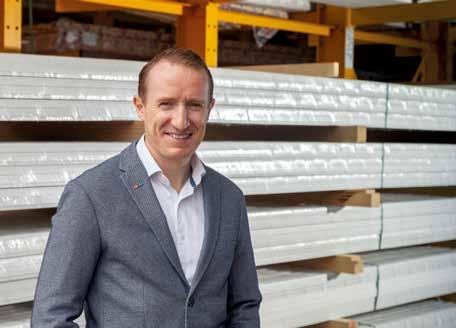
8 minute read
REFRAMING THE TIMBER HOMES APPROACH
REFRAMING THE
TIMBER HOMES APPROACH
Following the acquisition of Stewart Milne Timber Systems (SMTS), Andrew Donaldson, CEO of the Donaldson Group discusses their plans and what this acquisition means for the future of the business and the industry.
2021 was undoubtedly a transformational year for the Donaldson Group. The deal with SMTS marked the largest acquisition in our 161-year history, as well as our entry into the timber frame market.
As timber experts with an historic commitment to the timber market, we have long-considered venturing into timber frame but the timing was never quite right. Last summer, when we developed and completed our five-year strategic plan for the Group, we outlined our ambition to grow the business through an organic and acquisitive growth strategy, with timber frame being a strategic opportunity to explore. This was not only the natural progression for our business, but more importantly, we also recognise the importance of timber frame in meeting the sustainable housing agenda. This is an area we feel particularly passionate about, and we’re keen to support increasing the amount of timber in homes to play our part in achieving net zero.
01
While our plan was clear, we didn’t expect that within six months we would become the largest timber frame manufacturer in the UK. Around the time we were making the first steps forward, the opportunity with SMTS arose and it was a perfect fit for both the Donaldson Group and for SMTS. Fast forward a few months and the deal was made. The move has prompted us to expedite the plans we were working on regarding structure and synergies within the Group. Work is still underway on this, but there will be much more of a concerted focus on offsite construction as a business, and the individual parts of the Group will be working together to promote modern methods of construction (MMC).
To reflect the company joining a new family, the legal name of the business has been changed from Stewart Milne Timber Systems to Donaldson Timber Systems, with a full rebrand to follow in the coming weeks.
As a Group, we’ll be looking into the opportunities that MMC can provide the industry as a whole. Our Group businesses now have a significant capacity to offer the market, whether that it is in timber frame systems, door sets and stair manufacture or floors and roofs from our timber-engineering business. The Donaldson Group can help to support the development of MMC across the housebuilding market in the UK.
It’s an exciting move to venture into the timber frame market at a time when interest in the material has never been higher. As the only renewable building material, there has never been a more crucial time to utilise timber in construction and to deliver more innovative build systems through offsite manufacture.
Rising construction costs, increasing housing demand and the significant skills shortage provide a catalyst for new and more innovative building solutions. Timber within an offsite building system provides that solution and is a material that is recognised and valued by both housebuilders and consumers.
Our opportunity here is to promote the inherent values of offsite timber frame to both new and existing clients. Working in partnership with our clients, we can successfully help them convert their traditional masonry approach to a cost effective and sustainable method of home building.
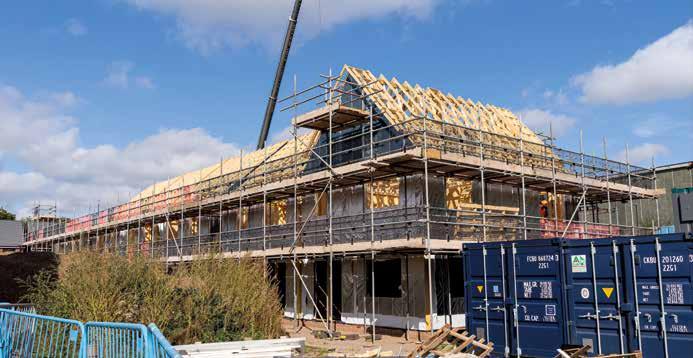
We are in the process of developing an offsite manufacturing division within the Donaldson Group that will utilise the years of expertise in our people and leverage our business experience and contacts, while offering an unparalleled breadth of products and services.
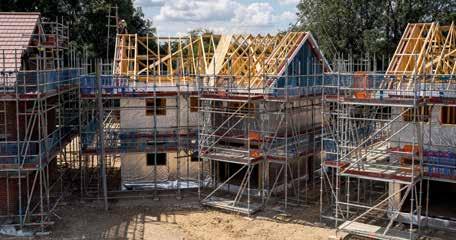
The three businesses that form this division will continue to operate individually with their own leadership teams and a focus on their own clients. However, we will bring together the combined strengths of our management teams to support the overall growth plans for the entire UK structural timber industry.
As a business, we are confident of the continued growth in the use of timber within construction – particularly in the housebuilding sector. To ensure we play our part in providing the capacity that the market will need in the future, we’ll be making investments in product development and innovation, as well as considering new manufacturing locations across the UK. We have exciting plans for the future and hope to push the boundaries of the offsite timber frame industry, while supporting the drive to use more MMC throughout the UK, which will be of benefit to the industry as a whole.
SMTS has always been a leading innovator and advocate for the timber sector. We will be continuing their work with industry partners such as Innovate UK, NHBC and Homes England to provide help developing guidance, standards, training and operating methods that give the market confidence to specify offsite systems in structural timber. This approach is consistent with the ethos of the wider Donaldson Group. We therefore expect the integration of SMTS into the business will enable us to contribute significantly to the future growth of the whole sector and the greater use of structural timber in construction. As we move forward, we are committed to playing a positive role in the complementary trade associations within our industry. We are fully aware of the work they do to ensure the timber industry is understood and appreciated by the full range of policy makers, industry influencers and specifiers of timber. This has been a superb move for our group, and we’re very much looking forward to seeing how our industry progresses over the next few years, as timber comes into its own.
02
03
www.jamesdonaldsongroup.co.uk
IMAGES:
01. Andrew Donaldson, CEO, Donaldson Group 02-03. Developing a timber offsite manufacturing division within the Donaldson Group will utilise years of expertise and business experience
FACE 2022 WITH A
SPRING IN YOUR STEP
David Hopkins, CEO of Timber Development UK (TDUK), reflects on a challenging 2021 and looks at the opportunities that lie ahead for timber over the next 12 months.
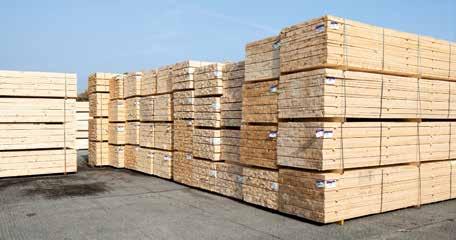
After two years where we, as an industry, have had to battle challenges from every direction, I think it’s safe to say that we’re all hoping for a slightly calmer, less stressful period ahead. Early indications are that things do seem to be settling down. Import levels have fallen back from the recordbreaking heights of 2021, when imports exceeded 3 million m3 for Q3, and were more than 10% higher than the last time imports for that quarter exceeded 3 million m3 – back in 2007.
Things were certainly difficult for a while as merchants scrambled to source enough product to keep up with demand, but despite all the upheaval the supply chain proved just how resilient it is, and we rode out the storm. More recently we’ve seen stocks return to merchant yards across the country, and we expect demand to return to more typical levels for the remainder of 2022. Even though demand this year may be less than we saw in 2021, there are still plenty of opportunities for businesses throughout the timber supply chain.
The Construction Products Association’s (CPA) latest quarterly forecast suggests that output across the entire construction industry will grow by a healthy 4.3% this year, demonstrating once again the impressive resilience that the industry has shown throughout the last few years. Housebuilding is expected to remain buoyant, as is private housing, while the infrastructure sector is predicted to be the major driver for growth – all good signs for timber businesses throughout the UK.
01
With Building Regulations changes coming into force later this year, and even tighter energy efficiency requirements expected to be introduced over the coming decade, it’s inevitable that architects, engineers and developers will be searching for more efficient, sustainable materials when specifying products for their projects.
As a low-carbon, low-energy construction material, we firmly believe that timber has the potential to become the material of choice in the creation of a more sustainable, circular economy, and at TDUK we will continue to promote the use of timber and its efficiency benefits to all our members, as well as through initiatives such as our University Design Challenge, which seek to educate tomorrow’s architects and designers on new ways of thinking.
This is all good news, but it doesn’t mean everything will be plain sailing for this year, as challenges do remain.
Global and UK/European Union Customs Regulations changed in January 2022, with new documentation requirements in place for companies who wish to import or export products. Companies must ensure that goods have the necessary ‘proof of origin’ when trading with the EU, or risk costly delays during customs checks. Changes have also been made to the customs codes for wood products, and companies would be wise to make sure they are fully up to speed with the changes to prevent any avoidable problems.
Despite the unprecedented two years we’ve just experienced, the timber supply chain is an inherently stable market, maintained by merchants holding good stock levels on the ground and being ready to supply timber to builders and developers as they kickstart their sites in 2022.
2022 is looking to be a particularly busy year as we continue to unite the Timber Trade Federation and TRADA under the banner of our new organisation. Bringing both entities together will help us to continue our mission to grow the use of wood as a UK construction material, strengthening our voice and encouraging greater dialogue and interaction throughout the entire supply chain.
Over the coming months you’ll hear even more from us as we work to create a single, central resource hub for the everyone who works with timber, from sawmill to specifier. We want to be the first port of call for any business seeking information, market statistics or guidance, while we actively represent the best interests of timber to government and other industry bodies on your behalf.
www.ttf.co.uk
IMAGES:
01. Timber stocks are returning to pre-pandemic normality