendo le tecnologie di precisione, a seguito della migliorata qualità e delle prestazioni più performanti delle macchine utensili, solo un approccio sistematico può aiutare ad individuare il portautensile ottimale per ogni singola lavorazione.
È chiaro, infatti, che non esiste “il portautensili” per tutte le applicazioni. La selezione di una determinata tipologia è sempre una decisione unica che dipende da una varietà di parametri. Nella scelta, infatti, occorre confrontare i vari portautensili, in funzione delle caratteristiche tecniche e delle interfacce per il mandrino della macchina. Il portautensile non deve essere considerato un componente isolato, ma come elemento facente parte dell’intero sistema, che comprende: pezzo, utensile, portautensili, interfaccia del mandrino e macchina. Data l’interazione privilegiata e considerata la vicinanza con il pezzo, il portautensili svolge un ruolo cruciale, poiché può compensare parzialmente i punti deboli all’interno dell’intero sistema.
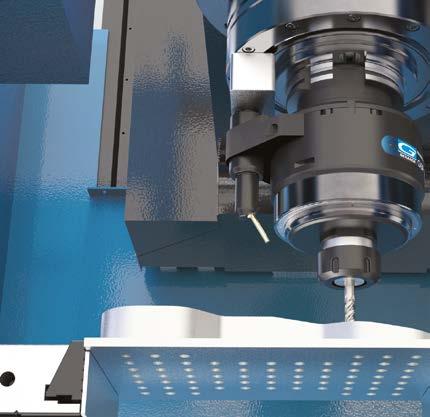
Bloccaggi sempre più sicuri
Le attuali macchine utensili di fresatura e tornitura richiedono componenti dagli elevati standard qualitativi anche in termini di resistenza alle aggressioni chimiche, oltre che alle sollecitazioni meccaniche e alle vibrazioni. In questo contesto, occorrono sistemi di serraggio che possano essere utilizzati universalmente e che assicurino i massimi livelli di precisione nelle lavorazioni. Per raggiungere questi obiettivi servono anche precisione nelle tolleranze e cura nelle finiture superficiali. Dal metodo meccanico a quello magnetico, passando per i sistemi a vuoto, le aziende del settore offrono una gamma completa per ogni tipo di esigenza produttiva per la presa del pezzo in tutte le sue modalità.
Il sistema di staffaggio del pezzo viene realizzato con varie soluzioni tecniche, in base al pezzo e alla tipologia della macchina. Le morse di serraggio - meccaniche, pneumatiche, idrauliche, autocentranti, con ganascia fissa e mobile – sono una delle soluzioni più utilizzate. Vengono impiegate nei centri di lavoro, soprattutto nella lavorazione di pezzi variabili, a causa del rapido posizionamento e del loro facile trasferimento da una macchina all’altra: alcune tipologie consentono l’immediato passaggio dal serraggio di un pezzo singolo a quello doppio, in quanto possono serrare contemporaneamente 2 pezzi anche di differenti dimensioni tra loro, grazie a particolari soluzioni di cui sono dotate, come ad esempio, sistemi flottanti della forcella e della vite. Analogamente, possono passare alla modalità bloccaggio autocentrante. Queste caratteristiche, unite all’elevata compattezza, ne fanno il prodotto ideale per l’utilizzo su qualsiasi tipo di macchina, da 3 a 5 assi.
Le morse ad alta precisione sono utilizzate prevalentemente su fresatrici e rettificatrici, dove è richiesta una precisione di serraggio elevata. Quelle più moderne sono caratterizzate da elevate forze di bloccaggio ed estrema rigidità del sistema che consentono di ottimizzare la presa di particolari e la loro lavorazione. Con i sistemi di bloccaggio più innovativi, sia i componenti cubici che quelli rotondi, vengono bloccati in modo concentrico ottimale. Questo consente di produrre i componenti in modo economico e di ottenere risultati eccellenti in particolare durante il bloccaggio di componenti sensibili alla deformazione.
Quando si tratta di lavorare piccoli pezzi, i collegamenti fissi sono particolarmente importanti per le morse, soprattutto a causa delle tolleranze estremamente strette che sono generalmente richieste.
Le morse modulari e i minibloccaggi rappresentano invece soluzioni ideali per il bloccaggio in spazi ridotti; consentono di sviluppare forze notevoli in tutte quelle situazioni in cui è importante limitare la dimensione del bloccaggio, senza rinunciare alla forza. Nel settore degli stampi, sono particolarmente efficaci i bloccaggi idraulici in quanto riducono i tempi di cambio stampi eliminando laboriose operazioni manuali e incrementano la sicurezza delle presse garantendo forze di bloccaggio elevate e costanti.
Sistemi di bloccaggio zero point
I sistemi di bloccaggio zero point, o a punto zero, nascono per ridurre i tempi di riattrezzaggio della macchina, che possono essere anche molto elevati. Sono di importanza fondamentale per realizzare processi stabili. Grazie alla definizione del punto di riferimento, pezzi, dispositivi e sistemi di serraggio possono essere serrati con un unico staffaggio, garantendo ottima ripetibilità.
Queste soluzioni, infatti, sono caratterizzate da un sistema d’interfaccia universale tra macchina utensile, attrezzatura di bloccaggio e/o direttamente il pezzo da lavorare, la cui estrema flessibilità consente il posizionamento e il bloccaggio in un’unica operazione. Nel settore degli stampi, il serraggio diretto dei pezzi da lavorare ha registrato un notevole sviluppo, diventando un vero e proprio punto chiave della produzione moderna. Il principio fondamentale è semplice: i pezzi da lavorare, una volta collegati ai perni di serraggio del sistema cambio rapido, possono essere fissati direttamente ai moduli di serraggio a punto zero. Per questo, il serraggio diretto si rivela decisamente superiore alle altre soluzioni di questo tipo nella produzione di pezzi singoli e piccoli lotti ed è la base per i cambi rapidi.
Disponibili nelle versioni pneumatica e idraulica, questi sistemi vengono utilizzati per soluzioni sia manuali che automatizzate. Per fissare il pezzo in lavorazione sulla base, è possibile utilizzare una morsa (meccanica, pneumatica o idraulica), una torre di serraggio, un dispositivo di serraggio modulare, un sistema di serraggio modulare, una piastra di serraggio magnetica o un dispositivo speciale in base alle esigenze del cliente.
Per ogni pezzo, quindi, indipendentemente dalla sua forma o dimensione, sono disponibili soluzioni globali ottimali ed economiche. Il sistema di serraggio a punto zero blocca il pezzo in modo preciso, garantendo così la massima forza di contrasto. Nello stesso tempo, l’usura e la manutenzione sono estremamente basse, perché vi sono solo tre parti mobili. Inoltre, in questo tipo di sistemi sono integrate le funzioni di movimentazione e spinta. Il design modulare garantisce la massima flessibilità e un enorme risparmio di tempo e costi in produzione.
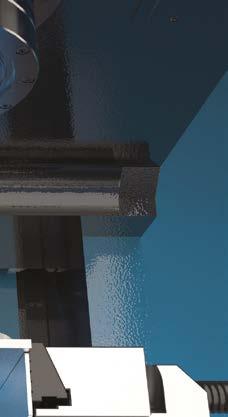