
18 minute read
Education, Education, Education
The government has set out a vision for the education sector to be world leading in sustainability by 2030. As Richard Hipkiss, Development Director of the Modular and Portable Building Association (MPBA) makes clear – central to shaping that will be the increased use of volumetric modular design.
All new school buildings delivered by the Department for Education (DfE) that are not already contracted will be net zero in operation. Recognising and finding ways to meet the requirements of changing regulations and policy demands is crucial in reshaping our approach to sustainability. The ecological clock is ticking, and we must take urgent action to mitigate the impact of global warming.
We have a proud legacy of innovation in the modular and portable building sector and many of our members are gearing up to face the biggest challenge of our generation – the climate crisis. To prevent the global temperature rising and avoid the worst impacts of climate change, the world needs to reach our 2030 Nationally Determined Contribution, and net zero by 2050.
So, what is net zero? Put simply, net zero is a target of negating the amount of greenhouse gases we produce by reducing emissions and implementing methods of absorbing carbon dioxide from the atmosphere. In November 2021 the DfE published a delivery framework so that all new schools and colleges can meet the same lowcarbon, climate-resilient standards as centrally delivered projects. From now on bids into the governments Further Education Capital Transformation Programme will also be assessed to determine if the new works will be net zero in operation.
With great challenges come opportunities and the construction sector is setting out road maps to deliver buildings that will be net zero in operation, but this is only part of the carbon equation.
According to the World Green Building Council, construction and buildings in use are responsible for 39% of all carbon emissions in the world. This is broken down into two elements with 11% being linked to the manufacture of materials and construction processes known as embodied carbon emissions and 28% associated with operational emissions caused by heating, cooling and lighting systems when a building is in use.
The challenge is therefore two-fold. Whilst there has been a drive to reduce operational emissions through the implementation of government legislation to improve the building fabric and the wider use of innovative technologies – little has been done to address the carbon inefficiencies in the construction process.
As an industry association, it is one of our objectives to demonstrate how the route to 2050 could follow many different paths. It is now established that volumetric modular approaches are a game changer for the construction industry – reducing
1
build times by an impressive 50-60% whilst increasing quality, productivity and safety. But what is not so widely understood is that compared to traditionally built projects it is easier to control energy use in factory settings than in an open construction site. On average 67% less energy is required to produce a volumetric manufactured building and up to 50% less time is spent onsite, resulting in up to 90% fewer vehicle movements which is less disruptive and reduces carbon emissions.
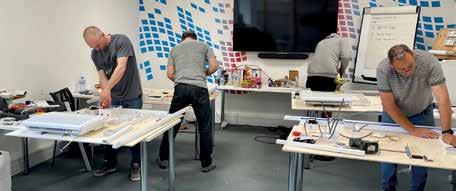
Not only is the actual construction of the building ‘greener’ but volumetric manufactured buildings are more energy efficient – reducing primary energy requirements and in-use operational emissions during the lifetime of the building.

Unlike factory manufactured buildings, there is significant evidence that traditional construction methods do not produce structures that perform as well as design expectations and there is a void between anticipated and actual in-use performance. Findings from studies such as PROBE (Post Occupancy Review of Buildings and their Engineering) reveal that actual energy consumption in buildings is often as much as twice of that predicted in the design. Providing a predictable pathway to net zero, the benefits of volumetric manufactured buildings begin in the factory, continue to the construction site and last through the lifetime of the building.
2
3
MPBA ACCREDITATION AND TRAINING CENTRE
The specialist MPBA Accreditation and Training Centre was created to deliver specific qualifications relevant to the sector it represents. Located in Coventry, West Midlands – it offers an environment for industry experts to share valuable knowledge away from the pressures of the workplace.
The centre provides National Vocational Qualifications, training and apprenticeships in partnership with local and national providers. The MPBA has developed a specific qualification for operatives, in addition to specialist training on electrical systems, and is now developing an apprenticeship for the sector through the Trailblazer Programme. Through the MPBA’s Learning Hub the association also provides specialist online courses.
The MPBA also works with key partners in specialist areas such as legal, insurance, employment, health and safety to offer industry specific business support together with technical and training services to help businesses reach their full potential. The MPBA has represented this highly innovative sector for over 80 years. Unlike regional training providers, course content is developed with members, for members.
To discover more about the MPBA, its training courses and how volumetric modular technology can benefit construction projects visit: www.mpba.biz
Images:
01-02. Polegate School. Courtesy Wernick Group 03. MPBA Accreditation and Training Centre
CASE STUDY GET READY TO CONNECT
1
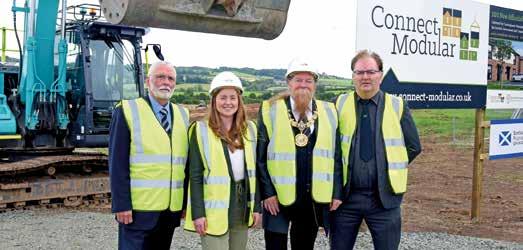
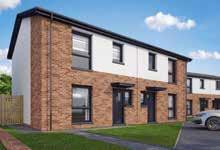
2

Work is officially underway on a large-scale, affordable modular housing development in Bridgehousehill, Kilmarnock, where Connect Modular will deliver 101 homes for Cunninghame Housing Association.
The £17million project will see a mixture of two, three and fourbedroom general needs houses constructed, together with ten amenity bungalows and five wheelchair bungalows. Located in the Shortlees neighbourhood of East Ayrshire, the homes are being delivered by Cunninghame Housing Association in partnership with East Ayrshire Council and the Scottish Government.
To mark the commencement of work on-site, an official sod cutting ceremony was held on 1 August, with the official duties carried out by East Ayrshire Council Provost Jim Todd, saying: “It was a pleasure to attend the sod cutting ceremony on at Bridgehousehill Road, marking the start of a new range of house types being built in the area.
3
It will be interesting to see the different approach being taken to building houses and I very much look forward to seeing them completed, which I am sure will be to a very high standard.”
Frank Sweeney, Chief Executive Officer for Cunninghame Housing Association, welcomed the new development, adding: “We are delighted to be working in partnership with Connect Modular to deliver this important development of 101 new modular homes. This is the first modular construction project undertaken by Cunninghame Housing Association and the largest modular low-rise housing development in Scotland.
“We are excited to be part of this innovative and efficient method of construction. We recognise the significant environmental benefits of the build and that the units will be built in Connect Modular’s Ayrshire factory, to a very high standard, and delivered to site. With the support of our strategic partners, East Ayrshire Council and the Scottish Government, we are able to provide these highly sought after affordable new homes in this popular area of Kilmarnock.” Housing Secretary Shona Robison is equally enthused by this new affordable housing development, commenting: “It’s fantastic to see this development underway which I know will provide high quality affordable homes within the local community and make a real and lasting difference to the lives of the new residents. We are proud of having delivered 111,750 affordable homes since 2007 with over 78,000 for social rent and these new homes will contribute towards our ambitious target of delivering 110,000 affordable homes by 2032, of which 70% will be for social rent and 10% in remote, rural and island communities These 101 new homes for social rent, supported by £10.5million of Scottish Government investment, are being built to a high standard using offsite construction methods. I recently visited the Connect Modular factory in Cumnock to see the quality for myself and I’m pleased people will benefit from these new homes.”
With houses constructed offsite, site preparation works can occur simultaneously, leading to a significantly condensed project timeline and earlier tenant occupancy. This approach also reduces waste, improves build quality and enables greater certainty over the project programme by eliminating variables such as adverse weather conditions. Jennifer Higgins, Managing Director of Connect Modular is incredibly proud to be delivering this brand new project, saying: “We are grateful for the opportunity to deliver a modular project at this scale. This project is a clear demonstration of Cunninghame, Scottish Government and the Council’s confidence in the ability of modular construction to provide better quality homes, to reduce construction waste and emissions, and to enable tenants to move in to their much-needed homes faster.”
For more information visit: www.theweehousecompany.co.uk/ connect-modular-ltd
Images:
01-03. The use of modular will be a first for Cunninghame Housing Association and the largest modular low-rise housing development in Scotland
WHEN ENERGY PERFORMANCE COUNTS
With bills set to rise by 80% this autumn, improving the energy efficiency of UK buildings is the most effective way to respond to rising prices. After several years in the making, sustainability and energy efficiency are at the heart of the MODULHAUS™ innovation.
Right from the initial concept stages, the decision was reached to develop a modular interim housing solution that would exceed the Future Homes Standard to relieve the burden of ongoing expenses associated with traditional temporary accommodation and negate fuel poverty. Created to meet the need for rapid-build housing, VOLUMETRIC™ has designed and developed this award-winning energy-efficient and secure modular accommodation solution. These hightech modular homes are now being used to great effect by local authorities and charities across the country for people who find themselves homeless and by NHS estates for onsite keyworker accommodation.
Energy-Efficient and Future-Proof Solution
Facilitating off-grid living, a revolutionary Energy Centre developed by VOLUMETRIC™, meets the energy requirements of up to six modules. This intelligent technology is digitally connected to each module – instantly responding to demands for hot water, heating and energy requirements. Although modules have mains connection, the Energy Centre can meet demands at most times of the year as energy generated during the day is stored in battery cells until required. Surplus energy goes back into the grid, carbon offsetting and creating net zero living. Modules achieve exceptional U-values (as low as 0.09W/m²K), in addition the airtightness achieved in using a volumetric modular approach enhances in-use energy efficiency and reduces carbon emissions for the lifetime of the building. Results of 3m³/hr/m² air loss at a 50 Pa are being routinely achieved during factory testing as part of QA procedures. With EPC rating A and B and emissions as low as 229.5KG CO2/year, modules are factory fitted with sustainable technologies, low energy lighting and white goods together with controlled flow shower mixers and dual flush cisterns to minimise energy and water consumption.
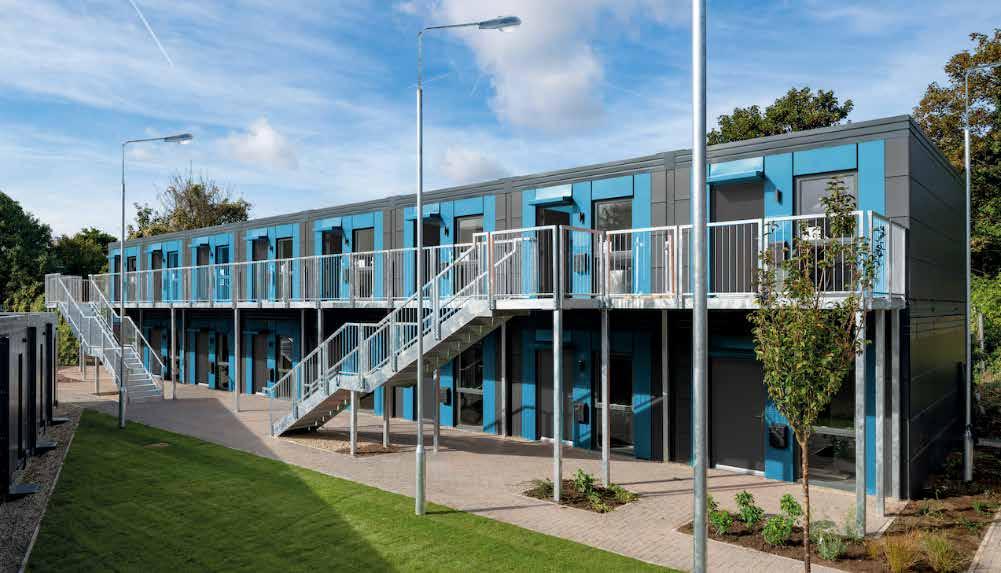
1
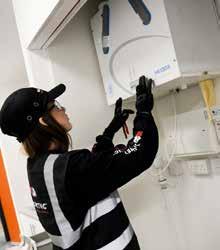
2
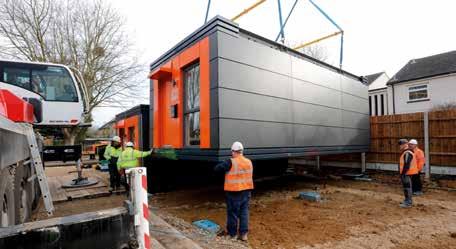
The embodied carbon assessment for MODULHAUS™ has been undertaken based on RICS and British Standard guidance. This includes information from relevant Environmental Product Declarations (EPDs), publicly available carbon data. LABC Assured with a 60-year BOPAS Certified design-life, MODULHAUS™ homes are futureproofed for Building Regulation changes and achieve 17% lower whole-life carbon impact than equivalent timber frame dwellings of the same size.
Modules are designed with a Design for Manufacture and Assembly (DfMA) layout and allow for the highest levels of offsite added benefits, with a PreManufacture Value (PMV) exceeding 90%, by adopting the maximum level of up-stream sub-assembly/prekitting and assuring consistent quality through robust manufacturing and assembly methods.
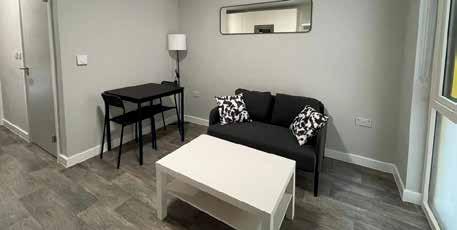
Volumetric modular technology can help deliver sustainability credentials in the entire construction value chain to improve resource and productivity efficiency. Designs are digitally constructed and virtually tested before moving onto the manufacturing phase. Any surplus materials are recycled or reused, virtually eliminating landfill waste. Materials are protected from moisture and extreme weather conditions, reducing the risk of disposal through water ingress and damage. Whilst widely recognised that volumetric modular technology has the potential to reduce overall construction programmes, it is not often acknowledged this approach can reduce up to 90% of site generated waste when compared with traditional construction methods.
3
4
Robust Processes and Quality Checks
All units undergo fully traceable factory inspections and test plans linked to unique serial numbers, with site installation inspection and test plans provided for maximum confidence. Optional extras and modifications are available to enhance the service with various purchase and lease arrangements to suit different sites and budgets. All options are available with a choice of fully integrated routine and reactive maintenance services.
The development and installation process has been optimised, from factory environment assembly to ground works, to ensure quality checks at each step. All units undergo a fully traceable factory inspection and test plan linked to a unique serial number, and VOLUMETRIC™ provides site installation supervision to ensure end to end quality control.
Long-Term Adaptable Solution
With single, double, and family options available, VOLUMETRIC™ work with local authorities, councils, NHS estates, project managers, and charities to deliver homes offering outstanding energy-efficiency and award-winning functional performance. Modules are delivered in one load to site 100% complete, ready for simple commissioning and connecting. Depending on site layouts and stacking requirements, modules can be installed in a matter of hours, enhancing operational improvements.
Fully relocatable, MODULHAUS™ provides a long-term adaptable solution to meet many unique requirements. High energy prices pose a significant financial risk to local authorities, charities and NHS estates budgets, MODULHAUS™ homes offer an investment in interim housing that is cost-effective, future-proof, and sustainable with running costs of less than £10/week.
For more information visit:
www.volumetric.co.uk
Images:
01-04. VOLUMETRIC™ has designed and developed an award-winning energy efficient and secure modular accommodation solution
CASE STUDY KITCHENER KEEPS MOVING
Located on the former site of an 18th century military barracks, the Kitchener Barracks project involves the construction of 300 residential units and is being delivered using advanced modular technology from TopHat.
With the 300-year-old Napoleonic Fortress, Fort Amherst, located at the entrance to the gated development, the site blends its historic military heritage with contemporary modular homes. Surrounded by 70 hectares of green space at Great Line Heritage Park and with some apartments overlooking the meandering River Medway, Kitchener Barracks benefits from a picturesque location. Just a fiveminute cycle away, Chatham rail station brings offers services to London St Pancras in as little as 38 minutes, ideal for commuters.
The homes are a mixture of one and two-bedroom apartments and two-, three-, four- and five-bedroom houses. All houses are either delivered to national space standards or above and all significantly exceed the requirements of Part L, which stipulates that newbuild homes built from last year much achieve a 31% reduction in carbon emissions.
The project is a development owned by TopHat and being delivered as a turnkey solution by TopHat Communities under a D&B JCT contract with the development SPV. The site involves the delivery of over 600 modules, across each of the different house types and phases.
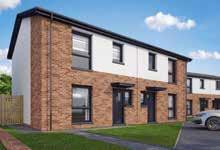
One of the challenges faced was the significant fall from the top to the bottom of the site. It has therefore been essential that the phasing and sequencing is cognisant of the site terrain. The project is being delivered in various phases, with Phases 1 and 2 now complete and Phase 3 due to complete in November 2023. The site also includes a heritage building, which TopHat is developing as part of the current works, demonstrating our ability to take on more complex sites than most offsite manufacturers.
All completed units have been sold by TopHat with 13 major high street mortgage lenders providing funding. The sales point of Kitchener Barracks has exceeded other local developments. The houses have been delivered to an outstanding airtightness, with less than 1m3/hr/ m2@50pa being achieved in some of the homes. This has been achieved using triple glazing and exceptionally high levels of insulation.
The homes have been delivered with a number of environmentally efficient technologies, including MVHR systems and wastewater heat recovery. This is in addition to the exceptional airtightness. Therefore, the completed units have all received excellent EPC scores. Most recently, TopHat announced they had sold 32 of development’s apartments to St. Arthur Homes’ shared ownership portfolio.
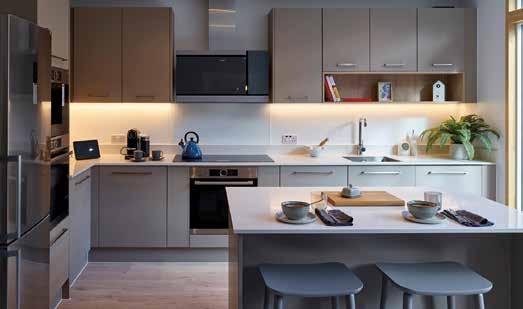
TopHat is a leading 3D modular housebuilder which has recently announced it is building Europe’s largest homebuilding factory. Homes at Kitchener Barracks are being manufactured in TopHat’s existing factory at Foston in Derby where robotics and lean manufacturing techniques are used to increase housing supply, improve quality, reduce costs and protect the environment.
TopHat’s new 650,000sq ft facility will be capable of delivery one-home-anhour. The factory will bring together the latest robotics and TopHat’s proprietary technology to manufacture and distribute up to 4,000 beautiful homes per year. One thousand new, green economy jobs across a wide range of roles will be created and a training academy will be established in partnership with local colleges. The new Corby facility will be the anchor tenant in the new Magna Park site being developed by GLP, the leading global logistics development manager, as part of a multi-millionpound investment in the site. Construction will begin later in the year, with the facility expected to be delivering its first homes by the end of 2023.
1 2
For more information visit: www.tophat.io
Images:
01-02. The project is being delivered in various phases, with Phases 1 and 2 now complete and Phase 3 due to complete in November 2023
CASE STUDY EDGE OF THE WORLD PERFORMANCE

Structural timber and modular design will provide a natural, energy efficient and demountable building in the extreme conditions at the fringes of Antarctica on South Shetland.
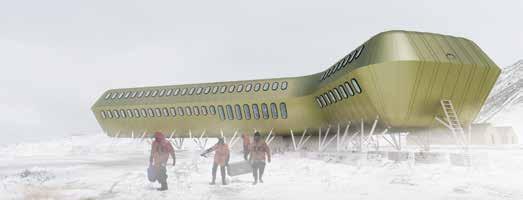
A unique research station is being constructed for the Institute of Biochemistry and Biophysics of Polish Academy of Sciences on King George Island in the South Shetland Archipelago, 120km off the coast of Antarctica. While milder than the Antarctic mainland, the island still endures sub-freezing temperatures, bitter strong winds and round-the-clock darkness for a significant portion of the year.
The Arctowski Polish Antarctic Station will accommodate up to 29 scientists studying the polar region, including the critical impacts on this vulnerable landscape caused by climate change.
Global engineering, consultancy and advisory practice Buro Happold was engaged to support the challenging project around multi-disciplinary concept structural design, as well as MEP services engineering. It worked closely with architects Kuryłowicz & Associates (general designer) on a prefabricated timber design for the structure, required to endure the worst of the region’s harsh climate.
The client’s objective was to provide comfortable and practical accommodation for a wide variety of researchers working across a broad range of disciplines, including oceanography, geology, geomorphology, glaciology, meteorology, seismology, biology and ecology. Together, they needed a holistic space for work, rest and technology, which would be comfortable, functional and welcoming, despite the extreme weather conditions. It must also be a fully flexible and extendable space. All elements of the building would need to be designed to be robust in the face of extremely low temperatures and strong winds, but quick to erect. The greatest obstacle is a construction programme limited to the three-month Antarctic summer weather window – the only moment when construction on-site is possible.
1
While busy in summer, during winter the building could house just a skeleton crew of scientists and needs to flex to this rise and fall in occupancy. This meant designing the MEP (Mechanical, Electrical and Plumbing) services in such way that the station would be fully self-sufficient in energy and water most of the year, and wings of the building could be shut down when occupancy was low.
It was decided early on that a mixedmaterial structure, comprising a glulam timber superstructure with a steel substructure and reinforced concrete foundation pads, could deliver all of the required benefits. Raised three metres high to stand above even from the thickest snow covers, computational fluid dynamics (CPD) digital simulations found an optimised shape provided by glulam that imitates the effect of an upside-down aircraft wing to keep it firmly on the ground in high winds.
2
The resulting highly efficient tripartite design provides scientists with a flexible range of spaces. Designed as a modular structure, all elements fit into standard 10 tonne shipping containers, with timber helping to limit their weight and eliminate the need for large cranes or heavy machinery on-site. The central common space was designed with an aesthetically distinctive glulam roof, which the investor embraced as a true ‘heart’ of integration, familiarity and high architectural quality.
Following a test build and disassembly in Poland, the first transport to install the foundation pads arrived during the 2021-22 Antarctic summer. Construction of the structure itself will take place following shipments over the next two summers, with completion by early 2024.
The modular design means the station can be easily disassembled at the end of its working life, which could be up to 50 years. The timber superstructure also has the benefit of being easily reusable on the site either for further construction or as fuel, reducing the need to remove waste materials by sea at the end of its life. Drawing on a breadth of knowledge and experience across structural and building services engineering, Buro Happold has helped tailor a unique and striking design for the construction, transport and weather challenges of working and living in Antarctica.
For more information visit: www.burohappold.com
Images:
01-02. The modular timber, demountable building will withstand extreme weather conditions