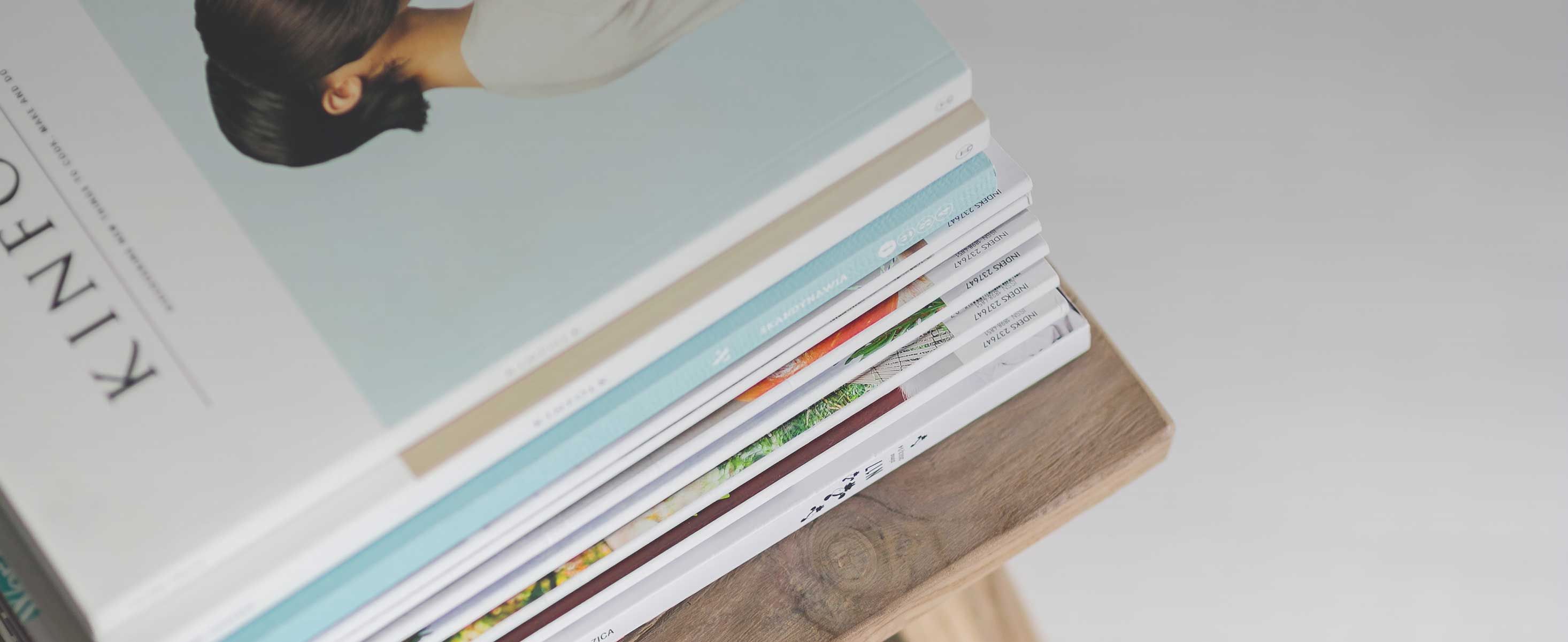
4 minute read
INTERFACING ISSUES
Dave highlighted several issues with interfacing the new trains with the depot, not least was the sheer length of the 12-car trains at nearly 237 metres, needing very careful set out of all the depot touch points – toilet and sand servicing points, for example – as well as the compatibility of wash plant brushes with a new train where the bodysides are lower than on the trains they replace. In addition, the first new depot facilities needed to be available before the new trains first ran and grew as the operational fleet grew.
Dave said that they were often “struggling to keep up” and “a high level of maths and planning was required”. But, in the end, there was a big gap between theory and practice. They found that servicing a 12-car train was a lot harder, and they sought and used alternative sites (Derby Etches Park, Ilford, and Bounds Green) to reduce the maintenance load for the legacy fleets when 70% of the maintenance sheds were lost to construction.
Dave described several of the bigger changes. On the older trains most of the maintenance was carried out from underneath, and vehicles were lifted on jacks for bogie changes. On the new trains, roof access was required for equipment displaced from underfloor locations because of the lower floors, side access to exchange diesel generators, and a bogie drop to facilitate bogie exchange on articulated vehicles that are not easy to split. Also, and inevitably, the shore supplies were different.
Managing all this safely proved to be a major task as the construction work fell under the CDM regulations and physical, interface, and management responsibilities between site management and the construction contractor, had to be defined.
There were many visitors to site including the new maintainer and commissioning teams (TSA and MSA), the transferred staff now working to the new maintainer’s rules, many construction contractor workers (in excess of 150 not familiar with depots and the OHLE environment). As Dave put it, “Piccadilly Circus moved to Crown Point”, but he noted that his responsibility as depot facility operator remained and there was a high risk to safety and operations. His advice for managing visitors included:
» Put in dedicated contractor controllers.
» Have a dedicated and separate safety team to take ownership of and investigate any accidents, incidents and near misses.
» Robustly audit and demand feedback.
» Check and approve work package plans, safety packs and lift plans.
» Make time to be out on the shop floor; don’t rely on the mountain of paper.
» Communication/briefing and toolbox talks to staff are vital.
» Have a robust induction programme (many visitors from outside the industry mean you need to act swiftly before any accidents occur).
» Have the confidence to remove/ban from site people who don’t behave safely.
Dave’s conclusion was that anyone managing a large fleet cascade will have to cope with big plans constantly changing; solutions that seem to have unacceptable compromises (e.g., bean counters say ‘no’); trying to run business as usual in the middle of a huge building site; all whilst introducing new stock and retiring and/ or cascading legacy stock. There will be a backdrop of conflicting requirements hour by hour, and uncertainty for many people such as TUPE, role changes, and possibly voluntary severance. And safety is only maintained by sticking to core principles.
Enabling Change
Finally in this section, Mark Knowles, leading on train maintenance/depot/stabling strategy for the Great British Railways Transition Team, outlined the emerging strategy for the sector. The current proposal assumes ‘targeted’ electrification roll out and decarbonisation objectives. The strategy is aimed at meeting the maintenance needs of a very rapidly developing mix and deployment of fleet traction types: electric, battery, diesel, bi mode, and hydrogen.
» ‘Principal depots’ will be a centre of excellence for rolling stock traction type.
» Existing commercial agreements would be re cast to align objectives/interests.
» There will be a template commercial model for new and cascaded stock to align interests.
» Stabling locations will be selectively developed to improve capability.
» The operator’s role as ‘maintenance controller’ will be enhanced with improved data, analysis, and knowledge.
» Operational excellence model will be developed and deployed throughout.
Mark said that deployment of this strategy will create better control for the operator, improve standards, create required flexibility, provide for growth, reduce operational costs, and equip maintenance operations for the future. He identified four ‘pillars’ that would be used to enable change:
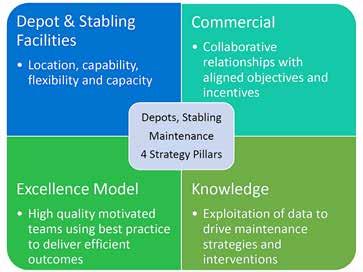
Pillar 1 is intended to help locate depots in the right place. Mark highlighted a depot and stabling facilities case study and said that once the train plan/ timetable is determined, the purpose of Pillar 1 is to define the future roles for depots and align capacity and capability for forecast needs (including growth) driven by electrification and decarbonisation objectives and traction solutions. This strategy also proposes an enhanced role for stabling locations reducing demand for further depot development, improving service delivery, and reducing ECS costs.
The purpose of Pillar 2 is to create more permissive agreements between asset owners, maintainers, and train operators which align objectives and create the environment for flexibility, innovation, and change which will be required in the future railway.
The purpose of Pillar 3 is to make full use of available data regarding train performance and faults to inform intelligent planning, deliver timely interventions, and avoid over maintaining rolling stock fleets in order to optimise reliability at lower cost.
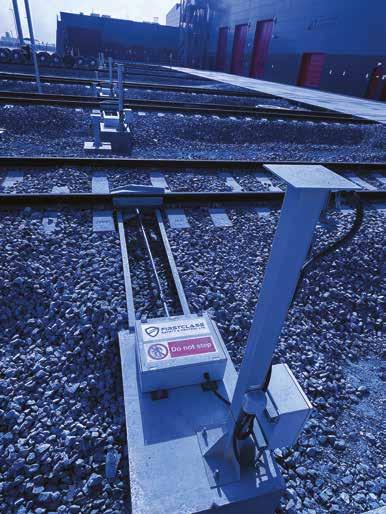
Finally, the purpose of Pillar 4 is to make rolling stock maintenance and service delivery a fully planned, resourced, and expertly delivered activity using best practice.
Mark concluded with expected benefits including efficient, cost-effective maintenance delivery; stable, highly trained and capable maintenance teams; lower industry costs per vehicle mile; fewer empty stock movements; greater flexibility/agility to deal with changes resulting from decarbonisation and electrification; and reduced need for depot development/ extension in response to increased demand. His final remark was that there would be opportunities for private the sector.
Roundup
This seminar and a subsequent new and cascaded fleet event were intended to provide lessons learned for others’ benefit and to publicise good practice guidance now available. A takeaway was that the message had certainly landed with the Great British Railways Transition Team which is working hard to deliver a strategy that will avoid the challenges caused to depots by the recent major programme of new and cascaded vehicles.
- Depot Protection Systems (DPS)
- Depot Control Systems (DCS)
- Combined DPS/DCS
- Locally Operated Points Systems (LOPS)
- SIL 2 Rated Systems as Standard
+44 (0)1621 743 743 info@ rstclass-safety-control.co.uk www.FirstClass-Safety-Control.co.uk