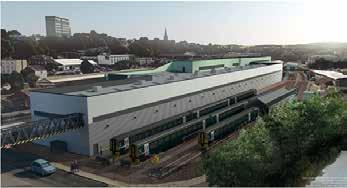
10 minute read
Exeter’s new depot – a tight squeeze

GRAHAME TAYLOR
Exeter St. David’s goods yard was a reasonable size when it was first established back in the 1840s. But then it soon started to be nibbled away. By 1864, additional platforms were constructed for the adjacent station, as a result of the arrival of three more railway companies.
Nothing much changed until the early part of the 20th Century, when further platform alterations took another chunk out of the southern end of the yard.
With the River Exe all along the western side, the engine sheds to the south west and the running lines on the east, there really wasn’t much room left, apart from a narrow sliver of land.
With the demise of steam, the engine sheds were converted into a diesel depot. This has room for a pair of diesel multiple units (DMUs) and a heavy maintenance shed that can take but a single carriage.
As goods traffic dwindled, the goods lines were removed and the site became the typical railway blend of informal car parking, abandoned ‘stuff’ and a smattering of portable buildings.
More seats, more trains
Then came the 2019 timetable change, which heralded an increase in passenger seating of over 50 per cent. Those additional seats meant additional and longer trains, and those additional and longer trains would need to be maintained.
Fiona Cane, GWR’s head of commercial development, explained: “The trains have been cascaded as a result of the delivery of new trains running under the wires between Paddington and Bristol - and the removal of the Class 143 Pacers that have…left the business.” Nice euphemism!
As already mentioned, the existing DMU facility can deal with just two 2-coach trains. The new trains will not fit and to split a DMU to make it fit would add two hours to any maintenance routine.
Something had to be done.
And the ‘something’ was a brand-new depot, built to 21st century standards, capable of taking two to five coach units. A scheme was developed to GRIP4 (single option development) by RPS Group and a contract valued at £34 million awarded to main contractor Hochtief in December 2017.
But, looking again at the diminished goods siding site, it was pretty obvious that it would all be a ‘bit of a squeeze’.
Tight
Fiona, who spent over three years as senior project manager at the new depot, knows the site well: “The footprint of the new depot is almost as big as the footprint of the existing goods yard.
“It isn’t just area that is a problem. Levels are critical. Trackwork has to join the existing connection into the main line. If the connection site changed, then this would have meant a change in the main line signalling. Timescales were tight enough, without bringing in an additional discipline.”
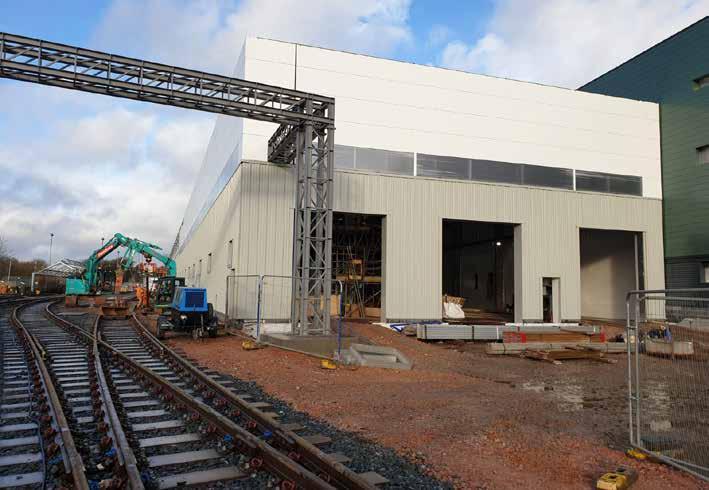
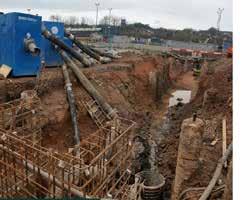
The new access roadway at the north end had to tie in with the existing Station Road. Normally, road levels are more forgiving, but on this occasion the entrance on to Station Road is within yards of the level crossing at the north end of St David’s station - so, no room to manoeuvre there. Given the need to have level maintenance lines within the shed, this meant that the level of the building was fixed. Despite the building structure being supported on piled foundations, there was still the need to excavate for the working areas below the tracks.
The final obstacle was a substantial (big enough to stand in) culvert that takes water from the hills to the east of the station, under the main lines, under the goods yard to discharge into the River Exe which, as well as a parallel relief channel, is tight against the western boundary. Needless to say, this outfall level too is fixed.
The challenge for Arup, Hochtief’s designer, was how to construct a ‘swimming pool’ type of structure with an underside that is lower than the soffit of the culvert.
The original plan was to divert the culvert around the shed outline. The adopted solution was to opt for a squashed, but wider, culvert beneath the maintenance shed, formed of precast concrete box sections. Ground conditions
As is typical for a plot of railway land, the ground conditions were predictably grim. An extensive and disruptive ground investigation by CC Ground Investigation took place which confirmed the likelihood of numerous unidentified services, obstructions and layers of toxic/unpleasant materials. There was no option but to take such ‘stuff’ away, as there was no room to bury it and cap it off.
An ordnance survey was carried out, but, despite intensive bombing of Exeter during the war, ordnance was well documented and had been dealt with at the time. The survey was limited to a desktop analysis. No substantial risk was identified - and, happily, no bombs were found!
Local firm JD Civil Engineering set to work temporarily diverting the offending culvert to allow the installation of precast concrete sections.
At the same time, most of the site drainage was established. This has no connection to the culvert. Surface and foul drainage from the southern end is pumped over the culvert and taken on to the outfalls in Station Road. Much of the site rainwater is captured and recycled - including that needed for the new carriage washing facility.
With the new building and its associated trackwork occupying all the site, there was no room for the normal village of welfare facilities, or compounds for stores, or for materials deliveries.
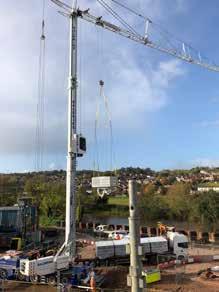
A Fresh Approach to Depot Safety and Control
• Depot Protection Systems (DPS) • Depot Control Systems (DCS) • Depot Control Systems (DCS) • Combined DPS/DCS • Combined DPS/DCS • Locally Operated Points Systems (LOPS) • Locally Operated Points Systems (LOPS) • SIL 2 Rated Systems as Standard • SIL 2 Rated Systems as Standard
01621 743 743 info@ rstclass-safety-control.co.uk
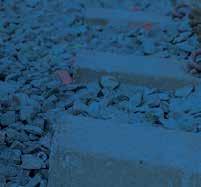
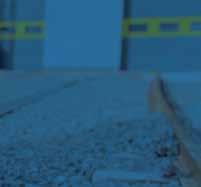


The main contractor set up site offices in a portion of railway land to the north of Station Road. This northern goods area had enough room for deliveries and storage, and further storage was available adjacent to a sidings complex further to the north.
Having cleared the site of extraneous clutter, the ground conditions were never going to improve. This had been marsh land originally and was incapable of supporting any building on normal footings. Piling was essential and these were 15-metre-long CFA (Continuous Fluid Auger) piles.
The process is virtually vibration-free and one of the quietest forms of piling, making it ideal for environmentally sensitive areas. There are several densely populated areas around the whole site, and hammered piling would have been unacceptable.
The system eliminates the need to use support fluid or casings in cohesive soils, non-cohesive or water bearing soils.
CFA piles are formed by drilling using a hollow stem continuous flight auger. After reaching the designed depth, a high slump concrete is then pumped through the hollow stem. While the concrete is being pumped, the auger is withdrawn at a controlled rate, removing the soil and forming a shaft of fluid concrete extending to ground level. A reinforcing cage is then inserted into the concrete.

Above ground
As the main building began to take shape, with steelwork fabricated and erected by Bourne Steel, space became ever-more a scarce commodity. In order to reduce site movements, the main contractor set up a large self-erecting tower crane, which needed a special license to ensure that loads were not suspended over the main lines.
The site of a new siding track to the west of the main building was used as a haul road until the final stages of the construction. This helped with access, but even this had its problems towards the southern throat of the site. A small patch of useful land could not be accessed, because the existing DMU maintenance shed blocked the way. With some imaginative staging, some of the main shed cladding at the southern end was delayed so that vehicles could drive into the shed to access the storage area.
The primary maintenance building contains a workshop area, a two-storey store area and a three-storey office/welfare area. Mechanical and electrical services were installed by N G Bailey. The maintenance workshop area accommodates two 5-car lines in a “swimming pool” arrangement with overhead cranes and a further three-car line with synchronised jack-lifting capability and a service pit underneath. There is no wheel lathe on site, but bogies can be swapped around and taken away for treatment. Two small turntables assist massively. Across the Station Road is a fuel farm, as there is no room in the main site. All the fluids, diesel and the various oils in the workshop are stockpiled and fed into the shed via a substantial fuel overbridge. It was deemed to be better to have an aerial route, which can be easily inspected and maintained, rather than having a buried route beneath the busy Station Road.
Within the depot, staff are protected by a DPS (Depot Protection System), which was designed and installed by FirstClass Safety & Control.
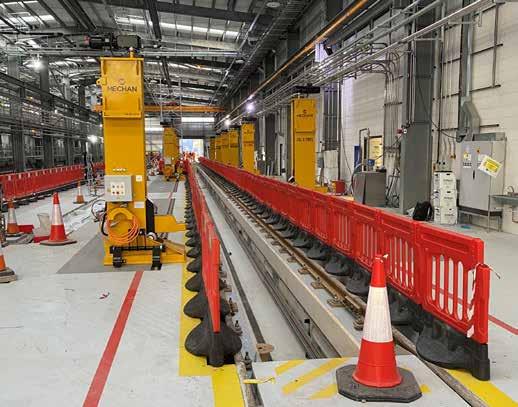
Ventilation
Ventilation of the shed was a particularly challenging issue. Regulations govern the nature and quantity of emission thresholds. The purpose of the shed is to service, maintain and run a wide variety of diesel engines. Emissions will occur and there is the potential that limits may be exceeded. This is not a depot dealing with just one type of brand-new train. Such depots can install specific ventilators that lower onto known exhaust outlets - a bit like cooker hoods.
GWR has inherited a mix of rolling stock with a mix of outlets within the vehicles. The alternative selected was whole-shed ventilation. Typically, fans that are used in these circumstances could be too noisy, both for those working inside the shed and also for the neighbours. Foreman Roberts, MEP designers along with RPS, recommended the use of closed-fan type units and these are housed in 26 enclosures on the roof. These need specific access for regular inspection. Concentrating on this one specific detail has made sure that the building is future proof. Any rolling stock can be accommodated in the shed.
Installed in parallel is a complex array of sensors to check the emissions levels in real-time and, if necessary, alert the production manager of hazards in good time to avoid harmful exposure.
Pedestrian access to the depot is via a bridge across to the northern station footbridge. This too had its own challenges. The main contractor worked around the clock to complete the link within a three-week window of opportunity whilst the lift access to the platform was temporarily closed.
Focussing on people
Fiona and the project team focussed hard on how to help people do their work well in the new facility. This extended to both the engineering depot staff and the train crew, who are moving into their new accommodation from ‘temporary’ (25-years temporary) cabins on the far side of the station, in order to be close to their frontline managers.
Uniquely for GWR, there are now shared facilities in one building.
At the time of writing, the site is soon to be handed over to GWR, trial running of trains having taken place in December 2020.
The transformation of the old yard from a brown field site (and that’s being kind!) to a 21st century train depot is impressive but, no matter what future technology might bring us, it won’t be easy to make it any bigger!

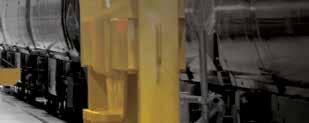
RAIL DEPOT & WORKSHOP EQUIPMENT
• RAILCAR LIFTING JACKS • BOGIE/EQUIPMENT DROPS • TRAVERSERS • TURNTABLES • BOGIE WORKSHOP
MACHINES • UNDER CAR
EQUIPMENT HANDLING • LASER MEASURING • SANDBOX FILLING • SHUNTERS • EXHAUST EXTRACTION • UNDER FLOOR
WHEEL LATHES
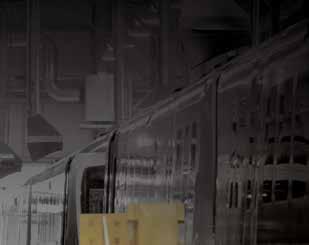
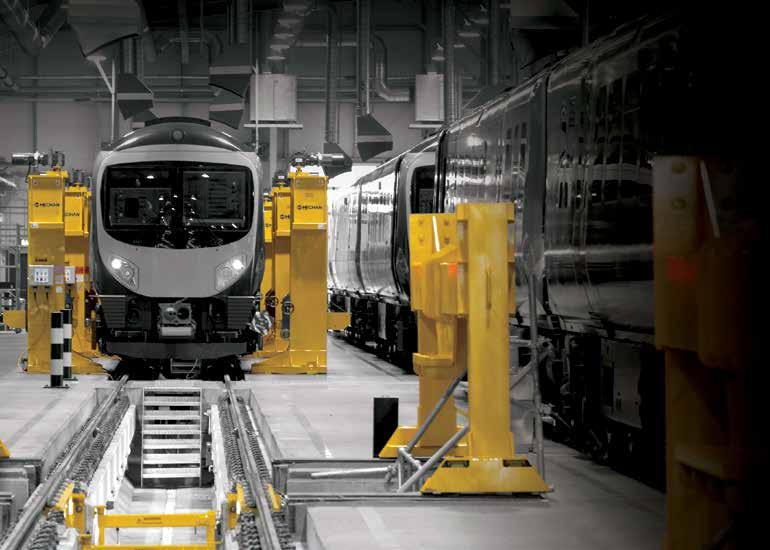

Davy Industrial Park Prince of Wales Road Sheffi eld S9 4EX