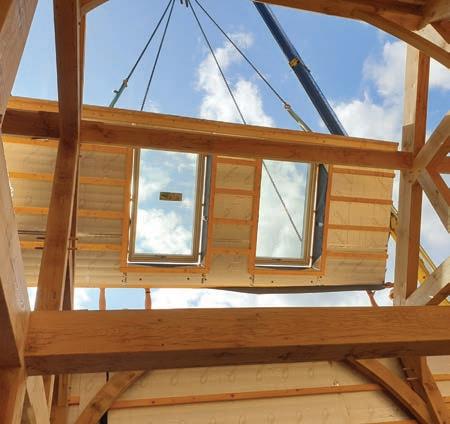
4 minute read
What is offsite manufacture?
I D Ut T E E E Ts Usi Stru Tur L Tim Er Uildi Systems I Ludi T Ry Ssured U Lity Tr L
Any structural method created in a factory or workshop away from the building site comes under the bracket of offsite manufacture. To put this into context: brick and block is a site-based method, as the structure forms in situ as bricks are built up. In contrast, a timber frame is cut and shaped offsite before being delivered to the plot and craned into place.
ou might equate offsite manufacture with post-war prefab homes, but times have moved on since the cheap and cheerful boxes that pervaded the mid-20th century. Offsite manufacture is a broad term covering a range of options – it doesn’t necessarily mean craning in entire prefinished rooms. It’s something of a hybrid
6
Right: The encapsulation panels for this Oakwrights home were manufactured offsite and include the windows, meaning whole sections of the house shell could be craned into place in one go
To Choose Offsite Construction
i ill t e d ersely i ue ed y i leme t e t er
2 Build cost & programme certainty site stru ti m es s eduli d sti m re predi t le t it tr diti l uildi met ds
3 Quality assurance Stri e t t ry u lity tr l e es t e m u ture uildi s e suri y u et m der i per rm e e el pe r y ur s eme
4 Energy usage erm lly e ie t i ly irti t mes redu e e er y sumpti r ss t e uildi s li e
5 Design flexibility it ide r e i ti e pr du ts d l ddi s luti s tim er systems meet t e spir ti s t r ite ts d sel uilders
6 Sustainability ll Stru tur l im er ss i ti mem ers use tim er r m C r SC ertified s ur es e suri resp si le m eme t t e rld s rests route, where much of the internal fit-out work can still be carried out onsite.
Built-in benefits
Near-enough every structural timber system is created offsite, and as time progresses, solutions continue to move towards a more factory-built focus, with greater levels of prefabrication. This means your new house can be delivered as part of a controlled process, with added benefits from factory-fitted insulation and pre-cut service channels through to panels that come complete with windows and doors already installed. Even internal finishes and e ternal cladding can be pre-applied.
Offsite manufactured timber systems have advanced greatly and offer genuine cost, programme and performance benefits for those building from scratch – especially when backed by the STA Assure Membership and uality Standards Scheme.
Intelligent, integrated construction systems such as closed panel timber frame, structural insulated panels SIPs and volumetric modular options (where a completed section of your building, such as a whole room or a big portion of your roof, is craned into place are driving innovation in the timber sector. This means there is much more choice now, from classic kit systems to highly prefabricated solutions. In this guide you will learn about all the varieties of timber structural solutions that can be used to make your new dream home. It’s not perfect for every project, of course if your plot suffers from restricted access, for e ample, it might be tricky to get large-scale panelised components delivered to site. But combine the enhanced energy e ciency of off site timber systems with shorter construction timescales, guaranteed build quality and vastly reduced ongoing running costs, and it’s clear that there are compelling reasons to specify these solutions.
Guaranteed performance
With the standards for energy e ciency constantly ramping up, the construction industry has faced a challenge in creating homes that achieve the actual performance specified in the design brief. The accuracy and control involved in using timber-based off site technology overcomes this issue.
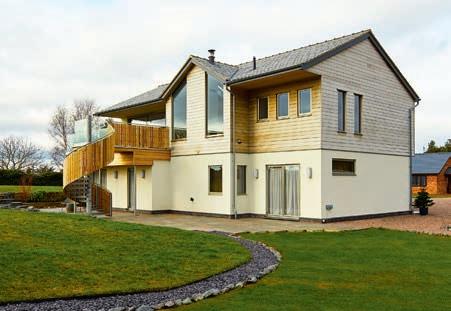
Factory-fi tting insulation prevents the performance gap that can happen if there are mistakes when fi tting these elements on site. Essentially, the more work that gets done in the factory, the more predictable the performance of the finished house will be. And as a major priority for self builders is an energy e cient home with e tremely low heating costs, this is a big benefi t for anyone looking to build from scratch.
Timber structural systems
There are three core types of timber building method, and we’ll be addressing each other these in much more detail throughout this guide. They are:
Timber frame: There are several varieties of timber frame, from open panels that require a bit more input on site, through to closed panel systems that come with insulation and sometimes even windows and services built in. Over on page we’re discussing all the reasons why timber frame is a great option and you can learn about how to design your timber frame home on page 4.
SIPs: Structural insulated panels are an energy e cient pre-insulated system that create large sections of wall, oor and roof. They can also be used as a thermal wraparound option for other systems, such as oak frame homes. Learn all about using this timber building method on page .
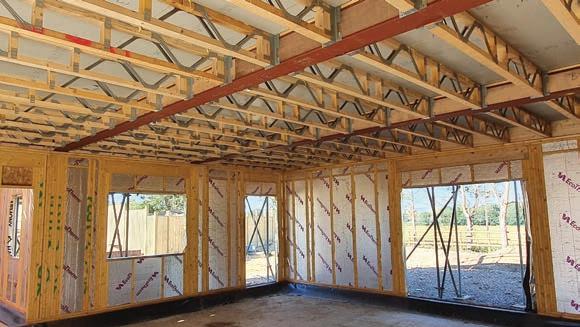
Oak frame: This building method boasts character and beauty but it isn’t just for lu ury budgets, as you’ll learn over on page 37. Go to page 2 to discover the benefi ts of this structural method, plus why oak is perfect for rural homes page 34 . Learn about how hybrid methods could help to cut costs further on page 42.
The Structural i ber ssociation e site (www.structuraltimber.co.uk) contains a wealth of information for self builders, from guidance on timber i ding syste s thro gh to top tips and an en iry syste to he p yo nd the right partner for yo r project. Learn more about STA Assure on page 45 and head to page 46 for contact details of STA members that could help with your bespoke home build.