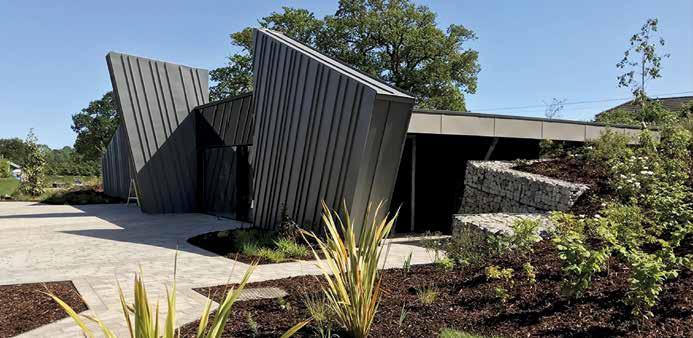
11 minute read
LIVING IN A SCULPTURE
Inspired by large sculptures in the countryside and the rocky outcrops of the nearby Dartmoor moors, The Hux Shard – as seen on Channel 4’s Grand Designs – offers a striking, geometric appearance and gave structural engineers a significant timber challenge.
With the building’s geometric architecture inspired by Dartmoor’s wild granite tors, The Hux Shard’s exterior walls are formed of 34 shard-shaped sculptural panels, set in a jagged 70m line following the contours of the hill on which the property stands. It is the combination of these immense-sized shards and the exposed rural landscape that was perhaps one of the key challenges behind the project, with TWP Consulting Engineers appointed as the structural engineers on the project.
It provided structural engineers, TWP Consulting Engineers, with a significant challenge. Speaking about the project, Nick Drew, Director at TWP said: “The Hux Shard was certainly a fascinating and an ambitious project, with a significant reliance on the engineering principle to create and bring the vision to life.”
The building design required a series of large concrete pad foundations and steel short columns, which in turn supported the gigantic timber frame’s floor structure and roof. The primary building frame consisted of 282 glulam timbers, which were bolted together with steel brackets to form a wooden skeleton reaching over seven metres into the air. The property’s exterior walls
01
were then formed from 34 insulated timber shards, each around 600mm thick and clad in zinc, and interspersed with 46 equally complex glazed panels. As if that wasn’t enough of a challenge, the whole structure was also partially suspended, raised between 0.5 and 1.5 metres off the ground.
Nick explained: “Perhaps the main challenge on this project was the shardshaped panels that formed the building exterior, and which served to create the dramatic geometric impact of the overall building. Due to the intended architectural aesthetic, there was no uniformity to the panels, no parallel elements and no true-90 degrees. Each of the shards was wholly individual and unique, all at different angles to one another, and the whole property was also slightly curved on plan.
“As if those design complexities weren’t challenging enough, the shards were also incredibly large – some as tall as a

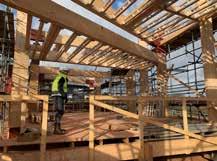
two-storey house. Given the exposed and elevated hill-top location, the concern was that the shards would effectively act as wind sails, capturing a lot of wind and putting more stress into the primary structure itself. As engineers, we had to ensure that this wind loading was accounted for in the engineered design and that the shards wouldn’t place unnecessary strain and deflection on the primary structure and glazing.
Having been a Tekla user for many years, TWP turned to its trusted Tekla Structural Designer software for help in bringing the client and architect’s dramatic vision to life. “Fortunately for us, Tekla Structural Designer has an automated wind loading feature, meaning that we were able to quickly and automatically model and calculate full building wind loads. In turn, this gave us a far better economy for an optimised design - rather than the alternative of manually considering the loads, which is often based off the worst-case scenarios and doesn’t necessarily provide the whole picture.”
Given that every timber shard was unique, with different heights, raking lengths and angles, each panel had to be modelled and constructed individually within the Tekla modelling environment.
“This, combined with the jagged layout of the shards and the uneven ground level, provided us with another challenge – mainly how to create clear layers in the software,” says Nick. “It was imperative that we were able to create clear layers and gridlines, as well as ensuring that the gridlines were named correctly, as this information then referenced back to the gridline’s respective shard. Without the ability to clearly and concisely complete and model this in the software, it would have presented some serious difficulties and confusion that would have affected the whole project delivery.”
In addition to the timber panels, there was also 46 equally large glass panels interspersed throughout the building’s exterior walls and roof, designed to help draw natural light into the property. Nick adds: “A priority for us as engineers was of course stability, ensuring that the overall building was stiff enough. Given the combination of glass and timber, it was vital that there

02
03 04
“As part of early discussions with the Local Authority regarding the planning application, under the then paragraph 55 piece of planning legislation, a reduction in embodied carbon and greener energy production were key to the long term aims of the project enhancing design in rural areas,” said Alex O’Connor from Architects Squirrel Design.
were no differential differences between the frames, as this then ran the risk of the glass shards cracking or shattering. Again, we were able to efficiently model and analyse all of this in Tekla Structural Designer, viewing all of the loads, deflections and stresses present in the building design.”
While Tekla Structural Designer is perhaps predominantly renowned for its use with concrete and steel design, the software is also continuing to expand its capabilities for timber design. Indeed, as the emphasis on sustainability and a building’s embodied carbon value continues, timber will inevitably become a more popular building material amongst clients, engineers and contractors.
Nick explained: “For us, we are seeing more and more timber being used on construction projects, such as this, as people become more focused on the importance of sustainability. With Tekla’s portfolio of software, we are able to analyse the timber building design in Tekla Structural Designer and understand all forces and potential stresses. Then, as a result of the software’s emphasis on integration and interoperability, we are then able to export the data and timber beams directly into Tekla Tedds, saving us considerable time.
“When you’re working on a project of this complexity, the ability to spin the 3D model around and interact with it, really understanding how it all relates, fits and connects together, is invaluable. Thanks to the software and the 3D environment that it provides, we were able to finish our engineering work within a threemonth period – without Tekla Structural Designer, I can only imagine how long it would have taken.”
www.tekla.com/uk www.squirrel-design.co.uk
IMAGES:
01. The shard of timber and zinc deliver a sustainable and sculptural impact 02-03. The primary building frame consisted of 282 glulam timber beams 04. Tekla software was integral to perfecting the design
BIO-BUILDING
THE FUTURE
Springfield Meadows is a project of 25 zero-carbon timber frame homes located in Southmoor, Oxfordshire and are all built to exacting Passivhaus standards.
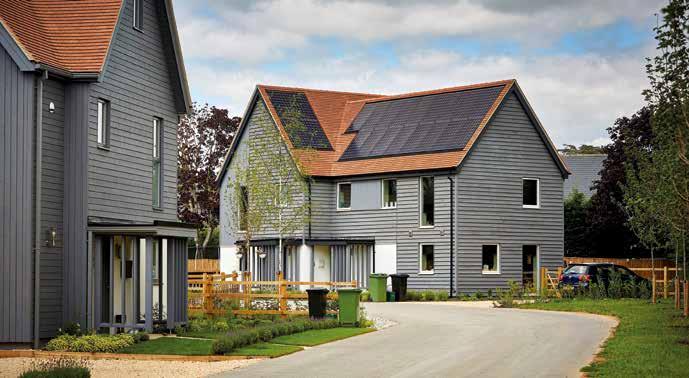
With housing responsible for approx. 20% of carbon emissions, and the construction of an average house responsible for embodied carbon of 50-60T from its manufacture, transport and construction, energy performance must improve both outside and inside the UK’s homes.
Greencore construction have used the economies of scale from its largest current project at Springfield Meadows to develop its building system from zero carbon, to ‘Climate Positive’. Climate Positive means locking up more carbon than the houses emit at the construction stage by using bio-based materials, the houses generating more energy than they use each year, the project increasing the biodiversity of the land and using local natural/bio-based products where possible, to create sustainable communities.
Springfield Meadows is a project of 25 zero-carbon homes and benefits from diverse shared outdoor spaces and private gardens, it consists of nice affordable houses and 16 private units, 12 of which are custom-build. These, high-performance homes, provide comfortable, low-carbon living, thanks to the Biond Building System. Biond is an offsite manufactured, closed panel timber frame, insulated with lime-hemp and natural fibre insulation.
01
The external wall panels lock up 32kg of CO2e/m2 of wall, with cross laminated timber (CLT) used for the upper floors (and any flat roofs). These lock up 125kg of CO2e/m2 of floor and roof and all 25 homes are built using the same Passivhaus principles with minimal thermal bridges, triple glazed timber windows, high levels of airtightness and a mechanical ventilation with heat recovery (MVHR) system. Additional PV panels can generate more electricity than is likely to be used, over the course of a full year.
Homeowners can customise their houses in different ways so even when the same base design has been used, the finished result is unique. Springfield Meadows has been awarded One Planet Living Global Leader status by the leading environmental charity Bioregional. Bioregional’s One Planet Living framework has been integrated
BUILD WITH BIOND
Biond is a 21st century hemp-lime construction system that delivers a high performance, comfortable living environment with a ‘social conscience’. The Biond project is aimed at expanding the market of lowcarbon construction by the development of a construction system that can be franchised by builders and developers across the EU and further afield. Biond had already established a preferred methodology for building with closed panel tim¬ber frames constructed within a factory and with hemp and lime insulation and had overcome the challenges of drying the hemp and lime material within commercially acceptable timescales.
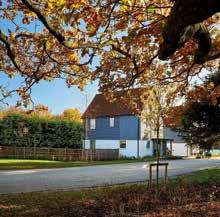
People who live in hemp-lime houses report higher comfort levels than people who live in conventional houses. This is in part due to the ability of hemp-lime to ‘buffer’ changes in humidity and temperature. Key benefits include:
• Walls are insulated in the factory with hemp and lime, and with woodfibre, to deliver U values of 0.15W/m2.K • Floor cassettes can also be manufactured in the factory to speed up the construction process and ensure high quality standards • Roof cassettes can also be manufactured in the factory, with insulation and roof lights fitted, also to speed up the construction process and ensure high quality standards.
www.biond.co.uk
02
from an early stage to ensure that the development covers all aspects of sustainability. Including an electric car club, links to local bus routes, use of local labour and creation of community features such as a community orchard and wildlife pond.
www.greencoreconstruction.co.uk www.ssassyproperty.com
IMAGES:
01-02. The homes are high specification and are hugely energy efficient being built to Passivhaus standards
INNOVATION IN LIFTING
Britlift are a designer and manufacturer of lifting equipment, specialising in the lifting of modular homes, bathroom pods, commercial modules, containerised structures and pre-cast components.
With a wealth of experience in the design and manufacture of lifting frames and lifting systems to the Offsite Construction sector, Britlift are the Offsite sector partner of choice.
BATHROOM POD LIFTING PRECAST LIFTING
Awards 2019 WINNER
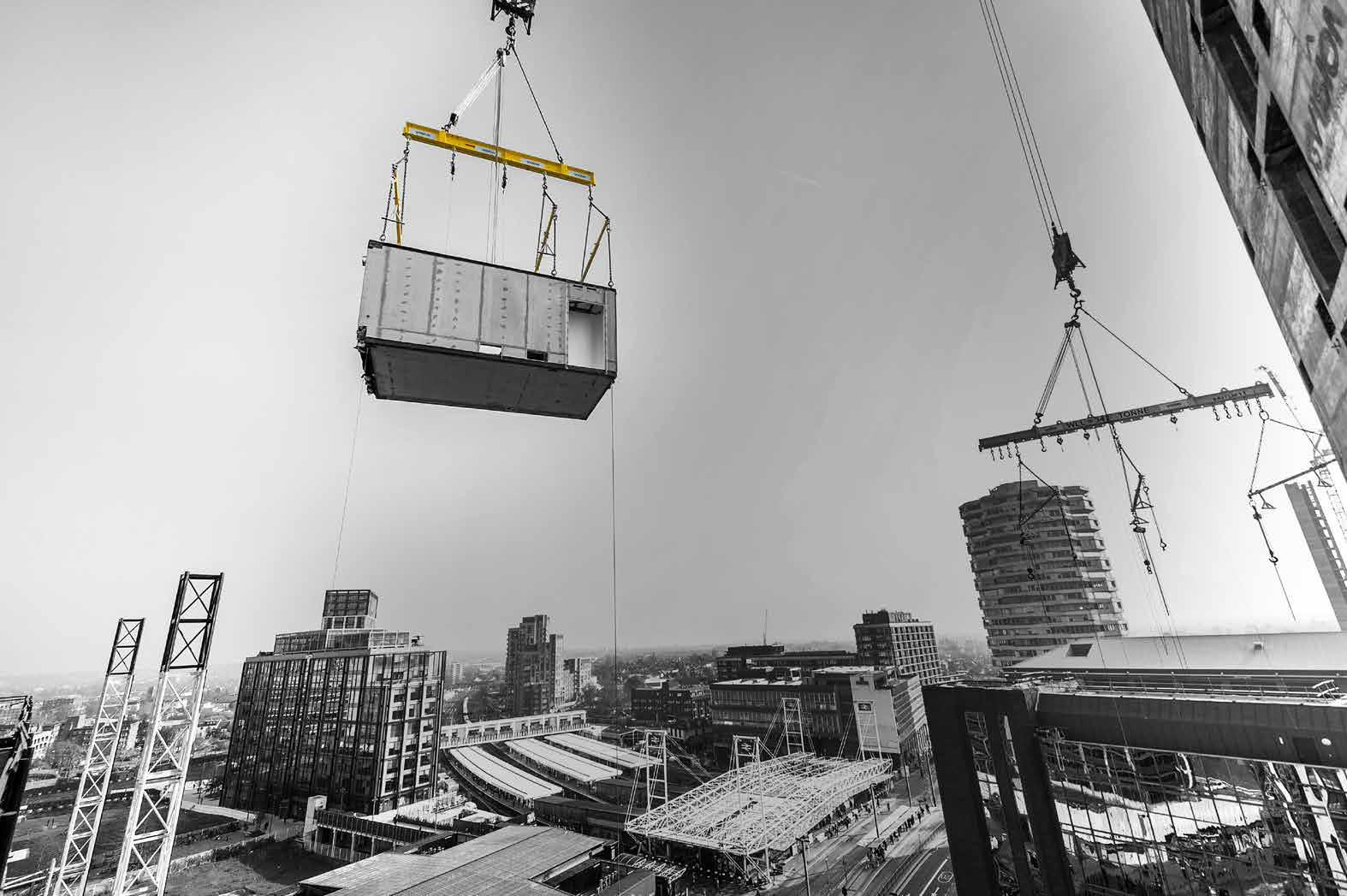
MAXIMISING TIMBER USAGE IN ROOF AND TRUSS DESIGNS
With timber shortages due to supply chain issues and with the costs of it increasing, it is now more important than ever to maximise the use of timber. So how can we best help prefabricators and housebuilders do just that?
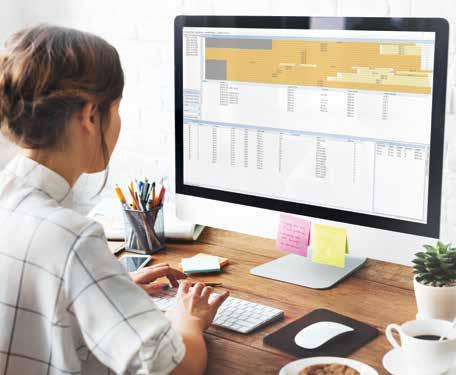
Implementing and using the right software
It is very important to implement and have the right software in place that will help you get the most out of your timber, especially during this difficult time within our industry. ITW Construction Products Offsite’s Gang-Nail Matrix software helps prefabricators and housebuilders optimise the use of timber.
01
With the timber optimiser feature, prefabricators can now calculate how to best utilise the timber within their stock for roof and truss designs at the click of a button.
This feature within the Gang-Nail Matrix software analyses your timber stock and calculates how to best utilise it for roof and truss design jobs. Once you’ve run the calculations, the software will produce a document that encompasses a pick list of what length of timber to use for the required job.
Minimise wastage
While we’re experiencing timber shortages within the industry, there is also a big focus on sustainability and greener building methods for both prefabricators and housebuilders. Using software that can help you build in a more sustainable way will in turn also help you to get the most out of your timber stock. Timber optimiser helps prefabricators and housebuilders meet their sustainability targets by minimising timber wastage and making more efficient use of materials within their supply chain. This feature not only supports with sustainable building methods and puts prefabricators in a better position within this climate, but it also helps save on costs.
Analyse trends and save on materials
Now that we’ve spoken about how the timber optimiser works within Gang-Nail Matrix software and how it can help with sustainability targets, let’s talk about how you can analyse trends using this feature.
For your roof and truss design jobs, the timber optimiser calculates what length of timber within your stock is needed for the required design jobs. With this feature, prefabricators can analyse trends and identify what lengths of timber is most needed and used within their stock. This can help businesses distinguish what length of timber they should and should not invest in, which helps with material savings.
To find out more on what the Gang-Nail Matrix software can do for your business, please contact Rebecca Bowen, Business Development Manager for Gang-Nail, email: rbowen@itwcp.com
www.itwcp-offsite.co.uk
IMAGES:
01. With the timber optimiser feature, prefabricators can now calculate how to best utilise the timber within their stock for roof and truss designs at the click of a button.