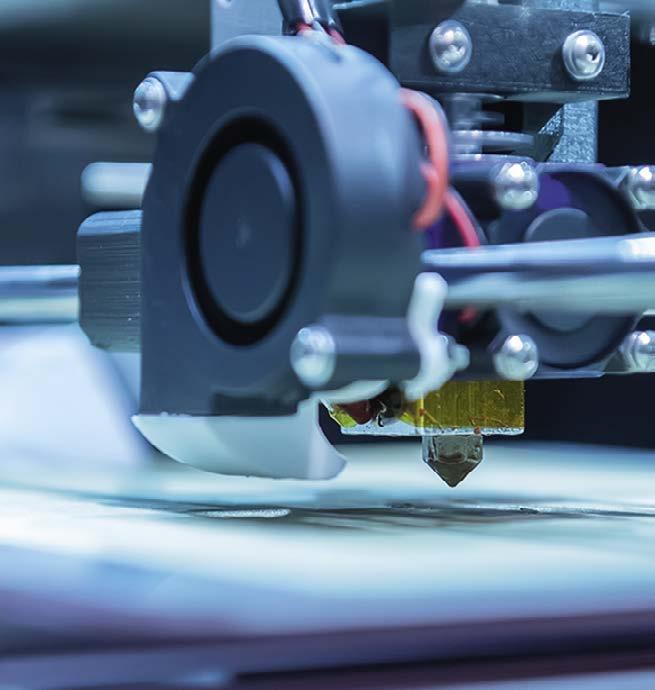
86 minute read
Dalla modellazione
DALLA MODELLAZIONE 3D ALL’OGGETTO stampato
L’AFFERMAZIONE DELLE STAMPANTI TRIDIMENSIONALI HA DIFFUSO LA CONVINZIONE CHE STAMPARE IN 3D SIA ESTREMAMENTE SEMPLICE E ALLA PORTATA DI CHIUNQUE
Di Patrizia Ricci
Una simile “sicurezza”, parzialmente vera per un impiego ludico, nasconde una serie di insidie quando la stampa additiva deve essere utilizzata per impieghi professionali e industriali. Realtà nelle quali assumono un’importanza determinante i tempi, la corretta esecuzione e la qualità della stampa stessa. Tutti questi fattori dipendono dal software, che assume un ruolo chiave all’interno di ogni valutazione relativa al panorama delle tecnologie di additive manufacturing. Per sfruttare al massimo il potenziale di una stampante 3D è essenziale conoscere anche gli strumenti software con cui si crea il progetto 3D da produrre. Cos’è un “software CAD”? Come funzionano? Cosa significa “slicing”? Queste sono solo alcune delle domande che ci si pone quando si ha a che fare con i software per la stampa 3D. Partiamo dalla base. Quando si guarda un oggetto 3D sul monitor di un computer quell’oggetto rappresenta il “modello 3D” ed ogni punto che lo definisce è calcolato matematicamente. I calcoli matematici che definiscono un oggetto 3D e lo rendono visibile sul monitor sono risolti dai software di modellazione 3D, i quali permettono di realizzare oggetti 3D digitali. Per creare e stampare modelli 3D occorrono tre tipi di software: uno per progettare l’oggetto (3D modeling/CAD software), uno per prepararlo per la stampa (Slicing/CAM software) ed uno per comandare i movimenti della macchina (Client Software).
Modellazione 3D/CAD software
Sono i programmi utilizzati per modellare in 3D. “CAD” sta per “Computer-Aided Design”, cioè “progettazione assistita dall’elaboratore”, ed identifica quell’area dell’informatica che raggruppa tutti i software di modellazione digitale nati per la progettazione di modelli in 3D. I sistemi di Computer
Aided Design hanno infatti come obiettivo la creazione di modelli, in genere 3D, di un oggetto. Ad esempio, un sistema Computer Aided Design può essere impiegato da un progettista meccanico per la creazione di un modello 3D di un motore. Nella stampa 3D, tramite un file STL o altro, il CAD chiede alla stampante 3D di realizzare degli oggetti fisici. Inoltre, permette la lettura del funzionamento e dell’effetto finale (render) di un oggetto prima ancora della sua realizzazione. Il
CAD è un linguaggio di programmazione orientato alla creazione di oggetti. Quindi, il destinatario del file, ad esempio una stampante 3D, lo legge al fine di concepire un prodotto reale, seguendo proprio le indicazioni fornite dal CAD. Con la messa a punto di un modello 3D, inoltre, si può procedere a calcoli sotto forma di analisi strutturali, di analisi dinamiche e di analisi statiche: si entra, quindi, nell’ambito del CAE, cioè la Computer-Aided Engineering (in italiano, “ingegneria assistita dall’elaboratore”). Il CAE può essere considerato come un insieme più ampio di cui il CAD fa parte. In un programma CAD/CAE, pertanto, la CAE ha lo scopo di segnalare le applicazioni software che permettono di giungere alla soluzione di problemi tecnologici basandosi sul calcolo numerico. La padronanza di un software CAD è un prerequisito fondamentale per la modellazione, mentre il file modellato lo è per la stampa 3D. In pratica, per stampare un oggetto in 3D, bisogna prima di tutto modellarlo, creandone la copia digitale in formato STL, leggibile dalla stampante. Esistono diversi tipi di software CAD, ognuno di essi funziona in modo diverso, anche se tutti hanno come obiettivo la modellazione dell’oggetto da realizzare. La differenza tra i software di modellazione 3D sta nel modo in cui avviene la modellazione stessa e la scelta di utilizzare un software rispetto un altro dipende da cosa dobbiamo modellare. Le tipologie di software CAD sono: solido, scultoreo, parametrico. Modellazione 3D solida: i software di modellazione 3D solida si basano sulla tecnologia CSG, ossia “geometria di costruzione dei solidi”. Questa tecnologia consente di avere delle forme prestabilite, chiamate “primitive”, attraverso le quali si definiscono oggetti più complessi grazie all’unione o alla modifica di una o più primitive. Per primitive si intendono cilindri, cubi, piramidi, sfere, ecc. Questi software, semplificando notevolmente l’attività di modellazione e produzione del modello 3D, risultano decisamente intuitivi e costituiscono un valido strumento per chi è alle prime armi. Modellazione 3D scultorea: i software di modellazione 3D scultorea permettono di creare oggetti scolpendo forme tridimensionali di base. Di solito le forme di base vengono scolpite a mano libera, permettendo di ottenere superfici più aggraziate e naturali. Si può quindi intuire come questa tipologia di modellazione 3D sia adatta per disegnare figure, facce, oggetti naturali o organici. Superfici piatte e regolari risulteranno meno precise rispetto all’utilizzo di altre tipologie di modellazione. Modellazione 3D parametrica: i software di modellazione 3D parametrica permettono di disegnare oggetti tridimensionali usando programmi di scrittura contenenti i parametri dell’oggetto. Grazie all’impostazione dei parametri, combinando diverse forme tra loro, viene definita in modo estremamente preciso ogni minima variazione di superficie o volume. Definito il modello attraverso i software CAD, il passo successivo è il salvataggio per la cessione del file al software slicer.
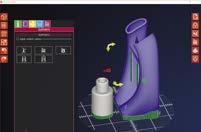
Quale formato di stampa?
Uno degli aspetti erroneamente trascurati, nella fase di pre-stampa 3D, è proprio la corretta scelta del formato del file da inviare alla stampante stessa. Non è infatti possibile inviare un progetto nel formato utilizzato per la progettazione CAD, ma occorre convertirlo in un formato adatto alla specifica stampante. In particolare, le macchine più moderne, accettano le estensioni .slt o .obj. Ma qual è il formato più adatto ad una stampa tridimensionale? Una risposta assoluta non esiste, in quanto occorre valutare le specifiche esigenze, partendo dalla corretta comprensione del funzionamento della stampa additiva. Uno dei formati più diffusi e divenuto ormai uno standard è sicuramente STL – STereo Lithography interface (.stl). Questo tipo di file permette di scomporre la superficie di un oggetto in triangoli per creare la sagoma. Le sagome più semplici richiedono meno triangoli, mentre l’aumento della complessità corrisponde a un incremento del numero di triangoli necessari. Un’alternativa che si sta progressivamente affermando è 3MF – 3D Manufacturing Format. A differenza dei modelli tradizionali, 3MF fornisce tutte le informazioni relative alla stampa: colore, orientamento, mesh, texture e materiali da utilizzare. Offre inoltre la possibilità di passare agevolmente da un filamento ad un altro. Una serie di stampanti, infine, richiedono l’estensione .obj. Si tratta di un formato open source, particolarmente utilizzato nelle stampe 3D multicolori, registra una serie di dati come coordinate, mappe di texture, informazioni sui colori e file di texture. Inoltre contiene un formato immagine tridimensionale standard, che può essere esportato e aperto utilizzando diversi programmi di editing di immagini 3D. Questi tre esempi di formati (ma ne esistono numerosi altri), fanno capire quanto il settore della stampa tridimensionale stia vivendo una fase di evoluzione, con la necessità di poter salvare i propri progetti nel formato più adatto alla specifica esigenza o alle caratteristiche della stampante che si andrà ad utilizzare. Anche per tale ragione, in fase di scelta del software di progettazione, occorre valutare la sua capacità di salvare il lavoro nel formato adatto.
Slicing/CAM software
Lo slicing è il passaggio intermedio tra la modellazione e la stampa 3D. Il “Computer-Aided Manufacturing“, che significa fabbricazione assistita da computer, converte i modelli 3D in comandi meccanici, i quali permetteranno alla stampante 3D di capire cosa deve fare e come deve muoversi. Il CAM software è comunemente chiamato “Slicer”. Molti programmi integrano strumenti CAD con quelli CAM, nel senso che permettono all’utente sia di disegnare modelli geometrici, che di generare le istruzioni per una macchina utensile. Questi programmi sono detti di CAD/CAM. I programmi di CAD/CAM non hanno bisogno di usare un file di scambio per passare il modello geometrico dalla funzione di CAD a quella di CAM.
A cosa serve uno Slicer?
Come già detto, i software slicer permettono di convertire il modello 3D in istruzioni che dialogano con la stampante 3D, impostando tutti i parametri di stampa. Le istruzioni sono recepite dalla stampante grazie ad un codice specifico, chiamato G-code. Durante il processo di slicing, l’obiettivo è quello di impostare e ottimizzare alcune caratteristiche di stampa del modello, fornendo attributi che, durante la stampa e a posteriori, possono influire sulla velocità di realizzazione e sull’aspetto/comportamento dell’oggetto stampato, oltre a quello di esportare il file 3D in un formato riconoscibile e leggibile dalla stampante. È possibile, ad esempio, impostare l’altezza dello strato (Layer Height);la larghezza delle pareti (Shell Thickness); la densità di riempimento (Fill Density) o il tipo di supporto (Support Type, per strutture a sbalzo che hanno bisogno di supporti per garantire l’integrità strutturale). Mentre alcuni dettagli a volte possono essere dettati direttamente dalla stampante utilizzata: ad esempio, la velocità (Print Speed) oppure la temperatura di stampa (Print Temperature, da determinare a seconda del materiale con cui si vuole stampare). Un’altra serie di impostazioni importanti da caricare nel programma di slicing sono le informazioni relative alle caratteristiche tecniche della stampante 3D in uso (chiamati “profili”), pressoché unici per ogni stampante e ottenibili di norma sul sito delle stesse.
Client software
È il software di controllo della stampante 3D. Serve per dare le istruzioni di stampa e per impostare la macchina che si intende utilizzare. Attraverso questo software è possibile lanciare un oggetto 3D in stampa, metterlo in pausa o bloccarlo, impostare parametri come le temperature del piatto e dell’estrusore. Solitamente, i client sono anche dotati di un’interfaccia che ci aiuta a livellare il piano di stampa e a correggere la posizione degli assi di stampa. Esistono client software open source e client software proprietari, ossia progettati esclusivamente per certi modelli di macchine. In questo scenario la scelta corretta dello strumento di progettazione diventa elemento strategico per l’azienda. La piattaforma software e hardware deve rispondere a precise necessità e avere anche la giusta dose di scalabilità necessaria ad assecondare la crescita dell’azienda.
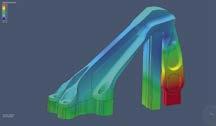
Pyramis nasce dalla necessità dell’azienda di interfacciarsi anche al mondo dell’additive manufacturing, ma sempre strizzando l’occhio alla semplicità di utilizzo. L’idea di partenza di sviluppo del software è stata quella di pensare ad un flusso di lavoro semplificato per l’utilizzatore finale. L’utilizzatore comune non dovrà necessariamente districarsi tra infiniti settaggi, settaggi che saranno solo a carico di chi con le macchine e i materiali ci lavora ogni giorno. Si è puntato sulla semplicità di utilizzo e su una serie di funzioni avanzate ad attivazione automatica, l’utilizzatore si trova quindi di fronte ad una interfaccia estremamente semplice, e dal workflow guidato per minimizzare il rischio di errore. Tra le funzionalità più importanti del software, spicca l’analisi automatica delle mesh del file tridimensionale durante la fase di importazione. In questa fase il software si incarica di analizzare la mesh al fine di trovarne difetti o imperfezioni, e successivamente di correggerli, sempre automaticamente, per non creare poi artefatti durante la fase di stampa. Altre funzioni molto apprezzate dagli utenti sono i potenti strumenti di nesting (posizionamento del modello nello spazio), di pinning (posizionamento dei connettori) e slicing (sezionamento). Il sistema, inoltre, utilizza in parallelo i processori delle schede grafiche (GPU), riducendo notevolmente i tempi di calcolo. Nesting: con un semplice comando, il software posiziona tutti gli oggetti presenti all’interno dell’area di stampa, per assecondare diverse necessità. Dalla possibilità di sfruttare al meglio lo spazio disponibile al fine di accomodare più oggetti possibili, oppure al fine di ottimizzare il posizionamento dell’oggetto per soddisfare delle caratteristiche di stampa ottimizzate all’oggetto da stampare. Pinning: al tocco di un pulsante il software è in grado di analizzare la geometria dell’oggetto, e andare a posizionare i supporti in maniera costante e intelligente, esattamente dove è necessario, con la densità specifica, e sorreggendo i punti fondamentali alla corretta realizzazione dell’oggetto da stampare. Slicing: è un’altra fase rilevante per la realizzazione di un manufatto corretto e di qualità. Pyramis, ottimizzando per ogni singola macchina e materiale i parametri, attua in base a ogni tecnologia di stampa una serie di accorgimenti al fine di eliminare o ridurre eventuali effetti negativi. La simulazione 3D permette una verifica accurata della costruzione. Grande impegno è stato profuso sullo sviluppo software in ottica macchine laser, laddove l’interesse professionale si sta sempre maggiormente orientando. Infine, per gli utenti con maggiore competenza e che vogliono avere la possibilità di intervenire nei parametri tecnologici dedicati che influenzano il risultato di stampa, è disponibile la versione “expert” del software, che oltre a garantire come in tutte le versioni un flusso di lavoro semplice e ottimizzato, permette di avere accesso a tutto ciò che sono le configurazioni di tutti i parametri, dai parametri macchina, a quelli dedicati al singolo materiale, o le caratteristiche di nesting e di pinning. CIMsystem offre la possibilità a costruttori di macchine o materiali, di avere delle versioni OEM del software Pyramis, con parametri dedicati alla propria linea di macchine per stampa, e ai propri materiali, avendo poi un occhio di riguardo verso la protezione dei dati facenti parte del know-how del costruttore stesso.
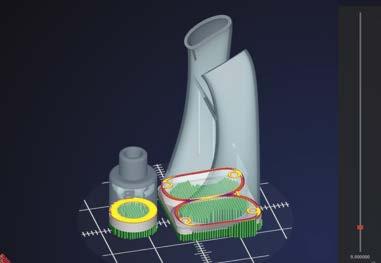
MSC SOFTWARE LA PIATTAFORMA INTEGRATA DI HEXAGON PER LA PRODUZIONE ADDITIVA
Negli ultimi anni Hexagon ha esteso il suo portafoglio prodotti con l’acquisizione di società come Vero Software, MSC Software, Volume Graphics, per citarne alcune. Così oggi, la divisione di Hexagon orientata alla produzione è in grado di aiutare i clienti a prendere il controllo della qualità in tutte le fasi chiave del loro processo, a partire dal CAE nella fase di progettazione e ingegnerizzazione, attraverso il CAD/CAM e il software complementare per le applicazioni di produzione, fino alle soluzioni hardware e software di metrologia incentrate sulla qualità. Come anche molti nostri clienti, crediamo che l’Additive Manufacturing sia un metodo di produzione altamente innovativo con un enorme potenziale dirompente. Solo recentemente, abbiamo visto l’AM svolgere un ruolo importante nella fornitura di materiali per dispositivi di protezione individuale (DPI) per proteggere le persone dal coronavirus. Questo esempio mette davvero in evidenza l’agilità che l’AM porta alla produzione - in un contesto commerciale questo potrebbe significare che un impianto medico urgentemente necessario può essere prodotto in tempi brevi, o un componente militare prodotto e sostituito sul campo. L’obiettivo della gamma di soluzioni di Hexagon è quello di aiutare le aziende a ottenere processi di additive manufacturing robusti, per passare dalla prototipazione alla produzione in serie. L’implementazione dei processi di produzione additiva su larga scala porta però nuove sfide complesse che richiedono un approccio connesso guidato dai dati. Stiamo lavorando per integrare le capacità delle migliori tecnologie Digital Twin di Hexagon in una piattaforma completa, che comprende: • Modelli digitali dei materiali da utilizzare per le simulazioni. • Progettazione del prodotto basata sulle ultime tecnologie di
Design for Additive Manufacturing (DfAM) e Generative Design. • Capacità di reverse engineering che permettono la creazione di gemelli digitali attraverso la scansione. • Ottimizzazione della stampa attraverso la simulazione del processo di costruzione • Simulazione del post processing e programmazione diretta della macchina. • Software di ispezione per convalidare il confronto della geometria finale e gli effetti volumetrici (come la porosità). Le soluzioni di simulazione, offerte dalla divisione Design & Engineering di Hexagon, includono: • MSC Apex Generative design: offre una vera soluzione end to end per i progettisti che creano componenti in metallo ad alta precisione. Passa rapidamente dallo schermo del computer alla stampa con intervento umano inferiore rispetto agli altri software. • Digimat AM: la recente versione del software Digimat permette alle aziende di simulare il processo di stampa 3D di materiali polimerici e calcolare il costo totale di produzione di ogni componente, compreso l’utilizzo del materiale, il tempo di lavoro dei dipendenti, il consumo di energia e le fasi di post-produzione necessarie. Consente inoltre di migliorare costantemente i metodi di progettazione virtuale verificando la microstruttura del materiale composito con scansioni CT dei componenti prodotti. • Simufact Additive è un potente ambiente di simulazione per l’ottimizzazione “al primo tentativo” dei processi di additive manufacturing a letto di polvere (SLS, SLM, LBM, DMLS, EBM).
Simufact Additive esegue la stima della distorsione e delle tensioni residue nel pezzo e fornisce agli ingegneri di produzione indicazioni su quali compensazioni applicare per ottenere un componente di qualità direttamente al primo tentativo. Permette inoltre di selezionare variabili di controllo per ottimizzare il processo di stampa in 3D e ridurre così tempi e sprechi. • Simufact ha recentemente introdotto la simulazione del metal binder jetting (MBJ), consentendo ai produttori di prevedere e prevenire la distorsione che avviene durante il processo di sinterizzazione sulle componenti in fase di progettazione. Il nuovo strumento di simulazione segna un significativo passo in avanti per l’additive manufacturing perché consente ai produttori di migliorare la qualità dei processi sfruttando al contempo i vantaggi esclusivi offerti dal MBJ per la produzione in serie. • A queste soluzioni, specifiche per l’Additive manufacturing, è possibile affiancare software di analisi strutturale come MSC
Nastran per valutare le prestazioni del pezzo finito. Per saperne di più visitare il sito: www.mscsoftware.com/it
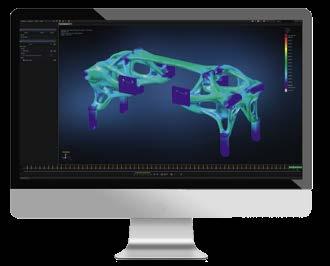
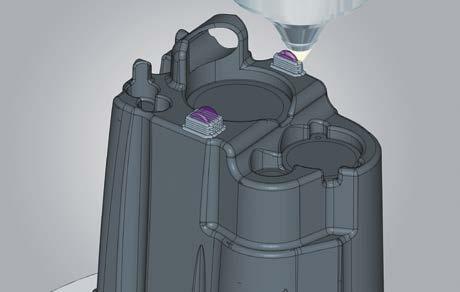
OPEN MIND SFRUTTARE IL POTENZIALE DELLA PRODUZIONE ADDITIVA E DELLA RIMOZIONE DEL MATERIALE È POSSIBILE…CON hyperMILL®!
OPEN MIND presenta un importante aggiornamento alla sua suite CAD/CAM hyperMILL®: hyperMILL® ADDITIVE Manufacturing amplia una delle soluzioni CAD/CAM leader mondiale per rispondere alle esigenze del processo industriale di stampa 3D. La soluzione software consente un’efficiente lavorazione ibrida con la contemporanea lavorazione additiva e sottrattiva in un’unica macchina. hyperMILL® ADDITIVE Manufacturing aggiunge al processo Direct Energy Deposition (DED) e al Wire Arc Additive Manufacturing (WAAM) la flessibilità della lavorazione simultanea a 5 assi ad alta complessità. Il software di OPEN MIND consente di programmare comodamente e di simulare per la prevenzione delle collisioni sia il controllo delle teste di lavorazione degli ugelli di polverizzazione sia la saldatura ad arco per l’applicazione puntuale del materiale. Ripresa ciclo e produzione ibrida in un unico processo Con hyperMILL® ora è possibile sfruttare appieno anche il potenziale nella produzione additiva mediante procedimento con letto di polvere (Powder Bed Fusion – PBF). Lì dove le parti stampate 3D non offrono la precisione desiderata o devono essere rimosse le strutture di sostegno, è possibile completare la lavorazione mediante la procedura di asportazione di trucioli a 5 assi. hyperMILL® consente una lavorazione sicura anche Nei punti più difficili da raggiungere. Come parte integrante della catena di processi, il sistema CAD/CAM di OPEN MIND supporta la ripresa ciclo: i componenti stampati vengono analizzati, fresati a misura e controllati. Lo specialista nel settore CAM OPEN MIND, però, si spinge oltre nella realizzazione di catene di processi integrate. Nei processi di produzione ibridi (Hybrid Manufacturing) la produzione additiva e quella sottrattiva vengono combinate in un’unica macchina utensile. L’utente con l’ausilio di hyperMILL® ora ha la possibilità di programmare insieme, la saldatura con riporto di materiale e la lavorazione di fresatura. Una simulazione particolareggiata del riporto e della rimozione di materiale e il trasporto di pezzi grezzi tra i diversi cicli di lavorazione garantiscono la massima sicurezza dei processi. Efficienza e sicurezza dei processi “Il nostro impegno tempestivo nei processi industriali della produzione additiva sta dando i suoi frutti. Con hyperMILL® ADDITIVE Manufacturing miglioriamo l’efficienza, la precisione e la sicurezza dei processi della produzione additiva e ibrida. Integrando le nuove procedure nelle catene di processi affermati, aumentiamo l’efficienza e le possibilità di utilizzo”, afferma Volker Nesenhöner, CEO di OPEN MIND Technologies AG. “In questo modo siamo sicuri di contribuire a numerose soluzioni innovative e di ampliare notevolmente le possibilità di applicazione dei nuovi processi”. Un’applicazione importante sarà la riparazione di componenti danneggiati, ad esempio nella produzione di stampi e progettazione di utensili, oppure la riparazione di pale di turbina, ad esempio nell’industria aerospaziale. Inoltre, si aprono opportunità completamente nuove nella combinazione di materiali diversi, ad esempio quando vengono applicati strati di materiale di alta qualità ai materiali di supporto.
TOPSOLID IL PROCESSO PRODUTTIVO PER L’ADDITIVE MANUFACTURING CON TOPSOLID’STRATO®
Il processo di stratoconcezione è una delle 7 famiglie di processi standardizzati (ISO 17296-2) dell’Additive Manufacturing. L’idea del “Design per strati” con un materiale composto da vari strati è stata brevettata (Brevetto C. BARLIER 02/1991). Il brevetto proponeva già la scomposizione del pezzo in vari strati (planari o irregolari) mediante un calcolo numerico eseguito a CAD, secondo la forma del pezzo, delle sue funzioni e delle sue sollecitazioni strutturali ed è stato oggetto di numerose pubblicazioni. Era quindi già previsto un progetto in rottura con i disegni tradizionali delle parti meccaniche: il materiale depositato al posto giusto poteva essere scelto per ciascuno degli strati secondo le diverse funzioni individuate, come nell’esempio della biella del compressore progettata con strati di acciaio per gli aspetti meccanici (trazione/compressione), strati di polimero per gli aspetti vibratori e inserti in bronzo per perni di collegamento. L’incorporazione di funzioni di circolazione dei fluidi, di aspirazione, o di miglioramento della resistenza meccanica diventa possibile, consente di ottenere un pezzo o un attrezzatura maggiormente ottimizzato per il suo raffreddamento, un’aspirazione meglio controllata o una sorveglianza integrata. Ciò ha permesso di dimostrare il miglioramento della produttività degli stampi prodotti, e l’ottenimento di nuove forme di pezzi grazie alla riduzione dei vincoli tecnologici. Questi diversi strumenti sono stati, sin dall’inizio, integrati nella processo digitale di stratoconcezione. Processo digitale per la produzione additiva di Stratoconception® La stratoconcezione è un originale processo di manifattura additiva per strati di tipo solido/solido che consiste nello scomporre per calcolo il modello 3D del pezzo in un insieme di semplici strati elementari, detti “strati”, nei quali vengono inseriti rinforzi e inserti. Gli strati 3D elementari vengono assemblati e prodotti in un materiale in lastra ottenuto dal taglio mediante micro-fresatura rapida, taglio laser, erosione a filo ecc. Gli strati vengono quindi assemblati utilizzando inserti, o anche imbricati, per ricostituire l’oggetto finale. Questo assemblaggio viene fin da subito considerato non appena l’oggetto viene decomposto. Questo assieme è parte integrante della struttura e resistenza meccanica delle parti. Il processo e il software associato sono stati sviluppati dai team CIRTES dal 1991. Le stazioni sono prodotte da partner di produzione. Il nostro team ha deciso nel 2016 di unire le forze con TOPSOLID per sviluppare TopSolid’Strato, un add-in dedicato in TopSolid e un bundle StratoTop. Questo lavoro è svolto nell’ambito del progetto nazionale PIA C-FAST guidato da BpiFrance. TopSolid’Strato è disponibile da aprile 2019, nell’ambito di questo progetto è allo studio anche una macchina completamente robotizzata con processo digitale completamente integrato, che sarà commercializzata nel 2020. Il software TopSolid’Strato®, integrato nel softwrae CAD/CAM TopSolid 7, consente di produrre parti mediante il processo Stratoconception® senza interrompere il processo digitale, liberandosi dal vincolo del formato STL e aggiornato istantaneamente ogni volta che il modello iniziale viene modificato. In questo modulo sono implementati diversi strumenti di scomposizione 3D in particolare per l’uso di più assi di taglio, o più spessori o materiali diversi, o per la pre-scomposizione di forme complesse. Strumenti per la scomposizione di aree
Figura 1 Figura 2


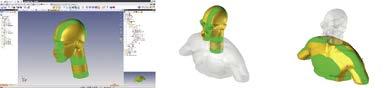
Figura 6
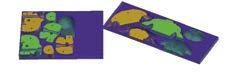

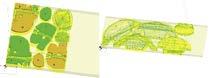
Figura 4
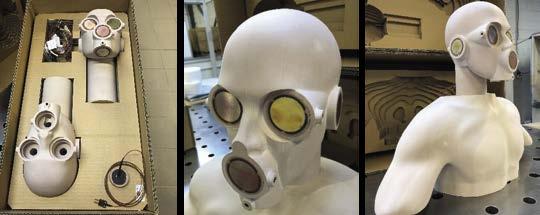
Figura 7
in più parti consentono la produzione di grandi strati su macchine con corse brevi, o dentro piastre di piccole dimensioni, o per ottenere un’ottimizzazione dell’uso del materiale. Infine, la generazione automatica di entità di assieme sugli strati viene eseguita da un algoritmo basato su una scheletrizzazione risultante dal diagramma di Voronoi generalizzato. L’arraying è ottimizzato per la riduzione degli scarti nella lastra di partenza tramite algoritmi ibridi euristici e genetici. Questo nuovo strumento è illustrato, attraverso la produzione di busti di misura strumentati, utilizzati da EDF R&D (per conto di Enedis) per testare i caschi protettivi. Applicazione di TopSolid’Strato® alla progettazione-produzione di un busto di misura per EDF - ENEDIS Il modello CAD è composto da due parti: testa e busto (Figura 1). In TopSolid’Strato® vengono effettuate diverse scelte di parametri di processo: asse di taglio, spessore del materiale, metodo di realizzazione (Figura 2) e generazione di un documento di taglio (Figura 3). Vengono selezionati diversi assi di taglio per ottimizzare la produzione e l’inserimento dei sensori. Un’integrazione di elementi di assemblaggio (inserti) consente l’assemblaggio degli strati (Figura 4). Successivamente gli strati vengono nestati in una piastra grezza (Figura 5) e vengono generati automaticamente i percorsi utensile per il taglio degli strati (Figura 6). I sensori di temperatura (calorimetri) sono fabbricati (la 2a specialità del team Cirtes) e integrati durante la produzione mediante stratoconcezione all’interno degli strati (Pelaingre et al.2018). Gli strati vengono quindi prodotti su una stazione di stratoconcezione in lastre di poliuretano e riassemblate per ottenere il manichino strumentato completo finale (Figura 7). I sensori sono integrati negli strati durante l’assemblaggio. Il ciclo continuo digitale per la produzione additiva (CAAM) è uno strumento che diventerà essenziale, come il CAD / CAM è lo è diventato per la lavorazione, e consentirà l’accelerazione di una progettazione per la produzione additiva consentendo l’implementazione delle principali innovazioni AM per fornire nuove possibilità per la progettazione di prodotti e di modelli di produzione (forme complesse, funzionalizzazione delle parti). I primi esempi di integrazione di queste tecnologie permetteranno di portare valore aggiunto alle aziende indipendentemente dal settore di attività. Inoltre le scienze cognitive permetteranno, grazie a questo ciclo continuo, un processo di apprendimento di fabbricazione assistita accessibile anche alle piccole aziende. Il busto e la testa di misurazione sono stati valutati con successo nei laboratori elettrici dei Renardières di EDF R&D al fine di perfezionare le tecniche di prova
Quando si parla di stampa 3D (o, più propriamente, di manifattura additiva o AM: Additive Manufacturing), spesso si pensa a piccole stampanti da tavolo che producono pezzi in plastica, oppure a grandi stampanti industriali all’interno delle quali miscele di polveri metalliche vengono fuse da potenti raggi laser. Tuttavia, ciò che spesso viene trascurato in questa immagine mentale è il software, che è in realtà un elemento indispensabile per guidare il processo di stampa additiva. Ora che il settore dell’additive manufacturing ha iniziato la transizione da un uso per la prototipazione in piccoli lotti verso la vera e propria produzione di livello industriale, il ruolo del software assume una importanza sempre maggiore. Al crescere del numero di pezzi prodotti, infatti, l’efficienza del processo produttivo può determinare il successo o il fallimento di un sistema di produzione. La disponibilità del software appropriato assicura un agevole flusso dei dati dalla progettazione fino alla produzione, consentendo di controllare l’intero workflow della stampa, attraverso tutti gli aspetti del processo. In effetti, per poter ottenere l’efficienza ed il livello qualitativo richiesti da uno scenario di produzione additiva su scala industriale, una gestione così accurata del processo di stampa è assolutamente indispensabile.
Alla base di tutto c’è la progettazione Naturalmente, il processo di stampa additiva inizia con la progettazione di un digital twin del pezzo fisico. La tecnologia dell’additive manufacturing, di per sé, consente di stampare quasi qualsiasi geometria immaginabile. Può capitare tuttavia che molti pezzi, pur essendo stampabili, non siano affatto ottimizzati per la stampa 3D. L’utilizzo di un software di progettazione dotato di funzioni pensate specificamente per la produzione con tecnologie additive si rivela in questi casi determinante. Una delle soluzioni di questo tipo è il software NX di Siemens. Grazie alle funzionalità integrate per la generazione di strutture reticolari e per l’ottimizzazione topologica, le aziende che utilizzano NX sono in grado di progettare elementi meccanici destinati alla stampa 3D che non sono semplicemente stampabili: sono ottimizzati per la stampa. La possibilità di integrare queste funzionalità all’interno del sottostante sistema CAD elimina inoltre la necessità di produrre file in formati “neutrali”, come l’STL, assicurando che il flusso dei dati non produca alcuna perdita di informazioni. In aggiunta, grazie alle funzionalità integrate di validazione, i progettisti possono continuamente validare il progetto dei propri pezzi, per assicurarsi che essi verranno stampati nel modo corretto, il tutto con ampio anticipo rispetto al momento in cui il progetto verrà consegnato al reparto di produzione. Questo è un aspetto chiave, poiché rimandare la validazione di stampabilità di un pezzo fino al momento della sua effettiva produzione (come avviene con molti pacchetti software) comporta che spesso, per ottenere una stampa di elevata qualità, si rivelino necessarie diverse costose revisioni del progetto.
Il pezzo e il processo La progettazione del pezzo da produrre, tuttavia, è solo la prima fase dell’intero processo di AM. Una volta che il progetto sia stato finalizzato, il pezzo dovrà infatti essere stampato, ed anche in questa fase il software è di fondamentale importanza. Sapendo che una corretta creazione dei setup di stampa ed una gestione efficiente dello stabilimento possono fare la differenza tra il successo o il fallimento delle operazioni, le aziende leader utilizzano del software opportuno anche per gestire il processo produttivo nel suo complesso. Il software NX integra anche specifiche funzioni dedicate alla creazione dei setup per la stampa additiva, mediante le quali un operatore può ottimizzare l’orientazione dei pezzi per garantire la qualità delle stampe, come anche massimizzare l’occupazione del vassoio di stampa, inserire elementi di supporto, impostare tutti i parametri della stampa, ed infine lanciare direttamente la stampa su un’ampia gamma di hardware di additive manufacturing. L’hardware supportato include sia le tradizionali stampanti da tavolo a filamento che le stampanti a polveri, ma anche modelli particolari di alta gamma, quali stampanti multi-assiali o stampanti ibride. Il fatto che tali funzionalità siano integrate all’interno del sistema NX comporta che, anche in questo caso, non vi sia alcuna necessità di produrre file in formato STL o in altri formati neutrali. I dati, quindi, fluiscono direttamente dalle fasi di progettazione e di validazione a quella di creazione dei setup di stampa, senza bisogno di transcodifiche. Ciò significa che, ogni volta che il progetto viene modificato tramite più revisioni, il setup di stampa può essere facilmente aggiornato, mantenendo le varie versioni sempre allineate alle revisioni del pezzo da produrre. Infine, quando i pezzi sono pronti per la stampa, le aziende possono utilizzare il software Opcenter di Siemens - una suite di sistemi per la gestione dello stabilimento produttivo - per ottimizzare l’efficienza della fabbrica, grazie alla possibilità di gestire il flusso delle materie prime e le schedulazioni dei job, nonché di monitorare l’efficienza dei diversi processi mediante potenti funzionalità di analisi.
Il software è l’elemento chiave per garantire la qualità della stampa Appurato quanto la qualità e la corretta esecuzione della stampa a livello industriale dipendano dal software, è imperativo che al software venga attribuito un ruolo chiave all’interno di ogni valutazione relativa al panorama delle tecnologie di additive manufacturing. Come illustrato, Siemens sta investendo pesantemente nella realizzazione di una soluzione software completa per l’additive manufacturing, con l’obiettivo di assistere le aziende di tutto il mondo nelle attività di progettazione e di stampa di elevata qualità su scala industriale.
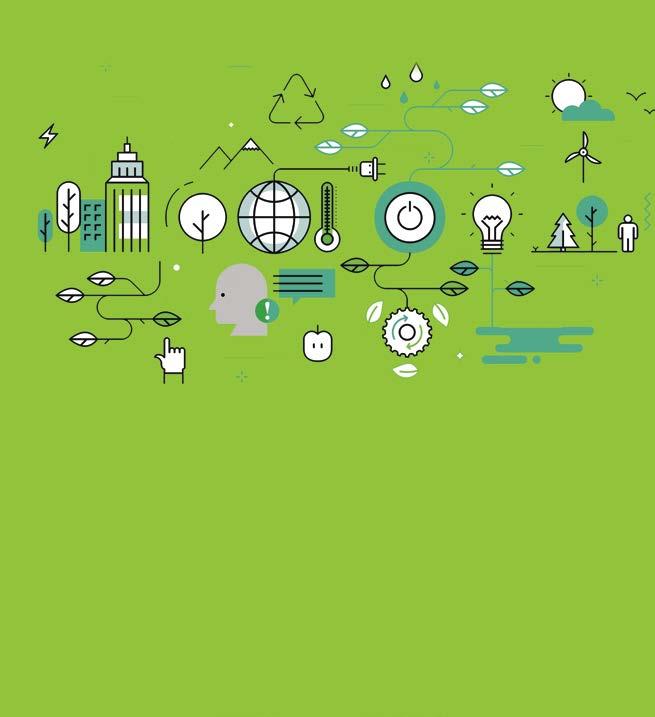
FORMARE TECNICI SUPERIORI ATTRAVERSO PERCORSI INNOVATIVI NELLA FILIERA DELL’EFFICIENZA ENERGETICA
A cura di Fondazione Green
GGli ITS Istituti Tecnici Superiori – scuole professionalizzanti post diploma della durata di due anni, rappresentano un’alternativa ai percorsi universitari e alla scelta di inserirsi nel mondo del lavoro subito dopo il diploma. L’alta specializzazione professionale che li caratterizza nasce per rispondere alla domanda delle imprese di nuove ed elevate competenze tecniche e tecnologiche in aree strategiche per lo sviluppo economico e la competitività in Italia
Al termine del percorso formativo i partecipanti che superano l’esame finale, ottengono il diploma rilasciato dal Ministero dell’Istruzione di tecnico superiore e di 5° livello riconosciuto in tutta Europa dall’ European Qualification Framework - EQF
La figura giuridica degli ITS è quella della Fondazione di partecipazione poiché sono costituiti dalla collaborazione del mondo del lavoro e della formazione. Le Il quadro europeo delle qualifiche (EQF) È stato sviluppato per comparare le qualifiche di paesi e istituzioni diversi allo scopo di sostenere la mobilità di studenti e lavoratori, per promuovere l’apprendimento permanente e lo sviluppo professionale in tutta Europa. L’EQF comprende tutti i tipi e tutti i livelli di qualifiche e l’uso dei risultati dell’apprendimento rende chiaro ciò che una persona sa, capisce ed è in grado di fare. Il livello aumenta in funzione della competenza, il livello 1 è il più basso e l’8 il più alto. https://europa.eu/europass/it/ european-qualifications-frameworkeqf
Fondazioni ITS sono 107 in Italia e danno possibilità molto ampie, operando in 11 filiere: Efficienza energetica, Mobilità sostenibile e mobilità marittima, Nuove tecnologie della vita, Nuove tecnologie per il made in Italy – Servizi alle imprese, Sistema agro-alimentare, Sistema casa, Sistema meccanica, Sistema moda, Tecnologie innovative per i beni e le attività culturali – Turismo, Tecnologie dell’informazione e della comunicazione.
I risultati dei percorsi ITS rilevati da Indire nel 2020 parlano di un sistema solido: 2856 soci delle fondazioni, di cui 1.244 imprese e loro associazioni; 83% degli allievi occupati a 12 mesi e il 92% con occupazione coerente; il 52% dei percorsi utilizza tecnologie abilitanti 4.0.
La Fondazione GREEN, ITS Energia, Ambiente ed Edilizia è una delle 20 fondazioni presenti in Lombardia, solo due di queste sono attive nella filiera dell’efficienza energetica.
Fondata nel 2014, delle sei aree tecnologiche nelle quali lavorano gli ITS, Fondazione GREEN è attiva nell’ambito efficienza energetica con lo scopo di preparare i tecnici specializzati che, nelle aziende, possano aiutare a governare e sfruttare il potenziale delle soluzioni di Impresa 4.0
La Fondazione ha 13 soci, ma le collaborazioni intraprese per l’organizzazione degli stage, riguardano un totale di più di
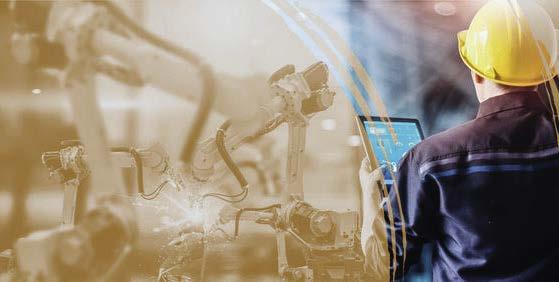
Un progetto innovativo degli studenti del primo anno del corso ITS Tecnico superiore per la fabbrica intelligente e l’industria 4.0 Al Maker Faire di Roma ( https:// makerfairerome.eu/it/) che a dicembre scorso ha avuto la sua edizione virtuale, è stato presentato questo interessante progetto di alcuni studenti della Fondazione GREEN. Il progetto nasce da un’esigenza reale di persone reali: le persone con disabilità motorie gravi che si muovono in autonomia in carrozzina elettrica hanno la necessità di riconoscere ed evitare gli ostacoli. I protagonisti sono gli studenti del primo anno insieme a due aziende partner: -Cooperativa Sim-patia, residenza sanitaria per persone con disabilità motorie gravi o gravissime che offre numerosi servizi tra cui la realizzazione di prototipi finalizzati al miglioramento delle qualità di vita di persone con fragilità -Caporali 2000 s.r.l., azienda specializzata nella commercializzazione e manutenzione di ausili per disabili e attrezzature ospedaliere -e al dipartimento STIIMA-CNR, Istituto Sistemi e Tecnologie Industriali Intelligenti per il Manifatturiero Avanzato – Consiglio Nazionale delle Ricerche socio della Fondazione GREEN. Il prototipo realizzato è un sistema di sensoristica utilizzabile con tutti i tipi di carrozzine elettriche, posizionabile in diversi punti, per una gestione consapevole dello spazio circostante. Consente una retromarcia innovativa e una manovrabilità sempre più sicura.

250 imprese del territorio attive nell’ambito prevalentemente energetico – elettrico e dell’edilizia. Oltre ad ospitare gli stage, le aziende forniscono docenze specializzate oppure mettono a disposizione i loro laboratori all’avanguardia.
I ragazzi non sono considerati dai docenti come studenti ma come futuri lavoratori. Aspetto dimostrato dai dati di occupazione dei diplomati che per i corsi 2019 ha toccato il 93,75% entro i dodici mesi successivi. Inoltre per il 92% dei casi il lavoro è perfettamente coerente con il percorso di qualifica. In un corso addirittura è stato raggiunto il 100% di entrambe le misurazioni.
La collaborazione del mondo del lavoro e della formazione è il punto caratterizzante di questo modello di formazione perché proprio a partire dalle esigenze del
Learning-by-doing, project work, problem solving, design thinking sono solo alcuni degli approcci didattici più utilizzati dagli ITS. Un altro punto fondamentale, caratterizzante dei corsi della Fondazione GREEN son i tirocini con durata pari quasi al 50% del percorso di studi che perciò prevede 1100 ore di aula e 900 di tirocinio. E’ proprio durante il tirocinio in azienda che gli studenti sperimentano le competenze acquisite, si mettono alla prova avviando il loro percorso professionale mentre sono affiancati e dal tutor dell’azienda.
Il lavoro degli studenti in azienda è in presa diretta: si lavora da subito con il personale più esperto in azienda e si diventa presto operativi, lavorando con i colleghi e contribuendo allo sviluppo grazie alle conoscenze e alle dinamiche innovative proprie dei Tecnici Superiori.
mondo del lavoro si progettano i contenuti dei corsi.
Tutti i corsi ITS sono pensati e studiati in questo modo e sono realizzati in collaborazione con imprese, università, centri di ricerca per sviluppare nuove competenze tecnico-tecnologiche considerate strategiche per lo sviluppo economico e per la competitività del Paese.
Viene privilegiata la didattica esperienziale: i corsi sono strutturati per competenze anziché per materie, intendendo la competenza come la capacità di applicare ciò che si sa per realizzare qualcosa. Insieme alle competenze tecniche, hanno molta importanza le competenze cosiddette trasversali cioè quelle che riguardano i comportamenti e la capacità di relazione perché anche questo è un sapere importante per il mondo del lavoro.

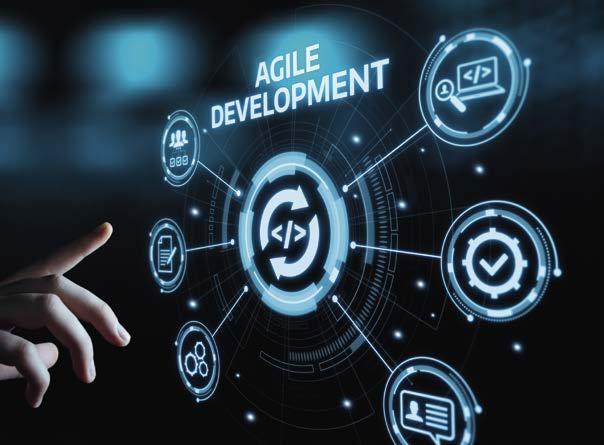
Altre competenze importantissime che gli studenti sperimentano in aula e sviluppano durante il tirocinio sono soft skills: i nostri studenti sanno lavorare in gruppo, affrontare e risolvere problemi.
Elisabetta Oliveri, ricercatrice presso Istituto STIIMA CNR e responsabile di un corso di Fondazione GREEN orientato alle esigenze dell’Impresa 4.0, descrive così le caratteristiche principali dei corsi ITS: “hanno un costo non elevato, un’alta percentuale di occupazione e danno la possibilità di fare uno stage presso un’azienda, sono molto adatti a quei ragazzi che non hanno voglia di frequentare l’università perché la ritengono troppo impegnativa ma al tempo stesso pensano che sia meglio studiare ancora un po’ prima di andare a lavorare. Offrono un’opportunità anche a chi vorrebbe continuare a studiare, ma ha problemi economici oppure a quei ragazzi che abbandonano gli studi universitari perché non si ritengono capaci, avendo avuto degli insuccessi con i primi esami. A tutti questi ragazzi l’ITS consente di acquisire non solo delle competenze specialistiche, ma anche di migliorare la fiducia in sé stessi e di essere quindi più strutturati e preparati per affrontare il lavoro. Il vero problema dei corsi ITS è promuoverli e fare capire la loro importanza ai ragazzi e alle loro famiglie; sono corsi poco conosciuti persino dalle scuole di istruzione secondaria superiore”.
Però, a fronte del milione di tecnici superiori del Canada, degli oltre 900.000 della Germania e dei 600.000 in Francia, in Italia gli ultimi dati INDIRE contano poco più di 18.500 iscritti ai percorsi ITS.
INDIRE
L’Istituto Nazionale di Documentazione, Innovazione e Ricerca Educativa (Indire) è da oltre 90 anni il punto di riferimento per la ricerca educativa in Italia. l’Istituto accompagna l’evoluzione del sistema scolastico italiano investendo in formazione e innovazione e sostenendo i processi di miglioramento della scuola. Sviluppa nuovi modelli didattici, sperimenta l’utilizzo delle nuove tecnologie nei percorsi formativi, promuove la ridefinizione del rapporto fra spazi e tempi dell’apprendimento e dell’insegnamento. Attraverso monitoraggi quantitativi e qualitativi, banche dati e rapporti di ricerca, l’Indire osserva e documenta i fenomeni legati alla trasformazione del curricolo nell’istruzione tecnica e professionale e ai temi di scuola e lavoro. https://www.indire.it
Due dei sistemi robotici proprietari di Caracol per la stampa in 3D di componenti avanzati di grandi dimensioni
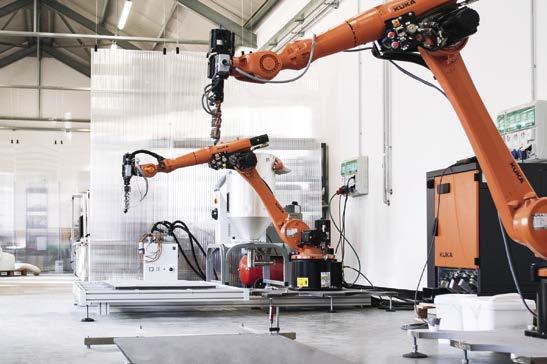
VERSO TECNOLOGIE DI ADDITIVE MANUFACTURING SEMPRE PIÙ SOSTENIBILI
UN PERCORSO PASSO A PASSO
Di Violetta Nespolo
CCaracol, azienda che offre servizi avanzati di additive manufacturing ad aziende in diversi settori industriali, ha l’ambizione di rivoluzionare i metodi tradizionali di produzione. Oltre all’aver sviluppato una tecnologia additive robotica proprietaria per la produzione di componenti di grandissime dimensioni con materiali compositi (i.e., tecnopolimeri rinforzati con fibre) e all’aver avviato il primo cluster di manifattura additiva robotica per applicazioni estreme in Italia, Caracol crede nella necessità di fornire ai propri clienti gli strumenti affinché possano sfruttare appieno le opportunità che derivano dalla stampa 3D.
In particolare, Caracol si propone per accompagnare i propri clienti lungo tutto il processo di produzione, offrendo la possibilità di esplorare e apprendere, toccando con mano i benefici che derivano dall’introduzione di queste tecnologie all’interno dei propri processi produttivi. Lo fa con progetti dimostrativi e di produzione, ma anche offrendosi come partner per l’acquisizione di competenze tecniche e offrendo soluzioni formative studiate ad-hoc per i propri clienti. L’azienda offre anche workshop e training sviluppati ad-hoc per i suoi clienti che vogliono integrare competenze legate ai temi dell’Industry 4.0 nelle loro filiere
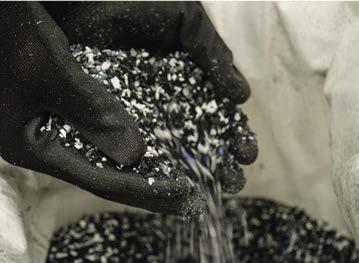
Scarti produttivi riciclati e tritati per produzione con robot proprietario di Caracol
produttive o nei dipartimenti di ricerca e sviluppo. L’azienda, infatti, studia alcune soluzioni di training che permettano ai dipendenti delle aziende clienti di internalizzare tecniche e approcci per la progettazione e produzione di applicazioni con soluzioni AM.
I workshop sono generalmente strutturati con un’introduzione generale ai temi dell’additive manufacturing, delle varie opportunità tecnologiche e progettuali che derivano da queste innovazioni. Includiamo poi dei verticali sulle tecniche di progettazione, generative e parametric design, e gestione di software per lo slicing – necessari per la trasformazione dei file dei modelli 3D in G-Code leggibili dalle macchine per la produzione. Il training solitamente verte sulla tecnologia più adatta al cliente (e.g., macchine FDM industriali, SLA, …) dove Caracol offre alcuni consigli e per la gestione in completa autonomia delle soluzioni tecniche. Per quanto riguarda poi il mondo dei materiali, Caracol propone il suo expertise per andare a proporre i materiali più adatti rispetto alle applicazioni del cliente, raccontando nei suoi training quelle che sono le caratteristiche dei materiali e offrendo consigli sul migliore utilizzo in fase di stampa (e.g., temperatura di estrusione, trattamenti pre e post), che permettano di ottenere i migliori risultati sulle applicazioni di interesse.
Caratterizzazione del materiale e riutilizzo degli scarti produttivi
Per andare incontro alle esigenze dei clienti, l’azienda offre anche soluzioni di caratterizzazione dei materiali. Lavorando con una vasta gamma di materiali compositi, tecnopolimeri (e.g., PA, PPS, PEEK, ABS, …) rinforzati con diverse percentuali di fibra (e.g., carbonio, vetro, kevlar), è possibile identificare un mix customizzato e ideale per determinate applicazioni. I tecnopolimeri sono ottimi per andare ad effettuare metal replacement, ottenendo anche dei benefici di alleggerimento e miglioramento della performance del componente. Infine, grazie al controllo integrato su tutta la supply-chain si potrà caratterizzare il materiale e qualificarlo per andare incontro ai requisiti tecnici del cliente.
È possibile anche customizzare dei materiali per la stampa 3D utilizzando materiali che il cliente già utilizza con altre tecniche produttive (e.g., injection molding o fresatura). Caracol ha anche studiato delle soluzioni che permettano di andare a riciclare il materiale di scarto del cliente, reimmettendolo direttamente in produzione con tecnologie come la soluzione robotica di Caracol o caratterizzandolo e filando il materiale per produzioni 3D più tradizionali, e dando vita a vere e proprie soluzioni di circular economy.
L’additive manufacturing per raggiungere obiettivi di sostenibilità
Uno dei vantaggi noti dell’additive manufacturing è legato alla sostenibilità del processo produttivo rispetto ad altre tecnologie tradizionali. Infatti, le tecnologie per la stampa 3D che sicuramente portano vantaggi in termini di sprechi di materiali in produzione e grazie al fatto che supporti e stampi sono spesso superflui. Inoltre, la possibilità di stampare in loco permette di ridurre l’impatto dei trasporti, della logistica e del magazzino.
Anche questi vantaggi di sostenibilità possono essere ottimizzati attraverso un utilizzo più consapevole delle tecnologie. Soprattutto, questo ha un forte legame anche con l’utilizzo il più limitato possibile dei materiali di base ed un efficiente gestione dei prodotti e riutilizzo degli scarti. Caracol ha l’obiettivo di ridurre al minimo anche l’impatto ambientale delle attività che segue per se e per i suoi clienti, adottando quindi un concetto di sostenibilità più ampio che copra l’ottimizzazione della filiera produttiva (dall’approvvigionamento dei materiali, all’utilizzo minimizzato di questi e alla logistica efficiente), la flessibilità della produzione (attivando le linee per una produzione on-demand e senza la necessità di fare stock di magazzino), fino ad eliminazione degli scarti e riutilizzo di prodotti dismessi, e attivazione di soluzioni di circular economy che diano nuova vita a materiali che altrimenti finirebbe in discarca.
Casi studio applicativi
Produzione di Guide, Dime, Tooling e Strumenti su misura
Spesso lavoriamo a stretto contatto con i nostri clienti per ingegnerizzare strumenti di lavoro come guide, dime, e attrezzi svi-
Dima di assemblaggio in PA CF (Rosso Carbonio) prodotta da Caracol
Caracol offre training per dipendenti di aziende interessate alle tecnologie additive manufacturing, comprensivi di progettazione e design, identificazione e utilizzo delle tecnologie ed approfondimenti sui materiali.
luppati su misura che facilitino alcune operazioni. Questo è possibile grazie all’approccio end-to-end che utilizziamo nell’accompagnare il cliente verso l’introduzione di tecnologie additive nei suoi processi produttivi. Ad esempio, questa maschera di posizionamento e assemblaggio serviva al nostro cliente per identificare velocemente la posizione in cui lavorare e doveva resistere ad alcuni sforzi meccanici durante le operazioni. Abbiamo selezionato un nylon rinforzato con fibra di carbonio in colore rosso, prodotto da Treed Filaments, che corrispondeva alle caratteristiche tecniche richieste dal progetto. La produzione in additive manufacturing ha permesso al cliente di ricevere un pezzo ingegnerizzato e su misura per le sue necessità in soli tre giorni.
Queste pinze servivano invece per facilitare la centratura di un oggetto fragile durante alcune operazioni con un traforo. La scelta del materiale è quindi ricaduta sul TPU (poliuretano termoplastico), materiale molto utilizzato in stampa 3D per la sua caratteristica flessibilità. Senza l’utilizzo di stampi e maschere, è stato possibile riprodurre digitalmente il calco del componente che viene supportato da queste pinze, ottenendo uno strumento performante in pochi giorni con molti meno sprechi.
Per un cliente che lavora nel settore oil and gas, Caracol ha sviluppato un giunto di un tubo che doveva resistere al contatto con alcuni liquidi e soluzioni chimiche. Per questa ragione è stato scelto il PEEK, ideale per il metal replacement grazie alle sue performance meccaniche, chimiche e termiche elevate. La geometria del componente era anche ideale per sfruttare appieno in vantaggi che derivano dalla stampa 3D, risparmiando su stampi ed evitando spreco di un materiale molto costoso come il PEEK.
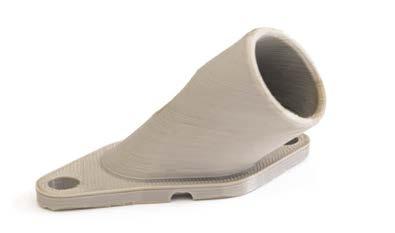
Produzione di giunti per oil and gas in PEEK, da Caracol
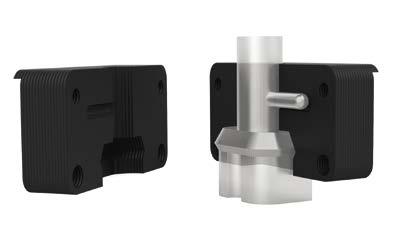
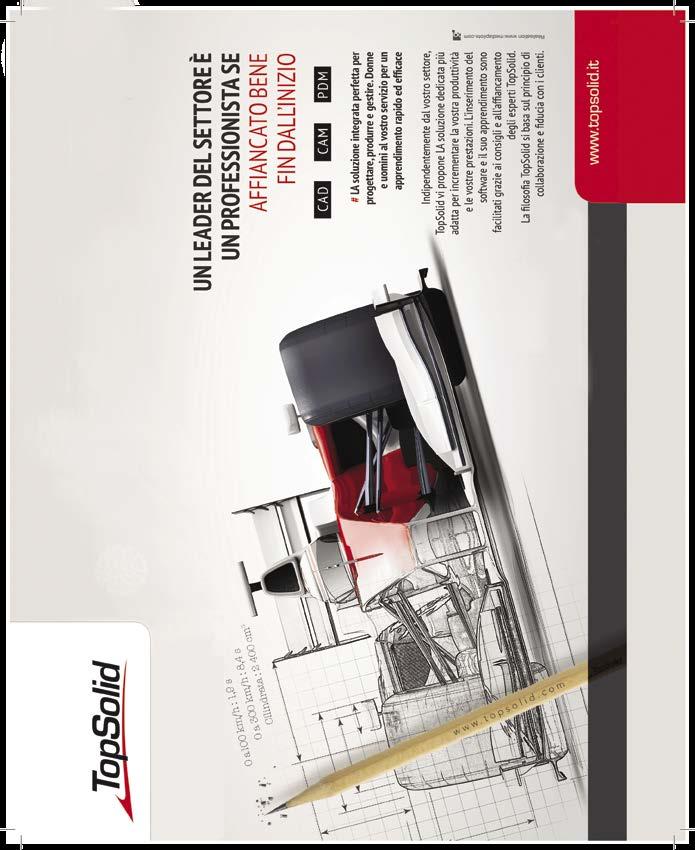

LE NUOVE FRONTIERE DEL PACKAGING FLESSIBILE
IL PROGETTO DI PFM PACKAGING MACHINERY
A cura di Service Group R&D in collaborazione con PFM S.P.A.
IIl mondo del packaging, in particolare Il tema della sostenibilità ambientale nel largo consumo non siano sufficientemente in Europa, sta affrontando una importante settore del packaging è di grande attualità. impegnati nello sviluppo di soluzioni di rivoluzione. Stiamo infatti assistendo alla L’Unione Europea si sta attivando per packaging più sostenibile. Inoltre, la magtransizione da un modello di business spingere le aziende ad adottare soluzioni gior parte dei consumatori (77%) risulta basato quasi esclusivamente sulla massi- più sostenibili e meno impattanti sull’am- disposta a pagare un prezzo maggiore per mizzazione della produttività e la mini- biente, generalmente tramite incentivi o un prodotto confezionato in un imballagmizzazione dei costi, a uno che cerca di disincentivi appositamente studiati. Anche gio meno impattante sull’ambiente (Pro bilanciare gli aspetti economici con quelli i consumatori sono sempre più sensibili Carton – European Packaging Perceptions sociali e ambientali, ponendo grande atten- al tema della sostenibilità ambientale e Study, 2018). La pressione esercitata dalle zione anche su quest’ultimi. In altre parole, tendono a direzionare i propri acquisti istituzioni e dai consumatori sui rivenditori nel mondo del packaging, come in molti proprio sulla base di questi fattori. La si riflette sui produttori dei beni, i quali altri settori, è in corso un’evoluzione a ritmi maggior parte dei consumatori in Europa devono necessariamente coinvolgere sia serrati verso un modello di sviluppo più (64%) ritiene che i responsabili per la i produttori di film per l’imballaggio, sia sostenibile. produzione e distribuzione di prodotti di i produttori di macchine confezionatrici.
Nuove tipologie di film per il packaging sostenibile vengono studiate per minimizzare l’impatto ambientale dell’imballaggio, cercando di rendere il materiale biodegradabile/ compostabile o facilmente riciclabile, ma mantenendo comunque le proprietà fondamentali del packaging. Caratteristica indispensabile del packaging è infatti quella di proteggere il prodotto in esso contenuto, facilitandone la conservazione e il trasporto, e massimizzando la shelf life, ovvero la vita utile prima dell’acquisto. Un packaging realmente sostenibile deve assicurare una shelf life elevata, altrimenti il danno causato dallo spreco del prodotto vanificherebbe qualunque altro tipo di sforzo. Inoltre, vanno sempre tenute in considerazione caratteristiche fondamentali quali il rispetto delle normative vigenti nel settore food, la lavorabilità dei materiali impiegati e l’aspetto estetico, che deve comunque risultare piacevole.
Il packaging flessibile è uno dei principali protagonisti della rivoluzione tecnologica in corso, in quanto rappresenta per il consumatore un grave problema ambientale, in particolare nel momento in cui deve occuparsi dello smaltimento. Il packaging flessibile viene utilizzato soprattutto nella grande distribuzione di alimenti e bevande, ma anche in settori come la farmaceutica, la cosmetica e l’igiene domestica. In Europa, sebbene il packaging flessibile rappresenti soltanto il 10% in massa sul totale del food packaging, viene impiegato per confezionare oltre il 40% dei prodotti alimentari (Flexible Packaging Europe – Sustainability Key Facts, 2018). Considerando i valori minimi di packaging-to-product ratio, ovvero il rapporto tra la massa dell’imballaggio e quella del prodotto, il packaging flessibile resta una delle soluzioni più economiche e sostenibili attualmente a disposizione.I principali problemi legati al packaging flessibile emergono nel momento dello smaltimento. I materiali utilizzati negli imballaggi flessibili sono molteplici: non solo polimeri plastici di svariata natura, ma anche alluminio e carta, assieme ad altri componenti secondari come collanti, adesivi e inchiostri. Nella maggior parte dei casi le confezioni sono costituite da poliaccoppiati, cioè film ottenuti combinando diversi materiali (anche profondamente diversi, come plastica ed alluminio) con lo scopo di conferire alla confezione particolari proprietà, difficilmente ottenibili con un singolo materiale. Il recupero, lo smistamento e il riciclo di questi materiali è un processo molto complesso e spesso poco conveniente, sia da un punto di vista economico, sia da un punto di vista ambientale, a causa della grande quantità di risorse ed energia necessarie.
I produttori dei film destinati al confezionamento di packaging flessibile si sono attivati negli ultimi anni per portare sul mercato soluzioni in grado di ridurre l’impatto ambientale del packaging. I nuovi film “sostenibili” sono concepiti per risolvere il problema attraverso approcci differenti, puntando ad esempio alla completa riciclabilità del rifiuto o alla biodegradabilità/compostabilità dello stesso. La natura diversa di queste soluzioni si traduce in una molteplicità di materiali e combinazioni, che deve essere quindi necessariamente presa in considerazione dai produttori di macchine confezionatrici, affinché sia possibile promuovere lo sviluppo del packaging sostenibile.
Il progetto
PFM S.p.A., azienda leader nel mercato delle macchine confezionatrici, è parte attiva del processo di miglioramento della sostenibilità del packaging flessibile.
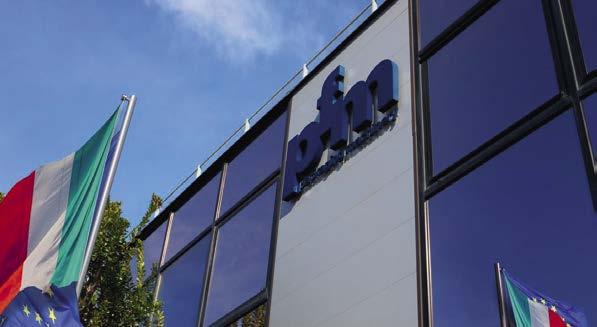
L’azienda è consapevole che l’introduzione nel mercato di una vasta gamma di film sostenibili comporta un grande cambiamento anche a livello di macchine per il confezionamento. I film infatti non si comportano tutti allo stesso modo durante il processo di confezionamento. Piccole variazioni delle caratteristiche chimicofisiche del film possono tradursi in una drastica perdita di efficienza, in un calo di protezione del prodotto o addirittura nella totale impossibilità di lavorazione. Il ruolo di PFM e dei produttori di macchinari per il confezionamento è quindi cruciale nel processo di miglioramento della sostenibilità del packaging. Il progetto nasce proprio dalla necessità di rinnovare le macchine e i dispositivi attualmente disponibili, sviluppando soluzioni che permettano di trattare nuovi film, mantenendo i più elevati standard qualitativi senza sacrificare la produttività. Il progetto si articola in 8 fasi consequenziali, nelle quali verranno analizzati tutti gli aspetti fondamentali riguardanti il trattamento del film durante il processo di confezionamento, dalla manipolazione dello stesso alla saldatura della confezione e verranno prodotti diversi prototipi all’avanguardia.

La sostenibilità ambientale
Per valutare l’impatto ambientale di un imballaggio, e più in generale del sistema prodotto-packaging, è necessario considerarne l’intero ciclo di vita. Un rischio che si corre quando si cerca di valutare la soluzione migliore in termini di impatto sull’ambiente è infatti quello di concentrare l’analisi su un determinato segmento del ciclo di vita del prodotto, trascurando aspetti rilevanti caratteristici di altri segmenti. È opportuno ricordare anche che il concetto di packaging sostenibile prevede l’integrazione dei requisiti ambientali con quelli di tipo economico e sociale, i quali non devono essere trascurati. La commercializzazione di un sistema per il confezionamento a ridotto impatto ambientale, ma completamente disallineato sul piano economico, andrebbe ad occupare soltanto una trascurabile nicchia del mercato, vanificando gli sforzi effettuati. Il progetto di PFM S.p.A. prevede uno studio del ciclo di vita del prodotto mediante tecniche di Life Cycle Assessment (LCA), in modo da valutare il miglioramento in termini di impatto ambientale, ottenibile grazie al confezionamento dei prodotti in packaging sostenibile. In particolare, verrà analizzato il ciclo di vita della confezione (packaging) dalla produzione allo smaltimento, prestando particolare attenzione alla fase di lavorazione del film operata dalle macchine di PFM. La valutazione dell’impatto del packaging verrà inoltre effettuata prendendo in considerazione diversi film “sostenibili” disponibili sul mercato. In questo modo sarà possibile effettuare un confronto quantitativo, oltre che qualitativo, tra le diverse tipologie di film e i relativi sistemi di smaltimento/recupero, cercando di definire infine quale sia la soluzione più ecosostenibile nei diversi contesti.
L’azienda e i partner
PFM S.p.A. è un’azienda multinazionale con sede operativa in Italia a Torrebelvicino, in provincia di Vicenza, leader nel settore delle macchine per il confezionamento di packaging flessibile. L’azienda progetta, costruisce e commercializza macchine flowrap, form fill & seal, stand-up pouch, pesatrici multitesta e linee automatiche di confezionamento per diversi prodotti, destinati sia all’industria alimentare (prodotti caseari, prodotti da forno, dolciumi, carne e pesce, prodotti ortofrutticoli, ecc.), che ad altri settori, come il farmaceutico e il cosmetico. Nel corso degli anni PFM ha sperimentato una crescita molto rapida, anche attraverso l’espansione su nuovi mercati e la costituzione o l’acquisizione di nuove società.
Il progetto, gestito e coordinato da PFM S.p.A., prevede la collaborazione con diversi partner, in un’ottica di open innovation. In particolare, è in corso una collaborazione tra l’azienda e l’Università degli Studi di Padova, la quale fornirà il proprio supporto nel campo dello studio dei materiali e in quello ingegneristico. Fondamentale è anche la collaborazione instaurata con Service Group R&D, una start-up innovativa specializzata nell’analisi degli impatti ambientali generati da prodotti e processi attraverso tecniche di valutazione del ciclo di vita. Per maggiori info: www.pfm.it info@pfm.it
INIZIATIVE E PROGETTI PER UN MANIFATTURIERO LOMBARDO CIRCOLARE

di Andrea Mazzoleni, Roberta Curiazzi – AFIL; Luca Gentilini, Marcello Colledani – Politecnico di Milano, Dipartimento di Meccanica; Giacomo Copani – CNR - STIIMA, AFIL
LL’Economia Circolare è un paradigma apportare all’economia dell’Unione Euro- e dei processi incoraggiando l’adozione di cardine per lo sviluppo sostenibile, inclusivo pea; si stima che sia possibile ottenere sistemi regolatori comuni in tutti i settori ed efficiente. Concettualmente, essa benefici annui fino a 1,8 miliardi di €, un economici, le cui prime misure sono state sottende un modello economico finalizzato aumento del PIL dello 0,5 % e la crea- introdotte in Italia con la legge di Bilancio ad una riduzione degli sprechi e a un zione di 700.000 posti di lavoro entro il 2020. ripensamento radicale nella concezione 2030 con risparmi netti per le imprese fino In tutto ciò, la manifattura assume un dei prodotti e del loro utilizzo secondo a 604 miliardi di €, pari all’8% del fatturato ruolo importante perché direttamente una logica di riuso, recupero, riciclo lungo annuo. legata all’impiego delle risorse e alla tratutto il ciclo di vita, dalla progettazione allo Per promuovere la circolarità, la Com- sformazione di esse in prodotti finiti; pur smaltimento. missione ha presentato nel Dicembre essendo tra le attività economiche che più
Notevoli sono gli aspetti positivi che 2019 il Piano “Green Deal” il cui intento consuma materiali ed energia, il manifatuna transizione verso la circolarità potrebbe è promuovere la sostenibilità dei prodotti turiero presenta elevate potenzialità di
Il Progetto Screen: “Synergic Circular Economy Across European Regions”
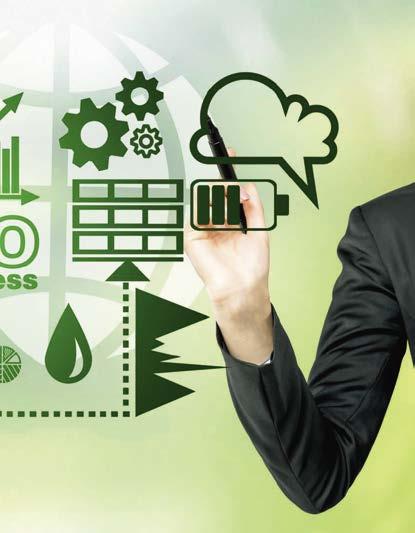
Screen è un progetto co-finanziato dalla Commissione Europea attraverso il programma Horizon 2020 in cui 17 regioni, fra cui la Lombardia, si sono riunite per definire un approccio sistemico e replicabile per la transizione verso una Economia Circolare nel contesto della Smart Specialisation Strategy. Il progetto, della durata di due anni e concluso nel 2018, si è articolato di quattro fasi principali. Nella prima fase è stata messa a punto una procedura per l’identificazione e la mappatura di catene del valore circolari reali e potenziali presenti, a livello locale, in ogni regione. Nella seconda fase, la metodologia precedentemente identificata a livello locale è stata scalata a livello interregionale. La terza fase, sfruttando il laboratorio sulle politiche (Screen Policy Lab), ha definito uno strumento denominato “Common Pot”, aperto a tutte le regioni Europee e che capitalizza e amplia il concetto di “Seal of Excellence” della Commissione Europea riguardante il finanziamento attraverso fondi strutturali di progetti con un solo beneficiario. In sinergia con la precedente, la quarta fase ha elaborato una serie di criteri comuni per la valutazione dei progetti di economia circolare.
Maggiori informazioni sono disponibili al seguente Link http:// www.screen-lab.eu/documents/ SCREEN%20Presentazione-It.pdf
circolarità, ad esempio nei comparti della plastica, del tessile, dell’elettronica, degli imballaggi, dei veicoli, delle batterie e dei beni strumentali.
L’Economia Circolare offre infatti il potenziale per la creazione di nuove catene del valore con una logica di simbiosi industriale che può contribuire al rinnovamento dell’industria comunitaria ed aumentare la resilienza supportando la continuità delle catene di approvvigionamento come evidenziato dalla recente emergenza sanitaria.
Ne consegue che lo sviluppo sostenibile e l’Economia Circolare, insieme alla digitalizzazione, siano aspetti di primaria importanza per il futuro e la competitività delle imprese.
Le tecnologie legate a Industria 4.0 come la manifattura additiva, la robotica, i big data – alle quali si aggiunge l’Intelligenza Artificiale – consentono la progettazione circolare di prodotti e componenti, la scelta di materiali idonei per mantenere nel tempo le funzionalità, il design di componenti che ne facilitino il disassemblaggio in maniera non distruttiva, l’adozione e l’implementazione di nuovi modelli di business (es. pay per use) e l’adeguamento delle infrastrutture lungo la filiera per la sincronia tra supply chains.
Nell’ambito della sostenibilità industriale, uno degli aspetti principali per un’industria manifatturiera efficiente è il tema del “De-and Remanufacturing” il cui potenziale di mercato in EU è stimato in 90 miliardi di € entro il 2030.
Il termine “De-and Remanufacturing” descrive l’insieme di attività, processi, tecnologie, strumenti e metodi per il recupero e il riuso dei prodotti a fine vita all’interno di applicazioni secondarie nonchè l’upgrade di funzioni e materiali dai rifiuti industriali e dai prodotti high-tech postconsumo, in una prospettiva circolare che pone il produttore al centro della catena del valore.
Nel concreto, il prodotto usato o una sua parte, subisce un processo di trasformazione o riconversione che varia a seconda del settore e della filiera con un processo che prevede il disassemblaggio, il recupero e la sostituzione di componenti per concludersi con il collaudo delle singole parti finalizzato al ripristino delle condizioni originali. I beni ottenuti possono essere
Il Progetto Fiber-E-Use: “Large Scale demonstration of new circular economy value chains based on the reuse of end-of-life fiber reinforced composites”.
FiberEUse è un progetto iniziato nel 2017, della durata di quattro anni e co-finanziato dalla Commissione Europea attraverso il programma Horizon 2020. Coordinato dal Dipartimento di Meccanica del Politecnico di Milano, FiberEUse raccoglie più di venti partner da otto paesi europei fra industriali, accademici e centri di ricerca per dimostrare su larga scala la sostenibilità economica ed ambientale di catene del valore innovative basate sul riciclo e recupero di prodotti in materiale composito a base vetro e carbonio. Il progetto si basa sulla validazione di tre use-case, tre filoni tecnologici che collegano diversi settori in input e output: il riciclo meccanico per ottenere fibre di vetro corte, il riciclo termico per ottenere fibre di vetro e carbonio di qualità superiore e il ricondizionamento di componenti attraverso soluzioni di joining reversibili. Le soluzioni tecniche sono sviluppate all’interno del progetto, scalando il livello di maturità tecnologica di soluzioni già validate in scala di laboratorio.La sostenibilità economica ed ambientale, e quindi l’appetibilità sul mercato, emerge attraverso otto dimostratori: prodotti che inglobano materiale riciclato e componenti second-life collegando in ottiche sia di ciclo chiuso che cross-settoriale i comparti automotive, costruzioni, energia, sportivo, sanitari, aerospaziale e design. FiberEUse è caratterizzato da una forte componente lombarda: oltre a Politecnico di Milano, anche l’istituto STIIMA-CNR, con sede a Milano, partecipa come centro di ricerca. Al progetto si uniscono Rivierasca, azienda bergamasca che da anni costruisce prodotti in vetroresina quali lastre e ondulati; GREEN COAT, attore mantovano esperto in coating e verniciature di prodotti plastici e compositi e Holonix, azienda ICT brianzola che sta sviluppando la piattaforma IT di FiberEUse, per identificare possibili sinergie fra attori di catene del valore diverse e fornire servizi software all’utilizzatore.
Maggiori informazioni sono disponibili al seguente Link http://www.fibereuse. eu/index.php
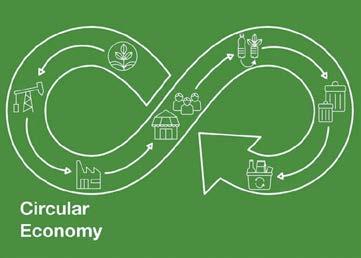
utilizzati per applicazioni nel settore di partenza o con un approccio di simbiosi industriale, come ad esempio l’utilizzo di fibra tessile nel settore edile garantendo la conformità agli standard tecnici e di sicurezza nonchè performance equivalenti a quelli iniziale.
Il Cluster AFIL – Associazione Fabbrica Intelligente Lombardia – promuove e valorizza sin dal 2015 la transizione del manifatturiero regionale verso il modello dell’Economia Circolare attraverso il coimanufacturing e riciclo, la ri-progettazione e il co-design dei prodotti, strumenti ICT a supporto della circolarità, nuovi modelli di business e aspetti legislativi e barriere da affrontare per l’adozione del modello circolare.
Grazie alle attività svolte all’interno della Strategic Community, gli stakeholders coinvolti hanno l’opportunità di approfondire le proprie competenze e conoscenze, entrando inoltre all’interno dei principali network di innovazione in Europa, attraverso i canali interregionali di cui il Cluster è protagonista.
Infatti, AFIL, su mandato di Regione Lombardia, coordina il Pilot “Efficient and Sustainable Manufacturing (ESM)” all’interno dell’iniziativa Vanguard, un network di più di 30 Regioni Europee, avviato nel 2014, con l’obiettivo di sviluppare una rete interregionale di impianti pilota che supportino le aziende nelle attività di testing e up-take di tecnologie innovative.
Tra le attività sviluppate nel Pilot vi è un demo-case, coordinato da AFIL, sul tema “De-and Remanufacturing” il cui obiettivo è contribuire alla creazione di nuove catene del valore circolare in Europa, indirizzando casi industriali rilevanti a livello comunitario, tra i quali il recupero e il riuso dei materiali compositi, delle batterie dei veicoli elettrici e di componenti ad alto valore derivanti dai prodotti elettronici. I
volgimento dei propri Soci nelle attività del Gruppo di Lavoro (GdL) “De-and Remanufacturing”, che raccoglie circa 30 membri in rappresentanza di Aziende, RTOs, Università e Associazioni Industriali. Le tematiche discusse dal GdL, che si è evoluto in “Strategic Community De-and Remanufacturing for Circular Economy”, riguardano tecnologie innovative per la gestione di prodotti e materiali a fine vita per massimizzare il valore residuo attraverso opportune pratiche di riuso, re-
membri della Strategic Community sono attivamente coinvolti in questa iniziativa contribuendo allo sviluppo del demo-case “De-and Remanufacturing” e alla realizzazione di specifici progetti di R&I, come ad esempio: SCREEN, FiberEUse, CarE-Service e DigiPrime, finanziati dal programma H2020. Le attività e gli scopi di queste attività di ricerca collaborativa hanno ricadute di impatto per il territorio lombardo, sia in termini di coinvolgimento delle imprese sia a supporto delle politiche di R&I come nel caso di SCREEN e del progetto INTERREG CircE che hanno fornito indicazioni metodologiche e linee guida per la redazione della recente “Roadmap per la R&I sull’Economia Circolare di Regione Lombardia”. Il documento, approvato da Regione Lombardia nel Maggio 2020, delinea le priorità di R&I ritenute essenziali per la transizione del territorio verso l’Economia Circolare. Esso è il risultato di un processo collaborativo che ha coinvolto un rilevante numero di attori del territorio coordinati da AFIL.
1Fonte: European Commission 2Fonte: Ministero dell’Ambiente 3Fonte: Roadmap per la Ricerca e Innovazione, 4Cluster Fabbrica Intelligente - 2014. 5Fonte: European Remanufacturing Network (https://www.remanufacturing.eu)
Il Progetto DigiPrime: “Digital Manufacturing Platforms for Connected Smart Factories”
Sviluppare e dimostrare l’impatto di una piattaforma digitale per favorire lo scambio di informazioni e servizi tra aziende, con ottica cross-settoriale, abilitando così nuovi modelli di business di economia circolare ad alto valore aggiunto. Con questo obiettivo è stato lanciato a gennaio 2020 DigiPrime, un progetto co-finanziato dall’Unione Europea attraverso il programma Horizon 2020, della durata di 4 anni, con un consorzio di 36 partner fra industriali e accademici da 11 diversi stati membri e coordinato dal Politecnico di Milano, Dipartimento di Meccanica. DigiPrime ha il doppio target di connettere attori industriali appartenenti a settori diversi attraverso lo scambio di informazioni in ottica win-win e di fornire agli stessi servizi IT sia orizzontali di coordinamento dell’intera value-chain che verticali per la singola azienda. Lo sviluppo della piattaforma parte da sei casi pilota che collegano diversi settori, tra cui batterie litio-ione, compositi e tecnopolimeri, componenti elettronici e meccatronici e prodotti tessili. Inoltre, il progetto gestirà due call aperte a nuovi attori esterni a DigiPrime che vogliano popolare ed arricchire la piattaforma con il meccanismo del “cascade funding”, cioè finanziamenti gestiti dal progetto stesso. DigiPrime rappresenta anche un importante moltiplicatore per risultati raggiunti e best-practices legate alle attività già mature sopra descritte: da un lato metodologie sviluppate e dati generati nei progetti FiberEUse, CarEService e Screen sono alla base dello sviluppo di alcuni servizi della piattaforma, dall’altro attori industriali già coinvolti nei progetti popolano i pilot e contribuiscono a definire come le funzionalità di DigiPrime debbano essere tarate per il mondo dell’Economia Circolare. La Lombardia è ben rappresentata nel consorzio DigiPrime, che oltre al Politecnico annovera Holonix e TTS Technology Transfer System fra gli sviluppatori IT e Centrocot e Rivierasca come campioni di Economia Circolare nei settori tessile e prodotti in materiale composito.
Maggiori informazioni sono disponibili al seguente Link https:// www.digiprime.eu/
Il Progetto CarE-Service: “Circular Economy oriented services for re-use and remanufacturing of hybrid and electric vehicles components through smart and movable modules”.
CarE-Service è un progetto di innovazione industriale volto allo sviluppo di modelli di business circolari per la valorizzazione di componenti ad alto valore aggiunto provenienti da auto elettriche. Il tutto attraverso l’implementazione di tecnologie abilitanti e la loro modularizzazione, per permettere sia trattamenti in-situ presso i dismantler, che presso impianto di per il remanufacturing ed il riciclo di materiali. L’obiettivo è il recupero di funzioni e materiali di tre componenti target del veicolo elettrico: il pacco batteria agli ioni di litio, che contiene materiali critici quali il cobalto e generalmente mantiene, alla fine della sua via utile in contesto automotive, proprietà elettrochimiche residue sufficienti ad un suo utilizzo in altri settori; componenti metallici di carrozzeria e telaio, riutilizzabili o ricondizionabili attraverso trattamenti a freddo per l’adeguamento a nuove geometrie o per il loro uso in contesti diversi da quello automotive; tecnopolimeri con alte proprietà meccaniche che sono introdotti nei veicoli in percentuali sempre maggiori per ridurne il peso. Nel progetto si stanno sviluppando e testando nuove tecnologie per il disassemblaggio, testing, remanufacturing e riciclo di questi materiali. Inoltre, è in fase di implementazione una piattaforma informatica per l’integrazione degli attori dell’End-Of-Life dei veicoli elettrici e per lo scambio delle parti recuperate attraverso processi che riducono l’incertezza tipica del fine vita. Finanziato attraverso il programma Horizon 2020, iniziato nel 2018 e con una durata prevista di tre anni, CarE-Service bene intercetta le necessità del mercato italiano di adattarsi ai crescenti volumi di auto elettriche immesse sul mercato, sia perché tante aziende del territorio popolano il settore automotive sia perché sempre più consumatori si stanno rivolgendo al mercato elettrico e ibrido per l’acquisto di una nuova vettura. Coordinato dall’Istituto STIIMA-CNR, con sede a Milano, CarE-Service annovera tra le aziende lombarde Radici Group, realtà di grande importanza nel settore plastiche, E-VAI, società di car sharing del Gruppo Ferrovie Nord Milano, CIA Robotics, integratore di sistemi robotizzati e Cobat, consorzio di raccolta e trattamento leader in Italia nella filiera delle batterie. Tra gli altri partner, Fiat Chrysler Automobiles, il Fraunhofer Institute, il JRC della Commissione Europea, il CSIC spagnolo, Envirobat, Università di Linkoping, IMA, Prodigentia, C-ECO, Avicenne.
Maggiori informazioni sono disponibili al seguente Link https://www.careserviceproject.eu/
PACKAGING ALIMENTARE, LA RIVOLUZIONE FOODTECH PARTE DAI MATERIALI

NELL’INDUSTRIA ALIMENTARE IL SEGMENTO DELL’IMBALLAGGIO RESISTE: IL MADE IN ITALY HA SUCCESSO ANCHE ALL’ESTERO. MATERIALI FORTEMENTE INNOVATIVI PER UN PACKAGING SEMPRE PIÙ ECOCOMPATIBILE E RICERCA DI NUOVE SOLUZIONI NEI MACCHINARI APPORTANO SLANCIO ALLA RIVOLUZIONE FOODTECH
di Alberto Buffon
Nel FoodTech, l’incontro tra l’innovazione tecnologica e la tradizione agroalimentaria, si è visto un fiorire di innovazioni trasversali capaci di unire ambiti anche molto diversi fra loro, come ad esempio lo studio di modelli di machine learning, l’aerodinamica e la topografia per istruire una flotta di droni ad analizzare e trattare un campo coltivato. L’Italia, motivata al mantenimento del suo status di patria per eccellenza della cultura alimentare, si sta organizzando per divenire il portabandiera di questo movimento socioeconomico. La già citata Talent Garden ha dedicato proprio al Foodtech un campus a Milano, aperto nel 2019 in zona Isola e che ospita attualmente oltre 150 membri tra startup, agenzie, freelancer, corporate e investor, mentre a Roma ha aperto “Startupbootcamp FoodTech Rome”, acceleratore d’impresa dedicato all’agroalimentare organizzato dall’azienda esperta di startup Startupbootcamp, la quale conta più di dieci incubatori sparsi in tutto il mondo. A Milano troviamo anche il percorso del “FoodTech Accelerator” coordinato da Deloitte Officine Innovazione, in collaborazione con alcune realtà italiane tra cui Amadori, Cereal Docks, Birra Peroni e COPROB Italia Zuccheri, che ha presentato nel Febbraio scorso nove startup internazionali scelte tra più di 600 candidature. Non mancano anche programmi dedicati all’interno degli acceleratori già presenti nel territorio, come quello proposto da UniCredit.
L’innovazione nel packaging
La spinta fornita dal Foodtech al mercato alimentare ha riacceso l’interesse delle aziende già solide nel settore portandole a scommettere nuovamente sull’innovazione e sulla ricerca, così da non farsi lasciare indietro dalle neonate imprese. I primi cambiamenti visibili di questa rivoluzione sono stati inerenti all’ambito del packaging, elemento comune a tutte le fasi finali della catena di produzione ed essenziale per la conservazione del prodotto. Per il mercato interno e ancor più per l’export, la flessione riportata in questa difficile congiuntura dal segmento del packaging alimentare è stata molto più contenuta rispetto ad altri settori, grazie a diversi fattori: dallo sviluppo di tecnologie di ultima generazione (Industry 4.0), per lo svolgimento di attività strategiche, come l’installazione degli impianti da remoto e l’assistenza virtuale al cliente, all’introduzione di prodotti a basso impatto ambientale. Nel corso del 2020, infatti, gli imballaggi ecologici hanno acquisito interessanti quote di mercato, forti dell’interesse dimostrato negli ultimi anni sia dall’industria, sia dai consumatori.
Confezioni sempre più green
Già oggi sono numerose le aziende che investono nella ricerca di nuovi materiali come le bioplastiche, a base di materiali sostenibili, come la cellulosa, l’amido, la fecola di patata, le alghe, i residui di lavorazione del latte, i rifiuti organici e così via. La sfida, per tutti gli operatori del settore, è produrre materiali resistenti, in grado
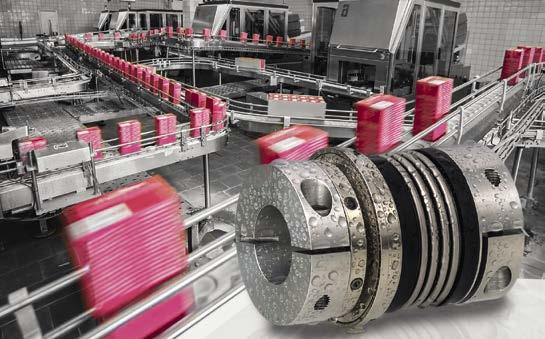

Igienizzazione macchinario
di proteggere efficacemente l’alimento, facilmente stampabili, accattivanti per il consumatore. Tra le idee più interessanti presentate al riguardo troviamo “Ooho” la capsula per il contenimento di liquidi trasparente, biodegradabile e commestibile, realizzata con un polimero sintetico ricavato dalle alghe marine. Questo speciale involucro è stato sviluppato dalla startup britannica Skipping Rocks Lab, la quale ha saputo trovare una soluzione al problema delle bottiglie di plastica, ormai sempre più presenti nei nostri oceani, che fosse sia economicamente che ecologicamente sostenibile. Altre novità riguardano per esempio una nuova pellicola per alimenti fatta con un tessuto biodegradabile realizzato con prodotti biologici certificati. Questo nuovo materiale beeopak potrebbe sostituire la pellicola di plastica per alimenti e la carta stagnola. Può essere utilizzato per avvolgere quasi tutti gli alimenti come pane, formaggi, frutta e verdura e per coprire i contenitori. Si tratta di un materiale ricavato con ingredienti biologici certificati, come la cera d’api biologica e l’olio di nocciola tonda e gentile Igp. È un tessuto naturale, modellabile e adattabile, lavabile e riutilizzabile per circa un anno senza perdere le sue caratteristiche.
La lotta allo spreco alimentare
In un periodo in cui la responsabilità sociale dell’impresa è sempre più sentita da consumatori, mercati e finanza, tra le sfide che si trovano ad affrontare le aziende del settore non poteva mancare lo studio e la realizzazione di confezioni in grado di migliorare la qualità dei prodotti alimentari, prolungare la loro durata di conservazione e avere un impatto economico inferiore rispetto ai costi di smaltimento degli imballaggi tradizionali. In questo ambito è stata sviluppata da Iuv – azienda italiana che sviluppa, produce e commercializza packaging innovativi, sostenibili e naturali – la soluzione chiamata Columbus’ Egg che si propone di abbattere le perdite e gli sprechi alimentari. Le pellicole sviluppate con questa tecnologie sono in grado di prevenire la comparsa di muffe, lieviti e batteri, di allungare la vita degli alimenti naturalmente. Sono applicabili per immersione e realizzate utilizzando componenti naturali, sostenibili e a basso costo, con la possibilità di inglobare prodotti funzionali al benessere del consumatore. Anche Ixon, startup di Hong Kong incubata presso l’acceleratore di Deloitte Officine Innovazioni, si è mossa in questa direzione, sviluppando una tecnologia di confezionamento asettico capace di trasformare gli alimenti sottovuoto in prodotti stabili, senza la necessità di utilizzare il frigorifero, eliminando così il problema logistico della catena del freddo e della conservazione.
Packaging connesso
Altro trend che guida il comparto è la digitalizzazione delle confezioni per essere sempre più vicino al consumatore. Come? Connettendo il packaging alla rete tramite un codice QR e altri indicatori grafici near field communication (NFC), identificazione a radio frequenza (RFID), Bluetooth e realtà aumentata (AR). Attraverso queste tecnologie sarà possibile infatti accedere a una quantità di dati e
informazioni impensabili sul prodotto: ingredienti, tabelle nutrizionali, consigli per l’uso, ricette e curiosità, oltre a un ambiente virtuale dove il produttore e l’intera comunità di consumatori potranno incontrarsi, confrontarsi ed interagire. L’obiettivo è arrivare a un packaging alimentare altamente personalizzato e personalizzabile, che porterà a un maggiore coinvolgimento dei consumatori, una rinnovata consapevolezza del prodotto con l’aggiunta dell’elemento esperienziale, tutti fattori che portano con sé nuove sfide di marketing e nuovi potenziali sviluppi di mercato.
Nuove sfide per il settore
Il mercato contemporaneo richiede di far fronte, oltre che alla già menzionata esigenza di imballaggi 100% riciclabili, anche al bisogno del consumatore di fruire di prodotti senza aggiunta di additivi e conservanti chimici; ciò rappresenta una sfida per le aziende, poiché fa emergere la necessità di ristudiare le strategie per rendere i processi di lavorazione, e di conseguenza gli alimenti, più protetti da contaminazioni microbiologiche. Il conseguente irrigidimento delle norme igieniche, con l’aumento della frequenza dell’attività di pulizia e igienizzazione, ha fatto emergere un effetto collaterale imprevisto: la corrosione anticipata dei macchinari impiegati, nonostante i materiali che li costituiscono siano acciai inossidabili e allumini. Negli ultimi anni, infatti, si è visto un aumento degli studi riguardanti tale fenomeno del settore alimentare.
Nuovi materiali contro la corrosione
Lo studio “AES and XPS investigations of thecleaning-agent-induced pitting corrosion of stainless steels used in the food-processing environment” di D. Steiner-Petrovič e D. Mandrino condotto sugli acciai inossidabili AISI 304 e AISI 430 usati nelle attrezzature a contatto con gli alimenti, ha rilevato la presenza di strati passivati gravemente danneggiati e non omogenei, indotti dall’ammoniaca contenuta nel detergente che reagisce con il cloro disperso nell’ambiente. Le analisi superficiali AES e XPS hanno dimostrato la presenza di Cl e N sulle superfici analizzate, soggette a frequenti pulizie approfondite, in cui il sale di ammonio dell’acido cloridrico, attraverso una reazione con l’acqua, aumenta la sua concentrazione di ioni cloruro nella soluzione, innalzando di molto il potere corrosivo dei detergenti. La distruzione localizzata dello strato passivante innesca il processo corrosivo denominato pitting, o vaiolatura a causa della sua distribuzione a puntini come la famosa malattia. L’attacco corrosivo è localizzato ma funge da innesco per l’azione della corrosione elettrochimica; le zone dove il film viene a mancare fungono da anodi (zona attiva) rispetto a quelle circostanti, che presentano uno strato di ossidi ancora integro, su cui invece ha luogo l’azione riducente (catodica). Anche lo studio “Microstructure investigation of premature corroded heat exchanger plates(Article)” di A.Wassilkowska, T. Skowronek, S. Rybicki, ha rilevato le stesse problematiche analizzando le piastre di uno scambiatore in acciaio 316L, corrose per pitting in appena cinque mesi di utilizzo. Entrambi gli articoli evidenziano la necessità di utilizzare leghe a più elevata resistenza alla corrosione in tutte quelle applicazioni per cui vi è la necessità di pulire frequentemente i componenti con detergenti a base di ammoniaca o in cui un guasto nel funzionamento della macchina possa causare uno sversamento di materiale organico; inoltre, raccomandano di ridurre il più possibile la rugosità superficiale poiché, altrimenti, le microasperità presenti potrebbero essere tali per cui un normale risciacquo con acqua dopo il trattamento di pulizia non sia sufficiente per rimuovere le piccole concentrazioni di sale di ammonio presenti in superficie.
Il ruolo del fornitore di componenti
Un’attività complessa come la realizzazione delle macchine per il settore del packaging alimentare può trovare un valido supporto nei fornitori di componenti. È il caso di R+W, azienda leader nella produzione di giunti e alberi di trasmissione, in grado di mettere la sua esperienza a disposizione del progettista. Il packaging, spesso considerato un aspetto minimale del prodotto, incide fino al 40% sul prezzo di vendita al dettaglio dell’oggetto, svolgendo un ruolo di primaria importanza dal punto di vista del marketing. Questo si traduce in un continuo rinnovo dei formati, dei materiali impiegati nel confezionamento e nella costruzione di macchinari custom per fabbricarli. Macchine sempre più smart, come vuole l’economia 4.0, che richiedono componenti evoluti, intelligenti e capaci di comunicare tra loro per ottimizzare la produttività e salvaguardare la competitività sui mercati internazionali.
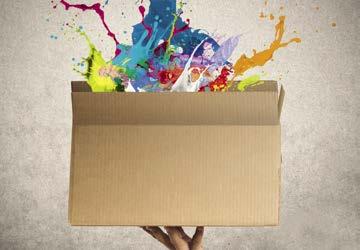
Allunghe per giunti della serie ZA
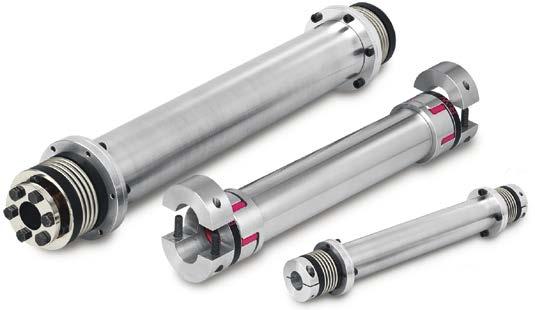
Nel settore della produzione o trasformazione alimentare, R+W Italia serve anche marchi di primo piano nel segmento dei derivati del latte che anche grazie a questi prodotti seguono sia il ciclo produttivo sia il confezionamento; ma il segmento dell’industria alimentare dove la presenza di R+W è maggiore rimane il packaging, dove i componenti dell’azienda trovano utile impiego nei sistemi complessi delle linee di imballaggio e nella gestione pallettizzata delle confezioni. L’industria sta attraversando un periodo di grandi cambiamenti dettati, come detto prima, dalla spinta green alla realizzazione e commercializzazione di imballi compostabili o nei quali il ricorso alla plastica sia il più possibile contenuto. Fra i clienti di R+W rientrano sia le società di stampaggio delle materie plastiche, sia molte altre aziende che invece stanno scommettendo sulla sostituzione della plastica. Sono i brand dell’alimentare e anche le scelte dei consumatori a orientarne le strategie, stimolando parte le ricerca, lo sviluppo, l’innovazione. Pur mantenendo invariate le rispettive caratteristiche originarie, i prodotti di R+W seguono i trend di mercato, fra i quali quello della sostenibilità è fra i più percepibili e condivisibili. Per soddisfare le esigenze dei clienti l’azienda propone i giunti di precisione a soffietto BK, i giunti a elastomero della serie EK, i giunti con allunga ZAE ed EZ nonché con i limitatori di coppia della famiglia SK. I giunti BK a soffietto metallico, precisi e senza gioco, sono molto apprezzati per il basso momento di inerzia, la totale assenza di necessità di manutenzione, la durata praticamente infinita e soprattutto la totale affidabilità. I giunti a elastomero della serie EK combinano elevata flessibilità e buona resistenza. Smorzano vibrazioni e impatti compensando i disallineamenti degli alberi. I giunti a elastomero EK combinano elevata flessibilità e buona resistenza. Smorzano vibrazioni e impatti compensando i disallineamenti degli alberi. Molti elementi condizionano la progettazione dei giunti a elastomero: da fattori quali il carico, l’avviamento e la temperatura dipende la durata dell’inserto. L’elemento elastomerico è disponibile in diverse durezze shore, per trovare sempre un compromesso adatto fa le proprietà di smorzamento, la rigidità torsionale e la correzione dei disallineamenti per la maggior parte delle applicazioni. I giunti con allunga della serie ZA-EZ sono ideali per collegamenti con grandi distanze assiali, eventualità spesso presente nelle macchine da imballaggio. Sono facili da montare e smontare senza che occorra muovere o allineare gli elementi da collegare. R+W ha in assortimento giunti con allunghe fino a 6 m, che non necessitano di supporto intermedio. Disponibili in versioni speciali per quanto riguarda materiali, tolleranze, dimensioni e prestazioni, i giunti con allunga R+W se ben dimensionati e montati correttamente non hanno alcuna necessità di manutenzione e una durata praticamente infinita. I limitatori di coppia SK sono in grado di svincolare la parte motrice dalla parte condotta nel caso di un sovraccarico. E questo allo scopo di tutelare non solamente i componenti coinvolti nella trasmissione del moto, ma anche il prodotto finale e naturalmente il suo packaging. In modo da evitare il suo danneggiamento durante la produzione e limitare la percentuale di prodotto che risulta non conforme alla vendita per la difettosità della confezione. La sfida raccolta da R+W è dar vita a oggetti che per tipologia del materiale, peso e prestazioni supportino l’ottimizzazione dei processi. Per esempio, il food predilige l’acciaio inox che dà ampie garanzie di igienicità nel contatto col prodotto. R+W ha dovuto portare a termine studi importanti che hanno però dato buoni frutti, perché sinora l’azienda è sempre stata in grado di consegnare agli utilizzatori soluzioni adeguate.
IGUS
E-SPOOL FLEX: ALIMENTAZIONE CONTINUA E SICURA DEL TOUCHPAD DI ROBOT INDUSTRIALI
Con l’e-spool flex è possibile arrotolare e srotolare con sicurezza il cavo del touchpad. L’azienda ARAGON Industrieelektronik GmbH ha scelto questa soluzione. (Fonte: igus GmbH)
Sono la “regia” per i sistemi robotizzati: i touchpad di controllo. Per agevolarne l’utilizzo, devono avere una lunghezza di cavo sufficiente, devono essere mobili, flessibili e sicuri. Proprio per questo, igus ha sviluppato il sistema e-spool flex. Questo speciale dispositivo funziona senza giunto rotante e può quindi trasmettere in modo continuo anche i segnali bus. Con questo sistema, è facile inserire il cavo, anche già cabalato, successivamente alla prima installazione del robot. Ecco i vantaggi che hanno conquistato il fornitore di servizi di robotica ARAGON. Con i suoi robot industriali, l’azienda propone un set completo composto dal sistema e-spool con un cavo standard e un supporto preassemblato per il pannello. Dare una seconda vita ai vecchi robot: ecco ciò che ARAGON Industrieelektronik GmbH si propone di fare. L’azienda, specializzata nelle soluzioni di robotica industriale, offre in tutto il mondo i suoi servizi per la riparazione, la manutenzione, il retrofitting e il revamping di robot industriali. Tra i clienti, ci sono piccole imprese che utilizzano non più di 10 robot, ma anche società più grandi oppure OEM del settore automobilistico che scelgono di avvalersi dell’expertise di questo fornitore specializzato. Proprio per le applicazioni dei touchpad, l’azienda stava cercando una soluzione pratica per i cavi: “Il nostro obiettivo principale è sempre quello di garantire la sicurezza dei clienti offrendo soluzioni innovative. Spesso, finora, il cavo veniva lasciato a terra, si danneggiava rapidamente e c’era il rischio di inciampare. Così cercavamo un avvolgicavo versatile che si potesse aggiornare in modo semplice, veloce e senza interruzioni”, spiega Iryna Geike, Country Manager presso ARAGON. La soluzione è stata trovata in igus. “Ci è stato presentato il nuovo sistema e-spool flex e ci ha convinto subito”, ricorda Iryna Geike. Il vantaggio fondamentale dell’e-spool flex rispetto ad altri dispositivi per cavi sta nel fatto che non viene utilizzato alcun giunto rotante. In questo modo, è possibile integrare nel sistema anche tubi, cavi dati, potenza e il segnale per l’arresto di emergenza. I cavi preesistenti del touchpad si possono inserire facilmente nella guida elicoidale del sistema e vengono arrotolati automaticamente. „Ora i nostri clienti, per il loro touchpad, ricevono un set preassemblato composto da e-spool flex, supporto per pannello ARAGON, cavo e una staffa sagomata per il fissaggio agli armadi dei comandi dei robot. Con l’e-spool flex, la durata d’esercizio del cavo si allunga notevolmente e migliorano sicurezza e ordine sui pannelli di controllo”, spiega Iryna Geike.
Arrotolare e srotolare i cavi: manualmente o in modo automatico
igus propone l’e-spool flex in diverse varianti. Una versione low-cost con una maniglia di avvolgimento o un avvitatore a batteria oppure una soluzione automatica con meccanismo di recupero a molla e una funzione di arresto. Su richiesta, viene fornito con un freno di entrata. ARAGON ha scelto la variante con molla di richiamo. L’avvolgicavo è disponibile in tre dimensioni, per cavo con diametro da 5 a 15 millimetri e per estensioni da 5 a 15 metri. Il cavo può essere sostituito in qualunque momento. Oltre alla possibilità di inserire un cavo esistente nell’e-spool flex, igus propone questo sistema già preassemblato con cavi flessibili chainflex appositamente progettati per le applicazioni in movimento. La durata dei cavi nell’e-spool flex viene attualmente testata nel laboratorio di prova aziendale di 3.800m2, attraverso numerose prove.
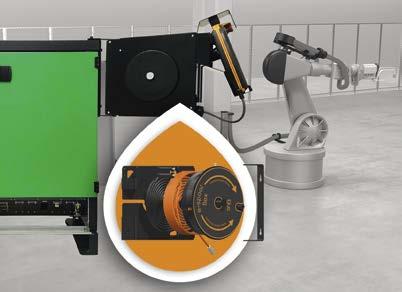
SCHUNK
MASSIMIZZA L’EFFICIENZA CON I NUOVI TOOL SCHUNK PER LA FINITURA SUPERFICIALE ROBOTIZZATA
Per ottenere prodotti perfettamente finiti, è necessario rimuovere in modo preciso ed affidabile spigoli vivi, irregolarità o eccessi di materiale che si presentano a seguito dei processi di asportazione o fusione dei metalli. Fino ad ora, questo tipo di operazioni delicate è stato condotto principalmente attraverso la lavorazione manuale. Oggi, invece, è possibile portare il processo di sbavatura ad un livello superiore, automatizzandolo. SCHUNK, leader di competenza in questo campo, ha ampliato il proprio portfolio di accessori robot dedicati alle operazioni di finitura superficiale per ottenere risultati di lavorazione perfetti, aumentare l’efficienza, risparmiare sui costi e sollevare gli operatori da un lavoro duro e faticoso.
Nel settore dell’asportazione truciolo, la finitura superficiale rappresenta solitamente una fase di lavoro ulteriore che richiede sforzi aggiuntivi dal punto di vista sia logistico che delle risorse umane. Contemporaneamente, tuttavia, molti robot svolgono nella stessa officina operazioni di asservimento macchina utensile. E’ proprio a questo punto che entrano in gioco i nuovi tool per la finitura superficiale robotizzata di SCHUNK. Oltre all’impiego per il semplice carico/ scarico macchina, lo stesso robot potrebbe essere impiegato per la realizzazione di operazioni di finitura robotizzata. La sbavatura di un pezzo lavorato può essere effettuata in parallelo alla lavorazione del pezzo successivo, evitando una fase di lavoro ulteriore, a seguito dell’asportazione. La sbavatura simultanea consente di ridurre i tempi di consegna e i costi unitari, e contribuisce a massimizzare l’investimento del robot utilizzato quasi esclusivamente nell’asservimento macchina. La precisione di ripetibilità del robot assicura risultati migliori in termini di omogeneità e riproducibilità, rispetto al lavoro umano. Utilizzando un robot per operazioni monotone e faticose, gli operatori, sollevati da tali operazioni, possono beneficiare di maggiore sicurezza ed ergonomia della postazione di lavoro. Con i nuovi tool SCHUNK, gli utilizzatori possono davvero ottenere tutti questi vantaggi.
Soluzione ideale per ogni tipo di esigenza
Con CRT, RCV e CDB, SCHUNK ha sviluppato tre unità per diverse operazioni di finitura superficiale, fornendo strumenti ottimali per ogni applicazione. La lima ad azionamento pneumatico, CRT, è particolarmente adatta per la finitura di componenti dalle geometrie piccole e strette. Anche in zone difficili da raggiungere come fessure, angoli o scanalature, l’eccesso di materiale può essere rimosso e il pezzo pulito con precisione e senza lasciare residui. L’angolo di compensazione di +/- 1,8 mm compensa in modo affidabile le imprecisioni di posizione e le tolleranze del pezzo e del robot. Poiché la lima può essere dotata di lame tradizionali, il materiale disponibile può essere riutilizzato e il passaggio a processi automatizzati risulta più semplice. Il mandrino di sbavatura pneumatico RCV è attualmente il prodotto più robusto sul mercato e dimostra le sue capacità durante la finitura di pezzi grezzi o fresati. Dato che possono essere utilizzati diversi strumenti rotanti, l’RCV può essere utilizzato in modo flessibile per varie operazioni di sbavatura. Grazie alla sua robustezza e alta qualità, è possibile ottenere risultati di lavorazione omogenei in maniera costante. Il motore a palette accorcia i tempi macchina con coppia elevata e tempi di arresto brevi, garantendo quindi una maggiore produttività. L’unità CDB facilita il passaggio da processi manuali a processi automatici. Per la prima volta è, infatti, possibile utilizzare lame di sbavatura manuali già collaudate e non sono necessari ulteriori investimenti in nuovi materiali. Grazie al bloccaggio utensile uniformato e alla possibilità di cambio lama automatico, il tempo di attrezzaggio è breve e quindi anche piccole serie possono essere lavorate in modo economico. L’unità è regolabile in direzione assiale e radiale ed è adatta per la sbavatura di vari pezzi. È possibile lavorare facilmente una varietà di materiali, come plastica, alluminio, acciaio o ottone, nonché diverse forme geometriche. Tutti i prodotti menzionati sono compensati. La regolazione dell’utensile può essere effettuata con pressione pneumatica. Pertanto, viene garantita una funzione di bilanciamento variabile e lo sforzo di programmazione per il robot si riduce notevolmente. La messa in servizio viene eseguita molto rapidamente e facilmente. Con il fissaggio opzionale dell’asse y, gli utilizzatori possono passare dalla compensazione oscillante a quella radiale. Questa flessibilità garantisce una lavorazione efficiente, anche di varie geometrie del pezzo. Meno scarti, tempi di inattività notevolmente ridotti e solo una esigenza molto limitata di ricambi sono i vantaggi del processo automatizzato. L’impatto di questi risultati sarà evidente in un risparmio notevole sui costi.
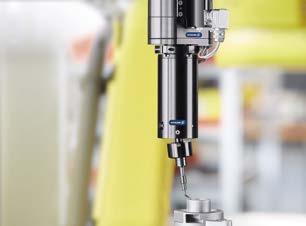
UNA COLLABORAZIONE “CABLATA” PER IL SUCCESSO
Il confezionamento di fine linea è un’operazione indispensabile per la movimentazione e il trasporto sicuro dei prodotti. Efficienza, flessibilità e precisione sono i requisiti che i moderni impianti per l’imballaggio secondario devono soddisfare al fine di assicurare massimi livelli di produttività, anche nelle ultime fasi operative della supply chain. Ne è perfettamente consapevole Officina Meccanica Sestese (OMS Group), player mondiale nella produzione di sistemi per il confezionamento di fine linea di prodotti pallettizzati, che da oltre 20 anni si affida a LAPP, leader nello sviluppo e produzione di soluzioni integrate nella tecnologia di connessione e cablaggio, per il cablaggio delle diverse tipologie di macchine che compongono la sua offerta. Una partnership all’insegna dell’eccellenza e della collaborazione reciproca, testimoniata anche dalla scelta da parte di LAPP di adottare le soluzioni OMS per il suo nuovo centro logistico di Hannover. Reggiatrici automatiche, incappucciatrici, forni per termoretrazione e avvolgitrici: in virtù della sua proposta completa, OMS Group soddisfa qualsiasi richiesta del mercato in molteplici settori, dalla singola macchina al più sofisticato impianto di imballaggio chiavi in mano. Una flessibilità produttiva che trova in LAPP un partner in grado di fornire dalle poche decine di m di cavi, fino al cablaggio completo dell’intera linea. “La qualità e l’affidabilità dei prodotti LAPP sono sicuramente i pilastri su cui si fonda il nostro rapporto consolidato” commenta Maurizio Alessi, Marketing Manager di OMS che continua “Inoltre, conoscere e utilizzare i cavi LAPP da così tanto tempo ci ha permesso di attuare delle economie di scala al fine di ottimizzare la progettazione dei nostri macchinari, in termini di componentistica elettrica, in funzione delle loro specifiche caratteristiche” e conclude “Da questo punto di vista, la facile reperibilità su scala mondiale rappresenta per noi, in qualità di Gruppo internazionale, uno dei principali vantaggi unitamente all’ampia gamma certificata UL e CSA per il mercato Nord Americano”.
Nello specifico, tra le soluzioni maggiormente apprezzate da OMS Group spiccano i cavi listed di controllo e comando ÖLFLEX® CONTROL TM, per posa fissa e i cavi di alimentazione e comando, ÖLFLEX® TRAY II, dotati di multi-approvazione conforme a NFPA 70/NEC e NFPA 79. Inoltre, per le parti delle macchine in movimento, OMS sceglie i cavi flessibili ÖLFLEX® CLASSIC FD 810, con isolamento dei conduttori e guaina esterna in PVC. Si distinguono, altresì, le soluzioni schermate: i cavi ÖLFLEX® CLASSIC 110 CY e ÖLFLEX® CLASSIC 100 CY, per bordo macchina e i cavi per servomotori ÖLFLEX® SERVO FD 781 CY, con costruzione a bassa capacità, che consente lunghezze maggiori tra convertitore e azionamento. Infine, per la trasmissione di segnale OMS si affida ai cavi del brand UNITRONIC®, ideali sia per posa fissa che mobile. “LAPP e OMS sono due realtà internazionali che condividono il fatto che sviluppare soluzioni custom sia un vero e proprio valore aggiunto per i Clienti” dichiara Gaetano Grasso, Head of Product Management and Marketing di LAPP, che aggiunge “Questo è il presupposto della nostra relazione che si declina altresì nel supportare OMS nella progettazione e realizzazione di macchine, per il confezionamento di fine linea, altamente performanti” e conclude “Per questo, nella selezione del supplier ideale per la realizzazione dell’imballo delle bobine di cavi del nuovo centro logistico di Hannover, LAPP Germania si è affidata alla validità delle proposte personalizzate di OMS”. “Grazie alla sua expertise, OMS è stata in grado di configurare la nostra “macchina dei sogni” che combina, in un’unica stazione di lavoro, sia la reggiatura, sia le operazioni per incappucciare, con film termoretraibile, consentendoci così di ridurre l’utilizzo di film, laddove consentito” afferma Andreas Gesse, Responsabile del centro logistico 3 di Hannover, di LAPP Germania che prosegue “Una soluzione che permette di imballare prodotti dal diametro anche fino a 120 cm, con una velocità di 80 confezioni l’ora, il doppio rispetto alle macchine utilizzate in precedenza” e conclude “Infine, dato il periodo storico particolarmente delicato, acquisisce ancor più valore che abbiano rigorosamente rispettato i tempi di consegna, oltre alla tempestività del servizio di assistenza tecnica locale”.

STARTER KIT IO-LINK ALLA SCOPERTA DELLA TECNOLOGIA
Turck Banner Italia, tra i principali fornitori di sensoristica, illuminatori e segnalatori industriali, sistemi bus e sicurezza, presenta uno starter kit compatto per tutti coloro i quali desiderino scoprire i vantaggi del protocollo di comunicazione digitale IO-Link. I dispositivi IO-Link contenuti nella confezione consentono di configurare il proprio sistema e quindi acquisire esperienza pratica con questa tecnologia.
I dispositivi IO-Link forniscono dati di manutenzione per il condition monitoring di macchinari e impianti insieme anche a dati utente. Grazie al master IO-Link TBEN-S con quattro canali PNP universali, tutti i dati sono facili da utilizzare e possono anche essere visualizzati con l’indicatore luminoso RGB IO-Link. Lo starter kit contiene anche un alimentatore da 230 V, i cavi per collegare un PC o per collegare il master IO-Link e i dispositivi IO-Link (M12-M12 e M8-Ethernet RJ45) e una memory stick USB per facilitare la messa in produzione. Il supporto di memoria contiene anche il software operativo PACTware, tutte le descrizioni dei dispositivi IO (IODD) e un interprete IODD DTM.
Rapida integrazione nei sistemi Profinet
Il software Simple IO-Link Device Integration (SIDI) consente di integrare i dispositivi nei sistemi Profinet senza la necessità di alcun software aggiuntivo. La libreria SIDI sui master IO-Link di Turck Banner include non soltanto tutti i dispositivi IO-Link in portfolio, sia quelli di matrice tedesca, e cioè di Turck GmbH, sia quelli di matrice statunitense originati dal partner di optoelettronica Banner Engineering, ma anche quelli di diversi dispositivi di altri noti produttori. Ulteriori altri dispositivi di altri ulteriori produttori possono essere integrati su richiesta. Questo significa che i dispositivi IO-Link possono essere selezionati dal catalogo hardware di un ambiente di programmazione come TIA Portal come se fossero sottomoduli di un sistema I / O. Caratteristiche e parametri importanti, come i campi di misura, i segnali di uscita o le frequenze degli impulsi possono essere modificati nel campo di testo in chiaro.
Le principali funzionalità
Con lo starter kit si accede a un modulo I / O multiprotocollo con 4 canali master IO-Link e a un Hub I / O a 8 canali per il collegamento di 8 segnali PNP digitali. Il kit presenta inoltre un sensore induttivo a grande distanza di commutazione e un sensore a fattore 1 per tutti i metalli. Completa la dotazione un sensore a ultrasuoni M18 con compensazione della temperatura e analisi dell’intensità degli ultrasuoni. L’accesso ai dati di processo, alla diagnostica e alle informazioni sui dispositivi avviene tramite IO-Link.
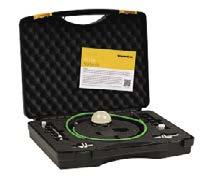
CT MECA
MAGNETI
I magneti sono utilizzati in diversi settori e applicazioni per risolvere problemi di fissaggio. Presentano un sistema magnetico permanente con una sola superficie di attrazione dove si concentra l’energia magnetica. Un sistema di schermatura circoscrive il lato magnetico evitando l’attrazione degli oggetti circostanti. Per risolvere i problemi di fissaggio permanente, Ct Meca propone una vasta gamma di magneti industriali utilizzabili in diversi settori applicativi. Nella gamma sono presenti magneti di diversi materiali e forme: piatti, cilindrici, con gancio o con foro liscio, filettato o passante. Proponiamo una gamma di magneti in Ferrite, AlNiCo, Neodimio e Samario. A seconda del materiale, i magneti presentano catatteristiche diverse in termini di capacità di attrazione, resistenza termica, all’ossidazione, alla corrosione ed alla smagnetizzazione. A completamento della gamma tre nuovi prodotti: le barre magnetiche porta utensili, le etichette e le viti magnetiche.

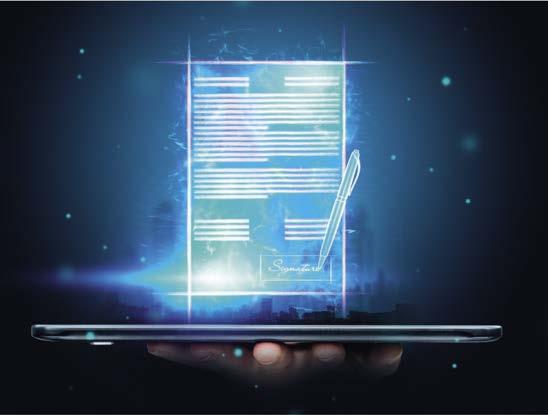
WOLTERS KLUWER TAX & ACCOUNTING ITALIA
AUMENTARE L’EFFICIENZA OPERATIVA CON LA FIRMA SMART DA REMOTO
FirmaWEB è una nuovissima soluzione in cloud di Wolters Kluwer Tax & Accounting Italia che consente al professionista una gestione semplificata del flusso delle firme, grazie ad una dashboard intuitiva ed un flusso operativo totalmente automatizzato. Con FirmaWEB, Wolters Kluwer Tax & Accounting Italia pone le basi per un progresso importante nell’efficienza dello Studio e offre alla Clientela dello Studio stesso un servizio altamente apprezzato. La soluzione FirmaWEB si basa sul concetto di firma elettronica avanzata (FEA). Per utilizzarla è necessario un numero telefonico riferito ad una SIM card, di cui il firmatario dichiara di avere esclusiva e piena disponibilità. Il tool digitale FirmaWEB identifica i documenti, generati da qualsiasi gestionale, e a ciascuno abbina i firmatari che riceveranno una mail con il link al documento.Il firmatario, cliente dello Studio, accede al servizio web da computer, tablet o smartphone e una volta avviata la procedura, FirmaWEB genera una password dinamica (OTP, One Time Password) valida solo per il tempo necessario alla firma e che gli viene recapitata attraverso un SMS. Il Cliente dello Studio, verificato e visionato il documento, firmerà inserendo il codice OTP. Nell’applicativo saranno presenti in automatico tutti i documenti firmati per poter procedere alla conservazione.
FirmaWEB solleva il Cliente dalla presenza in Studio per le firme e aumenta notevolmente l’automazione dello Studio stesso che non avrà più la necessità della documentazione cartacea e vedrà agevolato il processo di conservazione digitale dei documenti firmati. La sicurezza della password dinamica (OTP) e la gestione via posta elettronica faciliterà la comunicazione tra Studio e Cliente, che potrà firmare in qualsiasi momento anche in mobilità. Inoltre, niente affatto trascurabile per lo Studio il risparmio in carta, toner, usura delle stampanti e tempo dedicato alla stampa stessa dei documenti.
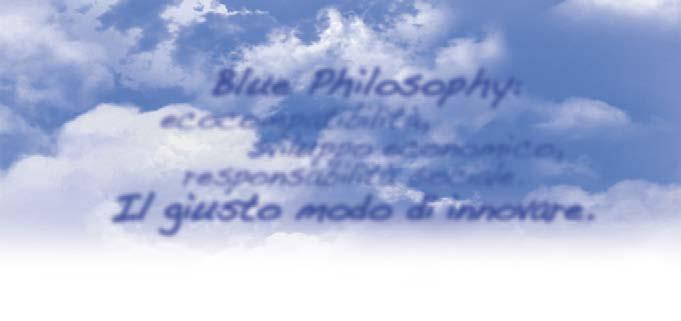
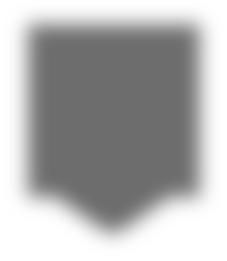

Direttore Responsabile Giorgio Albonetti Publisher Marco Tenaglia Direttore tecnico Chiara Tagliaferri Redazione Cristina Gualdoni (Coordinatrice) cristina.gualdoni@quine.it Eleonora Panzeri redazione.ma@quine.it Hanno collaborato a questo numero Chiara Tagliaferri, Patrizia Ricci, Eleonora Segafredo, A. Mazzoleni, G.Copani, M.Morgantini, R.Curiazzi Realizzazione grafica Fabio Castiglioni Direzione pubblicità Luigi Mingacci dircom@quine.it Responsabile produzione Paolo Ficicchia
Ufficio traffico Stefania Bruno s.bruno@lswr.it
Direzione, Redazione
Quine S.r.l. - via Spadolini, 7 - 20141 Milano Tel +39 02 864105 - Fax +39 02 72016740
Stampa Aziende Grafiche Printing srl
ABBONAMENTI Tel. 02.88184.317 - Fax 02.9366.4151abbonamenti@lswr.it Costo copia singola: euro 2,30 (presso l’Editore, fiere, manifestazioni) L’IVA è assolta dall’Editore ai sensi dell’Art. 74, 1° comma, Lettera C del DPR 26/10/72 n. 633 e successive modificazioni e integrazioni. Prezzo abbonamento annuo (9 fascicoli) in Italia euro 49,99, abbonamento Europa (9 fascicoli) euro 100,00. I numeri arretrati (seconda disponibilità) possono essere richiesti direttamente all’Editore, al doppio del prezzo di copertina. Non si effettuano spedizioni in contrassegno. L’Editore si riserva la facoltà di modificare il prezzo nel corso della pubblicazione, se costretto da mutate condizioni di mercato. L’IVA sugli abbonamenti, nonché sulla vendita dei fascicoli separati, è assolta dall’Editore ai sensi dell’Art. 74, 1° comma, Lettera C del DPR 26/10/72 n. 633 e successive modificazioni e integrazioni. © 2017 QUINE S.r.l. via Spadolini, 7 - 20141 Milano m&a meccanica&automazione - mensile (9 numeri annui) Registrazione del Tribunale di Milano n. 653 del 21.09.2005. Iscrizione al R.O.C. n. 12191 del 29/10/2005 Tutti gli articoli pubblicati su m&a meccanica &automazione sono redatti sotto la responsabilità degli Autori. La pubblicazione o la ristampa degli articoli deve essere autorizzata per iscritto dall’Editore. Ai sensi dell’art. 13 del D.Lgs. 196/03, i dati di tutti i lettori saranno trattati sia manualmente sia con strumenti informatici e saranno utilizzati per l’invio di questa e di altre pubblicazioni e di materiale informativo e promozionale. Le modalità di trattamento saranno conformi a quanto previsto dall’art. 11 D.Lgs. 196/03. I dati potrebbero essere comunicati a soggetti con i quali Quine S.r.l. intrattiene rapporti contrattuali necessari per l’invio delle copie della rivista. Il titolare del trattamento dei dati è Quine S.r.l. - via Spadolini, 7 - 20141 Milano Tel +39 02 864105 Fax +39 02 72016740, al quale il lettore si potrà rivolgere per chiedere l’aggiornamento, l’integrazione, la cancellazione e ogni altra operazione di cui all’art. 7 D.Lgs. 196/03. RESPONSABILE DATI PERSONALI QUINE S.r.l. - via Spadolini, 7 - 20141 Milano Tel +39 02 864105 Fax +39 02 72016740 Per i diritti di cui all’articolo 7 del Decreto Legislativo n. 196/03, è possibile consultare, modificare o cancellare i dati personali ed esercitare tutti i diritti riconosciuti inviando una lettera raccomandata a: QUINE S.r.l. - via Spadolini, 7 - 20141 Milano
Testata volontariamente sottoposta a certificazione di tiratura e diffusione in conformità al Regolamento CSST Certificazione Editoria Specializzata e Tecnica Per il periodo 1/1/2019-31/12/2019 Periodicità: Mensile
Periodicità: Mensile Tiratura media: 3381 Diffusione media:3103 Certificato CSST n. 2019-3050 del 24/2/2020 Società di Revisione: Fausto Vittucci
ABBIAMO PARLATO DI...
INSERZIONISTI
ABB AFIL Amaplast Berlin Packaging Celada CIMSYSTEM Ct Meca Danobat DKC DMG MORI FFG Fondazione Green GF Machining Solutions Goglio Heller Hermle ICIM igus LAPP Mewa MSC software OML Omron Open Mind Prima Power R+W Salvagnini Schunk Siemens SMC Soraluce Topsolid Turck Banner Wolters Kluwer Tax & Accounting Italia Yamawa 13 82 10 9 32 60 95 36 18 38 58 70 42 12 44 46 24 92 94 8 60 48 14 60 50 86 54 93 60 8 56 60 95 96 22
Amc Danobat DMG MORI Essity GF Mchning solutions KUKA MMC Pilz Procam Sensormatic Soraluce Sorma Tecnopiù Top Solid UCIMU
28 3 81 35 69 53 23 4 11 II cop 17 7 IV cop 77 97
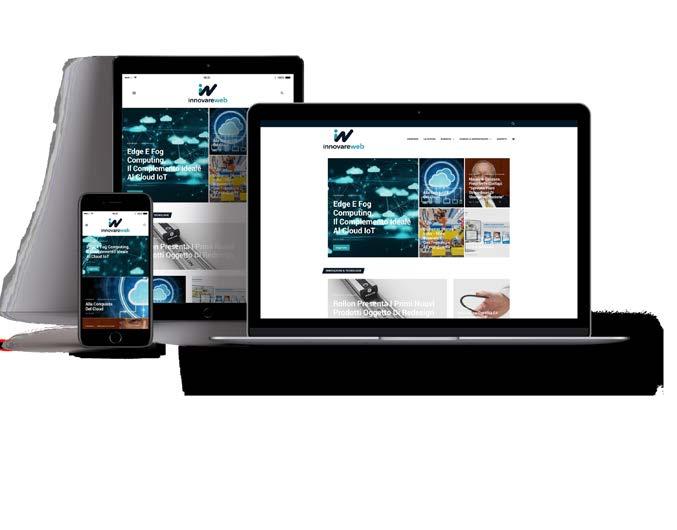
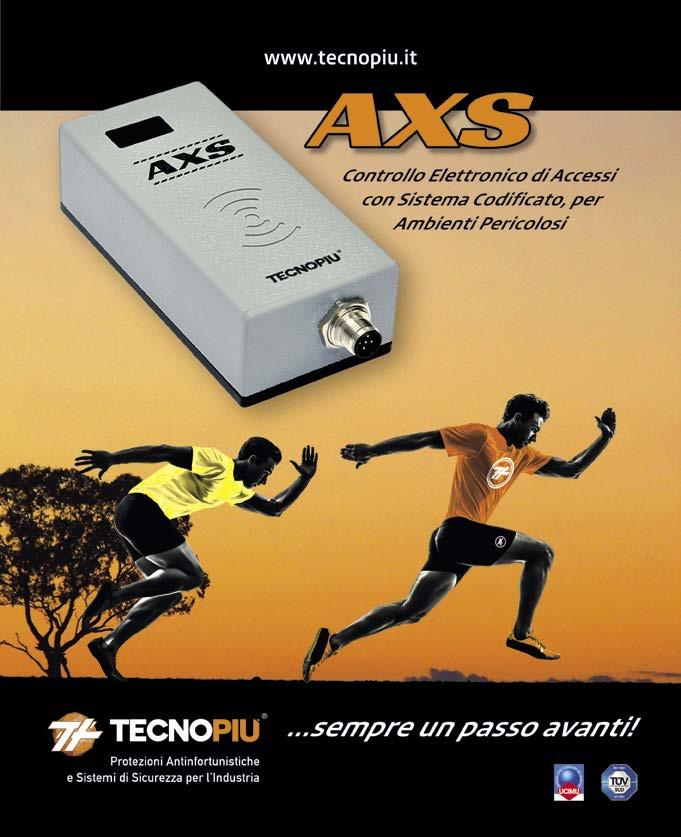