
14 minute read
Industry News
PLATFORM DESIGN TEAM ANNOUNCED
BARRATT TO BUILD ONE IN FOUR HOMES USING MMC BY 2025
The Construction Innovation Hub has unveiled the industry ‘players’ who will take forward its flagship Platform Design programme – a central plank of the Hub’s four-year Government-backed programme to transform UK construction.
Platforms will enable new buildings to be designed and configured using a pre-defined ‘kit of parts’, which are proven to demonstrate greater whole-life value, lower carbon and energy use, better safety and quality and which will improve the overall performance of buildings. This approach will support the government’s ambition to drive innovation and build industrial capability and capacity in businesses throughout the UK to deliver more sustainable buildings in the near future. The Platform programme will be driven by a collaborative team of integrators comprising some of construction’s biggest names: Skanska, BAM, PCE, MID Group, Kier/ VINCI Construction UK, Mace and Mott MacDonald.
Supported through every step of the programme by manufacturing, building performance and digital specialists from the three partners of the Hub – the Manufacturing Technology Centre (MTC), BRE and Centre for Digital Built Britain (CDBB) – Platform participants will develop and refine their products, technologies or services which will then be installed and widely showcased on a proof-of-concept building, demonstrating how these solutions can be applied across a wide range of UK government projects for vital new buildings including schools, hospitals and prisons.

Construction Innovation Hub Programme Director, Keith Waller, said: “Our flagship Platform Design programme is a game-changer for construction. With the right blend of expertise and collaboration across government and industry, we could see a critical mass of new-built projects like schools and hospitals constructed using the Platform approach in as little as ten years, driving improved productivity and performance for the sector and better outcomes for the environment and society. The innovative businesses joining us on our journey are the vanguard of transformative change, not just in terms of how we create buildings, but in how those buildings impact on our lives and the environment.”
The wider collaborative team for the Hub’s Platform programme comprises over forty businesses drawn from a range of disciplines, and includes a number of specialist SMEs, who will work alongside the Hub and the integrators, providing design, specialist consultancy services, sub-assembly, components and materials that will be showcased on the proof of concept building.
MMC Programme Director at the Infrastructure and Projects Authority (IPA), Will Varah, added: “There is a strong alignment between the IPA’s P-DfMA approach and the Hub’s Platform programme. We look forward to working together to deliver a more sustainable and productive way to meeting our ambitious investment programme.”
Britain's biggest housebuilder aims to build a quarter of its homes using modern methods of construction by 2025. Barratt has rolled out a series of new housing types to allow a switch to greater use of offsite production and standardised product use.
Its commitment to driving down build costs using modern methods of construction came as the volume housebuilder reported a 12-year high in completions, up 9% to 8,314 in the first six months of the financial year.
David Thomas, chief executive, said: “Barratt planned to increase volumes by 3-5% a year, against a backdrop of some of its rival housebuilders reining back completions.”
In the last six months of 2019, despite impacts from General Election and Brexit uncertainty, Barratt lifted revenue 6% to £2.27bn, generating a pre-tax profit up nearly 4% to £423m. Operating margin softened slightly over the period to 19%.
He added that Barratt had become the first major housebuilder to set a science-based target to reduce carbon emissions in its operations by around a third by 2025.
Rival Redrow also revealed its first-half trading today with legal completions down 14% to 2,554 homes. Pre-tax profit over the six months to December slid 15% to £157m on revenue down 10% at £870m.
John Tutte, executive chairman of Redrow, said that the market was fairly consistent across all of Redrow's operating areas with London showing some early signs of improvement. "The market in the first five weeks of the second half has been resilient with the value of reservations up 15% at £180m (2019: £156m)."
Shaping the
Supporting the Development of Light Steel Frame Construction
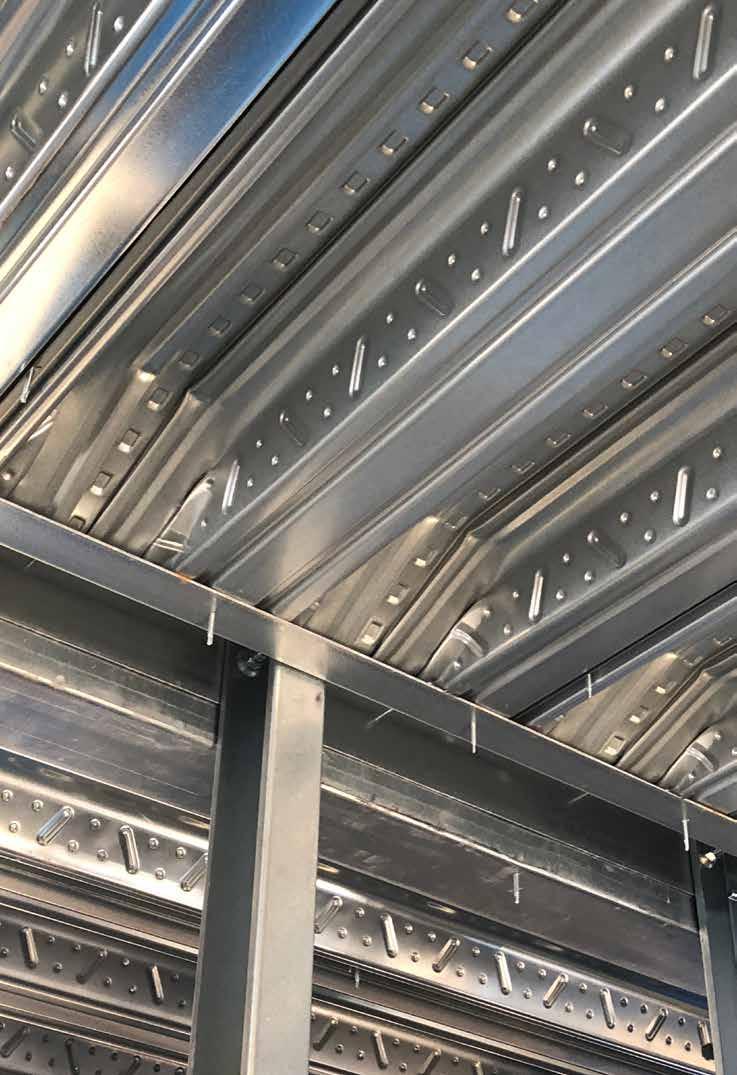
DEDICATED LIGHT GAUGE DIVISION
We have a dedicated supply only division, happy to help with customers design and installation queries.
FLOOR DECK SOLUTIONS
Our product range and crushed end finish is perfect for the light gauge solution.
DEDICATED PRODUCTION LINE
Due to demand our works have a dedicated production line to manage the large volume and quick turnarounds you require.
SMD
Structural Floor and Roof Solutions
www.smdltd.co.uk
NEW STUDENT ACCOMMODATION FOR COVENTRY
The Oaks is a 382-bedroom student accommodation scheme in Coventry built on the site of a former college building that was demolished to make way for this new development.
The building has two wings of student accommodation over four to six storeys with a mix of studio apartments and cluster bedrooms. McLaren Construction appointed MetStructures for the light gauge steel structure as they provided an in-house service from design through to on-site installation.
The pre-assembled external walls were pre-clad with 12mm Cementitious board in MetStructures factory so that as the building progresses the envelope was protected from the elements. The internal loadbearing walls arrived pre-assembled and as with the external walls were co-ordinated for a rapid installation process. On a floor by floor basis the external and internal walls were erected then the composite metal decking was installed from below, the staircases were also installed to allow safe access to the floor above for when the decking was complete.
Gary Donnelly, MetStructures Project Director, stated that: "Regular communication and meetings between the design and project teams led to the successful design, detailing and installation of the project. We are pleased to say that following on from the successful delivery of The Oaks project, McLaren Construction are now engaging with MetStructures on a number of other projects."
The MetStructures system is NHBC and SCI-certified to 15 storeys and has been fire tested to 60, 90 & 120 minutes which meets the new building regulation standards for fire resistance. During their most recent suite of fire testing MetStructures paid
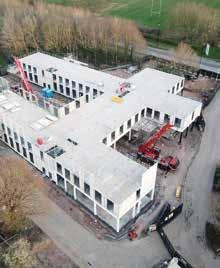
MYTHBUSTING GUIDE TO MMC SEEKS TO SOLVE AFFORDABLE HOUSING CRISIS
particular attention to the external wall fire resistance from outside to inside and achieved a 120-minute fire rating for their system.
For information on the MetStructures System: visit www.metstructures.uk.com

A new guide argues that modern methods of construction (MMC) are key to increasing the supply of affordable homes in the UK.
Published by The Housing Forum, 'MMC for Affordable Housing Developers', aims to help public sector organisations navigate the procurement, planning, design and post-build stages of MMC projects. It includes a detailed section on mythbusting, highlighting common assumptions people make about MMC, such as a lack of quality, difficulty in securing finance, and confusion over contracts.
Shelagh Grant, chief executive of The Housing Forum, said: "The guide challenges the myths surrounding procurement, contracts and costs, to help public sector organisations assess the business case for MMC, armed with accurate information.
"MMC will help the Government meet its commitment to deliver 300,000 homes a year, but also benefit affordable housing providers and its tenants. Using MMC effectively will future-proof housing supply. It leads to faster build times, minimises disruption to communities, and there are fewer defects, providing consistent quality and better as-built performance." Other benefits of MMC were highlighted within the report, including that it can offer more predictable thermal performance, improved cashflow and a reduction in the building's maintenance costs.
Despite these benefits, barriers do exist. Compliance with the procurement regime was identified as one of the biggest issues preventing public sector organisations from adopting MMC. It clarifies that the public contracts regulations 2015 can evaluate benefits including quality/price evaluation and ongoing maintenance costs.
Mike Fairey, director at Fusion Building Systems, wrote the foreword to the guide. He said: "This is a comprehensive guide developed by a cross-industry working group, with experts from all areas of the supply chain represented, including architects, manufacturers, contractors, housing associations, trade bodies, and government. It was essential to get a rounded view to understand the issues fully." Jeff Endean, director at Cast Consultancy provided the keynote at a launch event for the guide and discussed how the housing sector can take MMC forward.
Jeff Endean commented: "The emergence of MMC specific frameworks, alongside better understanding of delivery and contractual models, is already helping to create affordable and sustainable housing. The next challenge will be to achieve this at scale. With the support of the industry, MMC will become a mainstream housing choice. In order to achieve this, there needs to be more control over new build delivery. It will involve collaboration and innovation in how homes are designed and delivered across the housing association sector, as well as support from regulatory bodies feeding into the funding, insurance and warranty market."
The full report ‘MMC for Affordable Housing Developers’ can be downloaded via the Housing Forum's website: www.housingforum.org.uk
COREHAUS MAKING NATIONAL PROGRESS
An ambitious North East housebuilder is showcasing the benefits of an innovative modular building design on the national stage.
Newton Aycliffe-based Homes by Carlton has been trialling the new-style design, CoreHaus, on several local housing developments in a bid to slash build costs, reduce the amount of time spent on-site and lessen the impact on the environment.
The firm’s Managing Director, Simon Walker, has now embarked on a mission to spread the word about CoreHaus outside of the region. Simon Walker said: “Developers and other property professionals are trying to work out ways of building affordable, quality homes efficiently and at relatively low cost. Not only are we having to battle a skills shortage within the industry, there are also things we can’t control, like inclement weather which reduces the amount of time workers can realistically spend on-site. The market says we need to move towards a solution where part of the construction takes place offsite. With CoreHaus, this is possible.” CoreHaus homes offer the flexible combination of being part modular, with a standard, engineered core that can then be configured to different sizes. A modular core including a pre-finished kitchen, downstairs toilet, staircase, bathroom and central heating system are manufactured offsite before being delivered to the development. This is then followed by the external walls and roof being constructed to reduce build time. Assembled in factory-controlled conditions, this energy-efficient housing ‘pod’ can help reduce onsite construction time by 50%, increase flexibility in the design of the home and cut CO 2 emissions.
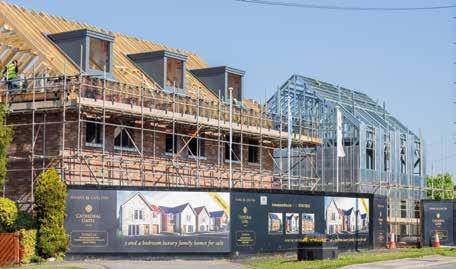
CoreHaus is a joint-venture company between Carlton & Co Group, the parent company behind Homes by Carlton, and national social enterprise Fusion21. The innovation has been trialled on Cathedral Gates, a mix of 14 three and four-bed detached and semi-detached homes in Chilton, eight miles from Durham City.
www.corehaus.co.uk www.homesbycarlton.com www.fusion21.co.uk
Your partner in delivering a to meet your project requirements LIGHT GAUGE STEEL FRAME
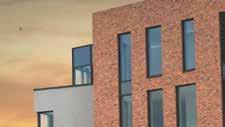
• MetStructures light gauge steel framing, NHBC and SCI approved to 15 storeys • 100mm external and internal LGSF walls • MetFloor composite metal decking and concrete • Fully finished balconies • Hot rolled steel podium structures • MetSafe accredited temporary edge protection system. • All elements designed, coordinated, supplied and installed on site.
Your exact project requirements Met
NEW MACHINE ADDS SIGNIFICANT CAPACITY TO HADLEY GROUP
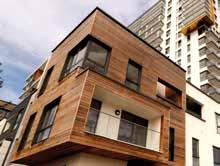
O’ROURKE LAUNCHES OFFSITE BENEFITS GUIDE
Following the acquisition of Hadley Steel Framing (HSF) in 2018, Hadley Group has further strengthened its position and improved its capabilities in the steel framing market by investing in a new purpose-built machine at its Oldbury production site.
The Purposed Built Steel Framing Machine joins Hadley Group’s extensive portfolio of world-class equipment and will allow the company to offer greater speed and flexibility in producing steel framing products. The new machine takes steel coil and processes it through a linear system of equipment, adding features to the strip before it is cold rollformed into a series of shapes, such as U’s, C’s and Z sections, angles and odd legged channels (either pierced or plain), depending on individual customer requirements. The custom rollformed profiles are then supplied for the construction of steel frame structures and buildings.
The coil-fed system offers superior product quality control of hole positions and end flare, which enables the components to be functionally fitted together with greater speed. Investment in many connection features within the punch system allows it to support low, medium and high-rise framed buildings. The machine can produce all types of metal framed profiles from S250 to S550 structural steels and in lengths from
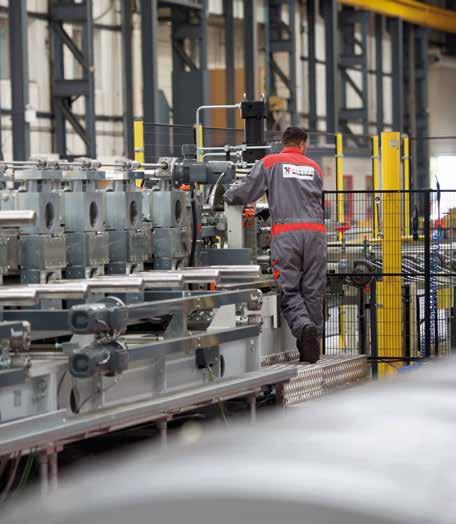
200mm to 12m, all with individual ink jet marks for product traceability.
Working closely with the supplier, the Hadley Purposed Built Steel Framing Machine came to fruition after a 10-month design and build process. The manufacturer collaborated with the Hadley Group to ensure that the machine would be able to optimise profiles and production processes to suit the company’s needs. The machine is now fully integrated into Hadley Group’s Building Products Division, based at Oldbury, and reduces scrap by more than 25%.
James Bishop, Regional Director of Operations – International, at Hadley Group said: “This is an exciting investment for Hadley Group, enabling us to strengthen our position in the steel framing market during such uncertain times. It streamlines the production of framing profiles, going from enquiry to production in a matter of hours and enabling profiles to be delivered to the customer efficiently. It will also strengthen the integration of the recent acquisition of HSF into Hadley Group and ensure that Hadley Group stays at the forefront of steel framed structures in the UK.”
www.hadleygroup.com
The Laing O’Rourke Centre for Construction Engineering and Technology at the University of Cambridge and CIRIA have launched a new report unveiling a new methodology for quantifying the benefits of offsite construction.
Uptake of offsite construction is still slow, despite the benefits it offers in terms of improved health and safety, speed, and predictability of cost and time. O’Rourke said this was in part due to there being no industry method for assessing the benefits of offsite techniques.
The new guide proposes a framework for comparing construction approaches, making it possible to keep consistent records across projects and identify all the possible benefits available. It also highlights the challenges that can be expected when assessing the performance of construction projects and developing robust benchmarks for comparison. It provides a framework for evaluating project performance that can be used by clients, construction management teams and designers to assess the value and benefits achieved on projects.
Professor Lord Robert Mair, emeritus Sir Kirby Laing professor of civil engineering and director of research at the University of Cambridge said: “There is compelling evidence for more widespread adoption of offsite manufacture in construction. Yet a methodology for quantifying its benefits is much needed. The process outlined in this excellent report provides an invaluable guide for industry professionals, such as contractors and project managers, as well as those who are influential in decision-making on construction projects, including clients, advisors and policy makers.”
The guide is available to download freely from: www.ciria.org/c792
INTELLIGENT APPROACH DELIVERS SUPPLY CHAIN SYNERGY
For the next generation of housebuilders, steel frame construction is a cost effective and efficient way to build upwards. Built offsite in its modular lightweight steel factory, Intelligent Steel is providing a modern construction solution for London developer Henley Homes’ Brent House scheme in Wembley.
By having steel frame manufacturing within the group, Henley Homes is ahead of the curve and able to cut the supply chain for its clients. At Brent House the developer is working with Notting Hill Genesis to provide a mixed-use development of 248 new homes including affordable and London Living Rent homes alongside substantial commercial space. The design and manufacture of the panels was carried out in the Intelligent Steel factory for the development’s two linear buildings of five principle blocks ranging in height from seven to 10 storeys high. Henley Homes’ construction arm then used two shades of brick to add visual interest to the external facades defining the variation in height. By controlling up to 40% of its supply chain, Henley Homes can offer modular steel frames for all its clients, including Housing Association builds at a more efficient cost to a tighter delivery programme, without compromising on design, quality and sustainability.
Tariq Usmani, CEO of Henley Homes, said “Thanks to significant time and cost efficiencies due to our in-house manufacturing capability, we are able to
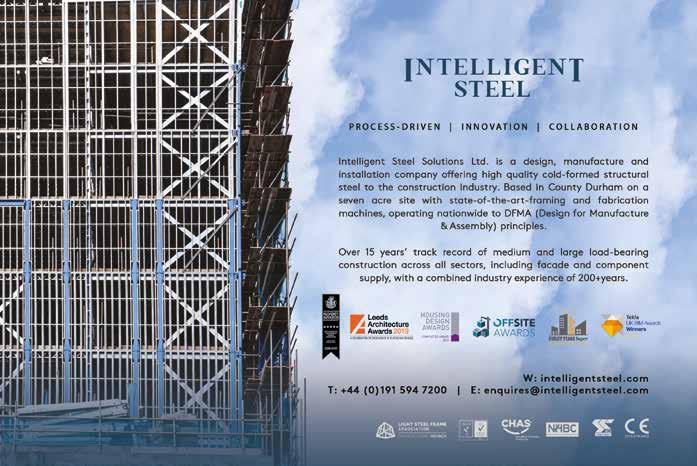
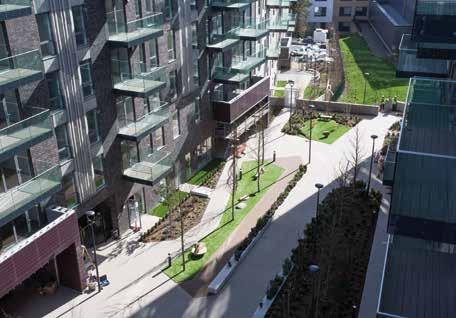
deliver precision engineered, high-quality housing of varying tenures at scale and pace both for our own developments and our partners such as Notting Hill Genesis. This ultimately reflects our ethos that everyone deserves quality housing, regardless of whether they are renting or buying.”