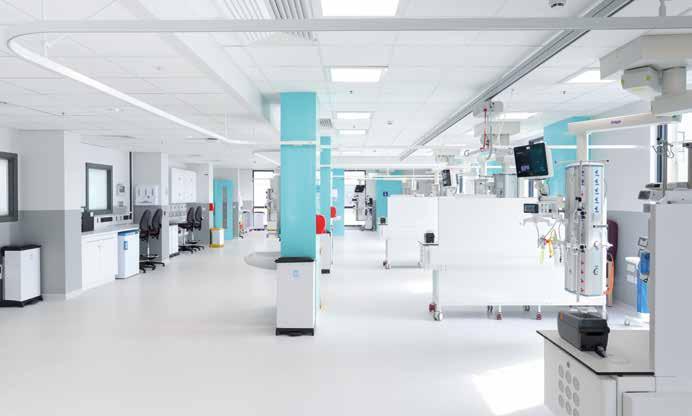
7 minute read
OCC Gets Volumetric Boost
A newbuild 48-bed critical care building delivered to the prestigious John Radcliffe Hospital in Oxford, saw a range of facilities delivered including five storeys of bespoke volumetric modular accommodation.
Healthcare construction specialists MTX have provided Oxford University Hospitals NHS Foundation Trust with a 5,450sq m new critical care building, achieving a pre-manufactured value (PMV) of 54%. The new five-storey facility, now called Oxford Critical Care (OCC), was part of a regional approach for managing critical care demand and activity throughout the COVID-19 pandemic, in addition to supporting and alleviating future seasonal and epidemic pressures for the Trust and its one million annual users.
Situated directly next to the hospital’s existing Trauma Department, the OCC connects directly into one of the main live corridors at ground floor level, proving a seamless flow between departments housing theatres and imaging and diagnostics facilities. Through offsite construction, MTX were also able to minimise disruption to the Trauma Department and allow for uninterrupted staff and patient access.
The use of volumetric modular construction, MEP services, virtual prototyping and speedy onsite installation minimised disruption to the Trauma Department and enabled uninterrupted staff and patient access 24/7. MTX’s platform approach, incorporating multiple MMC disciplines, quickly delivered this high-quality new hospital facility cost effectively, within budget and openly on time. MTX bespoke solutions are specifically created for medical and healthcare use, with advanced super-efficient mechanical heating and ventilation systems, which
1
optimise clean air flow and meet clinical needs, in addition to reducing energy consumption and protecting the estates power capacity, all whilst minimising the carbon footprint.
The new OCC comprises 3no 16 bed wards across the ground floor, first floor and second floor, with dedicated plant room and non-clinical accommodation (seminar rooms, offices and spacious staff rooms) across the remaining 2 floors. The top floor dedicated staff area, boasts enviable 360-degree views of the Oxfordshire countryside, providing staff with a beautiful and calming training environment.
Careful planning and logistics allowed the team to work out of hours to install and commission 148 modules to be
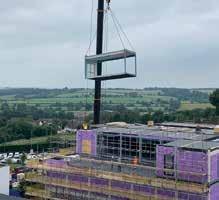
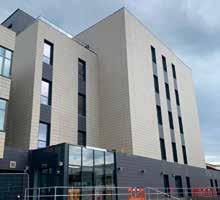
safely and efficiently craned into place in just five days by the experienced on-site team. Through continuous and close communication with the client, the team were able to work meticulously and successfully deliver the project in the shortest possible programme as well as continuity of intensive patient care.
Significant logistical challenges included tight site constraints, maintaining access to the Trauma Building and main hospital, creating the foundations and installing the piling on a pronounced slope, and obtaining the Execution Grade 3 steelwork. MTX also had to address the exacting ventilation requirements of a critical care building, divert the water and gas services, create the new sub-station and associated electrical infrastructure, and subsequently ensure vehicular access, including for cranes of different sizes.
Through excellent collaboration and teamwork between the key project partners – the Trust’s clinical, estates, and projects personnel, architects IBI Group, consulting engineers DSSR and Hoare Lee, civil engineers Rossi Long and structural engineers Alan Wood, the scheme progressed smoothly. Lyn Bennett, Matron for Adult Critical Care and Clinical Lead Advisor Nurse for the new building said: “This is a fantastic new building which has been constructed to a limited budget. We have been able to incorporate advanced 21st century designs that, from experience, will enable the clinical team to provide efficient and excellent clinical care for patients while working in a modern, bright, natural daylit and person-centred environment. The design of the new critical care building has attracted considerable external interest, including from NHSE/NHSI and believe it will prove to be a landmark building.” A combination of an extremely rapid design and planning process and strenuous on-site 14-hour working days, saw it take just 15 months to get the prestigious project from initial design to successful handover. This critical care building with such complex services requirements, would have taken up to three years to complete if traditional construction methods were used.

3 2
4
For more information visit: www.mtxcontracts.co.uk
Images:
01-04. MTX won Healthcare Project of the Year at the Offsite Awards 2022 for its work at John Radcliffe Hospital
MODULAR NHS UNIT FITS SEAMLESSLY
A £10million project for Ashford and St Peter’s Hospitals NHS Foundation Trust has been delivered by Premier Modular and provides a new priority assessment unit.
Premier Modular was appointed as the principal contractor for the 62-bed, priority assessment unit at St Peter’s Hospital in Chertsey, supported by delivery partner Claritas. Faced with increasing patient numbers and tight deadlines, the Trust needed the new building to support increased demand, especially during the busy winter period. St Peter’s chose to fasttrack the building project by using offsite construction, which reduced the overall programme time by nine months.
Designed by BDP and delivery architects P+HS, the new space purposefully reflects the existing environment, while matching the hospital’s modern needs, ensuring seamless integration. The new facility was linked to the emergency department with 62 patient bays, alongside nurse stations, staff rooms, seminar rooms, laundry and clean utilities and kitchenettes for staff. The new unit provides updated technology, with datacomms, security systems, CCTV and nurse call systems, which are all fully integrated with the main hospital.
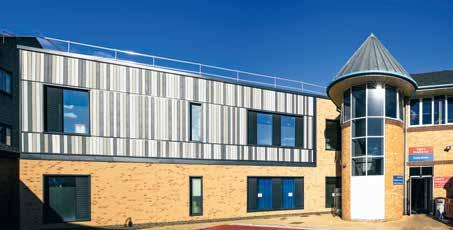
“This project shows how striking and unique architectural design, that is also in keeping with its surroundings, can
1
be successfully married with efficient delivery via offsite construction, bringing many benefits including speed and quality,” said Akshay Khera, Architecture Director, BDP.
The offsite solution was engineered to fit seamlessly into the existing hospital, maintaining flows between the existing facilities and the new unit, with continuous level floors throughout. Externally, the assessment unit is finished with vertical rainscreen cladding in grey and brickwork to complement adjacent buildings.
Andrew Grimes, Assistant Director of Property and Capital Development added: “This project responds to the urgent national need to increase capacity in emergency care. Offsite construction allows us to add space on our hospital campus more quickly. We estimate Premier reduced time on site by around six months and the overall programme by nine months. Less time on site also means less disruption to patient care, which is always a priority for hospital building projects.
“Premier had the capabilities to meet the technical constraints of this site and the brief very well, particularly to provide seamless connections at two levels to maintain patient flows and allow us to move beds easily between this building and the existing facilities. Premier was also the only offsite specialist who was able to meet our module height requirement without the addition of ramps. And the lightweight nature of steel-framed modular construction minimised groundworks which had time and cost savings. Premier demonstrated the flexibility and design capabilities to engineer a bespoke solution for this challenging site, with all the speed and value benefits of offsite construction.”
To support the Trust’s sustainability targets, the building envelope has been designed to be thermally efficient to reduce running costs and carbon emissions. It incorporates technology, such as solar control glass, integral brise soleil sun shading and a building energy management system (BeMS) to optimise energy usage.
“This scheme was ideally suited to offsite construction,” said Dan Allison, Divisional Director, Premier Modular. “It allowed the Trust to meet an urgent need to expand capacity for emergency care and the development of a very constrained site. The new building has been constructed in a courtyard and close to the emergency department, which required careful logistical planning from our project team. We maximised construction and fitout work offsite to radically reduce disruption to patient care and were only on site for around six months to produce a facility for the trust.”
For more information visit: www.premiermodular.co.uk
Images:
01. The new unit shows how modular construction can offer a striking and unique architectural design
OFFSITE CONSTRUCTION INFORMATION PORTAL
FREE TO ACCESS
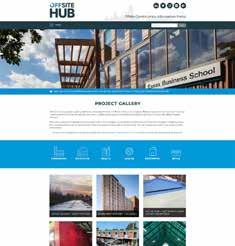
Digital Marketing Packages Available
The Offsite Hub receives over 5,000 unique visitors per month, complemented by 42,300 newsletter subscribers, making these digital opportunities an attractive proposition for marketers planning future activity.