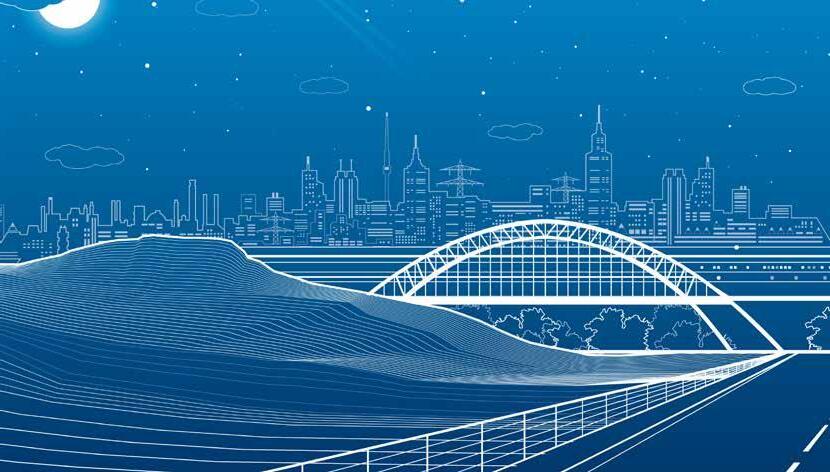
7 minute read
TRAIN DEPOTS FOR TODAY AND TOMORROW
Rail Partners, the trade body for train operators, organised the ‘Train depots for today and tomorrow’ event to bring train operators, suppliers, and other industry stakeholders together to discuss how to improve depot safety and productivity. It covered the importance of depots and the constraints within which they work, something not fully appreciated but critical to the performance of the railway. Late starts from depots, for example, affect network reliability.
Depots are safety critical environments and, although new build depots offer opportunity to get things right and improve safety, provide a better working environment, and complement the local landscape, the process of upgrading a depot can introduce safety challenges. The event also provided opportunities for sharing good practice and, looking to the future, considered plans for HS2 and how robotics can improve productivity and reduce workforce exposure to dangerous, dirty, unpleasant, or repetitive tasks, something covered in separate mini articles.
Challenges
Neil Bamford, fleet director at East Midlands Railway and formerly, West Midlands Trains (WMT), opened the event stating several challenges. Clearly, depots are there to achieve top class safety (both in terms of the depot production environment and the rolling stock itself), train performance, and train presentation. On some projects, he observed that civil engineers have, perhaps, “held sway” when building or upgrading depots and the engineer/ operator voice has not been heard loud enough. He also said that Network Rail route studies did not always consider the criticality and importance of train depots and outstations with the desired output of consistently delivering excellent operational performance.
Neil worried that engineers always find a way to deliver the service in the end, but asked: “Do we compromise too much, relying on a make do and mend approach, leading to 363 days (excluding
Christmas Day and Boxing Day) a year of work arounds and the consequential inefficiency and increased cost?”
He emphasised the importance of planning and management, making sure that required downtime for maintenance, servicing, and train presentation is delivered and that delays leaving depot (code MP701A, known as 701A) are correctly attributed so that the correct root causes are identified, understood, and acted upon. He added that we must move to depots that operate more efficiently and Train Servicing Agreements that are properly managed.
His final words were: “if you plan to run at 100% capacity then you’ll plan to fail; you must build in some contingency and headroom.”
Safety
Several speakers rightly highlighted safety; the prerequisite of all other activity. Neil Bamford drew attention to the fatal accident at Tyseley depot on 14 December 2019 where a driver was killed when passing between two units, just 350mm apart. The RAIB recommended improvements to hazard identification, risk assessment, and WMT’s safety assurance processes.
Dave Baston, in charge of Norwich Crown Point depot, described the safety challenges of an influx of construction workers unused to working in depots, together with another group of nonEnglish speakers involved in the commissioning and support of their new trains and completely unaware of UK safety law and practice. As a result, he had to put in place additional management resource just to help to manage these activities safely.
Seamus Scallon, operations and safety director for First Rail, cited the Tyseley accident as part of the catalyst that led to setting up a Depot Working Group. This and three other depot fatalities in very different circumstances reinforced the need to improve depot safety. There had also been expensive damage to trains in depot derailments and, in January 2020, the Network Performance Board challenged depots to improve wrong formation and 701A performance. At that time, the depot delay incident count across the network had increased by 86% since the start of Control Period 5 (CP5).

Seamus summarised the challenges. There had been limited industry focus on depots (including yards and sidings) and there was no clear industry-wide picture of risk, safety, and performance. They were often treated as a black box i.e., what went on inside was less clear. He added that a factory type environment with moving trains was an added risk and there was limited good practice guidance. The rail industry’s health and safety strategy, Leading Health and Safety on Britain’s Railway (LHSBR), recognises that there is no clear industry-wide picture of risk and safety performance in depots and calls for improved industry-wide understanding of depot risk.
Depot Working Group
In response, train operators created the Depot Working Group, a task and finish group reporting to the Passenger Operators’ Safety Forum. Initially, it included joint working between RSSB and The Rail Delivery Group but transferred to Rail Partners although retaining the RDG and RSSB links. With the challenges of Covid and lockdown the group rarely met face to face, but a great deal of useful work has been done. RSSB carried out a deep dive on depot safety – mostly slips trip, falls and issues such as a peak in accidents after the morning peak. The Depot Working Group has enabled improved collaboration between depots and has developed a Depot Good Practice Guidance Note (on the RDG website). There is also a Train Depot Good Practice Guidance note 07 available on request from Rail Partners.
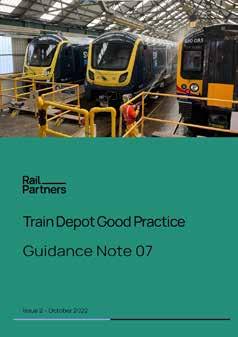
RSSB is currently working on understanding practical depot capacities, ensuring the timetable works for depots and depot performance benchmarking.
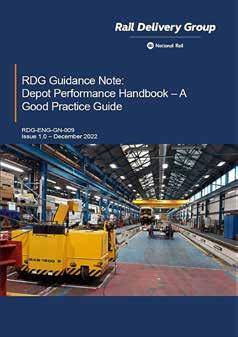
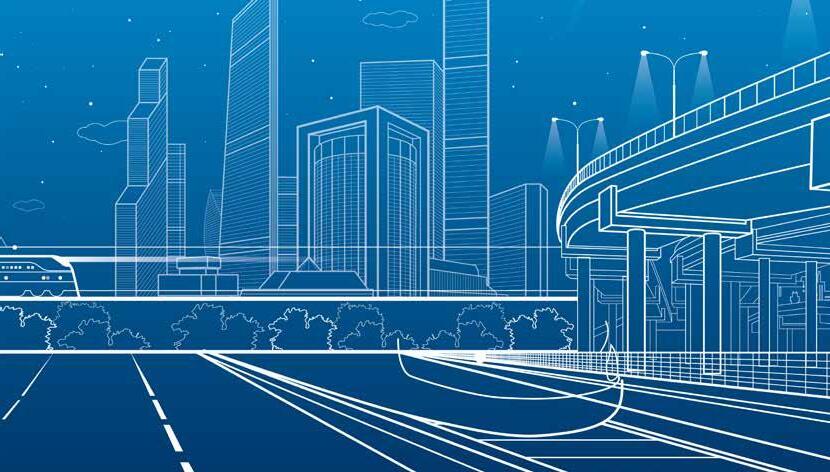
Seamus added that RSSB has delivered many activities such as economic modelling and bow tie safety/ hazard modelling.
Seamus said that the task and finish group has completed its work. There is much work still to do and will now link more closely with LHSBR and there is an opportunity to widen the work to HS2 and freight. He concluded that collaboration between train depots is still needed, and Rail Partners will link depot managers together via events, workshops, and webinars.
Lessons From The Past
Peter Williams, fleet and performance data manager at Avanti West Coast, took up the theme of Learning Lessons from the Past. Peter also chairs the subgroup aiming to reduce 701A delays of trains leaving depots. His theme was that depots were the ‘Cinderellas’ of the railway (according to the Collins Dictionary: “a poor, neglected or unsuccessful person or thing”).
This view came about because depots are not considered to be part of the ‘main line network’ with an inference of not being important. They tend to be treated like a black box with top management only interested in ‘what’ and not in ‘how’, and they are expected to work miracles. As Peter said: “Management thinks depots have supernatural powers to magically reset the clock at midnight, because irrespective of the carnage on the network the day before, the following day all the trains needed are expected to be offered for service on time, fully repaired, reliable, and clean”.
Peter said that depots are not adequately considered in timetable development and that not all Empty Coaching Stock (ECS) moves are even timetabled. “How can the depot plan for when trains are going to arrive?”, he asked. He added that some new trains have been ordered without any clear depot maintenance agreement and there have been examples where the trains are too long to be accommodated satisfactorily in the nominated depot(s). These two issues came as a shock to your writer with his 40+ years’ experience in London Underground, where trains are always timetabled for all moves, and where depot alterations are always part of new train procurement projects. In the general discussion, the need for closer working between depots, TOC operations, Network Rail Operations and Network Rail timetable planners was echoed by most present, including representatives from Scotrail where the TOC/ Network Rail relationship is closer than anywhere else in Great Britain.
Increasing Incidents
FIGURE 1 - Peter showed a 2019 graph illustrating the 86% increase in 701A incidents since the start of CP5.
Although 701A incidents are low compared with other causes, he said, they often trigger knock on delays. The delays fell to a very low value during the Covid lockdowns and have gradually risen since, but not to the same level as in 2019. Peter’s subgroup’s tasks were to review the national data and work towards providing the necessary insight in relation to filling the gaps in the depot performance data; consider and propose how the 701A data could be used to ‘fairly’ compare depot performance; consider and propose how depot performance can be improved; reduce the number of 701A incidents; and develop good practice proposals.
One team in his group is developing a methodology to determine depot capacity.
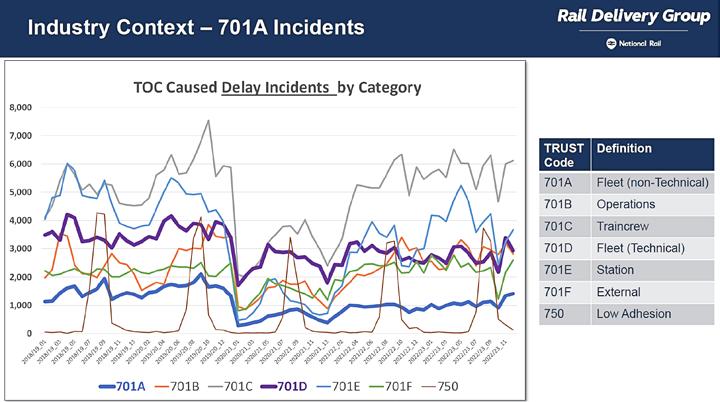
For example, a simple fan siding set might be capable of operating successfully if all sidings are occupied, but a depot might need to leave some roads vacant to allow trains to be moved around for servicing, fuelling, maintenance etc., and if those roads are filled, the depot will not be able to operate.
Some depots have defined Depot Rules (not unlike rules of the route/plan) that outline what each depot can: accommodate (frequency of incoming trains); store (capacity); maintain (maintenance activities/ requirements); and deliver (times/ frequency of departing trains). These rules will be used to confirm that new or changed timetables are compatible with these requirements.
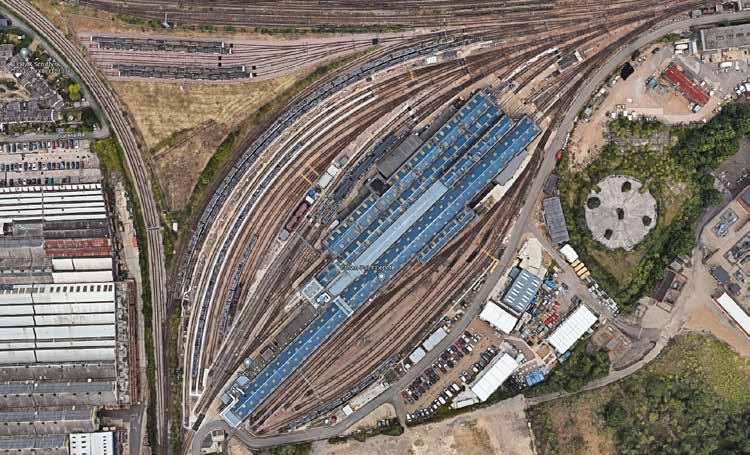
Peter asked attendees to help raise the priority of depot needs in relation to decision making, develop and enforce Depot Rules, review delay attribution processes, and make sure that incidents allocated to a depot are really within its gift to resolve.
Safety During Change
Dave Baston talked about Safety during Change drawing on his experience managing Norwich Crown Point depot which formerly looked after the London-Norwich loco hauled Mk3 carriage push pull sets and a motley collection of diesel multiple units.
Earth).
When the current Greater Anglia contract started, it was announced that all of these (and the Stansted Express) were to be replaced by 20, 12-car Stadler EMUs, 24 4-car and 14 3-car diesel electric bi-mode regional units, all from Stadler. They represented a significant change in technology and, for passengers, probably the single biggest innovations were train floors which were more or less level with the platforms and automatic sliding steps to bridge the gap between train and platform. Dave explained the pain involved with such a massive change, the more so because Crown Point was not originally planned to be the depot for these trains as the proposed site in Manningree proved to be unsuitable.
He summarised the depot team’s journey in three stages:
» Pre-October 2016 – Evolution.
» One team, stable facilities, availability matched to service, high performance, stable franchise environment.
» 2016-2022 – Revolution.
» Split teams (some existing staff transfer to Stadler under TUPE), major depot change, major fleet change, low performance.
» Present – Evolution.
» Common goals, stable fleet, stable facilities, marginal gains, one team.