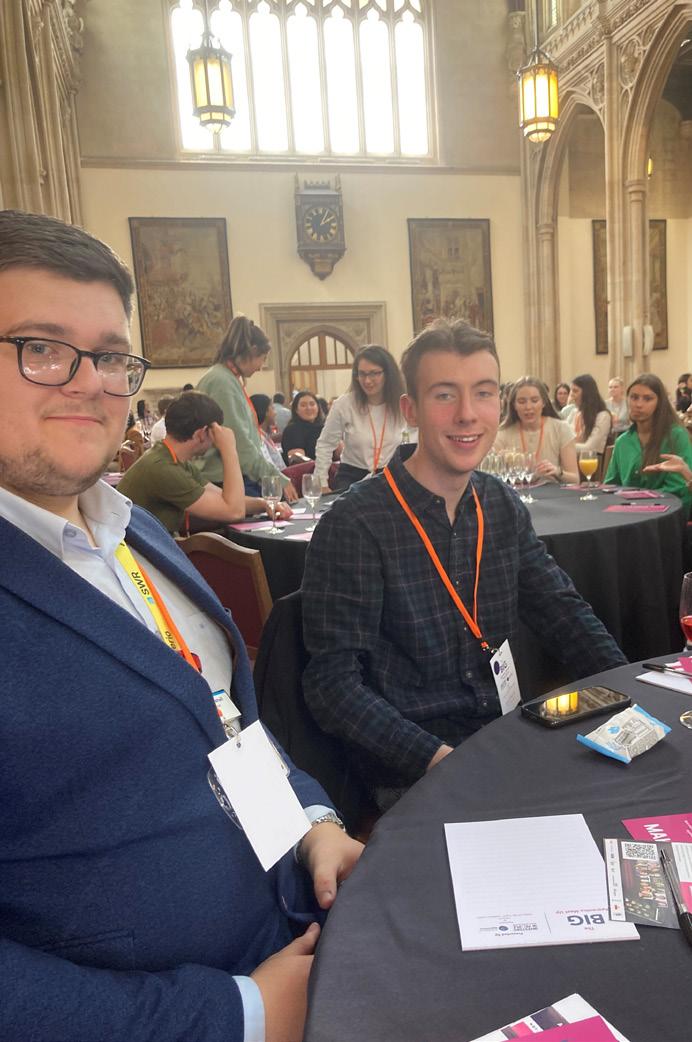
65 minute read
TRAINING
The SWR Employer Apprenticeship Challenge
Kirstie Thompson, Apprenticeship Compliance Manager at South Western Railway describes how apprenticeships form part of the business plan to develop a high performing workforce with succession planning
We recognise that there is an aging workforce in the railway and although our traditional programmes are aimed at bringing younger talent into the railway, our apprenticeships that are linked to job roles and upskilling apprenticeships are open to colleagues of all ages and backgrounds.
SWR’s dedicated Apprenticeship Team sits within the Learning & Development function within HR. This allows us to talk to about other development opportunities we have available and not just apprenticeships.
In early 2018, we introduced REACh (the SWR Railway Employer Apprenticeship Challenge) as the brand for our apprenticeship programme.
We know we are doing well – in 2020 we were shortlisted for the Personnel Today ‘Apprenticeship Employer of the Year’ and achieved silver in the Investors in People ‘We Invest in Apprentices’ accreditation. In 2022, we have been short listed for the Investors in People ‘Best Apprenticeship Programme’.
In September 2022, we celebrated our 100th colleague successfully achieving their apprenticeship. In recognition of the amount of time and effort we know our colleagues put into their apprenticeships, we decided to offer colleagues the opportunity of a meal out with other colleagues who have completed their apprenticeships. Our first event in October included colleagues who had completed their apprenticeships plus our Young Talent and Leadership Talent apprentices who used the event as a networking opportunity.
We use apprenticeships in three ways: • Traditional – bringing new talent into the business through our Young Talent
Rail Apprenticeship, Leadership Talent
Rail Apprenticeship and Engineering
Apprenticeship. • Linked to Job Role – we have aligned the train driver apprenticeship and customer service practitioner apprenticeship to our internal training programmes for Train
Driver and Customer Ambassador. • Upskilling – offering apprenticeships to upskill colleagues at any stage in their careers.
Engineering Apprenticeship
This has been our longstanding apprenticeship programme and is essential to ensure succession planning within our engineering function where the general age profile is higher than across other functions.
Although we primarily recruit younger people into the apprenticeship, there is no age limit and where we only recruit on average six apprentices per year, it’s always good to see a range of different age groups as they all bring different approaches and ways of working. We have a great retention rate within our engineering apprenticeship with many apprentices moving onto team leader and leadership roles as their careers have developed.
In February 2022, SWR introduced the Young Talent Rail Apprenticeship and the Leadership Talent Rail Apprenticeship programmes. We designed a bespoke recruitment process and reached out to local authorities and colleges to promote our programme and attract a wide range of candidates.
In designing the two-year programme, we collaborated with senior leaders across the business to understand their functional needs and how apprentices could support succession planning.
We worked closely with our training provider (Fareham College) to adapt the Level 2 Customer Service Practitioner apprenticeship standard to fit our needs - the college have listened to our feedback and introduced additional masterclasses (conflict management, team working and meeting targets) and to help ensure the apprentices have the skills and confidence they need to meet our customer needs.
Each apprentice has a flexible training plan – we are always adapting the plan to meet the needs of the apprentice and the business. This means that the apprentices can attend events and join business projects that support their learning. We encourage the apprentices to approach areas of the business and have input in their own development plan.
This programme is aimed at developing the apprentices and keeping them in the business longer term. This includes ensuring we have longer term development plans in place and opportunities for continuous learning and improvement. We build in monthly one-to-ones with the apprentices and encourage honest feedback and suggestions for improvement.
We have received some very positive feedback about our new apprentices from every area of the business they have had placements in.
Feedback has included: ‘The WICC Information Team has hosted three apprentices, who joined us in February of this year. Having them as part of the team has been a huge benefit – aside from the enthusiasm and dedication they have brought to the role, it’s also given some of our team a great opportunity to develop and learn how to coach others!
‘We share our apprentices with the stations team, and it has been great to see their customer service skills develop over the multiple mediums – in-person, over help points and on social media. Seeing them get more at ease at handling customer concerns, delivering network information and taking up a key role in disruption – that of making sure systems are updated with train alterations – is a testament to their adaptability too.
‘Our team has benefitted too – alongside the typical benefits of a fresh perspective from individuals who are new to the industry and to SWR, our team have also been able to take a role in training,
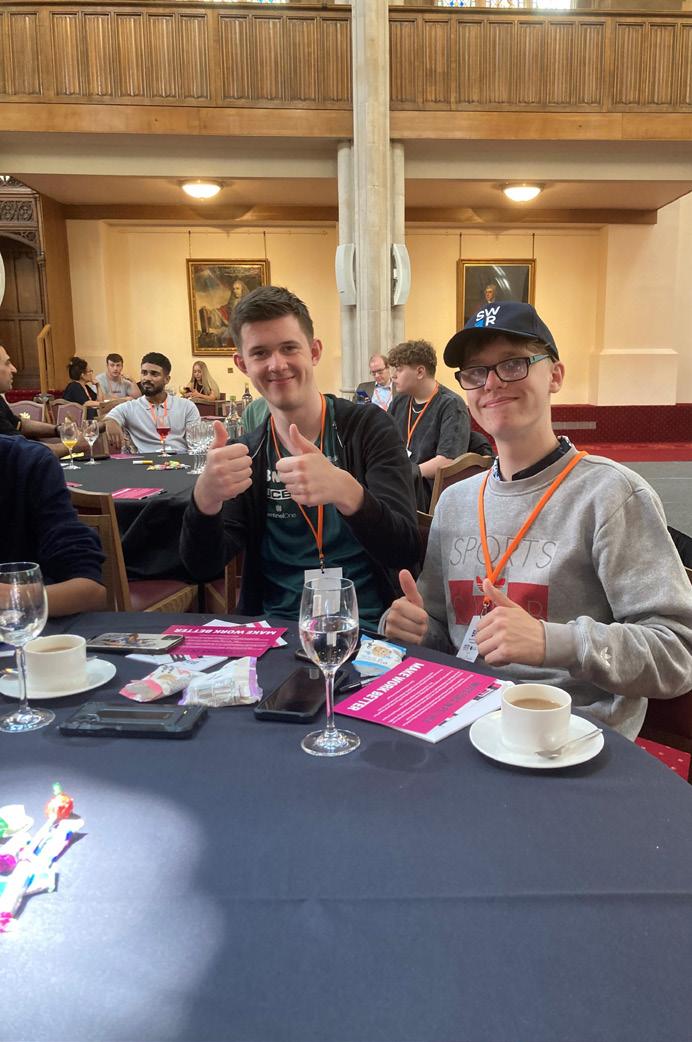
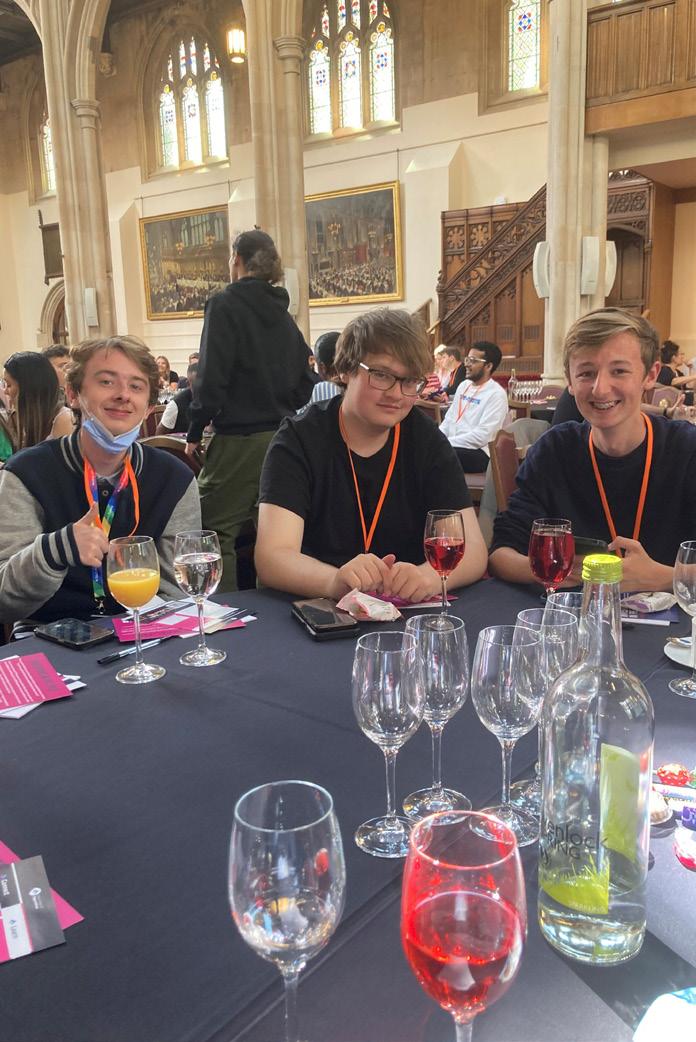
coaching, and developing our apprentices. This has boosted their confidence and helped us in developing individuals and identifying talent.
‘The flexibility of the programme is also a great help – we usually have the apprentices two days a week but have also relied upon their assistance for additional periods of time during planned disruption and arranged trips and visits for the apprentices, and our wider team, to develop valuable knowledge in areas and departments across the network we interact with on a daily basis. We also enjoy a great relationship with the Programme Manager Michael, who has been a huge help navigating this new experience for us all.’
The apprentices have been supporting the business during the recent Industrial Action. The Apprenticeship Team were initially apprehensive about letting the younger apprentices out during the industrial action as customers can be very challenging but they insisted on getting involved. Using the skills and knowledge they have developed over the last six-months, they were able to interact with our customers and provide support and assistance where they could. It was great to see them step up to the challenge.
Upskilling Apprenticeships
In addition to our traditional apprenticeship programmes, we offer a range of upskilling apprenticeships that are available to all colleagues.
Working closely with a range of training providers, we are able to offer upskilling apprenticeships in Team Leading, Leadership, Chartered Manager, Learning Mentor, Coaching Professional, Customer Service and Data – all of these apprenticeships support the development of our colleagues.
The railway industry is going through a period of significant change and, historically, we have a lot of ‘accidental managers’. The offer of the upskilling apprenticeships helps to ensure that our leaders have the underpinning knowledge and skills required to allow them to adapt to change.
Line Managers now understand the value of being involved in the apprenticeship programme of their team members and we have adapted our internal application processes to help ensure that the right support and understanding is in place to help ensure we get the right colleague on the right apprenticeship at the right time.
Prior to Covid, our Engineering Apprentices would regularly get involved with community activities such as beach cleaning and visiting local businesses. This was an opportunity for our apprentices to get together and do some team building.
The Apprenticeship Team engages with local schools and colleges in our local areas –we regularly attend careers events where we promote apprenticeships and railway careers and we also support with CV writing and interview practice. It is great to see younger people find out that the railway is more than just train drivers and engineers.
When we introduced our Young Talent and Leadership Talent Apprenticeship, our first step was to reach out to local authorities and schools to generate interest in the programme and encourage a diverse range of candidates. The aim of our Young Talent and Leadership Talent Apprenticeship is to help develop a diverse workforce which is reflective of our local communities.
SWR is in the process of moving into a formal collaborative relationship with Shaping Portsmouth where we will be a Patron member. Shaping Portsmouth is a charity in Portsmouth that supports employability and brings organisations together to support young people and disadvantaged people in the community. SWR is a large employer in the Portsmouth area and we can work with Shaping Portsmouth to support events and offer work experience opportunities. Shaping Portsmouth organises an annual ‘Apprenticeship Bus’ event where apprentices from business across the Portsmouth area get on the bus and visit several schools and college to promote apprenticeship opportunities and share their experiences. This activity links with SWR's Social Value commitments and supports our ‘Employer of Choice’ Sustainability initiative.
The Apprenticeship Team visited a community project in the Basingstoke area which is designed to offer advice on employment and career opportunities to young adults with physical and learning disabilities. Part of this experience was a learning experience for the Apprenticeship Team and how the railway can be more accessible to customers and colleagues with physical and verbal disabilities.
SWR is joining the Cornerstone Employer initiative – we work with thousands of businesses across the country. But our Cornerstone Employers are a flagship group of more than 300 businesses of every size, shape, type and sector who Transform the lives of young people in their area. Celebrated by government, Cornerstone Employers work collaboratively and strategically with networks of schools, colleges and local stakeholders to improve careers education.
Kirstie Thompson is Apprenticeship Compliance Manager at South Western Railway and supports the other First Group businesses with their apprentices.

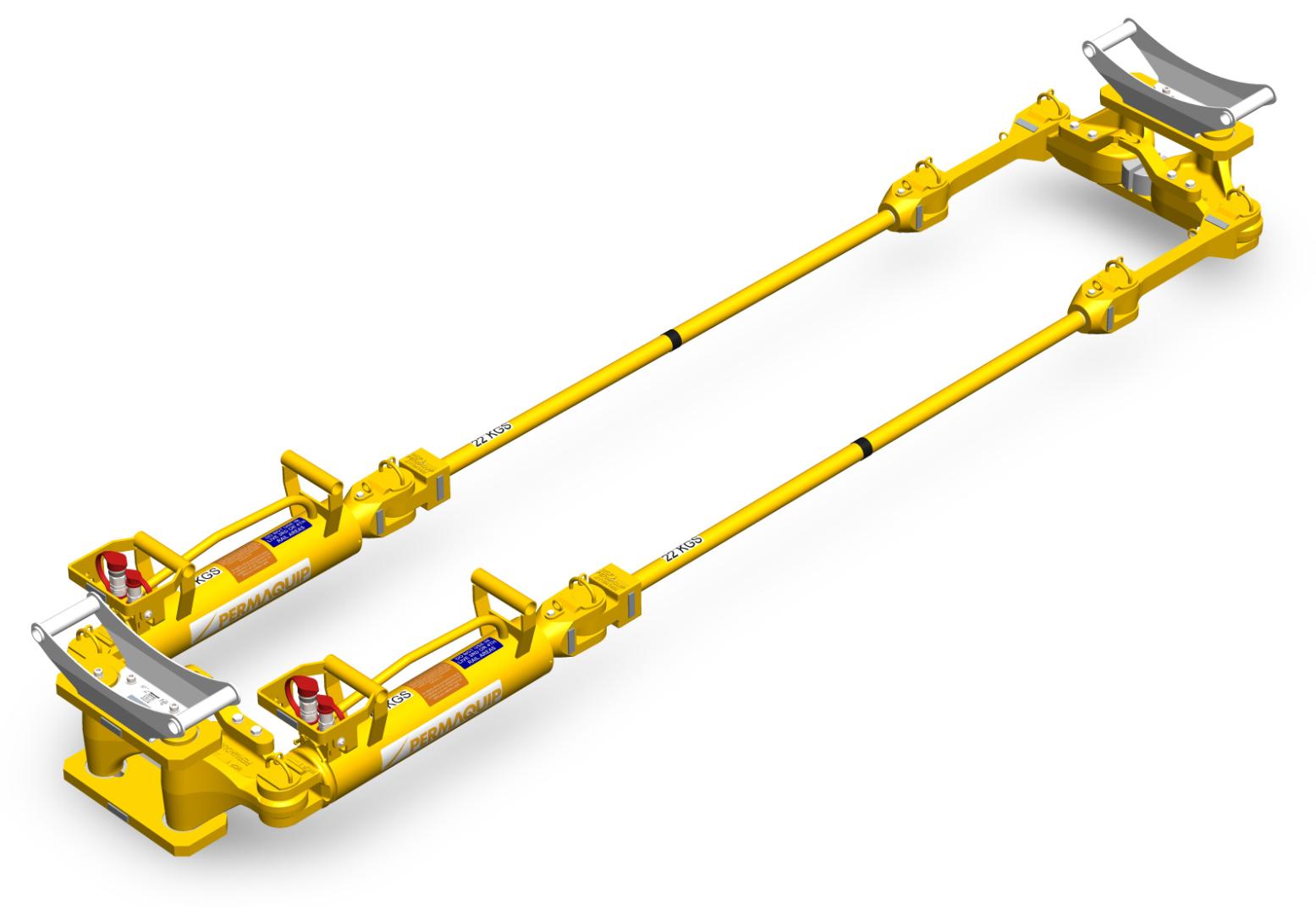

Adaptable Solutions from Aquarius Rail
Specialists in the design and manufacture of innovative highway-based road rail vehicles, trailers, and attachments
Aquarius Railroad Technologies provide safe and efficient transport solutions for track maintenance across the UK and around the world.
Innovation in the blood
Continually driven by problem-solving, Aquarius has developed a range of niche products, which offer the perfect solution for a wide range of reactive or scheduled track maintenance tasks, such as: • Cable pulling (power, communication and optical fibre). • OLE isolation. • Track asset scanning/data gathering. • Asset management. • Seasonal treatment (autumn leaf fall). • Weed spraying. • Trackside graffiti removal. • Transport of personnel and materials.
Making leaf mulch a thing of the past on Devon’s railways
Each autumn, thousands of tonnes of leaves fall onto tracks. Crushed leaves contaminate the railhead reducing the train’s braking efficiency and decreasing traction when setting off. Likened to ‘ice on the roads’ this can lead to significant train delays.
Aquarius is helping Network Rail keep train services running this autumn, with the adapted R2R 4x4. The vehicle, known as the ‘Sand Rover’, is being deployed on Devon’s branch lines following successful trials which saw an average reduction of 80 per cent in delays as a result of leaf fall on the tracks.

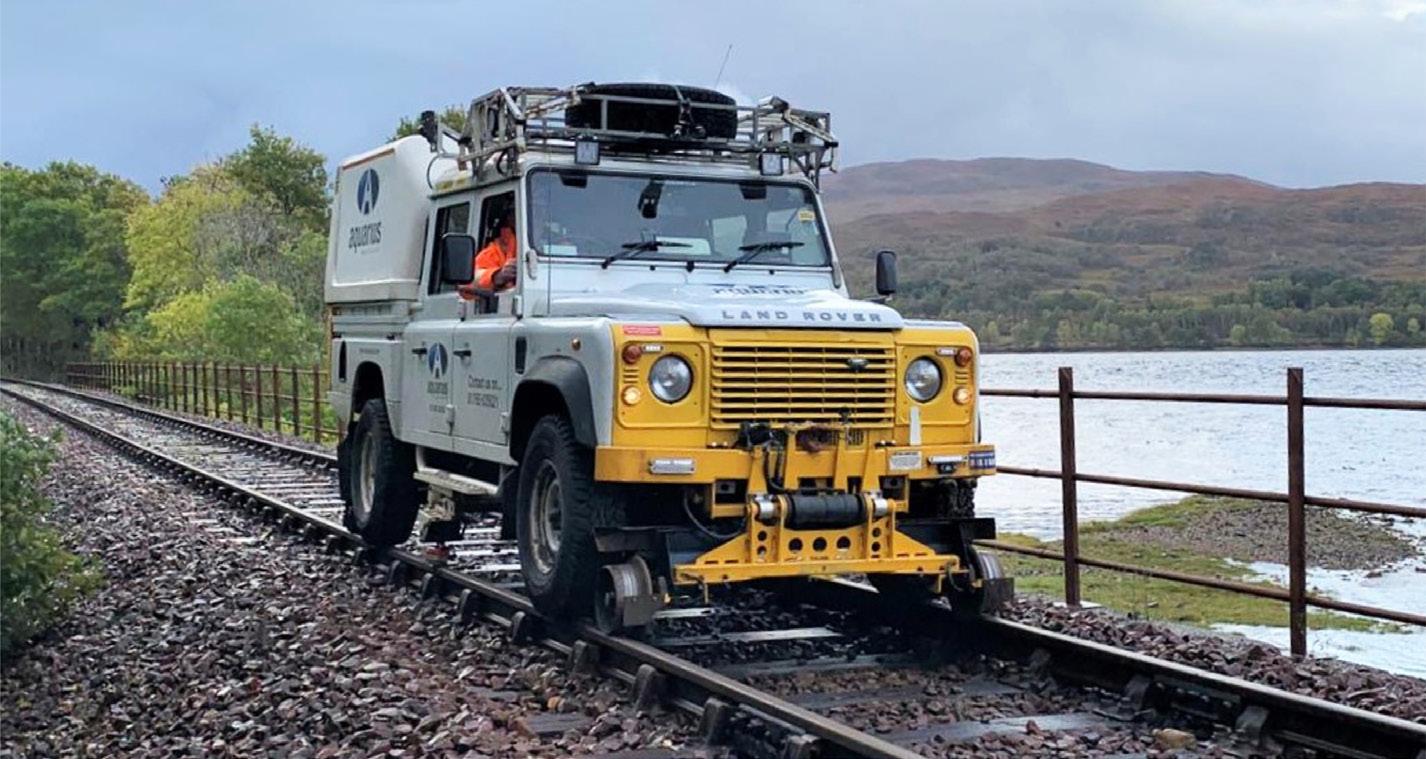
Aquarius Rail ‘Sand Rover’ R2R 4x4s are deployed on various lines across the UK each Autumn, to help combat leaf fall on the tracks and have been proved to reduce delays caused by fallen leaves by around 80 per cent.
Scott Harrison, Managing Director, Aquarius Railroad Technologies
The Sand Rover applies a citrus-based treatment to the track. Sweeps leaf mulch off the rails with wire brushes, and finally coats the rails with dry sand which helps trains to grip.
During autumn 2020 Network Rail trialled the use of a Sand Rover on the Tarka line, resulting in an 87 per cent reduction in delays caused by fallen leaves when compared with previous autumn seasons.
Last autumn, Network Rail widened the scope of the trial and the Sand Rover was also put to work on the Dartmoor line, with the equipment working in each area on alternate nights.
The lines, specifically chosen owing to their locations, both experience a high volume of leaf fall and are not accessible by the rail head treatment trains (RHTTs).
Simple and safe
Available to purchase or hire vehicles, trailers and attachments are designed to: • Improve Health and Safety. • Save Time and Money. • Maximise Productivity.
Contact Aquarius Rail to find out how the company can help you with your railway maintenance project.

Tel: 01765 635 021 Email: enquiries@aquariusrail.com Visit: www.aquariusrail.com Linkedin: aquarius-rail Address: Aquarius Railroad Technologies Ltd Old Sleningford Farm, North Stainley, Ripon HG4 3JB
Home of Innovation for over 50 Years
The Permaquip name is a byword in the rail industry for safe, rugged, dependable products, made in the UK to world-class standards
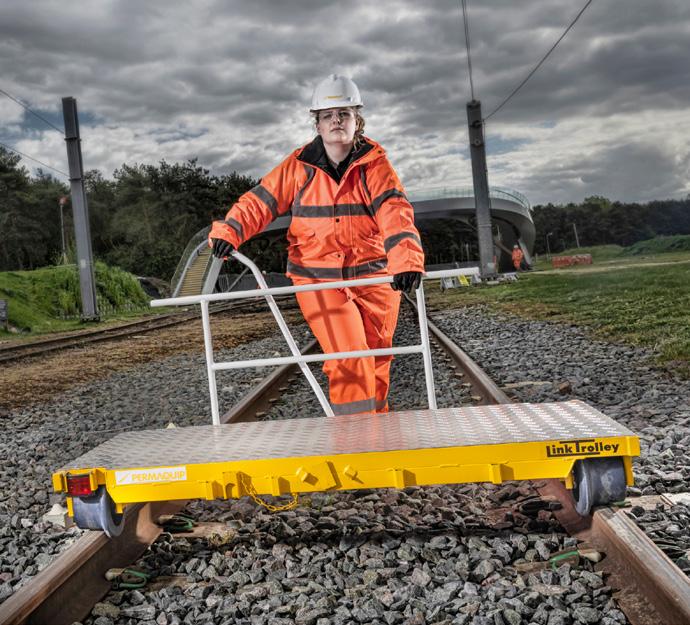
Permaquip Link Trolley
Permaquip’s innovations have solved railway maintenance tasks and challenges as they’ve emerged. Improving efficiency, productivity, and safety.
The design approach
Permaquip draws on its extensive knowledge and expertise in engineering and design. Using state-of-the-art technologies to bring new products to life and ensure they have the strength, agility and durability that have become Permaquip's hallmarks.
Extensive product range
The Permaquip brand is synonymous with fail-safe products that remain ahead of the curve. The range of products includes: • Road Rail Vehicles. • Trolleys. • Rail lift and move equipment. • Stressors and machinery. • Rail maintenance accessories and tools.
Quality matters
Permaquip’s business and products comply fully with UK and international quality management standards. Permaquip is ISO 9001 approved and holds RISQS (Railway Industry Supplier Qualification Scheme) accreditation. Designed and manufactured in the UK, all Permaquip products carry BS, EN and CE markings.

Permaquip Ironman
Permaquip’s NEW Stressor
Based on the Permaquip HSM70 Stressor, which is the most proven and durable Stressor on the market. The in-house engineering team has developed the NEW Stressor, an ergonomic breakthrough.
Used in full or half sets to adjust the gap between rail ends for rail stressing, rail welding, repairing rail failures, and installing insulated joints. • New ergonomic handle design for easier manual handling. Plus, carrying/lifting tongs (38854) for safer offset operation. • Ideal for use in conjunction with the
Permaquip Stressor Petrol or Electric
‘Zero Emissions’ Power Pack. • Accessories available: lifting/carrying tongs, side rollers and under-rail rollers. • Choice of Stressor Half Set FFC UIC60 (38871) or FFC STD (38872). • NEW Stressor Product Approval:
PA05/07595.
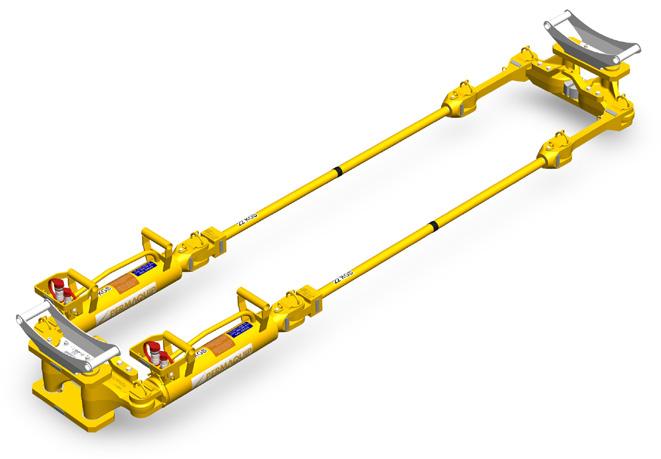

Permaquip Scaffold Trolley
Upgrade your HSM70 Stressor
Give your existing HSM70 equipment the ergonomic benefits of the NEW Stressor with Permaquip’s retrofit handle upgrade kit (38950), which includes all the parts you need to convert an HSM70 half set: • 4qty Ram Handles, 2qty Clamp Handles, 2qty Fixing Sets (for Clamp Handles) and 2qty Lifting / Carrying Tongs.
Relied on by the best
Available to purchase directly or via a global network of distributors, Permaquip’s products: • Improve Health and Safety. • Save Time and Money. • Maximise Productivity.
To find out how Permaquip can help you with your railway maintenance project.

Tel: 01623 513 349 Email: sales@permaquip.co.uk Visit: www.permaquip.co.uk Linkedin: permaquip Address: Permaquip Ltd, Old Sleningford Farm, North Stainley, Ripon HG4 3JB
Protecting Systems from Start to Finish
Relec Electronics’ three-phase sine wave dc-ac inverter series protects systems from start to finish
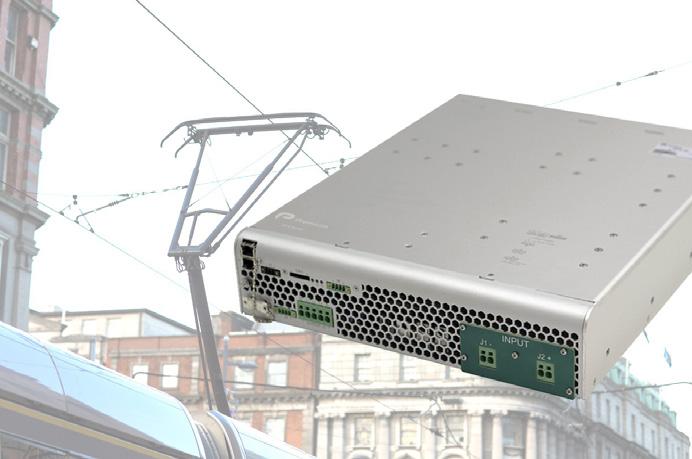
Information systems, enhanced communications and safety-critical equipment have all increased the electrical systems within trains. Yet too often, power design is something of an afterthought, risking compromise on performance to meet physical constraints. Relec is a specialist in power which supports engineers in the quest to meet the rail industry’s particular set of design criteria with the appropriate, high quality power supply.
Onboard monitoring sensors, climate control systems, lighting and door opening systems are all powered by the train’s battery system. Electronic equipment and the high voltage power supplies which power them must be integrated but engineers have to bear in mind several factors. For example, electromagnetic interference (EMI) can cause disruption to electrical signals, but there is also electrostatic discharge (ESD), transient surges and over-voltage episodes as well as shock and vibration resistance considerations.
Electronic equipment on rolling stock must therefore be rugged and able to support not only computing functions but also telematics, engine control or other vehicle functions. The international rail standards are based on a requirement that rolling stock systems will have to operate 24/7 for 30 years without failure. In addition, these systems must not interfere with each other when installed in close proximity, which is often the case in the limited space in control panels and cabin space.
Demanding standards
The EN50155 standard refers to the EN50121-3-2 standard (railway applications, electromagnetic compatibility, rolling stock) to ensure that the equipment does not produce noise levels that may interfere with other nearby devices.
To meet EN50155, systems must be able to operate over a wide temperature
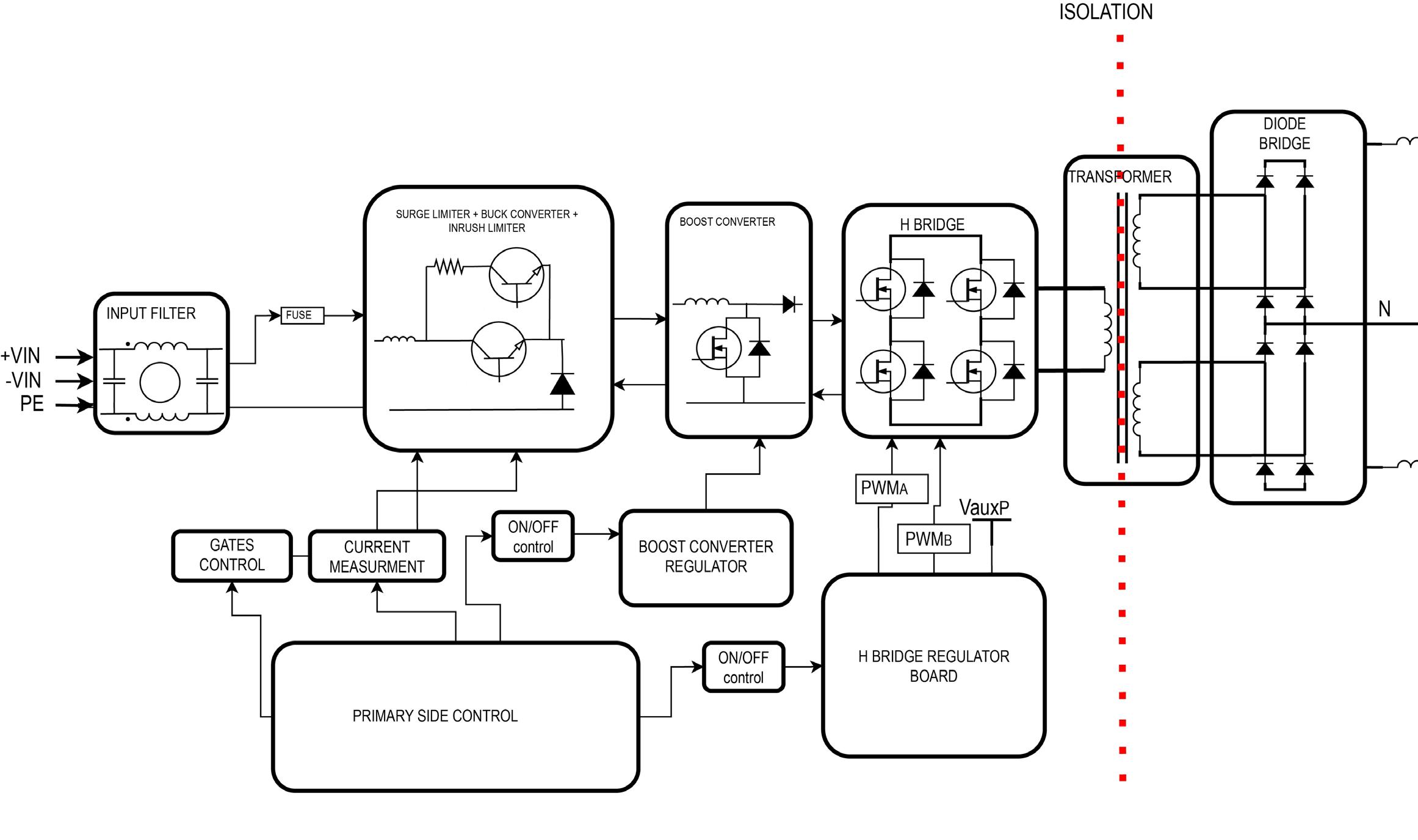
range (-40°C to +85°C). The power supply is required to operate at 85 per cent or above efficiently in order to reduce power consumption over a wide range of voltage and load conditions. It must also have reliable and robust thermal management.
There are also stringent shock and vibration requirements for equipment fitted on rolling stock in the specification. Shock and vibration requirements are divided into three categories: carriage-mounted, bogiemounted, and axle-mounted.
Critical and emergency systems are fed by batteries – a safeguard in the event of a power supply failure. The standard railway battery voltages are: 24, 36, 48, 72 and 110V and battery voltage needs to range from -30 per cent to +25 per cent with variations of ±40 per cent for 100ms, surges up to ±1kV and power interruptions up to 20ms.
Introducing the OVX-6400
Relec Electronics has introduced a threephase sine wave dc-ac inverter series which is designed to protect rail systems from start to finish.
The OVX-6400 dc-ac inverter is engineered to operate over a wide input range and to protect loads at start-up and mid-power modes. The rail-certified products are available from specialist power company, Relec Electronics and are the first designed by Premium to operate straight from the high voltage catenary power line.
The OVX-6400-7701 inverter is a rugged three-phase sine-wave dc-ac inverter which has an input range of 400 to 900Vdc and 400Vac 3ph output, delivering 6,400VA/8,000W pk. It has a high inputoutput isolation withstand of 5400Vrms.
It includes a soft start mode for the startup of high inductance motors, whereby the output voltage rises linearly from 0V to a set voltage and the frequency increases to a set limit. The start-up ramp slope can be changed to meet specific conditions via CAN-BUS control or a dedicated RS-232 port.
A programmable auxiliary Input allows either mid-power or reverse modes. In midpower mode, the voltage and frequency can be set to a percentage of the nominal in order to limit output power from the inverter. The input can also be used to enable reverse mode (phase inversion) which changes the phase sequence, reversing the rotation of the motor
The compact inverter measures just 85.8 x 372 x 450.3 mm. It is certified to EN50163:2006 (supply voltages of traction systems), EN50124-2:2017 (Insulation co-ordination over-voltages and related protection) and EN61287-1 (Power converters installed on board rolling stock). In particular, EN50124-2:2017 details simulation and/or test requirements for protection against transient over-voltages.
The OVX-6400 series inverter also meets EN50155 and EN62368-1 covering electronic equipment on rolling stock and safety standards for IT and AV equipment, respectively. OVX-6400’s certification to EN45545-2 (Fire and smoke) is pending.
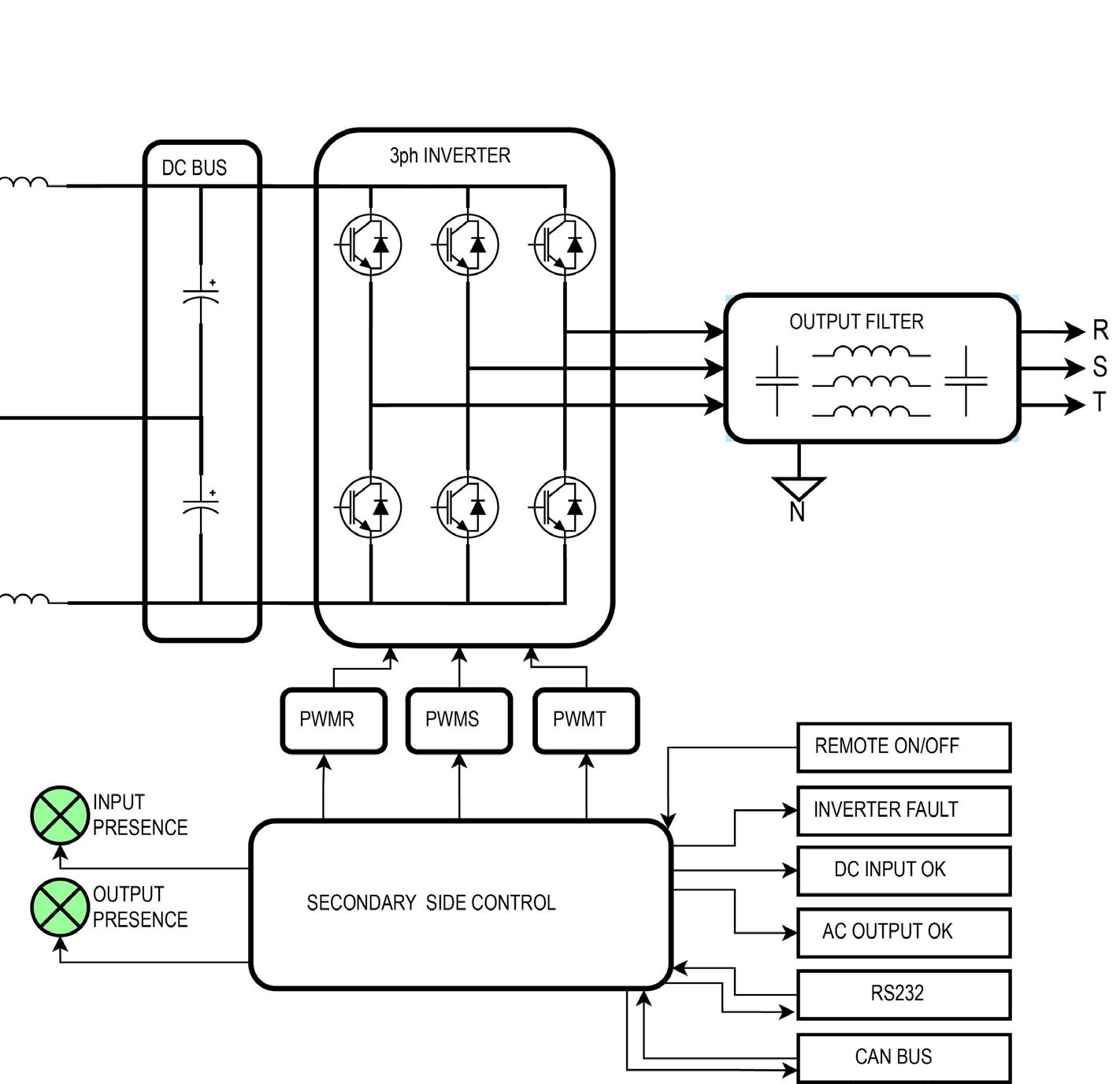
Rail power specialists
Premium PSU has a wide range of dc-dc converters and dc-ac inverters designed specifically to comply with EN50155 standard. It also has extensive experience developing custom designs to ensure protection and quality in the harshest environments.
Relec Electronics offers a wide and varied portfolio of high-performance, rugged ac-dc, dc-dc converters, dc-ac inverters, displays and EMC filters for the railway industry as well as for other demanding applications in other industrial sectors.
In addition to Premium PSU’s dc-ac inverters, Relec also supplies high quality ac-dc power supplies and dc-dc converters from industry leading manufacturers such as Bel Power, Artesyn,Mornsun and Cincon and a wide range of EMC filters, all designed for use in the rail industry.
Premium's OVX-6400 power supply is available from Relec Electronics.
Tel: 01929 555700 Email: sales@relec.co.uk Visit: www.relec.co.uk LinkedIn: Relec Electronics Ltd Address: Animal House Justin Business Park, Sandford Lane Wareham, Dorset BH20 4DY
RELEC ELECTRONICS
Relec Electronics is a specialist in power conversion and display products, representing leading brand names including Bel Power, Mornsun, Chinfa, Cincon, Premium, Advanced Energy (Artesyn and Excelsys) with key display partners, Digiwise and RockTouch. For over 40 years, Relec Electronics has worked closely with key suppliers and specialises in a wide range of industry sectors, including automotive, industrial, transportation, instrumentation and defence. A team of dedicated engineers is ready to support customers throughout the design process. The company carries stock of all standard modules and accessories for next day delivery. Relec’s team of specialist advisers can refine an initial specification for a given application to include bespoke features to meet the needs of a particular design or project. In December 2020, Relec Electronics became a UK subsidiary of Gresham Worldwide.
Keeping Rail Sector Performance on Track
Stäubli Group has become a trusted partner across multiple market sectors where end-to-end fluid, gas and electrical connection solutions are required
The rail sector, whether it is urban or intercity rail transport, passenger, or freight, faces significant environmental and demographic challenges in today’s fast changing world. Rail users are increasingly demanding services that offer superior comfort, safety, and speed, while operators continue to raise their demands for performance, productivity, and reliability.
Rail Sector Technology & Expertise
As an industry partner and key supplier in the international rail sector for over 30 years, Stäubli has a clear insight into the sectors’ unique challenges and expectations, such as service continuity, extreme weather conditions and mechanical stresses. This close partnership with the sector during this time has been the catalyst for the development of a series of connector products which are now generally recognised by many as industry standard solutions.
Stäubli designs and manufactures reliable, lightweight, and compact quickrelease couplings that are very easy to use, even in confined spaces, thereby minimising equipment maintenance processes and subsequent rolling stock downtime. The rail sector fluid and electrical applications covered by Stäubli’s connector technology include cooling of on-board electronic circuits, body-to-bogie and inter-body connections, hydraulic circuits, braking systems, battery pack connections and converters.
A key element of the Stäubli product offering to the rail sector is the Modular Power Connector (MPC) range, which facilitates electric connectivity between the various functions that are part of the electric traction chain on different types of rolling stock.
The Modular Power Connector (MPC) range has the advantage of delivering a universal multi-application, compact and modular solution, through the rationalisation and the standardisation of common components.
Thanks to the modular nature of the connector design, combined with a series of options, a complete customised solution can be configured for each specific application. The MPC connector solutions offer a range of benefits including the fact that all on-board power applications can be connected, the same system can be used for every power connection plus the fact that the range offers easy and fast assembly and maintenance. Stäubli connectors are certified for high voltage and high current applications and are tested to rail sector standards IEC 62847 – EN 61373 and EN 45545-2.
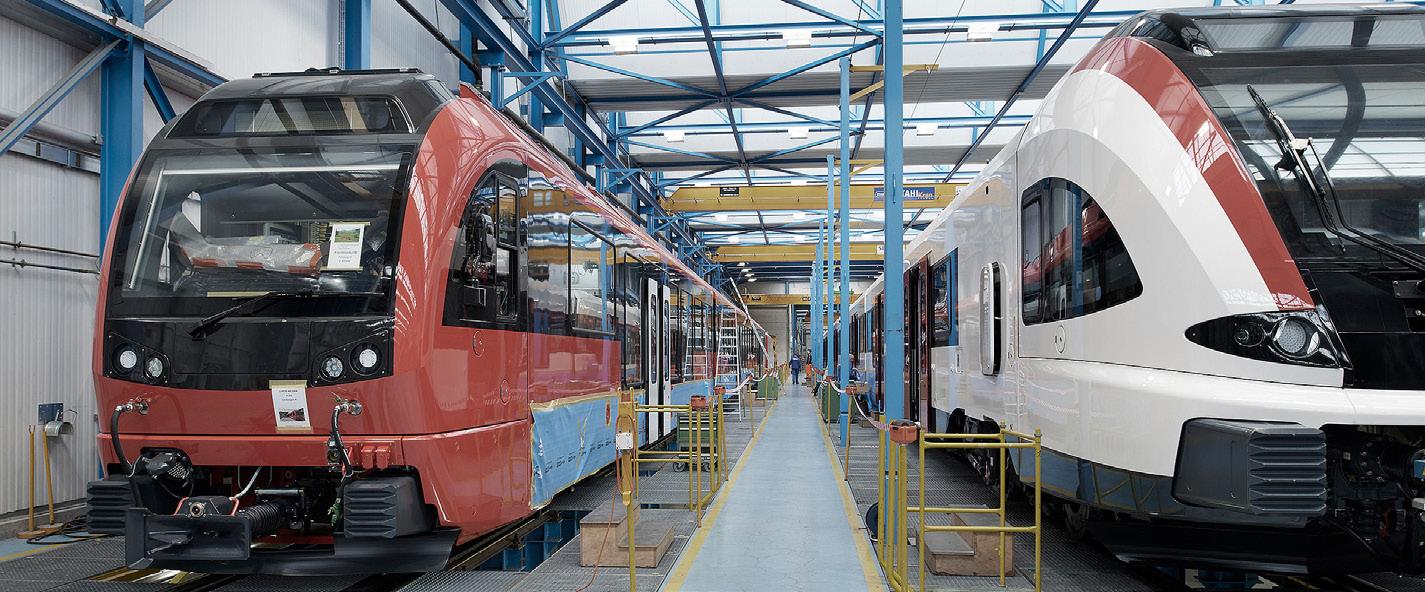

Stäubli’s MPC range has the advantage of delivering a universal multi-application, compact and modular solution
Tel: 01908 26 55 44 Visit: www.staubli.com Address: Staubli (UK) Ltd Staubli House, Presley Way, Crownhill MK8 0ES Milton Keynes
STÄUBLI GROUP
Stäubli is a mechatronics solutions provider with three core activities: Connectors, Robotics and Textile. It is an international group that currently operates in 29 countries, with agents in 50 countries on four continents. Stäubli’s global workforce of 5,500 shares a commitment to partnering with customers in nearly every industry to provide comprehensive solutions with long-term support. Originally founded in 1892 as a small workshop in Horgen/Zurich, today Stäubli is an international group headquartered in Pfäffikon, Switzerland, delivering innovative solutions to all industrial sectors around the world.
MEWPs Making Electrification Easy
Carl Abraitis explains how these versatile machines are perfect for OLE construction and maintenance
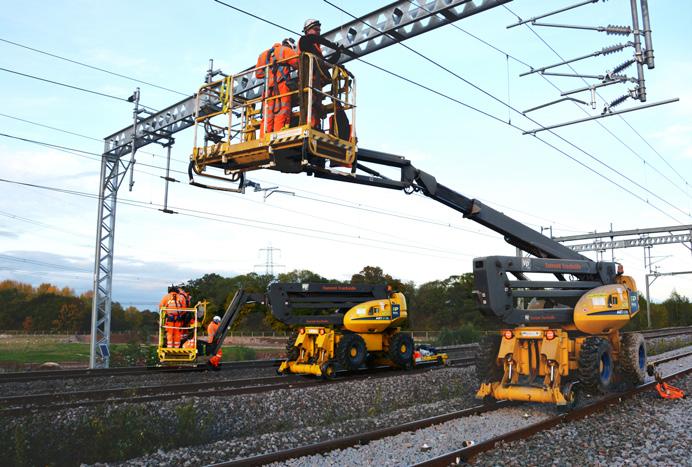
The MEWPs are perfect for overhead line construction.
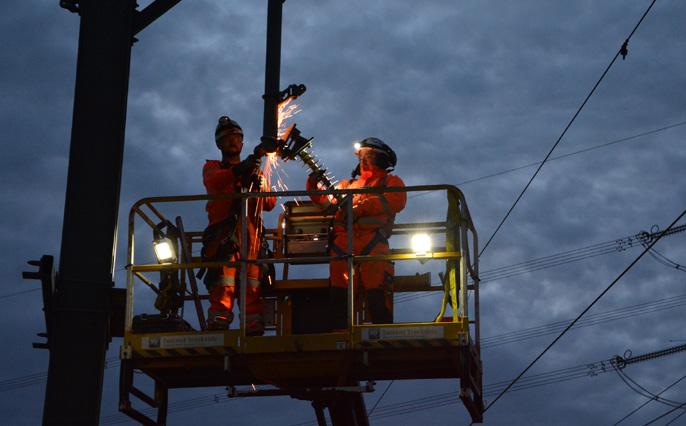
The MEWPs provide a stable platform for intricate tasks.
The electrification of the UK’s rail network continues at a pace. Electric trains are much better for the environment than the diesel trains they are replacing and with Network Rail’s pledge to become carbon neutral by 2050 this drive towards electrification must continue.
Electrification involves many engineering challenges that need to be addressed, trackside posts have to be installed to hold the overhead wires and bridges and tunnels may need to be raised to allow the necessary clearance for the wires. Once constructed the lines need regular monitoring and maintenance. Electrification needs specialist tools and equipment to get the job done efficiently, safely and to budget.
Torrent Trackside has an established OLE division to provide the majority of the equipment needed for these demanding projects. A major part of this division is comprised of their fleet of MEWPs (Mobile Elevated Work Platforms). The MEWPs are perfect for OLE construction, bridge and tunnel works or anywhere a stable working platform is required, especially in hard to reach areas.
The MEWPs are all-terrain and can easily travel on and off track. Four-wheel drive and four-wheel steer, gives great off road capability and fantastic manoeuvrability in tight spaces. Foam filled floatation tyres provide great stability on rough ground and makes them puncture proof, so less likely to suffer downtime due to poor ground conditions.
Challenging access points are easily dealt with before the machine rapidly switches to rail mode with the powerful 46hp Kubota engine propelling the MEWP across rail at up to 12 kph. The machines can also cope with a rail cant of up to 200mm.
The spacious basket can accommodate up to three people and carry a total weight of 400 kg. It has a three-way entry/exit that allows personnel the safest access from ground level. The MEWPs have a working height of 16.4 metres and a lateral outreach of 8.95 metres. The whole platform can rotate through 360 degrees. For further flexibility the basket can rotate 90 degrees and the jib can move 70 degrees.
The machines sophisticated hydraulic and electric systems combine to provide an exceptionally smooth platform operation, this is essential for delicate tasks and operator comfort.
An advanced pantograph can be fitted that will take height and stagger measurements while the machine is moving. The pantograph continuously shows measurements on a digital display and can also download them to an Excel file. A detachable trolley is available to carry equipment to the worksite. The trolley is easily attached to the MEWP and can carry a load of up to 1,000kg.
The machines benefit from a number of safety systems. An alarm sounds before travelling and they have a traffic light overload warning system to maintain stability. As the majority of the work is undertaken at night the MEWPs have excellent built-in lighting so additional external lighting is not required.
A team of service engineers ensure the machines are maintained to the highest levels. The company also has a complete range of OLE tools and equipment that can be ordered along with the MEWPs.
Torrent Trackside is a national company with nine depots serving the whole of the UK. Likewise the MEWPs have been employed on projects all across the country, most recently for Network Rail with the upgrading of the West Coast Mainline near Lichfield, Staffordshire.
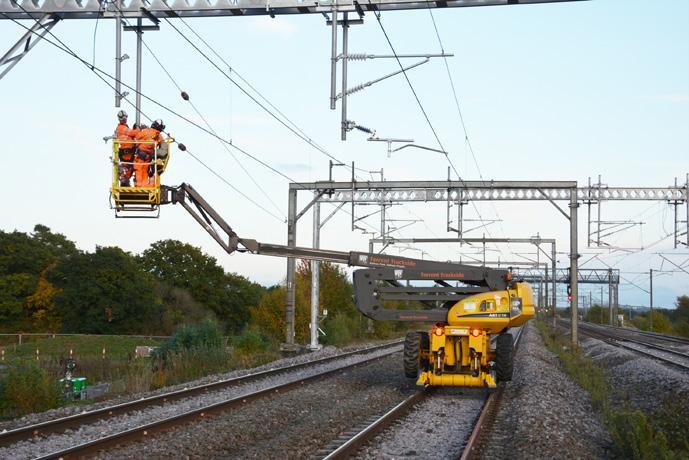
The MEWPs have exceptional manoeuvrability and reach. The spacious basket can accommodate up to three people and carry a total weight of 400kg.
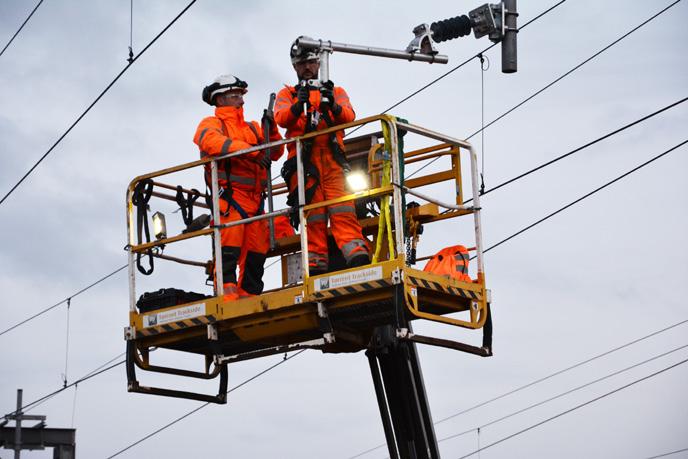
Carl Abraitis is Operations Directions, Torrent Trackside, get in touch via email at carl.abraitis@vpplc.com
Improving Depot Safety
‘There is no clear industry-wide picture of risk and safety performance in depots’ according to the RSSB’s most recent Annual Health and Safety Report
Given this lack of reporting and regulation, it might come as no surprise that more than 20 per cent of workforce harm and fatalities have occurred in maintenance facilities in the last five years.
Given this lack of reporting and regulation, it might come as no surprise that more than 20 per cent of workforce harm and fatalities have occurred in maintenance facilities in the last five years.
Leading safety expert, Christian Fletcher, Technical Director at Sheffield’s Zonegreen, has been striving to improve working conditions in rail depots for more than 20 years. He said: ‘We all know high speed vehicles, high voltage electricity and powerful machinery introduce significant elements of risk into the maintenance environment, but the stark findings of the RSSB show not enough is being done to focus on the safety of depot workers and provide conditions in which staff can fulfil their role without fear.’
Christian believes technology is the answer and can be used to automate and regulate depot safety, eliminating the margin for human error. As a result, he and his team at Zonegreen have developed the most advanced protection system on the market, allowing the safe and efficient control of vehicles in maintenance environments.
Protection and accountability
Zonegreen’s Depot Personnel Protection System (DPPS) safeguards maintenance staff from unexpected train movements via Network Rail-approved powered derailers.
Staff log onto DPPS using RFID tags, which record their location and activate the appropriate derailers. They remain in place until the operative has logged off and the road is once again opened to traffic.
Access permission for a train can only be granted by a supervisor, who uses a conveniently positioned road end control panel. They are usually situated next to depot doors, giving a clear view of incoming and outgoing vehicles. If the derailer has been lowered, the signal to proceed will be given and audible and visual warnings activated to indicate movement.
DPPS can also be linked to Zonegreen’s advanced Depot Manager software, offering an overview of the entire protection system and complete traceability. It provides key information to make operations easier and quicker to implement, for example, identifying peak movement times, so additional focus can be placed on safety during these highest risk periods.
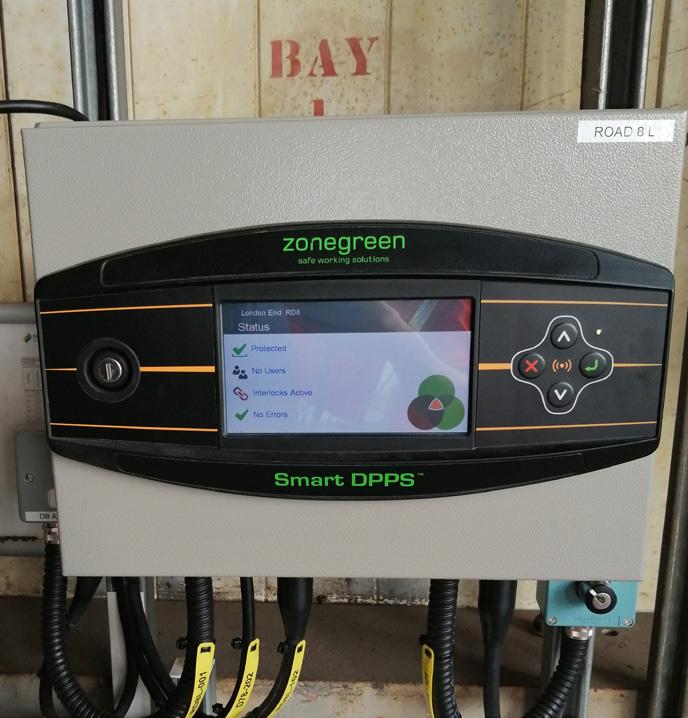
Zonegreen REP installed at Wimbledon Depot Zonegreen Derailer

A perfect match for Wimbledon
One of the latest facilities to be equipped with Zonegreen’s state-of-the-art technology is South Western Railway’s Wimbledon Traincare Depot in London. The firm worked with Octavius Infrastructure to deliver the project, which saw DPPS replace the existing obsolete safety system. The depot remained fully operational whilst the new technology was installed on five double ended roads and two singled ended roads.
Christian continued: ‘Due to its age, state and the availability of parts, an increasing number of faults and breakdowns were occurring on Wimbledon’s former safety system, making it difficult to safeguard the workforce and carry out maintenance activities. It is crucial in such a busy depot that staff are protected by reliable and effective technology and they now have that in DPPS. It works for the facility’s current needs and is futureproofed to allow further upgrades to be integrated seamlessly.’
Independent accreditation
thoroughly tested and proven in use, meaning it is the lowest risk option for depot protection.
The whole system has been independently certified to meet both the hardware and software requirements of SIL 2 – a reliability assessment of the relative risk reduction provided by a safety system. It is also compliant with the European standards for railway and radio emissions and uses intuitive technology to make it easier to maintain, modify and expand, extending the lifetime of the product.
Gemma Houghton, Zonegreen’s Sales Director, added: ‘We sell more safety systems than all of our competitors combined and thanks to our excellent reputation and longstanding relationships with clients, DPPS is regarded as the industry standard.
‘Our dedicated research and development team, led by Christian, works non-stop to enhance our depot protection technologies and we know these efforts are making a real and lasting difference to the wellbeing of workers.’
For information about DPPS or Zonegreen’s suite of safety solutions get in touch via the contact information below.
Tel: 0114 230 0822 Visit: www.zonegreen.co.uk Twitter: @zonegreen

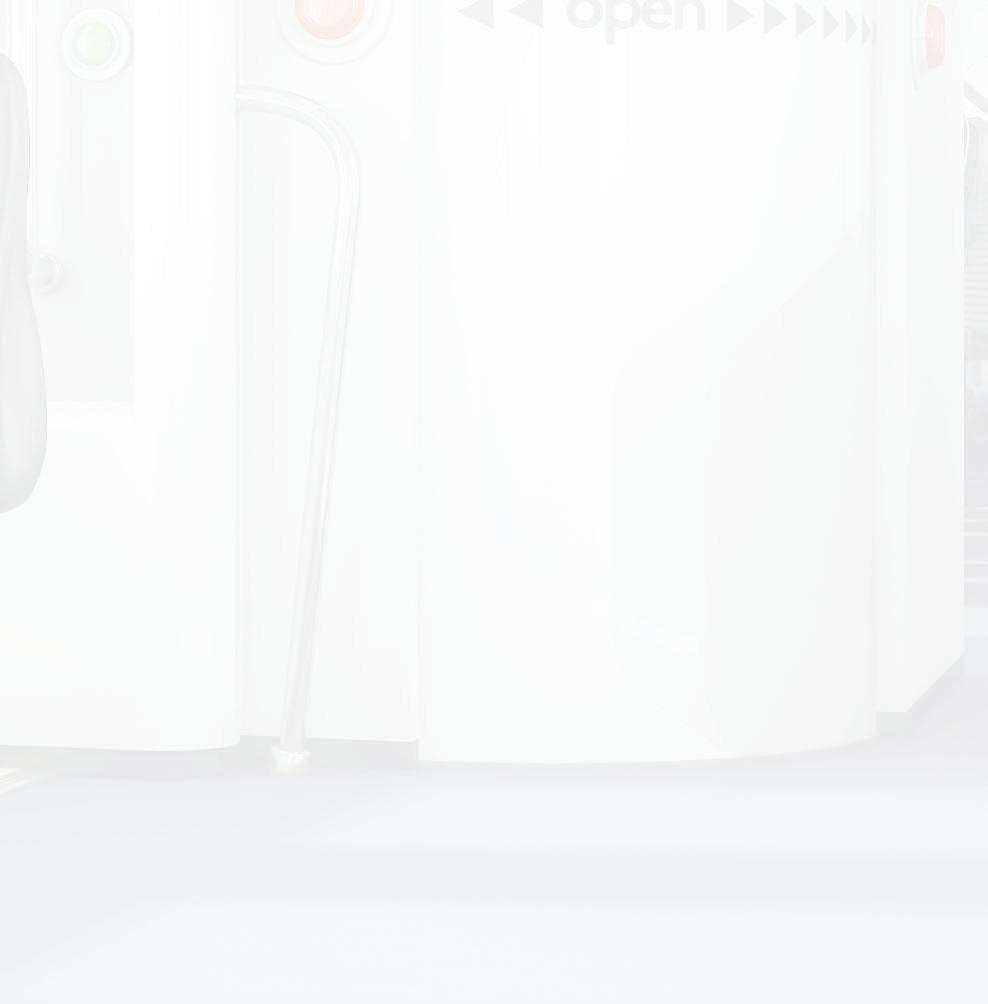
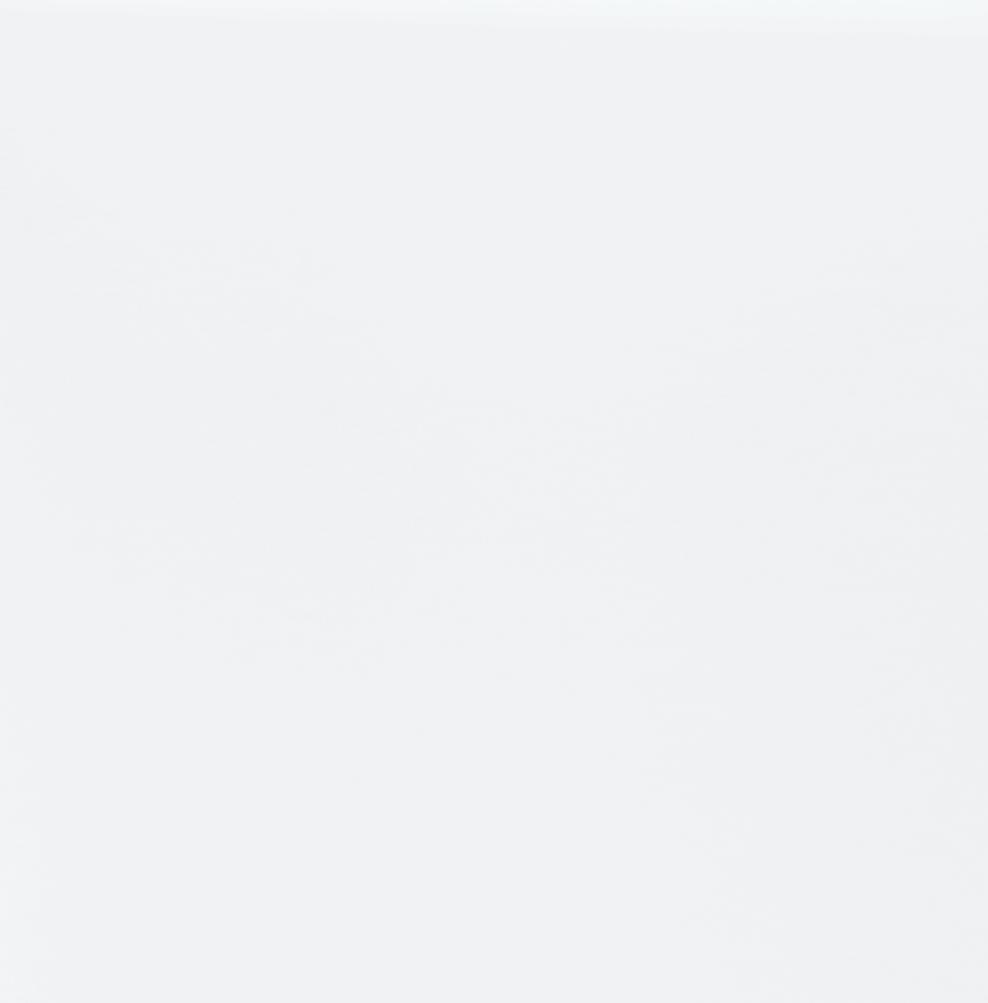
New Digitally Printed Carpet Designs
Designed specifically for rail interiors, ‘Coral Move Vision FR’ is an exceptionally versatile, premium cut pile carpet solution offering extensive design possibilities and colourways to complement a wide range of interior design schemes
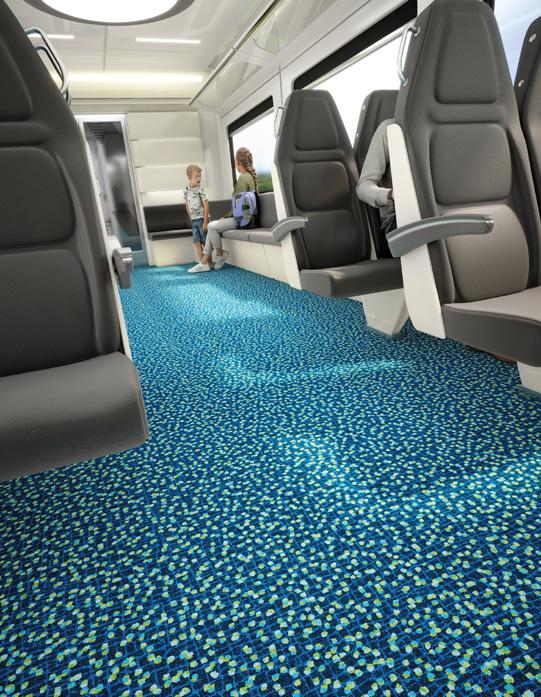

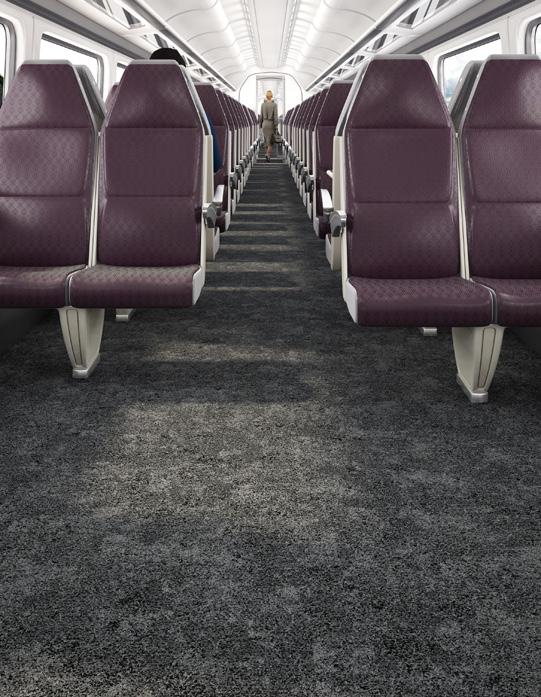
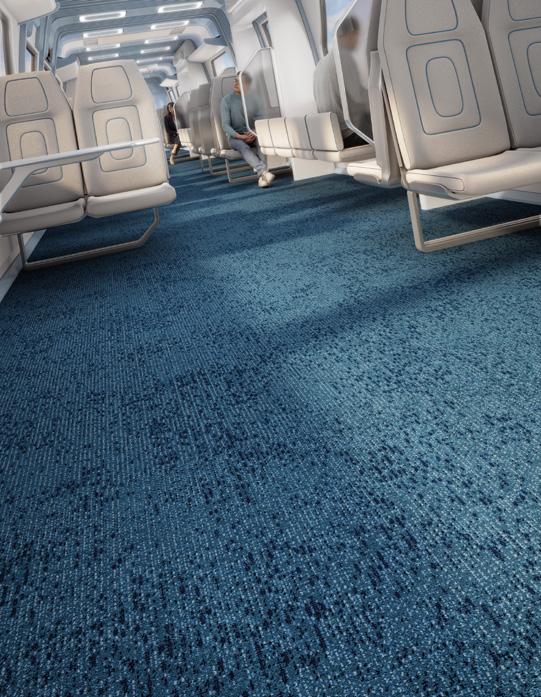
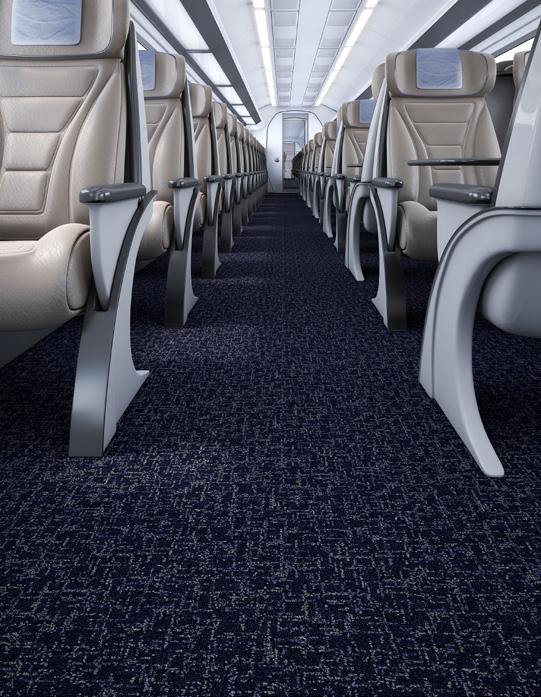
Shown above are five of the eight designs in the core collection. To view the full range of designs and colourways go to: www.forbo-flooring.com/rail or click on the QR code
Aluxurious made-to-order carpet, manufactured from 100 per cent regenerated Econyl yarn, that delivers aesthetic styling, durability, and long-lasting appearance retention, as required for heavily trafficked carriage interiors.
Being digitally printed, it allows for a virtually limitless number of aesthetic styles and makes non-linear type designs possible. It is perfect for more complicated designs or when there are many different colourways within a design. All Pantone and RAL colours can be matched to.
The new core collection consists of eight designs. Each design is available in several colourways, giving a total offering of 82 references. If you don’t see what you are looking for in this collection, Forbo Flooring Systems can re-scale/re-colour any of the designs or you can work with its dedicated design team on an individual project basis to ensure that the resulting Coral Move Vision FR carpet meets your bespoke design and colour requirements. • Extensive customisation possibilities. • Underfoot comfort, slip resistance and outstanding acoustic properties. • Durability and appearance retention due to 100 per cent nylon construction. • Made with Econyl 100 per cent regenerated yarns. • Natural latex backing from rapidly renewable source. • Ease of maintenance thanks to open cut pile construction. • Reaction to fire EN45545-2: HL2. • Available with different backing options for quicker installation.
Quicker installation solutions
As an alternative to fully adhering the floor covering to the subfloor, Coral Move Vision FR can also be supplied with different backing options designed to improve efficiencies in time, cost, and operation throughout the life of the rail vehicle. The ‘PRO-FIT’ hook and loop solution for example has numerous advantages over traditional fully bonded adhesive systems, resulting in cost savings for train operators thanks to: • Quicker and easier installation and replacement. • No need to wait for the adhesive to dry. • No waiting time before the carpet can be walked on. • Immediate use of the train after installation.
The optional backing solutions cannot be added to latex-backed material after production, so the required backing type must be clearly specified at the time of ordering.
From how they're made to how they perform, Forbo Flooring Systems makes outstanding floor covering products that are truly sustainable.
Of all the electricity Forbo Flooring Systems buys, 100 per cent comes from renewable sources. This means the Coral Move Vision FR production site is part of an effective environmental management system and has achieved ISO 14001 certification.
Zero landfill
Virtually zero landfill is achieved by the Coral Move Vision FR manufacturing plant.
Reuse waste
All the waste yarn from the Coral Move Vision FR production is re-used by the yarn supplier. The search for new ways to reduce its environmental impact has led Forbo Flooring Systems to work very closely with forward thinking suppliers who are able to incorporate ever higher levels of recycled content in their materials.
Econyl® yarn
Coral Move Vision FR floorcoverings use Econyl® yarn which is made from used and abandoned fishing nets. Using Econyl® is a way to reduce existing waste, avoid additional manufacturing-related pollution, and keep the consumption of natural resources and energy to a minimum.
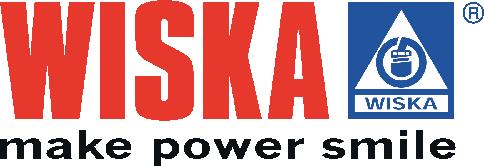
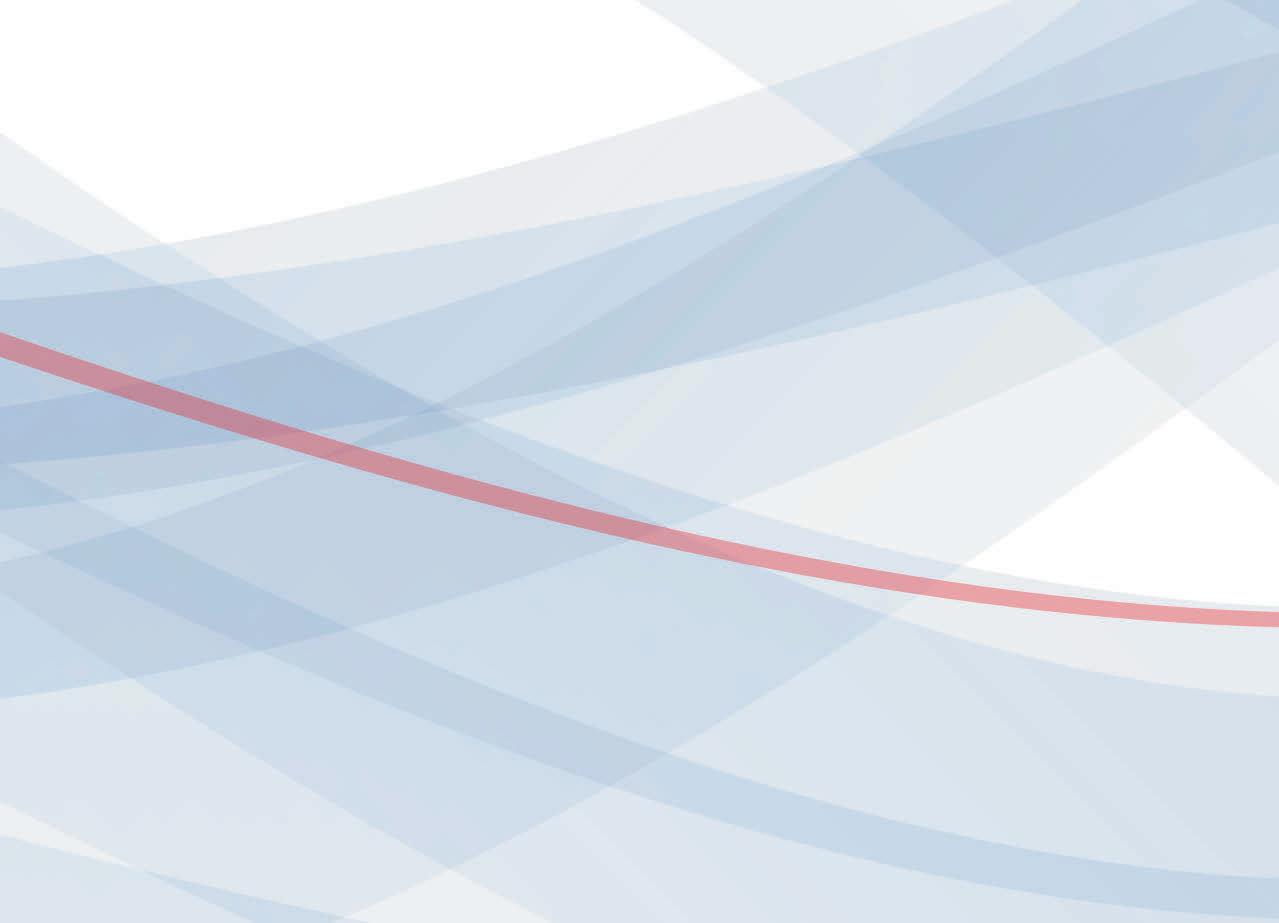
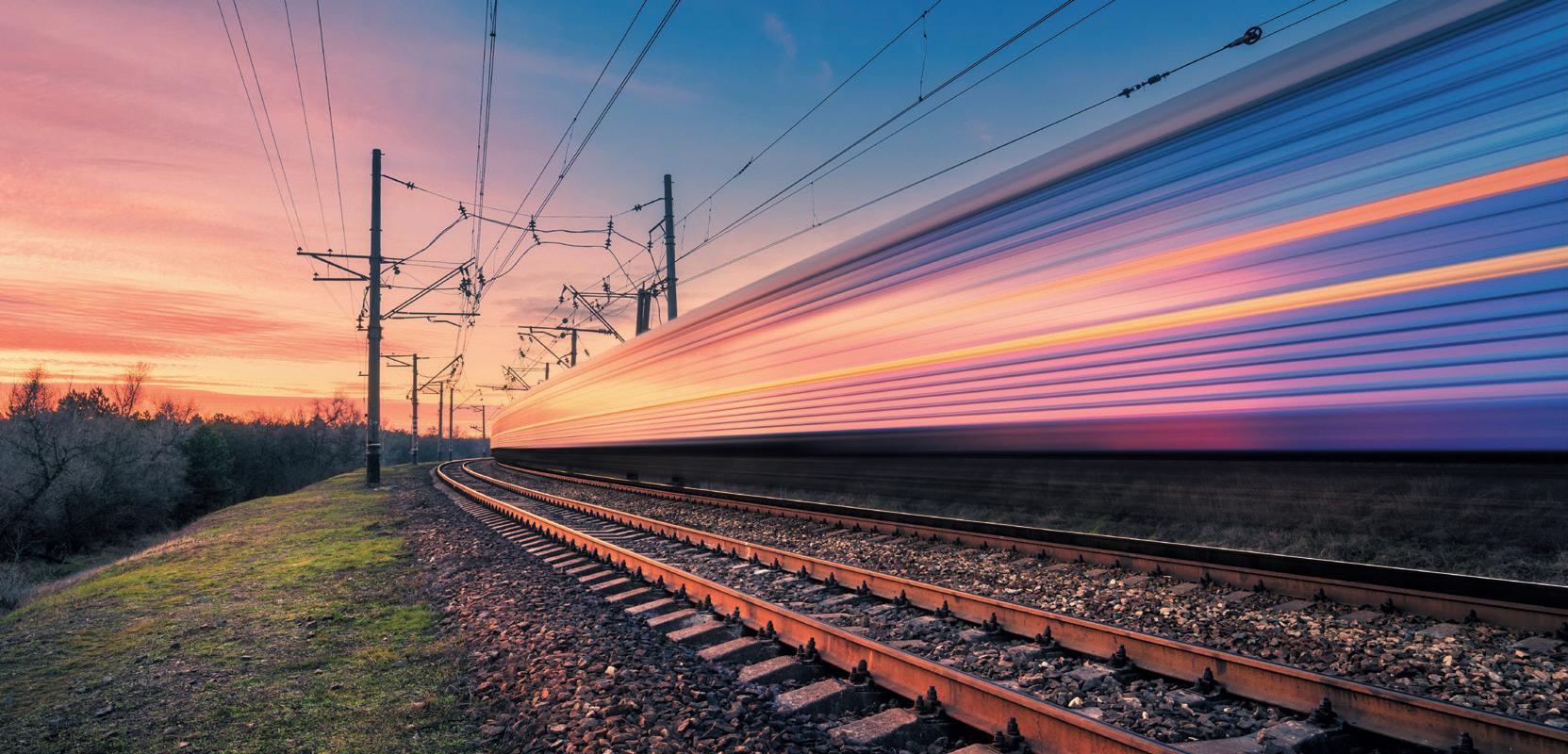
EN 45545 Approved Cable Glands and Entries...

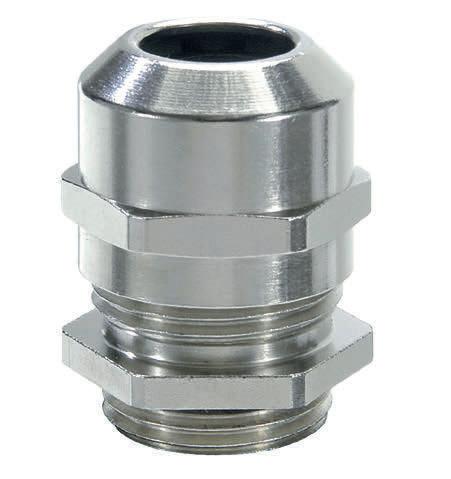
For over 100 years WISKA have been at the forefront of cable management design and innvoation. This level of expertise has resulted in the development of our lastest range of products, introducing The Railway Series by WISKA.
The Railway Series is a comprehensive range of industry-specific cable glands and conduit solutions in accordance with EN 45545.
Need an expert? Speak to us today.
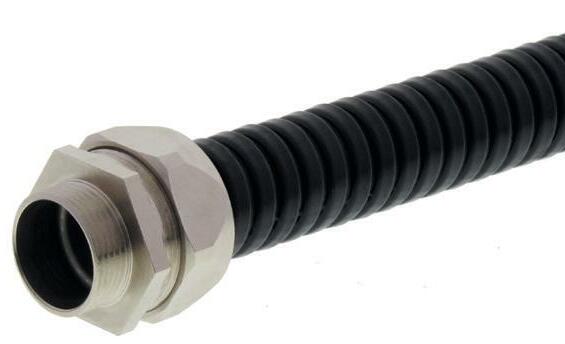
01208 816062 / 01208 816708 / www.wiska.co.uk / info@wiska.co.uk
Trusted Materials Promise Circular Future
The Department for Transport’s 2021 plan, Decarbonising Transport: A Better, Greener Britain envisages ‘a net zero rail network by 2050, with sustained carbon reductions in rail along the way.’ Alongside the removal of all diesel-only trains from the network by 2040, extensive, ongoing electrification works and the introduction of new battery and hydrogen trains will form part of a layered strategy to create a shift towards cleaner travel.
Whilst the uptake of new technology, better transport integration and new ways of operating are seen as key to encouraging an increase in annual rail mileage, the construction of new rail lines and the material improvements to existing networks are also important. The way we build and design these projects will significantly impact how better and greener the new vision can be, including the materials we choose, the local nature of the supply chain and the maintenance schedules that we build into the infrastructure.
Embracing circular principles will be key
Choosing adaptable materials that can be kept in a constant loop of use and which eradicate end of life scenarios is central to circular construction. But building for tomorrow does not mean overlooking the materials of today. Galvanized steel has contributed significantly to UK rail infrastructure for decades and is used abundantly in infrastructure, overhead line support steelwork, concourse structures and as a reliable solution for station construction and platform architecture. Going forward, the role of galvanised steel need not diminish as galvanized steel is ideally aligned with key principles central to circular design and construction:
Lasting many lifetimes
Galvanized steel offers the highest levels of durability, delivering once-only solutions that last the lifetime of a building,
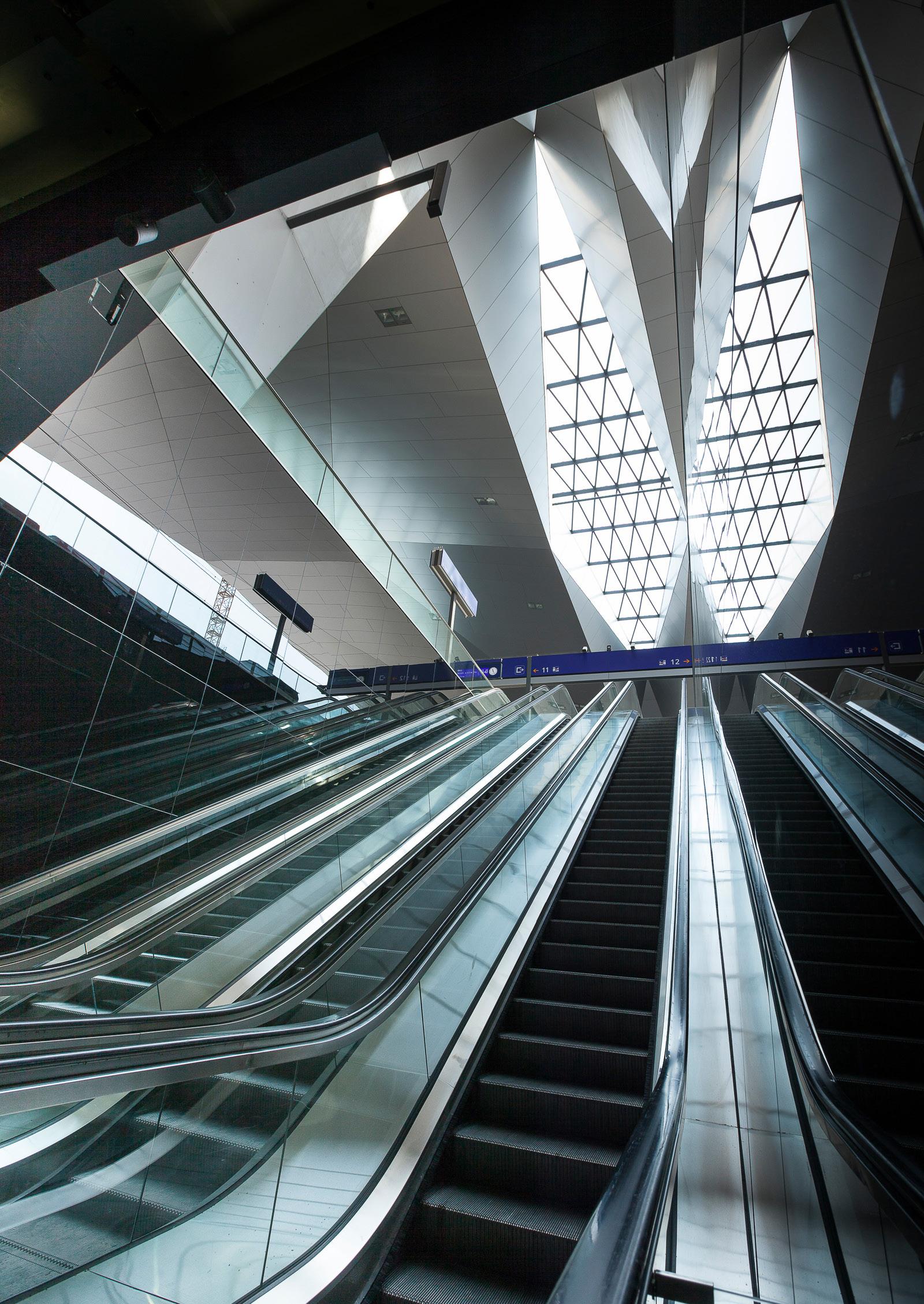
component or structure. This allows for an emphasis on avoiding the environmental impact of further unnecessary construction.
Reducing maintenance burdens
Data on the corrosion protection offered by a galvanized coating shows how the process of galvanizing steel components offers lifetime protection and reduces maintenance burdens over the lifetime of a project.
A modular material
Galvanized steel is an ideal material for reuse, as it is robust and does not damage easily. It is suited to modular design, is easily disassembled for reuse and can provide multiple life cycles of a building or structure. If a building is designed with reuse in mind, entire structures can be repurposed or individual components can be put to diverse use.
Perfect for remaking
When the limits of reuse of an existing component or structure have been exhausted, galvanized steel presents an excellent choice for remaking, as the coating stays with the steel and no additional coating is needed in any subsequent use. Galvanized steel components can be easily adapted, re-galvanized and put back into service – avoiding the environmental burden of new steel production.
Endless no-waste recycling
Galvanizers Association, the voice of the UK and Ireland galvanizing industry, gives clear end of life information on how steel and zinc are recycled together – without loss of properties – to produce new galvanized steel. As zinc self-sacrifices at a very slow rate, recycling will not happen for many decades and dependent on location, a galvanized coating can provide over a century of use.
Recent landmark projects in the UK and Europe highlight how galvanized steel is already contributing to ambitious infrastructure design that can last multiple lifetimes. The lozenge roof of the new Vienna Central railway station is a case in point. One of the most complicated steel construction projects in Austria and winner of the Austrian Steel Construction Prize, it incorporates approximately 7,000 tonnes of steel and is six times the size of a football pitch. It can be seen for miles around and is a prime example of what can be achieved when galvanized steel is selected as material of choice from the outset. As a public transport solution, it meets both a 100-year design specification and the need for zero maintenance. In addition, the use of bolted connections for the roof structure means that the steelwork can be readapted or reused for other infrastructure projects needs should requirements change.
Projects closer to home also show what can be achieved when future thinking our station architecture and how we can adapt existing station design to cope with the projected increase in rail capacity. Many of the innovative solutions for Leeds Station Southern Entrance, situated alongside the River Aire, lie unseen below the new building, including the foundations and galvanized steel that form the ground floor concourse. The foundations comprise two concrete piers supported on piles socketed into bedrock below the riverbed. A concourse deck formed from a grillage of deep steel beams, supports the superstructure. A sizeable fifty percent of this concourse is constructed below the existing viaduct, in inclement conditions directly above the river. Hot dip galvanizing was chosen as the only method of corrosion protection with enough proven reliability for the complexities of the environment. All steelwork located above the river forming the ground floor concourse, as well as the bridges linking the concourse to the riverbanks is galvanized, offering unbeatable corrosion protection where trusted, proven performance is critical.
These and many other infrastructure projects make visible what is possible when we use materials where their strengths lie. They emphasize that a final solution for UK Rail infrastructure will be about taking a mixed approach and prioritising the efficient use of durable materials that complement each other. Viewed over the long-term, hot dip galvanizing has a long list of systematic benefits that are both reliable and quantifiable. It is a material we have prioritised for many decades already, it is suited for use for many decades to come.
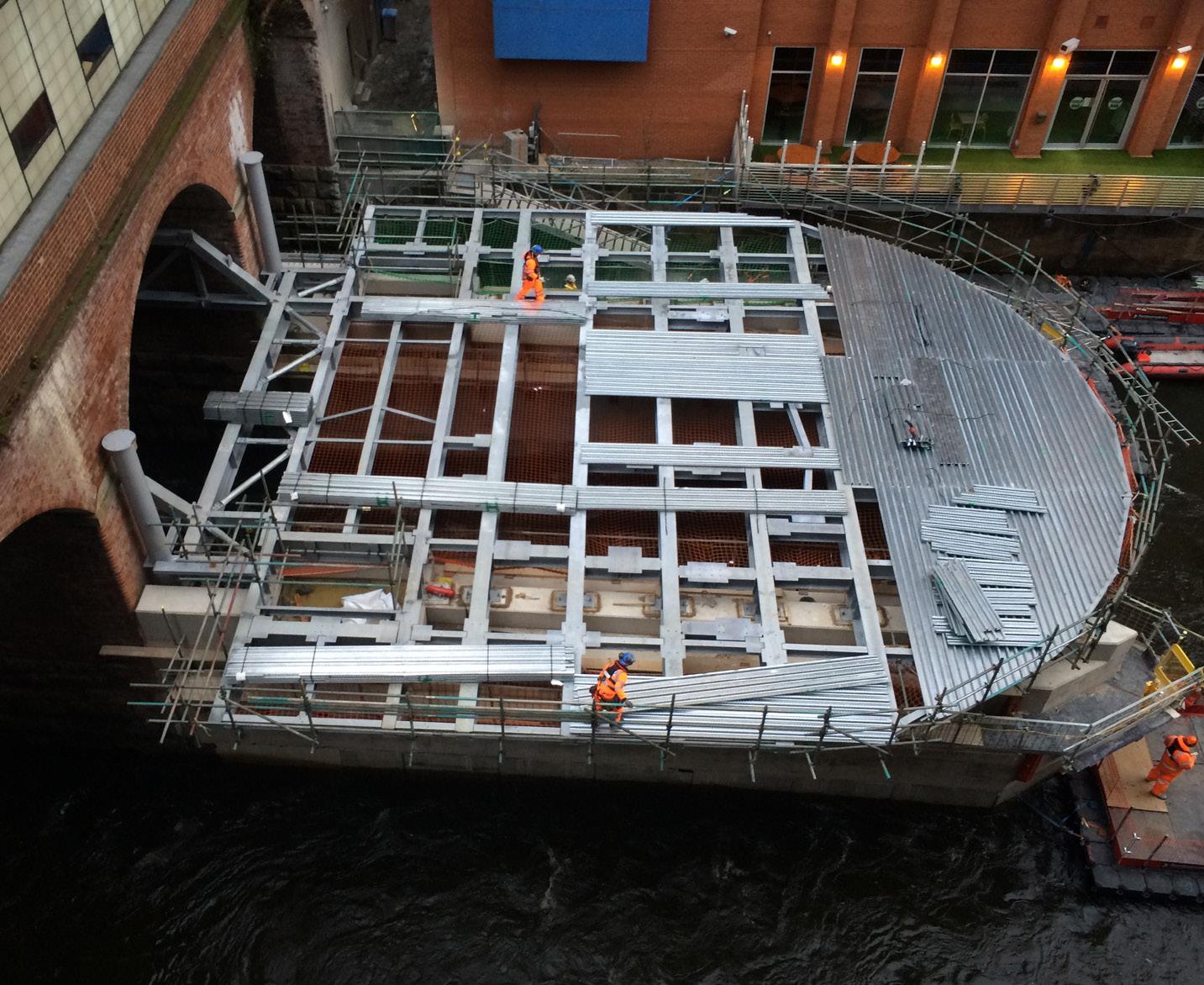
Ground floor concourse structure for Leeds station southern entrance
Tel: 0121 355 8838 Email: i.johal@hdg.org.uk Visit: www.galvanizing.org.uk
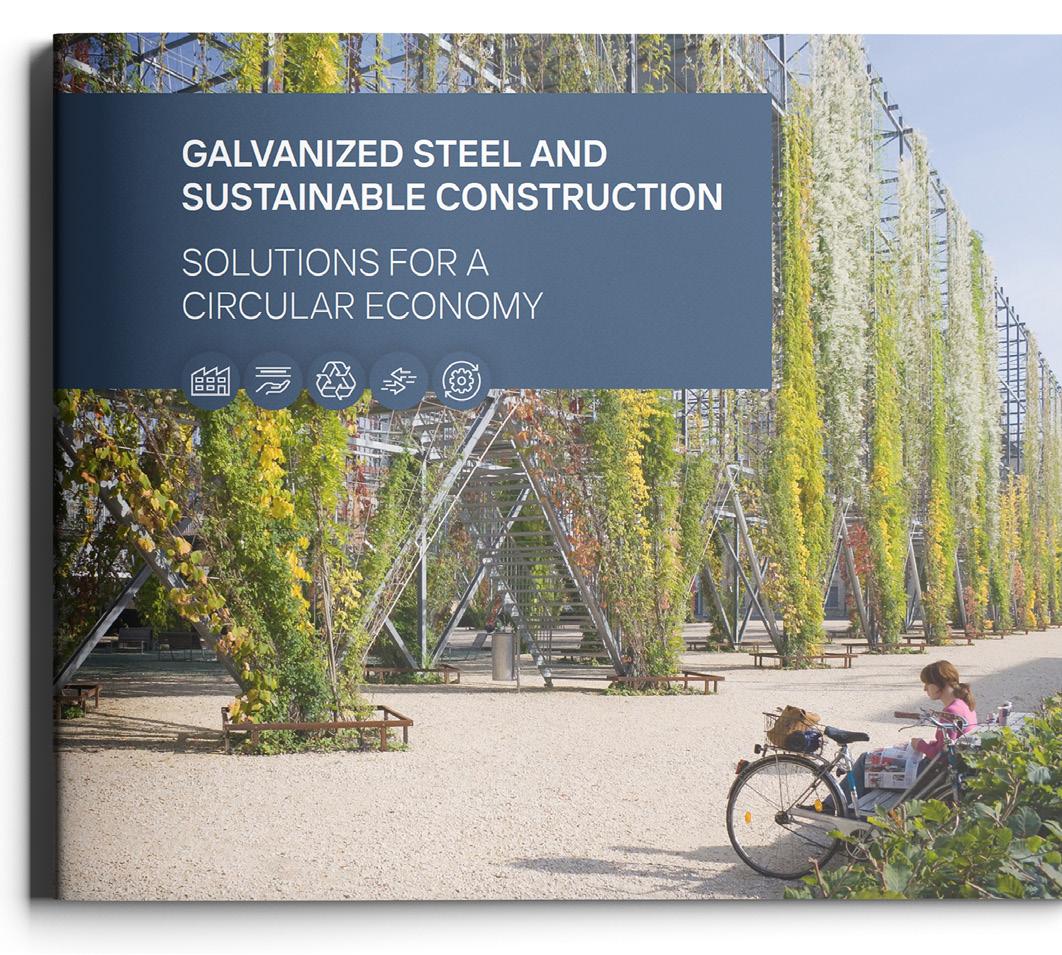
Hybrid Reality Delivers Human Factors Insights
Combining low fidelity mock-ups with Virtual Reality and pose estimation
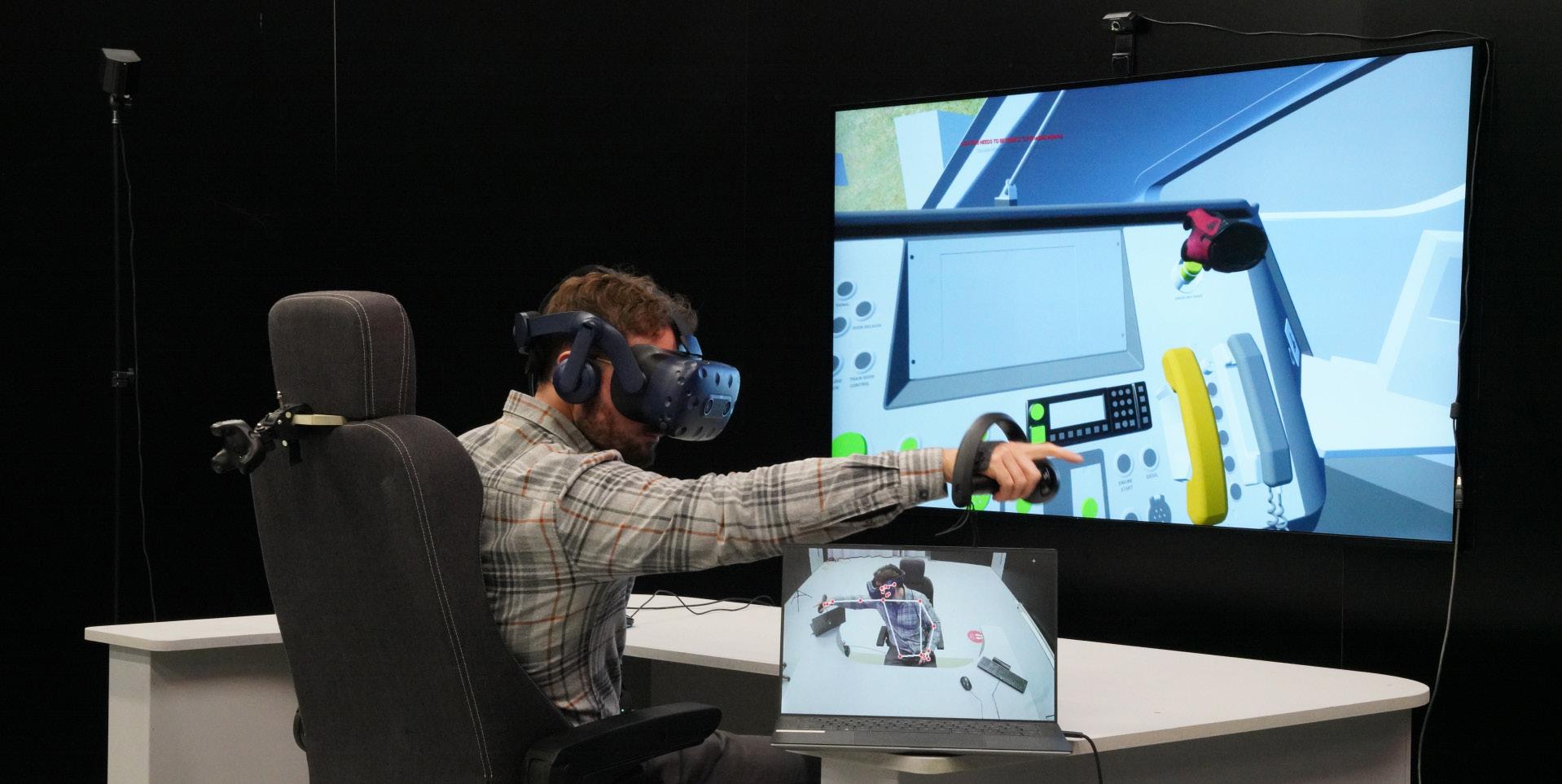
Human Factors (HF) is an integral part of successfully delivering any new rail vehicle to market. Compliance with ergonomic, usability and accessibility legislation and best practice needs to be addressed and evidenced in a fully integrated fashion throughout the entire development programme. A range of tools and techniques is available to achieve this, many involving the observation and assessment of trial users interacting with physical rigs and mock-ups.
These typically increase in fidelity as the train development progresses, most commonly culminating in a full size representative mock-up that closely emulates the production vehicle. Design changes at this late stage in a project can be costly and time consuming, so resolving as many potential HF issues as possible before the final mock-up build is essential.
To address this, we have recently been exploring the use of new technology to create hybrid prototypes, which combine basic, low-fidelity physical mock-ups with virtual reality (VR) and pose estimation to deliver a higher fidelity experience of the train and meaningful HF outcomes much earlier in the development programme. These hybrid prototypes are fully immersive, highly flexible and offer the potential for larger numbers of subjects to experience and interact with a range of proposed design solutions.
The video gaming industry has transformed what can be achieved using relatively standard high-end desktop computers and low cost VR headsets. This creates a fantastic opportunity to combine the benefits of basic prototyping and VR to create an environment in which we can interact with a concept proposal from the very start of the design journey.
In a recent example, DCA used hybrid prototyping to analyse specified train driver tasks and assess comfort and reach parameters for a new cab design and desk layout. However, for the purposes of this article we have used images of a cab that is already in the public domain to illustrate our process.
We were looking to see whether the driver could comfortably reach the controls used most commonly during driving operations without repetitive stretching and overreach, which can cause strain to the lower back and generate work related stress injuries.
Traditionally, train cab design, and the driver’s desk layout in particular, starts with the use of basic 2D reach envelopes to map out control layouts, before progressing to physical mock-ups. By definition, this initial 2D approach provides a limited view of the physical design. Now, with
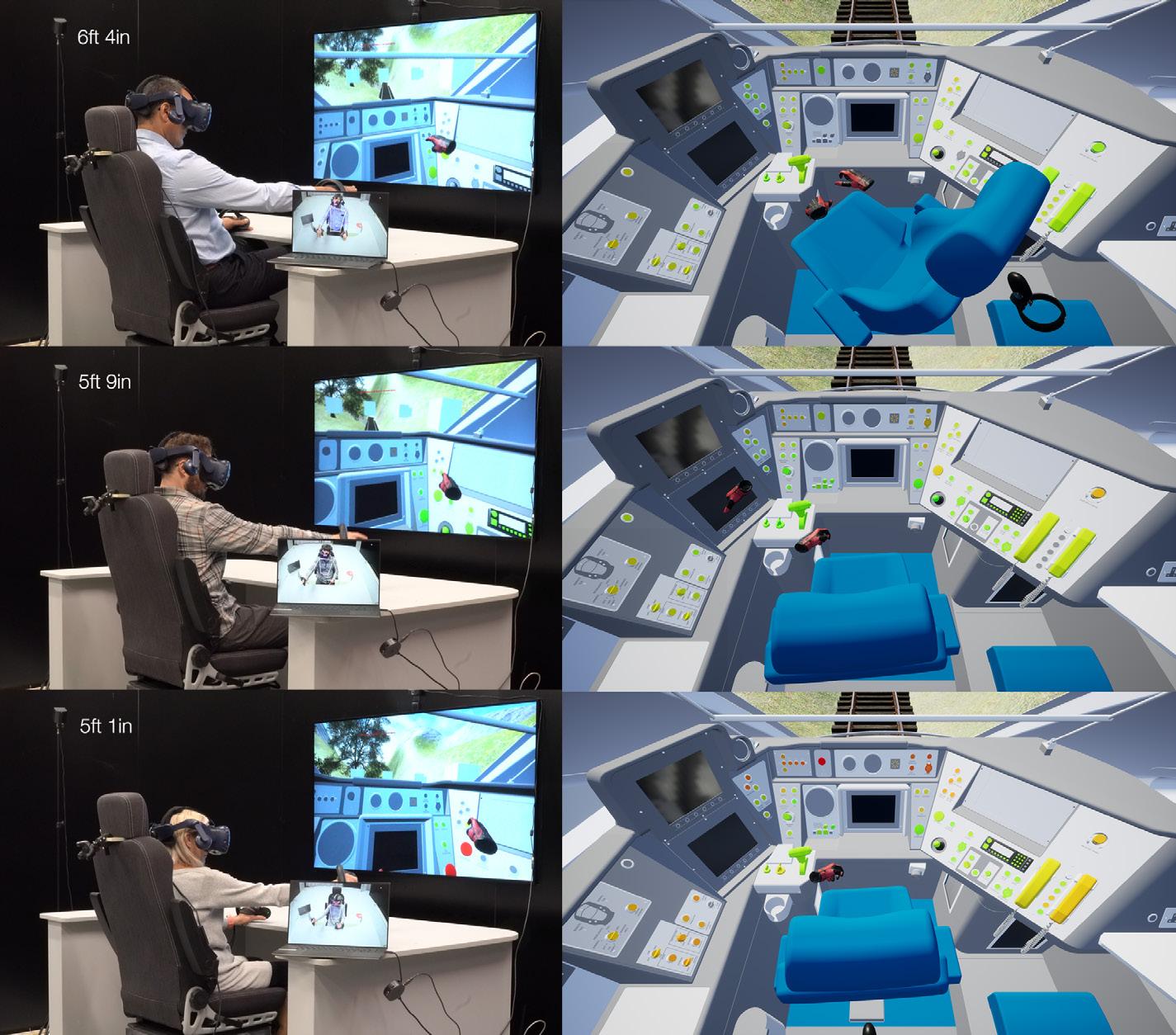
hybrid prototyping, we can perform this early reach analysis in a representative 3D VR environment, which gives a much more realistic and thorough assessment of whether the design is suitable and fit for purpose.
This potentially removes the need for some of the physical mock-ups and allows us to rapidly trial multiple design variants. Some of these may be bolder than normal because the VR environment allows us to assess innovative solutions with far greater confidence. We can also include larger numbers of users in our hybrid reality HF trials, and even scale the VR environment to allow any user to experience interactions as they would feel for a different sized user.
For this specific hybrid HF assessment, we synchronised the virtual train driver’s cabin with a simplified physical model of the driver’s desk and seat. An HTC Vive Pro VR headset was used with Valve Index controllers for the hands, which we selected specifically for their individual finger tracking capability. This allows the user to interact with buttons and controls in a more realistic, natural way.
The actual driver’s chair swivels between defined detents, so we wanted to ensure that this was reflected in the virtual world as well. To achieve this, we added a Vive Tracker 2.0 to the back of the chair and paired this with a virtual chair in the VR world. We have found from experience that adding tracked elements, which the user can interact with, increases the sense of immersion significantly.
Another key feature of our hybrid model for this project was the use of Google’s Media Pipe machine learning software as the platform for our pose estimation model. This looked at live image feeds from a webcam and worked out where the ‘bones’ and ‘joints’ of the test subject were. The image above shows how the ‘bones’ and ‘joints’ are overlaid in real time onto the captured webcam image.
The final hurdle to overcome was integrating the pose estimation data with the VR model within Unreal Engine, the software we use to produce and run our VR applications. We have found that web sockets, with a Raspberry Pi for the MQTT messaging service, work well for this task. The system is set up in a truly scalable way such that if we want to add more PCs to perform more pose estimation calculations we can. It also allows us to exchange and combine data from both Unreal Engine and Unity (another game engine) and even from Arduinos (small consumer electronics boards). Essentially, we can simulate any kind of interaction, whether it be physical or digital, in VR.
With the generated data inside Unreal Engine, we then needed to make it meaningful for our HF assessment. We used the movement of the subject’s shoulders from an initial ‘comfortable’ seated position to infer how far they were leaning or twisting in the seat. We added simple interactions to all the train controls and buttons such that when the user touched them in the virtual world they illuminated. The colour in which they illuminated was directly linked to how far the user was leaning or twisting at the time. If the user isn’t leaning during driving operations, all the buttons would illuminate green, but if the user were leaning or stretching significantly then the buttons associated with that task would go amber.
After a user trial was completed, we captured a final snapshot from above of the whole driver’s desk to provide a clear colour map that summarises which controls require a posture change to reach them. The results from trials for three users of very different statures and reaches are shown on the left.
The image for the very large subject (99th percentile male; 6ft 4in or 193cm tall) shows a mostly green control array, indicating that they were able to reach almost all the controls without adjusting their posture. However, even with this extended reach there are still some yellow controls on the left hand side of the desk, indicating that a small posture change was required to reach these low frequency HVAC and external lights controls. The average sized user (42nd percentile male, 5ft 9in or 175cm) shows many more yellow controls on both the left and the right, highlighting the need to adjust the posture to reach the less frequently used controls, while the smallest user (11th percentile female; 5ft 1in or 155cm) shows that more controls required a posture adjustment.
This data provided us with the necessary insight to improve or verify the design. Each control that requires a posture adjustment should be carefully considered, based on its frequency of use and criticality. Importantly, the hybrid prototyping technique allows us to make these changes and re-assess the outcomes early in the design process more quickly and at a lower cost than would have been possible with a full mock-up. Furthermore, it provides an excellent objective record of what is often perceived to be a rather subjective assessment.
This is just one example of how DCA is using hybrid prototypes to accelerate its design processes, improve design outcomes and de-risk future development programmes. We are finding the tools that games engines now provide, when run alongside artificial intelligence and machine learning, allow us to simulate a whole host of scenarios and address questions that were previously very difficult to answer until very late in the development process.
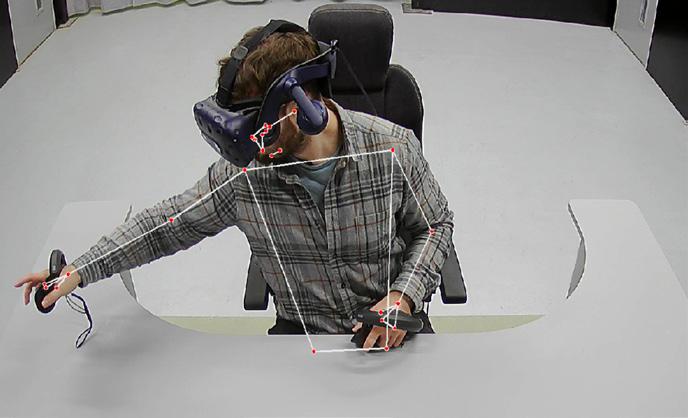
Tel: 01926 499461 Email: transport@dca-design.com Visit: www.dcatransport.com
What is an Occupational Health Assessment?
In our health and safety conscious industry, Occupational Health Assessments are common practice
However, individuals who are referred for an assessment often find it daunting as they are not always aware of the purpose of the assessment and what is actually involved. As the UK’s most trusted Occupational Health and Wellbeing provider, Medigold Health have cut through the jargon to give rail employees (and employers) a no-nonsense guide to what an Occupational Health Assessment is all about.
An Occupational Health Assessment (also known as a sickness absence referral, management referral or occupational health referral) is a medical examination carried out by a qualified Occupational Health clinician to assess a person’s fitness for work and their capability to fulfil the duties and responsibilities of their role safely and without detriment to their health.
Employers will usually request an Occupational Health Assessment when they require advice to help them manage an employee’s medical condition or disability or their return to work following a period of sickness absence. They may also refer an employee for an assessment if they have concerns that their health may be affecting their attendance or performance.
Occupational Health clinicians specialise in the interrelationship between work and health and have expert knowledge of both the specific health risks and hazards associated with different job roles and industries and of the various laws and standards that govern health and safety in the workplace. They can therefore provide employers with the objective, solutionfocused advice and guidance they need to be able to: • Support employees back to work as swiftly and safely as possible after absence due to ill health or injury. • Introduce appropriate adjustments and support to enable employees to better manage any health conditions or disabilities, so that they can remain in
work and continue performing their role effectively. • Reduce the risk of future sickness absence and any adverse effects of work on employees’ health. • Avoid any management action that may leave them in breach of employment or equality legislation.
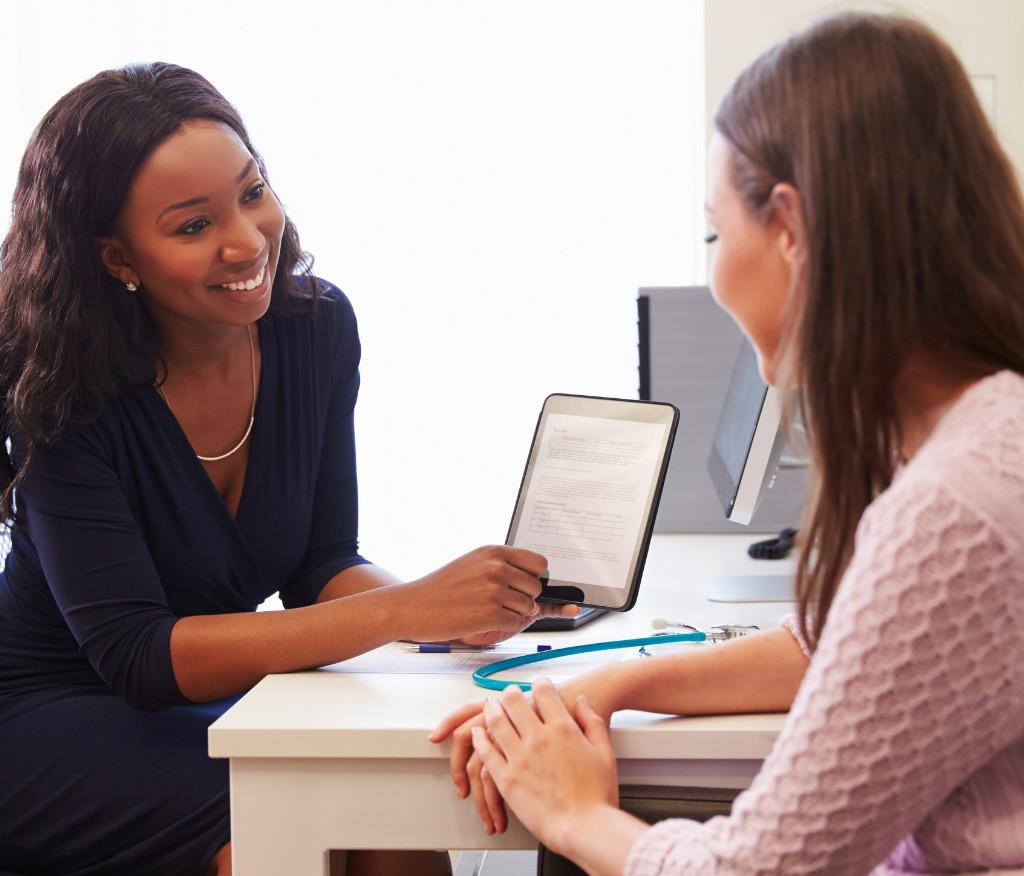
Occupational Health assessments can take place either face to face or remotely via a telephone or video consultation. The type of appointment you have will depend on a number of factors, but both offer an effective medium for conducting assessments, and both will follow the same format, usually lasting around 30 to 45 minutes.
In advance of the assessment, the clinician will have been provided with a referral form from your employer providing details of: • The reason for the referral, including any background information about your medical condition or diagnosis, how it is affecting you, both generally and at work, and any treatment or rehabilitation you are receiving. • Any information provided by your GP or other treating healthcare professional on your fit note. • Any action they have taken so far (for example, introducing additional support or adjustments to your duties or hours) and how successful these have been. • Any alternative duties or adjustments they are able to offer or accommodate. • Any specific questions they wish the clinician to answer.
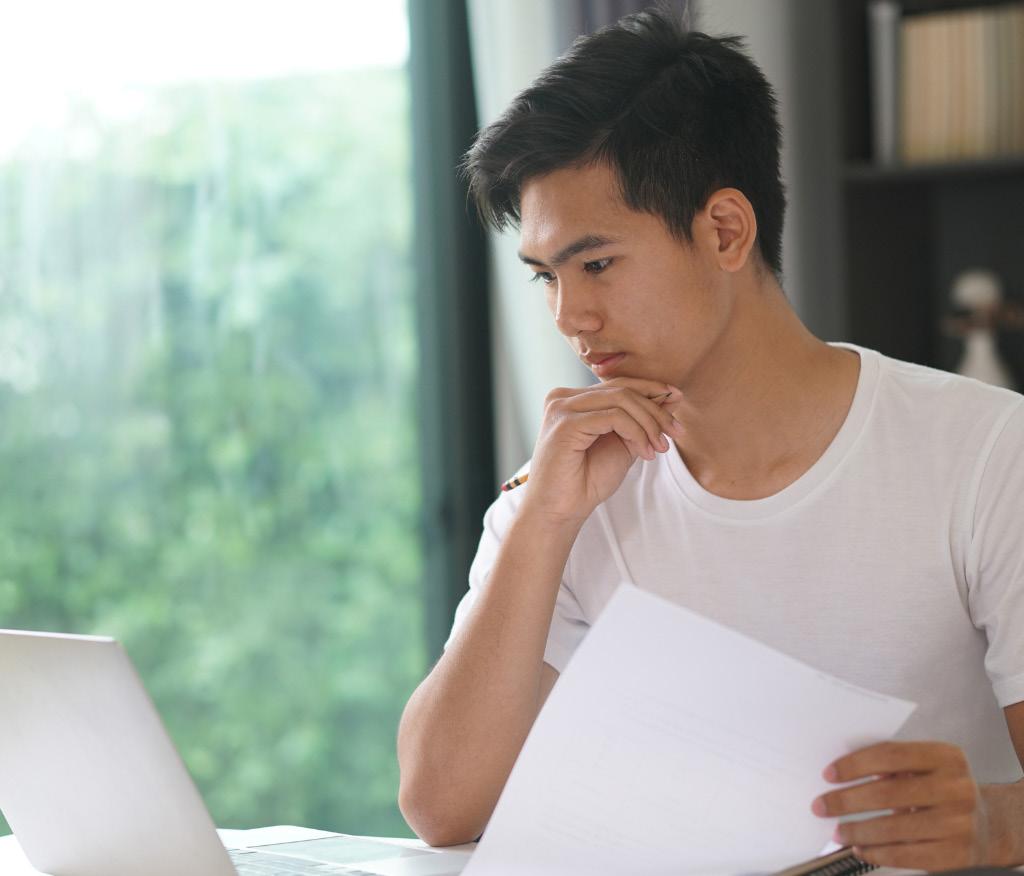
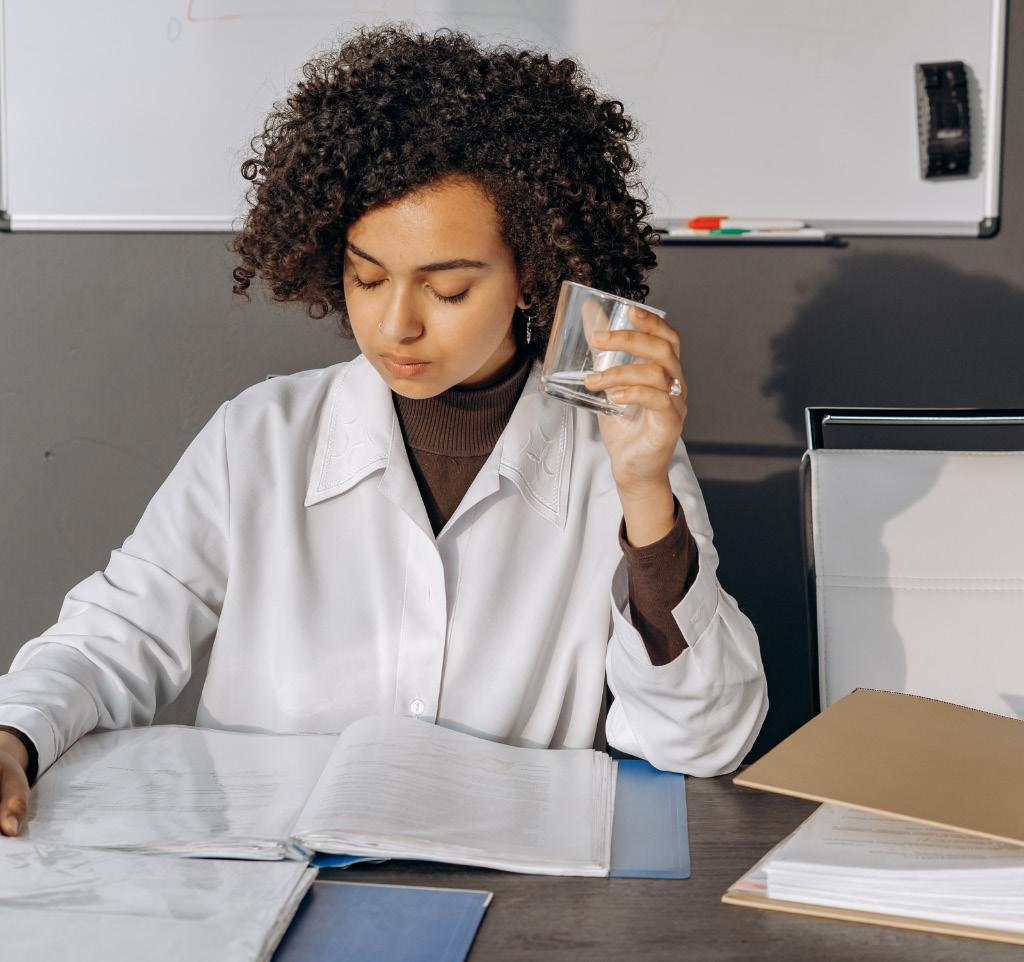
Occupational Health assessments rarely involve any form of physical examination. Instead, during the appointment the clinician will take a detailed medical, social and occupational history and discuss with you the information your employer has provided. They will also ask you specific questions to help them understand your perspective of your present situation and how your health is affecting you; your current functional capabilities; and what support you feel you need to help you get back to work sooner (if you are absent) or continue doing your role. At the end of the consultation, the clinician will talk you through the advice and recommendations they intend to include in their report. You will also be asked to confirm that you consent to their report being released to your employer (and may be requested to complete a written consent form).
After the assessment, the clinician will produce a report to your employer summarising what was discussed during your consultation and providing advice and recommendations on: • Whether or not you are fit to return to work and continue in your role (and if you are not yet fit, why that is the case and when they expect that you are likely to be able to return). • Whether a phased return is necessary and how to approach it. • Any workplace adjustments that are required (e.g. to your hours, shift patterns or duties), either on a temporary or permanent basis, or any additional support they could provide to help you return to work sooner. • Any action either they or you can take to aid your recovery and reduce any risk of future sickness absence (e.g. compliance with treatment, making lifestyle changes, maintaining open dialogue with your line manager and scheduling regular catchups to troubleshoot issues at work that may be impacting on your health). • Whether you are likely to be covered under the provisions of the Equality Act. • Whether any further guidance is required from your treating doctor or specialist.
It’s important to remember that Occupational Health assessments are a supportive process. The aim is always to help move forward the situation that has prompted the referral by identifying a solution that is not only commercially viable for your employer but also ensures both they and you feel supported to manage your health effectively at work, so you can continue making a valuable contribution in the workplace.
Are there any other types of Occupational Health Assessment?
Sometimes, if an employee is starting a new job or working in a certain type of role, they may require either a pre-placement assessment or ongoing health checks/ periodic medicals to ensure they are medically fit to carry out their duties safely, especially if they are returning to work after absence due to ill health. For more information about Occupational Health and other assessments, get in touch via the contact information below.
Tel: 0330 390 3370 Email: salesenquiries@medigold-health.com Visit: www.medigold-health.com
Colas Rail
Formerly known as Seco Rail, Colas Rail is a rail freight operator that is a subsidiary of French industrial group Bouygues
Colas Rail Limited is part of the Colas Rail Group, a Colas company – leading in road construction and maintenance, with the inside track on what makes for the ultimate rail infrastructure solution. Colas Rail is one of Europe’s leading suppliers of railway infrastructure services.
The organisation is split into four different sections: • Rail Infrastructure. • Rail Services. • Urban Rail. • High-Speed Rail.
Rail Infrastructure
Colas Rail is a leading provider of railway infrastructure services – providing design, engineering, project management, construction and maintenance solutions for the light rail, metro, mainline and highspeed markets.
Some of the schemes they deliver include: • Track Installation, Renewal and
Maintenance. • Signalling. • Electrification (Overhead Catenary
Systems and 3rd Rail). • High Voltage and Traction Power. • Rolling Stock Refurbishment and
Maintenance.
In 2019, Colas Rail UK won a ten-year contract for the South Rail Systems Alliance (SRSA) across three Network Rail regions in the South of the UK – Western & Wales, Southern and Anglia. The framework creates an alliance between Network Rail, Colas Rail Ltd, and AECOM providing an integrated delivery model for the development, design and construction of track renewals on plain line, switches and crossings.
Rail services
Their services include the operation and maintenance of On Track Plant, which includes operating and maintaining the largest, most advanced fleet of On Track Plant in the UK, and Rail Freight, Rolling Stock Refurbishment and Maintenance, as well as Rail Grinding and Milling services.
Their extended depot in Rugby accommodates On Track Plant and Locomotives up to 148 metres long and undertakes the servicing and repair of On Track Machines, On Track Plant and Locomotives.
Rolling stock
Colas Rail currently operates an extensive fleet of railway assets: 130 locomotives, 500 wagons and two track-laying trains. As well as three ballast clearing machines, 32 ballast tampers, three stabilisers, 13 ballast regulators, 55 road-rail vehicles, 15 loaders, and three concreting trains, across the 20 countries in which it operates.
Included in this collection are several ‘Specialist Wagons’ including eight ‘Slinger’ rail delivery and recovery gantry wagons, one high capacity 125T Kirow crane KRC 1200 UK, 16 PEM LEM switch handling units (PEMs/LEMs) and two Track Relaying Machines (TRM).
Urban rail
Colas Rail has over 25 years’ experience in designing and delivering Light Rail systems in more than 50 cities around the world. In the UK they deliver design, construction and maintenance for light/metro rail projects, they work in partnership with their customers to identify optimal engineering and value-based solutions through Early Contractor Involvement.
Urban Rail transit offers low energy consumption and high efficiency travel, opening up under-populated areas and aiding regeneration. Increasingly becoming an integral part of urban planning, it provides one of the most convenient and safest modes of transportation within inner city areas – enhancing regional quality of life and having a positive impact on the local community, the environment and the economy.
Urban rail works
The Midland Metro Alliance (MMA) was established in 2016 and consists of a consortium of partners including the West Midlands Combined Authority and Colas Rail Ltd. It was established to contribute to the social and economic regeneration of the West Midlands – with the aim of extending the tram network by a further 32 kilometres by 2026.
Construction started in June 2017 with the Birmingham Centenary Square Extension, completed in 2019. Further works include the tramway extensions to Wolverhampton City Centre and Edgbaston due to enter operation in 2021. The Wednesbury Brierley Hill Line will follow in 2023. Dependent on financing, the network will extend to the east of Birmingham, to link the future high-speed line, High Speed 2 (HS2) and towards the airport with the East Birmingham-Solihull branch.
High-speed rail
With over 35 years’ experience managing and delivering high-speed rail projects, the Colas Rail Group have delivered on a variety of projects harnessing a successful track record.
Colas Rail built 74 kilometres of new highspeed double track line from the Channel Tunnel to Fawkham Junction in north Kent, with a design speed of 300 kph, including the OCS and Mechanical and Electrical equipment and services.
Cities are being reinvented all over the world, with mobility being the key to connecting people and boosting local economies. In the UK, Colas Rail are proud to be a partner of choice – helping customers to put the passenger first.
KEY PERSONNEL CEO: Jean- Pierre Bertrand Deputy CEO: Stephens Haynes Rail Freight Director: Simon Ball
CONTACT INFORMATION Address: Dacre House, Dacre St, Westminster, London SW1H0DJ Tel: 020 7593 5348 Email: info@colasrail.co.uk Visit: www.colasrail.co.uk
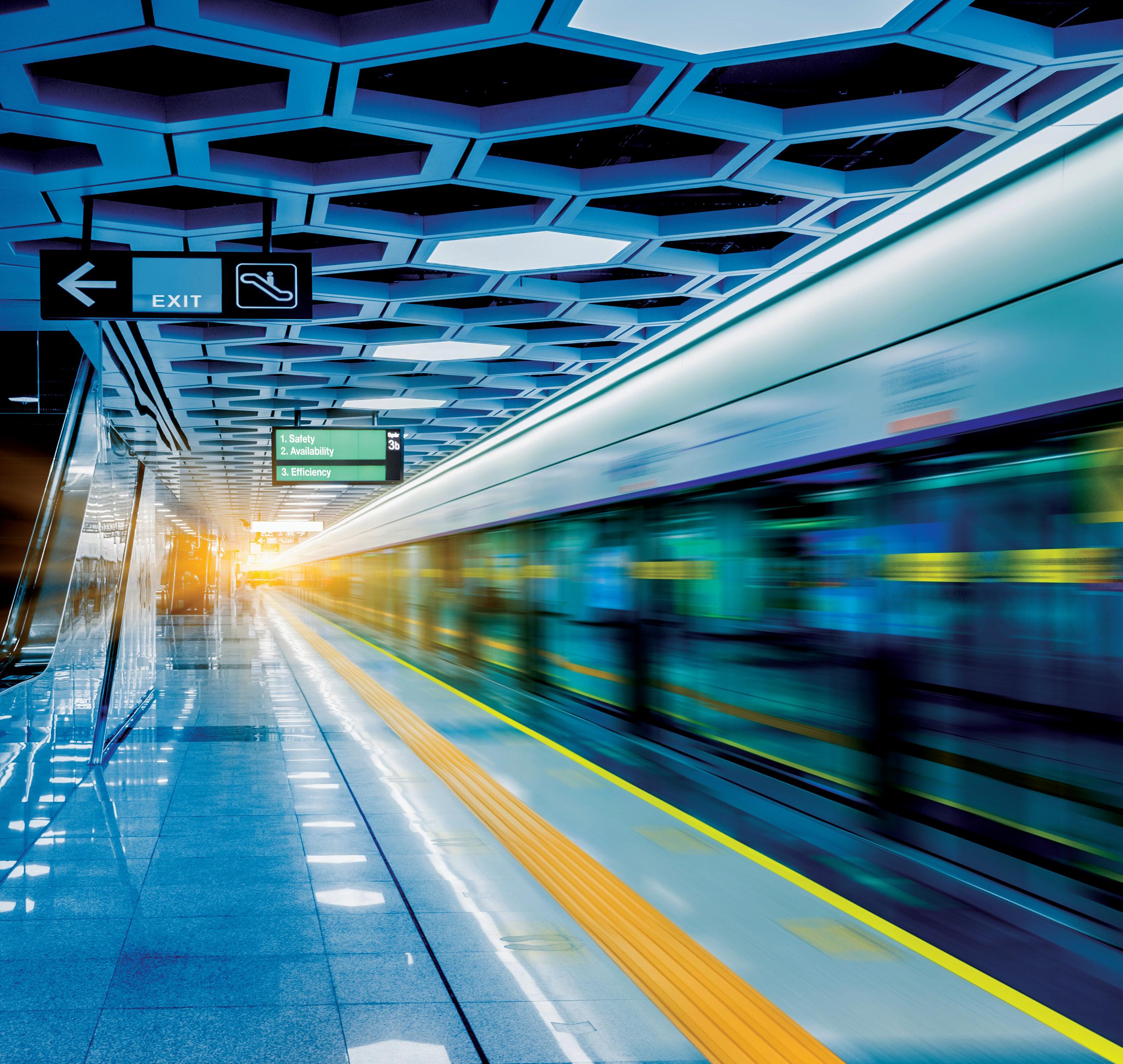
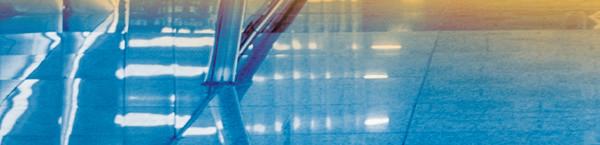

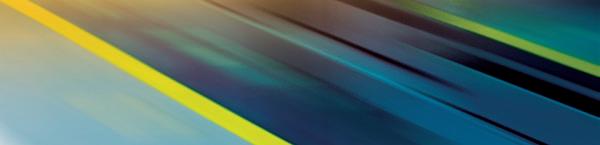
DB Cargo UK
DB Cargo UK is the largest rail freight haulier in the UK. It operates freight and infrastructure services, as well as passenger charter trains throughout the UK
The company was born in 1996 when assets from the former British Rail freight business were used to form English Welsh and Scottish Railway (EWS). In 2007 Deutsche Bahn AG acquired all shares in the company and in 2016 renamed it DB Cargo UK.
Maritime Intermodal
In October 2021, DB Cargo UK announced plans to lease its Mossend EuroTerminal rail freight facility to Maritime Intermodal. The Lanarkshire depot provides intermodal freight transfer between rail and road and is well-placed at the centre of Scotland’s road network, next to the M8 motorway linking Glasgow and Edinburgh. The announcement came two years after Maritime Intermodal took over the lease of DB’s intermodal rail freight facilities in Wakefield, West Yorkshire and Trafford Park in Manchester.
Under the terms of that agreement: • DB Cargo UK was contracted to run
Maritime Intermodal’s rail operations out of Felixstowe and Southampton. • Maritime Intermodal took on responsibility for DB Cargo UK’s terminals in Trafford Park, Manchester and Wakefield in West Yorkshire, thus strengthening the road haulier’s national network of strategic hubs. • Maritime Intermodal took responsibility for DB Cargo UK’s existing intermodal customers on its Felixstowe and
Southampton services.
Contracts
DB Cargo UK signed a ten-year contract with Brett Aggregates in 2020. The contract will see DB Cargo UK transport millions of tonnes of sea-dredged products every year from Brett’s marine aggregates terminals in Ipswich, Cliffe and Newhaven.
DB Cargo UK was awarded a five-year haulage contract with Tarmac in 2020. This has welcomed a boost for the rail freight company which already runs a range of services for Tarmac to and from Mountsorrel Quarry in Leicestershire and its aggregates facility in Angerstein Wharf, Greenwich, London.
DB Cargo UK has been awarded a twoyear contract to transport China clay for Imerys. DB Cargo UK also signed a fiveyear ‘hook and haul’ contract to transport supplies of sustainable biomass to Drax. Each train will carry around 1,650 tonnes of sustainable biomass to Drax Power Station, which provides flexible and reliable renewable power for millions of UK homes and businesses.
DB Cargo UK has also secured a new three-year deal with fellow rail freight company GB Railfreight (GBRf) to undertake the maintenance of ten Class 60 locomotives for them as well as providing technical infield support.
Logistics
In October 2018, UK manufacturing was given a major boost with the opening of DB Cargo UK’s new £6 million steel logistics centre in the West Midlands. Construction took more than twelve months and saw the German-owned freight operator more than double the size of its existing facility in Knowles Road, Wolverhampton, which receives imported steel from as far afield as Holland and Sweden.
The £6 million project was one of the largest investments in rail freight in the past five years and seen as a major vote of confidence in the UK’s continuing ability to trade and attract inward investment post-Brexit.
The new state-of-the-art logistics centre is now used by some of the world’s biggest steel companies including ArcelorMittal, Tata Steel and SSAB; providing a major boost to local businesses that use their products in their manufacturing processes.
Track infrastructure renewals
In August 2019, DB Cargo UK started work on a multi-million programme of investment to improve track and rail infrastructure at three key sites. The UK’s largest rail freight operator is replacing more than 20 kilometres of track at its depots at Immingham in North Lincolnshire, Rotherham in South Yorkshire and Toton in Nottinghamshire. The investment will further improve the safety and reliability of services.
The campaign intends to support the UK in reaching its climate targets as freight transport plays a key role in production of greenhouse gas emissions. The aim of the campaign is to encourage more businesses to choose rail freight over road haulage for their transport needs, thus assisting in the UK efforts to achieve its goal of net zero carbon emissions by 2050.
To encourage more companies to switch from road to rail, DB Cargo UK are asking the government to: • Set out in primary legislation a legally binding target for future modal growth, thus driving greater collaboration and innovation (as we have seen with decarbonisation). • Work with the rail industry to incentivise businesses to switch their goods from road to rail. • Establish an efficient logistics sector which has hubs and terminals in the right places, with strong rail connectivity to help avoid a road-led recovery. • Commit to investing in the infrastructure required to decarbonise rail freight including a long-term programme of electrifying the railways. • Ensure that the future industry structure supports rail freight growth and unlock continued third-party investment that will allow rail freight operators to deliver greater long-term economic and environmental benefits. • Make the best use of capacity on the network, using a benefits-led assessment that considers the relative value of different capacity choices and which maximises the opportunities for getting more freight on each train. • Upgrade Britain’s infrastructure to make it fit for the digital age, which can allow both freight and passenger trains to run more efficiently.
KEY PERSONNEL Chief Executive Officer: Andrea Rossi Chief Financial Officer: Deb Hardy Chief Transformation and Digitalisation Officer: Marie Hill Head of Sales: Roger Neary
CONTACT INFORMATION Address: Lakeside Business Park, South Yorkshire, DN4 5PN Tel: 01302 575000 Email: Uk.dbcargo@deutschebahn.com Visit: www.uk.dbcargo.com
Direct Rail Services
Operating for over 25 years, Direct Rail Services (DRS) is one of the UK’s leading national rail freight operators
DRS has a uniquely flexible and efficient fleet of locomotives and rolling stock. Their fleet of Class 88, 68, 66, 57 and 37 locomotives offer unbridled flexibility allowing them to deliver freight services across the network.
The Class 88 is their state-of-the-art bimode locomotive, the only dual powered locomotive in the UK. It can run on overhead electricity and offers industry leading CO2 savings, but also up to 500 miles on diesel power when no overhead lines are available.
Unique amongst UK rail freight businesses, DRS is not only fully accredited to ISO 9001 quality management and ISO 14001 environmental standards, but has also achieved the occupational health and safety approval BS OHSAS 18001.
With a unique blend of skills and experience, the company offers a comprehensive package of rail transport and related services, tailor-made to match a wide range of exacting customer requirements. DRS’s award winning UK-wide operations are delivered from a national network of fully equipped depots and facilities, supported by a 24/7 control centre.
Supporting DRS’s core business of delivering safe, secure and reliable transport services for some of the most sensitive and demanding loads is an ever-expanding portfolio of key rail activities.
DRS operates a unique fleet of locomotives matched with a flexible team of highly trained, fully experienced staff, providing a comprehensive range of infrastructure support services including: • Autumn Rail Head Treatment
Trains (RHTT). • Winter snow clearance utilising DRS’ own
MSP-fi tted locomotives and Network
Rail Independent Snow Ploughs and
Beilhack Ploughs. • Overhead line ‘ice breaking’ service. • MPV weed-spraying operations. • S&C Video MPV Operation. • A variety of Test Trains, including
Network Rail Saloon services.
In addition to these key services, DRS also supports Supply Chain Operations for Network Rail with the extensive resources required to facilitate its infrastructure renewal requirements, including the provision of Network Services, Bulk Ballast Services, Delivery Trains and Possession Services.
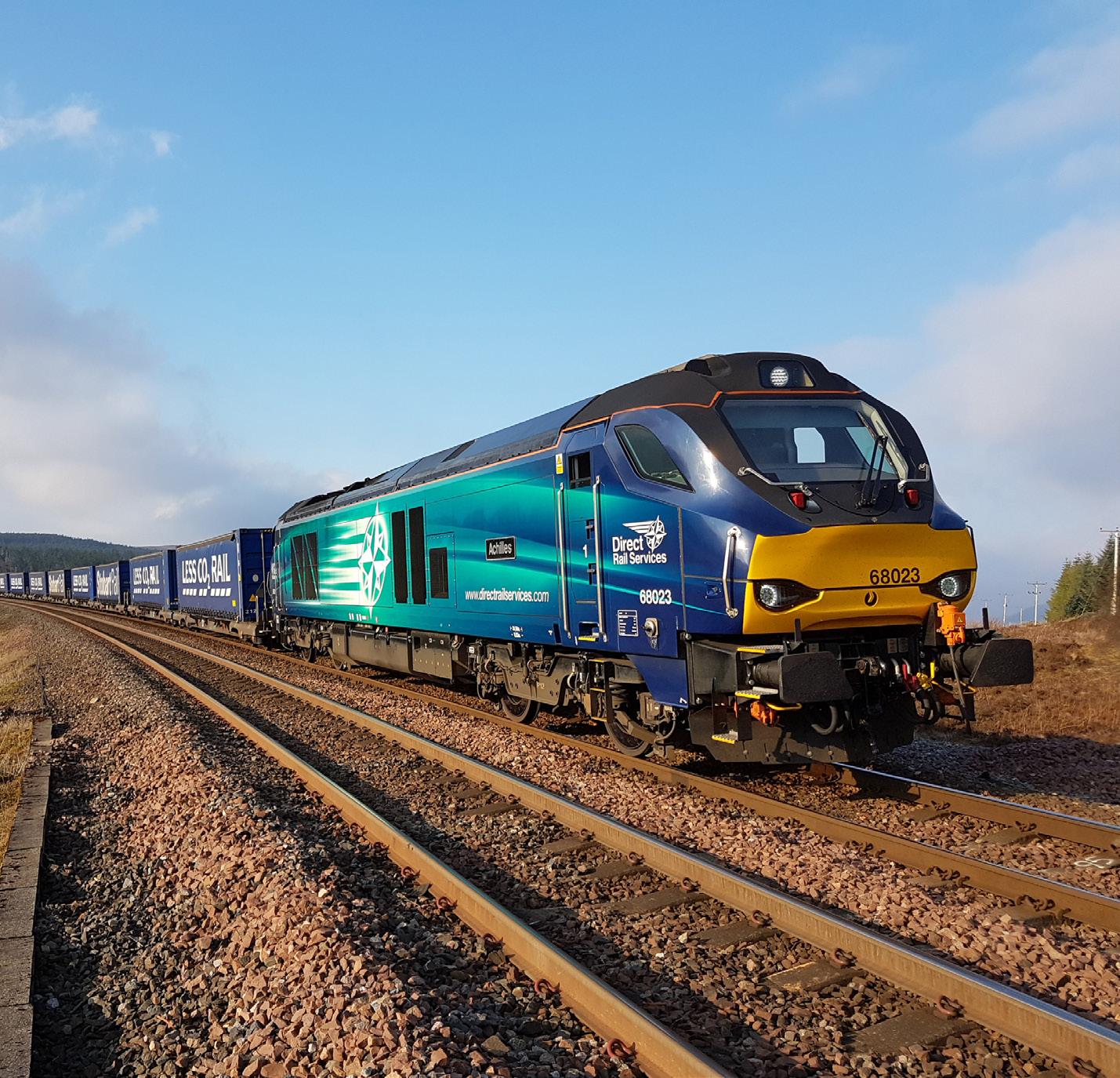
Nuclear Transport Solutions
In April 2021, Nuclear Transport Solutions (NTS), a specialist nuclear transport organisation, was launched. NTS is part of the Nuclear Decommissioning Authority (NDA) group and specialises in the operational, commercial, engineering, legal, and regulatory expertise that underpin nuclear transport and logistics operations.
Operating from a network of more than thirty depots and sites, from Georgemas in the far north of Scotland to Devonport on the south coast, Nuclear Transport Solutions operate seven fully nuclear capable regional railheads that are positioned to support decommissioning and new build activities, and safe, high-security stabling facilities at strategic locations.
KEY PERSONNEL Managing Director: Chris Connelly Senior Business Manager: Sabrina Brannan Senior Operations Planning Manager: Sam Dixon
CONTACT INFORMATION Address: Direct Rail Services, Regents Court, Baron Way, Carlisle, Cumbria CA6 4SJ Tel: 01228 406600 Email: communications@drsl.co.uk
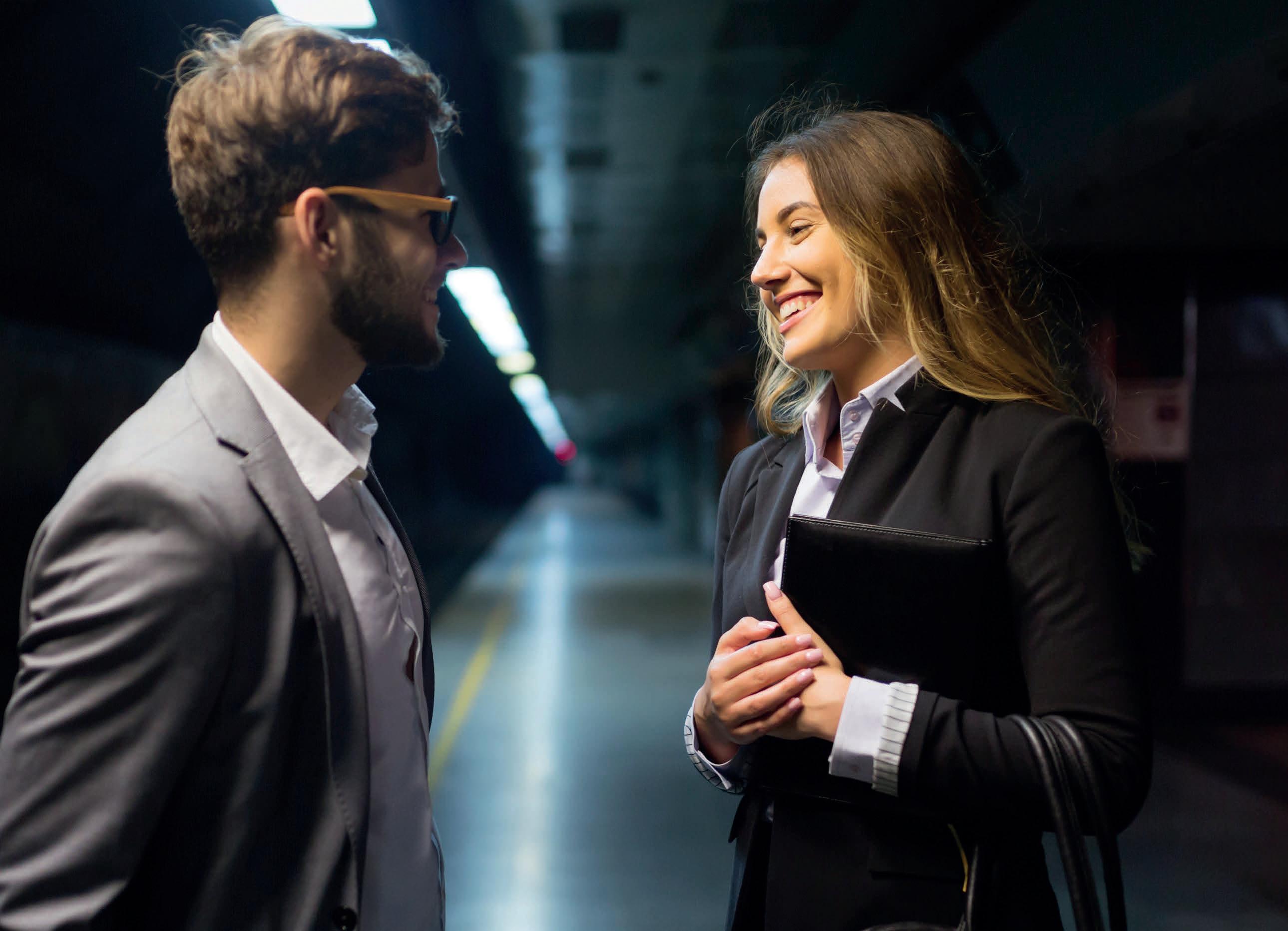
GB Railfreight
GB Railfreight (GBRf) is the third largest rail freight operator in the United Kingdom, transporting goods for a wide range of customers
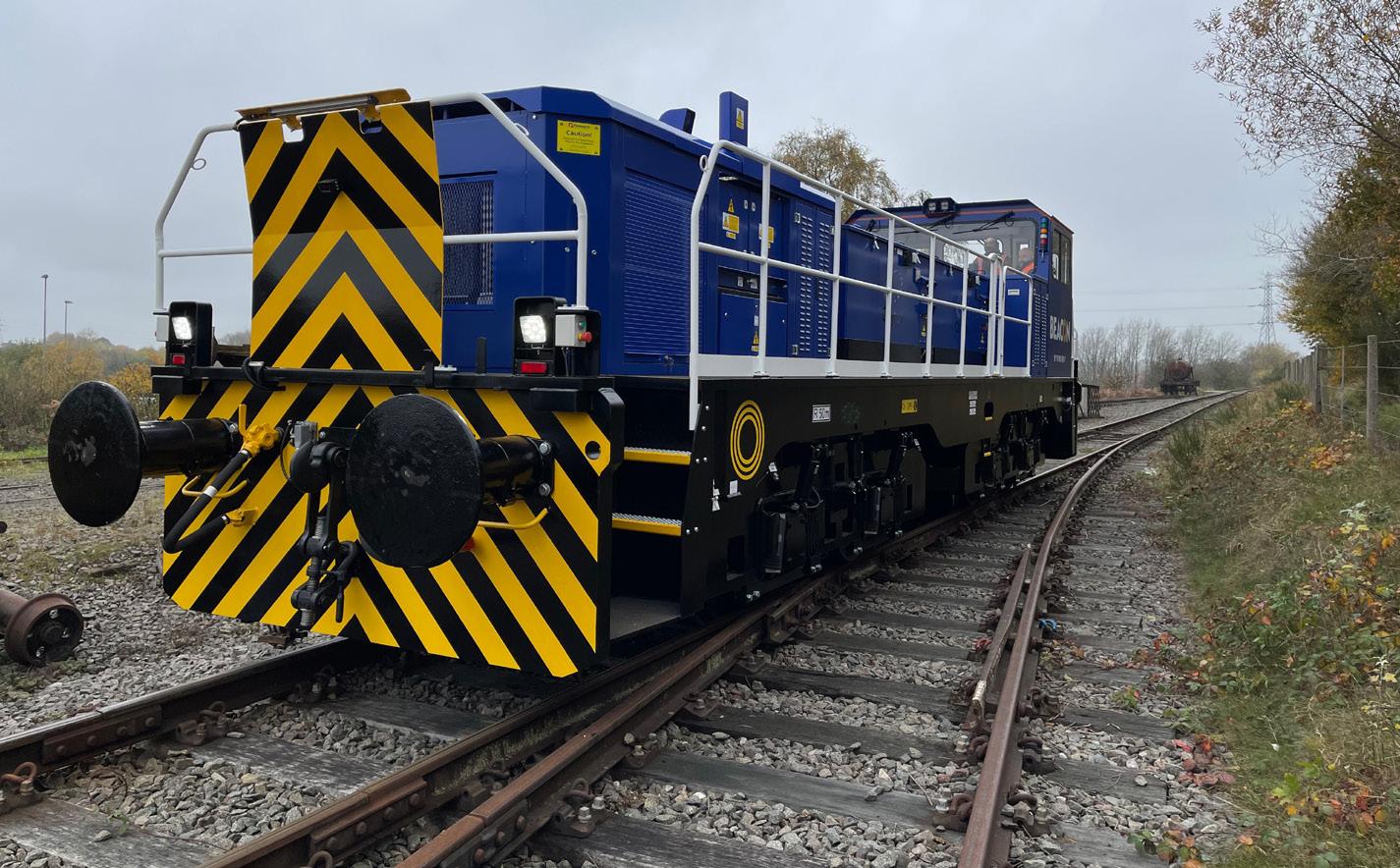
GBRf’s £3 million building opened in August 2021, accommodates GBRf’s traincrew and office staff including its 24-hour control centre, training and operations departments, as well as the asset management team. The building plays host to three new purpose-built classrooms and state-of-the-art simulators which will be used to develop future generations of talent from the local area and beyond.
Eastleigh and Bescot upgrades
GBRf has completed two major upgrade projects funded by Network Rail worth over £1.5 million, aimed at improving vital Local Distribution Centres (LDCs) in Eastleigh and Bescot.
Both LDC’s act as a focal point for the shunting, marshalling and preparation of trains needed to support vital engineering works carried out by Network Rail.
The work on Eastleigh LDC, in Hampshire, has been two years in the making with GBRf replacing old cabins with updated facilities that provide full recreational capability, offices for management, a meeting room, as well as a vantage point that overlooks the yard. Alongside this, GBRf undertook a car park overhaul, maximising the potential parking for those operating onsite.
Contracts
GB Railfreight (GBRf) renewed its contract with Tarmac for five years from January 2020 to 31 December 2025. GB Railfreight (GBRf) and Rail Stone Solutions (RSS) signed two contracts to support construction on the first phase of HS2.
The deals, with HS2 contractors EKFB (Eiffage, Kier, Ferrovial BAM Nuttall) and BBV (Balfour Beatty VINCI) will see GBRf join forces with RSS to deliver aggregates by rail to the high-speed rail project’s main construction compounds.
As part of the deal with EKFB, GBRf will support the training of new train drivers at their new state-of-the-art twin-simulators near Peterborough where the UK’s first and only full-cab freight European Rail Traffic Management System (ERTMS) simulator centre is located.
UK’s first rail freight electrification trial
The Decarbonisation & Electrification of Freight Terminals (DEFT) project, funded by the Department for Transport and Innovate UK, has seen project partners Furrer+Frey GB, Tarmac and GB Railfreight demonstrate a new way of decarbonising rail and lessen freight’s impact on passenger journeys.
Engineers from Furrer+Frey GB designed a Moveable Overhead Conductor system at Northamptonshire terminal where overhead equipment supplying electricity to the locomotives can safely move away once the train is in place and return when the train needs to move again. This would transform the terminal in Northamptonshire to become the first in the UK to demonstrate an innovative overhead electrification system, which indicates the end for diesel on electrified rail routes and boosts the industry’s net zero ambitions. If successful, the moveable overhead system could go on to be deployed at other freight terminals across the UK and support the full decarbonisation of Britain’s railways
New locomotives
In June 2019, GBRf announced three Class 66 locomotives were to be leased from Beacon Rail Leasing and introduced to the UK rail network from Sweden. The locomotives mark GBRf’s continued growth and investment in its fleet. These locos are the most widely operated modern freight locomotives in the European market and will further strengthen GBRf’s already reliable fleet. GBRf have considerable experience bringing locomotives from Europe to the UK. Previous conversions include 66 747/8/9/5/51 from European to UK specification with the assistance of Electro Motive Diesels (EMD).
GB Railfreight (GBRF) has taken delivery of a class 18 hybrid+ shunting locomotive as part of a three-month trial with Beacon Rail Leasing, marking the latest expansion of its growing fleet. Manufactured by Clayton Equipment Ltd, the Class 18 is powered by an onboard battery that provides emissionsfree operation where charging facilities are available, or through a regenerative braking system. When challenges with range or operation occur, an efficient onboard Stage V compliant engine can be utilised to increase the locomotives running time. This shunting locomotive will enable low noise and zero emissions, demonstrating a clear contribution to meeting the UK’s net zero carbon targets.
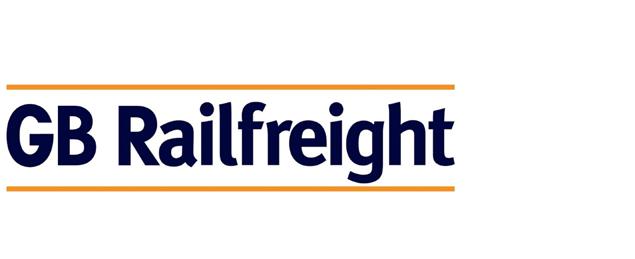
KEY PERSONNEL Chief Executive Officer: John Smith Commercial Director: Liam Day Production Director: Ian Langton Finance Director: Karl Goulding- Davis Asset Director: David Goulding Business Development Director: Tim Hartley General Infrastructure Manager: Alex Kirk
CONTACT INFORMATION Address: LONDON HQ, 3rd Floor, 55 Old Broad Street, London EC2M 1RX Tel: 020 7904 3393 Email: info@gbrailfreight.com Visit: www.gbrailfreight.com

Trio of new appointments for GCRE
The Global Centre of Rail Excellence (GCRE) has announced the appointment of Gail Hawthorne and Simon Blanchflower CBE as new Non-Executive Directors along with Rob Thompson as Director of Implementation.
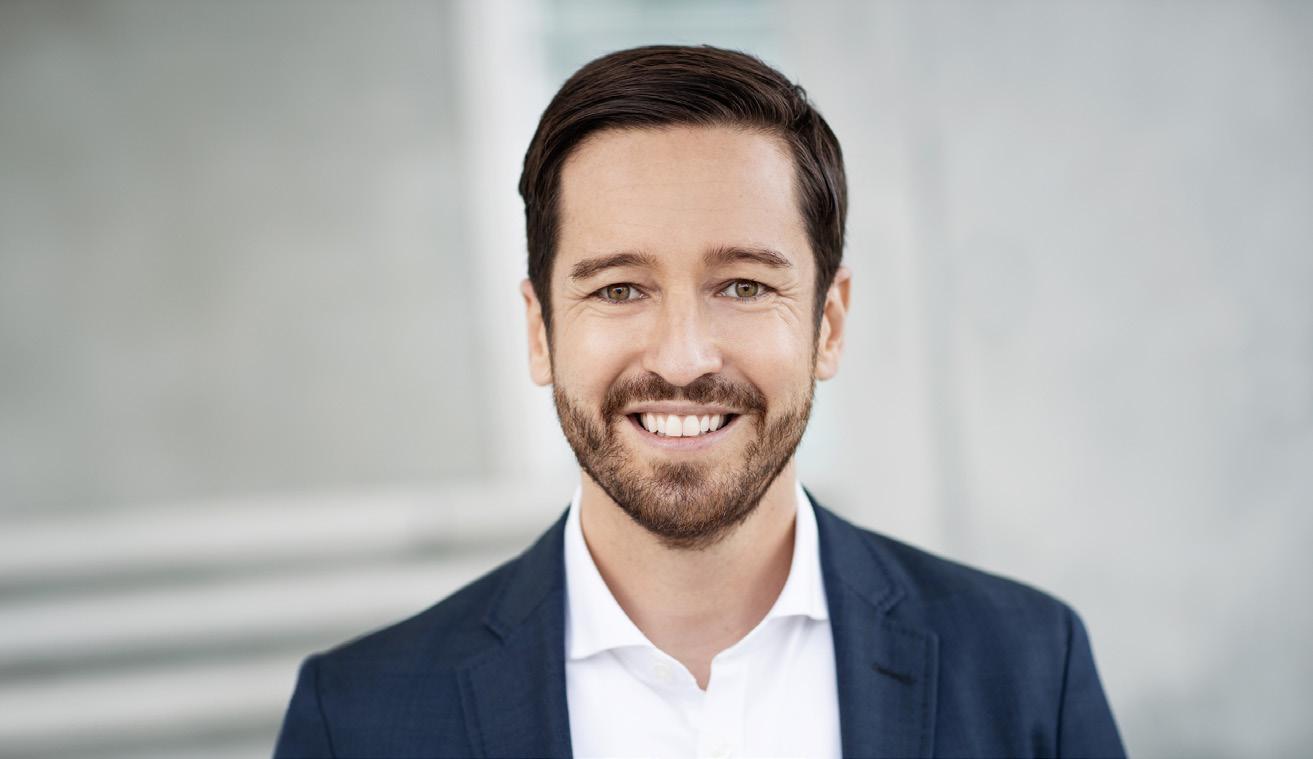
Rail Europe appoints New President and CEO
Rail Europe has appointed Björn Bender as President and CEO.
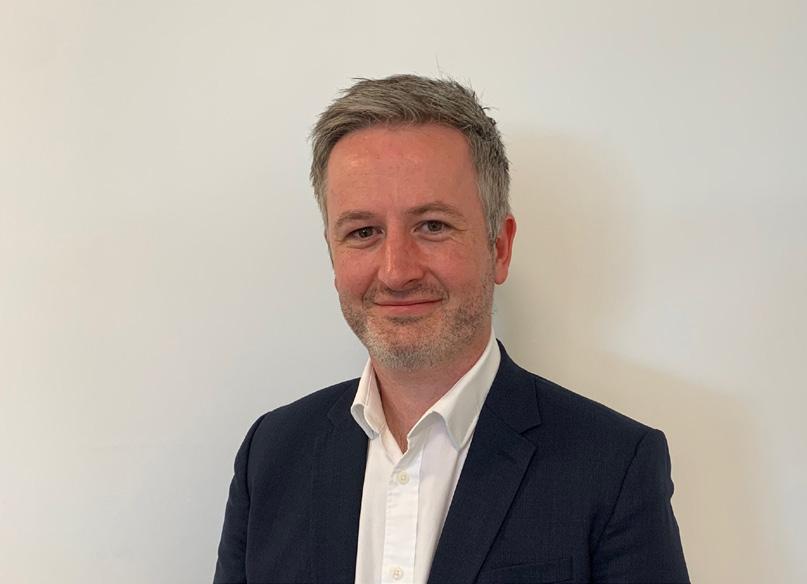
Greater Anglia appoints new Finance Director
Greater Anglia has appointed a new Finance Director to oversee the company’s Finance, IT and Procurement functions. Michael Robertson joins Greater Anglia from Abellio Group where he was Group Financial Controller.
New Chief Executive of London TravelWatch appointed
London TravelWatch has announced the appointment of Michael Roberts as its new Chief Executive Officer (CEO).
Future mobility, energy and innovation expert joins PA Consulting as a Partner
Michael Hurwitz has joined PA Consulting (PA) as a partner to further develop the Future Mobility practice, at the intersect of PA’s Transport and Energy and Utilities sectors.
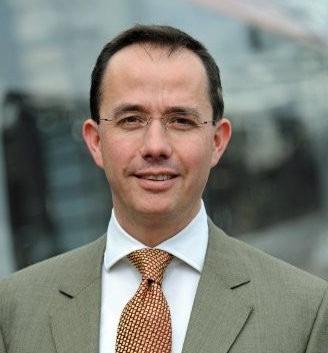
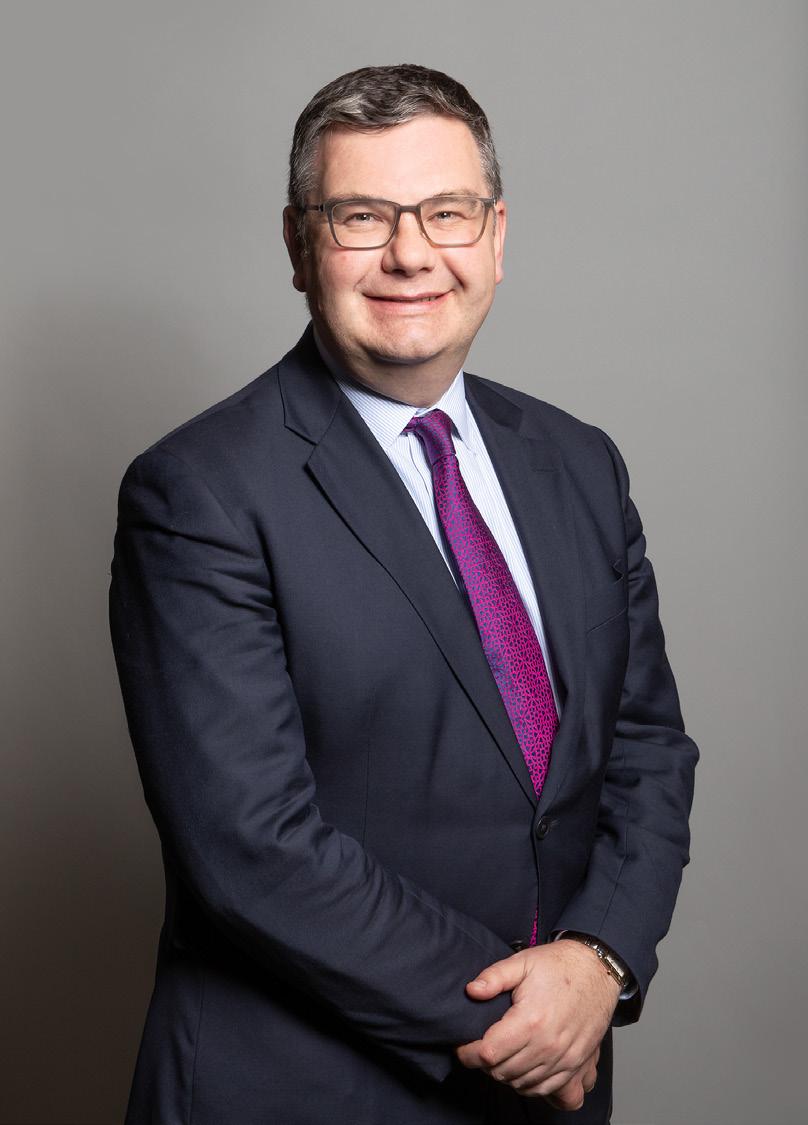
New Transport Committee Chair elected
The Deputy Speaker of the House has announced that Iain Stewart has been elected Chair of the Transport Committee.
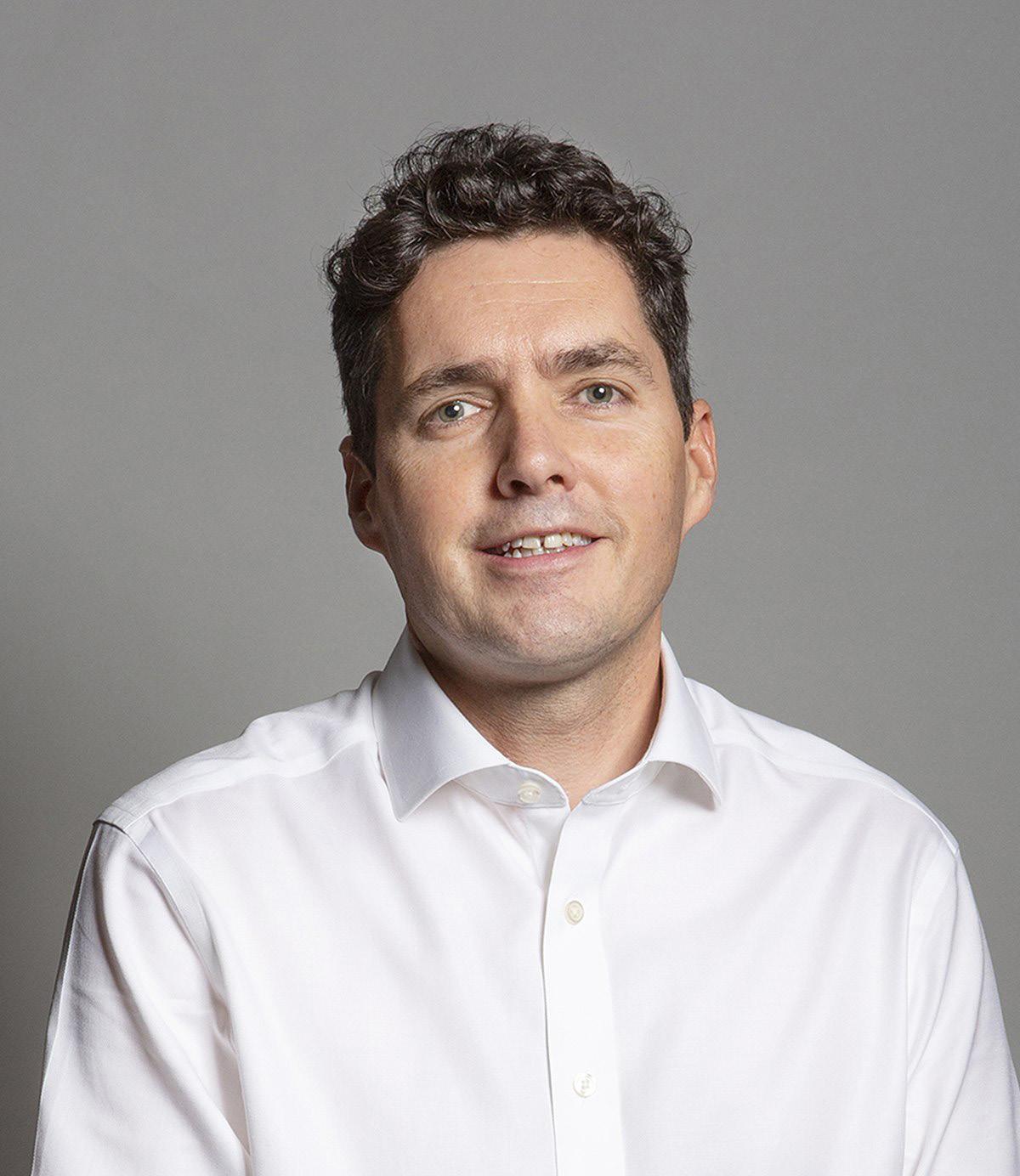
New Minister for Rail & HS2 at the Department for Transport
Huw Merriman has been appointed Minister of State at the Department for Transport. Huw previously sat on the Transport Select Committee and served as its Chair between 2020 and 2022.