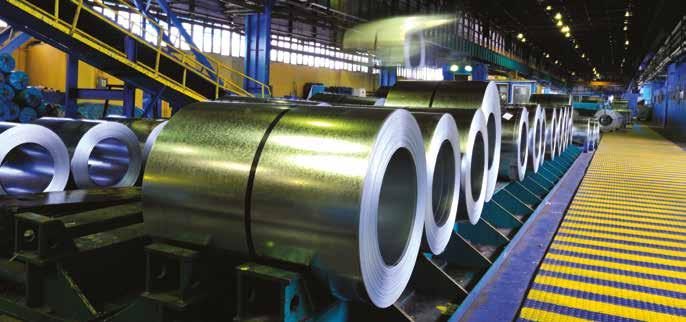
2 minute read
Sustainability into the Future
Sustainability now
Sustainability is already a key driver for the use of LSF technology, with manufacturers who have quality and environmental procedures integrated into all their business processes to ensure that waste is minimised. Manufacturers actively manage the products they use to minimise waste and ensure they are sustainably-sourced.
Each manufacturer has design and engineering teams who maximise the structural benefits of the products by using the smallest amounts of material possible and minimising waste. They use digital technology at the design stage of a project in conjunction with the quality processes used by the manufacturer. This ensures that all steel components used are formed from steel which is traceable back to the coil from which it was formed. This allows the gauge, grade and level of galvanising of the steel used to be clearly identified to ensure it can be repurposed in a safe and structurally sound manner.
Sustainability in the future
Looking to the future manufacturers are further developing a fabric first approach which allows the system users to achieve exceptional energy performance in their buildings. LSF manufacturers seek to partner with like-minded specialists to help their clients achieve and surpass their sustainability goals. This is achieved through early project engagement which enables clients to benefit from industry expertise to help deliver environmental solutions. Steel, being the core element of the LSF technology is provided by suppliers who are investing heavily in steel production and the likes of TATA are working in partnership with the LSF industry to develop the largest cluster of hydrogen powered plants in Europe to meet the goal of being carbon neutral by 2050.
TATA are also working on radical new technologies which will completely transform the way steel is made. These processes will use 50% scrap steel and reduce carbon emission by 80%. The steel industry is united around the recycling and reuse of components and are working together to offer significant embodied carbon benefits.
Steel has a well-developed and efficient recovery infrastructure, with current recovery rates from demolition sites in the UK at 99% for structural steelwork and 96% for all steel construction products. These figures far exceed those for any other construction material. Research carried out by the LSFA’s technical partner, the Steel Construction Institute (SCI) has estimated that there are around 100 million tonnes of steel in buildings and infrastructure in the UK. This ‘stock’ of steel is an important and valuable material asset that will be reclaimed and either reused or recycled in the future.
The UK is largely self-sufficient in steel, in that it can produce the steel needed through recycling the latent stock to satisfy market demand so well placed for the future.