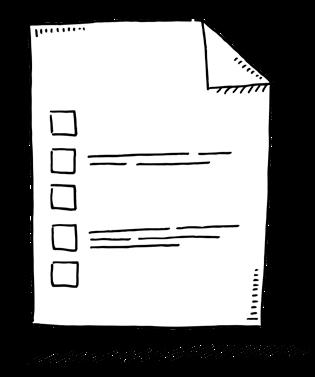
9 minute read
Rhomberg Sersa’s list of successes
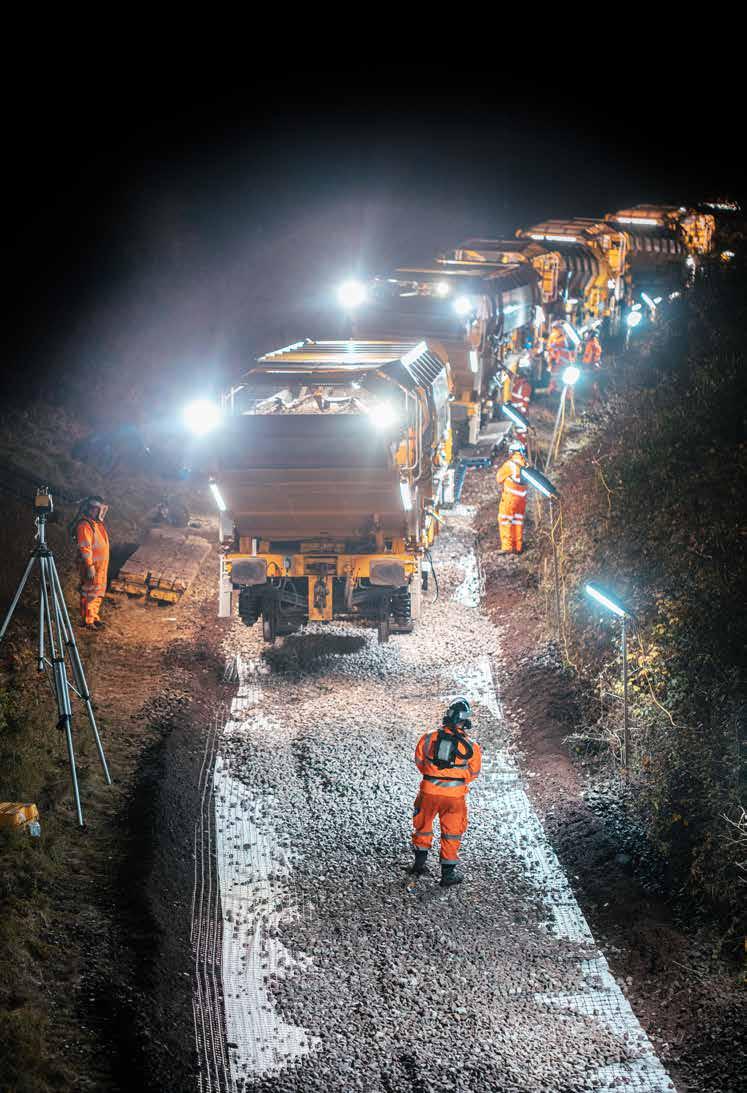
Rhomberg GRAHAME TAYLOR list of Sersa’s successes
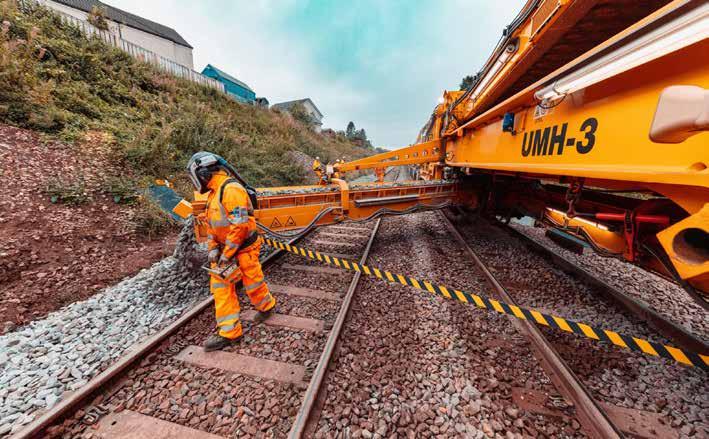
It seems a world away. December 2019 was so uncomplicated, with the agonies of Christmas shopping being just one of the rather minor issues to cope with. It was back in December that avid readers of the Rail Engineer magazine were introduced to the Rhomberg Sersa machine group project, with expansions on the theme being added in February, March and then May/June of this year.
This month we have a ‘Grand Summary’, a recap of the whole system along with some fine examples of where, when and how the machines - individually or in combination - have been used in real life.
But for new readers, or for those whose memory span is shortening by the day, here is a brief reminder of what is meant by the machine group and what those six machines can actually do. The ITC-BL4
At the ‘front’ of the machine group is the ITC-BL4. This is an upscaled ‘dustpan and brush’. Evolved from the tunnelling and quarry industries, it is used to excavate a track bed ahead of itself and to shift spoil between its legs into awaiting in-line material conveyancing machines.
It is transported by haulage contractors by road and does not need movement orders as it is neither over-length nor over-width. It runs on ‘caterpillar-type’ tracks as well as flanged rail wheels, and so can operate on the track bed where the rails have already been lifted.
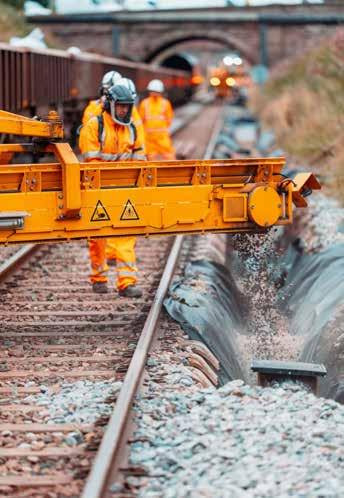
The MFS+ machines
These are special in-line material conveyancing machines. These have been based on conventional MFS wagons – the ones in a consist of hopper-cum-conveyor-belt vehicles that have been used for many years in re-ballasting works.
Their unique selling point is that they are fitted with caterpillartype tracks that can be lowered to carry the entire machine off-track and into an excavated worksite. In fact, this rather understates their true capabilities as, once released from the confines of the rail system, they can be manoeuvred with surprising nimbleness – or, at least, nimble for something that weighs up to 110 tonnes fully loaded.
The UMH
Finally, there is the UMH – Universal Materials Handling machine – or the ‘Swiss Army Knife’ of material distribution vehicles. The UMH is rail mounted but, unlike its companion machines, the ITC and the MFS+, it does not have retractable caterpillar tracks. It is marshalled conventionally within a rake of MFS wagons – usually at the end. It can travel at 60mph and has an RA1 route availability. It is a material handling machine kitted out with several systems of conveyor belts.
New or spent material is fed by the conveyors of adjacent wagons onto an initial lower handling conveyor at one end of the UMH. The UMH is thus direction sensitive - which is another way of saying that it has to be marshalled the right way round within a train and the whole train has to be the right way round as well!
From the initial handling conveyor, the material is directed to one of three other conveyor systems. The upper conveyor takes material and delivers it up to 6.5 metres either side of the track centre line. This has a capacity of up to 400 cubic metres per hour (about 800 tonnes/ hour) and can be used to feed materials into wagons on adjacent lines or onto an adjacent excavated track bed, such as depositing bottom ballast for spreading by dozers, or to the trackside. The upper conveyor can swing out to 90° to the machine - an arc of 180°.
Keep to just half a dozen...
These, then, are the machines. They are large, yellow... and unusual. Large, yellow and unusual machines have appeared before - several times over the years. Some are still with us. Some have been shunted into the long grass. So, how have the Rhomberg Sersa machines got on?
Who better to ask than Tom Cherryholme, lead supervisor with Rhomberg Sersa and someone who has been directly involved with their use for the past five years – right from the start, in fact.
When asked how many sites he’s been involved in and which ones would be best to include in this article there was a pause. Then, a muttered: “Two… three... six... eight... twelve... about fifteen probably... maybe more.”
OK, hang on. With a wordcount of about 1,500 words, perhaps we should concentrate on half a dozen!
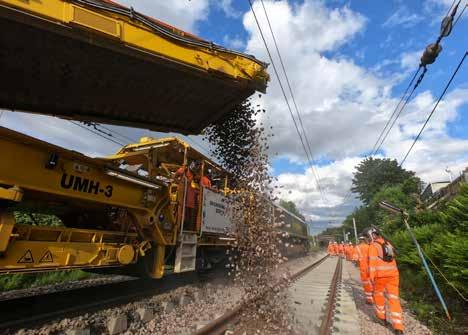
The single line platform
Liverpool Lime Street station Platform 7 is a single line platform in an extremely confined area. Approached through narrow tunnels, it was the first outing for the machine group. Ballast for the formation was placed by the MFS+’s taking delivery of material from a rake of conventional MFS wagons.
Single line platforms and the like are the system’s forte. They are forever on the ‘difficult’ pile. They cannot benefit from materials or plant being fed from an adjacent line using conventional machinery. Hitherto, the working methods have been clumsy, imprecise and timeconsuming.
On the other hand, an ITC can make short work of the excavation and materials are shifted straightaway into waiting MFS wagons. MFS+ machines can deliver ballast precisely.
The island platform
The ITC was first deployed on a platform track-relaying job ‘under the wires’ through the island platform at Acton Bridge in Cheshire. The overall project was a relaying job of about 500yds.
The track at one end of the platform was excavated conventionally, with the 265yds through the platform being dug with the ITC feeding the MFS+ machines which, in turn, fed the awaiting MFS wagons. Grading of the formation was done by a dozer feeding the ITC.
This first project was a composite effort between conventional and new methodologies.

Working with geotextiles
Geotextiles are great for separating layers of material – it is what they are designed for.
They are not so great at withstanding being trampled on directly by heavy machinery.
MFS+s are very large, very heavy machines and yet, with some clever research and experimentation, geotextile membranes easily survive their encounter.
The trick is to set the belts running and sprinkle a 4” layer of ballast on the geotextile just ahead of the MFS+ as it enters the excavation. Effectively installing its own haul road, the MFS+ makes its way to the far end of the excavation before gathering full loads of 60 tonnes which is then placed on the bottom ballast for dozers to grade. The offloading rate outstrips the dozing rate and so the MFS+ output doesn’t figure on the critical path for the project.
This method was used successfully on a single line at Park South curve near Barrow.
Working with high cant
A project at Holton curve in Cheshire showed that track/formation superelevation does not cause a problem with the precise dropping of ballast by MFS+ machines. The alignment of the top belt has an adjustment of about five degrees
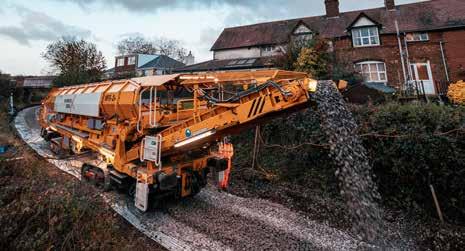
either side of the centre line. This is a feature designed primarily to allow precise alignment of belts in a marshalled consist.
Happily, it can also be used in the dropping of ballast so that there is no tendency for there to be a bias towards the low side of the formation and for there to be a need for further grading by a separate dozer.
Ballast spreading
At Cambuslang in Scotland, at a site called Hoover (it’s opposite a Hoover factory), the UMH, in a consist with MFS wagons, was trialled as an alternative for the SKAKO train. The SKAKO train has been used extensively to spread top ballast throughout Scotland, but it is now getting old. It runs in a formation of ten 60-tonne wagons, each of which has a small side-belt that reaches out 2½ metres – not quite far enough to reach the cess.
The UMH has a selection of belts, all have a distribution capability of reaching up to 6.5 metres from the centre line (that’s around 5.25 metres from the sleeper ends). The control of the output is precise so that ballast delivery can be started or stopped at any time.
At Hoover, the train ran through at a steady 1mph with the belts being adjusted to cope with high or low spots in the ballast. Even though the top belt is large, it was still possible to drop between the rails.
The drainage project
At Stanley Joiners Shop in Perth, two UMHs, working in tandem, were used in a drainage project. Each UMH was marshalled with a consist of MFS wagons. One MFS consist was loaded with pea gravel, for pipe bedding, and the other part of the consist was loaded with track ballast.
The bottom bed of pea gravel was laid by the UMH. The drainage pipes were then installed and the remaining pea gravel placed over the pipes. The second UMH then ran through the site placing ballast to backfill to cess level. There were no problems reaching any part of the drainage channel – even over the track on which the road-rail vehicles travelled. The bottom belt-end was over the sleeper ends. When the belt started running, the speed of the belt propelled the stone into the drain.
Is this a guess? Has this been tried before? Indeed it has. This method of drainage works has been trialled at Tyne Yard and so there is confidence that ballast placing will be effective.
Another job in Scotland using exactly the same method would have taken place already, but for the rapid introduction of the lockdown.
Off-loading large quantities in a small space
A novel use of the UMH was near Kincardine, where there was a requirement to concentrate 700 tonnes of excavated material in an area of about a tennis court. Again, the reach of the belts made this straightforward, with all of the material laid clear of the running lines and with no need for further dozing or double handling.
This ability to process and concentrate large quantities of material in a small area is ideal for backfilling earthworks and material distribution on bank slips. The 700 tonnes at Kincardine was placed in about an hour in a virtual quarry approximately four metres high.
The game changer
By now, Tom Cherryholme’s half a dozen sites has become seven, with crossreferencing to another two! Tom’s list was of real-life projects and real-life successes - the Rhomberg Sersa machine group has left its experimental stage far behind.
Right at the start of this series of articles, Network Rail’s Steve Featherstone called the project a ‘game changer’. Even though the world, as we presently know it, has been turned upside down, this deserved accolade remains as valid as ever.
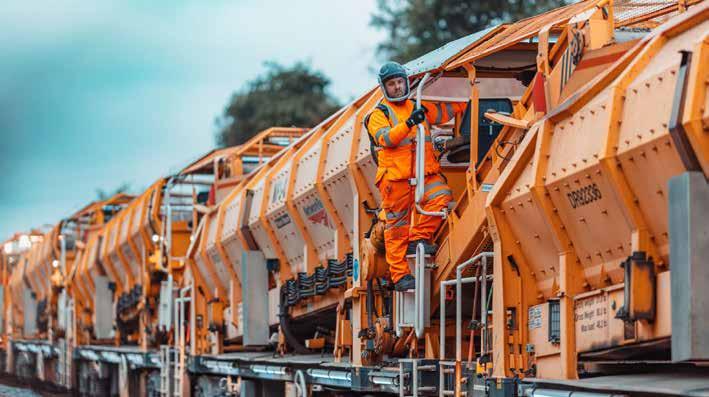