VANDECASTEELE
Leading
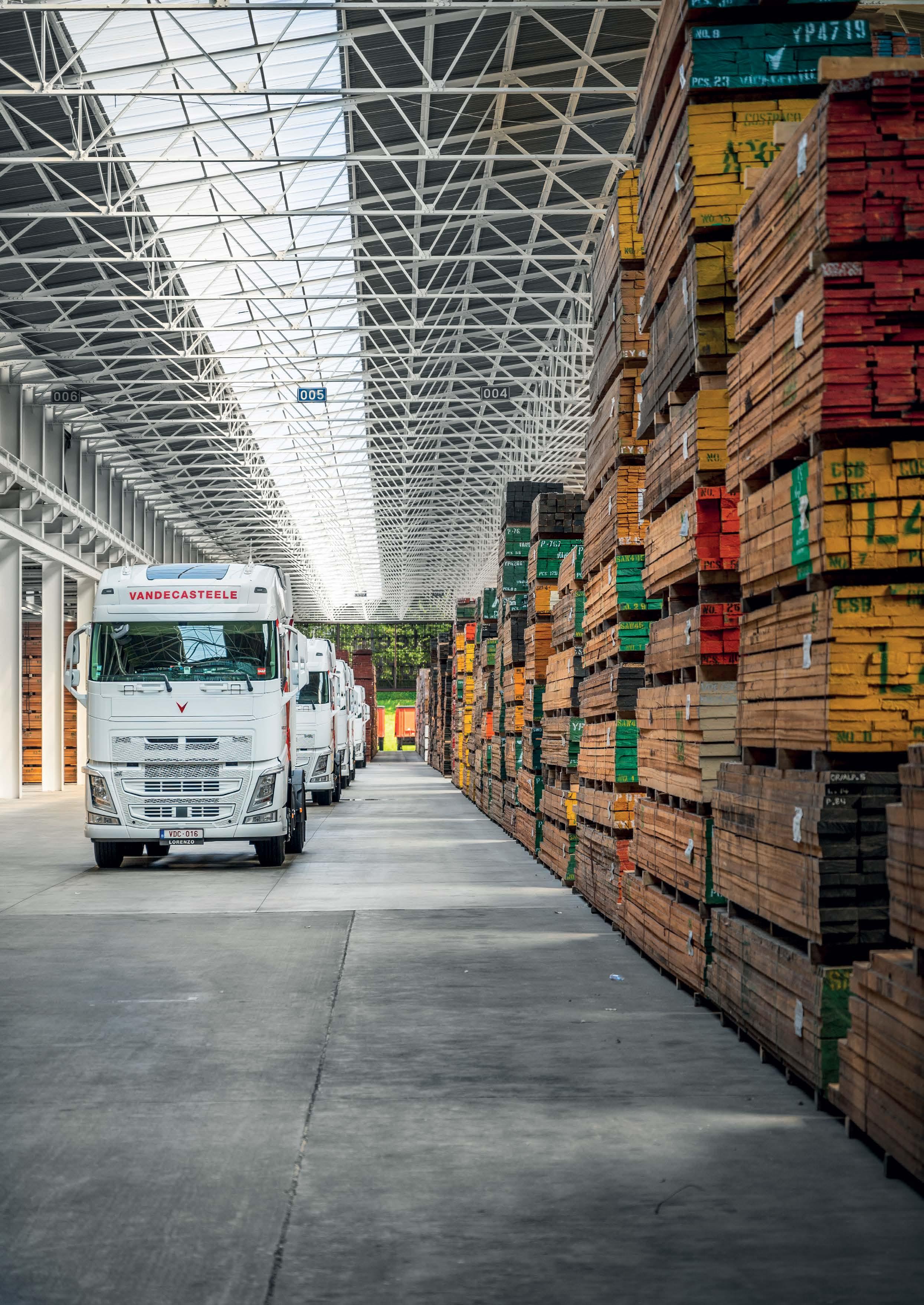
HOUTIMPORT 24
Demystifying
Leading
Demystifying
In many manufacturing facilities, extraction fans operate continuously, at full power, throughout the working day.
Even when some machines are not in use, and often during factory breaks, the powerful, energy-consuming fans continue to run at full speed – wasting valuable energy... and money!
With ECOGATE, the extraction system responds in real-time to variations in machine use. When a production machine is switched on, the greenBOX Controller opens a motorised damper to provide extraction for that particular machine.
With ECOGATE technology installed, an extraction fan will consume the minimum power required to provide optimum extraction – reducing electricity bills by 68% on average.
sales@ecogate.co.uk
05 Industry News
A
24 Cover Story: Vandecasteele Houtimport
With a blend of family spirit and global reach, Vandecasteele Houtimport are a familiar name across the timber sector and gave us a glimpse behind the scenes of this dynamic Belgian timber importer.
26 Volume Deficit Still Falling
According to the latest figures from TDUK, the deficit of timber import volumes during 2024 compared to the year before continues to fall.
28 Applause for Sweet Extraction
Dust and fume extraction specialists, Extractly have recently completed the installation and commissioning of a comprehensive new dust extraction system for Sweet Joinery.
30 Questions of Carbon
Kevin Underwood, Technical Director of the BWF explores the potential impact of new buildings consultation on the calculation of U-values for windows and doors.
32 Lessons in Lignum
Andy Ball, Founder Director at The Joinery Network explains how Lignum is now the go-to system for joinery companies to manufacture timber windows and doors profitably.
34 Championing Homegrown Timber
Mark Councill and Alec Laing founded Logie Timber in 2017 with a shared vision to establish a sawmill to bridge the gap between small estate owners, larger forestry sites and the public.
38 Using Woodland Differently
Our trees are our future and as John Orchard, Chief Executive of Woodland Heritage explains, we need to grow more of them and think differently about how we use them.
40 Striking and Sustainable
Sustainability doesn’t mean our buildings have to lack creativity, says Ruaridh Nicol, Associate at architectural practice Holmes Miller.
42 Plywood Under Scrutiny
The European Commission has announced the launch of a new anti-dumping investigation into unfairly priced imports of hardwood plywood from China into the EU.
Roof slating and tiling apprentices in colleges across the UK have received 9,800 linear metres of timber roofing batten donated so far this year from SR Timber as the business commits to assisting the next generation of roofing contractors.
As a leading importer of graded roofing batten, which they market as Premium Gold®, SR Timber has been supplying the UK roofing market since 2008. Based in Huthwaite, north Nottinghamshire, the business is led by co-founder Shaun Revill, well-known in the trade as a specialist in graded timber roofing batten with a mantra for promoting to roofers the importance of using only certified, quality batten.
During 2023 over 10,000 linear metres were donated to eight different colleges offering relevant roofing apprenticeships. So far this year 4 training providers, including Leeds College of Building, South Lanarkshire College, Rooftrain Melksham and (pictured) South West
Roofing Training Group in Exeter, have received or are about to receive timber donations.
“Investing in the next generation of roofing contractors is important for the business,” said Shaun. “These apprentices are the future of our industry, and we need more of them to consider this industry as a future career. Once on an apprenticeship programme, it is also important to educate on the benefits of using a correctly graded roofing batten that adheres to British Standards BS5534. So when we are approached by colleges running these training courses we have always been happy to supply our Premium Gold – a correctly graded roofing batten for apprentice roofers to work with. We have been doing it for years and will continue to help, it is our investment in the future.”
Leeds College of Building is the latest ‘CITB - IOC Timber Industry College Hub’ to organise a bespoke trade event with the Institute of Carpentry (IOC). The recent showcase day promoted the wealth of global career opportunities and experiences available to carpentry and joinery students as new IOC members. As well as exploring IOC benefits, students also gained meaningful industry connections as they start out in their profession.
After a welcome from Leeds College of Building CEO & Principal Nikki Davis and an introduction by President of The Institute of Carpenters Geoff Rhodes, students enjoyed fascinating talks by varied experts from across the sector.
Kickstarting the day, Ricky Sandoval from the Construction Industry Training Board (CITB) talked to attendees about their organisation’s support for students who are looking for apprenticeship employment and career opportunities nationally and regionally. Roly Ward from MEDITE SMARTPLY then explained the growing use of emerging technologies in MDF and OSB products in the construction and timber industry.
Emma Woodward from Historic England delivered an illuminating presentation about restoration projects, followed by a talk by Nick Boulton from the Timber Development UK (TDUK) & Trussed Rafter Association (TRA). Chris Jones from Lynn & Jones spoke about experiences and careers in shopfitting, and the day concluded with a presentation by Lucy Kamall from the American Hardwood Export Council, who introduced learners to a bank of useful resources.
Adam Sharpe, Leeds College of Building Curriculum Manager for Construction Crafts – Timber, said: “We were thrilled to host this event for timber specialists of the future. I am involved in the IOC mentoring scheme and excited to be part of a much-needed initiative to help inspire and motivate future carpenters and joiners. Above all, I’m excited to see how projects like this will help fill vital skills gaps and boost the construction industry and wider economy.”
The IOC is an established partner of Leeds College of Building with over 20 years of collaboration to date. The Institute ensures each generation of carpenters and joiners upholds the highest traditions of the historic craft, including wood trades such as furniture and cabinet makers, structural post and beam carpenters, wheelwrights, computeraided design carpentry design, woodcarvers and turners and boat builders
Geoff Rhodes, President of The Institute of Carpenters, said: “I was delighted to be at Leeds College of Building to deliver the CITB-IOC Mentoring Champions Scheme, a selective programme across ten colleges in the UK, ranging from South Wales to Inverness. This scheme aims to link qualified people in the IOC with young people coming into the trade to inspire them about the career pathways that lie ahead. The aim today was to bring the industry into the college to share knowledge and experiences whilst adding value to what the college is doing.”
Nikki Davis, CEO & Principal of Leeds College of Building, added: “We’re so pleased to support the IOC’s work and further grow our partnership. The IOC mentoring scheme will help learners develop confidence and knowledge about current issues and developments in the industry, as well as help boost performance and increase retention rates in apprenticeships. The construction industry is crying out for a highly skilled workforce, and critical work such as this is helping to bridge that gap.”
Leeds College of Building was established in 1960 and is the only specialist general further education construction college in the UK. Over 5,000 students attend a comprehensive range of more than 200 courses related to construction and the built environment. In total, the College trains nearly 3,000 apprentices across all areas of provision, working with around 800 employers across the UK.
More at www.lcb.ac.uk
Stephen George + Partners (SGP) in conjunction with AHR has submitted plans for the £20million redevelopment of Huddersfield’s bus station, fronted by a sweeping 120m-long glulam, green roof and Solar PV canopy. The bus station transformation is a partnership between Kirklees Metropolitan Borough Council and West Yorkshire Combined Authority to create an innovative gateway to the revitalised town centre along with enhanced passenger facilities.
Alistair Branch, Partner at SGP explained: “Huddersfield is the largest bus station in West Yorkshire and its redevelopment is a core component in an ambitious series of town centre interventions led by the Council to create a cultural heart for the town centre. The unique canopy structure has a contemporary design, reminiscent of the rolling Yorkshire landscape, elevating the importance of this key transport hub and gathering point within the town centre. SGP has been involved in the project for several years, developing the canopy from initial concept, through business case approval to the design now submitted for planning approval.”
SGP’s design for the canopy and the public realm beneath it was developed through extensive discussions with clients, the local authority and other stakeholders. The proposed canopy design is a simple sinusoidal timber lattice structure supporting a green roof that undulates along the length of the bus station, emphasising key
entrances and drawing the eye down from the imposing multistorey car park’s long concrete façade. Office and retail units in the station’s frontages will also be revitalised, delivering a harmonious continuity with surrounding businesses.
Matt Beaumont, Associate at SGP added: “The canopy uses a glulam lattice to support a mix of sedum roof and solar panel glass to create a light and inviting transition space from the public realm to the bus station itself. The integrated roof lights not only let natural light flow into the area but produce their own green energy, whilst the sedum promotes biodiversity, reducing rainwater runoff and helping improve local air quality. The solar glazing ensures energy generation is visible to users below for educational purposes whilst additionally diffusing direct sunlight.”
Beneath the canopy, enhanced public realm extends north towards the taxi ranks and Grade I listed Railway station. A secure, glazed cycle hub for green transport supports the Local Authorities’ commitment to modal shift, linking towns and villages across West Yorkshire and beyond as well as cycle and walking routes to the retail, civic and employment areas within Huddersfield town centre. If planning is granted, work is expected to start on-site in the Summer of 2025.
More at www.stephengeorge.co.uk
Perform Panel, part of the Donaldson Group, has published third party accredited environmental product declarations (EPD) for its full range of wet wall laminated panels.
Separate EPDs were completed for each of the Perform Panel ranges, which comprise over 48 designs. The EPDs, which transparently communicate the environmental performance of a product over its lifetime, show that Perform Panel outperforms its competitors in terms of Global Warming Potential (GWP).
The Global Warming Potential (GWP) of Perform Panel’s most popular 7-ply Birch plywood core panel and the Perform Panel Nu-Lock range is carbon positive, with an impact of -1.02kg CO2e and -3.89kg CO2e respectively. This means that 1.02kg of carbon dioxide is stored in every m² of plywood core Perform Panel produced and 3.89kg of carbon is stored in every m² of Nu-Lock panel.
A cost-effective and versatile alternative to tiles, Perform Panel can demonstrate that it is also more sustainable than ceramic tiles, which are more carbon intensive to produce. The measurements are based on volume produced and unit measurements, providing an accurate and fair representation. Measurements are independently verified and published in the public domain.
Valid for five years, the EPD is based on current available and published data for end-of-life assumptions. With advances in the industry over the next five years, along with improved building recycling processes and ongoing Donaldson Group investments in ESG, it is expected that performance will be even higher at the next review.
Stephen Murray, Managing Director, Nu-Style Products, said: “We’re extremely proud to be able to prove the sustainable benefits of our product, showcasing that Perform Panel is not only a cost-effective and stylish alternative to tiles, but also a more environmentally friendly one.
With a 35-year guarantee, Perform Panel is also long-lasting, so doesn’t need to be regularly replaced – further reducing its environmental impact.”
Steve Galbraith, Divisional Managing Director of Donaldson Retail and Distribution, added: “At the Donaldson Group, our goal is to become a leading independent Net Zero Carbon Business. This exercise is part of a wider project to understand our impact on the environment across all parts of our business, and a commitment to provide solutions that help our customers to be carbon neutral.
“We have been working to reduce energy consumption and act more sustainably for years, and things like production line efficiencies, use of LED lights and solar panels are all contributing to positive EPD results for Perform Panel and across the Group. This is the first time there has been an EPD for Perform Panel, and we’re thrilled with the results.”
Perform Panel provides a number of hygiene, cleaning and maintenance benefits, as well as versatility and ease of installation. The panels come with a 35-year guarantee, have seamless borders and are five times quicker to install than standard tiles. The panels are suitable for various internal applications within both domestic and commercial environments.
All manufacturing is currently carried out in Aberdeen, with a distribution network throughout the UK. Predominately supplied through the merchant base, it also appeals to contractors, bathroom showrooms, plumber merchants and joiners. Perform Panel has seen substantial growth in the last five years, with expansion into England as well as the Netherlands and Belgium.
More at www.performpanel.co.uk
Nine Zero Timber Windows and Doors has facilitated the planting of 750 trees in 2024, to coincide with this year’s FSC™ Forest Week and its theme: ‘The small steps that create big change.’ As a long-standing FSC license holder and advocate for timber’s standout sustainability credentials, Nine Zero is passionate about raising awareness around the vital role that sustainable forestry and timber products play in combating climate change and biodiversity loss.
In 2024 alone, Nine Zero has actioned the planting of 750 trees worldwide through the More Trees initiative, a platform that powers businesses and individuals to plant trees at the click of a button. The trees, which have been planted in Kent, Rwanda and Senegal, are forecasted to capture 1161.5 tonnes of future CO₂. This milestone not only embodies the spirit of FSC Forest Week, but also reinforces the responsibility Nine Zero embraces to advise, educate and demonstrate how timber is the springboard to reaching stringent Building Regulations – as well as our global Net Zero Strategy goals.
sourcing of FSC-certified materials, recycling timber waste, providing renewable energy to local homes, tree-planting initiatives, or simply keeping the conversation going.
Steve Winscott, Director of Nine Zero, is passionate about the timber industry’s role in driving change: “The timber glazing industry is uniquely positioned to lead the way in sustainability, and FSC Forest Week reminds us that even the smallest steps can have a profound impact on our environment. Nine Zero has long been committed to being part of the solution, whether that’s through our responsible
“As consumers become increasingly aware of the role they can play in combating climate change, Nine Zero continues to provide them with sustainable choices that make a tangible difference. We need to make sure the message is clear, that by choosing FSC-certified timber windows and doors, consumers are contributing to a larger movement, ensuring the future of forests – and the communities that depend on them.”
A project to build Europe’s first bamboo-timber composite gridshell at Edinburgh Napier University (ENU) has been successfully completed. The 9x8m structure was put up in just four days by a team of 31 visiting students from the Technological and Higher Education Institute of Hong Kong (THEi) in an engineering lab at ENU’s Merchiston campus.
The team used cutting-edge design and construction methods, including augmented reality technology to visualise the plans in real time. Project leaders hope to now replicate it at a larger scale, allowing researchers to investigate the use of bamboo-timber gridshells as a sustainable building design, and to train construction professionals.
Known for their structural efficiency and aesthetic appeal, gridshells are curved, shell-like structures made from an interconnected grid pattern. Experts believe their design – which makes the most of bamboo’s strengths as a sustainable building material – could be used to create large-span roofs.
This latest effort follows the construction of a similar structure in China by a team of ENU students last year. Professor Johnson Zhang, Head of International for Edinburgh Napier’s School of Computing, Engineering & the Built Environment, led the project saying: “The construction has gone really well. The last time we did something like this in China it took a month – so it has taken a huge effort to get it all done in four days.
“We were delighted to welcome the students to Edinburgh for the project. They have all learned a lot from the process, as have we. Using the technology allowed us to monitor the construction, so we could make changes and corrections in real time during the build. It has huge potential in the industry. It’s the first time something like this has been done in Europe, and we’re hoping to create an even bigger gridshell here in future. We first demonstrated the idea behind bamboo-timber gridshells at COP26 in Glasgow, and this is another step in the journey to realise its potential.”
As well as ENU and THEi, the project backed by the Construction Industry Council of Hong Kong and the British Council, alongside partners: Built Environment - Smarter Transformation, Xylotek Advanced Timber, Glenalmond Timber and Intelligent Wood Systems.
A group of academics from the Department of Architecture of Inner Mongolia University of Science and Technology (IMUST) also came to Edinburgh to support the construction. The finished structure was shown off during a closing ceremony for visiting partners at Merchiston. Plans are underway to develop bamboo-timber gridshell technology further at Edinburgh Napier University.
More at www.napier.ac.uk
As the number of green LOOP pallets in the construction sector continues to increase week on week, The Pallet LOOP has appointed a Merchant Account Manager. Rob Devonshire joins the business to help onboard merchant branches to The Pallet LOOP and ensure they are making the most of the circular economy scheme, which is helping to reduce pallet waste and provides a PayBack of up to £4 for every green pallet put back in the LOOP.
Rob is a national account specialist who has worked in the merchant sector for many years. Before joining The Pallet LOOP, he was National Buying Group Manager at Vado – a leading British bathroom brassware manufacturer. He has also held roles at Victoria Plum, Geberit, Travis Perkins and Marshalls.
Steve Ottaway, Chief Operating Officer at The Pallet LOOP said: “We are pleased to
welcome Rob to the team. Four months on from the roll out of the first LOOP pallets, we’re now getting lots of requests for collections – but there are definitely more of our green pallets out there and we want to really start driving up returns. Doing so will benefit the environment. It will also be hugely advantageous for merchants as well as housebuilding companies and principal contractors, who can make significant waste, carbon and financial savings. In the merchant sector, Rob will be championing our pallet collection service, making sure national and independent merchants – wherever they are in the UK – are driving as much value from The Pallet LOOP service as possible.”
Commenting, Rob said: “I’m really excited to be joining The Pallet LOOP – a truly innovative, forward-thinking company with a unique proposition for tackling what is a huge issue in the construction and material supply
Choose Tanalith® MF wood preservative with built-in contemporary colour for your treated timber.
sector. I can’t wait to get out and about and start helping our merchant partners as they, and the wider sector, work towards achieving the Government’s ambition of net zero emissions by 2050.”
With a continued focus on reducing the overall carbon impact of a project, we have developed Tanalith® MF. A water-based, high-pressure wood preservative, Tanalith® MF is both metal-free and VOC-free. www.trusttreatedtimber.com
BSW Group is proud to be a national partner of Forests With Impact, a social enterprise focusing on sustainability and community development. This programme establishes commercial tree nurseries in prisons, delivering valuable skills in horticulture, nursery management and environmental conservation, in turn supporting how we approach ecological restoration.
The primary goal of Forests With Impact, a community interest company, is to grow seedlings that will assist the UK in achieving its tree planting, nature recovery and biodiversity targets, while the surplus income made from the tree nurseries will be reinvested into targeted training and community resources for the prison and the local community.
This programme not only tackles local employment and skills development challenges, but also serves as a powerful force for environmental change, marking the start of an extraordinary journey toward ecological restoration, community empowerment and social wellbeing.
Forests With Impact aligns with BSW’s own operations, and the two businesses have already been working closely together, with Maelor Forest Nurseries, a member of BSW Group, providing expert insight to help HMP Haverigg establish its first polytunnel.
Andrew Henry, Nursery Director at Maelor, has supported the launch of the initiative with invaluable advice, along with Gavin McLaughlin, Head of ESG at BSW Group, and James Brennan, Head of Marketing at BSW Group.
Gavin McLaughlin expressed his enthusiasm for the partnership, saying: “We’re delighted to be a National Partner for Forests With
Impact and believe their objectives are very closely aligned with our own. Growing and planting trees promotes ecosystem restoration, helps combat climate change, and improves air quality, all while equipping prisoners with employable skills.
“Helping to provide valuable skills is an essential step in improving our communities and helping those in difficult situations turn their lives around. We’re incredibly excited about the programme and believe that by working together, we can help to change people’s lives for the better, while also raising awareness of the opportunities within our sector.”
Sarah MacGregor, Programme Lead for Forests With Impact, added: “Forests With Impact is a unique and innovative social enterprise, which is only made possible by our partners. Through collaboration across industries, we are creating meaningful change, which gives hope, pride and purpose to prisoners, whilst helping create forests across the UK. The expert support and advice from BSW have been incredible and crucial to our set-up and launch. We are forever grateful for the amazing legacy they are helping us to create and the impact we are making together.”
Gavin added: “So much progress has been made in a short space of time, but we are already excited about the future of the programme. Forests With Impact have some very ambitious plans – and we’re delighted to be part of it.”
With 250,000 saplings already planted, and a larger polytunnel being installed soon, the project is gearing up for a wide scale launch later this year.
Accoya fenders were recognised at the London Construction Awards (LCA). Circular design consultancy, 540 WORLD won the Excellence in Sustainability – Product category for the innovative Accoya wood fenders, designed for the Thames Estuary.
These fenders were developed for the Environment Agency’s TEAM2100 initiative by 540 WORLD in collaboration with Accsys. Notable contributions to their biodiverse design came from Glasgow University and King’s College London. Produced by International Timber and Jacobs Engineering, these fenders not only help manage flood defences in the Thames Estuary but also enhance local biodiversity. Special alcoves in the fenders support a diverse habitat for marine life and microorganisms.
The Environment Agency sought a resilient and durable alternative to tropical hardwood fenders that also prioritised sustainability. Accoya wood, being non-toxic, durability class 1, and Cradle to Cradle certified® at Gold level, proved to be the perfect choice. The LCA judges praised the fenders for being an
HMP Littlehay carpentry teacher Matthew Bysouth has won a prestigious national award. The tutor at the category C prison, which is located near Huntingdon in Cambridgeshire, was named overall winner in the Educator of the Year Award category at the third annual Skills for Justice – Inspire Justice Awards. Professional carpenter Matt joined the prison education provider PeoplePlus in 2012 and has since gone on to be rated ‘Outstanding’ by education regulatory body Ofsted. Matt’s dedication to teaching his craft is evident in his meticulous lesson planning and delivery says colleagues, with learners grateful for the impact that he’s had on their lives.
“impactful product that brings a number of wider innovative sustainability benefits.”
Chaline Church explained that for 540 WORLD, “the key benefit is that the Accoya fender exemplifies a regenerative circular design benchmark - that designing for positive impact is possible through Cradle to Cradle Certified products, and together we can create a circular world of good!”.
Laura Keily, Head of Marketing at Accsys Technologies, comments, “The Thames presents a challenging environment with its mix of brackish saltwater and active marine organisms that can rapidly degrade most wood types. It’s the ultimate endurance test for any wood product, and Accoya has consistently met expectations. Accoya’s outstanding performance in such harsh conditions is helping to set new benchmarks for durability in the construction industry.”
“Choosing materials that are sustainable and that consider the effects of their production on the environment is a key goal of our flood risk management program. Certification processes, such as the Cradle to Cradle Certified® Products Program, help achieve this and permit
identification of materials that consider the effects of their production on the environment, minimise energy and water use, and aid social fairness. Finding a viable, sustainable substitute for tropical hardwood has been an important goal of ours,” states Dr Jo Guy, of the Environment Agency’s TEAM2100.
More at www.accsysplc.com
“He is such a calm and good-humoured tutor, he has a lot of patience to demonstrate his own skills, and I have learnt so much from him, I will leave HMP Littlehey knowing that I have the carpentry skills to use confidently and hopefully find a job where I can use them,” said one.
“Matt uses real life scenarios as to when and how you make and how you make and build certain pieces, you always feel challenged and you don’t feel rushed, we have the time to practise, and Matt offers supportive guidance in doing so. He instils in us the importance of a tidy workshop and everyone works hard to make sure that it is, I have loved this course,” said another.
Accepting his award at an awards ceremony held in London Matt said: “Absolutely amazing – I seriously wasn’t expecting it from the very first minute that I was told that I was put forward for an award. Everything I’ve ever done has just been for my learners and to help other people.
And at no point do I do it for recognition. I’m just so humbled that I’ve won it, even being runner up I would have been chuffed, let alone winning it. I just can’t believe it.
“You see all the bad stuff in the news and all the bad stuff that’s going on and no one really sees inside prisons and the good stuff that’s going on. People have got such a fixed idea of what a prisoner is and it’s nothing like that in reality. When you see someone that comes in with no skills and you see them develop their skills and stuff like that, it’s amazing to see.”
The Inspire Justice Awards is the UK’s only awards programme dedicated to recognising the achievements of the entire justice sector. Organised by Skills for Justice, the awards are supported by BT, PeoplePlus, UNISON, Midlands Partnership University NHS Foundation Trust, HM Courts & Tribunals Service and SFJ Awards.
New Model Institute for Technology and Engineering (NMITE) was delighted to welcome The Duke of Edinburgh to the Centre for Advanced Timber Technology (CATT) at their Skylon Campus in October.
His Royal Highness, was accompanied by the Lord-Lieutenant of Herefordshire Mr Edward Harley CBE, will meet NMITE’s President and Chief Executive Officer, James Newby, academic staff and NMITE students, including those who have recently entered the workplace. The visit included a tour of NMITE’s Skylon Campus, providing an opportunity for His Royal Highness to get hands-on with NMITE’s unique approach to learning, and concluded with the unveiling of a commemorative plaque.
Ahead of the visit James Newby, President & Chief Executive said “This will be an amazing opportunity to show The Duke of Edinburgh how NMITE is a transformative force in UK university and technical education, redefining engineering and construction training on a national scale, how we are providing new educational opportunities for local people and helping to overcome the barriers to regional economic growth. Our overarching goal is to generate substantial employment, skills development, and economic impacts for Herefordshire, fulfilling the institution’s intended role as a catalyst for positive change in the region.”
During the visit, His Royal Highness met NMITE’s Foundation Year students, along with MEng and BEng Integrated Engineering students, some of whom showcases their engineering and technology projects. Several of NMITE’s Pioneers (NMITE’s first student intake from 2021) who have now entered the workplace were among those on-site to welcome His Royal Highness. Representatives from NMITE’s recent Retrofit programme, and Timber Technology Engineering Design (TED) short courses were also in attendance.
The venue for the visit, Skylon Campus, completed in 2021, has been recognised with a Construction Excellence Social Impact Award and is an exemplar of timber-based modern methods of construction. Designed as a demonstration of the benefits of using timber as a building material, the building is a ‘Living Lab’ and also stores 330,000 kg of CO2e, serving as a beacon for sustainability in the region and beyond.
Academic staff present included Professor Robert Hairstans, CATT Director, Professor David Oloke, Chief Academic Officer and Steve Bertasso, Associate Professor. CATT which was established as a partnership between NMITE and Edinburgh Napier University (ENU) has drawn particular praise from industry and government for its part in developing innovation in timber construction.
Professor Hairstans, NMITE’s CATT Director, is also a Professor of offsite and industrialised construction at ENU’s School of Computing, Engineering & the Built Environment (SCEBE). Robert Hairstans said:
“It is a privilege to have the opportunity to explain how CATT is being established as a nationally renowned centre for research and education excellence in timber construction for the delivery and upgrade of the built environment. Our work in collaboration with the sector and throughout the supply chain has an important part to play in achieving the net zero carbon ambitions of the UK whilst enabling a just transition by means of upskilling and reskilling the professionals of the future.”
More at www.nmite.ac.uk
Combilift secured awards in two categories at the recent UK Materials Handling Association Awards in Birmingham. Up against some of the biggest names in materials handling, they walked away with the ‘Ergonomic Innovation of the Year’ and the ‘Manufacturer Product Innovation of the Year’ awards.
The Combi-CB70E was celebrated for its groundbreaking ergonomic design. The 7-ton electric-powered, multidirectional counterbalance forklift is the shortest 7-ton capacity truck on the market, making it highly efficient with long loads in tight spaces. The truck’s surprisingly spacious cab, with floorto-ceiling panoramic glass, provides operators with excellent visibility and enhanced safety.
One of its standout features is the Auto Swivel Seat, which automatically swivels 15 degrees to the left or right, depending on the direction of travel. This feature significantly reduces driver strain, particularly when reversing.
Combilift’s independent electric traction system – previous Red Dot award winner –
provides 100% traction control for all front and rear drive wheels. This system eliminates the need for a differential lock on slippery surfaces, reduces load swing, and enhances safety and precision when transporting long, heavy loads particularly when navigating sideways, regardless of ground conditions.
Combilift’s second award, the ‘Manufacturer Product Innovation of the Year’, went to the Combi LC Blade, a cutting-edge machine designed specifically to address the growing challenges of transporting offshore wind turbine blades from the manufacturing plant to storage or transportation facilities. These blades, which can reach up to 115 metres in length and weigh up to 70 tonnes, have long posed logistical challenges due to their size, fragility and complexity.
Combilift’s Heavy Equipment Design Team, known for developing pioneering solutions like the Combi-SC Straddle Carrier and Combi-MG Mobile Gantry worked hand in hand with Siemens Gamesa, a leading
supplier of offshore wind turbines, the LC Blade ensures unparalleled stability and safety during transport. Now implemented in manufacturing sites across the world, Combilift has transformed the logistics of handling wind turbine blades and set a new industry standard.
Combilift CEO and Co-Founder Martin McVicar said: “We are more than delighted to have won not just one, but two prestigious accolades at this year’s Archies 2024, making this our 12th Archies to date. Competing against such high-calibre competitors highlights what a fantastic team we have, which are willing to push the boundaries of the material handling industry.”
The awards solidify Combilift’s winning momentum after taking home ‘Design Team of the Year’ for the LC Blade and the ‘Industry Leader Award’ – recognising McVicar’s transformative leadership at the UK EMA Awards in London, bringing a total of four awards for the Irish manufacture within weeks.
The Structural Timber Association (STA) launched a new Time for Timber Hub at Offsite Expo 2024 in Coventry in September, to provide a vital source of information and resources to those interested in building in structural timber.
With all eyes on the new Labour Government to deliver its ambitious commitment to building 1.5 million homes in the next five years, offsite manufacture and low carbon structural timber has an essential role to play - with the capacity to meet 30% of the Government’s pledge. To support in this effort, the new Time for Timber hub has been developed to provide the HOW – guidance on how to plan, design, cost and build in structural timber.
Andrew Carpenter, CEO of the STA, said: “With the Government’s pledge to building 1.5 million homes over the next five years, the dialogue has now shifted from whether to build more homes to how do we build more, and the only way to do this is to embrace change. Ultimately, the Time for Timber hub provides answers to this question and demonstrates how
we can build more higher quality sustainable timber frame homes, regardless of where you find yourself in that journey.”
As part of the Time for Timber Hub, the STA is also developing a series of How To guides that will provide practical advice on making the transition to using timber. The STA also took advantage of Offsite Expo to showcase the latest developments from several of its manufacturing members.
Donaldson Timber Systems is the first timber frame manufacturer to offer a published, third party accredited environmental product declaration (EPD) for its Alpha product, proving its sustainability credentials. The EPD, which transparently communicates the environmental performance of a product over its lifetime, demonstrates the benefits building with timber can bring.
MEDITE SMARTPLY, a leader in sustainable wood-based panels, has completed extensive testing with a UKAS-accredited lab on their SMARTPLY MAX DB and SMARTPLY SURE STEP DB flooring solutions. These OSB panels
meet the 40dB airborne sound insulation requirement set by Building Regs. KLH, with its overall water management solution comprising factory applied membranes to provide weather resistance during the installation period. This product is part of an overall water management solution.
Kirkwood Timber Frame has introduced FastBuild®, a new product designed to speed up and enhance construction efficiency. FastBuild® can cut construction times by up to eight weeks while boosting sustainability and energy efficiency. This comprehensive timber frame system includes wall panels, floors, roofs, windows, and insulation. Openwall® offers an innovative ‘true’ open panel timber frame wall system combining, enhanced performance, simple, flexible detailing and volume manufacture in a cost-effective package without compromise on time, quality or safety, enabling housebuilders to viably produce high-quality, thermally efficient homes at scale.
This year’s shortlist for the British Woodworking Federation (BWF) Awards has been revealed. The Awards celebrate the outstanding skills, talent and achievements of the UK woodworking and joinery manufacturing industry.
Helen Hewitt, Chief Executive of the BWF, commented: “As the BWF Awards enter their sixteenth year, I’m pleased to share that we’ve seen a record-breaking number of award entries – clearly demonstrating the wide range of skills, expertise and passion within our talented sector.
“It’s also exciting to see the enthusiasm for our new BWF Sustainability Award – where for the first time we’re shining a spotlight on the woodworking and joinery businesses who are committed to reducing their carbon emissions or improving their energy efficiency through innovative new processes. The BWF Awards give us a welcome opportunity to celebrate the projects, successes and brilliant individuals within our profession. I’m looking forward to a fantastic evening recognising the achievements from across the woodworking and joinery sector.”
The new BWF Sustainability Award shortlist includes: Surrey Wood Products – for their commitment to demonstrating lasting and sustainable change in their timber supply. James Latham – for the development of The James Latham Carbon Calculator, developed to help woodworkers and joiners select materials with greater confidence to meet regulatory, ethical, and aspirational requirements surrounding sustainability, and Gowercroft Joinery – for their commitment to continued improvement within its manufacturing processes, leading to tangible enhancements in sustainability practices and further reductions in the overall environmental impact using Life Cycle Assessments.
All the winners will be announced at the BWF Annual Awards, held at the prestigious London hotel, The Langham on Friday 22 November.
More at www.bwf.org.uk/awards-2024
The Builders Merchants Federation (BMF) has welcomed Kronospan – the global manufacturer of wood-based panels, as its thousandth member. The BMF’s merchant and supplier members, who together have combined sales of £50.2billion, employ just under 203,000 people.
The BMF’s latest member, Kronospan is a great example of the vibrant and innovative businesses within the Building Materials sector. The company has been processing timber for more than 100 years. Committed to sustainable production and reducing its carbon footprint, it uses alternative energy sources and takes recycled wood and residues from the sawmill industry to create engineered panel products designed to improve building performance.
John Newcomb, BMF CEO, said: “I am delighted to welcome Kronospan to the
BMF. A forward-thinking company, they have pioneered many of their industry’s key advances and committed to producing carbon negative products. I look forward to working with them.
“We take enormous pride in providing genuine value to members through business support, people and skills development, supply chain collaboration and government influence – and this is evidenced by the continuous growth in membership which has more than tripled from 324 when I joined the organisation twelve years ago. With 1,000 companies now in membership, the BMF is the only trade body that can truly speak and act with authority for the entire Building Materials sector.”
More at www.bmf.org.uk
Responding to the rising demand for battery-powered tools and outdoor equipment, Wood-Mizer is proud to introduce the industry’s battery-powered first portable sawmill.
The innovative lithium-ion powered sawmill offers a convenient alternative, providing users with a consistent, reliable, high-quality sawing experience. Available on the popular LT15WIDE model, this breakthrough sawmill enables woodworking enthusiasts and forestry professionals to embrace the future of fully portable sawmilling.
Building upon the solid foundation of the LT15 series, the new LT15 Battery Sawmill integrates cutting-edge features, including an intelligent power feed, power up/down functions, and an upgraded Setworks system with enhanced capabilities. Like its predecessor, the LT15CLASSIC WIDE, the battery-powered version handles logs up to 90cm in diameter, while its modular bed allows for cutting logs up to 5.4m long. The new sawmill is available in stationary and mobile versions.
Smart Power Feed: Innovative technology that continuously monitors sawing parameters, optimizing motor performance to deliver the best possible cutting results.
SW-B Control Panel: Features automatic cutting height adjustment and provides crucial data such as battery charge level, energy usage, and engine and battery temperatures.
Durable Battery Housing: Located in an easily accessible spot where a traditional engine would be mounted, the battery housing is dust-tight, moisture-resistant, and designed to withstand outdoor conditions.
Battery Configurations: The sawmill operates with 4, 5, or 6 batteries, providing flexibility and extended operational hours for large projects.
Fast Charging: The included charging station allows simultaneous charging of up to 6
batteries and can be connected to a standard electrical outlet. Charging four batteries takes approximately 4 hours, with each additional battery extending the charge time by an hour.
Mobile sawmilling: The sawmill is ready for transportation on public roads allowing sawyers to engage in remote projects and saw timber independently. The sawmill can be configured with up to six batteries for extended use, enabling an impressive 8-hour operating time, depending on wood type and cutting requirements.
Contact your local Wood-Mizer representative for more details on pricing, availability and product information.
Think Timber, a family-run timber supply business, has opened a new trade centre in Newcastle-Under-Lyme, offering a one-stop shop for bespoke timber solutions.
With more than 20 years’ experience working with some of the UK’s biggest staircase manufacturers, the trade centre will service local joiners and fitters looking for high-quality, innovative solutions for homebuilding projects. Specialising in bespoke staircase components, acoustic wall panelling and kitchen countertops, Think Timber is committed to delivering market-leading products to local trades.
Located on Parkhouse Industrial Estate, one of Newcastle-Under-Lyme’s busiest trade estates, Managing Director, Gavin Brown is confident now is the right time to be making this investment, he said: “We’re in a prime location when it comes to trade in Newcastle-UnderLyme. Every day, hundreds of independent contractors drive right past our doors without knowing what we do. It’s time we changed that.”
Leveraging strong relationships with the best timber mills around the world, Think Timber is committed to raising industry
standards with high-quality, sustainable solutions. Gavin continues:
“The opening of our new trade centre is a big milestone and the result of months of hard work behind the scenes. Our goal, from the beginning, was to open up access to innovative, high-quality timber products and this is just one more way we’re making that mission possible.
“Whether it’s a national staircase manufacturer or a local joiner, our approach is the same. We understand design, we know the market and, more importantly, we know
the materials. We take a consultative approach with our customers and pride ourselves on understanding their unique business requirements. Our partners feel that from the first interaction. With the trade centre and our entire suite of products under one roof, we are offering our customers a new way to buy from us, one that will make our products and expertise even more accessible to the local trade community- which can only be a good thing.”
Through innovation, modern technology and committed employees, Moelven Valåsen is taking big steps towards increasing production to 500,000m³. The new small timber line, advanced camera technology and updated standard machines have created a unique, high-tech production chain that sets a new standard in the sawmill industry.
Several major investment projects are taking place at Moelven Valåsen AB’s industrial sites, including a new small timber line, a kiln, a dryer and a new pellet factory.
In addition, investments have been made to secure the industry’s own energy supply through the establishment of a new energy center, which will be put into operation along with the pellet factory. This development ensures that Moelven Valåsen maximizes resource efficiency by utilizing the entire tree. All bark is now used to fuel their boilers, and the sawdust that was previously transported off-site is now used in the new pellet factory built adjacent to the industry, significantly reducing transportation distances.
Through these investments, they are creating a safer, faster, and more precise hightech production. Once the investments are operational, plans are to increase the production of sawn timber from approximately 350,000m³ to 500,000m³ by 2026.
The raw material is sourced locally from sustainable Swedish forestry, ensuring both a high standard of quality and an ambition to reduce the carbon footprint. On average, the wood used at their facilities is transported only 73.5km from the forest to the sawmill, contributing to both environmental sustainability and an efficient supply chain operation.
More at www.moelven.com
VWith a blend of family spirit and global reach, Vandecasteele Houtimport are a familiar name across the timber sector. Here they give us a glimpse behind the scenes of this dynamic Belgian timber importer.
andecasteele Houtimport stands out as one of Belgium’s premier companies. Based in Aalbeke, West Flanders, this timber importer has a storied history in both the local and international markets.
In addition to common timber species, they also provide a variety of lesser-known species. With a stock of 130,000m³ and over 120 different timber species spread across a 20-hectare site, this Belgian family business continues to flourish.
Vandecasteele Houtimport was founded in 1883 by Louis Vandecasteele and in those days, wagon making was the core business. In 1919, his son Désiré added a small sawmill. Urbain Vandecasteele, the next in line to lead, possessed sharp business acumen and an unrelenting drive. He was the one who started the timber trade. Partly via trade missions organised by the late King Albert, Urbain opened the door to the rest of the world. In the meantime, his son Stefaan had taken over the company and astutely overseen further international expansion. Louis Vandecasteele, the fifth generation, is now further reinforcing the firm’s family character.
Vandecasteele Houtimport has grown into the number one supplier of hardwood and softwood in Belgium and internationally. The Belgian company purchases hardwood and softwood in over 35 countries and continues to look for new opportunities. On the import side they buy from Scandinavia, South-East Asia, North America, Canada, Africa and South America. As regards export, the Vandecasteele Houtimport market comprises all of Europe, with Belgium, France, the Netherlands, the United Kingdom and Germany in the lead. In 2018, Vandecasteele Houtimport set up a separate company in the UK – Vandecasteele Timber Ltd – to help facilitate export after Brexit.
The number of timber species – more than 120 – both hardwood and softwood, grows each year. The company makes a distinction between mainstream timber species and lesser-known timber species (LKTS) the so called ‘secondary’ species. The support and marketing of LKTS boosts biodiversity and reduces the pressure on forests. For each timber species, we maintain a wide range of dimensions. This variety makes Vandecasteele Houtimport a valuable partner for both suppliers and customers.
Besides rough sawn timber, the company has a full range of finished products such as decking and cladding in stock. Customers include timber importers, timber traders, industrial joiners and DIY traders. With the own fleet of 17 company trucks, we deliver orders within one to three days.
The timber market is driven by supply and demand and by project requirements. However, there is one constant factor, namely the demand for quality. For instance, for under construction of decking you always need sustainability Class 1, regardless of the timber species.
“Our biggest assets are having the timber for prompt delivery and being able to deliver with our own fleet of company trucks alongside our knowledgeable and hugely experienced team.”
Vandecasteele Houtimport responds strongly to the quality demands of the market and therefore has various certificates. A commitment to certified timber is a priority and the certificates enable making the timber sector more sustainable, responsible and professional. For instance, purchasing FSC® certified timber contributes to 14 of the 17 sustainability development goals of the United Nations. Certificates include: FSC®, PEFC, OLB (origine légale du bois) and Legal Source.
Sustainability is in the company’s DNA. Since 2000, Vandecasteele Houtimport has committed itself through the Corporate Durability Charter by signing up to environmental objectives exceeding the applicable legislation. In 2020, Vandecasteele Houtimport was the first timber company in the world to obtain the ‘SDG Pioneer’ certificate from CIFAL Flanders, the local hub of UNITAR, the United Nations Training & Research Institute. Vandecasteele continues to make efforts to embed sustainability into their business. At the end of 2022, they received the ‘SDG Champion’ certificate, making Vandecasteele the first timber company in the world to receive these two internationally recognised awards.
Vandecasteele Houtimport is a family business and that typifies its way of doing business. We have the ambition of reinforcing our global reputation. At the same time, we are still a modest company in West Flanders with a family character and we welcome people personally and heartily.’ Amongst other things, Vandecasteele Houtimport will present its activities during the Dubai Wood Show, a trade fair in Dubai from the 14 -16 April 2025. Such opportunities are important milestones for our export ambitions. We hope to open doors in the Middle East through Dubai and establish contact with players from all over the world.
Vandecasteele Houtimport is clearly a company with sustainability in its DNA, a company which radiates ambition and at the same time has both feet on the Belgian ground.
According to the latest figures from Timber Development UK, the deficit of timber import volumes during 2024 compared to the year before continues to fall as we enter the final quarter of the year.
The latest figures, covering the first six months of 2024, show that although imports remain lower than in 2023, the deficit is continuing to narrow, raising hopes that 2024 as a whole may end up meeting – or even marginally exceeding – the previous year.
Volumes of the main timber and panel products from January to June 2024 were 3.6% lower than during the same period in 2023. However, it’s important to note that the deficit has reduced steadily every month since March 2024 and, with second-half 2023 volumes having been relatively weak, there is hope that if the market continues to improve during Q3 and Q4 this year, we could finish 2024 seeing marginal growth across the market.
Total import volumes during Q2 2024 were 1.2% below those seen in Q2 2023. There were more pronounced differences between solid wood imports (both softwood and hardwood), which were 1.2% higher in 2024 than in 2023, and panel products, which fell by a more significant 6.1% during the same period.
The first half of 2024 has been characterised by one month delivering volume below the same month of 2023, followed by one month delivering higher volume than the same month a year earlier. For June specifically, imports were 0.5% better than in June 2023, which was enough to help reduce the volume deficit from 4.3% between January and May, to 3.6% for the first six months. Within this deficit, engineered wood products saw the largest fall in volumes, and softwood imports the smallest.
Interestingly, the value of planed softwoods remained almost the same as in 2023, down by just 0.3%, while the value of sawn goods fell by 7%. The overall softwood decline was caused by the 2.6% reduction in volume, coupled with a 1.3% fall in the average price of the basket of softwood imports.
Hardwood imports were around 7% lower than in the first half of 2023, largely due to a fall in imports from Latvia, although increased volumes from other countries including France, Estonia Romania and The Congo
“The first half of 2024 saw a number of significant changes in particleboard imports. France and Germany have been the leading countries of supply for many years, but both have seen their volumes eroded as increases have been recorded from Belgium, Portugal and Spain.”
Republic have helped to partially offset this fall. Plywood import values have seen an 11% fall, with softwood plywood values falling 23%, and hardwood plywood 7% down on H1 2023. The 7% fall in the value of hardwood plywood was price related with an average reduction in price of 11% which drove values down, despite a 4% rise in the volume of hardwood plywood in the first half of 2024.
The first half of 2024 saw a number of significant changes in particleboard imports. France and Germany have been the leading countries of supply for many years, but both have seen their volumes eroded as increases have been recorded from Belgium, Portugal and Spain. France and Germany have each lost around 14,000m3 in 2024 to date while
Belgium, Portugal and Spain have increased volumes by around 8,000m3, 3,000m3 and 11,000m3 respectively.
The value of all particleboard imports in the first half of 2024 was 12% lower than in the same period in 2023. This was caused by an 8.5% drop in the average price of the basket of particleboard products as volumes fell by 4% compared to 2023. The 12% overall decline in value comprised a 5% decrease in the value of standard (unworked) particleboards, a 14% fall in the value of melaminefaced chipboards and a 15% decline in the value of other assorted products, including decorative laminated-faced chipboard.
“The continued timber import deficit remains disappointing but is nevertheless unsurprising given the wider construction outlook,” says TDUK’s Head of Technical and Trade, Nick Boulton. “The most recent data
The UK’s recognition of CE marking on construction products was due to end across Great Britain on 30 June 2025. However, the UK government has now announced an extension to the scheme beyond this date, ending years of uncertainty for the construction industry.
Back in January 2020, when the UK exited the European Union, the then-UK government said recognition of CE marked products would end ‘in the shortest time possible’, and that the UK would develop its own marking system known as UK Conformity Assured (UKCA). However, in the years since, the new legislation required to support this change was not introduced, and recognition for many products outside of construction materials were extended indefinitely.
Until now, recognition of the CE marking of construction products was still due to end on 30 June 2025, but this has now been extended for at least two years as part of a planned systemwide reform of construction product regulations.
Rushanara Ali, Parliamentary Under Secretary for Building
from the Ministry of Housing, Communities, and Local Government shows that housing starts in Q1 2024 were the lowest Q1 starts for 15 years and 39% below those seen in Q1 2023, with the picture further skewed by the short-lived race to register housing starts
Safety and Homelessness, announced the extension in a statement on building safety in Parliament on 2 September. The UKCA mark will remain a valid and accepted regulatory mark, sitting alongside CE marking until further notice, and timber and builders’ merchants can use be assured that both products remain valid symbols of conformity to all relevant safety, health and environmental requirements and legislation.
David Hopkins, TDUK CEO said: “We welcome the government’s decision, and in particular the announcement of the two-year transitional period to give manufacturers, suppliers and merchants sufficient time to adjust to any future changes. We have long been calling for the government to provide the clarity the industry urgently needed, and this decision gives all concerned time to create a regulatory system that is truly fit for purpose, without creating barriers to trade both into and out of Great Britain. We will continue to work with the Government and all timber industry stakeholders to support the wider reform of all construction products, including timber.”
in Q2 2023 before changes to the Building Regulation came into force.
“However, the latest Construction Products Association summer forecast is predicting growth will return in 2025, preceded by an estimated 11% decrease for
2024 as a whole. A strong finish to 2024 would be required to achieve these levels, but this does, we believe, offer some green shoots of hope that the worst is now behind us.”
860 & CSF 860.
Simple, Flexible and Absolute are three words that describe the CS 860 & CSF 860 from VOLLMER. Perfect for machining the sharpest clearance angles and sides, the new arrivals are easy to use and incredibly flexible. This gives you outstanding grinding results with optimal processes for all your circular saw blade requirements. The CS 860 & CSF 860 deliver the highest level of quality, productivity and user-friendliness with maximum flexibility.
www.vollmer-group.com
Dust and fume extraction specialists, Extractly have recently completed the installation and commissioning of a comprehensive new dust extraction system to maintain a safe, clean workspace for North Somerset-based Sweet Joinery.
OAlthough Sweet Joinery was incorporated as recently as 2017, the business has family roots going back over five decades. Company founder, Dan Sweet, started his career in the early 2000s as an apprentice carpenter for his grandfather’s company, H. Sweet & Sons, and later went on to manage the firm’s specialist joinery shop. In 2019, Sweet Joinery’s rapid expansion was bolstered with the acquisition of Woodhill Joinery – another local family concern, also established back in the 1970s.
In addition to a collection of traditional woodworking tools that are typically employed in the crafting of bespoke kitchen cabinetry and window frames, the company’s workshop, located just a few miles southwest
of Bristol, houses a comprehensive range of high-performance production machinery, including a Biesse Rover machining centre, Hebrock Edgebander and Altendorf F45 Panel Saw, along with SCM Spindle Moulder and Planer Thicknesser, and a Sedgwick Tenoner. This comprehensive set-up, teamed with a dedicated and experienced workforce, has enabled Sweet Joinery to build an enviable reputation for high quality bespoke joinery for their clients in the retail, education and transport sectors.
“To eliminate our wood waste disposal costs, and to get ‘free’ heating for the workshop in the process, we wanted to install a modern, efficient, waste wood burner, explains Dan Sweet. “However, to
effectively filter and collect all the wood waste material our machines were producing, which was necessary to make the installation viable, it was obvious that our existing extraction would require something of an upgrade. After discussing our requirements with other colleagues in the industry, it was recommended that we should contact Extractly for advice.”
The advice was provided by Ian Rayner, UK Sales Manager for Extractly and Ecogate: “This was a challenging but really interesting project to be involved with”, says Ian. “Key to the success of the installation was going to be a new and more efficient filter unit, including a more powerful main fan, but space and access at the site was particularly restricted. The wood burner was being installed internally, at the rear of the workshop, along
with a high-powered Reinbold Shredder, and there was just enough space here to site the 30kW ATEX fan unit we’d specified to provide the necessary maximum airflow volume of 17,000m³/hr.
This would provide effective extraction from all the current machinery, plus a margin of extra capacity for future additions, but siting the filter was going to require a more complex operation: as space in front of the factory needed to be kept clear for delivery vehicles and personnel access, and a narrow passageway to the rear of the premises had
already been earmarked for a vast, externallylocated silo which would store the collected waste before feeding it to the new burner.”
The solution Extractly’s design engineers provided was for the new filter unit to be mounted on top of the silo. The unit selected for the task was an LBR-S HJ2 reverse air baghouse weighing in at around 2 tonnes. The unit is fitted with XT15 ‘Superbag’ filter media, and two 1.1kW regeneration fans provide filter cleaning.
The modular, galvanised steel housing, with a 2.4m x 2.4m square footprint and around six metres tall, was craned-in over the roof of the factory and fixed into place above the silo. “The positioning of the filter unit is actually ideal”, says Ian Rayner. “Collected waste is discharged from below the hopper, then delivered directly into the silo, pressurefree, via an ATEX rotary valve.”
The installation not only provides Sweet Joinery with a renewable heating source and cuts the cost of woodwaste disposal, but it’s also a great way for the business to reduce its carbon footprint. And, to ensure the company derives maximum cost savings and reduces its carbon footprint even further, Ian Rayner also put forward a proposal to include Ecogate® energy-saving technology to control the dust extraction system, adding: “In common with all workshops involved in the production of bespoke joinery, the machines at Sweet
Joinery are never all in use at the same time, so demand for extraction is continually changing throughout the working day.”
With an ‘On-Demand’ Ecogate® system controlling the extraction system, a sensor fitted to each machine monitors machine usage and sends a signal to the Ecogate® greenBOX controller whenever an individual machine comes on or offline. In turn, the greenBOX controller, via the Ecogate® PowerMASTER™ Variable Speed Drive unit, immediately adjusts the fan speed to exactly match the change in demand – reducing power consumption and saving on electricity costs.
However, the level of savings a company like Sweet Joinery can achieve are quite significant, as Ian says: “By taking advantage of the Laws of Physics, Ecogate® technology can typically reduce electricity usage by at least 50% when the fan speed is reduced by as little as 20%. This sort of saving is easily achieved when machine usage is varying throughout the day and, when it’s break-time and all machines shut down, the fan also shuts down – automatically.”
“We were really pleased with the installation team from Extractly,” says Dan Sweet. “They worked efficiently around us, and I found them to be professional and very flexible when delays on other equipment installations inevitably impacted their installation work schedules.”
More at www.extractly.co.uk
Kevin Underwood, Technical Director of the British Woodworking Federation (BWF) explores the potential impact of The Future Homes and Buildings Standards 2023 Consultation on the calculation of U-values for windows and doors.
The Future Homes and Buildings Standards 2023 consultation outcomes will shape the future of the woodworking and joinery sector, as well as the broader construction industry, by establishing new energy efficiency requirements that will help the decarbonisation of newbuild homes.
In its October 2021 publication, Net Zero Strategy: Build Back Greener, the Government stated it: “aims to support action in the construction sector by improving reporting on embodied carbon in buildings and infrastructure with a view to exploring a maximum level for new builds in the future.”
When the ‘Future Homes and Buildings Standards: 2023’ consultation was published in December of that year the BWF was shocked to see that embodied carbon was to be out of scope. The consultation document stated: “Embodied carbon, the carbon emissions generated from the production and transportation of building materials,
construction process and maintenance of a building – is beyond the scope of this consultation and the existing Building Regulations. We recognise, however, that embodied carbon is a significant contributor to the whole life carbon of a building and that it is therefore crucial that we take steps to address it. The government intends to consult on our approach to measuring and reducing embodied carbon in new buildings in due course.”
At the same time, the Government published a policy paper, the ‘Timber in Construction Roadmap’, where it said: “Timber in construction can reduce the whole life carbon, the full carbon impact, of our built environment. The carbon impact of the built environment is made up of both operational carbon from the type of energy or heating systems within a building and the embodied carbon resulting from the manufacture, maintenance and disposal of the construction products that comprise the building or structure. Use of timber can reduce the embodied emissions in a single building by 20% to 60%.”
As the operational carbon of a building reduces, the embodied carbon becomes more significant. By not considering embodied carbon the government has lost an opportunity to further reduce carbon in the construction industry.
As the operational carbon of a building reduces, the embodied carbon becomes more significant. By not considering embodied carbon the government has lost an opportunity to further reduce carbon in the construction industry.
In the Future Homes and Buildings consultation the Government considered that it could keep fabric standards largely the same as the levels set in the 2021 amendments to Approved Document L as:
• It considered that level set in 2021 would ensure that (with adequate ventilation) new homes would not generally experience damp and mould or excessive temperatures
• The 2021 fabric standards allow efficient low carbon heating, e.g. heat pumps, to function well
• As the electricity grid is decarbonising, and the efficiency of heat pumps significantly reduces energy demand, further reducing total energy use is relatively less important than switching to electric sources of heat in efforts to decarbonise.
The notional (target) and limiting (no worse than) U-values for windows and doors in new dwellings are set out in the table below. For the reasons already highlighted, these values are no different to what they are today. But it is not the values that pose a problem for manufacturers, it is the proposed change in the way that U-values are determined that presents a challenge to the sector.
be calculated using either the actual size and configuration of the window or door, or it should be measured using the appropriate hot box method. This proposal would require a huge increase in heat transfer modelling or testing to be undertaken by manufacturers. For new dwellings, the U-value of a door or window should be either calculated using the actual size and configuration of the door or window or measured using the hot-box method set out in BS EN ISO 12567-1.
The Future Homes Standard 2025: dwelling notional buildings for consultation.
U-value (W/(m2.K))
Currently, ‘Approved Document L, Volume 1: Dwellings’ allows the U-value of a window or door to be determined using standard sizes and configurations, but the Future Homes and Buildings consultation introduced a new national calculation methodology for dwellings called the Home Energy Model. This new methodology aims to improve the accuracy of energy modelling and consequently requires greater accuracy of the input data.
This is based on the government’s view that when determining U-values for windows and doors, the use of U-value calculations based on standard sizes and configurations, or default values was not sufficiently accurate. The proposals for new dwellings recommend that the U-value of windows and doors should
Draft consultation-stage Approved Document L, Volume 1: Dwellings, Table 4.1 Limiting U-values for new fabric elements in new dwellings.
(W/(m2.K))
The Government’s proposal for the determination of U-values, however, appear to have missed two essential points.
Firstly, that windows and external doors are regulated under the construction products regulation and must be conformity marked –either UKCA or CE. As such, the determination of U-values must follow the requirements of the designated product standard BS EN 14351-1.
Secondly, that there are no UK Approved Bodies that can undertake hot box testing to BS EN 12567-1 and the governments post-Brexit rules do not permit the use of test evidence from laboratories that are not UK Approved Bodies for the purposes of UKCA marking.
Article 4 of the assimilated EU Construction Product Regulation (305/2011)
(the CPR) states that: “When a construction product is covered by a designated standard or conforms to a Technical Assessment which has been issued for it, information in any form about its performance in relation to the essential characteristics, as defined in the applicable harmonised technical specification, may be provided only if included and specified in the declaration of performance.”
This means that for windows and external doors their U-value, which is an essential characteristic, must be determined by a UK Approved Body and not determined by the manufacturer alone.
However, the Government is proposing that unique U-values are produced for each window or door installed into a new build home. This is therefore not only complicated by the number of calculations required but also by the requirements of the CPR.
Looking ahead, it is difficult for the sector to plan for what may not come to fruition. Until we see the final amendments to Approved Document L, we can’t be certain of what the guidance document will require. In the past, content put forward in a consultation, has not made its way into the final Approved Document so it is right for the sector to be cautious. The hope is that whatever changes are made, the sector is given sufficient time to put in place new systems to achieve the new demands.
Approved Document L could have a significant impact on our sector, and at the BWF, we are closely monitoring the proposed amendments. Once the document is finalised, the BWF will be ready to provide our members with the necessary guidance and support to effectively navigate the changes.
More at www.bwf.org.uk
Andy Ball, Founder Director at The Joinery Network explains how from the seed of an idea five years ago, Lignum is now the go-to system for joinery companies to manufacture timber windows and doors profitably.
Five years ago, five industry experts got together to set up The Joinery Network with the singular goal of helping joinery manufacturers make fully certified, superior timber windows and doors profitably. Fast forward to 2024, The Joinery Network has 50 joinery companies as members manufacturing the Lignum timber window and door system.
This success has been against a backdrop of increased legislation, declining sales and a skill shortage in the industry. The model has proven that by providing easy access to a window and door system that is fully tested and compliant with Building Regulations, is easy to manufacture with simple training and has a low cost of entry, Lignum can quickly become a profitable income stream for joinery manufacturers of any size.
The increased level of interest in manufacturing timber windows and doors through The Joinery Network was evident at the Materials and Finishes (MAF) Show earlier in the year at the NEC. Founder Director and joinery consultant Owen Dare’s daily demonstrations manufacturing the Lignum system attracted large crowds of joiners and, from this interest at the show, we are continuing to add new members.
At the MAF Show, we also brought together some of our key
partners in The Joinery Network to demonstrate the strength of the support we offer throughout the supply chain. This was followed by the network’s annual Partners Conference in September, where 28 delegates from leading suppliers in timber, joinery and glazing discussed the next steps in developing the UK timber window and door sector. There is no shortage of ideas of how to grow market share and support joiners looking to manufacture timber windows and doors.
We started with the founder partners originally investing in developing and fully testing the Lignum system. We brought together the technical expertise of Owen Dare as product designer, with specialists Leitz Tooling UK, Winkhaus and Deventer to create a complete suite of products which now includes five window styles, a range of entrance doors, French doors and bifold door products.
The Joinery Network provides advice, comprehensive operative training and licenses to joinery companies to manufacture the fully compliant system. Lignum is approved by Secured by Design, and members have the option to add this prestigious accreditation. This year we have added the new GUTMANN-LIGNUM wood-aluminium window and door suite, developed in conjunction with leading aluminium specialist GUTMANN. The timber Lignum entrance door system is also available either fully finished or in kit form for customers.
The Lignum range was created for UK homes and designed to be low maintenance for both replacement and newbuild sectors. We achieve this through continuous product development working alongside our partners. Carefully designed profiles, smooth-cut Leitz tooling, advanced paint technology from Teknos (UK) and Remmers, plus superior weatherseals, all combine to provide highly durable exterior weather protection. The Joinery Network has recently added Accoya French Doors to the range, achieving stringent PAS24:2022 certification for Accoya wood.
We are also at the forefront of vacuum glazed windows and doors, bringing practical, cost-effective and sustainable energy efficiency to glazing projects. All the products in the Lignum range are supported with a marketing suite, so that new customers can hit the ground running.
Typically, joinery companies manufacturing the Lignum system are finding that there’s a sea change in profitability for windows and doors. John Fanthorpe from JF Joinery reported that by moving to Lignum he was able to double production of windows and doors, with a significant increase in profit margin. John says: “Since we adopted the Lignum system our production times have decreased significantly, and we have more than doubled our revenue.”
As well as the growing interest in timber windows and doors from joinery companies, interest from homeowners is increasing as well. The Joinery Network member Timbawood Ltd reported its busiest stand ever at the recent Homebuilding and Renovation Show at Excel, London.
Timbawood’s Managing Director Ian Selby told us: “There was huge interest in our historic and contemporary product ranges, with strong enquiries for vacuum glazing. Visitors to our stand were searching for climate change solutions and motivated by the sustainability of our timber windows and doors.”
It’s impressive to see what The Joinery Network, working with our members and partners have achieved together in the first five years.
And the next five? We are looking forward to growing the number of UK manufacturers of Lignum superior, fully certified timber windows and doors to stay ahead of demand. More at www.thejoinerynetwork.co.uk
Mark Councill and Alec Laing founded Logie Timber in 2017 with a shared vision to establish a sawmill to bridge the gap between small estate owners, private garden owners, larger forestry sites and the public.
ur goal was to demystify hardwood timber processing,” says Mark, who was running a tree surgery business at the time. “Making it more approachable and less intimidating. We wanted to remove the barriers that often surround the industry, ensuring that anyone, regardless of their background or knowledge, could navigate the process with ease. I always envisioned it as the kind of place anyone with no experience in timber or hardwood production could visit, feel welcome and get all the information they need in a friendly, supportive environment.”
With around 82% of wood overall in the UK imported – and the figure is around two thirds for sawn timber – the need for increased amounts of homegrown timber
entering the supply chain has never been higher. With Scottish woodlands so important to this aim, how can requirements be better prioritised to create a healthier and less import-led supply chain?
“Although 82% of overall timber in the UK is imported, largely reflecting softwood imports,” says Mark. “When it comes to hardwoods, the percentage is significantly higher – well over 90%. This is a concerning statistic, and one we must address. It’s frustrating for a country with a rich natural resource base to rely so heavily on imports, especially when small companies like ours are committed to using only Scottish and UK-grown timber.
“One of the main challenges is consistency in quality across the industry. Currently, there
is no standardised grading system for Scottish timber, which can lead to inconsistencies. A construction company might buy from a competitor and receive timber that doesn’t meet the required standards. This leaves them with a poor impression of UK timber, pushing them back to relying on imports.
“Establishing a unified standard for timber quality would go a long way in building trust and encouraging the construction industry to choose locally sourced timber over imports.
Another key factor that could drive a shift towards UK-grown timber is the introduction of a carbon tax or some form of carbon-conscious purchasing. When you compare the carbon footprint of sourcing timber locally to that of importing it from places like Scandinavia, America, or even New Zealand, the benefits are clear. A shorter supply chain means significantly lower carbon emissions, making local timber an obvious choice.”
So, what can improve? Can our homegrown timber stocks provide enough timber for the domestic UK market and what are the blockers for the wider construction industry using more homegrown resource? “This is a challenging question because the exact figures aren’t clear,” says Mark. “I would hope that Scotland and the UK could one day produce enough timber to meet their own needs. However, with forest cover at only around 13-14% across the UK and 18-19% in Scotland, we’re significantly behind countries like Finland, where forest cover is an impressive 74%. Given these numbers, it’s unlikely that we currently have enough high-quality, usable timber to fully meet our needs, so it’s essential that we start working toward greater self-sufficiency in timber production.
“When it comes to structural timber, we tend to rely heavily on a few species, primarily Scots Pine and Spruce. While these are great for many applications, we should be exploring the use of other species, such as Douglas Fir and Hemlock, which could help diversify and stabilise the supply chain. By broadening the range of species used in construction, we can make better use of the forests we do have and reduce dependence on imports.”
A Mark points out, if we are serious about reducing our reliance on imported timber, we need to embrace innovation and look beyond traditional species. Combined with better forest management and planting initiatives, this will help the UK move toward a more sustainable and self-reliant timber industry. Of course, the timber material supply chain has been through many ups and downs over the last few years. Where have the pressure points been for Logie Timber?
“We’re in a unique position because of the diverse range of products we offer,” adds Mark. “Our line-up spans everything from hardwoods – like oak tabletops and elm skirting boards and shelving – to structural posts, beams, and large-scale cladding. This variety allows us to balance out the fluctuations in the supply chain. However, sourcing certain materials – particularly larch – has become increasingly difficult. The spread of ‘Phytophthora ramorum’, a disease that’s decimating larch trees across the UK, has made it much harder to get hold of.
“We have been working to shift demand toward Douglas fir as a viable alternative. All our structural posts and beams are now made from Douglas fir, and when we built a new shed on-site, we clad the entire structure in this timber. We’re also producing more Douglas fir planed cladding, and it’s proving to be a fantastic option. Of course, the rise in energy costs has impacted us, as it has across the industry and that has inevitably affected the pricing of our timber products.”
Logie Timber takes its commitment to sustainability and reducing carbon footprint very seriously, with a range of measures in place at the sawmill and they are Grown in Britain certified. They are determined to showcase the value of homegrown timber and be carbon conscious.
“Sustainability is embedded in every part of our operation,” says Mark. “We have installed a 22-kilowatt solar panel system on one of our sheds, which powers our machines when they’re running and feeds excess energy back into the grid when they’re not. We’re planning to expand our renewable energy infrastructure with a larger solar panel system on another shed, and we’re looking to install a biomass boiler system to heat new drying kilns for the sawmill.
“The biomass system will be powered by our own wood chips –essentially recycling waste from our production process to fuel our energy needs. This combined heat and power system will generate electricity for our machinery and heat for the kilns. The surplus heat from this system will even be used to warm nearby cottages on the estate, further expanding our efforts to create a sustainable, circular approach to energy use.
“We are also committed to keeping our processes chemical-free. All our timber is untreated – there are no chemicals involved at any stage. Even the lubrication for our bandsaw blades is plant-based, rather than the diesel commonly used in the industry. This not only works as well, if not better, but also creates a healthier working environment. At every step, we’re working to reduce our carbon footprint as much as possible. Our efforts to minimise emissions aren’t just about meeting industry standards—they’re about creating a responsible, forward-thinking business that values the environment and works to protect it for future generations.”
With a growing shift toward using more homegrown timber in the future, Mark, Alec and the team at Logie Timber have big plans as they continue to consolidate current operations and success. Mark says: “In terms of our sawmill expansion, we have already made a significant
The Logie Timber Festival took place on 7-8 September 2024, on the picturesque Logie Estate, near Forres. The goal for the festival was to inspire a love for timber, forestry, and woodworking, making it an engaging experience for everyone who attended.
“Over the course of the weekend, we welcomed around 2,500 to 3,000 visitors and showcased around 40 exhibitors, says Mark. “The festival featured a variety of engaging demonstrations, including timber
harvesting, tree climbing for children, axe throwing, archery lessons with Bow Hunter Archery, as well as trying their hand at green woodworking with Aaron Sterritt.
Festival goers had the opportunity to learn more about a range of organisations including the Highland Folk Museum, Forestry and Land Scotland, Mackintosh School of Architecture, and the Institute of Chartered Foresters. It also hosted talks from the British Deer Society and Grown
investment in a brand new Mebor saw line and a new building, which has increased our production capacity. Looking ahead, we do have a couple of potential directions we’re considering. One option is to expand into creating structural timber frame kits that customers could easily assemble themselves. This would be a new product line that could add significant value to our business and provide a more accessible way for people to build with timber.
“We’re also exploring the possibility of setting up a thermokiln to produce thermally modified timber here in Scotland. Given the challenges we’re facing with larch, finding alternatives for untreated external cladding is critical. Thermal modification offers an excellent solution, as it enhances the durability and stability of timber without using chemicals.
As larch becomes more of a premium product, we need to have other sustainable options available, and thermowood is a promising alternative. While we have plenty of exciting ideas for the future, right now, our focus is on consolidating. We need to get everything running smoothly – refining our processes, ensuring quality and making sure all systems are working as they should – before we consider any further expansions.”
in Britain, along with presentations from industry leaders such as Dan Ridley-Ellis from Napier University and Neil Sutherland of MAKAR. “These sessions provided invaluable insights into forestry and how we can encourage the use of homegrown timber. We had originally planned to hold the festival every two years, but given the enthusiasm and interest, it’s looking likely that we may return next year. Although nothing is confirmed yet, we encourage everyone to stay tuned for updates.”
Our trees are our future and as John Orchard, Chief Executive of Woodland Heritage explains, we need to grow more of them and think differently about how we use them.
You know we face a climate crisis. You might not know that at a time when so much of our woodlands aren’t sustainably managed, the UK is the third largest net importer of forest products, behind China and the USA.
It means we simply aren’t making the most of what we have. Woodland Heritage is doing something about this by championing the good use of homegrown timber from sustainable, productive woodlands for the benefit of present and future generations.
Through a combination of demonstration sites like James Wood in Somerset and Whitney Sawmills in Herefordshire, alongside research, education, membership and outreach programmes, the charity builds on the wisdom and skills of the past and present to weather the challenges of tomorrow. Put simply – grow trees and use wood – for our future.
Productive woodland is part of the answer to this conundrum. By selectively felling, the canopy is opened, new plants appear, attracting new insects, birds and wildlife. Through this traditional cycle, sustainable
forests produce beautiful timber for striking buildings, long lasting furniture and treasured objects. In addition to social benefits, a hectare of mixed broadleaf trees sequesters 596 tonnes of CO2 equivalent over the next 100 years. Of course, timber products and places are vital stores of carbon, too.
But to bring these benefits to life we must support and invest in the nation’s processing capabilities. This is where Whitney Sawmills enters the story. The business is a vital part of the charity, and Whitney
Sawmills demonstrate the value of productive woodland first hand. The sawmills are a well-established, keystone business offering a range of green and dried hardwood and softwood timbers. There is an impressive range of species and sizes of timbers in stock and the mill has a proven ability to meet demand for unusual and bespoke specifications, cut to order.
This track record means the company is as renowned for its involvement in restoration projects like HMS Victory as it is for supplying
leading furniture makers, construction projects and even timber bikes and yurts. Beyond providing this vital service at a time when over the last 30 years we have lost three quarters of our sawmills, the business routinely brings people together to share skills, experience and research.
The charity and sawmills are proud of their involvement in courses like ‘Woodland to Workshop’, which broadens horizons and raises awareness by educating participants from the forest through to the workshop and beyond.
This ground-breaking course is supported by knowledgeable practitioners and eminent speakers from the timber industry. Based in the woodland, timber yard, sawmill and joinery workshop, this is an intense, practical course that will give attendees knowledge to last a lifetime.
Places are available now and the hope is that by attending the course those that grow trees and use wood can take action to improve a healthy supply of homegrown timber from sustainable, productive woodlands. Building on the course, the sawmill and charity are walking the walk, too. Since the charity and sawmill joined forces the percentage of the
Whitney Sawmills
Whitney Sawmills supplies a range of different timbers specialising in oak, although douglas fir has become increasingly popular in recent years. Other hardwoods supplied include ash, elm, sycamore, sweet chestnut, cherry and poplar, with walnut, alder, lime and maple occasionally available as well.
The vast majority of planking stock is milled offsite and then air-dried in a large barn, although some stock is kiln-dried to reduce moisture content further for internal uses in particular. Kiln-drying takes over from the air-drying process which, with the most commonly supplied oak planking, can normally be assumed to take one year for each inch of thickness. Air drying goes down to 16-17% compared with10-12% moisture content with kiln drying.
Tongue-and-groove flooring as well as skirting, architrave and cladding have all been growing as sales products, although the other major product in demand besides planking is beaming, which is taken in as green logs and then milled on-site to order. Where possible ‘falling-boards’ coming off the saw will be retained for use as flooring or planking, but otherwise the main by-product created is firewood that is sold in bulk (slabwood), as well as by the sack to the general public.
Customers include joiners, cabinet makers, timber framers, builders, architects and DIY woodworkers and whilst a good proportion live and work within a 50-mile radius of Whitney, many orders are shipped each year across the UK; one of the attractions that draws customers to Whitney Sawmills is its ability to fulfil customised orders.
Whitney Sawmills has always supplied both UK and European timbers with Woodland Heritage’s aim being to increase the proportion of timber sourced from the UK and especially from the West Midlands and Wales. Whitney Sawmills isn’t just a supplier; it’s also a customer, buying timber from local landowners and helping to secure the jobs that they in turn offer.
sawmill’s timber supply, which is home-grown has changed dramatically, from an estimated two thirds five years ago, to over 95% at the time of writing.
Heritage comes from c.1200 Old French and means ‘that which may be inherited’. Old French was spoken hundreds of years ago, largely in northern France, and was a mesh of Romance dialects including Italic and Celtic. So, ‘that which may be inherited’. The charity feels the key word is ‘may’. It’s far from certain. Because the world of woodlands often changes slowly, the decisions we make today
directly affect the knowledge, skills, woodlands and timber we pass on to future generations. This in turn affects whether our children and grandchildren can create a thriving wood culture that benefits their environment, all people and their economy. This means woodland heritage is not the passive act of preserving the past. It is the active process of deciding what world our children and grandchildren will inherit. It requires action. Have you thought about your woodland heritage? What are you passing on?
Sustainability doesn’t mean our buildings have to lack creativity, says Ruaridh Nicol, Associate at architectural practice Holmes Miller.
As the climate crisis continues to drive one of the biggest calls for change across the globe, sustainability has become front and centre of every aspect of dayto-day life. The way we design our buildings, and use them, has changed dramatically as a result. But while architects and contractors are upping their game when it comes to sustainable design, strict turnaround times and tight budgets are still creating challenges in unlocking the full potential of buildings.
As specialists in creating architecture with people and the planet at its heart, we work with public and private sector clients on a wide range of projects, from stadiums and leisure facilities to schools and care homes.
Creating environmentally friendly buildings is engrained in our journey from the outset. We don’t just aim for the bare minimum when it comes to building standards, but we use these as our guiding template from the initial stages of planning, all the way through to delivery. Our clients want to create buildings that do good, but often, time constraints and tight budgets limit the opportunity to truly bring their projects to life. And most of the time, funding is the key driver. Ultimately, if the money is coming from another party, it’s them who will have the final say.
It’s understandable that people who are investing in buildings sometimes want to take the quick and easy route. They do it because it’s the safest and cheapest way to get the job done, but our buildings and the environment are suffering as a result. Creativity, and more leeway to think outside the box, can help to maximise their potential.
Creating something stand-out from scratch and watching it come to life is an exciting prospect, and something I know all architects are keen to do more of. It can be frustrating to watch our industry take the “same old” route, with the same old materials, to churn buildings out one after the other.
To create buildings with true meaning and value, we need clients to take a bold step outside of their comfort zone and think about the longterm gain. Giving them the confidence they need to do this, however, relies on more conversations between Government and industry to incentivise creative ways of working, while keeping in line with building standards.
Encouraging the use of new, sustainable products on the market, or reusing existing building stock, are just some examples of a change of approach. It sounds easy, but innovative products often come at a higher price point than traditional alternatives, so making them more affordable and achievable would go a long way.
Just last year, Michelin Scotland Innovation Parc’s Innovation Hub reached completion – an ambitious £4.75million joint venture between Scottish Enterprise, Dundee City Council and Michelin. The brief was to create somewhere that would drive innovation in the Scottish economy and address the global climate emergency, while also inspiring its users and creating a sense of togetherness. Moving away from the usual run-of-the-mill approach, our client wanted something unique, and was keen to explore different methods of design, putting in the time and money needed to achieve this.
We worked closely with them to identify their needs and created a new and exciting concept, which perfectly showcases Scotland’s ability to innovate. It incorporates everything they need, including labs, flexible meeting areas, an events space and a café. But most importantly, it successfully puts both people and the planet at its heart.
On first look, the building is wrapped in sinusoidal cladding, matching MSIP’s desire for an industrial look. But once inside, it breathes a raw and honest warmth and vibrancy, enhanced by the sustainable materials used throughout. The exposed mass timber frame which welcomes visitors as they enter is made from cross laminated timber (CLT) and glulam and is
one of the building’s most striking and recognisable features. Our client describes it as a building that gives you a hug and makes you feel warm and cosy. Not only does the timber create a showstopping interior, but it also significantly reduced the carbon footprint of the building.
At the core of the building, users are greeted by a stripped back Hellerup staircase made from reclaimed timber, which provides a vibrant informal meeting point to bring people together and spark new ideas. All in all, the entire primary structure of the building was erected in just four weeks. It’s a prime example of how sustainability and creativity can come together to result in something that’s truly inspiring. And it’s a good reminder of how pushing boundaries to take the innovative route, rather than the easy one, can often be the right decision. Sustainable buildings shouldn’t be boring, and there’s plenty of opportunity out there to do more with the designs we create. All that’s needed is a little bravery, education, collaboration, and a splash of imagination.
The European Commission has announced the launch of a new anti-dumping investigation into unfairly priced imports of hardwood plywood from China into the European Union.
Procedurally, the initiation of the investigation, for the first time ever, will require registration of all imports of Chinese hardwood plywood at EU borders. This would allow European customs officials to collect additional duties retroactively if they are imposed because of the Commission’s findings after the investigation.
The investigation was initiated at the request of nine leading European plywood producers who formed the Greenwood Consortium, saying: “The investigation will now examine whether Chinese producers are indeed dumping hardwood plywood in the EU, and what the consequences of those practices for European businesses are. Several other countries and markets, including the US, Morocco, Turkey and South Korea, have already taken action to protect their own industries from similar unfair trade practices.”
Established in 2023, as an ad hoc Consortium by leading EU producers of hardwood plywood from Bulgaria, Czech Republic, Finland, France, Hungary, Latvia, Italy, Poland, and Spain, Greenwood leverages trade policy instruments to further its commitment to fostering a level playing field that ensures fairness and sustainability in the EU hardwood plywood industry.
Jaroslaw Michniuk, CEO of consortium member Paged Morag – with plywood production facilities in Poland and Estonia – said: “We are pleased that the Commission has granted the Greenwood Consortium’s request and launched an investigation, the course of which we will be following closely. The investigation itself takes up to 14 months, however, as was the case in the proceedings against Russian birch plywood producers, the European Commission can impose so-called provisional duties after about six months. We also welcome the Commission’s announcement of the registration of hardwood plywood imports at the EU border, as this makes retroactive duties possible.
Paged has been an active supporter of fair competition in the EU plywood market for years. The company co-founded the Woodstock Consortium, at the request of which the European Commission conducted antidumping proceedings and imposed tariffs on
Russian plywood even before Russia’s invasion of Ukraine, as well as tariffs on Turkey and Kazakhstan for circumventing these regulations.
“The imposition of sanctions on plywood from Russia and Belarus has caused these countries to try to find ways to reach the EU market with their illegal goods,” added Michniuk. “One of the directions that is gaining dynamic importance today is China. Keeping in mind that already today China is the largest supplier of plywood to the European Union, it is so important that trade with this country takes place in accordance with WTO regulations.”
The Greenwood Consortium and its supporters are committed fully to co-operating with the European Commission to ensure a successful outcome for the industry and its workers.
More at green-business.ec.europa.eu/publications/ guidance-eu-deforestation-regulation_en
The upcoming EU Deforestation Regulation (EUDR) is set to reshape how businesses trade timber and wood products in the European market, with many implications for global supply chains.
The EUDR’s core requirement is straightforward. Companies supplying timber – either entering or leaving the EU market – must be legally sourced, free from deforestation or degradation, based on a cut-off date of 31 December 2020, and verified by a robust due diligence system. This includes sawn timber, wood-based materials, paper, and furniture, as well as rubber, palm oil, soy, coffee, cacao, and beef.
On 2 October 2024, the European Commission proposed to delay implementation a full year to 30 December 2025 for large companies and 30 June 2026 for and small and medium enterprises. The scope of implementation has been vastly underestimated, with a statement from the European Commission saying: “The Commission recognizes that three months ahead of the intended implementation date, several global partners have repeatedly expressed concerns about their state of preparedness, most recently during the United Nations General Assembly week in New York. Moreover, the state of preparations amongst stakeholders in Europe is also uneven. While many expect to be ready in time, thanks to intensive preparations, others have expressed concerns.”
Companies must still prepare to implement rigorous due diligence systems that trace the wood from harvest to the marketplace. This includes supplying geolocation data that pinpoints the exact areas where the timber is grown. The Commission update in October also stated: “The Commission is intensifying dialogues with most concerned countries, which will feed into the speedy finalization of the country benchmarking system through a proposed Implementing Act by 30 June 2025.”
From the wide choice of filter types and technologies available, we source the most appropriate and cost-efficient system to meet your requirements and, from initial consultation and design, all the way through to installation and commissioning, we will be with you at every stage of the process.
The wealth of practical experience within the company, together with an extensive range of proven products, allows Extractly to offer extraction systems which are individually tailored to customers’ specific needs.
Whether you need a small mobile extractor, or a high-capacity modular filter unit, an energy-efficient shredder or briquette press, or perhaps a modern spray booth or enclosure… from simply adapting ductwork to suit a new machine installation, to commissioning a complete waste-to-energy system, Extractly’s experienced engineers deliver the optimum solution.
ENHANCE THE SAFETY, STORAGE AND EFFICIENCY OF YOUR LOGISTICS WITH COMBILIFT
For 25 years, Combilift has been revolutionising the way companies handle and store goods. We help companies of all sizes and from every industry to maximise the capacity, safety and efficiency of their warehouse and storage facilities.
Our pioneering product range of multidirectional, articulated and pedestrian forklifts, straddle carriers and container loaders allows you to manoeuvre long loads safely, reduce aisle widths and increase the amount of space available for storage.
To find out how Combilift can help you unlock every inch of your storage space.