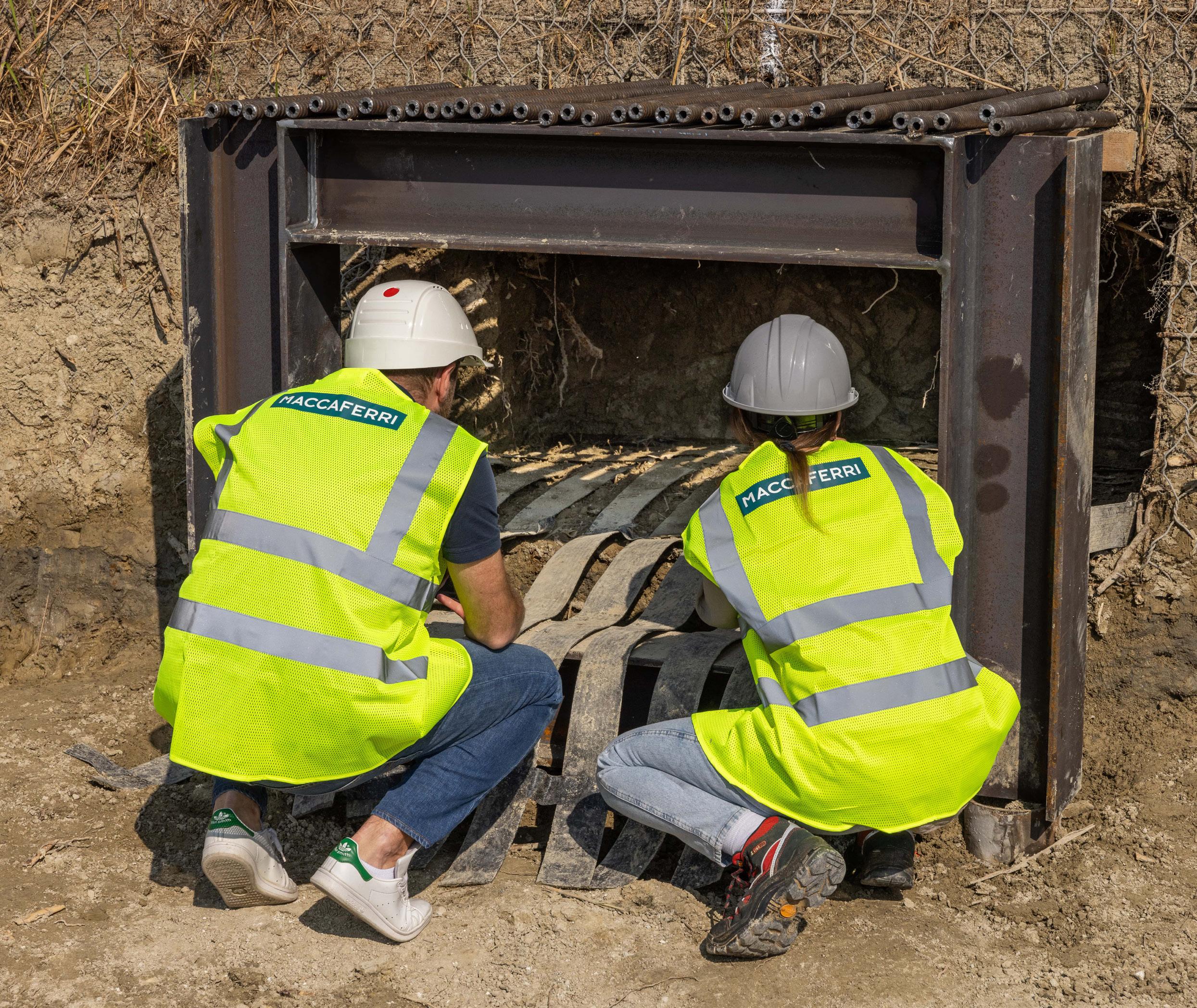
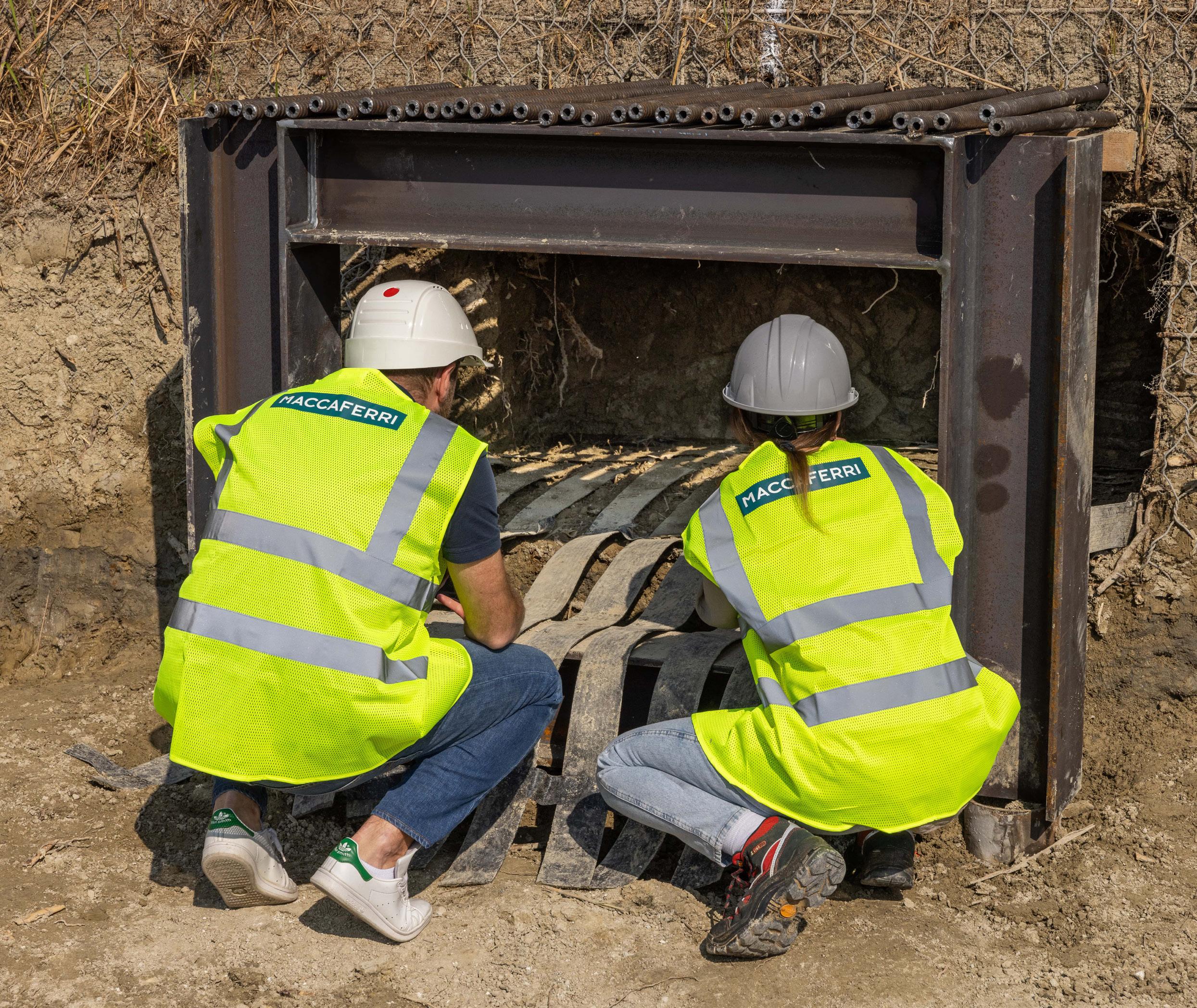
Breaking Ground



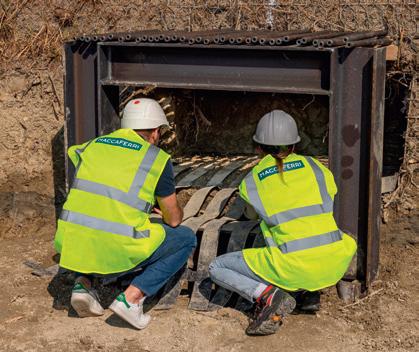
railprofessional @railpromag
PUBLISHER
RAIL PROFESSIONAL LTD
Hallmark House, Downham Road, Ramsden Heath, Essex CM11 1PU
Telephone: +44 (0) 1268 711 811
EDITORIAL
EDITOR
Sam Sherwood-Hale editor@railpro.co.uk
DISPLAY ADVERTISING
Adam Overall
Jamie Tregarthen sales@railpro.co.uk
RECRUITMENT ADVERTISING recruitment@railpro.co.uk
SUBSCRIPTIONS subscriptions@railpro.co.uk
ADMINISTRATION
Cherie Nugent info@railpro.co.uk
Lisa Etherington admin@railpro.co.uk
DESIGN & PRODUCTION
Jasmine Szaniszlo
Lukasz Saczek production@railpro.co.uk
COVER Image credit: Maccaferri
EDITOR’S NOTE
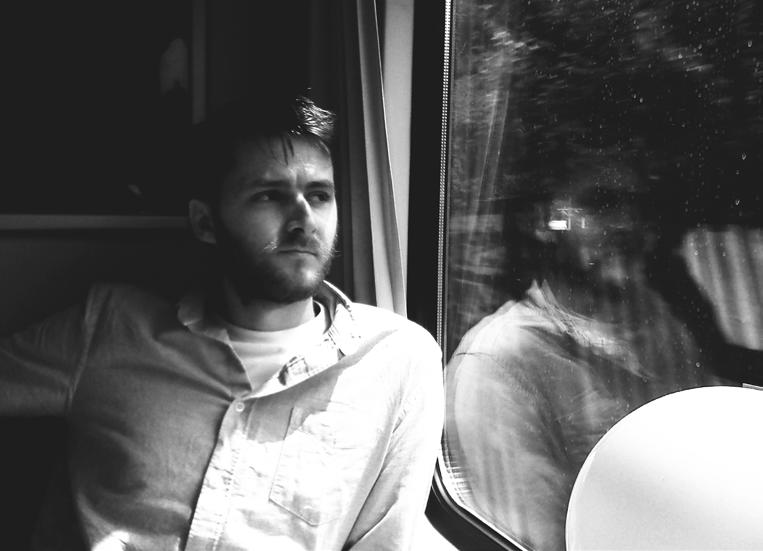
At the time of writing, The Transport Committee is holding the first session of its inquiry to scrutinise the Government’s draft Rail Reform Bill. The draft Bill, published in February, proposes legislation needed to deliver reforms included in the Government’s Plan for Rail. This includes giving Great British Railways new legal powers to manage and oversee the country’s rail infrastructure and franchising of services to train operating companies.
The Williams Review stated that ‘the railway has become fragmented and accountabilities are not always clear’ and has come to ‘lack a single strategic direction.’
To remedy this, RIA suggests removing the Secretary of State’s (SoS) open-ended power of direction and Rail Partners concurred by saying that Guidance and directions should be issued sparingly. For years our opinion writers have been calling for joined-up thinking and a single guiding mind, which we are expected to get from GBR, but what is currently being proposed is changing the designation of Network Rail Infrastructure Limited (NRIL) to the Integrated Rail Body (IRB). As always, we will continue to watch how this story develops.
My interview this month is with Colin Campbell of Mabey Hire on the innovations they came up with whilst working on the restoration of Barmouth Viaduct. We’ve also got a case study of the project itself to follow as well as several other major infrastructure stories looking at bridges, tunnels and the plant and machinery outlook for the year.
Alongside the usual collection of interviews of key figures within the industry as well as opinion pieces on Scotland’s railways from AECOM’s Rail Lead for Scotland Crawford Johnston and Rebecca Collings and Simon Young, both of Nichols explain how success happens when rail and regeneration programmes are aligned.
SAM SHERWOOD-HALE EDITOR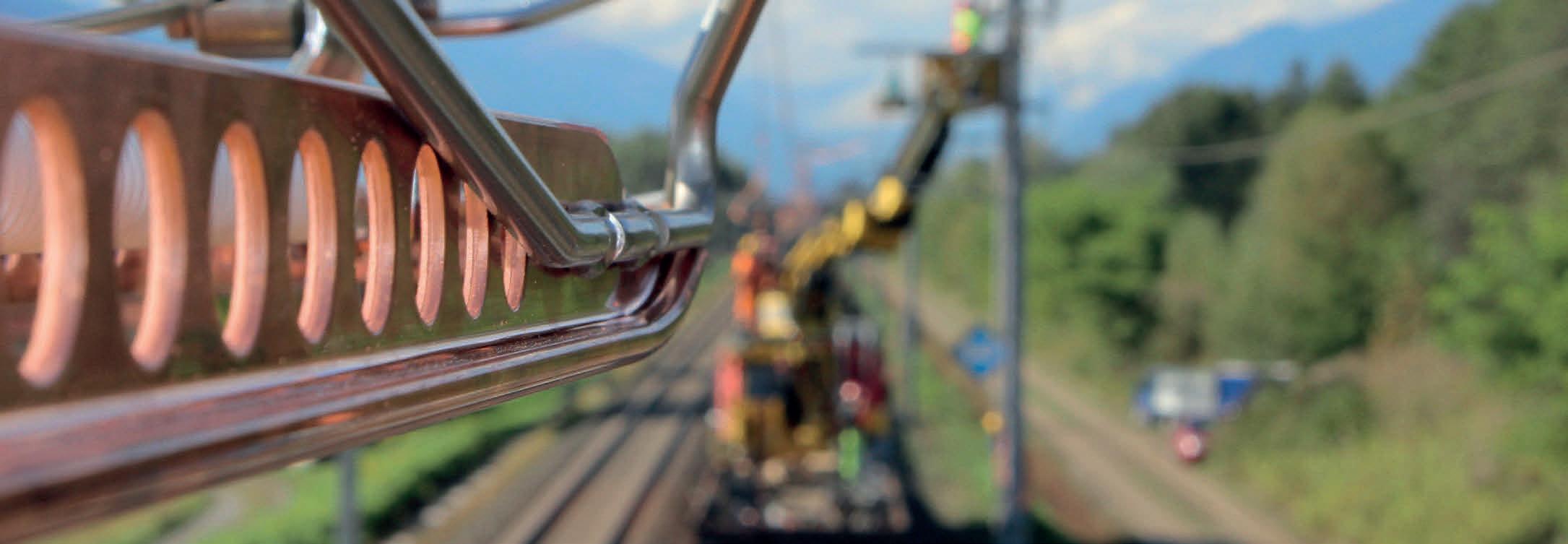
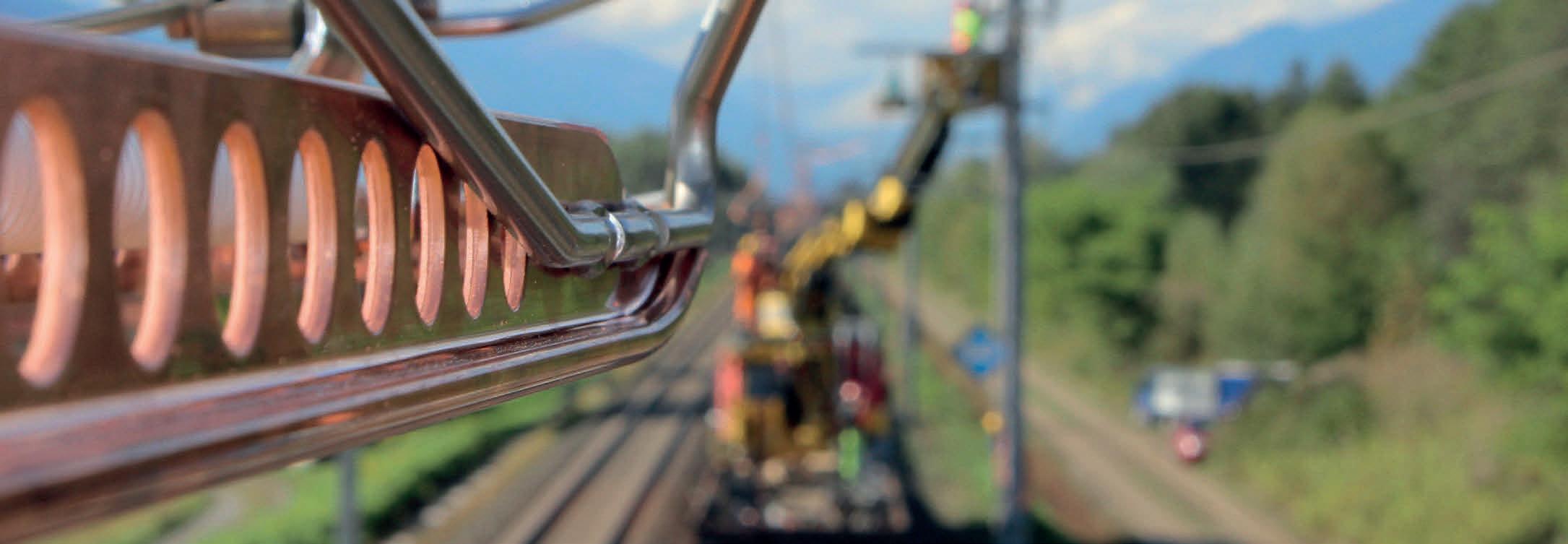
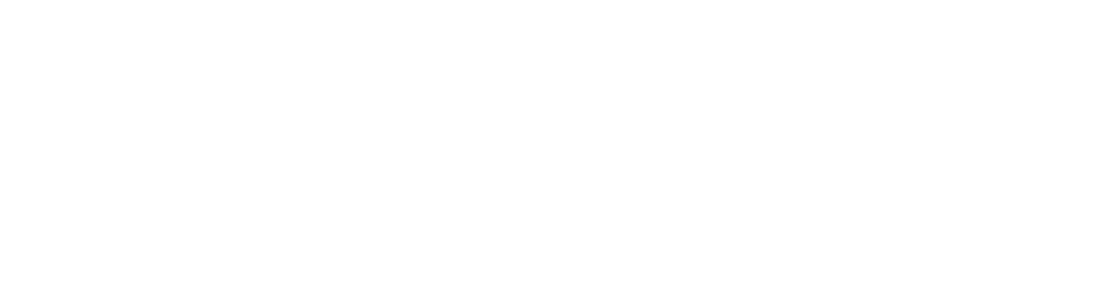
RIA Annual Conference 2024
A fresh start for UK Rail?
6-7 November
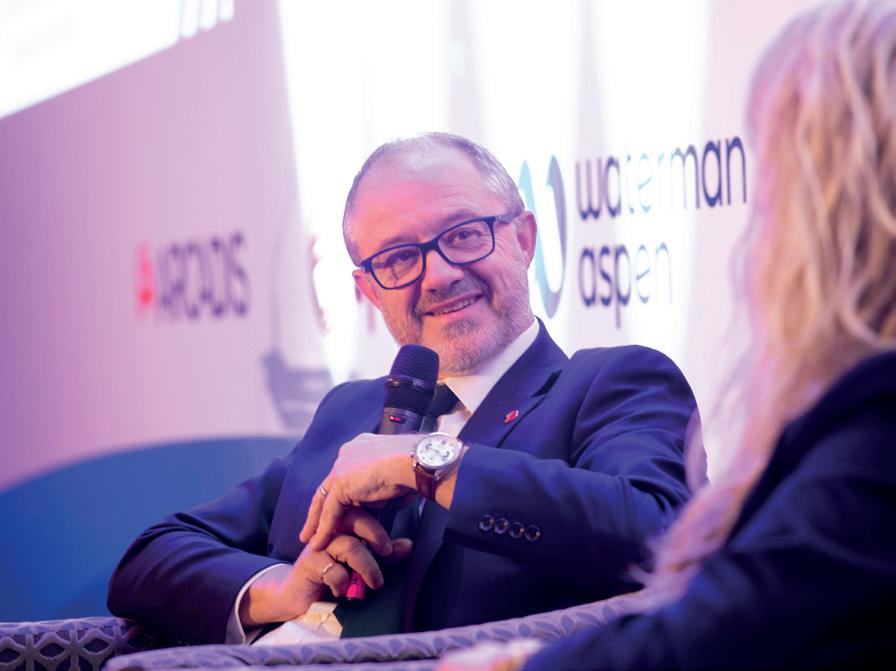
Leonardo Royal Hotel
London Tower Bridge
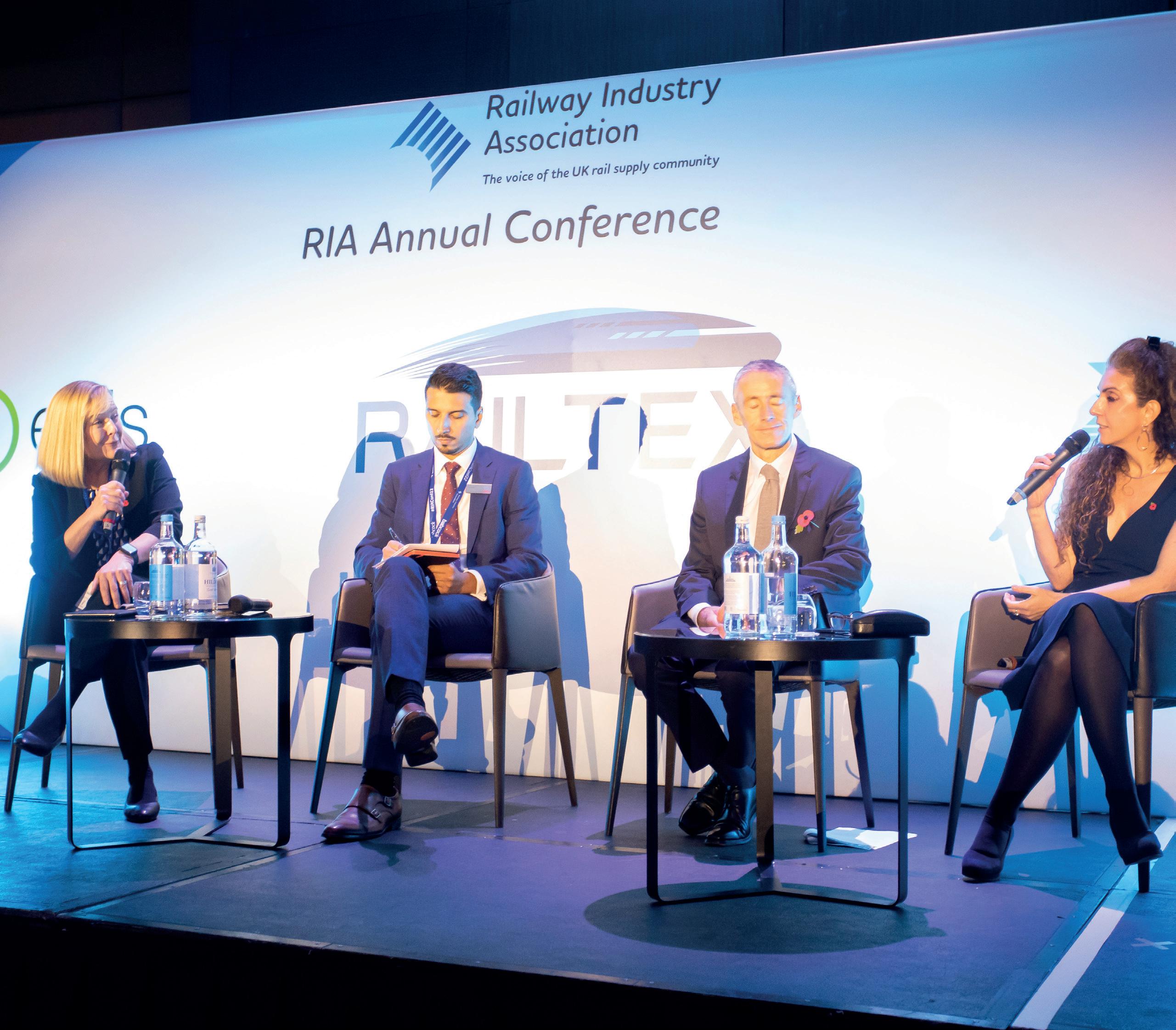
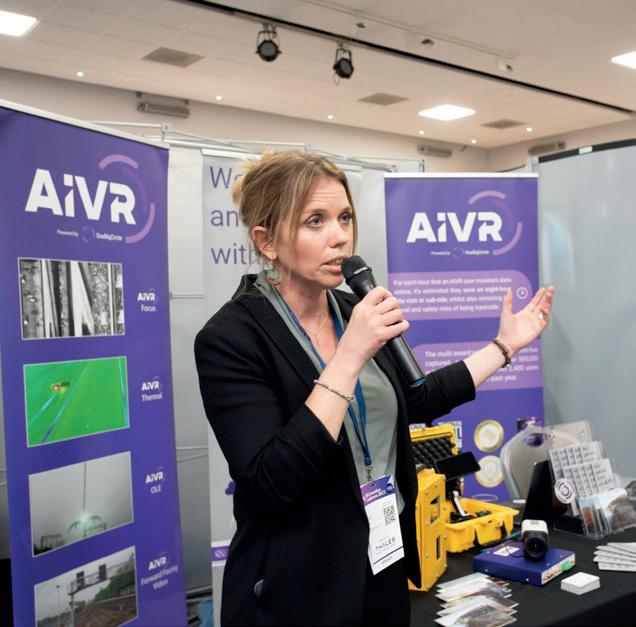
2-day conference with inspiring keynotes including: – Andrew Haines, Chief Executive, Network Rail
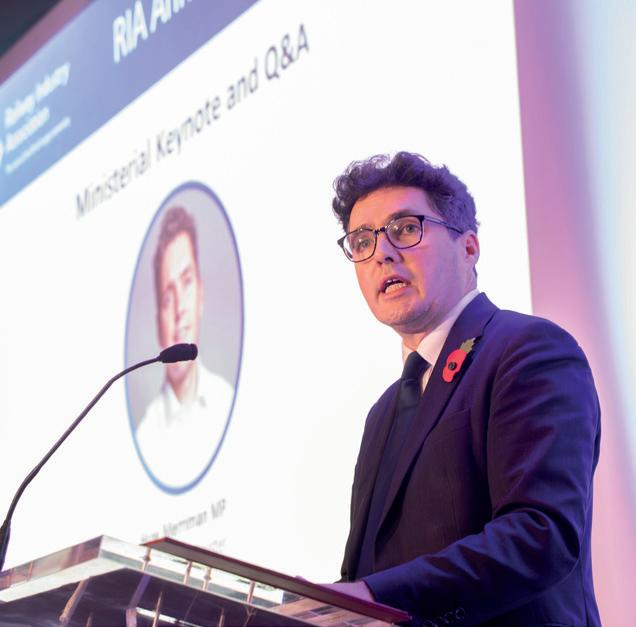
– Sir John Armitt CBE FREng FICE, Chair, National Infrastructure Commission – Sir Jon Thompson, Executive Chair, HS2
– And many more…
Large interactive exhibition area with spotlight pitches presenting services, products and solutions
Evening programme including networking drinks, dinner and entertainment

Dave Hersey, Technical Director at National Infrastructure Solutions, lifts the lid on the company’s new Signalling Academy in the
In Conversation with Denis Crehan, Managing Director of
In Conversation with John Greenhalgh, Sales Manager UK & Ireland at Bekaert Bradford UK Ltd (NV Bekaert SS)
, Senior Policy Advisor, Logistics
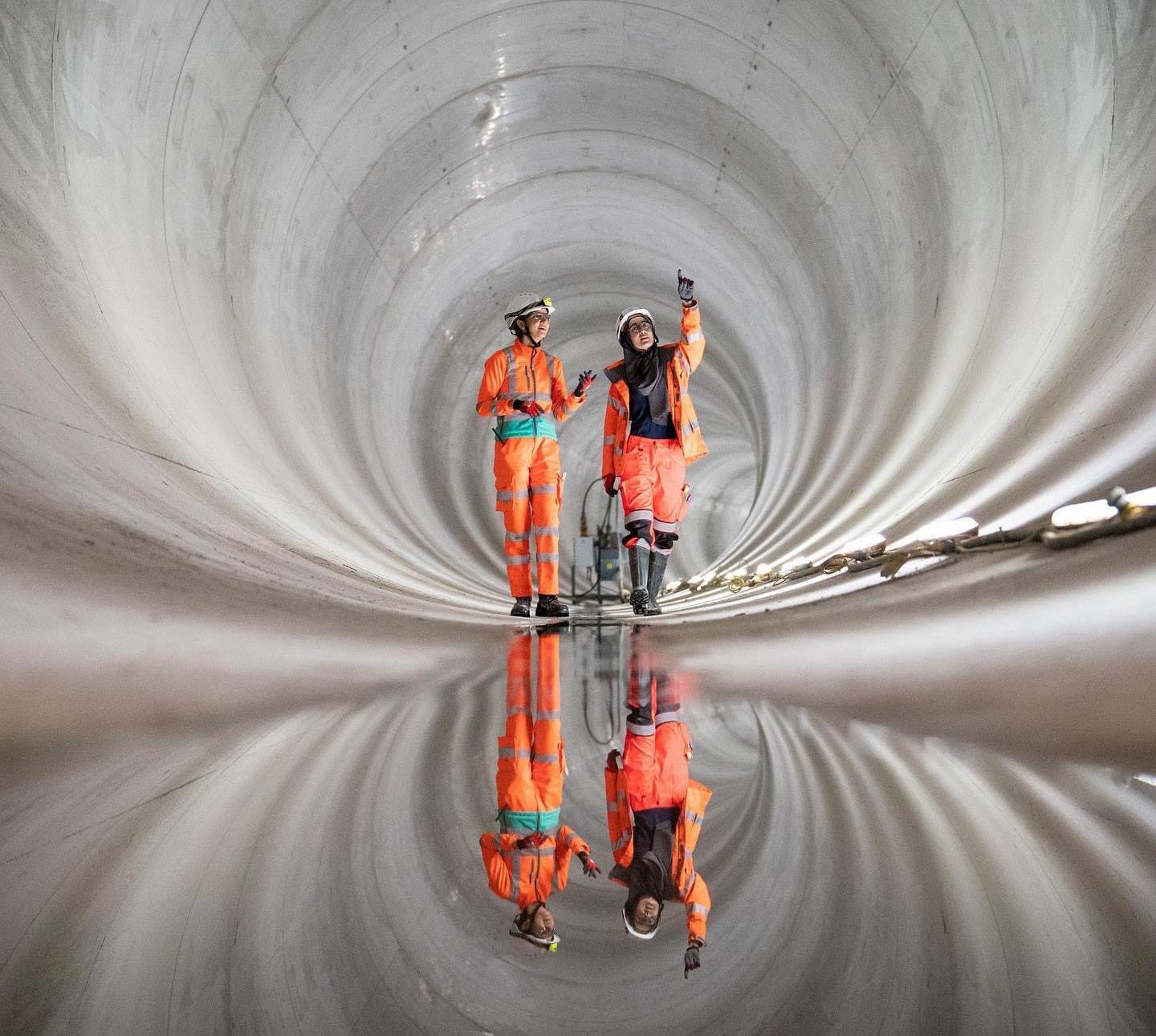

Healthy rail
Harmonised rail
Sustainable rail
Automated rail
Efficient rail
Digitised rail
Resilient rail
Insightful rail
GB Rail 2024-2029: Safe rail
We’re with you every step of the way
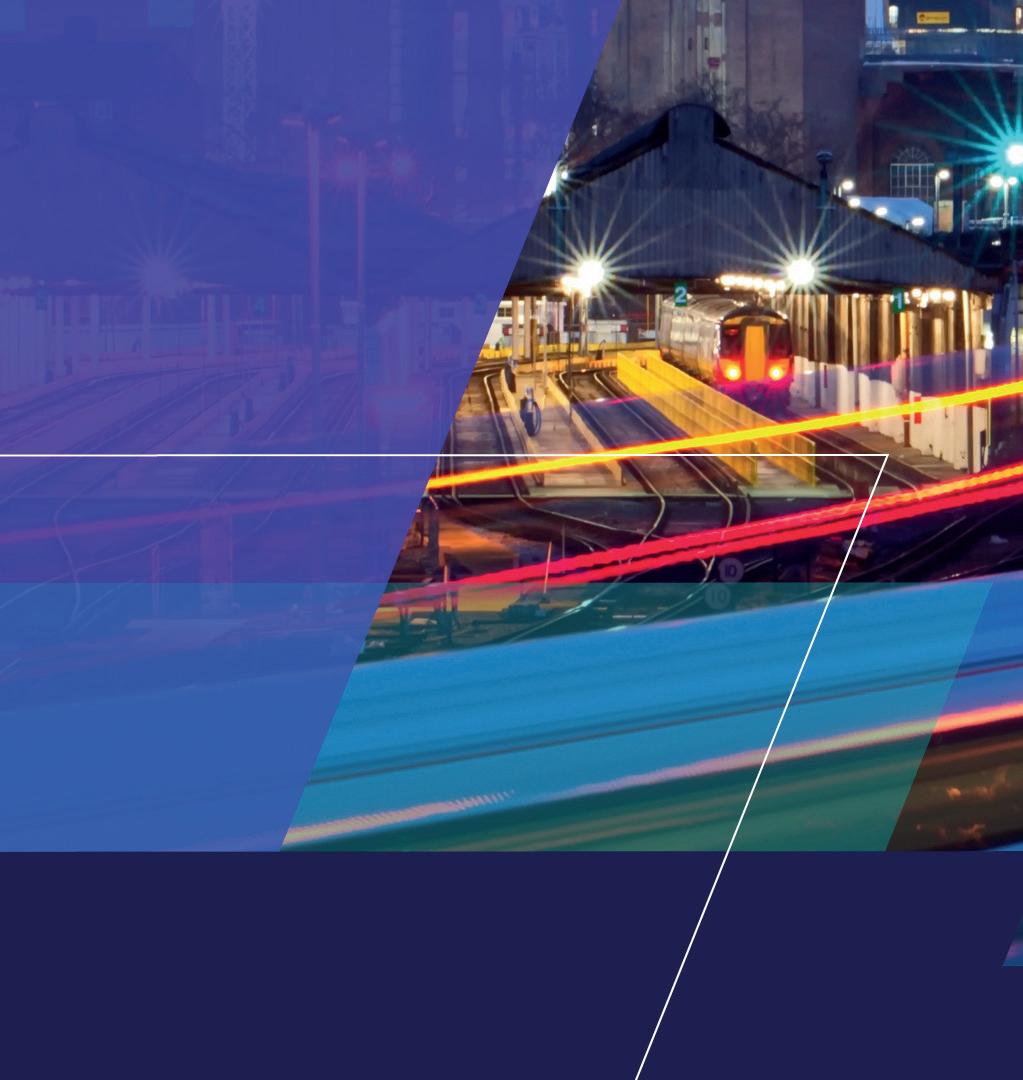
Continuity and change: the RSSB strategic plan
We’re used to providing continuity while embracing change – a vital balance that defines how RSSB operates. We preserve the industry’s institutional memory while encouraging innovation and our five-year strategic plan for 2024-2029 is designed to keep us on track.
Our ambition is that by 2030, every rail employee will use at least one RSSB tool or service every day, from the Rule Book to cuttingedge research. It’s a challenging target, but we believe we can achieve it – with your help.
To find out more about our latest strategic plan, visit www.rssb.co.uk/continuityandchange
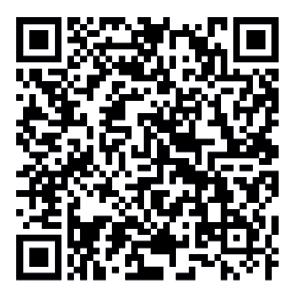
55 VIEWPOINT
Alan Kinsey, Country Manager, UK & Ireland at Opengear on the risks inherent in digital transformation 56 TUNNELING
Britain’s youngest tunnel came closer to reality in late March, whilst later this summer one of the country's oldest will receive essential repairs
The Plant and Machinery Sector in 2024
Direct trains to Ebbw Vale
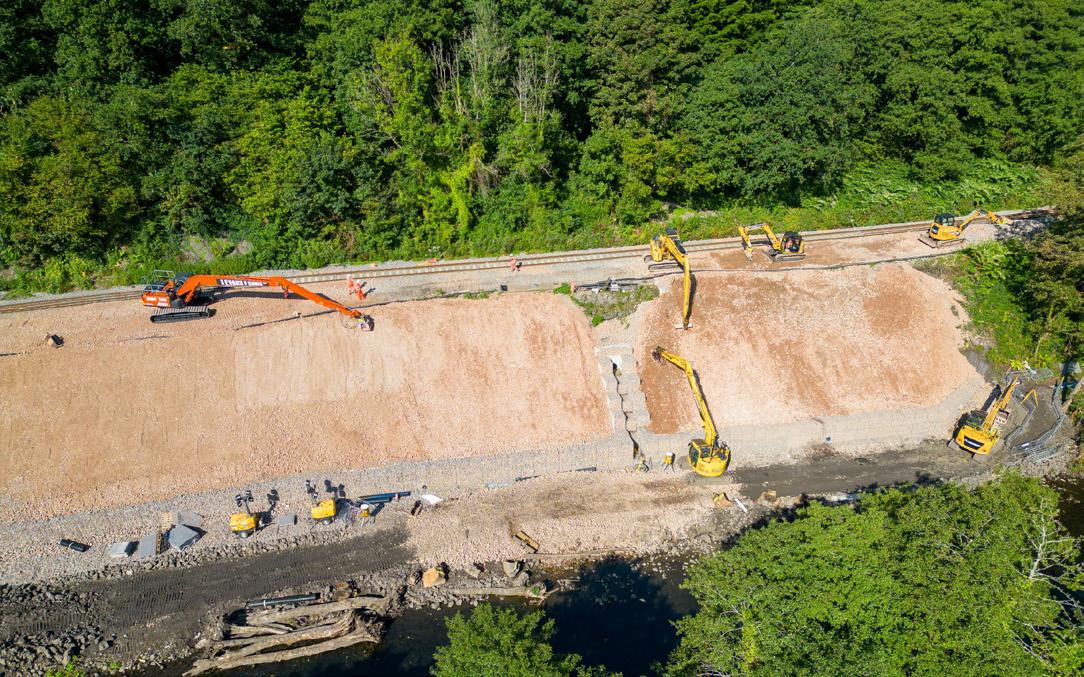
Susan Rashid, CEO of SR Supply Chain Consultants
AECOM’s Rail Lead for Scotland, Crawford Johnston on reviving the country’s railways for a greener future
Peter Ainsworth, CEO of Monirail
Honor Clough, Area Business Manager – Rail at Camira Fabrics
74 IN CONVERSATION
Michael Saunders, CEO and Co-Founder at Re-Flow Field Management 77 VIEWPOINT
Rebecca Collings and Simon Young, both of Nichols explain how success happens when rail and regeneration programmes are aligned
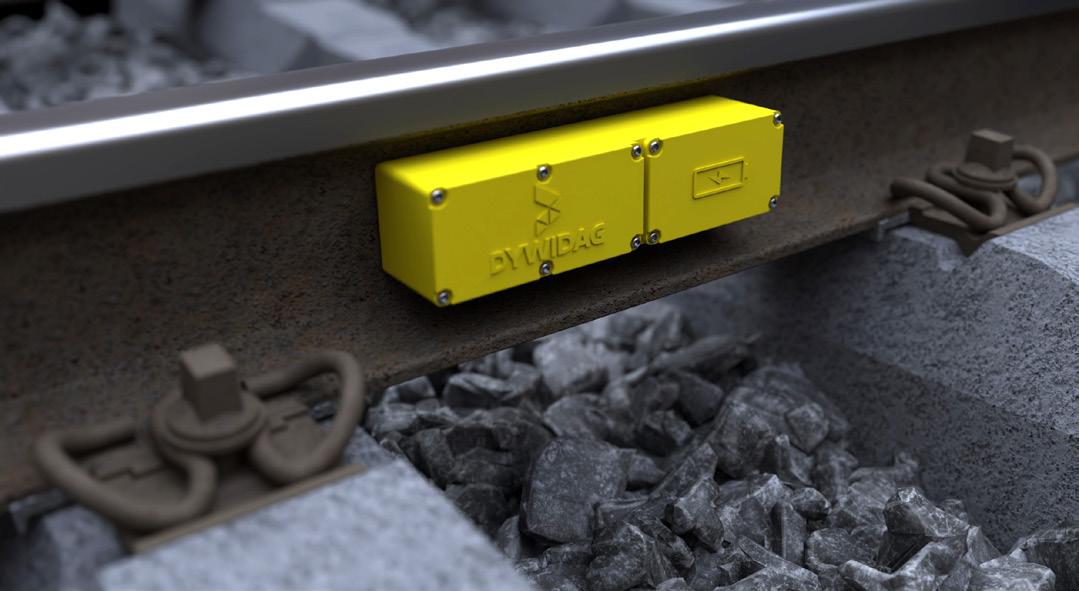
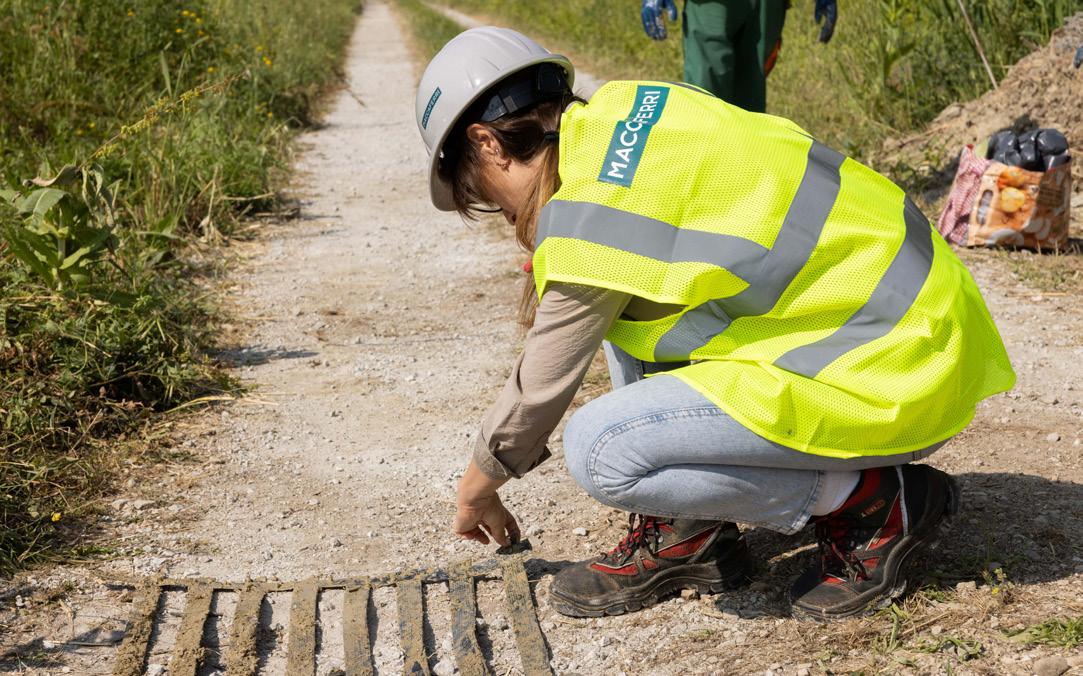
from the industry’s supply-side
Sjoerd van de Velde, Joanne Maguire, Dyan Perry OBE, Steve Scrimshaw, Stuart Harvey, Elvis Beric, Paul Garthwaite

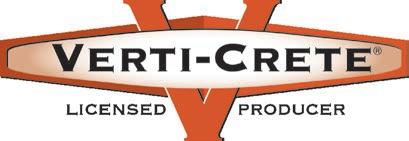


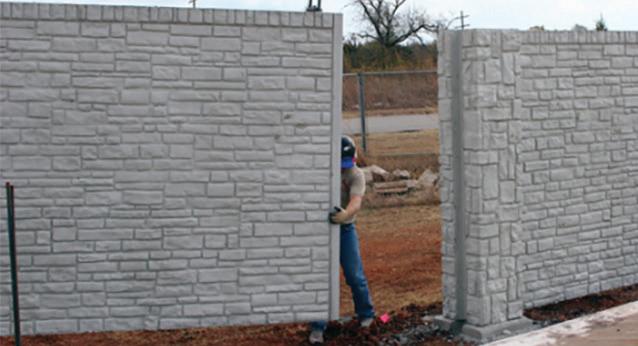
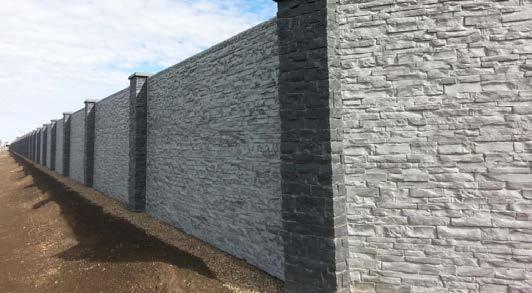


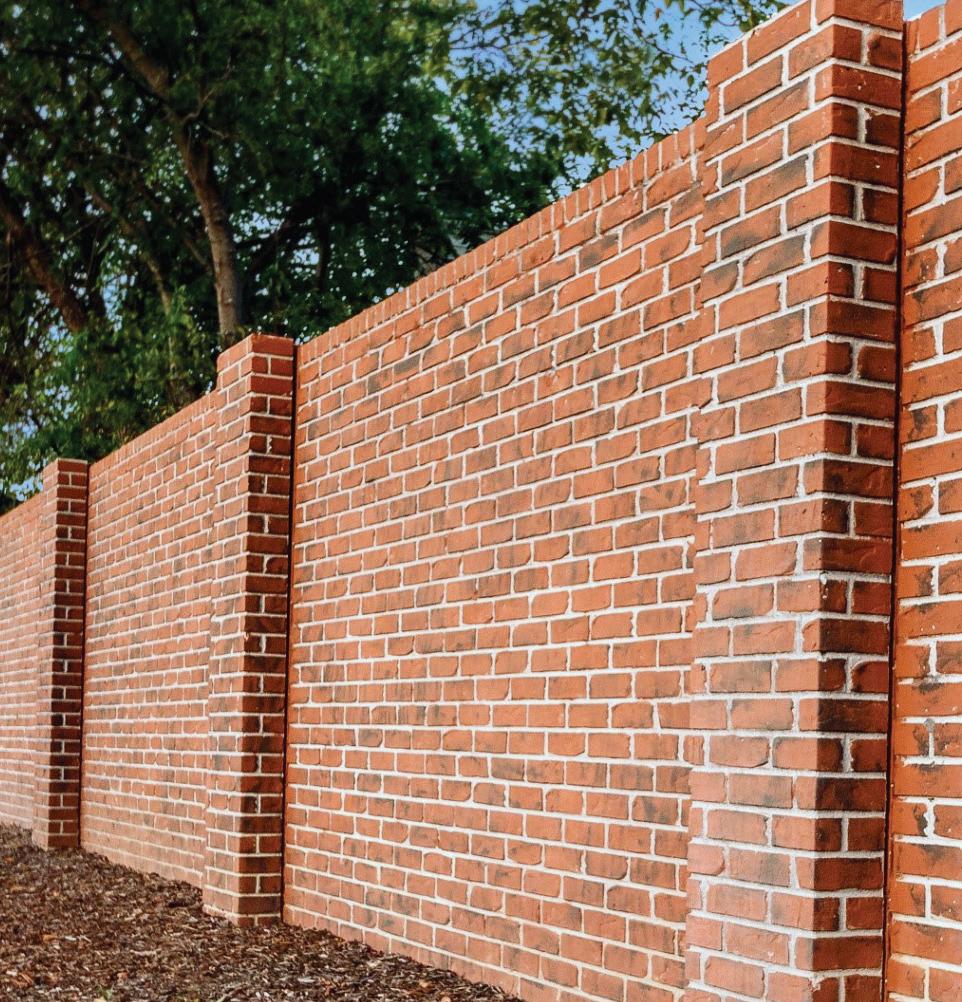


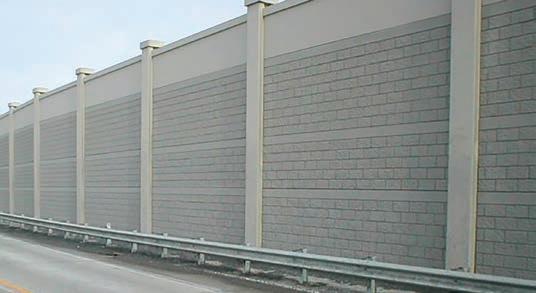
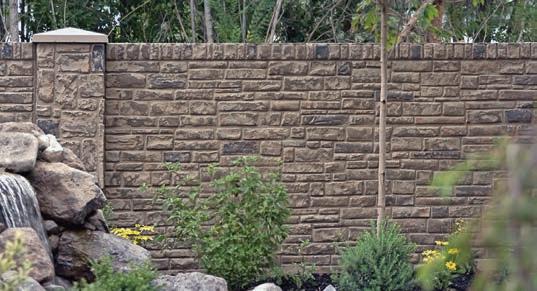
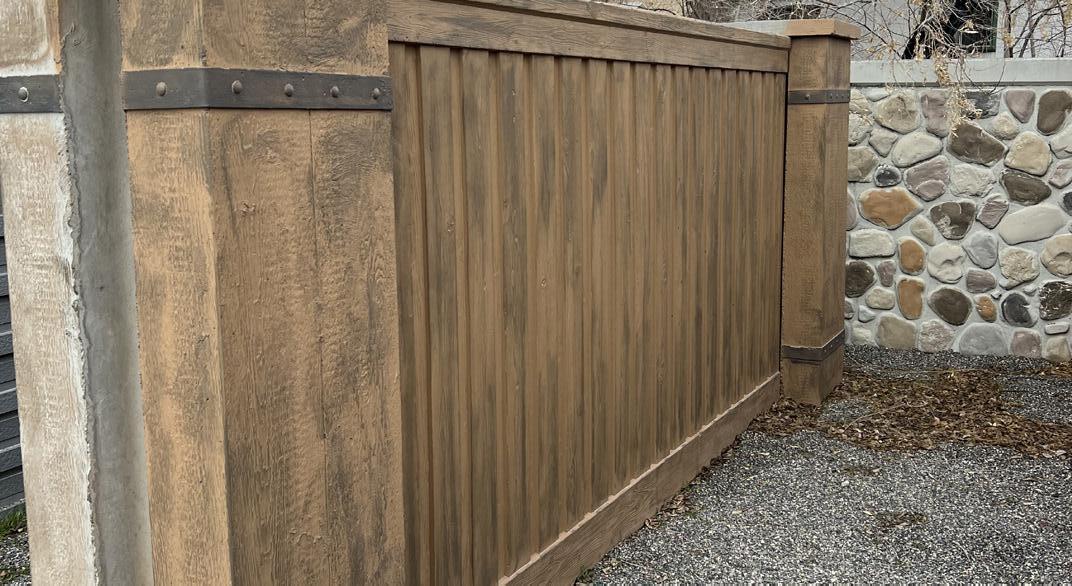
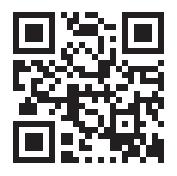



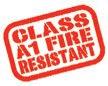
Blueprint for the North’s Transport Infrastructure
Transport for the North (TfN) has today (25 March) published an ambitious plan for sustainable and inclusive economic growth in the North, enabled by transformational connectivity.
The new Strategic Transport Plan (STP) was approved at Transport for the North Board meeting in Leeds by Northern leaders. It outlines how with the right investment and policy levers, together with transformational transport infrastructure we could have a Northern economy that will be £118 billion larger by 2050.
The blueprint which builds on the first plan published five years ago, sets out the case to transform the North’s transport infrastructure and services, demonstrating how better connectivity can enable economic growth, decarbonise our transport system and create more opportunities for all. The first STP enabled a step change in government funding for rail, by setting
out the case for Northern Powerhouse Rail (NPR).
TfN’s new Plan is focused on the outcomes needed for people and places, seeking to better connect communities and businesses with services and opportunities. It sets out robust monitoring and evaluation to measure progress year-on-year, making sure the Plan is on track. The new STP sets out the North’s ambition for near zero emissions from surface transport in the region by 2045, supports efforts to reduce car dependency and create the capacity required to grow patronage on our public transport networks. It als recognises the scale of change required in accessibility needed to unlock opportunity and reduce social exclusion by one million people by 2050 and puts in place a long-term ambition to treble the share of freight carried by rail.
Lord McLoughlin, Chair of Transport for the North, said: ‘Our Strategic Transport
The Rail Academy Now ORR-registered
The Office of Rail and Road (ORR) has confirmed The Rail Academy has been successful in its application to become an ORRregistered Train Driver Training and Examination Centre. The Rail Academy will now be added to the official ORR public register.
The Rail Academy, which is already one of only four companies approved by OFQUAL to carry out specialist Train Driver Apprentice End Point Assessments, is now also able to:
• Train and assess train drivers in all areas of general professional knowledge, rolling stock and routes.
• Provide this training and independent assessment to train drivers employed by themselves and others.
• Support new driver’s licence applications.
• Prepare and deliver train driver training materials, compliant with the required regulations.
• Register train driver assessors, competent to train and assess train drivers.
The approval follows a thorough and comprehensive review of the company’s systems, processes and capability assessed in line with the Train Driver Licences and Certificates Regulations 2010. These regulations stipulate UK train driver training, examination and licensing requirements.
Only organisations registered by ORR may assess and licence train drivers from street to seat. The Rail Academy is the only independent, ORR-recognised Train Driver Training and Examination Centre in the UK.
Plan sets out Transport for the North’s statutory advice to government on how the North, speaking with one voice, can reach a sustainable, socially inclusive transport network for the future, support growth and employment opportunities. The STP will lay the foundations for the transport infrastructure investment for the North for decades to come. We will provide further advice to government on how the plan can be implemented, from the pan-regional investment pipeline required, to efficiencies in how transport infrastructure and services are delivered. The evidence in this STP shows how with sustained investment, the right policy levers and enabling behaviour change, we can truly transform the North.’
The revised Strategic Transport Plan can be viewed at: www.transportforthenorth.com/ reports/strategic-transport-plan-transformingthe-north-2024
GB Railfreight Launches New Service Connecting Southampton to Hams Hall
GB Railfreight (GBRf) has started a new intermodal service connecting Southampton to Hams Hall Rail Freight Terminal in the West Midlands. This is the first time that GBRf has run an intermodal service from the UK’s second-largest deep seaport to the West Midlands. GBRf will be running five trains a week from Southampton to Hams Hall with a further option to connect Southampton with Mossend International Rail Freight Terminal in Scotland, with final mile delivery available at both terminals. For this service, GBRf is using its brand-new high-density FEA-G intermodal wagons, which will significantly increase the volume of cargo that can be transported on each journey.
The new train is part of DP World’s trial Modal Shift incentivisation programme for cargo owners to use rail within 140 miles of The Port of Southampton. It is hoped that the scheme will reduce 30,000 metric tonnes of carbon dioxide emissions per year and remove thousands of lorries from the road network.
Schemes like this will help the UK Government achieve its long-term freight growth target, to increase rail freight by at least 75 per cent by 2050 and GBRf to run c.80 intermodal services a day by 2025.
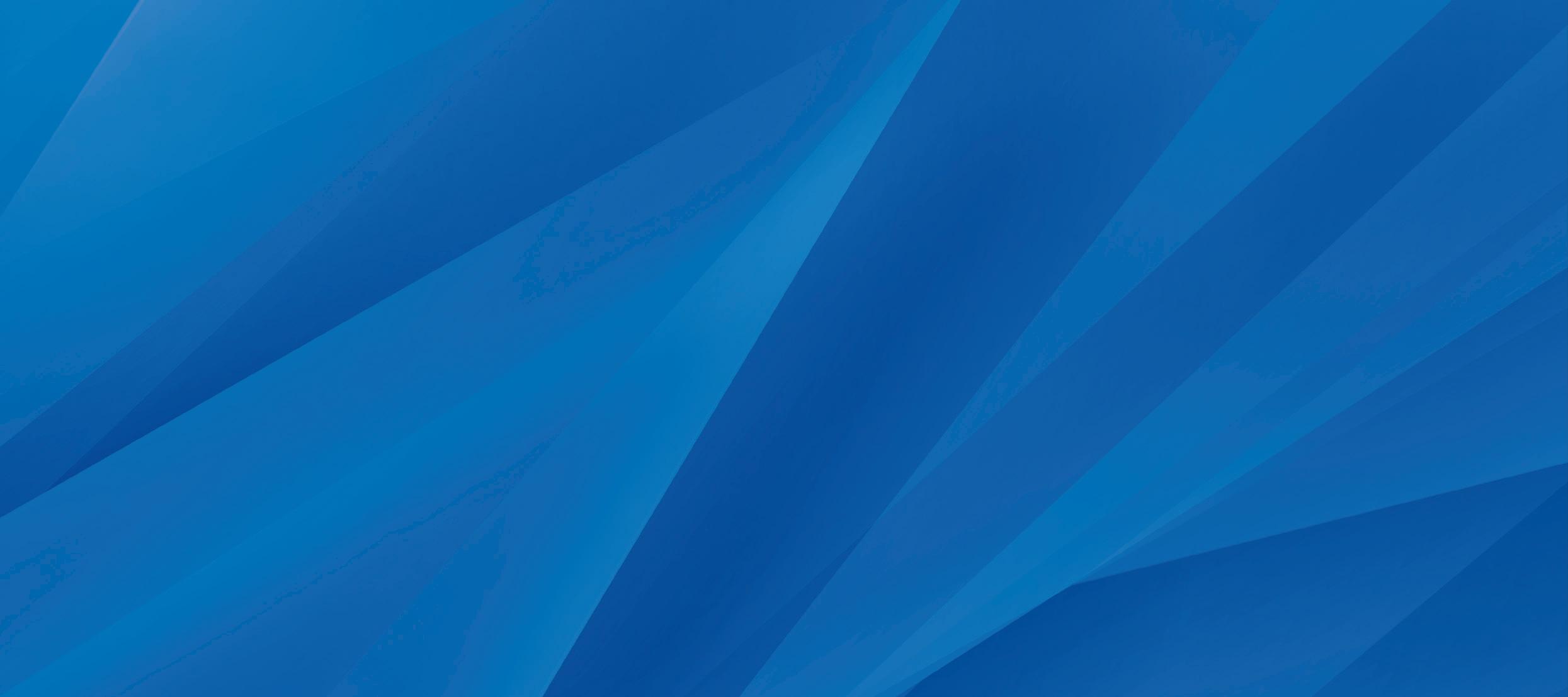
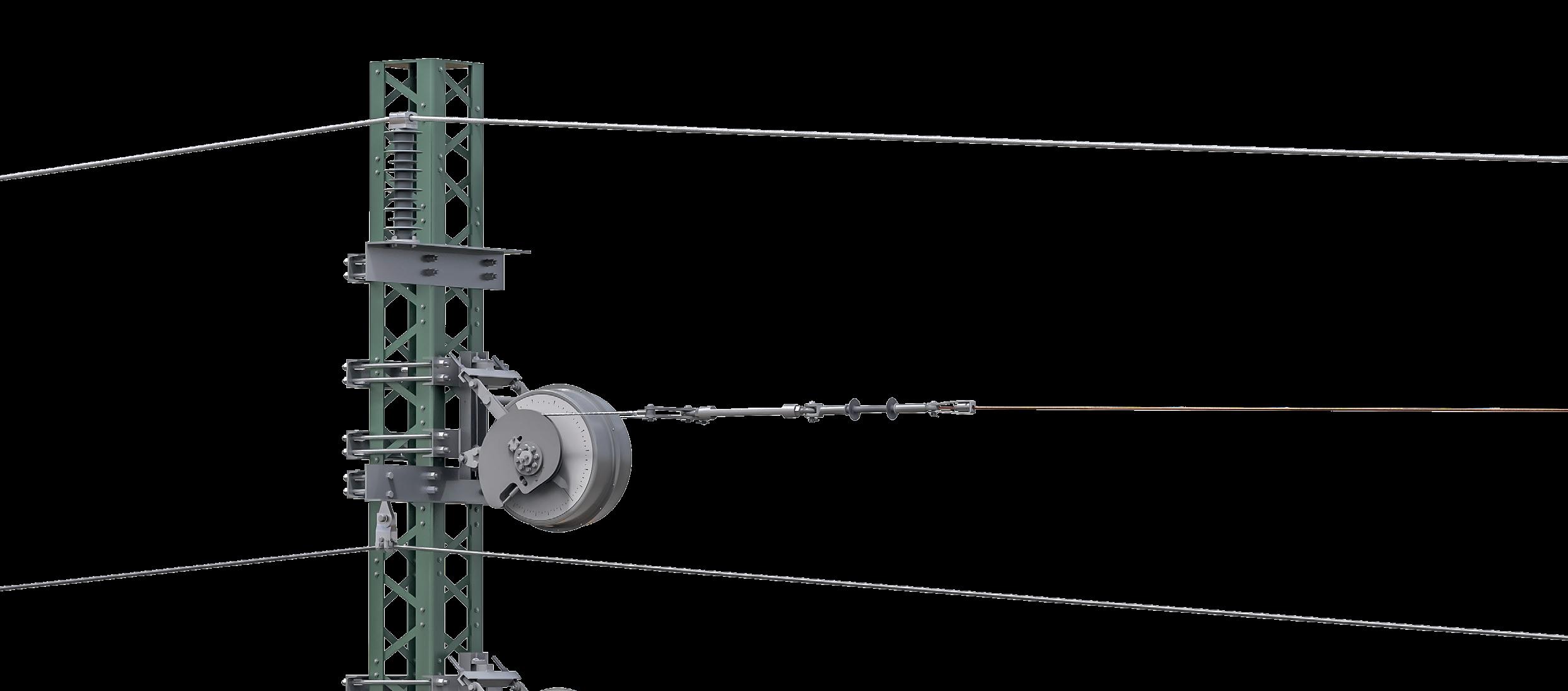
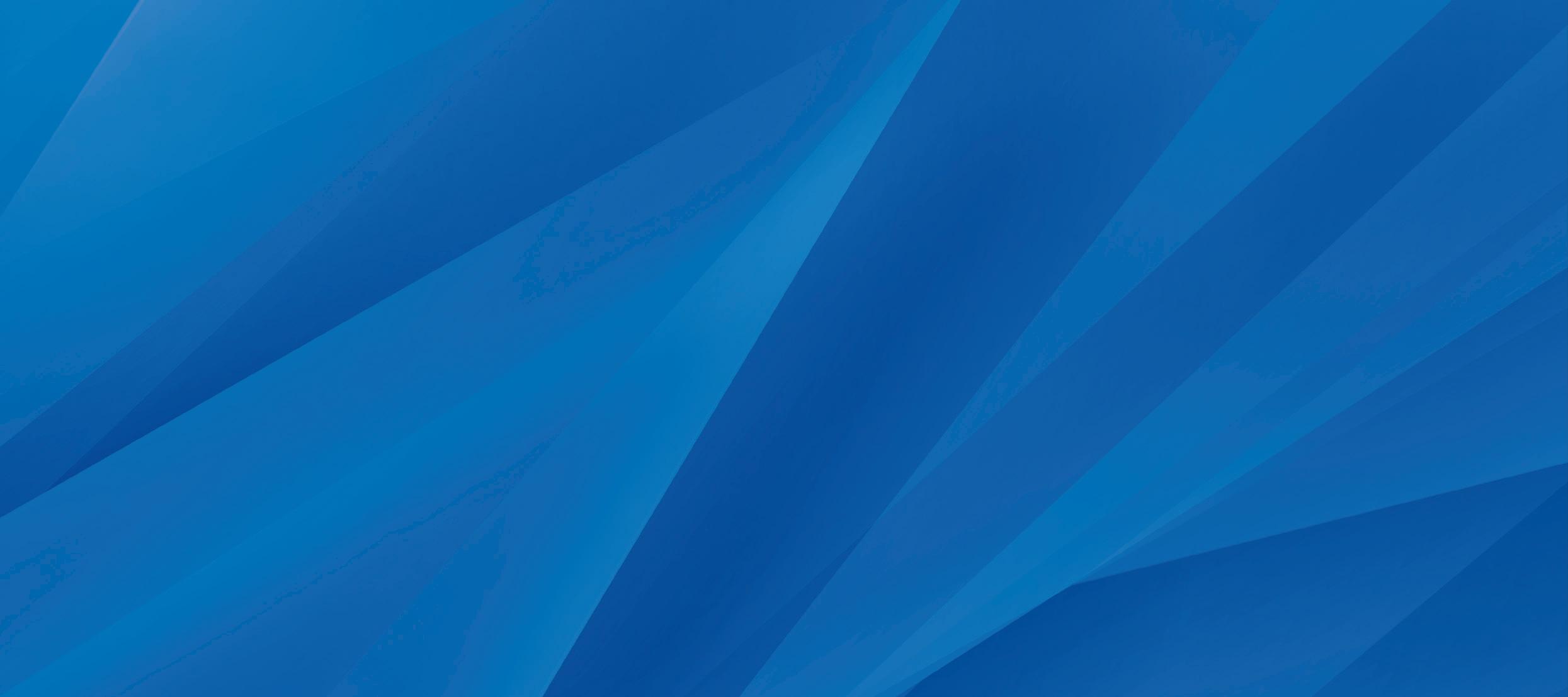
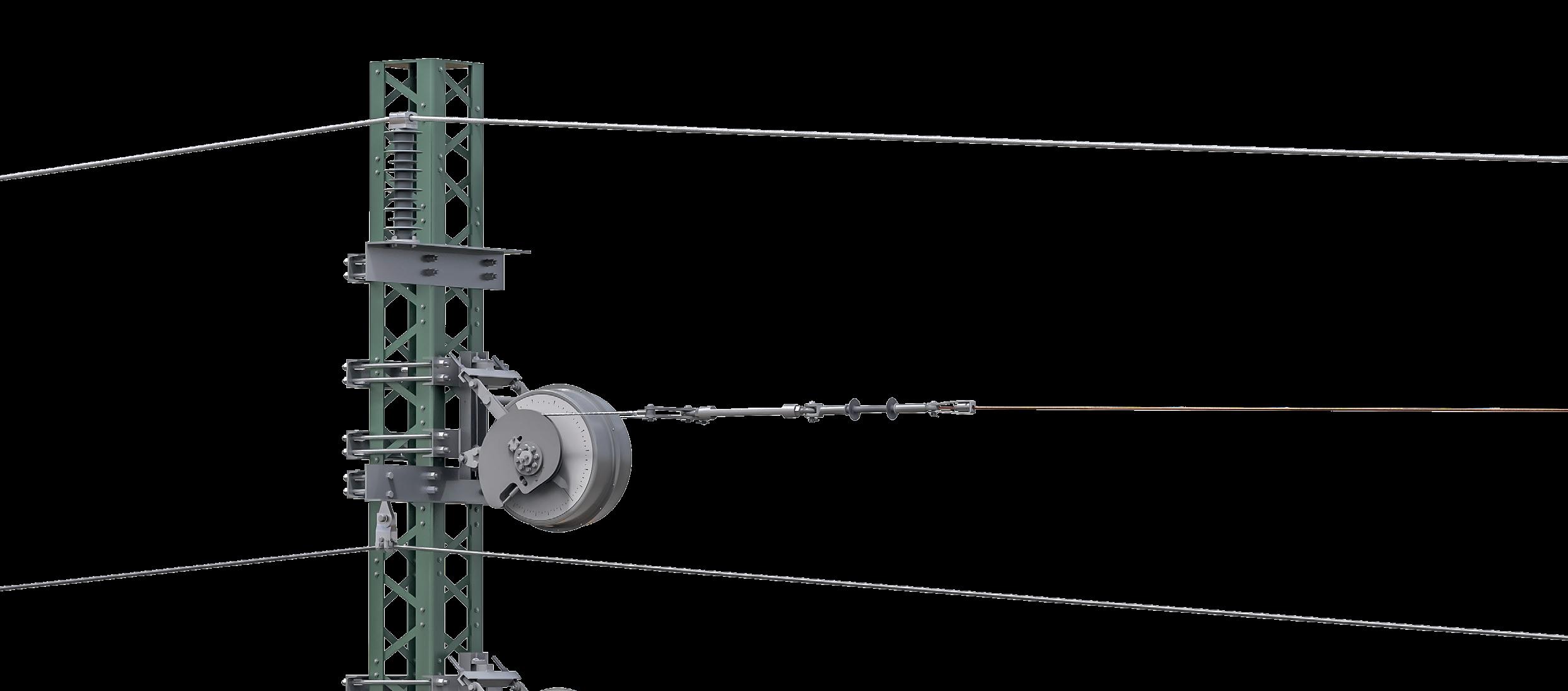
Automatic Tensoning Device
RAILWAY INFRASTRUCTURE SOLUTIONS
Our Expertise for Railway and Tramway:
Our Expertise for Railway and Tramway:
- Railway Catenary Systems
- Railway Catenary Systems
- Tensioning
- Tensioning
- Insulation technology
- Insulation technology
- Power supply
- Power supply
- Safety equipment
- Safety equipment

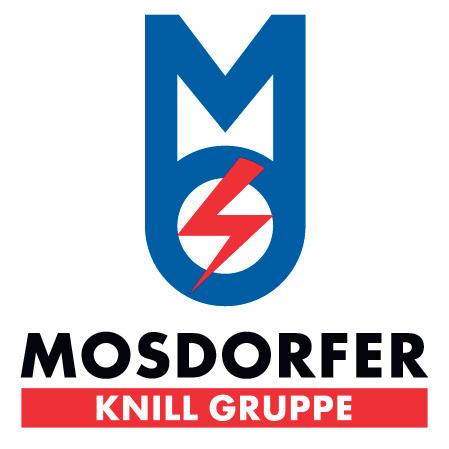
Mosdorfer Rail Ltd.
Mosdorfer Rail Ltd.

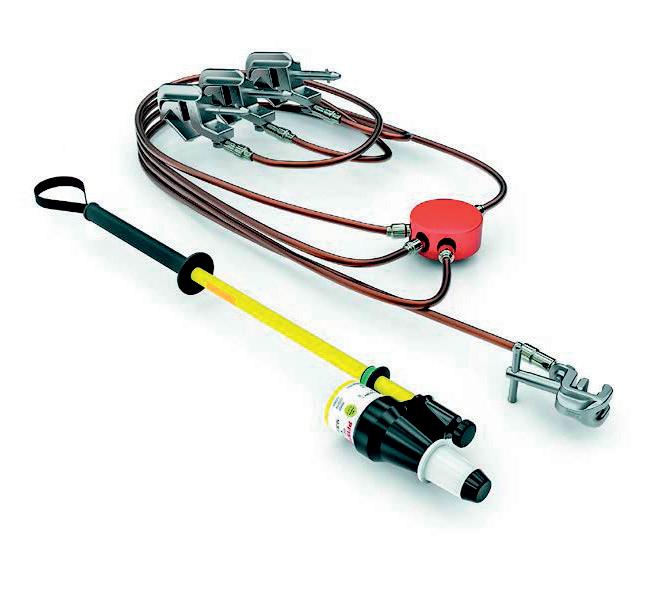
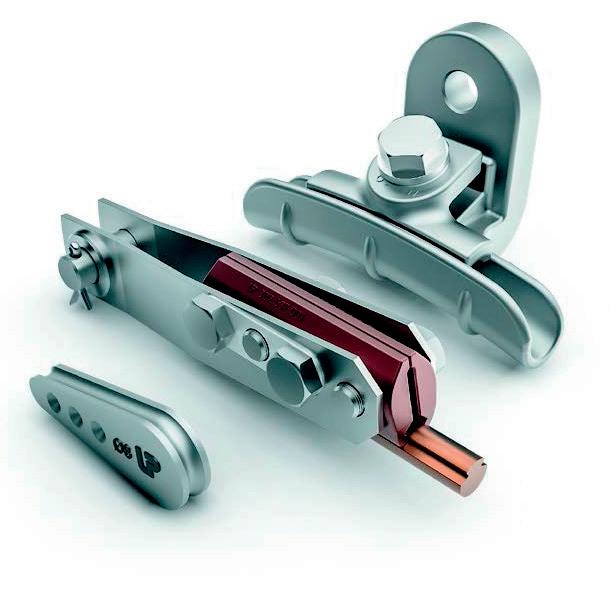

2 – 4 Orgreave Place, Orgreave
2 – 4 Orgreave Place, Orgreave
Sheffield S13 9LU, South Yorkshire, UK
Phone: +44 114 3878370
Sheffield S13 9LU, South Yorkshire, UK
Phone: +44 114 3878370
E-Mail: OrdersRailUK@mosdorfer.com
E-Mail: OrdersRailUK@mosdorfer.com
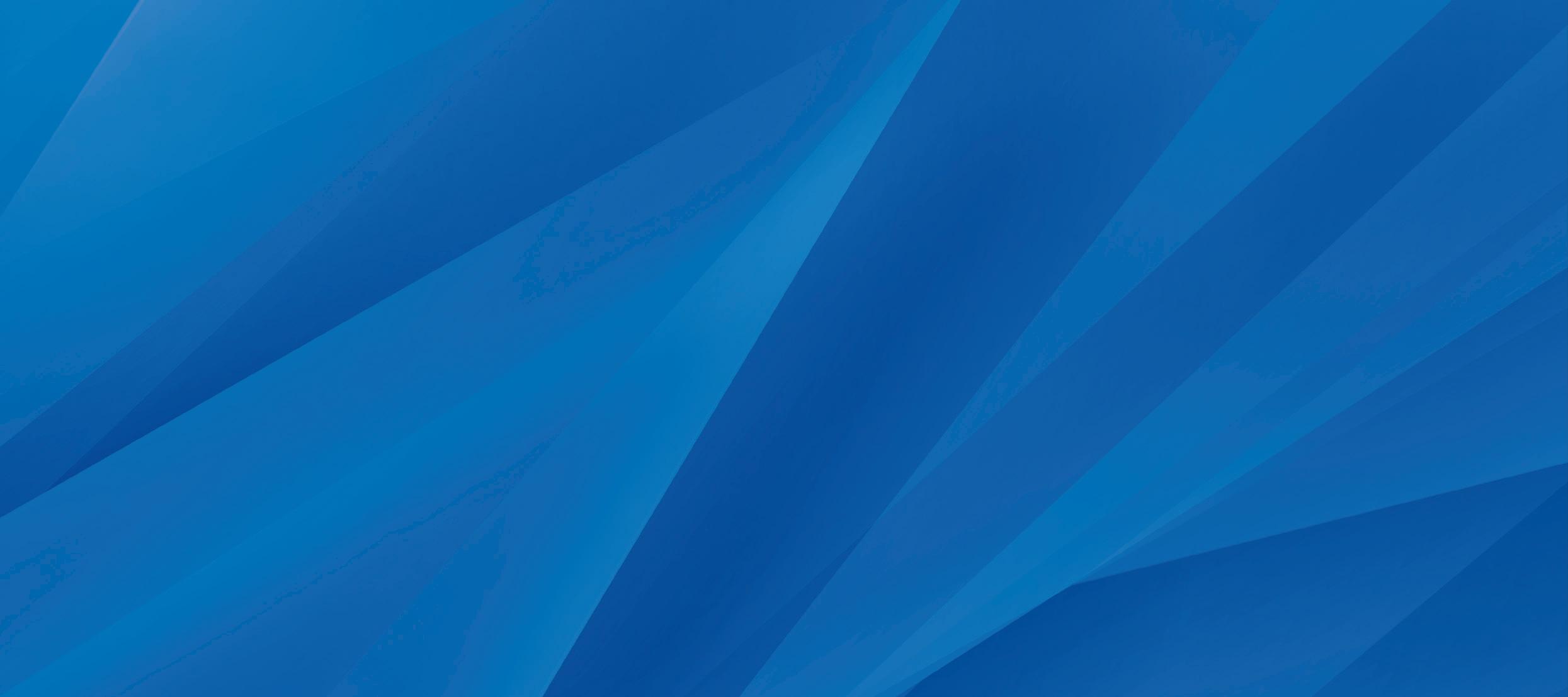
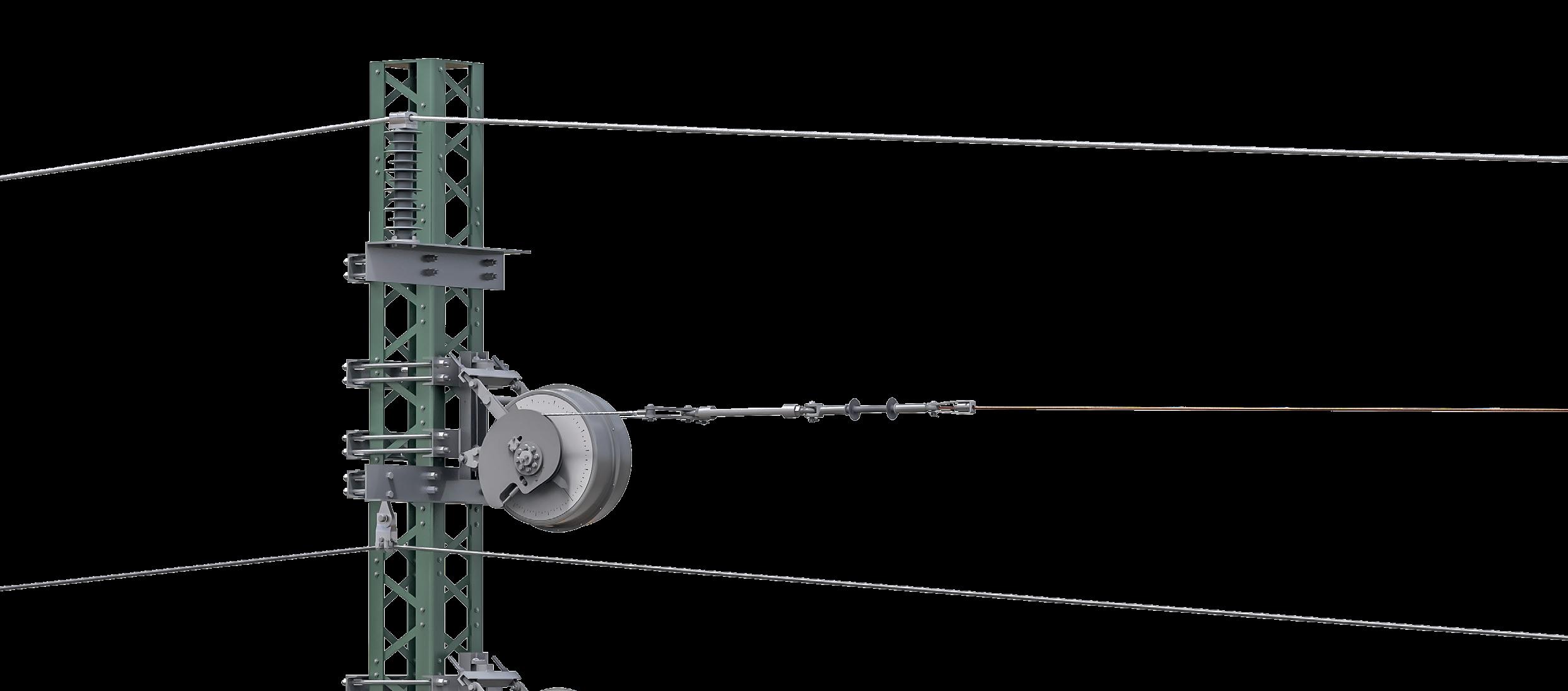
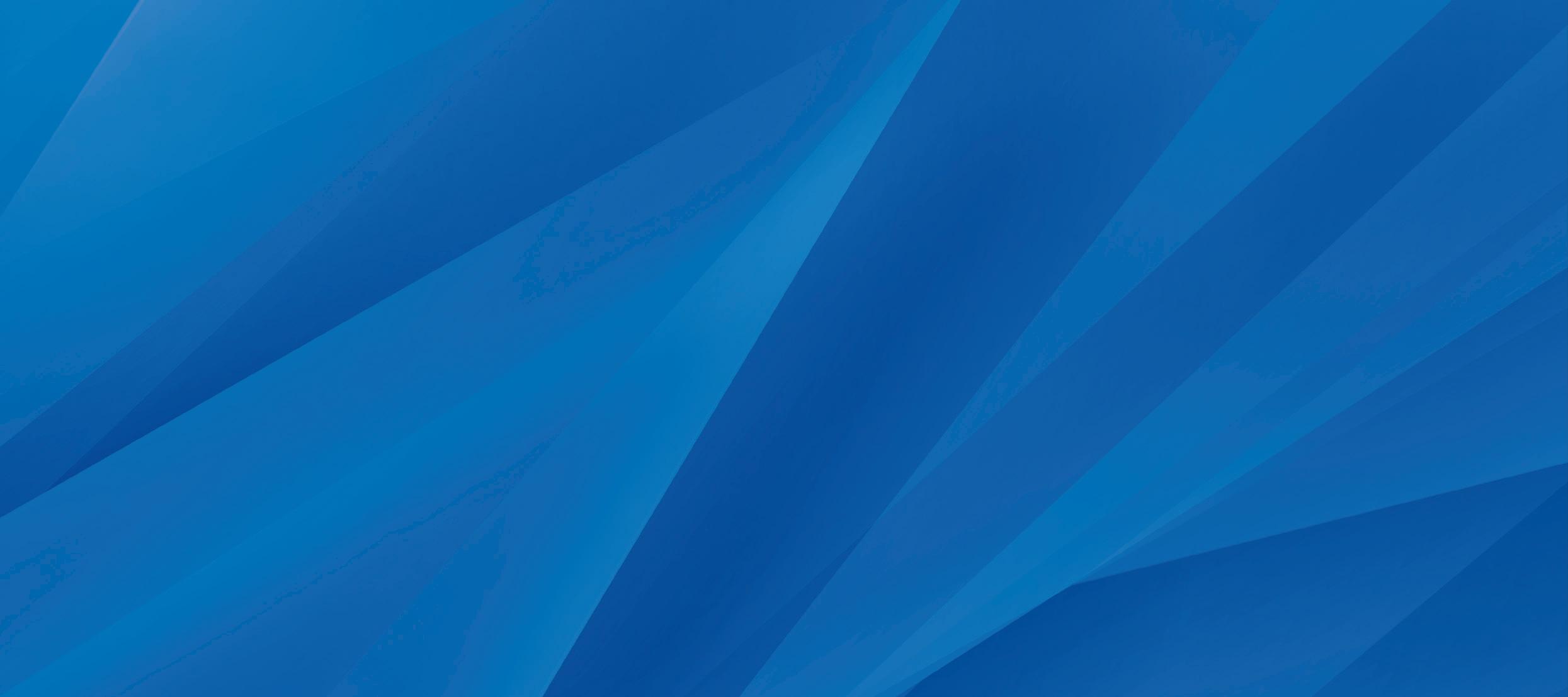
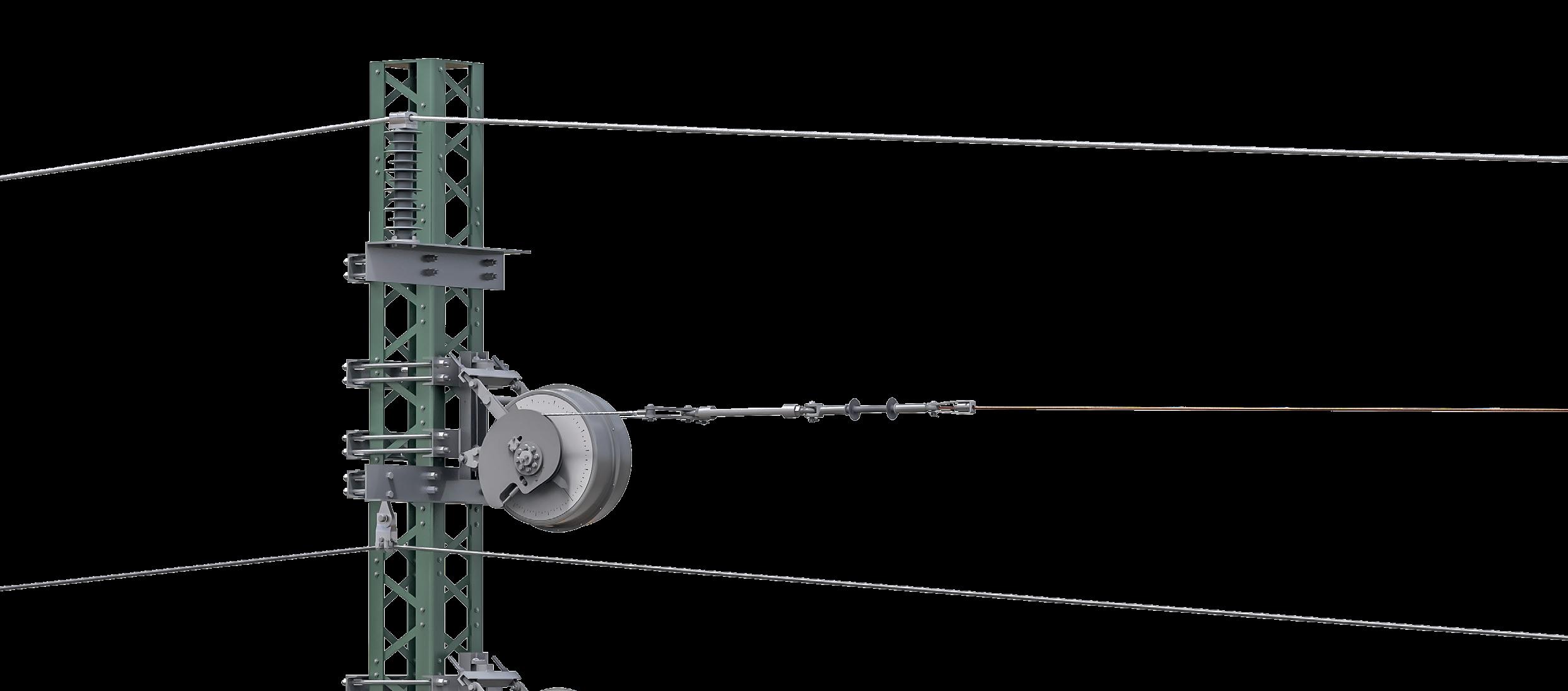
Cullercoats Metro Station Footbridge Re-opens Following Major Restoration Work
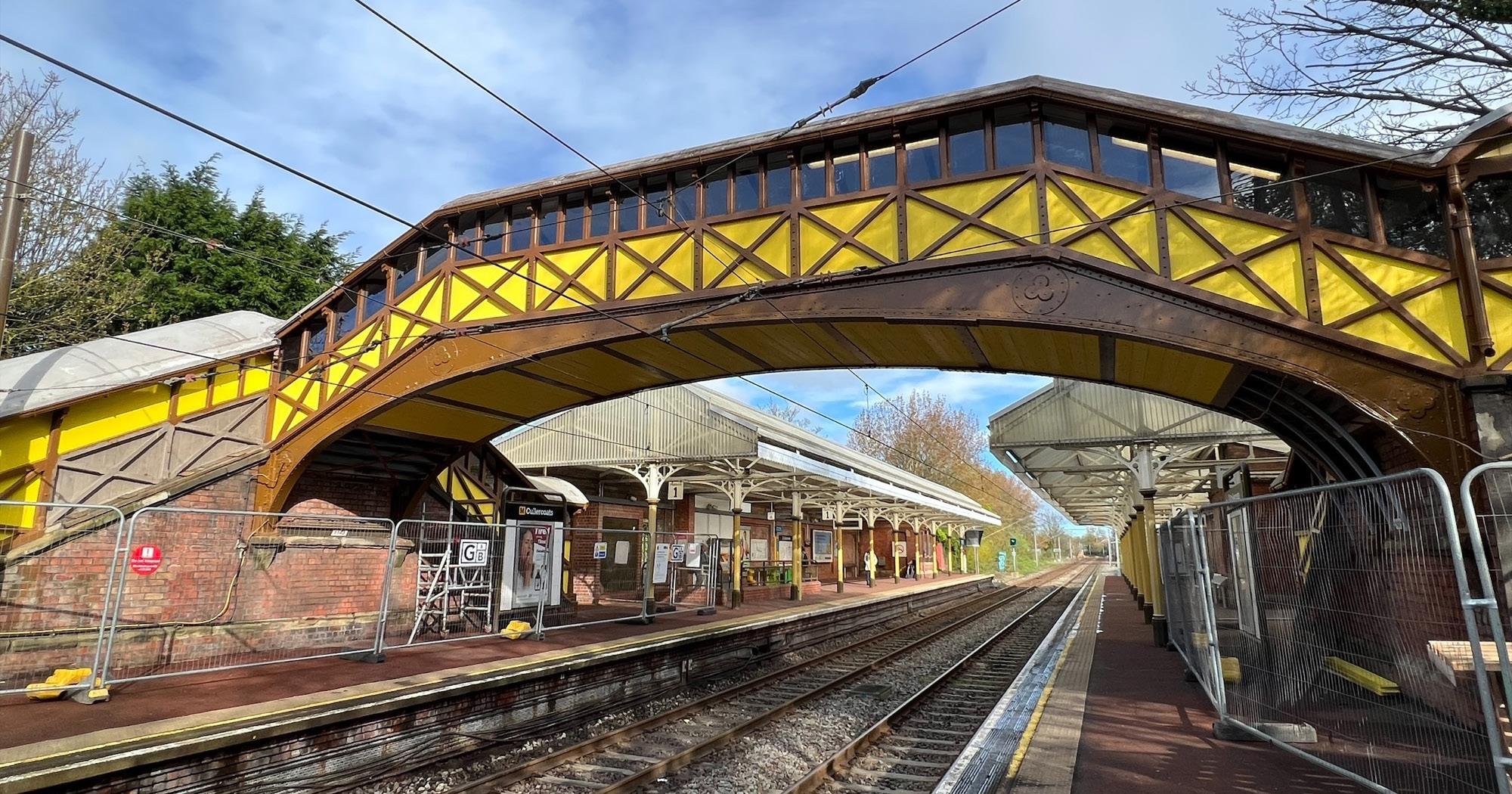
A major project to refurbish the historic footbridge at Cullercoats Metro station in North Tyneside has been completed, allowing it to reopened for customers. Nexus, the public body which runs Metro, has invested £579,000 in the works, which formed part of its infrastructure modernisation programme. Restoring Cullercoats’ Victorian-era footbridge was the main focus of the project.
Its wrought iron structure has been strengthened with new steelwork and the outer wooden panels and decking replaced to provide a fresher appearance and an improved customer experience.
The previously boarded-up windows have been fully renewed, with new glazing installed, vastly improving the natural light
within the footbridge, and new CCTV cameras have been fitted. The decorative dagger boards on the station’s canopies have also been replaced. The footbridge has been closed since August of last year, with an alternative walking route in place between the two station platforms. It re-opened to the public at 9am today, Wednesday 17 April.
Cullercoats station was opened in 1882 by the North-Eastern Railway and was converted to a Metro station when the network opened in August 1980. Gateshead-based G&B Civil Engineering have carried out the works on behalf of Nexus.
TramForward Puts Tram Proposal to East Midlands Mayoral Candidates
TramForward has submitted proposals to all the candidates for the position of elected Mayor for the East Midlands Combined Counties Authority (EMCCA), for extension of Nottingham's NET tramway into Derby, and a tram network within Derby. This is designed to suit Derby’s travel pattern, where most jobs are outside the city centre, and would greatly increase the public transport proportion of journeys to work from the very low present level of five per cent to over twenty per cent. This
would greatly benefit the economy and environment of Derby, making it much more attractive for investment and growth. Derby and Nottingham are similar sized cities fifteen miles apart. However, Nottingham has a larger adjoining urban area giving about 600,000 residents, compared with around 350,000 for the Derby area. Nottingham has much higher public transport use, largely through the Nottingham Express Transit (NET) tram network. Travel patterns for both cities
are different; Nottingham has much higher city centre employment, Derby has most employment outside the city centre in industrial and commercial sites. The proposal points to these being badly served by buses, resulting in most journeys being car-based, with buses only taking five per cent; resulting in high levels of traffic congestion, pollution and extended journey times.
First 756 Electric Train Runs on the Core Valley Lines
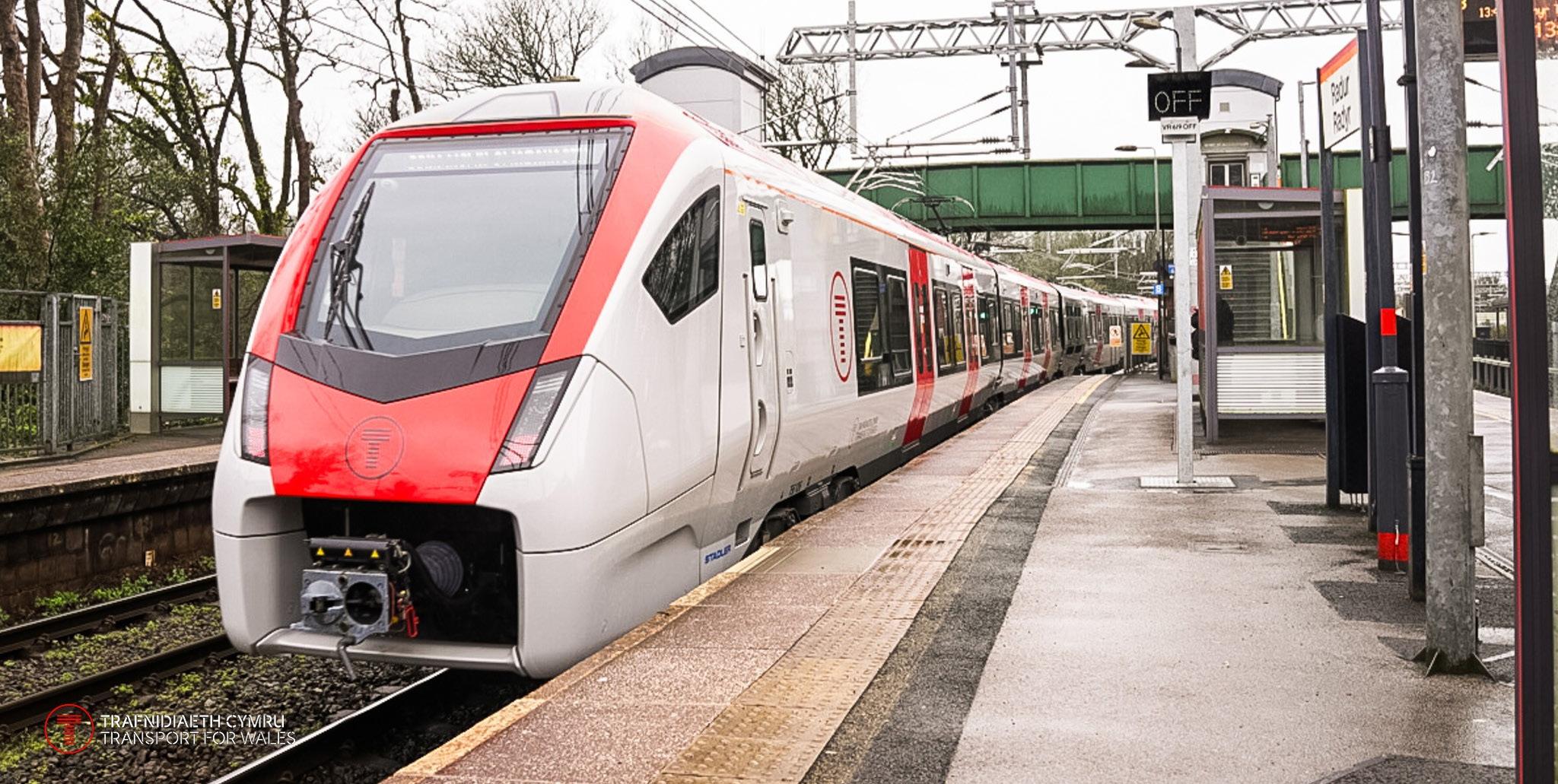
History was made this month as the very first electric train ran north of Cardiff to Pontypridd during daylight hours. The moment marked the next vital step in our vision to build a world class metro for south east Wales. On 3 April, a small crew successfully completed a test run from Canton Depot via the City line up to Radyr and Pontypridd using the brand new Overhead Line Electrification.
Following the test run, further routes on the Core Valleys Network will see testing take place in the coming weeks before the start of an intensive train crew training programme. The trains will then be entering public service later this year.
Boasting either three or four modern, spacious carriages, the Stadler 756 fleet are almost identical to the brand new trains we introduced on the Rhymney line in 2023, but with the ability to run on overhead or battery power, or as a diesel/battery hybrid.
They can travel up to 75mph and are also able to switch to run on battery or diesel hybrid power for sections of the network that are difficult or costly to electrify. Work began to electrify the Merthyr, Treherbert and Aberdare lines in 2020 and at various points the lines have been closed for extended periods to ensure the work is able to progress. The Merthyr and Aberdare lines were successfully electrified in 2023, with the Overhead Line Equipment now live. Alongside electrifying the network, significant transformation work has been undertaken to upgrade our railway infrastructure including upgrading our stations to ensure they’re ready for the introduction of the new longer trains and brand-new signalling. Major track work has also been undertaken to install new passing loops and track doubling in many areas, allowing us to begin increasing the frequency of trains on the South-East Wales network from Summer 2024.
Over 575,000 Customers Use Luton DART
East Midlands Railway's (EMR) Luton Airport Express has enjoyed great success in the last twelve months - growing the number of journeys by more than 50 per cent since its new link with the Luton DART shuttle service. The Luton Airport Express has carried 575,997 customers from the capital and the south, providing a convenient, fast, and environmentally friendly way to get to London Luton Airport (LLA).
Customers have taken advantage of quick journey times and cheap tickets, with
a trip from Central London to the London Luton Airport terminal taking as little as 32 minutes, and costing from just £10, when using the Luton Airport Express and Luton DART.
Services depart every 30 minutes, from early morning to late at night, Monday to Saturday, with regular services on Sundays.
When customers arrive at Luton Airport Parkway, they are able to use a lift or escalators for step-free access between the train platform and the airport's shuttle service – the Luton DART. The Luton DART
takes customers straight to the terminal in under four minutes, providing a reliable, quick, and greener connection.
Luton Airport Express customers are also set to benefit with the announcement that the electric Class 360 trains that operate the service will receive a refurbishment. The £27.6 million investment will see more brand new interiors, greater luggage space, new 2+2 seating, charging points, and new passenger information systems.
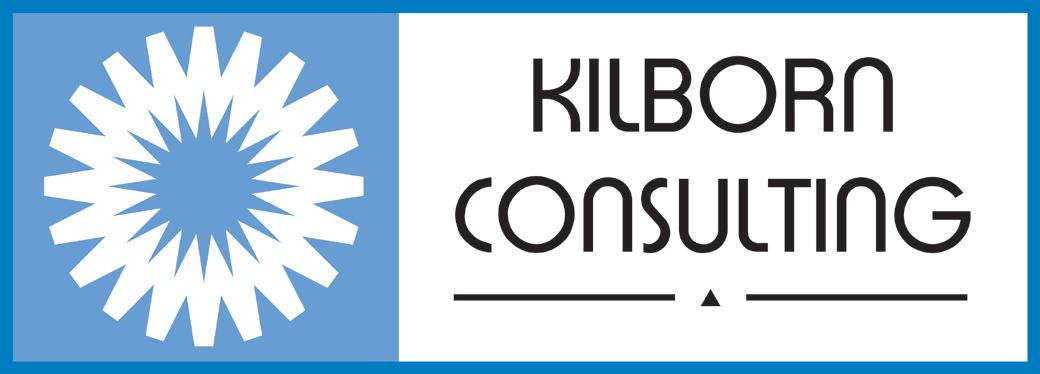
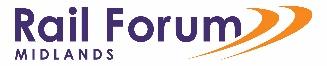


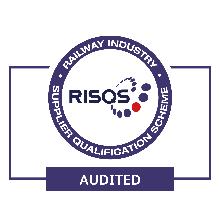
Kilborn Consulting Limited is an independent railway engineering consultancy and design business, with over 21 years of railway experience.
We specialise in the design of new and altered railway Signalling & Telecoms systems for the UK railway infrastructure.
Our areas of specialism are:
•Signalling and Telecoms Consultancy, including technical advice & support;
•Asset Condition Assessments, Correlation and Surveys;
•Signalling & Level Crossing Risk Assessments;
•Feasibility and Optioneering Studies;
•Concept and Outline Signalling Design;
• Telecoms Option Selection Reports (including AiP), Reference System Design and Detailed Design;
•Detailed Signalling Design;
•Competency Management & Assessments;
•Signal Sighting assessments, covering the full Signal Sighting Committee process with a competent Chair.
The new office which is located in the heart of Wellingborough can accommodate all staff and visitors alike and offer widespread views across Wellingborough and the surrounding green spaces. We would be delighted to welcome you to our office to discuss your requirements and how we can support you to achieve those.
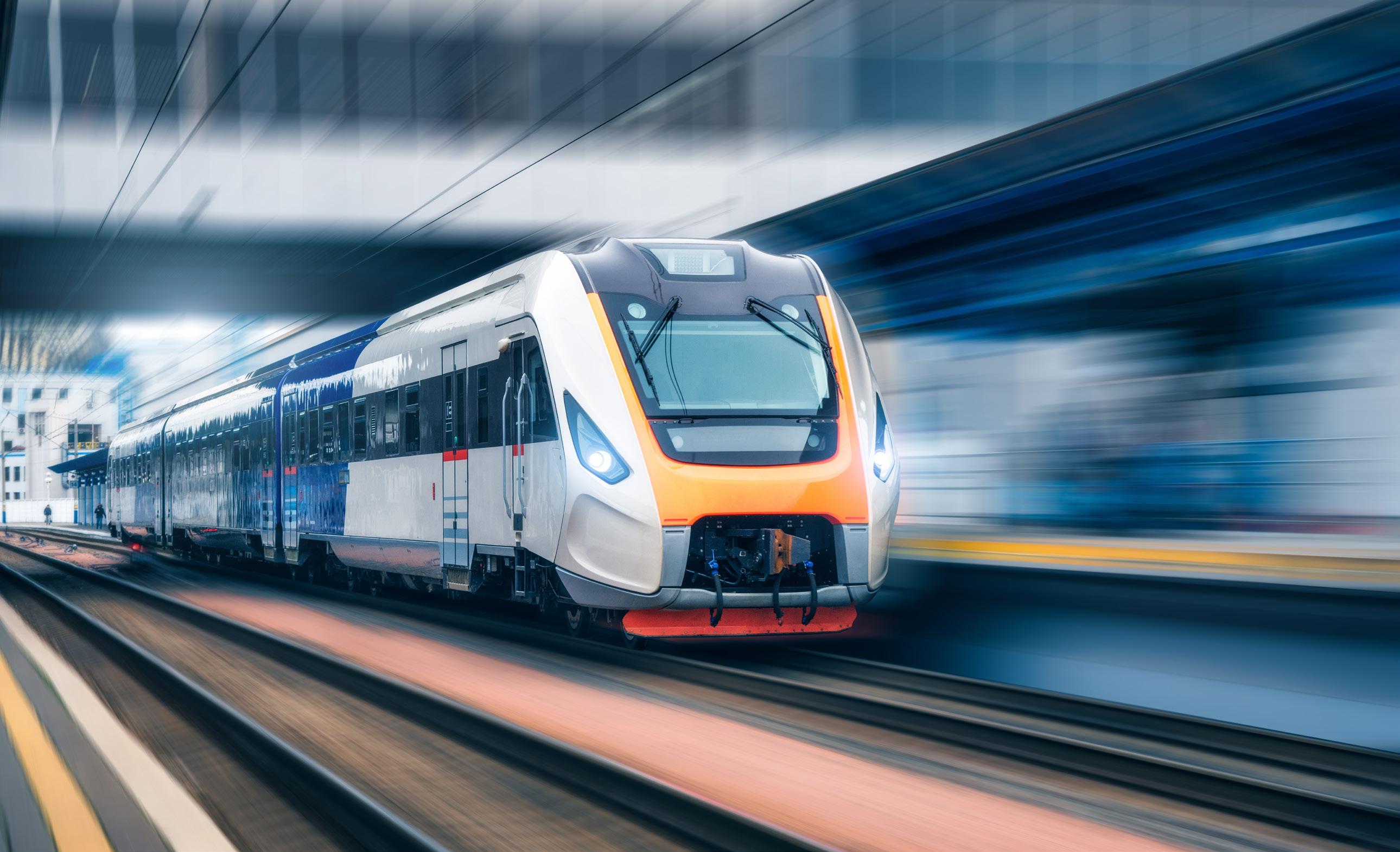
Norbar is a UK manufacturer of battery, electric, pneumatic and manually operated torque multipliers, wrenches, torque measurement equipment and bespoke torque control solutions specially developed for the rail industry Contact Norbar and speak to The Voice of Torque Control
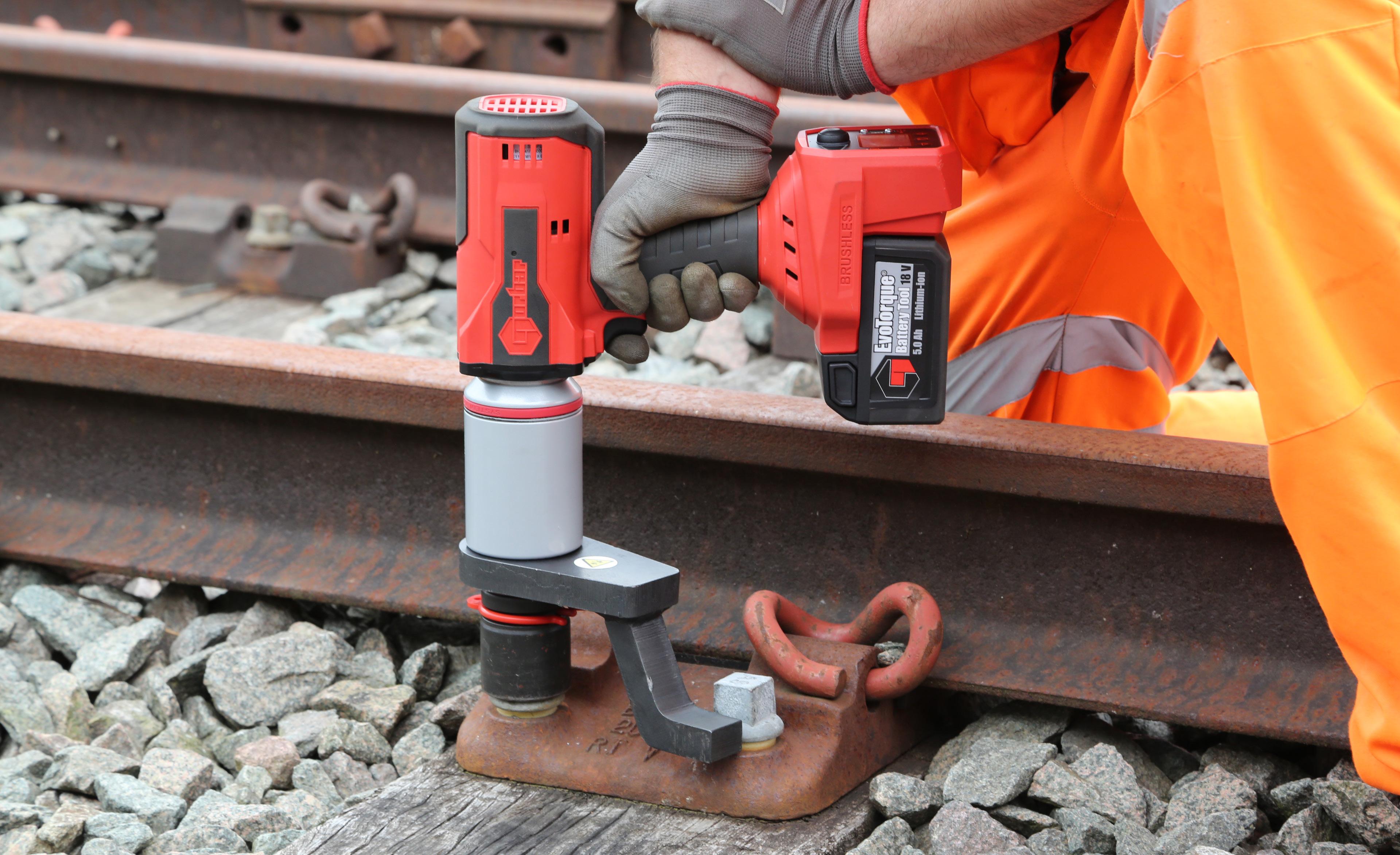
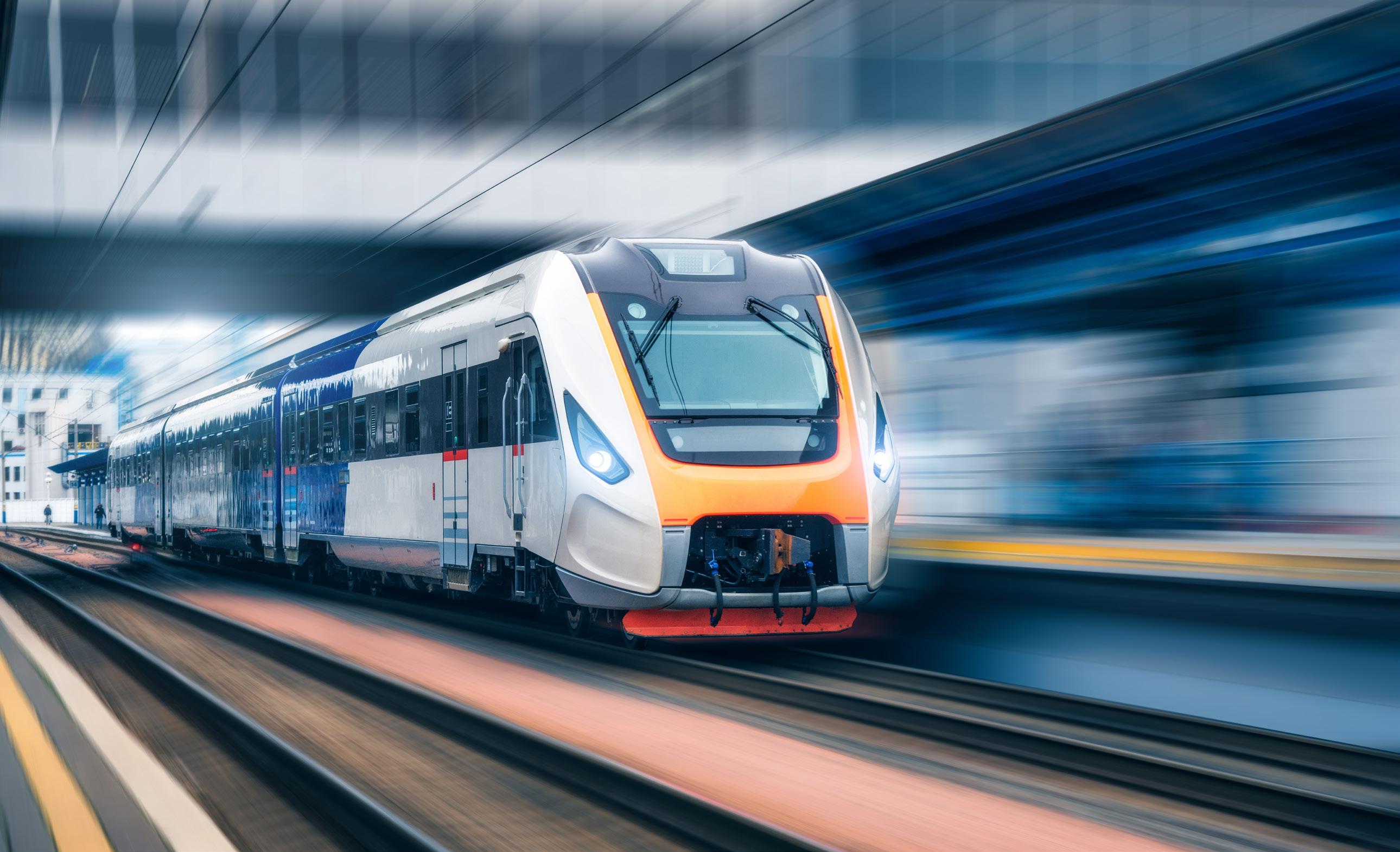
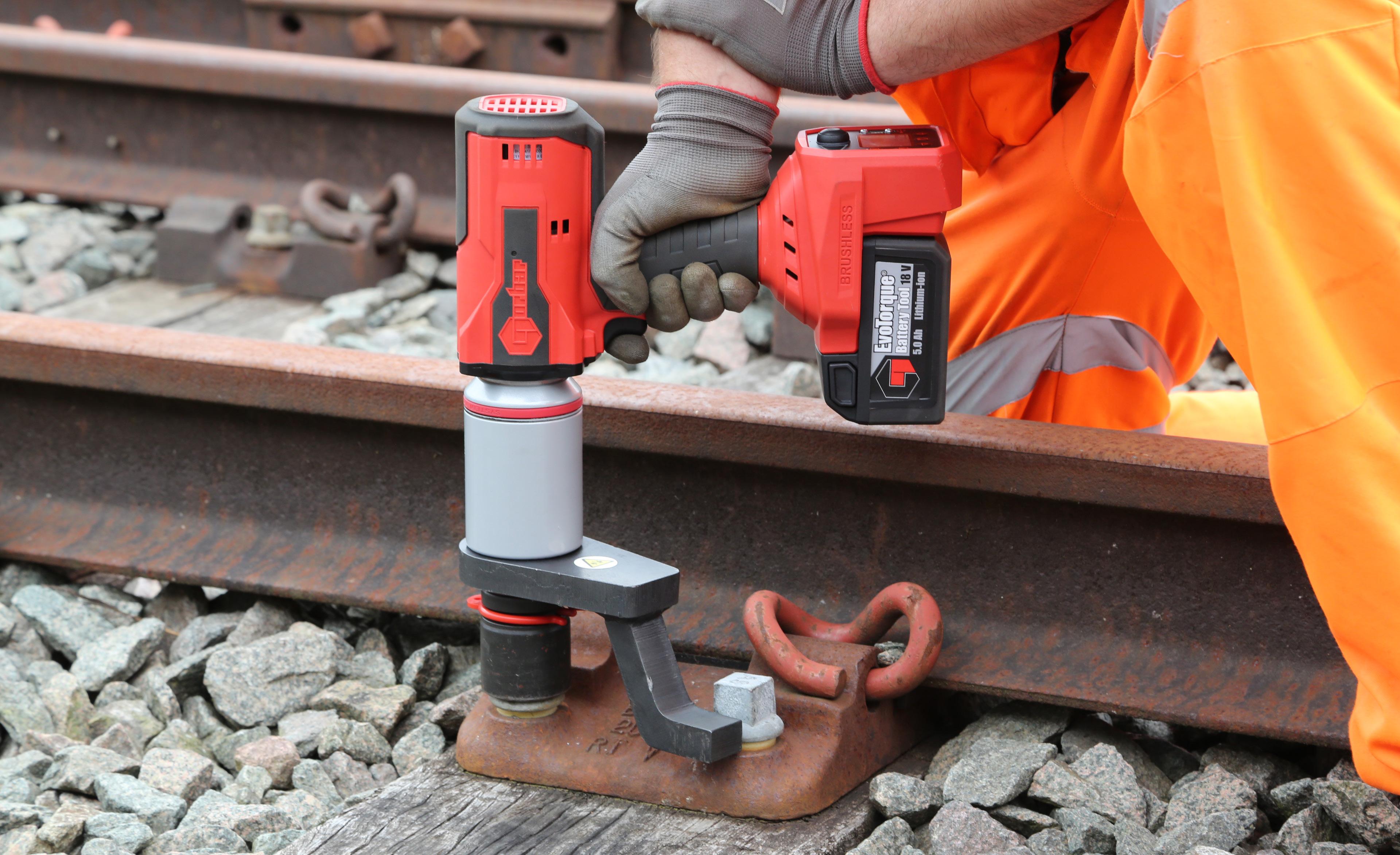
New Community Inspired Artwork Unveiled at Rugby Station
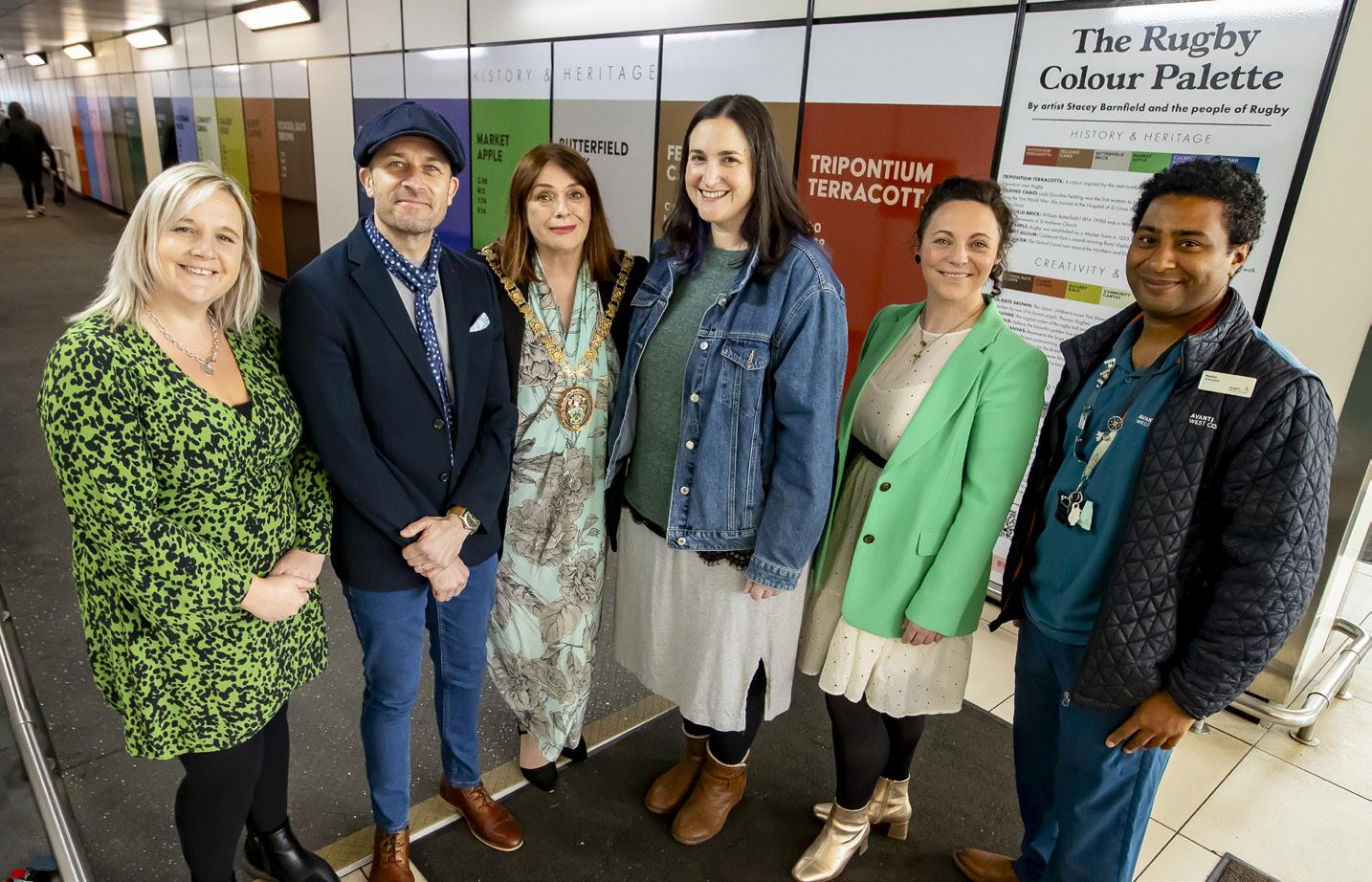
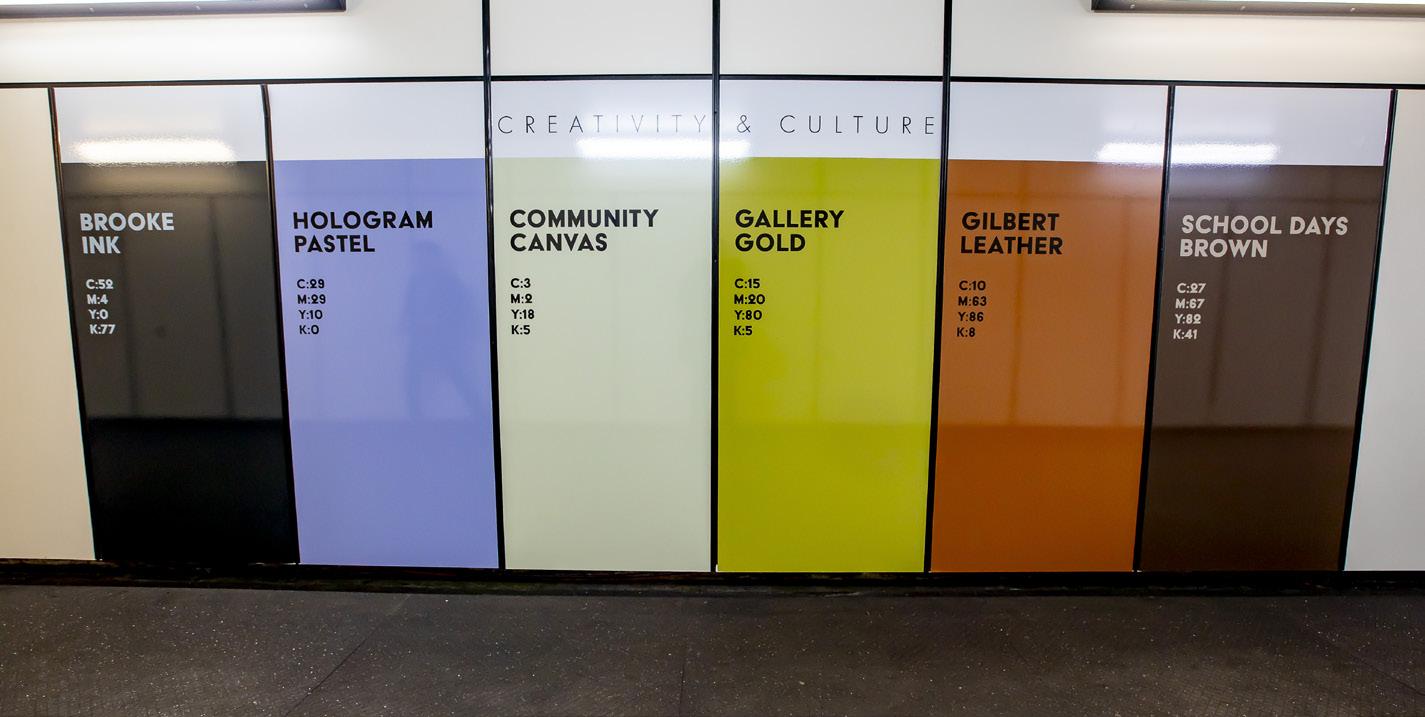
A new piece of community inspired artwork has been unveiled at Rugby station thanks to the backing of Avanti West Coast and the Heart of England Community Rail Partnership. The Rugby Colour Palette went on display last week at the station to help promote the character of the town. Funded by Avanti West Coast Project Fund, the Heart of England Community Rail Partnership worked with artist Stacey Barnfield from Draw My City, to develop the project. The colours were chosen from the ideas that arose from a public consultation, the aim of which was to get respondents to celebrate their hometown. At its heart were a number of school and community workshops delivered by Ruby Road, a Warwickshire based storytelling collective, and its creative producer Jo Chalkblack.
Working with the project partners, Stacey brought to life the many ideas, creating three colour palettes with the themes History and Heritage, Creativity and Culture, and Industry and Innovation. The colours chosen are a mix of direct references to suggestions from the public as well as more thought-provoking choices designed to encourage conversation around the palette. The colours include Market Apple referencing the fact that Rugby was established as a Market Town in 125, School Days Brown which references Tom Brown's School Days by Thomas Hughes – published in 1857 – which was set at Rugby School and Webb Ellis Bronze which nods to the bronzecast statue of William Webb Ellis, the Rugby schoolboy who is credited with inventing the sport.
HS2 Begins Foundation Works for Key A43 Bridge
HS2 has begun foundation works for a key bridge that will take a major A road over the new high-speed railway just outside Brackley, after successfully completing the temporarily realignment of both carriageways.
The A43 – which links Oxford, Brackley and Northampton – is a vital route, providing access to Silverstone and connections between the M40 and M1. Just
two weekend closures were needed during the seven-month realignment project, with HS2 working closely with National Highways to create an ‘island’ between the two carriageways big enough for the construction of the new bridge deck.
HS2 engineers have now begun work on the 52-metre deep piled foundation that will support the weight of the bridge. These will be topped with concrete pile caps and piers
supporting the 66-metre-long bridge deck that will carry the road.
Once the deck has been completed, the road will be moved back over the new bridge and excavation can begin to create space for the railway to pass underneath. This multistage approach was designed to keep traffic flowing and reduce disruption.
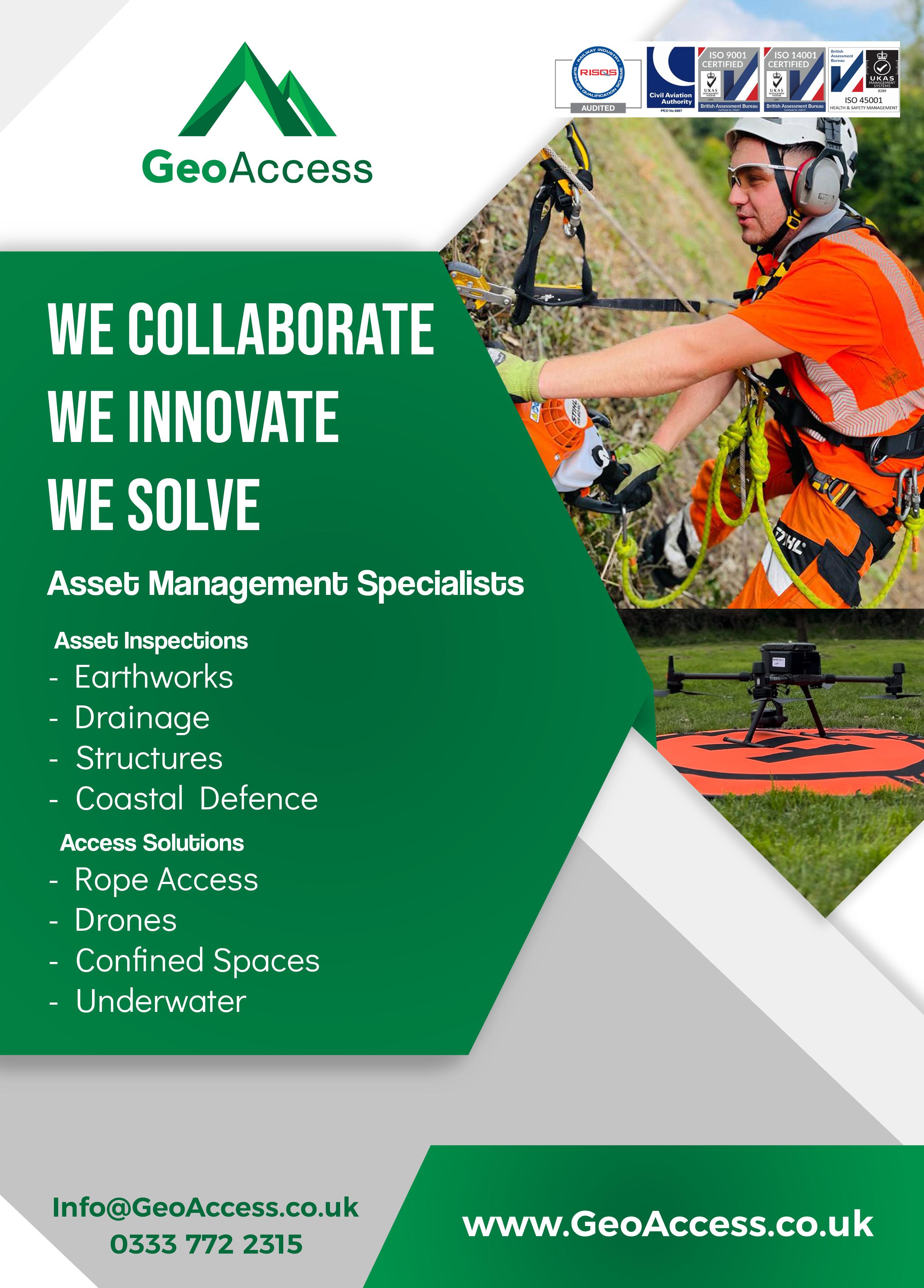
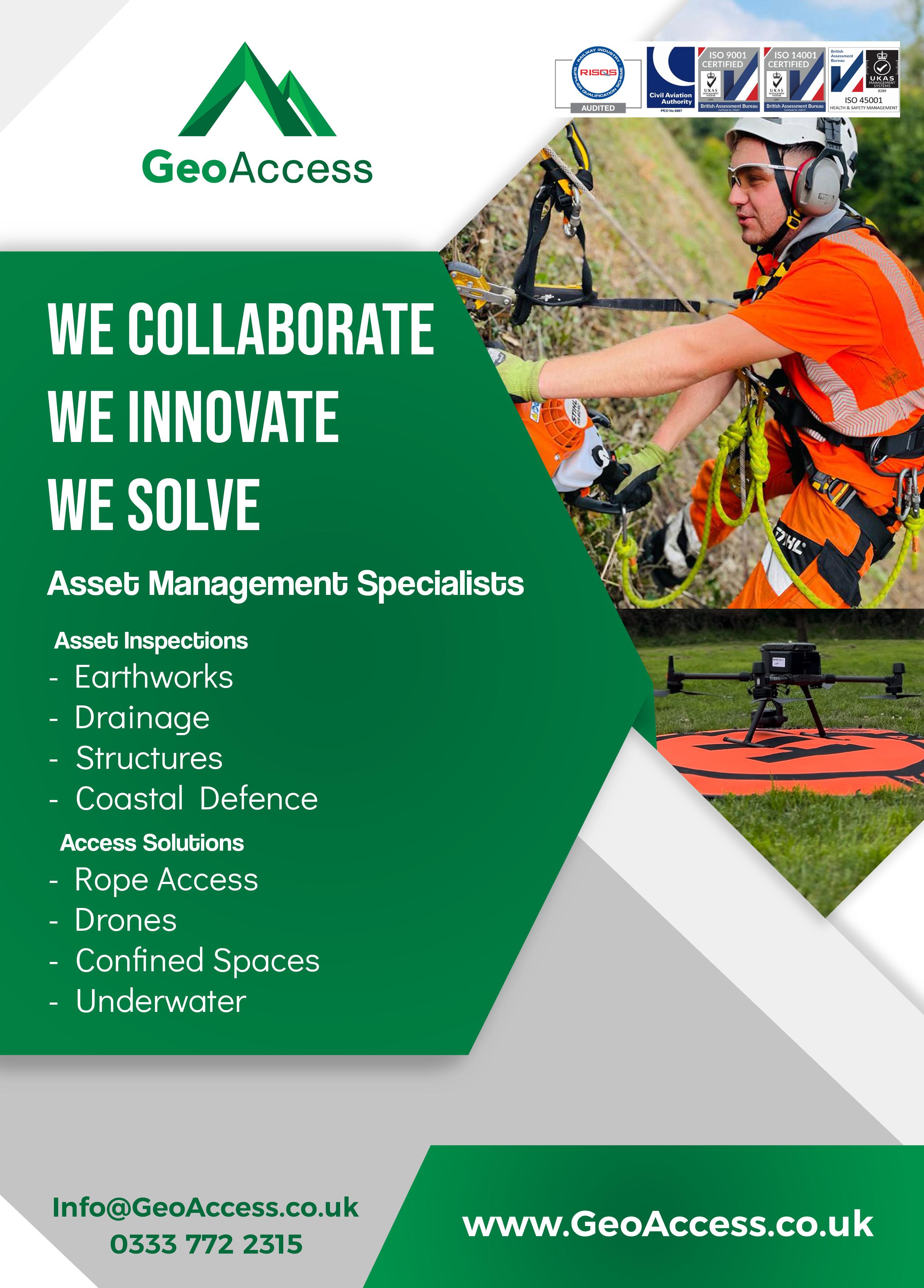
Nexus Unveils New Training Tool for Metro Level Crossing Safety Awareness
A new and interactive training tool is being used to promote level crossing safety on the Tyne and Wear Metro. Nexus, the public body which runs Metro, has installed a mocked-up Metro level crossing at the SafetyWorks teaching centre in Newcastle. It recreates the red stop lights and warning tones and will be used to educate thousands of children about the dangers of misusing them. The mock-up is a new part of an immersive Metro safety training facility, which includes a Metro station called West Fifteen, tracks, ticket machines, platforms, and a life-sized front end of a Metro train.
Safety Works, which is based in the west end of Newcastle, is a multi-agency training facility which is used by the Tyne and Wear Fire and Rescue Service, Northumbria Police, Nexus, and the local authorities to conduct safety awareness days for young people.
Courses, which are tailored for school visits, students and young offenders, include everything from road and railway safety, to fire prevention and criminal justice.
SafetyWorks prides itself on creating an interactive, informative day out. The classes are scenario-based, meaning children are immersed in realistic situations throughout their visit to learn about potential problems, how they arise and how to combat them directly. All classes are held in a life-sized ‘safety town’, so the resources that the students interact with are the physical areas around them.
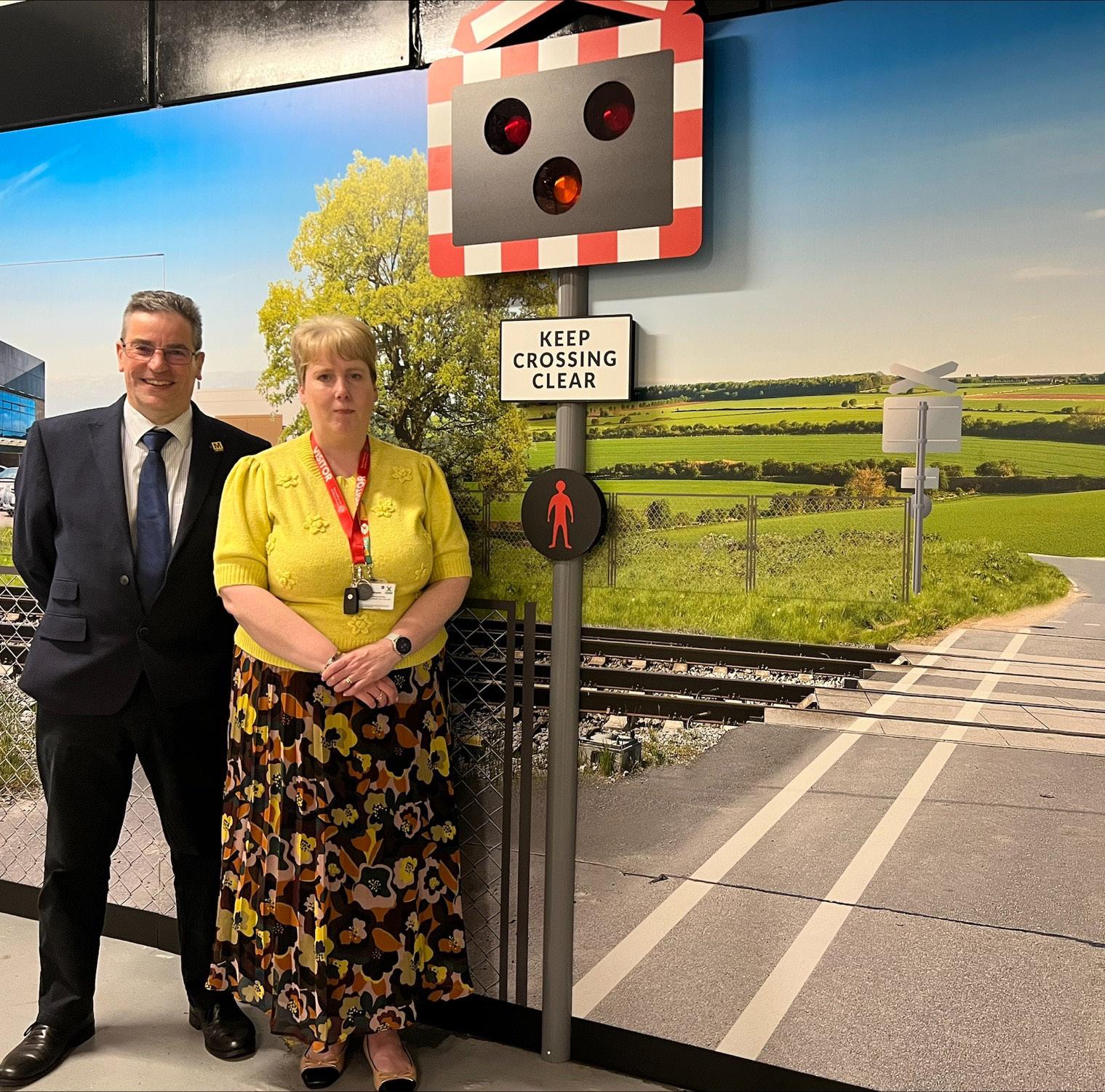
Support Grows for Flourishing Community Rail Movement in the Netherlands
Community Rail Network is supporting the creation of a new national community rail organisation in the Netherlands. At a celebration event in Utrecht, Chief Executive of Community Rail Network Jools Townsend joined members of Coöperatie Stationspark Deurne and other rail industry figures to share best practice from the community rail movement in the UK.
Michel Lintermans has been at the forefront of promoting community rail in the Netherlands since establishing Coöperatie Stationspark Deurne in 2014 alongside colleagues Jos van Wegen of Coöperatie Coopnet and Vincent Jacobs of LSA. Their initiatives have positioned Deurne Station as a vibrant hub at the heart of its community, with projects including a bicycle service point, a community
garden and artwork, a book exchange and a Fairtrade catering facility.
The team have now secured funding from the Ministry of Infrastructure and Water Management and are developing strong relationships with ProRail, the rail contractor responsible for the Dutch rail network, and NS, the main Dutch railway company.
To gain momentum for the proposed national organisation, the team have also reached out to 15 other groups who are currently carrying out social initiatives at stations across the Netherlands, highlighting a growing range of community rail activity.
Jools Townsend, Chief Executive at Community Rail Network, said: ‘The community rail movement strives to
put stations and railways at the centre of community life, increase rail use and support modal shift towards greener, healthier, more inclusive travel.
‘I was delighted to be invited to Utrecht to speak about the fantastic achievements of our community rail partnerships and station groups across Britain. It was an honour to be able to share community rail’s insights and exchange ideas with colleagues in the Netherlands, on empowering local communities and creating railways and stations that deliver maximum social, economic and environmental value.
‘We are proud to support the growing community rail movement in the Netherlands and can’t wait to see it go from strength to strength, and to be able to learn from its experiences and innovations.’
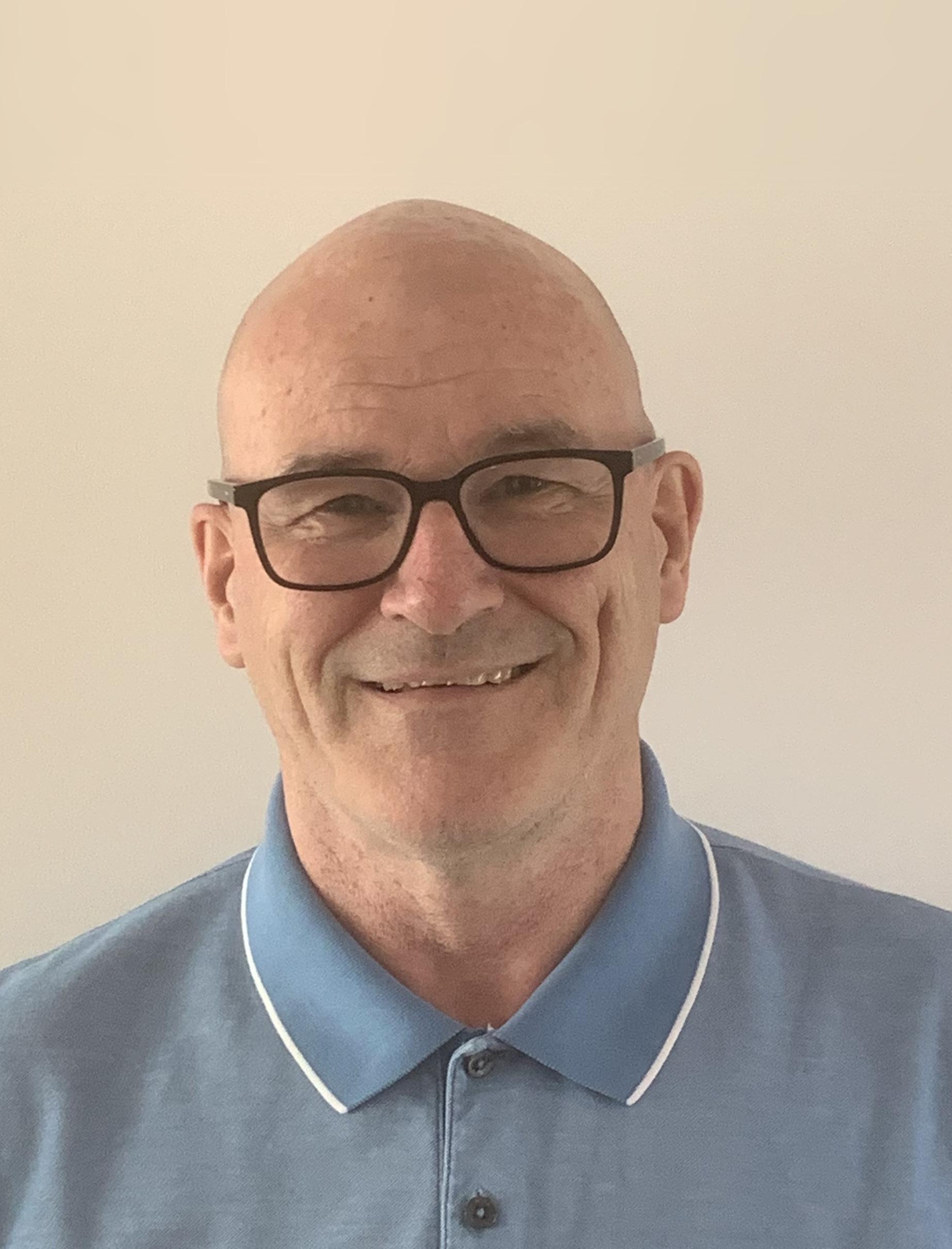
Colin Campbell Senior Engineer at
Mabey Hire
Sam Sherwood-Hale spoke to Colin Campbell, SeniorEngineer
at Mabey Hire about his work on the Barmouth Viaduct project
SSH: When dealing with a 150 yearold, Grade II listed single-track wooden railway bridge – what type of special considerations do you have to make?
The timber viaduct had to be strengthened first, which was an 18-month programme split into two phases. Phase One involved replacing timber crossheads and bracing and then Phase Two was the replacement of the metal structure. We had to jack from adjacent crossheads to lift out the middle crosshead, which was done on 19 or 20 of the timber structures.
We only had a 90-day blockade for possession, so rather than going in cold, Alun Griffiths set up a full size, 100-metre track in the compound, and we built the trusses, attached them to the new bridge beams, moved them along the track and then got them to a point where we could lift them off the rail bogies and down onto the simulation area at the other end.
It was about one and 3/4 miles from that track to where the actual bridge was. We had a jacking system with the bogies to keep the whole thing level as it was travelling because of the undulations on the track.
They couldn’t just use our temporary works at the full width of the bridge, it had to be narrow enough to pass through the existing structure and then allow them to dismantle the old structure around it and finally put the new structure into the footprint of the original structure.
SSH: What type of bespoke equipment did Mabey Hire bring to the project?
CC: The Mabey Hire components we used were bridging panels to create a truss. The beams were 60 or 70 tonnes each, so we had to clamp them to the truss whilst they were sat on the rail bogies and lift them all up. Then, once we’ve got possession, we had to replicate that on the track, so the trusses are loaded onto the bogies and the new edge beams are then attached either side.
Once that is all attached we then jack the system up 25mm to make sure it was on the hydraulics so that as it was travelling down, any discrepancies on the track were taken out by the hydraulics and then the jacks could be adjusted to suit the travelling conditions.
SSH: How did the test scenario differ to the reality on site?
CC: When you do that in a test scenario, the test track is built on a perfectly flat surface, it is only when doing it live on site that you encounter the undulations of the track.
Once it got to the bridge, passing through the bridge we had 55mm clearance on either side of the new structure going into the old structure. The swing span was travelled down first, once that was in line over the piers and then lifted off the bogies. The next job was the jack and pack, because the travelling height was 700 or 800mm
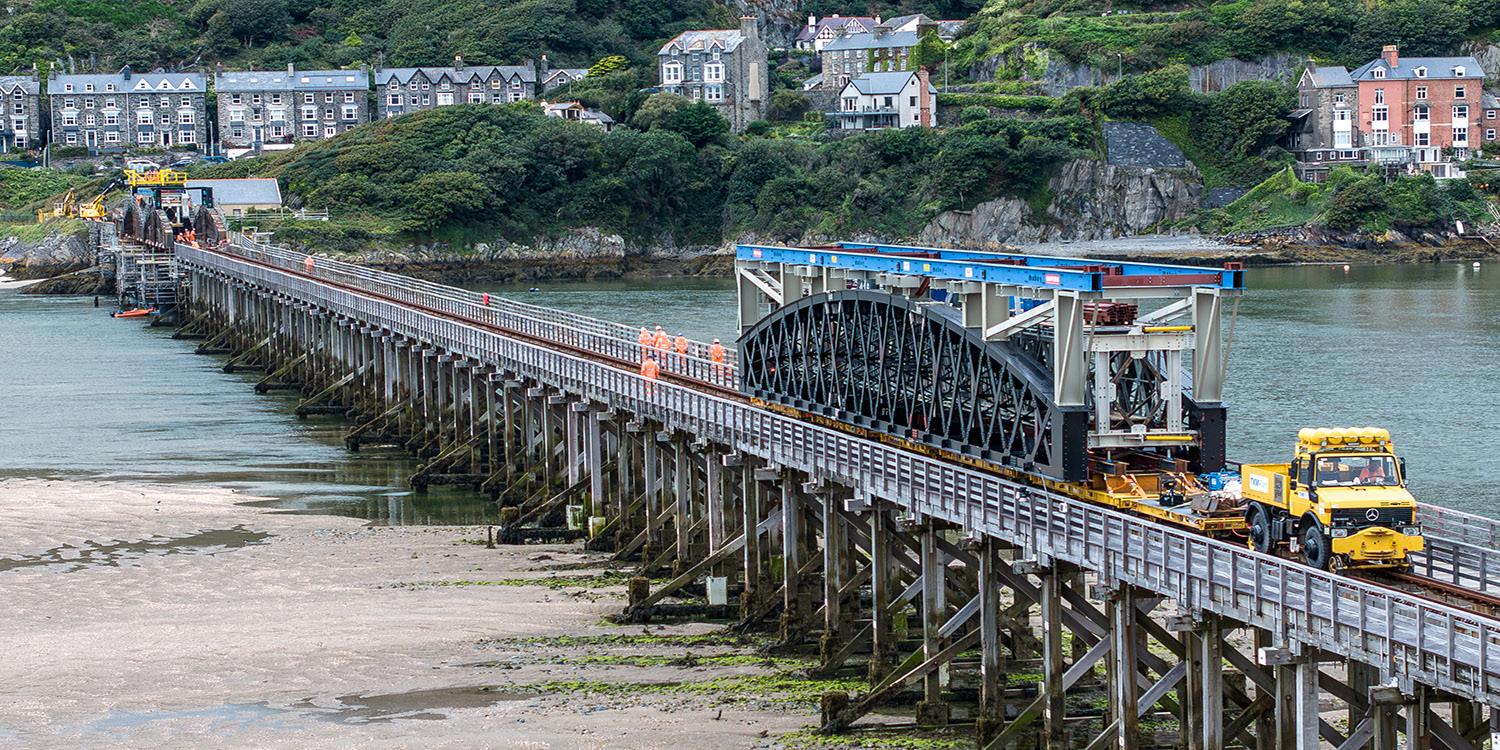
‘A typical bridge job might all be done over two nights but Barmouth was 60 days of jacking attendance which is quite unique as we essentially had to put aside a separate team for the eventualities that happen on site.’
as well. Once it was out to the correct footprint everything was bolted up to make it rigid again and then jacked up again, the sliding interfaces were removed and the new bearings were put in and the structure was lowered down into the footprint.
So there were five piers total, to get the jacking arrangements and the stool arrangements we had to do a cantilever jacking system from pier three. Once it was down and everything was in we lifted the new structure from pier three which allowed them to get the temporary steelwork out at pier two, install the new steelwork at pier two and the new bearings. We repeated this for pier four and five. The jacking frames were our proprietary equipment from Mabey Hire.
SSH: What sort of timeframe were you working to?
CC: From building the truss in the test area we had about four weeks per truss in the compound to prefabricate and then once the closure was on, we had about 60 days on site. Alun Griffths were working three gangs on 24 hour days and we slotted into that.
‘Even though we couldn’t replicate the 800mm (in the test scenario) the principle of getting it from one set of jacks to another set and then changing the packs was established in the test.’
higher than the actual pier height, so whilst the team was lowering the swing span the same process was happening back at the compound for the fixed span which was then driven in behind.
We had to come up with a jacking frame that allowed us to jack it up off the rail bogies but also be able to get it down to the phase one on temporary stools. Once there, Alun Griffiths could start the demolition. Obviously, they had to install the cranes on top of the temporary structure, once they had dismantled the old structure the next phase was to get it down to the bearing level. Where sliding interfaces with hydraulic jacks on the pier side were all engaged and it was slid out at 963mm, then we flipped them over to the estuary side and they were slid out the same way.
Incorporated into the system was a facility to allow the two girders to move out, but also for the gantry crane running across the top to widen with the structure
Generally, if we’re doing bridge jacking we’ll get the programme from the customer and then we’ll see where Mabey Hire fits in.
A typical bridge job might all be done over two nights but Barmouth was 60 days of jacking attendance which is quite unique as we essentially had to put aside a separate team for the eventualities that happen on site.
During the first phase in 2020 we did around 20 shifts and came up with two bespoke systems to shorten the programme down.
SSH: How did this job differ from other programmes you’ve worked on?
CC: On normal jacking jobs you’re reliant on whatever stroke of the jack you’ve got, which may be 100 or 200mm, when you go over 600mm you’ve got to think about how to energize the jack to take the weight of the structure and then allow it to come down the full stroke of the jack which might
only be 200mm, lock it off and then have a secondary jacking system alongside which can take the weight whilst you repack the process.
You can either jack and pack and make up your packs during the changeover, you can use strand jacking bars if you’ve got the space for winches, but if you’re working within the confines of an existing structure and a new structure then everything has to be made on site.
You’re governed by the space that is available so you’re trying to keeping the packs as small as you can whilst still being able to brace and make up a frame, this was all part of the test in the compound and so even though we couldn’t replicate the 800mm the principle of getting it from one set of jacks to another set and then changing the packs was established in the test.
SSH: How much of this information do you have access to prior to beginning the job?
CC: A customer will tell us the weight and dimensions of the structure and then how far down they need to go. From that you can think back to a previous job and see if the same rules will apply, it is a combination of a few restraints. No two jobs are the same because the weight won’t be the same and then it depends on what propping system you’ll use, if we do have to make fabrications to start the frame off we would do that and the incorporate it into the temporary steel that the customer has on site.
A lot of Mabey Hire’s jobs are through reputation and prior contracts, we tend to think outside the box with a lot of our stuff as so many jobs are one-off and bespoke.
£30 Million Restoration of Barmouth Viaduct
Mabey Hire’s temporary works solutions chosen again in renovations to 19th century viaduct

As part of the second phase of renovation works to Barmouth Viaduct, civil engineering contractors Alun Griffiths required a range of temporary works solutions to facilitate the replacement of the bridge’s existing hogback trusses. For this work, a variety of Mabey Hire’s equipment was specified to help manoeuvre the new supports into place.
First opened over 150 years ago, Barmouth Viaduct is a Grade II* listed single-track wooden railway bridge, one of
the oldest of its type still in regular use. To ensure longevity of the structure, Network Rail took the decision to run a major programme of upgrade works to completely restore the viaduct. These works aimed to maintain the bridge as a viable crossing for Cambrian line trains, as well as being sympathetic to the bridge’s great heritage and listed status. In keeping with this, components had to be swapped out on a ‘like for like’ basis.
The first stage of these works, carried out in 2020, involved an innovative bridge
lift to facilitate the replacement of 24 of the bridge’s crossheads. Alun Griffiths carried out these works, with assistance from Mabey Hire, who provided a bespoke jacking scheme to temporarily lift two deck spans of the bridge off its central support, while the crossheads were replaced.
Speaking about the second phase of the works, Steve Richardson, Operations Manager, at Alun Griffiths, said: ‘As part of the ongoing restoration and renovation programme, Network Rail wished to replace the two original 160 tonne metallic spans of

GRP RAIL SOLUTIONS

Our team of in-house experts create detailed solutions that exceed all Health & Safety requirements. With our extensive experience working with GRP, we provide the best solutions possible. From trackside to station car park, we have the perfect solution for all your needs.
Don't settle for anything less than the best. CONTACT US NOW!
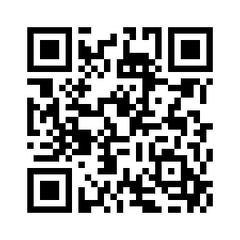
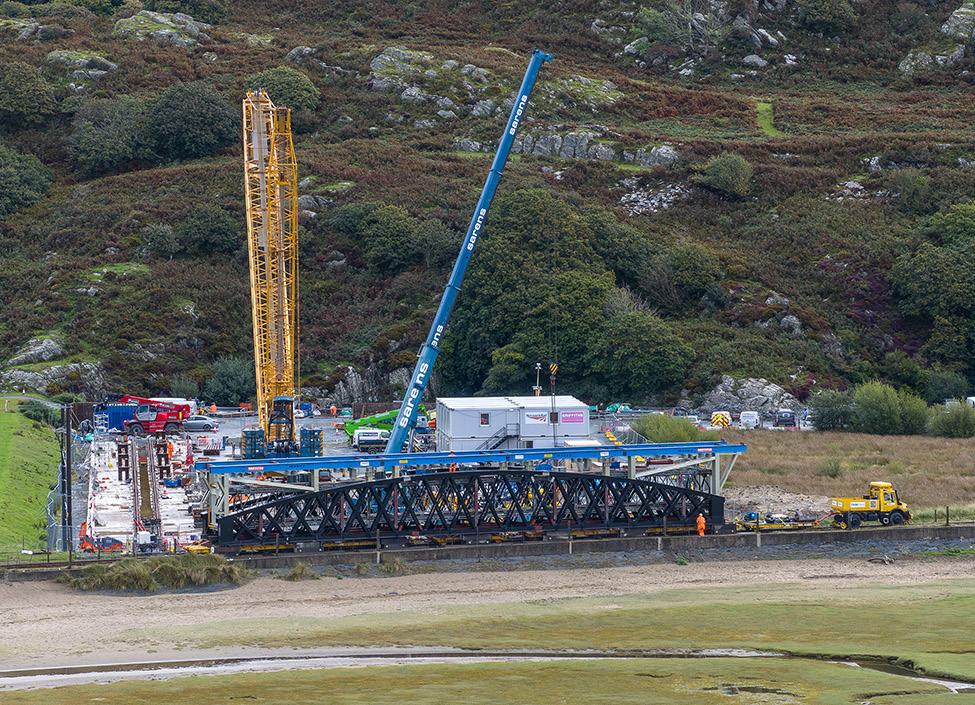
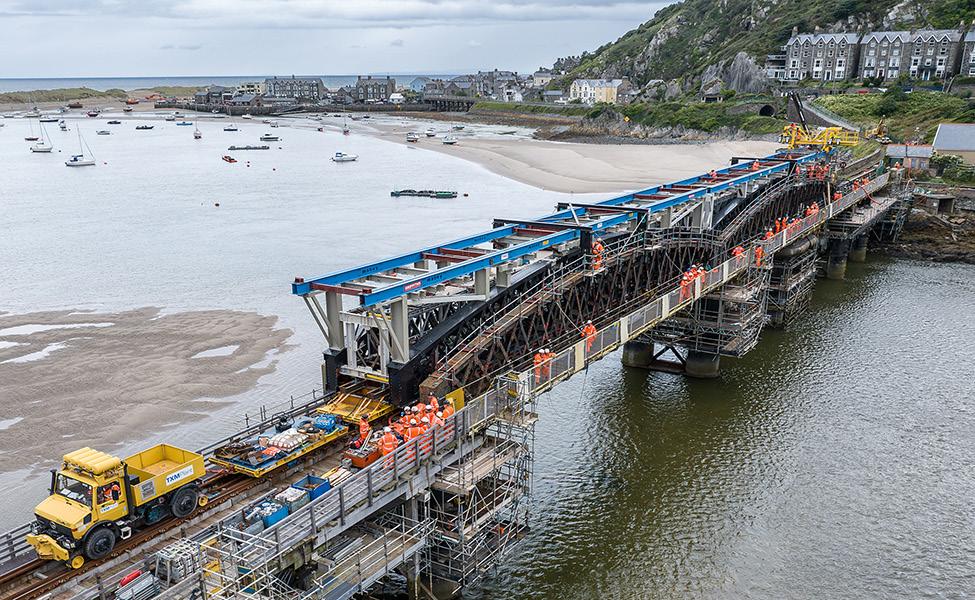
the bridge. As with the previous work carried out, everything had to resemble the original 19th century structure, with the new hogback trusses being specially fabricated.
‘Considering the complexity of the project, we decided to carry out a test run of the proposed method of installing these new spans. This test was conducted around half a mile away from the site, meaning we also had to devise a way to move the whole system from the test compound to the bridge, without damaging the new main spans.’
To facilitate this, a temporary works design was engineered by Tony Gee & Partners, with Mabey Hire designing the temporary jacking arrangements to simulate the actual system on the structure, as Colin Campbell, Senior Engineer at Mabey Hire explained: “To prove the proposed system would work, it was important that it was tested. To do this, Tony Gee & Partners designed a temporary works scheme featuring our bridge panels and corner brackets to create an eleven-bay truss. This was then connected directly to the bridge’s new trusses, which were placed on seven rail bogies, with our hydraulic jacks placed underneath the trusses. This whole system was then pushed 50 metres along the mock rail, proving that it did indeed work.
‘The second part of the test involved
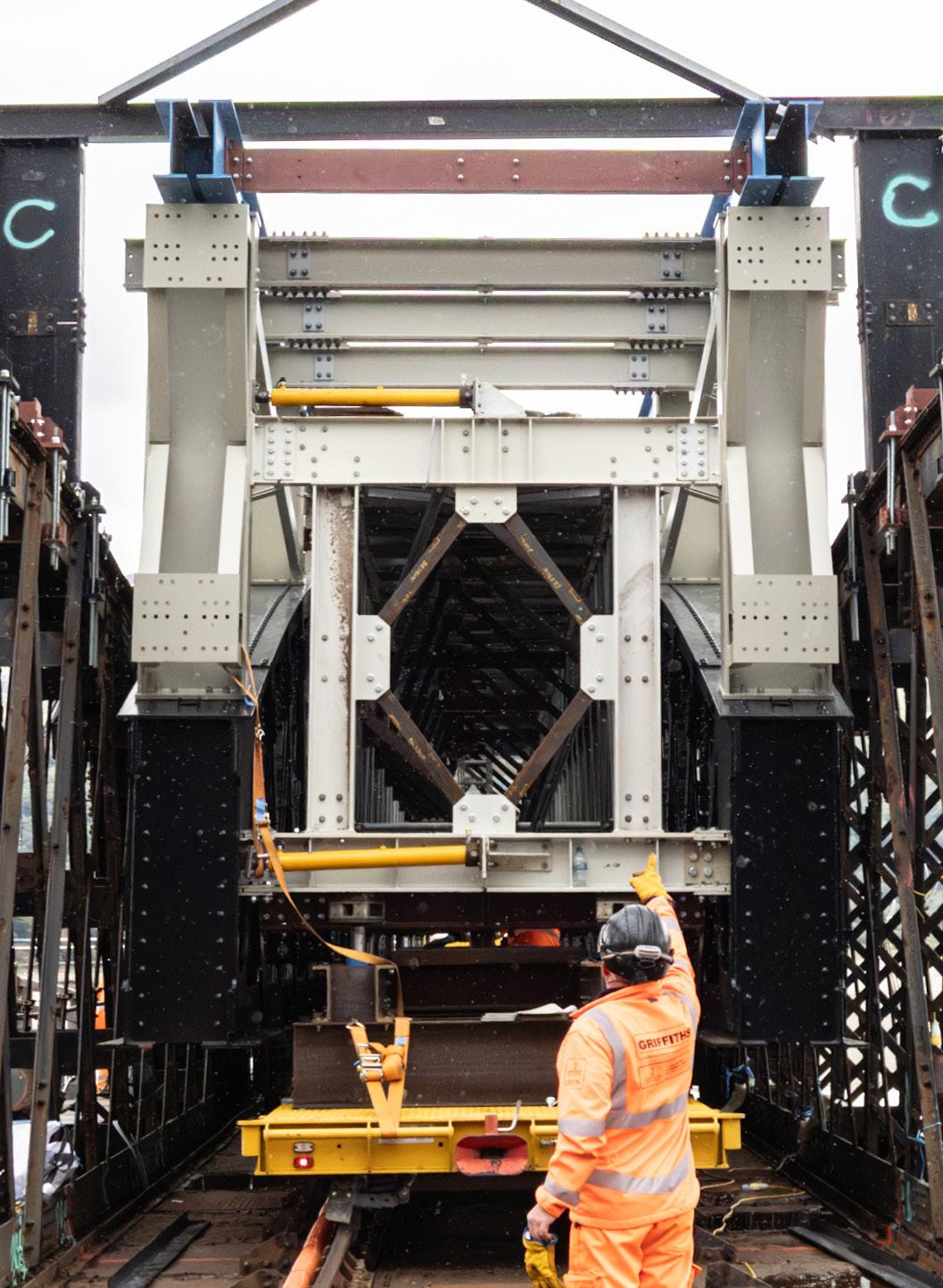
energising the jacks to lift up the edge beams and, using a slider system, move the main spans across onto mock piers, made using our Mass 50 propping and Hymat jacking solutions. We then de-energised the jacks to lower the spans back down, simulating the actual installation.’
With one of the main challenges being the movement of the trusses onto the bridge, Mabey Hire’s hydraulic jacks were crucial to these works, accounting for the undulations anticipated in the tracks during transport. With the jacks pre-set to accommodate for the weight of the beams, they acted almost as a suspension system, ensuring there was little to no movement during transportation.
Another issue that Alun Griffiths had to consider was the positioning of the finished trusses, as Steve explained: ‘With the plan being to move the new trusses onto the bridge inside of the existing spans, we had to allow for 75mm clearance on either side of the whole system. This would allow the new trusses to clear the originals and then be easily placed into their footprint. Once the new trusses were in position on the bridge, the old supports were cut into smaller pieces and lowered onto pontoons on the estuary below, where they were taken away. The new trusses were then installed using a push-pull jacking system, which was mounted on a
cantilever framework designed by Tony Gee & Partners.’
Steve concluded: ‘The project went well, with the temporary works system doing its job and successfully supporting the new bridge trusses. Having worked with Mabey Hire on the first phase of the renovation programme, we knew they had the capabilities to supply what we needed and they were very good to work with onsite.’
As a result of the Network Rail programme, the bridge now has an estimated further lifespan of 120 years and was reopened to trains in early December 2023.
Find out more about Mabey Hire’s temporary works solutions, here: www.mabeyhire.co.uk

RAIL LIFTING JACKS & PIT EXPERTS
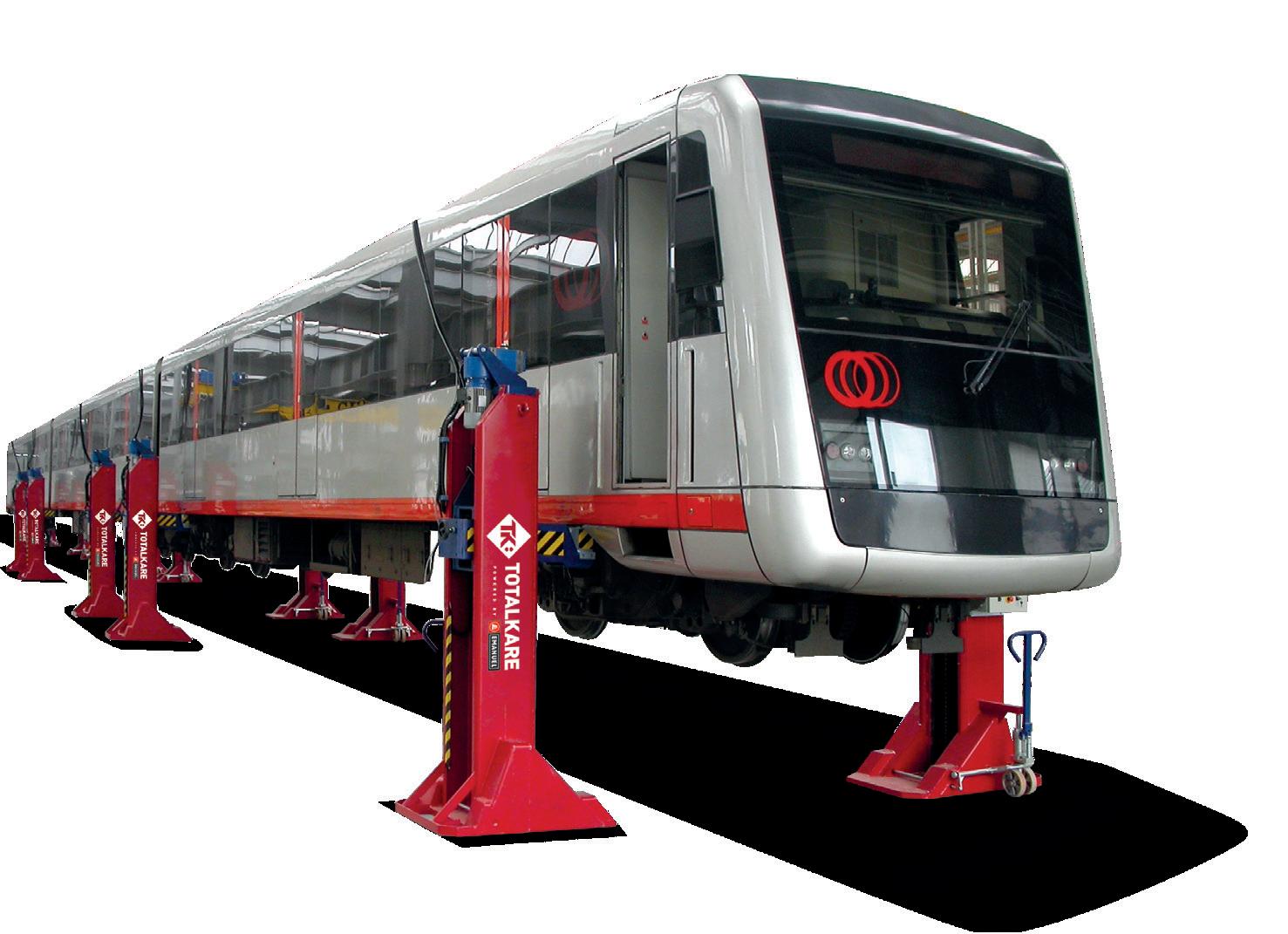
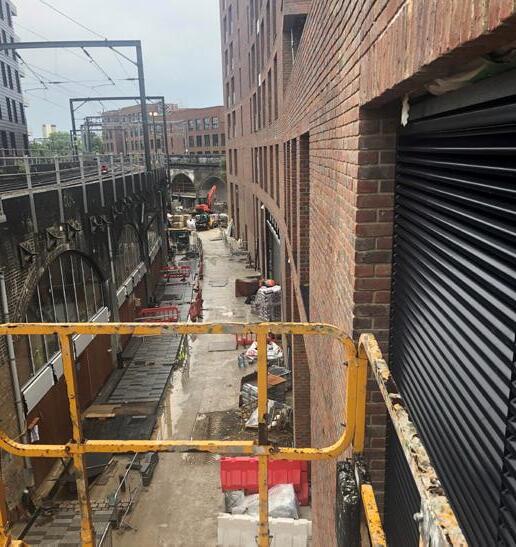
With clients and projects such as TFL, EuroTunnel, DLR, Crossrail and HS2, Sunray is the Rail Industry partner when specifying Steel Door and associated products. Our consultative and practical approach ensure bespoke product solutions to meet performance needs without compromise to design. With exceptional Door Size Ratios, Fire Ratings of 1-4 hours plus overrun and Security Levels 1-6 provide total
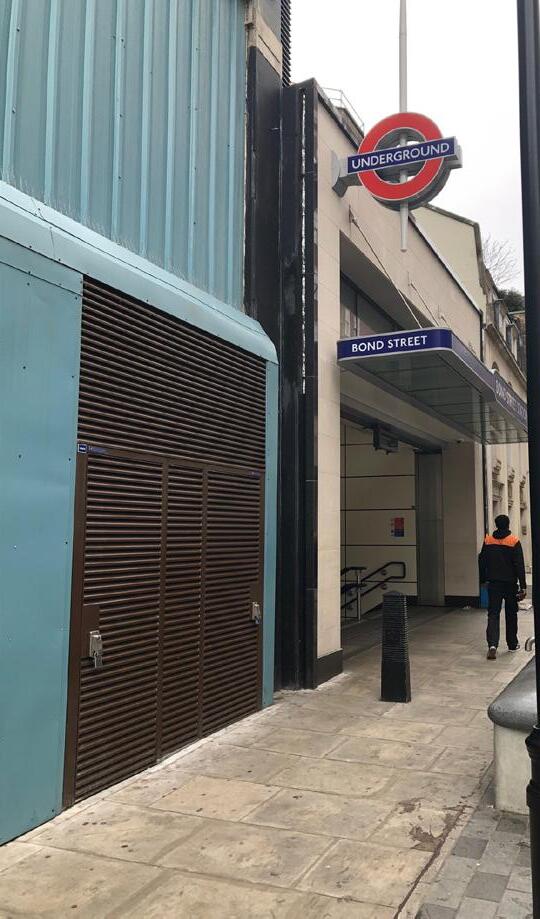
in today’s built environment together with extensive hardware and locking options, vision panels and overall RAL colours.
Durability Supports Decarbonisation
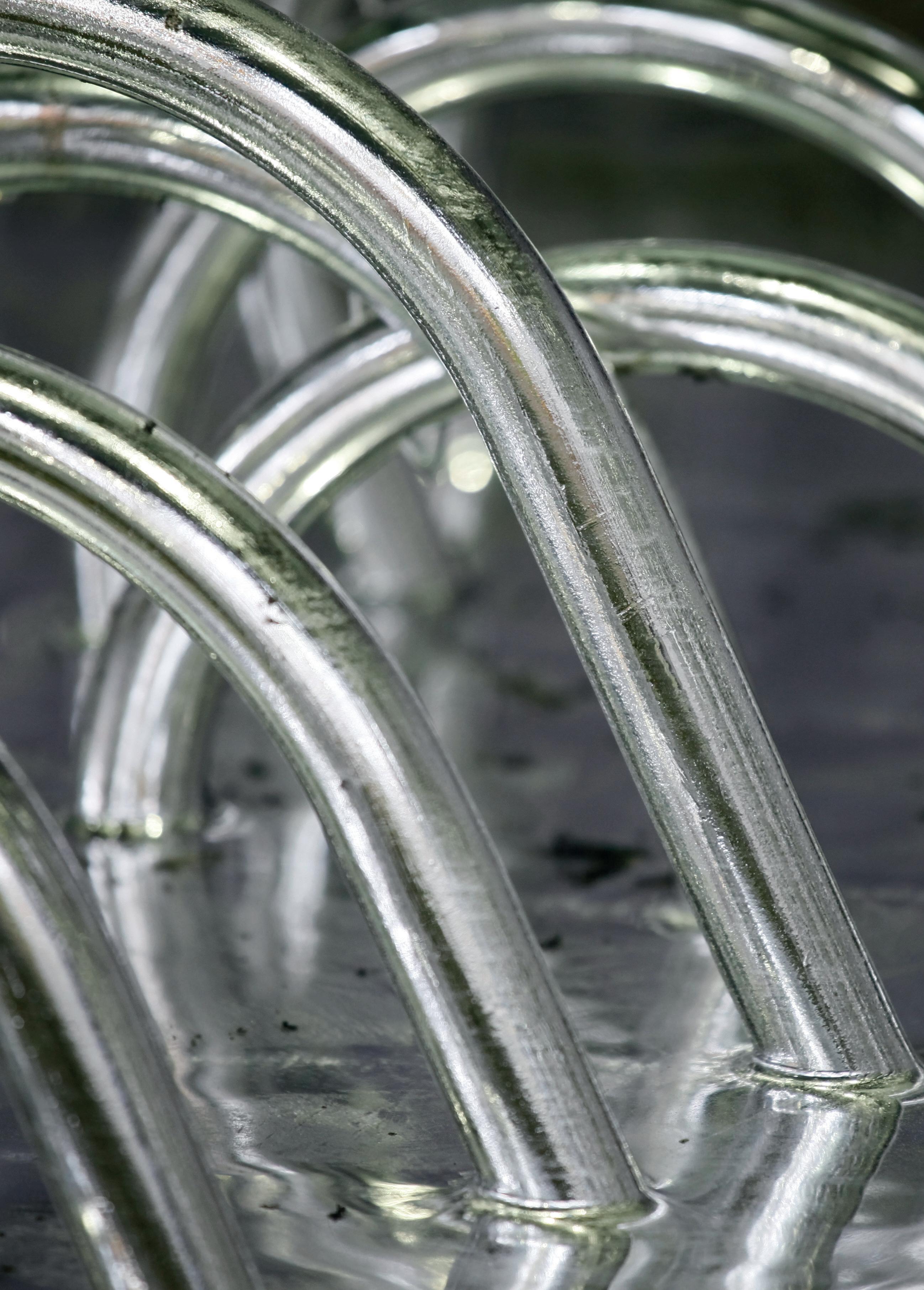
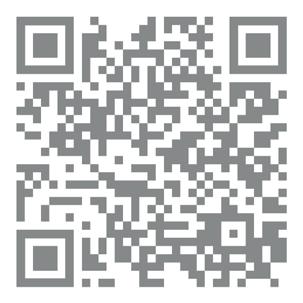




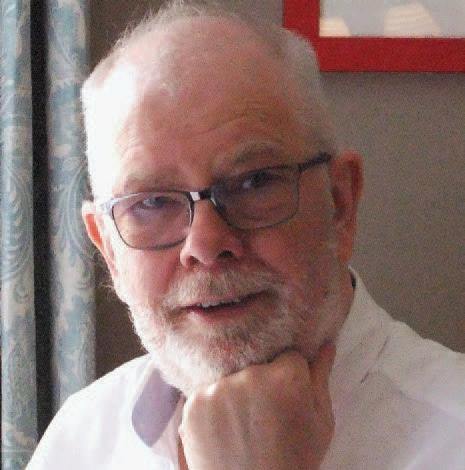
Busy Autumn Quarter Helps Demand Recovery
Forty per cent Elizabeth Line growth helps lift demand above 90 per cent of pre-Covid levels
The recovery in demand for rail services in Britain from the Covid pandemic continued into the autumn of last year, with the pace of growth accelerating a little. Non-Elizabeth Line passenger numbers were 17.1 per cent higher than the same quarter in 2022, reaching a new post lockdown high. Including traffic on the new line, growth was 19.9 per cent.
Overall, demand came rose to 90.9 per cent of pre-Covid levels, according to National Rail Trends statistics, published by the Office of Rail and Road (ORR). However, without the Elizabeth Line, the recovery is to 80.7 per cent.
The provisional figures cover the third quarter of fiscal year 2023/24, finishing at the end of December: across the network, 417.4 million passenger journeys were made during the twelve-week period, up from 348.1 million in 2022. Between them, they covered 15.2 billion passenger kilometres, 15.7 per cent up, and paid a total of £2.7 billion in fares, 24.7 per cent more than in 2022.
Looking at demand by ticket type, advance tickets were up by 37.8 per cent, taking sales 49 per cent higher than before the pandemic. Anytime peak and off-peak fares were up by 18.7 and 21 per cent respectively, leaving them 10.7 per cent and 18.9 per cent ahead of the pre-Covid figure. Season ticket holders made 7.3 per cent more journeys than last year, but the 56.3 million total remained 64 per cent below the 2019 figure.
Excluding the Elizabeth Line, services in London and South East moved ahead by 14.9 per cent during the quarter, but in fact it was the slowest growing sector. Between them,
the operators carried 234.2m passengers in 2023, but remaining 22.0 per cent below 2019. Double digit growth was the norm for the sector, with strongest quarterly growth coming at London Overground (20.4 per cent), followed by West Midlands (20.1 per cent) and Greater Anglia (18.4 per cent). The exception was c2c (6.1 per cent).
The Elizabeth Line carried 58.5 million passengers in its sixth full quarter of operation, 40.3 per cent up in the year. Figures for the line have been revised downwards following discovery of a tendency to overstate passenger numbers in the Lennon data. The revised figures show that the route accounted for 14.1 per cent of the national network’s patronage in the October to December quarter, second only to GTR’s 17.1 per cent.
Amongst the regional franchises, total patronage was 21.9 per cent up on 2022 and remained 18.4 per cent below 2019 levels. Amongst individual TOCs, Scotrail saw the strongest recovery, growing passenger numbers up by 33.9 per cent during the quarter, though still 22 per cent short of their 2019 figure. TransPennine, newly renationalised in the previous the quarter and delivering improved performance, was a close second in the growth stakes, seeing 33.3 per cent more passenger journeys, recovering to 87.3 per cent of the preCovid figure.
TfW saw growth of 19 per cent on the quarter and moved to within 17 per cent of its 2019 figures. Merseyrail saw growth of 15.2 per cent but demand remained almost 34 per cent short of pre-Covid levels. Northern saw a rise of 14.3 per cent in passenger journeys, leaving a shortfall of 23.6 per cent.
NEWS IN BRIEF
GB RAILFREIGHT EXTENDS HAULAGE CONTRACT WITH NETWORK RAIL
GB Railfreight (GBRf) has extended its haulage contract with Network Rail, the owner and infrastructure manager of the UK mainline railway network. Effective from 1 April 2024, the contract is a two-year extension with an option for a third year.
GBRf will continue to provide critical services essential for the smooth operation of Network Rail's engineering works and renewals. This includes the provision of possession trains and the movement of Network Rail wagons to support engineering trains, with up to 16 daily trains dedicated to network services.
In addition, GBRf will continue to operate bulk services, facilitating the transportation of stone from quarries to Network Rail's Logistics Delivery Centres (LDCs). With up to four daily trains allocated for bulk services, this essential function ensures a steady supply of materials to key locations, including the LDCs.
‘To put this quarter’s numbers into some form of historic context, annual patronage is now comparable with levels seen around 2014 and 2015, at around 1.5 to 1.6 billion a year.’
The long-distance InterCity sector saw demand increase by 21.1 per cent compared with 2022, leaving passenger numbers 6.7 per cent short of 2019 levels. Avanti West Coast saw the largest growth, on 38 per cent, coming therefore to 84.8 per cent of pre-pandemic levels. followed by Cross Country on 26.3 per cent, but still 16.5 per cent down from 2019. EMR grew by 22.5
per cent, taking passenger numbers 8.7 per cent above pre-pandemic levels. Caledonian Sleeper saw growth of 20.4 per cent, but still 13.0 per cent short of previous highs. GWR advanced by 10.1 per cent to 80.3 per cent of pre-Covid patronage, though the shortfall will also include some transfer of Thames Valley suburban passengers to the Elizabeth Line since 2022.
Though LNER saw the lowest growth at 6.4 per cent, the operation is the second to exceed 2019 passenger numbers, 2.3 per cent up.
Amongst the non-franchised operators, Hull Trains saw growth of 26.6 per cent and exceeded their 2019 number by 29.5 per cent whilst Grand Central grew numbers by 22.0 per cent and moved 18.4 per cent ahead of their pre-Covid patronage. Helped by the continuing recovery in air travel, Heathrow Express saw numbers grow by 4.8 per cent in the quarter.
This left patronage on the premium route still 21.6 per cent short of previous peaks, suggesting the effect of competition from the Elizabeth Line with its superior links between the airport and central London. Lumo grew by 28.7 per cent during the quarter.
Rolling year figures
The national totals for the twelve months ended 31 December show that, compared with the last pre-Covid year of 2018/19, the number of passenger journeys was 12.5 per cent lower at 1.6 billion. However, excluding the Elizabeth Line, passenger numbers remained 24.5 per cent short of the 2019 figure. Passenger kilometres travelled were 23.4 per cent lower at 51.7 billion, whilst passenger revenue saw a shortfall of 14.6 per cent at £8.8 billion.
As in previous quarters, performance varied between the sectors. Passenger journeys were still 27.4 per cent below 2019 levels in London and South East and 23.9 per cent on the regional networks but moved to within 15.3 per cent on the InterCity routes.
Comment
Last autumn saw more progress on the long road to recovery in the rail industry, with overall numbers now just above 90 per cent of the figure in the same quarter in 2018/19. That is a good headline, but it disguises a much patchier picture, where a combination of TfL concessions and open access operators lead the way.
The Elizabeth Line continues to go from strength to strength, and the 40 per cent plus growth achieved during the autumn is spectacular. It means that the line is already carrying passengers at an annual rate of over 230 million, ahead of with its original 200 million forecast. As noted above, though, stripping these numbers out of the national total leaves the other TOCs looking rather less healthy, at just over 80 per cent of prepandemic levels.
The problem continues to lie primarily with the fall in commuting. As a result, the London commuter lines are still behind in the recovery stakes, having a shortfall of 22 per cent. At 14.9 per cent, the growth seen during the autumn quarter was well behind that achieved on the long distance and regional routes.
The long distance InterCity routes achieved over 93 per cent of previous levels during the twelve weeks and saw demand levels more than a fifth higher than in the same quarter in 2022. But revenue remains a problem: after adjusting for inflation, these routes had a revenue shortfall of over 23 per cent, and inflation-adjusted yields (revenue per passenger kilometre) are still 13 per cent lower than pre-Covid.
In London and the South East, revenue recovery is slightly better than patronage –at 79.8 per cent against patronage of 78 per cent. A shift from season ticket purchase to full fare or off-peak tickets will have helped here. Yields rose by 0.9 per cent and are just 3.7 per cent down from 2019.
The regional networks are, like InterCity, suffering from a yield problem. Patronage has recovered to 81.6 per cent, but revenue is only at 78.5 per cent. Yields are 10.5 per
cent below pre-Covid levels after allowing for inflation.
The shift in the type of tickets purchased continues – and here the latest figures confirm several trends that we have noticed before. First the move towards advance purchase tickets – passengers using these increased by a whopping 37.8 per cent during the quarter, taking the numbers to more than 49 per cent higher than preCovid. Anytime/peak tickets saw passenger numbers up by 18.7 per cent, so that sales were 10.7 per cent higher than 2019, whilst off-peak fares were used by 21.0 per cent more people, now 18.9 per cent up on prepandemic. Journeys undertaken by season ticket holders remain in the doldrums. There was growth of 7.3 per cent in the quarter, but the total is still more than 63 per cent down on previous levels.
The patronage shortfall remains a problem – but recovery is still continuing, and would no doubt be helped by an end to strikes and disruptions caused by staff shortages and overtime bans. ORR reports strikes on some part of the network on seven days during the quarter.
To put this quarter’s numbers into some form of historic context, annual patronage is now comparable with levels seen around 2014 and 2015, at around 1.5 to 1.6 billion a year. So far so good, but then consider the money: revenue levels then stood at around £11.2 billion at today’s prices, twelve per cent or so above today’s £9.8 billion. TOC operating costs were around £10.6 billion, compared with £13.2 billion in 2022/23. Add the £1.4 billion revenue shortfall and the £2.6 billion cost increase and you reach £4 billion – which equates to the amount of revenue support paid by DfT to the train operators in 2022/23.
Things do seem to be moving in the right direction, but it looks as if times will continue to be tough on the railways, whoever runs them, especially in the light of the almighty spending crunch that awaits the next government within months of taking office.
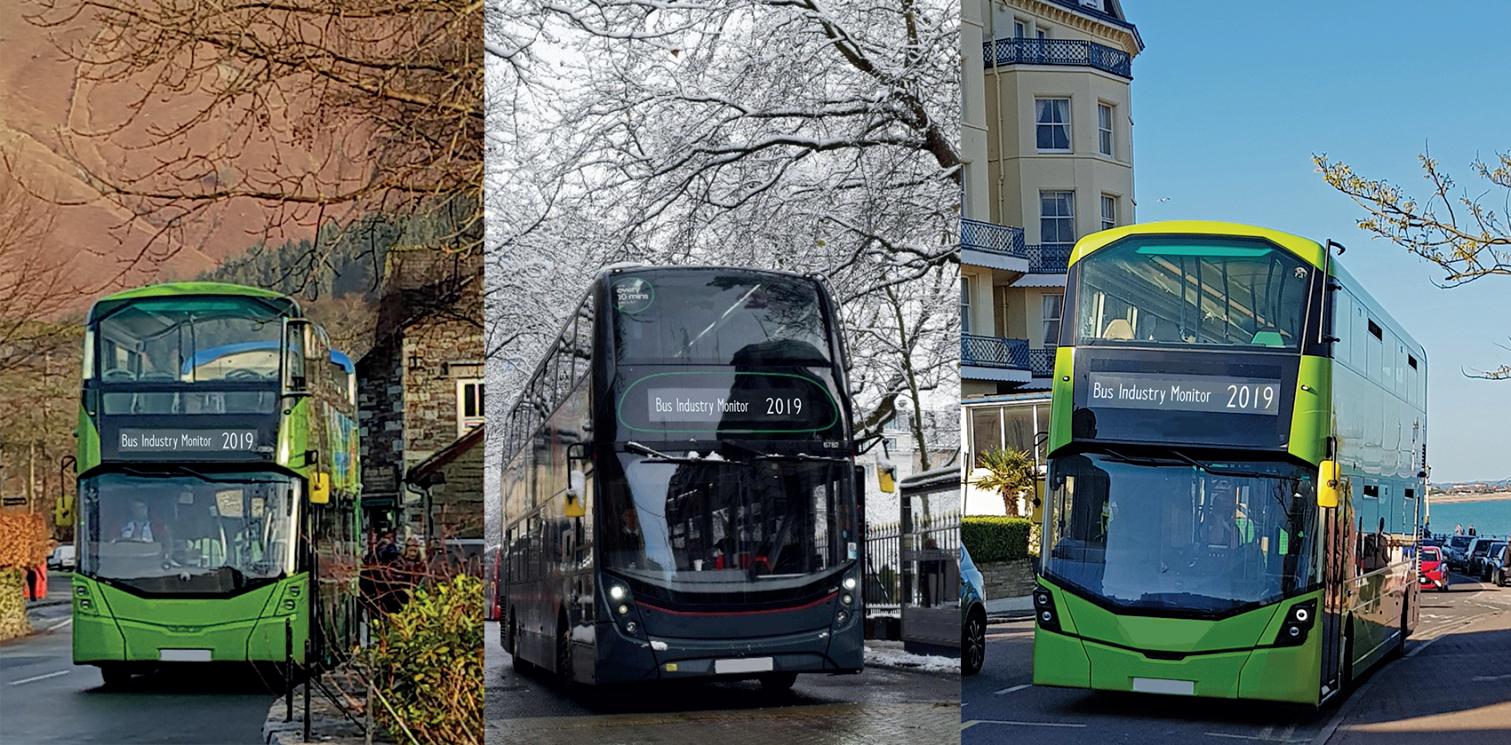
THE BIG PICTURE IN PUBLIC TRANSPORT



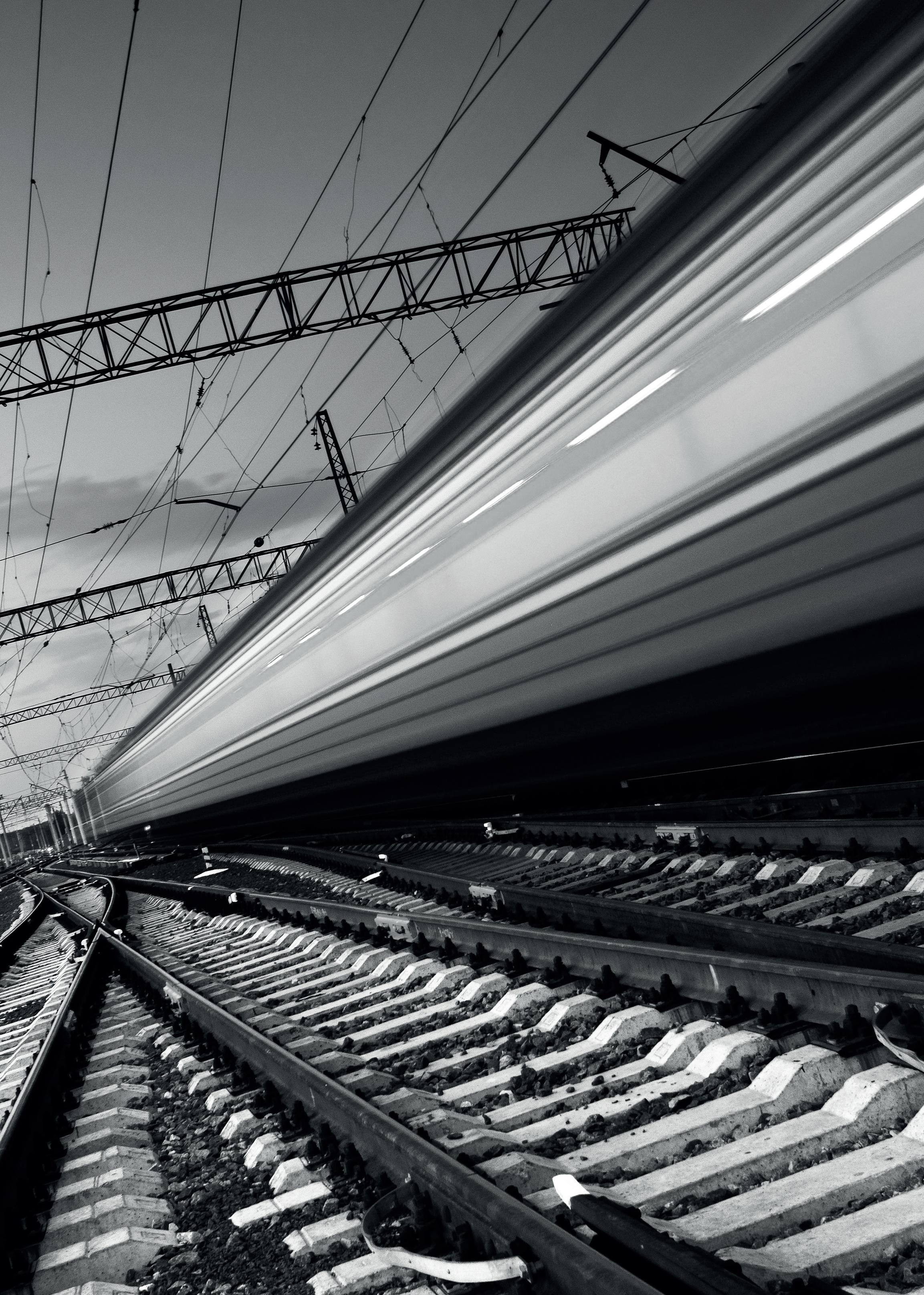

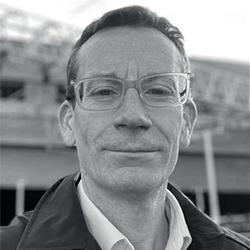

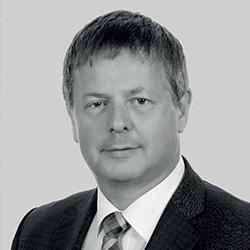
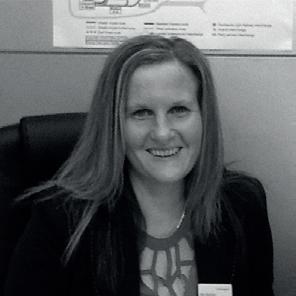

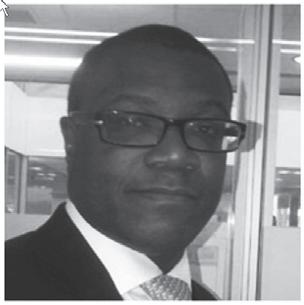
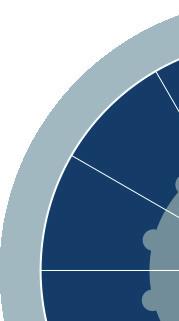
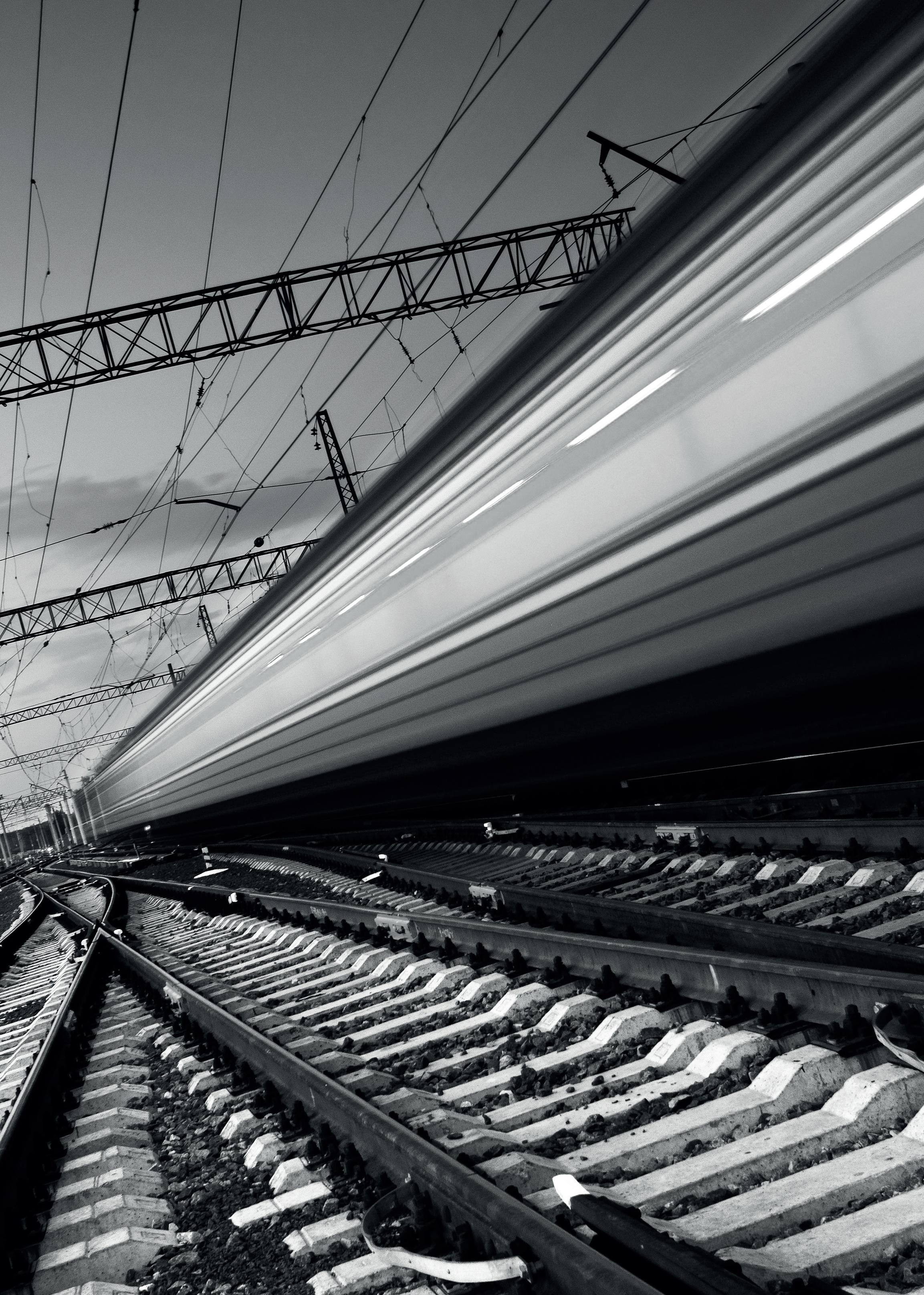
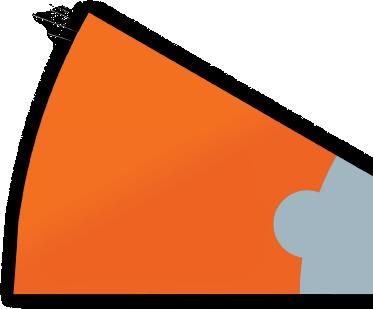
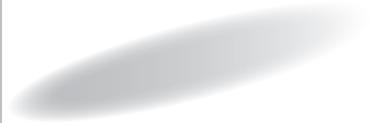
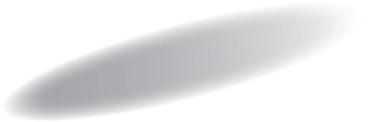
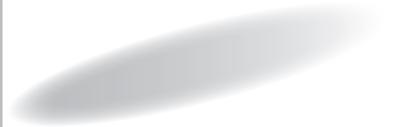
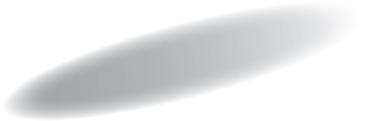
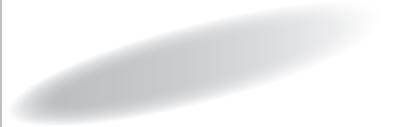
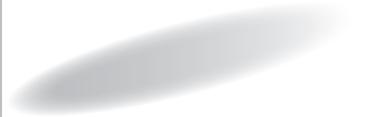


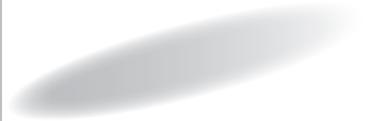
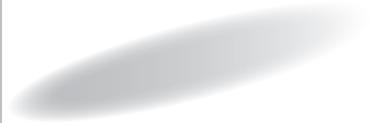
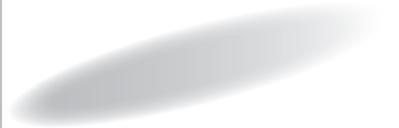

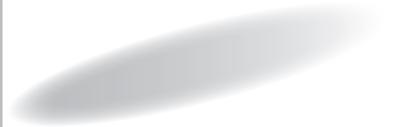

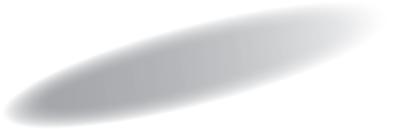
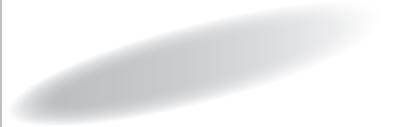
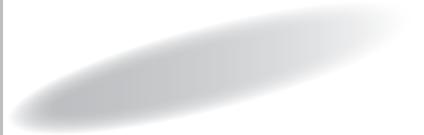

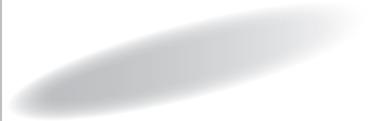

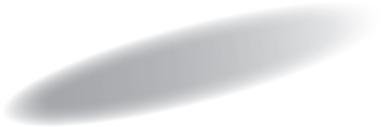
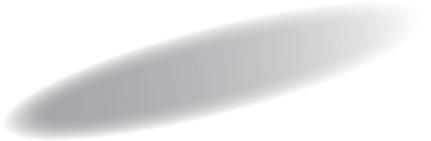
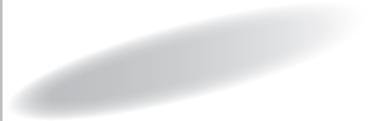
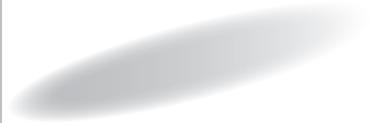

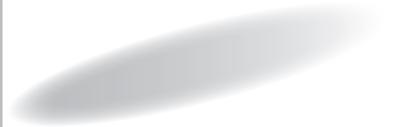
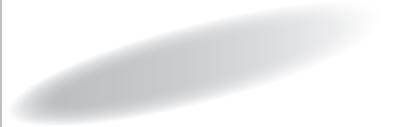
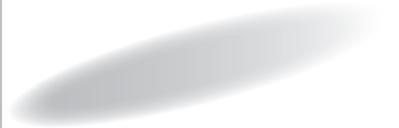
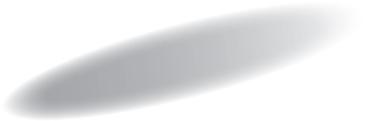
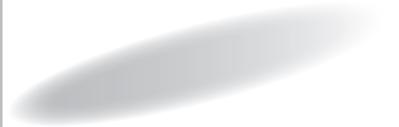
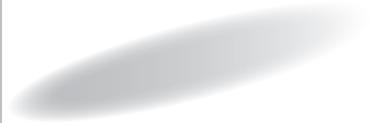
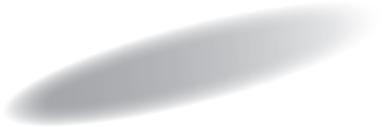
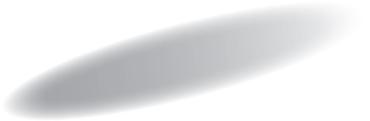
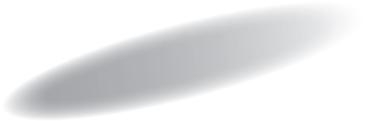



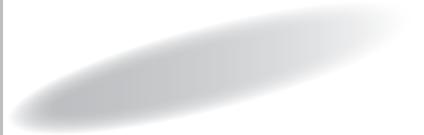
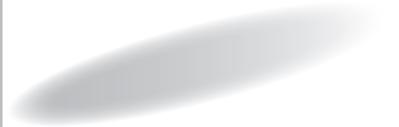
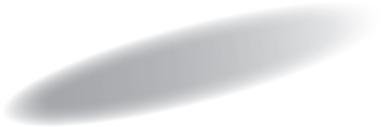

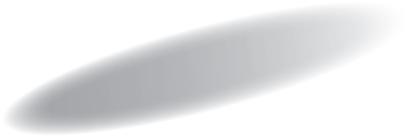
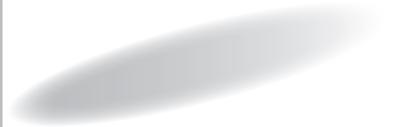
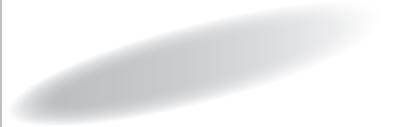
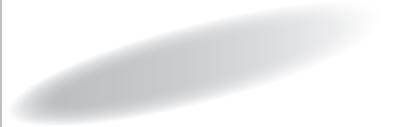
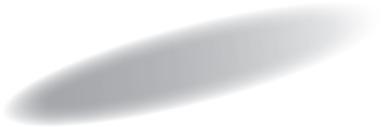

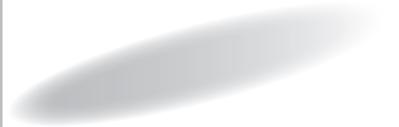
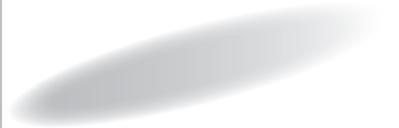
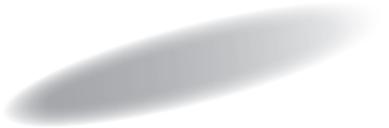

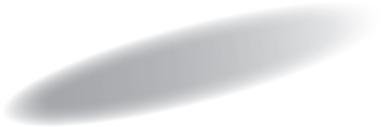
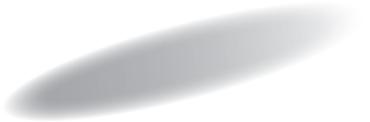

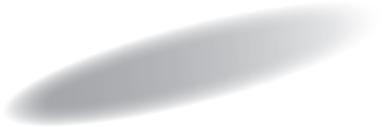
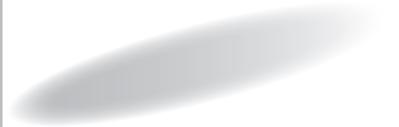
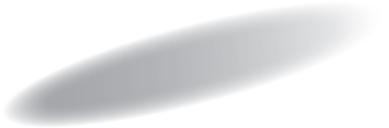

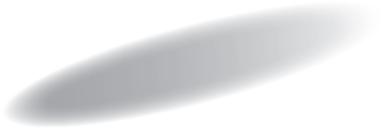
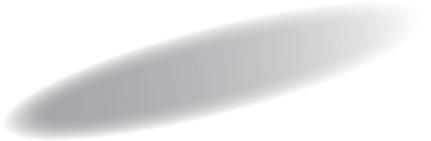
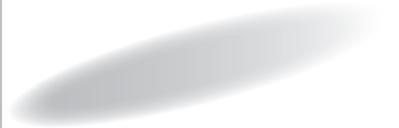

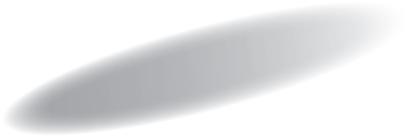
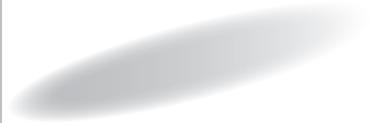
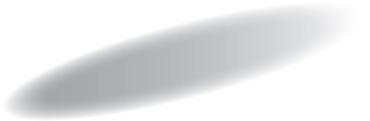

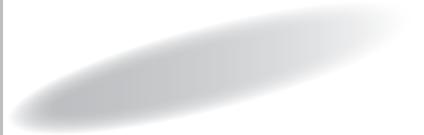
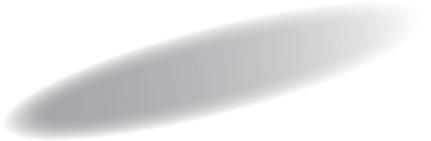


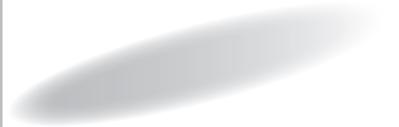
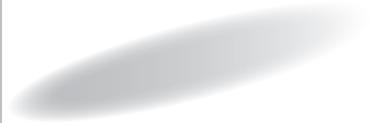
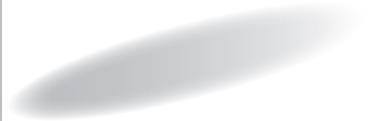

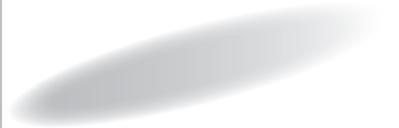
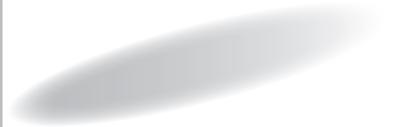
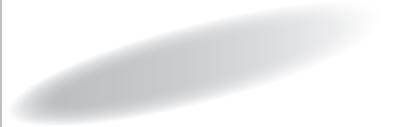
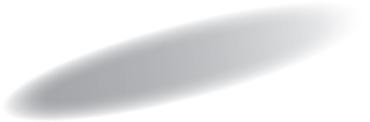
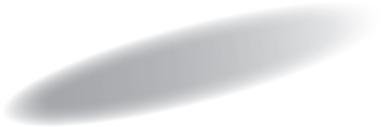
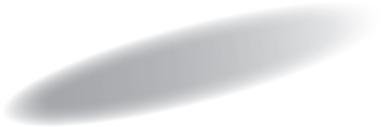

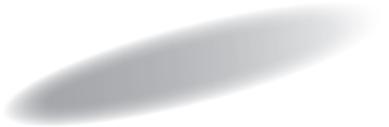

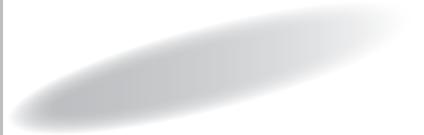
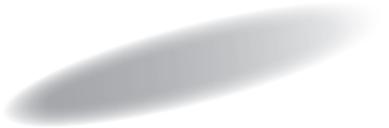
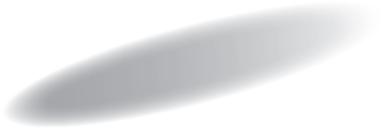
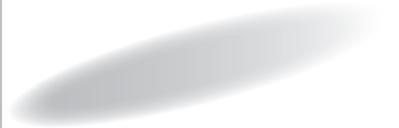

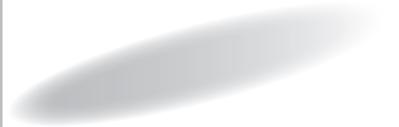
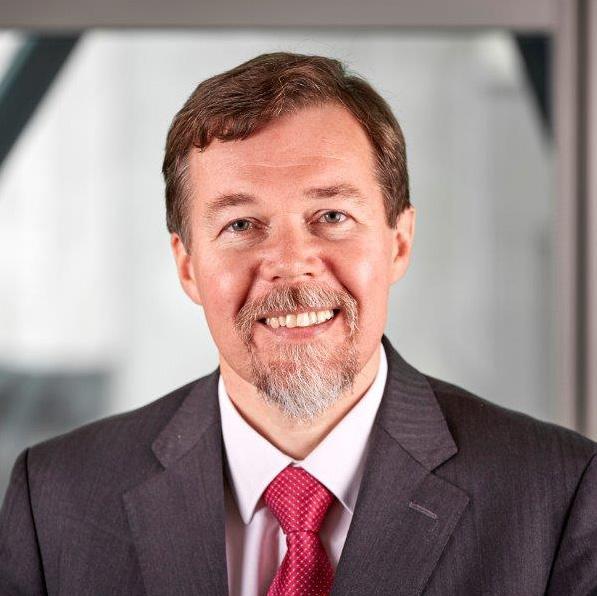
LAYING DOWN THE LAW
by Martin FleetwoodManaging the Rise of AI usage
Over the last year or so there has been a rise in the number of organisations taking advantage of the benefits of using Artificial Intelligence (AI)
With the railways being no stranger to introducing new technology, a number of organisations working in the sector have been embracing the various benefits that AI can bring. AI offers unprecedented opportunities to streamline processes, enhance productivity, and drive innovation. However, the integration of AI alongside employees also raises important considerations, such as ethical implications, potential job displacement, and the need for robust policies and strategies concerning its use.
Establishing control over outputs
Introducing AI into the workplace brings many benefits, including assisting in work planning, prioritising tasks, and optimising resource allocation. AI-powered algorithms can quickly analyse large amounts of data, saving time and cost, providing valuable insights for market research, customer behaviour analysis, and financial forecasting. It can generate written content, automate customer responses, and improve communication and productivity.
AI can also help with quality control, by swiftly finding mistakes and maintaining high standards, and improve customer service by handling common questions, reducing wait times, and providing personalised recommendations and targeted marketing. In addition, AI can contribute to cybersecurity by identifying threats and bolstering fraud detection.
However, while it sounds as if AI is the solution to so many issues, it is important to remember that much of AI is simply working through algorithms extremely quickly which can also produce unintended consequences
which will need to be managed before the output is used. These can include:
• Biases and discrimination – AI can perpetuate biases present in the data it is trained on (particularly if historic data is used), leading to discriminatory outcomes, such as biased hiring decisions, unequal treatment of employees, or unfair targeting of certain groups.
• Lack of transparency in decision making –AI algorithms can operate as ‘black boxes’ making it difficult to understand how they arrive at their decisions. This lack of transparency can be problematic when it comes to accountability, as it becomes challenging to explain or challenge AIgenerated outcomes.
• Data privacy and security – AI systems often rely on accessing vast amounts of data, raising concerns about privacy and security. Mishandling or unauthorised access to sensitive data can have severe consequences, including breaches of confidentiality, identity theft, or manipulation of personal information.
• Overreliance and dependency –overreliance on AI systems without human oversight can lead to errors or incorrect decisions. Trusting AI-generated outputs without critical evaluation can have negative consequences, especially in critical areas such as operations, finance or legal decision-making. Striking the right balance is important.
• Ethical considerations – dilemmas may arise when AI systems must make critical decisions affecting responsibility and accountability. For instance, if an autonomous vehicle is faced with an unavoidable collision, should its split-
Martin Fleetwood is a Consultant at Addleshaw Goddard’s Transport practice. The Rail Team has over 30 lawyers who advise clients in both the private and public sectors across a wide range of legal areas. As well as contractual issues, the team advises on operational matters, franchises, concessions, finance, regulatory, property, employment, environmental and procurement issues.
Disclaimer: This article is for informational purposes only and does not constitute legal advice. It is recommended that specific professional advice is sought before acting on any of the information given.
‘While it sounds as if AI is the solution to so many issues, it is important to remember that much of AI is simply working through algorithms extremely quickly which can also produce unintended consequences which will need to be managed before the output is used.’
second decisions prioritise protecting its passengers or other people outside the vehicle? Would human judgement reach the same conclusions and what legal ramifications would follow against the company providing the AI or the operator of the vehicle?
• Technical limitations and errors – AI systems are not infallible and can make mistakes or encounter technical limitations. These errors can lead to incorrect results, faulty predictions, or unreliable recommendations, potentially impacting business operations or decision-making processes, particularly if the results are not reviewed and tested, leaving the company exposed to legal challenge.
Latest developments on legal protections Without legal protections, the adoption of AI in the workplace can lead to a range of negative consequences.
In December 2023, MEPs and the European Council reached agreement on
proposed legislation for AI regulation in the European Union. It is intended that AI systems will be categorised into four groups: unacceptable, high, limited, or minimal risk. This grouping will be based on the potential harm to health, safety, fundamental rights, the environment, democracy, and the rule of law.
The final text of the European AI Act is expected during 2024, followed by a phased implementation period.
So far, the UK has adopted a more 'light-touch' approach, noting in its March 2023 White Paper (AI White Paper) that, for the time being, it will devolve the work of regulation to sector-specific regulators, such as the Information Commissioner's Office and the Health and Safety Executive (the latter's obligations flowing into the Office of Rail and Road). The Regulators are expected to start publishing guidance in 2024 explaining how these principles will apply within their remit, having regard to the underpinning principles set out in the AI White Paper of (1) safety, (2) security and robustness, (3) transparency and explainability, (4) fairness, (5) accountability and governance, and (6) contestability and redress.
Alongside UK government processes, the TUC has assembled an AI taskforce aiming to
establish new legal protections for employees and employers. This includes publishing a draft ‘AI and Employment Bill’ by early 2024, which is expected to cover:
• Duties on employers to consult trade unions on the use of high-risk AI.
• Rights for workers to have a human review of decisions made by AI systems.
• Amendments to existing legislation to guard against discriminatory algorithms.
What should companies do now?
• Develop clear policies – establish policies outlining ethical use of AI in the workplace and address issues such as fairness, transparency, accountability, bias mitigation, data privacy, and security.
• Retain human oversight – maintain human involvement and oversight in decision-making processes involving AI systems. Allow humans to intervene when necessary to ensure fairness and ethical decision-making.
• Regularly monitor and audit AI systems – implement monitoring and auditing mechanisms to assess the performance and impact of AI systems. Regular evaluations can help identify and address any biases, errors, or unintended consequences that may arise from the use of AI.
• Ensure transparency and explainability – make efforts to explain how decisions are made. This can involve using interpretable algorithms, providing clear documentation, and offering explanations of AI-generated outcomes.
• Continuously train and educate employees – ensure that employees understand about AI systems, their capabilities, and limitations. This will help employees manage the role of AI in their work, foster collaboration, and enable them to identify and address potential issues or biases.
• Regularly update and improve AI systems – AI technology is rapidly evolving, and regular updates are essential to enhance system performance, address biases, and improve overall accuracy.
• Collaborate and share best practices – engage in industry collaborations and initiatives to share best practices, insights, and lessons learned regarding responsible AI use. Collaborative efforts can help establish industry standards and guidelines for ethical AI implementation.
While the use of AI is still evolving, it is important for organisations to ensure that sufficient processes are in place to manage the risks associated with its usage.
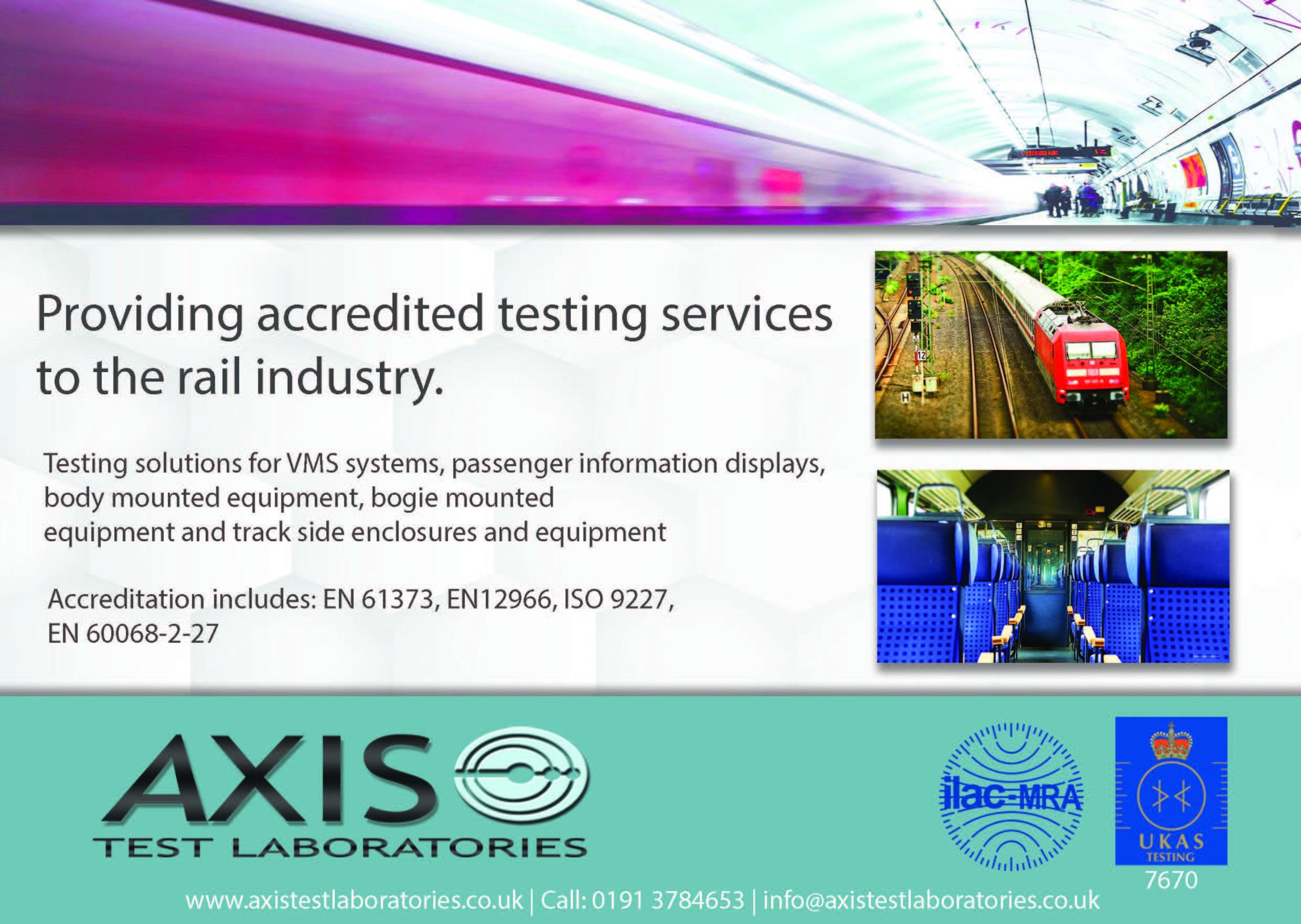

Derailing Progress
Ellis Shelton, Senior Policy Advisor, Logistics UK explains how the Scottish Government’s decision to scrap MSRS could see environmental goals left in the sidings
The Scottish Government budget, published in November 2023, referred only once to freight, which was a line showing that ‘support for freight industry’ was being axed from £700,000 per year to zero. Further investigation by Logistics UK got to the bottom of the cut, and it was confirmed by Scottish Government officials that this was in fact their contribution to the Mode Shift Revenue Support Scheme (MSRS), meaning Scottish operators would no longer benefit from grants encouraging the move of freight off the roads on to rail and water.
This was a somewhat bewildering decision for many and while the DfT have confirmed it will continue to subsidise the Scottish legs of any freight movement for 2024, it does seem to send out a conflicted message to discourage modal shift when the sector is doing everything it can to decarbonise and move to net-zero. The announcement is also at odds with the Scottish Government's High Level Output Statement for the railway, 2024-2027, which reasserts support for rail freight growth.
MSRS started in 2010 to assist companies with the operating costs associated with running rail or inland water freight transport, instead of road, where rail or inland waterway transport is more expensive and less polluting.
In 2022/23, the scheme helped remove 900,000 lorry journeys from Britain’s roads, saving almost 40,000 tonnes of carbon dioxide (CO2) emissions. A significant proportion of MSRS applications are within rail transport where the most supported movements are intermodal containers.
Rail in Scotland
Scotland’s location and geography meant the scheme enabled Scottish freight services to compete with road especially at a time when road costs have fallen significantly
as the cost-of-living crisis has impacted on freight volumes.
Unlike most regions of the UK, Scotland is a net exporter of goods with a trade balance of over £9 billion in 2021, the most recent year for which figures are available. Businesses in Scotland therefore need access to efficient and reliable transport routes to get their goods to market, and rail is a major part of this.
The Scottish Government’s decision to remove its support for MSRS is even stranger since it has generally been a bestpractice example of how government can support growth and has set targets for Network Rail for the last and upcoming control periods, and is supporting new flows with freight facilities grants.
Scottish markets are a long distance from the significant supply chain networks based in the English midlands and include more rural areas. The technology does not currently exist to serve these areas with electric HGVs so, with regard to the transition to net-zero, the opportunity is perfect for a combination of long-distance rail, and shorter haul road legs.
Mode shift grants review
The Scottish Government’s decision to scrap its support of MSRS also comes at the same time the UK Government issued a call for evidence for its ‘Mode shift grants review’. The call for evidence closed in January and will assess the MSRS and Waterborne Freight Grant (WFG).
These grant programmes currently allocate about £20 million annually and it is essential that Government support continues to promote sustainable transportation solutions within the country’s freight industry.
There is no doubt there is room for improvement to the current scheme and rail freight operators have been critical of the

Logistics UK is one of the UK’s leading business groups, representing logistics businesses which are vital to keeping the UK trading, and more than seven million people directly employed in the making, selling and moving of goods. With Covid-19, Brexit, new technology and other disruptive forces driving change in the way goods move across borders and through the supply chain, logistics has never been more important to UK plc. Logistics UK supports, shapes and stands up for safe and efficient logistics, and is the only business group which represents the whole industry, with members from the road, rail, sea and air industries, as well as the buyers of freight services such as retailers and manufacturers whose businesses depend on the efficient movement of goods. For more information about the organisation and its work, including its ground-breaking research into the impacts of Covid-19 on the whole supply chain, please visit logistics.org.uk.
application process. In the current scheme, the window for applying for the grant does not necessarily align with the demands of the freight network’s needs, and a route may need to apply for funding beyond the grant timelines. One solution that a future scheme should consider is an online system with shorter and more frequent assessment periods.
At the end of 2023, the UK Transport Secretary announced a rail freight growth target of 75 per cent growth in net freight tonne kilometres by 2050. Removing, reducing or restricting access to grant funding to support modal shift to rail would not only be detrimental to achieving that goal, but in direct contrast to the rail freight growth target.
The stated purpose of the mode shift grants is to “reduce road congestion, decrease carbon emissions and create a more sustainable and resilient freight network that benefits both the economy and the environment.” It cannot be overstated that without these grants, less freight will be moved by rail.
Importance of rail
Rail freight has the potential to facilitate and support the achievement of wider policy goals. Net-zero and levelling-up are prime examples. However, for rail freight to play its role the right decisions need to be made
concerning investment, capacity allocation and modal shift across the industry.
The sector is currently limited by network capacity. Additional rail connected terminals and improved capacity will be necessary to substantially grow the rail freight market. The majority of which will be largely driven by private investment. As such, an environment must be created that gives the private sector the confidence to make sizeable investments. This includes ensuring that there is capacity on the rail network to accommodate additional services and more productive heavier and longer rail freight services, to ensure that rail freight can compete with other transport modes.
Destination net-zero
Rail freight has the potential to play an important role going forward in supporting priority policy initiatives, such as net-zero. Rail freight reduces CO2 emissions by up to 76 per cent compared to road, whilst a single rail freight service can remove up to 129 HGV movements.
To decarbonise the railway, Logistics UK is in support of a rolling programme of electrification. Electrified rail transport is a fully mature, proven green technology which has been in use for more than 60 years. To enable 95 per cent of rail freight
Approved
Hydraulics have been supplying some of the largest rail build and maintenance firms for over 10 years. Now considered some of the best in the world!
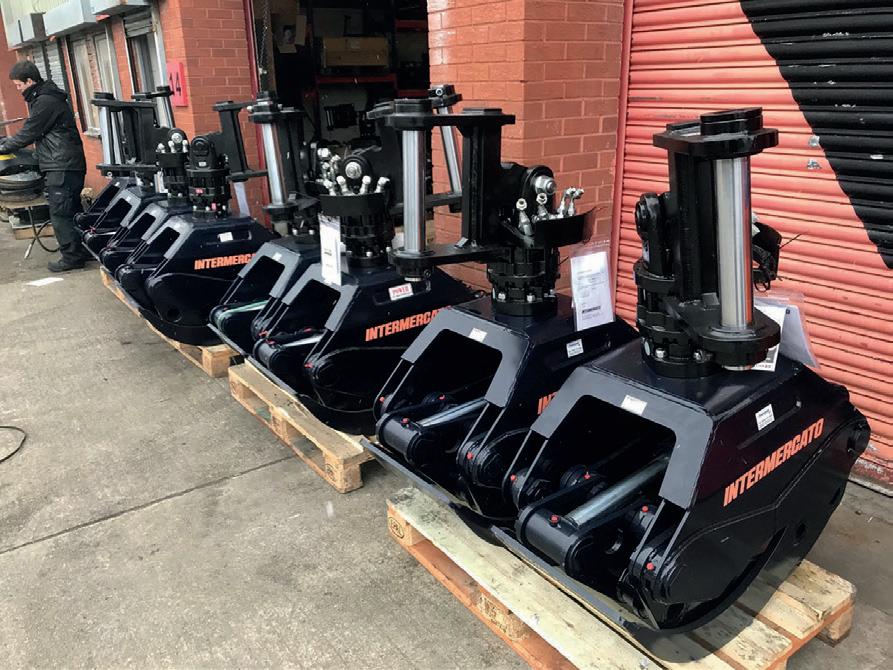
to be electrically hauled, only 800 miles of additional electrification is needed in the UK, according to the CILT Freight Electrification Map. Currently, only ten per cent of British freight trains are hauled by electric locomotives.
Rail freight also has advantages from an air quality perspective. Air pollutants produced by rail freight are generally emitted further away from people, and often in a contained environment where railway cuttings, tunnels, fencing and buildings can act as shields, limiting the impact on human health.
Conclusion
The Scottish Government’s decision to cancel its support for MSRS seems shortsighted and one that is at odds with Scotland’s environmental goals with the potential to create confusion as Scotland is the only part of the UK not using the scheme.
It comes at a time when the mode shift grants have played a vital part in moving freight from road, predominantly onto rail. Shifting to rail freight has led to many benefits including reducing road congestion, building resilience into the supply chain, and lowering carbon emissions. If less freight moves by rail, these benefits will be reduced.
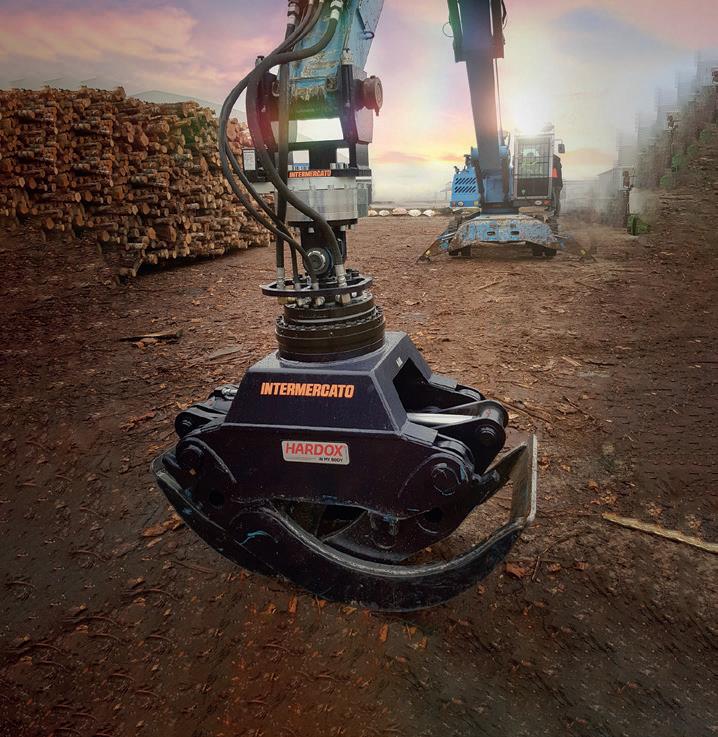
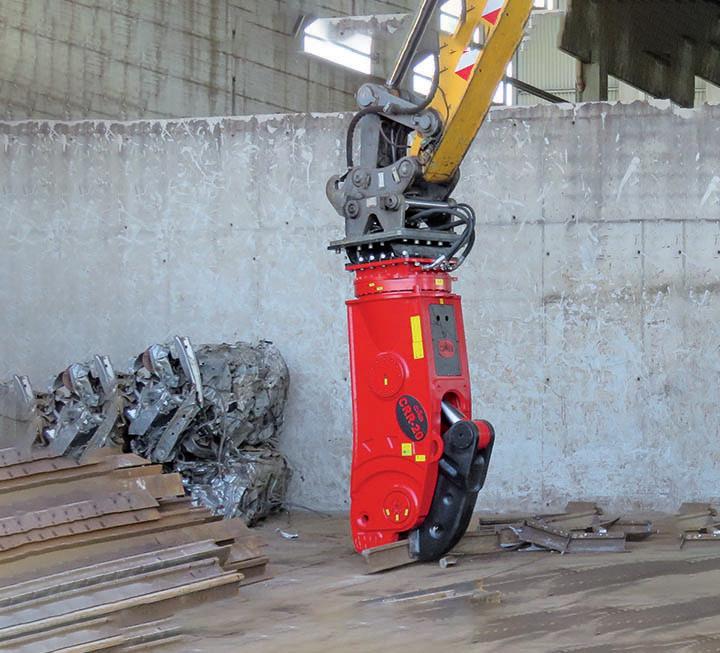
‘The Scottish Government’s decision to cancel its support for MSRS seems shortsighted and one that is at odds with Scotland’s environmental goals with the potential to create confusion as Scotland is the only part of the UK not using the scheme.’
The wider review of mode shift grants needs to position rail freight at a higher point in the national economic agenda and recognise the importance of a stable policy framework to enable rail freight to grow and achieve its potential.
The grants should not shift focus from their original intent to: ‘reduce road congestion, decrease carbon emissions and create a more sustainable and resilient freight network that benefits both the economy and the environment.’
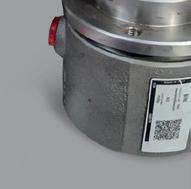
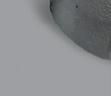
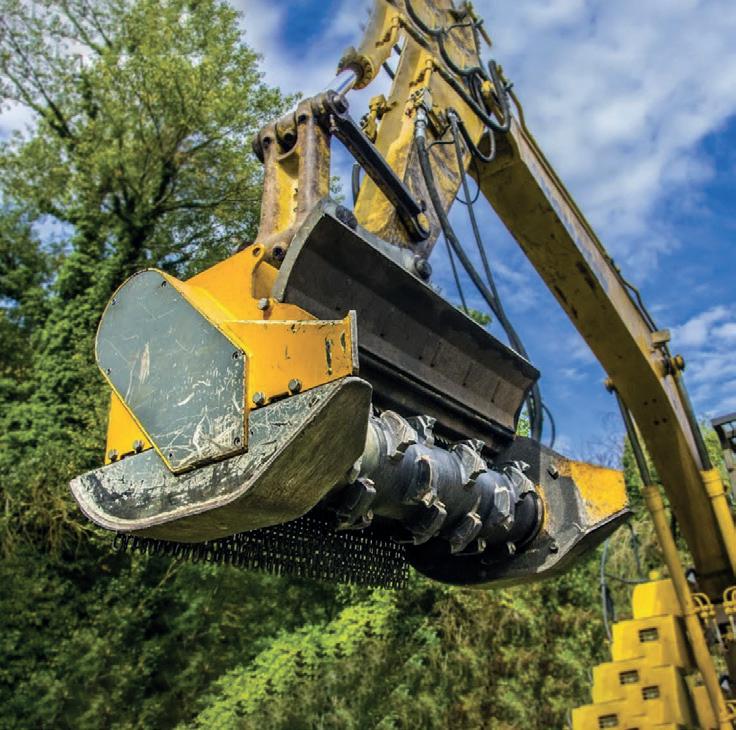
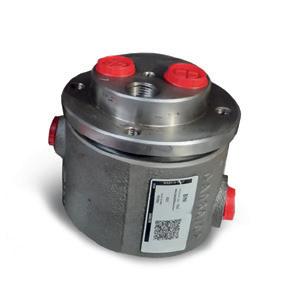


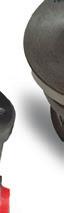
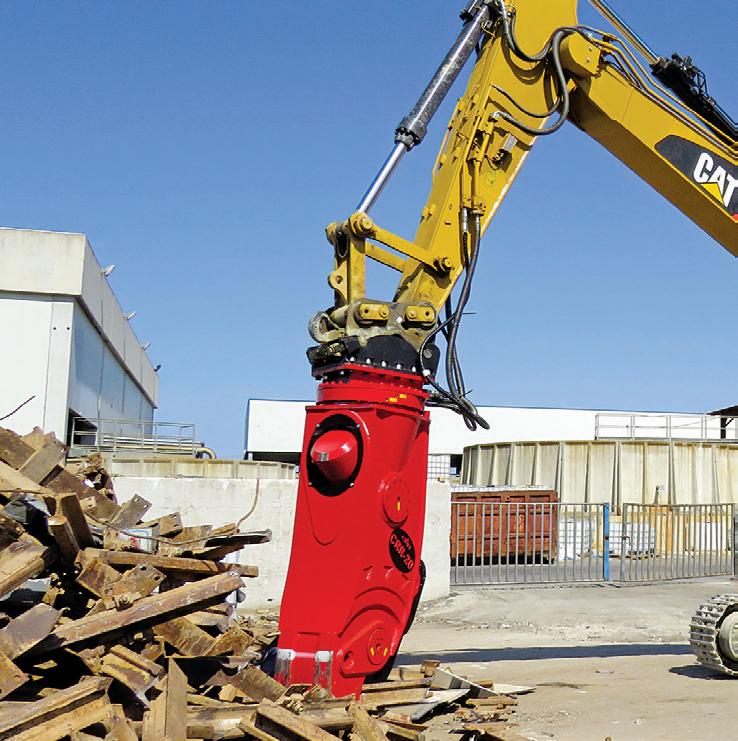












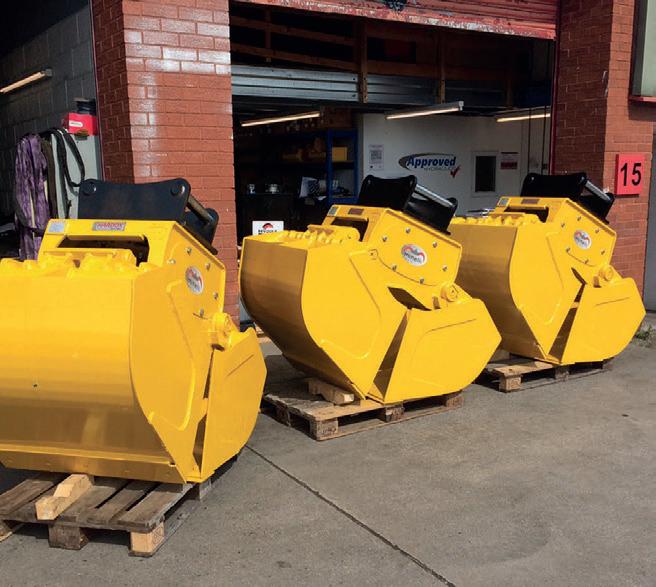
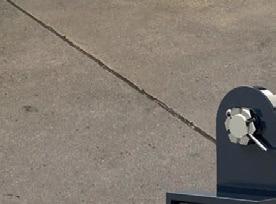
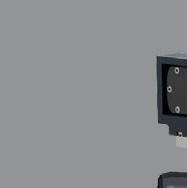
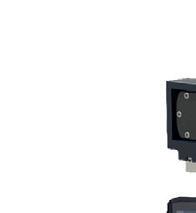










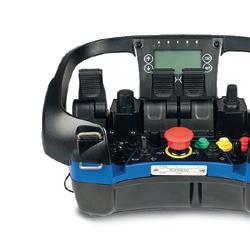
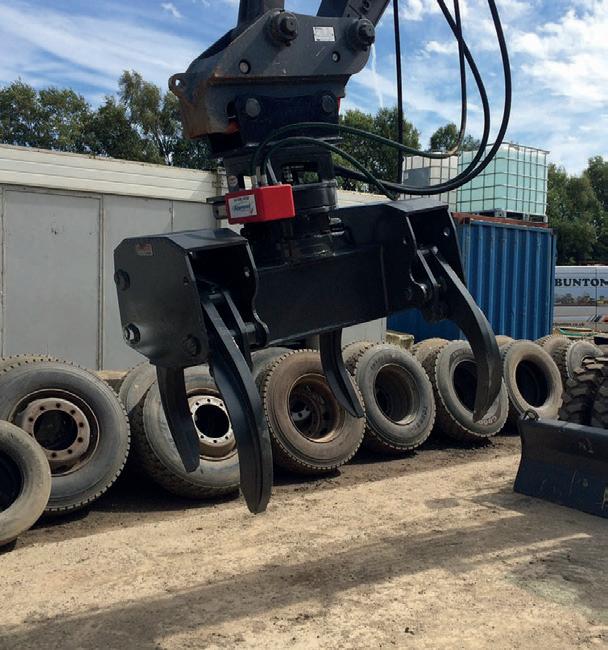
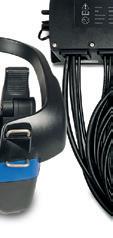
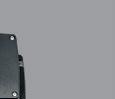
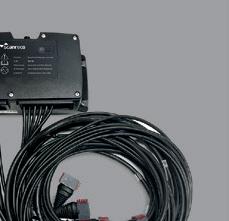
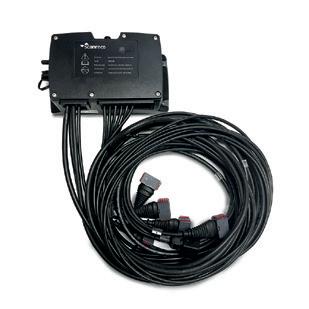

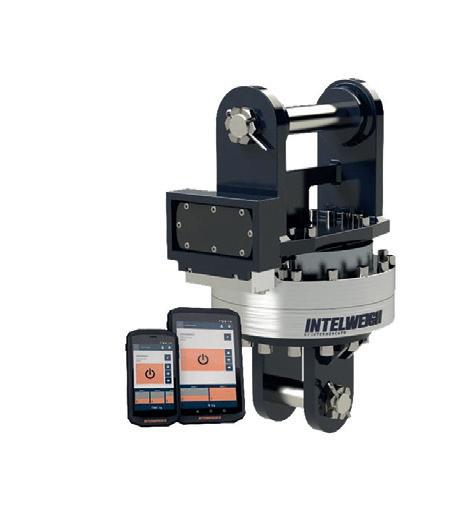
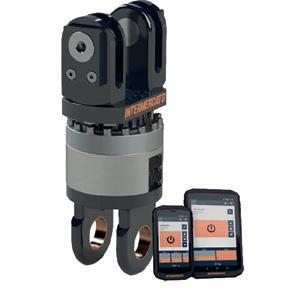
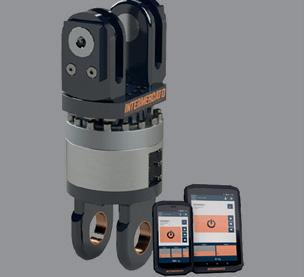

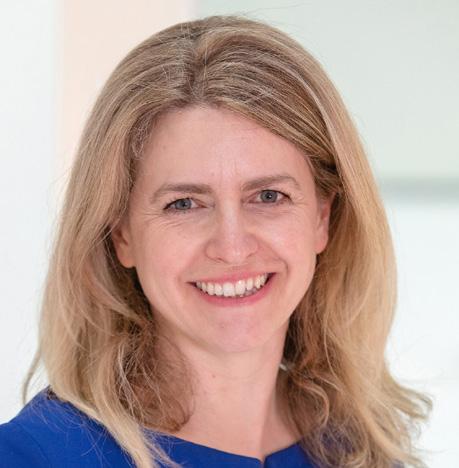
Brioney
Thomas is partner and Head of Burges Salmon’s Transport sector.
Is Your Business Ready?
Advances on ESG could be undermined by compliance failures within the supply chain, reveals new research, Brioney Thomas, partner and head of Burges Salmon’s Transport sector dives into the data
The findings from Burges Salmon’s ESG report show that organisations in the transport sector are somewhat prepared to meet corporate disclosure obligations, but only just.
As businesses continue to develop the application of robust ESG standards into everyday operations, efforts could be undermined by compliance failures within their supply chain.
This is according to new research published by independent UK law firm Burges Salmon.
In order to gauge how UK companies are reporting on the full ESG value chain of their operations, Burges Salmon surveyed over 360 business leaders from across sectors to shed light on how prepared businesses are to meet their supply chain-related ESG disclosure obligations, set to be further tightened by a raft of new legislation, including the EU Corporate Sustainability Reporting Directive.
The report – Supply chain ESG disclosure – is your business ready? – reveals that 32 per cent of all businesses surveyed are completely unprepared to meet their ESG supply chain disclosure obligations and among those, only 29 per cent, fewer than three in ten, believe their organisation fully understands the legislative and regulatory landscape governing ESG corporate disclosure.
Michael Barlow, partner and Head of ESG at Burges Salmon, says: ‘UK companies must first prove their commitment to ESG by complying with a range of mandatory disclosure obligations. Ensuring business partners meet ESG standards requires investment, resources and constant monitoring, and it is clear from our research that most companies still have some way to go.’
‘Many companies can use the information that they’ve already captured to help satisfy ESG requirements and then identify the gaps where they need to put in place new systems. For example, in my experience, transport businesses already hold themselves to quite a high standard in health and safety.’
‘UK companies must first prove their commitment to ESG by complying with a range of mandatory disclosure obligations. Ensuring business partners meet ESG standards requires investment, resources and constant monitoring, and it is clear from our research that most companies still have some way to go.’
For transport businesses, ESG credentials are incredibly important, and these organisations broadly understand that they will be held to account by their customers and other stakeholders. Many are well positioned to deal with ESG obligations and the credentials of their supply chain, but there are others that are finding it difficult, because of the sheer number of organisations that they routinely deal with.
The research highlights that when it comes to ESG legislation and regulations, various areas are being overlooked, which could be putting businesses in the transport sector at a greater risk of non-compliance. For example, over one in five of those surveyed in the sector say that contracts with their suppliers haven’t been adapted to enable them to gather the required information, and therefore to monitor ESG compliance in respect of their supply chain.
At the same time, only 22 per cent say their organisation has detailed procedures in place to assess the ESG compliance of prospective supply chain companies and the same percentage say their organisation doesn’t have a dedicated team that deals with ESG related matters, including in respect of its supply chain.
Brioney Thomas, partner and head of Burges Salmon’s Transport sector says: ‘Many companies can use the information that they’ve already captured to help satisfy ESG requirements and then identify the gaps where they need to put in place new systems. For example, in my experience, transport businesses already hold themselves to quite a high standard in health and safety.’
Leveraging its market leading ESG expertise, Burges Salmon has developed a number of practical tools to consolidate all ESG guidance, legislation and other useful resources into interactive and intuitive platforms. Amongst those is the firm’s ESG Corporate Disclosure Tool.
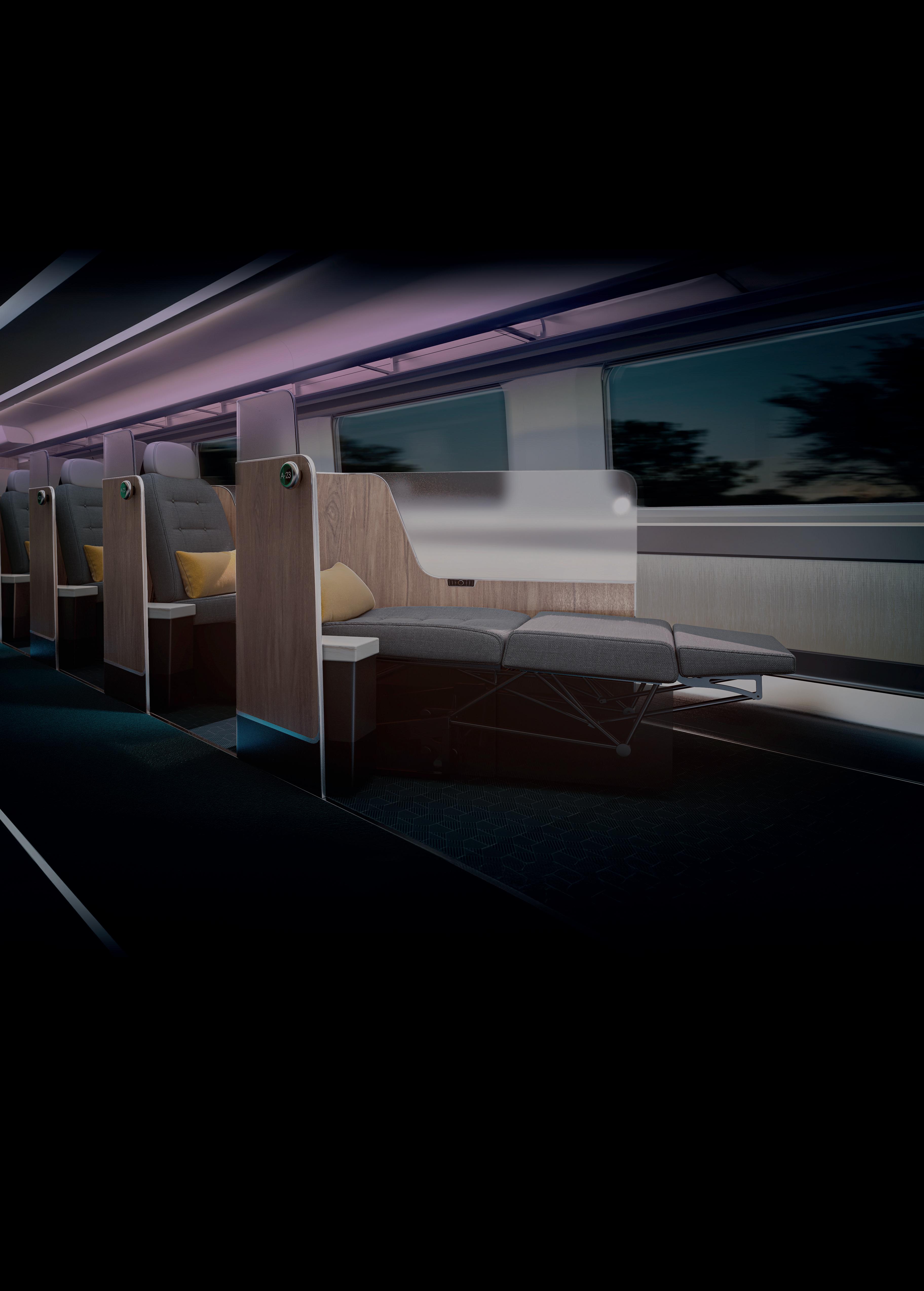
application GB 2208661.5)
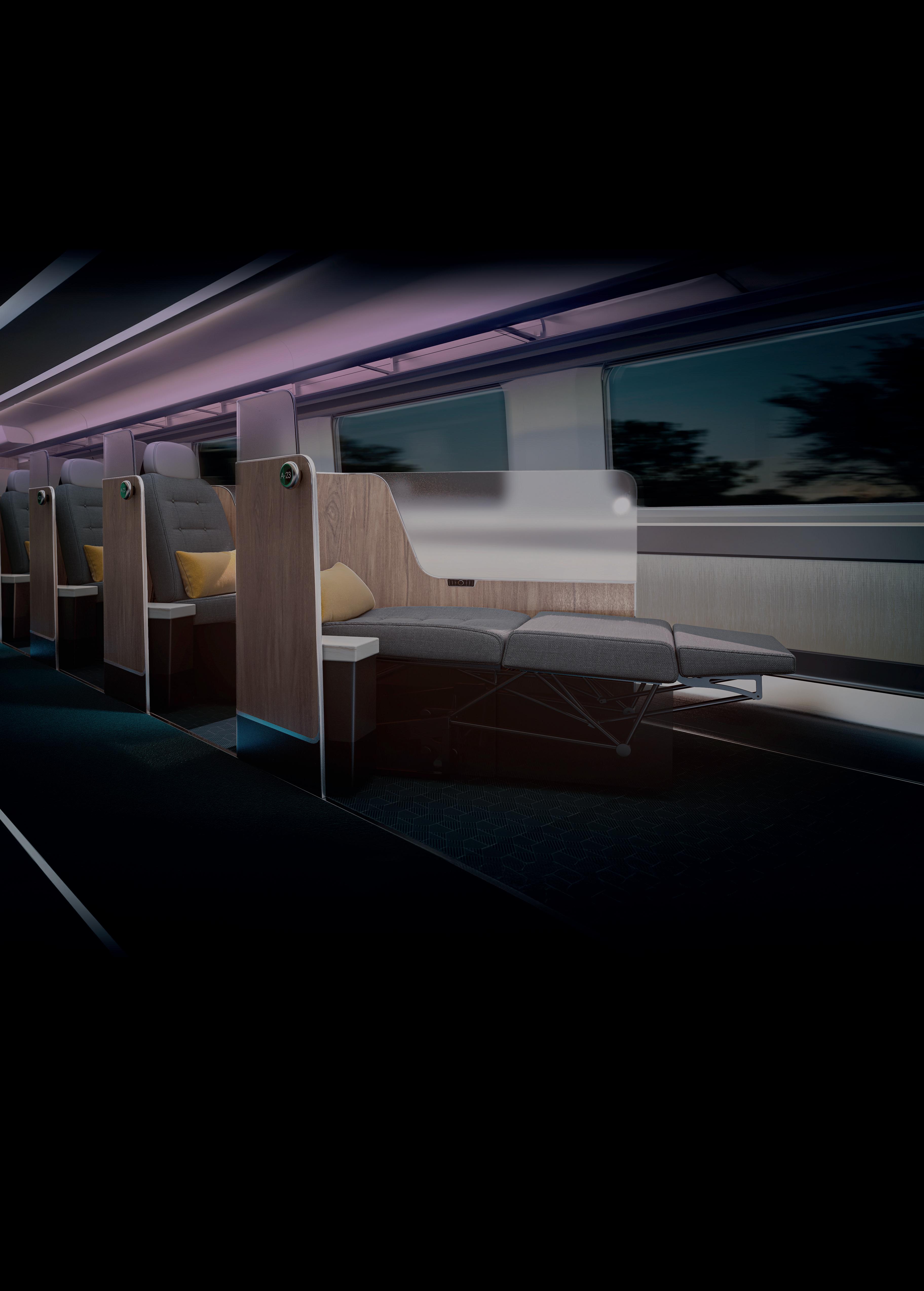
Creating a More Accessible Journey for Passengers
The railway network is important to everyone throughout the UK, but it’s even more important for the disabled community to get around the country quickly and efficiently
In the UK alone, there were over 242,700 Disabled Persons Railcards (DPRCs) in circulation at the end of March 2023, according to the Office of Rail and Road (ORR) data. With the number of disabled rail users throughout the UK being a consistent and significant presence throughout the country, it’s important to make sure their journeys are as seamless and accessible as possible. Technology will be a huge factor going forward, specifically the following solutions that will revolutionise the way we look at accessible rail travel.
AI,
machine learning and 5G 5G, Artificial Intelligence (AI) and machine learning are seeing continued evolution across several industries, and the rail industry could benefit from being transformed by it. A survey conducted by Analysys Mason has found that it’s expected that 5G will cover 68 per cent of the population by the end of 2023, so we may see massive changes in the sector towards the end of the year and the start of the new year.
Combining these technologies would allow railways to build a database of large amounts of information to better individual passenger experience through personalisation. AI algorithms could analyse data from passengers to address their specific needs, which would help those with disabilities significantly.
Say there were points within a passenger’s journey that would likely make
‘It’s expected that 5G will cover 68 per cent of the population by the end of 2023.’
things harder, whether that’s a lack of accessibility options at the destination or certain rail services that regularly see delays. This information can be used by railways to improve journey accessibility, which could include additional staff to aid or offer spaces that are dedicated to disabled passengers.
This would work in tandem with 5G, as it would offer high-speed connectivity on trains, so you’ll always be connected. Adding inclusivity for disabled passengers makes a world of difference for them. They can then enjoy on-board entertainment while feeling reassured their journeys will be seamless.
Mobility as a Service (MaaS)
One solution that could revolutionise travel for not just differently abled passengers is Mobility as a Service (MaaS). This is a huge fundamental shift in how journeys through transportation services are planned by integrating a variety of transport modes in a single platform centred around its users. This would include relevant information about trains, buses, trams, metros, and other travel like taxis and car-sharing, for passengers to plan their journeys seamlessly. This would allow for planning the most convenient and accessible options available.
MaaS solutions wouldn’t just include updates about service disruptions and arrival times but would provide the best options in real-time.
On-Board Information Systems
On-Board Information Systems (OBIS), as its name suggests, gives passengers live information on their rail journey while travelling to their destination. This ranges from scheduling changes, delays, and the platform and station you arrive in. These systems, having features that include information about arrival locations, like accessibility options, such as working lifts, ramps available and where they are, and disabled toilets, are game-changing. Having the assurance that when they arrive at their destination, they’ll have the necessary facilities available to them adds a level of confidence to their journey.
Seamless digital passenger experience
Public transport is part of the backbone of travel in the UK, and the seamless and efficient passenger experience is tantamount to the sector’s success. Research from transportfocus has found that passengers' priorities centre around the ‘reliability and punctuality’ of services, as well as ‘accurate and timely information’ on train arrival and departure times.
Technology and data can help to provide this for passengers in a single app through Mobility as a Service (MaaS) and Operator Business Information Systems (OBIS).
Monika Singh, Product Manager at Nomad Digital, an expert in passenger experience, have offered sector insight into how these systems provide an improved digital and physical experience for passengers on public transport journeys.
The basics of MaaS and how it benefits passengers
MaaS systems are conceptualised to integrate multiple modes of public transport into a single platform to provide users with a one-stop digital ecosystem for passengers. These systems are designed for passengers to plan and book a journey across different options.
This can range from train routes, buses, trams or undergrounds to taxis and ridesharing services, as well as smaller options like rental bikes and e-scooters. Convenience and streamlined organisation is the goal of these systems and can help to revolutionise travel, especially rail travel:
1. Booking made simpler – booking a full journey and storing tickets in a single place gives passengers seamless transitions between transport options with no hassle of buying multiple physical tickets.
2. Real-time information – passengers can use these platforms for updates on the journey, ranging from delays to schedules to changes in planned service while travelling in real-time, and feel less stressed.
NEWS IN BRIEF
RAIL STATION CAR PARKS IN ESSEX RECEIVE AWARDS FOR SECURITY
Greater Anglia and its station car park operator, NCP, have received ‘Park Mark’ awards, for three rail station car parks in Essex. Bishop’s Stortford station’s new multi-storey car park received a new accreditation, while Witham and Audley End station car parks received re-accreditations for levels of safety and security.
The Park Marks demonstrate that the car parks have measures in place to deter crime and anti-social behaviour, and have been risk assessed by the police, thus making the car parks safer environments for both customers and their vehicles.
Park Mark is the accredited logo of Safer Parking Scheme, which is given to parking facilities that have achieved the requirements of a risk assessment conducted by the Police and the British Parking Association.
3. Personalised experience – through personalised suggestions, MaaS can utilise passenger data to offer the best options for travel, including timings, prices, and environmental impacts.
4. Easy payment – passengers can make a single payment for their full journey rather than spreading it across multiple tickets, with fares automatically calculated for more convenient payment.
OBIS benefiting rail operators
On-Board Information Systems (OBIS) play a crucial role in successfully implementing MaaS solutions. OBIS provides rail operators with a centralised system for managing data, essential for delivering a seamless digital passenger experience.
OBIS will help integrate data into passenger experience like MaaS, offering rail operators a single system for managing collected data. This will become significantly important in improving digital passenger experiences:
1. Integrating the data – these systems collect and integrate passenger data from multiple network points to provide accurate and updated info to passengers. Utilising ticketing and schedules will help provide this information to those travelling on the services.
2. Efficient operations – by streamlining operations and automating processes, the quality of the delivery of services is greatly improved.
3. Customer insights and feedback – the data collected can be analysed to offer providers greater insight into the behavioural patterns and preferences of passengers who travel on their services. It can help to optimise the scheduling and experience of future journeys, collect feedback directly and inform how to improve going forward.
Embracing solutions like MaaS and integrating OBIS into processes can help rail operators push the sector forward through digitisation. Streamlining internal operations while meeting the demands and requirements of those making their journeys while offering a comfortable experience by killing two birds with one stone in technology is a no-brainer. Data lies at the heart of this, which is why collecting it and knowing how to best analyse it is crucial to building on improving transport. The faster these are implemented, the sooner more innovations will occur to improve operations for operators and make journeys easier for passengers.
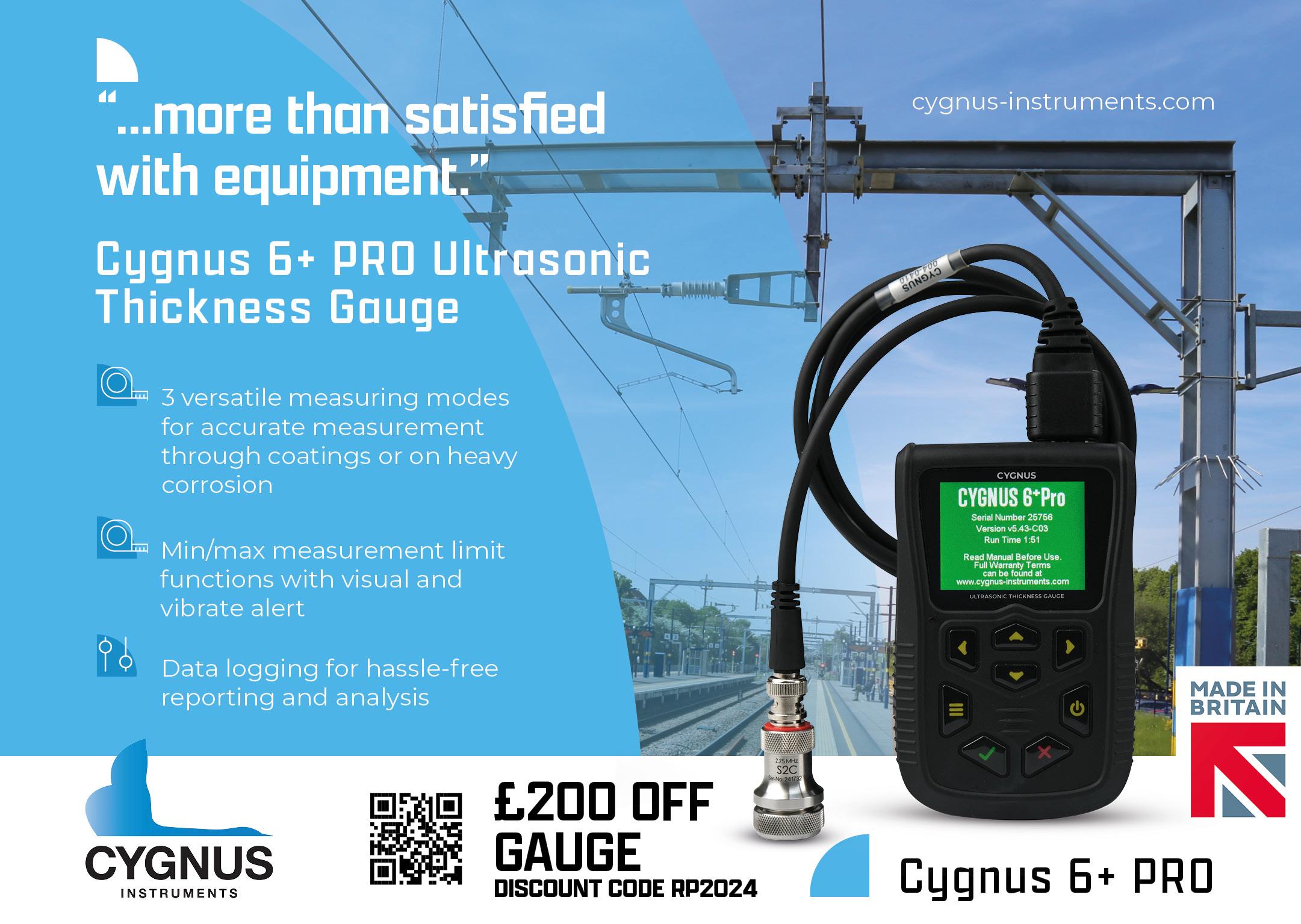
The Longer-term Legacy of the Pandemic on Rail in Britain
The Independent Transport Commission (ITC) has recently released its research report into the pandemic and its longerterm effects on travel, transport and land use. Dr Matthew Niblett, Director of the ITC and Sarah Kendall, Independent Consultant at ITC summarise the findings relevant to rail, and the implications for future rail policy
Four years ago, the world was disrupted as the Covid-19 pandemic rapidly spread. The immediate effect of lockdowns, uncertainty and strict public health measures had a profound impact on life in Britain and forced major changes to how we live, work and travel. Two years after the removal of the last public health measures, it is timely to reassess the impacts of the pandemic on behaviours, lifestyles and policy. The Independent Transport Commission (ITC) has recently released its research report into the pandemic and its longer-term effects on travel, transport and land use. In this article we summarise the findings relevant to rail, and the implications for future rail policy.
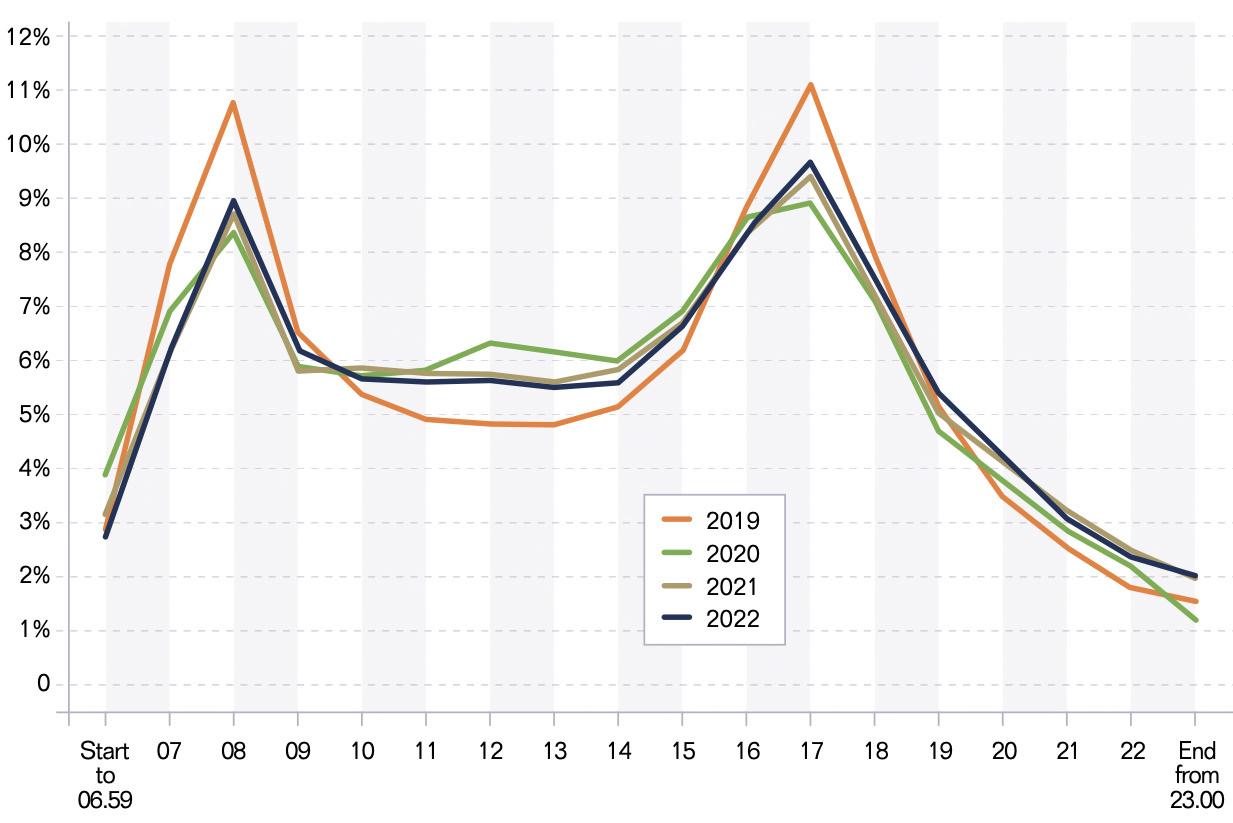
Percentage of Passenger Arrivals and Departures by Hour, Regional Major Cities, 2019-23 (Source: ORR)
Rail demand: from commuting to leisure
Rail travel was affected more substantially by the pandemic than other modes. After an initial collapse in rail demand caused by lockdowns and ‘do not use public transport’ messaging, rail travel recovered to about 75 per cent of pre-pandemic levels by early 2022, and passenger journeys have since risen gradually to more than 90 per cent of pre-pandemic levels. This figure is boosted by the inclusion of the Elizabeth Line across London, which opened in 2022, without which the figure is 79 per cent (Q2 of 2023/24 compared with Q2 of 2019/20).
Note that these reduced rail passenger volumes are still double those of 1995, being served on rail infrastructure that has not significantly grown over that period.
A crucial legacy of the pandemic is a shift of journey purpose. Before the pandemic rail had a significant reliance on commuting and
business travel compared to other modes, with over 50 per cent of rail journeys for these purposes. The rise in hybrid working with more working from home since the start of the pandemic has dampened demand for commuting travel, with some of this shortfall compensated by increased leisure travel.
This change has also affected the times of the day and week when people travel. Data indicates that weekend rail travel has recovered more strongly than weekday travel, and that Mondays and Fridays see fewer journeys than midweek. The peak hours of rail travel, traditionally between 07:00 and 09:00 in the morning and 16:00 to 18:30 in the afternoon, have flattened while off-peak rail travel in the middle of the day and evenings has increased since 2019. Rail freight did not see the same collapse in demand as passenger travel during the pandemic and rebounded to pre-pandemic levels by 2021, especially after construction projects resumed and intermodal demand increased. There has been a slight fall in rail freight volumes over the past couple of years, but this appears to be driven by wider
NEWS IN BRIEF
FREIGHTLINER SELLS COATBRIDGE TERMINAL TO JOHN G RUSSELL
On 13 April 2024 Freightliner confirmed that ownership of the Coatbridge terminal has be taken over by Russell Railroad Limited, a subsidiary of John G Russell, effective immediately. Following a strategic review of the Freightliner Coatbridge terminal, it was recognised that the Coatbridge facility would be better served under new ownership. Freightliner rail services remain unaffected by this sale and will continue to run into the Coatbridge terminal as usual.
£12 MILLION INVESTMENT INCLUDES LINCOLN-BASED RAILWAY SAFETY STARTUP, TENDED
East Midlands-based Tended, a follow-on investment by Blackfinch, is transforming workplace safety with its wearable technology designed to prevent accidents in high risk environments. Recognised by Time Magazine as one of the inventions of 2023, Tended has secured significant contracts, including a framework agreement with Siemens worth up to £7 million. With £2.8 million EIS and £1.1 million VCT investment since joining the Blackfinch Ventures portfolio, Tended is set to expand its impact, rolling out over 400 devices in the coming months. This fast growing company’s products are making heavy industry workplaces safer globally, demonstrating the scalability and international appeal of UK-based innovations.
NETWORK RAIL SCOTLAND AND NETBALL SCOTLAND PARTNER UP
Network Rail Scotland and Netball Scotland have extended their education partnership to spread vital rail safety messages to young people across Scotland. Over the next three years, Network Rail Scotland and Netball Scotland will work together to educate young people across Scotland about safety on the railway whilst they attend school and netball competitions. During the previous partnership, almost 1,000 young girls benefitted from the programme in 42 schools and five netball camps with 9,582 social media views.
NEWS IN BRIEF
SENSONIC EYES UP NEXT LEVEL RAILWAY SECURITY
Sensonic, a leading provider of intelligent sensing solutions for the railway industry, today announced the addition of CCTV functionality to its groundbreaking Distributed Acoustic Sensing (DAS) security system. This integration empowers railways to not only detect and locate track trespassers in real-time but also visually identify them, significantly enhancing security and situational awareness. Sensonic DAS technology acts as a virtual fence, utilizing fiber optic cables to detect vibrations and pinpoint suspicious activity along railway tracks.
NEW TRAINS ON THE EBBW VALE LINE
Brand new trains have been launched on the Ebbw Vale line. Built in Newport, the Class 197 trains have started to enter service on mainline routes around Wales and the Borders. They will run between Ebbw Vale and Cardiff Central, as well as Newport, following the introduction of brand-new services on the line earlier this year. The trains will be able to run up to a maximum of four carriages on the Ebbw Vale line. January marked the introduction of the new Newport services, almost doubling the number of trains operating on the line with two trains running per hour, one to/from Cardiff and one to/ from Newport.
GREAT WESTERN RAILWAY AND NETWORK RAIL DIRECTOR RECEIVES OBE
Inspirational Great Western Railway and Network Rail director Ruth Busby was at Buckingham Palace on Friday to receive her OBE from the Princess Royal. Ruth, People and Transformation Director (Regional) for GWR and Network Rail Wales and Western, was recognised in the New Year Honours ‘for services to diversity in the rail industry’. Her award recognises not only her work within GWR and Network Rail, but the numerous other organisations she represents to champion Equality, Diversity and Inclusion (EDI) in the rail industry. Ruth also remains a passionate supporter of Women in Rail, having previously served as co-chair of Women in Rail South.
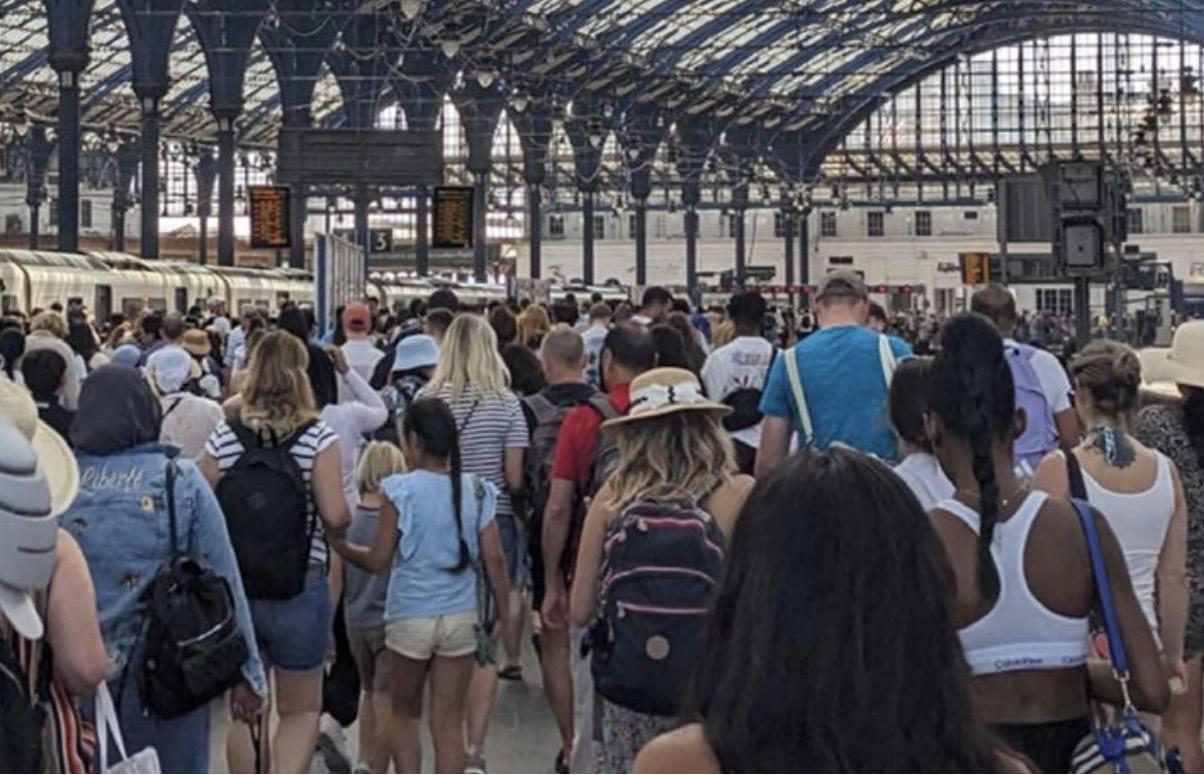
economic factors than the legacy of the pandemic. As the level of passenger services returned, the opportunities for more rail freight paths in the timetable receded, and capacity limitations on much of the network remain.
‘Government support was 52 per cent of industry income in 2022/23 compared with 32 per cent in 2019/20 and a peak of 82 per cent during the pandemic’
Recovery and revenue: new challenges for rail
Although passenger rail demand has proved more resilient than many feared during the pandemic, major challenges have arisen. The shift in travel patterns has resulted in a significant loss of fare revenue for the rail industry, as higher-yield peak hour fares (including season tickets) have reduced but the revenue shortfall has not been offset by the increase in passengers buying cheaper off-peak and advance tickets. Passenger revenue is just over 80 per cent of prepandemic levels, and for 2022/23 there was a revenue shortfall of £2 billion compared with the pre-Covid situation.
Government support was 52 per cent of industry income in 2022/23 compared with 32 per cent in 2019/20 and a peak of 82 per cent during the pandemic. It seems unlikely that the farebox will return to delivering the pre-pandemic level of over 65 per cent of rail income.
Meanwhile, railway operational costs have remained largely unchanged. Operating costs such as train leasing, track access and staffing are difficult to reduce without major structural changes.
The changed revenue position does, however, provide some important opportunities. Given that all ticket revenue currently accrues to the Government, there
is a current opportunity for a major restructuring of fares, which would generate customer benefits and potentially lead to savings in sales costs. Changes to rolling stock leasing could allow a more holistic and longer-term view of future requirements compared with the shorter-term outlook of individual TOCs on limited year contracts.
If higher weekend and offpeak rail demand continues, opportunities exist to make better use of the limited network capacity, potentially with shorter train planning timescales, and enabling a rethink of when maintenance and renewals are scheduled. Some of these challenges could be simplified by the creation of Great British Railways, although current and future Parliamentary commitment to this is unclear.
Infrastructure and investment: the future of rail policy in Britain
Rail has a crucial role to play if the Government is to meet its net-zero carbon and wider policy objectives. In spite of current funding challenges, it remains essential to take the long view given the lengthy timescales involved with delivery of new and improved infrastructure. Unfortunately, infrastructure projects have become relatively more expensive since the pandemic as a result of higher interest rates and cost inflation.
The part-cancellation of HS2 remains controversial but the success of the Elizabeth Line shows the capability of new infrastructure to boost demand through improved connectivity and new journey opportunities. The drivers of rail passenger demand remain strong and are likely to generate increased patronage in the coming decades.
Justification for additional rail investment could come from improved appraisal processes. The historic narrow focus on ‘journey time savings’ is less appropriate with reduced commuting and business travel. A revised appraisal methodology could better value rail’s contribution to reducing carbon emissions, ‘levelling up’ regional economies, and the social benefits from accessibility and connectivity.
The rail sector also requires a consistent pipeline of infrastructure investment projects to sustain its supply industry, which makes an important contribution to the UK economy. The future for rail should be bright but it requires a long-term view of the wider benefits our railways bring and commitment from Government policy makers.
The ITC’s new report can be downloaded from the following link: www.theitc.org.uk/ wp-content/uploads/2024/03/ITC-Impacts-ofthe-Pandemic-Report-March-2024.pdf.
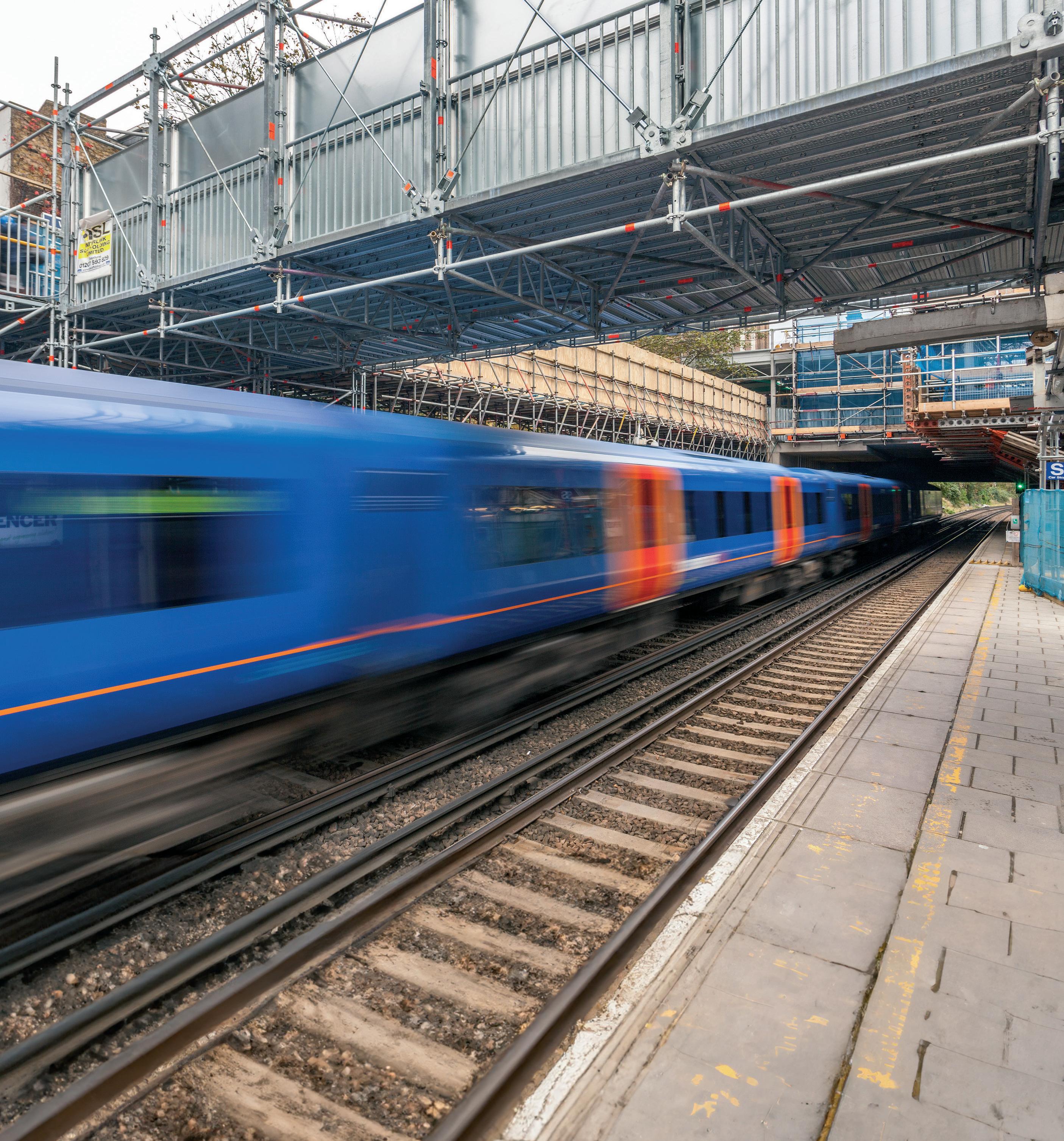
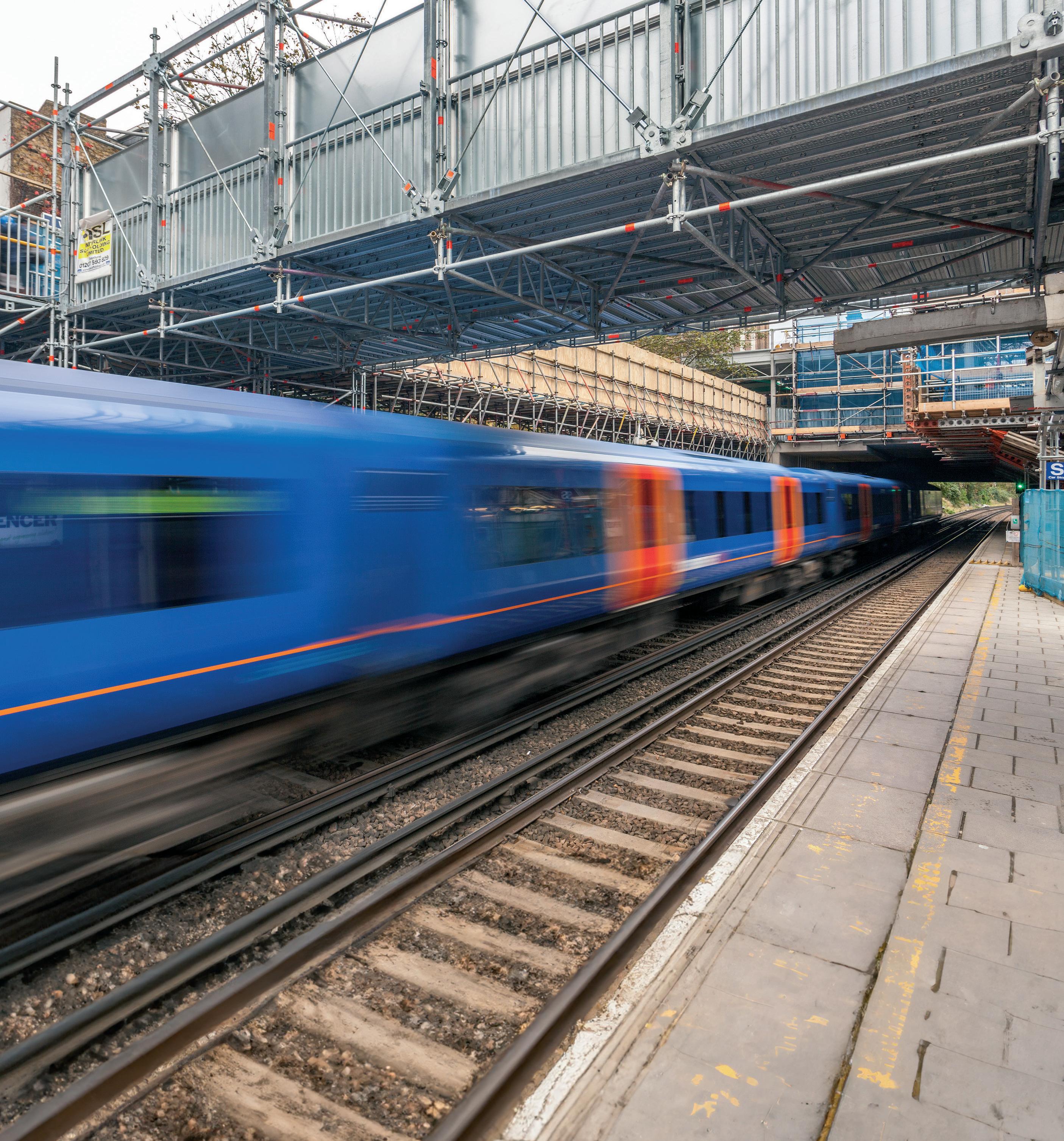
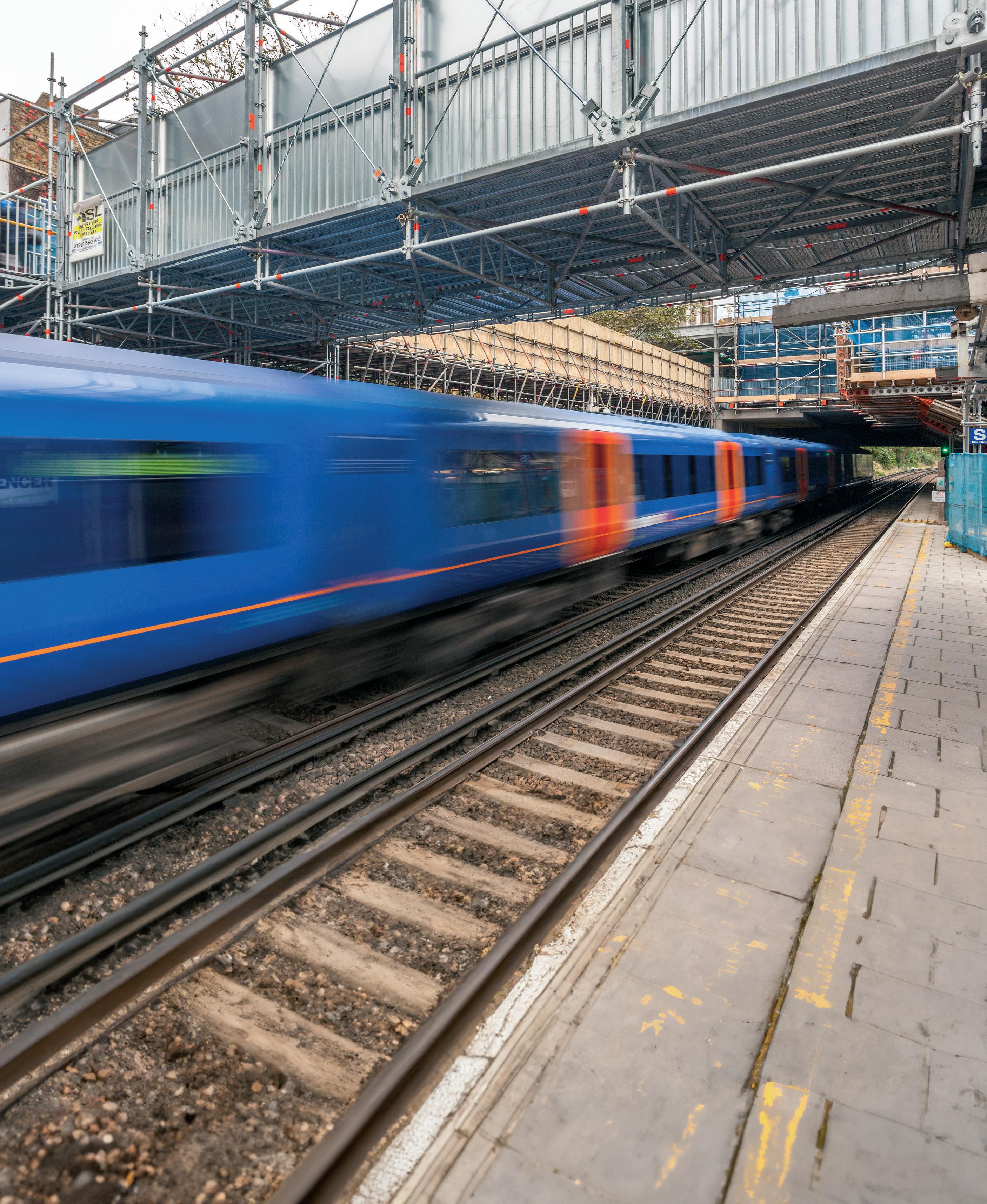
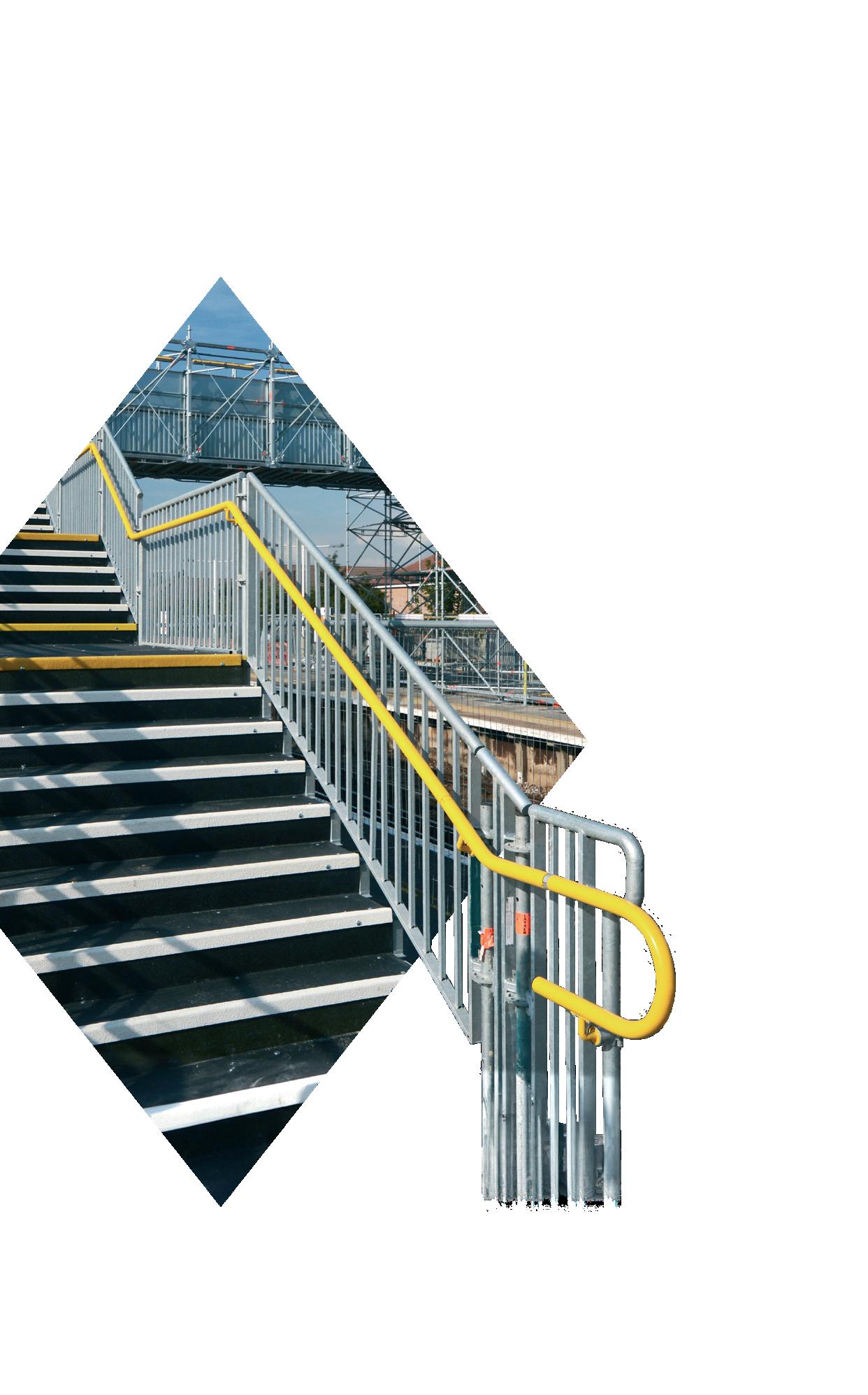
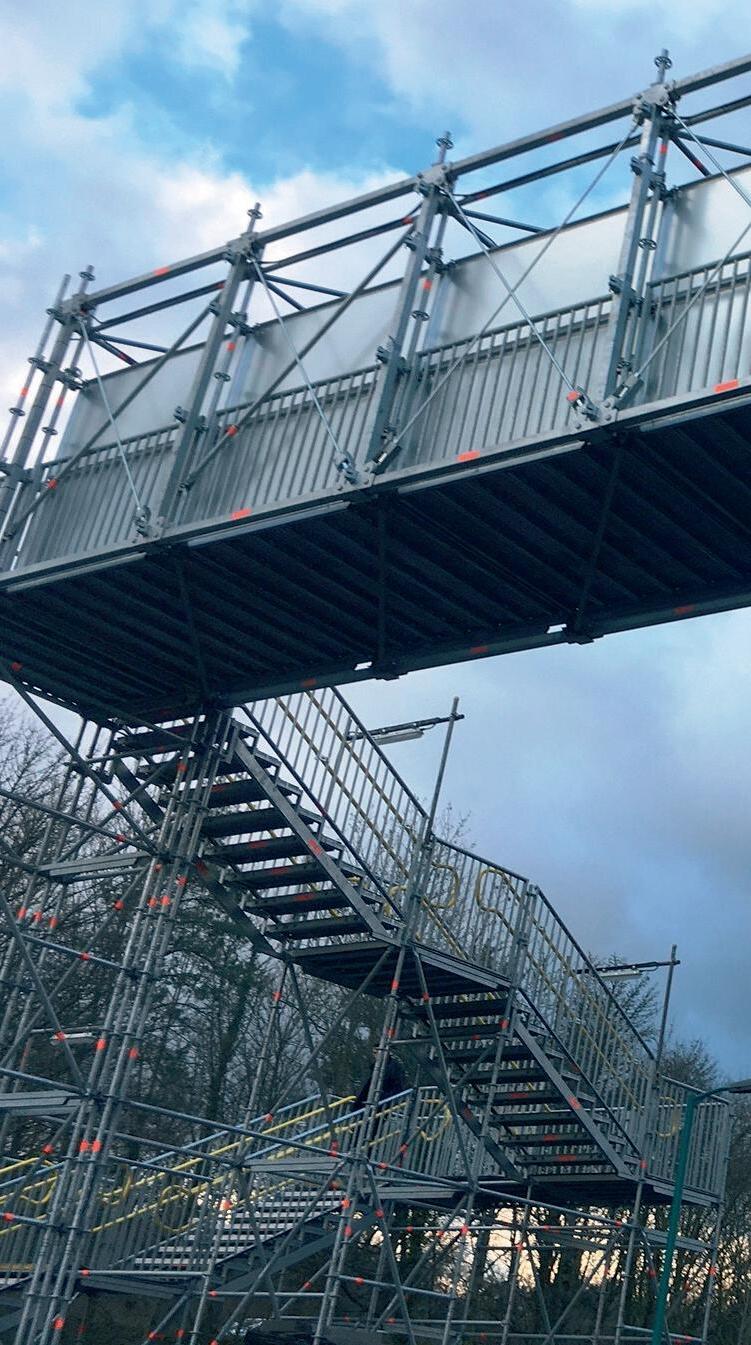
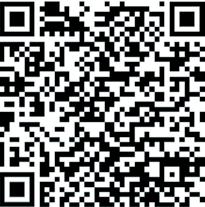
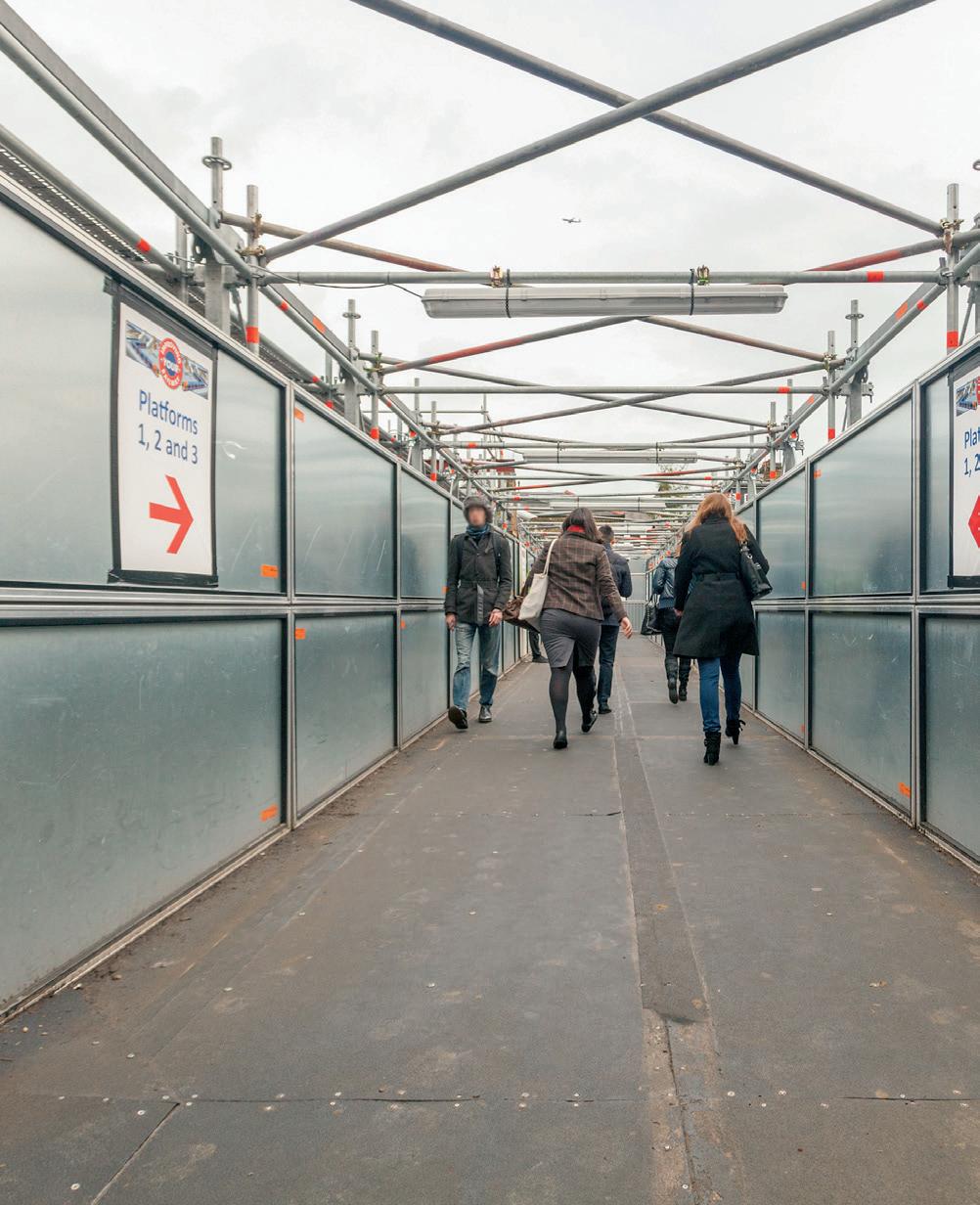
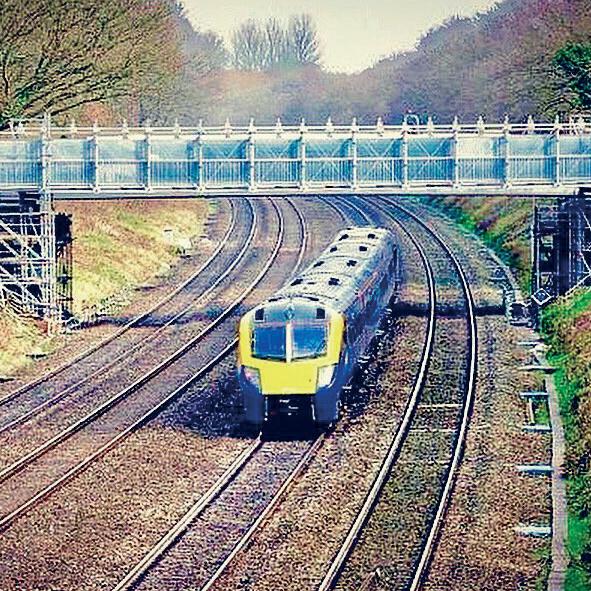

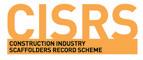

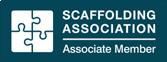
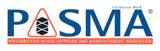
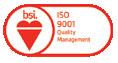


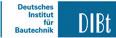



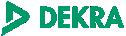




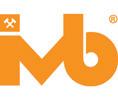
The Future of Rail by AtkinsRéalis Graduates
‘It’ll only happen if we’re proactive’: three AtkinsRéalis graduates speak about opportunities, obstacles and the shape of rail’s future
Rail needs a credible long-term strategy to build skills and engineering expertise, erode disciplinary boundaries, and ultimately become, once again, a truly desirable place to work. Through the eyes of three of our graduates, we look to rail’s big challenges, and how we can address them.
Rail has a demographics problem. Gradually but consistently, its workforce is ageing. Just eight years ago, our industry employed twice as many under-25-year-olds as it does now – just five per cent of the total. At the other end of the age spectrum, over 20 per cent of the workforce will retire in the next six years. The result is a steadily worsening skills crisis, and a daunting hurdle for an industry which urgently demands investment, growth and digital adoption.
But rail also has a diversity problem. Despite a strong consensus around the need for a workforce that genuinely looks like the people who use rail, the statistics indicate a worryingly static picture. As of 2022, only 14.6 per cent of the workforce was female (a dip against the year before), whilst the proportion of other than white workers hasn’t budged from around 12.5 per cent in the last five years (against 18.3 per cent in the general population).
These two concerns appear separate. But what they have in common is that they both can – and must – be solved by an impetus of young, diverse and innovative minds. Through our Graduate Development programme, we guide our graduates to aspire, achieve and advance, building skills, broadening horizons and working towards a professional qualification. Through a series of signature events, core training modules, mentoring and on-the-job experience, we equip our young professionals to overcome the thorny challenges of a difficult future –and find some unexpected buds along the way. The journey of three of our graduates shows how our industry is already changing.
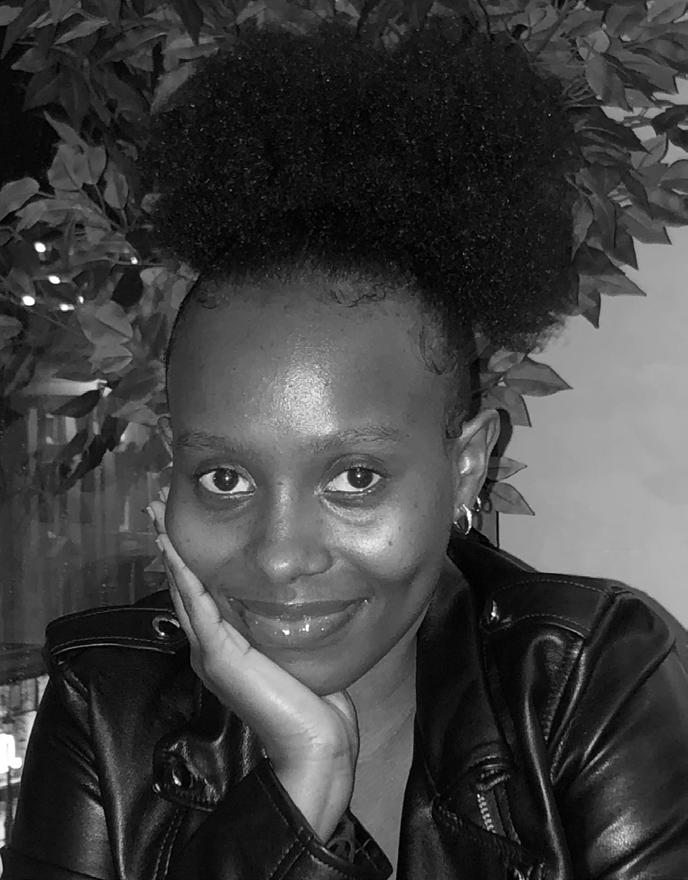
What are you currently working on?
Through AtkinsRéalis, I keep being exposed to interesting projects. Right now, I’m designing transportation systems for NEOM in Saudi Arabia, and project managing contractual compensation events for the National Highways East Region Design Services Contract. I’m really interested in something that’s revolutionary, that actually builds a sustainable future and for which you have to literally think outside the box! But I’ve really loved the challenge of project management, and my manager has helped me fulfil my desire for more of it.
What stands out about your experience at AtkinsRéalis?
There are so many opportunities to follow my passions, and I love that I feel positively encouraged to do that. I recently volunteered to be a Governor in AtkinsRéalis’ industryleading partnership with Governors for Schools (GfS). That’s been so amazingly
‘Through AtkinsRéalis, I keep being exposed to interesting projects. Right now, I’m designing transportation systems for NEOM in Saudi Arabia.’
impactful – we’re delivering an enhanced STEM curriculum into schools to inspire the next generation of engineers. I’m also a Wellbeing Champion for my local office in Leeds, organising mental health talks, and I’m involved in the Net Zero workforce, helping organise leadership training events to embed low-carbon thinking. As you can imagine, I'm quite busy!
How do you see change happening in our industry?
Along with everyone I work with, we know we actually need to go out and do more to make change happen. It’ll only happen if we’re proactive. So, I think it’s about small, intentional things. For instance, during Race Equality Week we had a five-day challenge to get people talking. ‘Okay, on this day, as a team, what are we going to do? What are we doing to bridge the gap?’ And that’s how we kickstart and continue cultural change – by getting people talking about things they don’t normally talk about.
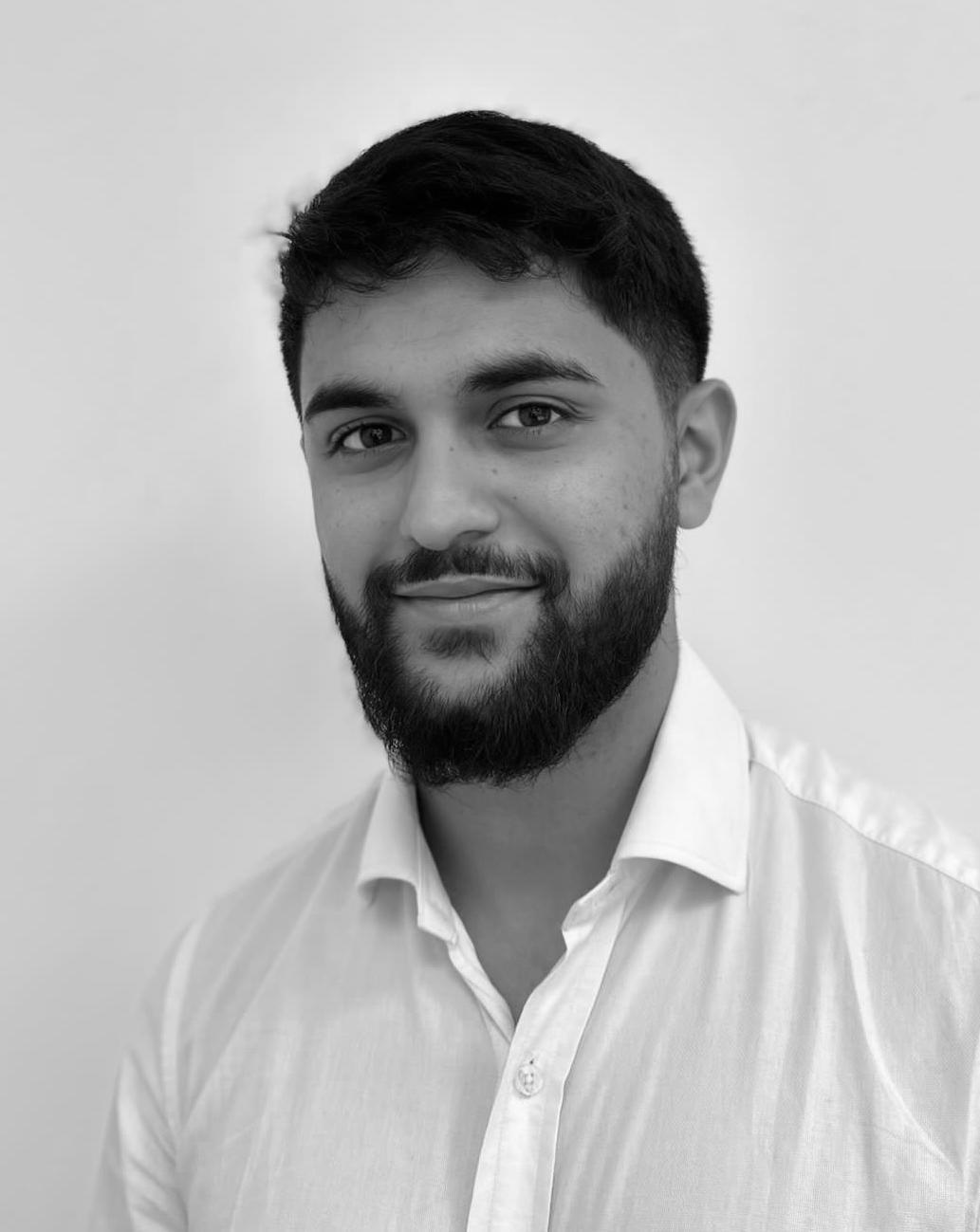
Can you tell us a bit more about your graduate scheme?
The structure of my scheme led in many different directions – it involved threeto-six-month long placements around all elements of the Signalling business over three years. You begin to understand how the disciplines operate, implement what you’ve learned and bring forward best practices into new teams. The result is I’ve seen the importance of connecting and integrating different viewpoints and technical skills, and I’ve felt really supported. Alongside your line manager, you have an allocated buddy – usually a secondyear graduate – and a mentor from the senior leadership team. I felt like I was heard right from the beginning. So regardless of the team I end up in, I have been given the support, the resources and the ability to work on exciting projects.
What stands out about your experience at AtkinsRéalis?
The culture at AtkinsRéalis is so focussed on people. As a young engineer, I wanted to be surrounded by people who would foster my development. But that focus on development – and providing the resources and opportunities for training – is unique. Unusually for such a large company, I feel part of a strong graduate community that is given the time and space to bond, share information and build relationships.
One year we had an autumn school experience, where me and nine other graduates from all three years of the programme came together to volunteer on heritage rail – that was amazing. And last year, I managed a project volunteering initiative which involved around 50 members from our staff, as well as our client and sub-contractors, to deliver meaningful social value in our local communities.
‘The culture at AtkinsRéalis is so focussed on people. As a young engineer, I wanted to be surrounded by people who would foster my development.’
NEWS IN BRIEF
‘BUG HOTELS’ TO SUPPORT BIODIVERSITY
Northern is set to open ‘bug hotels’ at three stations on the Bentham Line between Leeds and Morecambe as part of a project with local schools to support biodiversity. Undergraduates working for the train operator as part of their ‘Year in Industry’ will lead the sessions with local schools, which are designed to educate schoolchildren on biodiversity and the importance of caring for local habitats.
Since then, I’ve engaged with the business to ensure social value is a core part of our projects. I’ve also been given the platform to showcase my ideas – joining the Signalling Pathfinders programme has allowed me to work on strategic business objectives alongside the Signalling senior leadership team.
How do you see change happening in our industry?
I’ve always had a strong interest in equality, diversity and inclusion, as fostering a positive environment is key to maximising staff potential. But I wasn’t expecting that as soon as I arrived, I would join discussions with our senior leadership on how to build a more inclusive workplace! The result is I feel able to make a difference, not just day to day, but also through all the initiatives within AtkinsRéalis. I find I can always try something different, develop new skills, and give back to the community. I think that’s key to bringing about and spreading change.
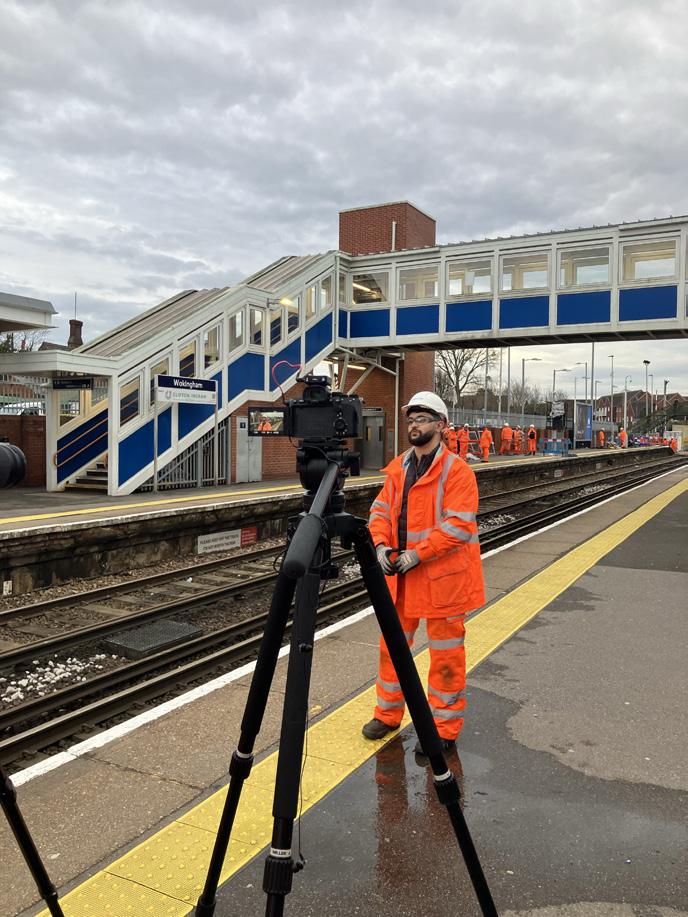
The workshops, which are being delivered in partnership with Bentham Community Rail Partnership, will take place at schools in Lancashire and West Yorkshire. The ‘bug hotels’ will be created from old wooden pallets and when complete will contain a variety of repurposed materials including twigs, bamboo canes and corrugated carboard.
PUBLIC CONSULTATION SHAPES EXCITING NEW TIMETABLE FOR FIFE, TAY CITIES, AND LEVEN
A number of timetable improvements for customers in and around Fife and the Tay Cities are set to be introduced in June this year after more than 700 responses to a public consultation. ScotRail held the consultation in September last year on a series of proposed improvements for services between Edinburgh, Fife, Perth, and Dundee and for the historic return of rail services to communities in Levenmouth.
SCOTRAIL INVESTS IN VITAL LIFESAVING DEFIBS ACROSS THE COUNTRY
Lifesaving defibrillators have now been installed at 87 ScotRail stations throughout the country, after the train operator completed the latest roll-out of new machines. The devices are now in place at stations all over Scotland, including Arrochar, Crianlarich, Nairn, Dunbar, and Dumfries. ScotRail has installed the defibs in accessible places wherever possible at stations, and they are available 24 hours day. There are exceptions where it has been necessary to install them in ticket offices due to security issues.
NEWS IN BRIEF
CUSTOMER IMPROVEMENTS FOR 112 SOUTHEASTERN TRAINS NOW COMPLETE
All 112 of the Class 375 ‘Electrostar’ trains that operate on Southeastern’s routes serving Kent, East Sussex and mainline London stations have received at-seat power sockets, including USB points, and new LED lighting. The new power sockets allow customers to charge their smartphones, tablets and laptops – supporting commuting and leisure trips throughout the network.
Meanwhile, the energy efficient lighting will produce the same level of light in carriages while using up to three-quarters less energy, furthering reducing the impact on the environment of Southeastern’s allelectric train fleet.
In addition, energy meters have been installed on the 42 trains that didn’t have them to better track usage and costs.
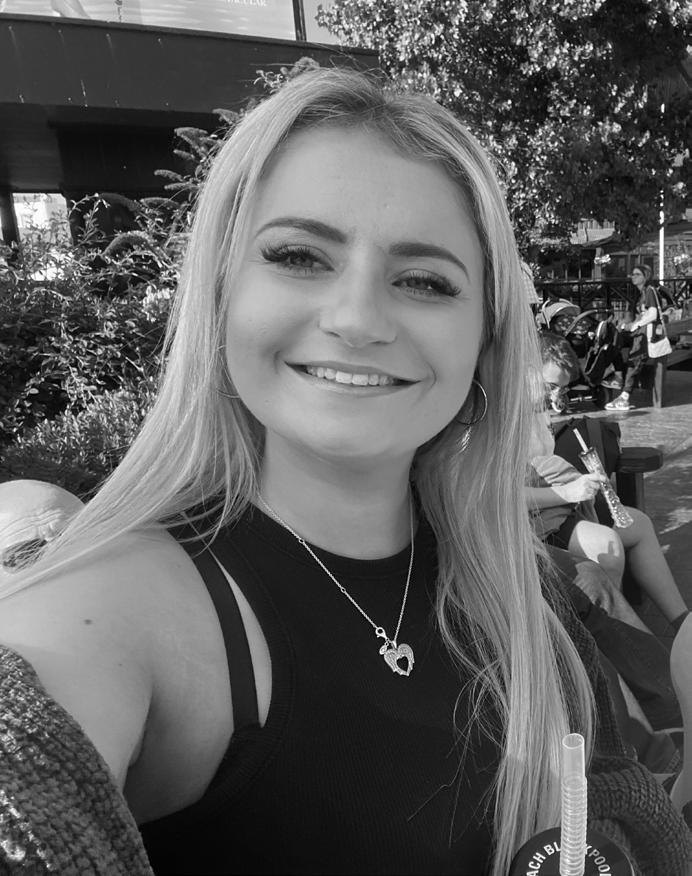
Natalie Halarnyk-Peet Civil Design Engineer
What are you currently working on?
Civils. During my secondment, I was the Site Design Engineer for Ancillary Civils, in which my role was to bridge the gap between the construction team and the design team. If any site issues occurred, I would help to resolve the issue collaboratively ensuring design standards were met, whilst remaining buildable. It’s been an incredible opportunity to be learning in this fully integrated Alliance environment working with Laing O’Rourke, VolkerRail and Network Rail – I’ve gained so much experience of major projects.
What stands out about your experience at AtkinsRéalis?
‘TRY A NEW ROUTE’: TPE OFFERS NEW RAILWAY APPRENTICESHIP ROLES
TransPennine Express (TPE) is seeking talented people to join its 1,800 strong workforce through its popular apprenticeship scheme – whether they are just starting out in the world of work or looking for a change of career. A total of eight apprenticeships are now available across the business, in areas including customer experience,
APPLICATIONS ARE OPEN UNTIL FRIDAY 31 MAY
performance, service planning, safety, corporate communications, retail, resourcing, and business management.
Last year the equivalent of nine out of ten apprentices obtained a full-time position within TPE upon completion of their qualification. Applications are open until Friday 31 May. More information is available at www.tpexpress.co.uk/about-us/ apprenticeships
I’m coming to the end of a two-year site secondment on East West Rail Phase 2 after working on the project for over five years. It’s been a thoroughly interesting project to work on due to the various aspects of design and construction i was involved with. The project objective is to re-open a section of railway between Bicester and Bletchley which was mothballed in the late 60s. My first role was involved with producing Highway Consents for the first year, before moving on to a Design Lead role in Ancillary
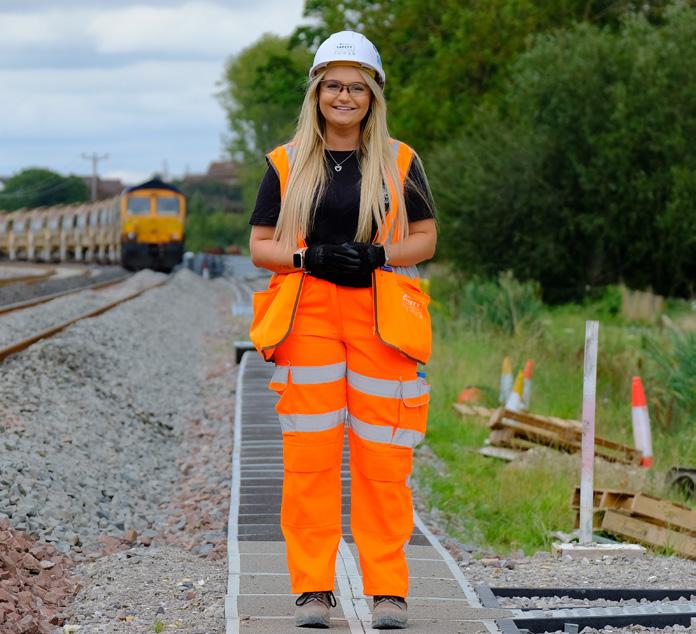
‘STEM wasn’t promoted to me when I was in secondary school, but I’d like to believe I can help change that, convince more young girls to set their sights on STEM careers.’
The first thing that comes to my mind is the graduate community. There is such a large, welcoming community where everyone is supportive and friendly. One of my highlights is annual graduate ski trip. This is something I never thought I would do, but I was fortunate enough to attend three of these trips, boosting my confidence, expanding my network and walking away with friends for life! By my second year I was organising the next ski trip for over one hundred graduates. It’s almost like a metaphor for AtkinsRéalis culture, that you’re encouraged to try new things without fear and that you’re surrounded by a big, well-structured and supportive community. I have also been fortunate enough to take part in the Women in Rail Mentoring Scheme. I had a mentor, Barry Tan, from RSSB (Rail Safety and Standards Board), who supported me through this programme. We had weekly chats which hugely boosted my confidence, even in just general life decisions. Having that honest relationship that wasn’t about business, which slowly developed my skills – that was really helpful. And one day I’d like to pay that forward and become a mentor myself.
How do you see change happening in our industry?
I think our outreach with schools is vital. I’ve used my volunteer days to go into schools to give introductions to STEM and showcase the work I do as an engineer These are the events that really do make a difference. Practical events are my favourite, those tend to be the moments that ignite that little spark in children, particularly with girls. It’s still a challenge to get older girls interested because they already know what they want, and we still don’t have that many women in our industry. STEM wasn’t promoted to me when I was in secondary school, but I’d like to believe I can help change that, convince more young girls to set their sights on STEM careers.

Email: atkinsrealis@atkinsrealis.com Visit: www.atkinsrealis.com www.atkinsrealis.com/en/contact
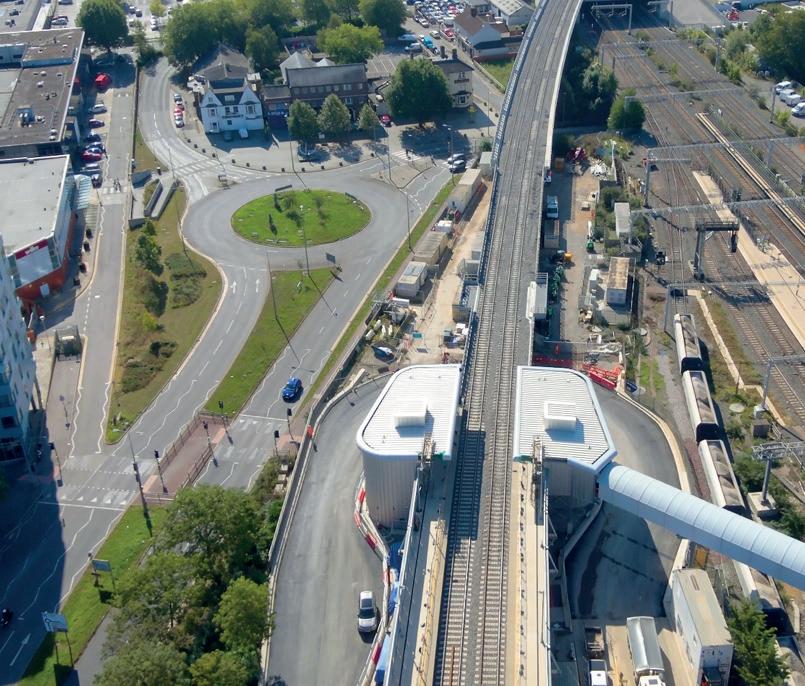
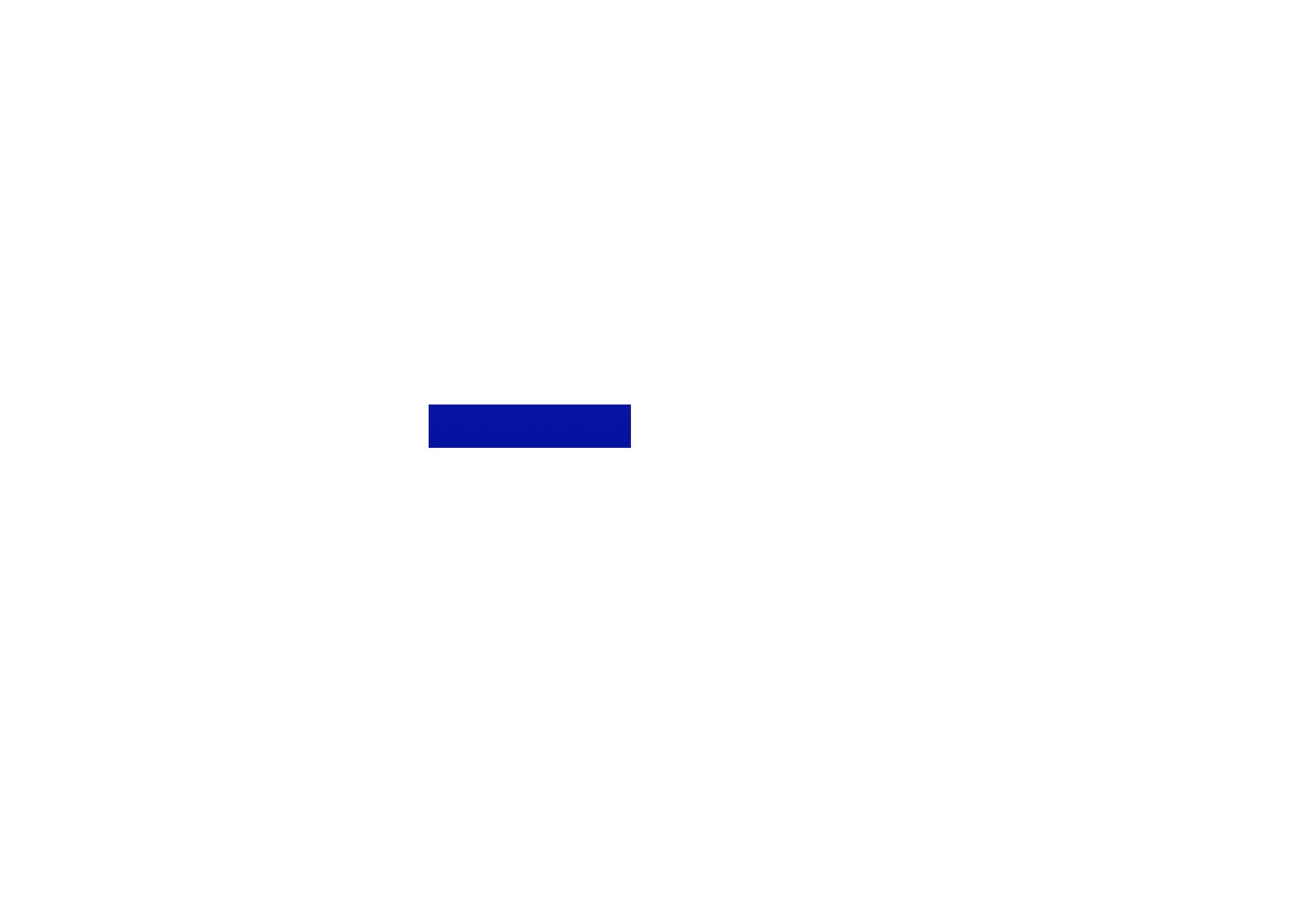
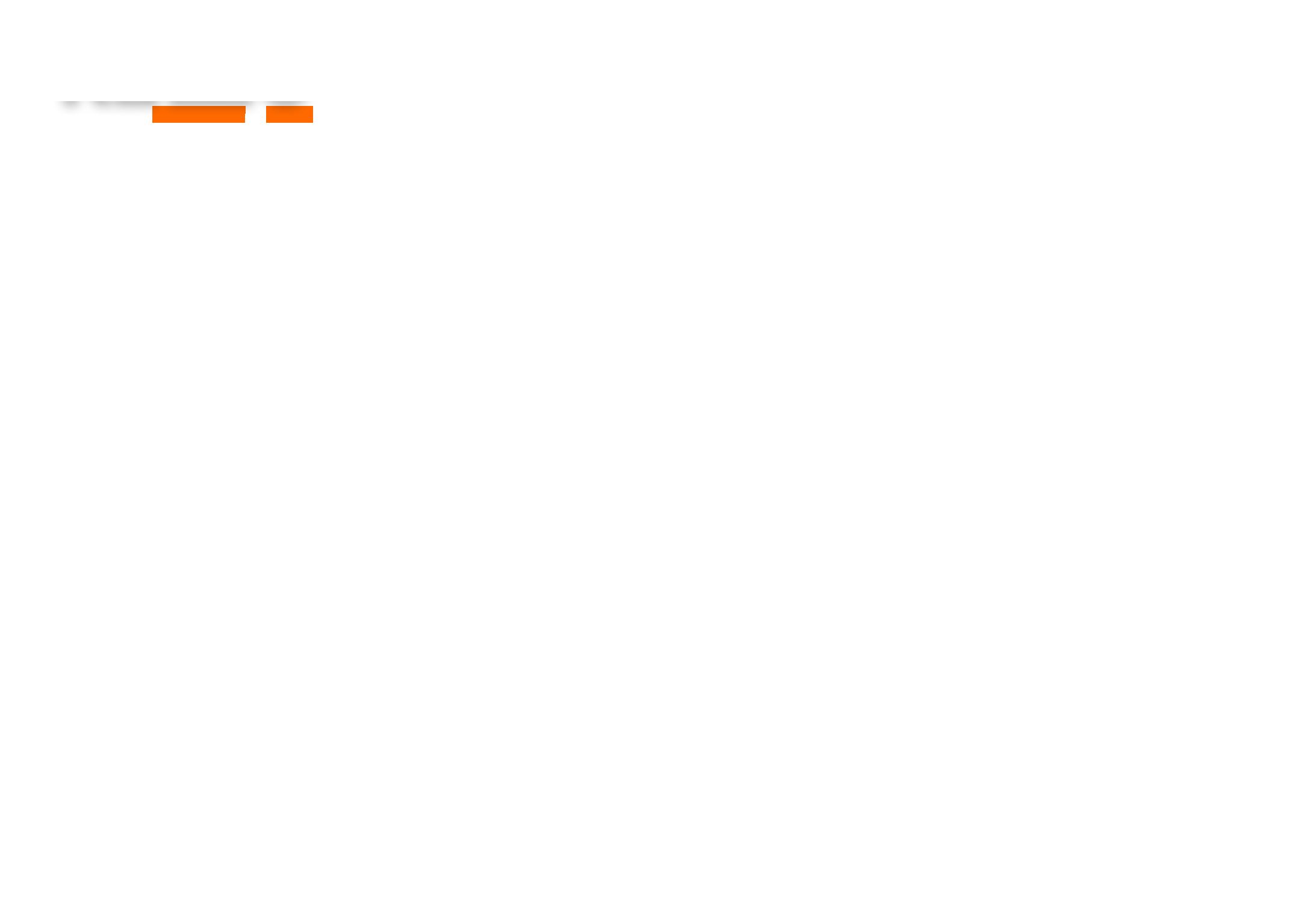
Critical Standards for Power Supply Design
In the realm of transportation, particularly within railway systems, the adherence to technical standards is non-negotiable for the development of power supply products that are both safe and reliable
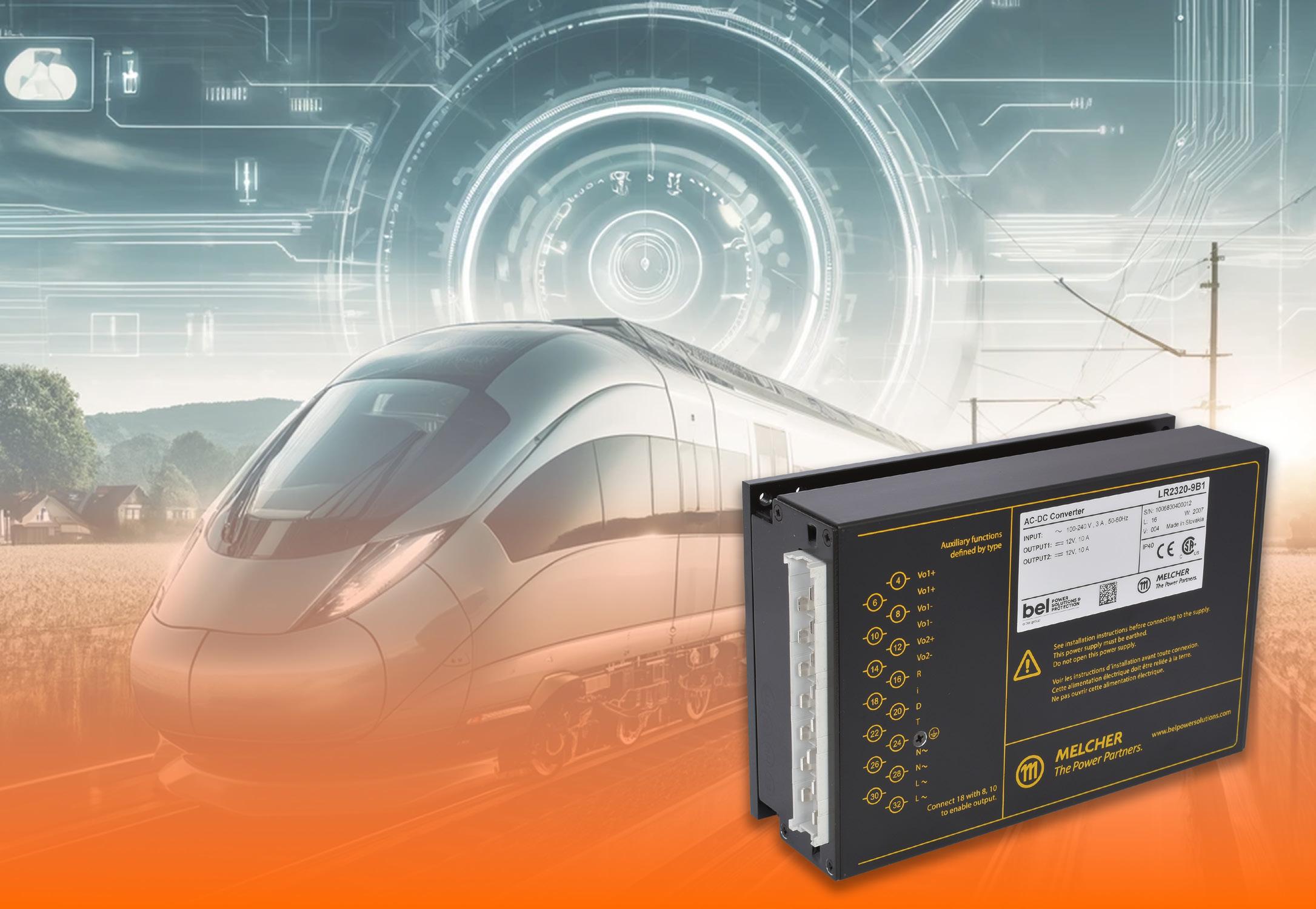
Among these, EN 50155 emerges as a pivotal European standard, governing the electronic equipment utilized in rolling stock. This standard, crafted by the European Committee for Electrotechnical Standardization (CENELEC), transcends its European origins to address the global railway market's needs, setting the benchmark for power supply design and testing in this sector.
Safety and reliability in modern rail networks
The integrity of power distribution systems in trains is paramount, necessitating compliance with rigorous standards, with EN 50155 standing out for its comprehensive coverage. This standard is applicable to a wide array of electronic equipment on trains, spanning power supplies, ensuring their safety and reliability across diverse railway applications. As
trains evolve, incorporating advanced engineering and enhanced passenger amenities such as onboard Wi-Fi and sophisticated climate controls, EN 50155's role becomes increasingly vital, necessitating periodic updates to align with technological advancements and complex electrical demands.
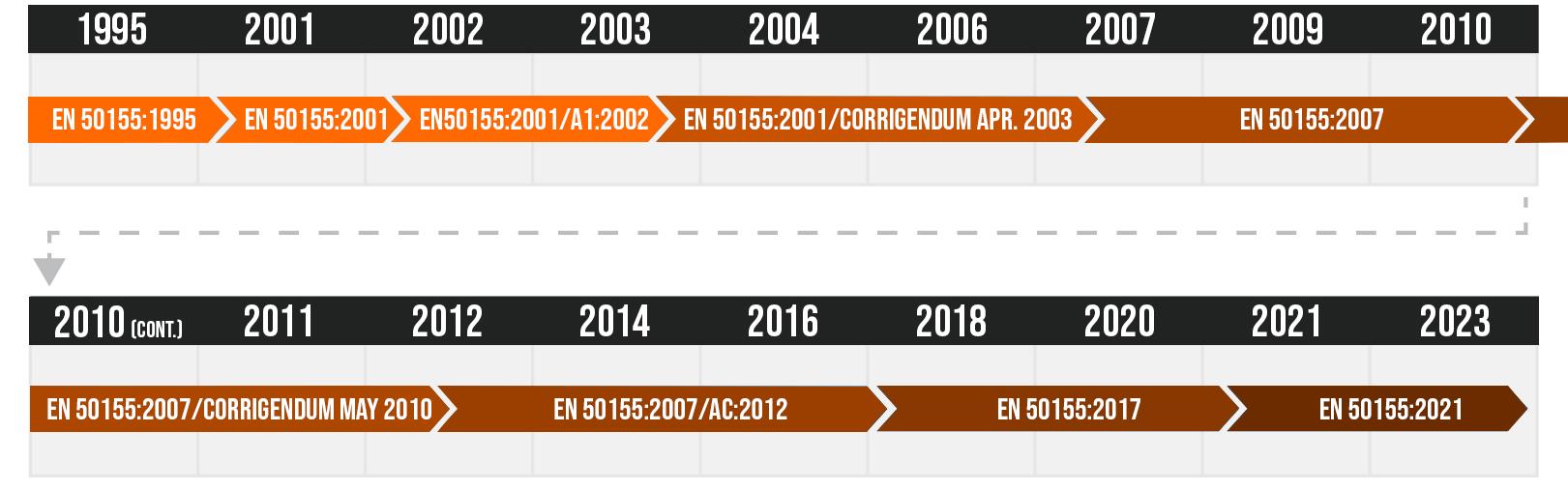
Comprehensive Scope of EN 50155
EN 50155 delineates requirements for electronic equipment involved in control, regulation, protection, diagnostics, and energy supply within rolling stock. It addresses various aspects including operating conditions, design, documentation, testing, integration, and software considerations for power supplies and converters. These components are crucial for delivering stable and clean power across the electronics spectrum in modern rail systems. The standard emphasizes key factors such as voltage variation, temperature extremes, shock, vibration, electromagnetic compatibility, and overall reliability.
Interconnected standards and updates
EN 50155 does not stand in isolation but references additional standards that tackle specific challenges, including fire safety (EN 45545-1), electromagnetic emissions and immunity (EN 50121-3-2), and shock and vibration resistance (EN 61373). These referenced standards ensure a holistic approach to safety and performance in railway power supply design.
Since its initial publication in 1995, EN 50155 has undergone several revisions to keep pace with the evolving landscape of power supply technology and railway safety. Noteworthy updates have introduced new testing categories, enhanced safety management requirements, and adjustments to operating temperature classes and equipment life expectancy, reflecting the standard's adaptability to changing technological and safety paradigms.
EN 50155's impact on power supply design
The standard's relevance extends to various facets of power supply design for railway applications, addressing supply voltage characteristics, environmental conditions, shock and vibration tolerance, electromagnetic compliance, and performance reliability. These elements are critical for ensuring that power supplies can withstand the rigorous demands of railway environments, contributing to the safety and efficiency of rail transport.
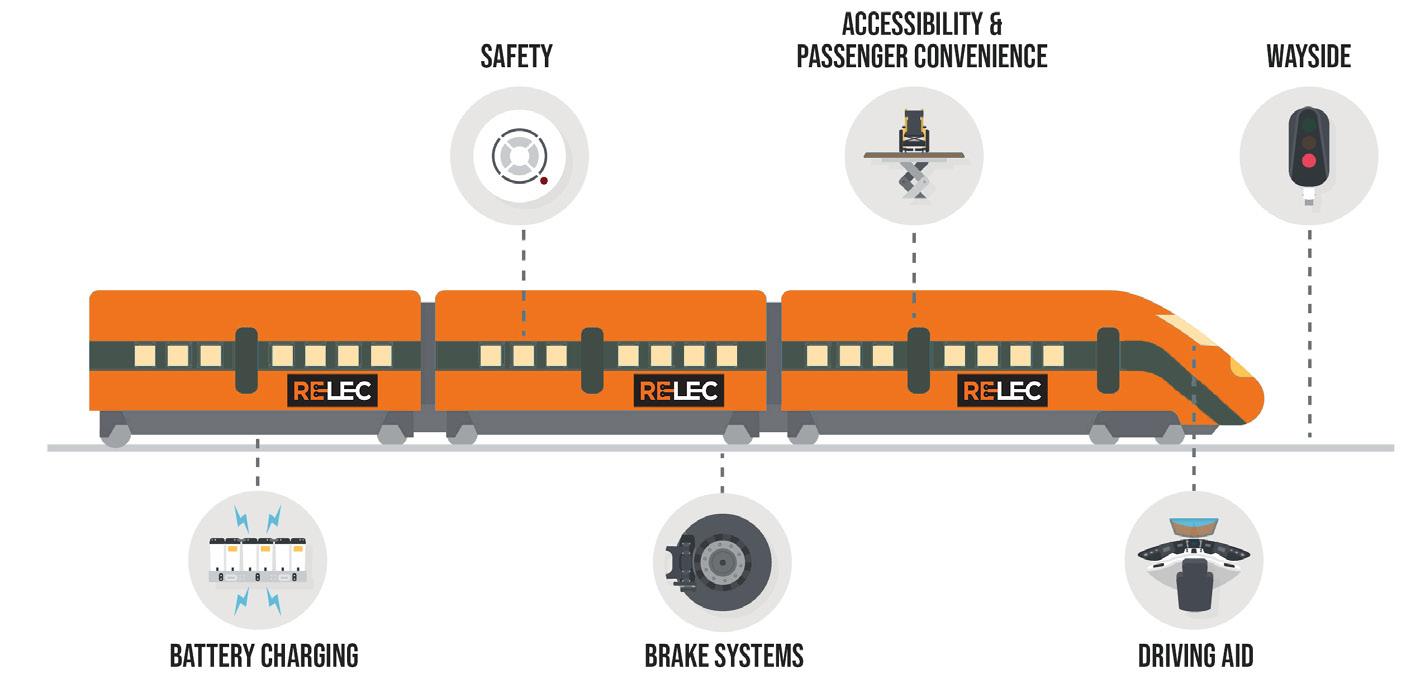
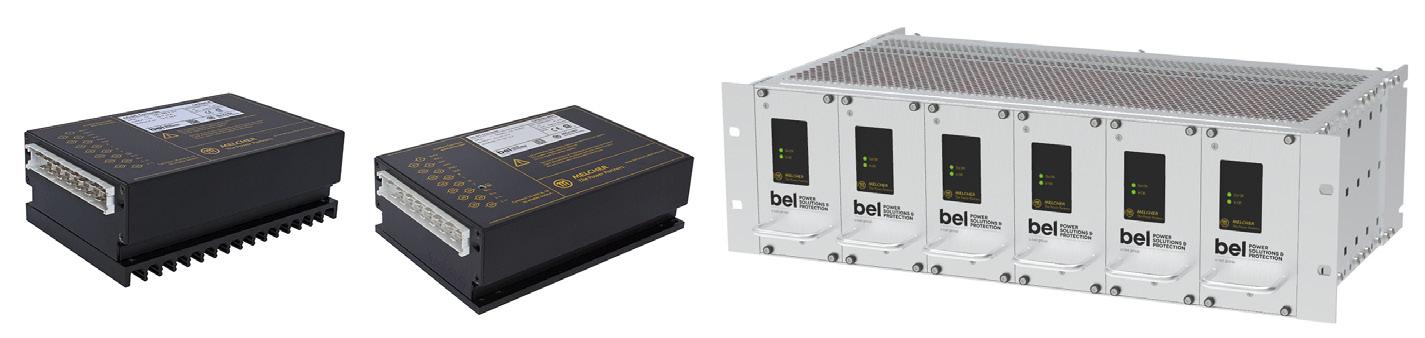
Guidance for compliance and innovation
For manufacturers and designers of railway power supplies, EN 50155 serves as an essential guide, ensuring that products not only meet stringent performance and safety criteria but also cater to the specific needs of the railway industry. Companies like Bel, through their Melcher brand, exemplify the commitment to designing and manufacturing power supplies that comply with EN 50155, offering customized solutions to meet the unique requirements of railway applications.
In conclusion, EN 50155 stands as a cornerstone standard for the design and development of power supply systems in the railway sector, embodying the principles of safety, reliability, and technological advancement. Its comprehensive scope and periodic updates ensure that railway power supplies keep pace with the evolving demands of modern rail systems, underpinning the safe and efficient operation of trains worldwide.
Bel-Power, with its extensive portfolio of power supply solutions and its collaboration with Relec Electronics in the UK, remains a definition of excellence in the railway sector. Their dedication to safety, dependability, and forward-thinking positions them as a crucial partner in the of railway industry.

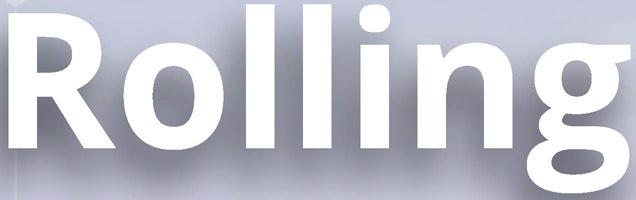
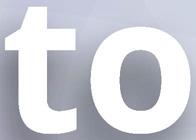
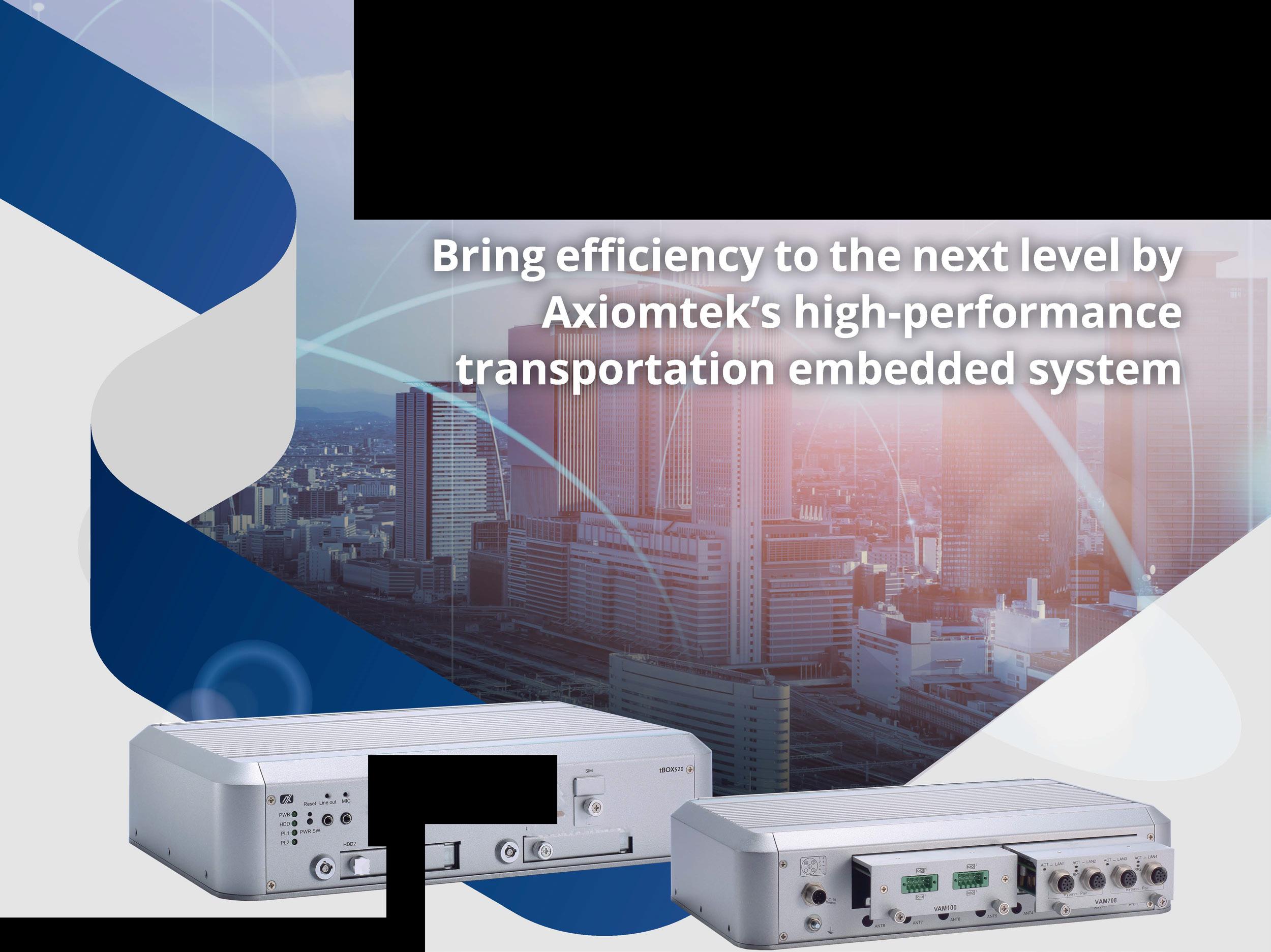
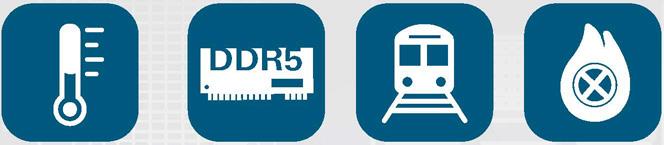
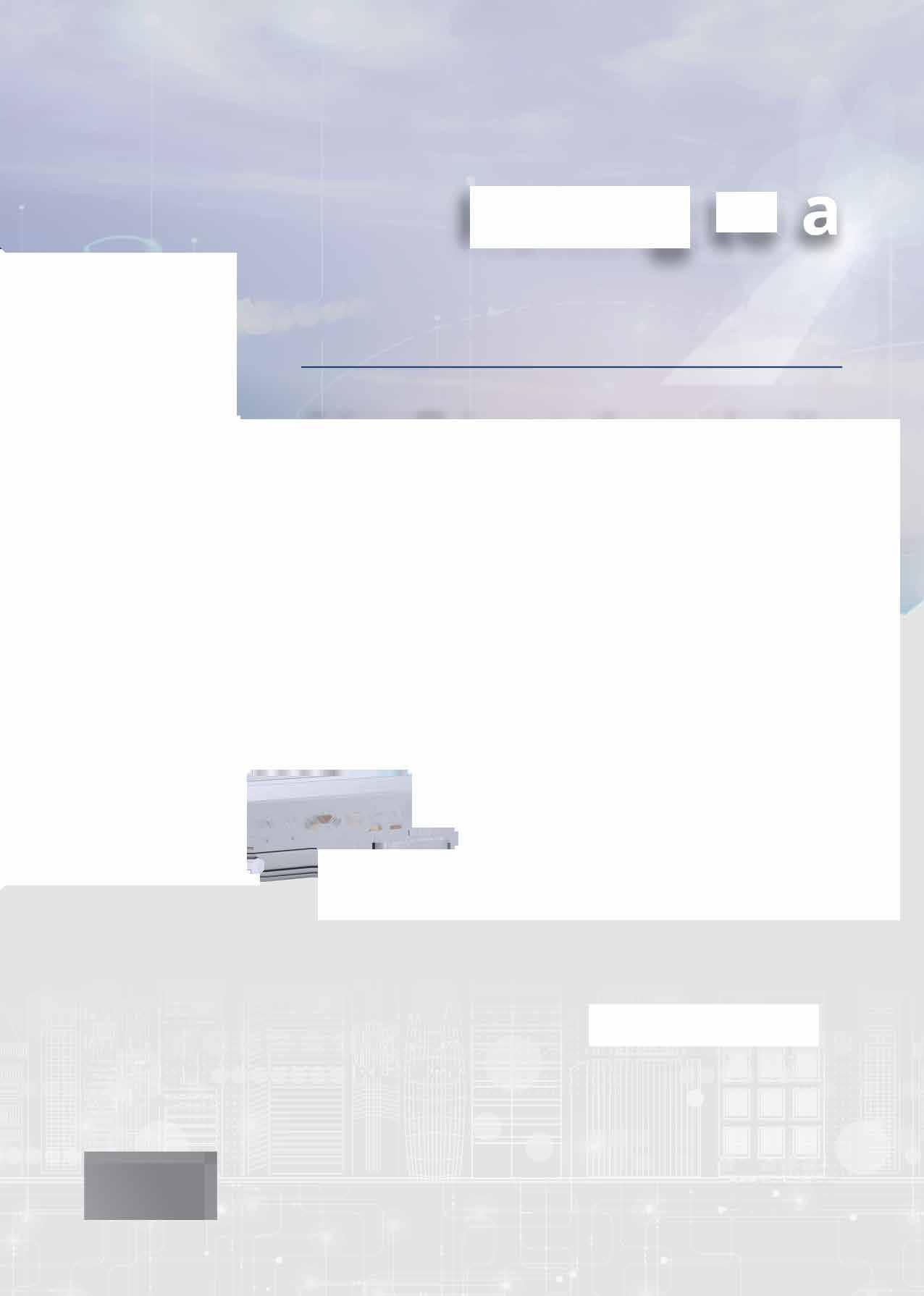
Inside the Signalling Academy
Dave Hersey, Technical Director at National Infrastructure Solutions (NIS), lifts the lid on the company’s new Signalling Academy in the Black Country and explains why it was only made possible thanks to the backing of rail employers
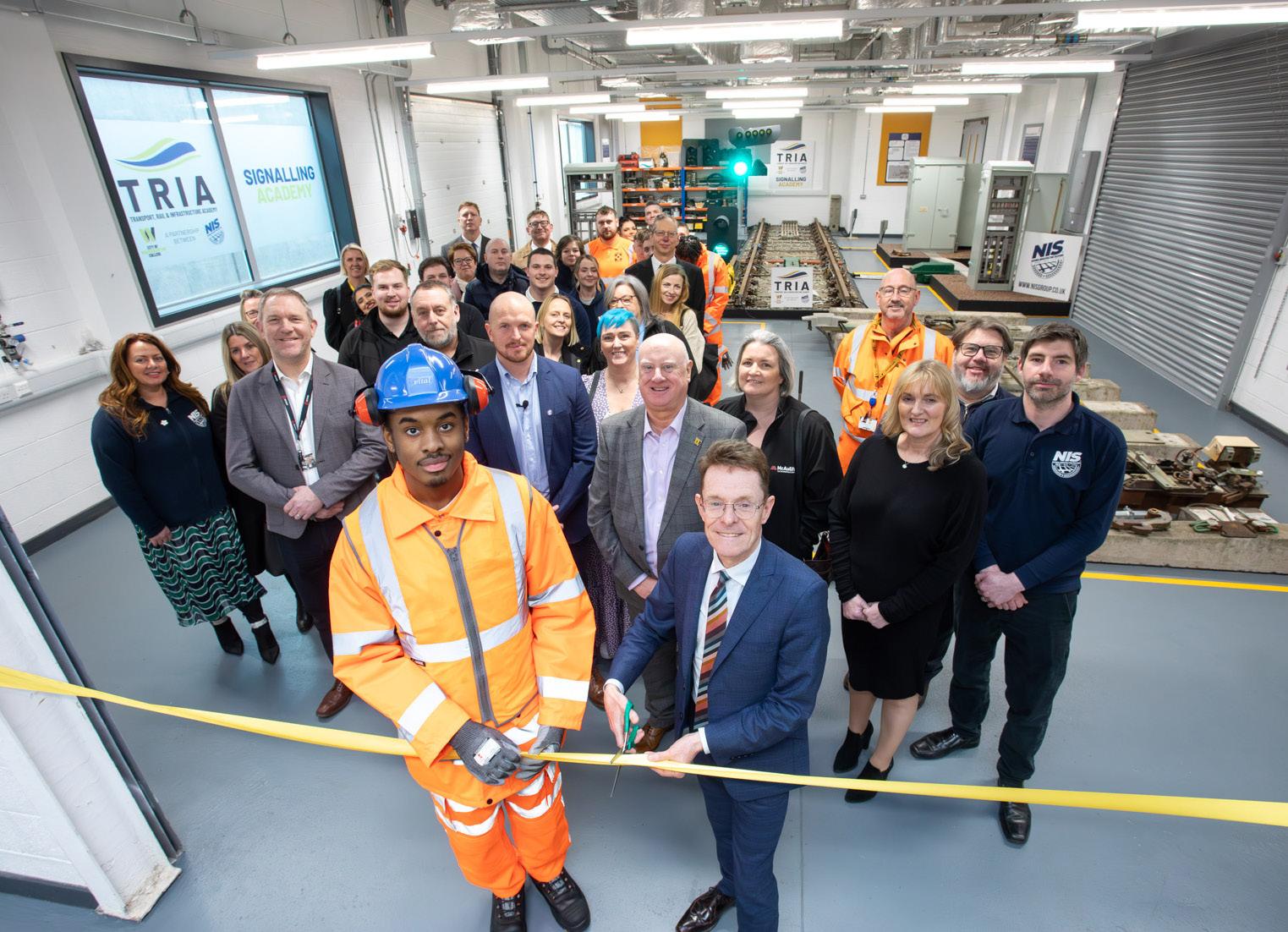
There was a lot of excitement and media spotlight at the recent launch of the Transport, Rail and Infrastructure Academy (TRIA), a milestone moment for National Infrastructure Solutions (NIS) and our strategic partners.
More than one hundred industry delegates listened to the Mayor of the West Midlands outline the importance of this venture that will see us take over part of the Black Country Innovative Manufacturing Organisation (BCIMO)'s Very Light Rail National Innovation Centre in Dudley.
To support residents into good jobs in rail, the West Midlands Combined Authority (WMCA) is investing £1.1 million to create 432 training places and this will deliver the entry and advanced skills people require to gain sustainable jobs.
Moreover, it also marks the creation of a wider brand that will help us move into new regions, with additional sites also in the process of opening in Aston and Coventry, with early conversations also taking place in the East Midlands and Wales.
However, TRIA represented the culmination of a personal project for myself
that consumed my working life for more than three months.
Our new Signalling Academy at BCIMO has been a real painstaking love affair that has involved several members of the NIS team and reflects the strength of our relationship with employers.
People in the signalling profession have a wealth of knowledge, honed through years of experience on the track. Unfortunately, the workforce is ageing and with more experts starting to retire there is an urgent need for ‘fresh blood’ and young people beginning to learn the discipline.
This skillset was identified as a priority for companies involved in track maintenance and they have backed it by contributing over £250,000 worth of industry equipment for our learners to use.
It was imperative that employers felt they were being listened to from day one and could tailor some of the modules of training we were going to deliver – in essence, this would ensure staff could fit seamlessly into sustainable jobs and have a positive impact on site and on track.
All equipment is configured in the same way as the real-world; therefore, students can see it, work on it, and understand it as it would be on site, accelerating the familiarisation of the track assets process considerably.
The Academy can deliver high-level, technical training, but the initial focus will be on getting people started in signalling and giving them basic skills and a flavour of what is involved – before moving through NIS’ skills escalator.
It’s an approach that has already worked in lots of other rail related roles, with 88 per cent of our 2,000 learners to date going on to gain employment.
Below is a guide to what you can expect from The Signalling Academy.
Plain Line
In the section on plain line, we have two Track Circuits separated by an IBJ. This is the most common method of train detection, which shows how train positions are identified back to the Signaller. The type of track connections (cables to rails) used in both Track Circuits are deliberately different to show the older (but still commonplace) and newer styles.
The bonding around the fish plates is also varied to show the types used in third rail, overhead line equipment and nonelectrified track.
The track also includes AWS (Automatic Warning System) and TPWS (Train Protection and Warning System), which are in use on most infrastructure to warn train drivers of upcoming speed reductions and to stop the train if the driver is going too fast.
Another use for this track is for nonSignalling courses, such as the practical element of PTS courses and, thanks to a section of third rail, it is ideal for the practical training of the DCCR course.
Signals
Signals are everywhere on the railway and play a critical role in telling the drivers whether they can go at full speed (green), slow down (yellow) or stop (red). We have three signals to show a full sequence: GreenYellow-Red, with them all acting together.
The third signal also has a Route Indicator. We have positioned the third signal on a Collis collapsible structure that are becoming more commonplace, as they allow the signal to be easily brought down to the ground rather than staff working at height.
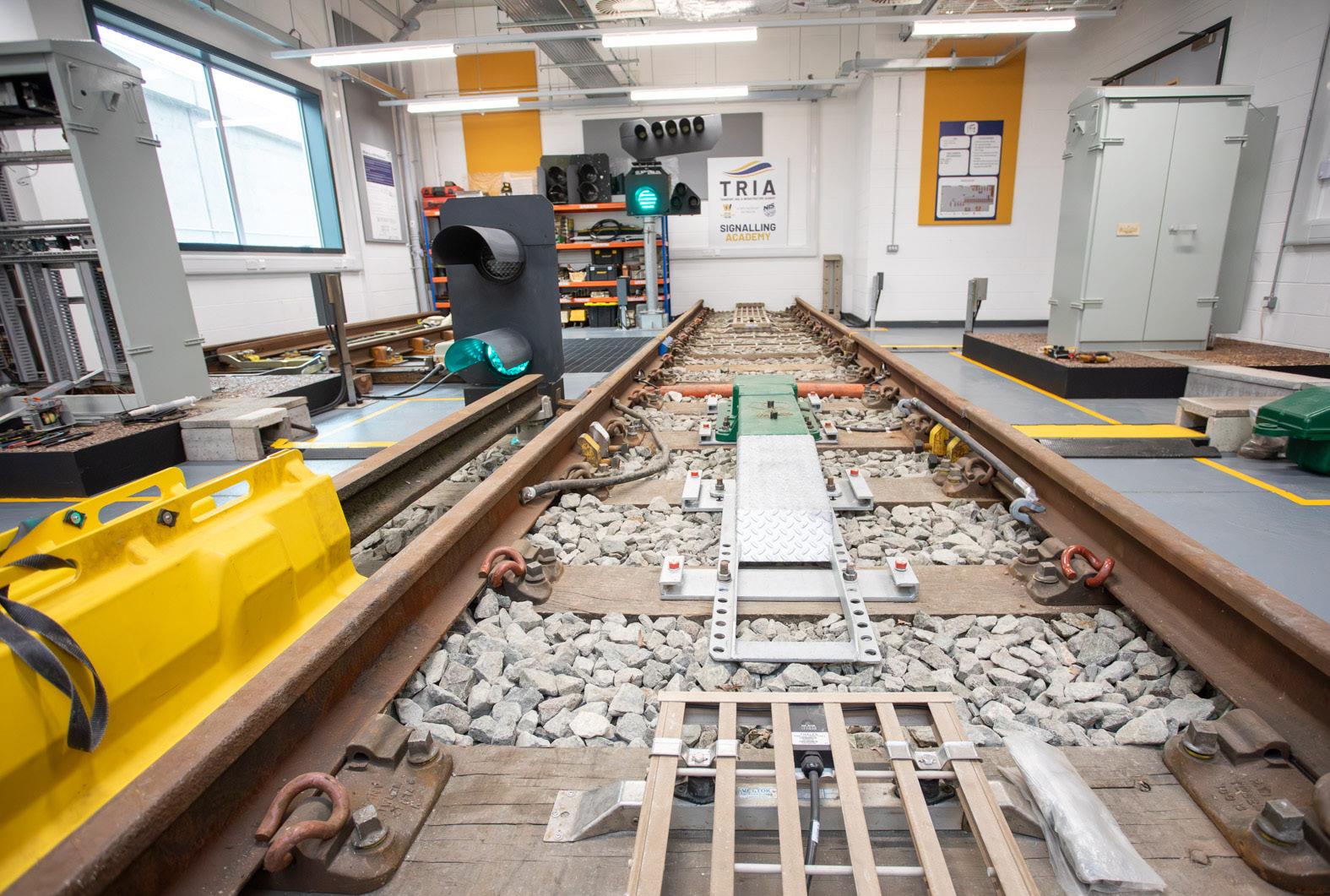
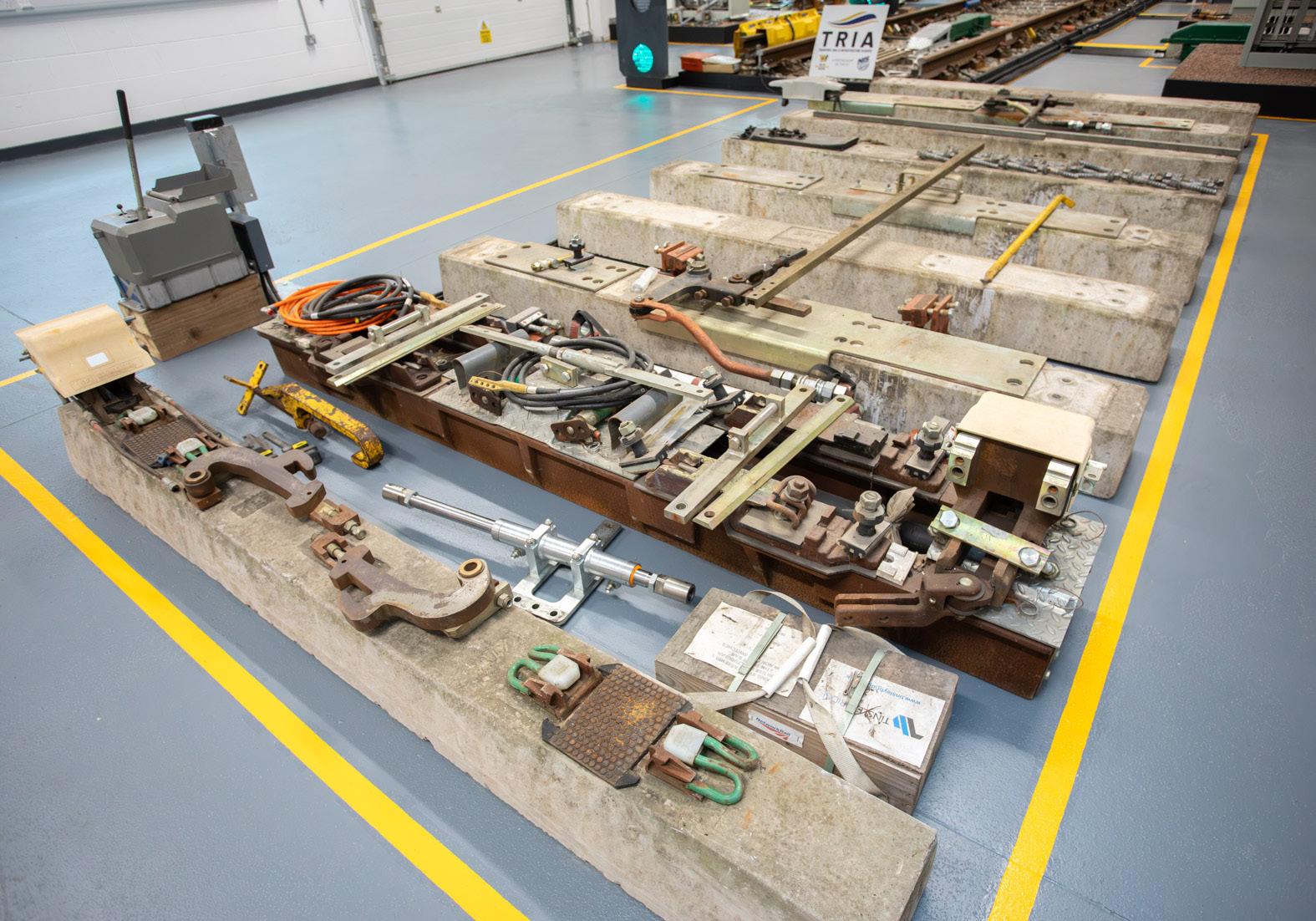
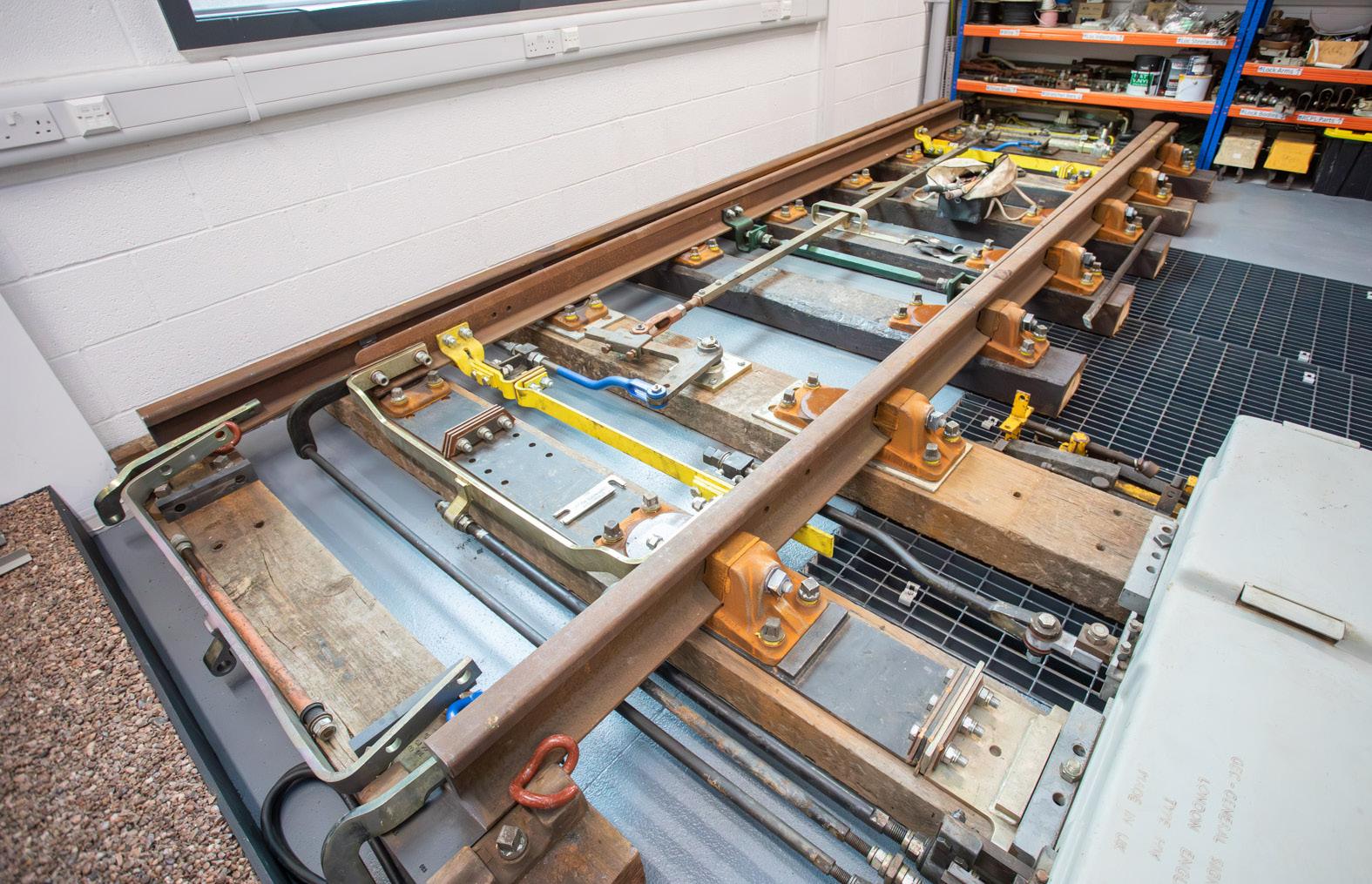
Location Cases (Locs)
The two full cases and one-half case are the connection point for all the cables coming back from the other equipment (points, signals, track circuits, AWS, TPWS).
They contain the different power supplies, fuses, and relays, with the latter allowing the systems to be interlocked, ensuring that one thing cannot happen if another thing doesn’t happen first.
For example, if the track circuit is interrupted (dropped) by something across the rails, the signal will turn to red as that means a train would be in section and the next train can’t come forward and the TPWS would activate to stop the train if it did.
The internal wiring of all three cases is deliberately different, using older and newer types of wiring and connections to illustrate the differences.
Dis-boxes are used for some of the cables running from the equipment to the Location Cases – these are used as an interface for cables that would run miles along the track in a protected route and then come to the surface to meet with equipment.
The dis-boxes give a point of connecting multiple cables, a point of testing and fault finding and reduces the need for longer lengths of cable to be renewed if damage occurs.
HW Points + Full Depth layout
HW Points, although first released in the late 1950s, are still pretty much the same today with a few internal components being improved, but the functionality and installation remaining the same.
They are still being installed brand new today all over the network. The Full Depth layout (switch and stock rails) is the type that has been used for decades but is still common for lower speed lines and use specific types of Stretcher Bars and fittings. This layout was selected to show these fittings.
IBCL Points + Shallow Depth layout
In Bearer Clamp Locks (IBCL) are now the preferred type of points for new installations – although a newer version of the Mark 1 Clamp Locks, first introduced in the 1960s, they are still based on the same technology.
The Shallow Depth layout is used in a lot of lower speed lines, but will also support higher speed lines. The types of Stretcher Bars and fittings are also different to those for full Depth.
Dave Hersey is Technical Director at National Infrastructure Solutions (NIS)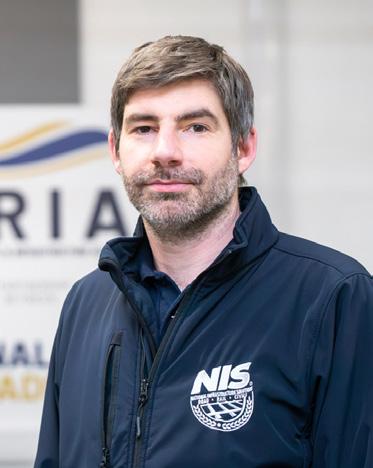
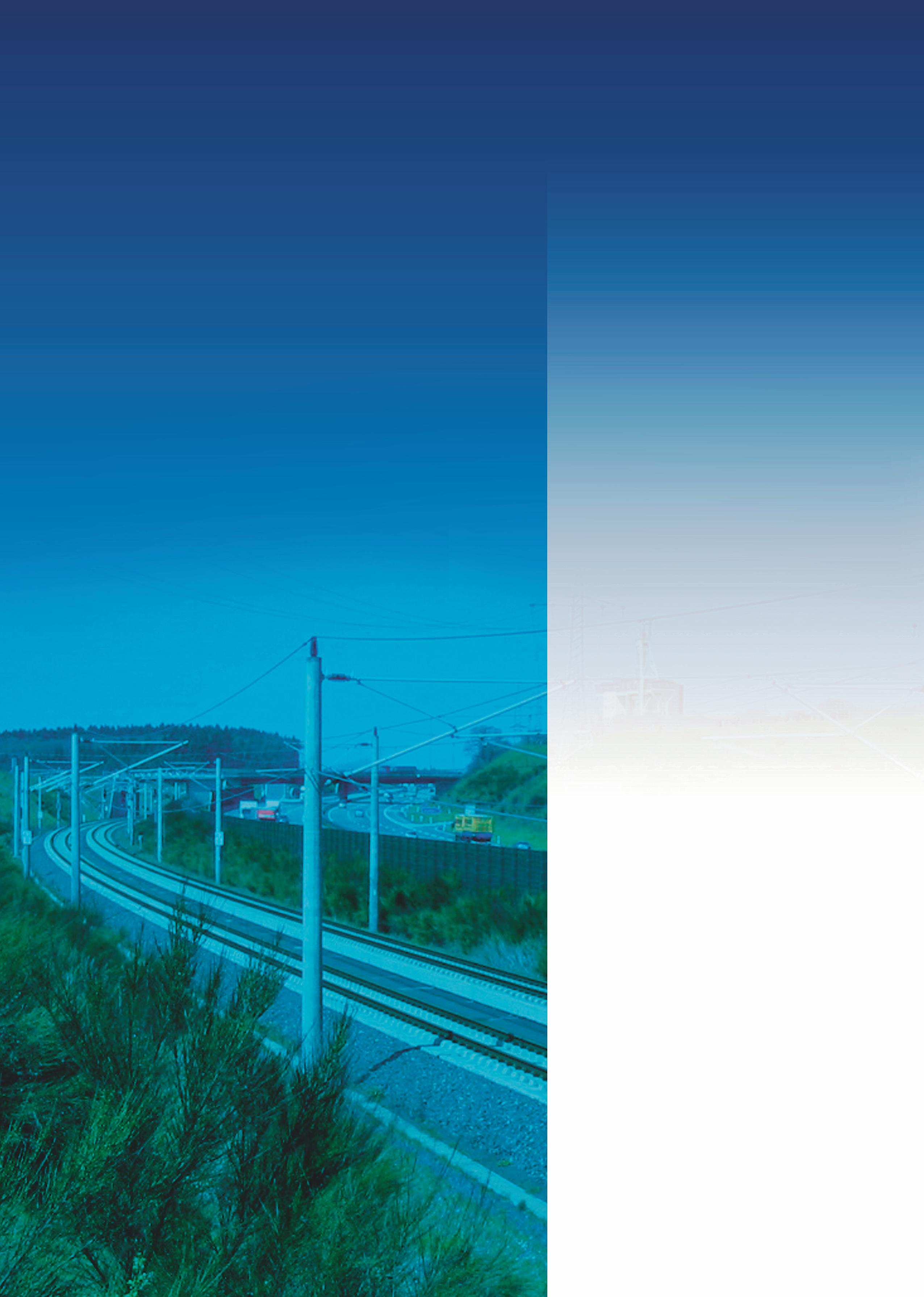
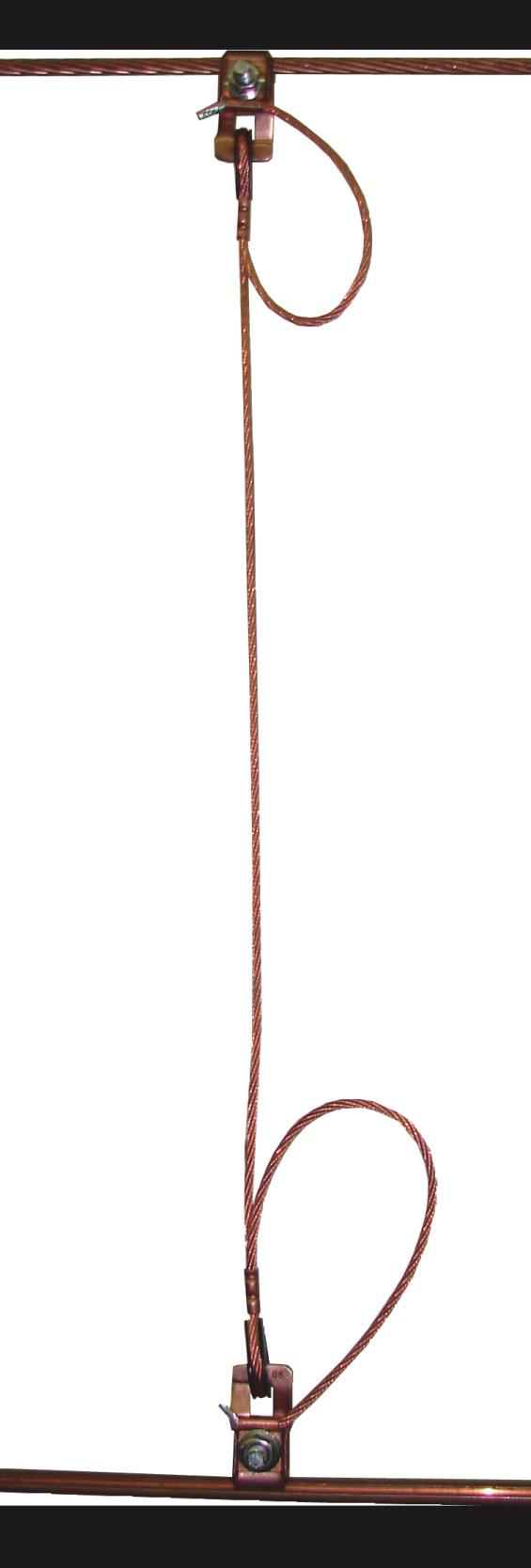
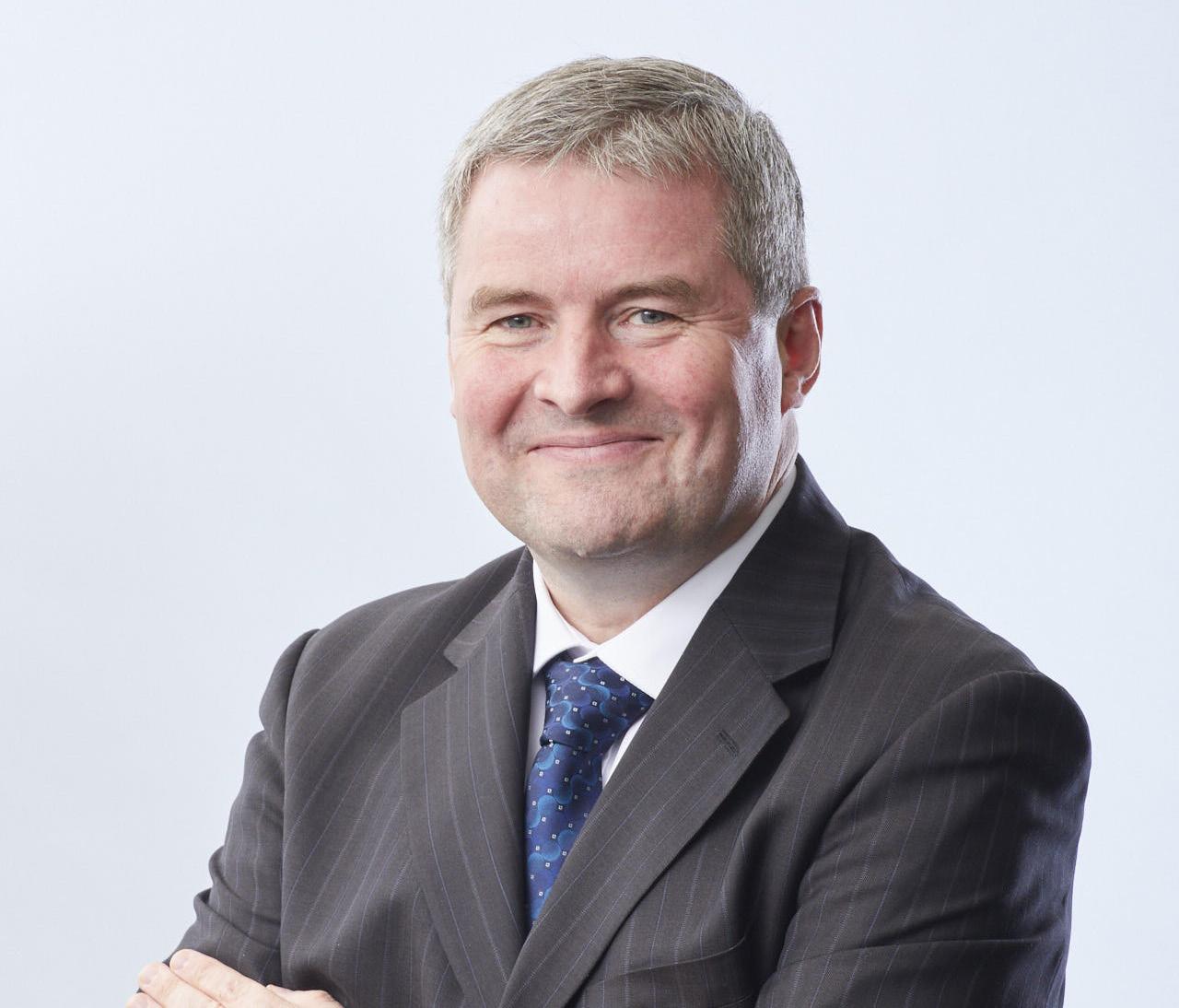
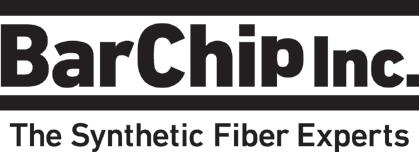
BARCHIP EMEA
Barchip is active in all kinds of civil infrastructure applications, typically in the rail industry it provides fibres for shotcrete, slab track and precast applications. The team has strong track record of delivering innovative and cost-effective solutions for complex and challenging projects across various sectors and geographies.
Want to know more about BarChip EMEA?
Tel: +353 (0) 1 4693197
Visit: www.barchip.com
Tell us about BarChip.
BarChip is a leading global manufacturer and supplier of macro synthetic fibre concrete reinforcement, specialising in high performance solutions for major infrastructure projects. BarChip fibre replaces steel reinforcement in concrete,
DENIS CREHAN MANAGING DIRECTOR OF BARCHIP EMEAAs the Managing Director of BarChip EMEA Ltd, Denis oversees the operations and strategy of the Europe Mid-East and Africa (EMEA) region for BarChip Inc. a global leader in the manufacturer of synthetic fibre reinforcement for concrete.
eliminating corrosion, reducing construction time and cost, improving crack control, and lowering carbon footprint.
BarChip is a wholly owned subsidiary of Hagihara Industries, a global leader in flat yarn and plastic extrusion technologies. Hagihara was founded in Japan in 1962 producing PE monofilaments for the local Okayama market and is today listed on the First Section of the Tokyo Stock Exchange with annual revenue of nearly 30 billion Yen (£157 million).
In recent years, BarChip has been investing considerable effort into the railway industry, developing solutions for fibre reinforced railway track slab. Eliminating steel reinforcement from track slab delivers many benefits, including reduced construction time and labour costs, reduced carbon footprint, improved crack control and reduced current leakage. These benefits have seen BarChip used in metro & light rail projects across Europe, Asia, America and Australia.
‘BarChip has been established as the fibre of choice in
rail track slab having successfully reinforced New York Metro, Halkali Metro in Turkey, Sydney metro, Parramatta light rail, Cross River Rail, Bukit Berapit, Osaka High Speed
Rail and more.’
What was the inspiration behind starting BarChip?
BarChip was introduced to market in the mid 1990s with a simple vision to eliminate the corrosion of steel reinforcement in concrete, with the initial target being the Australian mining industry. Steel fibre was commonly used in shotcrete ground support for mining excavations, but the extreme ground conditions and corrosive environments resulted in significant corrosion issues.
BarChip macro synthetic fibre is an inert material made from virgin polypropylene and will never suffer from corrosion. With the simple switch from steel to synthetic fibre reinforcement, mines were able to eliminate corrosion from their ground support reinforcement. Only a decade after being introduced, one hundred per cent of underground mines in Australia had transitioned from steel fibre to synthetic fibre reinforcement, establishing the BarChip brand on the market and provided a launching pad for BarChip to enter other regions and markets.
What types of products and services do you offer?
BarChip specializes in manufacturing high-performance macro synthetic fiber reinforcement for concrete, replacing traditional steel reinforcement. Our innovative fibres offer a multitude of advantages, including enhanced construction efficiencies, improved durability, cost reduction, and superior performance.
The BarChip fibre range includes BarChip48, globally renowned for its superior performance at low deflections and the preferred fibre in applications like railway track slab and segmental tunnel linings.
BarChip MQ58 has a unique multi-strand design that delivers a fiber-free finish in flooring applications. The patented design also delivers the same level of plastic shrinkage reduction as regular doses of micro fibre while being able to replace 2 layers of steel mesh or steel fibre in both jointed and jointless industrial floor slabs.
BarChip R-Series is made with recycled materials for low carbon reinforcement solutions and excels in shotcrete applications requiring performance at large deformations. Beyond simply supplying fibres, BarChip provides comprehensive support from fiber selection, engineering design and construction support, leveraging nearly three decades of experience and a global team of experts, all offered for free to every customer.
Has the market grown since the company was established?
In the early days, growth was mainly driven by increased adoption in the mining industry, but there was always a focus on the wider concrete industry. BarChip invested considerable resources developing fibres for civil applications and educating the wider engineering community, which has allowed BarChip to enter most sectors of the concrete industry. BarChip also opened offices in Europe, North and South America and Asia, in a major step towards the multinational corporation it is now.
Today, fibre reinforced concrete is widely accepted in most global construction markets, with multiple codes and guidelines existing. While the mining, infrastructure and flooring markets would be the most common place to see fibre, adoption is growing in all regions and across all sectors.
Which sectors do you work in?
BarChip’s impact in the wider construction market resonates globally, having reinforced more than 450 civil tunnels, major mine developments, over nine million square metres of industrial flooring, precast concrete, roadway paving and many other applications. Today, BarChip is used in nearly every sector of the construction industry.
In the last decade the use of BarChip in fibre reinforced railway track slab has gained significant momentum. Installing steel mesh in track slab is a time consuming and tedious process. By using BarChip fibre this entire process is removed, reducing construction time and cost along with the standard performance and durability benefits you can expect with a fibre reinforced solution. As an added benefit for rail track slab, BarChip synthetic fibres reduce the risk of
stray current leakage, a welcome benefit to contractors and designers.
Built in 2005, The Docklands Light Rail in the UK was the first use of synthetic fibre in a track slab in Europe. This project demonstrated the benefits to the wider community and was quickly followed with Szeged Light Rail in Hungary. Today, BarChip has been established as the fibre of choice in rail track having successfully reinforced New York Metro, Halkali Metro in Turkey, Sydney metro, Parramatta light rail, Cross River Rail, Bukit Berapit, Osaka High Speed Rail, PCAT and more.
What kind of challenges did you face in the early days?
For a new product to be successful it needs to solve a problem or deliver a service. Luckily, BarChip did both when it launched in the mining industry. The main challenge was proving synthetic fibre could match the performance of steel reinforcement. The mining industry has a large capacity for selfregulation and once customers believed in the performance it could be quickly adopted. The real challenge was in the transition to the broader construction market.
As a new product class, macro synthetic fibre was not included in any construction codes or guidelines. It was almost always misclassified as a micro synthetic fibre and for those who understood steel fibre at least, they did not understand the difference between the fibre classes. Educating the market and getting into codes was by far the biggest challenge when moving into the civil market. A challenge that is still ongoing.
Today, macro synthetic fibre is recognized around the world by the likes of British Standards, Concrete Society, CE, Rilem, ASTM, fib, American Concrete Institute, Australian Concrete Institute and more. Regardless of your concrete application, you can find a national standard or design guideline to fall back on.
How have the products and services you offer developed over the years?
The mechanics of macro synthetic fibres wasn’t really understood in the 1990s. The product was there to eliminate corrosion and the only thing that needed to be achieved was to match steel fibre performance. Since then the amount of research and understanding of different fibre characteristics has been tremendous. From bonding mechanisms to fibre shapes, tensile strengths, material composition and even manufacturing processes, every aspect of BarChip fibre has been analysed. Since our first fibre, BarChip has reduced dose rates by 70 per cent while increasing performance by 219 per cent.
This performance increase combined with unique fibres designed for specific applications has allowed BarChip to replace steel reinforcement in applications like precast segmental tunnelling linings,
jointless flooring, high deformation shotcrete and precast track slab.
What are some standout projects you’ve been involved in over the years?
Constructed in 2023, Parramatta Light Rail in Sydney, Australia, demonstrated both the cost and environmental benefits BarChip fibre could deliver. The highlight of the project was the 12-kilometre two-way light rail track and supporting works, including 16 light rail stops.
Contractors Downer & CPB Contractors were heavily focussed on sustainability, and this led them to specifying BarChip as a replacement for steel bar in the track slab. Eliminated the steel installation reduced labour costs by around 15 per cent and also reduced the overall construction time. BarChip was also able to reduce the carbon footprint by 4,815 tonnes of CO2e which was a significant contribution to the projects overall achievement of 28 per cent reduction in embodied carbon emissions in materials use.
What types of companies do you collaborate on projects with?
BarChip users are a who’s who of top tier global engineering and construction firms, including Rio Tinto, BHP, Newcrest, Vale, Freeport, Anglo America, Cadelco, Barrick, Jacobs, Acciona, Kiewit, CPB, AECOM. However, the benefits of BarChip’s fiber technology extend far beyond these industry giants. Local governments, general contractors, and firms of all sizes worldwide also leverage BarChip fibres to enhance their projects. Whether it’s reinforcing railway track slabs, precast concrete elements, or a local footpath, BarChip’s innovative solutions offer sustainable alternatives to traditional steel reinforcement.
What are some of the biggest challenges this sector currently faces?
Achieving Net Zero carbon on major infrastructure is one of the biggest challenges for the industry and requires analysis of every product and service in the supply chain. BarChip fibre can play its part in helping contractors achieve their targets, without sacrificing performance or adding costs.
BarChip’s adoption aligns with the construction sector's strategic shift towards low carbon materials and methods by reducing the reliance on conventional steel reinforcement, notorious for its high carbon footprint. Furthermore, BarChip’s durability and longevity contribute to lowering lifecycle emissions by minimizing maintenance and repair needs.
Overall, the increased use of BarChip represents another step towards low carbon railway infrastructure, offering both environmental benefits and long-term cost savings.
Low Cost, Low Carbon Concrete Track Slab with BarChip Fibre
• 15% Reduction in Labour Cost
• 4,815 Tonne Reduction in CO2e
• 96% Reduction in Fresh Water Consumption
• 86% Reduction in Non-Renewable Energy Consumption
• Simplified Construction Process
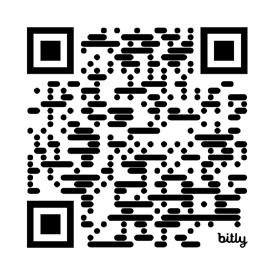
Eliminate Steel From You Concrete Track Slab Scan to find out more
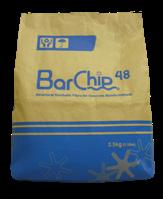
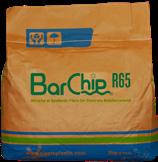
www.barchip.com
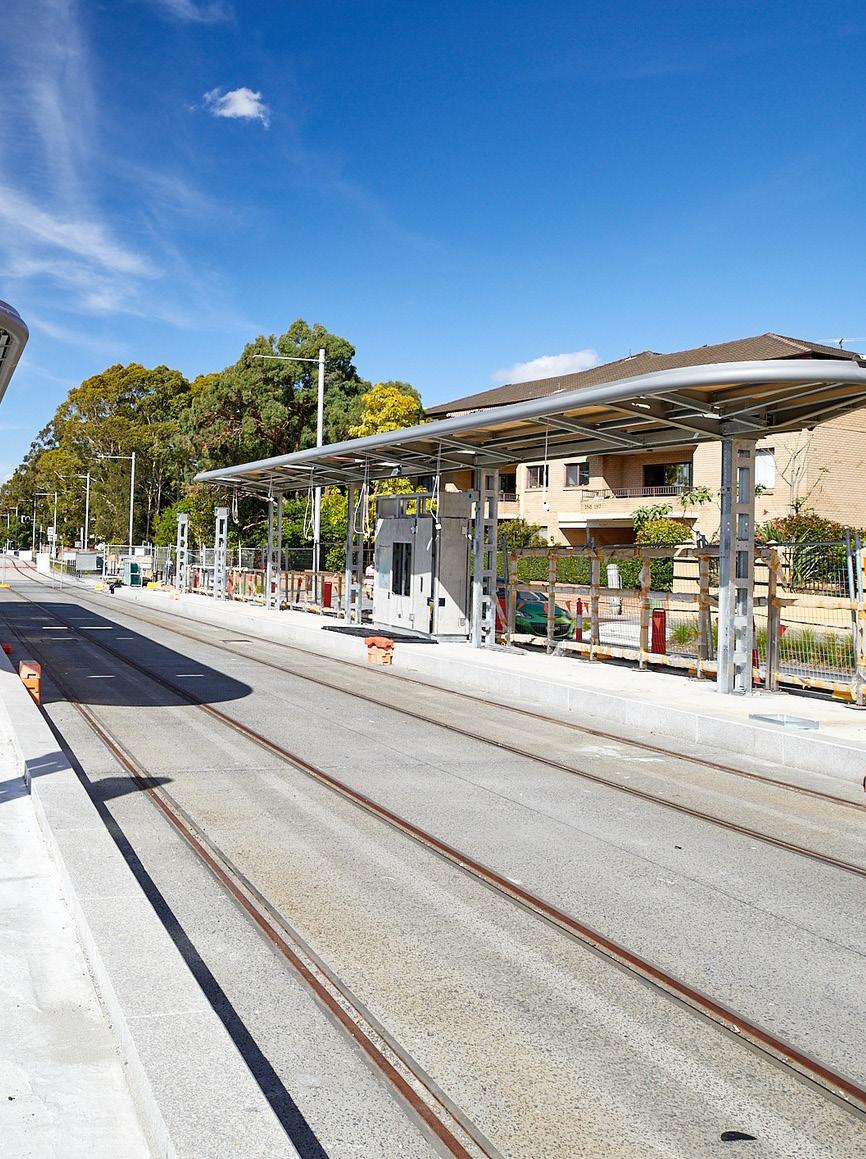

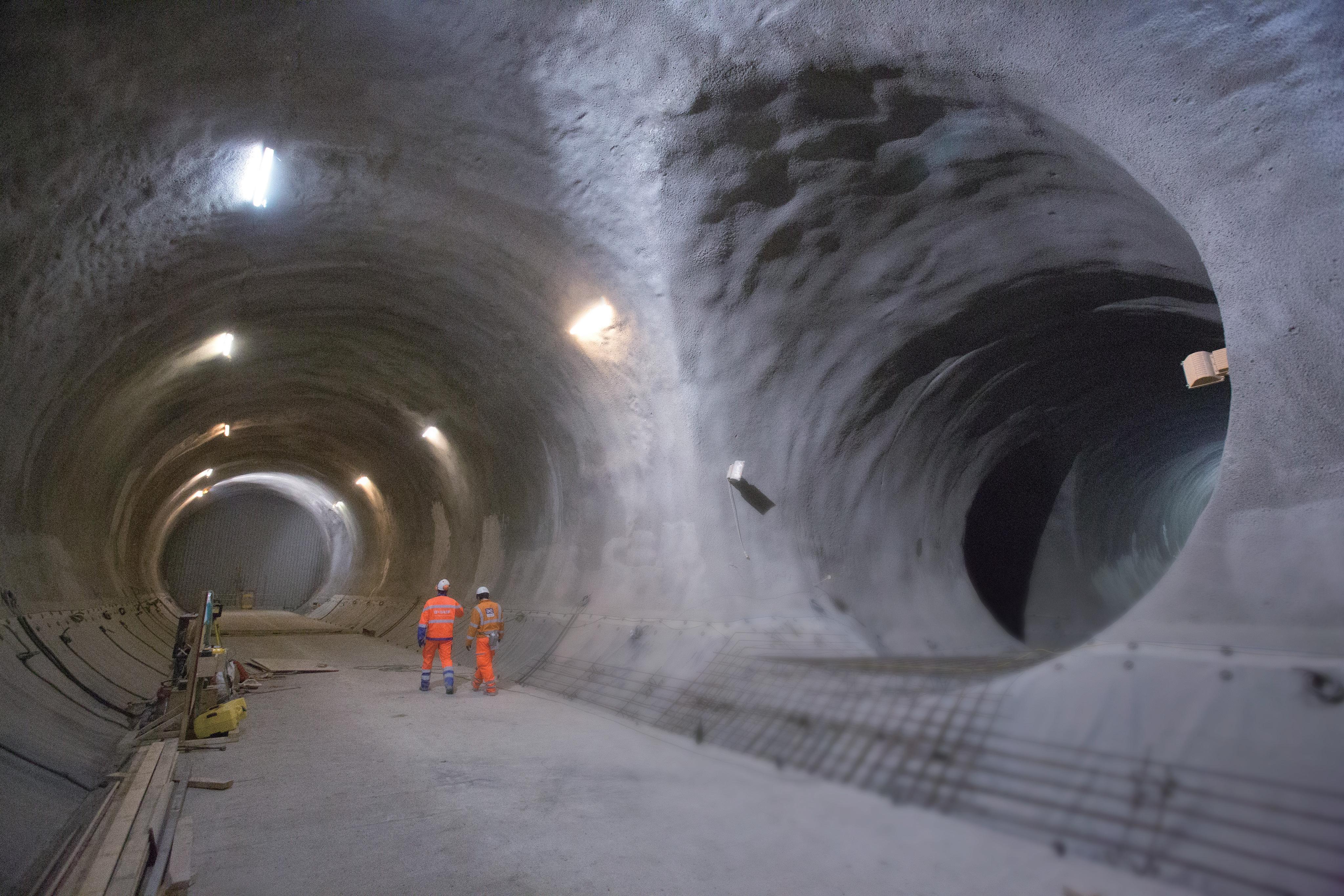
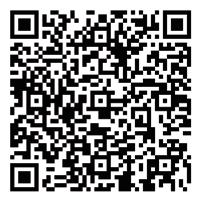
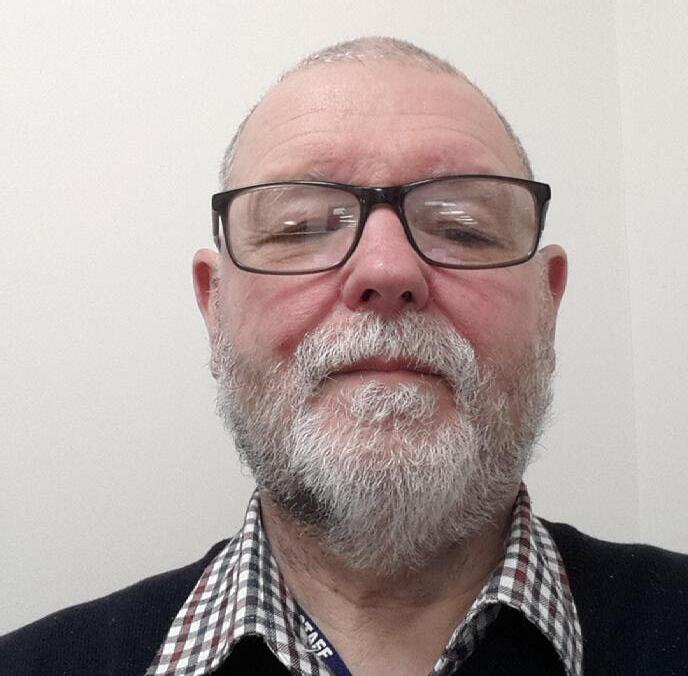
JOHN GREENHALGH
SALES MANAGER UK & IRELAND AT BEKAERT BRADFORD UK LTD (NV BEKAERT SA)
John joined the industry in the early 1970s and has been in the construction industry ever since, working for three major companies all tied to the construction industry. He has mainly worked in the South West of England, occasionally in Scotland and for the last 30 years or so in and around London involved with the major tunnelling projects.
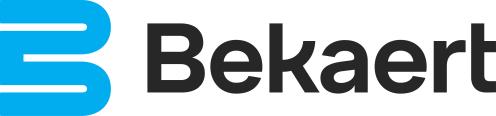
BEKAERT BRADFORD UK LTD (NV BEKAERT SA)
Founded in 1880 and headquartered in Belgium, Bekaert (Euronext Brussels, BEKB) is a global market and technology leader in material science of steel wire transformation and coating technologies.
Want to know more about Bekaert?
Tel: 07771-834241
Email: john.greenhalgh@ bekaert.com
Visit: www.bekaert.com/dramix
Address: Bekaert Bradford UK Ltd Park House Road, Low Moor Bradford, West Yorkshire BD12 0QB
Tell us about your career before you joined Bekaert – NV Bekaert SA – Now Bradford Ltd.
I received a sponsorship to attend the CITB operated Civil Engineering Collage (CECOL) at Bircham Newton in Norfolk in 1973 from George Wimpey Ltd. The one-year course was designed to provide the trainees and students with practical knowledge of the many skills required for the civil engineering industry, these ranged from scaffolding to steel fixing and bar bending, concrete production to laying concrete, pipe laying and formwork erection and dismantling, sheet piling.
So you would go into the classroom and were taught the theory and the terminology and the actual ‘how’ to do the operation and then as a gang you went out onto the training grounds and actually did it. Yes, you got your hands dirty and the programme was laid out so another gang would follow you and they would then complete their particular operation or item of work.
The trainees/students were split into working gangs of six operatives who worked together as a complete unit and so team bonding was important to make it work, this was promoted through sports in local leagues and we all had to complete one month’s outward bound at one of the four centres in various parts of the country, I ended up in Scotland in January.
Once my year was complete my now employer George Wimpey shipped me off to their department in Bristol and my first project was the new High Speed Diesel Depot at St Phillips Marsh that was built for the new APT train.
What challenges have you faced in the industry?
I brought a new type of concrete reinforcement to the industry that until then had only been seen by university academics used in concrete technology research, but never sold commercially into the UK concrete/construction market. So it was a shock to many that you could reduce the volume of concrete required to construct a ground supported floor slab as this was the main application for steel fibre reinforced concrete at the time and the manufacturers and suppliers of the traditional reinforcement steel and fabric meshes and the most of the flooring contractors laughed at the idea.
However through research and development with large scale testing of ground supported floors we were able to demonstrate the performance was equal to and sometime exceeded the traditional fabric mesh reinforcement solution with other technical benefits. We made progress with one or two flooring contractors who had seen the use of steel fibre reinforced concrete slabs in Europe where this type of reinforcement had been in use for some ten to twelve years already.
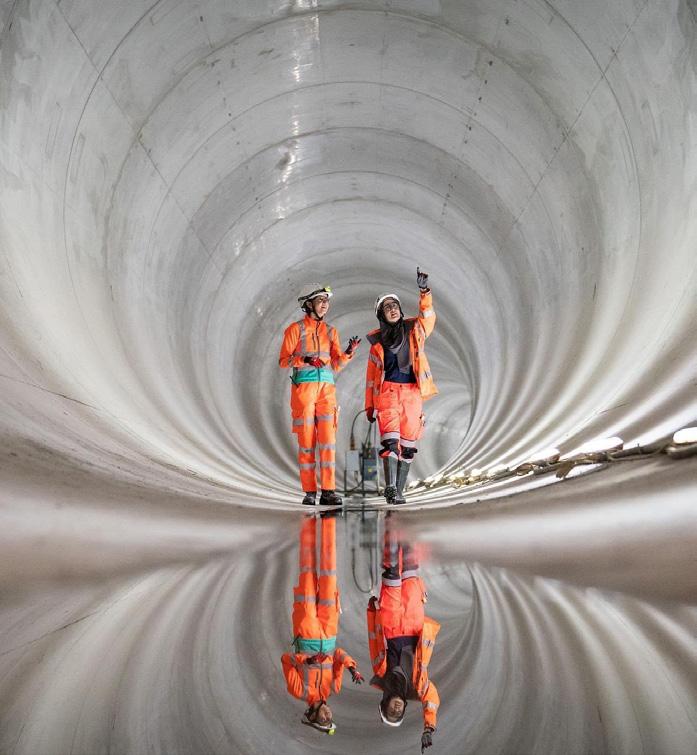
Also a few designers had begun to take notice of the published work regarding the research and as for myself attending a number of Concrete Society events with several technical publications showing the test results we were able to create some positive interest amongst the industry and a number of small projects came along and these began to grow in size and a number of external slabs were done followed by internal slabs.
How has technology developed since you started in the industry?
The technology has come on leaps and bounds over the years and even more so in recent years with global research and development in many applications by using simple beam testing to large specimen testing for major projects.
We now have Euro-codes for specifying steel and synthetic fibres for use in sprayed concrete and for describing the method of testing beam samples and plates to assist with the design of elements and monitoring the performance of the material. The Federation of International Beton (FIB) have also produced documents relating to the design of steel fibre reinforced concrete segmental lining for tunnels which is now generally accepted by most tunnel designers, certainly in most of Western Europe but also in parts of North America and some countries in Asia.
Tell us about NA Bekaert Sa.
Bekaert (www.bekaert.com) the parent group was established 140 years ago in Belgium, the founder Leon Bekaert began by making barbed wire for local farmers to stop cattle and sheep from wandering off.
We are a global entity with an annual turnover of over €5 billion (£4.3 billion) in recent years. The department I am attached to have been operational for almost 50 years producing the Dramix steel wire fibres for concrete reinforcement. The first application was for ground supported floors slabs for warehouse, factories and external
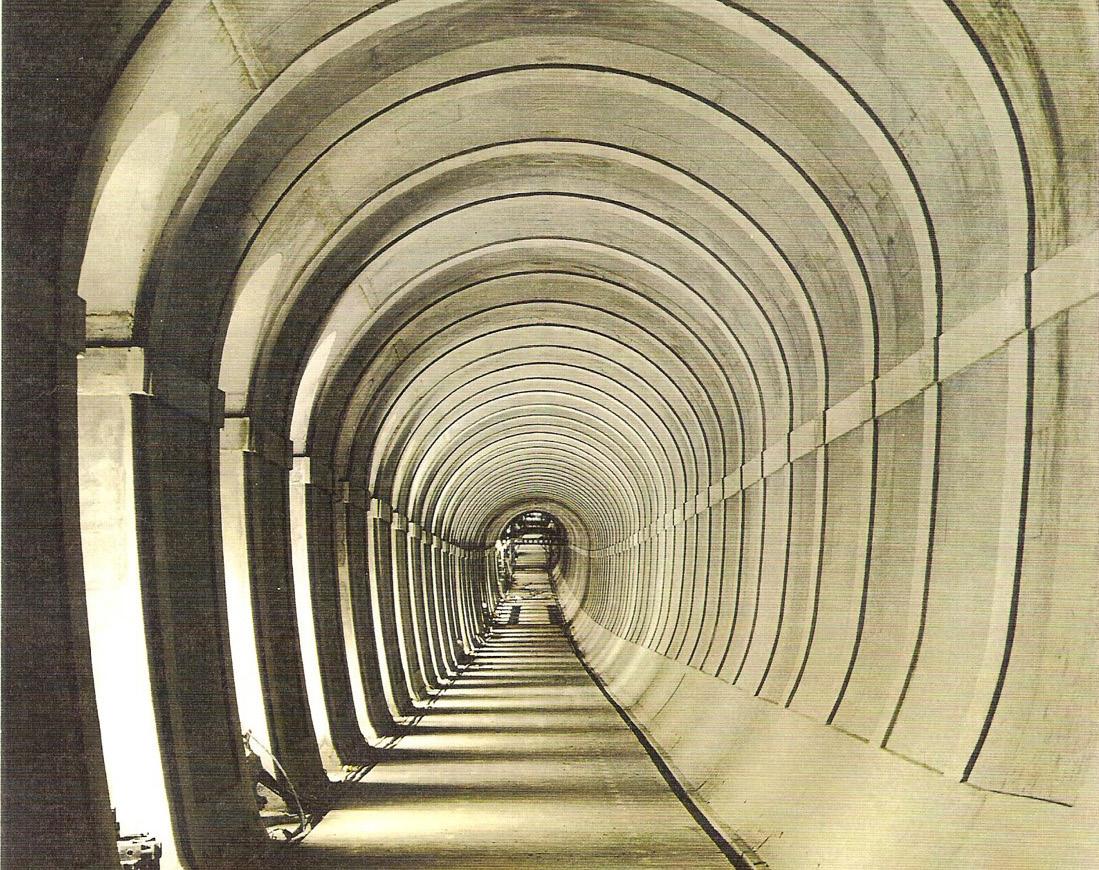
hardstanding and pavements – tunnels came a little later in the late 1980s. The first passenger tunnel was an extension to the Naples metro in 1993 and the first steel fibre tunnel in the UK was at London Heathrow Airport. This was the baggage tunnel that ran from Terminal 4 to the CTA or Central Terminal Area which was built by Miller Tunnelling now Morgan Sindall and was some 4.54 metres in diameter and 1.4 kilometres long – in fact this design was used for the extension to the Piccadilly into the Terminal 5 area and the extension of the Heathrow Express was also designed and built with the steel fibres as well.
Bekaert’s work is based on metal transformation mainly by drawing wire rod of various types and materials to be utilised in many products, I can guarantee every reader has most probably used or will use an item with Bekaert wire in it at some point.
We manufacture over 30 per cent of the reinforcement of vehicle tyre around the world so say one tyre on every car has Bekaert wire in it. Other products that use our wire include conveyor belt reinforcement and hydraulic hoses and many household products to industrial products such as gas burners in domestic and industrial boilers to shopping baskets and trollies, we don’t make the actual baskets and trollies but the chrome coated wire and one more product that everyone will have used or have been present is the wire that holds in the cork on bottle of sparkling wine.
Which sectors do you work in?
In the UK we work mainly in tunnelling. Our first real venture into the passenger based market was a section of the Jubilee Line extension in the mid 1990s, and then two sections of the Channel Tunnel Rail Link (CTRL) which is now HS1 or the Eurostar service into St Pancras and at the same time the extension out of St Pancras was also built. Other major tunnels using steel fibres were the Northern Line extension and very recently the Silvertown Road Tunnel and the currently ongoing construction Chiltern Rail Tunnels for the HS2 project under the Align JV. As well as steel fibres in the running tunnels, steel fibres are also being used on
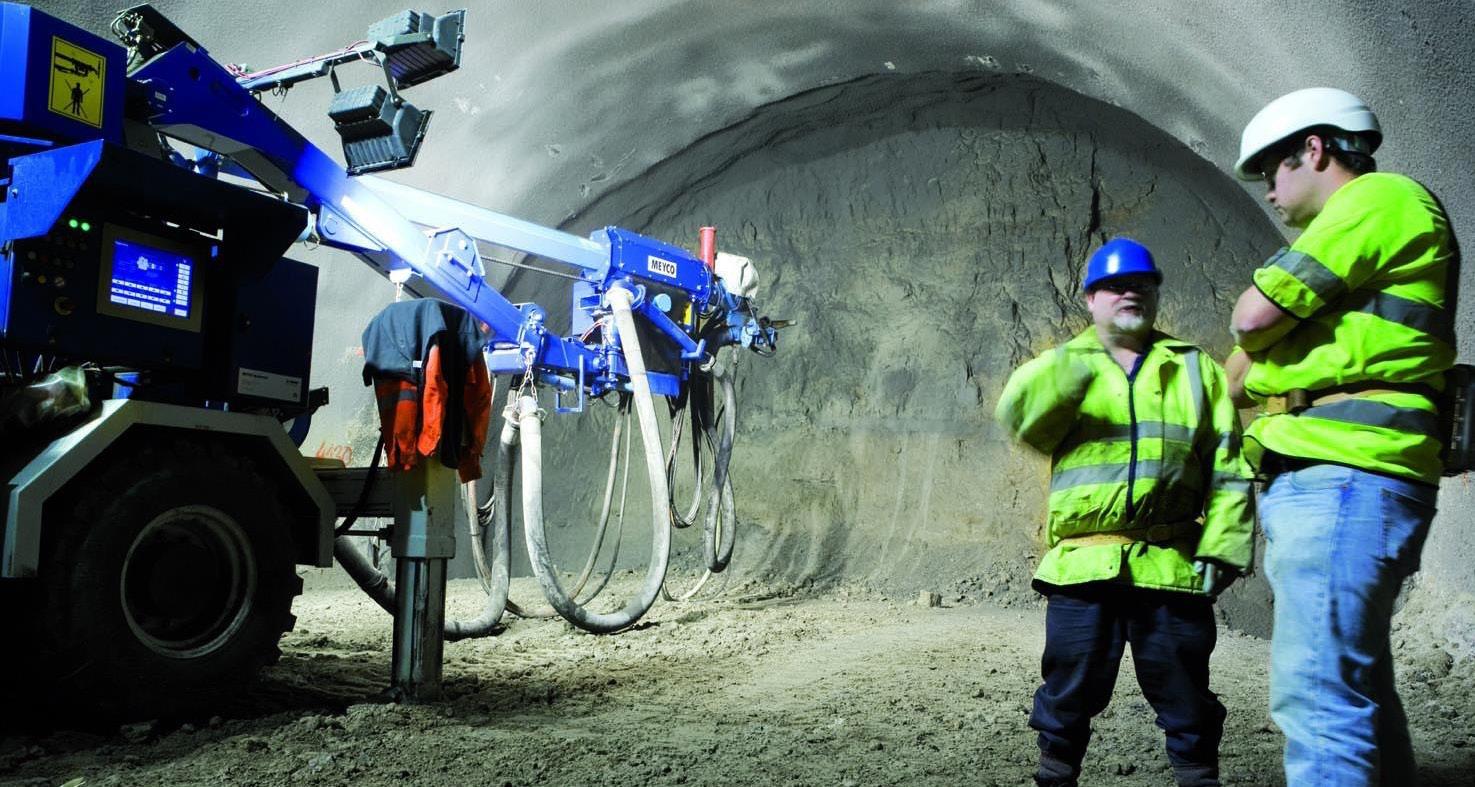
Steel fibres are incorporated in all sorts of tunnels such as utility, road, rail and metro tunnels. Dramix® steel fiber concrete reinforcement ensures the safety and reliability of underground concrete structures such as precast tunnel linings, castin-situ linings and permanent spray concrete lining.
this project in the crossover passages in sprayed concrete, plus the current HS2 works in sprayed concrete at Victoria Road with the JV of SCS in the tunnel linings.
What is your Unique Selling Point?
Originally it was the potential for saving concrete and traditional reinforcements such as fabric mesh in floor slabs, this horrified the ready mixed concrete companies as they just saw the volumes being reduced, it took some time to get them to think about the potential added value and so by including steel fibres they could actually make as much or even more revenue for less volume of concrete produced and delivered.
This was also the case to some degree in sprayed concrete linings, but this was more of a safety issue by removing the need of fabric mesh and the operatives having sometimes to place the fabric mesh in newly excavated areas and so by using steel fibres in the sprayed concrete they were actually spraying a ready reinforced concrete from a distance and in safety.
What eventually followed was the removal of the reinforcement cages from tunnel segmental linings and we’re able to make these savings in concrete and traditional steel reinforcements by substantially reducing the carbon content/ embodied energy in the concrete element of the project. This also saves time and construction costs and reduces the potential damage to the tunnel rings as steel fibre concrete is very resistant to impact damage when handling and storing the tunnel segments during the ring build.
By now being able to reduce the potential damage to these precast concrete elements, the need to repair these is thus reducing the potential carbon being consumed during the repair operations not only in the repair materials but also the access to the higher parts of the tunnel and the manpower required along with the additional financial burden.
How have the products and services you offer developed over the years?
Our steel fibres under the trade name of Dramix have been improved to provide a much better performance in the various applications in the market by increasing the tensile wire strength from 1100mpa to 1800 – 2200mpa in some of the fibres. We have changed the anchorage basis of the hooked ends that help resist the pull out of the fibres from the matrix of the concrete and so provide the bending softening behaviours but now we have Dramix steel fibres that will provide a bending hardening behaviour in some concrete applications as well as reducing the thickness of the concrete element/section.
What are your views on collaborative working?
Bekaert have always worked with several partners over the decades in many areas of our global activity. Not only in the construction industry but also in other areas of activity across our vast portfolio ranging from the automotive industry to rubber reinforcement for such items as vehicle tyre reinforcement, to electric vehicle charging points, wire for springs in chairs and beds to hydrogen energy, and in construction we also produce asphalt reinforcement and masonry reinforcement and render reinforcement, coated wire for products as ring binders and chain link fencing and countless more products – all have been researched with industry partners, universities and industry members. We also support students in their degree work and we hope they have gone on to achieve their goals in their working lives.
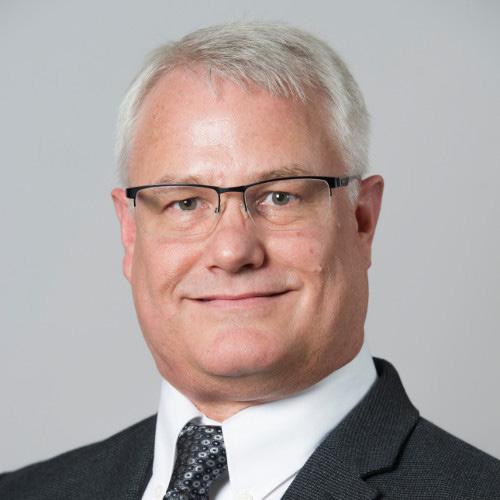
Alan
Kinsey is Country Manager, UK & Ireland at Opengear
Smart Strategies for UK Railway Cyber-resilience
Alan Kinsey, Country Manager, UK & Ireland at Opengear on the risks inherent in digital transformation
The railway sector's ongoing digital transformation, incorporating IoT, cloud computing, AI, and data analytics, promises to enhance operations, maintenance, routing, and passenger experiences. However, it also introduces new cybersecurity risks. In response, the industry is channelling more resources and money into protecting its data, systems and networks from emerging threats.
According to recent statistics from Market Research Guru, the global railway cybersecurity market size was valued at over $7.1 billion (£5.7 billion) in 2022 and is expected to expand at a compound annual growth rate (CAGR) of 8.65 per cent during the forecast period, reaching $11.8 billion (£9.5 billion) by 2028. These are figures that reflect increasing concerns about cybersecurity on the railways.
According to a study by rail cybersecurity firm Cylus, the rail industry has seen a surge in cyberattacks, with incidents rising by 220 per cent in the five years to 2022, resulting in financial losses amounting to billions of dollars globally.
In the UK, the potential threats to critical rail network infrastructure come from many sources. In April last year, the Government issued a heightened alert for critical infrastructure and services including railways due to potential threats from Russia-aligned attackers, suggesting railways were actively considered at risk.
Yet the threat to UK railways runs wider than that. In many ways, the issues coincide with those impacting businesses as whole. In recent Opengear research, 36 per cent of UK CIOs referenced ransomware as being among
the biggest threats to their organisation, with the same percentage referencing spam and phishing, and malware.
These are clearly among the biggest threats for railway networks also. The UK railway sector's increasing reliance on digital technologies for operations, maintenance, and customer services enlarges its attack surface. While technologies such as IoT, cloud computing, and automated control systems all improve efficiency and service, they also provide new vectors for malware and ransomware attacks. Furthermore, railways are especially susceptible to ransomware because they are considered critical national infrastructure, meaning disrupting these services can have significant societal and economic impacts.
Phishing attacks targeting the employees of rail operators are a significant threat to UK rail operators. Rail operations rely on access-controlled systems for essential functions. Gaining access to these systems through phishing can allow attackers to disrupt operations, steal sensitive information, or install malware.
To protect themselves effectively against cyber threats, rail operators need to focus on investing money in infrastructure and skills but that’s not easy for the cash-strapped sector, which, in common with many other industries, lacks funding and resources.
In the Opengear survey, UK engineers said that insufficient investments are increasing the risk of cyberattacks and/or downtime (38 per cent). This suggests that lack of budget spent on software upgrades and network upgrades, for example, leaves organisations vulnerable to attack and has the potential to affect business continuity.
‘36 per cent of UK CIOs referenced ransomware as being among the biggest threats to their organisation’
Finding a solution
In seeking to prevent cyberattacks, UK rail operators would be well advised to prioritise cost-effective cybersecurity measures. This includes employee training on cyber threats, implementing basic cyber hygiene practices like regular software updates, secure passwords, and multi-factor authentication.
Beyond this, however, rail operators need to ensure that they can get up and running again quickly in the event of an attack that brings their networks down. That’s where Out-of-Band Management (OOBM) comes in. OOBM refers to the use of a dedicated management channel for device, server, or network infrastructure administration, separate from the primary network or data channel used for everyday operations.
Smart Out-of-Band solutions enable organisations to manage their networks at all times from local and remote sites. This enables quick diagnosis and recovery without physical device access. By enhancing network resilience, Smart Out-of-Band ensures that rail operators can maintain visibility and control over their network infrastructure during cyberattacks.
This resilience is key to assessing the attack's scope, preventing further penetration, and systematically restoring network services. Using Smart Out-of-Band, rail operators can significantly improve their ability to respond to and recover from cyberattacks, minimising downtime and ensuring that rail services can be restored as quickly and securely as possible.
Steering towards cyber-resilience
As the UK railway sector navigates its journey to digital transformation, the escalation of cybersecurity threats demands both innovative and pragmatic responses. By prioritising cost-effective cybersecurity measures, including employee training and basic cyber hygiene, and leveraging technologies like Smart Out-of-Band for network resilience, rail operators can fortify their defences against an ever-evolving cyber threat landscape.
The strategic investment in these areas is not just about safeguarding operations but also about ensuring the continuity and reliability of services that are critical to the nation's infrastructure and economy, through active risk mitigation practices. Embracing these approaches will enable UK rail operators to not only mitigate the risks of cyberattacks but also recover swiftly and securely, minimising impact and upholding the trust of millions who rely on their services every day.
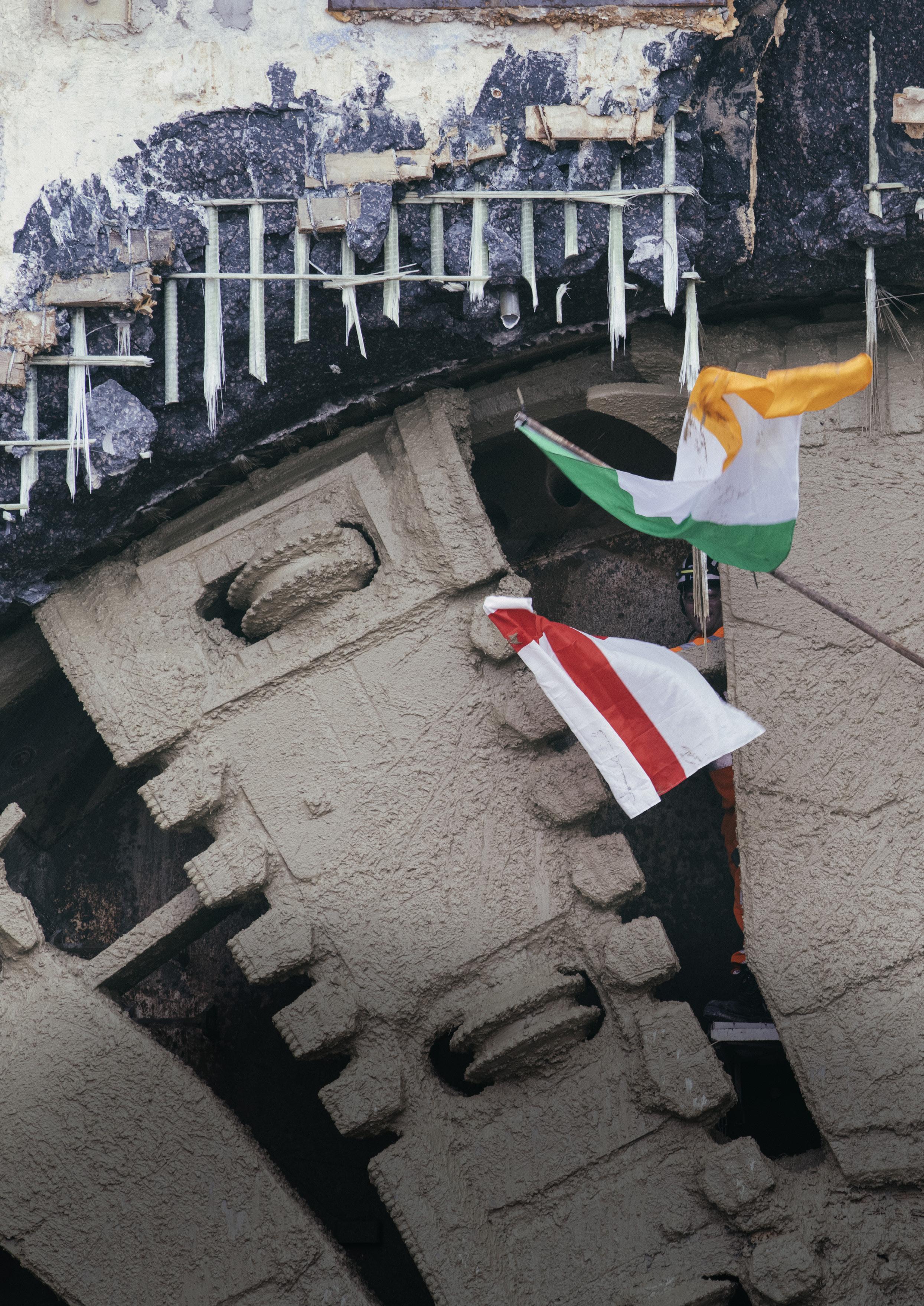
A Tale of Two Tunnels
Britain’s youngest tunnel came closer to reality in late March, whilst later this summer one of the country's oldest will receive essential repairs
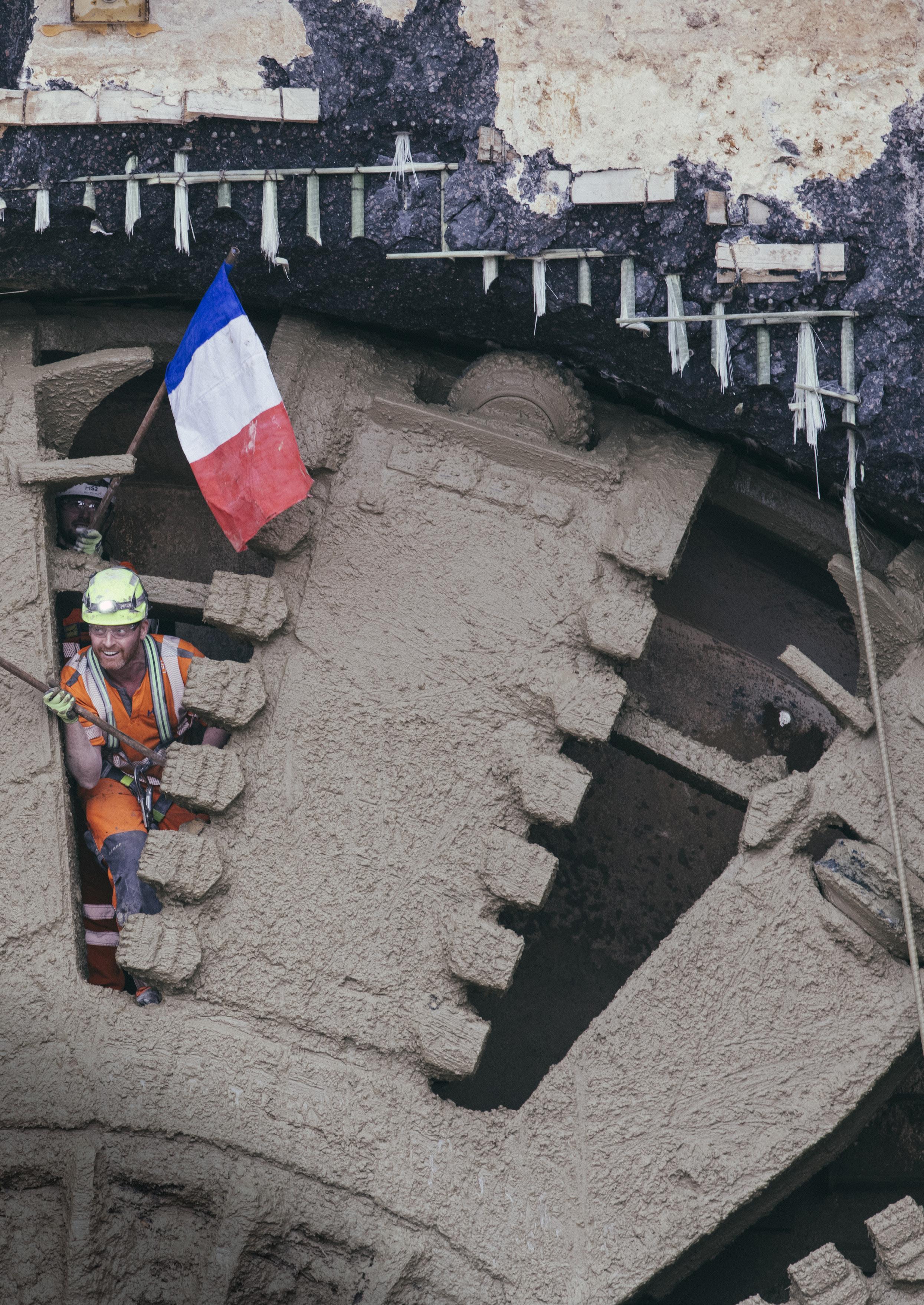
The second giant boring machine (TBM) building HS2 under the Chiltern Hills broke through at the tunnel’s northern portal in late March, completing a journey that began in June 2021. Meanwhile, in less than one month the Blackheath tunnel between Blackheath and Charlton will close as Network Rail begins £10 million of essential repairs to the 175-year-old Victorian-era structure.
Named Cecilia, the TBM has driven for ten miles underground to join twin sister machine – Florence. She arrived at the site near the Buckinghamshire town of Wendover on 27 February, after completing her adjacent tunnel drive.
Between them, the two 2,000 tonne machines have built the twin bore tunnel at depths of up to 80 metres and excavated three million cubic metres of chalk. Each machine operates like an underground factory, able to excavate the tunnels and line them with 56,000 pre-cast concrete tunnel segments, grouting them into place and moving forward at an average speed of 16 metres per day.
Compare this to the work being done on the Blackheath tunnel where Network Rail will replace tens of thousands of bricks damaged by the freezing and thawing of rainwater and install a new concrete tunnel lining to stop water leaking into the tunnel, which will be crucial for the reliable running of the railway long into the future.
They'll also strengthen several filled-in construction shafts that were used during the tunnel’s construction, rebuild drainage systems and carry out other essential track work including ‘wet bed’ removal –waterlogged sections of track that cause bumpy train rides for customers. These extra works will mean less disruption for passengers in the long term.
A closure of ten consecutive weeks is needed because carrying out work in cramped and narrow tunnels is incredibly difficult. If traditional weekend working was used, engineers would spend 50 per cent of the time available bringing materials

and plant in and out of the tunnel, leaving limited time for actual repair work.
When HS2 is operational trains will travel through the Chiltern tunnel – the line’s longest – at speeds of up to 200mph, helping to almost halve journey times between Britain’s two largest cities.
The new high-speed line will relieve traffic the West Coast Mainline, freeing up space for more local services on the most crowded part of the important Victorian route. It will almost double rail capacity between London and the West Midlands, providing a more reliable service and driving economic growth.
Both machines launched from the tunnel’s south portal, near the M25 motorway, were operated by HS2’s main works contractor, Align – a joint venture formed of three international infrastructure companies: Bouygues Travaux Publics, Sir Robert McAlpine, and VolkerFitzpatrick. The machines are made in Germany by TBM specialists Herrenknecht.
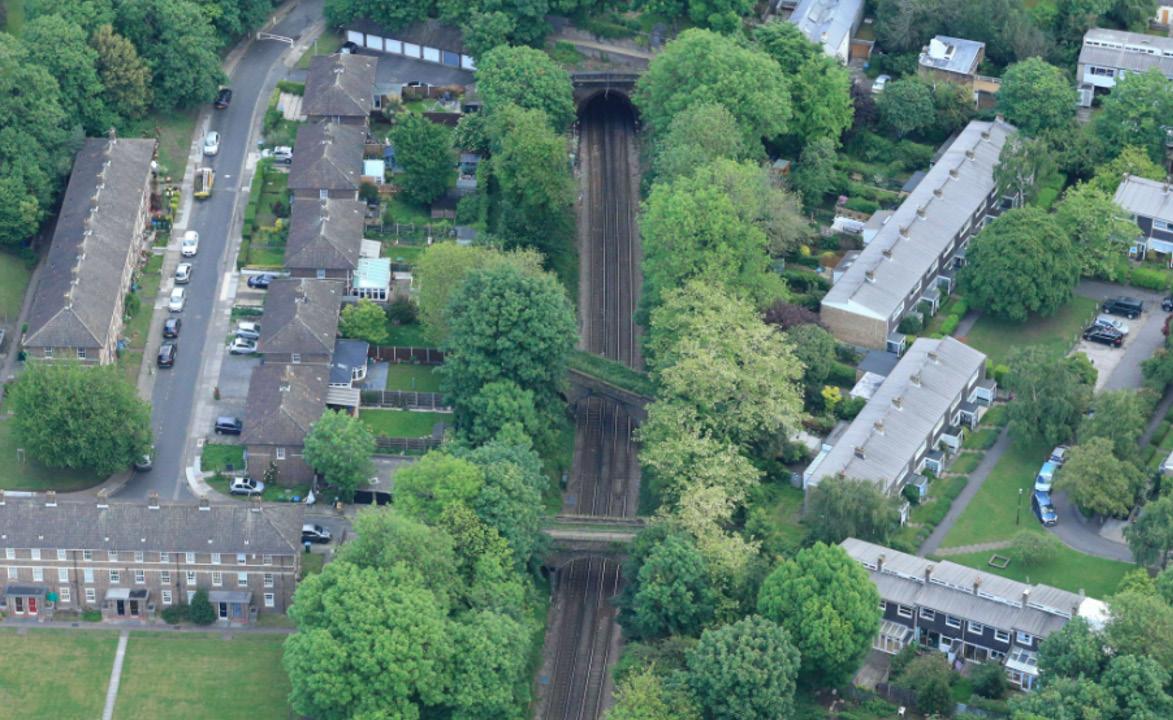
Each TBM is operated by a crew of around 17, working in shifts to keep the machines running when required 24/7. They are supported by over 100 people on the surface, managing the logistics and maintaining the smooth progress of the tunnelling operation.
In total over 450 people have worked on the tunnels over the last three years, including a dedicated production team who made 112,000 precision-engineered, fibrereinforced concrete tunnel wall segments on site at a purpose build temporary factory – and a team processing the spoil from the tunnels.
Completion of tunnelling under the Chilterns follows recent publication of HS2 Ltd research showing how high-speed line’s arrival in the West Midlands will give a £10 billion economic boost over the next decade, with new development around its stations at Birmingham’s Curzon Street and near the city’s airport and the NEC.
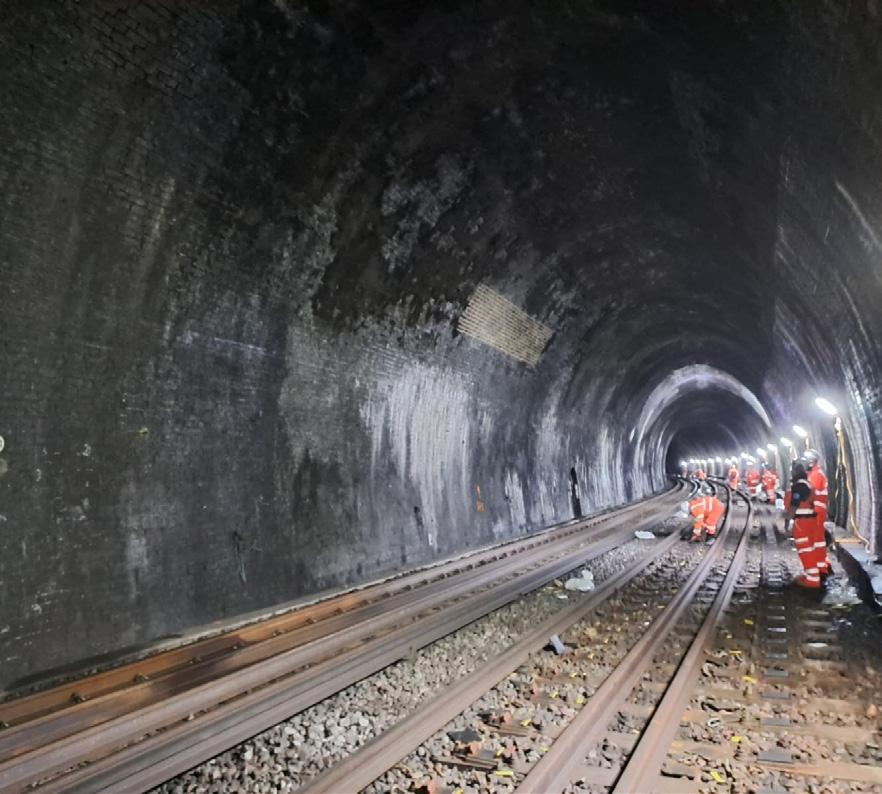


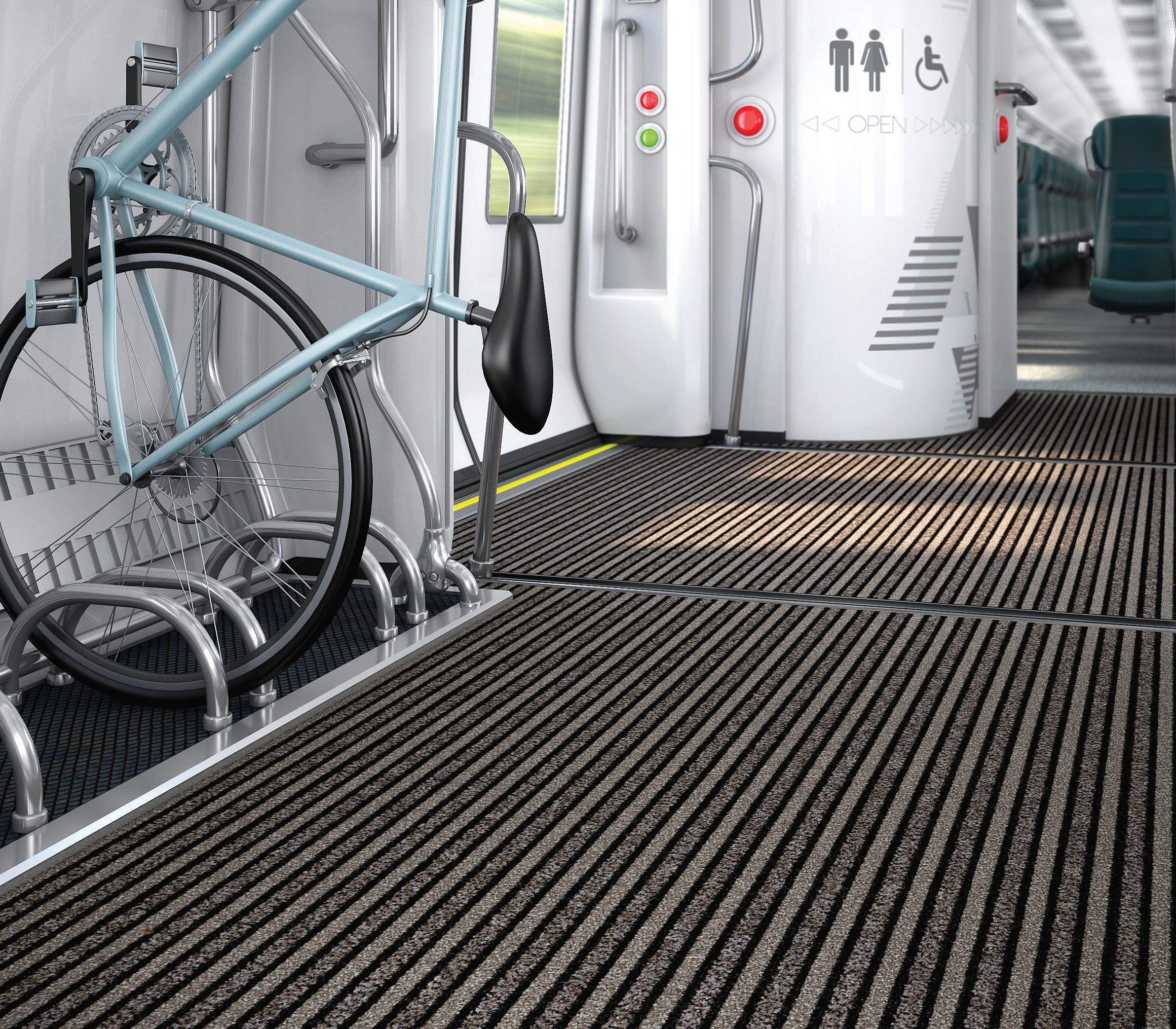
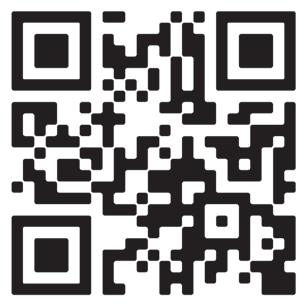
The Plant and Machinery Sector in 2024
The UK's largest rail plant exhibition will be taking place next month at the Long Marston Rail Innovation Centre, here we look at what is in store for the plant and machinery sector in 2024
Visitors to Rail Live 2024 will get to see cutting-edge innovation and technology in action with live plant demonstrations.
In response to Chancellor Jeremy Hunt’s Spring Budget earlier this year, Brian Jones, President of the Construction Plant-hire Association (CPA) said: ‘The announcement by the Chancellor in today’s Spring Budget, that the government will publish draft legislation to extend Full Expensing to assets for leasing when
fiscal conditions allow, is a positive step. However, it is vital we know what these fiscal conditions are and when they will be met.
‘We urgently need a timetable of action for this legislation that sets out when CPA members can invest with confidence in new equipment and boost business investment and productivity. The announcement to freeze fuel duty will be welcomed. With oil prices volatile, and the wider economic outlook still uncertain, this is a positive move.’
CPA Conference 2024
The CPA Conference 2024 will take place on Thursday 7 November 2024 at the Heart of England Conference and Events Centre in Fillongley near Coventry. The theme of the CPA Conference 2024 will be ‘Shaping the Future: Insights for the Plant-hire Sector’.
Last year’s conference looked at the challenges facing the plant-hire sector at a time of ongoing political and economic uncertainty. Solutions and strategies to address these issues were suggested in four

panel discussions during the event, chaired by former BBC news presenter Merryn Myatt who will return to host the 2024 edition alongside well-known content, social media and PR specialist, journalist and vlogger Peter Haddock.
Last year’s conference speakers were unanimous in the view that the Special Interest Groups played a key role in representing member interests and needs, especially at times of challenge and change – but individuals had to make their views known and get involved in a spirit of collaboration.
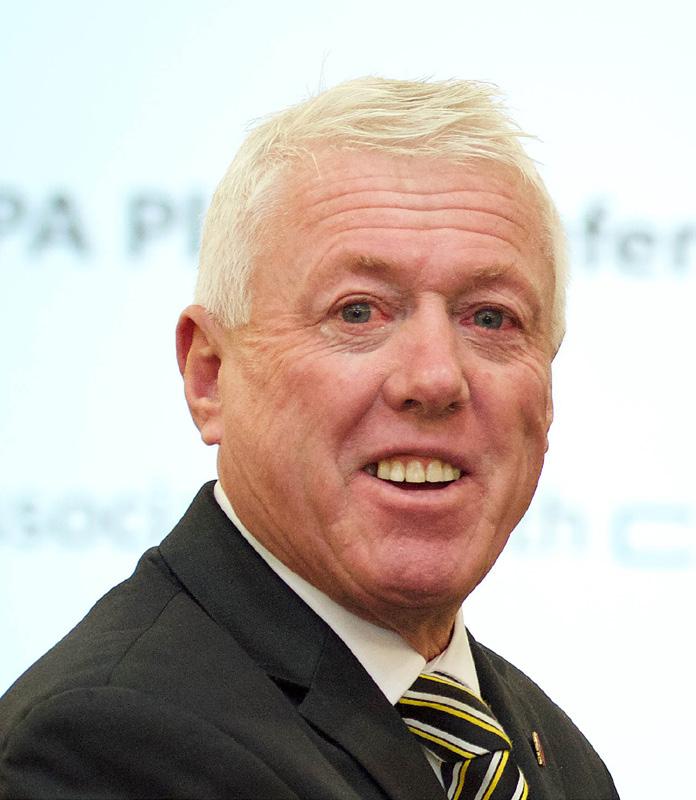
‘We urgently need a timetable of action for this legislation that sets out when CPA members can invest with confidence in new equipment and boost business investment and productivity. The announcement to freeze fuel duty will be welcomed. With oil prices volatile, and the wider economic outlook still uncertain, this is a positive move.’
Brian Jones, President of the Construction Plant-hire Association (CPA) ’
SCOTPLANT 2024
The most important event in the Scottish construction equipment industry calendar took place at the Royal Highland Centre, near Edinburgh at the end of April. With Scottish dealer Molson showcasing six XCMG machines for the first time at a Scottish trade show – a range of excavators and a wheel loader. The Marubeni-Komatsu stand featured nine of the latest Komatsu machines, including a wheeled excavator with a drastically reduced tail swing to meet the demands of safe and productive work on sites with limited space.
German manufacturing giant Liebherr celebrated its 75th anniversary by bringing with it a lineup that showcased the company’s range of equipment for the earthmoving, materials handling and crane sectors.
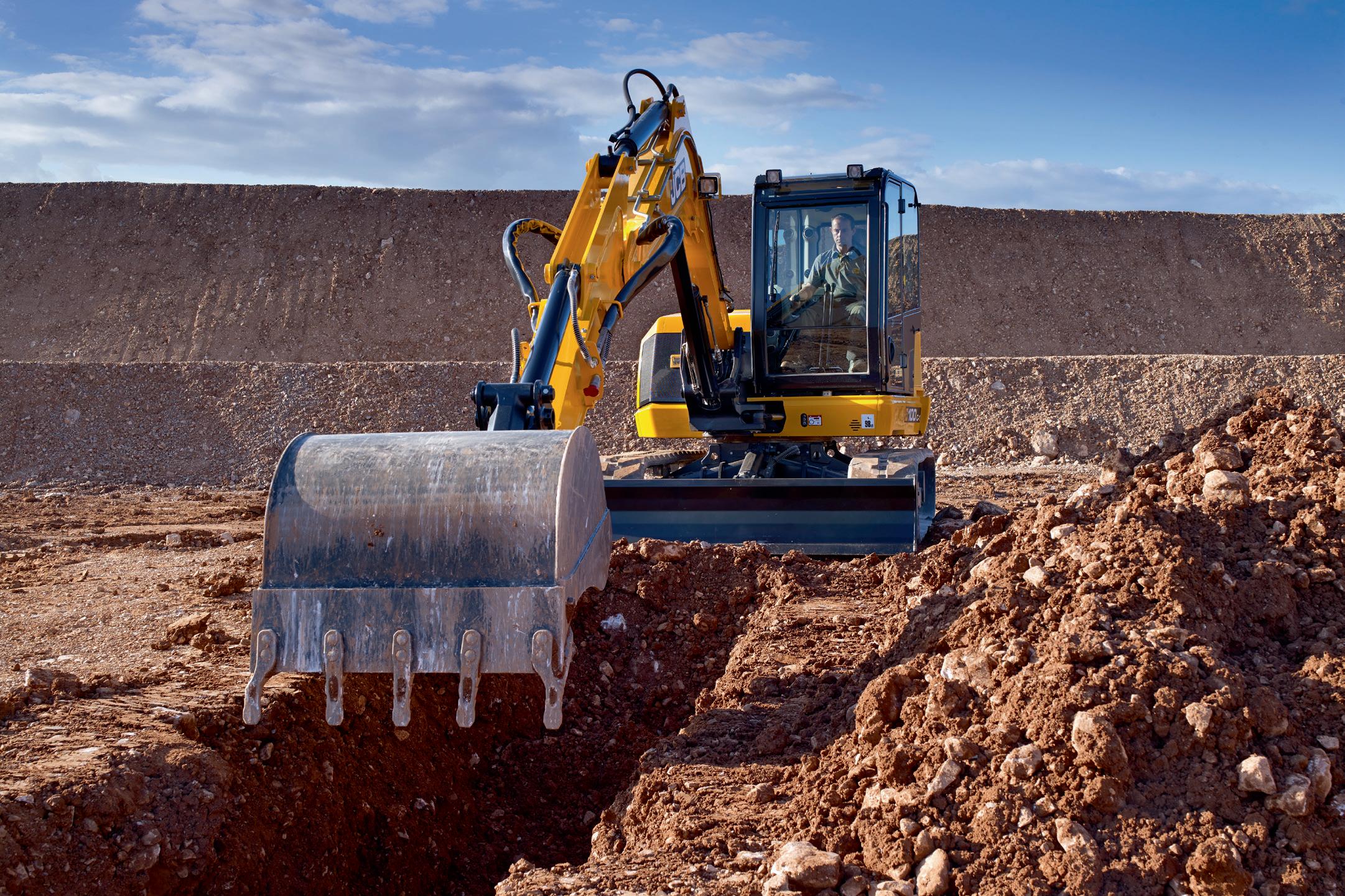
Direct trains to Ebbw Vale
Upgrades to the Ebbw Vale line which will double the frequency of services into Newport and Cardiff, aim to revive the South Wales valley’s fortunes once more
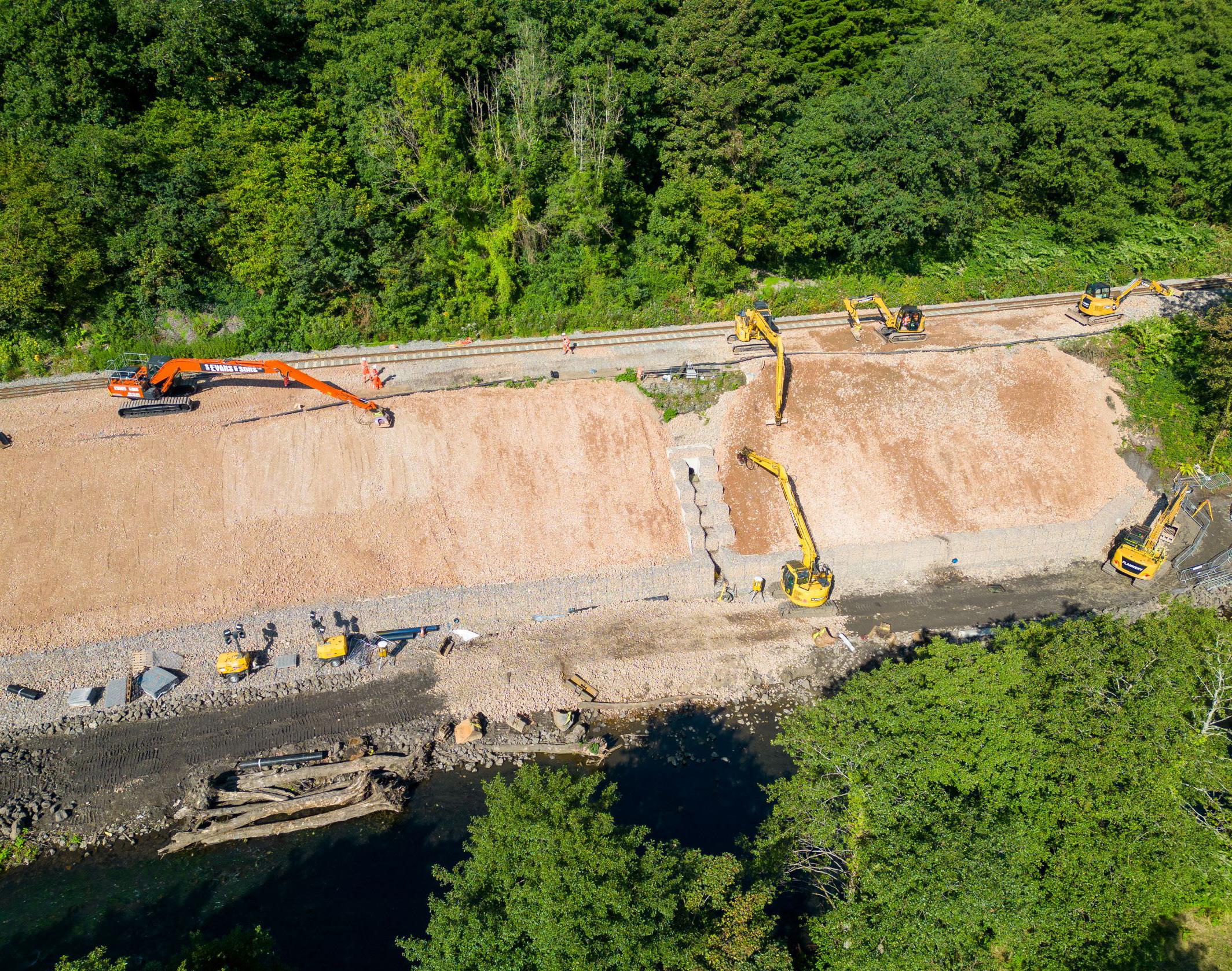
There have been many chapters to the story of the Ebbw Vale line since it opened in 1855. Like the economy of the valley through which it runs, it expanded to serve the burgeoning mining and steel industries once situated there – and then faded away, as those activities have reduced and eventually stopped altogether.
‘Like the whole rail network, the line has been through various financial stages, with funding from the private and public sectors over the years’ says Gerard McArdle, engineering geologist at SYSTRA. ‘Parts of this alignment have been six track, four track and two track over the years. The line went from a mixture of passenger and goods railway to just a goods railway and then to a single-track passenger railway.’
The latest chapter sees modifications which doubles the level of train services from the town of Ebbw Vale at the top of the valley. The Ebbw Vale Frequency Enhancements project has added a second service to the hourly one which was already running to Cardiff.
Now there is a second train each hour which heads to Newport, meaning that there are two trains an hour and more than 60 services running on it each day. The goal is to further re-boost the local economy by providing the people along its route with better access to jobs, businesses, education and leisure.
Long time coming
The people who live along the towns and villages along the Ebbw valley have been waiting a long time for their passenger service to return. British Rail stopped the existing one in 1962, retaining freight services for the Ebbw Vale steelworks and collieries. Once the coal mines closed the line was reduced to mostly single track in the 1990s to serve the steelworks which closed in 2002.
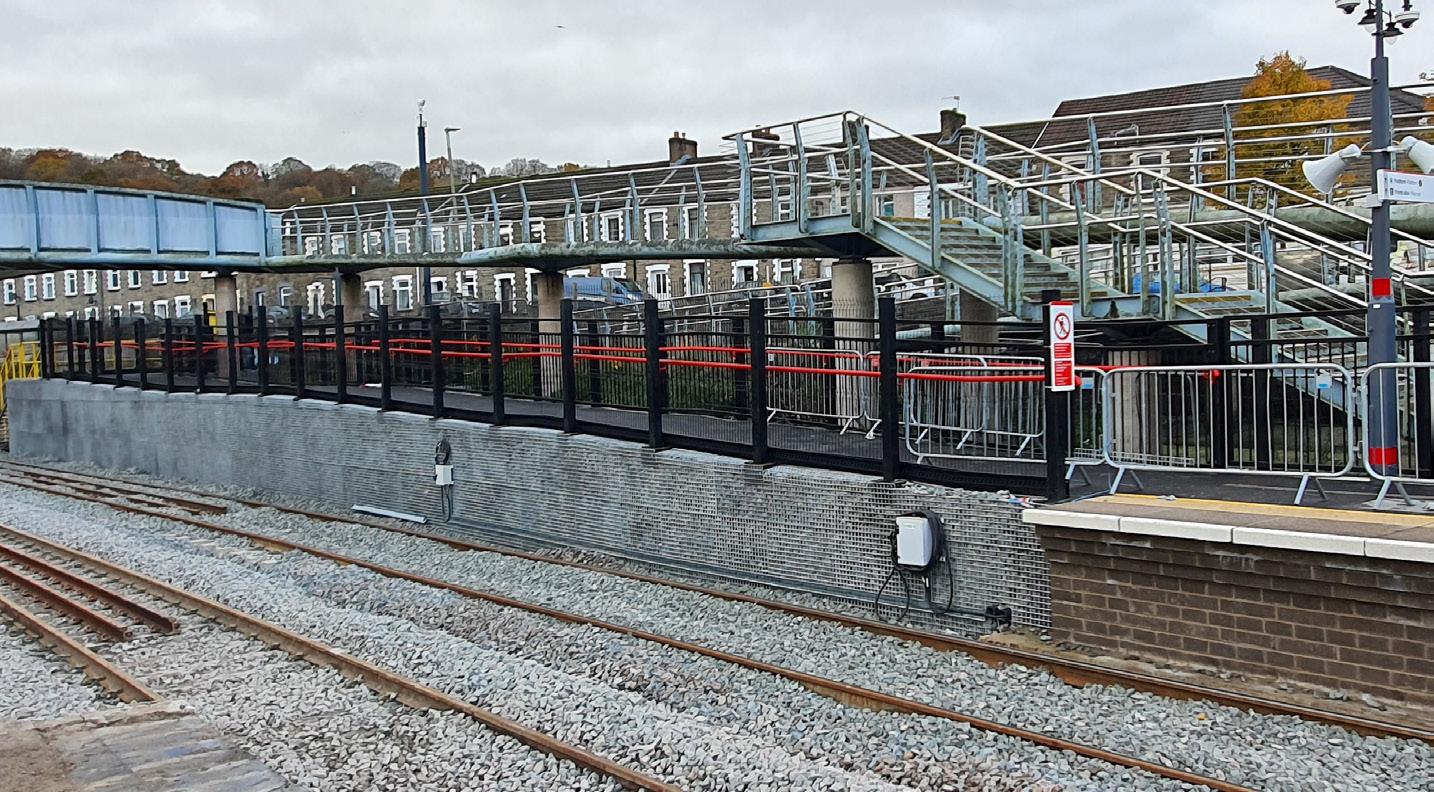
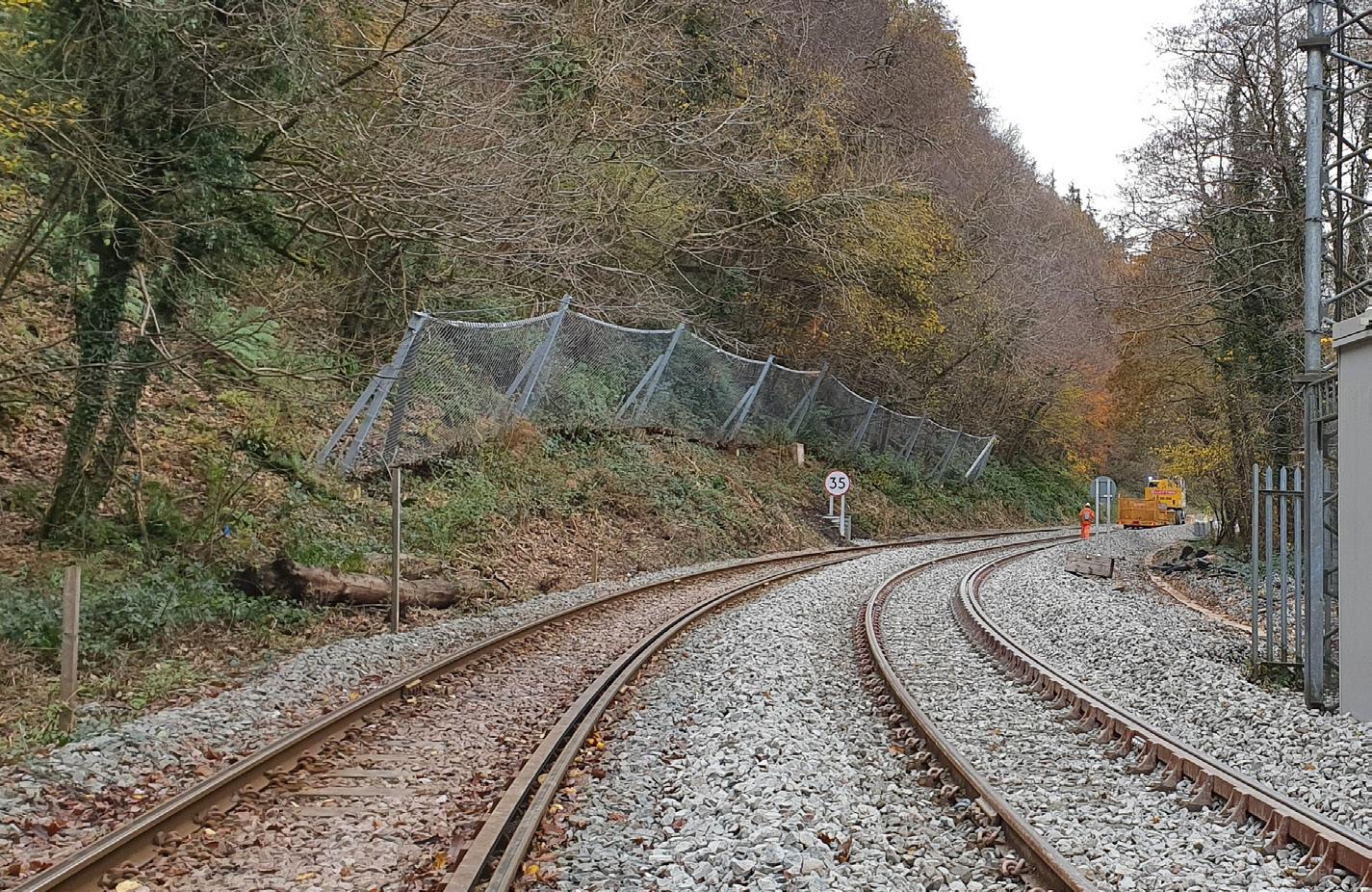
As far back as 1999, the Welsh Assembly Government – as it then was - promised to reopen the line to passengers. In 2005, the Welsh Government announced that this would be delivered in two phases. The first phase of works saw the line reopen in 2008 with Network Rail subsequently adding a new station, Pye Corner at the Southern end of the line and a new 1.5-kilometre (just under one mile) section at its Northern end to a new station at Ebbw Vale Town.
Ridership on the re-opened passenger service far exceeded expectations with the service carrying twice as many passengers as forecast in its first year of operation. This many have been due to the forecasting model being based on passengers switching from cars – but car ownership in the area was among the lowest in the UK.
The second phase of works took longer to mobilise. In May 2021, Network Rail awarded a £25 million construction contract to AmcoGiffen, with Siemens contracted to upgrade and renew signalling. The Welsh Government loaned the £70 million of investment needed to Blaenau Gwent Council with the Department for Transport and Network rail provided a further £22 million of funding for the signalling work at the south end of the line.
AmcoGiffien’s package of works included the creation of a seven-mile passing loop between Crosskeys and Aberbeeg, building a new footbridge at Llanhilleth station, a new rail bridge at Newbridge, new platforms at Llanhilleth and Newbridge stations and extending existing platforms to accommodate longer trains in the future. Systra is AmcoGiffen’s engineer, delivering a £2.5 million design package, including civil, structural, geotechnical and architectural engineering.
Victorian earthworks
Work began on site in early 2022. One of the most technically demanding elements of AmcoGiffen’s contract was
the reinforcement and modification of the 170-year-old embankments which would carry the rails for the passing loop, which themselves had seen changes over the years due to the valley’s industrial activities.
Some of the embankments contained sandstone quarry waste, in other places deposits of ash from the railway and slag from the valley’s steelworks had been added, with everything hidden under a thick layer of vegetation. As well as taking the loads from modern-day trains, and coping with forces of nature in coming years, the embankments had to provide a safe working platform for AmcoGiffen and take the loads of its construction equipment during the works.
SYSTRA’s ground engineering team, led by Charlotte Woodhall-Jones, assessed the proposed works along the embankments and made changes to reduce risk, while staying within the original budget. ‘For the track design my team’s knowledge of engineering geology lead to the creation of a geomorphological hazard mapping system so that we could create the right interventions based on the level of risk. We managed the hazards better and kept within the same budget envelope’ explains Woodhall-Jones.
AmcoGiffen’s works also included some substantial civil engineering. At Newbridge Station, the contractor replaced an existing rail bridge over Bridge Street, requiring a 950-tonne crane and a nine-day closure, during which other track and platform works were also completed.
Newbridge station also benefited from the innovative use of a reinforced matrix wall, Ramwall, used for the first time in this application. Swapping the Ramwall for a precast concrete retaining wall, meant that there was no need for the need for concrete foundations, which would have extended onto the track and could have been damaged by the ballast cleaners used for maintenance. An added bonus was that it reduced the
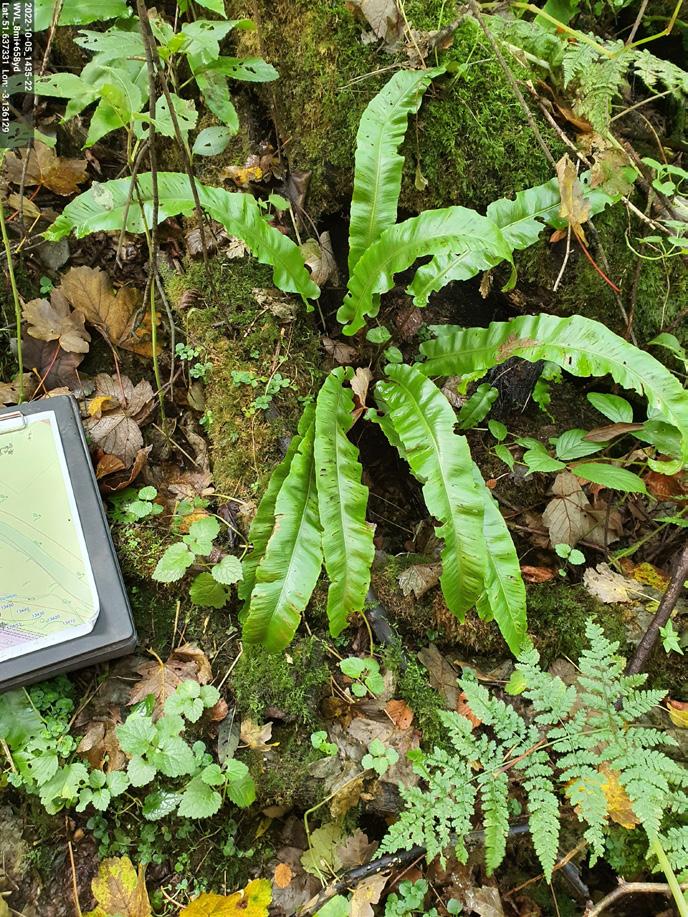
‘With a new fleet of trains on the way from French manufacturer CAF, the Ebbw Vale Enhancements project promises to transform travel for the communities served by the rail line.’
embodied carbon of the structure by two-thirds – and its components can be repurposed in the future.
In April 2023, AmcoGiffen installed a new, fully accessible, steel footbridge over the tracks at Llanhilleth. During a five-day closure, engineers from the contractor and Network Rail oversaw the installation of the bridge in 15 sections, using a 230-tonne crane. An alterative SYSTRA design to support the extended platform at Llanhilleth swapped ground anchors for inclined piles, simplifying the build and saving money.
New era
With all the works completed by early 2024, the new service to Newport was launched on 1 February 2024. Now the inhabitants of the valley can travel direct to Newport by train, rather than going into Cardiff and back out again, or changing to a bus service from Pye Corner in Rogerstone.
With a new fleet of trains on the way from French manufacturer CAF, the Ebbw Vale Enhancements project promises to transform travel for the communities served by the rail line. It will be interesting to see when the extended platforms – and trains –are called upon to carry more passengers.

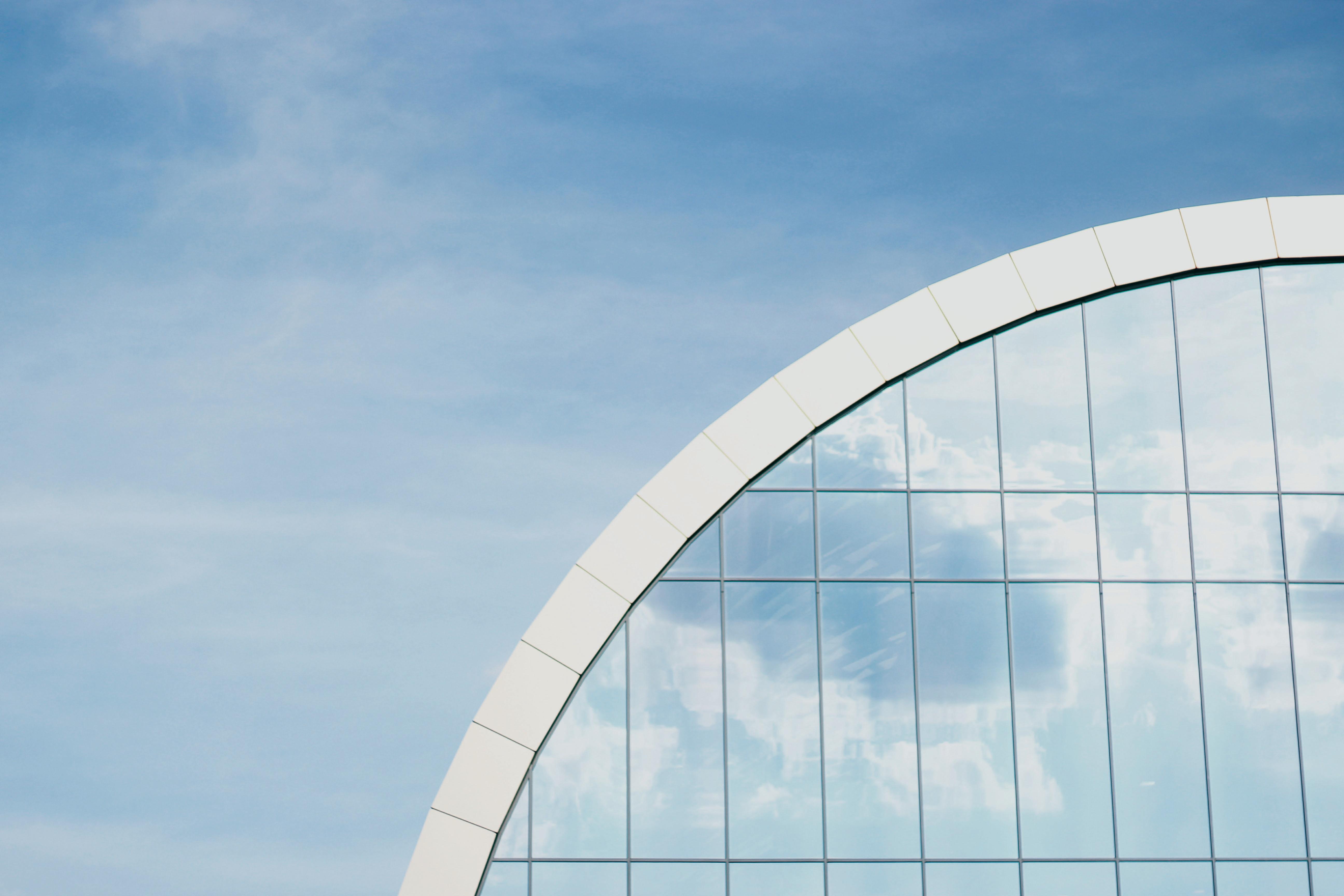
CIPS
CIPS Level 4 Diploma
CIPS Level 5 Advanced Diploma
CIPS Level 6 Professional Diploma
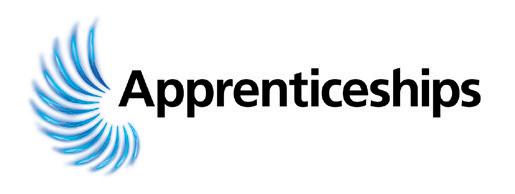
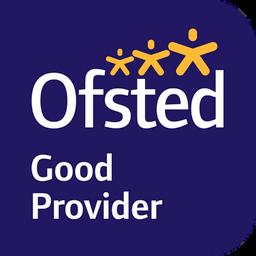

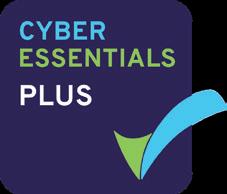
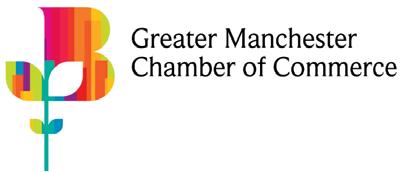
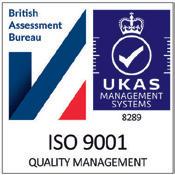
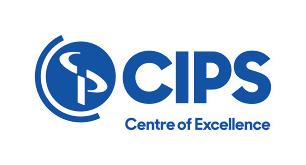
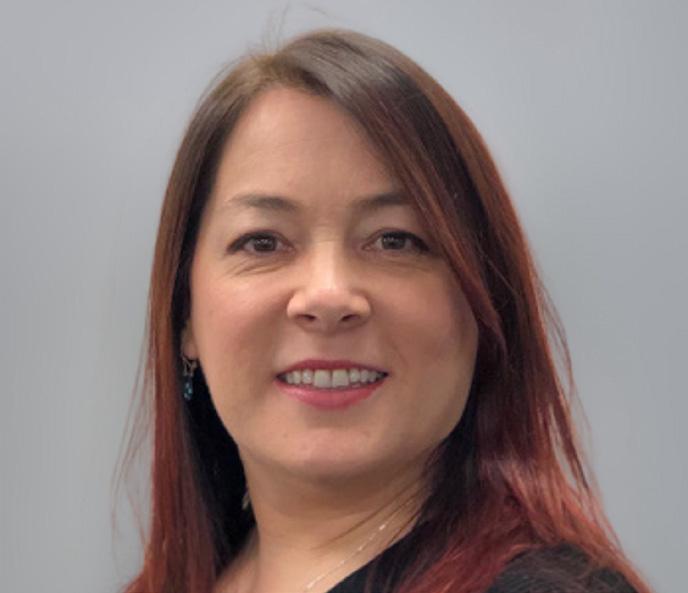
SUSAN RASHID CEO OF SR SUPPLY CHAIN CONSULTANTS LTD
Susan boasts extensive experience in various procurement and supply chain management roles, specialising in JIT, Kaizen, Lean, Agile, Leagile, and Total Quality Management methodologies. After many years in the industry, she transitioned to a full-time lecturer and exam team member for CIPS before founding her own training company, SR Supply Chain Consultants Ltd.

SR SUPPLY CHAIN CONSULTANTS LTD
SR Supply Chain Consultants (SRSCC) Ltd is a training provider that specialises in procurement and supply chain management. SRSCC operates four study centres and two exam centres across England. It has been awarded the 'Centre of Excellence' status by the Chartered Institute of Procurement and Supply (CIPS) and is a Main Provider on the Register of Apprenticeship Training Providers (ROATP). Additionally, SRSCC is rated 'Good' by OFSTED as a provider of apprenticeships.
Want to know more about SR Supply Chain Consultants?
Tel: 01772 282555
Email: info@srscc.co.uk Visit: www.srscc.co.uk
What is your role within SR Supply Chain Consultants Ltd?
I am CEO and Head of Business Development, I head up the business and work with our Leadership Team to develop the Vision, Mission and Goals whilst ensuring implementation of the strategic plans and priorities. As Head of Business Development, I am responsible for the development of new products and services and spend a lot of my time working with Procurement and Supply Chain Leaders, Employers and Industry Experts to identify skills gaps and challenges.
How did you start SR Supply Chain Consultants Ltd and tell us about your career before you founded the company?
With a career beginning in London at 16 as a purchasing clerk in the automotive industry, I quickly developed a passion for procurement and supply chains, particularly within the automotive and FMCG sectors. This early experience in a fast-paced manufacturing environment fuelled my love for the field, prompting a significant career move to Lancashire to delve deeper into materials management.
Over the years, I have held various roles, from Office Manager to MD, gaining expertise in methodologies like JIT, Kaizen, and Lean across both private and public sectors. My journey into training began while pursuing Chartered Institute of Procurement and Supply (CIPS) qualifications, leading to a career shift as a full-time lecturer and member of the CIPS examination team.
In 2007, I founded SR Supply Chain Consultants Limited, expanding services to include procurement apprenticeships and developing a team of 35, allowing me to focus on strategic growth and the future of procurement and supply chains. My qualifications include a teaching certification, Prince2 Practitioner, Chartered Procurement Professional status, a Fellow of CIPS, and an MBA focused on the relationship between procurement qualifications and job satisfaction. Now, as CEO, I'm dedicated to advancing procurement and supply chain education, continuously striving for excellence and improvement, evidenced by maintaining ISO9001 and working towards ISO27001.
What challenges have you faced in the industry?
Over the past year, my interactions with leaders in the procurement and supply chain sectors, including notable figures such as Ben McCluskey from AmcoGiffen, highlighted industry challenges. A key issue is the perception of procurement and supply as mere transactional functions rather than strategic components.
The industry's focus often leans heavily on safety and cost, sidelining important
elements like social value and sustainability. There's an evident need for training to help professionals incorporate these aspects into their sourcing strategies, enhancing supply chain resilience. Ben McCluskey's efforts with AmcoGiffen’s procurement programme, which seeks a more ethical and value-driven approach, underline the potential benefits of such training.
The Price Iceberg model by Baily et al. is crucial, illustrating the need to consider hidden costs and values beyond mere pricing, including safety, sustainability, and service. Recognising these factors allows for better-informed decision-making and value creation. Upskilling procurement and supply chain professionals can significantly improve supply chain resilience, promote sustainability, and mitigate risks. Effective training equips professionals to navigate complex challenges, spearhead strategic projects, and cultivate meaningful supplier relationships, driving positive organisational change.
What does sustainability mean to you?
Sustainability is a cornerstone of my role in procurement and supply, especially as the head of a training company. It's a broad concept that underpins our business operations and our mission to educate future procurement professionals.
Environmental sustainability is critical, focusing on reducing our ecological footprint through lower carbon emissions, resource conservation, waste reduction, and the adoption of eco-friendly practices. Social sustainability is equally vital, advocating for fair labour practices, ethical sourcing, and community well-being, including adherence to labour laws and human rights. Economic sustainability emphasises making procurement decisions that ensure long-term organisational and stakeholder prosperity, optimising costs, and fostering innovation for resilient supply chains.
Supply chain resilience is fundamental, preparing organisations to handle disruptions from various sources by diversifying suppliers and implementing risk management strategies. Sustainability is an ongoing journey of improvement, setting and pursuing ambitious goals, measuring performance, and adapting strategies for better outcomes. Our commitment involves embedding sustainability principles into our training programs, aiming to drive positive change in the procurement and supply field.
We strive to cultivate a culture of sustainability and responsibility among professionals, harmonising environmental, social, and economic considerations with resilience and continual progress.
What was the inspiration behind starting SR Supply Chain Consultants?
The inspiration behind starting SR Supply Chain Consultants (SRSCC) stemmed from a passion for the field of procurement and
‘We’re known for blending Traditional and Live Virtual Classrooms with our unique Independent Learning Zone (ILZ), offering flexible, blended learning options to suit diverse needs.’
learners to improve their workplace skills and advance their careers with our supportive, professional training.
Our tutors, experts in procurement and supply, bring real-world experience and qualifications such as MCIPS or FCIPS to the classroom, ensuring our training is both engaging and practical. SRSCC's quality is affirmed by our OFSTED 'Good' rating and over a decade as a CIPS Centre of Excellence, reflecting our dedication to excellence in education. At SRSCC, we pride ourselves on being innovators and supporters of our learners' success in the evolving procurement and supply field.
Which sectors do you work in?
a genuine love for witnessing individuals' personal and professional growth. With years of experience in procurement and supply chain management, the realisation that this sector is not just about transactions but about strategic decision-making, relationship building, and sustainable practices, fuelled the desire to share this knowledge and expertise. Seeing the transformative impact of quality education and training on professionals –how it equips them with the skills to make impactful decisions, innovate, and drive their organisations forward – motivated the creation of a platform dedicated to nurturing these talents.
The goal was to empower professionals by providing them with the tools, knowledge, and confidence to excel in their careers, contribute to the success of their organisations, and, ultimately, influence the procurement and supply chain industry positively. Witnessing the development and success of learners, knowing that they are equipped to tackle the challenges of today and tomorrow with a forward-thinking and strategic mindset, is a source of immense satisfaction and continues to be a driving force behind our mission.
Tell us about SR Supply Chain Consultants Ltd.
SRSCC, founded in 2007, is a leading provider of procurement and supply chain training, including CIPS qualifications, apprenticeships, and bespoke training for a broad audience, from individuals enhancing their careers to organisations upgrading their teams' skills. Our growth from the first study centre in Preston in 2009 to additional centres in Manchester, Birmingham, and London demonstrates our commitment to accessible, quality education across England.
We’re known for blending Traditional and Live Virtual Classrooms with our unique Independent Learning Zone (ILZ), offering flexible, blended learning options to suit diverse needs. Our mission is to empower
Private, Public and Third Sector; including industries such as the rail industry, construction, health, energy, FMCG, health care, manufacturing, retail, food and beverage, professional services, central and local government, NHS and many more.
What is your Unique Selling Point?
Our Unique Selling Point lies in our unparalleled expertise and dedication as specialists in procurement and supply chain management. Recognised as a CIPS Centre of Excellence, we set ourselves apart by offering an educational experience that is not just about acquiring knowledge but about fostering a deep understanding and passion for the field. Our approach is characterised by flexibility, friendliness, a caring attitude, and a strong ethical foundation, ensuring that every learner receives a personalised and supported educational journey.
We pride ourselves on creating an environment where learners are not just numbers but valued members of a community striving for excellence in procurement and supply. This blend of specialist knowledge, recognition as a centre of excellence, and our commitment to a flexible, friendly, caring, and ethical approach defines our distinct position in the market and underlines our dedication to advancing the careers of our students and the efficiency of the organisations we work with.
What types of products and services do you offer?
We offer CIPS Qualifications:
• CIPS Level 3 Advanced Certificate.
• CIPS Level 4 Diploma.
• CIPS Level 5 Advanced Diploma.
• CIPS Level 6 Professional Diploma.
And Apprenticeships:
• Level 3 Procurement and Supply Assistant.
• Level 3 Supply Chain Practitioner.
• Level 4 Commercial Procurement and Supply.
• Level 6 Senior Procurement Professional.
What are some of the biggest challenges this sector currently faces?
The rail industry and its supply chain grapple with challenges affecting operations, efficiency, and sustainability. Key issues include aging infrastructure needing continuous maintenance and modernisation, safety concerns, and rising maintenance costs. Capacity constraints also pose difficulties in maintaining infrastructure and service levels. The integration of new technologies demands substantial investment and expertise, while environmental regulations push for reduced emissions, energy consumption, and sustainable practices.
Safety and security remain critical, compounded by a skilled labour shortage as experienced workers retire. Supply chain resilience is vital, necessitating diversified suppliers, risk management, and contingency plans. The industry must navigate a complex regulatory landscape, ensuring compliance with safety, environmental, and labour laws. Financial sustainability is another concern, with rail projects requiring significant investment amid fluctuating fuel prices and economic challenges.
Addressing these challenges calls for stakeholder collaboration, including governments, industry players, and labour unions, emphasising innovation, investment, and strategic planning. SR Supply Chain Consultants contributes by raising awareness and offering training on procurement strategies, logistics management, technology sourcing, green procurement policies, supplier relationship management, risk management, and contract negotiations, aiming to enhance the industry's sustainability and competitiveness.


Reviving Scotland’s Railways for a Greener Future
Reopening railway stations in Scotland after many decades brings huge social and economic benefits to previously cut off communities, but projects must put sustainability at their core to drive down their carbon impact, says AECOM’s Rail Lead for Scotland Crawford Johnston
East Linton is Scotland’s latest railway station to reopen, bringing back rail services to the local community after nearly 60 years. Sitting on the East Coast Main Line, which runs from Edinburgh Waverley to London Kings Cross, the station connects passengers to new employment, education and business opportunities and offers a more sustainable travel option that will encourage people away from their cars.
After many decades without passenger services, the new station is set to help transform this area of East Lothian, supporting economic growth and acting as a trigger for more investment and further development in the community. Opened in December last year, the station is part of the Scottish Government’s ongoing investment to expand the rail network and open-up Scotland’s railway to new communities.
The new station boasts two 158-metrelong platforms and is fully accessible with step-free access across the railway via a footbridge with lifts connecting both platforms for pedestrians and cyclists. It includes 114 parking spaces, including blue badge priority parking, and 18 electric vehicle charging points.
AECOM was appointed by contractor BAM Nuttall to deliver the detailed design of the station, footbridge, car park and access road, as well as the associated retail power, lighting and telecoms infrastructure.
Our team also delivered the detailed design of the track and overhead line equipment (OLE) alterations needed to facilitate the installation of the station.
A significant challenge was to design the new station in a way that could be installed in line with available access on the East Coast Main Line. Through collaboration with Network Rail, BAM Nuttall and their supply chain partners, we designed the track adjustments, OLE modifications and a steel and concrete composite station platform structure that could be installed with minimal disruption to existing services on this key rail corridor.
To achieve this, early in the design programme we proposed to amend the design solution from a concrete construction to the modular steel and concrete composite solution. This meant that the existing cable route could remain, and the signalling staging works could be significantly reduced.
This modular form of construction also allowed us to incorporate reclaimed oil and gas pipes as the piled foundations for the station and footbridge. Minimising waste was a key element of our approach to improve the sustainability of the design.
During the tender phase for the detailed design, it was identified that the outline design solution comprising a standard concrete slab construction could not be built with the available access and achieve the project programme.
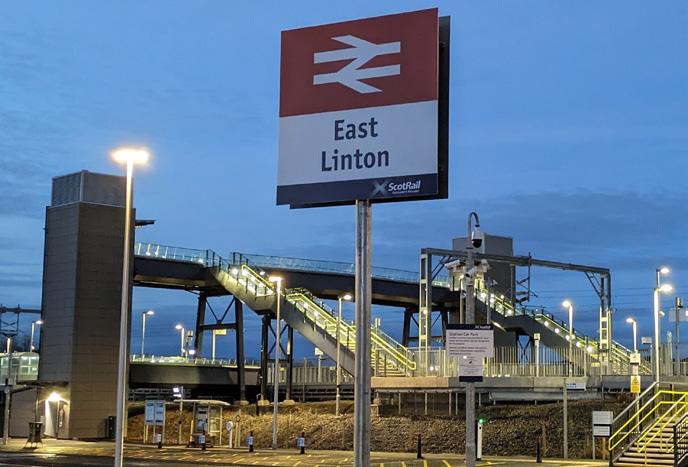
Our team developed the bespoke steel and concrete platform slab as an alternative solution that allowed larger prefabricated slab units to be made, reducing the number of supports that were required. We then used steel driven piles to shorten the duration of piling activity on site and enable some piling activity to take place with the adjacent railway still open to traffic.
When specifying the steel piles, we identified an opportunity to reuse pipework that had previously been used in oil and gas production. We prepared a testing specification and inspected the procured pipework for suitability. Avoiding the need to manufacture entirely new steel piles had a significant impact on the sustainability of the design and the overall carbon impact of the station.
During design development we also sought inputs from the steel and concrete fabricators to identify the readily available materials, steel plate sizes and concrete mix types to incorporate these into the design. Consultation with the fabricators also allowed us to incorporate their preferred fabrication methods into the design, which influenced the connection types and led to more standardisation of the platform components.
Our team also designed an OLE arrangement that modified the current OLE masts to make them suitable for the amendments needed to introduce the station, reducing the additional materials and disruption that would have been needed if new masts were to be installed.
By working closely with Network Rail and BAM Nuttall during design development, we were able to develop a programme for the detailed design of the new solution that allowed us to release design information in a staged manner and support the construction progressing in parallel with completion of the design.
Undoubtedly, challenging the scope of the project at an early stage and continuing to interrogate the requirements helped to improve both the efficiency and the carbon impact of our design.
Working on the new East Linton station and helping to restore vital rail services for the local community was a particularly rewarding project for our team to deliver. But equally fulfilling was designing a solution that put sustainability at its heart, driving down the project’s carbon impact and enhancing the legacy that this new station is set to bring.
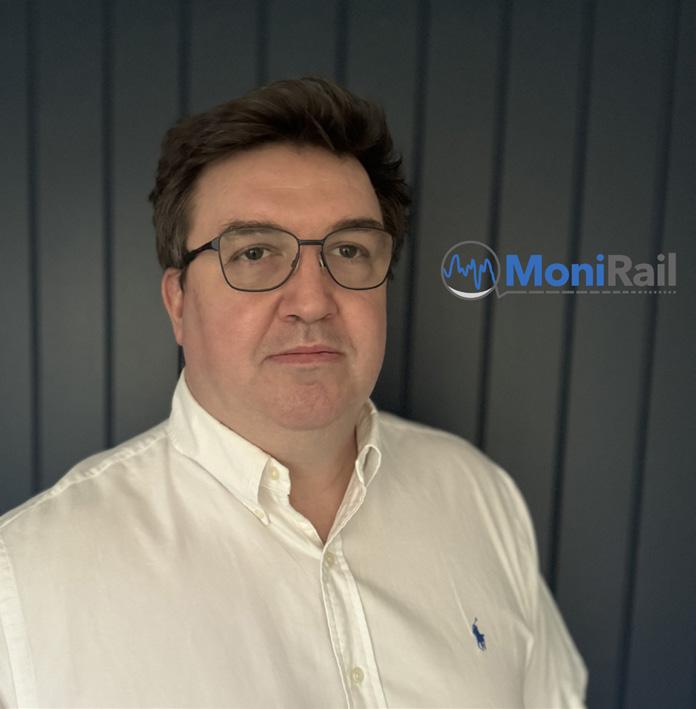
PETER AINSWORTH CEO OF MONIRAIL
Peter Ainsworth, CEO of MoniRail, has been working with the academic founders since 2019 to commercialise the University of Birmingham research that underpins MoniRail products. He has more than 10 years’ experience in the rail sector and prior to MoniRail, led the £100 million innovation programme at RSSB.
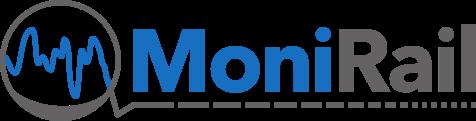
MONIRAIL
With over 50 years of combined rail experience, University of Birmingham spinout MoniRail is comprised of a team of academic and industry experts with a proven track record, that are dedicated to delivering non-intrusive track monitoring solutions through comprehensive knowledge of the infrastructure and its challenges.
Want to know more about MoniRail?
Tel: 07875 544898
Email: peter@monirail.co.uk
Visit: monirail.co.uk
LinkedIn: MoniRail X (formerly Twitter): MoniRail_Ltd
What challenges have you faced in the industry?
Encouraging the rail industry to embrace innovation and new technologies has always been a challenge. It is why organisations such as MoniRail exist – to create solutions that overcome the key issues the industry faces, such as how to effectively harness data and make better-informed decisions.
The industry structure is also a challenge; our solution utilises in-service vehicles, but the benefit of the solution generally sits with a combination of the infrastructure owner, operator, and vehicle owner. As such it has sometimes been difficult to organise the fitment of equipment to all stakeholders.
How has technology developed since you started in the industry?
When MoniRail started, the research device weighed around 3kg and was the size of a shoe box. This has been completely reengineered to provide a solution that can be easily manufactured, weighs less than 1kg and fits easily in the palm of your hand. It has also been redesigned with standards and fitment in mind; the solution can be easily retrofitted to both passenger and freight vehicles and meets all necessary standards (i.e. EN50155).
Alongside this, a core element of our product suite, the data collection and analysis, has significantly evolved since we started and is a core element of our product suite. Recognising that the information provided to our customers is a central component of how their businesses operate and undertake informed decision making.
Our offering is now a cloud-based solution, and we recognise that customers may not want a plethora of different user interfaces for their maintenance activities. As such we can either provide our own user interface or integrate with existing user interfaces.
We are proud to develop software solutions that place a significant focus on this. Our tools interpret data from multiple sources supplying reproduceable information to those who need it. As a result, this ensures the safe and efficient running of the rail network, something that we are proud to play a part in.
‘The rail industry is notoriously conservative and averse to change and innovation. MoniRail was formed through the ICURe programme at the University of Birmingham and supported by Innovate UK.’
How have the products and services you offer developed over the years?
At our core, we provide solutions for monitoring the condition and degradation of railway track from on-board operational passenger and freight vehicles. Our team of experienced data interpreters and rail experts supply scientifically proven, costeffective, in-service monitoring solutions for rail, tram, and metro infrastructure.
We have also developed products that overcome key challenges, such as rough rides using data from our sensors, thus enhancing the overall passenger experience.
We are working hard to continue to support the delivery of the digital railway and a network that prioritises maintenance, and improves the overall customer experience, through automated data collection, processing, and analysis.
What are some standout projects you’ve been involved in over the years?
We are collaborating with Network Rail High Speed and Eurostar to enhance ride and track quality on the High Speed 1 track in the UK. The dynamic interaction between high-speed trains and the track yields critical insights for both the track maintenance team and the train operator. Our system offers unique information not captured by the measurement fleet, playing a crucial role in maintaining superior ride quality on highspeed lines.
Our equipment is installed on shuttles within the Eurotunnel fleet, offering insights into the wheel/rail interface and enabling predictive maintenance.
We are collaborating with our partner in America, MxVRail, to introduce this system across North America. Our equipment is installed on an American freight wagon, generating valuable data for the research and engineering team at their test facilities.
We are working with Fishbone to develop The Freight Wagon Condition Monitoring System (FWCOMS) project which employs remote condition monitoring to enhance rail freight wagon and infrastructure maintenance. Through FWCOMS, we've demonstrated the effective use of Internet of Things (IoT) technology in railways, enabling seamless integration with onboard systems. This approach provides valuable insights into fleet maintenance, track quality, and safety, aligning with the EN 14363 standard for stability and safety requirements.
Railway vehicles are fitted with MoniRail proprietary hardware – compact, lightweight sensor units – used to continuously produce accurate measurements of the railway track and vehicles.
The MoniRail system simultaneously collects data from body, bogie and, if required, axleboxes to monitor track geometry, ride comfort and rolling stock performance. A data analytics software platform converts collected data from the IMU into actionable condition information.
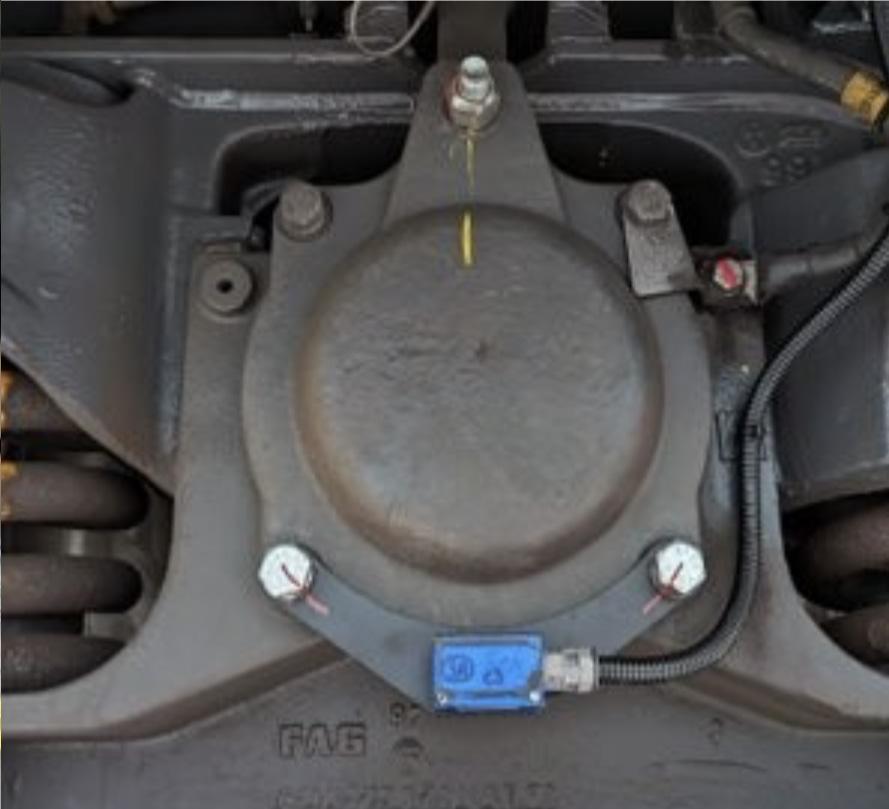
Monitoring the quality of the track from in-service trains in this way gives a better understanding of the evolving condition of the assets, helping users to build up a clearer picture of the train and track conditions over time. This enables accurate prediction of potential problems and allows for early detection of railway track degradation.
Preventative maintenance can therefore be implemented accordingly, and problems can be tackled promptly, before they escalate into causing a major fault or delay. We believe this project has a tangible, positive impact on the rail network and we look forward to evolving it further this year.
What kind of challenges did you face in the early days?
The rail industry is notoriously conservative and averse to change and innovation. MoniRail was formed through the ICURe programme at the University of Birmingham and supported by Innovate UK.
This provided initial financial support to undertake initial market studies and form the business. Given the challenges bringing the rail market, the founders took a conscious decision not to seek venture capital investment but instead seek an industrial partner who had strong links and connections with the rail sector. This obviously meant the pool of potential investors was smaller and the opportunities less so, but MoniRail managed to make a positive breakthrough and secured a partnership with Unipart Rail.
This partnership helped us in our manufacturing design process and provides MoniRail with greater reach into rail organisations both in the UK and internationally.
In partnership with Unipart, MoniRail won the Network Rail design competition, which should have been a key opportunity to demonstrate the technology and approach and a route to further trials and funding. Unfortunately, it took more than 18 months to make the necessary commercial arrangements for train fitments and a project that had originally been due to be completed by March 2021 did not conclude until Summer 2022; of course, the pandemic didn’t help.
Nevertheless, the project delivered valuable insights to NR regarding the use of in-service monitoring and its capabilities, particularly on driver reported rough rides, removal of temporary speed restriction and in-service track geometry monitoring. It has opened the door to further opportunities across the Network Rail regions and the UK rail sector, as well as for potential international customers with strong evidence-based use-cases of our approach.
What are your plans going forward to ensure MoniRail services are still around for years to come?
A significant factor in our success so far has been the close collaboration we’ve been fortunate to establish. As a spinout from the University of Birmingham, we are in a privileged position to engage with key industry players on a variety of new and exciting projects.
Moving forward, we plan to continue building on this foundation in 2024 and beyond, by not only maintaining our existing partnerships but also by exploring innovative technologies and market opportunities that ensure MoniRail's services remain relevant and in demand for years to come.
We have also recently secured a £2.5 million SBRI award from Innovate UK in partnership with London Underground (TfL), Imperial College London, University of Birmingham, University of Sussex, Qinetiq and Unipart to investigate the potential application of quantum sensors in condition-based maintenance for highly accurate positioning in underground environments. This is an exciting project enabling MoniRail to work at the cutting edge of science and technology and partner with world leading UK research institutions and corporate entities to develop a new approach for positioning.
Funded by the Department for Science, Innovation and Technology, and Innovate UK, this coveted endorsement will help us to take the next step on our journey to develop technologies that make a real-world impact. Something that had the industry not shifted to embrace, may not have happened.
How do you work with the supply chain within this sector?
MoniRail works collaboratively with the supply chain. To truly deliver a conditionbased maintenance regime and enable Network Rail to deliver the potential maintenance savings available, MoniRail only provides part of the solution. As such we recognise that working with partners who have different technologies for monitoring other aspects of the railway is critical.
We have worked with several other SMEs in this space to deliver projects collaboratively both here in the UK and
abroad, enabling us to develop our solution into new markets. Alongside this, we work collaboratively with our end-user customers to deliver the solutions that they require.
Through our collaborative working with Eurostar and Network Rail High Speed, we have developed our solution such that the operator can gain important insights into wheelset and suspension performance as well as delivering critical track information to NR.
Similarly with Eurotunnel, we work collaboratively with the University of Birmingham and a French SME to help deliver solutions that improve the performance of the Eurotunnel service.
We believe that the value we create is in the data we provide to our customers, and we work with them to help them both visualise this data in appropriate and informative ways that are useful to them. We harness this data to resolve underlying problems and issues they may have while maintaining close partnerships with sensor manufacturers, ensuring we select highly accurate sensors that deliver valuable information. Finally, we also work closely with cloud service providers and data analytics tools to ensure that we provide the best performance for our customers.
With the coming launch of Great British Railways, how do you anticipate your place within the supply chain changing?
Time will tell what will happen and how our position will change, however what is guaranteed is that we will continue to place a significant focus on close industry collaboration. It is important for us to retain the relationships that we built since our inception, to understand the challenges and complexities that our clients face and how we can develop solutions that overcome these.
What are some of the biggest challenges this sector currently faces?
Adopting new technologies is challenging in the traditionally cautious railway sector. MoniRail is addressing this by showcasing the reliability and benefits of our innovations to encourage broader acceptance.
Securing investment for new technologies in the rail sector is also a major hurdle due to high initial costs and the highly regulated, risk averse nature of the industry not being attractive to many investors. MoniRail navigates this by building partnerships with investors and demonstrating the long-term value of our solutions.
Finally, conducting trials and testing for new technologies is complex and regulatory-heavy. MoniRail simplifies this process through close collaboration with regulators and the use of advanced simulation technologies to meet safety and performance standards efficiently.
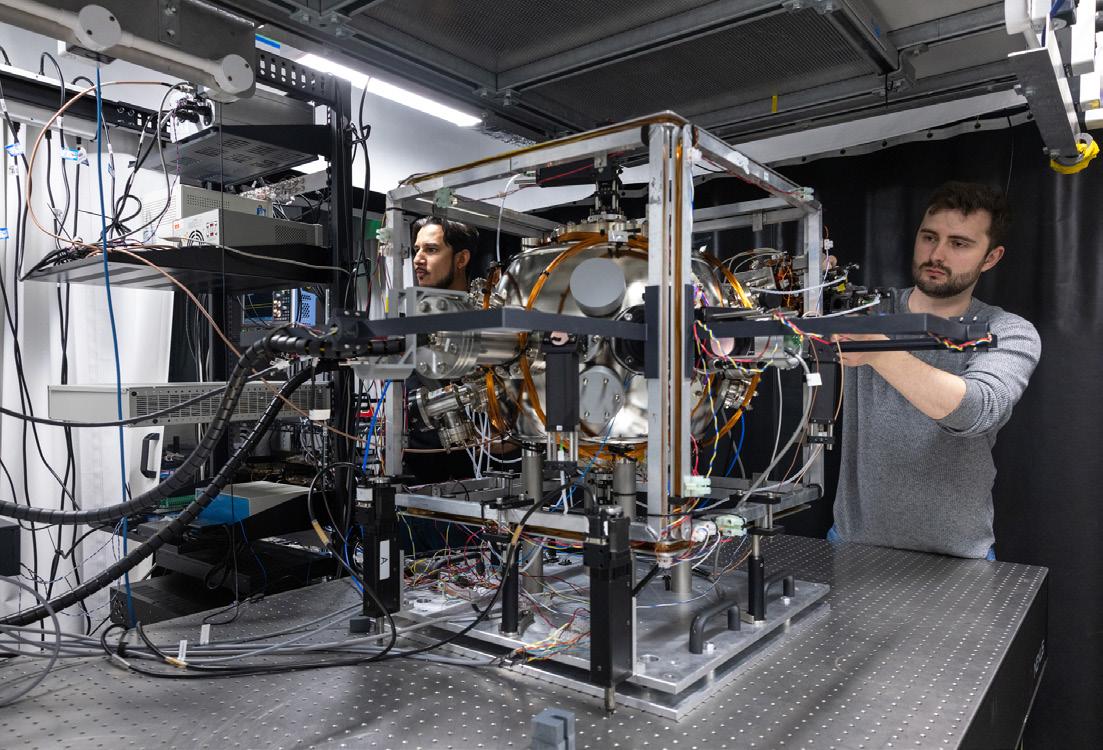
How have you seen the industry change over the years?
Over the last ten years, there has been significant investment in new technologies and innovation as evidenced by the range of funding competitions that have taken place over this time. Such initiatives never used to be available. However, many of the technologies funded through these initiatives are still working their way through the system to full adoption.
In addition, the way the railway is used by its passengers has also changed due to the impact of Covid and the change in working habits for many in the UK and worldwide. This has brought challenges for funding which means there is now an incentive and a need to reduce costs within the industry and one way to do that is through innovation and adoption of new technologies and approaches.
The MoniRail solution directly addresses this by providing the necessary data and information to engineers to make more informed decisions about maintenance regimes for their track and vehicle assets, helping to reduce maintenance costs and having the added benefit of reducing disruption to passengers.
Our recent award for the SBRI quantum project evidence how the industry is changing, and the fact that Transport for London (TfL) have partnered with us to help deliver the testing and trialling on the TfL network of the proposed quantum solution is a huge benefit in developing the technology. Five to ten years ago it would have been highly unlikely that such equipment would have been allowed onto any rail network, aside from perhaps a heritage network, to enable testing in the operational environment.
Where do you think the industry will be in the next 10 to 15 years?
We envisage that the industry will be utilising data and technology far more than it currently is. Through this step change we will hopefully see a shift in how technology
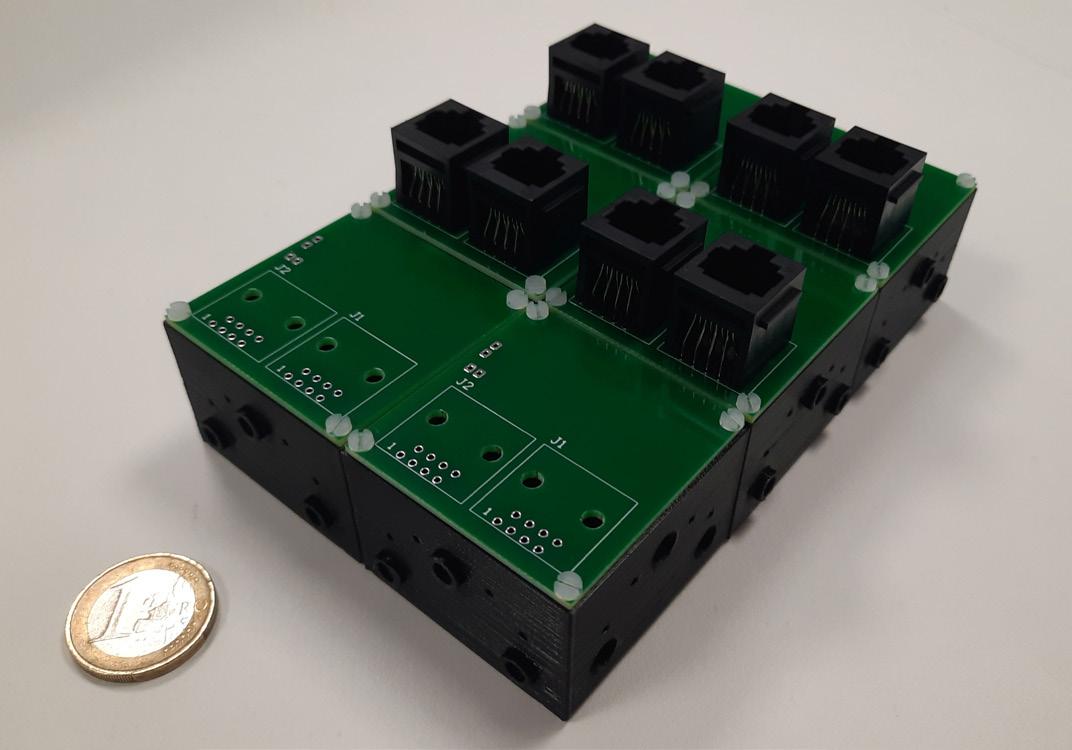
is harnessed; helping to create a more efficient, digitally enabled, and safer rail network, resilient to emerging challenges such as climate change and evolving passenger behaviour.
How can we make the rail industry a place people want to work in?
The rail industry has always been a fantastic place to work, as many will testify. However, to continue to nurture this and attract emerging talent, it is vital for the industry to continue to invest in its people, through training programmes and be more open to adoption of new technologies and approaches.
It is also important to continue its work in embracing academic partnerships – companies such as MoniRail have truly benefited from this, and it is a prime way for the industry to find and mould new talent.
What do you expect to be the biggest challenges that come from this transformation of the railway industry?
The ongoing adoption of technology presents a continuous challenge, as the railway industry needs to stay abreast of rapid technological advancements to maintain efficiency and safety. MoniRail anticipates the need for a proactive approach in integrating emerging technologies, whilst ensuring that these innovations seamlessly enhance our existing operations.
Ensuring there is a steady flow of investment in new technologies is also critical for sustaining innovation within the railway sector. MoniRail understands the importance of establishing and maintaining a consistent investment pipeline. We are focussed on fostering relationships with investors and stakeholders who are committed to the future of rail, thereby securing the financial backing necessary for ongoing technological advancement.
The advent of AI technology also brings its own set of challenges, particularly concerning ensuring quality and deciding between investing in human capital versus
‘The fact that Transport for London (TfL) have partnered with us to help deliver the testing and trialling on the TfL network of the proposed quantum solution is a huge benefit in developing the technology. Five to ten years ago it would have been highly unlikely that such equipment would have been allowed onto any rail network.’
automation. MoniRail recognises the importance of balancing investments in AI with the need for skilled professionals who can manage, interpret, and leverage these technologies effectively. We are committed to navigating these emerging challenges by prioritising both quality assurance in AI applications and the continuous development of our team’s expertise.
In terms of technology, how do you anticipate things might change in the next five to ten years?
The adoption and uptake of AI may significantly alter how things are done. Whilst it poses some benefits, it also poses some challenges and the key will be to navigate this in a way that enables technology such as the solutions we develop at MoniRail, to continue to evolve and grow and provide its users with the wealth of benefits that it has done to date.
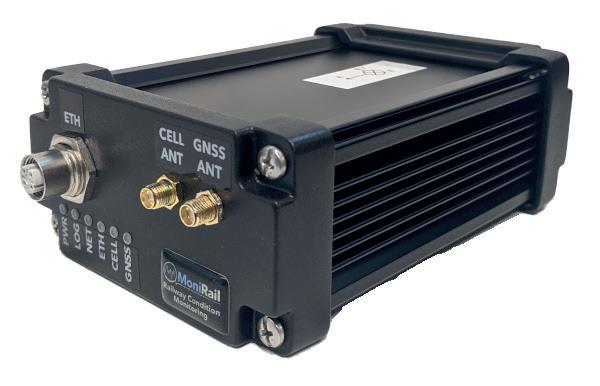
In-service track and ride quality monitoring
Non-intrusive track and train monitoring based on 20 years of academic research from the University of Birmingham, the MoniRail solution harnesses advanced vehicle-mounted sensor technology to deliver insights into track geometry and ride quality, enabling continuous monitoring and predictive maintenance.
Improves Efficiency
The integrated hardware and software solution supports continual data analysis, helping to improve performance and reduce maintenance costs.
And Forget
Designed for easy installation and low-maintenance, the solution monitors track conditions in real time without disrupting daily operations.
Data
Processed sensor data delivers accurate track condition and vehicle performance data combined with accurate position information.
Maintenance
MoniRail empowers railway operators to undertake predictive maintenance, by providing early detection of potential issues. Ensuring the longevity of rail assets and enhancing ride quality.
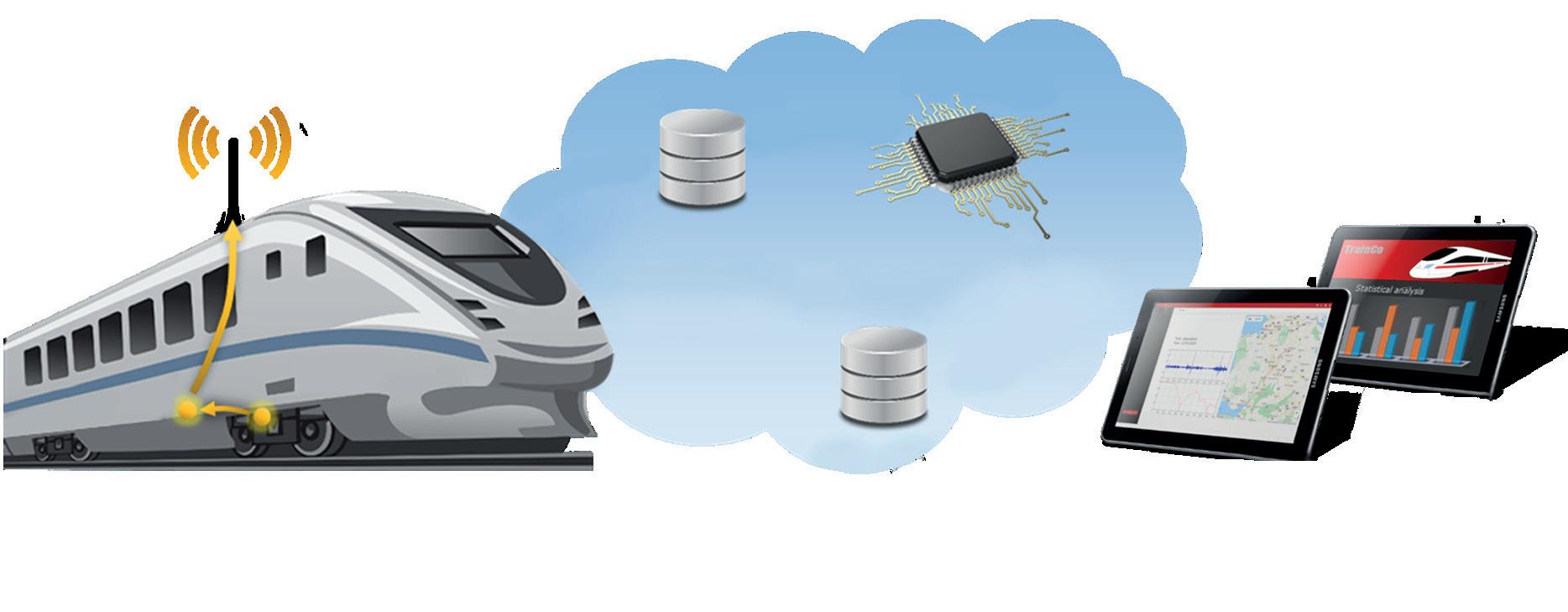

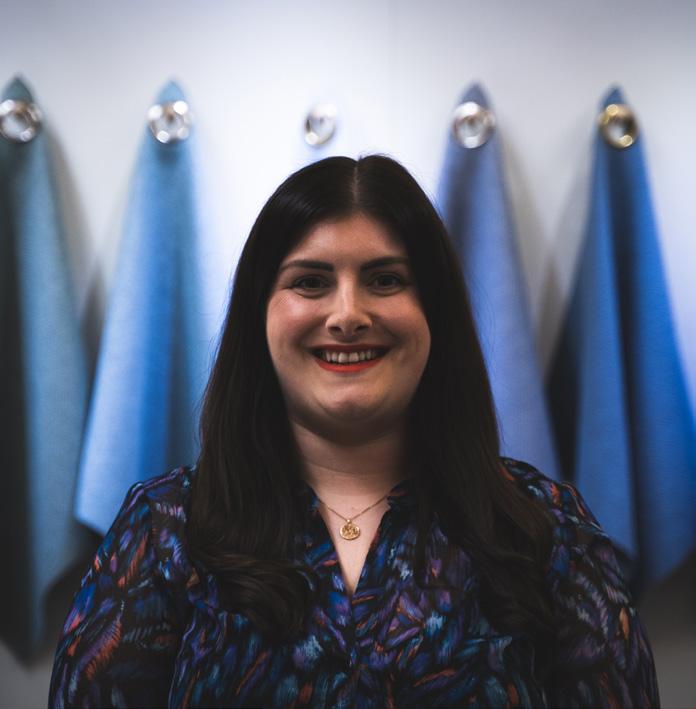
HONOR CLOUGH AREA BUSINESS MANAGER –RAIL AT CAMIRA FABRICS
Honor recently passed her Sales Executive course. She has worked on the new fabric for Transport for London’s Deep Tube Upgrade Programme with Siemens and the East Midlands Railways Aurora launch film. She also worked to get Camira Print on to the new Tyne & Wear Metro.

CAMIRA FABRICS
Camira is a privately-owned UK textile group founded in 1974 under the name Camborne Fabrics, but its heritage goes back to 1783 through various acquisitions. From offices to universities, hotels to hospitals, trains to buses, and shopping malls to cinemas, Yorkshirebased textile manufacturer Camira Fabrics spins, dyes, warps, weaves, knits, finishes, cuts and sews.
Want to know more about Camira Fabrics?
Tel: 03330 324 568
Email: info@camirafabrics.com
Visit: www.camirafabrics.com
Social: @camira

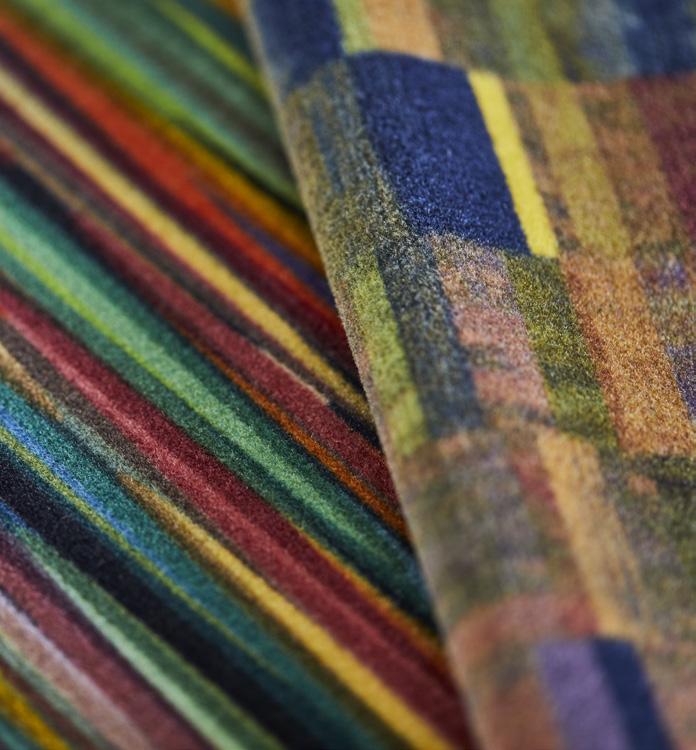
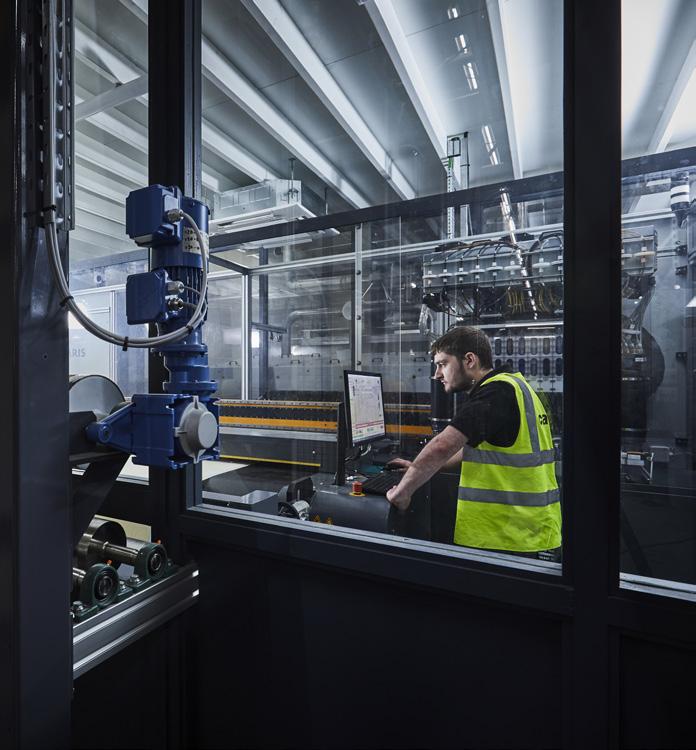
How did you get started in the industry?
I started in Camira’s transport customer services team in 2015 and then moved into the sales department in 2019. Joining Camira was a great move for me as I had studied textiles in school and had a real interest in the products. Prior to working at Camira I worked in administrative role in the product sampling and legal sectors.
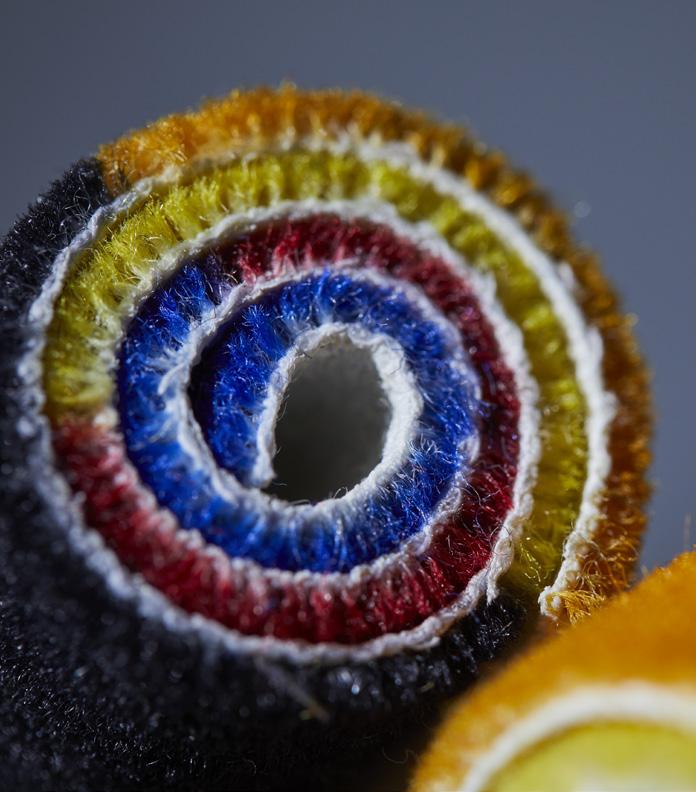
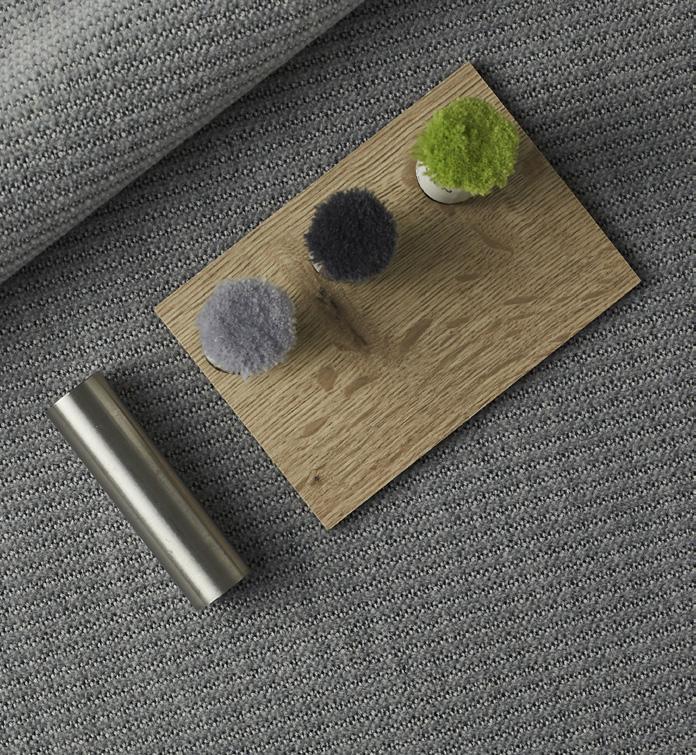
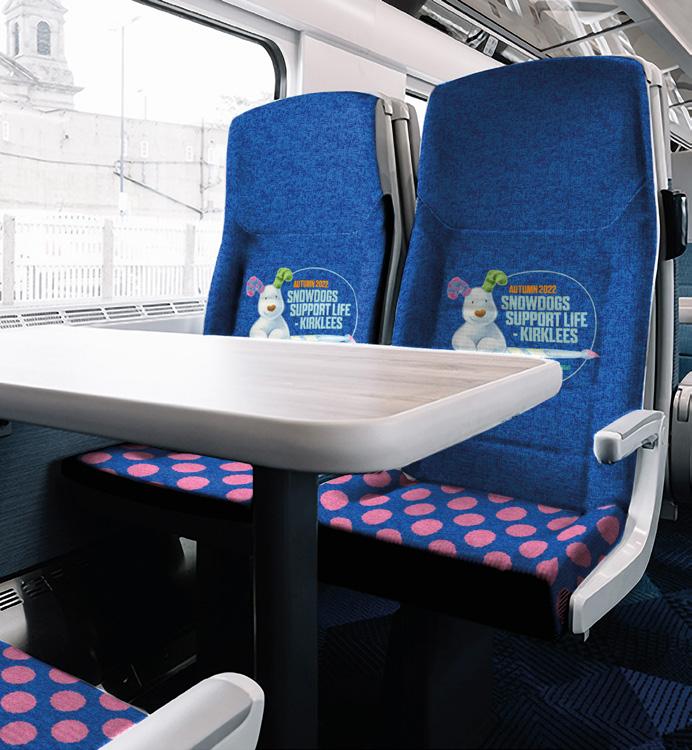
When did you join Camira Fabrics and what is your role within the company?
I started in April 2015 and I am the Area Business Manager for Rail; this involves nurturing relationships with our transport customers, growing business in the transport sector and collaborating with other departments to provide excellent customer service and promote our textile products for the transport sector.
What would you say is the most exciting technology in the industry?
Camira Print transforms what is possible in rail interiors. With cutting edge capabilities, Camira Print creates fabrics using state-ofthe-art digital print technology that delivers design and manufacturing freedom.
Applied to a lightweight British wool moquette fabric, it provides the ultimate in durability, and meeting the highest of standards, there’s a reason why moquette is part of the transport sector’s past, present, and future.
An industry rich in heritage and iconic in its textiles, the fabrics of bygone transport eras can be brought to life with Camira Print which makes recreating existing designs simpler than ever before using images, logos and branding.
What are some of the biggest challenges this sector currently faces?
Transport accounts for around a fifth of global carbon dioxide emissions and has the highest reliance on fossil fuels of any sector, it’s a challenge for transport designers to create an interior that is sustainable whilst remaining durable and aesthetic for years to come.
Rail already has strong credentials for sustainability, with lower emissions compared to other modes of transport. What we get asked by customers is what can interiors do to address sustainability, and more specifically how can we provide them with sustainable textile solutions.
Hybrid, Camira’s wool rich composition is one of our most sustainable transport textiles. Its renewable fibres are highly durable, supremely technical, ultraintelligent, and can even enhance the air quality of transport interiors with its ability to absorb harmful gases. With an everincreasing need to embrace sustainability in each element of our lives, Hybrid marks the future of transport textiles.
What types of products and services do you offer?
Camira offers moquette, leather, vinyl and faux leather fabrics.
What are some standout projects you’ve been involved in over the years?
Elizabeth Line, Avanti, East Midlands, Central Line, DART Irish Rail, COP26. We are involved in most of the projects in the UK rail market.
Camira, a longstanding supplier to Transport for London, worked with the organisation and design house Wallace Sewell to develop the fabric, which is now installed across the route’s 70, 200-metrelong trains. Designed to have a distinctive look and feel, with pinstripe details creating a sense of speed, and coloured to match the purple Pantone shade 3515C used to denote the route on the London Underground map, the Elizabeth Line fabric is set to be a well-known and well-loved addition to the city’s transport network.
Expertly designed for rail interiors
A flat-woven, British wool fabric destined to transform transport interiors. With the durability of a moquette and a contemporary look and feel, Hybrid is robust, lightweight and imbued with sustainability credentials. Scan the QR code to find out more.

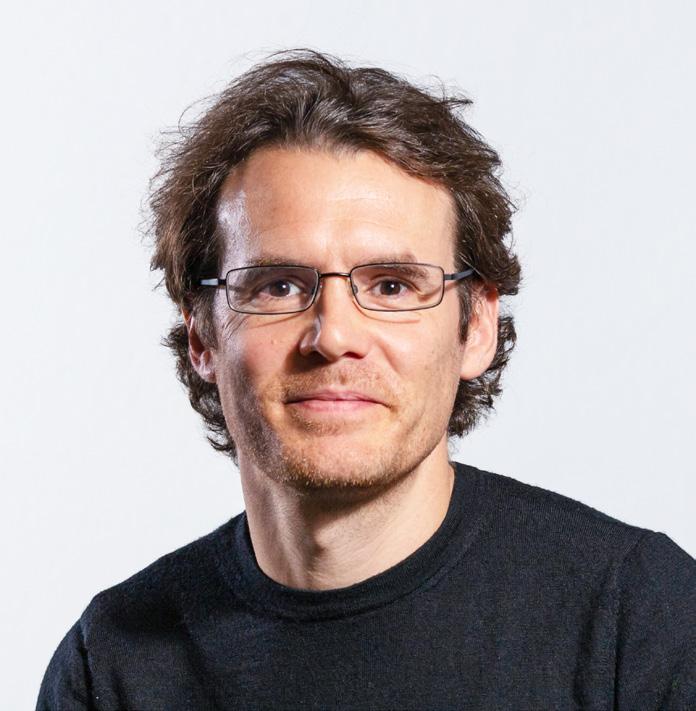
FIELD MANAGEMENT
Michael co-founded Re-flow alongside CTO Leandro Wade in 2018. He is responsible for overseeing the company's direction and specialises in negotiating partnerships, managing finances and working with the sales team to further expand adoption of the software.
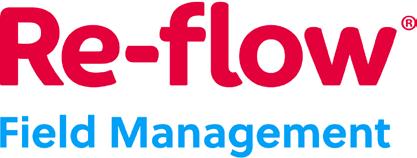
RE-FLOW FIELD MANAGEMENT
Re-flow Field Management provides field operations teams with a world-class field management solution that enables them to grow rapidly – save time, increase productivity and ensure compliance..
‘Last year we won The Sunday Times Best Places to Work Award and hope to achieve the same this year.’
What is your role within Re-flow?
I am the CEO and Co-Founder of Re-flow Field Management, one of the UK's leading field management software providers. I cofounded Re-flow alongside CTO Leandro Wade in 2018, building the business together from scratch. These days, I'm responsible for overseeing the company's direction and specialise in negotiating partnerships. I manage finances and work with the sales team to further expand adoption of the software.
Tell us about Re-flow.
Re-flow Field Management offers a comprehensive software solution for companies operating in large-scale infrastructure projects. We enhance their processes, safety protocols, and operational efficiencies.
Our software seamlessly connects office teams and on-site operatives through an integrated cloud-based system that consolidates essential field management functionalities. We deliver a configurable SaaS solution that can adapt to meet the needs of small and medium-sized enterprises as well as larger businesses.
Companies operating in highways, civils, utilities and commercial landscaping are rapidly embracing our digital solution.
These days companies are striving for improved compliance, safety, profitability, and industry leadership. We have the same values, so we’re an ideal partner. We’re preparing to expand our reach globally in the near future, and our growth trajectory seems promising.
What was the inspiration behind starting Re-flow?
team capable of creating bespoke elements. Our clients inspire us to keep growing the software and to make Re-flow the best digital solution on the market.
What success have you experienced in the last twelve months, and how do you measure success?
Re-flow has grown exponentially over the last year. In the last three months alone, we’ve hired twelve new members of staff in our marketing, support, development, and sales teams. We’ve recently moved to a bigger office as a result.
Also, with the recent launch of our 1.7 update, and with more features on the way, we’re confident the best is yet to come.
We measure success through our evergrowing team, clients re-signing with us, and our ability to keep on taking on new customers, with plenty of new users across our sectors.
With over 20,000 users, across 325 companies, already using Re-flow, what started as an app idea between friends has grown into a tool used all over the UK and Ireland to help streamline workflows.
What is your Unique Selling Point?
Our support team is second to none. From the moment companies speak to our software specialists we try to identify the gaps that are costing them money, time, and added stress, and we offer them a solution. Companies then move to a trial period where they see our software in action, build custom forms, or try out our pre-built forms. They work with our support team to address any queries and to understand the full capabilities of the software. Clients often digitise their existing forms – for example, timesheets or vehicle checks – and immediately see the benefits of Re-flow.
After the trial period, clients are passed on to our onboarding team, who guide clients through the software in an easily digestible and understandable way. At every step of the implementation journey, clients have access to our experienced support team, who are capable of handling any scale of challenge, big or small.
Want to know more about Re-flow?
Tel: 01392 574001
Email: info@re-flow.co.uk
Visit: www.re-flow.co.uk
First, we developed a rudimentary system for handling the transfer of digital forms between site and office for a company suffering from data loss. This simple project would lay the groundwork for what Re-flow has evolved into today. At Re-flow we’re tirelessly committed to listening to client needs and putting them into practice, and the system has grown exponentially ever since.
Client relationships remain at the core of everything we do. Without our clients Reflow wouldn’t just be an inferior product, it simply wouldn’t exist.
Re-flow is about working with businesses and scaling the software to meet our clients’ needs. We’re adaptable and have a talented
Customers also have access to detailed documentation and in-depth tutorial videos about using the app. These resources break down the software and its features in a simple way, without any unnecessary technical jargon. When issues or requests arise, our support portal is primed and ready. Clients submit a ticket, send an e-mail, or get in touch by phone – and our team is there to help.
How do you make your business a good place to work?
Last year we won The Sunday Times Best Places to Work Award and hope to achieve the same this year. What makes Re-flow a good place to work is that we are
continuously seeking out new talent, while also ensuring that we remain a tight-knit team. We foster a friendly and welcoming environment, and we work together to achieve collective goals.
When you spend the majority of your time at work, it is important to enjoy what you do and like where you are. Re-flow’s culture is inclusive, warm, and makes you want to come to work each day. Everyone shows passion for what they do and works hard. Re-flow's open-door policy and general culture create an inspiring environment. Each member of the team wants to excel personally and professionally.
Re-flow also provides an array of employee benefits, including bonuses, life and critical-life cover, the Cycle to Work scheme and an EMI Share scheme. The company also offers flexible remote working and recognises the value of face-to-face interactions. This approach allows the team to strike a healthy balance between remote work and office collaboration.
We’re committed to supporting our team within the workplace and beyond. For professional development, we pay for staff certifications, training, and courses. From first aid to role-relevant training, Re-flow provides the funds and time needed to complete the course.
It’s also important to take care of our team outside of the office. With YuLife Insurance employees have access to dental and medical care, and with EdenRed they can get benefits from savings across hundreds of the UK’s biggest vendors.
What are some of the biggest challenges this sector currently faces?
I think three of the biggest challenges the sector is facing are:
• Changing climate and green initiatives.
• Rail strikes.
• A lack of investment.
With rising tides, drainage issues, and extremes in temperature and weather, infrastructure is facing a constant battle against the elements. Finding new ways of innovating on and updating old infrastructure, as well as installing new infrastructure, needs to be addressed. And with net zero targets, better and greener ways of working need to be found.
With ongoing rail strikes over better pay, hundreds of millions of journeys have been cancelled, and billions of pounds have been lost from the UK economy. Passengers have been left stranded, unable to get to work or school, and attitudes towards rail have become negative. Confidence in transportation needs to be restored.
Infrastructure is the backbone of society and investment in these services has a positive effect on economic growth and development. With the HS2 leg from Crewe to Manchester being cancelled and budget cuts happening left, right and centre, there has been quite a lot of friction
between industry and the government – as demonstrated by an impassioned Henri Murison, CEO of Northern Powerhouse Partnership, at the Interchange Conference.
What are some potential solutions?
Looking at greener alternatives during the procurement stage of a project could be a possible solution to achieving net zero targets. Before work even begins, research should be undertaken to find greener materials, suppliers, and contractors. In this way, the overall carbon footprint of a job could be minimised. Although this may add to costs and make a project more expensive, we should weigh this up in relation to the health of the planet.
Another solution could be keeping our finger on the pulse regarding new technologies, and working with other industries to see how they are addressing the same problems.
Collaboration is very important in moving the industry forward and if we can learn from other sectors and replicate their efforts, why wouldn’t we?
Digitisation is another drum we bang at Re-flow. Improving efficiency through streamlining workflows, communication processes, and data sharing leads to less time spent sweating the small stuff, and more time spent thinking of big ideas and ways to make significant improvements. An extra hour here or there to sit down and come up with solutions to ongoing problems can make all the difference.
How can the industry tackle its skills shortage and how do you recruit/retain/ train your staff?
Staff and skills shortages are an ongoing issue in many of the sectors we serve. Attending exhibitions and shows has given
‘Looking at greener alternatives when in the procurement stage of a project could be a possible solution to achieving net zero targets. Before work even begins, research should be undertaken to find greener materials, suppliers, and contractors.’
us an insight into the current state of the industry and the location of any gaps and challenges. It is clear that the industry needs to be made more attractive to young people looking to start their careers, but also to those already working in the sector. This can be done with incentives and training.
Looking at reports from the CITB, they suggest retraining current staff to fill roles. And listening to Julie Davidson, Head of Quality, Safety, Health & Environment at Jointline at the recent RSMA Annual Conference, she said that improvements can be made by being transparent and upfront about the challenges – being truthful and matter-of-fact is a quality most people in the industry appreciate.
Embracing technology is also something that can make a vast difference to companies. The younger generation are tech savvy and, with data being the new oil, investing in digital solutions where possible seems like a positive move forward. At Re-flow we’ve seen time and time again

how adopting technology has helped staff. If an operative wants to change their role, understanding field management software like Re-flow puts them ahead of competitors who may never have used this type of technology before. They have more chance of moving up the ranks.
What are your views on collaborative working?
Collaboration is the only way forward. The industries we work with at Re-flow are siloed and sometimes reluctant to share knowledge, but to bring change in infrastructure we need to work together. As a tech company, we understand the importance of data and how, when data is shared, it can bring positive change, efficiencies, and growth to a company. The better the quality of the data collected and shared, the more trends and challenges can be identified and solved. When you have a clear picture of where you are, you can better address where you’re going. This same attitude should be taken within infrastructure. The old adage, ‘a problem shared is a problem halved’ comes to mind. During a talk at the recent Interchange UK conference, Martin Riley, SVP Climate Performance at CRH, spoke about a supply-
chain collaboration led by Tarmac, Shell, Volvo, JCB, Benninghoven, Certas Energy, and Zappshelter. They delivered carbon savings of up to 80 per cent on a road project through use of the best available materials and plant. As a case study, they proved how cross-collaboration can really work and make a big difference in achieving the net zero targets set for 2050.
In terms of technology, how do you anticipate things might change in the next five to ten years?
I think that there will be an increased adoption of digital signalling, control systems, and train management platforms to enhance operational efficiency and safety. There will be an integration of Internet of Things (IoT), devices, and sensors for the real-time monitoring of train components, infrastructure, and track conditions.
There is a lot being said about the development and implementation of autonomous and semi-autonomous train technologies, the leveraging of artificial intelligence, and the integration of augmented reality and virtual reality systems for enhanced driver training, maintenance, and passenger entertainment experiences.
Thinking about green issues, there’s a need to electrify rail networks and to connect renewable energy sources – such as wind and solar – to power infrastructure.
Of course, we also need to upgrade and modernise existing rail infrastructure –tracks, bridges, tunnels, and stations – to accommodate high-speed trains and increase capacity.
With tools like Re-flow, rail companies could undertake predictive maintenance, asset management, and real-time monitoring systems, to optimise performance and reduce downtime.
I think more collaboration between governments, industry stakeholders, and regulatory bodies will promote innovation, improve investment, and encourage sustainable growth in the rail sector. I hope to see a future where we can work together to build infrastructure that will not only stand the test of time but impact the planet positively.
This collaboration would also be prevalent in the development and implementation of regulatory standards, guidelines, and frameworks to govern the deployment and operation of new rail technologies. Industry standards should be continually reviewed and improved.
Field management software that puts you in control and your team to work
Re-flow delivers easy-to-use Field Management software rooted in collaboration with the rail industry. Re-flow arms companies with an effortless workflow around everything rail maintenance workers need. Including: worker qualification libraries dynamic scheduling job progress photo uploads instant in-app communication on-site streamlining of HSE processes, risk assessments, and asset check
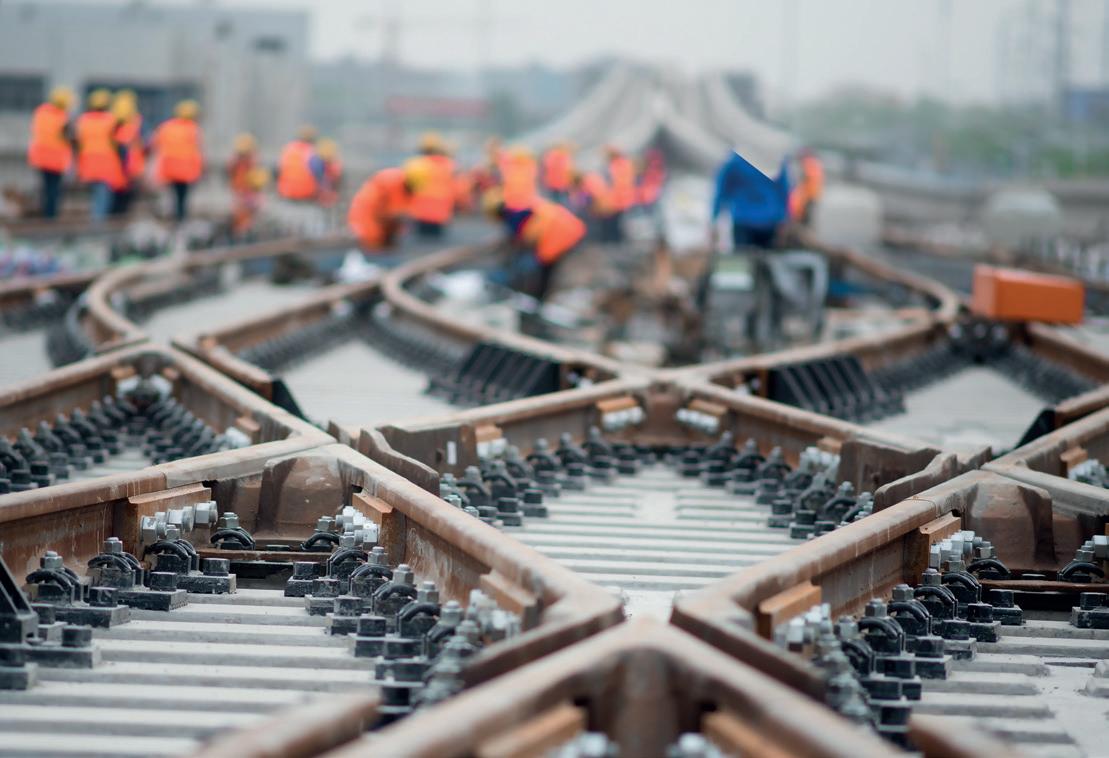
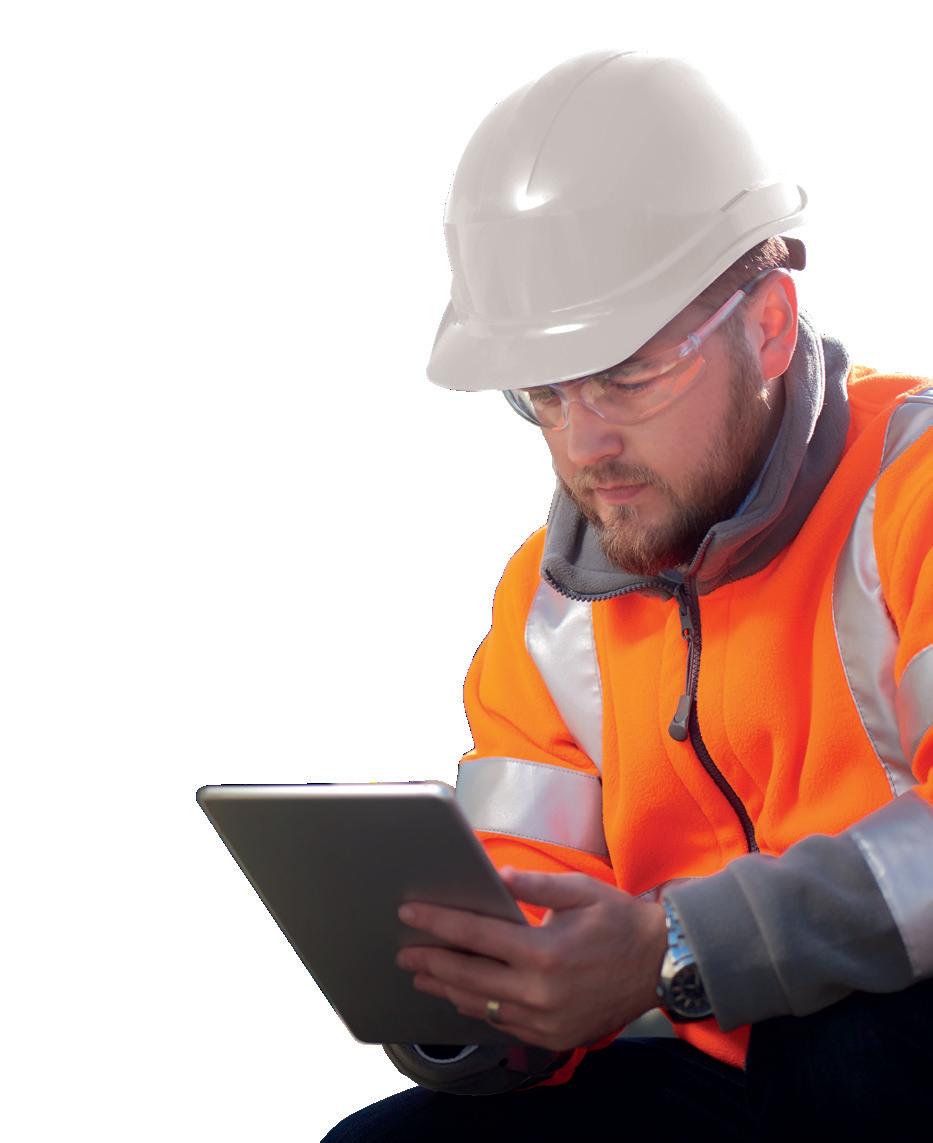
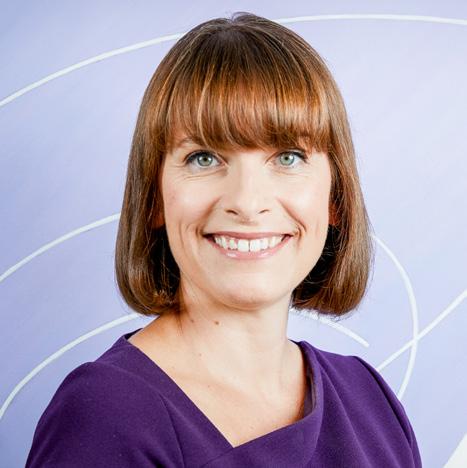
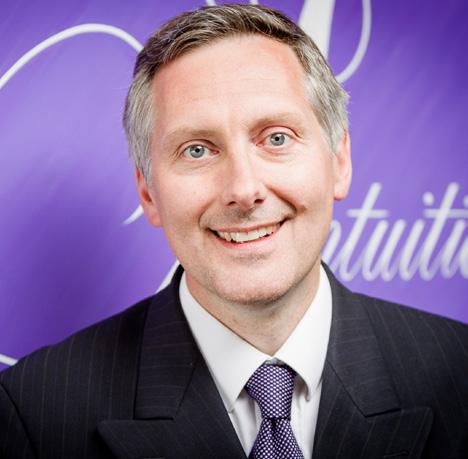
Rebecca Collings is Nichols Regeneration Lead offering strategic advice to clients involved in regenerating towns and cities. Previously, Rebecca worked in central government, with two decades of experience in senior roles.
Simon Young has been with Nichols for over two decades providing specialist expertise in rail and regeneration. He led the successful Programme Partner on Crossrail to deliver the Elizabeth Line. Previously, Simon worked for London Transport in operations.
What Comes First: a Station or Regeneration?
Rebecca Collings and Simon Young, both of Nichols explain how success happens when rail and regeneration programmes are aligned
Academic research has shown that when stations are closed, such as during the Beeching closures of the 1960s, economic growth in surrounding areas declines. There is increased understanding of the value of integration and joined up planning between rail and regeneration in creating growth.
For five decades Nichols have advised and delivered on large, iconic programmes, complex projects and major business change initiatives, operating in a wide range of industries, especially regeneration, transport, environment, and technology.
We are strategic advisors involved throughout the development and delivery lifecycle of unique programmes. Through helping revitalise urban and rural areas we have enabled many opportunities and economic growth for years to come. We have worked nationally and internationally on cities, levelling up towns, universities, roads, railways and airports. Through a combination of creating business cases, strategic advice, planning and programme management we have been able to reawaken and bring renewed life to many communities.
More can be done to ensure that the full potential for regeneration is explored, assessed, and realised as rail projects compete for investment funds. We believe regeneration benefits should be a key consideration from the outset and at the core of station business cases. Accounting for wider social and community value, as well as economic growth benefits, makes for a more compelling business case for rail projects, broadening the focus beyond transport and connectivity. Integrating rail and regeneration programmes also attracts private investors and so increases opportunities to bring benefits to communities and areas.
Nichols recently hosted an event in West Yorkshire with transport experts and representatives of local and combined authorities working in growth and development. We introduced the concept that regeneration benefits should be at the heart of any station business case. We discussed that the opportunity for regeneration should be a key priority when developing the case for investment on rail projects, with improved transport and connectivity seen as only one element of the strategic rationale. It was highlighted that
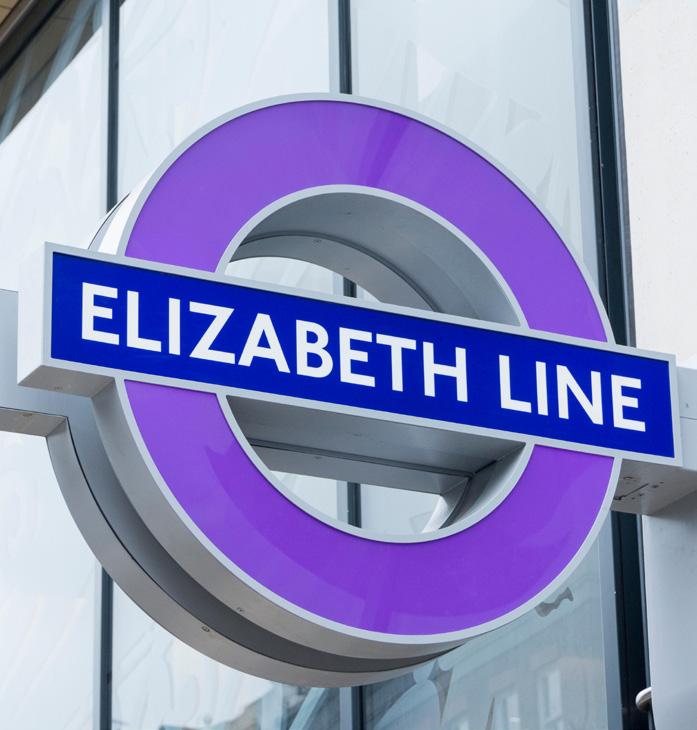
more could be done to bring stakeholders together earlier to consider those wider opportunities.
Diverse sets of stakeholders are driven by different agendas, priorities, and financial objectives and constraints. We have found on many projects, stakeholders such as councils, rail companies, central government and local business and community representatives were not sufficiently aligned from the outset. A lack of appetite, confidence, and tools to take on the significant challenge of gaining alignment, co-creation and ownership of business cases and plans presents a barrier to getting to an optimum solution.
We prioritise stakeholder engagement and aligning plans to develop a vision, requirements and cases for rail and regeneration projects. We focus on enabling stakeholders to find the ‘golden thread’ between their varying priorities and agendas so that they can come together to create a single strategic vision and case for investment funding.
Our framework encourages early stakeholder engagement and provides guidance on the long term economic and social benefits. This enables the potential that station projects present to be leveraged to shape opportunities that underpin the case for funding.
Station projects should be funded at the lowest possible cost and be attractive for private sector investment. Private sector funding is more valuable than its monetary contribution, it expedites and prioritises the investment case through the investment process.
Private sector investors bring a sharper focus on managing risk and cost. Unit rates for construction works in a rail environment carry a safety premium compared with UK ‘high street’ construction work. There is an opportunity to apportion works to enable more non-rail construction companies to undertake works at ‘high street’ rates.
We believe that neither the station nor the regeneration should come first. Stations and regeneration are perfect partners and when considered together from the outset make a compelling investment case.
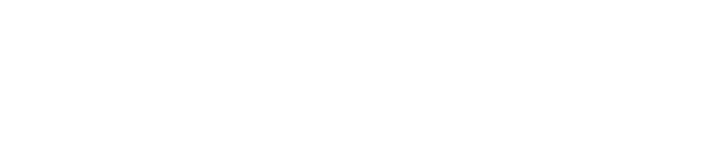
Keep passengers in the know and not in the dark
The RailSmart Dynamic Route Map keeps passengers informed using a completely customisable interactive route map that displays disruption updates, station information and much more.
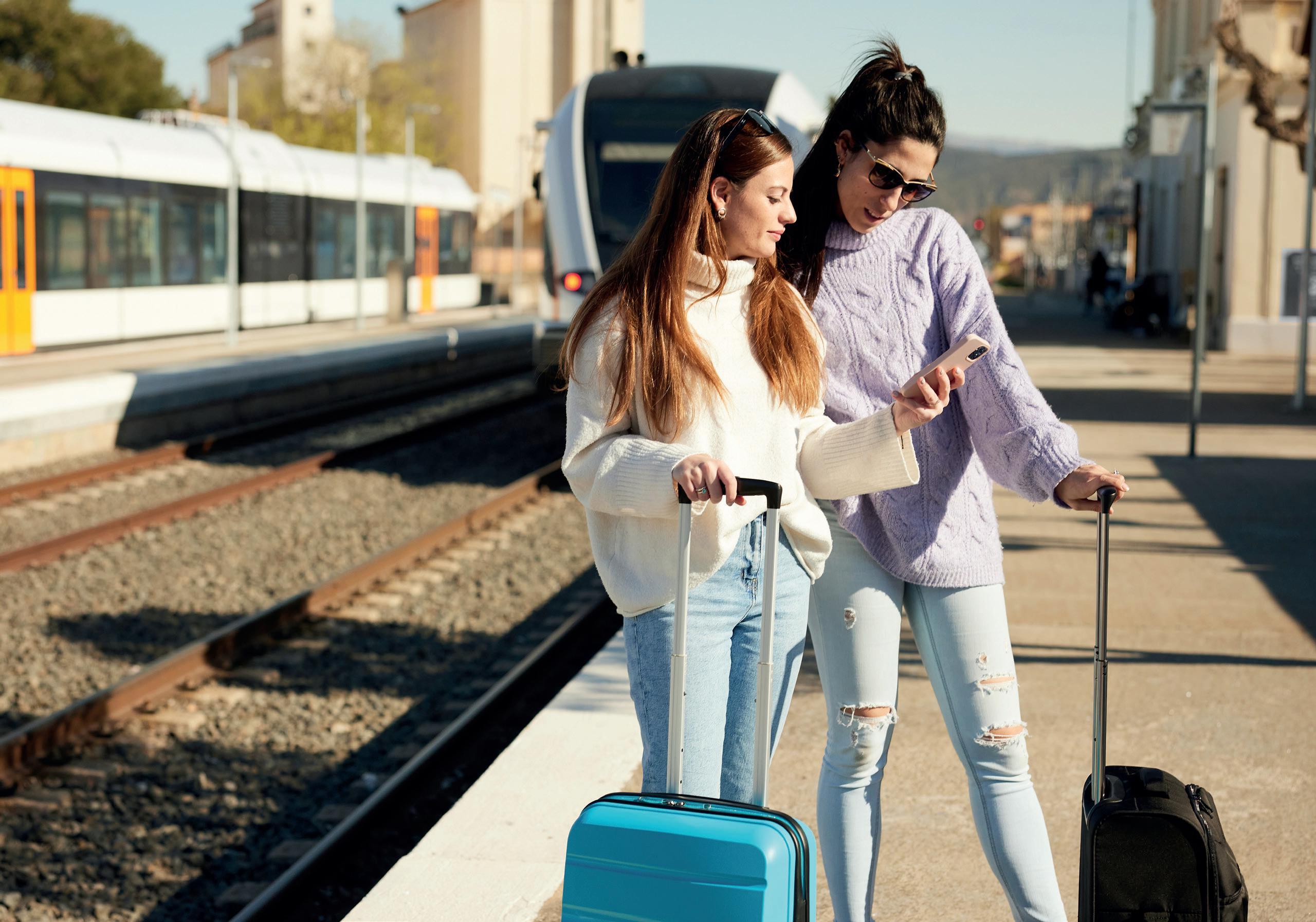


Improve Passenger Communications
When passengers have the information they need, they can make informed decisions, putting them in control of their journey
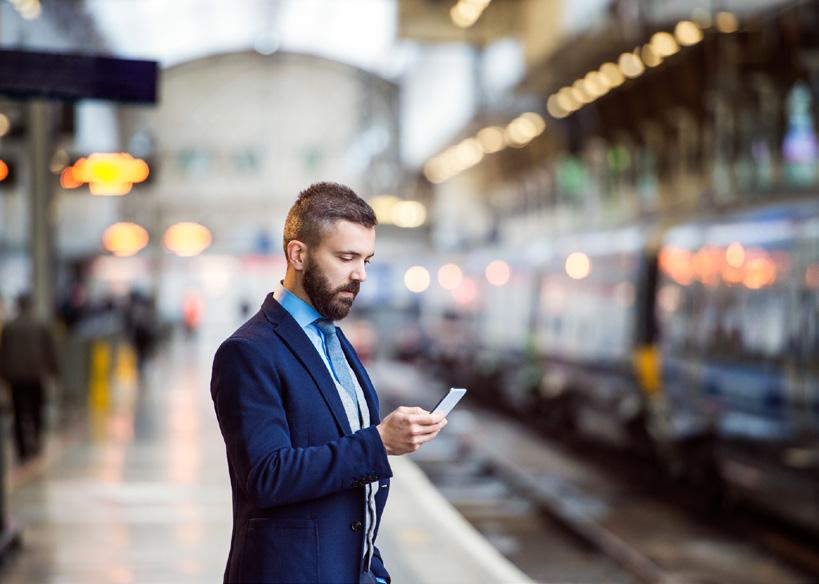
Research suggests that passenger information is one of the top priorities for people using the railway. The 2022 Transport Focus report What Matters to Passengers reveals that out of twenty-five factors which matter most on a rail journey, ‘Being kept informed about delays and the options I might have’ is ranked seventh in importance.
For passengers aged between 18 and 35, it’s the third most important factor, coming just below value for money and punctuality and reliability. Hardly surprising when you consider how we’ve all come to expect instant and accurate information about just about everything on our smartphone screens.
But how can TOCs provide the information passengers need in a more automated, streamlined way?
Provide real-time information when service is disrupted
In times of disruption, passengers want to know if it’s worth waiting on the platform a few minutes longer, or if there’s time to grab a coffee. They definitely want to know if they have to re-plan their journey or reorganise their day. Your customer support staff can provide passengers with this information but it involves accessing data from different sources – such as signalling systems and live departure boards – and rekeying it into
the customer information system. Even then there’s no guarantee your customers can locate the information easily enough to plan their journey.
In an ideal world, passengers could access a map on their smartphone showing the service status on the rail network they use. A quick tap on their station would bring up real-time information relevant to their journey, giving them an accurate picture in both summary and detail.
Instant access to the status of the service goes a long way towards alleviating the pain of disruption and puts the passenger back in control.
Give passengers the tools to plan in advance
Planned engineering works can be an unwelcome surprise for even the best prepared passenger, particularly if part of their journey is covered by a rail replacement bus service, or their train is cancelled altogether.
However, when a passenger knows in advance how their journey will be affected, it becomes a much less frustrating experience.
A journey is easier to plan if passengers can see on a map which section of their trip is disrupted and how that is likely to affect their arrival time.
Increasingly TOCs are offering their passengers a calendar view of scheduled changes or disruptions to the service so passengers know what to expect well before they travel, giving them the option to either tweak their journey, factor in more travel time or decide to travel on a different day.
Consider all the other factors which help people plan their journeys too. Knowing whether the lifts are working at the station, which carriage they need if the train is too long for the platform or which side the doors will open.
Having this simple yet very practical information easily to hand is a gamechanger for rail passengers.
Save time for customer information staff
All this information may already be available on different data feeds, but pulling it together to present to customers can be complex and time-consuming for staff. The aim of RailSmart Dynamic Route Maps is to automate that process, freeing up time for customer information teams to spend on more strategic communications tasks.
Instead of accessing data from multiple sources and manually sending out messages, TOCs can give passengers clearly presented, colour-coded live maps on their smartphones, so they can plan their journeys in real time and in advance.
RailSmart Dynamic Route Maps provide complete flexibility, allowing operators to customise the maps with their own branding and define delay times, for instance a minor delay could be defined as ten minutes and a major delay as twenty or more.
Operators can also set parameters in advance, so a major delay could automatically trigger a certain type of message. The advantage is that the maps update themselves using existing information feeds with very little need for human intervention.
You know what works best in your region, and we can work alongside you to create a better way to share information tailored to passengers’ journeys.
Disruption happens, but by giving your passengers their own personal live route map for planning their journeys, straight to their smartphone, you can transform their travel experience.
To find out how 3Squared can help you deliver better passenger information, visit: 3squared.com/our-solutions/customerinformation/
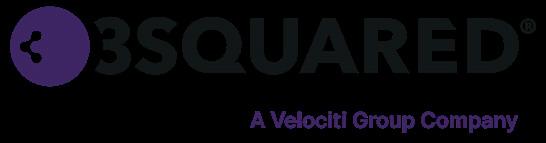
Email: hello@3squared.com
Visit: www.3squared.com
Social: @3Squared

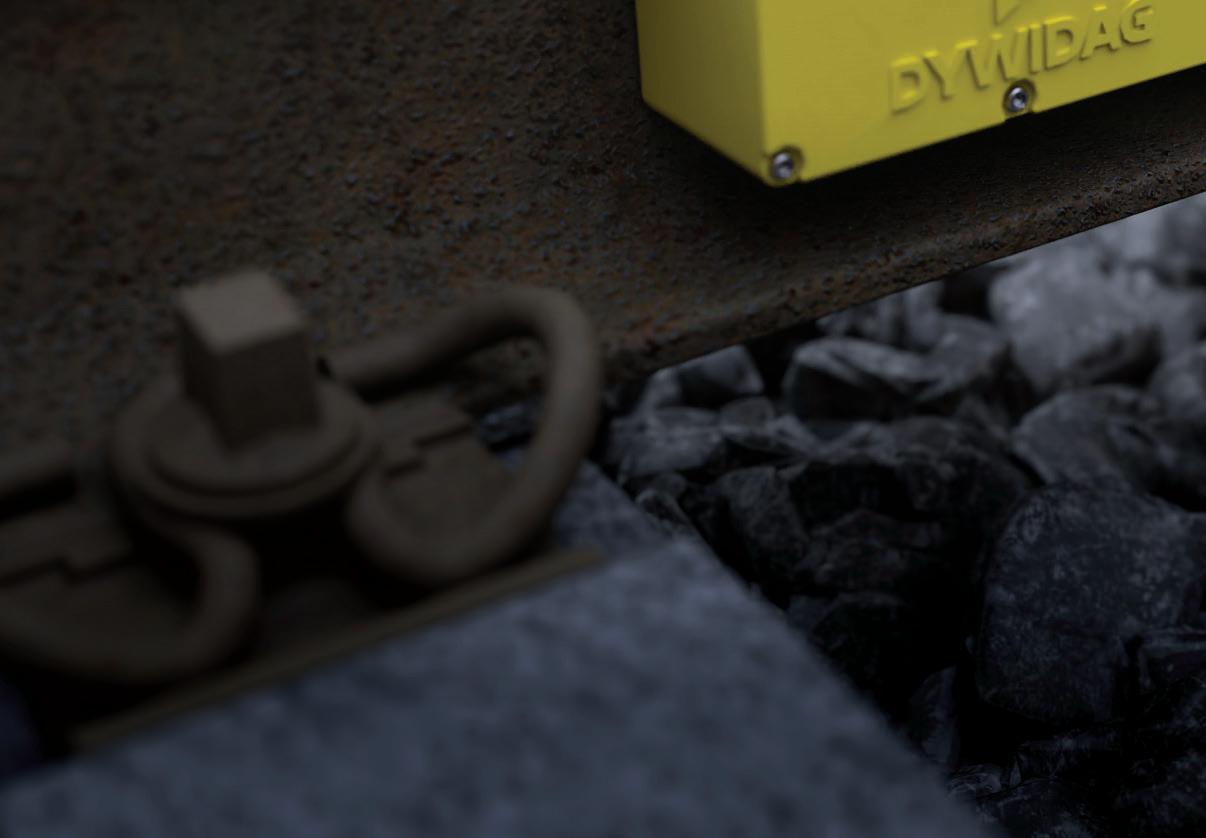
Transforming Rail Safety.
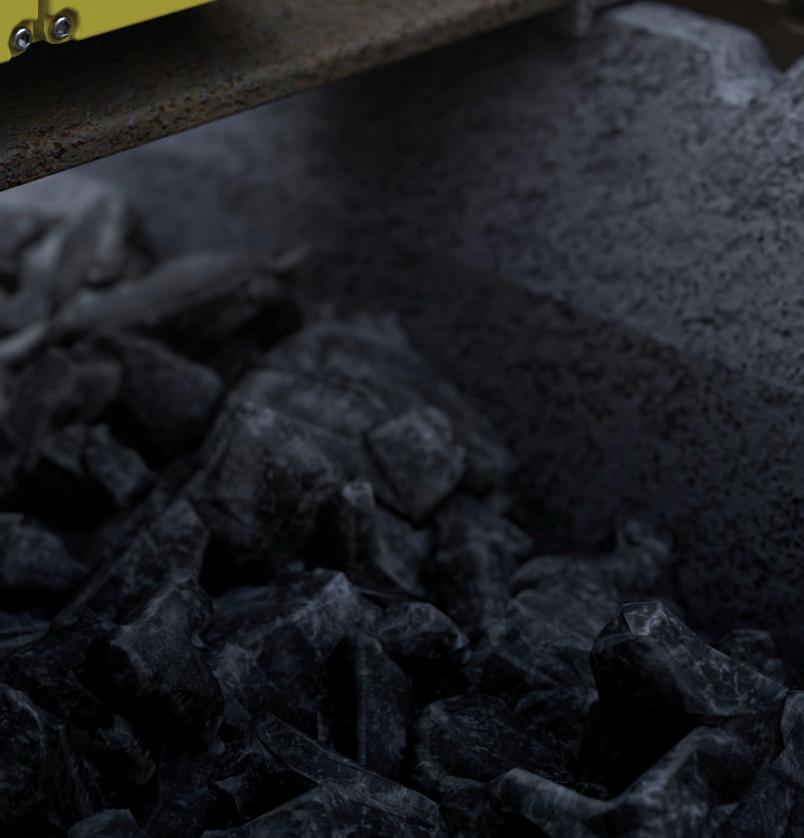
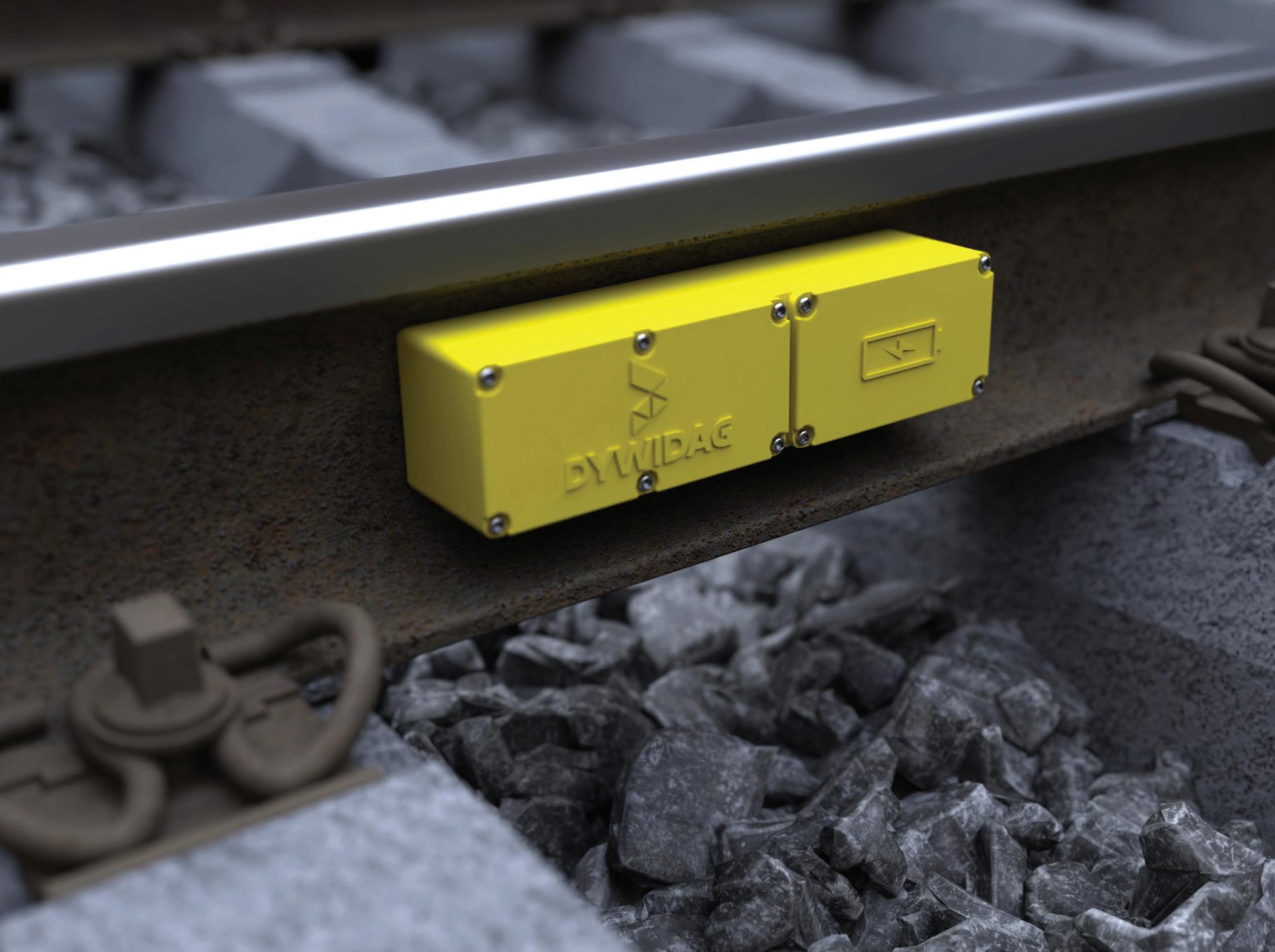
The NEW DYWIDAG Smart Temp Critical Rail Temperature monitor revolutionises rail safety, minimises train delays and eliminates unnecessary speed restrictions. It provides real-time temperature data, GPS positioning and seamless integration with Network Rail’s RADAR and DYWIDAG’s Infrastructure Intelligence platforms.
• User configurable temperature thresholds
• Immediately sends data as thresholds are crossed
• Real-time data every 15 minutes
• Fully compliant with NR/L2/TRK/011 Mod 14 managing track in hot weather
MONITORING | SURVEY | SENSORS | INFRASTRUCTURE INTELLIGENCE
Transforming Rail Safety
Understanding the imperative for enhanced rail temperature monitoring on the modern railway
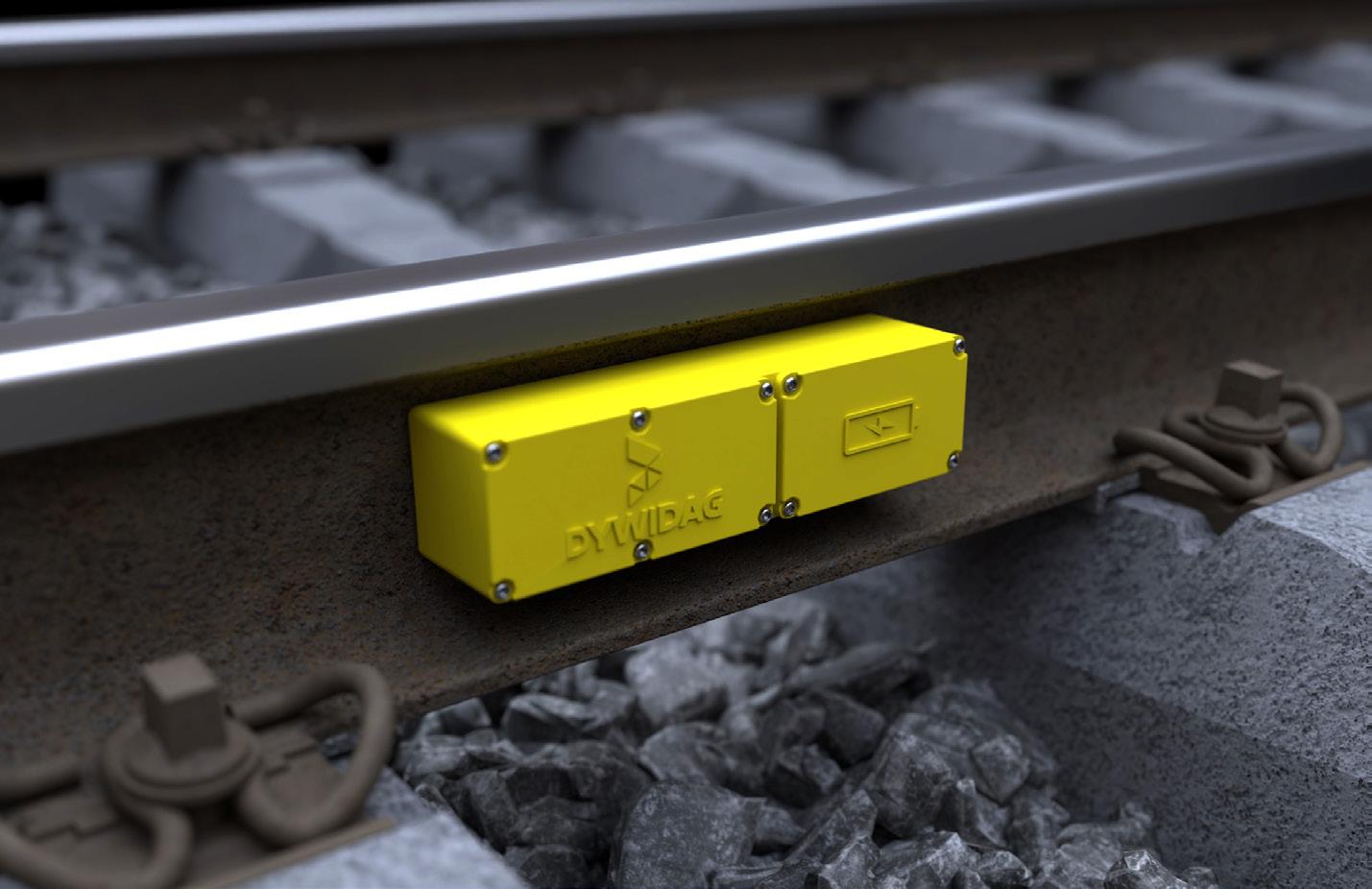
In the railway industry, safety remains the paramount concern, transcending all other operational priorities.
According to Network Rail's Challenge Statements*, weather-related impacts result in 1.5 million delay minutes annually, amounting up to £100 million in delay and cancellation costs alone for Network Rail. Monitoring track temperature is crucial for reducing such train delays. The introduction of the DYWIDAG Smart Temp CRT monitor represents a significant advancement in this area, offering real-time rail temperature data every 15 minutes to enable prompt and informed decision-making.
Elevating safety standards through real-time data
The evolution of rail temperature monitoring technologies is marked by an increased emphasis on real-time data accuracy. The DYWIDAG Smart Temp CRT monitor provides this level of precision through advanced sensor technology, empowering permanant way managers to pre-emptively address potential safety risks and operational inefficiencies. By obtaining timely data, rail operators are empowered to make informed decisions that prevent accidents, reduce the need for speed restrictions, and decrease onsite maintenance work. This strategic shift
not only boosts safety but also minimises operational disruptions, thereby ensuring a smoother and more reliable service for passengers and freight.
Reliable and accessible temperature monitoring
For the railway industry to successfully navigate the challenges posed by temperature fluctuations, the deployment of reliable and easily accessible monitoring solutions is crucial. The DYWIDAG Smart Temp CRT monitor, with its robust design featuring high-strength magnets for secure attachment and seamless integration with Network Rail's RADAR platform and DYWIDAG’s Infrastructure Intelligence platform, embodies the ideal solution. Its compact size and vibrant yellow casing ensure both practicality and visibility, making it a firm companion in the quest for enhanced rail safety.
The collective benefit of industrywide adoption
The adoption of the DYWIDAG Smart Temp CRT monitor enhances rail safety and efficiency, setting a new standard for temperature-related risk management in the industry. It aligns with broader objectives of enhancing safety, operational
efficiency, and passenger confidence. As rail operators increasingly look to technological innovations to address complex challenges, the DYWIDAG Smart Temp CRT's userfriendly design, long battery life, and quick recharge time further minimise maintenance needs, allowing focus to remain on safety and reliability.
As the industry moves forward, the focus on accurate, reliable, and accessible temperature monitoring technologies will continue to play a key role in shaping the future of rail safety, ensuring that railways remain a safe and dependable mode of transportation for all.
*Source: Challenge Statement – Environment – Weather Resilience and Climate Change (networkrail.co.uk)
Join us at Rail Live 2024 on June 19th and 20th where you'll get to see the new DYWIDAG Smart Temp CRT Monitor along with our full range of products.
Make sure to stop by Stand B25 to engage with our experts and discover how this state-of-the-art monitoring solution enhances safety and efficiency in rail projects.
Register now to attend. We look forward to meeting you at Rail Live 2024.
www.raillive.org.uk/registration-2024
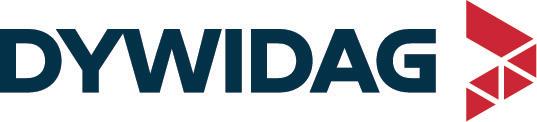
Tel: 0161 797 5511
Email: sales.uk@dywidag.com
Visit: dywidag.com/products/dywidag-smart-temp

Scan me to learn more about the new DYWIDAG Smart Temp CRT
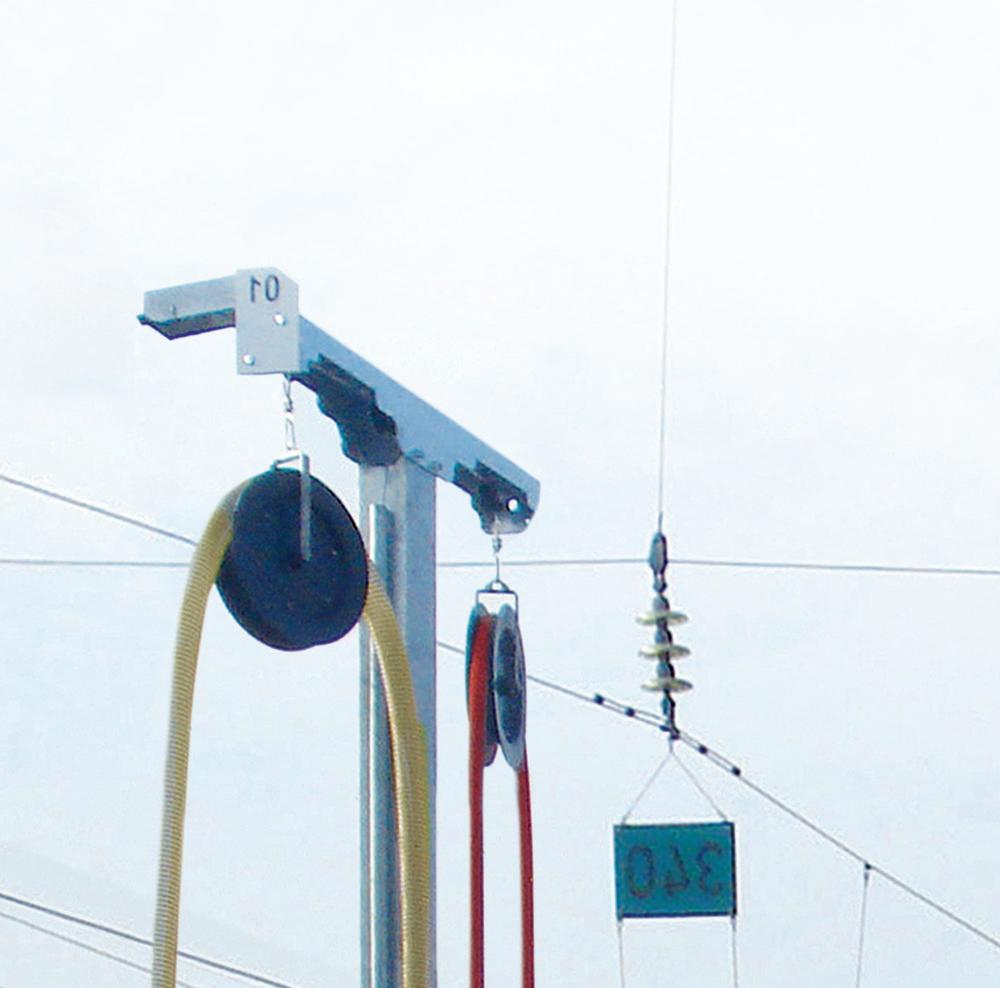
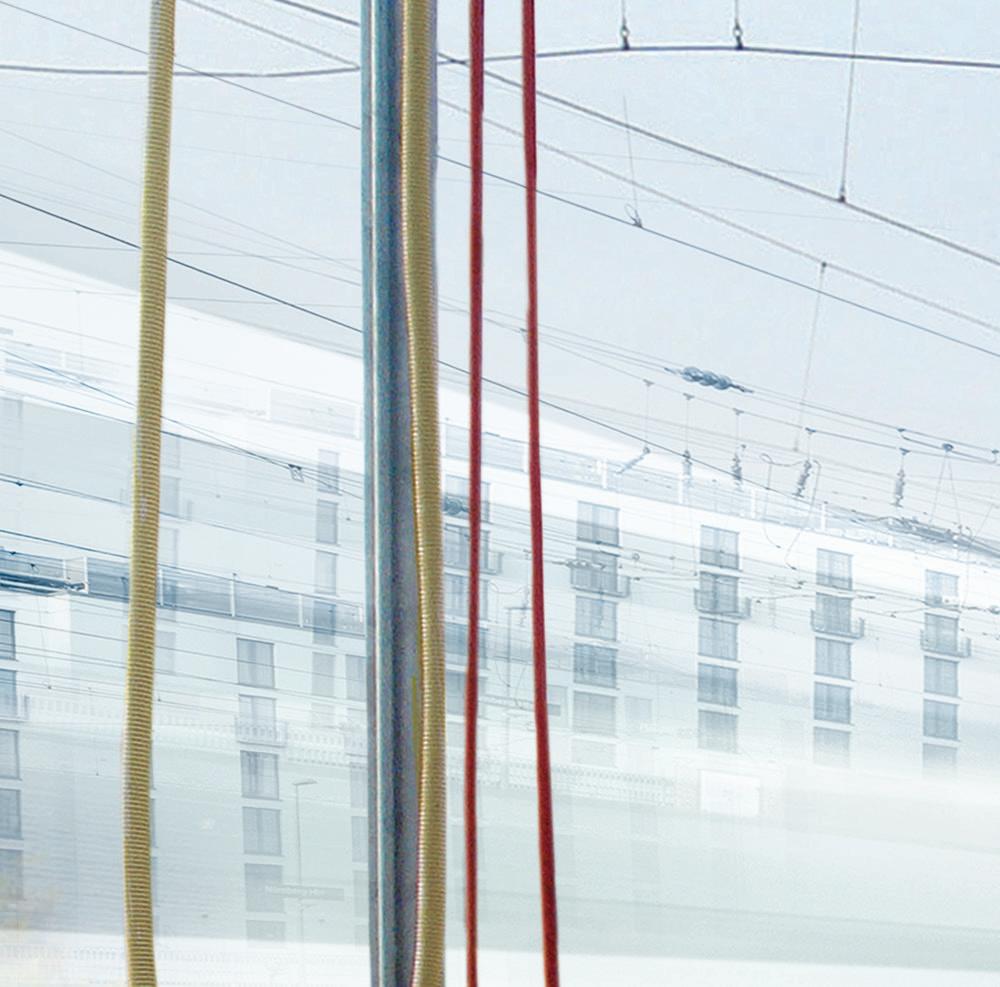
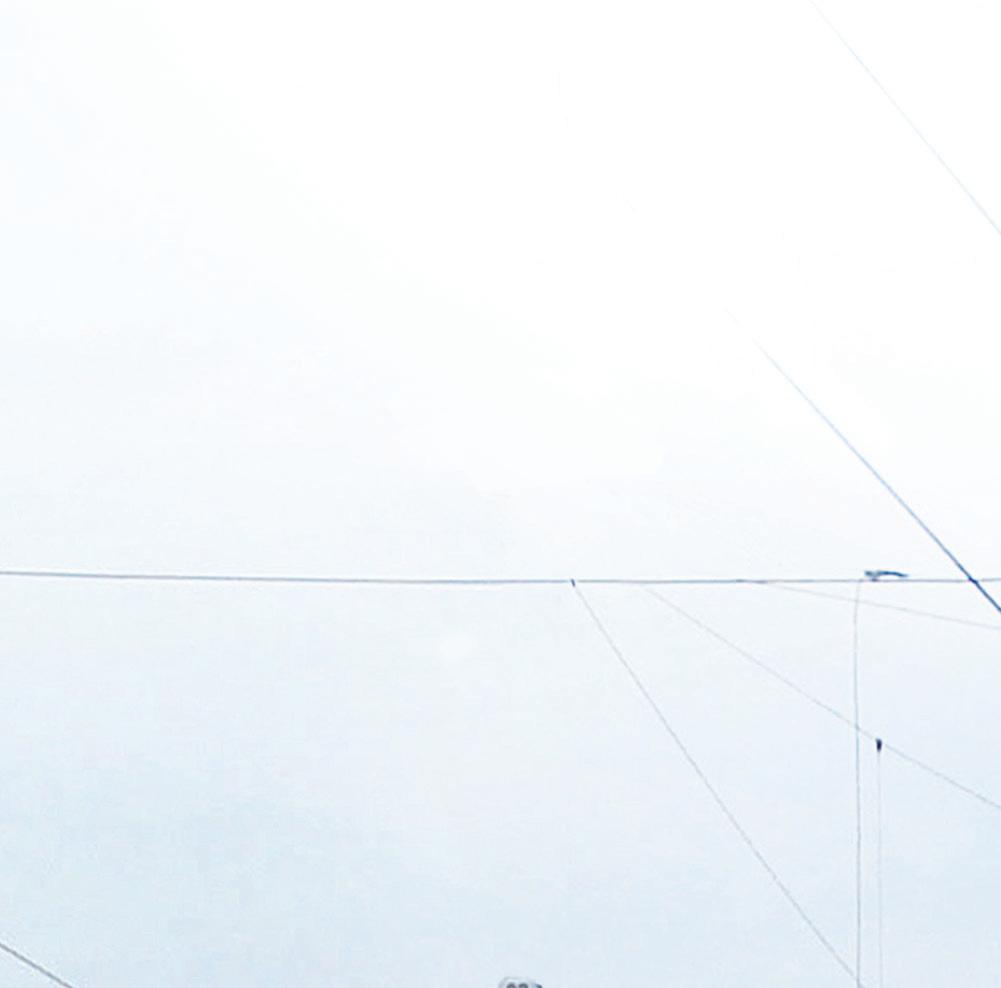
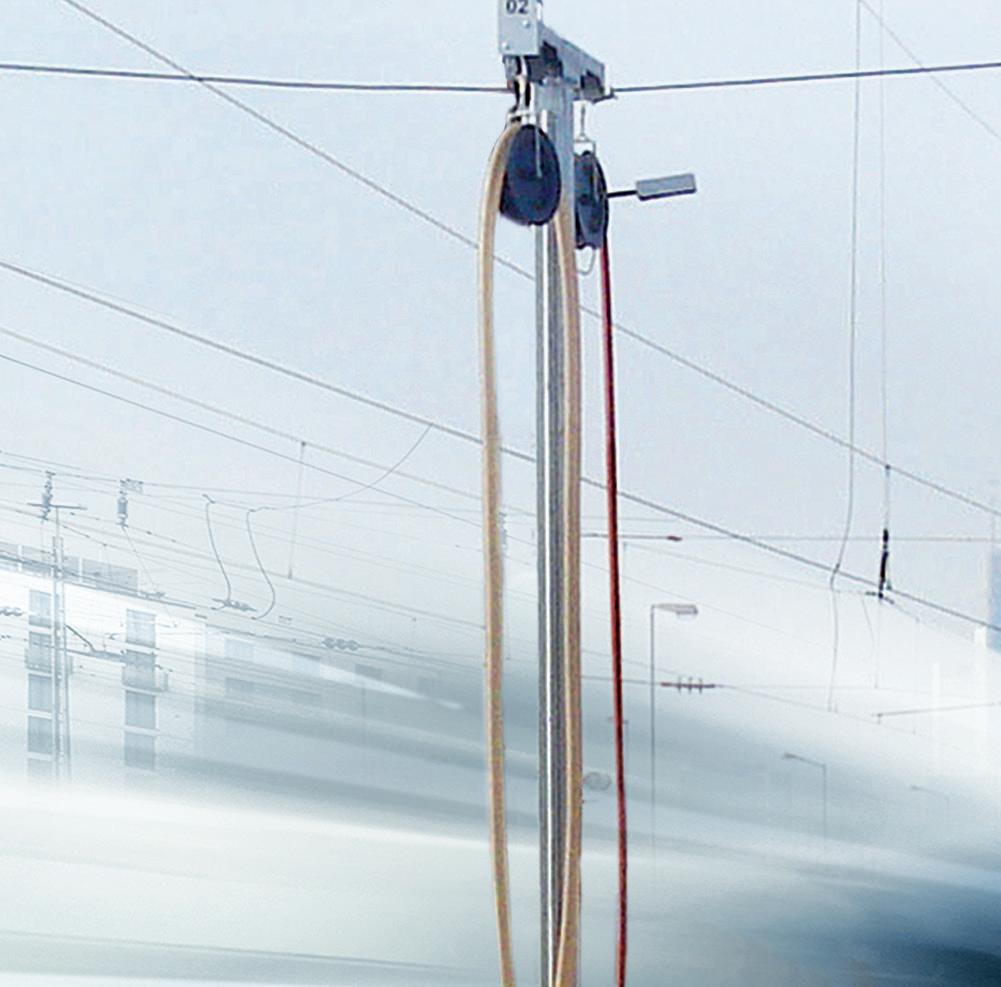
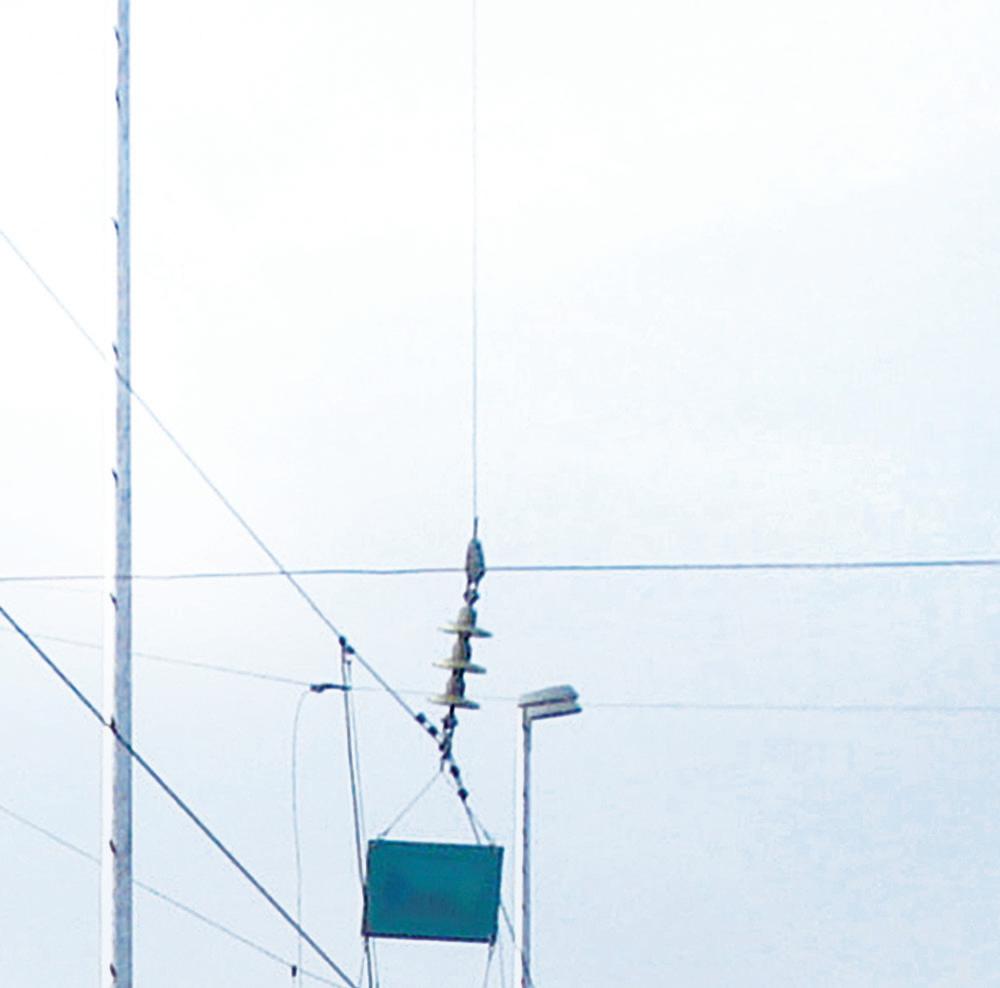
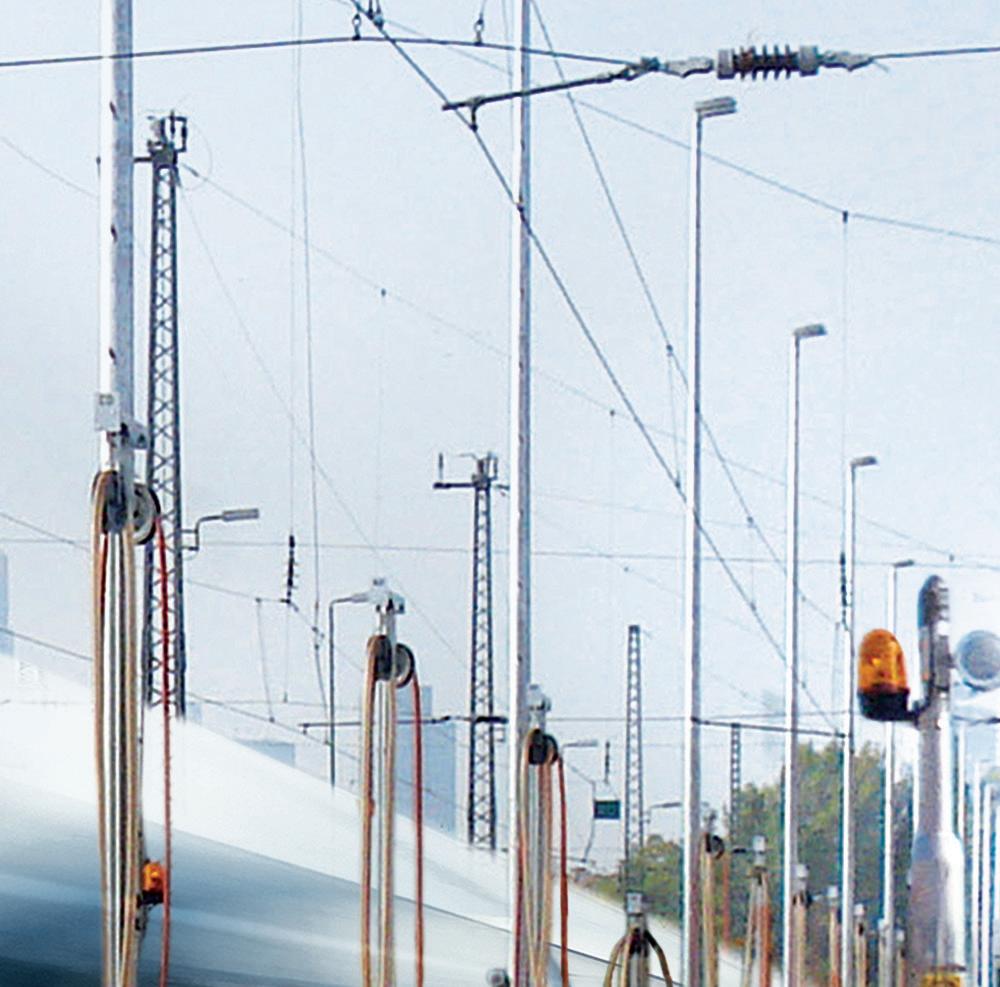

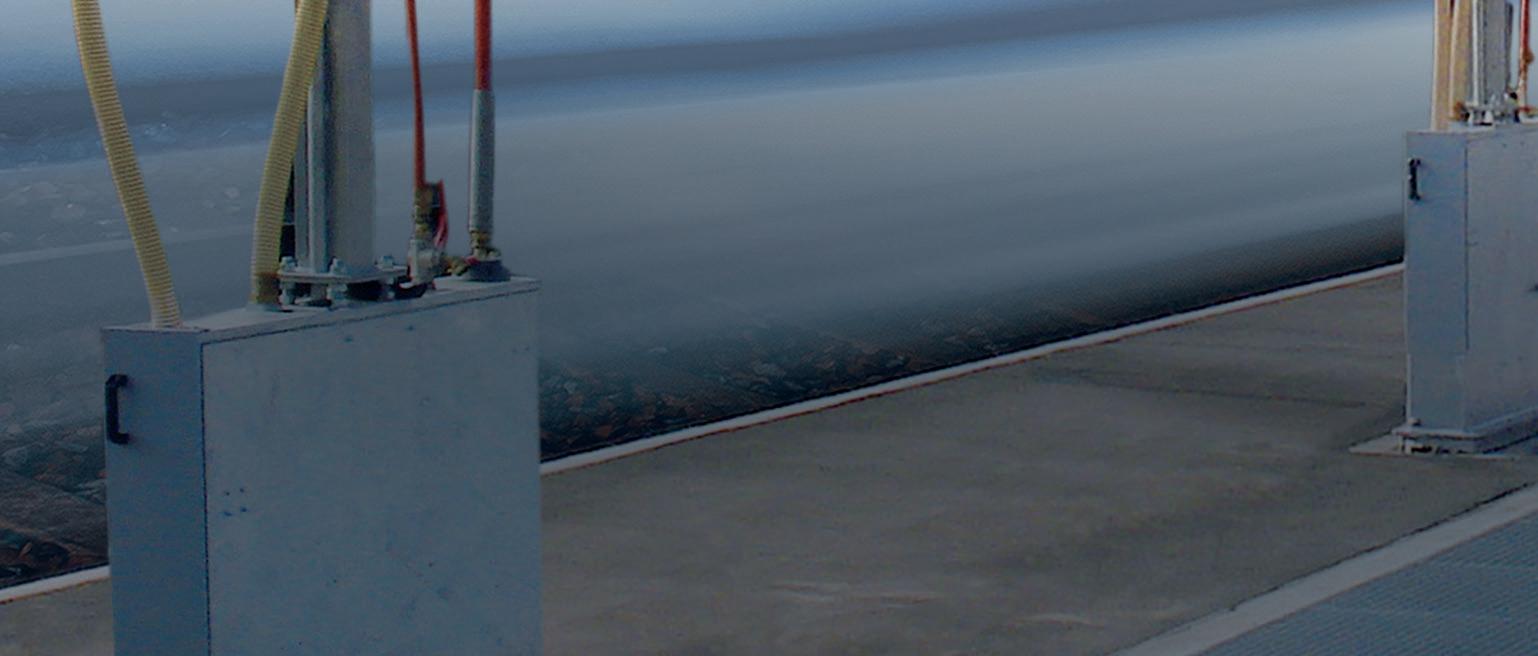
PROGRESS IS A MATTER OF STAYING ON THE RIGHT TRACK
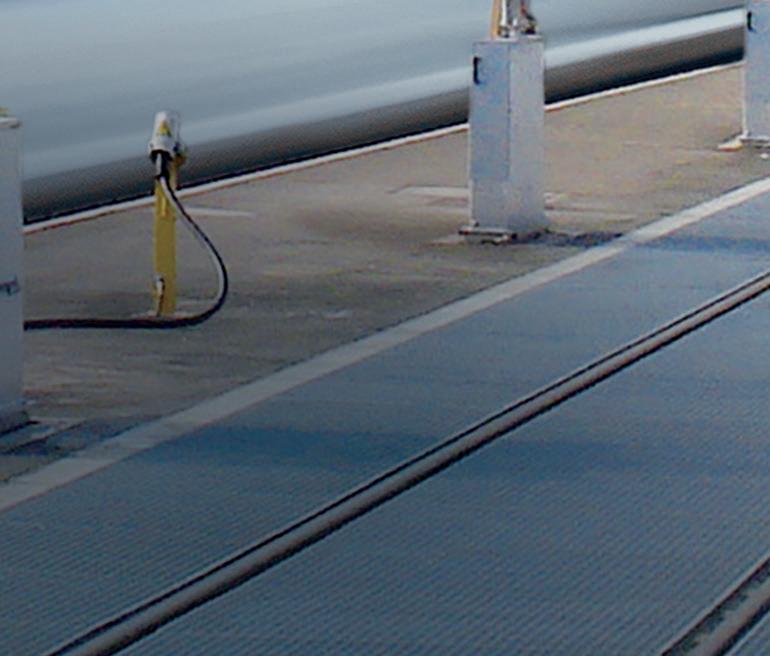
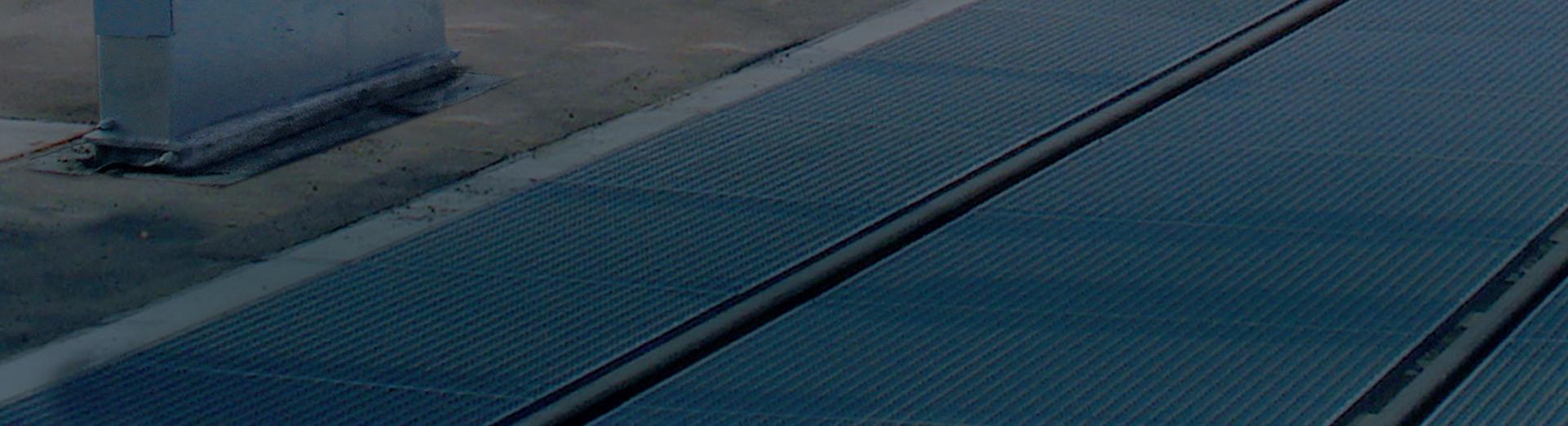
In everything we do, we never lose sight of what is essential to you: working economically with reliable technology.


As the inventor of the elastomer-coated rotary lobe pump and a pioneer in the area of wastewater technology, we have been supplying technical solutions whose functionality, quality and reliability set the benchmark for our competitors. Leading railway operators put their trust in our intelligently designed pumping stations and Vogelsang’s demand-oriented technical equipment. These include systems for water supply and wastewater disposal as well as servicing and cleaning for passenger trains to ensure the highest standards regarding hygiene, usability and cost-efficiency.
VOGELSANG – LEADING IN TECHNOLOGY
Contact person: Wayne Carrington
Tel. 07845 541 429 | wayne.carrington@vogelsang.info vogelsang.info



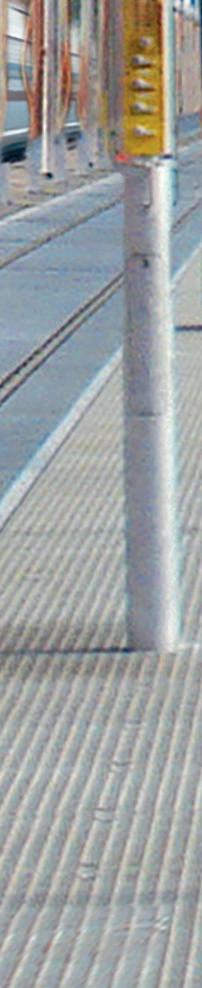
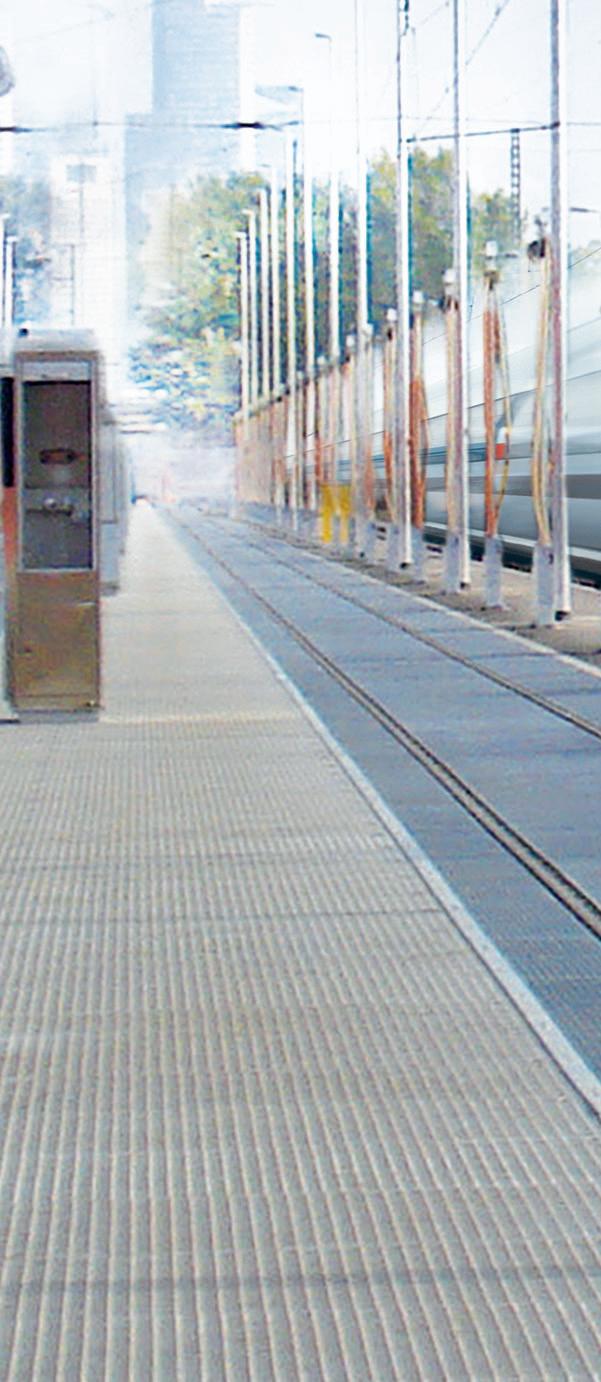
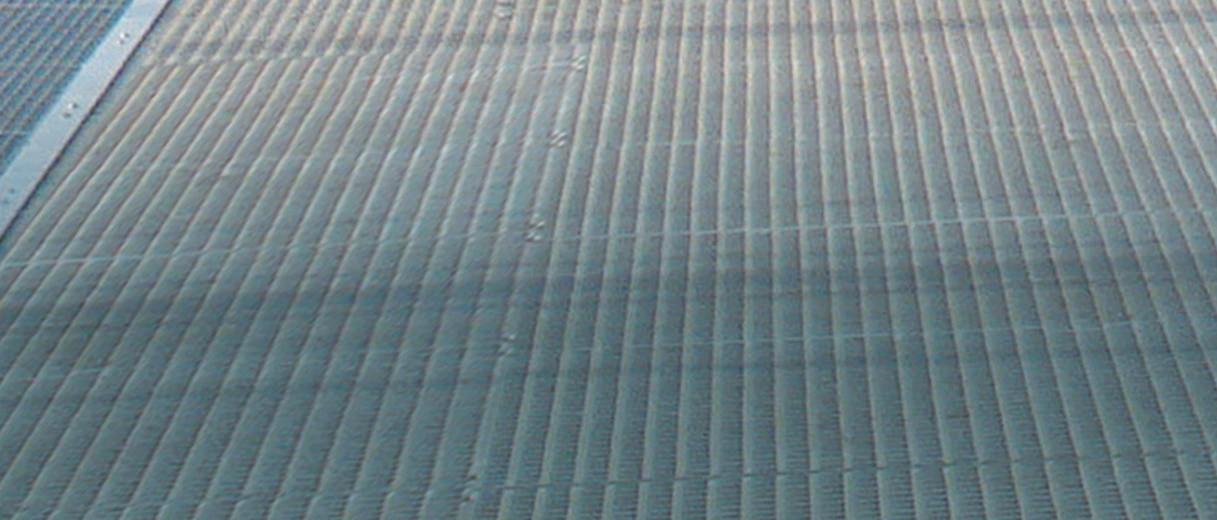
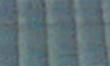

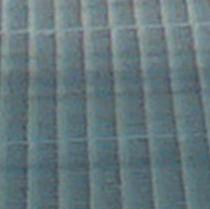
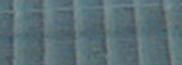
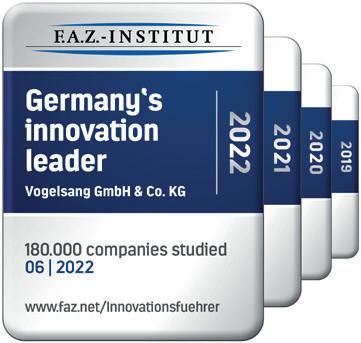
Trains Stay Clean with MobileUnit
Clean carriages are part and parcel of a well-maintained train, but as many train care depot managers know, keeping them to a high standard takes work
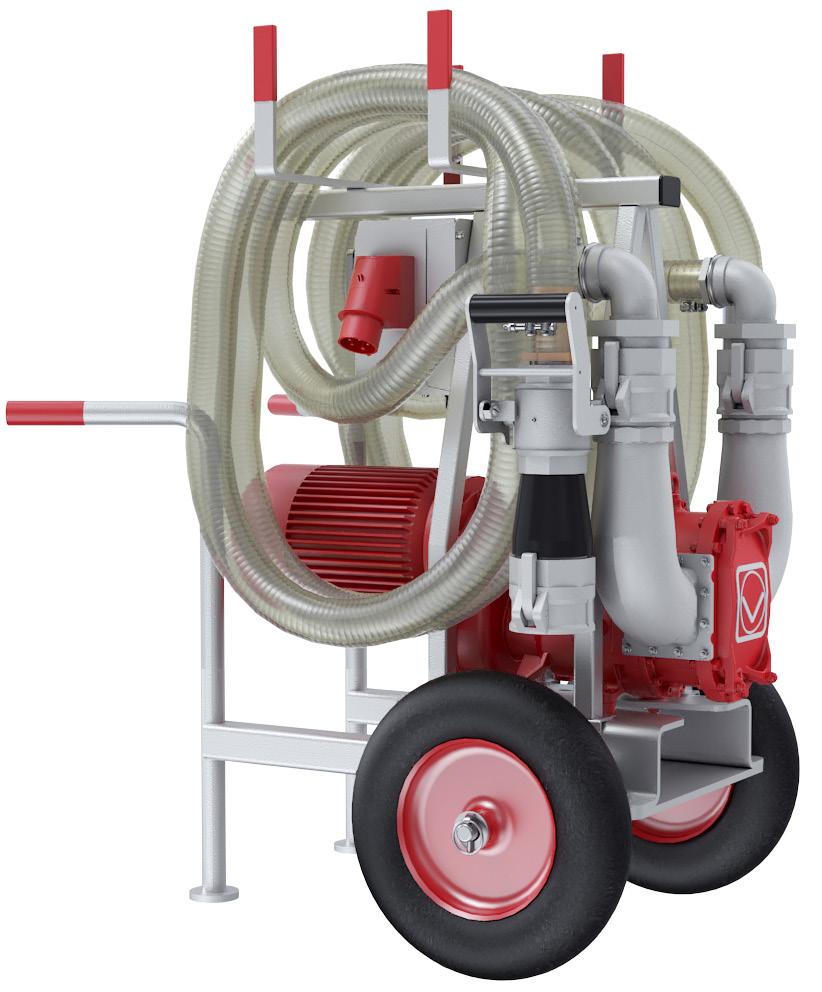
Out-of-service toilets can mean delays and fines, as well as disgruntled passengers. They are the railway’s customers after all. The cleaning of carriages is often a well-oiled machine, but things can go awry when the cleaning apparatus breaks down or is out of action for maintenance, there are scheduling problems, or carriages need cleaning on the platform.
Whilst Vogelsang’s railway customers enjoyed the TUnit CET system, particularly the non-drip coupling, that the pump manufacturer supplied, the company recognised there was a gap in the market for an easy-to-use cleaning system that wasn’t stationary. Hence, the MobileUnit was created.
‘We saw there was a real need for a reliable and durable emptying system’ said Wayne Carrington, of Vogelsang. ‘We have a lot of experience in the railway sector and have worked closely with depot managers for decades. We applied our knowledge and expertise to creating a portable pump in a variety of sizes and options, as we knew a ‘one size fits all’ solution wouldn’t work for all depots and stations.’
One such depot that has benefitted from the Mobile Unit is a depot run by Northern Rail. Fitted onto a self-propelled trailer, the MobileUnit can be used in the depot shed or at the site of the carriage if it’s unable to be moved, significantly reducing stoppage time.
‘The MobileUnit works a treat’ said a Depot Operator at Northern Rail. ‘It’s a vital piece of equipment for us. It’s not always possible to use a fixed CET pump; for instance in winter the CET pumps and pipework often freeze, however the MobileUnit can easily be within the shed so this eliminates service delivery stoppage time. The same thing applies when a train carriage needs to be emptied internally and can’t be moved from its current protected position.
‘Because, by its design, a closed system, it has the ability to suck and pump source to source, it’s very clean and everything can easily be flushed to the drainage system - which can be up to 1,000 litres a night when it’s in use. The unit itself is easy to manoeuvre, has a braking system, can be power isolated and is robust enough to cross rail tracks with ease. During our possession, and in use we’ve never had an issue with it.’
Another problem for traincare depots was what to do during maintenance or refurbishment works. Whilst stationary CET systems are the mainstay for most depots, when these are out of action, the MobileUnit has provided a solution, as Northern Rail discovered.
‘We had to replace our CET system, which was originally installed in the 1980s, and was no longer working properly. The refurbishment work took twelve months and we needed a carriage cleaning system in the meantime’ said the Depot Coordinator for Northern Rail.
‘We used a Vogelsang MobileUnit for the whole time that the refurbishment was underway. It worked hard! It’s simple to operate and we never had any issues with it. I’d recommend the MobileUnit as an excellent temporary or emergency CT unit.’
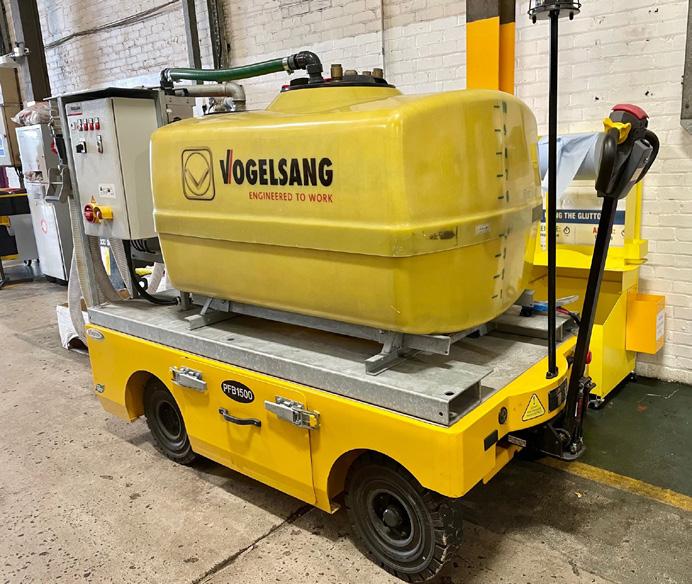
Other train operators are also using the MobileUnit as a standby system for when the traincare team is unable to use the CET systems. West Midlands Trains has been using the MobileUnit since 2016 at two of its train care depots. The Property Manager for West Midland Trains said: ‘Where and when the trains are stabled is changeable due to timetabling, so to have the MobileUnit ready for use at the train care depot is helpful for our maintenance teams. It does the job perfectly; empties sanitary waste and replenishes water cleanly and easily. We’ve also used the unit on station platforms when we’ve needed to empty busy trains.’
Prices start from £8,500. For more information about the MobileUnit, get in touch via the contact information below.

Email: wayne.carrington@vogelsang.info. Visit: www.vogelsang.co.uk
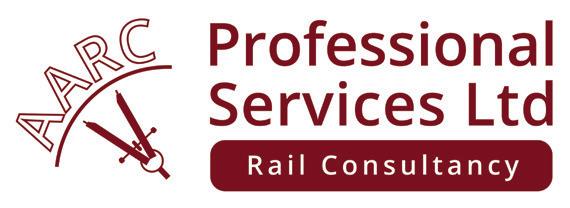

AARC Professional Services Limited draws from over
We are a railway consultancy bringing together likeminded rail professionals with a common aim to deliver outstanding outcomes by..
• Helping clients achieve their goals...
• Through strategic and technical expert advice...
• Across a range of disciplines...
• From the frontline through to the boardroom
Whether you’re looking for high level advice & guidance or direct project support, we’re here to help you deliver excellent outcomes.
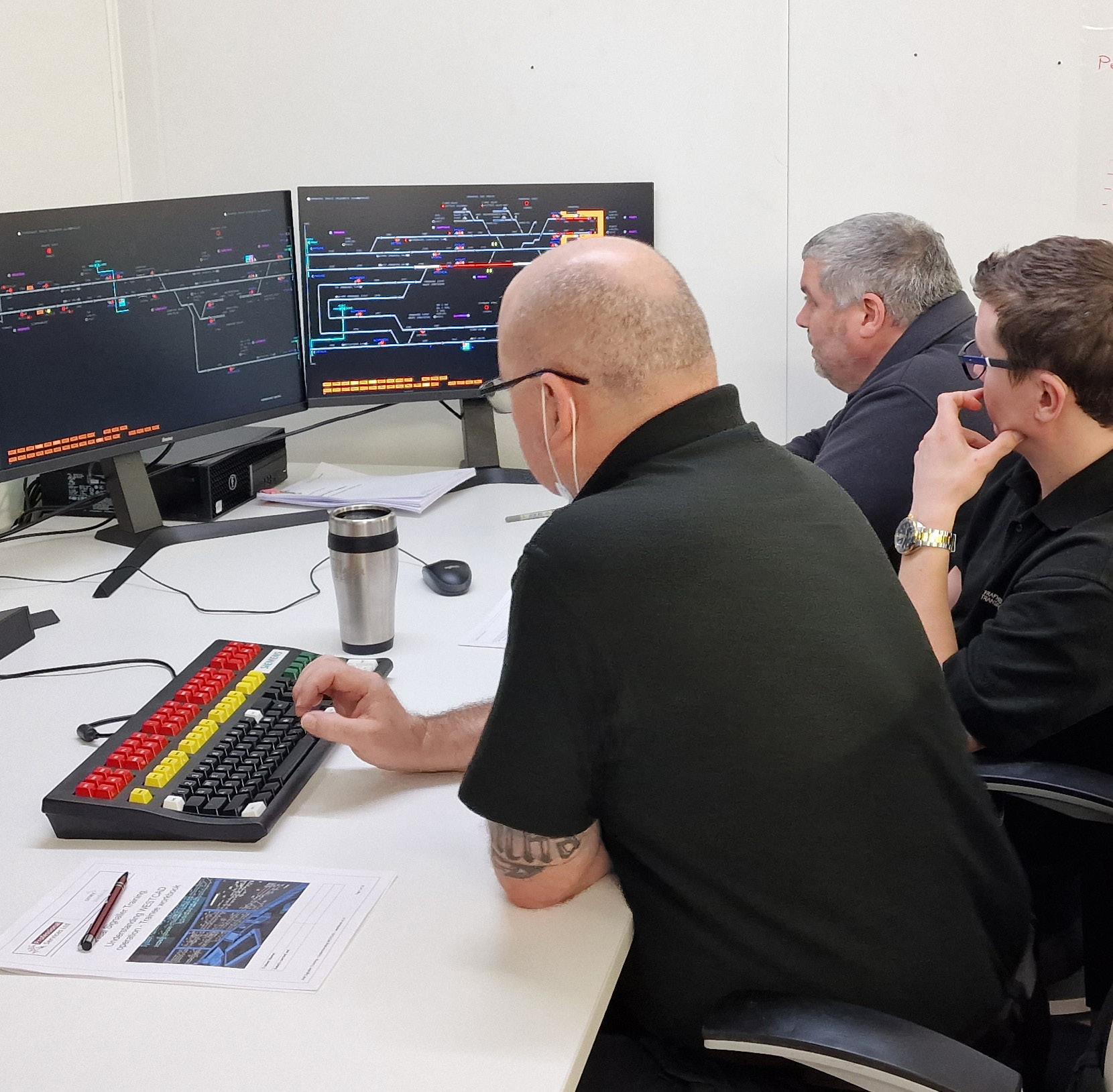

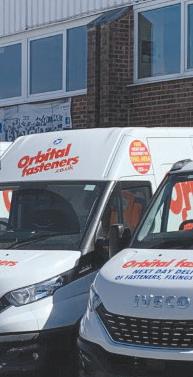
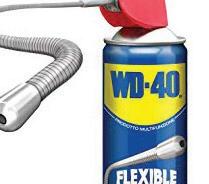
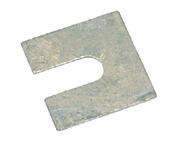
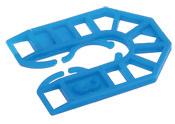
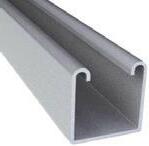
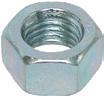
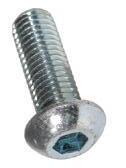
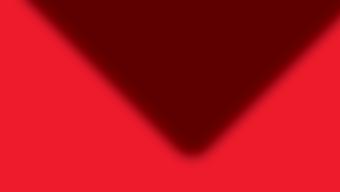
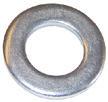

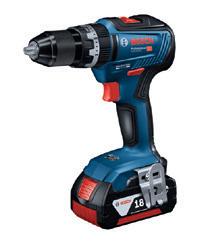
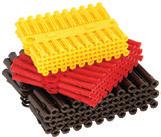
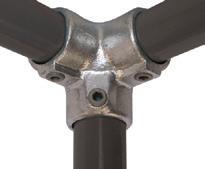

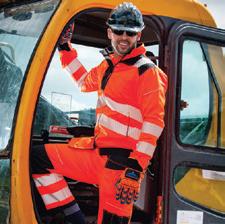
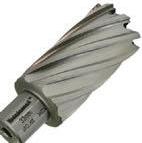
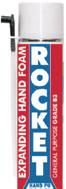
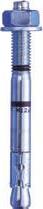

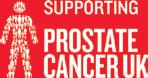
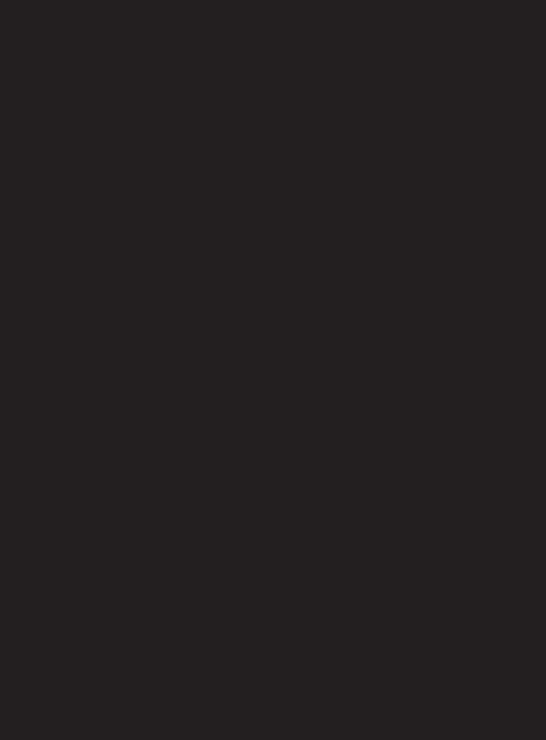
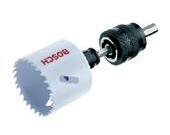
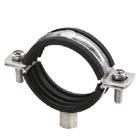


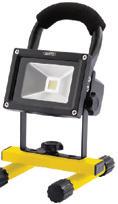
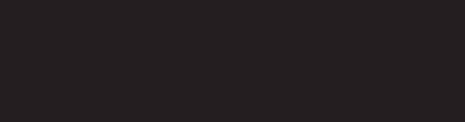
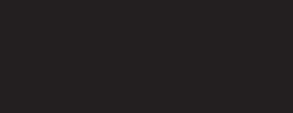
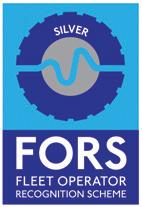
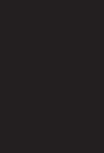
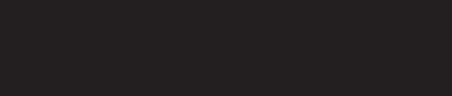
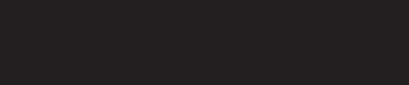
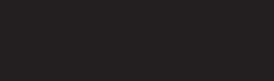


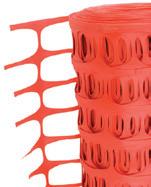
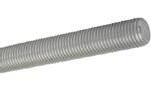


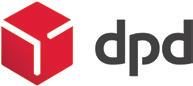
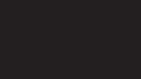
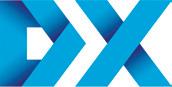
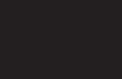
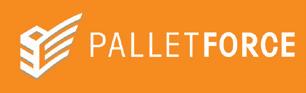
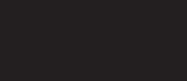



Exceeding Expectations
Network Rail’s System Operator (SO) function turned to rail consultancy AARC Professional Services (AARCPS) and its Safety and Assurance specialists when it needed support with the production of a new Health and Safety Guide
Responsible for making sure the network operates as ‘one seamless and high performing organisation,’ the System Operator’s role includes strategic planning for the future, provision of highquality analysis and advice, production of the timetable and managing industry wide relationships including freight.
To help highlight its continuing commitment to health, safety and wellbeing, the System Operator set out to produce a dedicated guide, aligned to Network Rail’s lifesaving rules and covering all business activities potentially affecting the health and safety of its workforce, suppliers, passengers, the public and freight customers.
Supporting production of the document was AARCPS, a specialist consultancy run by railway people for railway people, with Transport Systems and HSQE Specialist Liz Parkes and Change Consultant Emma Somers taking the lead. Liz had also helped Network Rail remodel its overarching health and safety management systems last year, into an accessible tool for continuous improvement in risk management.
Liz explained: ‘For this latest assignment, the key objectives were to successfully communicate the health and safety processes, standards and interfaces, as well as ‘the what to dos’, ‘how-to dos’ and systems for continuous improvement. The guide also had to support Network Rail’s broader health and safety management system, as well as meeting the System Operator’s strategic business objectives and safety strategy.’
Production of the guide involved liaison with over 25 members of the System Operator team, including individual interviews, working groups and consultations, with the document set to be reviewed annually and developed into an action plan.
The guide itself features:
• ‘One-stop-shop’ for readily accessible information.
• Practical tips and resources based around those activities that carry a health and safety risk, including working from home, display screen equipment, site visits, travelling alone and driving.
• Organisation based information including strategic and system level health and safety arrangements at Network Rail, plus details of how the different teams within the System Operator impact on the railway, workforce and customer safety.
• Examples and reflections using real life scenarios, intended to challenge people’s knowledge and behaviours, encouraging discussion and action.
Liz added: ‘The guide has actually been written to highlight the relationship between the System Operator function and health, safety and wellbeing and, in particular, how, from an individual and activity perspective, everyone works together to manage the issues, prevent accidents and improve the collective safety and wellbeing of the organisation.’
The guide has been welcomed by project sponsor Richard Weatherstone, Operations Safety Manager for the System Operator.
‘From the outset, AARCPS has been extremely professional, giving advice throughout, whilst playing an integral part in managing and developing what has been a challenging project through to its conclusion’ said Richard.
For further information about this press release, please contact Nigel Barber on 07590 806 143 or at nigel.barber@ aarcps.co.uk
Company profile
AARC Professional Services Limited (AARCPS) is a rail consultancy drawing from over five decades of experience to provide expert support to the industry. It brings together likeminded rail professionals with a common aim to deliver outstanding outcomes by:
Helping clients achieve their goals through strategic and technical expert advice across a range of disciplines, from the frontline through to the boardroom, from high level advice and guidance through to project support, AARCPS helps deliver excellent outcomes.
For further information about AARC Professional Services Limited, get in touch via the contact information below.
NETWORK RAIL SYSTEM OPERATOR
The role of the System Operator is to make sure the network operates as one – seamless and high performing. It does this by working as a partner across the railway to support the delivery of high levels of safe and efficient operational performance – contributing to an excellent experience for passengers, freight and other customers. The System Operator’s focus is on improving what the network is capable of by planning for the future, providing high quality analysis and advice, producing the timetable and managing industry wide relationships.
‘From the outset, AARCPS has been extremely professional, giving advice throughout, whilst playing an integral part in managing and developing what has been a challenging project through to its conclusion.’
Richard Weatherstone, Operations Safety Manager for Network
Rail’s
System Operator.
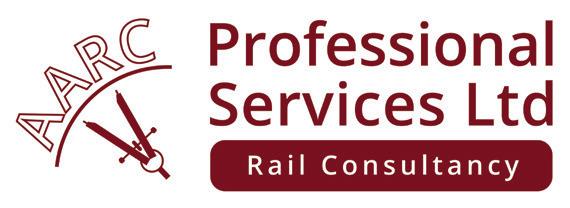
Tel: 07841 611657
Email: info@aarcps.co.uk
Visit: www. aarcps.co.uk

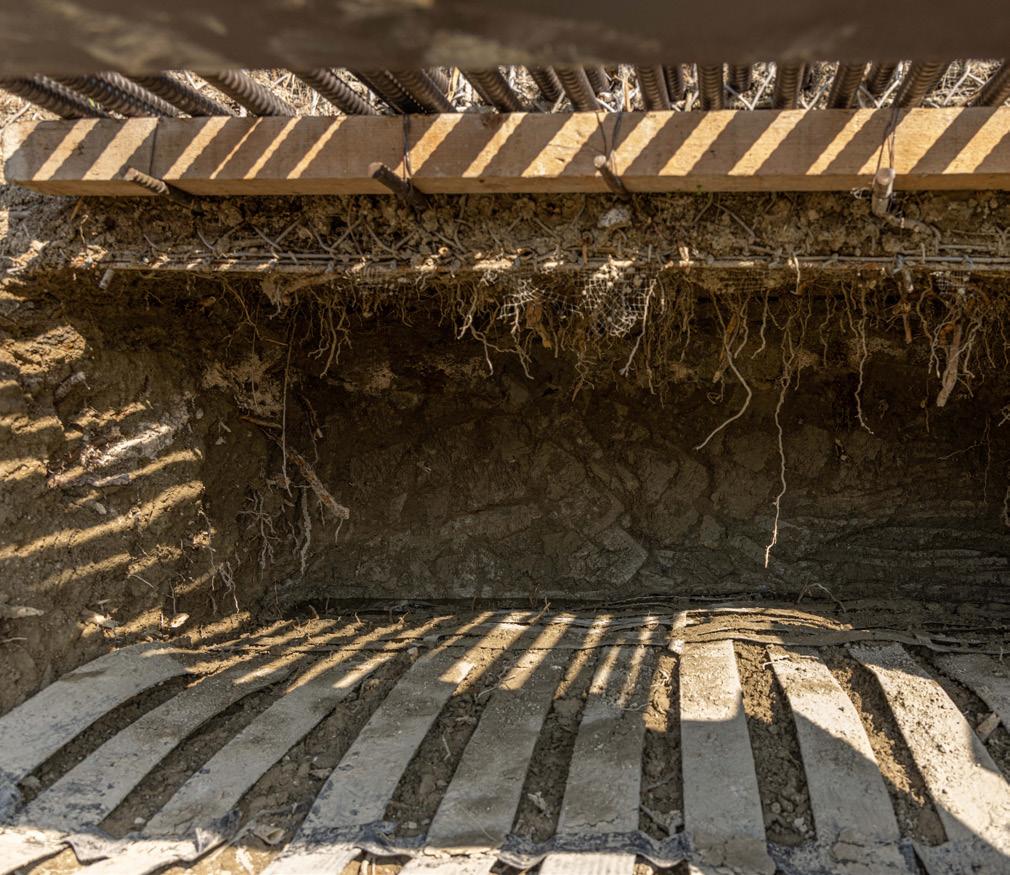
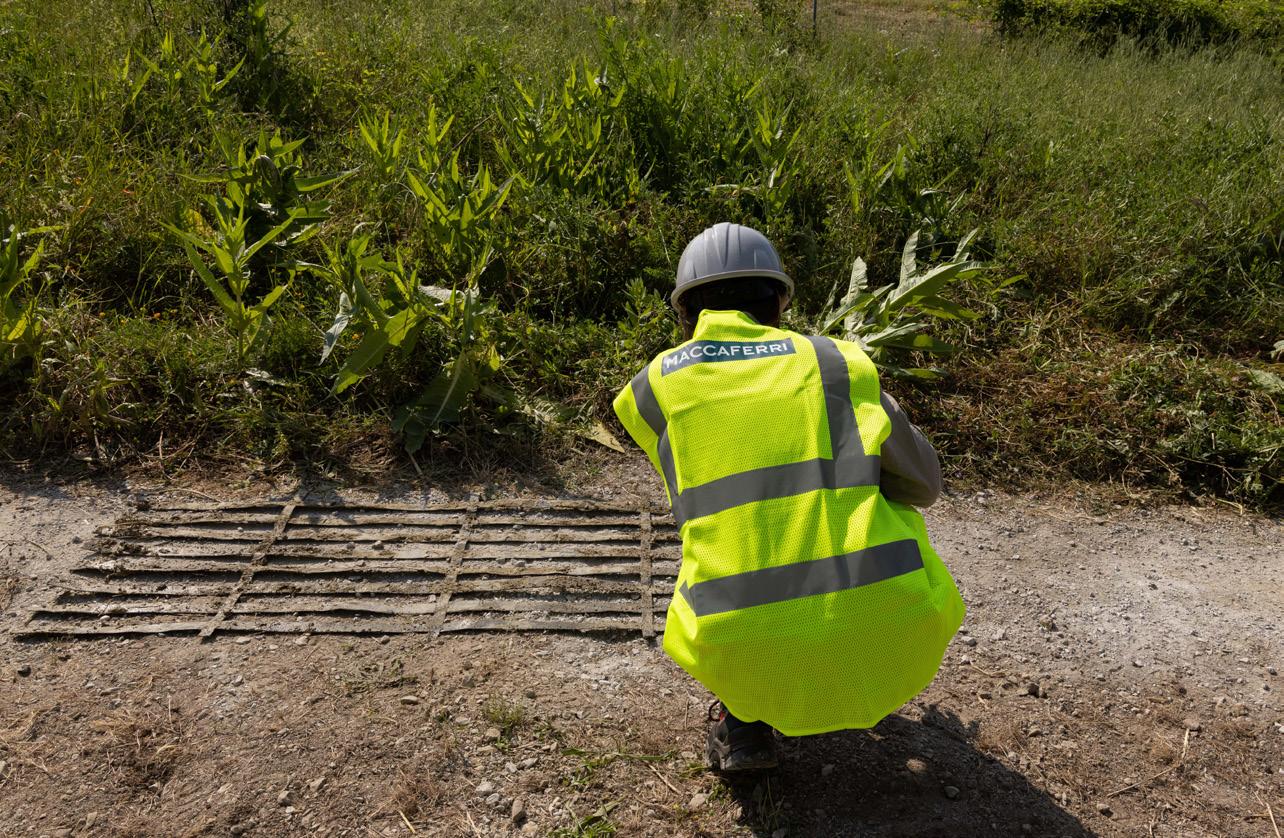

ParaProducts’ Alkaline Res
In the realm of civil engineering and geotechnical solutions, understanding and mitigating the impacts of soil conditions are crucial for the sustainability and success of any project. Highly alkaline soils, with pH levels exceeding nine, represent one such challenge, known for accelerating the degradation of materials. These conditions can arise from both natural causes, such as the presence of certain minerals or geological formations, and human activity, often occurring in projects where materials such as lime or cement are added to the soil to improve its mechanical properties, inadvertently raising the soil's pH and creating a more corrosive environment for geosynthetic products.
A groundbreaking testing initiative
In this challenging landscape, the ParaProduct High Alkalinity Testing Initiative by Maccaferri emerges as a pioneering venture. Aimed at rigorously assessing the durability and efficacy of its ParaProducts under highly alkaline conditions, the initiative has brought to light the resilience and reliability of these geogrid solutions.
Insightful
campaign
Spanning over three years, the initiative focused on evaluating ParaProducts that had been deployed in the field for up to two decades. Concentrated in the UK and Italy, these projects provided a realworld backdrop to assess the geogrids'
performance in alkaline conditions, where soil pH was initially set at a formidable twelve. The campaign entailed the careful exhumation of materials from several job sites, with subsequent analysis conducted by accredited laboratories. The British Board of Agrément (BBA) supervised these tests, ensuring rigorous evaluation standards.
Revealing remarkable results
The campaign's findings were striking. Despite the high alkalinity, which could potentially compromise material integrity, the tested ParaProducts exhibited outstanding durability. The residual tensile strength of these materials impressively exceeded 95 per cent of their certified characteristic value. For instance, in both
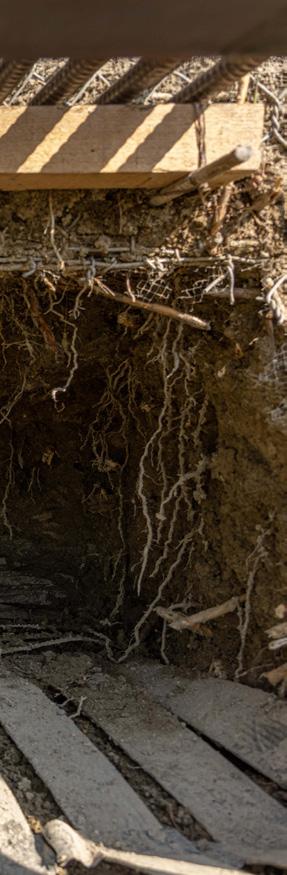
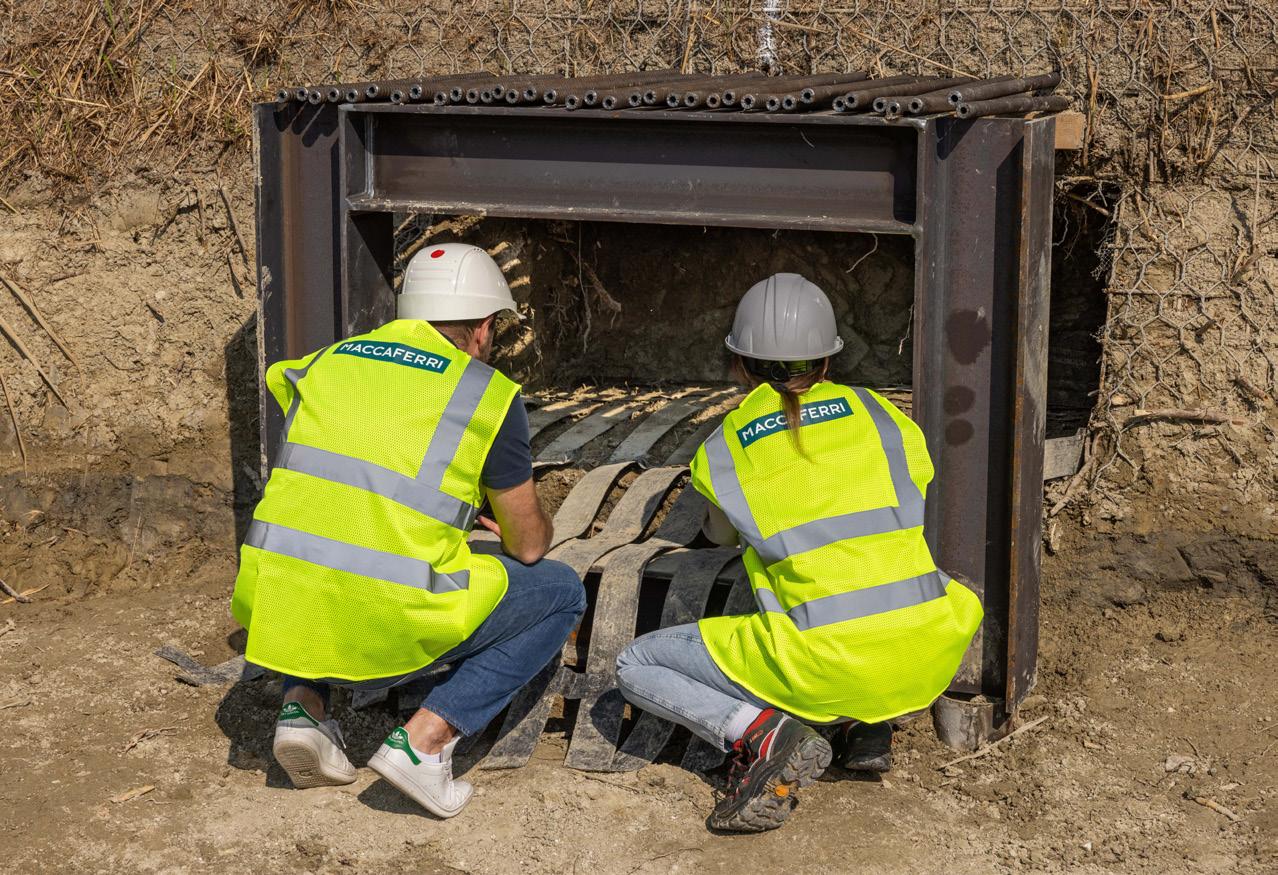
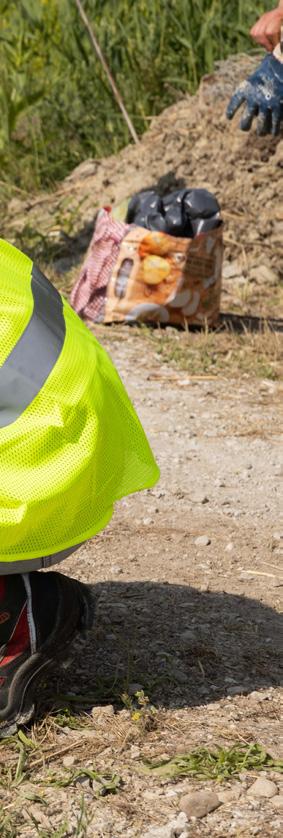
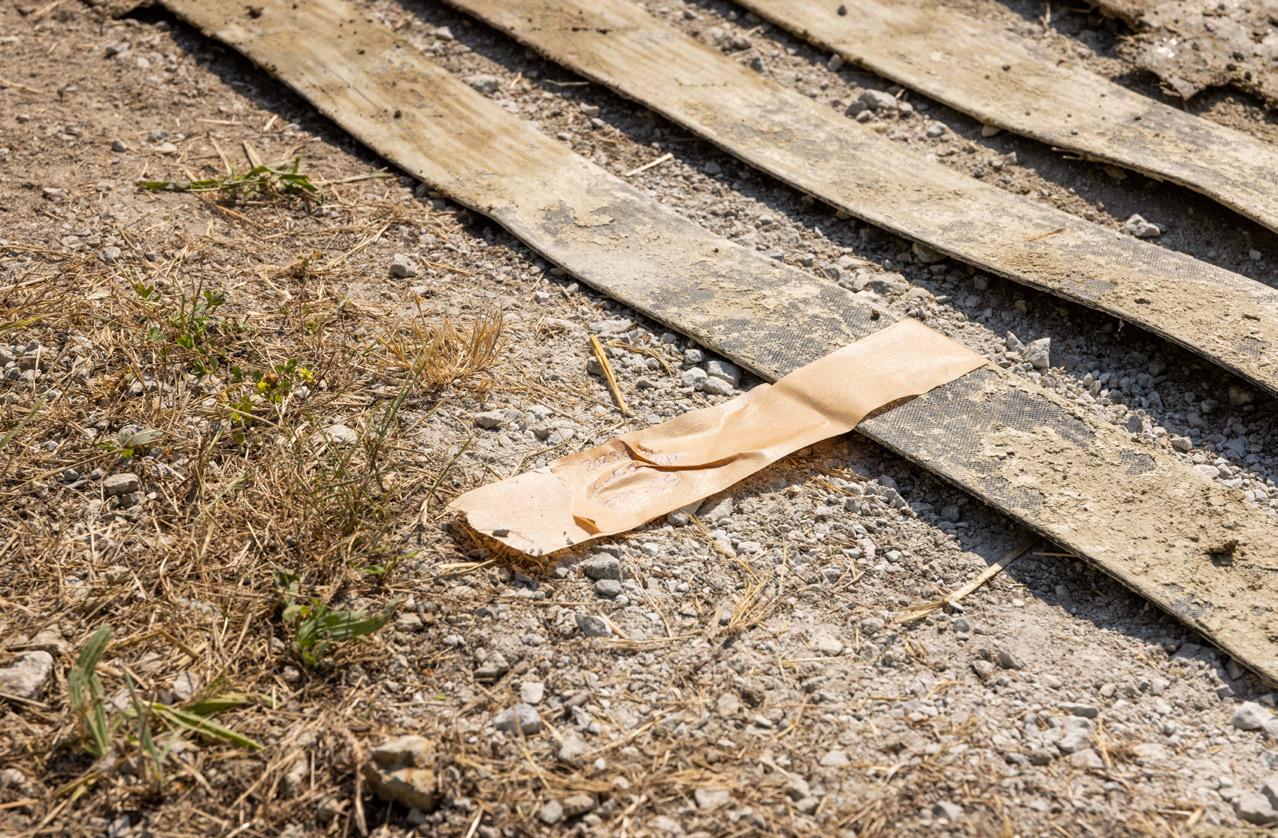
ilience
THE BRITISH BOARD OF AGRÉMENT
The British Board of Agrément (BBA) drives industry safety by providing services that help clients create accountability and mitigate risk. Since 1966, the BBA has built its position as an independent certification body in the Construction and Civil Engineering Industries. The Agrément Certificate is a UKAS-accredited product and system certificate scheme which enables manufacturers of products used in the construction industry to demonstrate a product’s fitness-forpurpose.
Unveiling the long-term durability of ParaProducts in alkaline soils
the Moodiesburn project in Glasgow and the Tangenziale di Forlì in Italy, the geogrids not only met but significantly surpassed the demanding requirements set for geosynthetic materials.
Such results are particularly illuminating, given the high pH conditions encountered at these sites due to the use of lime and cement for soil stabilization. These outcomes underscore the efficacy of ParaProducts in maintaining structural integrity and performance, even in environments that have undergone chemical alterations to enhance soil mechanics.
Forward-looking commitment
The ParaProduct High Alkalinity Testing Initiative underscores Maccaferri's
unwavering dedication to innovation and quality. As shared by Giulia Lugli during a specialized webinar, this initiative provides a roadmap for future projects, illustrating the adaptability and resilience of Maccaferri's solutions in the face of geotechnical challenges.
With a legacy of pioneering engineering solutions, Maccaferri remains committed to pushing the boundaries of geosynthetic performance. The geotechnical community eagerly awaits further advancements from Maccaferri, promising to redefine durability and reliability standards in the industry.
Stay tuned for more updates on Maccaferri's cutting-edge developments in geotechnical engineering.
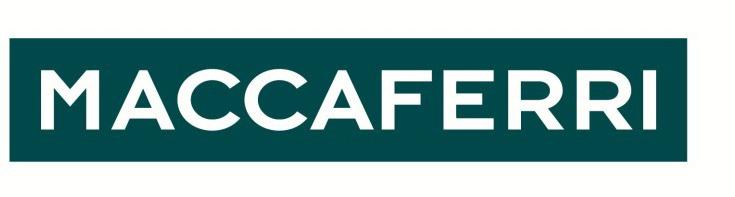
Tel: 01865 770 555
Email: info.uk@maccaferri.com Visit: www.maccaferri.com/uk
Network Rail’s Plan for the Next Five Years
Network Rail recently published its delivery plan for Control Period 7 which will run from 1 April 2024 to 31 March 2029
Five key challenges highlighted in the plan were inflation, climate change, train performance, income and rail reform. Inflation has eroded the value of CP7 funding by £1.3 billion since the SoFAs (Statements of Funds Available) were published using the November 2022 OBR forecast.
Regarding climate change, to mitigate the impact of extreme weather and climate change on the network, Network Rail will be investing £2.8 billion on activities that will improve the network’s resilience to extreme weather and climate change.
There are a number of inputs that are known to materially impact train performance that remain uncertain (e.g. train operator service patterns and passenger numbers). This level of uncertainty creates risk to delivering train performance targets. The targets set are whole-system measures, requiring delivery from train operators as well as Network Rail. ORR’s final determination confirmed that there will be a regulatory review during year two of CP7 (2025/26) to reset passenger train performance metrics for years three to five of CP7, recognising the uncertainty in forecasting train performance particularly for the latter years of the control period.
There is a risk of lower levels of income (from access charges and property income) as a consequence of lower service levels and footfall than the plan currently assumes, which could be a railway specific cause or due to wider economic factors.
Finally, around 30 per cent of total planned CP7 efficiencies relate to Network Rail’s share of the industry savings expected from rail reform. There is expected to be far greater alignment in decisions about infrastructure and train services once GBR is established.
Commenting on the plan, Railway Industry Association Chief Executive Darren Caplan said: ‘As we have regularly said, a rail investment strategy needs to include a comprehensive enhancements plan, given the significant infrastructure upgrades which lie ahead. We again urge the Government to publish a plan which sets out which rail schemes in Network North, the Integrated Rail Plan for the North & Midlands, and the Rail Network Enhancements Pipeline
it intends to bring forward over the next five years. Doing so will enable NR and rail suppliers to ensure they are ready to carry out and co-ordinate both renewals and enhancements work in CP7, in a way which delivers maximum value to both rail customers and taxpayers.’
Enabling programmes
During CP7 Network Rail plans to invest £126 million in further developing and rolling out several tools from the CP6 II programme. Tools such as insight, Network Enterprise Structures and Tunnels (NEST) and Geotechnical Asset Insights Application (GAIA) will provide its maintenance and asset management teams with better access to data to support their decision making. Predictions of when assets will fail inform its renewals plans, allowing for the extension of asset life where possible and the efficient allocation of resources. During CP7, additional capability will be added to allow for colleagues to identify all sites with specific faults or risk profiles giving them the information needed to understand root cause analysis and plan a coordinated maintenance or renewals approach.
Network Rail will also modernise how it takes possessions. Technology innovations to remove the use of detonators and stop boards, removing staff from the track and protecting worksites using highly reliable signalling systems.
A low-emission railway
Planning and delivery of railway possessions is traditionally very manual and painstaking with siloed data and stakeholders.
Our possession data ecosystem will deliver a full end-to-end
‘digital possession’ capability
Planning
Amara is the PLANNER, their visibility of the dynamic work plan over a longer time horizon is improved, enabling resolution of issues earlier in the planning lifecycle and development of optimised work plans for approval.
Operations
Dennis is the ODM, streamlined preparation and validation of safety critical documentation helps them to optimise the safe and effective use of access opportunities.

In 2020, Network Rail published an Environmental Sustainability Strategy, a Biodiversity Action Plan, and became the world’s first railway company to sign up to the most ambitious targets in the United Nations’ Science Based Targets initiative. Network Rail will achieve net zero carbon emissions by 2045 in Scotland and 2050 in England and Wales, in line with government policy. By 2035 its entire road vehicle fleet will be ultra-low-emission vehicles. A target by the end of CP7 is for harmful pollutants to have been reduced by 25 per cent in Network Rail managed stations.
Our Possession Data Ecosystem
Route Control
Piran is the ROUTE CONTROLLER, they have better insight and can be more responsive to issues impacting the possession, ensuring customers can travel with as little disruption as possible.
Works Delivery
Samir is the ES, they’re able to maximise ‘time-on-tools’ by communicating in real time with multiple COSS simultaneously. Working digitally, they save themselves time and improve data integrity as arrangement forms are auto-filled.
Possession Delivery
Cerys is the PICOP, their situational awareness is improved, making it easier to continuously monitor progress and safely oversee delivery of the possession.
Aiden is the PSS, they can always access the latest possession arrangements digitally and are alerted to safety critical comms via mobile device, so protection can be placed and removed in a safe and timely manner.
WillBaxter.com
£293 million investment in the Electrical Safety Delivery (ESD) programme.
£43 million industry performance innovation fund in England & Wales.
£53 million targeted performance fund in Scotland.
£2.8 billion in improving the resilience of our assets to extreme weather events.
£15 million to its 21st Century Operations programme.
£141 million contribution to Office of Rail and Road to cover the economic and safety regulation of Network Rail.
£78 million to Rail Safety and Standards Board.
£19 million to Rail Delivery Group. The Possession Optimisation Programme, which is being jointly delivered by Network Rail’s Wales & Western Region and https://assetinsights.co.uk/, is set to revolutionise the planning and delivery of possessions on the railway. For more info see https://info.railai.co.uk/podflo/.

New SMART Wrench Takes Quality Assurance for Safety-critical Joints to the Next Level
Giving manufacturers real-time quality assurance analysis of manual safety-critical joints is the primary benefit of a brand new digital smart wrench, launched by Atlas Copco Tools and Industrial Assembly Solutions.
Wi-Fi enabled with the largest touch screen interface in the industrial tools market, that’s also designed to be used with safety gloves, Atlas Copco’s new STRwrench Advanced delivers precision residual torque and breakaway torque checks. Featuring an integrated controller, STRwrench Advanced enables joint check analysis in real time, reporting data to Atlas Copco’s bespoke quality assurance platform, QA Supervisor (QAS), that provides manufacturers with full assembly traceability. This software can be integrated into customer QA systems for auditing even the most challenging assembly processes.
Consistency of critical joints is essential to ensuring product quality and safety. Incorrect tightening and torque checks can lead to product failure, resulting in costly rework. Research by Atlas Copco has found that a single minute of downtime due to a safety-critical joint failure can cost up to £10,000 in lost production.
With enough data storage for 50,000 checks and a built-in selection of different quality strategies for specific product types, STRwrench Advanced can still collect data in the event of a network shutdown. Durability on the assembly line is assured, thanks to Atlas Copco’s rigorous product testing process, which includes drop tests.
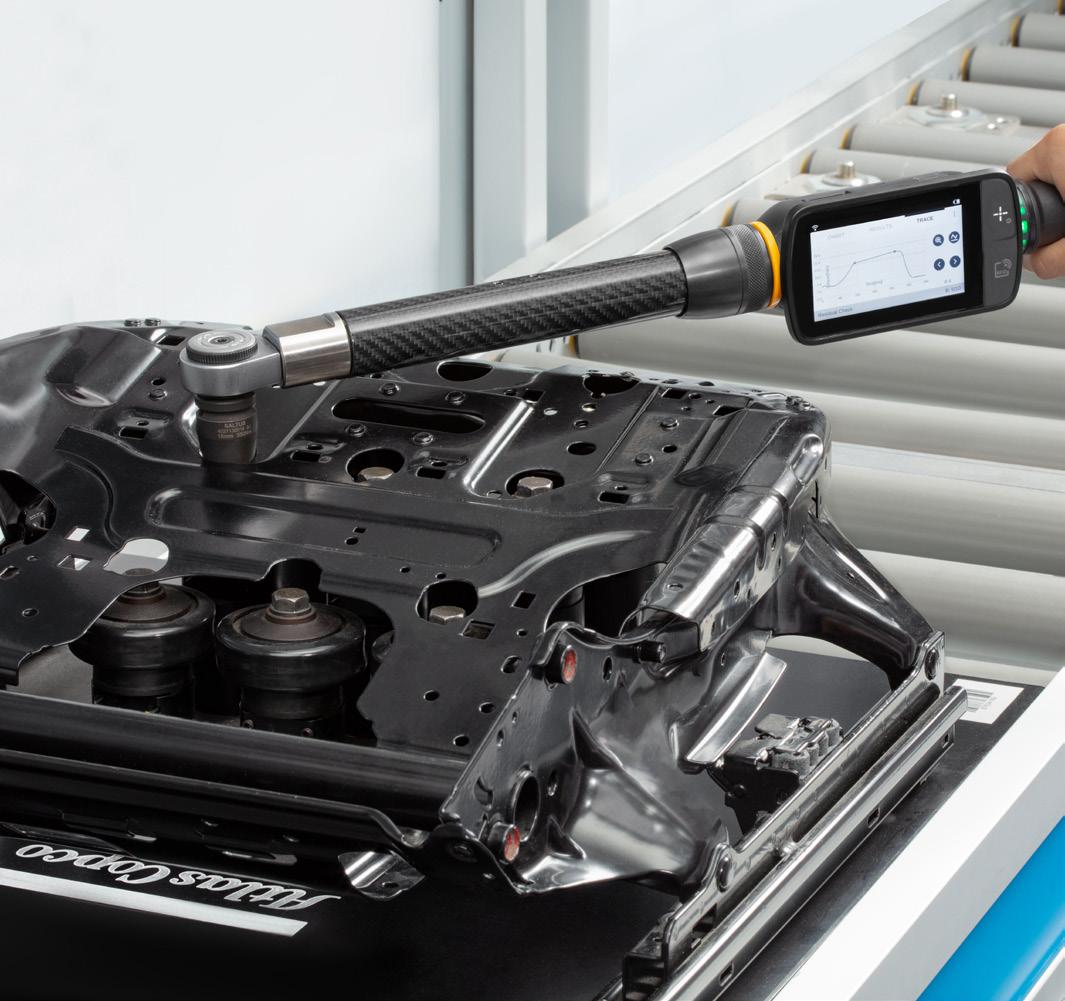
Rail Giant Set for Move to State-of-the-art
York Office Hub
A high-quality complex of modern office suites situated in the historic city of York is close to achieving full occupancy after Grand Central Rail announced it would be relocating to the premises.
Set within York’s famous medieval walls, the 23,091 sq. ft GradeII listed building at 20 George Hudson Street is home to the likes of First Bus, Jacobs, RotaCloud and Simpson Associates.
Grand Central is due to complete its move from Northern House at the start of May, taking up a 2,740 sq. ft second-floor suite with open-plan accommodation, two part-glazed meeting rooms, fitted kitchen and staff areas plus comfort cooling and heating.
New Nylon Constant Torque Hinge
Southco has expanded its successful line of E6 Constant Torque Hinges with a compact, nylon version designed for small applications. The newest addition to our E6 50 Constant Torque Position Control Hinge series measures 45mm with a torque range of 4-16 in/lbs and is 65 per cent lighter in weight compared to our standard E6 50 Hinge. Southco’s line of Constant Torque Position Control Hinges provide constant resistance throughout the entire range of motion, enabling users to easily position doors, display screens and other mounted components and hold them securely at any desired angle – fully opened, fully closed or anywhere in between.
Constructed of robust nylon and stainless steel, the new E6 Constant Torque Position Control Hinge provides the benefits of constant torque and contemporary styling in a compact, economic package for smaller doors and panels. The nylon E6 series is available with both symmetric and asymmetric torque, offering a more refined feel in any application. Southco’s line of position control hinges are available in a wide variety of torque ranges, sizes and materials to satisfy application needs across industries. Southco position control hinges provide reliable positioning and consistent operating efforts, and guaranteed performance without adjustment for the lifetime of most applications.
UK first: Lumo Leads the Way for a Plastic-free Future
The East Coast Main Line train operator, Lumo, is proud to announce a UK first for any train company in eliminating plastic bottles onboard its services which connect Edinburgh and London. To coincide with Earth Day which took place on 22 April 2024, Lumo’s all-electric fleet of trains will now offer cartons of water in a bespoke 100 per cent recyclable carton, reducing the many thousands of plastic bottles produced each week.
The Newcastle based operator worked in partnership with North East England entrepreneur Callum Mather from Everdurance to make the switch away from plastic become a reality; thought to be the first of any major long distance travel provider.
Martijn Gilbert, Managing Director of Lumo, said: ‘We already know that travelling by train is a very green way to get around and at Lumo our all-electric train fleet delivers the very best rail sustainability footprint, backed up by sustainability being at the heart of all we do from paper free work practices to more than 50 per cent of our food and drink menu being plant based.’
This is the latest move by the company to further establish itself as the most sustainable way to travel the East Coast route. Earlier this month plastic bottles of wine and fruit juice were replaced by sustainable alternatives as part of the popular onboard ‘LumoEats’ at seat food and drink offer. The pioneering move to introduce Flawsome juices made from ‘wonky’ fruits in a carton is sustainable from both a raw product and packaging perspective.
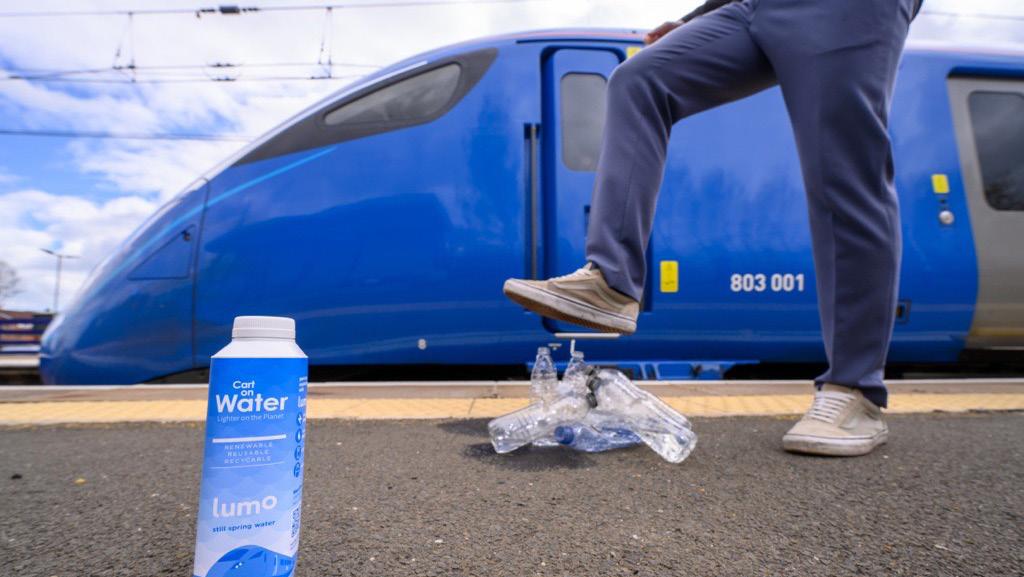
Customers will be able to purchase Lumo’s carton water when travelling onboard services from this week. Lumo has also become the latest member of Transform Scotland; Scotland’s alliance for promoting sustainable, accessible and affordable transport.
Callum Mather, Customer Success Director at Everdurance, said: ‘Our journey began with the goal of replacing plastic bottles with carton water solutions addressing environmental concerns so it’s a proud moment to see our cartons of water available on Lumo’s high-speed services on the East Coast route.’
Choosing rail travel is a notably more sustainable choice over air, specifically
traveling on a Lumo train is 25 times greener than flying thanks to the all-electric fleet. No UK domestic airline currently offers a sustainable alternative to plastic water bottles.
Earlier this year a report by Arup commissioned by Lumo revealed the operator saved 60.6 kilotons of CO2 last year - the equivalent of taking 13,475 petrol-powered cars off the road for a year or powering 7,632 homes for the same duration. The results also established that the open access operator saved eight times the carbon emissions it produced, as it attracted passengers from other, more polluting, modes of transport and continues to see people make the switch to rail.
CPC Transfers Ownership to EOT
CPC Project Services LLP (CPC) has transferred ownership to its employees, through an Employee Ownership Trust (EOT), to become CPC Project Services Ltd.
Over the past 12-18 months the shareholders of CPC have considered a number of options regarding the future ownership of the business and how best to prepare for its next stage of growth. The transfer of its business structure to an EOT means that CPC will be owned by each and every one of its employees, enabling them to share in the future success of the business, as well as having a greater say in how it is run.
CPC Project Services Ltd (CPC) is an independent, award-winning project and cost management consultancy in the UK. CPC Systems Ltd is a subsidiary of CPC Project Services Ltd delivering rail systems consultancy, engineering and technological solutions for railway operators and asset owners;
CPC’s HQ is Wood Street, London, EC2V 7AN (St. Paul’s). CPC’s recent projects include Transport for London’s £5.4 billion Four Lines Signalling Modernisation Programme (CPC and Mace Joint
Venture), Elizabeth Line Readiness (Stations & Systems) and London Borough of Enfield’s Lee Valley Rail Programme (LVRP) – Phase 2 – delivering new rail infrastructure on the West Anglian Mainline to increase service frequency and capacity as part of a £6 billion regeneration programme.
Steve Mole will continue to lead CPC, alongside the current Board of Partners. The Board is, and will remain, responsible for managing the day-to-day operations and business interests of CPC. The EOT will be governed by a Board of Trustees, who will be responsible for ensuring the success of the Trust for the benefit of CPC’s employees.
Steve Mole, CEO, CPC Project Services Ltd, said: ‘I am thrilled to be able to announce CPC’s transition to an Employee Ownership Trust. We’ve been working for many months to ensure that this change in business structure is in the best interests of our employees and clients, as well as cementing CPC’s long-term strategic commitment to remain an independent and agile project and cost management consultancy.’
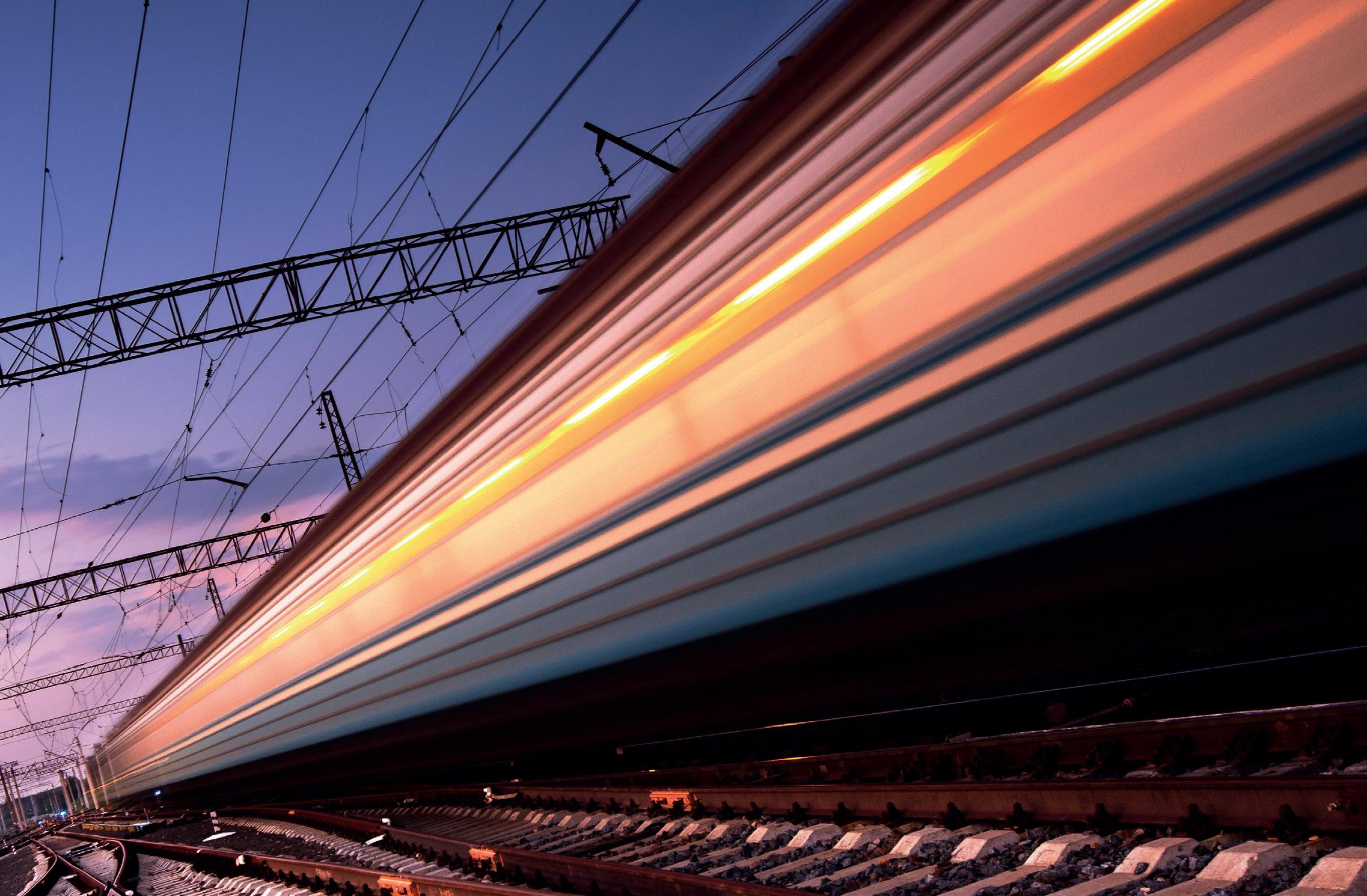
STAUFF are a premier global manufacturer of components and kits for railway applications.
STAUFF Line
A comprehensive range of quality products and innovative services delivered to your production line side for the manufacture of rolling stock.
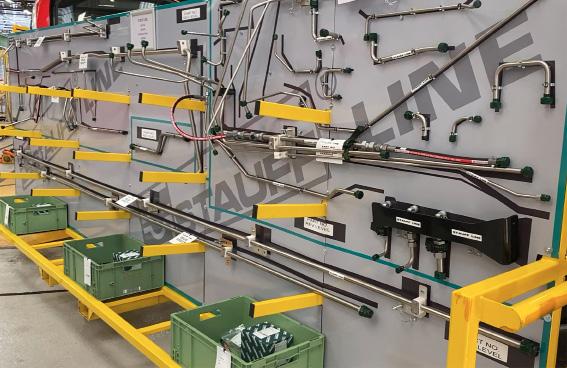
Presented in kit form, tested and ready for immediate installation, reducing logistic, production and inventory costs.
The STAUFF Line process is adopted by global OEMs to successfully achieve cost savings in rolling stock manufacture.
Sheffield Tel: 0114 251 8518
Email: uk.sales@stauff.com
Aberdeen Tel: 01224 786166
Email: uk.absales@stauff.com
Ireland Tel: 02892 606900

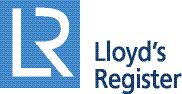

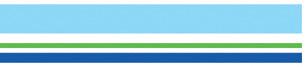

Email: uk.irsales@stauff.com www.stauff.co.uk
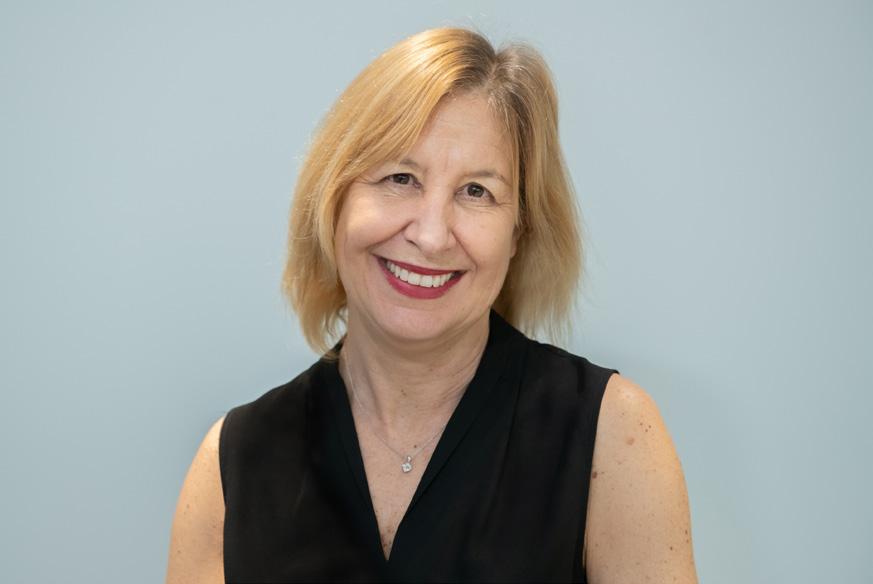
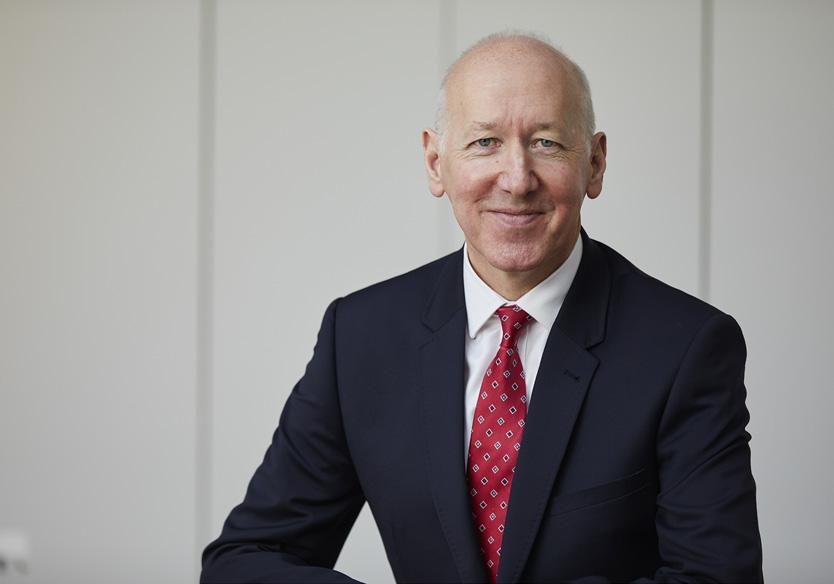
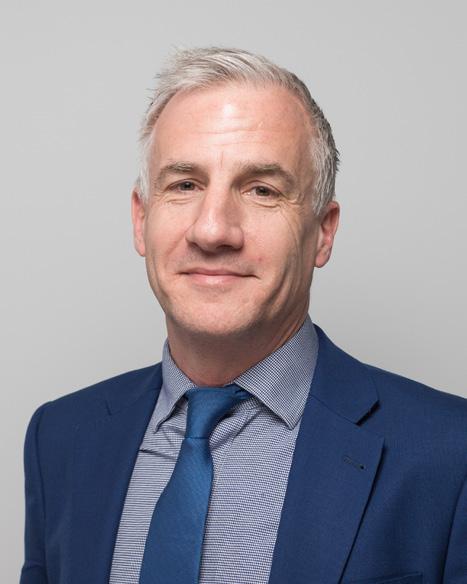
Network Rail announces appointment of three new non-executive directors to its Board Network Rail has today announced the appointment of three new non-executive directors to its Board. Dyan Perry OBE, Steve Scrimshaw and Stuart Harvey will join the Board from July, and will be bringing with them a wealth of knowledge and experience from a variety of public and private sector roles.
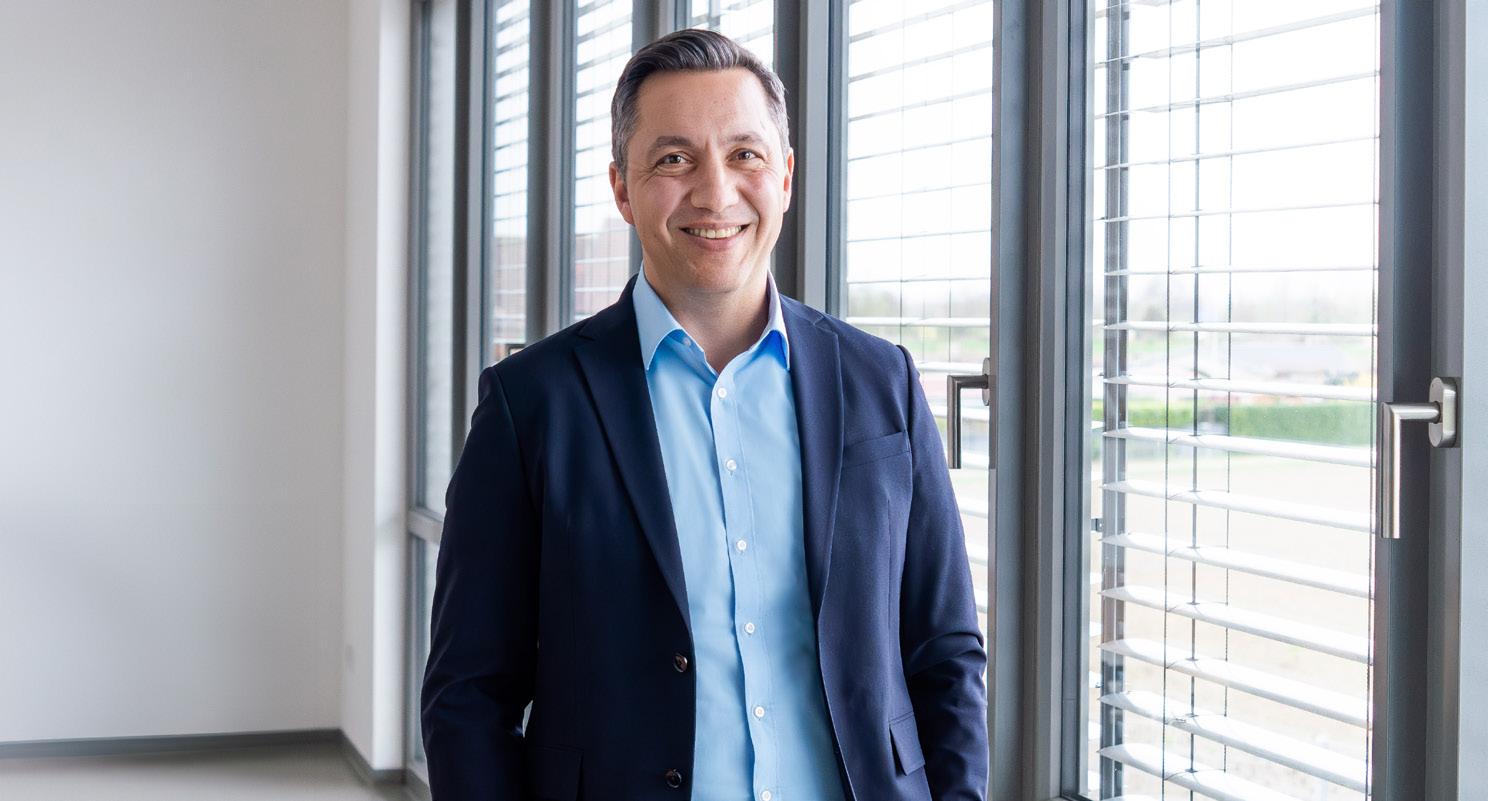
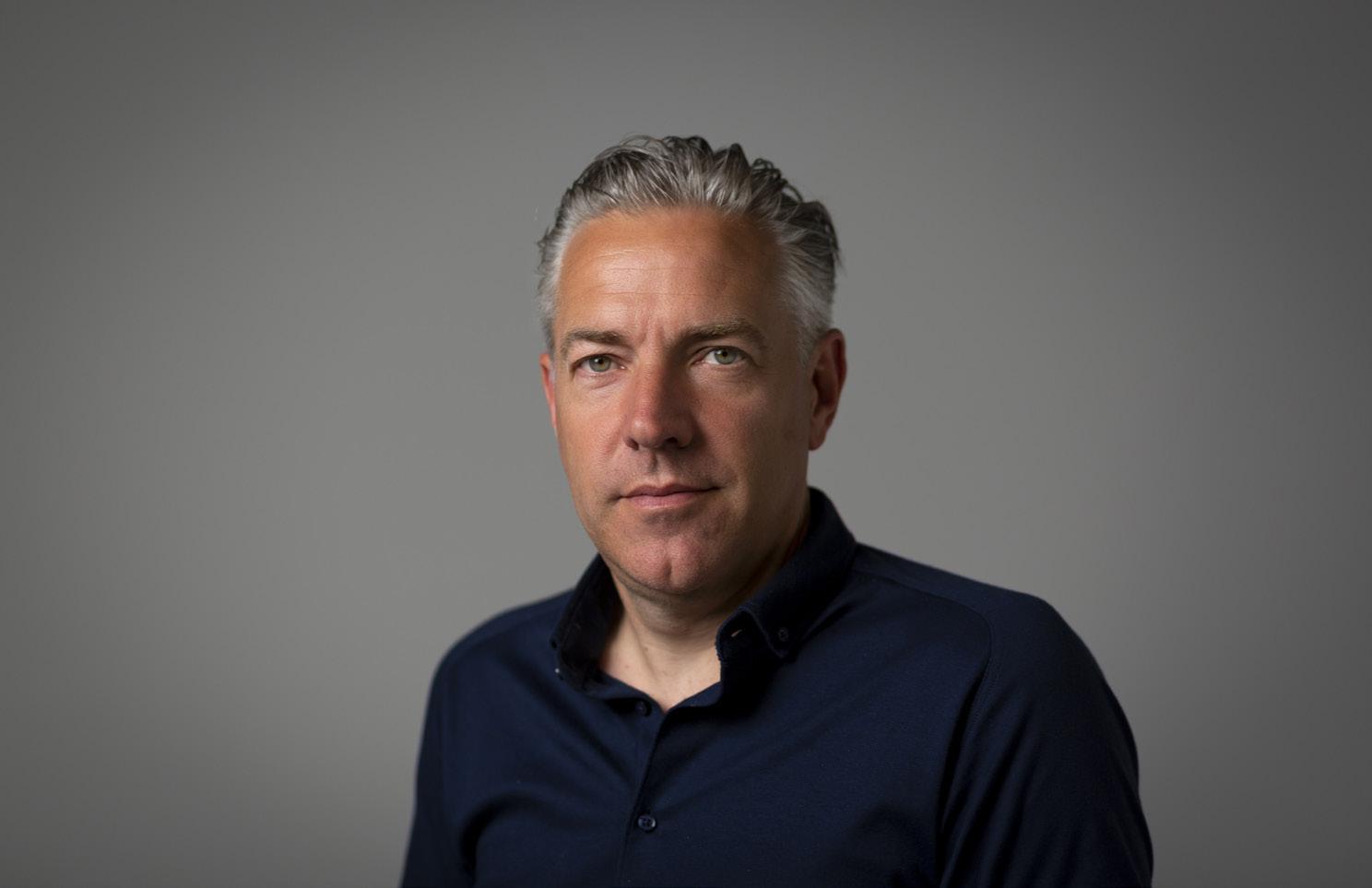
Briggs & Stratton appoints Managing Director for EMEA region
Sjoerd van de Velde, previously Managing Director for the Turf & Consumer Products division of EMEA, has been appointed Managing Director of EMEA with immediate effect.
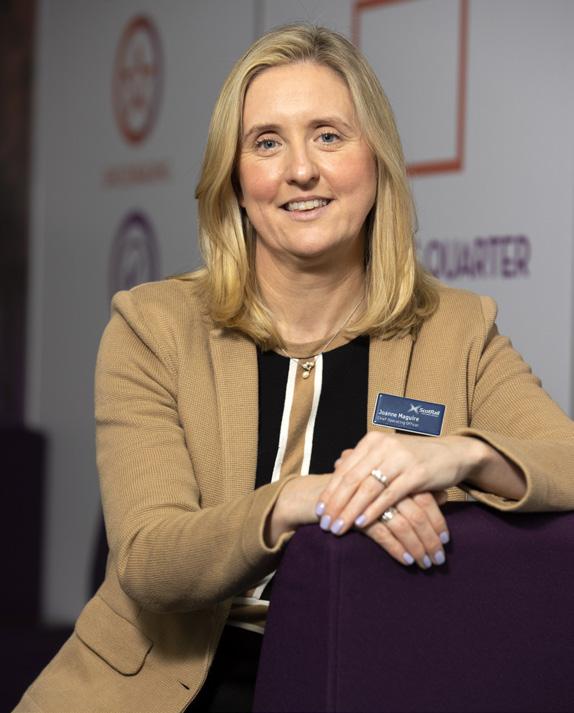
ScotRail appoints Managing Director Scottish Rail Holdings has announced that Joanne Maguire has been appointed interim Managing Director of ScotRail following Alex Hynes’ two-year secondment to the UK Government Department for Transport.
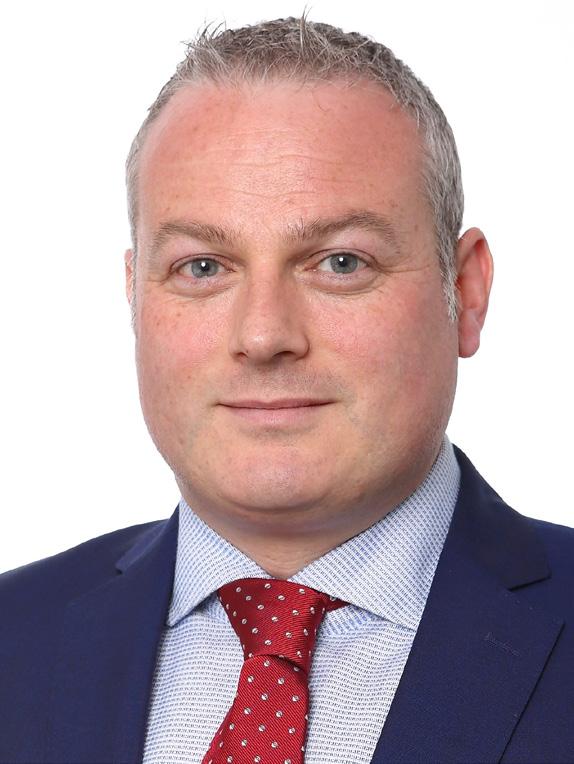
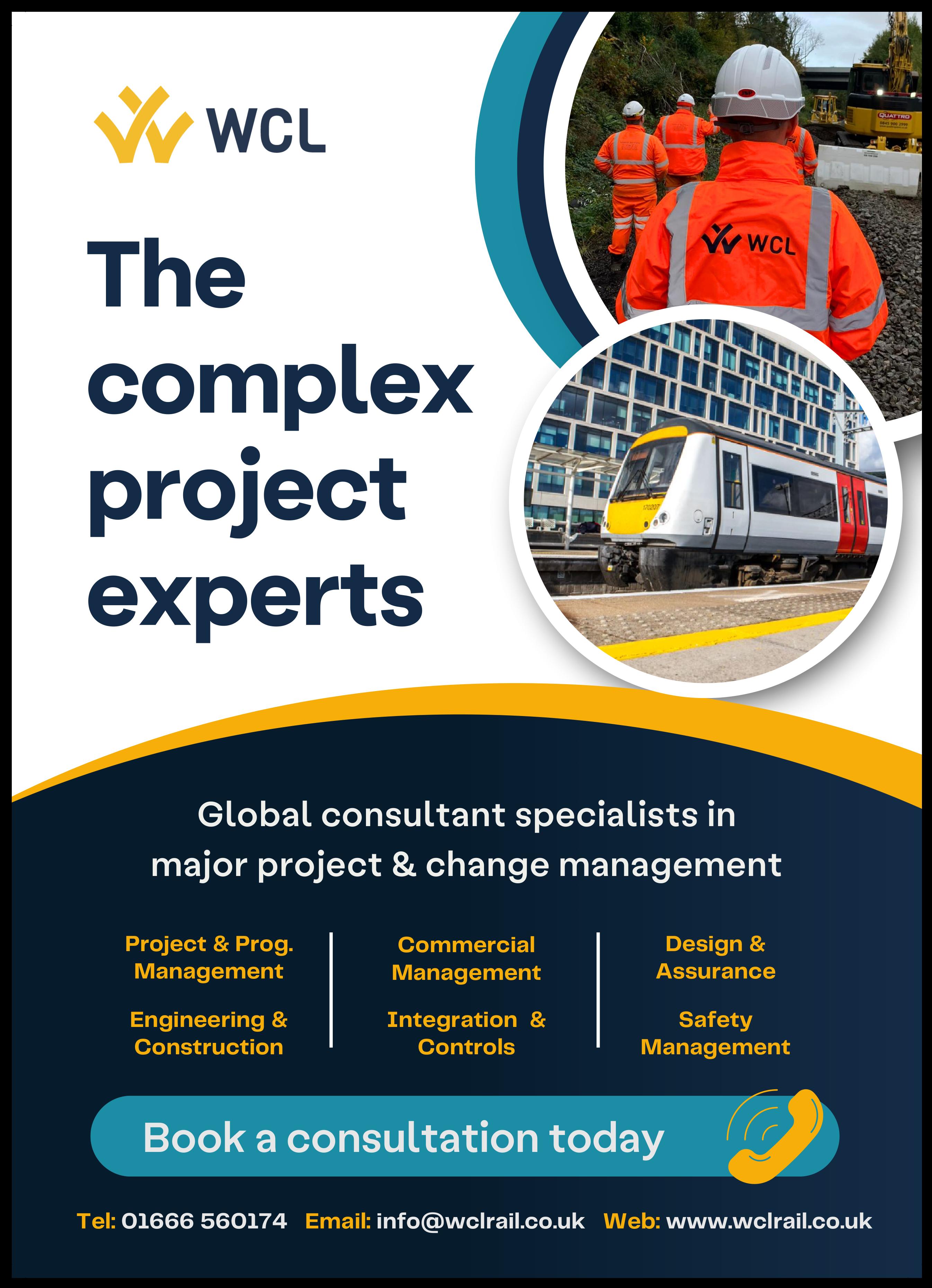

Delivering a sustainable future for high speed rail
We are dedicated to leading our clients towards a Net Zero future, championing greener initiatives in the rail industry.
Our team of experienced professionals are equipped with the knowledge and expertise to tailor our innovative solutions to your unique needs and objectives.
Together, let’s make a difference and build a better, more sustainable tomorrow.

Scan here to get in touch