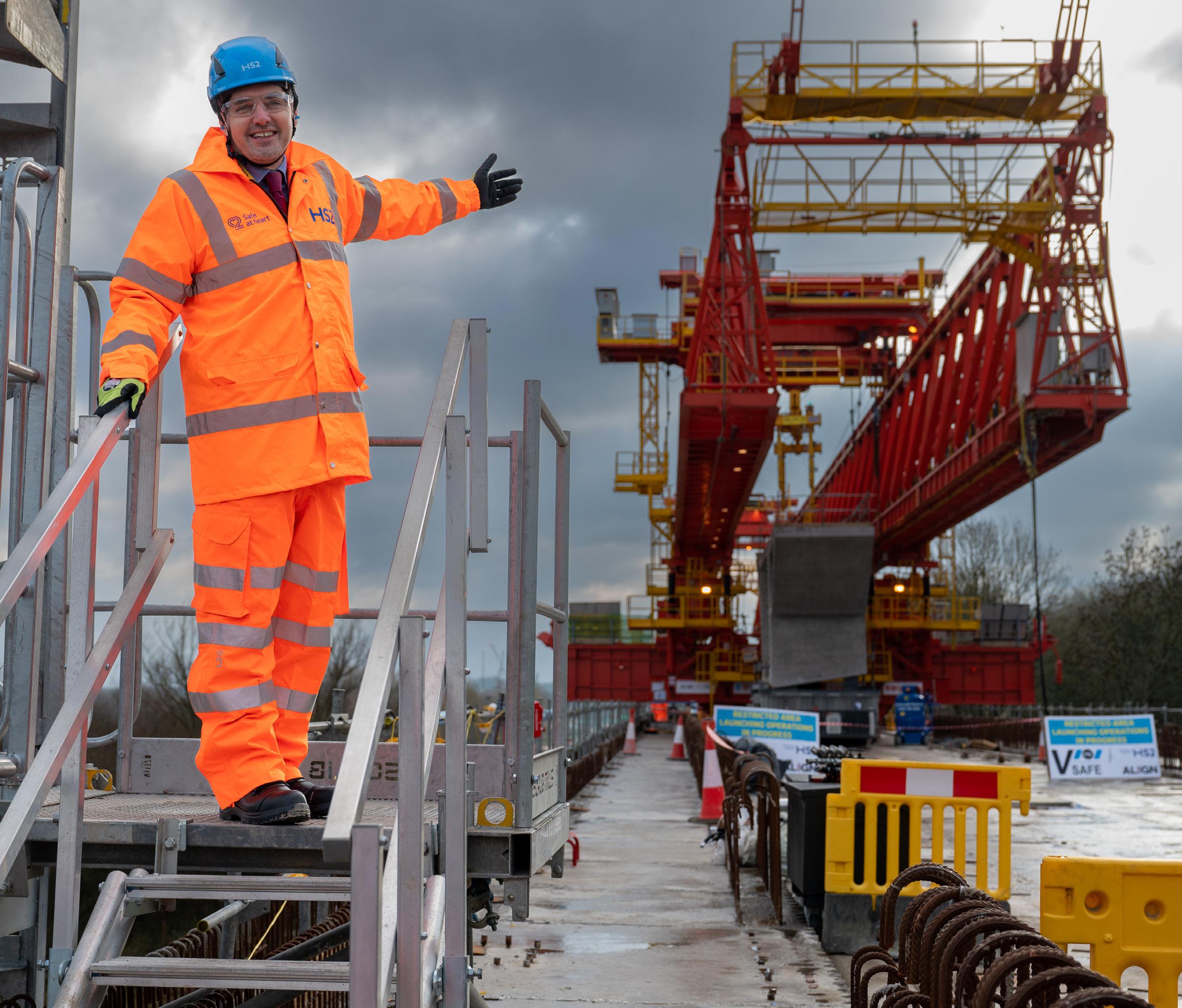
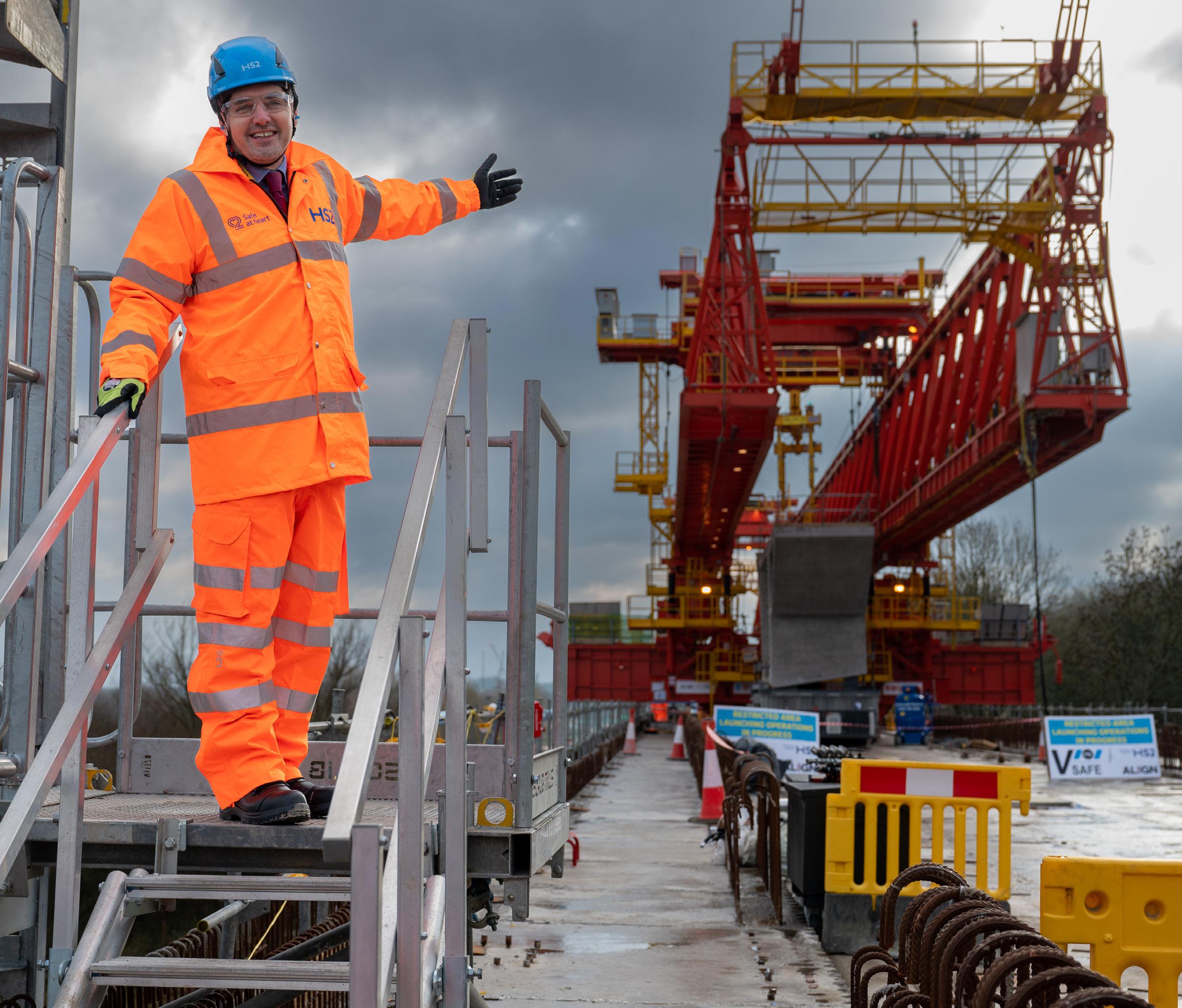
Discover potential. Drive performance.
With over 30 years’ experience working in the rail industry, specialising in the safety sector, the OPC provides practical, reliable ways of improving performance and assessing ability.

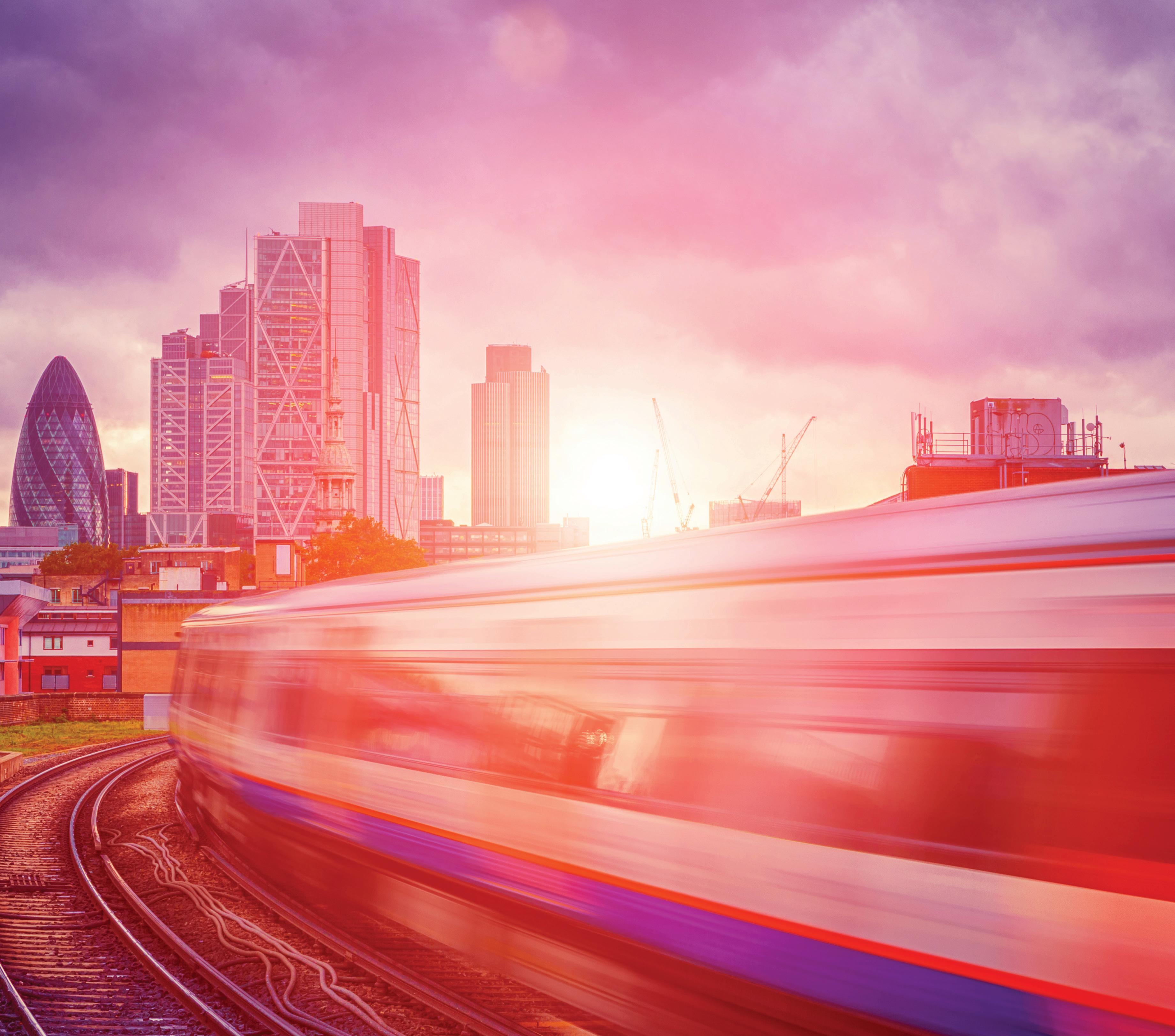
railprofessional @railpromag
PUBLISHER RAIL PROFESSIONAL LTD Hallmark House, Downham Road, Ramsden Heath, Essex CM11 1PU Telephone: +44 (0) 1268 711 811
EDITORIAL EDITOR
Sam Sherwood-Hale editor@railpro.co.uk
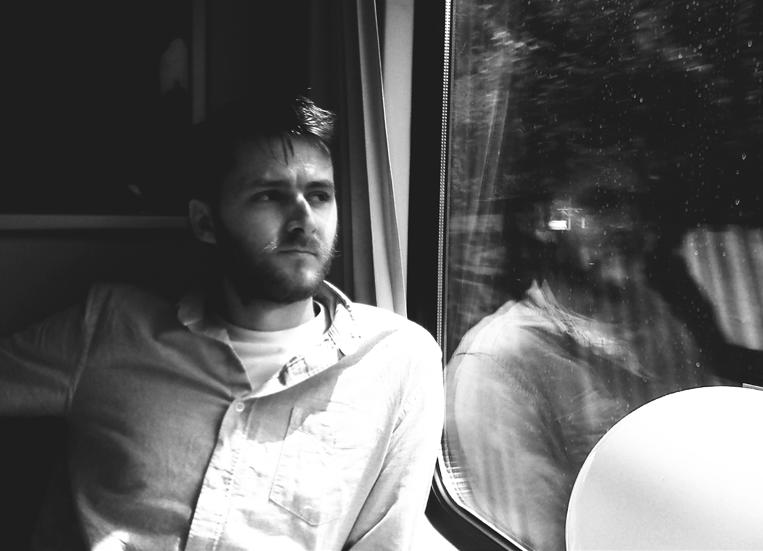
DISPLAY ADVERTISING
Adam Overall adam@railpro.co.uk
Jamie Tregarthen jamie@railpro.co.uk
RECRUITMENT ADVERTISING recruitment@railpro.co.uk
SUBSCRIPTIONS subscriptions@railpro.co.uk
ADMINISTRATION
Cherie Nugent info@railpro.co.uk
Lisa Etherington admin@railpro.co.uk
DESIGN & PRODUCTION
Alicia Bannister Lukasz Saczek production@railpro.co.uk
minister,
EDITOR’S NOTE
It’s conference season! With Summer right around the corner, we’re kicking off with Railtex which takes place in the middle of May at the NEC in Birmingham – you can read a full breakdown of the event in the opening pages of this month’s issue.
As the days get warmer we’ll be heading outside for Rail Live, the outdoor event will be taking place at the Long Marston Rail Innovation Centre, Warwickshire in June. We close out that month with Rolling Stock Maintenance & Depot Optimisation Europe and Rail Station Development & Regeneration both taking place in London.
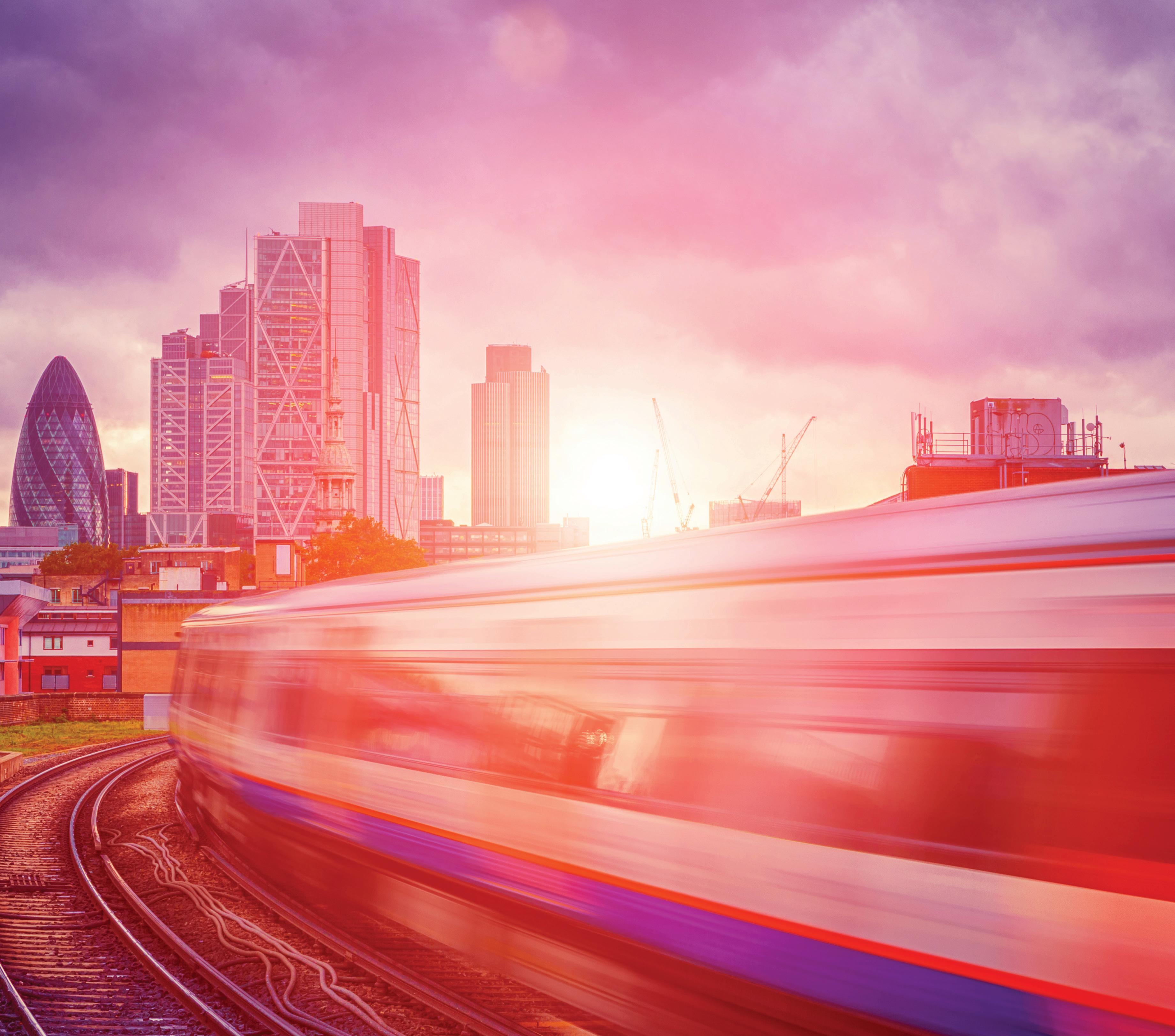


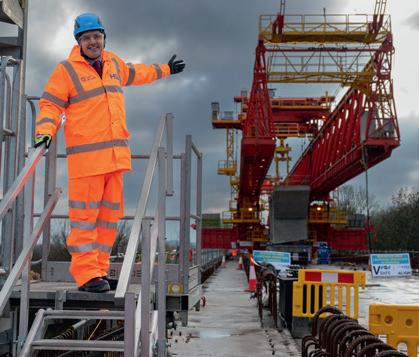
My interview in this issue is with the CEO of MTR UK, Steve Murphy We talked about environmental sustainability, Big Data and MTR trenolab. I particularly liked his comment about living in an era where ‘bad news sells’ and how rail transport has made itself an easy target for the media. This doesn’t just affect how the industry is seen by the public, which can impact political decisions about HS2 and other major projects, but also how it is seen by young people looking to join the workforce. This question seems to be a perennial one and we should all continue to look for an answer.
Our focus this month is on bridges and tunnels and we have some great spreads on two major projects from recent months.
We also have a selection of opinion pieces from Amy Marshall and Neil Kirkby of PA Consulting, Jonathan Spruce of the Institution of Civil Engineers and Michelle Craven-Faulkner of Shoosmiths. We also have a piece from RSK Biocensus Technical Director and Aquatic Ecology Lead Dr Peter Walker on aquatic ecology who provides us with a great selection of photos from a few different case studies.
SAM SHERWOOD-HALE EDITORKilborn Consulting Limited is an independent railway engineering consultancy and design business, with over 21 years of railway experience.
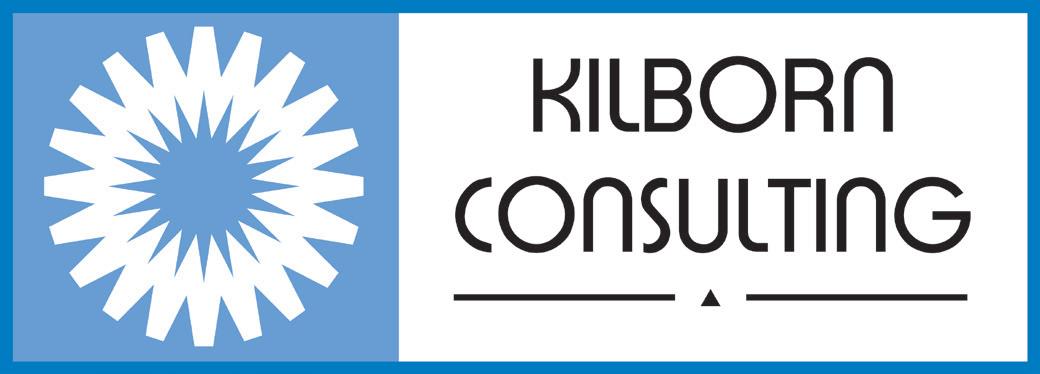
We specialise in the design of new and altered railway Signalling & Telecoms systems for the UK railway infrastructure.

Our areas of specialism are:
•Signalling and Telecoms Consultancy, including technical advice & support;
•Asset Condition Assessments, Correlation and Surveys;
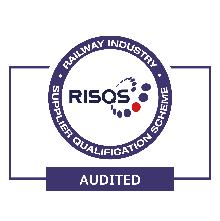

•Signalling & Level Crossing Risk Assessments;
•Feasibility and Optioneering Studies;
•Concept and Outline Signalling Design;
• Telecoms Option Selection Reports (including AiP), Reference System Design and Detailed Design;
•Detailed Signalling Design;
•Competency Management & Assessments;
•Signal Sighting assessments, covering the full Signal Sighting Committee process with a competent Chair.
The new office which is located in the heart of Wellingborough can accommodate all staff and visitors alike and offer widespread views across Wellingborough and the surrounding green spaces
We would be delighted to welcome you to our office to discuss your requirements and how we can support you to achieve those. Kilborn Consulting Limited 6th Floor, South Suite, 12 Sheep Street Wellingborough, Northamptonshire NN8 1BL
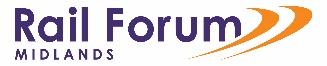
In this issue
11
15 RAILTEX Conference programme 16 SAFETY Safety Solutions for Depots and Workshops 18 RAILTEX Exhibition profile 21 SUSTAINABILITY Hydrogen Power for a Greener Future 24 RAILTEX How to get there and who you will be seeing on stage 28 INFRASTRUCTURE The Green Railway Revolution 31 NEWS
All the latest from Network Rail, the Department for Transport the Railway Industry Association and more

VIEWPOINT
41 WOMEN IN RAIL
Women in Rail Conference Marks End of Tenth Anniversary Celebrations
45 Steve Murphy, CEO, MTR (UK) celebrates the successful Rail + Property model, which removes risk and burden on the taxpayer, whilst delivering innovation
47 Connected communities: Enhancing the UK’s rail resilience for future generations
49 Decarbonisation in the Rail Sector
51 RSK Biocensus Technical Director and Aquatic Ecology Lead Dr Peter Walker draws on case study experience to illustrate the benefits of planning ahead
55 Jonathan Spruce, ICE Trustee for policy and external affairs considers the current planning climate for rail and asks if a national strategy is the answer
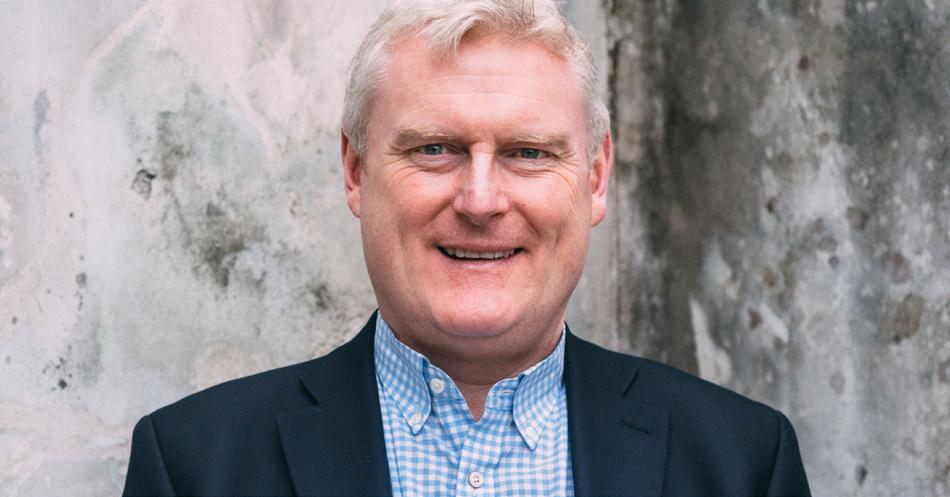
57 For every two steps forward, it feels like the UK’s rail industry takes one step back, says Michelle Craven-Faulkner, a partner and rail lead at Shoosmiths
59 And our industry needs to respond, says Champa Magesh, President of Trainline Partner Solutions
61 A new study reveals 47 per cent of UK-based adults have concerns surrounding germs on public transport
63 DELIVERING THE GOODS
Ellis Shelton, Policy Advisor, Logistics UK on the need for innovative and integrated infrastructure to deliver an increasingly productive and strategic logistics network
65 2023: the Year of Sustainable Transportation?
FEATURES
36 INTERVIEW
66 SPECIALIST SKILLS
The OPC shares some reflections and extracts from interviews with outstanding driver team managers (DTM); the special leadership skills needed to do this pivotal safety-critical role and what the industry might do to better support them
Want to further your planning career development and expertise?
Rail Operational Planning Masterclasses 2023
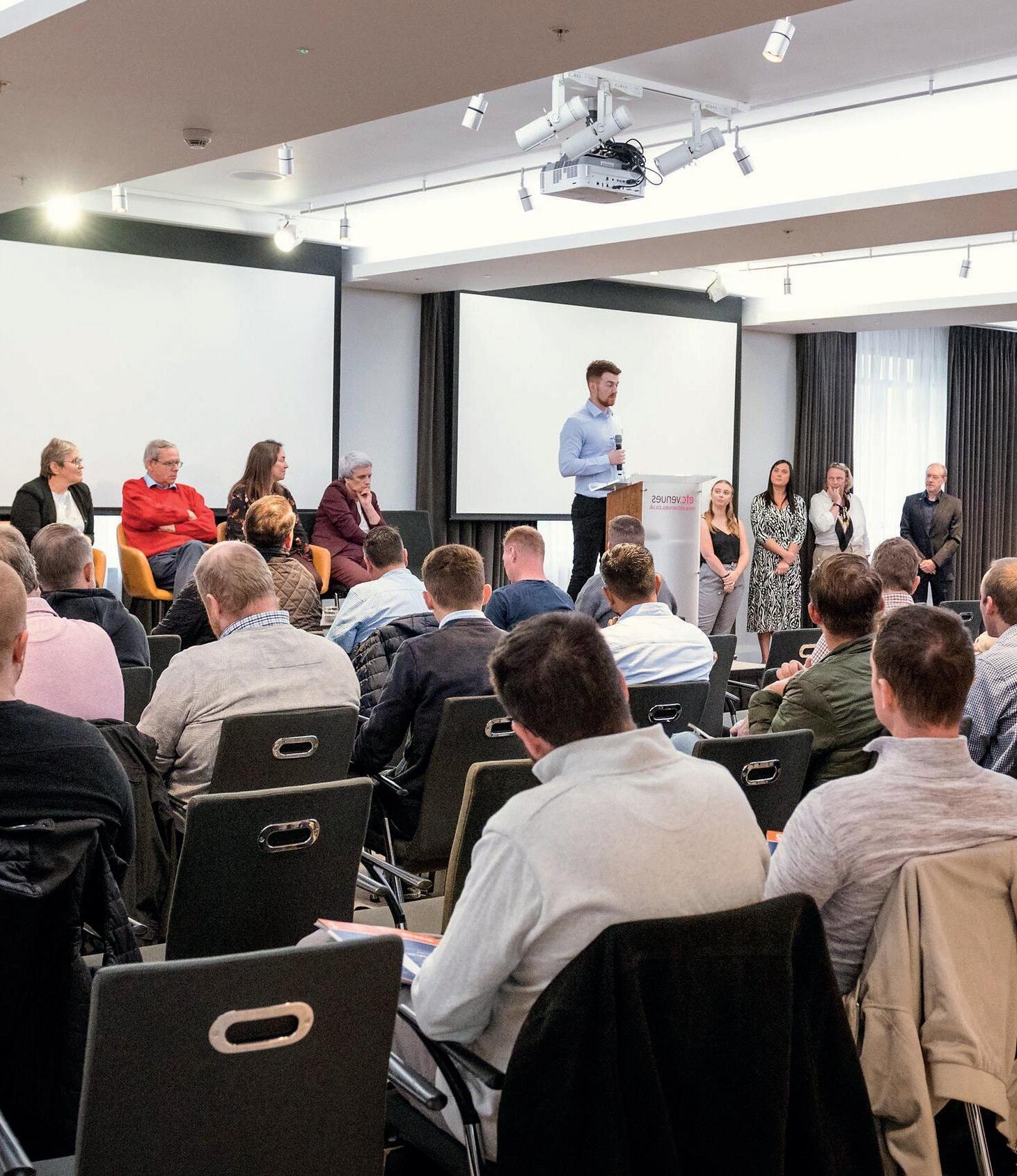
What will I learn?
The Operational Planning Masterclass will introduce the specific tasks of operational planning, this course illustrates how the timetable is fundamental to a railway business, generating revenue and influencing costs.
When and where is the training?
19th - 21st May
Friday 18.00-21.00
Saturday 9.00-17.30 (evening meal at 19.00)
Sunday 9.00-15.30
24th - 26th November
Friday 18.00-21.00
Saturday 9.00-17.30 (evening meal at 19.00)
Sunday 9.00-15.30
Location: Beacon Building 2nd Floor, Stafford Enterprise Park West, Weston Rd, Stafford, ST18 0BF
Refreshments and a light lunch will be provided for attendees.
What is the cost?
Members: £1200.00 inc VAT
Non Members: £1300.00 inc VAT


Book to Attend
To book your place on one of the Operational Planning Masterclasses or for more information about the course content, contact our learning and development team at learnserve@railwayoperators.co.uk.
learnserve@railwayoperators.co.uk
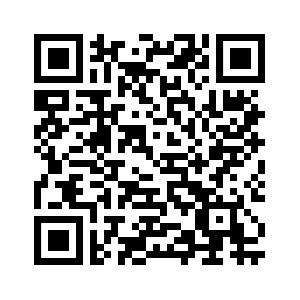
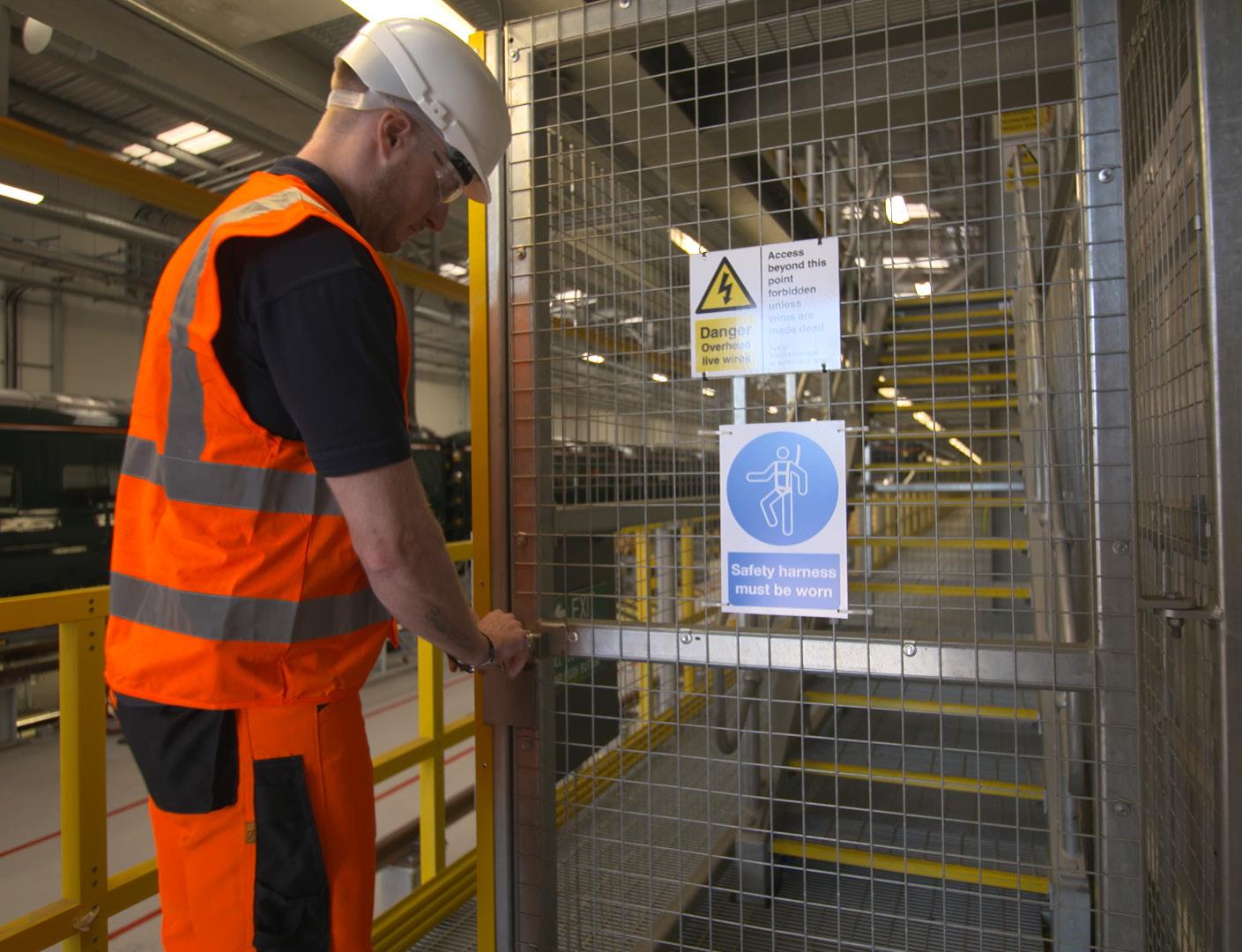

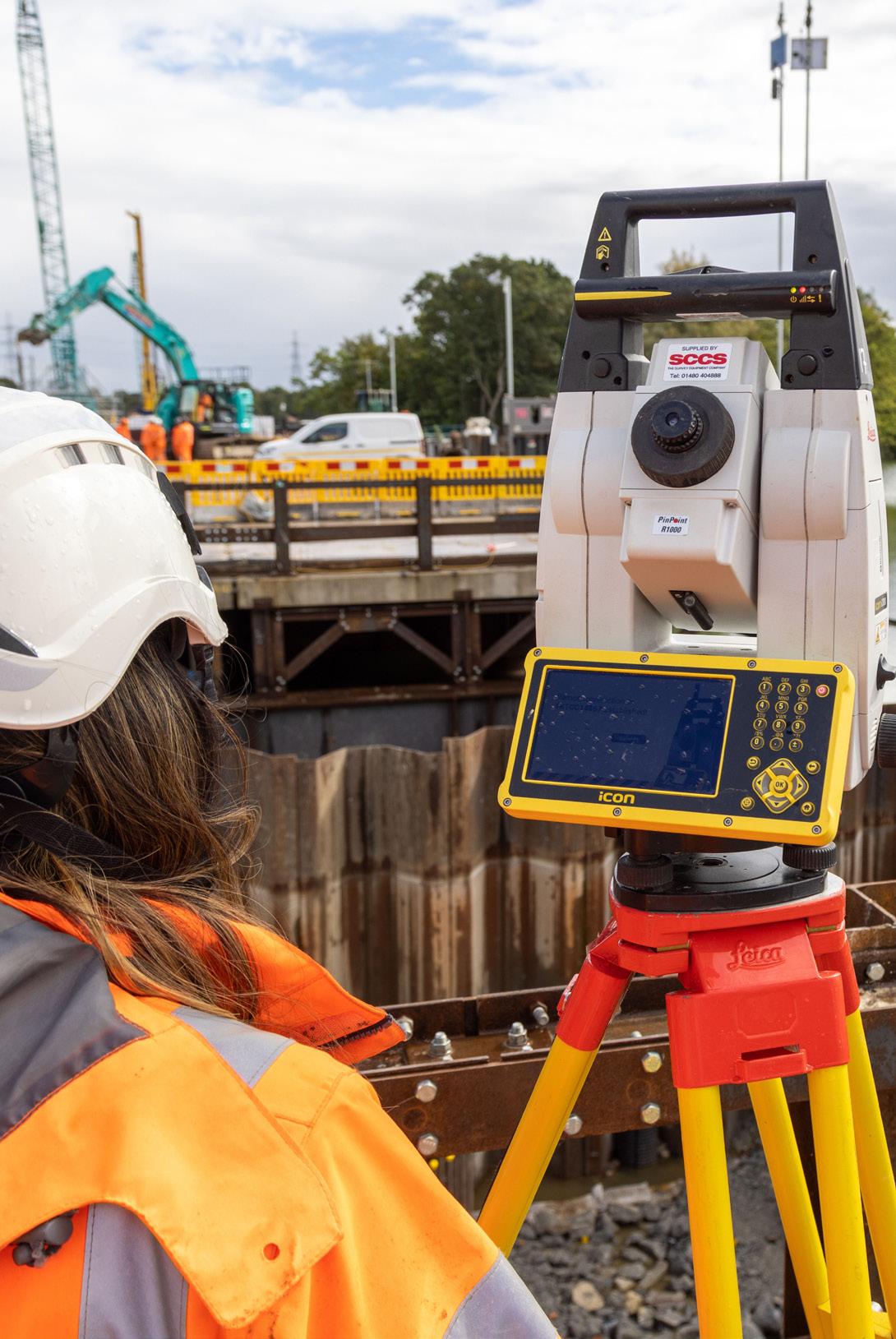
KEEP PRODUCTIVITY ON TRACK
When critical industry processes and concerns require the elimination of lost tool issues, the solution is to minimise human error. Let Snap-on ATC handle the control and tracking automatically
CUSTOMER BENEFIT
• Standardise Work
• Improve Productivity
• Control Inventory
• Reduce Losses
• Control FOD
• Improve Security
• Audit Trail
• Increase Accountability
• Oversight Prevention
• Calibration and Maintenance Reminders
AUTOMATED TOOL CONTROL
With advanced digital imaging technology and proprietary software, Level 5 Automated Tool Control System (ATC) scans the tool drawer and records which tools are removed and replaced in real time. You know where everything is at all times without your techs being slowed down for a second. The system also knows when tools are broken, allowing you to replace or repair them right away. It’s tool control that works hard to keep your techs working at their best.

snapon-industrial.co.uk snaponlevel5.com
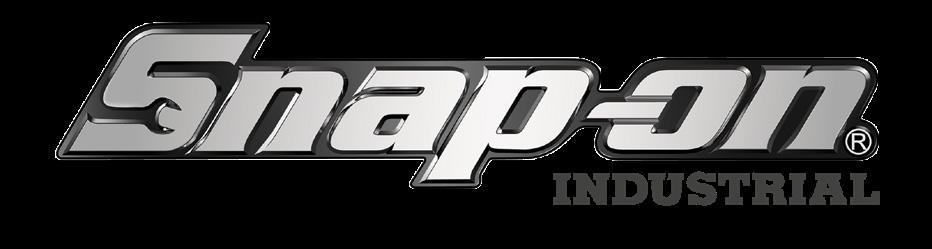
ATC BOX
PRODUCTS AND SERVICES
• Automated Tool Control Box

• Automated Tool Control Locker
• Value Add: Networking
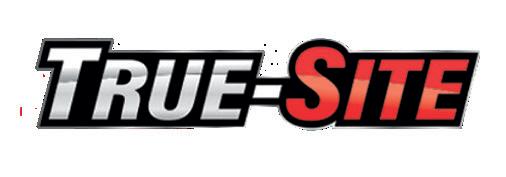
• No individual scanning required
• No RFID tags to install
• No limitations on tool sizeif it fits in the drawer, it works
• Optional polyurea elastomer coated top vs. stainless steel
WORKS WITH
AUTOMATION
FEATURES & BENEFITS
CONVENIENCE
• Intuitive touchscreen interface
• Audible voice confirmation of tool removal and replacement
• Automatic locking
• Errors announced and displayed for incorrect tool position
• 10.1” widescreen, 16:9 LED, resistive touchscreen
• Dual wireless antennas for improved connectivity
• Hardware – 64-bit processor with 8GB RAM
ATC LOCKER
• Track irregularly shaped items like extension cords, tools kitted in plastic or fabric carrying cases, personal protective equipment and more
• Track serialised items like torque wrenches, multimeters or micrometers
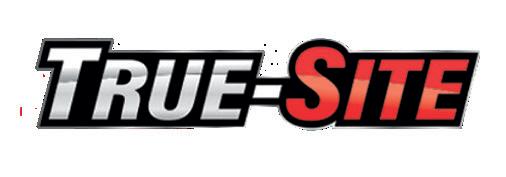

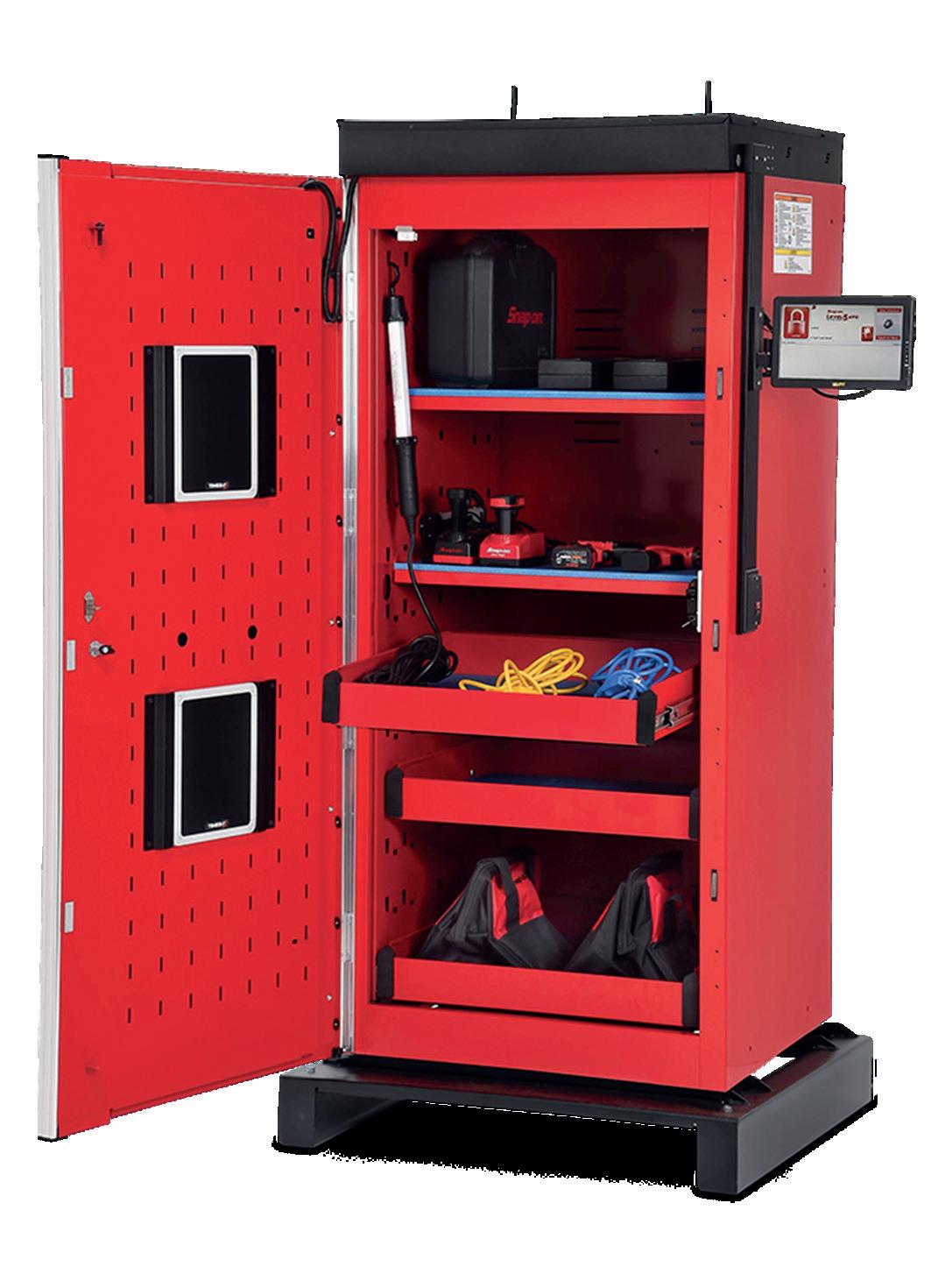
• Fully networkable – connects to Level 5™ administrative interface
• Recharge while storing power tool
ALL THE ACCESSORIES YOU NEED
• FastFlag™ adds status display lights
• ZoomID™ gives you the ability to track serialised, certified and calibrated assets in the ATC Box
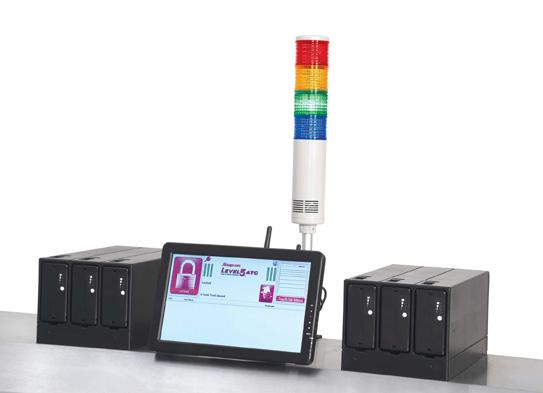
ZoomIDTM
FastFlagTM
Tel: 01536 413 904
industrialuk@snapon.com
POWERFUL ADMINISTRATIVE SOFTWARE WITH REAL TIME REPORTING
• Comprehensive analysis, reporting, and inventory tracking can be performed from administrator workstations located anywhere on the network in real time
• Reports are fully customisable and exportable to Excel or PDF
• Registers transactions in real time – both at the box and between the box and the admin client
• Real time communication includes email alerts when tools are used, when calibration is required, when tool status changes and lost or broken events
STATE-OF-THE-ART BATTERY POWER
• 16+ hours of battery run-time; 30 minutes of backup power for uninterrupted power supply
• Snap-on rechargeable batteries feature state-of-the-art circuit protection that prevents overload
SPECIFICATIONS
• 1 year electronics warranty
• Extended warranty available
• Unlimited number of assigned users
• Networking through Ethernet or wireless
• 1 copy of ATC software required for each administrator

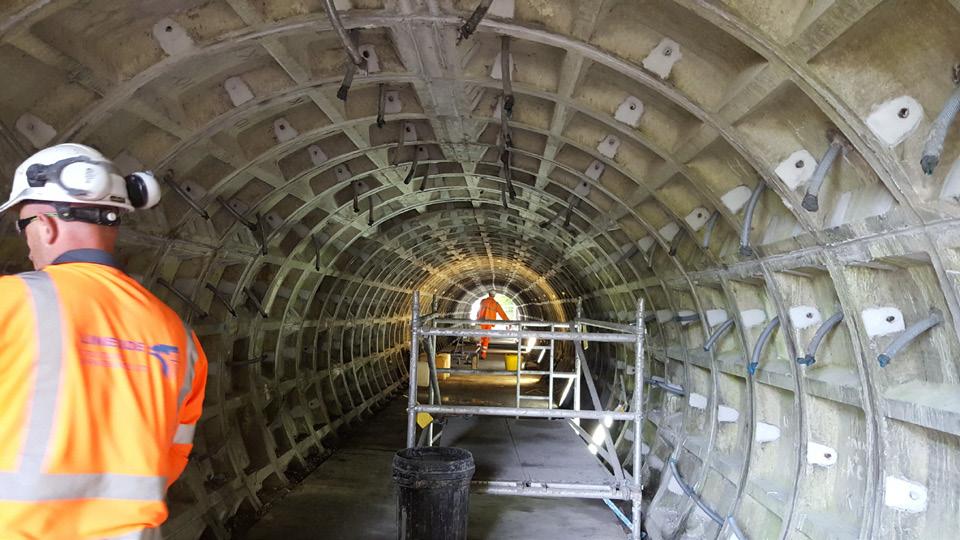
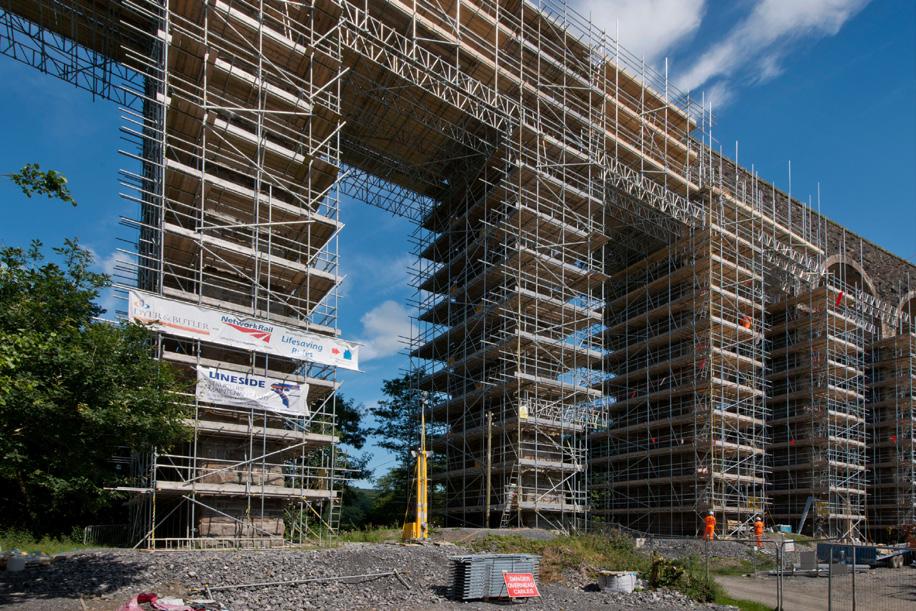

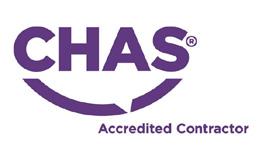



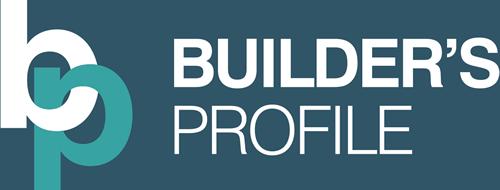
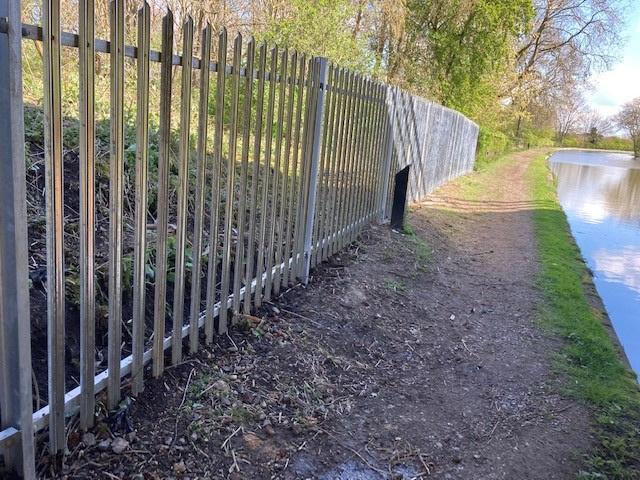
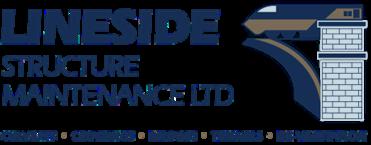
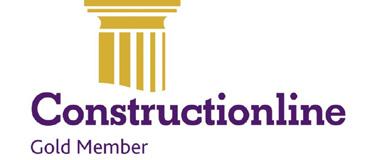
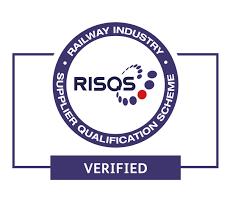

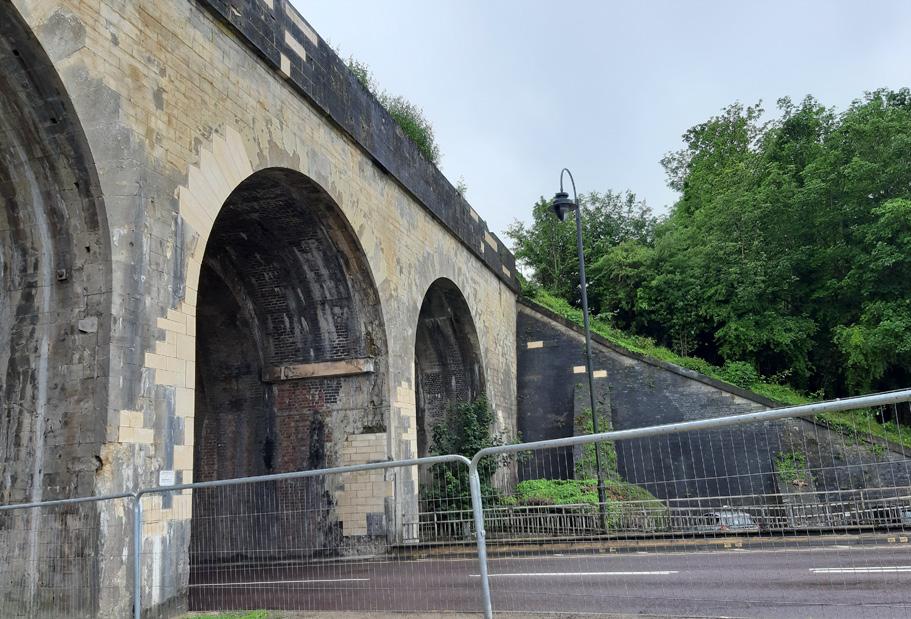
Railtex 2023
Full steam ahead with powerful partnerships, a strong line-up of new exhibitors and an exciting programme
From 9 to 11 May 2023, the rail industry will gather for Railtex 2023 at the NEC in Birmingham. The show provides a unique opportunity to meet with national and international players and thought leaders, all looking to enhance the passenger experience, freight logistics and the overall efficiency of railway operations.
Participants can expect live demonstrations of new machines and systems, technical in-person discussions and a rich supporting programme packed with keynote speakers from leading industry names. Railtex will once again reinforce its role as the central marketplace for the industry to come together and discuss both challenges and opportunities in the light of current developments within the rail industry.
Keeping the current rail market in mind, it is particularly important to focus on crucial topics such as decarbonisation and investments to create a more sustainable rail industry, the digitalisation of rail transport, as well as the passenger experience. It is essential to not only address and mirror these topics, but to also come together to find common solutions and shape a
successful future for the rail industry. This is precisely what Railtex facilitates.
Olaf Freier, the Transport Portfolio Director said: ‘Railtex 2023 is the place to be with all key players gathered in one place. We are glad to have the great support from our main show partner RIA – the Railway Industry Association, as well as our show partners, Rail Forum, Railway Benefit Fund, Department for Business & Trade, British Steel, the CPD Certification Services, our media partners, and many more.’
Network Rail and The Great British Railways Transition Team (GBRTT) as part of an extensive supporting programme
As the leading one-stop-shop event for the entire railway industry in the UK, Railtex reflects the dynamic developments in the sector and the vision of the rail network of the future via an exciting supporting programme.
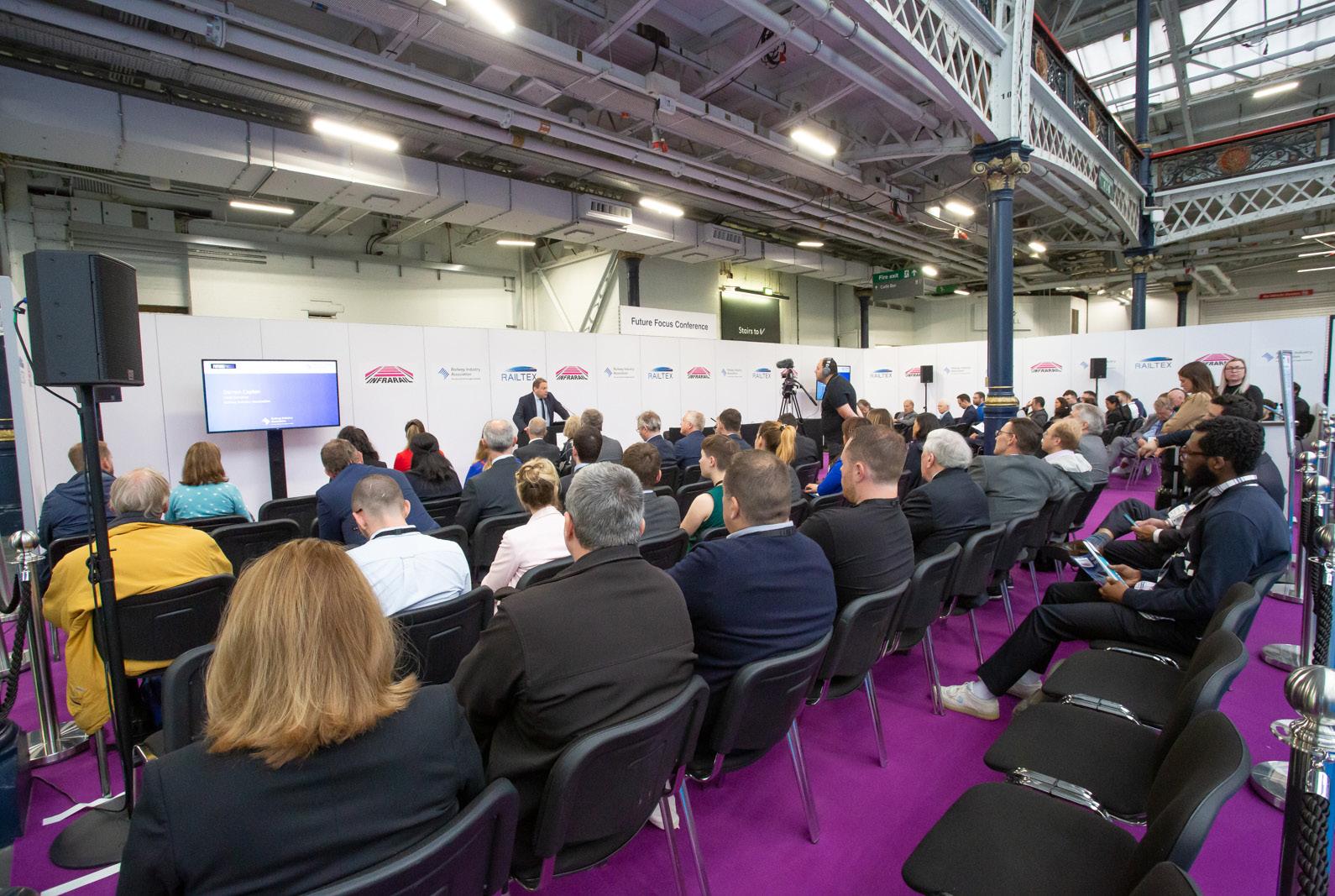
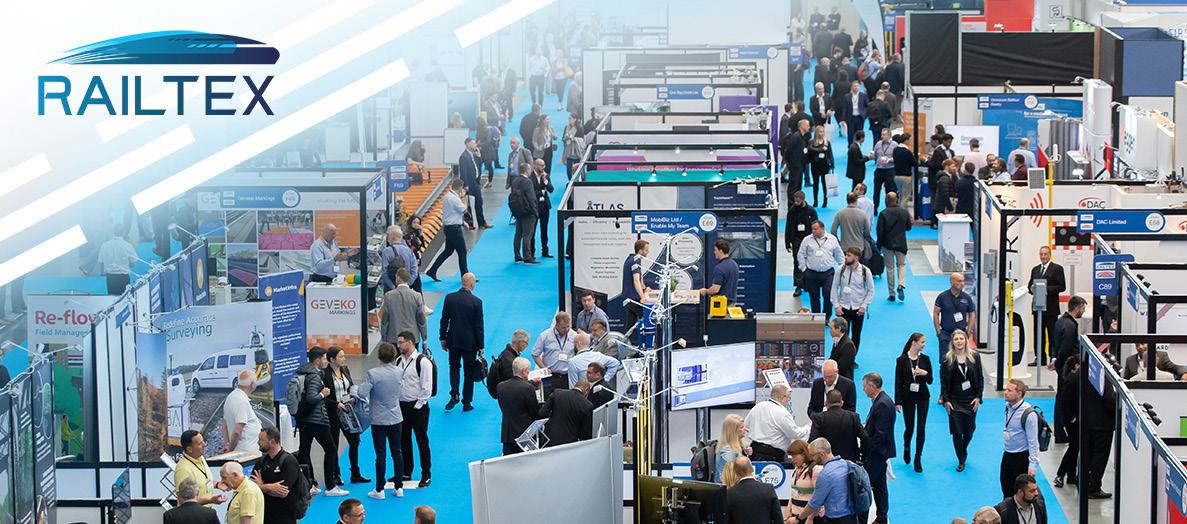
Darren Caplan, Chief Executive of the Railway Industry Association said: ‘We are delighted that the Railway Industry Association will be the main show partner at Railtex 2023, providing an extensive programme across the event. Our programme this year is bigger than ever and includes a Future Focus Conference, to provide an environment where strategic discussions on the future of UK rail can take place, an Innovation Village, where key clients, stakeholders and suppliers will showcase what they are doing on innovation, the RIA Networking Zone and Meet the Buyer programme to support companies looking to get new products and services onto the network, and a Young Rail Professional Conference, bringing a new generation in rail to the show.’
The programme will include keynotes, Q&A sessions and panel discussions held by a remarkable line-up of speakers, including leading figures from politics and industry and many other valuable actors from the rail industry, with the participation of Network Rail and The Great British Railways Transition Team. All sessions are free to attend and CPD certified. More details
will be published in the run-up to the show. The Innovation Village will be part of the ‘Unlocking Innovation’ programme, organised by RIA and supported by Network Rail’s R&D Portfolio.
Furthermore, the show features the popular On-Track Display area, sponsored by long-standing partner British Steel. It demonstrates tools and equipment in an authentic rail setting.
Strong line-up of new exhibitors
So far, 50 new companies are amongst the exhibitors that have already confirmed their participation at Railtex 2023, all serving the future development of the UK railway industry with their products and services. Both the Railtex Exhibitor List tool and the Online Show Preview with detailed information on the many exhibitors and products are regularly updated and available at www.railtex.co.uk. The Exhibitor List tool helps users to effectively prepare for their visit by finding the companies and products most relevant to them.
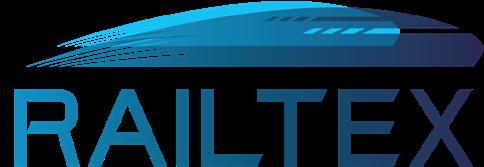
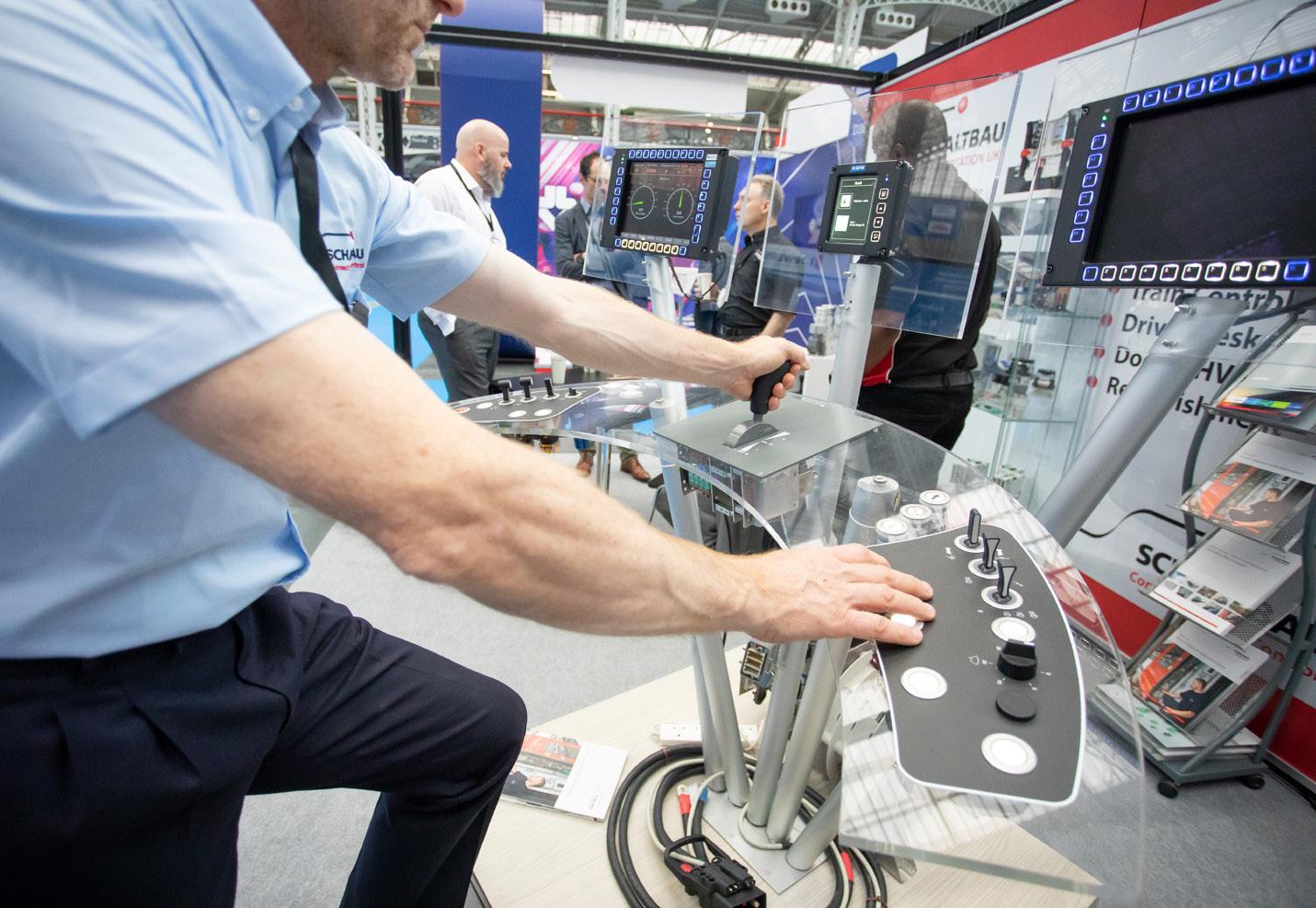
The Online Show Preview provides an overview of the wide variety of innovations, technologies and systems on display at the event.
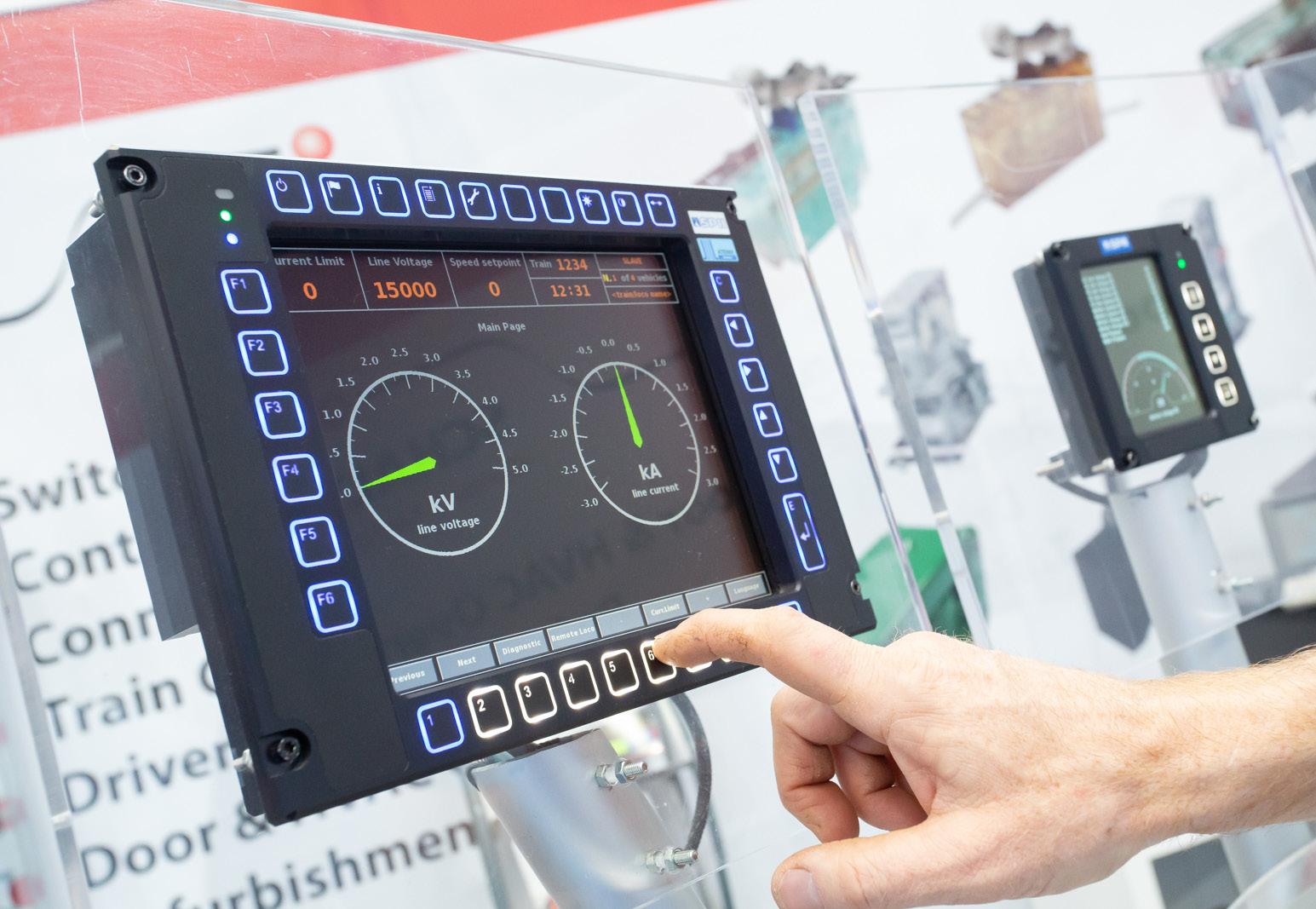
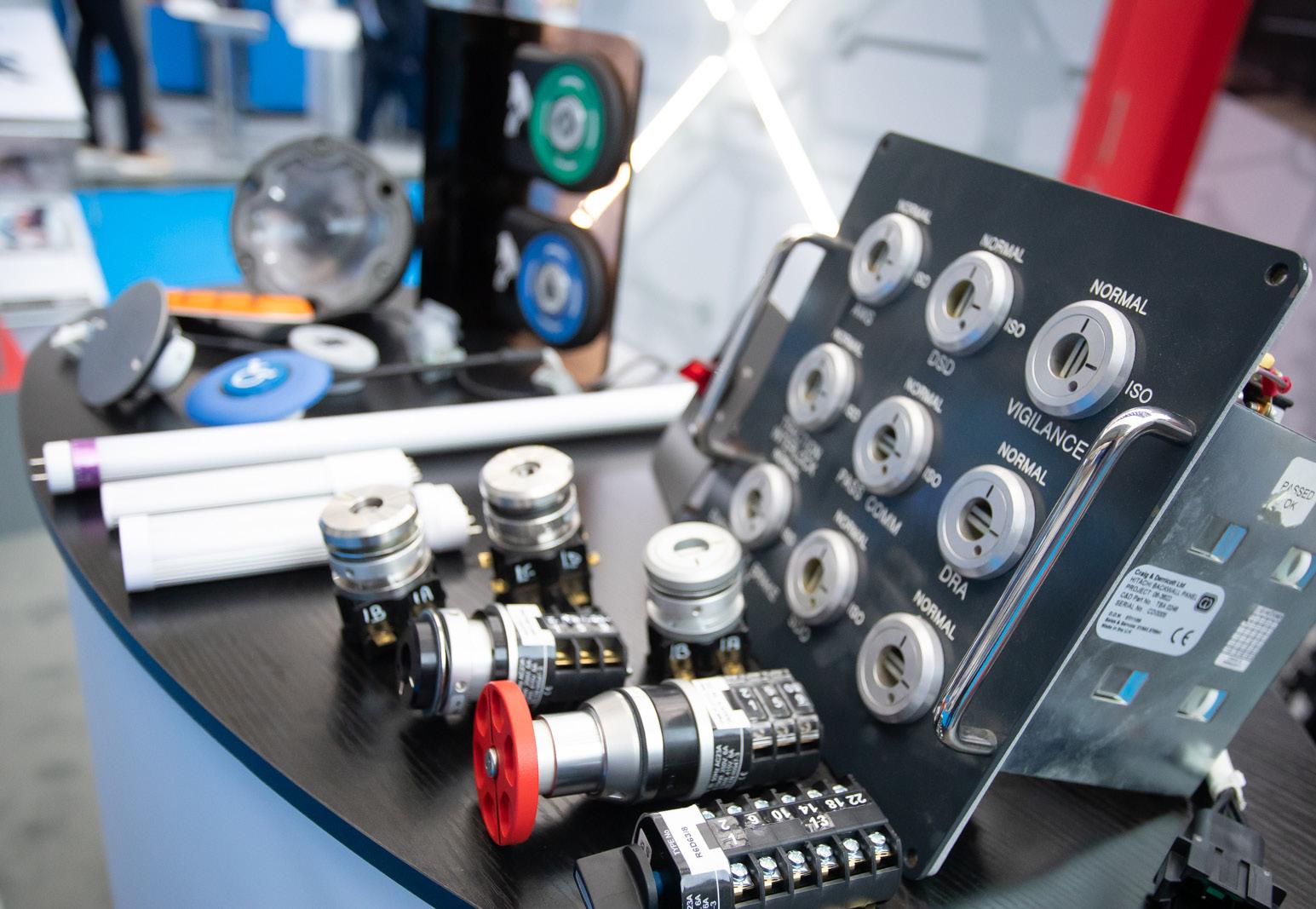
Visitor Information
The visitor registration is now open, and free tickets can be ordered online ahead of the show. During the exhibition, tickets can be purchased on-site or via the online ticket shop. For smooth entry, visitors are advised to print out their e-ticket or download their mobile ticket prior to the show. Show opening hours are from 10:00 to 17:00 on Tuesday, 9 May 2023, and Wednesday, 10 May 2023, and from 10:00 to 16:00 on Thursday, 11 May 2023. More information is available at www.railtex.co.uk
About RX
RX is in the business of building businesses for individuals, communities and organisations. We elevate the power of face to face events by combining data and digital products to help customers learn about markets, source products and complete transactions at over 400 events in 22 countries across 42 industry sectors. RX is passionate about making a positive impact on society and is fully committed to creating an inclusive work environment for all our people. RX is part of RELX, a global provider of information-based analytics and decision tools for professional and business customers.
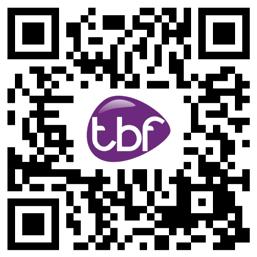
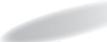


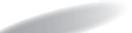

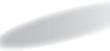


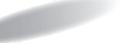


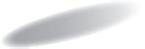
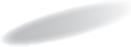
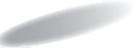




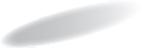


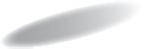


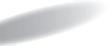
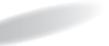
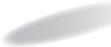

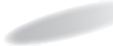


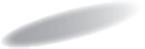


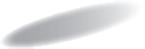

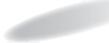
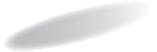
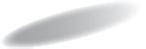
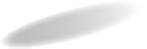
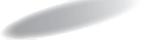
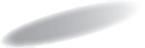
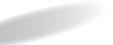
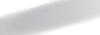
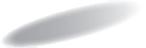
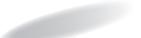

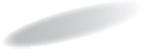
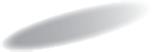
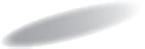

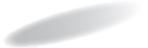
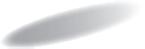

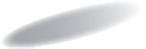

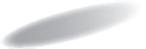
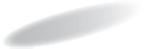
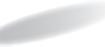


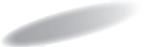

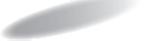
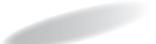




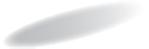



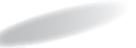




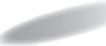




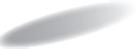


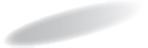
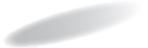

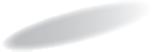
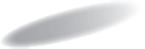
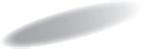
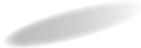
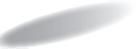

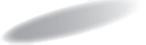
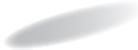
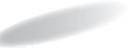

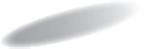
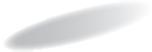
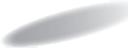




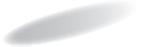
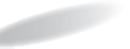



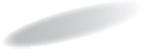

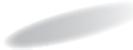

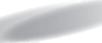
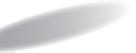


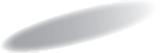
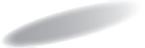
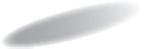
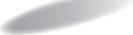
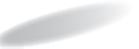
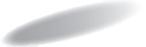
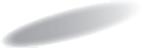
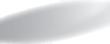


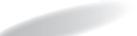
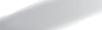
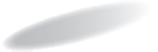

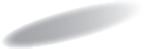
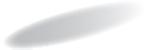
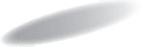
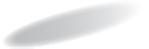

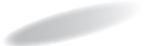
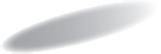
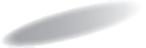
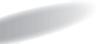
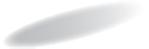
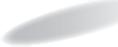



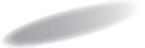
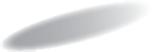
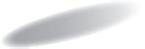
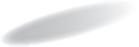
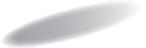

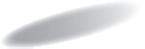
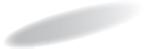
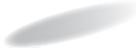


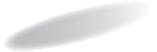
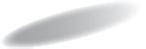
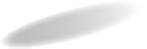
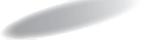
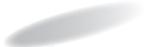
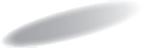
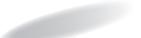

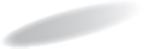
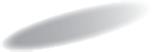
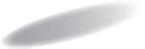

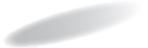
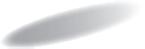
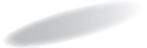
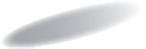

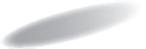
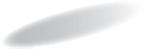
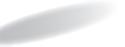

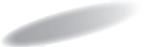

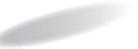









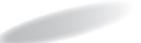



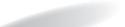

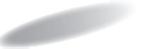


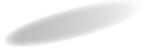
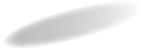
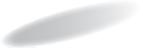

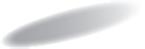
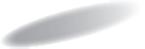

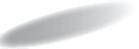

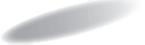
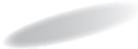
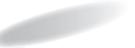



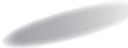
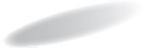
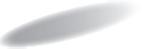


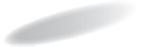


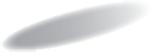
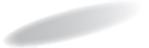
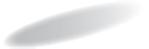
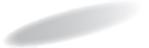

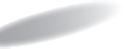
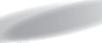
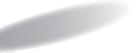



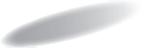
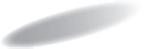
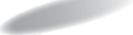
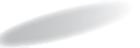
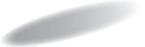
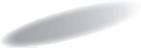


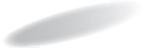
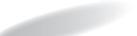
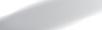
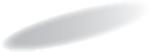

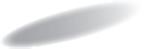
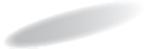
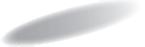
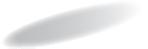

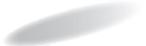

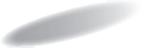

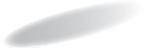
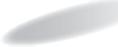



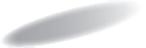
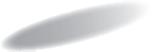

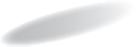
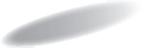

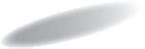



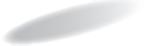

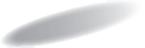
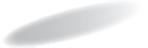

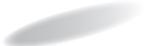
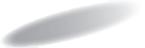
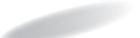

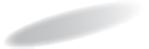
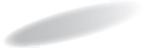
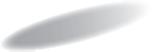
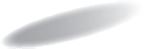
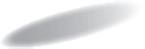
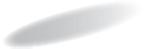

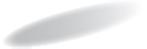
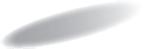
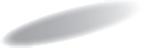
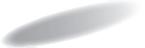
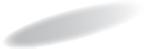
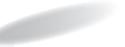

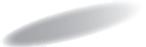






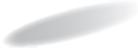
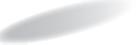

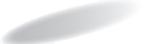

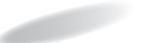
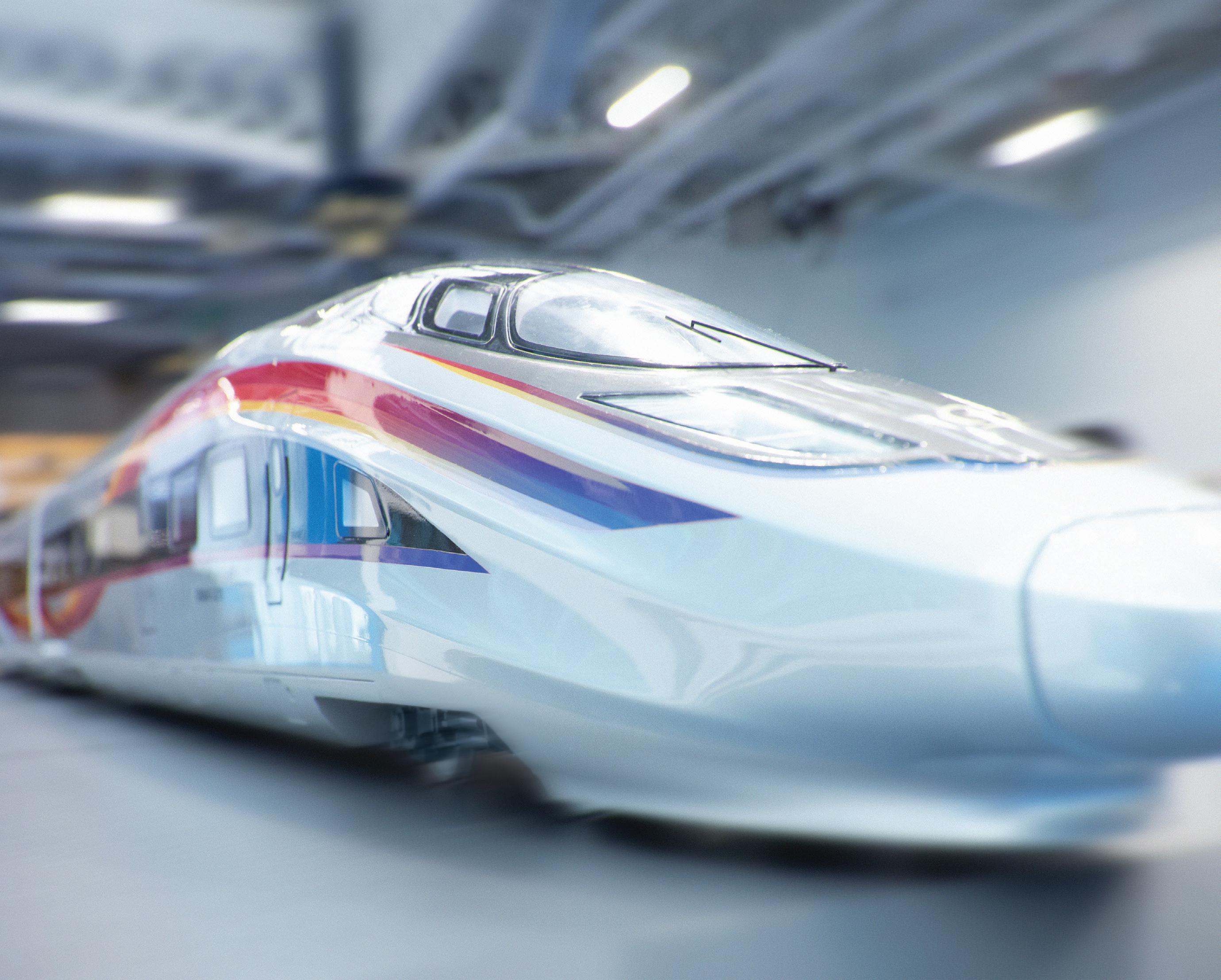
CONFERENCE PROGRAMME
TUESDAY 9 MAY at Conference Zone Stand U11
11:00
Opening Ceremony
Darren Caplan, Chief Executive Railway Industry Association (RIA)
Nicola Hamann, Managing Director, Mack-Brooks Exhibition Ltd
11:30
Minister Speech and Q&A
12:00 Keynote speech and Q&A
12:30
Presentation and Q&A
Gareth Evans, Head of Rail Technology, Network Rail
14:00
Decarbonisation Panel discussion and Q&A
Ruth Humphrey, Head of Business Development and Strategy at Siemens Mobility
David Clarke, Technical Director at Railway Industry Association
Jo Lewington, Chief Environment and Sustainability Officer at Network Rail
Rich Fisher, Head of Strategic Planning on the Great British Railways Transition Team
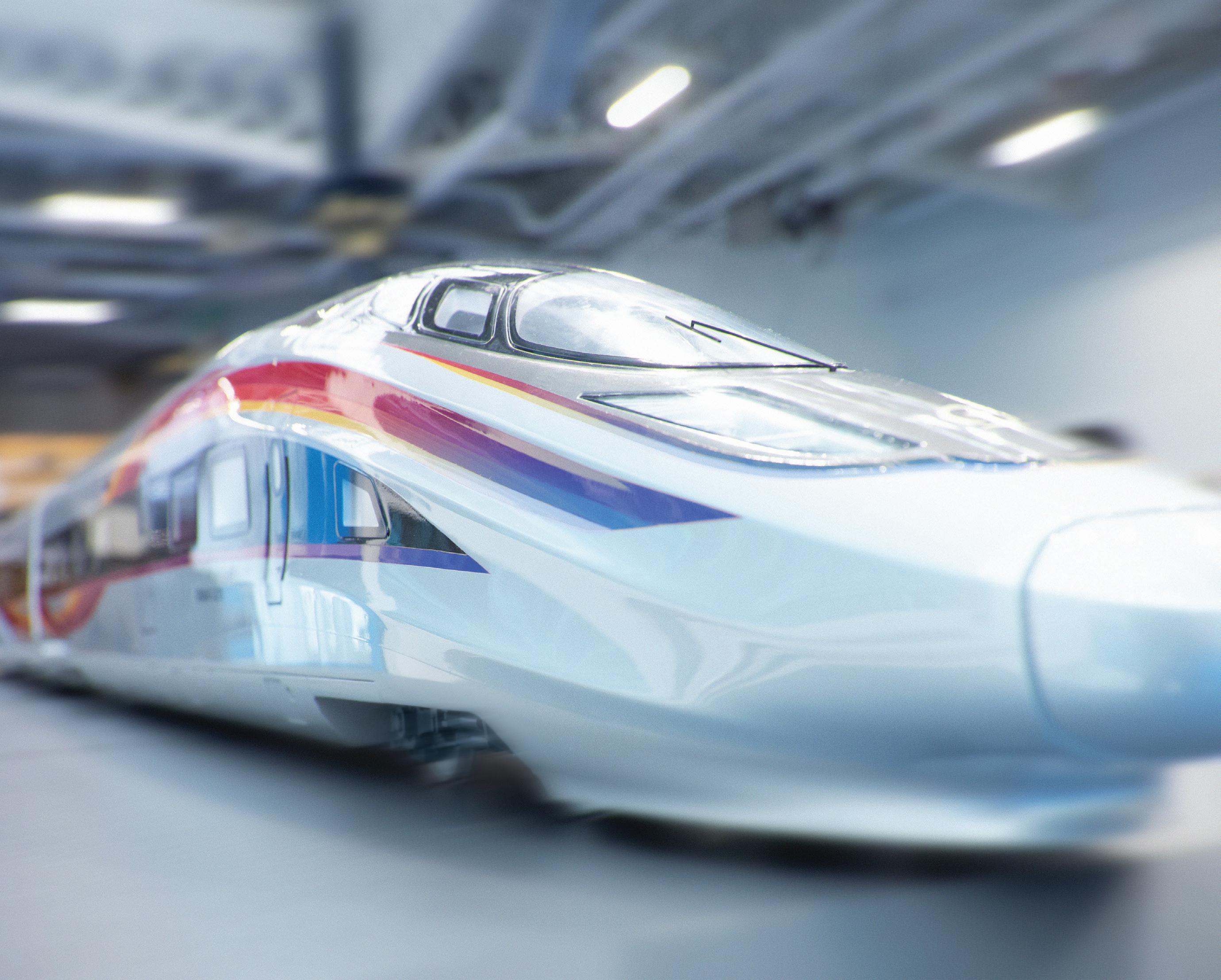
Simon Green, Engineering Director at Great Western Railway
TUESDAY 9 MAY at Innovation village Stand B51
11:00
Network Rail R&D Portfolio
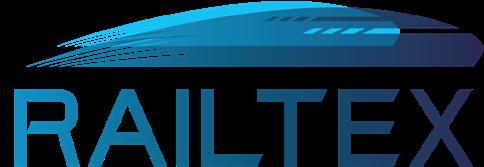
15:00
Presentation and Q&A on Railway Industry Supply Chain Health Check ahead of CP7
Phil Smith, RISQS Manager at RSSB
Network Rail’s Research, Development and Innovation (RD&I) Portfolio is working across the railway infrastructure to improve quality and value for passengers and freight customers. Investment is targeted at £357 million when Network Rail’s direct investment is combined with investment from other sources.
WEDNESDAY 10 MAY at Conference Zone Stand U11
WEDNESDAY 10 MAY at Innovation village Stand B51
12:30
Presentation and Q&A
Maria Machancoses, Chief Executive at Midlands Connect
14:30
Presentation and Q&A
THURSDAY 11 MAY at Conference Zone Stand U11
10:00
Young Rail Professional Conference
11:00
Lab by Transport for Wales
Transport for Wales Rail Limited is a Welsh publicly owned train operating company, a subsidiary of Transport for Wales, and they operate the Wales and Borders railway franchise. As part of their innovation work, they operate a twelve-week accelerator programme (TFW Lab) to help creative and ambitious start-ups pivot their existing solutions and ideas to improve customer experience and business efficiency across Transport for Wales Rail.
THURSDAY 11 MAY at Innovation village Stand B51
11:00
TOC Innovation Community
Train Operating Companies (TOC) Innovation Community works together to share innovation learnings including successes and failures, and to inspire ideas. The community builds a network of contacts, defines shared challenge statements and aims to have a closer collaboration on projects. South Western Railway, LNER, Avanti West Coast and other TOCs will showcase their innovation programmes and innovative solutions.
All information on the conference programme may be subject to change
continued on page 18
Safety Solutions for Depots and Workshops
SAFEMASTER STS offers protection options for plants, and combines the advantages of safety switches, guard locks, key transfer and command functions all in a single system
In depots and maintenance plants for railway technology, danger zones on trains must be protected with isolating protective devices. These are large-area installations over several levels and maintenance personnel are often exposed to hazards during maintenance work including:
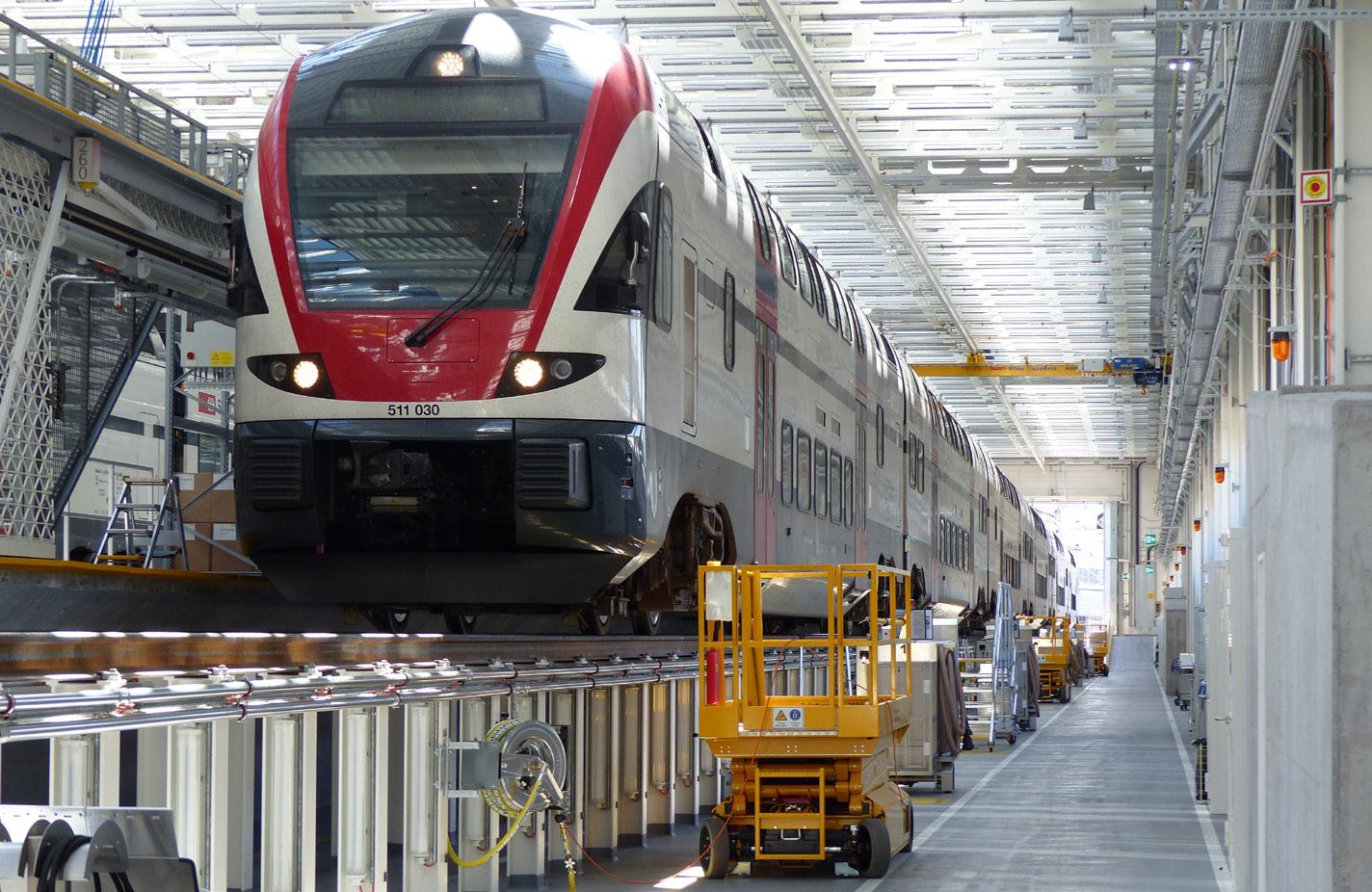
• Electric shock.
• Danger of falling.
• Danger of being locked in.
• Fire hazard.
Safeguarding these extensive depots with electrical components requires a large amount of wiring, which can be prone to faults. There are currently no specific standards for railway maintenance depots. However, working platforms and machines are generally planned in accordance with the requirements of the Machinery Directive 2006/42/EC. The safety devices must generally achieve a Performance Level d or PL e in accordance with EN ISO 13849-1. In maintenance depots the high voltage must be switched off via manual operating points or control systems.
In addition it must be ensured that there is no danger of falling (in pits, lifting platforms and roof-mounted work platforms), operating sequences must be adhered to particularly when accessing the train roof. It is often necessary for operating personnel to put on safety harnesses, use extend folding steps and ground / earth overhead lines using telescopic rods. Due to the size of these installations and the different access levels, it must be ensured that when the train is moved, the maintenance personnel have all left the danger areas and that all maintenance and safety doors are closed. In addition, any locked in operators must have a means to escape.
With the SAFEMASTER STS safety switch and key transfer system, predefined processes can be enforced. This is achieved by the key transfer function. The ability to
protect access and safety doors mechanically and without wiring saves installation cost and increases the availability and ergonomics of the plant, so improving productivity.
SAFEMASTER STS combines the advantages of safety switches, guard locks, key transfer and command functions in a single system. The new fibre reinforced polymer (FRP) variant impresses with its sleek functional design and its ability to be combined with the established stainless steel system. You can select the FRP variants for the control panel and use the robust stainless steel versions in rough environmental conditions.
SAFEMASTER STS is tested and approved according to statutory requirements, and as a stand alone or monitored system is suitable for use in safety applications up to Cat. 4 / PL e in accordance with EN ISO 13849-1.
Essex-based firm, DOLD Industries, is proud to have an almost 100-year track
record in the production of quality products to the manufacturing industry. Founded in 1928 by Emil Dold, the company’s origins are rooted in the best of Black Forest traditions. While the main manufacturing plant remains in Germany, the company’s base in Essex distributes the full range of safety and automation solutions for the UK.
Guaranteed electrical safety and reliable availability represent prerequisites for smooth railroad operations. This applies to locomotives and wagons just as much as to signalling systems, signal boxes, tunnels and bridge constructions. This means that system solutions are needed that ensure the continuous monitoring of electrical equipment and railroad facilities. Besides this, early warnings must enable troubleshooting before critical conditions arise.
Other products in DOLD’s repertoire include level monitoring for water tank monitoring and relays for trackside switching.
Systems and equipment are becoming more and more complex, due to growing automation, rationalisation, and the increasing use of control electronics in machines. Required maintenance work is increasing, making it more difficult for humans to modify such systems. Preventative maintenance which helps avoid malfunctions or reliably correct them in a short time helps to save costs. Using measurement and monitoring relays is becoming more and more economical, as lost production time is difficult to make up.
The situation is all too familiar –complex production systems, high demands for quality, delivery time, and delivery reliability, with permanent cost pressure. Today more than ever, these kinds of pressures require comprehensive operational readiness to maintain and even improve international competitiveness. In practice, however, comprehensive operational readiness is often difficult to achieve; ageing, moisture, contamination, mechanical damage, and other factors can lead to creeping insulation failures. Such undiscovered issues can lead to costintensive system and operational standstills, repair costs, and typically high follow-up costs due to production shutdowns. In the worst case scenario, insulation failures can even be a frequent cause of fires and personal injuries.
DOLD has a range of solutions including insulation monitors and fault locator units, with the multifunction measuring relay for Modbus UG 9400 simultaneously monitoring up to nine different measured variables such as voltage, voltage asymmetry, current, cos phi, active, apparent and reactive power as well as frequency and phase sequence.
Reliable switching and controlling is a mainstay of the product line, with
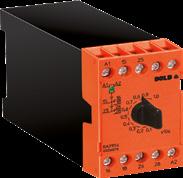
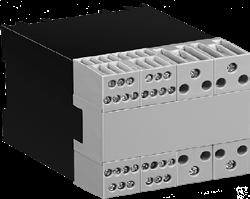
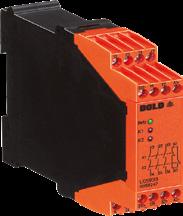
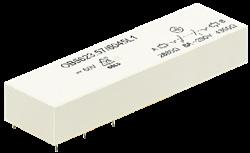
semiconductor contactors which have proven themselves in industrial applications in any situation where high switching frequencies or high switching cycles are required. With their long service lives and wear-free switching, they handle switching and controlling tasks in specific applications in a highly economical manner.

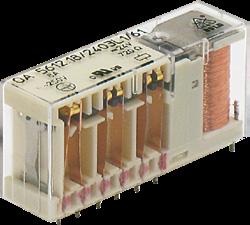
Safety technology is becoming more and more important in machine and equipment construction. Safety modules or even safety controllers are being used everywhere.

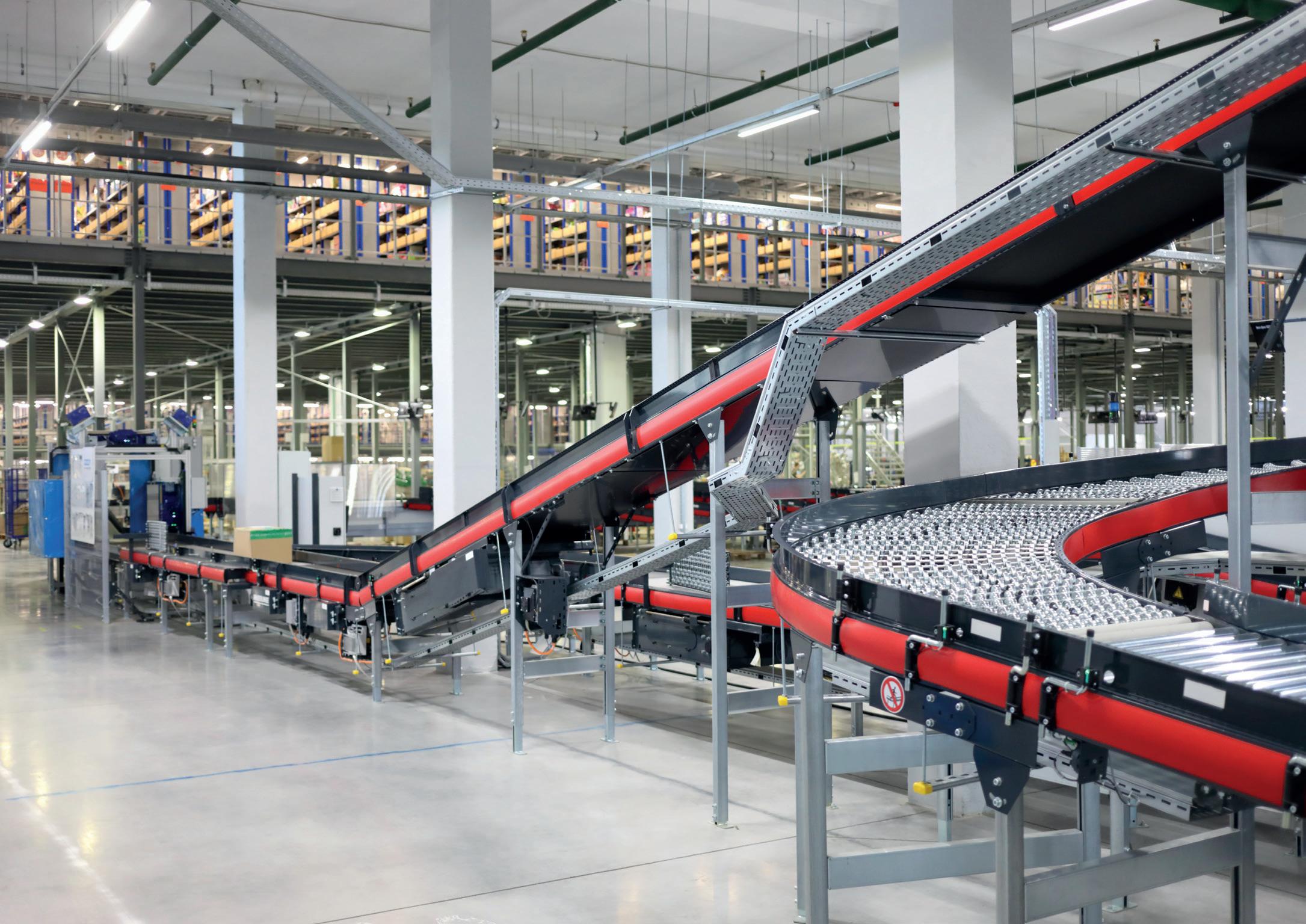
A pioneer in the production of Switchgear, E. Dold & Söhne GmbH & Co. KG is one of the leading European manufacturers and is certified to ISO 9001. DOLD develops, manufactures and distributes high-quality components and complete solutions for safe automation, electrical safety and smart drive technology worldwide. The product range includes safety relay modules, safety relays with forcibly guided contacts, electronic enclosures as well as safety switches, safety guard locks and key transfer systems.
Tel: 01245 324432
Email : admin@dold.co.uk
Visit: www.dold.co.uk
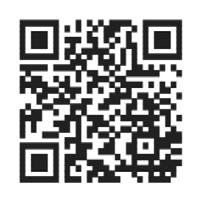
BCIMO RECEIVES A ROYAL SEAL OF APPROVAL
The Black Country Innovative Manufacturing Organisation (BCIMO) welcomed His Royal Highness the Duke of Gloucester to the Very Light National Rail Innovation Centre (VLRNIC) on 19 April. His visit cemented the centre’s status as an important new transport innovation hub, just four months after it opened for business on the site of the former Dudley railway station in the West Midlands.
Exhibition Profile
Railtex covers all aspects of railway technology and provides a showcase for manufacturers in the major fields of rolling stock technology, track and infrastructure and signalling and communications
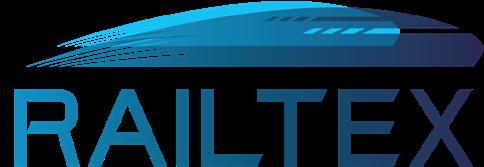
HS2’S MULTI-BILLION-POUND BOOST FOR UK BUSINESSES
HS2’s construction is helping to keep over 2,000 UK businesses afloat as they continue to tackle difficult economic conditions. Latest figures from HS2 show that tier two subcontracts totalling £7.9 billion have been awarded to over 2,000 UK-based companies, with SMEs securing £3.6 billion worth of orders – a 45 per cent share.
TWO
SUBCONTRACTS
Businesses in every UK region have won work supporting HS2’s construction, with the East of England, West Midlands, Greater London and the South East each amassing over £1 billion worth of contracts.
Firms of all sizes have stepped up to deliver – £1.9 billion worth of work has been awarded to medium sized businesses (50-250 employees), £677 million to small businesses (11-49 employees) and just over £1 billion to micro businesses (one to ten employees).
The exhibition also serves as a shop window for suppliers of the many other specialised products essential to the efficient and safe operation of railway and public transport systems. Among these are vehicle maintenance equipment, fare collection systems, rolling stock leasing, electronics for rail applications and cable technology. More than 180 categories of products and services will be represented at the event. If you supply products and services in any of the following areas, then exhibiting at Railtex 2023 should be part of your marketing plan:
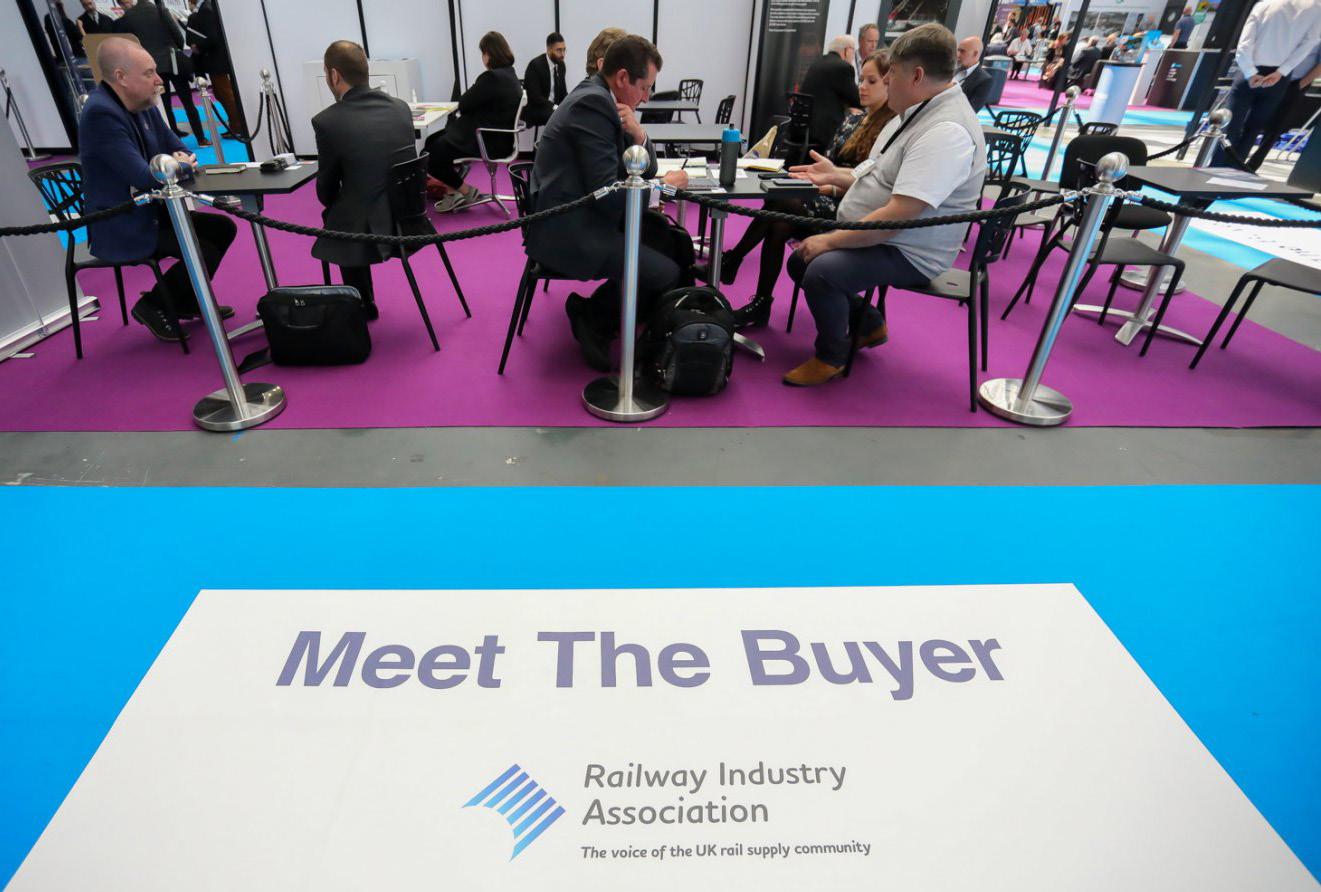
• Rolling Stock.
• Railway Civil Engineering.
• Track Design, Supply and Construction.
• Track and Infrastructure Maintenance.
• Electrification.
• Signalling and Communications.
• Depot and Workshop Equipment & Services.
• Plant and Equipment.
• Safety and Security Systems.
• Electrical products and Equipment.
• Measurement, Monitoring and Testing Systems.
• Information Technology.
• Station Equipment and Passenger Technology.
• Human resources and Occupational Health.
• Consultancy and Specialised Services.
See more at www.railtex.co.uk
TOTALLING £7.9 BILLION £1.9 BILLION WORTH OF WORK
We connect trains
Trackside
• Radio frequency connectivity
Rolling stock
• Wires and cables
• Cable systems
• Radio frequency connectivity
• Fiber optic connectivity

Our market-leading connectivity solutions for data and power transmission are designed to meet the unique requirements of the railway industry, including space-saving and lightweight RADOX® cables, high performance SENCITY® Rail antenna portfolio as well as future-proof fiber optic systems. Moreover, they are keeping operating costs down and the environmental impact low.

BIGGER BETTER BRIGHTER
To find your nearest Buckbootz supplier, call 01382 82 82 00 or email info@buckbootz.com The full Buckbootz range can be seen at buckbootz.com
If you thought that our pioneering BuckzViz products were show stoppers, feast your eyes on our sensational new high visibility rigger and high leg lace styles: two stunning safety footwear products whose specification combines our groundbreaking BuckzViz high visibility and reflective specification with our BangGuardz ankle protection technology.
That’s only part of the story but it’s the part which really jumps off this page. The rest of the specification brings you the latest EN/UKCA S7 waterproof standards plus enhanced scuff toe protection and truly impressive anti-slip performance from heat and fuel oil resistant non-marking outsoles which come complete with ladder grips.
On top of all that BuckzViz 5 and 6 are super lightweight and super comfortable thanks to their Buckbootz foot cushion insoles. Quite simply, no other outdoors workplace footwear on the market makes a safety statement like them.
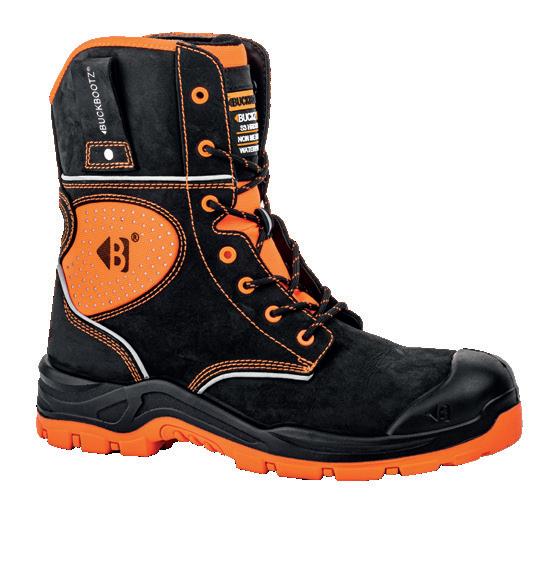
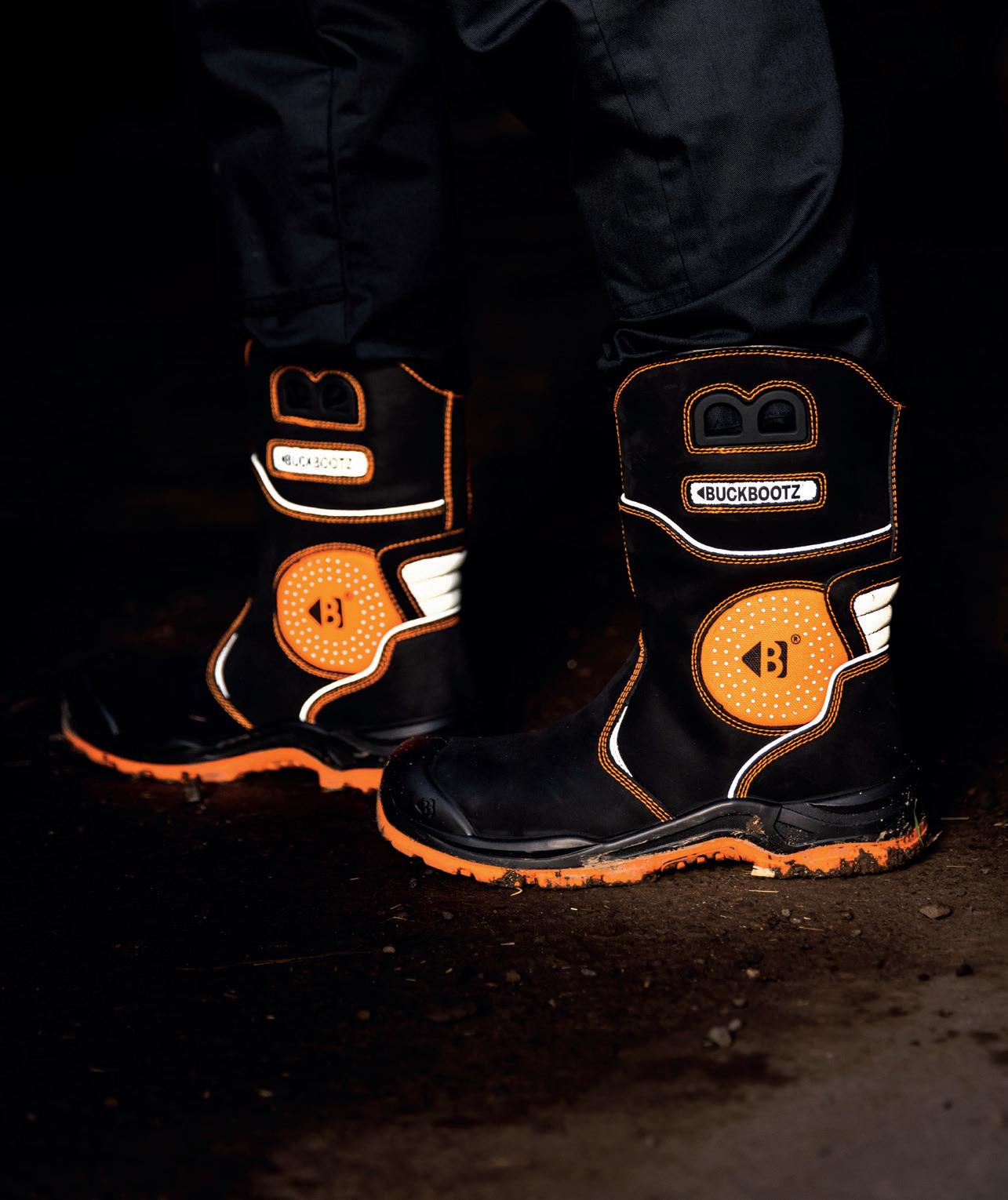
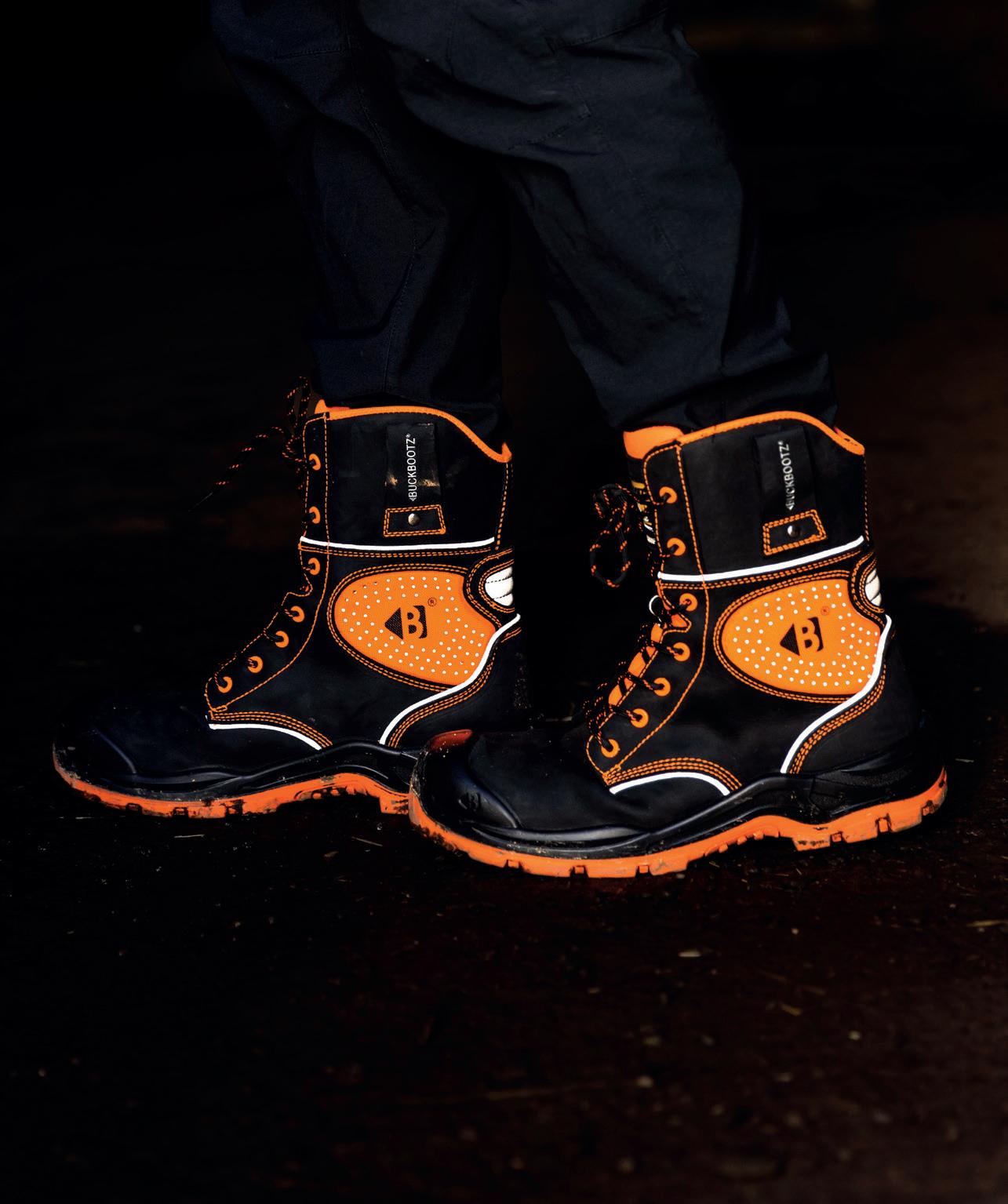
Hydrogen Power for a Greener Future
Rail continues to be one of the most environmentally friendly modes of transport available to commuters, says HUBER+SUHNER
Compared to airplanes and automotive vehicles, trains emit between 66 and 75 percent fewer carbon emissions. With the railway industry constantly in pursuit of greener services, using alternative fuels such as hydrogen may hold the key for further improvements.
Greater sustainability for rail transportation
Hydrogen-powered trains remain a relatively new concept, but are already in use on railways around the world. The first passenger train powered by hydrogen was put in service in Germany in 2018. The Avelia Coradia iLint can reach a maximum speed of 140 kph and is able to carry approximately 150 seated passengers per journey. Since then, there have also been successful deployments of similar trains within the United Kingdom, with the HydroFLEX project, devised by the University of Birmingham, carrying out their first successful mainline test at the end of 2021.
The use of hydrogen as an alternative fuel source enables rail operators to utilise a clean energy source capable of supporting low-carbon strategies. Energy is generated through the electrochemical reaction of both oxygen and hydrogen. As a result, no nitrogen is emitted, with water the only by-product. The technology also provides increased energy output as opposed to traditional sources such as fossil fuels, making hydrogen-powered trains a perfect solution for operators to reduce the amount of carbon within the environments they offer services in.
Achieving environmental goals
In 2020, the Chinese government announced its goal to peak carbon dioxide emissions by 2030 and achieve total carbon neutralisation by 2060. To achieve this, the government laid out plans to develop and maintain a low carbon and circular economy and promote high-quality green economic developments and accelerate
the development of economically friendly technologies.
CRRC Changchun Railway and the Chengdu Railway Group (CRG) quickly realised the potential of hydrogen-powered trains to create a greener, more sustainable solution for urban rail networks across China. Analysis carried out by experts within the country quickly found railway
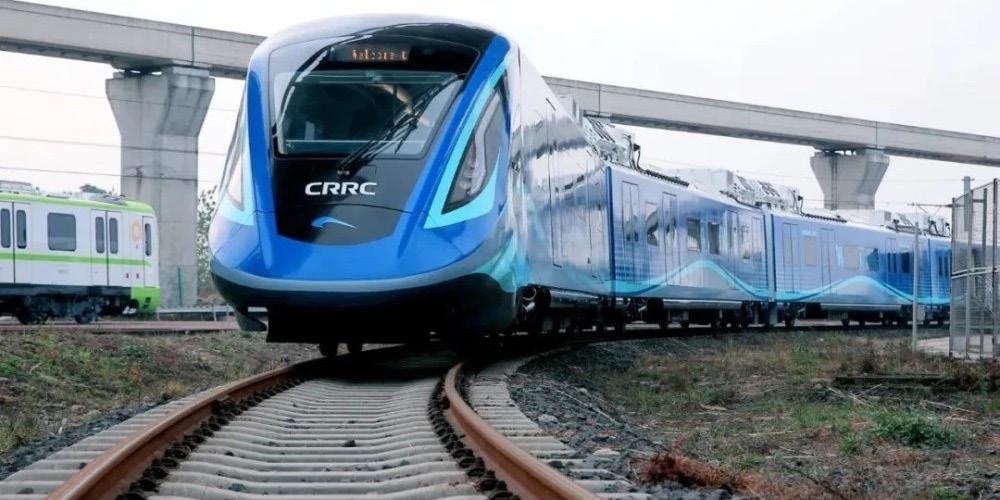
transportation to be the most appropriate application scenario for hydrogen powered fuel cells when compared to other passenger vehicles such as cars. Fixed railway lines –with point-to-point routes within railway systems – make the transportation and storage of hydrogen easier, avoiding the need to construct and establish expensive refuelling stations.

To help the government achieve their aims of a green future for China, CRRC and CRG joined forces to develop an inter-city, hydrogen-powered train for commuters travelling to and from Chengdu, the capital city of the Sichuan Province. Their plan was to create a hydrogen-powered train capable of operating at speeds up to 160 kph, making it the fastest of its kind once in service.
Overcoming the challenges
To make the project a success, both CRRC and CRG required a reliable hydrogenpowered service. This required the power and weight of the train’s engine system to be perfectly balanced. Optimal traction power could only be attained so long as there were no further increases to the train’s weight, else the range of the system would be negatively affected.
Due to the sheer number of power modules found within the hydrogen power supply system, the fuel cell had to be equipped with various sensors to precisely monitor temperature, pressure and the hydrogen concentration. As a result, any electrical systems deployed needed to be relied upon in order to accurately control these elements. This was especially crucial
for the connectivity system responsible for signalling and the transmission of power which required quality cabling to work efficiently.
If the operators were to provide a superior experience, especially when compared to traditional train offerings, cutting-edge technologies were required. These included autonomous driving capabilities, alongside intelligent passenger information systems (PIS) and 5G highcapacity train-to-ground communication. These would help establish and maintain a reliable service for staff and passengers alike, reducing the likelihood of disruption, providing precise information to the workforce and commuters regarding the status of the train, as well as increased incarriage connectivity.
Unique requirements, unique solutions
To overcome the demands of the project, HUBER+SUHNER were called upon due to its extensive experience within the rail sector. A bespoke harness was provided not only to meet the specific requirements of CRRC but also to ensure the train was compliant with the industry safety standards expected of rail braking systems. The electrical and passenger information
systems on the train were also enhanced through the use of RADOX® 3 GKW and 4 GKW and TENIUS cables, which help maintain reliable and stable signal transmission and electrical connections between the hydrogen power system and the other relevant sub-systems. These cables also helped to reduce weight and save crucial space within the train, which was a key requirement from the customer.
HUBER+SUHNER supplied two SENCITY® Rail MULTI 7-Port rooftop antennas for the train’s PIS and Wi-Fi system, alongside a SPUMA Radio Frequency (RF) cable with technical indicators to enable multi-network integration and accurate data analysis. These solutions were tailored for the project to further optimise the available communications and empower rail operators to continually and precisely assess the status of the train, improving the safety and efficiency of the service offered.
The project culminated in a successful rollout, with CRRC and CRG launching the inter-city train in Chengdu in December 2022. The organizations involved achieved their goal of developing a train not only offering a four-car configuration to increase the number of commuters able to use the service, but one that reached a speed of 160 kph. This makes it the fastest hydrogenpowered train in the world presently.

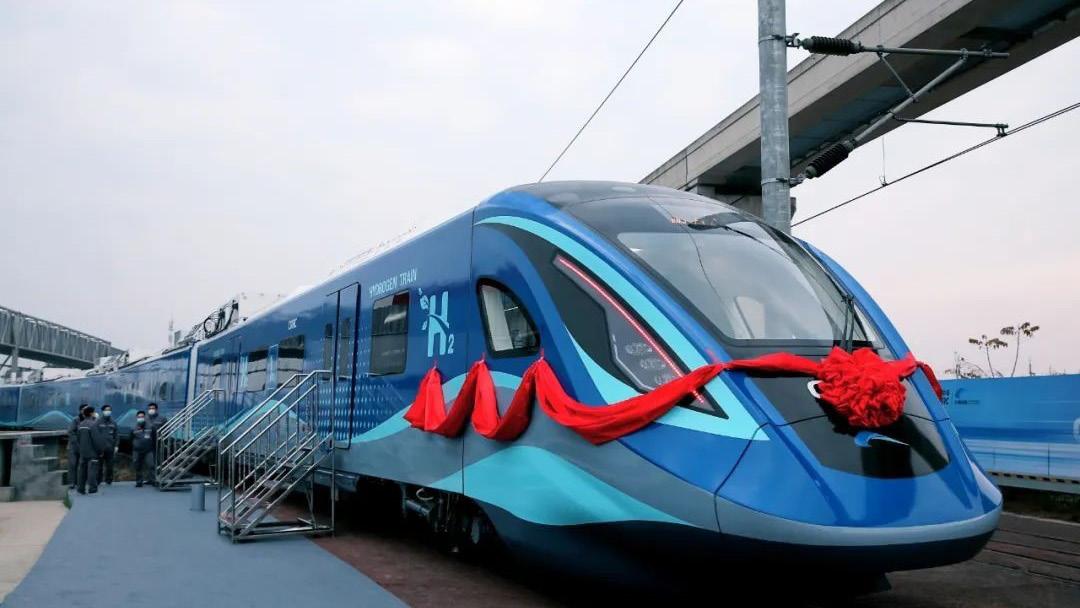
With a built-in power system capable of up to a range of 600 kilometres on a single charge, the combination of this technology –alongside a super capacitor – improved upon the catenary power supply traditionally seen in trains. All of this resulted in a reliable, eco-friendly service that aligns with the government’s environmental aims while delivering an improved service for commuters.
Green railways across the globe
Governments now face more scrutiny than ever regarding their approaches to decarbonation. In March 2023, the Transport Committee placed increased pressure on the UK government to adopt a better approach towards backing greener technologies within the transport sector, including recommendations to implement hydrogen-powered, battery-powered and bi-mode trains.
Solely developed to provide a new solution for the Chinese inter-city railway market, the Chengdu inter-city train is yet another example of a successful hydrogenpowered train roll-out. Governments looking to create a greener ecosystem may soon use the project as a benchmark of success, and we can soon expect hydrogen-powered trains to play a crucial role in modern railway networks across the globe.
Email: railway-marketing@hubersuhner.com
Visit: hubersuhner.com/en/solutions/railway
Safety
Efficiency
Health and wellbeing
Innovation Emerging technologies
Research Data insights
Sustainability Standards
RSSB
Leading and facilitating continuous improvement for rail
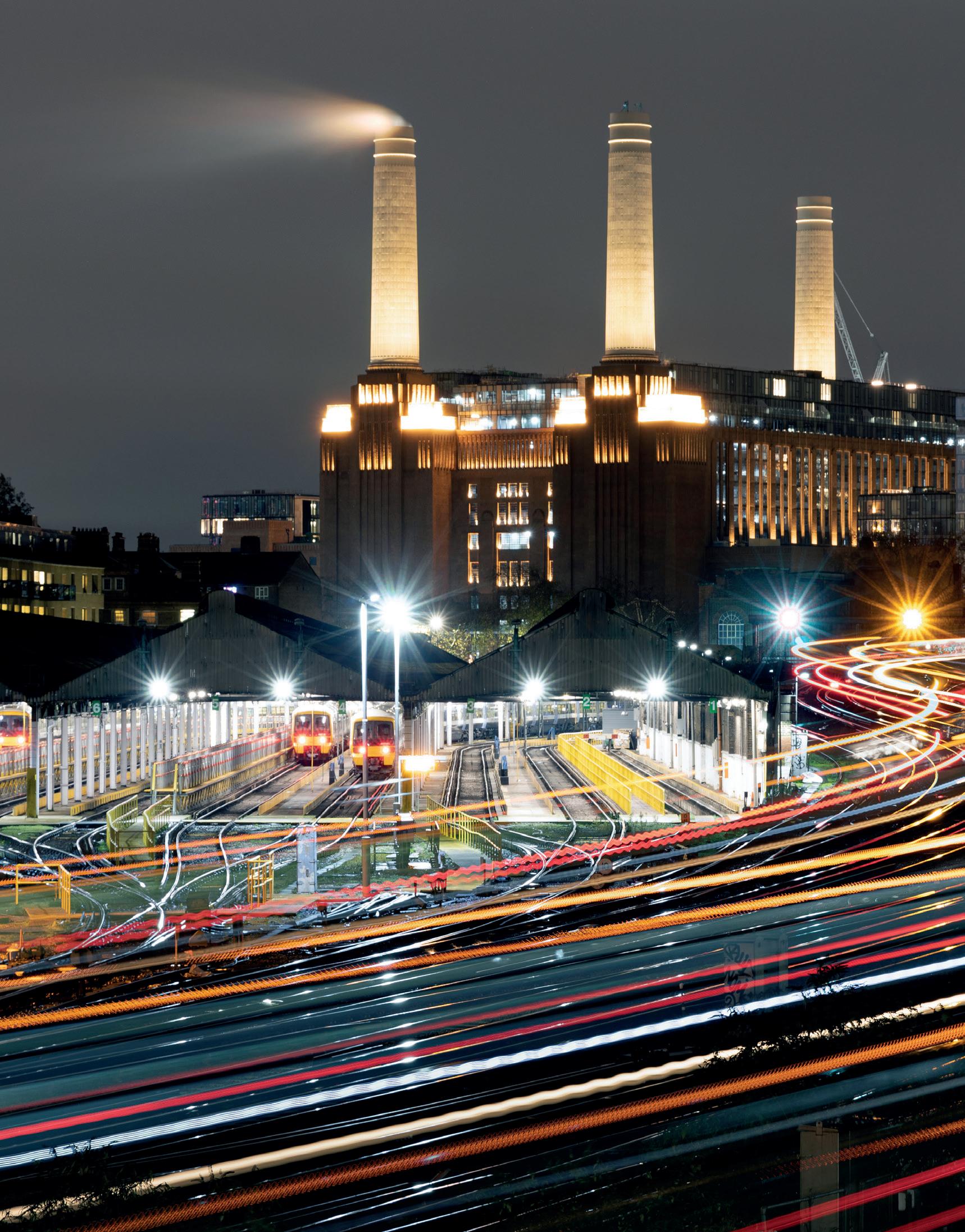
Twenty years ago this month, the Rail Safety and Standards Board was born. RSSB was created after the Ladbroke Grove crash, as a direct recommendation of the Cullen inquiry.
For two decades, we’ve worked hand-in-hand with the rail industry to make the network safer, more efficient and more sustainable. Now our materials and insights form a dynamic, impartial link between innovation, standards and safety. We close knowledge gaps, ensure new technology can be used safely and efficiently, and help codify and share best practice.
For more about our plans for the future, visit rssb.co.uk/RSSBat20

We’re with you every step of the way
How to Get There
By Train
The NEC is right next to Birmingham International rail station. The NEC entrance is on the right hand side as you exit the station, and clearly signposted. Many services run direct to Birmingham International. If yours doesn’t, you can catch a connecting train at Birmingham New Street. There are regular services, and the journey only takes 10-15 minutes. Buses to the NEC can be caught at Birmingham Moor Street and Solihull stations. For further information visit National Rail.
By Car
The postcode to use for satellite navigation is B40 1NT. The NEC is eight miles east of Birmingham city centre and has 16,500 parking spaces available. Follow the electronic signage or directions provided by their traffic team to get you to the right car park area for Railtex. Once you’ve parked you can either take a free shuttle bus or walk to the halls using the sign posted footpaths.
By Plane
The NEC is just minutes away from Birmingham Airport (BHX). From the airport, simply take the free and fast AirRail Link to Birmingham International railway station and then it’s just a short walk to the entrance of the NEC.
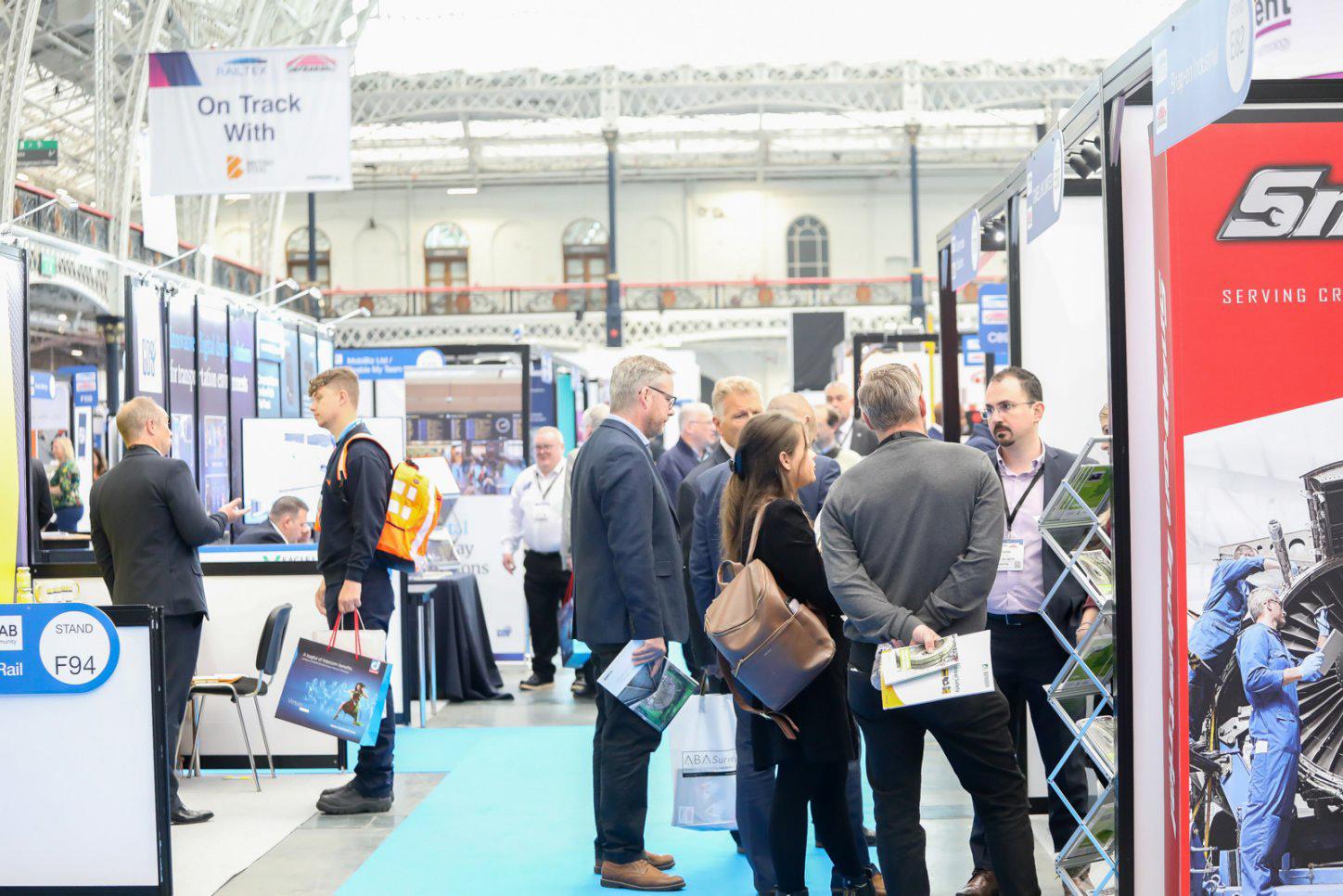
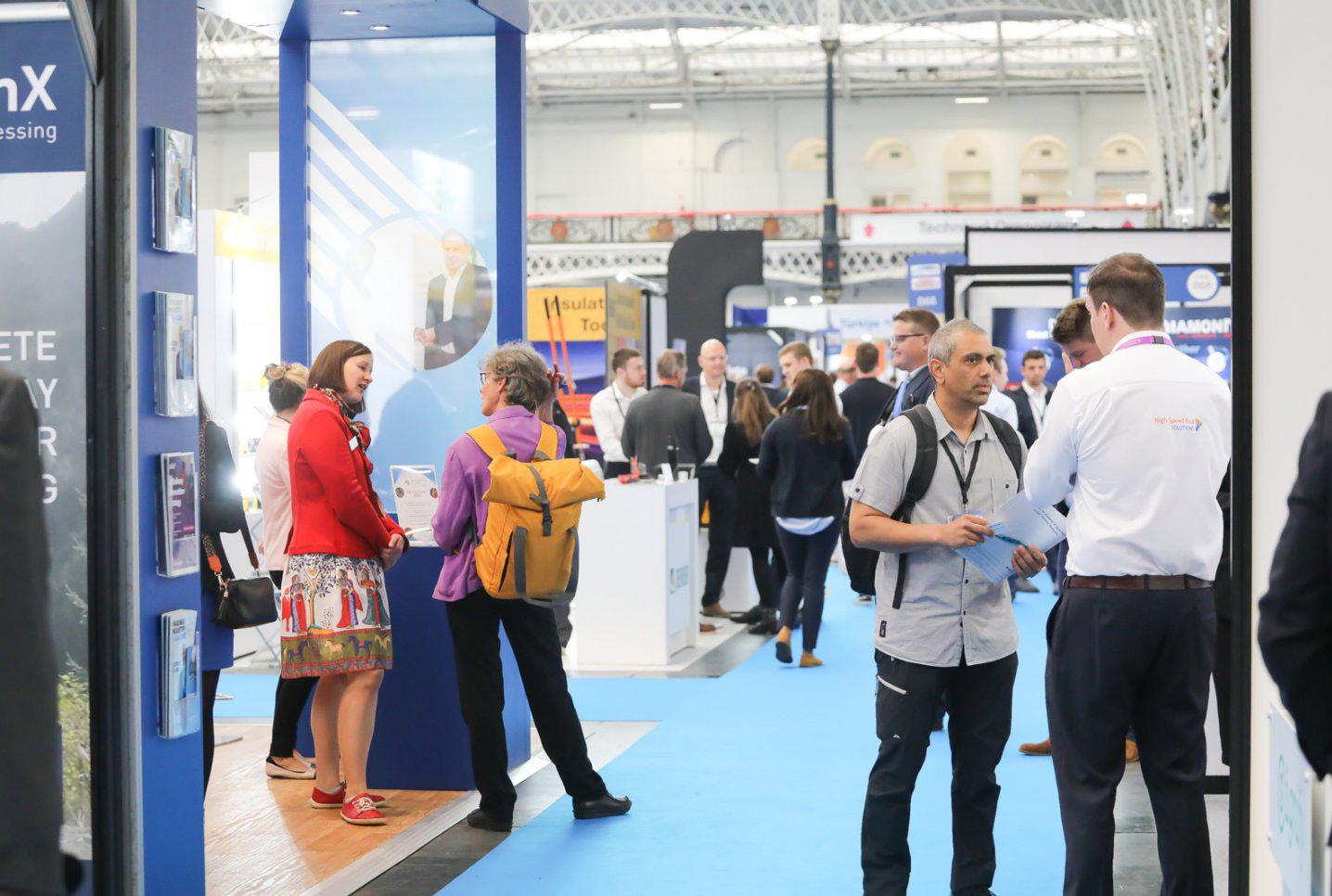
The Air-Rail Link runs every two minutes and takes just 90 seconds to reach the NEC. It leaves the airport from the upper level of Terminal 1 and operates daily between 05:15am and 02:00am. East Midlands Airport (EMA) is 40 miles away from the NEC.
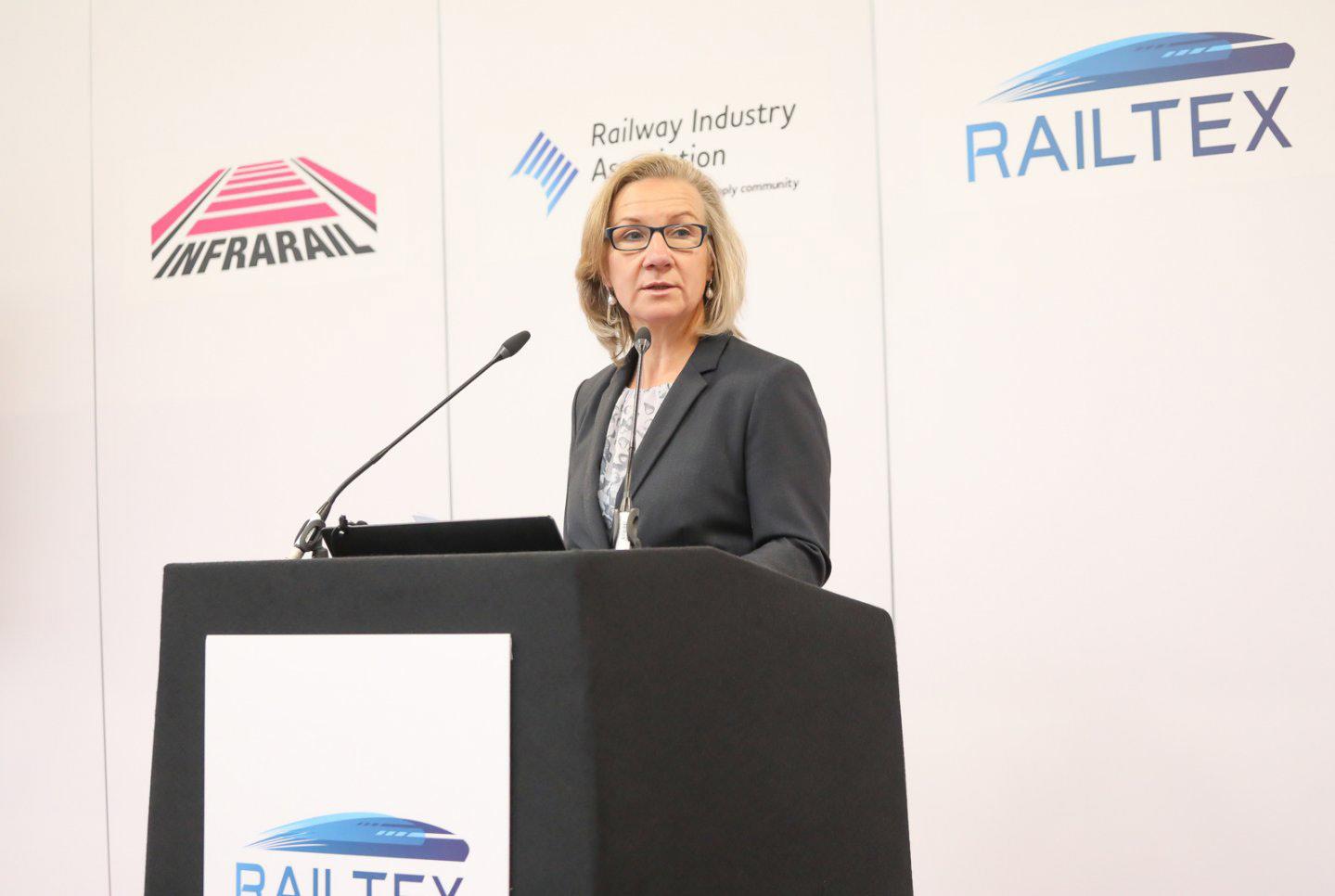
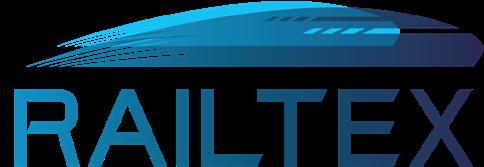
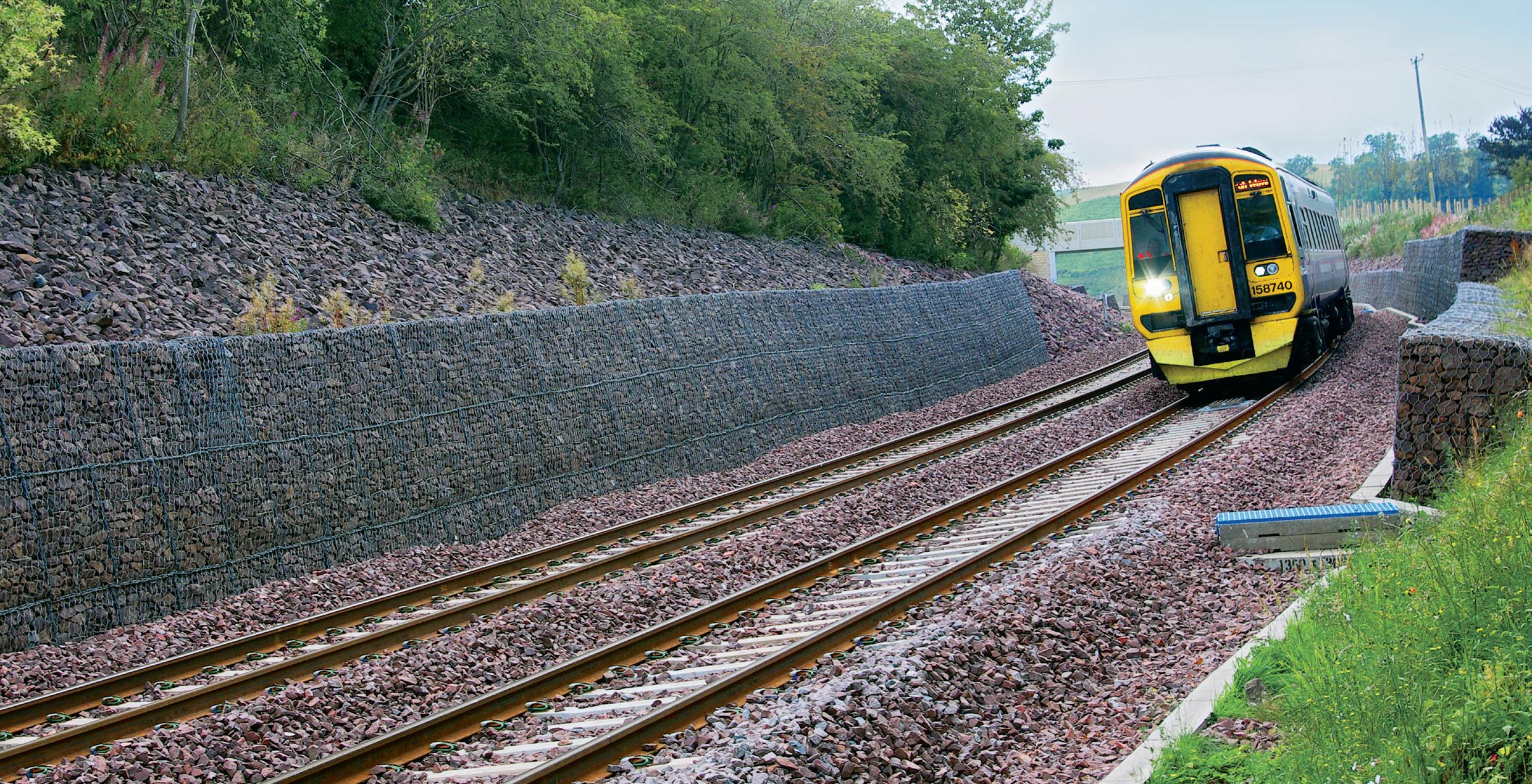
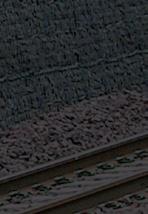
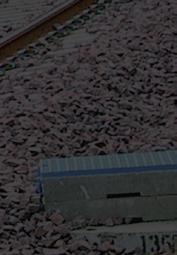
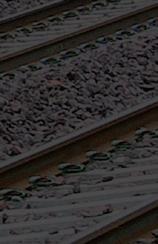
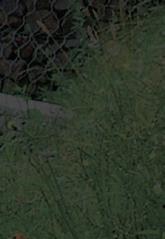
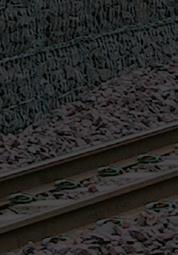
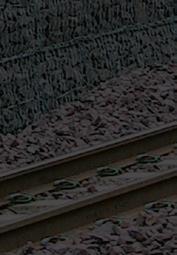










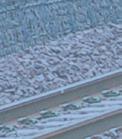
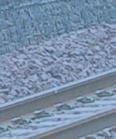
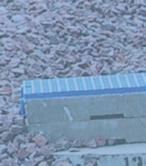
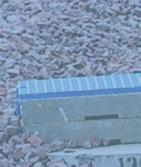
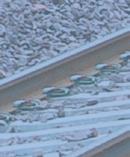

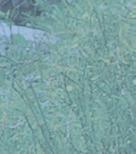




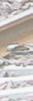
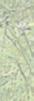
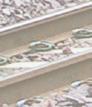
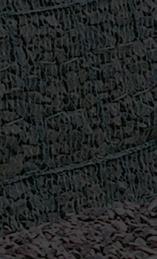


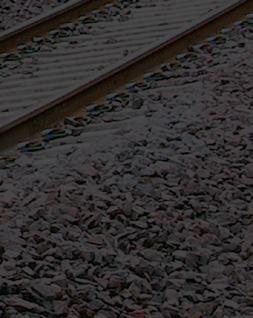
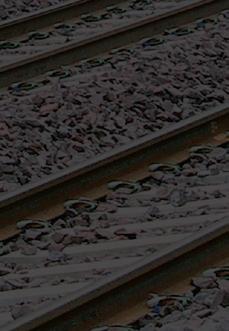
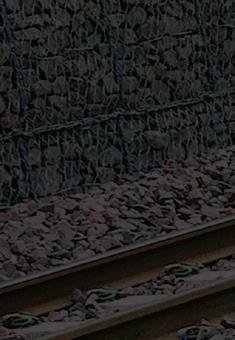
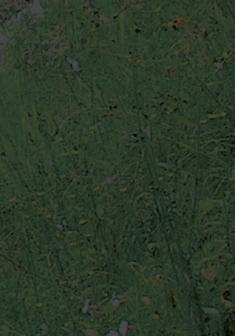






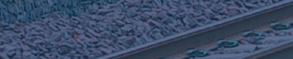
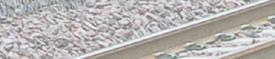

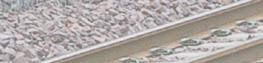
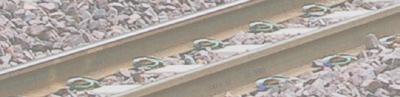
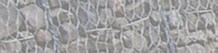



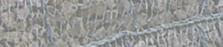




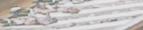
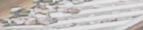










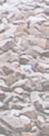

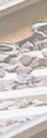
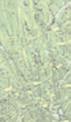
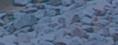
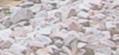

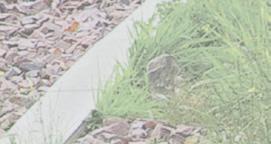
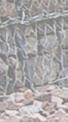
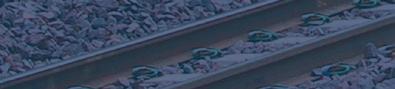
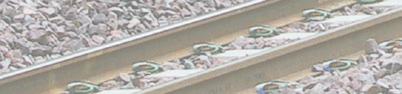
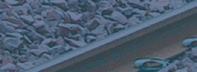
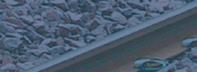
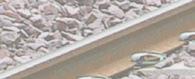
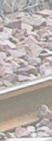
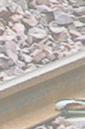
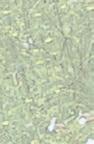

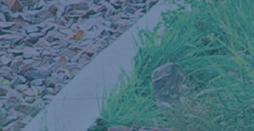


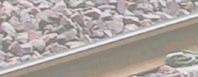
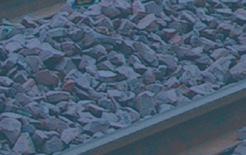
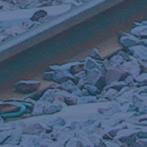

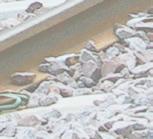
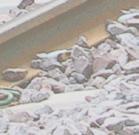
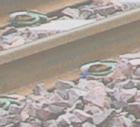
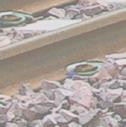
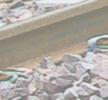

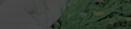


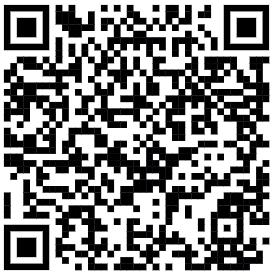
EN 45545 Approved Cable Glands and Entries...
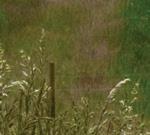
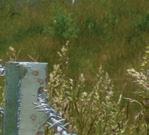
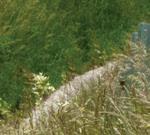
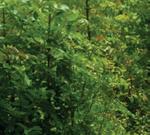
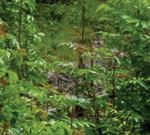
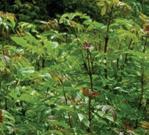

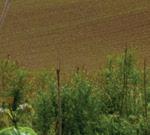
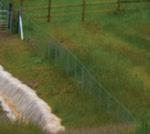
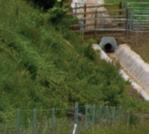
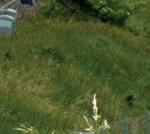
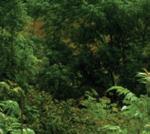
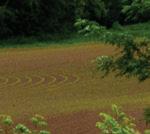
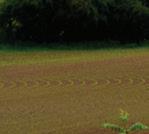
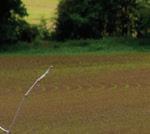
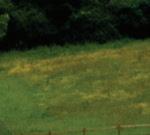
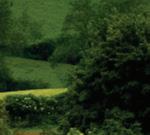
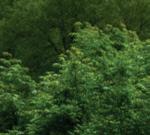

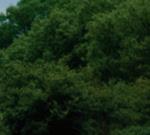
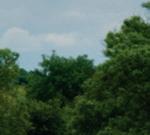
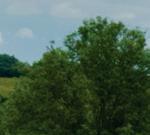
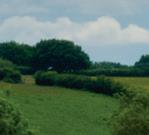
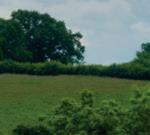
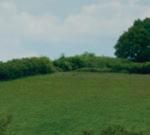
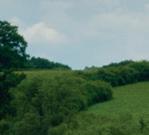
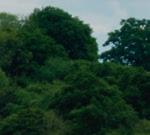
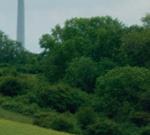
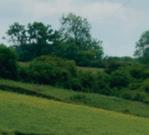
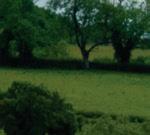
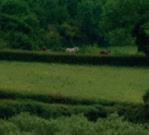
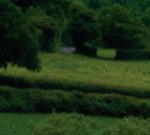
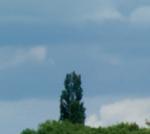


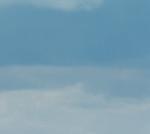
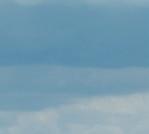
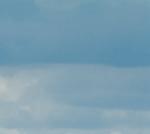
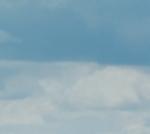
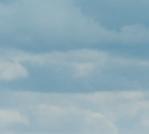

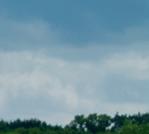
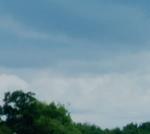



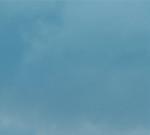
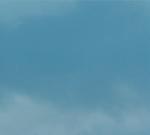
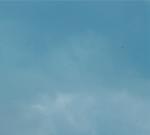
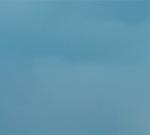
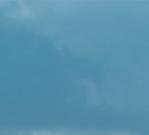
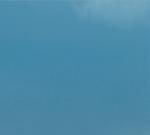
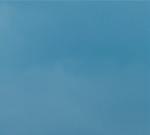
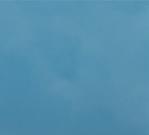
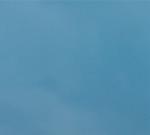
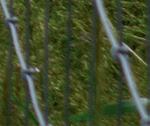
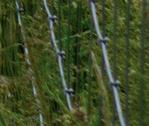
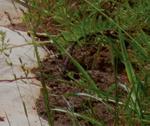


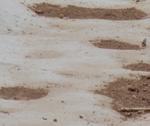

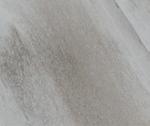
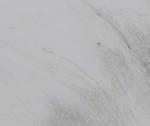
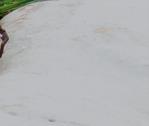
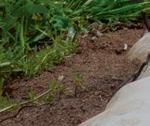
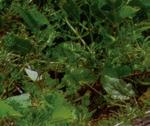
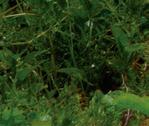
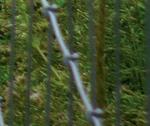
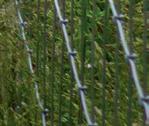

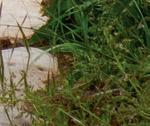


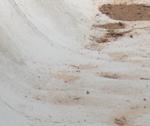
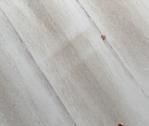
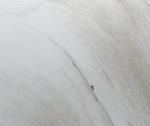
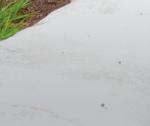
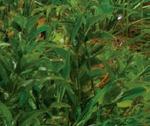
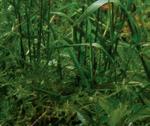
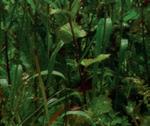
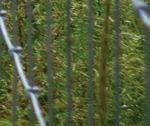


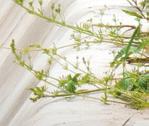
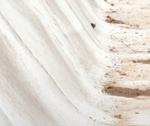
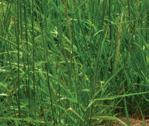
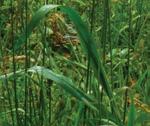
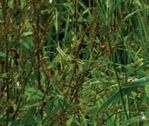
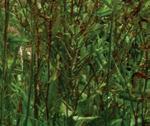

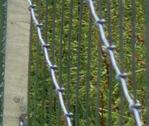
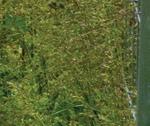
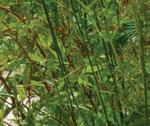
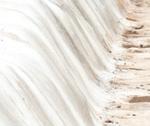
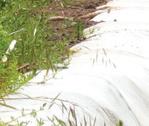



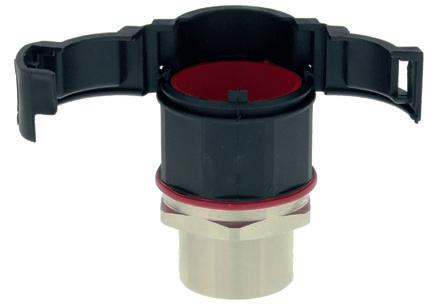

For over 100 years WISKA have been at the forefront of cable management design and innvoation. This level of expertise has resulted in the development of our lastest range of products, introducing The Railway Series by WISKA.
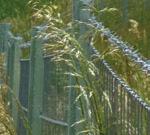
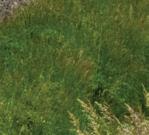

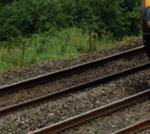
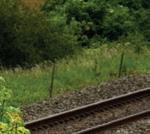
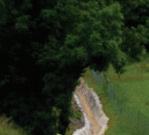

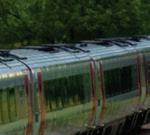
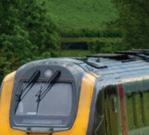
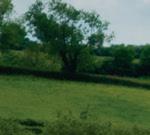
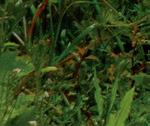
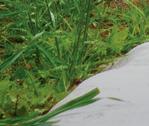
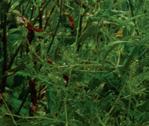
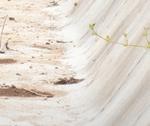
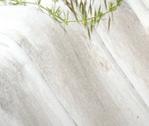
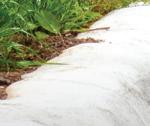
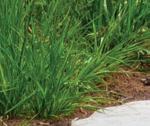
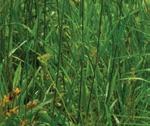
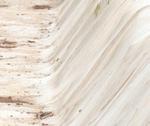
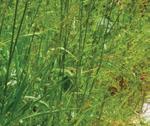

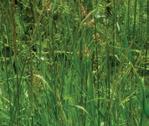
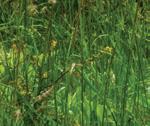
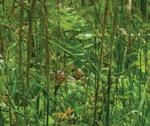

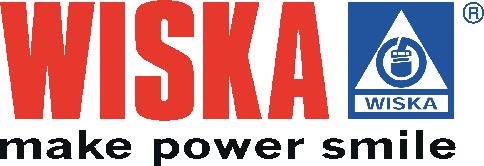
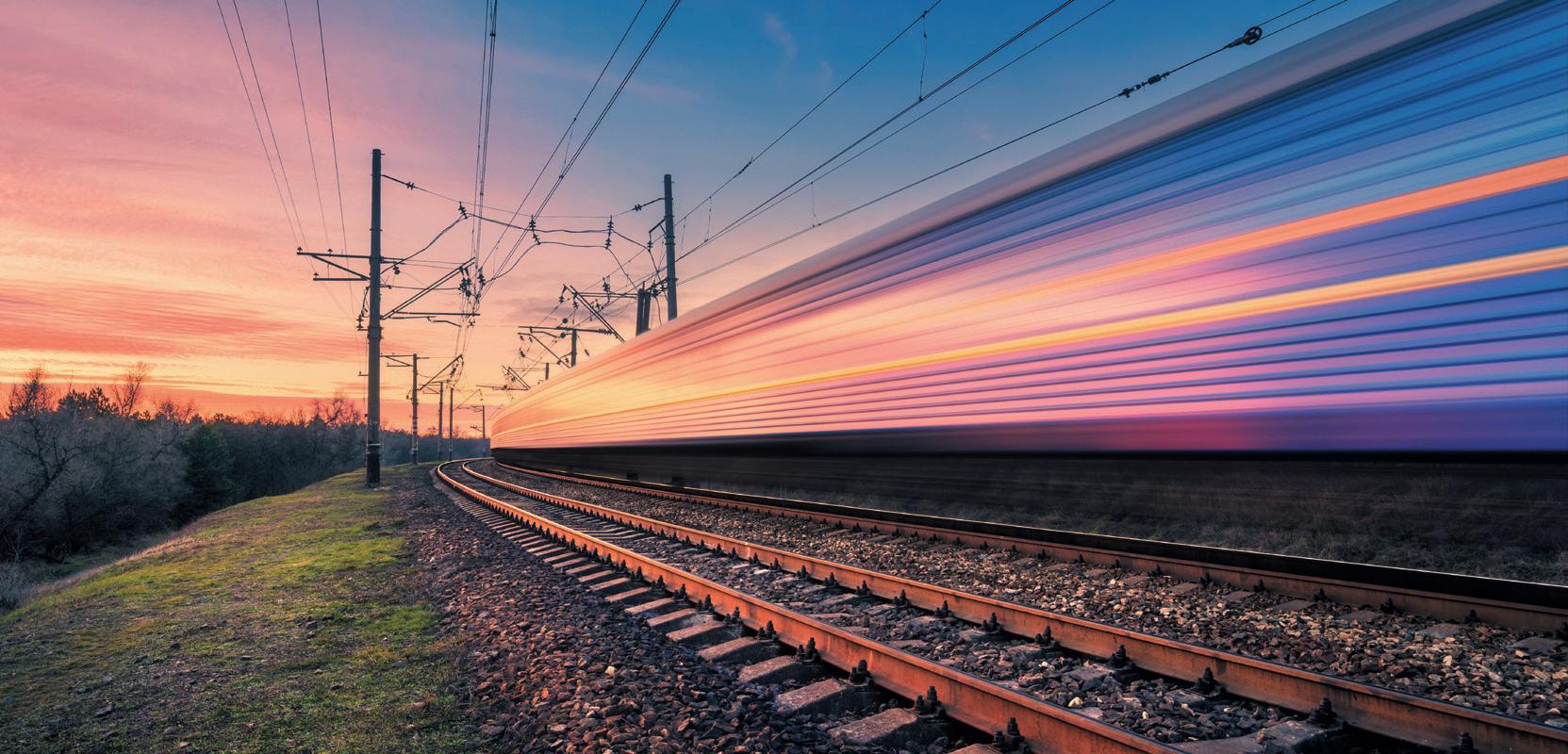
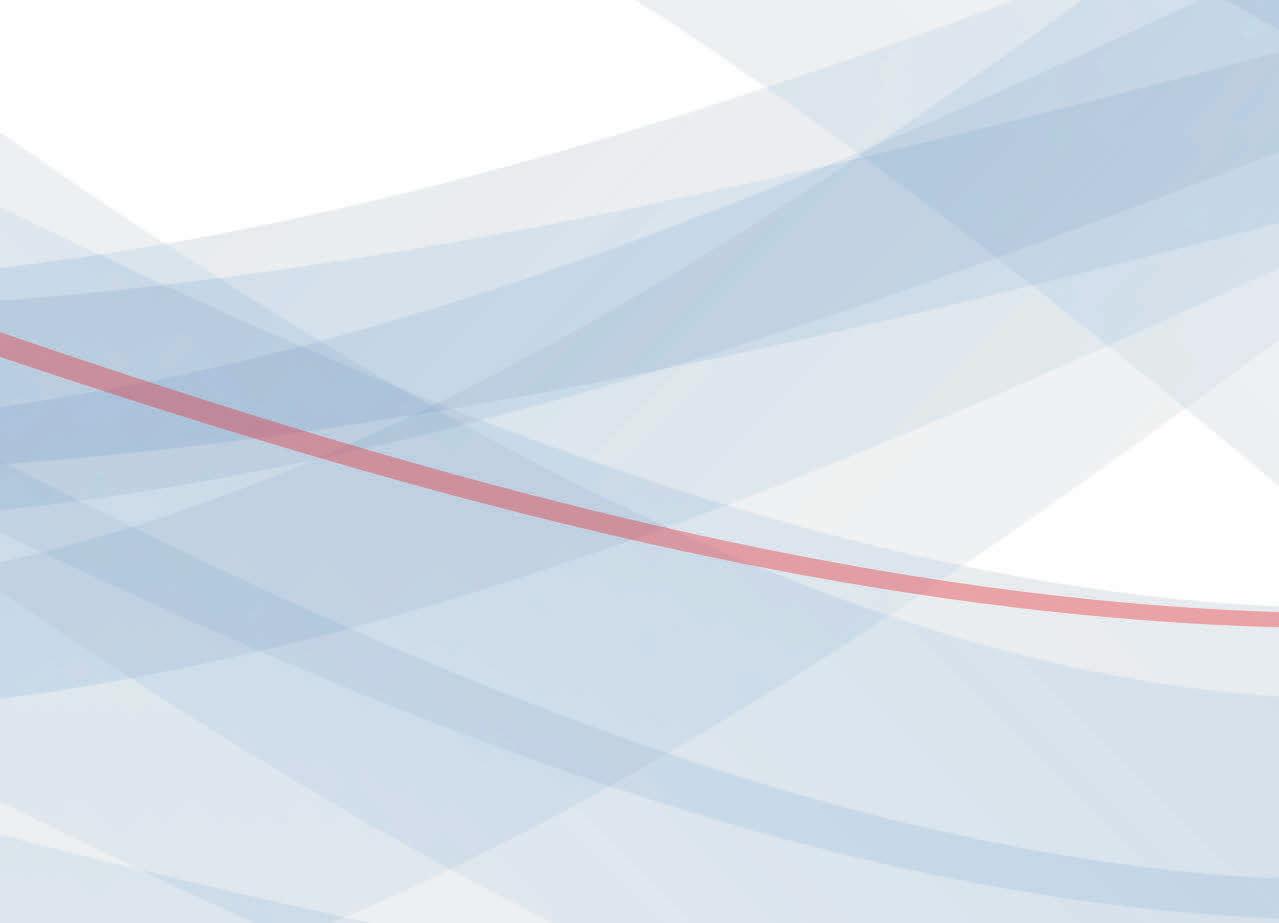
The Railway Series is a comprehensive range of industry-specific cable glands and conduit solutions in accordance with EN 45545.

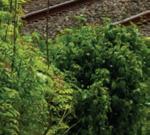

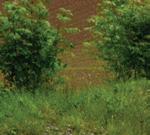
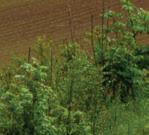
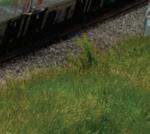
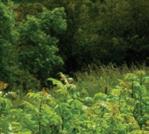
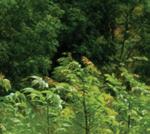

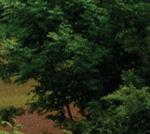


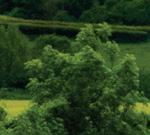
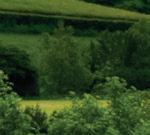
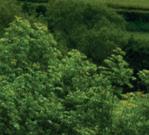

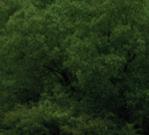


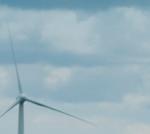
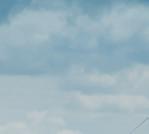
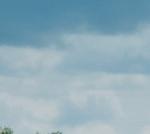


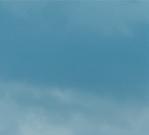

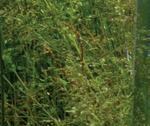
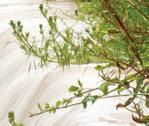
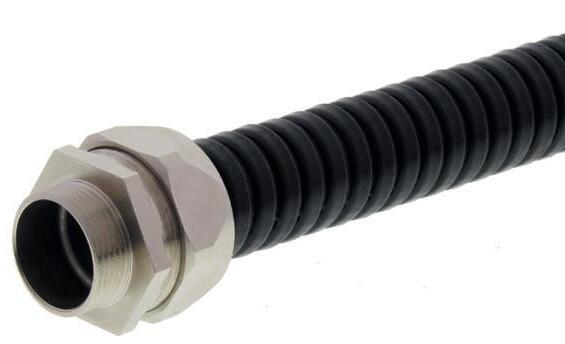
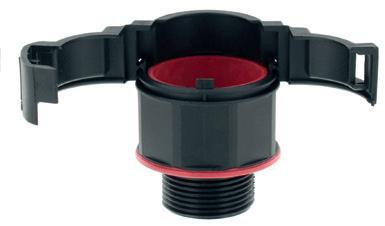
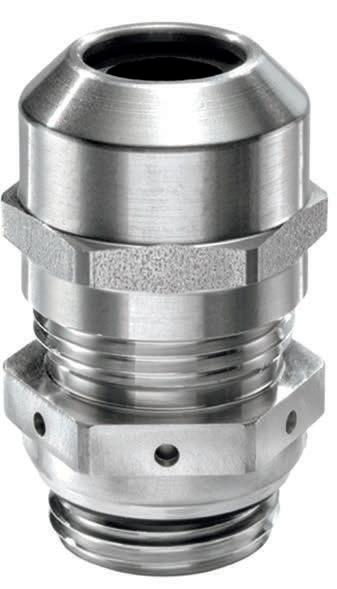
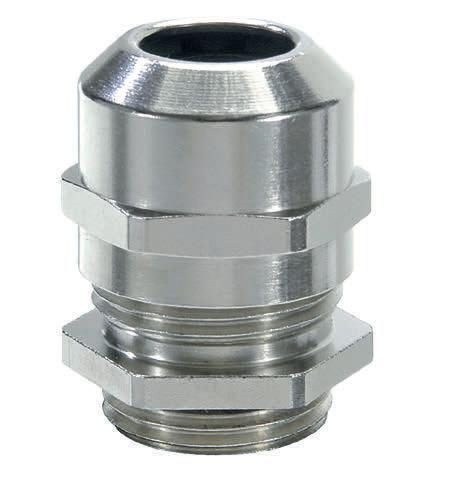
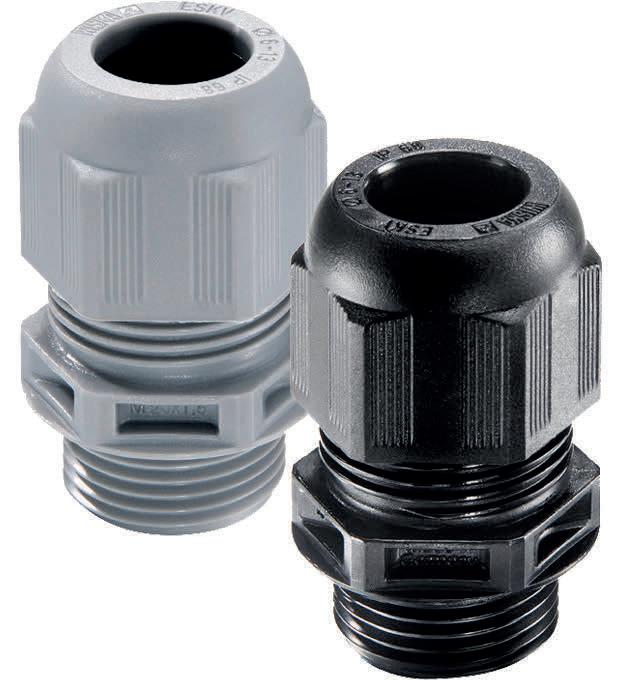
Who You will be Seeing on Stage
Darren Caplan, Chief Executive Railway Industry Association (RIA)
Darren Caplan joined RIA as Chief Executive in January 2017. Since then he has led the RIA team, with a mission to promote rail supply sector growth, increase RIA’s visibility amongst political and stakeholder decision makers and influencers, and ensure RIA develops into the very best trade association it can be for its members. Since 2017, RIA has won several awards including, in 2019, the ‘Overall Best Association’ category at the Association Excellence Awards and, in 2022, the Trade Association Forum ‘Leadership Award’.
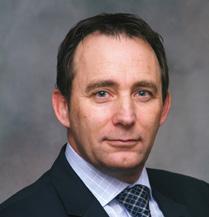
Nicola Hamann Managing Director, Mack-Brooks Exhibition Ltd
Nicola Hamann was made Managing Director at Mack-Brooks Exhibition Ltd in 2014. Prior to that she had been show director of several international trade exhibitions at Mack Brooks Exhibitions for ten years, including leading brands such as EuroBLECH, inter airport Europe and ICE International Converting Exhibition.
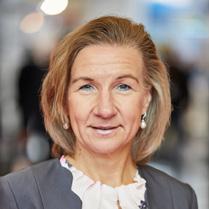
Gareth Evans, Head of Rail Technology, Network Rail
Gareth Evans joined Network Rail in 2009 and has been Head of Rail Technology since January 2023.
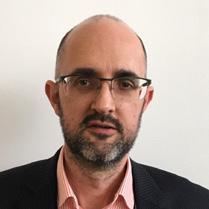
Ruth Humphrey, Head of Business Development and Strategy at Siemens Mobility
Ruth Humphrey was made Head of Business Development and Strategy at Siemens Mobility in 2018. Prior to that she was Project Director for six years Delivering the depots for the Thameslink Upgrade Programme.
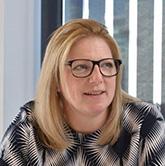
David Clarke, Technical Director at Railway Industry Association
David joined RIA in 2016 as the Technical Director. His role focuses on representing members interests in the important areas of safety, technical standards, technical strategy, research and innovation. David is a chartered engineer and a Fellow of the Institution of Civil Engineers and the Permanent Way Institution with over 30 years rail industry experience.
Jo Lewington, Chief Environment and Sustainability Officer at Network Rail
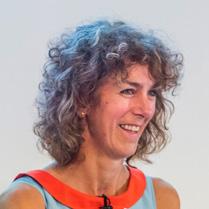
Jo Lewington is the Chief Environment & Sustainability Officer at Network Rail, based at the company’s national centre, The Quadrant in Milton Keynes. Jo is also a member of the My Milton Keynes BID Board and is committed to supporting the work of the BID making Milton Keynes an amazing place to work. Jo is a Chartered Surveyor and with 25 years professional experience, has a solid understanding of the land and property industry.
Rich Fisher, Head of Strategic Planning on the Great British Railways Transition Team
Rich Fisher was appointed Head of Strategic Planning on the Great British Railways Transition Team in February 2021.
Simon Green, Engineering Director at Great Western Railway
Simon joined Great Western Railway in 2018 having undertaken a number of roles, both inside and outside the rail industry, latterly at GTR. He is responsible for the supply and maintenance of the GWR fleet of trains, including the management of GWR’s maintenance depots and train service provision contracts.

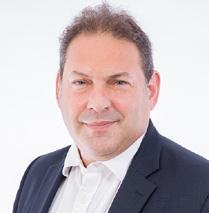
Maria Machancoses, Chief Executive at Midlands Connect
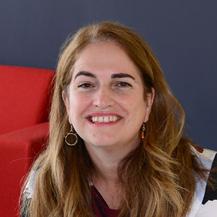
Maria Machancoses has been instrumental in the success and development of Midlands Connect since helping to set up the partnership in 2014. Maria has also worked as Director of the Midlands Engine and managed the West Midlands Integrated Transport Authority’s input into the HS2 Hybrid Bill.
Phil Smith, RISQS Manager at RSSB
Phil Smith is RISQS Manager at RSSB
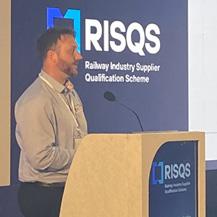

The Green Railway Revolution
BREEAM Infrastructure is supporting rail's sustainability goals
The railway system in Great Britain is the oldest railway system in the world, with the first locomotivehauled public railway opening in 1825. Network Rail has set out an ambitious 30-year strategy for delivering a sustainable railway that puts passengers first and supports local communities in both the north and south of England. The company’s vision is to serve the nation with the cleanest, greenest mass transport, and they have four core priorities to deliver it needing Government backing and local authority support:
• A low-emission railway.
• A reliable railway service that is resilient to climate change.
• Helping plants and wildlife flourish.
• Recycling and reusing everything.
However, delivering this vision is a complex challenge that requires both a comprehensive and integrated approach to sustainable rail management. To achieve these priorities, Network Rail needs to embrace new approaches and frameworks that promote sustainable rail development and maintenance.
BREEAM Infrastructure has a global proven credit rating to help partner organisations achieve ambitious goals and innovate through collaboration. It provides a robust framework that assesses a wide range of sustainability issues to manage programme of works and promotes environmental stewardship, supporting wider sustainable development goals including social value. The scheme is embedded in a number of the current high profile rail schemes connecting north and south.
By using BREEAM Infrastructure Term Contracts, rail professionals can demonstrate their commitment to carbon reduction that goes beyond current industry standards, delivering a sustainable railway that serves the nation with the cleanest, greenest mass transport.
Case Studies of BREEAM Infrastructure Assessments
Spanning three Boroughs, the London Bridge Railway Systems project demonstrated a comprehensive approach to sustainable rail management, achieving sustainability targets by reducing
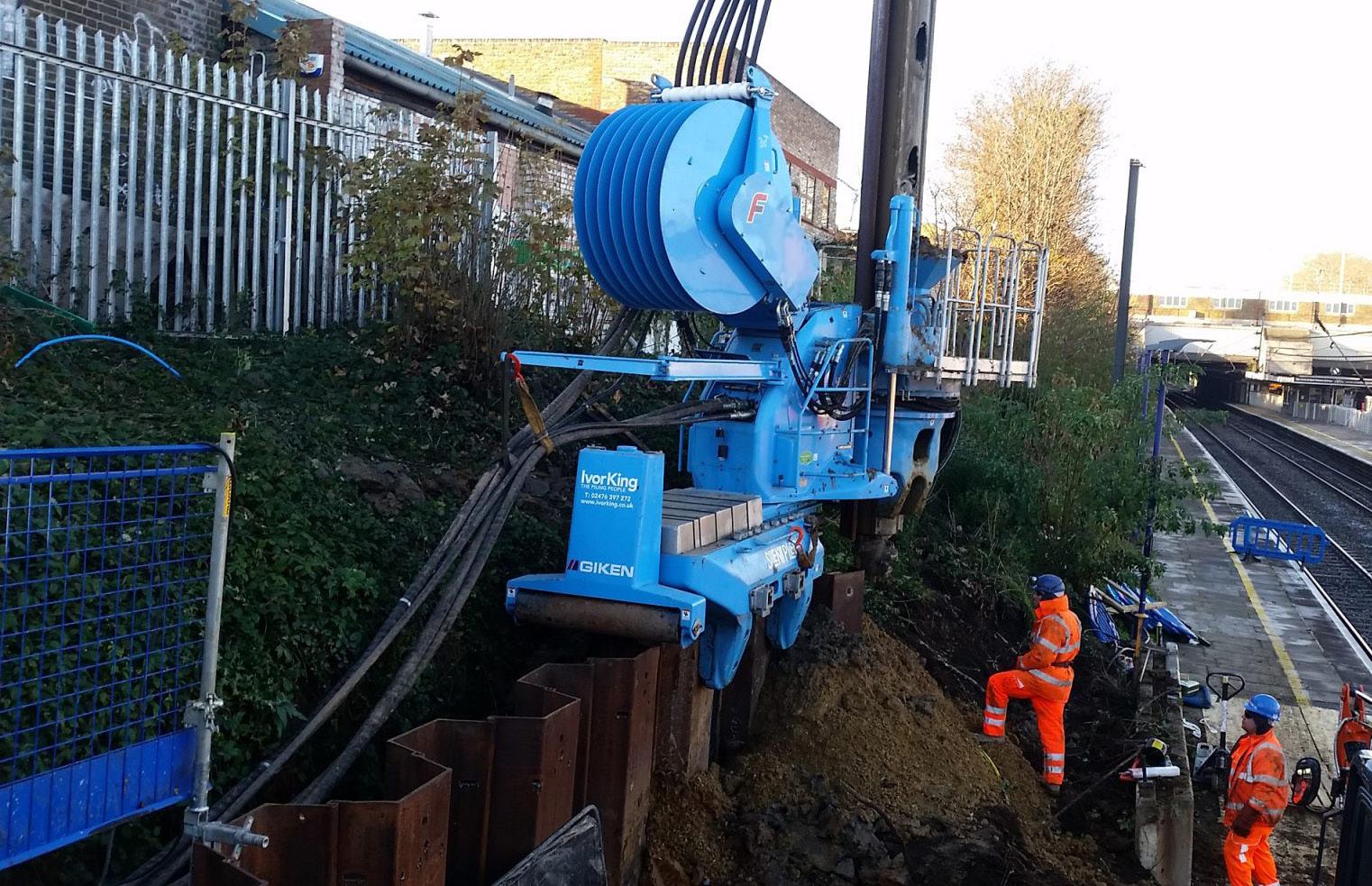
environmental impacts, saving on materials and embodied carbon, and as a result benefiting local communities. BREEAM Infrastructure Term Contracts provided criteria to achieve the strategic aims for sustainable rail management and deliver the wider development goals.
The Thameslink Programme’s London Bridge Railway Systems project included track, signalling, and civil works. Sustainability was a key driver, with contractors tracking progress against Thameslink Sustainability Strategy targets, capturing best practices and lessons learnt to share with the wider rail industry.
In Worcestershire the Parkway Regional Interchange project was designed to provide the wider South Midland’s area direct rail access to people and reduce car usage on the strategic highway network by 6 million kilometres per annum by 2031. The new station addresses the increasing demand for rail services to and from Worcestershire, contributing to the growth of the local economy and improving access to the rail network.
BREEAM Infrastructure enables the project teams to focus on managing the delivery of the scheme, protecting the local environment, efficiently using resources, and supporting the local communities.
The Infrastructure Assessment enabled the project to demonstrate best practices in retained and enhanced biodiversity, site waste management efficiency, reduced import and export of site materials, reuse of reclaimed oil pipes for piled foundations, flood risk management, and sustainable drainage.
Finally, Crossrail assessments included the West Stations Project, to accommodate the new Elizabeth Line trains, modifying 13 existing stations along the Great Western Railway network from Acton Main Line to Maidenhead station. The Project Team received an Excellent assessment rating for implementing sustainability throughout the project. Their initiatives were innovative, including noise reduction and community engagement exceeding contractual requirements. The project team also received further recognition through the Great
Western Rail and Crossrail Sustainability award and the Green Apple award.
The Eleanor Street and Mile End Road Shafts project was part of the larger Crossrail initiative that involved building a new railway for London and the Southeast. The project faced challenges, such as the need to mitigate noise and the impact on local communities. The Biodiversity module was a success, with the project team implementing sustainable practices such as creating wildflower meadows, green roofs, and planting trees. They also managed resources efficiently by recycling and reusing materials, leading to a positive impact on energy, water, materials, and waste.
The BREEAM Infrastructure scheme can improve Network Rail’s operational efficiency and promote environmental stewardship through a comprehensive and collaborative approach to sustainable rail management, as committed to by many projects in Scandinavia. The criteria in the V6 Manuals encourage considering wider aspects of sustainability to create a railway that prioritises clean and green mass transport, whether through inclusive economic growth, carbon reductions or building resilient and sustainable communities. It is a crucial time to embrace

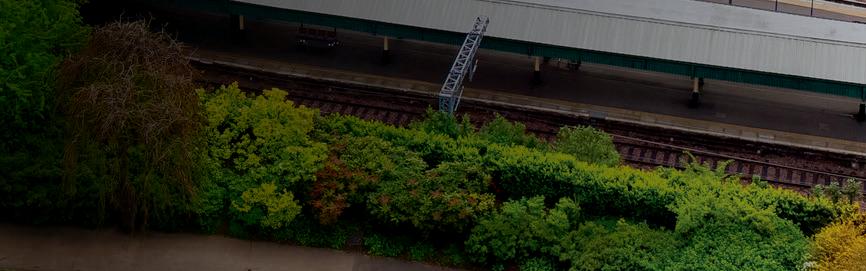
new solutions and challenge current thinking to create a railway industry with a sustainable and affordable future.
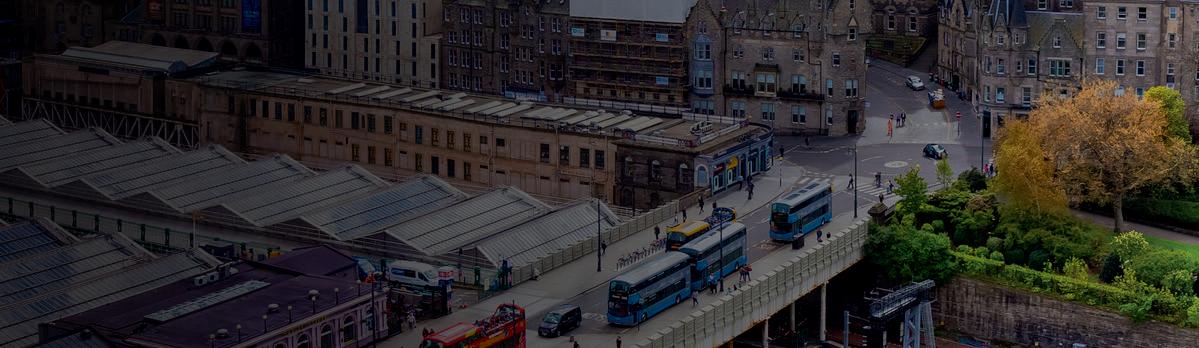

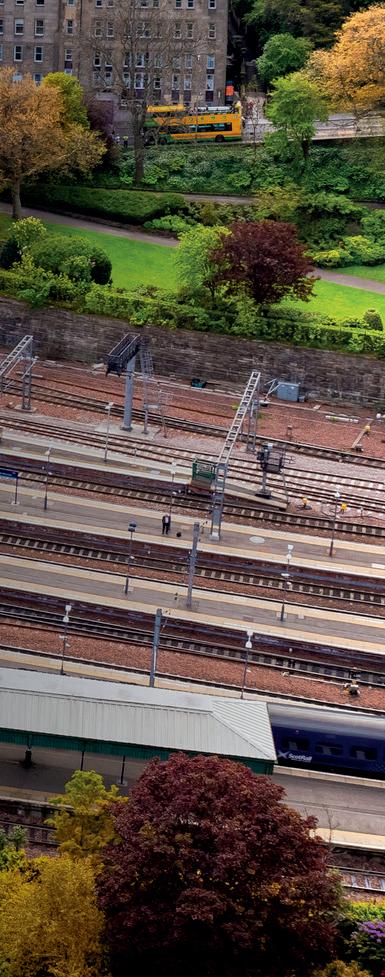
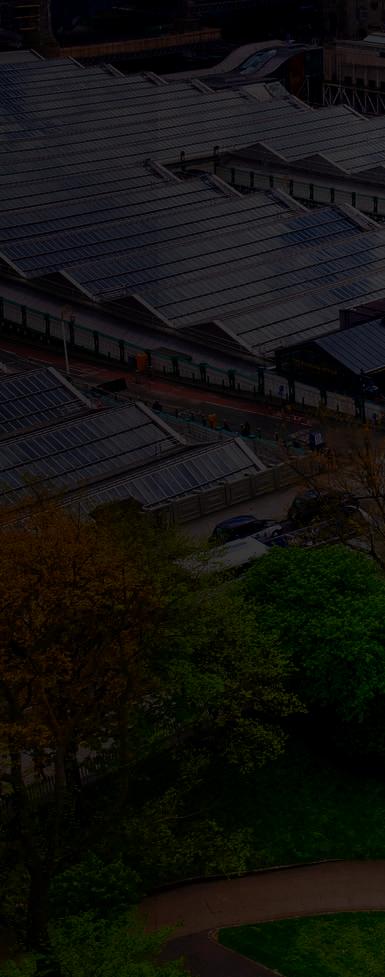
The scheme started its life as CEEQUAL (the Civil Engineering Environmental Quality Assessment) and was created to award and drive improvements in the environmental impact and quality of civil engineering. In 2015, it was acquired by BRE and rebranded into the BREEAM suite of schemes, to demonstrate the holistic approach to sustainability across different sectors and asset life cycle stages. The methodology uses two technical manuals BREEAM Infrastructure Projects V6 and BREEAM Infrastructure Term Contracts V6. The rebrand brings infrastructure into the BREEAM suite of schemes, further expanding the BREEAM approach to sustainability and reduced carbon footprint.

If you are interested in learning more about BREEAM Infrastructure and how it can benefit your rail projects, please don't hesitate to contact Melanie Manton or Billal Din. The team of experts is here to provide a scheme that drives your sustainable rail management goals.
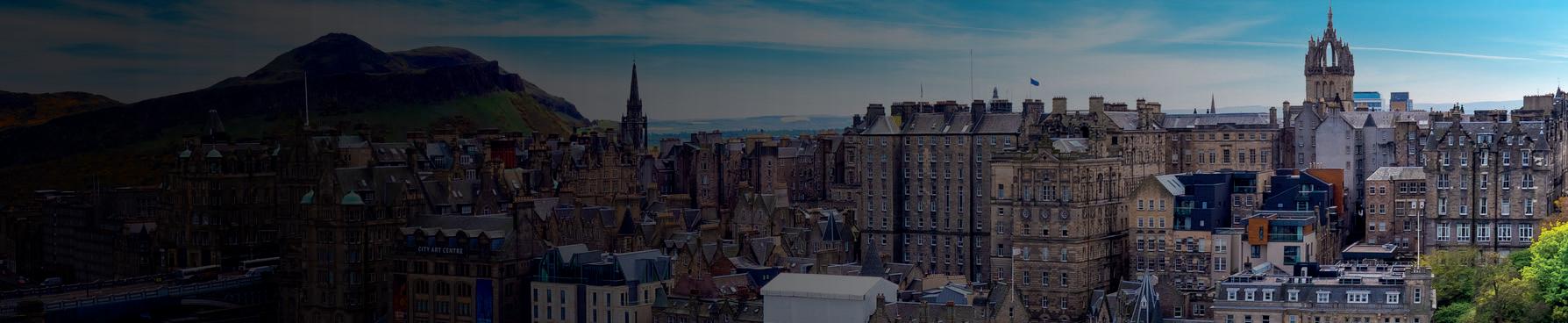
http://www.bre.ac/breeam-infrastructure/

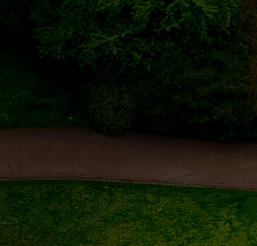
The original “warm to the touch” DDA handrail (“not cold to the touch ”)
4mm (4,000 mocrons) thick PVC sleeved over galvanised steel tube, resists knocks and bumps and will not chip or “flake”

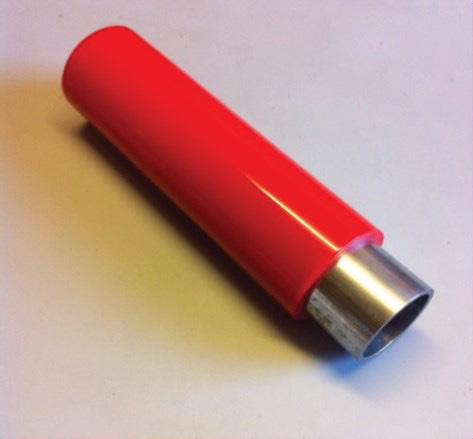
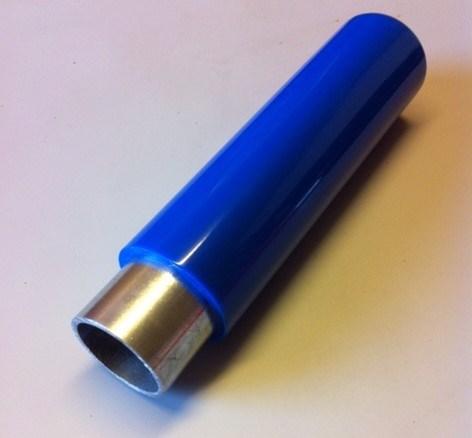
Vandal resistant Individual LED lights spaced to suit lighting levels required
A range of colours with the colour consistent throughout the thickness of the PVC sleeving.
New or re furb projects with or without LED lights
Re furb project: Double handrail
New Build: Double handrail, LED lighting, glass panels and stainless balusters
Single, double or curved handrail
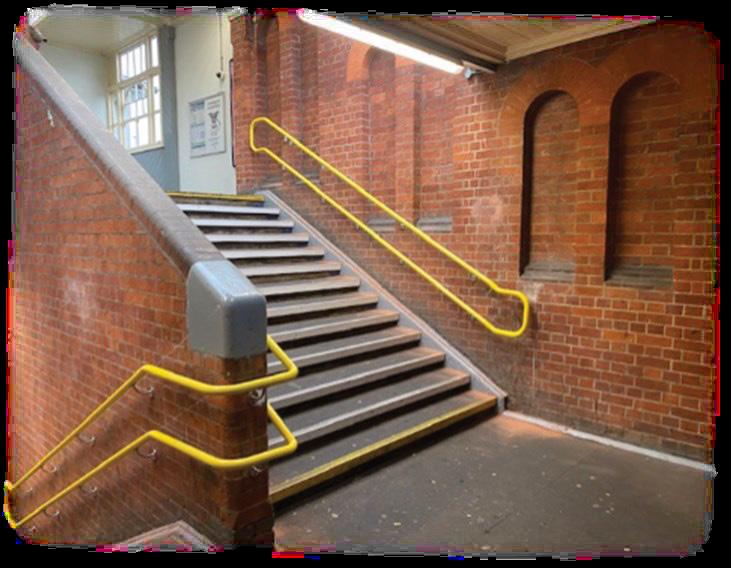
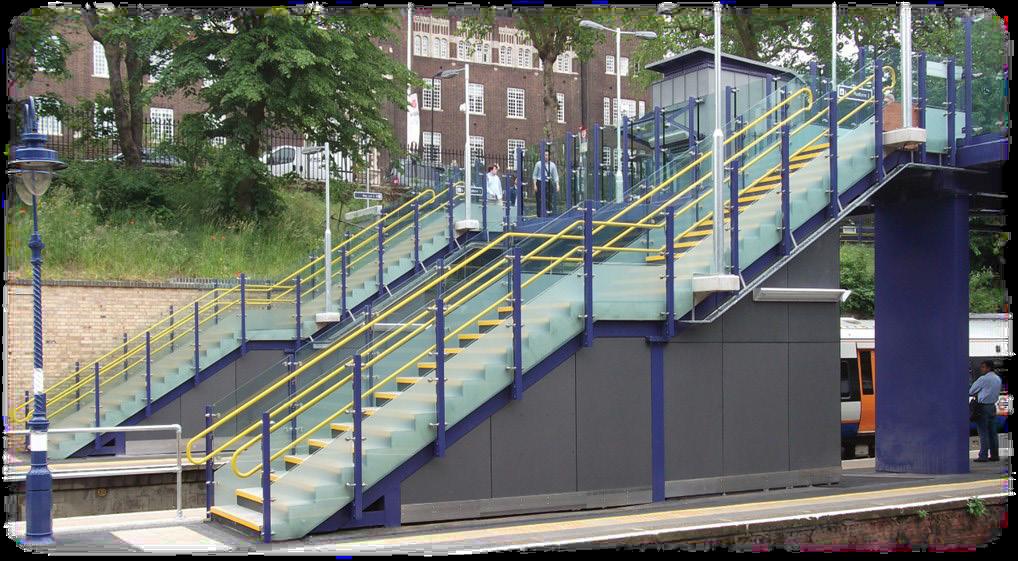
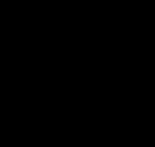
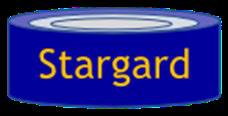
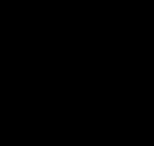
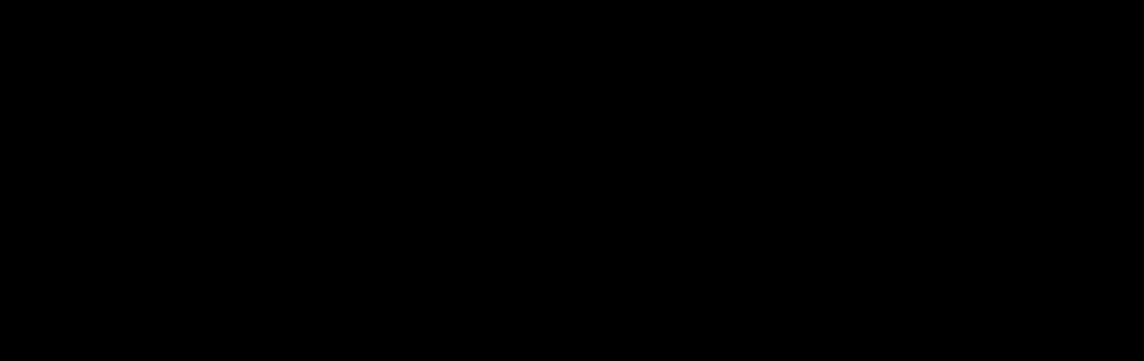
Stainless or galvanised steel balusters
Access Ramp: Double handrail, LED lighting, stainless balusters and glass panels
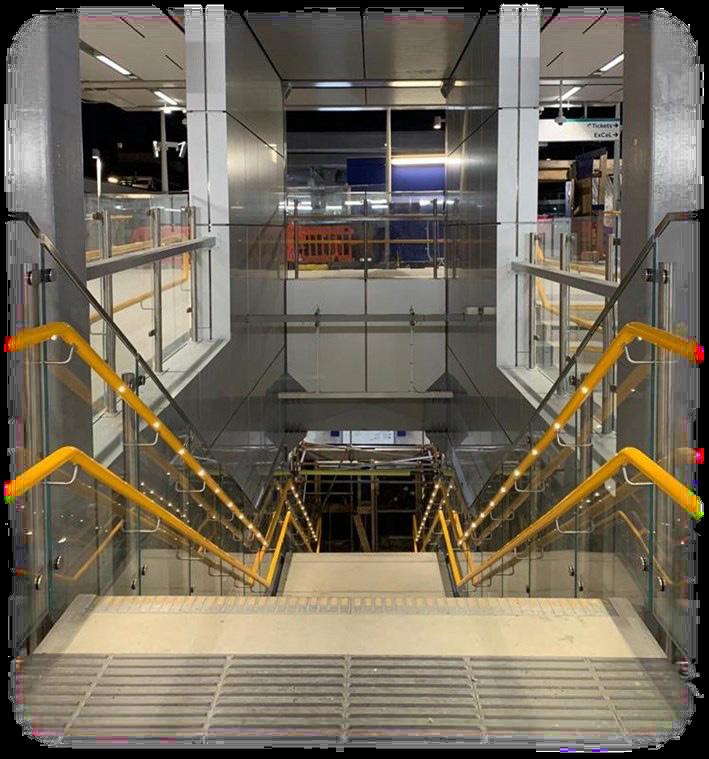
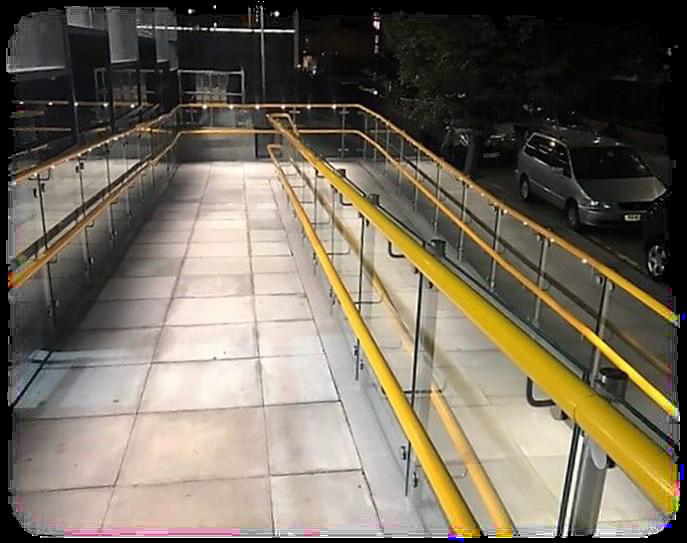
Suffolk Rail Stations Receive ‘Wildlife Friendly Station’ Status
Four rail stations in Suffolk have received a ‘Wildlife Friendly’ accreditation, recognising the work of community volunteers to improve biodiversity and support nature. Greater Anglia has partnered with the region’s Wildlife Trusts to formally recognise the achievements of its team of volunteer ‘station adopters’ to create wildlife havens at stations across its network through the new ‘Greater Anglia Wildlife Friendly Stations Accreditation Scheme.’ Needham Market, Saxmundham, Somerleyton and Westerfield
stations became the first ones in Suffolk to receive the awards, following assessment by a Suffolk Wildlife Trust Conservation Officer to determine how well they support local flora and fauna.
Each station is looked after by a team of volunteer ‘station adopters’ – members of the community who work with Greater Anglia to improve their local rail station for community benefit –who have focused on creating wildlife friendly areas to help support fragile local wildlife populations.
On-time Completion for New £16 Million Ravenscraig Rail Bridge
Work to install a new railway bridge at Ravenscraig, on the West Coast Mainline (WCML), has been completed on-time over the Easter weekend. Engineers worked around-the-clock for nine days, from 1 April to the early hours of 10 April, to successfully move the new 5,000-tonne bridge into position as part of a £16.9 million investment from North Lanarkshire Council and Glasgow City Region City Deal.
Network Rail and STORY Contracting have been working since May 2022 to construct the enormous concrete structure at a compound next to the WCML and had a tight window of opportunity to move it into position over Easter.

The new bridge deck was installed on 4 April after engineers had excavated over 36,000 tonnes of material from the railway embankment to create space for the new structure. Once in position, the structure was built into the embankment and over the Easter
weekend the overhead line equipment and track were reinstated before tamping compacted the new ballast under the railway track.
The bridge enables North Lanarkshire Council to construct a new dual carriageway, with pedestrian and cycle paths from Airbles Road/Windmillhill Street to Robberhall Road, as part of a wider investment to open the area for future development.
John MacArthur, Managing Director of Story Contracting (Scotland), said: ‘The successful delivery of Europe’s largest concrete structure lift at Ravenscraig is a significant milestone for Story Contracting and testament to the hard work and dedication of the team and our supply chain partners. This project showcases our commitment to excellence and our ability to collaborate as Scotland’s Railway to deliver high-quality solutions. I am extremely proud of everyone involved in bringing this ambitious project to life.’
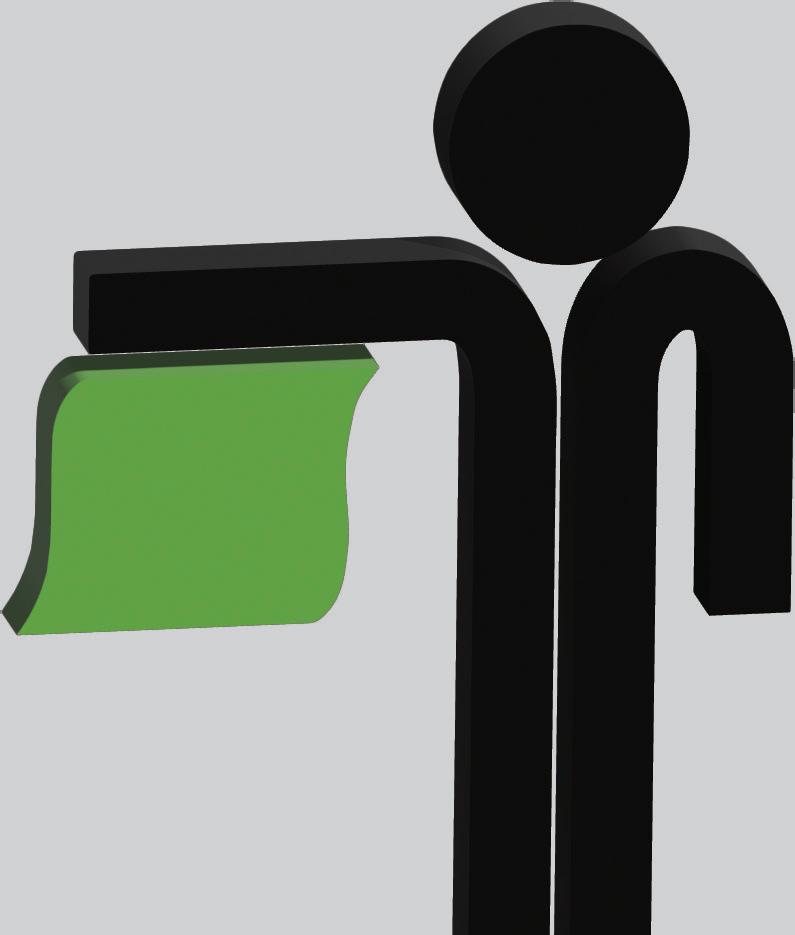
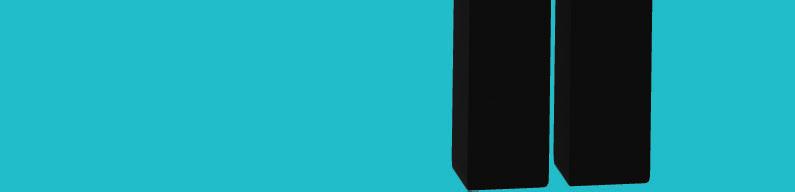
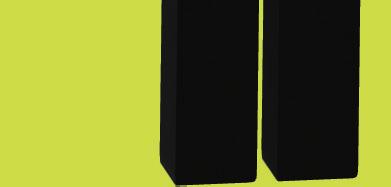

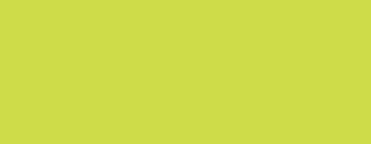

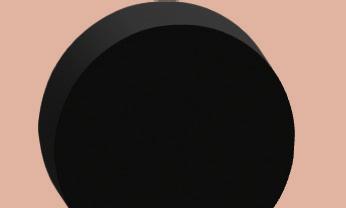
Intelligent CCTV Analytics Upgrade at 60 ScotRail Stations
ScotRail is increasing the safety and security at 60 stations across Scotland by installing new CCTV cameras with upgraded intelligent video analytics. The new cameras can analyse movements of customers on the platform to determine if members of the public are in unsafe situations, allowing the CCTV monitoring team to alert station staff, signallers, and British Transport Police, if necessary.
Everything from monitoring passenger numbers which will assist with crowd management to behavioural analytics which can identify people lingering in stations can be controlled via the new camera units.
GB Railfreight Sign Contract with Stadler
GB Railfreight (GBRf) and Stadler have signed an agreement that will see Stadler Rail Services be responsible for all aspects of service and maintenance GBRf’s latest hybrid locomotives from 2025. The news follows GBRf’s contract with Stadler and Beacon Rail to manufacture and deliver 30 new Class 99 bi-mode Co’Co locomotives. This deal marks the start of a long-term partnership between the organisations.
Beacon Rail will own the new hybrid fleet, and GBRf will be the lessee. The UK government’s electrification rollout, when complete, will enable the Class 99s to run on electricity across all UK routes and reduce emissions by 585,000 tonnes of carbon per year. High quality and reliable servicing is critical to ensuring the fleet can deliver this impact.
GBRf has agreed with Stadler that they will maintain the 30 locomotives at a new depot in Leicester, where they will receive tailored maintenance solutions to ensure a high quality of service. Stadler will manage overhauls, spare parts, material supplies, vehicle repairs, mobile service support, data and maintenance software.
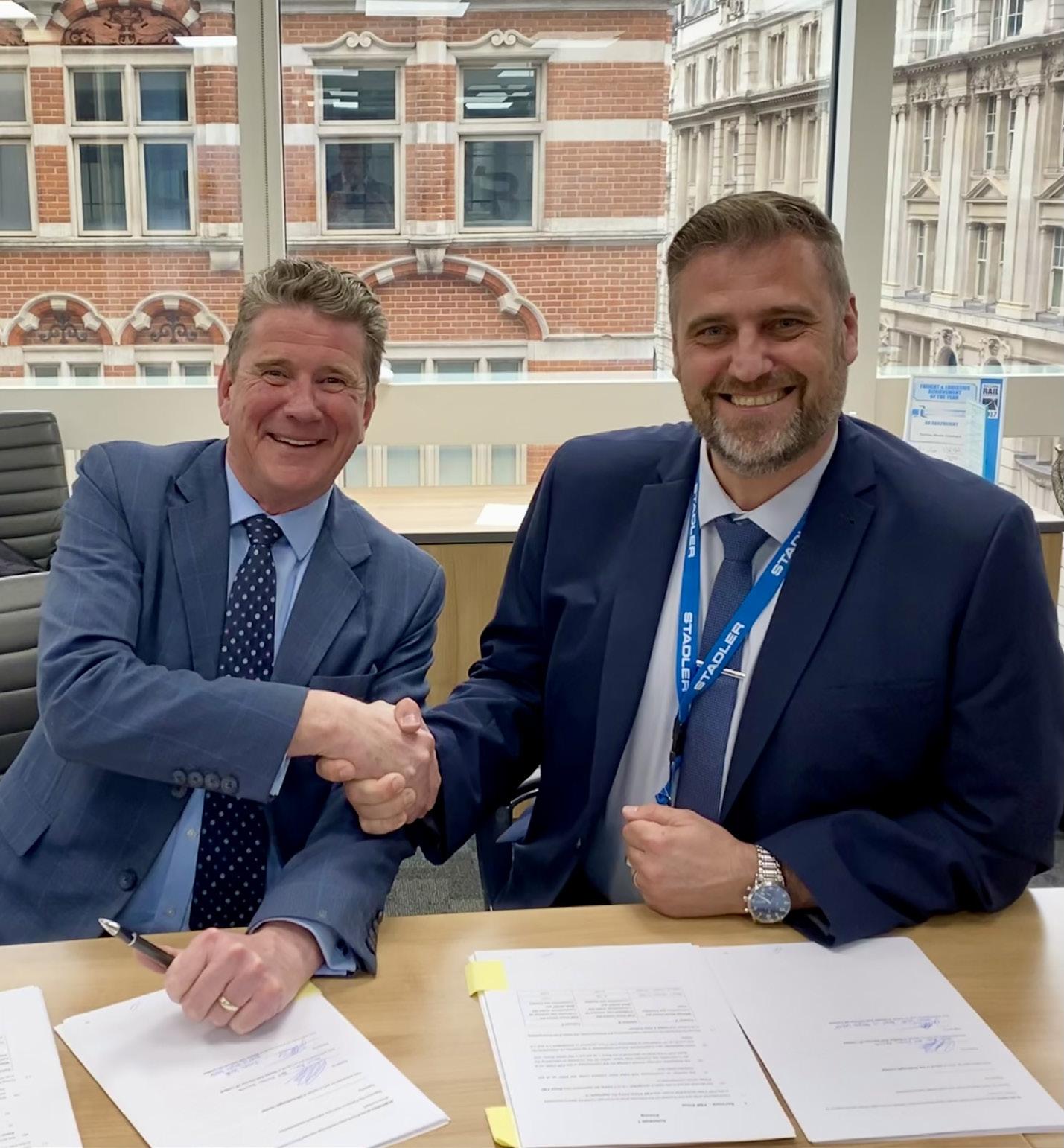
John Smith, CEO of GB Railfreight, said: ‘The service agreement with Stadler for the Class 99 locomotives brings together its design and maintenance divisions to ensure that rail freight continues to lead the decarbonisation of supply chains.
‘Continued private sector investment in the industry-leading Class 99s and their maintenance facilities, demonstrates a commitment to modernising and
It’s hoped that the new equipment will help ScotRail identify vulnerable people and reduce fatalities on the railway, as well as combatting anti-social behaviour.
The upgrade is part of a £2 million investment in the CCTV network on Scotland’s Railway, which, in 2018, saw ScotRail move from 220 scrolling CCTV monitors covering more than 280 stations to a 24-screen intelligent video wall in the customer service centres.
growing the rail freight sector in the UK to help deliver the government’s net zero ambitions.’
Paul Patrick, Managing Director of Stadler Rail Service UK, said: ‘We have established a strong foothold in the UK over recent years, and are delighted to have been awarded another Service contract, based on our proven track record and expertise in this
field. The locomotives that Stadler will be responsible for will pave the way to a greener and more efficient rail network, supporting the industry’s ambition of promoting modal shift from road to rail. We are pleased to be supporting the government’s targets to decarbonise the UK railway by 2040, which will benefit our clients, British business and society alike.’
Gloucestershire Community Rail Partnership Launch TrainTripper
TrainTripper, the innovative platform from Gloucestershire Community Rail Partnership (GCRP), aims to promote car-free leisure trips in and around the county, integrating transport information, promoting local businesses, and highlighting some of the incredible local attractions Gloucestershire has to offer.
Starting from the nine countywide train stations of Gloucester, Cheltenham, Kemble, Stroud, Stonehouse, Ashchurch for Tewkesbury, Moreton-in-Marsh, Cam and Dursley and Lydney, users can build a personalised itinerary of places to explore, eat and stay. With train travel at the heart of the platform, GCRP aims to promote sustainable travel and active forms of transport such as walking and cycling, for visitors to reach their chosen destination.
TrainTripper has received funding from train operators Great Western Railway and Cross Country Trains who operate train services across the county and beyond. The new website has been developed in partnership with Visit Gloucestershire as part of their sustainability and Climate Action agenda.
Hannah McDonnell, Executive Director at Gloucestershire Community Rail Partnership, said: ‘Supporting sustainable, car-free travel sits at the heart of what we do at Gloucestershire Community Rail Partnership. The long-term aim of TrainTripper is to generate sustainable tourism across the county, support local business and help people fall in love again with their journeys by train. We’re delighted to have received such fantastic support from Great Western Railway, Cross Country Trains and Visit Gloucestershire to launch this exciting new resource for the local area.’
Steve Gardner-Collins, Director of Visit Gloucestershire said about the launch: ‘I’m thrilled to see the launch of such an innovative and fun platform to drive tourism in Gloucestershire. The list of carefully curated places to eat, stay and explore make it really easy for users to find great places to visit, and support local businesses at the same time. By promoting travel by train, the platform and our work with GCRP supports Gloucestershire’s aspirations to reduce carbon emissions and be net zero by 2045.’
Huw Margetts, CrossCountry’s Regional Director, said: ‘We’re pleased to have helped fund the development of the TrainTripper service. Its launch will open up new ideas and opportunities for people to take car-free journeys for leisure and pleasure around Gloucestershire.’
GWR Business Development Portfolio Director, Tom Pierpoint, said: ‘We have a specific pot of money designed to support the Community Rail Partnerships on our network who in turn work with their local communities. TrainTripper is a fantastic, pioneering project which will help to encourage rail travel to a glorious part of the GWR network, boosting local economies at the same time.’
TrainTripper encourages people to leave the car at home and to consider the train journey as part of the experience, whether they are planning a day out with the kids, a short getaway or a longer break in Gloucestershire, find out more at www.TrainTripper.co.uk.
RIA Celebrates Reaching New 350 Membership Milestone
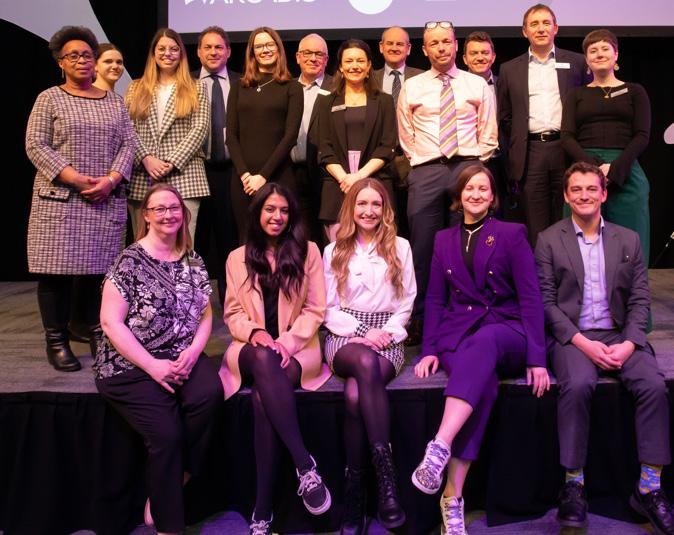
membership of the Railway Industry Association (RIA), the national
has just reached 350
member companies. This represents an increase from 190, or 84 per cent, since 2017.
Commenting, RIA’s Chief Executive, Darren Caplan said: ‘We are really excited here at the Railway Industry Association to see membership increasing so much since 2017 when we had 190 members, now reaching the milestone of 350 in April. It is particularly heartening to see this healthy growth considering the pandemic and the political and economic turbulence of recent years.
‘We believe this is a reflection of both the hard work Team RIA carries out for members and the broader supply sector, and the wideranging and impactful member benefits RIA offers. This includes access to award-winning networking events, a unique Nations and Regions network around the UK, and the unrivalled expertise of the team itself, whether lobbying senior politicians and other policy influencers, or conducting high quality policy, technical, innovation and exports work.
‘We are tremendously grateful to our 350 members for being with us and informing the work the association does, and hope that any rail supply businesses not currently in membership consider joining us as we move ever closer to our 150th year in 2025. The future for rail really is bright, as passenger numbers, freight, and revenue recover towards pre pandemic levels, and we look forward to working with the RIA membership to help the railway industry become even bigger and better in the months and years to come!’
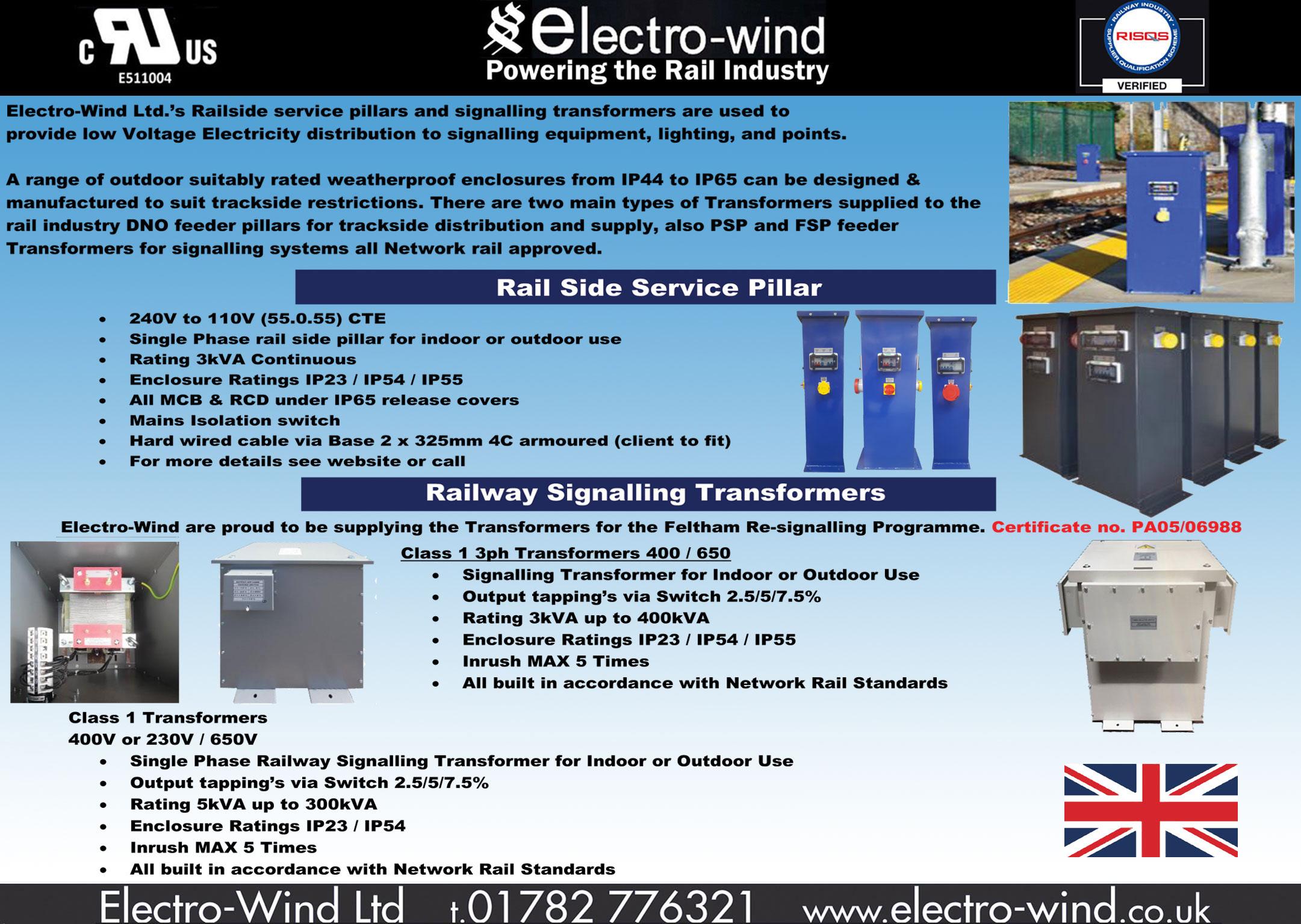
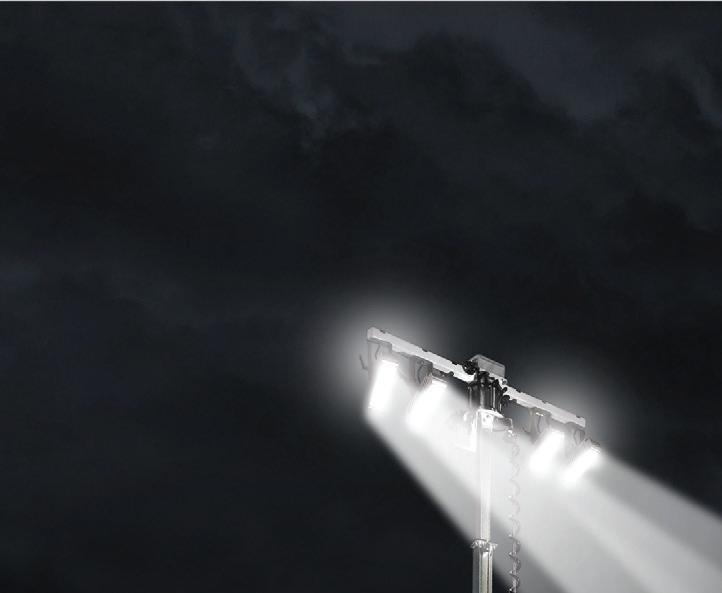


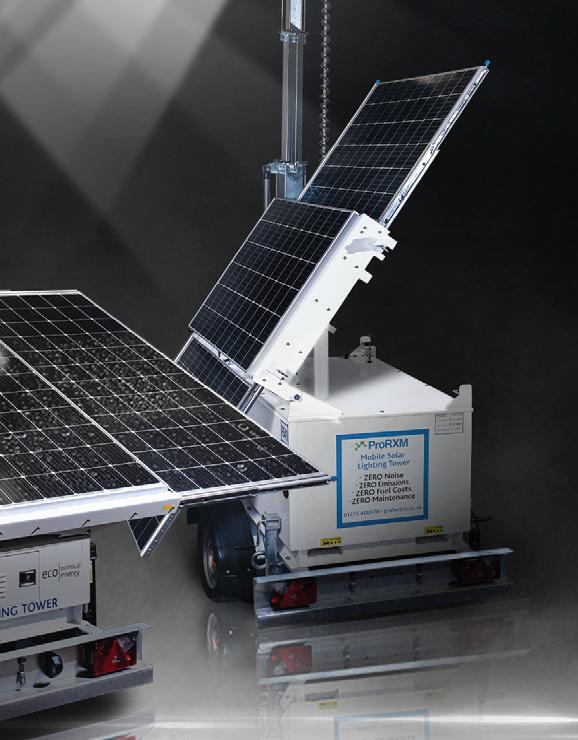
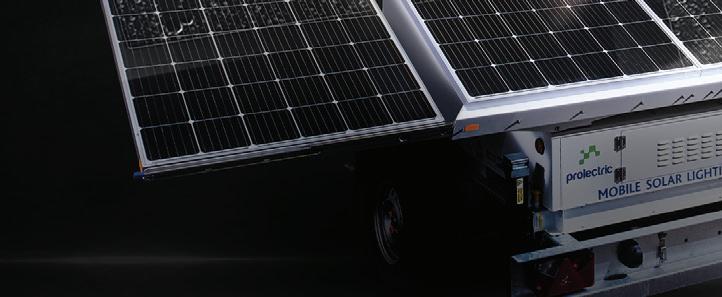

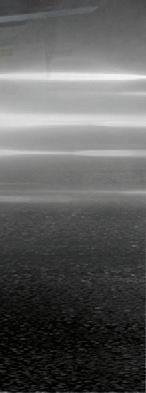
Steve Murphy Chief Executive Officer of MTR UK
Steve Murphy is the CEO of MTR UK. He joined MTR in 2014, as Managing Director of MTR Elizabeth line. He subsequently became CEO of MTR UK in 2020.
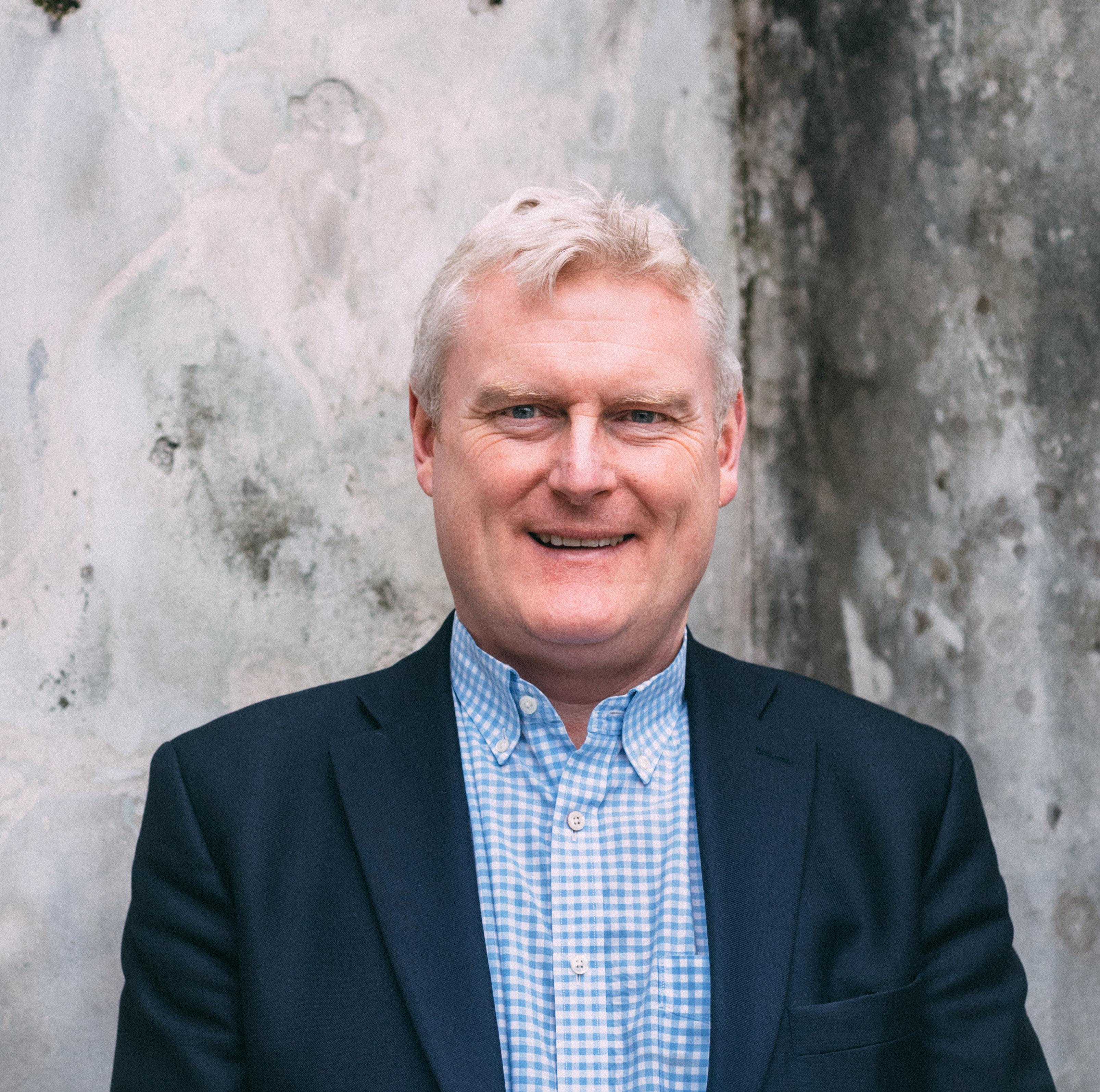
Sam Sherwood-Hale spoke to Steve Murphy, CEO of MTR UK about environmental sustainability, Big Data and MTR trenolab
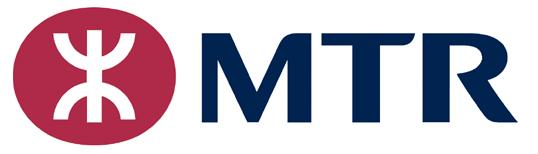
SSH: How did you get started in the industry?
SM: I started my career with British Rail, as a Graduate Trainee, just as the industry was being privatised. It was a great time to be in the industry with such seismic changes taking place across the sector and gave me the opportunity to not only learn a lot, but to add new perspectives and try out different things. While learning from the past is an essential element in any career – it
is equally important to question how we can do things differently and to innovate.
I joined MTR in 2014, as Managing Director of MTR Elizabeth line. I subsequently became CEO of MTR UK in 2020.
SSH: Tell us about your career before you joined MTR UK?
SM: My first management role was as Marketing Manager for Chiltern Railways.
My career to-date of 30+ years has included senior posts at Chiltern Railways, Iarnród Éireann (Irish Rail), the Arriva Group and London Overground Rail Operations Limited (LOROL).
SSH: What challenges have you faced in the industry?
SM: The nature of the rail industry demands constant change and innovation. Part of my job is to lead change and improvements that
benefit our passengers and stakeholders while also ensuring our people are taken care of. It is a privilege to be challenged in this every day!
SSH: What success have you experienced in the last twelve months and how do you measure success?
SM: Success only comes about through leading a team effort. There are many areas of the business where we are demonstrating this but I’m particularly proud to have led a team responsible for the highly successful passenger launch of Europe’s biggest infrastructure project – London’s Elizabeth line, now the most punctual and popular rail line in the UK, according to ORR statistics. In a transport business, a crucial way to measure success is in customer satisfaction. Ultimately, that’s what drives repeat business, profitability, and shareholder value. I’m pleased that we have a positive track-record in that area! After driving improvements during the phased opening of the Elizabeth line, our trains had an average 94.4 per cent punctuality during the summer of 2022, compared to 87.6 per cent for all London and Southeast Operators.
SSH: What does sustainability mean to you?
SM: One definition of sustainability is that it is about maintaining and improving our way of life whilst respecting nature and avoiding the long-term depletion of natural resources. From a business perspective, this means recognising that environmental, social and governance (ESG) issues are vital considerations for companies operating and making business decisions.
With increasingly stringent regulatory requirements for risk management and disclosure and increasing stakeholder expectations, ESG is no longer optional, but a prerequisite for companies to maintain their social licence to operate. MTR has set several environmental and social objectives to embed ESG principles across its business to create long-term value for its stakeholders and the cities it serves. These include:
• Environmental sustainability – One of MTR UK’s key areas of focus. Across all our business units, we seek to improve the way we interact with the environment around us and ensure our business keeps sustainability at the forefront of all we do.
• Social inclusion – We look to provide key transport links and develop supporting infrastructure to enhance the lives of the customers and communities we serve. The company supports social inclusion by committing to providing a safe, accessible, and sustainable transport system for all. Improvement works to stations, and trains can provide fit-for-purpose and easy-access facilities for people with additional needs, luggage, and small children. We apply the same rigor with our internal team, where equality, diversity and inclusion underpin all we do.
• Advancement and opportunities –Economic sustainability runs through our business processes and ensures we make considered decisions in line with our ecological and social values. MTR has sustainable financing thanks to its Rail plus Property (R+P) business model. We aim to develop integrated communities along rail lines that generate diversified revenue streams, including property development.
From a social perspective, urban mobility is closely linked with social inclusion. MTR’s aspiration is to keep cities moving by managing our business sustainably with best-in-class governance and helping individuals and communities thrive.
SSH: How has technology developed since you started in the industry?
SM: There has been a quantum leap in information available – ‘Big Data’. We are ensuring that MTR leads the way in delivering innovative technologies to the UK market in areas as diverse as performance modelling, capacity analysis and passenger behaviour analytics. For instance, MTR trenolab is a newly established Joint Venture, that will use technology to revolutionise timetable planning. MTR trenolab merges the best in modelling software technology with the best in industry operations experience to provide a new level of analysis to reduce the performance risk associated with introducing new timetables. There’s a difference between planning software – which allocates timetable paths, and modelling software, which looks at real life implications – such as the impact that one late train might have on another.
Our driver Academy uses virtual and augmented reality for operational training, and this will be developed across the business.
SSH: What are some standout projects you’ve been involved in over the years?
SM: At Iarnród Éireann (Irish Rail) I led a team that delivered a 15 per cent increase in punctuality on all intercity routes, secured over £300 million of investment in new rolling stock to completely replace the existing Intercity fleet, and increased customer satisfaction on Intercity services to record levels. Our investment and efforts created the fastest passenger growth – 15 per cent – for any European railway at the time.
As MD of London Overground, I raised punctuality from near the bottom of UK train operators to the top, achieving 96.5 per cent, increased customer satisfaction to the highest level of any UK train operating company. I also project managed the implementation of the new East London line – one of London’s biggest ever rail projects. One of my career highlights was leading the team to deliver outstanding performance as a key part of the 2012 Olympics Transport plan.
SSH: What would you say is the most exciting technology in the industry?
SM: It’s impossible to narrow this down to just one. But going back to ‘Big Data’ as one example – analysis will, for the first time, allow us to understand passenger needs and actual behaviours. This will inform future investment decisions as well as future timetables that will ultimately deliver positive benefits to our customers. I’m delighted that MTR trenolab is at the forefront of this thinking.
SSH: How can the industry tackle its skills shortage and how do you recruit/retain/ train your staff?
SM: We are in an era where ‘bad news sells’, and unfortunately rail transport has made itself an easy target for the media. We need to make the sector more attractive to a wide range of people. Improving perceptions – starting with school age children – is important, when so many positive things are happening. By modernising and embracing new technologies, we can make it an attractive place to work and an option for them to consider.
Similarly for graduates or those looking for a career change or for a change of employer, we need to demonstrate such innovation and change. For instance, on the Elizabeth line we demonstrated a modern and innovative system, with innovative, forward-thinking people. There was a huge amount of recruitment needed; we started with no employees and now have nearly 1,300.
We have developed engaging and innovative training and development, with our in-house specialists working with industry to produce new apps and methods that maintain engagement and a high level of knowledge retention.
Our initial focus was on training drivers, and because it enables remote learning, our system was a success, despite the blight of Covid elsewhere. As the world becomes more digitally-integrated, rail needs to embrace such change – to train and retrain, to address the skills shortage, and to maintain interest.
Employees and potential employees are increasingly looking for companies that share their ESG (Environmental, Social, and Governance) values, and that are committed to reducing waste and pollution – as well as to making a positive impact on society and the environment.
Companies that prioritise ESG practices also are often seen as more ethical and trustworthy by customers, investors, and the media - which can lead to increased loyalty and positive ‘word-of-mouth’.
Future employment strategy must increasingly emphasise sustainable practices that will benefit society and the environment while generating long-term profits for the business.
SSH: What do you think is one of the biggest challenges currently facing the rail industry?
SM: One of the most important, defining challenges for railways around the world is performance/reliability – this should be a constant, all-consuming obsession! If your railway is unreliable, every day should be defined by plans to improve. If you are running a reliable railway, it’s all about how you maintain that and mitigate the everpresent and changing risks to performance. As a specific example, when starting London Overground in 2007, that railway had the lowest customer satisfaction ever recorded, on the back of dreadful day-to-day performance. The excellent management team I led were obsessive and ruthless about changing the unreliability of the railway, as were our partners in TfL – every day we implemented ideas to improve performance and then developed new ideas – a great many of these came directly from frontline colleagues. In this sort of environment good leadership refuses to allow any distractions to the team in the pursuit of better reliability.
SSH: Where do you think the industry will be in the next ten to fifteen years?
SM: In the next ten to fifteen years I’d love to see a railway carrying double the number of customers today and with a significant part of its funding being independent of government and derived from a different use of railway assets – I see our London Liverpool Street station project being a crucial pioneer in developing this independent funding capability for the railway.
The reason doubling the number of customers is both achievable and desirable is that rail’s current market share of all UK passenger journeys is only around two to three per cent – less than half of many of our European neighbours. Efficiently building this sort of demand will re-establish rail as a major success story and at the forefront of the UK’s plans to achieve its national environmental and carbon reduction targets.
The industry quite clearly needs to have creative and innovative funding models to be sustainable and if it is to develop to suit the needs of the UK economy and a growing, mobile population. Our highly successful Rail plus Property (R+P) model enables MTR to build new railway lines and plan and create integrated commercial and residential communities around existing railway stations. MTR has used this model for over 40 years and I am very keen to see it developed here in the UK. Our model connects communities, whilst contributing to lower government spending through more efficient land utilisation and reduced spend on railway infrastructure.
We’ve delivered over one hundred million feet of rail plus development in Hong Kong. Now – in partnership with Sellar (one of London’s leading property developers) we are proposing to revitalise London Liverpool
Street station. The proposed plans will turn a challenging and overloaded passenger experience into something that better serves everyone – whatever their mobility and personal requirements. Liverpool Street is London’s third-busiest station, and is set to get busier. The plans will include an enhanced concourse to sustain future growth, with new commercial, retail and leisure facilities too. Most importantly, this development will be delivered at no cost to the taxpayer or rail user. I believe that this model can be utilised in many parts of the rail network – even opening up opportunities for new lines and connections.
SSH: How can we get more use of the rail assets and what is your vision of rail in ten or twenty years?
SM: In the short-term, the ground-breaking approach delivered by MTR trenolab offers operators the opportunity to deliver more capacity and more reliably, on existing railway assets.
As a railway company, if your entire model is ‘I’m going to go to government and ask for more money to do what I want to do’ … it’s not sustainable. Wherever possible, rail must find private sector solutions to grow and be successful. MTR’s highly successful Rail plus Property (R+P) model enables MTR to improve infrastructure and to build new railway lines and plan and create integrated commercial and residential communities around existing railway stations – at no cost to the taxpayer.
Established over 40 years ago as a way of financing MTR’s first railway line, the Rail plus Property (R+P) model helps to fill funding gaps for new railway lines and generates revenue for railway operations through land and property developments adjacent to, and above, the railway. We’ve recently started to employ this model in a joint venture, to deliver a transformational scheme at London’s Liverpool Street station.
Not just a source of railway financing, elsewhere the model has become a critical part of a city’s urban-development approach where well-planned, high-quality communities can flourish. MTR’s Rail plus Property (R+P) developments support thriving communities and local businesses through improved accessibility, greater connectivity, and enhanced public and green spaces.
SSH: How can we make the rail industry a place people want to work in?
SM: By making it exciting, innovative, and rewarding – and by showing what a great future it can have driven forward by the right people. We also have a responsibility to ensure we continue to drive equality, diversity and inclusion to support and retain the great people already within our industry and to attract the diverse leaders of the future our industry needs. Ultimately rail will have a far larger role to play in the success of the UK. Who wouldn’t want to be part of that?
SSH: What are your views on collaborative working?
SM: Is there any other kind? Every organisation needs a leader, but part of that role is to inspire and bring out the best in others. At one end of the scale, it is important to avoid the inertia of ‘decision by committee’ and ‘groupthink’ – but at the other end, it is essential to foster new ways of thinking and to encourage people to inspire the best in each other.
SSH: How do you make your business a good place to work?
SM: Lead by example, share a vision and common purpose, and trust people to use their initiative and to make the right decisions. There’s something very wrong if you have people hanging around ‘waiting to be told what to do’. That’s not why we are all here. We are here to find solutions to difficult challenges, and to keep going until we do.
SSH: What do you expect to be the biggest challenges that come from this transformation of the railway industry?
SM: We must get away from ‘normalising the abnormal’. It is very easy for some internally – and for our political masters –to accept long-term train delays, Industrial Relations unrest, and a variety of other challenges almost as ‘occupational hazards’. We are here to restore the railway. If we make the trains run on time, we then have more time to think strategically and plan for the future. It’s a virtuous circle – and the least that passengers should expect!
SSH: At some point, every company will face the question of how to continue maximising earnings from their current business practice whilst also investing enough in innovation so they can turn a profit in the future. How can a company achieve the necessary creativity to innovate without compromising their existing business?
SM: It is important to employ people not only with the right skillsets, but with the vision to see how these may need to change over time. If a company stands still, it will be overtaken. And if an industry stands still, it won’t be sustainable. Historically, the rail industry has been mixed in how it responds to customer needs and changing circumstances. However, there are numerous examples of the importance of focusing on longer-term vision. For example, during my time at Chiltern Railways, we challenged the ‘status quo’ of the steady-state railway, by effectively creating a new mainline railway between London Marylebone and Birmingham. At the same time, we upgraded services on the route for traditional ‘Home Counties’ commuters. By investing in infrastructure, listening to our customers, and concentrating on detail, we delivered a clean, punctual service that people wanted to use.
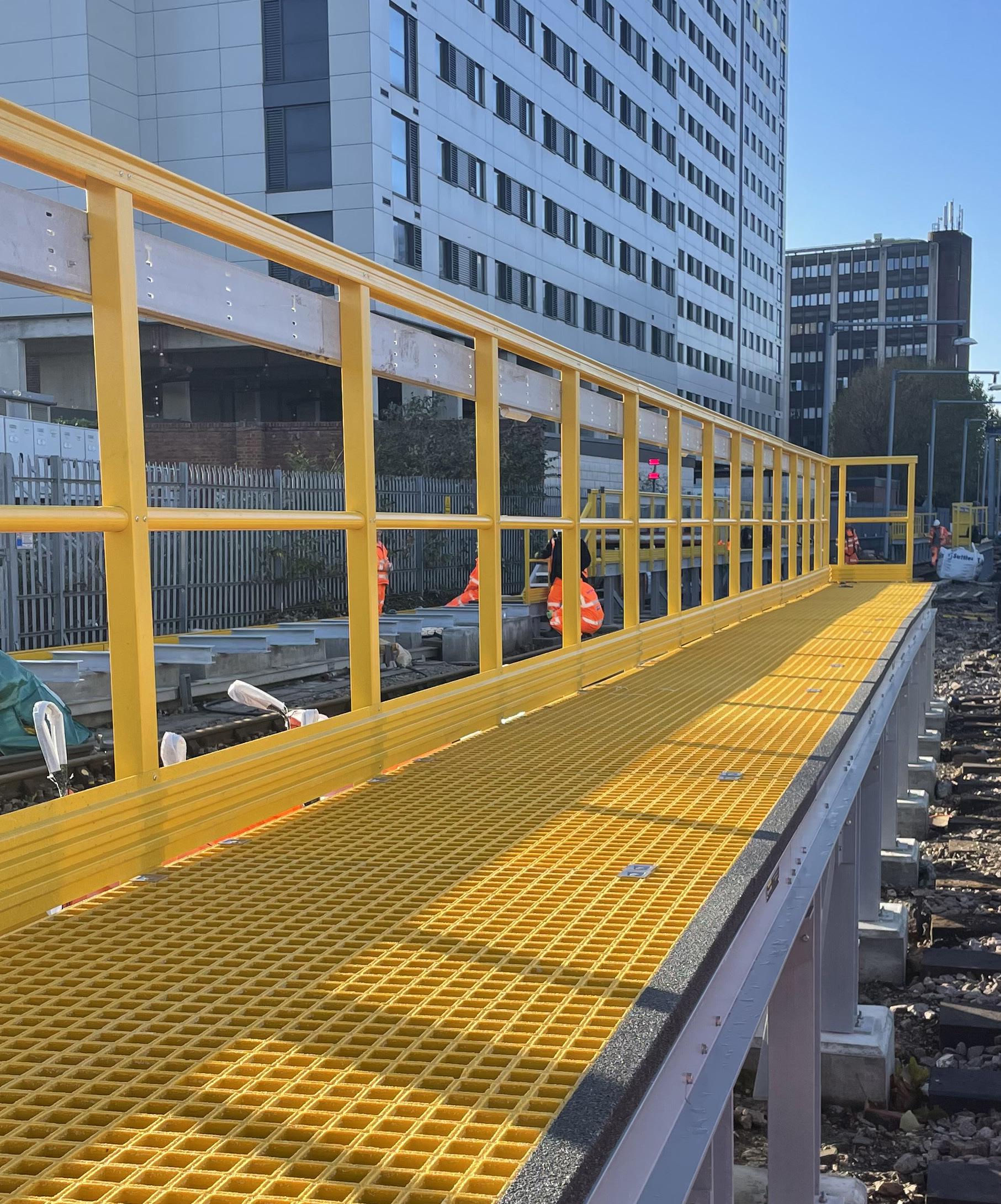
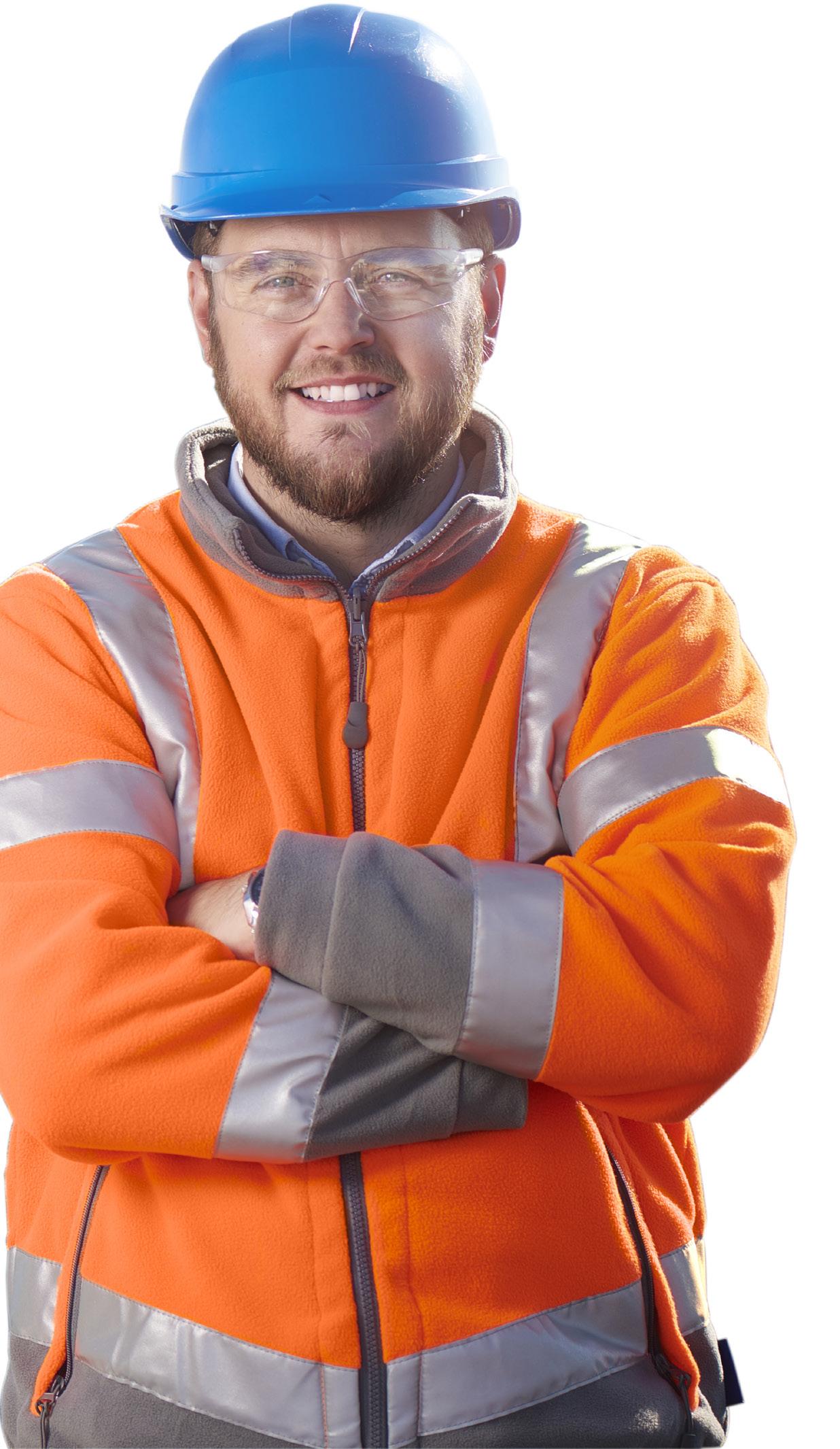


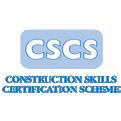
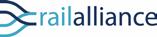
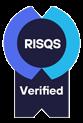
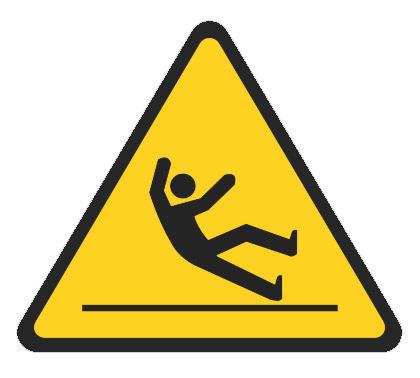
OPTICAL FIBRE TUNNEL CABLES
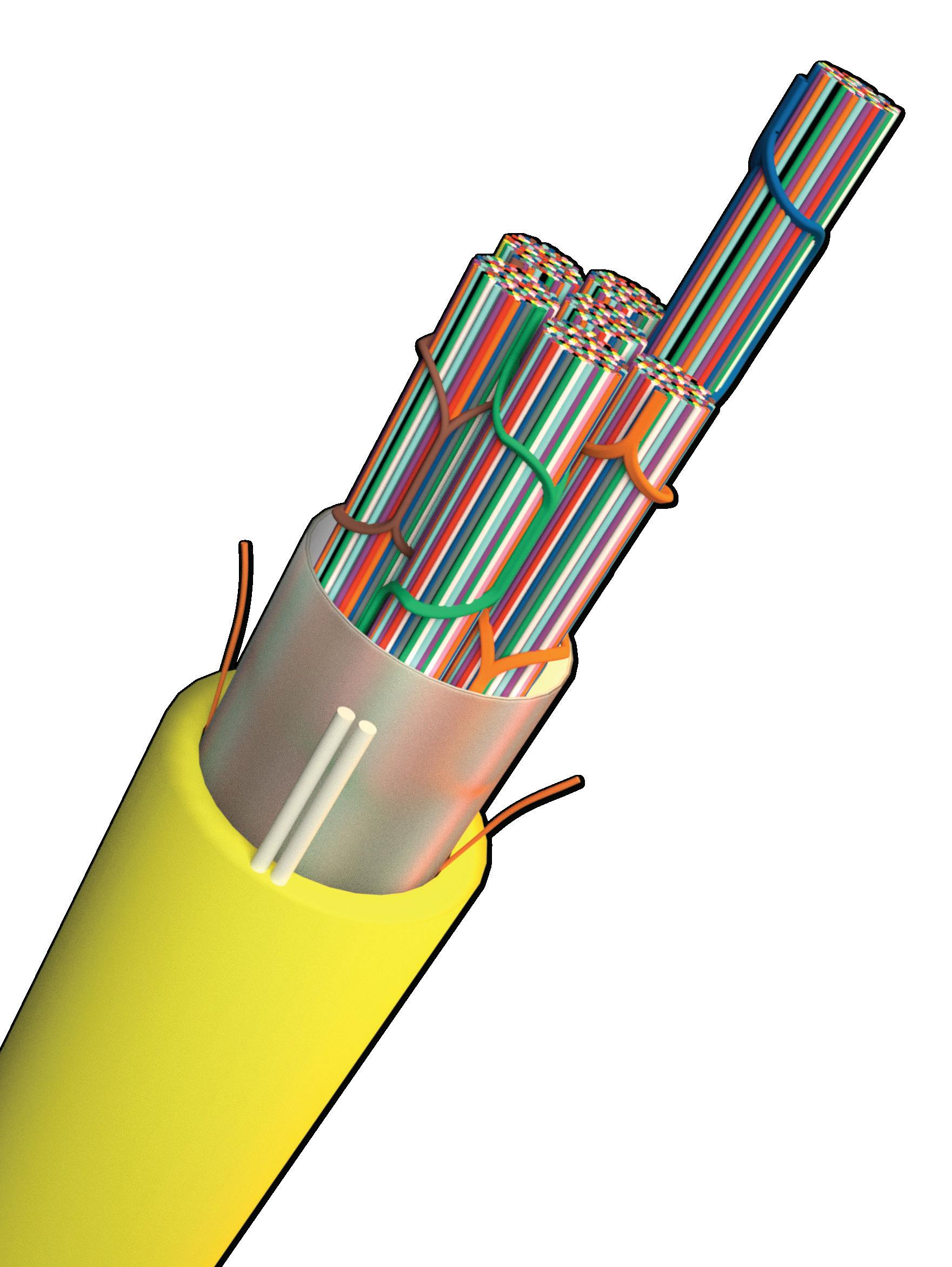
Non-armored and armored Flame-retardant Wrapping Tube Cable using SpiderWeb Ribbon (FR-WTC-SWR) for rail, underground and metro applications.
Range of ultra-high fibre density cable designs including 288, 432 and 864 fibres both non-armored and armored variants specifically intended for OVERGROUND RAIL TUNNEL and UNDERGROUND network applications.
www.fujikura.co.uk
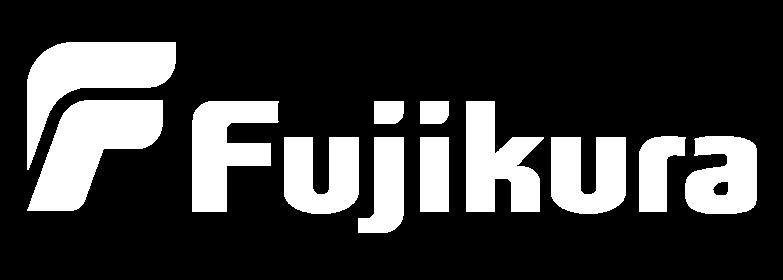
• Illustration is 432 fibre over-ground double-jacket design
• Cable can be jointed in 4-5 hours compared to 20+ hours using traditional loose tube cables and conventional installation methods.
• Small and lightweight compared to traditional designs
• Fully dry (gel-free) construction
• 12 Fiber Spider Web Ribbon (SWR)
• CPR Class B2ca-s1a,d0,a1
Inner sheath (FRPE, Yellow)
Corrugated steel tape
12F Spider Web Ribbon in each bundled unit
Water blocking tape
Strength member (FRP)
Water blocking material
Ripcords
Outer sheath (FRPE, Black)
Women in Rail Conference Marks End of Tenth Anniversary Celebrations
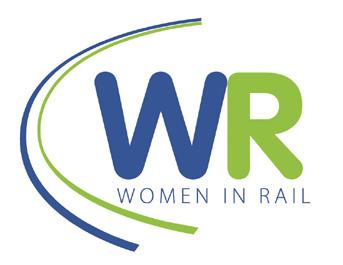
Women in Rail formally marked the end of the organisation’s tenth anniversary celebrations with the annual Women in Rail Conference 2023
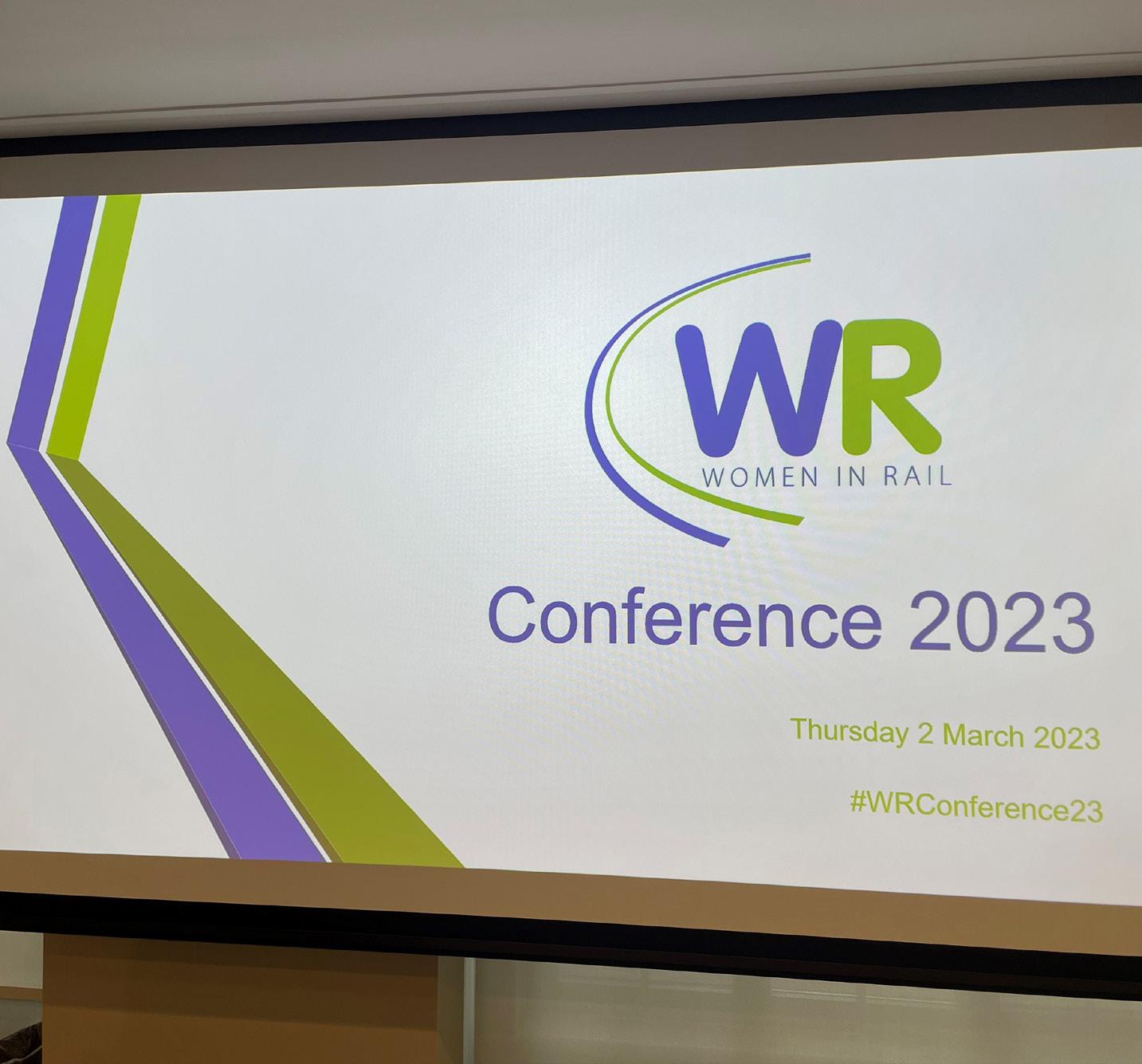
The event, which took place Thursday, 2 March, presented an opportunity for Women in Rail (WR) members to reflect on equality, diversity and inclusion (EDI) achievements during the past decade and to look forward to innovations and improvements over the next ten years.
Organised as a hybrid event hosted by London law firm Stephenson Harwood, with 120 in-person attendees and a virtual
audience of almost 100, attendee tickets sold out within 48 hours of their release.
The conference started with a fun and enlightening EDI-related ice-breaker hosted by Lucy Dyer, an Apprentice Civil Engineer at SLC Rail and member of Women in Rail West Midlands Committee.
Keynote speaker Adeline Ginn MBE, who founded WR in 2012 to improve gender balance, female diversity and broader EDI across all grades and roles
For more information about WR visit https://womeninrail.org/.
within the UK railway sector, shared the organisation's remarkable journey and achievements to date.
Other speakers from across the rail industry presented on EDI topics including: EDI Charter Working Group; the Great British Railways Transition Team (GBRTT) on attracting new talent; apprenticeships and Young Rail Professionals (YRP); Southeastern on progress and allyship; guest speaker Leon Llyod on high performing
WOMEN IN RAIL HIGHLIGHTS
2016 – North West, Yorkshire, East Midlands and West Midlands Rail regional groups launch.
2016 – WR gains charity status.
2016 – Inaugural Big Rail Diversity Challenge promotes the message 'Gender Diversity – Better for Business, Better for People, Better for Rail'.
2017 – WR Jobs Board launched with vacancies from employers actively seeking to recruit women for full or part time jobs.
2018 – Prestigious Women in Rail Awards launches to reward industry excellence.
2019 – The first cohort engages in the WR cross-company mentoring scheme.
2020 – WR joins forces with the Railway Industry Association (RIA) to launch the Equality, Diversity and Inclusion Charter, which now has more than 200 signatories.
2022 – 2023 WR programme of activities focused on celebrating the organisations ten-year journey.
teamsBritish Transport Police's support of White Ribbon – the UK’s leading charity engaging with men and boys to end violence against women and girls.
A lively panel discussion considered a variety of EDI talking points including sharing ideas and greater collaboration between networks such as Rail Unites for InclusionWR and EDI Charter Group.
Attendees had the opportunity to network during lunch and refreshment breaks – for some an opportunity to meet face to face for the first time.


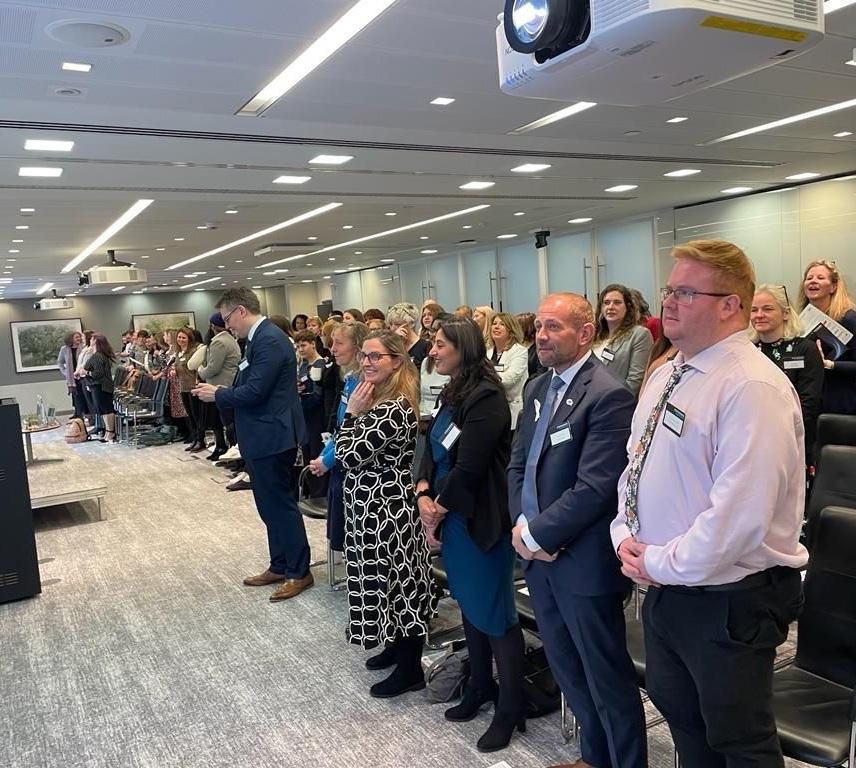
Shona Clive, WR Vice-Chair said: ‘In line with our ten year anniversary celebrations, the conference reflected on WR's journey so far and addressed the significant progress in EDI in UK rail, with a particular focus on how organisations and individuals across the sector have implemented EDI as a key business imperative and the benefits this has realised.
‘Our speakers provided valuable insight into the industry’s thoughts on what the next decade will bring in terms of EDI activity and how we can all contribute collectively to making change happen across the industry and that allyship will play a central role.
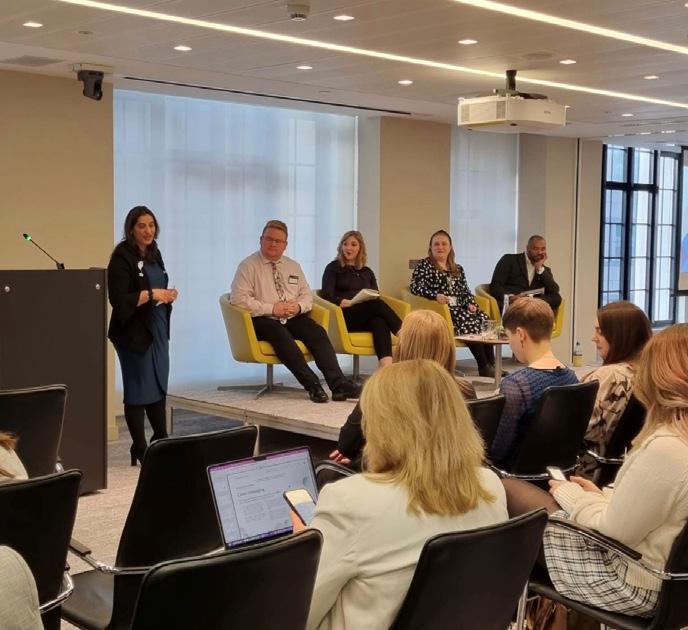
‘While much has been achieved, there is still more to be done, and we are now looking to the next decade and where we, as an organisation, can add most value and give best support.’
The conference was sponsored by CAF Rail UK, Egis Transport Solutions, Morson Group, Alstom Transport UK Limited, Great Western Railways and Porterbrook.
‘We would like to thank the conference's corporate sponsors and the team at Nimble Media Ltd for supporting and delivering what was a hugely successful and wellattended event’ added Shona.
CONFERENCE SPEAKERS
• Alexandra Batey, HS2 Ltd Phase 2b Development Director.
• Lydia Fairman, Head of Capability and Skills Development for Network Rail and Great British Railways Transition Team (GBRTT).
• Rachel Fullard, Rail Delivery Group National Rail Service Analyst, and Chair of WR RIA EDI Charter Working Group.
• Mark Johnson, Southeastern Engineering and Major Programmes Director.
• Leon Lloyd, Director of Centrum Solutions and former England international rugby player.
• Nia Mellor, Detective Chief Inspector in the British Transport Police.
• Mandeep Singh, D/Gauge Marketing Manager and Vice-Chair, WR RIA EDI Charter Working Group.
• Fi Westcough, Atkins Consultant (Strategic Rail) and National Chair YRP.
PANEL MEMBERS
• Shane Andrews MBE, Network Rail Project Manager and Chair of Archway, Network Rail LGBTQI+ network.
• Jess Bates, Atkins Network Rail Client Account Director and Atkins Global EDI Lead.
• Laura Donnelly, West Midlands Trains Head of Sales and Marketing and Chair of Engender, West Midlands Trains group dedicated to gender-related topics.
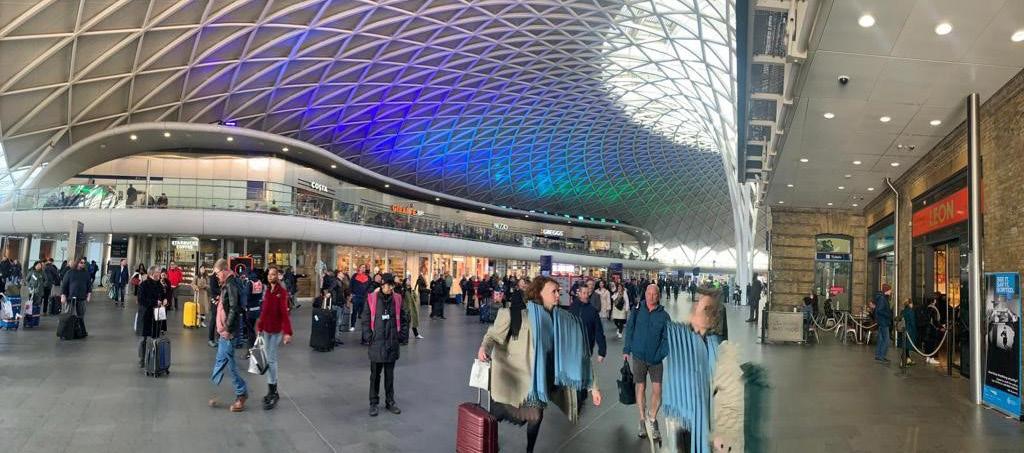
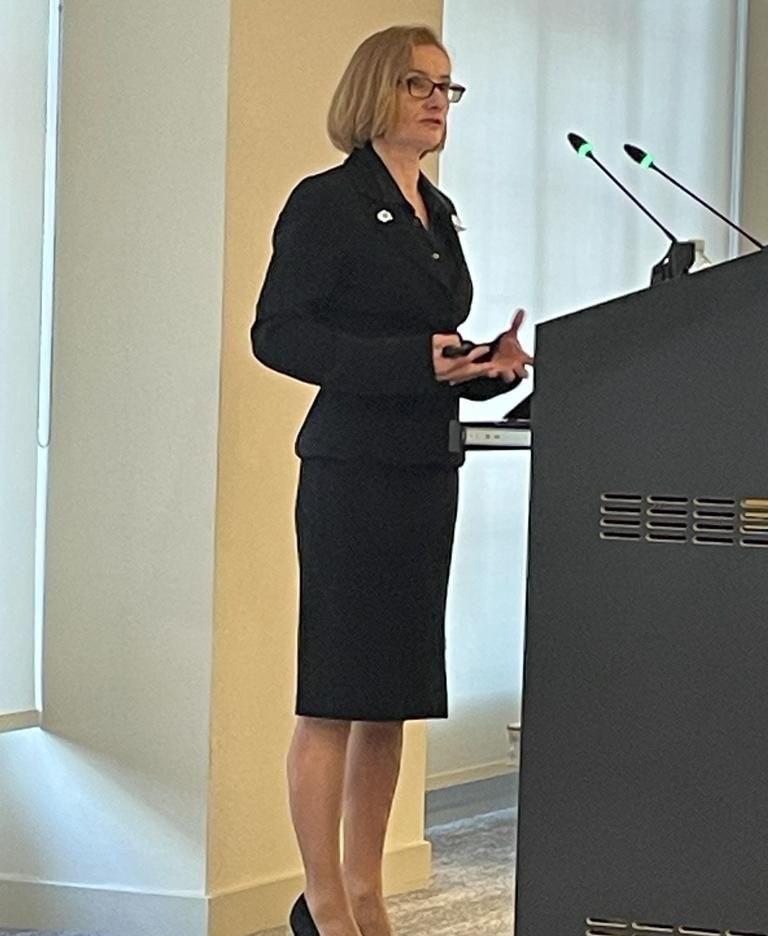
• Odis Palmer, GBRTT EDI Project Manager, I&D Manager at GWR and Co-Chair of Rail Unites for Inclusion.
• Facilitatated by Rajinder Pryor MBE, Lead Delivery Manager (Customer) Network Rail, Trustee, Women in Rail.
SECURITY DOORS FOR THE RAIL INDUSTRY
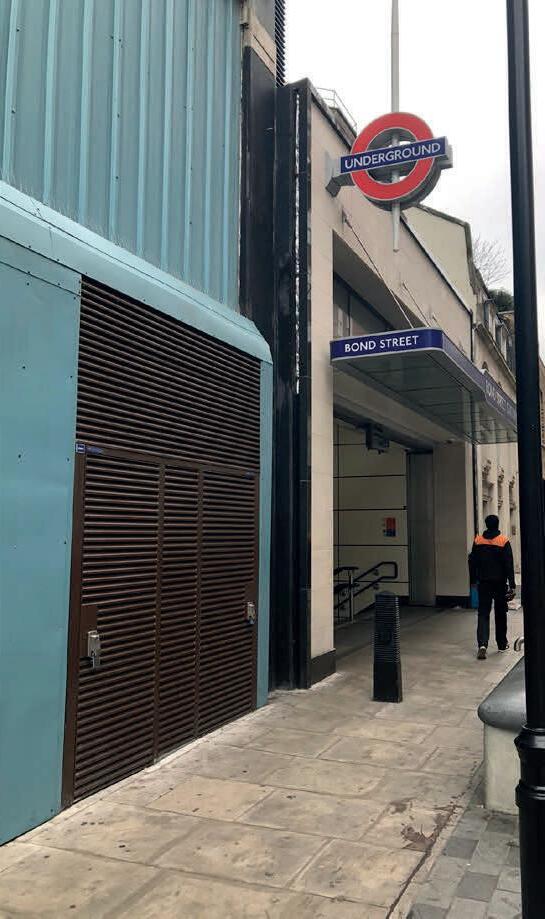
CF Booth Ltd was established in 1920 by Clarence Frederick Booth and since that time has continued to be passed down through the generations of the Booth family.
● SPECIALIST RAIL SOLUTIONS - Overground, Underground/TFL, DLR
The company has been associated with the scrapping of diesel and electric locomotives since the 1960s and has an excellent reputation as one of the largest rolling stock recyclers in the UK, winning nationally released tenders from several of the main rail operating companies.
● REFERENCE PROJECTS - Crossrail, DLR, TFL, EuroTunnel
● BESPOKE SOLUTIONS - Tailored designs to meet project criteria
● INSTALLATION & MAINTENANCE - Qualified, Compliant & Trained Operatives
● TECHNICAL SUPPORT - Consultative advice with complete back up concept to installation
For more details, call our specialised team to discuss your particular project on:
01233 639039
sales@sunraydoors.co.uk
www.sunraydoors.co.uk
CF Booth Ltd was established in 1920 by Clarence Frederick Booth and since that time has continued to be passed down through the generations of the Booth family.
The company has been associated with the scrapping of diesel and electric locomotives since the 1960s and has an excellent reputation as one of the largest rolling stock recyclers in the UK, winning nationally released tenders from several of the main rail operating companies.
The head office is located in Rotherham, South Yorkshire at Clarence Metal Works with the company’s gantry cranes and three derrick cranes making the site quite distinctive.

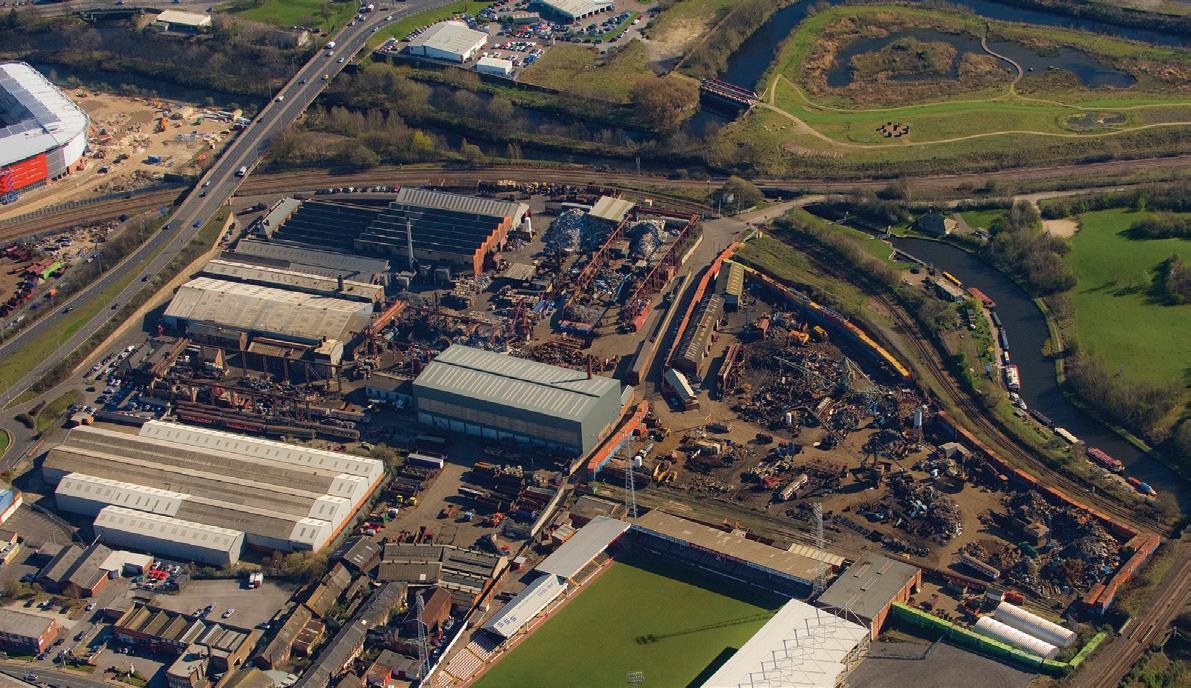
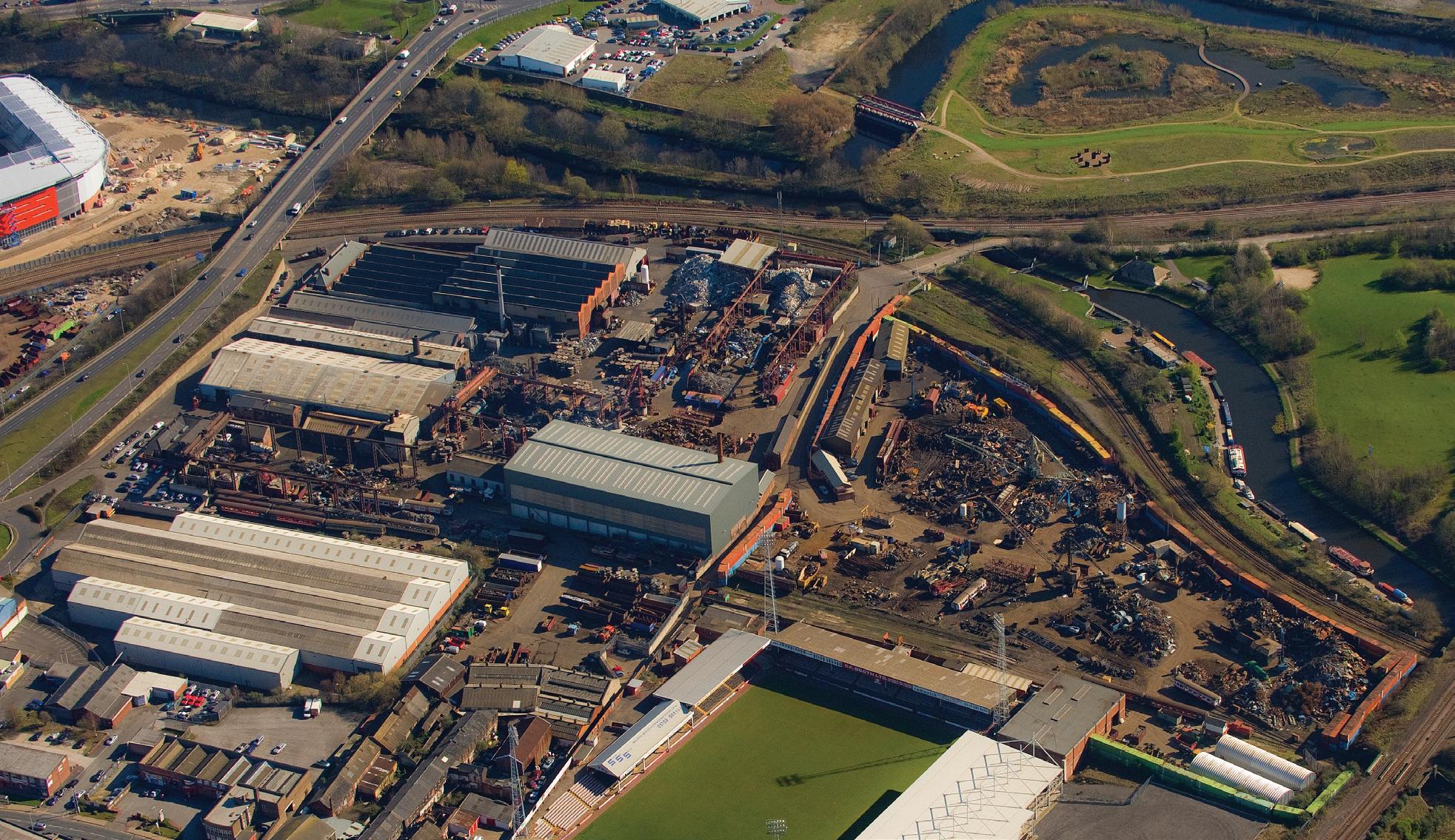
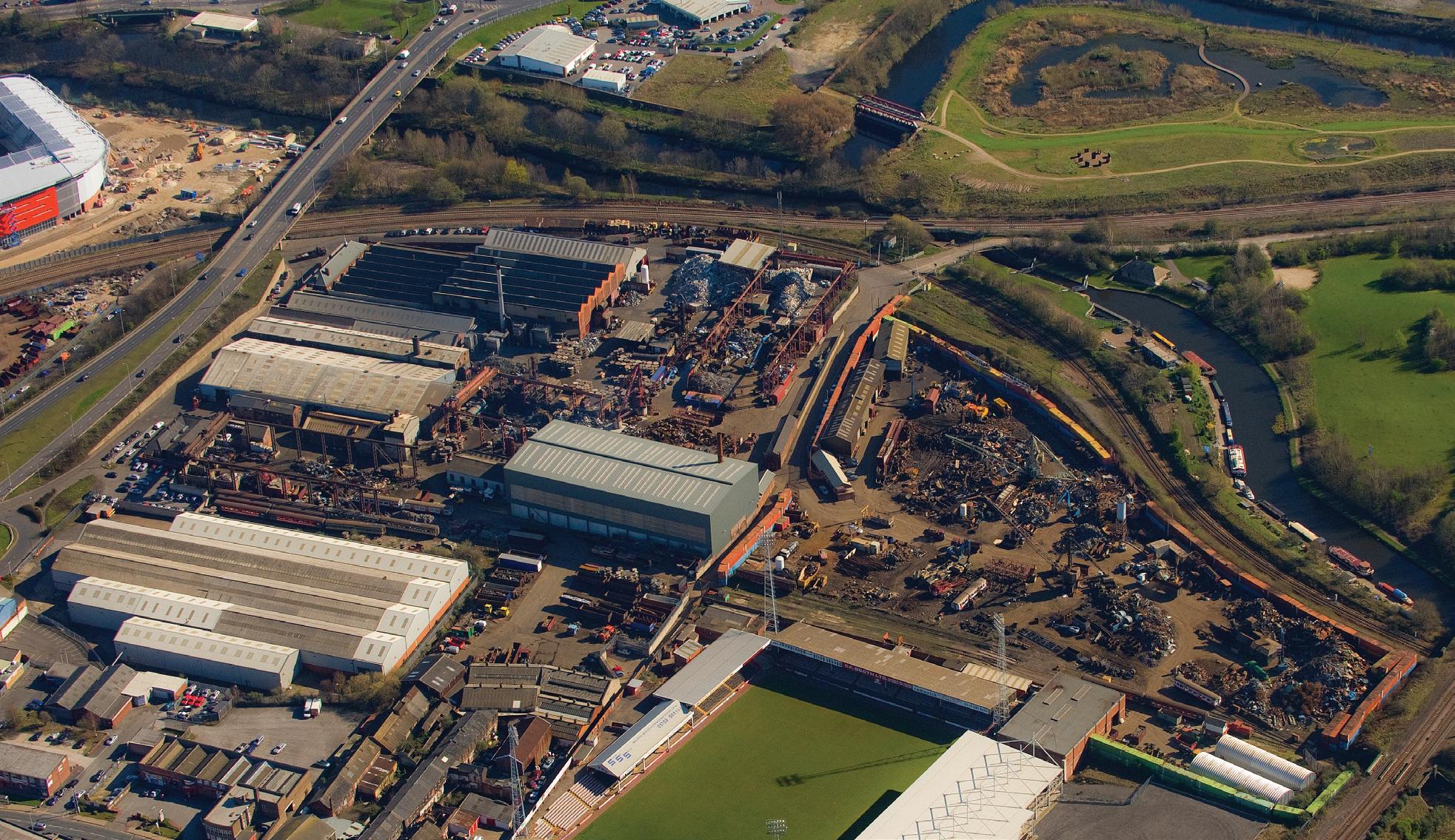
established in 1920 by Clarence Frederick Booth and since that time has continued to be generations of the Booth family.
CF Booth rolling stock division has achieved both ISO 9001 and 14001 standards and has invested heavily in developing the infrastructure to handle all kinds of rolling stock including more than 1,500 metres of rail sidings, which allows us to accommodate a substantial amount of rolling stock. Work continues at present with rail vehicles being brought in through a connection to Network Rail and the proximity of the railway sidings to roads give this side of the business a high profile with many wagons, carriages, underground and departmental stock being processed.
associated with the scrapping of diesel and electric locomotives since the 1960s and has an the largest rolling stock recyclers in the UK, winning nationally released tenders from operating companies.
Rotherham, South Yorkshire at Clarence Metal Works with the company’s gantry cranes making the site quite distinctive.
CF Booth Ltd is one of the leading metal recycling companies in the UK. Established in 1920 by Clarence Frederick Booth, the business has grown from a local metal trader into one of the largest independently run recycling companies in Europe and is nearing its 100th year anniversary. CF Booth has been associated with the scrapping of diesel and electric locomotives since the 1960’s and is now one of the largest rolling stock recyclers in the UK, working with several of the main rail operating companies.
In addition, our extremely competitive buying process and quick payment terms mean that for many companies wishing to dispose of their rolling stock, CF Booth Ltd is the first port of call. Besides processing rolling stock for their residual ferrous/non ferrous metals, we also salvage any or all components that may be required by railway preservationists.
The current Rolling Stock Manager, Christopher Davis, says: “We are proud to be playing a major role in supporting the UK national rail industry and extremely proud to provide a valuable service to railway enthusiasts and preservationists throughout the UK as they continue to restore rolling stock vehicles to their former glory for future generations to enjoy. We value the relationship we have built up with preservationists and enthusiasts over the years’’.
We are more than just a metal recycler, our continued investment in infrastructure and quality personnel has put us at the forefront of the metal recycling industry. Working with global businesses and international brands has made us think differently and strive to continue our development.
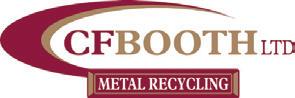
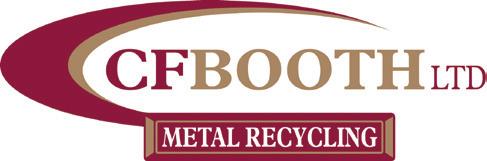
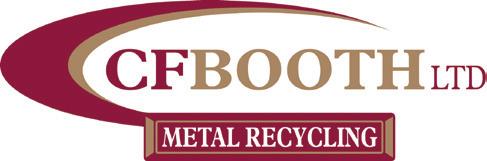
Our rolling stock asbestos removal/disposal service is supported by Demex Ltd a part of the CF Booth Group. Their fully trained and accredited operatives use the very latest equipment and techniques to safely strip out and dispose of asbestos. Besides processing rolling stock for their residual ferrous/non-ferrous metals, we also salvage any or all components that may be required by Railway Companies and Railway Preservationists.
CF Booth rolling stock division has achieved both ISO 9001 and 14001 standards and has invested heavily in developing the infrastructure to handle all kinds of rolling stock including more than 1,500 metres of rail sidings, which allows us to accommodate a substantial amount of rolling stock. Work continues at present with rail vehicles being brought in through a connection to Network Rail and the proximity of the railway sidings to roads give this side of the business a high profile with many wagons, carriages, underground and departmental stock being processed. In addition, our extremely competitive buying process and quick payment terms mean that for many companies wishing to dispose of their rolling stock, CF Booth Ltd is the first port of call. Besides processing rolling stock for their residual ferrous/non ferrous metals, we also salvage any or all components that may be required by railway preservationists.
The current Rolling Stock Manager, Christopher Davis, says: “We are proud to be playing a major role in supporting the UK national rail industry and extremely proud to provide a valuable service to railway enthusiasts and preservationists throughout the UK as they continue to restore rolling stock vehicles to their former glory for future generations to enjoy. We value the relationship we have built up with preservationists and enthusiasts over the years’’.
Limited, Clarence

What Success Looks Like
Steve Murphy, CEO, MTR UK celebrates the successful Rail + Property model, which removes risk and burden on the taxpayer, whilst delivering innovation

Recent postponement of certain work on High Speed 2 (HS2) has highlighted the stop-start funding and delivery problems that have blighted UK rail infrastructure for decades. When schemes are downsized, does there remain a clear, unified vision of ‘what success looks like’?
A recent report from the National Audit Office revealed over £100 million of design costs that were no longer required, as well as risk that delay to the project would further increase cost overruns – to potentially double the original estimate. All such risk is ultimately carried by the UK taxpayer, so it’s hardly surprising that some of our political representatives get queasier as the next General Election approaches.
Taking taxpayer risk out of huge infrastructure schemes may appear to be impossible; however, MTR has quietly been doing that for over forty years, and is now poised to deliver the same in the UK.

Our Rail + Property (R+P) model is a business strategy that involves combining the development and management of railway infrastructure and services with property development around stations and transit hubs. The idea behind this model is
to make public transport more attractive and accessible to commuters and travellers, while creating value from the real estate opportunities that arise from the increased demand for connectivity and accessibility.
MTR’s model should not be viewed in isolation. It is more than a transport solution and has become a critical part of a city’s urban-development approach. Our R+P developments support thriving communities and local businesses through improved accessibility, greater connectivity, and enhanced public and green spaces.
It may seem obvious, but the key to success is in defining ‘what success looks like’. MTR’s property R+P model thus depends on careful planning, coordination, and stakeholder engagement throughout the process. It is critical to align, balance and mitigate the social, economic, and environmental impacts of any development, not just to ensure the long-term sustainability and resilience of the project, but to maintain support at Governmental level.
In Hong Kong, MTR operates a Metro comprising of nine railway lines serving Hong Kong Island, Kowloon, and the New Territories. In addition, a Light Rail network serves the local communities of Tuen Mun and Yuen Long in the New Territories while a fleet of buses provide convenient feeder services.
The Corporation also operates the Airport Express, a dedicated high-speed rail link providing the fastest connections to Hong Kong International Airport and the city's newest exhibition and conference centre, AsiaWorld-Expo. MTR has applied the R+P model extensively. Buildings sit over about half of the rapid transit system’s 98 stations, totalling around 13 million square metres of floor area.
The financial advantages of the R+P model have been proved over more than forty years. Instead of taking on the risk, the government exports it to the developer, whilst still being able to generate increased revenues from enhanced land values and taxation on commercial activity.
In Hong Kong, MTR has worked with stakeholders to plan and deliver mixed-use development projects that integrate walking and cycle routes, walkability, public space, and leisure with commercial, residential, or office accommodation. The result – ‘what success looks like’ – is the creation of a live-work-play environment that benefits everyone, by increasing ridership, relieving urban congestion, and generating economic activity.
Seeking to apply this model locally in the UK, MTR has entered into a Joint Venture with Sellar, the developer of London Bridge Quarter and Paddington Square, andworking together with Network Rail - plan to transform London’s Liverpool Street station. A significant upgrade is required to the last development, which was completed in the early 1990s when there was little expectation that passenger numbers would grow.
Now Liverpool Street is one of London’s busiest stations, with up to 135 million people using it annually in recent years. The station suffers from extreme congestion at times, and access is hugely problematic for people with additional needs, luggage, and small children. There is only one accessible lift serving the main line station and no step-free access to most of the Underground platforms.
The Joint Venture will enable the delivery of £450 million of vital station upgrades, resulting in an improved passenger experience at no cost to passengers or the taxpayer. The wider project, costed at £1.5
Steve Murphy is CEO of MTR UK
‘The financial advantages of the R+P model have been proved over more than forty years. Instead of taking on the risk, the government exports it to the developer, whilst still being able to generate increased revenues from enhanced land values and taxation on commercial activity.’
‘In Hong Kong, MTR operates a Metro comprising of nine railway lines serving Hong Kong Island, Kowloon, and the New Territories.’
NEWS IN BRIEF
CROSS CITY LINE FLOOD PROTECTION WORK TO BRING MORE RELIABLE RAIL JOURNEYS
Railway improvements on the Cross City line south will bring faster and more reliable journeys for passengers thanks to upcoming work to prevent heavy rainfall flooding tracks and causing delays. Network Rail is carrying out major drainage upgrades between Barnt Green and Longbridge throughout the month of May. The weekend improvement work will reduce the risk of flooding and prevent speed restrictions on the busy route between Birmingham and Cheltenham Spa.
billion, will deliver not only a new accessible world-class station but also a new retail and leisure hub for visitors, passengers and the local community, supporting the City of London Corporation’s Destination City ambitions by creating a landmark seven-daya-week destination.
MTR is proud to draw on our international expertise of creating transport-focused property development to enable thriving communities across our network. Designs have evolved following months of consultation and discussions with the City of London, heritage organisations and other stakeholders, including members of the public, which have led to several amendments and improvements.
The proposed designs will not only establish Liverpool Street station as a worldclass destination but will offer accessible, inclusive spaces for everyone to enjoy, including passengers, visitors, office workers and significantly, the local community. We share the same values as our partners, and through working with some fantastic people at Sellar and Network Rail, our teamwork is making this project possible.
Whilst it is easy to see how this model may be employed in Global Cities, with ‘critical mass’, the MTR team believes
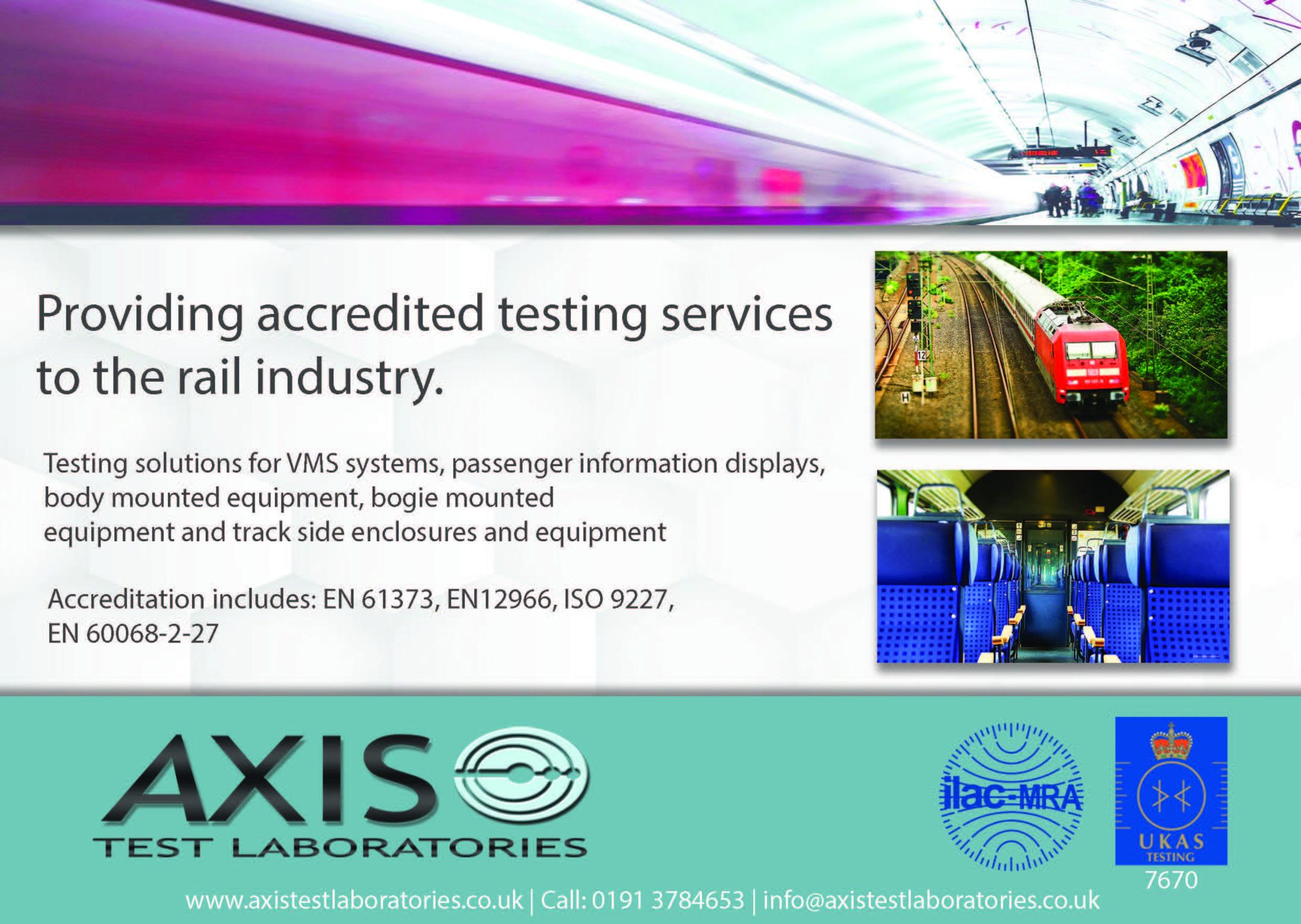
that there are many other opportunities across the UK where the R+P model can be deployed. Encouraging commercial and residential development near transit hubs is scalable. Profit-sharing deals with developers, partial ownership of new developments, and on-site property rentals can all yield revenue to help pay for new investments in transport.
New railway lines or spurs (perhaps to airports or new centres of population) are ideal candidates. However, there are plenty of less ambitious projects, to which the model may apply. MTR’s R+P developments offer positive community amenities that meet people’s needs; everything from a supermarket, gym and swimming pool to a coffee shop or a bar, to safe and friendly pedestrian corridors linking railway stations to surrounding buildings and parks.
MTR’s model seeks to be more than a source of railway financing; it is an integral part of urban-development where wellplanned, high-quality communities can develop. It removes risk from the taxpayer, works with clear vision and consensus, and avoids the ‘death of a thousand cuts’ that so many UK infrastructure schemes have faced in the past.
That’s what success looks like.
Connected Communities: Enhancing the UK’s Rail Resilience for Future
Dario Feliciangeli, Transport Market Leader at GHD, identifies the key issues facing the UK’s rail infrastructure and what more needs to be done to ensure a resilient and connected system for future communities
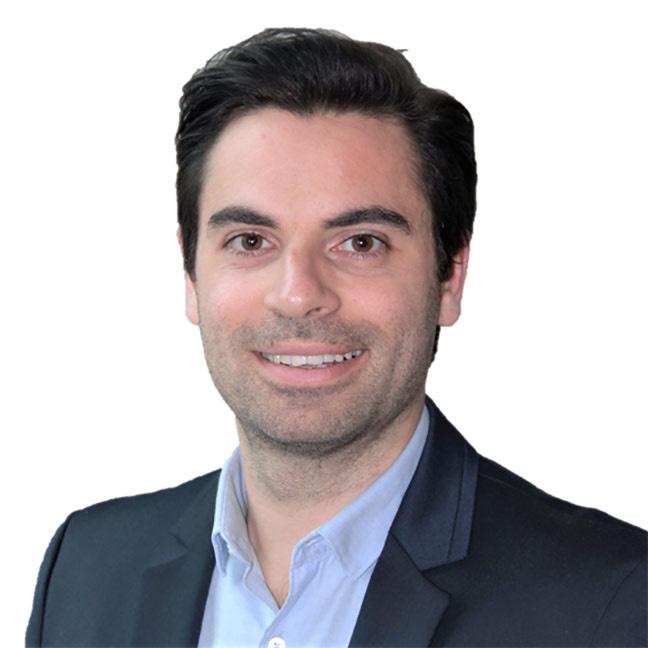
The UK’s rail network is the ‘backbone of Britain’ – it connects communities, promises convenient travel options, delivers employment opportunities, and is a critical piece in the puzzle of delivering on Net Zero ambitions. Recognising all of these benefits, demand for train travel has bounced back post-pandemic – just under one billion passenger rail journeys were made in 2022, a 155 per cent increase on the previous year.
As Great British Rail continues on this growth trajectory, acting on concerns around delays and disruption that have dominated headlines under new Transport Minister Mark Harper, it’s clear that the resilience of the UK’s railways must be prioritised.
One of the biggest challenges facing the public transport system’s resilience is ensuring new infrastructure is futureproofed. Somewhat surprisingly given increasingly volatile weather conditions including record rainfall, frequent heatwaves, flooding, and heightened erosion – designing the UK’s transport systems with the evolving climate in mind hasn’t always been a common approach. It’s in this context, and in response to the damning results as recorded in the latest IPCC report, that it has become imperative to analyse climate risks and how they can be mitigated to ensure that new infrastructure is designed to adapt to changing climates for future generations.
At GHD, climate change modelling is one of the bedrock principles we build into each of our designs. From the awardwinning Pooley Bridge replacement with a future- and flood-proof, first-of-its-kind stainless steel design, to the utilisation of agile technology along major railway lines to manage and mitigate against flooding and landslides, developing weather-resilient transport infrastructure is part of our design ethos.
But, there is arguably an even more pressing need to modernise, and decarbonise, existing infrastructure. Transport infrastructure is generally designed to last, however ensuring the design is done in the most sustainable way is paramount. Not only from an environmental perspective, but to ensure that investment is maximised.
One way of addressing that is by understanding how the infrastructure is being used, by who, and when. As seen in Network Rail’s recently launched ‘Nothing Beats Being There’ campaign, getting passengers back on the railways is of paramount importance, and is supported by a commitment to improve stations and the surrounding infrastructure, rail stock, and the end-to-end passenger experience. Having access to, and utilising passenger and community data is key here to ensuring that these much-sought after upgrades and innovations are not only made in the right areas, but that the design is future-proofed.
Resilient transport infrastructure is nothing without people connectivity, however. A resilient transport system is crucial for both individual and public health, a source of social cohesion integrating groups of people that might otherwise remain disconnected. It also has a huge impact on personal wellbeing, allowing us to meet friends and family and enjoy activities. Whilst innovative design, data analysis and application are imperative, connection and mobility in the wider community must take precedence. A well-designed urban environment with connected multi-modal transport is integral to supporting social and economic development in communities, particularly in new investment zones.
From bustling cities to rural towns, our transport system is the lifeblood connecting the UK. At GHD, we believe communities thrive when they are connected, resilient, productive, and inspired. The demand for safe and reliable public transport system has never been more pressing, and a pointed strategy, proactive partnerships and funding must be at the heart of government policy to ensure infrastructure can withstand future shocks. Now and in the future, transport systems require improved resilience to fulfil its role of reconnecting people, places, and spaces.
Dario Feliciangeli is Transport Market Leader at GHD
‘One of the biggest challenges facing the public transport system’s resilience is ensuring new infrastructure is futureproofed.
Somewhat surprisingly given increasingly volatile weather conditions including record rainfall, frequent heatwaves, flooding, and heightened erosion – designing the UK’s transport systems with the evolving climate in mind hasn’t always been a common approach.’
Premier global manufacturer of components and kits for railway applications

In addition to supplying individual components, the global companies of STAUFF and their authorised system partners use the STAUFF Line approach to support Original Equipment Manufacturers with the supply of custom-designed and ready-to-install fluid power lines from connection to connection and also provide supplemental services that create added value: · Components · Systems · Services · Contact
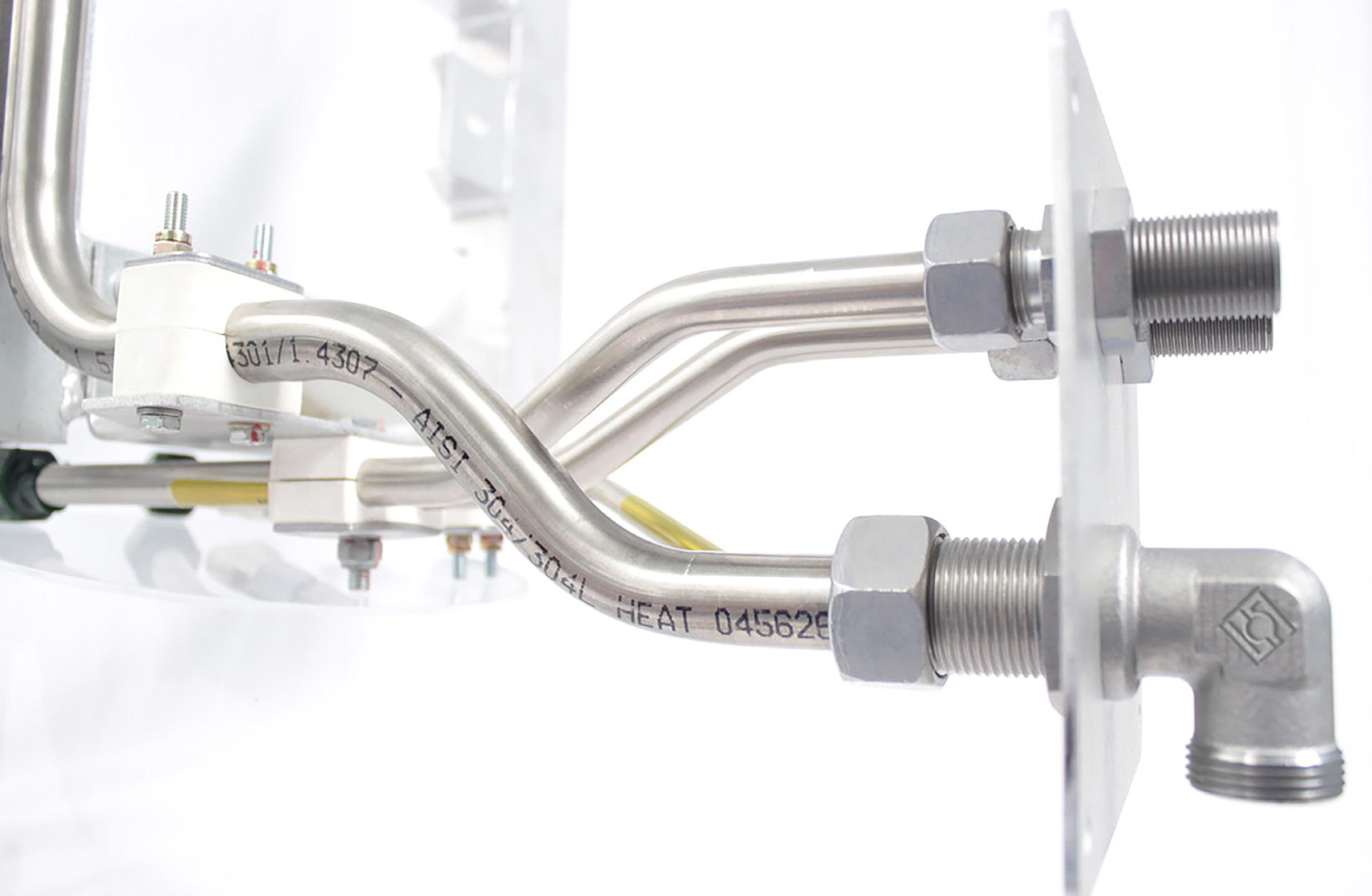
The STAUFF Line process is adopted by global OEMs to successfully achieve cost savings in rolling stock manufacture.

Sheffield Tel: 0114 251 8518
Email: sales@stauff.co.uk
Aberdeen Tel: 01224 786166
Email: sales@stauffscotland.co.uk
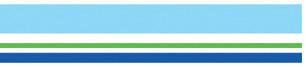
Ireland Tel: 02892 606900
Email: sales@stauffireland.com
Southampton Tel: 023 8069 8700
Email: sales@stauffsouthampton.co.uk
www.stauff.co.uk
Decarbonisation in the Rail Sector
The UK rail sector is not only a critical component of the country's transportation infrastructure but also one of its largest energy consumers: the rail industry was responsible for 0.5 per cent of the entirety of UK emissions in 2020 and Network Rail’s energy costs are expected to cross the unprecedented £1 billion threshold in 2023-2024. The rising cost of electricity and mounting pressure to meet sustainability and net-zero targets have brought the sector's energy consumption under increasing scrutiny and hastened the need for action. This is also compounded by the UK’s ambitious goal of net zero carbon emissions within the rail industry by 2050. Given the sheer size of the rail sector, and its strong green credentials, it is perfectly positioned to lead the race to net zero, creating more sustainable supply chains, sourcing more energy from renewable sources, and speeding the adoption of new technologies along the way.
Tackling financing and skilling barriers
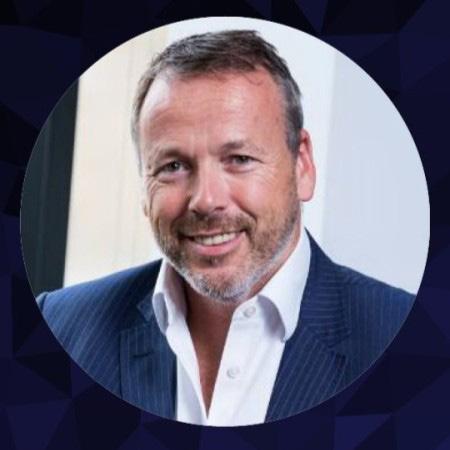
The decarbonisation of any transport industry is inevitably complex, with an evolving regulatory landscape, high investment requirements, and disparate assets to be considered. Critically, however, these challenges are not unique to the rail industry and have not prevented other transport industries from taking significant steps towards decarbonisation. Whilst these challenges are not small, they are certainly not insurmountable.
Finance is one of the significant hurdles facing by the UK rail sector in its decarbonisation efforts; improving energy efficiency, infrastructure electrification, and sourcing renewables for energy all require new and clean technology upgrades that require substantial investment. For the
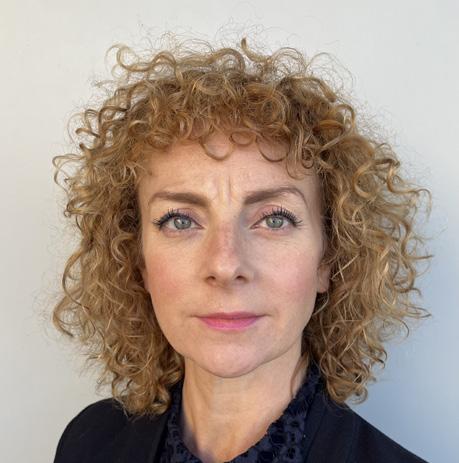
sector to attract necessary investment, a base level of policy and regulatory stability is required to allow private finance to take a considered view of returns on long term assets.
Fortunately, this challenge has been met by a growing trend of investment – from private and public institutions – into green energy infrastructure which can be leveraged by the rail sector. SSE, for example, is investing £25 billion into this, from which the UK rail sector could certainly benefit.
In conjunction with infrastructure investment, a large and country-wide up skilling initiative is required to deliver these installations across the network. Currently, a lack of expertise and a London-centric workforce creates a production bottleneck in delivering the necessary infrastructure. To meet this challenge, we must take this opportunity to train and bring people into the workforce which will ultimately provide them a valuable and highly translatable set of skills. SSE believe that investing in communities can help tackle this problem and will soon be announcing a new regionally focussed strategy designed to better connect us with communities. It plans to collaborate closely with local authorities and support organisations to diversify the workforce.
It is essential to upskill a new generation and take everyone with us as part of a fair transition to renewable energy. This, importantly, includes some of the UK’s industrial heartlands which traditionally served as the production backbone of the rail industry. SSE’s plans for new business hubs in cities including Liverpool, Manchester, Birmingham, and Leeds have already been met with considerable enthusiasm from prospective trainees and are part of its wider Net Zero Acceleration Programme which is expected to create over 1,000 jobs in 2025, alone.
Seizing unique opportunities
Despite the challenges, the race to net zero also creates a set of unique opportunities for innovation, growth, and sustainability. With a clear commitment to reducing emissions and increasing energy efficiency, the rail sector can position itself as a leader in the transition to a low-carbon economy.
One of the most promising opportunities lies with scaling and implementing innovative and exciting technologies that have demonstrated their technological proofof-concept. The UK, with a rich history and fondness for trains coupled with its globally recognised expertise in driving innovation, is well-positioned to scale up new rail technology. For example, the hydrogenpowered trains have already been showcased to deliver significant environmental benefits in the form of reduced emissions but are yet to see a substantial scaling-up agenda.
In addition, the sector should consider diversifying its energy asset portfolio (for example, solar panels or heat pumps). By investing in self-generation, the industry can reduce its dependence on the grid and reduce its exposure to risk and price volatility; together, these can improve cost-efficiencies as well as overall risk management. There are promising pilot projects, already, involving the utilisation of the rail network’s large land coverage to install solar panels. Gova Thameslink Railway, for instance, in partnership with Network Rail, installed 526 solar panels at Denmark Hill Station and Streatham Hill Depot producing the energy equivalent of 45,713kg of CO2 – that is enough to power nine homes for a year. These solar panels can also be used to match power demand more flexibly and even serve as a new revenue stream through ‘give back’ to the electric grid during periods of electricity production surplus.
Furthermore, the challenge of decarbonisation also provides an opportunity for the rail industry to establish long-term, productive, and trustworthy partnerships to help deliver the required changes and remain at the forefront of technological advancements. Establishing trust and productive relationships with private sector organisations, will be crucial for establishing a shared vision for the industry, reduce costs and risks, and drive innovation to keep the UK at the forefront.
As the UK rail industry steams ahead with its decarbonisation efforts, there are an abundance of opportunities for innovation, diversification, and partnership. Whether it is scaling up promising technologies like hydrogen-powered trains, diversifying the energy asset portfolio with solar panels, or up-skilling the UK’s workforce and creating 1000s of jobs, the industry is on the right track to deliver sustainable transport. While financing remains an obstacle, the industry is seeing significant investment from various organisation, paving the way for a cleaner and greener rail network.


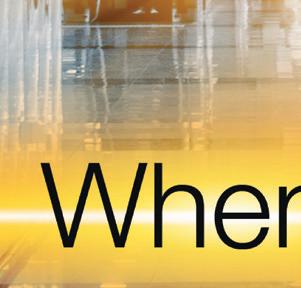
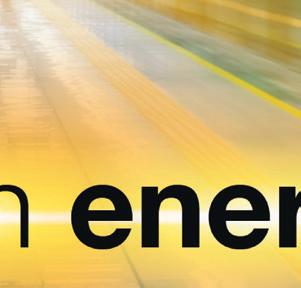
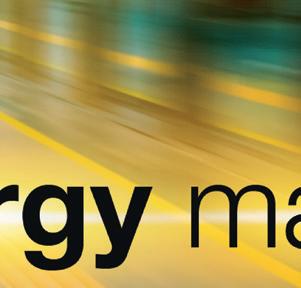
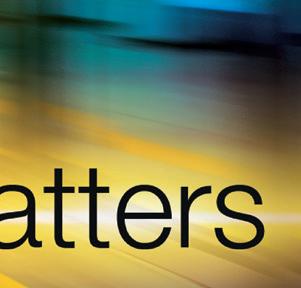
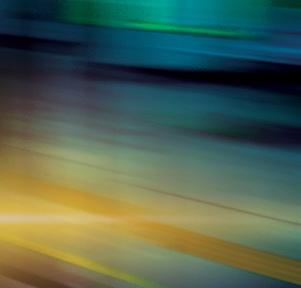
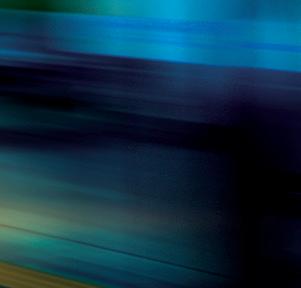

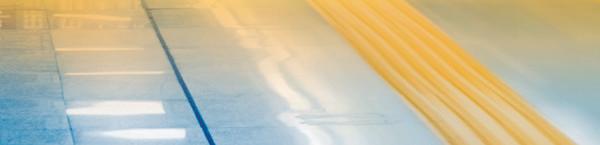
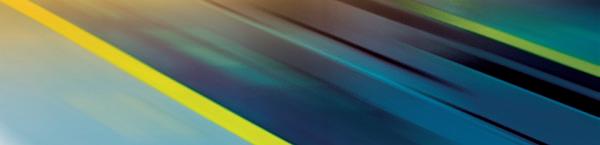

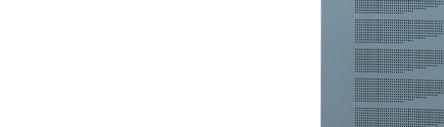
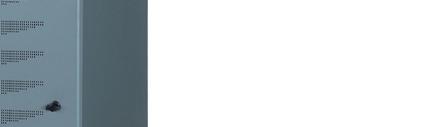
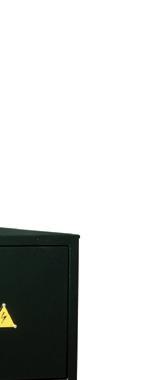

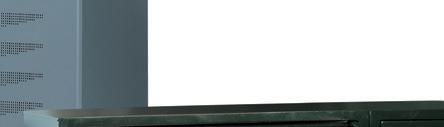
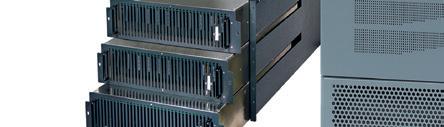
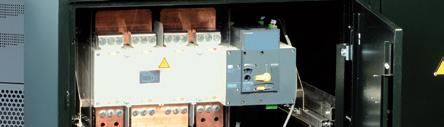
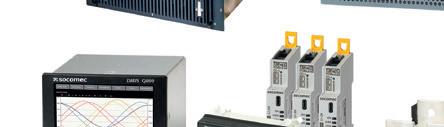
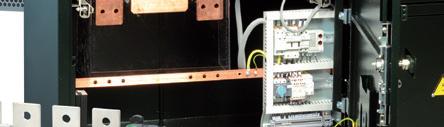
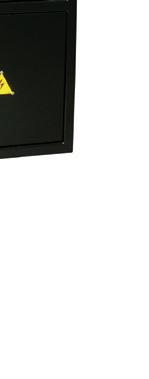

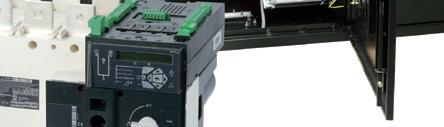
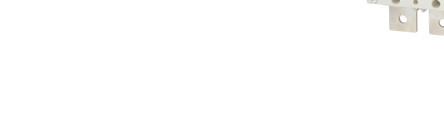
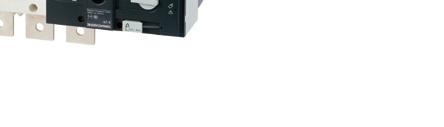
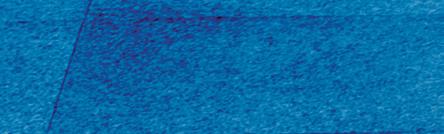



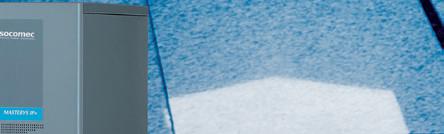
Dr Peter Walker is a chartered environmentalist, technical director and aquatic ecology lead at RSK Biocensus. He is also chairman of the Institute of Fisheries Management West Midlands Branch and has held positions at leading academic institutions and rivers trusts.
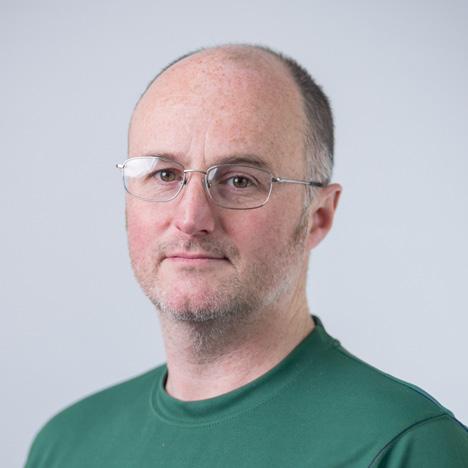
Don’t Forget the Fish!
RSK Biocensus Technical Director and Aquatic Ecology Lead
Dr Peter Walker draws on case study experience to illustrate the benefits of planning ahead
Aquatic ecology might not be the first thing than springs to mind in considering large rail infrastructure projects but factoring in this habitat at the start of project planning offers considerable benefits – informing impact assessments and mitigation and, crucially, avoiding costly delays.

During my time as an aquatic ecological consultant, I have worked in every type of UK freshwater (and marine) environment and several locations abroad. This includes rivers and streams, canals and ditches, ponds, lakes, reservoirs, estuaries and intertidal areas and coastal and offshore waters.
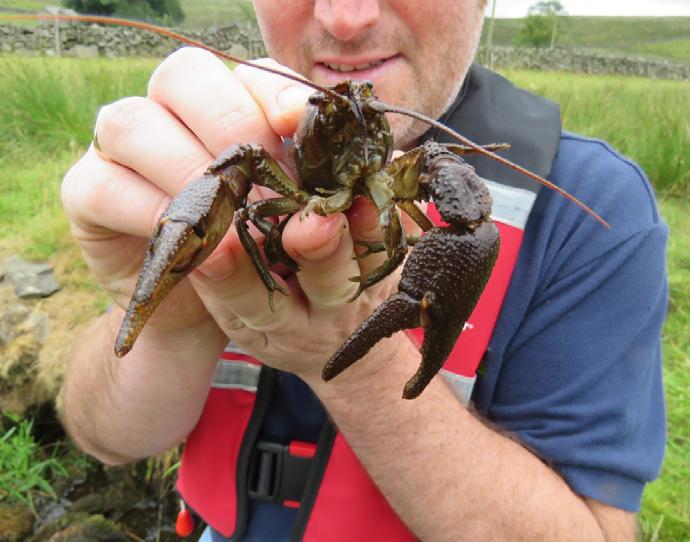
A notable number of these projects involved the rail industry. These ranged from small-scale repair works on culverts to monitoring sea defence improvements or large-scale baseline ecology data gathering for larger infrastructure projects such as Rail Central or HS2 to help inform impact assessments and mitigation.
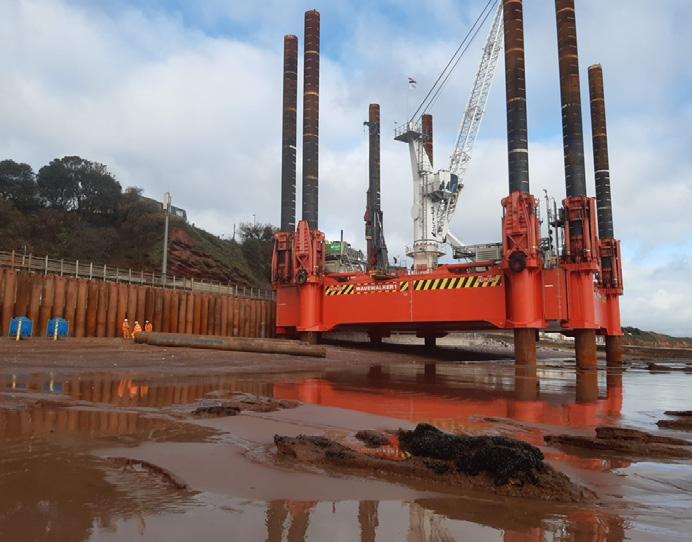
I am committed to applying this experience to identify key considerations with respect to aquatic ecology which may help with future rail project planning and avoid unnecessary delays, reduce the risk of falling foul of the law and, hopefully, help protect and conserve our diverse and valuable aquatic habitats and the organisms residing within them.
From the offset, it is important to understand the relevant legislation. Some species and habitats are protected by the Wildlife and Countryside Act or the Conservation of Habitats and Species Regulations. The Salmon and Freshwater Fisheries Act makes it an offence to disturb or damage spawning areas or spawning fish and the Eels (England and Wales) Regulations are in place to help this
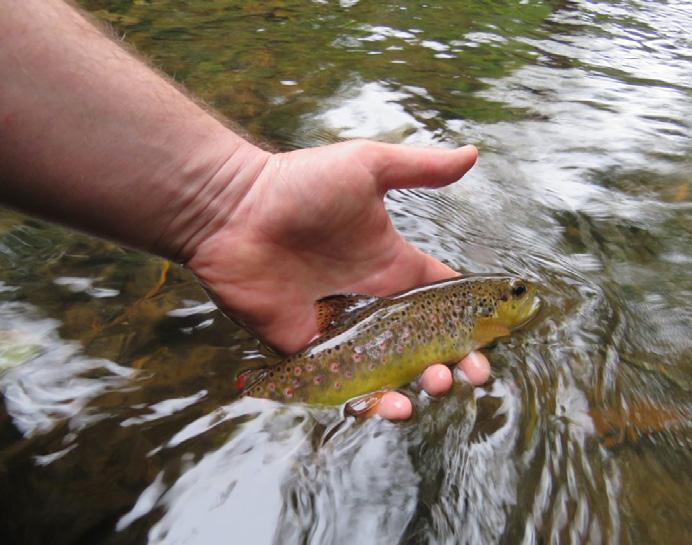
species complete its life cycle by improving opportunities for eels to navigate through river systems and preventing them being entrained into water abstractions.
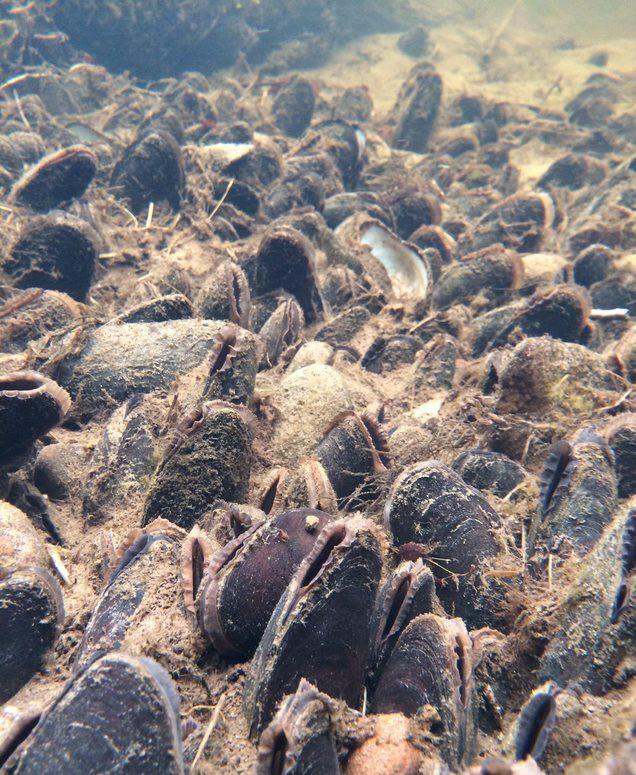
The Water Framework Directive is likely to require a detailed assessment if any proposed activities might cause a deterioration in (or prevent future improvements to) water quality, habitat quality or connectivity or adversely affect species within a watercourse. This includes aquatic invertebrates, fish, aquatic plants and diatoms for example. If you’re unsure as to whether your proposed works / activities may impact aquatic life, you should consult an (aquatic) ecology specialist early in the process, much the same as you would for terrestrial ecology considerations such as bats, badgers or great crested newts.
With rail projects, more often than not it is linear waterbodies such as streams, rivers and ditches that are affected. However, stillwaters such as ponds, lakes and reservoirs should be considered if they are close to and could potentially be affected by works. Similarly estuaries and coastal areas require consideration.
In addition to the habitats, it’s often necessary to consider individual species or groups of species, the potential impacts on them and the mitigation that can be employed. Some species that are specifically protected include white-clawed crayfish, freshwater pearl mussel and, in some waterbodies, fish species such as Atlantic salmon or lampreys. It’s also important to understand whether invasive non-native species are present and if the proposed activities at a given site have potential to result in the spread of those species away from the works location, which would be an offence.
So what sort of activities might require aquatic ecology surveys, advice or
mitigation? Essentially anything that may affect the physical, chemical or biological components of an aquatic (freshwater, estuarine/brackish or marine (salt water)) environment.
This might include:
• Physical alterations to a waterbody, watercourse or it’s banks (e.g. Installation of bridge footings, retaining walls, sheet pilings or other in-river structures).
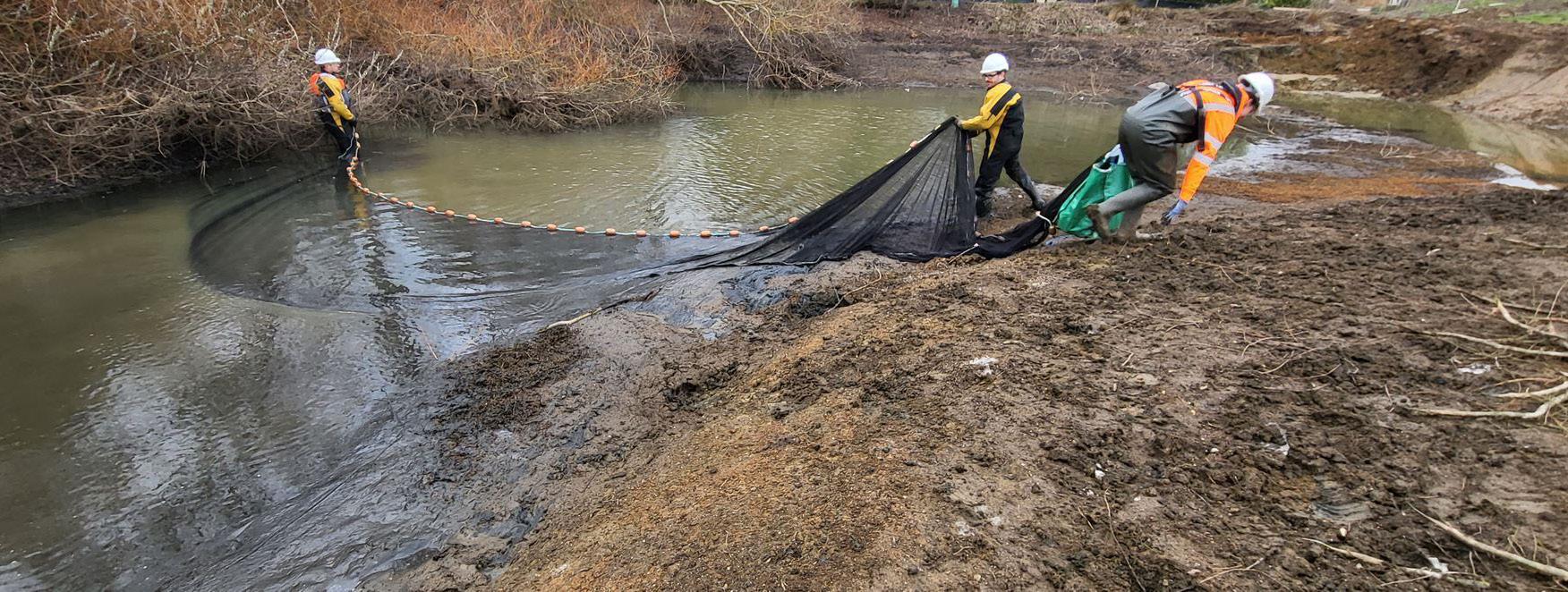
• Replacing or altering/repairing existing in-river structures (e.g. Culverts or bridges).
• Temporary or permanent dewatering.
• Temporary or permanent channel diversions.
• Undertaking works within a channel, including works to the underside of bridges or culverts which require access from within the channel.
• Undertaking works which could affect water quality, disturb bankside or in-channel sediment, cause noise or vibrations or artificially illuminate the aquatic environment.
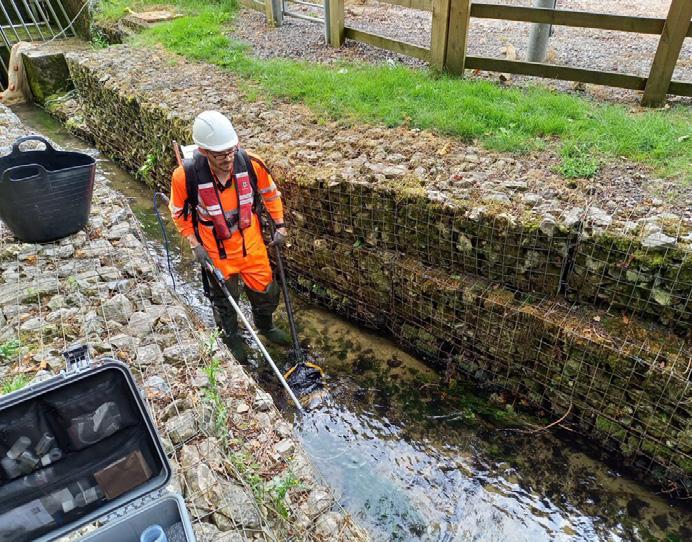
• Actual pollution incidents (e.g. Fuel or chemical spills, runoff or sewage discharges / leaks).
I’ve highlighted a couple of case studies to illustrate the importance of considering all waterbody types and sizes and of consulting relevant specialists early.
Case study – the honeycomb worm

Works were being undertaken to repair and improve sea defences which protect a railway line running along the coast. The planned works involved large plant and
machinery accessing the seashore. RSK aquatic ecologists undertook a Phase 1 habitat survey which identified the presence of Sabellaria sp. (honeycomb worm) colonies at various locations which were at risk of damage from plant operating along the shore.
Sabellaria reefs are protected and so RSK prepared a method statement for the client which enabled works to progress while minimising the risk to the colonies. Monthly monitoring was undertaken to ensure that the works were being undertaken in accordance with the method statement and weren’t causing harm to the Sabellaria colonies.
Case study – fish rescue

As part of ongoing works to create construction storage areas and compounds a moderate-sized pond was being dewatered prior to infilling. The client was not aware of any fish in the pond and had not consulted an aquatic ecologist. During the dewatering process several fish were observed, and all works had to be stopped until a team of aquatic ecologists could be called to the site to undertake a fish rescue and translocation. This took over a week as a receptor pond had to be found for the rescued fish to be released into. The delay to works had additional knock-on effects for other works, affecting other schedules and costing the client time and money.
The case studies highlight that waterbody size can often incorrectly be seen as an indicator of whether or not aquatic ecology is an important consideration. In fact aquatic life, including fish, can be found

in very small, very shallow waterbodies, sometimes in just a few centimetres water depth. Furthermore, consulting aquatic ecologists early in the process can save considerable time and money.
The take home messages here are:
1. Polluting watercourses is an offence.
2. Causing harm or disturbance to aquatic species or habitats can be an offence.
3. Size of watercourse / waterbody doesn’t necessarily affect the likelihood of sensitive features or species being present.
4. If you are planning works at a site that has aquatic features present (including ponds, lakes, streams, rivers, estuaries, the coast etc) and your works have potential to affect those features or organisms within them you should get advice from an experienced aquatic ecologist.
5. Speak to the relevant specialists early in the project/works planning process to avoid delays once works commence.
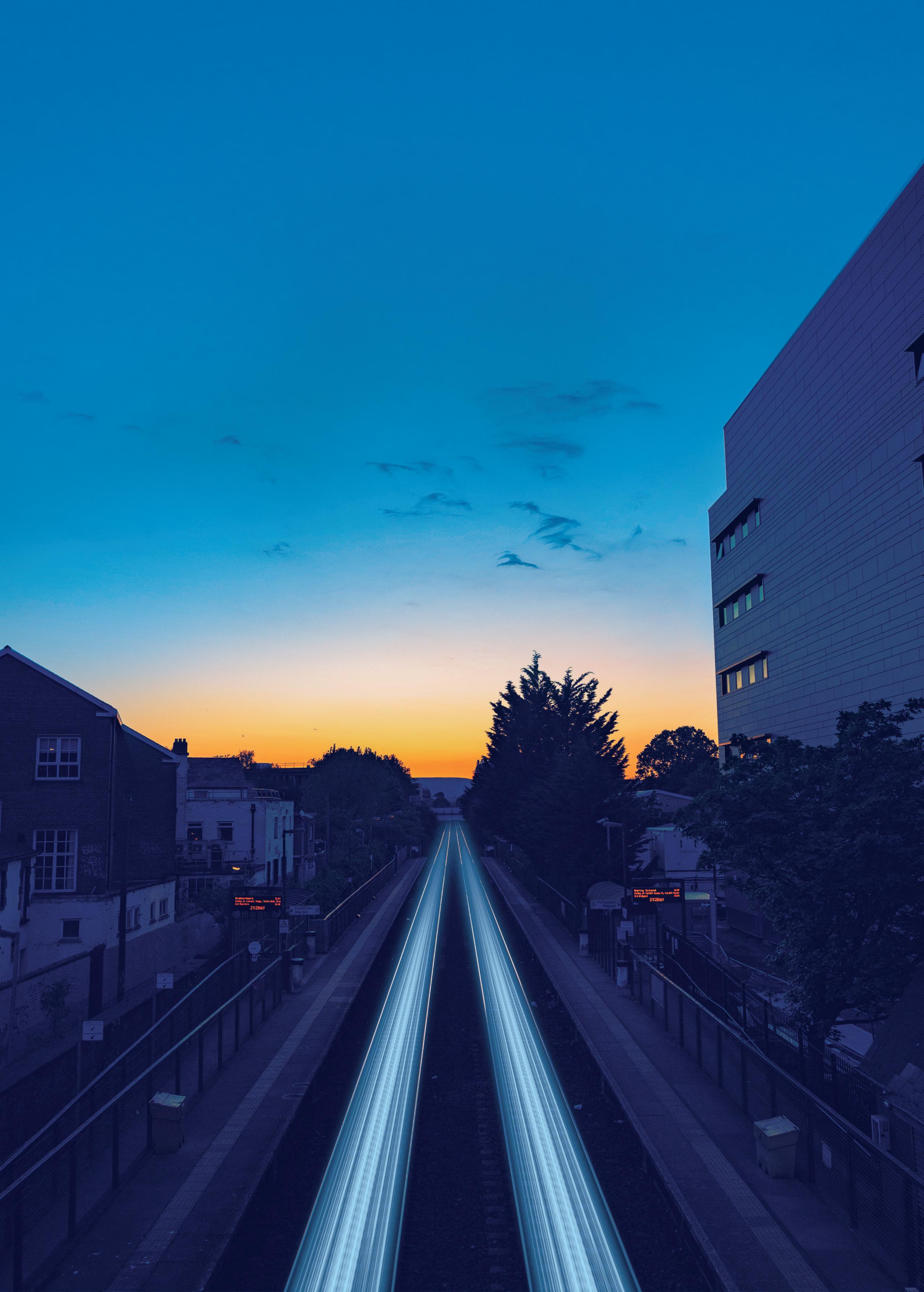
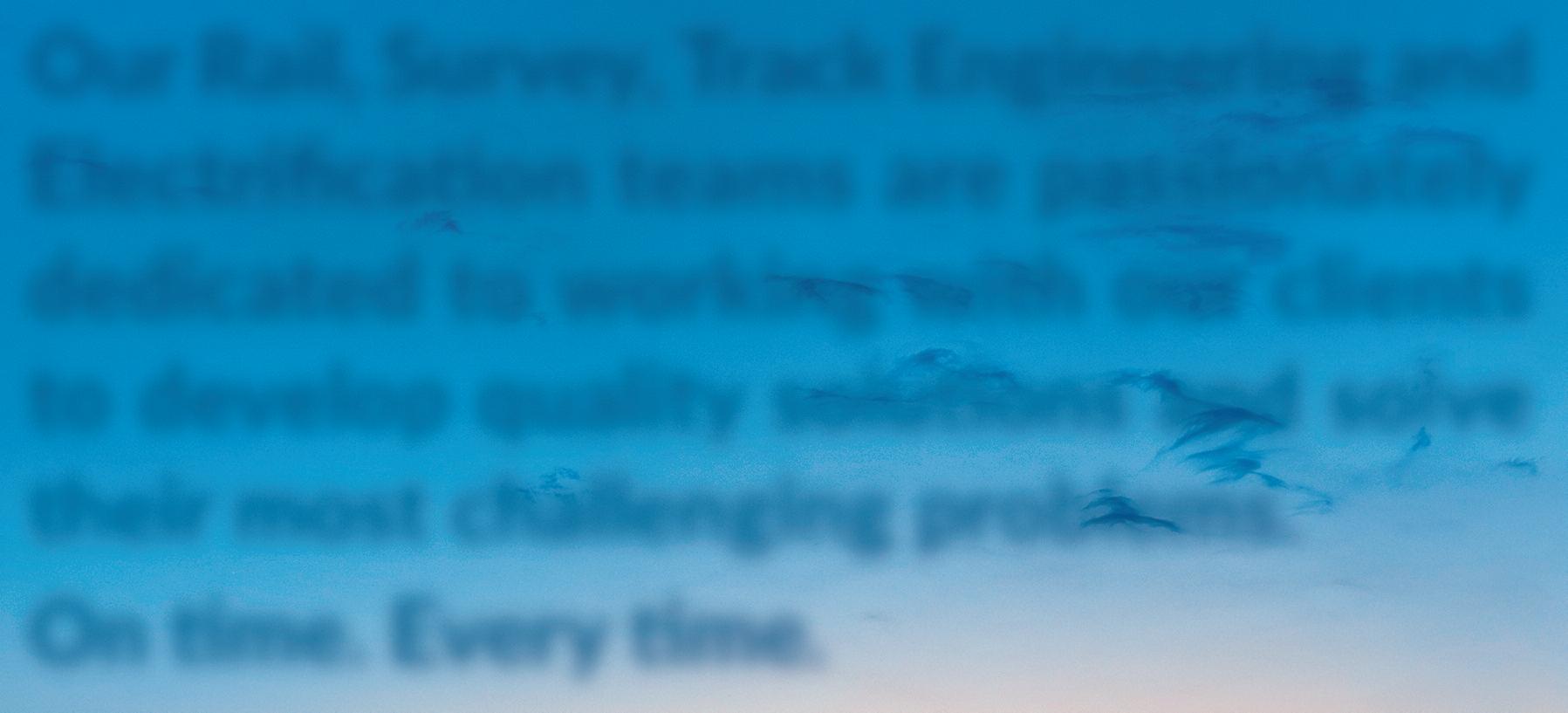
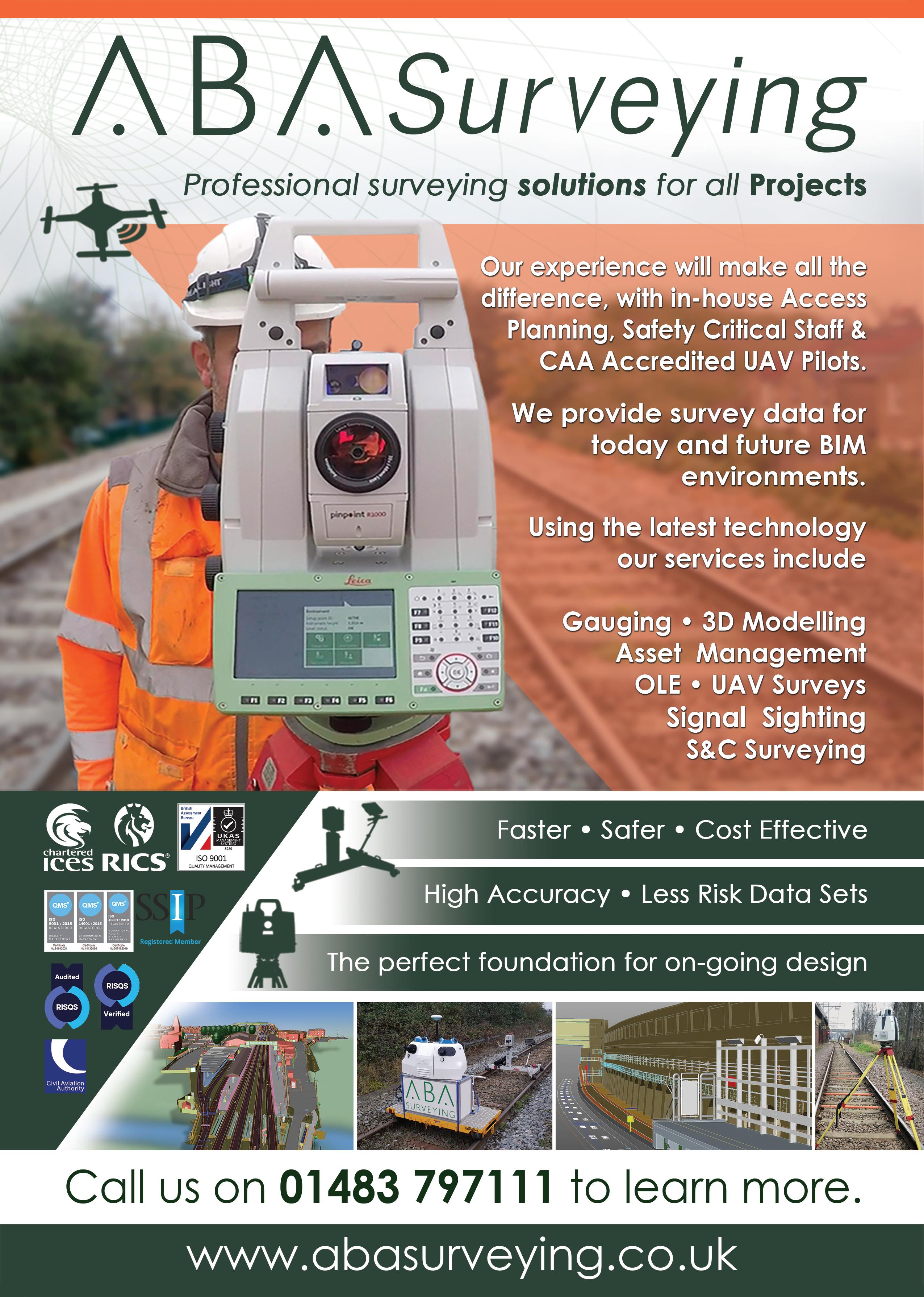
Does England Need a National Transport Strategy?
Jonathan Spruce, ICE Trustee for policy and external affairs considers the current planning climate for rail and asks if a national strategy is the answer
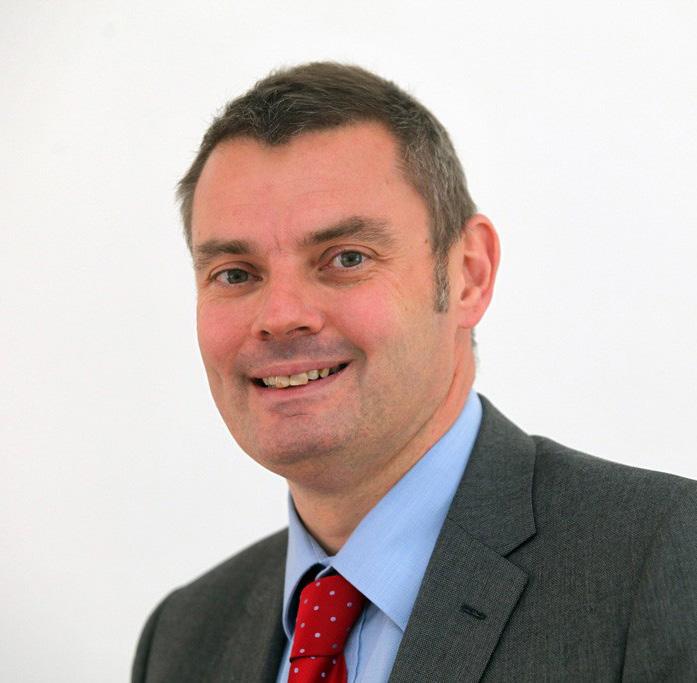
The UK is tackling a series of long-term strategic challenges, including reaching net zero, adapting our infrastructure in preparation for climate change and levelling up the economy An accessible, reliable, low carbon transport network is vital for achieving these objectives.
But the government’s recent decision to delay several major projects, including parts of HS2, risks that vision.
The decision to delay HS2 suggests we still think of public infrastructure projects as a cost, rather than an investment in our future. This mindset is symptomatic of the way we currently plan our transport networks.
A patchwork of strategies
Planning and prioritisation of transport investment in the UK is too often undermined by our fragmented system of strategies across regions and modes of transport.
Scotland, Wales and Northern Ireland all have national transport strategies, as do many of England’s cities and regions.
But England itself, despite having a far larger population, does not have its own national transport strategy to tie its regions and modes together in a coherent plan.
Nor does the UK have an overarching vision for how its transport network should operate.
Two years ago, Sir Peter Hendy published the Union Connectivity Review – but the government has not yet responded to its recommendations.
Maximising investment
At a time when we need to maximise every pound of investment in infrastructure and accelerate progress towards achieving national goals we cannot afford inefficiency in transport planning.
Decision-makers need to be able to assess the benefits and trade-offs between schemes and which investments to prioritise. That process should be guided by a country’s strategic objectives.
The Welsh government’s recent decision to halt all road-building projects was directly informed by the priorities in its national transport strategy.
But England has no such set of principles to guide decision-makers. Instead, siloed thinking means investments can appear contradictory to the UK’s long-term objectives.
Reducing uncertainty
The decision to freeze capital spending in cash terms from 2025/26, effectively a cut, means prioritisation and efficiency become even more important.
However, the scope of key road and rail programmes, such as the Integrated Rail Plan, have been subject to long-term uncertainty.
This means the supply chain cannot efficiently manage the resources and capacity needed to deliver projects.
Subnational governments cannot properly plan contingent projects that will unlock the wider benefits of major infrastructure investment.
Businesses are reluctant to commit to the investment regional economies need to level up. In addition to increasing uncertainty, delaying major programmes like HS2 won’t reduce costs. In fact, the UK's ability to deliver projects effectively may become more difficult as construction firms shift their focus to other countries due to the global competition for talent.
Infrastructure decisions need to be guided by long-term strategic objectives, rather than short term political expediency.
User-centred outcomes, focused decision-making
Which brings me back to the need to reframe public infrastructure projects as investments in our future.
To fix how we plan our transport network we need to think more strategically about what outcomes we need that network to deliver.
We need to define what outcomes we are working to before agreeing which projects should move forward, and which should be delayed.
We need to understand how transport will help us achieve our economic, social and environmental goals and our decisionmaking framework must also reflect the multi-modal reality of how users – people and freight – interact with the network.
Better decision-making that links investment to strategic goals will help ensure the country gets the transport infrastructure it needs.
It will also provide greater certainty to subnational governments, the supply chain and other stakeholders to help us deliver those projects more efficiently and unlock the wider benefits of investment.
Tell us what you think a national transport strategy should look like
That is why the ICE has launched a consultation on whether England needs a national transport strategy.
We want to understand how a national transport strategy would help address the systemic challenges in transport planning, what it should look like, and how it should be implemented.
Our consultation is open until Friday, 12 May, please visit ICE’s website (ice.org.uk) to contribute.
‘The scope of key road and rail programmes, such as the Integrated Rail Plan, have been subject to long-term uncertainty. ’
Approved Hydraulics have been supplying some of the largest rail build and maintenance firms for over 10 years, now considered some of the best in the world!
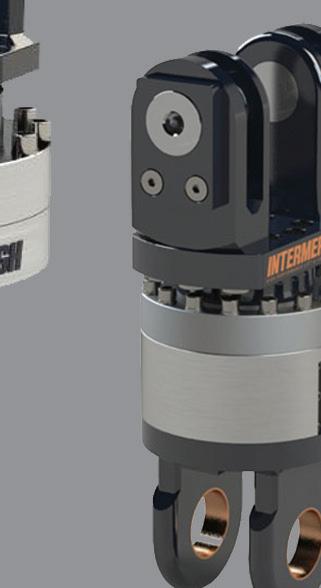










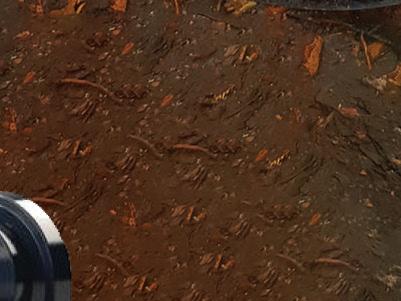
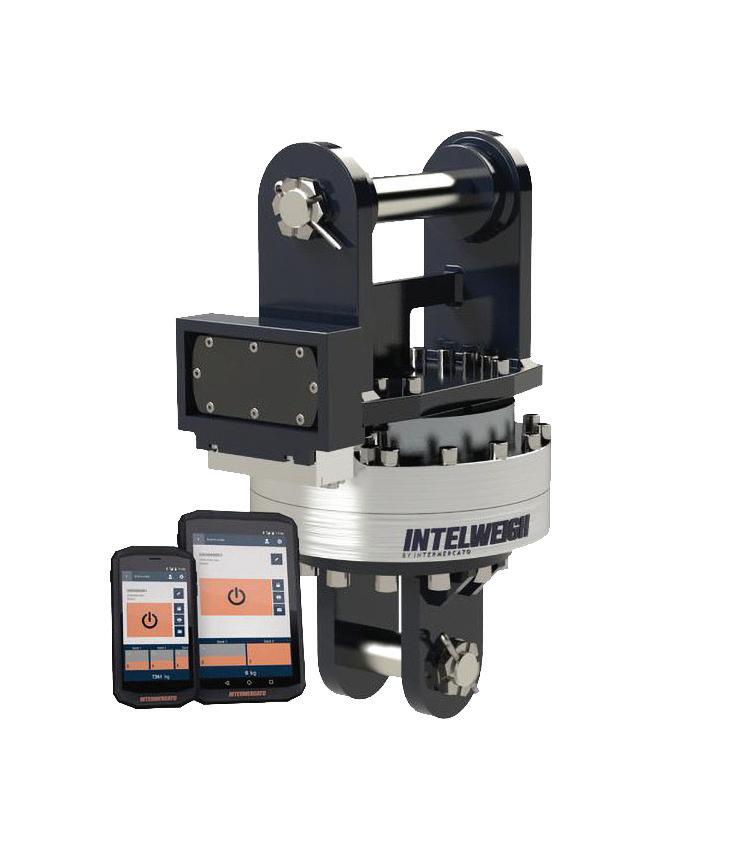
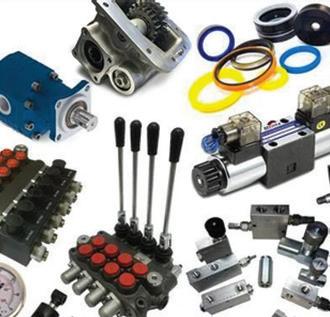
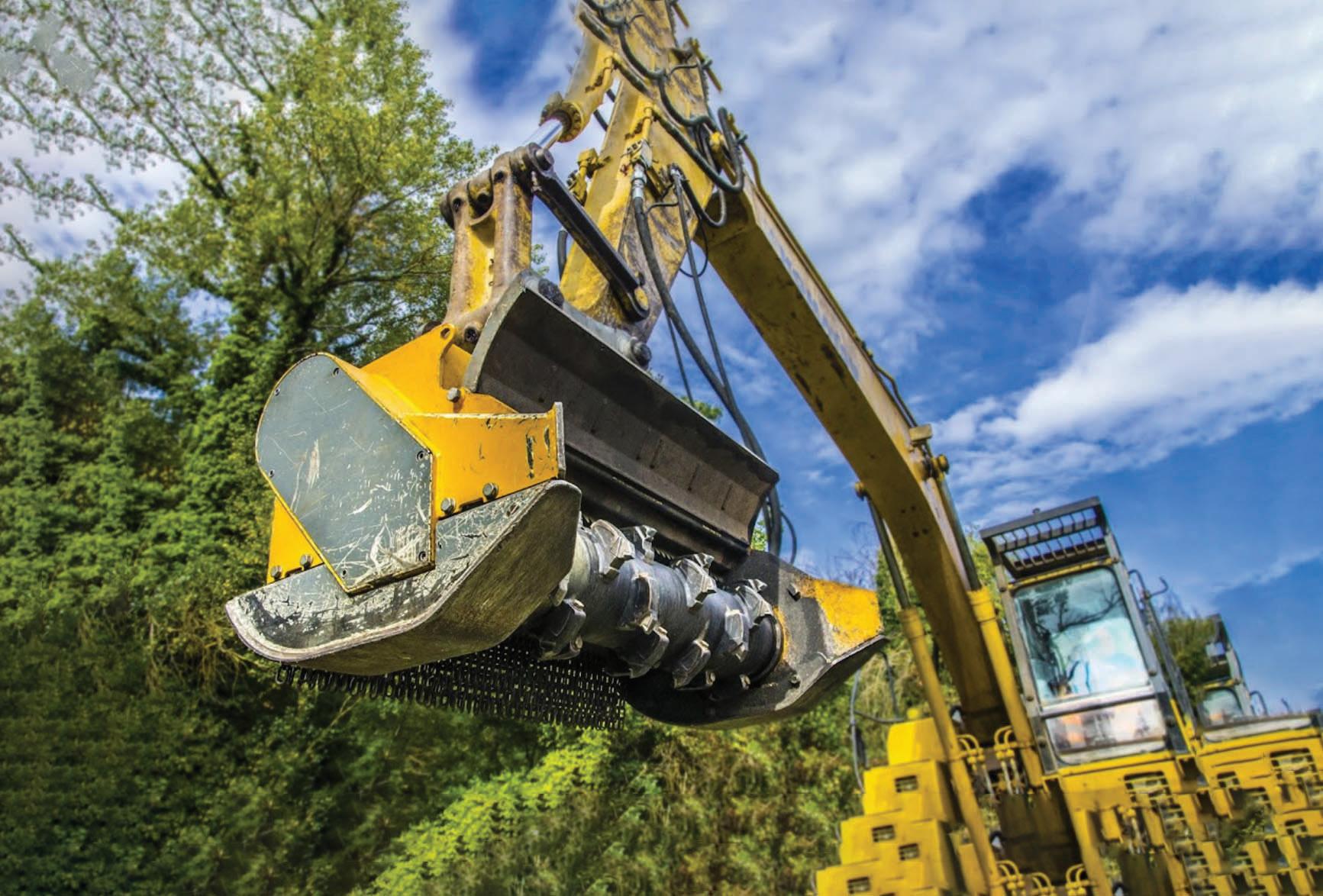
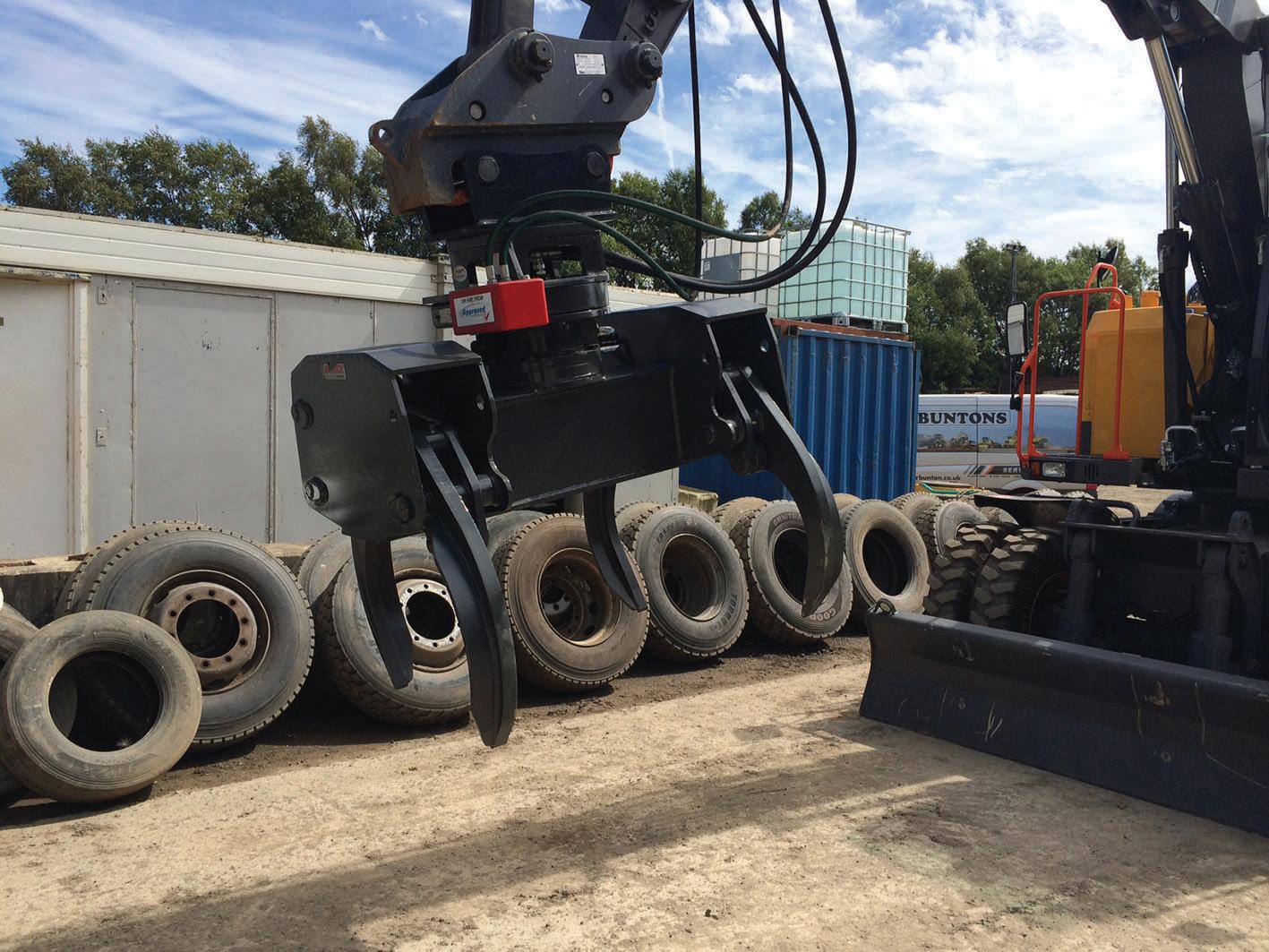


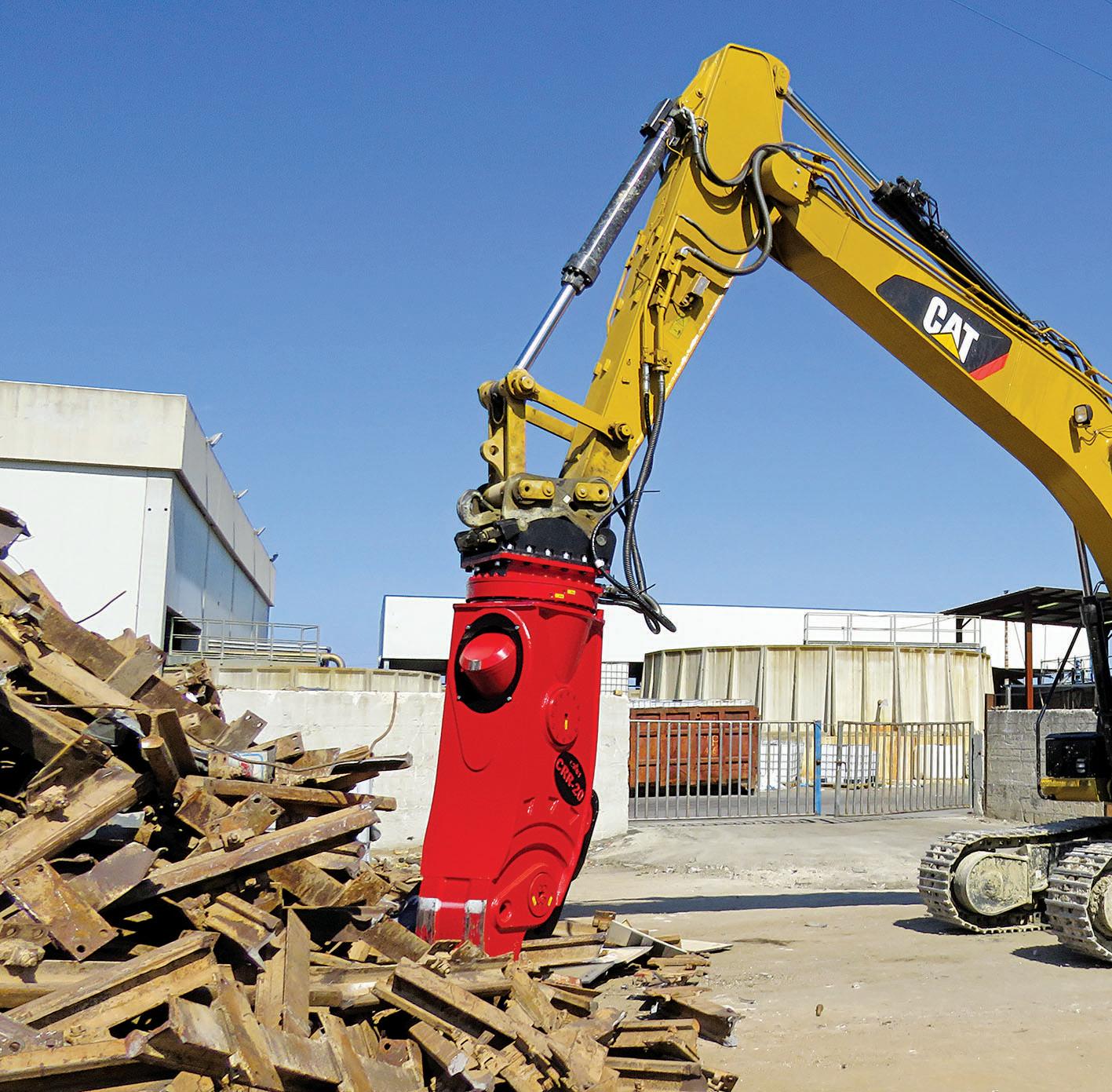
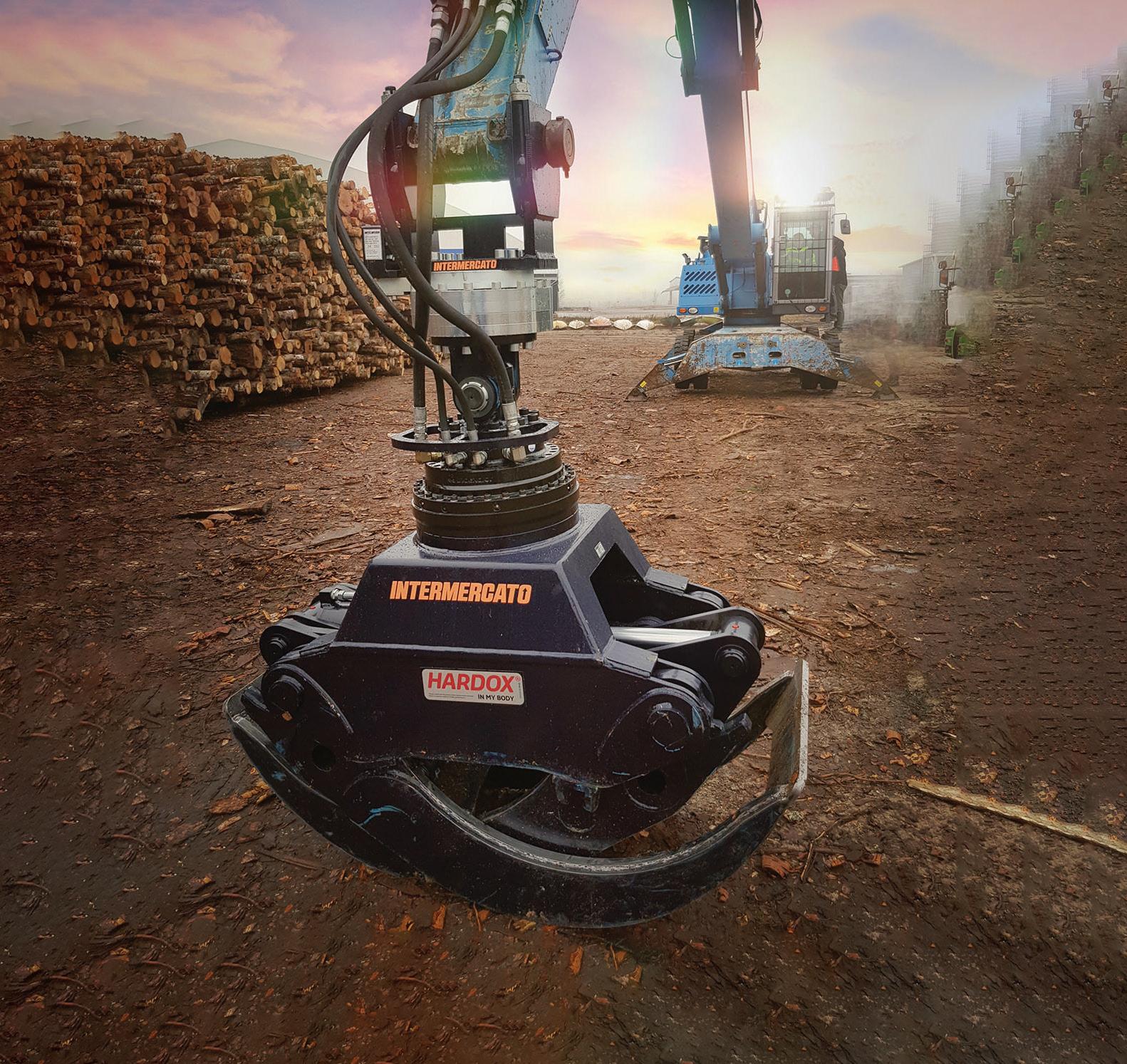
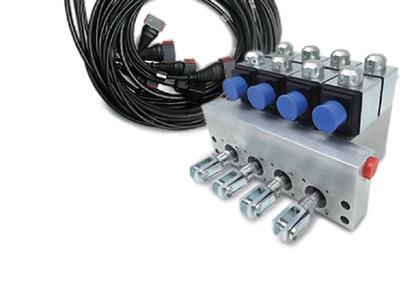
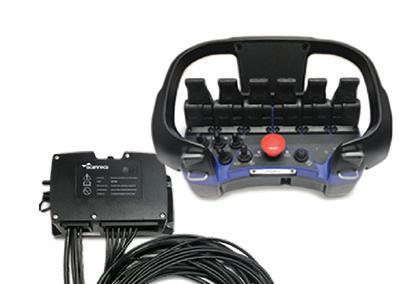
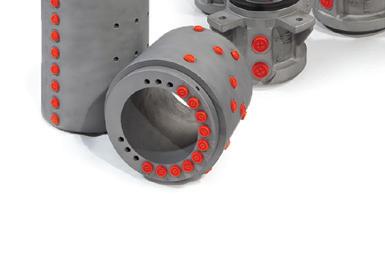

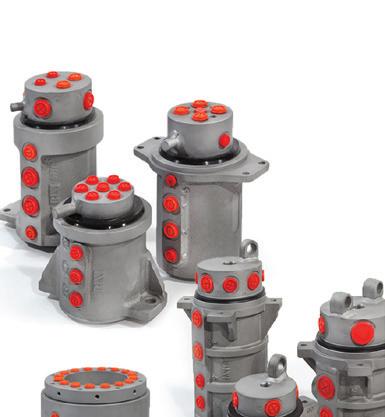
Building a Better Rail Network Starts Now
For every two steps forward, it feels like the UK’s rail industry takes one step back, says Michelle Craven-Faulkner, a partner and rail lead at Shoosmiths
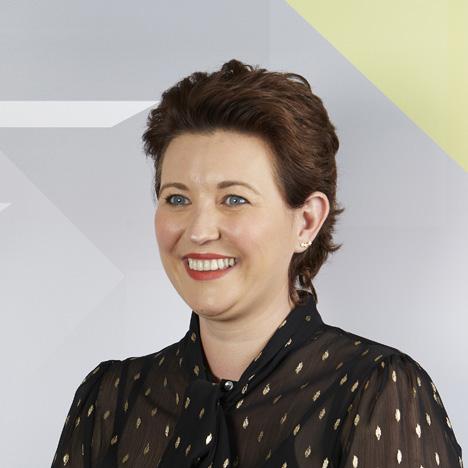
The government’s decision to ‘rephase’ parts of HS2 means the line to Crewe may not open until 2036, and Manchester not until 2043. There’s also the possibility that HS2 will not reach London Euston until 2040, instead stopping further out of the Capital at Old Oak Common.
That said, with inflation remaining above target levels and construction costs rising, the reasons for these actions are entirely understandable as the government grapples to control public spending. It is important to, however, remember that these rail links are critical to improving connectivity and driving economic growth across the UK. By delaying sections, after plans were already scaled back, there is a risk of limiting the full potential of high speed rail. Progress has been made elsewhere though, with the Great British Railways’ (GBR) headquarters announced – putting Derby and the wider East Midlands at the centre of the rail industry.
Great British Railways
While confirming the location of GBR’s HQ brings to an end months of uncertainty for bidding regions, the news also represents a major turning point for the rail sector.
It cements the commitment to move forwards with the establishment of GBR as the guiding mind of the rail network. The organisation will set its strategic direction, and if successful, could have a major impact on the rail network, passenger experience and ticketing.
On ticketing alone, the integration and reform delivered through GBR could be key to simplifying rail travel, overhauling a
system consisting of an estimated 55 million different fares. GBR has a transition team in place and with its HQ now confirmed, many in the industry, as well as the wider public, will be asking: Why isn’t it full steam ahead on reforming and improving the rail network? Unfortunately, there are hurdles that still need to be overcome.
Legislation
The establishment of GBR hinges on legislation and the passing of the Transport Bill.
While the Bill is not rail specific, dealing with other matters including legislating for the use of e-scooters, and pedicabs in London, it will introduce a series of provisions relating to GBR. Despite initially being mooted for implementation during the current parliamentary session, it has been confirmed that the Bill will not be brought forward until May 2023 at the earliest.
Without the Bill, the Department for Transport and GBR’s transition team will only be able to progress the parts of GBR that do not require legislation – effectively choking its full roll out.
Considering the delays to the Transport Bill, it is now likely that GBR will not be fully operational until 2025 or later. This poses a real danger for the rail industry, which is already dealing with the aftereffects of industrial action, ongoing economic disruption and increasing customer complaints.
Data from the Office of Rail and Road shows 86,385 complaints closed by train operators between 1 July to 30 September 2022 – an increase of 18.8 per cent on the
same quarter in 2021, and fuelled in part by a drop in train punctuality and reliability.
It is, therefore, critical that the rail industry avoids entering a period of stasis as it awaits the establishment of GBR. Forward momentum must be sustained, with a focus on upgrading the network, improving the passenger experience and attracting new talent into the sector.
Vision for the future
The rail industry has battled huge challenges in recent years. Its ability to bounce back from the Covid-19 pandemic shows its resiliency and the adaptiveness of those working in rail. While it may not always seem it, there are opportunities emerging for the rail sector. Passenger numbers are now exceeding pre-pandemic levels, reaching up to 103 per cent on 22 February 2023. Travel habits may have altered, but what remains clear is that people continue to see rail as a vital method of transport for both work and leisure purposes. There are also the environmental benefits of rail travel – arguably one of its main strengths. Per kilometre travelled, domestic rail emits less CO2 emissions than a passenger in an average diesel car, or domestic flight. There is progress still to be made, however, with the vast majority – over 60 per cent – of the UK’s rail network reliant on diesel power.
Fully electrifying UK rail is not only key to meeting the government’s long-term target of removing all diesel-only trains by 2040, but could also enable the industry to secure immediate efficiency gains. This is alongside cost savings per vehicle, and on a fleet basis.
The government must support these efforts by providing more information, including on the status of the Midland Main Line electrification and East Coast Main Line power upgrades.
A statement is also needed confirming which elements of the Integrated Rail Plan will continue and when, alongside the longawaited publication of the Rail network enhancements pipeline. By doing so, the government can provide much-needed clarity over the future development of the rail network – enabling those in the sector to plan accordingly.
Even without these announcements, the industry is moving forward and innovating.
Porterbrook’s hydrogen powered train – HydroFLEX – continues its trials, and with Great Western Railway recently agreeing to purchase assets from Vivarail, new technology could soon be brought into mainstream use and adopted across the network.
Electrification and hydrogen power represent only parts of what the future of rail could look like. The advent of GBR, delivery of HS2 and industry reforms have the potential to truly transform train travel in the UK. That is why further delays must be avoided, with the public and private sectors ensuring that the process of building a better rail network starts now.
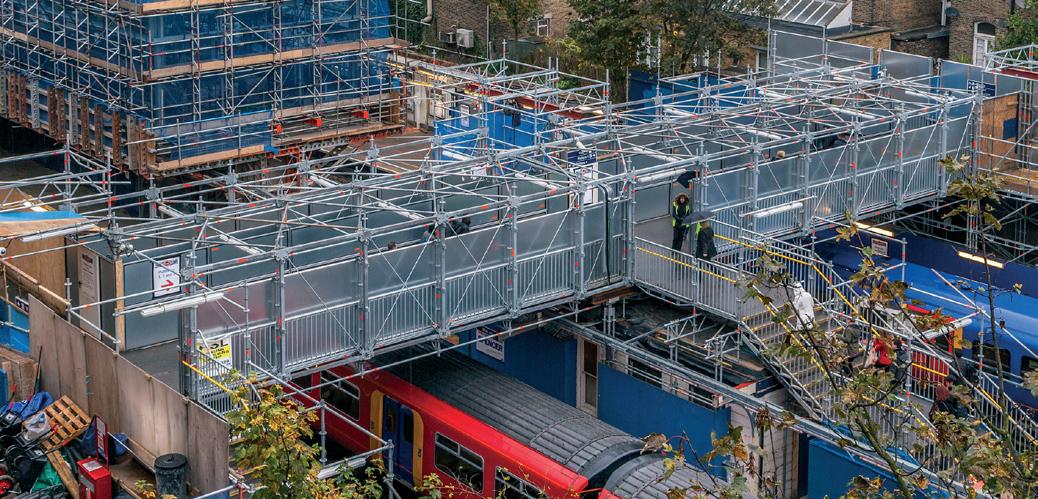
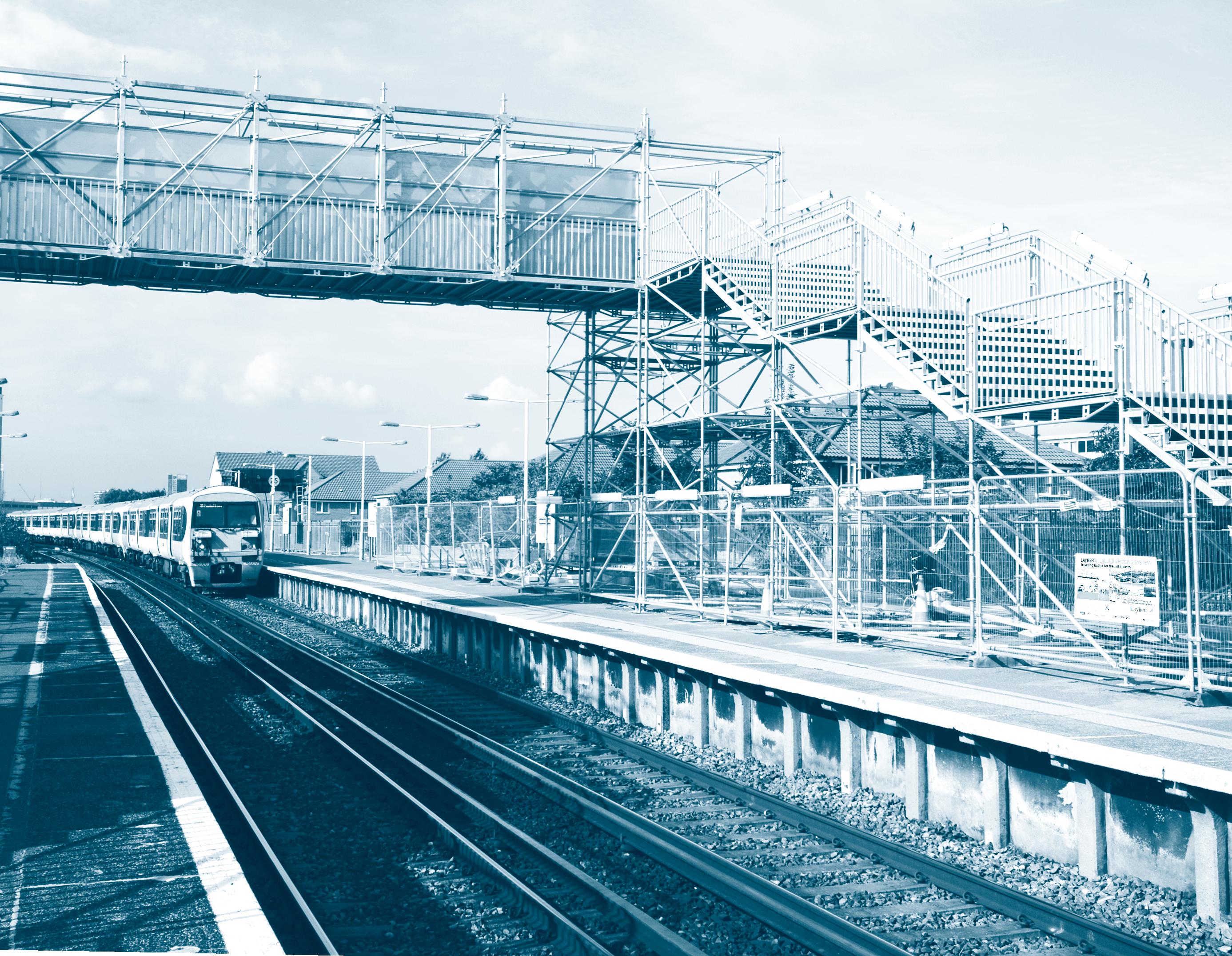
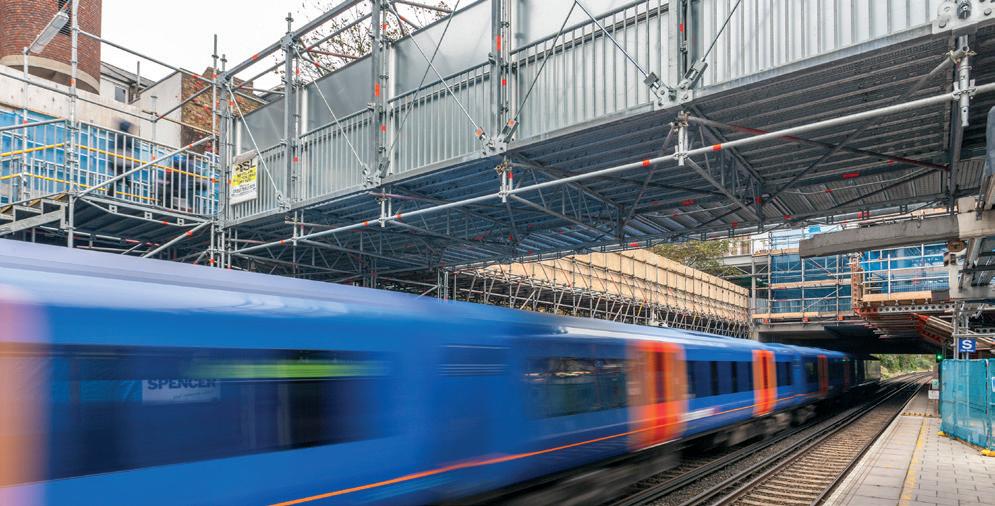
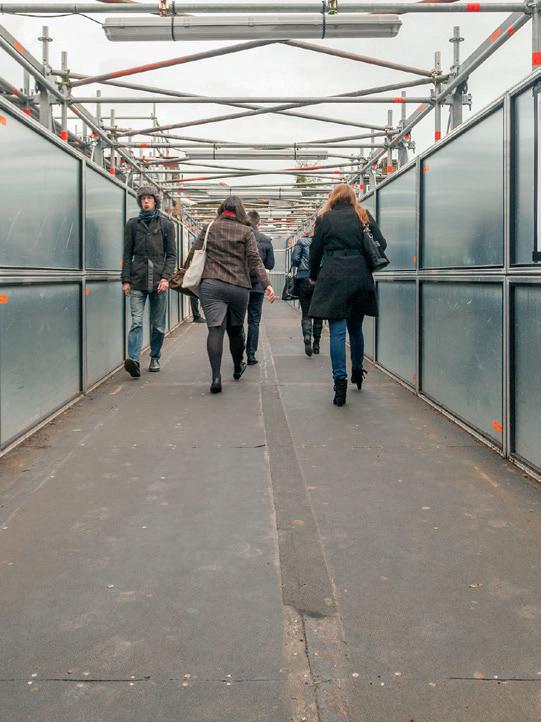
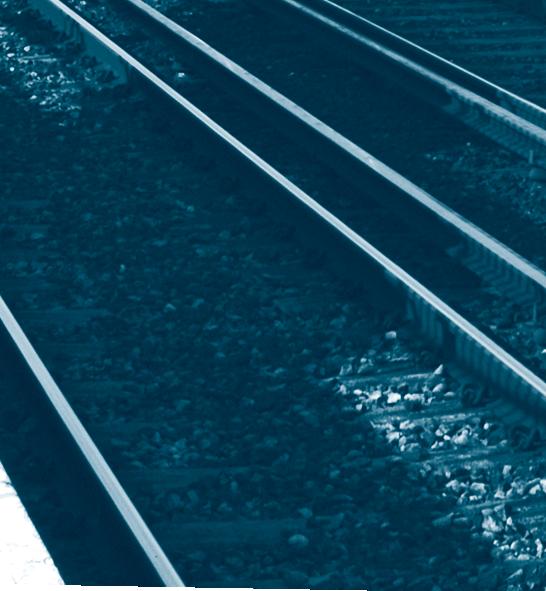
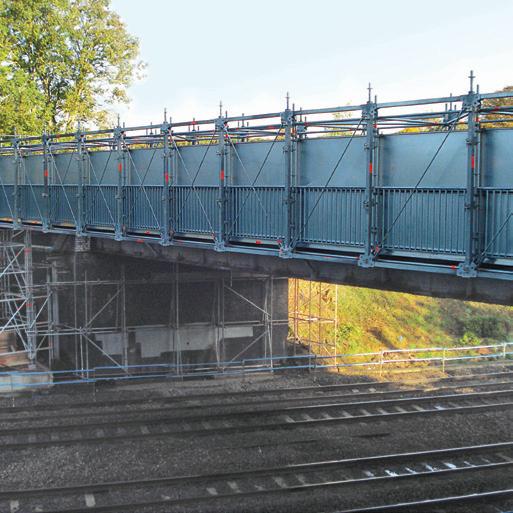
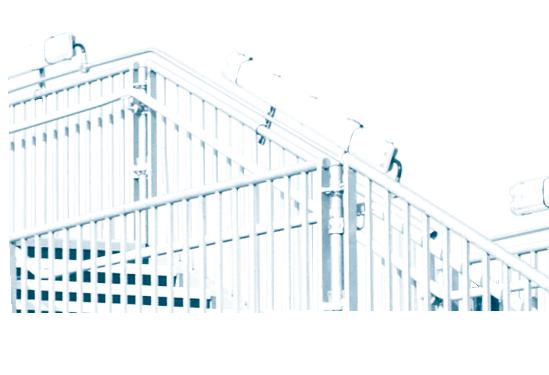

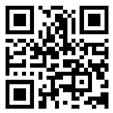
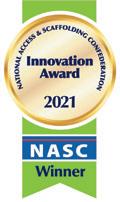



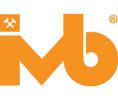



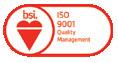
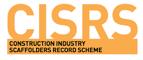

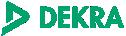
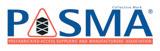

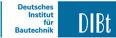



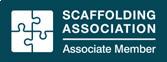
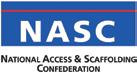
Rail Travel is Fast Becoming a Business
And our industry needs to respond, says Champa Magesh, President of Trainline Partner Solutions
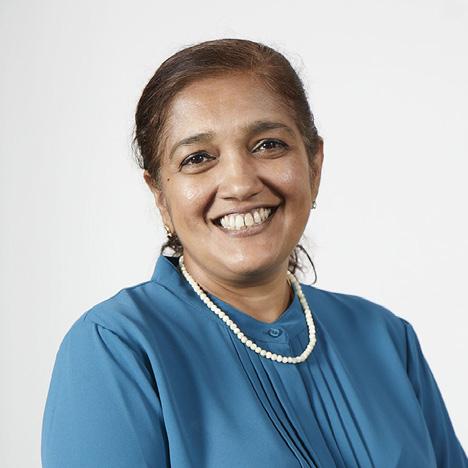
It’s more of a business imperative than ever that companies embed support for lower carbon modes of transport in their business travel policies. Thanks to a combination of growing awareness of sustainability issues amongst employees and growing policy and legislative pressure on businesses to act, there has never been stronger impetus for the corporate world.
As an industry, we should also take this as an opportunity to reflect on where we can better support businesses in choosing rail – and act on the changes that need to be made. Only by making rail travel as accessible and easy a choice as possible for business travellers will we see a true modal shift to rail.
Rail can help businesses respond to sustainability pressures
Whilst the pandemic undoubtedly changed both the way we work and the way we travel for work, there many are seeing a gradual return to their pre-pandemic business travel habits. In a Trainline Partner Solutions survey conducted in January, we found that over half (53 per cent) of UK business travellers surveyed had taken either a similar amount or more trips in 2022 than they had pre-pandemic.
However, what this survey also found was a correlative worry amongst business travellers about their carbon footprint, with over two-thirds (67 per cent) expressing concern over the environmental impact of their 2022 travel.
As we see greater societal awareness around sustainability issues, this is naturally permeating into people’s working lives. Employees increasingly want to work for companies that align with their values,
with broader career trends such as ‘climate quitting’ testimony to this. For those who travel frequently for business, we are seeing an increasing desire for access to more sustainable travel options – almost three-quarters (72 per cent) of the business travellers we surveyed in January said they would like to increasingly use lower carbon modes of transport, such as rail, for business trips in 2023.
As well as answering to shifting priorities amongst employees, it’s also in the best interest of organisations to increase access to rail options for employees who do have to travel for business. Taking sustainability issues seriously isn’t simply an expectation for businesses, but it is now enshrined in UK law. As of April last year, over 1,300 of the UK’s largest companies began measuring and reporting on their emissions, with the indirect ‘Scope 3’ segment – including business travel – recommended as best practice. In 2025, the legislation’s remit will be expanded further to cover a wider range of companies.
With a clear business imperative for ensuring employees feel supported to make more sustainable travel choices, now is the time for companies to start placing rail at the heart of their business travel policies.
Making the shift to rail a modal one
Getting businesses on board with rail is just part one part of the rail industry’s challenge; we now need to make sure rail is consistently a competitive option with the likes of air travel.
The first step is greater consumerising of the booking experience. We need to make it as easy and attractive as possible for business travellers to choose rail, so for TMCs the focus should be on using tech
to provide seamless access to the widest possible range of routes and fare options. Features such as multi-modal booking and fare splitting can boost the competitiveness of rail, and are enabled by industry collaboration and open AIs.
At a more structural level, we also need to see greater liberalisation and competition in our industry across Europe. We have seen the positive impact in the Italian market, which was one of the first to liberalise its rail market. This opened the gateway for competition between operators, and the success of newcomer Italo encouraged incumbent Trenitalia to improve its services – the result being that the Italian rail sector is now one of the most competitive in Europe. This has driven down prices, encouraged modal shift and made travellers – including business travellers – the winners.
As well as liberalisation of services, we need to liberalise the distribution model for ticketing. Third parties are valuable partners who can unlock increased ticket sales, but in some markets outdated licensing conditions that require TMCs to obtain licences individually from carriers have been an obstacle to making rail attractive. This is bad for retailers, bad for business travellers – and bad for the market. Liberalising this distribution model, so that accredited specialists like Trainline can streamline retailing, would represent a major breakthrough in simplifying rail business travel.
We know the support for rail travel is there; as an industry, we need to focus on making rail as attractive an option as possible. Open collaboration between carriers, travel tech platforms, OBTs and TMCs will help us to overcome many of the challenges we face and enable a truly modal shift to rail.
‘As of April last year, over 1,300 of the UK’s largest companies began measuring and reporting on their emissions, with the indirect ‘Scope 3’ segment – including business travel –recommended as best practice. In 2025, the legislation’s remit will be expanded further to cover a wider range of companies.’
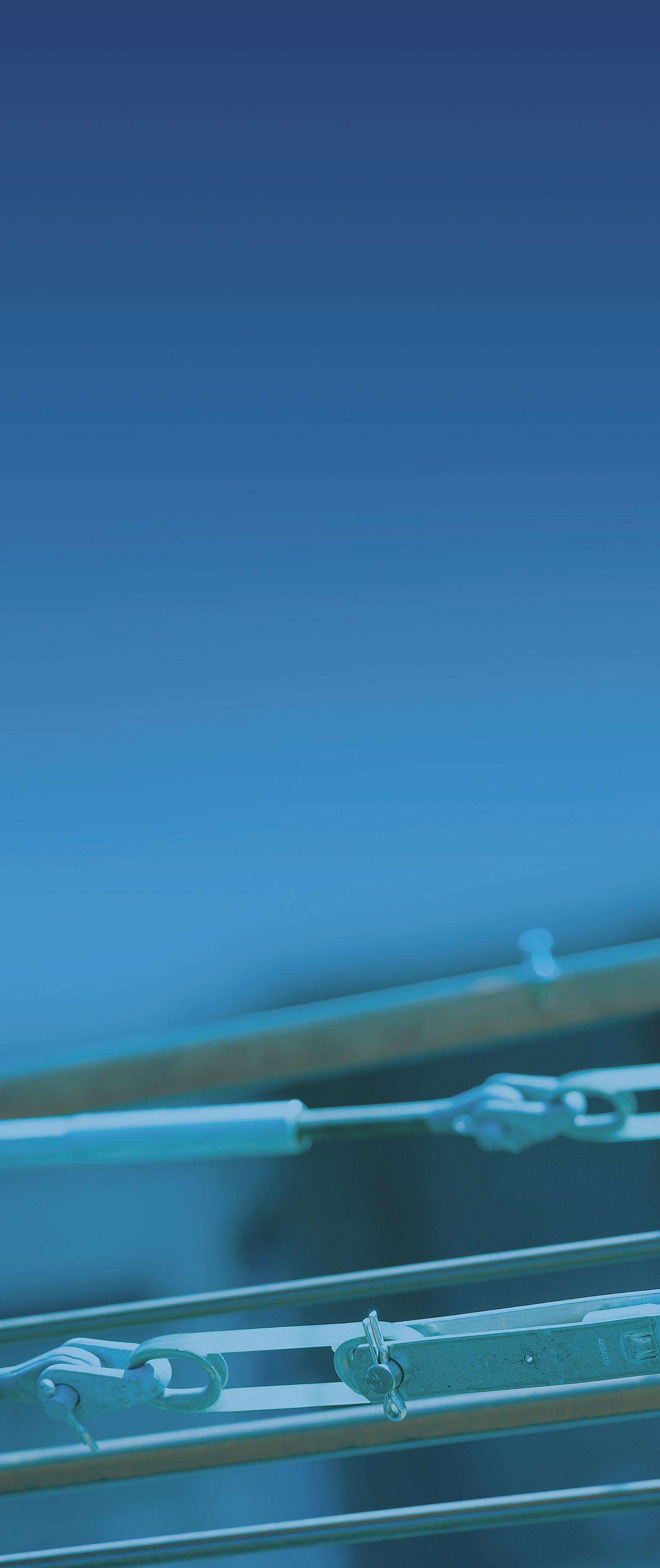

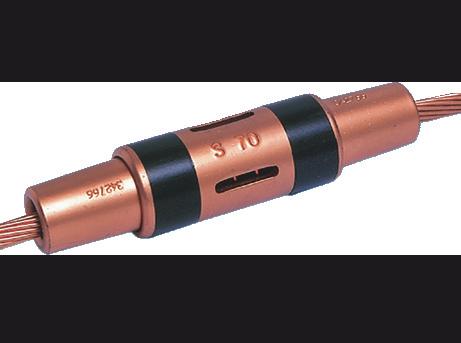
Nearly Half of the UK Worry about Germs on Public Transport
A new study reveals 47 per cent of UK-based adults have concerns surrounding germs on public transport
One in five say they’re still wearing masks on buses, trains and other forms of public transport, while a third are still sanitising their hands. Research conducted by commercial cleaning service provider, Perfect Clean, found that 14 per cent of people are ‘very concerned’ about the impact germs and bacteria on public transport might have on their wellbeing, while 33 per cent report being conscious and ‘somewhat concerned’.
The survey findings conclude that almost half of the UK express a level of concern about public cleanliness on public transport.
Just ten per cent of people across the UK use public transport every day, and a further 14 per cent said they use it once or twice a week. When using public transport, 18 per cent of all respondents said that they still wear masks – five per cent of which said that they did so ‘every time’.
A larger 35 per cent say that they still use hand sanitiser when using public transport, with a little over one in ten (14 per cent) saying they do so ‘every time’.
A quarter of those still taking precautions say that their reason is due to continuing Covid concerns, while 36 per cent say that it is part of their everyday hygiene routine.
Those aged 60+ represent the largest percentage across all age groups taking precautions due to continued Covid concern, with 35 per cent admitting to it being their main reason for continuing to wear masks and sanitise on public transport.
Regionally, 22 per cent of those living in the North of England share the largest voice of concern over germs and how clean the transport is, versus those in Wales, where concern is as little as six per cent.
In addition to Perfect Clean’s survey, recent Government data shows that while public transport methods have seen a gradual increase in use over the course of 2022, these figures are still below the preCovid base level.
Public transport use in 2022 (Against pre-Covid base)
As of February 2023, use of rail services was only 73 per cent of the figures seen in the same week in 2019 – a reduction of 27 per
by
cent. Buses outside of London have fared slightly better, with usage figures now at 81 per cent of their 2019 equivalent, while use of London buses is at a larger 85 per cent.
London’s tube service has fared slightly worse, sitting at just 74 per cent of its preCovid base level.
The introduction of remote and hybrid working models to post-Covid normality might offer some explanation as to the reduction in overall use of public transport, but 39 per cent of all respondents said that they viewed public transport as ‘too unreliable’, often making them late.
Regionally, 33 per cent of those in both the South and East of England report ‘terrible’ service as one of their main complaints with public transport, while one in five (22 per cent) of those aged 25-39 feel uncomfortable travelling with strangers.
On the other hand, 31 per cent of all survey respondents said that public transport was the most convenient form of transport for them, while 24 per cent praised its cost efficiency. These numbers rise in London, where 56 per cent say it’s the most convenient method and 36 per cent say it’s the most cost effective. As might be expected, 39 per cent of Londoners say that public transport is the fastest way to travel the capital.
Commenting on these findings, Managing Director of Perfect Clean, Emilia Ferenc, states: ‘As our research has shown, public transport remains a convenient and cost-effective mode of travel for much of the British public, used by many on a daily basis. With the global pandemic still lingering in people’s minds, it’s perhaps unsurprising that we have seen half of our respondents saying they’re concerned about cleanliness and hygiene on buses and trains, or continuing to take precautions such as wearing masks and using hand sanitiser. Companies such as ourselves are on-hand to provide fast, effective cleaning services for public transport and other commercial sites, but we would always advise the general public to take care of themselves and others, especially if they are unwell, in order to avoid the spreading of viruses and infections.’
DATA AND STATISTICS
Data and statistics drawn from a bespoke survey of 1,000 participants, conducted via yougov.co.uk. For more information please contact via email. Perfect Clean is an expert team of commercial cleaners based in Scotland, specialised in cleaning everything from offices and schools to aircraft and industrial machinery. Our mission is to deliver high-quality commercial cleaning services at affordable rates. We work with companies big and small, delivering a top cleaning service that meets our exacting standards. And, with a lot of experience under our belts, no job is too big or too challenging for us to tackle – we like to get stuck in and get the job well done.
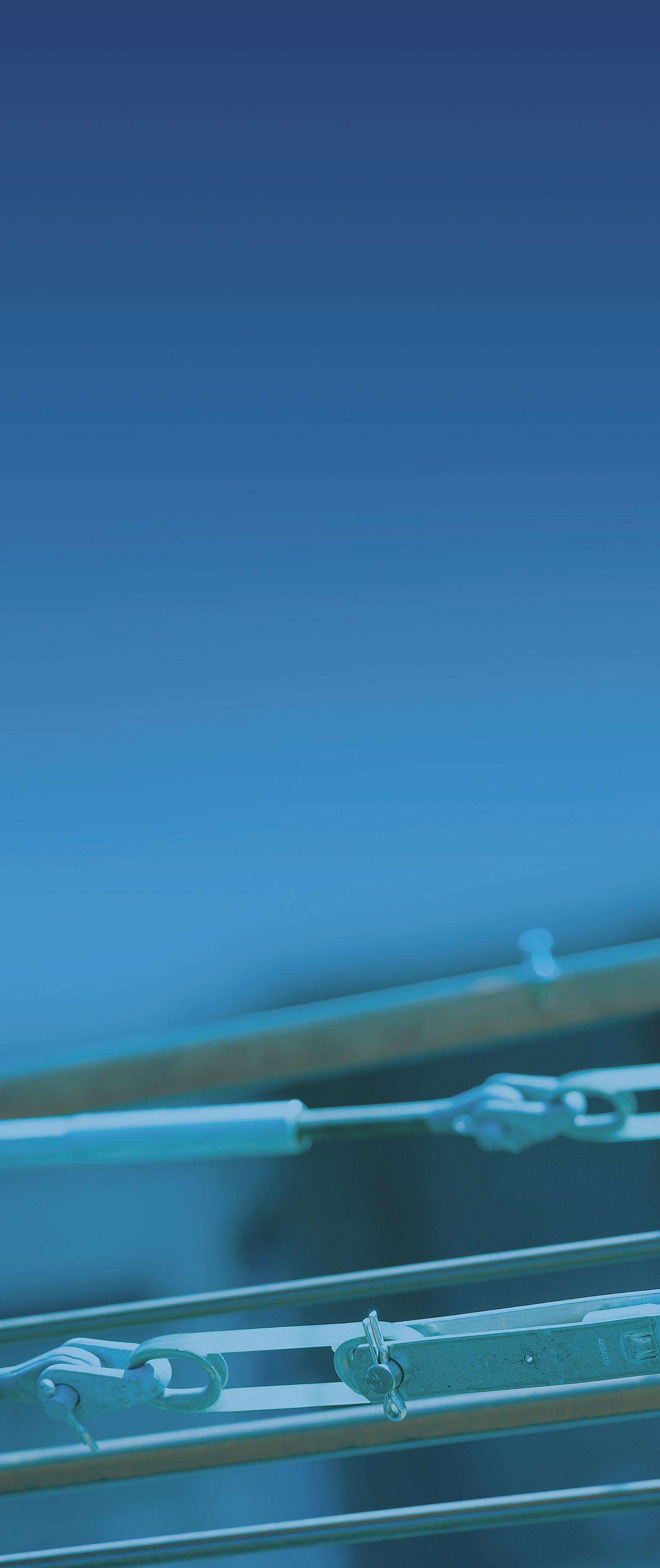
‘As our research has shown, public transport remains a convenient and cost-effective mode of travel for much of the British public, used
many on a daily basis. With the global pandemic still lingering in people’s minds, it’s perhaps unsurprising that we have seen half of our respondents saying they’re concerned about cleanliness and hygiene on buses and trains, or continuing to take precautions such as wearing masks and using hand sanitiser.’
Emilia Ferenc, Managing Director of Perfect Clean
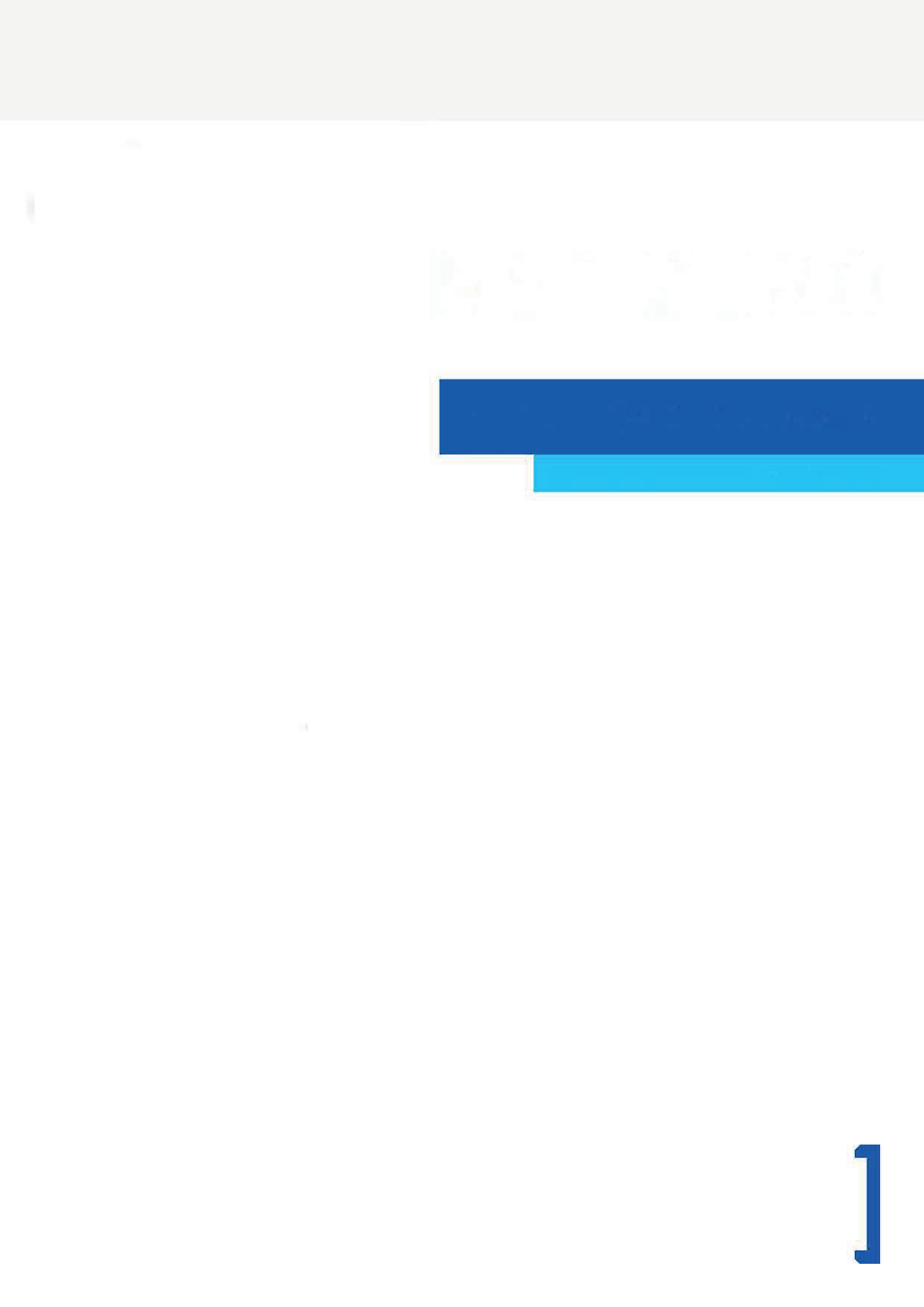
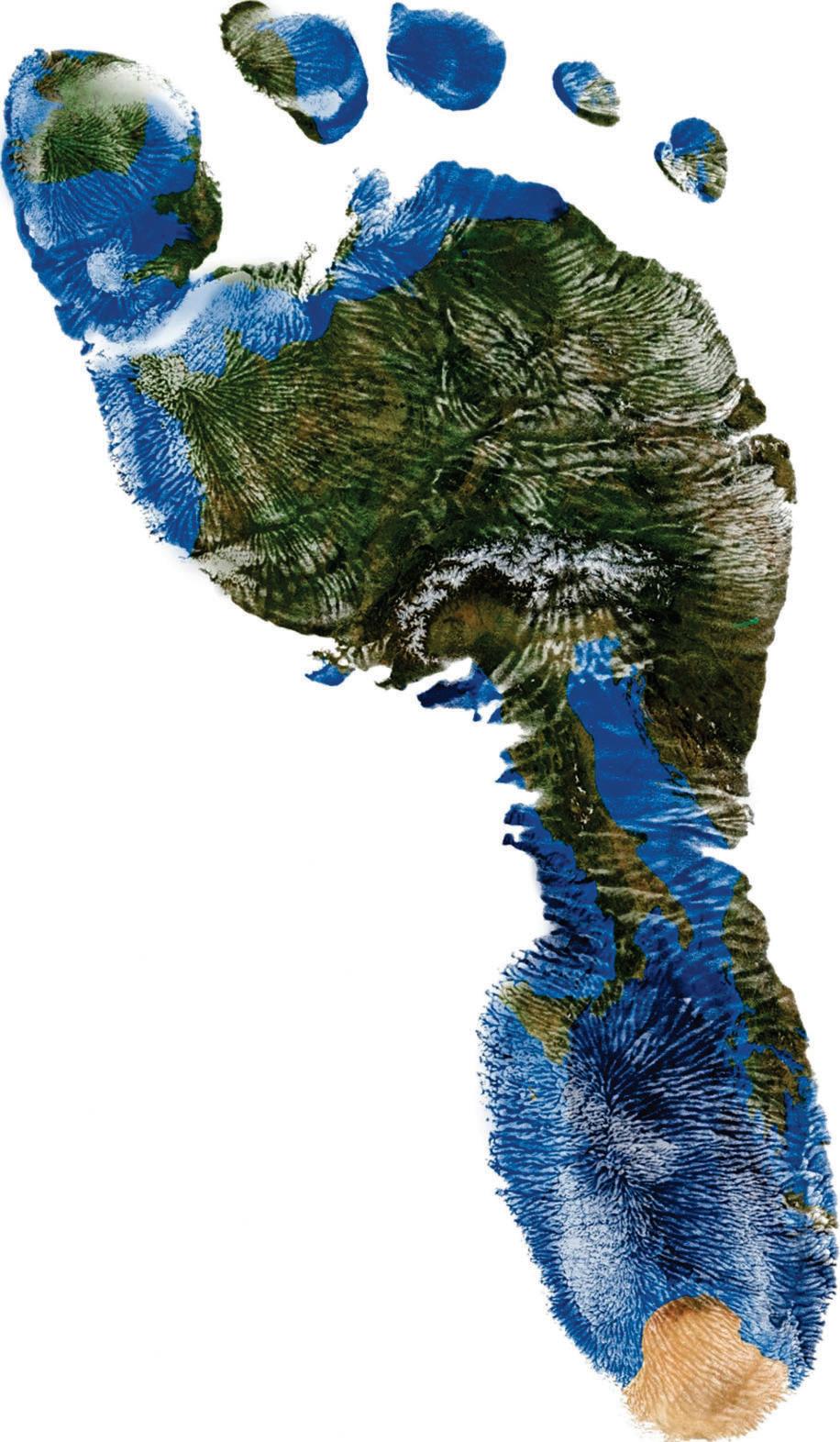
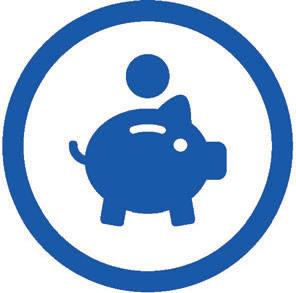
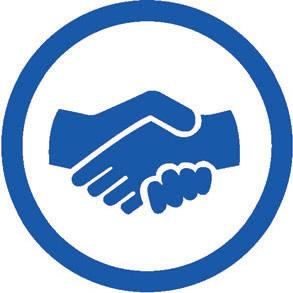
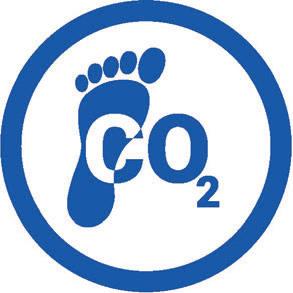

Further Delays for HS2 Impede Rail Freight Growth
Ellis Shelton, Policy Advisor, Logistics UK on the need for innovative and integrated infrastructure to deliver an increasingly productive and strategic logistics network
Rail continues to pave the way for decarbonising transport and helping the UK to reach its targets for achieving net zero by 2050. Driving modal shift towards low-carbon freight improves air quality and reduces road congestion particularly in urban areas, and it is estimated that rail freight removes 1,000 Heavy Goods Vehicle (HGV) movements per day from London’s roads alone. Rail is vital for supporting the construction of major infrastructure projects, carrying waste from urban areas for conversion into renewable energy and moving containerised consumer products through London and across Britain.
With the commencement of High Speed 2 (HS2) in 2009, Britain’s new high speed rail line being built from London to the NorthWest to decrease journey times, rail was set to receive a significant increase in network capacity and investment to deliver growth. This project has the potential to transform the rail network and provide the economy with a much-needed financial boost.
Currently, there are over 350 active sites between the West Midlands and London, supporting jobs and delivering benefits before a single train has started running. It is therefore a blow to the industry that UK government have announced a further delay, with elements of the project already cancelled or postponed indefinitely.
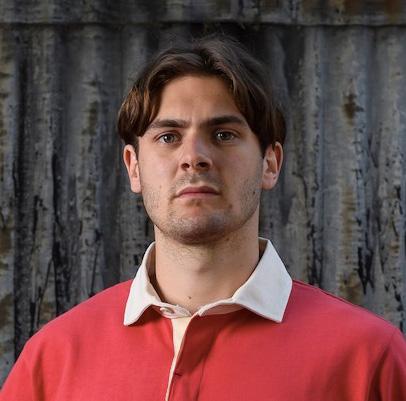
Due to numerous setbacks caused by significant inflationary pressure and

increased project costs, the main LondonBirmingham stretch is now set to be delayed by a further two years as a ‘rephase construction’ initiative.
With the first train now not operating until 2033, rail freight operators have been quick to criticise the delay, following Transport Secretary Mark Harper’s announcement on 9 March 2023, stating there is little gain for rail freight capacity given the additional wait time and unpredictability around the Crewe and Manchester expansions (Phases 2a and
Logistics UK is one of the UK’s leading business groups, representing logistics businesses which are vital to keeping the UK trading, and more than seven million people directly employed in the making, selling and moving of goods. With Covid-19, Brexit, new technology and other disruptive forces driving change in the way goods move across borders and through the supply chain, logistics has never been more important to UK plc. Logistics UK supports, shapes and stands up for safe and efficient logistics, and is the only business group which represents the whole industry, with members from the road, rail, sea and air industries, as well as the buyers of freight services such as retailers and manufacturers whose businesses depend on the efficient movement of goods. For more information about the organisation and its work, including its ground-breaking research into the impacts of Covid-19 on the whole supply chain, please visit logistics.org.uk.
2b). This delay will significantly affect the amount of capacity that will be available, particularly if new HS2 trains are to be forced to run on the existing tracks, as the West Coast Main Line is the most important route for rail freight in the country.
However, with the deadline being extended once again, rail freight businesses who are supporting the construction of HS2 with materials supply and engineering services are now facing uncertainty. Furthermore, the potential benefits of HS2 are diminishing as government continues to reduce the scope, by abandoning longer routes and delivery dates being extended. Government must consider the repercussions this decision will have on the rail freight sector and find a way forward which supports it as HS2 is critical in terms of freeing up capacity for freight on the network.
Logistics UK has recently highlighted to the Chancellor, Jeremy Hunt, and the Labour party, that the UK needs innovative and integrated infrastructure to enable the sector to deliver an increasingly productive and strategic logistics network. This will support economic growth by keeping costs on shelves down and reducing emissions. However, to cement rail freight’s position within reliable, green supply chains across the country, industry needs government to set an ambitious rail freight target. New analysis calls for rail freight to treble by 2050, delivering £5.2 billion in economic benefits every year and taking 20 million
‘New analysis calls for rail freight to treble by 2050, delivering £5.2 billion in economic benefits every year and taking 20 million HGV journeys off the roads which would help with road congestion relief and air quality improvement.’
NEWS IN BRIEF
RAIL INDUSTRY WORKS TOGETHER TO RAISE £200,000 FOR MARTIN HOUSE CHILDREN’S HOSPICE
Yesterday (Monday, 17 April), colleagues from Network Rail and DB Cargo UK handed over a cheque for £200,000 to Martin House Children’s Hospice. The huge sum is the culmination of four years of fundraising by the rail industry. The money has been raised through the organisation of special charter train tours for the charity, which have taken place up and down the country. The most recent tour ran last month between Whitby and Derby, and raised over £3,000 for the charity.
HGV journeys off the roads which would help with road congestion relief and air quality improvement.
If rail freight is to meet the needs of modal shift and dramatically expand traffic, significant capacity augmentation on the national network is required. This includes delivering investment in rail to increase the capacity for freight, such as through HS2 and making more strategic decisions on existing capacity, where Network Rail and Great British Railways (GBR) support is needed. Government needs to set out long term infrastructure plans and reforming planning to unlock private sector investment in rail freight, such as the inland freight terminals that enable the road and rail networks to work as one, supporting modal shift.
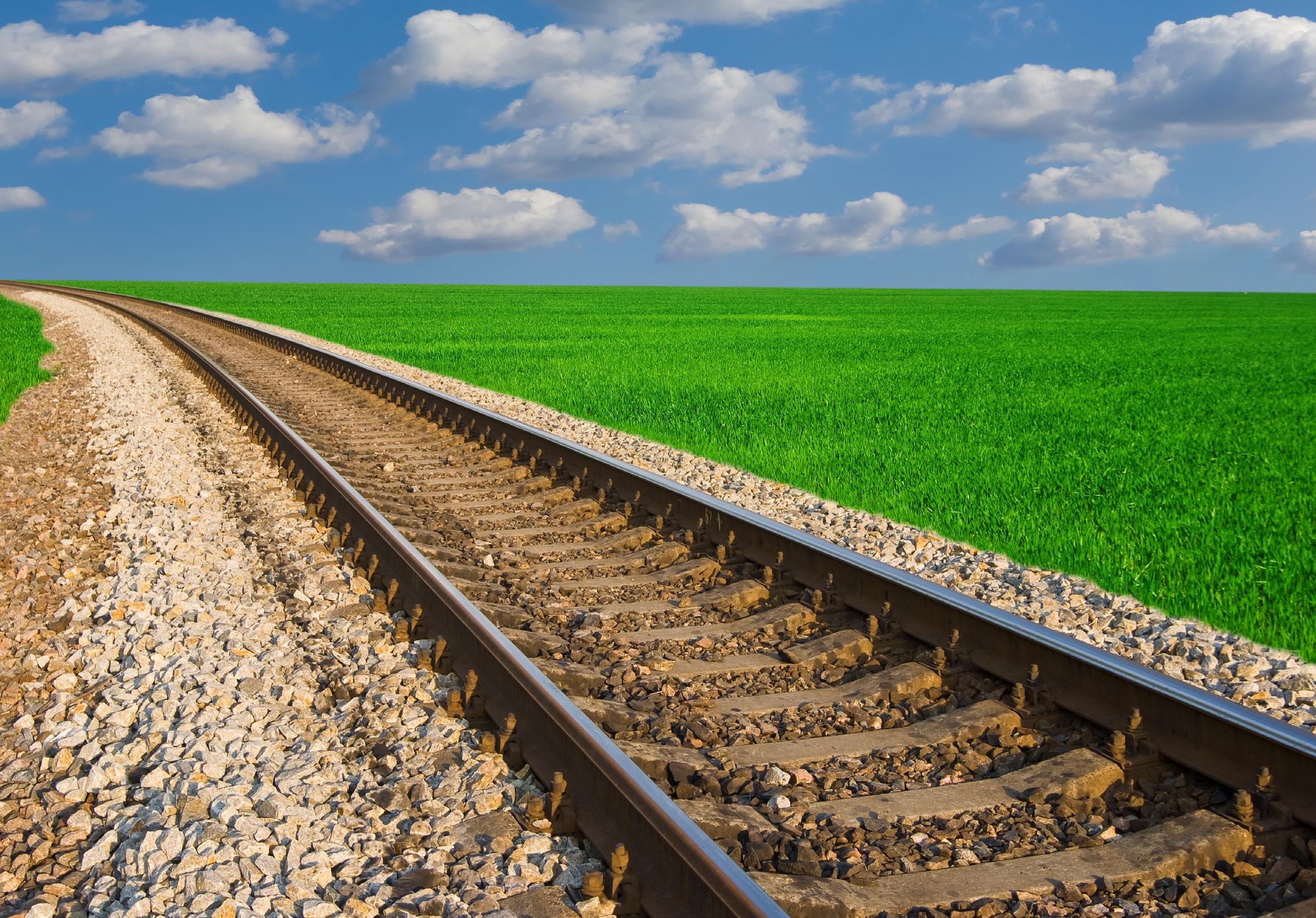
On 21 March 2023, Derby was selected by government to be the new home and national headquarters of Great British Railways (GBR) following its demonstration of strong links to the wider network, wellestablished connections with the industry, supply chain and customers, as well as an extensive local cluster of private sector rail businesses. This announcement follows on from the Transport Secretary’s Bradshaw address last February on setting a long-term
freight growth target this year, and marks a key milestone in the government’s plan to reform the nation’s railways. As Europe’s largest rail hub, Derby will soon become the heart of Great Britain’s rail industry too, bringing track and train together and delivering high-skilled jobs to the region.
It is vital that government collaborates with the private rail freight sector to achieve the ambitious goal of tripling freight. For the freight sector to expand and become carbon-free, freight operators and their clients will need to make investments in new resources and infrastructure, as a growing rail freight market has the potential to deliver even greater economic and environmental benefits between now and 2050. Logistics UK will continue to work with government on maximising the benefits of rail freight advancements and support members along the way.
• Powertrain modelling
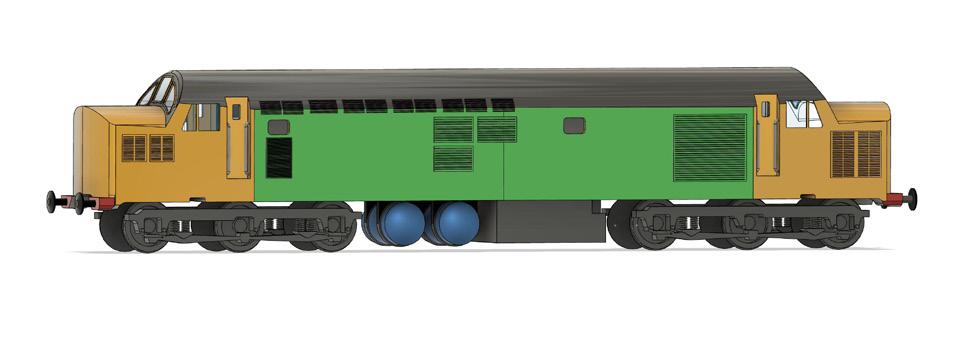
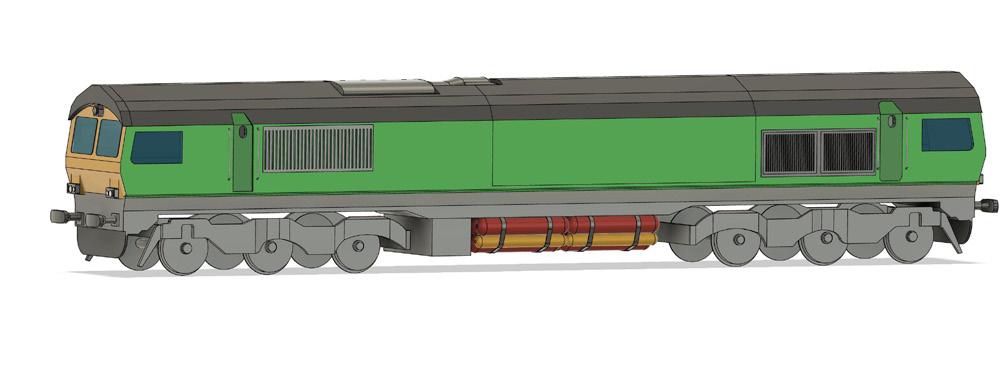
• Route simulations
• Packaging studies
• CAD modelling
2023: the Year of Sustainable Transportation?
There can be no doubt, as climate records continue to tumble and extreme weather events cause ever-increasing damage, that sustainability has a key role to play in humanity’s future
However, making a sustainable vision a reality is easier said than done, especially when it comes to transportation.
What progress can we expect in 2023, asks Audrey Denis, Senior Manager, Strategy & Strategic Partnerships, Cubic Transportation Systems?
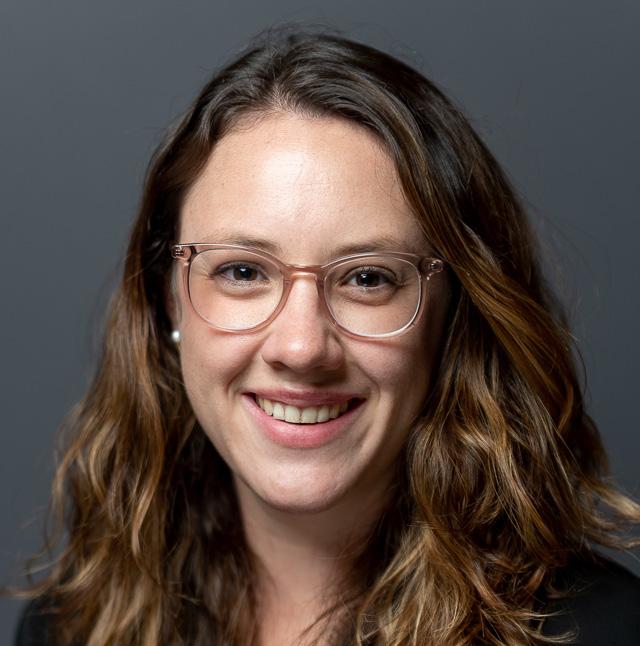
New research from Free Now reveals over half of the UK public plan to increase their use of sustainable transport choices in 2023 – as a way of reducing spending and looking after the planet. Almost a third say that sustainable transport – including shared mobility (micromobility, taxis and private hire vehicles) and public transport –is increasingly important in the wake of the current cost-of-living crisis.
The findings also show a marked shift in travel priorities across the UK. The UK’s top New Year transport resolutions include using more shared mobility, with 14 per cent of people pledging to use this form of transportation further. People are also increasingly likely to live without a car by using taxis, private hire vehicles, e-scooters and e-bikes. At the same time, 37 per cent of respondents said they will rely more on public transport this year.
The rise of sustainable transit
Does this really mark a sea change in how the public views sustainable transport and why is it important? It isn’t surprising that people want environmentally friendly, locally available, efficient and affordable mobility options. However, there are numerous factors to bear in mind, including
fluctuating demand, cost, maintenance and fuel prices. That means we must plan carefully to ensure public transport networks work effectively.
Whether you are going to a hospital appointment, doing the school run or commuting to work, ideally there should be a wide range of public transport options available, as well as the use of bicycles or private vehicles. The sad reality, however, is that outside of major urban areas, public transport in the UK is woefully limited. This is where perhaps private mobility service providers (MSPs), such as ride-sharing or electric scooters, can play a role in helping rural and urban communities expand their mobility options.
Behavioural impact
Because of these variables, local government and transport officials tend to focus on objectives that will enable regular, low-stress public transport while reducing congestion and emissions. A noble goal, but not an easy one because modern transit systems are largely fragmented, which makes it difficult for transport officials to coordinate a holistic strategy.
Instead, passenger behaviour can be changed – or ‘nudged’ – to make an impact on traffic and pollution. This approach requires the right tools to guide passengers to make more sustainable choices. That’s where digital mobility comes into play: solutions that can synchronise siloed transport systems across the mobility network, enabling regional, national and international stakeholders to collaborate
effectively and make well-informed decisions.
Digital mobility has the potential to integrate each mode of transport into a unified operating network across the whole transportation ecosystem. Therefore, we can connect everything, from local buses to ridesharing to traffic management, to provide one efficient, coordinated journey. As an example of how this might encourage proactive tactics, we might use dynamic congestion pricing to reduce traffic on days with poor air quality.
Technological advances
Across this integrated ecosystem, we can deploy digital tools, including integrated ticketing, real-time network data and dynamic pricing, to make sustainability a reality. Harvesting data from multiple sources, such as ticketing systems on public transport, digital toll booths, and traffic light cameras, enables total visibility in realtime of network demand and bottlenecks. That means transit managers can plan more efficiently and introduce flexible, adaptive and responsive incentives to optimise traffic and encourage passengers to choose the most sustainable option.
Technically speaking, digital mobility is available today: all the requisite tools to enable real-time, coordinated, and integrated mobility across multiple transport modes can be deployed through infrastructure upgrades and cloud-based SaaS solutions. Putting in place the foundational elements, like a unified account-based ticketing and payment platform which is interoperable between all transit options, is no longer a pipe dream or prohibitively expensive.
Despite chronic underfunding in the public sector, the increasingly impactful threat of climate change is driving adoption. Improving public transportation equity, access and usage is an honourable aim and the technology that connects passengers, services, vehicles and agencies exist to make it a sustainable reality.
We face an ever-more complex challenge to provide our citizens and neighbours with reliable, low-carbon, efficient and safe transport options, wherever we find ourselves in the world. Digital mobility, micromobility and MSPs, offer a clearly defined path to consistent availability and dependability. Now is the time to fund and promote them as a faster and more affordable alternative to private vehicles.
‘New research from Free Now reveals over half of the UK public plan to increase their use of sustainable transport choices in 2023.’
Highly Skilled Driver Team Managers
The OPC shares some reflections and extracts from interviews with outstanding driver team managers (DTM); the special leadership skills needed to do this pivotal safety-critical role and what the industry might do to better support them
Following on from the OPC’s article in the March issue of Rail Professional about Future Leaders Who Love the Railway, this feature focuses on the crucial, pivotal and special role of the managers responsible for crews of train drivers. Depending on the train operator these roles may sometimes be done by an individual manager, or some operators split the role in two, each with a different focus – driving competence or people management. Titles vary, but they might be known as driver managers (DM), driver train managers (DTM), competency development managers (CDM), driver line managers (DLM) or driver standards managers (DSM).
It takes experience and special skill to be in a leadership role looking after a team of drivers. Some team leaders may have moved direct into the role from being a train driver, others may have spent time as driver trainers or driver mentors/instructors, and some may have taken the long and winding road of wide industry experience gathered in station roles; being an on-board crew member; a guard or driver roster clerk, and some bring expertise from roles external to the railway. What is amazing in all cases is the passion with which they do the job and love their teams.
What’s so important about driver management?
It may be perceived that moving from a safety-critical role as a driver into a team managers’ role that they’re no longer in a safety critical job. But that’s far from true. Regardless of differing structures, getting the best from a driver to ensure driving competence or developing their Non-Technical Skills (NTS) after an incident or tenaciously managing a difficult conversation with a ‘human’ touch are all important skills that can impact on a drivers’ safe and consistent performance.
The OPC has undertaken hundreds of Post Incident Assessments (PIA) with
drivers who may have had an incident. The manager driver relationship is crucial to a driver’s return to safe and effective driving performance going forward. In many cases it’s only a positive, productive and trusting relationship between a driver and their manager that means the implementation and adherence to a competency development plan or an NTS development. So, the DM’s role, skills in their job and driver support can have a massive impact on safety.
Highly skilled people management
Fundamentally, it’s a tough job! Being the leader of a driver team and being responsible for them is critical in the rail industry. Whether a split or combined role, there’s a need to balance the key aspect of delivering safe and effective driving alongside keeping a team of drivers happy and motivated, thus ensuring trains run on time for customers. It can be a role that is very undervalued and unappreciated. Driver training is costly and can take up to two years to full qualification.
For some time thereafter, they have a high degree of support with competency assessments, ongoing training, mentor or instructor driver support and lots of contact with their DM or CTM. Yet DTM don’t always receive the same level of training support. Their role may require technical and analytical skills, behavioural and performance management skills and most importantly communication and people skills, which all take time to learn and hone – but sometimes they start in the role with little or no formal training.
What special skills make a really good driver team manager?
For a long time, OPC psychologist have worked closely with lots of train operator’s DTM, across numerous projects. These have included NTS training, Post Incident Assessments and Investigation training. They also undertook research with industry experts to form an in-depth understanding of a Driver Standards Manager (DSM) role.
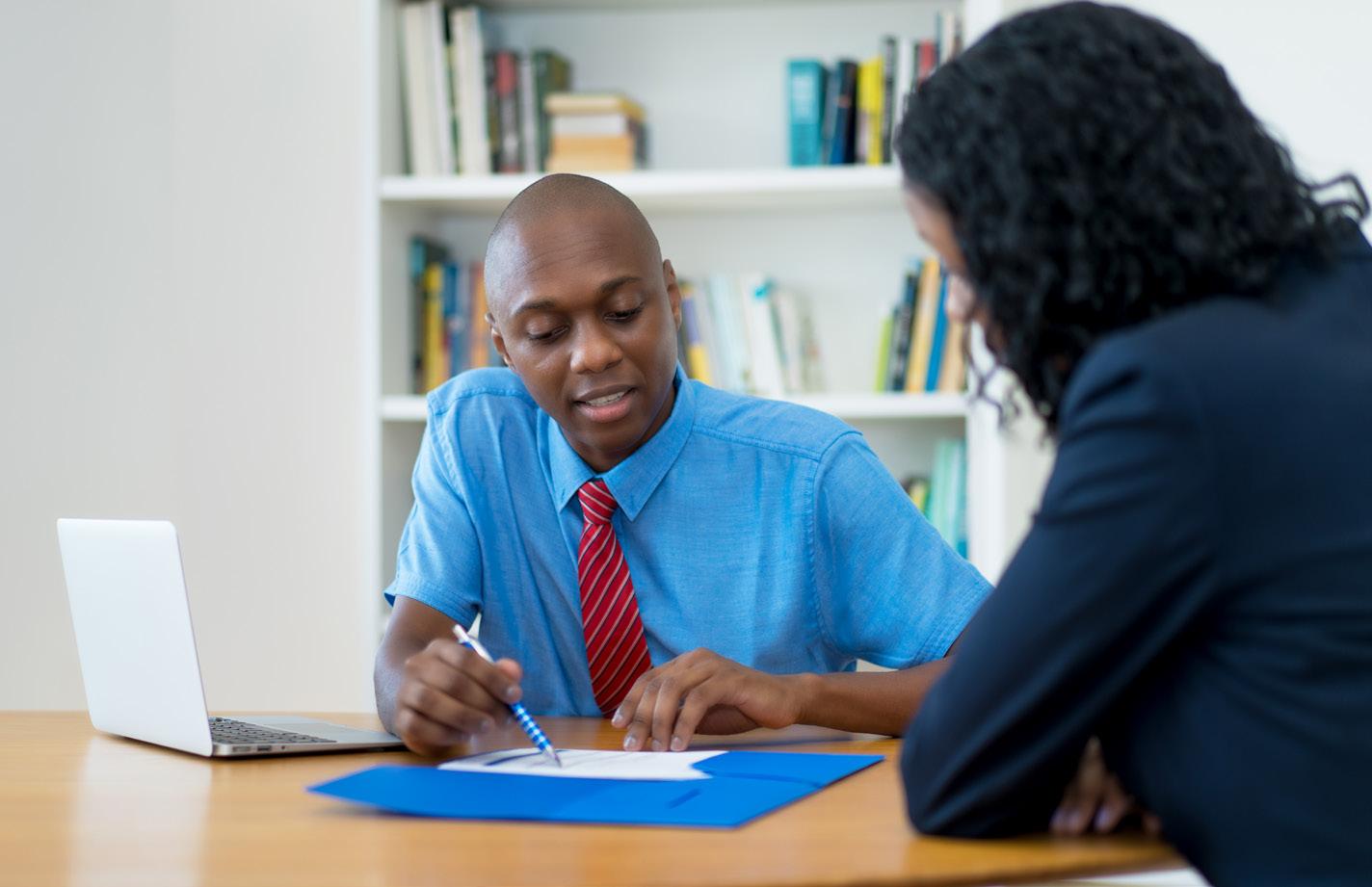
These experts helped OPC Psychologists to prepare a competency profile for the role. Additionally, OPC Assessment’s development work on the recently launched Leadership Potential Indicator Test (LPI) has informed what competencies are crucial to any of the roles responsible for leading a team of drivers. The OPC team also undertook some face-to-face interviews with some DMs, and their line manager to hear what made the job special and the skills needed to do it.
Some key leadership skills and what that really looks like for some DMs:
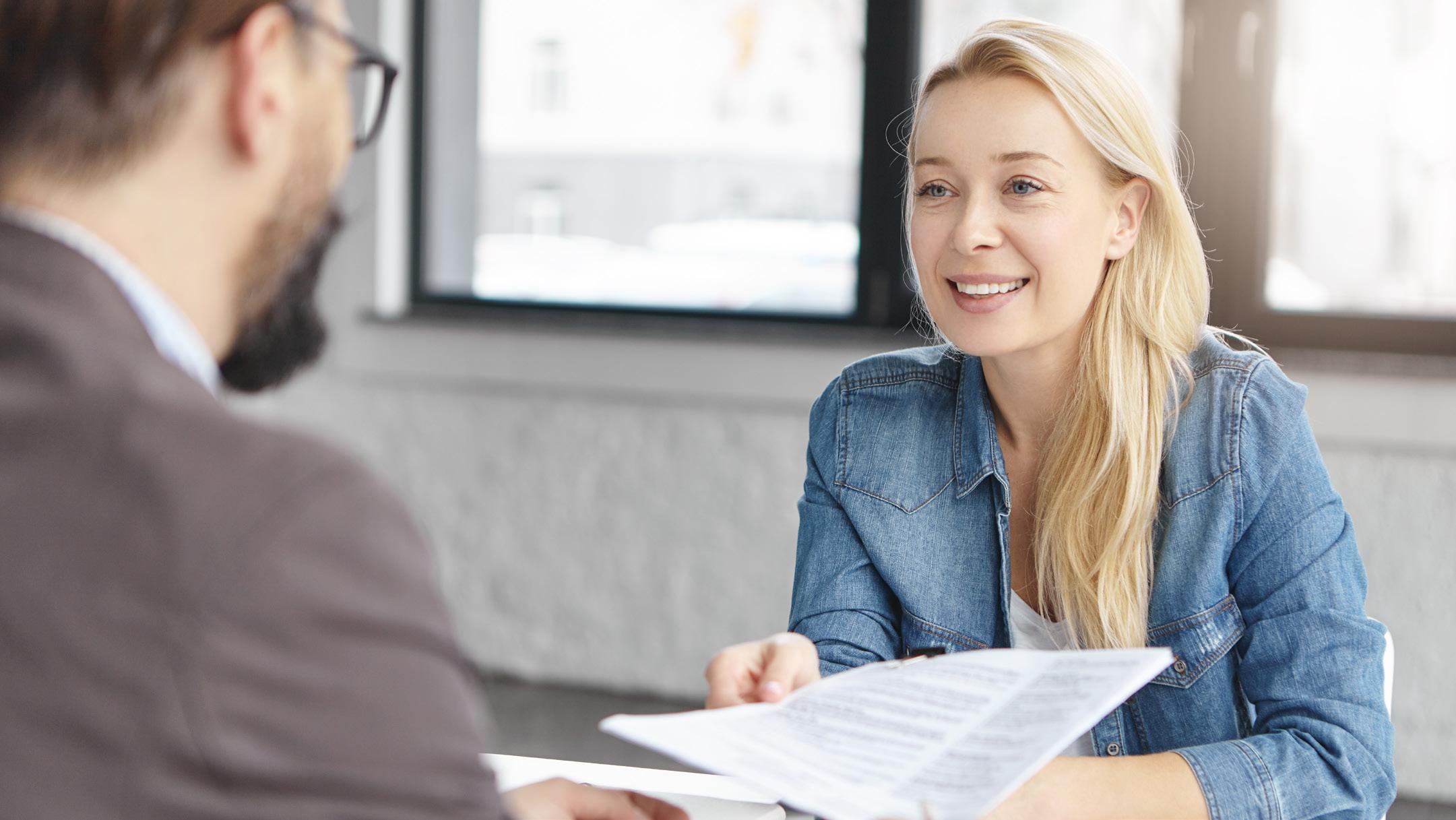
• Leading others.
• People skills.
• Thinking skills.
• Strong customer focus.
• Driving improvements.
Leading others
Leading others to deliver results may include managing and directing others through confident and assertive behaviour. Influencing and persuading people to take action. Effective communication through verbal, face to face or written methods.
A DTM said: ‘Building that strong rapport with a driver takes time. It’s not a ‘glancing’ relationship. You have to be in it for the long haul and you have to earn your stripes’.
‘Regardless of whether the role is split, it’s really necessary that the manager is skilled at building a high level of engagement with a driver to get the very best from them. You have to give more of yourself away to get the best in return.’
An operations manager said: ‘We have to achieve standards and safe performance through a low threat, high target approach.
It’s no good punishing a driver for an incident, saying you didn’t achieve X, therefore you’ll be disciplined. It’s much better to say, this is the target, and we’ll strive to get there together.’
People skills
People skills that build positive relationships and successful teams by using personal emotional intelligence, empathy and understanding. These leaders are good at motivating others. They can demonstrate independence and fairness when dealing with difficult situations, particularly when questioning drivers to establish facts and evidence during an investigation.
A DTM said: ‘Managing the driver team is the biggest delight but also the hardest challenge. We feel the pressure to make sure we’re doing our jobs properly, but that’s when we’ll sound ideas off or check each other’s work. You know the team have got your back.’
A DM said: ‘When we need to put a competency development plan or NTS development plan in place after a safety incident, it’s essential that drivers are nurtured and cared for. There needs to be proper consideration for the driver’s welfare to help them, and make sure the plan really works.’
Thinking skills
Thinking skills for effective problem-solving decision making, and planning. Managers are able to prepare and implement effective plans, using analytical skills to make informed decisions. They are flexible and can prioritise effectively as the job needs change – sometimes constantly!
A DM said: ‘Sometimes things snowball in the job. You need to be flexible and adaptable without being wedded to your day’s tick list. You could be implementing rules and procedures, doing a driver’s development plan, or admin for a return to work after long-term sickness. Then there’s a safety incident. That takes priority and everything else goes on hold.’
Strong customer focus
DMs have a strong customer focus with external and internal customers.
A DTM said: ‘I find it really rewarding, especially working with a driver who may be quite challenging. I love to work with someone who may have been struggling; help turn things around alongside them; change their attitude and see their driving performance improve – it makes me so proud of them.’
Driving improvements
Another important factor is driving improvements in themselves and others, particularly in relation to competence and performance.
A DTM said: ‘It’s hard to make standards match and work the same for each and every driver in the team. As a manager, you
‘When you first get into the role, it’s a massive ocean and it’s pretty quick to drown out there!’IMAGE CREDIT: ISTOCK
need to be able to translate them to fit the scenario and the person – that takes a lot of competence, skill and a gentle touch to deliver a front-line change.’
A DM said: ‘I love helping to grow a person, training and developing them –whether that’s about enriching their current role performance or helping them develop for a future opportunity.’
A DTM said: ‘Things that help us develop away from the day to day are continuous training and development opportunities, like signal sighting courses, risk assessment or special projects.’
Finding and recruiting the best
When thinking about recruiting the best candidates for this skilled and varied role, the OPC have a number of assessment tools and exercises available that cover a range of competencies and abilities. Some of these have been designed bespoke for the driver manager role. They would recommend including the Leadership Potential Indicator Test (LPI) that can help to measure leadership potential, and assess for key management competencies. The Investigation Exercise (InEx) can help provide evidence of a candidate’s ability to gather information and establish facts through a systematic and thorough approach – a significant skill requirement for this role. The Rules Acquisition Aptitude Test (RAAT) can help assess the ability to understand and reason with basic written rules, regulations and procedures which would be necessary when driving or implementing standards. As the role relies heavily on interpersonal skills to motivate people, deal with conflict, as well as persuading and influencing skills, it’s important to see how a candidate may behave in a face-to-face situation. Therefore, in addition to an interview, it may be useful to include a role play exercise in the recruitment process. Other assessment tools measuring planning, organising, or communication skills could also be considered as part of a recruitment process.
Growing talent in-house
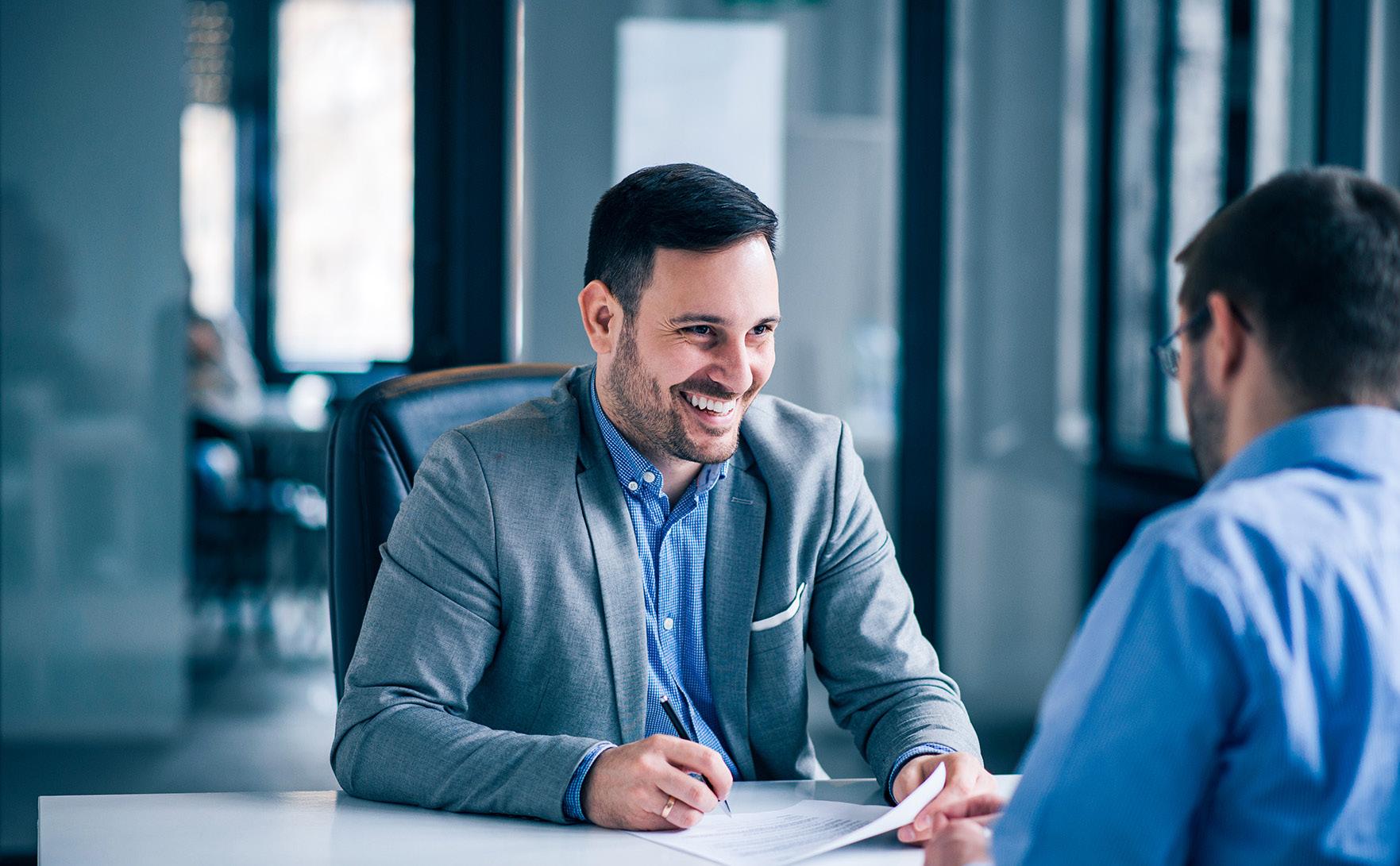
Whether the role is split or combined, a potential new driver manager may not necessarily have all the skills to make a good team leader straight away – particularly if they need help developing communication and people management skills. Managers interviewed by the OPC reflected there’s sometimes a lack of formal training prior to starting in role and that there is considerable up-front hours investment to get a good handle on the role. In most cases, unlike drivers’ training, there is little or no ongoing development for a DTM once in post.
A DTM commented: ‘When you first get into the role, it’s a massive ocean and it’s pretty quick to drown out there!’
In some cases, there’s a lack of formal induction training linked to standards or even simple ‘how to’ tech. This would include training in how to operate key assessment software or undertake and interpret an OTDR download. The current IR issues have also highlighted the need for more robust and informed learning in this key area so managers feel more prepared and protected.
One leading train operator mentioned offering short-term secondments for drivers into their DTM role, to learn particular skills and shadow an existing DTM. However, this can be quite draining on an already stretched team, plus it creates a driver gap. But it did prove most beneficial for those who took part with one subsequently moving into a DTM role and others into leadership posts too.
Another option may be to consider a Leadership Development Centre (LDC) for individual driver managers or groups of managers. An LDC can either support the transition of those potential managers into their new role, or up-skill managers who may have been in post for some time and need additional development. The OPC can run development centres that are a hybrid mix of personal self-assessment and learning, online learning and face-to-face skills development and practice. These can include
leadership skills, coaching and mentoring skills development; communication skills; giving positive, relevant and empathic feedback, personal leadership styles and learning interpersonal skills.
Why can’t we find people willing to fill these roles?
Laura Hedley, Occupational Psychologist at the OPC said: ‘When listening to those who lead these rare and crucial teams of managers, it’s easy to see why it may be hard to fill some of these gaps in the industry. Regardless of whether the role is split or combined, the job is extensive. The breadth of tasks is wide, needing an ability to multi-task, prioritise and self-manage, whilst coping with the stress of the position. The role can indeed be challenging and this might explain why some managers either don’t stay in this leadership role or return to driving. It takes a special, very skilled manager to take on this pivotal and safety-critical role for the industry. With more secondments, a robust selection process, effective induction training and ongoing coaching and development we might be able to encourage more managers to stay and flourish in this vital role.’
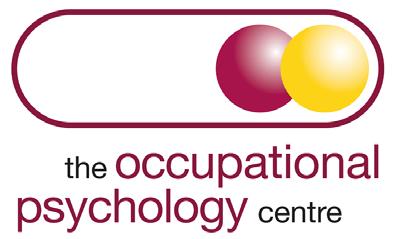
An Operations Delivery Manager concluded saying: ‘Driver team managers are under huge pressure every day. They have very strong competence and extensive knowledge of what it really takes to drive a train safely and get the best out of their drivers. They rapidly flex and adapt their plans to whatever the day throws at them; what’s the highest priority and which of their drivers need them the most. Driver team managers can sometimes be seen as a ‘Jack of all trades’ however, they are probably the most skilled managers in the business.’
Tel: +44 01923 234646
Email: admin@theopc.co.uk
Visit: www.theopc.co.uk
‘Driver team managers can sometimes be seen as a ‘Jack of all trades’ however, they are probably the most skilled managers in the business.’
Designing interiors for future generations

HS2 will Deliver UK’s Longest Railway Bridge
At the beginning of 2023, the last of 292 concrete piles that will form the foundations for the UK’s longest railway bridge were installed at the site of HS2’s Colne Valley Viaduct
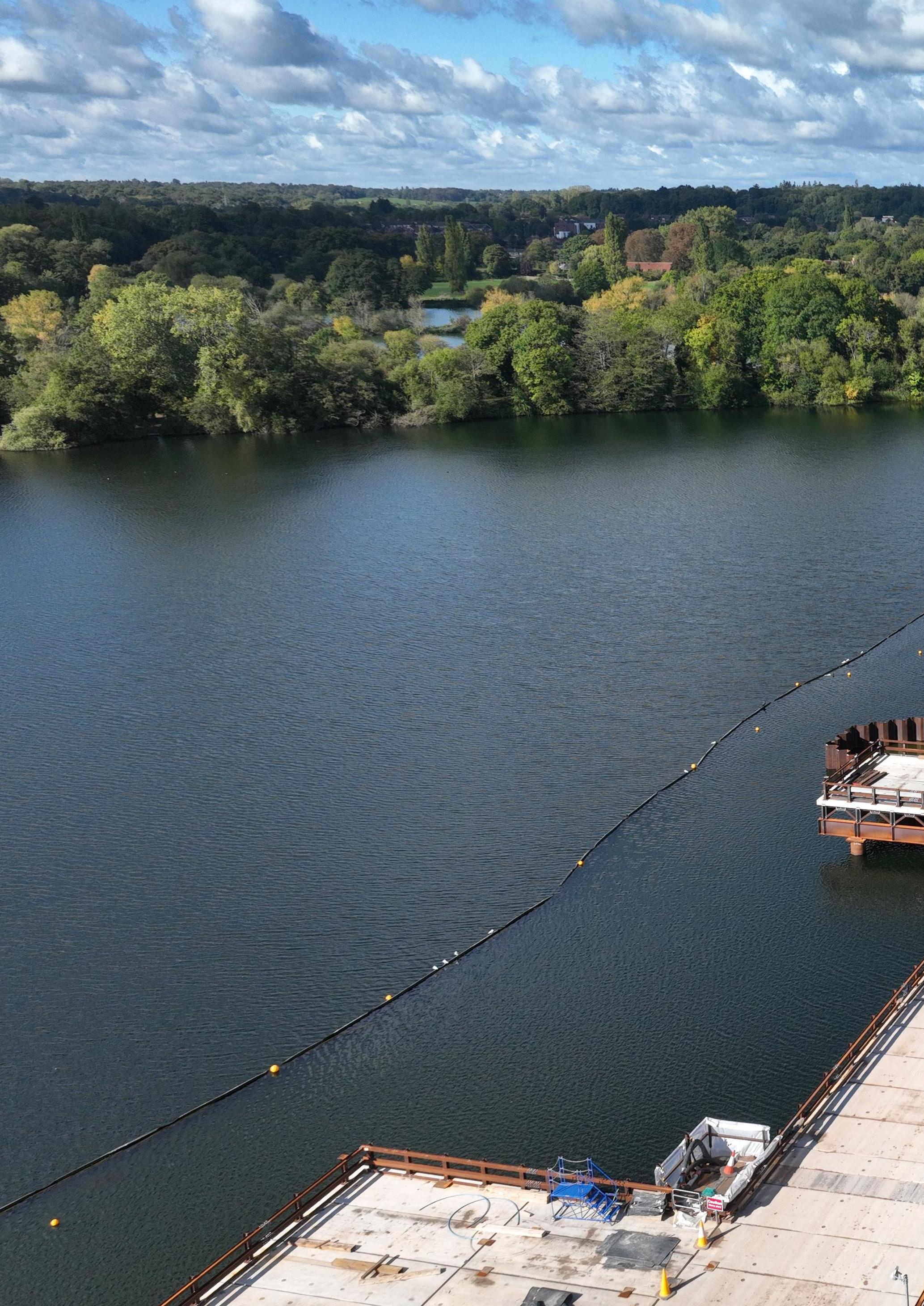
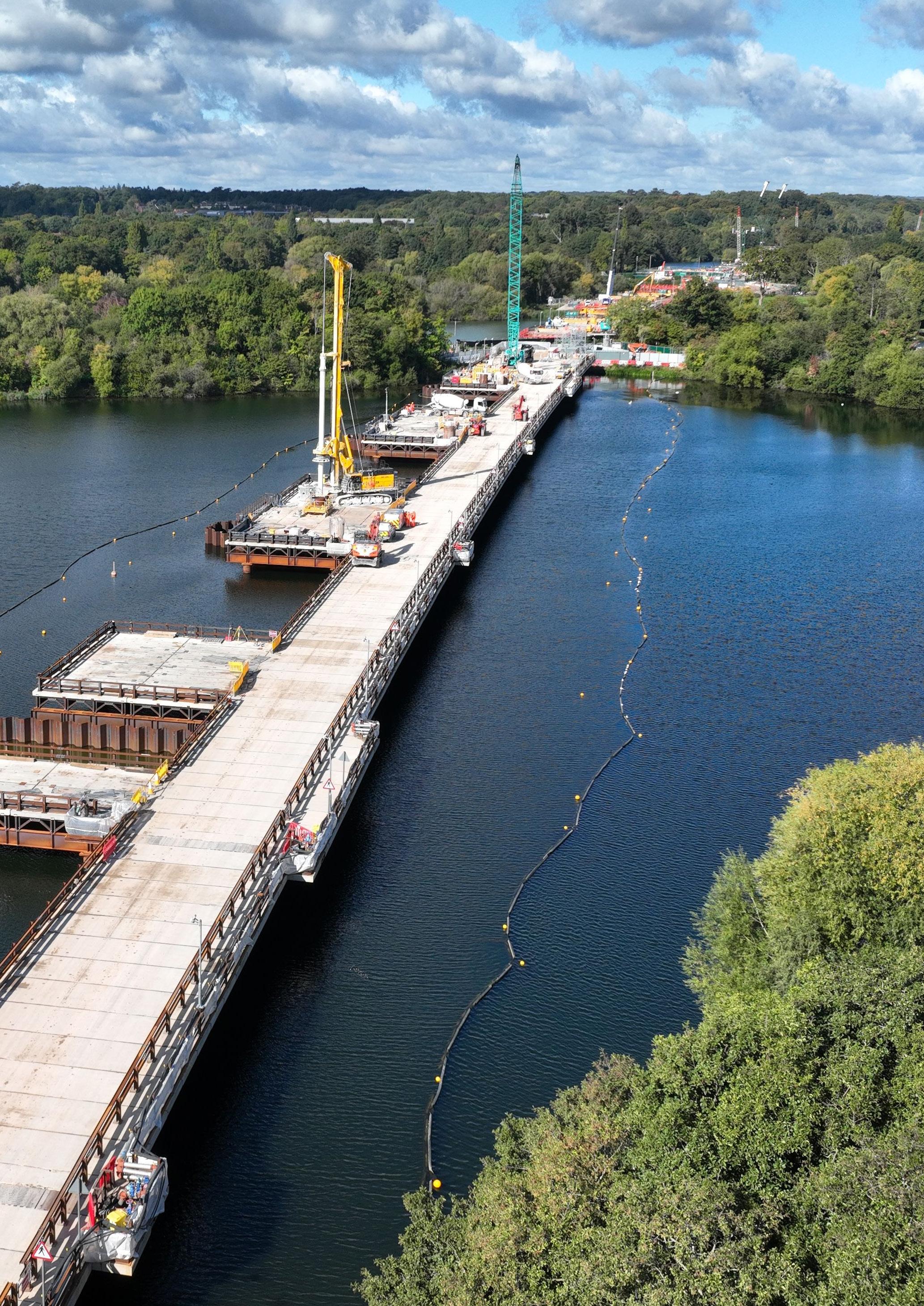
Once complete, the 3.4-kilometre-long bridge will carry the new high-speed rail line across a series of lakes and waterways near Hillingdon on the north-west outskirts of London.
The construction of the foundations, the 56 huge piers and the deck on top, have all been happening in parallel – with separate teams working from north to south. Deck assembly began last year, with more than 500 metres of the viaduct structure now complete.
In order to deliver the 66 piles in the lakebed, the team first had to construct over a kilometre of temporary jetties, with cofferdams to hold back the water around each set of foundations. The jetties are also used to transport materials and equipment during the construction of the piers and viaduct deck, keeping vehicles off local roads.
The viaduct is being built by HS2 Ltd’s main works contractor Align JV – a team made up of Bouygues Travaux Publics, Sir Robert McAlpine, and VolkerFitzpatrick, working with its contractor KVJV – who
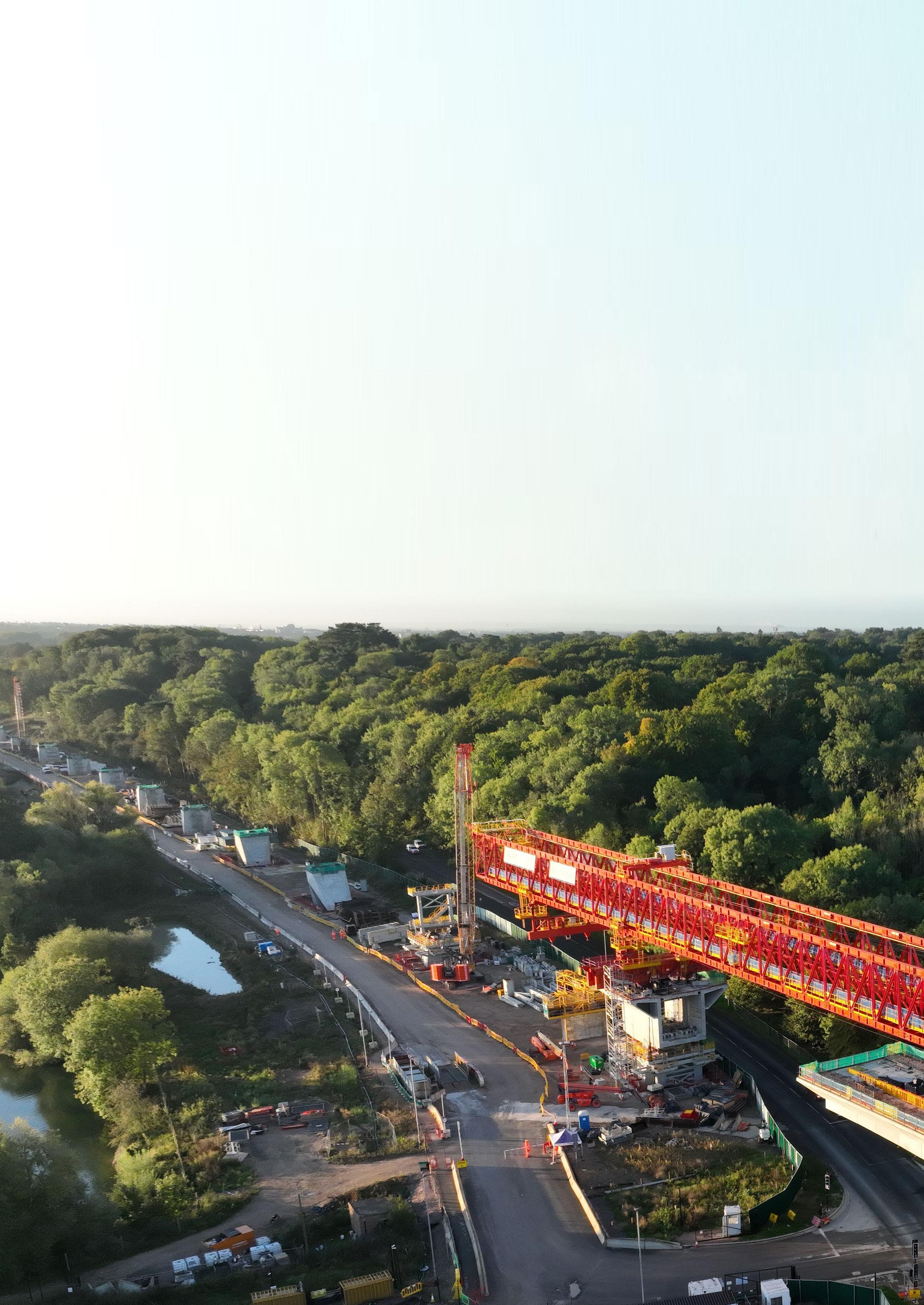
spent almost two years on the piling. KVJV is a team made up of Keller Group and VSL International.
On top of each group of piles – some of which are to a depth of 60 metres into the ground – a concrete pile cap will support the pier which will in turn support the weight of the bridge structure above. Instead of hammering the piles into the ground, holes were bored before being backfilled to create the piles.
The main deck of the viaduct is being built in 1,000 separate segments at a temporary factory nearby and assembled using a bridge-building machine which lifts each piece into position before shifting itself forward to the next pier.
Align’s Surface Operations Director, Derek van Rensburg said: ‘Completing the piling is a great achievement for both Align and the team at KVJV, working over the lakes and waterways across the Colne Valley. We were able to complete the piling with no significant impact on the environment, a great result for the whole team.’
Set low into the landscape, the widest spans reserved for where the viaduct
crosses the lakes, and narrower spans for the approaches. This design was chosen to enable views across the landscape, minimise the viaduct’s footprint on the lakes and help complement the natural surroundings.
The design was inspired by the flight of a stone skipping across the water, with a series of elegant spans, some up to 80 metres long, carrying the railway around ten metres above the surface of the lakes, River Colne and Grand Union Canal.
HS2 worked closely with Affinity Water and the Environment Agency to monitor water quality and agree working methods. These were monitored by a team of specialist engineers during construction in order to protect the natural environment.
Before work began, an extensive programme of test piling was completed with engineers sinking twelve piles at two locations with geological and structural data from these tests fed back into the design of the viaduct. This resulted in a 10-15 per cent reduction in the depth of the piles and associated time and cost savings.
‘This is an extraordinary feat of engineering and architecture, designed to enable spectacular views across a beautiful part of our British countryside which is being preserved and protected by this project. It was incredible to be the first person to officially walk on top of it today –another milestone for this monumental project which will transform journeys for people up and down the country, creating almost 30,000 jobs and providing a low carbon alternative to cars for decades to come.’

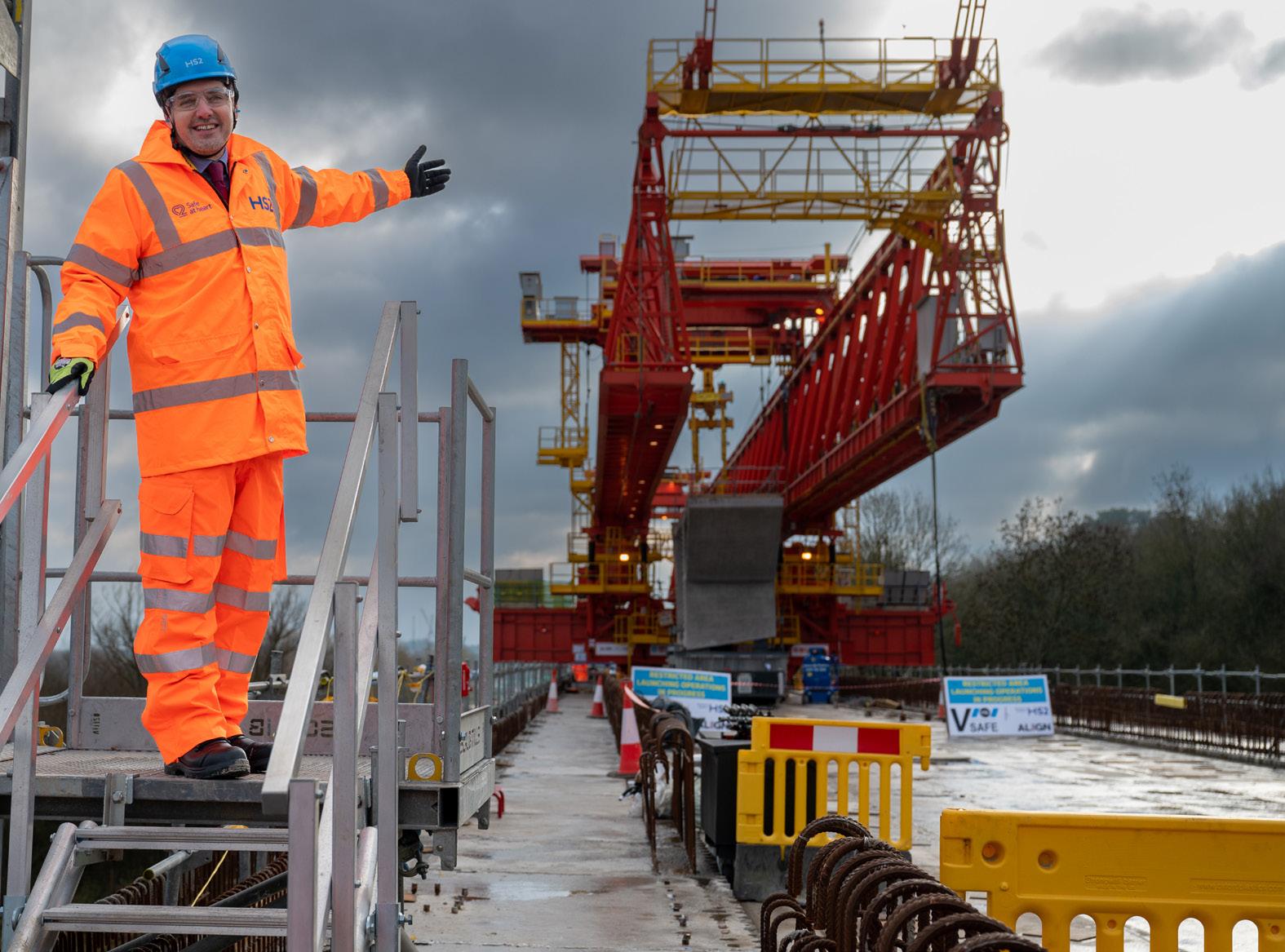
Launching girder
Known as a ‘launching girder’, the 160-metre long bridge-building machine is the only one of its kind operating in the UK and is used to lift the giant concrete deck segments that form the viaduct’s arches into position. Once each section is complete, the machine inches itself forward to build the next stage.
Each deck segment weighs up to 140 tonnes. To allow for the gentle curves of the viaduct as it crosses the valley, all the segments are slightly different shapes and made on site at a purpose-built temporary factory close to the north abutment.
Originally built in 2004, the launching girder was first used during the construction of the Hong Kong East Tsing Yi Viaduct. Specially designed to handle complex viaduct construction, the machine is named ‘Dominique’ in memory of Bouygues engineer Dominique Droniou who played a leading role in its design and development.
56 piers each weighing around 370 tonnes are being constructed along the Colne Valley ahead of the girder, with the machine moving from one pier to the next, installing the deck segments as it goes.
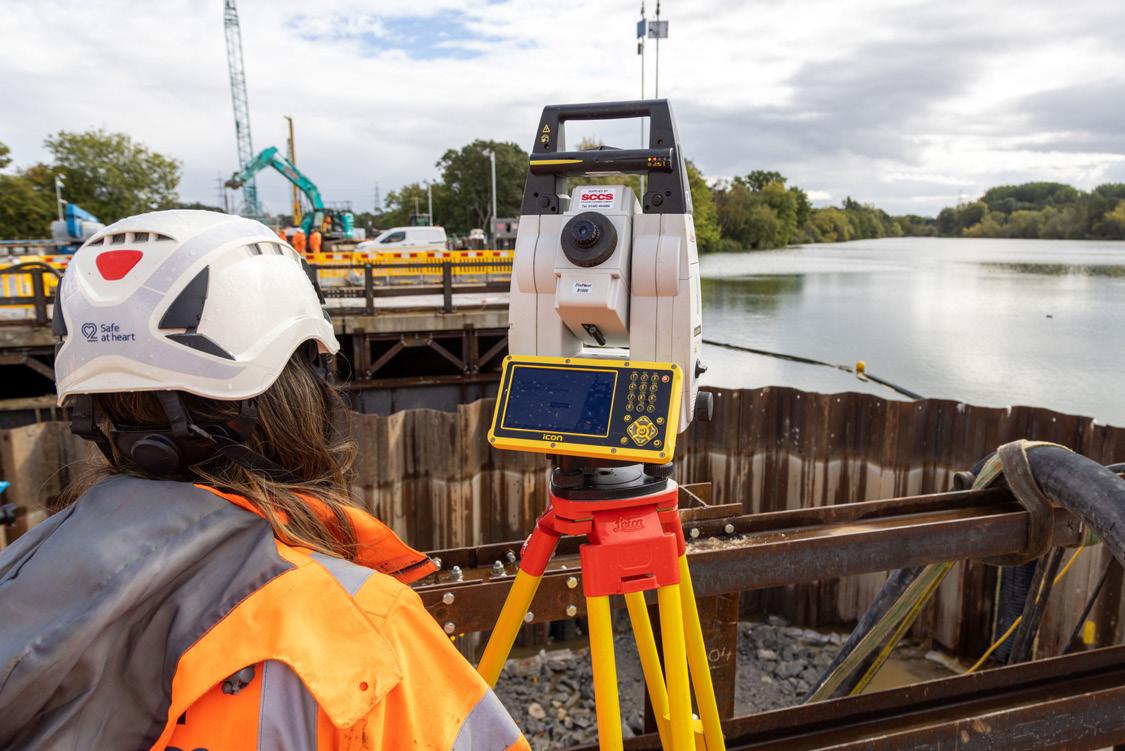
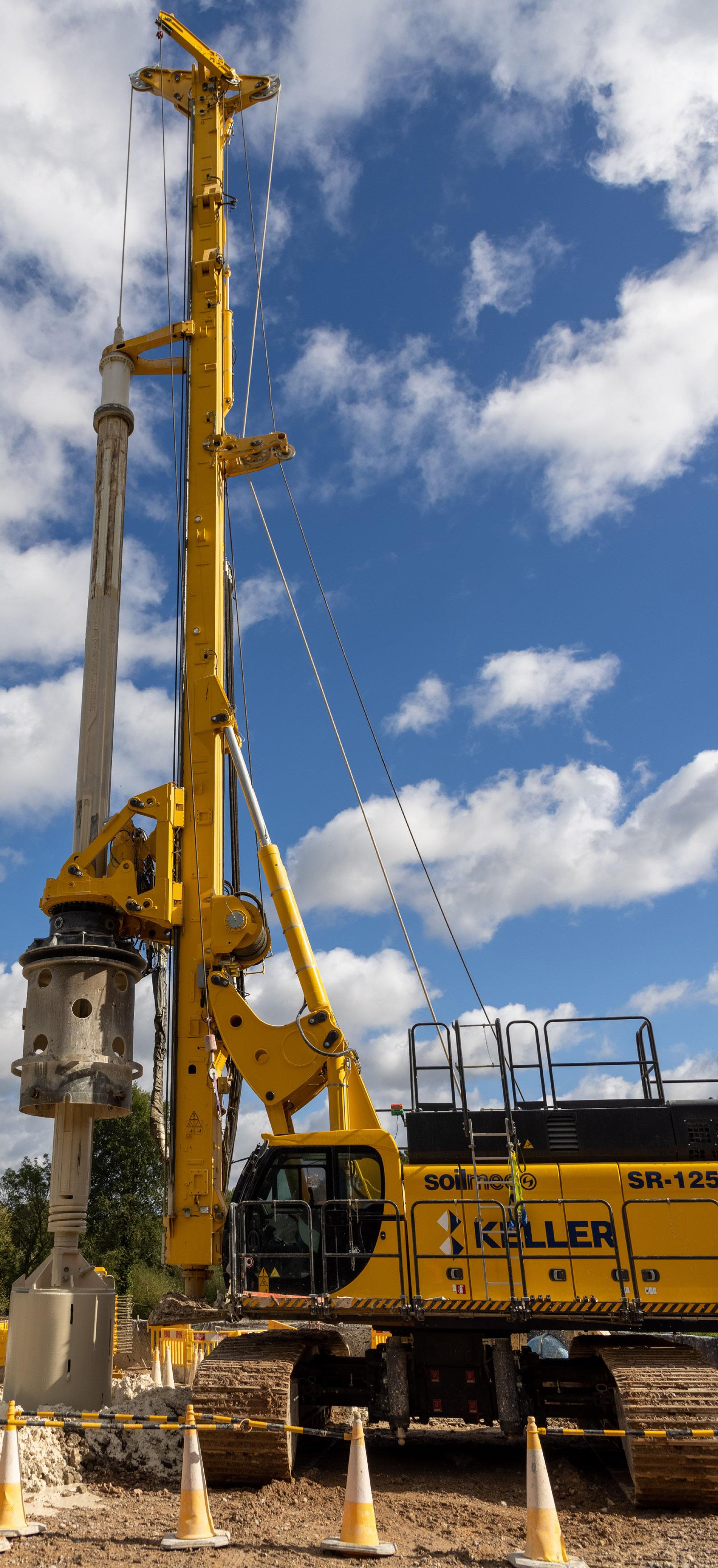
Segments are placed alternately on each side of the pier, using a cantilever approach to balance the structure, as two half-arches are constructed simultaneously. Steel tensioning cables are then threaded through the segments to strengthen the bridge.
The viaduct pre-cast factory where the one thousand segments are made uses a ‘match-casting’ technique. This approachwhere each segment is poured against the previous one – will ensure the whole deck fits perfectly when assembled on the piers. Up to twelve segments a week can be cast at the mammoth 100-metre long factory, which has an internal volume of 105,000 cubic metres – making it larger than the Royal Albert Hall.
Once construction is complete, the factory and surrounding buildings will be removed and the whole area between the viaduct and the Chiltern tunnel will be transformed into an area of chalk grassland and woodland as part of HS2’s ‘green corridor’ project.
RIA Annual Conference 2023
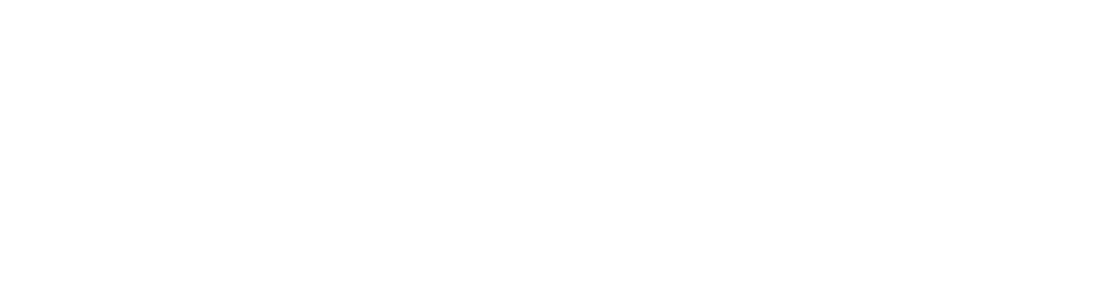
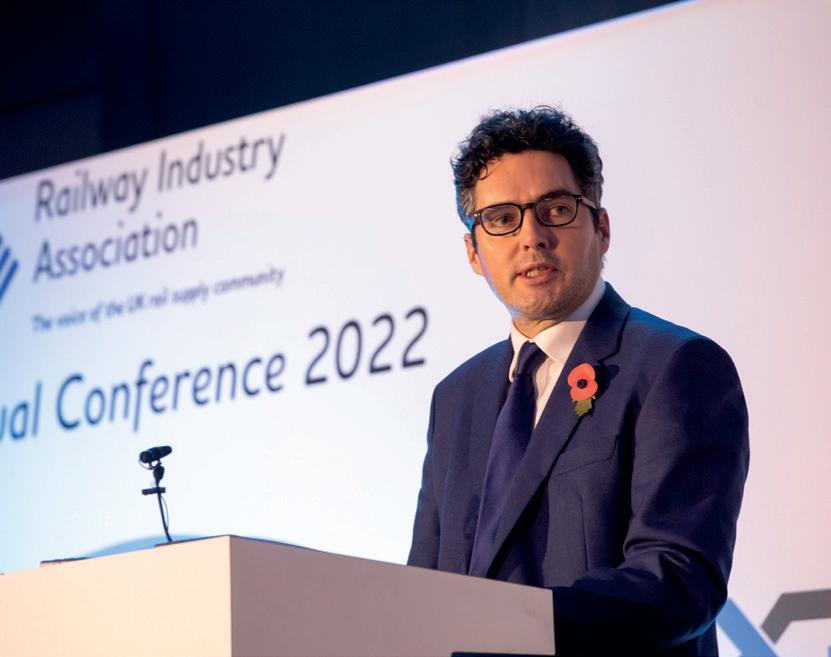
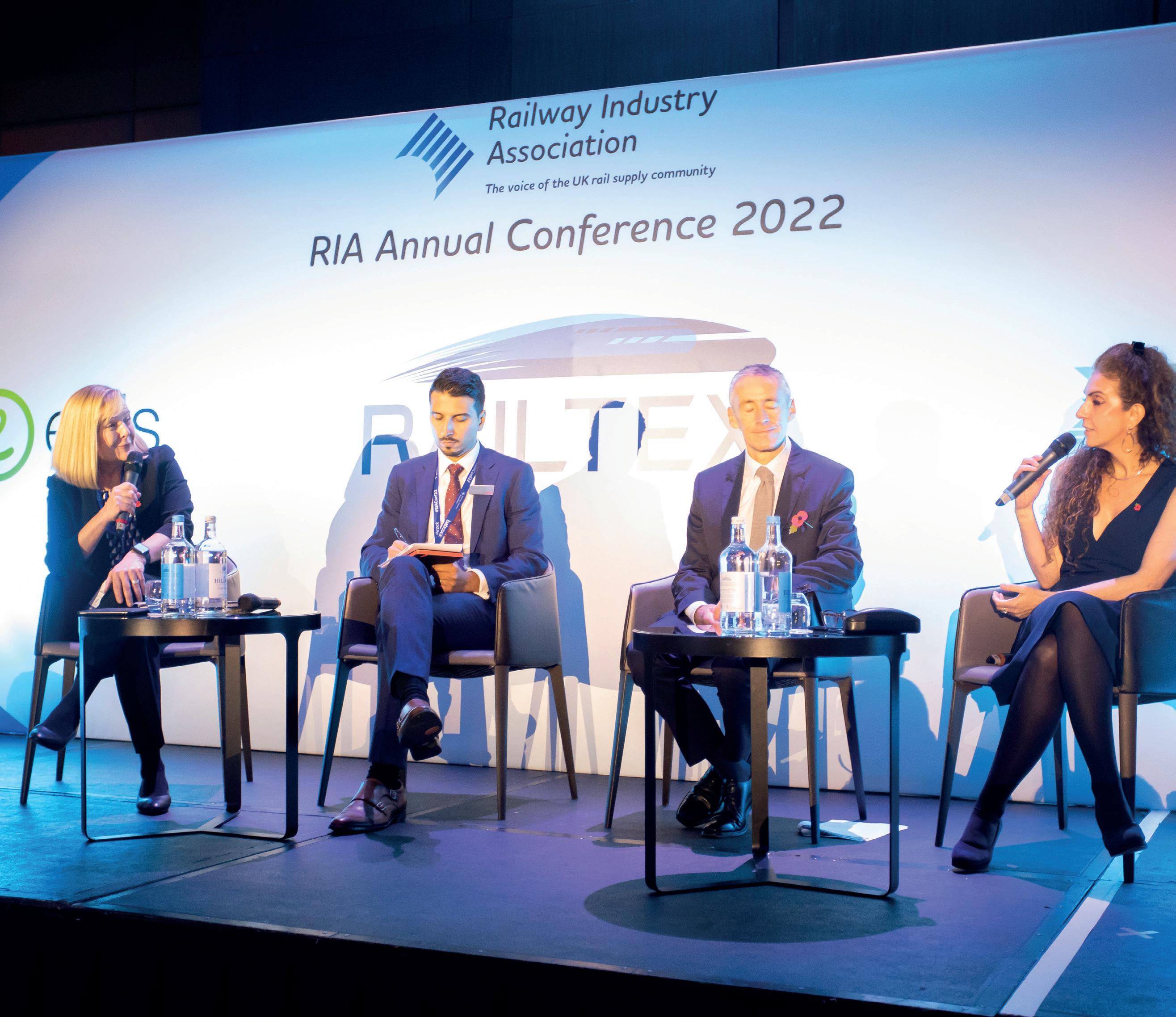
Promoting the case for rail and investment in uncertain times
1 and 2 November
Early Bird tickets now available!
2-day conference with inspiring keynotes, interview sessions and panel discussions
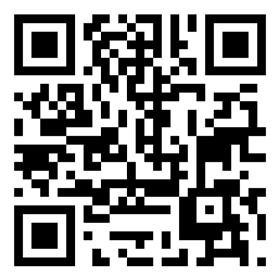
Large interactive exhibition area with spotlight pitches presenting services, products and solutions
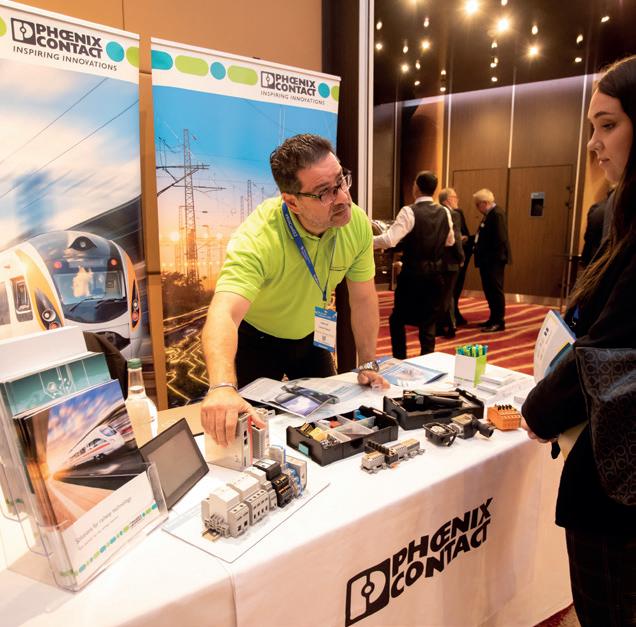
Evening programme including networking drinks, dinner and entertainment
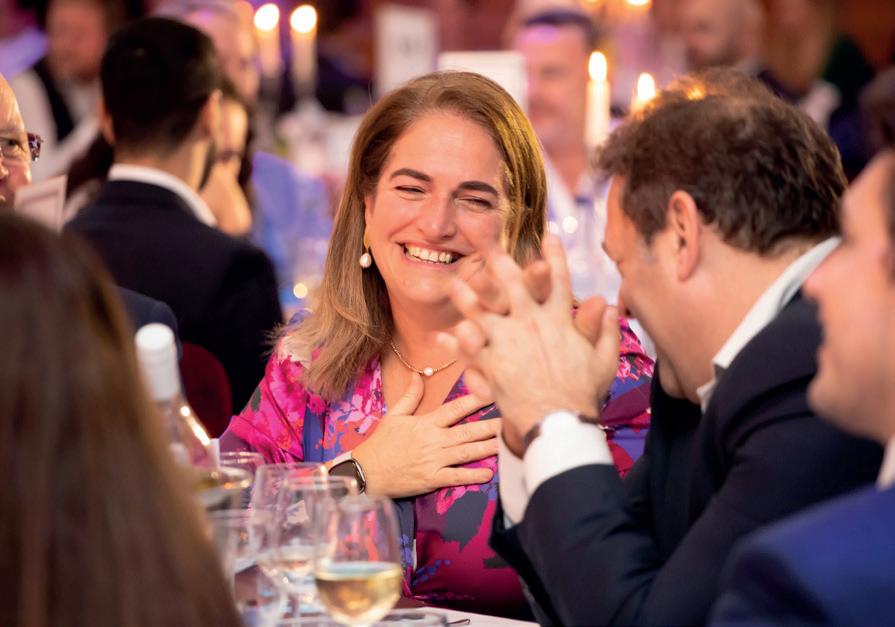
Going with the FLOW
Innovative ‘first-of-its-kind' railway footbridge opens to the public – replacing dangerous level crossing
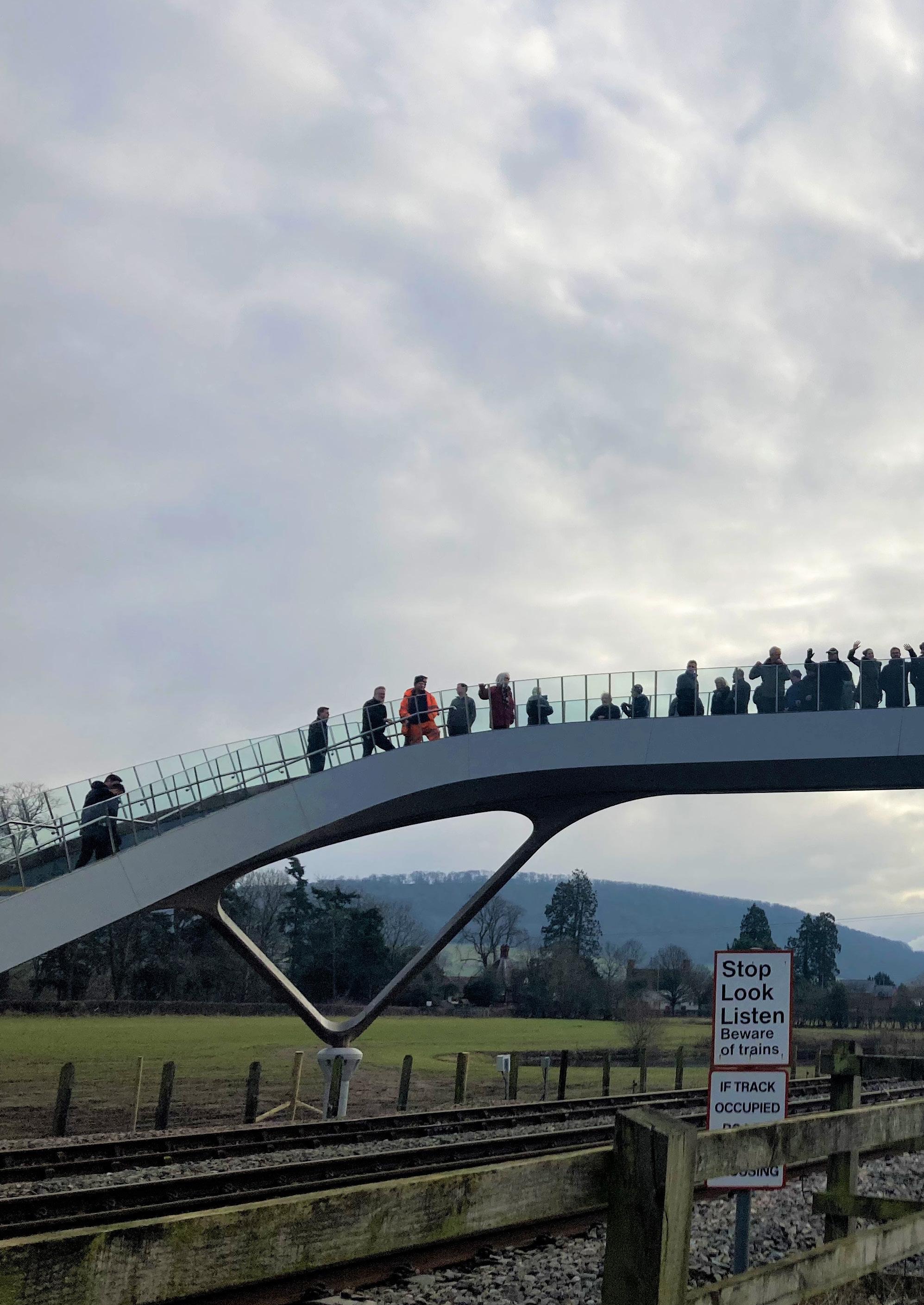
AShropshire village has had a major safety boost with the installation of a Network Rail designed eye-catching ‘FLOW’ bridge – a low carbon, lightweight and affordable safety solution.
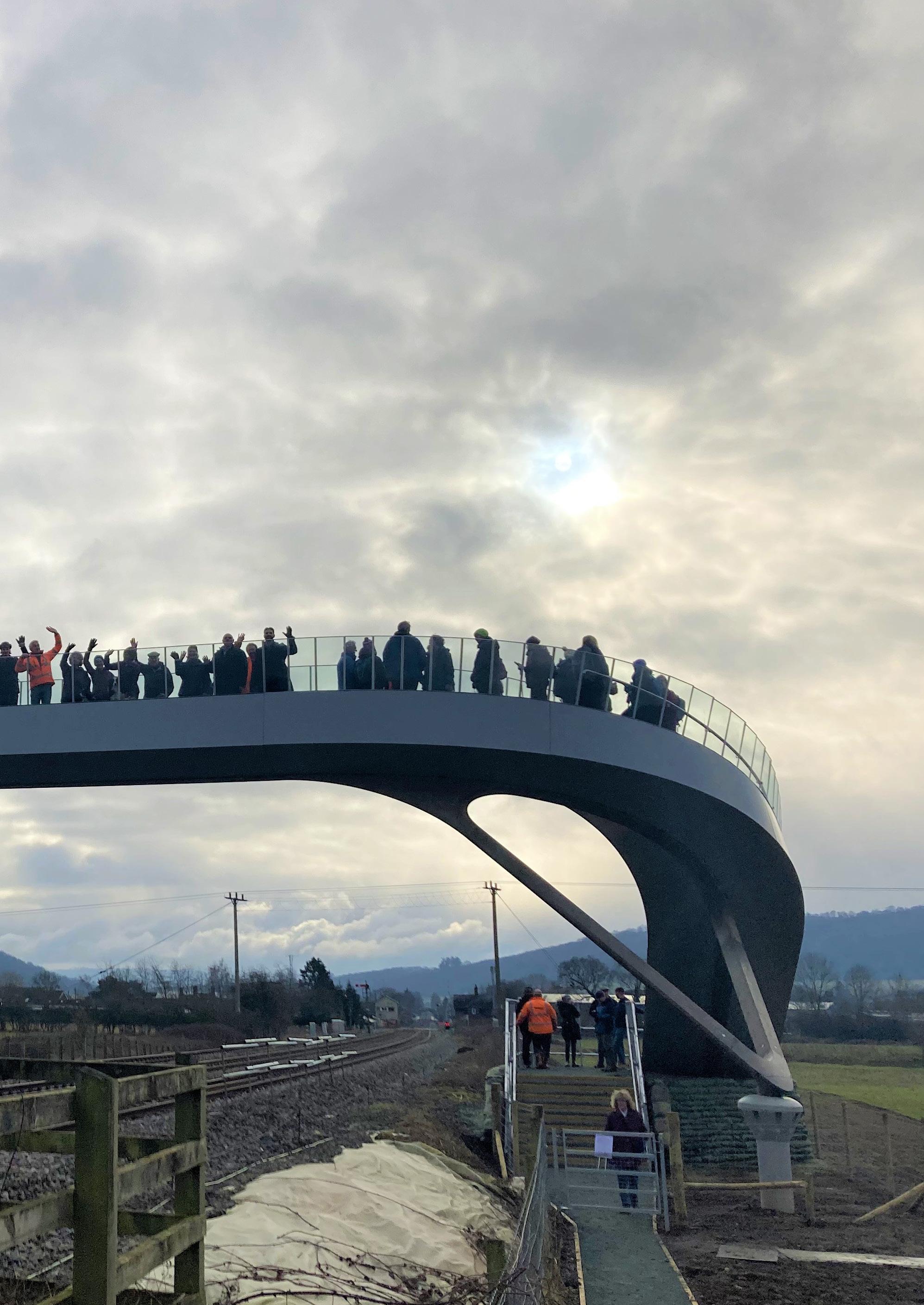
Designed and funded by Network Rail’s Research and Development (R&D) team, alongside leading industry specialists, the bridge aims to provide a faster, more sustainable, and affordable option to assist with the closure of dangerous railway foot crossings around the UK. The first location to benefit from the prototype is a rural crossing, just north of Craven Arms, in the Shropshire hills.
The footbridge replaces an extremely high-risk level crossing that closed a number of years ago after it was deemed unsafe for use. This was due to the position of the loop – the layby to the side of the main track – at this location, which prevented
pedestrians from having clear visibility of oncoming trains.
FLOW stands for fibre-reinforced polymer (FRP), lower cost, optimised design, working bridge, but the name also underpins its striking and modular design.
The 21-metre long bridge has been designed to save time and money – costing around 40 per cent less than traditional steel structures. No concrete is used in the foundations, reducing its carbon footprint, and it weighs half of a traditional steel bridge, meaning lower transportation and installation costs.
With the majority of construction taking place off site, installation is able to take place without disruption to passenger services.
The bridge is equipped with a real-time structural health monitoring system (SHM) which records how it performs, allowing future improvements to the design and
more efficient maintenance, as well as tracking its use.
Knight Architects was first appointed by Network Rail to develop a concept design in Spring 2020, and went on to develop the prototype with the wider team of specialists: Network Rail Design Delivery (NRDD) Jacobs, FoFlo, KS Composites, Sui Generis, Q-Railing, Rapid Root, Epsilon Optics, Sentry Systems and Mabey Bridge.
The team continues to work alongside Network Rail to develop ‘MK2’ of the system, which will include an updated stepped solution, as well as a wider range of ramped and lift configurations to suit a variety of sites. The team believe that ‘standardised design can be excellent design’. With a user-first ethos, the system incorporates a range of variability to see that it fits different site constraints, users and contexts.
Using composite materials
Knight Architects’ ‘Flow’ Bridge design uses modern composite materials which have numerous benefits – they are lightweight, cost-effective, and strong. They also offer a great deal of freedom in design – a widerange of forms are achievable. Given this flexibility, the team wanted to develop a solution which significantly enhanced the user experience of crossing the railway, starting first by thinking about people using the bridges, rather than the object itself. This approach is echoed in Network Rail’s ‘Principles of Good Design’ which sets out the ambitions for new structures across the network.
People first design
Network Rail’s bridges play a vital role as part of a holistic end-to-end passenger journey. They have to provide a safe crossing of the tracks, yet often the safety and security requirements of the railway can lead to bridges which are unwelcoming, and are seen as a negative part of the journey. Knight Architects subsequently developed the Flow Bridge concept, alongside the rest of the team, to focus on greatly improved user experience. It is designed to meet the required standards, whilst also creating a welcoming, enjoyable, and safe crossing for all.
Modular aesthetics
It is essential that any modular solution carefully considers the identity of the railway and also the identity of the specific sites in which the bridges will sit. Local stakeholders often view standardised solutions as insufficient, utilitarian and inward-looking – focusing only on the requirements of the rail, often at the expense of local objectives. The Flow Bridges are inherently outwardlooking. The crossings are designed to be assets within their communities, with each design taken as an opportunity to provide a beneficial, tangible link between the railway and the people which surround it.
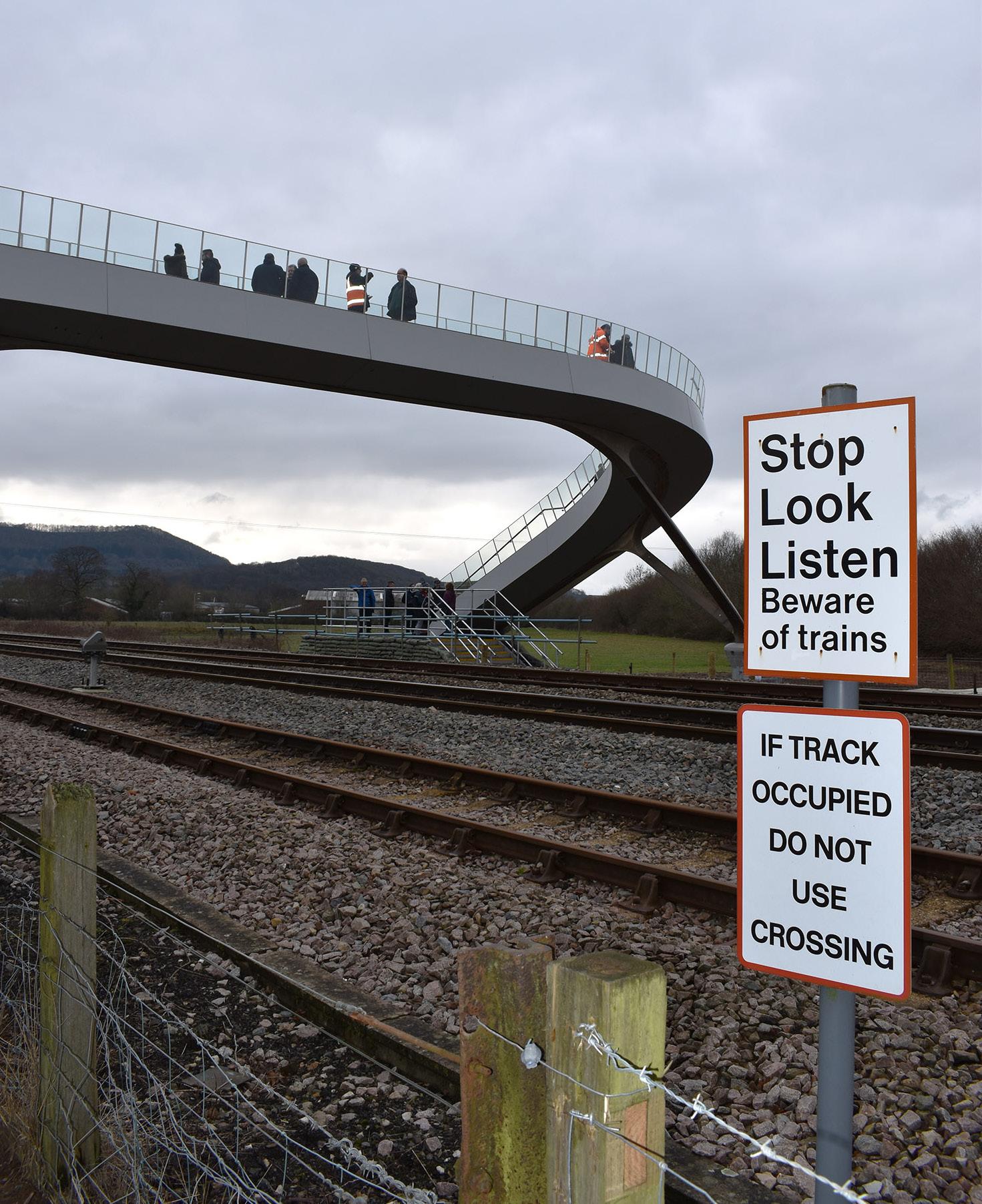
One of the key challenges for any ‘standard’ bridge solution is how one design can ‘fit’ a variety of sites. Standardisation is driven by consistency and repetition, yet good design traditionally seen as a specific response to context. The Flow Bridge addresses this with contemporary, refined forms paired with careful detailing and a ‘human-scale’, all driven through enhancing the user experience. The aim is to ensure that even the ‘base’ design offers an attractive, fitting and welcomed addition to new sites. To respond to the specific characteristics of a site, the system offers a wide-variety of configurations. These extend from geometric adaptability such as altering the span or width of the deck, through to texture, pattern and colour modifications all of which are readily achievable with composites. The Flow Bridges will demonstrate that by embedding variability into the system, and focusing on user experience, modular design can be good design.
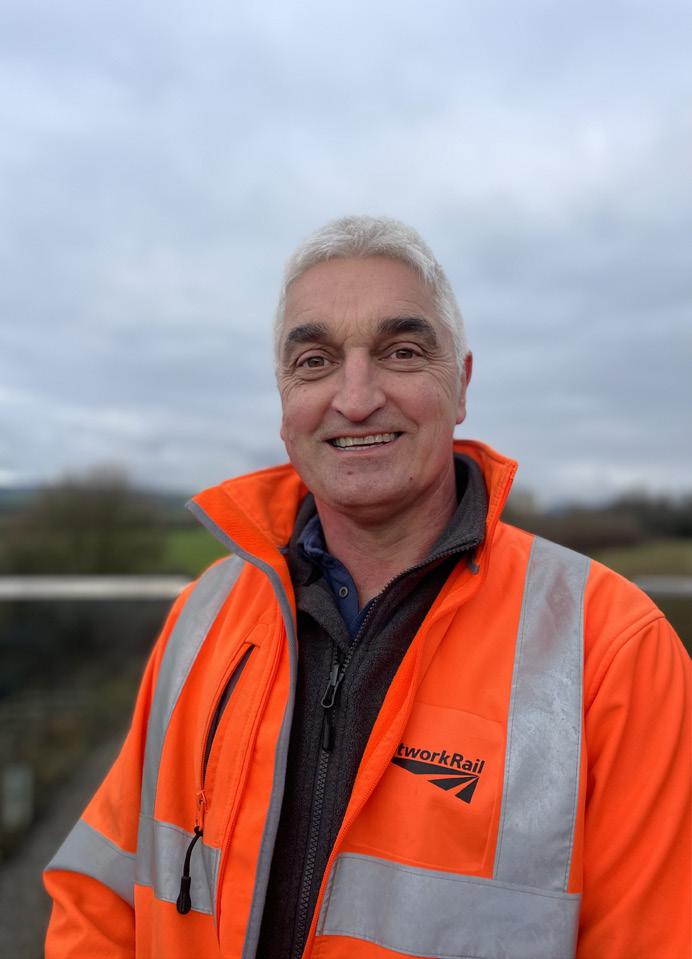
‘The flow bridge was designed, first and foremost, as a safety solution but our teams have also gone above and beyond to create a quicker and more sustainable option for the future of the railway. Its versatile design means we have already started looking at fully accessible versions, with lifts and ramps, for other locations where that would be a suitable option.’
Andy Cross, Programme Manager at Network Rail Wales and Borders
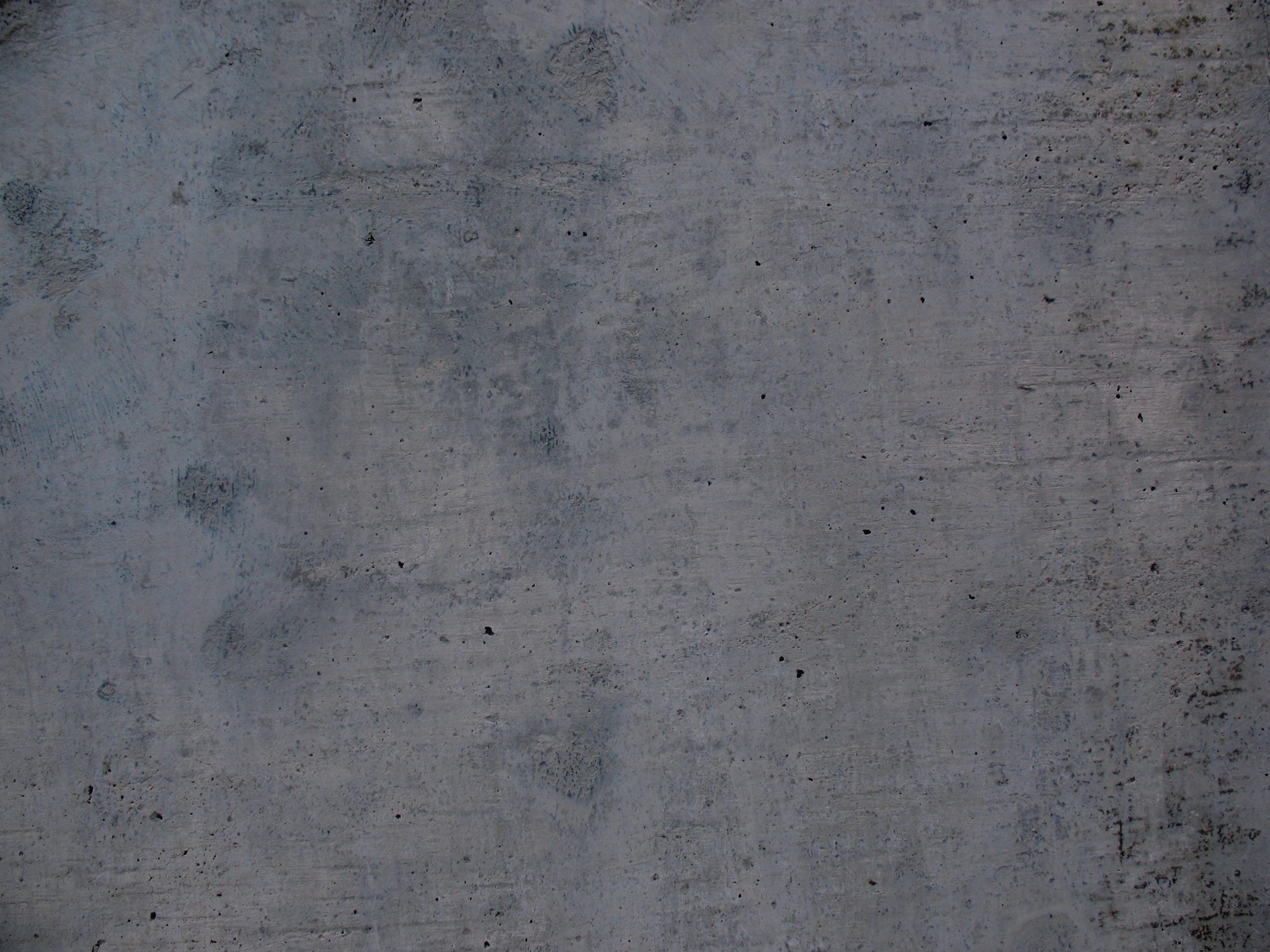

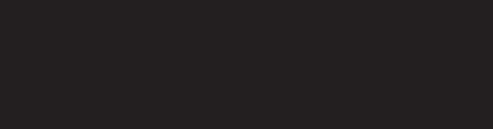
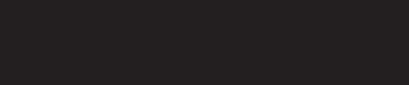
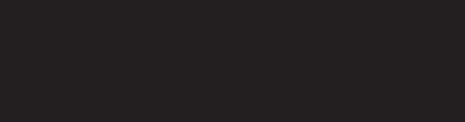




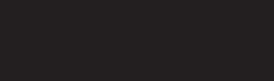

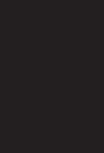
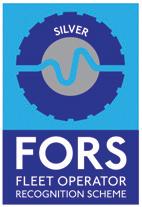


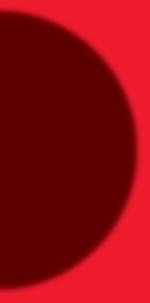
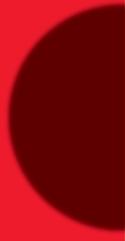

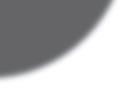

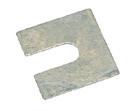




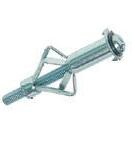
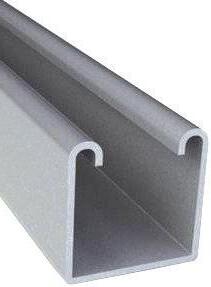


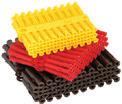


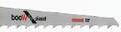
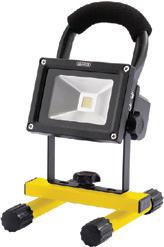
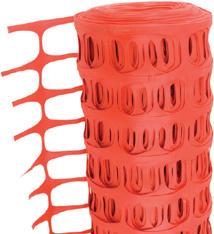
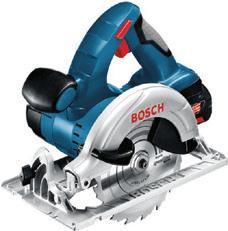
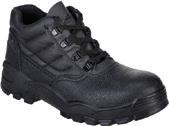
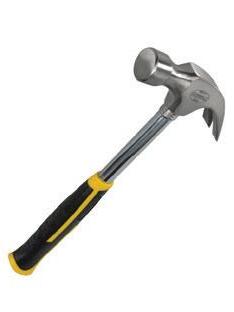

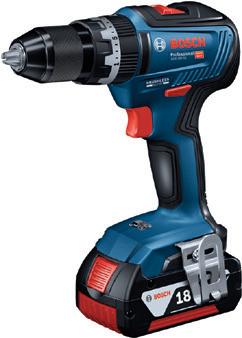
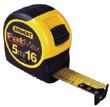
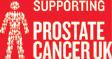
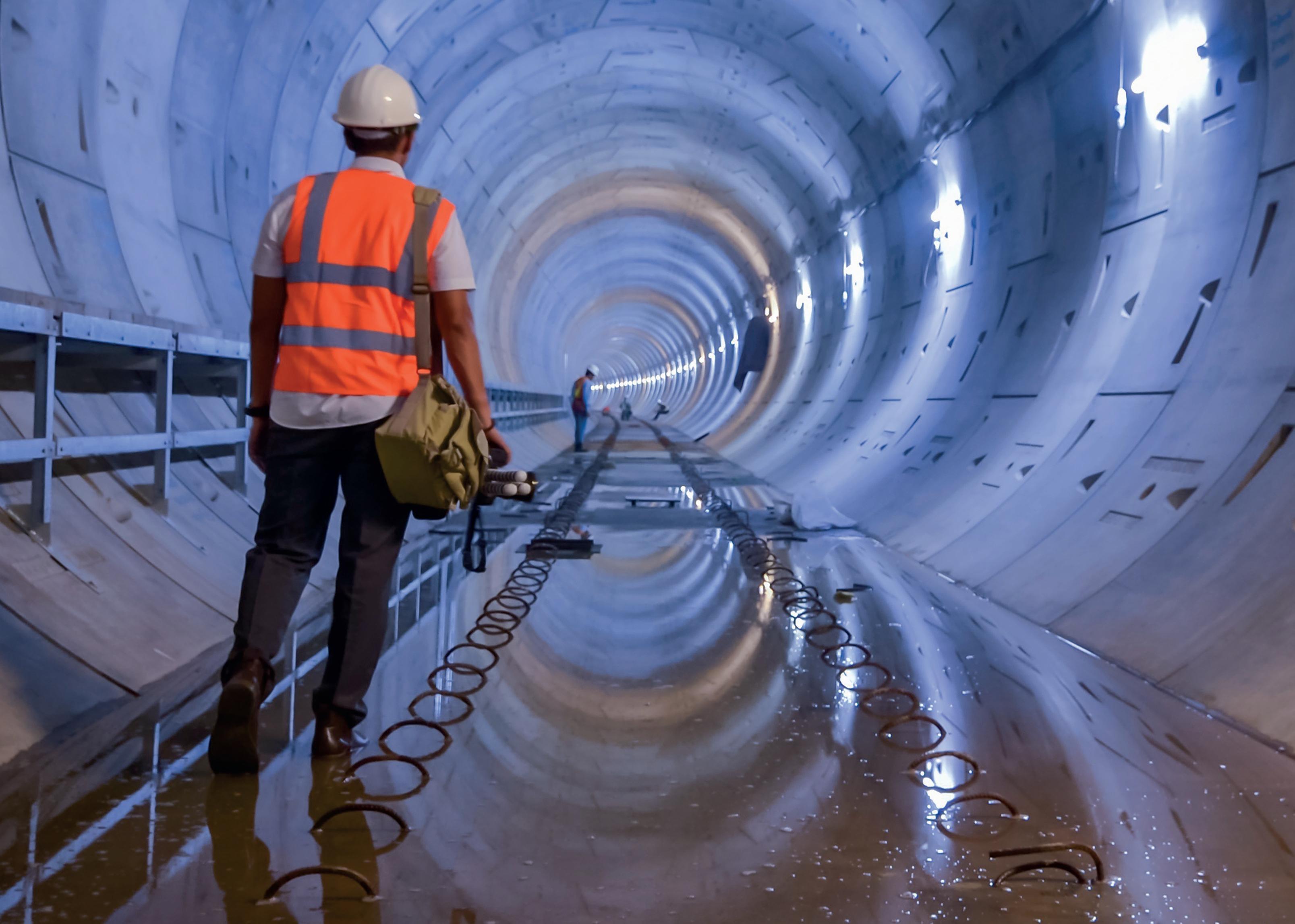
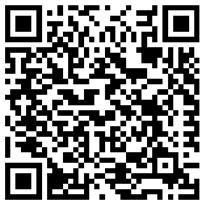
Key aspects of the design
Traditionally, ramps and stairs are positioned at 90 degrees to the main span which when combined with high-containment parapets creates a ‘blind corner’ to turn around. This creates an uncomfortable moment for users, unable to see who or what is around the corner. Smoothing this corner out is important, as it creates a much safer, more welcoming user experience. However, doing so can lengthen the bridge, pushing the stairs/ramps away from the rail fence line and clearance envelope. This increases the cost, material use, and the land required for crossings.
The Flow Bridge resolves this with the addition of a structural ‘spine’. Whilst the deck turns smoothly around the corner, the supporting spine remains orthogonally aligned to the railway. This ‘disconnect’ between spine and deck allows the deck to ‘flow’ around the corner, whilst maintaining a minimalistic structural footprint.
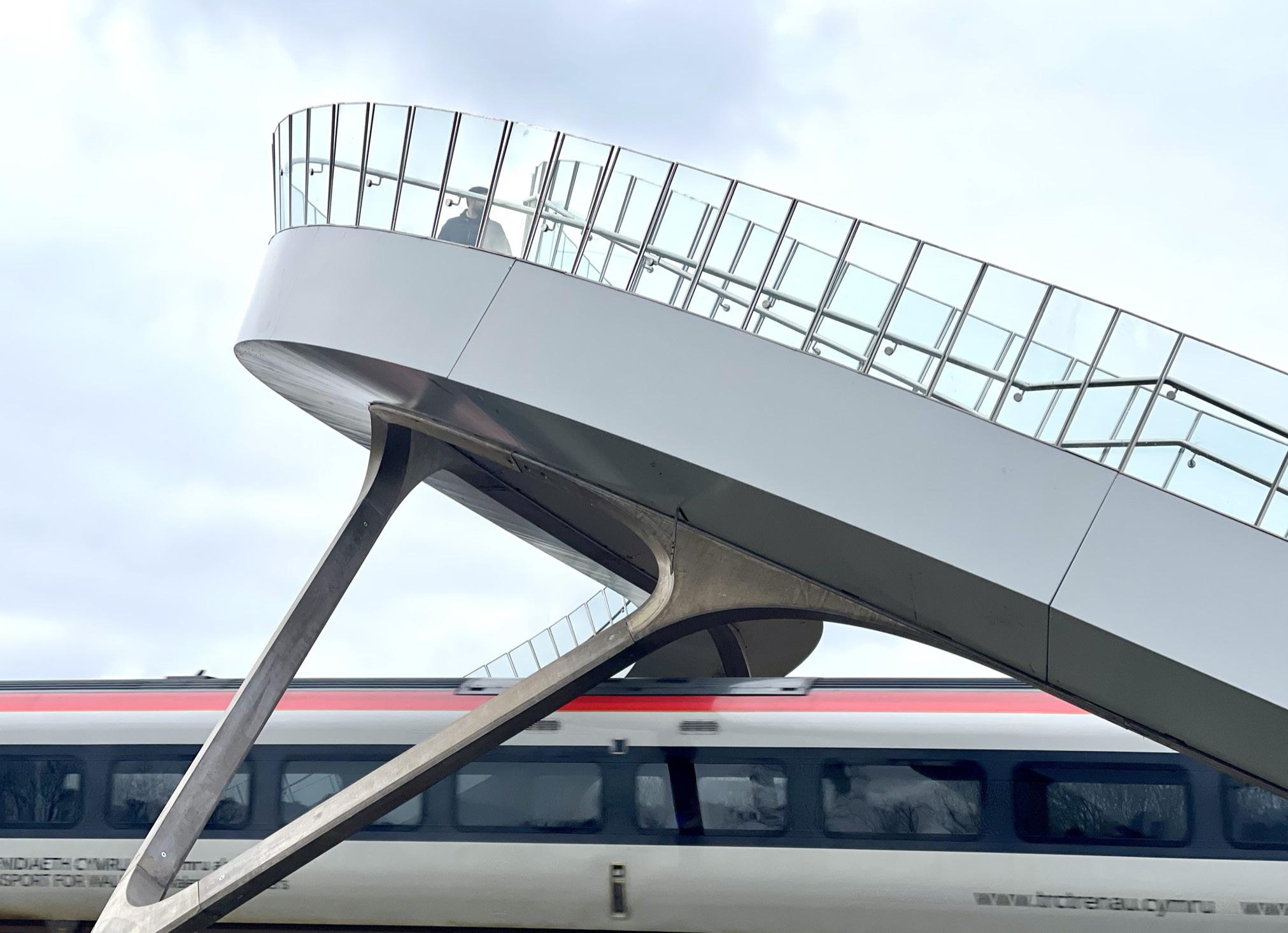
The addition of a spine also unlocks other benefits. On site, it allows deck modules to be lifted in incrementally, allowing for smaller, more manageable components to be transported and installed, or even replaced if necessary. It provides rigidity between deck modules, resulting in more
refined connections, and allows precise connection to the concrete-free ‘Rapid-Root’ foundation system.

The containment requirements of the railway often lead to solid, tall parapets, which create an oppressive, tunnel-like experience. The view from the structure is restricted, and the resulting enclosed space being poorly overlooked can even feel unsafe. In response to this, the team wanted to return bridges to being enjoyable ‘moments’ within a walk, opportunities to take in a new view, a vantage point from which to experience the surrounding environment.
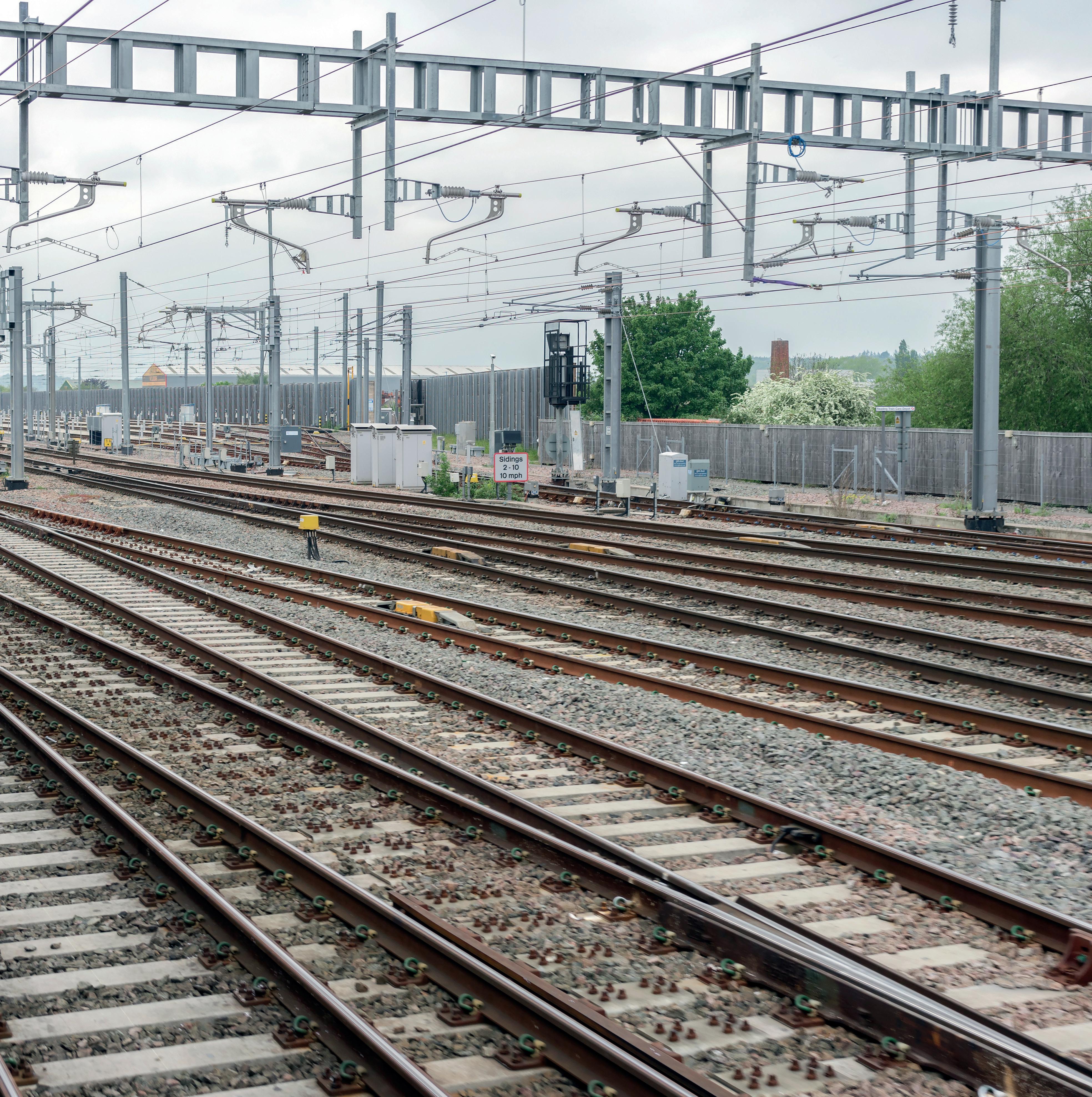
But this is also about safety – the view of the bridge is also opened up, and with more visibility of who is on the bridge, people can see their entire route before they embark upon it. Knowing that they can be seen on the bridge will make people feel safer when using it.
Opening up these views requires transparency, and so a glazed parapet system has been developed. At low level the composite material extends up above the deck, but only as far as is necessary from a structural standpoint. Beyond this, the containment is achieved through laminated frameless glazing, held by an aluminium channel; a system designed by Q-Railing.
The glazed element is one of the ‘variables’ of the scheme, with a multitude of options available to suit all site conditions. For example, a layered glass/composite solution has been developed to improve the glazing durability in sites particularly prone to vandalism.
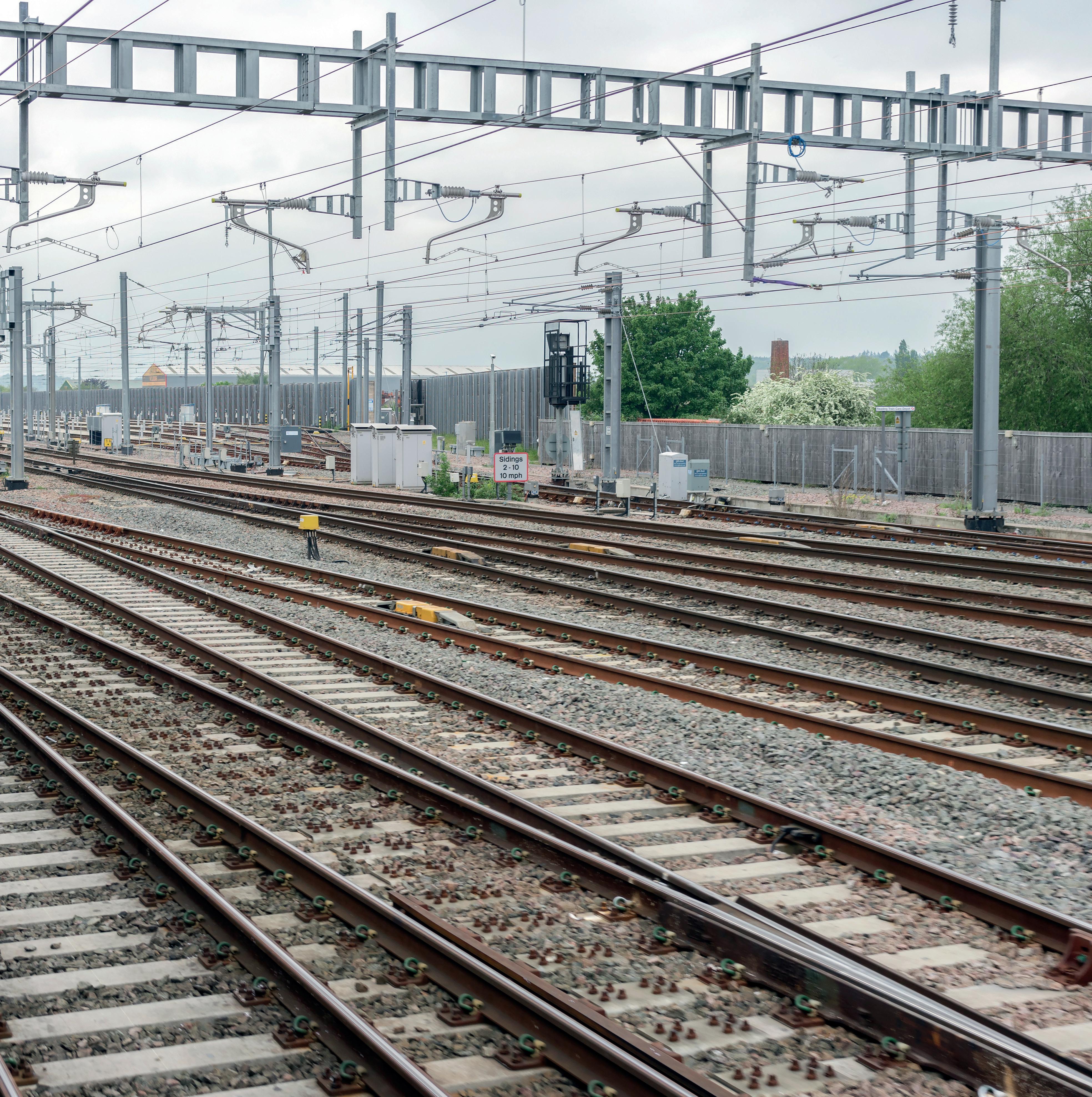

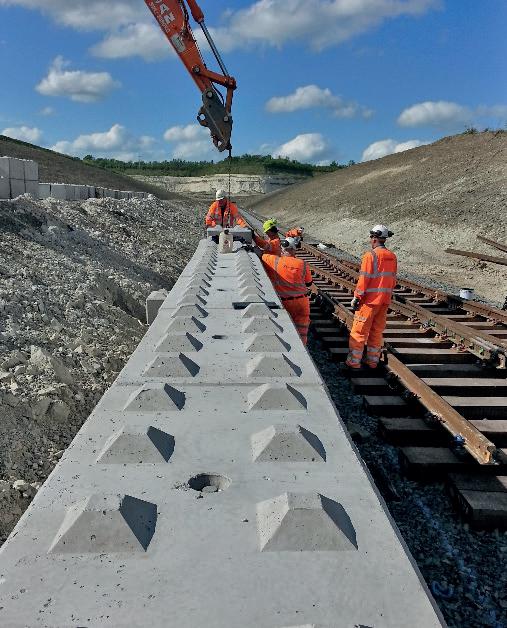

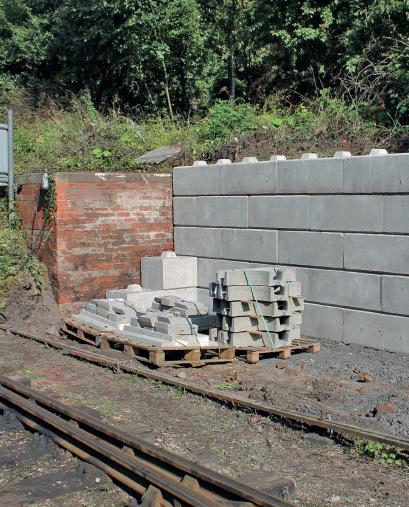



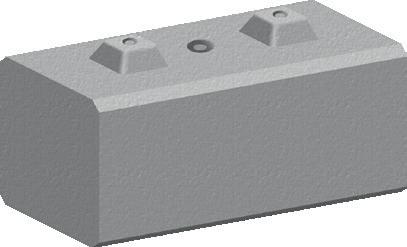
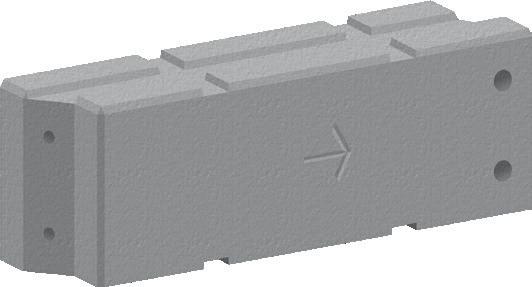
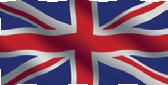
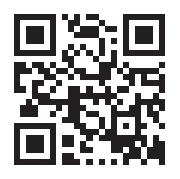
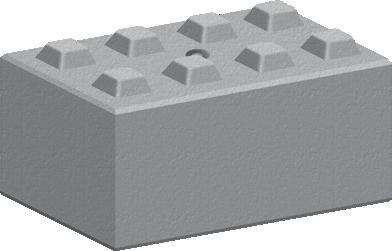
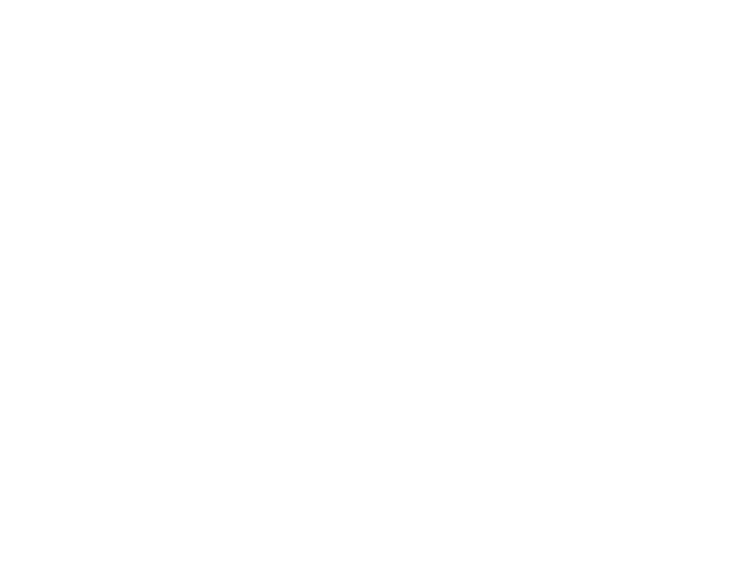

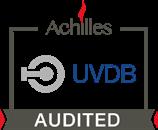

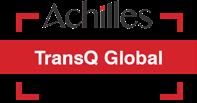


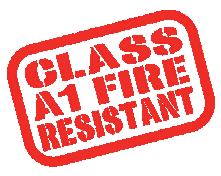
Kaymac has been a specialist in the rail industry since 1989. We are experts in delivering challenging marine civil engineering solutions while minimising disruption to rail services. When a rail track runs over a culvert, river, or watercourse, Kaymac are experts in temporary works design and installation, inspection, survey, repair, and protection of structures.
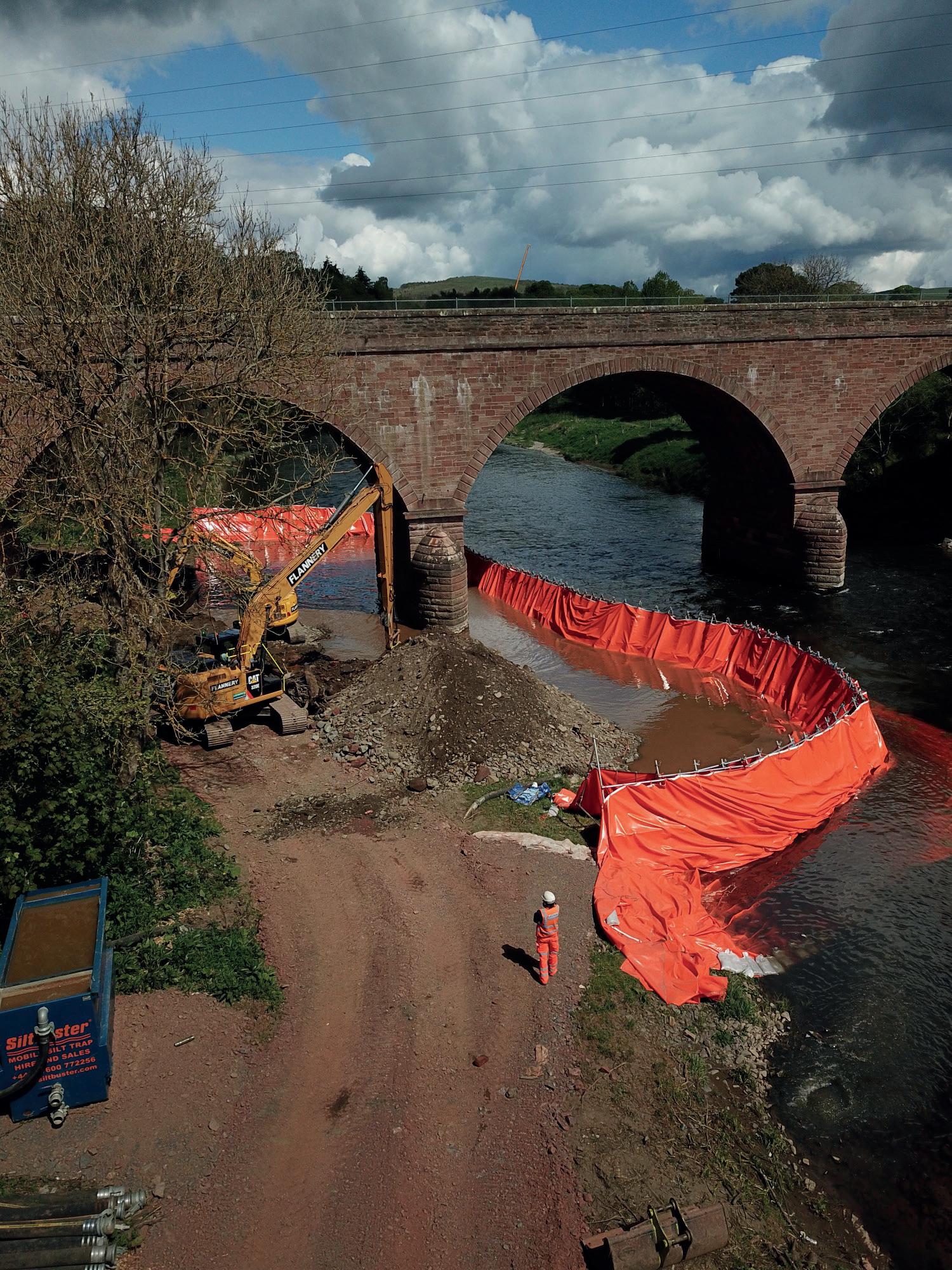
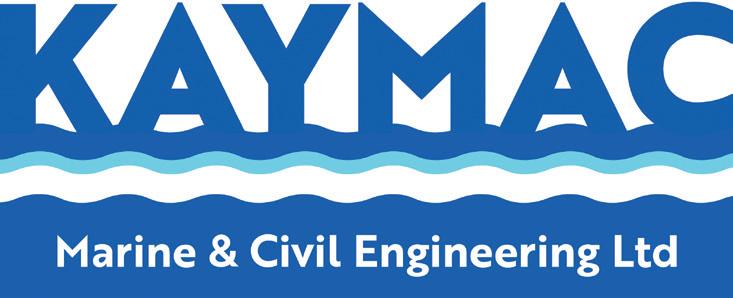

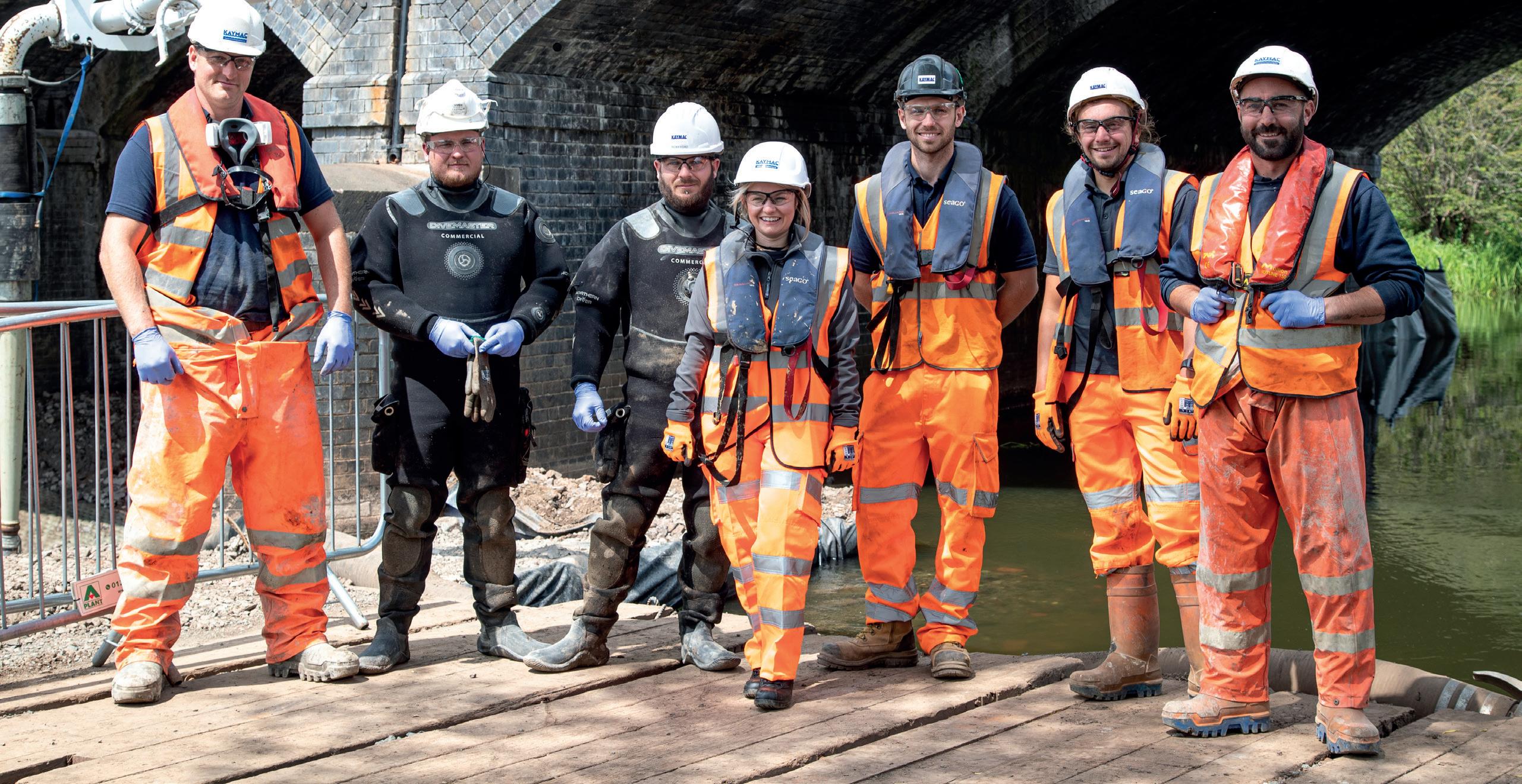
Scour repair and protection
Culvert repairs and re-lining
Fluvial erosion repairs
Commercial diving services

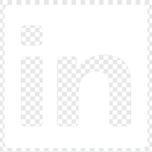
Confined space engineering
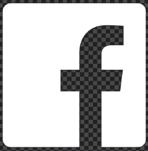
Connecting Communities
Specialist marine contractor delivers unique solutions for repairing and maintaining structures in water
turnkey solutions to construction challenges within watercourses. This has enabled Kaymac to integrate its offering, and work as a specialist subcontractor on larger schemes to Network Rail Tier 1 delivery partners as well as Principal Contractors.


In recent years, Kaymac has repaired and maintained some iconic bridges situated in tidal and fluvial environments. The Kaymac team have delivered complex scour protection projects that have involved temporary work designs, installations, and highly skilled, multidisciplined construction teams that include Commercial Divers, plant and skilled civils operatives to deliver the permanent scour repair and protection works within watercourses.
Going off track and winning awards
The structures within the rail network infrastructure; particularly rail bridges over water, are engineering marvels that have been connecting communities for centuries. These structures not only serve as vital transport links, but also showcase the creativity and ingenuity of the engineers who design and build them. However, the rail industry has challenges. One of the industry’s biggest obstacles is the need for infrastructure development and modernisation. As well as ageing infrastructure, climate change has also had a detrimental effect on inland and coastal rail infrastructure. Many railways in the UK require significant investment to upgrade and maintain them properly.
Kaymac Marine and Civil Engineering Ltd. has made it its business to deliver water infrastructure solutions in ways which minimise disruption to rail services. Demonstrating its continued commitment to being at the forefront of developments in this discipline, Kaymac has sourced and trialled new technologies and innovative methods to ensure that it has the most productive and effective ways of managing transport projects, even highly regulated and time-sensitive ones. Kaymac guarantees the best results for clients whilst reducing downtime for users.
Multidisciplined team
Over the years Kaymac has grown significantly and now delivers multidisciplined schemes across waterway infrastructure and the UK rail network. Due to its experience and expertise in controlling water flow, Kaymac can deliver unique
Kaymac is not just a rail engineering specialist and has an equally impressive portfolio of work and clients in civil engineering, coastal and inland waterways, confined space services and diving operations. To give an indication of how diverse and specialised its areas of expertise are here are a couple of examples of awardwinning projects outside of rail engineering. On the coastal engineering front and energy sector, Kaymac was contracted to install a
fish deterrent system at Pembroke Power Station in West Wales, which is the biggest gas-powered power station in Europe, it received an award for ‘Excellence’ and a plaque to commemorate the inauguration of the power station.
The Swansea Tawe Barrage project comprised of scour protection for the quay wall above and below the waterline, refurbishing the main barrage lock gates and installation of new post and rail fencing. The work was undertaken with a multidisciplined approach and was completed on schedule and within budget, which resulted in Kaymac winning a prestigious ‘Best Project’ award in 2019. In 2021, following the unprecedented flood conditions experienced, structures across the UK’s watercourses had been left in dilapidated states, with asset owners determining whether repairs can be undertaken safely,
or in some cases whether a full structural demolition is required.
The Grade II listed structure at Escob West was such a structure earmarked for demolition before Kaymac was given another great opportunity to showcase its innovative approach to solving complex inwater engineering problems. Kaymac saved the bridge with a creative temporary works and repair solution that saw them win the National Bridges Awards 2021 Category: The Bridges Award for New Life – Project Below £5 million. Most recently, Kaymac won a Team100 award for quality for its involvement in the pintle replacement on the £34 million flood defence scheme at Tilbury Docks.
The future is bright
Kaymac will continue to offer turnkey innovative marine civil engineering

KAYMAC’S SPECIALIST SERVICES
• Scour protection.
• Culvert repairs and relining.
• Confined space engineering.
• Repair of timber structures.
• Concrete repairs and bridge strengthening.
• Commercial diving operations.
• Design and installation of floating access systems.
• Flood alleviation.
• Design and installation of temporary works within watercourses.

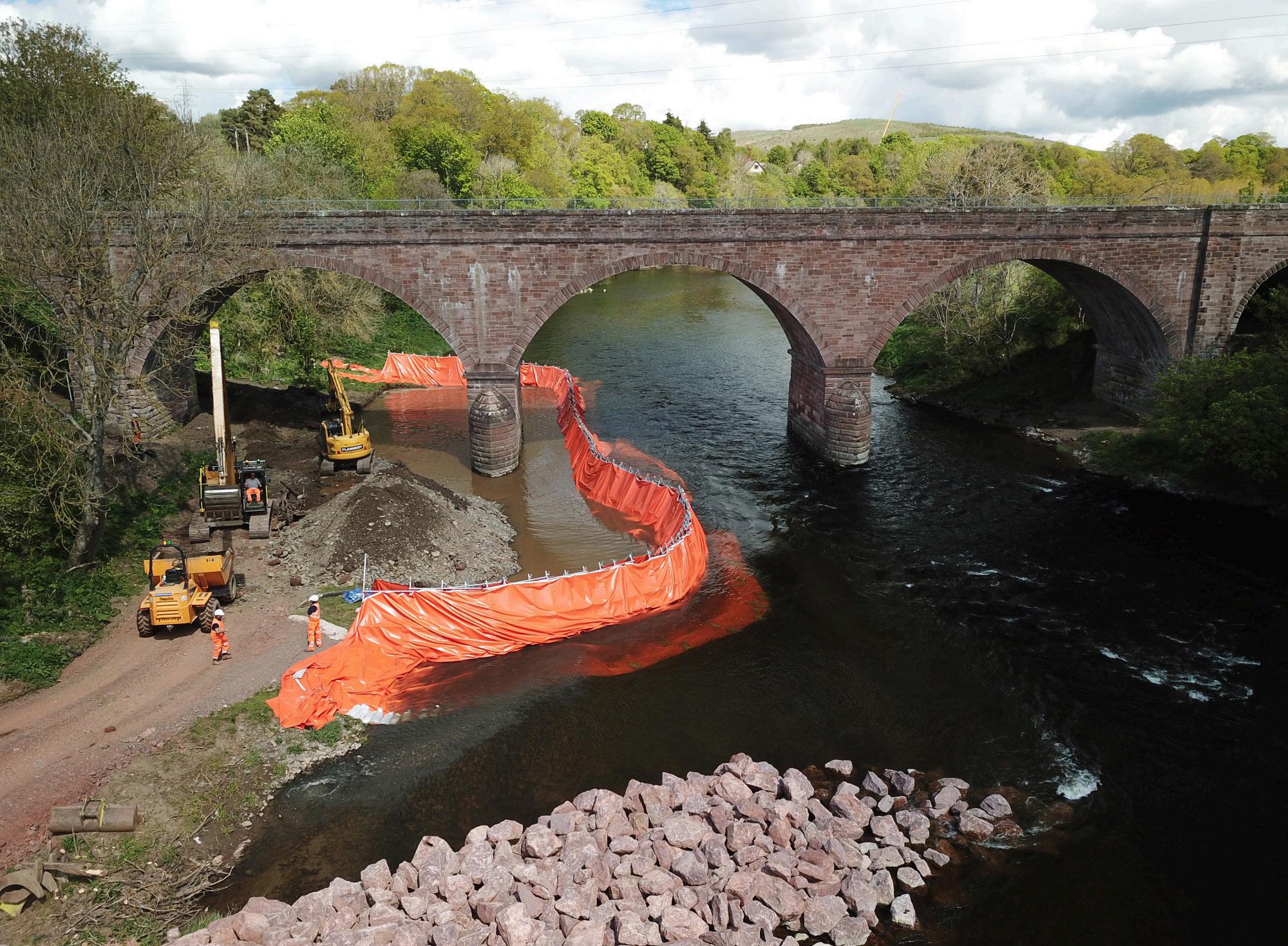
• Inspections and survey.
solutions to Private and Public sector clients UK Nationwide. The company recently secured its place on Lot 10. Of the £1 billion South West Wales Regional Civil Engineering Framework which has secured a healthy pipeline of work over the next four years.
Rhiannon Crees-Moore, Business Development Director, Kaymac Marine & Civil Engineering Ltd: ‘Out of the five contractors that tendered for the Lot. 10, there were just two successful bids; We are extremely proud of the hard work and dedication that has gone into this achievement, and we couldn’t have done it without the support of our amazing team. As a first-generation framework contractor, we have had the privilege of working with some incredible clients over the years, and we are grateful for the strong relationships we have built with them. We look forward to continuing these partnerships and providing exceptional service and support to our clients. At our core, we are committed to delivering excellence in everything we do, and this latest contract win is a testament to our unwavering commitment to quality and customer satisfaction.’
Following the UK fisheries embargo, construction work In Salomon Rivers will commence in April and continue through to October, and Kaymac is very much looking forward to another exciting summer delivering high-profile scour protection projects in collaboration with Network Rail Tier 1. Contractors and Consultants.
As well as project delivery, Kaymac will be exhibiting at the Flood and Coast Exhibition at Telford International Centre on the 6, 7 and 8 June.
Tel: 01792 301818
Email: enquiries@kaymacltd.co.uk
Visit: www.kaymacmarine.co.uk
TENSOREX C+: Spring Automatic Tensoning Device

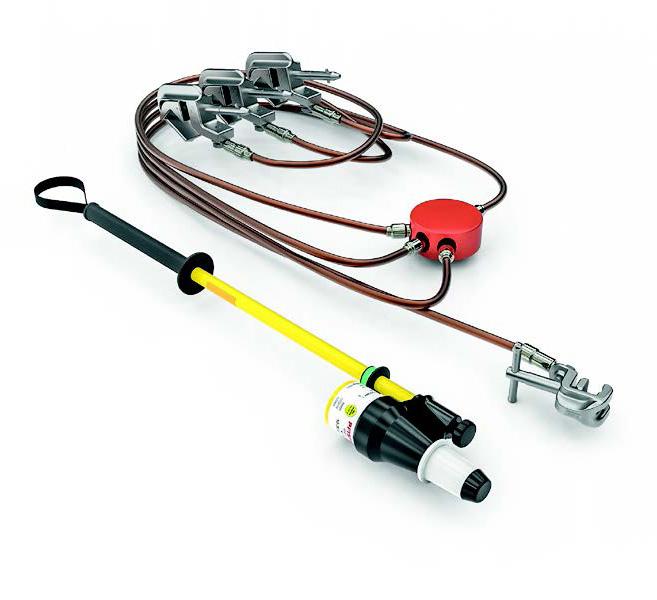
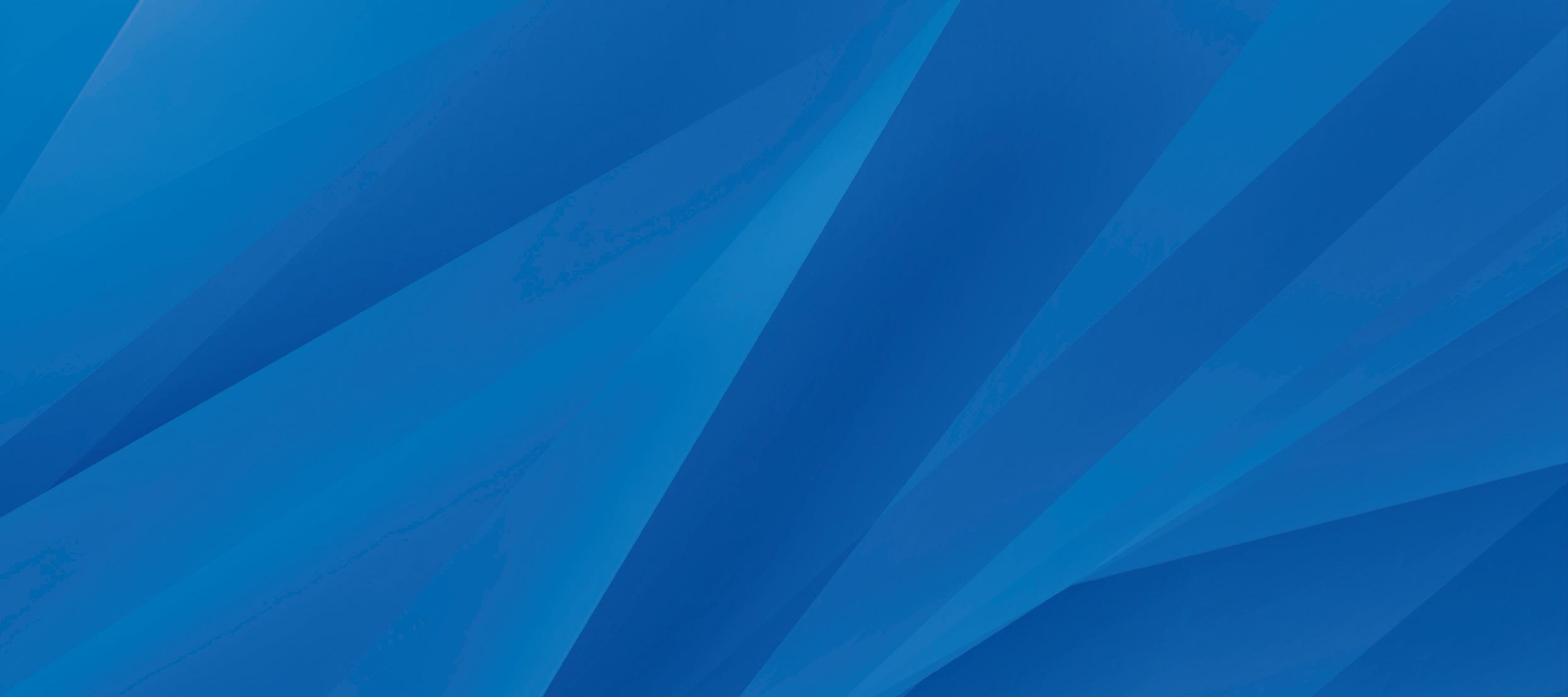
RAILWAY INFRASTRUCTURE SOLUTIONS
FOR TODAY´S AND FUTURE CHALLENGES
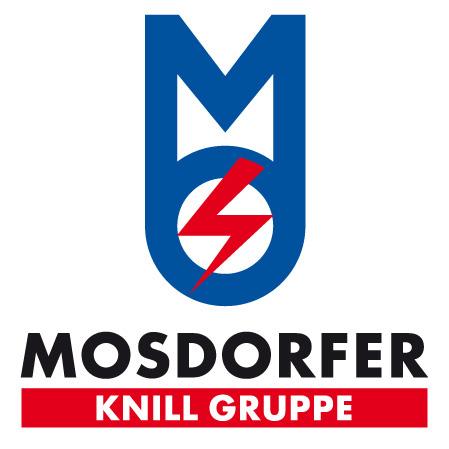
Insulators
Safety Equipment
Bonding Connectors


Catenary Clamps

Droppers

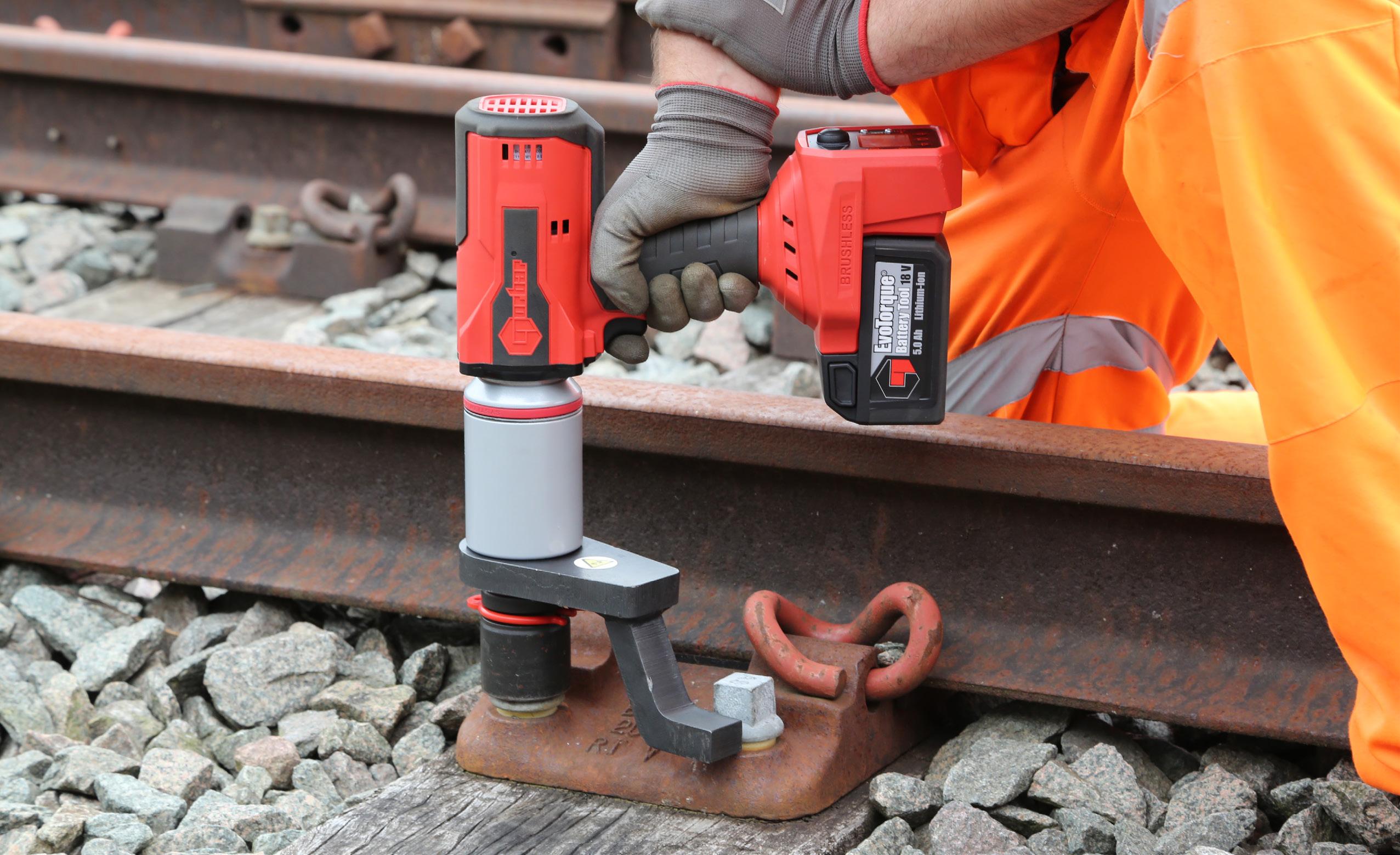
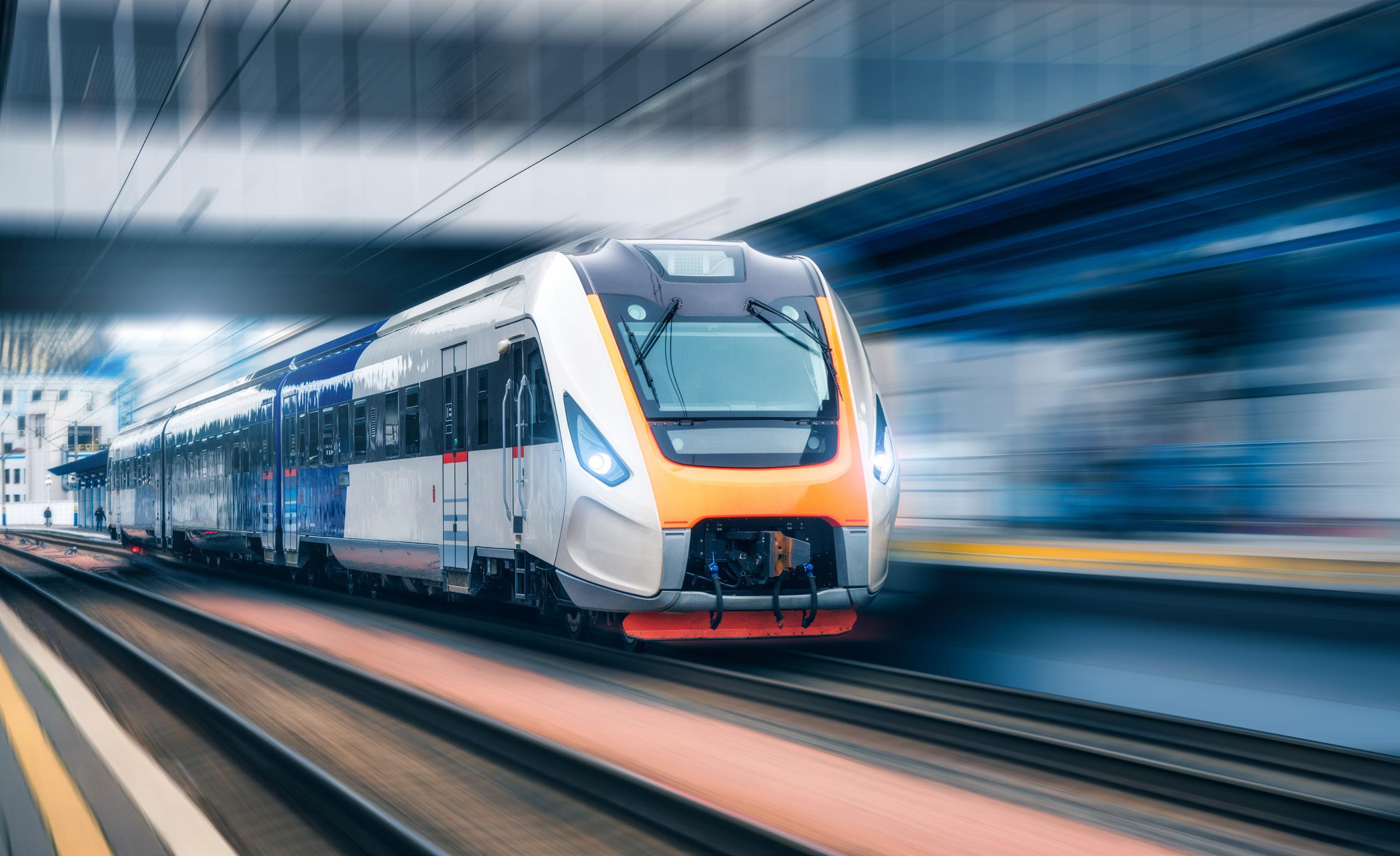
Q&A with Marco van der Linden
Country Sales Manager at PULS UK Ltd
For the last six years Marco has been heading up PULS UK Ltd as the Country Sales Manager. PULS UK is part of PULS Power a privately owned German manufacturer. Under Marco’s leadership PULS UK has received several Business and Industry Excellence awards.
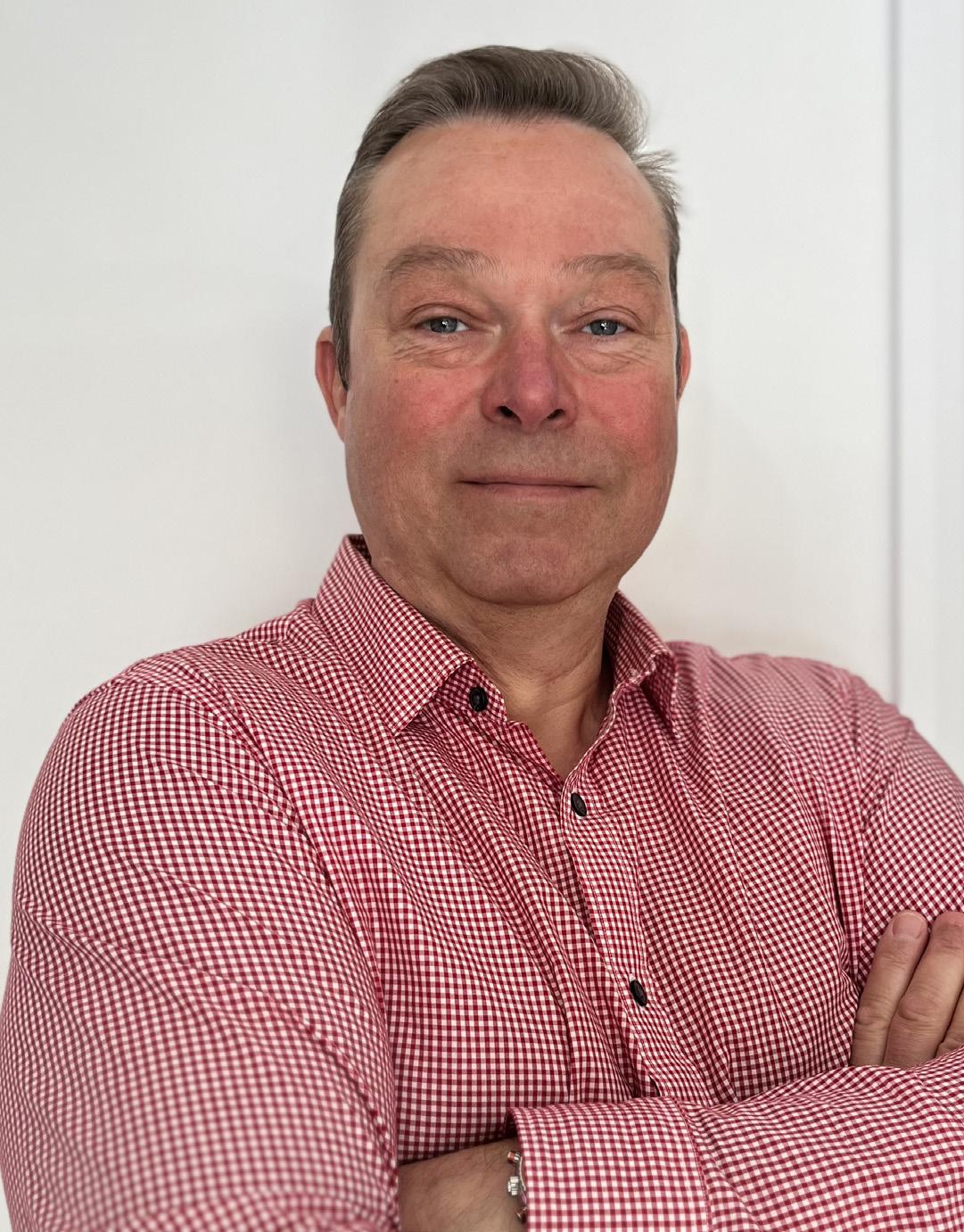
What is your role within PULS UK Ltd?
I am the Country Sales Manager at PULS UK but I have a much broader remit in that I oversee the entire UK operation. I have been with PULS since 2016 and I manage the day to day running of the company. I wear many hats and my role includes strategic planning, P&L, sales and marketing, recruitment and staff management and much more.
Another area that has become a focus is import and export, especially since Brexit. We have a UK warehouse and we import stock from our PULS manufacturing facilities. We distribute these products within the UK but we also export to the Republic of Ireland and this requires me to liaise with customs and excise to make sure our products arrive into the UK in a timely fashion.
My job is very dynamic and I don’t have a typical business day which is really exciting.
Tell us about PULS UK Ltd?
PULS UK is a subsidiary of PULS GmbH which is part of the PULS POWER Group. PULS was founded by Bernhard Erdl in Germany in 1980. PULS UK is based in Cranfield and has been in the UK since 2012.
We have a sales team covering the UK and Ireland. Our sales team work closely with customers, either over the phone/ via video call or face to face, to better understand
the customers’ needs and offer applicationspecific advice. Our team is highly trained and will review the customer’s requirements to ensure they have the product solution that’s right for them. Where necessary, they will advise customers on alternative solutions which are often more efficient in terms of cost, energy or space-saving. We offer UK based technical support from design-in stage to improving and modernising existing applications. We also hold stock here in the UK which is a huge benefit to our customer as we are able to fulfil the majority of orders from locally held stock within 24 hours.
What sectors do you work in?
We cover a wide range of markets and supply any industry where power needs to be converted from AC to DC or DC to DC. In the UK we are particularly strong in Rail (trackside and rolling stock), Panel Building and Renewable Energy. Our products are particularly suited to the Rail industry because they have very high reliability. Our products have been chosen by Network Rail as the preferred power supply to use in trackside applications. There certificates are available, for all the PULS power supplies approved by Network Rail, and can be found on their website. We also supply a selection of EN50155 certified power supplies for rolling stock.
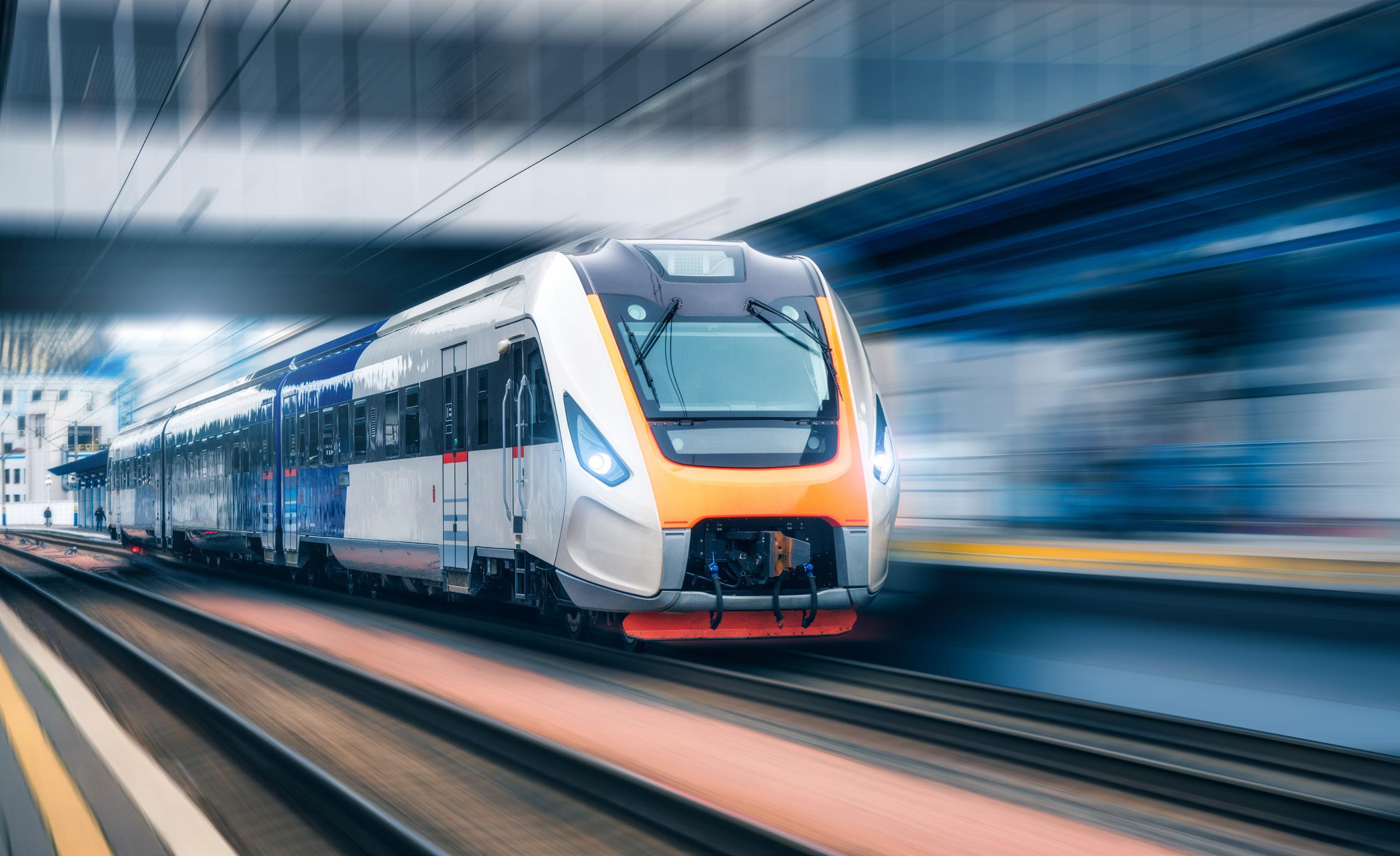
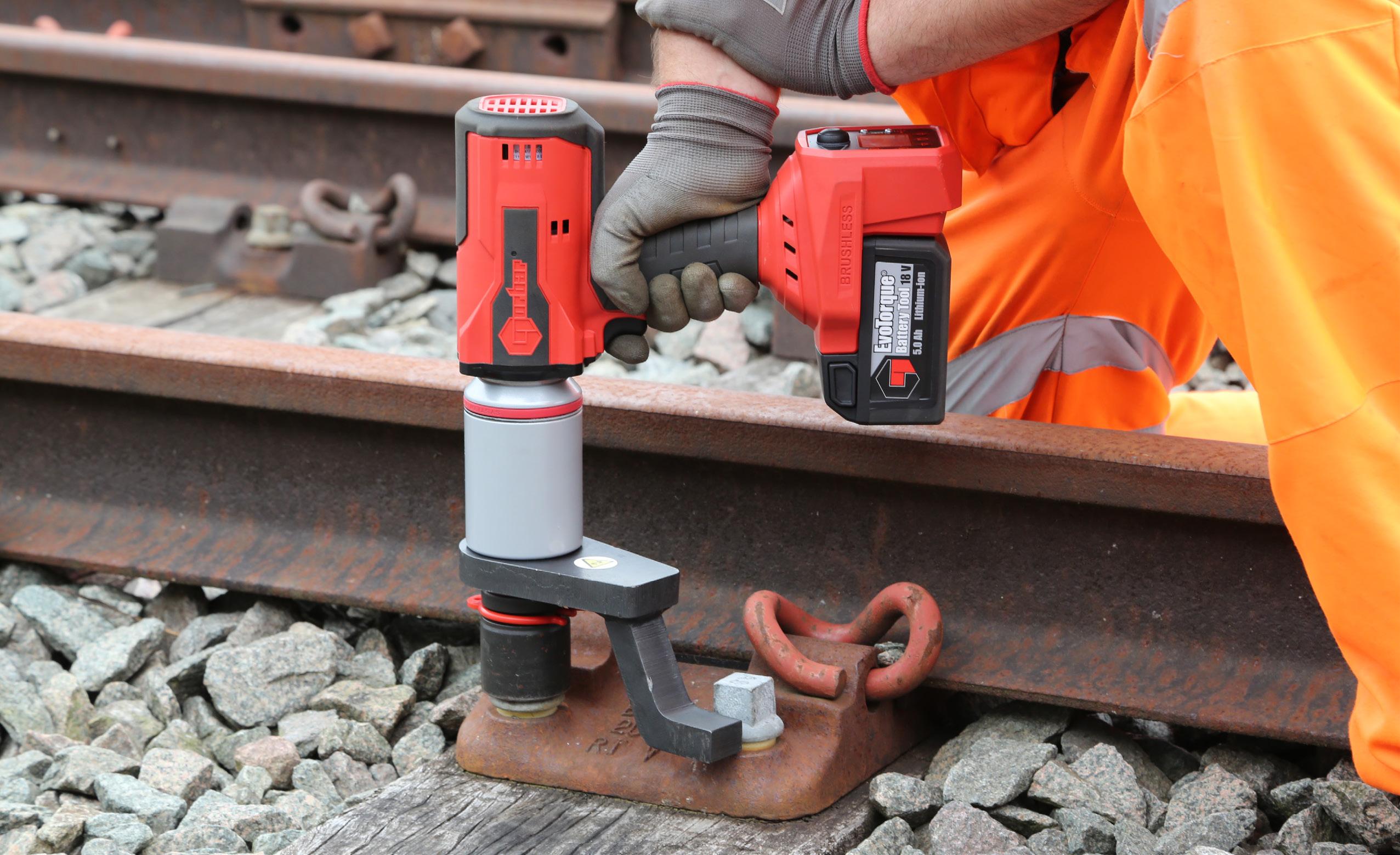
Globally our strongest markets are Automotive, Intralogistics and Medical devices. We are very strong in the Automotive industry due to the efficiency and reliability of our products. Major car manufacturers choose to implement our power supplies in their manufacturing machines which significantly reduces cost in terms of energy consumption and maintenance. For intralogistics, our development of the FIEPOS decentralised unit, has made it easier to bring power to any motor driven part of any logistics setup. There is no longer a need for cabinets as the units are sealed up to IP67 rating.
What is your USP (Unique Selling Point)?
Our primary USP is the product range itself. Due to the smart design and architecture of the circuit boards and the choice of quality components, PULS power supplies have the highest efficiency, smallest footprint, lightest weight, longest lifetime and highest MTBF of any on the market.
We are the only DIN Rail power supply manufacturer to test every other power supply on the market against our own and these results are available upon request. Secondly, many of our products are in stock in the UK which is a credit to our smart ordering system. This is a great achievement despite the current issues regarding the availability of components in
the market which has driven delivery times up to and over six months for many of our competitors.
What types of products and services do you offer?
The PULS product portfolio contains the following solutions:
• Single phase AC/DC DIN Rail power supplies ranging from 15W to 960w, 5Vdc to 72Vdc.
• 3 phase AC/DC DIN Rail power supplies ranging from 90W to 960w, 12Vdc to 72Vdc.
• DIN Rail DC/DC converters ranging from 92w to 480w, 12Vdc to 600Vdc.
• PoE units. 4 or 8 channels with or without built-in power supply.
• Redundancy units ranging from 2x 5A to 2x 40A based on DIODE or MOSFET.

• Single phase AC/DC DIN Rail power supplies, 10A and 20A, with built-in MOSFET redundancy.
• DIN Rail electronic fuses with 4 or 8 channels, fixed or individually adjusted up to 12A.
• DC-UPS DIN Rail devices. In combination with VRLA batteries up to 200Ah, or with built in Electrolytic or ‘Super Cap’ capacitors.
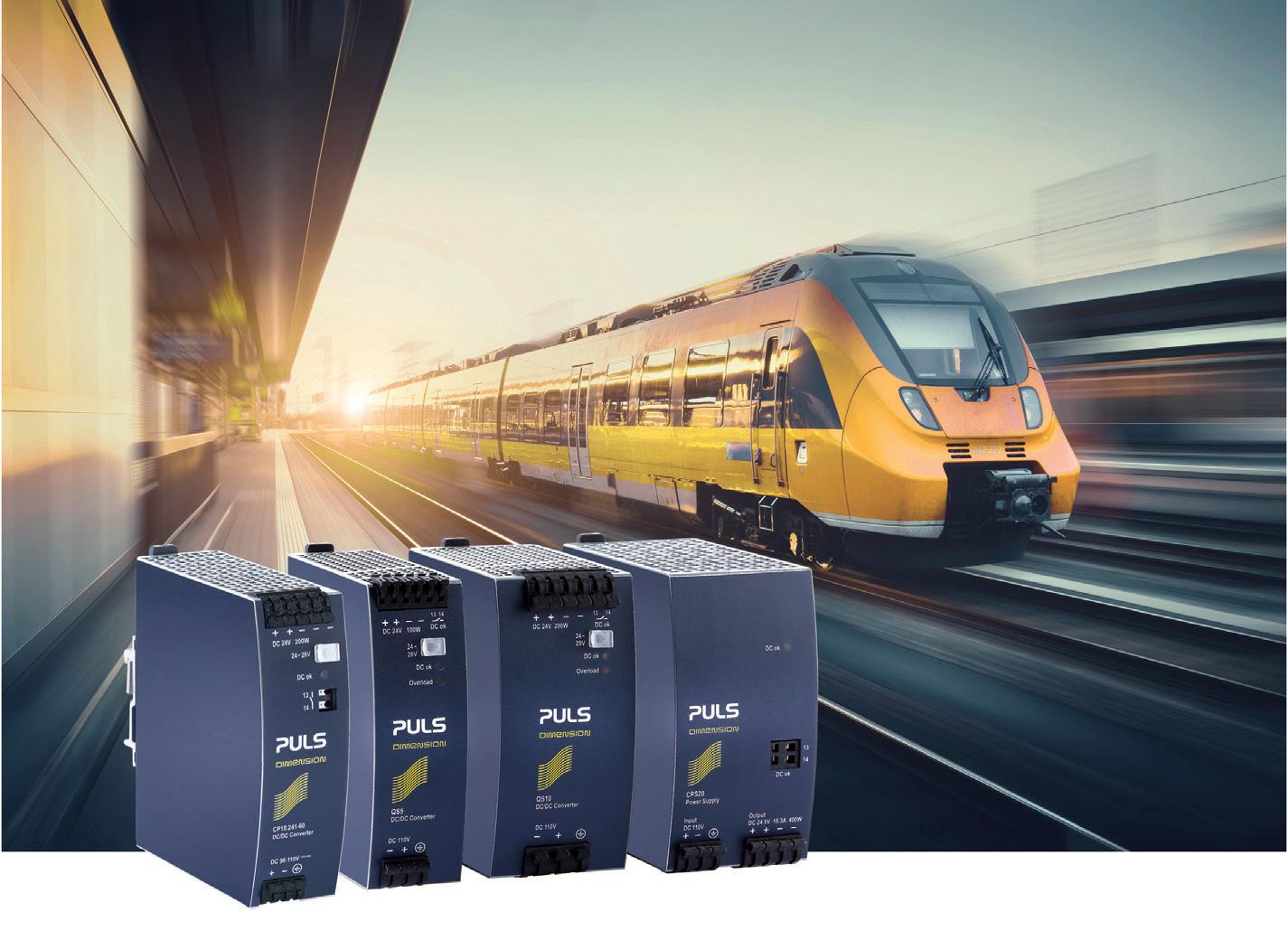
• Our FIEPOS waterproof range from IP54 to IP67. 300W and 500W. Soon in 1200W and 48Vdc.
What type of companies do you collaborate on projects with?
We work with many different types of companies from design companies and consultants who are at the very beginning of a project through to end-users who implement the designs into a finished solution.
For the rail industry, we work mainly with Tier 1 suppliers for both trackside and rolling stock applications. We work closely with Network Rail as we are their preferred brand for trackside applications and we make sure they are always up to date on our latest products.
Besides Network Rail we work with companies either installing trackside applications like signalling, safety control, networks and wireless, lighting projects and various types of crossings. Additionally, our products are used on rolling stock for heating/cooling and other DC/DC applications.
We always endeavour to keep our customers and partners informed about our product range, the benefits to their application and any new products that could be of interest. This ensures they are informed from the outset of the latest technology available to them from PULS so they can design in the right product from the outset.
Have you changed your approach to work at all since Covid?
We have certainly changed how we work since Covid. We now have a hybrid working week with the team working both from home and the office. We can optimise our work time by reducing travel but we still come to the office during the week to keep everyone connected personally and professionally.
There has also been a huge process change in the way we work since we went paperless which was directly as a result of the pandemic. Prior to Covid, our order processing involved a lot of paperwork and we had lever arch files coming out of our ears. However, once we went into lockdown we were not in the office and we had to quickly adapt and find a new and more efficient solution.
We reviewed the capability of our ERP system and we took printing out of the equation and implemented a system whereby we used all forms digitally and started filing digitally too. We faced some initial stumbling blocks but ultimately, we have a more secure and more efficient solution for handling and storing files.
How do you make your business a good place to work?
I am constantly looking at ways to make sure my team enjoy what they do and feel empowered and valued. It’s vital my team are happy in what they do. I have an opendoor policy so the team can feedback and talk to me at any time.
Now we are all back in the office, I am looking at a refurbishment to make the office a welcoming place. It’s important the team have an environment they enjoy being in. We are planning to invest in new ergonomic office furniture, a new kitchen and a relaxing breakout area.
Is there one thing you would advise the rail industry?
For many years now much of the rail industry has been using the same technology it has always used and there is often some hesitancy, even fear, of embracing new and modern solutions. I’m aware that changes can’t be made overnight, but just being open to new solutions could bring so many benefits including energy cost-saving and space saving which is becoming ever more important.
The older products are often bulky and many contain old components that are difficult to source. They can also be incredibly inefficient, big and very heavy compared to more modern products. If we consider trackside cabinets, they are full of these dated products. By starting to test new and smaller, smarter and more energy efficient products sooner rather than later, means they could be implemented in new applications after having been fully tested and proven within just a few years.

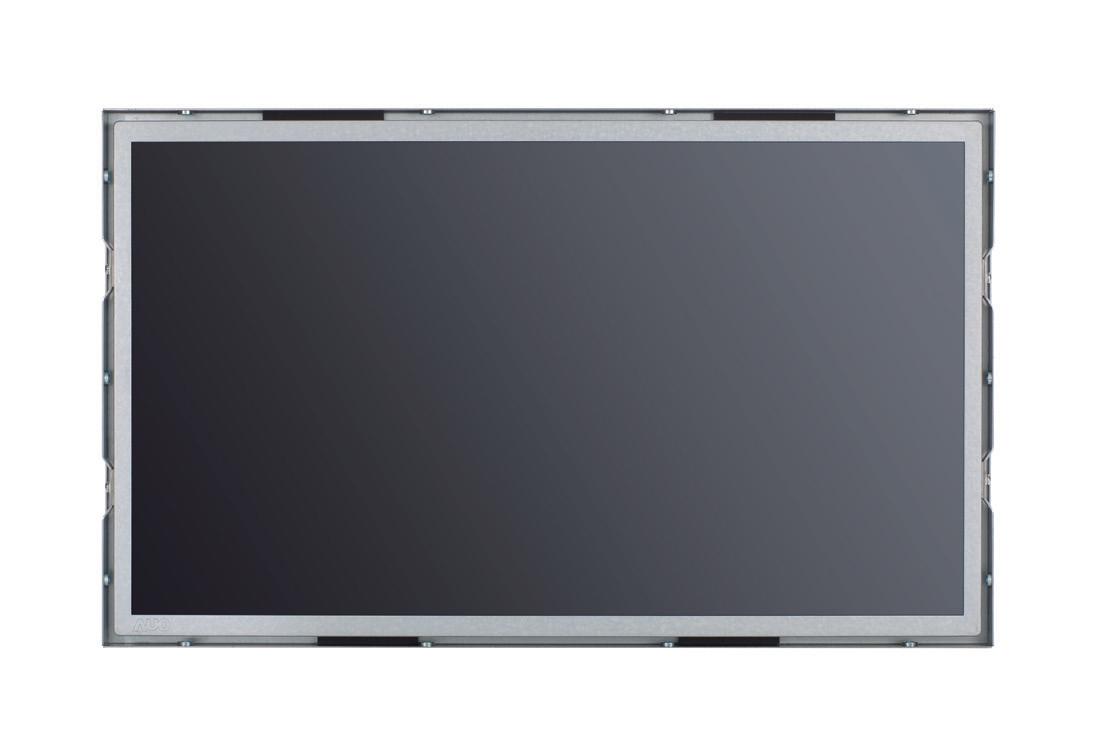
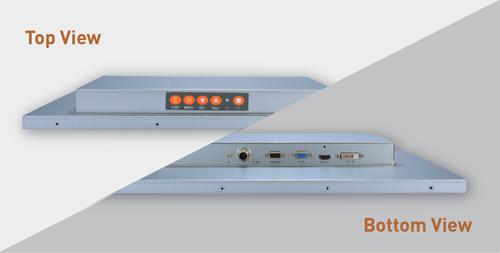
KEEP ON TRACK
Bender is a leading authority in electrical safety, with proven experience in the rail industry.
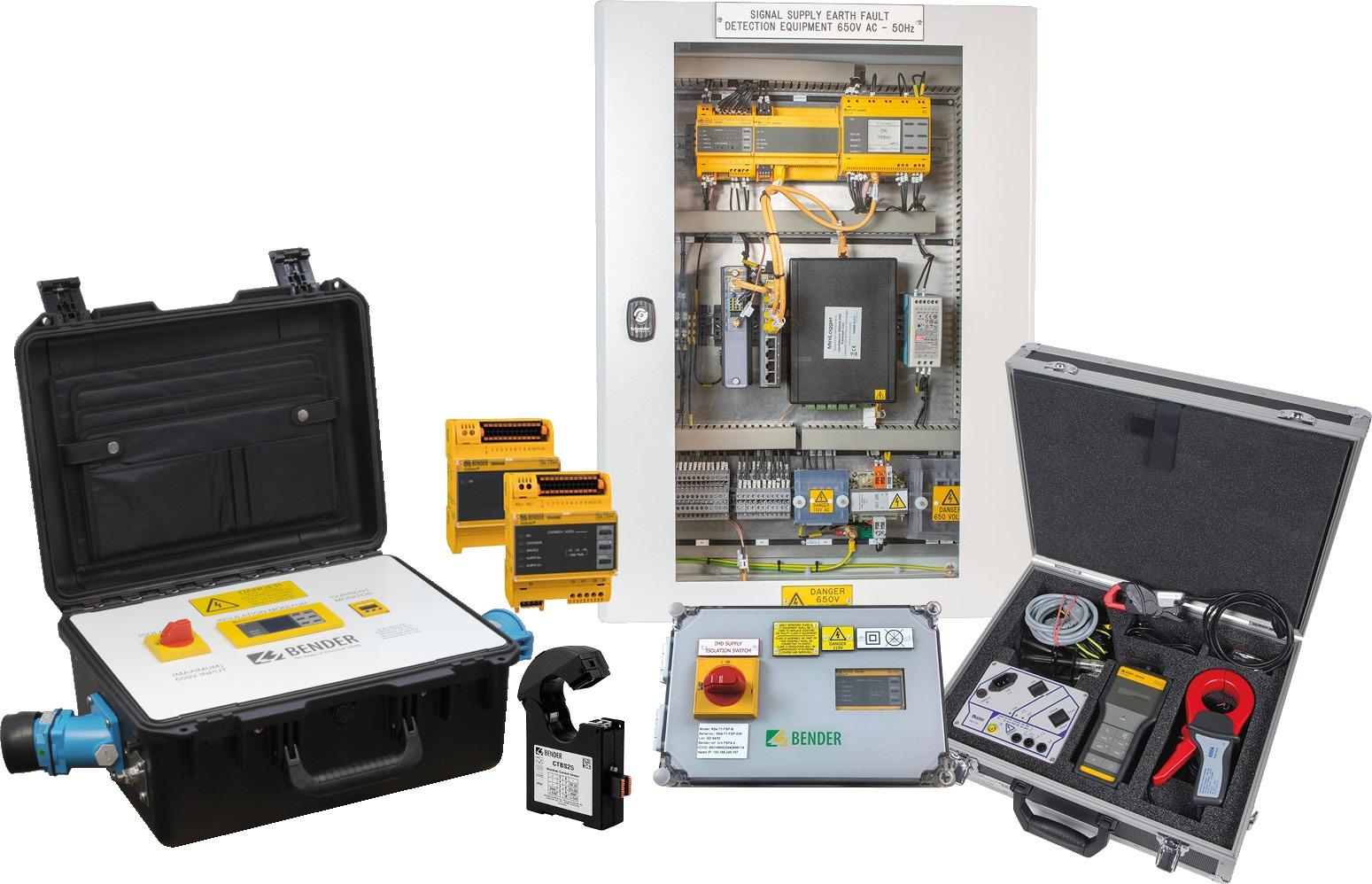
An approved Network Rail supplier, Bender UK has worked in the industry for over two decades to ensure maximum availability, prevent downtime, maintain uptime and to ensure operational efficiency. Bender continuous insulation monitoring and earth fault location solutions measure system status and pinpoint the location of failure and degradation and issue warnings and alarms, to improve rail safety, and ensure timely rail services for passengers.
Bender’s rail capability includes monitoring of signal power, points heating, rail crossings, underground networks and rolling stock, supported with predictive maintenance and software solutions.
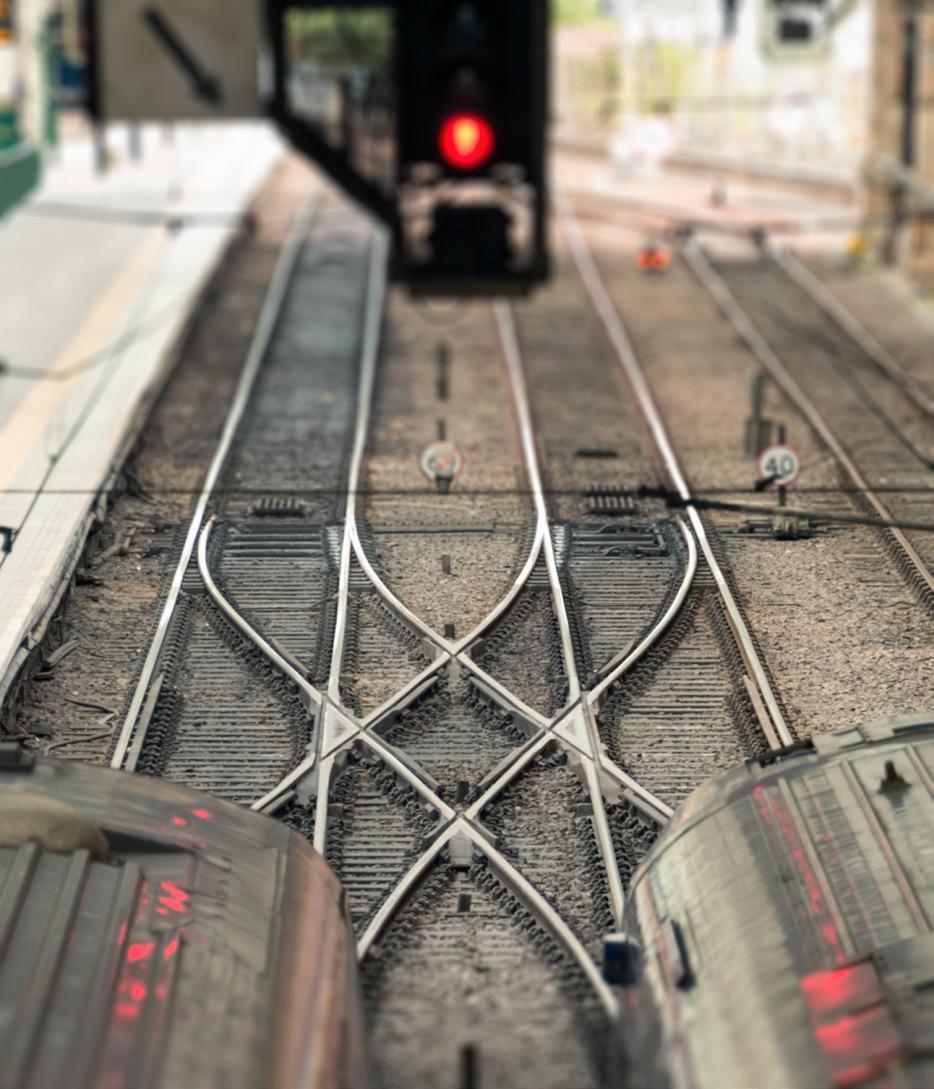

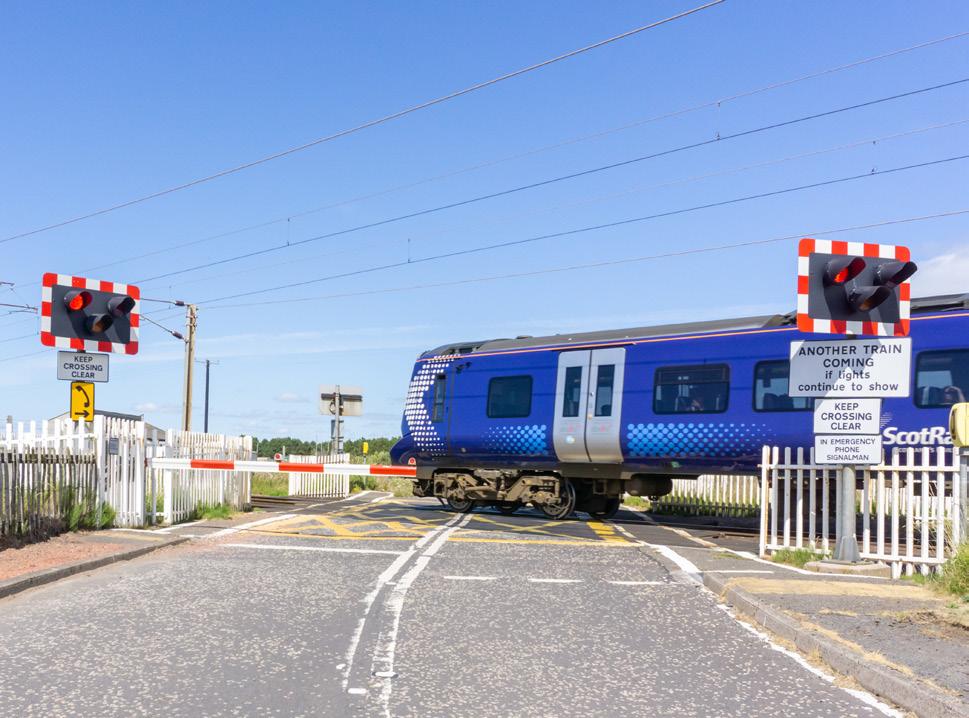
Advanced Monitoring and Insulation Fault Location
Approval of Tier 2 and Tier 1 Rail System insulation monitoring has paved the way for widespread upgrades across the UK
Full approval of Rail Safety technology from Bender has enabled more widespread investment in intelligent insulation monitoring of signal power systems in the UK.
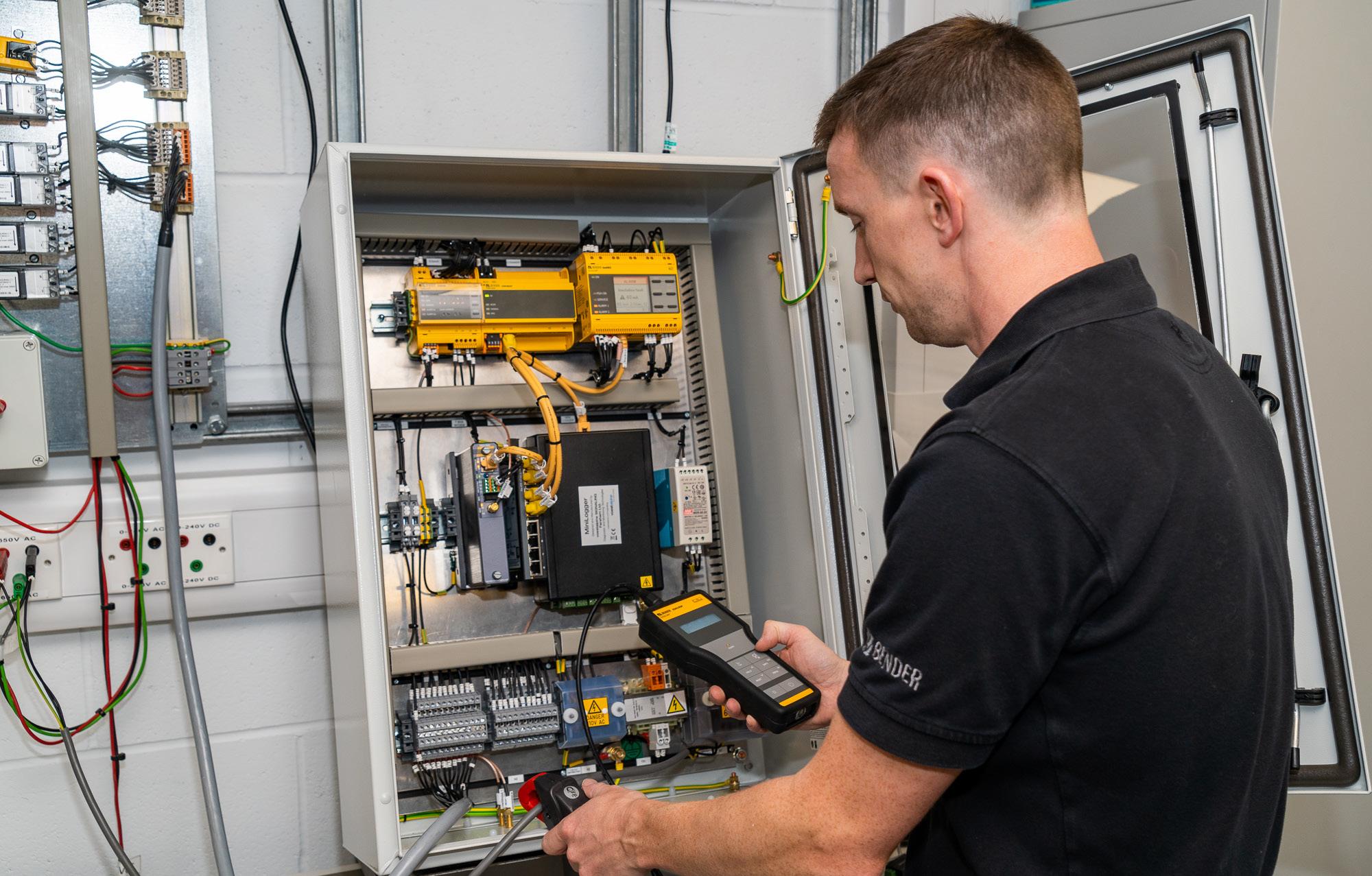
The new generation multi-tier RS4 Rail Signalling Power Monitoring delivers increased sensitivity for first fault location and remote condition monitoring of coreto-earth failures, which accounts for most faults on signal power systems. RS4 helps to reduce maintenance, infrastructure and service failures and improve staff safety by
minimising trackside intervention (‘boots on ballast’).
Bender RS4 technology was developed in collaboration with Network Rail in response to the standard NR/L2/SIGELP/27725 which defines requirements for insulation monitoring and fault location for use on IT Electrical Systems where the nominal system voltage does not exceed 1,000 V a.c. or 1,500 V d.c.
Network Rail regulation NR/L3/ SIGELP/50001 requires an increase in intervention windows. Faults identified at critical stages (20 kΩ or lower) require
immediate intervention within 24 hours. Advanced monitoring and insulation fault location at up to 100kΩ increases intervention time, enabling fault identification within a prescribed six-week window. More importantly, it also offers the option of dealing with the fault over a longer timescale through planned and predictive maintenance.
Bender systems were the principal method of tracking and locating faults on the UK rail signalling power network for two decades. However, less critical emerging faults at lower intervention/insulation
limits have been difficult to track and pinpoint. The new generation multi-tier RS4 Rail Signalling Power Monitoring system offers increased sensitivity for first fault location and remote condition monitoring of core-to-earth failures, which account for most faults on signalling power systems.

Network Rail demands maximum visibility to assess the health and condition of its power systems to support signals, points, and communications infrastructure. Manual cable testing on a five-year cycle continues to be a requirement, but RS4 is a key step forward in enabling Network Rail to move from periodic testing to a realtime condition-based approach through continuous monitoring.
Tony Edwards, Rail Business Manager from Bender UK commented: ‘The response from our customers to the Tier 1 and 2 RS4 approval has been very positive. It is being taken on board across the rail network as a straightforward way of upgrading legacy installations to deliver the extra functionality and sensitive monitoring that is set to be the new base level going forward. It is the area where we expect to see growth from companies carrying out improvements – with less new rail developments planned, any future investment is being concentrated on improving existing systems.
‘For example, the standard has not yet been reviewed but the future architecture for new Principal Supply Points (PSPs) may be a single transformer for every single feeder. If that is adopted as the new standard, RS4 Tier 2 is the ideal equipment to monitor the systems because the Tier 2 standard
is automatically achieved with functional insulation monitoring. Alongside that, routes are already indicating they prefer to upgrade to RS4 Tier 2 as a bare minimum.
‘Data analysis and trending is also becoming increasingly important and an easy way to access current data is via the cloud using Tier 2 equipment. Bender can enable cloud access as part of its managed service package, which means customers can access data uploaded every 15 minutes from each feeder.’
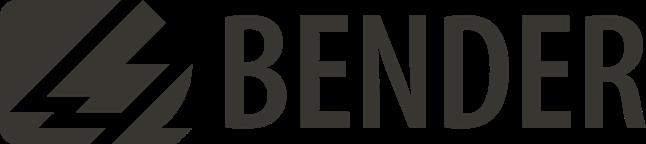
RS4 Tier 2 system measures insulation resistance and leakage capacitances to individual feeder levels on rail IT electrical systems up to 690V, in addition to delivering the overall system resistance and capacitance provided by the RS4 Tier 3 system. Comprehensive data readings and information on the status of miles of networked cables enable operators to make a clearer overall assessment of the system condition and plan predictive and preventive maintenance to prevent downtime.
RS4 Tier 2 is the most cost-effective solution for upgrading previous generation Bender rail technology and can be installed with simple mechanical and wiring modifications onsite. Tier 2 compliance is achieved through the incorporation of Bender Type B current transformers (CT) and Bender COM465IP condition monitor to enable complex individual feeder measurements. It is also fully upgradeable to deliver a Tier 1 solution.
Bender also offers a range of support systems and services, including remote condition monitoring designed to integrate
seamlessly with future smart infrastructure, and advanced analysis of data collected by Bender and third-party devices. This supports end users with the identification of warnings and trends to help minimise failures, improve the efficiency of rail network maintenance, enhance safety and reduce operating costs for the network.
Condition monitoring data from Tier 3 systems is reported back to the Network Rail central system known as RADAR. This is monitored 24/7 by Intelligent Infrastructure technicians who utilise the information to predict an asset failure, providing guidance to front line teams.
RS4 Tier 1 increases the functionality level to provide accurate individual cable section and FSP switchgear level insulation resistances. RS4 is an approved Tier 1 solution that doesn’t require trackside connection to 650V for safer and more costeffective installation without the need to switch off power. Bender’s Tier 1 solution is capable of separately reporting on the insulation status and performance of the switchgear and cable.
This unique solution enables unobtrusive working with dual end fed reconfigurable systems, so that in the reconfigured state, monitoring can be changed to match the new systems without trackside intervention.
‘The future architecture for new Principal Supply Points (PSPs) may be a single transformer for every single feeder … Data analysis and trending is also becoming increasingly important and an easy way to access current data is via the cloud using Tier 2 equipment. Bender can enable cloud access as part of its managed service package, which means customers can access data uploaded every 15 minutes from each feeder.’
Tony Edwards, Rail Business Manager at Bender UK
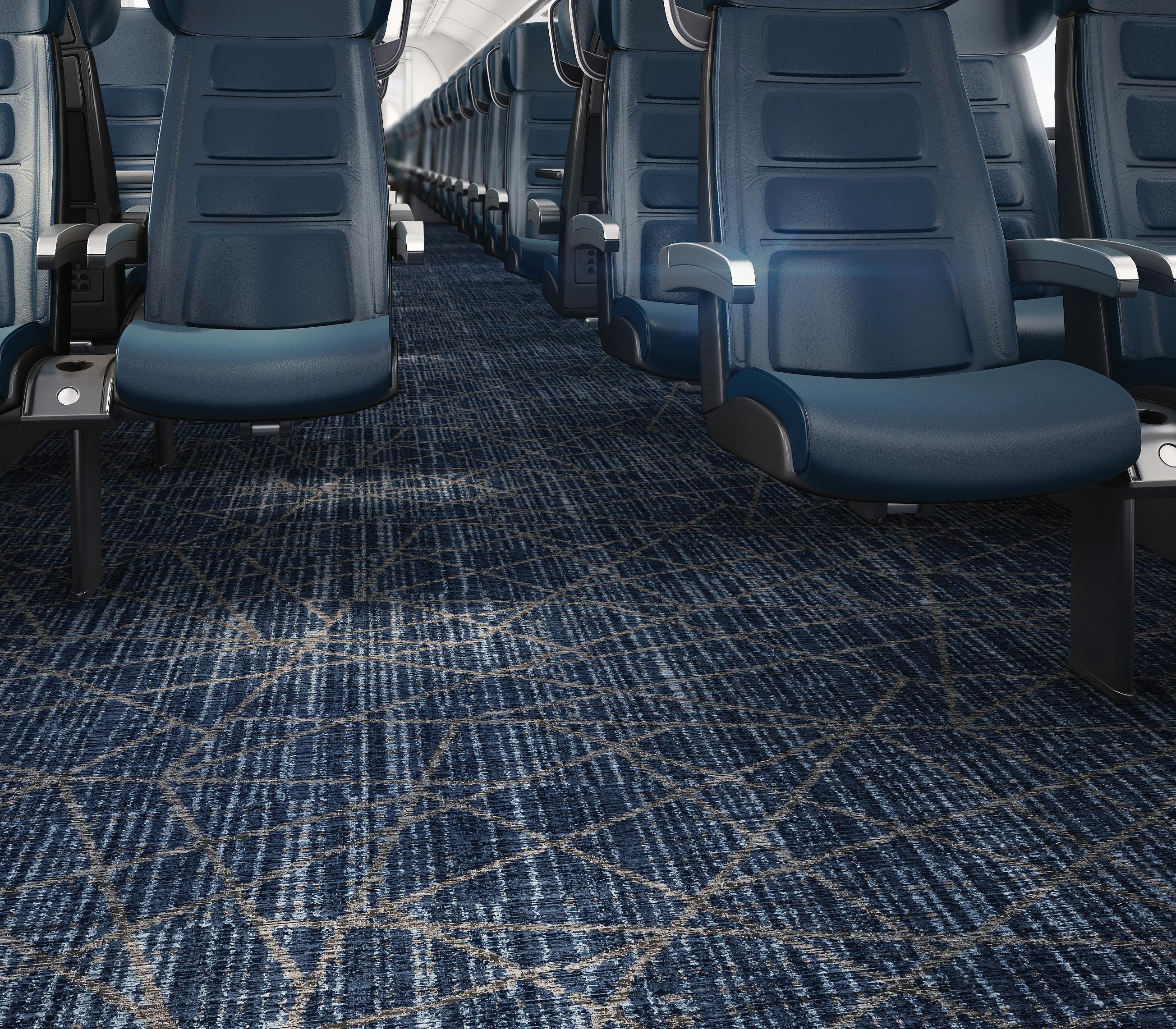


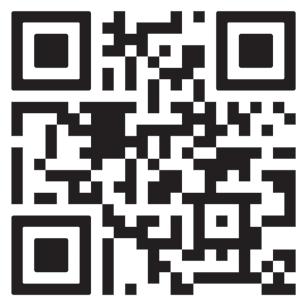
Flotex FR – Functionality Meets Style
A unique high tech textile – Flotex FR combines the warmth, underfoot comfort and acoustic properties of a textile with the durable cleanability of a hard-wearing floor covering

The only available product in the flooring market that brings together the appeal of a textile floor covering with the hygienic practical advantages of a resilient one. Withstanding extreme wear and high traffic makes it the ideal floor covering for rail vehicle applications. With a unique blend of qualities, Flotex FR will maintain its superb aesthetics for many years to come. Designed to support high traffic, Flotex FR cleans up like new every time without fading or wearing, achieving both style and performance without compromise.
Custom colourisation and bespoke design capabilities
Thanks to its high-density, flocked surface pile, Flotex FR can be rotary or digitally printed, offering endless design possibilities as well as high performance. Digital printing enables vibrant designs and true to life visuals that can be produced in high level photographic resolutions.
Select from an array of striking designs in the Flotex Vision FR online collection (with over 500 references), or simply create your own masterpiece. The bespoke design process is available to any designer wanting to create their own unique rail floor covering design or anyone who would like the support of the Flotex Design Team in developing custom designs from initial concepts or at any stage in the design process.
Cleanability
Whether it’s water-soluble stains such as coffee, ketchup, coca cola, wine, etc. or greasy stains like butter, engine oil or permanent marker, all can be removed easily from Flotex FR flocked flooring. Flotex FR can save you time and cut your cleaning costs as it is easy to clean, quick-drying and typically needs less water/chemicals than other textile floor coverings.
Unlike most textiles, Flotex FR can be easily cleaned and maintained using standard cleaning equipment and its
impervious backing also makes it suitable for wet cleaning. Flotex FR is durable due to its dense surface pile and can be cleaned down to its base due to its upright nylon fibres and impermeable PVC backing. Having been awarded the prestigious Allergy UK Seal of Approval, Flotex FR is also proven to reduce allergens, improving indoor air quality for passengers.
A recent Cleaning Research International study compared the cleanability of a flocked pile floor covering with both a loop pile and a cut pile carpet. The results clearly demonstrated the superior cleanability of the flocked floor covering, showing that a 77.7 per cent mean of soil was removed after the use of a contra-rotating brush cleaner. This meant it had the least amount of soil remaining after each cycle.
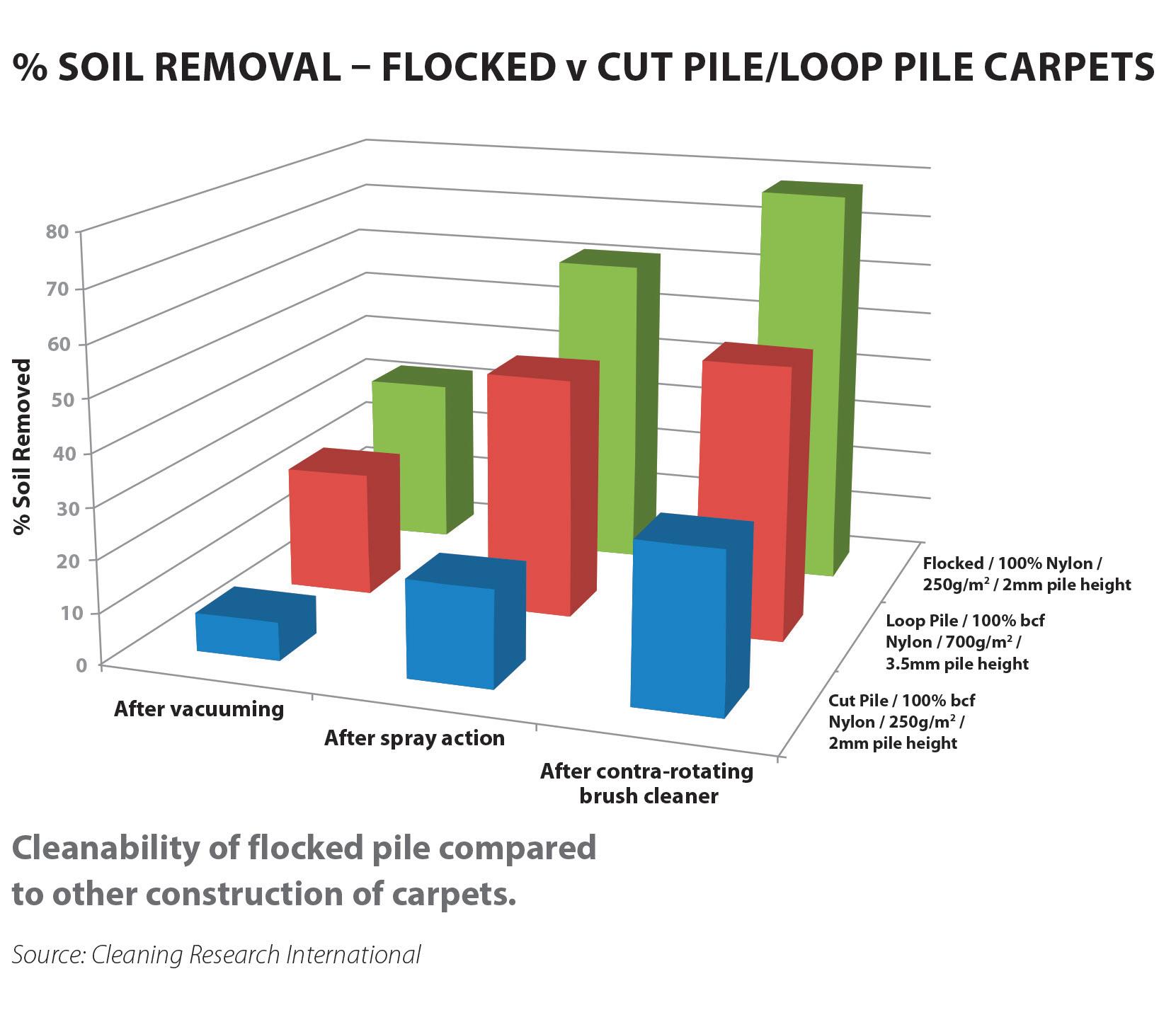
Forbo Flooring appreciates that the amount of time it takes for a floor covering to dry is also a major concern for operators who are keen to minimise turnaround times. The study also looked specifically at this aspect and tested the drying characteristics of flocked floor coverings alongside six different carpet constructions. After just two hours, the flocked pile sample was substantially drier than all the other constructions of carpet, with only 0.57 per cent of moisture remaining, and after five hours, the pile was almost completely dry. Other samples still retained significant amounts of moisture.
Thanks to its hard-wearing properties and durability benefits, Flotex FR flocked flooring has a product lifetime that surpasses that of ordinary textiles. Longer
PERFORMANCE
• Flotex FR has an impermeable backing. You can also steam clean when hygiene standards demand it.
• Flotex FR is proven to have a positive effect on the lives of allergy sufferers and is the only textile floor covering to receive the prestigious Allergy UK Seal of Approval™.
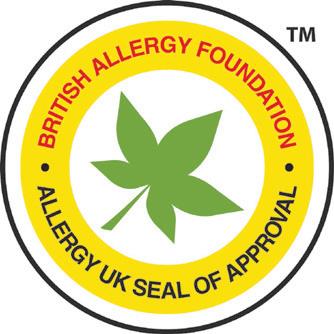
• Research by Cleaning Research International has shown that the cleanability and durability of flocked floor coverings is unsurpassed amongst textile floor coverings.
• Slip-resistant and offering up to 22 dB impact noise reduction, Flotex FR is a reassuringly safe and sound floor covering solution.
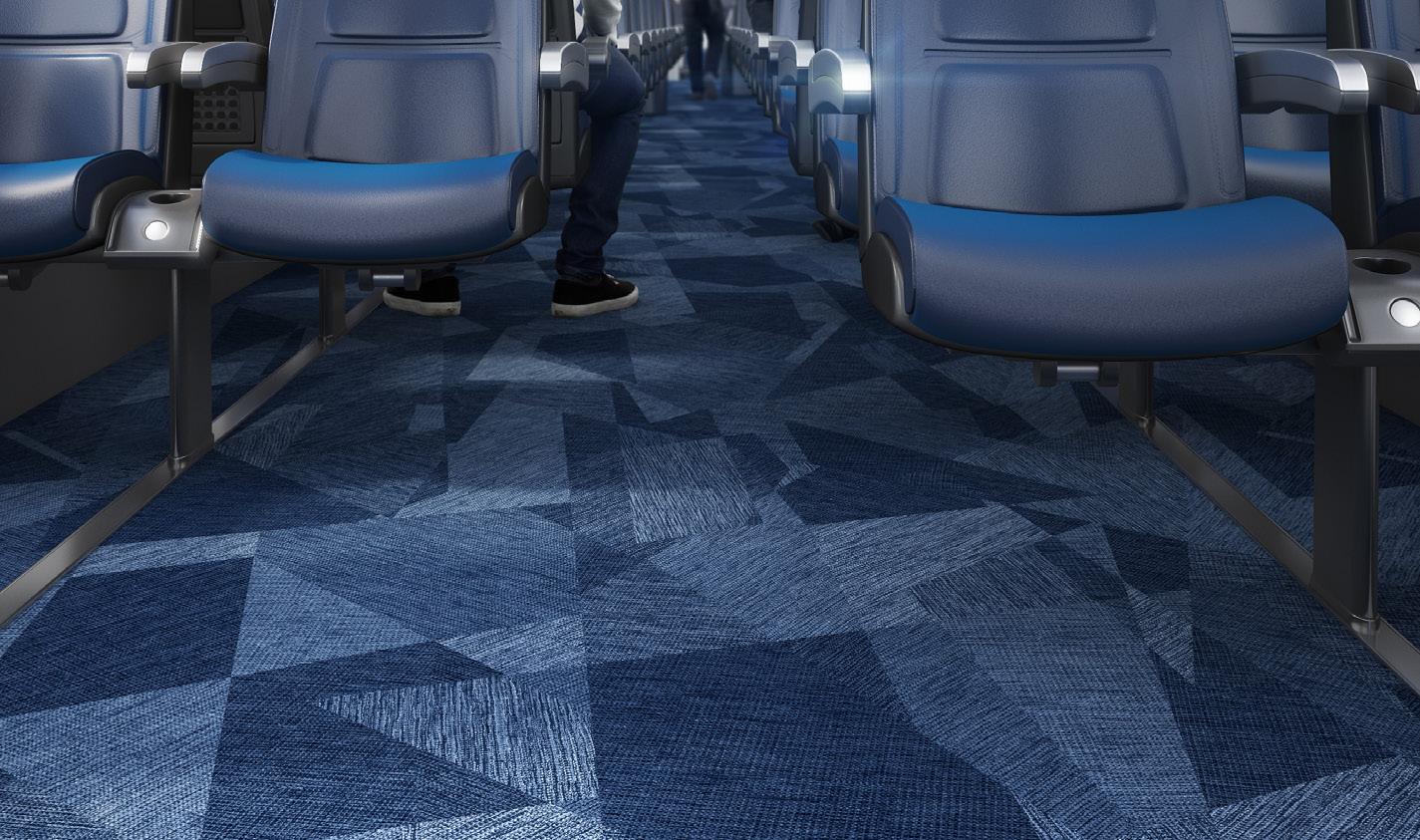
• Flotex FR is is phalate-free and has undetectable levels of emissions.
• Flotex FR is waterproof and washable.
• Lightweight compared to many other flooring materials at approximately 1,225gram/m2, it helps reduce overall vehicle weight, thus allowing for running efficiencies.
lasting, Flotex FR can help you to reduce cleaning, maintenance and refurbishment costs whilst retaining its visual appearance.
Flotex FR floor coverings are clearly different to any other textile floor coverings on the market in terms of cleanability and performance. Factor in the faster drying times, durability, allergy benefits, acoustic and slip resistant properties, wide design options and it is clear to see why this innovative floor covering is popular with rail designers worldwide.
Tel: 01773 744121
Email: transport@forbo.com
Visit: www.forbo-flooring.com/rail

The ‘Rapid Route’ Elevated Cable Carrying System
Anchor Systems (International) Ltd are pleased to introduce the ‘Rapid Route’ elevated cable route system and their collaboration with Scott Parnell the leading specialist supplier to the Rail industry
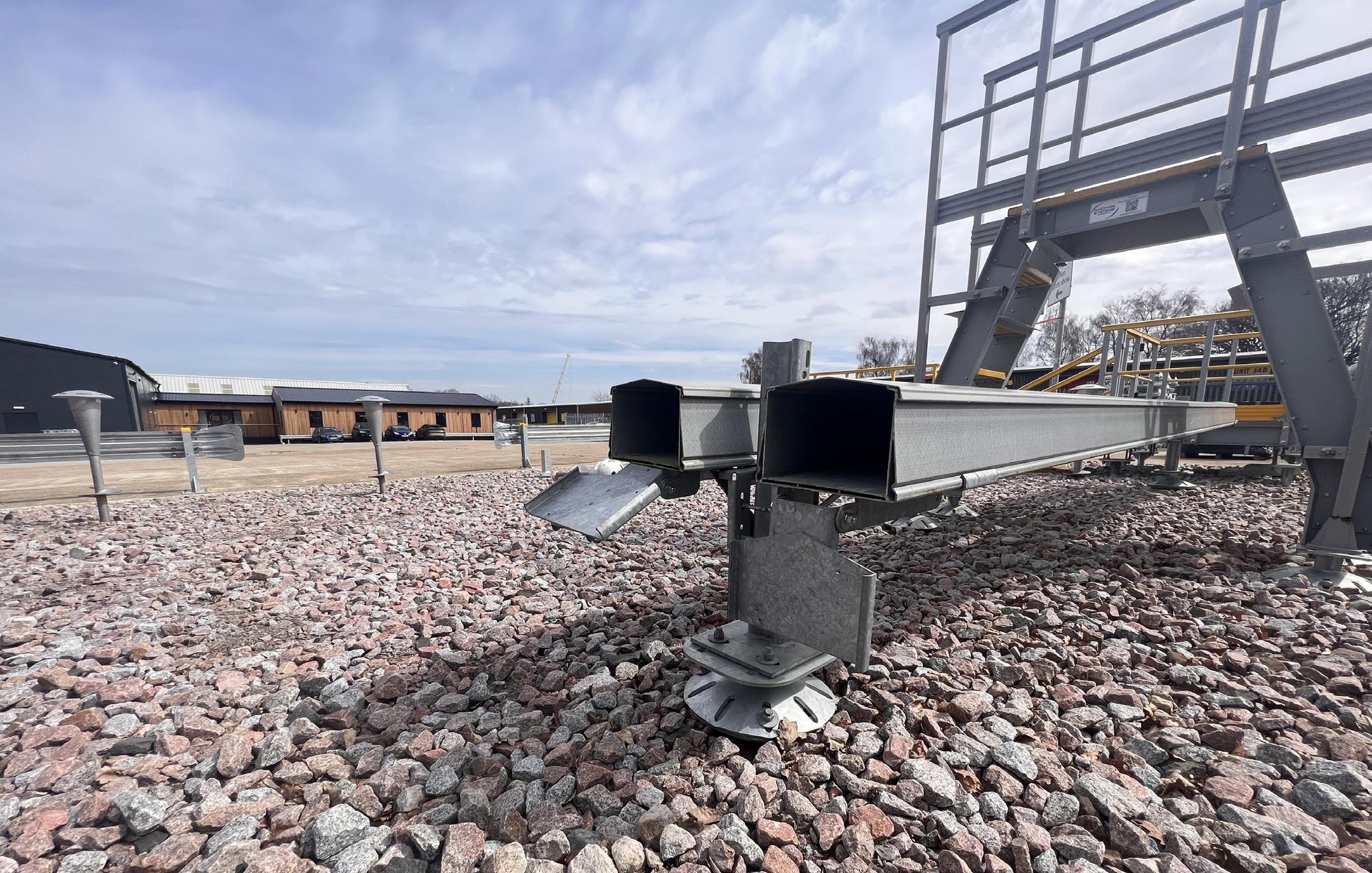
The ‘Rapid Route’ comprises of two main elements, the ARCOSYSTEM® cable carrying trough and lid and the Anchor Screw foundation system.
ARCOSYSTEM®
The ARCOSYSTEM® is a cable trough capable of spanning 6m between support posts and comes in two sizes. It has full PADS approval and has been extensively used in the UK Rail industry on Network Rail and London Underground as well as Transport for Wales and ScotRail infrastructure.
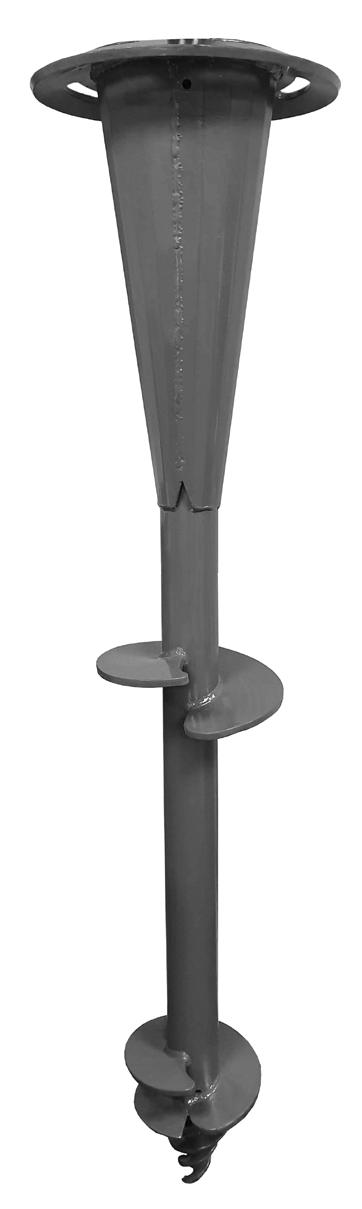
It can carry signalling cables as well as HV cables and is made from GRP that is UV stable, water resistant and provides a 50-year service life which requires zero maintenance.
Anchor Screw
The patented Anchor Screw is a rapidly installed foundation system that negates the need for concrete and all its associated negative aspects like digging, spoil removal, drying times etc. After proving borehole clearance through ground penetrating radar (GPR), the Anchor Screw is wound into
the ground using lightweight, handheld equipment, in less than ten minutes with no HAVS risk.
The Anchor Screw’s domed head, in conjunction with a bespoke interface plate, allows the supporting posts to easily achieve a level and accurate position.
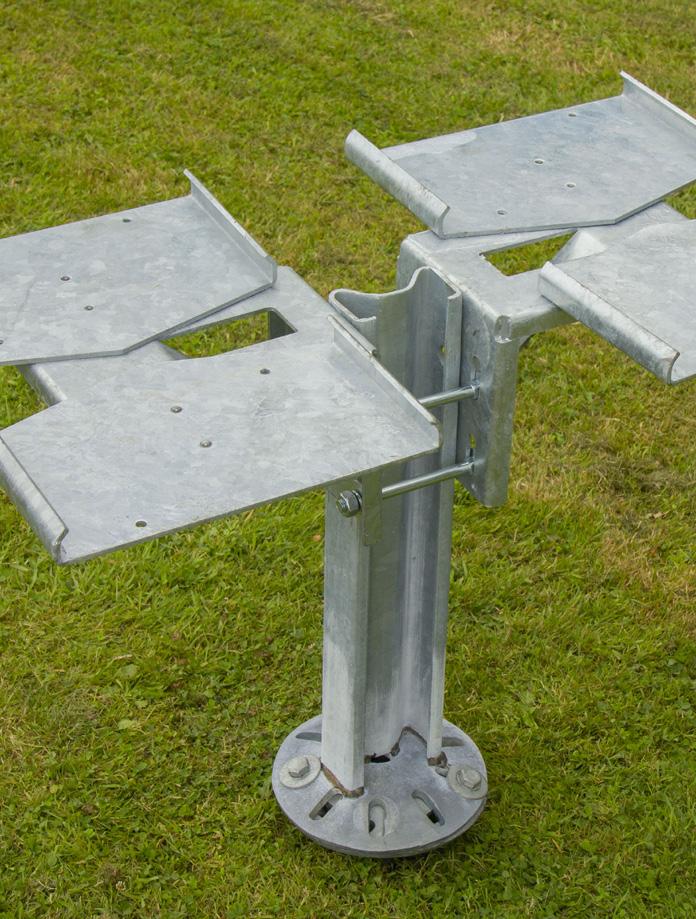
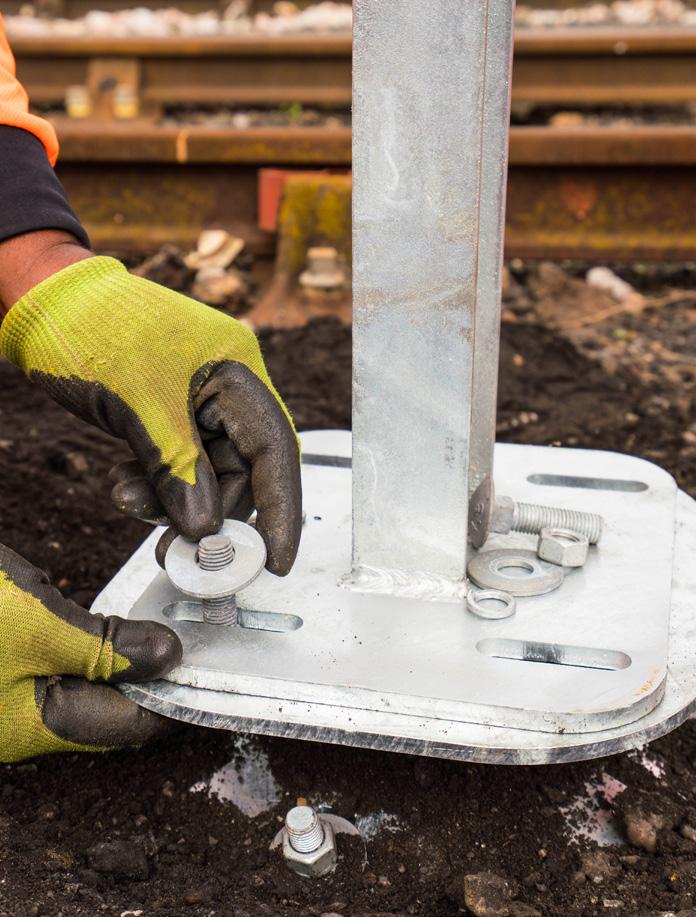
Anchor Screws have been utilised as a foundation system throughout the UK Rail industry on Network Rail and London underground infrastructure for many years and offers a 50 year plus service life.
Rapid Route
Together, the ARCOSYSTEM® and Anchor Screw form the Rapid Route. The most rapidly installed elevated cable route system available. It is cost effective over its life cycle, saving and de-risking on installation and maintenance as well as providing a demonstratable huge reduction on a projects carbon footprint. The Rapid Route system can be installed in areas that are prone to flooding and have the benefit of being added to once the initial installation has been carried out. I.E. Once the foundation system is in place with the first trough run in place, more can be installed at a later date.
The system comes with a selection of brackets that allow the ARCOSYSTEM® trough to transition in height, direction and into and out of other cable carrying systems. Support from CPDs, training and on-site support is also offered along with the Rapid Route System.
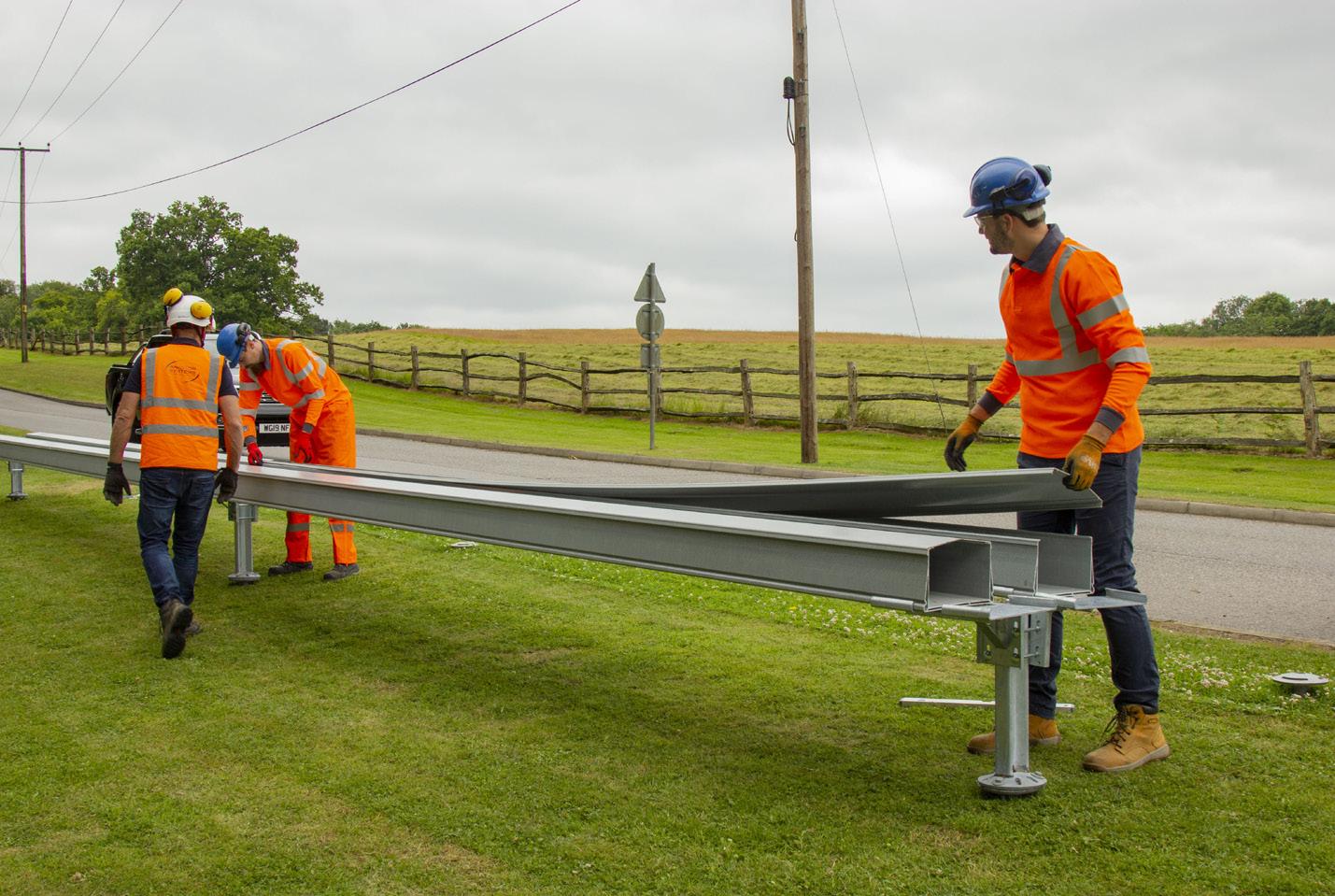
Collaboration
Anchor Systems (International) Ltd and Scott Parnell have collaborated in offering this system to the UK Rail industry. Anchor Systems providing the Anchor Screw foundation, technical and on-site support and training. Scott Parnell providing the ARCOSYSTEM®, sales and marketing.
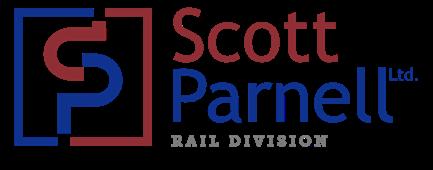
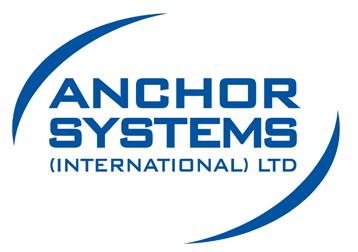

Sharon Meek, Scott Parnell’s Head of Rail says: ‘I’m absolutely thrilled Anchor Systems Ltd have chosen ARCOSYSTEM® to work with the Anchor Screw. We now have two of the very best systems working together to offer the sector significant cost savings, work force safety and sustainable cable management installation.’
For all your enquiries please get in touch via the contact information below.
Tel: 01342 719 362
Email: info@anchorsystems.co.uk
Visit: www.anchorsystems.co.uk
Flexible, Cement-filled Fabric
Concrete Canvas’s unique properties make it an ideal solution for a wide range of rail applications, including crest drainage, slope protection, weed suppression and erosion control. It’s easy installation and durability make it a popular choice for rail infrastructure projects.
of existing infrastructure. CC can improve the industry by utilising existing assets, reducing waste and contractor burden. One Bulk Roll of CC equals two ready mix trucks; therefore, one 40ft vehicle movement would cut down on 32 mixer trucks.
CC is an industry-accepted alternative to conventional concrete that has been widely used by Network Rail across the UK for over 14 years and is one of a few products included in the Network Rail Standardised Task Portal. Route Directors, Senior Asset Engineers (Drainage) and minor works teams across the five Network Rail regions and their 13 routes have specified the geosynthetic.
CC has been extensively used through CP4, CP5 and CP6. Most route network framework contractors have installed CC, including QTS, Balfour Beatty, BAM Nuttall, Costain, AmcoGiffen, Alun Griffiths and Story Contracting. CC has been specified on numerous projects for Network Rail, Transport for London, Translink NI Railways and others. Typical applications for Rail in the UK include channel lining, culvert repair and weed suppression.
Concrete Canvas® (CC) is a flexible, concrete-filled geosynthetic that hardens on hydration to form a thin, durable and waterproof concrete layer. CC combines the robustness of a precast or poured concrete solution with the ease of installation and reduced permeability of a geomembrane. CC allows concrete construction without the need for plant or mixing equipment, offering a rapid, lower carbon, environmentally sensitive solution for erosion control and weed suppression applications. Essentially, it's Concrete on a Roll™.
CC is manufactured in South Wales and exported to over 80 countries worldwide from its purpose-built headquarters, incorporating state-of-the-art R&D laboratories and a demonstration park.
The speed and ease of installing CC mean it is well suited to time-critical track-side work, reducing line possession and improving safety. Eliminating issues associated with rebound from shotcrete and the large plant and equipment required for traditional concreting methods means rail works can continue without line closures. CC is certified with a durability of over 120 years when used in erosion control applications - HS2 requires a 120-year design life for products; this provides vital accreditation to the physical properties, design and installation guidance of CC, enabling designers to ensure they are specifying a quality material.
With tightening budgets and a greater focus on increasing the efficiencies of current assets rather than building new ones, CC offers a unique solution for the remediation
During three control periods, the company has been fortunate to be involved in over 600 Network Rail schemes across the UK. Some recent standout projects include the installation of Concrete Canvas® for the rapid lining of crest drainage channels across several Network Rail routes, including work at Slochd, Charfield and Bath Road Cutting. It was specified over ST4 poured concrete to line crest perimeter drainage channels on different compounds at HS2; this application is typically required to prevent saturation of embankments and potential slip onto a track below as a result. For all projects, the ease and speed of installation allowed contractors to increase workers' health & safety by minimising the time on site, reducing line possession during the works and providing a lower carbon alternative to conventional concrete lining methods.
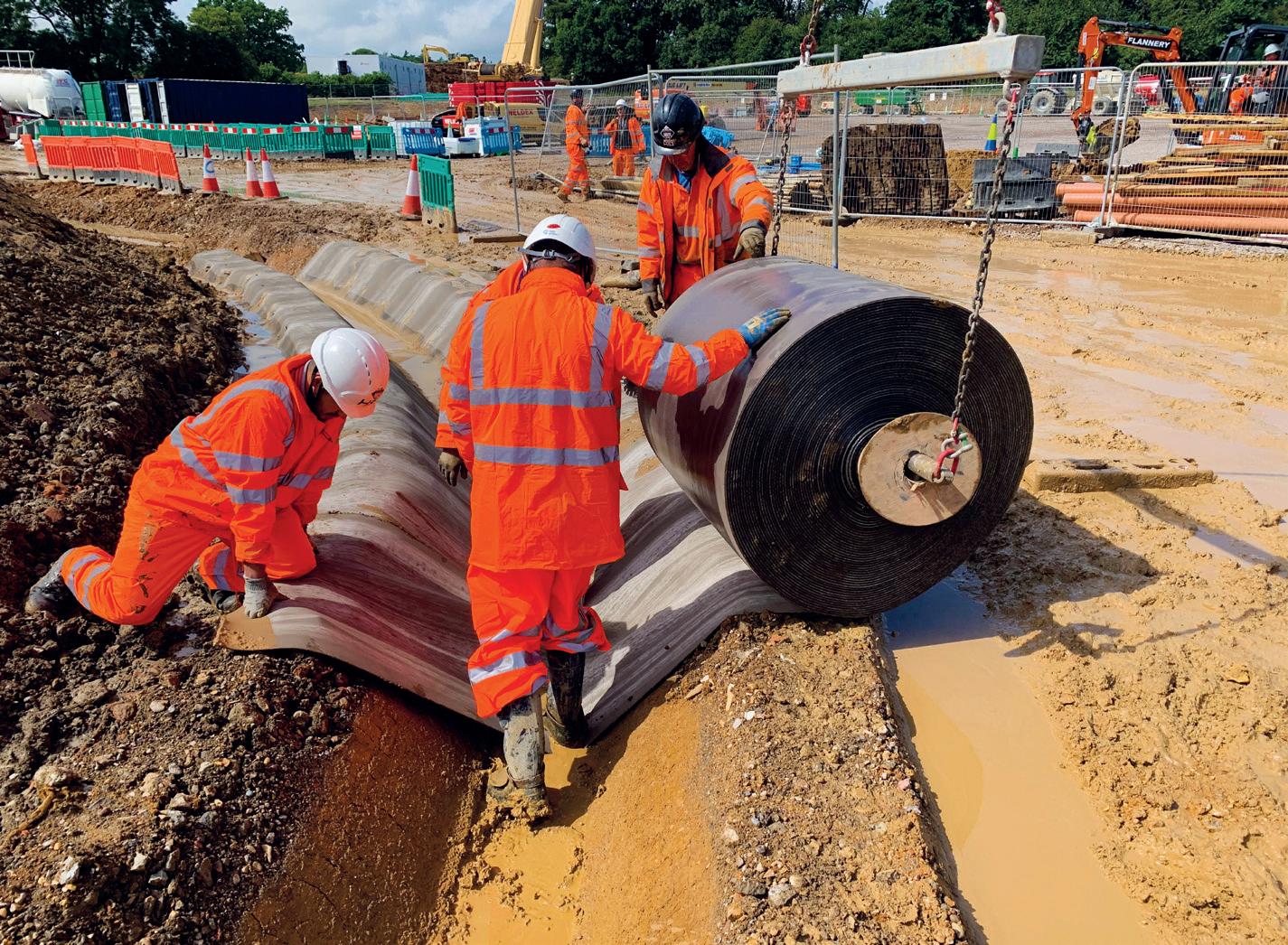
As a supply chain partner with Network Rail since 2009, CC has worked and collaborated with most Tier 1 and Tier 2 consultants and contractors in the rail sector across the UK. As a manufacturer, CC can provide expert support at all project stages, from pre-design to completion, with regional technical sales support, specification and installation guidance.
A new product range has been developed to reduce further the environmental impact of the original Concrete Canvas® material whilst delivering even higher performance for the customer. The new T-series has 33 per cent less embodied carbon than standard CC, providing more than 63 per cent savings when used to replace conventional poured concrete for erosion control applications. The new material also has 25 per cent higher abrasion resistance providing longer-lasting protection.
The T-series was a vast project for Concrete Canvas, with thousands of hours
in research by the R&D team with well over 150 documents carefully being checked, updated and re-issued by the Marketing Department to launch successfully in June 2022.
CC Ltd is working hard to reduce the company's environmental footprint and is proud that by replacing conventional concrete solutions, CC products sold to date are estimated to have saved over 3000 tonnes of CO2 emissions globally. The T-series product line mentioned previously has 33 per cent less embodied carbon than the original CC and is building on this legacy as we advance.
The introduction of the T-series has already seen several of its key benefits utilised by clients in the Rail Sector and beyond to help them deliver their KPIs and objectives to reduce embodied carbon on projects.
One of the biggest challenges to the railway network in recent years has been
extreme weather conditions. Long-term trends show changing weather patterns with increasing average and maximum daily temperatures with drier summers, wetter winters, and severe storms. The increased risk of weather-related events such as floods and landslips causing delays, rising operating costs and increased safety risks along the network is a genuine issue.
There has been increased investment in CP6 and a focus on weather resilience, which has led to long-term asset resilience improvements, reducing the number of assets susceptible to adverse weather. Drainage management has also been enhanced, focussing on the importance of water management around rail infrastructure to prevent saturation of slopes and minimise the risk of landslips.
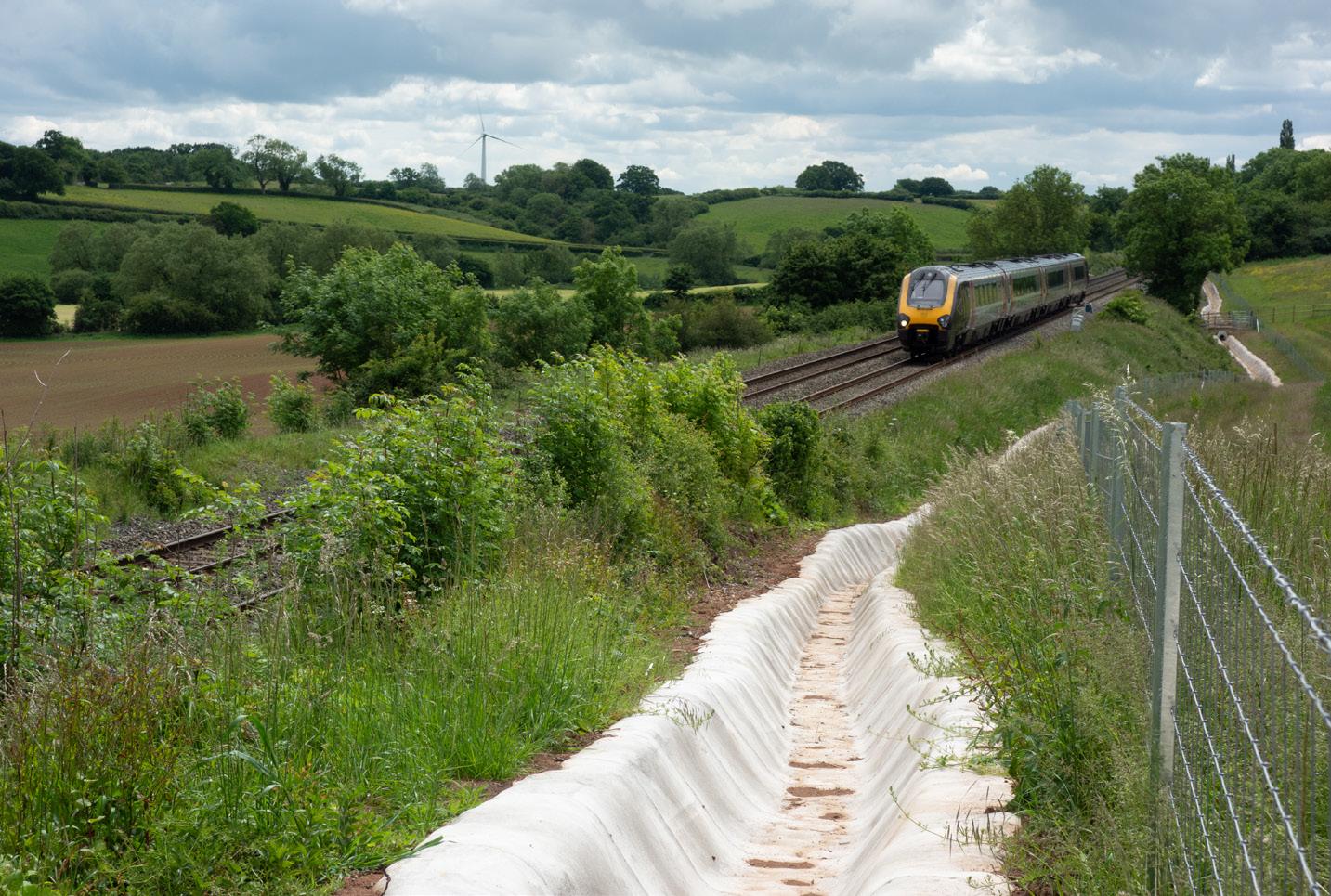
An example of use is a recent multiagency scheme, headed by the Environment Agency with National Highways and Network Rail collaboration to provide an erosion protection solution to a Network Rail embankment as part of an overall flood alleviation scheme in Birmingham. The use of Concrete Canvas showed the materials' innovative approach to solving issues the original poured concrete design presented to the contractor regarding the project's buildability.
The GWP saving on this scheme alone, compared to ST4 poured concrete was a massive 66 per cent. All parties had approved and accepted the original material. Still, after the launch of the new T-series formulation, even better-embodied carbon savings than initially expected were achieved.
CCT-series is already reducing the amount of embodied carbon emitted by the rail sector. Since launch last year, Concrete Canvas has sold over 11,600m² of material to the rail sector across the UK at just under £300,000. The switch to the T-series has saved 160 tonnes of CO2, equivalent to approximately 26 days of airline flight or 7,500 trees absorbing CO2 in a year.

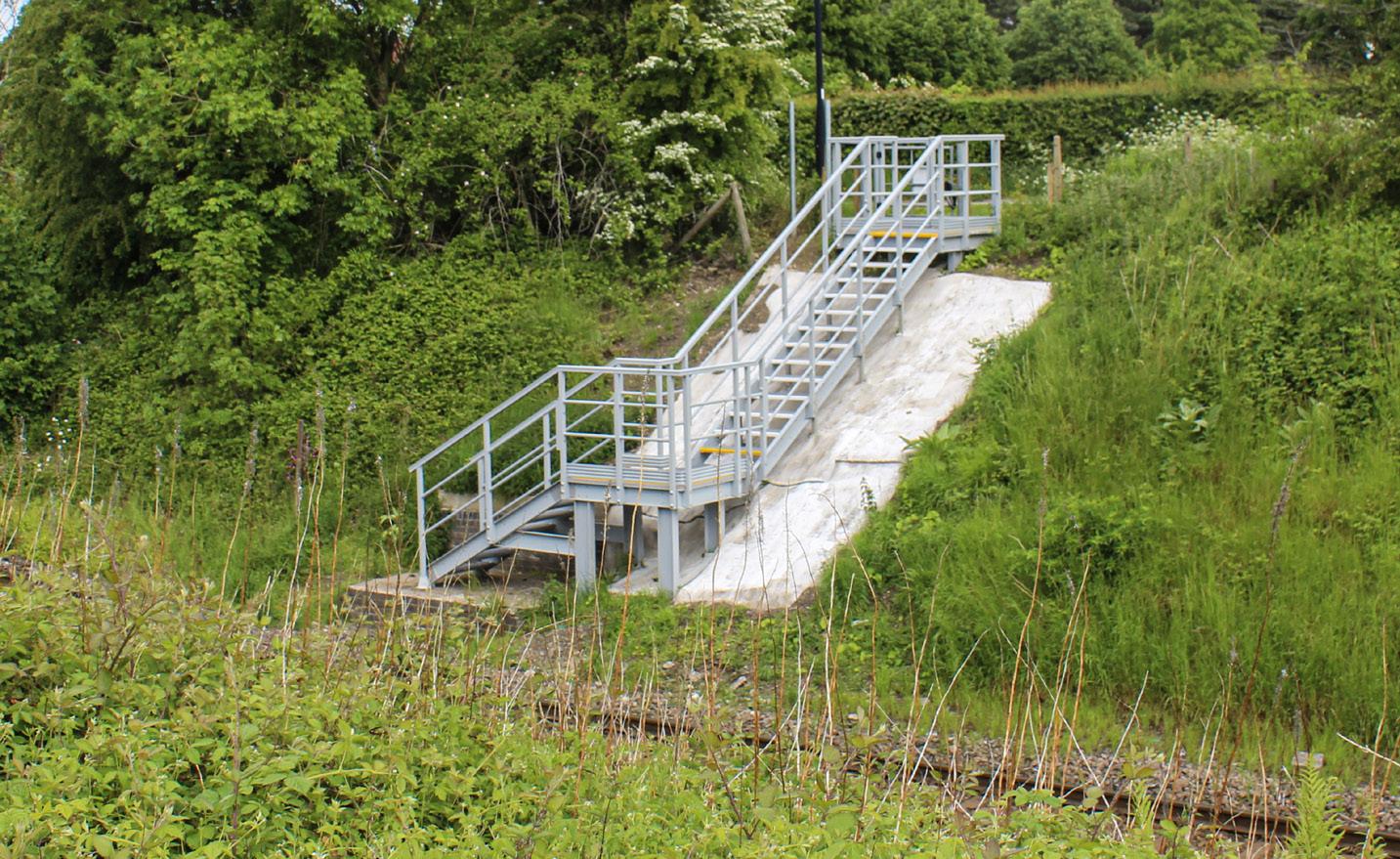
The new product ranges are a large step forward in evolution for the GCCM material class used in the rail sector, and the company is still innovating. Since day one, Concrete Canvas has strived to provide the best material possible for erosion protection with continuous innovation critical to the company's growth, evolving and moving towards a better, greener, and brighter future for the rail sector.
Visit CC at RailLive stand E13.
On Track for a Greener Future
Torrent Trackside is a business built for rail We are committed to investing in the latest battery powered tools, lighting and equipment which provide outstanding levels of power and efficiency. The advantages of battery power include:
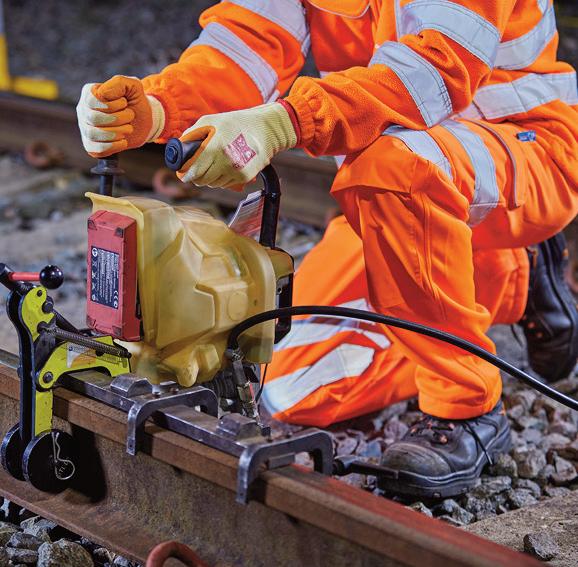

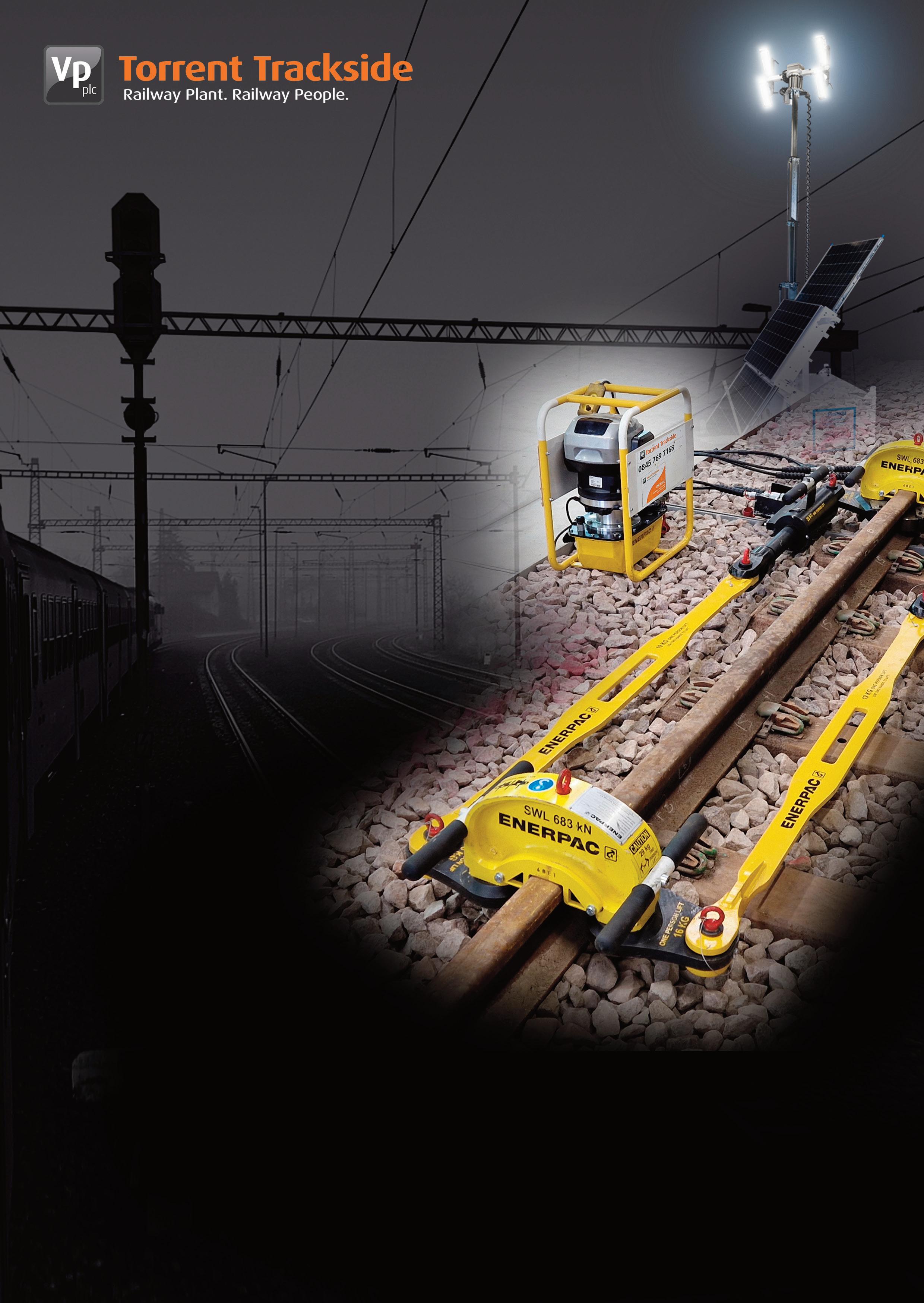
l Zero emissions - better for the environment and safer for the operator
l Instant power at the flick of a switch - no tugging on pull cords
l Significant reduction in HAVs - up to 80% for some tools
l Battery tools are smaller, lighter and easier to transport
l Quieter than petrol tools - ideal for built up areas and night work

l Battery and solar lighting is powerful, lightweight and silent
r contact our 24hr helpline 0845 769 7168



Reaching New Heights for the Rail Industry
Torrent Trackside is introducing a range of modern and efficient telehandlers for hire
The UK rail network consists of over 20,000 miles of track, 30,000 tunnels, bridges, viaducts and thousands of signals, level crossings and stations. With this much infrastructure there is constant demand for large and heavy materials and goods to be moved and manoeuvred safely around sites and over obstacles. Telehandlers are the ideal solution for this demand. The machines combine the lifting capacity of a forklift truck with the reach and elevation of a crane. Torrent Trackside has teamed up with its fellow Vp plc company UK Forks to offer these machines to the rail industry. Torrent Trackside will coordinate the hires through its experienced hiredesk to ensure a seamless service to its new and existing rail customers.
The fleet is one of the largest in the UK consisting of over 2,000 machines chosen from the industry’s leading suppliers such as JCB, Merlo and Manitou. They are located at six strategic locations across the UK from Glasgow to Exeter, meaning that customers are no more than a couple of hours from a suitable machine. The fleet can be broadly broken down into four main types:
• Telehandlers – Four-wheel drive machines fitted with a telescopic boom that can carry up to 4,000kg up to a height of 20 metres, depending on the
machine model. These machines offer unrivalled manoeuvrability and excellent ground clearance.
• Roto Telehandlers – Larger machines fitted with a 360 degree rotating boom that can carry loads of almost 5,000kg up to a height of 35 metres, depending on machine model.
• Heavy Lift Telehandlers – Powerful machines for shifting heavy loads up to 12,000kg up to a height of almost ten metres.
• Electric Telehandlers – Near silent operation with zero emissions capable of lifting up to 2,500kg to a height of six metres. These machines are perfect for indoor and night projects.
With many telehandlers costing over £100,000 hiring can be a much more cost effective option. Servicing, depreciation and repairs are not an issue. Machines can be handpicked for different tasks ensuring projects are run most efficiently.
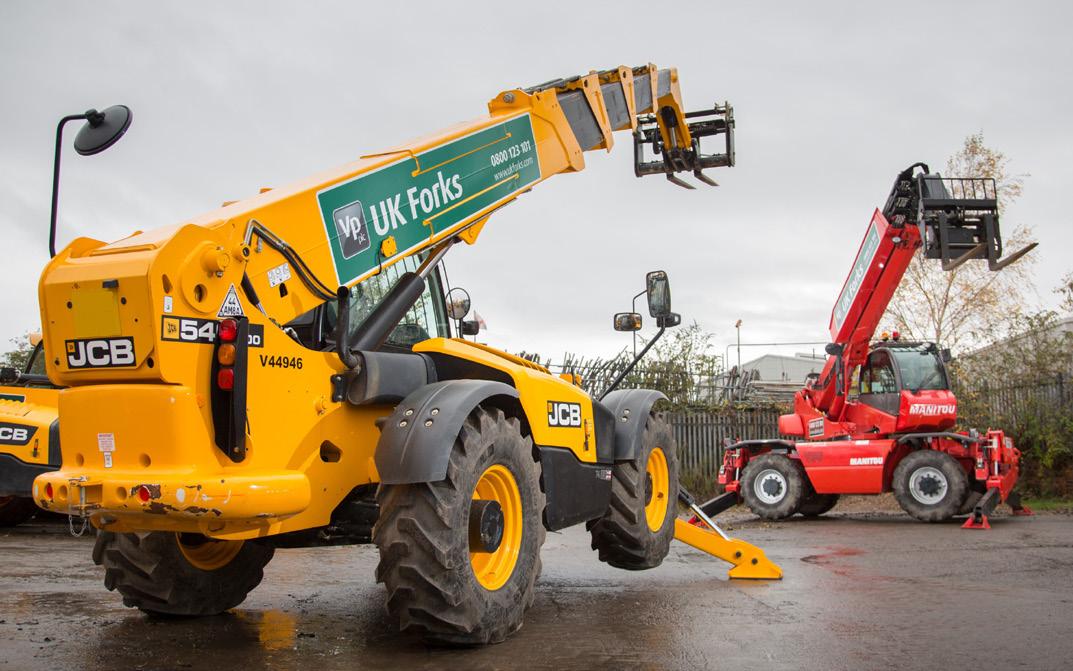
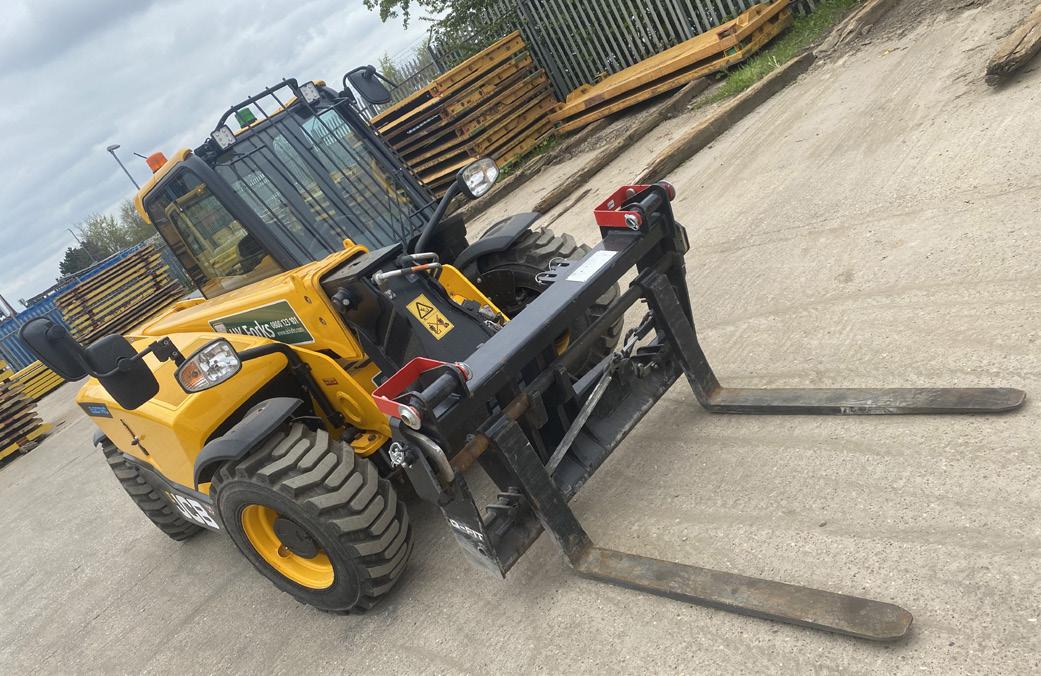
Minimising downtime is a key focus. Continuous investment in the latest machines provides customers with unrivalled quality and reliability. All machines are subject to a rigorous pre-hire inspection. The field service engineers are manufacturer trained and their support vans are tailored for telehandlers, meaning many
issues can be fixed on the spot. Machine performance reports can be provided to further improve efficiencies on site.
A complete range of manufacturer supported and approved attachments are available to be delivered with the machines from man platforms, sweepers, forks and jibs to a host of electronic equipment such as reversing cameras, remote control devices and tracking equipment.
Torrent Trackside’s Operations Director Carl Abraitis commented: ‘Torrent Trackside is the leading supplier of portable plant and equipment to the rail industry. These telehandlers will be a welcome and versatile addition to our range of innovative equipment.’
A number of telehandlers will be exhibited at the Vp stand G7 at this year’s Rail Live. Carl Abraitis is Operations Director at Torrent Trackside, get in touch via the contact information below.

Control and Decontamination
Dr. Uri Stoin of Alpha Cleantec AG, Switzerland describes how one in-situ holistic solution worked for three challenges of railway maintenance
Railway tracks, roads, and other infrastructures must be vegetation-free to comply with safety and operational requirements. Several wellknown methods to prevent and treat vegetation include biological, mechanical, and electro-thermal processes. The standard market solution to prevent and treat vegetation on railway tracks is the use of soil herbicides and leaf herbicides.
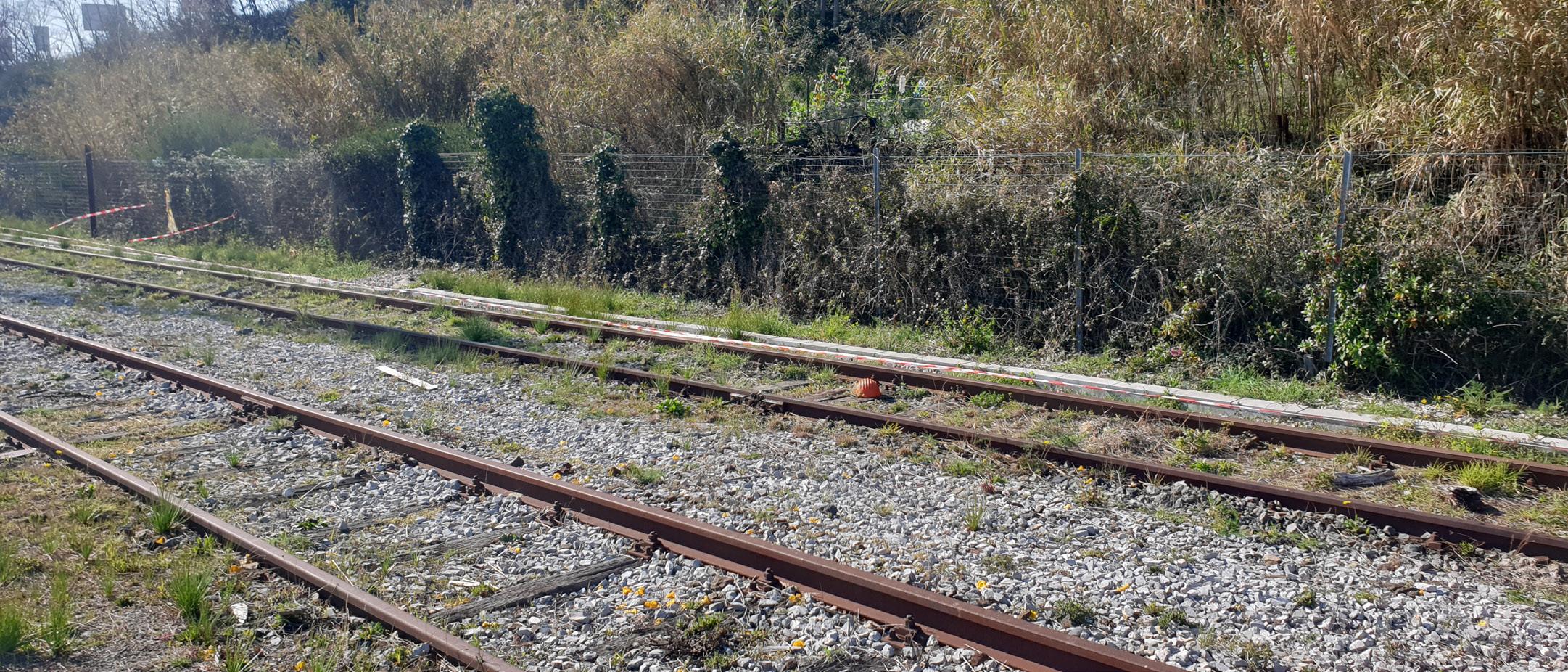
For decades, glyphosate-based materials such as Roundup and Dominator Ultra have been the most efficient and cost-effective solutions. These methods are rapid, efficient, cost-effective, and straightforward to use. However, due to their environmental and health impacts as well as the resistance of part of the plants, it was recently decided to stop using Glyphosate-based materials in EU countries.
In December 2022, The European Commission extended the current approval for the herbicide Glyphosate by a year until 15 December 2023. This decision was made official through EU Regulation 2022/2364, which amends the approval period for
the Glyphosate active ingredient. The amendment has been made to Regulation 540/2011, which deals with the list of Active Ingredient Substances (AIS) approved in the EU. However, it is clear that times for common aggressive and environment damaging use of Glyphosate-based materials are coming to an end. New environmentally friendly, safe, rapid to implement, efficient and cost-effective non-Glyphosate herbicides that can be applied with the existing spaying equipment are in great need.
In addition, decades of aggressive application of Glyphosate-based materials have generated a new persistent environmentally damaging contamination of subsoil and groundwater with Glyphosate leftovers. EGEIS summarized groundwater monitoring on over 8.900 European locations between 1993 and 2009 and found a percentage of samples above the maximum concentration permitted in drinking water (0.1μg/liter) in several EU countries such as Germany, Denmark, Norway, France and Hungary. For example, in France, Glyphosate accounted for 2.9 per cent of all samples exceeding the concentration limit
in raw water sources used for the production of drinking water (2000-2002). In Denmark, 3.4 per cent of wells exceeded this limit. In Catalonia, between 2007 and 2010, Glyphosate was found in 41 per cent of 140 groundwater samples, with a maximum concentration of 2.5μg/liter.
The situation in the subsoil is even worse, and each rain increases Glyphosate concentrations in groundwater and drinking water, with contamination rates constantly rising over the years. However, Glyphosate leftovers are only part of the organic contaminants present in the subsoil and groundwater. Other sources of organic pollution are found in railway ballast contaminated with, among others, used oil, lubricants and petroleum leftovers. Therefore, holistic solutions for vegetation control, ballast decontamination, subsoil and groundwater treatment are in great need.
Alpha Cleantec AG (ACT) is a Swiss technology company providing various safe, green, rapid, efficient, and cost-effective technologies to resolve environmental harms and hazards caused by human and
industrial activities. The company offers one holistic solution package for the above mentioned three challenges. Vegetation Control (VC) process for efficient Glyphosate free vegetation control and Railway Ballast Oxidation (RBO) for ballast, subsoil, and groundwater decontamination. The technologies can be applied separately or as one global solution during one single vegetation control spraying. ACT is a certified technology provider operating internationally based on flexible business offers adapted to the specific requirements and constraints of local operators, e.g., license agreements.
VC solution is based on an environmentally friendly mixture of inorganic salts that generates concentrated (non-Glyphosate) herbicide. The salts penetrate the plant´s stem (absorption by the plant), change in a first stage the ion balance inside the plant and, in the second stage, dehydrate the plant (water absorption), drying plant and roots. The material works as a non-selective herbicide or ‘total weedkiller’ that destroys in a nonselective manner all types of plant material with which they come in direct contact (contact herbicide), including a wide range of glyphosate-resistant species. The solution can be applied with standard market manual and automatic spraying tools (as used for Glyphosate-based materials). The company successfully completed compatibility studies with several manufacturers of spraying trains.
RBO is an in-situ physico-chemical technology based on the generation of superoxide radical that can simultaneously decompose organic pollutants and herbicide leftovers on the ballast surface, in subsoil and groundwater without excavation or replacement of the ballast. The solution can be combined and applied simultaneously with VC technology. The process efficiency was certified by independent laboratory tests carried out by TÜV Süd, Germany.
To date, the RBO process was tested in field tests in Switzerland, and the VC application is in a very advanced stage of piloting in Austria and Italy. ACT plans to carry out additional pilots in the Netherlands, Belgium, France, and the UK by the end of 2023. These technologies do not damage railway infrastructure and can be applied with existing spraying trains and tools as part of usual rail maintenance proceedings. The company is with great interest looking for new partners in the UK.
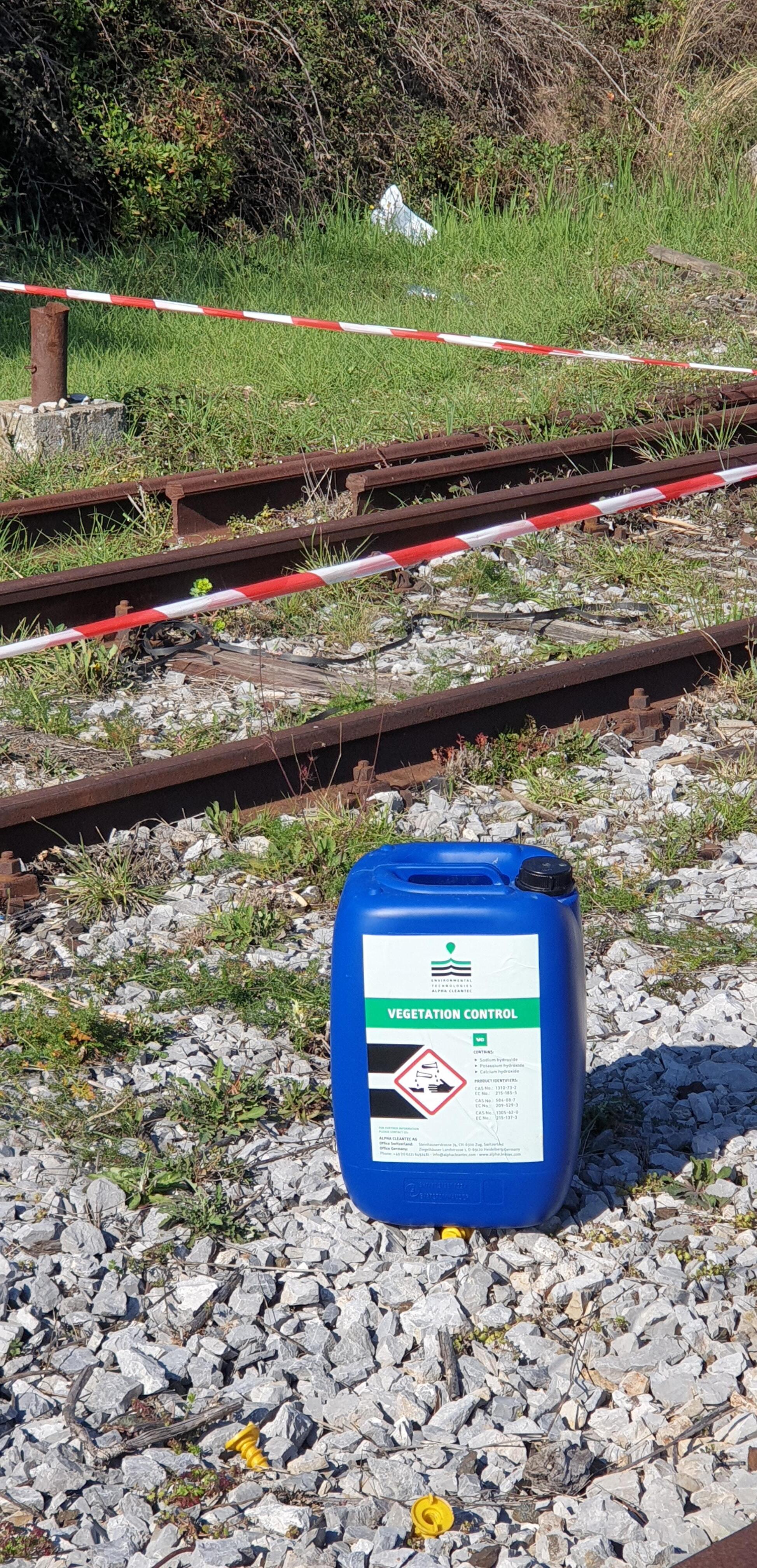
For more information please get in touch via the contact information below.
Tel: +49 (0) 6221 6492481
Email: info@alphacleantec.com
Visit: http://alphacleantec.com/contacts/ LinkedIn: https://www.linkedin.com/company/alphacleantec-ag/about/
YouTube: https://youtu.be/iVjxCV-l6J8
Providing Safe Passage
Thousands of supply chain members supported Crossrail in its delivery of the Elizabeth Line. They included safety seal manufacturer Roxtec, who played a specialist role in the creation of its tunnels’ cross passages, a vital safety feature
infrastructure project of its generation. The new line, named in honour of Queen Elizabeth II, was officially opened in May last year.
The company’s industryleading products were integrated into the door and frame designs and used to seal against fire, air pressure, gas tightness, cable retention and moisture ingress.
Roxtec UK is the British subsidiary of the Swedishheadquartered Roxtec Group and has a long history of supporting rail infrastructure projects around the world.
Founded in the garage of entrepreneur Mikael Blomqvist in the Swedish city of Karlskrona in 1990, the business has grown to become the world leader within sealing solutions for cable and pipe transits.
Anetwork of tunnels created by eight giant boring machines today carry the new Elizabeth Line’s trains as they move across London, linking the east and west of the capital.
Each tunnel, built as part of the £19 billion Crossrail project, is 21 kilometres long, 6.2 metres in diameter and up to 40 metres below ground.
The tunnels’ cross passages, built into their design and construction, are critical to life safety. Created at regular intervals, they enable the safe evacuation of passengers in the event of an emergency, allowing people and rescue services to move safely from one tunnel to another.
Safety seal manufacturer Roxtec played a specialist role in the £300m project to deliver the cross passages’ doors. These doors not only have to provide fire protection, but they must also withstand the constant pressure created by trains passing within metres of them at high speed.
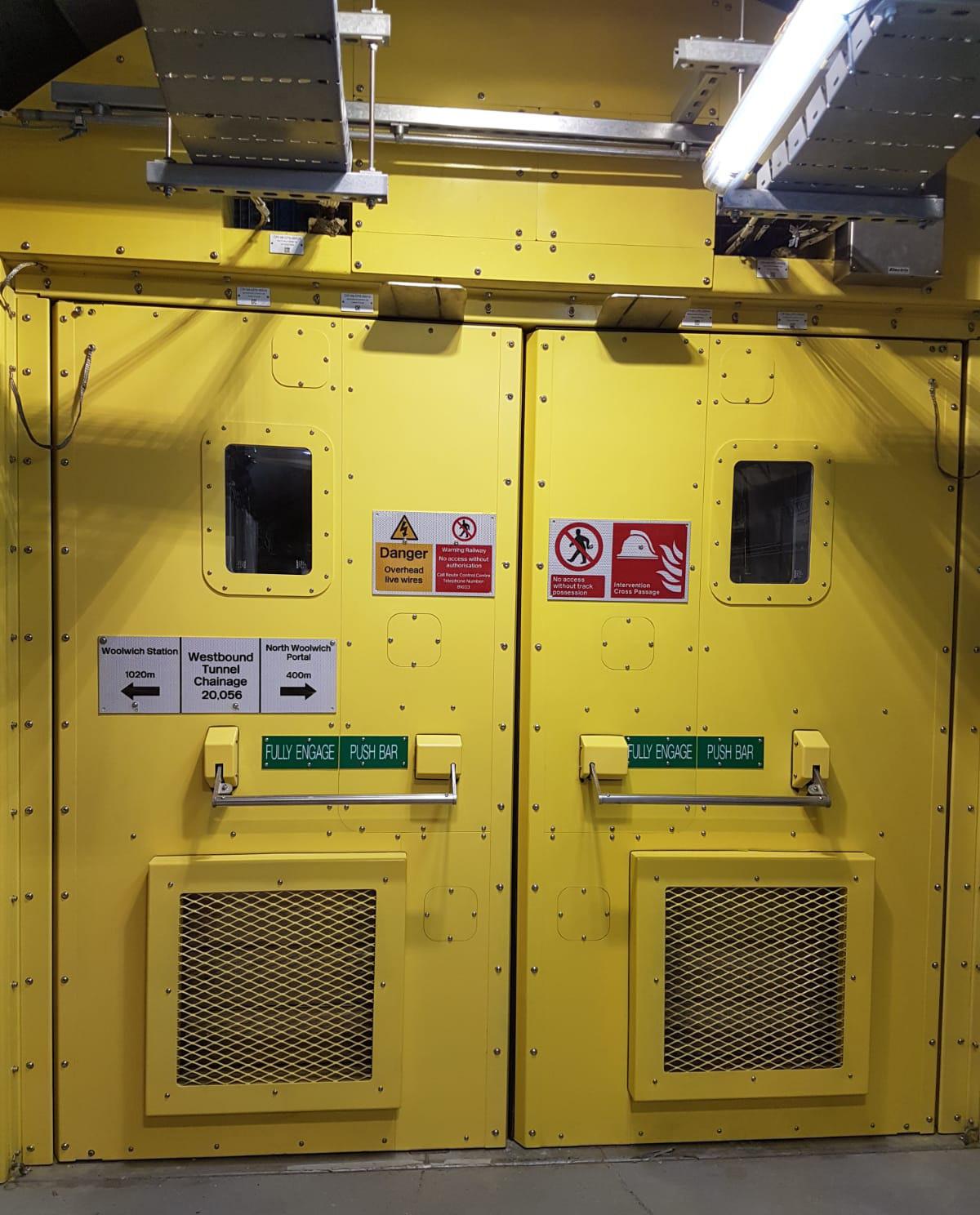
Roxtec was one of thousands of supply chain members using its expertise to support Crossrail, the UK’s biggest
Today the group has in excess of 250 registered product certificates and more than 500 registered tests and approvals and is active in more than 80 markets around the globe. With a team of 20, based in Bury, Greater Manchester, the UK operation’s turnover is more than £6 million and it is on the track to further growth.
Within the rail industry, Roxtec products can be found everywhere from the London Underground to Sydney’s metropolitan rail network. As well as rail infrastructure projects, its flexible sealing products are also used on board rolling stock.
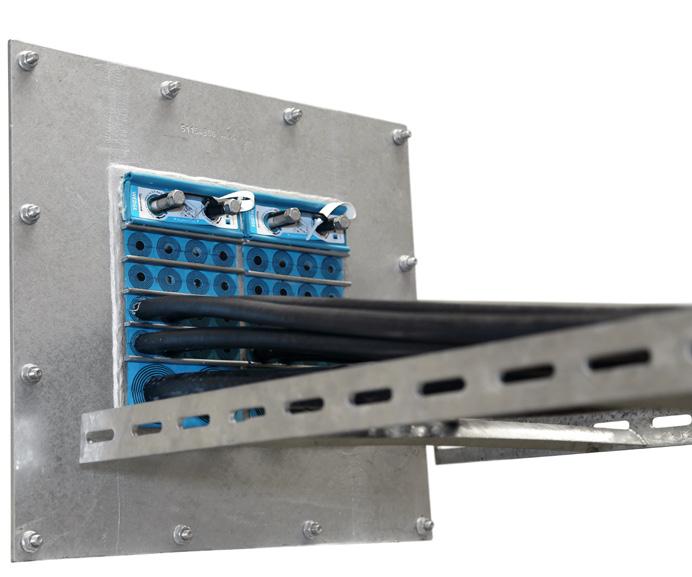
Its seals are used to protect people and assets wherever pipes, cables or conduits need to pass through walls, floors, foundations and bulkheads, as well as into cabinets, enclosures and junction boxes.
Depending on project requirements, these sealing solutions can provide certified protection against a vast range of hazards including fire, gas, water, electromagnetic disturbance and the risk of explosion.
Rail sector expertise
Working closely with specialist UK firm Booth Industries, the chosen manufacturer for doors in the Crossrail programme, the
Roxtec team incorporated its systems into the cross passage door designs, leading on the frame design section of the project.
They also supported the delivery process by carrying out detailed installation training for the project’s engineers.
Onsite support saw Roxtec working with the design team to configure the cable layouts, as specific cables had to pass through at exact points in the transits.
The company’s experts were on hand to inspect the installed transits and were on site when the first were installed to ensure the process was carried out correctly.
Continuing Professional Development (CPD) presentations were also given to the design engineers as part of the project, showcasing Roxtec’s high level of rail industry expertise.
The knowledge-sharing exercise covered such subjects as protecting assets and ensuring reliable operation with certified cable sealing systems.
David Chalmers, Divisional Manager, Infrastructure and Industry, Roxtec Ltd,
‘The cross passages are escape routes in case of a blaze in the tunnels or on the trains, so sealing them against fire is crucial’
says: ‘We used our knowledge and our wide range of products to deliver the sealing solutions needed here when it came to the cables that had to pass through the doorways.
‘There were a number of factors that had to be considered. The cross passage doorways are escape routes in case of a blaze in the tunnels or on the trains, so sealing them against fire is crucial. They are also under constant air pressure caused by the trains passing so close to them at speed.’
He added: ‘The company is proud to have played a role in this high-profile, landmark UK rail sector project.
‘It is incredibly rewarding to know that our seals are helping to keep people safe and vital transport infrastructure operational.’
Roxtec has also worked on a major programme to upgrade the London Underground. The £5 billion Four Lines Modernisation project (4LM), is a project to update the Tube network’s Circle, District, Hammersmith & City and Metropolitan lines with hi-tech signalling equipment capable of boosting the frequency of trains and cutting down on delays.
That project has seen 51 new signalling rooms created, as well as equipment to house signalling cabinets along the 161
kilometres of track, with Roxtec products sealing cables going into and out of these buildings and cabinets.
Each station’s signal equipment room or removable electrical building has been individually designed.
Other recent key UK projects the business has been involved in include the delivery of heavy-duty cable seal solutions for Network Rail’s London Bridge Station.
The firm is also involved in the supply of cable and pipe seals for use within tunnels, substations, flood defences and signalling infrastructure as part of the UK’s HS2 project, linking London to the North of England and Midlands, and it has supported
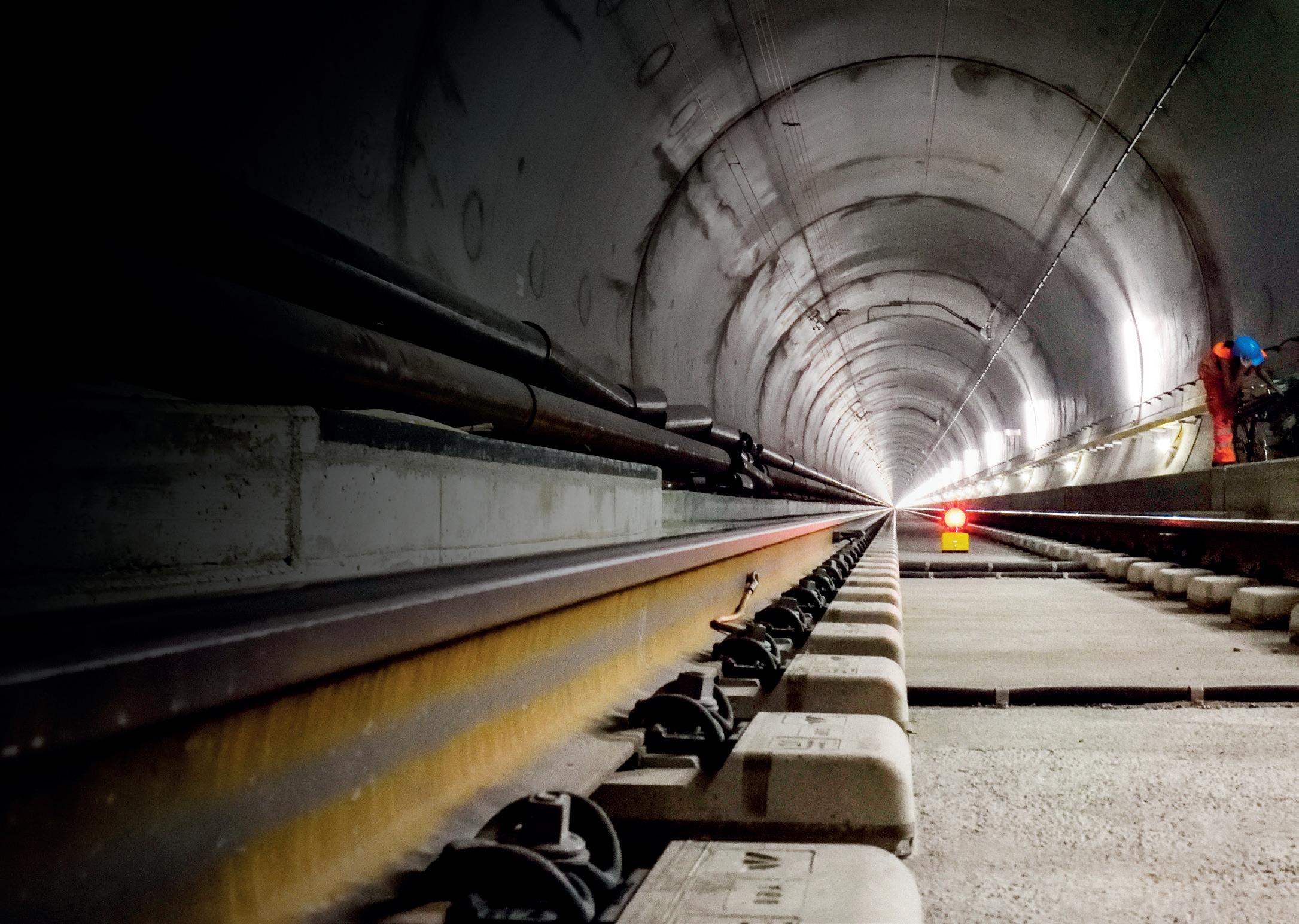
several high-profile rail infrastructure developments across Europe.
David Chalmers adds: ‘We have seen sustained growth in the rail sector, with increased demand for our solutions across the infrastructure and rolling stock markets.
‘As part of our ongoing commitment to rail infrastructure we have appointed Phil Jones as Rail Infrastructure Market Manager.’
Roxtec has a Triple-A credit rating and is actively expanding into new areas offering innovative and safe sealing solutions to a variety of industries.
For further details contact Roxtec UK at Waterfold Business Park, Bury.
Tel: 0161 761 5280
Email: info@uk.roxtec.com
Visit: www.roxtec.com/uk

‘It is incredibly rewarding to know that our seals are helping to keep people safe and vital transport infrastructure operational’
Zonegreen Proves Rail Risks can be Reduced
Britain’s railways remain the safest in Europe, but high voltage equipment, heavy machinery and moving vehicles make maintenance depots, in particular, dangerous places to work
When coupled with an inconsistent approach to staff safety and some facilities still relying on ad hoc risk control arrangements, it is undeniable that more can be done. Technological developments offer great opportunities to improve safety. This philosophy is at the core of Zonegreen’s working practises and the Sheffieldbased depot safety specialist continues to develop highly sophisticated systems that protect personnel, without impeding depot operations or productivity.
Protection via prevention
Perhaps best known for its market leading Depot Personnel Protection System (DPPS™), which is installed extensively across the UK, Australasia and the Middle East, Zonegreen is also a leading expert in interlocking, combining intuitive functionality with easy to use controls to improve worker safety.
The firm provides advanced interlocking systems that prevent personnel and
equipment entering dangerous areas and coming into contact with live third rails or overhead lines. It has developed a safe system of work that absolutely prevents access to high level platforms by means of a fully guarded stairway and interlocked gate that can only be opened with a key that is released from a control panel when the OLE is isolated. The sequence of unlocking and removing keys, which in turn allows other keys to be released, ensures prohibition of access to areas unless they are safely isolated and earthed. It is also possible to monitor the position of the gate locks to ensure that they are all closed and locked prior to enabling the reenergisation of the OLE.
Interlocking is far superior to ‘permit to work’ systems that rely entirely on everyone operating within the area of risk to follow procedure continually. One lapse of concentration is all it takes to place a member of staff in danger. Taking away the margin for human error, therefore, can potentially save lives.
Further refinements can be included within an interlocked OLE system to protect
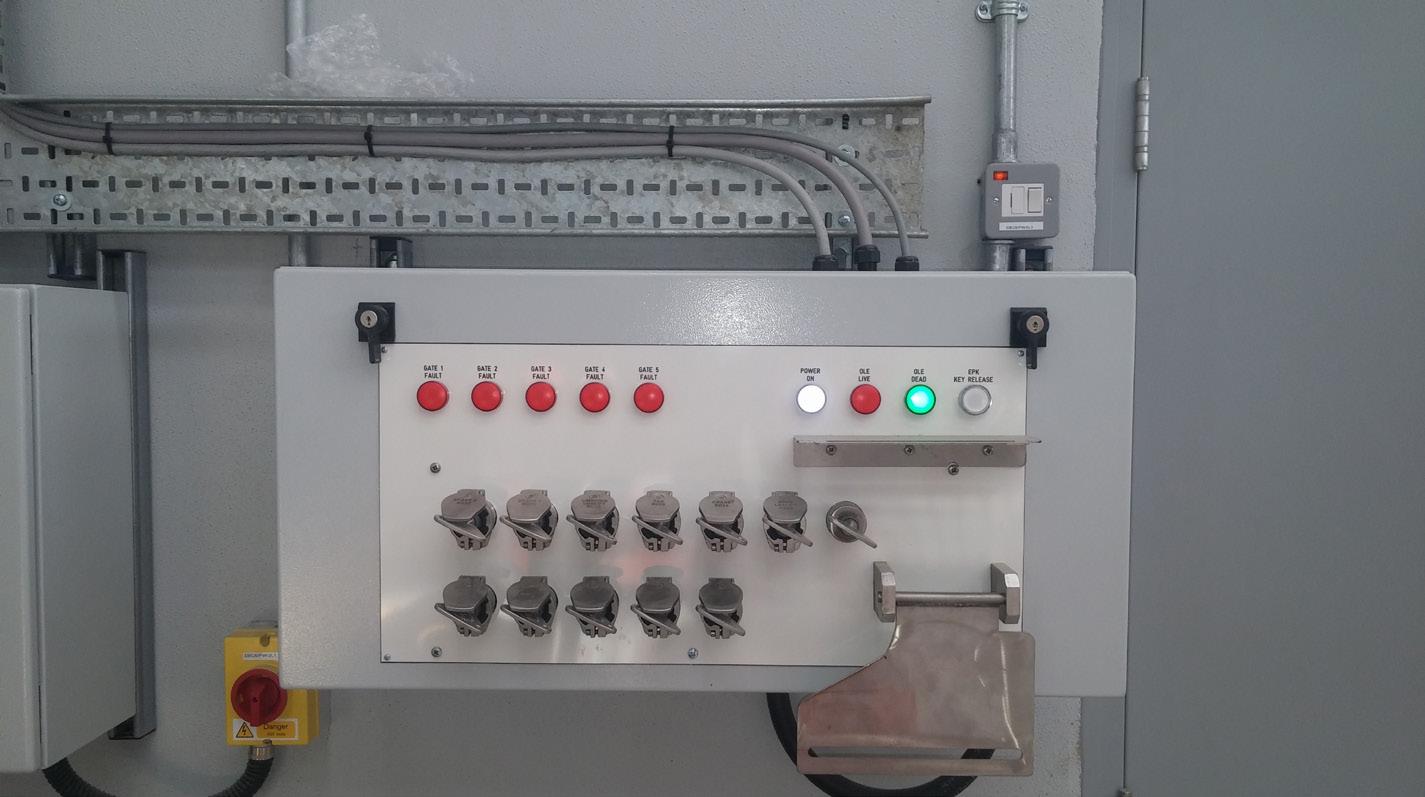
third party depot equipment. For example, to eliminate hazards from trains with two pantographs or multiple pick up shoes and to ensure the safe placing and removal of earth loops. In the past, failure to remove earth loops has caused numerous incidents, subsequent injury to workers and damage to equipment.
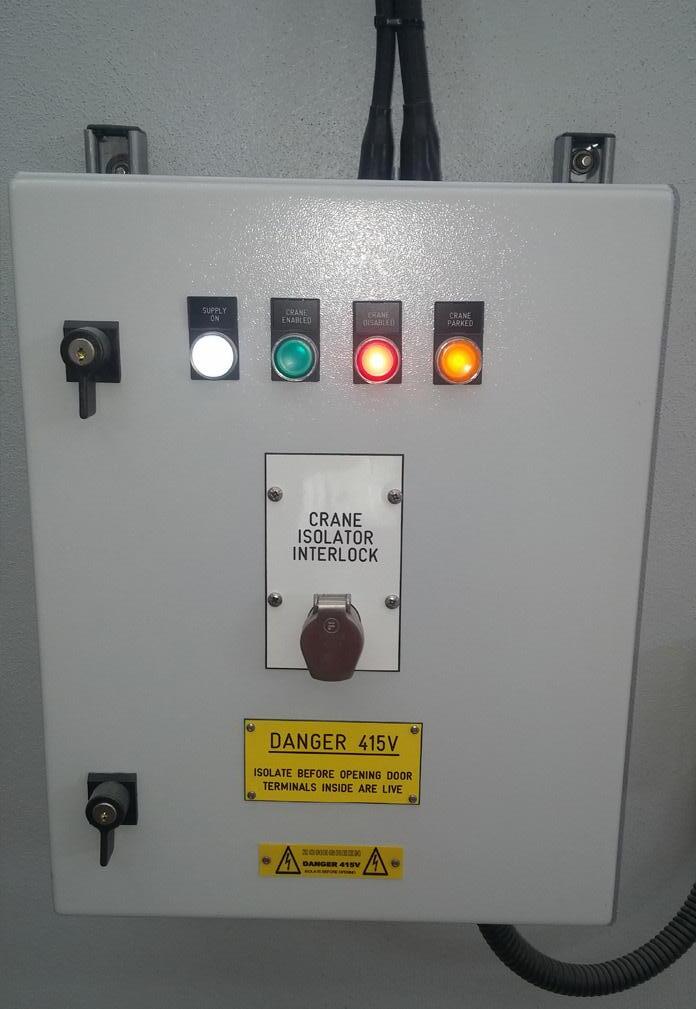
Specialist depot equipment that has the potential to come into contact with a live OLE, such as cranes, pressure washers and mobile gantries, can also be interlocked to prohibit their operation in potentially unsafe conditions.
The future
Whilst many UK depots already benefit from Zonegreen’s technology, there is still room for improvement.
Christian Fletcher, Zonegreen’s Head of Engineering, said: ‘The safest way to
protect personnel is to keep them out of dangerous areas. It is vital, therefore, to have properly engineered systems that can play a major role in staff safety, but also have the ability to improve efficiency. By applying our expertise, experience and adaptable technology to the issue, we are helping to prevent personal injury and the associated costly damages.
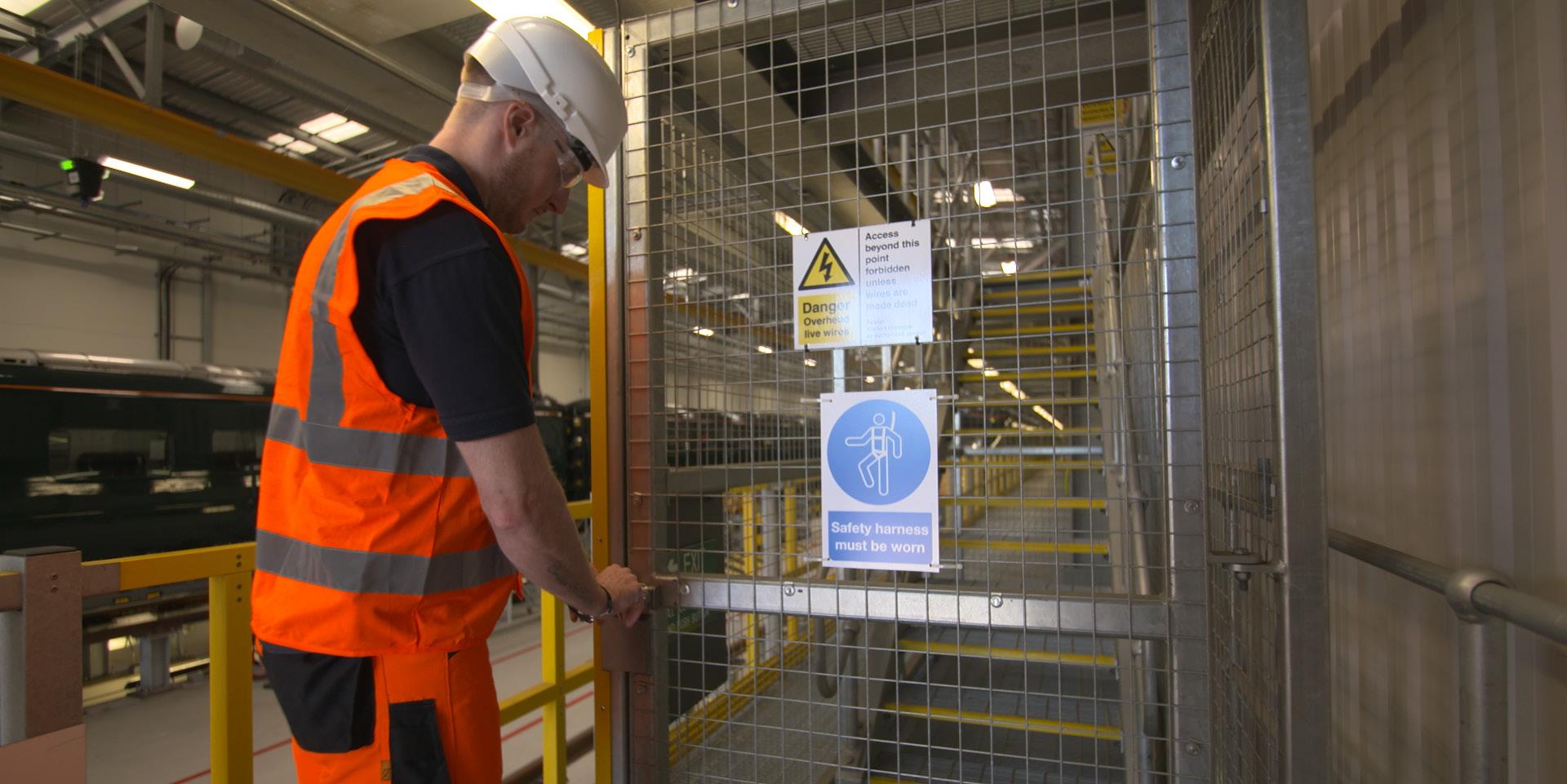
‘At the moment, the rail industry still has an inconsistent approach to keeping workers
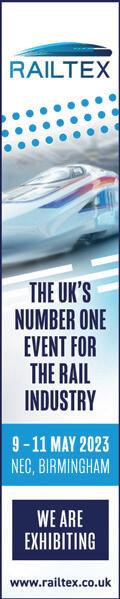
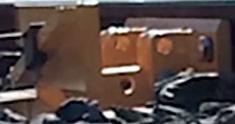

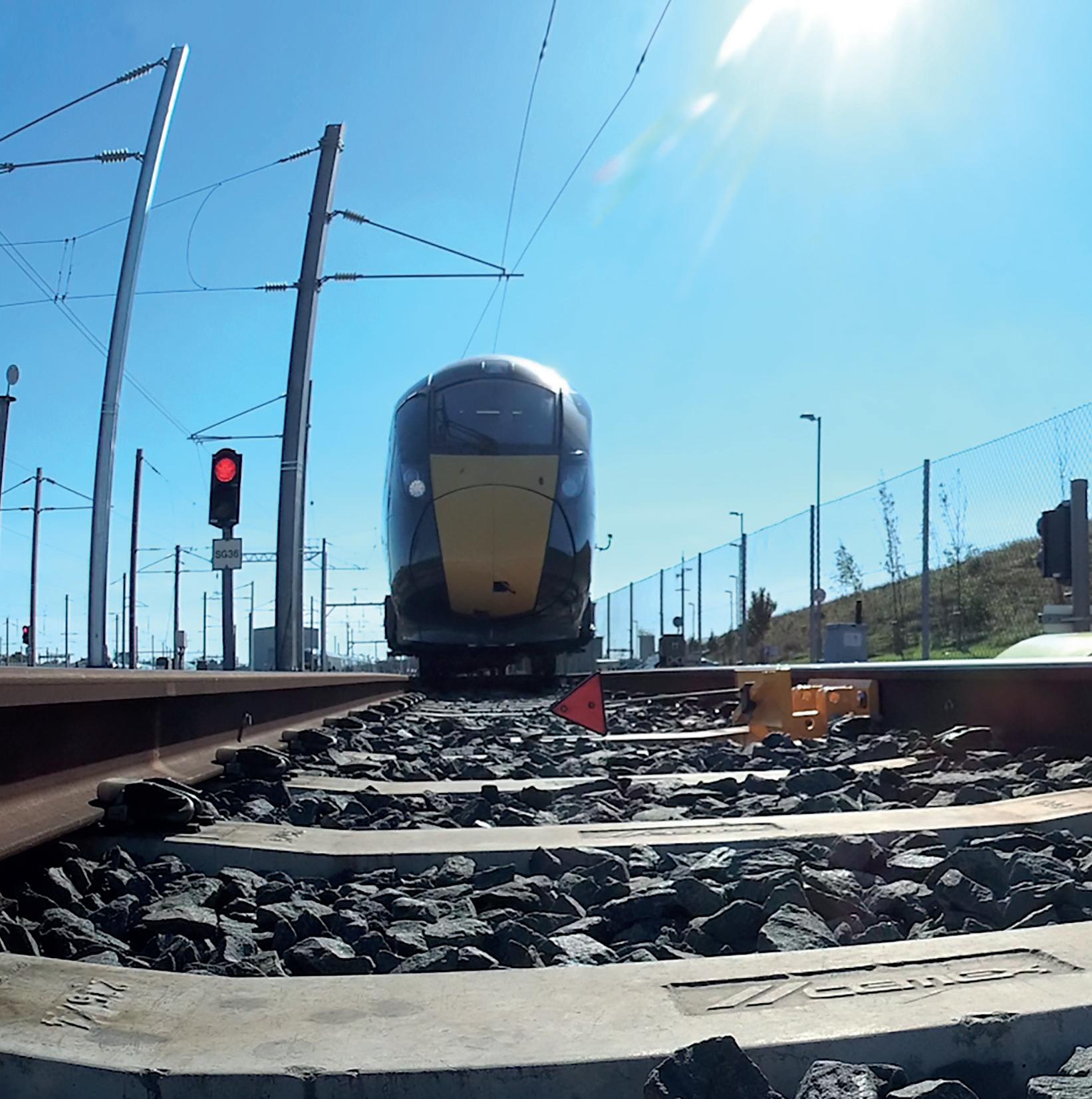
safe. Until the failings of manual systems are addressed across all rail depots, the potential for loss of life remains all too real. Our user-friendly DPPS™ can be developed to encompass both electronic and mechanical interlocking, providing proven protection against the risks identified.’
Safety demonstrations
Zonegreen will be exhibiting its market leading depot protection system and
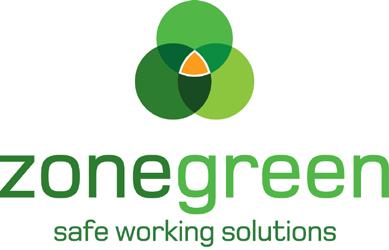
interlocking solutions at Railtex this year, on stand M11 at NEC in Birmingham, from 9 to 11 May. Throughout the event, the firm’s Head of Engineering and global expert in depot protection, Christian Fletcher, will be delivering informative and educational workshops about the risks to staff in maintenance depots.
Gemma Houghton, the firm’s Head of Sales, said: ‘We are really looking forward to catching up with old friends and introducing our DPPS and interlocking solutions to new contacts at Railtex.’
To register your interest in attending Zonegreen’s Railtex workshops or for more information about its suite of safety systems get in touch via the contact information below.
Tel: 0114 230 0822
Visit: www.zonegreen.co.uk
NON-GLYPHOSATE
RAILWAY VEGETATION CONTROL

RAILWAY TRACK, SUBSOIL AND GROUNDWATER DECONTAMINATION
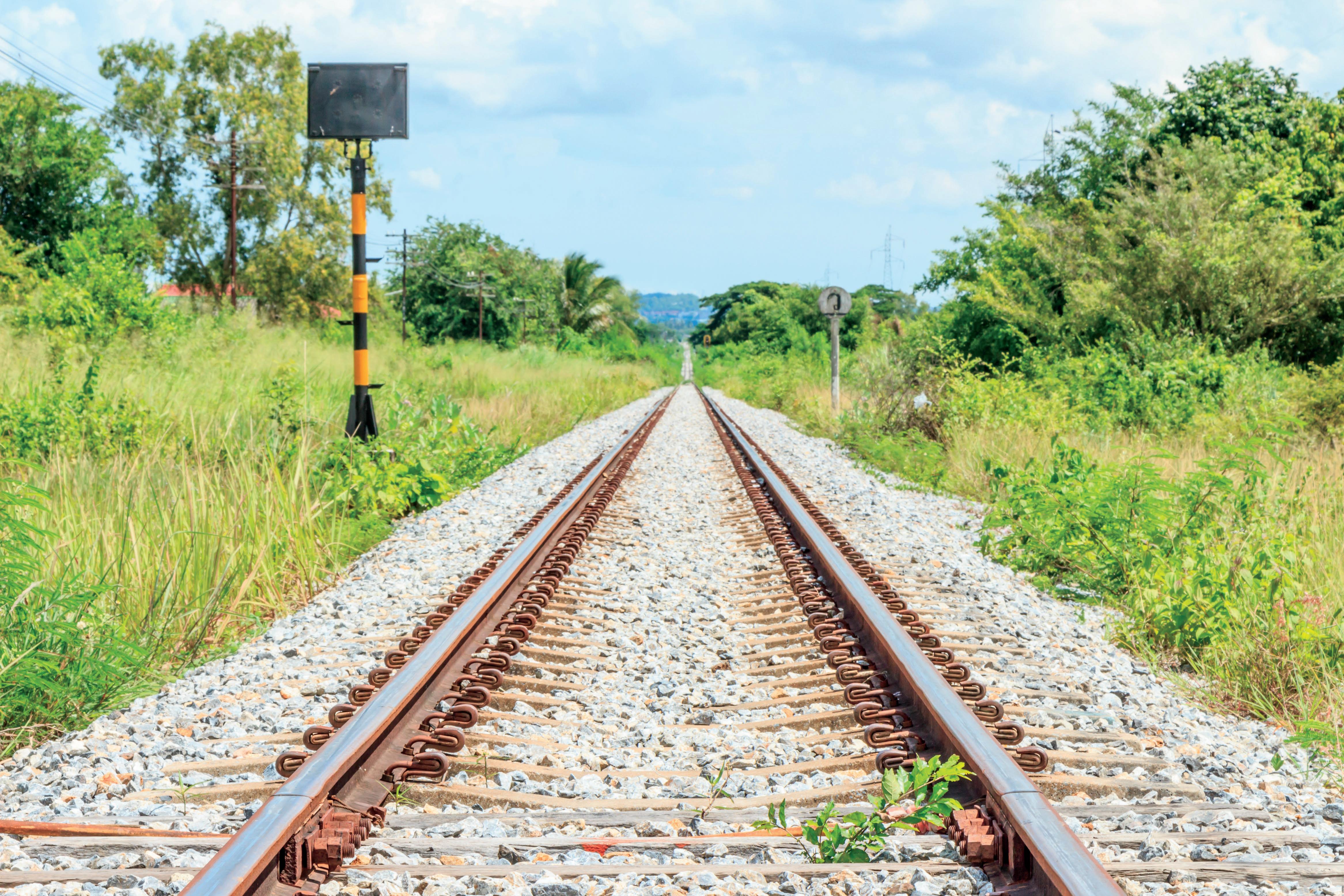
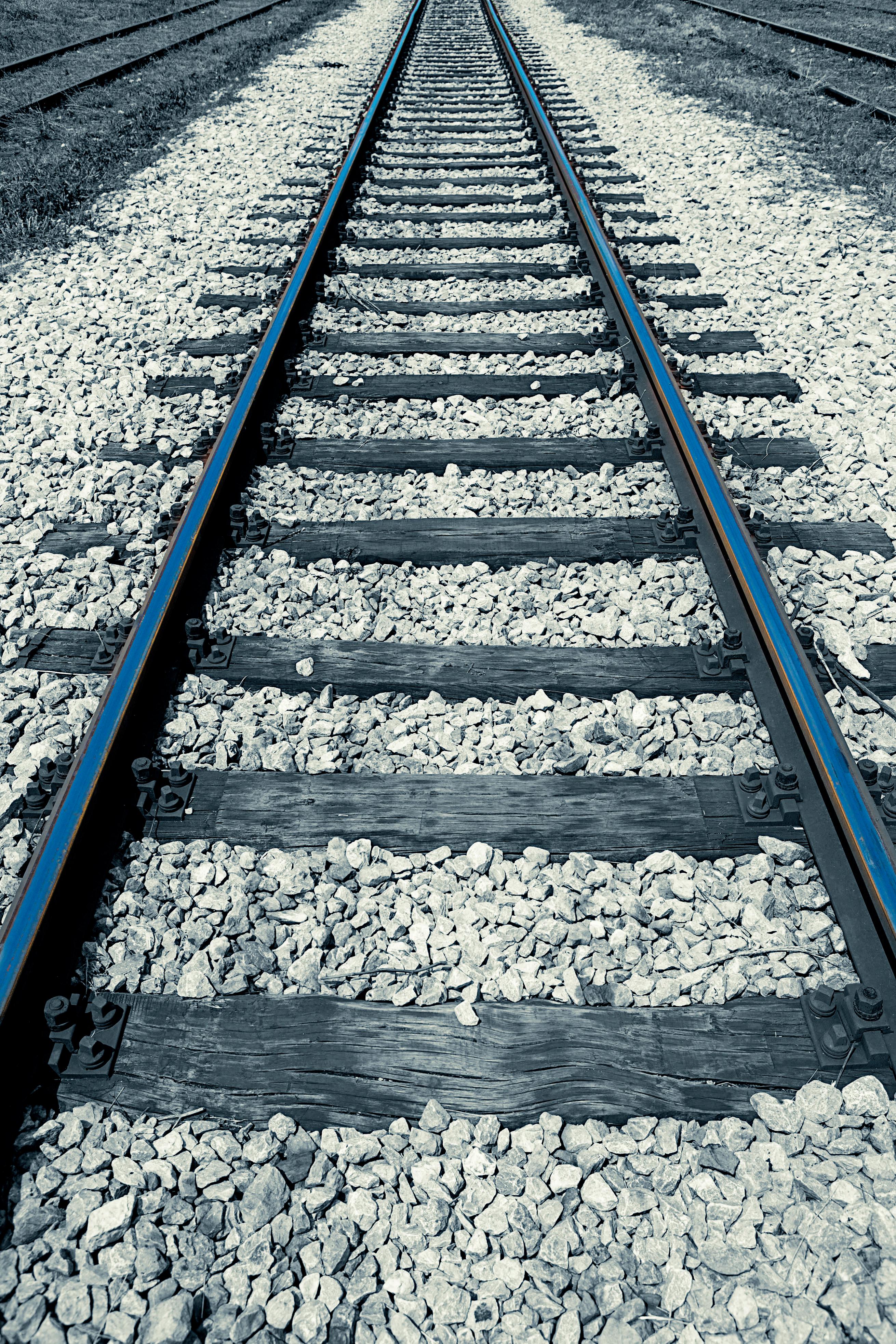
WWW.ALPHACLEANTEC.COM
INFO@ALPHACLEANTEC.COM
Over the past 20 years Gall Zeidler Consultants has completed 550km of tunnelling projects across the globe, establishing our position as a world-leader in tunnel design and consultancy services.



Our specialists relish a challenge and always deliver – it’s why we’re a leader in innovative underground solutions, geotechnical engineering, bespoke tunnel design, tunnel rehabilitation, and project/construction management.
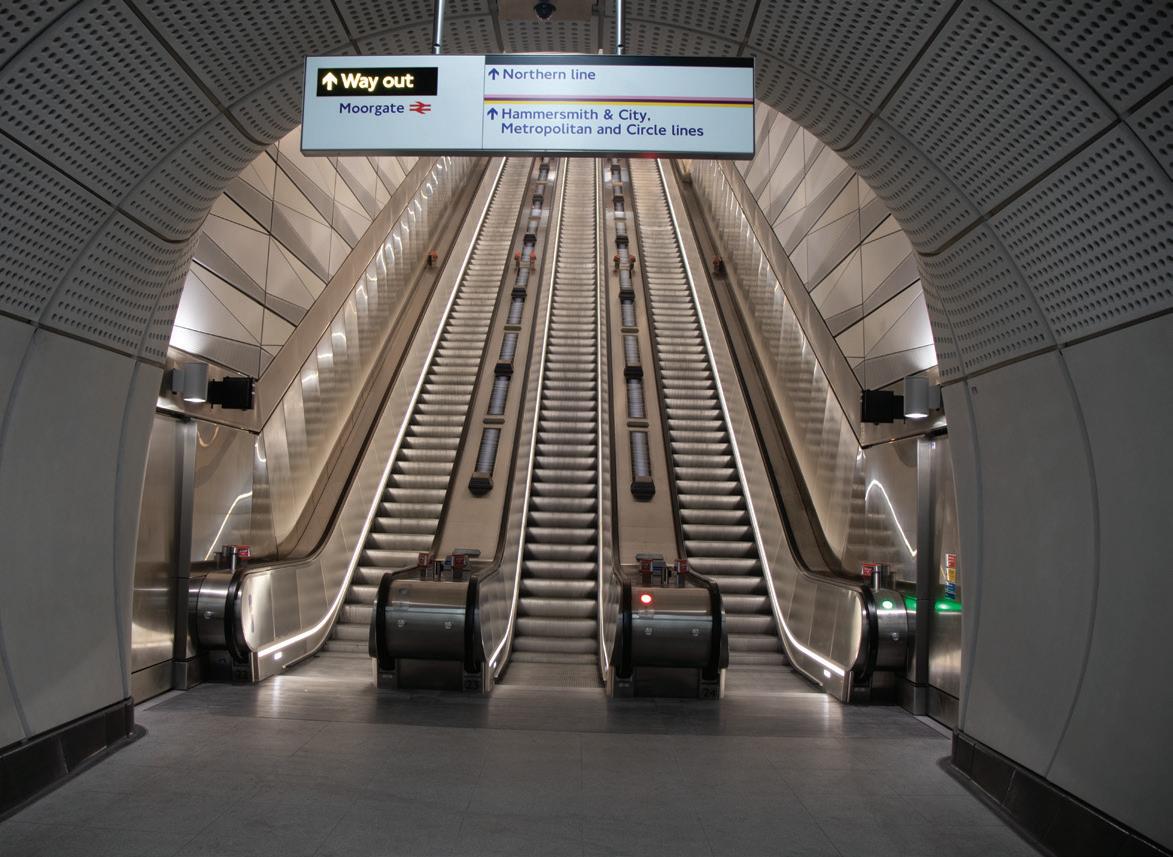
Feltham and Wokingham Re-signalling Project
In early 2016, Electro-Wind was approached by Devontech to collaborate on the design, build and obtain approval for a range of PSP transformers for the Feltham and Wokingham projects
For over 35 years ElectroWind has been designing and manufacturing single and three phase transformer products for customers in the UK, Europe and Global Markets, having a well-established reputation as one of the UK’s leading specialists the company has fulfilled many contracts for companies such as Alstom, Tata, Corus, Mitsubishi and Toyota.
Electro-Wind, Devontech and Atkins global; have been working on the project which covers some 80 miles of railway and 500 pieces of outdated signalling equipment, which is being replaced as part of Network Rail’s commitment to transforming the UK’s entire network through the deployment of digital signalling and train control technology, transforming signalling for
passengers, business and freight operators. The new signalling equipment which uses digital technologies will bring a number of benefits such as increased capacity for trains on the network, fewer delays, enhanced safety and lower costs.
To date Electro-Wind has manufactured 57 transformers for this project ranging from 5kva up to 60kva. The Transformers have been 400v/650v signalling transformers that Devontech and Electro have worked closely together to get PADS approval for the Network rail Infrastructure.
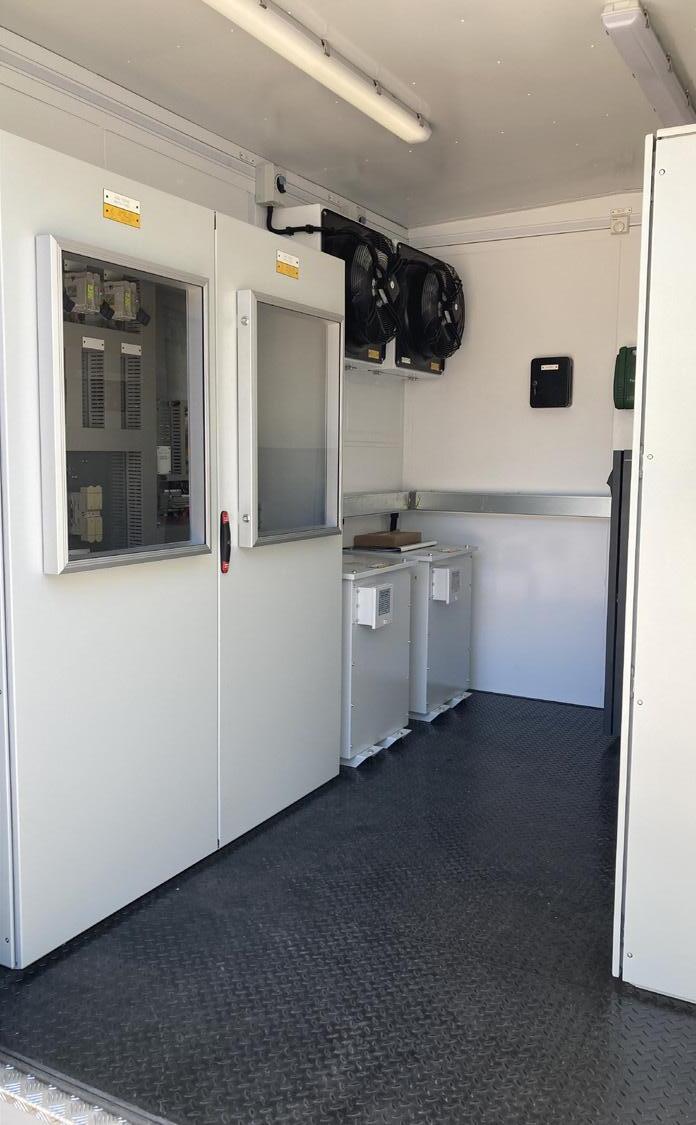
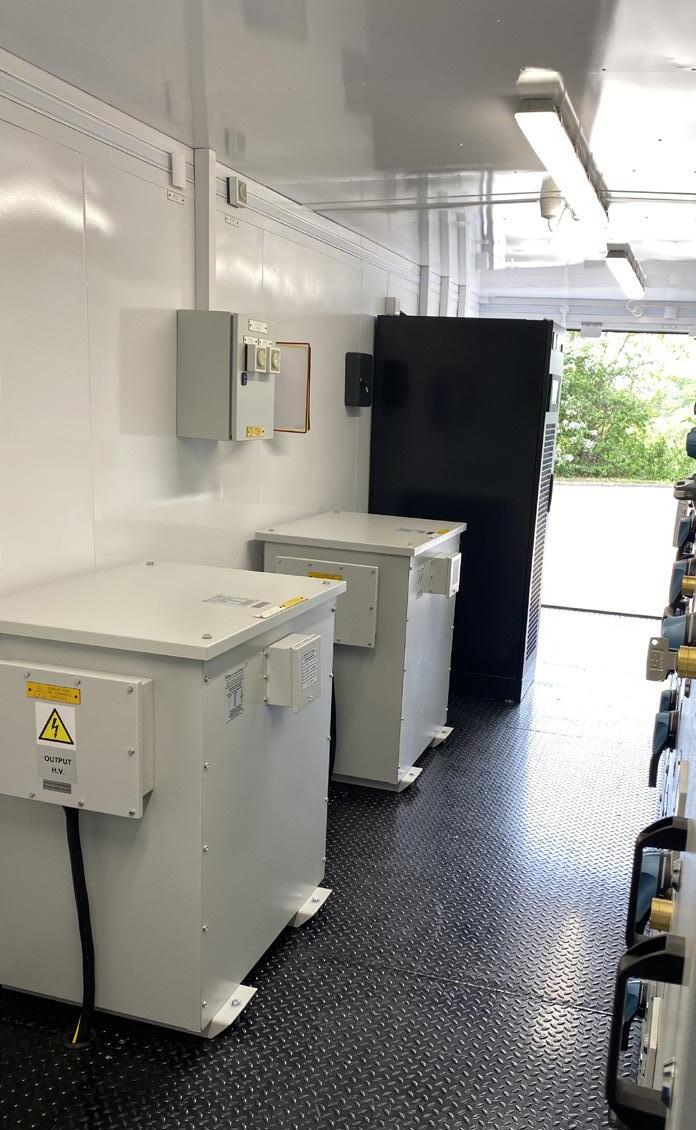
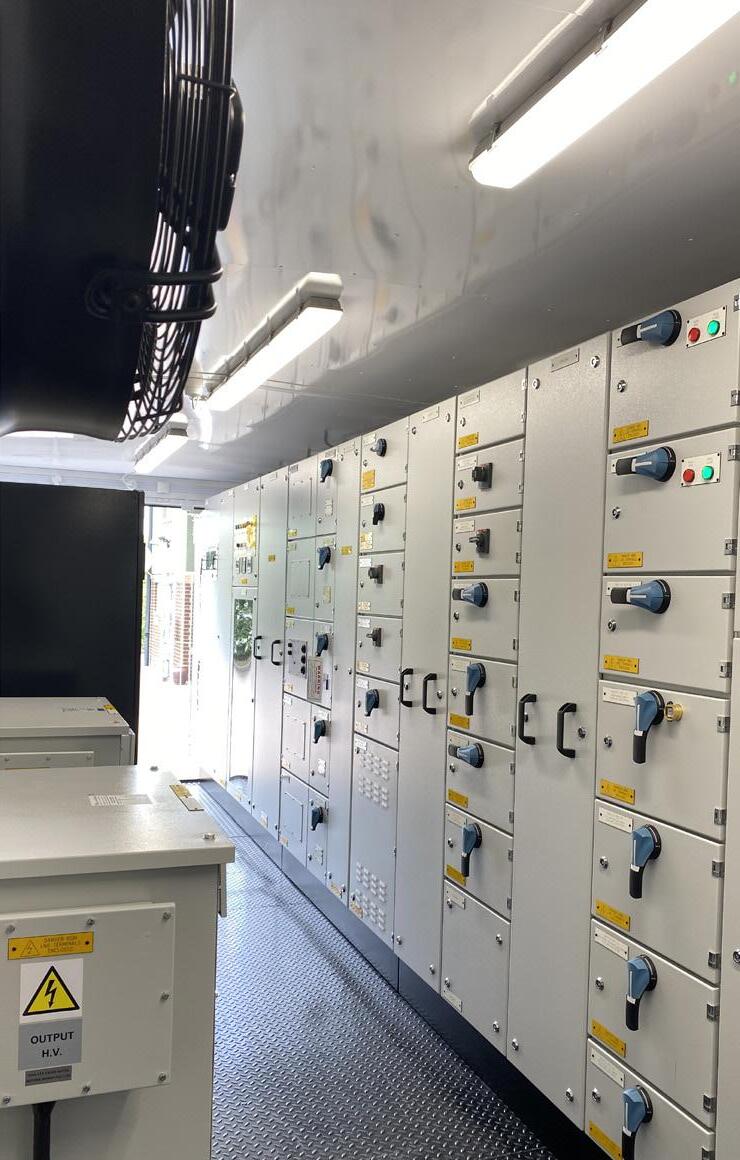
The project started in December 2015 and is now completed with final commissioning for the project into service in August 2023.
Electro-Wind has over 35 years of experience in transformer repair and
manufacture. The company offers a repair service that spans from control transformers to large three-phase distribution transformers. A rapid response repair service is available which includes a 24-hour service when required, as well as enclosure repairs and replacement options that are part of the repair service.
Electro-Wind prides itself on exceeding customer expectations, delivering on time and within budget. All of its standard transformers are manufactured to IEC61558 and IEC60076. For further information, get in touch via the contact information below.
Tel: 01782 776 321
Email: sales@electro-wind.co.uk
Visit: www.electro-wind.co.uk

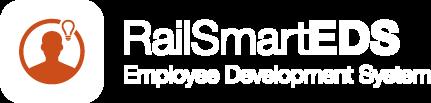

Delivering Digital Transformation

Cultivating a green and digitally enabled railway of the future with 3Squared, a Sheffield-based rail software and solutions specialist, founded in 2002
With over two decades of experience in the industry, 3Squared understands rail – from the multitude of organisations involved, to the complex rules and regulations. Through the expertise the company has developed, it has the foresight and understanding to create and implement solutions that make a positive impact on the rail network’s day-today operations and to Make. Change. Work.
3Squared collaborates closely with key players from across the rail industry, from Network Rail to HS2, to understand the problems they are experiencing, and how technology can play a key part in overcoming them.
The team is comprised of industryleading specialists, enthusiastic about keeping the rail industry moving and innovating.
The vision is geared towards the creation of a greener, digital rail network, that runs efficiently, safely and on time.
Innovative solutions
Through the RailSmart suite, 3Squared delivers digital transformation, drives efficiency and streamlines operations across the industry. The flagship RailSmart solution is EDS (Employee Development System), it is a competency management solution that has delivered tangible results for a diverse range of organisations, including London North Eastern Railway (LNER), East Midlands Railway (EMR), Alstom, and more.
Designed with efficiency in mind, RailSmart EDS enables its users to lower business risk and reduce incident rates through digital-based, reliable competency management. Since LNER began implementing EDS, seven years ago, they have seen improvements across safety and performance.
Simon Reading, Driver Team Manager at LNER commented that: ‘Every driver manager, every station assessor, every train
manager assessor uses RailSmart EDS – even our training team now use it.’
EDS enables clear organisation and oversight for users, creating a smoother process which drives significant operational improvements. In Simon Reading’s role as Driver Team Manager he reports: ‘As RailSmart EDS is an electronic system, I always have information at hand and can look at competency with ease.’
No longer do teams have to file complicated paperwork or travel up and down the country to review files. This solution acts as a digital hub of information which can be accessed at the office, onboard rolling stock, onsite and beyond. This drastically saves time and reduces the administrative burden of compliance.
LNER’s Safety & Environment Programme Manager, Melanie Sewell has also described the benefits EDS has established: ‘We have been using RailSmart EDS for the last seven years and it has made a significant change to our business. Bringing in an electronic system means we have a better oversight of our competency management arrangement.’
3Squared strives for continuous improvement, which is why it works
together with clients to drive developments. Following a focus group last year, 3Squared has some exciting new enhancements to EDS tailored to meet its users’ evolving requirements. This includes interface enhancement, further customisation capacity, reporting tools, and more.
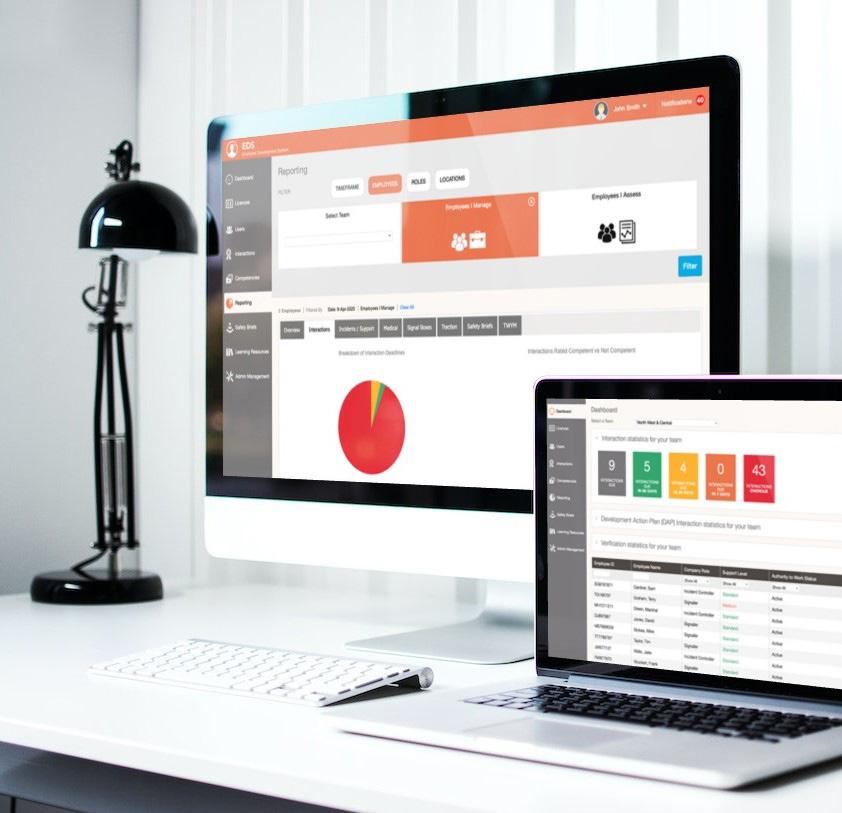
To support organisations with the effective implementation of competency management systems (CMS), 3Squared has released a free guide which focuses on the following:
• The benefits of a good CMS implementation.
• The key drivers for change to CMS processes.
• How to plan for success.
Download the guide from the website: https://3squared.com/freeimplementation-guide/
Railtex
Make sure to visit 3Squared at this year’s Railtex to learn more about the RailSmart suite of solutions, discover how competency management can drive improvements across your business, and hear how to Make. Change. Work. in the industry. 3Squared is delighted to join Rail Forum and five other Rail Forum members at Stand D17.
If you would like to find out how 3Squared can support your digital transformation, get in touch via the contact information below.
Q&A with Claire Thompson
Business Manager – Rail at Mallatite Rail (formerly VMS)
With over 15 years of experience Claire has established herself as a respected professional and leader in the industry. Her deep understanding of the rail sector, combined with her expertise in commercial, operational and customer focused roles has enabled Mallatite Rail to deliver effective solutions for clients across the UK.
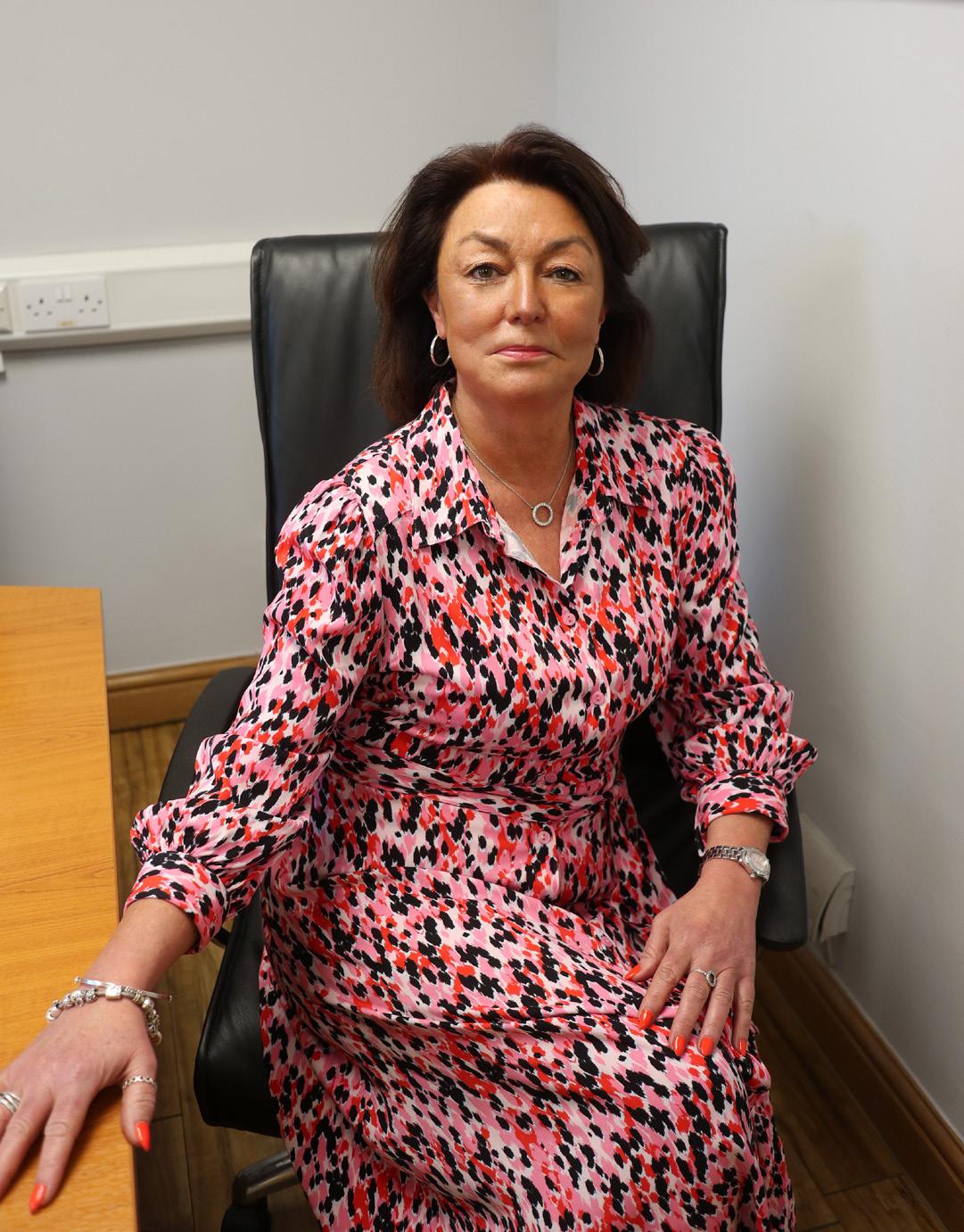
When did you join the company?
I joined VMS in 2008 as Financial Controller and became involved in the Rail Business around the time that the lightweight products gained acceptance in 2011. My early involvement was mainly supporting customers and making sure orders were delivered on time. The opportunity then arose to become the Business Manager in 2014 and I did not hesitate to move out of finance and become involved in all aspects of the Business.
How long has your company been in business?
Formerly part of Rolls Royce, the business commenced in 1989 supplying reflective flip dot signs. In 1994 the first LED signs were supplied and this was shortly followed by Highways Agency deployed LED signs in 1995.
We then became involved in the rail industry when Railtrack employees observed these new VMS LED Motorway signs and were extremely impressed by the readability and high contrast ratios they presented (even in direct sunlight) and approached RollsRoyce to ask if we would consider applying our in depth knowledge of optoelectronics
and LED control, to design and manufacture products which would replace the existing lineside signals with LED equivalents.
The business departed Rolls Royce in 2003 when the management team acquired it and VMS was established. Our first rail products continued to be developed throughout this transition and a series of trials commenced. While the fundamental challenges of the optical design of road and rail products were similar, the road signs consisted of dozens of processors and communication links providing fault status and logging. Therefore, the technical challenge for VMS was making a complex LED signal which would mimic the simple failure modes of an SL35 lamp with no possibility of presenting a wrong side failure condition. This allowed the VMS signals to be backwards compatible with the extremely limited status reporting of the existing filament lamp control infrastructure. However, these issues were soon overcome and tested and resulted in our first product acceptance in 2006.
What types of products and services do you offer?
All types lineside signals, indicators and accessories, starting in 2006 with a stacked
colour light signal. These signals tell the driver when it’s safe to proceed and following this we now offer a wide range of signalling products which we supply either direct to Network Rail on a Framework contract or to their contractors.
How have the products and services you offer developed over the years?
Once our first product was accepted and deployed, we rapidly introduced more, our banner signal was developed and on-trial within a year and in 2011 we were awarded the Network Rail Partnership Award for Innovation for our range of lightweight signalling equipment. Since then, our product portfolio has continued to increase as we reacted to signalling challenges, most recently addressing different types of environment and space constraints for station areas.
What are some standout projects you’ve been involved in recently?
We are proud to say the resignalling of Birmingham New Street Station and Manchester Piccadilly Station. These projects gave us an opportunity to collaborate with Network Rail and develop products
which solved the particular challenges of station areas.
We introduced a compact version of our colour light signal which took all the optical performance of the exiting products but housed them in a smaller enclosure for deployment in lower sector installations and tunnels or even anywhere where there are space constraints. In addition to the size reduction which solved the spatial challenge, VMS also introduced a reduced brightness variant to ensure the signals would function optimally in a station environment which has numerous reflective surfaces. The existing product we offered presented the risks of a train driver misreading the signal, confusion to platform departure staff and dazzling drivers and customers on the platform. We understood these risks and took on the challenge to adapt our products further and, after a series of readability assessments and stakeholder feedback we introduced a short-range signal which is now deployed throughout the station.

Alongside the colour light signal, space constraints also impacted on our existing route indicator range. We were able to navigate the hugely challenging standard required on readability and develop a route indicator which combined the aspects from two products (our Standard, Alphanumeric Route Indicator and Miniature, Alphanumeric Route Indicator) into one, (Combined, Alphanumeric Route Indicator) another space saving solution which has resulted in these products being installed in many station areas. Not only does this product save on space it also saves money as it reduces the cost of deploying two signals.
What is your USP (Unique Selling Point)?
Definitely our collaborative attitude and ability to problem solve and develop new products to meet industry challenges. We never go back to our customer with ‘well that’s what’s available’ we listen, are keen to understand the problem and we apply our innovation skills and industry knowledge to deliver new products.
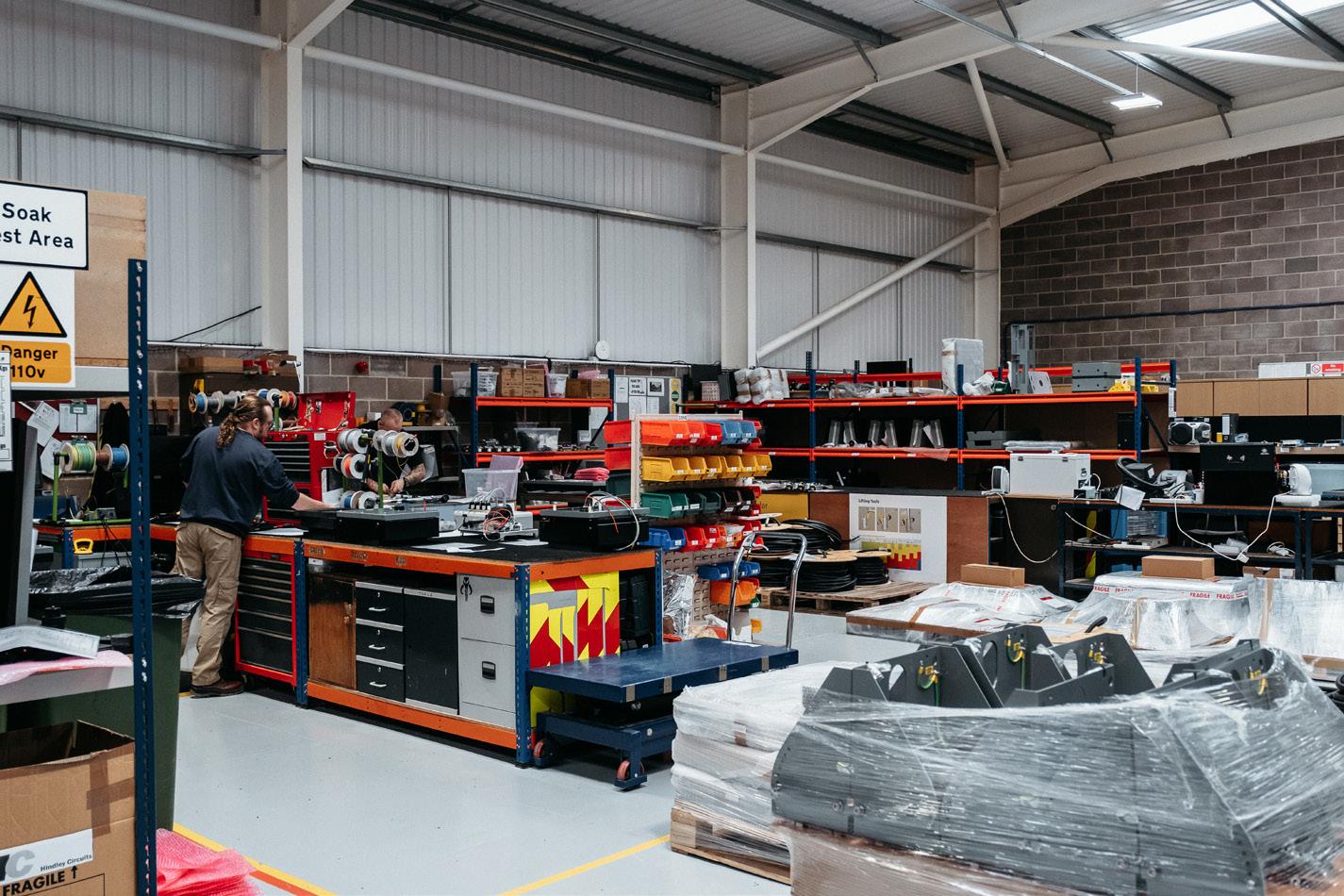

What do you have planned for the year ahead?
We are currently developing a 12V DC variant of our existing 24V DC colour light signal for a customer who has identified a number of 12V signals in their existing infrastructure which will require imminent replacement. Switching these systems over to the currently established voltages of 110V AC or 24V DC would be both complicated and expensive. It is our intention to deliver this product to solve their problem, but furthermore to ultimately offer this product as a “universal” DC signal which will be capable of being installed in both 12V and 24V applications with no modifications to the product, greatly simplifying ordering and spares holdings.
NEWS IN BRIEF

HITACHI PARTNERSHIP WITH GLOBAL CENTRE OF RAIL EXCELLENCE WILL DELIVER ENERGY SECURITY AND UK INNOVATION
Hitachi Rail and Global Centre of Rail Excellence (GCRE) have signed an agreement to test the latest in rail technology. This follows Hitachi Energy winning a competitive tender to provide a Static Frequency Converter to manage the power grid and provide energy security. This strategic partnership exemplifies Hitachi’s collaborative approach, using its wide expertise in Green Energy and Mobility to deliver innovative solutions from wind to wheel in the UK.
New appointment gives boost to East Suffolk Lines Community Rail Partnership
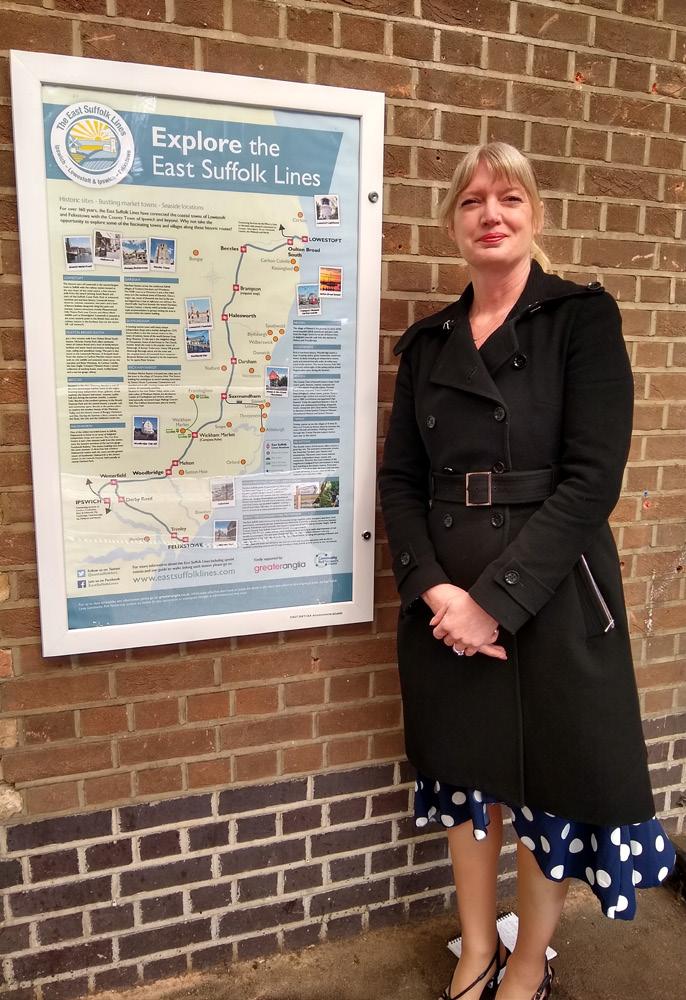
ISLE OF WIGHT: RYDE PIER HEAD STATION TO REOPEN BY 10 JUNE
Network Rail and South Western Railway (SWR) can confirm that the station and line between Ryde Pier Head and Ryde Esplanade stations will open no later than 10 June, in time
172 METRES OF TRACK AND 280 SLEEPERS
for the start of the summer holidays and the Isle of Wight Festival. Work is progressing well and is now entering the final stages with engineers reinstating 172 metres of track and 280 sleepers following the repairs and painting of the steelwork.
Thalia Rushmore joins the East Suffolk Lines Community Rail Partnership to focus on promoting the railway and working with the communities along the lines between Ipswich and Lowestoft and Felixstowe for their mutual benefit – as well as maximising the positive impact of the new trains now providing a regular, high-quality service for communities and customers along the line.
New appointment to the GEODIS executive committee
GEODIS, a world leader in transport and logistics, is pleased to announce the appointment of Camille Porgès as EVP Governance, Risks and Compliance. She will join the Group’s executive committee, which is chaired by Marie-Christine Lombard, Chief Executive Officer of GEODIS.
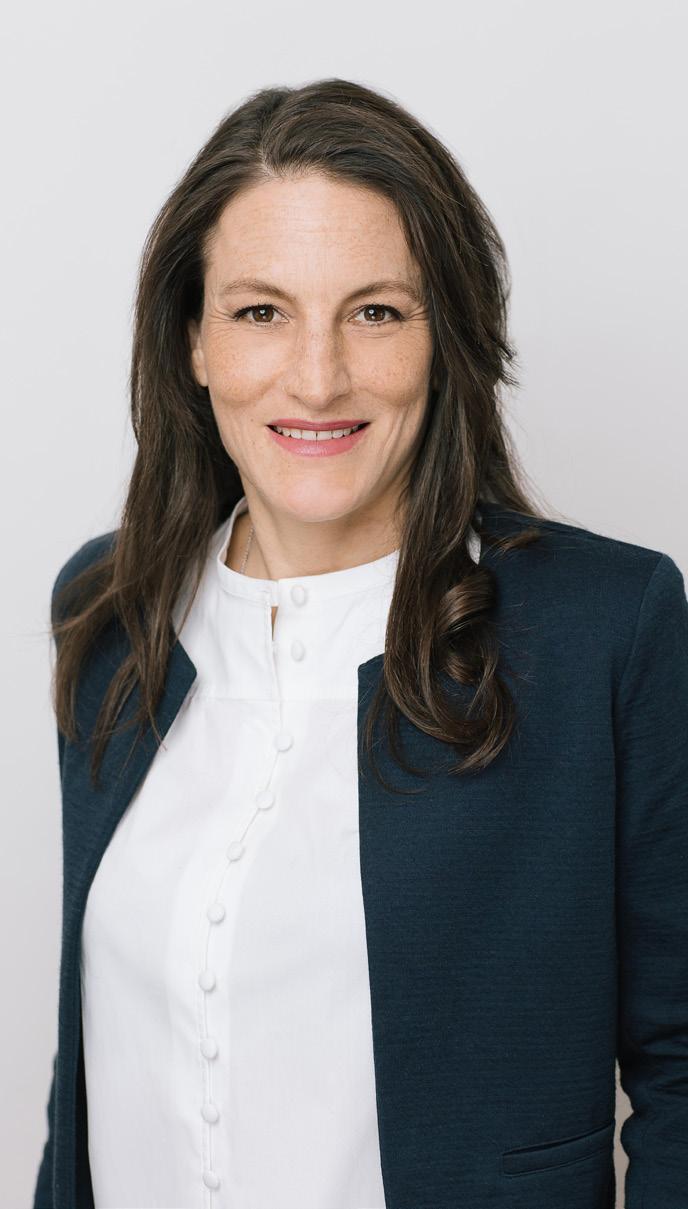
GREEN LIGHT FOR HS2’S SMALL DEAN VIADUCT
A key viaduct that will take HS2 trains across the A413 and local rail lines south of Wendover has been given the green light by Buckinghamshire Council. The striking 345 metre long viaduct is the latest major structure to gain design approval, as construction continues to ramp up on the UK’s new high speed railway.
New Group CEO joins Hitachi Rail at the start of an exciting new chapter Giuseppe Marino has begun work as the new Group CEO of Hitachi Rail, as the global leader in rail enters an exciting new chapter delivering innovative digital technology and sustainable transport around the world.

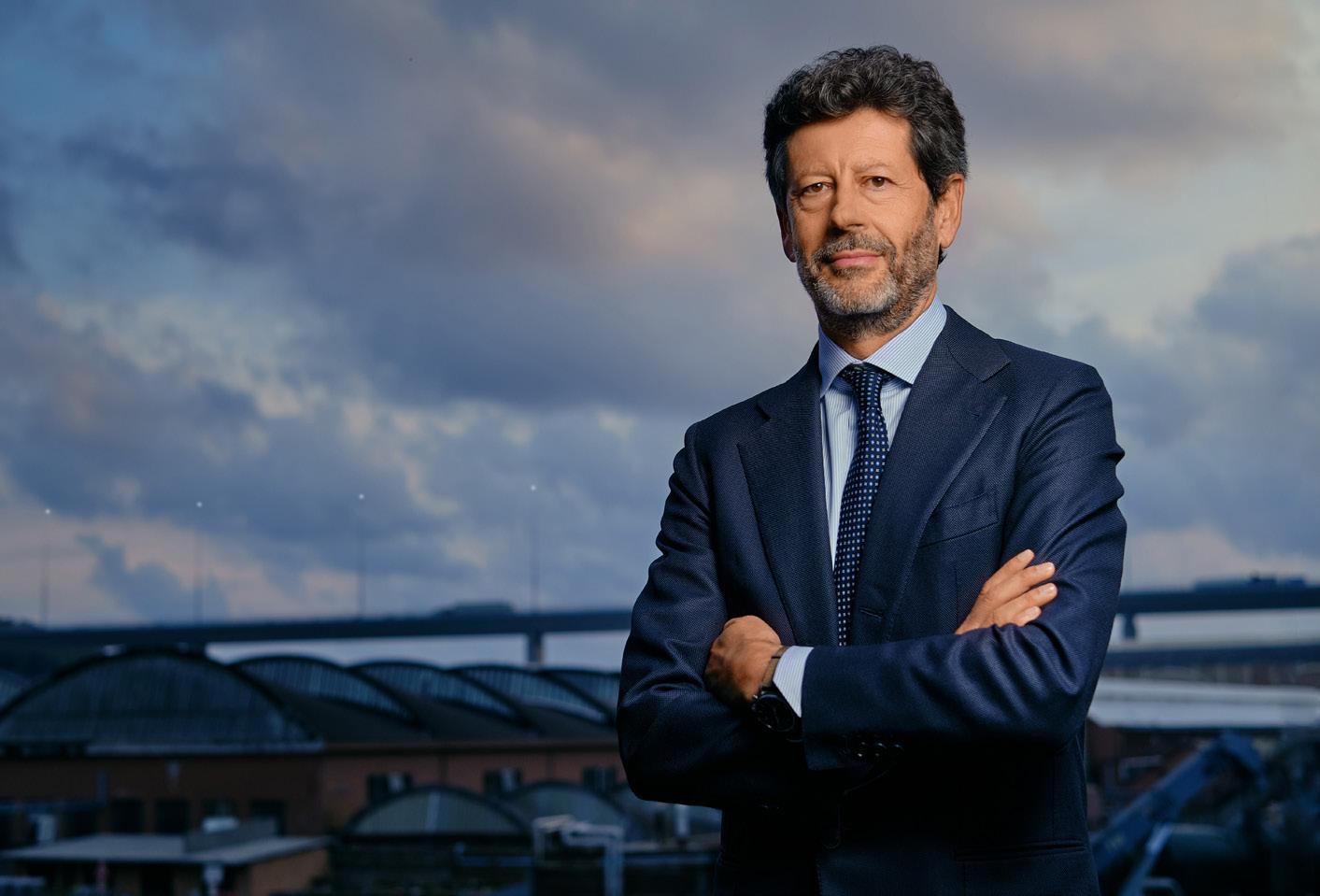

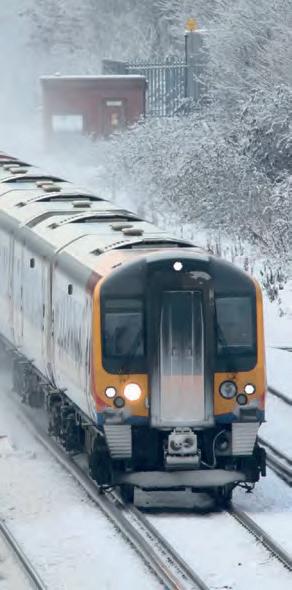



