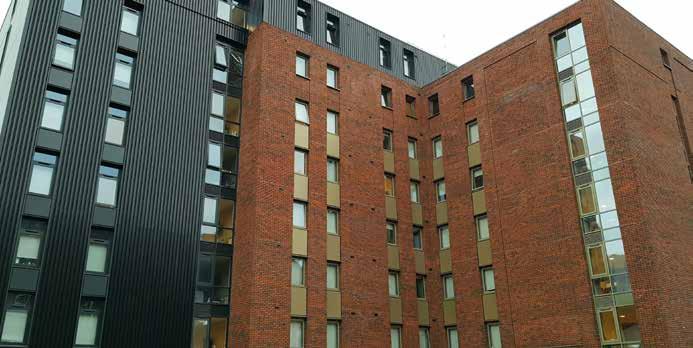
5 minute read
Bailey Street
A HUB FOR STUDENT ACTIVITY
LOCATED JUST AN EIGHT-MINUTE WALK FROM BOTH SHEFFIELD HALLAM AND SHEFFIELD UNIVERSITY, THE NEW BAILEY STREET DEVELOPMENT BOASTS A HIGH-END 220-BEDROOM STUDENT ACCOMMODATION BLOCK.
A hub for student activity, the eight storey Bailey Street development boasts seven different room types incorporating facilities including: ensuite bathrooms, gym, bike storage, laundry room and games room.
Sigmat were appointed by Yorkshirebased developer and contractor Torsion to deliver the light gauge steel frame for the new student accommodation building. Managing the design, manufacture, assembly and installation, Sigmat delivered a complete source-to

site solution, preassembling the panels at their in-house Leeds manufacturing facility.
Comprising 8.5km of Sigmat panels, 191 hot rolled steel members and 533m 3 of concrete the project was completed two weeks ahead of programme.
Sigmat’s Operations Manager John Ritchie commented: “This is a great example of how offsite processes can really benefit construction on a busy city centre site facing various logistical restrictions. The speed of erection and programme surely demonstrates why light gauge steel is the fast-emerging solution of choice – not just for student accommodation, but also hotel, residential apartment, retirement living/ care sectors too.”
The £1.1 million project also included the installation of steel staircases each comprising 12 flights and six half landings. In addition, Sigmat supported the installation of 315 bathroom pods and 367 plasterboard packs, aiding follow-on trades to commence their work early on in the project schedule. Other notable statistics from the project include the installation of 4,600m 2 of decking, 32t of reinforcement and the roof structure which incorporated 598m 2 and 2.7t of cold rolled steel.
Early planning with Torsion enabled other trades to commence work sooner, facilitating early completion and increasing profitability for the client. Planning for and achieving these goals demonstrates the versatility of the Sigmat light gauge steel frame
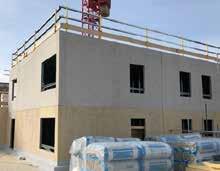
system, and the important role offsite construction has to play.
Dan Spencer, CEO of Torsion Group, commented on the success of the project, saying: “Engaging with Sigmat early on in the design process allowed us to take full advantage of the offsite manufacturing process, giving certainty in delivery of the frame and allowing us to accurately procure follow-on trades. Sigmat managed their works extremely diligently and handed sections of their works over early. By working in partnership, we were able to take advantage of this as we could plan for the follow-on trades to commence
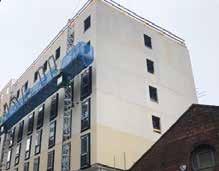
works earlier and take advantage of the great work carried out by Sigmat.”
Bailey Street offers high-end, safe and homely accommodation for both local, national and international students, opening in September 2019 ready for the new intake of students. This was the first Sigmat project with Torsion and the success has strengthened the relationship, with more schemes planned for 2020 and beyond.

For more information visit:
www.sigmat.co.uk www.torsion-group.com
www.cogent-consulting.co.uk

Delivering efficiency and competitive advantage using offsite construction technology and DfMA principles
We develop and improve: Business strategies Product & service portfolios Manufacturing operations Supply-chain integration Business processes Management systems
Ask the experts...
FIRE TESTS

RECEIVE HIGH ACCLAIM
01
AS PART OF ITS ONGOING REVIEW OF MODERN METHODS OF CONSTRUCTION (MMC), THE NHBC HAS ACCEPTED FUSION BUILDING SYSTEMS LIGHT STEEL FRAME SOLUTIONS FOR RESIDENTIAL BUILDINGS UP TO AND OVER 18M IN HEIGHT.
Fusion Building Systems has recently undergone a new series of fire performance tests to demonstrate how its bespoke offsite manufactured light steel frame solutions can be used in buildings up to 18m.
The offsite manufacturer has also introduced a new product, called FusionX which excludes the use of combustible materials, to extend the height to 30m. These systems have both been accepted by the NHBC. Since April 2019, Fusion has been working closely with the NHBC.
Independent fire test data has been submitted to meet new criteria for both its Thermashield 162 external wall solution for buildings up to 18m in height, and its new high performance FusionX system for buildings up to the height specified and over 18m. The process also assessed Fusion’s system for situations where the use is not restricted to the loads imposed during fire testing – including an approved method to extrapolate loads, beyond fire testing requirements.
“The cladding ban has seen significant changes throughout the construction industry and we have all had a responsibility to review our systems and materials to meet the new standards,” says Mike Fairey, Fusion Director. “The Ministry of Housing, Communities and Local Government (MHCLG) has set relevant new criteria for residential buildings and we’ve worked hard to prove the performance of our existing systems, as well as placing significant investment in new products. We’ve worked with the NHBC for many years and they understand the Fusion system. I hope their confirmation of the system acceptance, will lead to housebuilders opting for Fusion as a tried and tested offsite method of construction.”
Richard Lankshear, NHBC’s Innovation Manager added: “Our review of MMC is designed to give confidence to homeowners in the quality of homes built with MMC. We frequently reappraise MMC systems and our review of the Fusion Building Systems has included the structure, performance in fire, durability and factory production controls. Only systems that are rigorously and frequently reviewed are listed on the MMC Hub.”
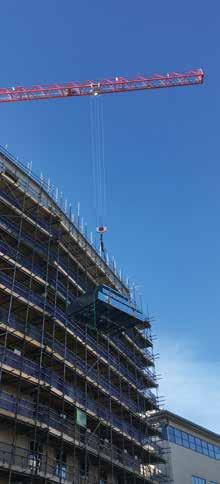
03

02
Independent fire testing of Fusion’s Thermashield 162 external wall solution passed 60 minutes for fire from inside of a building, below 18m in height. Its new FusionX system has passed both the 90-minute and 120-minute test for fire from the inside with 3 x 12.5mm fire boards – as well as 90 and 120-minute tests for fire from the outside with 100mm mineral wool slab and a 12mm sheathing board.
For more information visit:
www.fusionbuild.com www.nhbc.co.uk/mmchub
IMAGES
01 The NHBC has accepted Fusion Building System’s new FusionX product, which excludes the use of combustible materials in buildings over 18m in height 02-03 Thermashield wall panels at Fusion’s manufacturing facility are insulated using its patented system before being transported to site and installed
With digital technology at our core, combined with a fully non-combustible system, 20 years of experience and more than 50 projects delivered using concrete composite metal decks, we’re working towards a future built with Fusion.
www.fusionbuild.co.uk
25
schools
2,000
care homes

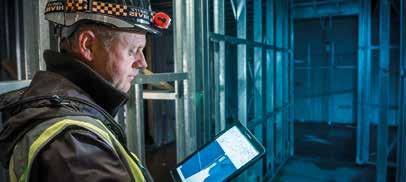
3,000
houses
4,000
apartments
9,000
student beds