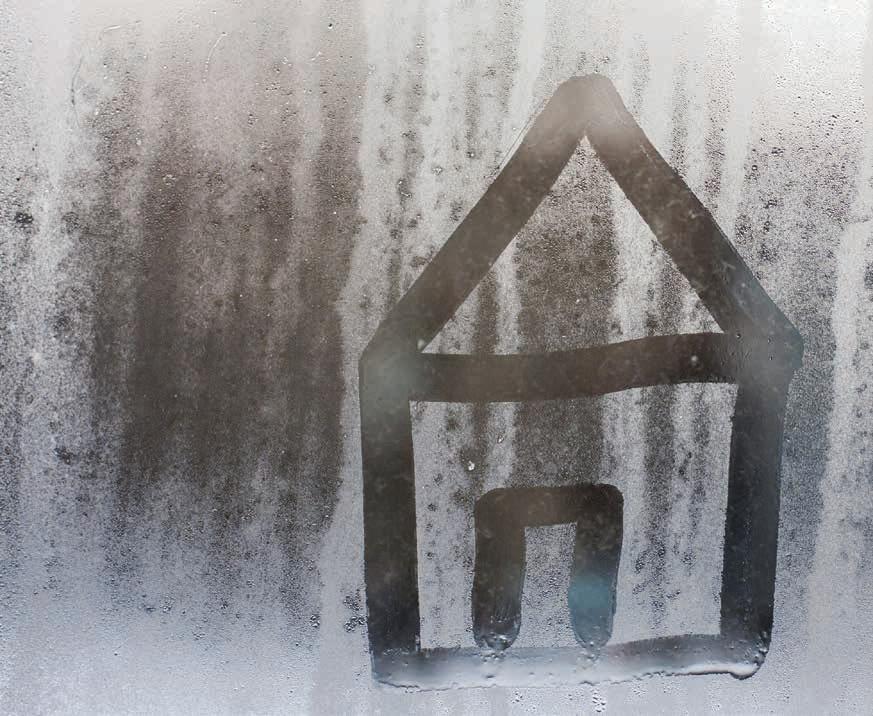
21 minute read
Piani di posa con sorprese
DISATTENZIONI CHE NON POSSONO ESSERE TOLLERATE
di Mauro Errico*
Ipiani di posa per pavimenti in legno, di qualsiasi genere (massetti cementizi di qualunque natura, in graniglia, in marmo, in cotto, in legno etc.) da sempre sono stati oggetto di discussioni tecniche su come verificarli, controllarli ed eventualmente correggerli se necessario.
Ebbene, nonostante ormai si dibatte da anni con ogni mezzo sull’argomento e sul quale sono stati pubblicati – ritengo – decine e decine di articoli tecnici vari, ancora oggi si continuano a registrare problemi di ogni genere. Nel caso in questione possiamo renderci conto come sia estremamente facile ritrovarsi in una problematica, anche piuttosto grave, a seguito di una serie di malintesi o presunte dimenticanze che io definirei disattenzioni, che non possono essere tollerate in un parchettista professionista.
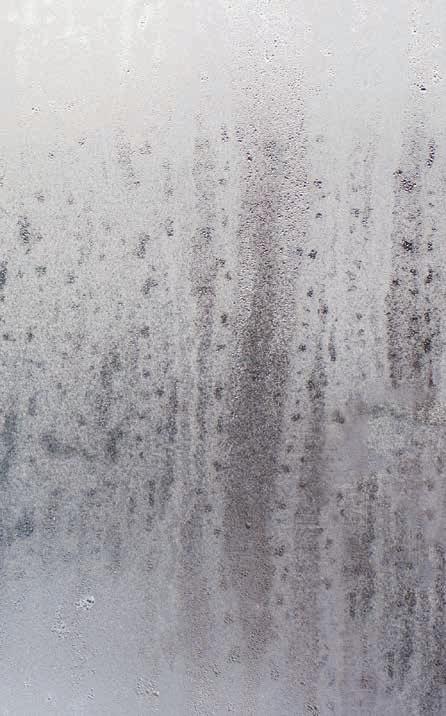
LAYING PLANS WITH SURPRISES Inattention which cannot be tolerated
The laying surfaces for wooden floors have always been the subject of technical discussions on how to check them and possibly correct them if necessary. Despite the fact that we have been debating this subject for years on which – I believe -–dozens and dozens of various technical articles have been published, even today problems of all kinds continue to be recorded. In the case in question, we can realize how extremely easy it is to find oneself in a problem, even a rather serious one, following a series of misunderstandings or presumed forgetfulness that I would define inattention, which cannot be tolerated in a professional parquet player.
La disamina della pavimentazione
La pavimentazione, oggetto dell’indagine, era una tipologia di massello prefinito in rovere con uno spessore nominale pari a mm 10, posta in opera per incollaggio totale con apposito adesivo specifico sintetico. Il piano di posa era costituito da varie tipologie di materiali ovvero: pavimenti in grès nei quali erano state realizzate diverse tracce per il passaggio delle tubazioni e impianti vari ricoperti poi con del cemento tradizionale. In altri vani, invece, il piano di posa era stato costituito con una nuova stesura di cemento, sempre tradizionale, in quanto avevano dovuto smantellare i vecchi pavimenti esistenti. L’intervento di posa in opera era stato condotto nel periodo invernale e risultava che durante le operazioni di pavimentazione, l’impianto di riscaldamento fosse regolarmente in funzione sia pure a regimi bassi. Tutte le altre opere edili, compreso le imbiancature, erano già state ultimate; avevamo quindi, come risultava da dichiarazioni di varie persone addette ai lavori, un
ambiente regolare e ottimale per iniziare la posa in
opera di un materiale igroscopico. Anche per i controlli sulla idoneità del piano di posa, in termini igroscopici, veniva riferito da parte del parchettista, che erano stati fatti (in particolare la misurazione del contenuto di umidità in peso) e non vi erano valori negativi. Un particolare però, non sussisteva alcuna documentazione fotografica di quanto eseguito e, per di più, questa operazione di verifica era stata fatta (ma riferito verbalmente) da un altro parchettista che poi aveva lasciato il lavoro ad altra azienda. Dalla disamina dell’intera superficie del pavimento in legno, qualche dubbio cominciava a presentarsi, infatti tutta la pavimentazione in legno si presentava con una
deformazione dimensionale dei propri listelli, i quali
avevano assunto una conformazione concava. Non solo, ma diverse porzioni del pavimento erano già totalmente distaccate, mentre altre sottoposte ad una percussione manuale denotavano un suono a vuoto rivelando quindi zone sollevate. Vi erano anche porzioni di pavimento, già totalmente asportate e in una parte di questi ultimi vi era la pre-
senza di adesivo, sia sulla superficie del piano di posa che nella contro faccia delle doghe, che al tatto non
era ancora totalmente reticolato. Al contrario, sussistevano altre porzioni di pavimento
sempre sollevato dal piano di posa, dove il medesimo adesivo, risultava al tatto regolarmente reticolato ma di facile asportazione dalla parte inferiore delle
doghe. Evidente comunque, nelle parti di pavimento asportato, la cosiddetta rottura della linea collante.
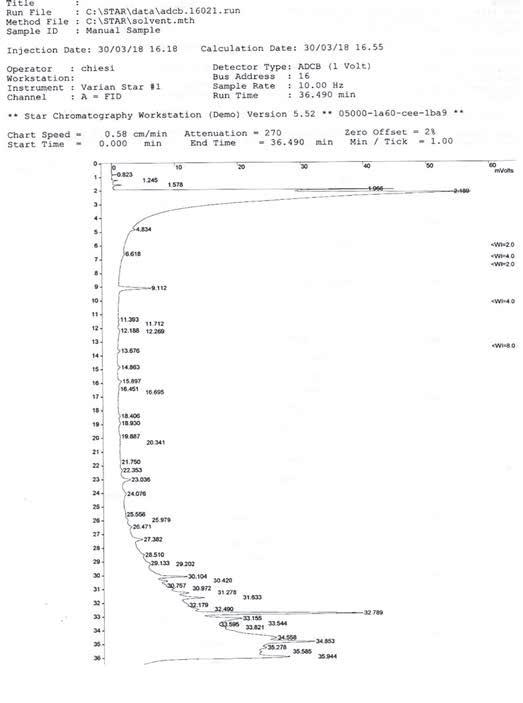
Tracciato A1 e A2 - Trace A1 and A2
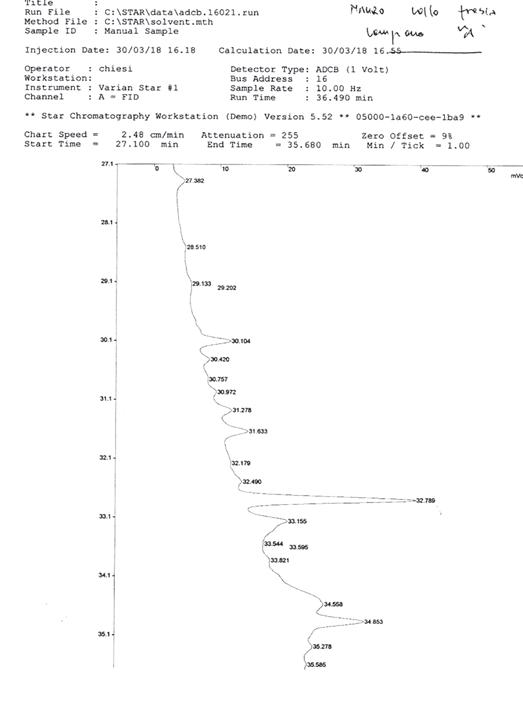
Per quanto concerne il materiale fornito, oltre alla pavimentazione in legno che ricordiamo essere un prefinito in rovere, era di riferimento la norma EN 13228 che così identifica il prodotto: “pannello composto da doga in legno massello a tutto spessore con unioni maschio-femmina su entrambi i bordi e le teste, con faccia trattata con vernice poliacrilica caratterizzata da elevata resistenza al graffio e contro faccia, bordi e teste trattati con vernice poliacrilica)”; non sussistevano contestazioni particolari da parte di nessuno, inoltre il medesimo fornitore, aveva fornito anche l’adesivo necessario. L’adesivo, come da schede di sicurezza e tecniche che mi sono state inviate successivamente al sopralluogo, era un bicomponente di natura sintetica, regolare e idoneo per il lavoro al quale era destinato. Durante il sopralluogo comunque sono state prelevate alcune doghe, già distaccate dal piano di posa, che presentavano nel proprio adesivo rimasto una differente compattezza al tatto; ovvero una parte ancora abbastanza “morbida e pastosa” e un’altra invece “compatta ma apparentemente friabile”. Alcune aliquote di questo adesivo, sono state sottoposte a una verifica in gas cromatografia al fine di avere un primo responso su alcuni dubbi che erano emersi, ovvero se i due componenti dell’adesivo fossero stati regolarmente e ottimamente miscelati fra di loro, per la regolare catalizzazione dell’adesivo medesimo. Come si può osservare nei tracciati chimici (Tracciato A1, A2 e B1, B2) l’adesivo presente nei due diversi campioni prelevati in sito presenta quanto segue:
•Il tracciato A1 è completo, mentre nel tracciato A2 parte “alto bollente” dove dovrebbero ritrovarsi i residui del catalizzatore e della base non reticolata; • Il tracciato B1 è completo, mentre per il tracciato
B2 (come per la parte A) parte ad elevati tempi di ritenzione. • Non si osservano grandi differenze fra le due aliquote di adesivo, ovvero anche nella colla più compatta (solida) e catalizzata (riferimento tracciati con la lettera B) non si rilevano grandi picchi del catalizzatore.
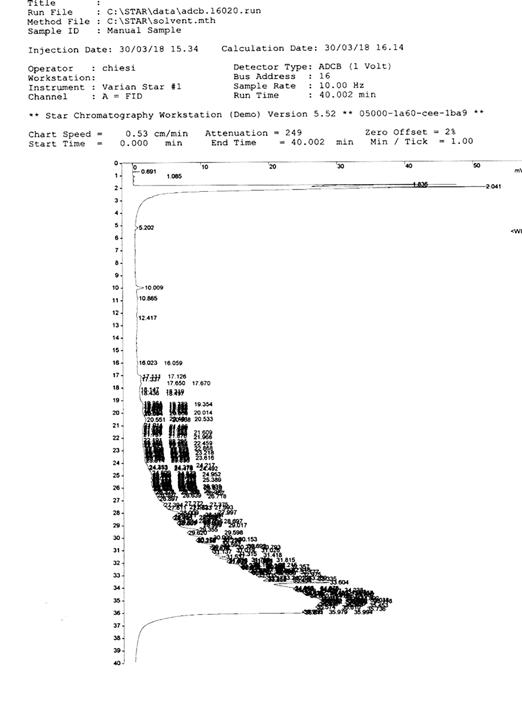
Tracciato B1 e B2 - Trace B1 and B2
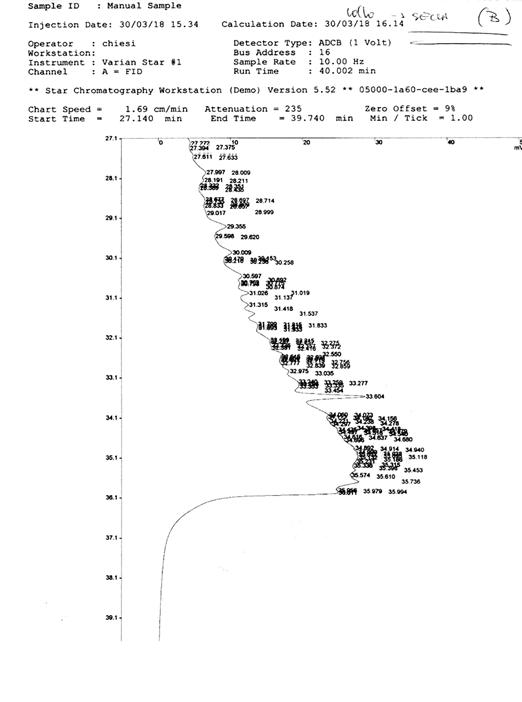
The examination of the pavement
The subject of the investigation was a type of pre-finished solid oak with a nominal thickness of 10 mm, installed by total gluing with a specific synthetic adhesive. The laying surface was made up of various types of materials, namely: stoneware floors in which various traces were made for the passage of pipes and various systems then covered with traditional concrete. In other rooms, however, the laying surface had been made up with a new layer of concrete, always traditional, as they had had to dismantle the old existing floors. The installation work had been carried out in the winter period and it appeared that during the paving operations, the heating system was regularly in operation, albeit at low speeds. All the other building works had already been completed; we therefore had, as was clear from the statements of various people involved in the work, a regular and optimal environment to begin the installation of a hygroscopic material. Also for the checks on the suitability of the laying surface, in hygroscopic terms, it was reported by the parquet installer that they had been made (in particular the measurement of the moisture content by weight) and there were no negative values. One detail however, there was no photographic documentation of what was carried out and, moreover, this verification operation had been carried out (but reported verbally) by another parquet operator who then left the job to another company. From the examination of the entire surface of the wooden floor, some doubts began to arise, in fact all the wooden flooring showed a dimensional deformation of its strips, which had assumed a concave shape. Not only that, but several portions of the floor were already totally detached, while others subjected to a manual percussion denoted an empty sound thus revealing raised areas. There were also portions of the floor already completely removed and in a part of the latter there was the presence of adhesive, both on the surface of the laying surface and on the counter face of the slats, which to the touch was not yet totally cross-linked. On the contrary, there were other portions of flooring always raised from the laying surface, where the same adhesive was regularly cross-linked to the touch but easy to remove from the lower part of the slats. However, in the parts of the removed floor, the so-called breaking of the glue line is evident. As regards the material supplied, in addition to the wooden flooring which we remember being a pre-finished oak, the EN 13228 standard was of reference. There were no particular complaints from anyone, moreover the same supplier had also provided the necessary adhesive. The adhesive, as per the safety and technical data sheets that were sent to me after the inspection, was a two-component synthetic, regular and suitable for the work for which it was intended.
During the inspection, some staves were removed, already detached from the laying surface, which had a different compactness to the touch in their remaining adhesive; that is, one part that is still quite “soft and mellow” and another part “compact but apparently crumbly”. Some aliquots of this adhesive were subjected to a gas chromatography check in order to have an initial response on some doubts that had emerged, i.e. whether the two components of the adhesive had been regularly and optimally mixed together, for the regular catalyzing the adhesive itself. As can be seen in the chemical traces (Trace A1, A2 and B1, B2), the adhesive present in the two different samples taken on site has the following: • Trace A1 is complete, while in trace A2 the “high boiling” part where the residues of the catalyst and the non-cros• slinked base should be found; Track B1 is complete, while for track B2 (as for part A) it • starts with high retention times. No major differences are observed between the two adhesive aliquots, or even in the more compact (solid) and catalyzed glue (reference marked with the letter B) there are no large peaks of the catalyst.
Questione di umidità
Oltre a quanto esaminato dal laboratorio, e a quanto osservato presso l’immobile dove si trova la pavimentazione in legno oggetto di sollevamento e distacco dal piano di posa, si è proceduto comunque a eseguire alcune verifiche, in alcuni punti del piano di posa, con metodo di reazione chimica (Norma UNI 10329:1994) questo se erano trascorsi diversi mesi dall’ultimazione dei lavori. Il piano di posa non presentava umidità in peso al di sopra del minimo previsto del 2%, va anche tenuto conto che la proprietà e la D.L., presente al sopralluogo, concordavano sul fatto che, durante i lavori di posa in opera, i vani erano regolari dato che gli stessi erano

Misurazioni - Measurements completamente ultimati nelle lavorazioni edili e che anche l’impianto di riscaldamento era in funzione. Questa situazione ci portava, con ragionevole certezza, a escludere la presenza continua di umidità ambien-
tale sopra il massimo previsto anche dalla scheda prodotto del materiale fornito (valore indicato oltre il 60%) che potesse avere inciso sulla stabilità dimen-
sionale delle doghe in opera. Quindi, apparentemente, avevamo valori di umidità (ambientali e nel piano di posa) nella norma. Un solo dubbio sussisteva per quanto riguardava la lavorazione dell’adesivo, eppure l’intera pavimentazione in legno era completamente deformata e distaccata dal piano di posa. Occorre però precisare, per dovere di informazione, che la misurazione del contenuto di umidità è stata eseguita, da vari tecnici, ma a distanza di quasi cinque mesi (Immagini 1-4) dall’inizio dei lavori di posa in opera; pertanto non sussistendo prove fotografiche dei rilievi fatti prima dell’inizio dei lavori (come riferito dagli addetti ai lavori) è probabile che il contenuto di umidità nel piano di posa potesse essere maggiore di quanto accertato. Per quanto si attiene alla individuazione del nesso causale che può avere dato origine ai difetti così come lamentati, risulta evidente che il differenziale termico
tra l’appartamento dove era posizionato il pavimento in legno e i locali al piano seminterrato (umidi e freddi, Immagini 5-6) sia inequivocabilmente all’origine di una condensa formatasi sulla superficie più fredda (vedi mattonelle e cemento) al di sotto delle doghe di parquet. Il conseguente assorbimento di umidità in eccesso da parte del materiale igroscopico (legno) e l’inevitabile aumento di volume delle singole listelle hanno originato il relativo sollevamento e distacco
dal piano di posa. Infatti, la posa in opera del pavimento in legno è stata iniziata in pieno inverno e le condizioni ambientali di cantiere (mai contestate da nessuna delle parti coinvolte) erano più che ottimali. Si precisa infatti che tutte le lavorazioni interne quali imbiancature e/o piccole opere murarie erano state ultimate da tempo, gli infissi di nuova fattura erano tutti installati e, come già anticipato, anche l’impianto di riscaldamento era già in funzione all’interno dell’immobile. Quindi, è “possibile tecnicamente” che una pavimentazione di legno, presumibilmente posta in opera su di un piano idoneo dal punto di vista igroscopico, ovvero con una umidità residua in peso inferiore o uguale al 2%, possa poi risentire della formazione di umidità da condensa. Ritengo che proprio le ottimali condizioni del luogo di lavoro (riscaldamento in primis) abbia innescato in maniera veloce quel problema del differenziale termico
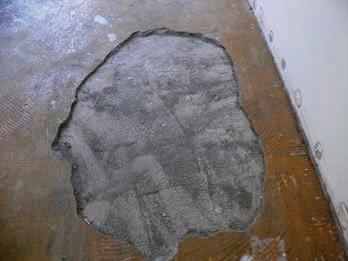
Immagine 1. Situazioni piani di posa - Situations of laying plans
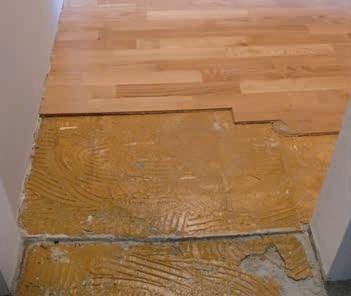
Immagine 3. Situazioni piani di posa a distanza di 5 mesi -
Situations of laying plans after 5 months Immagine 2. Situazioni piani di posa a distanza di 5 mesi - Situations of laying plans after 5 months
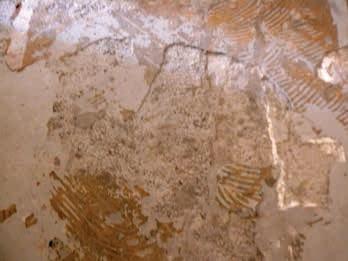
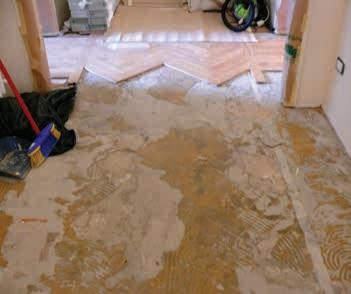
Immagine 4. Situazioni piani di posa a distanza di 5 mesi
- Situations of laying plans after 5 months
con i locali sottostanti; si ricorda che quando sussistono 5°C di differenziale termico tra due locali, si avvia la formazione di condensa.
La mancata interposizione di una adeguata barriera al vapore, in conseguenza di una evidente sottovalutazione o addirittura nessuna valutazione da parte del termotecnico prima e della D.L. poi della situazione di possibile formazione di condensa, sia la causa principale di quanto successivamente avvenuto.
Per quanto sopra si ricorda che se un elemento ligneo assorbe umidità in eccesso dal piano di posa, aumenta di volume si deforma e si solleva distaccandosi violentemente dal piano medesimo; al contrario se un elemento ligneo assorbe umidità dall’ambiente (in termini appena superiori al proprio stato di equilibrio igroscopico) tende ad aumentare leggermente di volume per poi ritirarsi dimensionalmente in larghezza alla cessione di umidità a seguito del proprio equilibrio ambientale. Quindi, il movimento dei listelli originato da umidità proveniente dal piano di posa può creare, come nel caso in disamina, delle tensioni trasversali perpendicolari al supporto di posa con cedimento del massetto (come avvenuto) ed anche sollevamenti dal piano come infatti sono stati rilevati.
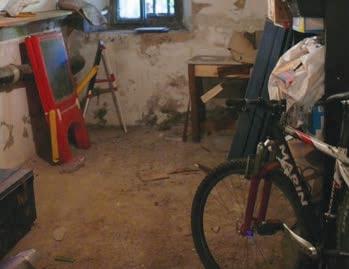
Immagine 5. Locali seminterrati Immagine 6. Locali seminterrati
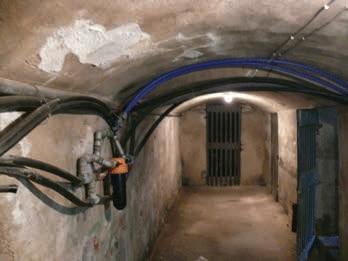
Tuttavia, l’aumento di volume che il legno subisce a seguito dell’aumento di umidità intrinseca, porta i singoli listelli a “crescere sempre” in larghezza; nel caso in disamina abbiamo una specie legnosa che varia la propria dimensione di circa 0,23 mm per ogni grado di umidità assorbita o desorbita. Si tenga conto che la geometria di posa adottata nel caso in disamina, è denominata “a tolda di nave” comunemente indicata come “cassero sfalsato a correre”; evidente, quindi, che tutto l’aumento di volume si sia manifestato sul lato lungo ovvero in senso longitudinale dei listelli con conseguente “arrivo” al muro perimetrale e sia rimasto invece invariato nel lato corto ovvero di punta (assiale) dei medesimi listelli. Infatti, le variazioni dimensionali del legno in senso assiale sono assolutamente minime e insignificanti per la stabilità di una pavimentazione di legno, per la specie legnosa del Rovere si parla di 0,1 mm su 1 m.
A matter of humidity
In addition to what was examined by the laboratory, some checks were carried out in some points of the laying surface, using the method chemical reaction (UNI 10329: 1994 standard). The laying surface did not present moisture by weight above the minimum expected of 2%. This situation led us, with reasonable certainty, to exclude the continuous presence of environmental humidity above the maximum foreseen also by the product sheet of the material supplied (value indicated over 60%) which could have affected the dimensional stability of the staves in place. So, apparently, we had normal humidity values (environmental and in the laying surface). There was only one doubt regarding the processing of the adhesive, yet the entire wooden flooring was completely deformed and detached from the laying surface. However, it should be noted, for the sake of information, that the measurement of the moisture content was carried out by various technicians, but almost five months later (Images 1-4) from the start of the installation work; therefore, as there is no photographic evidence of the surveys made before the start of the work (as reported by the experts) it is likely that the moisture content in the laying surface could be greater than what was ascertained. As regards the identification of the causal link that may have given rise to the defects as complained, it is clear that the thermal differential between the apartment where the wooden floor was located and the rooms in the basement (wet and cold, Images 5-6) is unequivocally at the origin of a condensation formed on the colder surface (see tiles and concrete) underneath the parquet slats. The consequent absorption of excess moisture by the hygroscopic material (wood) and the inevitable increase in volume of the individual strips have resulted in the relative lifting and detachment from the laying surface. In fact, the laying of the wooden floor was started in the middle of winter and the environmental conditions of the construction site (never contested by any of the parties involved) were more than optimal. It should be noted that all internal work such as whitewashing and/or small masonry works had been completed for some time, the newly made fixtures were all installed and, as already anticipated, the heating system was already in operation inside the immovable. Therefore, it is “technically possible” that a wooden floor, presumably placed on a suitable surface from the hygroscopic point of view, or with a residual humidity in weight lower than or equal to 2%, can then be affected by the formation of humidity from condensation. I believe that it is precisely the optimal conditions of the workplace (heating) that quickly triggered that problem of the thermal differential with the rooms below; remember that when there is a 5° C temperature differential between two rooms, the formation of condensation starts. The lack of interposition of an adequate vapor barrier, as a result of an evident underestimation or even no evaluation by the thermotechnician before and then the situation of possible condensation formation, is the main cause of what subsequently happened. As regards the above, it should be remembered that if a wooden element absorbs excess moisture from the laying surface, it increases in volume, deforms and lifts, detaching itself violently from the surface itself; on the contrary, if a wooden element absorbs humidity from the environment (in terms just above its state of hygroscopic equilibrium) it tends to slightly increase in
volume and then shrink dimensionally in width due to the release of humidity as a result of its environmental balance. Therefore, the movement of the strips originating from humidity coming from the laying surface can create, as in the case in question, transversal tensions perpendicular to the laying support with subsidence of the screed (as happened) and also lifting from the surface as in fact they were detected. However, the increase in volume that the wood undergoes as a result of the increase in intrinsic humidity, leads the individual strips to “always grow” in width; in the case in question we have a wood species that varies in size by about 0.23 mm for each degree of humidity absorbed or desorbed. It should be borne in mind that the laying geometry adopted in the case under examination is called “ship deck” commonly referred to as “staggered running formwork”; evident, therefore, that all the increase in volume occurred on the long side or in the longitudinal direction of the strips with consequent “arrival” at the perimeter wall and remained unchanged on the short side or the tip (axial) of the same strips. In fact, the dimensional variations of the wood in the axial direction are absolutely minimal and insignificant for the stability of a wooden flooring, for the wood species of Oak we speak of 0.1 mm on 1 m.
Conclusioni
Riassumendo abbiamo rilevato una serie di errori nei quali sono incorsi diverse figure operative in un cantiere, ovvero impresa edile, termotecnico, direzione lavori etc. senza dimenticare l’ultimo ovvero il parchettista. L’indagine tecnica, condotta anche in contraddittorio con altre figure tecniche, ha permesso di accertare anche dopo avere fatto eseguire delle verifiche termo-igrometriche, la necessità di una barriera vapore sotto il massetto di nuova realizzazione e quanto meno di una impermeabilizzazione liquida (tipo primer o similari) sul massetto esistente al fine di contrastare problematiche di condense superficiali e/o interstiziali, vista l’adiacenza con locali sottostanti freddi, non riscaldati e soprattutto molto umidi. Vi è inoltre l’errata realizzazione dei piani di posa del parquet, caratterizzati da una resistenza meccanica non sufficiente (Rck < 200 daN/cm2); un’eccessiva friabilità; uno spessore non adeguato (< 4 cm); la presenza di numerose tubazioni al suo interno (peraltro isolate con uno spessore non conforme alle prescrizioni del D.P.R. 412 del 1993 per tubazioni correnti entro strutture confinanti con ambienti non riscaldati) ben visibili soprattutto nell’ingresso e nei disimpegni. Non solo, è stata accertata anche l’assenza di bandella perimetrale, un’eccessiva umidità residua (> 2%), sicuramente in alcune zone del massetto esistente (e non è da escludere che lo fosse anche in alcune zone di quello di nuova realizzazione visto il valore limite rilevato del 2% a ben cinque mesi dalla posa). Per ultimo abbiamo anche una carenza di tenuta dell’adesivo, sia pure limitata ad alcune zone, originata da una sfortunata ma errata miscelazione dei due componenti del collante. Una serie quindi di errori tecnici e manuali, che si sono manifestati tutti insieme in un unico cantiere; una situazione che non sempre avviene ma che è possibile che avvenga.Quindi prima di iniziare un lavoro di installazione di pavimenti in legno, occorre sempre eseguire una serie di verifiche e, soprattutto, documentarle oltre che confrontarsi con le varie figure tecniche presenti in cantiere.
Conclusions
In summary, we found a series of errors in which various operational figures have incurred on a construction site, i.e. construction company, thermotechnician, construction management etc. without forgetting the last one or the parquetist. The technical investigation, also conducted in contradiction with other technical figures, made it possible to ascertain, even after having carried out thermo-hygrometric checks, the need for a vapor barrier under the newly built screed and at least liquid waterproofing (such as primer or similar) on the existing screed in order to counteract problems of surface and / or interstitial condensation, given the proximity to cold, unheated and above all very humid rooms below. There is also the incorrect implementation of the parquet laying surfaces, characterized by insufficient mechanical strength (Rck <200 daN / cm2); excessive friability; an inadequate thickness (<4 cm); the presence of numerous pipes inside (moreover insulated with a thickness that does not comply with the requirements of Presidential Decree 412 of 1993 for pipes running within neighboring structures with unheated rooms) clearly visible especially in the entrance and in the corridors. Not only that, it was also ascertained the absence of a perimeter strip, an excessive residual humidity (> 2%), certainly in some areas of the existing screed (and it cannot be excluded that it was also in some areas of the newly built one. given the limit value of 2% five months after installation). Lastly, we also have a lack of adhesive strength, albeit limited to some areas, originating from an unfortunate but incorrect mixing of the two components of the glue. Therefore, a series of technical and manual errors, which manifested themselves all together in a single construction site; a situation that does not always happen but that it is possible that it does. Therefore, before starting a work of installing wooden floors, it is always necessary to carry out a series of checks and, above all, to document them as well as to deal with the various technical figures present on site.
*Perito Esperto C.C.I.A.A. Firenze nr. 957 Categoria Legno – Pavimenti in legno e Metodologie Posa in Opera
Fonti e Bibliografia consultata all’epoca dell’indagine tecnica
• Norma UNI EN 13228:2004 pavimentazioni in legno massiccio con sistema di assemblaggio; • Norma UNI EN 10329:1994 Misurazione del contenuto di umidità negli strati di supporto cementizi o simili; • D.L. nr 206 del 06 Settembre 2005 Codice del Consumo; • DOP dichiarazione di prestazione – Regolamento europeo n° 305/2011; • D.P.R. nr 412 del 26 Agosto 1993 Regolamento norme per progettazione, installazione, esercizio e manutenzione impianti termici degli edifici.