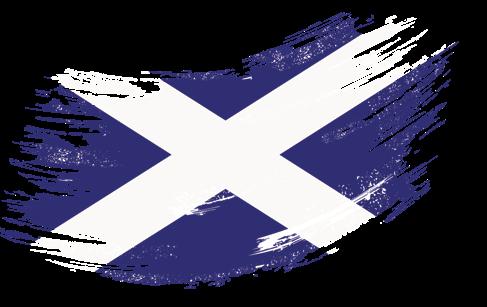
14 minute read
Scotland’s hydrogen train
SCOTLAND’SHYDROGEN TRAIN

DAVID SHIRRES
Rail Engineer’s recent feature on hydrogen trains mentioned plans to produce a hydrogen demonstrator train in Scotland, but it went to press before the announcement of the contract award. As this initiative has much of interest, in both the train and the UK’s decarbonisation strategy, we hope readers will agree that it is worthy of another hydrogen-train article.
Both the Committee on Climate Change’s Net Zero report and the National Grid’s Future Energy Scenarios conclude that hydrogen will have a key role in the decarbonisation of the energy system. They consider that replacing fossil fuels requires an increase in both zero-carbon electrical generation and hydrogen production. This would provide power beyond the fixed electrical distribution system and could also be used for heating, for example for high temperature industrial processes and domestic heating using the existing gas grid.
In November, HM Government published its Ten Point Plan for a Green Industrial Revolution. One of these points was driving the growth of lowcarbon hydrogen, which it considers will potentially unlock 100,000 jobs by 2050.
In Scotland, the devolved government’s ‘Scottish Hydrogen Assessment’ was published in December. This concluded that Scotland could produce significant quantities of green hydrogen from offshore wind. It also considered three scenarios for hydrogen production in 2045, which ranged between 20 and 127TWh. In these scenarios, transport would consume between 7 and 22TWh of hydrogen production and the value to the economy was estimated at between £5.7 and £25.9 billion resulting in between 68,000 and 313,000 jobs by 2045. Accelerating hydrogen
In July, the Scottish Government announced that it was to invest £300,000 in a hydrogen accelerator at the University of St Andrews to support delivery of its target of net-zero carbon by 2045. This requires the University to collaborate with relevant Scottish institutions to drive hydrogen technology innovations and to encourage knowledge sharing and the development of expertise to support transport applications. It also aims to maximise the economic opportunities from the shift to zero or ultra-low emission transport by fostering new partnerships between industry and government.
Thus, this supports Transport Scotland’s transport decarbonisation plan and Scottish Enterprise’s requirement to develop the supply chain to support Scotland’s green recovery.
In September, the University of St Andrews announced that it was seeking a partner for the next phase of the production of a hydrogen train demonstrator. This scheme had been developed by Scottish Enterprise and Transport Scotland. Its first phase had been a concept design for conversion of a Class 314 EMU that had been jointly developed by Brodie Engineering of Kilmarnock and Arcola Energy. The contract notice for the second phase required a hydrogen train to be demonstrated on the Bo’ness and Kinneil heritage railway and available for the COP26 world environmental summit in Glasgow in November. It had an estimated contract value of £2.74 million and stated
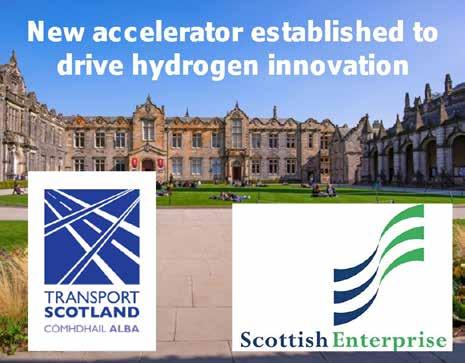
that the contract objectives were to: 1. Prove, or work towards proving, that Scotland has the capability of modifying an existing item of rolling stock to install hydrogen fuel cell (FC) technologies, batteries and control equipment; 2. Work with the regulatory bodies to develop the necessary standards and controls for the use of hydrogen fuel cell electric power on passenger rolling stock; 3. Inform rail policy on the application of such technology on the Scottish passenger rail network in advance of the decarbonisation target of 2035 for Scotland’s passenger rail services; 4. Demonstrate, or work towards demonstrating, to Scotland’s rail community, through practical application, the operation of hydrogen fuel cell electric passenger rolling stock; 5. Provide Scotland’s supply chain with the opportunity to develop its skills and advance its knowledge of the application of hydrogen fuel cell electric technologies on passenger rolling stock, as well as issues relating to hydrogen supply and refuelling infrastructure; 6. Provide educational institutions with the opportunity for research and practical application of hydrogen fuel cell electric technologies within the rail industry.
In December, this contract to convert a surplus Class 314 EMU into a hydrogen train was awarded to an industry consortium led by Arcola Energy working with partners Arup, Abbott Risk Consulting and Aegis.
The big picture
Rail Engineer was glad of the opportunity to have a Zoom call with Arcola Energy’s founder and CEO Dr Ben Todd and the company’s head of rail engineering, Glenn Daniel, to discuss the Class 314 hydrogen train project and the wider role of hydrogen in a net-zero economy.
Ben founded Arcola Energy in 2010 to bridge the gap between evolving clean energy technologies and end-user needs. The company is a Tier 1 supplier that offers zeroemission solutions for heavyduty vehicles and transport. To do so, Arcola Energy has developed powertrains which integrate fuel cells, batteries, hydrogen storage, power electronics, motor, and brakes. These can either be retrofitted or installed on new vehicles.
The company has been part of various engineering partnerships which have seen their powertrains fitted on buses, HGVs and refuse collection vehicle (RCVs). He notes that Glasgow City Council has a project for 23 hydrogen-powered RCVs, one of which will be operational in Glasgow during the COP26 summit.
The company’s fuel cell system was also used in the Surf ‘n’ Turf project on the Orkney Islands. This demonstrates how hydrogen can be used as an energy vector by generating it from tidal and wind power on offshore islands and transporting it to generate electricity on the Orkney mainland. 314209 at Yoker Depot in Glasgow waiting for its hydrogen conversion.


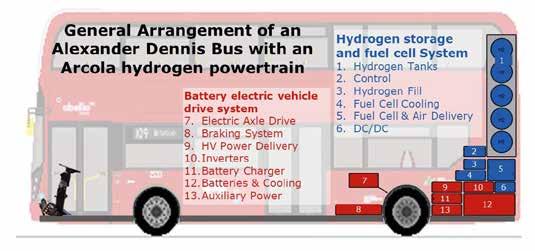

(Above) Alstom’s Breeze, the proposed UK iLint equivalent, has hydrogen stored inside the train. (Inset) Roof mounted hydrogen tanks on Alstom’s iLint.
Ben pointed out that the objectives of the Scottish hydrogen train project do not include building a train. There they are all concerned with the much bigger picture, which is about building Scottish hydrogen capabilities, helping industry to understand where hydrogen fits and overcoming natural reluctance to adopting this technology.
He considers that there is extraordinary potential for renewable electricity in Scotland, which he feels is currently constrained as promoters cannot secure sufficiently strong electricity purchase agreements. These need to be of at least ten-years duration to make renewable power investments sufficiently attractive.
A zero-carbon economy requires more renewables and decarbonised transport. His view is that hydrogen is an energy vector, stuck between these requirements, which realises both of them. Also, the more projects that use hydrogen, the better the economics. Trains are great in this respect as they offer a predicable demand and return to base which simplifies hydrogen supply.
We discuss the poor efficiency of hydrogen traction, which Ben feels is not an issue as it does not detract from hydrogen’s role as an energy vector, as he had described. He also considers that this explains why the economics of hydrogen need not depend on the use of surplus overnight wind power, which Ben feels is a “nice to have.” Furthermore, this would require electrolysers to run at a low percentage utilisation.
Ben is convinced that, with economies of scale, the price of hydrogen generated from renewables can only be reduced, whereas the volatile cost of fossil fuels is likely to increase. He considered Alstom’s €500 million contract to supply 27 trains in Germany, which includes the supply of hydrogen fuel for 25 years. No company would enter into such an agreement unless there was reasonable certainty of fuel costs over such a long period. This is the case for hydrogen, as its costs are the capital and maintenance costs of the electrolyser and renewable power installation. Hydrogen storage
One of the limitations of a hydrogen train is that, compared with diesel, it requires much more space to store its fuel. As a result, this may encroach upon the train’s passenger space, which is a particular problem in Britain. For example, each coach of Alstom’s German iLint stores 98kg of hydrogen in roof mounted hydrogen tanks. However, as the constrained British loading gauge precludes the use of roof tanks, Alstom’s “Breeze” proposal for a UK hydrogen train has hydrogen stored within the coach body.
The iLint stores hydrogen as a compressed gas at 350bar, which is the norm for heavy-duty hydrogen applications and requires what Ben described as a “quite straightforward” pressure vessel. Hydrogen cars generally store it at 700bar, as consumers want maximum range and are prepared to pay for it. However, this requires more expensive cylinders and is not an efficient way of storage as doubling the pressure from 350 to 700bar only stores 60 per cent more hydrogen.
Alternative ways of storing hydrogen are by chemical storage, such as Ammonia or metal hydrides. However, these present practical problems such as long refuelling times.
The 3-car Class 314 hydrogen train will store 80kg of hydrogen, which is sufficient for its use as a demonstrator train. Doubling this amount for passenger use would require some hydrogen to be stored within the coaches, where Ben feels there is scope to create appropriately ventilated spaces that do not take up too much passenger space. He feels that, in the short term, a lot can be done to efficiently package 350bar hydrogen within a train, possibly including the development of rectilinear tanks to maximise storage space.
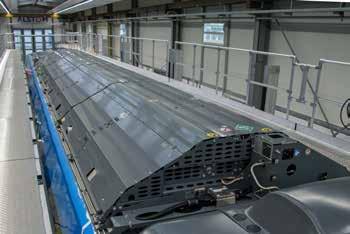

Artemis energy recovery test vehicle outside a workshop at Bo’ness. The railway also hosted a test of a Vivarail battery train so is becoming a testbed for decarbonisation initiatives.
Class 314 driving motor coach 64600 on the M9 motorway passing the iconic Kelpies at Grangemouth en route to Bo’ness. Moving to Bo’ness
The three-car 25kV AC Class 314 units were second generation British Rail EMUs that were built in 1979. They were withdrawn in 2019 due to their lack of compliance with the persons of reduced mobility legislation, which became law in January 2020. The outer coaches have driving cabs with powered bogies and an unpowered pantograph trailer coach is in the middle of the unit. Of the 16 units built, all have been scrapped except for unit 314209, which was moved to Yoker carriage sidings in December 2019, ready for its conversion to a hydrogen unit.
It stayed there for a year until it was moved under its own power from Yoker to Shields Depot in a regular empty stock move on 16 December. The next day it was moved by road from Shields Depot in Glasgow to Bo’ness on the shore of the Firth of Forth. The train was moved shortly after Arcola was engaged to undertake the hydrogen train conversion. Ben was impressed at that way everyone client-side recognised the urgency to get project started and pulled all the stops out to get the train to Bo’ness before Christmas.
He felt that the requirement to complete the hydrogen conversion before COP26 in November was challenging. However, his team had previously replaced diesel engine/transmissions with hydrogen powertrains on similar projects within a ninemonth timescale, and so he was confident that this was achievable.
The heritage Bo’ness and Kinneil railway has workshop facilities to maintain its collection of steam and diesel locomotives. Its five-mile line has a challenging gradient and is connected to the main Edinburgh to Glasgow railway. The Arcola team has an agreement with the railway that its train can use the diesel locomotive workshop whenever required. There is also the potential to engage the railway’s experienced engineering volunteers on the project.
Another benefit of basing the project at Bo’ness is familiarising the railway community with hydrogen trains, as required by the project’s fourth objective. Many volunteers at Bo’ness have extensive contacts within the Scottish railway community.
A hydrogen fuelling station to compress, store and dispense the gas will also be provided at Bo’ness for the train. Hydrogen will be delivered by road on a tube trailer.
Converting the 314
Glenn Daniels advised that the first step was to weigh the train. It is important to ensure that the converted unit is neither too light, which presents a derailment risk, nor too heavy, due to axleload and dynamic gauging constraints. Hence, during the conversion
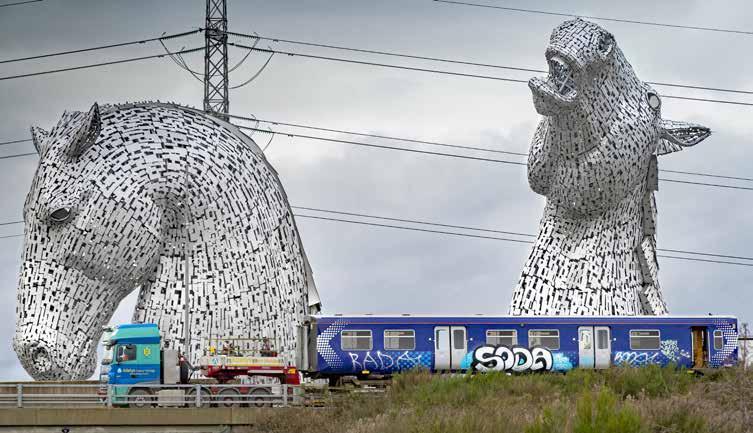
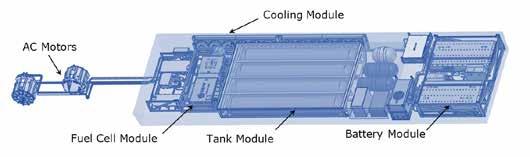
Water vapour from the Bo’ness and Kinneil Railway’s steam trains is more visible than that from hydrogen trains.
work, all components removed and fitted will be weighed. Although the unit was designed to carry a 25-tonne passenger crush weight, he is sure that the converted unit would not add anything like this crush weight. Indeed, it is possible that replacing the electrification kit with hydrogen equipment may result in a lighter unit. Hence, there may be a requirement to add ballast.
The conversion will fit an Arcola A-Drive hydrogen fuel cell powertrain with hydrogen tank and battery modules under each coach. Once the old equipment is removed, there is plenty of space to fit a steel frame with these modules underneath each coach. The powertrain will be the PP70 variant which provides a peak power of between 200 to 300kW. It will use fuel cells supplied by Ballard.
The Class 314 motors presented a particular challenge. These DC motors are powered by an AC feed from the 25kV transformer which is converted into the required DC voltage by thyristor control. Unfortunately, there is nothing available off the shelf to marry the A-Drive powertrain’s DC output to this thyristor control. It was felt that the option of developing the software and power electronics to do this presented an unacceptable risk to the project timescale. Hence it was decided to replace the DC motors with permanent magnet AC motors of a type used with Arcola’s powertrain.
This then presents the mechanical problem of fitting the new AC motor to the old bogie’s suspension tube to drive the motorised axle’s gearwheel. Arup will design the required fitments, which will be manufactured by an external supplier. Although this is a non-trivial task, the timescale for it can be quantified. In this respect, mechanical engineering is much less risky than software engineering.
Raising awareness
Like many visitor attractions, the Bo’ness and Kinneil railway has been hit hard by the severe restrictions imposed during the COVID pandemic. Hopefully, its trains may be able to operate normally in the not-too-distant future. When they do, the railway’s steam locomotives will be joined by another train that exhausts water vapour, as hydrogen combines with oxygen in its fuel cells. Having a hydrogen train running on its railway may also help put Bo’ness on the map, even though the train won’t be carrying passengers.
No doubt Bo’ness will see a good few visitors from the railway community as the project aims to familiarise them with the concept of a hydrogen train. It’s possible there may be distinguished visitors in November, as delegates at COP26 travel the 35 miles from Glasgow to see the train. This is likely, as certification to run on Network Rail’s infrastructure is not required until the next phase of the project.
Ben considers that Arcola’s proven hydrogen engineering and the consortium’s risk-based approach should satisfy main-line certification requirements. From his perspective, the key point is understanding what these are. He hopes that this should now be clear after Porterbook and the University of Birmingham’s Hydroflex received approval for mainline testing in England in September. So perhaps, by November, it might be possible for Scotland’s hydrogen train to run under its own power to COP26 in Glasgow after all.
No doubt, it will be widely acclaimed there. Yet, for many railway engineers, the jury is still out on hydrogen trains. With their poor efficiency and the need to store hydrogen inside the train, they have their limitations and should certainly not be considered as an alternative to electrification. Yet, they are the only potentially net-zero traction that have a reasonable range on lines for which electrification is uneconomic or is not possible for many years.
Furthermore, any meaningful assessment of the value of fuel-cell-powered trains must consider the UK’s decarbonisation strategy and the role of these trains in a future hydrogen economy. Scotland’s hydrogen train should raise awareness of these issues and is part of the drive to develop a hydrogen supply chain to support a net-zero future. Rail Engineer looks forward to following the development of this hydrogen train project.
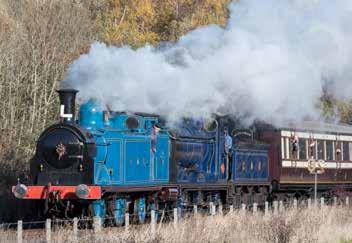