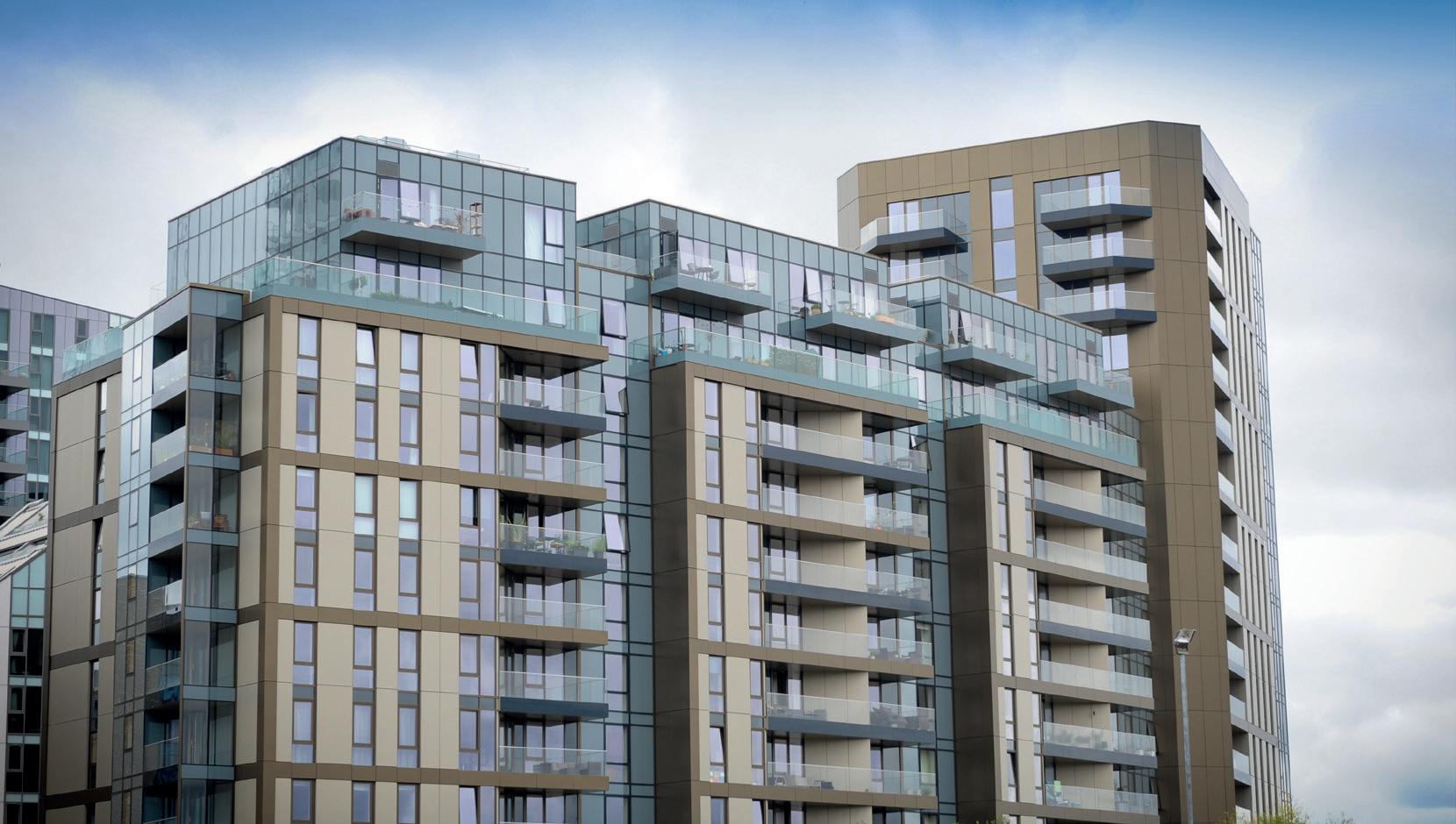
2 minute read
Case Study - Riverside Quarter
CASE STUDY
Riverside Quarter, Wandsworth
CONSTRUCTION PARTNERS
Client
Frasers Property
Main Contractor
Galliford Try
Architect
Carey Jones Chapman Tolcher
Steel Framing Systems Supplier
EOS
Type of Solution
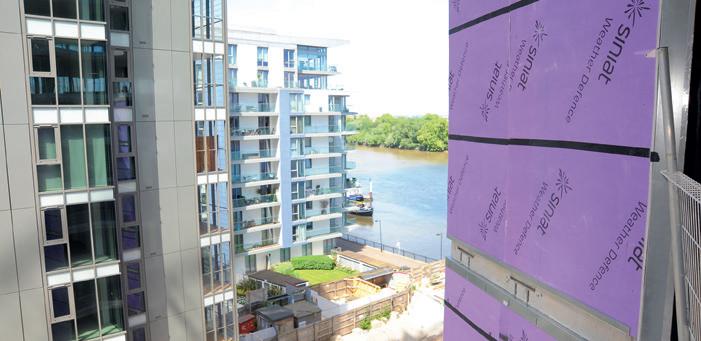
OVERVIEW
Riverside Quarter in Wandsworth is a £250 million mixed use development located on the south bank of the River Thames. Delivered in four phases, it comprises six buildings ranging from 11 to 15 storeys, as well as commercial accommodation and leisure spaces.
Galliford Try has been working with Frasers Property to deliver the prestigious project with construction work starting in 2014 and finishing in January 2020. The project has created over 750 new apartments, including 197 affordable homes.
Pioneering a new systems approach, the final phase of Riverside Quarter was the first development in the UK to specify our Pre-Assembled Frames (PAF) – a non-loadbearing infill system.
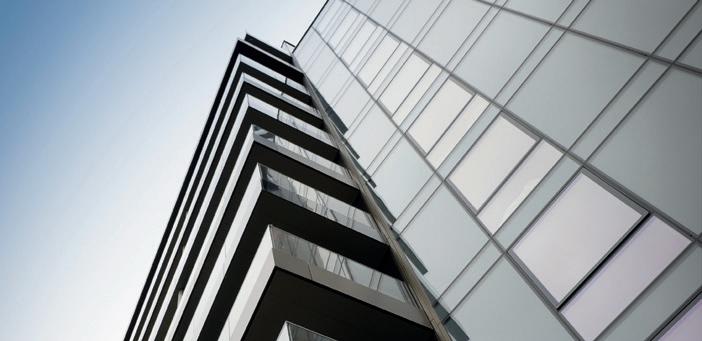
MITIGATING RISK
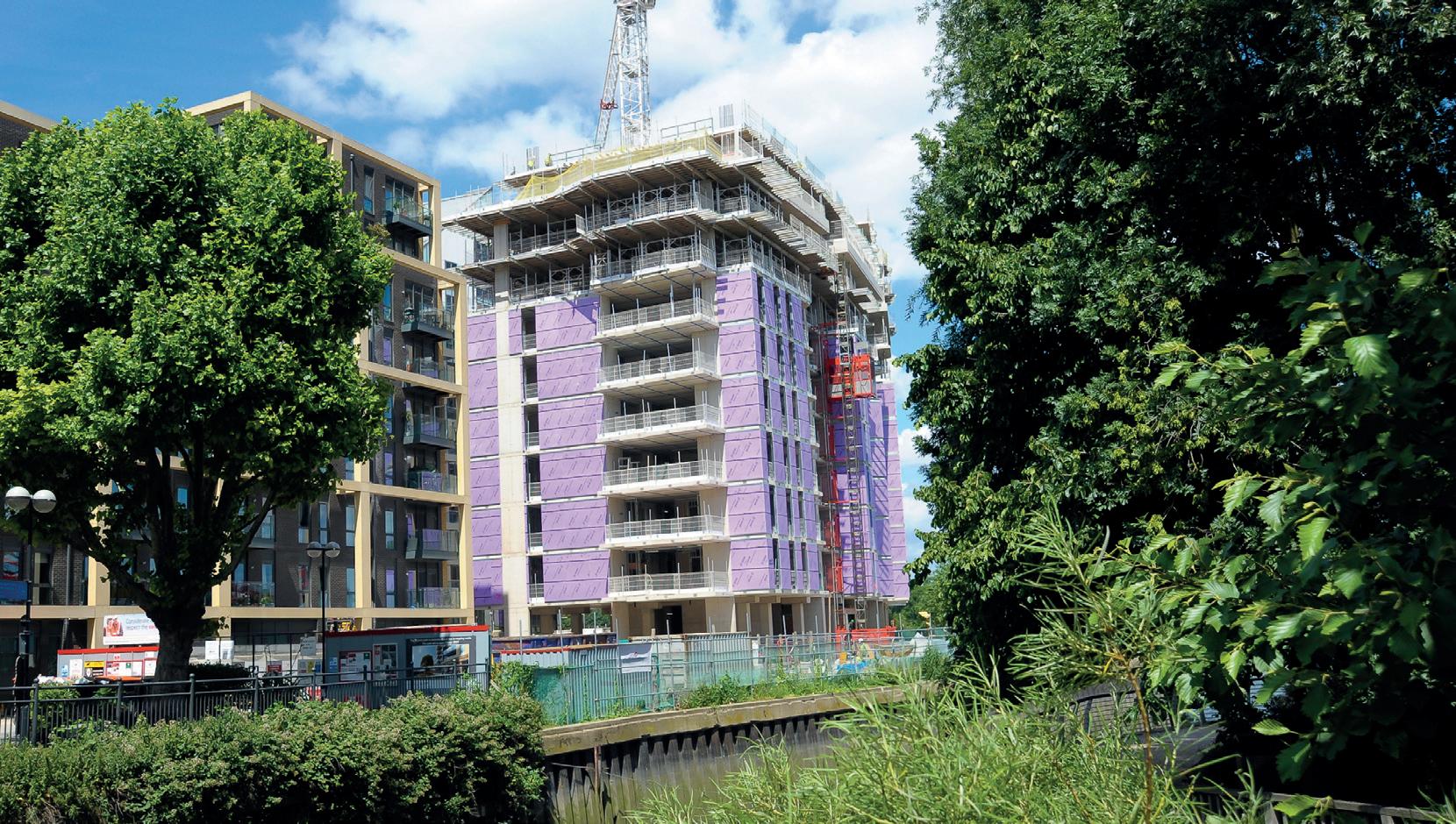
The performance of building materials is under an unprecedented spotlight. Architects, designers, specifiers and ultimately, clients – are feeling exposed. We believe material providers should have full-scale testing regimes that study the performance of products working together to see how they interact in ‘real’ circumstances, like under fire conditions or when exposed to wind and rain.
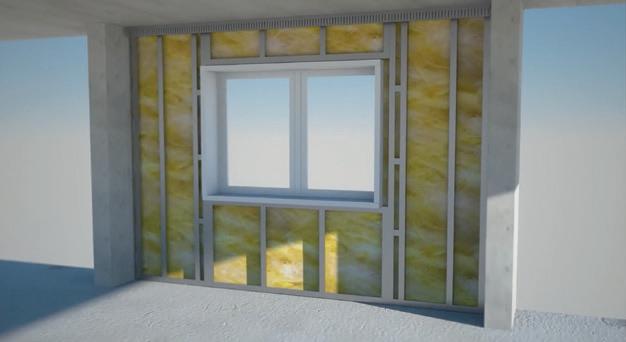
WATCH OUR CASE STUDY VIDEOS GO TO: www.eosframing.co.uk/informationcentre/#video-library SYSTEMS APPROACH
After rigorous testing of the complete system, Pre-Assembled Frames achieved 60-minute fire resistance and was awarded a product and performance 30-year Etex warranty following a specification and validation process. This approach provided the Riverside Quarter specifiers with complete confidence and peace of mind knowing that the PAF system has been subjected to relevant testing for fire, acoustic, weathering, energy efficiency, airtightness, durability and mechanical performance.
Meeting building performance requirements in a unitised solution, the systems were delivered to the Riverside Quarter site as assembled panelised units. The system performance balance was achieved through tested configurations of factory prefabricated light steel frame and Siniat Weather Defence external sheathing together with site applied glass mineral wool insulation at a minimum thickness of 100mm and Siniat internal wall lining.
Just in time deliveries reduced the requirement for site storage and the systems approach reduced cutting and reworks onsite. Installation from inside the concrete mainframe enhanced Health and Safety by reducing working externally at height and also offered vast savings for the Riverside Quarter development by reducing mast climber and scaffolding requirements.
Delivering crucial cost and time benefits making programme savings of up to 30%, the prefabrication of the individual steel elements took place under controlled, highly regulated and safe factory conditions. With so much work completed offsite, the onsite construction schedule for Riverside Quarter was reduced – delivering a faster return on investment for Frasers Property.