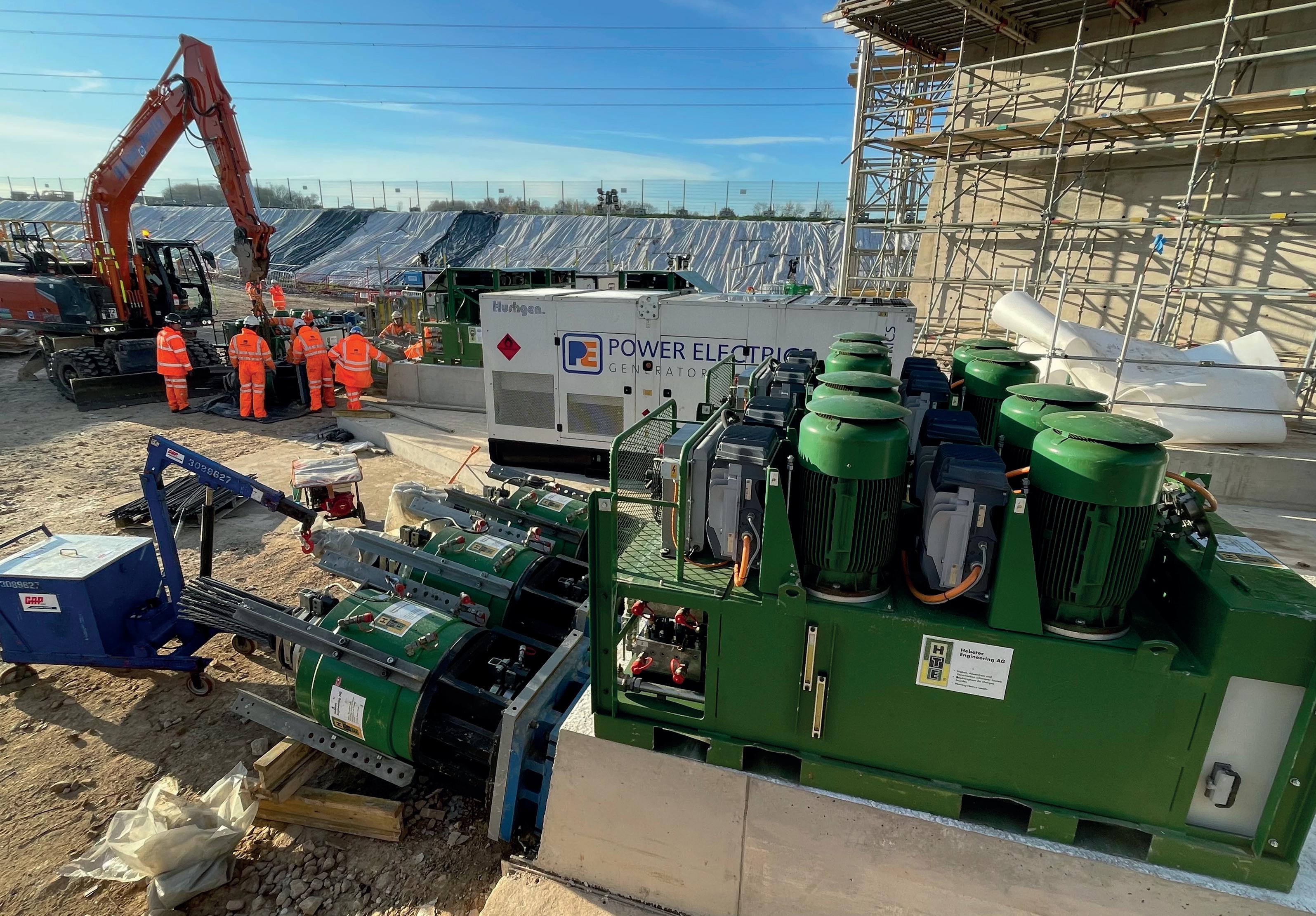
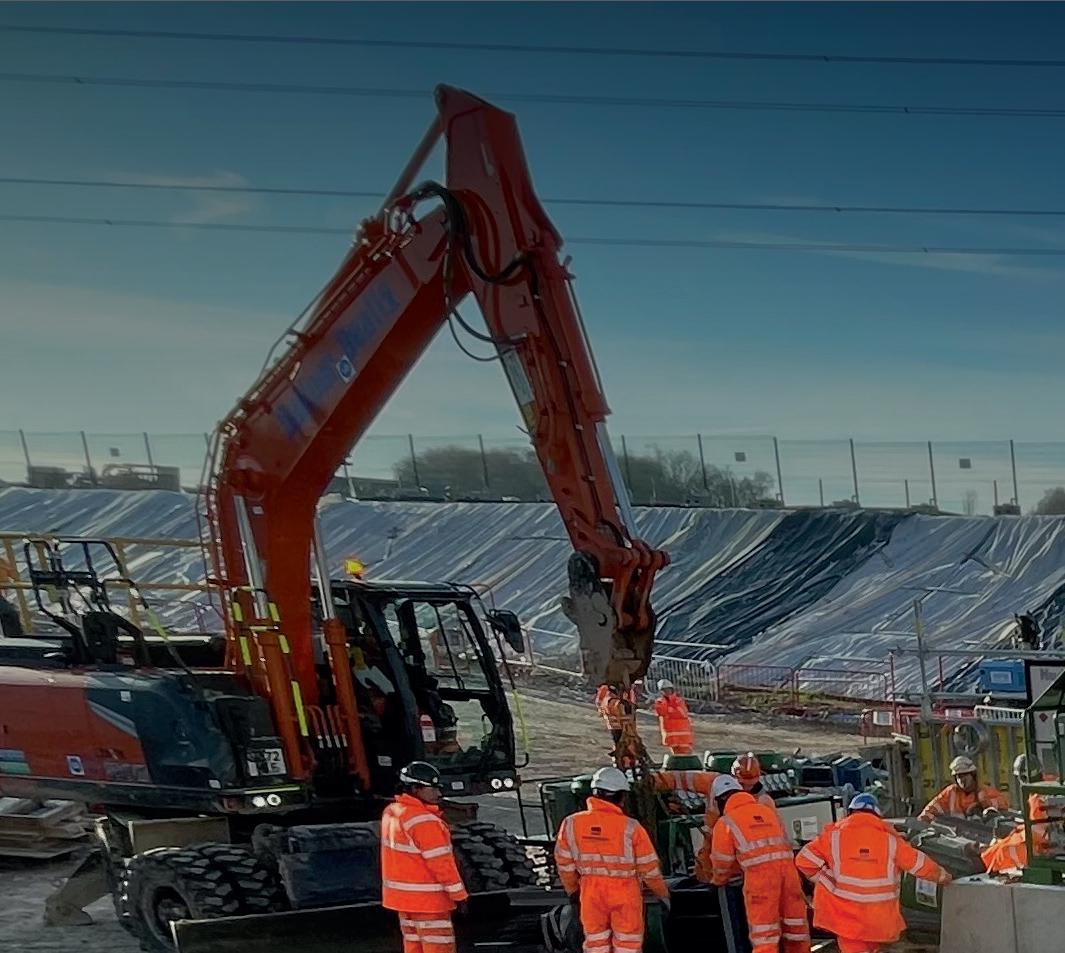
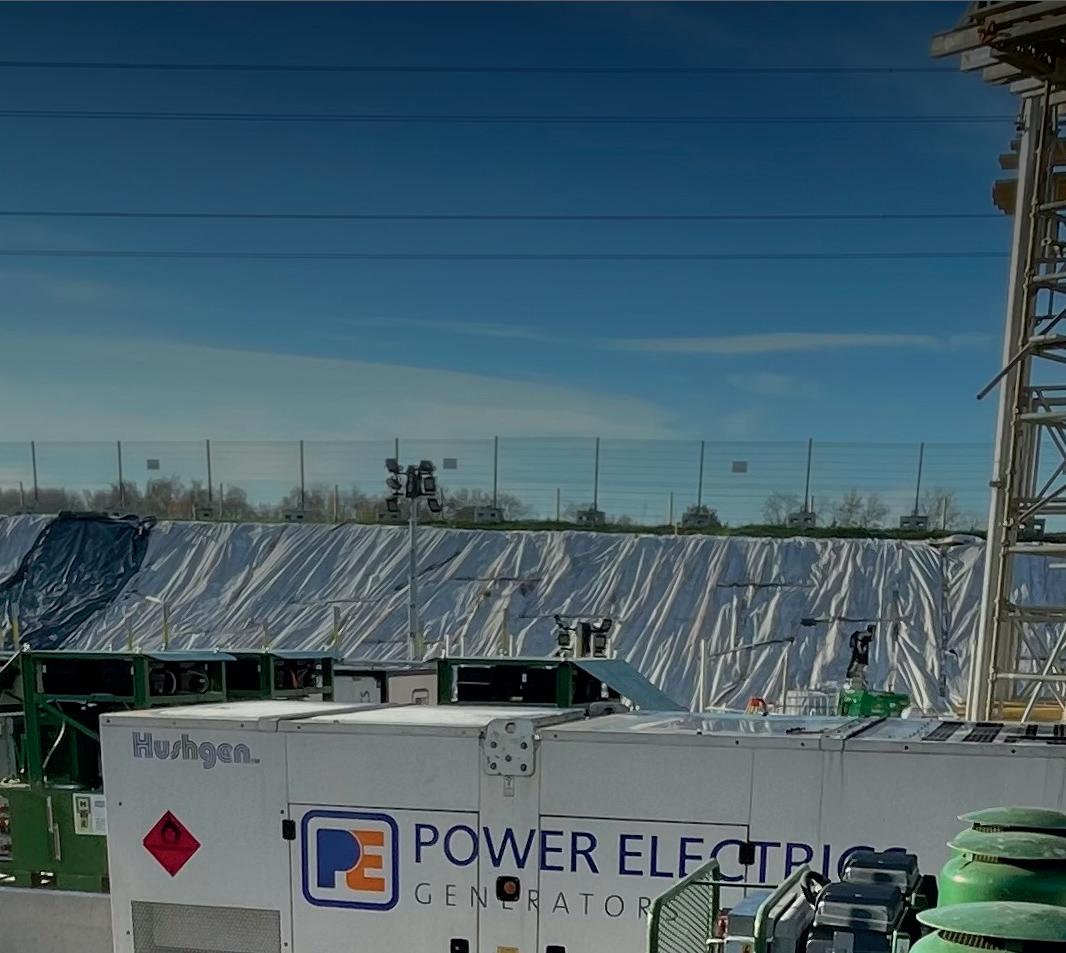
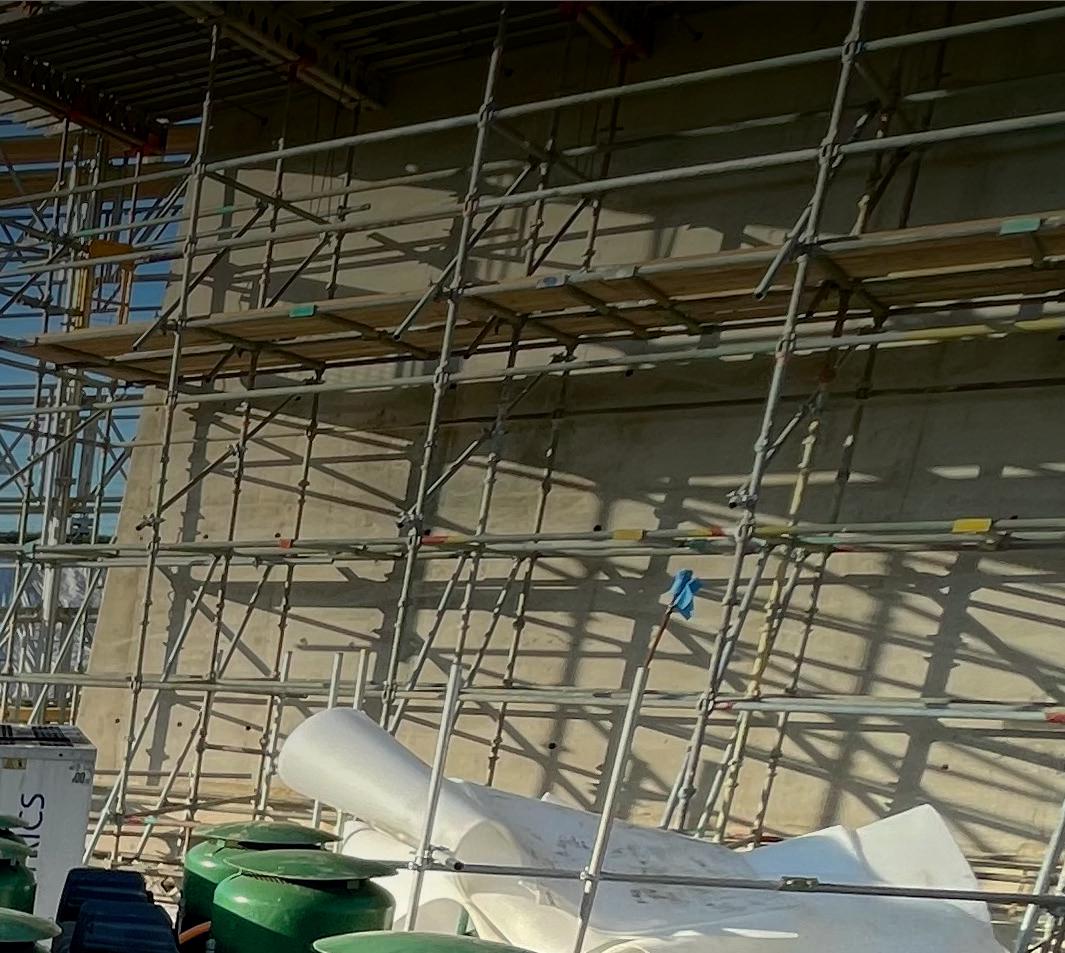
Over Christmas 2022, the bridge that will take HS2 over the M42 motorway slid into position – all 12,600 tonnes of it
Over Christmas 2022, the bridge that will take HS2 over the M42 motorway slid into position – all 12,600 tonnes of it
The M42 motorway is a key part of the Midlands highway network. From its junction with the M5 West Midlands to Exeter motorway just north of Droitwich, it runs eastwards along the bottom edge of the Birmingham metropolitan area.
Just past Redditch, the road forks. One leg continues eastwards, becoming the M40 that passes Banbury, Bicester and Oxford on its way to the M25 London orbital. The other turns left, running up the eastern side of Birmingham, crossing under the A45 close to Birmingham airport and the National Exhibition Centre and then over the M6.
Now down to two lanes in each direction, the M42 continues northwards, past Tamworth, to Measham. Here it is downgraded to the A42 dual carriageway, which continues to East Midlands Airport where it joins the M1 at junction 23A.
Like London’s Elizabeth line, the M42 is a good example of how infrastructure will attract more users than the planners predict. The northern section –only two-lanes and an A road for half of its length –is regularly congested at peak periods, with queues at the A5 junction near Tamworth and the M6 interchange a regular feature.
All of which made two things certain – the new
HS2 high-speed railway from London to Birmingham and the North would have to cross it somewhere, and there was no way that construction could be allowed to close the road for an extended period.
The first bridge that the HS2 project built over the M42 was installed in August 2020. A concrete and steel bridge, 65 metres long, was built alongside the motorway by HS2 enabling works contractor, LMJV (Laing O’Rourke and J. Murphy & Sons Joint Venture) and specialist engineering contractor Expanded.
Made up of 1,130 tonnes of steel plate girders and 1,610 tonnes of precast and in-situ concrete, the structure was ‘driven’ up the closed motorway and into position in just two days on top of two selfpropelled modular transporters. This bridge will be a road bridge, part of the new road layout being created around HS2’s new Interchange station.
The bridge that would carry the HS2 line itself, capable of carrying 200-metre-long trains running at 360km/h (226mph) would have to be much
sturdier – and heavier. Too heavy to be carried into place atop transporters. A new solution would have to be found.
The Marston Box bridge will connect with the Dunton Wood Embankment to the south and the Birmingham and Fazeley Canal Viaduct, which crosses the canal, to the north. The completed structure will be approximately 190 metres in length, of which approximately 82 metres is the Marston Box structure itself.
Above: Architect’s impression of Marston Box rail bridge over the M42
Image: HS2
Opposite: The world’s longest box bridge slide across the M42 in Warwickshire
Image: HS2
The rapid, cost effective lower carbon alternative to conventional concrete
The original HS2 Environmental Statement scheme design required the bridge to be constructed ‘in situ’ on a live motorway over a 20-month period. The lengthy closure periods would require a defined diversion route to be active for a three-month period, increasing traffic volumes, congestion and delays on the local road network. Even when the motorway was open, there would be around two years of reduced lane widths, 50mph speed limits and weekend and night closures. A new plan was needed.
“We looked at a number of options,” Sasan Ghavami, Balfour Beatty Vinci’s construction director for the project, explained. “There was always more than one option – in-situ construction, a combination of in-situ and precast and so on. Our considerations revolved around workforce safety – if we built it in-situ we would be doing so alongside a live motorway. And the motorway is only two live lanes and a hard shoulder, so if we took too much for the safety of our workforce it would cause immense disruption for road users as the M42 is very busy there.”
After much consideration of options, HS2 and its contractor Balfour Beatty Vinci (BBV) decided to build the bridge alongside the motorway along the line of the new railway and then to ‘slide’ it into place using a system known as ‘jacking’. The bridge would be pushed in a straight line using huge hydraulic jacks, inching the structure into place.
To do this, several hurdles would have to be overcome. For a start, the structure would have to be rigid enough to slide while maintaining structural integrity. A ‘box’ design, incorporating the bridge deck, two abutments, a central pier and a ‘floor’ was selected so as to give the required rigidity.
As the railway will cross the motorway at an angle, the whole box was built as a parallelogram, which added to its overall length.
It will also give passive provision for a third motorway lane in each direction, in case the M42 is widened later.
The floor slab of the structure would also have to sit below the motorway road surface, and on ground that is strong enough to support the box’s massive weight.
To prepare for this, the motorway was closed for a week in December 2021 between junction 9 (Dunton interchange) and junction 10 (Tamworth interchange). The motorway was dug out to a depth of three metres, new drainage was installed, a redundant fuel pipeline removed and a surface of compacted Type 1 aggregate laid ready to take the box. The ground was then restored and the road surface replaced so that the motorway could reopen to traffic.
Early in 2022, two tower cranes were erected on land next to the motorway to service the construction of the guide raft and the box structure. The guide raft – a reinforced concrete slab – was constructed first and then the reinforced concrete box structure, with part of the jacking mechanism cast into the base of the box.
Over the next six months, the 86-metre-long structure took shape. Developed by a design joint venture of Mott MacDonald and Systra, working on behalf of BBV, the box was manufactured alongside the motorway some 163 metres from its final position, further than any slide yet attempted.
Opposite: The Marston Box bridge will connect with the Dunton Wood Embankment
Image: Freyssinet
Below: M42 road bridge being moved into position August 2020
Image: HS2
By the time we started the excavation of the northbound carriageway, the box was already on its way to us
The box slide itself would involve an ‘Autoripage®’ jacking system, designed by specialist civil and structural engineering company Freyssinet, capable of pushing the 12,600 tonne box along the guiding raft at speeds of over four metres per hour.
The jacking system also had an influence on the design of the box itself.
“The tolerances were very tight,” Sasan recalled. “We are talking about plus or minus three millimetres for the base slab because a flat surface gives the least resistance to sliding. You’ve also got to bear in mind that this is a railway bridge, so the amount of reinforcement that went into it made it quite dense compared with other bridges.
The reinforcing bars are large to withstand the vibration and that all adds to the weight.”
“We built a flat guide raft first, with a number of troughs cast into it to take the jacking cables and upstands to guide the bridge box to slide in the right direction.
“Then we laid a grease film on that base, and a polythene membrane on top of that, and then we built the bridge box on the membrane, so it would later slide on that film.”
Three-day slide
The motorway closed southbound on Friday 23 December so that engineers from BBV and its contractors could begin excavating the road down to the level that had been prepared one year earlier.
The following day, the northbound carriageway was also shut and work moved over onto that side of the
road. Also on the 23rd, the jacking itself commenced. The bridge structure slid along the concrete raft on which it had been constructed.
That was around 120 metres long and then the bridge slid onto a very dense granular material,
similar to a Type One base material, across the motorway verge and into position.
The front of the bridge box curved upwards, rather like the curve on the front of skis, to stop it digging into the foundation material.
Bentonite – a naturally occurring clay that absorbs water and is also used for lubrication for deep-hole drilling for oil and gas – was forced under the box to help it slide and nine 1,000-tonne jacks were connected to the box by cables.
“We did a trial run on the 23rd,” Sasan said. “We established the box was moving and everything was good. We started gradually getting ourselves into position then, as soon as we had closure of the southbound carriageway, we started pushing forward. So, by the time we started the excavation of the northbound carriageway, the box was already on its way to us.
“That worked very well because we had to do certain things immediately in front of it and we didn’t want to expose the surface to the weather – we didn’t want wet ground. Luckily, the weather was with us while we were sliding and the ground was reasonably dry so, by the time the box was arrived at its final location, we were a shift ahead at that point, which was really, really good.”
Late on Boxing Day, Monday 26 December, the Marston Box finally settled into place. All that was left to do was to waterproof the base (a job made more difficult by a sudden downpour), to remove all the jacking equipment, flush out all the bentonite and seal off all the tubes. The motorway reopened on Sunday 1 January, 36 hours ahead of schedule.
Rail Minister Huw Merriman said of the team’s achievement: “This is yet another astonishing achievement by HS2 – a project which is already changing lives through employment and regeneration
and will completely transform the way we live and work once trains hit the tracks.
“Thank you to the 450 people working over the Christmas period on this incredible operation, who are playing their part in bringing this pioneering project to life. What a way to end the year.”
The life of a director can be a stressful one. In among the day-to-day running of the business and compliance obligations like PAYE, VAT and corporation tax (CT), they also must consider their own personal tax matters and legal responsibilities.
And failure to comply on both counts has consequences.
Late filing of Corporation Tax returns, for example, can result in a fine of up to 20 per cent of total CT liability, while providing inaccurate or late PAYE information, or failing to report information on time also has penalty fines. In some circumstances, directors have even been prosecuted for not fulfilling legal or tax obligations.
Of course, similar consequences exist for neglecting personal tax matters, but it’s not uncommon for these things to slip; just before the 31 January self-assessment deadline, HMRC estimated that around 3.4 million returns were still waiting to be filed.
At best, this last-minute rush will lead to mistakes being made, incorrect or estimated returns being filed, and potential loss of tax savings. At worst, penalty fines will be received.
There’s one key tax decision that needs to be made if you’re a company director: whether to withdraw money as a salaried employee, or through dividends.
It’s MPA’s recommendation that directors at least take a small salary and are enrolled on the company’s payroll.
The main drawback of taking a salary (above an annual income from salary and bonuses over £11,908) is that both the individual and company will be subject to National Insurance contributions. Salaries may also attract a higher income tax rate, dependent on how much you earn.
If you take a salary below the £11,908 threshold, you will need to consider paying voluntary class 3 NIC contributions, which can fill gaps in your contributions record to qualify for benefits like the State Pension.
Advantages to taking a salary may include Corporation Tax liability reductions, access to employee benefits like maternity leave, entitlements to higher pension contributions, and being able to take a salary even if no business profits are made.
An alternative way to draw income from a business is through dividends.
Subject to a profit being made (post liabilities and tax) then a company may choose to pay these to directors and other shareholders. Currently, no income tax is due on the first £2,000 of dividend income received, and the remainder attracts more preferential rates than income tax. Furthermore, unlike salary, no NIC (employer’s or employee’s) is payable up to the £2,000 threshold, reducing both the cost to the company and individual.
Personal cash flow needs now and in the future are the number one thing to consider when deciding whether to take dividends or salary, and each decision has tax and administrative implications.
Other things that could influence this decision include what you want to happen to the business in the future – e.g. sale, closure, family or alternative takeover; pension needs; and inheritance.
The most common question we receive from directors is ‘do I need to file a self-assessment tax return’?
Directors are not classed as self-employed, so they only need to worry about reporting additional taxable income via self-assessment.
Additional income could be from savings, other dividends, investments, sole trader activity, or taxable pensions, for example.
If all income is taxed through PAYE there’s no need to register and submit a self-assessment tax return. Sometimes HMRC will request one, but if there’s no additional taxable income to report you can ask for that notice to file to be withdrawn. That request may be granted or denied.
Above the £2,000 dividend allowance and up to £10,000, directors can request HMRC change their tax code to cover tax payments via PAYE if they don’t want to file a self-assessment. Over £10,000 that’s not an option and a self-assessment tax return is mandatory.
So, as you can see, there are tax, administrative and personal planning implications to consider when deciding whether to become a director, and how to receive funds from a shareholding.
The best thing to do is to seek advice to ensure tax efficiency now, and in the future, from an advisor like MPA who can help you make efficient tax decisions at the start, middle and end of your financial journey.
Visit www.mpa.co.uk for more information
There are tax, administrative and personal planning implications to consider when deciding whether to become a director, and how to receive funds from a shareholding. Jessica Cowling, assistant tax manager at MPA, explains
Five years since construction started (in April 2018), London Luton Airport’s new DART people mover is now carrying passengers between the airport terminal and Luton Airport Parkway railway station
Luton Airport has always been a bit different from other UK regional airports.
For a start, it is owned by the local council. London Luton Airport Ltd is owned by Luton Borough Council and trades under the name Luton Rising.
It is the fifth largest airport in the UK in terms of passenger numbers but is also one of the smallest in physical size at 196 hectares – under half that of the new Global Centre of Rail Excellence (GCRE) which is being built in South Wales and is on a 550-hectare site.
Although it handles 26,000 tonnes of air freight every year, London Luton is primarily a tourist airport, attracting passengers from all over the UK who want to fly out on package holidays or use budget airlines. Pre-COVID, passenger numbers peaked at 16.7 million passengers per annum.
As an Internationally recognised rail infrastructure service supplier, we offer a comprehensive range of services, covering S&T, civils, operational communications & overhead line equipment.
Numbers have since recovered somewhat, now running at around 13.5 million.
The airport receives positive reviews from passengers and also has its place in British folklore. Readers with a long memory may remember the Campari television advert from 1976. Produced for advertising agency J Walter Thompson, a suave Jeremy Clyde asks stunningly beautiful Lorraine Chase: “Were you truly wafted here from paradise?”
Her reply “Nah – Luton Airport!” became an instant catchphrase and inspired a hit record from the all-female band Cats UK.
10,000 rail passengers per day
The airport’s very success causes it some problems (challenges). There is car parking on site, but around 20 per cent of passengers arrive by train –Thameslink or East Midlands Railway – at Luton Airport Parkway station, which opened in 1999. In a good year, that’s 3.6 million passengers with luggage, or around 10,000 a day.
There are plans to expand the airport further. Future LuToN is the name of the proposed project to expand London Luton Airport’s maximum passenger capacity to 32 million by building a second terminal and making best use of the single runway. If the airport hits growth expectations and reaches 32 million passengers a year by 2030, the number of rail arrivals will double – more if passengers cut
back on car use as fuel prices rise and the need for decarbonisation becomes more widely recognised. And, of course, a number of the airport’s 10,000 employees also commute by train.
Passengers were being carried to and from Luton Airport Parkway station by bus/coach. It was clear that a more sustainable method of transport, and one which can carry more passengers, bags and workers, would be needed.
The selected solution was a twin track automated shuttle system. Running on rubber-tyred wheels on concrete track, the cars would be hauled/powered by an endless wire cable loop, running around pulleys at each end and each driven by a large electric motor. The two ‘trains’ can run independently, so having one out for service doesn’t affect the other. Both can run at peak times.
The civil engineering contract was awarded to a joint venture of Volker Fitzpatrick and Kier. That for the shuttle cars, drive train and control system went to Doppelmayr, an experienced supplier of such equipment that has already supplied shuttles to airports all over the world (including Birmingham airport). Siemens was appointed as a subcontractor for control room systems and Arup was brought in by Luton Rising to design the stations and act as system integrator.
Each shuttle consists of four cars and can carry 170 passengers – 34 seated, two disabled bays, everyone else stands.
Luton is the fifth largest airport in the UK in terms of passenger numbers
The two shuttles travel between the railway station and the airport, a distance of 2.1km with an elevation change of 40 metres between the Midland main line station at the lowest point and the airport terminal at the top.
If demand increases, two additional cars can be added in the centre of each consist, meaning the shuttle will then have a capacity of 240 people. Station platforms have been built long enough to handle six-car sets and, with the possibility of trains making 16 runs an hour, that works out at 3,840 passengers per hour in each direction.
New concourse
Working in conjunction with Network Rail, owner of Luton Airport Parkway railway station, a new passenger concourse has been built to service both stations.
Travellers arriving by train will exit the main line station through a gateline, cross about 30 metres of concourse, and then enter the DART (Direct Air-Rail Transit) gateline. DART services are not free, a single non-concession ticket costs £4.90.
However, through tickets can be purchased from the originating station straight to the airport and, in those cases, the same ticket that allows passengers to exit the main line station gateline will grant them access to DART.
The two tracks terminate in bay platforms, with a row of platform screen doors along each side. One platform face is designated as giving access to the shuttle, the other is for exit.
The journey itself is undramatic, quiet and smooth, and takes about three minutes. Towards the top, the shuttle passes into a tunnel. This is under a live taxiway, which had to remain operational through construction. The tunnel, built using a cut-and-cover technique, was therefore constructed in stages, allowing the taxiway to stay open, for part of its width at least, throughout the process.
On reaching the terminal level, the doors on the exit side open first, allowing passengers out, and only then do the doors on the other side of the shuttle. The terminal building is only a short walk away.
Behind the scenes, there is a control room under the new Parkway station, where the system is constantly monitored with CCTV in the stations and the shuttle cars.
At the Central Terminal station, shuttles in normal operation go back the way they came – they stay on the same track and the cable drive is reversed. However, if needed, they can proceed onwards, through a doorway and into the maintenance bay. Here, both light and heavy maintenance can be carried out – engineers have already removed a bogie from one of the shuttles “just to prove they can do it”, project director Ruud Haket commented.
With all of the infrastructure in place and test runs complete, safety checks and approvals were carried out by the Department for Transport. Interestingly, rail regulator the Office of Rail and Road was not involved – DART is neither a train nor a road vehicle.
Instead, it was approved by the team that looks after cable cars because, with its cable operation, that’s essentially what it is – Doppelmayr also built the London Cable Car (now the IFS Cloud Cable Car, formerly the Emirates Air Line). Passenger safety, however, has to conform with light rail requirements.
King Charles III has already given his approval – he visited on Tuesday 6 December and took a ride from Parkway station to the airport terminal.
Now the travelling public can give their own verdict. Luton DART opened, without fanfare, for four hours on Friday 10 March. It will now start to open for a little longer each day until it is in full operation, running 14 services an hour, 24 hours each day.
And that’s just the start…
The journey itself is undramatic, quiet and smooth
The Department for Transport released its strategy document “Decarbonising transport: a better, greener Britain” in July 2021. It set out the government’s commitments and the actions needed to decarbonise the entire transport system in the UK, including the pathway to net zero transport in the UK, the wider benefits net zero transport can deliver and the principles that underpin the UK Government’s approach to delivering net zero transport.
This strategy is about more than just railways. Part 2 of the document covers decarbonising all forms of transport, with sections on increasing cycling and walking, zero-emission buses and coaches, decarbonising the railways, a zero-emission fleet of cars, vans, motorcycles, and scooters, accelerating maritime decarbonisation and accelerating aviation decarbonisation.
Grant Shapps, who was Secretary of State for Transport at the time, wrote in his foreword: “Transport decarbonisation is a dull way of describing something much more exciting and far-reaching.”
He went on to say: “Decarbonisation is not just some technocratic process. It is how we fix some of that harm. It is how we make sure that transport shapes the country and the economy in ways that are good. It’s about taking the filth out of the air and creating cleaner,
quieter, healthier places. It’s about a second, green, industrial revolution, creating hundreds of thousands of new, skilled jobs, in some of the proud towns and cities that were the cradle of the first one.”
It’s a very big subject and has some very big goals. These include:
Increasing cycling and walking by investing £2 billion over five years with the aim that half of all journeys in towns and cities will be cycled or walked by 2030;
Supporting delivery of 4,000 new zero-emission buses and the infrastructure needed to support them;
Leading by example with 25 per cent of the government car fleet ultra-low emission by December 2022 and 100 per cent of the government car and van fleet zero emission by 2027;
Delivering a net-zero railway network by 2050, with sustained carbon reductions in rail along the way, and removing all diesel-only trains (passenger and freight) from the network by 2040;
Consulting on the Jet Zero strategy that will set out the steps needed to reach net zero aviation emissions by 2050.
To discuss what is being done to achieve these goals, and review the challenges they present, global design and engineering consultancy Arup recently hosted an event on the topic ‘Tackling Decarbonisation with Purpose – The race to decarbonise transport’, with speakers from four of the transport sectors highlighted in the government’s strategy paper.
Opening the event, Arup’s global transport lead Isabel Dedring said: “The purpose of this evening’s discussion is to explore how we can accelerate the decarbonisation of our sector – the transport sector. We all want to do the right thing. We know about the carbon targets. We know the pressures from investors, from ESG (Environmental, Social and Governance) reporting and finance. But, for all of us, I think we know how hard it is to achieve change with pace and with purpose in any sphere of our lives, and this is no exception and is a particularly knotty problem.
“So, what can we learn from each other? And how can we accelerate real change at scale on the ground?”
She then introduced the first of the evening’s speakers, representing the walking and cycling sector. Chris Boardman is the UK’s national active travel commissioner. A former professional cyclist, he held the Yellow Jersey in the Tour de France on three separate occasions, took three World titles on track and road and broke several world records.
As the government’s target of zero carbon by 2050 gets closer every day, the transport sector is considering what still needs to be done
After retiring from active competition, he helped set up and lead the R&D branch of the Great Britain Olympic Cycling team, a squad that then dominated the international scene, becoming the most successful British sporting team of all time.
Chris explained that, not only is walking and cycling the greenest form of transport, it is also healthy and inexpensive. “It costs £20 a year to service my bike,” he said.
“We have to remember that just under one third of people in this country don’t have access to a car,” he continued, “so it’s an incredibly versatile, useful form of transport for our local journeys.”
Andy Burnham, Mayor of Greater Manchester, asked him to become walking and cycling commissioner and to help put in place the improved provisions for both activities that he had been advocating for years.
“We found out that just under one third of all car journeys in Greater Manchester were of less than one kilometre,” Chris stated. “250 million journeys a year were less than a kilometre. And the cost of those journeys was £2.75 billion.”
So, his team analysed where people wanted to travel, and asked the public to draw up a map of where they wanted cycleways and safe walking routes to shops, green spaces and other amenities. The result was a network that was 1,800 miles long, took 10 years to deliver and cost £1.5 billion. And, because the public drew up the routes, they owned it and they used it.
Using the routes, and walking and cycling to his local station, has enabled Chris and his family to go down from two cars to one, and that one is electric, which is what decarbonisation on a local basis is all about.
John Fagan, Arup’s UKIMEA transport leader, next introduced Karen Dee, chief executive of the Airport Operators Association, to comment on decarbonisation from the point of view of the aviation sector.
Globally, aviation represents two per cent of carbon emissions, or seven per cent within the UK. As other sectors start to decarbonise, then aviation’s share will increase. However, the sector has pledged to reach zero carbon by 2050, with a 20 per cent reduction in net emissions by 2030 and 40 per cent by 2040.
“What’s clear for us is that aviation is quite a hard sector to decarbonise,” Karen continued. “A lot of our decarbonisation will come as we ramp up once we get into the 2040s. But there are game-changing technologies out there. Sustainable aviation fuel (SAF) will make a big difference.
“We have a Jet Zero council that has been established by government, joining with industry, focused entirely on getting to 2050. We have seen the first sustainable aviation fuel plant given planning permission for Immingham, we have seen airspace modernisation, which is really crucial – motorways in the sky – and we are seeing hydrogen/electric planes being given their first test flights. Last November, the RAF flew a plane entirely on SAF and Virgin Atlantic is planning to fly a plane from London Heathrow to JFK New York on SAF.”
At airports, there is an increasing use of electric vehicles, reducing the overall carbon footprint of the sector.
Nick Harris, CEO of National Highways, joined the conversation at this point. “We have a similar kind of story and similar timescales,” he started. “By 2050, we need road transport to be carbon neutral. And what progress have we made on that.
The vast proportion of carbon that we emit comes out of the tailpipes of cars and lorries
“It’s quite a challenge because, collectively, we are responsible for something like 25 per cent of all greenhouse emissions in this country. So, we we’ve got a huge responsibility to make a difference and to hit those targets by 2050.
“Something like 90 per cent of all journeys in this country take place on roads and, if you look forward to 2050, that’s still going to be largely the case. If you look at freight, it’s a factor of something like nine to one, road versus rail.
“So that’s our reality. Our challenge is how do we maintain that flexibility, with all of the support that provides to the economy, and still meet the 2050 targets? We are seeing a lot of really innovative ideas around road building and road construction, but of course the vast proportion of carbon that we emit comes out of the tailpipes of cars and lorries. So, we are looking to zero-emission vehicles, at hydrogen and other fuels. But thinking of what Chris Boardman said earlier, people are going to have to change how they live their lives, change the pattern of the way they use things, because the road is not always the right solution for journeys.”
Attention turned to rail, the fourth sector represented on the panel, and to Shamit Weinberger Gaiger, managing director of the West Coast Partnership, which both provides rail services on the West Coast main line and is the shadow operator for HS2.
“Network Rail published its Decarbonisation Strategy two years ago, and it was pretty much electrification, electrification and electrification,” she began.
“On the operations side, train operating companies have had targets to reduce carbon for many, many years – over 10 years now – and they are slowly getting there. They have targets they need to meet and they are slowly delivering them.
“In Scotland, where the government has more ambition, they have a much bigger appetite and are willing to invest, they are electrifying.
“However, if we really want to take it to the next level, we need to have commitment from Treasury to give us the money for further electrification. According to a report published last year, we have got 71 per cent of our train fleet electrified – we need to make sure that the rest is.
“And we need to be proactive as an industry and understand that not everything is going to be electrified. So, for example high-volume-high-speed must be electrified. On lines that are not high volume or high speed, maybe there is not enough demand. So, hydrogen and batteries and bi-modes can supply the short-term solution.”
After the introductions, the panel continued the discussion and answered questions from the floor. But the crux of the evening’s discussion was that all the transport sectors have similar challenges, with the possible exception of walking and cycling.
All need to learn from each other, but they can’t do everything and people are going to have to change their lifestyles and their approach to transport in the future, so we can ALL benefit from the progress being made to get to zero carbon by 2050.
We need to have commitment from Treasury to give us the money for further electrification
ust two months ago, in the January issue of Rail Director, the article “What now for GBR?” examined the issue of rail reform, which had commenced with the publication of Keith Williams’ report and the William-Shapps Plan for Rail in May 2021.
That article answered the headline in another publication “GBR is dead but reform lives on” and outlined how people were talking about rail reform. The consensus was that reform was still needed, but the jury was out on what form it would take and the ‘Great British Railways’ descriptor would probably not survive.
However, over the last 60 days, a number of speeches around the country have brought Great British Railways back onto the agenda.
It started with Secretary of State Mark Harper’s George Bradshaw address, delivered on 7 February.
He began by commenting that nothing ever seems to change. The annual George Bradshaw address gives industry leaders a chance to express their opinions and, to an extent, climb onto their soapbox to address the challenges of the day. And it is those challenges that seem fairly constant.
The last Secretary of State to give the address
was Patrick McLoughlin in 2016. Six years later, on the same platform, Mark Harper said: “Patrick’s 2016 Bradshaw Address – a passionate call for a more flexible, more accountable and more joined up railway – still rings true today.
“As do the reflections of previous Bradshaw speakers – Lord Hendy’s case for a whole system railway in 2018, Keith Williams a year later, with his relentless focus on passengers, and even (Network Rail chairman 2009-2012) Rick Haythornthwaite’s warning, at the inaugural Bradshaw Address in 2011, of a disillusioned public not trusting the way our railways are run.”
The Transport Secretary then stated that the railways, currently mired in industrial action, routinely letting passengers and freight customers down and historically unable to deliver major improvements at good value for the taxpayer, aren’t fit for purpose. What Britain needs, he said, is a modern railway that meets the needs of the moment, one reliable enough to be the seven-day-a-week engine for growth businesses expect, nimble enough for post-pandemic travel while allowing more flexibility for freight and
efficient enough when public spending is being scrutinised like never before.
“The railways need fundamental reform,” he announced, and then proceeded to tell his audience what he and the government intend to do.
He said that Keith Williams’ blueprint for a more customer focused and joined up railway was a good way to start, but he added that he intends to go further and actually enhance the role of the private sector, not just in running services, but in maximising competition, innovation, and revenue growth right across the industry, benefits that he suggested the private sector has delivered time and again.
Ticketing will be one of his first targets. It is, he noted, the issue which tops passenger lists of biggest concerns. “With 55 million fares available, how can anyone feel confident they’re getting the best value for money?” he asked. “Ticketing should be hassle free, something you don’t even have to think about.
“This is not about increasing fares,” he commented. “I just want passengers to benefit from simpler ticketing that meets their needs.”
Mark Harper made sure his audience realised he was talking about reforming the railway for the benefit of its customers, not just its passengers.
The scepticism of the past couple of months has been replaced by a real appetite for rail reform
“Carrying tens of billions of pounds worth of goods, we cannot overstate rail freight’s untapped potential for green growth,” he said. “So, I intend to create a duty to ensure the new industry structure realises that potential, with a dedicated Strategic Freight Unit tasked with creating better safeguards, more national co-ordination and, later this year, setting a long-term freight growth target.”
He didn’t shrink from talking about Great British Railways, and the reforms it could bring. “By the summer, we will respond to the consultation on GBR’s legislative powers,” he promised. “The industry has long called for a guiding mind to co-ordinate the network, so GBR will be responsible for track and train, as well as revenue and cost.
“It means finally treating the railway as the whole system it should be, rather than the web of disparate interests that it’s become. Passengers will no longer face the excuse-making and blame shifting of years past. Instead, GBR will be wholeheartedly customer focused, serving as the single point of accountability for the performance of the railway and, crucially, following Ministerial direction.”
He also answered some of GRR’s critics. “There remains a lot of misinformation about GBR,” he said, “so let me tackle some of these myths head on.
“This is not Network Rail 2.0, nor a return to British Rail. Taking politics out of the railways is the only way to build a truly commercially led industry, and, for me, that is non-negotiable. That’s why GBR will be an arm’s length body, ensuring a balanced approach to both infrastructure and operations, with both sides getting a seat at the table and both sides ultimately delivering an efficient, high-performing railway for customers.
“The role of ministers is to provide strategic direction and be accountable to Parliament, it is not the role of ministers to pore over operational decisions. For example, I shouldn’t need to approve whether a passenger train ought to be removed from the timetable to allow a freight train to run instead. That will be left to industry experts in five regional GBR divisions working in partnership with regional bodies such as the Greater Manchester and the West Midlands Combined Authorities.”
The role of the private sector in the reformed railway interested many in the audience. “Under privatisation, and thanks to a resilient and world-class supply chain, passenger numbers doubled to 1.75 billion by the eve of the pandemic, with private sector investment in rolling stock reaching nearly £7 billion over the past 10 years,” Mark Harper explained, adding: “I am not prepared to turn my back on that commercial expertise.
“The National Rail Contracts and current overcentralised approach are temporary, a shortterm fix that has helped steer the industry through the pandemic, and this will be phased out. Instead, I want the private sector to play its most important role in our railways yet, to reinvigorate the sector, drive innovation and ultimately, attract more customers to the railway. It will do so in partnership with GBR, which will help set the right commercial conditions across several key areas.
“The GBR Transition Team will develop the guiding long-term strategy for rail, which will be published later this year and I hope will provide strategic direction to the sector.”
He then rounded off his address with one very important piece of information, stating that his words “have the full support of the Prime Minister and the Chancellor”.
“So, as a whole government, we are pressing ‘go’ on rail reform,” he concluded. “Day to day work will be ably led by the Rail Minister, Huw Merriman, who has long championed the need for a reformed railway. He will provide the stability and leadership needed, while also giving the industry freedom to deliver meaningful change, to put customers first, to realise the benefits of GBR, to help enhance the role of the private sector. Because only then can the railway earn the public trust it needs to grow.
“This is our chance to resurrect some national pride in our railways. A chance to harness the political will, the economic imperative and the industry buy-in to build the modern railway Britain deserves.
“It’s a chance we cannot waste.”
GBR is therefore very much back on, after some of the uncertainty resulting from the many changes of government during 2022.
Support from the Prime Minister will ease the path of the necessary legislation through Parliament, which the Chancellor’s backing will have obvious benefits in terms of funding the changes that are needed.
Speaking a few days later, Andrew Haines, Network Rail’s chief executive and also leader of the GBR Transition Team, said he was particularly impressed how quickly Mark Harper had understood the need for rail reform once he had been been appointed Secretary of State on 25 October 2022. He rapidly understood the opportunities it presents and then arranged for both the Prime Minister and Chancellor to get on board with the process.
“Mark came to this quite sceptically at the beginning of November,” Andrew Haines remembered, “but by the week before Christmas he had written to the Chancellor saying that he bought into rail reform, he understood the logic, he understood the compelling case. Considering that he was also dealing with industrial relations and a lot of other things at the time, that gives me confidence that the fundamental logic behind rail reform is good and robust and withstands a lot of real scrutiny.”
Although not all of the intended reforms need new legislation, some do. Ticketing reform, for example, does not, but the transfer of the ability to sign contracts with train operators from the Department for Transport (Secretary of State) to GBR certainly does. At the same time, some adjustment of the regulatory regime will also be required to make it fit with the new management organisation.
It looks likely that this legislation will be introduced to Parliament in the fourth session, probably in the late autumn. Once the Bill has received its second reading, preparations can be put in hand, including the recruitment of senior GBR executives. Expectation is that GBR will be up and running late in 2024.
Top: Andrew Haines Bottom: Jonathan FoxPassage of the legislation would appear to be uncontentious. The Labour opposition may have different ideas on how GBR should run, and how much control it should have, but the basic concept of some sort of ‘guiding mind’ seems to be accepted, so the same primary legislation will need to be in place to make that happen.
The idea of GBR has, of course, to be sold to the whole nation, not just railway executives and politicians. Wales and Scotland have transport devolved to their own local Parliaments, and various English regions are also now getting involved in setting targets and managing rail transport, most notably Transport for the North and Midlands Connect.
At the latter’s recent annual conference, Jonathan Fox, lead for partnerships at GBRTT, highlighted the need for regional cooperation.
“I keep coming across people who ask is GBR actually going to happen? Is reform dead? But I believe that the Secretary of State (speaking at the George Bradshaw Address) made a very clear statement about the future of the railways.”
Jon focused on three topics – the importance of customers, including ticketing and ticket pricing, freight and a rail freight growth target – structure and structural reform of the industry, including a strong focus on regionalism – and the role of the private sector.
Finally, he talked about capital investment. He said that it was all very well planning new infrastructure that will connect up centres of population and industry, but
it was also important to plan in, at the same time, the services that will run on that infrastructure.
“Unless and until we have a holistic approach to making sure that, whatever the business case said, the services that were expected to run, when new infrastructure is invested in, do run, then we will only have completed half of the job,” he concluded.
“I believe that a future that looks at Great British Railways with an integrated, holistic approach to both services and infrastructure will bring better
railways, better connected railways and better regionally focused railways.”
So, there are many expectations from the rail reforms that Great British Railways will bring about. More focus on customers, both passengers and freight, simpler ticketing, more reliable services, better regional connections, reduced costs and improved efficiency. But, whatever anyone’s personal ambitions in those regards, the only way they will get delivered is by Great British Railways, which is far from dead.
Digital ‘in-cab’ signalling has several advantages over traditional coloured light signals – and the earlier semaphore types that are still in use in some locations.
For a start, putting all of the signalling instructions on the driver’s desk means that lineside signals can be removed. Conventional lineside signalling systems are costly to install and maintain and, despite their high construction and maintenance costs, signalling asset failures are a major cause of delays. In any one year, there are something like 15,000 signalling failures that are severe enough to affect a service –that’s about 40 a day spread around the network.
Digital signalling systems remove a lot of trackside physical infrastructure and are operated by on-board equipment, which is placed in train cabs. This provides better information for drivers and is more cost efficient to operate.
The signalling system being used to upgrade Britain’s railway is the European Train Control System, or ETCS. Although developed in the EU – hence the E of ETCS – the system is, in fact, used worldwide.
Equipment made to the ETCS standard should be interoperable between manufacturers, so one company’s on-train system will talk to another company’s trackside sensors, giving train companies and infrastructure owners flexibility when choosing suppliers.
UK installations are to level 2 of the ETCS standard. This uses trackside equipment to monitor the train’s position and GSM mobile-phone technology, albeit to a GSM-R railway standard, to communicate between the control centre and the train.
However, all movement authorities are passed to the train’s driver via the signalling system, so conventional signals are no longer required. Because of this, the so-called ‘blocks’ between signals are no longer a fixed length, dictated by the position of the conventional signals, so trains can run closer together more safely, increasing capacity.
The combination of ETCS signalling and GSM-R train-shore communications is known as ERTMS or the European Railway Traffic Management System.
As a further enhancement, Automatic Train Operation can be overlaid on top of the ETCS. This effectively allows the train to drive itself, shortening
stopping distances and improving the accuracy with which the trains stops at a particular point, important if stations are fitted with platform screen doors.
The ATO does not replace the driver, who will still close the doors and launch the train when it is safe to do so, be ready to take over if there is a fault or an incident, and drive the train manually outside of the ATO area.
In the UK, there are already some lines fitted with ETCS signalling. The Cambrian line in Wales, linking Shrewsbury with Aberystwyth and Pwllheli, came into full service in 2011 operating at ETCS level 2. Two signaller positions were implemented in Machynlleth to control the route, which is supported by the deployment of a GSM-R system, axle counters, motorised point machines and balises along the track and a single Radio Block Centre (RBC) installed at the control centre in Machynlleth.
The Thameslink project running North-South through London is controlled using ETCS Level 2 and ATO in the central section. The utilisation of ATO over ETCS allows the achievement of a very ambitious timetable in the core.
At the southern end of the East Coast main line, the Northern City line out of Moorgate is now fi tted with digital ‘in-cab’ signalling
The Elizabeth line across London uses a proprietary CBTC (computer-based train control) system through the tunnels under London, which is similar in concept to ETCS but is designed for high-capacity metro systems. However, when trains emerge from the western portal onto Network Rail tracks and run on to Heathrow, they switch to an ETCS level 2 system.
In addition to these operational systems, ETCS is also installed on the Hertford Loop, a five-mile stretch of line near Hitchin between Molewood tunnel and Langley South junction. This has been used for testing, particularly regarding the level of interoperability between equipment from different manufacturers.
The latest ETCS line is the Northern City line from Moorgate to Finsbury Park. This is the first phase of installing ETCS on the East Coast main line, from King’s Cross to Stoke tunnel, just short of Grantham and a distance of 105 miles, as part of the billionpound East Coast Digital Programme.
Northern City line services are run by Great Northern, part of Govia Thameslink Railway (GTR), which also runs the trains on Thameslink using ETCS between Kentish Town, Blackfriars, and London Bridge or Elephant & Castle.
While much attention has been paid to the installation of the lineside infrastructure and control equipment, and the fitment of ETCS computers and displays to the train, GTR’s drivers have had to be trained up to use the equipment.
Driver training on the Northern City line will begin during the summer, once the ETCS is passed fit for passenger service on the route. Currently, for the Thameslink section of ETCS, just over 250 of the company’s 900 drivers have been through the required training course, a process which was delayed by the COVID pandemic and is also governed by the need to keep drivers in the cab of passenger services –take too many out for training at one time and service levels will suffer.
A suite of rooms has been set aside for this training at GTR’s Hornsey depot. Drivers are introduced to the concept and then given hands-on experience using simulators before being taken out on the live railway, all as part of a one-week course.
One advantage on both Thameslink and – for the future – the Northern City line is that drivers can and will be able to start using their new skills the moment they qualify. They can straight away drive trains using both ETCS and, in the Thameslink core, ATO. There is therefore no delay after qualification, which could possibly lead to a loss of competence and the need to retrain.
In fact, the current team of drivers has a mixed skill set. Some can only drive the trains manually, some are ETCS-trained and others also have ATO qualifications.
When a driver logs into the train, they also log their competency, and the train is driven accordingly. So successive trains in the schedule can be driven by drivers with different qualifications. It will take time to train the entire roster, current estimates are that training will not be complete until 2025.
Peterborough
Huntingdon
St Neots
Sandy
Biggleswade
Arlesey
Hitchin
Stevenage
Knebworth
Welwyn North
WELWYN GARDEN CITY
Hatfield
Welham Green
Brookmans Park
Potters Bar
Hadley Wood
New Barnet
Oakleigh Park
New Southgate
Kings Lynn Watlington
Downham Market
Littleport Ely
Waterbeach
Cambridge North
Cambridge
Foxton
Shepreth
Meldreth
Royston
Ashwell & Mordon
Baldock
Letchworth Garden City
Watton-at-Stone
HERTFORD NORTH
Bayford
Cuffley
Crews Hill
Gordon Hill
Enfield Chase
Grange Park
Winchmore Hill
Palmers Green
Bowes Park
Thameslink Core
Kentish Town
LONDON ST PANCRAS INTERNATIONAL
Farringdon
City Thameslink
LONDON BLACKFRIARS
Elephant & Castle
Alexandra Palace
Hornsey
Harringay
FINSBURY PARK
LONDON KING’S CROSS
LONDON BRIDGE
Selecting ETCS and ATO is as simple as the qualified driver pressing a button when the train reaches the transition point on the approach to St Pancras at the northern end and to London Bridge and (from Elephant & Castle) to Blackfriars in the south.
To ensure that testing and commissioning drivers have experience of driving on a fully ETCS railway – one without lineside systems – they have spent time at the Cambrian line, driving Class 158 service trains solely by ETCS. In return, Cambrian line drivers experience big-city driving on a hybrid railway when they visit Thameslink. Oliver Turner, GTR’s head of ERTMS integration manager, called it “industrial tourism” and recalled that, on one visit, the entire Cambrian line service was being operated by five GTR drivers – a real eye-opener!
At a recent visit to Hornsey depot, Inside Track was talked through the current status of ETCS/ERTMS on both the Thameslink core and the Northern City line. Oliver Turner was joined by Matthew Teller, GTR’s ERTMS integration manager, Sarah Hewlett, change programme manager for Network Rail, and Daniel Hill, Siemens senior project engineer at Siemens.
Drayton Park
Highbury & Islington
Essex Road
Old Street
MOORGATE
February 2023
Previous page: A Class 717 Northern City line train waiting to depart Highbury & Islington for Welwyn Garden City,
Opposite: Driving the simulator
In any one year, there are something like 15,000 signalling failures that are severe enough to affect a service
On Thameslink, both ETCS and ATO have already been deployed. All of the trains are fitted with the requisite equipment and the only reason that some services aren’t using it is that not all drivers have been trained yet. On the Northern City line, the trackside infrastructure is in place and the trains are all fitted with ETCS. The Class 717 are not fitted with ATO as this won’t be used on the line or indeed on the ECML. Testing is taking place and the line will start carrying passengers using ETCS in 2023 and become fully digital in 2024.
Driver trainer Jim O’Donnell, who manages the simulators at Hornsey, was keen to show how the process worked. Trainees sit in front of a large screen showing a realistic view of the track ahead and are then shown how driving under ETCS differs from conventional driving. The panel in front of them shows speeds, distance to the next point of interest, upcoming speed restrictions and a host of other information that allows them to drive the train to its optimum.
Effectively, they can “see round corners”, as Jim explained. The next stop point may be out of sight, yet the distance counts down and gives the driver all the information needed to reduce speed or bring the train safely to a stop. After spending some time trying out the simulator, and stopping the virtual train ‘almost’ at the correct position alongside the platform, it was outside to Finsbury Park station to see ETCS driving in practice. The Thameslink service departed under conventional AWS/TPWS signalling (Automatic Warning System/ Train Protecting and Warning System).
As it approached King’s Cross, it was directed to the right through the Canal Tunnels towards St Pancras.
Once in the tunnel, the yellow ATO light shone brightly. Jim pressed the button and we were under ATO control – it was as simple as that. Without the driver touching the controls at all, the train came to a halt at St Pancras.
It is easy to see the benefits, both in terms of capacity enhancement and service regularity and reliability. ‘All’ GTR has to do now is train another 650 drivers, which will keep Jim and his team busy for a few months yet!
Drivers can start using their new skills the moment they qualify
Selling tunnel is in Kent, midway between Faversham and Canterbury on the line from London Victoria to Dover Priory. Opened in 1860, when the line was built, it is 663 metres (33 chains – 726 yards) long, twin track and brick lined.
The tunnel was dug through Thanet sands, or Thanet beds, which form a layer between London clay above and chalk beneath. The line approaches the tunnel in a deep cutting. And therein lies the problem.
Derek Butcher, Network Rail’s principal geotechnical engineer for the Southern region, explained the problem. “It’s a sandy cutting, and it has spring lines coming out of it,” he told Inside Track. “It’s a wet tunnel as well, with a lot of water in the drainage system, which is in a poor condition.
“The rainwater filters down through the sand, hits an impermeable layer and then come out as a spring – it hits a clay layer that forms the base or bed between the Thanet sands and the chalk and
then runs out the face of the cutting. When that happens, it saturates the bottom of the cutting as the water can’t get away unless the drainage is effective, and the drainage isn’t particularly good at that location.
“There is a drain in the six-foot that is meant to transmit water from the cutting through the tunnel and beyond.
“The drain is on quite a good slope, but the water isn’t finding its way from one end of the tunnel to the other.”
Full end-to-end capabilities, as a trackside POS and Principal Contractor; From ground investigation, design, and temporary works through to all types of ground engineering and geotechnical solutions
A track record of 450+ completed Network Rail projects; Including over 200 stations, major electrification schemes, re-signalling projects, track bed stabilisation, slope retention, sheet piling and ground investigation
Track Bed Stabilisation is a system unique to Van Elle and is used to stabilise the track bed without the need for removing the track or ballast
Van Elle has the in-house ability to design and manufacture off-site, for both steel and precast concrete in our in-house factories and workshops
Off-site manufacturing and other modern methods of construction (MMC) has the potential to transform the delivery of construction activity
ScrewFast Foundations, the UK’s leading helical piling and steel modular company, is now part of the Van Elle Group, offering additional design and construction solutions for the rail network.
STRATA Geotechnics, part of the Van Elle group, has the expertise and specialist equipment to perform on and off-track ground investigation (GI) projects for the rail network
INSIDE
TRACK:
As well as resulting in a wet tunnel, the quality of the track and the ride for passengers were affected, leading to the imposition of a speed restriction. The faces of the cutting also experienced problems with the lower half tending to slide, as happened recently alongside the Severn estuary, described in Rail Director/Inside Track February 2023 issue
The decision was taken to close the railway to address the problems.
Other areas along the route were experiencing similar difficulties, so a line closure would allow everything to be done at once.
The work was scheduled to coincide with school half term in the area, from Saturday 11 to Saturday 18 February 2023.
The line was also closed for the weekend of 7/8 January for preparatory works. Six sites between Faversham, Canterbury East and Dover Priory would be upgraded – at Faversham, Selling, Aylesham, Snowdown, Shepherds Well and Bekesbourne – as part of a £3 million upgrade programme.
Fiona Taylor, Network Rail’s Kent route director, commented: “The change in weather patterns means that we’re experiencing drier summers and much wetter winters, and this has a huge impact on a railway that was largely designed and built in the Victorian era when the understanding of construction materials and geology was less advanced than today.
Above: Constructing the king-post retaining wall
Image: Van Elle
Opposite: One of the new catch pits
Image: Van Elle
Previous page: Constructing the king-post retaining wall
“We constantly monitor embankments and cuttings to keep passengers safe, cautioning trains when sensors detect any movement. However, this has an impact on the punctuality of
“The work over February half-term will provide a long-term solution to the risk of landslips on this section of track and allow trains to run at full speed and will also improve the reliability.”
The monitoring of the line so as to have early warning of slips is a major undertaking, as Derek Butcher explained: “Our earthworks are measured in five-chain lengths – that’s 100-metre lengths –and we are currently monitoring 355 five-chain lengths, that’s around 17,000 nodes grouped into 350 gateways. The gateway is the system that sends the signal from the node back to the control centre, and there are also 670 cameras so each of the sites is monitored by a camera at each end.
“If we get an alarm going off, then control will look at the cameras before they caution trains. Only if they see that material has moved or is on the track will they caution a train, so it’s a secondary system that prevents us from stopping trains if there’s a false
When the line was first built, not only were geotechnics and civil engineering processes less sophisticated than they are now, but railways were under financial pressure so they bought the minimum amount of land they could get away with.
As a result, the overall footprint of the line is quite narrow, resulting in cutting slopes that are steeper than would be thought advisable today.
Derek Butcher believes that the Victorian builders had trouble from the beginning. It is quite a short tunnel, and could easily have been replaced by a deep cutting, which would have been cheaper to build.
“We think it’s probably because of the ground conditions that they encountered that they felt that they didn’t want cuttings, they wanted a tunnel instead,” he pondered.
“If they’d have built some deep cuttings, they would have been forever dealing with landslips. They were thinking about long-term management of the line.”
One hundred and sixty years later, Network Rail and its contractors had to tackle the problem. At several locations, the solution proposed was to remove thousands of tonnes of earth from sections of the cuttings to reduce the steepness of the slopes leading down to the track and instal rock netting to prevent rocks and earth from falling onto trains.
■ Quickly measure the track and rail corridor to Band 1A accuracy
■ Significantly reduce the risks associated with trackside working
■ Avoid disruption to rail services by removing access possessions
To find out more visit fugro.com/raildata
Previous page: Work inside the tunnel was difficult in constrained conditions
Image: L&W Contractors/Pro Rail
Above: Constructing the king-post retaining wall.
Image: L&W Contractors/Pro Rail
Opposite: Constructing the king-post retaining wall
Image: L&W Contractors/Pro Rail
However, that would not suffice at Selling tunnel, where more substantial work was needed.
To reduce the angle of the slope, two actions were taken. A strip of land eight metres wide was purchased from the local farmer at the top of the slope and a substantial king-post wall was built at the bottom. King-post walls are suitable for many earth retaining structures and are a fast and cost-effective way of building permanent or temporary retaining walls.
In this case, specialist contractor Van Elle installed a king-post retaining wall, consisting of 31 universal columns at lengths of up to 11 metres. The piles were constructed to depths of up to 7.5 metres using the continuous flight auger (CFA) piling technique. Van Elle used its VESPA piling mast attachments to carry out the all-important works, which used a methodology for which Van Elle is the only provider on Network Rail infrastructure with product acceptance.
The 56-metre-long king-post wall was constructed from concrete planks stacked between the H-beam piles and the ground then backfilled behind it. The combination of that four metres of fill at the toe of the slope and pulling the top of the slope back almost eight metres would allow the slope to be regraded, preventing the risk of future movement.
Active badger sets on the slope were to be filled with grout and then netted to prevent the badgers returning, so encouraging them to move to less sensitive parts of the railway environment. Finally, the slope would have a layer of topsoil added and be seeded to encourage vegetation that would bind the ground together and prevent it being washed down onto the track.
Many Network Rail drainage assets were installed during the Victorian-era and are deteriorating with age. This site was no exception and required the replacement of 330 metres of tunnel drainage and 17 catch-pits in order to mitigate the flood risk of the operational railway due to blockages, collapses, and fractures in the existing drainage assets within the tunnel. The condition of the drainage had been responsible for a poor quality track formation within the tunnel and repeat track circuit failures due to standing water, which develops where surface-water cannot drain effectively as intended and instead sits above ground level in a stagnant manner.
Local framework contractor BAM Nuttall carried out the work on behalf of Network Rail. As the access points at either end of the tunnel were a couple of miles away, meaning that using a road-rail vehicle with a flatbed trailer to transport materials to and from site would be complex and time consuming, a work train hauled by a Class 66 locomotive was used to bring in all the new material, including the piles and concrete planks for the fence and the drainage popes and catchpits. It stayed on site to act as a store during the work, and to carry the spoil away afterwards.
A specialist contractor was brought in to install a ventilation system in the tunnel – needed to ensure that those working were breathing clear air and any fumes from on-track plant were safely managed.
Selling tunnel is an unusual shape. As well as being fairly short, it is also relatively high and narrow. The height comes from it being a single-bore twin-track tunnel, so the crown is higher than the clearance needed above each of the two tracks.
The space between the tracks, often called the sixfoot because, in general terms, that is what it usually is, measures only about 5.3 feet inside Selling tunnel (1.6 metres). That not only means that the trains run very close together, hence the low speed limit inside the tunnel (40mph for passenger trains, 20mph for freight), but also doesn’t give much room for the between-tracks drainage system.
With the work train parked on one track, and thirdrail conductors also in the six-foot area, there was even less space as the team started to dig out the old drain. Once the ballast was removed from between the tracks, it was found that the old catch pits were substantial concrete structures and there was more concrete covering the old drainage pipes, all of which had to be broken up and removed.
This was accomplished by changing the method of working – for example exchanging the bucket on L&W Contractors’ excavator for a narrower one – and the concrete protective slabs and 11 catch pits were removed, with the rubble going into wagons on the work train.
We constantly monitor embankments and cuttings to keep passengers safe, cautioning trains when sensors detect any movement
Six catch pits could be repaired. The other 11 were replaced with bespoke ‘Stafford’ catch pits manufactured and supplied by Aqua Fabrications. These enable fitment of larger-diameter pipes than in a rectangular chamber and also allow those pipes to have varying input and output angles. The installation at Selling was similar to one that Aqua had developed for Somerton tunnel on the Reading
to Taunton line in Somerset, which has similar size constraints.
Mounted on Aqua’s ‘Derby’ GRP (glass-reinforced polymer) raising frames, which are only one-quarter of the weight of traditional frames and therefore much easier to lift into position, the 11 units had been manufactured in only five days, once the need for them became obvious.
This allowed the work in the tunnel to be completed on schedule, with the new plastic perforated pipe allowing water to enter the drain and be carried safely away. Signalling and telecommunications cables through the tunnel were not impacted in the work.
Despite the challenges, work proceeded quickly. The team even found the time to install an extra 18 metres of drainage outside of tunnel, London side, which was originally planned to be completed in the upcoming months during future possessions. Completing this extra work increased the flood resilience outside of the tunnel as it dealt with a localised low spot that was prone to the development of standing water – which can deteriorate the track quality if not managed.
Outside, the king-post wall was in place before the line reopened. Regrading, netting and replanting the slope behind the wall can safely be carried out with trains running.
While the line was closed, netting and regrading was also completed on the other five at-risk slopes, and some station work, including the resurfacing of platforms at Kearnsey, was carried out.
In total, 33 projects were completed over the 22 miles of railway between Faversham and Dover. These included a boost for local biodiversity as diseased and invasive trees were removed and areas around stations reseeded with native plants and wildflowers.
Trains commenced running again, as planned, on Sunday 19 February.