
17 minute read
Maintaining the 385s
DAVID SHIRRES
Two 4-car class 385 units on a Glasgow to Edinburgh service.
In December, ScotRail accepted into service the last of the 70 Class 385 EMUs that Abellio had ordered from Hitachi in a £475 million contract. This was signed in April 2015, just before the company took over the ScotRail franchise.
The completion of this order, together with the introduction of HSTs on Scottish intercity routes, brings the number of passenger coaches operated by ScotRail to 1,016, an increase of 28 per cent since the start of the Abellio franchise. These extra vehicles have enabled ScotRail to use the diesel multiple units (DMUs) they replace to strengthen services and to withdraw its Class 314 EMU fleet that was built in the late 1970s. ScotRail’s Class 385 fleet comprises 46 three-car and 24 four-car units. These operate services between Edinburgh and Glasgow via Falkirk High, Cumbernauld and Shotts as well as the Dunblane/Alloa, North Berwick/ Dunbar, Lanark and Cathcart circles services. The manufacture of the Class 385s and their introduction into service is described in issues 157 (November 2017) and 162 (April 2018).
Under the contract, the first train was to be operational in Autumn 2017, with all trains on the main Edinburgh to Glasgow line via Falkirk High operated by Class 385s from December 2017. However, for various reasons, including a much-publicised windscreen problem, the first unit did not enter service until July 2018. Since then the number of diagrams worked by the units were: November 2018 - 10; December 2018 - 32; May 2019 - 58 and after the December 2019 timetable change - 62.
This new timetable also saw the widespread use of eight-coach trains on the Edinburgh to Glasgow main line, which was made possible by platform extensions at Glasgow Queen Street station. The eight-coach Class 385 trains have 546 seats. This is 45 per cent more seats than the six-coach Class 170 DMUs that operated this service before the line was electrified.
At the time of writing, ScotRail’s Class 385 fleet has accumulated 8.5 million miles running. The fleet ran 727,000 miles in just one four-week period before Christmas.

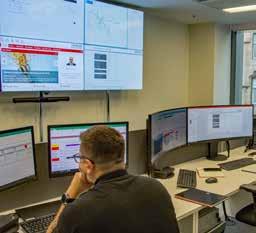
The contract between Hitachi and Abellio also included a 10-year contract for the maintenance of these units. This is managed at Hitachi’s central planning contract office in Glasgow and undertaken at the company’s Craigentinny train maintenance centre, which also does maintenance work on LNER’s Azuma fleet. Whilst it is not unusual for new train contracts to include maintenance agreements, this is the first time that ScotRail has relied on another company to maintain its trains. Furthermore, as is the case with all new trains, the Class 385s have numerous sensors and are software controlled.
For these reasons Rail Engineer was glad of the opportunity to visit both Hitachi’s Glasgow office and its Craigentinny depot to see how the class 385 units are maintained.
Host for these visits was Tim Olton, Hitachi’s general manager for Scotland, who advised that the company established itself in Scotland in April 2016 and now has 300 people supporting its Scottish train operations, of which around 40 are based in Glasgow and across Scotland’s central belt. Tim explained that the central planning contract office was essential to maintain close contact with ScotRail’s head office for there to be effective collaboration in the delivery of the train service agreement.
Hitachi Glasgow
Our tour started at the Glasgow office. Here we meet Stephen Williams, who is responsible for control room and outstations, and Craig Morrison, the fleet performance and planning manager responsible for the central planning cell. Reporting to Stephen are six maintenance controllers and 25 riding inspectors.

The maintenance controllers are co-located with ScotRail’s maintenance control in the West of Scotland signalling centre at Springburn, close to Glasgow city centre. They can speak directly to the train crews, resolving any issues as quickly as possible in order to limit delays to the service. The 25 riding inspectors check the trains in service and undertake repairs around the clock at ScotRail’s berthing locations.
Craig has a team of six fleet planners who plan maintenance examinations, fleet checks and modifications at Craigentinny depot and ScotRail’s berthing locations. He also has two contract performance technicians who manage delay attribution and fleet performance, including the management of in-service defects and the monitoring of repeat defects.
The work of the Glasgow office is supported by two key systems - SOROS and HFMT. SOROS is a web-based fleet maintenance planning tool, designed to optimise control and coordination of operations, maintenance and safety management activities, developed by Danburykline.
The Hitachi Fleet Monitoring Tool (HFMT) uses condition and fault information data transmitted from the train management system (TMS). This is an autonomous, decentralised, integrated system that has a 100-Mbit/s ethernet backbone and controls traction, braking, passenger information and air conditioning, as well as providing functions such as selective Hitachi’s Glasgow central planning contract office.
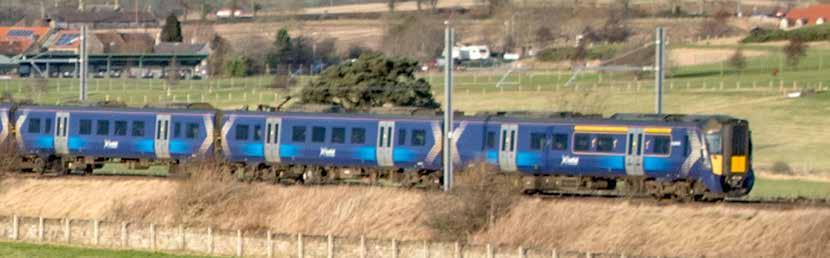
Class 385 and HST at Craigentinny.
TransPennine Nova 1 unit at Craigentinny. door opening and driver advisory systems. It is designed to reduce the amount of wiring, consolidate on board equipment and provide extensive fault detection and automatic testing.
The information obtained from the HFMT is used to proactively manage performance of the fleet by providing real-time information on system health and notification of train faults. It also provides remote fault finding and defect analysis. As an example, this ensures that units with incipient faults are not unnecessarily removed from service. This is possible as HFMT provides information about such things as gearbox oil levels and water tank levels. It also sends an alert in certain situations such as an emergency brake application and the activation of a pantograph automatic dropping device.
Relevant information from HFMT is also passed on to Network Rail. This includes adhesion hot spots, as indication from frequent wheel slide protection activation, and OLE over-voltage.
Weekly meetings are held with drivers and train crew to provide them with advice and information about technical incidents. Tim advised that the rapport that has developed between the technical riding technicians and train crew has proved particularly useful by, for example, reducing the number of coupling/uncoupling incidents.


Craigentinny
Hitachi took over the operation of Craigentinny depot from LNER in November 2018. At the time, the depot had its full fleet of LNER’s 15 diesel HSTs to maintain and also serviced the company’s IC225 trainsets as well as the occasional Hitachi-built Azuma, which had not yet entered service.
The depot also had contracts to maintain Voyager units for CrossCountry trains, Class 73 locomotives for Caledonian Sleeper and Class 350 EMUs for TransPennine Express. It had also started to maintain Class 385 units, of which about 30 were in service at this time. The variety of work undertaken by the depot is explained in issue 139 (May 2016).
At the time of my visit, the depot was about to lose its last HSTs. Two sets had been rebranded, ready to be sent to East Midlands Railway, and two power cars had been repainted in British Rail colours ready for their last LNER passenger service, a four-day “Let’s go around again” farewell special.
With almost half LNER’s Azuma fleet operational, the depot also had an increasing number of Class 800/801s to service. Another change was that it was also about to lose its TransPennine Class 350 units, although the depot was just starting to maintain the new Nova 1 units which are Hitachi-built Class 802s. These units operate a new TransPennine service on the East Coast main line from Edinburgh and Newcastle.
Tim advised that one result of all these changes was that, other than some Class 73 maintenance, the depot no longer maintains HST power cars and locomotives. As a result, much of the depot repair shop space where this work was done is now not required. This provided an opportunity to establish a new technical training facility for the Hitachi-built Class 385, 800, 801 and 802 units, which share many common components.
Class 385 maintenance
Class 385 engineering manager, Alasdair MacPherson, advised that the depot has 270 skilled maintenance engineers and fitters who are all qualified to work on every fleet. He considers that the Class 385s are a great step forward from the Voyagers and Class 350s even though the new ScotRail units require a different approach - the first step when fault finding is to plug in a laptop. The training required an integration overview with modules for every system including the TMS, doors and toilets. For a technician with no railway experience, around six months training is required. Alasdair advised that Class 385 maintenance is undertaken by a balanced examination system which ensures the amount of work in each examination is about the same. This requires an examination to be undertaken every 20,000 miles or 40 days, whichever comes first. These exams are denoted XN where N is the exam sequence number. The last examination is X36.
Given the amount of information available from the TMS, we discussed the feasibility of introducing a condition-based monitoring maintenance regime rather than the conventional fixed examinations. Tim commented that Hitachi is open to this idea and that TMS data is being used to review maintenance intervals. However, for now, the emphasis is on using tried and tested techniques to ensure reliability. Alasdair makes the point that train component maintenance periodicities will always be a compromise, as the work has to be done when the train is in a depot. Furthermore, any changes to the maintenance regime must be approved in accordance with the ROGS regulations (Railways and Other Guided Transport Systems (Safety) Regulations 2006, updated 2011 and 2013).
At the Millerhill servicing depot, there is a condition monitoring station supplied by MRX Technologies which is due to be commissioned in January. When this is operational, it will enable the Glasgow project office to further refine its maintenance plans with information the monitoring station provides on the wear of pantograph carbons, brake and disc pads as well as wheel profiles.
Improving reliability
The bathtub curve shows the reliability of a fleet throughout its life and identifies three stages of failure: infant, constant and wear out. During the Class 385’s infant failure stage, there
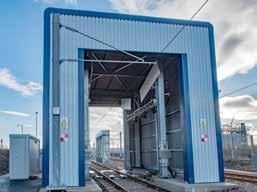

had been initial problems with the units involving the TMS, brakes, door setup and speed control unit, all of which have been largely resolved, mainly through software fixes.
TMS updates can be done within a couple of hours at most. These do not require units to come to Craigentinny as technicians can do this at stabling points. However, the speed control unit had to be returned to the manufacturer for its software update.
Alasdair explained that maintenance challenges include evening out the maintenance workload as the fleet is introduced and understanding the intricacies of the IFE electric door system.
Another problem is the different mileages accumulated by the three-car and four-car fleets. This is because the four-car units are primarily used on the main Edinburgh to Glasgow expresses where, each hour, they shuttle between the two cities. Prior to December, this service was a seven-car consist (a three and a four car-unit). However, as many of the threecar unit diagrams are also on lower-mileage stopping services, the three-car fleet has a lower mileage. At the time of my visit, the respective average mileage of the three and four car units was 306 and 572 miles per day.
This mileage disparity increased with the December timetable, which saw the Edinburgh to Glasgow service primarily formed of two fourcar Class 385 units coupled together to form an eight-car train.
During my visit, there were six units out of service: two were having X6 and X13 examinations, three needed tyre-turning and one was at Edinburgh Waverley with a TMS fault. In period 10, the Class 385 fleet achieved a record 89,438 miles per technical incident (MTIN) compared with 60,160 in the previous period. As Alasdair pointed out, “the top end of the bathtub curve has now bottomed out”. 385 007 undergoes an X13 examination at Craigentinny. The roof access platform was built to enable Class 385s to be maintained at the depot.
Expansion BEGINS AT

40
Afortieth birthday is always something to celebrate. It’s a milestone, whether it’s for a person, a company or a product. In this case, it’s a product. The company, Walter Somers Material Handling, was formed in 1953, but it wasn’t until 1980 that the firm, by then known as SomersHandling, introduced its first mobile column lift – the model RG with a lifting capacity of 4,000 to 6,500kg.
That same company, now named Totalkare to reflect its dedication to aftermarket service as well as its highquality product portfolio, is still supplying mobile column lifts to the commercial vehicle market as well as now supplying railway depots.
To celebrate the birthday of its lifting-jack business, Totalkare is giving itself a birthday present, by investing £750,000 into the business and pressing the button on a five-year expansion plan that will see it target more business in the rail sector.
Planning ahead
“It is the right time to lay the foundations for our next four decades,” explained David Hall, who joined Totalkare just 18 months ago, leading a management buy-out of the Halesowen-based firm.
In that short space of time, the likeable Midlander has overseen a 25 per cent increase in sales and the introduction of new testing solutions into the product portfolio for the first time ever. “The business will always be based on the founding principles of customer care and being experts in our field and we wanted to build on this philosophy by putting a marker in the sand for the next stage of our development.
“We have already started the process of implementing a new ERP (enterprise resource planning) system that will give us lots of internal and external efficiency improvements and this will pave the way for our
Rail Engineer | Issue 183 | April 2020 relocation to a new purpose built-site in the Midlands. There is also investment being channelled into enhanced service management software to further improve our service capabilities.”
The lifting and testing specialist, who has been involved in the sector for more than 25 years, continued: “In total, this is a significant spend for us and we are in the final stages of negotiations on a great location that is close to our current home in Halesowen.
“It’s a necessary move to give us the ability to optimise the workflow on the shop floor and increase our capacity to hold stock of mobile column lifts, railway lifting jacks and new testing products.”
Excellent reputation
The company is respected throughout the UK for being an industry-leader in the supply, service and

maintenance of two and four post lifts, mobile column lifts and forklifter ramp systems. Many of its clients have benefitted from its lifting solutions for 40 years, a customer base that covers some of the biggest names in the bus and coach, commercial vehicle and heavy haulage sectors.
Last year, Totalkare signed a deal with Italy-based manufacturer Emanuel to supply a range of railway lifting jacks with capacities up to 50,000kg that also conform to Machine Directive 2006/42/CE and European standard EN1493. Easily customised, they can be used to lift any rolling stock - from wagons and carriages through to complete trains - providing a safe, flexible and comfortable position for operatives to carry out maintenance, repairs and servicing.
David explained: “We have been working with Emanuel for five years, supplying its heavy-duty four-post lifts into the bus and coach and commercial-vehicle sectors. “Following a number of conversations, we saw the opportunity to take its manufacturing expertise into the rail sector, where they have similar requirements to provide a safe and fast means of keeping rolling stock operational.”
David, who is joined by Mike Lord, James Radford and Peter Geobey in the new-look leadership team, continued: “There’s a reason our customers have been with us for many years and that stems from the quality of the product and this flows through the aftercare experience. “We really do care, a mentality that you would normally find in a family-run business. This makes a real difference and we have built on this culture by investing in new technology and by strengthening our service David Hall.
offer with additional engineers now operating all over the country, ably supported by product specialists. The plan is to continue our recruitment drive to grow this team by an additional 20 per cent over the next 12 months.

“It’s a full lifecycle from purchasing the Totalkare product and regular servicing to preventative maintenance, planned refurbishment and swift repairs to ensure we minimise workshop downtime.”
RAILWAY LIFTING JACKS RAISING STANDARDS
With 40 years’ experience in heavy duty lifting solutions, Totalkare combines world class products with industry leading support to facilitate effective maintenance and repair, keeping you on track for success.


Global connections Hitachi Rail, a fully integrated, global provider of rail solutions across rolling stock, signalling services and turnkey solutions, is the latest company to benefit from the Totalkare experience. Its assembly plant at Newton Aycliffe, Co Durham, employs 700 people and has recently introduced eight new 15,000kg railway lifting jacks that will give it flexibility for future projects.
Initially, the jacks will be used to lift metro-style carriages during the manufacturing process.
“We’ve manufactured these lifting jacks in line with Hitachi Rail’s bespoke requirements, with specific attention paid towards the size of the outriggers, height of the anvil and the lifting capacity of each product,” explained area sales manager Adam Bowser. “This install will be supported through our comprehensive Afterkare service package, which includes two visits per year.”
Wayne Abbott, manufacturing engineer for Hitachi Rail, commented: “We have an existing relationship with Totalkare’s European manufacturing partner Emanuel, having previously used their lifting jacks in Italy. “Totalkare was the only supplier who could tailor a solution specifically to our requirement and we’re keen to make the most of the additional flexibility it will provide at our Newton Aycliffe facility.”
Moving forward
With numerous birthday celebrations planned for 2020, it’s only right to give David Hall the final word on what the year has in store for Totalkare. “Like I said before, it’s about laying foundations for the next five years, but that doesn’t mean we haven’t set ourselves ambitious targets. 25 per cent growth is expected again over the next twelve months.
“Personally, I’m really keen to push our online training platform more and increase adoption of technology that can make our workshops
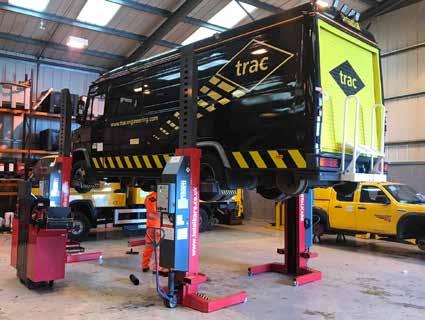
safer and help to minimise the number of accidents.
“R&D continues at pace and we are already planning the introduction of another new range of products and increasing the capabilities of our existing ones. We’ve got to stay ahead of the competition - great products with excellent service, that’s the Totalkare way.”
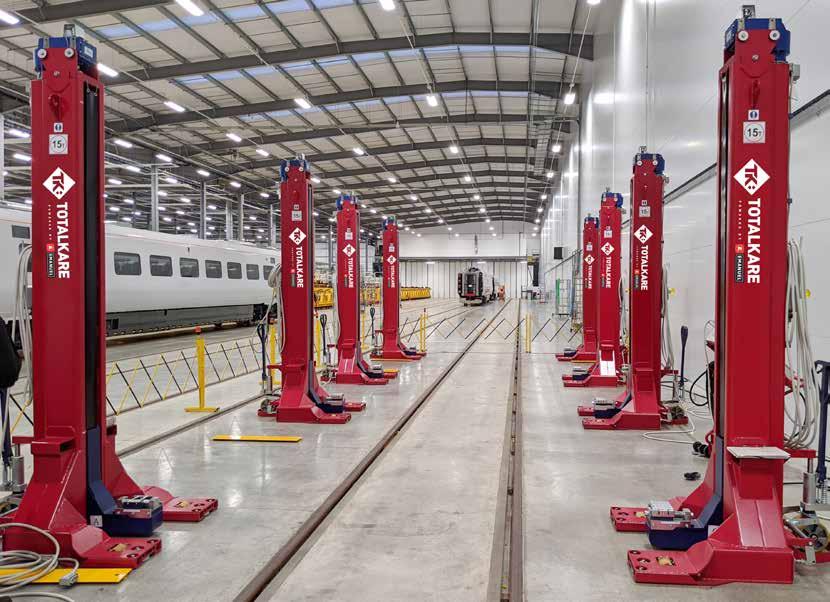
LIFE IS PRICELESS.

zonegreen safe working solutions
SMART DEPOT PERSONNEL PROTECTION SYSTEM (DPPS™)
Renowned as the global market leading depot protection system, the SMART DPPS™ delivers physical protection from vehicle movements to rail depot staff whilst providing visual and audible warnings. The Smart DPPS™: • Protects staff and equipment • Ensures safe and controlled movement of rail vehicles into and out of the depot • Allows train maintenance operations to be conducted without endangering the safety of staff or damaging infrastructure It is: • Fully configurable, flexible and functional • Proven in use and installed globally • Capable of interfacing with third party equipment including signalling systems. • Adaptable to the safe requirements of the depot