
3 minute read
Best Use of Concrete
CATEGORY SPONSOR
BEST USE OF CONCRETE TECHNOLOGY
Category: This category will reward the exemplar use of precast concrete in a project across any UK construction sector. Including floor and wall panels, cladding, volumetric and pod technology, pre-stressed units and formwork systems, the entrant will have used concrete as a major factor in delivering quality, factory controlled, robust and sustainable offsite manufacture. Special attention will be given to material performance levels and any project should clearly demonstrate how cost-predictability, economy, accuracy, transportability, speed of installation and principles of lean manufacture have been achieved. Sponsor: The Concrete Centre provides material, design and construction guidance. Our aim is to enable all those involved in the design, use and performance of concrete and masonry to realise the potential of these materials. The Concrete Centre, part of the MPA. Mineral Products Association (MPA) is the trade association for aggregates, asphalt, cement, concrete, dimension stone, lime, mortar and silica sand industries.
BEST USE OF CONCRETE TECHNOLOGY
For all general enquiries, please contact: www.concretecentre.com
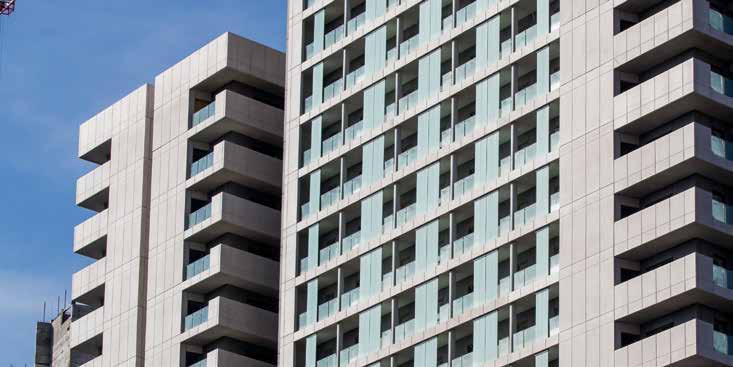
Providing guidance on offsite solutions
The Concrete Centre offers a wealth of resources including best practice guides, sustainability data, webinars and case studies – www.concretecentre.com/offsite Choosing concrete offsite solutions provides the inherent benefits of concrete: it does not burn; it provides energy-saving thermal mass and resilience to climate change risks such as overheating and flooding; it is 100% recyclable at end of life. The Concrete Centre is also the proud sponsor of the ‘Best Use of Concrete Technology’ award at the Offsite Awards.
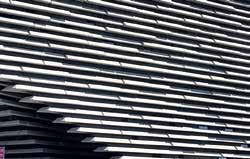
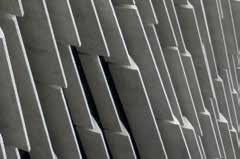
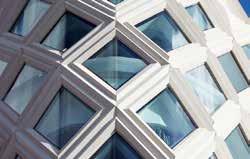
BEST USE OF CONCRETE TECHNOLOGY SHORTLIST
CHAPMAN TAYLOR: MANCHESTER GOODS YARD
BEST USE OF CONCRETE TECHNOLOGY
Manchester Goods Yard is set to become the fulcrum for Enterprise City at St. John’s, a new digital media technology hub which will soon be home to a mix of SMEs and multi-corporation technology and creative industry organisations in the heart of Manchester City Centre. The ultra-modern, flexible workspaces will be supplemented by a mix of café bars, restaurants and leisure facilities, with the aim of creating a vibrant neighbourhood in which to live, work, shop and relax.
The MFS team have formulated an offsite construction rationale, which we trademarked as the MFS i-Form Solution™. We combine large scale calcium silicate elements and pre-cast concrete components with MMC methodology to drive forward the concept of P-DfMA for offsite manufacture and building design. Our suite of ‘platforms’, or standardised & repeatable offsite components, enable us to deliver a bespoke solution to the client’s needs, in terms of building function and site demands.
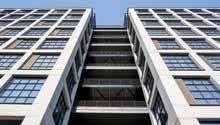
MASONRY FRAME SYSTEMS: THE MFS i-FORM SOLUTION™
BEST USE OF CONCRETE TECHNOLOGY

NUSPAN FLOORING: VARIOUS PROJECTS
BEST USE OF CONCRETE TECHNOLOGY
Nuspan Flooring’s offsite alternative to block and beam offers high-performance, primary, structural, insulated closed floor panels for suspended ground floors. The units comprise structural-grade reinforced concrete bonded to high-performance expanded polystyrene (EPS), offering an uplift in build speed of 500%, a saving of up to 83% in onsite labour and an elimination of onsite waste. They can achieve U-values as low as 0.10 W/m2K, already meeting Future Homes Standard Part L requirements.
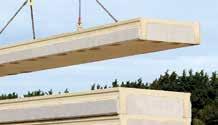
PCE: ASSEMBLY - BUILDING C
BEST USE OF CONCRETE TECHNOLOGY
PCE Ltd has designed, manufactured and constructed a 14 storey HybriDfMA office building using offsite manufactured structural steel and precast concrete components together with in-situ reinforced concrete, forming the PCE Hybrid Frame System. The HybriDfMA framed building provides 92,000 sq. ft. of office space utilising PCE’s experience of Modern Methods of Construction (MMC), Offsite engineering and providing as much Offsite construction as possible in a very busy city centre location.
PCE: LODGE ROAD - ST JOHN’S WOOD, LONDON
BEST USE OF CONCRETE TECHNOLOGY
Purpose-built 13 storey building that introduces a sophisticated and high-end design set to challenge the concept of affordable housing for London’s over 55s. Located next to the prestigious Lord’s Cricket Ground, the building provides world class standard of retirement living. The building is home to 170 new apartments to help residents stay social and active. Each home is specifically designed for both the lifestyle needs and aspirations of its residents with private balconies to each apartment.

