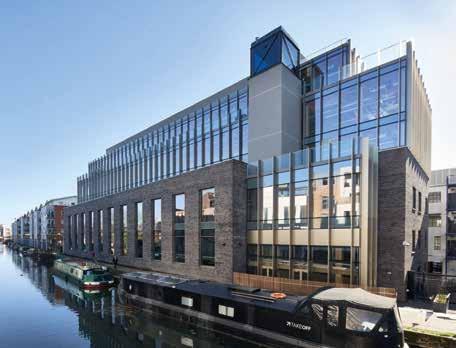
5 minute read
CHOOSING THE RIGHT MATERIAL IN THE RIGHT PLACE
Alex Brock, PreConstruction Manager at B&K Structures (BKS) explains why hybrid mass timber structural systems can improve sustainability and help meet financial requirements.
Growing concerns about climate change have forced many into action. The responsibility to reduce the environmental impact no longer falls solely on construction firms, but architects and building designers too. However, the question over balancing bottom line with environmental impact remains at large. Put simply, a sustainable building is one where the structure and processes are environmentally responsible and resource-efficient throughout the lifecycle of the building; everything from design and construction, maintenance and renovation, through to demolition. Sustainable building design is therefore crucial with the rise in construction developments, from newbuilds to office buildings and the need for new habits, natural resources and habits are dwindling, with the planet being unable to match the pace of modernisation.
According to the UK Green Building Council, around 10% of the country’s carbon dioxide emissions are directly associated with ongoing construction activities, with that number rising to
01
45% when the whole built environment sector is considered. But it isn’t just the construction process that is having an environmental impact. The majority of a building’s carbon footprint is from energy used in buildings. Heating alone represents 10% of the nation’s carbon footprint, with homes a more significant contributor than all other building types put together.
The Government has responded and the target to achieve net zero by 2050 is now familiar to everyone in our industry. However, this deadline is rapidly growing closer, and the UK has also set an ambitious legally binding target to cut emissions by 78% by 2035 compared to 1990 levels. Lowering the environmental impact of our buildings is an important step in achieving the required reductions.
While minimising the operational carbon emissions of buildings through heating, lighting and power is often the primary focus, embodied carbon – the greenhouse gas emissions associated with the production of materials and the construction process – is a significant issue. In fact, in its ‘Embodied and whole life carbon assessment’ document, the Royal Institute of British Architects (RIBA) advises that for a UK office, warehouse or residential building, embodied emissions can represent around 70% of the building’s lifecycle emissions.
One of the best ways to address the issue of embodied carbon is to maximise the use of low carbon materials, such as timber, as well as to ensure that materials are used as efficiently as possible.
Timber is an ideal option for several reasons. Firstly, it is a well understood, natural material that has been used in construction for centuries and does not require energy-intensive processes to turn it into a building component. In addition, timber acts as a carbon store. This is because trees absorb a significant amount of carbon as they grow and sequester it for the life of the material. The environmental benefit of storing this carbon increases the longer the timber is in use. Therefore, to maximise the positive impact of timber as a material choice, it is important to design the building to last by selecting high quality solutions.

In addition, the embodied carbon of engineered timber solutions is decreasing rapidly as processes become more efficient and energy switches away from fossil fuels. This has been demonstrated in the revised carbon factors being published by organisations such as the Institution of Structural Engineers (IStructE).
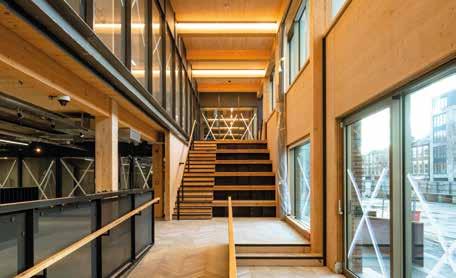
There is also a range of different engineered timber systems available, allowing the choice of solution or combination of solutions that aligns with the objectives and requirements of the project. These include glulam, cross laminated timber (CLT) and timber cassettes. Engineered timber systems like these can also be easily combined with other materials, such as steel, in a hybrid solution that can harness the benefits of both materials. Additionally, a hybrid approach can help navigate budgeting, scheduling and architectural challenges as well as remove the constraints associated with other solutions.
At BKS, our approach is focused on ensuring ‘the right material in the right place’ to find the most cost-effective solution that maximises building and material efficiency as well as fulfilling the design requirements. For example, extensive use of timber may be desirable to create a warm and welcoming atmosphere in the building. In these cases, glulam beams could be combined with steel columns to create a structurally efficient and visually attractive structure.
A hybrid structure could also consist of a steel supporting frame with CLT used for floor and wall panels, meaning the steel and timber then share the gravitational and lateral load transfer. This combination of steel and CLT could also be selected to achieve specific project aims. As engineered timber components are typically lighter than those manufactured using other materials, approximately one-fifth the weight of concrete, the required size and strength of supporting structural elements can be reduced, including in areas such as the foundations. This provides the opportunity for value engineering as it minimises the amount of material required and therefore reduces the costs, as well as embodied carbon.
Finally, the lower weight of timber compared to other options has another additional benefit. It can increase the efficiency of moving the required materials and components to site. For example, our study on a 10-storey building found that switching from concrete to a hybrid steel-CLT
02
03
solution with offsite manufactured components reduced lorry deliveries to site from around 700 to 111. The lower weight also means reduced cranage requirements for the installation.
Construction using hybrid engineered timber solutions can provide the answer to many of the challenges facing architects and developers. However, it requires specific knowledge and experience. Working with specialists such as BKS to get the correct advice in the early stages of the project will help ensure a building is optimised for a hybrid approach.
www.bkstructures.co.uk
IMAGES:
01-03. The need for new habits in sustainable building design is crucial from newbuilds to office buildings and beyond