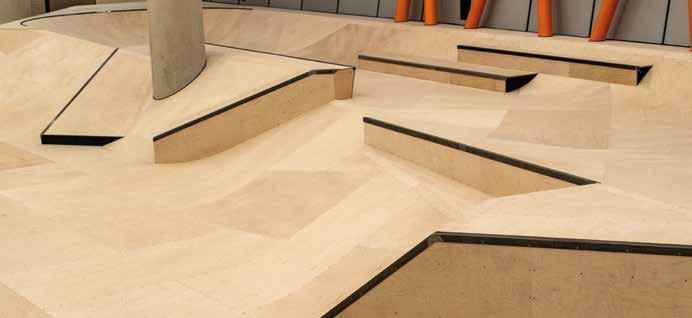
4 minute read
A MARRIAGE MADE IN CONSTRUCTION
A MARRIAGE
MADE IN CONSTRUCTION
A quick overview of two impressive projects that show why offsite design and build and timber are perfectly matched to provide hugely successful buildings.
Timber building and offsite construction go hand in hand and have done so for many years. Engineered timber products such as cross laminated timber (CLT) are now well understood and specified across many timber-led construction, alongside the commonly used panel-based solutions. So it’s not surprising that 2022 has seen a particularly inventive slew of buildings completed in the UK which really make the most of the possibilities of offsite methodology, prefabrication and modular construction using wood.
F51 Urban Sports Park
The F51 Urban Sports Park – more specifically, its second and third floors – is one great example. When you think ‘timber construction’, you probably don’t immediately picture a skateboard park. But two indoor skateparks made of timber is what Cambian Engineering Solutions delivered for Folkestone’s F51 building, a hugely impressive indoor sports facility.
The two skate floors at F51 are an oasis of engineered wood in an otherwise concrete, steel and aluminium building. Effectively, this is the world’s first purpose-built multi-storey skatepark. And it would not be the success of architecture and function that it is without employing prefabrication. “Our offsite methods take the wellproven practices of applying factory conditions to architectural scale construction to the next level,” states Piers Chapman of Cambian Engineering Solutions. “We produce all our walls and parks in an almost completely modular format, achieving exceptional accuracy and speed of installation.”
The designs used digitally intensive methods, employing pioneering methods of CAD detailing, along with highly automated CAD/ CAM workflows and CNC machining. The modular structures, comprising tens of thousands of unique parts, were almost exclusively produced from birch and spruce plywood. Offsite assembly of the modules was essential given the building’s restricted access, and also enabled parallel production as the building was being erected.
These structures, many of which are compound curved, were then clad in a process combining digital production with highly skilled fitting, bringing craftmanship and automation together. The herringbone ply – which Chapman describes as “a curved parquet floor on steroids” – and the detailing and workmanship of the compound curved surfaces are a testament to well thought out use of offsite design.
01

March House
A more commonplace use of offsite and timber – though no less stylish – can be seen in March House, a private home designed by architects Knox Bhavan. March House was built using a prefabricated oriented strand board (OSB) cassette system which required only a small team to put together. The house’s OSB cassette system was developed by structural engineers Price & Myers and BlokBuild, a digital manufacturing company, together with the Knox Bhavan studio. Their system’s principle is to make hollow objects filled with insulation which become the building blocks of the house. “The cassettes slot easily toge ther,” explains architect Simon Knox. “A digital clone is made of the planned building, and they are cut from OSB boards to very tight tolerances which fit, like a jigsaw puzzle, together.”
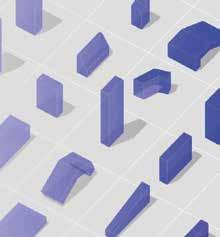
A series of variously shaped cassette components were designed by Price & Myers to make up the floor, walls and roof. These were then cut from sheets of SMARTPLY OSB and assembled, using digital assistance, by BlokBuild at their factory in Hull. By systematising and co-ordinating the templates on the OSB sheets the team were able to reduce wastage on the production line. The accuracy of the digital modelling and cutting process also meant that later, at the installation stage, complex junctions at the eaves and the sills were reliable and tightly fitting, resulting in improved thermal bridging performance. One recurring theme in projects that use offsite manufacturing is that it provides a perfect solution for constrained sites. And March House had several constraints: it is on a Thamesside site that regularly floods. Until the 1980s, it was accessible only by boat. It was important that the wall and roof modules were small enough to be comfortably handled and delivered in small vehicles. Once onsite, the cassettes could be manually lifted and stacked using specially designed chunky plywood pegs that aligned the boxes, pulling them tightly together. The boxes were then screwed in place using nail plates to make them more resilient.
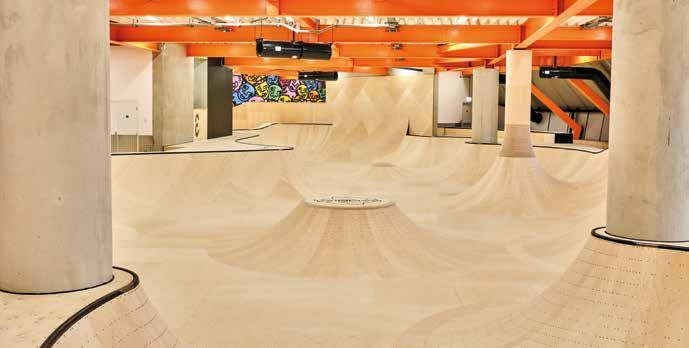
02
03 04
The benefits of prefabrication were appreciated by the project’s main contractors, Phillian. A narrow access road, limited space and the everpresent risk of flooding made storing large quantities of timber onsite risky. So working with components able to be delivered in batches and easily installed had obvious logistical advantages. Both superstructure and enclosure were able to be quickly erected.
The project is a great example of the collaborative nature of many offsite and timber projects, with the architect, engineer and contractor learning a great deal from the process and using the experience to take their system further on new projects together.
www.cambian-engineering.com www.knoxbhavan.co.uk www.pricemyers.com
IMAGES:
01-02. F51 Skatepark, Folkestone 03-04. March House where a series of variously shaped cassette components were designed to make up the floor, walls and roof. All images courtesy TDUK