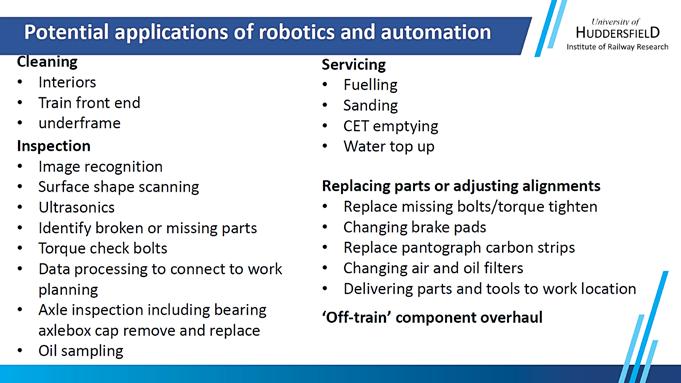
4 minute read
THOW CAN ROBO S MAKE DEPOTS MORE EFFECTIVE?
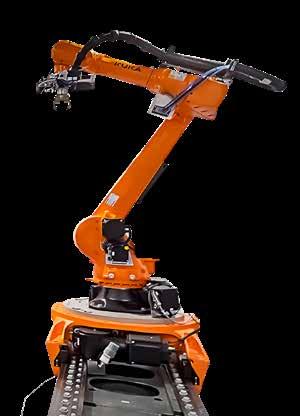
The Rail Partners Depots for Today and Tomorrow event offered a glimpse of a possible future.
Professor Gareth Tucker and Dr Hamidreza Faham from the University of Huddersfield, and Dr Mingfeng (Ming) Wang from Brunel University London, described and demonstrated how robotics might automate certain maintenance, inspection and servicing tasks. Initial priorities will be to automate tasks which are repetitive, unpleasant, or relatively unsafe.
Gareth highlighted how robots have transformed manufacturing of mass-produced automobiles and are being used for nondestructive testing of air frames, automated bricklaying, and even concrete printing. Drones and other remote-controlled vehicles are also increasingly being used for inspection on railways. Other devices including visual and other sensing systems to assess the condition of trains are already in use in some depots.

QUICKER, SAFER
Gareth presented a long list of potential applications, and benefits could include increased accuracy and repeatability of maintenance tasks leading to increased productivity and train reliability. Robotics could also reduce workforce exposure to previously mentioned dangerous, dirty, unpleasant, or repetitive tasks therefore improving safety and reducing the risk of long term muscular-skeletal injuries for train maintenance staff.
For some tasks, maintenance could be carried out more quickly, all this leading to improved availability. The systems would automatically record what they’ve seen and done and, with direct connection to maintenance management and Remote Condition Monitoring (RCM) tools, they would help achieve maximum component life and minimum resource usage.
Gareth presented slides and videos of the robotics workshop that has been built in the University of Huddersfield, an element of the ‘Smart Rolling Stock Maintenance Research Facility’, part funded by the European Regional Development Fund. In addition to research into robotics for train maintenance, the facility also focuses on the use of AI for optimised depot operations such as planning and processing of remote condition monitoring data to work towards prognostic maintenance.
The robotics lab includes a short section of a standard gauge pit road with an industrial robot on each side and another, smaller, collaborative robot in the pit. This is supported by a digital twin to help programmers test their ideas without using workshop time.
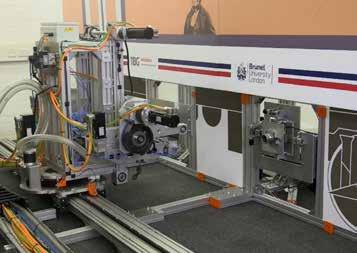
Gareth illustrated a variety of applications including a laser scanning head on the robot to assess the condition of pantograph carbons. Another early demonstration was the automated removal of brake discs from wheels already removed from the axle, for application in a bogie overhaul facility.
Cyberfluids
Ming presented Brunel’s work to develop automated methods to deal with train fluids service (e.g., CET). CyberFluids, a prototype autonomous robot for servicing the fluids on trains, is funded by Innovate UK and RSSB. In early work, Ming’s team had identified that misalignments between the train fluid port and attachment head of the automated operation device (e.g., CyberFluids’ robot) always exist. The train might not stop accurately for maintenance at the depot, and the height of the attachment points might vary. They had assumed that trains would stop inaccurately and that the attachment heads would be mounted on tracks that would allow reasonably accurate longitudinal alignment. The heads would then be designed to accommodate small longitudinal and vertical misalignments without damage or excessive insertion or removal force.
Ming’s team proposed and developed a proof-of-concept, novel compliant endeffector (a device the robot uses to perform its proposed task) for robotic train fluid servicing, which can accommodate large misalignments with significantly reduced insert force. So far, full scale prototypes and field testing are in progress, but commercialisation is some way off. Gareth outlined many of the challenges to be overcome.
Technical Challenges
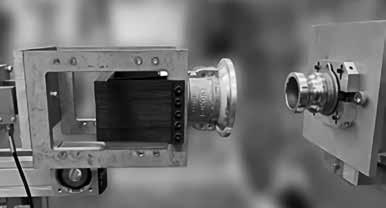
As Ming had highlighted, trains do not stop in the same place every time they arrive in a depot road, sidings, or fuel point. Components may be dirty, worn, damaged, or missing and, up to now, trains have not been designed to accept robotic maintenance. Gareth suggested that due to the limited volumes of work for each specific task (compared to an automated manufacturing line in a car factory) each robot arm will likely need to do multiple jobs to create the required cost benefit and might have to work on multiple fleet types and vehicle types within a fleet at a given depot. For some more complex jobs, it might be necessary for multiple robot arms to interact. And for cleaning or working outside, robot systems will require a suitable IP rating.
Business Concerns
Currently there is a lack of demonstrators to clearly show feasibility and realistic benefits, so it is hard to demonstrate a business case, although Ming’s team is working on field trials of novel compliant end-effectors for train fluid servicing with Chiltern Railways. This compounded by shorter contracts which can make it difficult to justify investments where the benefits are only delivered in the longer term. There is no clear leadership, drive, or critical mass in this area and Gareth highlighted that it can be difficult to implement significant changes to working practice in the rail industry.
Gareth isn’t daunted though, and outlined next steps with the labs at the University. There will be further familiarisation with the existing equipment and further lab-based demonstrations, further research into inspections using vision systems and into robot programming to accommodate worn and dirty components and allow for adjustments to accommodate train stopping position and worn state of components (e.g., wheels).
A digital twin/simulator will be used for larger scale off site concept development. Gareth wants to build a larger robotic demonstrator in a more realistic depot/ overhaul factory environment, conduct research into the application of AI to plan robotic tasks and modify robot code, integrate robot control with a condition monitoring/asset management tool, and integrate robotics with a ‘virtual depot’ scheduling tool.
Finally, there’s the all-important task of developing a cost benefit analysis for the application of robotics to rolling stock maintenance and overhaul.
Rail Engineer will watch developments with interest.