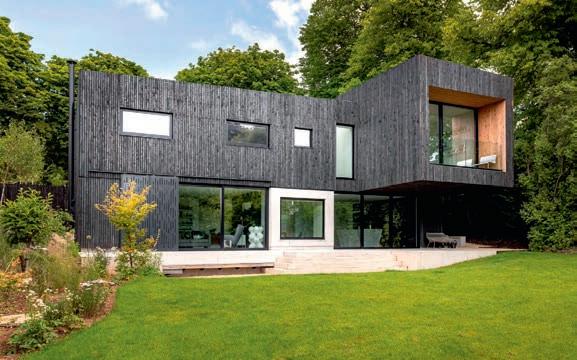
8 minute read
Why choose timber frame?
Timber frame is a leading contender for the creation of high-quality oneoff homes. Among other benefi ts, this factory-manufactured system offers high sustainability standards, speedy construction and e cellent energy e ciency in use all in a value-for-money package. So, it’s no surprise timber frame has cornered a strong share of the market. According to a survey by NaCSBA in 2022, it accounts for just shy of a third of all K self builds. STA research suggests that, in Scotland, take-up rises to a massive 3 of all new housing. So, could it be the right investment to support your dream home goals?
What is a timber frame?
Modern timber frames are engineered and manufactured as bespoke house shell kits. The core component is the storey-height walling panels, which form the inner loadbearing leaf of your home’s external walls ready to accept your choice of decorative cladding . A typical frame package will also include the internal stud walls, intermediate oors and roof structure all precision-cut and ready for assembly onsite – along with the insulation, membranes and sundries required for construction.
There are two main types of timber frame system available. In both cases, the lightweight engineered panels are formed of a network of studs, rails and sheathing. The key difference is the level of prefabrication involved. Open panel versions, as the name suggests, are left
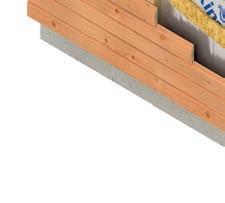
Top: Kingspan’s Ultima closed panel building system is available in three variants, achieving U-values down to 0.14 W/m2K
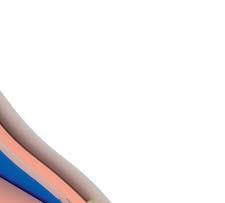
Above: This cantilevered woodland build features the Passiv Innovations factoryinsulated timber frame system from Timber Innovations. The pro e t is nished in Shou Sugi Ban charred cladding open on one face. Insulation is then added on site to your agreed specification, whereupon the panel is then finished with ply or OSB boarding. According to the STA, this approach can achieve -values a measure of thermal performance, where lower numbers indicate better heat retention down to around 0. 5 W m2K.

Closed panel systems bring more of the work into the factory. The insulation is prefi tted under controlled conditions, ensuring full coverage and making it easier to achieve e cellent -values down to 0. 0 W m2K or better . Some providers can also install windows, door linings and even claddings plasterboard prior to delivery. This makes for an even quicker build phase, as well as giving you a single point of responsibility for more of your project. However, it does mean you’ll need to nail down more of the design detail prior to manufacture.
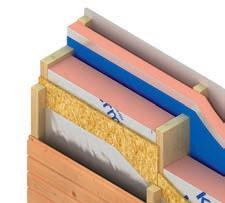
Your timber package
One of the most seductive elements of buying a timber home is that you’re dealing with a single company for a big chunk of the main superstructure – rather than pulling together a cornucopia of trades and suppliers. Manufacturers can provide varying levels of service depending on your needs and location. A typical package takes in the engineering, design, manufacture and assembly to weathertight stage – using either the supplier’s own team or trusted contractors they’ve worked with before. This ensures they can offer a warranty on the completed house shell.
Some timber frame suppliers offer follow-on joinery elements as part of their services, such as windows, staircases, architraves, internal cills and plasterboard. The big benefit of this is that it gives you access to proven products from trusted
5 Key Benefits Of Timber Frame
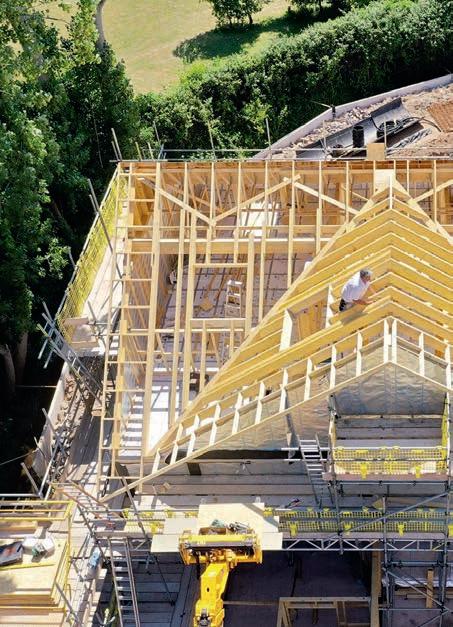
1 It’s eco friendly, combining sustainably-sourced timber with high-quality thermal insulation and straightforward airtightness detailing. So, you can enjoy a low-carbon build along with minimal heating bills once you move in.
2 Factory quality is assured, s y u e fide t you’re buying a consistent, accurately-manufactured product. This means you’re not as reliant on the skills of onsite labour to achieve the performance and quality you expect –plus it can enable early ordering of follow-on components, such as windows and glazed doors.
3 Quick build times. Your prefabricated timber frame house shell will be erected onsite much faster than with traditional masonry construction, reducing the risk of weather delays and meaning internal works can start sooner.
4 Design flexibility co es as standard with a host of impressive architectural features readily achievable. You fi is tim er r me e ter lly i yt i r m d cladding to brick, stone, render and more – so, from the outside, you’d be hard-pressed to identify exactly what building system lies underneath. For more on designing your timber frame home, see page 14.
5 Value-for-money. Price-wise, building with timber frame is very competitive with masonry construction. That’s partly because the factory fabrication process ensures greater predictability and improved visibility over costs, as well as reducing the labour requirement on site. Combine that with etter ert i ty er t e fi is ed u lity d it s e sy t see why this method holds so much appeal.
suppliers via a single intermediary. This means you’ll gain access to the sort of buying power you wouldn’t have as an individual self builder, potentially bringing savings versus a solo approach. Your frame manufacturer will also take care of quantities and snagging issues for their part of the package, reducing the complexity and stress of specifying your build.
A number of timber frame companies can support you with project management –either in-house or through trusted partners – deeper into the works, and potentially right up to completion. Known as a turnkey build, this route puts you in charge of the specification and design of your home, but leaves it up to the professionals to deliver it.
As with any building contract, always take the time to check your timber frame quote includes everything you’re expecting – and not just the materials, specification and who’s doing the install. For instance, who’s responsible for things like steelwork and crane hire, and what it will cost? A good supplier will hold your hand through this process, as well as provide you with detailed handover advice so that you know what to expect once their part of the work is done.
The build
Once you’re happy with the engineering design and your quote, it’s time to sign the drawings off to enable manufacture. Lead times to produce all the components for a timber home are typically eight to 2 weeks but the build itself will be lightning-quick. On site, a standard house shell can take anything from a few days to several weeks to assemble, depending on size and architectural comple ity. According to the STA, this process is around 45 faster to reach weathertight than using conventional blockwork.
The manufacturing lead time won’t impact on your overall project schedule. In fact, it gives you the ideal window to prepare your site for the frame’s arrival by completing the groundworks just as soon as you have the sole plate design . This is a crucial stage, as the foundations must be highly accurate and level to enable installation of the precision-engineered timber kit. So, it pays to use an e perienced groundworks crew. our frame supplier may be able to recommend trades in your area.
For many self builders, the day the frame arrives on site is the most e citing part of
Insulation Options
tim er me s impressi e e ie y stems r m t e m i ti i u lity i sul ti d pre ise m u ture deli eri ri first ppr t e er y s i stru ti tly t pr du ts re spe ified ill depe d y ur ud et d per rm e ls re y u ee t ie e ssi us st d rds r i st e
RIGID INSULATION e m st mm tim er r me i sul ti type i t e is p lyuret e i pr ides e elle t t erm l per rm e i t i er ll ll pr files e pl i s Sim rrells r me e l ies deed li e r li e t tim er r me d S s ie e re t lues it slimmer ll uild up t m s ry ity lli i uld elp m imise r sp e i y ur pr e t
NATURAL OPTIONS y suppliers ls er t e pp rtu ity r tur l re t le i sul ti s su s s eep s l ellul se d emp sed pr du ts ey ll st little m re ut urt er st y ur pr e t s sust i ility rede ti ls y u t t use tur l m teri ls spe t y ur tim er r me spe i list e rly s it ill re uire s me d ustme ts i t e desi det il d e r i y u ill eed t ept sli tly t i er lls t it pl sti sed i sul ti s
MEETING YOUR PERFORMANCE GOALS st d rd tim er r me ill m rt ly e t uildi e s re uireme ts r t erm l e ie y ut it s ls re t i e r t se l i t ie e e epti l per rm e epe di t e pr e t d m u turer t is mi t e d e y ryi t e t i ess t e p el t ept m re i sul ti r y ddi e tr l yer i sul ti r t e m rity tim er r me pr e ts i sul ti is fitted et ee d i side t e studs t e r m side t e p el s ys Sim e e efit t is ppr is t e se d i ter l l yer t redu e t erm l rid i d impr e irti t ess e ser i e tte s re t e fitted s t t ll ser i es sit t e rm side t e i sul ti d d t pier e t e ri the process, as the project will rapidly go from drawings to a recognisable house. The panels, joists etc will typically be marked up and provided in the order they’re required on site making assembly straightforward for an e perienced team. A fringe benefit of the quick, panelised construction process is that there’s fewer individual materials to store on site reducing the risk of damage, waste and theft, and ensuring a tidier, safer site. A timber frame house typically goes up storey-by-storey, with the intermediate oors and any internal load bearing walls installed as construction proceeds. Once the walls are assembled, the roof trusses will be installed, decked and counter battened. If you’ve chosen an advanced closed panel system, the doors, windows and some claddings might be pre-fi tted but at the very least, the openings will be prepared and the whole building wrapped in a waterproof membrane. At this point, you’re at weathertight stage, ready for your follow-on trades to start their work.
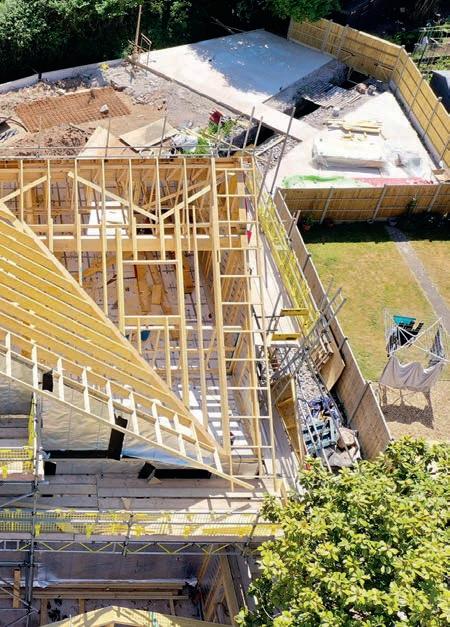
Quick Guide Timber Frame Costs
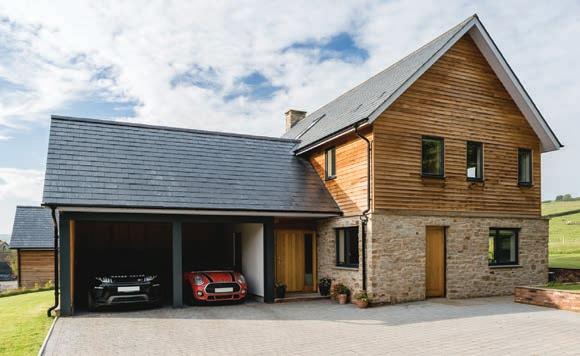
Building with timber frame is a coste e ti e pti r sel uilders it pr e t pri es mp r le t l r t s m re t ere re s me le r ud eti e efits t i t e tim er r ute t t e le st i is st ert i ty s t e pri e is reed up r t S pr ided y u press t e ree utt it i t e u te s lidity peri d y u t t s t y u ll p y r t e ser i es y u e mmissi ed It’s worth being aware that the cash prem u tured uild l s little di ere t t m re site sed ppr es ur m u turer ill e pr du i use s ell spe ifi t y ur esp e re uireme ts s t ey t ust d sell it s me ere else s result y u s uld e pe t t pre p y r y ur r me i ere t suppliers ill split t is i di ere t ys ut e mple mi t e t trigger fabrication and the remaining pri r t ssem ly site
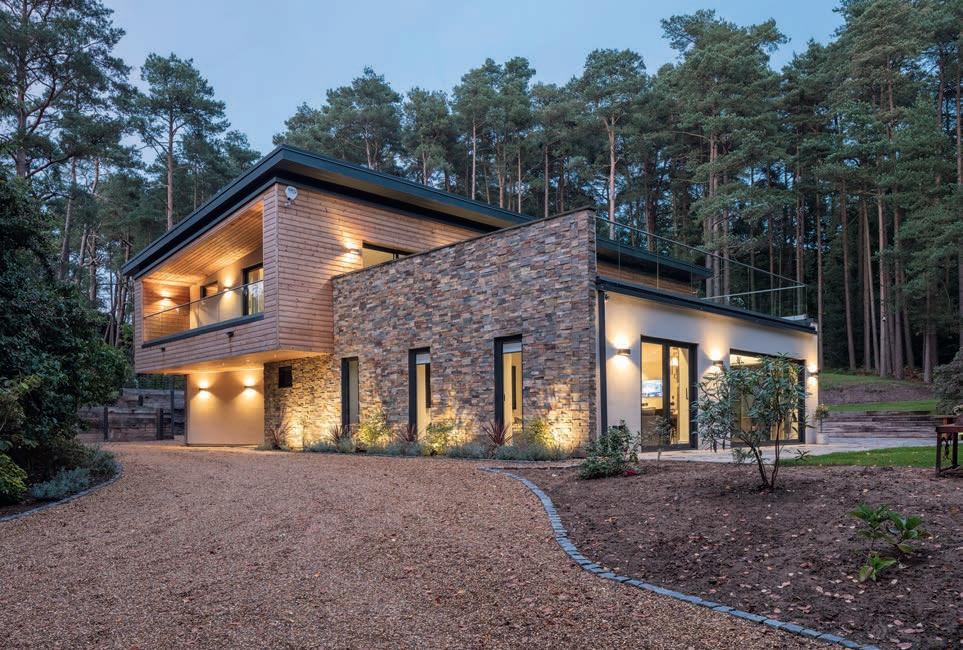