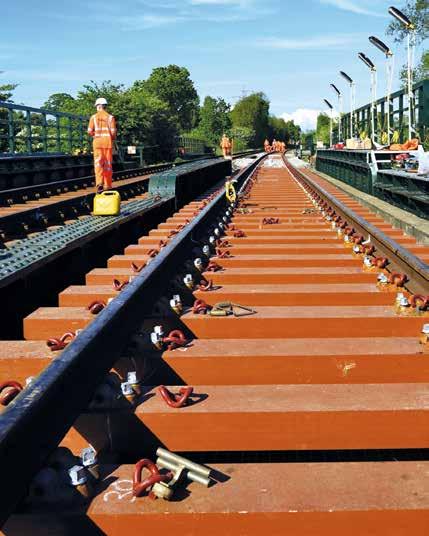
7 minute read
State of the Art
Synthetic Sleeper
Simply working & sustainable
Since 1985 we have installed more than 1,850 km of track 1.7 billion load tonnes | equivalent of 50 years use
Application: Ballast, Slab Track, Steel Construction and Direct Fastening
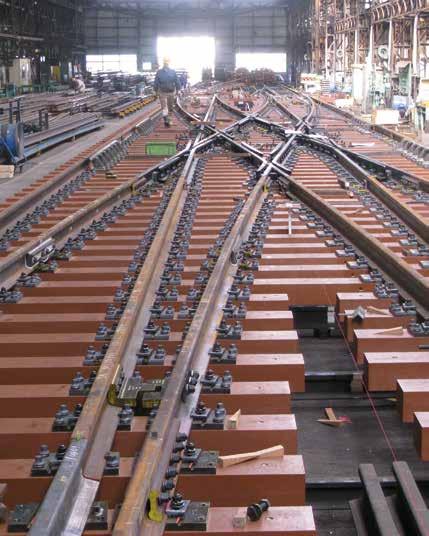
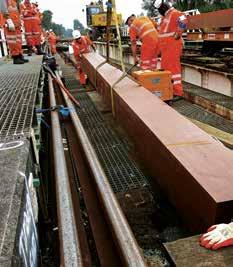
Can carry Axle loads of up to 65 tons
Use on High Speed Rail up to 300 km/h
Maintains long term track geometry
Contact with ballast similar to timber sleepers
Workable properties like timber sleepers
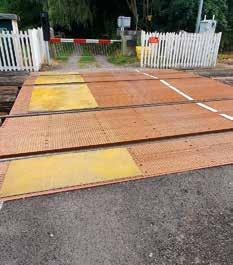
26|
32|
34
RAIB’s annual report shows no room for complacency 2022 saw 16 railway accidents on the main line network. RAIB’s report addresses its most significant areas of concern.
New fleet introduction and fleet cascades
With 8,000 new vehicles ordered in the 2010s, their introduction and the cascade of older vehicles was far from smooth.
Train depots for today and tomorrow
Rail Partners brought operators, suppliers, and other stakeholders together to discuss depot safety and productivity.
Designing a safe and efficient depot
The Train Depots for Today and Tomorrow event examined the concept for HS2’s forthcoming Washwood Heath depot.
34|
How can robots make depots more effective?
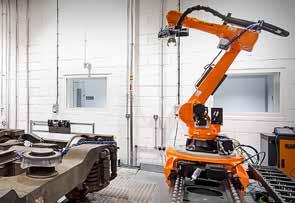
Our final report from the Rail Partners depot event gave us a glimpse of the future.
66
36|
44|
48|
54|
60|
And then there was AI Malcolm Dobell reports from the Rolling Stock Maintenance and Depot Innovation conference held in June.
The connected asset –when a cab radio is not (just) a radio
The GSM-R cab mobile asset could be used to reduce costs, increase operational efficiency, and improve customer benefits. Customer information developments
Accurate information is essential for customers, as Paul Darlington discussed with Network Rail and the Rail Delivery Group.
HS2’s future stations
We take a look at the progress made at HS2’s new stations in London and the West Midlands.
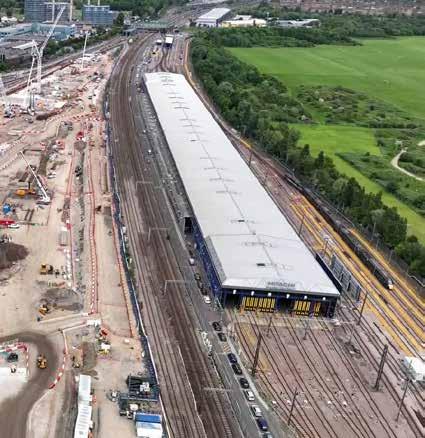
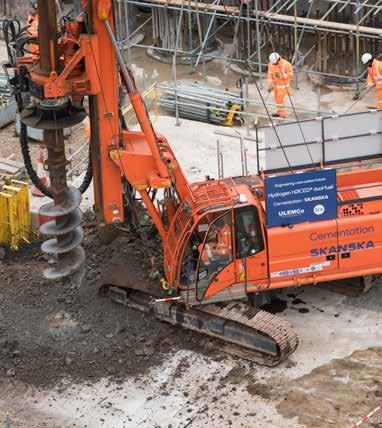
Rail Live 2023
The UK’s largest outdoor rail show returned in June to Porterbrook’s Long Marston Rail Innovation Centre.
64|
66|
Energy harvesting & ‘fit and forget’ wireless sensors
Intelligent infrastructure and remote condition monitoring systems are essential for the maintenance and management of today’s railway assets.
HS2: an eco-plant test bed
HS2 is collaborating with the industry and its supply chain to accelerate innovation in low carbon plant and equipment.
68| Best challenge yet
76|
The quality of entries at this year’s Railway Challenge was the highest the judges have ever seen.
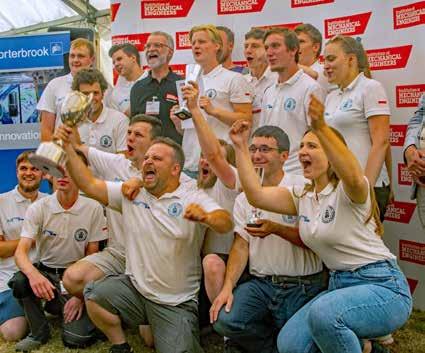
Unlocking innovation at the robotarium
RIA’s latest event brought a wide range of delegates together at Edinburgh’s Heriot-Watt University.
DAVID SHIRRES
2018 saw the last Long Term Passenger Rolling Stock Strategy (LTPRSS). Yet with the UK’s rolling stock fleet comprising of 14,000 vehicles and costing £3 billion per annum, there is clearly a need for the overview that LTPRSS used to provide.

In 2021, the Government’s Transport Decarbonisation Plan committed to an ambitious electrification programme and the deployment of battery and hydrogen trains. Yet there is no visibility of any such plans. That year also saw the Williams Shapps report which bemoaned the absence of strategic planning which the McNulty Review highlighted in 2011. It noted that work had started on a 30-year Whole Industry Strategy Plan (WISP) to be produced in 2022.
Infrastructure schemes are part of the Rail Network Enhancement Pipeline which was published in 2018 and has not been updated since 2019 despite the promise of annual updates.
The Great British Railways Transition Team (GBRTT) is expected to publish a WISP, of which rolling stock is a subset, by the end of the year. Yet, with no sign of a rolling electrification programme, and no orders for conventional rolling stock for almost four years, decisions are needed now. Doing nothing is an expensive option. Against this background, the Railway Industry Association (RIA) has done the industry a great service by publishing its report ‘The UK Rolling Stock Industry – making 2023 the year of opportunity not crisis’. It shows how the ‘boom and bust’ procurement that characterises
UK rolling stock orders has resulted in factory closures and downsized the UK’s train upgrade capability. The current lack of orders will increase costs in the longrun as the lack of continuous production reduces productivity and reduces the skilled workforce. In addition, increasingly elderly trains will become significantly more expensive to operate and maintain.
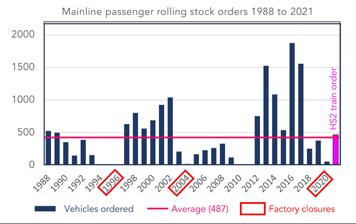
In 2011, the UK had one new build factory. Following a glut of 7,300 vehicles ordered between 2012 and 2017, there are now five. These factories, and thousands of jobs, are now at risk. One has already run out of work and two will do so next year. The RIA report shows that UK rolling stock is a high productivity industry with the average employee generating gross value added of almost £105,000. This compares to an average of £65,000 in the manufacturing industry.
FIG 1
case for new trains can be disputed, ‘no brainer’ would be a better description.
Introducing the 8,000 new vehicles ordered in the 2010s presented many notso-obvious challenges both for their new operators and those receiving cascaded older vehicles. In a comprehensive feature, Malcolm Dobell explains how train fleet introduction is a major business change programme for which detailed planning and building effective collaborative relationships is essential.
By 2030, around 2,600 vehicles will be over 35 years old. New trains are needed, not only to reduce costs, but to improve passenger services and meet decarbonisation commitments. ETCS also has to be considered given the cost of retrofitting old trains. Another issue is the lack of electrification plans which makes it difficult to specify the type of trains, though such uncertainties can be partly addressed by procuring battery EMUs and bi-mode trains.
RIA’s report also points out that, unlike infrastructure investment, new trains don’t need a large upfront public investment as the use of private finance to procure rolling stock is common practice. It explains why ordering new trains is a ‘no regrets’ decision. As it is difficult to see how RIA’s
A recent seminar considered how these large new fleets presented many challenges for depot operators. This included a GBRTT presentation on the emerging strategy for train maintenance, depots, and stabling to address the rapidly developing mix of all traction types. It focuses on location, aligned objectives for all concerned, best use of data, and best possible maintenance delivery.
On a much smaller scale, producing, modifying, maintaining, and operating miniature locomotives for the Railway Challenge has provided hundreds of young engineers with an excellent development opportunity. As we report, this event has been run by volunteers from the IMechE’s Railway Division since 2012 and was the best challenge yet.
Continuing the depot theme, we describe how HS2 is designing its Washwood Heath depot to be as safe and efficient as possible and how Artificial Intelligence (AI) and robots can make depots more effective. The National Robotarium was the location of a wide- ranging RIA Unlocking Innovation Event which showed how the widespread use of robots may not be many years away.
Fitting 12,000 upgraded GSM-R cab radios also presented significant challenges for which improved quality of communications is just one benefit. Others include Connected Driver Advisory Systems, and train-borne condition monitoring. Perhaps most importantly, they are future proofed as they can be upgraded to use the Future Railway Mobile Communication System.
The cross-industry Smarter Information, Smarter Journeys programme aims to communicate better and simpler customer information. As Paul Darlington reports, effective collaboration has delivered a range of initiatives. He also considers the latest in customer information displays at stations.
Our article on HS2’s stations includes the sad saga of HS2’s London Euston terminus where high costs have forced a pause and a third design rethink. The resultant abortive design work was cost hundreds of millions of pounds.
Correction: Controlling the Elizabeth line
The Controlling the Elizabeth line feature included in the printed edition of Rail Engineer 202 (May/June 2023) unfortunately contained an incorrect statement that the Rigid Overhead Conductor (ROC) system used instead of a catenary was installed because it was perceived to require less maintenance and that in practice this was not the case.
In the public discussion about Euston, hardly anything is said about how terminating at Old Oak Common or reducing Euston’s platforms reduces HS2’s capacity. Tens of billions are being spent on the HS2 phase one line which will provide benefits of an equivalent value and free up a large amount of capacity on the existing railway.
As this is intended to be the trunk of Britain’s high-speed rail network, it is designed to carry 18 trains per hour. The latest leak suggest that Euston may only have seven platforms. If this is true, it would significantly reduce HS2 phase one’s capacity and so throw away benefits worth billions. This would also irrevocably reduce the capacity of any future high-speed network.
Safety on our railways is a good news story, though as the Railway Accident Investigation Branch’s (RAIB) annual report shows there is no room for complacency. Our feature highlights the key issues in this report which we hope will encourage readers to study the incident reports and summaries of learning published by RAIB that relate to their work.
The reality is that the ROC system was chosen primarily for the management of limited clearances and has given such good performance that it has been possible to double the period between maintenance inspections as a result of operational experience.
Although the online version of the article and the online PDF of the magazine contains the correct statement, Rail Engineer would like to assure readers of the printed edition of the magazine that the ROC system offers significant clearance and maintenance benefits.
Rail Engineer apologies for this error.
Editor
David Shirres david.shirres@railengineer.co.uk
Production Editor
Matt Atkins matt@rail-media.com
Production and design
Lauren Palin lauren@rail-media.com
Adam O’Connor adam@rail-media.com
Engineering writers bob.hazell@railengineer.co.uk bob.wright@railengineer.co.uk clive.kessell@railengineer.co.uk david.fenner@railengineer.co.uk graeme.bickerdike@railengineer.co.uk malcolm.dobell@railengineer.co.uk mark.phillips@railengineer.co.uk paul.darlington@railengineer.co.uk peter.stanton@railengineer.co.uk

Advertising
Asif Ahmed asif@rail-media.com Craig Smith craig@rail-media.com
Rail Engineer
Rail Media House, Samson Road, Coalville Leicestershire, LE67 3FP, UK. Switchboard: 01530 816 444 Website: www.railengineer.co.uk
Rail Engineer Videos http://rail.media/REYouTube
Editorial copy to Email: news@rail-media.com
Free controlled circulation
Email: subscribe@rail-media.com
The small print
Rail Engineer is published by RailStaff Publications Limited and printed by PCP Ltd.
© All rights reserved. No part of this magazine may be reproduced in any form without the prior written permission of the copyright owners.
Part of: ® www.rail-media.com
DAVID SHIRRES