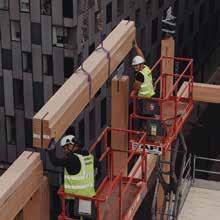
7 minute read
THE NEXT STAGE IN THE NEW TIMBER AGE
01
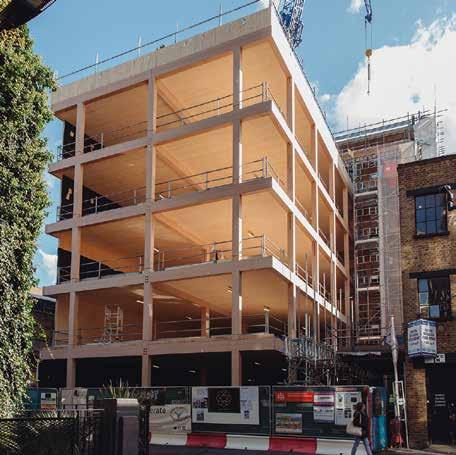
Laminated veneer lumber (LVL) is the least well-known of the glue laminated systems (the others being CLT and glulam) but is arguably the one most likely to take the spotlight by the end of this year. Peter Wilson, architect and founding director of the Mass Timber Academy explains more.
Before environmentally sensitive and climate change aware readers turn the page at the mention of ‘glue lamination’, we need to have a grown-up discussion about modern adhesives and their use in combination with the principal renewable construction material we have available to us: wood. In parallel with extensive R&D in the manufacture of mass timber, adhesive technology has advanced dramatically in recent years, with MUF and PUR being the most commonly used in laminate systems today. Put simply, these are solvent-free formulations with zero adhesive-related formaldehyde emissions in the finished wood products. Like glulam, LVL is formed from layers of wood in which the grain in every layer runs in the same di-rection. Unlike glulam, however, LVL’s layers are only 3mm thick and are produced by putting a long blade against a rotating log to peel a continuous veneer that is subsequently glued and pressed into boards or beams. There are two advantages to this over CLT or glulam – the resulting LVL products have significantly greater strength than their two mass timber siblings, plus they make far more efficient use of the raw timber (i.e. greater yield from each log than if they were sawn into boards).
Some readers may not be aware of LVL projects in the UK, but there are some remarkable examples, not least the five-storey Black & White Building currently being completed in London’s Shoreditch area that is attracting considerable attention from commercial developers. Its prefabricated beech hardwood LVL post and beam structure supports a CLT core and slabs, but the apparent simplicity of this fullyengineered, precision-built timber construction belies its groundbreaking innovation. Sitting on a very tight site and erected at remarkable speed with no major plant and with practically no
02
03
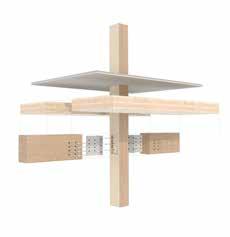
noise and no waste, its optimisation of material delivers a powerful sustainable agenda with only 410 kgCO2e/m2 embodied carbon (A1-A5).
Designed by Waugh Thistleton Architects, the practice is currently completing a major Horizon 2020 ‘Build-In-Wood’ research project for industry-wide publication in September, whilst recently starting a four-storey LVL commercial building on-site in Milan that is intended to demonstrate the findings from their investigations.
The practice had previously utilised Pollmeier’s Baubuche product in its design for the remarkable Vitsoe Factory in Leamington Spa. This project was very much a hybrid of hardwood LVL with CLT and steel used for their respective efficiencies in the building’s elegant and highly rational structural de-sign. The same might be said of the Black & White Building, but here the efficiency is achieved without the inclusion of structural steel. Much more is likely to written about the innovative use of engi-neered and modified timber products in this project and we may well look back on its completion as being as ground breaking for LVL as was the practice’s 2009 nine-storey Stadthaus in London’s Murray Grove for the extensive use of CLT in the evolution of tall mass timber buildings.
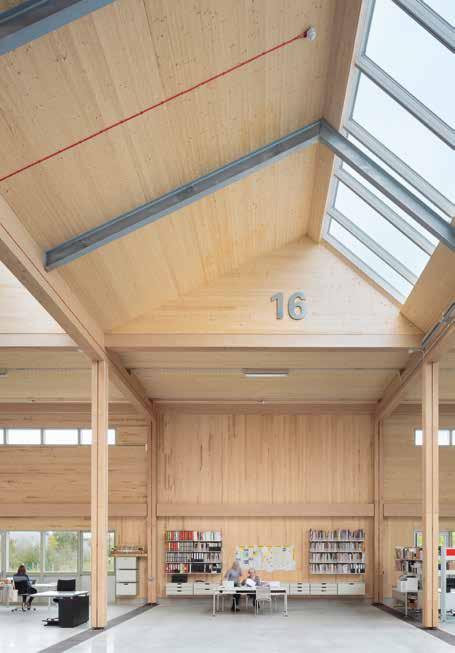
Softwood LVL has of course been widely used in domestic housebuilding projects and provides much of the day-today, bread-and-butter use of LVL but, notably – in board form – also in larger commercial structures such as the widely regarded Cheshire Oaks superstore for Marks and Spencer where Steico’s 57mm LVL X grade flooring panels provided one-hour fire resistance without addition treatment and its 33mm panels used elsewhere in the building where 30-minutes fire resistance was required. It’s post and beam credentials can be seen in the 2012 visitor centre and restaurant at Abbotsford, Sir Walter Scott’s House in the Scottish Borders, where its straightforward post and beam use by LDN Architects in the building’s portal frames provide visible simplicity to its structure.
Over the past 15 years or so, considerable exploration of the different LVL products and their respec-tive structural properties has taken place. At small scale, the 2005 temporary Serpentine Pavilion in London by renowned Portuguese architects Alvaro Siza and Eduardo Souto de Moura, working with ARUP engineers was an ingenious structural feat using traditional techniques such as mortice and ten-on joints to interlock 427 LVL elements in a self-supporting gridshell structure.
The opposite end of the structural engineering spectrum saw the emergence in 2011 of the Metropol Parasol (locally referred to as ‘las Setas’) in Sevilla. Designed by Jurgen Meyer H Architects and ARUP, this enormous gridshell fabricated from Metsä Wood’s glued Kerto-Q product remains the largest LVL structure in the world, its massive scale sheltering a covered market and archaeological excavations and protected by a thickly sprayed intumescent coating, the latter unfortunately concealing the true nature
04
of the structural product employed. More recently, Pollmeier’s Baubuche beech hardwood LVL product has been used to great advantage in two performing arts centre in the UK to deliver the roofs of large span, columnfree auditorium spaces. At Wells Cathedral School, Eric Parry Architects working with Momentum Consulting Engineers and Inwood Developments in 2016 created the visible and acoustically-beneficial inverted LVL diagrid above the Cedars Hall recital space. The one-way spanning structure is made up primary and secondary LVL ribs, the whole supported on only four columns at the corners.
Two years later, Haworth Tompkins Architects, Price and Myers engineers and Constructional Timber employed the Baubuche product to exemplary effect in the Peter Hall Performing Arts Centre at the Perse School in Cambridge. Here the externally and internally visible roof structure uses 126 identically sized members connected at 75 node points to create a two-way spanning diagrid laid out at a 45-degree angle over a 10 x 24m grid. Both this and the Cedar Hall have undoubtedly set the bar for new theatre and performing space roof structures.
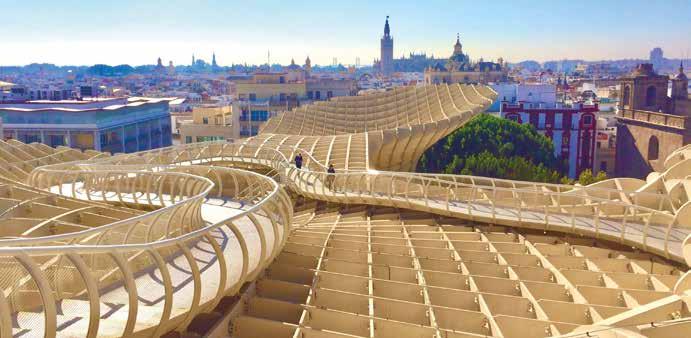
But why the emphasis on the use of hardwood as opposed to softwood LVL? Essentially this product has massive structural strength benefits compared to softwood glulam and, as mentioned earlier, delivers a more highly efficient yield from the log its veneers are sourced from than is possible in the manufacture of CLT and glulam. Because it can be produced in long sheets as well as beam and column form, its potential to be curved and twisted in two directions at once offers considerable design potential to conceive and construct building forms never previously possible with wood.
But the opportunity lies not only in the creation of new building forms, but in LVL’s potential to for designers to rethink and reshape the way in which we build out towns and cities. Two of the world’s leading LVL manufacturers are busily exploring these possibilities: Metsä Wood and Stora Enso are not only talking the talk, but they are also walking the walk, the latter constructing its ‘Wood City’ in Helsinki, the largest sustainable urban wooded district in Finland and a demonstration to the wider world of the efficiency and high quality that can be achieved with LVL.
Over the next few years, LVL demand in Europe is forecast to have a projected average annual growth rate of 6+%. This substantial LVL consumption increase will likely be driven in the main by several key factors, including growing LVL usage rates and volumes in domestic house construction both as beams and headers as well as I-Joist flanges – builders’ needs to shorten building erection times, to avoid expensive on-site equipment (e.g. cranes) and to reduce the cost of on-site labour. This base level demand will undoubtedly benefit from greater
05
awareness amongst architects and engineers of LVL’s properties and benefits and its consequent use in larger commercial and public projects.
Amongst these benefits are the continuing advances being made in peeling and lamination technology that allow manufacturers to produce lighter and smaller LVL sections with a greater strength and longer span than sawn timber. As wood defects (i.e. strength reducing knots) have been removed and randomised within thin layers, LVL is stronger, straighter, and more uniform than traditional sawn timber. The phenomenon of shrinkage and swelling is hugely reduced, making for more dimensionally stable and accurate construction. Due to its composite nature and pre-graded veneers for stiffness, LVL is also much less likely to warp, twist or bow than tradition timber.
To ensure architects and structural engineers get up to speed with LVL, Timber Development UK (TDUK) in collaboration with the Mass Timber Academy will shortly be announcing details of an in-depth online course to take place in late Autumn 2022. Look out for more details at: www.masstimberacademy.com
IMAGES:
01-03. The Black & White Building has a prefabricated beech hardwood LVL post and beam structure supporting a CLT core. Courtesy Waugh Thistleton 04. Vitsoe Factory, Royal Leamington Spa. Courtesy Dirk Lindner 05. The Metropol Parasol, Sevilla is the largest LVL structure in the world. Courtesy Robin Cross