
4 minute read
FABRIC FIRST
SUPERSTRUCTURE
Stoneham Park Academy is a brand new £5.6million, 1.5 form entry school, designed by Hampshire County Council’s (HCC) award-winning Property Services team, which successfully used a compact and energy-efficient design through modern methods of construction.
Constructed by Morgan Sindall Construction, the project used the innovative Streif advanced timber panel system and was delivered to meet HCC’s design standards – providing a sustainable school which is fit for future expansion into a two form entry school for 420 pupils.
The primary school was built to serve North Stoneham Park, a new housing development of 1,100 homes to the south of Eastleigh. Awarded through the Southern Construction Framework (SCF) and sponsored by the University of Winchester Academy Trust, the school will provide 315 school places for pupils aged four to 11 within the Hampshire area.
Hampshire County Council Model Stoneham Park Primary Academy is
01
the pilot project for the HCC model. Conceived as a lean, compact and energy efficient two-storey form the building is modest in scale and futureproofed for expansion. The Hampshire model can be scaled ranging from 1.5 form entry to three form entry and due to its compact form and footprint can be adapted to suit a variety of sites and contexts as well as the client’s brief and budget.
The compact design is based on ‘fabric first’ principles combined with a mechanical ventilation heat recovery (MVHR) system to improve thermal comfort, indoor air quality (IAQ) and dramatically reduce energy consumption. An options appraisal for the superstructure concluded that an offsite timber frame was the preferred solution for the project.

Why the Streif system?
Streif was the preferred option for the delivery of the complete building superstructure. This was primarily based on the key benefits of an offsite factory manufactured panelised system that had the potential for replication on future projects. In particular, the integration of factory-installed components including triple glazed windows/doors, internal and external insulation, sheathing, membranes and conduits was a major factor in terms of quality control and programme benefits on-site.
With production undertaken at their factory in Weinsheim, Germany, the pre-construction team visited the factory to gather information on the production process and a live construction site to witness works in progress. The team also undertook a robust review of key details in collaboration with HCC’s in-house technical services team. This included the review of on-site sample details and processes to ensure quality control measures were maintained.
Benefits of the Streif system
The innovative Streif advanced timber panel system is a robust and highly sustainable framed timber construction that is based on low carbon/energy use and ‘fabric-first’ design principles. Its numerous benefits include improved quality and running costs, significant savings on the programme and preliminaries, while minimising the risk of co-ordination errors when working internally.
Despite the impact of weather, Brexit and COVID-19 pandemic restrictions the project was completed on-time, on-budget and to a very high standard.
02
On-time manufacture and delivery allowed the building to rapidly achieve the key milestone of watertightness; enabling access to all working areas of the building and allowing internal finishing trades to complete works in multiple areas at the same time in safe and dry working conditions. Internal partitions were robust, dimensionally stable, and easy to finish with a skim coat of plaster. Floor and ceiling finishes were also able to rapidly proceed in dry conditions. Externally, the cavity brickwork facades could safely proceed unhindered by other trades due to the factory-installed cavity insulation and membranes on the external face of the panels.
Manufactured in controlled factory conditions, high quality standards were met right from the production stage where the Streif quality management is audited to ISO 9001 standards. All panels and cassettes were thoroughly checked for quality before being loaded on to specially designed lorries and distributed to site.
The system provides a very well-insulated and airtight building, improving thermal performance and energy consumption which ultimately improve running costs. With pre-manufactured panels made offsite, this dramatically reduced the number of operatives on-site, thereby reducing construction phase health and safety risks, as well as reducing waste on-site.
Methodology of the Streif system
Early co-ordination of the M&E with the Streif timber frame system was vital to the successful delivery of Stoneham Park, as all panels arrived as fully-sealed components with first fix wire ways including electrical conduits and cable ways for the wall panels as well as
03
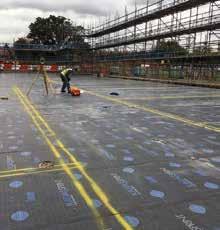
04
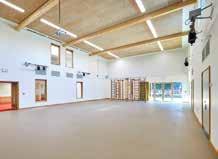
cut-outs for sockets and switches. This was pinned on the collaborative working and coordination with Morgan Sindall Construction, HCC, Streif and the M&E sub-contractors through M&E co-ordination, to ensure the fully made-up panels were correct on delivery.
Scaffold was erected entirely before the Streif system arrived on-site and was placed in the correct position using a third-board bracket, which was then removed to enable brickwork construction.
The panels and cassettes were delivered from Germany, arriving on-site in strict order and safely craned into position and fixed, providing a quick weathertight building. All wall panels were placed into position using a theodolite station to gain mm accuracy. All elements were manufactured with a high degree of dimensional accuracy, with other elements incorporated such as windows/doors, minimising co-ordination errors when working internally.
www.morgansindall.com www.streif.co.uk
IMAGES:
01-04. Stoneham Park Academy used the innovative Streif advanced timber panel system and provided a sustainable school fit for future expansion