Work at Height Solutions
Bringing Light to the World’s Darkest Places
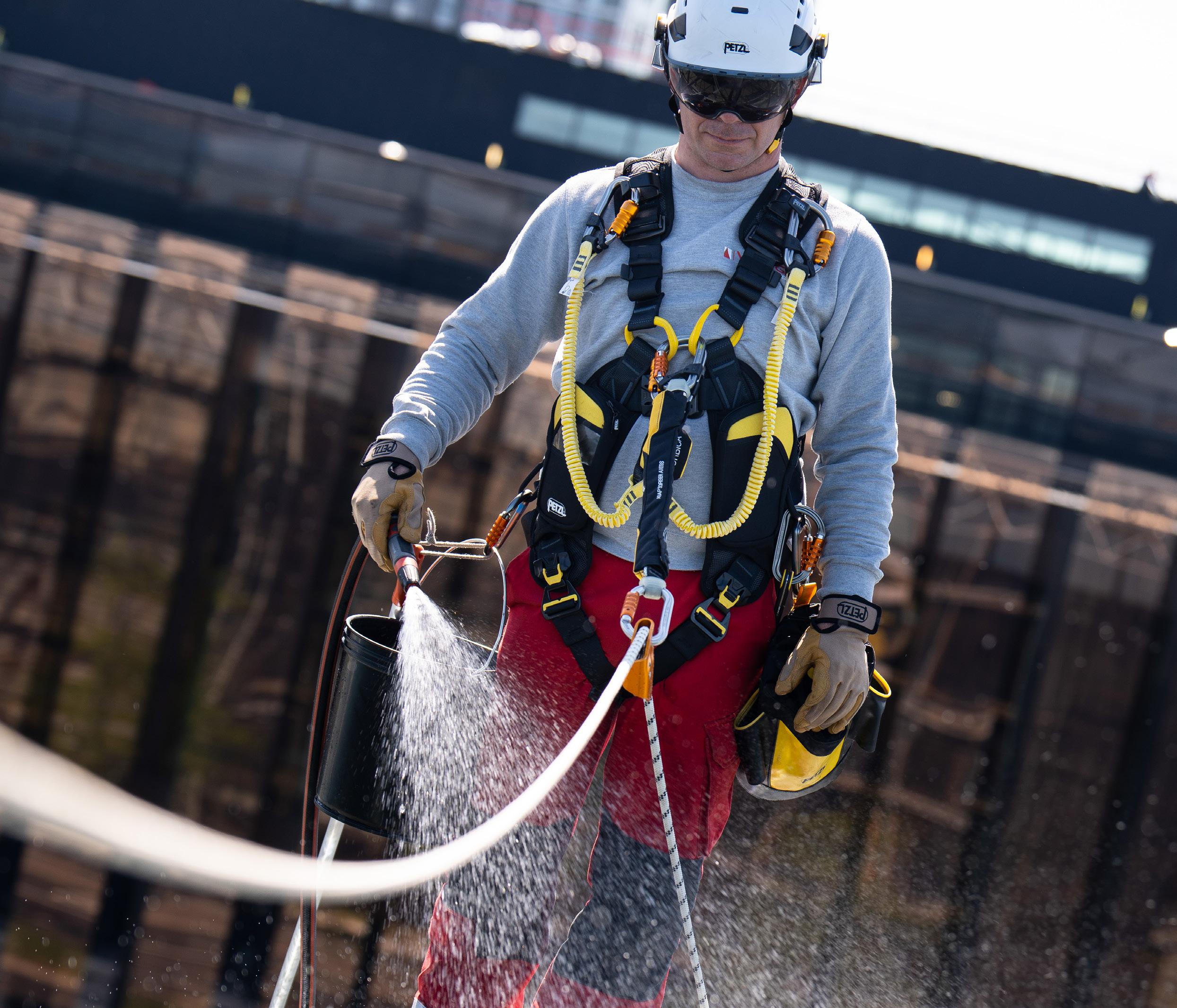
SIGNALLING What Makes an Outstanding Signaller?
HIGH-SPEED RAIL
HS2’s Northern Leg Is Off, What Can We Learn?
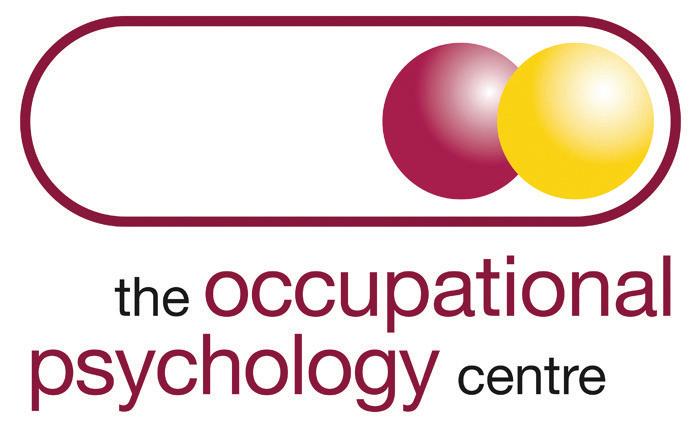
SIGNALLING What Makes an Outstanding Signaller?
HS2’s Northern Leg Is Off, What Can We Learn?
With over 30 years’ experience working in the rail industry, specialising in the safety sector, the OPC provides practical, reliable ways of improving performance and assessing ability.
railprofessional @railpromag
PUBLISHER
RAIL PROFESSIONAL LTD
Hallmark House, Downham Road, Ramsden Heath, Essex CM11 1PU
Telephone: +44 (0) 1268 711 811
EDITORIAL
EDITOR
Sam Sherwood-Hale editor@railpro.co.uk
DISPLAY ADVERTISING
Adam Overall
Jamie Tregarthen sales@railpro.co.uk
RECRUITMENT ADVERTISING recruitment@railpro.co.uk
SUBSCRIPTIONS subscriptions@railpro.co.uk
ADMINISTRATION
Cherie Nugent info@railpro.co.uk
Lisa Etherington admin@railpro.co.uk
DESIGN & PRODUCTION
Jasmine Szaniszlo
Lukasz Saczek production@railpro.co.uk
COVER
As I’m writing this, we’ve just had the announcement that next General Election is to be held on 4 July. Commenting, Director of Operations for the Civil Engineering Contractors Association (CECA) Marie-Claude Hemming said: ‘It is more important than ever that we take the UK’s infrastructure needs out of party-political considerations, and work to ensure the requirements of businesses and communities will be met irrespective of the make-up of the next UK government.’
There’s a lot going on in Whitehall currently, with the Transport Committee holding sessions on the draft Rail Reform Bill with Rail Minister and devolved transport leaders the same day the election was announced. The Government’s draft Bill, published in February, proposes legislation needed to deliver reforms included in the Government’s Plan for Rail. This includes establishing an Integrated Rail Body, which we know as Great British Railways (GBR) and giving it new legal powers to manage and oversee the country’s rail infrastructure and franchising of services to train operating companies.
Alongside that, the Department for Transport is currently running an open consultation on adapting the UK’s transport system to the impacts of climate change. The transport adaptation strategy includes actions and policies to enhance climate adaptation planning across the sector, ensure these plans are achieved and lead to improved climate resilience in the transport system. These policies will be developed over the next five years to enable progress ahead of the fourth National Adaptation Programme. Responding to the open consultation (which will be ended by time of publication) a statement from Greengaue 21 said: ‘There is a risk that the Department’s planned new guidance on Climate Change adaptation will be applied line by line, or one section of highway at a time without due regard to existing or potential adjacent infrastructure networks.’
We will be looking at sustainability in the July issue and Jim Steer, Director and Founder of Steer Group consultancy and Director of Greengauge 21 will be featured in that issue along with the various opinions on the above-mentioned topics.
Coming to this issue and we’re looking at electrification, signalling, high-speed rail and track and trackside. David Hawkes, the Institution of Civil Engineers’ Interim Associate Director of Policy will be asking ‘what went wrong with HS2’, Wendy Spinks, Commercial Director of HS1 Ltd explains why she believes high-speed rail is the future of travel to Europe and John Butterworth, Head of Infrastructure Products at Gripple, explores the challenges that are leading to delays in electrification.
My interviews this month are with Matthew Jenner and Peter Mitchinson of Atlas Copco where we discuss collaborating with industry and getting rail up to code on data-driven technology and with Darren Jackson on supporting rail stakeholders in navigating the complexities of tailored monitoring strategies.
See you all at Rail Live!
SAM SHERWOOD-HALE EDITORLaurent Bonnaud, Economic Historian and Director and Founder of Sponte Sua Srl on the greatest engineering project of the 20th
Network Rail Completes Final Phase of £375 Million
Project
Laura Hedley, Senior Occupational Psychologist at the OPC and a Rail Operations Director discuss the key skills required to be an excellent Signaller and some of the pitfalls to avoid
High-speed rail is the future of travel to Europe – let’s work together to achieve the ambition, Wendy Spinks, Commercial Director of HS1 Ltd explains how
David Hawkes, the Institution of Civil Engineers’ Interim Associate Director of Policy, looks at some of the questions raised by HS2’s cancellation
Burges
Why
58
Kathryn Adams, Commercial Director at Prolectric
Charlotte Lane, Office Manager at Grommets Ltd
In Conversation with Ross Tucker, Construction Sales Manager at Propump Engineering Ltd
The UK's largest and only immersive rail exhibition returns
The Railway Industry Association (RIA) at Rail Live 2024
Nikki Amers-Delph discusses the sustainable movement in modular construction and its opportunities for the
In conversation with the MOSDORFER rail group
In conversation with Daniel Palmer, Business Development Manager at Chevron Green Services
In conversation, with Micheal Russell, Managing Director at Transit Handrail Lighting Ltd
TVS Rail Spares celebrate first birthday 96
Ric Kirman, Business Area Manager Rail & Monitoring at Korec Group
Steve
,
Elevating Station Environments with Urbis Schréder's Smart Lighting Innovation for Modern Stations
Developments from the industry’s supply-side
Tricia Williams, Matt Rice, Jane Cole, Noel Travers, David Tonkin, Sir Philip Rutnam KCB
Our in-house design team, based in Central London, has significant knowledge and experience of working in the light and heavy sectors of the rail industry for clients such as Network Rail and Transport for London. Operating nationally, we can help with:
• Initial project scoping and development
• Surveys – topographic, GPR/buried services, geotechnical etc.
• Various assured design GRIP stages
• Providing AFC and as-built drawings on completion
We are a specialist contractor for the rail industry and also offer a range of other high-quality services that include high pressure jetting, CCTV surveying, UV and hot cure pipe lining, civil engineering services and vegetation management.
Come and see us at Rail Live (19 - 20 June 2024)
Scan here to download our brochure or get in touch
The Construction Plant-hire Association (CPA) has written to the Secretary of State for Transport, Mark Harper, outlining its concerns on embargo times – police enforced movement orders which are preventing the movement of construction plant and equipment at the beginning and end of the day.
CPA members increasingly fear these movement orders are being applied in a disproportionate manner, which in turn, are having an impact on their day-to-day operations and the smooth and efficient movement of construction machinery across the country.
The letter highlights the inconsistent approach being adopted by different police forces, with several being particularly stringent and inflexible in their interpretation and enforcement of embargo times. Mobile crane hire companies in particular, are seemingly being targeted.
One CPA member was notified by their local force, they had infringed their movement order by just 49 seconds. As part of its research, the CPA has also received reports of police vehicles
sitting outside hire depots and construction sites, monitoring the movement of construction equipment.
A newly published report by the Centre for Economics and Business Research (CEBR) ‘The Costs of Increased Police Enforcement of Abnormal Loads Regulations’ highlights the impact this is having on the wider haulage industry – with high end estimates citing a £1.5 billion loss of economic activity over a ten year period due to these regulations. Longer journey times due to the current enforcement practices, alongside the associated costs which could well cost businesses upwards of £2.4 billion over the same period. The CEBR estimates UK plc would eventually be over £5 billion better off if a more consistent approach was taken.
The letter from the CPA calls for next month’s review of the Association of Chief Police Officer’s (ACPO) 2010 ‘Guidance on the Movement of Abnormal Indivisible Loads’ to take a sensible and consistent approach to their application and enforcement, with the review working with the construction industry.
Lumo is celebrating that 95 per cent of its workforce began as apprentices recruited in partnership with provider, Train’d Up. Lumo’s 95 per cent milestone follows a fiveyear partnership between Lumo and Train’d Up, which has seen many successes. This includes 16 drivers in one cohort, the largest number of driver trainees Train’d Up has seen in its 20 years of operation.
The welcomed announcement follows news that the UK has seen 2.5 per cent overall boost in apprenticeships in the last year. Yet, there is still work to be done in the North East due to an ongoing decline in uptake from 23,260 in 2018 to 18,450 in 2023.
To date, a total of 78 Lumo Customer Drivers and Customer Experience Ambassadors have successfully enrolled through the apprenticeship completing a range of training modules.
The custom designed programme prepares Lumo colleagues beyond their day-to-day roles. Additional ICT training is included to ensure they have the skills required to advance internally from day one and, adapt to the quickly approaching digital future.
The apprenticeship partnership with Train’d Up began in 2020, ahead of the business’ launch date on 2021. It was created and, has continued to give the local workforce new opportunities and, the chance to develop new skills to readily enter the rail industry.
c2c has announced that its near-term (2030) and netzero science-based targets (2050), outlined in the company’s Decarbonisation Strategy, have been validated by the Science Based Targets initiative (SBTi), the global body responsible for enabling businesses to set ambitious emissions reduction targets in line with the latest climate science. The SBTi, which is focused on accelerating companies across the world to half their emissions before 2030, and achieve net-zero emissions before 2050, is a collaboration between the United Nations Global Compact (CDP), World Resources Institute (WRI) and the World Wide Fund for Nature (WWF) and is one of the We Mean Business Coalition commitments.
The SBTi also defines and promotes best practice in sciencebased target setting, offers resources and guidance to reduce barriers to adoption, and independently assesses and approves companies’ targets.
Commenting on c2c’s sustainability targets, Managing Director, Rob Mullen, said: ‘c2c remains fully focused on reducing harmful emissions, while providing a sustainable and successful railway for our customers, colleagues and communities. Our ambitious near and long-term science-based targets, recently validated by the SBTi, clearly demonstrate our commitment to reaching net-zero Greenhouse Gases (GHG) emissions right across the business by 2050.’
Stadler has announced the first public appearance of the new trimodal rescue train. The roll-in of the special train featuring innovative drive and safety technology took place today at the ÖBB training campus in St. Pölten. Stadler is to deliver 18 of the multifunctional, low-emission firefighting and rescue trains to ÖBBInfrastruktur AG (ÖBB). Under the name ‘Servicejet’, these will then be stationed at Austrian tunnel portals and deployed on site to assist firefighters. The vehicles were developed and produced at the Swiss sites in Bussnang and St. Margrethen.
68 metres of state-ofthe-art rolling safety, a top speed of 160 kph in both directions and a trimodal drive concept – this is the basic data for Stadler’s new rescue train. Its electric hybrid drive system can run on several energy sources: the overhead line, powerful traction batteries and diesel generators. This enables the rescue train to realise a completely new firefighting and rescue concept. It can fight its way through a smoky tunnel to the source of the fire, rescue people from damaged trains, tow damaged trains, fight fires and get itself and everything it is carrying out of the danger zone to safety.
Johann Pluy, Member of the Board of Management of ÖBB-Infrastruktur AG said: ‘Our new Servicejets enable us to provide assistance even faster than before. They provide more power in a larger operational area. The new concept also enables a reduction from 21 to 18 vehicles.’
Peter Spuhler, Chairman of the Board of Directors of Stadler added: ‘With the launch of the rescue train, we have put a highly innovative concept on the rails that meets ÖBB Infrastruktur’s specifications and satisfies all the customer’s quality and safety requirements. That’s why we will now take the next steps towards the mobility of the future together. Stadler has been commissioned by ÖBB to build longdistance trains from the KISS brand, as well as intercity and regional multiple units from the FLIRT.’
The new Stadler rescue train combines versatility with operational tactics. It has to be equipped for the worst-case scenario, which would be a firefighting and rescue
operation in a railway tunnel. As well as being able to recover passengers from other trains during an evacuation, it is also suitable for carrying out maintenance work. In an emergency, there is enough room for over 300 people in the three cars, which have uninterrupted access along the entire train. 18 seats are fitted with SCBA brackets for firefighters. An HVAC system with special filters protects people on the train from smoke gases. What is more, the entire train is pressurised, which means that there is a slight overpressure inside to keep it free of smoke in tunnels. The front part of the train where the driver’s cab is located is protected by a water spray system on the outside.
Metro customers are getting their first chance to see the new trains out on the system as daytime testing gets underway –marking a new major milestone for the £362 million programme. Nexus said this was the next significant step in getting the new Stadler trains ready to enter service later this year.
The daytime testing began at 2pm on Wednesday 15 May, when a new Metro train operated in the gaps between timetabled services provided by the current fleet on Metro’s coastal route between Newcastle and North Tyneside.
It allows for a process known as kilometre accumulation, putting the trains through their paces by simulating customer service, and follows a detailed testing phase which has been talking place during the night.
The public will be unable to get on board the new trains at this stage. Special netting has been fitted to each set of doors to prevent anyone getting on should the train stop at a station. Announcements will also be made over the public address system and Nexus employees will be in the carriages to advise customers the train is in test.
Stadler, the Swiss train manufacturer, are building 46 new Metro trains, which are set to herald a new era of comfort, quality and reliability. Two more new trains arrived in April, bringing the total number now delivered up to seven. Stadler has now built 23 new Metro trains, half of the total order it is delivering for Nexus.
North East Mayor, Kim McGuinness, said: ‘The North East deserves the best public transport system. I have promised to deliver the best connected and greenest network in the UK and that’s exactly what we’ll do. Our region’s new £362 million fleet will be transformational by improving comfort and reliability for the people who use the Metro every day to travel to work or to get to school or college.’
Testing the Stadler Class 555 Metro trains includes 90,000 individual checks. This had previously been taking place overnight when the Metro network is closed. It covers everything from seats and windscreen wipers, to more big-ticket items like brakes, CCTV, doors, wheels, and power supply.
There are approximately 19,000 hours of training time, with the first few trains completing 37,000 kilometres of running, as part of the testing phase.
There are around 22,000 standards and clauses to comply with and 480 staff to train up. Testing is there is to ensure that the new trains work safely and
seamlessly with Metro’s 60 stations and 77 kilometres of track. All of the on-board customer information systems need to be checked and be working correctly, along with the emergency settings and fail-safe systems. Power consumption, ride quality, and performance reliability are all being scrutinised thoroughly.
This started with some basic functionality testing within the depot and the first trains started to be tested on the Nexus network in May 2023. It involves the same level of detail that a big car manufacturer undertakes when bringing a new model to the market, Nexus said.
Northern has recycled 10,390kg of old uniforms in the last twelve months. In 2023, the train operator announced it had signed a deal with recycling specialist Avena so that its ‘end of life’ uniforms could be shredded and turned into ‘further life products’. The arrangement has saved 4,364kg CO2e of carbon emissions in the last twelve months (May 2023 – April 2024) than if the same volume of material had been sent to landfill.
That’s the equivalent of over 11,159 miles driven by an average petrol car or 2,181kg of coal being burned. It’s also the same carbon emissions generated from charging 288,031 smart phones.
Northern has tens of thousands of pieces of uniform and workwear in use by colleagues across the business at any one time.
Many of the items feature the Northern logo and therefore have to be disposed of safely for security reasons – to avoid the possibility of items being used by those looking to impersonate rail workers and gain access to restricted areas of depots and stations.
As part of the new recycling drive, 'end of life' uniforms have been collected from 25 depots and train crew centres across the Northern network on a regular basis over the last year.
We take care of everything from site survey to completed installation
We provide you fully or part fabricated modules for your teams to install
We’re happy to supply the materials and fixings needed for your own projects
For specialist environments we can simply be on site to support your teams
We provide specialist GRP training courses to enable your teams to understand its unique properties
Kilborn Consulting Limited is an independent railway engineering consultancy and design business, with over 21 years of railway experience.
We specialise in the design of new and altered railway Signalling & Telecoms systems for the UK railway infrastructure.
Our areas of specialism are:
•Signalling and Telecoms Consultancy, including technical advice & support;
•Asset Condition Assessments, Correlation and Surveys;
•Signalling & Level Crossing Risk Assessments;
•Feasibility and Optioneering Studies;
•Concept and Outline Signalling Design;
• Telecoms Option Selection Reports (including AiP), Reference System Design and Detailed Design;
•Detailed Signalling Design;
•Competency Management & Assessments;
•Signal Sighting assessments, covering the full Signal Sighting Committee process with a competent Chair.
FirstGroup plc has submitted the first phase of an application for a new open access rail service between Rochdale and London to the Office of Rail and Road (ORR), restoring this direct link for the first time in almost a quarter of a century.
FirstGroup plans to expand its open access rail operations as part of its successful Lumo business, building on Lumo’s existing service which has transformed long-distance connectivity between London and Edinburgh and helped support a growth in passenger numbers for all operators on the East Coast Mainline. All of the trains on this new route will be electric and battery powered, and the service will be operated by brand new trains built in the UK.
FirstGroup’s proposal for six return journeys a day aims to restore a direct Rochdale to London link via Manchester Victoria which last ran in the year 2000. The trains will run from Rochdale to
London Euston, calling at Manchester Victoria, Eccles, Newton-leWillows and Warrington Bank Quay. The station at Eccles provides connectivity for other parts of the City of Salford, including the fast-growing MediaCity area, via the nearby interchange with Metrolink and services to Newton-le-Willows will deliver greater rail connectivity for St Helens. It is estimated that this new service would provide 1.6 million people in the North West with a convenient and competitively priced direct rail service to London from stations that are more local to them, helping to stimulate a shift in transport mode from coach and car travel to rail.
FirstGroup has submitted a formal application to the ORR. A consultation period will now follow, as well as discussion with Network Rail to secure the required approvals. It is anticipated that services could begin in the 2027 calendar year.
The seventh Women in Rail Awards took place on Thursday 16 May at the stunning and iconic Roundhouse in London.
The evening saw 13 awards being presented across team and individual categories, with a further 10 Highly Commended and a Judge’s Special Mention awarded to exceptional shortlisted nominees.
Delivered by Nimble Media, the event was attended by over 780 individuals from across the rail industry, coming together to celebrate colleagues, teams and companies, who work hard to support others and to help create a more gender-balanced, diverse and inclusive work culture in the industry.
Following the Champagne Reception, guests were serenaded to their seats by the Southeastern TRAX Choir. A welcome address from Chair of Women in Rail, Marie Daly followed by a keynote address from Nia Mellor, Detective Chief Inspector for the British Transport Police, marked the opening of the ceremony. Host, Kate Bottley – Vicar, Journalist, Media Presenter and Reality Television Star – added a witty commentary to the evening.
Ian Watson of TransPennine Express was presented with the Adeline Ginn Unsung Hero Award. A tragic event whilst driving a train changed Ian’s life forever. He is now a key advocate for mental health at both TransPennine Express and in local communities. Ian helped to launch ‘Chatty Benches’ and his work with men’s suicide prevention charity ‘Andy’s Man Club’ led to extensive media coverage.
Charity work, local community engagement and peer support were just
some of the outstanding feats mentioned in the nomination for the 2024 Adeline Ginn Lifetime Achievement award recipient –Debra Iveson of Network Rail High Speed. Her passion, selflessness and dedication are described by colleagues as ‘truly unparalleled’ – as is her willingness to take on challenges beyond the job description, tackling extra projects with unmatched enthusiasm, and displaying a true passion for work that goes far beyond mere duty. This has included becoming a Mental Health First Aider to enable Debra to better support her peers; raising money for breast cancer charities through walking challenges and collecting bras (which not only helps raise vital funds
for pioneering breast cancer research but also offers a new lease of life to bras in developing countries); and organising school assembly sessions in her local area – personally visiting schools to engage children in discussions about the risks associated with trespassing on the railway.
The judges specifically requested that all the nominees be commended for their hard work, selfless dedication, and commitment and that a huge thank you be directed to all those who were nominated for this year’s Women in Rail Awards.
The full list of Winners, Highly Commended and Shortlist is available to view on the Women in Rail website.
As it enters a new membership year, Rail Forum welcomes the Global Centre of Rail Excellence (GCRE) as an Export Partner for 2024-2025. With growing international opportunities and worldleading rail capability across its membership, Rail Forum is pleased to launch enhanced exporting support. With 50 per cent of members as current or potential exporters Rail Forum anticipates strong interest in developing international growth and partnership opportunities.
Kelly Warburton, Chief Commercial Officer at GCRE said: ‘The Global Centre of Rail Excellence is delighted to partner with the Rail Forum as its Export Partner and is looking forward to playing a full role in the Steering Group to enhance the export potential of UK rail. GCRE will be a world class facility for research, testing and product development that will be a very powerful platform from which to showcase the very best in UK rail innovation for an international export market.
‘Rail is a critical strategic asset for the UK not only in terms of public transport, but also in how it can help to grow the UK economy
and enhance our national exports. With an international portfolio of customers and partners using the facility, GCRE will add important new capability to UK exports and so we are excited to partner with the Rail Forum for this critical programme.’
Catherine Appleby, Membership & Engagement Director at Rail Forum said: ‘We’re delighted to welcome GCRE as our Export Partner and value their support and engagement. We recognise our role as an important instrument to support members’ international journeys and facilitate access to wider support, funding, opportunities as well as our own export community.’
Together with its Export Partner, Rail Forum’s recently launched Export Steering Group is developing initiatives to promote the extensive export capability of the UK rail supply chain and bring Rail Forum members and international opportunities together.
Members involved in this group include Anturas, AtkinsRéalis, GCRE, HÜBNER, J-Flex Rubber Products, LPA Group, Portaramp, Railstons, Transport Design International and TRB Lightweight Structures.
of
fastest growing areas. The new
Mayor Rotheram has also pledged to build three new stations at Daresbury in Halton, Woodchurch on the Wirral and Carr Mill in St Helens, with work to develop all three underway by the end of the decade. It means that every borough of the city region will have had a brand-new station since Mayor Rotheram took office in 2017.
Plans for Liverpool Baltic station include step-free access from street to train, passenger waiting facilities, fully accessible passenger toilets, secured monitored cycle parking and links to an enhanced local active travel network.
The new station is part of Mayor Rotheram’s ‘Merseyrail for All’ commitment to reach communities that are currently not connected to the local rail network by utilising the region’s new pioneering battery powered technology, which has made it possible to extend the lines beyond current boundaries.
The images have been unveiled ahead of a public consultation in June and July over plans for the new station. As part of the consultation, a new virtual reality (VR) walkthrough will allow members of public to place themselves within the station and view its facilities and points of interest. The engagement period will run until 5pm on Friday 26 July, with those interested invited to submit their views.
station is one of four planned by recently re-elected Liverpool City Region Mayor Steve Rotheram, who has committed to completing the project by the end of 2027 –a year ahead of its current schedule.
Information gathered from this will be used to finalise the designs ahead of the planning application. Subject to approval, it is expected work will begin on site in 2025, with the station planned for opening by the end of 2027.
PoliMac® polymer coating for Gabions, Reno Mattresses, Rockfall protection systems and Double-Twist Products designed to last
• Longer Life
• More Abrasion resistance
• More UV resistance
• More Chemical resistance
• More Environment-friendly
Atlas Copco
Sam Sherwood-Hale spoke to Matthew Jenner and Peter Mitchinson of Atlas Copco about its innovative equipment, collaborating with industry and getting rail up to code on data-driven technology
SSH: Tell us about these innovative solutions from Atlas Copco.
MJ: What we’re trying to do is transform the way that customers not only produce equipment for the rail industry but also how they maintain it in MRO facilities. The impact of our smarter solutions for assembly and maintenance is creating efficiencies for the customer, as well as creating opportunities to move towards a decarbonised rail network.
Our customers are companies that produce the rolling stock and also those which operate MRO facilities, so we support both manufacturers and operators. Atlas Copco can deliver solutions across the whole sector, so if there is a factory building digital signalling equipment, then we are able to provide solutions for them to enhance
what they do. As a holistically focused business, we're looking at the rail industry as a whole, although much of our growth to date has come from supporting rolling stock manufacture.
We break down our general industry portfolio into segments. One of those segments specifically looks at Rail and we've designed bespoke products to support that industry. As the rail sector has moved towards digitalization and having smart factories that produce their equipment, we've come along with them by offering those solutions that can transform them to that point.
SSH: So what kind of solutions are we talking about?
PM: If you look at how the rail sector operates, it is still using basic equipment like hand torque wrenches and air powered nutrunners that tighten to specific, often high, torques. So one of the products that we have introduced is our smart torque wrench. This is a transducerized, calibrated instrument that can apply torque across a range of values, which means that one smart wrench can replace three or four basic click-type torque wrenches, and give them traceability of the tightening data which can be sent to the network and stored for reference and analysis.
Another product is our transducerized high torque nutrunners, these are power tools that apply torque across a range and records data on the network. These are usually used on safety critical and quality critical tightening processes.
SSH: What kind of leap forward does this represent, what is the innovation within this technology?
PM: Previously the torque value might have been recorded in paper form, so there’s a reliance on the operator to record that information, whereas our technology records the tightening data automatically, during the tightening process. Once it's complete the information is then stored in the controller or it's sent directly to the customer’s own network. There is a lot of reliance on the operator to apply the correct torque value and then record that as well. With the tooling that’s being used now, such as basic torque wrenches, there's also a lot of over processing. For example, it’s not uncommon for the user to take the torque wrench, then walk to the end of the factory, test the wrench to make sure it's set to the correct torque and then they’ll go back to do the job. Despite doing this, we still don't know if the correct torque has been applied, so an operator could over torque a bolt and there's no real control or traceability of the process.
SSH: How important is that data that they can collect? Do you have access to it?
PM: The data that is available from the tools is an important selling point of the solutions that we're offering. At the moment, there's a lot of paper documentation, so having this data means that they can show their customers they’ve had a specific carriage into maintenance and correctly overhauled it, and reassembled it with the correct
torque values based on the data obtained from the tools on the line, all recorded against the rail car number or the job number that they're working on.
This kind of documentation gives their customer peace of mind that they're carrying out the process in the right way, but it also reduces the risk of assembly errors and any costs for them further down the line.
MJ: It goes beyond peace of mind; their customers are now mandating that they must gather that data and they must have that level of traceability. So that if there is an issue out in the field, it can be traced back.
The data is there for the customer and it's there for the manufacturer to make improvements to their tightening processes. In terms of whether we have access to the data as the tool supplier, generally the answer is no, but that's the next evolution that some customers are working to now where we are able to support them with predictive maintenance through systems that can learn from the data that's being generated and then help customers to take
proactive steps. That's where we're starting to see development going, provided the customers are willing to work with us and offer us access to that level of data.
SSH: So the data has multiple applications and presumably the more eyes on it the better?
MJ: Exactly, our data collection tool is actually a data analysis tool. The manufacturing engineer can look at the analysis produced and see how things are trending. They're really empowered to be able to analyse their work with our software tools and then make improvements to their own processes. The next level on top is that we can give them the capability for either us to look at it and make proactive recommendations and support them with our AI engine which does the same thing. It's a case where other industries are a little bit further ahead; Atlas Copco serves a varied amount of manufacturing from automotive production to building wind turbines to building electronic boards for
‘At the core of it, we're tightening the bolt, but we're actually offering everything that allows the customer to record and analyse the data to control the quality and to guide the operator and fully connect to their plant.’
smartphones. The learning and that breadth of product that we put into developing other industry segments is something that we can offer straight away into rail customers as they come on their journey with data.
SSH: What's the direction of travel for this technology?
MJ: There is the pull coming from the very end rail operator, up to the manufacturer and then up to us and there’s also a push from what we know we can offer. So, we're actively promoting ourselves into the rail industry with that in mind.
The core of what we do is very assembly centric, so torque tightening and then all the systems that support that which is expanding all the time. For example, we offer location systems that will control where the tool is and only activate it when it's in the right location to be doing that particular joint. We offer operator guidance to make sure things are done right first time. Then beyond that, we talked about the AI technology that recommends real time predictive maintenance activities to the customer. All of this builds into fully integrating it into the customer’s MES or Manufacturing Execution System. So that connectivity element is really important. We offer complementary technologies. At the core of it, we're tightening the bolt, but we're actually offering everything that allows the customer to record and analyse the data to control the quality and to guide the operator and fully connect to their plant.
That level of integration is the peak of the pyramid, but not every customer wants that right now, so we're certainly flexible in our approach.
SSH: How have you found working with those different companies in the rail industry, specifically the openness to data sharing?
PM: The rail industry is notoriously resistant to change, they are traditional in the way they do things. This transformation that we're doing is something that is probably going to take a number of years. There are
different segments like repair and overhaul and then there’s freight and the passenger side of the business, so there's a lot to cover but we feel there's good potential to transform the industry.
SSH: What were your expectations coming into this and have they been realised?
PM: One customer was looking for better process control which fits in perfectly with what we could offer and do for them. We always knew that for rail there was a better way to work but the hard bit was convincing them and getting them to understand the technology and understand the benefits of working this way. So that's still a challenge in terms of developing our business within rail, to get them to understand the benefits of what we can do and how it can help them be more efficient.
The traditional supply chain relationship within an industry is being redefined. This is not a case of a customer just wanting a supplier to provide something. What Atlas Copco is demonstrating is, through strategic partnership, they are helping a customer and de facto an industry to really make significant advancements, not just from a product quality perspective but also from a business, cost efficiency and general industry advancement. By embedding in with customers and saying we can help you with costs, we can help you with quality, we can help you with sustainable operations by using tooling that takes out the traditional pneumatic style of tools. It creates so much added value beyond simply supplying a prepackaged solution.
SSH: What are some successes you have had in other areas of the rail industry?
MJ: We talked about one of the drivers for the rolling stock itself being the classification of the joints, some of which are safety critical and then we need the right solutions and data to support that. Similarly, if you’re looking at digital
infrastructure like signalling, this is a safety critical device that the industry is using, and to support the manufacturing of something like that we use very similar technology but applied at a different level. If you're talking electronics, we have our micro-torque screwdrivers which are capable of delivering very, very small but accurate torque to screws that might be using electronics. And we've got the full quality control to ensure correct torque and angle and the data is recorded.
Before this they might have been using a very basic clutch screwdriver that would maybe not be accurate in terms of the torque level it was delivering, and then you potentially face problems with that joint later on.
Also, as Pete said, the level of consistency would depend on the operator. So you might have one operator that potentially could be in a position where they over-torque something, another operator hits it bang on and another operator might slightly undertorque, but we won't know until after the event if ever it came back to the rework, which obviously has its associated costs in labour, time and materials. That's really expensive for a rail operator or an MRO. This is what this whole system is designed to help the customer alleviate.
With the smart solutions you take out the possibility of errors, because the tool will not allow the operator to move on in the sequence unless the correct torque value is met. The tool can help the operator to follow the work sequence, which improves efficiency as well as consistency.
PM: In terms of identifying opportunities within rail, what we've experienced with other industries is that human beings will make mistakes. So, the idea is that our solutions will eliminate errors and guide the operator through the process and then also give them the information to support that as well in terms of data.
It’s the ultimate provenance, you can trace that tightening all the way back, so
‘Previously the torque value might have been recorded in paper form, so there’s a reliance on the operator to record that information, whereas our technology records the tightening data automatically, during the tightening process.’
in situations further down the line there is that all important traceability to show that a particular bolt was done up in accordance with the correct procedure which stops it from becoming a point of failure. The data is there in black and white for perpetuity.
MJ: Atlas Copco’s ‘Alture’ system is already being used with customers outside the rail industry. It’s a compelling application because there should be a lot of consistency in manufacturing, so it should be something that can spot those trends and if you were working the tools a bit harder over a certain period, it's going to pick up on that and inform you to do the maintenance now because something is about to fail, rather than waiting for your annual review. So it’s giving you that intelligence to do the maintenance at the right time and not costing more than it needs to.
IT stakeholders are much more a part of our conversation with customers now. They can run much of what we do in isolation on their factory network and then any security concerns are mostly alleviated. When you start to talk about Alture and us connecting in to be able to give them this insight, that’s when there's increased cybersecurity considerations, and that's when we need to have a more in depth conversation with those stakeholders and make sure they understand that we as a business have considered those issues and that the required security measures are present.
SSH: How does this align with the Network Rail ESG programme?
PM: For delivering a sustainable railway, you'll have lower emissions by moving from air to electric which would obviously reduce the carbon footprint and help companies to achieve their science-based targets. And having a railway service that is safe and reliable comes back to traceability and data collection, as well as a reduction in waste because they're using predictive maintenance.
Our patented system that removes and replaces rail panels swiftly and safely.
Specially designed to effectively lift, transport, and dispense cable from pre-wound reels.
The industry’s safest and most efficient way to move and install lengths of rail and iron work.
Self-mounting, self-propelled, self-loading vehicle that can complete a variety of tasks.
Our all-electric solution to move and install lengths of rail and iron work.
Our McCulloch Turnout Solution is the perfect solution to move and replace S&C.
The UK’s rail infrastructure is facing significant challenges, from ageing assets and climate impacts to evolving safety requirements. DYWIDAG, the global construction and infrastructure services provider, delivers solutions that are crucial in understanding the lifespan of these rail assets, while also ensuring public safety and maintaining trust with its stakeholders.
This support is vital as it aims to strengthen the nation’s railways against both current and -future challenges. Sam Sherwood-Hale spoke to Darren Jackson, who recently stepped into the role of UK Sales & Business Development Director at DYWIDAG, about how its tailored monitoring strategies are supporting rail stakeholders in navigating these complexities.
Could you share some insights into your professional background before you joined the structural health monitoring team as the UK Sales Director at DYWIDAG?
I've had a varied and interesting journey across several industries, including financial services, telecoms, and sports management. Regardless of the sector, the focal point has always been on people—understanding how to engage with and collaborate effectively with them has been key to shared success. I believe that active customer engagement is crucial not only for growth but also for innovation in any business. By working closely with customers to really grasp their needs and priorities, we can drive new innovations into the market that make a difference.
Before joining DYWIDAG, I spent nearly six years at Taziker, a leading rail infrastructure contractor, where I served initially as the Group Business Development Director and then as the Strategy, Sales & Marketing Director. Taziker were successful in the delivery of several major rail projects during my time there. This exposure gave me an invaluable understanding of the immense challenges rail stakeholders face in dealing with ageing assets, climate change impacts, and stringent safety requirements.
‘At DYWIDAG, we're proud to be collaborating with major rail clients and contractors on some truly pioneering infrastructure projects across the UK.’
‘Using our advanced sensors and imaging technologies, we can precisely track movements and deterioration on critical rail assets like tunnels, bridges, and viaducts to facilitate timely interventions and maintenance.’
How is DYWIDAG helping rail professionals address these challenges?
We provide a range of products and services tailored to ensure the safety, efficiency, and reliability of the rail sector. From specialised rope access, surveying, InSAR technology, Infrastructure Intelligence, and void monitoring to ground stability assessments, our technologies offer precision and reliability in rail asset management. Our dedicated team, comprising expert surveyors and monitoring technicians, is committed to understanding each client's needs and collaborating to enhance the resilience of rail assets throughout their lifespan.
We're always available, prepared to adapt and meet our clients' requirements, guaranteeing the smooth and secure execution of their projects. In addition to structural health monitoring, DYWIDAG has a wider portfolio that encompasses geotechnical solutions, repair and strengthening, and concrete technologies all geared towards guaranteeing stability and resilience across diverse infrastructures.
DYWIDAG has a unique position as both manufacturer and integrator of cuttingedge sensor systems. How does this benefit the rail sector?
As both the manufacturer and integrator, we deliver monitoring solutions that rail stakeholders can trust. We use InSAR technology to keep a close eye on asset performance at scale. This method combines radar satellite imagery with advanced algorithms, offering precise measurements of ground deformation and structural integrity. Working hands-on with technologies from start to finish gives us unique insights into user needs, shaping our products to be more user-friendly and effective. This close loop allows us to continuously improve and tailor our solutions to better meet industry demands.
Can you elaborate on the end-to-end services DYWIDAG provides for the rail industry?
Our services cover every aspect of the monitoring process, starting from the initial scope identification and design, through to installation, automated monitoring systems, surveying, testing, and project management. With our in-house rope access capabilities, we can swiftly respond to projects with difficult access. We also conduct inspections, evaluate conditions, and undertake repair and maintenance across a range of projects. With the flexibility to work autonomously or collaborate with specialist contractors, we ensure that even the most diverse project needs can be accommodated.
How does the integration of data from the DYWIDAG Smart Temp monitor into the Infrastructure Intelligence cloud platform enhance the ability of rail stakeholders to proactively manage asset health?
We've invested in research and development to automate traditional manual operations leading to increased product reliability and safety. Our DYWIDAG Smart Temp monitor is a perfect example of this investment in the rail sector. It tracks rail temperatures to quickly pinpoint potential problems like thermal expansion or buckling, helping us stop rail defects before they start.
Alongside, our Infrastructure Intelligence cloud platform brings this data to life with powerful visualisation and analysis tools. By pulling together data from the Smart Temp and other sources, the platform gives rail stakeholders a clear, actionable view of asset health and performance. This means they can manage risks, keep operations smooth, and plan proactive maintenance from anywhere making it easier to make smart, timely decisions that keep the rails running safely for longer.
I'm sure you have great insight into the types of projects DYWIDAG is currently engaged with. Can you give us some examples?
At DYWIDAG, we're proud to be collaborating with major rail clients and contractors on some truly pioneering infrastructure projects across the UK. Thanks to our Principal Contractor’s license, we have the flexibility to operate independently within the network or collaborate as a subcontractor, adapting to the unique requirements of each project.
A few key examples of these projects include comprehensive ground monitoring and remote sensing deployments for HS2, the first new intercity railway to be built north of London in over a century. We have also provided our monitoring services on structures such as the Hammersmith Flyover and the Britannia Bridge.
We work directly as a principal contractor with Network Rail on several monitoring
‘With the flexibility to work autonomously or collaborate with specialist contractors, we ensure that even the most diverse project needs can be accommodated.’
frameworks through to supporting designers and contractors across all stages of the project lifecycle. Using our advanced sensors and imaging technologies, we can precisely track movements and deterioration on critical rail assets like tunnels, bridges, and viaducts to facilitate timely interventions and maintenance.
What’s next for DYWIDAG in the rail industry?
As the rail sector navigates unprecedented challenges and opportunities, we will continue investing in research, embracing new technologies and work closely with our rail stakeholders to drive innovation.
Join me and my colleagues Robert Paterson, Regional Director, James Stewart, Technical Director, Brian Coogan, Sales Manager, and Jayson Pape-Jones, Design Engineer, at stand B25 during Rail Live in Warwickshire on 19-20 June. We're excited to celebrate 25 years of expertise in structural health monitoring within the rail industry. Our team will be delighted to share DYWIDAG's journey in structural health monitoring, which started in 1999 with the founding of Datum Monitoring Services Ltd in Bury, Lancashire. Following DYWIDAG's acquisition of Datum in 2018, we've experienced remarkable growth and development. Additionally, don't miss the chance to get a preview of latest innovation, the New DYWIDAG Smart Temp CRT monitor, along with our other products and services.
Tel: 0161 797 5511
Email: sales.uk@dywidag.com
Visit: www.dywidag.com/monitoring
The NEW DYWIDAG Smart Temp Critical Rail Temperature monitor revolutionises rail safety, minimises train delays and eliminates unnecessary speed restrictions. It provides real-time temperature data, GPS positioning and seamless integration with Network Rail’s RADAR and DYWIDAG’s Infrastructure Intelligence platforms.
• User configurable temperature thresholds
• Immediately sends data as thresholds are crossed
• Real-time data every 15 minutes
• Fully compliant with NR/L2/TRK/011 Mod 14 managing track in hot weather
MONITORING | SURVEY | SENSORS | INFRASTRUCTURE INTELLIGENCE
Norbar is a UK manufacturer of battery, electric, pneumatic and manually operated torque multipliers, wrenches, torque measurement equipment and bespoke torque control solutions specially developed for the rail industry Contact Norbar and speak to The Voice of Torque Control
A growth in education and leisure travel offset business travel losses, according to the National Travel Survey
The Department for Transport (DfT) has published new data from its National Travel Survey, combining data from the last six months of the 2022 survey with the first six of 2023. The limited number of tables predates publication of the full 2023 data later in the year. The figures point to a continuing recovery from the Covid-19 pandemic, with overall trip rates increasing between the 2022 survey and these interim results.
The public as a whole made an estimated 882 trips per person per year (tpppy) by all modes in 2022/23, up by 3.4 per cent compared with 2022. However, the figure remained 8.2 per cent below the 952.6 trips recorded in the 2019 survey. Shopping trips,
for long the backbone of travel demand, also increased, up 2.7 per cent to 165.4 tpppy, compared with 2022’s figure of 151.1. Again, however, this was substantially down on pre-pandemic levels, when 180.6 tpppy were recorded. That’s a shortfall of 15.4 per cent.
Looking specifically at the rail market in England, the overall trip rate forged ahead by 37 per cent, reaching 15.4 tpppy compared with 11.2 in 2022. The last preCovid figure recorded in 2019 was 22.1, leaving a shortfall of 30.6 per cent.
Analysis of responses on people’s reasons for making their journey, trip rates for all purposes except personal business increased between 2022 and the latest data, with the overall increase being 12.7 per cent. When comparing the 2022/23 trip
rates with those of 2019, we see a sharp fall in many categories, but increases in travel for education and for leisure. The falls range from 44.8 per cent for business travel and 37.3 per cent for commuting to 3.4 per cent for shopping. The chart at Figure 1 illustrates the changes, but also shows the same figures for 2010, and we see that many of the gains made between 2010 and 2019 have been wiped out. The two purposes which show continuing falls across all three sample years – shopping and personal business – are those which have been most affected by the growth of online transactions.
Translating those trip rates into estimated passenger numbers, we see from Figure 2 that the importance of commuting has diminished, now accounting for 36.2 per cent of trips, ten points lower than in 2019. The growth in leisure travel means that this now accounts for 35.8 per cent of passenger journeys, less than one per cent behind commuting. Business travel has fallen back from 9.8 per cent to 6.7 per cent, a fall that is particularly damaging in revenue terms. The change has wiped out a decade of steady growth and taken the market share back below 2010 levels. The increased importance of education is notable, as is a small rise in the importance of shopping.
There have been some major shifts in the demographic profile of bus users, according to the survey, with trip rates falling amongst older people (see table). The overall recovery in 2022/23 was not universal: there were continuing falls in trip rates amongst those between 40 and 49 and between 50 and 59. The highest year-on-year growth came from those over 70, showing an increase of 44.3 per cent, closely followed by the under 17s on 41.2 per cent.
Comparing trip rates with the last prepandemic year, two age-groups, the under 17s and between 21 and 29, actually show an improvement of 33.8 per cent and 9.9 per cent respectively, but the others show sharp falls: this is as high as 43.4 per cent amongst the over 70s and 43.2 per cent for those in their fifties. All the age groups over 30 show a fall of over 30 per cent since 2019.
There are some significant differences in behaviour between men and women, with the latter showing much more significant falls in bus use since 2019 across all age groups, with the gap widening with age, so women in their sixties are making twothirds fewer trips since the pandemic. Even so, women continue to have higher trip rates than men across all age groups save one, the twentysomethings.
This latest update to the National Travel Survey offers further confirmation, if it were needed, that the onset of the Covid-19 pandemic turned the market for rail services upside down. Historic patterns of use by journey purpose and demography changed completely, and almost two decades of steady growth in rail trip making were slammed into reverse.
This both echoes and reinforces figures from the DfT show that in the first three months of this year, which suggests if anything that demand started to go backwards. Patronage averaged just under 83 per cent of pre-pandemic levels excluding the Elizabeth Line between January and March. This compared with 87 per cent across the whole of 2023 and 79.3 per cent in 2022. This makes full recovery still seem a long way off.
The NTS update goes a long way to explaining the shortfall, mapping both the changes in journey purpose and in the age and gender of rail users. The loss of commuting trips is well known and understandable, given the moves towards working from home and hybrid working. It accounts for some 300 million trips a year compared with 2019 – pretty much the whole of the 307 million national shortfall. Business travel accounts for 76 million more but this loss is offset by gains in education and leisure travel.
The shifts in the age profile of users both reflects and influences this. The fall in commuter trips can be linked with the decline in trip rates amongst those between
30 and 59, whilst the increased amongst the under 17s can be linked to the rise in leisure travel, associated with more weekend family trips. The fall in trip rates amongst older people mirrors that seen in bus travel and can be attributed to ongoing nervousness about infection risks, but the strong recovery in 2022/23 amongst the over 70s offers hope of a further revival.
As so often in the past, then, the rail industry has had to withstand a storm whipped up by factors outside its control – not helped, though, by self-inflicted wounds of ongoing strikes and poor reliability in some areas. There are still many uncertainties about the future, but at least this sort of analysis enables greater understanding of where we’re at and helps identify some target markets for future growth.
Meanwhile, the future is very uncertain, driven by a further tech revolution from AI, the difficult economic and fiscal outlook post this year’s General Election and the need
to do more to achieve Net Zero targets. All these and more impinge on our ability to see into the future. It’s already clear that this will have profound and unknowable impacts on the way we live and the way we travel. Flexibility and speed of response will be essential. Let’s hope that the new ownership framework can deliver this.
The NTS is a household survey of personal travel, from data collected via interviews and a seven-day travel diary, which enables analysis of patterns and trends. The statistics for the year ending June 2023 include data from the second half of 2022 and the first half of 2023. In the year ending June 2023, the survey captured responses from 10,351 individuals covering 167,916 trips. The National Travel Survey mid-year estimates are available at https://www.gov.uk/government/statistics/ national-travel-survey-mid-year-estimatesyear-ending-june-2023
Rail is already one of the most sustainable forms of transport. Nothing else can move people and goods so far, so fast and so efficiently.
But huge technical and social challenges are still on the horizon as we strive for Net Zero. Not least the need for cost-effective green approaches. RSSB will continue providing rail’s technical leadership, as we deliver on the Sustainable Rail Blueprint we created with the industry. We’ll supply the whole-system research and analysis needed for efficient, sustainable decision making.
For more on RSSB’s approach to sustainability: www.rssb.co.uk/realisingsustainablerail
STAUFF are a premier global manufacturer of components and kits for railway applications.
A comprehensive range of quality products and innovative services delivered to your production line side for the manufacture of rolling stock.
Presented in kit form, tested and ready for immediate installation, reducing logistic, production and inventory costs.
The STAUFF Line process is adopted by global OEMs to successfully achieve cost savings in rolling stock manufacture.
Sheffield Tel: 0114 251 8518
Email: uk.sales@stauff.com
Aberdeen Tel: 01224 786166
Email: uk.absales@stauff.com
Ireland Tel: 02892 606900
Email: uk.irsales@stauff.com www.stauff.co.uk
The rail sector is a broad spectrum of different businesses, some of which are more heavily unionised than others
Some recent decisions related to the provision of the Trade Union and Labour Relations (Consolidation) Act 1992 (TULRCA) should give employers some pause for thought.
Working towards union de-recognition needs to be treated with care.
The facts of Smith and Others v London Ashford Airport began when London Ashford Airport in-sourced its air traffic controllers in 2020 and it inherited a collective bargaining agreement. It is not unusual for this to happen, or for the receiving employer in a TUPE situation to feel negatively towards a union deal struck by others. This agreement with the Prospect trade union covered the small but distinct bargaining group of the air traffic controllers (nine in total), giving them rights to negotiate on pay and holidays once a year.
During Covid, there were no pay rises, but in late 2022, Prospect sought pay talks. They were told to wait until late Spring 2023 when financial data would be available.
While Prospect was waiting for the financial data, the employer served six months' notice on Prospect’s collective bargaining agreement in January 2023, as they were entitled to do under the voluntary agreement. In February the employer wrote to all staff announcing across-the-board standard pay rises worth five per cent that year with a further rise the following year.
In April 2023, workers received a follow up letter, inviting them to sign to confirm, and the pay rises were processed to staff that month.
Prospect was unhappy with the situation and took the matter to the Employment Tribunal. The collective agreement was still in force when the offers were made and the Tribunal decided that both the February and April communications were ‘unlawful offers’ under s145b TULRCA as they were made directly to employees covered by the collective agreement but had not been agreed with the union. As a result, the employer was required to pay each union member financial compensation of £9,108.
That was not all. Because of the level of membership amongst the air traffic controllers at the airport (Prospect enjoyed one hundred per cent membership), the union was able to immediately apply to regain its position as the recognised bargaining entity by applying to the Central Arbitration Committee (CAC). It acted the day after its old agreement expired, making an initial statutory recognition request on 19 July 2023, applying to the CAC on 3 August 2023 and having formal statutory recognition declared by the CAC on 21 September 2023 covering the usual formula of pay, hours and holiday.
As the original recognition agreement was just for pay and holiday it appears that the union gained ground by adding deals on hours too.
Martin Fleetwood is a Consultant at Addleshaw Goddard’s Transport practice. The Rail Team has over 30 lawyers who advise clients in both the private and public sectors across a wide range of legal areas. As well as contractual issues, the team advises on operational matters, franchises, concessions, finance, regulatory, property, employment, environmental and procurement issues.
Disclaimer: This article is for informational purposes only and does not constitute legal advice. It is recommended that specific professional advice is sought before acting on any of the information given.
‘Article 11 of the European Convention on Human Rights (ECHR) sets out the freedom of assembly and association and protects certain trade union freedoms.’
Before looking to remove union recognition for collective bargaining, employers should note:
• Unions are very willing to bring claims for statutory recognition to the Central Arbitration Committee (CAC) as thresholds for recognition are fairly low. Only ten per cent membership is required to get an application off the ground, leaving unions time and opportunity to agitate to attain the necessary support from the workforce.
• The CAC recognition mechanism moves quickly (in the above case Prospect was essentially reinstated within two months).
• To avoid being ‘back where you started’, take a realistic view of the membership density within the bargaining group.
• The CAC only grants rights to negotiate on pay, hours and holidays. For some more complicated heavyweight legacy collective agreements with sweeping
negotiation rights the CAC option may still be better.
• If trying to avoid collective bargaining, a successful group claim under s145b TULRCA will be more costly to the employer than a conventionally negotiated pay rise.
• There may be cases where it is appropriate and lawful to impose a pay rise on staff in a true stalemate. However, to avoid liability under s145b the employer needs to exhaust the collective bargaining procedure first (including any disputes procedures in the collective bargaining agreement). Bespoke legal advice should be taken in this situation.
In the case of Secretary of State for Business and Trade v Mercer, Ms Mercer was suspended by her employer after taking part in lawful industrial action. One of the results of this was that she was unable to earn overtime pay which she would normally have earned. While section 146 TURLCA prohibits employers from subjecting employees and workers to detriment short of dismissal when taking part in the activities of an independent trade union, the Court of Appeal had decided that
activities of an independent trade union could not be interpreted so as to apply to industrial action.
However, Article 11 of the European Convention on Human Rights (ECHR) sets out the freedom of assembly and association and protects certain trade union freedoms.
This created an unusual gap in the legislation which appears to permit employers to impose detriments on workers taking part in industrial action (as long as they don't dismiss them) where protection elsewhere in TULRCA does provide protection. Ms Mercer claimed that imposing a detriment on her must breach s146 TULRCA – if it did not, then that meant s146 TULRCA was not compatible with her rights under Article 11 ECHR.
The Supreme Court considered the claim and decided that s146 TULRCA is incompatible with Article 11 ECHR. In the Supreme Court's view, to comply with Article 11 ECHR, the Government has a positive obligation to provide some protection from detriment resulting from industrial action.
The Supreme Court's declaration of incompatibility firmly puts the next step in the Government's hands. It is now for ministers to determine whether TULRCA should be amended, or other legislation passed to address the gap in the current
legislation. The decision will not be straightforward and once Government has decided on a solution any proposed changes must then be approved by Parliament. With a General Election on the horizon, new legislation before a change of Government is unlikely.
How do employers manage the issue?
In purely legal terms, nothing has changed for private sector employers until new legislation is passed. Public sector employers are in a different position because they have a duty to act in a way compatible with ECHR. In addition, trade unions have already been vocal in expressing their view that employers should no longer impose detriments on workers who take part in industrial action.
Any employers who are considering imposing detriments on workers taking part in industrial action must also beware of breaching the Blacklisting Regulations 2010. These make it illegal for employers to compile a ‘prohibited list’ of workers who are members of trade unions or take part in trade union activities.
Taking a cautious view is likely to be the best course of action until the gap in the law is closed by a new Government (of whatever colour).
After 45 years in public transport from running his own business, senior roles in major companies and as MD Surface Transport for Transport for London, Leon Daniels now advises and works inside governments, agencies and nice companies like Thames Clippers, RATPDEV, and Optibus. Leon is also President of The Chartered Institute of Logistics and Transport in the UK and host of the monthly bite-sized transport podcast Lunch with Leon.
As part of its election promise push, Labour will renationalise all of Britain’s rail services within five years of being in power, Leon Daniels OBE explains
Under its blueprint, a new arm's length body, Great British Railways (GBR), would take over service contracts currently held by private firms as they expire in the coming years. GBR would operate services and set timetables, and eventually take over responsibility for maintaining and improving rail infrastructure from Network Rail.
Labour leader Sir Keir Starmer denied the plans stem from an ideological drive for nationalisation, referring to the mess of the past three decades of privatisation and a problem which ‘we have to pick up and fix’.
Although I’m reticent to support a full ‘nationalisation', Labour’s promise to ‘Fix Britain’s Railways' would at least remove the confused and useless hybrid arrangement currently operating between our private and public sector.
When transport companies are operating on a 'cost plus’ basis with a fixed fee, there’s no longer any incentive for the private sector to push revenue, which ultimately costs the passenger. Labour’s proposed changes to bring all the existing contracts directly ‘in house’ would, at least, eliminate the costly bidding and evaluation process all of which becomes redundant, but in rail terms those savings don’t build you much track.
All of the rail functions of the Office of Rail and Road, Transport Focus and the Rail Ombudsman, will be retained despite our transport being under state control, as will all of the other agencies currently involved. Surely one benefit of full government control could have been a more streamlined governance and standards structure?
Industrial unrest has been across the rail industry now for a couple of years. Full state control removes one separation between government and employee. Labour
has widely criticised this government for failing to engage directly. Now any new Labour government will have to. How will a Labour government deal with the powerful Trades Union without incurring more cost? Moreover, how will these negotiations proceed with people with generous pension arrangements on one side of the table and representatives of the union members on the other? If the political pundits are correct about Labour winning the next election, these are the critical questions the transport sector will need answers to.
Scotland’s rail network has been almost completely nationalised by the SNP, and there is no improvement whatsoever. Instead, there is decline, a cut in the number of services, trains running late and worse service for the passenger.
Will Whitehorn, former CEO of Virgin Galactic and close colleague of Richard Branson, spoke of a ‘managed decline’ of our rail network on a recent episode of my podcast Lunch with Leon, going as far to say that it’s a ‘tragedy’.
‘Before the impact of Covid, we'd already begun a slippery slope where the state took back control removing any profit incentive for operators to operate anymore’ Whitehorn said. ‘The railways were going somewhere positive for a while but have slipped back into mediocrity.’
Despite the benefit of shifting from the current, broken system, the reality is enterprises are better managed in a mixed economy that responds to market signals, rather than being controlled by central planning from the government. Even if a business is state-owned, it will perform better if it operates based on market forces and profit incentives, rather than just following dictates from the central government.
£6 MILLION INVESTMENT TO FUTUREPROOF CAMPS VIADUCT NOW COMPLETE
A 13-month project to strengthen the 160-year-old Camps viaduct has been delivered successfully. Nestled amidst ancient woodland, the 11-span viaduct serves as a crucial artery for passengers travelling between Glasgow and Motherwell by train. Along with Story Contracting, Network Rail began work to extend the lifespan of the historic landmark, which towers 35 metres above the River Clyde, in spring 2023.
Engineers completed 1370 repairs, replaced more than over 10,000 rivets and added 65 tonnes of new steel during these extensive strengthening and refurbishment works. Essential scour protection works were also carried out to both the east and west river banks and this included the installation of over 800 tonnes of rock armour.
To protect the surrounding environment from dust or pollution, including the River Clyde which flows underneath, work on the structure was completed while the viaduct was encapsulated and sealed. Pontoons were built in the river so that the scour and masonry repair work could be done most safely and to limit disruption during work on the riverbed and underwater.
‘At the end of the day, the laws of economics won’t change under a new government. Regardless of who owns what, the railways will continue to require substantial Treasury support.’
At the end of the day, the laws of economics won’t change under a new government. Regardless of who owns what, the railways will continue to require substantial Treasury support, and as ever, the argument will come down to the proportion raised in fares and the proportion paid by taxpayers. Regardless of the contractual arrangements, that is on what the argument turns.
Chris Simms is a partner at Independent UK law firm Burges Salmon. Burges Salmon and West Midlands Trains (WMT), part of the Transport UK Group, have a longstanding relationship and recently worked together to bring in a total of £116 million of private financing to enhance two of WMT’s rail depot facilities.
Burges Salmon and West Midlands Trains unlock private financing to support Net Zero fleet and infrastructure investment programme, Burges Salmon partner Chris Simms explains
Last December Burges Salmon’s Sustainable Transport team advised WMT on a £50 million investment by Angel Trains to support the upgrading of its Tyseley, Birmingham rail depot and maintenance of WMT’s new fleet of Class 196 trains.
Furthermore, in April this year, the firm acted on a £66 million investment by Porterbrook into the Bletchley rail depot in Milton Keynes, supporting the modernisation of the facility so that it could accommodate the long-term maintenance requirement of WMT’s fleet, comprising 36 brand new electric five-car Class 730 Aventra trains, infrastructure that is essential to support a Net-Zero railway in the future.
In a time of constrained public finances, attracting private sector investment into rail assets is crucial to enable the industry to make the transition to Net Zero. The key to successfully attracting that investment is to be able to structure projects in a way which provides clarity to the private and public sectors on the investment required and the returns available. That is made more complex in the rail environment by the regulatory regime which applies to railway assets and the wide range of stakeholders involved.
Building on similar infrastructure projects which the team delivered in 2018/19 for Greater Anglia, another network operated by Transport UK Group, the Burges Salmon team helped deliver a structure which provides for the financiers to take a long-term interest in the depots
‘Real estate transactions can be complex in the railway environment due to the number of interests in the property.’
‘In a time of constrained public finances, attracting private sector investment into rail assets is crucial to enable the industry to make the transition to Net Zero.’
from Network Rail, and then in turn sublease the depots back to the current operator and then future operators. This provides certainty for the financier that they have a route to recover their investment while ensuring that each operator of the depot does not incur the significant cost of carrying out the upgrade over its relatively short operating contract.
In this structure, the leasing arrangements between Network Rail and the Financier, and between the Financier and the Operator are a key plank of the deal. Real estate transactions can be complex in the railway environment due to the number of interests in the property, the very long tenure enjoyed by Network Rail and the wide range of stakeholders.
This was, in particular the case at Tyseley, where the financing project had to take account of the interests of a heritage railway which is situated in part of the depot site.
Another challenge in this structure is the regulatory aspect, and in particular the need to provide for the Financier’s interests in the regulated documents which apply to the depot. Given the nature of those documents, this is a complex exercise which requires indepth knowledge of the regulatory regime. Working with the WMT team and the other parties in the deal, Burges Salmon’s sustainable transport team were able to deal with all of these challenges, and deliver the projects to the required timescales.
Both transactions are a shining example of the private sector investing in and supporting the national rail network, and demonstrate WMT’s ongoing commitment to the West Midlands and its rail passengers, whose customer experience will be significantly improved as a result of the investment.
The Burges Salmon team advising on the transactions was led by myself, Colin Ligman and Pat Parkin and supported by solicitors Louis Bothamley and Madeleine Henson. The firm provided finance, real estate and rail regulatory expertise. At the time I said it had been a pleasure to advise WMT on these significant projects, which will further add to the modernisation of the UK’s rail network along with contributing to a Net Zero railway for the future. These were both complex transactions, involving many parties, from investors and Network Rail through to the Department for Transport and the Office of Rail and Road. Our understanding of the rail sector, and our experience acting for both private and public sector bodies, meant we had the expertise to guide our client through these ambitious ventures.
Robert Stansfeld, the Financing & Treasury Director of Transport UK Group, added: ‘Both of these deals are a critical part of our wider fleet and infrastructure investment programme across the West Midlands. We would like to thank the Burges Salmon team for their ongoing support and excellent advice on these projects. The firm understood our objectives from the outset and collaborated with all parties to get us to a successful outcome.’
RSK Environment Technical Director Rachael Riley has 20 years’ experience in the construction, rail and manufacturing sectors, having worked with both contractor and client organisations. She leads a team of environmental management and sustainability professionals and is an active member of key industry bodies, including Women in Rail and the Rail Infrastructure Sustainability Forum.
The UK construction and engineering sectors have come a long way in the more than 20 years that RSK Technical Director Rachael Riley has spent in the industry. However, she believes that much more still needs to be done
With women still representing, at most, only around 16 per cent of both the rail and the engineering sectors’ workforce (Women in Rail 2024 and EngineeringUK 2023). Women in Rail offers an effective vehicle to deliver a better gender balance while addressing the skills shortage.
A great deal of work and commitment across our industry means that it is a much more fair and inclusive workplace on the whole in 2024; however, the gender balance represents a powerful reminder that we are still not attracting and retaining women as effectively as we could and should be. I believe that this indicates a similar situation for people with other protected characteristics, and this was highlighted in the Supply Chain Sustainability School employee diversity report in 2023.
Women in Rail, and its cross-industry mentoring programme, is well established now and has a mature understanding of what a fair and inclusive workplace looks like for women. Crucially, this includes the support and tools that benefit women taking ownership of their career paths.
I have a long history with the organisation and was one of the first Women in Rail Award winners in 2016 at the Rail Business Awards, something that is deeply meaningful to me. It came at a time in my career when I was starting to take on more leadership responsibilities. I had been
working for some truly inspirational leaders, men who supported me through coaching and mentoring and ensured I challenged myself with new opportunities. I’ve also had the privilege of some excellent leadership training over the years and have learned to recognise that coaching and mentoring skills are an incredibly useful way of helping people take ownership of their careers.
This didn’t come naturally to me. I come from a family of business women and was brought up to expect to have a career: my right to one was never in doubt. However, a fantastic line manager changed my perspective. He suggested that I had a duty to get involved in supporting women I worked with in this way.
That was pretty transformational for me and, once I started looking at the data, I realised that I had zero chance of ever making it into a senior leadership position – there were no women on the board of that company at the time. This realisation galvanised me, motivating me to engage with the gender equality agenda in a much more constructive way. This was also around the time that the Supply Chain Sustainability School was developing its fairness, inclusion and respect programme, which is very important to me, and coincided with the launch of the Women in Rail organisation, founded by Adeline Ginn.
I began to better understand the connection among the crisis in recruitment and retention, the skills shortage for the
For more information about WR visit https://womeninrail.org/.
construction and engineering sector and the general lack of diversity. It was clear that we were never going to recruit the numbers we needed to deliver the UK infrastructure programme if we continued to recruit only from the same limited talent pool.
Having recently joined RSK, I was delighted to be invited to support the business case to renew the group’s membership, and we are proud to be silver members for 2024. I have previously worked for contractors and client organisations, and when I joined RSK I was struck by two key facts – that it has a much more balanced gender split (28 per cent women) and it is successful in attracting and retaining talent. Many businesses strive for a fair and inclusive culture, but RSK has added to this with a long history (pre-Covid) of supporting flexible and agile work patterns. It’s food for thought, isn’t it?
Our membership allows us to participate in the fantastic mentoring programme, delivered by experts in structured mentoring, Moving Ahead, and we have registered five mentees and four mentors from across RSK. It is a cross-business programme, which means that we are paired with people from other organisations. This is a great way to make sure the mentoring experience is mutually beneficial for both the mentees and the mentors. It also exposes us to different ways of doing things and fresh perspectives from outside our organisation, which is hugely beneficial and a unique opportunity. The impact this programme creates is impressive: 56 per cent of mentees from the 2022–2023 cohort have been promoted, expanded their responsibilities or moved roles; 59 per cent of mentees reported feeling more confident as a result of the programme; and over a third of mentors were driven to make change having participated.
The programme runs for nine months, and I think most of us have had our initial introductory meetings with our partners now. The initiative provides excellent guidance and support to ensure the
Grand Central, has submitted an application to the ORR that could result in a significant uplift in capacity, around 30 per cent, for its services along existing routes connecting both the North East and West Yorkshire lines to London’s King’s Cross station. The application includes a proposal for two additional daily return services between Bradford and London (with up to eight stops in between), bringing the total to six a day. It also includes an additional early morning connection from York into London King’s Cross, with a late evening return, bringing much needed additional capacity onto a key route, used by both business and leisure travellers. Subject to approval, the new services could see more than 550,000 additional seats made available, a total uplift of more than 30 per cent compared to what is available today. Services could launch around May 2025.
Commenting on the National Infrastructure Commission’s annual review published on 16 May, which includes new analysis of the railway network in the North and Midlands post-HS2 north of Birmingham cancellation, RIA Chief Executive Darren Caplan said: ‘The National Infrastructure Commission’s findings fire a warning shot to both current and future governments about the need for more investment in rail capacity in the decades ahead.
‘The report clearly says that without investment in transport infrastructure like rail, growth in cities around the country - particularly the North and Midlands - would be constrained, and it cites the recent RIA-commissioned Steer report forecasting that rail passenger demand will grow between 37 per cent and 97 per cent to 2050, depending on which policies are adopted in the coming years. RIA has consistently warned that the absence of a strategy for north-south rail capacity and regional connectivity risks holding the country back, whether the economy, connectivity, local growth, or the UK’s ability to deliver Net Zero.’
mentoring relationship is successful for everyone. This is a learning experience that will benefit all participants, as mentoring is a crucial leadership skill to develop. The programme also includes the opportunity to network, which is another great tool for career and personal development.
In order to achieve our gender balance goal and simultaneously address our recruitment needs, I have several priorities for the industry.
We need to find out why there continues to be a drop-off at each stage of a girl’s academic life. I understand that science, technology, engineering and mathematics (STEM) subjects at A-level tend to be 50:50, but the gender balance changes for STEM subjects at degree level, then post graduate and then gradually erodes at early career stages and onwards. What happens to those women, and why are they not supported and encouraged to stay and progress in STEM careers and into leadership roles if they want to? The sector needs to understand the root causes and barriers and what it means to the next generation entering the workplace now. The good news is that organisations, such as EngineeringUK, are studying this issue and sharing what they have learned, including the need to start engaging girls with engineering and technology activities at a young age, including activities that challenge gender stereotypes around engineering and technology and using role models of a similar age to bridge the developmental gap between students and professionals.
Consider different routes into the sector for different talent pools, and think about transferable skills, particularly for green careers within the sector. Not all roles require a degree, although we traditionally mandate this in job descriptions. For a site environment adviser or a construction supervisor, for example, the majority of the role is about effective communication and relationships, not just technical civil engineering detail.
It’s great to see that the sector is increasingly supporting the apprenticeship route so that new entrants have the opportunity to learn and develop through blended learning and work experience, rather than a purely academic approach. It’s interesting to think about career change opportunities, for instance, as well as the chance to tap into talent from hard-toreach groups or people with barriers to entry into the workforce. It’s important to have diversity of thought and experience in a team.
Achieving transparent recruitment will ensure our processes are fair, open and accessible to everyone in the communities in which we are working. We want to break the mould of what we traditionally think of as someone working in the construction and engineering sector. My favourite example is one of the major client organisations that used an image of a man’s shirt collar and tie in an advert for its graduate scheme. Fortunately, the CEO intercepted the advert
– they had teenage daughters themselves and had a penny-drop moment about what this image was portraying to women.
Consider adopting flexible and agile working practices as standard and learn what worked well in this respect during the pandemic, although most businesses recognise the benefit of building collaboration back in, as well as face-to-face team time.
Upskilling leaders and line managers will help them understand their own communication preferences and leadership styles, how they work best, how they behave under pressure and how that translates into their team management. Give line managers and leaders coaching and mentoring skills so that they can properly support women in their career progression. Undertake reverse mentoring as well: leaders need to be prepared to listen to feedback.
Make sure employees are able to call out poor, unfair and disrespectful behaviour that is not inclusive. Senior leaders must model this and people should be supported to speak up. When people leave the business, it is important to understand why they have done so.
Acknowledge the importance of male allies. Most managers and colleagues want to support women in their careers. This comes back to making sure they have the tools they need and they share what works well.
Encourage women to network as part of their career development. Line managers and leaders can help by making introductions, as well as encouraging women to take part in industry events and groups, perhaps even to chair working groups or committees. It’s a good way to grow a group of allies, buddies and informal mentors; to have conversations with people you wouldn’t otherwise have the opportunity to talk to; and to get new and different perspectives. This is something that I think comes more easily to male colleagues, so it’s good to encourage and remind women to do it. This was another leadership top tip that was shared with me in my career.
The skills shortage is impacting on many areas of our sector, and there is a need to recruit new talent over the coming years, so it is important to invest in initiatives such as Women in Rail now. We need to make it clear to women and girls that this is a sector that will support and invest in their career development and demonstrate this with meaningful programmes and commitments. The rail sector has some incredible role models, and giving these women a greater profile is another way of attracting and retaining talent in our sector, one that is so important in the UK’s infrastructure development and where innovation and sustainability provide excellent career options. Our participation in the Women in Rail cross-company mentoring programme is a fantastic example of a practical initiative that can achieve tangible results and impact – I can’t wait to share what our participants this year achieve.
Jeremy Woolridge is Chairman of B.E. Wedge Holdings which owns a number of successful galvanizing businesses across Europe and the USA. Driven by growth, expansion and innovation, the company actively explores potential opportunities for business development worldwide, as well as heavily invests in the future of steel protection and corrosion prevention.
Chairman of B.E. Wedge Holdings, Jeremy Woolridge, shares why he believes the rail network is at risk of regressing to the 'rusty railway' of the 1960s, and what he believes the industry can do about it
Some of the railway sector’s most important components are made of steel, including: gantries, platforms, and overhead signalling systems – even down to the intricate nuts and bolts used to join rails and fasten track. However, due to its innate nature, steel is highly susceptible to corrosion, which is why an appropriate coating must be selected to ensure it can withstand the elements and remain fit for purpose – especially so during the current cost-of-living crisis where businesses are seeking solutions that provide true value for money.
The galvanizing industry has partnered with the Rail sector for decades – providing a robust, long-lasting, and durable galvanized finish of choice.
With steel boasting qualities such as being able to withstand immense weight, intense pressure and endure harsh weather conditions (when finished appropriately), it’s clear why it’s the material of choice for the rail industry. But without a sufficient coating, it’s highly susceptible to corrosion. And I’m sure it’ll come as no surprise that as a galvanizer, I don’t like rust.
As a veteran in my field, I recall how in the 1960s our rail network was dubbed the ‘rusty railway’ due to its premature corrosion. Paint was typically used at the time due to being both easily accessible and the most affordable (in the short term), but typically only had a lifecycle of around ten years. As a result, the components started rusting relatively quickly and began flaking, creating an unappealing appearance
‘Due to its innate nature, steel is highly susceptible to corrosion, which is why an appropriate coating must be selected to ensure it can withstand the elements and remain fit for purpose’
worldwide. As a completely unique process, galvanizing allows components to be evenly and entirely coated with molten zinc ensuring a permanent finish is applied, which boasts the greatest resistance to damage. Galvanizing will last for more than 70 years without the need for maintenance or downtime, meaning the overall lifecycle costs remain low – significantly saving time, labour and resources: particularly important during the current economic climate. Plus, it caters for even the most eco-conscious customer, as galvanizing is the original green solution.
In recent months and years, the rail sector has certainly been in the spotlight. The development and implementation of the UK’s new high-speed rail line (the largest infrastructure project in Europe), is set to form the backbone of our transport network by providing zero-carbon journeys from Birmingham to London. However, it’s interesting to note the increasing use of weathering steel for bridges throughout the project.
Over the years, we’ve collaborated with alternative coating companies in completing some of the UK’s biggest projects in this sector, including those who provide weathering steel. Especially when dealing with bigger articles that cannot fit into the galvanizing bath, (significant bridge structures, for example), or for projects where the finished item needs to blend into its environment and complement its surroundings, such as woodland.
However, aesthetically, it looks very different to the galvanized steel that customers and the wider public have come to know and love. Instead, it begins to surrender its outer coating and starts to corrode almost immediately, causing it to have a rust-like appearance for its entire lifetime.
To counteract the loss of this surface layer, steel sections are designed oversize from the outset, with the additional metal thickness resulting in as much as 17 per cent more steel being needed. Therefore, this incurs more costs, more time, and more waste – meaning it’s potentially unsuitable for an entire project.
that required significant continuous maintenance, and was widely mocked –not just in the industry but by the general public too.
Since then, thanks to its abundance of benefits, galvanizing has become the prominent choice as a solution for the Rail industry.
Following its introduction in the mid1700s, hot-dip galvanizing companies have worked closely with the rail sector, supporting projects and businesses
With HS2 being the biggest infrastructure project of modern times, as a nation we – of course – want it to be a resounding success. But as we progress through 2024, I’m intrigued to witness further industry changes including how (and where) weathering steel will be used. Will HS2 become the ‘new rusty railway’? And will this unusual design choice tarnish the perception (and future) of steel in general?
This is our chance to shine – our time to showcase this exciting project to the world, and to be seen as the true innovators and leaders in this arena. For me, personally, I want to ensure that we embrace this wholeheartedly, and collaborate to ensure that the completed project is one we can all be proud of for generations to come. And not a new rusty railway for the 21st century.
Rail Ops 2024, the largest free virtual learning conference in rail, highlights ‘Performance Excellence in Rail’. Featuring leading industry experts, attendees can expect a dynamic and vibrant event focused on industry best practice and fostering collaboration and idea sharing.
“ I cannot overstate the importance of the knowledge I acquired listening to experts and colleagues on a variety of topics, challenges, and potential solutions in the rail industry”
Scan the QR code or visit www.ciro.org/whats-on
Dr Laurent Bonnaud is director and founder of Sponte sua srl, a strategy and communication consultancy based in Brussels. Among its recent achievements, Sponte sua srl has coordinated the international research programme "Twenty Years under the Channel, and beyond", an initiative by Rails et histoire, the railway history agency. An economic historian and MBA with expertise in European transport infrastructure, railways and aerospace, Laurent Bonnaud was educated at the University of Paris-Sorbonne and at ESSEC business school. During the « Chunnel » construction phase, he was the recipient of a Franco-British Council Fellowship to study at St Antony’s College, Oxford University. You can reach him at laurent.bonnaud@essec.edu and read his work at www.amazon.co.uk/Tunnel-sous-Manche-si%C3%A8cles-passions/dp/B00QH7UGNG or at www.ahicf.com/product-page/pack-anniversaire-du-tunnel-sous-la-manche-rhcf-48-49-et-52
Laurent Bonnaud, Economic Historian and Director and Founder of Sponte Sua Srl on the greatest engineering project of the 20th century
For a century and a half, projects for a fixed cross-Channel link were a succession of visions by engineers and entrepreneurs, strategic polemics and shattering abandonments. Albert Mathieu-Favier, a mining engineer, submitted a project for a bored tunnel to Napoleon Bonaparte in 1802. On a completely different scale, the major railway companies financed a first project in the early 1880s. But the tunnel became the focus of British invasion panic and work was halted.
London, a recent member of NATO, abandoned its military objections in 1955. In the early 1960s, as part of the Channel Tunnel Study Group (CTSG), engineers from the SNCF and British Railways developed a shuttle system for cars and lorries, inspired by services offered in the Swiss Alps in the 1930s. Roger Hutter, inventor of the car-sleeper train, perfected it with a closed loop. The second project, begun in 1973, accompanied the United Kingdom's accession to the EEC. It was abandoned by Harold Wilson's Labour government in 1975: the country was going through a critical economic and social situation and had to finance another costly Franco-British project: the Concorde supersonic aircraft.
A window of opportunity, an integrated transport system
The French and British governments once again agreed to build a fixed link in 1984. This was an exceptionally favourable period: Margaret Thatcher and François Mitterrand, both supporters of the project, remained in power throughout the decade. In Brussels, the Delors Commission provided the
impetus for the Single Market, the euro and European enlargement. Civil servants and promoters had to square the circle: how to accommodate passengers and goods under the Channel in optimum conditions of safety and comfort? The project reached all its technical and financial limits and met with strong opposition in England: the loss of insularity, the cost of the tunnel and of the railway line to London, threats to jobs in the ports, an increase in traffic in Kent, the ‘garden of England’, etc.
What's more, Margaret Thatcher wanted to ‘drive across the Channel in her own car’ and finance a fixed link privately. The French side favoured a rail tunnel, a showcase for the TGV, and did not rule out public funding. Several projects were in the running. In the Channel, the busiest strait in the world, a tunnel was preferable to a bridge, which is vulnerable to maritime collisions. Furthermore, an underwater road tunnel over forty kilometres long posed safety and ventilation challenges. In 1986, Eurotunnel was awarded the concession for a privately financed and operated railway. The banks' requirements were decisive in this choice.
The main features of the new tunnel are the same as those abandoned in 1975: two rail tunnels and a central service and emergency tunnel, accessible via two terminals connected to the land transport networks of the two countries. Two interconnections, cathedrals under the sea, allowed traffic to be switched. The tunnels are 50.5 kilometres long, including 37.5 kilometres under the Straits of Dover.
Work began at the very end of 1986. On 1 December 1990, the French and British teams joined forces under the English
Channel with an historic handshake. The work was handed over to the concessionaire on 10 December 1993, a record time, and inaugurated on 6 May 1994. Ten years after the political decision, and at the end of a titanic engineering project, involving more than ten thousand workers and seven tunnel boring machines, the Channel Tunnel was a reality.
It was home to direct passenger trains (Eurostar), freight trains and shuttles (Le Shuttle). The Eurostar was a prototype GECAlsthom high-speed three-current train to run in France, England and Belgium, with a narrow gauge to comply with British Rail standards. The two countries financed the accompanying infrastructure: a complete overhaul of the Lille service, at the instigation of mayor Pierre Mauroy, motorway connections in Pas-de-Calais and Kent, the TGV Nord ready for the inauguration of the tunnel, and the Belgian high-speed line in 1997. The high-speed rail link between London and the tunnel was not completed until 2007. The Eurostar then arrived at St Pancras instead of Waterloo Station. The train became more attractive than the plane between Paris, Brussels and London.
Since 1994, the concession holder, renamed Getlink in 2017, has overcome the challenges of an unprecedented ramp-up in traffic. The financing of the project, which was entirely private, was restructured with the help of the public authorities, with the original shareholders and lenders losing part of their stake. The project's security issues have been kept under control.
Two serious fires, in 1996 and 2008, caused no casualties, demonstrating the resilience of the technical concept. The Channel Tunnel has become the busiest railway line in the world. By making possible direct crossings of the Straits of Dover and in all weather conditions, it has revolutionised mobility between the British Islands and the continent: by high-speed Eurostar train for around ten million tourists and business travellers a year, in Le Shuttle, for a similar number of accompanied passengers and for millions of HGVs. By contrast, direct freight trains remain marginal.
Train journeys between London, Paris, Brussels and, since 2018, Amsterdam, have multiplied and have captured most of the air traffic between these cities. Ferry
EUROSTAR TO INVEST IN UP TO 50 NEW TRAINS AS IT REPORTS STRONG FINANCIAL PERFORMANCE
Following strong financial results in 2023 and successful debt refinancing, Eurostar is now preparing to invest in up to 50 new trains as it looks boldly to the future. As demand for sustainable travel continues to grow, this milestone investment will ensure there is enough capacity to encompass the 30 million annual passengers Eurostar expects by 2030 and for future growth. The new fleet will eventually operate alongside Eurostar’s current fleet of 17 e320s, providing a total fleet of up to 67 trains (a 30 per cent increase compared to the 51 trains Eurostar operates today). While the detailed design elements are to be confirmed, the new trains will set the standards for customer experience and comfort. It aims for the first new trains to be in service from the early 2030s.
Both Eurostar customers and staff will be involved in the design process and all trains will be created in the most eco-friendly way. The new fleet will be required to have improved energy consumption versus the current fleet. The news comes following a successful year for Eurostar. Today, it can report that for 2023, Eurostar Group exceeded €2 billion (£1.7 billion) revenue for the first time and achieved EBITDA of €423 million (£363 million). This success was due to a ramp up of operations from 2022 to 2023, and overall growth in passenger numbers reaching nearly 19 million. This strong performance in 2023 means Eurostar can now confidently invest in its future fleet. Eurostar Group successfully refinanced its existing debt of €963.7 million (£826.9 million) in April 2024. This was achieved via strong cash generation following its post-Covid recovery and a new €650 million (£558 million) fiveyear Green Term Loan with a €100 million (£86 million) Green Revolving Credit Facility (RCF).
services retain a significant market share after modernising, restructuring and concentrating on the Straits of Dover. New logistics chains are linking British industries to their customers and suppliers across Europe. EU nationals residing in the UK in the year ending June 2020 was an estimated 3.6 million including over 160,000 French nationals in London and 1.2 million British nationals in EU member states, led by Spain and France.
Despite this growing integration and against the vision of the tunnel's promoters, who wanted to ‘tie Britain to Europe’, a majority of Britons voted on 23 June 2016 to leave the European Union. This is not the least paradox of Brexit.
The cross-Channel fixed link, the UK's only border with the continent, is at the heart of this economic and political upheaval. Knowing its history means delving into the collective narratives that build each generation, and which are embodied to a rare degree in the ‘construction site of the century’.
The concessionaire employs 3,500 people. Also active in rail freight services and electrical interconnection, it now generates enough cash to repay its debt and pay its shareholders. By 2023, it had generated sales of €1.8 billion (£1.55 billion) and carried 18 million passengers, divided equally between Eurostar and shuttle services, 2.25 million cars and 1.2 million lorries.
The tunnel is only being used at half capacity, and the concession runs until 2086. Market share gains are possible in HGV transport, and there is significant potential in direct freight trains. However, rail services are constrained by the narrower gauge in the UK and by the different power supply and signalling systems in the countries served. Only very busy lines are profitable, unless there is equalisation of profits or public funding.
Eurostar's new Siemens Velaro trains are designed to meet these challenges: 20 per cent more spacious, four current, they can travel as far as the Netherlands and Germany. In addition, the recent merger with Thalys has changed the scale of the incumbent operator, making it possible to envisage new strategies. The High Speed 2 line to the north of Great Britain, planned back in the 1980s, should generate traffic for the tunnel. There is demand for interregional links, for example between Kent and the Hauts de France and between South East England and the continent (French provinces, western Germany, Geneva/ Lausanne), which are dominated by low-cost airlines.
New entrants may encourage competition: the Spanish public operator Renfe began negotiations at the end of 2021 for the operation of Paris-London trains, and in October 2023, the Evolyn group of investors has announced its intention to open cross-Channel services. Led by Alsa,
‘The cross-Channel fixed link, the UK's only border with the continent, is at the heart of this economic and political upheaval. Knowing its history means delving into the collective narratives that build each generation, and which are embodied to a rare degree in the ‘construction site of the century’’
the Cosmen family's Spanish road haulage group, it has been allied since 2005 with National Express Group. Dutch investors have also signalled their interest.
The history of the Channel Tunnel is rich in lessons for the design, financing and operation of major infrastructures, which Europe, Britain and the world massively need in the coming decades. A recent research programme by Rails et histoire, the railways history association, has established the state of knowledge about the Channel Tunnel Fixed Link, measured its achievements and drawn lessons for the future. It underlined the importance of governance, accompanying infrastructure and wider economic and social effects for major projects.
Indeed, the profitability of an infrastructure project cannot be assessed solely in terms of its direct costs and benefits, but must also take into account the wider externalities, such as the reduction in CO2 emissions during the crossing or the reduction in maritime accidents.
Understanding this history, from the Mathieu-Favier project to the present day, also means gaining a better understanding of the changes taking place in the UK, France and Europe, and their relationships over the long term.
The cross-Channel fixed link is a strategic European route, reinforcing the age-old importance of the Straits Dover for Europe and the world. Its economic and commercial importance should not obscure the fact that it is also a major supply route in the event of conflict, as seen by many witnesses to its long history.
City & Guilds Training's Environmental Initiatives are playing a key role in shaping a more sustainable future for the UK rail sector
With the recent launch of the Sustainable Rail Blueprint, an industry-wide framework designed to reduce carbon emissions, improve air quality, conserve biodiversity, and improve quality of life for Brits, it’s never been more important to be part of the shift toward a greener world. As such, City & Guilds’ training courses place a particular focus on rail electrification, so students are equipped with the skills needed to work in a zerocarbon industry. They also recently launched a digital training course (an industry-first) in an effort to make the rail sector more accessible and sustainable to students across the country.
Online learning: shaping a sustainable future
City & Guilds recently partnered with Intertrain to launch the Small Plant Training programme for the rail sector. The course is split into a mix of in-person practical training and online learning, which is a first for the industry and a significant move toward a sustainable future. Online learning is beneficial for the environment in and of itself. In fact, online learning has been found to use as much as 87 per cent less energy and reduce carbon emissions by 85 per cent, compared to full-time, in-person courses.
Students can also benefit from cheaper travel expenses and the flexibility to fit the course around their schedule.
The online modules teach students key occupational skills for the rail sector, while they also have the opportunity to put their learning into practice at nationwide Intertrain training centres, worksites, and railway sidings. Students can choose to attend practical training sessions at the site that’s closest to them. The course is designed in line with Network Rail training standards, and students receive a City & Guilds digital credential once completed.
A promising partnership
Intertrain is a National Railway Safety Training and Assessment provider who’ve
successfully delivered engineering training and apprenticeships for over five years.
Just like City & Guilds, Intertrain is committed to providing seamless hybrid learning opportunities that make training in the rail sector more accessible to students. Their partnership is built on a strong foundation of shared values and is set to only go from strength to strength.
‘Intertrain are delighted to announce the launch of the first industry Small Plant blended learning programme’ comments
Alex Pond, Managing Director of Intertrain.
‘The first of its kind, blended learning aims to offer efficiencies to the industry while streamlining quality and practicality at all levels’. Together, Intertrain and City & Guilds plan on launching more collaborative training programmes, including courses on Railway Technical, in the near future.
In particular, City & Guilds’ Level 3 Rail Engineering Technician Knowledge course places a strong emphasis on rail electrification, so students are trained in the safe construction, installation, maintenance, and renewal of sustainable electric railways. The UK aims to electrify 162.5 kilometres of railway track by the end of 2025, which is in keeping with the country’s overall goal of achieving net zero greenhouse gas
emissions by 2050. In particular, the course module Features and application of electrical machines aims to teach students all about ‘the legislation, regulations and standards related to working with electrical apparatus’, as stated in the qualification handbook.
Upon completion of the module, students will: be able to successfully spot hazards associated with working with electrical apparatus; have a strong understanding of the control measures required to work safely on electrical apparatus; and also have a strong grasp of all the relevant legislation, regulations, and standards that surround electrical apparatus in the rail sector. And, once they’ve completed the course, students also have the opportunity to develop their newly-acquired skills, and move onto further training in sustainable areas like electrification construction and electrification maintenance.
City & Guilds is playing a key role in shaping a more sustainable future for the UK rail sector. Their groundbreaking hybrid training course, along with their strong focus on rail electrification modules, are two key initiatives designed to successfully prepare students for work in a greener, zerocarbon world.
John Butterworth, Head of Infrastructure Products at Gripple, explores the challenges that are leading to delays in electrification and looks at the innovative solutions being developed to address these
The UK rail network requires significant electrification and the government has set ambitious targets to electrify lines nationwide as part of its commitment to achieving a net-zero-carbon economy by 2050.
According to the Office of Rail and Road Rail Infrastructure and Assets Report, the total amount of electrified track available for use in the UK stands at 6,042 kilometres, which is around 38 per cent of the total network.
Data shows that plans to electrify the UK’s railways are running far short of what is needed to reach the net zero goal, with estimates stating that 448 kilometres of rail track must be electrified every year and around 13,000 kilometres of track in total requires electrification. Without significant improvements in the speed of electrification, it is estimated that the network will not reach net zero until the 2090s. These delays will no doubt have consequences for the environment, as well as for the efficiency and reliability of the country’s rail network.
Despite the importance of electrification, progress towards meeting the targets has been slow. Cost is one of the major obstacles
to electrification, as infrastructure upgrades and equipment installation are undoubtedly expensive.
Another challenge is the increasing demand for electrical power on the railway network due to longer and more powerintensive trains. This presents issues in managing the supply and demand of electricity and ensuring the network can handle the increased power requirements.
In addition, limitations around availability and costs of possession windows for electrification works can be challenging. These windows are short and expensive, making it difficult to complete necessary tasks within the allocated time using current processes, which is why rail contractors are looking for alternative, innovative solutions to increase productivity.
To overcome the costs associated with electrification, the rail industry is focused on driving down costs through improved project management, standardisation, and optimisation of resources. By streamlining processes and adopting innovative technologies and techniques, the industry aims to reduce complexity and improve efficiency.
One area of focus is reducing the cost of electricity. Network Rail is developing technologies and processes to manage electrical energy demand more effectively. This includes the use of Smart Grid technologies, energy harvesting, storage, and recycling through regenerative braking. These initiatives will help to reduce electricity costs and increase the energy efficiency of the rail network.
In response to the need to accelerate electrification, whilst also achieving cost efficiencies, a number of innovative solutions are being developed.
One such solution is the SwiftLine Rail Dropper from Gripple, a game-changing technology that simplifies and speeds up the installation of overhead line equipment (OLE). This innovative, Network Railapproved product has been developed in collaboration with OLE engineers and contractors and offers significant advantages over traditional methods.
The current challenges around slow and expensive electrification roll out and maintenance was the starting point for the development of this new pre-assembled rail dropper. Trials have proven that time and
labour can be saved with its use, costs can be minimised, and projects can be completed faster and within budget.
The rail dropper enables much faster installation on site, thanks to the simple but secure quarter turn catenary fixing and the Auto Torque contact wire clamp, which ensures the correct torque every time. This not only reduces project durations but also enhances safety and enables more work to be completed within possession windows, optimising the use of limited time.
While the challenges of electrifying the UK rail network are significant, the development of innovative solutions and collaborative efforts offer opportunities for accelerating progress. Collaboration between suppliers, industry experts, and contractors is crucial in driving innovation and finding solutions to electrification challenges.
A great example of this is the collaboration between Network Rail and Gripple in the development of the SwiftLine Rail Dropper. Seeing the value of innovation within OLE installation, Network Rail were keen to support the development of the new rail dropper, providing insights and feedback throughout the process.
The adoption of supplier innovations will play a significant role in achieving targets, making electrification a more viable and attractive option for the rail industry. To successfully overcome the challenges of electrification, strong government support is crucial in providing a clear regulatory framework and favourable policies that encourage investment in this important area. By creating a supportive environment, the government can attract private sector participation and drive innovation in the rail industry.
Despite the challenges faced, the electrification of the UK rail network remains a top priority. The industry is committed to finding innovative solutions to overcome obstacles and drive forward electrification efforts. By embracing new technologies, improving efficiency, and fostering collaboration, the rail industry can create a sustainable and low-carbon transportation system for the future.
New solutions, such as the recent developments in rail dropper technology, are undoubtedly going to play an important role in driving the electrification of the rail
network forward. But they are just one part of the wider approach that’s required. By driving down costs, improving efficiencies, securing government support, and fully embracing innovation, the UK can accelerate its electrification programme and work towards achieving its net zero carbon emissions goals. For more information about the new Gripple Rail Dropper visit, gripple.com/rail/
Network Rail and South Western Railway have officially switched on new signalling equipment to bring more reliable
As part of the five-year programme, Network Rail moved control of the signalling equipment between Feltham and Wokingham and transferred it to Basingstoke, into the Rail Operating Centre (ROC), as well as upgraded 16 level crossings and installed 500 pieces of signalling equipment, which covers 80 miles of railway across Feltham, Hounslow, Shepperton, Twickenham, Windsor & Eton Riverside and Wokingham.
Moving control to the ROC allows signallers to communicate more effectively with each other as they are in the same room rather than remote signal boxes and is more cost efficient to operate.
The first phases were completed in 2021 and 2022 with phases 3 and 4 of the project extending across 40 miles of track and signalling in the Feltham area. This was completed in 2023. It comprised the installation and re-control of 144 digital signals, staged upgrade of seven level crossings, laying of 260 miles of cabling, and 234 axle counters, amongst other signalling infrastructure, to support the new digital signalling technology.
The programme is being delivered by AtkinsRéalis through its innovative Advanced Signalling Method (ASM), the company’s unique end-to-end delivery approach that is the only solution in the UK capable of integrating multiple signalling systems. ASM is also the sole method which has received full product approval by Network Rail meaning it can be deployed efficiency anywhere in the UK making it one of the most cost-effective and reliable rail signalling systems on the market.
Recent phases of the project have also demonstrated significant advancements in technology including a new innovation developed by AtkinsRéalis that enables the
automated development and testing of signalling software. This is the first time this has been achieved in the industry and is dramatically improving the quality, integrity and efficiency of application software which runs the railway signalling.
Scott Kelley, Managing Director for AtkinsRéalis, commented: ‘The FelthamWokingham resignalling programme was a complex project which required extensive collaboration across the supply chain and with our client Network Rail. Its completion is a significant achievement for the UK rail industry, as demonstrated by industry awards for innovation and collaboration for the brilliant team. We pioneered several cutting-edge digital solutions, including advanced systems engineering and automated testing and data compilation.
‘The modern signalling system provides advanced fault detection and prediction capabilities, meaning this key passenger and freight network now provides improved levels of reliability and safety.’
Matt Pocock, Network Rail’s Wessex route director, said: ‘It’s fantastic to see the completion of our Feltham to Wokingham resignalling programme. We've worked closely with SWR and our contractors over the past five years to bring the signalling system up to modern standards and I’m pleased to see the completion of the final piece of this complex and challenging jigsaw puzzle.
‘The new digital signals have replaced the old equipment which became unreliable and harder to maintain and the new state of the art signalling will improve the reliability of this key stretch of railway and in turn help reduce delays for our customers.’
‘We pioneered several cutting-edge digital solutions, including advanced systems engineering and automated testing and data compilation.’
Scott Kelley, Managing Director for AtkinsRéalis
Laura Hedley, Senior Occupational Psychologist at the OPC and a Rail Operations Director discuss the key skills required to be an excellent Signaller and some of the pitfalls to avoid
Over the years, psychologists at the Occupational Psychology Centre (OPC) have worked closely with many Signallers and control room operatives from around the world to understand the intricacies of their roles and identify the skills and behaviours essential in an outstanding Signaller. Recently, the OPC had the opportunity to interview an industry expert, an Operations Director with over two decades of signalling experience. Together, they share some of the core attributes and essential skills required for this pivotal, safety-critical role.
‘Being a Signaller is more than just a job; it's a crucial role at the heart of rail operations. Signallers are the gatekeepers and custodians of safety for their track sections’ said our industry expert.
‘Depending on their level, Signallers manage extensive responsibilities and navigate fluid, challenging situations
daily. They ensure the safety of everyone passing through their section of the track— train drivers, passengers, and engineers alike. They control the safe and efficient movement of trains, regulating them and keeping them apart while holding the tension of getting them to their destination on time for paying customers.’
So, what are some of the key skills of a high-performing Signaller?
Laura Hedley said: ‘Situational awareness is crucial for any Signaller regardless of their level or signal post, whether that’s a busy signalling centre with up-to-date technology, or a quieter, single person location. It means ‘knowing what’s going on all around you’, retaining key information about train schedules or essential maintenance work and focusing on the details that regulate train movements through a Signaller’s section. However, it’s also about a higher
cognitive processing ability, using situational information to decide how to act. In essence, it’s central to effective decision-making.’
The Operations Director added: ‘An outstanding Signaller won’t panic or flap! They remain composed in the face of unexpected challenges, or when under pressure. Their situational awareness and comprehensive understanding of others’ roles helps their decision-making. A quiet confidence and familiarity of what’s ‘happening on the ground’ in their area of control, enables them to make the right decisions to keep passengers and colleagues safe, and trains running smoothly.’
Attention to detail and vigilance are key Non-Technical Skills (NTS) for Signallers, tied closely to situational awareness. Laura said: ‘As Psychologists, we’re interested in safety behaviours and we know the key behavioural markers for attention to detail
‘Despite the pressure, there's a sense of satisfaction knowing that your work directly contributes to the safety of passengers and the smooth running of the railway’
A Signaller
and vigilance. Signallers must be focused on details, identify the essentials and the unnecessary, while being systematic in their approach. They’ll care about accuracy and precision, recognising the importance of working at a steady pace. They rigorously and habitually check information, often more than once, without relying on past experience or assumptions. Despite time pressures, they consistently verify details and maintain precision in their work.’
Our industry expert added: ‘A highperforming Signaller remains vigilant in their signal box and workstation, always focused on the train schedule and fully aware of all the train movements running through their section. A passionate Signaller will be watchful and ready for trains about to enter or leave their section as well. They meticulously review and cross-check information and paperwork for line blockages to ensure safe access for trackworker colleagues. By consistently demonstrating vigilance and thoroughness, Signallers uphold safety standards and maintain the smooth operation of the network.’
‘The NTS of risk anticipation is paramount for Signallers, ensuring safety on the railway. It involves actively managing known
‘I enjoy figuring out and problem-solving situations when something happens.’
A Signaller
hazards and emerging risks to reduce the likelihood of a safety incident. Starting at the beginning of each shift and continuing throughout the day, Signallers must remain vigilant to various risks, covering work-related, environmental, and/or personal factors. OPC Psychologists, having undertaken hundreds of Post-Incident Assessments (PIA) with employees who have had safety incidents. They have observed that incidents often result from multiple subtle risks accumulating over time, rather than a single factor. Therefore, Signallers must be adept at recognising and mitigating these potential hazards to maintain a safe environment’ said Laura.
‘Some top Signallers in my team prioritise punctuality. They’re never tardy, their time keeping is exemplary and that isn’t just running trains to time! They arrive at their post un-flustered and organised enabling them to complete up-front risk assessments – either mentally or as part of a written handover before the shift starts. It also reflects in their critical time-focus of train movements, communications with drivers or track engineers – particularly when the pressure is mounting. They’re unhurried in their paperwork. They demonstrate accuracy and discipline that inspires confidence in colleagues and managers alike’ added the Operations Director
‘Activity levels vary, with some signal centres being bustling hubs while others are quieter. Newly qualified Signallers often start in a quieter environment where their challenge can be to remain
vigilant during slower periods. However, excellent performers take the opportunity to conduct additional checks and ensure line blockage records are accurate and up to date. Newly qualified individuals may have the opportunity to review their training and refresh their knowledge of operating procedures and emergency protocols, ensuring they’re well prepared for any potential issues. Their commitment to personal development prepares them for busier roles and a potential promotion’ said our industry expert.
During an incident such as trespassing or track faults, effective communication skills are essential. Signallers must communicate effectively with drivers, track teams, and/or the Control centre, conveying crucial information clearly and concisely. Efficient train operations rely on Signallers gathering critical information and relaying it to Control for action, whether that’s dispatching an engineering team to fix a fault or summoning appropriate response teams to deal with a trespasser. Effective communication is an essential NTS for Signallers especially in the event of an unforeseen problem.
Laura shared several key behaviour tips on good communication skills:
• Stick to safety protocols and procedures for communications.
• It can be helpful to prepare communications in advance.
• Be an active listener. Pay attention and provide feedback when necessary.
• Seek clarity and confirmation to avoid misunderstandings and agree actions.
• Be clear and concise, avoid unnecessary details.
• Accuracy is key. Verify information before relaying it.
• Communicate promptly to help decisionmaking and action.
• Be professional by maintaining a respectful demeanour and speaking clearly.
‘Being a Signaller is more than just a job; it's a crucial role at the heart of rail operations. Signallers are the gatekeepers and custodians of safety for their track sections’
In a recent Post-Incident Assessment (PIA) with a Signaller employed by an overseas rail operator an OPC Psychologist identified negative interpersonal working relationships as a key concern. Laura said: ‘Strong team-working and interpersonal skills are crucial alongside communications. Weak or fractious team relationships can’t hinder the sharing of vital safety-critical details. Signallers need both an assertive yet approachable manner to encourage open communication. They also need adaptability working alongside different roles and people. Other employees can’t be hesitant or afraid to talk to a Signaller. Conflict, aggression or disrespect can break down trust, cooperation and communication between team members, potentially leading to a safety incident and undermining the overall safety culture for that section.’
The Operations Director said: ‘We’re all human. We all make mistakes. In a busy signalling centre, when the pressure mounts a Signaller must stay on top of train movements, planned maintenance, and colleagues accessing the track. If unplanned incidents such as a signal fault or a trespasser on the line happen, then the pressure of juggling all those tasks can mean something has to give. A high performing Signaller will recognise they can no longer
Weak or fractious team relationships can’t hinder the sharing of vital safety-critical details’
manage their workload, remain calm, and take a ‘pause’. They’ll use key NTS like risk anticipation, prioritisation and decisionmaking to review and prioritise the train plan, re-schedule planned maintenance and associated line blocks, so the problem can be fixed. Then they’ll communicate with Control to discuss and agree a plan. An experienced Signaller will also know when their workload is at an intolerable level and there’s a risk of something going seriously wrong. They’ll be confident enough to escalate their concerns and ask for support from either their line manager or Control to prevent the risk of an incident.’
Signallers undergo extensive initial training. Some OPC rail clients also use simulators to practice key tasks and the application of rules and regulations under an assessor's guidance before starting in a live signal position. This really helps assessors and line managers sign off a trainee as ‘fit to perform the role’ as well as equip trainees and grow their confidence.
The Operations Director added: ‘To support new Signallers, we also conduct cross-functional simulations and tabletop exercises that really enhance teamworking and interpersonal skills. Although Signallers may need to phone an adjacent Signaller along the track, they may never actually meet face-to-face. These exercises really help build relationships, provide insight into others’ roles, develop effective communications and remove some of the barriers that stop people asking key safetycritical questions – thus helping to improve overall safety culture.’
‘Situational awareness is crucial for any Signaller regardless of their level or signal post’
An outstanding Signaller is likely to have a mix of both experience and natural aptitude. Years on-the-job may have exposed them to many different daily pressures and challenges to develop their skills. However, natural abilities and key NTS play an important role in their make-up. OPC Assessment has a range of innovative assessment tools that can help identify and evaluate key Signaller attributes.
Some of these include: The Risk and Time Focus Questionnaire (RTQ) that profiles a candidate’s behaviour and attitude towards risk anticipation, including their consideration of time. The Visual Search Exercise (VSE) is an innovative test that identifies individuals who have the ability to focus and respond to numerous things simultaneously while remaining situationally aware.
The Safe Personality Questionnaire (SAFEPQ) which profiles four personality factors; Cautiousness, Conscientiousness, Resilience and Rules Focus that are linked to safe behaviours in the rail industry.
The OPC provide a range of tailored NTS training programmes to help employees and managers to harness the power of NTS critical in a Signaller’s role. These have been received by Signallers with considerable praise. OPC Psychologists also undertake PIAs with Signallers who have had safety incidents for which they were wholly or partly responsible. The aim is to help uncover the human factors behind a safety incident, along with development plans to support a safe return to work.
In addition, the OPC can provide training and development through bespoke crossfunctional simulation exercises to enhance operational performance as well as review emergency procedures.
Get in touch with the friendly OPC team if you think they can help you identify and develop outstanding Signallers.
Tel: +44 (0) 01923 234646
Email: admin@theopc.co.uk
Visit: www.theopc.co.uk
High-speed rail is the future of travel to Europe – let’s work together to achieve the ambition, Wendy Spinks, Commercial Director of HS1 Ltd explains how
We all know the feeling. Jetting off for a short-haul holiday to the Continent on paper seems painless, but the reality is often the complete opposite.
From getting to the airport, navigating security, the long walk to the boarding gate, waiting to board, touching down, more queuing and waiting around before finally getting outside – short haul flights feel less like luxury and more a disjointed series of journeys, steps and tiresome queues.
Not to mention the significant impact on the environment, with a whopping 92kg of carbon emitted per passenger on an average flight from London Heathrow to Paris Charles De Gaulle.
So it’s no surprise that increasingly, travellers are turning to high-speed international rail services as a more relaxed and seamless alternative.
Polling by HS1 – the owner of Britain’s first and only high-speed rail line – has found that two-thirds of people would prefer to make their journey by rail instead of air: a total of 66 per cent said they planned to travel to Europe by train for business, increasing to 77 per cent for holidaymakers.
Recent research from Hitachi Rail also found that Brits expect to travel more by train over the next five years than any other mode of transport.
It’s not just the polls telling us this, we can see it in passenger numbers too. Last year, Eurostar reported a record 22 per cent upturn in passenger numbers, with yearon-year across its three main routes serving London St Pancras: Amsterdam (up 38 per cent), Brussels (up 33 per cent), and Paris (up 25 per cent).
But to reap the full benefits of a green modal shift to travel by rail, the growth in demand for high-speed rail must be matched by the ambition of the rail industry. At HS1, we have a two-fold strategy to meet demand and position the UK at the epicentre of international rail growth.
Our first mission is to utilise the existing 50 per cent capacity on the HS1 line. We welcome competition which will mean more services to more destinations, benefitting the regional, UK and international economies combined with lower prices, lower emissions and greater choice for the travelling public.
Secondly, we are preparing to welcome a growing number of passengers and are developing plans to upgrade and futureproof the beautiful, historic and iconic St Pancras International – the place where every international rail journey from the UK starts and ends.
St Pancras International is the green gateway to Europe with thousands of passengers moving through the station every hour. Currently the station has capacity to process 1,800 international passengers per hour, however new technological upgrades could see this number significantly increase.
We know that passengers love St Pancras for its unique atmosphere and beautiful architecture, and retaining this sense of awe is important for all of us at HS1.
The upgrades to St Pancras should be bold, embracing modern approaches and technological solutions, using the space we have in a smarter and more efficient way but at the same time protecting the history and integrity of the building.
The UK has a strong railway heritage spanning almost 200 years, and we must
capitalise on the growing desire from the public to make high speed rail the preferred choice of travel to the Continent.
At HS1 we are fully preparing for the exciting possibilities ahead, and as an industry, we need to work together to fully realise the opportunities and benefits more high-speed rail can bring.
Wendy Spinks is Commercial Director of HS1 Ltd. As Commercial Director, Wendy works closely with train operating companies, local stakeholders to each of the HS1 stations and leads the strategy for the commercial property and retail ventures. Alongside her role, Wendy sits as Chair of Urban Partners, a voluntary business partnership, as well Chair of Camden Business Board.
at some of the questions raised by HS2’s cancellation
It’s now been over six months since Prime Minister Rishi Sunak cancelled the Northern leg of HS2. Despite the time that’s passed, questions about HS2 continue to dominate headlines and many conversations in the infrastructure space. The sustained interest is undoubtedly partly to do with the scale of the project – so far reaching that it’s virtually impossible to identify a senior leader in UK transport who wasn’t involved in some capacity.
Why was the Prime Minister able to solely cancel a project of this scale? Why had political support evaporated so significantly? Can the UK still deliver largescale infrastructure projects? These are just some of the questions raised in the wake of the cancellation.
As a professional engineering institution, some of these questions are beyond the Institution of Civil Engineers’ remit, but understanding why this flagship project was cut short is key to improving how infrastructure is planned, promoted, developed, and delivered in the UK.
Developing that understanding is firmly within the ICE’s scope, which is why it launched a policy programme to explore what went wrong and what lessons can be learned.
As part of the programme, the team hosted a public Question Time style session exploring the question Can the UK do major infrastructure projects anymore? You can watch a recording of that discussion on the ICE’s website.
In addition, the ICE policy team is running a consultation to hear from HS2 stakeholders and others in the know to understand what went wrong with the project and what needs to be done differently on future major projects.
The consultation allows individuals, businesses, and stakeholders who contributed to this project and who were impacted by its cancellation to give feedback on the processes and decision making that
led to this outcome. Some early lessons are emerging from our initial conversations, such as the need for better corporate governance on who makes decisions, and how and when these decisions are made. Uncertainty about HS2 Ltd’s role, the loss of corporate memory, duplication of functions and lack of technical design oversight all undermined HS2’s development.
There’s a need for stronger client and departmental capability – particularly on technical assurance and ‘owning the project’. Departmental sponsorship of major projects works – but only if there’s strong departmental capability, consistent advocacy and robust challenge.
The contracting approach didn’t set the project up for best-practice delivery. The size and scope of contracts allowed for cost increases and prevented the standardisation of project assets, such as bridges.
Major projects and programmes require clarity and consistency on outcomes to achieve political and public buy-in. A focus on transport, not outcomes, and a shifting narrative harmed support for HS2 and made the decision to cancel the northern leg easier.
Any programme of this scale and significance needs to spend more time in development. In the design stages, flexibility is high and costs are low, but HS2 moved quickly from concept to being greenlit, reducing opportunities to examine different options.
These lessons are a good beginning and will undoubtedly provide a good foundation for discussing what needs to be done differently in the future. But this may not be the whole story.
The ICE policy team is eager to hear from infrastructure professionals and other experts about the above points, and from anyone with insights on evidence we may have missed. We’re also keen that positive learnings don’t get lost in the frustration around the cancellation and associated challenges.
While it’s right to ask questions about skills and capacity to deliver infrastructure projects, there’s much about HS2 that was positive. Phase 1 has already shown that there is impressive civil engineering and construction problem solving happening in the UK, e.g., there has been pioneering work to reduce carbon emissions at HS2 construction sites. The project also generated investments along its route, upskilled thousands of workers, and pushed delivery practices forward. If there are insights you’d like to share along these lines, we’re keen to hear those, too.
Robust lessons can be gleaned from healthy debate, so we invite people to challenge what we have found so far. What isn’t up for debate is the fact that the ability to plan, communicate about, and deliver the right infrastructure is key to the UK’s future economic, environmental, and social prosperity.
It’s worth taking the time to analyse what we can from the experiences of those who were involved in HS2 so we can apply them to future projects. It’s essential for all our futures that we get this right.
Please get in touch with policy@ice.org.uk to contribute your views to the consultation. Anonymity will be respected.
The consultation closes on 31 May, but submissions made in response to this article will be included in the ICE’s updated briefing paper, which is scheduled to be published this summer.
DAVID HAWKES is Interim Associate Director of Policy at the Institution of Civil Engineers.-
-
-
- Cybersecurity to protect data and systems
SLC has partnered with the Rail Safe Friendly programme, which seeks to educate young people on the many dangers that are present on the railway
Rail Safe Friendly was launched in March 2023 and delivers video safety content about the dangers of trespassing on railways directly to schools via digital education provider Learn Live, which, since 2019 has reached more than 21 million young people in over 12,500 schools across the UK in partnership with the Trespass Improvement Team at Network Rail.
SLC’s partnership with the programme will see young people from ten schools educated on the risks of trespassing on or close to Britain’s railways.
Sam Uren, Director of SLC said: ‘As we help our clients to build new rail stations and open new rail lines, we believe that our partnership with the Rail Safe Friendly programme will help us to have an even bigger social value impact in the communities in which we work by ensuring more school children are educated about rail safety. This learning will help encourage a younger generation to be confident rail passengers in the future.’
Already, over 4,000 UK schools are on board with the Rail Safe Friendly programme and more than 80 industry partners from across the rail sector have sponsored and become partners in it.
The Rail Safe Friendly broadcasts are delivered through live or on demand content digitally into classrooms and assembly halls via the Learn Live channel. The channel also has a moderated, GDPR compliant LIVE CHAT facility to promote interaction and involvement from the schools and colleges taking part in Rail Safe Friendly.
The programme was launched last year by Stuart Heaton, Learn Live and Rail Safe Friendly Managing Director, following the tragic death of eleven-year-old Harrison Ballantyne who received a fatal electric shock after climbing over a fence to retrieve his football at a train depot.
Stuart Heaton, Managing Director of Learn Live and Rail Safe Friendly, said: ‘SLC works on many projects across the UK
and we are delighted to welcome them to Rail Safe Friendly. The support of the rail industry is pivotal in ensuring rail safety education is delivered to as many schools and youth organisations as possible.
‘Since Rail Safe Friendly launched in March 2023, it has been embraced by more than 80 train operating companies, freight operating companies and small to large organisations working across the rail supply chain, with one goal, to ensure children receive vital education to keep them rail safe.’
The Rail Safe Friendly programme seeks to teach children and young people about the many dangers that are present on the railway. For example, nearly half of the UK rail network is electrified and more than 30 per cent uses a third rail to power the train. The third rail has 750 volts running through it, which is enough to kill or seriously injure someone if they stepped on it.
Overhead cables that power trains carry 25,000 volts, more than 100 times the power of electricity in the average home. Electricity from overhead lines can also jump or arc through the air, meaning someone does not have to be touching the line to be electrocuted and killed.
Businesses and organisations that want to partner with Rail Safe Friendly, or schools that want to be certified, can register their interest at www.railsafefriendly.com
SLC celebrates its 15 year anniversary in 2024. SLC Rail started in 2009 with the aim to help clients better understand how the railways can contribute to social, economic and sustainability goals. Since then, SLC has worked on making over 100 projects and specialises in helping third party scheme promoters develop strategic plans, win industry support, develop business cases that secure funding, and develop and deliver their aspirations. The company is working in a JV with AECOM on the Northumberland Line, which is the biggest
third party-funded rail upgrade project in the UK directly developed and promoted by a local authority. Other SLC businesses include SLC Property and SLC Investments. SLC Rail is also working in partnership with Alstom, global leader in smart and sustainable mobility, on plans to operate a new passenger rail service across England and Wales. The open access operation will be known as Wrexham, Shropshire and Midlands Railway (WSMR).
Learn Live runs innovative, interactive, moderated online news channels that bring a world of opportunity and experiences directly into the classroom, home, or business. Each interactive Learn Live broadcast can be attended by an unlimited number of schools/colleges, job seekers or businesses simply by logging into the channel online. The Learn Live News Channels continuously link schools/ colleges/universities to employers and are working successfully with companies like Network Rail, Balfour Beatty, DWP, Gatwick Airport, Brook and The NHS amongst others to deliver PSHE broadcasts across the UK.
Rail Safe Friendly is run by Learn Live, and it was launched in March 2023 to deliver Network Rail’s video safety content directly to schools via the Learn Live Channel. Already, over 4,000 UK schools are on board with the programme and industry partners from across the rail sector have sponsored and become partners in it.
AARC Professional Services Limited draws from over five decades of experience to provide expert support to the industry.
We are a railway consultancy bringing together likeminded rail professionals with a common aim to deliver outstanding outcomes by..
• Helping clients achieve their goals...
• Through strategic and technical expert advice...
• Across a range of disciplines...
• From the frontline through to the boardroom
Whether you’re looking for high level advice & guidance or direct project support, we’re here to help you deliver excellent outcomes.
Approved Hydraulics have been supplying some of the largest rail build and maintenance firms for over 10 years. Now considered some of the best in the world!
Essential TfL project completed by ADS Laser Cutting and UB Infrastructure partnership with significant time, cost and environmental savings
Leicester-based metalwork firm, ADS Laser Cutting has successfully delivered a project in partnership with UB Infrastructure (UBI) that is set to revolutionise how upgrades to essential trackside infrastructure are delivered across the UK’s rail network.
Responding to a brief from Transport for London (TfL) to deliver a safe and efficient upgrade to a lineside electrical switch box near the Willesden Depot in West London, UB Infrastructure devised a modular concept to clad the existing building in non-corrosive aluminium that was then manufactured by the team at ADS Laser Cutting.
The critical lineside building had experienced water ingress due to poor design and without urgent replacement or remediation, was in danger of a catastrophic failure. However, mindful of potential disruption to rail services whilst the work was carried out, TfL turned to UBI, experts in modular construction solutions, to deliver an innovative building wrap solution.
Charlie Davies, Managing Director at UBI, commented: ‘To remove and replace the existing building would have involved lengthy design and planning approvals, whilst more traditional remediation processes would have carried risks due to the site’s proximity to the live rails. Both options would have incurred significant costs.
‘In comparison, our UBI Shell solution has been designed with sustainability, longevity of lifespan and ease of installation as paramount considerations. Consequently, it is also 85 per cent cheaper.’
Comprised of a series of aluminium panels that were laser cut, folded and fabricated off-site, their low weight meant that the individual components could be easily sent to site for assembly in just two days. The solution is also more environmentally friendly than other more traditional approaches with the completed building delivering a forecasted energy efficiency saving of 97 per cent.
ADS Laser managed all manufacturing processes ensuring seamless integration of the components, and Stuart Rowan,
Production Director, commented: ‘Modular and off-site solutions within construction are growing at pace and it has been a privilege to partner with the UBI team to deliver what we believe is a game changer for UK rail infrastructure.
‘As one of the only UK metalwork companies to boast the ability to manage laser cutting, folding, fabrication, finishing and assembly on sheet metal up to six metre all in-house, we were well-placed to partner with UBI on this project. Unusually, we powder coated the parts when fully assembled to mitigate any damage to the components during either the deliver or assembly process.’
With up to 12,000 trackside structures requiring similar upgrades across the UK rail network, Charlie concluded:
‘The team at ADS Laser is more than simply a manufacturing supplier to UBI. We consider them partners in our work and benefit hugely from their expertise within the sheet metal industry.
‘The fact that they have invested heavily in market-leading technologies positions them perfectly to adapt and scale to the varying requirements of projects such as this one.
‘Witnessing our modular concept come to fruition, thanks to ADS Laser, places us favourably to complete similar rail infrastructure projects across the UK.’
Installation of the modular cladding system at Willesden was carried out by Walker Construction.
KATHRYN ADAMS COMMERCIAL DIRECTOR AT PROLECTRIC
Kathryn Adams is the Commercial Director at Prolectric and she supports the Sales, Marketing and Product Development departments to develop the products and services its customers need. For the last 20 years she has worked in roles across B2C and B2B that span these fields, from Business Development and National Account Management through to Channel Marketing and Head of Insights.
What types of products and services do you offer?
As the first to specialise in off-grid, renewable lighting and power, we’ve made it our mission to build the world’s cleanest, most advanced, sustainable products. We’ve been powering the UK’s off-grid energy needs with smart, clean, renewable technology for almost a decade.
We’ve invested heavily in developing and bringing to market the most advanced and capable fleet of temporary and permanent lighting units. They can be utilised across multiple environments, controlled remotely and deployed as part of our ultra-efficient ‘setup-and-forget’ model that doesn’t require fuel, refuelling or regular servicing.
We introduced the first solar street lighting to the UK in 2011, as a like-for-like alternative to traditional mains powered lights. With no need for trenching or cabling and with no ongoing costs, they are a perfect replacement for streetlights that have come to the end of their life or new installations. Our temporary lights autonomously adapt to ensure they stay on throughout the night, our batteries don’t need draining to maintain their lifespan and our Smart Remote Portal offers the most indepth diagnostic and remote management functionality on the market.
Our products are engineered in Britain to the highest standards, our products provide unparalleled performance, which reduces or eliminates carbon, fuel and noise, whilst also saving costs and meeting carbon saving goals. Since launching our first solar lighting tower in 2016, we have saved customers 27 million kgs of CO2 and reduced diesel usage by more than 10.2 million litres, which represents a customer saving of more than £10 million.
Our Solar Hybrid Generators and Solar Lighting Towers are like-for-like alternatives to Diesel. They have been engineered using the latest autonomous software to ensure they work perfectly in the UK, whatever the weather and season. We lead the way in this sector - not least because we pioneered it – but because we’re the only ones to have mastered the art of engineering the only solar, battery and hybrid systems in the UK to truly work autonomously, all-year round. Our products are the smartest on the market. They interpret advanced telematics, historic weather and GPS location data to autonomously adapt, based on their battery state of charge, ensuring optimum performance – meaning the lights work all night. Our smart batteries require no battery draining or a monthly ‘maintenance’ programme.
All of these attributes make us truly unique and demonstrate how we are always leading the way, powering the route forward for off-grid solar technology.
As the leading manufacturers of sustainable solar lighting and solar hybrid power generators, our units have been widely adopted across UK infrastructure. Our products have been specially designed to suit a wide range of urban and multi-site applications from rail and airports and large commercial estates to local authority car parks, large campus, residential housing developments, parks and pedestrian walkways.
Our ProRXM and ProRXM Hybrid temporary tower lights have been developed specifically to support rail, highways and other space restricted sites, where tower light footprints need to be minimised without sacrificing the quality and capability of the lighting. Our temporary power provides a perfect solution for tracksides, as well as in densely populated urban areas, as it operates silently and has zero risk of spillages. And when it comes to making an investment the whole life cost is worth considering compared to traditional diesel units. Including the initial investment, our customer is cost-neutral after only twoand-a-half-years on average – and makes an average total saving of £18,000 year on year after that.
Our permanent Solar Lighting is genuinely revolutionary, as our solar streetlights and bollards, are simple, quick and economical to install. With no labour required to dig trenches or install trunking for cables, labour costs and carbon footprints are significantly reduced. Installation time is minimal compared to conventional mains power alternatives.
What types of companies do you collaborate on projects with?
We work closely with a range of companies across UK infrastructure who want to make a positive change to their business and the environment. As problem-solving solar and battery experts, from 1W to 30kW, we work collaboratively with customers and business partners in that space to continuously improve and develop new solutions to overcome their unique challenges in the market. We further guide businesses, to support them on their sustainability journey and help them transition away from diesel and mains power. Helping organisations to achieve their carbon-saving goals and sustainability commitments, as well as saving money, is our primary goal.
How passionate are you about sustainability?
Sustainability is in our DNA. In 2021, we received the prestigious Queen’s Award for Enterprise (Sustainable Development) and we also hold the Gold Corporate Social Responsibility Accreditation for our contribution to the environment, workplace, community and philanthropy. As such,
‘Even on overcast days, solar panels can still capture diffuse sunlight by efficiently converting it into usable energy, allowing customers to effectively harness solar power in lowlight conditions.’
we are committed to an environmentally and socially conscious culture. We design and build products for our customers with a determined focus on reducing carbon emissions – and we practice what we preach. Our Prolectric operations are actively managed to minimise our environmental impact, monitoring and measuring all our scope 1, 2, and 3 emissions. With a relentless pursuit, we work hard to foster a sustainability-focused culture where we challenge ourselves to behave in a way that reduces our carbon, improves efficiency and reduces the amount of power we use within our operation.
What are some standout projects you’ve been involved in over the years?
We were delighted to be involved in an ambitious project led by Network Rail and Colas Rail used innovative solar lighting and power generation to prove the viability of a sustainable ‘Site of the Future’, achieving 97 per cent diesel-free operation in support of a major rail renewal project at Llanwern, South Wales.
Our clean, silent solar lighting and power generation technologies covered more than 21 acres across the site. This included access roads, the welfare cabin area, car parking and the track working area, where the London to Cardiff main line meets the Llanwern steelworks spur near Newport. The set-up and core works spanned 14 days leading up to and following a 72hour possession. More than 70 rail staff were employed on site and benefited from reduced noise and fumes because of the use of our solar powered products.
Two Propower Solar Hybrid Generators replaced conventional diesel generators, providing light and heat for seven welfare cabins, including site offices, a canteen, toilets and a drying room. A total of 21 Prolectric ProLight solar tower lights illuminated the site compound, car park and work preparation areas. The ProTemp column street lights were positioned along the access road to the site. We also deployed 200 metres of ProTrack on the trackside.
Using our smart solar and battery technology, the joint initiative saved 6,000 litres of fuel and more than 15 tonnes of CO2 during a 14-day project centred around a 72-hour possession over the May Day Bank Holiday weekend.
The results are being viewed as a significant achievement that marks an environmental milestone towards clean, carbon-free off-grid working, supporting Network Rail’s CP6 target to reduce nontraction energy consumption by almost 20 per cent and carbon emissions by 25 per cent.
When a client comes to you with a particular problem, what’s your process for coming up with a solution, and how closely do you work with clients throughout the projects?
Collaboration is a critical part of the Prolectric approach. It is in our values to ‘work as one’; ultimately in partnership with our customers to help them meet their carbon reduction targets. Our units can be adapted to the customer need, working closely as one team to find the right solution. In addition, customers can commission completely bespoke units for specialist applications and site conditions. By taking a ‘software-style’ approach to collaborative working, we are able to continually launch, get feedback, iterate, and refine our products and services. This fosters an environment where we can build close, trusted relationships.
As problem solving solar power and battery experts, we pride ourselves on being able to employ a completely flexible approach which caters for individual customer requirements. As such we also share our five-year NPD roadmap with our key customers and invite them to be part of it.
What are some of the biggest challenges this sector currently faces?
Sustainability and carbon reduction are the two critical drivers and challenges for all global industries. And as we travel closer to 2030 and 2050, the rail sector, like many others has a vital role to play on its journey to meet its ambitious Government zerocarbon targets. We are fully supportive of the environmental measures that have been taken across the rail industry to date, but so much more can be done to accelerate this – and making a commitment to increased alternative power use is a great place to start.
What are some potential solutions?
Clearly, there has never been a better time to move away from polluting fossil fuels, to transition away from diesel and switch to solar. Solar lighting offers many advantages, including lower fuel costs and no fumes or greenhouse gas emissions. By adopting solar
‘Since launching our first solar lighting tower in 2016, we have saved customers 27 million kgs of CO2 and reduced diesel usage by more than 10.2 million litres, which represents a customer saving of more than £10 million.’
power and solar lighting solutions, the rail industry can reduce its carbon footprint even further and mitigate the environmental impact of energy generation.
These technologies contribute to achieving net zero by replacing fossil fuel-based energy sources with clean and renewable alternatives. Working in close collaboration with its rail partners, Prolectric expects future advances in the design, function and versatility of solar and battery technology, with telematics driving forward the capabilities of off-grid solar light and power generation.
Do you think the rail industry could be greener and what is your organisation’s green strategy?
A critical part of our green strategy, at the forefront of the solar industry is our commitment to driving positive change – and we see it as our duty to educate the market. This year we have been invited as guest of Network Rail to attend Rail Live where we will continue to fly the flag for solar.
At Prolectric, we are incredibly proud to be part of the solar revolution transforming the sustainability of the rail and infrastructure sectors, alongside the health and safety of its workers and local communities. It is encouraging to witness the appetite and the significant strides that have been made towards a cleaner, greener rail sector, but as we said before, the race is far from complete.
Adoption rates have been slower for many factors, but a lot of this is concerned with a huge lack of accurate information. We are making it our mission to right this. Challenging the norm is never easy. There are many misconceptions when it comes to solar and alternative power use, so we have to work hard at myth busting.
On a wide range of applications, solar lighting has come a long way from its early days and today offers a reliable and ecofriendly solution, without compromising on quality, reliability and brightness. Even on
overcast days, solar panels can still capture diffuse sunlight by efficiently converting it into usable energy, allowing customers to effectively harness solar power in lowlight conditions. To date, we have provided over 8,000 solar streetlights across the UK, brightening up car parks, walkways and streets, round the clock, 365 days a year.
Cost is often highlighted as a barrier to change, and whilst the initial outlay of a solar unit is often higher than traditional options, the lifetime costs are significantly cheaper and the dividends are quickly clear to see. Helping the rail sector to move away from using polluting fossil fuels is a longstanding commitment. Unlike the light emitted from our solar towers, it isn’t happening overnight, but we are certainly enjoying the ride.
Prolectric was the first company to introduce permanent, solar-only streetlights to the UK in 2011. In 2016 the business, with its vast knowledge and experience of solar, pivoted to create temporary solar lights, the ProLight and ProRXM, alternatives to traditional diesel tower lights, alongside the already successful permanent solar streetlight.
The award-winning ProPower Solar Hybrid Generator was launched in 2020, continuing our innovation and development of solar alternatives for the industrial market.
In March 2021, Prolectric became part of Hill and Smith PLC, a FTSE 250 £1 billion international group providing sustainable infrastructure; this has further enabled our business to innovate and grow at pace.
Want to know more about Prolectric?
Tel: 01275 400 570
Email: info@prolectric.co.uk
Visit: www.prolectric.co.uk
LinkedIn: Prolectric Services
Charlotte has worked for her family’s business Grommets Ltd for almost 15 years, although her work experience started much earlier than this, gaining invaluable experience from her mother (Managing Director, Joanne Boorsma) throughout her school years. Charlotte worked within the banking industry and for a Chartered Surveyor’s firm before returning to Grommets Ltd in 2009.
What is your role within Grommets Ltd?
I am the Office Manager for Grommets Ltd, a UK leading manufacturer of rubber cable Grommets, washers, plugs, bushes, and other small rubber components. The company was founded by my Grandad, Sidney Wells, in 1993 when I was just 9 years old. Throughout my childhood I would spend school holidays at the office with my Mum, Joanne, and my Grandad Sid, so I quickly adapted to an office environment. I gained experience over the years and started my employment in the family business in 2009 as an office junior.
I gained knowledge of the products and joined the sales team as well as being the office administrator and assisting Joanne with the accounts. I love my current role as the Office Manager, following in Joanne’s footsteps I have taken over all the managing of the company accounts, having trained in Xero. I also manage all the company HR and our team of employees.
How long has Grommets Ltd been in business?
From humble beginnings to worldwide markets! Grommets Ltd was started in 1993 by Sid Wells with our HQ in a draughty shed in Horsham with the factory several miles away! Today we operate from our brand new £550,000 office and dispatch building in Henfield with our factory next door. As well as our UK based customers we export around the world.
The late Sid's daughter Joanne (or Mrs. Grommet!) has, despite some bumps, pushed the business to success. A fourthgeneration British rubber moulding business that makes grommets and associated mouldings for a wide market with a longstanding presence in the rubber moulding manufacturing industry.
Tell us about Grommets Ltd.
Grommets Ltd are a UK leading manufacturer and stockist of grommets and custom moulded products. We stock a wide range of Rubber & PVC products, all manufactured and stocked in the UK but available for European and Worldwide export.
Want to know more about Grommets?
Tel: 01273 493355
Email: sales@grommets.co.uk Visit: www.grommets.co.uk
Frustrated with the lack of progress working in engineering, Sid went into partnership with two friends to start RTS, a rubber moulding company. Over the years, Sid’s friends left or retired from the business. Coupled with the early 1990s recession a new direction was sought and a plan to concentrate on the smaller product market was hatched.
Sid started again in 1993. Phoenix would have been an apt business name but instead Sid chose Grommets as it ‘did what it said on the tin’! Little did he realise what an act of brilliance the name was as, with the advent of the World Wide Web, and a Grommets website the ‘hit’ rate is very high. Headquartered in a ‘shed’ in Horsham with the factory a few miles away Sid recruited daughter Joanne in the early 1990s as a delivery driver, serving some of the 50 or so customers we had at that time. Branching out by working in all other areas of the business, including moving accounts from
‘If we don’t have a stock item to suit your requirements, we can offer a bespoke solution using custom tooling produced by our tooling engineer.’
old-style ledgers onto accounts software. Joanne was appointed MD by her late father in 2009. Grommets Ltd now has over 7,000 customers on its database.
Joanne was sadly handed the role of matriarch, after the sudden loss of her mother in 1998. Grace was Sid’s ‘rock’ she was only 62 when she passed away, and both she and Sid had looked forward to taking steps into retirement after Grace had served 25 years working for Marks & Spencer in Crawley as well as always being on hand to help in the business if required.
In 1998 the business moved to Henfield to bring it under one roof in the beautiful setting of West Sussex and shortly after Sid’s son Robert joined the business. We have been an ISO9001:2015 accredited company since 2009 specialising in producing highquality rubber moulded components for various industries. Joanne’s husband Mark joined the business in 2013. He re-wrote the quality manual and has main responsibility for maintaining our ISO9001 accreditation, by updating our systems and working with auditors. We manufacture our parts using compression moulding and whatever your requirement large or small we will aim to find a solution for you. We keep a vast range of items in stock and can offer quick lead times for non-stock items.
On the manufacturing side, the team of press operators is managed by Andy whose hands on approach, engineering skills and knowledge to make and repair tools is highly valued. The ‘hot off the press’ moulded products head off over to our despatch team, who are enjoying the ease of navigating the new stock and despatch area, enabling them to finish our products, pick, pack and send in a very productive way. We use sustainable packaging and, along with our own fully electric fleet, are making progress on environmental, sustainability and governance.
Sadly, Sid passed in 2010. Joanne had a vision of the future which Robert did not share so she bought him out in 2013. To move the business forward Joanne brought in family members with outside industry experience to share. Today, the business is one hundred per cent family owned with four generations represented – Joanne is MD; husband Mark (quality director); daughter Charlotte (office manager); stepson Josh (sales and factory planning) and granddaughter Saskia (social media).
Joanne is now a proud mother, grandmother, and great grandmother. Juggling her family alongside the busy manufacturing company has been challenging but rewarding. The joint efforts of family and our reliable workforce have all been instrumental in bringing Grommets Ltd as a market leader to a worldwide distributor of our products manufactured in the UK.
What success have you experienced in the last twelve months and how do you measure success?
Over the past year, we have achieved several milestones, including the completion of a new building for our office and despatch operations. With our extra space we could now introduce additional moulding presses (and employ more operators) and/or diversify into PVC injection moulding. This expansion allowed us to streamline our administrative processes and improve efficiency in delivering products to customers. We measure success through various metrics, including customer satisfaction surveys, production efficiency, and financial performance. Additionally, the positive feedback from our employees on the new work environment is a testament to our success in fostering a supportive workplace culture. Along with increasing our marketing budget, in his semi-retirement, Mark will attend many conferences, meetings and exhibitions. This, along with increasing social media presence and implementing a new sales and marketing strategy to promote our business and attract new customers and keep our present customers happy.
Which sectors do you work in?
We serve a diverse range of sectors, including automotive, aerospace, electrical, medical, military as well as supplying to rail industry distributors. Over the last few years, we have also seen a large demand for our parts from green industries such as wind farms and electrical car charging unit manufacturers. Our customers use our products for many applications including ventilators and other medical appliances; Royal Navy ships; road bridges; film sets which demonstrates a range of uses for our parts. Our expertise in rubber moulding allows us to cater to the unique needs of each sector, providing customised solutions for our clients.
What type of products and services do you offer?
We offer a comprehensive range of products, including but not limited to Open Grommets, Blind Grommets, Bungs, Bushes, and Washers, you can find our full range of parts on our website www.grommets. co.uk. We have tooling for several thousand different products. Often this can be easily
‘Over the past year, we have achieved several milestones, including the completion of a new building for our office and despatch operations. With our extra space we could now introduce additional moulding presses (and employ more operators) and/ or diversify into PVC injection moulding.’
adapted to produce several different sizes off the same tool. If we don’t have a stock item to suit your requirements, we can offer a bespoke solution using custom tooling produced by our tooling engineer where we can provide design assistance and quality assurance to ensure the highest standards of excellence in every product we deliver.
We have a simple part numbering system where the dimensions are the part number! For example, G10 R100-10-25 is an open rubber grommet to fit a hole size of 10mm in a panel thickness of 1mm and a cable hole of 2.5mm. This makes it easy for customers to quickly identify the part they require.
We mould in three main materials Nitrile (NBR); EPDM and Neoprene to suit the customer’s needs but we can also use silicone and FKM (a viton® equivalent).
How do you make your business a good place to work?
We prioritise creating a positive and supportive work environment by fostering a culture of collaboration, respect, and continuous improvement. We invest in the wellbeing and professional development of our employees through training programs and open communication channels. Additionally, our implementation of a fourday workweek for factory staff demonstrates our commitment to promoting work-life balance and employee satisfaction.
This also recognises that moulding is a tough, hot, and physical job. By valuing our team members and providing a conducive workplace, we strive to make Grommets Ltd a great place to work. We still follow Sid’s family business values of inclusiveness, honesty, and respect. However, we are a family so there will be disagreements (yes, and sometimes arguments!) but these are not allowed to fester and dealt with openness and respect. There are regular formal management and less formal staff meetings.
Grommets Ltd are a UK leading manufacturer and stockist of grommets and custom moulded products. We are proud to be a fourth generation family run business based in Sussex.
We stock a wide range of Rubber & PVC products, all manufactured and stocked in the UK but available for European and Worldwide export. We produce a wide range of standard catalogue items and custom made parts. We supply all areas of industry including rail, motor and electronic companies with “Just in Time” parts for their production.
Please visit our website www.grommets.co.uk to view our range of Grommets and other products, all stocked in a range of materials including Nitrile, Neoprene, EPDM, Silicone and PVC. Our products can be manufactured in any rubber listed on our website. -10%
on orders using the code “RailGrommets10”
Please call our friendly sales team with your enquiry or email sales@grommets.co.uk and make use of our 10% off discount code!
T: +44 (0)1273 494 400
E: sales@grommets.co.uk
W: www.grommets.co.uk
Ross has worked within the construction industry for over 10 years now, originally within the renewables sector Procurement before become Ops Manager and then Commercial and Contracts Manager. After many years of working in the renewable energy sector Ross joined Propump Engineering Ltd to head up their sales team.
Foamed concrete specialists ProPump Engineering Ltd design, supply and place or pump, light weight foamed concrete (also known as foam concrete) for permanent void infill, abandonment, or temporary structures all over the UK, London, Home Counties, Midlands, and Northern Counties.
Want to know more about Propump Engineering
Tel: 01322 429900
Email: info@propump.co.uk
Visit: www.foamedconcrete.co.uk
Tell us about Propump Engineering Ltd.
Established in 1991 and independently owned, Propump Engineering were the first foamed concrete specialists in the United Kingdom and today offer a nation-wide service from our purpose-built premises in South London. This pioneering attitude toward foamed materials has enabled a steady expansion using our own labour, specialist plant, and equipment, all of which is designed and manufactured in-house.
We have developed a range of materials for many applications and are continually enhancing these products, this on-going development is concerned with further improving the properties of foamed concrete including its potential use in high grade structural applications, thermally insulating blocks, and the production of foamed concretes using non primary aggregates.
What types of products and services do you offer?
We offer and specialise in the supply of many different grades of foamed concrete. Foamed concrete is a lightweight, free flowing, self-compacting, and highly insulating material. It exhibits good load bearing capacity and resistance to freeze thaw exposure. We provide a versatile product, which is highly flowable and yet when set can be tooled to provide access for services, piled through, bored through, and even driven over.
From strengthening weak bridges to infilling abandoned mine workings and everything in-between, foamed concrete in its many forms is a versatile and proven solution. Designed as a void fill material, typical densities are normally between 450 kg/m³ to 1500 kg/m³, with corresponding strengths ranging between 0.50 N/mm² to 10 N/mm².
Alongside our core business of foamed concrete, we also manufacture and sell both 100mm and 150mm polystyrene cube moulds for sampling and testing of cementitious grouts.
What is your Unique Selling Point?
Our Inline Foamed Concrete System (IFCS). These systems are site based and enable full deliveries of a specified base material to be delivered to us on site via ready-mix mixer trucks. The IFCS processes these base materials by injecting a preformed foam under pressure into the base material as it is being pumped. The injection of the foam is carefully controlled and added on a continual basis to produce a consistent foamed concrete material, this coupled with the ability to pump the material to a distance of 150 metres plus means we are well suited for even the most challenging of projects.
The IFCS enables us to produce up to 35m³ of foamed concrete from a 7m³ load of
‘We work with many different organisations from joint ventures, that head up projects such as HS2 and Thames Tideway, through to large Civil Engineers and smaller scale construction firms and anything in between.’
base material (mix design dependant). This greatly reduces the number of trucks on the road and truck movements on and off site, which in turn reduces the CO₂ footprint associated with site deliveries. Having a dedicated IFCS means that we are a one stop solution, there is no need to have additional concrete pumps hired in, we are able to complete the project with one piece of plant and a highly skilled team.
What are some standout projects you’ve been involved in over the years?
Gerrards Cross – Gerrards Cross Tunnel is a new railway tunnel in Buckinghamshire, over the Chiltern Main Line. The purpose of the tunnel was to cover some 300 metres of railway track which would then enable a new supermarket to be built over the railway. Unfortunately, during the initial construction of the tunnel, it partially collapsed.
After this initial collapse, the damaged section of the tunnel was rebuilt and Propump were approached to provide an ultra-lightweight material that could be used instead of the original specified fill material to fill the void, thus reducing the dead weight loading on the tunnel structure. The foamed concrete specified was 450 kg/ m³, this being approximately five times less dense than a traditional infill material whilst still achieving 1 N/mm² strength at 28 days. By reducing the weight of the void infill, the loading on the structure was reduced drastically. Propump had two IFCS’ on site, each producing over 300m³ per day of foamed concrete. Over 25,000 cubic metres of foamed concrete were manufactured and pumped in total.
Crossrail – Crossrail provides a commuter rail and rapid transit system, known as the Elizabeth line, that crosses the capital from the West to East and connects two major railway lines.
We manufactured and placed over 30,000m³ of foamed concrete for various applications throughout the Crossrail
‘From strengthening weak bridges to infilling abandoned mine workings and everything in-between, foamed concrete in its many forms is a versatile and proven solution.’
project. These included filling redundant shafts, adits or linking tunnels used during the main construction phase.
An innovative use for foamed concrete was as a medium for the TBM’s to drive through on a number of station chambers, this meant that the TBM’s didn’t have to stop, they could continue boring through the foamed concrete and back into the surrounding strata. It was much more efficient to do it this way than to dismantle the TBM at one side of the station chamber and re-assemble it on the other side to continue the tunnel boring process.
Foamed concrete was also used to permanently bury several of the TBM’s after their final drive.
Dawlish – A 109-metre-long rock fall shelter constructed at the North end of Parsons Tunnel near Holcombe in Devon to protect the rail line from falling rocks and debris from the steep cliffs.
After the new rock fall shelter was constructed as an extension to the existing Parsons Tunnel along the coastal rail line at Holcombe, Devon, Propump were contracted to infill the large void area between the cliff face and the new rock fall shelter.
Over a course of seven weeks, we placed over 5,000 m³ of foamed concrete, coming up to a total height of approximately eight metres. This project presented its own set of unique challenges, as we had to set up the IFCS at the top of a cliff and pump down 30 metres via a fixed concrete line and then horizontally up to 170 metres to the point of discharge without compromising the materials density, which was specified to be 600 kg/m³.
This was made even more challenging as this project was carried out in the middle of summer with increased temperatures on the exposed concrete pump lines, which potentially could have resulted in an accelerated curing time for the foamed concrete. However, working closely with the main contractor meant that we found safe, reliable, and effective, workable solutions to the challenges faced. These solutions included a delivery system that incorporated vehicle tracking to enable base mix deliveries to be managed and monitored from batching plant to site, meaning that foamed concrete could be produced at the required daily rate to the specified program.
Propump Engineering Ltd are a manufacturer and supplier of foamed concrete. Working on some world class projects, including the largest foamed concrete project in Europe at Combe Down near Bath, as well as on HS2, Thames Tideway and the Crossrail project. With dedicated in-house training and a forwardthinking approach, Propump Engineering Ltd are the go-to when foamed concrete is needed on a project anywhere in the United Kingdom.
Established in 1991 Propump have pushed the boundaries of foamed concrete production and placement and in doing so have left their competition behind. Propump Engineering Ltd have continued to be at the forefront of new developments all whilst not losing site of what their clients require and expect from them.
Want to know more about Propump Engineering Ltd or more information on foamed concrete?
Tel: 01322 429900
Email: info@propump.co.uk
Web: www.foamedconcrete.co.uk
What types of companies do you collaborate on projects with?
We work with many different organisations from joint ventures, that head up projects such as HS2 and Thames Tideway, through to large Civil Engineers and smaller scale construction firms and anything in between. We also work across multiple sectors. To us, it doesn’t matter who our client is, we treat everybody with respect, and approach our work with the same professional manner, whether we are manufacturing 5m³ or 5,000m³.
What are some of the biggest challenges this sector currently faces?
With cement production being a major contributor to CO₂ emissions as well as a key component of foamed concrete, we face a challenge in reducing the products embodied carbon. Continued and further R&D at Propump means that we are constantly developing new mix designs to meet the challenges of modern construction. At present, a foamed concrete with a kg CO₂e/m³ as low as 130 is available on a national basis.
Utilising over 7 years of historical data, PathPlanner seeks out unused paths across the network to unlock capacity and generate new opportunities for the freight sector to transport more goods seamlessly and sustainably. Make. Change. Work.
Rail freight is getting ready to deliver a customer-focused, competitive and sustainable option for the business world
For the first time ever, the Office of Rail and Road has set targets for rail freight growth across Great Britain, of 7.5 per cent for England and Wales, and 8.7 per cent for Scotland over the next five years.
These targets show that policymakers are backing sustainable transport. With research outlined in a 2023 Rail Partners report suggesting that a single freight train can remove up to 129 HGV journeys, the environmental benefits are clear.
The challenge now is to encourage more freight customers to make the shift from road to rail.
Many businesses consider rail to be a complex, unwieldy and uncompetitive way to move goods around the country. However, some pioneering digital solutions are set to change the minds of logistics customers by making rail freight a more streamlined, accessible choice.
These are some ways technology can make rail freight a more competitive option for business.
The difficulties in finding new paths on the rail network at short notice make freight planning a challenge. Digital technology is improving the way operators can plan their freight services by identifying available paths which they can bid for directly from Network Rail through the Very Short-Term Planning (VSTP) process.
Finding a path to run an additional freight train is also difficult because rail timetables show little free capacity on the network. However, our research shows that around 45 per cent of timetabled freight paths are not used. Predictive analytics based on historical timetables and operational data can help operators identify unused paths on the network which would otherwise go to waste.
Rail freight needs to be more flexible in order to compete with road. Technology
could help operators make sure those unused paths they identify on the network don’t conflict with other services. So, if an operator finds an existing path that’s available but doesn’t exactly suit their customer’s needs, the operator can adjust the departure time or build in breaks to fit around other scheduled services.
To grow their customer base, rail operators need to tailor their services to customers of all sizes and budgets. Better visibility of data can help operators respond more quickly and cost-effectively, making their services more competitive. A tool which can identify space on partially filled wagons could support better planning for customers with lastminute orders or smaller loads.
Logistics firms are increasingly expecting Amazon style order tracking. Operators can respond to these demands by providing greater visibility through virtual booking systems. These systems allow customers to place rail freight orders online and access accurate departure and arrival times. A simpler, more transparent ordering process helps customers plan and manage their own business commitments.
Businesses with complex logistics requirements need information on the movement of their containers, but what happens on the yard can sometimes seem a bit of a mystery. Some operators provide customers with an app which enables them to view the number and locations of the wagons where their containers are carried. The app can also update customers on the loading of the wagons and confirm when their load is ready to go.
Late deliveries can make or break a business in today’s competitive environment. If there’s a tree blocking the track or the overhead lines are down, getting that
information to the control team in real time allows them to make better decisions. Digital communication allows controllers to notify the customer of the likely length of delay, while real time alerts assist in identifying capacity on another train, or taking a different route to the destination.
By analysing data on why incidents happen and how they affect customers, operators can identify solutions to reduce incidents and minimise their impact. Operators can also use data on the relationship between capacity and demand to anticipate and meet their customers’ evolving needs.
The environmental case for rail freight is compelling. With advancements in digital technology, the rail freight sector can take advantage of the opportunities presented by the decarbonisation agenda, and help customers make the shift from road to rail.
To find out more about how digital technology can drive growth in rail freight, with insight from leading voices in the industry, download our eBook: https://3squared.com/ebook-how-digitaltransformation-can-shape-the-future-of-rail/
Visit: www.3squared.com
Social: @3Squared
Join over 6,000 rail professionals at Rail Live 2024 on 19 and 20 June, held at Porterbrook’s Long Marston Rail Innovation Centre
At the UK's largest outdoor rail exhibition, immerse yourself in a vibrant atmosphere, which blends networking with the latest advancements in rail technology, all set against the authentic backdrop of a real railway environment. This year's event features cutting-edge technology, engaging panel discussions, and excellent networking prospects.
You’ll be able to explore the latest rail innovations and see technology you didn't know existed that can help you with your work practices, from safety, to productivity, to sustainability.
Innovations for Rail Live 2024 include the introduction of a dedicated engineering theatre for the first time, and filming of an instalment in Network Rail’s Freight Escape series. The Railway Industry Association will also be filming (in its case the next episode of RIA Rail TV) and running a showcase on unlocking innovation in its dedicated RIA Lounge.
You can join a variety of in-depth content sessions led by experts from Network Rail, the Government, and more. A full list of speakers is available overleaf.
A key question being asked at this year’s event is: How do we retain and build on learnings from the innovative engineering involved in the construction of High Speed 2? That will be one of many topics debated in the new engineering theatre being introduced for the first time at Rail Live 2024.
With future recruitment to the railway of increasing concern, this year’s Rail Live will also include a focus on attracting new people to the railway. Network Rail Group HR director Pauline Holroyd and East West
Rail Innovation Manager Daisy ChapmanChamberlain will be among those advising business leaders about how the railway can increase its appeal to a younger, more diverse workforce. Held at Porterbrook’s Long Marston Rail Innovation Centre on June 19/20, Rail Live will also host the rolling stock company’s ‘Primary Engineer’ programme, which allows children to investigate and build their own model trains.
Porterbrook’s Long Marston Operations Manager Phil Handford said of the programme: ‘I’m hoping that some of these
young kids today, from what they’ve taken in this experience, will become an engineer – whether it’s in the railway, car industry, or wherever.’
Rail Live will also include a dedicated Railway Industry Association Innovation Lounge, displays of ‘yellow plant’. Rail Live is also the only rail event in the UK with real rolling stock on display in a real railway environment with a presentation of one of the new Class 93 tri-mode locomotives being built by Stadler for Rail Operations Group (ROG). Class 153 monitoring train.
Han® HPR HPTC – Especially developed for railway applications.
High performance transformer connectors
■ Longer lifetime due to Han® HPR metal hoods and housings for harsh environments
■ Time savings due to easy installation and shielding without shrinking or taping
■ Cost savings due to minimum inventory needed based on efficient coding system
■ Secure solution according to relevant railway standards (EN 50467, EN 50124-1, EN 61373, EN 45545, EN 60137)
■ Shock- and vibration proofed system
One Range. No Limits: www.HARTING.com/hptc
The UK’s largest outdoor rail exhibition, Rail Live, takes place over 19 and 20 of June at the Long Marston Rail Innovation Centre in Warwickshire
The Railway Industry Association (RIA) is pleased to partner with Bauer Media for the event where over 6000 visitors from across the sector are expected to attend.
The annual rail show is an industry highlight and brims with visually engaging displays such as live plant demonstrations, rolling stock and examples of the latest technological developments and innovations in the rail industry. In addition, there are lots of opportunities to meet and connect with decision-makers and gain insights from rail experts.
For the first time, RIA will be hosting an Innovation Showcase this year at the RIA Lounge, which visitors will find located at stand P75, and will include a variety of member companies exhibiting their latest rail products and services.
The Rail Live exhibition will feature a diverse range of senior level speakers, supply chain innovations and thought leaders from across the industry. Key contributors include RIA Chief Executive Darren Caplan, Rufus Boyd, Interim Lead Director at the Great British Railway Transition Team, Andrew Haines, Chief Executive Network Rail, RIA Innovation Director Milda Manomaityte, Lucy Prior MBE, Business Growth Director at HIRD Group, Huw Merriman MP, Rail & HS2 Minister and Stephen Morgan MP, Shadow Rail Minister.
Both Huw Merriman and Stephen Morgan will be visiting the RIA Lounge and meeting rail suppliers. The politicians will then have a tour of the site with Darren Caplan, RIA Chief Executive.
Chris Lester, Event Director, Rail Live – Bauer Media said: ‘We are excited
to announce that RIA has become a show partner of our leading Rail Exhibition in the U.K. RIA is an essential organisation within the Rail industry, and we are proud to have them as our official partner. We are eagerly looking forward to welcoming them to Long Marston in June. The positive experience for exhibitors in 2023 has already led to a record number of rebooking’s for this year's event. It is encouraging to hear that many of our exhibitors met and exceeded their targets for the event and even took several orders on their stand.’
This year will also see the return of RIA Rail TV, with an episode set to be filmed at the event. Last year’s episode featured appearances from Huw Merriman MP and Lord Peter Hendy, Chairman of Network Rail.
Lord Hendy said of RIA: ‘You need a good trade association to represent the member’s interest and also to do political advocacy about the long-term future of the railway.’
Full details of the Rail Live programme can be found at www.raillive.org.uk/2024features.
French manufacturer Petzl is renowned the world over for its technical equipment and today it offers a complete package from helmets and headlamps to work at height harnesses for professionals
‘One
of the long-standing missions of Petzl has been to improve ergonomics and efficiencies.’
There’s no question Petzl is a company with a fascinating story behind it. Developing out of one man’s passion for caving, the safety equipment manufacturer has grown to become one of the world’s biggest names in climbing gear and personal protective equipment for those who work and play in darkness or at height.
The Petzl company was established by Fernand and his son Paul in 1975, and today it continues to be owned and operated by the same family. Petzl headlamps have brought light to the world’s darkest of places for over four decades.
Petzl produce an extensive range of products and integrated solutions designed for a variety of disciplines involved with industry, height and vertical environments including the ‘pro’ markets of rail, wind energy, arborism, rope access and rescue operators through to ‘sport’ markets of climbing, trail running and mountaineering.
One of the long-standing missions of Petzl has been to improve ergonomics and efficiencies, whether that’s offering integrated helmets and headlamps for rail, working on a wind turbine or pushing the limits of difficulties on an Alpine climb, it’s about looking at the touchpoints of the products, how they’re handled and how they feel, so they are as simple and as seamless to use as Petzl can possibly make them, but also so they make the job as efficient and stress-free as possible.
Petzl's philosophy for design and production is also based on accelerating change, transforming, and innovating in order to provide professionals and sports enthusiasts with the quality products they demand. Testing tower, experimentation centre, individual inspections, LEAN manufacturing process – Petzl was a pioneer in all of these innovations.
Petzl headlamps can be installed on any helmet by using the headband, adhesive plates, or mounting plates at the front or rear of Petzl helmets for inserting the headlamp. With a power source that comes either from disposable batteries and/or rechargeable batteries, you can be sure that you'll have the light you need, when you need it.
The ultra-compact ARIA headlamps save space, are extremely lightweight, and small enough to slip into your pocket while the DUO performance headlamps are particularly durable and powerful. They are designed for intensive use in industrial environments, or for maintenance and inspection purposes. Petzl also has models that are ATEX certified, designed for use in hazardous areas to endure the rigours of high-risk zones and confined spaces.
When safety is a priority, so is industrial excellence. Petzl has a deep responsibility to the people who trust it with their lives, and it develops, tests, and qualifies all of its products above required standards. Petzl’s objective is to allow zero defective products to leave is facilities, to give you high quality products and peace of mind at work.
Petzl Work at Height Solutions offer a full range of helmets, harnesses, lanyards, fall arrest, headlamps and equipment to make your work easier. Email:
Nikki Amers-Delph discusses the sustainable movement in modular construction and its opportunities for the rail industry
Atotal of 417 million rail passenger journeys were recorded in Great Britain in the latest quarter of 2023, with a total passenger revenue of £2.6 billion. With continuous growth and evidence of substantial investment projects including HS2 and EGIP, it’s vital that we acknowledge opportunities where sustainability developments can be introduced.
In the realm of rail infrastructure development, sustainability is paramount. Wernick Hire and Wernick Power Solutions are pivotal players, offering solutions that prioritise environmental responsibility while enhancing project efficiency.
In today's global landscape, sustainability has transcended from a mere trend to an imperative. Environmental concerns and heightened awareness about the impact of human activities have developed the movements of sustainability. Our customers, now more than ever, demand products that align with their values and contribute positively to the planet. Embracing sustainability isn't just a choice for us; it's a responsibility. By integrating eco-friendly practices into our products and processes, we not only meet the evolving expectations of our customers but also contribute towards a healthier, greener future for generations to come.
Wernick's commitment to sustainability extends seamlessly into the rail industry, with its welfare units indispensable to
rail projects. Prioritising the well-being of the workforce is paramount within the fast-paced and demanding world of rail construction and maintenance. Wernick's welfare units, equipped with toilets, changing facilities, and comfortable break areas, serve as vital sanctuaries for railway personnel. Our welfare units are designed with sustainability in mind, integrating energy-efficient fixtures and environmentally friendly materials to foster a conducive environment for productivity and safety. Prioritising comfort while minimising environmental impact, these units contribute to a healthier and more sustainable rail work environment.
At the forefront of Wernick's sustainable site accommodation solutions is the GreenSpace® Sureguard Cabin, representing the pinnacle of energy efficiency and environmental performance with its EPC A rating. Exemplifying Wernick's commitment to sustainable construction practices, the cabin features advanced insulation, energy-efficient fixtures, and options for renewable energy integration. It offers occupants a comfortable and environmentally responsible workspace, supporting productivity while minimising carbon footprint.
So that we can deliver service excellence to our customers, Wernick must ensure investment is made into sustainable assets to accommodate the permanent demand. In 2023, Wernick Power Solutions (WPS) invested £10.8 million into volt banks, flybrids and solar frames amongst other products. May of 2024 saw another £2.1
million investment acquiring 36 battery storage units; another ethical move to offer clients products which will substantially reduce their carbon emissions. The new units will significantly reduce generator runtime, resulting in a decrease to emissions output, noise levels and fuel costs. The Rail Safety and Standards Board (RSSB) have presented the rail industry's view on how to make the railway even more sustainable, and the industry is already working to implement the Blueprint. Leveraging of renewable energy sources and optimising energy usage in rail projects with Wernick's temporary power solutions highlights more than just convenience, it projects movement to a more sustainable rail industry.
The Wernick Group of Companies have made the ambitious commitment to become net-zero by 2040, ten years before the UK government initiative. Within the Carbon Management Plan, Wernick is targeting a 45 per cent reduction in scope 1 and 2 emissions by 2030, and an annual carbon emissions reduction of 6.7 per cent. Not only are we making conscious efforts to enhance the current impact of sustainability, but we’re also continuously working to guarantee a sustainable future for modular construction and its opportunities for the rail industry.
Milwaukee tools, which has built its reputation on the supply of high quality power tools for professional site workers, has turned its attention to the railway sector and launched the lightest, cleanest and most end user friendly powered railway wrench on the market
The M18 Fuel Railway Impact Wrench with Friction Ring is designed for workers to use without having to bend when fastening and unfastening railway bolts at ground level. It provides a fast solution to this traditionally backbreaking task.
A completely new concept for Milwaukee, the wrench was designed after extensive research with workers to find out what they were looking for. The design team believes that using this new wrench will make bolt fastening faster and easier while also significantly reducing the physical challenge for the operative.
Light weight and comfortable
Battery powered rather than using petrol, the M18 Fuel Wrench weighs in at just 7.8kg in use. It is 780mm in height, allowing the user to work in an upright position to significantly reduce fatigue. Comfortable rubber-covered handles plus carrying handles also make it the easiest tool to move around.
Despite the ergonomic design, this is no lightweight when it comes to performance. The M18 Fuel Wrench gives 2,000Nm of maximum torque, easily equalling petrolbased equivalents in terms of power performance. Sufficient power to loosen even the oldest, most rust-bound bolts quickly and easily.
It’s the latest in the range of high performance M18 Fuel power tools that are based on the market leading M18 HIGH OUTPUT batteries – engineered by Milwaukee to deliver more power, run cooler and provide more run-time versus previous battery technology. When used with the M18 12Amp HIGH OUTPUT battery, the wrench should give a runtime of approximately 300 bolts without any fading
of performance. The battery is also designed for fast charging, minimising downtime. For main contractors looking to control carbon emissions, the battery powered Wrench is another clean contribution from Milwaukee. It is also designed to be extremely durable, requiring less maintenance than similar tools, making it a cost-effective as well as CO2 free choice.
Users will appreciate the range of speed settings, ensuring that each use is completed at optimum speed, while an auto shut-off function will prevent over tightening of bolts. The wrench is even designed to cope with low light levels, having two LED lights at the bottom of the tool to give visibility in dark conditions such as in tunnels.
Milwaukee believes that this tool will help make the working day easier, more productive and far less exhausting for operatives, contributing to cost-effective project delivery for contractors.
The M18 Fuel Railway Wrench is supplied with two M18 HIGH OUTPUT 12.0 AH BATTERIES, an M12-M18 fast charger and a robust kit box. It is available via most major distributors. To find your nearest stockist, visit the Milwaukee website at https://uk.milwaukeetool.eu/
Automatic Tensoning Device
Our Expertise for Railway and Tramway:
Our Expertise for Railway and Tramway:
- Railway Catenary Systems
- Railway Catenary Systems
- Tensioning
- Tensioning
- Insulation technology
- Insulation technology
- Power supply
- Power supply
- Safety equipment
- Safety equipment
Mosdorfer Rail Ltd.
Mosdorfer Rail Ltd.
2 – 4 Orgreave Place, Orgreave
2 – 4 Orgreave Place, Orgreave
Sheffield S13 9LU, South Yorkshire, UK
Phone: +44 114 3878370
Sheffield S13 9LU, South Yorkshire, UK
Phone: +44 114 3878370
E-Mail: OrdersRailUK@mosdorfer.com
E-Mail: OrdersRailUK@mosdorfer.com
The MOSDORFER rail group has companies in the UK, Spain, Italy and India. It is part of the Knill Gruppe which is based in Weiz, Austria. The Knill Gruppe is family-owned organisation with over 310 years of experience within the Engineering sector but specialises in Energy and Technology.
Want to know more about MOSDORFER Rail?
Tel: 0114 387 8370
Email: ordersrailuk@mosdorfer.com Visit: www.mosdorfer.com/en/about-us/
What types of products and services do you offer?
We are a provider of complete overhead line electrification systems for high speed, mainline, light rail and tramway systems. Our products include all elements of overhead line equipment from cantilever system, insulators, tensioning system, droppers, electrical clamps and fitting and safety equipment.
What are some major projects you’re currently working on?
We are currently working on several global rail projects. The two largest projects are Tren Maya in Mexico and Mersin-AdanaGaziantep in Turkey. In the UK we are supplying products to the decarbonisation projects in Scotland and the Core Valley Lines in Wales.
What are some standout projects you’ve been involved in over the years?
We have been involved in most mainline electrification schemes throughout the years but we are probably not given credit for our international presence and recent significant projects include:
• Yerkoy Sivas project Turkey
• Dar es Salaam – Morogoro Project Tanzania
• Bandirma-Osmaneli project Turkey
• Midland Mainline electrification
• The Great Western electrification
What challenges have you faced in the industry?
Over the past decade we have faced a number of significant challenges. Instability of the UK domestic market has necessitated strategic adjustments due to unpredictable volumes and demands. Add Brexit, the conflict in Ukraine and the Covid pandemic into the mix and as a business we have faced unprecedented challenges. The uncertainty around the 2050 net zero decarbonisation delivery is the biggest challenge we currently face. We need clear commitment to a strategic delivery plan.
How has technology developed since you started in the industry?
The industry has rapidly moved into the digital age with the key drivers being reliability, whole life cost, environmental sustainability and AI utilisation to provide predictive maintenance models instead of planned/reactive maintenance.
What is your Unique Selling Point?
Our USP is being able to combine value with innovation while maintaining small business flexibility, think local and act global!
When a client comes to you with a particular problem, what’s your process for coming up with a solution, and how closely do you work with clients throughout the projects?
We aim to provide an end-to-end delivery service based on the customer needs and specifications. We often adapt our product to suit the customer specific application and pride ourselves on our customer service level. With this approach we strive to achieve customer retention and product loyalty.
What new developments/strategies do you have?
We have several new product developments currently in the final stages of the product design life cycle. These include the following:
• New spring tension device with up to 40 per cent increase in compensation.
• Lightweight low-cost cantilevers for high speed and tramway applications.
• Smart tension products with predictive maintenance technology.
• In-house manufacturing of balance weight anchors.
• A range of product related installation tools.
• Dedicated Tensorex C+ Installation Training course.
What are your plans going forward to ensure Mosdorfer Rail services are still around for years to come?
We intend to invest in people, plant and customer partnerships to ensure that we do not stand still and that we will remain in business for another 300 years. We also see synergies within the Knill Gruppe in similar sectors such as transmission and distribution systems that can transfer directly to the railway sector.
What are some of the biggest challenges this sector currently faces?
Uncertainty over the correct current or future technologies to be used on UK decarbonisation projects is creating a whole new level of concern as a supplier. The sector needs a clear long-term commitment and delivery strategy, without this we face further loss of skills and expertise.
What are some potential solutions?
The solution is to have a long-term railway strategy which is independent to political party and introduce competition to certain routes.
What do you think is the biggest challenge currently facing the rail industry?
We believe the rail industry faces two large challenges which are linked. Firstly, the UK is losing its UK-based railway manufacturing capability, the number of UK based railway manufactures is dwindling as a result of the uncertainties concerning rail strategy and investment. We are far from the railway powerhouse we once were! The resultant effect of this lack of manufacturing can be seen in the industry knowledge base. There is a significant skills and knowledge shortage.
What are your hopes for the new regulatory bodies, such as Great British Railways?
To embrace innovation and UK manufacture by making the approval process and route to market more efficient and having accessible testing facilities that support this approach.
In terms of technology, how do you anticipate things might change in the next five to ten years?
In the next five to ten years batteries and fuel cells are going to challenge electrification systems and the general mode of moving people. Autonomous railway systems and predictive maintenance systems through digitisation are also going to have a huge impact on the industry.
Daniel joined Chevron Green Services in 2022 following an 8-year tenure as the Asset Manager for National Highways. Following the completion of a Civil Engineering Degree Apprenticeship, Daniel has achieved Fellow Membership of the Chartered Institute of Highways and Transportation for his contributions to the industry.
Chevron Green Services deliver unrivalled, future focused green infrastructure services and consultancy. With over three decades of experience in environmental consultancy, commercial vegetation management, landscaping, and arboriculture. Their focus is on helping clients to create and maintain sustainable environments.
Want to know more about Chevron Green Services?
Tel: 0330 174 4386
Email: info@ChevronGS.com Visit: www.chevrongs.com
‘There are huge opportunities to enhance the green infrastructure on the rail network.’
gives us scale, where scale matters most. Covering the UK, our sister companies are experts in critical infrastructure safety services. Which means through our Group, we can offer specialist solutions in traffic management, barrier services, fencing, digital technologies, and design services. A caring force for a safer world is the mission that runs through every interaction. A core strength across our group is collaboration, whether that’s with each other, with our clients or with other contractors to complete the job safely.
What is your role within Chevron Green Services?
My role as Business Development Manager is varied from working on bids and tenders, to client support and advice, to ensuring projects and maintenance activities are delivered with maintenance in mind. It’s important to CGS that we’re offering solutions with longevity and maintenance front and centre, so supporting clients to design or adapt projects to include that way of thinking is an important part of my role. I’m also privileged to have opportunities to work with our teams on research and development projects alongside organisations such as Grown in Britain, supporting how the industry captures asset data.
What does sustainability mean to you?
Personally, I approach sustainability holistically, via each of the three pillars; environmental, social and economic. We always incorporate the three pillars into daily routine tasks and even more so when working on larger projects where our clients have sustainability targets to reach. The way our business operates allows us to have a positive impact on the environmental pillar, from our contributions to biodiversity net gain support and calculations, to the way we utilise our plant and where required, hire in the latest models with lower emissions.
Being part of Chevron Group allows us to be involved with social value projects such as assisting HMP Lindholm with their modules regarding arboricultural training, providing specialist NVQ guidance that inmates and ex-offenders would previously have had difficulty accessing.
The business must also make decisions of economic sense whilst following our core mission statement: ‘To safely create, maintain and care for biodiverse habitats for generations to come’. For me, it’s about changing the approach from thinking about a short-term financial gain to looking at the lifecycle cost of works.
Tell us about Chevron Green Services.
Chevron Green Services has been operating across England and Wales for three decades. We are built on knowledge, respect and appreciation for nature and our planet. We are part of the Chevron Group which
What types of products and services do you offer?
Our Consultancy division offers a full range of environmental, ecological and arboricultural consultancy services which can be delivered as standalone services to our customers or can be combined with our operations teams for all vegetation management, tree and landscape works. We offer design support to customers from full site scoping assessments, preparation of specifications, and production of bills of quantities.
Our ecologists carry out Biodiversity Net Gain assessments, Preliminary Ecological Appraisals, European Protected Species licence applications and Ecological Clerk of Works. Our experienced team of consultants have strong connections in the industry which enable us to be involved with research and development projects meaning as a company, we are at the forefront of developments within the industry.
Our Operations teams deliver a variety of future focused green infrastructure services. Including vegetation management, arboriculture services, creating and managing planting schemes and asset management.
How passionate are you about sustainability in the rail sector?
Sustainability is key for our business which is supported by the Chevron Group sustainability strategy. Chevron Green Services benefit from the support of our Group ESG team for baselining our activities and supporting our drive towards Net Zero. There are huge opportunities to enhance the green infrastructure on the rail network. A long narrow asset may seem difficult to create biodiverse habitats, but there are so many efficient and effective options for landscape creation and management that these activities should become day-to-day maintenance activities undertaken across the network. Proactive asset management and planning will be the key to creating biodiverse habitats, understanding the asset condition and proactively planning and implementing interventions. Creating and managing a cyclical works programme will also allow clients to secure and allocate sufficient funding to establish important linear habitats.
‘Being able to demonstrate that the rail industry is concerned about the environment and is making positive changes to the way it operates will also help in enticing new people into the industry.’
When a client comes to you with a particular problem, what’s your process for coming up with a solution, and how closely do you work with clients throughout the projects?
Chevron Green Services are typically brought in to create solutions for our client’s problems. Whether the problem is an urgent European Protected Species or a client not
knowing what they want from a site, we always engage with the client early to allow us to understand what they want or envisage the outcome will be from a project.
We work with clients to meet project requirements, understanding any KPIs and support them to deliver these. This can start from producing a specification and bill of quantities, to producing method statements to prevent unnecessary damage to wildlife and undertaking the ecological clerk of works role and finally producing biodiversity net gain calculations. The importance of understanding that proposals put forward by our consultants will need to be approved by individuals outside of our field means we have to be clear with our explanations using visualisations and concept designs where required to reaffirm our message to deliver on the project goals.
Sometimes our clients come to us not really knowing what they want or what would be most useful for them at a particular point in time. Our professional and honest approach is grounded in integrity. If you don’t need what you’re asking for, we’ll tell you.
Our open and collaborative way of operating means that we have clients returning to us time and again as they know we provide a safe pair of hands.
What are your plans going forward to ensure Chevron Green Services are still around for years to come?
Chevron Green Services will continue to deliver works to the highest quality whilst building on our reputation of excellent customer service. Enhancing our existing relationships whilst engaging with new clients is critical to our success. We’ll continue to use our expert knowledge whilst collaborating with experts outside of our industries to bring new working methods into transportation to ensure we are leading the way within this important sector.
To ensure the success of the business, we will continue to diversify into new sectors, growing into these through our existing client relationships and integrating our teams into contracts, projects and client organisations. This collaborative approach with our clients will pass on our knowledge and understanding of the environmental requirements to ensure the success of their projects.
What’s next for Chevron Green Services?
Chevron Green Services are always looking to innovate, to develop and to secure additional work that we believe in, and we
We deliver unrivalled, future focused green infrastructure services and consultancy.
Every day, through nature’s lens we care for their world, and our planet.
Our mission is to safely create, maintain and care for biodiverse habitats for generations to come.
With a bespoke, client focused approach, we work with you to plan for the long-term, beyond the life cycle of your projects.
Over three decades of experience in:
• Environmental Consultancy
• Landscaping and Arboriculture
• Commercial Vegetation Management
Because we care. With us you get more. Contact us on info@ChevronGS.com To find out more go
care about delivering. We are taking our expertise, gained within three decades of highways work and are transferring this knowledge into other sectors. Our team of ecologists and environmentalists have already taken this knowledge forward into the rail and defence sectors and we will look to do the same with our operational delivery teams. The support we have from Chevron Group will allow us to grow, develop and innovate as a business.
Our mission to safely create, maintain and care for biodiverse habitats for generations to come means that we always have an eye on the long-term. We want to enable our clients to conserve the habitats they own for as long as possible.
What are some of the biggest challenges this sector currently faces?
One of the biggest challenges is the cost of projects. Many projects are awarded on price where the most economically advantageous price for the work is awarded to that bidder. This is particularly notable with Tier 1 to Tier 2 procurement activities. Where forward thinking companies are trying to reduce their impact, implementing sustainable procurement policies and therefore may increase the price of work delivery, this puts the company at a disadvantage where cost is the deciding factor. It’s a straightforward solution though, carbon emissions, sustainability and the whole life cost of projects needs to be considered at design and ECI states of a project.
Changing behaviours and ways of doing business means we can improve as an industry and drive sustainable targets at the forefront of every project. Safety plays a big part in this too, if a project is devised with maintenance and longevity in mind, there are often safety benefits too. For example, in the use of biodegradable tree guards, they reduce the need for return visits to remove the guards in years to come once the tree is established. This not only removes the
carbon associated with the return trip, but with no return trip, we are removing the need for someone to be working in a safetycritical environment.
Do you think the rail industry could be greener and what is your organisations green strategy?
It’s always possible to be greener, whether that’s offsetting your carbon emissions, using low emission plant or vehicles or diverting waste from landfill. There are always additional small steps or changes organisations can take or make. There are opportunities to reduce the impact of our industry on the environment and improve our surroundings. Retrofitting green roofs on station buildings would be a fantastic opportunity to reduce the impact of water into positive drainage as well as increase local biodiversity in generally non-diverse environments.
The Chevron Group aim to decarbonise by design, initially avoiding carbon intensive activities, then by reducing the number of these activities where possible. Thirdly, we’ll replace the high-usage activities with low carbon energy sources and finally will offset where emissions cannot be eliminated.
How can we make the rail industry a place people want to work in?
The rail industry, like any part of the transportation industry, is a constantly evolving sector. With new innovations for working methods, new technologies developing to improve the way we survey and understand our asset and state of the art development projects, existing and potential employees should be excited to work in the industry.
However, with other technologies developing outside of the industry, it is key to engage people at a young age whilst also making the rail industry enticing for people looking for a career change. This can be achieved through engagement with schools and colleges to allow young people to understand the opportunities available to them as they are so broad within the rail industry.
I started within the transportation industry at a young age and didn’t know the wide offering of career prospects available to young people, therefore it is key to show these so people can understand where their career could progress to.
The younger generations care deeply about the environment and the impact society has on the planet. Being able to demonstrate that the rail industry is concerned about the environment and is making positive changes to the way it operates will also help in enticing new people into the industry. If we as an industry can show that we are working to reduce climate change and create biodiverse habitats, then we will be in a good position moving forward.
Michael Russell is the Managing Director of Transit Handrail Lighting Ltd. With over 30 years of experience designing and developing lighting products he believes he has a lot to offer the rail industry.
Transit is a U.K. based company specialising in the design and manufacture of LED handrail lighting. All products are in-house designs made from solid metals – materials such as marine grade 316 (A4) Stainless Steel and Aluminium.
Want to know more about Transit Handrail Lighting?
Address: Innovation Centre
St Cross Business Park
Newport
Isle of Wight PO30 5WB
Tel: 02081 500 015
Email: info@transitlighting.co.uk
Visit: www.transitlighting.co.uk
Tell us about your career before you joined Transit Handrail Lighting Ltd.
I started in the lighting industry in 1992, providing lighting designs for Architects and Designers. Very quickly, the company grew into custom manufacturing, and in the late 1990s, I became involved in an innovative technology to create large, uniformly illuminated panels. A high-performance panel was developed in collaboration with ICI and with Clear Channel as a potential customer. I cannot say it was a eureka moment, but this 20mm thick acrylic panel was ideal for a new product – an illuminated glass floor.
In 1999 the design was granted a Patent and at once won a DTI Smart Award. I came up with a suite of interlocking aluminium extrusions and the combination created System Tread. A thin, evenly lit floor using 13mm glass and so strong you could park a car on it! I remember Harrods gave us Christmas window space for a James Bond theme and then a Honda Accord. It was a popular product in the UK and abroad.
Development also included a wall system with a shallow profile System Muro. Another suite of extrusions with panels up to 1.2 metres by 2.4 metres. One project of note was Money Zone, at the Millennium Dome, a 680 square metre lightbox, 21 metre high at its apex, weighing 28 tonnes, installed in time for New Years eve.
One more derivative was Paviour, an inground illuminated glass tile for external applications. Its development highlighted the challenges of ingress protection and how supply cables react to the slightest presence of moisture over time, all important insights for the products I have developed for Transit.
Producing a product that consumes the least amount of energy in operation, performs for an exceptionally long time and where the body can be refurbished/repurposed at little cost. At present, we cannot escape the need to mine and process the earth's resources, but we can ensure that products have a long life and that elements can be re-used for as long as possible.
I consider myself an environmentalist. This perspective stems from childhood when I was privileged to grow up in a semi-rural environment. Being able to experience the natural world at first hand has given me a deep sense of wanting to preserve it.
The things to do list for saving the planet continues to grow and whilst I cannot achieve all of them, I can have some influence on preserving the night sky.
I have designed products to make the most of an efficient one-watt LED. Instead of using a scatter gun approach, every product is designed to focus light from each LED and deliver it to precisely where it is needed, the right amount of illumination in the right place.
I am especially proud of Transit’s range of asymmetric projectors, which feature zero upward light to ensure the skies above the handrail remain dark, protecting nocturnal wildlife as moths, bats, and fish under bridges.
When did you first start the company?
Transit was born from a handrail project we were invited to work on in central London in 2012. Until then, we had worked extensively with LEDs in edge-lit lighting panels. The project was Brown Hart Gardens in central London, and we worked with Building Design Partnership, handrail lighting was part of the package.
The installation was a success, and I decided to explore this niche market further, developing a range of products for B2B sales to handrail fabricators.
Over the years, we have had a lot of experiences, so many good and, of course, a few not so, but both have shaped our products and the services we offer today.
Tell us about Transit Handrail Lighting Ltd
Transit is a specialist company with U.K.-based manufacturing. It provides high-performance lighting products with all-encompassing design and installation services. We are passionate about reducing light pollution and achieving darker skies.
Transit offers a range of luminaires that are designed to maximise the output from the LED source. With any light source in order to maximise performance you need to point it in the right direction, and that is what we do.
In 2012, I developed the projector system we use across the entire range. It includes a comprehensive choice of focused lenses with beam spreads from spot to wide flood, that enable us to control the light. The next part is direction.
Every project is simulated (in software) to calculate the best angle at which the projector achieves the best light intensity and uniformity; this angle is then machined into the body of our asymmetric products at a fixed position. These are installed at the nadir point of the handrail and project light from an almost invisible source, creating darker skies above and glare-free illumination for pedestrians.
We have recently introduced two industry leading products: one, that offers the projector angle at anywhere between 0-60 (beam centre) and another for emergency tunnel lighting that projects light along the handrail achieving fixing centres at six metres.
All this sophistication and dedication pays off. Pointing the light in the best direction means less energy is consumed and fewer light fittings are needed. Therefore, cable loss is reduced, leading to greater distances from a single LED driver position. In addition, our products take less time to install which reduces project costs.
‘We are passionate about reducing light pollution and achieving darker skies.’
Our client base is varied, but our work is within the commercial sector with installations in areas such as education, transport, and public infrastructure, in this country and overseas.
Around a year ago I re-looked at Transit, its products, markets, and direction. I can sum up our USP in one word: ‘Precision’. The way we deliver the right amount of light to the surface, deliver power to the projectors, and deliver the projects.
Transit’s primary objective is to project the precise amount of light to precisely where it is needed, with effective, accurate illumination at maximum efficiency.
To me, precision means reliability, longevity, and performance. Our products are designed to operate the LED light source at lower temperatures to ensure long life. Precision engineering and a carefully considered design ensure IP67 ingress protection and IK10 vandal resistance. Our instant fit flush finish mechanism ensures the correct fit and retention every time making insertion and extraction in secondsbut only with a key.
Over time I have recognised that wiring creates the biggest problems. We have recently introduced a custom wiring loom service that elegantly delivers connecting wires to every aperture. No bulky splice
connectors to be made on-site, in our looms every slim profiled splice is waterproof, does not snag within the handrail and does not affect the structural integrity of the conductor. Installation times have been dramatically reduced, whilst reliability and longevity have increased to fit and forget dependability.
When a client comes to you with a particular problem, what’s your process for coming up with a solution, and how closely do you work with clients throughout the projects?
My principal role in Transit is product designer and after so many years of product development experience has taught me to be pragmatic and to keep it simple.
There is a voice in my head from High School, my Design and Technology teacher continually repeating his mantra: first, listen to the client, and secondly accept the problem. It seems obvious but accepting the problem is so important, the need to keep focussed.
With our handrail fabrication and installation partners, we take total responsibility for the illuminated handrail. Whether we are using our standard lighting products and handrail components or designing a new solution.
From the lighting perspective if a standard product is not suitable, we look to re-work one of our modules or create a new product. Unfamiliar problems are great, the solutions grow our catalogue.
We work closely with our handrail partners, who carry out load calculations and handrail design, creating custom elements as required. Partnerships require some commonality, dedication and passion seems to sum up our working relationships.
The client is king, they are paying the bill! Our commonality means we work very closely with our clients and their consultants to deliver their expectations.
‘I am especially proud of Transit’s range of asymmetric projectors, which feature zero upward light to ensure the skies above the handrail remain dark, protecting nocturnal wildlife as moths, bats, and fish under bridges.’
What’s next for Transit Handrail Lighting Ltd?
More products for our portfolio. Currently we are developing a fireretardant version of our Tri-linear luminaire in parallel with creating looms of FT 120 fire retardant cable to be run and connected within the handrail.
We have almost finished development of a twin version of another of our
products RAILled that will provide twice the luminous intensity with greater dispersion, projecting light +/- of the centreline, made in 316 stainless steel.
To aid with fabrication of the handrail and retrofitting we are continuing to develop more jigs and tooling.
How can we get more use of the rail assets and what is your vision of rail in 10 or 20 years?
Being a humble lighting supplier I am probably too far down the supply chain to give a truly informed answer but, from the point of climate change I would like to see a return to the railways of past centuries.
Whilst the initial expansion of the railways was due more to competition than precisely calculated profit it did provide branch lines to more remote areas as climate change takes hold, we need to reduce vehicle emissions and the obvious way to achieve this is rail.
Collecting and delivering goods and people as close to their destination as possible. Ongoing transport may still require a vehicle, but this also could be carried by train over the greater distance of the journey.
I believe we need a bigger infrastructure, not necessarily speed. Increasing the network will of course raise objections and will have an impact on wildlife but, nature recovers faster and more robustly around railway lines where it is undisturbed.
It may mean losses in profits for some lines, but it is better than losing our planet. I read that during lockdown without air and land traffic, the carbon content of the world’s atmosphere only returned to levels recorded in 2014. I believe rail is the only way forward and whoever is in government needs to commit to long-term expansion.
Anything else you’d like to add?
Looking forward to seeing you at RAIL Live!
It’s been a busy twelve months in the life of TVS Rail Spares since the service launched at Rail Live 2023. We examine the successes of the first year of the UK’s newest online rail One Stop Shop and the timetable for future innovation in the sector
It’s that time of year again, when we all prepare to flock to the Long Marston Rail Innovation Centre for another edition of Rail Live. This time last year, TVS Rail Spares was gearing up for its launch into the rail industry and a lot has happened since that landmark moment.
The fledgling service has gained traction in the industry, with over one hundred unique rail companies now signed up to the TVS Rail Spares online catalogue. Virtually all of the Tier 1 signalling contractors have formally onboarded TVS Rail Spares as a supplier and placed orders, as well as customers from Train Care depots and subcontractors from Telecoms, OLE, and Civils disciplines.
Grant Jones, Managing Director TVS Supply Chain Solutions said: ‘We are delighted with the progress that we’ve made over the past year. The team have worked really hard to develop our proposition to the sector and we’re proud of the achievements and milestones that we’ve already reached. As we move through the next control period, we are ready to the be the rail industry’s CP7 Partner of Choice.’
TVS Rail Spares supplies over 10,000 PADS approved or rail industry recognised spare parts with free next-day delivery, powered by their innovative IT solutions for maximum supply chain efficiency. They manage more than 400 rail suppliers and deliver solutions in the rail sector across infrastructure, signalling, rolling stock and maintenance support.
‘When I first joined TVS fifteen months ago, we already had the capability in the rail sector to deliver a great service’ explains Steve Welch, Commercial Manager, who manages TVS Rail Spares and developed the proposition.
‘We wanted to think differently and tried as a team to set out a philosophy for the service, based upon what the rail
industry desperately needed. We came to the conclusion that there are three key principles at the forefront of our proposition: customer service, value for money and above all, being easy to do business with.’
As part of TVS Supply Chain Solutions, a global leader in end-to-end supply chain services for various industries including automotive, beverage, health, industrial, rail, utilities, and defence markets, the building blocks were already in place to be successful on all three fronts.
With the online catalogue offering world-class material availability and delivery
performance, fast quote turnaround and cost-effective pricing, it’s clear that the service ticks all the boxes. But what have been the key challenges faced in launching TVS Rail Spares?
‘The journey for us has been about spreading the word of what we offer, as much as anything else’ says Steve Welch.
‘We had a great start at Rail Live last year and got to meet many of the Tier 1 contractors in the industry. Since then, it’s taken a lot of hard work trying to get to see as many customers, and attend as many events as possible, to make sure everyone in the industry knows what we can do.’
With the online catalogue providing lots of benefits for the industry, with real time availability and pricing, as well as nearly 6,000 safety datasheets and more than 17,000 product images. However, the most critical of all the features is the speedy supply of products.
Steve Welch agrees: ‘The free next day delivery is really important for our customers. We know the cost and pain our customers face when they haven’t got the material they need, so having this as a standard feature for over 3,500 items we have on the shelf, is vital.’
TVS SCS has a long-standing reputation for innovation and unlocking value through technology, with many more developments planned for the TVS Rail Spares journey.
Andy Lawrence, Head of Business Development picks up the story.
‘We see ourselves as disruptors in the marketplace and the rail sector has been long overdue some innovation in the supply chain’ he explains.
‘We see TVS Rail Spares as part of a long-term journey and there’s still a lot of work to do. We’re looking to add many more products to the 10,000 that we already supply, increasing our portfolio into the Traction & Rolling Stock market, as well as working with suppliers to help them bring innovative infrastructure products to the market. There’s so much potential for us to benefit the whole industry, from the contractors to the train builders and operators, so we can collectively deliver a better passenger experience.’
It's clear that they have great ambitions in the industry and a track record to back it up. With many stops still to go on their rail journey, TVS Rail Spares are on the right track.
It’s going to be a great ride.
To find out more, go to www.tvsrailspares.com or get in touch via the contact information below.
Tel: 01257 265531
Email: rail@tvsscs.com
Visit: www.tvsrailspares.com
Social: www.linkedin.com/showcase/tvsrailspares/
Address: Logistics House Buckshaw Avenue Chorley, Lancashire PR6 7AJ
A VERTEX helmet and DUO RL headlamp in use while performing tunnel maintenance near La Pelonière, France.
Petzl’s advanced headlamp technology and range of helmets and modular accessories offer solutions for whatever your requirements may be.
9:30 - 10:15
Recruitment & retention: attracting new people to the railway 45 min session
• Nina Lockwood, CEO, Intuitive Interim & Executive Search
• Neil Robertson, Chief Executive, NSAR
• Pauline Holroyd, Group HR Director, Network Rail
10:30 - 11:00 Collaboration at SPEED in CP7 30 min session
• Mike Wright, Programme Director, Network Rail
10:00 - 10:45
11:15 - 11:45 Building a bridge to GBR: rail’s relevance in 2025 and beyond 30 min session
• Rufus Boyd, Lead Director, GBRTT
12:00 - 12:30 Reimagining the railway's role in the local transport ecosystem 30 min session
• Andrew Scott, Deputy Director of Regional Partnerships, GBRTT
13:15 - 14:00 Safety on the railway 45 min session
• Johnny Schute, Chief Operating Officer, RSSB
• Richard Hines, HM Deputy Chief Inspector of Railways, ORR
9:30 - 10:00 Tackling a rapidly changing climate –capacity and resilience 30 min session
11:00 - 11:45
Playing politics with the railway 45 min session
• Huw Merriman, Transport Minister
Freight Escape Live: Accelerating the shift to rail 45 min session
• Guy Bates, Head of Freight Development Strategic Freight, Network Rail
• Daniel Ashville Louisy, Director, Ashville Group of Companies
• Kathryn Oldale, Head of Strategy & Policy & Communications, DB Cargo UK
• Steve Naybour, Head of Programme Controls & Programme Management, Wales and Western, Network Rail
• Mark Wyborn, Head of Freight and Route services, Porterbrook
12:15 - 12:45 Rail Reform: securing a long-term and successful future for the railway 30 min session
Andrew Haines, CEO and Transition Team Lead, Network Rail
13:00 - 13:45 A railway in crisis...? Discuss 45 min session
• Darren Caplan, Chief Executive, RIA
• Martin Tugwell, Chief Executive, Transport for the North
• Shamit Gaiger, Managing Director, West Coast Partnership Development
14:00 - 14:45 Playing politics with the railway – part 2 45 min session
• Stephen Morgan, Shadow Transport Minister
• Mona Sihota, Network Technical Head – Drainage and Off-Track, Network Rail
10:15 - 10:45 Retaining what we've learnt from HS2 30 min session
• Giles Thomas, Ph1 Engineering
13:45 - 14:15 How do suppliers get ahead of the railway's needs 30 min session
10:00 - 10:30 Solving the track access equation 30 min session
• Ben Brooks, Portfolio Delivery Director, Network Rail
• Tony Morgani, Technical Lead (Track), J Murphey & Sons
• Emma Porter, Managing Director, Story Plant
10:45 - 11:15 Real-world uses of machine learning 30 min session
• Speaker to be confirmed
• Speaker to be confirmed 14:00 - 14:30 Future signalling - progress & prospects 30 min session
• Speaker to be confirmed
14:30 - 15:00 Unlocking rail freight's potential 30 min session
• Simon Kendler, Regional Freight manager, Network Rail Engineering theatre sponsored by Pandrol
For more information, visit raillive.org.uk This agenda is subject to change at the discretion of event organisers.
Ric Kirman is the Rail & Monitoring Manager at KOREC Group and the driving force behind this growing area of the business. With a background in business development, team leadership and customer engagement and with extensive experience within the rail industry, he is renowned for his motivational skills and excellent communication.
KOREC specialises in providing measurement solutions, surveying equipment and mapping systems for the geospatial, engineering and construction sectors in the UK. If you want to know more about KOREC, get in touch via the contact information below.
Want to know more about KOREC Group?
Tel: 07966251781
Email: ric.kirman@korecgroup.com
Visit: www.linkedin.com/showcase/ korec-rail/
What is your role within KOREC Group
I am the Business Area Manager for Rail and Monitoring. Rail and Monitoring is one of the specialist business areas within the KOREC Group; each area offers industry specific advice, support, training and consultancy ensuring we can deliver the very best service for our customers. KOREC Group offers an award-winning service in geospatial solutions to its varied customer base as well as a range of digital construction solutions.
We are one of Trimble’s largest distributors which enables us to bring world class rail solutions to our customers but always tailored to the demands of a UK market.
Key to the success of this team is our focus on using dedicated industry specialist sales consultants and industry certified Applications Engineers. Within my team alone we have over 50 years’ experience in the rail industry and over 70 years’ within the monitoring sector, this is what helps set us apart from our competition, we really do understand your challenges.
Tell us about KOREC Group
Our mission statement sums up KOREC Group perfectly – Our mission is to empower you to measure, map and manage the natural and built environment.
We’ve been established for over 50 years and our strength lies in the relationships we have with our customers and our partners. We have a strong company culture, (KOREC Group is an Investor in People and an Investor in Wellbeing). Our customers often share their appreciation of the KOREC team’s willingness to go ‘above and beyond’ to help support them in the more challenging situations.
In your last interview, you talked about general trends in the Rail Industry –what’s new this time around
In my last interview, we talked about the GEDO Track Measurement Survey system and some of the more recent iterations of this solution and its benefits. We also outlined the key areas where surveying technology could contribute to significant gains in track safety and efficiency whilst making best use of any site access or possession time. In particular, I feel one of the most exciting developments is the ability to collect, use and share point cloud data captured by 3D Laser Scanners.
As I mentioned previously, the use of point cloud data is not standard practice yet, but I predict that within five years it will become the norm. Since our first interview, we’ve been working with KOREC Rail customers who’ve not only been using 3D Laser Scanning in their operations but have committed to the future of this methodology by investing in Trimble’s Network Rail approved GEDO GX50,
‘If the industry is to meet the demands of CP7 head on then it must look for new workflows and ways to collect and view the data it needs to design, construct and maintain the UK rail network.’
an advanced and flexible laser scanner, optimised for use with Trimble GEDO track measurement systems.
In short, the Trimble GX50 is the only rail dedicated scanner to fit on a TMD. It’s made to measure, not a system that’s been put together to fulfil random jobs. Scanners in the past have been compromised in their ability to create a full field of view, with the GX50 rail dedicated scanner that simple isn’t the case because it’s on a TMD – this benefit is huge.
Some of the tangible technical benefits of the GEDO GX50 are the creation of full 360° point clouds allowing for more data to be captured (one million points per second) which in turn creates more detailed cross sections used for clearance analysis. The GEDO GX50 provides the ability to map/ survey assets within 4ft without additional equipment and the enclosed scan heads give greater weather resistance so our customers can get great results in areas they were previously unable to (damp wet tunnels mainly). Additionally, the working speed increased from 0.6m/s to 1.2m/s which allows much more data to be captured in the track time available, again efficiently reducing the need for boots on ballast.
Who is using the GEDO GX50 scan system both in the UK and globally?
It’s worth noting that the UK is one of the leading lights in adopting rail innovation because we face such a unique set of challenges. Individually, these challenges are reflected around the globe but here in the UK they are compounded! They include our ageing infrastructure, geological factors such as the climate, land slips and coastal erosion and of course the demands of a dense, freight heavy rail system on, what is actually quite a small island – these are vital transport links that must be maintained making any closures a particularly time sensitive undertaking. During whatever track or possession time is available, it’s vital that this is made the best use of and therefore, whatever technology is used has to be reliable, accurate, safe and operator friendly, all criteria for which the GEDO GX50 has a proven track record.
In the UK, Network Rail has led the charge in adopting innovative laser scanning technology. Since the GEDO GX50 was Network Rail Approved, they’ve bought a number of systems, an investment that sends a strong message to the industry that this is the way forward.
Consequently, where Network Rail leads, others will follow and we’re seeing a growing take-up from independent rail survey specialist companies of which SEP Rail Services is a prime example (more on them below). We’ve already seen this happen in Germany with Deutsche Bahn leading the way and independents following and there’s no doubt the UK market will enjoy the same trajectory.
Are there any proven benefits to using the GEDO GX50 scanning system?
The most obvious benefit is an overall reduction in risk to human life because rail workers spend so much less time on track – one site visit is often enough to collect sufficient data to create a high-quality digital twin. This one site visit can generate a single data set that can be used across a number of departments for a collaborative approach for asset management, track quality surveys, OLE height measurement etc, filling the needs of Design, Construction and Maintenance functions.
It may sound too good to be true but a typical job using traditional methods could include five separate teams, three site visits/possessions, extended exposure of staff being trackside and of course hotels and travel. Alternatively, a single
shift of just two workers using the GX50 (although it requires just a single operator) could accomplish much, much more. A more collaborative workflow is vital for the industry as it moves forward into this next control period and beyond.
What sort of application areas are we seeing this technology used in and what sort of results are these users achieving?
We’re seeing it used everywhere but predominantly in works delivery, civils, maintenance and OLE. However, we’re even seeing it used in design and tamping because it allows you to scan an area or length of rail, create a new design and still test the clearance of that new design in the existing scan back in the office – a huge time saver. This brings the ability to make and correct any mistakes in the office, not on site, another way to keep people out of potentially dangerous environments.
It’s therefore a far more financially responsible approach enabling budgets to be stretched further. The ROI is massive and feedback from GX50 users is wholly positive.
SEP Rail Services, what’s their story?
KOREC Rail has always worked closely with SEP Rail Services and in particular, Managing Director Rikki Morrow, attending their stand down days and providing insights into new ways of working. They are an extremely forward-looking company, something that we’ve seen first-hand, and it’s therefore no surprise that with their
prior laser scanning knowledge, they have become the first UK independent survey business to invest in the GEDO GX50 dedicated rail scanning system.
We’ve recently heard interesting feedback from Chris Lyon, the company’s Head of Delivery, who says that the GX50 is a significant step forward in their operational capabilities, especially compared to their previous scanning system being faster, more robust and with less shadowing ensuring that more features can be accurately captured.
SEP Rail Services are discovering more and more applications and want to use the system as much as they can because they have found it to be the simplest, fastest, safest and most accurate way of capturing data for collaborative working between its multiple rail departments
Has the market grown in this area?
Yes, the market has grown because the challenges of working on rail have grown and if the industry is to meet the demands of CP7 head on then it must look for new workflows and ways to collect and view the data it needs to design, construct and maintain the UK rail network. In the UK, efficiency is a massive driver of innovation
and its take-up. SEP Rail Services is leading the way here and as the benefits become evident, others will follow.
What do you expect to be the biggest challenges that come from this transformation of the railway industry?
A primary future challenge lies in data storage and sharing. Collaboration must be the path forward. Currently, operations are confined within individual teams across departments. We must explore ways for teams to de-isolate; the era of a siloed team is coming to an end if we are to aim for greater efficiency as a whole. Although technology for data sharing exists, its adoption is lacking and that’s where KOREC Rail can play a part.
We aim to contribute to the rail industry's awareness of available solutions and our key message is to encourage industry partnerships and support for new processes, influencing standards and fostering improvement within the rail sector. However, we're only one part of the equation, which is why it's encouraging to see Network Rail and SEP Rail Services embracing technological advancements. Their example sets a standard for others to follow.
It would have been understandable if the idea was to save money. But that’s not why HS2 was chopped. Its funding went mainly to road projects, some of it to be spent filling pot holes
Two excisions were made at either end of HS2. At the London end, Euston would only now proceed if it could be funded by the private sector. Otherwise high-speed trains will get no further than Old Oak Common, a station not designed to act as a terminus.
Careless at one end, careless at the other, where the section from Lichfield in the Midlands to Crewe in the North has simply been thrown on to the compost heap.
Perhaps its name (Phase 2a) was too anodyne for its significance to be grasped. So let’s call it for what it is: the NorthMidlands Link. It links the West Midlands to North West England. And it is of huge significance to the operation of the national transport system.
It is a crucial section of new railway because it allows longer-distance trains to bypass a two-track bottleneck on the country’s busiest route, the West Coast Main Line (WCML).
Without the North-Midlands Link, this is where 4 WMCL tracks will now be joined by two HS2 tracks, only to be squeezed onto two tracks at Colwich Junction. An existing bottleneck made worse.
The Government’s cost estimate for the North-Midlands Link that bypasses the bottleneck is £5.2-7.2 billion (in 2019 prices). That’s roughly ten per cent of the cost now quoted for the Midlands-London section of HS2, say roundly £1 billion/year through its intended construction period.
As Phase 2a, the North-Midlands Link already has Parliamentary Consent and roughly half of the land needed for it has been acquired. This may be contrasted with the smörgåsbord of schemes across the country – misleadingly titled ’Network North’ – dreamt up in short order to spend the funding allocated to pruned sections of HS2. Most of the smörgåsbord schemes don’t even have business cases.
The North-Midlands Link is ‘shovel ready’. It has been through nine years of careful planning scrutiny. All such projects of course have local impacts, but this one has been the subject of the most careful of environmental assessments and treatment. It avoids urban areas, National Trust property, SSSIs –carefully planned, carelessly pruned.
The North-Midlands Link broadly parallels the ever-busy M6 motorway. Already subject to an application of the unloved ‘Smart Motorway’ roll-out, there is
no scope to add further capacity to the M6. It too is a network pressure point, where, from the south, the M5 joins the M6 and the M6 Toll.
Although the North-Midlands Link is designed to carry long-distance intercity rail services, it will free up capacity for more and better local/commuter rail and railfreight services too. Connected to the surviving section of HS2, it provides key transport capacity the nation needs in pursuit of its economic growth agenda.
In December 2023, the DfT announced a rail freight growth target of 75 per cent growth in net freight tonne kilometres by 2050. Welcomed because it sets a positive direction for the railfreight industry, it is in truth woefully unambitious. For railfreight to become, as it must, the routine alternative to long haul 44T HGVs by 2050, the switch from road to rail will need to be much greater. But how hard will that be, with the nation’s most important railfreight line so constrained?
When Government pruned HS2, it didn’t see fit to propose any alternative rail investment in the area, oblivious to the need to act on what is a crucial and current constraint on the national rail system.
City Mayors Andy Street and Andy Burnham have stepped into the breach, and asked Sir David Higgins to oversee what else might meet fit the bill. This will include consideration of using private sector finance. We must applaud their endeavour.
But the North-Midlands Link (NML) has already progressed through its nine-year planning process. It might be wise to revisit and reuse what remains in place, particularly the Parliamentary powers which will survive until 2026.
Jim Steer is Director and Founder Steer Group consultancy and Director Greengauge21
Steve Stocks is the managing director of WCL Rail, an agile management consultancy with a global reach. He’s played key roles in some of the UK’s major rail infrastructure projects in recent years, from the Bristol Temple Meads Resignalling project to Network Rail’s CP6 and a range of significant works for TfW.
WCL specialises in big projects and their unique challenges. With roles including lead strategic support for the £738 million multi-disciplinary overhaul of rail infrastructure in South Wales, as well as lead consultancy services for Network Rail’s CP6 Wessex Works Delivery.
Want to know more about WCL Rail?
Tel: 01666 560174
Email: info@wclrail.co.uk
Visit: www.wclrail.co.uk
Tell us about your career before you joined WCL. What was the inspiration behind starting the company?
It all started at 16, when I left school on an apprenticeship with British Rail – over 32 years ago! Sponsor funding dried up partway, so I did a degree in Electronics off my own back and then did a graduation scheme with the Defence, Engineering and Science Group instead. It took me all over, from Bristol sites to Australian submarines.
I returned to the world of rail as a project engineer for Amey, then a project manager with a focus on signalling. It was a great career, but the travel and workload was very demanding on family life – so eventually we decided to sell everything and travel around the world for two years.
As part of our travels, what was meant to be a few months in New Zealand turned into six and half years. I worked on the railways over there, getting involved in major resignalling and electrification projects before we moved back to the UK.
I started WCL Rail in 2012. While in New Zealand, I’d seen how the flexibility of specialist contractors could address specific project or organisational skill gaps – and could make the difference between success and not getting off the ground. I carried that ethos back to the UK, forming the roaming band of WCL experts which allowed me to satisfy my love of tackling the biggest, knottiest challenges in the entire sector.
It’s been twelve years since then – I can say with certainty that WCL has lived up to its founding purpose, now more than ever.
What types of products and services do you offer – what is your USP?
At its heart, WCL are specialist problem solvers and change makers for large and complex rail projects. We untangle the impossible knots. We’re a network of expert consultants and engineers that you can plug into your project – and get results.
WCL is a highly agile, low overheads, outcome-focused toolbox. We bring focused firepower. We don’t bring bloat. We’re the expert response team for large works that are stuck in the mud or sinking under their own weight.
WCL works across four areas:
1. Project management and consultancy.
2. Engineering and construction.
3. Commercial management.
4. Integration and controls.
Our clients can bring us in for a specific output, such as design review or Entry Into Services documentation, or have us develop a bespoke route to achieving a certain goal or overcoming a challenge. In the case where expert resource is required as part of our service delivery, fulfilment is fast and impactful through our wide industry network and suite of in-house talent. When you engage WCL, you aren’t just getting an output or a bum in a seat. We operate as a
leading provider of comprehensive, turnkey packages spanning project, programme, technical and consultancy services. When you work with us, you’re plugging your project or organisation into the entire network of WCL experts.
What are some major projects you’re currently working on, or standout projects from over the years?
We’re working on a large programme of works for Transport for Wales at the moment. As part of a £738 million multidisciplinary overhaul of South Wales infrastructure, we’re involved in major resignalling and re-control, introduction of 25kV overhead lines, track re-doubling and re-modelling and major civils interventions including station upgrades, a new depot and new ICC facilities at Taffs Well.
WCL is also centrally involved in the KiwiRail Wellington Resignalling project in New Zealand. We’re working on signalling design and integration as part of the Wellington Master Plan, plus project management of major resignalling upgrades for Wellington Station and the Wairapa lines. That’s on top of engineering support for the TransPennine Route Upgrade (TRU) works, a multi-billion programme that promises to completely transform travel across the northern region.
The Bristol Area resignalling enhancements was a fantastic achievement for us in recent times – I worked as lead project manager on some of the biggest signalling enhancement works that the country had seen up to that point, with the Bristol Temple Meads Station Stage 4 signalling commission being the biggest single commission ever done in the UK.
What’s your typical process for working with clients, coming up with solutions to their problems and delivering success?
Our work on Wessex Works Delivery for Network Rail’s CP6 work bank is a textbook example of the WCL approach. A sponsor may come to us and say, ‘we want a signal here, we want a signal there’, ‘we want a location case with equipment here’, ‘we want five more planners’ – but we reflect it back
and ask ‘do you? Or do you want to run ten trains an hour, reliably and with cost savings against last year?’
Once we’ve identified the requirements at their root, we define and deliver the optimal solution.
For the Wessex Works Delivery Unit, another WCL director and I went into their struggling signalling department. By adding just two new posts and a suite of process reforms, we took them from completing £10 million of work to completing £20 million of work in a year. Another year later, we disengaged, leaving a signalling department delivering £30 million of work annually.
We achieved this 200 per cent productivity increase without an ocean of recruitment, or fresh wallpaper stuck over old processes. Rather, we looked at what was going on from root to branch, systematically streamlined, restructured, and adapted it for efficacy. Through this work we also delivered over a year of operation without a single safety incident, making it one of best performing Network Rail teams in the UK at that time.
We cover this in depth on our website, for anyone who wants more detail.
What’s next for WCL?
WCL has experienced rapid growth in recent years, especially across the Wales area. We’re looking to continue this expansion, deepening our involvement and broadening the scale of our activities across the region. Recent wins in this area include the renewal of our framework services contract with Amey Infrastructure Wales, which has set the groundwork for a range of exciting works throughout 2024 and 2025. It represents the single biggest purchase order in the company’s history, and we’re thrilled to continue collaborating with Amey and TfW.
Our activity is also gaining momentum around the world – we’re winning more work in New Zealand, including further work with KiwiRail. We’re providing programme management and strategic oversight to develop new station and network upgrades, as part of the LNIRIM rail programme. Through this work we’ll enable the full potential a new fleet of efficient and sustainable tri-modal trains operating across the Wairarapa and Manawatū lines, which connect the capital city to the surrounding regions. We’re also having exciting conversations with potential partners in Canada, taking us closer to being a leading rail consultant with a presence that circles the globe.
WCL is placing a greater focus on frameworks and funding sources outside of the Network Rail ecosystem. We’re identifying a myriad of opportunities for us to get involved in exciting areas like urban transportation networks and intermodal innovations.
WCL is also expanding its team, supporting our continued growth through
a larger roster of highly skilled permanent staff. Recent hires include Jonathan Davies, as our new Business Development Director. He brings an unparalleled level of experience with him, having worked in the rail industry for more than 30 years and run his own consultancy since 2022.
We’re actively looking for the best and brightest to help us take on even bigger challenges right now, including project and scheme project managers, as well as engineers from several disciplines, to help us accommodate even larger contracts and works for our growing roster of clients.
With the coming launch of Great British Railways, how do you anticipate your place within the supply chain changing?
We have great hope that the move to Great British Railways is going to be a huge benefit to the industry. In terms of our positioning, I expect the reforms to drive up the requirement for managing agent style works as the industry and Network Rail push more reliance on Tier 1 contractors.
This will decentralise expert intelligence, creating more need for consultants like us to support clients, provide expertise to navigate the changing risk landscape, and guide the industry through the uncertainty that comes with major changes like these.
While it will absolutely be a challenge, the potential benefits are immense. Bringing track and train under one management umbrella is critical to tackling inefficiency at its root. Most importantly, it will get investment flowing outwards from the main lines, unlocking new transport opportunities and driving up service quality in all parts of the country.
With longer investment horizons and connected decision making, we can finally turn system-wide integration and efficiency from aspirations into realities. We’re optimistic about the possibility of a unified
national body, but one that has devolution and effective public-private collaboration as built-in features.
Whether it’s before or after a general election, I think the Integrated Rail Body needs to become a reality – sooner, rather than later.
What are some of the biggest challenges this sector currently faces – and what are some potential solutions?
Skills shortage is one of the biggest challenges we see in the industry at the moment. As with any big changes in an industry, you never retain one hundred per cent of your talent as you go through them. Whether by naturally encouraging retirements or driving technical experts to areas or sectors of greater stability, the rail industry will likely find specialist resource even more scarce. Against a backdrop of major reform, expanding investment and a number of mega programmes of investment, this becomes a critical bottleneck.
WCL is a leader in the provision of technical expertise – a core part of that is our energetic approach to identifying and securing the best talent available. We’re recruiting from a wide range of parallel industries, nurturing the best and brightest minds to become rail experts. Whether it’s from defence, energy, transport or elsewhere, each brings invaluable practices and perspectives from their unique backgrounds. Through this, they enable innovation and prevent tunnel vision across rail.
We’ve also secured a visa sponsorship licence to secure specific overseas specialists as required. Altogether, the skills shortage is one of the challenges we focus on most as a consultancy, working to support the Achilles heel of the industry and ensuring we have the expertise available to help our clients solve any problem, no matter how knotty.
Elevating Station Environments with Urbis Schréder's Smart Lighting Innovation for Modern Stations
Rising fuel prices, the growing problem of road congestion and the need to move towards sustainability make rail more than ever the most appropriate means of transport. There has never been a better time to reduce costs and build confidence in outdoor areas.
Money is often wasted on poorly designed systems which don’t benefit the comfort of the commuters/travellers or your finances, and what people don’t know is that installing the optimal lighting solution for each area of the station also offers significant financial savings too.
In March 2023, Billingham Station introduced an unobstructed accessible route connecting the two platforms and a stepfree solution with two new lifts to support those with limited mobility, heavy luggage, bicycles, pushchairs etc. To make the station more accessible and encourage more people to travel by train, this project was delivered by AMCO GIFFEN, who designed and chose Urbis Schréder’s ALINEA LED HANDRAILS to illuminate the footbridge and serve its intended purpose.
Unrivalled Performance, Coupled with Seamless Aesthetics, to Deliver the Best Experience. The ALINEA LED HANDRAILS used to illuminate the Billingham Bridge and drive footfall, is a robust solution that provides a safe and pleasant experience for passengers travelling. By Illuminating bridges, pathways, and stairways you can drive footfall to new areas and therefore providing benefits to the local economy. It can also have a profound effect on its presence at night.
Whether it is a 200-year-old stairway, or a new pedestrian bridge a long-lasting scheme can provide benefits and recognition for decades to come.
When clients are spending large sums of money on new infrastructure, it is easy to forget the lighting. However, to protect the investment made it is critical to illuminate the infrastructure properly both to highlight the development but most importantly ensure it remains, safe and usable during the darker hours.
As energy prices soar, local authorities seek to cut costs, enhance safety, and boost confidence in outdoor areas. Often, money is wasted on poorly designed systems that fail to improve commuter comfort or financial efficiency. What many overlook is that installing optimal lighting solutions for each station area not only enhances comfort but also yields significant financial savings.
Enter Schréder’s EXEDRA: a remotecontrol system enabling monitoring, metering, and management within a lighting network. This comprehensive solution, built on open standards and protocols, merges cutting-edge technology with user-friendly
web interfaces for seamless luminaire control via secure internet connections. With bi-directional communication, users can monitor operating status, energy consumption, and potential failures in real-time, resulting in up to 85 per cent energy savings.
Whether it is the station forefront, carparks, platforms, footbridges, tunnels, junctions, or maintenance pits, Schréder’s dedicated systems offer solutions to suit your space. Urbis Schreder’s expertise enables any environment to be transformed into a safe, sustainable, and cost-effective place where the commuters can travel with ease and no worries. Schréder’s lighting systems also require less maintenance than traditional discharge lamps, which means another reduction in costs.
However, connecting your luminaires is not just about adding in a control system to the products you are having installed, it’s much more than that. It is about control of the area you are lighting, it’s about the space the lights are in and the people who are using that space, it’s about delivering solutions beyond lighting for electric mobility, security, information, and entertainment. Is the light right for type of areas? Are you lighting an area to reduce the crime rate? What type of lighting will attract people to use that space? And do you need to dim the light during certain hours of the night but have the control to be able to make them bright again should there be an emergency? Are you wanting to look for energy efficient lighting, a more sustainable solution that reduces your costs?
High quality, yet energy-efficient and lowmaintenance lighting provides a strategic asset for the development of a sustainable and beneficial railway infrastructure. Urbis Schréder’s wide range of lighting solutions for the rail industry, combined with the company’s expertise and outstanding heritage in delivering breakthrough projects, creates the best possible experience for passengers and staff in the station environment.
Critical to delivering a safe and pleasant passenger experience inside and in the vicinity of a station is appropriate lighting solutions. New technology also offers the rail industry the ability to improve station lighting and significantly reduce cost. By combining traditional street lighting, LED handrails, continuous tiled lighting, and ground level inclination lighting; it is possible to create a bright and effective environment. The improved visibility reduces the risk of crime in a station environment and increases passenger confidence.
Urbis Schreder’s solutions are not just limited to rail, but also extend to interior
‘With bi-directional communication, users can monitor operating status, energy consumption, and potential failures in real-time, resulting in up to 85 per cent energy savings.’
and exterior lighting such as workspace, roads, architectural buildings, urban deco, sports, cities/communities etc. As it has done so for many years, Urbis Schreder provides beneficial LED alternatives to luminaires with fluorescent lamps and can offer a uniform and comfortable lighting suited to any area of choice, whether that’s interior or exterior, helping enhance spaces and create places, people love to live, learn, travel, and play in.
Bright solutions for greener transport
Schréder's commitment to sustainability extends beyond mere energy efficiency. Urbis Schreder’s systems are designed with longevity and environmental impact in mind, utilizing durable materials and innovative designs to reduce waste and carbon footprints. By choosing Schréder, local authorities not only invest in superior lighting solutions but also contribute to broader environmental goals, fostering greener communities and promoting a healthier planet for future generations. Together, we can create smarter, safer, and more sustainable urban environments.
To find out how Urbis Schreder can support your vision for connected, safe and sustainable places get in touch at sales@ urbis-schreder.com
Urbis Schréder
Sapphire House Lime Tree Way, Basingstoke RG24 8GG
Tel: 01256 354446
Email: sales@urbis-schreder.com
Visit: schreder.com
LinkedIn: Urbis Schréder
Geotechnical and ground source heat specialist supplier, MGS, have expanded their Thermo-Loops® range to include larger diameter pipes that meet the growing demands for higher capacity ground source heat pump systems.
Previously only available in 32mm and 40mm, their Thermo-Loops® pipes can now be supplied in 45mm and 50mm diameters to support more demanding ground source heat applications.
The new diameters of MGS ThermoLoops® are supported by a full range of electrofusion fittings, including those for the 45mm Thermo-Loops®. Ground source heat pumps are an increasingly popular form of low-carbon heating systems which extract ambient warmth from the ground to heat buildings and properties. A borehole is drilled in the ground, into which the Thermo-Loop® is installed. Powered by a pump, a glycol fluid is circulated around the loop to extract heat from the ground and deliver it back to the heat pump where
it passes through a compressor to increase the temperature. It is then passed through a heat exchanger and transferred to radiators or underfloor heating to heat the building. Thermal loops can also help provide cooling by reversing the process to transfer excess heat from the building to the ground.
Produced in the UK, the Thermo-Loops® are made from virgin grade PE100-RC, which is a very durable crack resistant polyethylene material, ensuring a maximum lifespan. The MGS Thermo-Loops® are
manufactured in accordance with Ground Source Heat Pump Association standards to ensure the underground heat exchange system is built to last.
Rail bolt manufacturer Tension Control Bolts Ltd (TCB) has been recognised by His Majesty The King. TCB has been honoured with a King's Award for Enterprise in the International trade category. TCB supplies bolting assemblies for safety-critical infrastructure including rail track joints, and train and truck chassis. The firm currently exports some 20 million bolts to over 30 countries around the world each year. Tension Control Bolts are widely used throughout the rail network. Primary applications include new rail bridges, bridge strengthening, track joints/ permanent way, temporary works, signal gantries and overhead line electrification (OLE).
Tension Control Bolts Ltd have the Railway Industry Supplier Qualification Scheme (RISQS) accreditation and is also accredited for rail station regeneration, station carparks, and stairwells
and approved for use by Transport for London (TfL). The firm’s environmentally friendly coating called Greenkote® is longer lasting, harder wearing and more cost effective than conventional types of Zinc coating. Greenkote® is approved by international motor manufacturers including General Motors, Mercedes-Benz, VW, and Audi.
TCB Managing Director Tim Stokes said: ‘We are thrilled to be recognised by His Majesty the King for our contribution to UK exports. We are a great trading nation. The UK is home to so many manufacturing companies shipping their goods to major infrastructure projects around the world. This is something as a country we should be incredibly proud of. I’d like to pay tribute to our dedicated staff who put in long hours to produce some of the most advanced bolts available on the market today.’
A consortium of mechanical and civil engineering, and robotic automation industry leaders, including Tunnel Engineering Services (UK) Ltd (TES), i3D robotics (i3D), the Manufacturing Technology Centre (MTC), Costain, and VVB Engineering, has developed the first robotic and AI solution set to revolutionise the installation of mechanical and civil services in tunnels.
Traditionally, installing these services in tunnels is hazardous, labour-intensive and time-consuming. The prototype Automated Tunnel Robotic Installation System (ATRIS) can autonomously select brackets, locate where they need to be mounted along a tunnel wall, and install them. In doing so, the automated solution can improve onsite health and safety by reducing the risks associated with manual labour at the tunnel work face, for example, working at height in confined spaces, and hand-arm vibration experienced by workers during installation.
Once fully developed, the final system can be deployed in tunnel construction for a variety of sectors including transport, water and energy. It is expected to increase productivity by 40 per cent due to faster installation, reduce installation costs for new mechanical and electrical (M&E) systems by 30 per cent, and cut construction plant movements by 40 per cent to decrease embodied carbon.
The 22-month project, partly funded by Innovate UK’s Smart grant, was led by TES, which developed the initial concept in partnership with the consortium. Leveraging its expertise in robotics and automation, MTC spearheaded the design and
manufacture of the robot's end effectors. i3D developed crucial visualisation software for precise navigation, whilst Costain and VVB provided industry knowledge and expertise in tunnelling and fit-out requirements.
Alan Worsley, Design and Project Manager at Tunnel Engineering Services (UK) Ltd said: ‘TES has over many years designed and manufactured Mechanised Tunnelling Machines and special purpose equipment for the construction industry. Over this time, innovation has been at the forefront of our business, and the need for automation in traditionally manual M&E fit-out techniques has led us to develop ATRIS and make it commercially viable for the market. We believe the system can offer a safer, more cost-effective and sustainable solution for future infrastructure projects.’
Steve Nesbitt, Chief Technologist for the Built Environment at MTC, said: ‘Like many sectors, construction has faced labour challenges over the past few years which has driven greater interest in using robots, beyond manufacturing and logistics, to address these issues. By contributing our expertise to this project, we are paving the way for construction companies to adopt technology for greater control and structuring of on-site works, making infrastructure delivery safer, more productive, and more sustainable.’
Dr Jon Storey, Lead Engineer at i3D, said: ‘Developing an automated system to install infrastructure in tunnels has been a long-standing ambition for the construction sector. ATRIS has moved us significantly closer to that goal. The use of stereo vision with machine learning and robotics to place
bolts precisely on a curved surface is an unprecedented achievement, with potential applications beyond the construction sector, such as nuclear decommissioning and defence.’
Lee Bateson, Mechanical and Engineering Manager and Robotics Lead at Costain, said: ‘Teaching the robots to learn seemingly simple tasks – such as how to avoid crossthreading the screws that go into the sockets – has been hugely fulfilling, thanks to the consortium’s collaborative spirit. Whether it’s carbon reduction, increasing productivity or improving workforce health and safety, this is transformative technology that will have enormous benefits for the customers that we build tunnels for.’
Nicholas Beedle, Group Operations Director at VVB Engineering, said: ‘Tunnel works historically are expensive to build and maintain, and in the higher risk bracket for safety during construction and operation. It is important that ongoing improvements are made to address both of these issues. The development of the robotic AI solution is a step towards solving both of these industry challenges.’
All change at Northern Northern has appointed Tricia Williams as Managing Director and she is succeeded in the Chief Operating Officer role by Matt Rice
Appointment further strengthens LRSSB board
The Managing Director of Blackpool Transport has become the latest highprofile figure to be appointed to the board of the organisation responsible for light rail safety. Jane Cole joins the Light Rail Safety and Standards Board as a Non-Executive Director.
The Independent Transport Commission (ITC) welcomes new Patron
The Independent Transport Commission (ITC), Britain’s leading research charity covering transport and land use policy, is delighted to announce the appointment of Sir Philip Rutnam KCB as a new Patron.
RIA appoints new Chairman
The Railway Industry Association (RIA) is pleased to announce that – following a competitive interview process – its Board has appointed Noel Travers as RIA’s new Chairman. He succeeds David Tonkin, who is standing down after seven years in the post.
The UK rail industry needs to adapt their existing energy infrastructures to keep up with evolving customer demand.
We take the time to understand individual rail energy requirements which allows us to develop technologically advanced solutions tailored to our clients needs to increase productivity and decarbonise infrastructure.
Scan here to get in