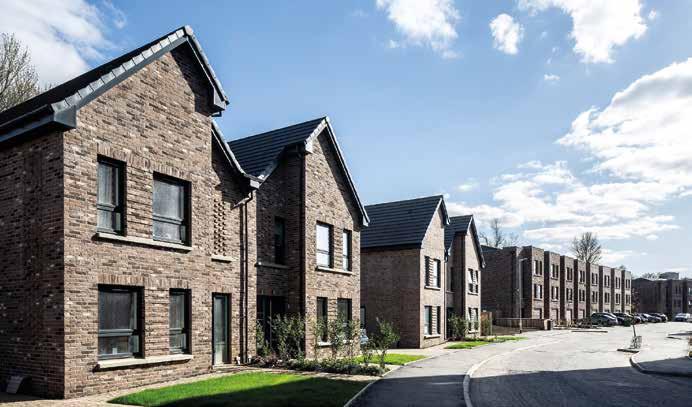
3 minute read
PRIORITISE MOISTURE MANAGEMENT
Drawing on the collective and wide expertise of the STA Technical Steering Group, the guidance enables the industry to benefit from the experience that is needed to connect the ideas of the design team with the outcomes of site installation. The aim is to present a more formal and effective process for industry-wide adoption to ensure that durability of structural timber buildings fulfils whole-life and sustainability objectives.
Andrew Orriss from the Structural Timber Association (STA) explains why a planned approach to moisture management and durability, is an essential part of building design and construction.
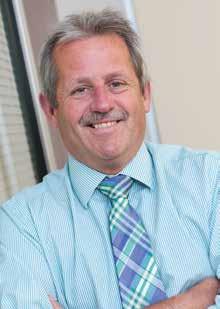
Durability is a key concern when investing in the construction of any building and it must be carefully accounted for throughout the planning, design, build and maintenance process. Buildings that do not prioritise durability run the risk of system failures from issues such as moisture ingress –problems that can be avoided by taking a strategic approach from the outset.
There are numerous examples of structural timber buildings that have stood the test of time, with many having been in-situ for centuries. But what is it that distinguishes a truly durable building from one that is vulnerable to deterioration, particularly when it comes to moisture ingress? The answer is a focus on good practice throughout the entire construction chain – from initial design conception to in-use life – all applied with a solid understanding of the materials being used. Crucially, those involved in a building’s construction need to approach the issue of durability from the perspective of ‘what if?’ at all stages of the process.
Managing moisture
Embarking on a project with clearly defined roles and responsibilities related to moisture management avoids confusion and minimises ingress risks. To help achieve this – and in recognition of the growing popularity of structural timber and the many new businesses entering this market – the STA has produced a ‘layman’s guide’ to moisture ingress, which outlines the steps required to develop an effective moisture management strategy.
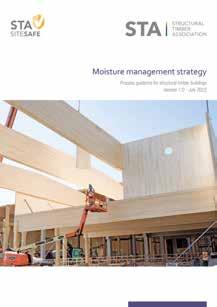
Critically, the guidance emphasises that prevention is better than cure, therefore it’s important to identify the key causes of excessive moisture and the steps that can be taken to mitigate this risk. For example, from fabrication to delivery there is the potential for rainwater to collect on inadequately protected timber panels during storage and transportation. This can be overcome by thoroughly inspecting materials on receipt and allowing for ventilation and drying time during the storage and build process.
Similarly, during construction heavy rain or snowfall can leave unprotected materials and pre-assembled elements vulnerable to moisture absorption, particularly if they are left in standing water or if trapped moisture is encased before it has been given a chance to dry. A thorough programme of protection, moisture inspections, ventilation and allocated drying out periods can avoid these issues.
Once the building is in use, the key risks are around long-term condensation, repeated humid conditions and potential floods. Avoiding these issues is down to good practice at the conceptual stage, such as ensuring adequate drainage is available in the event of a flood or service system failure and designing-out areas where condensation could collect.
RIBA Plan of Work
With these foundations in mind, the STA’s moisture management guidance states that, above all else, all parties must understand and clarify the design and build responsibilities on a project. To achieve this, the STA has set out a systematic seven-step process that is aligned with the RIBA Plan of Work 2020. Each step of the process is closely tied to the comparable RIBA stage and clearly outlines who has responsibility for moisture management and what the expected output should be. For example, linking to RIBA Stage 1 Preparation and Briefing, Step 1 of the moisture management strategy requires the principal designer to outline a responsibility matrix and produce a design life statement, taking into account the durability objectives and targets for the building.
By consistently applying the steps laid out in the moisture management strategy, relevant parties will be able to put in place plans, designs, materials and construction processes that, if executed properly, will avoid moisture defects in new structural timber buildings.
No material or building is designed to last forever but by taking a strategic and joined up approach, it is possible to create durable and sustainable structural timber buildings that will stand the test of time. Adopting an effective moisture management is key to achieving this, providing assurances to all parties and delivering a consistently high standard of structural timber construction.
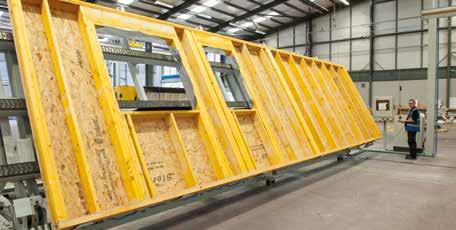
For more information and to download the STA Moisture Management Strategy document visit: www.structuraltimber.co.uk
IMAGES:
01. Andrew Orriss, Structural Timber Association
02. The guidance document ‘Moisture management strategy: process guidance for structural timber buildings’ 03-05. Timber construction is key to the UK’s net zero carbon ambitions
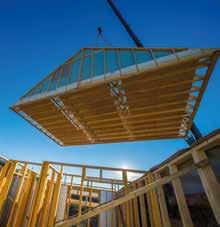