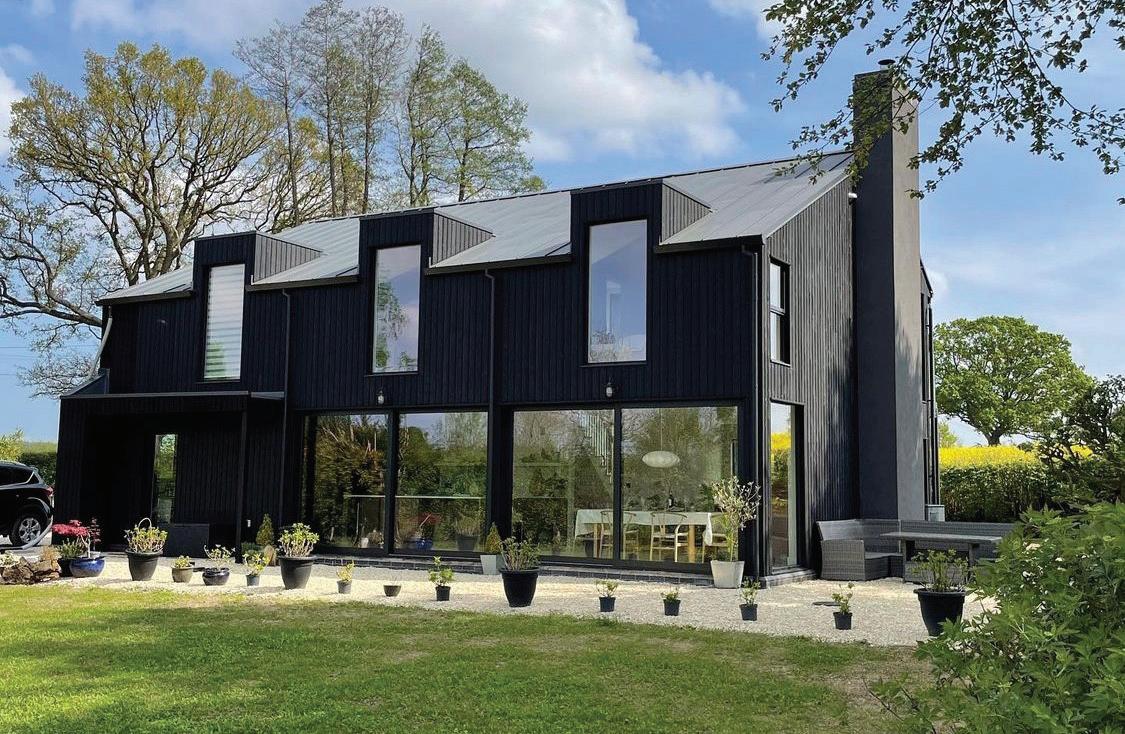
7 minute read
Making the most of SIPs
e r ut t e e efits t is m der met d stru ti d t m imise its p te ti l r y ur uild
The structural insulated panels system (better known as SIPs) is a premanufactured building method that shares many similarities with closed panel timber frame. It uses factoryengineered, load-carrying, timber-based panel products to form the superstructure of a bespoke home. Manufactured offsite, the lightweight system can be used for walls, roofs and even oors. It delivers both the structural capacity and thermal envelope of the building in one neat package offering super-quick construction speeds and confidence over the performance of your finished house.
SIPs are gaining traction in the UK self build market as a premium option wellsuited to low-energy homes. As such,
Above: Glosford SIPs provided the wall and roof envelope, plus the structural partitions and oors for this striking black timber-clad 240m2 self build you can expect to pay slightly more in comparison to systems like blockwork and timber frame. Don’t be put off by the upfront price, however. It’s important to consider whole-life costs when you’re building your own home, and SIPs can guarantee a predetermined level of insulation and airtightness out of the box. Plus, you’ll be able to plan the rest of your self build schedule around a highly-predictable, factory-controlled manufacturing and assembly process.
What’s in a SIP?
Most structural insulated panels are formed by sandwiching a core of high-quality rigid foam insulation in between two skins of structural timber – typically oriented strandboard (OSB) – as the facing material. The factory manufacturing process creates exceptionally strong panels without as much studwork as timber framing; enabling a continuous core of built-in insulation. This combination delivers excellent performance alongside impressive versatility. As a result, SIPs are often a preferred choice for many self builders looking to achieve Passivhaus and similar low-energy standards. “Heat loads in a SIPs house can be kept to a minimum, which
Key Benefits Of Sips
1
2
High levels of insulation and airtightness within a slim panel thickness. This can deliver Passivhaus and zero-carbon levels of energy performance without i t s rifi e r sp e
Ultra-quick assembly on site, with reduced reliance on skilled labour, enables smooth and predictable delivery of the main construction phase. There’s also less eed r pl t d s ld mp red t s me systems, helping to ease some preliminary costs.
3
4
Suitable for roof structures, creating pre-insulated lofts and vaulted ceilings that can add valuable extra space and design panache to your project.
A versatile system that’s capable of being used as a standalone house shell or to provide insulating encapsulation for other construction methods (oak frame wraps being a prime example).
5 equates to low running costs,” says Derek McIntyre, SIPs home director at JML SIPs. The system also offers a straightforward solution for creating coveted design features like vaulted ceilings without the need for trussed rafters.
Excellent whole-life costs due to the ease with which S s e les deli ery i per rm e e ie t home. So, while it may cost more upfront than building with traditional options like blockwork, you will reap the rewards of ongoing low energy bills.
There are variations on the theme. For instance, some SIPs suppliers use expanded polystyrene (EPS) as the insulation, which is fully-bonded with structural adhesive to the OSB skins. Others use polyurethane (PUR) or polyisocyanurate (PIR), which are foamed in between the sheathing to create an integral bond. The different insulations offer slightly different performance characteristics, which will be re ected in the price PIR offers the best insulation values as standard). The other area of choice is around the sheathing different manufacturers use: plywood and cement particleboard are among the alternatives.
SIPs can deliver U-values right down to 0.1 W/m2k, along
Below: An example of the Kingspan TEK SIPs building system, which is available in 142mm or 172mm thicknesses an features a rigid urethane insulation core. Note the insulated splines to underpin the system’s energy performance with superior airtightness thanks to their detailed jointing arrangements (it’s these qualities that make it a great solution for wrapping other building systems, such as oak frame . Some manufacturers even offer insulated splines to further underpin the system’s performance advantages. Coupled with the panels’ innate strength, the highspec insulation enables thinner walls and roofs compared to traditional construction systems. This can increase the finished oor area of your home within the same overall building footprint, while also keeping roof build-ups to a minimum, potentially increasing head height in loft spaces.
Design basics
SIPs have become a mainstream option in the self build market. Nevertheless, it’s sensible to choose a designer who has worked with SIPs before, putting them in close contact with your system provider. Each company has different details and panel thicknesses, which will in uence the drawings,” says Derek Mcintyre. “Bringing your supplier on board early saves time and money, as opposed to having to rethink plans to suit the system afterwards.” plans to suit the system afterwards.”
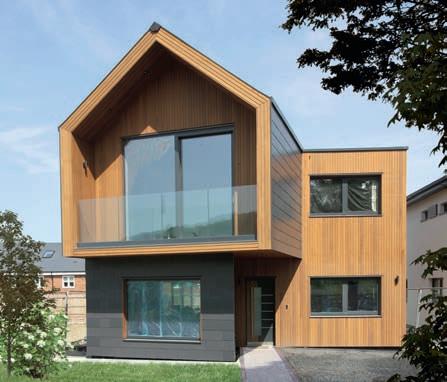
As everything is precision-engineered, you can be assured your house shell will be accurate to the drawings –enabling you to get ahead with the project schedule by ordering core components off-plan. Products
Schedule
on long lead times, such as windows and doors, can be ordered early knowing that, once the SIPs package is complete, glazing can be immediately installed,” says Mike Fleming, sales director at Glosford SIPs.
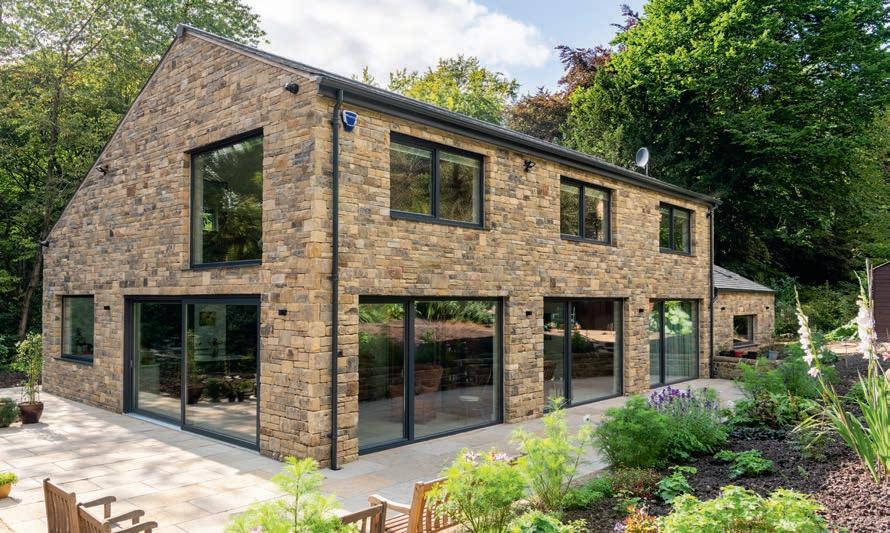
Standard SIPs panels are manufactured 1.2m wide and 2.7m (storey-height) in length, with smaller sections used to form the openings. Working to those sizes will be the most cost-effective option, minimising cutting in the factory. Panels can also be produced in wider spans and lengths up to 7.5m to suit particular design features, with window and door openings pre-cut.
The size-to-strength ratio is what enables those dramatic vaulted ceilings. The loadbearing work in the roof will done by the
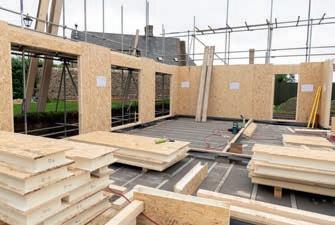
This 268m2 self build showcases some of the key ene ts of s he ays install used 142mm-thick panels with 50mm of extra insulation on the inside face of the walls, and 100mm on the roof he latter was a key feature – its asymmetric design is vaulted internally to enhance the sense of space, with the glulam purlins left exposed for added character ridge beam and any purlins – which are often formed in glulam. The SIPs panels then span from ridge to eaves with minimal need for extra support. So, you can easily achieve double- or triple-height zones. What’s more, unlike with conventional trusses, you’ll gain a clear and pre-insulated loft void that can be ideal for achieving extra habitable space.
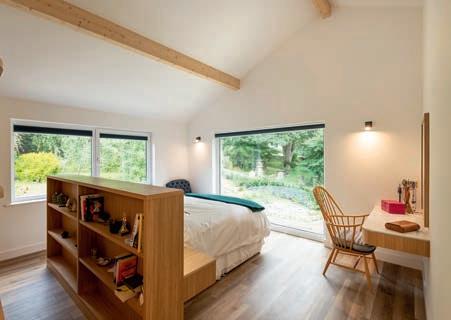
Building with SIPs
Lead times differ between suppliers, but a typical weathertight package for a four-bed house might be manufactured in around eight to 10 weeks. The kit will bring together all the core components to complete your house shell: walls, roof and oor structures, plus membranes according to the technical design. While the panels are being fabricated, it makes sense to get your groundworks sorted. A SIPs home can be built atop any mainstream foundation system, but the slab must be very accurate and level some providers require a tolerance of just +/- 5mm).
Once the foundations are signed off, the structure will be delivered and erected in sequence from soleplate upwards. First the
MAXIMISING SIPS’ PERFORMANCE BENEFITS
SIPs is widely acknowledged as a fast-track option for achieving low-energy standards such as ssi us is is ertified desi approach based around high levels of insulation, very low levels of air leakage, and the use of mechanical ventilation with heat recovery to enable a fresh, healthy living environment. But what do you need to know to ensure you hit the performance levels you want?
“There are plenty of systems on the market so make sure you u derst d t eir e efits s ys Clay, partner at SIPS@Clays. “Look at the thermal qualities – in particular the jointing system, which is key to creating an airtight envelope, as well s ertifi ti s fire per rm e stre t d st ility ut t e pr perly assembled SIPs structural shell ie es e elle t irti t ess e jointing arrangements inherent in
While some manufacturers er e tr t i p els t achieve lower U-values, it’s more common to stick to a standard t i ess d i ste d dd e tr layer of insulation internally. This will provide a further boost to airtightness and thermal bridge detailing. Insulation coverage is factory-guaranteed, but can be further enhanced by options such as insulated splines (joining sections between the panels) that make detailing straightforward on site.
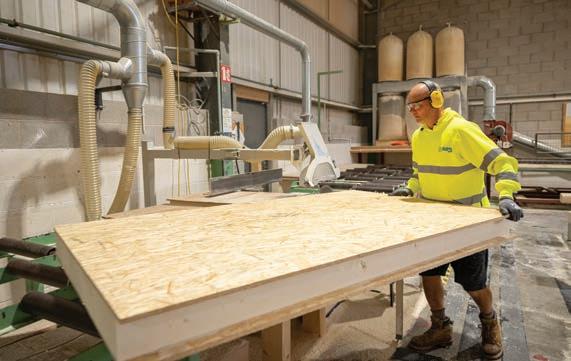
SIPs can provide air leakage rates as good as 1m3/hour/m2 e pl i s tt e s e d technical GB at Kingspan Insulation. “Once airtightness tape is applied to junctions, this can be reduced even further to beat the 0.6 air changes per hour required by the ssi us st d rd is tte ti to detail needs to be maintained further into the build, for instance ensuring windows and doors are installed at the optimum depth in the insulation zone and properly taped before plasterboarding.
To protect the insulation and airtightness performance, it’s vital t use e perie ed i st llers r ground oor load-bearing walls, then the intermediate oor structure, upper storey, ceiling joists and finally the roof. A typical SIPs house shell can be erected in as little as one to two weeks. The only thing that might slow a build down is very high winds.
SIPs are lightweight and easy to handle, so the ground oor can often be slotted together by hand. pper storeys, roofs and larger panels require lifting equipment so you’ll need access for a crane or telescopic handler. If you’re worried this might cause disruption for neighbours, in fact the opposite is true: the impressive speed the follow-on works. Services are typically run through the internal p rtiti lls d r stru ture to minimise penetrations through the thermal envelope. Where wiring, pipes etc do need to be run l e teri r ll p els it m y be possible to include service ducts during fabrication – but a more common solution is to batten out a service void (which is then hidden by plasterboard). of assembly means there will be fewer deliveries and trades coming and going compared to traditional build methods.
Open-web positjoists are often spe ified r t e rs s t ey re available in a range of sizes to easily accommodate ventilation du ts et st S s uses ill use mechanical ventilation with heat re ery t ptimise e ie y e tr t ste ir d pr ide constant fresh incoming supply.
The moment your SIPs home reaches weathertight, you’ll can bring in internal and e ternal trades to work simultaneously. So, your chosen cladding can be installed while first-fi plumbing, electrics etc proceed internally a benefit you don’t get with systems like masonry. our trades will have solid, clean and straightforward surfaces to work off, says Ian. Progress is therefore swift and predictable, bringing the advantage of easy sequencing of works.