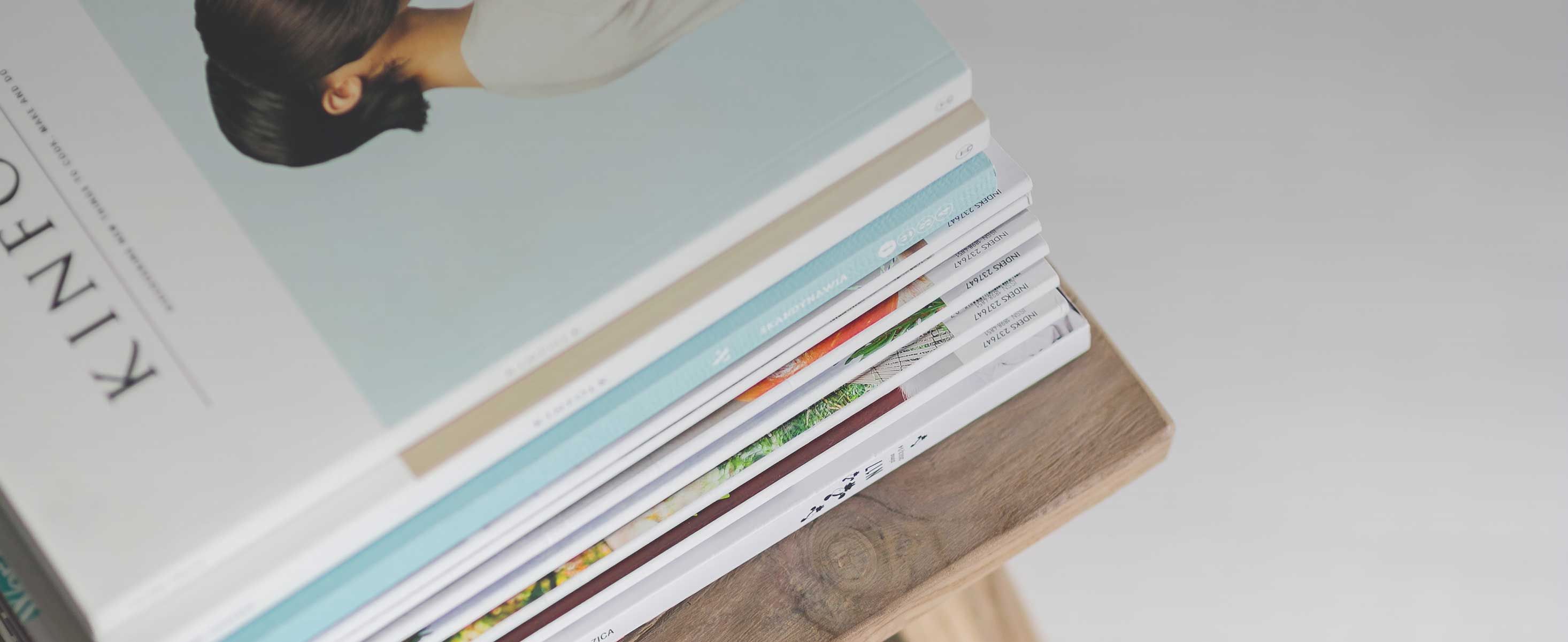
2 minute read
Embodied Carbon
There is a misconception about LSF construction and steel in particular in the embodied carbon debate, that steel is not as good an option as timber where sustainability is concerned. However, the strength of the LSF structure when assessed against the low weight of the steel used equates to improved efficiencies as a lot of structure can be formed with not a lot of weight. This reduces embodied carbon and is where LSF technologies come to the fore as lighter structures not only reduce material consumption but reduce the concrete required in the ground* .
Embodied carbon assessments (also known as carbon foot-printing) look at materials used, energy use/performance, waste, transportation and are based on RICS and British Standard guidance and include information from relevant Environmental Product Declarations (EPDs) and publicly available embodied carbon data. These assessments review the structure from facilitating works/demolition through to fixtures and fittings/ building services as part of the 60-year whole-life embodied carbon assessment including: product, construction process, in use – maintenance/repair and refurbishment, in use – water and energy and end of life.
Embodied carbon assessments are quite straightforward involving the multiplication of quantities of construction products and materials (generally on a weight basis) with embodied carbon coefficients or carbon emission factors. Quantities are generally derived from a ‘take off’ from construction drawings or directly from Bills of Quantities. Increasingly, design software is being developed to automate the assessment process.
Embodied carbon assessment is a subset of a full Life Cycle Assessment (LCA) which is the tool used to develop Environmental Product Declarations (EPD) which are increasingly used to quantify the environmental impacts of construction products.
To validate these positive statements, whole-life carbon cycle analysis have been carried out to assess credentials/performance when compared to structures formed using other methods of construction. These assessments show that light steel frame structures demonstrate a substantial reduction in the overall carbon footprint of a building of up to 20%.
An assessment of a medium scale residential property has been carried out by the LSF industry and can be found in a report on the SteelConstruction.info website. The figures in this report show the breakdown of the key elements are as follows:
Operational Energy 67%
Transport 2%
Product Materials 21%
End of life disposal 1%
Maintenance 8%
Construction <1%
It is clear that the ‘big wins’ are in the operational energy and product/materials and these areas are where benefits of LSF technology can be seen. Embodied Carbon Assessments and LCA’s may be available from manufacturers which can demonstrate the green credentials of the relevant LSF system.
*Manufacture of concrete generates 9% of the world’s carbon emissions - almost 3 times as much as the entire aviation industry.