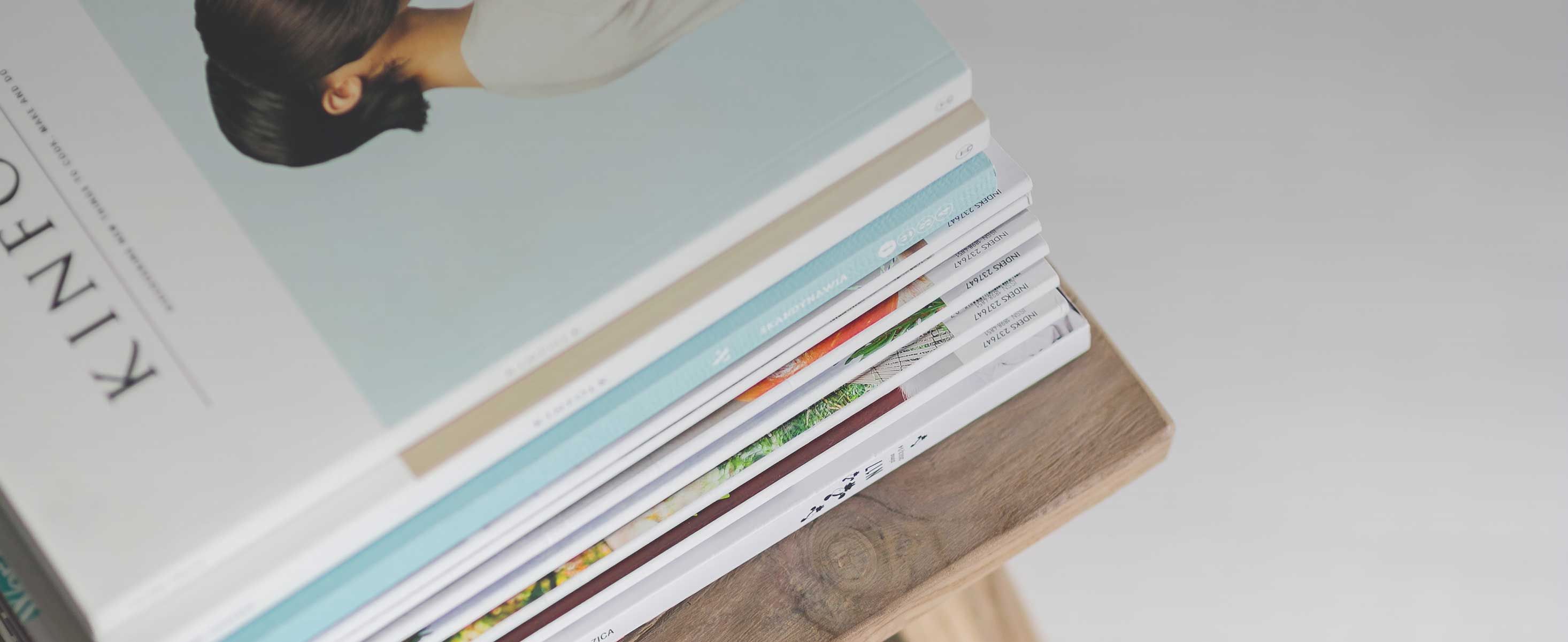
2 minute read
MANCHESTER AESTHETICS
Manchester Goods Yard is the fulcrum for Enterprise City, a new digital media technology hub in Manchester city centre that has used precast concrete to provide stunning new work and leisure facilities.
Architects Chapman Taylor paid attention to detail and reflected Manchester’s industrial vernacular as key factors in ensuring this scheme's context. They were able to define the design, assembly, logistics and quality at a very early stage which also included the installation of the windows in the factory, in factory conditions to create a complete modular assembly ready for hanging on the building.
The ultra-modern, flexible workspaces will be supplemented by a mix of café bars, restaurants and leisure facilities, with the aim of creating a vibrant neighbourhood in which to live, work, shop and relax. Manchester Goods Yard (MGY) is a significant new office scheme at the heart of the St. John’s regeneration development, a new city centre neighbourhood underpinned by enterprise, culture and living.
Techrete precast panels were used that are 100% recyclable at the end-oflife stage fulfilling the futureproofing and circular economy approach. Techrete also promotes the use of partial cement replacement in their mixture to minimise embodied carbon impact. The collaborative offsite approach between the façade suppliers meant that the overall embodied carbon implication from transport was significantly reduced. Each panel provides a deep concrete reveal – vital in emphasising the industrial aesthetic. The 400mm thick precast concrete panels with 200mm mineral wool insulation behind them provides a betterment against current Part L U-values. Offsite manufacture enabled cost certainty, as materials are quantifiable, and less wastage occurred due to the production process.
A mix of construction techniques were used for the building superstructure. The two satellite cores were constructed with twin-wall precast concrete panels and the main core was cast in-situ. This hybrid approach allowed areas of the building to be accelerated to improve commercial viability, and to improve programme by allowing different disciplines to safely work on elements at different phases and stages of the building.
The façade subcontractors, Lindner Prater and Techrete worked collaboratively to facilitate the installation of the curtain wall systems into the precast concrete panels at the Techrete’s factory before being transported to the construction site. This benefitted offsite manufacturing processes – e.g. waste mitigation and controlled quality, and importantly lessened the number of lifts that were required by combining two separate components.
The level of automation, factory consistency and quality provided by the offsite manufacturing process of the precast panels ensured consistency in the appearance, performance, and finish. The precast panels have increased lifecycle capability with minimal maintenance required due to their durability. No applied finishes were added to the exposed concrete, reducing maintenance requirements whilst evoking an industrial feel in a contemporary environment. The precast concrete donut panels have been designed to interlock into one another for both ease of assembly and future disassembly.
MGY is rated BREEAM Excellent and used offsite manufacture and assembly to maximise opportunities to reduce waste, improve quality and minimise its carbon footprint. This innovative approach to designing new office space has provided c.31,000m² of shell and core commercial space across 10 floors, two levels of basement parking and cycle facilities.
For more information visit: www.chapmantaylor.com www.techcrete.com
Images: 01-03. Precast concrete has given a contemporary feel to Manchester’s latest multi-purpose commercial project