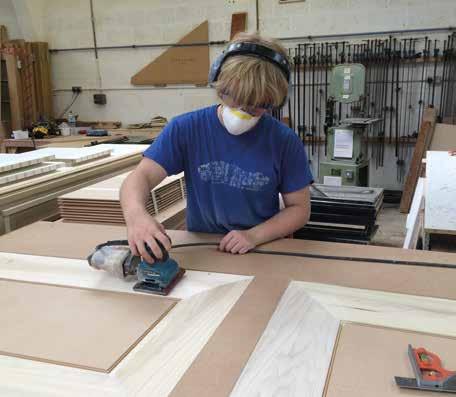
7 minute read
BWF PROVIDE POSITIVE MESSAGES ON WINDOWS AND RECYCLING
Helen added: “With the cost of living and energy crisis ongoing, it comes as no surprise that cost and energy efficiency are the primary concerns for homeowners when selecting windows for their property. But while it’s encouraging that timber is viewed positively by many against these criteria, there are still some outdated assumptions over how timber windows perform.
“When it comes to cost, the improved durability of wood window frames means they can last longer – when maintained properly – and therefore actually provide better value over their lifetime than alternatives. In terms of energy efficiency, timber has naturally insulating properties, meaning timber windows can offer improved thermal performance. We want to challenge these misconceptions and help show that whether a property is a new build, a period home or anything inbetween, wood windows and doors are the natural choice and can add value for any homeowner.”
New research from the British Woodworking Federation (BWF) reveals signs that timber windows and doors are viewed positively by homeowners, but that misunderstandings over their performance persist. The survey of 1,500 homeowners unearthed the main factors guiding product choice. It found that, aside from cost, for both windows and doors energy efficiency was the main priority for homeowners when selecting products (50% for windows and 39% for doors).
When it came to windows, cost and energy efficiency weren’t the only significant factors for homeowners. Aesthetic appeal was most important to almost a third (32%), while the source and sustainability of timber was an important consideration for almost half (48%) of all homeowners, and almost three quarters (73%) of period property owners.
For doors, aesthetic appeal was also a prominent factor, a top priority for 32%, with product lifespan (31%) and security features (24%) also important. Encouragingly, 59% of homeowners felt that timber windows offered a wider opportunity for design and style options than alternatives, and 56% thought timber windows were more sustainable.
Helen Hewitt, CEO at the BWF, said: “The beautiful aesthetic of timber has always been its enduring appeal, whatever the property type. And with timber products being designed to be repaired rather than replaced, they are a naturally sustainable choice. It’s hugely encouraging that the benefits of timber are recognised by those who may be considering replacing windows or doors in their homes or buying properties in need of renovation.”
Despite positive perceptions, research also revealed a number of misconceptions over timber windows as compared to alternatives:
• Fewer than half (40%) believed timber windows offer high energy efficiency performance
• Only 35% thought timber windows have the same U-value performance
• More than half (57%) believed timber windows cost more to purchase and install www.bwf.org.uk
• 70% of homeowners believed timber windows have a shorter lifespan.
The BWF has also joined forces with the Glass and Glazing Federation (GGF) and Community Wood Recycling to support timber window frame recycling across the construction industry. Open to all BWF members, the recycling scheme will collect any waste wood for recycling – including timber frames and off-cuts – where a designated volume has been accumulated.
Through Community Wood Recycling, 100% of the wood supplied is reused or recycled, meaning none of the waste collected will end up in landfill. Not only does this make timber a more sustainable construction material than ever, but the scheme also creates jobs, training, and volunteering opportunities for disadvantaged people. The UK creates 4.5 million tonnes of waste wood each year. Last year, Community Wood Recycling retrieved nearly 24,000 tonnes of wood, a figure the scheme’s partners aim to increase through this initiative.
Passivhaus pioneer and modular construction specialist Beattie Passive has been included in J.P. Morgan Private Bank’s annual list of the UK’s Top 200 women-powered businesses. J.P. Morgan Private Bank and research provider Beauhurst analysed 46,300 companies in the UK and found that 13,255 are either founded, led, owned or managed by women. Beattie Passive was ranked at number 171 in the Top 200.
The report recognises the tremendous contribution that female-led businesses make in terms of development and innovation, raising £5.75billion of private equity investment across 2,097 deals in 2022. Beattie Passive’s inclusion underlines the high number of women-powered businesses in the East of England, which accounts for 26.7% of the total population by region.
Rosemary Beattie, a Director at the Norwich-based firm, said: “We’re very proud to be named in this report. Construction has traditionally been a maledominated sector, but that’s changing and addressing the gender imbalance will have many benefits. A shortage of skilled workers is one of the biggest challenges facing our industry, so encouraging more women into construction will help to close the skills gap and widen the talent pool. There’s a very broad range of opportunities out there, so I would urge more women to consider a career in construction.”
In other news, Beattie Passive has been appointed to three major modular construction and retrofit frameworks over the past six months. Most recently, the firm was named on LHC’s £1.2billion Modern Methods of Construction (MMC) of New Homes (NH3) Framework. Beattie Passive secured a place on the Offsite Homes Alliance’s £2billion offsite national modular construction framework. It has been appointed to deliver Category 1 MMC over the next four years on the OSHA Framework, administrated by Great Places Housing Group, to supply homes to its 23 members and to future new members of the alliance.
Matthew Harrison, Chief Executive of OSHA member Great Places Housing Group, said:
“We’re delighted to be working with Beattie Passive on the new OSHA framework. We’re confident they will be able to work with us and the OSHA clients in delivering the sector’s extensive development ambitions. We were pleased with the positive response from the market and received high quality proposals and substantial social value pledges for our communities. We are now looking forward to mobilising the framework and working together on new projects to realise our ambitions of delivering muchneeded affordable homes.”
Image: L-R Rosemary and Isabel Beattie www.beattiepassive.com
HOW MUCH DO WE KNOW ABOUT SCREWS?
Theory, practice, experimental campaigns: putting it all together on screws takes years of lectures, workshops and construction sites. We make it available to you in 70 pages that are extra catalogue. Because our experience is in your hands.
rothoblaas.com
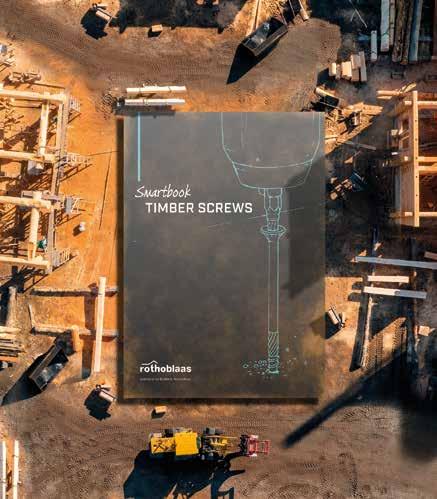
Persimmon Get Green Light For Timber Frame Factory
NEW ADDITION TO JJI-JOIST PRODUCTS
Approval has been granted by Charnwood Borough Council for the creation of a new Space4 timber frame factory – believed to be the biggest in the UK – on the edge of Loughborough. Following approval from Charnwood Borough Council on 22 June 2023, the state-of-the-art facility will bring up to 120 new jobs to Loughborough and the surrounding areas, whilst also utilising the latest automation technology as part of the manufacturing process.
The factory will produce timber frame units for up to 7,000 homes a year and is set to be in full operation towards the end of 2025. Utilising modern methods of construction (MMC) systems within Space4’s products places sustainability at the core of our build practices. Utilising timber over other materials enables the homes to be more environmentally friendly; all the timber used is from sustainable forestry sources. The factory-assembled nature of the product will also help to improve the speed and consistency in quality of the homes built, with timber frame homes being around 20% more efficient to build than other methods.
Gareth Wicks, Managing Director Designate at Space4, said: “We’re delighted to have received approval for our new Space4 facility and I want to thank Charnwood Borough Council for their support. Not only will the development deliver up to 120 new jobs, it will also further our goal to place sustainable practices at the very heart of our developments. We’re committed to creating vibrant, successful communities with the environment in mind. We’ll continue to work in partnership with the Council and other stakeholders to ensure our new Space4 factory delivers real benefits for local industry and the wider Loughborough community.”
The new Space4 facility will be placed on the Garendon Park Sustainable Urban Extension (SUE), a community of over 3,000 homes on the Garendon Park estate where our North Midlands team is master developer. Across the whole of the SUE, a cumulative figure of over £43million will be paid to support local infrastructure delivery and ensure economic development.
Dan Endersby, Managing Director of Persimmon Homes North Midlands, added: “Approval for the new Space4 facility at our Garendon Park development comes at a particularly exciting time as we welcome our first residents and continue to build our presence in Loughborough. Garendon Park will be one of Persimmon’s flagship communities, with over 3,000 homes, employment and leisure facilities, and a range of preserved historic monuments around the site.” www.persimmonhomes.com
The Timber Systems Division of forestry and sawmilling business, James Jones & Sons Ltd, has announced the addition of a new product – the JJI Wall Stud. James Jones & Sons operates the largest, fastest and most efficient I-Joist line in Europe. Made in the UK at its engineered timber manufacturing plant in Forres, the JJI Wall Stud offers a low carbon solution to the UK and European construction market.
Angus Macfarlane, General Manager of Timber Systems Division, said: “The JJI Wall Stud has been developed to complement changes in Part L legislation that requires more efficient insulation in timber frame and modular homes. More than ever there is a need for highly insulated, healthy homes and the JJI Wall Stud, in combination with different types of insulation, helps achieve this. We will manufacture the JJI Wall Stud in easy to handle and easy to cut lengths to offer flexibility to the offsite manufacturing process. The JJI Wall Stud is available via our existing distribution network throughout the UK and Europe.
“We are committed to supporting a programme of continued investment and other recent innovations have included development of our JJI Design and Joist Master Software, in addition to the expansion of a new stock yard in 2022 to enable us to ensure security of supply within industry best delivery timescales.”
