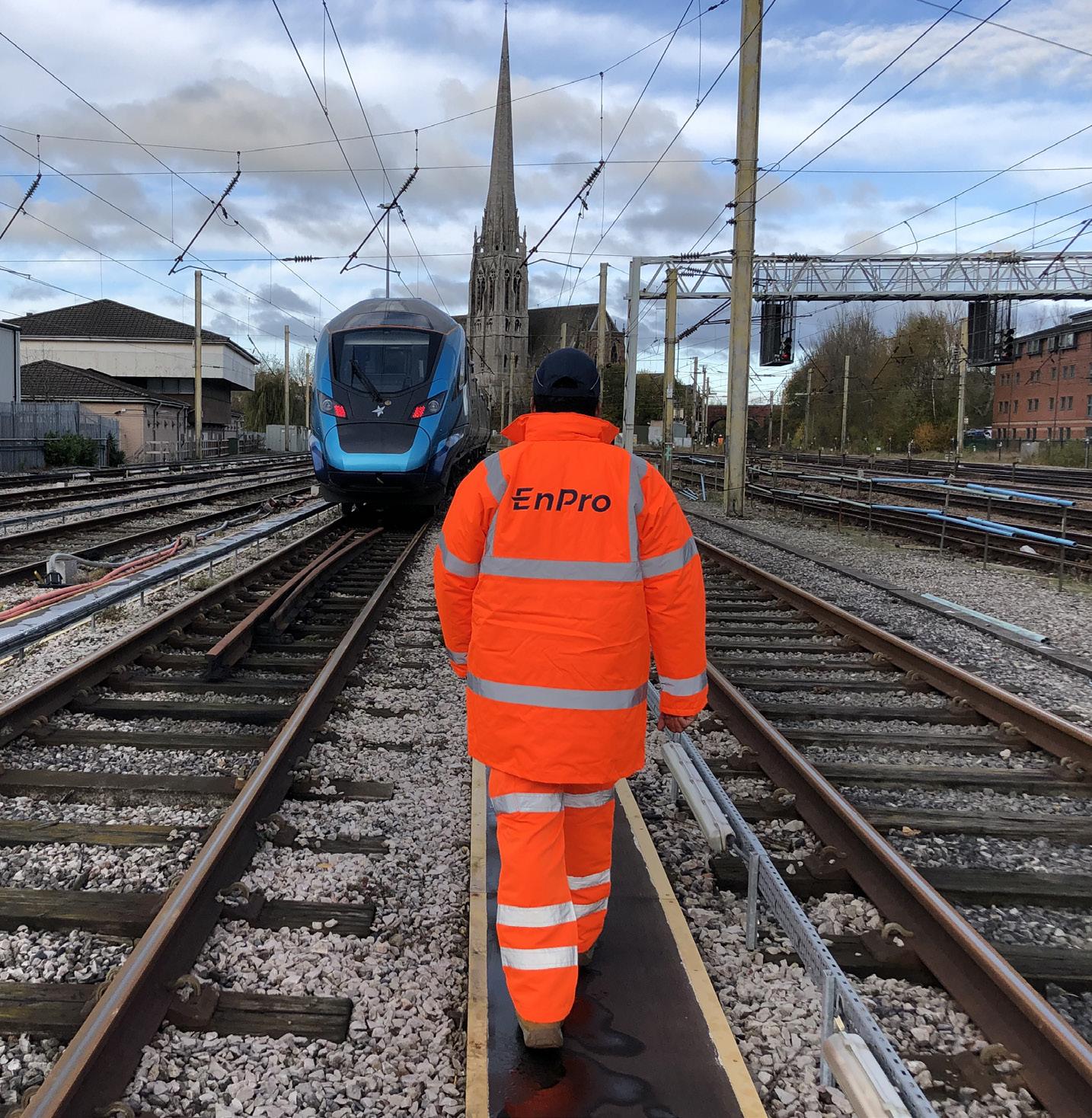
8 minute read
EnPro: Growth through Adversity
Established in 2017 by career railwaymen Daniel Cartwright and Craig Speed, EnPro Group provides bespoke, project-managed solutions for rail industry clients across the UK
With a mission to be ‘the best at what we do’, the founders of EnPro have created an organisation that focuses on inter-business relationships, collaboration, innovation, quality and consistent delivery across five complementary service divisions:
• Railway Projects – Traction & Rolling Stock (T&RS) turnkey projects, new technology installations and rail vehicle modifications.
• Train Presentation – Rail vehicle cleaning, asset protection and dilapidation repairs.
• Facilities Management – Office, premises and industrial site services.
• Security Provision – Uniformed security guard presence.
• Support Services – Provision of experienced management professionals and consulting services.
The business has proven remarkably resilient, enjoying continual growth despite challenging political and economic factors including the pandemic, the current transition from rail franchises to National Rail Contracts and a rising cost base owing to the ongoing cost of living crisis.
EnPro’s Head office is centrally situated in the Chubb Buildings at Wolverhampton Interchange with a second industrial facility located in north east Glasgow. However, most of the workforce operate at thirdparty sites - from London Underground and ScotRail depots, to GB Railfreight yards and sidings across the UK. Experienced and competent project teams integrate seamlessly with incumbent depot facility operational staff and activities. This approach is a key component of EnPro culture.
Operations are regularly delivered to tight timescales. Project mobilisation often includes the installation of temporary welfare and storage facilities which can be installed nationwide and within a matter of days.
Rolling Stock Experience
With a portfolio of rolling stock projects spanning five years, EnPro has successfully supplied modification designs and attained approvals, procured material and projectmanaged system installations across a range of passenger fleets, freight locomotives and track maintenance machines.

Case studies include Driver Only Operation reversal modifications to electric units at Bournemouth depot; internal and external modifications to fleets at Stewarts Lane (London) for Person with Reduced Mobility (PRM) compliance; CCTV installation packages, (including passenger saloon, forward-facing and pantograph cameras); LED lighting campaigns; plus, numerous relay renewal and wiring schemes to manage obsolescence of safety-critical systems, including sanders and brakes.
EnPro provides high quality service whilst striving to identify cost-effective solutions which delight the customer. For example, at Inverness and Corkerhill (Glasgow) depots, EnPro technicians performed a suite of works concurrently (HVAC controller upgrade, door system safety modification and CCTV renewal). The train operator realised savings through synergies in project cost, reduced downtime and increased availability of their diesel fleets.
EnPro vehicle builders have undertaken significant bodywork and roof corrosion repairs, incident damage and exterior paint works on passenger vehicles. They also offer Cab front end damage repair services, including GRP quarter panel renewals and paint.
Internal dilapidation repair and restoration capabilities include removal of saloon seats, dado panels and tables for strip and repaint before rebuilding. Paint repairs have also been completed on vestibules and in toilet compartments where the renovation of a whole panel is quicker and looks more aesthetically pleasing than patch repairs. Dilapidation repairs like these may be augmented with specialist cleaning (carpet cleaning and chewing gum removal) by our Train Presentation team. These are the benefits of EnPro’s one-stopshop approach and complementary service divisions.
Collaboration
A delivery pack of ‘project, communication and planning’ tools assures successful management and integration of complex projects with multiple stakeholders. This methodology was employed effectively on the Scottish GSM-R radio upgrade programme to provide progress review updates, manage issues and ensure deliverables were met to budget and on time. Interfaces between ScotRail, Network Rail, Siemens and SNC-Lavalin were governed to control float, logistics and installation across every ScotRail fleet from Inverness to Edinburgh.
EnPro also has demonstrable experience of seamlessly integrating with system suppliers to deliver rail vehicle modification packages. Working with Cibest, (a global leader in rail-rated, IP-based CCTV and Communication Systems), EnPro has been awarded the contract to upgrade video systems onboard Rail Grinders and Milling Trains. This collaboration has proved to be a compelling solution for Colas Rail, combining the on-site installation and project management pedigree of EnPro with access to the Cibest technical resource and know-how. EnPro will provide the client with a single point of contact and manage material supply through Cibest, (where all equipment will be covered by an extensive obsolescence management plan).
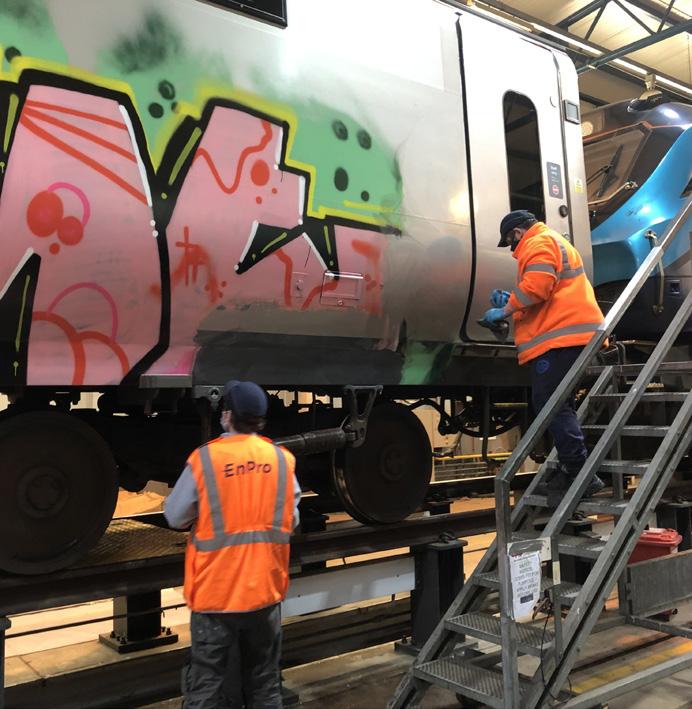
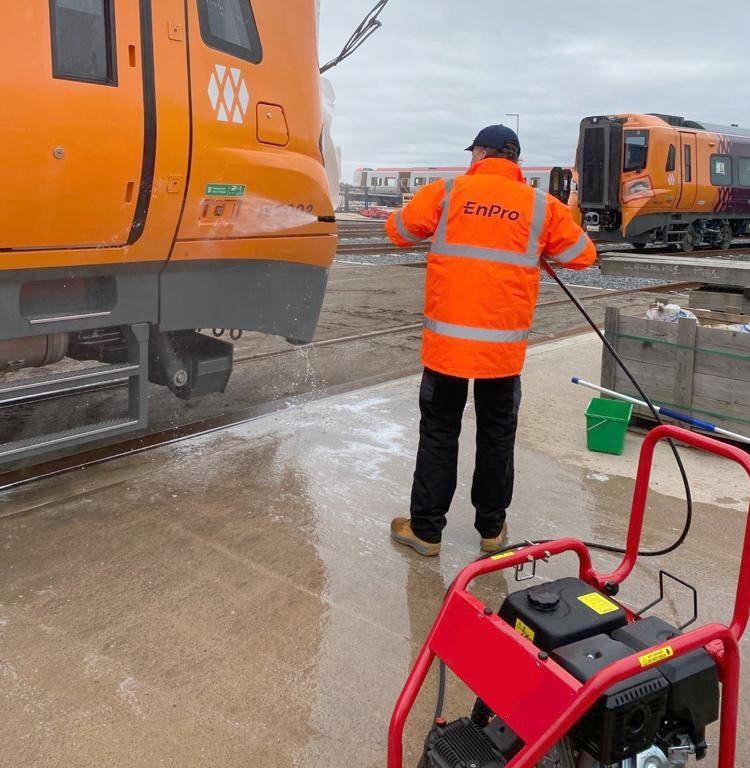
Shop Window
EnPro understands that cleanliness and presentation standards are the ‘shop window’ for train operators and our team are passionate about providing prestigious levels of service.
Current high profile contracts include the periodic heavy cleaning of locomotive cab interiors for GBRf. Works are centred on Doncaster, Peterborough and Tonbridge and augmented by mobile operatives in fully equipped vans, who will deliver services at outstation locations.
Mobile teams also perform cleaning and servicing of Britain's most luxurious train – the Northern Belle (on which customers experience luxury rail travel at its very best). This requires a unique kit of train cleaning chemicals, including metal polish and nonsilicone bees wax for the brass touch points and marquee woodwork.
When new trains are delivered, they require a thorough valet-type clean prior to acceptance by the customer. EnPro has a long history of completing these handover cleans on rail vehicle interiors and exteriors for new train builders CAF and Stadler.
New trains for Caledonian Sleeper, TransPennine Express, Greater Anglia and West Midlands Trains have all been cleaned to the highest standards by EnPro at locations including Polmadie (Glasgow), Wembley, Manchester, Cambridge, Tyseley (Birmingham) and Newport.
EnPro staff also conduct overnight cleaning and servicing of trains for East Midlands Railway in Boston and for TransPennine Express at Preston and Doncaster. The latter contract includes Train Preparation Pre-service Checks and Fitness to Run exams, so EnPro teams will be wholly responsible for making trains available for the morning service.
SQR Prepared
SQR (Service Quality Regime) audits are now being conducted by independent auditors to measure customer experience on trains and at stations. Incentives and penalties encourage train operators to maintain and improve standards.
Cognisant of how important SQR is to its clients, EnPro has invested in a fully digital smart compliance platform (mpro5), which can be used on desktop or mobile devices. Whilst it has already been implemented by Network Rail and several train operators, EnPro is the only SME to have made the financial commitment to adopt this software.
The implementation of processes, auditing and proving compliance is assured through mpro5. After completion of work, EnPro Operatives use the application to complete a quality audit (based on the SQR template). Supporting photographs are attached showing ‘before and after’ condition or vehicle defects that require rectification. Audit scores with GPS and time-stamped images are stored against rail vehicle painted numbers and results are presented in dashboard form, providing surety of standards to the operator.
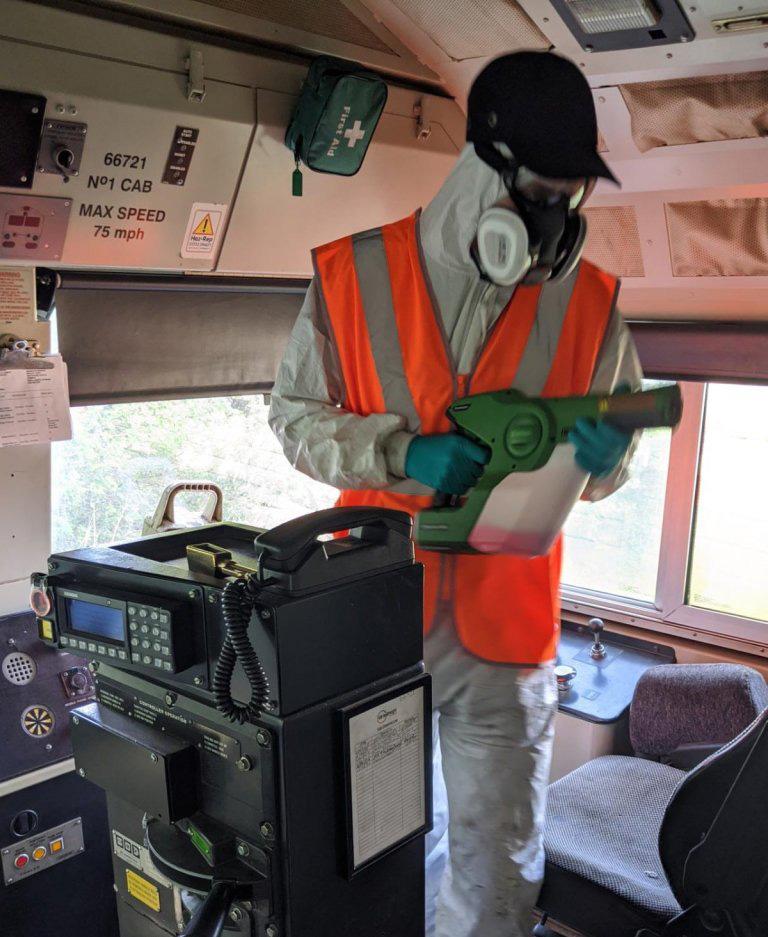
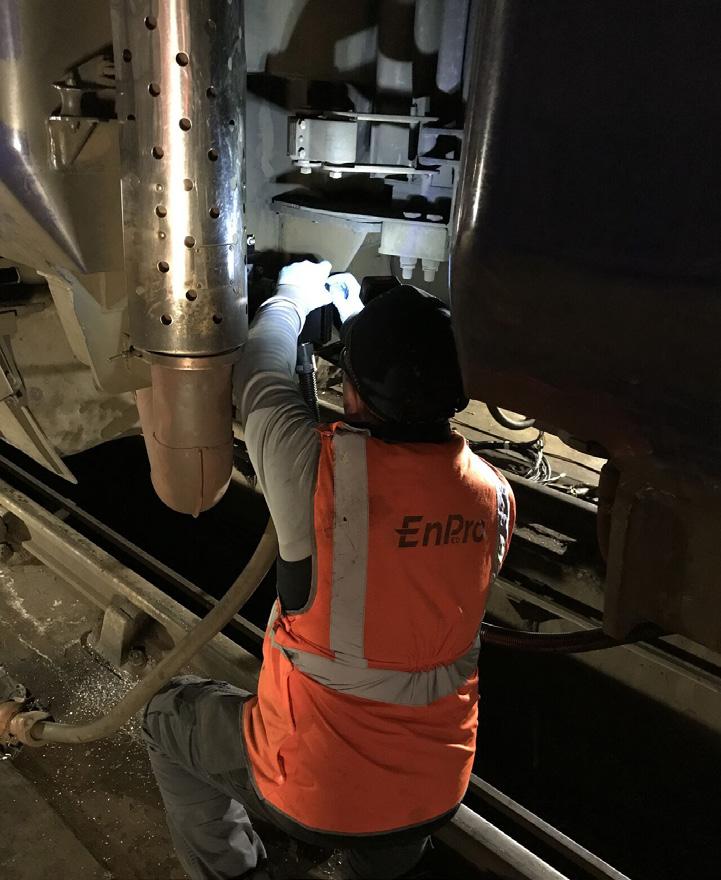
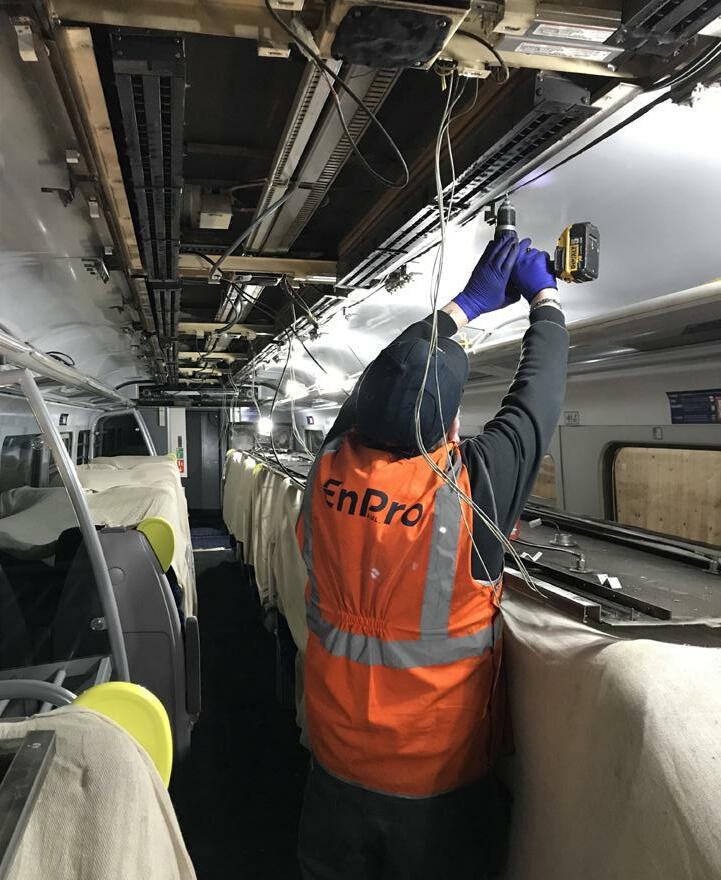


Keen to collaborate with operators to further drive improvement in SQR scores for trains entering service, EnPro has requested that operatives be issued with a float of mandatory labels so that any damaged stickers within passenger areas can be renewed immediately. Operatives have also been instructed to wash exterior bodyside doors and glazing in their marginal time and where practicable (in addition to the planned scope of cab front washing only).
Analysis of Big Data
EnPro’s Support Services division has placed experienced consultant auditors with rolling stock leasing companies to carry out condition assessments and dilapidation surveys. These reports are required when an operator hands rail vehicles back at the end of a lease and inform dilapidation repair requirements.
Online train presentation audits undertaken by EnPro operatives are creating a statistical and visual history of fleets serviced. This will be expanded as procedural documentation, including handover / handback for rolling stock modifications, is migrated to the software application and updated by EnPro technicians.
Whilst conducting system overhauls in the past, EnPro technicians have removed panels, fixtures and fittings from rail vehicle interiors. Campaigns like these could represent an opportunity to record rail vehicle condition in areas not easily accessible except at overhaul.
The management team at EnPro are constantly looking at areas where value can be added to existing services efficiently, effortlessly and cost effectively. The management of unstructured, multimedia data from EnPro audits (both technical and cleaning), could be utilised to produce comprehensive vehicle survey information. Exploring this opportunity might enable operators and leasing companies to dispense with traditional, time-consuming and costly condition assessments, whilst providing increased visibility of issues to stakeholders.
In conclusion and based on the first five years of growth, the future looks exciting for EnPro.
The Future
EnPro’s management team are confident that their plan to further invest in people, technology, equipment, and facilities will reinforce business capability. This strategy will, in turn, assure its existing projects and help the business to win further medium and long-term contracts – securing its future for both staff and customers.
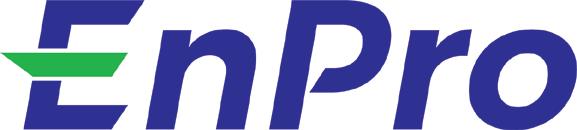
Tel: 01902 925307
Email: enquiries@enprogroup.co.uk
Visit: www.enprogroup.co.uk