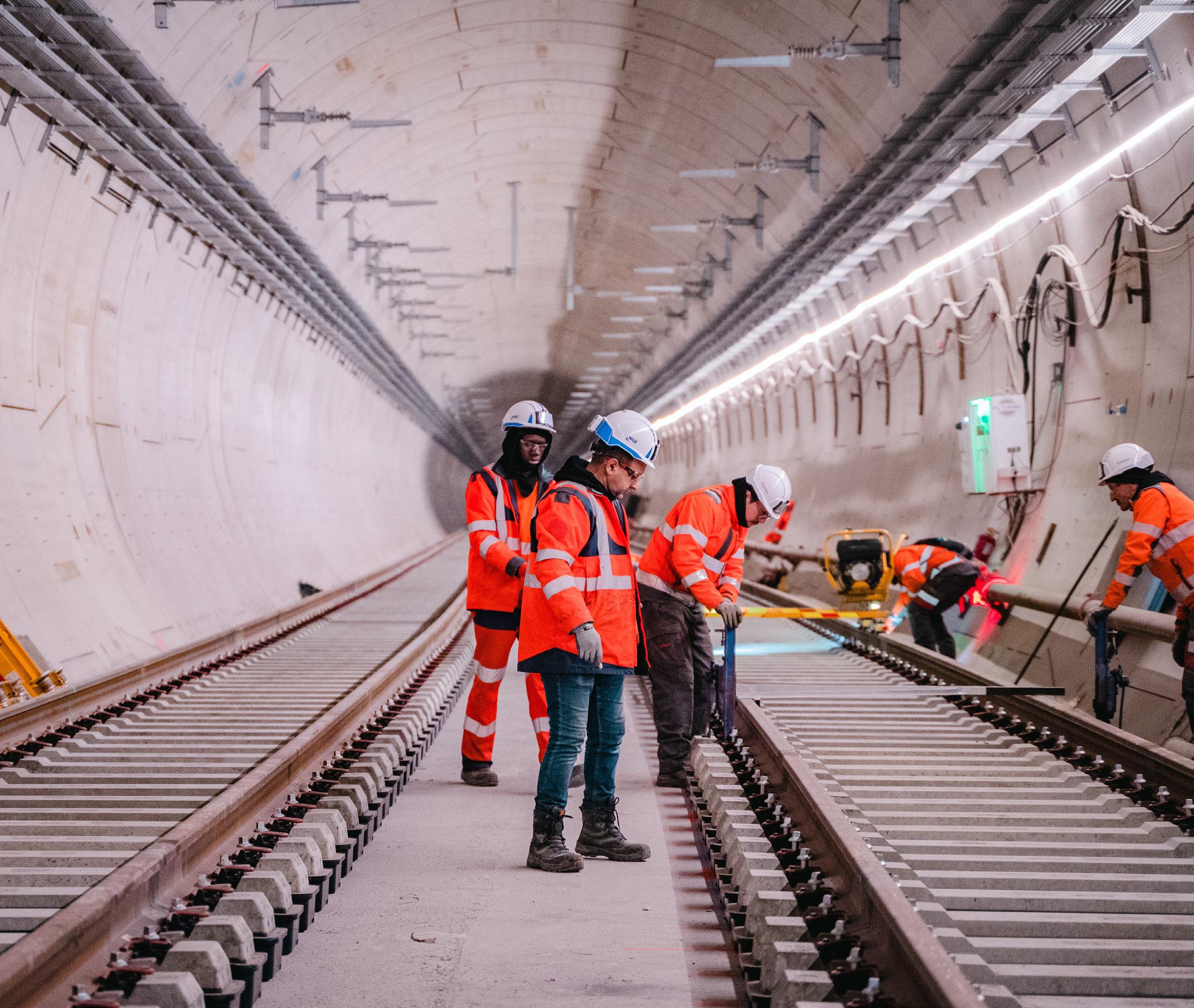
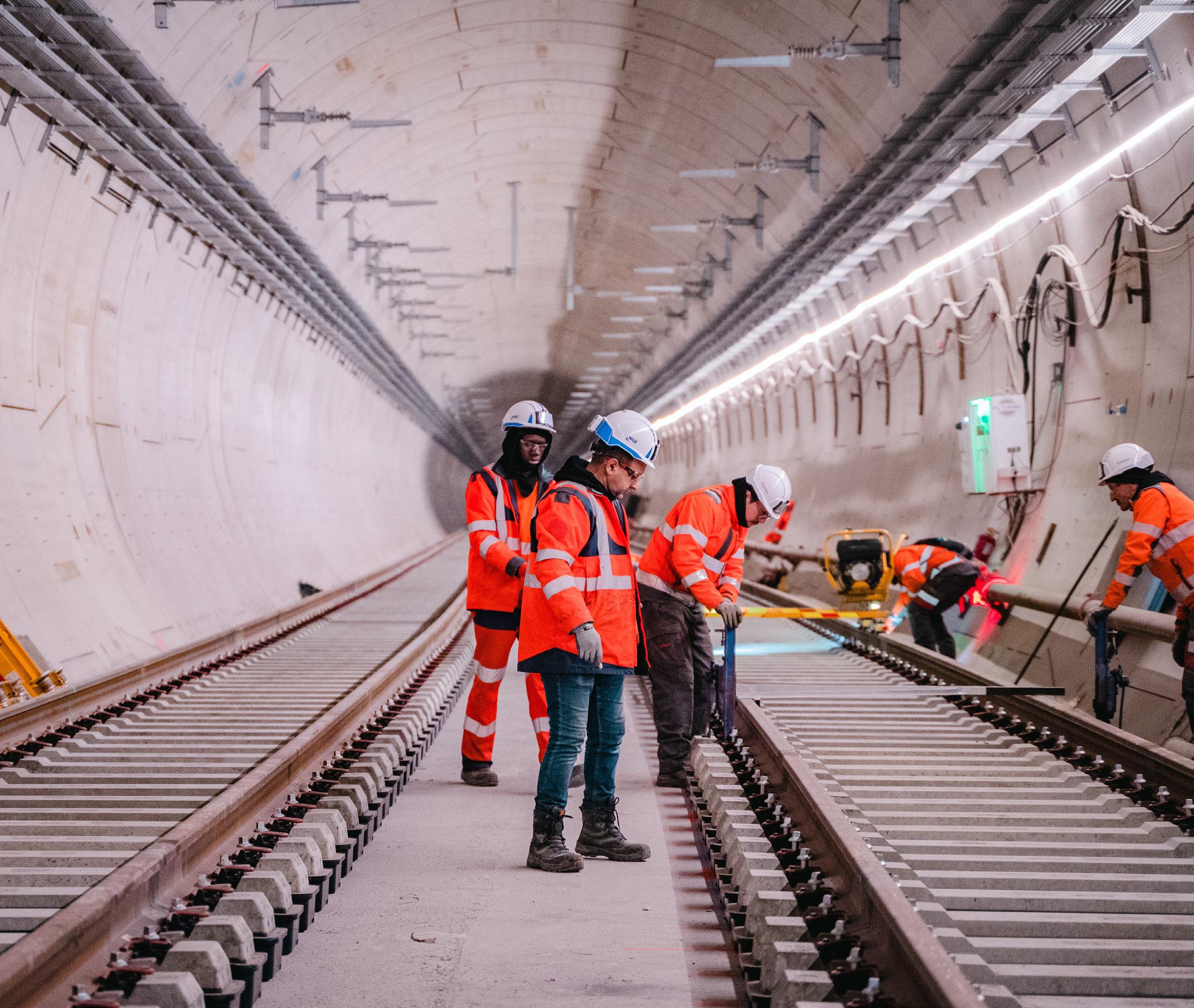
The Shifting Competitive Landscape
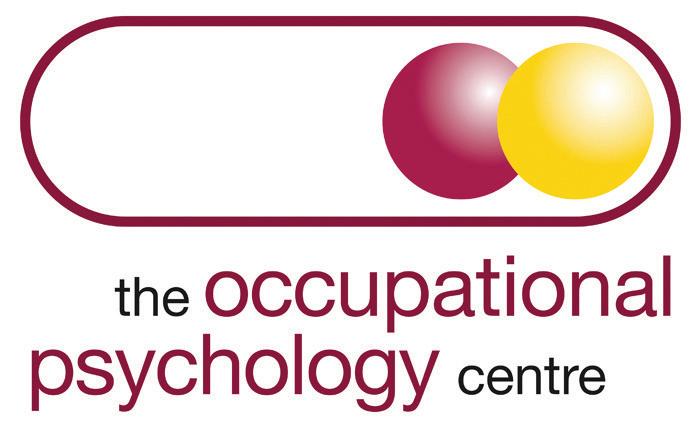
Discover potential. Drive performance.
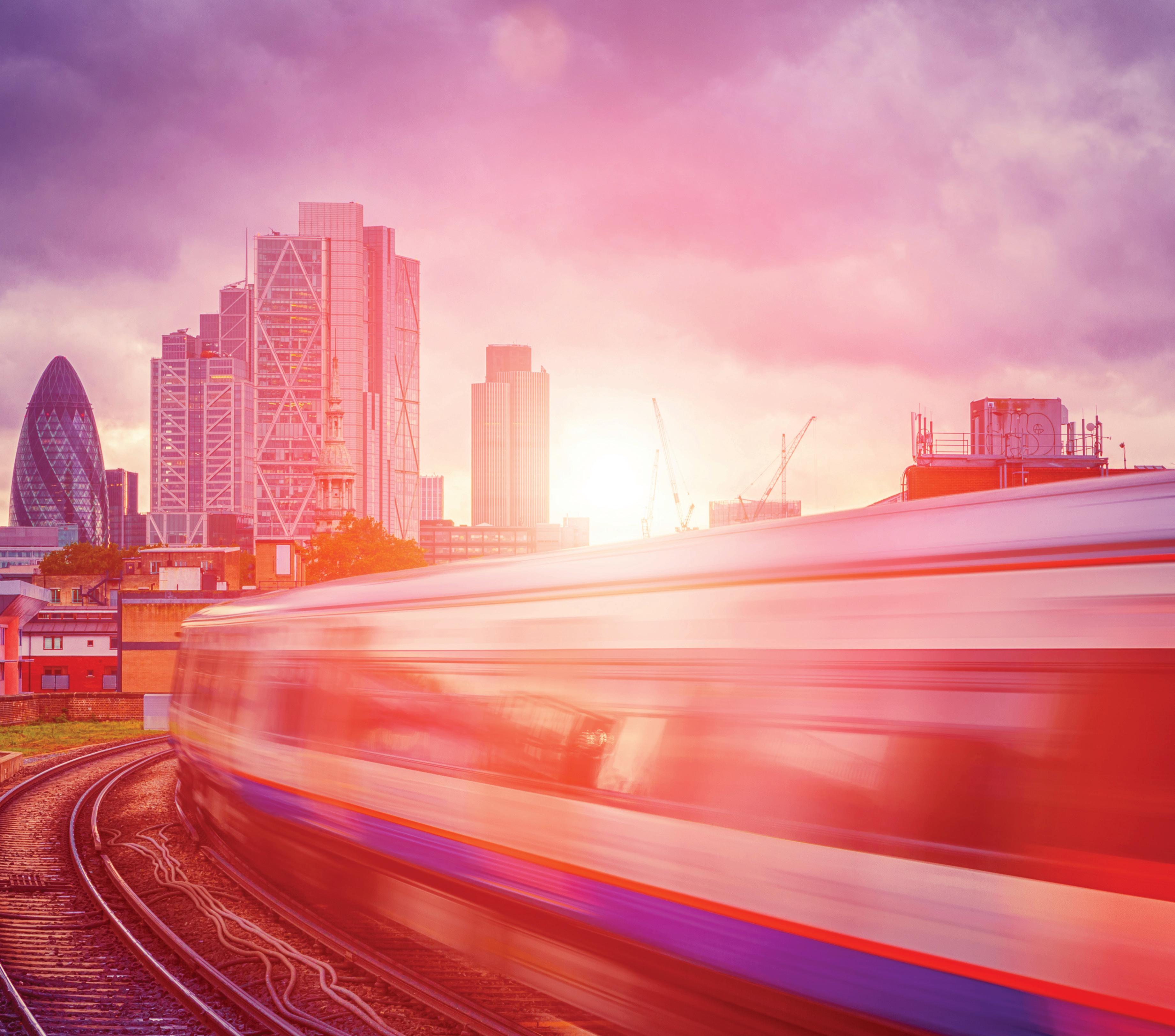
With over 30 years’ experience working in the rail industry, specialising in the safety sector, the OPC provides practical, reliable ways of improving performance and assessing ability.
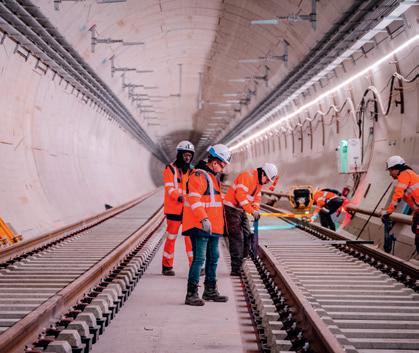
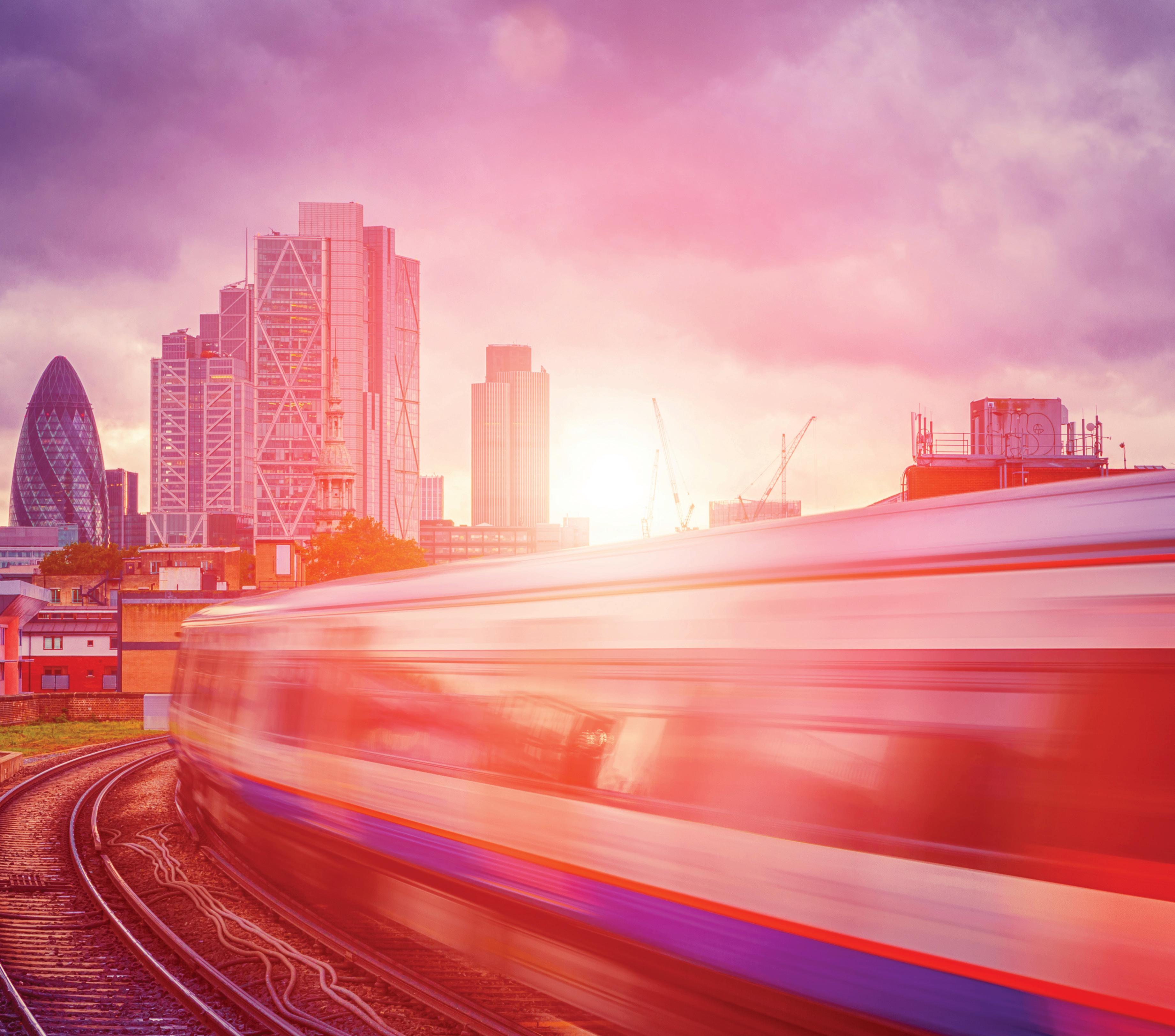
PUBLISHER
Hallmark House, Downham Road, Ramsden Heath, Essex CM11 1PU Telephone: +44 (0) 1268 711 811
EDITORIAL
EDITOR
Sam Sherwood-Hale editor@railpro.co.uk
DISPLAY ADVERTISING
Adam Overall
Jamie Tregarthen sales@railpro.co.uk
RECRUITMENT ADVERTISING recruitment@railpro.co.uk
SUBSCRIPTIONS subscriptions@railpro.co.uk
ADMINISTRATION
Cherie Nugent info@railpro.co.uk
Lisa Etherington admin@railpro.co.uk
DESIGN &
Jasmine Szaniszlo Lukasz Saczek production@railpro.co.uk
EDITOR’S NOTE
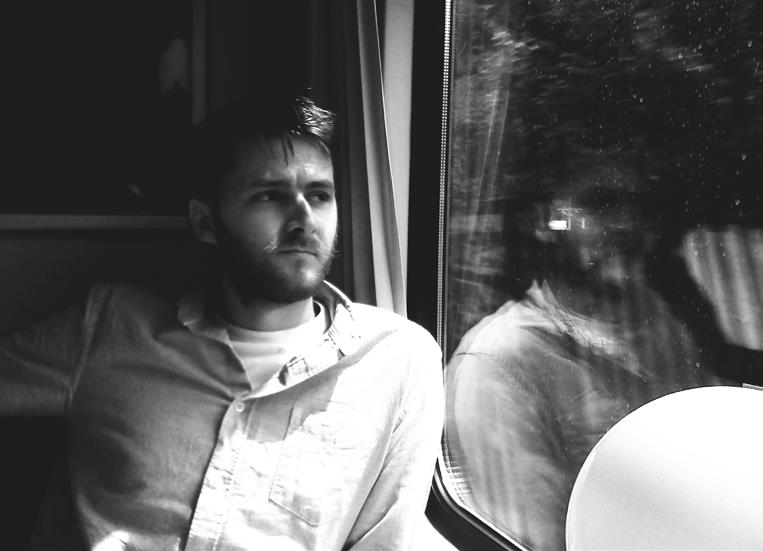
We’re back from a rather wet and windy summer break. There were some warm days sprinkled in there but for the most part this year’s summer was a literal washout. I took a family holiday to Jersey for a cousin’s wedding and we faced sideways rain almost every day –mercifully the weather held on the actual wedding day. The bad weather delayed our ferry home as well so we were forced to spend another day hiding behind a giant windbreaker on St Ouen’s Bay!
I’m assuming that those of you who ventured further south found the opposite problem as we’ve heard all about the heatwave they’re facing on the continent.
Here’s to a mild autumn though and with that comes our September issue which is focussing on stations and safety and security – we have stories from TransPennine Express, Greater Anglia, Mapei, The OPC and more.
My interview this month was with John Sheehy, Chief Executive Officer at Transport Benevolent Fund CIO. The charity is celebrating its 100th anniversary this year so we looked back at its history and how it functions in the modern world.
We also have interviews with Ralf Warwel of Stadler, Phil Evans of Pre Metro Operations Ltd, Kevin Webb of Step On Safety and many more alongside all the usual opinion pieces from Steve Murphy at MTR, Samantha Greer at Setfords and others.
SAM SHERWOOD-HALE EDITOR
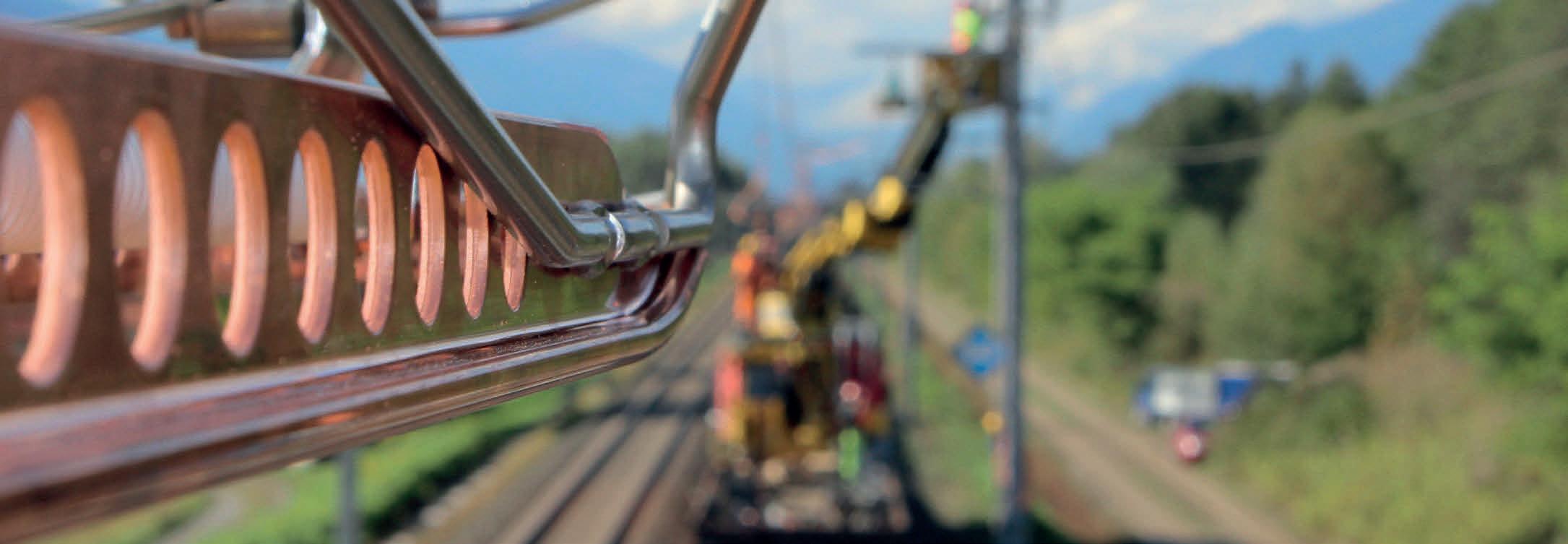
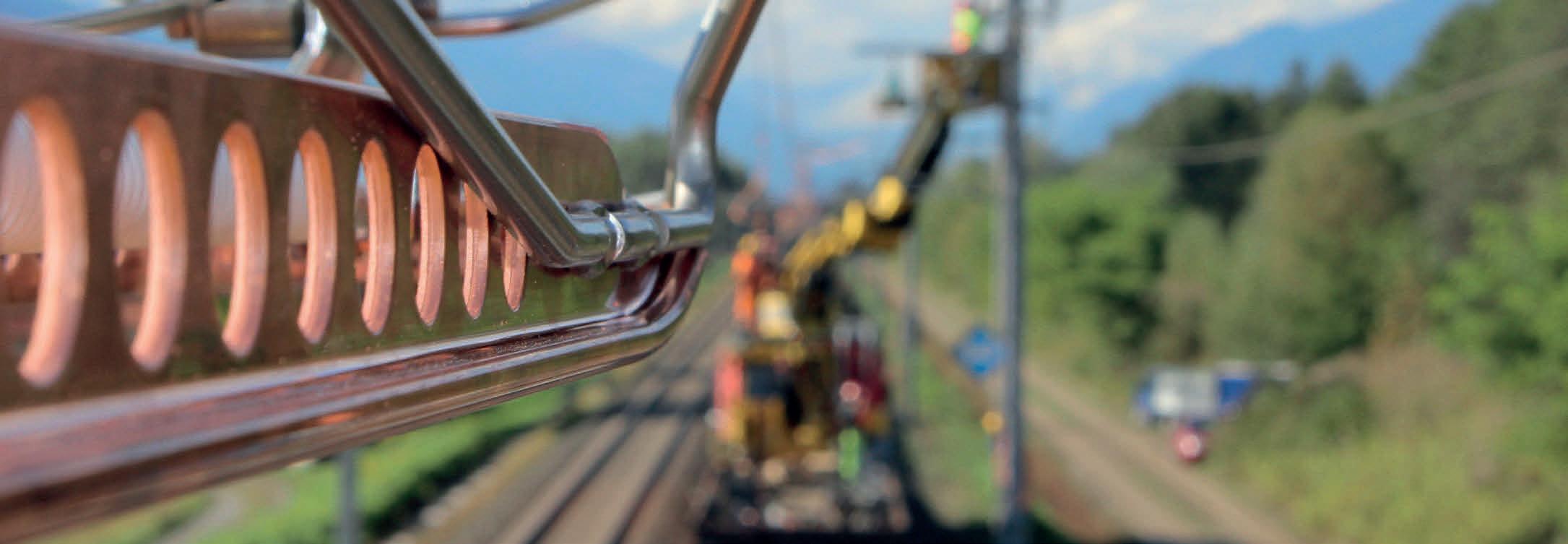
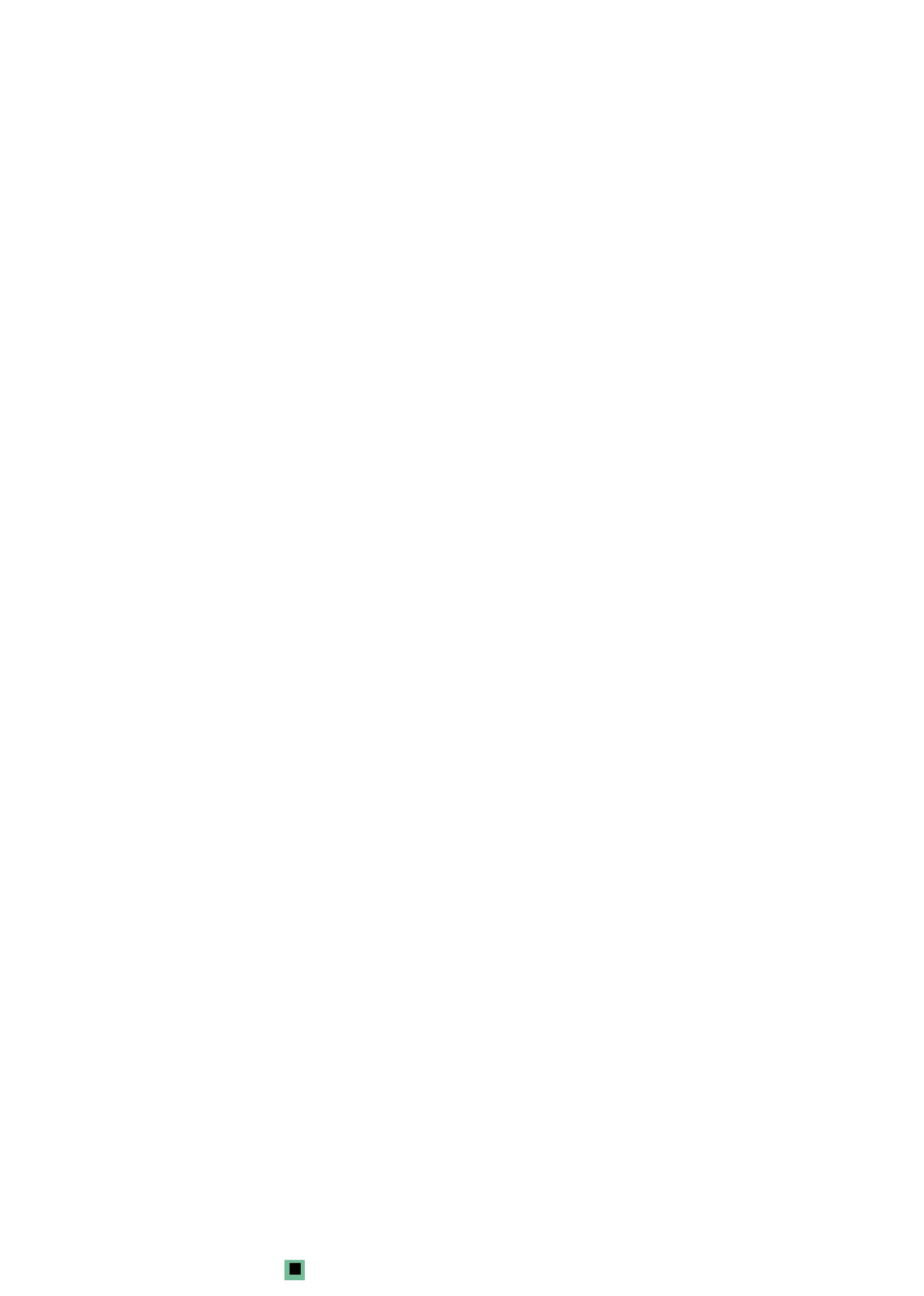

Steve Murphy, CEO of MTR
celebrates
years of the Anglo-Japanese Railways

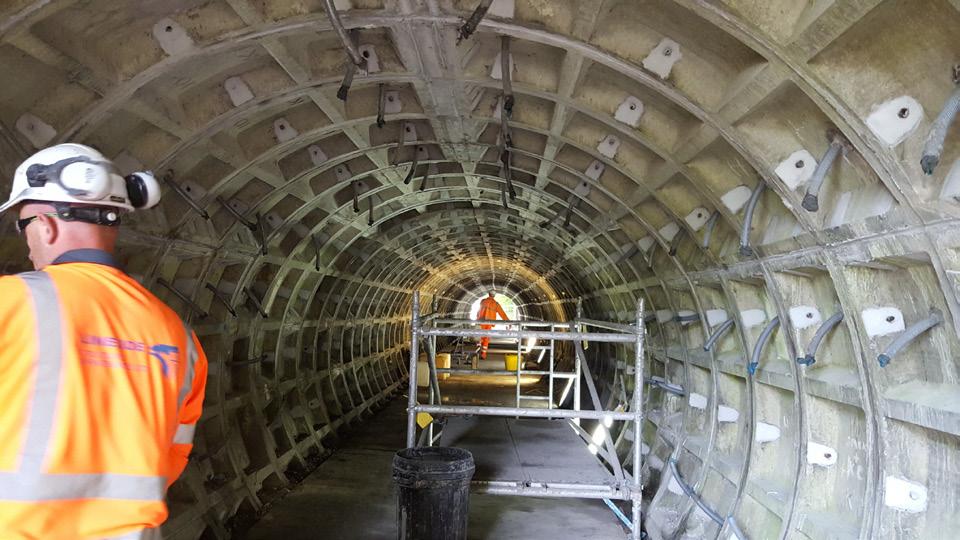
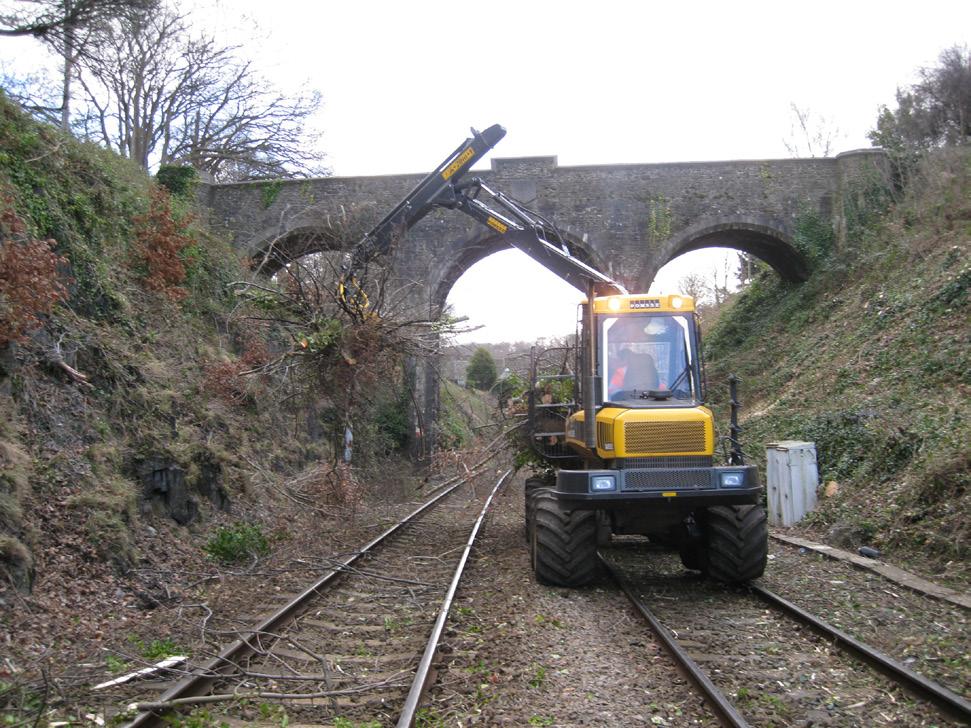

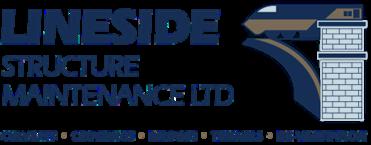

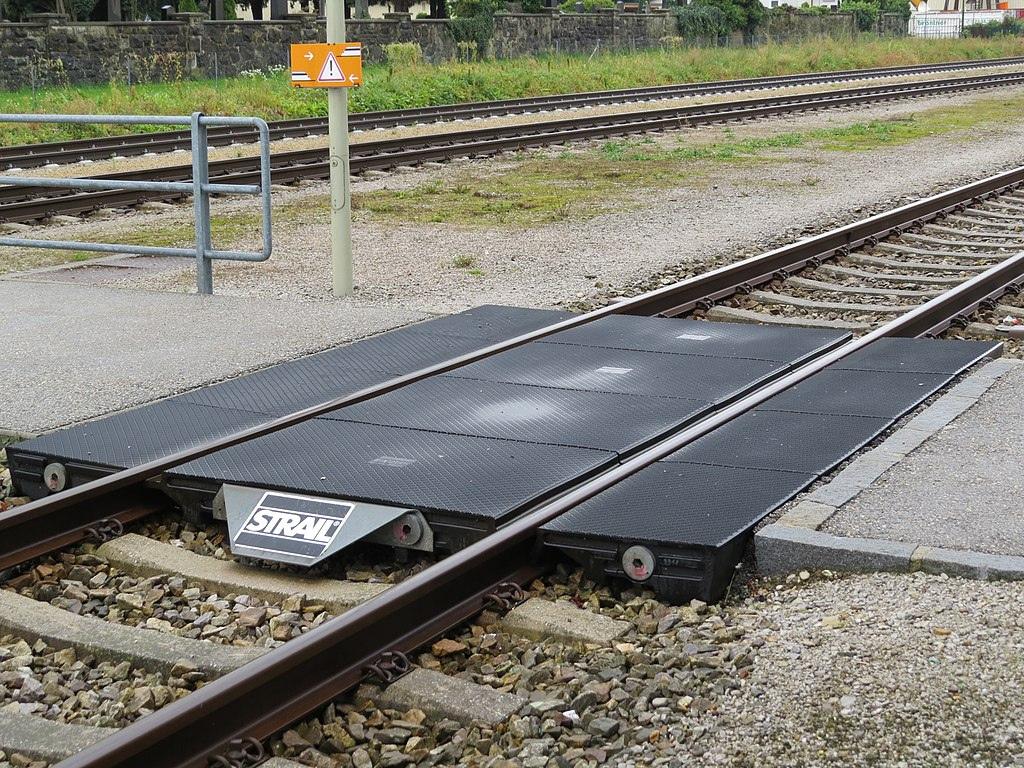
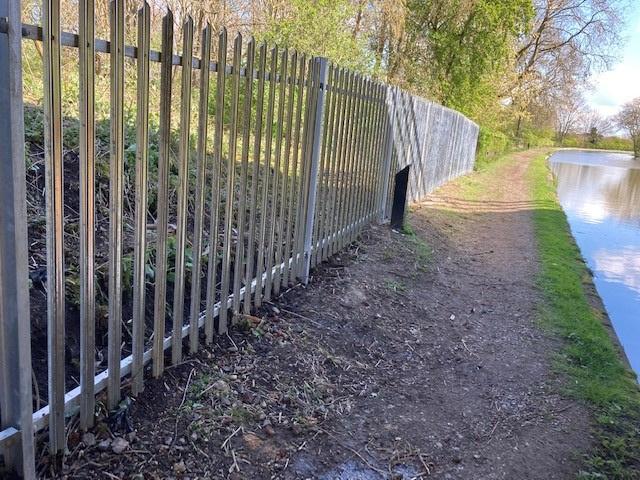
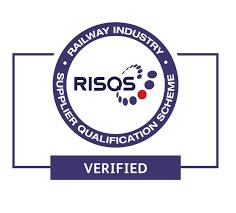

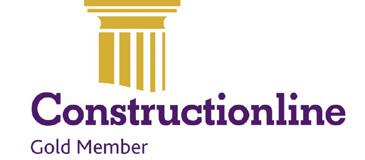
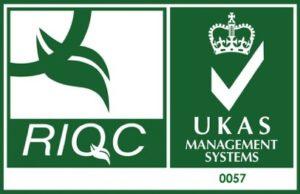
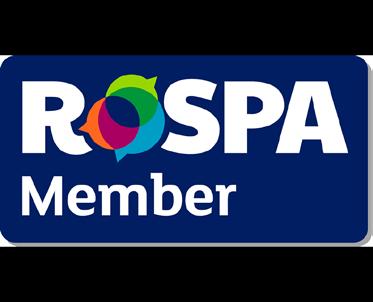
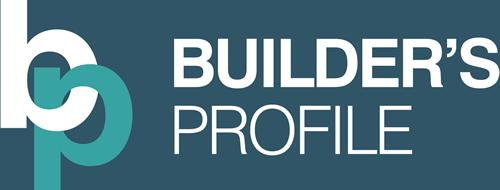

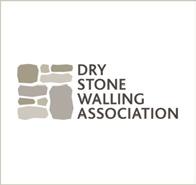
61 STATIONS
Smart integrated lighting solutions
65 STATIONS
Station receives ‘Wildlife Friendly Station’ status
69 STATIONS
Bespoke waterproofing at Bank Station
71 STATIONS
TPE Maps the Future to more Accessible Stations
73 SIGNALLING
Prime Rail Engineering Ltd
76 IN CONVERSATION
Ralf Warwel, Sales Director for UK and Ireland at Stadler
78 IN CONVERSATION
Phil Evans, Co-Founder and Managing Director of Pre Metro Operations Ltd
80 IN CONVERSATION
Minesh Naran, Head of Transport at 1Spatial
82 IN CONVERSATION
Callum Davidson, Head of Business Development – UK at Senceive
Dave Speakman, Engineering Director Rail and MD
Wentworth House Rail Systems at Keltbray
Digital accessibility
Is it time to change the railway narrative?
Sarah Kay, High Performance Textiles – Business Development Manager at Tba Protective Technologies Ltd
IN CONVERSATION
Wendy McCristal, Managing Director of The Mental Wealth Company
IN CONVERSATION
Stefani Dupree, Human Resources & Communications Manager at TSO
Andy Haynes, Director at Servo Group
Kevin Webb, Managing Director of Step On Safety
BUSINESS PROFILES
IN CONVERSATION
Martin Balcombe, Rail Director at Lanes
The most ‘on time’ railway in the country
IN CONVERSATION
Bob Hardwell, Rail Engineering Expert and Director of Linsinger UK Ltd
Roland Weinhart, Director of The Transportation Business Unit at Lubricant Consult Gmbh
All the latest from the industry supply chain
Eleni Jordan, Rohan Kapoor, Rob Forde, Neil Grabham, Ellie Burrows, Rob McIntosh, Jake Kelly, Tricia Williams

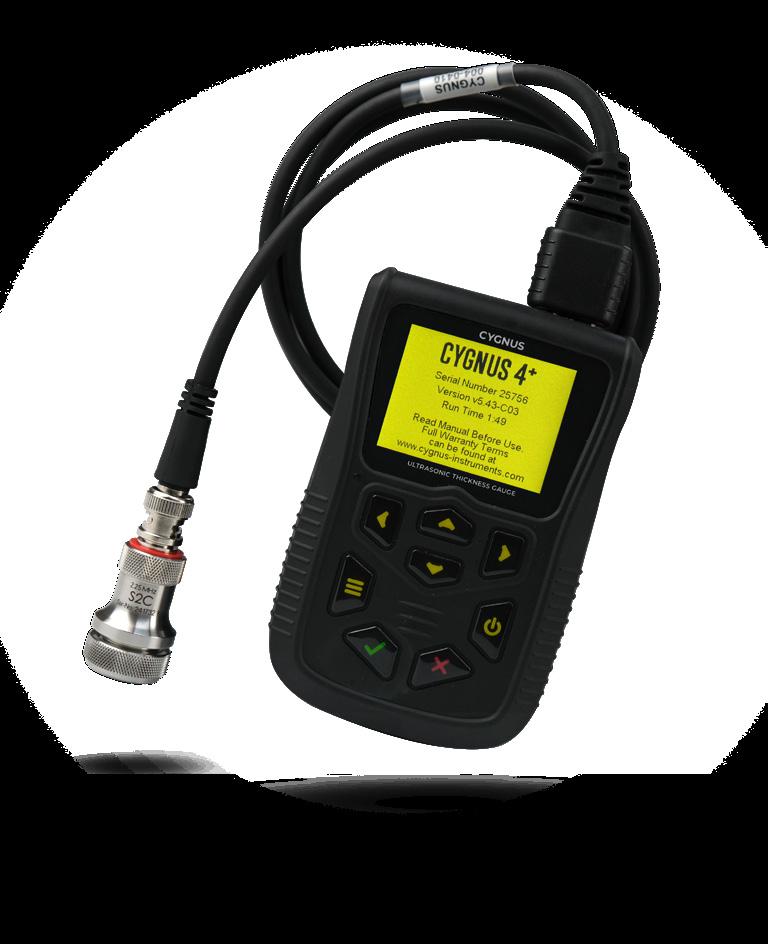
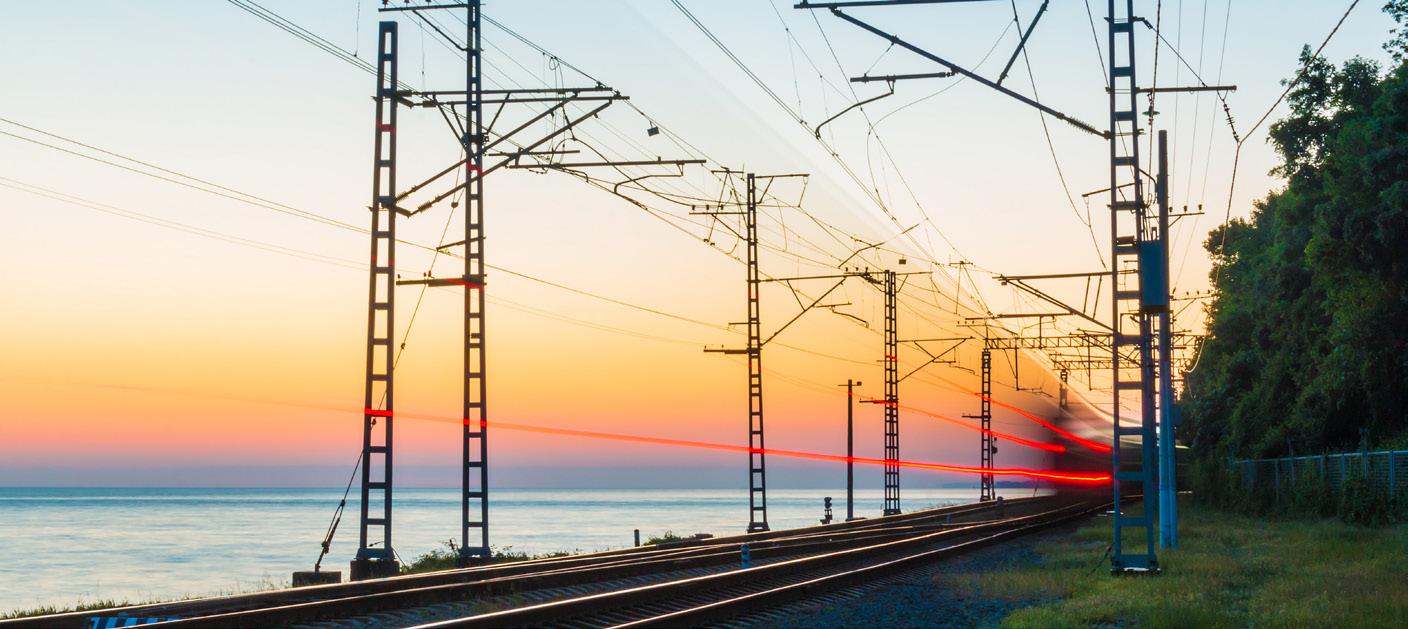
The best choice for versatility
Cygnus 4+ General Purpose Ultrasonic Thickness Gauge is our number 1, affordable all-rounder
• Extremely robust and simple to use
• Multi-measuring modes for accurate through-coat measurements – even for heavily corroded metals
• Sunlight readable display with Live A-Scan for visual verification
• Data logging with Auto-Log
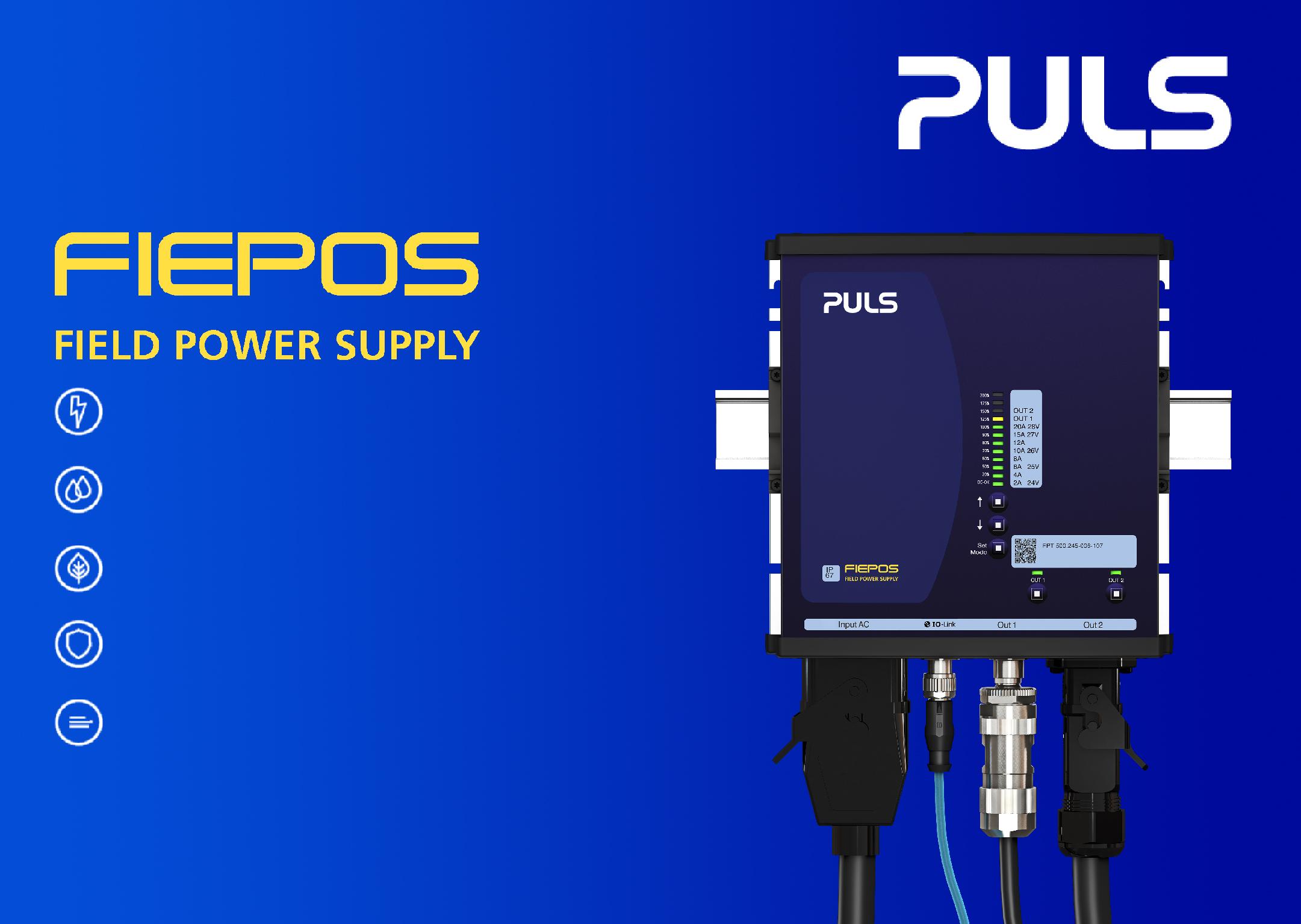

DISCOUNT CODE: RAIL23
Major Rail Innovation Competition Moves into Second Phase
The £7.4 million ‘Innovation in Railway Construction’ competition has moved into its second phase as teams were briefed on the next stage of the programme. In October last year UK organisations were invited to apply to Innovate UK for a share of up to £575,000 for feasibility studies as part of the ‘Innovation in Railway Construction’ competition funded by the Department for Business and Trade in the UK Government.
24 projects involving 36 organisations were successful in the initial round, allowing feasibility studies to be funded on their ideas. In August, successful teams held a briefing with Global Centre of Rail Excellence (GCRE) and Innovate UK about the next steps of the competition.
Projects successful in the second round will receive funding to further develop their ideas to concept stage at the new GCRE facility being constructed in South Wales.
GCRE Limited Chief Executive, Simon Jones, said: ‘The Innovation in Railway Construction competition represents one of the most exciting and interesting research and development projects in UK rail. It is a
glimpse into the future and a look at the new ideas and concepts that will be the backbone of tomorrow’s railway.
‘For us at GCRE this is especially exciting because these will the first project teams innovating at our site. Even before we are operational for commercial clients, we will have teams working on site and developing their new products and ideas.
‘It was great to see how the different teams have interpreted the challenge and hear how they are progressing with their innovations. There are some very creative and fascinating ideas being developed through the first phase and it’s exciting to think that we can take some of the very best through to development at our new GCRE facility.
Head of Innovation at GCRE Limited, Kelvin Davies, said: ‘What’s very exciting about the proposals teams are taking forward is the way they are aimed at tackling some of the biggest challenges in rail. Many of the projects successful in the first round are pitched at helping to decarbonise our railways or developing more cost effective
and sustainable rail infrastructure. That’s hugely exciting and also very beneficial for the future of the railways both here in the UK and across Europe.
‘This is a unique opportunity for the teams involved as we offer up the prospect of developing the best ideas on the page to construction at the Global Centre of Rail Excellence facility. That ethos of being a facility that supports innovation at every level – including small innovation teams – is one that is very important to the GCRE team and it’s great to seeing it being realised here.’
The Innovation in Railway Construction competition is a phased competition, with a number of successful projects progressing in 2024 to fully develop their ideas and delivering a demonstration on the GCRE site. The successful first round projects vary in scope from development of new rail drone technology to self-healing concrete.
When it opens, GCRE will be a facility providing world class research, testing and certification of rolling stock, infrastructure and innovative new technologies that will fill a strategic gap not just in UK rail, but across Europe.
GCRE was established in 2021 with an initial commitment of £50 million from the Welsh Government. The UK Government is supporting the project with funding for research and development along with capital funding of £20 million. GCRE is currently progressing a major public procurement to attract private funding for the project.
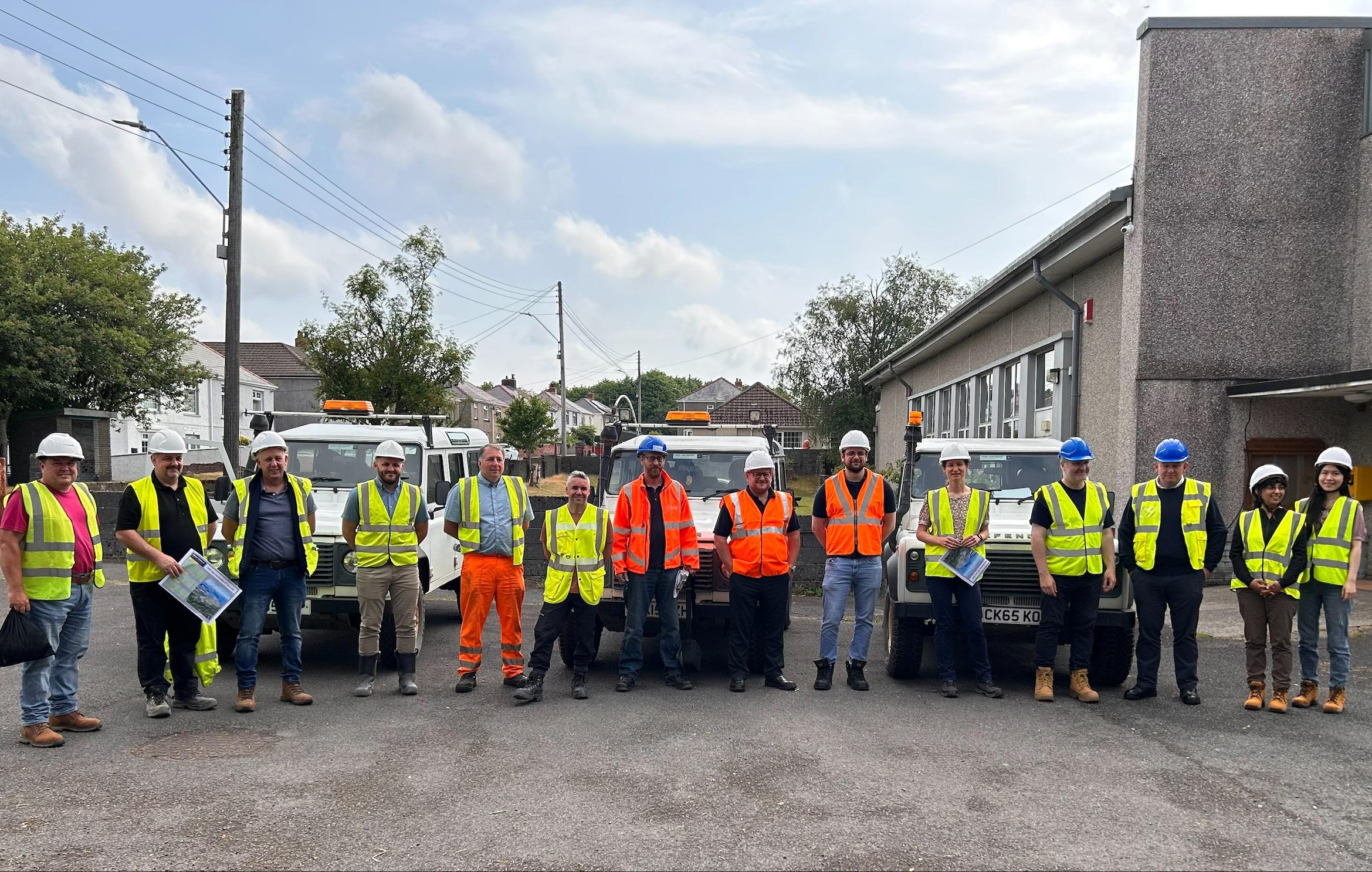
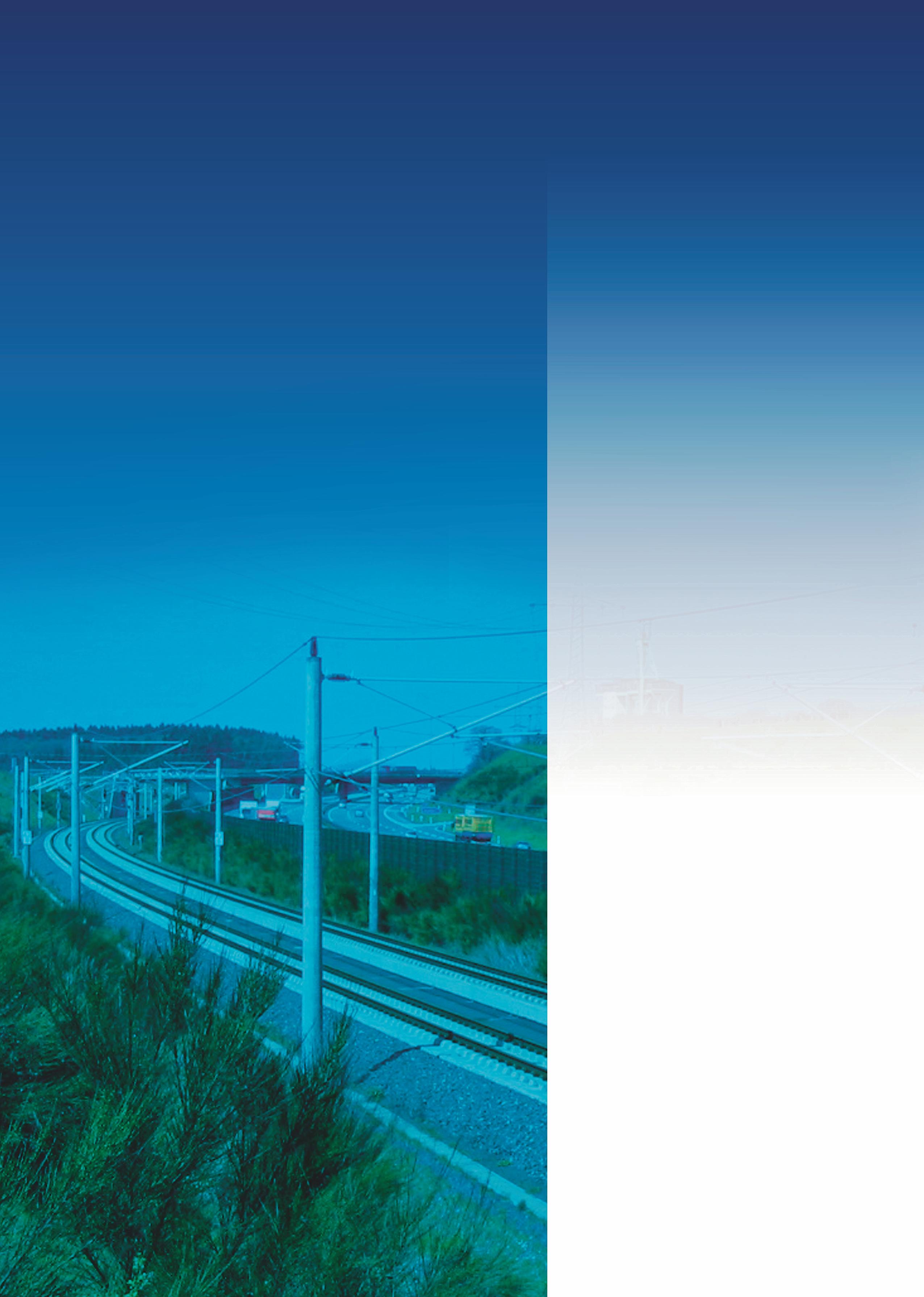
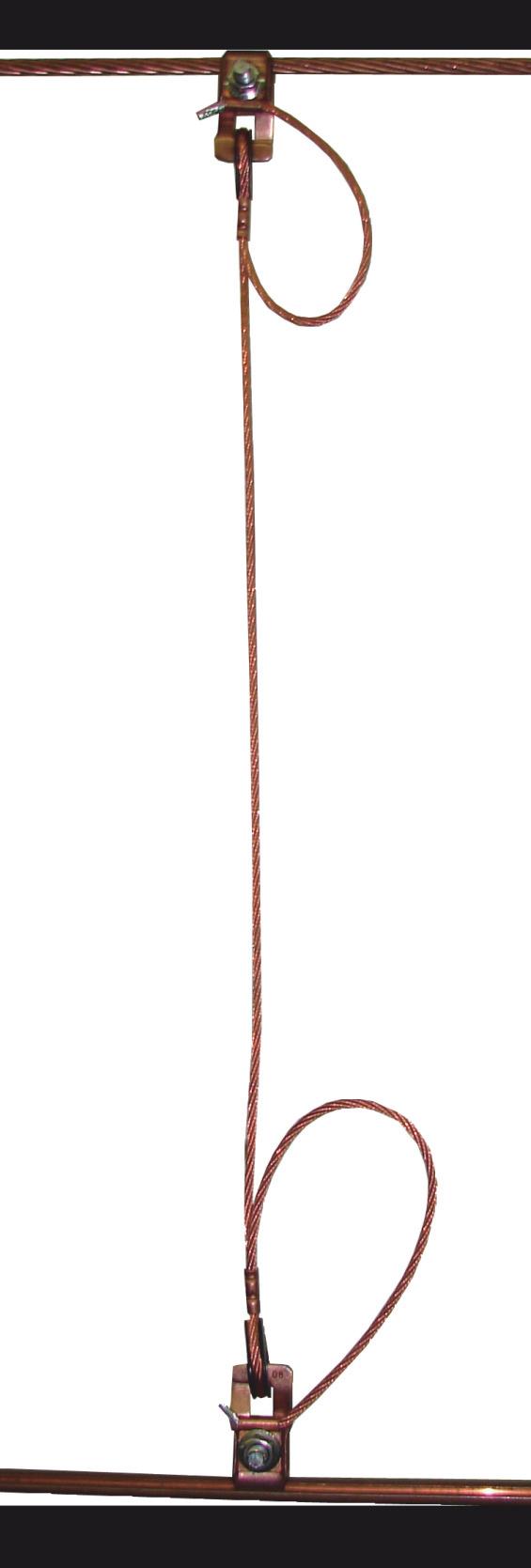
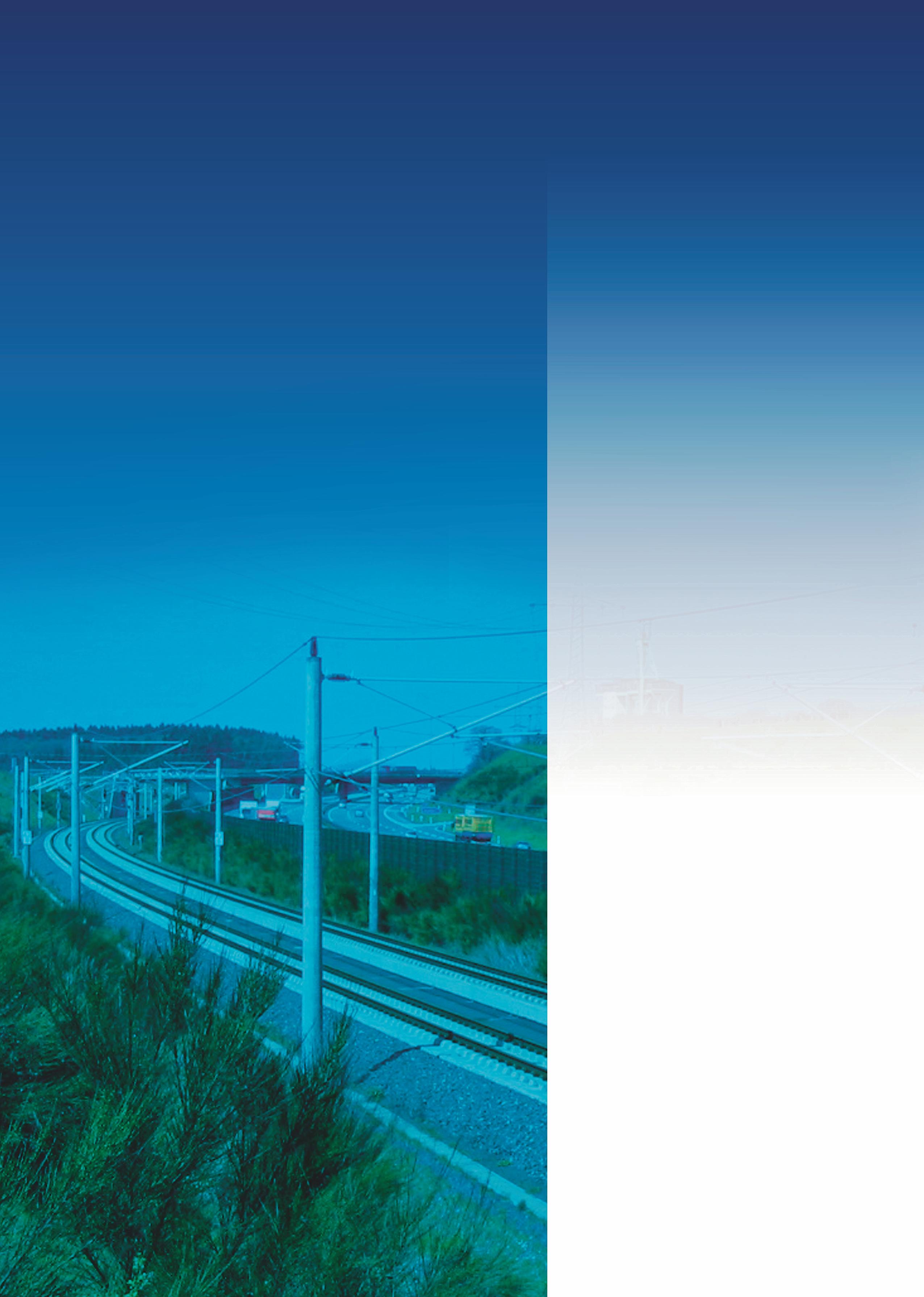
HS2 ‘Marathon’ Bridge Construction
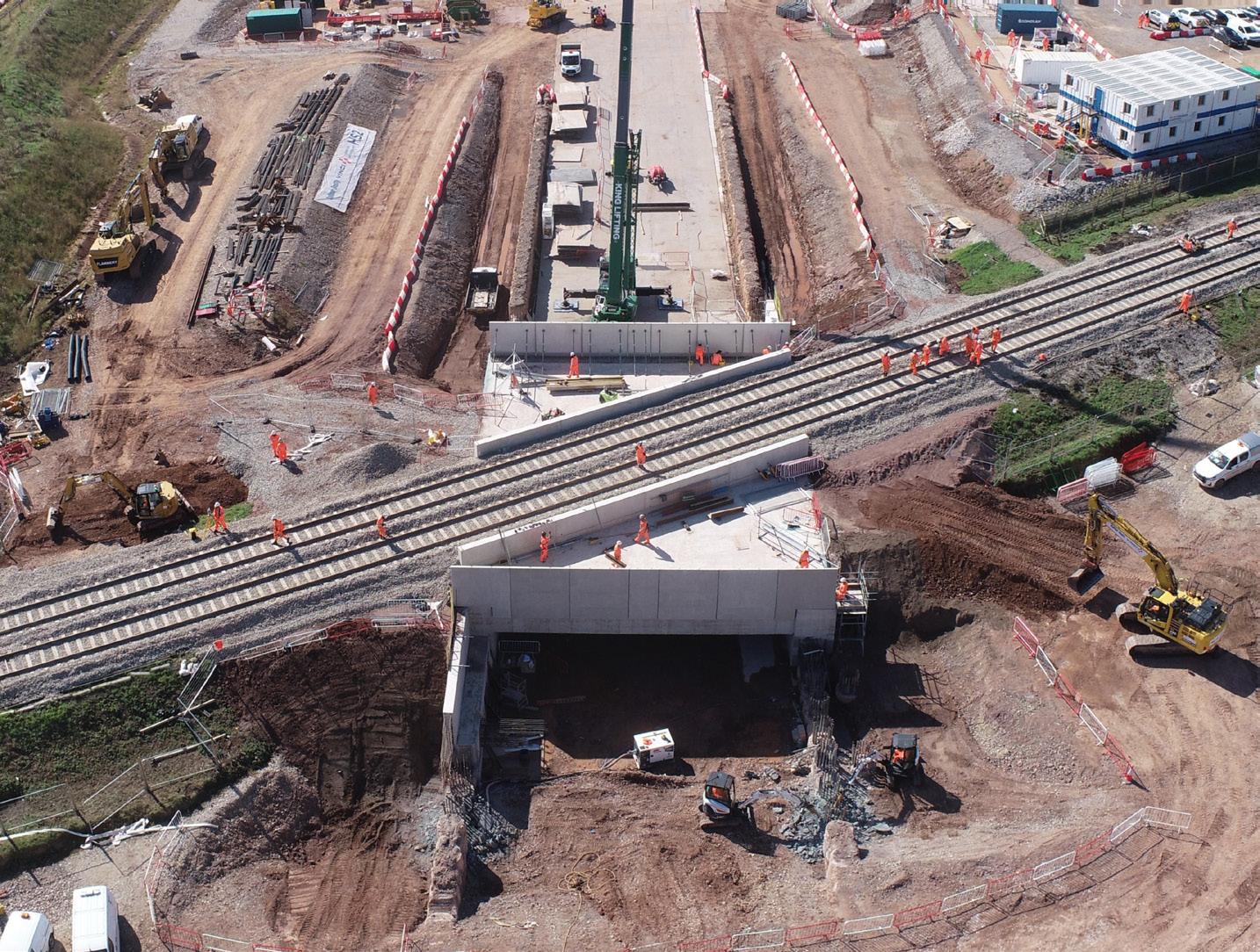
delivering design, surveys, piling works, bridge build, concrete pouring, crane operations, reinforcements, modular transportation, track and systems removal and reinstatement.
The work was delivered in parallel to the construction of the nearby Fulfen Wood bridge, which involved moving a giant 6,200 tonne single span structure under the West Coast Main Line – the UK’s heaviest drive to install an intersection bridge.
MP Shows Support for Worcestershire Rail Plans
Representatives from Midlands Connect and GWR met with Mid Worcestershire MP, Nigel Huddleston at Worcestershire Parkway station to discuss how their plans for the Midlands Rail Hub could benefit his constituency.
Midlands Rail Hub is an ambitious £1.5 billion rail scheme set to transform rail travel across the whole of the Midlands. It includes improved access from the West Midlands to the South West, Wales, and the East Midlands.
This will create an additional two million seats on the network per year; as well as giving more people access to HS2 when it is complete. When Curzon Street station in Birmingham is up and running, connections from Moor Street station to the high-speed network will be seamless.
The rail scheme will see the frequency of trains from Cardiff to Birmingham doubling, with stops at Newport, Gloucester, Cheltenham Spa, and Worcestershire Parkway. When plans are built, Mr Huddleston’s constituents will also benefit from faster and more frequent services from Hereford to Birmingham, which stop at Droitwich Spa.
Nigel Huddleston, MP for Mid Worcestershire, commented on the plans: ‘These proposals are so important for improving connections for the residents of Worcestershire. More services to Cardiff and Birmingham will create amazing opportunities for my constituents. I support these proposals and look forward to the development of the Full Business Case.’
Rail Trail 2023 Celebrates 160th Anniversary of the Metropolitan Line
Rail Trail, a fundraising event organised as part of this year’s Rail Aid is celebrating the 160th anniversary of London Underground’s Metropolitan line by walking a length of its route –and is looking for eager participants!
The Metropolitan line Rail Trail, a 20-kilometre walk above ground from Wembley Park to Aldgate on 29 September is generously supported by Transport for London and will raise vital funds for the rail industry’s favourite charity, Railway Children.
At every station along the way there’ll be a checkpoint to collect a stamp as well as marshals en-route to keep everyone on track. There’ll also be information hubs to point out local landmarks as well as tell participants about the kind of projects and children their fundraising will support. Each participant will receive a fold-out map containing walk information and an event T-shirt. And a celebratory drink and medal will be waiting for everyone at the finish line.
The Metropolitan line Rail Trail is just one of a whole host of events put on as part of Rail Aid 2023. First launched in 2020 as a response to Covid-19 restrictions wiping out Railway Children’s
popular events calendar, Rail Aid has become a much-loved part of the rail industry’s calendar. Alongside the Rail Trail, there will be golf events, luxury train experiences, Santa trains and much more –keep an eye on the activities as they are announced at www.railaid. co.uk/events
Last year’s Rail Trail raised over £42,000. And at a cost of just £20 to register and a £100 minimum sponsorship pledge, it is hoped this year’s Metropolitan line Rail Trail will raise even more. Every penny raised helps Railway Children reach and protect vulnerable children on the streets and railways of India, Tanzania and here in the UK.
The walk is suitable for individuals and groups, young and old, friends and colleagues, humans and their furry friends! The route is also suitable for mobility scooters and wheelchairs. Every pound raised will genuinely make a difference to children around the world who desperately need our support.
Find out more or sign up now at www.railaid.co.uk/metropolitanline-rail-trail/
West Yorkshire Residents Given Opportunity to Try Out a Career in Rail
The Rail Safety and Standards Board has developed a suite of metrics to help Great Britain's rail industry measure performance across the circular economy, waste management, and resource management.
A group of twelve people from across West Yorkshire that have been long-term unemployed began a three-week training programme with the train operator Northern on 29 August. They are the latest in-take to Northern’s ‘Get Into Rail’ scheme, which was open to anyone aged 18 and over that was receiving Universal Credit.
The scheme, which is delivered in collaboration with Network Rail, Carlisle Support Services and Shipley College, includes the opportunity to shadow operational colleagues at Northern and the chance to gain qualifications in employability and customer service.
At the end of the course, they are guaranteed an interview for roles advertised at Northern – with the train operator hoping the experience gained will help break the cycle of unemployment.
Lisa Leighton, People Director at Northern, said: ‘We’re incredibly proud of our ‘Get Into Rail’ scheme and the opportunity it offers to people considering a career in rail. It provides valuable experience in the workplace and the chance to develop job-specific and transferrable skills in an environment that recognises ability, not just academic achievement.
‘We hope through the ‘Get Into Rail’ scheme they will see for themselves how fulfilling a career in the rail industry can be whilst boosting their CV and employment credentials with some hands-on experience.’
Recycled Steel Supports Jobs while Cutting Carbon in Construction
Old car parts, radiators and shopping trolleys are being given a new lease of life in the construction of Britain’s new railway – HS2. The UK recycled steel initiative, which is helping HS2 to cut carbon in construction, is also supporting hundreds of jobs in South Wales, Yorkshire and Nottinghamshire.
Over the last two years, the UK steel industry has benefitted from a pipeline of orders worth over £170 million from HS2’s construction partners building the first phase of the high-speed railway linking London and the West Midlands.
As the backbone to HS2’s two-decade construction programme, over one million tonnes of steel are forecast to be needed for
standard construction materials, a further 200,000 tonnes for steel rail, switches and slabtrack, and an additional 15,000 tonnes for rolling stock.
CELSA Steel UK is the UK’s largest manufacturer of steel reinforcement and a driving force behind new sustainability standards for the industry. 750 staff work at the two Cardiff-based sites where recycled scrap metal is melted in an electric arc furnace to produce 80 per cent less carbon emissions than basic oxygen steelmaking. The molten steel is then turned in to billets and rolled to make reinforcing bar (rebar) for use on HS2 construction sites.
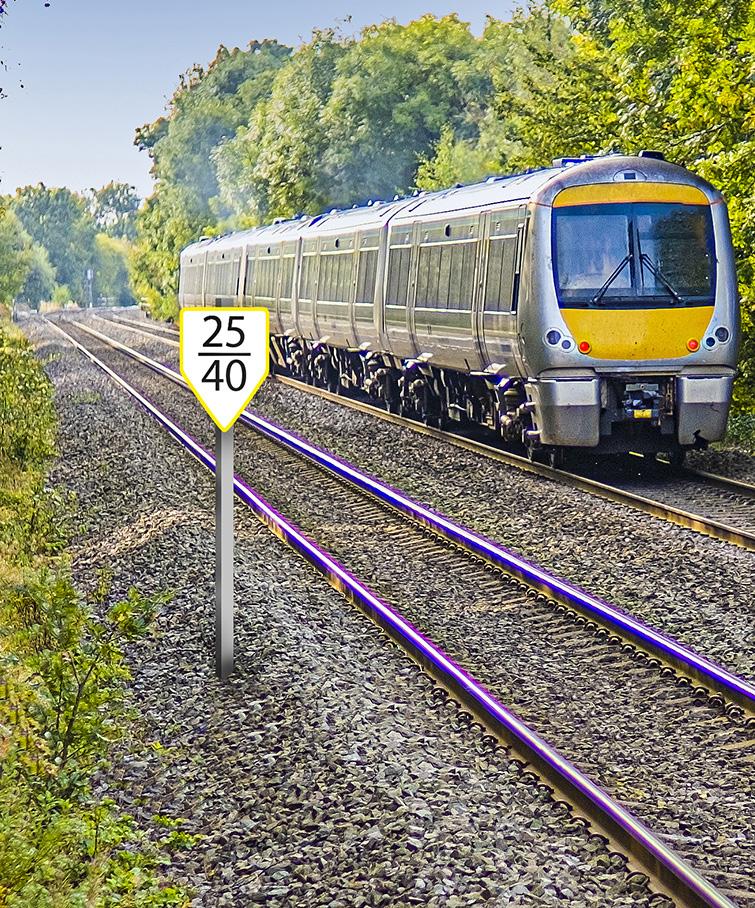
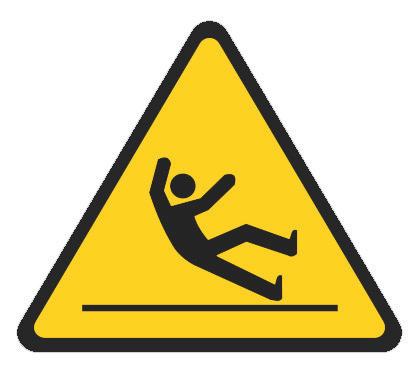
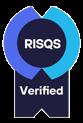

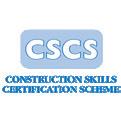


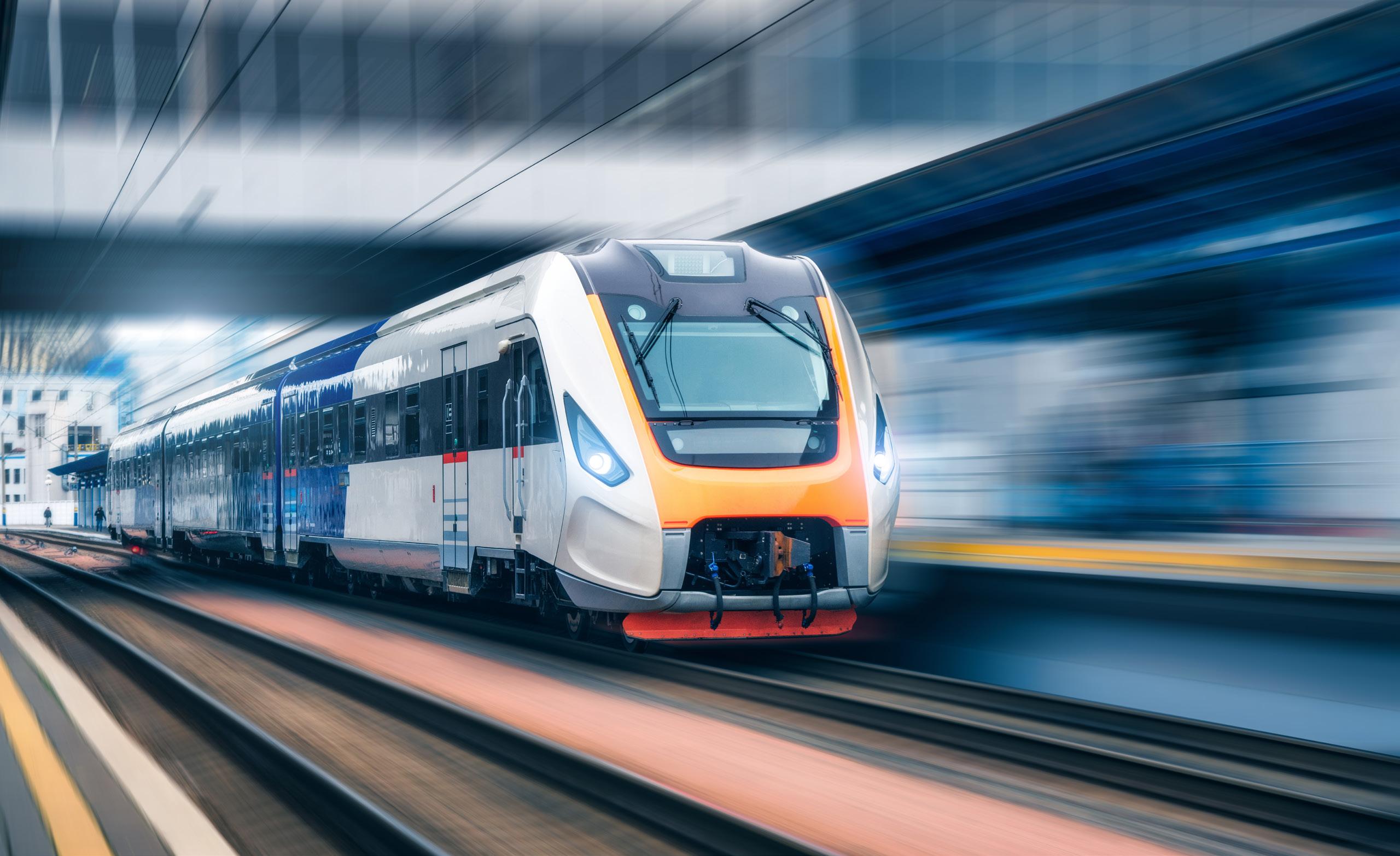
Norbar is a UK manufacturer of battery, electric, pneumatic and manually operated torque multipliers, wrenches, torque measurement equipment and bespoke torque control solutions specially developed for the rail industry
Contact Norbar and speak to The Voice of Torque Control
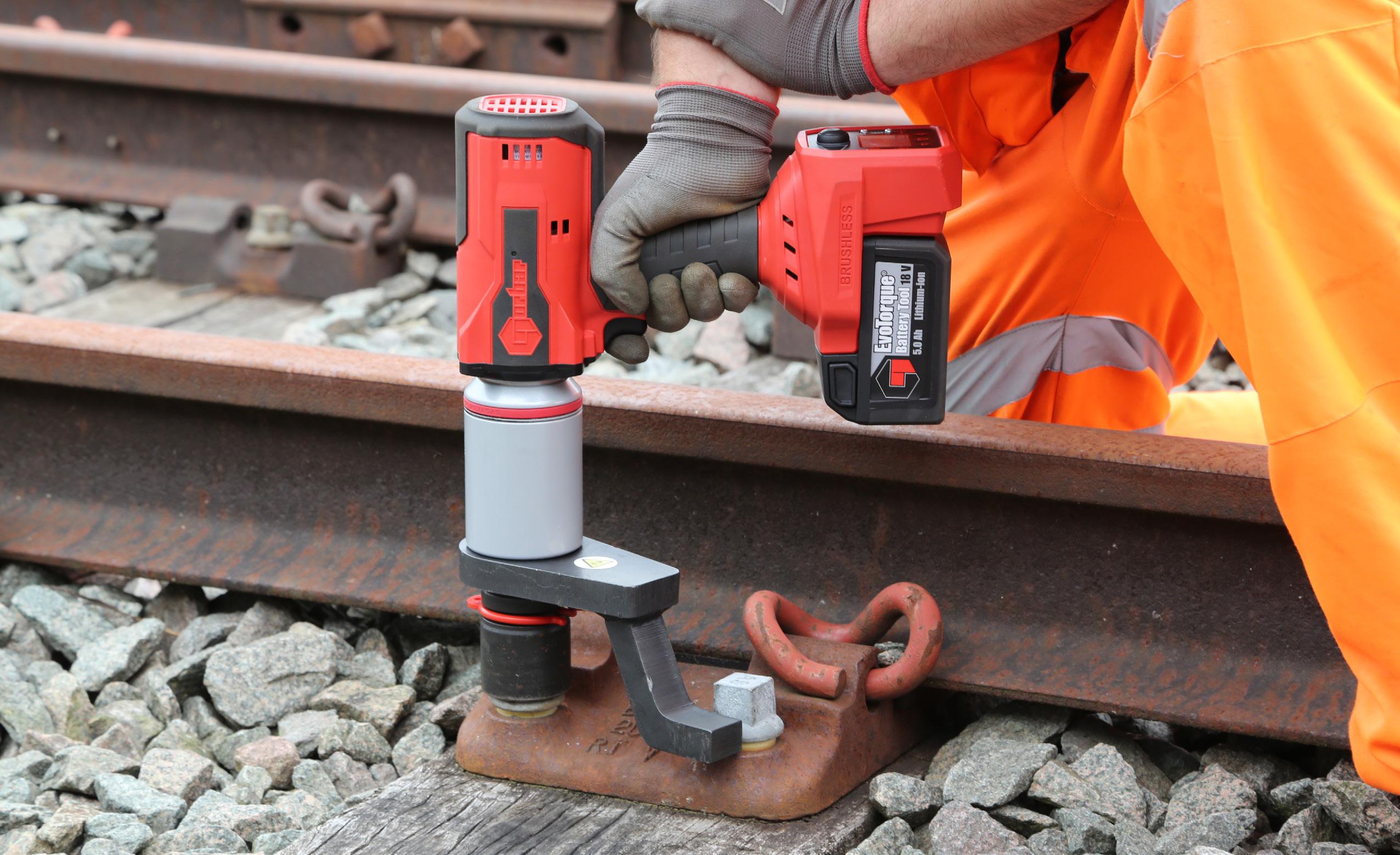
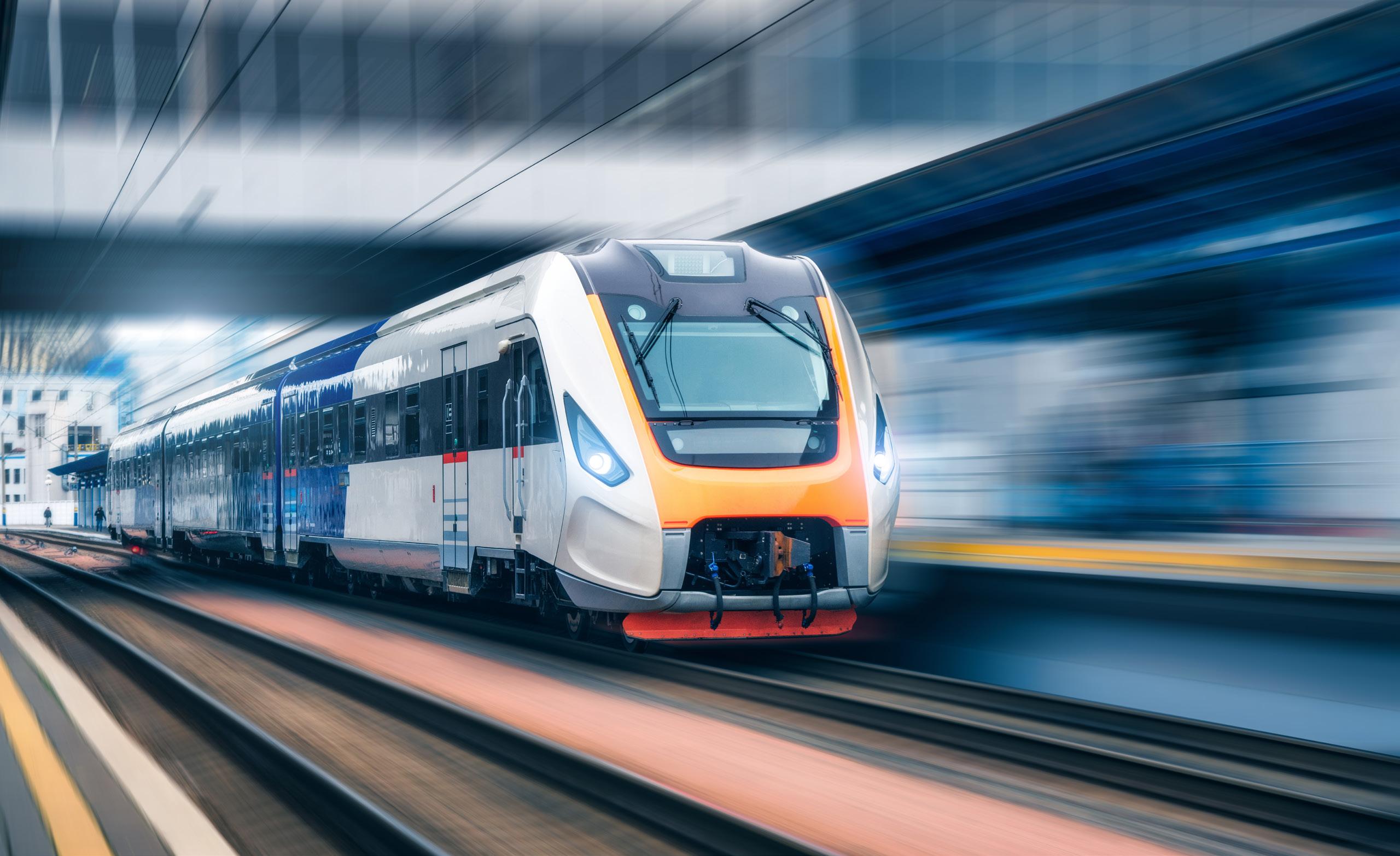
RSSB Develops Rail Industry Zero Waste Metrics
The Rail Safety and Standards Board has developed a suite of metrics to help Great Britain's rail industry measure performance across the circular economy, waste management, and resource management.
The Rail Safety and Standards Board (RSSB) working with the rail industry and global consulting experts Ricardo, has completed the first phase of a project to develop a suite of metrics to help the rail industry measure its performance towards reaching a zero waste goal of using its resources efficiently and supporting a collaborative circular economy. , Integrating these metrics across the rail industry will enable consistent measurement and support wide scale adoption of circular economy principles across its assets, infrastructure, and operations.
The project has:
• Identified the existing reporting, data flows, and metrics used across rail and other sectors to measure waste management.
• Created a shortlist of metrics – using multi-criteria analysis to prioritise the metrics according to their relevance, feasibility, and practicality.
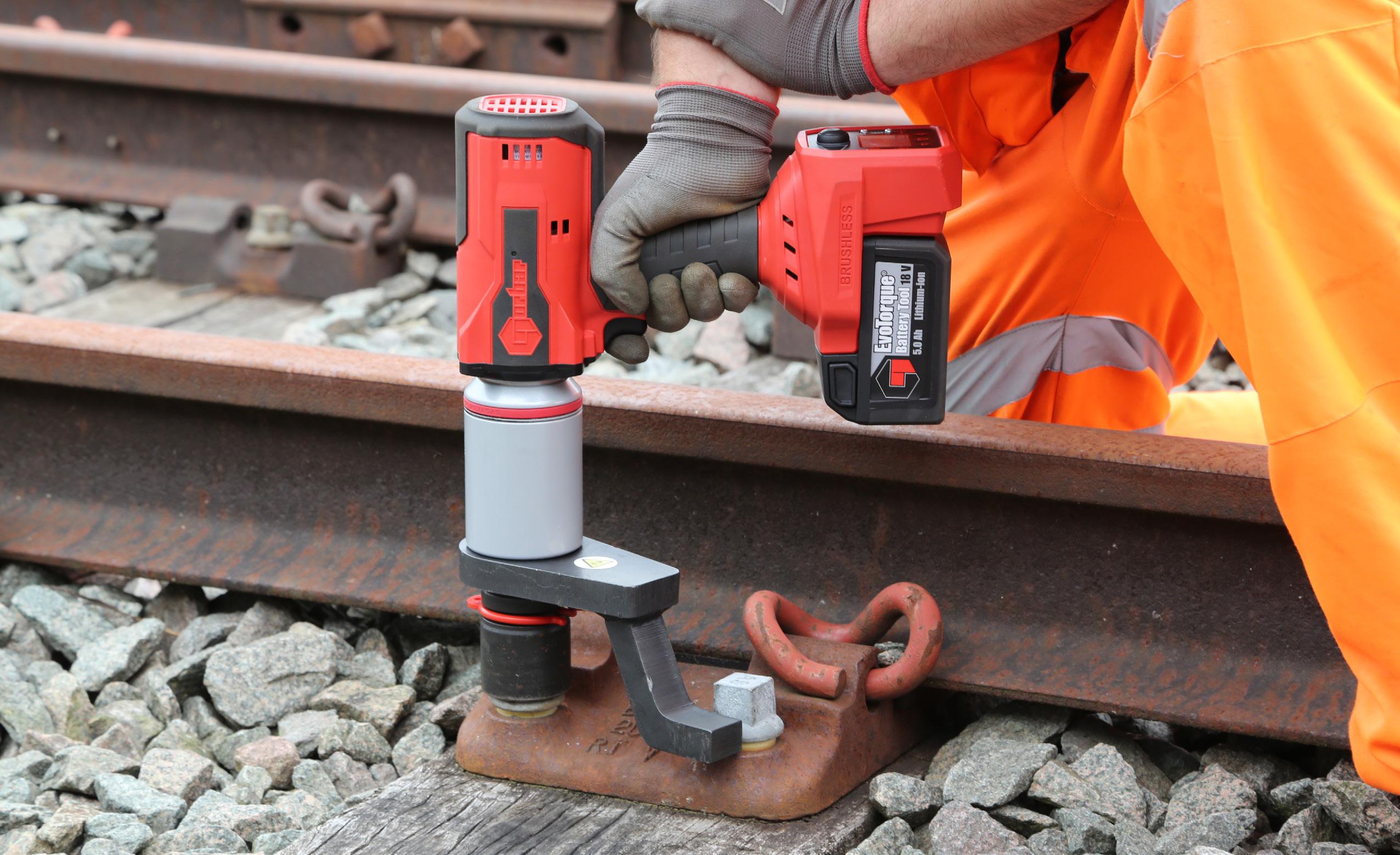
• Developed data collection plans for the implementation of metrics.
Core metrics have been selected as being the highest priority for the rail industry to adopt, based on the findings from stakeholder interviews. They include:
• Station waste generated, reported by treatment method.
• Proportion of surplus food redistributed.
• Level of recycled content in rail assets and infrastructure.
• Weight of materials in train models that can be reused or recycled at end-of-use.
• Depot waste generated, reported by treatment method.
• Provision of environmental training.
• Proportion of procurement activities/ contracts which include sustainability criteria in the selection criteria.
Progressive metrics have also been identified for implementation in the longer-term, including materials efficiency, the use of critical materials, and the amount of end-ofuse batteries retained for reuse. A headline metric was also developed to support the monitoring of the overall progress and
performance of the industry.
RSSB and Ricardo are now working with rail organisations to pilot the implementation of these data collection plans and metrics. The results will allow us to refine the recommended metrics, and develop guidance to enable our members to consistently and effectively collect, measure, and report on the industry’s circular economy performance.
RSSB’s Sustainable Rail Strategy Lead, Thom Rawson said: ‘This project has established tangible and measurable metrics for the rail industry’s management of waste and recycling, and represents a significant step forward towards achieving the goal of zero waste.
‘Ricardo’s systematic and collaborative approach has produced the right results, most importantly ensuring that the recommendations are supported by the rail industry. This is key to ensuring they are put into practice.
‘The information gathered using these metrics will be an important element of RSSB’s Sustainable Rail Data Framework, through which we are building a dataled understanding of rail’s sustainability credentials.’
Innovation in the Black Country
Nicola Richards, Member of Parliament for West Bromwich East, recently embarked on a visit to the Black Country Innovative Manufacturing Organisation (BCIMO) located in Dudley, as part of the Railway Industry Association's (RIA) Rail Fellowship Programme, which links politicians with rail supply sites across the country.
BCIMO, a not-for-profit organisation, is the driving force behind a new state-of-the-art rail research and development facility based in Dudley in the West Midlands.
Built on the site of Dudley’s former railway station, the £32 million pound multi-purpose centre of excellence, offers a host of unique facilities including a Rail Development and Test Site, Engineering Laboratories, Serviced Offices and an Events Suite – all of which can now be used by both local and national companies, including those looking to develop and test new rail products.
During her visit, Richards was impressed by the commitment to advancing the rail industry through hands-on research and development. She had the opportunity to meet the Coventry Very Light Rail (CVLR) project team who are undertaking R&D activity at the centre. The Coventry Very Light Rail project aims to create an innovative track design and vehicle that will deliver an affordable light rail system for Coventry and beyond. This is expected to provide an alternative to personal vehicles, contributing to improved air quality and reduced congestion in the region.
Richards also experienced the centre’s Transport Systems Simulator, which is used to train new VLR drivers and conduct research in VLR and transport technology. The simulator plays an important role in the development of new VLR systems by allowing the evaluation of new routes and the training of drivers. It is also being used to showcase the planned Coventry VLR first route to interested parties.
Another key project, the Clean Futures Accelerator, is promoting sustainable technologies in transportation across the West Midlands. Led by the Connected Place Catapult, BCIMO and Coventry University are partnering organisations providing facilities, expertise, and technical support to this programme. Over the course of the two-year programme, 40 SMEs will be selected to join a six-month, challenge-led accelerator where they will receive funding to trial their solutions. The challenges in the accelerator will be built around rail and automotive manufacturing, along with related supply chains.
Toby Williams, Public Affairs & PR Manager at RIA, said: ‘It was great to team up with the BCIMO to host Nicola Richards MP and showcase some of the best rail engineering innovation. Through purposeful conversations bridging industry stakeholders and policymakers, we are actively shaping a technologically advanced and sustainable rail sector.’
Network Rail and Dutch Rail Infrastructure Manager
ProRail Sign New Deal
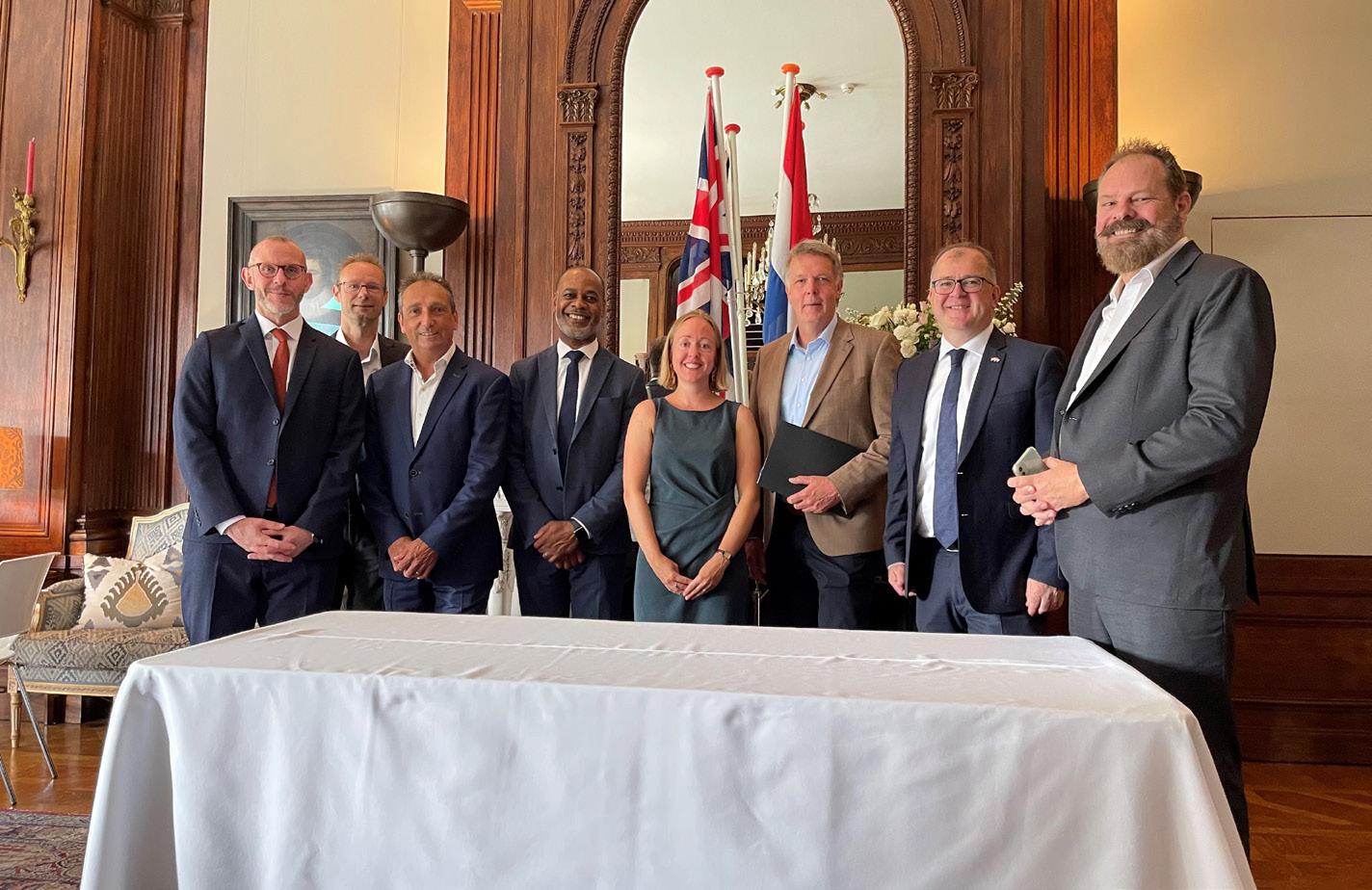
Automated inspection, acoustic monitoring using fibre optic cables and other technological improvements are among the developments being worked on as part of a partnership between British railway infrastructure company Network Rail and its Dutch equivalent, ProRail. The pair signed a Memorandum of Understanding at The Hague on Friday, August 18, to continue their partnership.
The MOU follows several years of close working on new tech including cab signalling system ERTMS Level 3 and Fibre Optic Acoustic Sensing, and builds on a previous MOU signed five years ago.
Robert Ampomah, Network Rail’s Chief Rail Technology Officer, said: ‘Network Rail and ProRail are both dedicated to running more reliable railways for passengers and freight customers, and we share many of the
Train Delays Cut in Half Following South London Signalling Upgrades
same challenges and opportunities. As well as new tech, we already share information on trespassing, managing our assets and even the impact of how Artificial Intelligence can help improve the way we work.
‘Our focus is always to make journeys easier for customers and by sharing information we can check our findings against another operator, get a better spread of data and test our ideas on different infrastructure too.’
Karel van Gils, ProRail Director of Innovation and Technical Renewal said: ‘ProRail and Network Rail have similar challenges in modernising and transforming their railway. Capacity needs to grow, whereas the railway systems and assets are aging and work forces are scarce. Both Network Rail and ProRail are committed to digitising the railway systems as it will be key for a future proof, interoperable and reliable, high-capacity railway. We will enhance each other’s efforts in the necessary research and development.’
Keith Allan, Deputy Head of Mission at the British Embassy, The Hague, said: ‘I was delighted to host representatives from Network Rail and ProRail at the Ambassador’s Residence for the MoU signing. I wish the teams every success with their further technical exchange and cooperation. Another great example of the strength of the relationship between our two countries as North Sea Neighbours.’
Network Rail has revealed that delays to Southern and Gatwick Express passengers travelling into London Victoria have fallen by 55 per cent following the switch-on of a brand-new signalling system in South London.
The new signalling – the railway’s traffic light system – which controls the safe movement of trains on the network, came into use on the lines between Balham, Clapham Junction and London Victoria (platforms 9-19) last Christmas. It replaced the old and unreliable equipment which had been signalling trains through the area since the early 1980s.
Howden Platform Improvements Completed
MP for Howden, David Davis, cut the ribbon to reveal new-look platforms at Howden Station which will ensure better accessibility for all passengers. The huge local investment made by Hull Trains was welcomed by a host of stakeholders who had gathered to see the outcome of months of redevelopment work.
Platform levels have been raised to reduce the stepping distance on and off passenger services and tactile paving has been installed
which alerts passengers, particularly those with vision impairments, to their distance from the platform edge. The works, made possible through the Hull Trains’ £3 million Passenger Infrastructure Improvements Fund, also a saw a new non-slip surface put in, better drainage and white and yellow safety lining painted on the platforms.
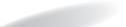


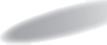

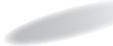


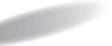
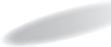
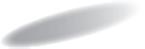
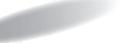

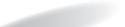


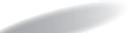







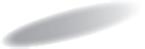

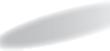





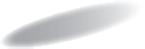
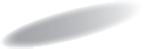
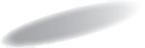
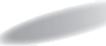







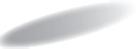
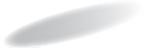

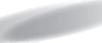
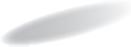


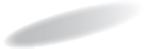
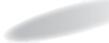
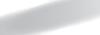
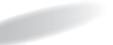

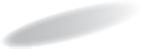


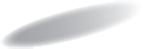
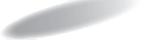
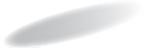
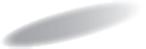
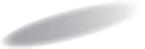
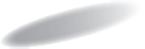
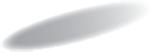
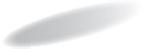


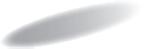
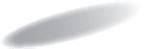
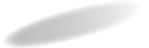

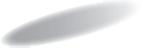

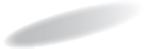
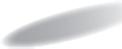


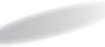
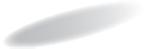

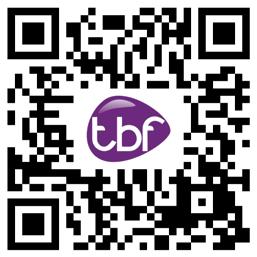


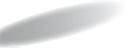






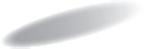

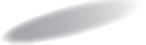
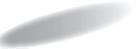

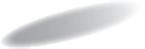

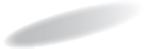
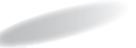



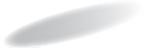
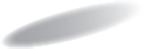



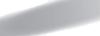
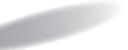
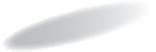
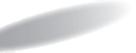



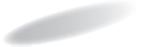

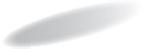
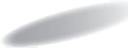
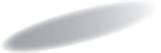

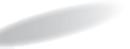
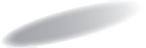
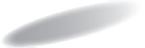
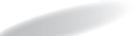
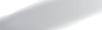
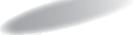




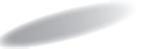


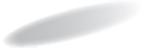
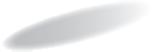
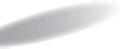

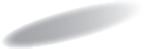
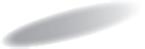
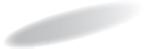
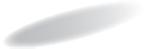
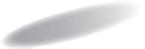
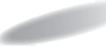
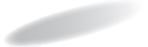


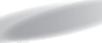
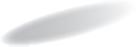
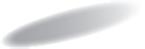
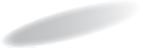

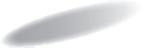

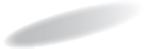
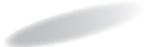
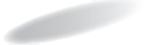
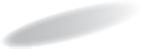
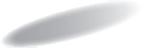

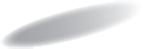
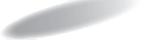
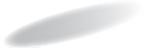
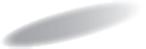
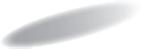
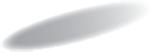



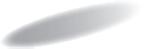
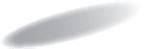
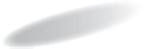



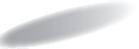


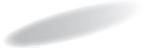


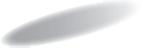


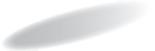


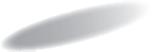

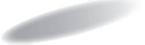

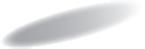
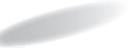
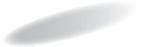
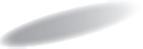
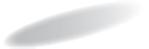
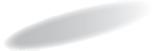
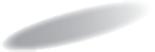
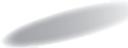
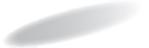
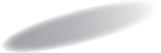
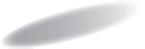
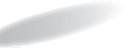

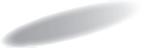

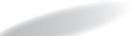
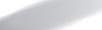
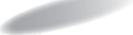
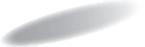
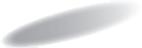
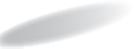



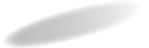
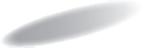

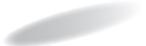
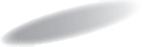
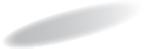


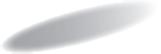
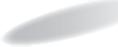


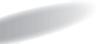
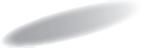

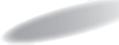

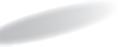
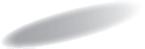


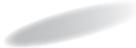
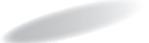

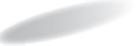

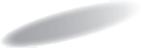
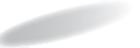
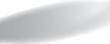

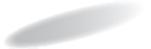
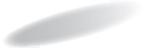
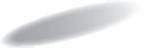

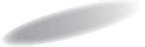
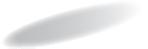


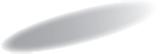
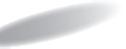
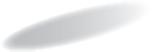

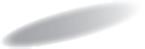
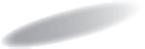
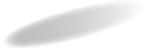
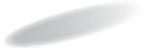
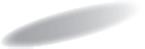

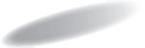

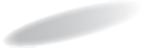
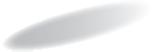
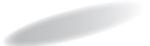
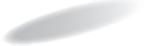



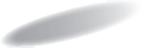

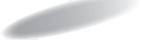
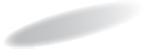
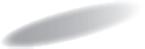
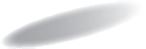
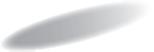

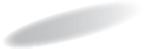
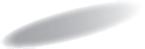
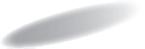
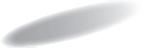
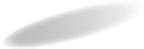

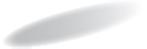
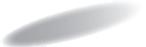

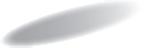

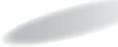


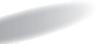
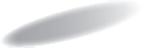
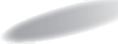


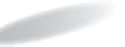

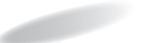
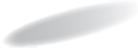
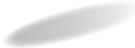
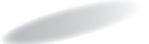



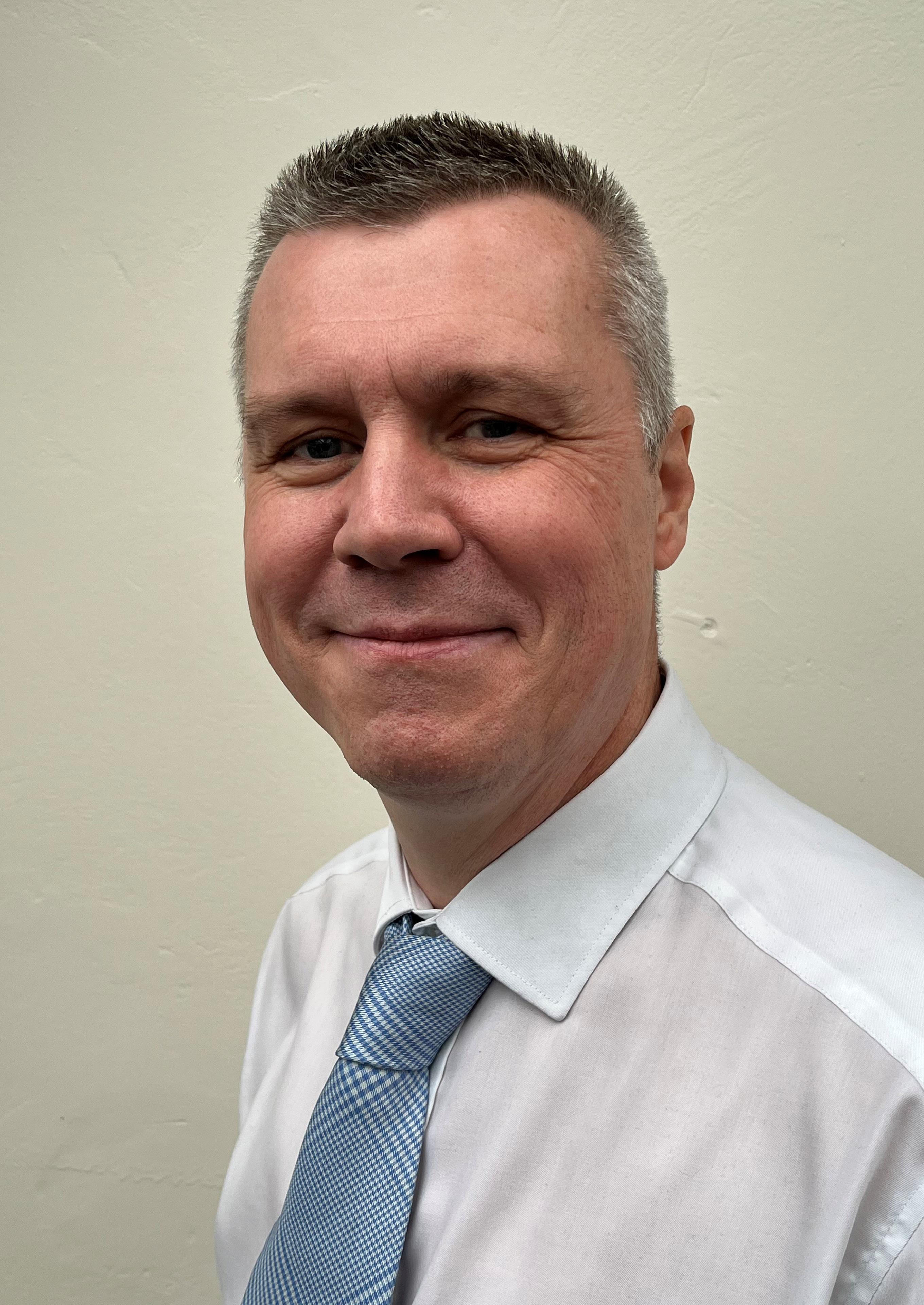
Sheehy Chief Executive Officer at
John
Sam
Sherwood-Hale, Editor of Rail Professional spoke to John Sheehy,
CEO
at Transport
Benevolent
Fund CIO about the charity’s history, its purpose in the 21st Century and its relationship with the industry
SSH: This year, TBF celebrates its centenary – how has the work TBF does changed during the last 100 years?
JS: The roots of the charity date back to the First World War when, in order to supplement the income of the dependants of those called to service with the armed forces, the Train, Omnibus and Tramway Group of London passenger transport companies set up the T.O.T. Mutual Aid Fund. Subscriptions were paid on a voluntary basis and were matched penny for penny by the participating companies. This enabled the service pay of employees to be supplemented so their families would not suffer undue hardship. Special help was also provided to relieve domestic difficulties and to offer medical and legal advice.
Today the charity helps beneficiaries and dependants by:
• Making cash grants to relieve short-term hardship.
• Signposting members on where/how to obtain advice on debt related issues and, where necessary, enabling them to enter into arrangements which will relieve their burden.
• Providing items of equipment required in order to ensure the maintenance of a reasonable standard of living.
• Making available complementary medical treatments.
• Helping with the cost of medical consultations, scans and tests if the NHS is unable to deliver within an acceptable time frame.
• Providing legal help (except, normally, on employment matters and conveyancing).
• Helping with the cost of mobility equipment not generally available from the state.
• Helping towards the cost of convalescence or recuperation.
• Helping towards the cost of prescription pre-payment certificates.
SSH: What do you personally see as the underlying ‘mission’ of the charity?
JS: To relieve need, hardship and distress among beneficiaries and their dependants. So, what is need, hardship and distress? We know what that means today but it might have a different form in another 20 or so years, in the same way that the problems facing our members a century ago would have been very different.
In the modern world, there are more things to be stressed over – we’ve seen an
increase in alternative therapies and part of our job has been to look at these treatment options and determine whether we can support with that and invariably we can. So, if you have a bad back we can support you up to £300 over a rolling twelve-month period with osteopathy but then if you also need counselling as a result of the suffering you’ve had to deal with as a result of the bad back we can also support you with another £300 for that over the same twelve-month period.
We get over 300 emails a day requesting help and our mission is to get those members reimbursed whenever possible.
SSH: In terms of the charity’s structure, how has that developed and evolved over the years?
JS: Following the success of the T.O.T. Mutual Aid Fund in World War 1, the T.O.T Group (by then consisting of twelve public transport and associated companies) entered into a Declaration of Trust, the result of which was the formation of the Train, Omnibus and Tramway Benevolent Fund on 1 January 1923.
Ten years later the T.O.T. Group and other undertakings were amalgamated to form the London Passenger Transport Board (‘London Transport’) and the name of the Fund was changed to the London Transport Benevolent Fund.
In January 1990, as a result of the fragmentation of London Transport, a new Deed was adopted, by which was formed the Transport Benevolent Fund (Registered Charity No 1002586). The transfer of assets from the London Transport Benevolent Fund to the first Transport Benevolent Fund was not successfully achieved, the Transport Benevolent Fund was finally established on 27 August 1996, to take over the assets of the earlier one of the same name and (insofar as they had not been transferred earlier) those of the London Transport Benevolent Fund.
The transfer took place in accordance with a Charity Commissioners’ Scheme of 19 December 1996, together with the transfer of the assets of the associated London Transport War Comforts Fund Association (‘LTWARCO’). This charity had been established on 29 November 1939 to provide relief for London Transport staff while on active service as well as their families or following death or disablement as a result of the Second World War or any extension of it. At the time of transfer to the new charity, LTWARCO still provided relief to eleven
‘We get over 300 emails a day requesting help and our mission is to get those members reimbursed whenever possible.’
widows whose husbands had been killed either while on service or in air raids. The final beneficiary passed away during 2008.
On 1 March 2006, the charity acquired the assets of the TfL Staff Welfare Fund, which had been established in 1948 to provide help for staff of the London Transport Executive (a predecessor body of Transport for London). These assets were accepted on the general trusts of the TBF but are held separately and used only for the relief of need, hardship and distress among the classes of persons specified by Transport for London in the Deed of Grant.
Following the unincorporated charity’s successful application to become a Charitable Incorporated Organisation, all assets from Transport Benevolent Fund a registered charity in England and Wales (1058032) and in Scotland (SCO40013) were transferred to the new entity Transport Benevolent Fund CIO a registered charity in England and Wales (1160901) on 1 October 2015. The unincorporated charity ceased operation on 1 October 2015 and the new Transport Benevolent Fund CIO started operating on 1 October 2015. On 25 November 2016 Transport Benevolent Fund CIO was registered with the Office of the Scottish Charity Register, registration number (SCO47016).
SSH: How have the needs of rail industry staff evolved over that time?
JS: I have noticed in the last five years that more and more people are suffering some form of debt, most people are just about managing, but it only takes one unexpected thing to happen to the beneficiary, partner or dependant child, to tip them over the edge and into debt very quickly. Mental health, as we know, is top of the agenda, and we have seen a greater call from our beneficiaries for help towards counselling. There has been a steady increase in requests for convalescence for beneficiaries with cancer in the last ten years.
SSH: How does the relationship you have with your patrons work?
JS: In recent years we have worked with the patrons more, I wrote to the patron in TfL because we were after a Trustee who had financial experience – he contacted the relevant person within TfL and then now
he’s a Trustee. So when we have a board meeting with our investment manager, we can use his skills in that area to put the right questions to him that we might otherwise not have known.
All our patrons work in the industry, which ensures they stay up to date with what workers in the industry need. We try to ensure a spectrum of all fields so we can have a full view of what our membership is actually like.
SSH: What do you see as the areas of biggest concern for the charity?
JS: The deterioration of the NHS and cuts in the state welfare benefits system ultimately means a greater call on charities like TBF. We generally say, if you’re waiting six to eight weeks for treatment on the NHS we can provide assistance for an alternative route. If you need convalescence and your GP signs off, we can also contribute to that.
SSH: What type of assistance are you providing more of?
JS: Cash grants to relieve short-term hardship while on reduced sick pay, and there is also an increase in grants for arrears on priority bills. Year after year, there is an increase in alternative therapies.
SSH: How do you make decisions around benefits?
JS: It is not practicable (nor desirable) for the Trustees to manage the charity on a day-to-day basis. For this, they appoint senior staff who advise them, implement their policies and decisions and refer issues to Trustees where necessary. In turn, other staff report to these senior staff and take instruction from them. The Trustees exercise control through a document (titled ‘Authorities’), which they review regularly. This includes limits on individual benefits; controls over such items as accounting for assets; securing supplies; and procedures that enable the Fund to be effectively managed without the need for Trustees to constantly be involved in detail, provided the levels of authority granted are not exceeded.
SSH: How do beneficiaries apply for relief?
JS: A beneficiary must contact TBF first to obtain the necessary authority for any benefit/help sought. Once authority has been granted a form will be sent to the beneficiary to complete. Our friendly team of advisors will do whatever they can to help. TBF does not have a call centre and no push-button options for callers. A great many requests are now received by email and predominantly our forms are sent, completed and returned electronically. However, we will always have paper forms available for those who cannot complete forms electronically.
SSH: How many members do you currently have and how much do you pay out in relief in a year?
JS: Currently we have 59,000 contributing members but if you add live-in partners, dependants, and retired members, this means we have approximately 180,000 people able to call on the fund, unlikely but possible. We expect to spend £2.9 million on direct benefits to TBF beneficiaries in the coming year.
SSH: Presumably the strict lockdown period brought new challenges for you, how did TBF rise to that occasion?
JS: When we realised the enormity of the pandemic, we initially thought the call on the charity would be overwhelming and result in expenditure being over budget again. We were amazed that this did not turn out to be the case due to the Government’s financial measures put in place to help individuals and companies throughout the pandemic.
We certainly expected an increase in requests for financial help, but this never materialised mainly due to the Government’s Furlough Scheme. Many people’s outgoings were reduced in lockdown, this meant receiving 80 per cent of pay through the Furlough Scheme was enough to help them through these unprecedented times. We were underspent on treatments because lockdown and social distancing meant people could not go out and access treatments. We were underspent on convalescence for the same reasons.
Like many industries, the public transport sector was affected, and understandably this impacted the Fund. TBF’s recruitment had dramatically been affected because our Organisers, who recruit new members, have been unable to access public transport sites.
All our office staff worked from home throughout the pandemic. Despite the challenges, it was very pleasing to see that we continued to fulfil our purpose in helping beneficiaries. We know that working from home for more than twelve months was not easy, especially with home schooling, lack of social interaction and the staff’s general well-being. We are very proud of their efforts to help keep the charity active. We were very thankful for our staff’s efforts in helping the charity meet its objectives and very grateful for the many thanks received from our beneficiaries, who appreciate us still being able to help them through the pandemic, even though it took longer to deal with requests for help.
A big issue was achieving growth when the pandemic had caused so much uncertainty; this resulted in our first decrease in membership for 20 years. As touched on earlier, our Organisers could not access public transport sites to recruit new members, resulting in all Organisers being put on the Furlough Scheme. However, due
‘I am immensely proud to be CEO of TBF and it warms my heart to see the difference TBF makes to its beneficiaries’ lives on a daily basis.’
to the Fund’s strong image within the public transport industry, TBF still managed to recruit a few new members every week.
SSH: As the rail industry continues to evolve, with new skills being required and new structures being followed – how do you anticipate TBF’s role will change in the years to come?
JS: It is difficult to say but we are always ready to react and help our beneficiaries with what need, hardship and distress arise within the resources available to TBF. We have arrangements with approximately forty-two companies whereby contributions are met by the employer as they see it as an affordable benefit they can provide for their employee. They understand that TBF membership has a positive impact on their staff’s well-being.
SSH: How do the Trustees manage their responsibilities with the charity?
JS: TBF aims to be a democratic organisation. The Rules state there shall be no fewer than three or more than fifteen Trustees at any time, who shall be appointed in accordance with clauses 12 and 13 of the Constitution, either by an AGM or, where vacancies remain, by the Trustees under Clause 13[4]. Trustees shall make such appointments only after taking into consideration any perceived need to increase diversity among the Trustees.
Written notice of the call for nominations for the election of Trustees at an AGM shall be sent by the Secretary to the registered address of each Local Committee Member or other CIO Member. They shall be given no less than fourteen days from the date of the despatch of the invitation to submit nominations which shall then be included in the formal notice of the AGM.
In order to ensure the Board collectively reflects the diversity of the membership, the Board always keeps in mind the following:
• Maintenance of representation from existing minority groups; or
• Improved representation for minority groups; or
• Involvement of a further major employer group; or
• Involvement of a Train Operating Company or Network Rail; or
• Bus workers (from companies where they are under-represented).

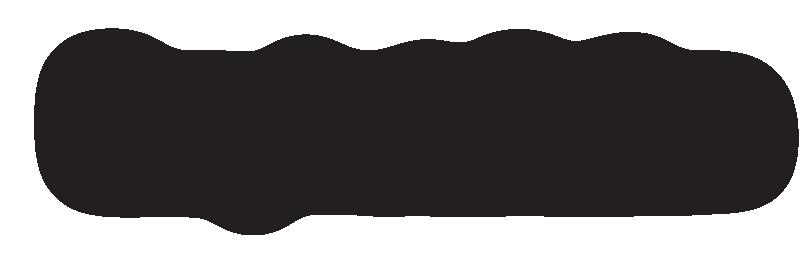


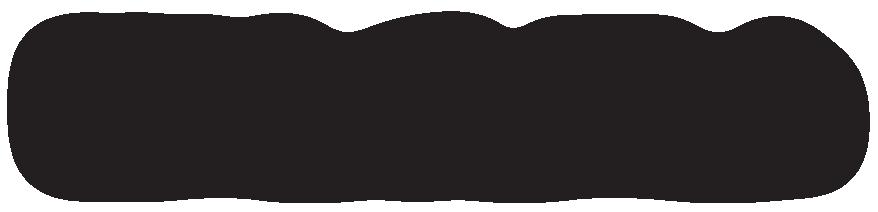

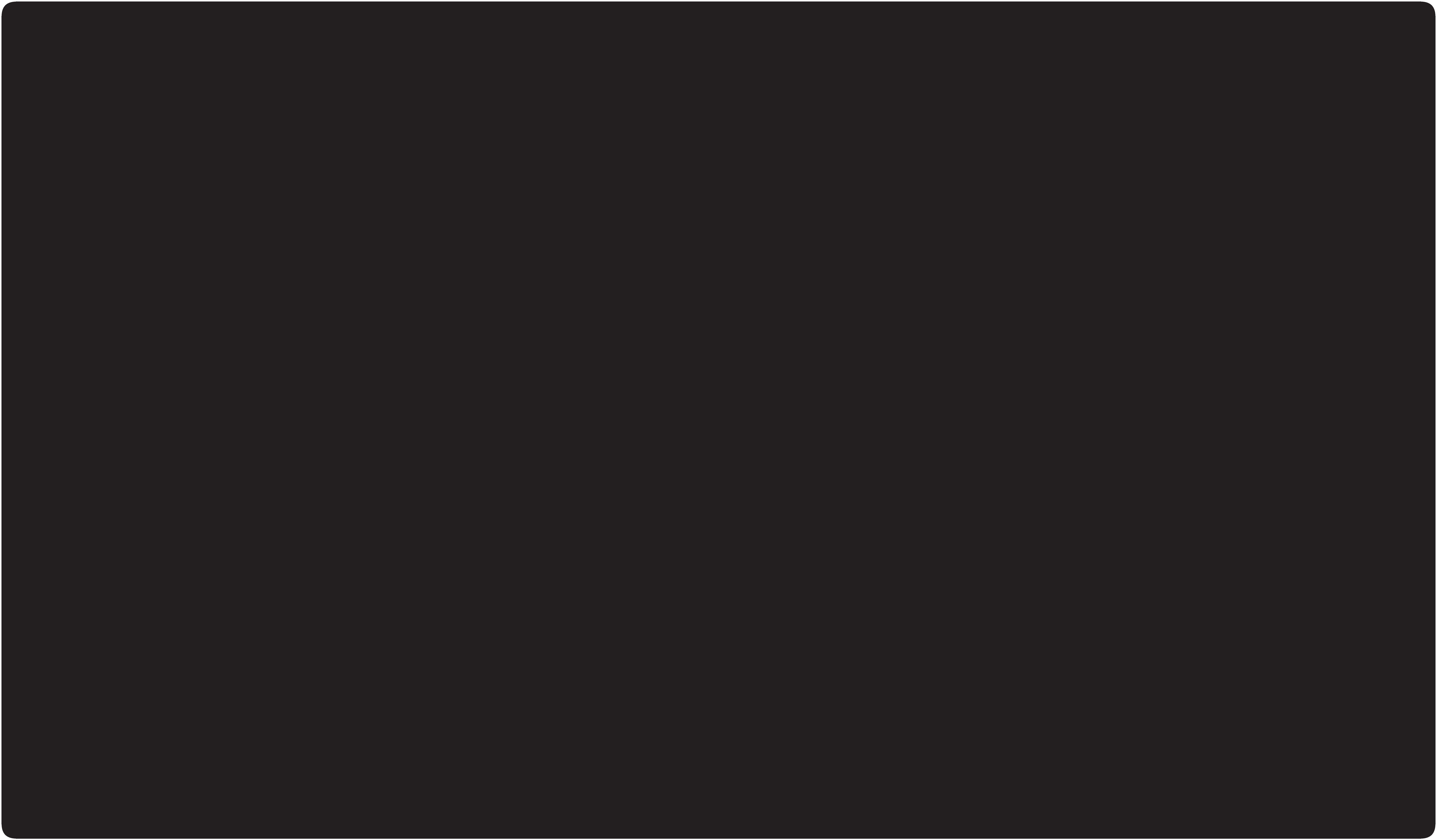
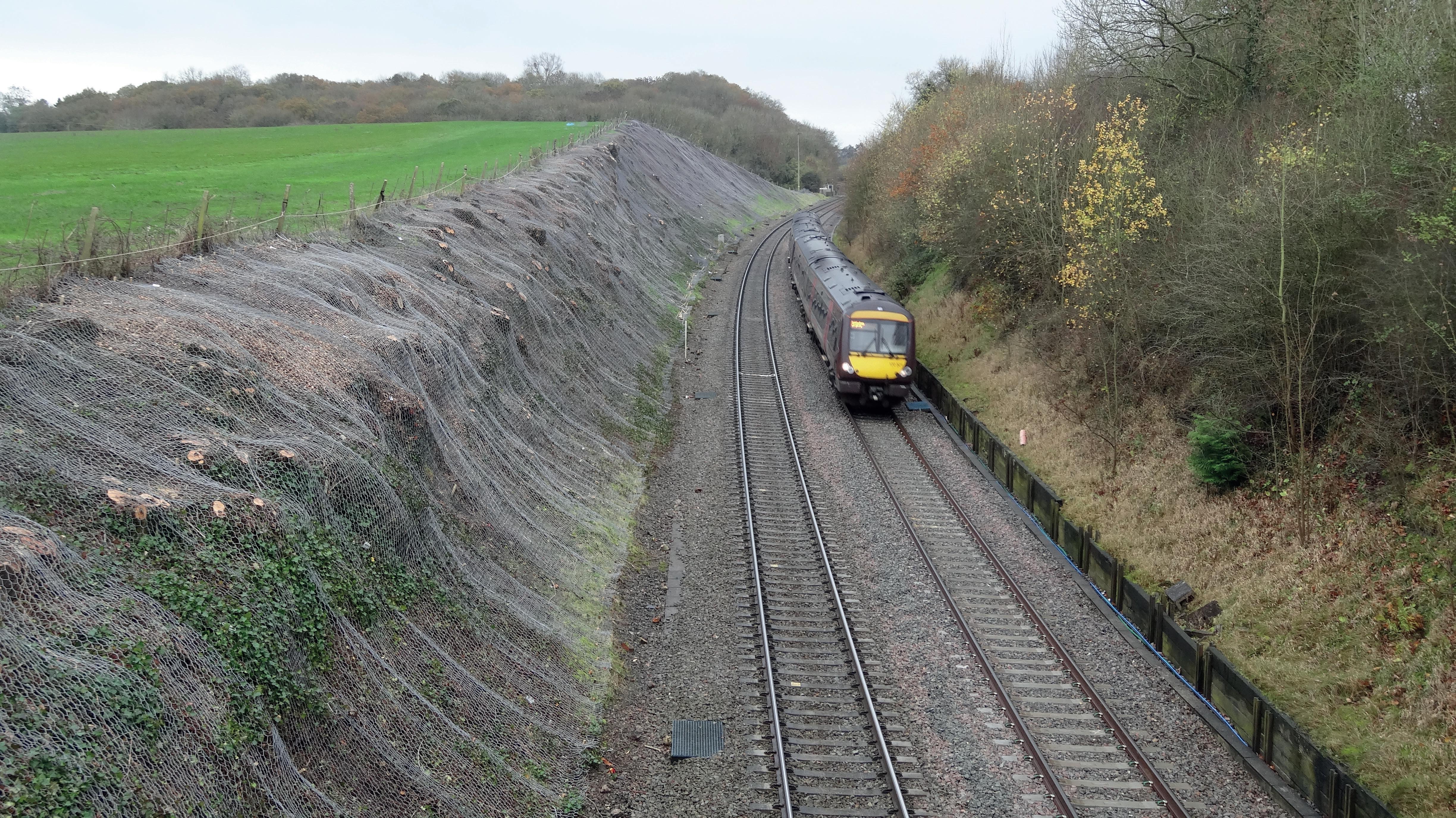
Apart from these employment categories, minority groups may be based on disability, gender reassignment, marriage and civil partnership (in employment only), pregnancy and maternity, race, religion or belief, sex and sexual orientation.
In addition, Trustees will be sought from younger age groups, to help ensure the smooth continuation of the charity as existing Trustees retire.
Trustees are elected because of their commitment to the charity and the support they enjoy from their peers. While a proper balance of skills is required on the Board, Trustees are not generally elected because they possess any particular practical or professional skills.
Collectively they control the Secretary, who is required to ensure that the necessary skills are available to them, either from among the staff or by the purchase of services in the market.
The Secretary as scrutineer is responsible for ensuring that those elected are not barred from office.
SSH: Tell me about Trustee Induction and Training.
JS: The Secretary is responsible for ensuring that all Trustees understand their powers and responsibilities, providing them with copies of appropriate Charity Commission publications and identifying further training needs.
The Chair is responsible for maintaining a climate in which all Trustees may raise questions or issues of concern and discuss matters relevant to their stewardship of the charity. He also ensures that meetings are conducted in such a way that all Trustees may take part in determining policies. They are expected to attend meetings regularly, both in order to control the charity effectively and to learn by experience and exposure to issues.
A lay expert on trusteeship issues addresses the Board annually on these issues, when all Trustees are able to raise any questions or items of concern and to identify what they believe to be shortcomings in the way in which the charity is run, or in their own development and training. There are also occasional questionnaires to the Trustees, to ascertain areas in which they feel that further training is needed. The Board considers the outcome and the Secretary pursues matters as necessary.
Arrangements are made for Trustees to attend external training courses as necessary. Some also have opportunities to undergo related training by other bodies on which they serve.
SSH: What is the organisational structure of the charity and how are decisions made?
JS: The basic unit of organisation is the Local Committee which also forms part of the CIO membership and each contributing Fund Member is covered by a Local
‘Mental health, as we know, is top of the agenda, and we have seen a greater call from our beneficiaries for help towards counselling.’
Committee. Each Local Committee consists of members employed in that area but, exceptionally, there is a Local Committee administered by TBF staff which covers areas not currently able to support a separate committee; this is known as LC2. It is the duty of each member of the CIO to exercise their power as a member of the CIO in a way they decide in good faith would be the most likely to further the purposes of the CIO.
The Secretary is charged with the establishment of as many viable Local Committees as possible. She determines the number of members to serve on each, taking into account the views of members in that area, of CIO membership (see below) or the Trustees. The Trustees are able to over-rule any decision of the Secretary in respect of the establishment or membership of Local Committees. Together, all members of Local Committees form part of the CIO membership. They elect the Trustees, have the power to consider all aspects of the charity's business and may make recommendations to the Trustees. If the Trustees do not adopt any recommendation of the CIO membership, they must explain why.
The Chair and Vice-Chair are elected at the first Trustees’ meeting in each calendar year from among the existing Trustees. Trustees, who must number between three and fifteen are elected by the AGM for rolling three-year terms. They must be members of the CIO and are eligible for re-election as long as they retain this qualification. TBF staff are not eligible to serve as CIO members.
The Trustees are accountable for all activities undertaken on behalf of the charity. They normally meet six times a year, including the AGM, to establish policy and review progress and developments. Within strictly defined limits (which are set down in a document that is reviewed regularly) they delegate responsibility for the dayto-day running of the charity to their staff (generally through the CEO).
Local Committees can consider recommendations in respect of initial grants for members in their areas who are in financial need, but the final decisions rest with the Trustees. A small sub-committee of Trustees determines whether to grant further help and its decisions are notified to all Trustees. The main aim of the Trustees is to ensure that, through the system of
delegated authority, requests for help are considered expeditiously, compassionately and fairly. Only in exceptional cases is it necessary for them as a body to consider individual requests.
SSH: You’ve been with TBF for over seven years, what was your experience of the rail industry before you joined?
JS: I joined LUL in August 1989 as a Direct Recruit Guard on the Northern Line, Golders Green Depot. I then passed out as a Train Operator. In 1998 I was diagnosed with Type 1 Diabetes, which meant I was not allowed to go anywhere near the track, which ended my operations career. After joining the pool for alternative employment, I applied for a role with TBF. I will forever be grateful to Chris Godbold, TBF Chief Executive, for taking me on; that was the start of a wonderful journey in helping the fund grow into what you see today. I am immensely proud to be CEO of TBF and it warms my heart to see the difference TBF makes to its beneficiaries lives on a daily basis.
ALL ABOUT PEOPLE
1923 TO 2023: ONE HUNDRED YEARS OF SUPPORT FOR PUBLIC TRANSPORT WORKERS DURING TIMES OF NEED.
TBF offers financial and medical benefits, a wide range of complementary and alternative therapies, bereavement grants and welfare advice. Supporting members during times of need, hardship and distress for less than 20p per day.
£1.25 a week covers you, your live-in partner and dependent children.
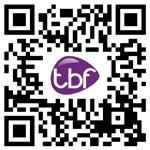
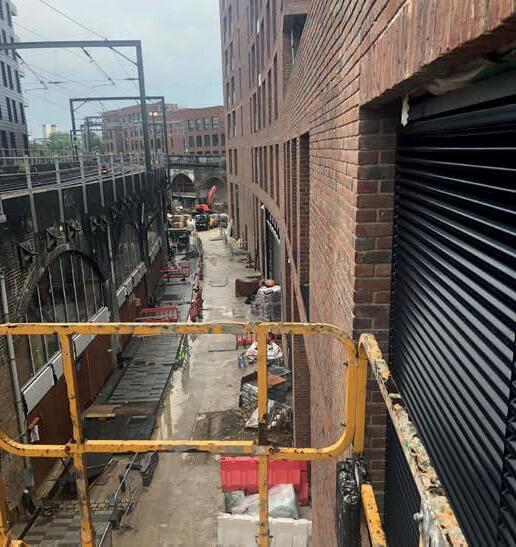
●
● REFERENCE PROJECTS - Crossrail, DLR, TFL, EuroTunnel
● BESPOKE SOLUTIONS - Tailored designs to meet project criteria
● INSTALLATION & MAINTENANCE - Qualified, Compliant & Trained Operatives
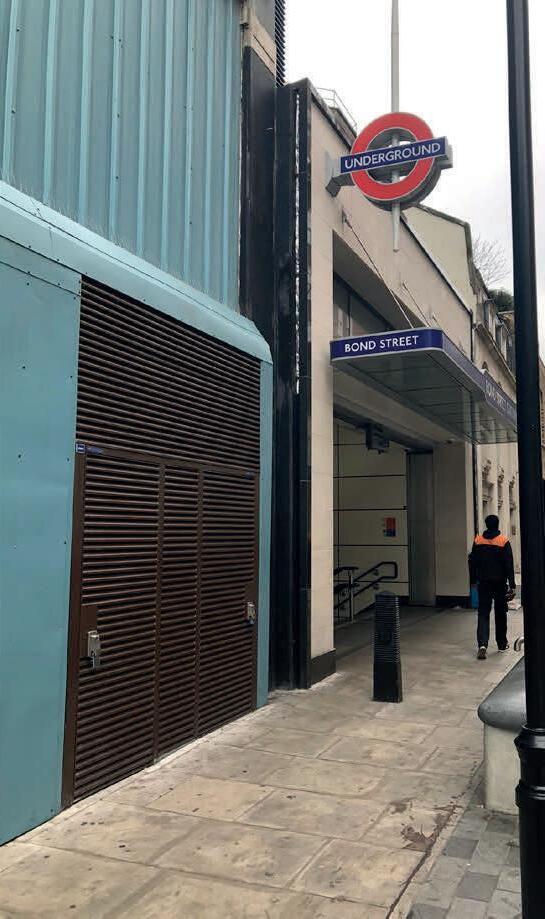
● TECHNICAL SUPPORT - Consultative advice with complete back up concept to installation
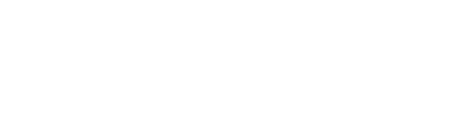
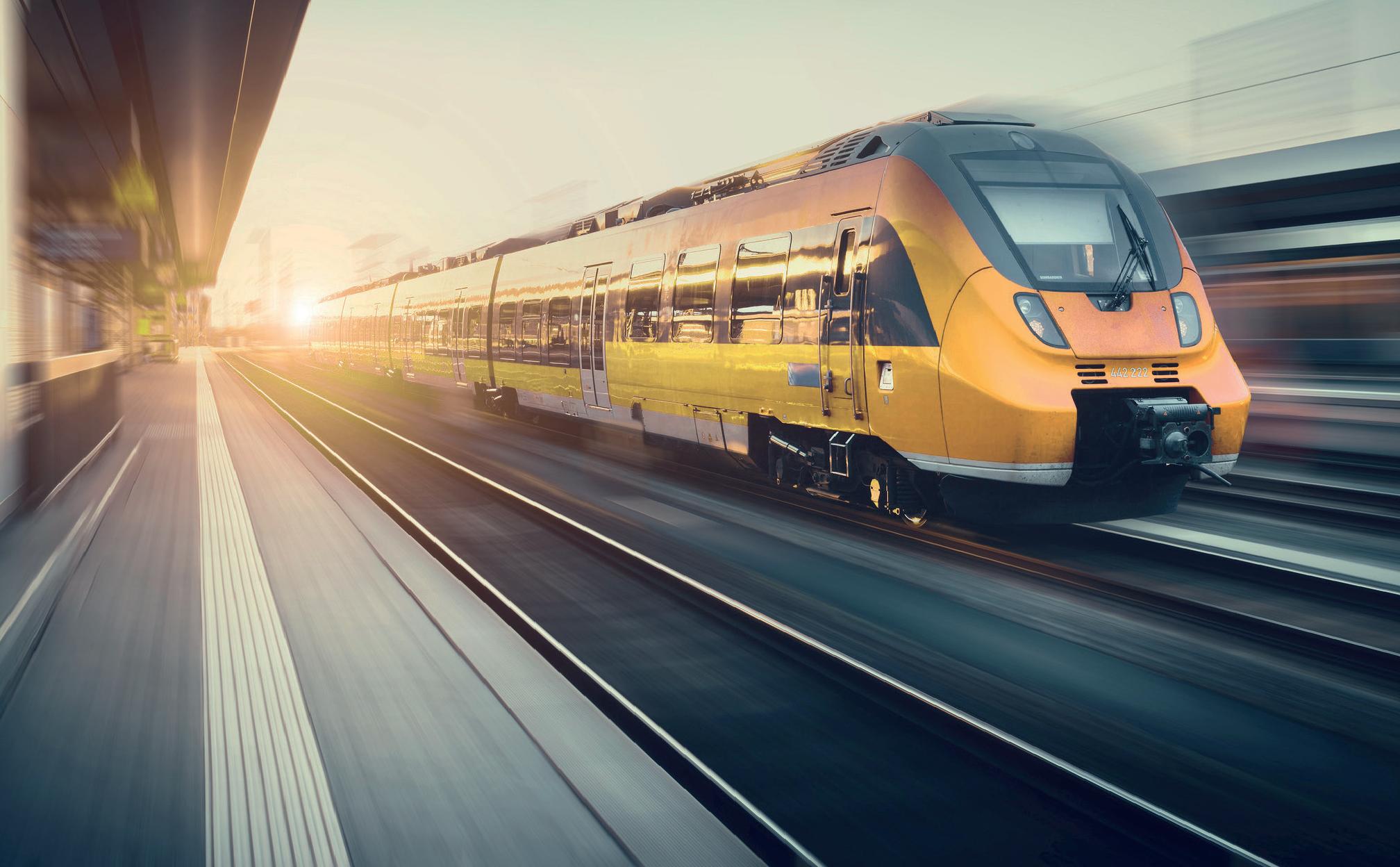
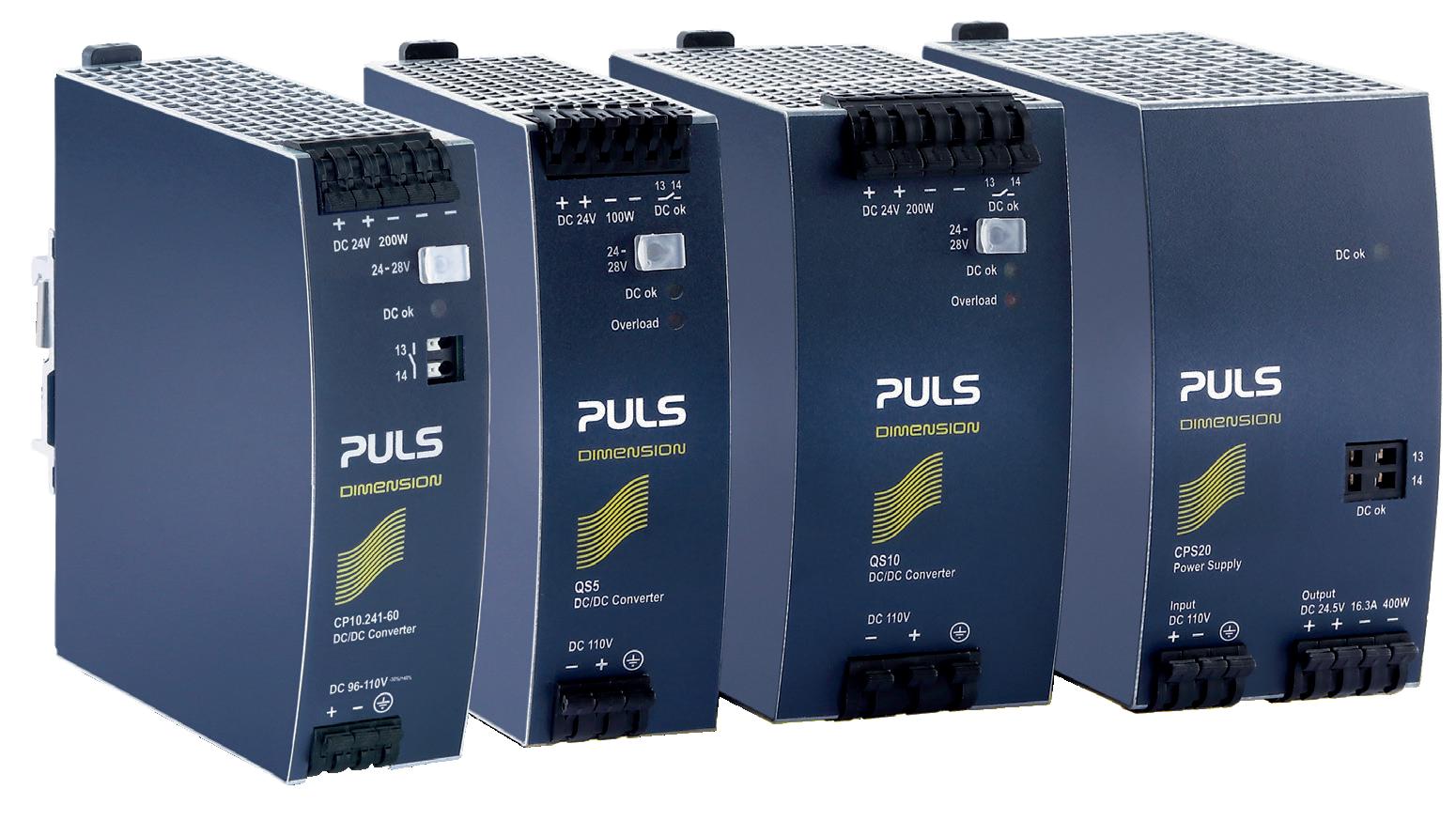
Level Crossing & RRAP Specialists

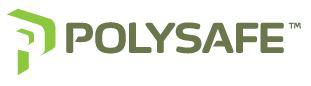


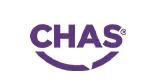
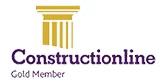
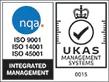
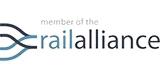


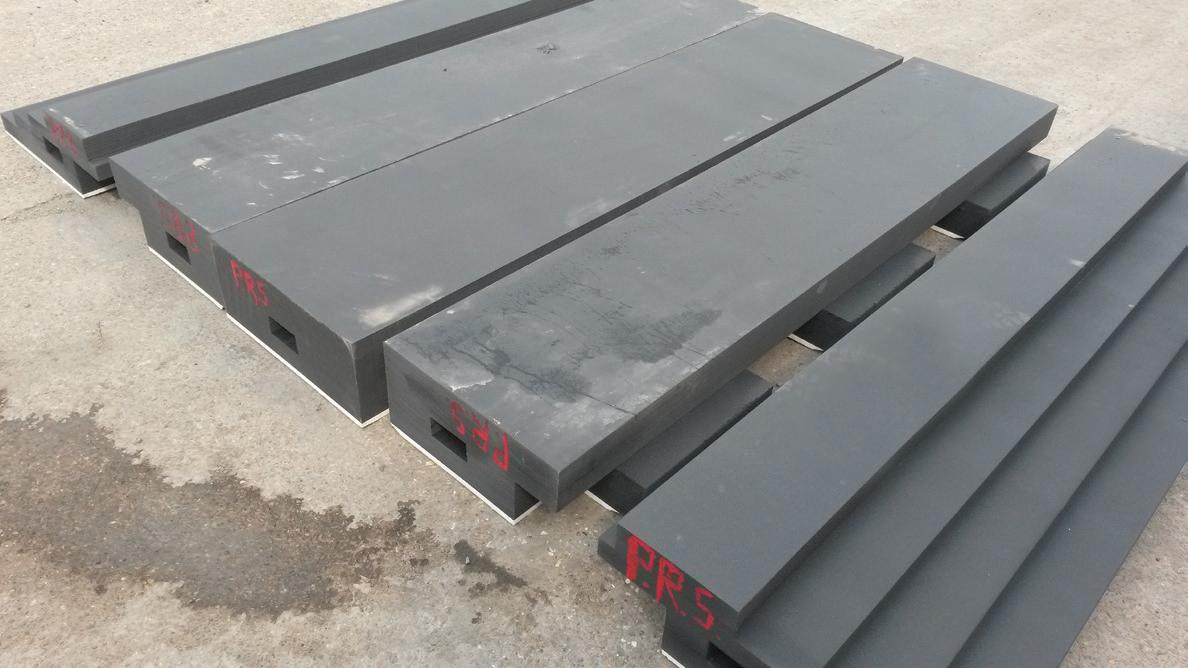
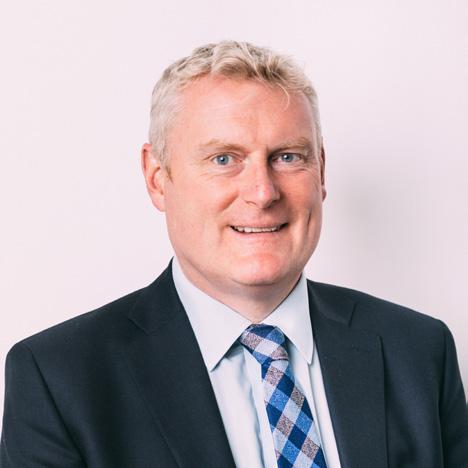
Steve Murphy is the CEO of MTR UK. He joined MTR in 2014 as Managing Director of MTR Elizabeth line. He subsequently became CEO of MTR UK in 2020.
Postcard from Japan
Steve Murphy, CEO of MTR UK, celebrates 30 years of the Anglo-Japanese Railways Exchange Programme
Ask any rail organisation in the UK if anyone has ever experienced the Anglo-Japanese Railways Exchange Programme and you can bet that a number of hands will shoot up.
Launched in 1993, by the late great Adrian Shooter whose love and fascination for the Central Japan Railway Company
prompted him to set up the programme, the ten-day exchange trip sees approximately eight UK delegates visit Japan and host their contemporaries in return each year. It is arguably one of Adrian’s greatest legacies.
Adrian hardly needs an introduction in a rail magazine. Former British Rail manager and founder of Chiltern Railways, he was one of the greatest engineering minds and
entrepreneurs in the industry. He was also a colleague, mentor and close friend who passed away in 2022 and is sadly missed.
So, in late 2021, when an email popped into my inbox from him asking if I’d oversee the future Anglo-Japanese Railways Exchange Programme, it was a task I was happy to step forward for.
As a former graduate of the programme, I’m well aware of just what a massive eye opener it is for rising stars in the early stages of their railway career.
Back in 1999, when I was Customer Services Director at Chiltern I got the opportunity to head to the Far East and learn from, as Adrian described it, ‘the best in the world’.
Make no mistake, it’s a fast-paced ten day tour, surpassed only by the speed of their own bullet train that we travelled on from Tokyo to Kyoto.
But it’s ten days of complete immersion in a country and culture for whom the railway is a symbol of huge national pride. From Operations to control room to maintenance depots to training to HQ, we got to see everything and did not fail to learn something at each stage of the trip.
While the peers in my cohort brought back new ideas and systems, one of the standout things I brought back was a philosophy. The idea of a ‘countermeasure’. And that is: ‘What could possibly go wrong?’
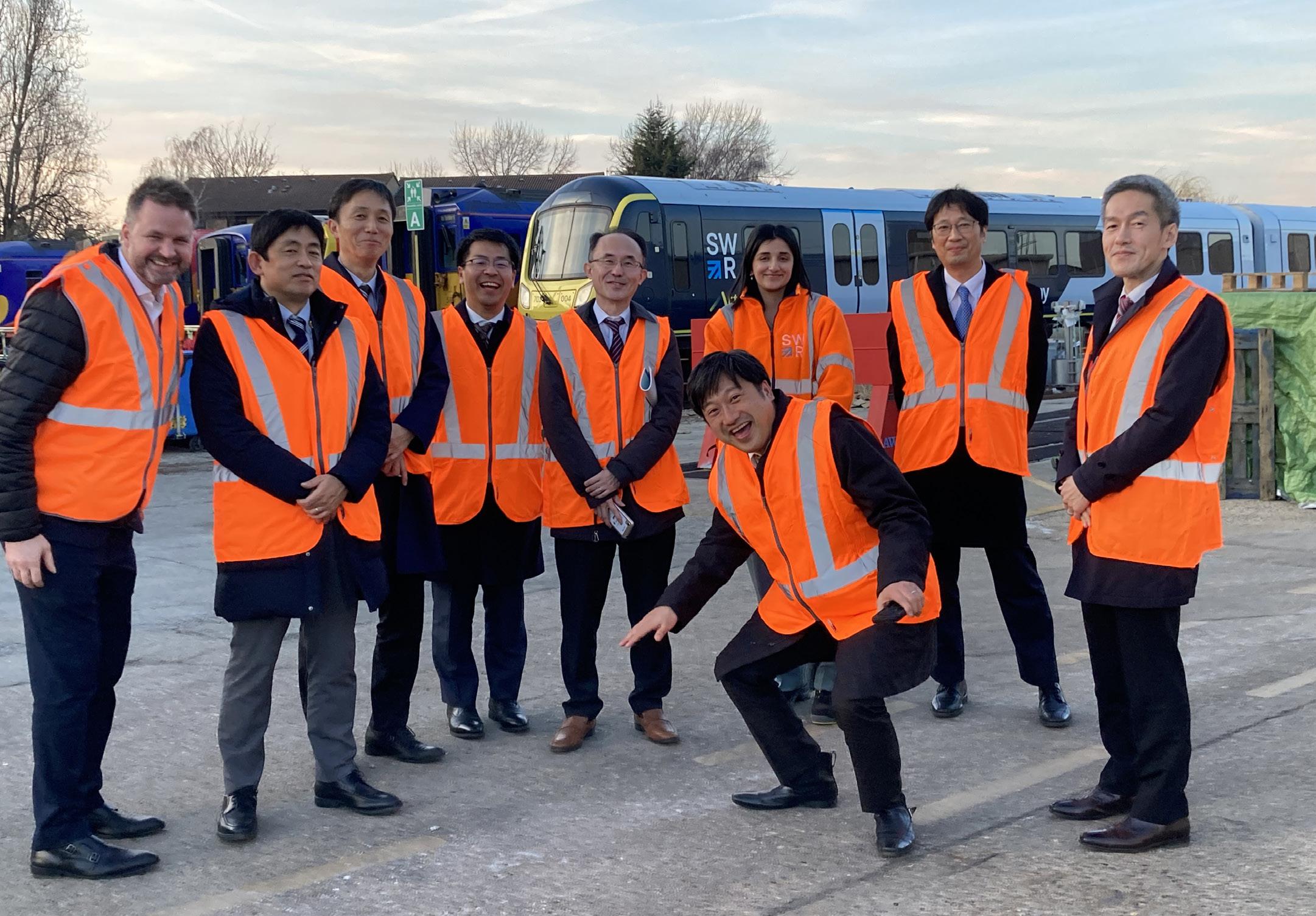
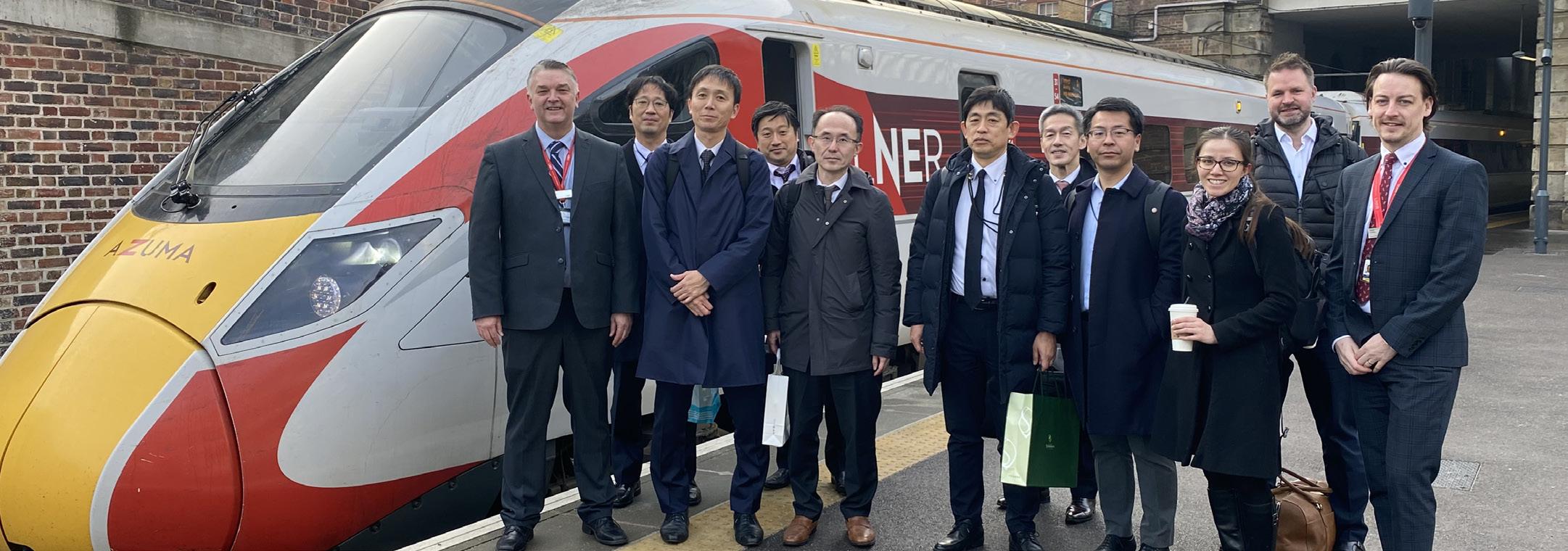
Everything in JR Central is developed with Murphy’s Law in mind. In fact, you can’t proceed with any project in Japan until for each of the problems you’ve identified, you have assiduously identified a corresponding countermeasure.
I recall visiting the Train Planning team on my trip in 1999 and asking them if they included any contingency in their schedules for when things go wrong (I fully expected them to say no, indignantly, because nothing ever goes wrong), however, they amazed me by saying that they routinely added ten per cent to the scheduled running time, just in case something went wrong! When I returned to Chiltern, I asked our planners what contingency we included into schedules, as disruption management was a regular challenge (as in the rest of the UK), the answer back was that we had about 60 seconds of contingency between Birmingham and London!
The philosophy of not leaving anything to chance is an approach I’ve taken in all the significant projects I’ve been involved with including the London Olympics, East London Line and getting Crossrail into operation.
And, almost 25 years later, the idea of the counter-measure is still at the heart of railway operations in Japan as my colleague Paul Breese discovered when he took part in the Exchange Programme last year.
Paul led planning for MTR Elizabeth line for four years (recently becoming Head of Service Delivery) and was one of those selected to head for Tokyo in 2022.
Here Paul shares a window into his experience: ‘The relentless focus on mitigation is almost cultural in Japan”, explains Paul. ‘When I visited Shinkansen, it became clear that ‘planning for the worst’ is still intrinsic in every decision at JR Central.
‘As part of our trip we got to see the control room in operation, but then, we discovered there is a completely identical control room kept entirely under wraps in case of emergencies! The cost of a dormant control room (albeit used periodically for training) is second to the value placed on safety in Japan.
‘And, in a country prone to earthquakes, the emphasis on preparedness is seismic. There is a blade underneath the train cars designed to hook the cars to the rails preventing derailment and collision in the event of an earthquake. Every single bullet train in Japan’s Central Railway is equipped with these parts.’
But what can our Japanese exchange partners expect on their reciprocal trip to the UK? It’s hard to believe we have something groundbreaking to share with a country currently testing a 500kph maglev train that should be in passenger operation by 2027.
Actually, there’s a lot. Paul took part in hosting the return Japanese delegation that visited the UK in February of this year and included a visit to the Railway Museum in York, the Elizabeth line and safety demonstrations across the network.
‘In the UK and Europe we are obsessed with technology in running our railways’ says Paul. ‘Interestingly, in Japan they are only just introducing QR codes and, in some areas of the business, shun tech entirely preferring a pen and paper to keep the railway operating. It’s all part of the mitigation ethos that runs through everything but coming to the UK and witnessing just how technology keeps our railway running - from timetable modelling to ticketing – was a huge eye-opener for the visiting Japanese delegation.’
It’s not just about learning however, it’s also about networking. Many of my contemporaries who I made the trip with back in 1999 are still in the industry and we are all still in touch. Paul regularly meets with his UK cohort from 2022 and no doubt future exchange groups will do the same.
Both countries have learnt so much from this exchange programme since 1993. We are now gearing up for the programme’s 30th anniversary celebrations at the Japanese Embassy in September and planning this year’s visit.
It’s incredible to think that 30 years on, a project that was set up by one man’s passion and long-term vision, is still inspiring people today. So put your hand up, it could be you next.
2024 ANGLO-JAPANESE RAIL EXCHANGE PROGRAMME
While places in this exclusive programme are limited to a small group of rising industry stars, if you are interested in nominating a colleague to take part in the 2024 Anglo-Japanese Rail Exchange Programme please email scott.mcloud@mtrel.co.uk for further information.

MTR UK is a subsidiary of MTR Corporation. We demonstrate our reputation for operational excellence, exceptional customer service and innovation across our UK portfolio, bringing together railway operations, rail infrastructure and transport-focused property development.
With a consistent track record of delivering through collaborative partnerships and joint ventures, we offer ground-breaking, technologyled approaches. The company's UK rail operations includes oversight of MTR Elizabeth line, the operator of the Elizabeth line (on behalf of Transport for London), covering all aspects of train and passenger service operations. MTR UK has operated South Western Railway, one of the largest UK franchises, as a joint venture with First Group since August 2017.
For more information about MTR UK, please visit mtr.uk.com
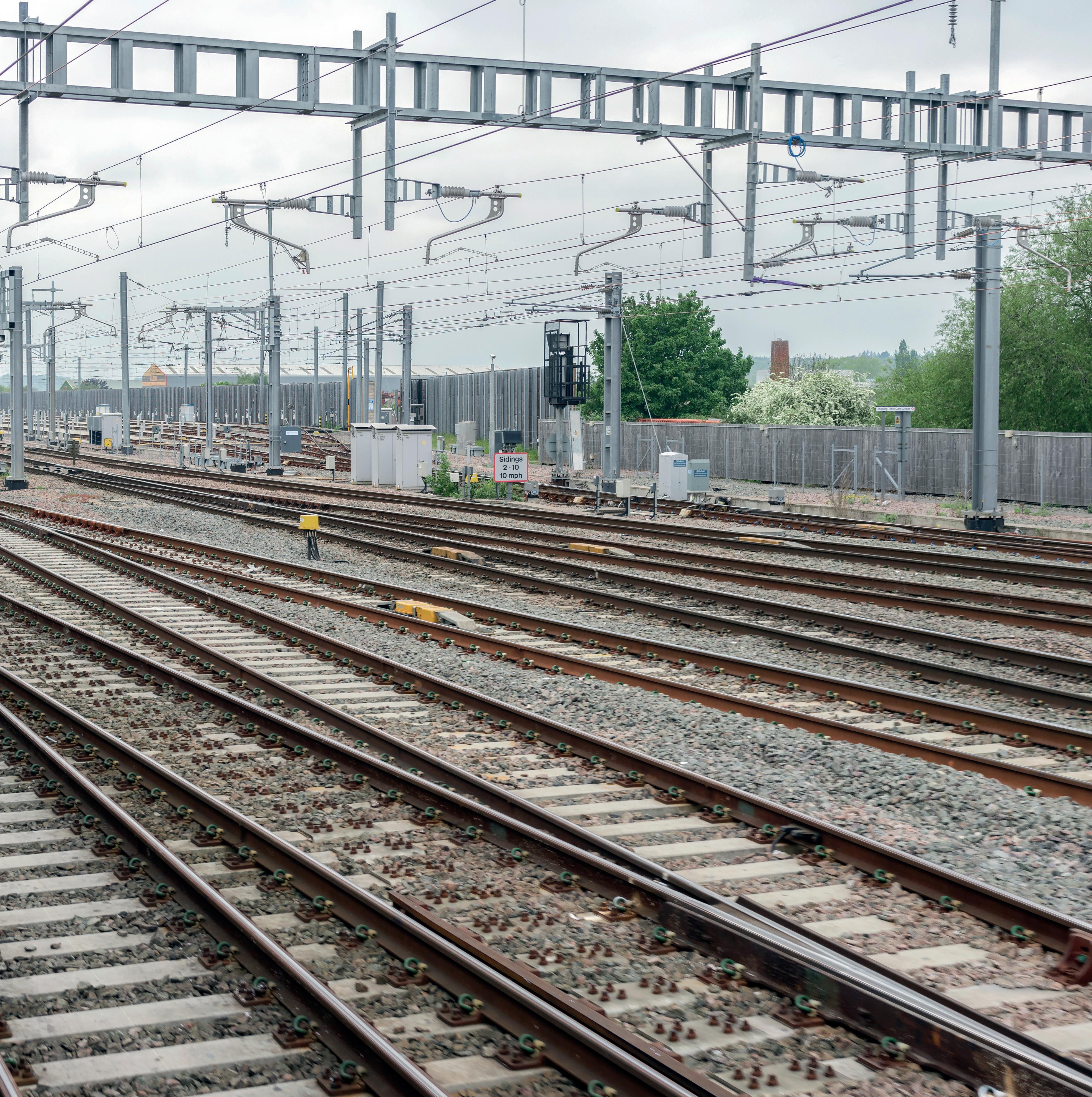
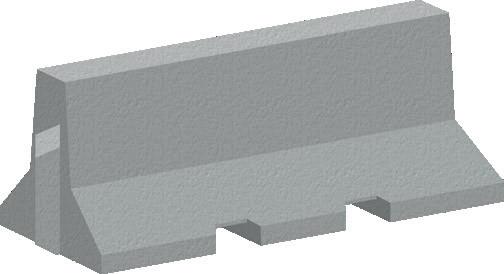
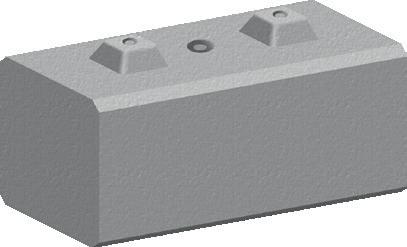

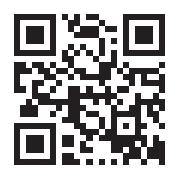
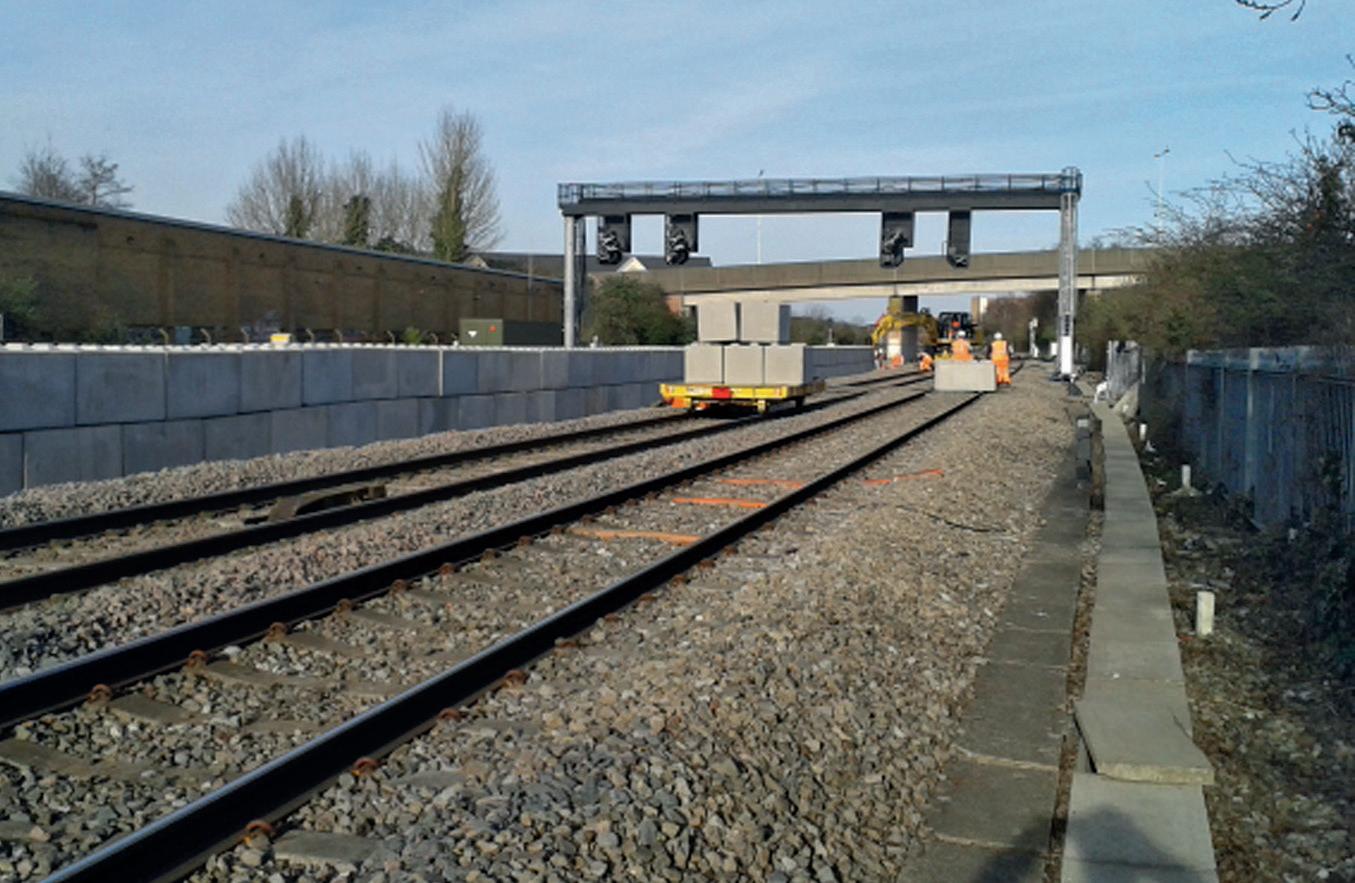
Workforce protection barriers avoiding all line closures with adjacent line open
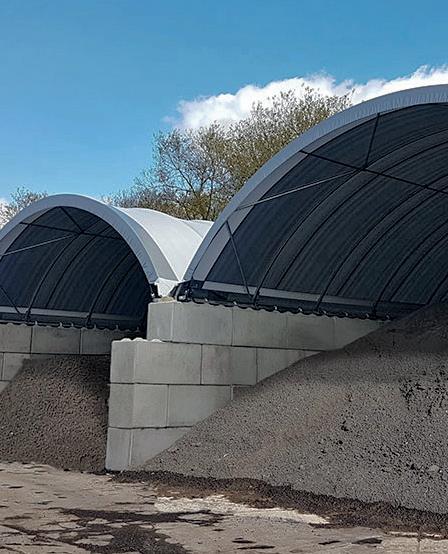
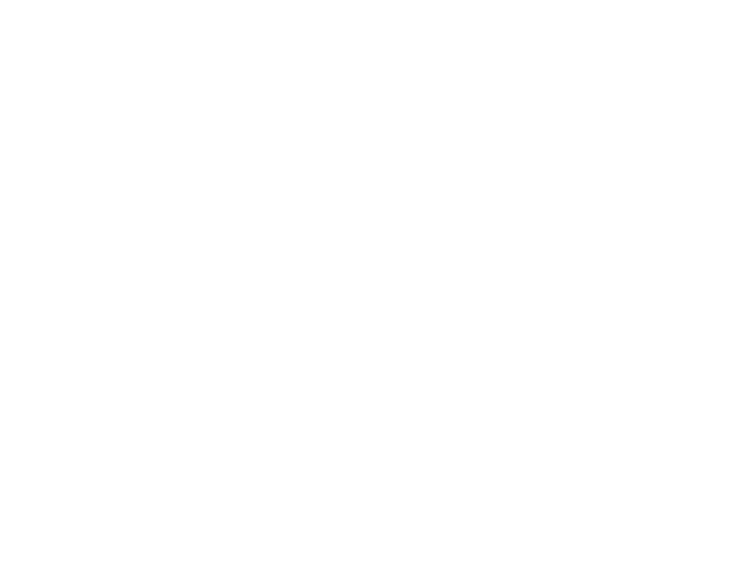
Rockfall prevention with our multi-purpose Jersy barriers
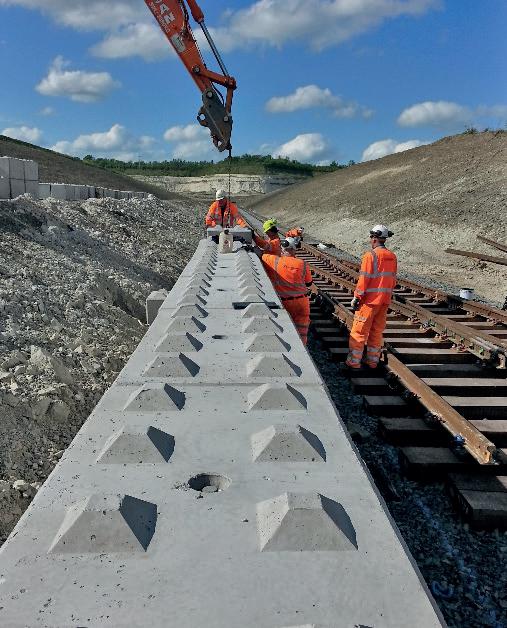
scale
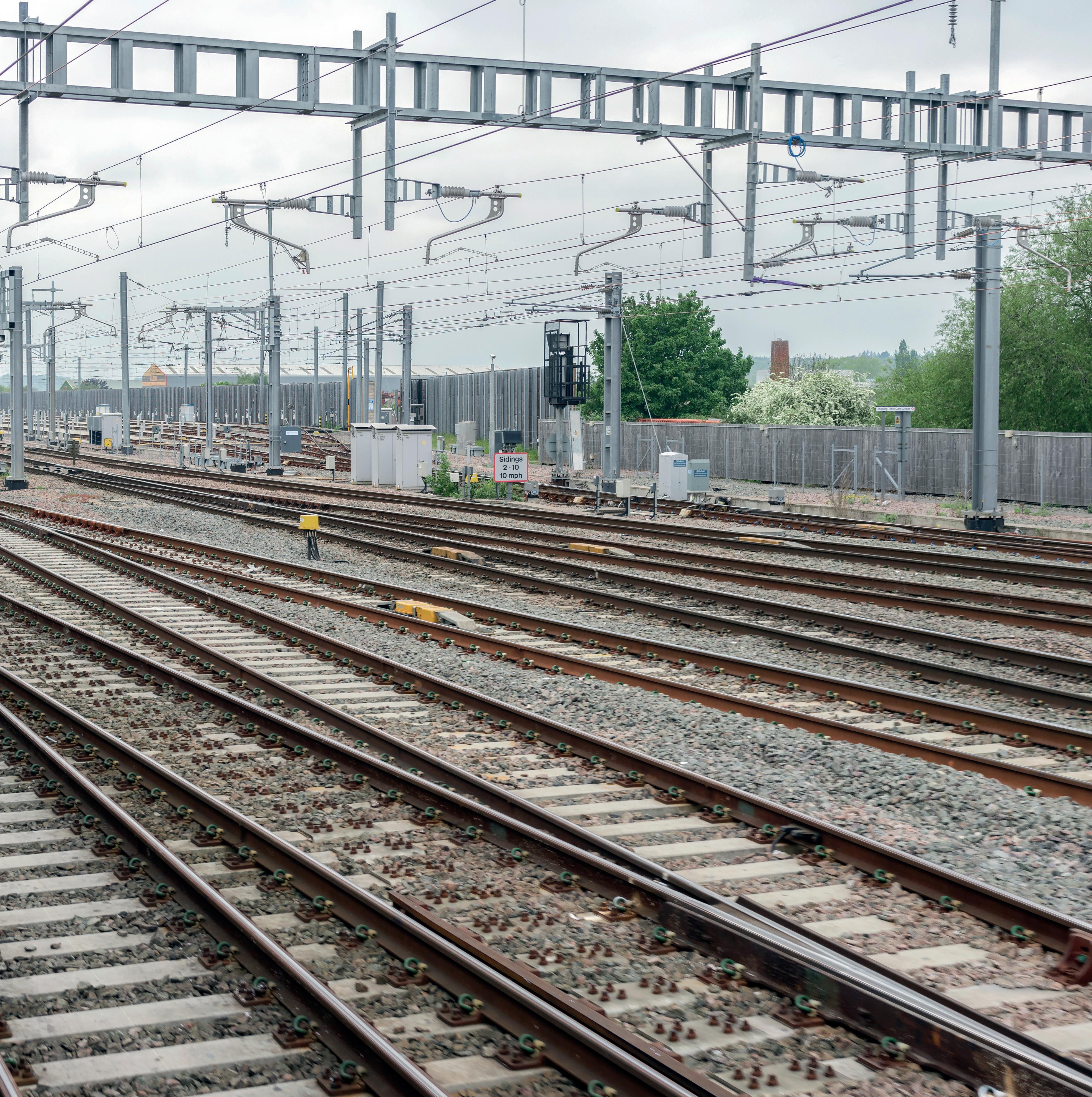
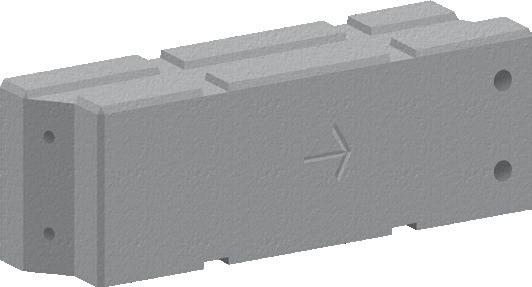


Hoarding stabilisation utilising Elite Duo interlocking blocks

safety
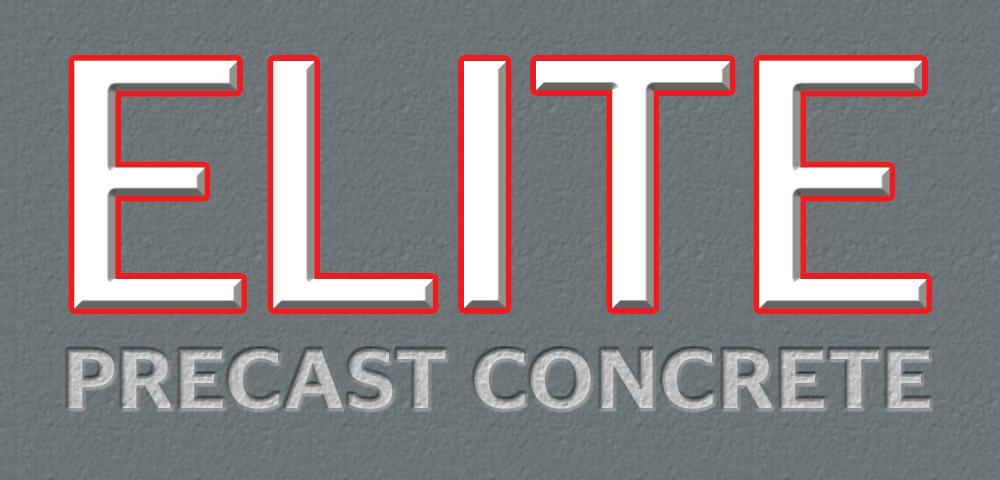
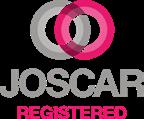


For more information phone 01952 588 885 or browse www.eliteprecast.co.uk or email sales@eliteprecast.co.uk

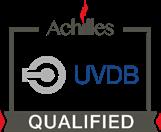
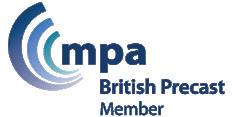
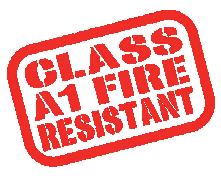
Large ballast bays with walls constructed from our Legato interlocking blocks
Large
embankment retention using the versatile Legato blocks
Workforce
refuges built from Elite Duo blocks
Excellence Showcased at RIA RISE Awards
A broad range of rail supply companies scooped Railway Industry Supply Excellence (RISE) Awards at the Railway Industry Association’s (RIA) Annual Dinner, highlighting excellence within the sector
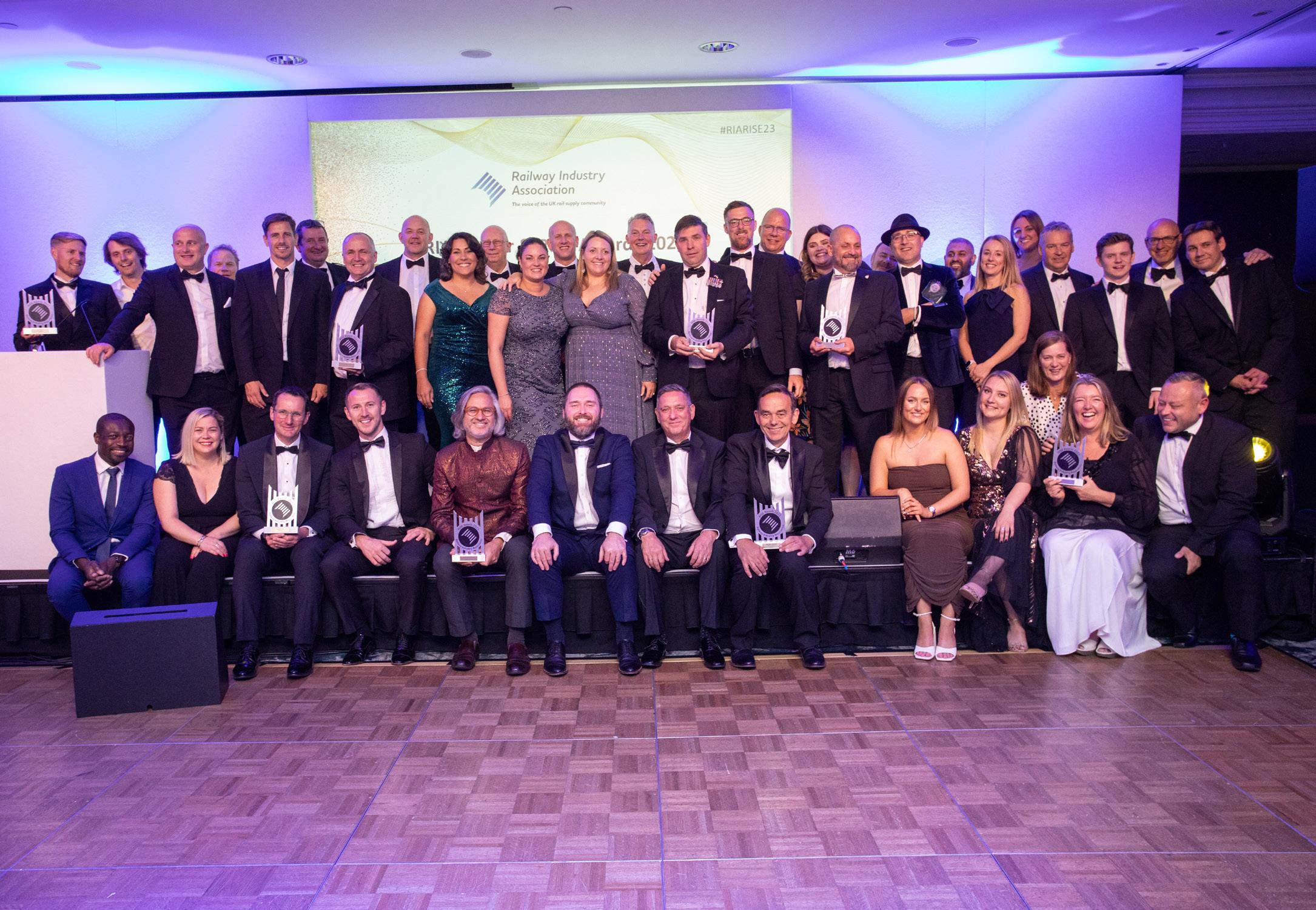
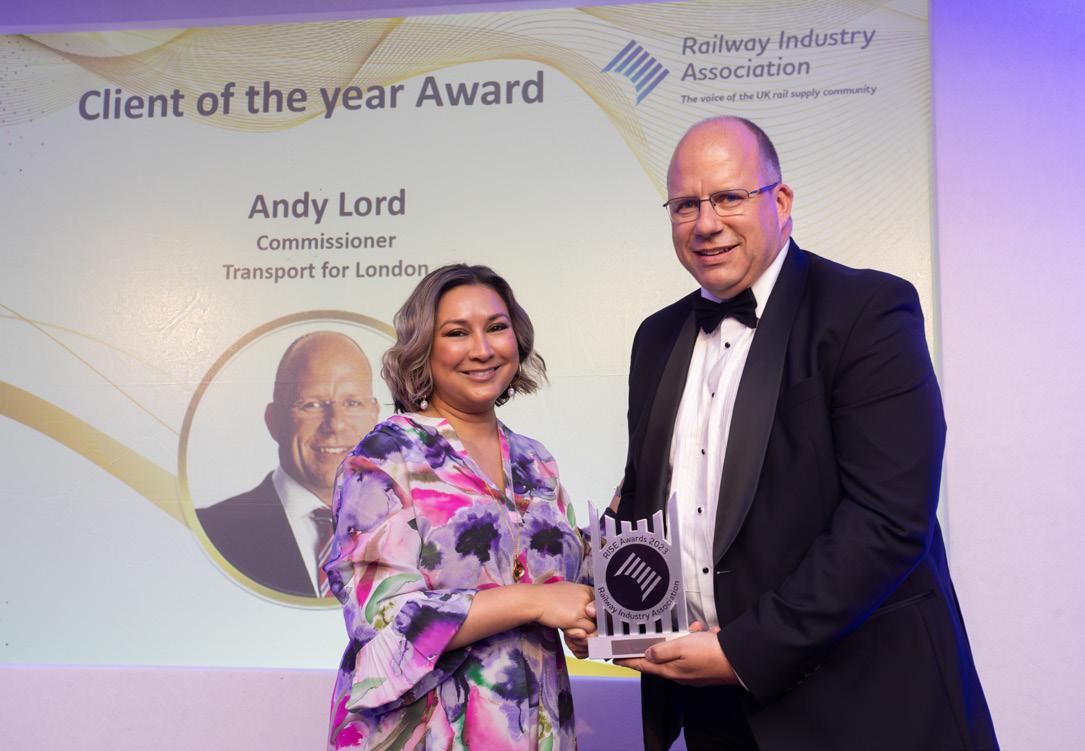
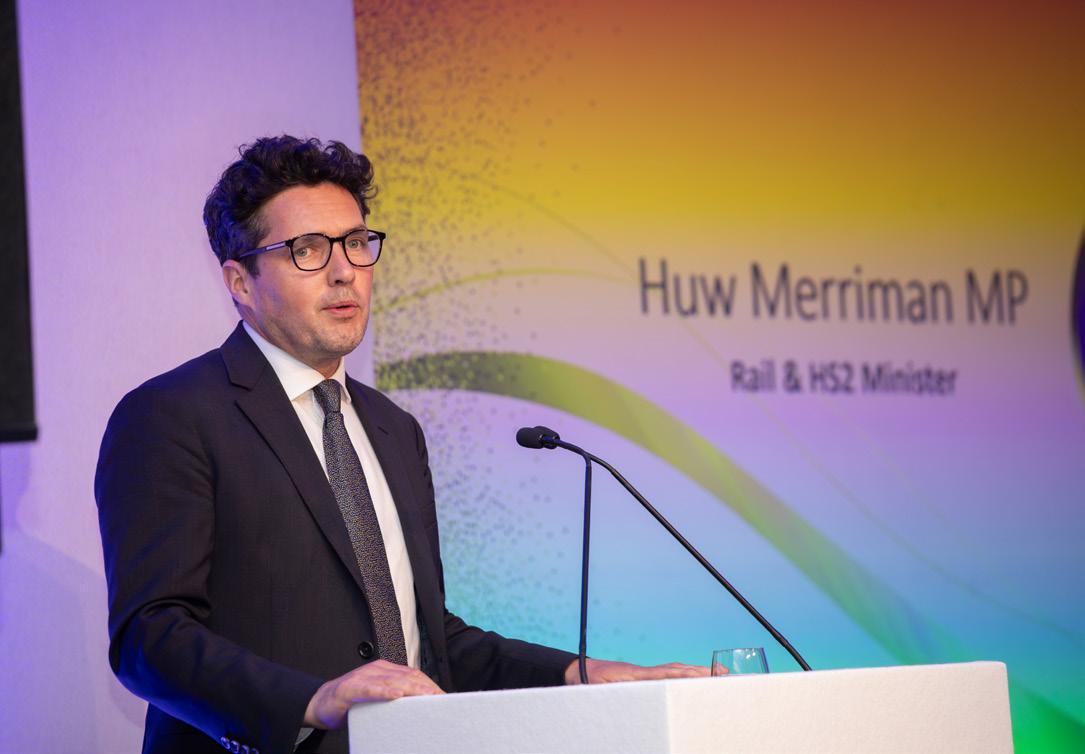
An independent judging panel of senior industry figures picked the winners after a record number of over 90 entries were submitted across eleven categories. Amongst the winners, Andy Lord, TfL Commissioner, picked up the ‘Client of the Year’ Award, regarded by the RIA Board as the rail client individual who had done the most to deliver rail in their area and build strong supplier relationships over the year.
The Dinner and Awards ceremony took place tonight at the Intercontinental Park Lane, Central London, with over 400 people in attendance. As part of the Dinner and Awards ceremony, guests were treated to some quality entertainment in the form of the ‘Fireflies’ – a troupe of classically trained ballerinas performing in custommade LED tutus – a violinist, and a DJ, as well as a charity raffle appeal in aid of the Railway Mission.
The evening was hosted by comedian, broadcaster and former political advisor, Ayesha Hazarika MBE, and featured keynote speeches from Rail & HS2 Minister, Huw Merriman MP, and RIA’s Chief Executive Darren Caplan and Chairman David Tonkin.
Commenting, RIA Chief Executive, Darren Caplan, said: ‘We would like to warmly congratulate all of tonight’s winners, as well as those who were Highly Commended, and everyone who took part. The judging panel were presented with a record number of highquality entries, and the standard was very high right across the board.
‘These Awards truly demonstrate the value of the rail supply chain. The industry faces a bright future, with suppliers not just delivering transformational rail projects to serve a growing number of passengers and freight customers, but also creating jobs and generating economic growth in the process.
‘A special congratulations should go to Andy Lord, TfL Commissioner, who won the ‘Client of the Year’ Award. This was awarded by the RIA Board for achieving a strong initial funding settlement for rail in the capital, ensuring friendly passenger services during events like the Queen Elizabeth II funeral and the recent Coronation, achieving the full running of Crossrail and providing new rolling stock for the DLR, and getting the Underground restored so well postCovid, with patronage returning to record post pandemic levels. Truly exceptional achievements for a first year in office!
‘We hope that the unprecedented number of people who attended the RIA Dinner & RISE Awards this year had a fantastic time, and we’re already looking forward to planning for an even bigger and better event in 2024!’
Transport for London Commissioner, Andy Lord, said: ‘I was deeply honoured to be recognised as part of RIA’s RISE Awards. The rail supply chain plays a crucial role in keeping London moving, and we at TfL look forward to continuing our constructive relationship with RIA over the coming months and years.’
THE ELEVEN AWARD WINNERS
• L.B. Foster (Equality, Diversity & Inclusion Award)
• Network Rail & 7 suppliers (Environmental, Social & Governance Award)
• Connected Places Catapult partnered with Network Rail (Safety Award)
• Angel Trains partnered with Transmission Dynamics (Partnership Award)
• Revolution VLR (Innovation Award)
• WSP (Application of Digital Technology Award)
• Croftstone (SME Growth in Rail Award)
• Xrail (SME Exporter in Rail Award)
• Josie Cheeseman, WSP (Rising Star Award)
• Pradeep Vasudev, WSP (Employee of the Year Award)
• Andy Lord, TfL Commissioner (Client of the Year Award)
THE BELOW ENTRIES WERE HIGHLY COMMENDED
• Atkins (Equality, Diversity & Inclusion Award)
• Trainline (Environmental, Social & Governance Award)
• Tended (Safety Award)
• L.B. Foster (Partnership Award)
• The University of Sheffield (Innovation Award)
• Cognizant (Application of Digital Technology Award)
• One Big Circle (SME Growth in Rail Award)
• Infinitive Group (SME Exporter in Rail Award)
• Kirsty Maule, Gleeds (Rising Star Award)
• Alex Nelson, Atkins (Employee of the Year Award)
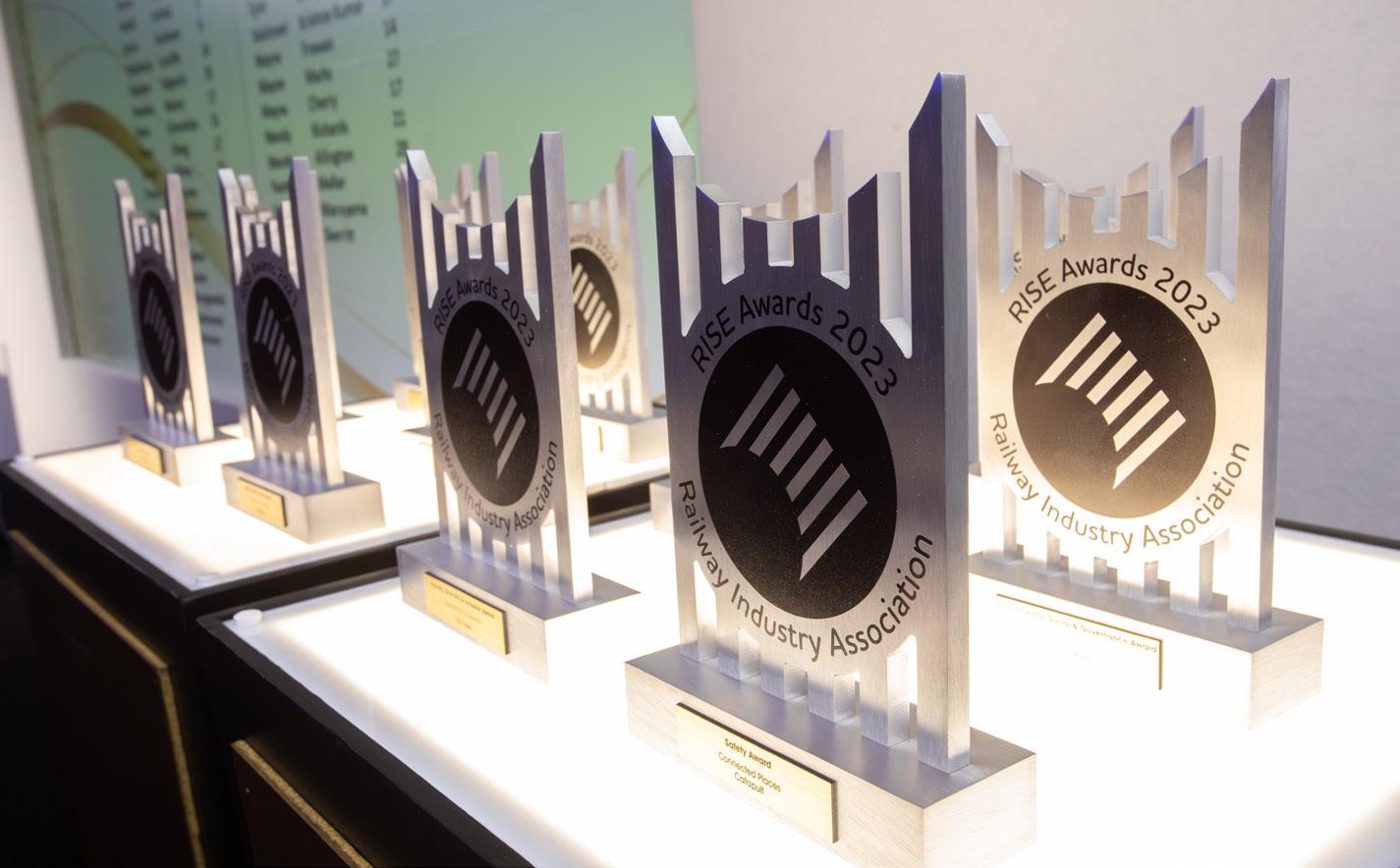
The RISE Awards judging panel consisted of:
• Robert Ampomah, Chief Technology Officer, Network Rail
• Dyan Crowther, Chief Executive Officer, HS1 Ltd
• Gareth Evans, Head of Rail Technology, Network Rail
• Rachel Fullard, Service Analyst at Rail Delivery Group and EDI Charter Working Group Chair
• Jo Lewington, Chief Environment and Sustainability Officer, Network Rail
• Klara Ludinova, Innovation Lead – Rail, Innovate UK
• Toufic Machnouk, Director, Industry Partnership for Digital Railway, Network Rail
• Justin Moss, Head of Business Development, Electrification at Siemens Mobility, Rail Infrastructure and Chair RIA North
• Ian Prosser CBE, HM Chief Inspector of Railways and Director of Railway Safety, Office of Rail and Road
• Wendy Richards, Railways Infrastructure Lead, Department for Business and Trade
• Fi Westcough, Chair, Young Rail Professionals
RIA would like to thank the sponsors of the RIA Dinner & RISE Awards 2023: Gleeds (Equality, Diversity & Inclusion Award), Tratos (Environmental, Social & Governance Award), Atkins (SME Growth in Rail Award), Kier (Employee of the Year Award) and Xrail (Silver Sponsor).

RIA Annual Conference 2023
Promoting the case for rail and investment in uncertain times
Millennium Gloucester Hotel
1 and 2 November
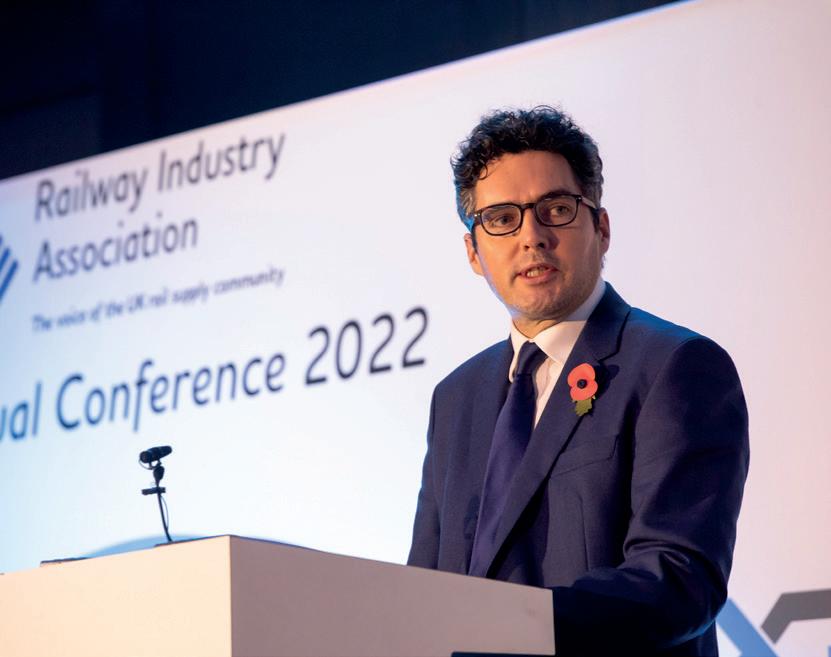
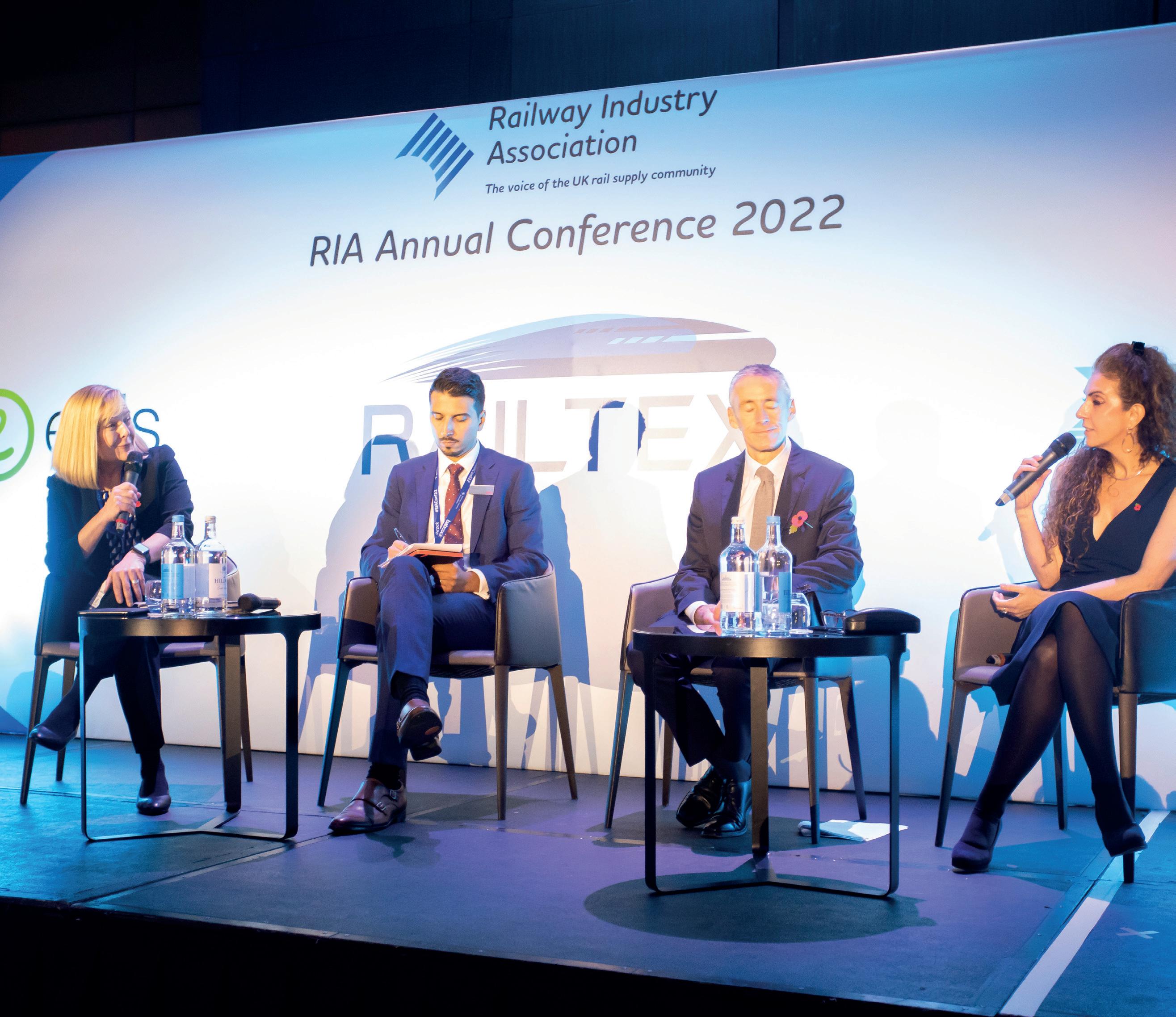

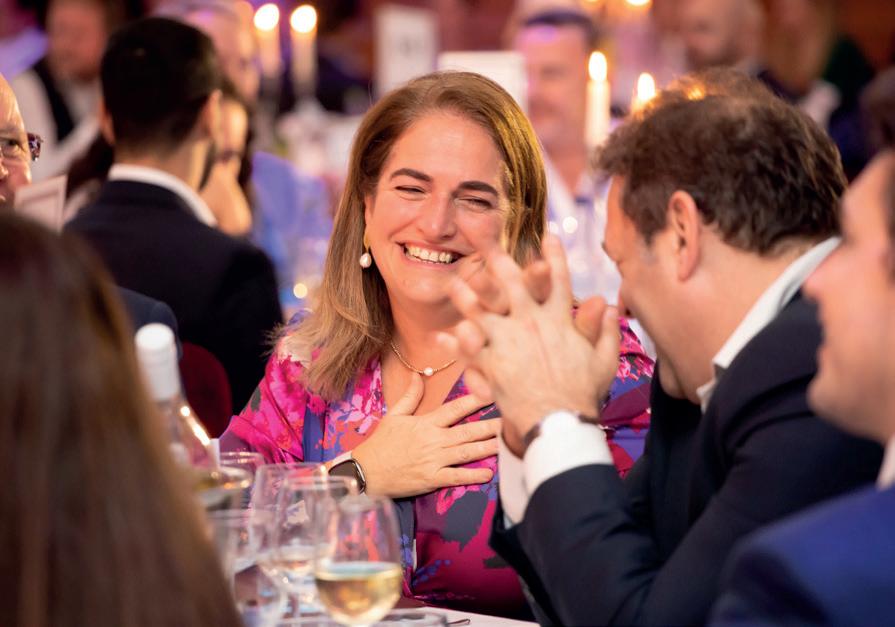
2-day conference with inspiring keynotes including: – Huw Merriman MP, Rail and HS2 Minister – Andrew Haines, Chief Executive, Network Rail – Baroness Grey-Thompson DBE, DL, Member of the House of Lords – And many more…
Large interactive exhibition area with spotlight pitches presenting services, products and solutions
Evening programme including networking drinks, dinner and entertainment
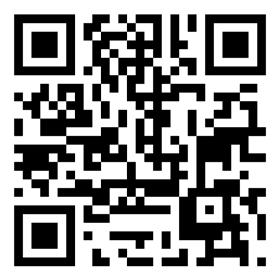
London Kensington Scan the QR code to register today
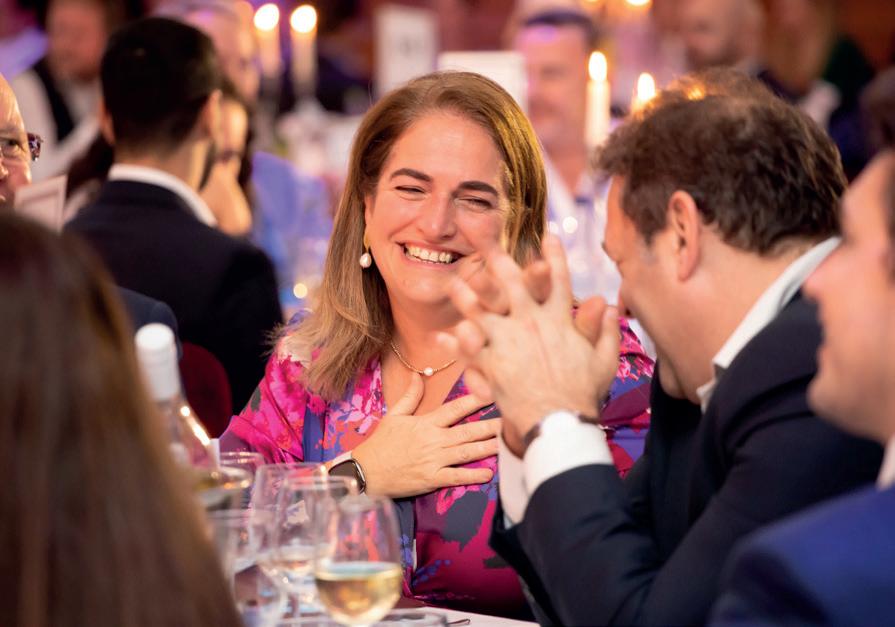
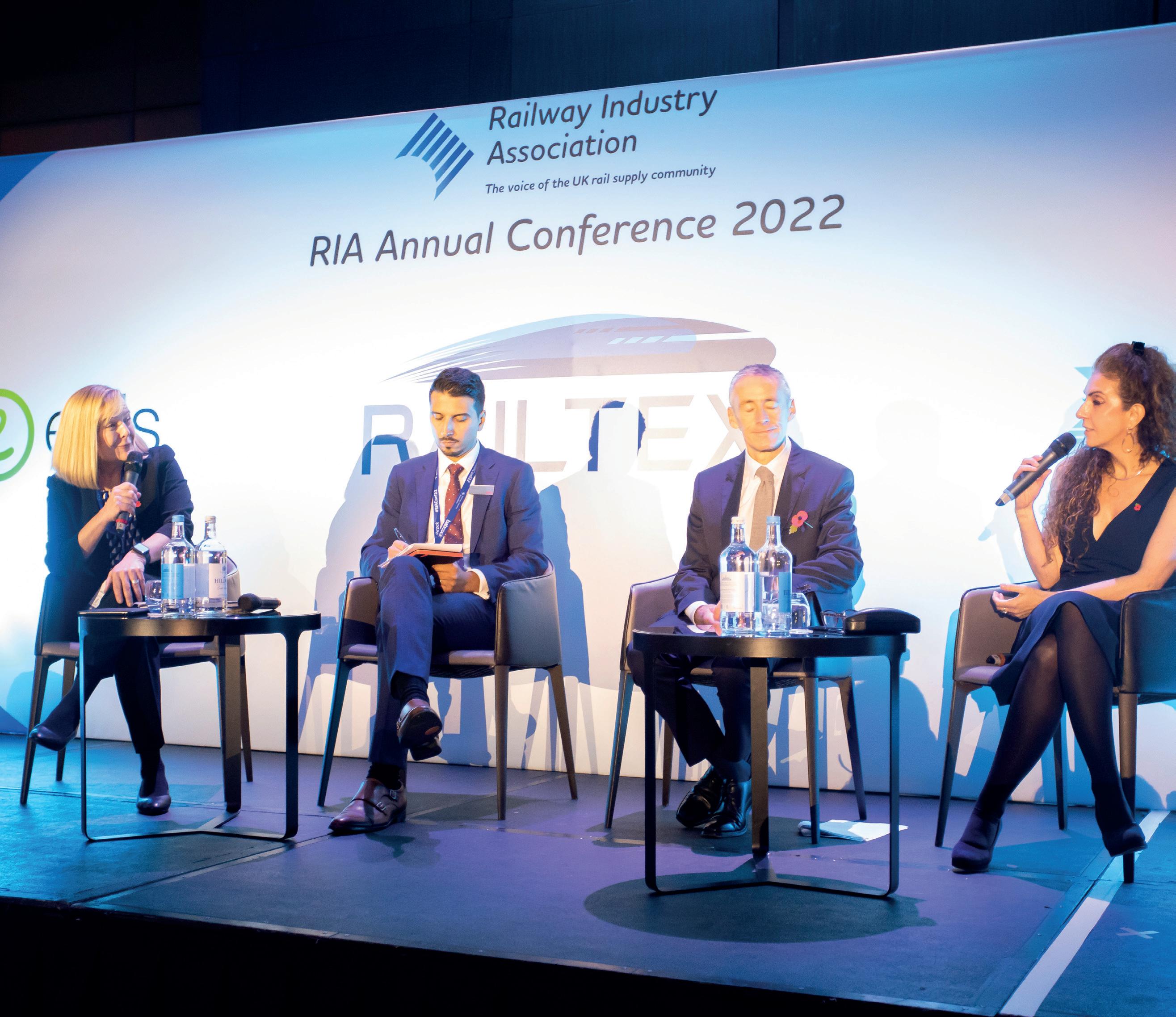
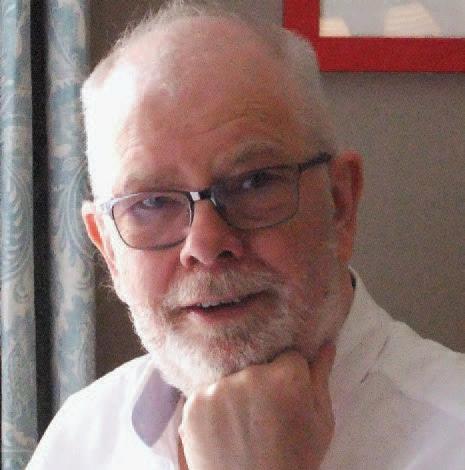
THE CHEEK OF IT
by Chris Cheek
What’s in a Number?
Transport Secretary Mark Harper’s Bradshaw Address in February fired the starting gun on rail reform once more, but one statistic he quoted has caused some fluttering in the dovecotes
When the Secretary of State for Transport Mark Harper sat down after delivering the Bradshaw lecture in London at the beginning of February, his speech was widely praised. At long last, he ended the uncertainty over the future of the Plan for Rail (previously known as the Shapps-Williams Plan) which had been launched with great fanfare in May 2021 but was quickly shunted into a legislative siding during the convulsions which hit the Tory party for most of last year.
As a result, we are assured that Great British Railways (GBR) will definitely happen, and that the micro-management of the rail network from Marsham Street will come to an end 20 years after it had started with the abolition of the Strategic Rail Authority in 2005. In an ironic twist which I am sure will not be lost on him, the vision then put forward by Richard Bowker of a single authority looking after tracks and the trains will actually come about. Harper said: ‘Taking politics out of the railways is the only way to build a truly commercially led industry and, for me, that is non-negotiable.’ Well amen to that – except I don’t think anybody has really taken the politics out of railways since 1844. He continued that the industry had long called for a guiding mind to coordinate the network, ‘so GBR will be responsible for track and train, as well as revenue and cost.’
Earlier in the speech, he had referred to current state of the industry’s finances, which he described as ‘unsustainable’. ‘It isn’t fair to continue asking taxpayers to foot the bill’ he continued. ‘Most of them don’t regularly use the railways, including plenty of my constituents in the Forest of Dean.
But they find themselves subsidising an industry that delivers between only 1.5 per cent and two per cent of all journeys that are taken by the public. That disproportionately serves commuters in the south-east and whose funding comes at the expense of other vital transport upgrades.’
It was this quote that set alarm bells ringing in some quarters, especially Richard Harper from consultant Steers in a social media post. So what got Richard and others so bothered? Was the Secretary of State wrong?
Well, no. He was factually correct to say that. According to the most recent National Travel Survey (sheet NTS0303), published last summer, average trip rates for surface rail stood at 11.2 trips per person per year (pppy), out of an all modes total of 757, giving rail a 1.5 per cent market share. Prior to Covid, the figure had been 21.2 trips pppy out of a total of 953 – a share of 2.2 per cent.
However, looking only at the number of journeys, without considering their length, significantly underplays rail’s importance. After all, nobody expects national rail services to cater for short urban journeys to the supermarket or the local High Street. This can be seen clearly in another table from the National Travel Survey, sheet NTS0317, which looks at the market share of different modes for longer distance journeys. This shows that, for journeys of over 50 miles, rail enjoys a 12.6 per cent market share, rising to over 18 per cent in the 150-250 mile range. Pre-Covid, rail’s overall share of 50+ mile journeys stood at 15.8 per cent, rising to 19.3 per cent in the 150-250 mile range, and up to 25.1 per cent in the 250-350 range.
This was one reason why, for many years, the government has had a preferred measure
NEWS IN BRIEF
NEW ASSISTED TRAVEL LOUNGE AT LONDON PADDINGTON
The new lounge, which is adjacent to the taxi rank on the upper deck at London Paddington, provides passengers who use the assistance programme with accessible wheelchair spaces, reduced mobility seating and a customer information screen.
The Assisted Travel Lounge (ATL) is being operated by Network Rail’s Passenger Assistance team, who will have a customer ambassador on hand to help any passengers requiring the use of the facility. It will be open from 8:00am until 8:00pm on weekdays, and from 10:00am until 6:00pm on weekends. When the waiting room is not staffed, there is a Help Point located on the taxi rank area adjacent to the ATL that connects passengers directly to the Network Rail reception on platform 1 for assistance.
The facility provides a safe, convenient and accessible waiting room which improves comfort for passengers of restricted mobility and helps to make their journey quicker and easier.
CHELTENHAM SAMARITANS MARK 60TH ANNIVERSARY
Cheltenham Samaritans has marked its 60th anniversary by installing two new planters at the town’s railway station. The branch successfully applied for a £1,000 grant from Great Western Railway’s Station Adoption Fund to add a touch of colour to Cheltenham Spa. The planters, which include Samaritans roses grown specifically to celebrate the branch’s 50th anniversary in 2013, are branded with the Samaritans contact number which is clearly visible to customers.
3.5 MILLION TRAVEL WITH SCOTRAIL
More than 3.5 million customers travelled on ScotRail services in the first two weeks of August, with the 2023 UCI World Cycling Championships helping to deliver the busiest period since before the pandemic. During the ten days of the cycling championships, 647,000 more journeys were made compared to the same period last year, with people taking advantage of the thousands of services ScotRail provides.
of passenger kilometres or miles in looking at market shares or growth targets. This has been true in a whole range of documents, including John Prescott’s famous ten-Year Plan of July 2000 back in the halcyon days of the Department for Transport, Local Government and the Regions (DTLR). This referred to a preferred measure of passenger kilometres (or passenger miles, as we have to say in these post-Brexit days) and set a target of 50 per cent growth by 2010. (As an aside, the 50 per cent target was missed –the growth by 2010 was 38 per cent. The 50 per cent figure was not reached until 2013).
Including distance makes rail’s market share much more significant than Mark Harper’s ‘one to two per cent’. According to the latest edition of Transport Statistics Great Britain (sheet TSGB0101), the 47 billion passenger kilometres travelled by rail and Underground in 2021 represented 7.3 per cent of the 645 billion travelled by all modes. Stripping out the Underground, National Rail’s total of 39.1 billion represented a 6.1 per cent market share. Once again, the pre-Covid figures were much higher: 67.7 billion by National Rail out of 831 billion in total, representing a market share of 8.2 per cent.
On the one hand, picking up such a relatively minor moment in Harper’s speech could easily be seen as a piece of nit-picking. On the other, it could also be seen as representing a right-wing, motoristdominated government’s wish to belittle rail as a mode as part of a process to soften the public up for service reductions and fare increases to come.
And before anybody gets too carried away about how insignificant these numbers are, just think about the alternative scenario – in which all those journeys transferred to car and bus, further clogging up the streets of London, the South East and our big urban areas. It doesn’t bear thinking about.
The difficulty is, of course, that the Secretary of State’s point was well made – the finances of the industry are
‘Mark Harper’s speech was well-received, and the hope must be that the Government now gets on with implementing its own plan, albeit two years late. The reaction from the Opposition was fairly muted, too – implying that they haven’t got much of an alternative policy either (especially since GBR would effectively give them what they want).’
unsustainable, and the amounts being pumped into revenue support on the railways are excessive compared with other modes such as bus. It is also true, unfortunately, that – as Sir Michael Holden recently pointed out in a recent article – it is nigh-on impossible for train operators to make major savings when around 75 per cent of their costs are fixed and/or regulated and the other 25 per cent has been cut to the bone over the last 25 years. (I note in passing though that everybody keeps avoiding mention of one of the industry’s biggest problems, its unaffordable pension scheme).
It all adds up to a pretty toxic set of circumstances, into which has to be stirred the current increasingly toxic industrial relations situation, and the ongoing failure of patronage to recover to pre-Covid levels in the face of economic stagnation. Any lingering hope that there would be a return soon is looking increasingly forlorn – not helped, of course, by the disruption caused by strikes and staff shortages.
The latest of the DfT’s now monthly statistics on post-Covid use of transport modes shows a mixed pattern. During the autumn, weekly averages hovered around and even exceeded 90 per cent of the prepandemic base on several occasions. The New Year got off to a slow start with the industrial action, but then reached a postlockdown peak of over 93 per cent in the two last weeks of January before slipping back to 88 per cent during the strike-hit first week of February. Numbers slipped further to 76 per cent during week ended 11 February: worryingly, that was a strike-free week.
Mark Harper’s speech was well-received, and the hope must be that the Government now gets on with implementing its own plan, albeit two years late. The reaction from the Opposition was fairly muted, too – implying that they haven’t got much of an alternative policy either (especially since GBR would effectively give them what they want). All of which must give some hope that there might just be a period of consistency and stability in policymaking – at least until the next General Election and maybe even after that. Though whether the primary legislation needed to set up GBR will get through Parliament before the dissolution likely in the autumn of 2024 remains to be seen. Meanwhile past experience suggest that there will be at least one more Secretary of State and several handbrake turns in policy between now and then. Hang on to your hats!
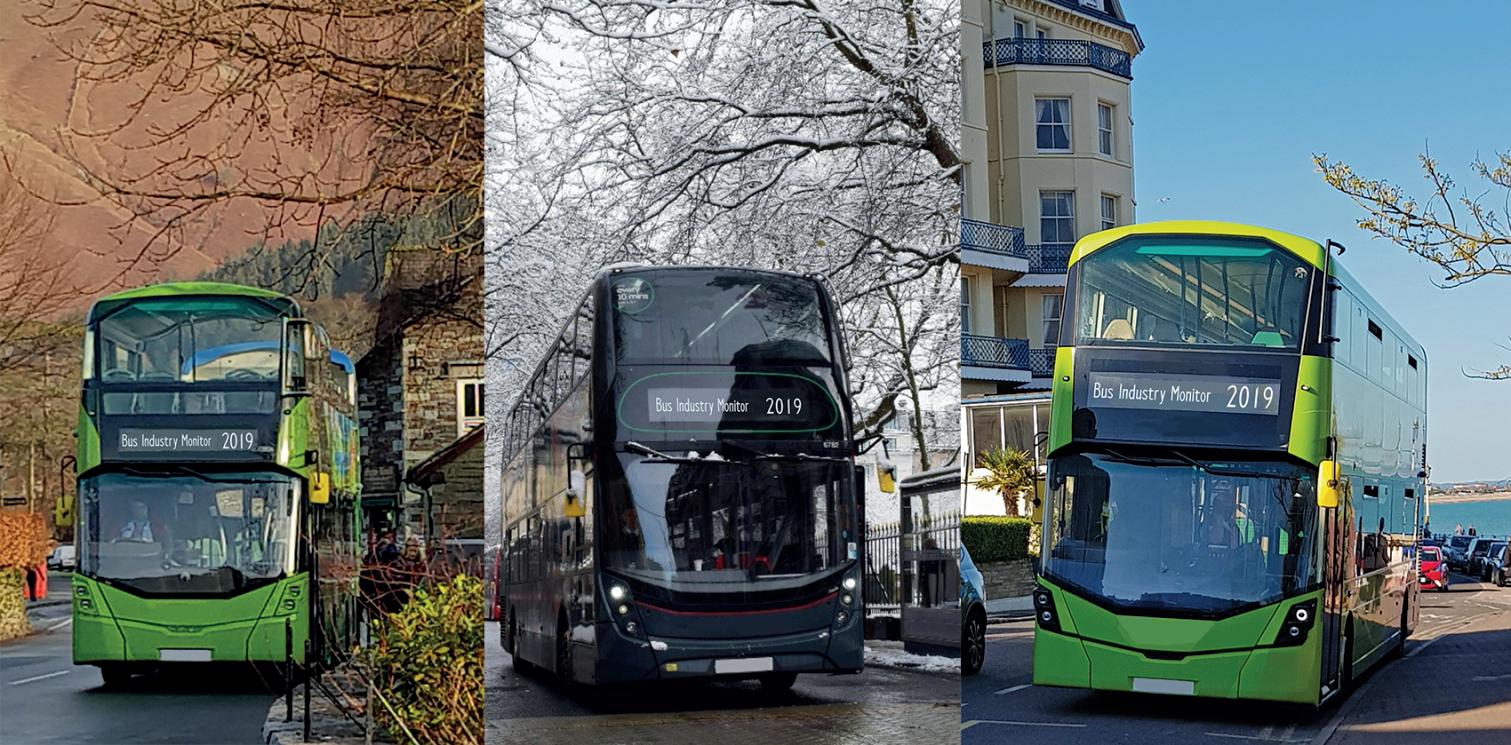



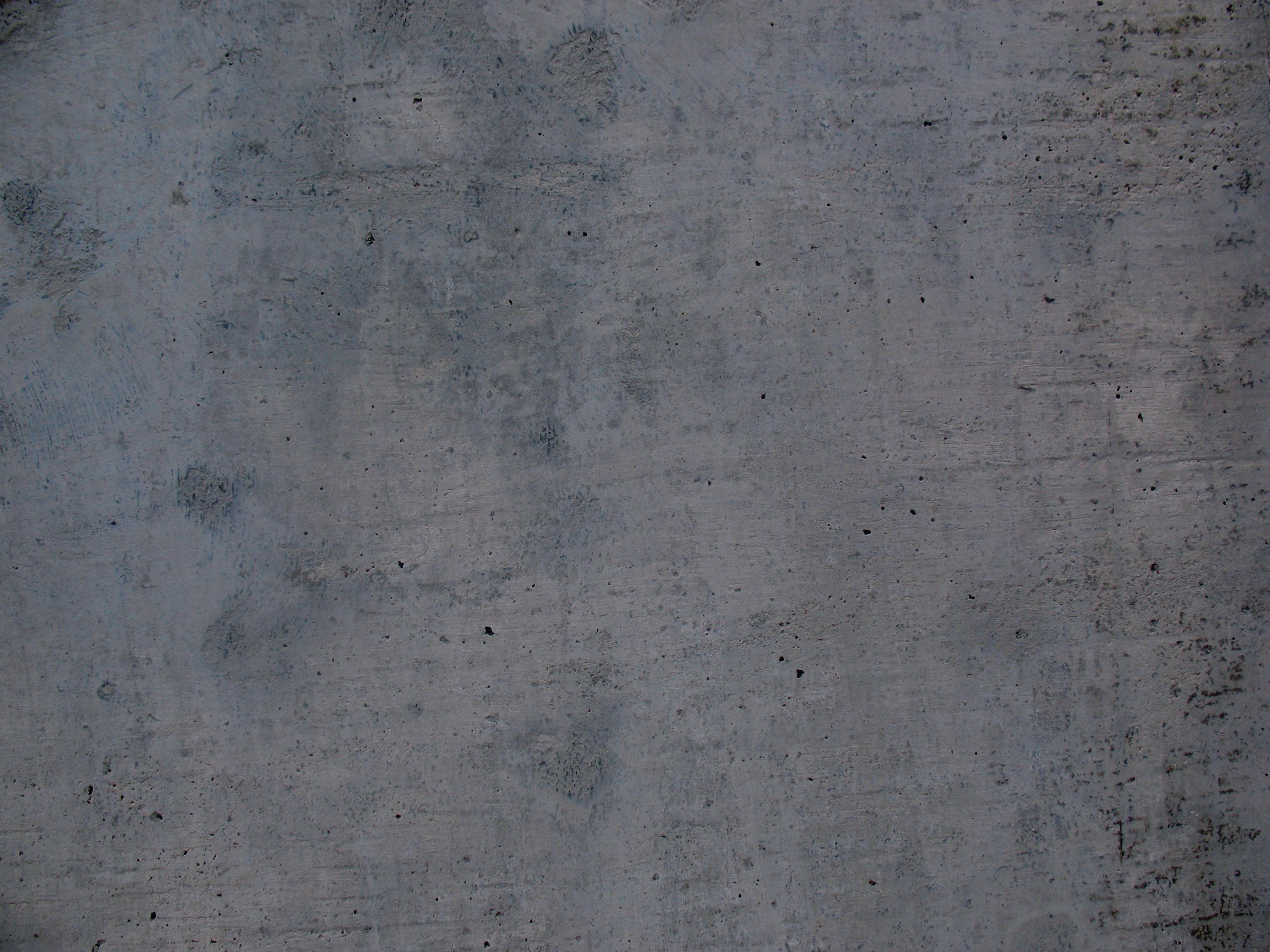

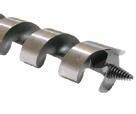


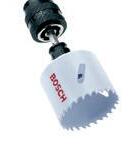
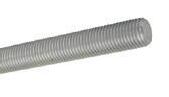
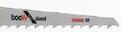
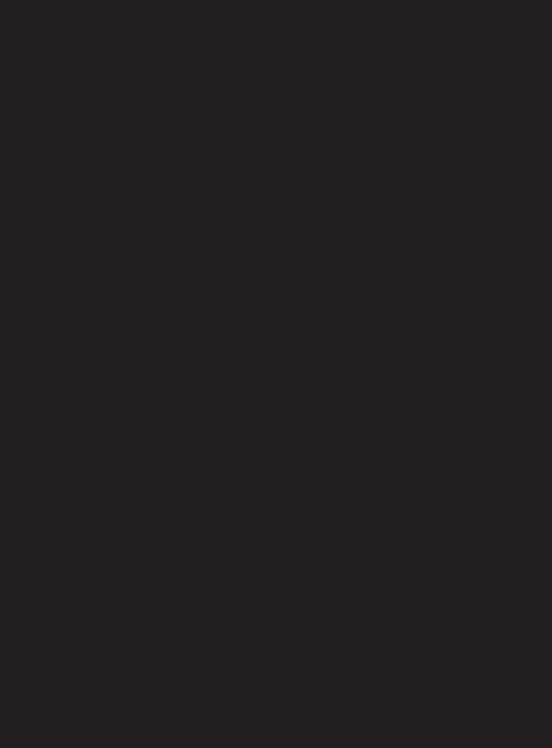
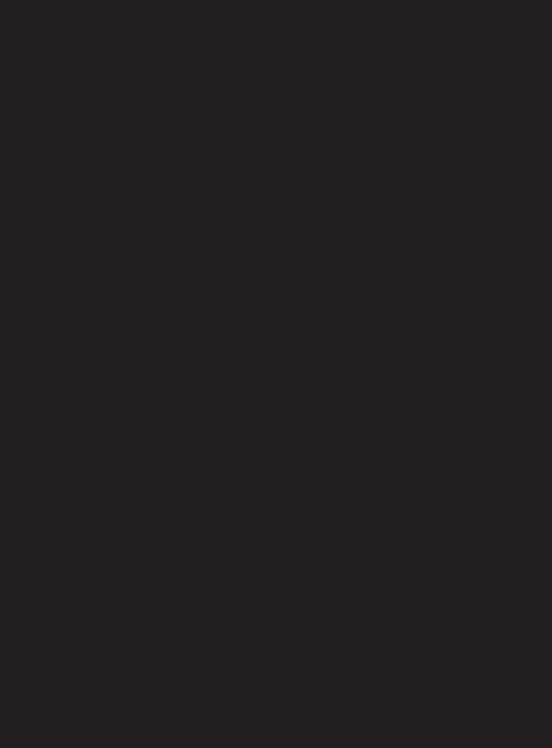

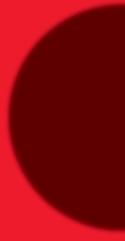
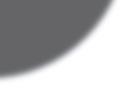
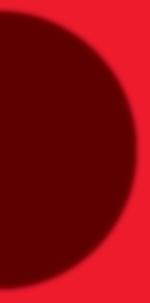
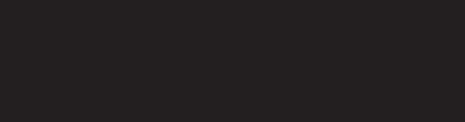
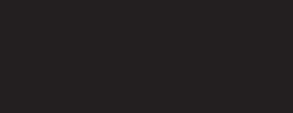

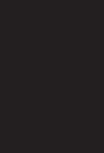
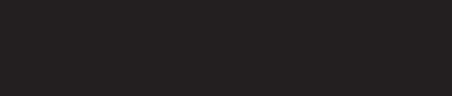

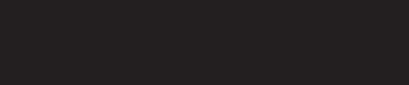
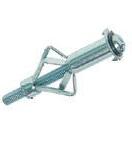


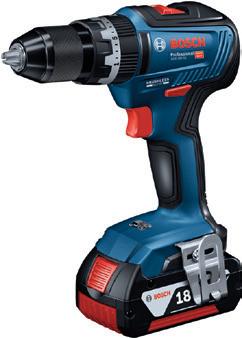

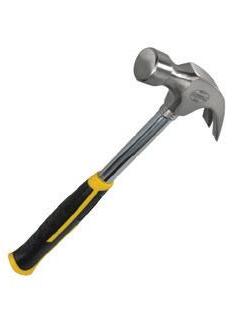
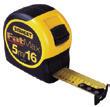
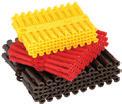
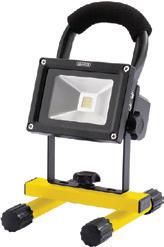

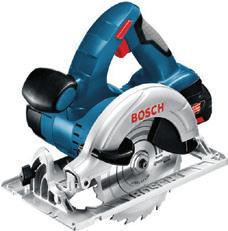
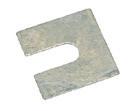
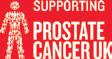


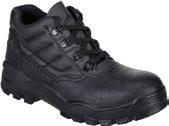
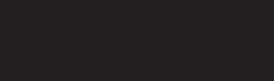

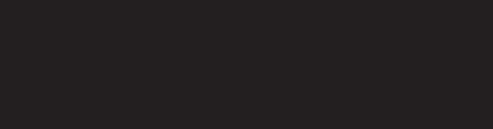


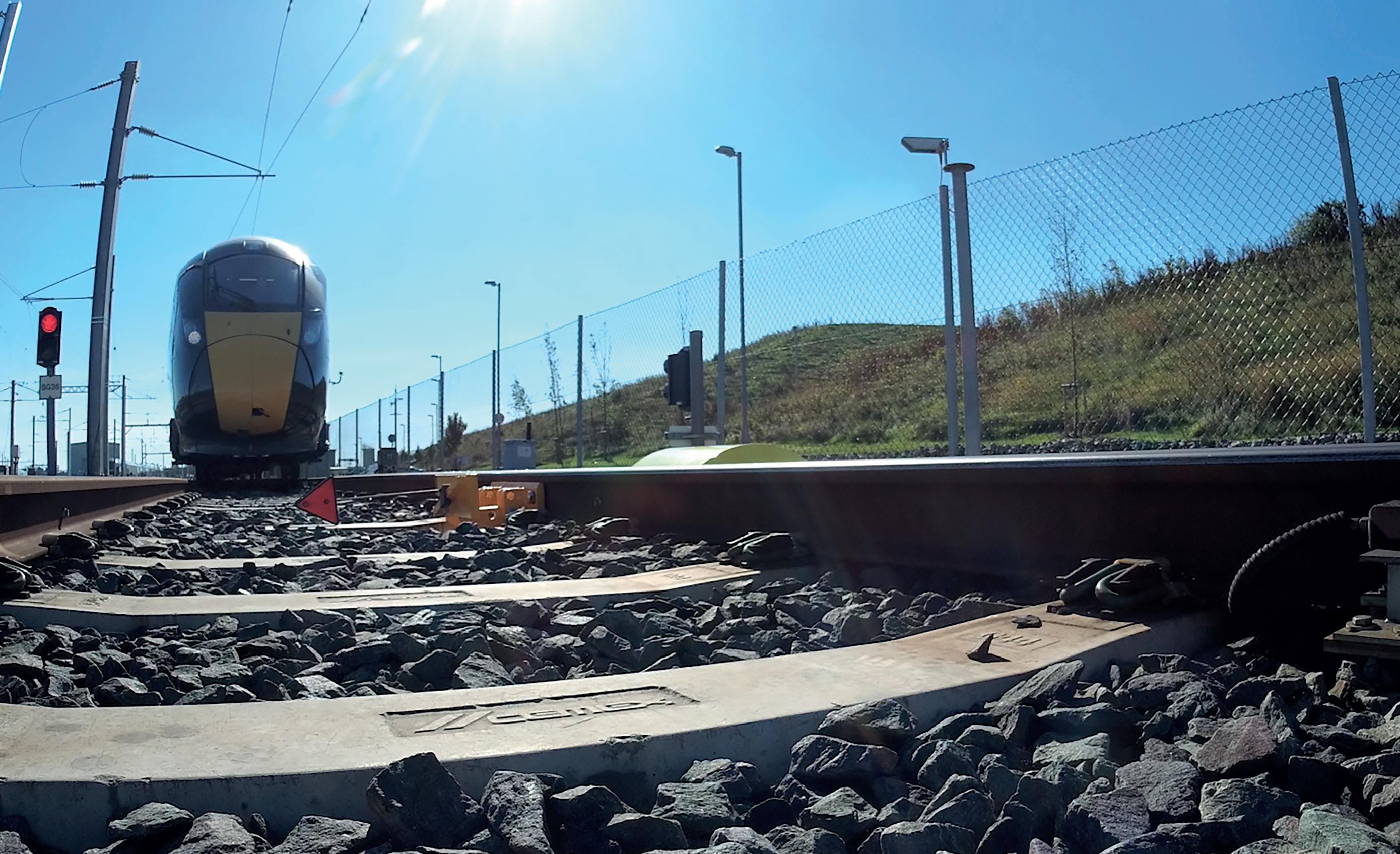
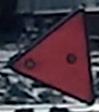

Rail Decarbonisation
How can you meet your decarbonisation goals with galvanized steel?
Download our guide to find out.
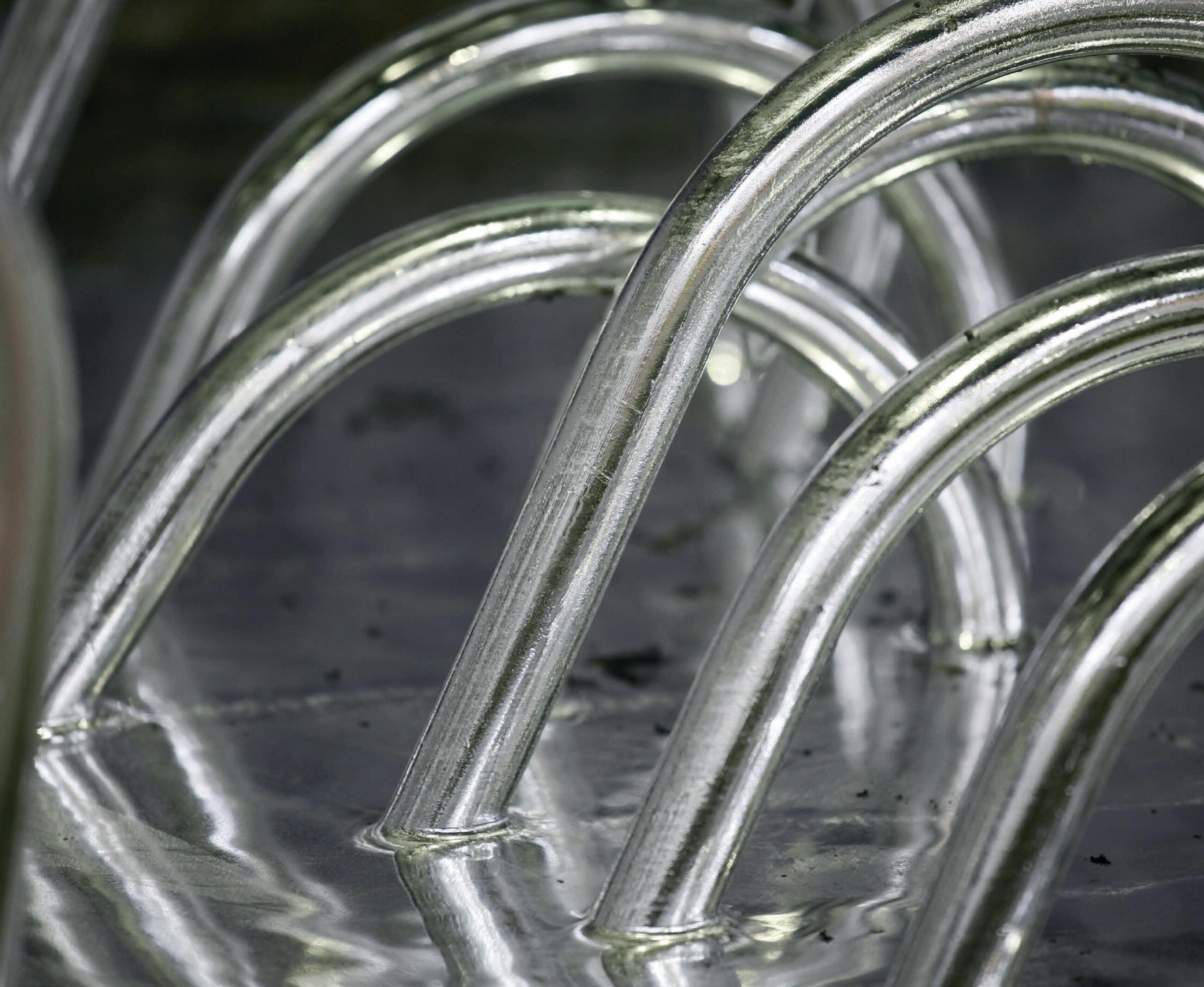
As the UK and Ireland seek to transition to a low carbon future, the challenge of sustainable construction is clear: we need to move to a circular economy.
How galvanizing can help you decarbonise your projects:
• It is durable and robust
• Avoids maintenance
• Facilitates reuse
• Avoids replacement
Read more in our guide...
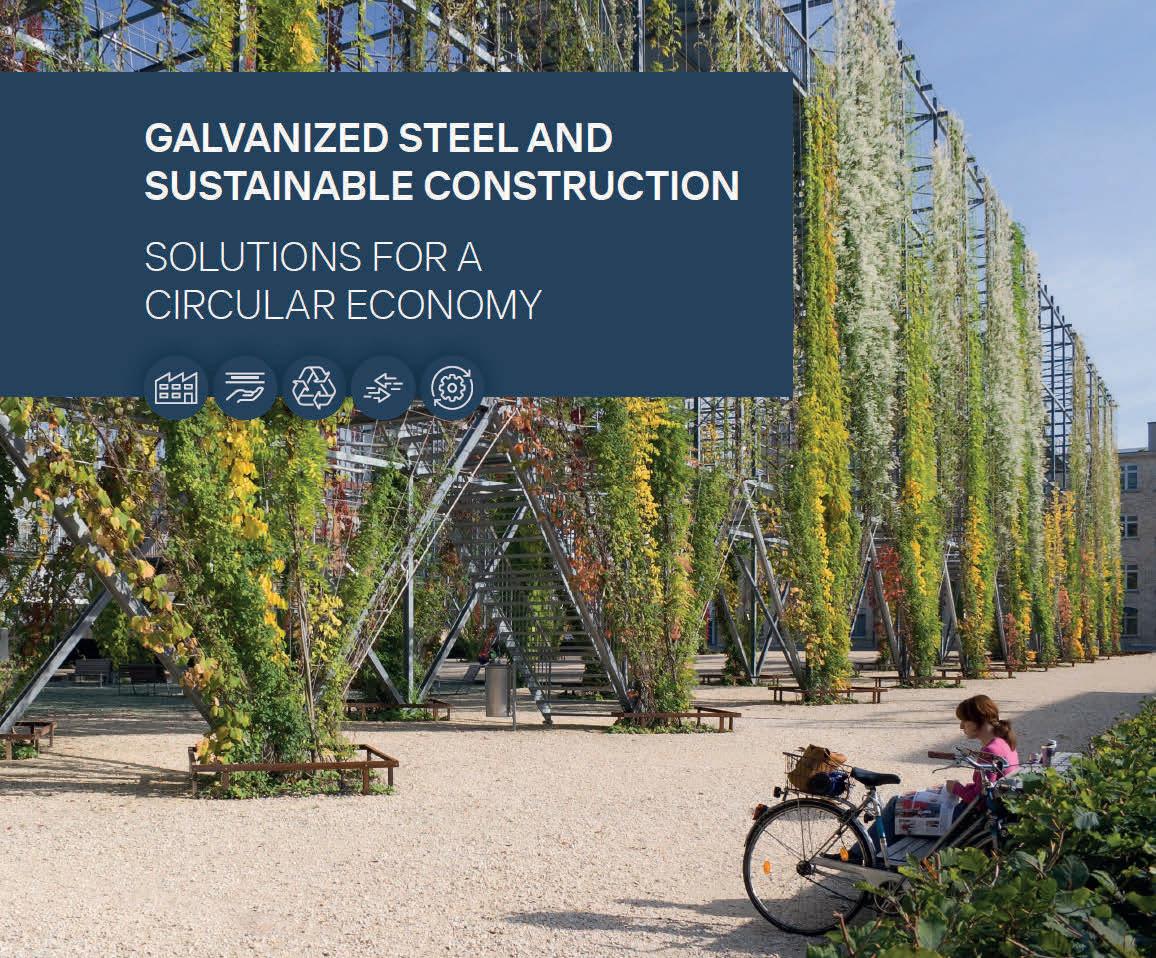
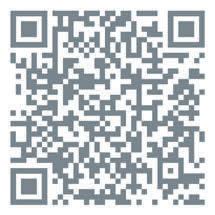
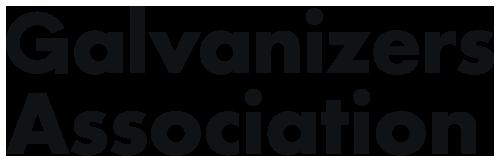



Light Rail Safety and Standards Board
Established in 2018, the Light Rail Safety and Standards Board (Light Rail SSB) is committed to further improvements to what is already one of the safest forms of public transport
Drawing on experience and expertise from across the sector, it brings all aspects of light rail safety under one roof while providing a central resource where colleagues can access the latest guidance and standards documentation.
In a report published in 2022 on the organisation’s work to date, the Office of Rail and Road (ORR) said the Light Rail SSB is adding value to the light rail sector and supporting continued improvements in managing safety.
In assessing whether the Light Rail SSB is on track to deliver Rail Accident Investigation Branch (RAIB) recommendations that followed the fatal Sandilands derailment in 2016, the regulator also found that the organisation is providing guidance and tools to improve the sector’s understanding of risk.
At the heart of this approach is the development of an Integrated Risk Management Framework that has been developed in partnership with key stakeholders, including its members and statutory organisations such as the ORR.
It also incorporates a series of interconnected projects that run in parallel with each other to deliver a comprehensive platform that is already making a significant contribution to light rail safety.
Key elements of the framework include the continued development of a Tram Accident and Incident Reporting (TAIR) database, a pioneering online reporting system aimed at enhancing tram safety. As well as the integration of the ORR’s Risk Management Maturity Model (RM3) into the light rail sector.
Whilst all tramway and light rail services have different challenges and potential hazards, the TAIR database enables them to add their own data to the platform and contribute to the most comprehensive risk management tool developed for the light
rail industry in the UK. With strong support from across the wider light rail community and funding from the Department of Transport, the LRSSB is also taking the lead on numerous research projects.
These initiatives have been fully incorporated within a sector-wide Risk Model and the introduction of new Bowtie Risk assessment database. Combined, these projects provide a continual development cycle that progressively drives down industry risk to as low as reasonably practicable (ALARP) levels.
LRSSB continues to support research and development projects in a number of important areas in particular in technology providing obstacle detection and avoidance systems. The initial results are promising for the UK light rail sector as the technology is now being utilised in Europe.
LRSSB is structured by the LRSSB Board which consists of the Chief Executive Officer (CEO), Non-executive Chair, 4 Bonexecutive Directors, the Managing Director of UKTram and an ORR Observer. In May 2020, LRSSB appointed a new Chair, Sue Byrne, and a new CEO, Carl Williams, in October 2020.
The current management structure of LRSSB consists of a CEO, Administration Manager and Safety and Assurance Manager, with the intention to recruit further posts in safety engineering and data analysis. LRSSB has also been supported by UKTram colleagues during the year.
Case study
In Spring 2022, LRSSB was invited by Transport for West Midlands (TfWM) and Midland Metro Alliance (MMA) to conduct a compliance review of their processes against the Railways and Other Guided Transport Systems (Safety) Regulations (ROGS) to help ensure a safe and smooth handover of the multi-million-pound extension to West Midlands Metro to the operator, West Midlands Metro.

MMA utilised LRSSB’s BowTieXP software system to develop a comprehensive database of assessments as it prepared for the opening of extensions to Edgbaston Village and Wolverhampton Railway Station.
Named after the shape of graphics to illustrate its core principles, BowTie contains eight elements: hazard, top event, threats, consequences, preventive barriers, recovery barriers, escalation factors and escalation factor barriers.
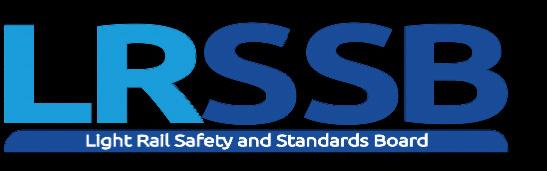
KEY PERSONNEL
Chairperson: Sue Byrne
Chief Executive: Carl Williams
Administration Manager: Erica Pearson
Safety Assurance: Mark Ashmore
Head of Engineering Safety & Innovation: Craig O'Brien
Head of Commercial: Jamie Swift
CONTACT INFORMATION
Email: info@lrssb.co.uk
Visit: www.lrssb.org
Address: LRSSB, 16 Summer Lane, Birmingham, B19 3SD
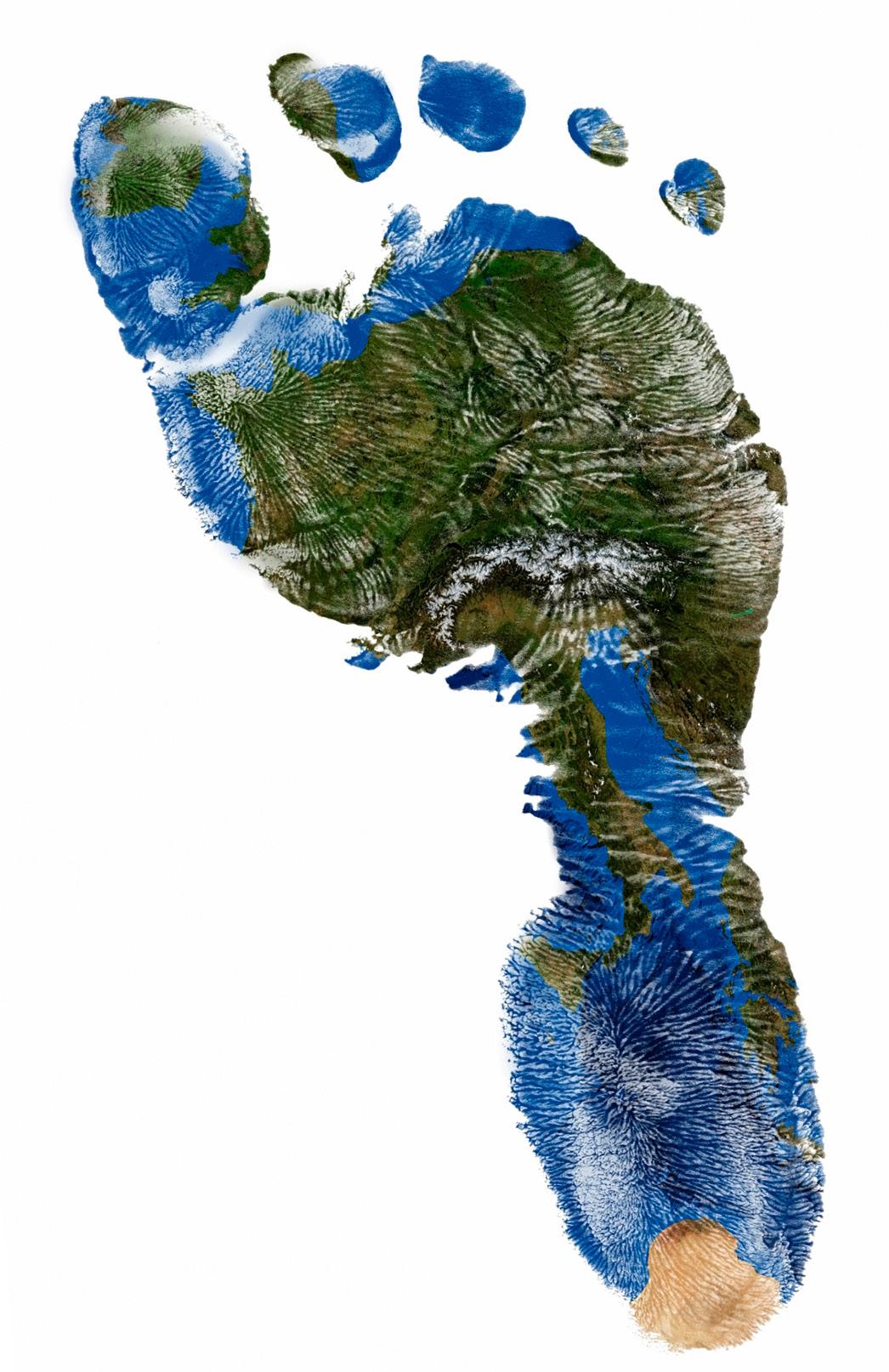
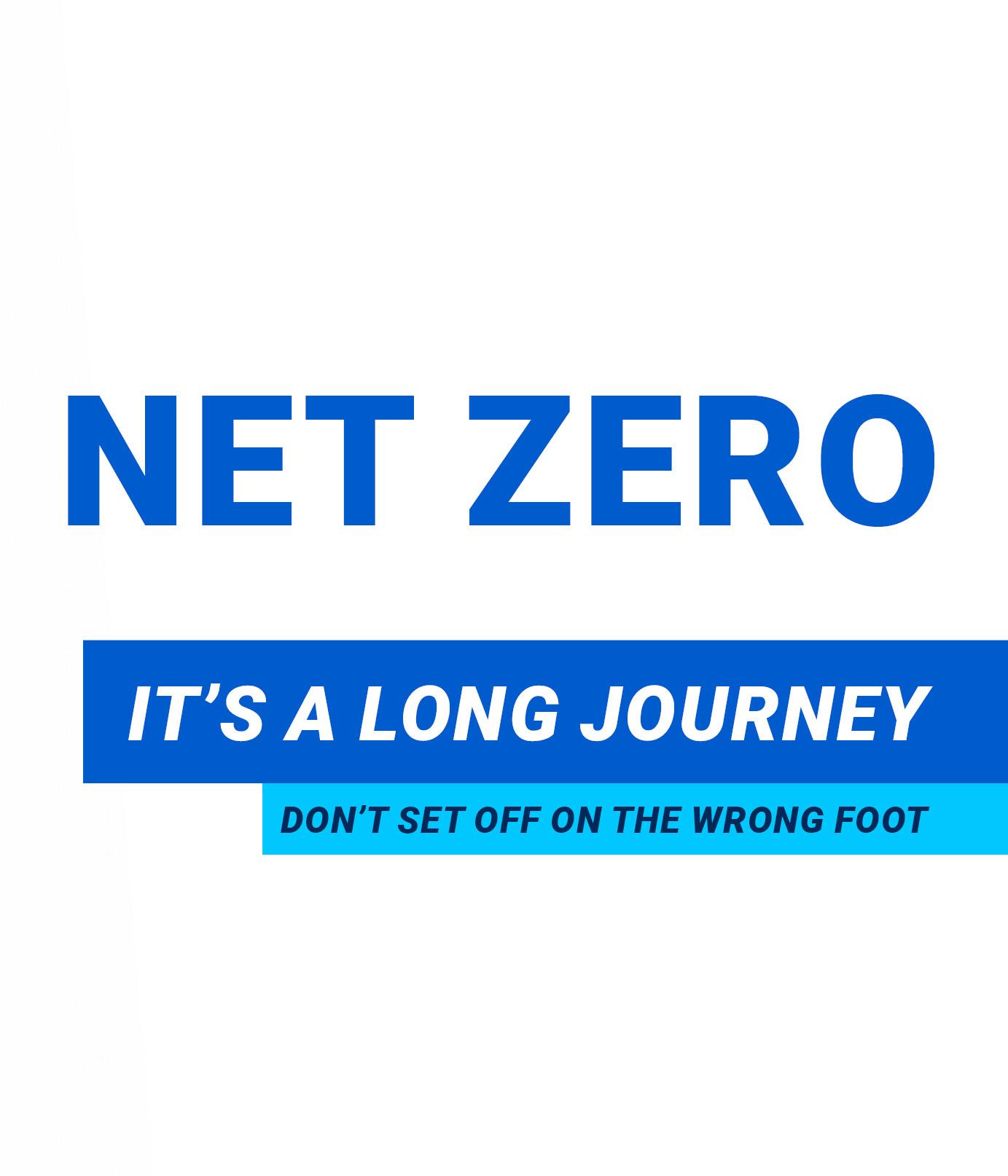
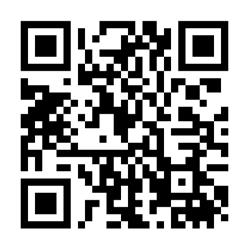
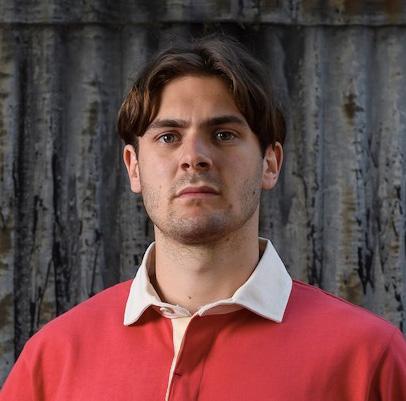
by Ellis Shelton
Rail Capacity Improvements at Ely Junction are Vital
Ellis Shelton, Policy Advisor, Logistics UK explains why the enhancements at Ely junction are crucial
In the modern era, where cities are expanding and populations are growing, the demand for reliable and high-capacity rail systems has never been greater. Railways are vital for the movement of goods and people across the UK, as well as facilitating trade, connecting businesses, and enabling productivity gains. However, as the logistics industry continues to decarbonise in response to the government’s 2050 net zero deadline, increased capacity is urgently needed to accommodate businesses shifting their logistics operations from road to rail. Improving rail capacity at significant bottleneck locations such as Ely Junction – where restricted speeds, signalling limitations and level crossings are a barrier to meeting increased demand for freight paths – is essential for supporting economic growth, addressing regional inequalities, and achieving net zero.
Ely Junction is a crucial railway interchange in the UK with multiple railway lines that connect important economic hubs such as London, the East of England, the Midlands, and beyond, however, struggles with frequent delays and congestion due to low capacity. East Anglia is home to significant economic cities such as Cambridge and Norwich but suffers from poor transport infrastructure compared to other regions due to limited accessibility. Rail improvements would ensure smoother operations along these key routes, which in turn would help foster
‘If the proposed changes outlined in the EEH report are made, it is approximated that carbon emissions will be reduced by 1.7 million tonnes of CO2 over the next 60 years and congestion will be alleviated by 5.6 million hours per year.’
economic prosperity, attract new businesses, encourage investment and create new job opportunities.
If modifications to the current infrastructure are not made, then the junction’s lack of capacity will continue to hinder and limit its vast potential. If capacity upgrades are implemented at Ely Junction enabling higher levels of freight to be accommodated, trains could run more frequently and at higher speeds, reducing travel times significantly and encouraging modal shift from private vehicles to rail. This would result in reduced road congestion and lower carbon emissions – rail transport is

Logistics UK is one of the UK’s leading business groups, representing logistics businesses which are vital to keeping the UK trading, and more than seven million people directly employed in the making, selling and moving of goods. With Covid-19, Brexit, new technology and other disruptive forces driving change in the way goods move across borders and through the supply chain, logistics has never been more important to UK plc. Logistics UK supports, shapes and stands up for safe and efficient logistics, and is the only business group which represents the whole industry, with members from the road, rail, sea and air industries, as well as the buyers of freight services such as retailers and manufacturers whose businesses depend on the efficient movement of goods. For more information about the organisation and its work, including its ground-breaking research into the impacts of Covid-19 on the whole supply chain, please visit logistics.org.uk.
widely recognised as a greener alternative to road or air travel, contributing to lower carbon emissions and improved air quality.
In Spring 2023, England’s Economic Heartland (EEH) and Transport East published their report ‘Keeping Trade on Track’, outlining the importance of delivering the Ely Area Capacity Enhancement scheme. Logistics UK is urging government to recognise the importance of the upgrades and act upon the points highlighted in this report to support growth in global trade. Ely supports businesses right across the country and is critical to the UK’s growth and role in global trade. While Logistics UK recognises that the cost of upgrading Ely Junction is estimated at £466 million, this is relatively low for rail network improvements and the benefits outweigh the costs tenfold, with research from EEH showing a return of £4.89 for every £1 invested.
Encouraging more freight to move to rail from less environmentally friendly modes where possible will help contribute to the UK achieving net zero carbon emissions by 2050. Improving capacity on the railway line will align with the country’s net zero agenda and has the potential to remove 98,000 HGVs off the road every year. In addition, more capacity will enable 2,900 extra freight services operating to and from Felixstowe, Britain’s biggest and busiest rail freight port. At Present, 70 per cent of containers arriving through the port are destined for a high-concentration belt of distribution
NEWS IN BRIEF
460,000 RESPONSES TO TICKET OFFICE CONSULTATION
One week before the public consultation on proposed changes to ticket offices ends, Transport Focus and London TravelWatch have received more than 460,000 responses. Independent watchdogs, Transport Focus and London TravelWatch are reminding passengers to respond to proposals before the deadline.
The consultation on train operator proposals to close the majority of ticket offices in England ended on Friday 1 September, following an extension on 26 July. Over the coming weeks, the two watchdogs will continue to analyse carefully the train operator proposals and consultation responses before they report their decisions on whether to support or object to the plans.
hubs stretching across the Midlands and the North of England. Currently, Ely Junction adds costs and carbon to every single container being moved out of the UK, but if the proposed changes outlined in the EEH report are made, it is approximated that carbon emissions will be reduced by 1.7 million tonnes of CO2 over the next 60 years and congestion will be alleviated by 5.6 million hours per year. Furthermore, by enhancing rail capacity it will enable Ely Junction to accommodate more trains, leading to increased rail freight services and passenger transport.
This will benefit the sector by facilitating the transfer of goods from road to rail, reducing the carbon emissions attributed to the logistics sector as a single freight train removes up to 129 HGV movements, with an average diesel-hauled freight service producing 76 per cent less CO2 per tonne than road transport.
Alongside its net zero deadline, government is also prioritising its levelling-up initiative aimed at reducing regional disparities and boosting economic opportunities across the country. Expanding rail capacity at Ely Junction will align with this initiative by boosting regional connectivity and accessibility which in
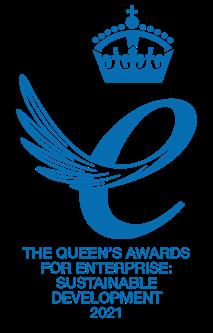
turn will foster stronger links with the rest of the UK. The Ely Area Capacity Enhancement (EACE) programme, developed by Network Rail, covers the railway through Ely and several lines radiating across Cambridgeshire, Norfolk and Suffolk with the aim to boost network capacity by nearly a third per hour. Efficient and reliable transportation infrastructure plays a fundamental role in supporting economic growth, and increased capacity will significantly elevate the amount of rail freight on the network, allowing crucial counties such as Norfolk and Suffolk the ability to unleash their full economic potential.
Logistics UK is in full support of Ely Junction increasing its rail capacity via the recommended infrastructure improvements to prevent further delays and remove the restrictive barriers for freight at this bottleneck. These modifications will significantly support economic growth, attract investment and create much needed job opportunities to help plug the sector’s ongoing skills gap. Logistics UK will continue to work with its members to ensure the rail sector has the infrastructure it requires to grow and accommodate the UK’s freight needs.
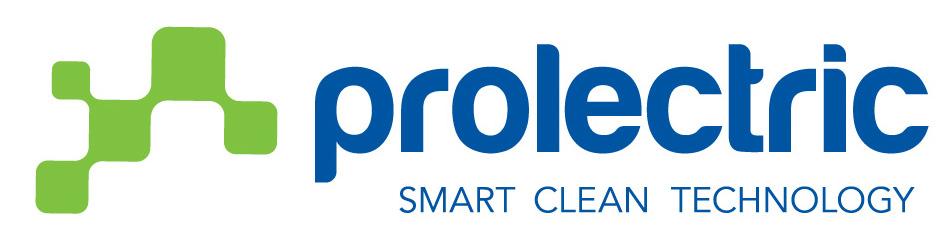
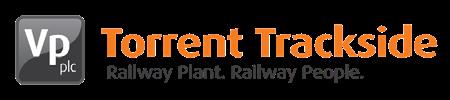


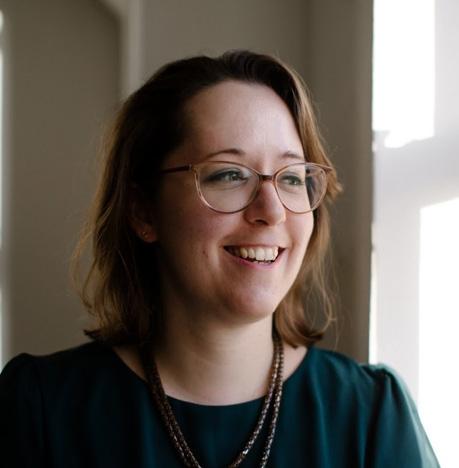
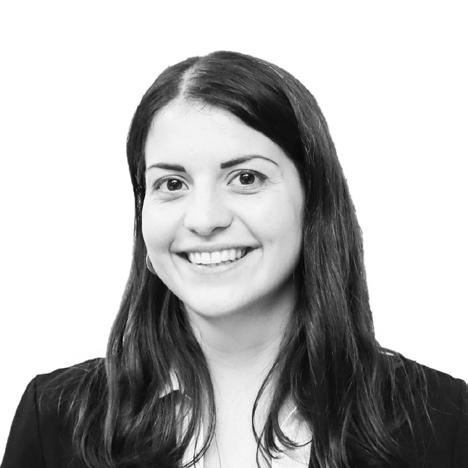
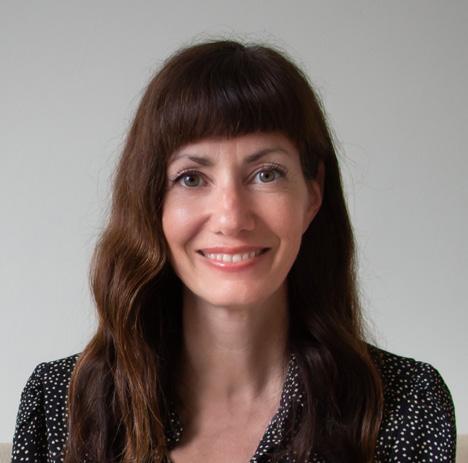
Driving Gender Inclusion in Transport and Mobility
The transport and mobility sector plays a crucial role in shaping the world we live in, yet it remains one of the most gender imbalanced industries
Despite women comprising 47 per cent of the total workforce in the UK, only 20 per cent of employees in the transport industry are women. This gender gap can lead to missed opportunities for businesses and hinder the industry’s progress towards a more sustainable future.
Motivated to help the sector become more diverse and inclusive, Women in Mobility UK (WiM UK) organised an inperson workshop on ‘Improving inclusion in the workspace in London’. The key aim of the workshop was to explore ways in which public and private sector companies working in transport and mobility can improve gender inclusion in the workplace. The workshop had 20 participants from across the sector.
The topic was broken down into three areas:
1. What works well?
2. What stops change?
3. The ideal, inclusive workplace – what does it look like?
It was mentioned throughout the workshop that a holistic approach is needed. Leadership teams need to educate themselves and foster an environment of trust and learning, provide budgets, general resources and enshrine inclusion in their policies. Clear KPIs and targets can help the organisation evolve and move forward.
What works well?
A lot of positive, tried and tested policies and initiatives were mentioned and can be recommended. Participants highlighted the importance of mentorships, knowledge
sharing, women’s groups, and buddy systems. Involving men in the conversation to foster better understanding of issues and having male champions within an organisation were also deemed essential. Regarding recruitment, inclusive job descriptions were a highlight, while for existing employees regular anonymous satisfaction surveys help ensure employers understand and listen to their employees. Participants also pointed to transparency about an organisation’s values.
What stops change?
Lack of awareness, accountability and resources were raised as blockers, for example a lack of budget, fear of change, poor policies, few women in senior management. Some applied to all sizes or types of organisations, while some impacted particular areas, such as for many startups and SMEs there is no established HR department to oversee change.
The ideal, inclusive workplace – what does it look like?
Participants in the workshop identified a variety of aspects that can make a workplace more inclusive, such as training, mentors, flexibility in working hours and location, and equal parental leave policies. Some priorities varied by age or career stage, but were agreed to benefit all at some point, even if they are not directly impacted (e.g. the need for fair parental leave even when not all choose to have children).
The full report can be accessed here: https://www.womeninmobility.org.uk/ resources
Annie Reddaway, Olga Anapryenka and Sandra Witzel are co-founders, WiM UK
Women in Mobility UK
WiM UK works to raise the visibility of women in the UK transport sector and improve diversity and inclusivity across all aspects of the mobility ecosystem. The network is run by three mobility enthusiasts with a wealth of experience, drive and determination to make our planet a better, more inclusive place.
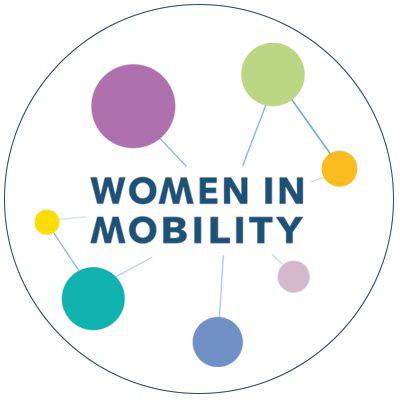
NEWS IN BRIEF
NEW BRIDGE FOR BALGRAY RESERVOIR WALKERS
A £2.9 million project to replace a bridge on a key walking route over the Neilston railway line has taken a big step forward. That’s after the replacement bridge deck was lifted into position at the start of this week. It's the first time this has happened in Scotland, with engineers working around the clock from the early hours of Sunday until Tuesday morning.
TWO RECENT TENDERS FOR ROLLING STOCK
The Railway Industry Association (RIA) has welcomed two recent tenders for rolling stock; up to 70 new or refurbished multiple units for Chiltern Railways and 450 new multiple units for Northern Trains. This comes following a recent RIA report, The UK Rolling Stock Industry: Making 2023 the year of opportunity not crisis, which highlighted the risks to the UK supply chain if orders for new rolling stock were not forthcoming.
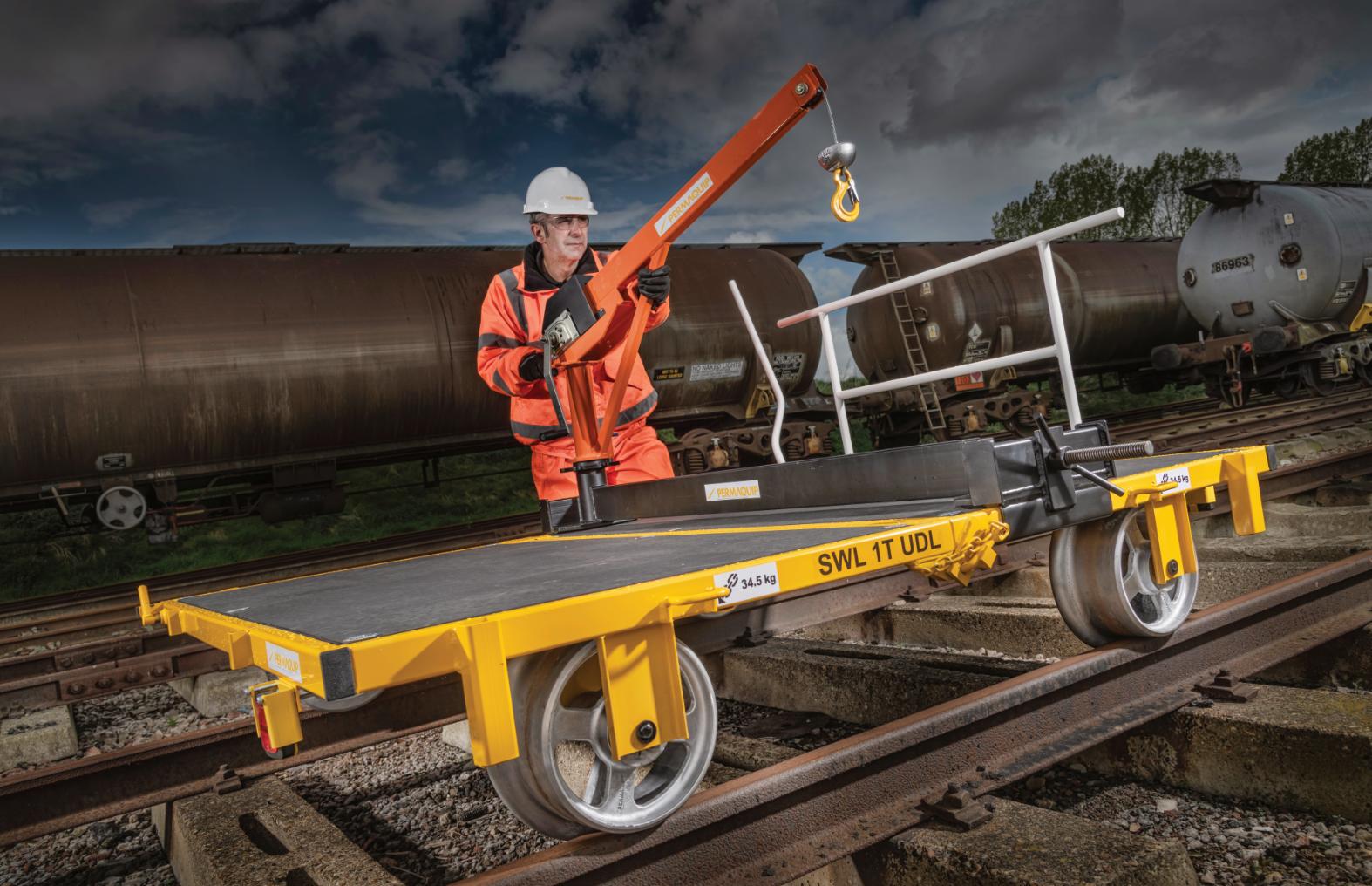
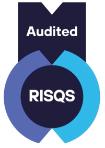

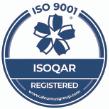
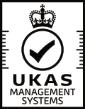
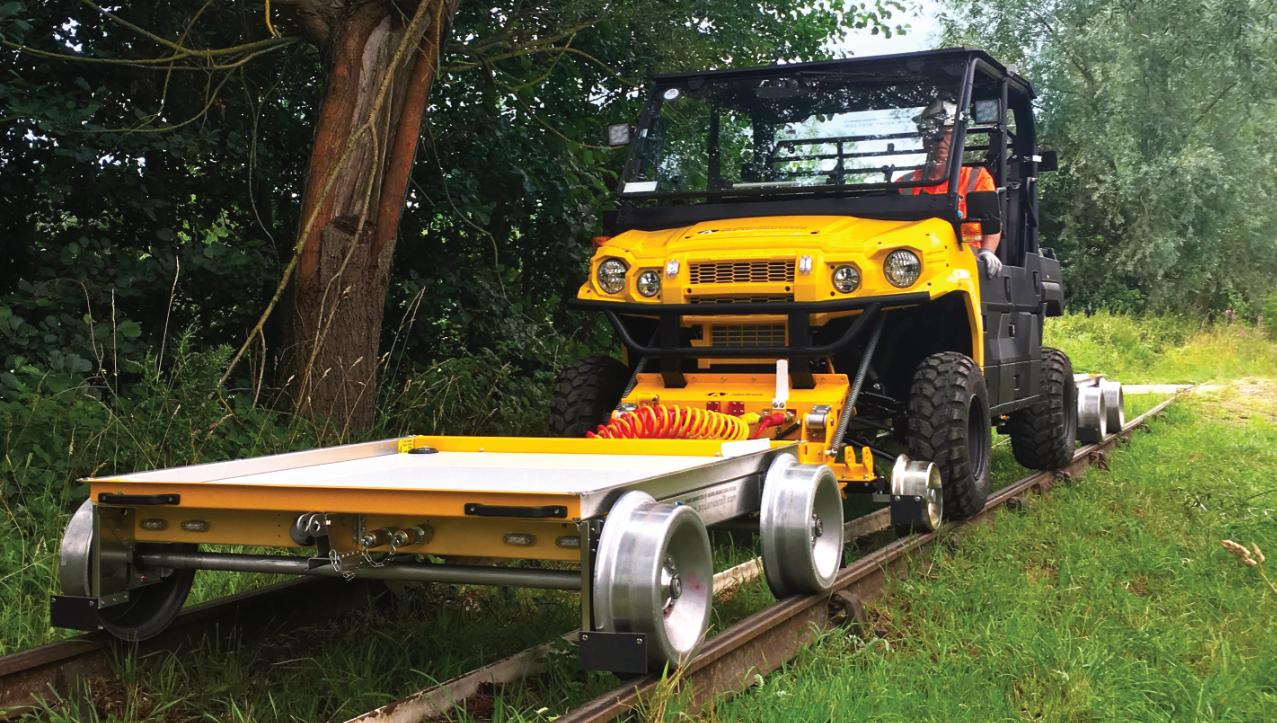
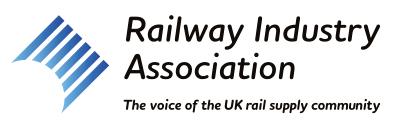
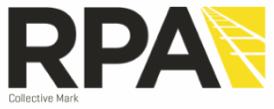
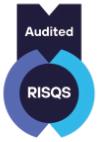
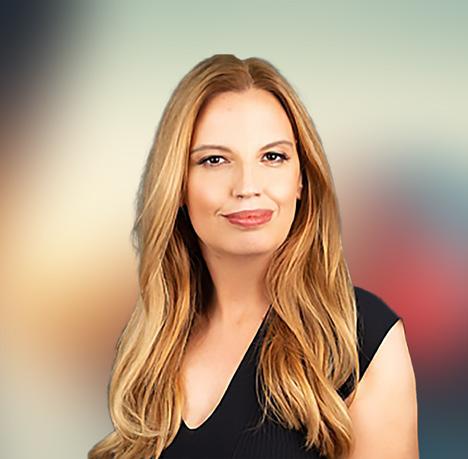
Samantha Greer, Senior Consultant Commercial Solicitor at Setfords explains how it can affect your business
Data Protection
Samantha Greer, Senior Consultant Commercial Solicitor at Setfords explains how it can affect your business
Data protection probably isn’t the most glamorous of subjects to be on your reading list, but consequences of noncompliance can have huge implications on businesses in the rail sector, particularly when engaging with Public Sector clients. It has been a little quiet in the media about the knock-on effect of Brexit to the Data Protection laws in the UK, so let’s refresh ourselves on where things stand now.
Since the UK left the European Union, the UK created the UK GDPR legislation which is a retained EU law version of GDPR ((EU) 2016/679 UK GDPR) and the Data Protection Act 2018 and is now a single legislative regime for general processing of personal data that applied after the Brexit transition period.
If you are considering working with clients or suppliers internationally and personal data is being ‘processed’ then there are strict rules to follow to ensure your business is compliant with UK laws and in some cases, the local laws of the country where the personal data is being transferred to.
Adequacy decisions
The secretary of state (SoS) has the power to amend a list of permitted countries that appear on the ‘List’. The List names a number of countries decided upon by the Secretary of State as having sufficient protections in place for UK personal data to be sent to. Sufficient protections such as local laws on data protection are very similar to those in the UK, and there are sufficient judicial remedies to enforce any breaches of data.
If you are sending any personal data of your employees, whether it is the name of your commercial manager, phone numbers, identity or pockets of information likely to give rise to the identity of a certain
individual, then you would need to ensure that that jurisdiction has been afforded an adequacy decision by the SoS.
Every four years, the SoS is obliged to review the List and may remove any jurisdiction if they feel that those jurisdictions do not have sufficient protections to protect UK citizens’ data. As such, it might be worth checking with your Data Protection Officer to ensure this has been reviewed internally. Ensure that you map your flows of international data and your privacy policies have been updated to reflect any changes.
The List
You do not need to take any other actions if you are sending personal data to countries within the EEA/EFTA, because the EEA/ EFTA member states have an adequacy decision from the SoS. For example, if you are entering into a collaborative bid with a partner in Spain but you need to transfer employee data to Spain to do so (unless this is in relation to immigration control).
Under the Adequacy Decision, there are no further protections needed to be carried out as the protections in Spain are sufficient enough to safeguard UK citizens. However, what if you were to send personal information over to the US? One would think that given the close ties that the UK has with the US government, this would be okay, right? Wrong.
At the moment, the UK does not have an adequacy decision by the SoS on transfers to the US, so in order to transfer data there, British companies need to show that they have adequate protections in place.
Transferring data to a country without an adequacy decision is called a ‘restricted transfer’. There are two types of Adequacy Decision: a full or a partial decision. Japan is considered a partial decision because it only relates to private sector businesses (not public) and Canada only covers data that is
subject to Canada's Personal Information Protection and Electronic Documents Act –not all personal data falls under this Act.
In the news we have heard a number of trade deals taking place involving the UK, therefore, we are to expect a shift in the number of adequacy decisions in the near future.
If there are no UK adequacy regulations about the country, territory, international organisation, or particular sector in a country or territory for your restricted transfer, you should then find out whether you can make the transfer subject to 'appropriate safeguards'.
There is a list of appropriate safeguards in Article 46 of the UK GDPR. Each ensures that both you and the receiver of the restricted transfer are legally required to protect people’s rights and freedoms about their personal data. We refer to these as Article 46 transfer mechanisms. A description of each Article 46 transfer mechanism is set out below.
Have you undertaken a transfer risk assessment?
Before you may rely on an Article 46 transfer mechanism to make a restricted transfer, you must be satisfied that the relevant protections in the UK GDPR are not undermined for people whose data is transferred.
You should do this by undertaking a risk assessment, which takes into account the protections contained in your selected Article 46 transfer mechanism and the protection afforded to data subjects in the destination country.
If your assessment is that the Article 46 transfer mechanism does not provide the required level of protection, before making the transfer you must take extra steps and protections so that it does provide the right level of protection. This assessment is undoubtedly complex in many situations.
An Article 46 transfer is likely to include satisfactory evidence that it is covered by either:
• A legal instrument – you can make a restricted transfer if it is covered by a legal instrument between public authorities or bodies containing ‘appropriate safeguards’. The appropriate safeguards must include enforceable rights and effective remedies for people whose personal data is transferred.
• UK Binding Corporate Rules (UK BCRs) – the concept of using BCRs to provide appropriate safeguards for making restricted transfers was developed under EU law and continues to be part of UK law under the UK GDPR, specifically Article 47.
• Standard data protection clauses – you can make a restricted transfer if you and the receiver have entered into a contract incorporating standard data protection clauses recognised or issued in accordance with UK data protection law. Standard data protection clauses
impose contractual obligations on the sender and the receiver, and grant rights to people whose personal data is transferred. People must be able to directly enforce those rights against the sender or receiver, or both. However, I caution businesses from relying solely on standard data protection clauses alone if there is a restricted transfer — see the Schrems II case below.
• Enter into an IDTA with Addendum – the IDTA and Addendum were laid before Parliament on 2 February 2022 and came into force on 21 March 2022. If you relied on the old EU SCCs as set out above before 21 September 2022, then these will continue to apply until 21 March 2024, at which point they cease to be satisfactory and you must enter into a new IDTA with addendum for any restrictive transfer.
There are eight exceptions to the rules on restricted transfers under Article 49:
1. You have the explicit consent of the person the transferring data is about.
2. You have a contract with the person the transferring data is about, and the restricted transfer is necessary so you can carry out your obligations in that contract. Or, the restricted transfer is necessary so you can carry out pre-contract steps as requested by that person.
3. The restricted transfer is necessary for you to enter into a contract or to carry out your obligations under a contract. And that contract benefits the person the transferring data is about — in this case the contract is not with that person.
4. The restricted transfer is necessary for important reasons of public interest.
5. 5. The restricted transfer is necessary to establish whether you or someone else has a legal claim or defence, to make a legal claim or to defend a legal claim.
6. The restricted transfer is necessary to protect someone’s vital interests— this may or may not be the person the transferring data is about. To use this exception, the person the transferring data is about must be physically or legally incapable of giving their consent to the restricted transfer.
7. The restricted transfer is from a public register and meets the relevant legal requirements relating to access to that public register.
8. The restricted transfer is a one-off transfer which is necessary to meet your compelling legitimate interests.
In the example I gave above regarding a collaboration with a party which would be deemed a restricted transfer, it may be possible to rely on Article 49: ‘so that you can carry out any pre-contract step as requested by that person’. That said, I do strongly suggest you take sensible legal advice if relying on any exception to the general prohibition on restricted transfers.
Exceptions 2, 3, 4, 5, 6 and 8 contain the word ‘necessary’. This does not mean that the transfer has to be absolutely essential. However, it must be more than just useful and standard practice. It must be a targeted and proportionate way of achieving a specific purpose. The exception does not apply if you can reasonably achieve the same purpose by some other means. An example of this could be that you are looking to set up an agreement with your Bond holders and therefore one could argue that while it is not absolutely essential, it forms part of standard practice to work with international financial institutes.
It is not enough to argue that the transfer is necessary because you have chosen to operate your business in a particular way. The question is whether the transfer is objectively necessary and proportionate for the stated purpose, not whether it is a necessary part of your chosen methods.
• The reason why the transfer is needed;
• The alternatives available;
• The protections which will be in place; and
• The potential harm to people.
Schrems II
Schrems II was a fascinating case highlighting the importance of making sure that the protections in place do what each country thinks it is doing. A lawyer and privacy activist Maximillian Schrems sought to challenge Facebook that it deprived users of the rights and protections they enjoy under the EU's privacy law, the General Data Protection Regulation (GDPR), by treating consent as a contract that empowers it to use their data to deliver targeted ads.
Privacy Shield framework between the EU and the US was supposed to provide for the possibility of lawful transfer of personal data from the EU to the US, while ensuring a strong set of data protection requirements and safeguards. On the basis of this framework, EU (and later European Economic Area, EEA) businesses were able to (then) legally transfer personal data to US-based companies that were listed in the Privacy Shield list. However, on July 16, 2020, the ECJ ruled that Commission Decision 2016/1250 on the adequacy of the protection provided by the EU-US Privacy Shield was invalid on account of invasive US surveillance programmes, thereby making transfers of personal data on the basis of the Privacy Shield Decision illegal.
The CJEU said: ‘The Privacy Shield does not provide adequate protection, and invalidated the agreement. The court also ruled that European data protection authorities must stop transfers of personal data made under the standard contractual clauses by companies, like Facebook, subject to overbroad surveillance. This decision has significant implications for U.S. Companies and for the US Congress because it calls into question the adequacy of privacy protection in the United States.’
Therefore, it was no longer good enough for data exporters and data importers simply to include the SCCs in their contracts. They must also now assess whether the SCCs will be effective in protecting the data once transferred to a third country. That requires the data exporter, with the help of the data importer, to review the laws and practices in the third country to assess whether they undermine the effectiveness of the SCCs. If they potentially do, then the data exporter and the data importer have to assess whether ‘supplementary measures’ are necessary to ensure that the transferred personal data will nevertheless enjoy ‘essentially equivalent’ protection as required by the GDPR.
Are the EU and US friends again?
It appears that Max did a good job! On 10 July 2023 the European Commission adopted its adequacy decision for the EUUS Data Privacy Framework. On the basis of the adequacy decision, personal data can now flow freely from the EU to companies in the US that participate in the Data Privacy Framework.
The adequacy decision followed the adoption of Executive Order on ‘Enhancing Safeguards for United States Signals Intelligence Activities’ by President Biden. This was in addition to a regulation issued by the US Attorney General following an agreement between President Von de Lyn for the EU member states and President Biden on 22 March 2022. These instruments introduced new binding safeguards to address the points raised by Court of Justice of the European Union in its Schrems II decision of July 2020, ensuring that data can be accessed by US intelligence agencies only to the extent necessary and proportionate. It also established an independent and impartial redress mechanism to handle and resolve complaints from Europeans concerning the collection of their data for national security purposes.
These safeguards also facilitate the use of other tools, such as standard contractual clauses and binding corporate rules as mentioned above.
Has the UK lost out on this opportunity?
Although the UK has been working hard over the last two years in technical discussions, progress was made on 8 June 2023 whereby a ‘commitment in principle’ was agreed between senior officials of the US and UK. Here, a data bridge between the two countries (called the ‘UK-US Data Bridge’) was created for transatlantic flows of personal data, something which could drive innovation, particularly in the rail sector. So we may see a UK version of the EU/US Data Framework – provided US businesses meet the criteria for acceptance of UK personal data.
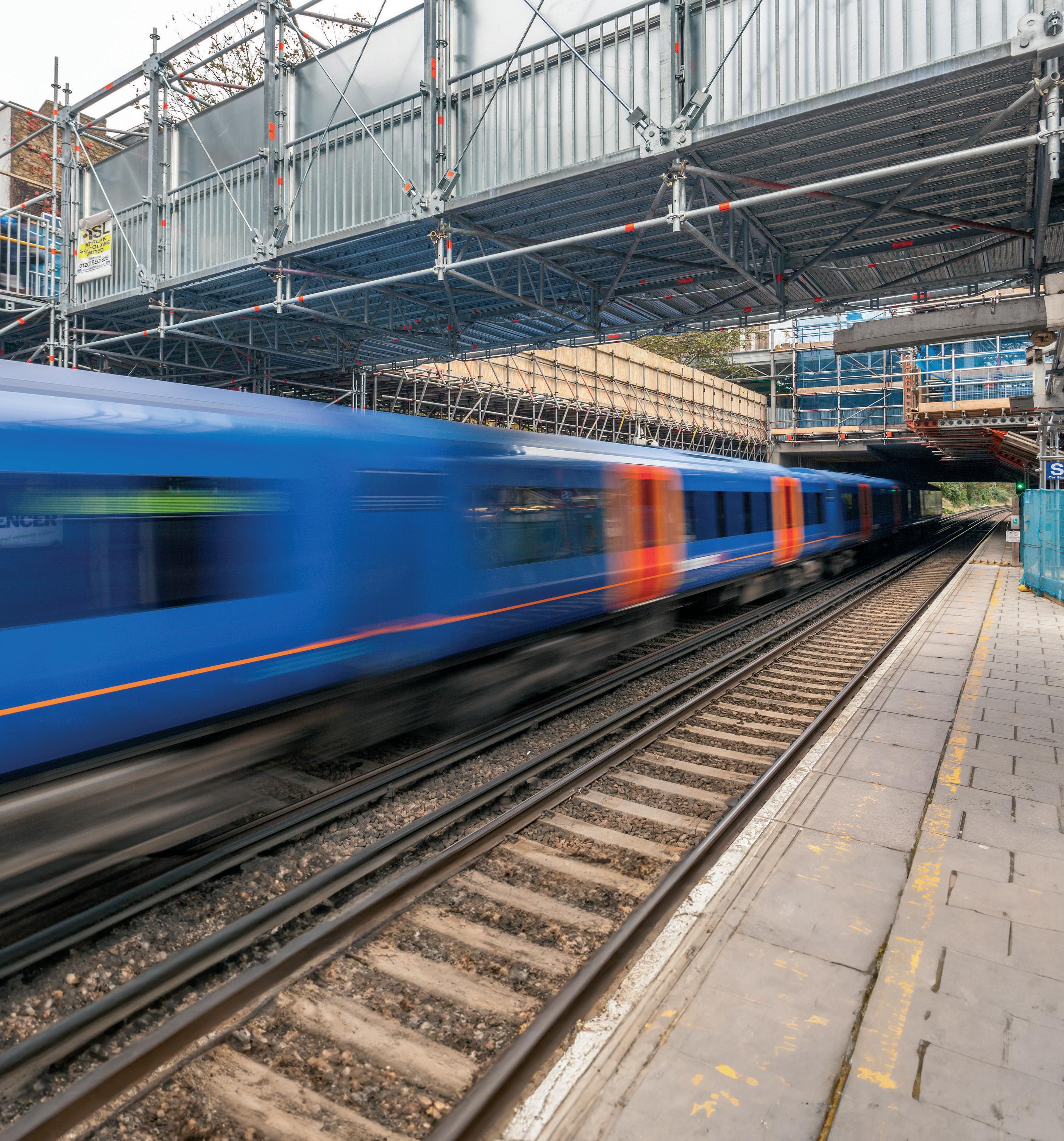
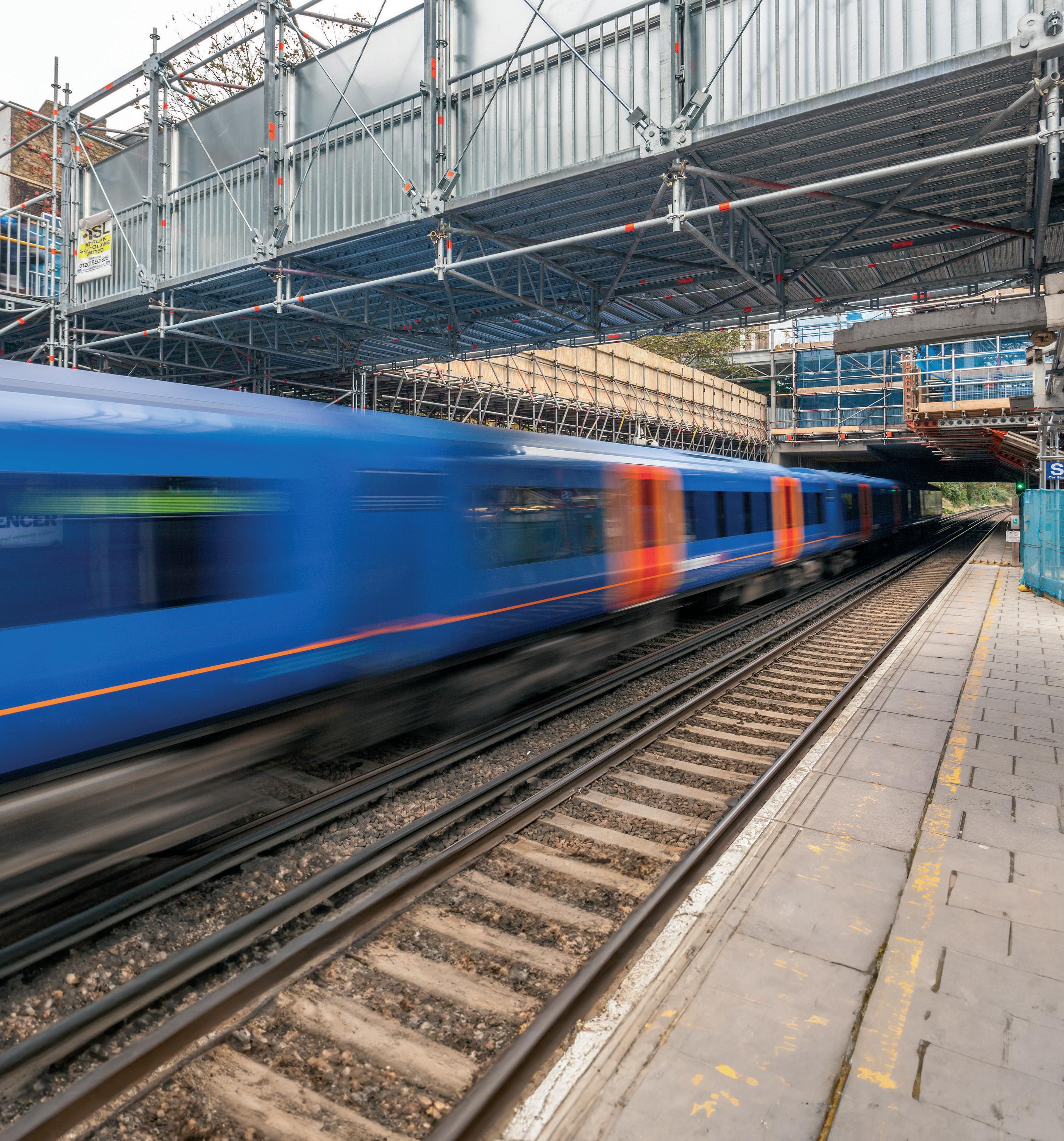
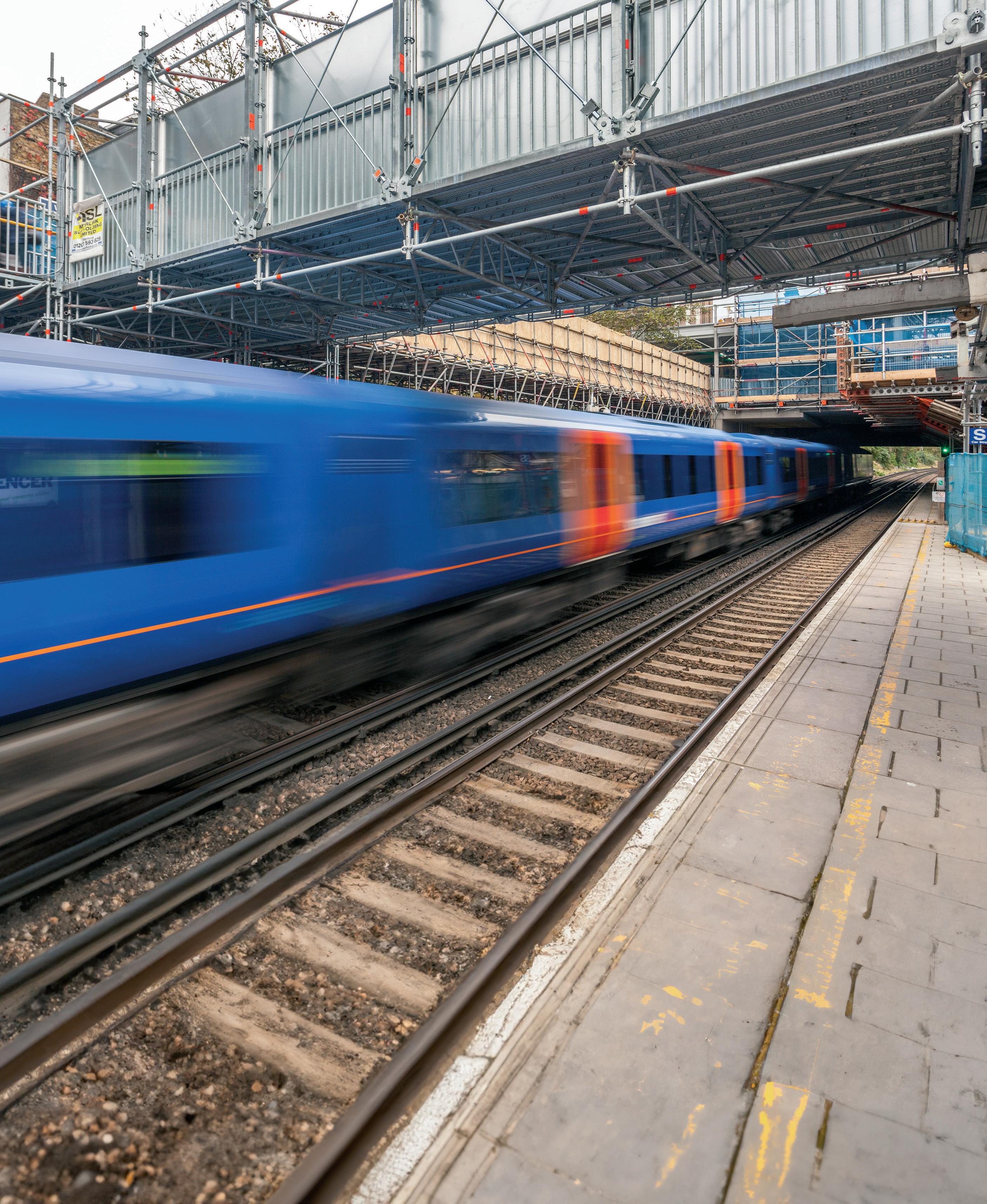

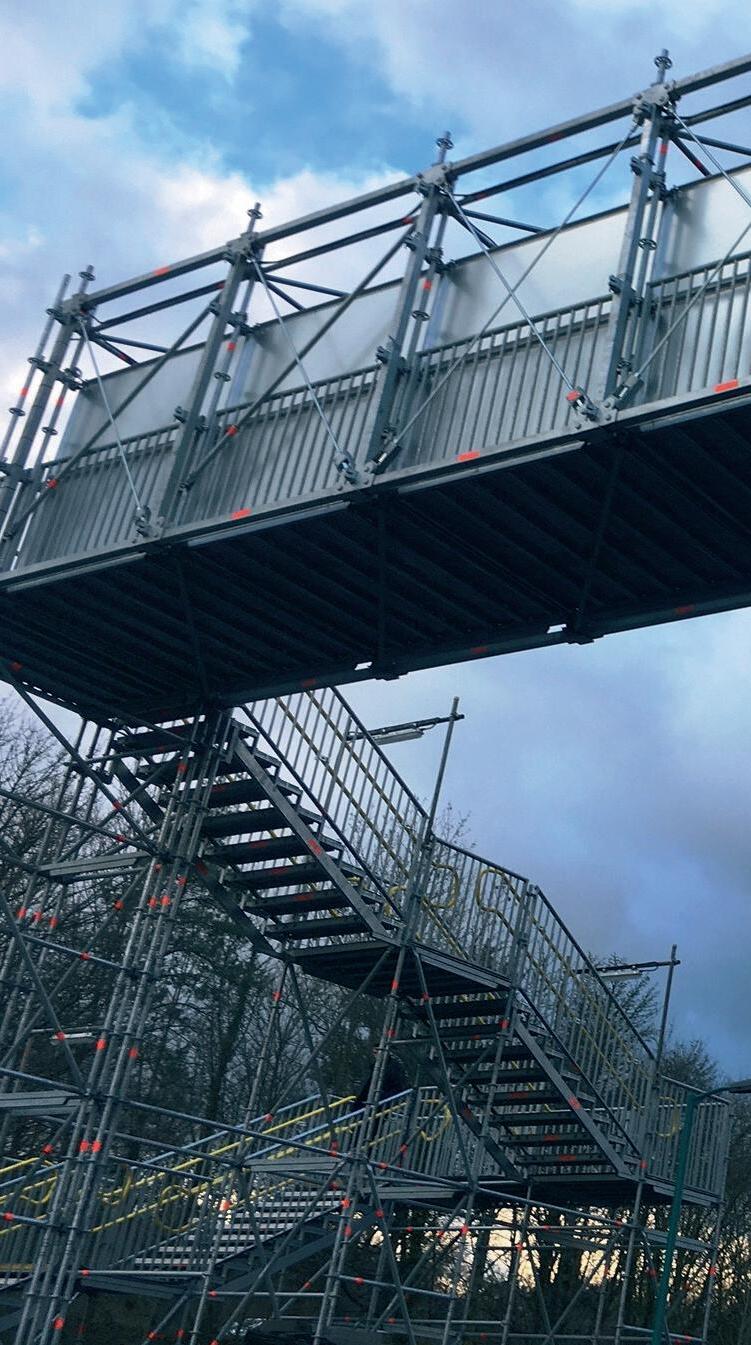

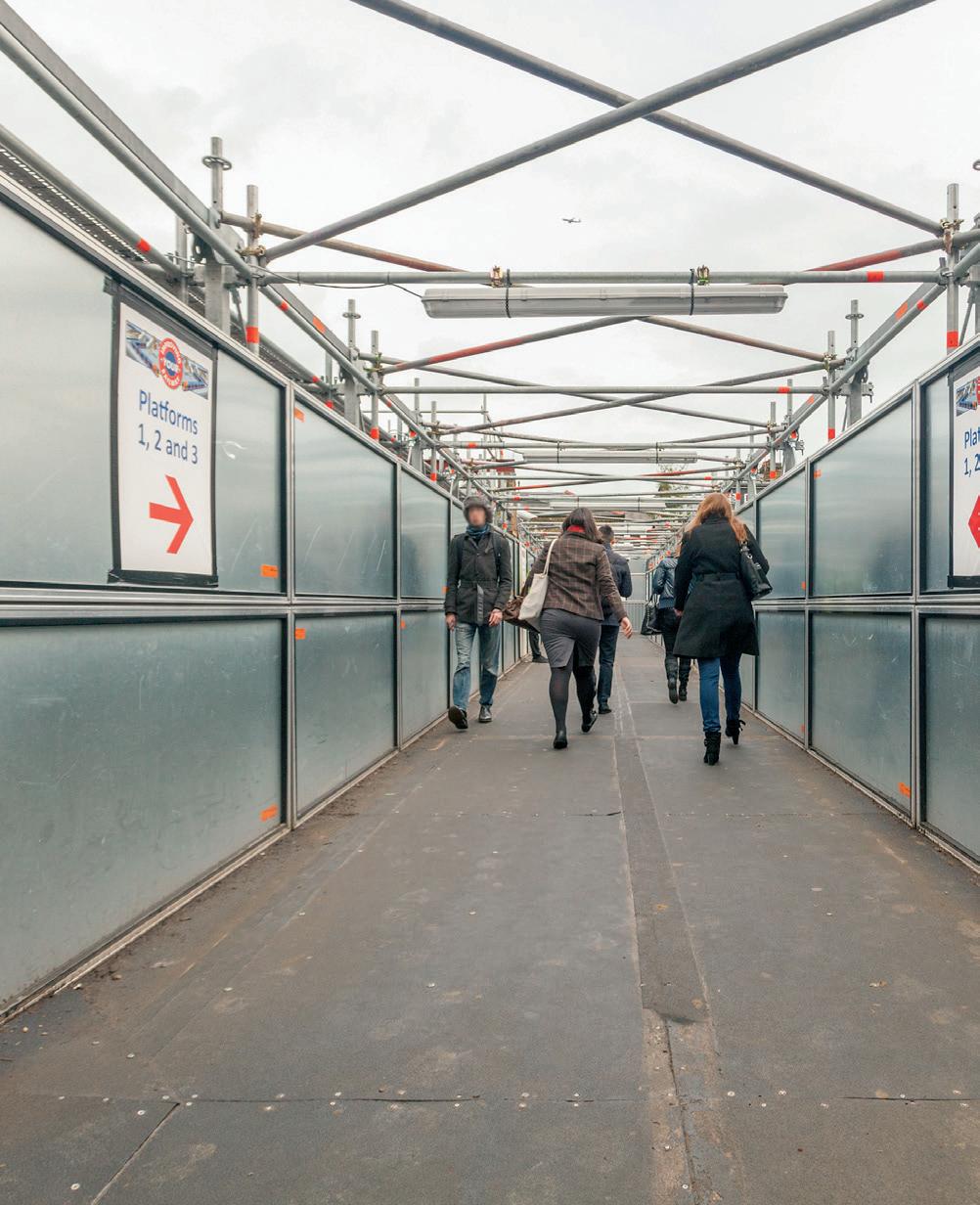
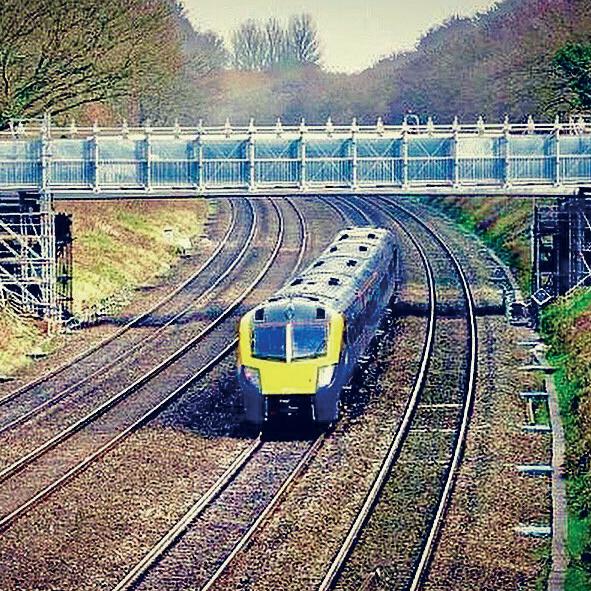
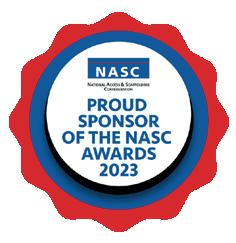
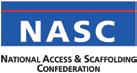
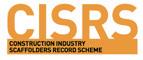

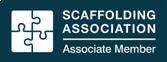

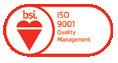











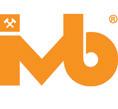
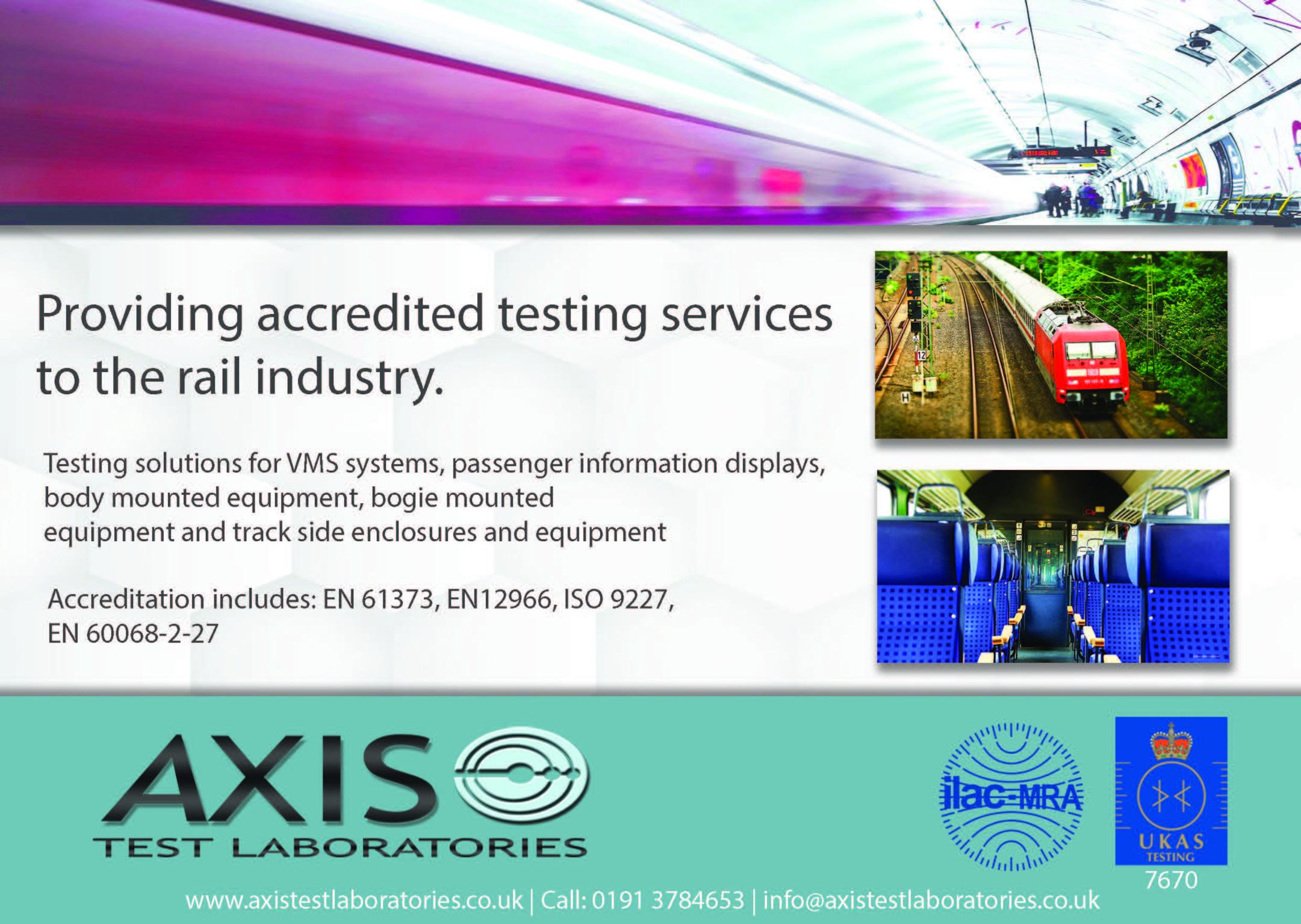
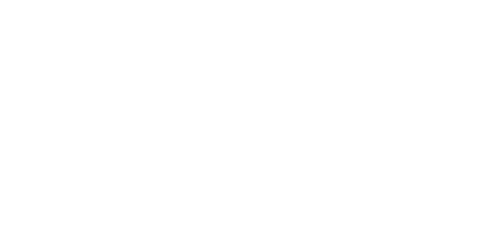
ENGINEERING A BETTER FUTURE FOR OUR PLANET AND ITS PEOPLE
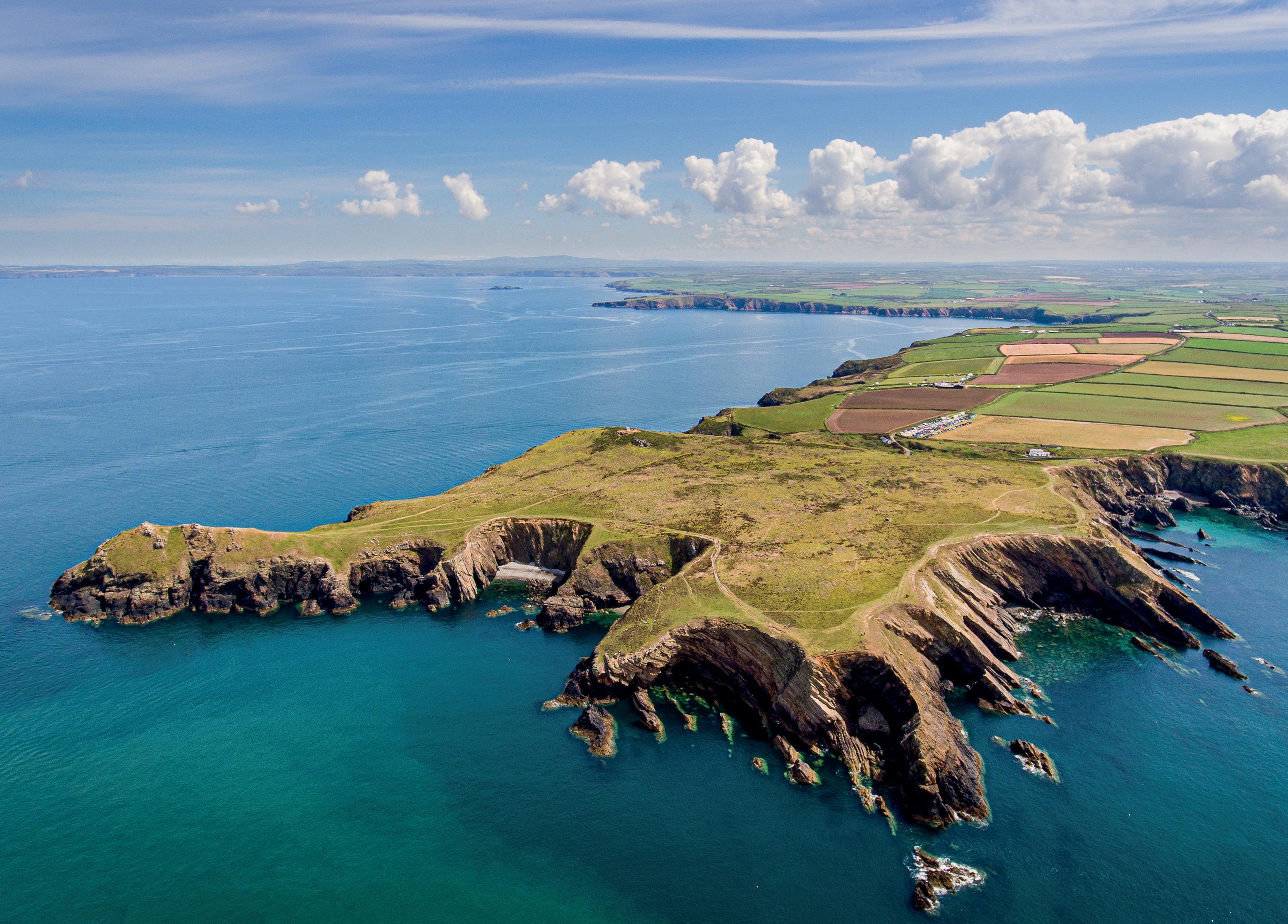
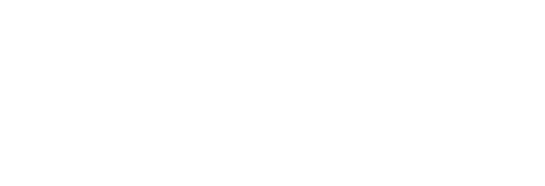
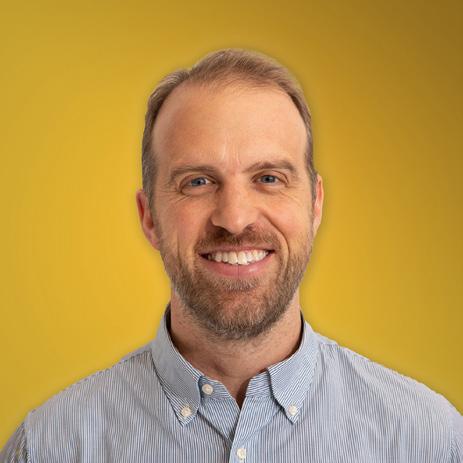
Colin
Bryce is Managing Director of Cobry, a Glasgow-based digital transformation company and Google Cloud partner.
Is your Business being Crushed by Big Data?
Don’t worry, help is at hand says Colin Bryce, Managing Director of Cobry
From being the preserve of actuaries and statisticians a generation ago, suddenly we have all become big data handlers. Even the smallest of businesses and organisations are now expected to handle and organise flows of information from multiple channels every day and, for many, it can feel overwhelming.
The reality is that it’s only going to intensify. By 2025, it is estimated that we will be generating 175 zettabytes – or 175 trillion gigabytes – of data globally every year.
Since one gigabyte is equal to one thousand million (109) bytes, 175 trillion gigabytes is expressed as 175,000,000,000,000,000,000,000 or 17.521 bytes, representing a fivefold increase in data generation since 2018, and 180 times more than was generated 20 years ago.
To put that figure into some kind of perspective, the Apollo 11 moon landing was achieved using around 4,000 bytes of computing power. A modern smartphone typically uses four gigabytes of randomaccess memory (RAM).
Big-data technology is transforming almost every industry by creating actionable information and, because of its effectiveness in helping to generate new business, even small companies, usually slow to adopt new technologies, are coming on board, helping them to leverage up 15 per cent more sales, according to a recent study.
An increasing amount of data is already generated by artificial intelligence (AI), to map the performance and output of the growing number of digital things in our lives.
As 5G communications become more widely adopted, these will soon include driverless transport, Internet of Things (IoT) devices including sensors in our bodies, homes, factories, and cities, as well as high-resolution content for 360 video and augmented reality.
Companies and organisations that are early adopters of big data analysis tools are more likely to benefit from reduced costs –including by optimising pricing strategies – increased operational efficiency and an improved ability to identify weaknesses and failures in their operations.
They will also be better able to design new products and services, conduct 360-degree customer reviews and identify and prevent fraud.
As a provider of Google management tools and services, the main bread and butter of our business has, until now, been platforms that help our clients handle documents, email files, video calls and other communication tools.
We estimate that, within two years the bulk of our work will be helping those same businesses to cope with the enormous flood of data they can expect to receive.
All companies have data; most have a lot of data and quite often the way it is organised is chaotic or not fully thought through. There’s not much governance and thought currently give to how that data is collected and organised and shared.
Our first step with new clients is to help them collect data in a consistent way – which means it’s easier to make sense of – and then to feed it through into what are called data lakes. We effectively pipe all of their data, from different sources, into one place, so that it can be more easily interrogated.
‘By 2025, it is estimated that we will be generating 175 zettabytes – or 175 trillion gigabytes – of data globally every year.’
Depending on the business, data can come from a range of different sources. Here are just some of the different types of intelligence that is routinely gleaned about its customers.
• Personal data – includes information such as their gender, occupation, age, and social class as well as non-personal material such as their IP address, web browser cookies and IDs of devices including laptops and mobile phones.
• Engagement data – this helps businesses to understand how their customers interact with their website, mobile phone apps, text messages, social media pages, emails, paid ads, and other customer service routes.
• Behavioural data – provides companies with transactional details, including purchase histories, product usage information, such as repeat custom as well as qualitative data, such as mouse movement information.
• Attitudinal data – encompasses metrics on items such as consumer satisfaction, buying criteria, product desirability and more.
Giving all that data structure and coherence helps businesses to better understand what it means, to visualise it and to create dashboards, charts and graphs so that nonexperts are able to see and understand what is happening with their customers.
Providing them with live intelligence and insights into customers habits and behaviour, means they can make better informed, data-driven decisions in a useful way, rather than flying blind.
Some businesses that have yet to perform any data analyses often worry that they don’t have enough information to analyse. Most have more information than they can handle and, as the business grows, big-data systems become more relevant.
Few business owners can expect to gain any meaningful insight by reviewing data manually; they need the right tools and methods provided for them and explained by a specialist.
If they don’t have the budget for a fulltime analyst, hiring a consultant who can point them in the right direction is a useful alternative.
As well as creating statistical summaries of their data analyses, an expert will also help them to understand what’s causing the
NEWS IN BRIEF
SCOTRAIL LAUNCHES INSPIRATION HUB
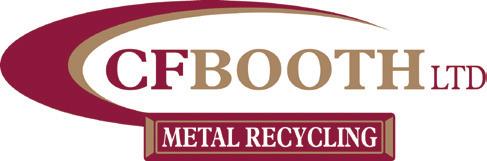
After they have analysed their data, they will need to have it presented in a way that non-technical staff members can comprehend and use to make informed decisions. Again, Google has a range of data visualisation tools that will work with their current technologies.
CF Booth Ltd was established in 1920 by Clarence Frederick Booth and since that time has continued to be passed down through the generations of the Booth family.
ScotRail is launching a new campaign, ‘Go by train’, to encourage more people to choose rail when planning days away in Scotland. The train operator’s new Inspiration Hub is an exciting new online resource with hundreds of ideas for things to do, upcoming events, discounts, and offers all within easy reach of more than 300 train stations across Scotland.
‘All companies have data; most have a lot of data and quite often the way it is organised is chaotic or not fully thought through.’
The company has been associated with the scrapping of diesel and electric locomotives since the 1960s and has an excellent reputation as one of the largest rolling stock recyclers in the UK, winning nationally released tenders from several of the main rail operating companies.
patterns in their data. Business owners and senior managers will also need to know what may happen in the future and technologies such as predictive and prescriptive analytics can help them to achieve that.
It’s generally accepted that Big Query is the best tool for gathering data and they also have arguably the best data visualisation tool in Looker. It’s more than a visualisation tool, it also takes care of governance and sharing of data.
The head office is located in Rotherham, South Yorkshire at Clarence Metal Works with the company’s gantry cranes and three derrick cranes making the site quite distinctive.
Everyone has their strengths in different parts of the cloud but I think everyone would accept that Google has the lead in data.
hundreds of ideas, all showing the nearest train station, details on train tickets, and other information, the Hub aims to make it as easy as possible to help plan an exciting day trip or short break in Scotland.
Using real-time analytics can provide
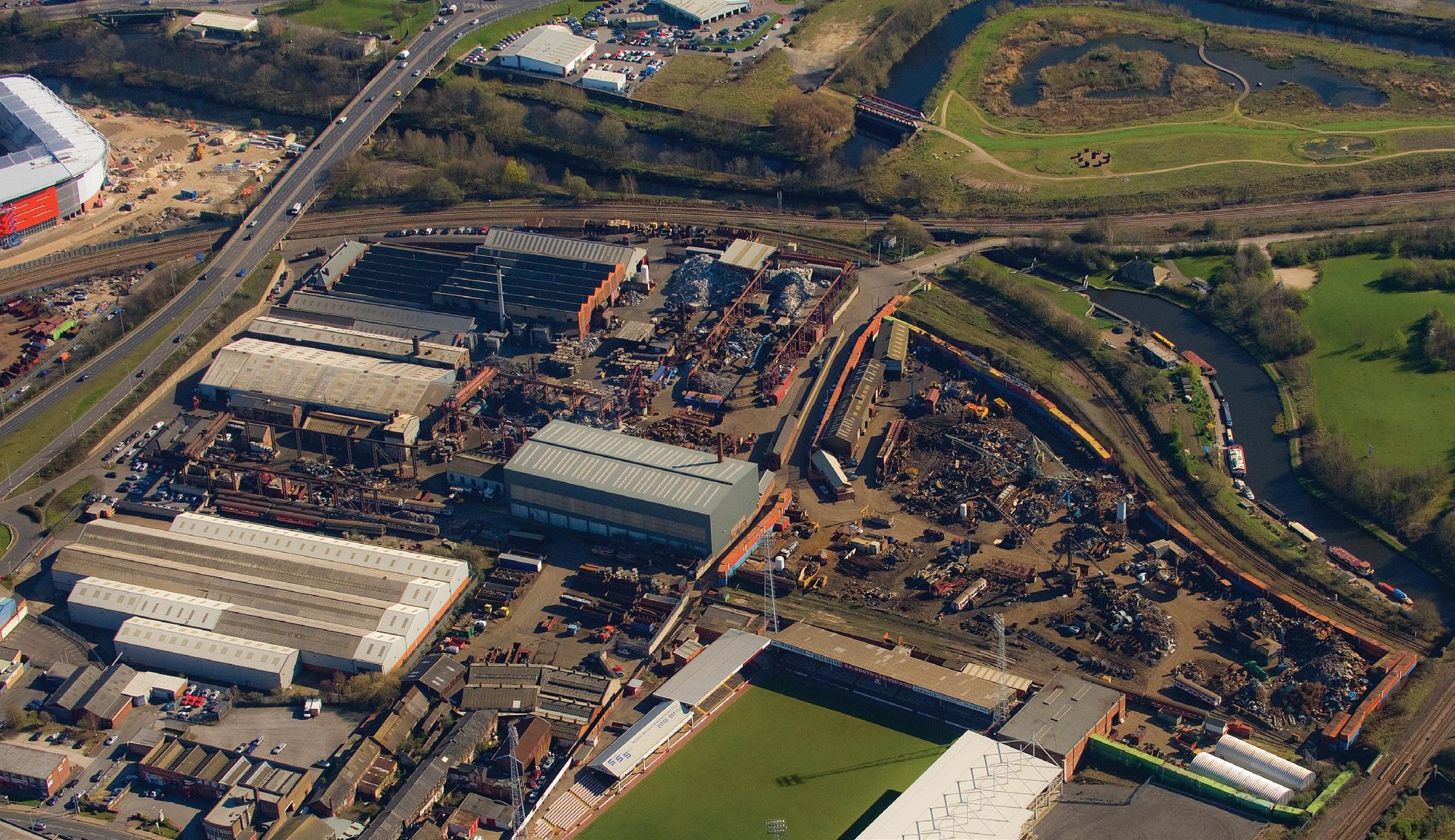
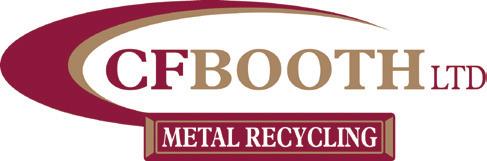
Change management is something that we have long standing expertise in and we have noticed that the techniques we have developed over a decade in helping people move to Google Workspace translate perfectly in helping them, to make sense of their data challenges, such as communicating with them, giving them a clear picture of what the pathway is going to be, training people and upskilling them and
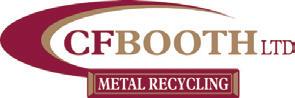
As we all strive to become big data handlers, it’s comforting to know that there are tools available to help lighten the load.
since the 1960s and has an excellent reputation as one of the largest rolling stock recyclers in the UK, winning nationally released tenders from several of the main rail operating companies.
The head office is located in Rotherham, South Yorkshire
and three derrick cranes making the site quite distinctive.
Clarence
established in 1920 by Clarence Frederick Booth and since that time has continued to be generations of the Booth family.
CF Booth rolling stock division has achieved both ISO 9001 and 14001 standards and has invested heavily in developing the infrastructure to handle all kinds of rolling stock including more than 1,500 metres of rail sidings, which allows us to accommodate a substantial amount of rolling stock. Work continues at present with rail vehicles being brought in through a connection to Network Rail and the proximity of the railway sidings to roads give this side of the business a high profile with many wagons, carriages, underground and departmental stock being processed.
associated with the scrapping of diesel and electric locomotives since the 1960s and has an the largest rolling stock recyclers in the UK, winning nationally released tenders from operating companies.
In addition, our extremely competitive buying process and quick payment terms mean that for many companies wishing to dispose of their rolling stock, CF Booth Ltd is the first port of call. Besides processing rolling stock for their residual ferrous/non ferrous metals, we also salvage any or all components that may be required by railway preservationists.
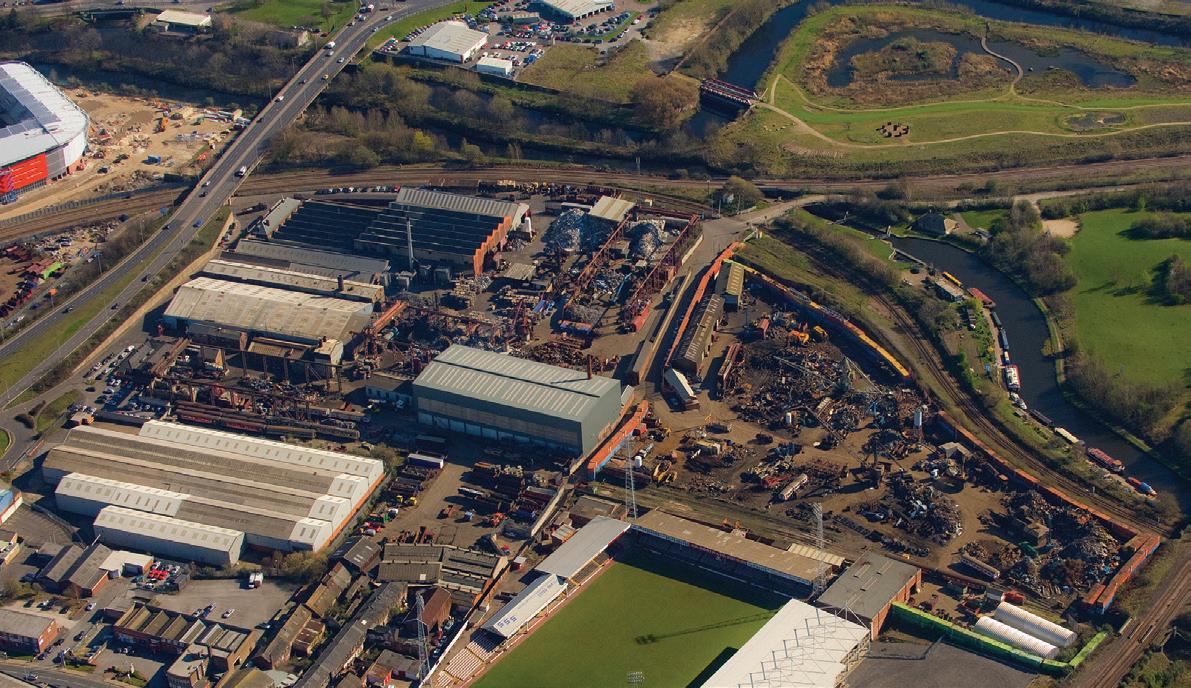
Rotherham, South Yorkshire at Clarence Metal Works with the company’s gantry cranes making the site quite distinctive.
CF Booth Ltd is one of the leading metal recycling companies in the UK. Established in 1920 by Clarence Frederick Booth, the business has grown from a local metal trader into one of the largest independently run recycling companies in Europe and is nearing its 100th year anniversary. CF Booth has been associated with the scrapping of diesel and electric locomotives since the 1960’s and is now one of the largest rolling stock recyclers in the UK, working with several of the main rail operating companies.
The current Rolling Stock Manager, Christopher Davis, says: “We are proud to be playing a major role in supporting the UK national rail industry and extremely proud to provide a valuable service to railway enthusiasts and preservationists throughout the UK as they continue to restore rolling stock vehicles to their former glory for future generations to enjoy. We value the relationship we have built up with preservationists and enthusiasts over the years’’.
CF Booth rolling stock division has achieved both ISO 9001 and 14001 standards and has invested heavily in developing the infrastructure to handle all kinds of rolling stock including more than 1,500 metres of rail sidings, which allows us to accommodate a substantial amount of rolling stock. Work continues at present with rail vehicles being brought in through a connection to Network Rail and the proximity of the railway sidings to roads give this side of the business a high profile with many wagons, carriages, underground and departmental stock being processed.
We are more than just a metal recycler, our continued investment in infrastructure and quality personnel has put us at the forefront of the metal recycling industry. Working with global businesses and international brands has made us think differently and strive to continue our development.
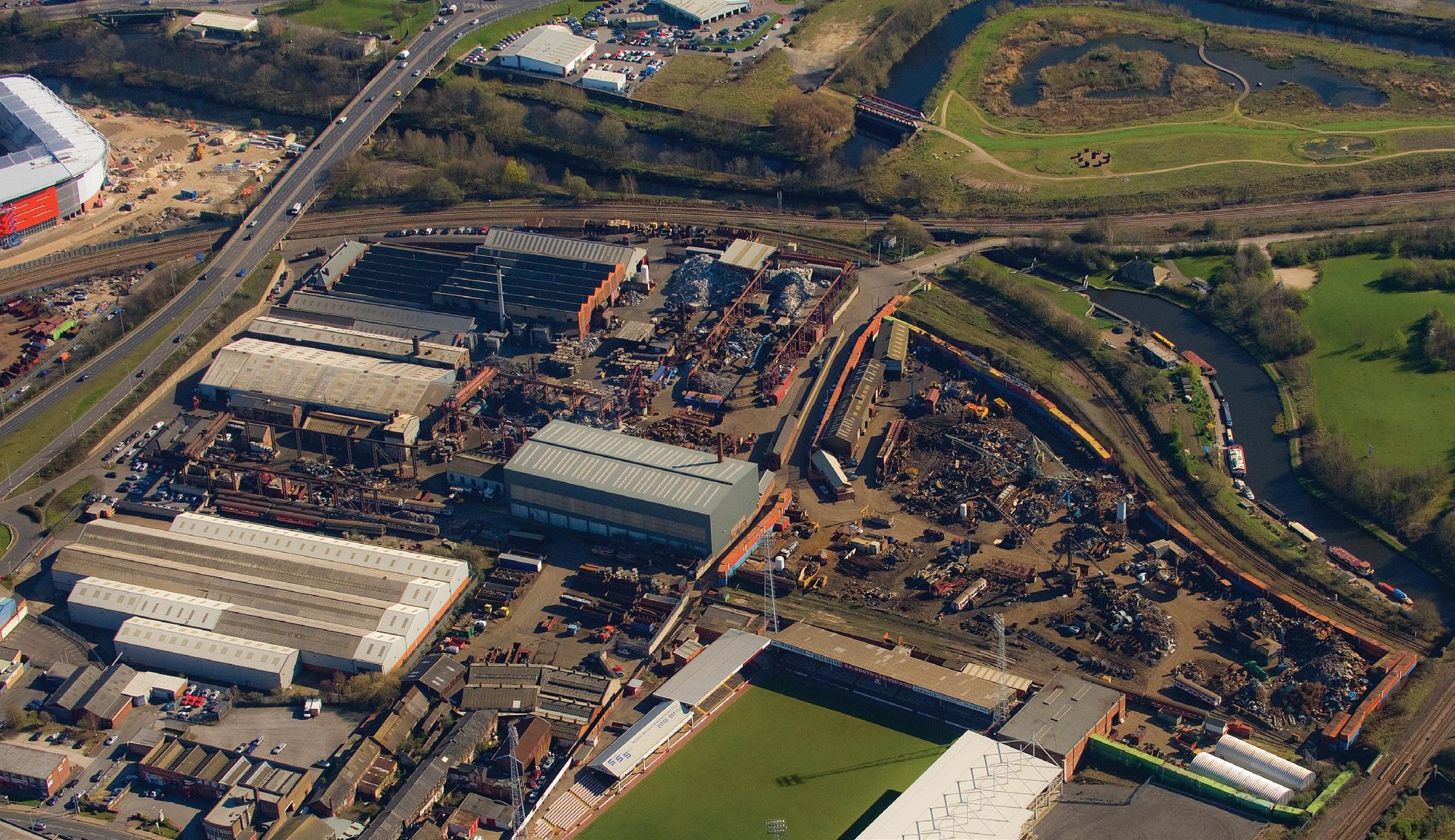
In addition, our extremely competitive buying process and quick payment terms mean that for many companies wishing to dispose of their rolling stock, CF Booth Ltd is the first port of call. Besides processing rolling stock for their residual ferrous/non ferrous metals, we also salvage any or all components that may be required by railway preservationists.
Our rolling stock asbestos removal/disposal service is supported by Demex Ltd a part of the CF Booth Group. Their fully trained and accredited operatives use the very latest equipment and techniques to safely strip out and dispose of asbestos. Besides processing rolling stock for their residual ferrous/non-ferrous metals, we also salvage any or all components that may be required by Railway Companies and Railway Preservationists.
The current Rolling Stock Manager, Christopher Davis, says: “We are proud to be playing a major role in supporting the UK national rail industry and extremely proud to provide a valuable service to railway enthusiasts and preservationists throughout the UK as they continue to restore rolling stock vehicles to their former glory for future generations to enjoy. We value the relationship we have built up with preservationists and enthusiasts over the years’’.
at
Metal Works with the company’s gantry cranes
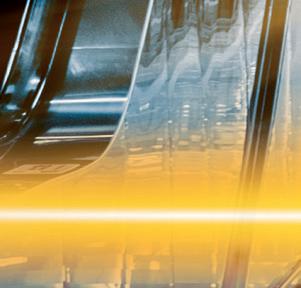
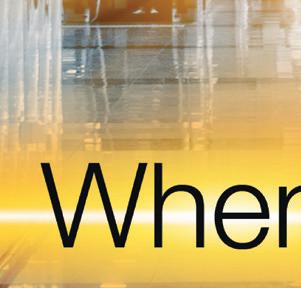
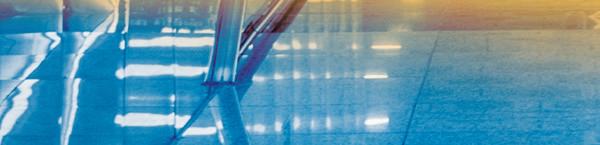
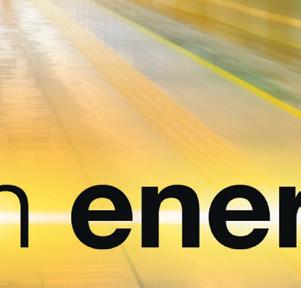
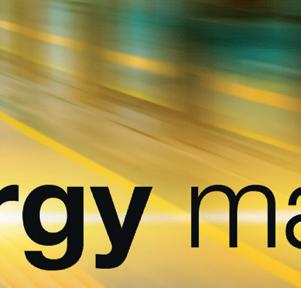
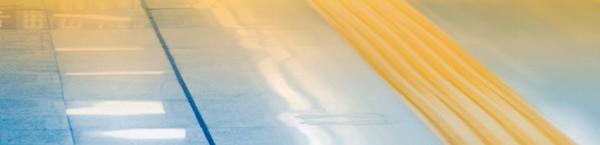
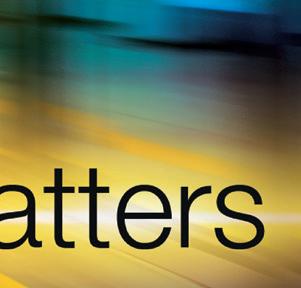
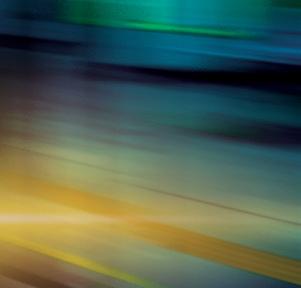

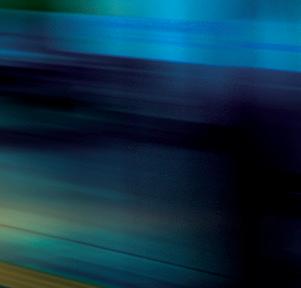
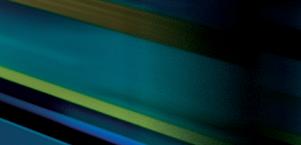
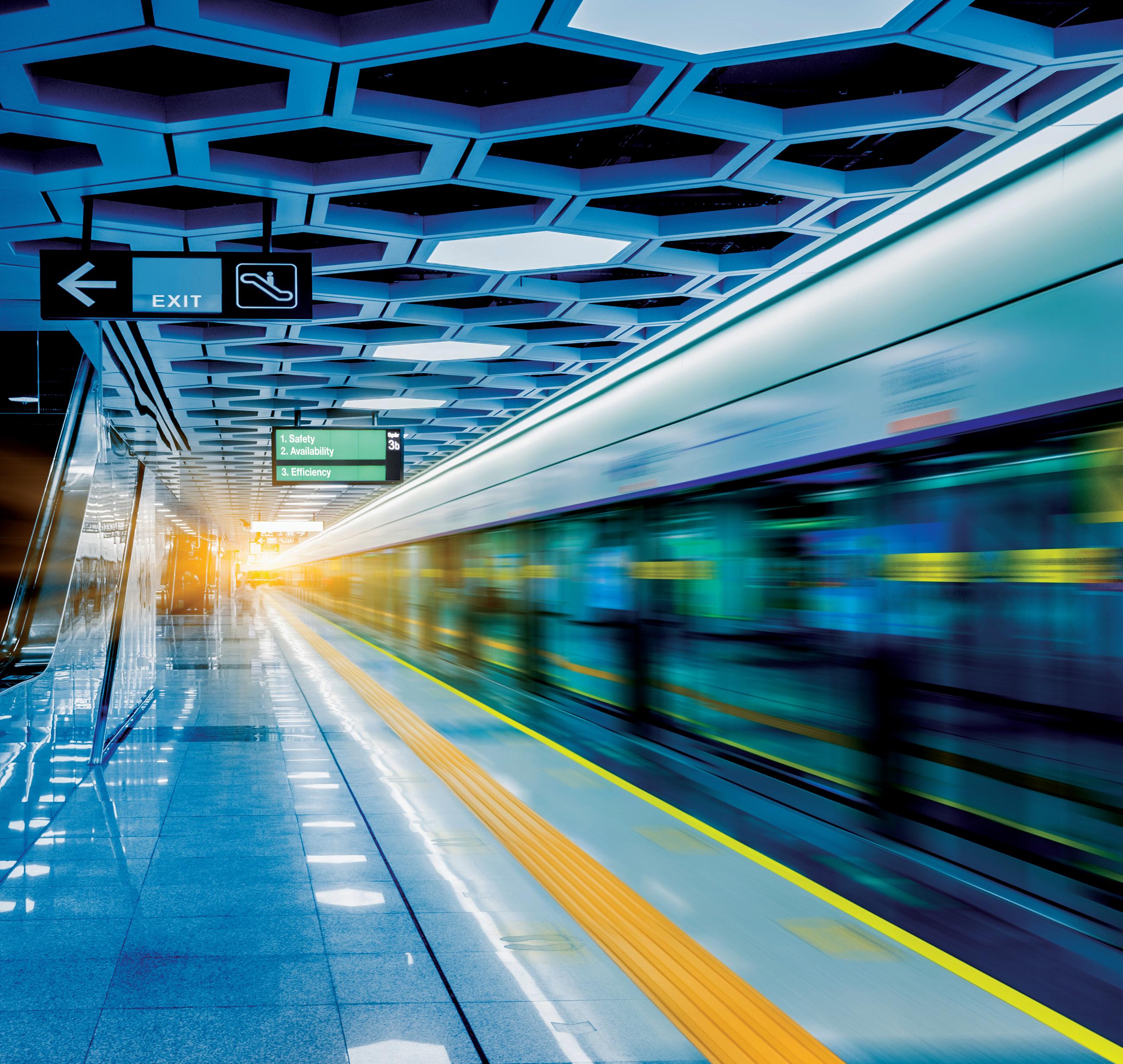
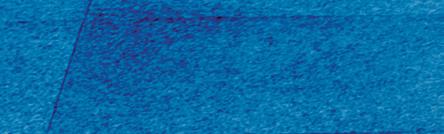

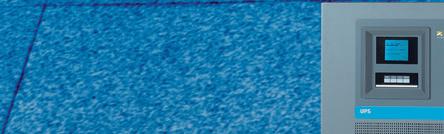
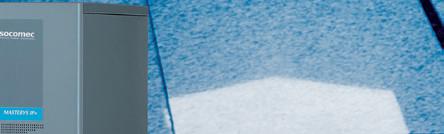
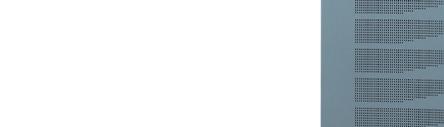
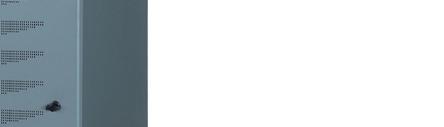
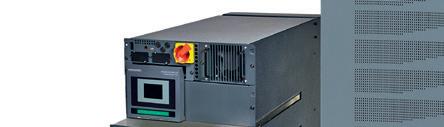
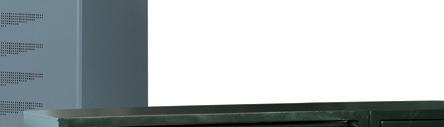
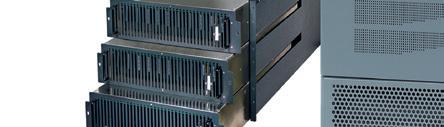

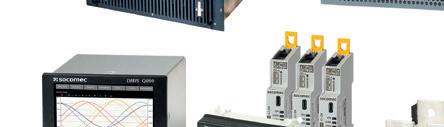
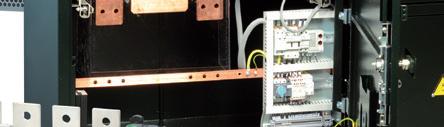

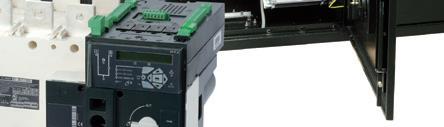
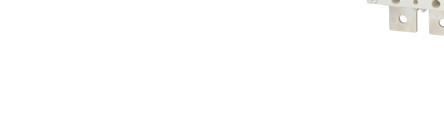
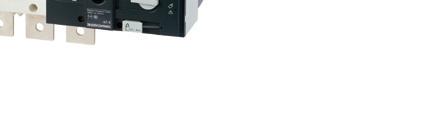
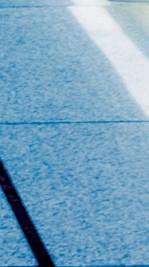
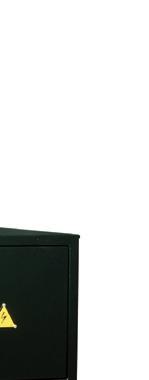
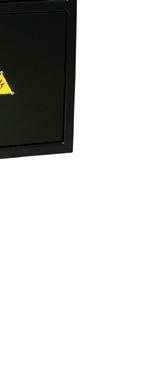
Approved Hydraulics have been supplying some of the largest rail build and maintenance firms for over 10 years, now considered some of the best in the world!
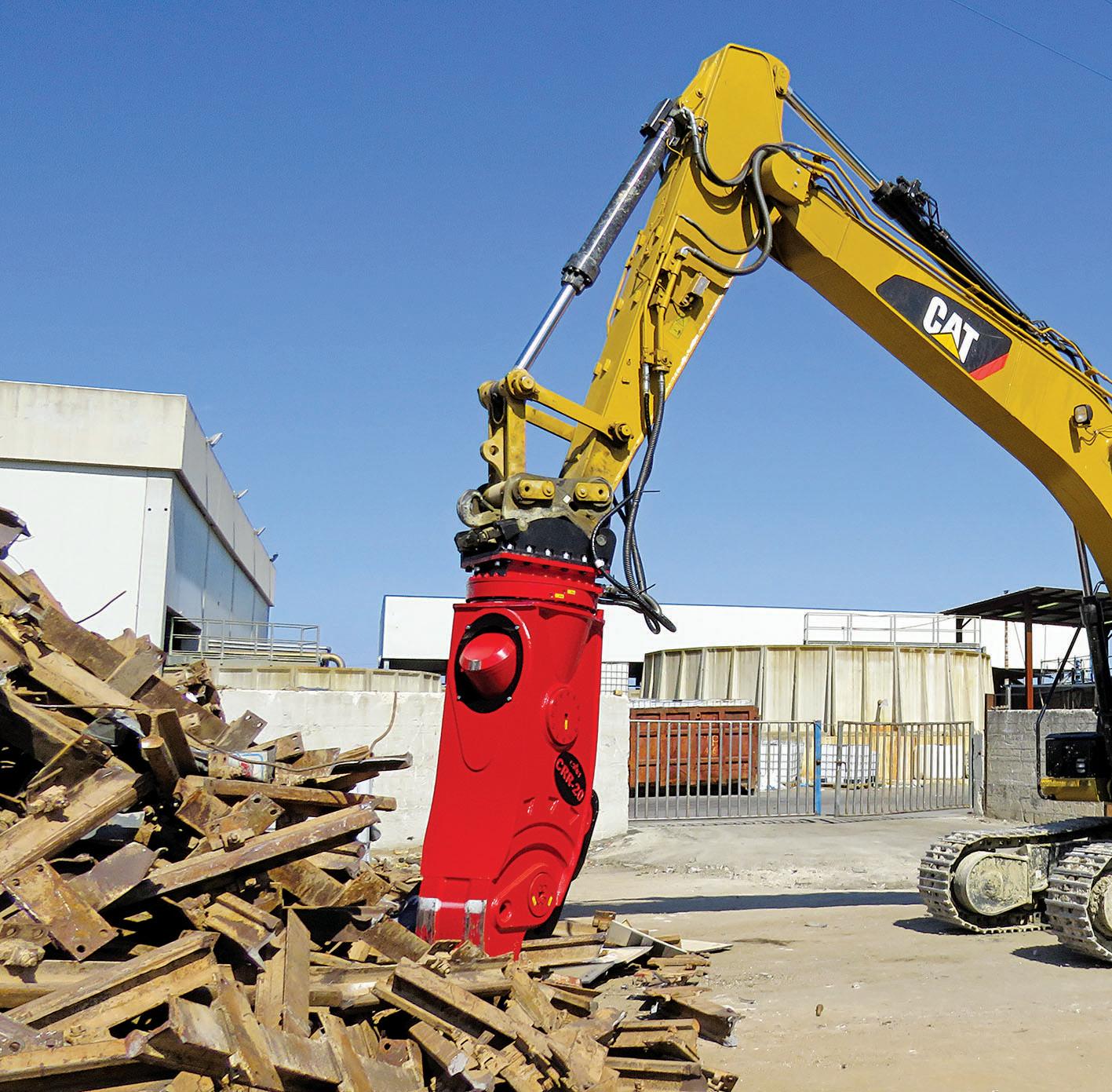

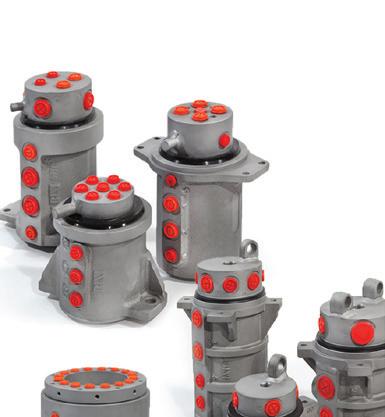
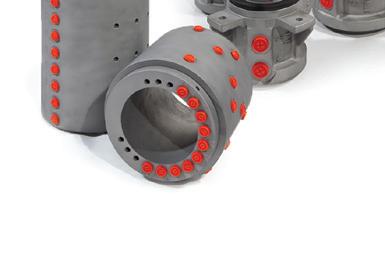
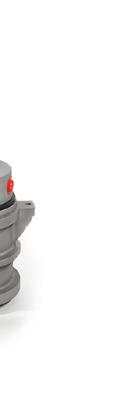
TechnicalBack-up

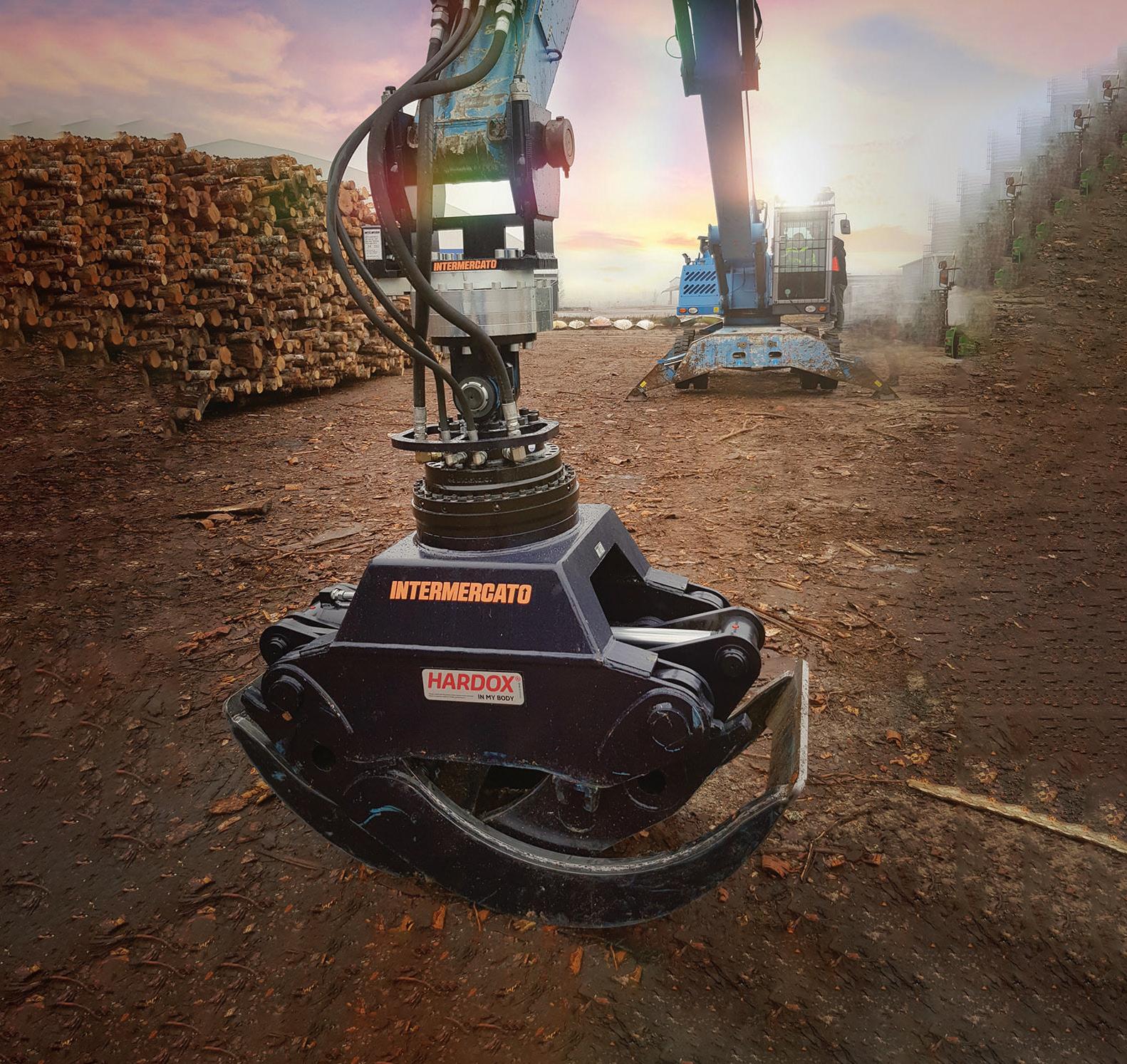
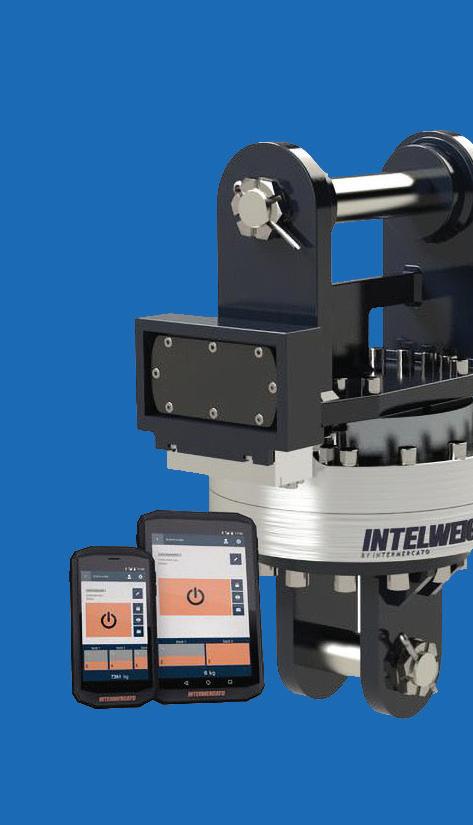
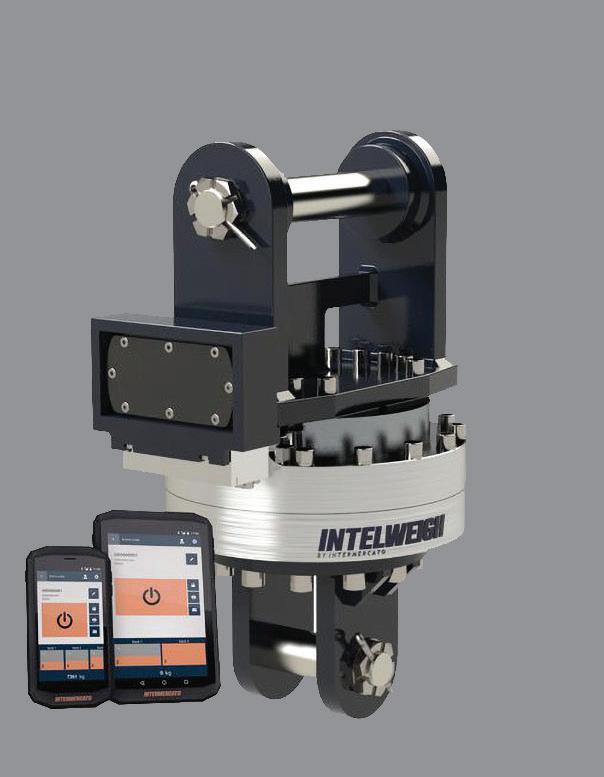
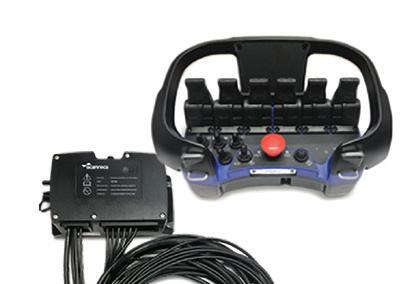
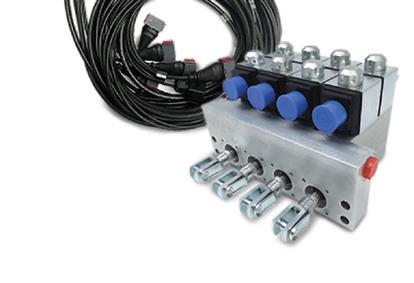
IntelligentWeighingSystems
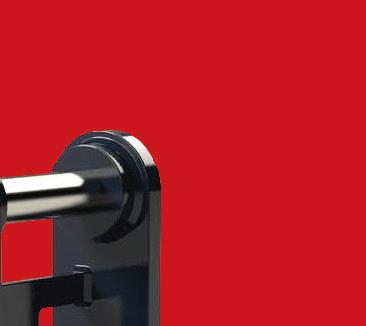

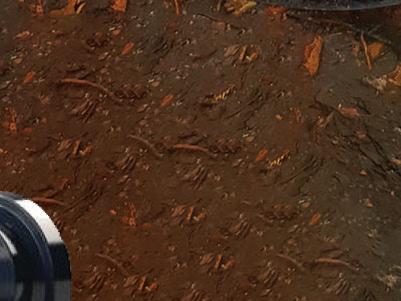


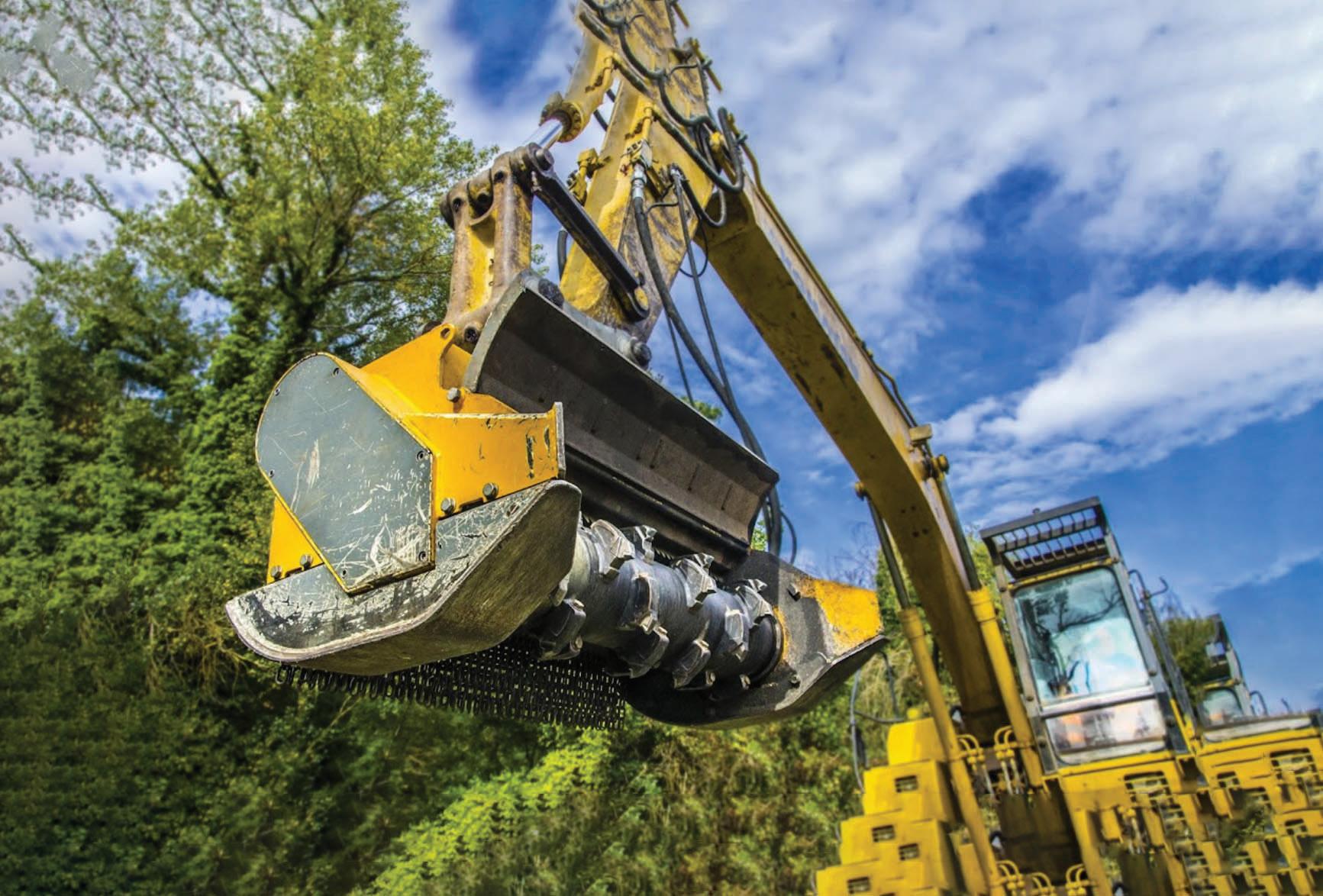
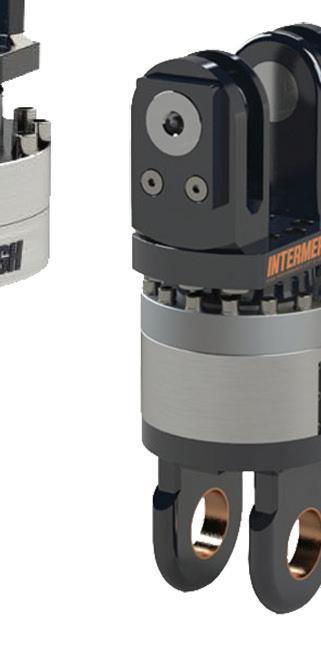
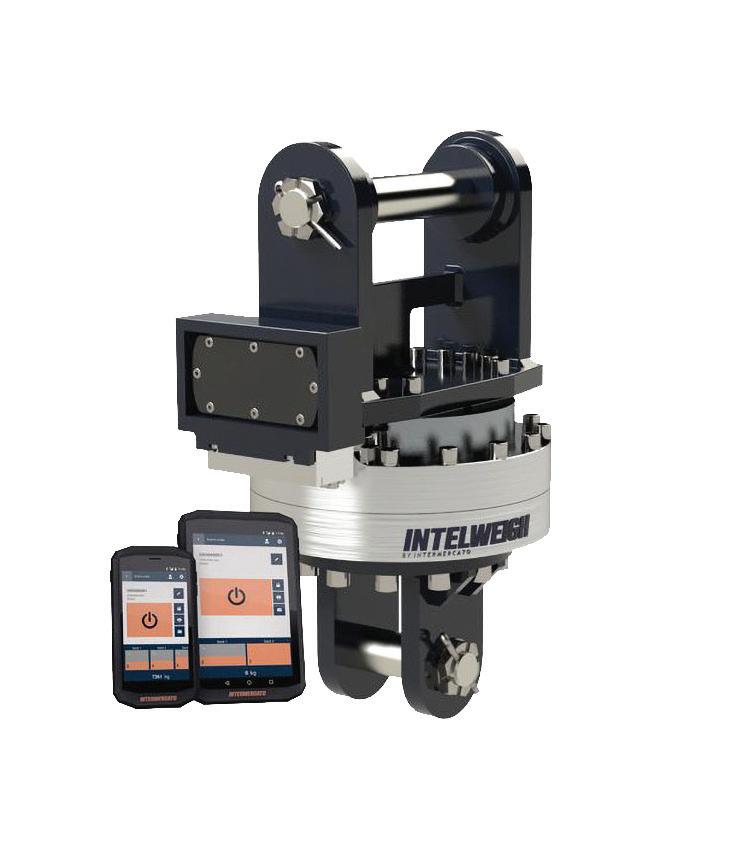
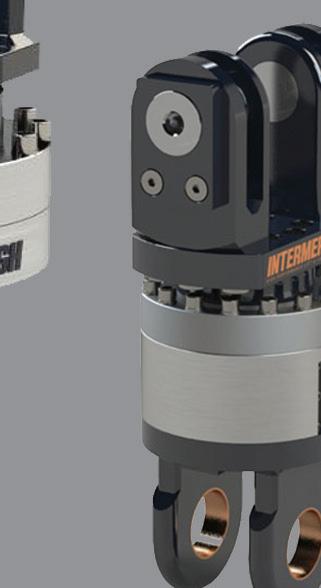
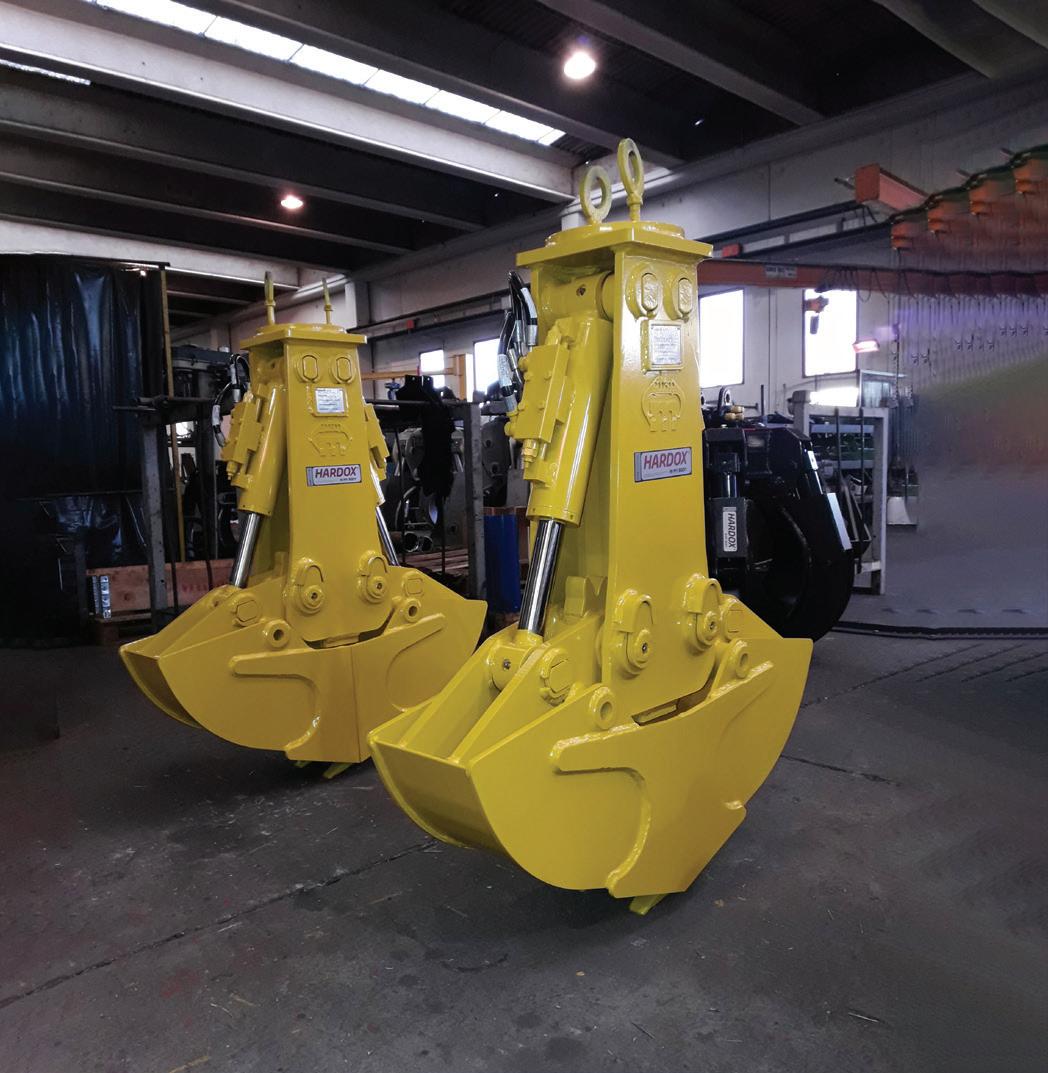


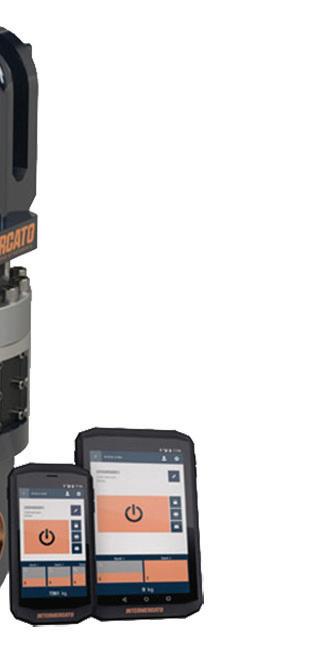
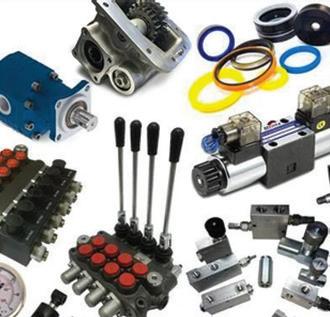
Creating Curiosity
Generation Logistics is on a mission to raise the profile of logistics and build interest and excitement about the prospect of a career in the industry amongst young people

Generation Logistics is a major careers awareness campaign designed to keep the nation’s supply chains protected by addressing skills shortages and attracting more talent into roles across the industry. The campaign launched in August 2022 and results to date are really encouraging – these first eleven months have created over three million engagements with the campaigns, generationlogistics. org has attracted over 640,000 visits, and the activity has created over 450 million opportunities to see the message.
The aim is to increase awareness of logistics and to get more people considering it as a career of choice. The team is helping to build the future for freight and a longterm plan for skills and attractiveness of a key part of the economy. But if we want to avoid a rapid return to critical shortages, shore up the supply of talent across a wide range of jobs across the whole sector, and compete for people against other industries
experiencing skills shortages, then we need to make logistics a leading destination for jobseekers – like media, tech, healthcare and business management.
Year two is shaping up to be equally exciting. There are plans to deepen awareness amongst young people of all backgrounds, by engaging with educators in schools and colleges and making generationlogistics.org a one-stop shop for information, advice and support about careers in logistics. There has also been a rapid expansion of the network of Generation Logistics Ambassadors, representing their employers, and primed to deliver their personal messages of endorsement for our industry to those curious to find out more.
The journey so far
At the start of last year, Generation Logistics was just an idea. By Easter 2022, the DfT had injected significant funding into the campaign. By June, most of the visionary
founding sponsors and partners were on board. Generation Logistics had a small dedicated project team, and had appointed a leading marketing and PR agency.
For the first time, the industry had come together to fund and deliver a high-profile, national campaign to shift perceptions and recruit the next generation of key workers. To target these hard-to-reach groups, including young people, career switchers and other underrepresented groups, the campaign has been very social and very digital, combined with more traditional PR and live events. The team has used Tik Tok, Instagram, Snapchat and Facebook, worked with social influencers, and tapped in to popular culture references and icons. It’s not the type of campaign our industry is used to, but it’s the one it needs to reach the next generation and change thinking.
The year ahead
For the second year, Generation Logistics will focus on young people from all walks of

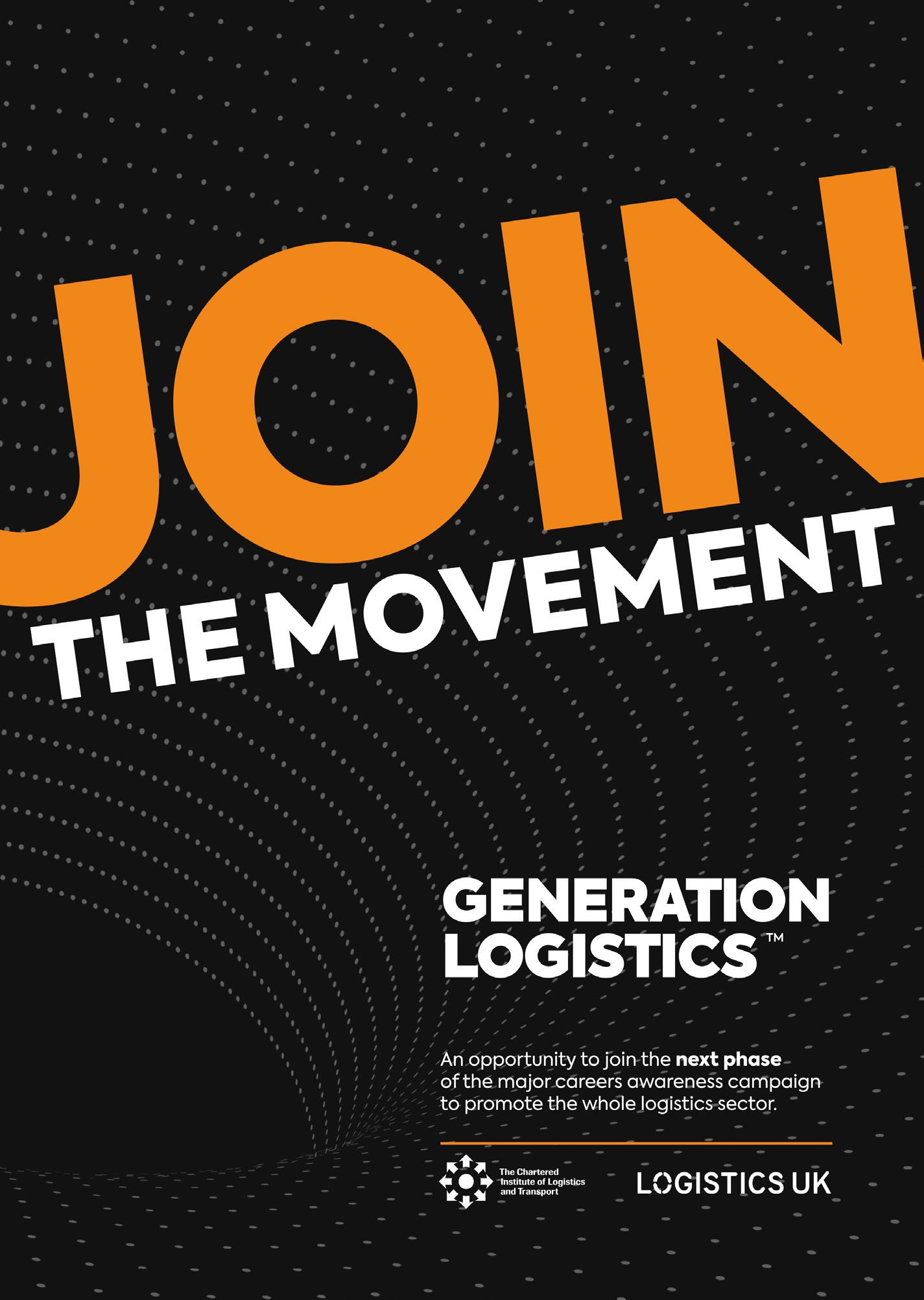
life aged between 13 and 24. It will do that by building on the innovative campaigns across different social media platforms – and start reaching and inspiring young people by providing curriculum-relevant material to educators in schools and colleges.
The goal is to reach as many young people as possible, change how they think about logistics, and give them the inspiration and the tools to build their careers. Generationlogistics.org will be expanded to be the one-stop shop for anyone thinking about a career in logistics. With new resources for educators, and the only place bringing together information on available entry schemes, including apprenticeships and graduate opportunities, it hopes to build the impact and the engagement of the site.
‘For the industry to thrive and attract the next generation of talent, it is vital that the whole sector comes together behind Generation Logistics. We are passionate about representing the whole sector which is why we have introduced a substantially discounted opportunity for smaller companies. Over the last year, the industry has delivered a high-profile, national awareness campaign – the first time this has happened - and we are definitely shifting perceptions. Year Two is going to be even better and I would urge companies of all sizes to come forward and support the campaign in its second year.’
Phil Roe, Generation Logistics Executive Sponsor
THE VALUE OF LOGISTICS
in 2021 the logistics sector contributed £163 billion (twelve per cent) to the UK economy (Gross Value Added, or GVA) and at last estimate in 2022, it employed over 2.7 million in logistics occupations, around 8.2 per cent of the UK’s total employment. For the first time, leading logistics brands have come together, along with unified support from leading trade groups, to raise awareness and consideration of a career in the sector.
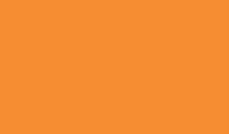


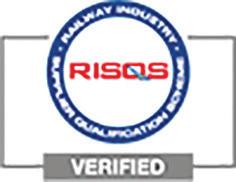


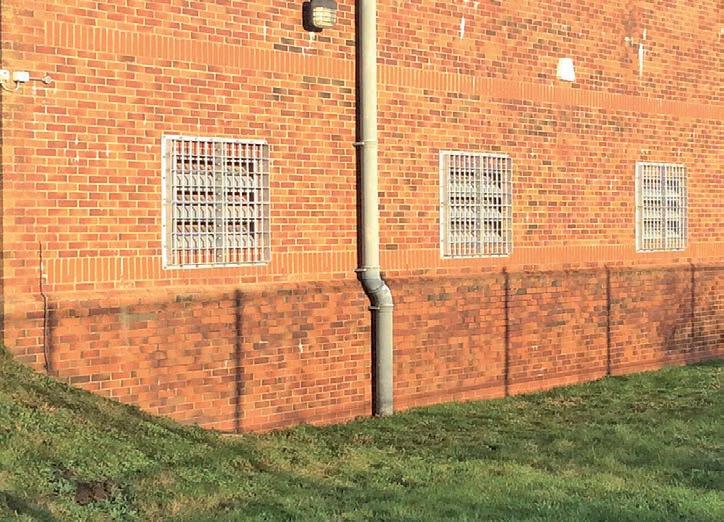
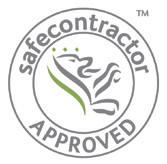
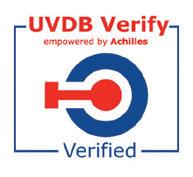
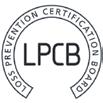
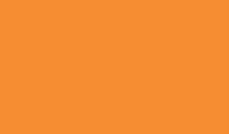
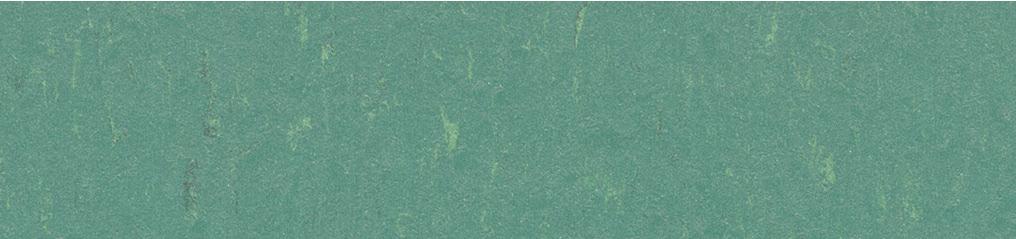


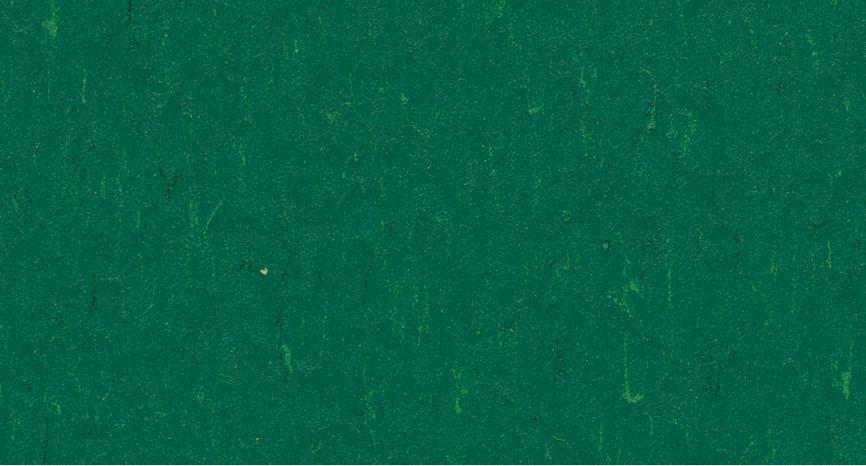
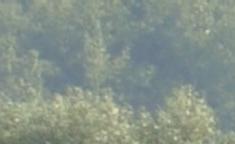


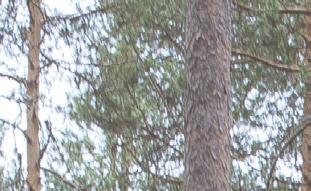




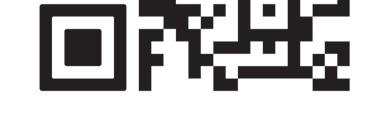

Addressing the Gender Disparity in Workwear
The primary role of PPE and workwear is simple – effective protection for the user
However, despite the growing number of women in the rail industry, many are having to ‘make do’ with workwear designed primarily for men. Here, Sangeeta Aeri, Technical Manager at Supertouch, covers the issues surrounding inclusive safety workwear and how industry can move forward.
The last decade has seen positive steps in the number of women entering the rail industry, with the benefits of a more diverse workforce on company culture and employee empowerment well documented. However, with the sector still heavily male-dominated, plenty of work remains to be done; especially given the findings of a recent survey by Women in Rail which revealed 60 per cent of respondents were either 'very dissatisfied' or ‘dissatisfied’ with the current gender balance.
A ‘day-to-day’ area where the gender gap has tended to manifest is PPE and workwear, particularly when out on site. It is not uncommon for women working at or visiting a site to have to make do with whatever workwear was available, the majority of which is typically designed and manufactured in male sizes.
This presents several challenges, especially from a site safety and user comfort point of view. While there is no such thing as an average female body type, there is undoubtedly a difference when it comes to waist ratio, limb length and chest size versus male counterparts.
Put simply, there is no guarantee that workwear designed for men will offer sufficient protection and comfort to the female workforce. Loose fitting clothing represents a real safety risk, either through trips and falls or getting caught in machinery. As is always the case when cutting corners on safety, this leaves female workers at greater risk of serious injuries.
Moreover, with many major infrastructure tenders now requiring contractors and suppliers to demonstrate their ESG credentials, it is important to remember that equality and diversity is a major pillar of ‘governance’ in ESG. For

instance, while today 19 per cent of Network Rail’s workforce is female, its target is to reach 26 per cent female by 2024.’
However, increasing the gender diversity within an organisation is only one piece of the puzzle and women should not only be more present, but more empowered. After all, protective workwear is both an essential component of workplace safety and crucial for employee wellbeing. The fact that so many female stakeholders, myself included, have had to wear protective clothing designed for our male counterparts reaffirms that there remains a lot of work to be done.
Levelling the playing field
Female workwear and PPE is not a new concept. However, the real trouble is the lack of supply, with many existing lines concentrated at the higher end of the market. This means women are essentially paying a premium for safety. Breaking this
mould and expanding the female workwear supply chain will not only positively impact female workers, but also offers substantial commercial benefits.
Consequently, manufacturers, such as ourselves, have a responsibility to drive the market forward by designing and bringing a broader portfolio of products to market. As a result, this month will see Supertouch launch its first ever range of ladies’ workwear suitable for a wide variety of industrial sectors.
The products within the range have been tailored to female body types with a view to maximising comfort and optimising ergonomics. To offer flexibility around sizing, each garment will be available in eight different sizes, and where appropriate, will incorporate adjustable cuffs and hems to enable the wearer to truly tailor each item of clothing to their personal fit.
The hi-vis elements of the range feature strategically positioned and stretchable reflective tape to ensure compliance with EN ISO 20471. Importantly for the rail industry, the range also includes ‘Rail Spec’ orange RIS-3279-TOM compliant workwear – required for all trackside work.
Each item in the range has also been named after the daughter of a Supertouch employee involved in the development process. By doing this, we hope to inspire future generations of women to enter the industry while highlighting the need for female input into the design processes.
Breaking down barriers
Ultimately, while landmark initiatives Women in Rail and Females in Transport Engineering (FiTE) are playing an important role in rebalancing the gender split across the sector, generational change requires buyin from stakeholders across the industry.
While to some it may seem small, the reality is the gender PPE gap is a tangible, daily reminder of the work that needs to be done to improve equality across rail workers. However, closing it is also one of the easiest steps to take.
For more information, please visit www.supertouch.com.
The Value of a Safety Culture Survey
Laura Hedley, Senior Occupational Psychologist at the OPC, shares work around a safety culture survey with a global, maritime client that can be a useful ongoing tool to review and improve an organisation’s safety performance
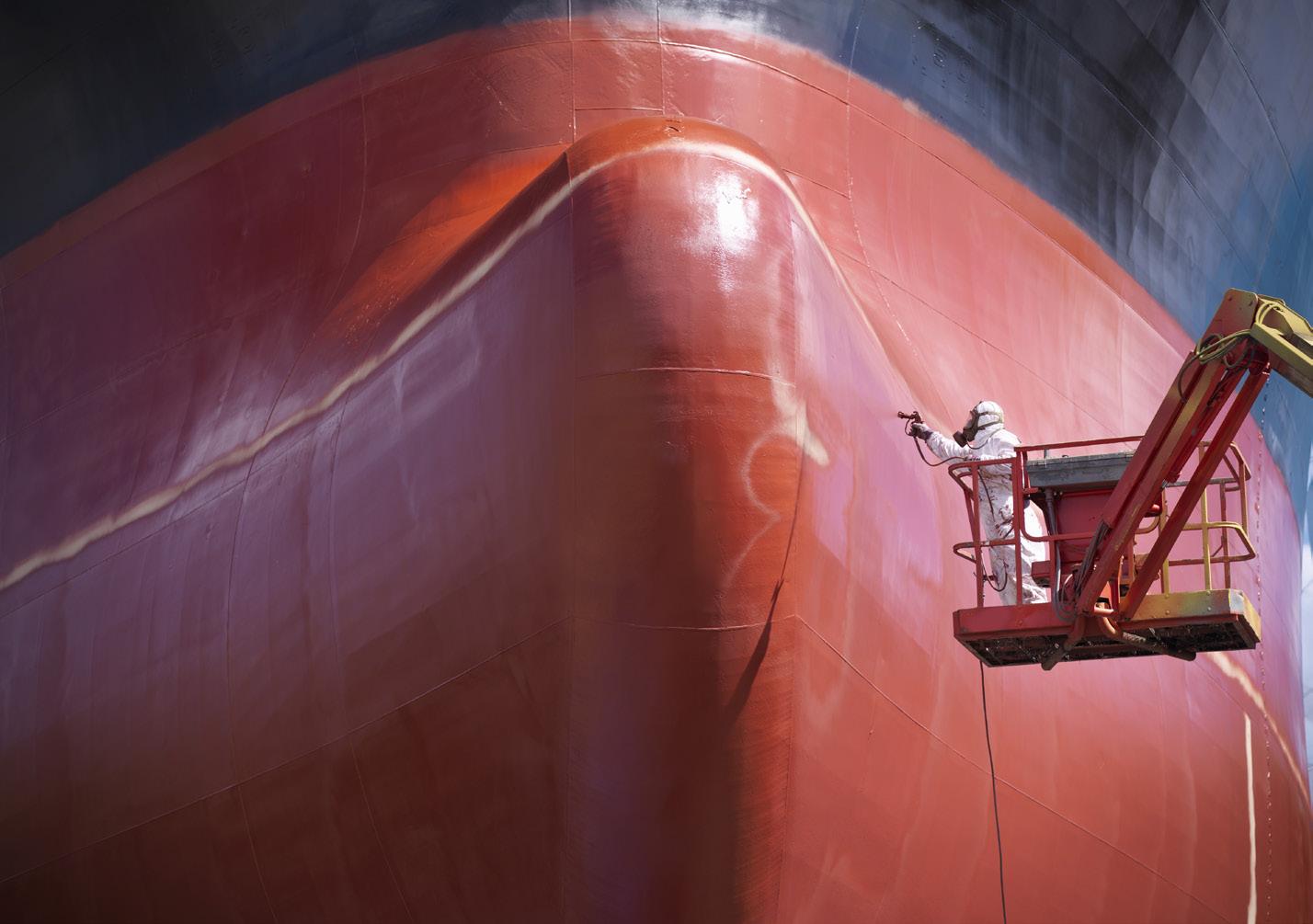
At the end of 2022, the OPC was approached by V., a global shipping business, to design and implement a bespoke Safety Culture Survey (SCS) across their entire organisation. V. is an independent global leader in ship management and marine services. They are based in 30 countries, have over 40,000 employees and operate in every ocean. Their operations encompass ship and crew management, crew and technical services, as well as additional marine services including supply chain and specialist marine insurance. The OPC was approached because of their independence, safety specialism and their non-maritime background. V.’s senior team wanted to understand their current safety culture and how they could continuously strive for improvement in relation to safety culture; safety behaviours, safety practices and safety performance.
The aim was to engage as many employees as possible to provide their views, opinions and experiences about safety in their workplaces – ashore and onboard vessels. To create an initial benchmark view of safety opinions from which to corroborate and influence their existing safety initiatives; as a new empirical source to help generate new safety initiatives, as well as identify any areas for safety improvements.
The survey
Using OPC Assessment’s Safety Culture Questionnaire (SafeCQ) tool, as a base, Laura Hedley, Senior Occupational Psychologist at the OPC worked with the V. team to create a bespoke survey that has twelve building blocks about safety and safety culture. The survey was specifically designed to be anonymous and inclusive –enabling all V. employees from across V.’s entire geographical and operational diversity
‘A safer organisation is an open one, that encourages open, honest discussion about safety performance with managers and peers alike, that is free from fear of reprisals.’
to take part – providing open and honest feedback without any concerns.
The questions were designed to be as easy as possible and quick to complete online or via an interactive pdf. To further encourage employee engagement the OPC conducted, collated and analysed the entire survey, ensuring impartiality and employee anonymity and confidence. The survey answers were a simple seven-point agreement scale.
At the end, there were some optional, free-text, opinion questions. Over 3,000 employees left valuable comments that have been analysed for themes for review by the V. HSSEQ team. This is a longterm investment plan for V. with the aim of repeating the SCS annually for three years, and then potentially on a rolling programme. The second wave of the survey is already well under way for 2023.
A positive start to the Safety Culture Survey for V.
Overall, there was a good response for the SCS amongst V. employees. Over 9,300 employees completed the survey. Initial response rates were encouraging for a first time undertaking of the SCS. They
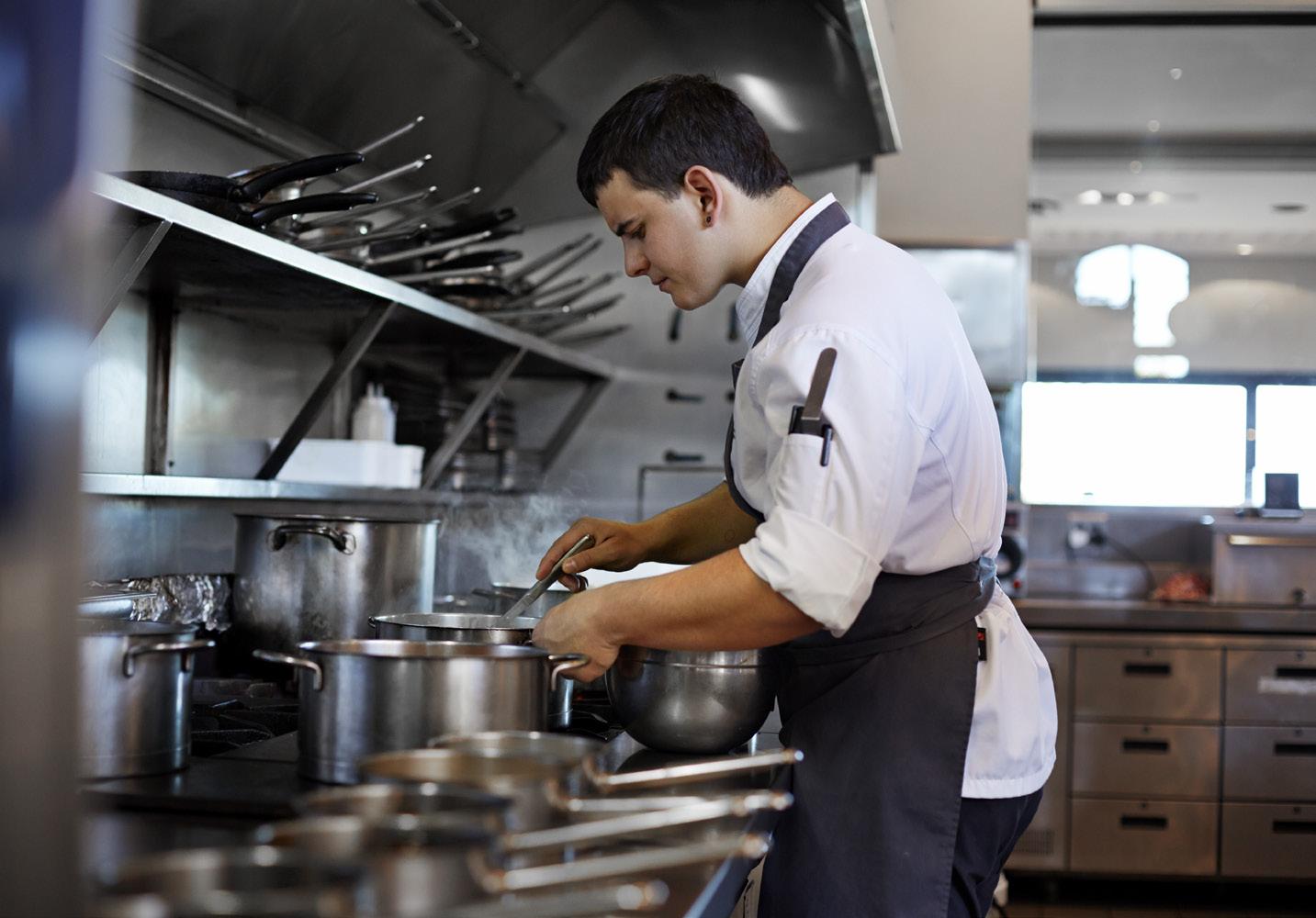
can provide an initial view of how well employees are already engaged with a safety agenda in their organisation. It also bodes well for future surveys where there’s still room for further employee engagement. As the SCS is repeated in the future, employees already engaged are also likely to be more confident in raising more challenging safety concerns.
The participation was strong across all V. divisions, all levels – from frontline employees to director level, and across all geographical locations with the strongest participation in Asia and Europe.
Once the results of the 2022 survey were in, OPC psychologists analysed them for each of the safety culture building blocks, assessing the views of the global organisation, plus the differing views by organisational function, business sector and geographical location.
The building blocks were rated as high, medium or low performing, based on the grouped views of those who responded to the survey. A low performing area
would necessitate some work and focus to improve this area of safety culture.
The survey indicated a strong initial view of safety culture performance across V. with no building blocks being rated as low performing, but there were some opportunities to improve on existing safety activities and therefore to improve safety culture. The OPC also provided insight into any emerging trends about safety and made some recommendations and suggested some possible initiatives for consideration. The end ‘free’, opinion questions were also analysed for specific themes. These are always a rich source of employees’ views, and initiatives for review.
Some detail behind the safety culture building blocks
A key building block is Safety Profile. This can be a general indicator of the focus given to safety by an organisations’ managers, and employees’ perceptions about their senior/ director level managers’ commitment and prioritisation of safety issues.
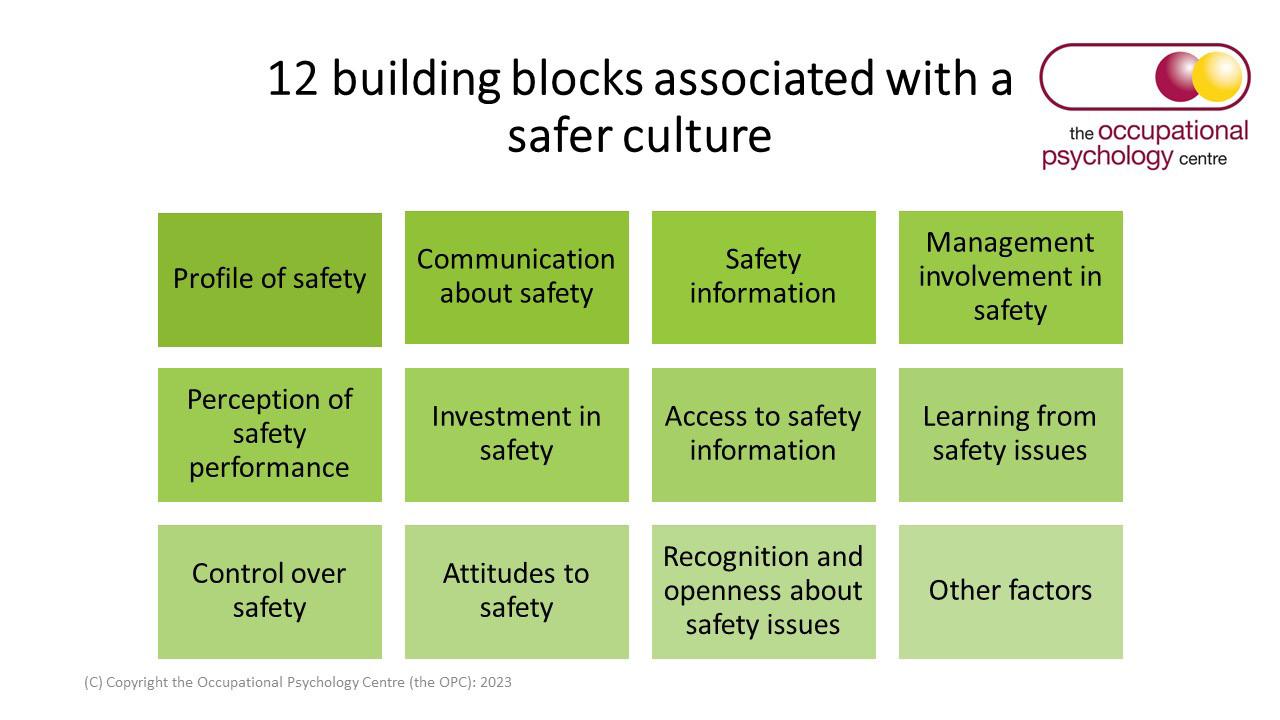
‘Extending representation outside of just functional and divisional ‘safety experts’ and across all employee levels – director through to front-line operatives can help to support safety responsibility, impact and communication.’
Attitude to Safety is about how well employees feel enabled, valued and motivated to engage with safety matters, training and working practices. Managers with strong safety leadership are essential to the success of this building block. An organisation with strong safety culture is where everyone, whether an operative, functional manager, divisional director or an office clerk all feel responsible and accountable for safety performance in their area.
Control over safety is about employees feeling they have charge and responsibility over their own safety, and that of their colleagues. Safety control is also about whether they feel they can influence and impact on their personal, divisional and overall business safety performance.
Recognition and openness to safety can be explained by how openly safety issues may be dealt with; how managers may approach a safety incident with employees and the outcomes and resolution of an incident – epitomised by a ‘blame vs a learning’ culture. A safer organisation is an open one, that encourages open, honest discussion about safety performance with managers and peers alike, that is free from fear of reprisals. This includes a belief that incidents will be managed in a fair and just manner. ‘Whistleblowing’ may be encouraged, as well as recognition for good safety performance.
Management involvement in safety – a healthy organisational safety culture is where everyone feels ownership and responsibility for safety issues. Regardless of function, level of responsibility or seniority, employees see that all managers care about and prioritise safety, doing so through strong safety leadership. Effective managers are accessible, approachable and active in both raising safety concerns themselves or they readily support in resolving them for, or with employees. In addition, a good safety leader will not compromise task completion time or profitability over the safety of their team employees.
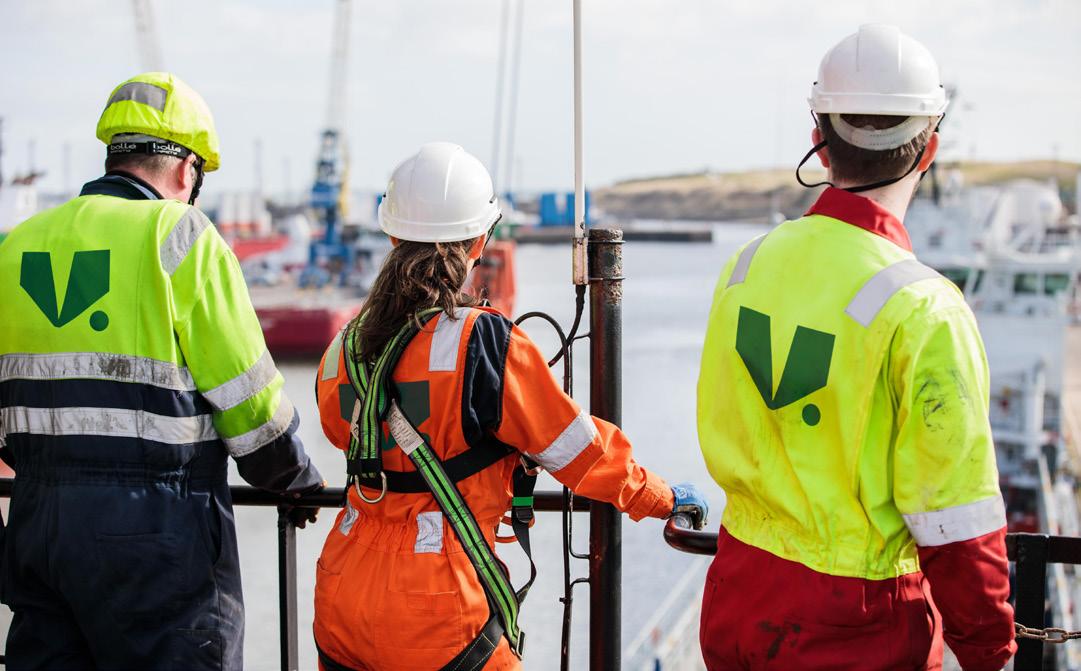
Investment in safety can be typified by physical resources, e.g., PPE, safety signage, ongoing repairs/maintenance works etc., but it also applies to time and people. For example, safety training and the degree to which it’s accessible, available, and relevant. A strong safety culture may be evident through time and investment in new initiatives or methodologies that maintain or enhance employee safety as well as the ‘back office’ activities such as accurate and timely updating of safety protocols. Investment in safety is also the balance between productivity and profitability vs employee safety.
Communications about safety – in the OPC’s experience downward communication is typically more apparent than upward communication from employees to more senior organisation levels. A ‘safe’ organisation needs to have both effective downward and upward communication processes actively working. Poor upward communication processes tend to have a detrimental effect on motivation and organisational learning. In some cases where there’s excessive downward communications it can be onerous and stifling for employees. Positive attitudes towards safety communication can be a good indicator of safety performance.
Some initiatives that can help improve safety culture
• Some organisations may have a specific cross-functional HSSEQ committee responsible for safety in the organisation with specific safety adviser divisional representatives. Extending representation outside of just functional and divisional ‘safety experts’ and across all employee levels – director through to front-line operatives can help to support safety responsibility, impact and communication. It can also drive motivation and engagement for some employees with the kudos this additional responsibility it can bring.
• Investment in new ideas and safety initiatives, or a review of existing methodologies can identify areas for improvements. Sometimes, the employees responsible for the work
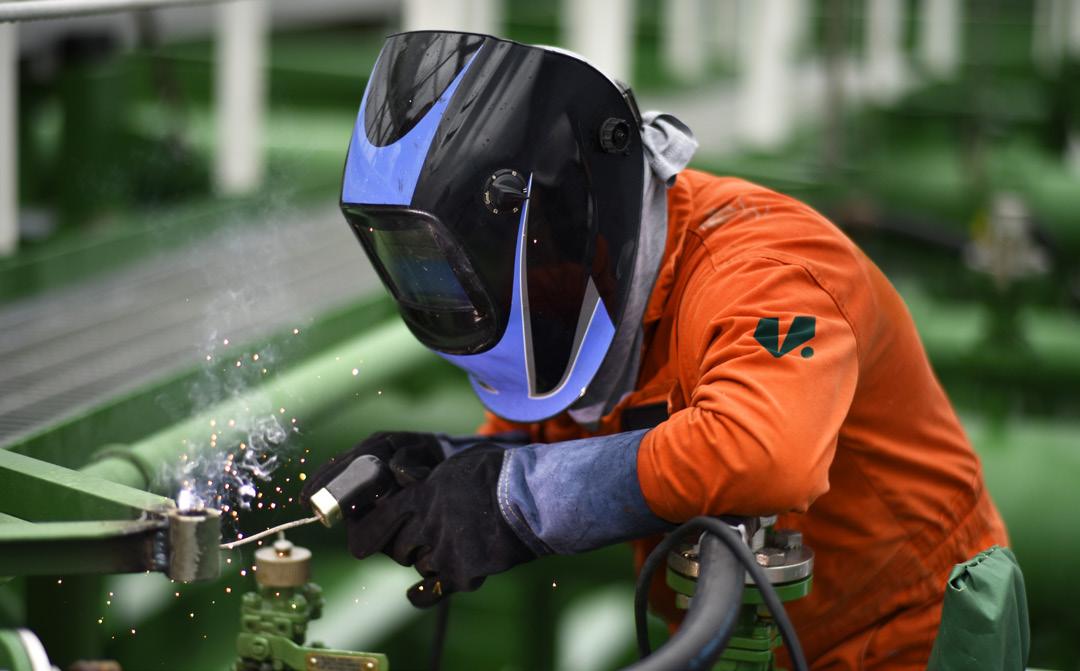
‘Safety culture can have a significant impact on preventing a major incident.’
area, can have some of the best safety improvement ideas.
• A review of all safety training (involving employees) to ensure it is fit for purpose; identify areas for improvements.
• Corporate employee recognition and reward schemes for either new Safety initiatives or outstanding safety performance.
• Regular process and procedure reviews to check compliance, update to improve, communicate effectively and keep well written records.
• Continuing to build strong safety leadership – the OPC offers a bespoke Safety Leadership workshop for all levels of managers and directors – including both safety-critical operational and non-operational roles. It aims to help test their operational safety focus and behaviours to help look for safety performance improvements.
There is empirical evidence to suggest that safety culture is directly linked to an organisation’s safety performance, but more importantly safety culture can have a significant impact on preventing a major incident. The absence of a strong safety culture has previously been implicated in some major rail accidents. Many organisations take their safety culture seriously and regularly undertake safety culture audits. Having them as part of a continuous improvement programme is very advantageous in preventing safety breaches; acting as a catalyst for safety performance learning, identifying hazards and safety improvements – contributing to employee well-being and overall organisational success.
Ian Trebinski, Group Director – HSSEQ at V., said: ‘I have worked in partnership with the OPC for several years now, and I’ve witnessed the value of the SafeCQ
tool in practice. I’ve experienced it helping international maritime operators and service providers to measure, influence, and improve safety cultures across multiple varying personal and operational cultures. The OPC’s manner of engaging colleagues, providing clear and concise insights, and of helping develop and deliver tangible initiatives that frontline workers can connect with and relate to is invaluable. Their involvement is another extremely beneficial toolset that HSSEQ leaders and teams can leverage to improve safety performance and cultural growth over time.’
Laura Hedley sums up by saying: ‘It’s really motivating and fulfilling to support an organisation with their Safety Culture project. It’s a change management project that can influence the whole organisation. Impacting employees’ personal safety; functional safety performance and contributing to an organisation’s success. V. is a leading global maritime organisation, equipping and enabling its seafarers to be future leaders in safety performance. Running an impartial Safety Culture Survey helps corroborate what’s already working, provides insight and empirical data for areas that may need some attention; is a catalyst for new initiatives, as well as motivating an organisations’ entire workforce to put the ‘spotlight’ on safety.’
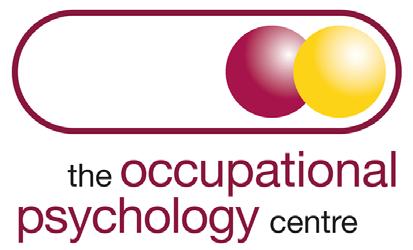

Tel: 01923 234646
Email: admin@theopc.co.uk
Visit: www.theopc.co.uk
Rhona Little – Marketing Manager marketing@v.group
Mobil Baustoffe GmbH
Trimburgstr. 2, 81249 Munich
Tel. +49 89 8954574-0
office@mobil-baustoffe.com
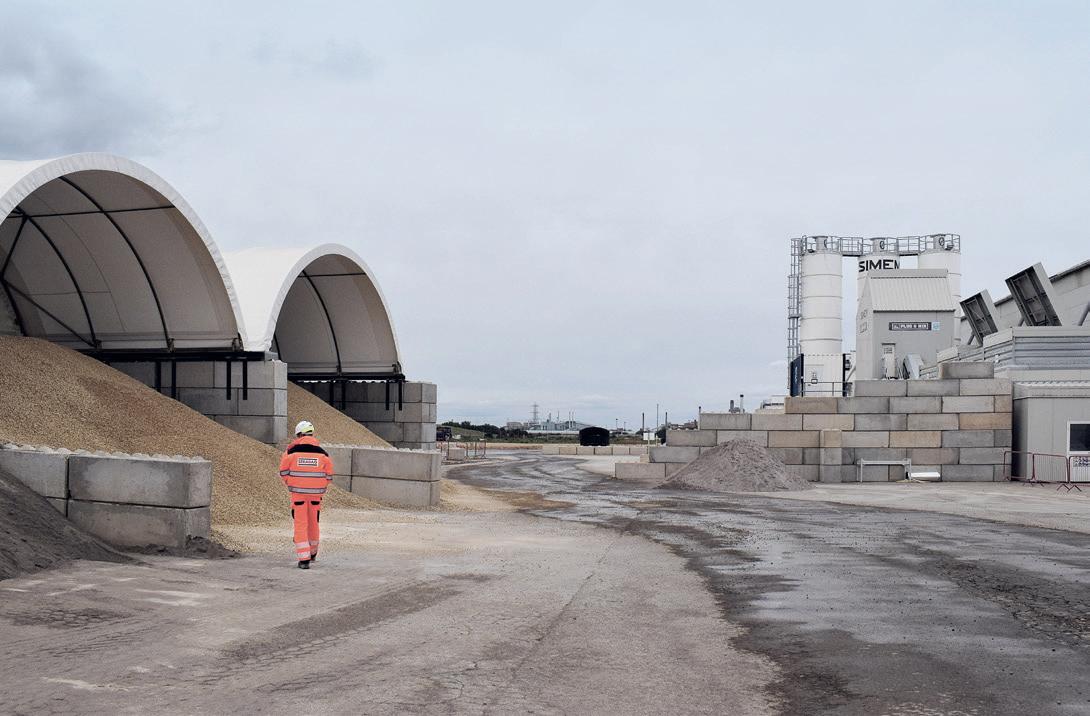
Work On Progress
We are shaping the future of construction. STRABAG subsidiary Mobil Baustoffe specialises in the production of on-site concrete for large scale construction projects such as tunnels but also produces high precision prefabricated segments for TBM drives (“tubbings”).
Mobil Baustoffe has been in operation for around two decades and has produced over 15 million cubic meters of concrete in many countries around the globe. Clients can be found across the whole spectrum of contractors, from large groups to small businesses.
In the UK Mobil Baustoffe experts have been involved in the Crossrail sites C300 and C410; are currently working for the North Yorkshire Polyhalite Project and are part of the team for the upcoming segments production for the HS2 S2 East and S1 tunnels.
To find out more, visit our website: www.mobil-baustoffe.com

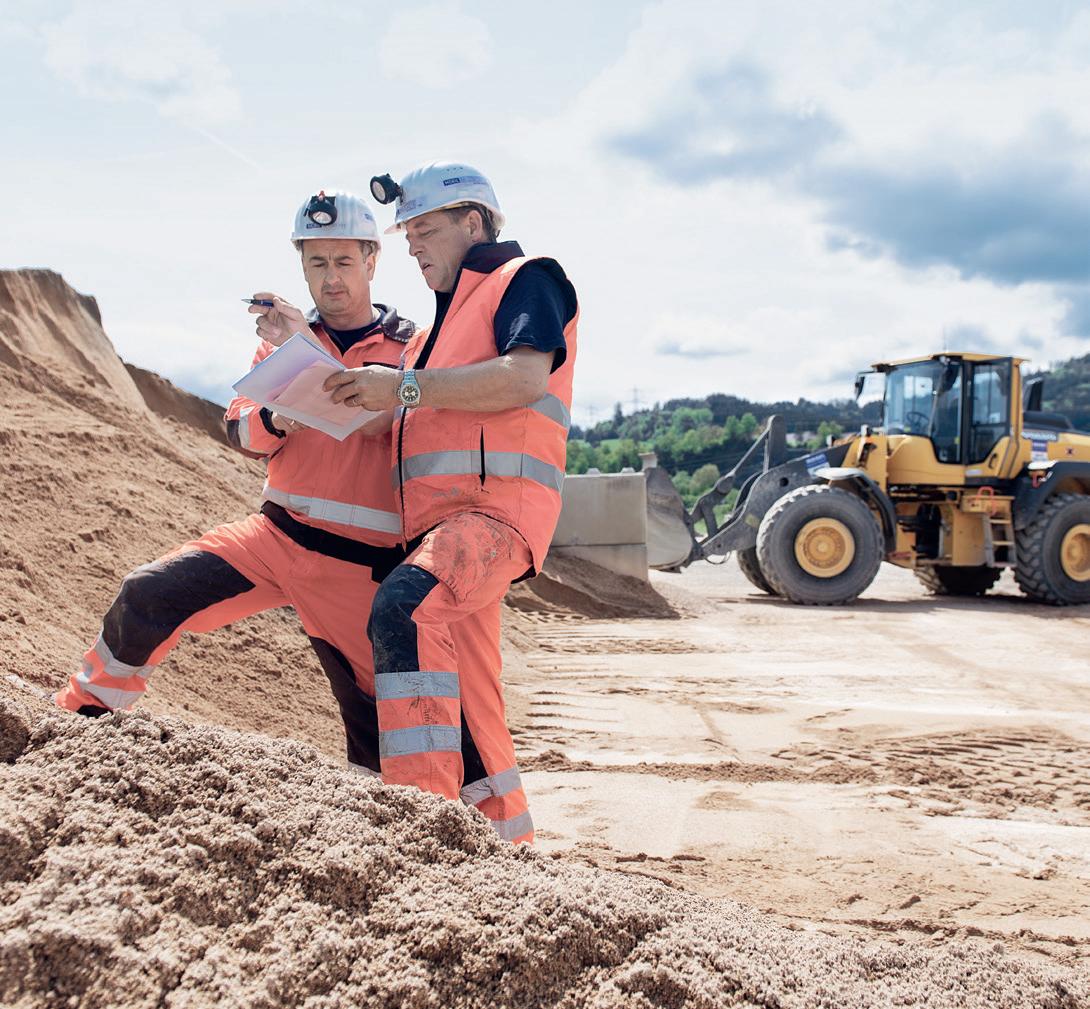
Realising the Potential of AI in the Rail Industry
Synoptix Limited’s AI/ML Optimus automated census system for Security and Safety Application
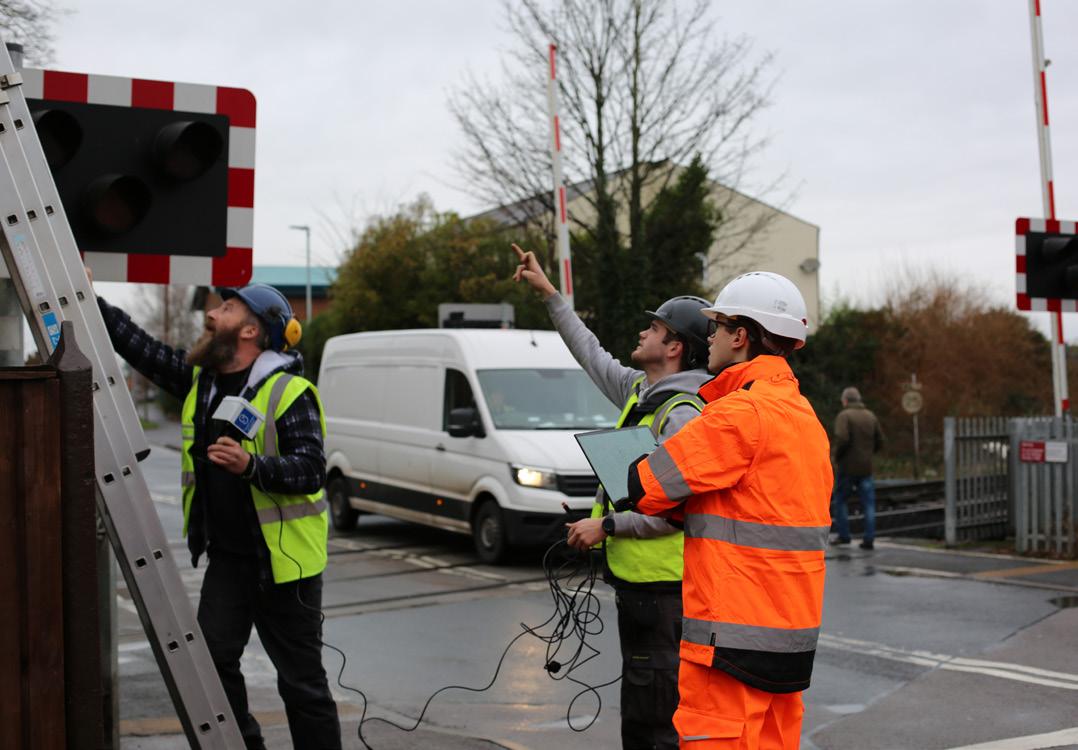
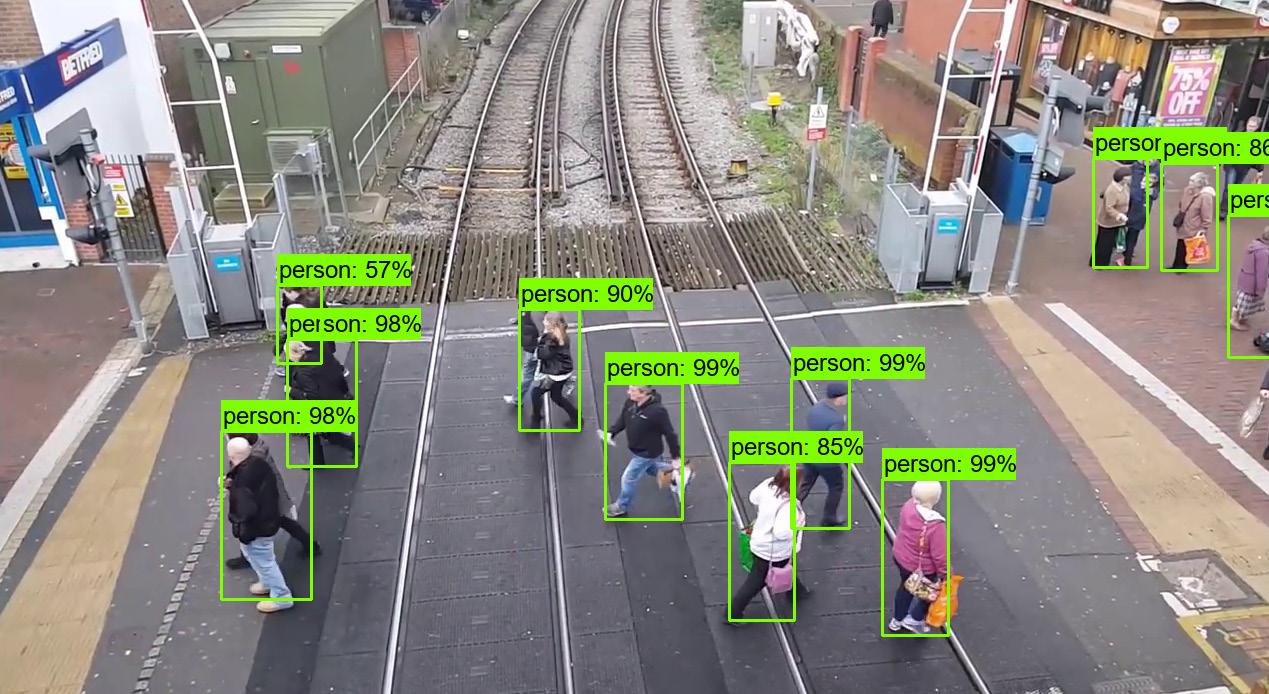
The specialist Bristol based Systems Engineering consultancy; Synoptix have been actively developing product lines around the Cyber Security, Artificial Intelligence / Machine Learning, Simulation and Modelling space. They have an extensive track record of successfully delivering, work packages for clients across a range of sectors including Defence, Security, Transport and Infrastructure where they deliver complex, multi-disciplinary Engineering work packages in Safety, Reliability and Technical Project Management. This expertise has been enhanced with its collaboration with UK academia including
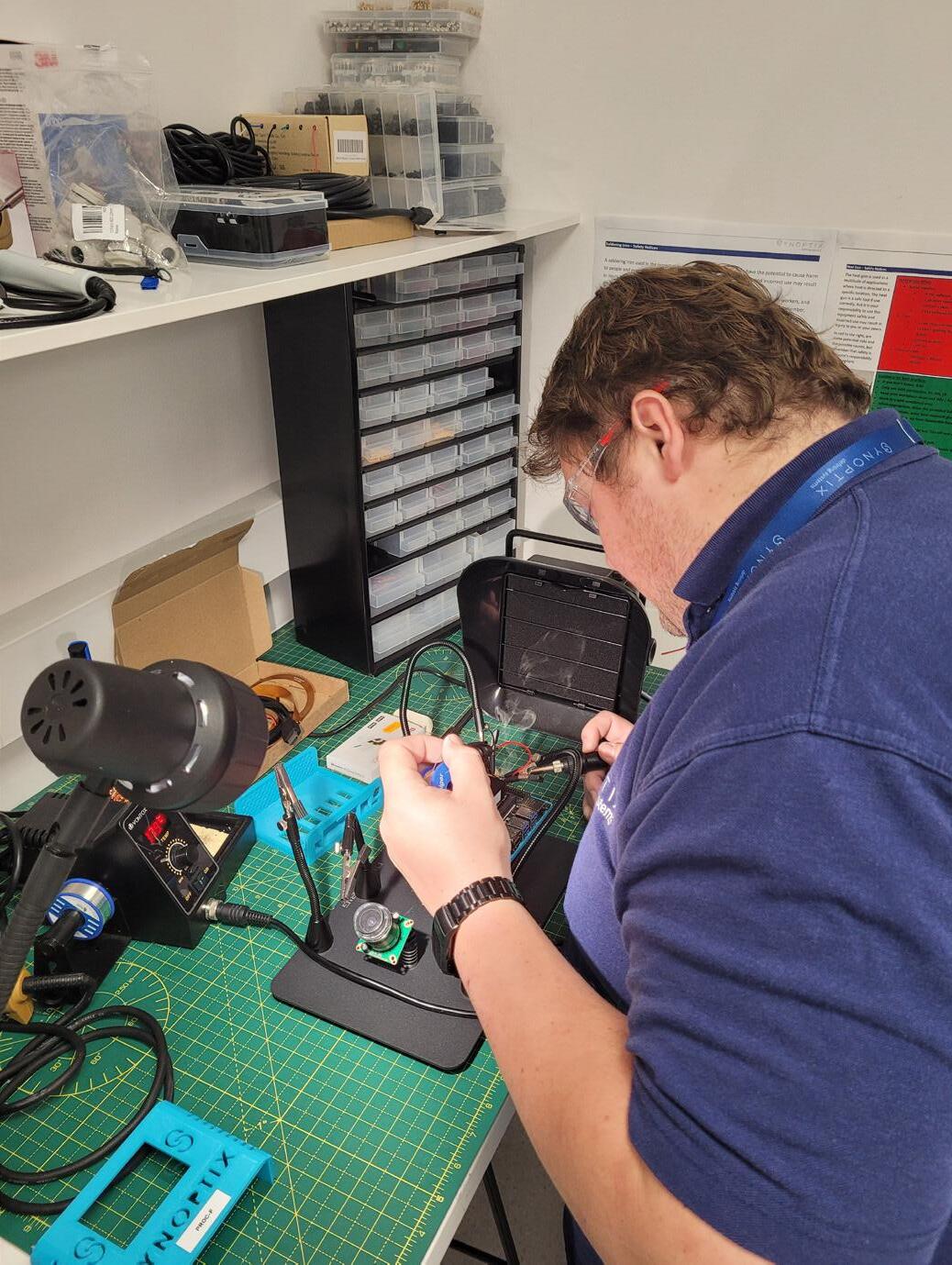
Bristol University, Kings College – London and The University of Leicester, where it has been developing cutting edge technology and innovating Engineering solutions. One product that has emerged from research conducted with the University of Leicester is the nationally recognised AI/ML Optimus automated census system.
Level Crossing Safety
Despite the UK rail network being one of the safest railways in Europe, serious and fatal accidents still occur. In the 2022/23 period the UK rail network saw 5 accidental fatalities at level crossings. In order to assess the risk at individual crossings, Network Rail
performs manual censuses; these can range from 60 minutes to a full 9 days. This data is then extrapolated to give the level crossing manager an idea what the total usage of the crossing is over a year, which informs risk assessment and crossing maintenance along with crossing closures.
While these censuses have helped make the UK rail network safer, they supply limited information about the pattern of life at the crossings. As the only information being collected is a limited time tally of the different types of crossing users, information such as average transit time or peak usage hours is missed. Synoptix, along with the University of Leicester,

have identified this issue and worked collaboratively to produce the Optimus automated census system to address these problems.
Optimus Automated Census System
The Optimus census system uses an object detection AI to identify crossing users in real time and monitor their journey across the crossing. The system processes all of this information “in-situ” using proprietary
software developed by Synoptix; only sending the processed usage data across to the user. As no images are being sent the system doesn’t use a significant amount of bandwidth; useful if the system is being deployed in rural and remote areas. This also has the added benefit of ensuring the privacy of the level crossing users, an important consideration in the modern world.
The data sent is equivalent to an activity log at the crossing, with each crossing user being assigned a profile which contains information regarding crossing time, speed and position of the crossing user during transit across the crossing. Through this the system can report class by class statistics, such as average crossing time or average route taken, as well as overall pattern of life for the crossing, including data like peak usage times or average day by day totals. The ability to do this also allows for the identification of outlier events, including abnormal or suspicious behaviours of individuals at the crossing.
Through the depth of information that the Optimus census system can supply Network Rail would be able to gain a better understanding of what happens at their level crossings and make more informed decisions regarding level crossing safety. The Optimus system can be used for census in other areas of the rail network, providing insights on high-risk areas like platforms or rail depots. International opportunities for the Optimus system within Australia and India are also being explored, with discussions having taken place regarding the usage of the system in rural and remote areas.
For more information on the Optimus census system, or how Optimus could help your business, please email our Business Development Executive Tom Sharma at tsharma@synoptix.co.uk, or visit our website www.synoptix.co.uk

Tel: +44(0) 117 943 0707
Email: info@synoptix.co.uk
Visit: www.synoptix.co.uk
Address: Synoptix Ltd, 530 Bristol Business Park, The Crescent, Stoke Gifford, Bristol, BS16 1EJ

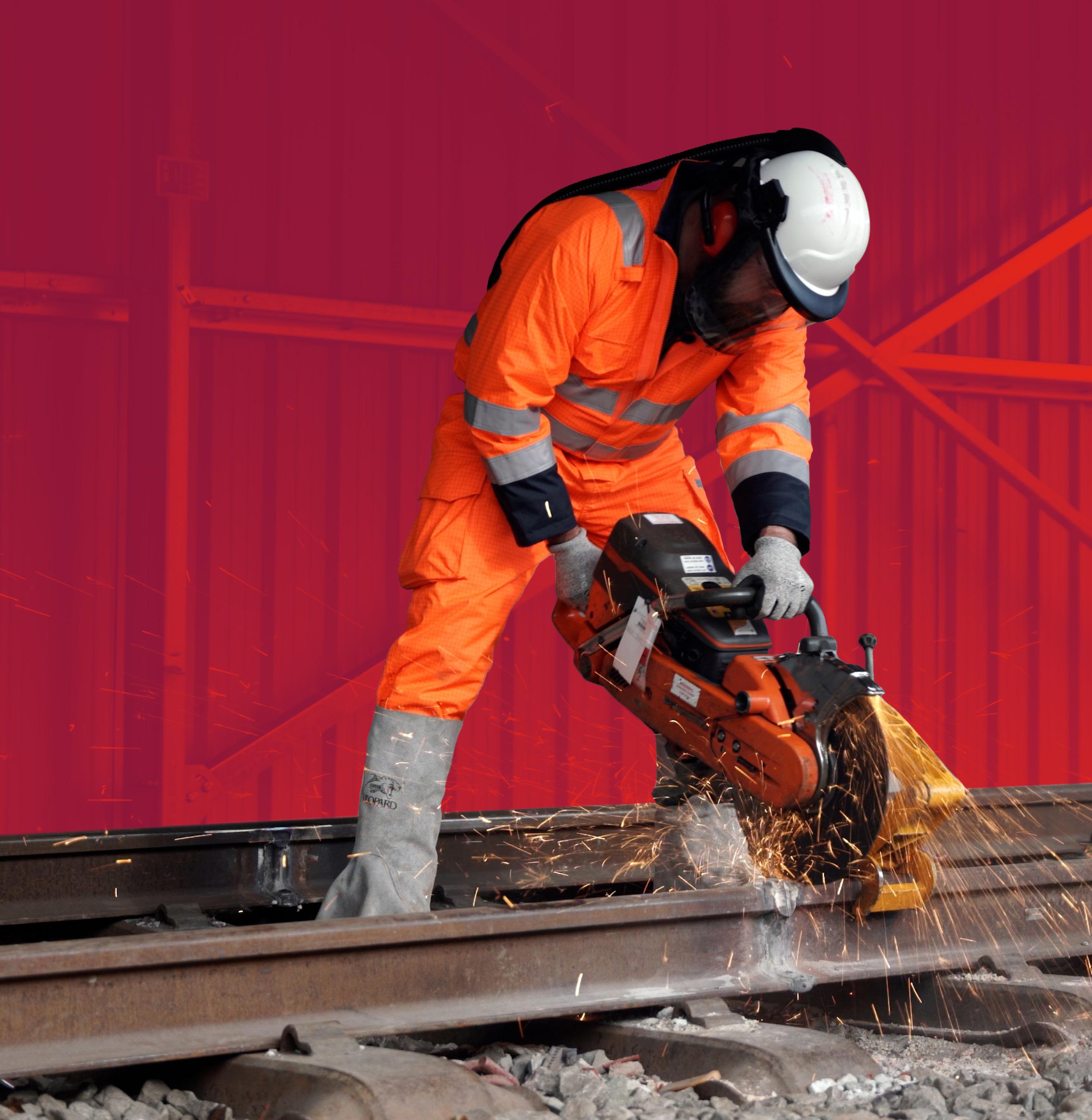

Smart Integrated Lighting Solutions
Rising fuel prices, the growing problem of road congestion and the need to move towards sustainability make rail more than ever the most appropriate means of transport
There has never been a better time to reduce costs and build confidence in outdoor areas.
For more than 115 years, Schréder, an independent, familyowned company, has dedicated itself to exploring everything there is about the potential of light, constantly pushing the boundaries of technological innovations. Expertise, passion, innovation, and sustainability drive 2,600+ employees to use the power of light for the safety and wellbeing of all, from public spaces to higher-risk environments, such as railway stations, commuter routes and carparks, where the consequences of a dark or dimly lit area can lead to injuries.
A
versatile lighting solution
Situated between Terminal 1 and Terminal 3, Manchester Airport Railway Station centres the airport campus with all three terminals within a ten minute walking distance from each other. Lifts, escalators and moving walkways connect the train station and terminal buildings, along with overhead signs to help guide passengers through the airport.
Following a fast lead time, Urbis Schréder were approached by AMCO-GRIFFIN to replace all old, expired SON lanterns in and around the ramp - and the 2No escalators down to the platform from the ticket line at the concourse level to platforms 1-2 and 3-4 - and install new modern
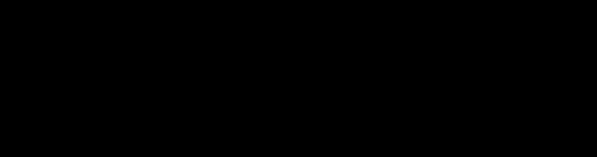
energy efficient LED lights that enhanced the user experience and helped guide commuters/passengers to their desired destination safely.
For this project we used our INDU FLOOD GEN 2 which was the ideal tool to provide an efficient multi-purpose LED lighting solution, especially in transport environments, considering its versatility for high-mast applications in indoor and outdoor areas.
The airport train station will not only benefit from its efficiency and versatility for indoor and outdoor area lighting, but thanks to its robust and compact design, highenergy savings and low operating costs will be significant.
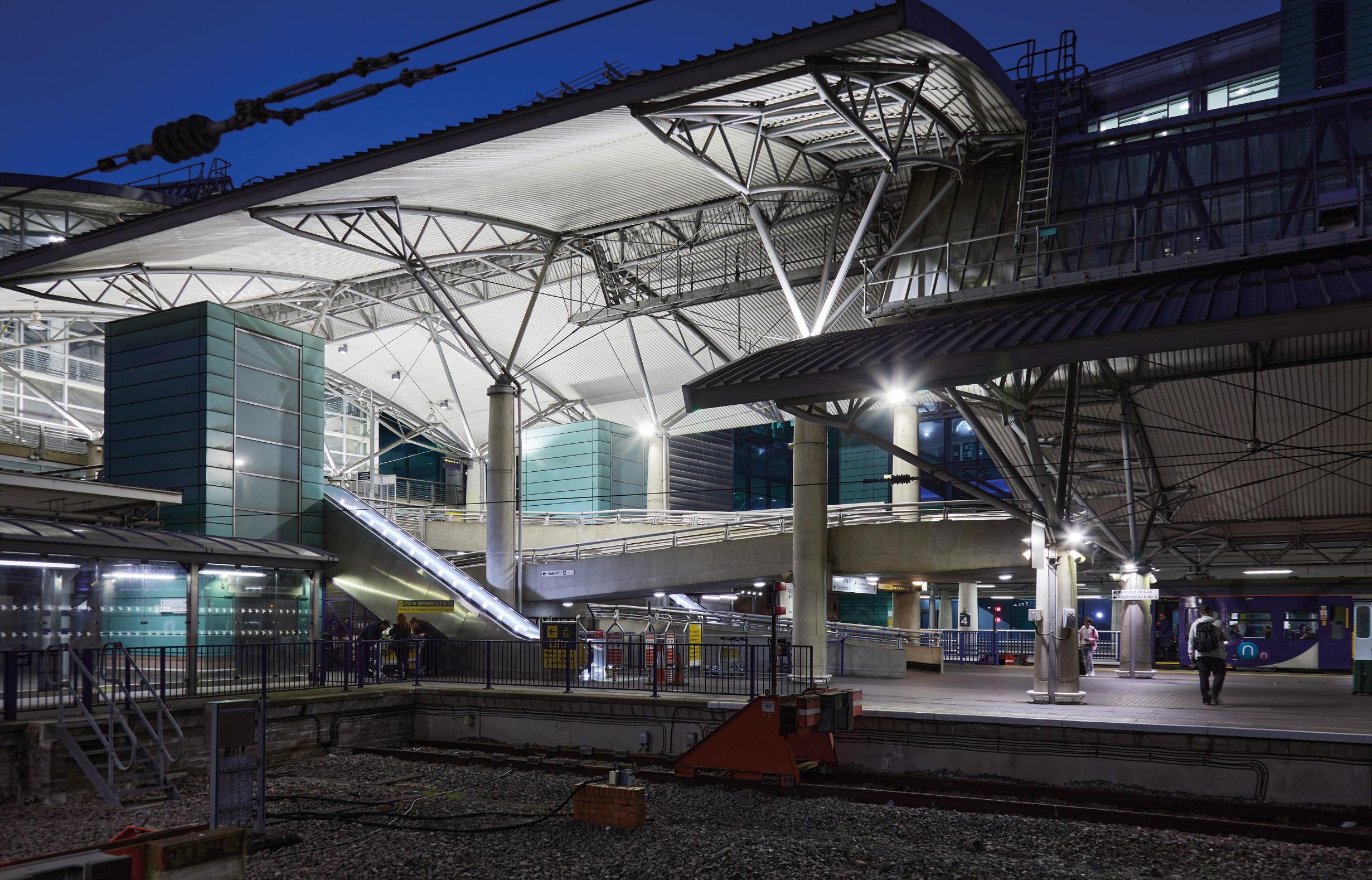
This project is a great example of proper industrial lighting application in railways, operating as a vital tool to enhance space, visibility, and safety. Creating an environment where passengers and travellers can easily be directed and guided to their desired destination, with a peace of mind.
Bespoke lighting to support your decarbonisation transport initiatives
With energy prices relentlessly rising, there has never been a better time for local authorities to reduce overhead costs, prioritise safety and build confidence in outdoor areas. Money is often wasted on poorly designed systems which don’t benefit the comfort of the commuters/travellers or your finances, and what people don’t know is that installing the optimal lighting solution for each area of the station also offers significant financial savings too.
Schréder’s EXEDRA, is a remote-control system which allows you to monitor, meter and manage in a lighting network. It is a complete solution based on open standards and protocols. Schréder’s EXEDRA offers a unique combination of state-of-the-art technology and an easy-to-use web interface to control each luminaire, at all times, through a secure internet connection. With bi-directional communication, the operating status, energy consumption and possible failures can be monitored. As a result, this improves efficiency: accurate real-time data and energy savings of up to 85 per cent.
Whether it is the station forefront, carparks, platforms, footbridges, tunnels, junctions, or maintenance pits, Schréder’s dedicated systems offer solutions to suit
your space. Our expertise enables any environment to be transformed into a safe, sustainable, and cost-effective place where the commuters can travel with ease and no worries. Schréder’s lighting systems also require less maintenance than traditional discharge lamps, which means another reduction in costs.
However, connecting your luminaires is not just about adding in a control system to the products you are having installed, it’s much more than that. It is about control of the area you are lighting, it’s about the space the lights are in and the people who are using that space, it’s about delivering solutions beyond lighting for electric mobility, security, information, and entertainment. Is the light right for type of areas? Are you lighting an area to reduce the crime rate? What type of lighting will attract people to use that space? And do you need to dim the light during certain hours of the night but have the control to be able to make them bright again should there be an emergency? Are you wanting to look for energy efficient lighting, a more sustainable solution that reduces your costs?
So, by taking all of this into consideration, the place, the space, the people, the light, the control, let’s get connected!
Schréder
takes the smart LED
High quality, yet energy-efficient and lowmaintenance lighting provides a strategic asset for the development of a sustainable and beneficial railway infrastructure. Urbis Schréder’s wide range of lighting solutions for the rail industry, combined with the company’s expertise and outstanding
heritage in delivering breakthrough projects, creates the best possible experience for passengers and staff in the station environment.
Critical to delivering a safe and pleasant passenger experience inside and in the vicinity of a station is appropriate lighting solutions. New technology also offers the rail industry the ability to improve station lighting and significantly reduce cost.
By combining traditional street lighting, LED handrails, continuous tiled lighting, and ground level inclination lighting; it is possible to create a bright and effective environment. The improved visibility reduces the risk of crime in a station environment and increases passenger confidence.
Our solutions are not just limited to rail, but also extend to interior and exterior lighting such as workspace, roads, architectural buildings, urban deco, sports, cities/communities etc. As we have done so for many years, we provide beneficial LED alternatives to luminaires with fluorescent lamps and can offer a uniform and comfortable lighting suited to any area of choice, whether that’s interior or exterior, helping enhance spaces and create places, people love to live, learn, travel, and play in.
To find out how we can support your vision for connected, safe and sustainable places get in touch.
Address: Sapphire House Lime Tree Way, Basingstoke RG24 8GG
Tel: 01256 354446
Email: sales@urbis-schreder.com
Visit: Rail Lighting Solutions | Schréder (schreder.com)
LinkedIn: Urbis Schréder

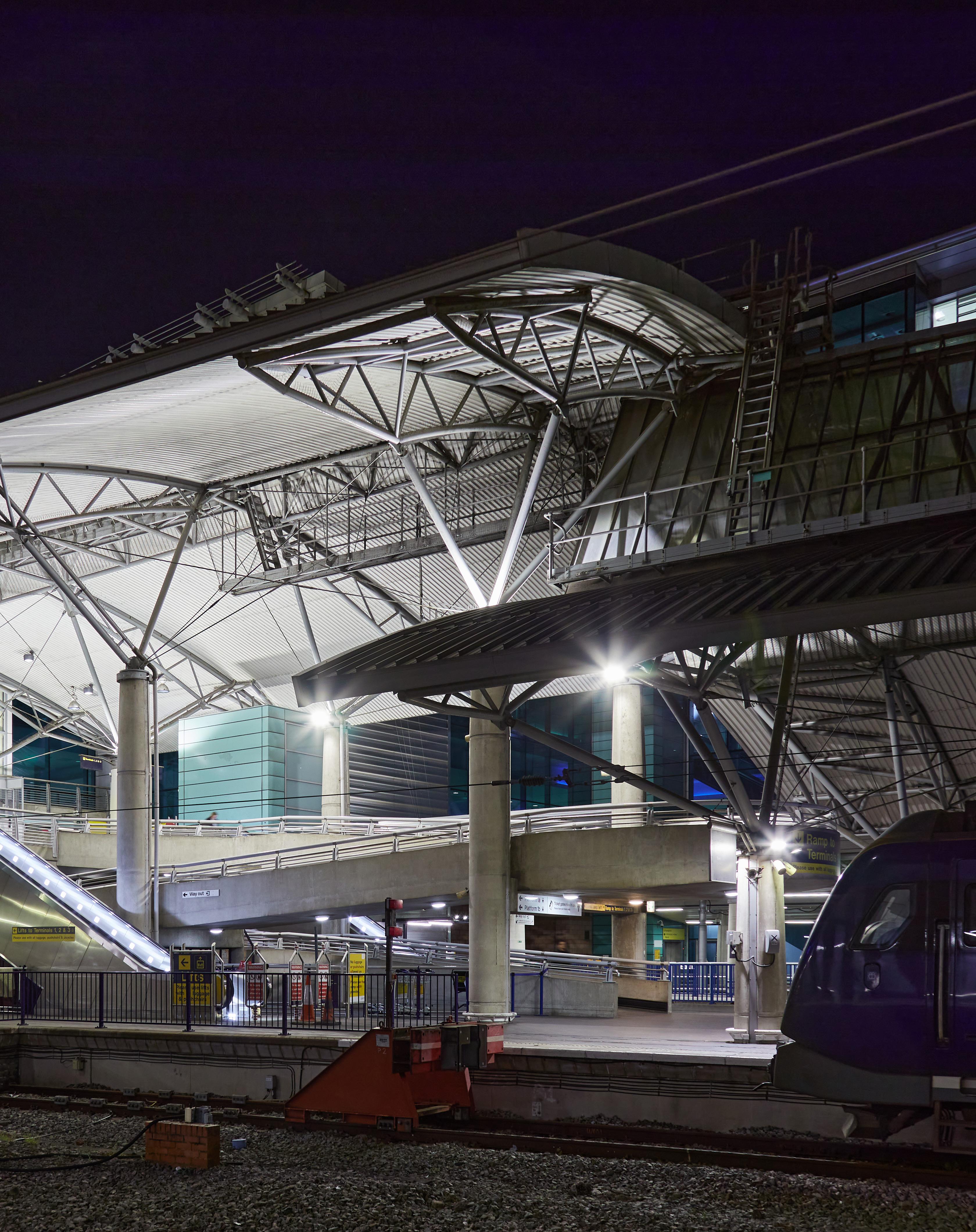




Network Rail and CIRO Partner to Launch Capacity Planning Qualifications
Following years of intensive development, Network Rail and CIRO have come together to launch three new capacity planning qualifications for use in Network Rail’s internal training programme.
The new qualifications, which will be awarded by CIRO and delivered by Network Rail‘s Capacity Planning Training and Development Team in Milton Keynes, will standardise capacity planning and offer a clear path of potential progression and developmental experience for the community of Operational Planners and Specialists, through the following tiers:
• CIRO AO, Level 2 (Certificate) in System Operator Timetable Development
• CIRO AO, Level 3 (Certificate) in System Operator Strategic Timetable Development
• CIRO AO, Level 4 (Diploma) in System Operator Strategic Timetable Development and Production
The development journey started back in 2019, with the appointment of Training and Development Manager (Capacity Planning) Carolyn O’Sullivan, who recognised the need for a more robust framework. Network Rail and CIRO collaborated on a third capacity planning paper to utilise the knowledge of several subject matter experts and to supplement the existing two competencies.
Forming the third level means that there’s now a comprehensive training plan which all new entrant Planners must complete to achieve the full Level 4 Diploma.
Following a successful pilot scheme of the new paper, discussions began with CIRO, who had received a Royal Charter in 2021, allowing it to award qualifications and enabling it to become the only sector specific standard setting body for rail. The opportunity plays to CIRO’s strengths of utilising the quality assurance disciplines from its successful EPA service whilst
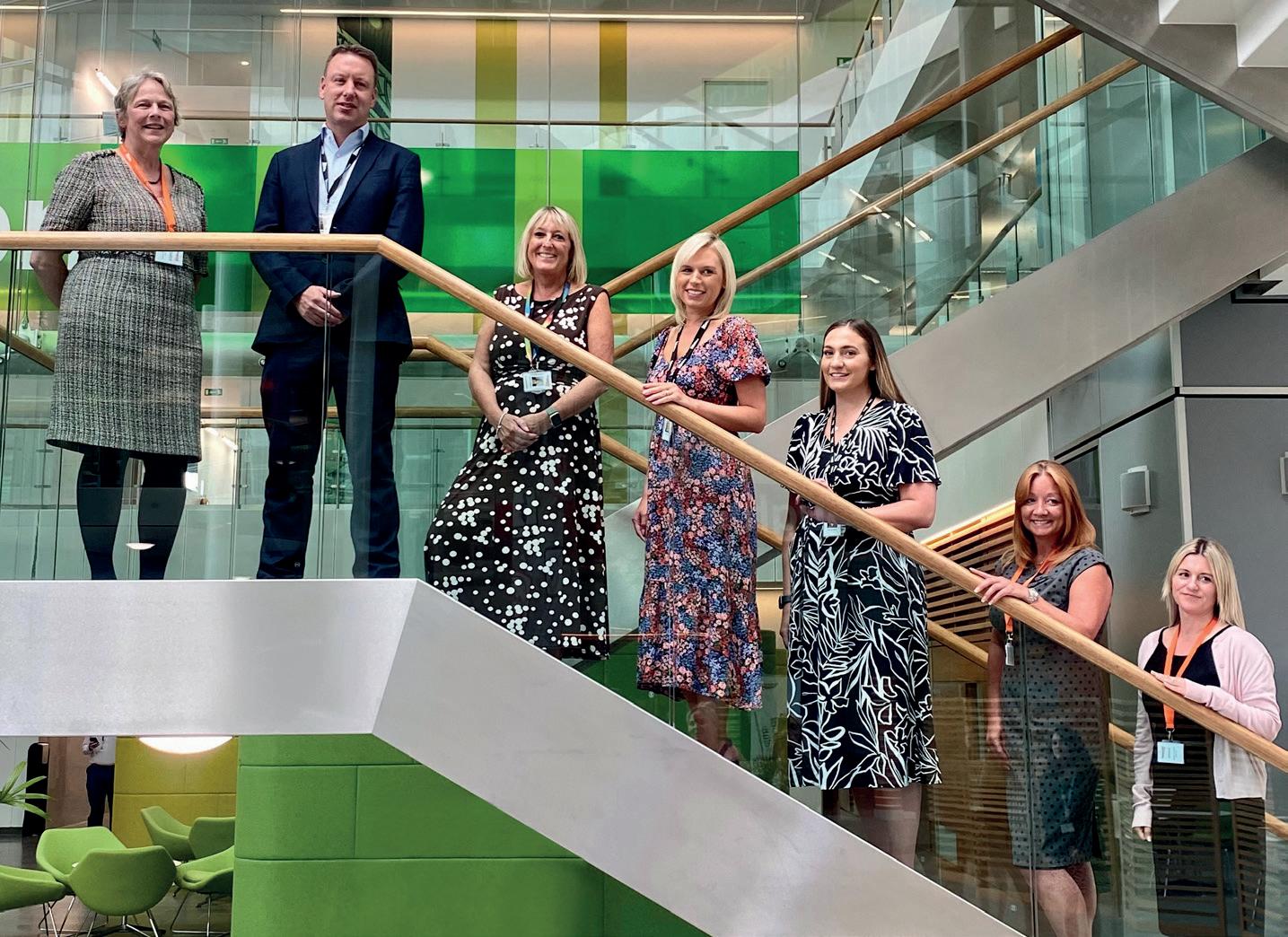
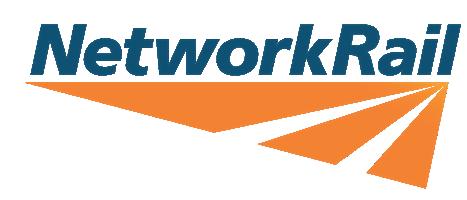

offering a unique, employer led solution connecting this important workforce to professional development and recognition.
Carolyn O’Sullivan, who led the project, explained the partnership:
“By collaborating closely and harnessing our collective expertise, Network Rail and CIRO have created something which will enhance the training experience of our Operational Planners, and ultimately raise the standards for our organisation and wider industry. Our teams have worked hard over the past few years to bring this to reality and we’re delighted to see the first Operational Planners and Specialists coming through the programme”.
The first certificates (level 2 and 3 certificates) will be awarded during the Autumn as Operational Planners and Specialists complete the course and competencies.
Thanks to the success of the programme, Network Rail and CIRO are currently looking at further opportunities for collaborative training product development.
If you would like more information on Network Rail careers or training opportunities, visit: www.networkrail.co.uk/careers
For more information on how a partnership with CIRO can help your organisation with speciailised training and development solutions, visit: www.ciro.org/awarding-organisation
Our teams have worked hard over the past few years to bring this to reality and were delighted to see the first Operational planners and Specialists coming through the programme”.
Carolyn O’Sullivan Training & Development Manager, Network Rail
Station Receives ‘Wildlife Friendly Station’ Status
Great Bentley rail station has received a ‘Wildlife Friendly’ accreditation recognising the work of community volunteers to improve biodiversity and support nature there
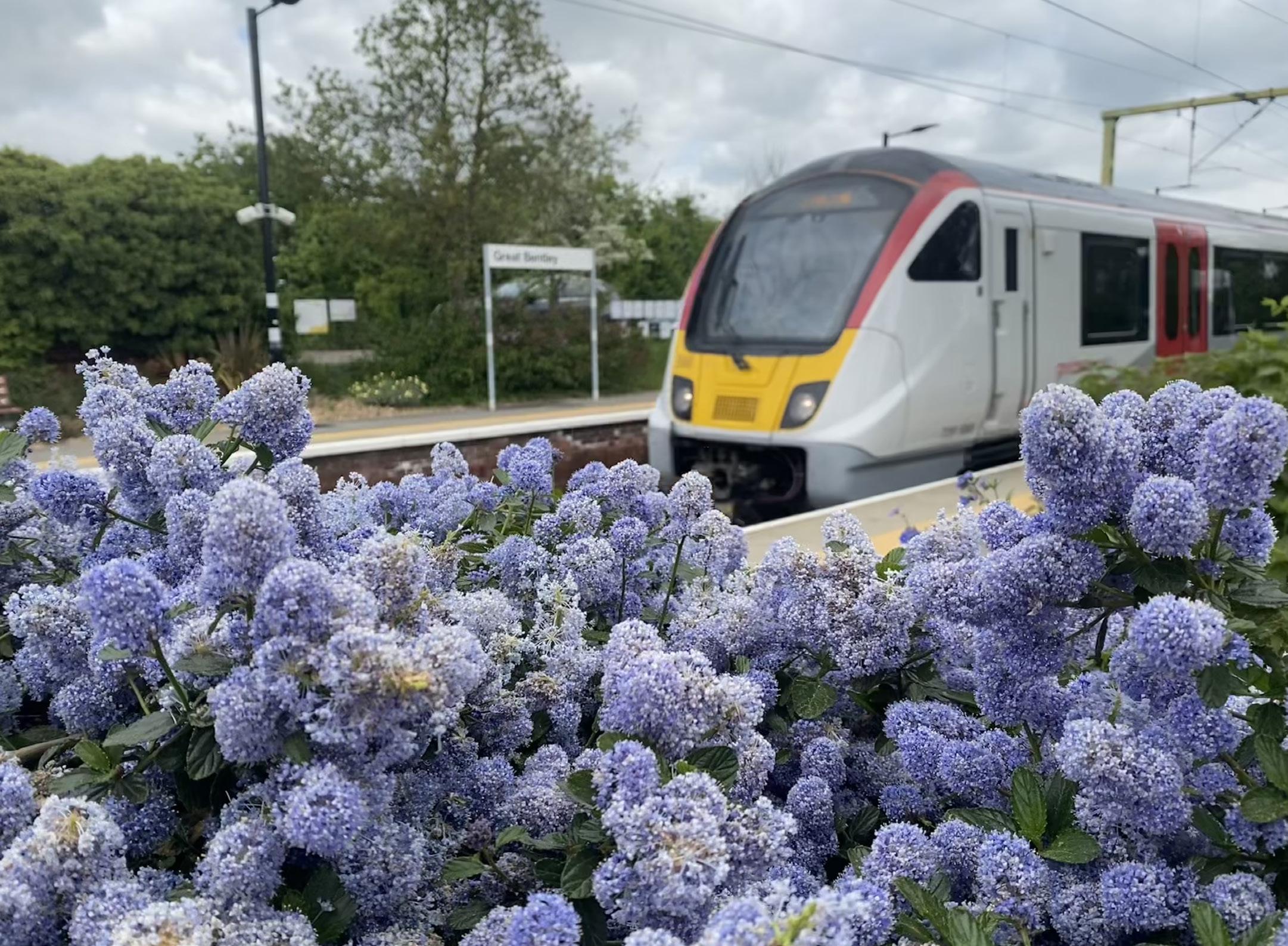
Greater Anglia has partnered with the region’s Wildlife Trusts to formally recognise the achievements of its teams of volunteer ‘station adopters’ to create wildlife havens at stations across its network, through the new ‘Greater Anglia Wildlife Friendly Stations Accreditation Scheme.’
The Great Bentley station adopter team, Peter Neale, Dawn Vinn, Jane Ryland and Daniel Ryland, received the award following assessment by an Essex Wildlife Trust Conservation Officer to determine how well the station supports local flora and fauna.
The ecologist’s report noted that Great Bentley station has great potential to make a difference to local biodiversity due to its
location, which can act as a stepping stone to woodlands to the south and south-west of the village.
The station also features ‘bee friendly’ planters, installed in partnership with the Bee Friendly Trust, which are filled with nectar rich plants to support pollinating insects, an insect hotel, and a community herb garden - where people can help
Greater Anglia train passes through Great Bentley station.
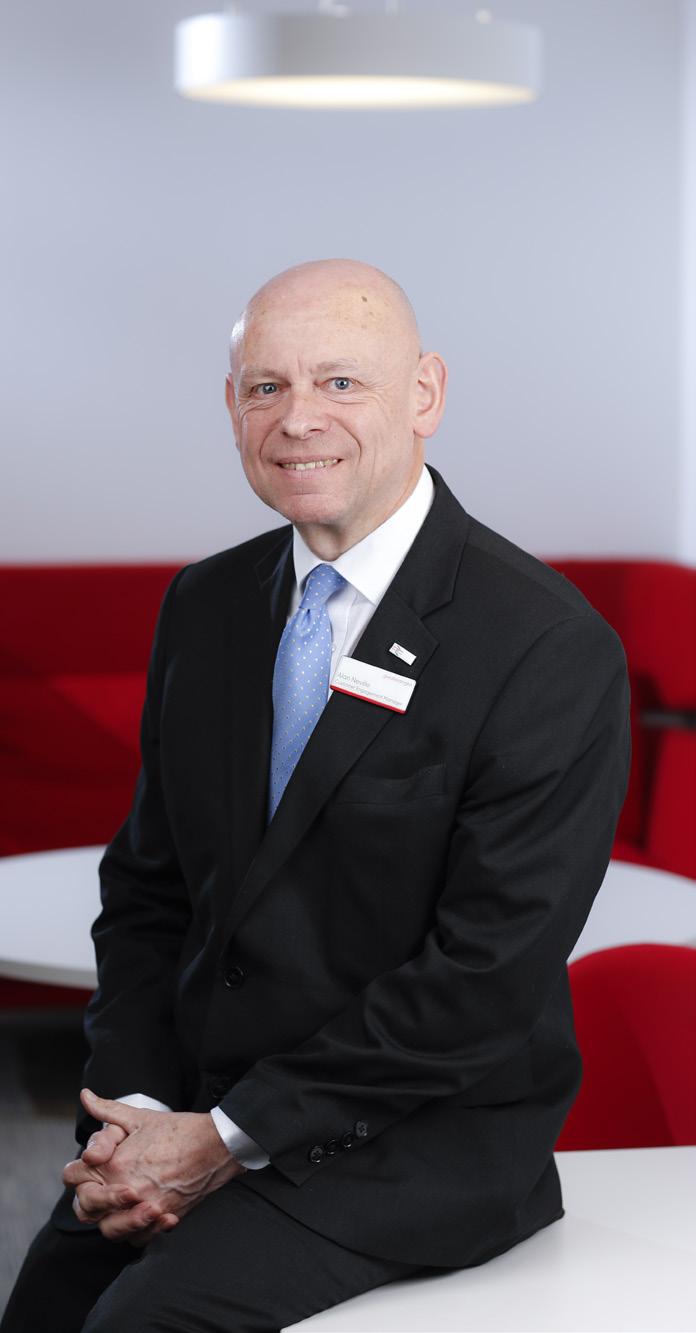
‘We are delighted to partner with the region’s wildlife trusts to formally recognise the valuable work of our station adopter volunteers in supporting wildlife and improving their local environment. I’d like to congratulate the volunteers at Great Bentley station on receiving this recognition and thank them for the incredible work that they are doing that is helping to support biodiversity locally.’
Alan Neville, Greater Anglia Customer and Community Engagement Manager
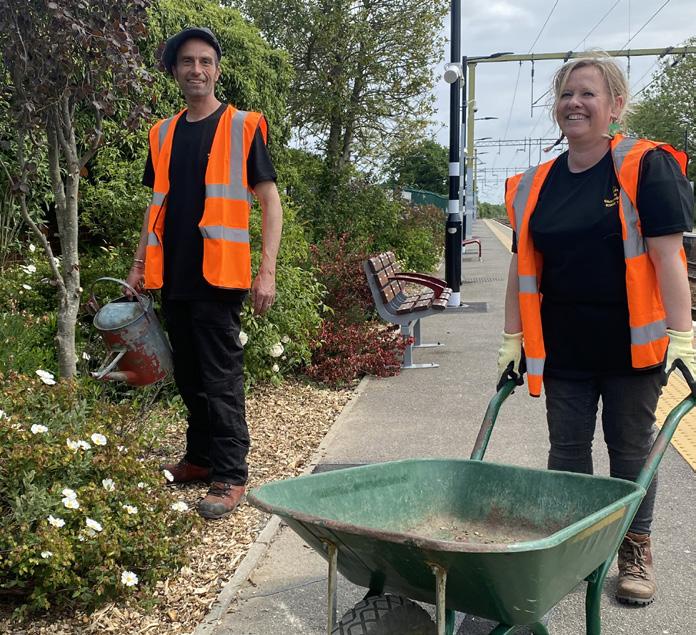
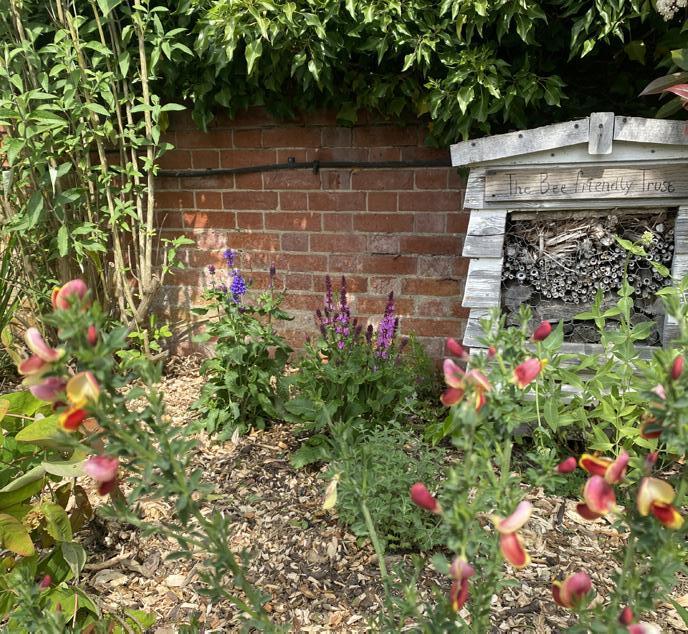
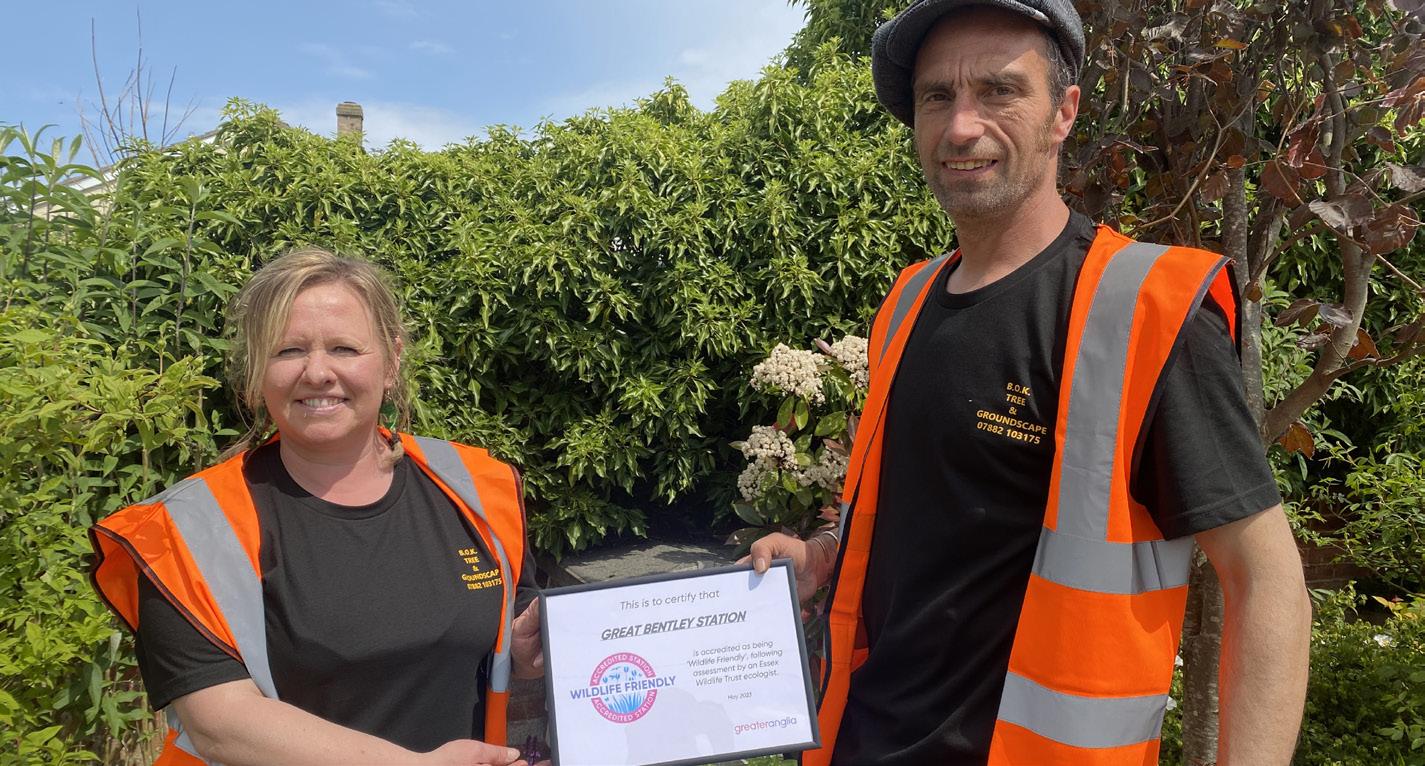
themselves to the herbs, which also provide a good food source for pollinators.
James Hogg, Development Officer at the Norfolk Wildlife Trust, the lead Trust for the initiative, said: ‘The alarming decline in the abundance of wildlife and the plight of species under threat means that just protecting the nature we have left is not enough; we need to put nature into recovery, and to do so at scale and with urgency.
‘This project with Greater Anglia is a fantastic example of how people can transform nature-poor areas into new nature-rich places – and change the way we think about land, seizing opportunities to help nature outside traditional nature reserves.’
Each assessment also offers tips and advice for how to make the stations more wildlife friendly and the reports can also be used as examples of best practice, to help spread good ideas around all Greater Anglia’s stations.
There are now 19 stations across the Greater Anglia network which have received the ‘Wildlife Friendly’ accreditation, with more expected to be certificated over the next year.
Rail stations in East Anglia are increasingly becoming havens for local wildlife thanks to the efforts of over 300 volunteers who last year transformed over
7,400 square metres of land into thriving wildlife gardens.
In a recent survey, Greater Anglia station adopters reported a wide range of creatures visiting their stations, including many different types of butterflies as well as bees, slow worms, bats, foxes, toads, lizards, deer and many varieties of birds, recording more than 200 different species.
Over the last 20 years, since the start of station adoption in East Anglia, the initiative has thrived, so that the vast majority of Greater Anglia stations now have station adopters. These ongoing increases in the areas adopted and the wildlife being seen on the stations show that the adopters are really playing their part in helping to make stations more biodiverse, as well as becoming more attractive gateways to the communities they serve.
Greater Anglia has also joined the rest of the rail industry in pledging to make stations across Britain more sustainable.
Action to reduce waste, support local wildlife and cut the carbon footprint of railway stations will be informed by the industry’s Sustainable Stations: Best Practice Guide, which details ways in which train operators can meet this commitment in support of global goals of decarbonisation, reducing waste and supporting local plant and animal life.
Insect refuge in the garden at Great Bentley station.
Great Bentley adopters, Jane and Daniel Ryland.
Great Bentley adopters, Jane and Daniel Ryland, with their Wildlife Friendly Stations accreditation.
Premier global manufacturer of components and kits for railway applications

In addition to supplying individual components, the global companies of STAUFF and their authorised system partners use the STAUFF Line approach to support Original Equipment Manufacturers with the supply of custom-designed and ready-to-install fluid power lines from connection to connection and also provide supplemental services that create added value: · Components · Systems · Services · Contact
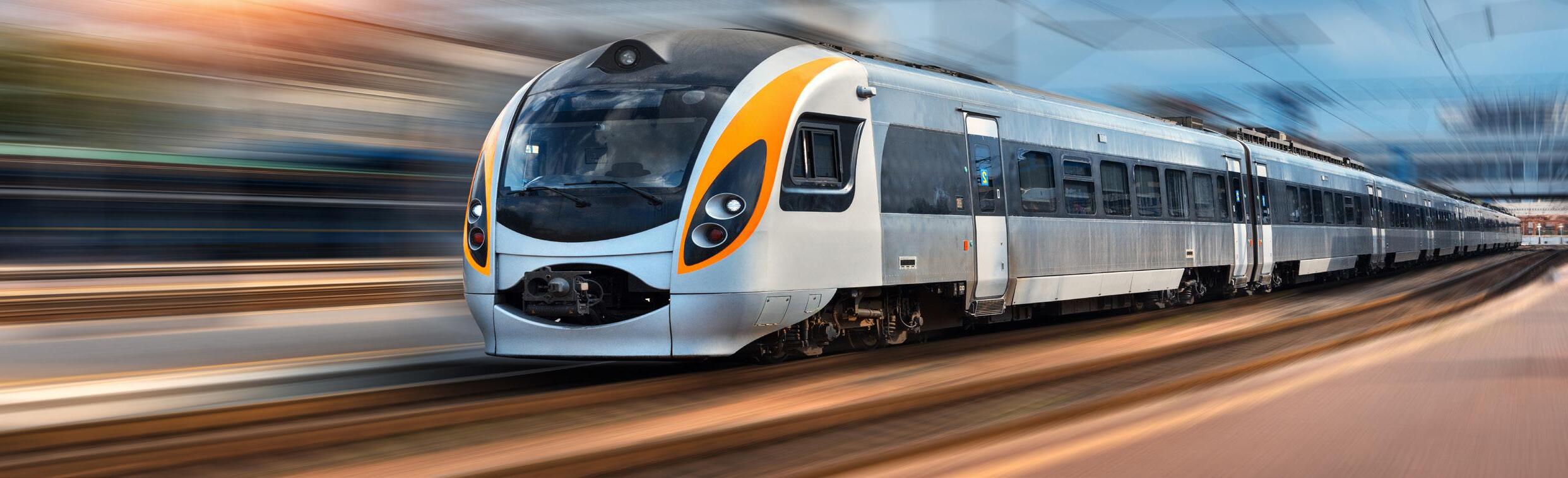
Sheffield Tel: 0114 251 8518
Email: sales@stauff.co.uk
Aberdeen Tel: 01224 786166
Email: sales@stauffscotland.co.uk
Ireland Tel: 02892 606900
Email: sales@stauffireland.com
Southampton Tel: 023 8069 8700
Email: sales@stauffsouthampton.co.uk
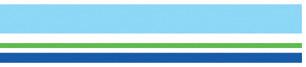

The STAUFF Line process is adopted by global OEMs to successfully achieve cost savings in rolling stock manufacture.
“We have the hose world in our hands”
Bespoke Waterproofing at Bank Station
A Mapei waterproofing solution has been installed as part of London Underground’s Bank Station Capacity Upgrade to increase passenger capacity and provide step-free access
The system – which included Mapegrout Gunite FSD and Mapelastic TU – was developed by Mapei’s Underground Technology Team (UTT) in collaboration with main contractor, Dragados; Transport for London and Engineers, Dr. Sauer & Partners. It ensured that the new infrastructure was watertight and maintained a safe and secure environment for passengers.
An ambitious and complex project, the Bank Station upgrade has increased the station’s capacity by 40 per cent. It includes a new railway tunnel and wider southbound platform for the Northern line; step-free access to the Northern line for the first time and improved step-free access to the DLR platforms; new station entrances and interchange routes, moving walkways, lifts and escalators, and approximately 1,400 metres of new tunnels. The installation, by Dragados, spanned a tunnel surface of approx. 24,000m2; it featured a low dust regulating layer of Mapegrout Gunite FSD and spray-applied of Mapelastic TU. The system was also used to waterproof reinforced concrete works in areas including shafts.
Mapegrout Gunite FSD is a fast-setting, ready-to-use fibre-reinforced cementitious mortar developed for concrete, stone and masonry structures including tunnel linings, shafts and foundations. It provides excellent bonding strength and speed of application, with low dust emissions. Waterproofing membrane, Mapelastic TU system is a onecomponent ready to use sprayable synthetic membrane developed for tunnels and underground structure waterproofing. Featuring excellent tensile strength and adhesive properties, the membrane creates a flexible, seamless waterproofing barrier and can be used in new tunnels and to replace existing systems. Other Mapei products specified included two fast drying hydraulic binders – Lamposilex, a water plug and Topcem for screeds – and two paint

finishes: Silexcolor – a silicate based, vapourpermeable protective paint - and Mapecoat ACT – a mould, virus and bacteria-resistant cleanable enamel paint.
Throughout the project, Mapei UTT provided technical support and training to ensure the project's unique challenges were met. The system accommodated heavy reinforcement, restricted access and low temperatures and the dust-free application – which was recognised in the NCE Tunnelling Award received by Mapei UTT –ensured a safe application in a challenging environment.
About Mapei and Mapei UK
Founded in 1937 in Milan, Mapei is now one of the world’s leading manufacturers of chemical products for the building industry and has contributed to the construction of some of the most important architectural and infrastructural works worldwide. With
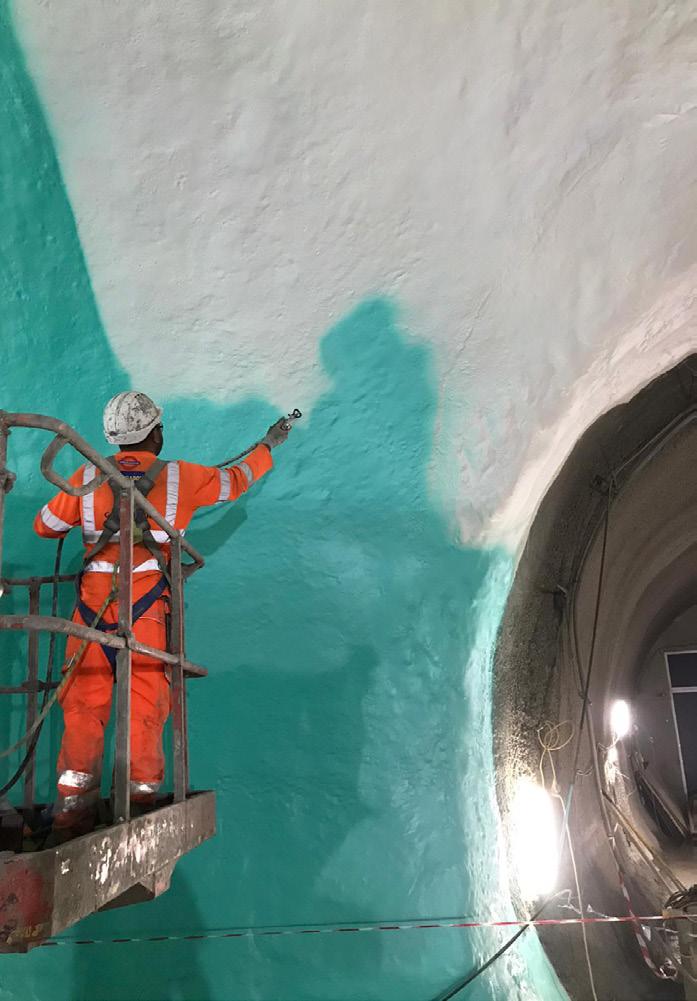
100 subsidiaries operating in 57 countries and 86 manufacturing plants in 35 different nations, the Group employs more than 11,000 staff worldwide. In 2021 Mapei had a consolidated turnover of €3.3 billion (£2.8 billion). The foundations for the success of the company are specialisation, internationalisation, research and development and sustainability. www.mapei.com
Headquartered in Halesowen, West Midlands, Mapei UK has a workforce of more than 300 employees. Mapei facilities have been certified to ISO 9001, ISO 14001 and ISO 45001 standards. An environmentally conscious manufacturer that reinvests significant revenue into R&D, Mapei offers training for architects, contractors, installers and distributors through Mapei Academy. For more about Mapei, please contact: info@mapei.co.uk or visit www.mapei.co.uk
TENSOREX C+:
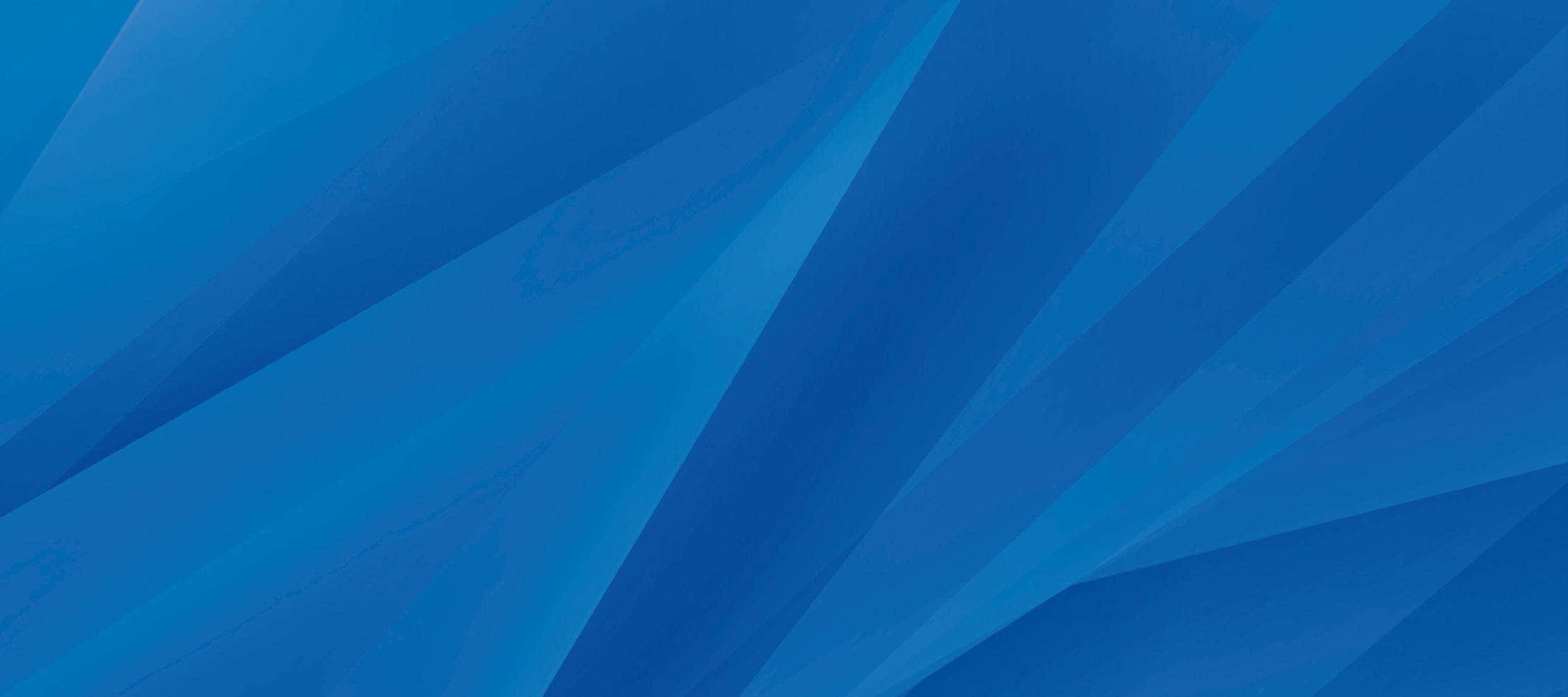

Spring Automatic Tensoning Device
RAILWAY INFRASTRUCTURE SOLUTIONS
FOR TODAY´S AND FUTURE CHALLENGES
Our Expertise for Railway and Tramway:
- Railway Catenary Systems
- Tensioning
- Insulation technology
- Power supply
- Safety equipment
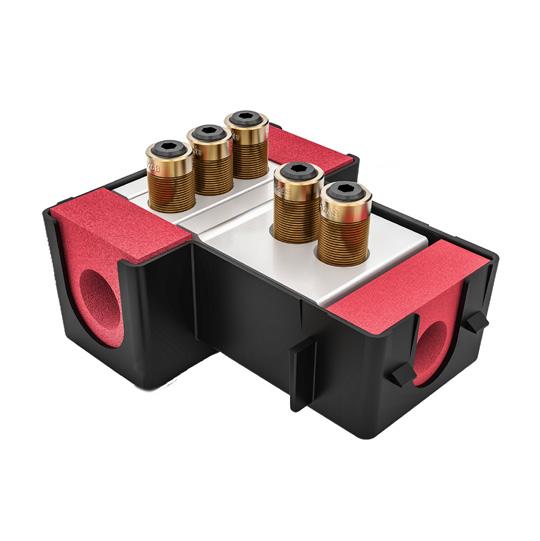
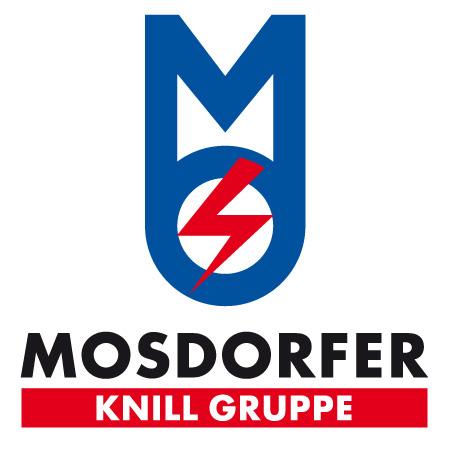
Mosdorfer Rail Ltd.
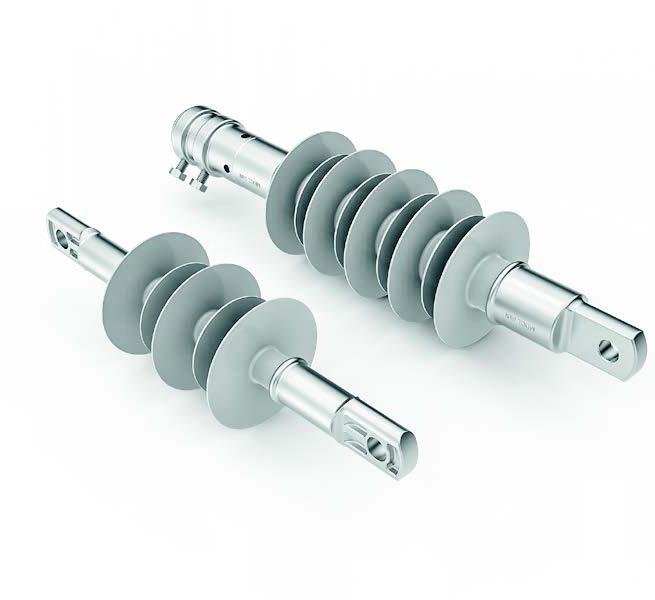
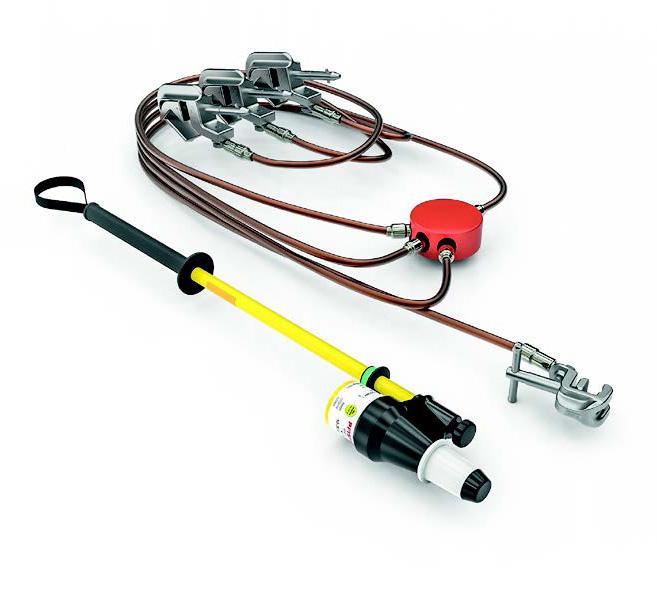

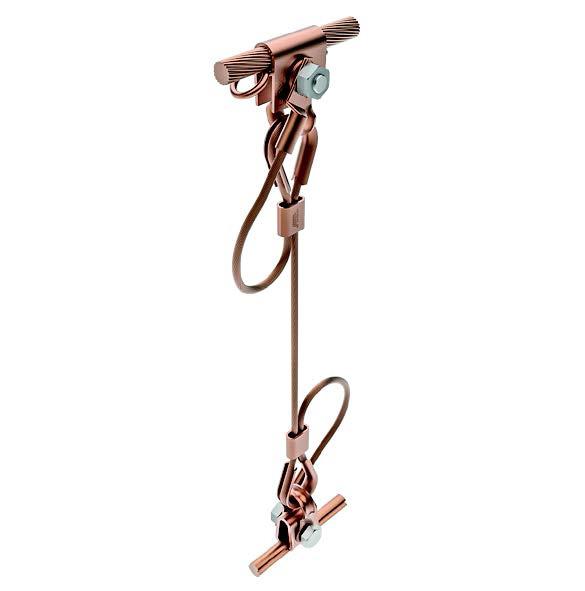
2 – 4 Orgreave Place, Orgreave Sheffield S13 9LU, South Yorkshire, UK
Phone: +44 114 3878370
E-Mail: OrdersRailUK@mosdorfer.com
Catenary Clamps Droppers
Bonding Connectors
TPE Maps the Future to more Accessible Stations
New tactile maps have been installed at Hull Paragon, Dewsbury and Manchester International Airport (MIA) as part of TransPennine Express’ (TPE) commitment to help blind and partially sighted passengers find rail travel even more accessible
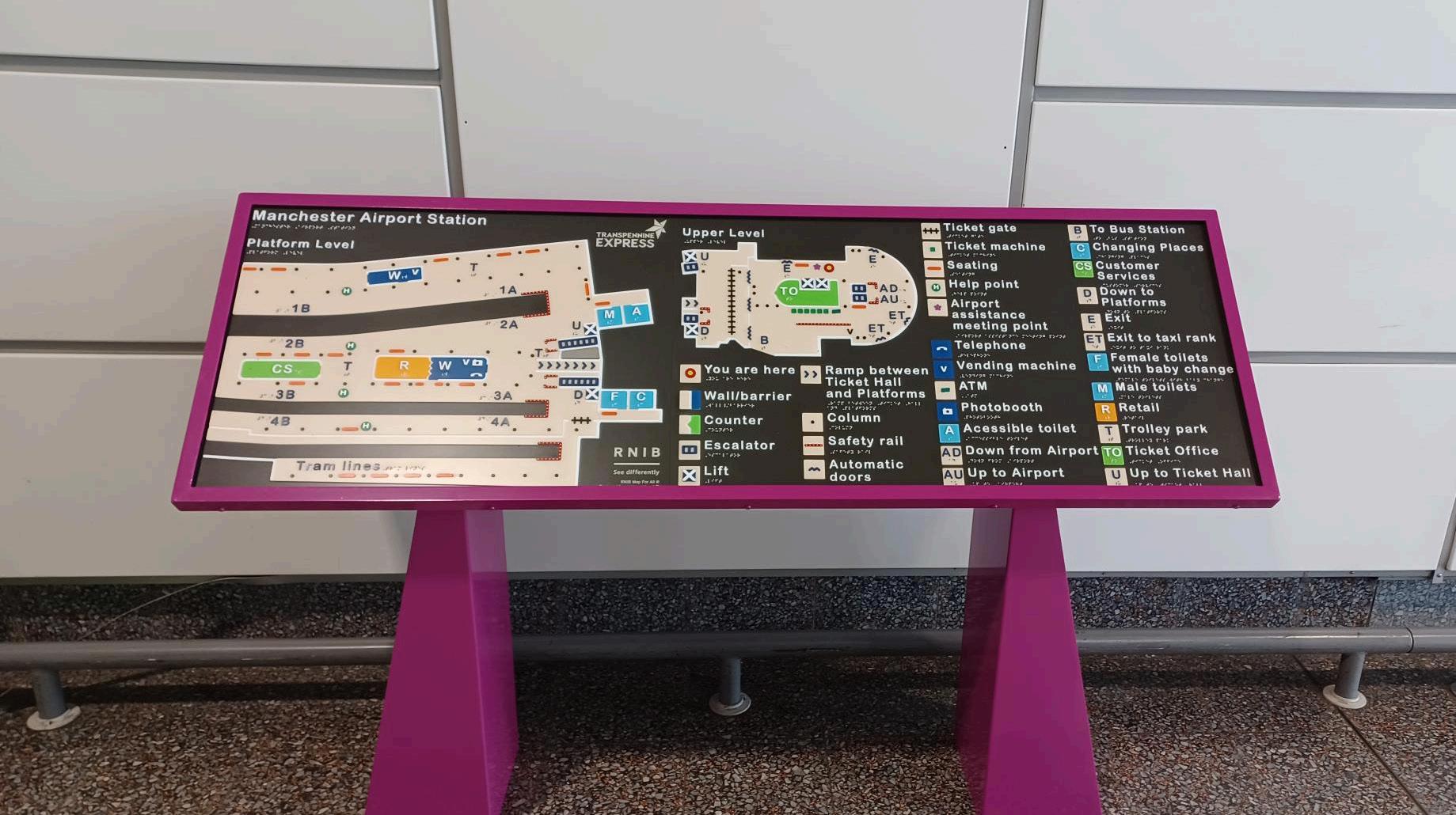
The tactile ‘Map for All’ is a unique product developed and produced by the Royal National Institute of Blind People (RNIB) and is intended for use by people of all ages and abilities. They can be read by sight, by touch, or a combination of both and are designed with ‘access for all’ as the core principle.
Chris Jeffrey, Accessibility & Transport Integration Manager for TPE, said: ‘I am delighted that we now have RNIB Maps for All at at our Hull Paragon, Dewsbury and MIA stations. We are committed to making our services as inclusive and accessible as possible and are continuously looking for new and innovative ways to achieve this.
‘We installed the maps following feedback from our Customer and Professionals Accessibility Panel who suggested a physical alternative to the many digital wayfinding innovations TPE already has in place.’
Each map is carefully created to combine both visual and tactile elements resulting in a map that is a mixture of layers, visual contrasts, textures, raised large print and braille lettering, as well as tactile and visual symbols.
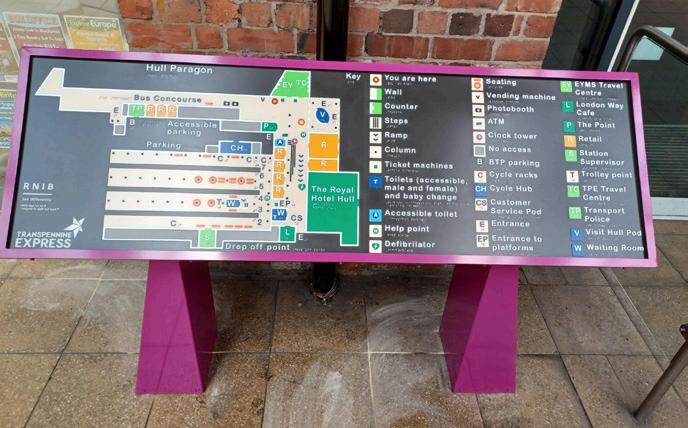

Chris added: ‘These maps will help blind and partially sighted people navigate our stations more easily and independently, but they are also great for anyone who is new to a station and needs visual directions.’
TPE has plans to expand its Maps for All to Huddersfield, Middlesbrough, and
RNIB Map for All is manufactured from exterior grade signage plastic that has a non-glare matt finish over a layer of rich colour that resists fingerprints, is stable under ultraviolet light and is suitable for use indoors and outdoors.
RNIB Map for All allows blind and partially sighted people to be more independent when visiting a wide variety of buildings and venues, contributing to a more inclusive lifestyle.
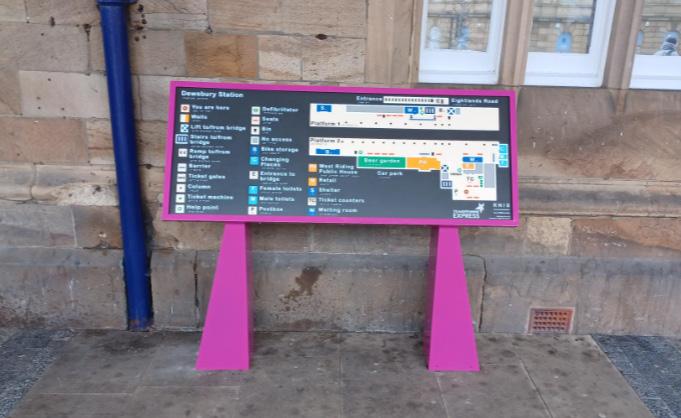
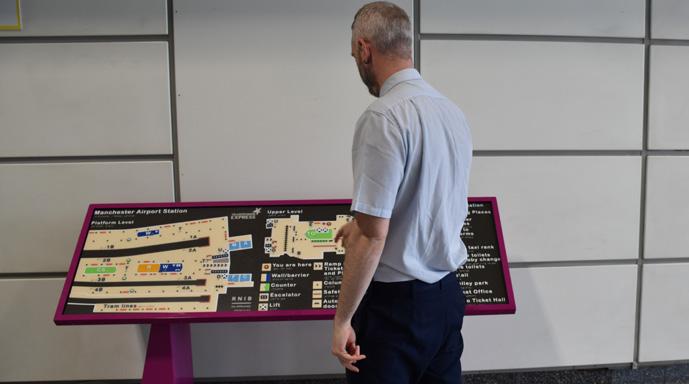
Scarborough stations in the future. Earlier this year TPE launched two new technologies, My Station View and GoodMaps Explore, are both designed to help customers navigate TPE’s managed stations across the north.
RNIB MAP FOR ALL

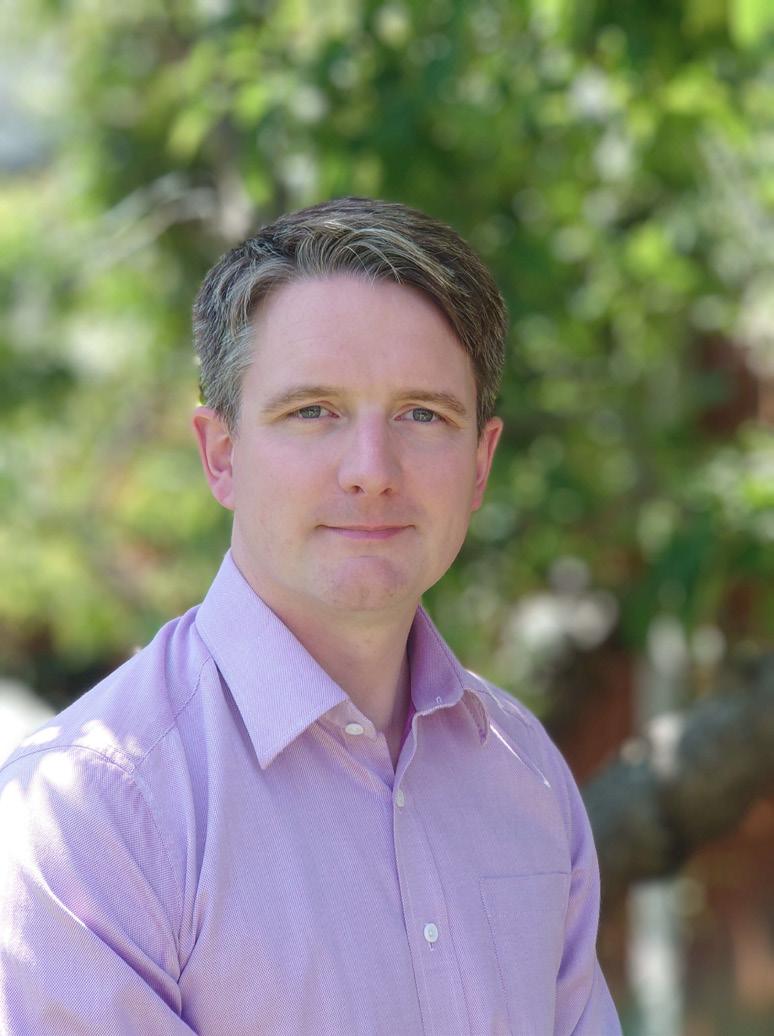
with over 20-years’ experience delivering signalling upgrades and enhancements in a variety of signalling design and project engineering roles. David is an IRSE licenced signalling principles verifier and engineering manager. David is a specialist in complex interlocking systems and signalling scheme design having delivered such projects consistently over the past 20 years.

ROBERT HAY OPERATIONS DIRECTOR AT PRIME RAIL ENGINEERING LTD
Rob started his rail career in recruitment before entering London Underground’s (then Metronet) engineering graduate scheme in 2004. After choosing to specialise in signalling, he crossed over to mainline principles, starting with Alstom in 2013. He has worked primarily for Siemens and Alstom since this date, before seeking a new challenge and forming Prime Rail Engineering in 2021.
How did you come to work in the rail industry?
DY: My railway career started aged 18 when I joined the London Underground engineering apprenticeship scheme in 1999. I enjoyed virtually every minute of this four-year scheme and was privileged to be awarded apprentice of the year in 2001. Originally, I trained to become a signalling technical officer, mid-way through I switched to the design office following advice from a colleague at the time. I then forged a successful early career in the LU signalling design office following completion of my apprenticeship. As an individual, the apprenticeship scheme was a perfect fit for me. I am excited by the emergence of degree apprentice schemes throughout the industry and have seen first-hand the talent that these schemes can help to nurture.
RH: My initial experience was fairly incidental to the engineering side of the industry – I was offered a job working for a recruitment agency after they were unable to find me an opening in the aerospace sector. This turned out to be a blessing in disguise as I worked on the rail desk and got to know the rail industry from the outside, seeing the fantastic opportunities available to young engineers in this field. As soon as the next round of graduate recruitment came round, I applied for, and was fortunate enough to procure, a graduate position with London Underground and the rest is history!
Tell us about your career before you joined Prime Rail Engineering?
DY: Following completion of my apprenticeship I worked as a signalling design engineer for the next ten years. I was fortunate to work on a number of complex and high-profile signalling schemes in the UK and abroad throughout this period. After establishing myself as a signalling design engineer on a number of LU projects (including the Piccadilly Line extension to Heathrow Terminal 5), I moved to Parsons Brinckerhoff in Sydney for the next three years. Exposure to different signalling technologies (including Computer Based Interlockings for the first time) and different systems broadened my signalling and project delivery experience. After returning to the UK, I worked as signalling design verifier for a number of organisations including Invensys, London Underground and Alstom. Over the past seven years, I have assumed lead engineering management roles in various signalling projects on Network Rail infrastructure.
How has technology developed since you started in the industry?
DY: I established myself as a signalling engineer producing designs to enhance legacy mechanical interlocking installations on London Underground. These were already
very much antiquated systems when I first entered the industry. It is remarkable that the robustness of these systems means that many mechanical installations still remain in operation today. Despite this, the emergence of digital systems including CBIs (Computer Based Interlockings), CBTC (Communications-Based Train Control) and ETCS (European Train Control System) have opened up virtually endless potential to improve headways, increase availability and provide safety enhancements throughout the railways.
These systems can be configured to provide redundant systems and can offer technicians remote diagnostic facilities. This can include fault prediction systems to prevent faults from affecting the train service. Digital systems also provide the potential for improved headways with a reduction in the number of lineside assets. This reduction of lineside assets, combined with a more centralised signalling system architecture has reduced the number of hours that technicians are required to access the railway.
Enhanced staff protection systems will also continue to improve safety to railway workers. It has also been interesting to see the way that signalling and interlocking principles have evolved over the years. The trends I have seen have helped to maintain the railway in non-degraded mode working or more elegant degraded modes than in years past. This ensures that safety critical systems will still protect the safe movement of trains during the most common failures.
I am confident that this, combined with a reduced dependency on procedural based hazard mitigation, will continue to improve the safety of signalling systems throughout the railways. What’s next? Cloud based systems? We at Prime are excited to see what advances the years to come will bring and will work hard to keep our skills and knowledge aligned with the new signalling technologies as they emerge.
What was the inspiration behind starting Prime Rail Engineering?
DY: As signalling engineers we have always been passionate about delivering signalling projects in the most safe and efficient way possible. We have been fortunate to work with some excellent organisations and individuals over the years who we know share that passion. Having seen the remarkable contribution other SMEs have made to the industry in recent years we feel the time is right for Prime and our engineers to do the same. After more than 20 years working on signalling projects, we know we have the knowledge and expertise to build and manage our own team of signalling professionals. Starting Prime Rail Engineering has allowed us to deliver signalling projects the way we believe they should be. We have a clear focus on delivery and a decisive approach to decision making based on our collective experience and knowledge within the industry.
What is your USP (Unique Selling Point)?
RH: Prime Rail Engineering has positioned itself as a provider of signalling design expertise. While there are, of course, many excellent designers across the industry working for various firms, as an SME we felt we had to really focus on our core skills: the complex and non-routine aspects of signalling delivery. We offer our clients solutions to the ten per cent of the signalling work that takes up 50 per cent or more of the thinking time and we offer this on a flexible basis.
We carry out services to clients from consultancy roles to delivery of full packages of work, avoiding the many pitfalls that can beset a signalling project when complexities that may not have been accounted for or fully understood at the start come into play. Our network of connections built up over twenty years puts us in an excellent position to bring the right resource to bear on any interlocking type, or signalling related issue, allowing us to provide value-added solutions to our clients.
What types of products and services do you offer?
DY: We offer signalling design and project engineering management solutions. We can deliver turnkey signalling design packages from early scheme development phases all the way through to detailed design and commissioning support. Our hands on approach to stakeholder management is designed to provide a service that will make our customers’ lives as easy as possible.
Our resource pool includes engineers with specialist expertise including the design and verification of computer based interlocking systems (including SSI and next generation systems). We also have signalling project engineers and engineering managers with experience in co-ordinating the integration and assurance of signalling projects and signalling-biased multidiscipline projects.
What are some standout projects you’ve been involved in over the years?
DY: I have had the privilege to play a key role in the design and delivery of many complex, large-scale and high-profile signalling upgrades. This includes, but is not limited to, the Piccadilly Line extension to Heathrow Terminal 5, Gap to Narrabri capacity improvements; Glenfield Junction remodelling; Victoria Line re-signalling; Bristol Area Signalling Enhancements and renewals, and the ongoing South Kirkby resignalling and Transpennine Route Upgrade.
RH: A now-retired ex-British Rail signalling engineer once told me that it was a privilege to work on category A station renewals and those words very much stuck with me throughout my career. I am proud to say that I have had key roles in the signalling design
delivery of Bristol Temple Meads, Liverpool Lime Street, Paddington and Leeds station renewals. Other highlights include the Victoria Line resignalling, Thameslink ETCS (KO1) and the ongoing Victoria signalling renewals.
What types of companies do you collaborate on projects with?
RH: We have a diverse client base from Network Rail itself and Tier 1 contractors through to collaborations with companies not much larger than ourselves and we have an equally diverse range of outputs with these clients. We are proud to work with NR, Siemens, WSP and Linbrooke (now Q1tm) among others, however, I would like to make special note of Park Signalling. I got in touch with Ian Allsion at Park (who was interviewed in this magazine back in July) as Park are local to Prime Rail Engineering with us both being based in Stockport. Ian has been highly encouraging and supportive and it has been very interesting working with Park who are primarily a signalling technology company, giving us an insight into part of the industry rarely seen from a design perspective.
What’s next for Prime Rail Engineering?
DY: Our first goal is to continue to maintain the high standards we set ourselves when delivering our services to our existing clients. We are also working hard to increase our signalling design portfolio and are always very keen to discuss opportunities to build new relationships with prospective clients. While we already hold a strong resource pool of signalling design staff, we will expand our capacity when our workload demands it. One of our objectives as an organisation is to pass down our experience and knowledge to the next generation of engineers.
As such, we are currently making plans to recruit new talented individuals within a signalling focused apprenticeship scheme. We feel that by doing so this will help us to provide an efficient and professional service to our clients for years to come.
With the coming launch of Great British Railways, how do you anticipate your place within the supply chain changing?
RH: That is a tough question to answer as there is very little information currently available on how GBR plans to organise itself and the ramifications for the signalling design industry and for companies such as ourselves within that. I would hope that the reforms lead to a higher degree of engagement with SMEs like Prime Rail Engineering and less red tape in the bids and tendering process across the industry. I am sure that Prime Rail Engineering – along with our peers – will be able to continue to provide quality solutions to our clients after the reforms have been enacted though and we look forward to this new chapter in the
history of UK rail. If you were in charge of the UK rail industry, where would you target investment and/or look for improvement?
RH: It probably goes without saying that we are passionate believers in UK rail, and we feel investment in our railways is the only way to meet net zero targets and ease congestion on the road network. It is a difficult question as there are so many areas, but I would target the completion of HS2 (and if we are discussing a wish list, I would include the scrapped northern leg to increase the cost/benefit ratio), the improvement of freight provision and, of course, the implementation of the digital railway/ETCS.
While we are about it, I would also be keen to reverse the Beeching cuts where there is a clear benefit to doing so – the railways should be run for the benefit of the British people and not always assessed on a profitability basis. I must admit that the above would not be cheap but (perhaps fortunately) it is unlikely that I will be making these decisions so I may as well go big!

PRIME RAIL ENGINEERING LTD
Prime Rail Engineering has extensive experience in delivering signalling projects with multi-discipline aspects which require the coordination and management of a plethora of stakeholders and actors.
Want to know more about Prime Rail Engineering?
Tel: 07960277185 and 07714259740
Email: david.young@ primerailengineering.com and robert.hay@ primerailengineering.com
Visit: www.primerailengineering.com
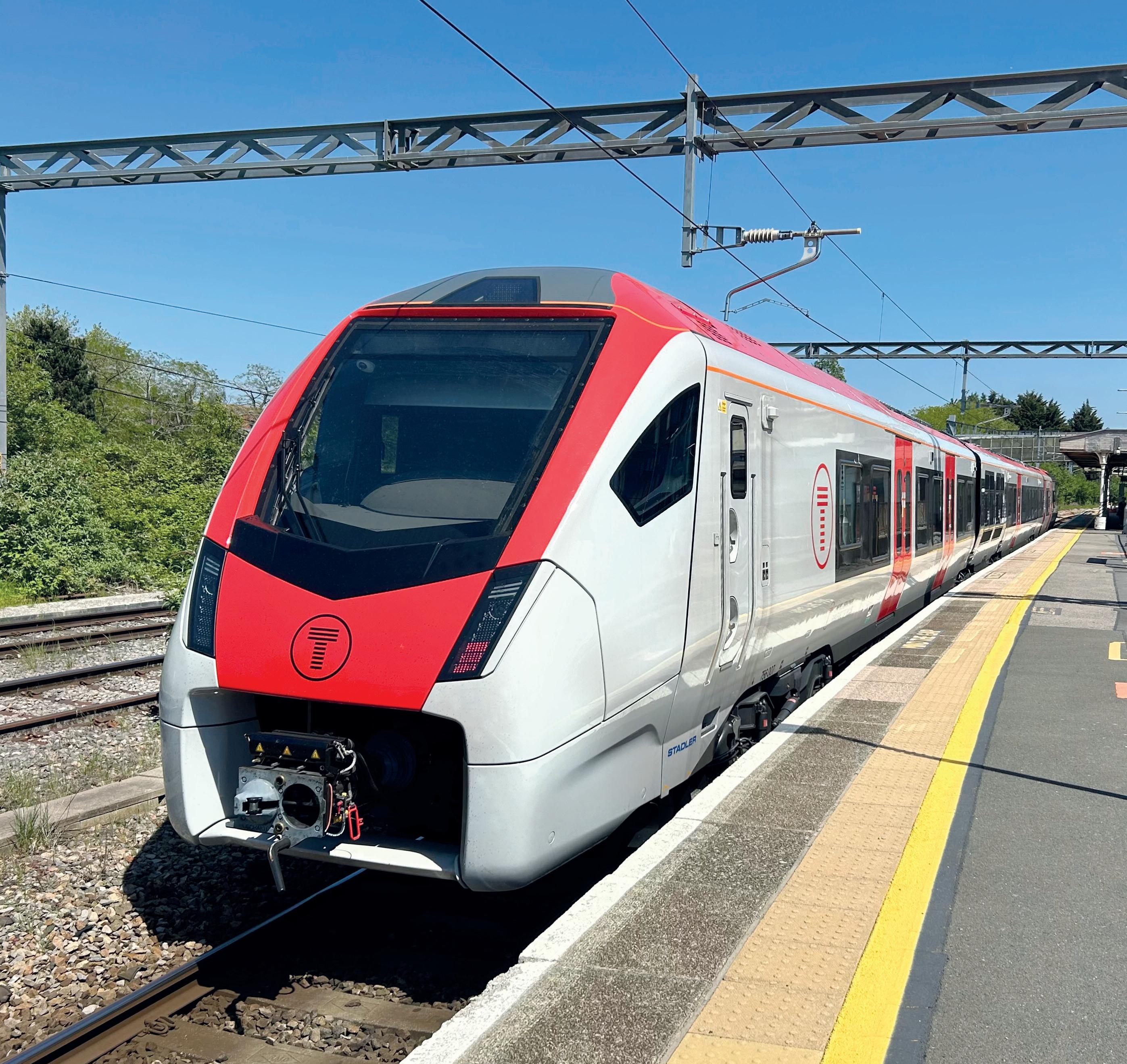

RALF WARWEL SALES DIRECTOR FOR UK AND IRELAND AT STADLER
Ralf is responsible for business development and sales in the UK and Ireland. Joining Stadler in 2010, he oversees major rolling stock projects. Previously, he was a project manager at Alstom. Ralf started his working life in 1985 as a mechanical engineering apprentice at rolling stock manufacturer, LHB in Salzgitter, Germany.
Tell us about Stadler.
Stadler produces innovative, sustainable, high-quality rolling stock and associated rail products and services. We are a market leader in emission-free traction and are playing a critical role in helping governments around the world achieve net zero targets.
Providing high-speed trains, intercity trains, regional and commuter heavy rail trains, underground trains, tram-trains and trams, Stadler also offers Service and Signalling solutions. With a keen focus on the environment, our products feature stateof-the-art technology, offering maximum comfort for passengers. They are safe, reliable, innovative and built to last.
13,500 people work for the business at production, component and Service locations around the world. Stadler was founded in 1942 and has its headquarters in Switzerland.
What is your USP (Unique Selling Point)?
As well as lightweight design, highly adaptable products and our focus on energy efficiency, a key feature of all Stadler passenger trains is the sliding step, which is installed on every unit that we manufacture. This design innovation improves safety, promotes accessibility for everyone, and makes getting on and off a train easier. It is a game-changer for wheelchair-users and people with pushchairs, bicycles or luggage.
A retractable step beneath the doors extends outwards when doors open, filling the gap between the train and the platform when a train is at a station. Steps are fitted with a sensor, allowing them to extend to varying degrees, depending on the size of the gap between the train and platform. They are particularly beneficial in the UK, where much of the railway infrastructure was developed in the Victorian era. During
STADLER
Stadler has been building rail vehicles for over 80 years. It is present at 15 production and component locations as well as over 80 service locations.
Want to know more about Stadler?
Tel: 071 626 21 20
Email: stadler.rail@stadlerrail.com Visit: www.stadlerrail.com
this period, stations were not built to a standard template, and some were even constructed on a curve. While most new trains are now produced within a standard kinematic envelope, the technology that enables the step to fill the gap makes a huge difference for passengers.
The new trains that Stadler delivered for Greater Anglia from 2019 were the first in the UK to have both low flooring and a retractable step, taking away the need for a ramp to board on the majority of Greater Anglia’s regional, intercity and Stansted Express services. The retractable step also features on the trains that Stadler is delivering for Transport for Wales, the Liverpool City Region and Nexus.
What types of products and services do you offer?
Stadler manufactures high-speed trains, intercity trains, regional and commuter heavy rail trains, underground trains, tramtrains and trams. We produce main-line locomotives, shunting locomotives and passenger carriages, and are the world’s leading manufacturer in the rack-andpinion sector.
Offering whole-life-cycle-cost effective rail solutions, including Signalling and Service, we deliver a wide range of greener drive systems to avoid the use of diesel on non-electrified lines. This makes the rail industry more sustainable and drives competition.
Stadler’s range of Signalling products enable trains to operate safely, efficiently and in an environmentally sustainable way. They demonstrate how the digitalisation of both trains and rail infrastructure can increase passenger capacity, enabling more people to use what is already the most environmentally friendly mode of transport.
We provide full Service, including modernisation and overhauls; spare parts
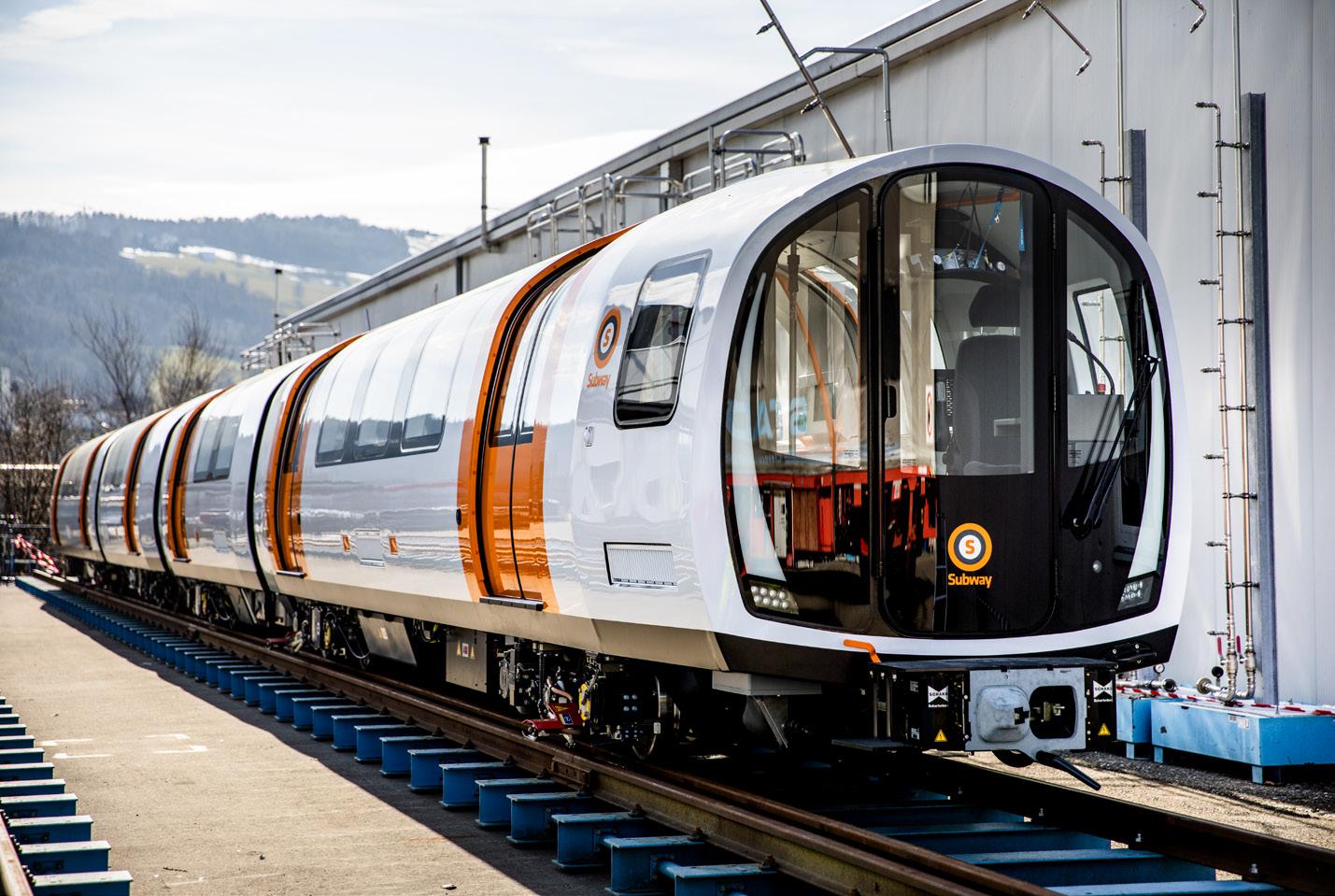
and material supplies; vehicle repairs; service support; rail data and maintenance software. This comprehensive portfolio enhances availability, reduces the number of spares, improves reliability and helps foster passenger satisfaction. In the UK, there are three full Service contracts operational in Liverpool, Norwich and Newcastle upon Tyne. For Transport for Wales and Glasgow Subway trains, we are providing technical support and materials.
What are some major projects you’re currently working on?
There are seven ‘live’ rolling stock-build projects in the UK. They are:
• 53 electrical multiple units for the Liverpool City Region Combined Authority, including a sub-class of seven independently powered electrical multiple units (IPEMU).
• 46 METRO trains for the Tyne and Wear Metro.
• 17 METRO trains for Strathclyde Partnership for Transport.
• 36 CITYLINK tram-trains for Transport for Wales.
• 35 tri-mode and DMU FLIRT trains for Transport for Wales.
• 10 tri-mode locomotives for Rail Operations (UK).
• 30 bi-mode locomotives for GB Railfreight and Beacon Rail.
So far this year, two fleets have been introduced into passenger service: the METRO trains for the Liverpool City Region and the FLIRTs for Transport for Wales. METRO trains for Glasgow Subway and METRO trains for the Tyne and Wear Metro are also scheduled to start entering into service by the end of 2023. Passengers on all underground trains in the UK outside London – in Liverpool, Glasgow and Newcastle – will soon be travelling on Stadler trains.
What are some standout projects you’ve been involved in over the years?
In 2016, we signed a contract with Abellio for a fleet of 58 trains serving the Greater Anglia network. The order was for 38 bimode trains and 20 electric trains, with units delivered from 2019. One of Stadler’s biggest contracts to date in the UK and our first for the mainline network, it consolidated our position as a key player in the UK rail industry. These bi-mode trains run on electricity as well as diesel and are equipped with environmentally friendly, modern technology to help reach net zero targets. They have replaced all of Greater Anglia’s diesel trains on rural routes, promoting more sustainable travel.
The electric Class 745 trains, EMUs, serve both the Stansted Express line as well as intercity routes into London. They are made up of twelve carriages and 236 metres long, and are the longest train of their type

in the UK. Operational in the south east of England, they serve the powerhouse of the national economy, and we are very proud of this.
All 58 of these trains for Greater Anglia are FLIRTs, Stadler’s best-selling product. They boast high levels of safety and are very popular with clients all over the world. To date, Stadler has sold more than 2,500 FLIRT units in 21 countries.
What are some of the biggest challenges this sector currently faces?
The rail industry’s biggest challenge continues to be the climate emergency. Rail is the most efficient mode of transport, and Stadler’s mission is to make the industry more sustainable, more efficient, more attractive and more competitive. It promotes modal shift, and encourages more people to travel by rail and more freight to be transported by rail. This cuts carbon emissions, saves energy and helps our clients, transport authorities and governments all over the world meet decarbonisation targets.
What are some potential solutions?
Our commitment to de-carbonise the railway covers products and services, production sites, employees, business partners and other stakeholders. By offering durable transport solutions, we promote a greener railway for generations of passengers to come.
We provide state-of-the-art signalling systems and service packages, and the equipment and materials we use are lightweight and recyclable. We select suppliers in part based on their proximity to our production sites and their own green credentials.
Electrification is still the greenest way of operating a railway, however for lines with
low patronage, it makes economic sense to operate battery trains or adopt a hybrid solution.
Do you think the rail industry could be greener and what is your organisations green strategy?
Stadler is focused on finding ever greener solutions to tackle the climate emergency, and broadly, we approach decarbonising the railway in two ways. First, we work with clients to make existing trains running on non-electrified lines more sustainable, and second, we are leading on the transformation from diesel-powered trains to zero-emission rolling stock.
Over recent years, we have invested heavily in alternative drive solutions, offering a range of options, including electric, battery and hydrogen. Stadler has sold approximately 300 trains, trams and tram-trains, as well as locomotives, with traction batteries, in ten countries, including the Netherlands, the UK, the US, Germany, Italy, Austria, Norway, Spain, Poland and Switzerland. The framework agreement Austrian Federal Railways (ÖBB) signed with Stadler in July 2023 for up to 120 batterypowered, FLIRT Akku trains consolidates Stadler’s position as a market-leader in battery and hydrogen green propulsion technology.
Stadler’s activities are underpinned by the Paris Climate Agreement, as well as market-specific sustainability and decarbonisation targets.
Our approach is three-pronged:
• Economy – foster economic solutions and increase competitiveness within the rail industry.
• Ecology – increase the design life of our products by up to 30 years.
• Society – improve the passenger experience for all.

PHIL EVANS CO-FOUNDER AND MANAGING DIRECTOR OF PRE METRO OPERATIONS LTD
Phil Evans is Co-founder and Managing Director of Pre Metro Operations Ltd, Phil was the Director of Finance, Centro (West Midlands Passenger Transport Executive) and put together the financial structure of operations, obtained all relevant operating agreements and obtained approval for the Safety Management System. Phil now leads discussions to expand VLR operations elsewhere across the UK.
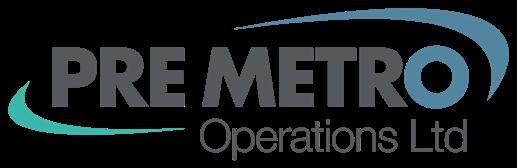
PRE METRO OPERATIONS LTD
Pre Metro Operations (PMOL) was founded in 1999 as an independent train operation company with the aim to establish innovative and low cost light rail transit services on branch lines across the UK.
Want to know more about Pre Metro Operations?
Tel: 01384 441325
Email: info@premetro.org
Visit: www.premetro.co.uk
What was the inspiration behind starting Pre Metro?
Pre Metro Operations Ltd was founded as an independent Train Operating Company with the aim of establishing innovative and lowcost light rail transit services on branch lines across the UK. No other TOC was willing, at that time, to use innovative light rail rolling stock on traditional heavy infrastructure, so we did it ourselves.
Pre Metro first saw the potential to help link the Stourbridge community with light rail technology using the Stourbridge Town to Stourbridge Junction branch line. The idea was supported by the West Midlands Passenger Transport Authority in 2002 and plans evolved from there.
Fast forward almost 25 years and the Stourbridge Shuttle has become one of the most reliable railway operations in the UK. We have also continued our trailblazing within the industry and are involved in numerous new Very Light Rail projects. Now, we are actively pursuing a second Stourbridge service to reconnect Brierley Hill with the main line railway.
How has technology developed since you began in the industry?
The Class 139 railcars we use to operate our Stourbridge Shuttle service are light-weight LPG-fuelled, flywheel hybrids, which were innovative at the time and still are today. Industry ideas on how we evolve rolling stock technology has followed suit, primarily with alternative methods of power.
This includes the pursuit of batterypowered technology and hydrogen fuel cells, with the principle of energy storage becoming the focus for the industry’s technical achievements in recent years. We fully support these developments for environmental and economic sustainability reasons, but there is a temptation to overcomplicate this process. The Class 139s are much more basic in function than next generation rolling stock, but we expect they’ll still be just as efficient, more reliable, and easier to maintain.
What are some standout projects you’ve been involved with in recent years?
We operate the Stourbridge Shuttle, which has become one of the most effective, efficient, and frequent light rail services in the UK. For almost 16 years, we have been an active member of the local community and we are providing the best service the line has ever seen. Our work at Stourbridge has also attracted attention from other industry members and we have been willing to provide support and advise to enable further innovations.
This includes the Revolution VLR project; a sustainable, lightweight system developed by Transport Design International and Eversholt Rail. We have been working with colleagues there to provide our expertise in
an operational capacity and through mileage accumulation at their Ironbridge Test Site.
We’ve assisted our colleagues at UltraLight Rail Partners in their development of the STEAMUltra and BioUltra projects. The STEAMUltra was a prototype vehicle with similar structure to the Class 139s and was powered by biomethane. The next aspiration is to create a larger, light-weight railcar capability of carrying 100 to 120 passengers.
We also are awaiting a green light to assist our colleagues working at the newly built VLR National Innovation Centre in Dudley and provide our expertise and mileage accumulation for the Coventry VLR railcars.
Our work on railway restoration projects over the years has also varied, but with many awaiting ‘Restoring Your Railway’ business case responses, we anticipate further news in the coming months.
What new developments/strategies do you have?
As mentioned earlier, we are actively pursuing a second service between Stourbridge and Brierley Hill, titled the Stourbridge Dasher, that can build upon our success with the Shuttle and provide a mixed-use case for the dual-track heavy rail freight line between Stourbridge Junction and Round Oak Steel works.
We are working on a strategy document for transport professionals regarding transport integration within Stourbridge and Brierley Hill, and we truly believe our solution will not only tick boxes in terms of supporting local policy and public investments, but it can provide a template for light rail integration at sites across the country and reestablish the Stourbridge to Walsall transport corridor.
How has the market grown?
The type of VLR operation we’ve conducted has grown the market organically, resulting in higher efficiency, lower costs, and increased patronage on the Stourbridge Branch Line. It has provided a template for branch line restoration projects, with many now capable of similar operation with the recent ‘Restoring Your Railway’ schemes.
We believe there is untapped potential for rural-to-urban VLR as a sustainable solution to the nation’s various connectivity needs, alongside its capability to support urbanised growth and create an exportable light rail industry within Britain.
The market is still in its infancy, and we believe it has the potential to revolutionise urban transport, offering a sustainable, costeffective, and accessible solution for growing cities.
What do you think is the biggest challenge currently facing the rail industry? (Waste of infrastructure?)
There are general assumptions about light rail technology and heavy rail being incompatible, the reality is that there has been a distinct lack of vision and ingrained thinking which has stifled many projects at a local level. This is a shame because many communities have lost out on effective public transport. There needs to be a greater understanding of the benefits of VLR at both local and national levels.
The Country is blessed with a plethora of railway lines, many under-utilised, and with strategic investment and innovation it is wholly practical to level-up communities, achieve carbon reduction and provide the connectivity which we all appear to aspire to. An obsession with reducing expenditure and staffing is not helpful.
How can we get more use of the rail assets and what is your vision of rail in 10 or 20 years?
Well, we seem to be at a turning point where there is an obsessive demand for service cuts and the reduction of facilities. Ticket offices
will become storage spaces or commercial lots whilst disused Branch Lines become overgrown.
If we really want to get more use out of our assets then we need a strategic plan for protecting transport corridors, empowering the human factor and local guidance on the integration of new and existing transport systems and services. This would accommodate the transfer from road to rail, with an overarching aim to transfer a high proportion of private travel to widely available public transport in both rural and metropolitan areas.
What do you expect to be the biggest challenges that come from this transformation of the railway industry?
The challenges of urban transport are growing increasingly complex, with traffic congestion, air pollution, and a lack of accessible public transport options becoming more prevalent as cities continue to expand.
As such, it is crucial for local authorities and policy makers to find innovative and sustainable solutions to address these issues. We believe that Very Light Rail (VLR) is one promising solution to these problems, as a transport system that can combine
the best features of conventional light rail and bus systems. Such systems would be affordable to small and medium-sized towns and cities.
The industry as a whole seems to approach the subject of Very Light Rail tentatively, perhaps due to the current economic climate, or our overly cautious attitude to what could go wrong rather than what will go right. The old proverb ‘if it ain’t broke don’t fix it’ seems to be an attitude that stifles innovation within the industry.
Regardless, we truly believe VLR represents an exciting new chapter we ought to embrace and genuinely consider the opportunities it presents to us before other countries take the lead and export our own inventions back to us. Our model is suitable for many branch lines across the UK and if we want see the industry and light rail innovation continue, then we need to ensure VLR can develop.

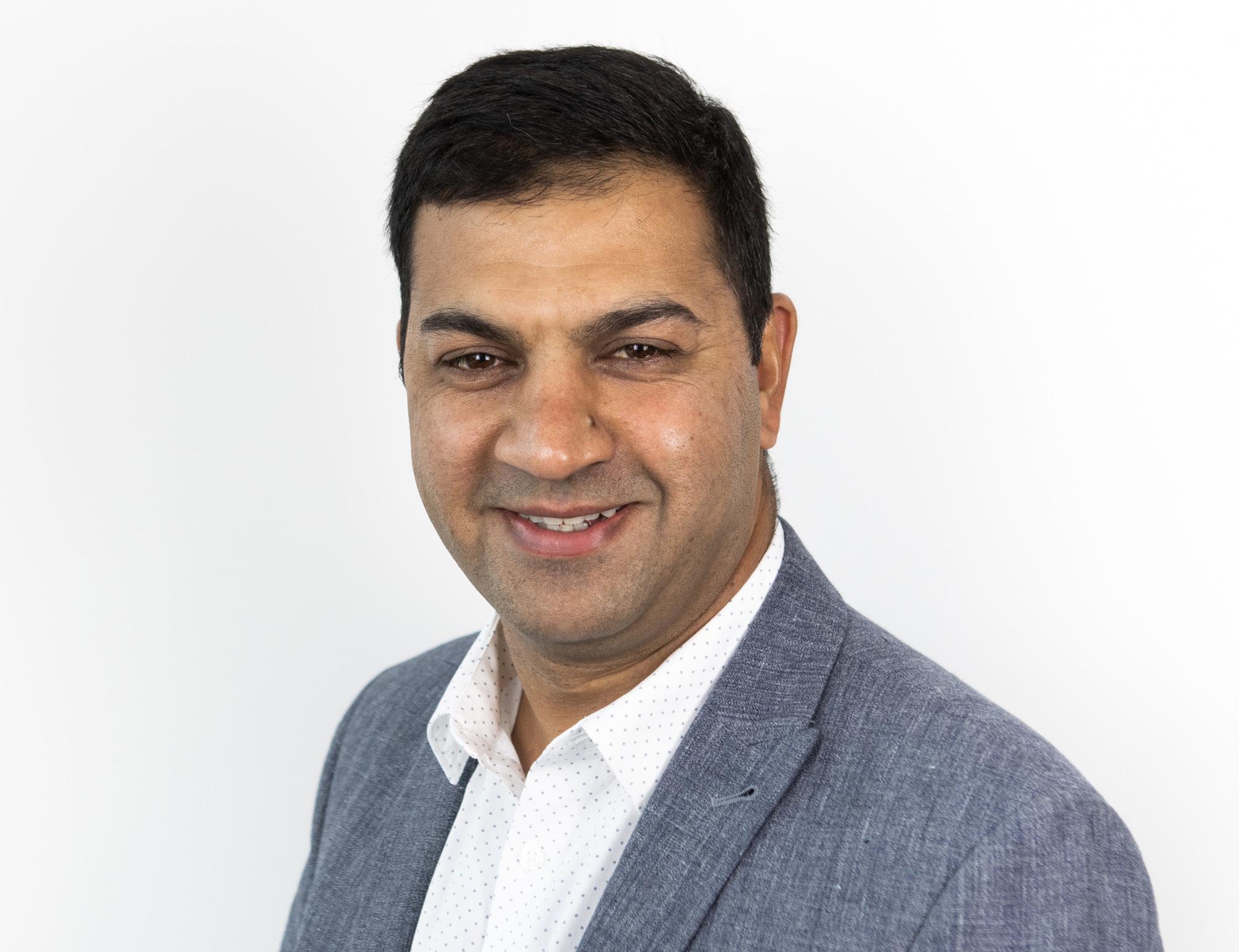
MINESH NARAN HEAD OF TRANSPORT AT 1SPATIAL
Minesh is passionate about helping his clients with their challenges by recommending effective technology-based solutions. With a wealth of consultative experience spanning over a decade, he continues to work with 1Spatial’s client base across national transport infrastructure owners, local government, and private sector consultants.
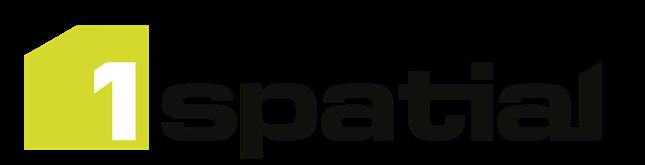
1SPATIAL
Pioneers in Location Master Data Management (LMDM), 1Spatial is already working with the likes of HS2, TfL, Network Rail, and others in the industry.
Want to know more about 1Spatial?
Email: transport@1spatial.com
Visit: www.1spatial.com
What is your role within 1Spatial?
As the Head of Transport within the Commercial Team at 1Spatial, I am responsible for overseeing and driving the company's efforts in the transport sector. It encompasses various strategic and operational responsibilities, with a focus on delivering spatial software solutions tailored to the specific needs of the transport industry.
Some of the areas I am focused on are:
• Client Engagement – this is the most enjoyable part of my role where I focus on building and maintaining strong relationships with key clients in the transport sector. Understanding their unique challenges and requirements would be essential in tailoring 1Spatial's solutions to meet their specific needs.
• Industry Collaboration – using my experience and knowledge of Geospatial Data and Transportation, I am engaged with transport industry associations, conferences, and forums to establish thought leadership and foster collaborative partnerships with other stakeholders in the sector.
Tell us about your career before you joined 1Spatial.
I started off my career in the UK as a Geospatial Technician, where my primary role was to analyse and visualise data, which involved consolidating information from various sources. However, I found myself spending excessive time manually checking, cleaning, and fixing the data, which hindered my productivity.
Recognising the importance of client engagement and face-to-face interactions, I decided to transition into a sales role within
‘We are working with HS2 to build a data validation gateway. The gateway will enable HS2 to validate the … data submitted by their supply chain.’
the same domain. This move allowed me to leverage my technical expertise while also enjoying the opportunity to work closely with clients, understand their unique needs, and provide tailored solutions. By combining my geospatial knowledge with effective sales strategies, I am now able to deliver value to clients while helping them make informed decisions through the power of geospatial data validation, integration and sharing.
Can you tell us more about 1Spatial?
Since its inception in 1969, 1Spatial has had a proven track-record in very large-scale spatial data management and data quality assurance. The company works with some of the largest spatial databases in the world and delivers innovative data management solutions and component technologies that underpin the successful business of its customers.
Our software architects and developers, project managers, consultants and support engineers work as an integrated team to design, develop and implement industryleading solutions that support major digital transformation and data management changes. We work closely with our customers to deliver the knowledge transfer necessary to ensure that they acquire the skills and expertise that provide them with a strong degree of control of the solution and ownership of our future evolution.
What are some major projects you’re currently working on?
We are working with HS2, the company responsible for developing the UK's new high-speed rail network, to build a data validation gateway. The gateway will enable HS2 to validate the quality, conformance and design of construction-related data submitted by their supply chain which in turn, will contribute to the efficiency and effective information delivery on Europe's largest infrastructure project.
The gateway comprises 1Spatial's 1Data Gateway product as a web portal for data uploading, and 1Integrate to check the compliance and quality of the data against stringent HS2 standards and criteria.
This will enable validated data to then be passed onto a Common Data Environment (CDE) to ensure compliance with wider UK government Digital Engineering initiatives. Through 1Spatial's products, the gateway will create greater reliability of data and reduce risks by delivering consistent and accurate geometrical, geospatial, and nongeometrical data ingested across the full Common Data Environment domain.
We also work with Network Rail, Transport for London, Transport for Wales, and East-West Rail.
What success have you experienced in the last twelve months and how do you measure success?
1Spatial is establishing itself as a trusted advisor and solution provider within the transportation sector. We are working with large transportation infrastructure asset owners and with well-known Tier 1 contractors within their supply chains. We measure success by the positive feedback we have had from across the stakeholder hierarchy into which we continue to expand our contracts.
What is your USP (Unique Selling Point)?
1Spatial's unique selling point lies in its innovative and comprehensive approach to spatial data management and governance. As a leading global provider of spatial software solutions, 1Spatial offers cuttingedge technology that enables organisations to harness the power of location-based data effectively.
What sets 1Spatial apart is its ability to automate, validate, and optimise complex geospatial processes, ensuring data accuracy, integrity, and compliance. Our people and products empower businesses to make informed decisions, improve operational efficiencies, and gain valuable insights from spatial data, enhancing their overall productivity and competitiveness. With a strong focus on data quality and intelligent automation, 1Spatial remains at the forefront of spatial data management, catering to verticals such as government, utilities, built-environment, defence and of course, transportation.
When a client comes to you with a particular problem, what is your process for coming up with a solution, and closely do you work with clients throughout the projects?
I take a consultative approach, working closely with both the client and several 1Spatial teams. My process begins by actively listening to the client's specific problem and understanding their unique needs and goals. I focus on their business and user requirements detailing, process, data flows and formats, honing in on bottle-necks and pain-points. Once I have a clear understanding of these, I develop a
‘Smart technologies, IoT sensors, and predictive analytics will play a crucial role in optimising operations, enhancing safety, and improving the overall passenger experience.’
What are some of the biggest challenges this sector currently faces?
The UK's rail system has witnessed significant modernisation efforts in recent years, with advancements in technology, safety measures, and infrastructure upgrades. However, the industry also faces challenges, such as capacity constraints, funding issues, and the need to reduce its environmental impact.
Despite these challenges, the UK rail industry remains a vital component of the nation's public transport, contributing to economic growth, connectivity, and sustainability. Continuous efforts are being made to enhance its services and address the evolving needs of passengers and businesses across the country.
customised and comprehensive plan that outlines the steps and strategies required to address the challenges effectively. I work collaboratively with experienced colleagues that sit within Enterprise and Solution Architecture, Presales, Product, Professional Services and Support.
Throughout the sales cycle and project delivery, I believe in maintaining a close and collaborative relationship with the client. Regular communication and updates ensure that both parties are on the same page regarding progress and any adjustments needed along the way. I actively seek feedback from the client during each phase of the project, valuing their insights and incorporating them into the solution whenever possible.
This collaborative approach ensures that the outcome aligns with the client's vision and meets their expectations. Additionally, I remain readily available to address any concerns, provide clarifications, or make modifications as needed, ensuring a successful and satisfactory project delivery.
With the coming launch of Great British Railways, how do you anticipate you place within the supply chain changing?
As an organisation that already works with players in rail, Great British Railways will undoubtedly have a significant impact on our place within the supply chain. With the centralisation of operations and infrastructure management under this new entity, we anticipate a more streamlined and standardised approach to procurement and collaboration.
Our role may evolve to align with the changes in the supply chain dynamics, and we are optimistically foreseeing increased opportunities for partnerships and collaborations with other stakeholders in the rail ecosystem.
While there might be challenges ahead, we are committed to leveraging our expertise and experience to continue providing high-quality products and services that support the efficiency and growth of the reimagined rail network under Great British Railways.
Where do you think the industry will be in the next 10-15 years?
The rail industry will undergo continued evolution over the next 10 to 15 years. I would draw out these predictions:
• Digitalisation and Automation – the rail industry is likely to undergo significant digital transformation, with an increased focus on automation and data-driven decision-making. Smart technologies, IoT sensors, and predictive analytics will play a crucial role in optimising operations, enhancing safety, and improving the overall passenger experience.
• Electrification and Sustainability – there will likely be a stronger push toward the electrification of rail networks to reduce carbon emissions and dependency on fossil fuels. Advancements in battery and charging technologies may also lead to more efficient and sustainable hybrid or battery-electric trains.
• Integration with Mobility-as-a-Service (MaaS) – rail transportation is expected to be integrated into broader Mobility-asa-Service platforms, allowing passengers to seamlessly plan, book, and pay for multi-modal journeys, combining trains with other forms of transportation like buses, taxis, and shared mobility services.
• Urbanisation and Rail Integration – as urban populations increase, there might be a greater emphasis on integrating rail networks with urban planning, creating seamless connections between residential areas, business districts, and key transportation hubs.
Overall, the rail industry is likely to evolve rapidly over the next decade. It is important to note that the predictions above will all be underpinned by the need for greater data integration and sharing, but importantly, with an increased need for high-quality data. This need will unlock innovation, embrace technological advancements and sustainability initiatives to meet the demands of a changing world and deliver efficient, eco-friendly, and interconnected transportation solutions.
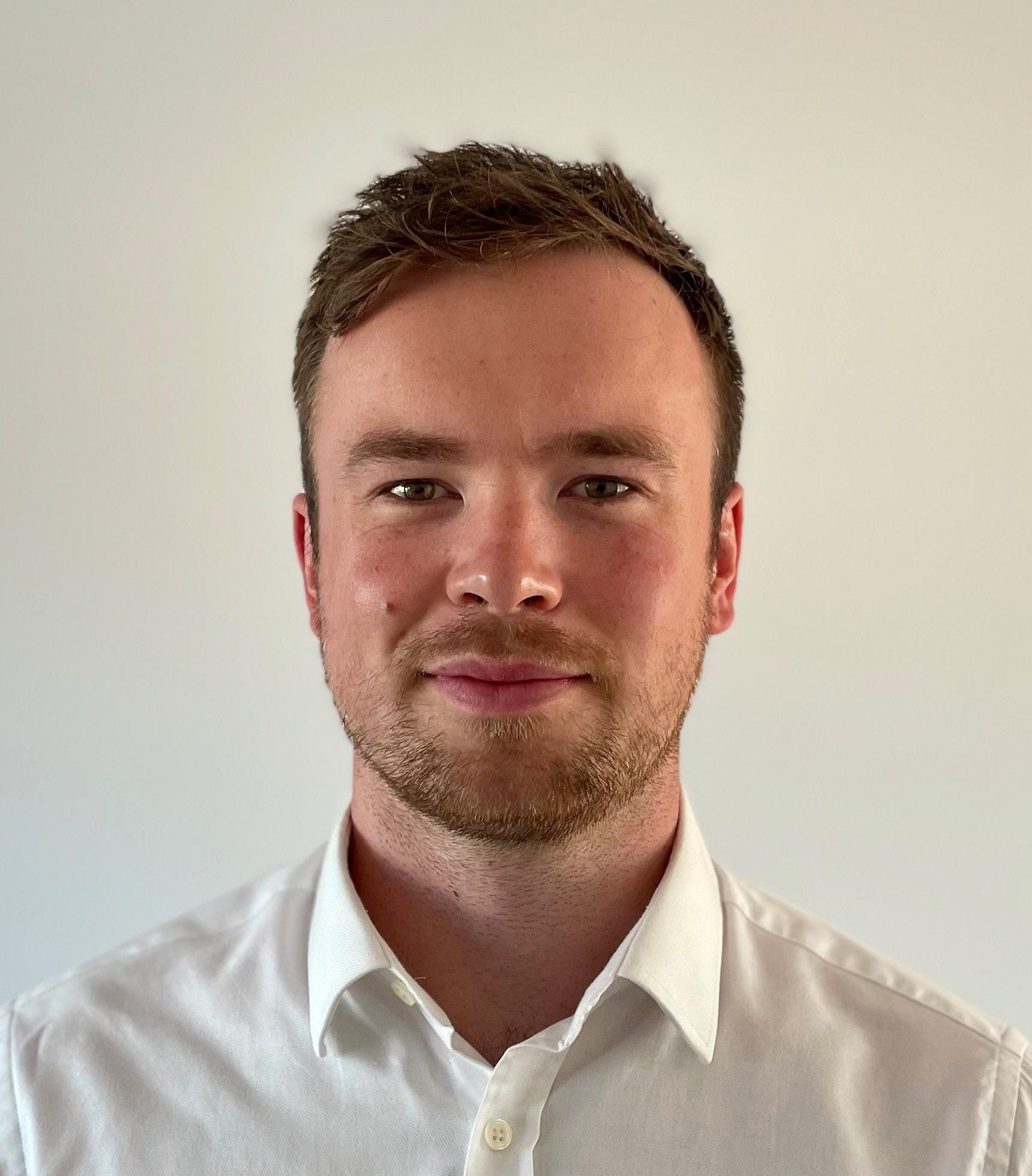
CALLUM DAVIDSON
HEAD OF BUSINESS DEVELOPMENT – UK AT SENCEIVE
Callum draws on a decade of experience in instrumentation and monitoring, geotechnics, site investigation and non-destructive testing, in both the UK and USA. Prior to joining Senceive as Head of Business Development for the UK Callum has held roles at Geo-Instruments, GEI Consultants and Lankelma.

SENCEIVE
Senceive designs, manufactures and continuously improves wireless condition monitoring systems and technology.
Want to know more about Senceive?
Tel: 0800 033 7731
Email: info@senceive.com
Visit: senceive.com
What is your role within Senceive?
I am currently the Head of Business Development for the United Kingdom, Ireland, Netherlands and Oceania at Senceive. In my day-to-day activities I work with asset owners, partners, specialist monitoring companies, contractors and consultants to promote, design and install precise, reliable and wireless remote condition monitoring systems.
Tell us about your career before you joined Senceive?
Before joining the Business Development Team at Senceive I worked in the United States for an Instrumentation and Monitoring Company, Geo-Instruments and an Engineering Consultancy, GEI Consultants. During this time I worked on many construction projects across the country from inspecting and evaluating the structural integrity of dam spillways in California, to designing and installing rail-based automated monitoring systems in Boston.
What challenges have you faced in the industry?
Because our product is not as mainstream as some conventional survey and monitoring technologies a big part of business development is building awareness and convincing people that there is another way. The best results usually happen when there is early engagement. If the end user talks to the instrumentation and monitoring expert early in the process there is a good chance that specifications and tender documents will encourage bidders to offer innovative solutions
What success have you experienced in the last twelve months and how do you measure success?
My remit includes the UK rail sector, and that has historically been the biggest part of our business. That has generally been the case over the last year and its been great to see routes and companies adopting our technology that have not used it before. I’m also responsible for our business in the Netherlands and we’ve had enormous success with major track monitoring projects underway on the ProRail network. Even further afield we have seen growth in Australia, particularly from mining railways and metros.
How has technology developed since you started in the industry?
What we offer is an IoT (Internet of Things) solution. Like most things in this space, the hardware has become smaller, faster and easier to use, generating ever more data.
Tell us about Senceive
We trace our roots data back to a 2005 technology spinout from University College London. The original Senceive engineering team pioneered the use of wireless mesh communications technology to connect sensors monitoring critical infrastructure such as rail track and tunnels with remote users.
These sensors detect movement with sufficient precision to monitor changes in track geometry, detect the early signs of landslides and identify deformation of bridges and tunnels. The sensor portfolio has grown to cover a wide range of engineering and geotechnical parameters, providing engineers with continuous data that helps them protect infrastructure and the people who use it.
Which sectors do you work in?
Senceive technology is used across the engineering spectrum of construction, infrastructure and mining. But by far the biggest user is the rail industry.
What types of products and services do you offer?
We design and build wireless remote condition monitoring technology. This includes a range of sensors and wireless communications platforms that provide users with a continuous flow of data.
What is your USP (Unique Selling Point)?
Within our niche field we have a relatively large and highly capable team of more than 80 experts that is able to deliver at scale (e.g. our recent record-breaking monitoring project in the Netherlands). The same applies to customer support team which covers all time zones from bases in Europe, the Americas and Oceania.
And in terms of technology, we can offer users unique options, such as the choice between our highly responsive FlatMesh™ and long-range GeoWAN ™ communications platforms.
How have the products and services you offer developed over the years?
Our FlatMesh™ communication platform is a great example of how our products have evolved. Its been our core technology since the early days, connecting sensors in the field with engineers wherever they may be, but has been improved year-on-year. The ethos of continuous improvement has seen it become more reliable, more responsive and easier to use. That’s why it’s the system of choice where users need a monitoring system that can sit in low power mode for many years but wake up instantly when a sudden event such as a landslide takes place, even sending photos of the site to stakeholders so they an assess the situation.
‘The best results usually happen when there is early engagement’
What are some standout projects you’ve been involved in over the years?
Network Rail has been a lead-user of this technology for many years and the earthworks team on Southern Route has rolled out a large scale programme of monitoring using the InfraGuard system that provides early warning of potentially dangerous and disruptive landslips and embankment failures. They’ve instrumented more than 40 kilometres of track using over 20,000 sensors and 700 automated cameras.
A recent installation in the Netherlands saw 3,600 track sensor nodes and the supporting cellular comms hardware installed in just four days – as far as we’re aware this is a record for a single deployment and is a great indication of how the business has grown from startup to established market leader capable of building, testing and delivering this volume of hardware in just five weeks.
But most large, complex rail projects around the world need a serious monitoring solution so you’ll find our nodes and gateways on railways as far afield as Grand Paris Metro, Vancouver Boadway and Santiago Metro.
Has the market grown since the company was established?
You could argue that the wireless remote condition monitoring market did not really exist before Senceive. As with any technology sector, there are now many players around the world providing different types of product, but the market is big and its growing. The need to extend the life of ageing assets, to manage risk and to address the challenges of an increasingly volatile climate mean it will continue to grow for years to come, with new applications emerging as time passes.
What’s next for Senceive?
At Senceive we put serious resources into product development and there are a string of innovations in the pipeline. Many of these have been specifically requested by our users in the rail sector and they will help tackle issues such as temperature related track buckle, rockfall and changing ground conditions. We are making it easier for users to integrate monitoring data with other asset information and to handle it within data analysis and visualisation tools of their choice. I think we’ll also see growth in some exciting new geographic regions such as Africa and Latin America.
‘Reliable condition data is therefore critical in allocating scarce maintenance and upgrade resources.’
What are some of the biggest challenges this sector currently faces?
An unavoidable challenge faced by the UK rail sector is that we are running 21st Century trains on 19th Century infrastructure. We cannot afford to replace our tunnels, bridges and embankments but have to keep them in safe working order. Reliable condition data is therefore critical in allocating scarce maintenance and upgrade resources.
At an asset management level, the rail sector is seeing all sorts of pressures, particularly associated with climate, budget and safety. A wetter, hotter climate increases the risk of landslides, debris flows, flooding and scour damage to bridges, and it increases the likelihood of rails buckling dangerously due to high temperatures. All this comes at a time when there is pressure to save money and to get boots off ballast.
What are some potential solutions?
At a general level, the sector needs to embrace technology and be prepared to try new ways of solving problems.
Wireless remote condition monitoring is just one of many technologies with big potential to be more widely used to improve safety and performance. Across the UK network our sensors are already feeding millions of data points into the system each year. Add that to the data collected from the various survey trains and mobile monitoring platforms and you have both a goldmine of data and a big headache. No human can make sense of all this information so we need to harness the power of AI to spot the patterns and guide us where to target scarce resources for maximum effect.
In terms of technology, how do you anticipate things might change in the next five to ten years?
The coming years will see smaller, faster, smarter data collection tools that will gather more data. If the sector is smart enough we will find ways to integrate and analyse that data and share the findings openly.
A great example is the way that some railways send the automated alerts from our InfraGuard system directly to route control centres – so within moments of a line blockage controllers are able to see the issue and slow or stop traffic.
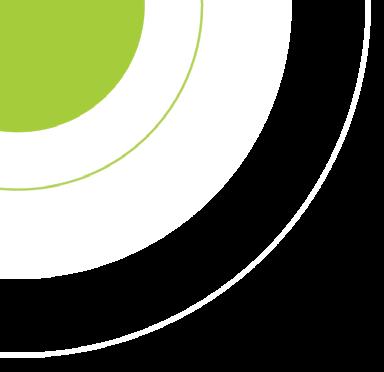
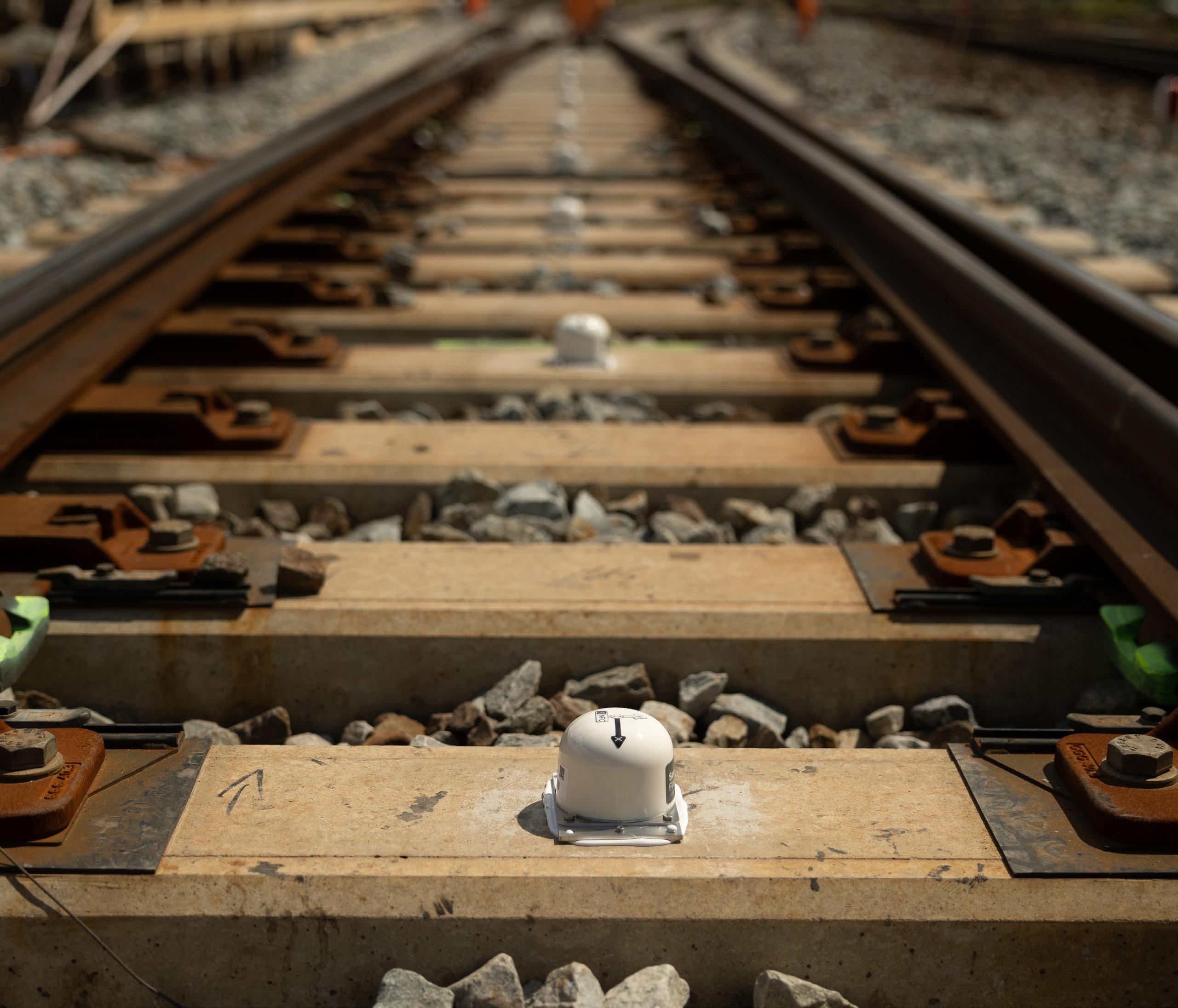
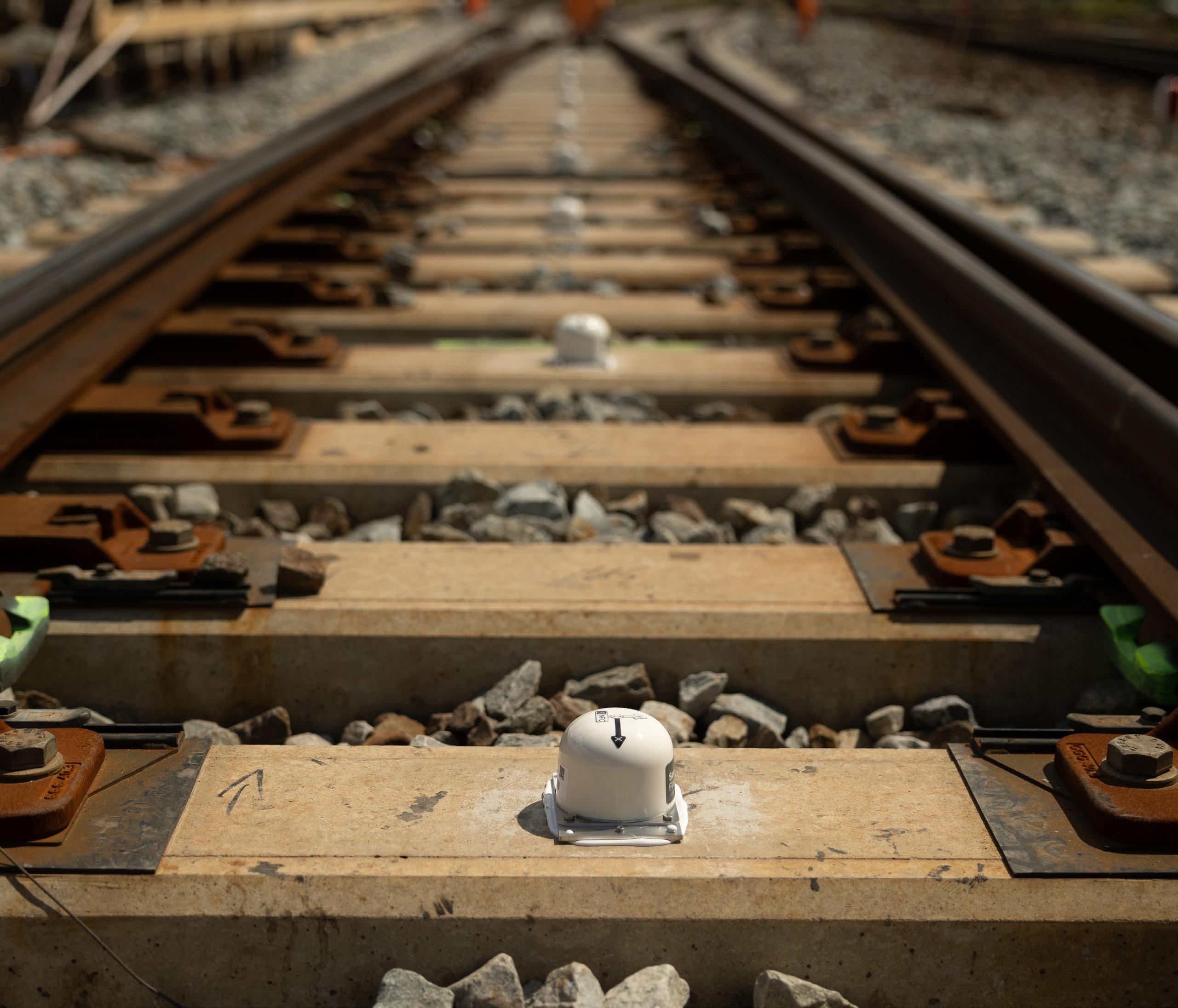
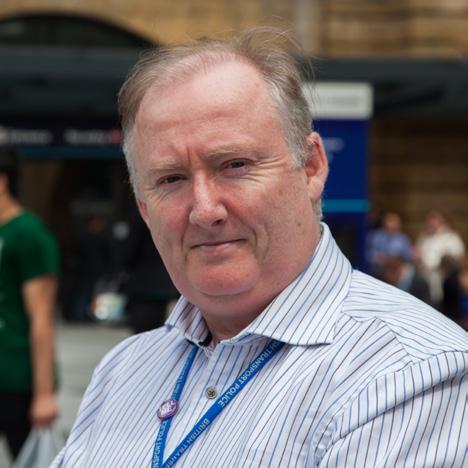
Liam Johnston is Executive Director of the Railway Mission
‘Let’s change the narrow narrative from faster journey times to a more all-embracing narrative of value and rail capacity.’
Is it Time to Change the Railway Narrative?
Fixed in steel and stone, the United Kingdom's railway network holds a narrative that is intertwined with the nation's economic and industrial development
However, that narrative in recent years has switched to one simply of speed; but is that all investment in the railway is for; faster journeys?
Today, as we navigate a rapidly changing world, the railway remains an invaluable asset, connecting communities, easing congestion, reducing carbon emissions, and bolstering economic growth. Even if you don't currently use the railway for travel, it is crucial to understand why investment in infrastructure and supporting its development is vitally important for everyone, even those who don’t travel by train.
While some may perceive the railway as a mode of transport reserved for daily commuters or long-distance travellers, the truth is that an efficient and expanded railway network benefits everyone. A robust rail system ensures improved connectivity between towns, cities, and rural areas, helping to solve the transportation needs that exist within the countries of the United Kingdom and via the Euro Tunnel far beyond our shores. By enhancing accessibility, railways enable people to reach employment opportunities, education centres, healthcare facilities, and leisure destinations more easily, irrespective of their mode of transport.
Traffic congestion is a pervasive issue in many urban areas, resulting in increased
journey times, stress, and harmful emissions. Investing in rail infrastructure offers a sustainable alternative that helps alleviate congestion and reduce the environmental impact of transportation. By encouraging more people to use the railway, particularly for daily commuting, we can significantly decrease the number of cars on the road, leading to smoother traffic flow, reduced air pollution, and a healthier living environment in urban areas and beyond.
In an era of increasing environmental consciousness, it is crucial to prioritise sustainable modes of transportation. Railways are renowned for their lower carbon emissions compared to road or air travel. By promoting rail as a preferred mode of transport, we can contribute to the national effort to combat climate change. Supporting the development of the railway network and investing government funds in improving its infrastructure is an effective step toward achieving a greener and more sustainable future.
Moreover, the railway industry plays a vital role in stimulating economic growth and job creation. Investment in rail infrastructure not only improves existing lines but also opens new avenues for business expansion. As connectivity improves, businesses gain access to a wider pool of customers, and regions that were previously isolated can attract investment and development.
The rail sector itself is a significant employer, supporting a wide range of job opportunities, from engineers and construction workers to station staff and train drivers. Expanding the industry leads to a ripple effect, benefiting the overall economy and providing stable employment prospects.
Regional development and social cohesion are also important but sometimes overlooked aspects of the value of the railway industry. The railway network has the power to bridge the gap between urban and rural areas, fostering both regional development and social cohesion. By providing efficient and affordable travel options, the rail industry can enhance opportunities for individuals living in remote regions, connecting them to essential services and cultural hubs. This connectivity promotes a sense of inclusivity and equality, allowing people from all walks of life to access educational, cultural, and economic resources.
Furthermore, investing in the rail sector stimulates technological advancements and innovation. As we strive for a smarter, more connected future, the railway network presents ample opportunities for developing cutting-edge technology and digital solutions. From high-speed trains to intelligent ticketing systems and real-time information platforms, advancements in the rail industry have far-reaching effects beyond transportation itself. By supporting the development of the railway network, we encourage the emergence of groundbreaking technologies that benefit society as a whole.
The railway system is not solely for the benefit of those who use it daily but for everyone and it is this message that seems to be failing to cut through the entrenched mindsets of politicians and the public. The development and investment in the UK's rail infrastructure have far-reaching implications for everyone. Improved connectivity, reduced congestion, economic growth, job creation, sustainability, regional development, and technological advancements are just a few of the many advantages that arise from a thriving railway network. So let’s change the narrow narrative from faster journey times to a more all-embracing narrative of value and rail capacity.
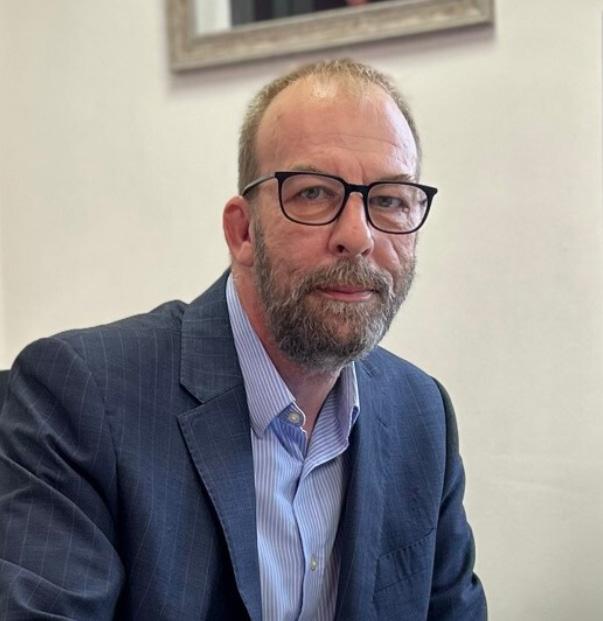
MARTIN BALCOMBE RAIL DIRECTOR AT LANES
Martin Balcombe joined Lanes in 2017 as a Project Manager, progressing to Rail Director in 2021. With involvement in both private and public sectors, he has in-depth knowledge of the industry, and invaluable experience in the field.
How did you come to work in the rail industry?
I joined Lanes Group as Project Manager in 2017 before progressing to General Manager and Rail Director in 2021. I trained as an electrical engineer and worked in the public and private sectors before moving into IT within facilities management businesses, most recently as a performance engineer for MJ Quinn.
At the time, they were carrying out facilities management for various companies, including London Underground, where I was involved in process performance and IT system installation.
The big challenges in rail maintenance are all about identifying what needs to be done and setting priorities, given the short working windows needed to keep passenger services running.
Of course, planned maintenance is preferred, but you have to also be able to respond decisively to reactive maintenance demands which will always arise. There is a fascinating mix of requirements –experience, skill, determination and ability to use advanced technologies, operating in a highly-controlled space, where safety is paramount. I’m glad to say, our teams have the attributes needed to do this in spades.
What does Lanes Rail do?
Lanes Rail has operated in the rail industry for more than 30 years. Over that time, there has been a strong focus on supporting London Underground, but we also work for Network Rail. A key strength is drainage services, including track drainage surveying, cleaning, repairs and replacement, minor civils as well as seepage.

LANES GROUP
Lanes Group is the leading wastewater utility solutions provider and largest independent drainage specialist in the UK.
Want to know more about Lanes Group?
Tel: 0800 526 488
Email: sales@lanesgroup.co.uk
Visit: www.lanesfordrains.co.uk
Also, since 2017, Lanes Rail has operated a major FM contract, covering building maintenance along underground lines, as well as depots, train crew accommodation, engineering works and power sites.
Services include fabric repair, vegetation control, pest control, and lock and gate management. We also deliver drainage services for Network Rail and various tram networks across our national depot network. We have teams across the UK that are experienced at working on rail sites, whether that be supporting station upgrades, tunnel track drainage cleaning or supporting development of rail sites.
That includes working with contractors busy constructing HS2, delivering CCTV drainage surveys, culvert cleaning and extensive tankering services. We certainly hope that work continue to grow as HS2 progresses.
What are some big successes you’ve experienced over the last twelve months?
One of our biggest projects over the last year involved delivering value for customers, by combining our two great strengths.
‘Knowledge and experience is everything when working on rail assets’
Until recently, Lanes Group plc has had two rail maintenance operations. Lanes Rail has focussed primarily on services for Transport for London, on the London Underground, London Overground, London Trams and the Elizabeth Line. Meanwhile, UKDN Waterflow (LG) has worked solely on Network Rail assets, working directly for Network Rail or tier 1 contractors, from a base in Slough.
Now, we’ve brought the UKDN Waterflow (LG) team over to join the Lanes Rail team in Rainham.
We have always worked together on projects. But now we can work even more closely together, so clients can have the benefits of the skills and capabilities of both teams.
It means we can control costs, with savings passed on to the clients. We can deliver better-coordinated solutions and work programmes. And we have more flexibility to quickly put together the best teams to deliver the best results.
UKDN Waterflow (LG) also has a principal contractor licence, so brings that authority to the Lanes Rail operations. Going forward, this creates a more powerful, capable, and agile maintenance operation, with opportunities to bid for more and bigger contracts.
What are your strengths as a service provider?
The starting point is the expertise and the capabilities of our teams. Knowledge and experience is everything when working on rail assets.
For example, the London Underground has multiple legacy systems. They are highly complex. In terms of drainage, they are hidden from view but are crucial to keeping the railways open.
Understanding how they work, having worked on them for many years, knowing what needs to be done, and when, is highly valuable. If not essential. We have very stable, dedicated experienced maintenance teams who work effectively and safely in the most challenging environments.
They are supported by brilliant project managers who understand what the client needs and wants and how to deliver.
Also, I would say, especially with UKDN Waterflow (LG) integrated into the team, the scope of our capability. We can deliver an end-to-end service.
We are also supported by Lanes Professional Services, an engineering and design consultancy within Lanes with a strong rail and transport infrastructure
focus. Its services include drainage and hydraulics investigation and design, drone surveys, and site and structural engineering surveys. Lanes also has its own sewer and culvert rehabilitation division, with the capability to install the UK’s largest cured in place pipe (CIPP) liners. Its teams have worked on numerous rail projects.
All this is done while setting the highest possible standards and using exemplar operating systems.
For example, our teams use a bespoke version of a remote working platform that helps us plan and control our work – which, during a TfL audit was praised as an example of exceptional practice that other suppliers could learn from.
We also very recently passed our ISO 9001 and 14001 audits with no nonconformities for the third year in a row, an achievement most other businesses cannot match.
Describe one of the biggest challenges of your work.
As a rail drainage contractor, a big challenge is water. Sometimes lots of it. Climate change is already a big factor in delivering drainage maintenance on all rail systems –but especially on below ground networks like London Underground.
Flash flooding attributed to climate change is an increasingly common occurrence in London. When it happens, it is our teams that are called in to remove water and put in mitigation measures to try to keep services running or get them operational again as quickly as possible.
Lanes Rail takes great pride in responding quickly and decisively to these emergencies 24 hours a day, seven days a week.
Our teams are among the hidden heroes of the capital’s rail network, helping TfL keep services running under increasingly extreme weather conditions.
Lanes has invested a lot of money to provide Lanes Rail with the latest, most capable specialist drainage vehicles so we can do this job.
They include new recycler jet vac tankers that can operate for longer on site, reusing water, which allows us to tackle flood clearance and a wide range of other tasks more sustainably.
What project have you been particularly proud of in recent times?
We were very pleased to be selected to deliver maintenance services for Crossrail even before the Elizabeth Line opened last year. As the newest railway line through London, it carries a significant prestige and is strategically vital to the future of the London and south east rail network. The Elizabeth Line team (known as RfLI or Rail for London Infrastructure) recognised our expertise, so we’re now the maintenance contractor for fabric maintenance and
drainage along the line, meeting all KPIs set for us. This includes working in partnership with RfLI teams on asset checking to verify its planned and preventative maintenance programmes.
The Elizabeth Line may be brand new but maintenance of newly installed assets has specific challenges, not least because some may not be as tried and tested as established systems.
There is a learning curve for all involved, and we’re very pleased to be using our experience and expertise to support RfLI teams as they nurture what is the rail equivalent of a newborn baby compared with the rest of the London Underground and overground system.
I would also say that Lanes played a big part in TfL’s response to the Covid 19 pandemic – putting in place thousands of signs and hundreds of hygiene points across the London Underground network and bus interchanges.
This work was planned and implemented by our teams, working under the most intense pressure and in difficult circumstances, and praised by TfL for its effectiveness. It’s this can-do approach that defines Lanes Rail’s maintenance work –while observing the highest health and safety standards.
What are the opportunities for your business?
Our railways are clearly an essential component of the UK’s drive to deliver carbon net zero by 2050. Passenger rail journeys almost doubled (96 per cent) in the 20 years before the pandemic. The pandemic was a big shock. All networks were badly hit, with passenger numbers falling off a cliff. London Underground was hit hardest of all.
However, they’re now recovering, and will continue to do so. I would expect further investments to be made in the rail network under Great British Railways over the next decade, both to meet passenger demand and the requirements of our climate change commitments.
This means maintenance work is as essential as ever, at a time when climate change is making drainage maintenance even more of a priority.
In March, the government released extra specific funding to cover flood alleviation work. Climate change will have been a factor in this decision-making. That money will be incorporate in CP7 allocations and spending decisions.
We aim to attract some of that work over the coming months. We’ve already won a sizeable new contract with Colas to provide drainage investigation services across the West and Wales region to enable Colas to plan works under a CP7 contract.
Drainage investigations are almost always the first task when planning rail maintenance or upgrades. So we aim to keep our teams very busy over the coming years.
NEWS IN BRIEF
‘CARBON LITERACY FOR RAIL’ TRAINING COURSE
The new tailored course for the rail industry has been prepared by RSSB’s sustainability experts for anyone working in rail infrastructure, train operating companies and the supply chain. It provides delegates with the knowledge and skills to lower their personal and organisational carbon footprint in line with rail industry targets.
The training course is accredited by the Carbon Literacy Project to meet the ‘Carbon Literacy Standard’, with delegates successfully completing the course certified as ‘Carbon Literate’.
GREAT NORTHERN’S CLASS 717 FLEET SET FOR SIGNALLING UPGRADE
Govia Thameslink Railway (GTR) has received authorisation from the Office of Rail and Road (ORR) to upgrade its Great Northern Class 717 fleet to the latest specification of European Train Control System (ETCS). It is the first fleet to receive authorisation to upgrade the onboard digital signalling system to this most recent version. Upgrading the software to the latest version of ETCS BL3 R2, also referred to as 3.6.0, will allow the trains to make use of the latest digital infrastructure to be installed on the East Coast Main Line, as part of the next phase of the government-funded East Coast Digital Programme (ECDP). The programme will see traditional lineside signals replaced by state-of-the-art in-cab signalling technology (ETCS) which will create a more reliable railway with lower emissions.
Final testing for the upgrade will take place this autumn, ahead of upgrading the entire fleet early next year, so that the trains are ready to operate in ETCS on the East Coast Main Line from 2025.
PW150-PVC-6.83m
A2AS_SO9133_5405A
EC100-CO-47.55m
A2AS_SO9133_5502A
PW600-CO-91.63m
A2AS_GU2000006767
PW150-PVC-6.38m
A2AS_SO9133_5400B
A2AS_GU2000006764
A2AS_GU2000006765
PW150-VC-1.03m
A2AS_SO9132_5799A
A2AS_GU2000006761
A2AS_GU2000006759

A2AS_SO9132_5490B
A2AS_SO9132_5490A
PW600-CO-89.66m
A2AS_GU2000006766
PW225-PP-13.29m
A2AS_SO9133_6402A
A2AS_SO9133_6501A
A2AS_SO9133_6401B
A2AS_SO9133_6400B
A2AS_GU2000006763
A2AS_SO9132_6199A
CF-PP-12.84m
A2AS_SO9133_6500D
A2AS_GU2000006762
A2AS_SO9132_6599A
A2AS_SO9132_6398B
CF225-PVC-13.42m
A2AS_GU2000006760
A2AS_SO9132_6497B
A2AS_SO9132_6396B
A2AS_GU2000006758
PW600-CO-91.96m
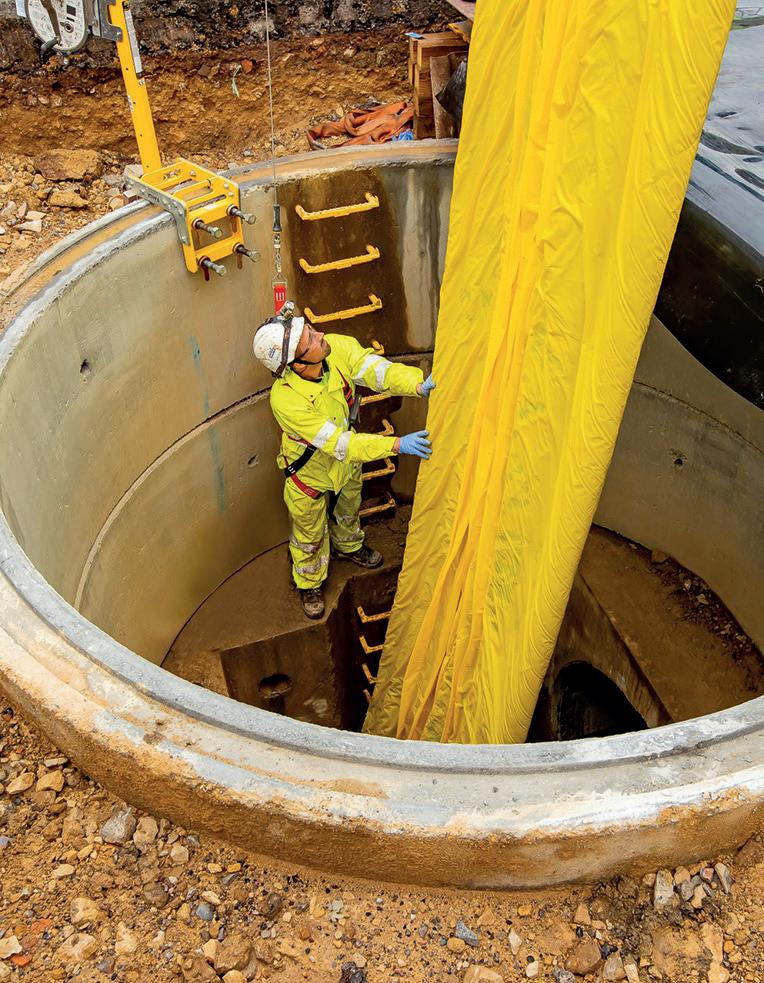
A2AS_GU2000006749
CF-PP-13.35m -PP-13.11mCF
A2AS_GU2000006755
A2AS_SO9132_6292B
A2AS_GU2000006753
Roddingeye13
A2AS_SO9132_6496A
A2AS_GU2000006757
A2AS_SO9132_6495E
A2AS_SO9132_6295B
A2AS_GU2000006750
A2AS_SO9132_6188B
PW150-VC-2.09m
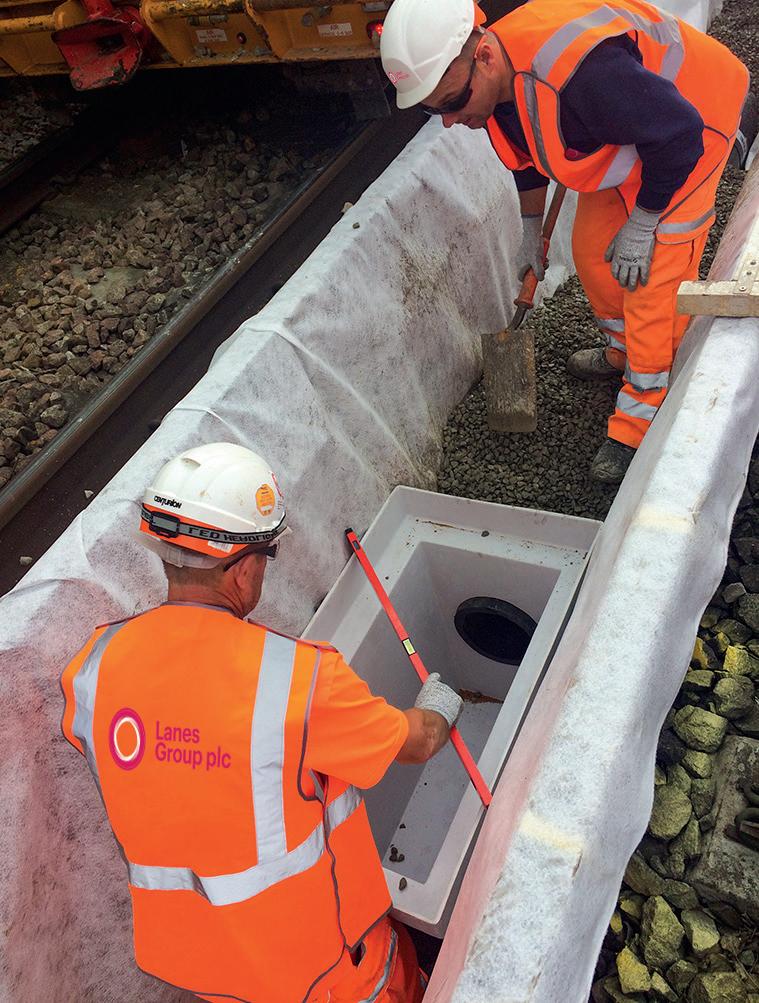
A2AS_GU2000006748
Roddingeye10
A2AS_GU2000006747
Wide range of rail maintenance services Latests CIPP technology for culvert lining Proven rail capabilities and experience
EC0-CO-505.83m
PW675-CO-89.23m
PW150-VC-8.28m
A2AS_SO9132_5385A
A2AS_GU2000006745
A2AS_GU2000006746
A2AS_GU2000006744
A2AS_MH2000000622
A2AS_GU2000006743
CF225-12.99m
PW600-CO-92.03m CF225-PVC-27.92m
Our expertise is tested and proven on the UK’s largest infrastructure projects – from smart motorways and nuclear sites to Crossrail and HS2, our customers trust Lanes to deliver. Delivering services for

PW150-VC-7.41m
A2AS_SO9132_5382A
A2AS_SO9132_5482E
A2AS_GU2000006740
A2AS_SO9132_5581A
Roddindeye11
A2AS_SO9132_6084C
A2AS_MH2000000621
A2AS_SO9132_6184E
A2AS_GU2000006742
PW225-PVC-13.29m
PW150-VC-3.62m
PW0-PVC-20.21m
PW150-PP-8.15m
A2AS_SO9132_6183D
roddingeye12
PW225-PP-16.49m
A2AS_SO9132_6181A
A2AS_SO9132_5382B
PW675-CO-20.19m
A2AS_SO9132_5981B
0800 526 488 | sales@lanesgroup.co.uk |
PW150-PVC-7.47m
A2AS_GU2000006739
A2AS_SO9132_5381A
PW150-PVC-7.44m
A2AS_SO9132_5380A
A2AS_GU2000006737
A2AS_GU2000006738
CU4000-CO-68.53m
PW150-VC-2m
PW675-CO-8.61m
PW150-VC-0.84m
A2AS_SO9132_6079C
A2AS_SO9132_6180C
A2AS_SO9132_5980A
A2AS_SO9132_6180A
A2AS_GU2000006735
A2AS_GU2000006734
PW150-PVC-8.54m
A2AS_SO9132_6179A
A2AS_SO9132_6179B
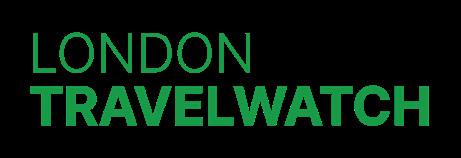
David Murdoch is Head of Communications at London TravelWatch
The Most ‘On Time’ Railway in the Country
Back when it first opened in the spring of 2022, after years of project delays and significant overspend, we heard from senior transport figures that the Elizabeth line was going to be a ‘game changer’
It is true that the Elizabeth line has been truly transformative for Londoners, connecting east to west with faster, accessible and more comfortable train journeys.
According to Transport for London Commissioner, Andy Lord, speaking at our board session at City Hall, in the first fourteen months of operation an incredible 185 million passenger journeys have been made.
The Elizabeth line has truly surpassed expectations. It recently came top in national tables for being the most ‘on time’ railway in the country.
The passenger improvements have come in several phases. Since the final timetable iteration was introduced in May 2023, trains now run roughly every two and a half minutes between Paddington and Whitechapel stations at peak times (with frequencies of up to 24 trains per hour in both directions). Twelve trains run every hour between Canary Wharf and Abbey Wood in peak times – a train every five minutes.
Passengers can now also travel directly from Shenfield to Heathrow, without having to change trains. All this has unlocked opportunities for Londoners in terms of work and leisure that simply didn't exist before.
There are also many journeys being made on the Elizabeth line that simply were not happening before. In other words, passenger growth has not come exclusively from passengers moving from other transport lines or modes. The Elizabeth line seems to have become a tourist destination or experience in its own right.
‘We would like to see a firm commitment to build Crossrail 2 in full by TfL and all of the London mayoral candidates.’
The success of the Elizabeth line shows that we can still deliver first class infrastructure projects in this country. While Crossrail was a very expensive and complex project - with more bumps along the way than anyone anticipated – it will surely pay off many times over.
We are glad that Crossrail 2 has been safeguarded by TfL as a project to prioritise in future when conditions allow. We know that big ticket items are not on the immediate horizon due to financial constraints, but to support growth in greater London - and across the country in terms of jobs via supply chains and transport interconnectivity - we must be ambitious once again.
We would like to see a firm commitment to build Crossrail 2 in full by TfL and all of the London mayoral candidates. A ‘Crossrail 2’ would have to be fully accessible (as the ‘core’ section of the Elizabeth line is) with lifts direct to platforms and level boarding across the entire route. And it would have to be built with net zero as an integral part of the project. We think it could then be just as much of a game changer as its elder sibling, the Elizabeth line.
NEWS IN BRIEF
HS2 COMPLETES PIER FOR WATER ORTON VIADUCTS
HS2 has completed the first of 32 giant piers for the first Water Orton Viaduct as work ramps up to build the Delta Junction, the project’s most complex network of structures in the West Midlands. HS2’s main works contractor for the West Midlands, Balfour Beatty VINCI (BBV) is building the 1,400 metre long northbound and southbound structures, which will connect HS2’s Birmingham Curzon Street Station with Crewe and Manchester.
JACOBS SELECTED TO PROVIDE ADVICE TO DFT
Jacobs has been selected as a PRIME Consultant by the U.K. Department for Transport (DfT) on its latest Specialist Technical and Commercial Advice for Rail and Other Transport Modes (STARThree) Framework to support the DfT’s portfolio of rail and other transport mode agreements, major projects and programs, and its policy and strategic work in transport. The DfT expects the framework to run over an initial two-year period with an option to extend by one or two years.
NORTHERN RE-RECORDS STATION NAME ANNOUNCEMENTS
Northern has re-recorded the onboard announcement for 34 of the stations across its network following a public appeal to ensure local pronunciation was respected. The train operator received 47 formal requests to rerecord announcements, with multiple submissions for Aspatria in Cumbria (to be pronounced as ‘As-spay-tria), Kirkham and Wesham in Lancashire (to be pronounced Kirkham and Wessam), Ilkeston in Derbyshire (to be pronounced Il-kes-ton) and Sowerby Bridge in West Yorkshire (to be pronounced Sowby Bridge).
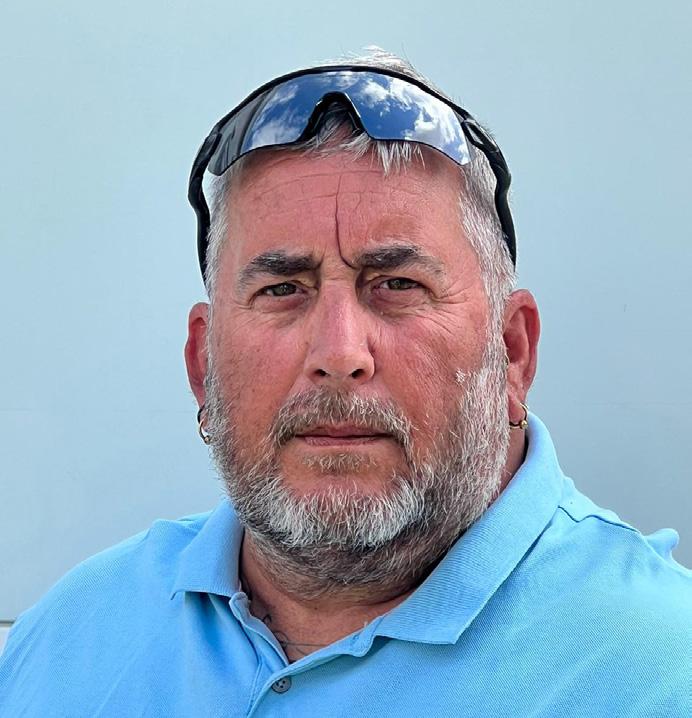
BOB HARDWELL RAIL ENGINEERING EXPERT AND DIRECTOR OF LINSINGER UK LTD
Bob Hardwell is a railway engineer who has worked on the UK railway network for over 30 years. He is currently the Head of Linsinger UK and responsible for providing specialist rail engineering advice for the business. Bob has a wealth of experience in the railway industry. He started his career as a trainee with British Rail in 1988. He has held a variety of engineering positions, including Track Inspection Supervisor, Route Rail Engineer, and National Rail Expert. He is a member of the Permanent Way Institute and gives talks on rail management innovation regularly.
How did you get started in the industry and what is your role within Linsinger?
I started at Linsinger GmbH in September 2020 and my role is to support all their activities within UK and Ireland for rail engineering expertise and machine introduction, commissioning, and customer support.
Tell us about your career before you joined Linsinger?
Before I and many other colleagues started at Linsinger in the late 1980s, work in other industries was not stable, my mum worked for British Rail (Great Eastern), she suggested I apply for a track job. I started my railway career in 1988 as a maintenance trackman working for British Rail on the Great Eastern Route (now Anglia) based at Kelvedon in Essex.
My career has mainly been track maintenance based, I was always keen to learn new things and the railway does support this approach, I started at the lowest grade in maintenance and as I increased my knowledge and skills I moved upwards through the grades. Little did I know at the start that this would provide good foundations to build on for the future. Post privatisation I had moved from the area of general track maintenance to rail specific roles, track welder and then also Ultrasonic examination gave me a great understanding of the rail material, failure modes and possible preventative measures that were achievable. We were the first team in the UK to encompass such stills and this allowed us to find and fix small defects within the same shift. After several years I became a supervisor for the rail department, started to get involved with UK working groups and progressed to route rail engineer. This role was to look at not just how to inspect and fix rail but also to start to understand preventative strategies and whole life cost engineering.
LINSINGER UK LTD
Linsinger has a tradition of more than 80 years as a global leader for milling and sawing technology.
Want to know more about Linsinger UK Ltd?
Tel: 07515620280
Email: r.hardwell@linsinger.com
Visit: www.linsinger.com
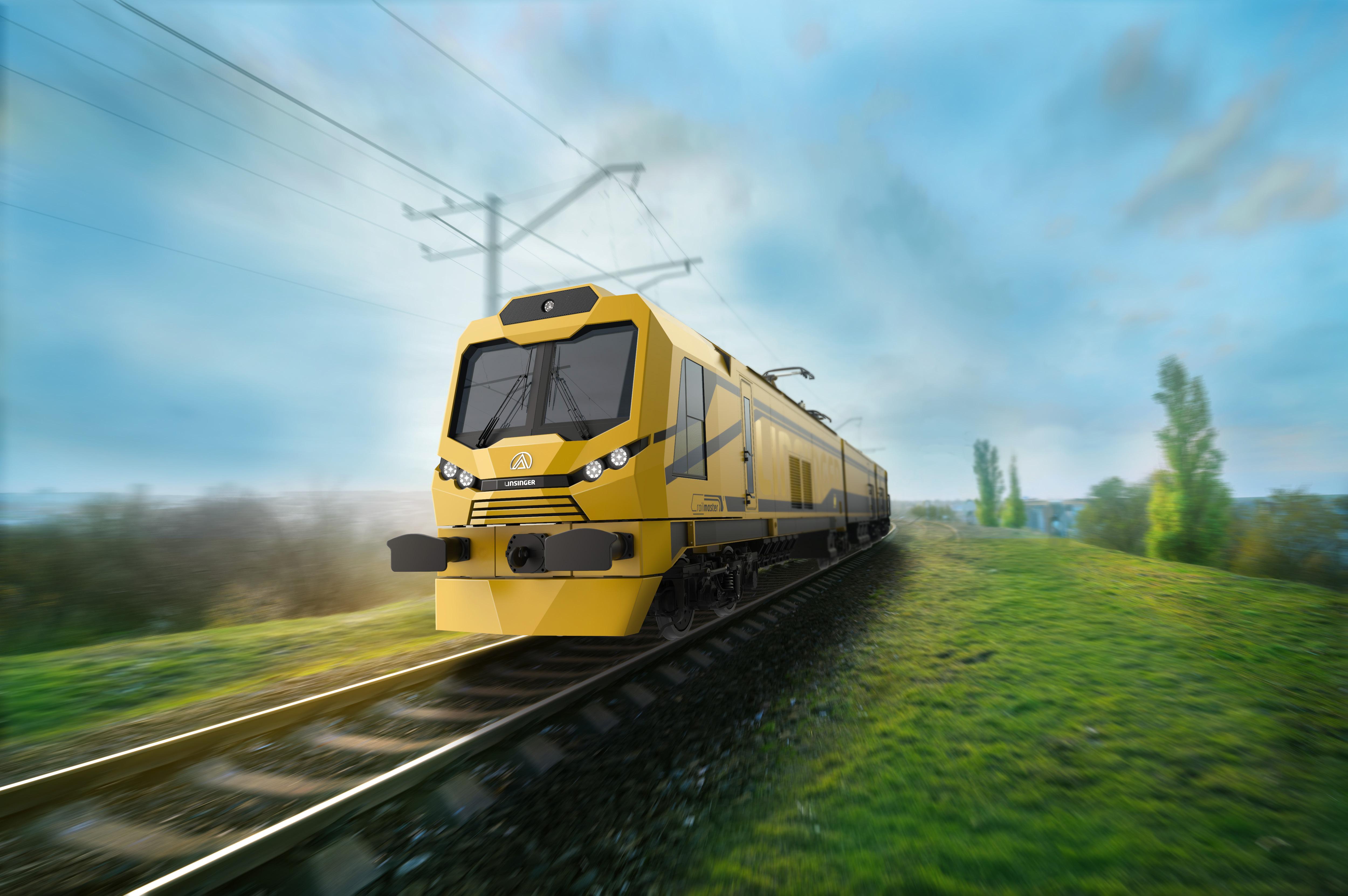
As different challenges were faced by the business and different contracts were awarded I became the route rail engineer, responsible for specialist support to the route asset management team and building the strategic route maintenance and renewal plans for rail in conjunction with representing the British Standards Institution as a rail expert on several European working groups. During the last seven years before leaving Network Rail I worked as a national rail engineer within the Technical Authority.
What challenges have you faced in the industry?
Change!! Change and innovation is the biggest challenge within the UK rail industry. The national rail sector is slow to adopt change and can be restrictive to new innovation. A good example of this was the introduction of rail milling: it took eight
Manual ultrasonic with analogue handsets has progressed to ultrasonic test trains identifying suspect areas and staff with digital systems confirm the defects. Artificial Intelligence will be the next step and reduce the need for manual verification. Rail profile management was not something that happened much in my early days as the benefits of good wheel rail interface wasn’t fully understood. I can remember seeing the results of plaining machines working in the area, where rail shaped cutters were lowered onto the railhead and dragged by on track machines, leaving long lengths of swarf lying in the track. Post the Hatfield derailment saw the introduction of cyclic grinding trains and now the UK has rail milling which delivers the next generation in precision of rail profile management.

RAILMASTER
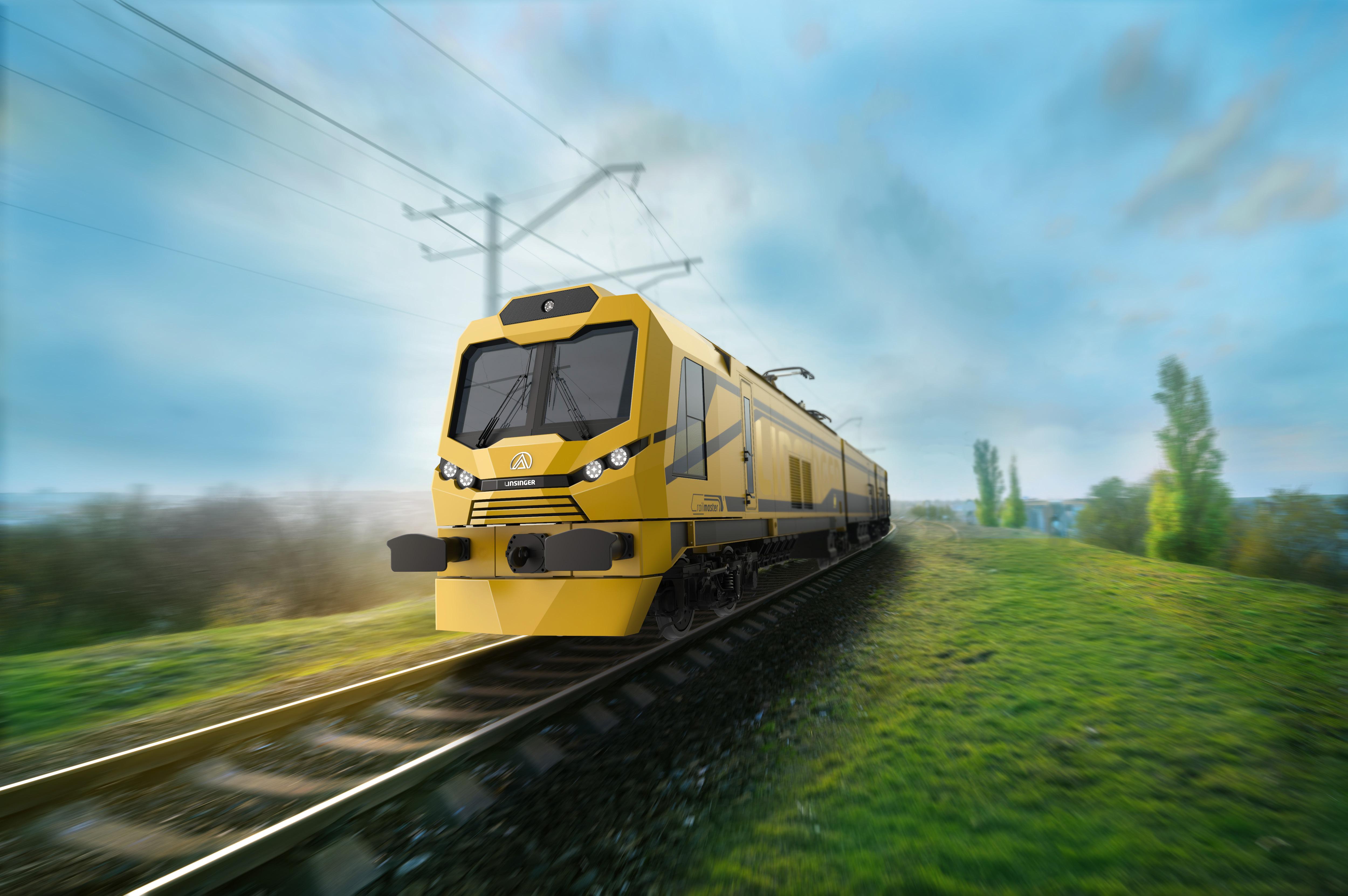

Linsinger´s latest development the ”RAILMASTER ” is the perfect fusion of the most advanced rail milling technology powered by zero emission propulsion systems. This is our contribution to a better future.
‘The Rail Master has the option to be powered by hydrogen or electric power units delivered via the pantograph / catenary system and can adopt different configurations of the
milling
and finishing units.’
Tell us about Linsinger.
Linsinger Maschinenbau GmbH is an Austrian company that specializes in the development and manufacture of machinery for the rail industry. The company was founded in 1946 and is headquartered in Laakirchen, Austria. Linsinger has a global presence, with offices in Europe, UK, Asia, and North America.

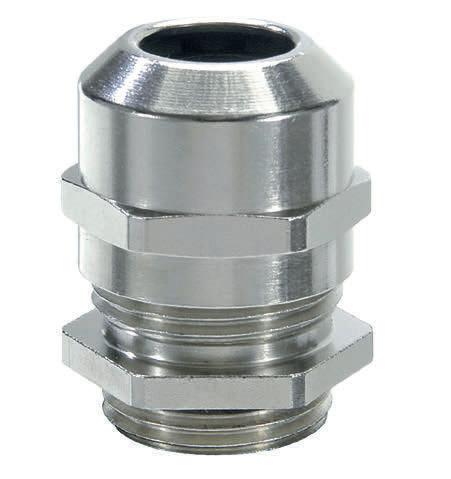
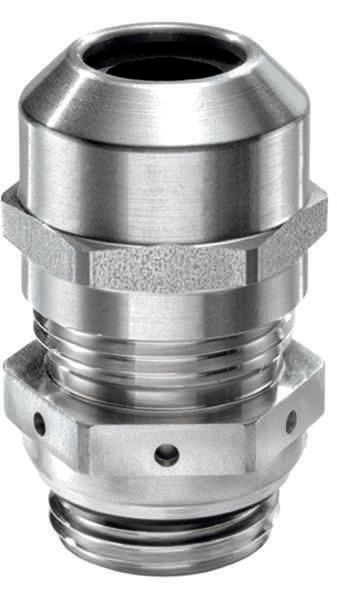
The company's product range includes rail milling and surface finishing machines, Linsinger also make sawing and drilling equipment and static rail machining plant. Linsinger's machines are used by railway operators and maintenance companies around the world to improve the safety and efficiency of rail operations.
Linsinger is a leading supplier of rail milling technology and has a reputation for innovation and quality. The company's products are used by some of the world's largest railway operators, including Deutsche Bahn and Network Rail.
Linsinger is committed to providing its customers with the best possible products and services. The company invests heavily in research and development and has a team of experienced engineers who are dedicated to developing new technologies that can improve the safety and efficiency of rail operations.
Do you think the rail industry could be greener and what is your organisation’s green strategy?
A lot of conventional rail plant within the industry is historically diesel/electric powered and we at Linsinger strive to
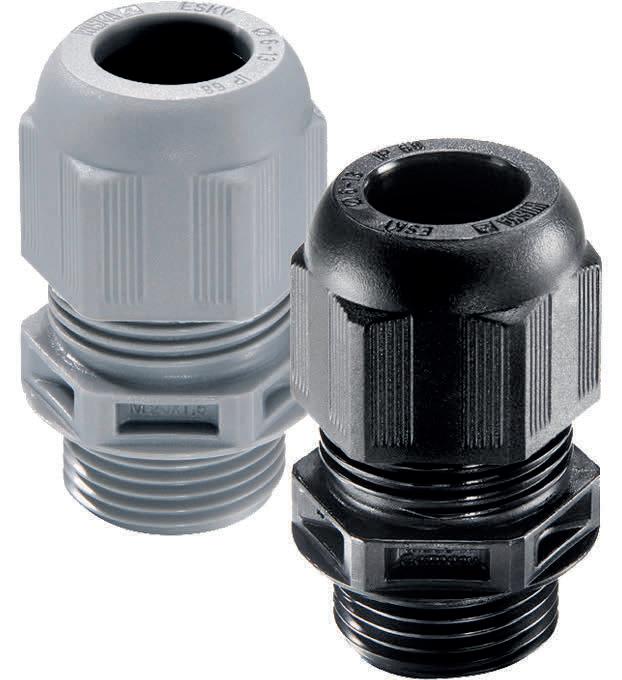
change this with our machines. Our green strategy is to have the ability to deliver power from multiple net zero sources to suit our customers’ needs. We choose hydrogen as the first alternative fuel source to be developed into fully hydrogen powered MG11 machine, this technology change delivers zero emission options for our customers and the first machine is now in North America.
To build on this success and give our customers the benefit of a choice of zero emission options the new Linsinger Rail Master has been developed. This machine is designed to ‘plug and play’ regarding its power source and the full consist can be flexible to suit the customers’ needs.
The Rail Master has the option to be powered by hydrogen or electric power units delivered via the pantograph/ catenary system and can adopt different configurations of the milling and finishing units.

EN 45545 Approved Cable Glands and Entries...

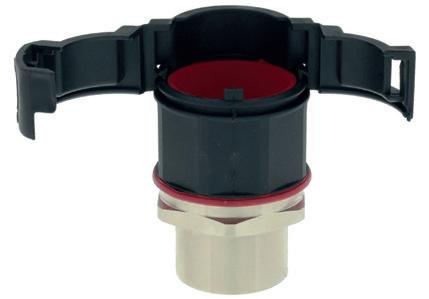
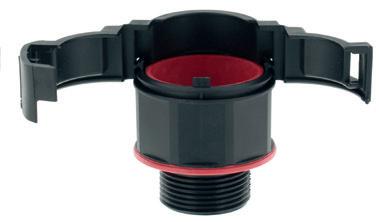
For over 100 years WISKA have been at the forefront of cable management design and innvoation. This level of expertise has resulted in the development of our lastest range of products, introducing The Railway Series by WISKA.
The Railway Series is a comprehensive range of industry-specific cable glands and conduit solutions in accordance with EN 45545.
Need an expert? Speak to us today.
01208 816062 / 01208 816708 / www.wiska.co.uk / info@wiska.co.uk
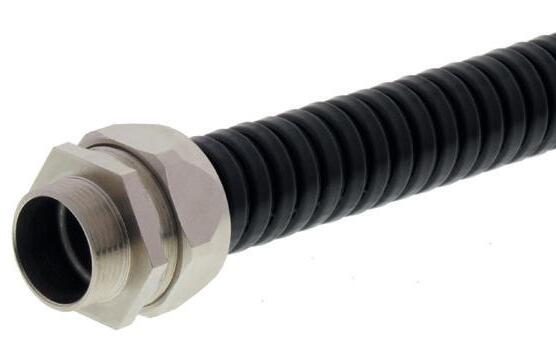

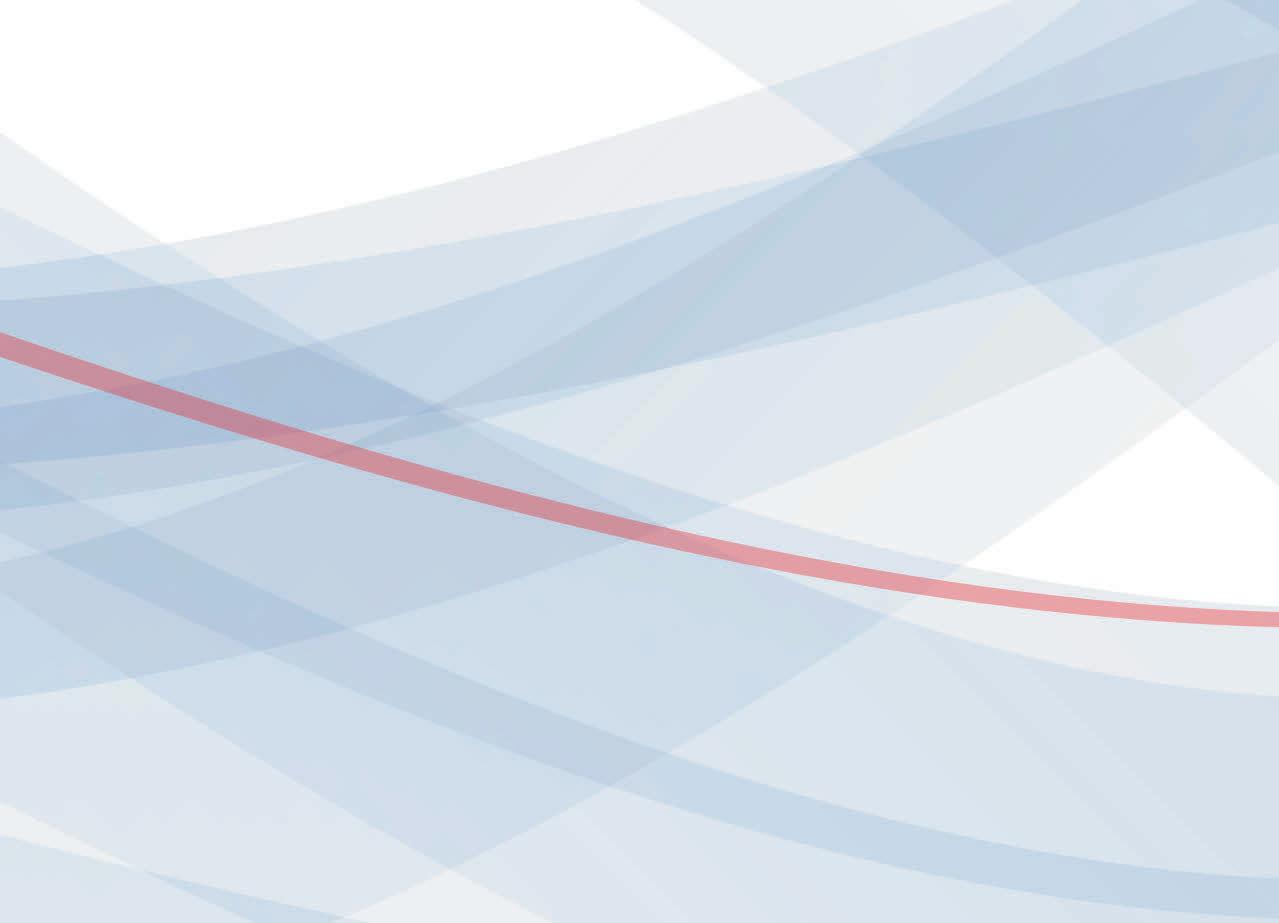
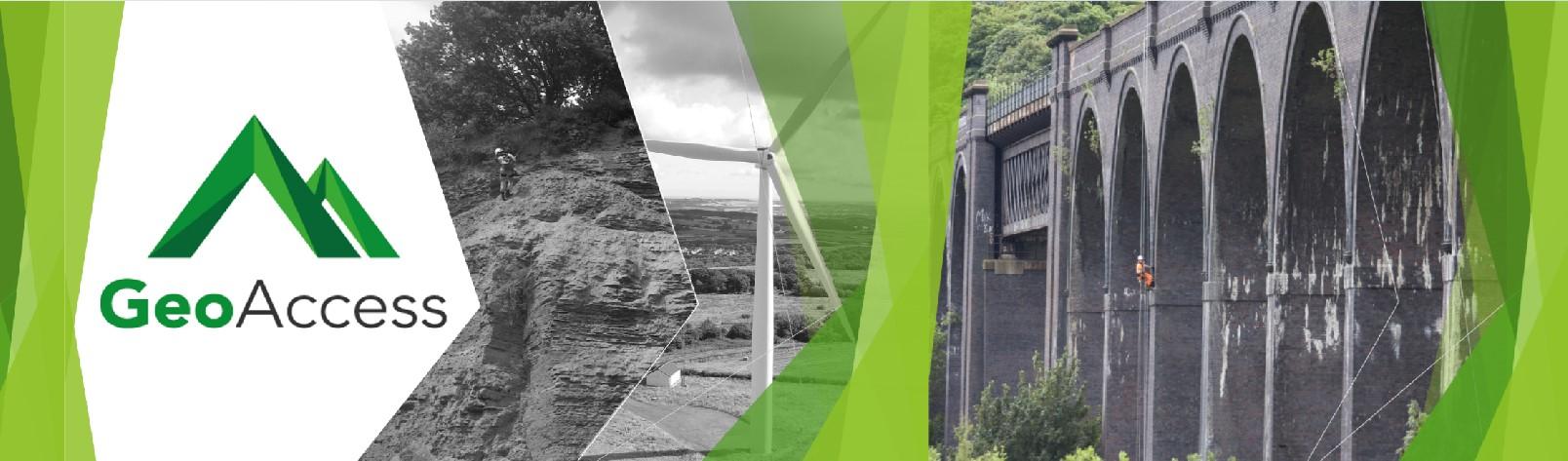
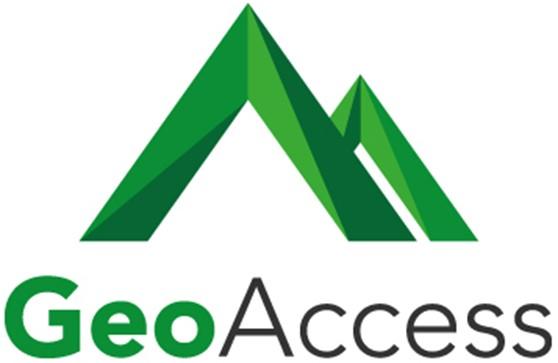

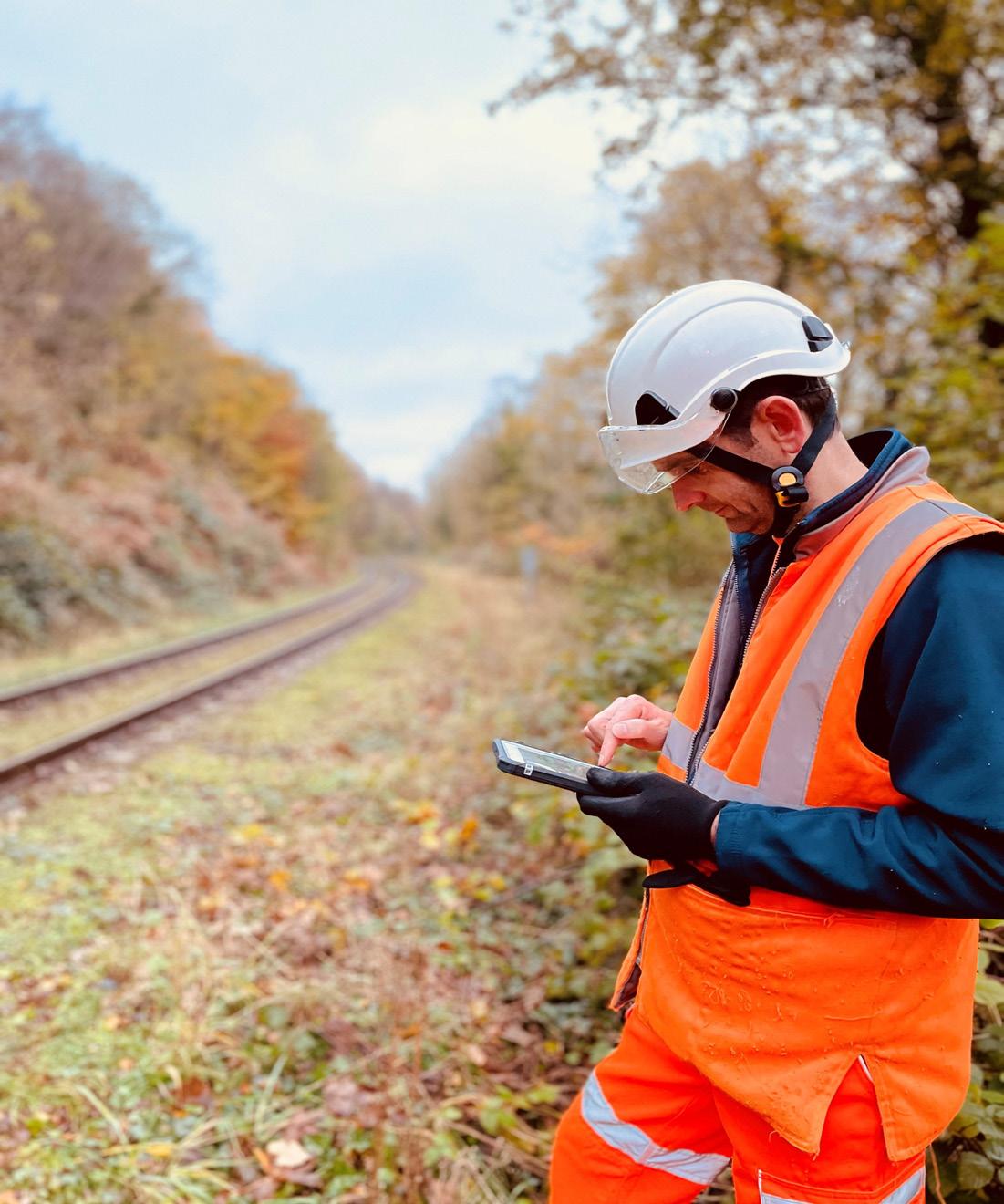
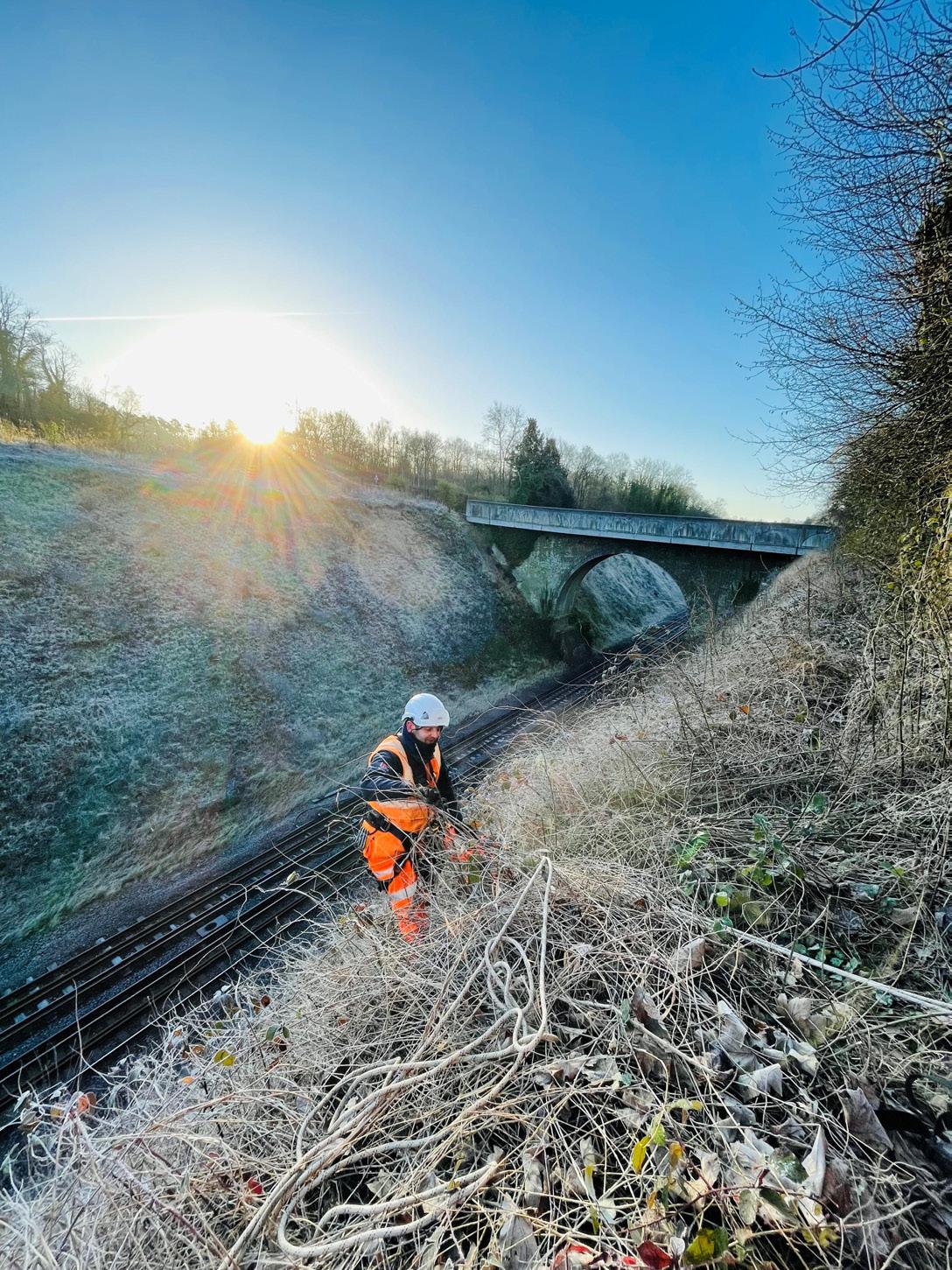
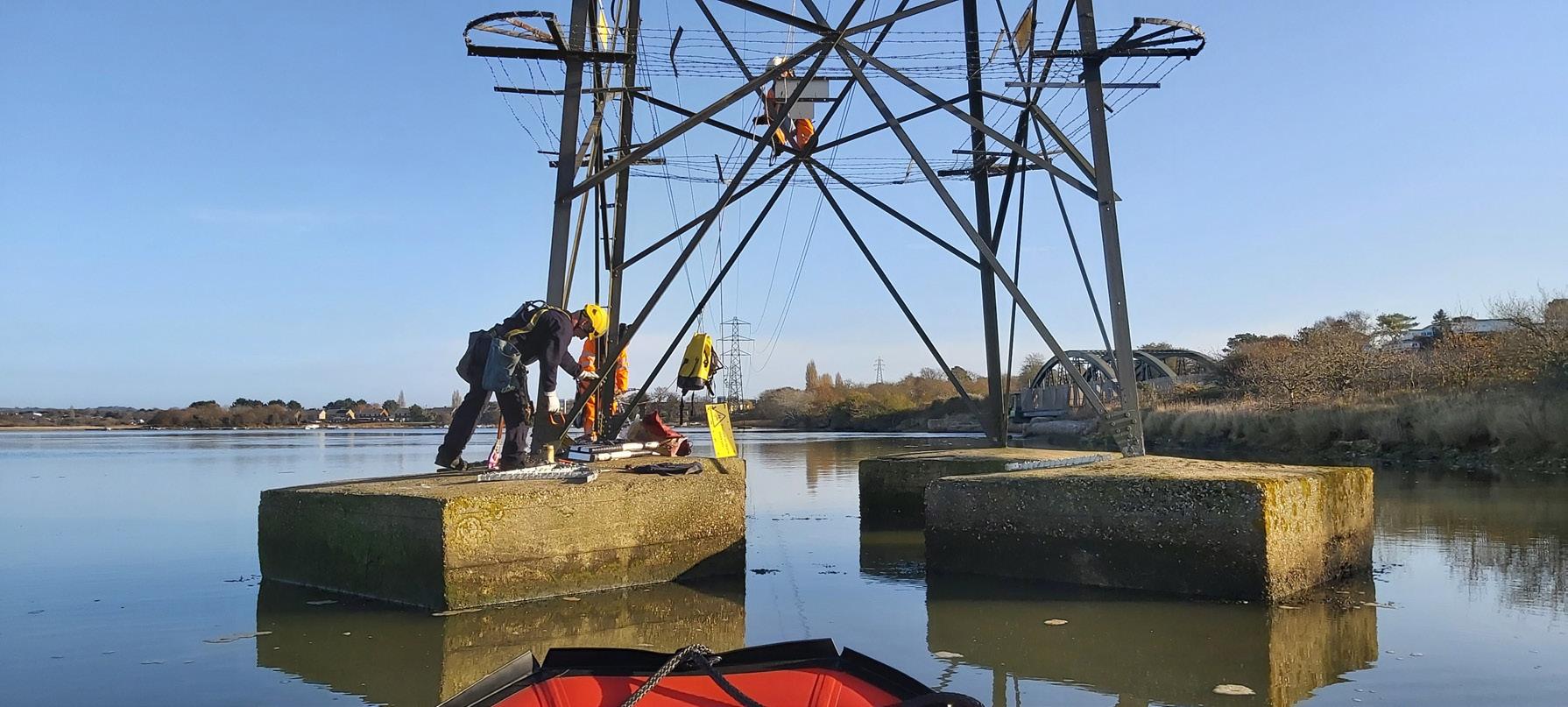
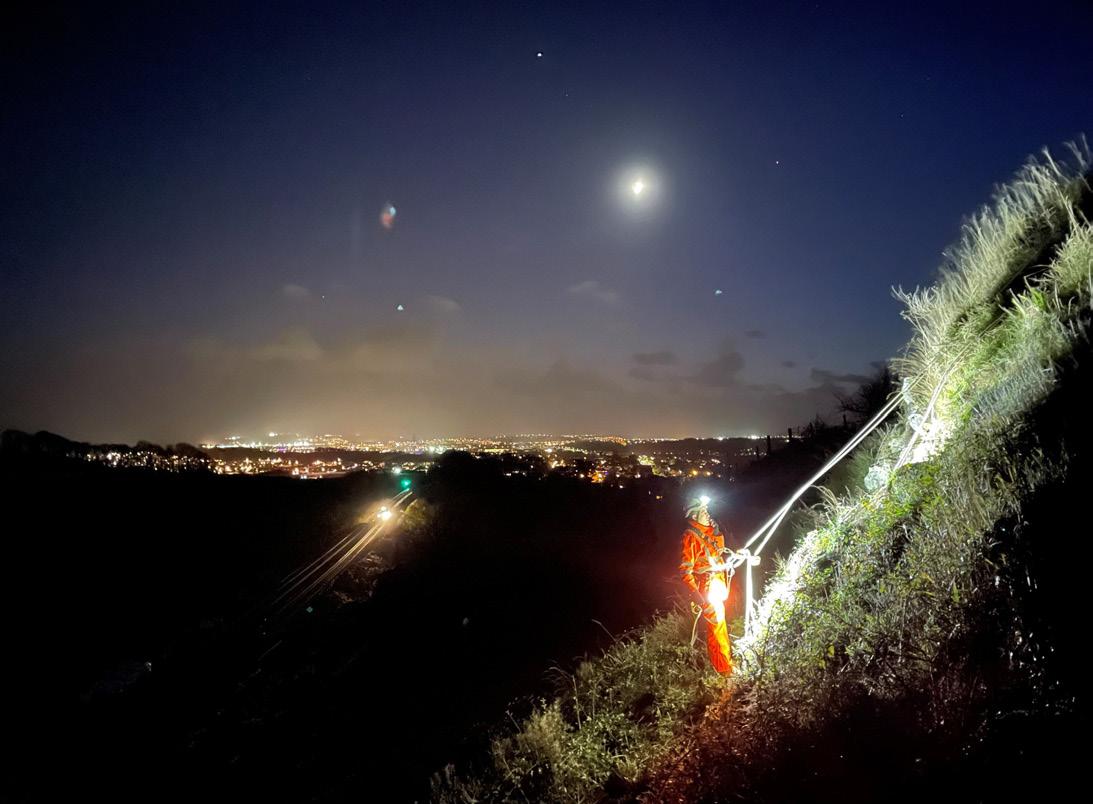
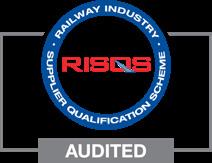
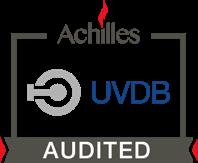

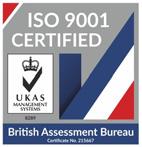


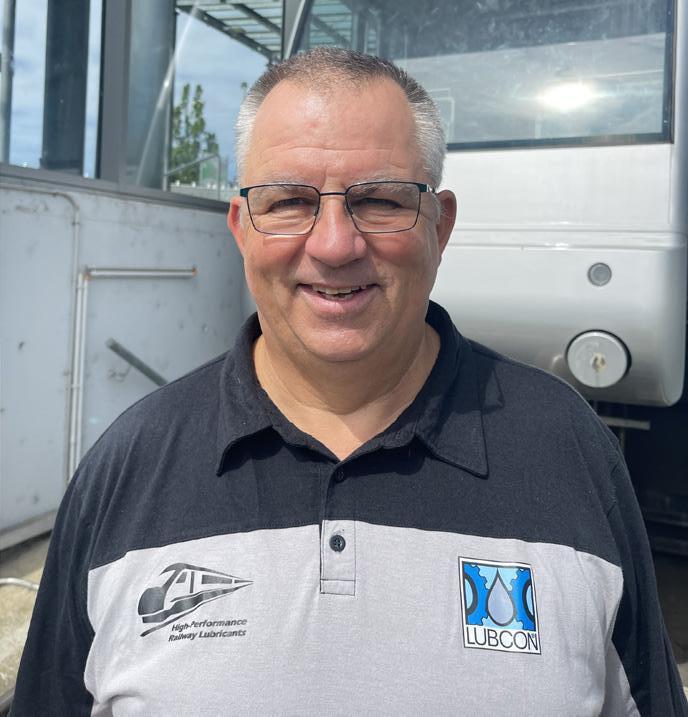
ROLAND
WEINHART
DIRECTOR
OF THE TRANSPORTATION BUSINESS UNIT AT LUBRICANT CONSULT GMBH
Roland Weinhart is a mechanical Engineer with qualifications in R&D specialties. He previously worked for US company AMISTAR as International Service technician in Microtechnology. In 1995 he received the Certificate of Sales Administration and in 2000 the Swiss Federal Diploma of Export Management. He joined LUBCON in 2021, taking over responsibility for the Transportation business unit.
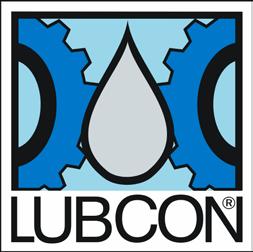
LUBRICANT CONSULT GMBH
LUBRICANT CONSULT GmbH is a worldwide operating lubricant manufacturer developing, producing and distributing high-grade greases, oils, pastes and sprays for nearly all industrial applications and manufacturing sectors.
Want to know more about LUBCON?
Tel: 01323 561030
Email: sales@lubcon.co.uk
Visit: www.lubcon.com
How did you get started in the industry?
The combination of my technical engineering background and bachelor’s degree in Business Administration has provided me with a unique perspective to work in the railway industry. I can bridge the gap between engineering expertise and effective business management, driving innovation, efficiency, and sustainability within the railway sector.
For me, engineering marvels are proof of human ingenuity and engineering prowess. Building railways often involves overcoming challenging terrains, construction intricate bridges and tunnels and implementing sophisticated signalling systems. The sheer scale and complexity of railway projects have drawn my admiration ever since.
What is your role within LUBCON?
I am the Director of the Transportation Business Unit since 2021, educating and supporting our own subsidiaries, resellers and customers worldwide in railway and general transportation projects.
Tell us about LUBCON.
Lubricant Consult GmbH, also going by the brand name ‘LUBCON’, was founded in August 1980 with the vision of supplying high quality lubricants and a unique customer service. We also have a separate business unit, to develop and manufacture specialised lubrication systems. LUBCON is represented in over 50 countries around the globe, with ‘LUBCON Lubricants UK Ltd’ being the branch in the United Kingdom. Additionally, there are regional production sites to ensure a full coverage of product availability worldwide. Our portfolio currently includes around 2,000 distinct products.
What types of products and services do you offer?
We focus on three main industry sectors, which are packaging, food and beverage and transportation. However, over the years, we have developed customised specialty lubricants for other applications and industries with the goal to improve service life and overall efficiency. LUBCON not only assists in selecting the best lubricant, but also provides advice regarding appropriate lubrication techniques. With expertise in both lubricants and application techniques, we are able to meet individual requirements and offer innovative solutions for all needs.
We have a dedicated R&D division, focussing on new sustainable developments such as easily biodegradable lubricants, which are environmentally friendly and minimise disposal costs. Finally, we offer hands-on training and seminars for maintenance personnel, engineers and management to provide a better understanding in the field of tribology and lubrication technology.
What are some major projects you’re currently working on?
I am currently working on various railway projects around the world. In metros, trams and commuter trains the current focus is clearly on the wheel-rail contact. As noise, wear and performance are key factors for a fully functional system, an increasing number of railway companies have a higher focus on those topics. Wheel-rail interaction can produce noise and vibration, impacting passenger comfort, environmental noise pollution and structural integrity of nearby infrastructure.
Focussing on the wheel-rail contact is crucial for understanding and optimising the performance of railway systems. The wheel-rail interface is a critical area because it directly affects train dynamics, safety and maintenance costs.
Together with railway companies, universities and government departments, LUBCON has developed specialised products to reduce the typical squealing noise and wear, increasing the performance and safety.
When a client comes to you with a particular problem, what’s your process for coming up with a solution, and how closely do you work with clients throughout the projects?
We usually begin by analysing the particular problem together with our customers. This can be done by video conferences and on-site visits. As every situation might be different, it is very important to take specific local and environmental circumstances into consideration. With our expertise and experience from many previous case studies, we help our customers to find the optimum solution.
On-site, we can take noise measurements to get an idea of the circumstances and the current situation. Furthermore, break tests are often required to evaluate safety and performance of a friction modifier. Once the tests are done on the plain track, we manually apply a friction modifier in defined areas and measure the achieved results again for a comparison of the break performance. In average, we can lower the squealing noise by 10 – 20 dBA, which is an impressive value.
The third step is then to find the best possible solution how to apply the product. Collaborating with designated system manufacturers we ensure the most suitable lubrication system is chosen and installed. We follow the project closely together with our customers to ensure 100 per cent functionality of our products and the implemented solution.
What types of companies do you collaborate on projects with?
Regarding the wheel-rail contact issue, we work closely with systems manufacturers worldwide. We ensure, that our products are
‘For me, engineering marvels are proof of human ingenuity and engineering prowess … the sheer scale and complexity of railway projects have drawn my admiration ever since.’
working perfectly with the various onboard or stationary systems, which are currently available on the market. So whatever preference our customers have, we make sure they are met with the perfect solution at the end.
What are some of the biggest challenges this sector currently faces?
Many of our customers face the problem of an aging infrastructure. This requires
constant maintenance and upgrades. Safety and operational efficiency are absolutely mandatory and whatever improvement needs to be done, it has to be cost efficient and reliable. When we look at lubricants, these are also called ‘soft factors’, which can be improved at comparably low costs, yet these changes can result in a tremendous performance advantage and significant cost savings.
What’s next for LUBCON?
Our focus clearly lies on the development of new sustainable lubricants, also known as eco-friendly or green lubricants. These lubricants are developed with a focus on reducing their carbon footprint, minimising waste generation and using more environmentally friendly ingredients. The goal is to provide effective lubrication while also promoting environmental responsibility and sustainability.
What are your hopes for the new regulatory bodies, such as Great British Railways?
Greasing of wheel flanges is widely accepted in the rail industry. We are currently
working in a joint group, to get the same acceptance level for top of rail treatments with friction modifiers. Therefore, the CENTR 15427 is currently being revised and hopefully approved in the near future. This would ensure, that more railway companies have the ability to test and implement such solutions in the future.
At the time being, any approval procedures using advanced technologies are immensely time consuming and therefore very costly for customers and suppliers.
In terms of technology, how do you anticipate things might change in the next five to ten years?
Besides heavy investments in infrastructure and rolling stock, we expect a much higher level of digitalisation and automation in the railway industry. There will be a more complex integration with various mobility services and an increased capacity demand. By following the new developments closely, we ensure that we are part of the process and can add value with our knowledge and key competencies.
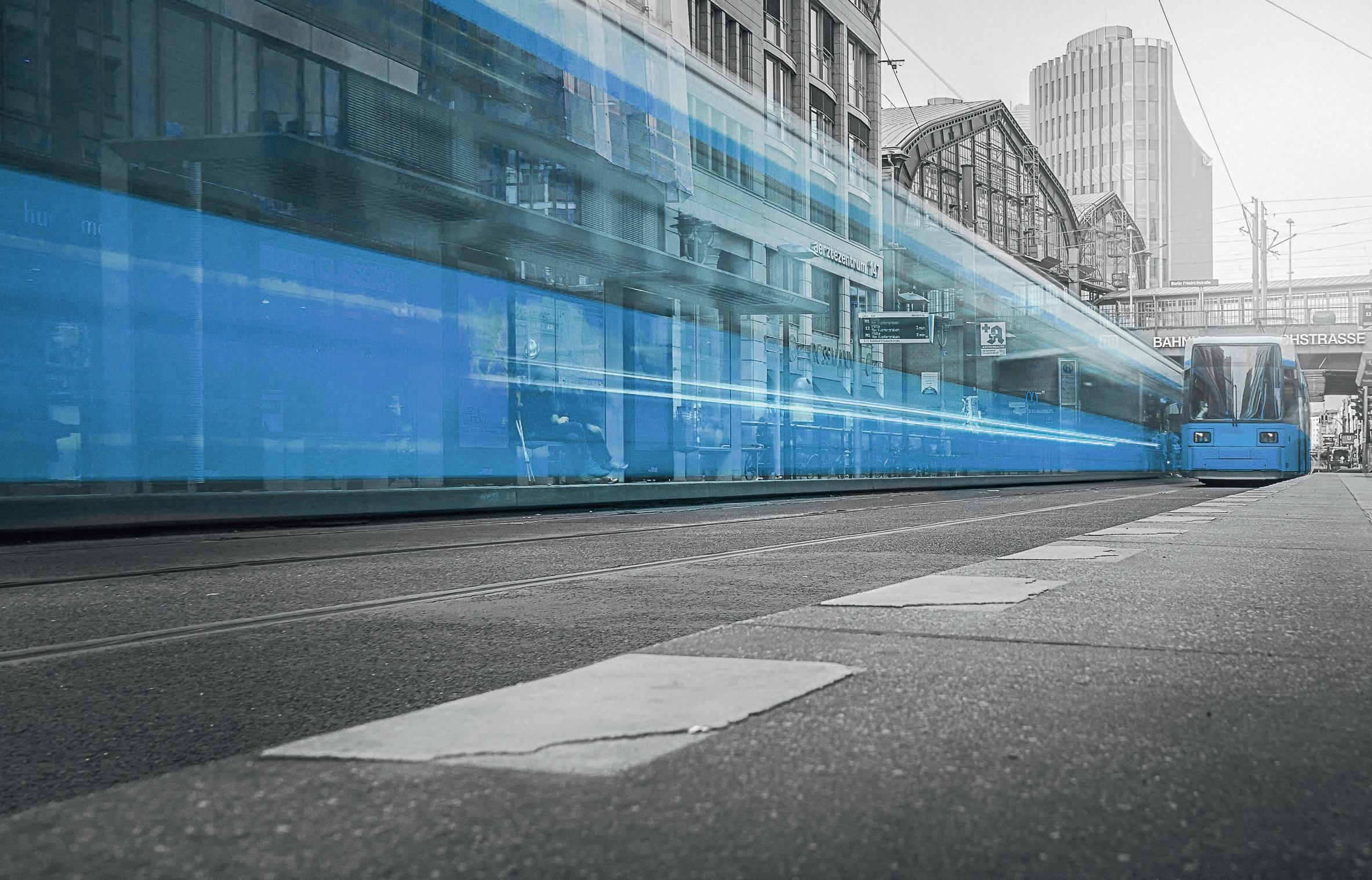

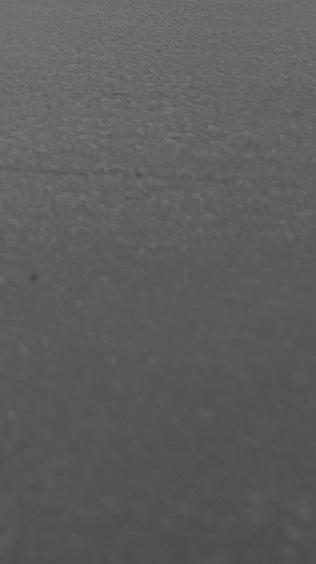

DAVE SPEAKMAN
ENGINEERING DIRECTOR
RAIL AND MD WENTWORTH HOUSE RAIL SYSTEMS AT KELTBRAY
Dave Speakman is an electrification engineer with over 34 years’ service in the rail industry. Dave has experience in design, construction, project and most recently engineering management roles prior to starting his dual role as MD of Wentworth House Rail Systems and engineering director for Keltbray Rail.
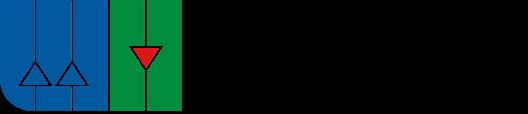
WENTWORTH HOUSE RAIL SYSTEMS
Wentworth House Rail Systems, a Keltbray Company, is a leading provider of Overhead Line Electrification (OLE) Design and Consultancy services.
Want to know more about Wentworth House Rail Systems?
Wentworth House Rail Systems Limited
Unit 2 Wellfield Business Park, Preston Brook, Runcorn, WA7 3AZ
Tel: 01270 448405
Email: enquiries@ railelectrification.com
Visit: www.railelectrification.com
LinkedIn: Wentworth House Rail Systems
How did you get started in the industry and when did you join the company?
I started in 1989 at age 16 as an apprentice Civil/Structural Draughtsman at Balfour Beatty TGD in Kirkby. I then joined the Keltbray/WHRS team in April 2022 but retained my role as CEM on TRU Project W1 until release in June following the successful completion of Entry into Service stage B.
What is your role within Keltbray/ Wentworth House Rail Systems?
I am the Engineering Director for Keltbray Rail and the MD for Wentworth House Rail Systems
Tell us about your career before you joined Keltbray/Wentworth House Rail Systems?
I am a civil engineer by profession with a 34year career within the railway electrification industry. I have worked on several high profile multi-disciplinary electrification projects in the UK and overseas for a wide range of clients.
I have been fortunate to have had many career/development opportunities within design, construction assurance, project management, construction management and more latterly engineering management prior to appointment in the dual role as Engineering Director for Keltbray Rail and MD for Wentworth House Rail Systems
What challenges have you faced in the industry?
The electrification industry has historically suffered through lack of continuity, investment and political indecision resulting in a cyclic ebb and flow for infrastructure investment. This creates uncertainty, ultimately deterring businesses from sustained staff development/investment.
Too often the downturn in work has resulted in key skills leaving the industry or emigrating in search of better/longer term opportunities outside of the UK.
What success have you experienced in the last twelve months and how do you measure success?
Prior to starting my current role, my biggest success in the last twelve months has been my role as CEM for Project W1 on the TRU Alliance.
More recently, I have established an engineering training programme within Keltbray Rail/WHRS providing guidance for apprentices, graduates, and existing engineering staff to upskill and achieve professional accreditation within the engineering council.
The true measure of success will be an established network/community of engineering staff within the business.
What does sustainability mean to you?
Investment. Not just money but time and development – if we get this right, we will provide a route for development/ progression of our existing staff and recruitment of more local talent that will ultimately leave a positive legacy to the rail industry.
How has technology developed since you started in the industry?
Immeasurably. I started work on drawing boards, I progressed to a state of the art ‘green screen’ CAD station, colour monitors followed with more advanced/progressive CAD and engineering packages.
My first memories of construction include setting out using ‘chainage and offset’ dimensions to position lineside assets prior to the adoption of a coordinatebased system.
Digitised design and construction now yield massive benefits/improvements in planning/assurance and reporting, through the HELIX system Keltbray provide RTI enabling remote visibility of progress/ issues and completion status. The real measure of success here is the speed in which information is available to both site operatives, the client and designer providing greater confidence in build quality/assurance and H&S file submissions.
The introduction of BIM and the CDE has introduced a heightened level of efficiency and control into the rail industry.
In 34 years I have seen incredible advancement in design/ construction and project management tools/equipment driven by constant improvement/ development of new technologies ultimately making the working environment more efficient, safer and driving economies.
How long has your company been in business and which sectors do you work in?
WHRS has been trading since 2012 and Keltbray Rail has been trading since 2009 and we cover Rail Electrification (Design and Construction).
What is your USP (Unique Selling Point)?
Keltbray Rail are an established electrification and civils construction business with an in-house design capability providing key benefits to potential clients. Early Contractor Involvement (ECI) of construction resource into the design arena helps drive efficiency in the design and planning process enabling a right first-time solution.
What types of products and services do you offer?
Keltbray’s specialist rail services delivery businesses are at the forefront of innovation
and best practice solutions in rail design, engineering, and operational delivery. The business has been involved in the construction of several of the UK’s most prominent and successful infrastructure projects.
Our direct-delivery philosophy in design, project management, engineering, construction and and rail plant supply allows us to control all aspects of a project delivery, minimising delivery risk and providing greater certainty for our clients.
Wentworth House Rail Systems (WHRS), has unrivalled expertise in existing and new build railway electrification design From commencement to completion on all infrastructure projects, we focus on our clients’ key performance drivers. Our practical experience and design-led philosophy are brought together to drive innovation, health, safety and wellbeing, time, and quality benefits from the very earliest engagement on a project.
How have the products and services you offer developed over the years?
The Keltbray Infrastructure group (of which Keltbray Rail is a part) has, through strategic acquisition, developed a multidisciplinary design and construction, Rail, capability in Power Distribution and Transmission, Highways and, heavy civils and renewable energy capability.
How passionate are you about sustainability in the rail sector, and how do you go about sourcing the materials for your products?
Sustainability is at the core of the Keltbray business model; we are one of the few companies within the construction industry with PAS 2080 accreditation. We support investment in renewable energy/ alternative sources and have, as a UK first, introduced hydrogen fuel cells on our M621 Highways site.
In 2023 Keltbray was awarded the Green World Awards, Building Construction: Sustainability Global Gold title in recognition of our innovation focus on alternative fuels.
We are aligning our business with the UN 17 Sustainability Goals.
What are some major projects you’re currently working on?
TRU (Transpennine Upgrade) Alliance and Cardiff Valley Lines are the two largest projects currently, but we are also active on several smaller rail schemes for NR and internationally in Canada.
What are some standout projects you’ve been involved in over the years?
I have fond memories of all the projects I have worked on but if I were to pick a couple of favorites if would have to be Hong
Kong as a young civil engineer – being part of a mega project and witnessing massive infrastructure development including the creation of a new airport on reclaimed land, LRT rail and road connectivity through cable stayed, suspension and fixed bridges, immersed tube and cut and cover tunnels, top-down construction of new combined skyscrapers/railway stations – all within a five-mile radius. Very exciting times and framed by the handover of the territory into Chinese stewardship, forming the SAR in 1997.
And then more recently, NWEP (Northwest Electrification Programme) Phase 2C, the electrification between Manchester Victoria station and Ordsall Lane Junction where I was part of an exceptional delivery team with an incredible work ethic and very strong focus on installation quality, we developed relationships with the client (NR) and interfacing contractors including the NR OCR team and Siemens Signaling.
Has the market grown since the company was established?
The market has grown however it is very cyclic – the agenda for greener transportation and megaprojects like HS2 have established the requirement for faster, greener reliable services to increase connectivity.
How can the industry tackle its skills shortage and how do you recruit/retain/ train your staff?
Investment in time/mentoring and training – no real secret. The rail industry needs better promotion at schools/colleges and careers fairs – we need to attract more talent. Fundamentally the rail industry can offer job security and development so should be an attractive path for school leavers/ graduates.
Keltbray and WHRS are keen to get the right candidates, we have an early careers team and have established a training programme that offers support and guidance for the route into the engineering council accreditation.
What do you think is the biggest challenge currently facing the rail industry?
Skills. When the work starts in earnest we will have a skills shortage – the lack of continuity in the electrification industry has driven a feast or famine culture – this inevitably leads to a skills shortage. The work has to come if we are to make that modal shift to greener energy.
What are your hopes for Great British Railways?
Consistency in approach and continuity of work, we need to see a rolling programme
of electrification and less of the stop/start mentality – if we are serious about being carbon neutral by 2050 there is lots to do! We need to reduce design timelines through a combination of MVP and reduced/ streamlined assurance timeframes – well defined requirements and local agreement with asset owners are at the heart of this.
How can we make the rail industry a place people want to work in?
The rail industry needs a stronger focus on staff training and development with a defined career path for progression. We need to get people more engaged with the Engineering Council and raise the profile of the railway to encourage more interest.
How do you make your business a good place to work?
Investment in people – whether through upskilling, training or development it is key to a sustained and engaged workforce. Keltbray and WHRS are investing heavily in engineering training for apprentices, graduates, new starters, and existing experienced staff.
What do you expect to be the biggest challenges that come from this transformation of the railway industry?
Structure and coherence – any fledging/ newly transformed business needs time to settle – this is seldom afforded in the rail industry, the media spotlight will focus on delivery through design to cost and control of CAPEX – both elements have proven difficult to manage during the last two NR control periods, this trend will continue unless we, as an industry, adapt and do things differently through competence/ innovation and experience.
Have you changed your approach to work at all since Covid?
We are more agile than pre-Covid. Where possible, we have adopted flexibility into our working patterns with a blend of remote, project and office working – it is, however, key to the development of the junior staff to ensure that there are senior staff on hand to provide guidance/advice.
In terms of technology, how do you anticipate things might change in the next five to ten years?
AI is undoubtedly going to become a factor in the design environment – this seems inevitable, we need to learn how best to harness its potential for the betterment of projects and the greater railway.
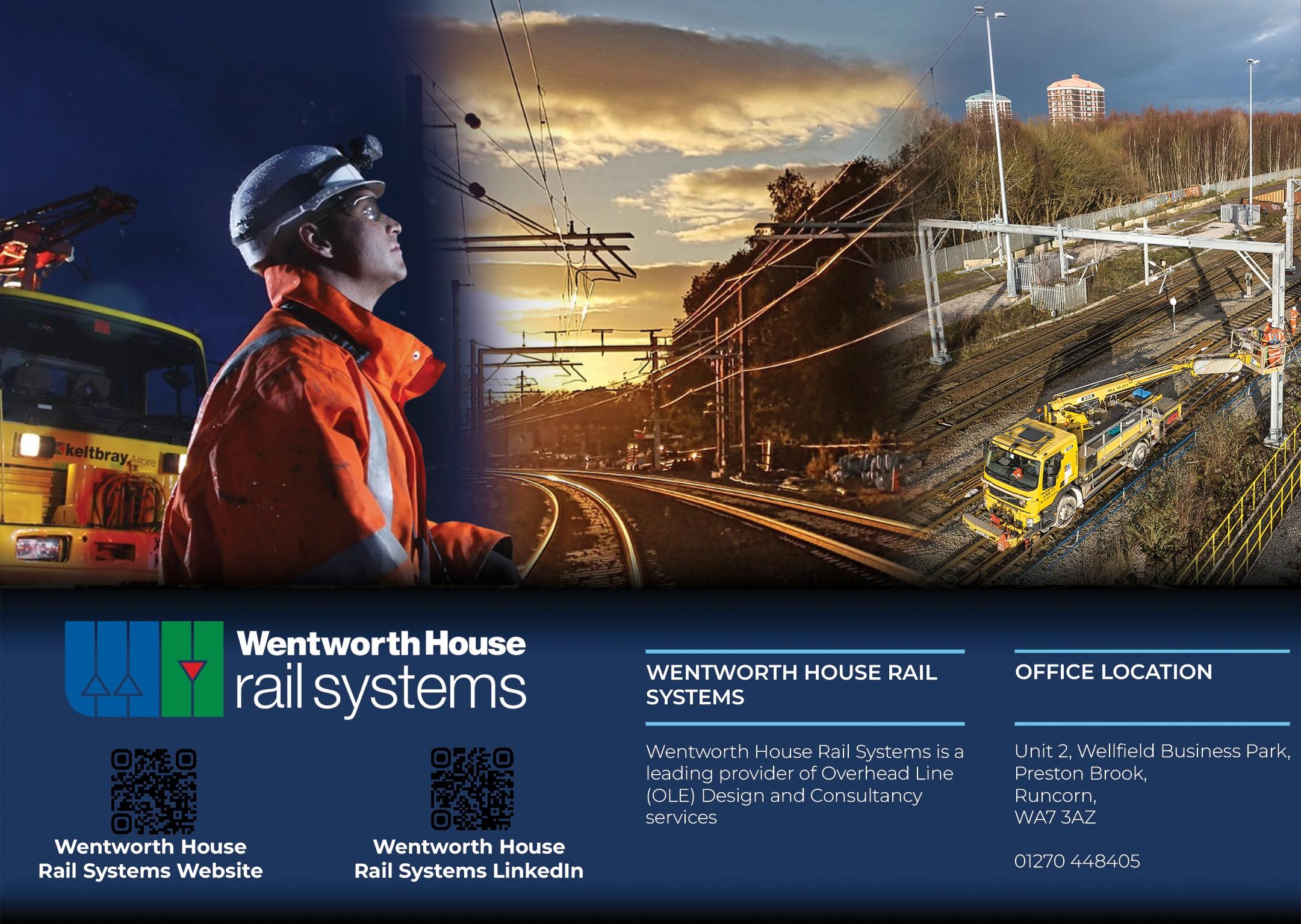
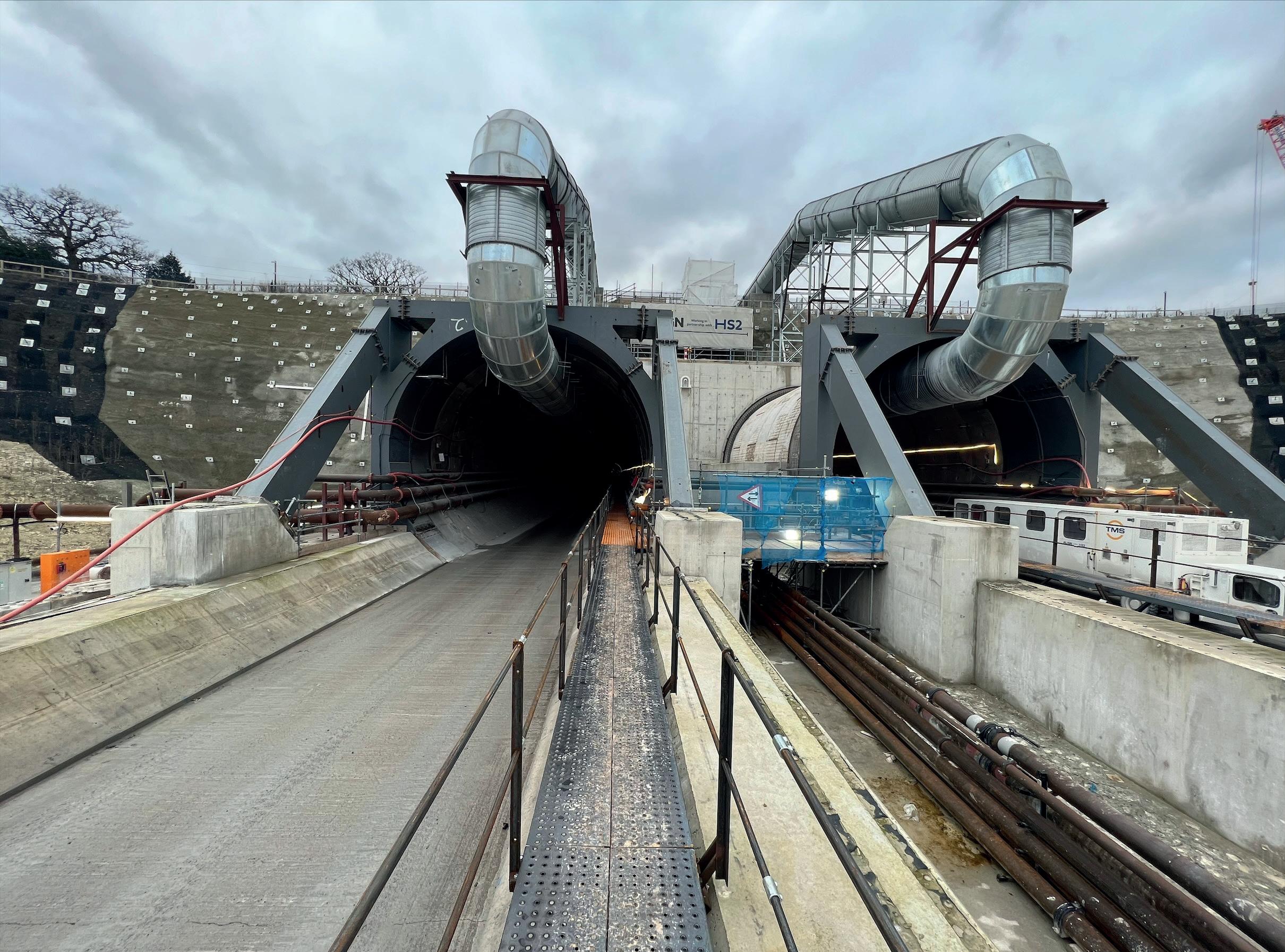
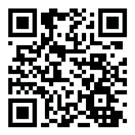
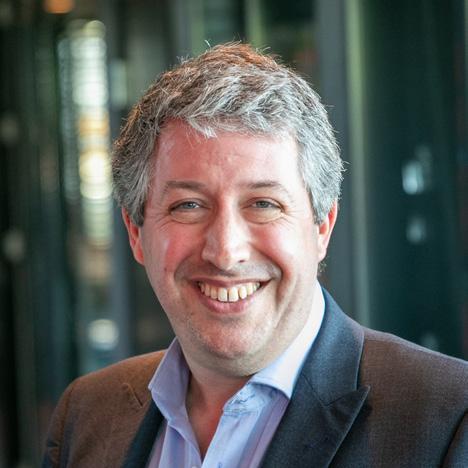
Jonathan Hassell is CEO at Hassell Inclusion
Digital Accessibility
From websites to ticket machines, Jonathan Hassell, CEO at Hassell Inclusion explains why it’s time for the rail industry to focus on digital accessibility
In July this year, it was confirmed by the Rail Delivery Group (RDG) that plans to close hundreds of ticket offices across the UK would go ahead over the next three years. Although this has been badged as an initiative to cut costs, the RDG also said that this was in response to the significant shift to online purchases, stating that just twelve per cent of tickets are now bought at inperson offices.
However, while this may seem like a relatively small number, in a subsequent debate in the House of Lords, Baroness Randerson said that: ‘In the past year there were 1.4 billion separate rail journeys, so 168 million tickets were bought in ticket offices. Passengers who use ticket offices will be inconvenienced and deterred by the closure of those offices. That will hit elderly, disabled and poorer people most of all.’
While, rightly, the majority of the focus has been on what this could mean for these groups while they are physically at a station, it also raises the wider issue of digital accessibility and whether online products including websites and apps, as well as instation ticket machines, adequately cater for those with physical and cognitive conditions.
That is not to say that using new technologies to modernise the UK’s railways is a bad thing. Digital transformation can be an overwhelming force for good, very often leading to an improved customer experience.
However, for those who find navigating the digital and online worlds challenging, it is more important than ever that the RDG, station and train operating companies (TOCs) take digital accessibility seriously.
Addressing digital accessibility
This is not a new issue. In July 2022, a review from the Office of Rail and Road (ORR) looked at the accessibility of 24 TOC websites to track the progress made
following a similar review in 2020. The ORR’s Accessible Travel Policy (ATP) states that TOCs must commit to working towards the Web Content Accessibility Guidelines (WCAG2.1 – AA level) and must also highlight the accessibility of their website, providing information on how the website will work with assistive technology.
The ATP also identifies 18 requirements for the provision of accessibility information online. Of the websites audited, six met all the obligations. While this was an improvement on 2020, where no website met these obligations, there are clearly still accessibility gaps to be addressed.
As the lead author of the International Standard on Digital Accessibility Maturity, ISO 30071-1, too often I see that digital accessibility is an afterthought that requires a product (a website, app or ticket machine) to be retro-fixed, when it would have been much more effective if it was embedded as a value right from the beginning of the design process.
In fact, Hassell Inclusion’s recent report, An Immature Response? Why organisations are failing to build digitally accessible product and services, shows that there are often major accessibility gaps throughout the process of designing digital products. Over a third (35 per cent) of organisations involved in the research said they would launch digital products with known accessibility issues, while just 14 per cent check that digital products created for them by external suppliers meet accessibility requirements.
So, how can TOCs and the RDG make sure their digital services and tools are available to all?
Adopt a strategic approach
Being great at digital accessibility requires a strategic approach to ensure that accessibility is ‘baked in’ to your processes
so it is not seen as a tactical add-on. Otherwise, you will always find yourselves having to retro-fix elements of your services that don’t meet accessibility requirements, which is inefficient.
Focus on user experience across all digital channels
Digital accessibility can mean different things for different people across multiple user touchpoints in user journeys. When looking at the rail sector, consumers may need to navigate websites, emails and apps, as well as social media messaging and instation ticket machines and barriers. All these things need to be accessible to ensure a smooth end-to-end user experience.
Define responsibility and get senior buy in
It is important to have a champion for accessibility at a senior level. Having a digital accessibility programme manager who can lead a project team to own, run and report progress against your strategic plans is essential. You should ensure your plan includes adequate training, and embedding of accessibility in your policies and processes, and their communication, to embed digital accessibility into your organisation’s DNA.
Require
accessibility from suppliers and partners as well as internal teams
Great accessibility is only possible if the whole organisation is aware of it and actively ensures it is part of the design and creation of any digital product or communication. Key to this will be taking your wider supply chain – your external digital suppliers and partners – on this journey with you, by ensuring digital accessibility is a key part of procurement processes and contracts.
Design for accessibility throughout your development process
Our analysis shows that there is often an ad-hoc approach to accessibility in the development of digital products. Rail sector leaders need to ensure it is embedded throughout the development process of all products, from websites to apps to social media and PDFs, and that their accessibility is regularly monitored, checked and fixed after launch. In short, make things inclusive by design, across each product’s lifecycle.
Towards a more digitally inclusive future
By undertaking regular audits, the ORR clearly takes digital accessibility seriously. But this has to be followed with tangible, coordinated action from the TOCs and the RDG to ensure all customers have a positive user experience. That isn’t the case right now and, as the rail sector moves towards becoming increasingly reliant on digital channels, both online and at the stations themselves, there is a real danger that this will exacerbate digital inequalities, particularly for disabled, elderly and other customers with additional needs.
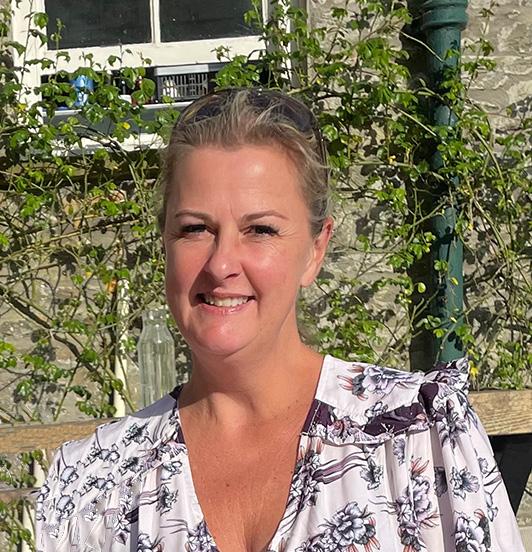
SARAH KAY HIGH PERFORMANCE TEXTILES – BUSINESS DEVELOPMENT MANAGER AT TBA PROTECTIVE TECHNOLOGIES LTD
Sarah Kay, Business Development Manager at TBA Protective Technologies Ltd., has 25 years experience developing specialist fire-resistant textiles for customers in the rail industry, working with many clients to develop bespoke solutions for use in seating and beyond.
How did you get started in the industry?
Having completed a BSc (hons) in Textile Technology, I joined TBA Protective Technologies in 1998. This role was within the High Performance Textiles division and focused very much on specialist product development, building a range of very specialist high temperature resistant materials. Since those early years my work and the company business has been intrinsically linked to the wider rail sector, especially within seating manufacture.
What is your role within TBA?
I endeavour to make best use of my 27 years’ experience in specialist thermal, heat and flame textiles to engineer the ideal bespoke solutions for our customers. Working with rail seating manufacturers, this is invariably a really collaborative process. There are always project specific elements and I am able to utilise all the in-house expertise we have to get the perfect fit. We literally manufacture from yarn all the way through to textile and fabricated products, and also have several other specialist textile businesses within the Group who are all connected by specialisms in high thermal performance – so we really have the biggest toolbox you could wish for. It’s my role to genuinely understand what our rail customers need and get the best outcome using the considerable expertise and clever manufacturing plant we have.

TBA PROTECTIVE TECHNOLOGIES LTD
TBA Protective Technologies Ltd is a specialist manufacturer of high performance textiles for use in critical fire, thermal and protective applications, based in Rochdale.
Want to know more about
TBA Protective Technologies Ltd
Tel: 07710 232618
Email: skay@tba-pt.com
How do you measure success?
Obviously in my role it’s ultimately sales, but really for us it’s when we can get a client to lean hard on our expertise and we deliver them something really unique – they get their perfect production materials, we get a valued relationship.
How long has you Company been in business?
A very long time actually! TBA has its roots in the Lancashire weaving industry going back over 150 years now. Obviously, it’s a very different business now with some very different production equipment, but we really value our history and while we have never added it up, the collective years of employee experience we can apply to developing our specialist high performance, high temperature materials must be quite staggering. We cherish that and hopefully our customers benefit too.
What sectors do you work in?
Our TBA HPT fabrics are used widely within rail seating to provide both flame and cut resistance, while another part of our business, FIREFLY®, manufactures flexible fire barriers used within the built environment and increasingly used in many station refurbishments across the UK. Different materials but the same offer really – a manufacturer with really specialist knowledge to provide fire-resistant materials to improve the safety of passengers
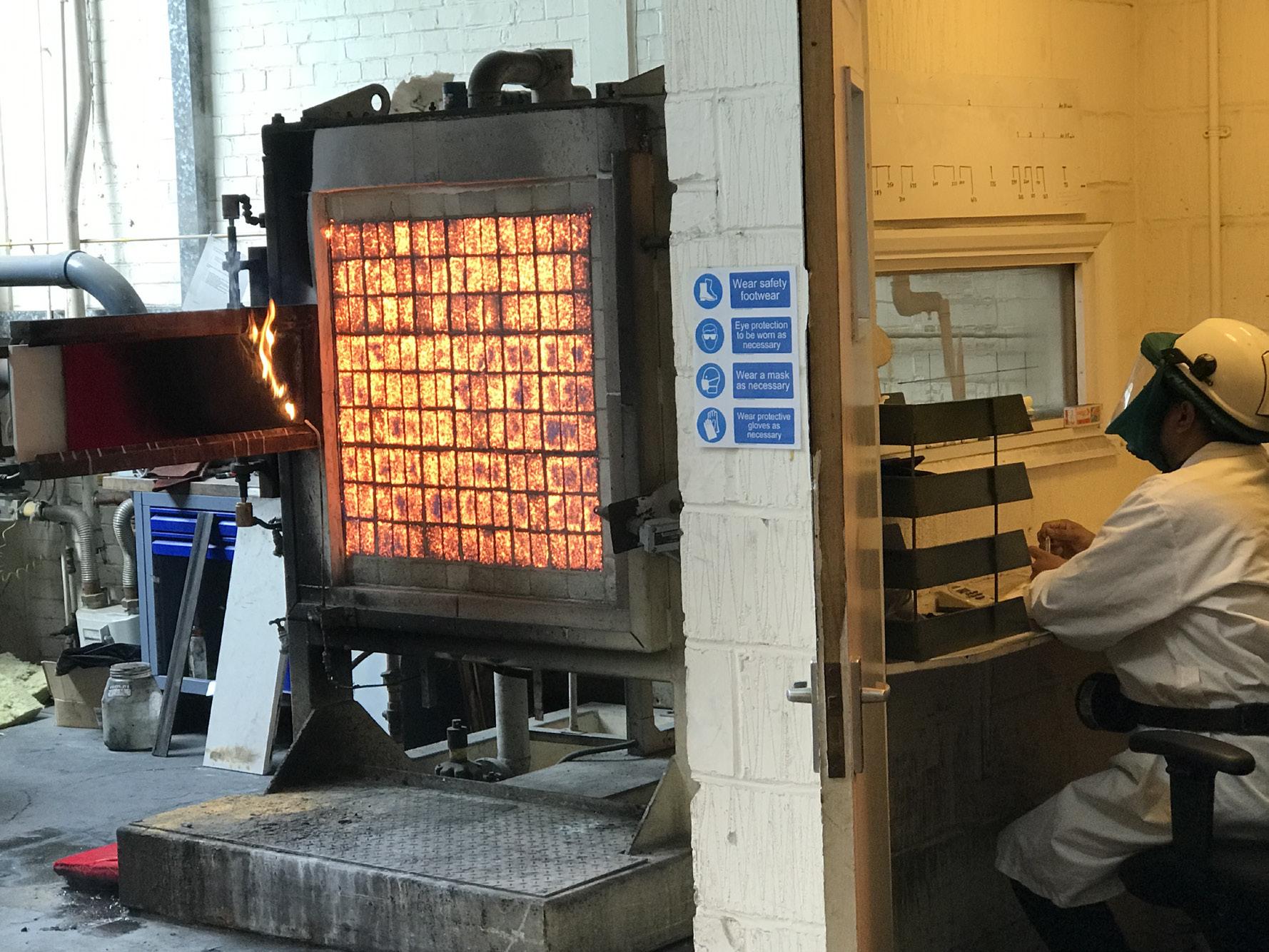
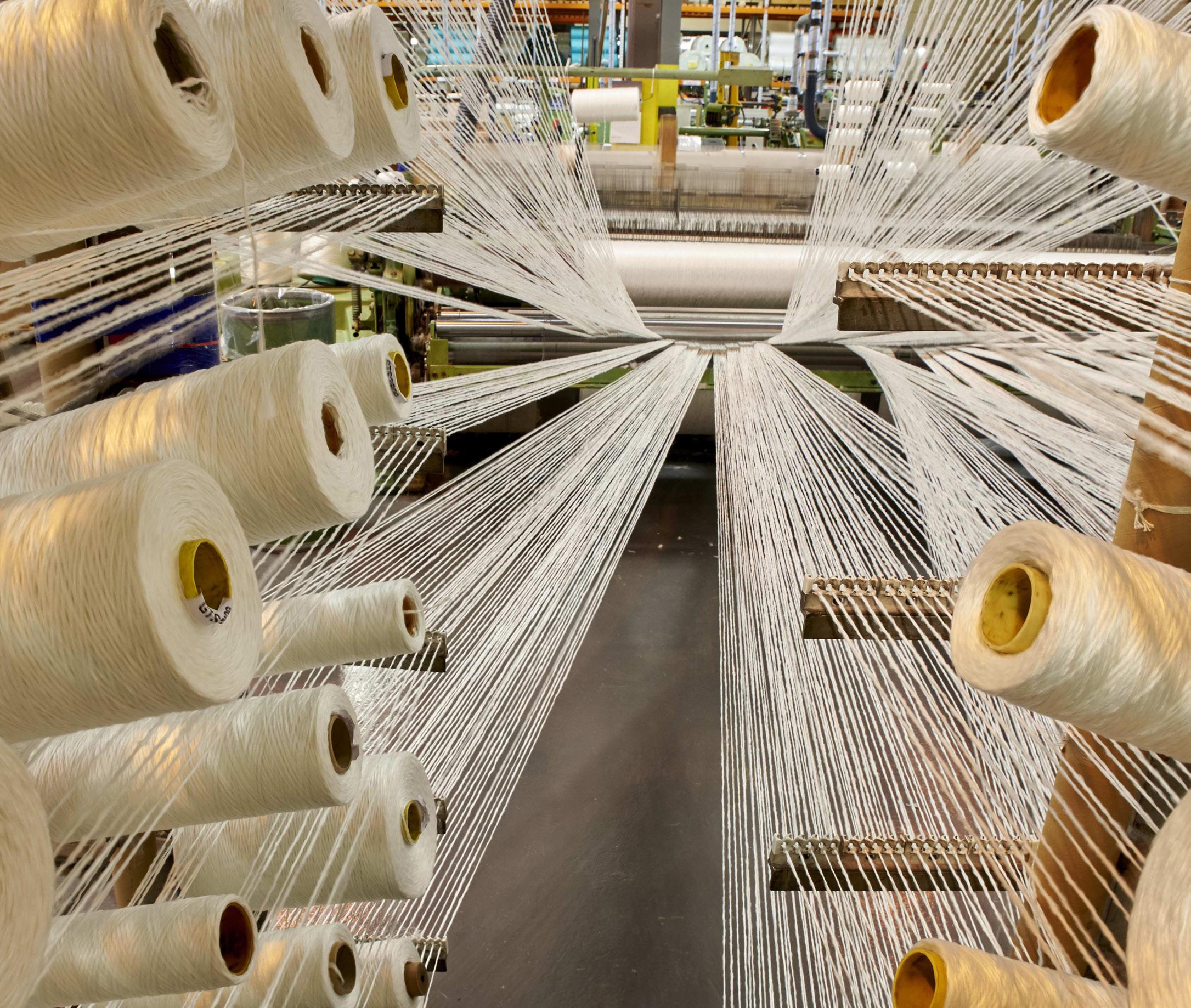
What is your USP?
I think we’d say that is the easiest question for us to answer – it’s our genuine expertise and vast experience. Manufacturing textiles and materials with fire and safety critical applications is a serious business and we treat it as such. The knowledge we have gained over the years is immense – our ambition is to get customers to utilise that! And I’d also say we remain nimble; we develop and manufacture in the UK and we are geared up to run lots of bespoke developments, not just generic products.
What are some of the biggest challenges faced?
Compliance and meeting safety standards – both on train and in station – becomes ever more demanding and complex. We manufacture textiles which are typically a component of a solution, albeit often the vital component in delivering fire safety. But
we need to understand the bigger picture the customer sees. We deal with rail customers in around 30 countries, often meeting different standards, so it is hard work to keep abreast of all these – but we recognise this collaborative approach to external challenges is where we can add our best value.
Currently of course, there is a lot of focus on EN45545 and ensuring we support our customers to ensure their seating meets the fire performance requirements of this standard. Increasingly this also means meeting the EN16989 cut/vandal resistant standards to retain the fire safety integrity of the seat. But again, that is our world, these are the specialist materials we process every day.
What type of products do you offer?
Whether seating inserts or fire barriers used within stations, all our products have a textile foundation to them, made using woven and nonwoven materials; from glass
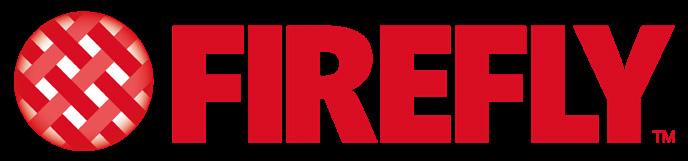
based products, inherently fire-resistant fibres, aluminium foils and specialist fibres like Kevlar® and other aramid fibres. So they are flexible and light but employing some pretty high-tech materials in a well proven production process. Our FIREFLY® barriers can offer up to a two-hour fire rating in buildings and obviously our seating insert layers maintain their performance properties for life.
What projects are you currently involved in?
TBA is constantly dealing with rail seating manufacturers, flying the flag for specialist British textile manufacturing across the globe. Our seating materials have been used in rail projects from Kuala Lumpur airport
TBA manufacture from yarn to fabricated finished products.
‘Our seating materials have been used in rail projects from Kuala Lumpur airport to TransPennine Express and from Indian Railways to the new Norske Tog Norwegian train fleet.’
to TransPennine Express and from Indian Railways to the new Norske Tog Norwegian train fleet. In the UK our FIREFLY® fire barriers have been used in various stations. A particular area we are seeing real growth is in many UK station refurbishments, especially the large glass roofs, where our fire barriers are used to provide worker protection from fire risk below – so the work can safely carry on above while the trains and stations continue to operate below.
What are your views on collaborative working?
Simple – we couldn’t operate without it. We know enormous amounts about textile manufacture and fire resistance but rely on our customers to inform us about the rolling stock or infrastructure needs. When it comes to fire safety, co-dependent, trustful relationships are the best place to be.
What makes your business a good place to work?
For me it’s just perpetual variety and challenge. So many of our orders are built on a specially developed solution – that’s what I trained to do and its what we do best. Never gets boring!
What are your future plans for the business?
Spreading the word - lean hard on the expertise of the supply chain! With EN45545 for example, we know we have tested solutions that can ensure our seating customers meet all elements of this standard and we see a future where fire safety compliance in all applications is sacrosanct
TBA has its roots in the Lancashire weaving industry going back over 150 years.
as it should be, but also demonstrable, tested and verifiable – we strongly believe we are well placed to deliver on this challenge. Our FIREFLY® fire barriers in the built environment are in a similar position – the ability to provide the technical support to work through the most intricate details at one level and have comprehensive independent certification of fire performance in all applications at the other is the clear direction of travel of the market. Again, it comes down to us as a manufacturer adding value – the product is only half of it, the expertise and collaboration count just as much and increasingly will do so.
Oh, and our fire barriers are being used in the seats of Hydroflex – the UK’s first hydrogen-ready passenger train showcased to the world at the COP26 climate summit –exciting times!
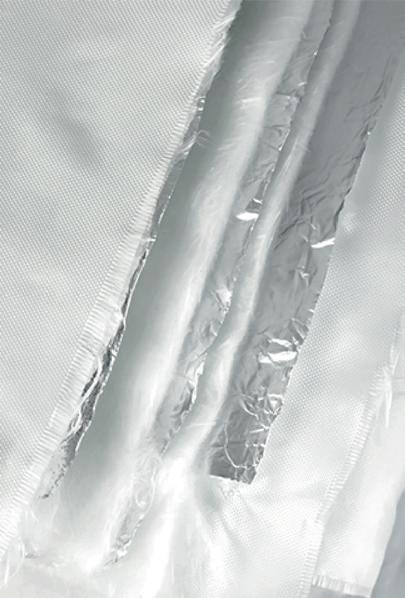
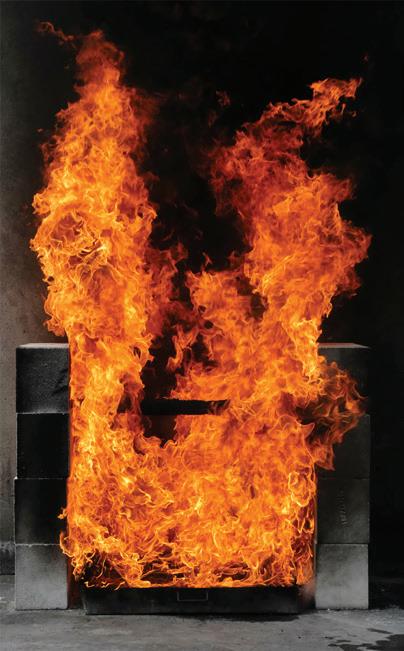
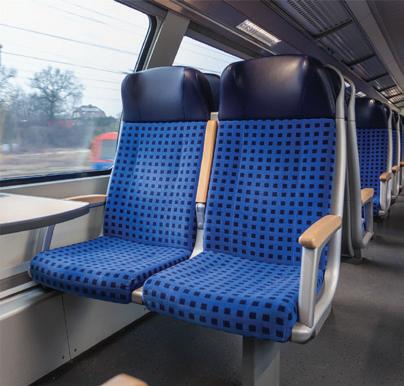
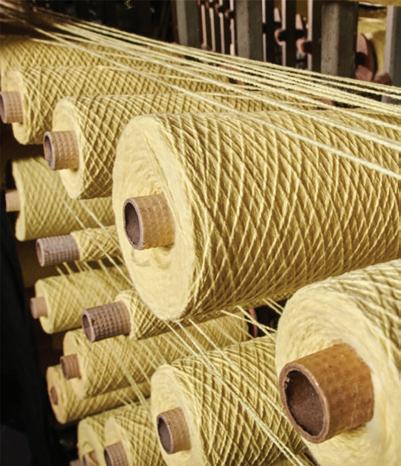






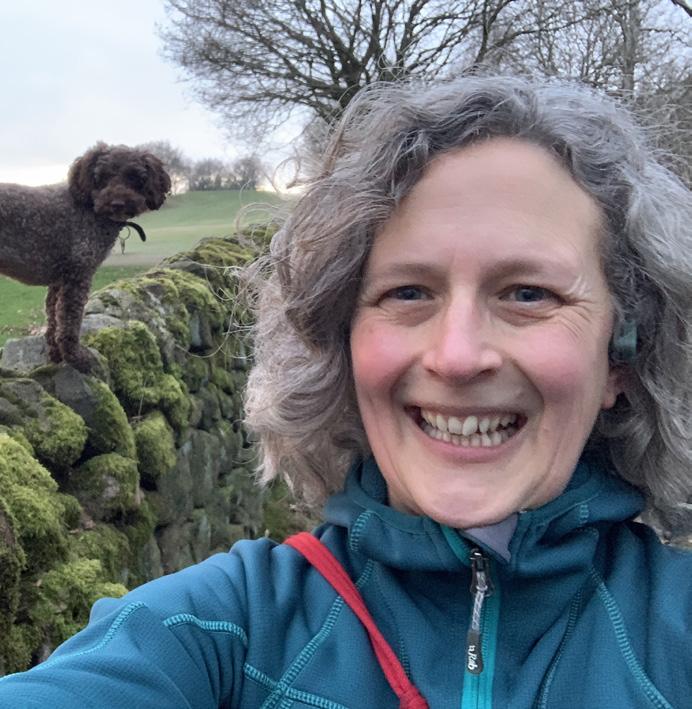
WENDY MCCRISTAL MANAGING DIRECTOR OF THE MENTAL WEALTH COMPANY
Wendy has 25 years’ experience across a variety of rail environments from specification and engineering through to incident investigation and assurance. After recovering from burnout in 2018, she founded The Mental Wealth Company and works with organisations to support their staff to thrive at work through their consultancy, training and coaching services.
What is your role within the company and what was the inspiration behind starting The Mental Wealth Company?
Back in 2018 I found myself in a ‘midlife crisis’. I was working as a senior manager in a large rail engineering consultancy, a mother to two amazing but demanding kids and my husband and I had bought a house to renovate. Although I generally thought I was looking after myself, the various stressors on me at that time caused my body and brain to pack up and I found myself chronically tired, unable to think and on a daily emotional rollercoaster. I was desperate to feel better and although my doctor signed me off work to recover, I needed to address the root causes that had led me to having too much to do, being pulled in multiple directions and really not enjoying my life much at all.
Luckily, I found a fantastic organisation, One of many® who helped me get my life back on track, and helped me develop the life skills I needed. At the time I thought ‘Why has nobody told me this before?’ Those new skills really did change my life, how I viewed the world, how I reacted to the world around me and importantly how I treated myself. I started the journey to become an accredited coach and trainer for One of many® and I decided that I wanted to bring these tools into the rail organisations I used to work with. Much as though my manager had really wanted to help me, they, nor the organisation knew how to really support me to get better. I realised there were many organisations that didn’t have the right knowledge to help people not only to recover from physical and mental ill health but more importantly to keep well at work in the first place.
THE MENTAL WEALTH COMPANY
The Mental Wealth Company help businesses raise awareness of the impact of poor wellbeing and help individuals, teams and organisations to integrate better wellbeing practices into what they do on a daily basis.
Want to know more about The Mental Wealth Company?
Tel: 07305 843993
Email: wendy@ thementalwealthcompany.co.uk Visit: www. thementalwealthcompany.co.uk
From being a line manager for many years, I already knew that the policies and processes that we had just weren’t serving us and we needed to understand the problem statement a little bit better. My lived experience of being the ill employee…the way I felt, the way my brain was at the time had given me a real insight into how we can improve things.
Whilst I was off, I had talked to many people in confidence who had had similar experiences in their lives and I was inspired to start The Mental Wealth Company to help organisations to understand how to support people to keep well at work. It made me mad and sad too that although we were brilliant at contributing to the UK rail network, we were also very good at breaking people in the process…BUT it’s not all the fault of the organisations we work for – our cultural paradigm also has an influence –the decisions we make as a result of the expectations of society, our families and our communities all play a part in the jigsaw puzzle that we need to solve.
I founded The Mental Wealth Company in 2019 – and we started by raising awareness in our Mental Wealth Café events (in collaboration with RSSB, Porterbrook and Rail Forum amongst others) about
wellbeing issues and how they can manifest for individuals, the incumbent cost to organisations and importantly, how we could address and challenge the status quo – I now manage a team of wellbeing facilitators who work in several industries including rail.
What challenges have you faced in the industry?
When we first set up, wellbeing was much less talked about and it wasn’t yet a topic that we were good at talking about at work, let alone in our families and communities. The stigma of mental ill health was so bad within some companies I talked to that I was actively discouraged from disclosing my experiences publicly. Some rejected completely the notion that their organisations could be in any way be responsible or indeed have employees who weren’t anything but OK – surprising when the statistics tell us that 1/6 of us will experience a common mental health problem such as anxiety or depression in any given week (Mind, 2017).
When Covid-19 hit everything changed. At the time we were a start-up and whilst we had had some success with informed organisations delivering Mental Health and Resilience Training to their employees, we were soon busy with requests from organisations big and small struggling with a range of wellbeing challenges. We ran a series of Mental Wealth Café webinars through lockdown for many including Rail Forum, Network Rail and Atkins, addressing issues from loneliness and keeping in touch with your team to managing overwhelm and setting healthy work/life boundaries. Lockdown had completely levelled the field and threw everyone a huge raft of new wellbeing challenges. Employees, HR and directors alike needed to understand the new range of wellbeing challenges upon them in order to keep their organisation operating effectively.
What are some major projects you’re currently working on?
In 2022, we expanded the team to five and are currently delivering a twelve-month resilience programme designed specifically for the Supply Chain Operations team at Network Rail (the team that operate ontrack machines and plant). We're about halfway through that programme and so far, has been incredibly successful in helping the team to develop positive, sustainable wellbeing habits.
We have also been supporting MTR Elizabeth Line to expand their network of peer-to-peer support within the operational community – by the end of 2023 we will have trained 85 more Mental Health First Aiders within front line, management, and office-based staff. This is part of a bigger strategic piece of work to develop and embed non-technical skills within their competency

management system, which is helping to sustain safe behaviours in the operational environment.
We’ve also supported 28 Practice Managers within the Atkins Transportation Engineering business. Between them they look after over a thousand employees and deliver some significant and challenging projects. We took them through a two-day deep dive into some of the core wellbeing challenges that they deal with on a daily basis – including how to keep themselves well and supporting remote staff. Every single delegate left with a clear, tangible action to support them in their role.
When a client comes to you with a particular problem, what’s your process for coming up with a solution and how closely do you work with clients throughout the project?
Every organisation and every person we work with is different. Whilst we have a core offering, we are essentially seeking impact and we adjust our approach to suit. Many of our clients work shifts and are under delivery pressure – creating plans that fit into their working day and can be delivered without creating another workload issue is critical. We spend time listening at the start of the project, and helping the client to engage at the right level and at the right pace for the people we are aiming to support.
Many organisations want to do something about improving well-being but don't know where to start. One of the first things that we do is identify what they're doing well already – for instance many have comprehensive but underused Employee Assistance Programmes (EAPs) – sometimes it's simply a case of helping them to work out why they aren’t being used. Some people we work with just need some simple guidance on how to talk to someone who is mentally unwell – it’s really common to feel out of your depth or be scared that you could make the situation worse. We help people to
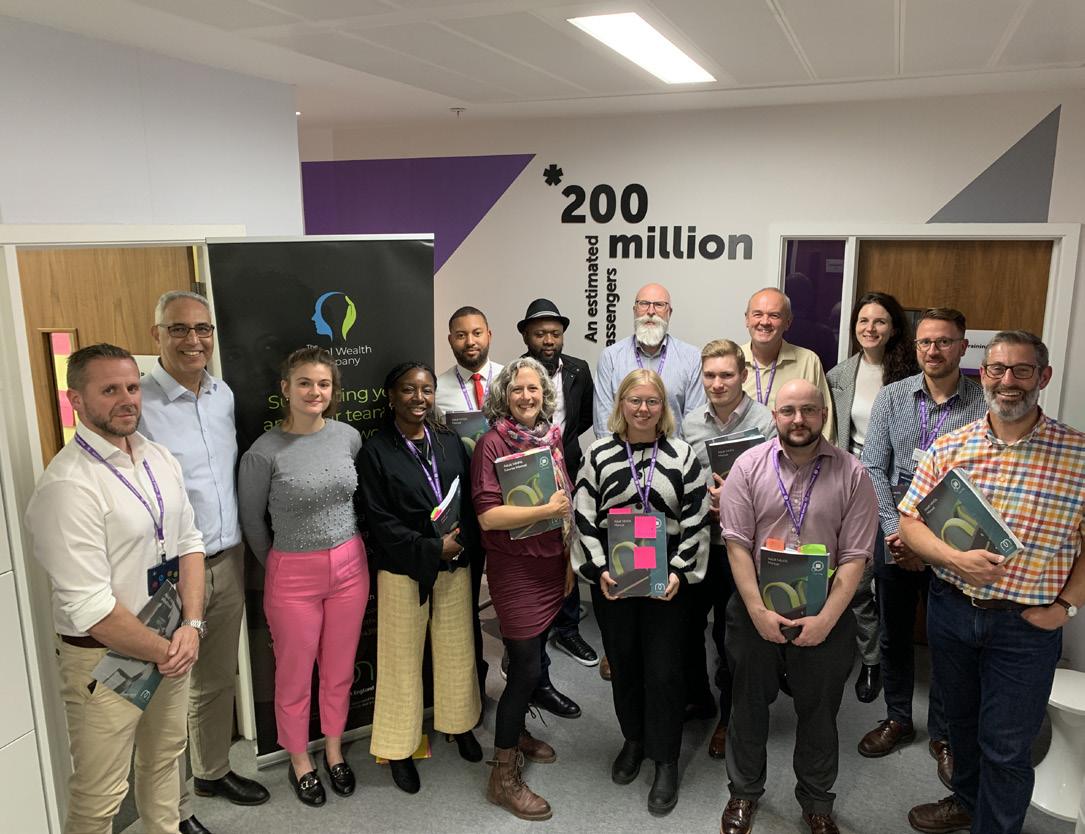
increase their confidence to start meaningful conversations that will help improve the situation.
Key to our success is our ability to initiate discussions within the senior leadership team about the role of well-being and its impact on the bottom line. Whilst significant financial returns are possible, senior teams can quickly become stuck on the practical next steps to improve things – a simple audit of the key areas of the company can be a helpful first step in building a sustainable wellbeing plan. We often get asked for training – and whilst this can be an important part of the solution, core organisational understanding and leadership is required to really drive wellbeing initiatives, so we also offer consultancy, training and executive coaching, to help business leaders to navigate this element.
Allie Moors – Principal Trainer & Coach
What makes The Mental Wealth Company a good place to work?
The team of course - the team! There's a wealth of knowledge and shared core values of openness, non-judgement, willingness to listen and learn and more than anything a shared enthusiasm to make what we do at The Mental Wealth Company creative, participative and impactful. Seeing people take on board the tools that enhance wellbeing and getting feedback on the way that this has helped them - both in small ways that make day-to-day life easier and bigger transformations is incredibly rewarding.
What is your USP?
I have a background in rail so understand some of the challenges from the industry, I also have a degree in Psychology, coaching qualifications, and a natural fascination with the way our brains are hard-wired to both help us be efficient, but also lead us astray. I guess what makes me different to others is a willingness to make a bold leap of
faith. In 2018 I packed some cycle panniers with camping gear and took off with my partner on our tandem and cycle explored our way across four continents for a year. I discovered so much about the world, made friends in unexpected places and learned many lessons about myself.
What are the standout projects you've been involved in over the years?
My most recent challenge has been as a member of the Human Factors team with Siemens Mobility, enabling the fitment of ETCS to the UK freight fleet. It’s a huge project as many different classes of vehicles are being fitted, all presenting variations and challenges and involves many stakeholders that have different perspectives. This gives me the first-hand knowledge of the pressures and frustrations of large rail projects, but also the difference it makes to bring well-being tools and practices into the workplace. Working in a technical rail environment is also helpful when delivering our wellbeing work as it helps me to find relevant language, stories and analogies to help our clients to understand and adopt the wellbeing strategies that we use.
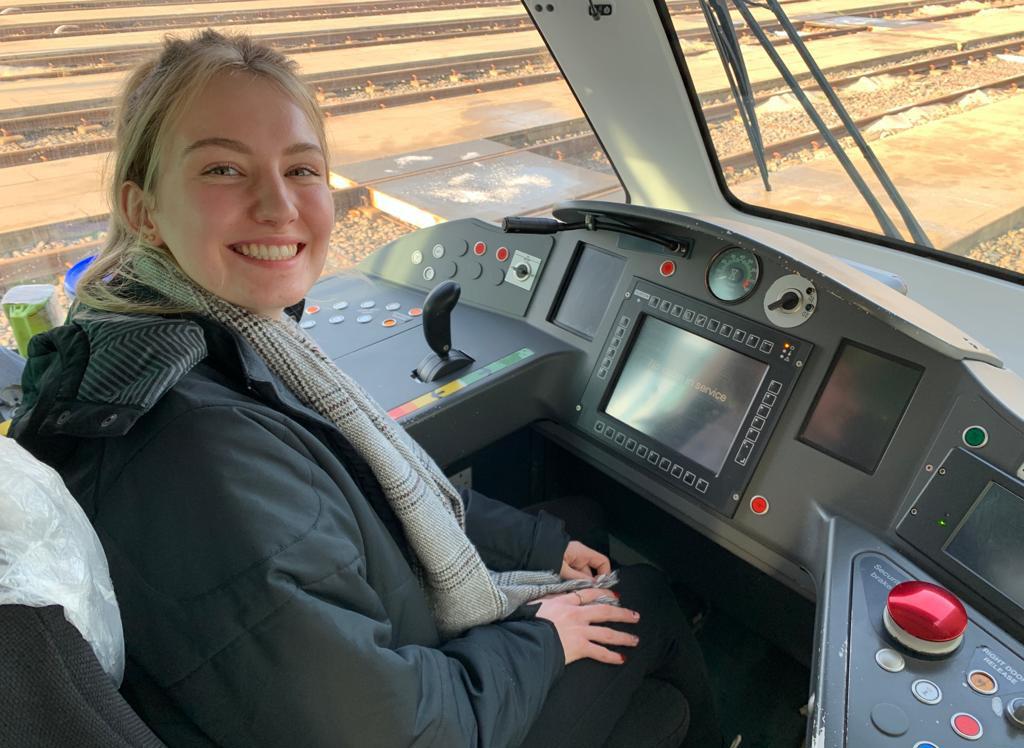
Emily Skinder – Consultant Occupational Psychologist
Tell us about your work within The Mental Wealth Company.
I work along Wendy, Allie and Andy to design and create wellbeing training
Supporting you to help your staff thrive at work
Want to improve employee wellbeing but don’t know where to start? Every organisation we work with is unique ... we work with you to tailor effective and practical wellbeing solutions that you can implement today.
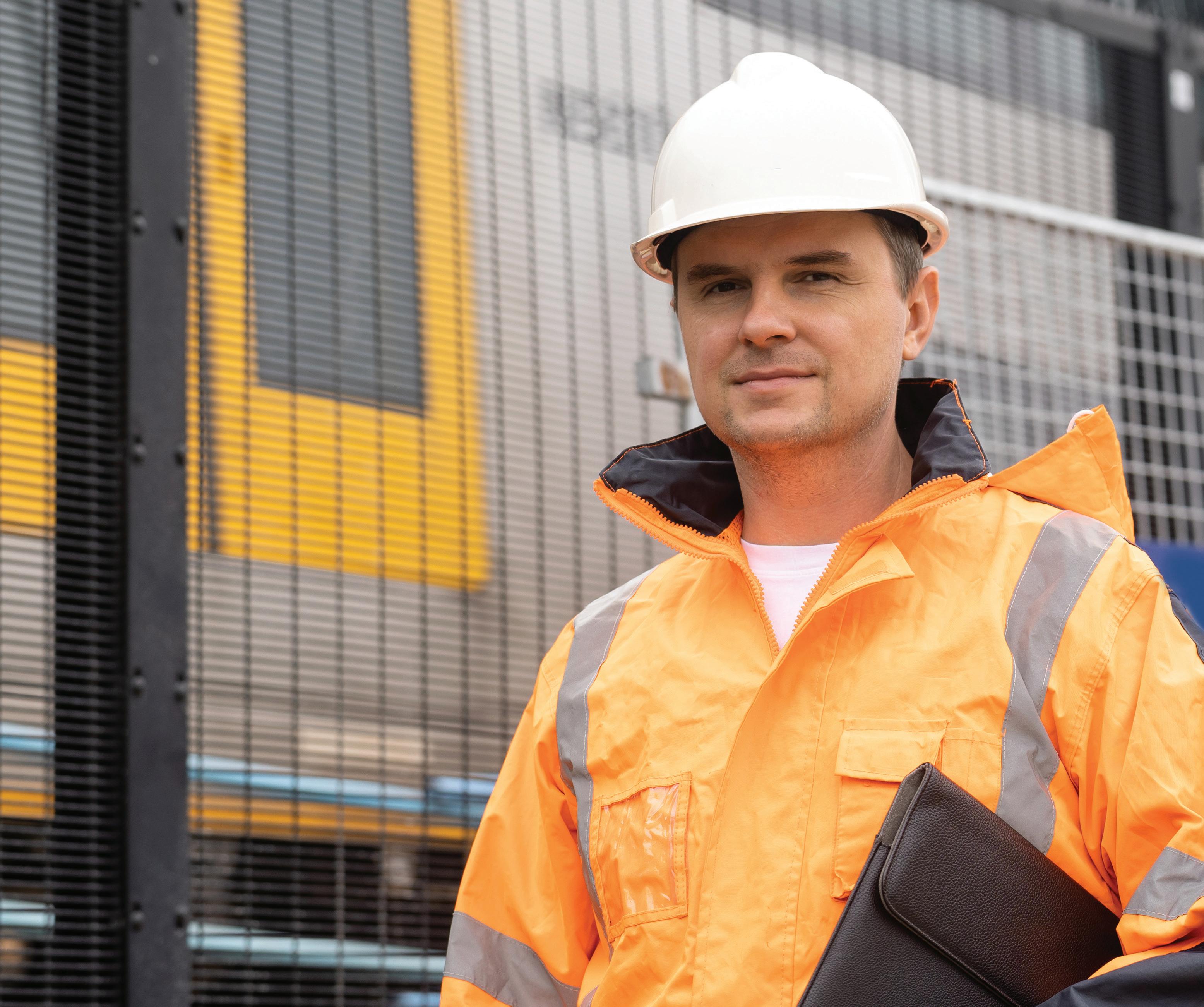
Business Partner Services
» Strategic wellbeing planning
» Practical support and advice
» Corporate event facilitation and speaking
» Lunch ’n’ Learn events
Training
» Mental Health First Aid
» Resilience and wellbeing programmes
» Non-technical skills for safety critical workers
» Train the trainer
Coaching
» Leadership teams
» Operational and project teams
» Individual wellbeing, life and executive coaching
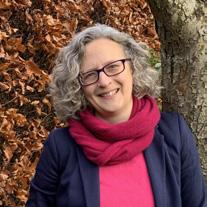
“The resilience training course has helped me focus on my priorities, and on how to better manage work-life balance. Well recommended.”
Phil Court, Certification Director, AEGIS Certification Services Ltd.
programmes tailored for our clients. Beyond the design and development phase, I also play a role in providing support and coordination for training days, which involves creating a fun, safe and professional environment which aids learning and growth. Additionally, I take charge of recording and analysing feedback from our training sessions. This feedback enables us to improve our programmes and ensure they resonate with the needs of the participants, ultimately enhancing their well-being.
We can also measure the impact of the wellbeing initiatives that have been put in place. Embracing the dynamic nature of my role, each day presents new and exciting challenges. Within my first six months it has been an incredibly rewarding experience to witness the positive impact our training programmes have on individuals and the organisations they work in. I have also been entrusted with the responsibility of designing the communication hub for the organisations we collaborate with. This platform is an external space for participants to quickly access curated resources and further support.
What attracted you to The Mental Wealth Company?
During my MSc in Occupational Psychology, an interest was sparked about the module on workplace wellbeing. This area of study stuck with me and resonated with both my personal interest and a want to help others. I discovered an interest in creating a positive change within the work environment, promoting mental health and wellbeing among employees.
The Mental Wealth Company’s mission and ethos aligns perfectly with my own values and purpose to make a difference in people’s personal and work-life. It has been incredibly fulfilling to work for a company that shares my passion and actively strives to create a healthier, more supportive work environment. Moreover, the organisation’s focus on the railway industry holds a special significance for me. Coming from a family with a long history of working on the railway, I have witnessed first-hand the unique challenges and demands individuals face within the industry. The personal connection further fuels my motivation to make a positive impact within the railway and support workers within the sector. Overall, the company’s alignment with my interests, purpose and family history within the railway industry is a variety of reasons to fuel my commitment to the work we do.
What kind of challenges have you faced during your first six months?
Being relatively new to the industry – it has been a steep learning curve with many challenges but with the help and guidance from the team I have managed to overcome these. Other than learning to work my
way around Microsoft (!), some challenges I have faced include learning to building our website and putting together a client resources hub. With the help of the team (and our tech support guy!) we have since launched both and used successfully by the participants on the training courses to access further support and resources. I am new to working in a consultancy business, there has been a lot to learn here – from speaking with clients and dissecting an organisational issue, helping them scope out what they need, to helping them to brainstorm potential solutions.
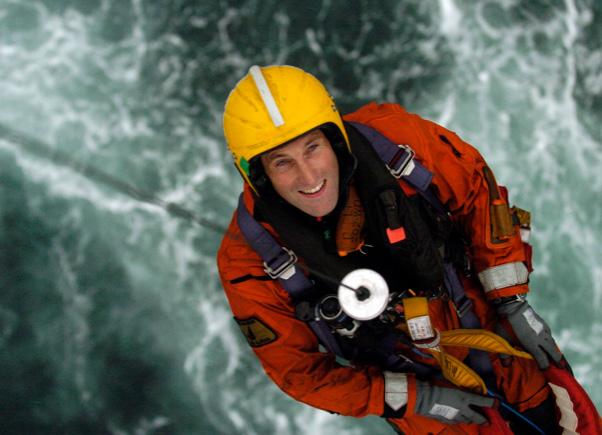
Andy Elwood – Mental Health
First Aid Instructor
How has the wellbeing market changed in the last five years?
There has been a massive shift in the wellbeing market since before Covid-19. I would say that ‘Wellbeing is now core business’! It’s much more normal now to hear someone talking about their own mental health in a work setting, which is an incredibly positive thing. More organisations are realising the importance of wellbeing, not only for their staff, but also for the long term success and performance of the business. ROIs of 11:1 are entirely possible (Deloitte, 2020) when organisations fully engage with the wellbeing agenda.
Mental Health First Aid England have trained over 600,000 MHFAiders® which are a fantastic help supporting colleagues, but we still have 33 per cent of managers reporting feeling out of their depth when it comes to supporting their team with mental health concerns (MHFA England, 2023). So there is still a need to do more to support our colleagues. Shift changes in organisations are possible and it’s remarkable to see how open and supportive a culture can become in a relatively short period of time. The real wins I’ve seen are when wellbeing is openly spoken about by the senior team in the business and every manager is competent in having wellbeing conversations with their team. This requires training to increase knowledge and understanding around the subject and to help them grow in confidence.
As Wendy stated, we often hear that EAPs are underutilised – we can never promote them enough. Sharing positive stories of how your EAP has helped staff is a fantastic way to share the practical
tools available to support lots of real-life challenges (not just about mental health concerns). Sharing that message of hope and bypassing the long wait-times for NHS help can really help employees to take control.
Tell us about your career before you entered this sector.
I used to be a ‘dope-on-a-rope’… getting winched out of helicopters to rescue people in the mountains, on sinking ships or in the sea. I have operated as a paramedic in the Royal Air Force and with HM Coastguard. I’ve also been a paramedic on the RAF battlefield rescue helicopter in Afghanistan. After 20 years, I had a pivot and now love to share what I have learned in my Search and Rescue days with people in the corporate organisations so that they can improve their health, wellbeing and performance of their team. I facilitate this in three areas for The Mental Wealth Company, namely instructing and training Mental Health First Aid, Nontechnical skills and Psychological Safety. Focusing on positive mental health, team safety and performance means that I save more lives now than I ever did dangling under rescue helicopters (even though that’s the best job in the world…).
What success have you experienced in the last twelve months and how do you measure success?
I believe that ‘all the magic happens outside your comfort zone’. Professionally, I am incredibly proud of the work that we have delivered over the last three years. It is so rewarding to see the positive changes that we have made to so many and the ripple effect that that has on their everyday lives. I have also been improving myself throughout 2023 with new challenges and learning in many aspects of my life. These range from rescuing a cocker spaniel, Bella, doing my advanced rider course on my motorbike to acquiring new accreditations in a work setting, especially in the field of Psychological Safety with the Academy of Brain-based Leadership.
On a deeper personal level, I have also progressed so much with Eye Movement Desensitisation and Reprocessing (EMDR) therapy to process many traumatic events into memories I can live with. This means that I am feeling full of energy each day and looking forward to the challenges my work brings and the people I meet as I enjoy my biggest adventure in life, which is to live the life of my dreams.
Success is measured when Bella comes back first time when I call her, that I am sleeping well, when I receive amazing feedback for my courses and when clients come back to book more training. I’ll let you know about the advanced rider test, which will be in the next few weeks…then I will be planning some further adventure rides to explore a little bit further than I have before.
A COMPANY ON A HUMAN SCALE
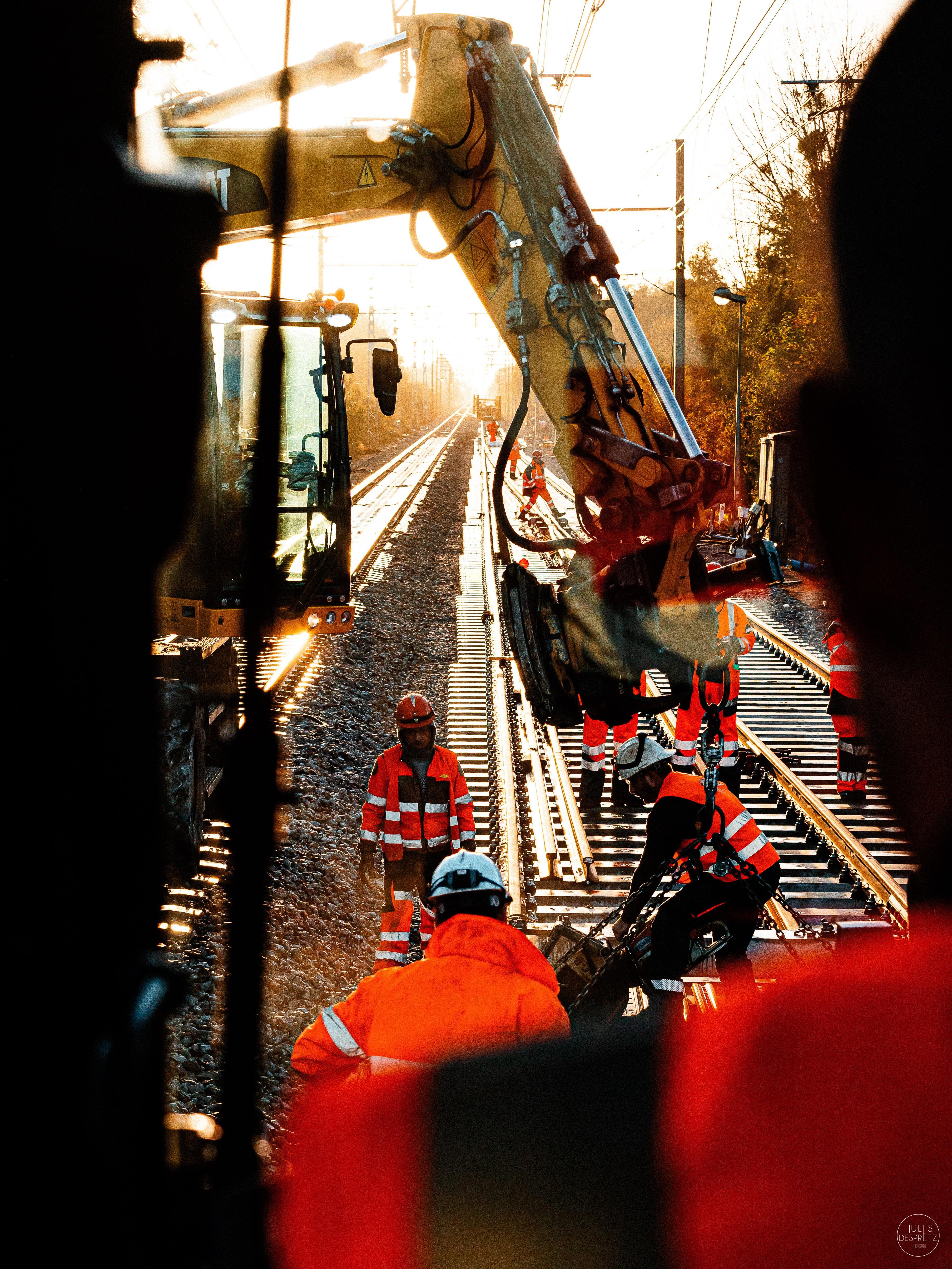
TSO develop, design and deliver rail systems renewals and railway enhancement projects across the UK, from London to the Scottish Border Being a part of The Central Railway Systems Alliance provides us with the unique chance to be involved in some of the UK’s most exciting projects, with a variety of work that is a oncein-a-lifetime opportunity for career development. www tso fr/en
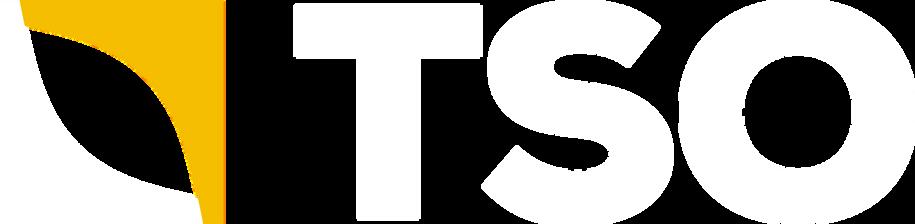
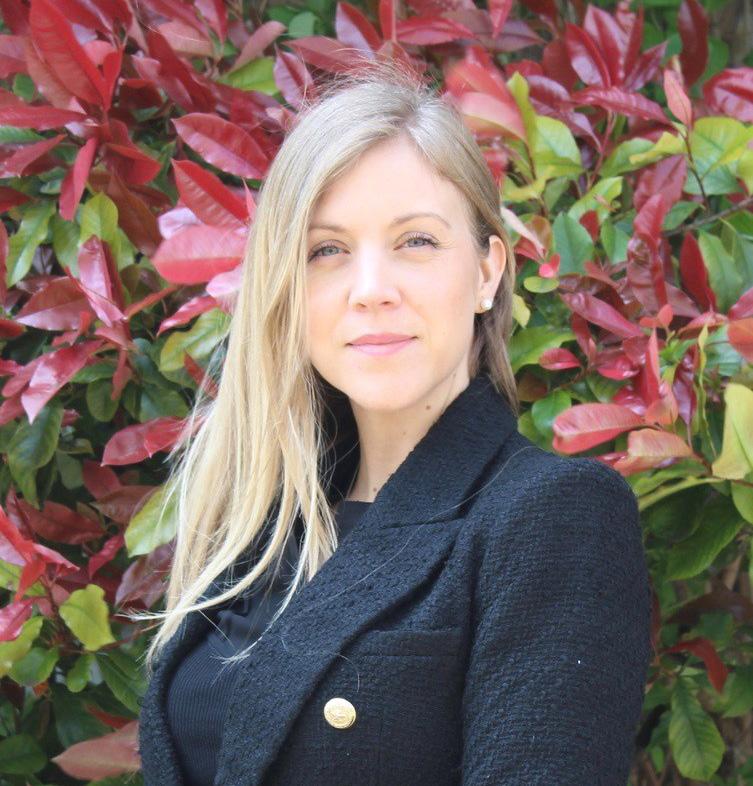
STEFANI DUPREE HUMAN RESOURCES & COMMUNICATIONS MANAGER AT TSO
Stefani Dupree is involved in various initiatives and recruitment programs across the rail sector. She has always sought to create an environment where everyone feels valued and respected, and where their differences are celebrated. She is committed to promoting inclusion in the workplace and beyond, regardless of gender or any other personal characteristic.
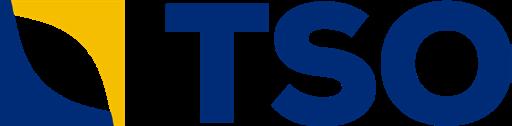
TSO
With more than 90 years’ experience in France and internationally, TSO puts its expertise to work on track construction, renewal and maintenance, electrification and catenary upgrades, survey and rail software development, rail safety and rail signalling.
How did you start at TSO?
I started at TSO after a short career break to raise my family, I knew that I was eager to step back into the rail space and TSO seemed like the perfect fit. Being a working mum can be a challenge, but as Human resources and communications manager here at TSO, I am so passionate about being involved with many areas of the business and find it extremely rewarding to grow alongside the industry.
What challenges have you faced in the industry?
From my perspective of being a female in the rail sector, I believe that it is important to address the challenges I have faced throughout my journey, as the gender imbalance within the industry should be a key part of the agenda when we conversate about the future of rail. Whilst I may be optimistic to say that when I look towards the future of the industry, I can see the workforce becoming much more diverse and accommodating for women, especially if companies agree to do their part and provide the right tools for progression into senior roles.
What success have you experienced in the last twelve months and how do you measure success?
Over the last twelve months, I was overwhelmed with gratitude and immensely delighted to have been shortlisted for the UKCW Role Model campaign and nominated as a Gender Role Model in the National Diversity Awards. Championing for gender equality is something I include at every opportunity within our workplace and beyond, as I see diversity and inclusion as being vital for success Especially within the rail industry. Sometimes it can be hard to find the time to reflect on and quantify the success in my career, but being nominated for such campaigns is an absolute honour.
What does sustainability mean to you?
Sustainability is always at the forefront of what direction I want to go in with the business. TSO is committed to reducing their impact on the environment, by creating an environmentally conscious workplace. This means having policies and procedures in place that encourage greener behaviours to reduce our carbon footprint.
What types of products and services do you offer?
out by TSO. Other specialist services, such as topographic studies, rail industry software development, the rebuilding of mainline and shunting locomotives, and rail safety, enable us to offer a comprehensive range of services.
What types of companies do you collaborate on projects with?
We are proud to be a part of the Central Railway System Alliance (CRSA), with which we collaborate on a variety of projects, as it brings together the collective strength of the four parent companies: Akins, Balfour Beatty, Network Rail and TSO. It is with these partners that we are able to develop, design and deliver rail systems renewals and railway enhancement projects across the large geographic regions of the North West, Central and Eastern regions, from London to the Scottish Border. Being a part of The Central Railway Systems Alliance provides us with the unique chance to be involved in some of the UK’s most exciting projects, with a variety of work that is a once-in-a-lifetime opportunity for career development.
How can we make the rail industry a place people want to work in?
We can make the rail industry a place where people want to work by being committed to fostering a diverse and inclusive workplace, where colleagues can thrive and feel comfortable in bringing their whole selves to work. We aim to support our employees through organised training, progress review around career advancements and open conversations.
How can the industry tackle its skills shortage and how do you recruit/retain/ train your staff?
At TSO we proactively search for the potential that can come from investing in the youth, through our apprentice and graduate schemes we have in place. The rail industry has a lot to offer in terms of the opportunity to work on impactful projects that shape the UK’s transport systems. Training at NGE is a proactive commitment by the company, which believes that professional training and development are integral to the fundamental rights of its employees.
What are some major projects you’re currently working on?
Want to know more about TSO?
Tel: 07891 650247
Email: lmarks@ nge-contracting.co.uk
Visit: www.tso.fr/en/
Our specialist services are involved in the construction, upgrading and maintenance of rail tracks. The work of this core business serves rail networks, high-speed rail line projects and urban networks, such as metro and tramway systems. Electrification and civil engineering signalling works are carried
Some major projects we are currently working on involve modernizing our rail infrastructure through the Central Rail Alliance, this includes upgrading track, signals and power systems. We are also developing strategies to improve efficiency and on-time performance through better scheduling, coordination across our workforce on both Eastern, North West and Central routes, and the use of new technologies and modern methods of construction.

What are your plans going forward to ensure TSO’s services are still around for years to come?
Going forward, our plan is to ensure the longevity of our services focusing on continued infrastructure investment, forming strategic partnerships, embracing innovation, and developing our workforce. We aim to provide safe, efficient and sustainable transportation options that meet changing market demands and exceed customer expectations.
How have you seen the industry change over the years?
Over the years I've seen the industry change tremendously in terms of safety, technology and competition. Safety is always the top priority and new technologies have made operations much more safe and efficient. The competitive landscape has definitely shifted as well, requiring us to find new ways to improve service, control costs and provide value to customers. Overall, it's an exciting time to be in the rail industry with many opportunities ahead.

TSO Underground Works, 2022
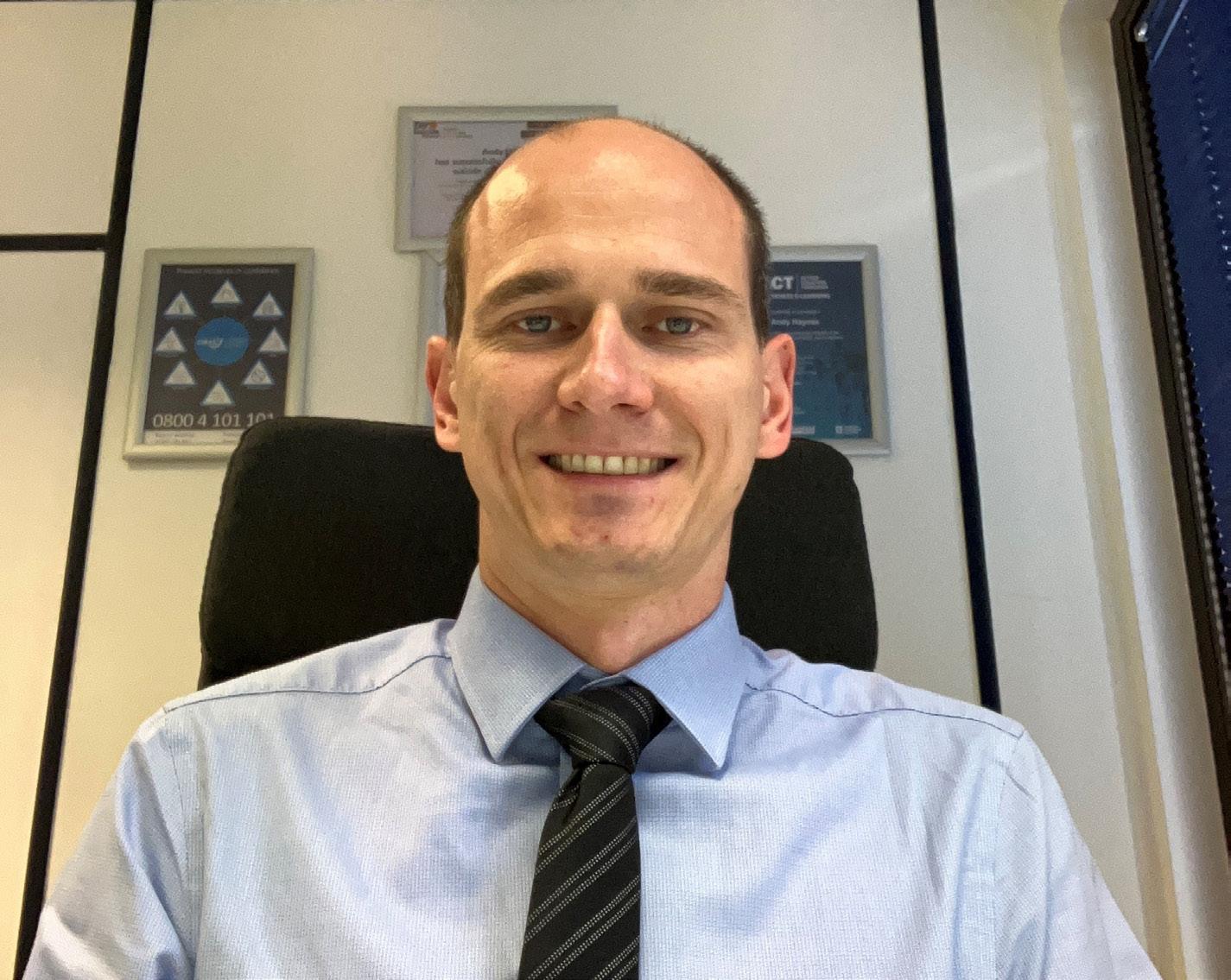
ANDY HAYNES DIRECTOR AT SERVO GROUP
With 13 years’ experience working in the rail industry across ten different train operating companies, Andy Haynes joined Servo Group in July 2022 to head up the Rail Division and launch the company’s London and South Office to drive forward further growth in the rail sector.
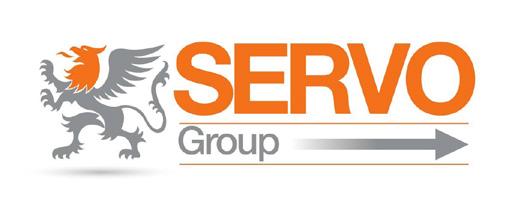
SERVO GROUP
With more than 50 years’ experience, Servo Group offers a broad selection of services – from full security packages to FM, Rail Labour, Cleaning and more. Its operations centre is staffed 24/7 making communication seamless throughout.
Want to know more about Servo Group?
Tel: 0845 450 0401
Visit: www.servo-group.co.uk
How did you get started in the industry?
I started my career through another security company, joining them as a supervisor with a portfolio of train stations to look after, which then developed into a portfolio which spanned stations, depots and track. Initially I’d never intended to work in rail but once you get into rail it seems you never want to leave.
When did you join the company?
I joined Servo Group in July 2022. It’s a very dynamic muti-faceted company which allowed me to take on the role of Director, tasked with growing our rail division. I was looking to keep myself involved with stations but also play a bigger role in trackside operations, so finding Servo Group already had an established trackside
operation spanning the UK, and a very prestigious contract with Network Rail, looking after Welfare and Trespass, made it the perfect move for me.
What is your role within Servo Group and how did you start?
I was very aware of Servo Group, as I had come across some of their teams over the previous year or so across the routes and so I made a few connections from the company on LinkedIn. It was clearly noticeable from that first link, how vibrant the team was, and how active they were across LinkedIn. Many of their social posts were about business growth, sustainability or people and this resonated with me as their values seemed closely aligned with mine.
I am a Director and my day to day remit is Director of London and South for Rail. It is my responsibility to ensure our teams that operate across the industry do so safely and supported by us.
It was hugely encouraging to see that their posts received a lot of interaction from their front-line teams, for me, this just felt like a great team who cared about their people, so I made some enquires through Linked In to set up a meeting with the owners. A couple of months on from that first message and we were launching a brand-new office in Highams Park London to service the whole of London and the South.
What success have you experienced in the last twelve months and how do you measure success?
One of our greatest successes is the continued growth of our Rail Division – since opening our London office in Highams Park, we have seen a rapidly increasing number of clients turn to us to supply track labour. We have also managed to re-secure our contract with Network Rail for Trespass and Welfare Officers for an additional two years which is a phenomenal achievement. An integral part of our vision for future growth is the success of large tender submissions and our team work relentlessly to make this happen.
Ultimately though, one of the greatest measures of success for me is the achievement of our frontline teams as they are the lynchpin of our business and one of the biggest drivers of our growth. I think our relationship with them, the tools and training we have invested, and their performance represents one of our biggest achievements – our team in London and the South have received over 3,000 hours of training delivered by external companies and their exemplary service delivery has resulted in 32 individual members of the team being recognised with outstanding achievement awards.
In amongst this we have celebrated many weddings, new babies, birthdays, anniversaries, and new homes with our teams and built up strong, mutual respect and that’s what really matters at the end of the day.
When did you first start the company?
Servo Group was initially started in 2013, as Servo Securities, with just one security guard manning a construction site in Leeds. The company grew its security offering rapidly, building up a strong reputation for pro-active, speedy service and quickly growing its weekly guarding hours. It launched its own CCTV division a couple of years later in response to technological advances and the needs of its customer base, which is now thriving with a huge range of installs in place from temporary towers on construction sites to complex, permanent infrastructures on solar farms. Around the same time, we attracted some interest from potential rail clients and decide to expand with a specialised rail division, obtaining full RISQS accreditation and Sentinel Approval in 2017, which allows us to supply track operatives to support the rail infrastructure.
At this point, thanks to the burgeoning but cohesive growth across our main divisions – staffed guarding, rail and CCTV – we decided to change our name to Servo Group. Since then, we have gone from strength to strength, with over 30 staff based at our Head Office in Leeds, offices in London, Manchester, Darlington and, most
recently, Scotland, along with the addition of a growing cleaning division.
How passionate are you about sustainability in the rail sector, and how do you go about sourcing the materials for your products?
At Servo, we’re immensely passionate about sustainability, across the whole of the business, and we always strive to reduce our carbon footprint, as well as working with our clients to meet their targets. As an ISO 14001 accredited company, its imperative that we have clear, documented eco-targets to work towards and we’re always exploring new ways of integrating sustainability into our projects.
We recently attained a Gold Safe Contractor verification from Alcumus, to add to our ISO 14001 accreditation, further boosting our ESG credentials, and we have some clear, defined eco-targets which include a commitment to reducing the waste we send to landfill by ten per cent year-onyear, transforming to a fully electric fleet of vehicles and investing in eco-friendly innovation exploring sustainable, creative solutions.
What are some standout projects you’ve been involved in over the years?
We’ve been lucky enough to accumulate a really diverse portfolio of brilliant clients since our rail division was set up giving us the chance to work a multitude of standout projects. One that we’re particularly proud of though is our provision of Trespass and Welfare Officers for 32 stations in Network Rail’s LNW region. We won this contract in 2021 and we have just been awarded a contract extension of two years.
It’s really satisfying to see the great work our welfare officers perform on this contract – more than 412 crisis interventions have been performed since 2021, preventing an estimate 274,000 minutes of delay and even more importantly, saving lives by intervening to prevent fatalities. Many of our officers have received awards for their work in the past two years, which is an amazing testament to the work they’re performing and something we take great pride in.
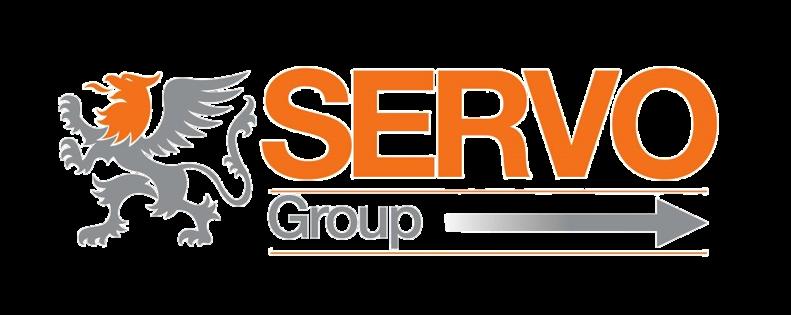
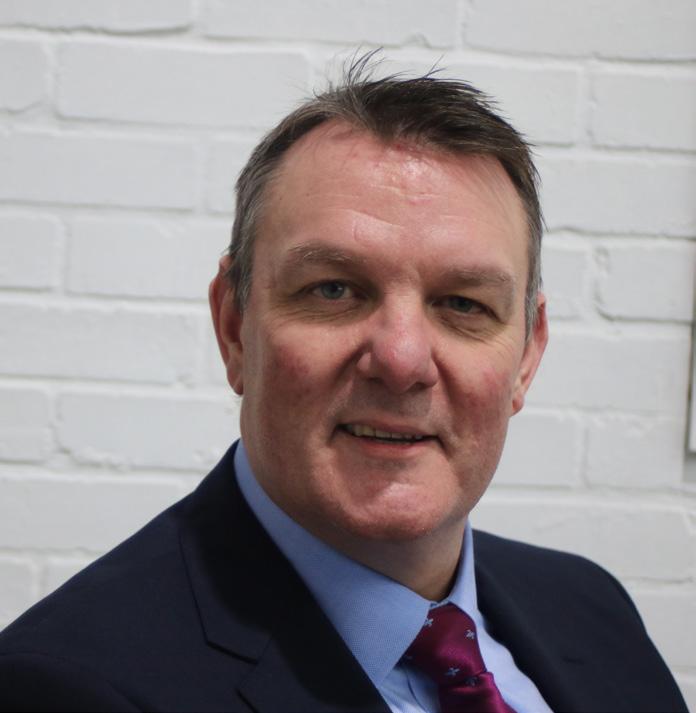
KEVIN WEBB MANAGING DIRECTOR OF STEP ON SAFETY
Having worked both in the UK and overseas for the past 18 years, Kevin Webb brings a wealth of experience from UK Construction and Civils to the GRP industry. He’s worked closely with architects, end customers, engineers, designers and contractors around the world.
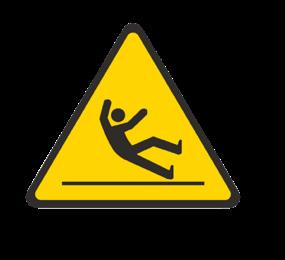
STEP ON SAFETY
Step on Safety was founded in 2007. It is an ISO 9001-accredited supplier of composite (GRP) slip-resistant access structures and flooring and provide a variety of industries with design, fabrication and installation solutions, including the Education, MOD, Rail & Transport, Public, Health, Motor, Stadium, Industrial, Office, and Construction sectors.
Tell us about your career before you joined Step on Safety?
The beginning of my management career was spent at Altro Flooring – a truly pioneering company which is still a family organization, but moreover embodies a philosophy that puts people’s needs at the centre of everything it does, influencing me to bring a human-centred approach to the roles I have had since.
What challenges have you faced in the industry?
Safety is at the forefront of why our company exists. However, there is not enough joined up thinking between manufacturers about how to tackle the larger problems the industry faces. Only by working together and sharing innovation can we move GRP and overall Network safety forward. Our company has a carbon fibre derivative on the Mars Rover but only seems to be able to share innovation in isolation.
What success have you experienced in the last twelve months and how do you measure success?
Only one person has left our business for another job in the last twelve months out of a team of nearly 100. This is testament to a new culture set up only three years ago where have recruited inside and outside of our industry from John Lewis, Ford, Virgin and others to enhance our talent mix. Our business philosophy is simple and all pervasive; ‘the key is we treat our staff how we would like to be treated.’
What does sustainability mean to you?
Sustainability is embossed on our board meeting notes as the first point to discuss at every meeting. Having worked for LOCOG at London 2012 and alongside BREEAM, I believe that everything we design and produce at Step on Safety should encompass the very latest technologies.
‘GRP is misunderstood because it lasts so long and on a Whole Life Cycle basis knocks alternative products for six.’
Want to know more about Step on Safety?
Tel: 01206 396 446
Email: sales@steponsafety.co.uk
Visit: www.steponsafety.co.uk
GRP is misunderstood because it lasts so long and on a Whole Life Cycle basis knocks alternative products for six. Step on Safety has been working with Lafarge and Hochim (SA) as to how to recycle 100 per cent and not on a tertiary basis. But sustainability has to be industry wide – I helped set up Recofloor many years ago and see the GRP industry following the same path. Once we begin to see this as an industry-wide problem and not one to be wrestled with in isolation, then truly inspirational things can happen.
What are some major projects you’re currently working on?
We’ve just signed a three-year contract with Network Rail to supply replacement track access points throughout Wales. Instead
of using contractors to install the steps, NWR will be providing their own teams who will be trained by us to work with the GRP modules we’ll be supplying.
Other projects include:
• Scotland Embankment Staircases – we’ve built over 200 rail access points for tier one contractors.
• GOOGLE HQ (London) – just one of our many landmark construction projects. We install over a thousand service riser floors every year across the UK.
• We’ve just started a three-year agreement with the American military to supply the GRP access solutions they require on their UK bases.
• The Beast (Saudi Arabia) – we are supplying over £1.5 million of bespoke GRP grating for a project in the Middle East.
What’s next for Step on Safety?
Step on Safety has just celebrated 16 years in business and has grown from the three original owners to a business working on all continents. But our approach hasn’t changed. We will continue to listen to our people and our customers and, by consistently turning creative thinking into practical, real-world solutions – that maintain the highest standards of safety and durability – Step on Safety has become synonymous with quality.
It is a history, that means we value the bold, the brave and the new. From focusing on how the different sectors we serve need their spaces to perform, to the call for more environmentally sustainable materials, Step on Safety is constantly challenging what is possible and seeking new ways of inspiring our customers and answering their biggest challenges.
What are your latest developments for the Rail Industry?
Launched at Rail Live this year, GRP LitePost™ has been designed to reduce installation time on-track and provides an alternative solution to traditional materials and installation methods. The lightweight post can be manually handled and hand excavated into position as opposed to using heavy duty plant equipment.
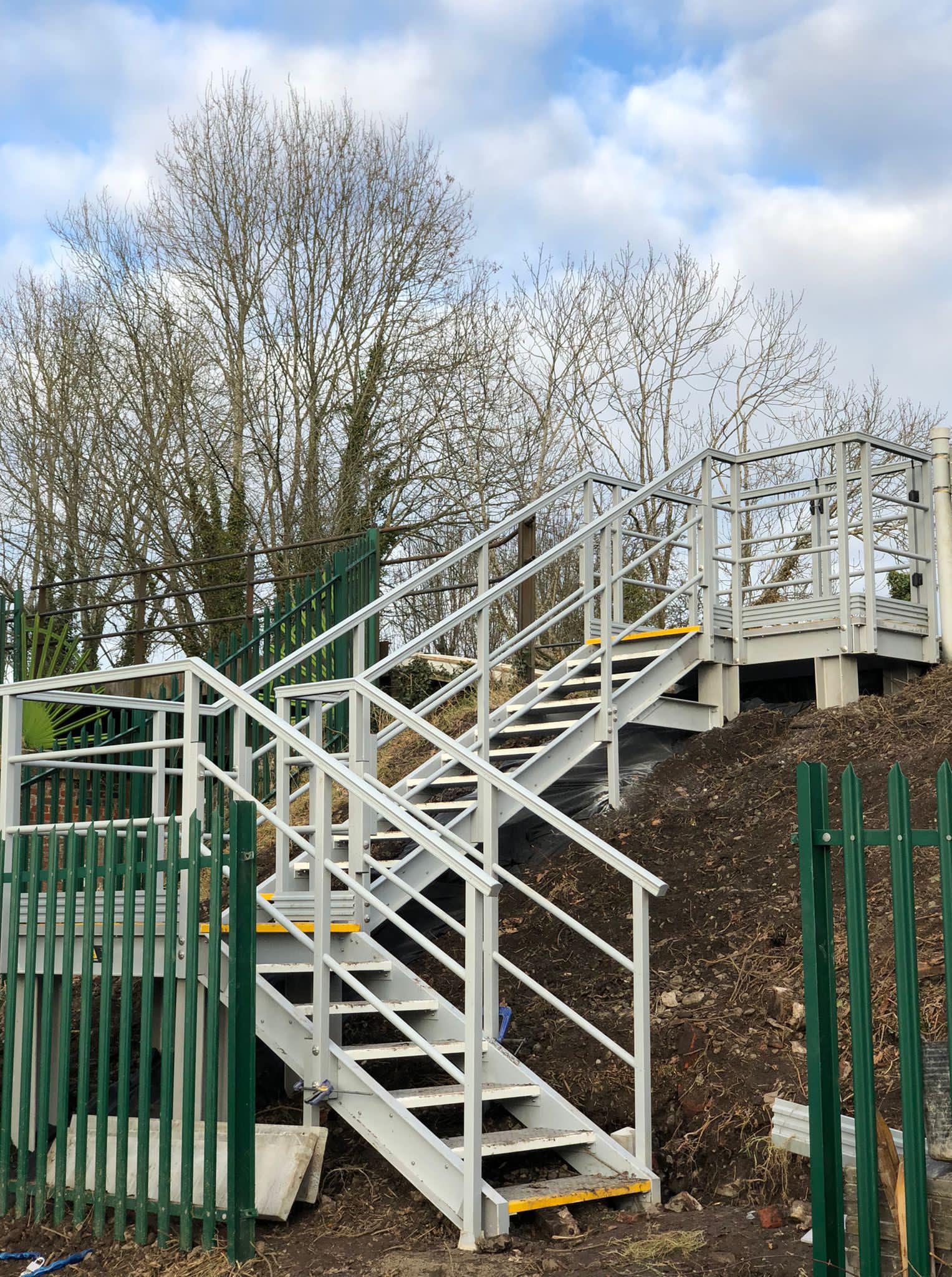
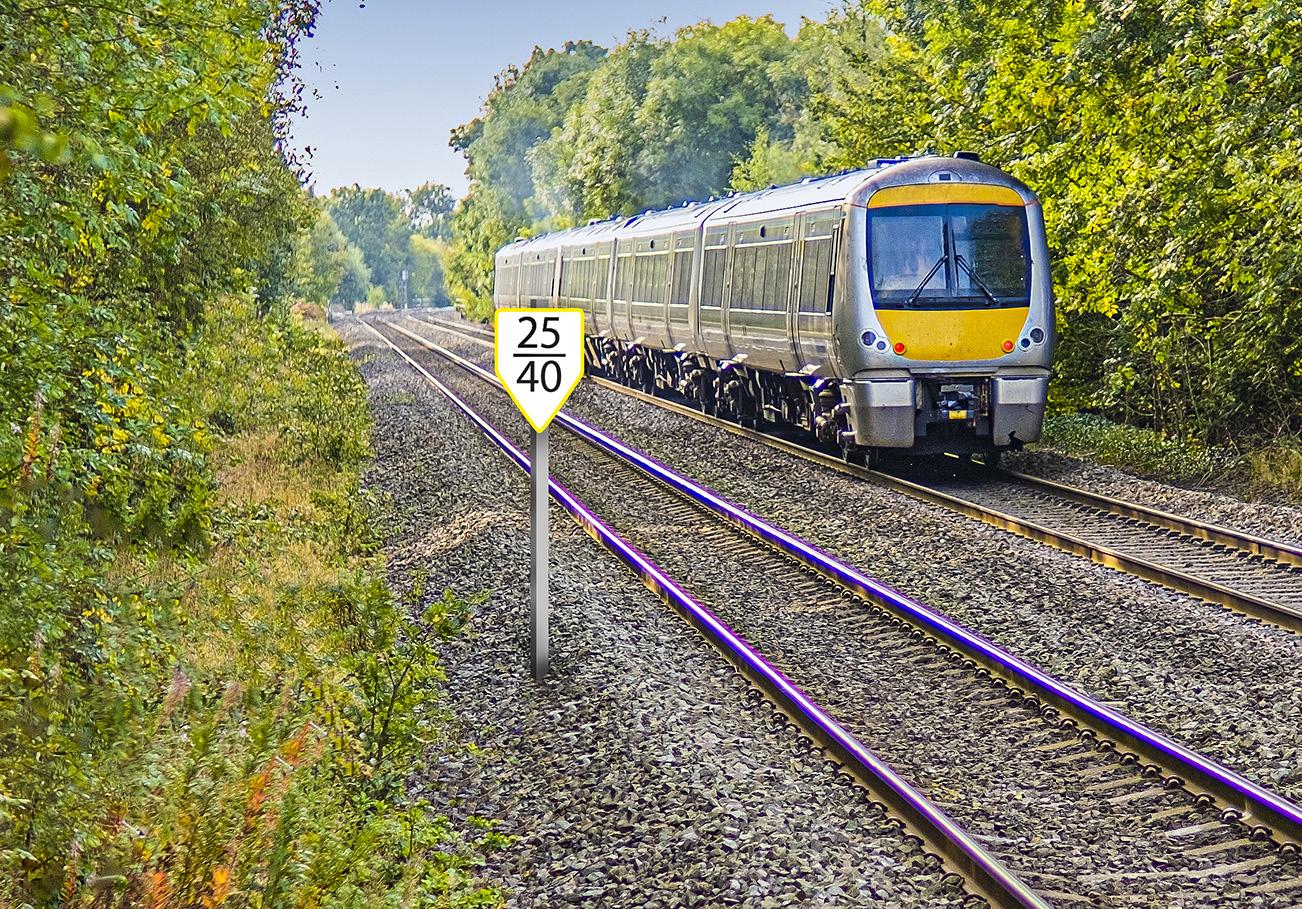
‘We believe safety for all should be at the centre of everything we do.’
Case studies suggest up to five GRP LitePosts can be installed in one night shift, previously three nights shifts would be required for one steel post. Suitable for digital or traditional signage to display temporary speed limits which are vital when the network needs to adapt to operational and environmental challenges.
Manufactured from GRP and delivered fully assembled, the LitePost™ is nonconductive, chemical resistant and noncorrosive with a suggested design life between 25-50 years. Supplied in either small or large versions, the LitePost has a maximum weight of 35kg and offers low to zero maintenance, making it the preferred option for future rail projects. In terms of sustainability, not only will it last longer than a steel post, it can be dug up and relocated if the signage is no longer required.
What do you think is the biggest challenge currently facing the rail industry?
Access, maintenance and maintenance time. The Rail infrastructure is under continuous use meaning the network needs constant maintenance and repair. Certain areas can be challenging to access whether that is logistically, through busy timetables or sufficient maintenance time. Upgrading the rail access points in the first place also faces its challenges: hundreds of locations need upgrading so that maintenance staff can safely access railway equipment and undertake the upkeep of the railways.
Which company do you most admire and why?
In 1959 Nils Bohlin at Volvo invented the three-point seatbelt. Volvo patented the designs; standard practice, to protect their investment from copy-cats. Volvo were in a position to charge significant license fees to rivals, or indeed, to promote their cars as the safest on the road, by retaining exclusivity.
Remarkably, however, Volvo did neither, but made the patent immediately available to all. Having sponsored the R&D, they gifted their designs to competitors, to encourage mass adoption and to save lives. This altruistic gesture changed the face of the car industry forever and we believe safety for all should be at the centre of everything we do.
Data Transmission in Train Control
Axiomtek’s Modular EN 50155 railway computer for driver machine interface applications – the tBOX510-518-FL
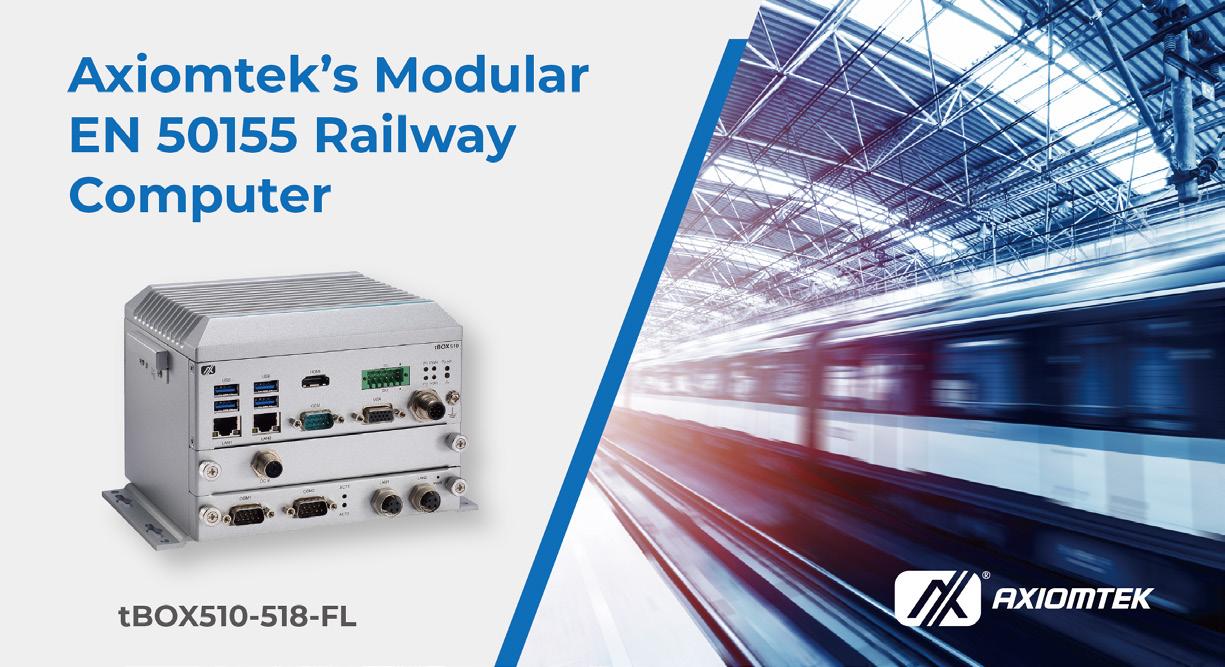
Axiomtek has released the tBOX510-518-FL, its new modular fanless railway computer with EN 50155, EN 60950-1, CE (Class A) and FCC (Class A) certifications and compliant with EN 50124 for railway-related applications. The rugged railway box PC is built to withstand harsh operating environments with a wide operating temperature range of -40°C to +70°C and vibration endurance for up to 3Grms with SSD.
Thanks to overcurrent, overvoltage, under-voltage and reverse polarity protection as well as 24V to 110V DC wide voltage input support, this heavyduty embedded computer is suitable for rugged industrial and railway applications with varying voltage input requirements. In addition, the tBOX510-518-FL has an optional Plug-in I/O Module (PIM) slot to meet different customization requirements.
The fanless tBOX510-518-FL is powered by the 7th generation Intel® Core™ i7/i5/ i3 (code name: Kaby Lake) or Celeron® processor 3965U. The high-performance embedded system comes with multifunctional expansion slots, modular design and abundant single-sided I/O connectors. Its rugged and ultra-slim structure ensures easy installation in limited space but requiring I/O flexibility and enhanced performance. The tBOX510-518-FL is an
ADVANCED FEATURES
• CE, LVD, FCC, and EN 50155 certified.
• 7th generation Intel® Core™ i7/i5/i3 or Celeron® processor (code name: Kaby Lake).
• Fanless and wide operating temperatures from -40°C to +70°C.
• Compact size with one Plug-in I/O Module (PIM) slot for various I/O requirements.
• Single-sided I/O design for easy maintenance.
• 24V to 110V DC wide range power input for railway applications.
• OVP, UVP, OCP, RPP power protection design.
ideal solution for data transmission in train control and rail signalling.
Axiomtek is dedicated to designing and manufacturing products that specifically cater to rolling stock applications for many years. Our tBOX510-518-FL is specially designed for the driver machine interface (DMI) in the communications-based train control (CBTC) system installed in a locomotive. This rugged railway embedded system provides control, monitoring and diagnostics over the train and its subsystems. More importantly, the rugged tBOX510-518-FL supports an optional function of 10ms interruption to protect the system against unexpected power outage or power source change to meet the requirements of EN 50155 S2. As a communication gateway system, the tBOX510-518-FL delivers enhanced flexibility, reliability, and stability for intelligent railway applications.
The tBOX510-518-FL has one DDR42133 SO-DIMM slot for up to 16GB of memory. It has flexible wireless communication options - with two fullsized PCI Express Mini Card slots and one external SIM card slot. The I/O interfaces of this fanless box system are single-sided design for easy access and maintenance. The multiple I/O interfaces include one DB9 serial console or RS-232/422/485, two Gigabit LANs with Intel® Ethernet
controller I210-IT, one M12 A-code USB 2.0 port, one HDMI port, one VGA port, an optional Plug-in I/O Module slot, one terminal block isolated DIO (4-in/4-out) port, one M12 power input connector, one reset button and four antenna openings. For diverse applications with limited space that still demand rich I/O connectivity, the tBOX510-518-FL’s compact design offers flexible configuration that dramatically simplifies deployment. Moreover, the highperformance embedded system supports one swappable 2.5-inch SATA drive bay and one CFast™ for enhanced storage capacity. The tBOX510-518-FL is compatible with Windows® 10 and Linux.
Axiomtek’s new tBOX510-518-FL is available now. For more product information get in touch via the contact information below.

Tel: +44-161-2093680
Email: info@axiomtek.co.uk
Visit: www.axiomtek.co.uk
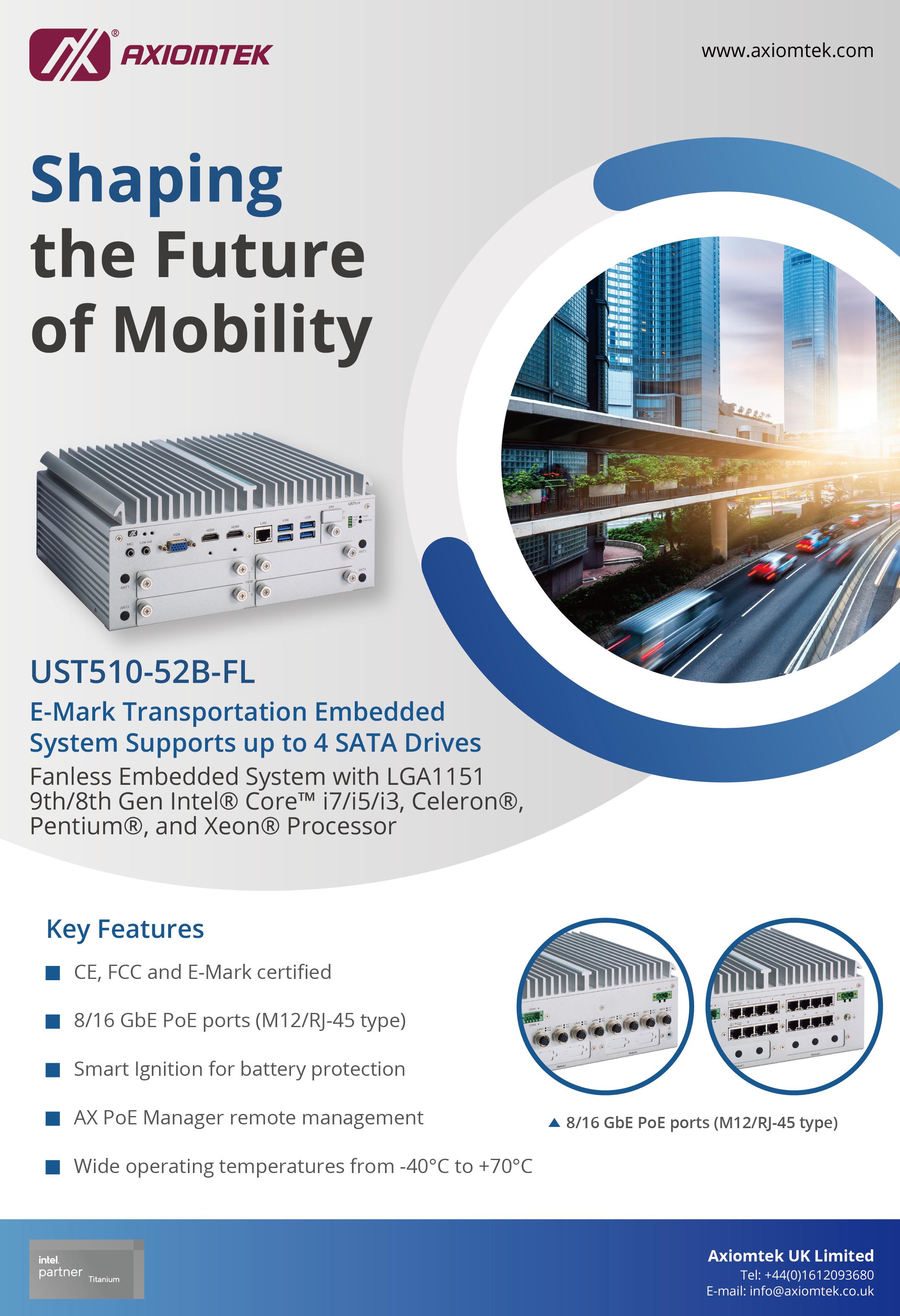
Rail digitisation
Biological hazards
Workforce expertise
Economic uncertainty
Extreme weather events
Digital and cyber security
Supply chain management
Climate change adaptation
Autonomous systems
Artificial Intelligence
Rail resilience

We’re with you every step of the way
Our Futures Lab helps rail become more resilient
The rail industry has seen significant change recently. It’s likely this will continue – from the rise of artificial intelligence (AI) to the increase in extreme weather events.
At RSSB Futures Lab, our horizon scanning and modelling experts identify and explore the emergent risks and potential vulnerabilities facing GB rail. Collaborating with the rail industry and learning from other sectors, we cover topics as diverse as asset integrity, complex software, and location setting without GPS.
To discover more about our rail resilience work and how to get involved, visit: rssb.co.uk/railresilience



A Proven Track-record of Rail Reliability
From new construction to refurbishment, the rail sector’s needs are as wide as the UK network is extensive
Safety is of paramount importance – the need to ensure safe and efficient use of all equipment and methods extends both to the workforce and rail-users alike. In these instances, proven scaffolding systems and experienced back-up are vital and integral to contractors’ successful project completion. A system capable of adaptation to a range of operational needs is a fundamental requirement.
Layher’s Allround equipment, featuring the widely used Bridging Truss, is a prime example. Developed to integrate fully with the Layher system and designed in response to the need for fast, controlled installation, bridging spans of up to 30 metres can be achieved – typically to provide temporary access between platforms, and for installation across active lines.
Supplemented by stair systems with DDR-compliant handrails and the versatile
Layher Protect panel design – used, for example, to create effective screens between bridging structures and the rail lines below – mean the majority of rail installations’ access needs can be met.
Possession time: an essential factor Sean Pike, Layher’s UK MD comments: ‘From our choice of scaffolding designs to purpose-developed equipment, we have always been fully aware of rail users’
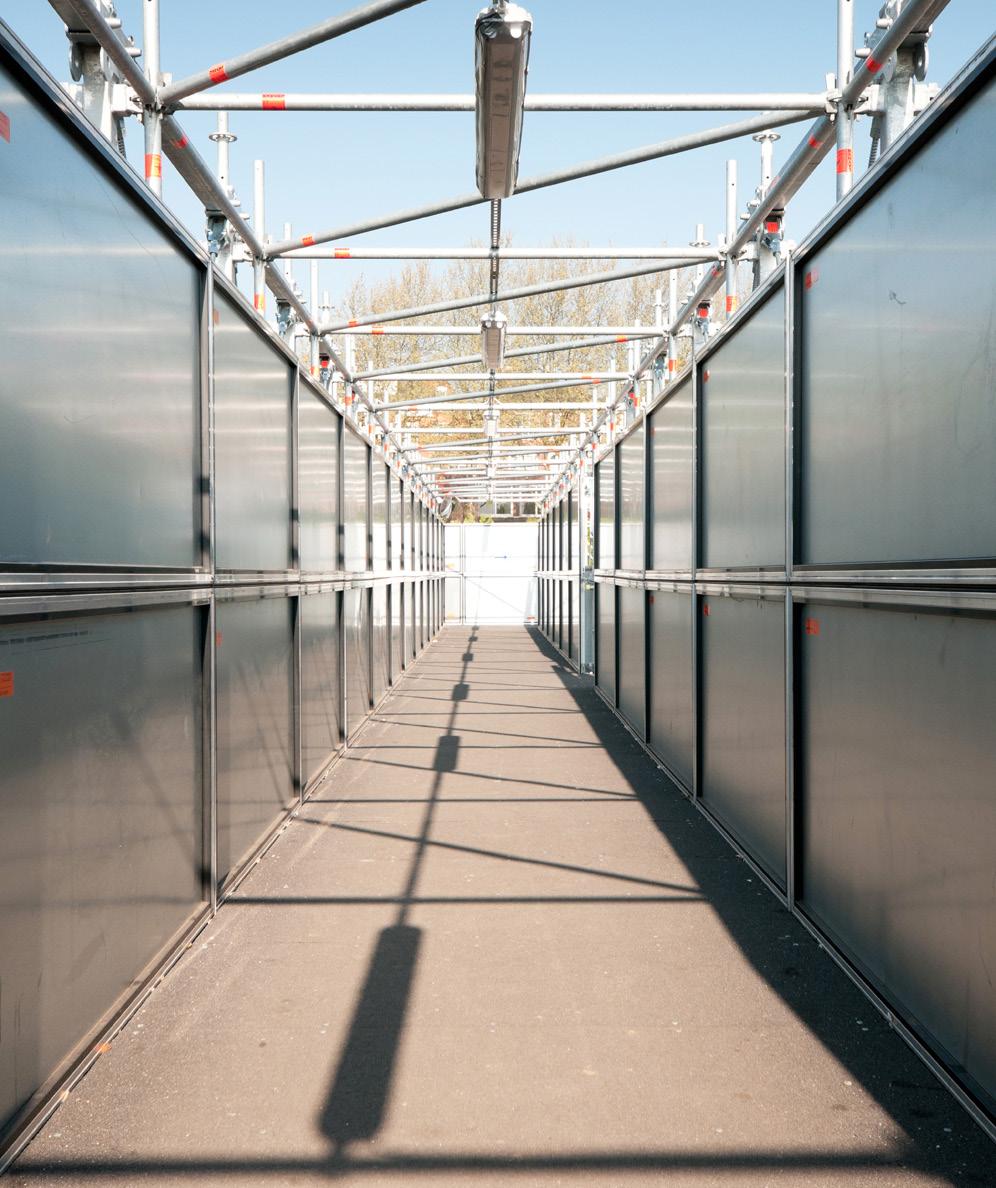
needs and work closely with contractors and operating companies to deliver optimum results.
‘We are fully aware, that possession times are key during rail works and can often be linked to penalty clauses arising from project overruns.’
The installation speed and simplicity of Layher designs have been proven to make a major contribution in this regard, “particularly as many of our structures can be assembled trackside or even offsite for craning into position during closure periods,” Sean Pike concludes.
Benefits Allround
The light weight, ease of handling and minimum components of the Layher system, together with equipment storage and transportation efficiencies are key planning and operational considerations. The proven gains arising from the use of the Layher system throughout the rail sector have been recognised by contractors across the UK.
A 16-metre span was required to provide passenger access between platforms during repairs of an existing bridge. The system was installed between two Layher stair systems, each featuring non-slip GRP surfaces, temporary lighting and Layher’s Protect screening panels. The structure was installed at a greater height than normal to enable drivers to maintain clear sight of the signalling system, and the contractor was able to complete with just one overnight possession.
Two sections of Layher Allround Bridging spanning six and 14 metres respectively were to be supported by a central tower to

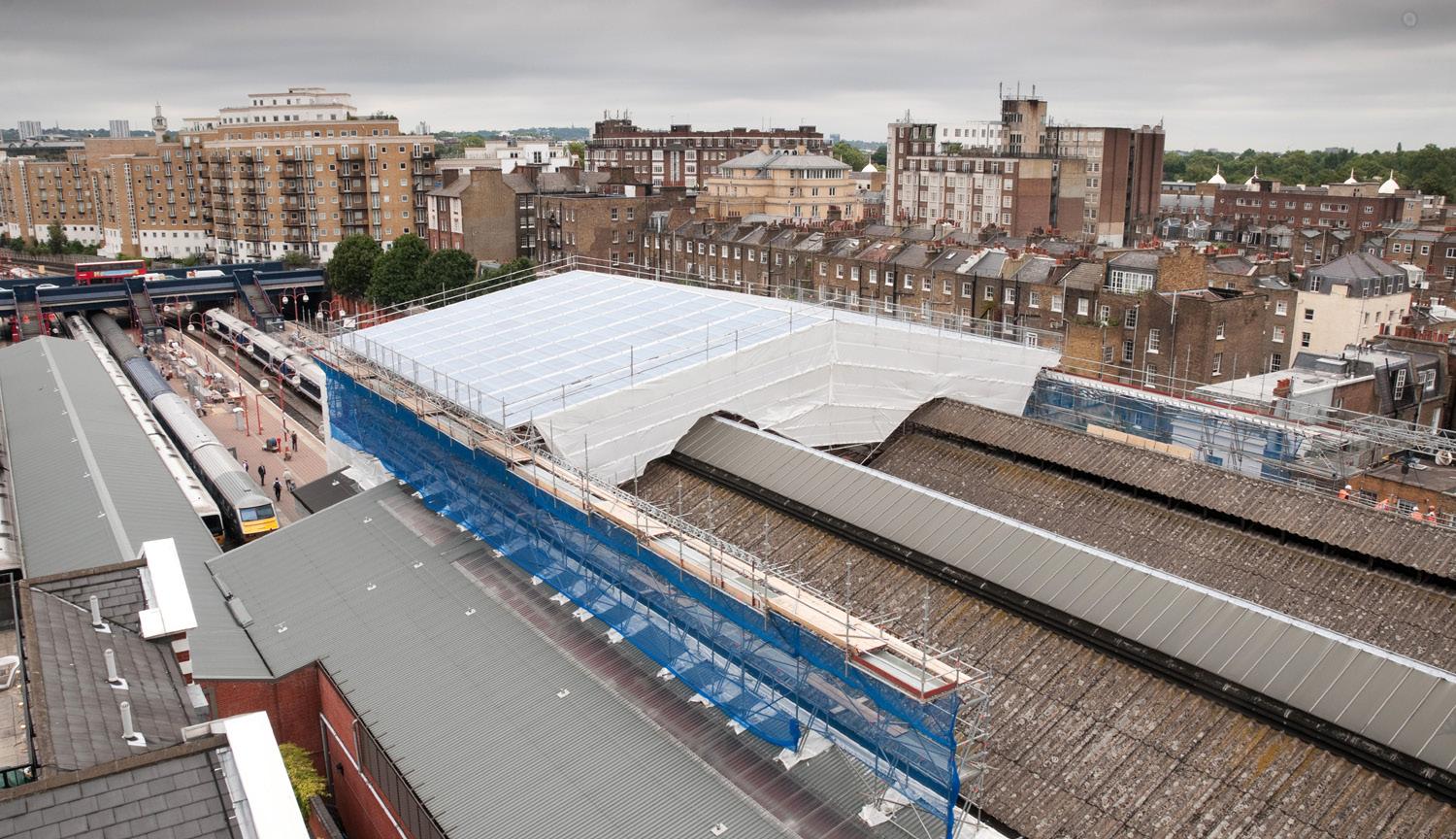
create a wide public walkway alongside service connections via two external cantilevered scaffolds. This build took place at ground level for the two spans to be craned into position overnight – minimising possession time – while the design also accommodated loading that allowed the central support to have been removed if required.
A team at another location carried out a full pre-build of a structure off-site to ensure track possession requirements were kept to a minimum. The bridge was craned into place during a single overnight possession. Two DDA-compliant Layher public access staircases were also fitted. By combining previous experience gained by using Layher equipment with the commitment of their specialist team, delivery was completed safely, on time and within budget.
A structure spanning some 30 metres across two train lines, and incorporating two bridges – one for construction use, the other to carry some of the location’s 60,000 commuting passengers daily – had highly complex design, health and safety and programming requirements. The Layher design was erected in a total of just four days but remained in position for some 18 months. The structure was an excellent example of the Layher bridging system’s versatility in accommodating stringent site conditions including the absence of access for crane usage and intermittent track closures resulting directly from such a busy train line.
A mobile temporary roof was required to follow refurbishment work as it progressed along a structure above a primary rail
hub. The contractor employed the Layher Allround system, including decking panels in order to provide protection below and as support for a rolling birdcage giving access to the roof. Movement of the entire roof structure was undertaken each time in an average of just 40 minutes, and by only four people.
For another contract, just two weekend periods were allocated for installation of a Layher bridge in contrast with the three weekends that would be needed with traditional material. In the event, only one weekend was required. Additionally, the two days anticipated for fitting ply-board screening along a 31-metre total span was completed in just 90 minutes by instead using Layher Protect panelling. Protect panels create an appearance that is markedly removed from that of a building site.
With storage and transportation benefits also to the fore, the gains arising from the use of Layher equipment throughout the rail sector are clear-cut and are well set to enable our work with contractors in the field to stay fully on track.
Tel: 01462 475 100
Email: info@layher.co.uk
Visit: www.layher.co.uk
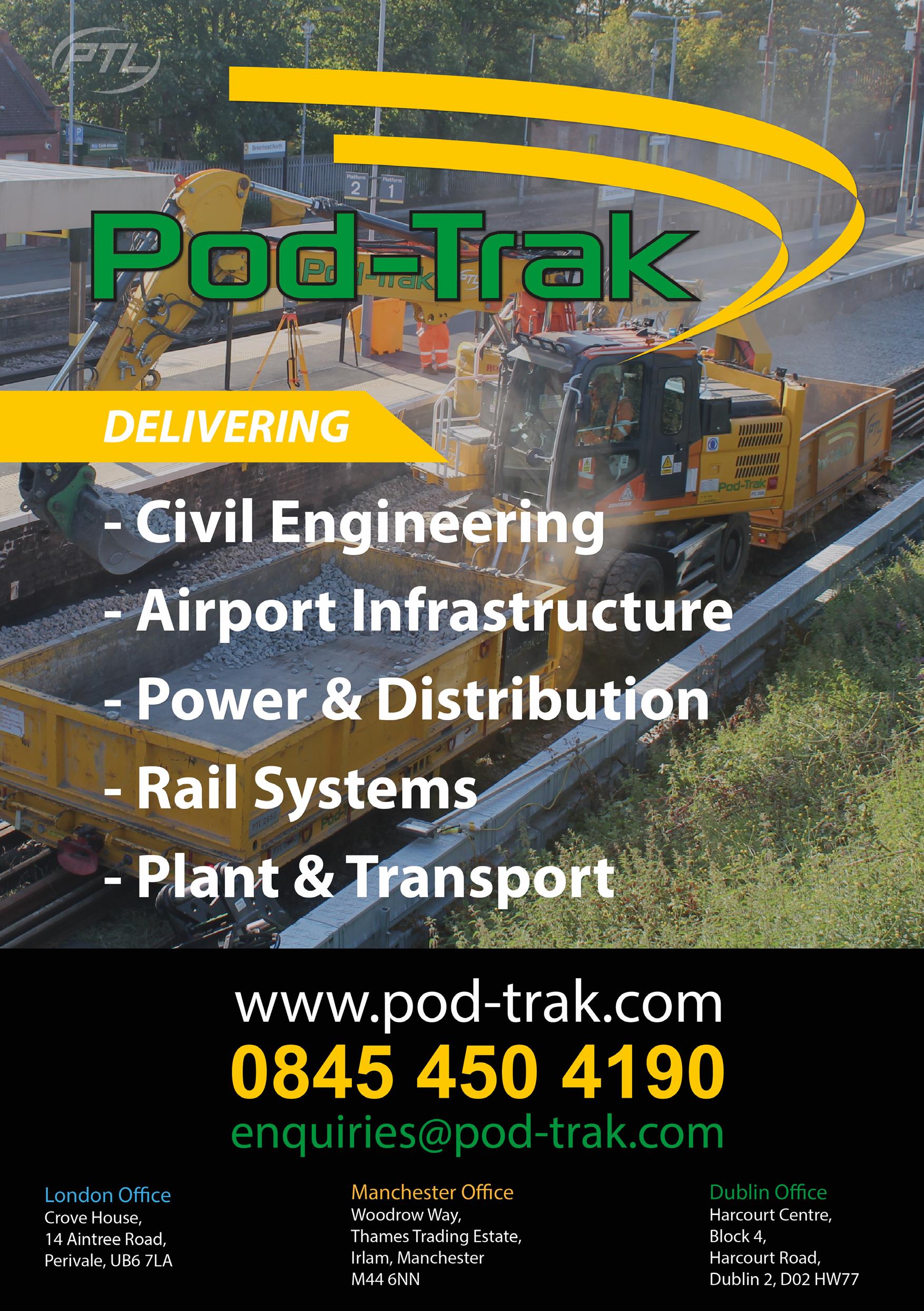
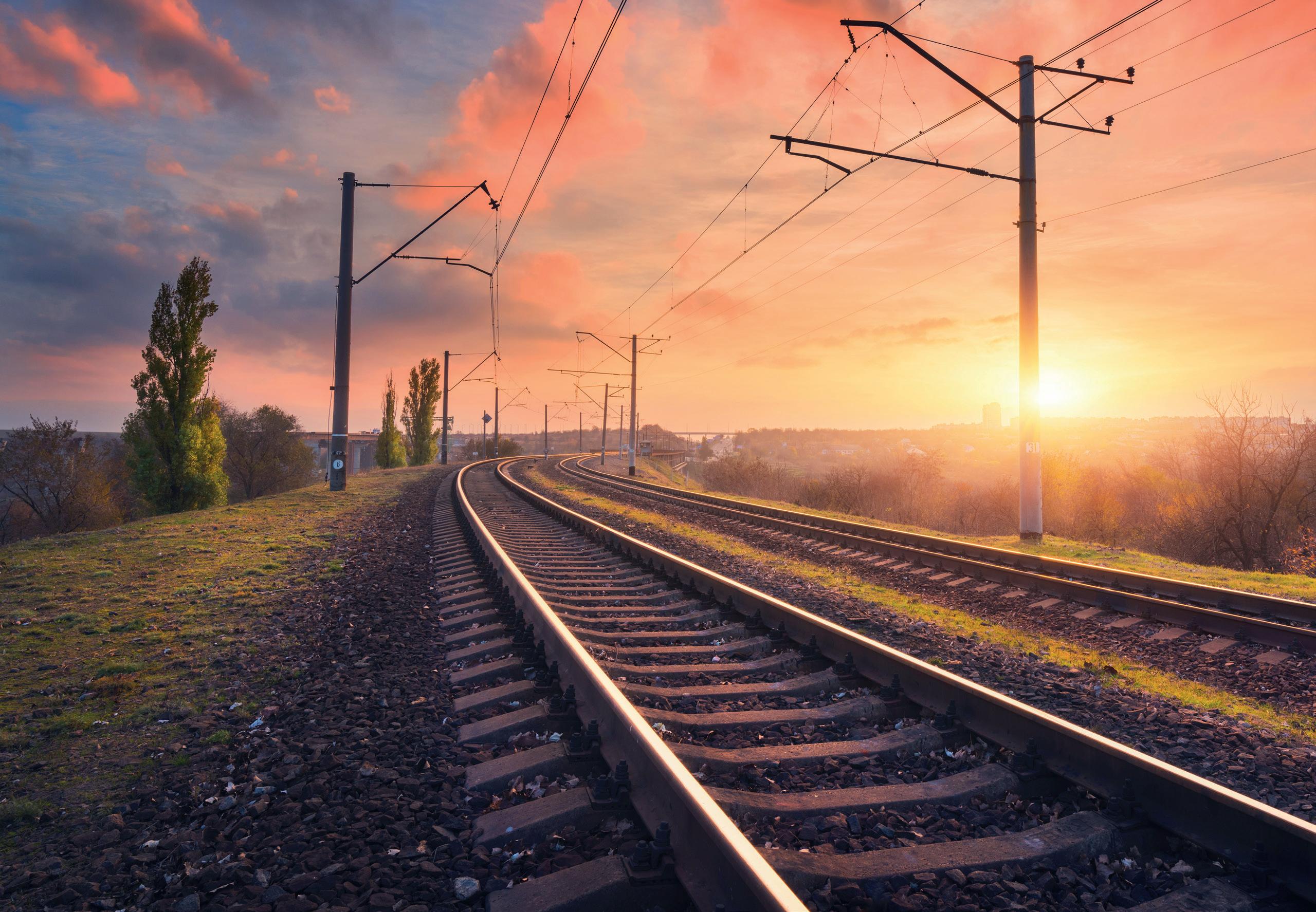
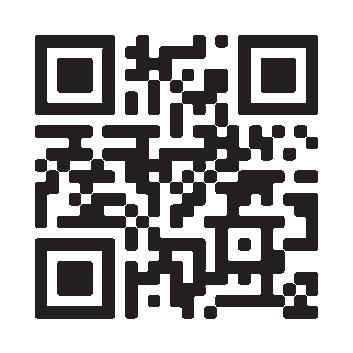
The Green, Digital Railway of the Future
3Squared is a Sheffield-based rail software and solutions specialist, founded in 2002, and part of Velociti Group – a key player in driving the transport sector forward
With over two decades of experience in the industry, 3Squared understands rail and has the foresight to implement solutions that make a positive impact on the rail network’s day-to-day operations. The company’s overarching goal is to ‘Make. Change. Work in rail’. It does this by collaborating closely with major influencers from across the rail industry, like Network Rail and HS2, to understand the problems they are facing, and how technology can play a crucial role in overcoming them.
The team is comprised of industryleading experts, passionate about revolutionising the rail industry. The vision is geared towards the creation of a greener, digital rail network that runs efficiently, safely and on time.
RailSmart Solutions
Through the RailSmart suite, it delivers digital transformation, drives efficiency, and streamlines operations across the industry.
The flagship RailSmart solution is EDS (Employee Development System) – a competency management solution that has delivered tangible results for a range of organisations including, London North Eastern Railway (LNER), East Midlands Railway (EMR), Alstom, and more.
Designed with efficiency in mind, RailSmart EDS enables its users to lower business risk and reduce incident rates through digital-based, reliable competency management.
Since LNER began implementing EDS seven years ago, they have seen substantial improvements across safety and performance.
Simon Reading, Driver Team Manager at LNER commented that: ‘Every driver manager, every station assessor, every train manager assessor uses RailSmart EDS – even our training team now use it.’
The solution acts as a digital hub of information which can be accessed at the
office, on board rolling stock, on site and beyond. This drastically saves time and reduces the administrative burden of compliance.
LNER’s Safety & Environment Programme Manager, Melanie Sewell also commented: ‘We have been using RailSmart EDS for the last seven years, and it has made a significant change to our business. Bringing in an electronic system means we have a better oversight of our competency management arrangement.’
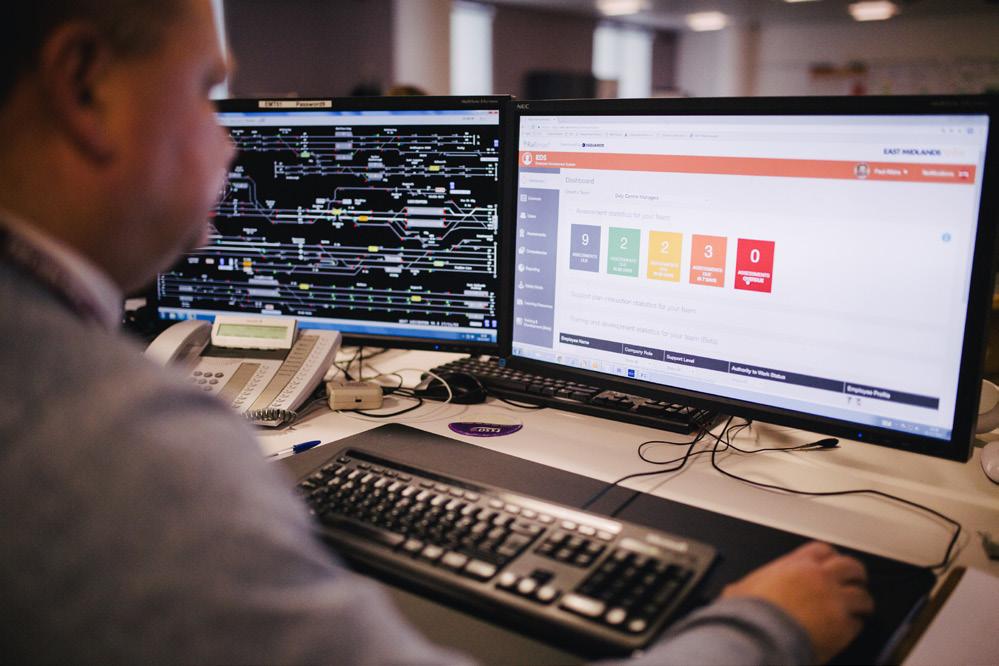
3Squared strives for continuous improvement, which is why it works together with clients to drive developments. Following on from two focus groups, 3Squared implemented several exciting upgrades to EDS – tailored to its users’ evolving requirements. This includes interface enhancement, further customisation capacity, reporting tools, and more.
Innovative PathPlanner solution
Through the new PathPlanner solution, launched this month, 3Squared is supporting the efficient, greener movement of freight across the UK. This First of a Kind (FOAK) winning solution enables planners to quickly identify available paths which can be bid to Network Rail.
PathPlanner seamlessly integrates with external systems and harnesses seven years of historical data of train schedules, enabling operators to take advantage of much-needed spare, and potentially wasted capacity.
The project has seen 3Squared working collaboratively to solve problems with both Network Rail and Solent Stevedores (with crucial input from Logistics UK, Stobart,
DP World and GB Railfreight) to help them realise the benefits of their investment by finding available paths to run longer and more frequent trains to and from Southampton. It is something the team is exceptionally proud of, and a key milestone achieved in PathPlanner’s journey.
To enable the shift to sustainable, greener travel, PathPlanner aims to take HGVs (Heavy Goods Vehicles) off the roads and onto the tracks, in turn, reducing carbon emissions and delivering on the Government’s commitment to reaching Net Zero by 2050.
Be part of the PathPlanner launch
In September 2023, 3Squared is showcasing PathPlanner in a live demonstration event at The Port of Southampton. To find out more, contact Jason Durk jason.durk@3squared.com

Email: hello@3squared.com
Visit: 3squared.com
Social: @3Squared
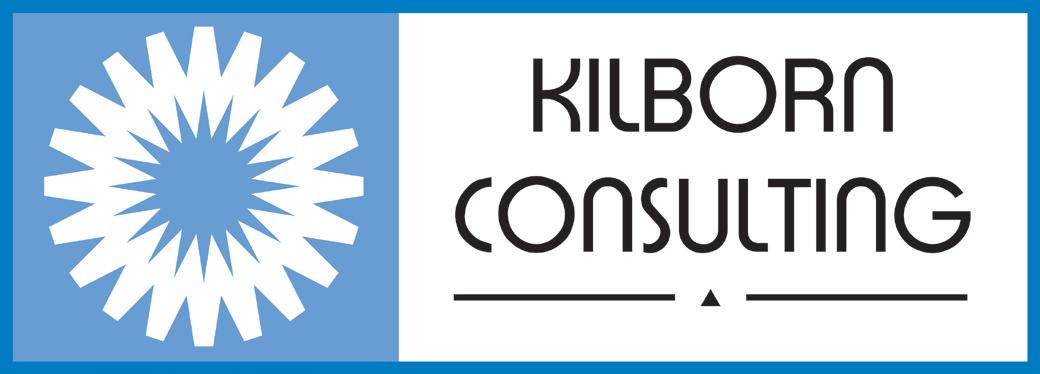

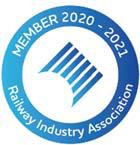
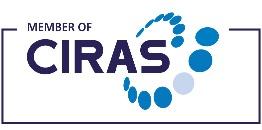
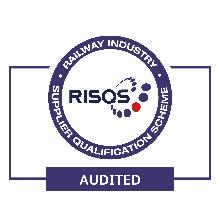
Kilborn Consulting Limited is an independent railway engineering consultancy and design business, with over 21 years of railway experience.
We specialise in the design of new and altered railway Signalling & Telecoms systems for the UK railway infrastructure.
Our areas of specialism are:
•Signalling and Telecoms Consultancy, including technical advice & support;
•Asset Condition Assessments, Correlation and Surveys;
•Signalling & Level Crossing Risk Assessments;
•Feasibility and Optioneering Studies;
•Concept and Outline Signalling Design;
• Telecoms Option Selection Reports (including AiP), Reference System Design and Detailed Design;
•Detailed Signalling Design;
•Competency Management & Assessments;
•Signal Sighting assessments, covering the full Signal Sighting Committee process with a competent Chair.
Hubken Group and Arriva PLC Clinch Global e-learning Award
Hubken Group, a leading UK provider of innovative e-learning solutions, is thrilled to announce its recent triumph at Totara’s prestigious Global e-learning Awards. Hubken, in partnership with Arriva PLC, secured the coveted accolade for delivering the Best Compliance Experience using Totara Learning’s Learn LMS platform.
The award recognises the exceptional impact of Hubken's Learning Management System (LMS) in improving compliance practices within Arriva PLC's pan-European operations, benefiting nearly 40,000 users.
Under the tutelage of Hubken's award-winning LMS solution, Arriva PLC has experienced a transformation in its compliance procedures, leading to substantial savings of both time and money. By enhancing previous compliance processes, the Hubken-powered LMS has propelled Arriva PLC compliance rates to new heights, achieving an astonishing compliance rate of nearly 100 per cent, against a target completion rate of 95 per cent, a substantial increase from their previous levels.
Robert Waggot, Arriva’s Business Applications Team Lead, commented: ‘We’re absolutely thrilled to receive Totara’s award for
having the Best Compliance Experience. It has been a pleasure to work with Totara and Hubken to create an online learning solution that not only meets the demands of our organisation today but also has the adaptability and scalability to support Arriva for years to come. We will continue to adapt and develop its potential to help our business in every way we can.’
Hubken's Director, Grace Lawrence, expressed immense pride in the recognition, stating: ‘We are honoured to receive this prestigious award alongside our esteemed partner, Arriva PLC. This achievement is a testament to our unwavering commitment to delivering innovative e-learning solutions. We look forward to continuing our journey of transforming organisations and delivering real change for our clients.’
This achievement demonstrates Hubken Group's dedication to delivering transformative e-learning experiences, empowering organisations to achieve compliance success while driving substantial cost and time savings. The Global e-learning Award serves as a testament to Hubken's commitment to e-learning and the significant impact it is having on all its clients.
Mechan Wins Key Contract with Transport for Wales
Sheffield-based rail depot equipment experts, Mechan, have secured a major contract with the public transport arm of the Welsh government. The specialist manufacturer will be designing, building and installing a bespoke bogie drop at the Canton rail depot in Cardiff, on behalf of Transport for Wales (TfWRL).
The custom-made unit enables bogies to be changed without decoupling trains, saving valuable maintenance time. It will be used to remove underframe equipment, including bogies, wheelsets, transformers and cooling units, from the diesel and trimode class 231/756 Stadler Flirt vehicles that are being introduced on South Wales Metro services. It will also accommodate all of TfWRL’s existing rolling stock.
The Canton bogie drop will enable underfloor units to be changed at track level, whilst allowing traffic to move freely when it is not in use. It has a rollover capacity of 60 tonnes and incorporates mini jacks that act as car body supports, to accommodate Stadler’s articulated bogies.
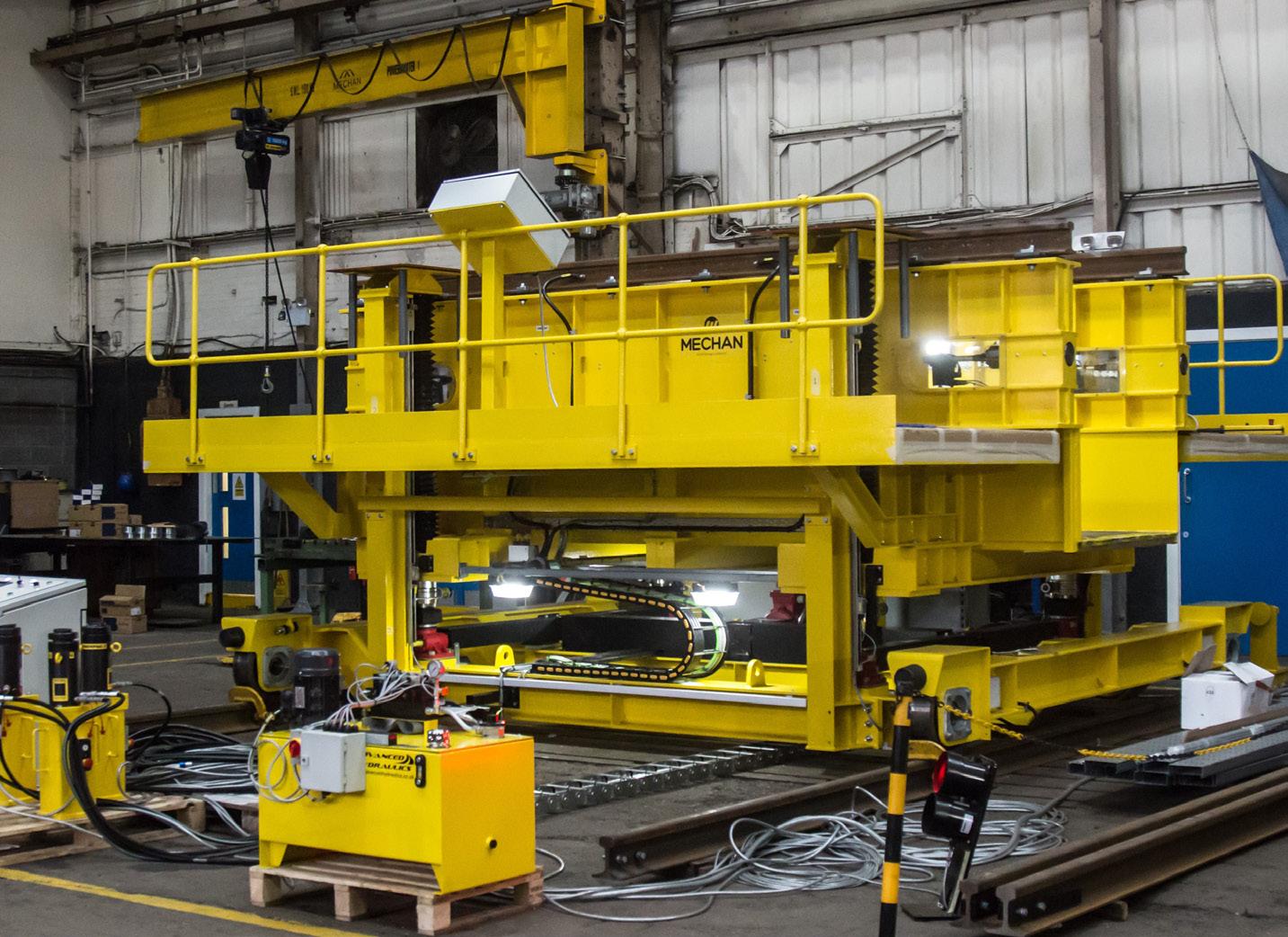

HUBER+SUHNER Success at the 2023 Reader’s Choice Awards
The SENCITY® Rail ACTIVE Rooftop antenna from HUBER+SUHNER has beaten competition from across the globe to be named ‘most innovative product’ at the 2023 Progressive Railroading Reader’s Choice Awards. The 50,000 readers of Progressive Railroading’s Daily News were asked to rank products submitted by suppliers in terms of innovation, standing out and meeting industry needs.
Developed in partnership with McLaren Applied, the SENCITY® Rail ACTIVE Rooftop antenna is a first-of-its-kind, 5G-ready omnidirectional solution, with an integrated edge compute module, Wi-Fi access point, GNSS receiver and cellular radios. Providing power and data via a single ethernet cable, the antenna has been designed to overcome the traditional challenges of railway applications, delivering highly performant connectivity for both on-vehicle data offloading and enhanced passenger Wi-Fi. It is certified for the EN 50155, EN 45545-2 and NFPA-130 standards.
The SENCITY® Rail ACTIVE Rooftop antenna simplifies deployment of train-to-ground systems on trains without the need for RF cabling, instead replacing them with just a single POE cable. The removal of RF cables also means that RF losses are reduced, improving the signal strength to the train and significantly improving the connectivity capability onboard. In addition, the antenna, with its integrated edge computing capability, enables rail operators to remove the need for a standard router in the train itself. As a result, rail operators can deliver reliable communication regardless of environmental factors, saving crucial space, money and overall vehicle weight during installation.
Progressive Railroading is the leading magazine for the North American Railroad industry. Published twelve times per year, each issue provides information on trends, technology, and industry news covering all disciplines of the railroad market. The Reader’s Choice Awards program is designed to highlight products that best meet the rail industry’s needs, as selected by their subscribers.
CWE Ltd and DB Cargo UK Strengthen Relationship with New Framework Agreement
CWE Ltd, an independent supply, maintenance, and logistics partner to the rail industry, has signed a twelve-month framework agreement with DB Cargo UK, one of the UK's largest rail freight operators. The agreement, facilitated by CWE's Centre of Excellence for Rail, will offer new and refurbished parts and services for DB Cargo UK's freight locomotives and wagons.
CWE’s business strategy and sustainable practice centres around repairing, overhauling, and reusing reconditioned parts instead of newly manufactured ones, wherever possible. This commitment ensures that CWE reduces waste and carbon emissions in its operations, which is then passed on through the supplier chain via framework agreements, without compromising reliability or durability.
CWE’s operational approach aligns perfectly with DB Cargo UK's goal of providing sustainable and innovative rail logistics solutions to its customers. The framework agreement will assist DB Cargo UK in delivering its strategy and support CWE’s commercial growth.
It is CWE and DB Cargo UK's first arrangement of this kind and is an extension of a strong existing customer relationship built by CWE Commercial Manager, Ricky Ravenhill and Sam Stewart, Procurement Manager at DB Cargo UK. The partnership will ensure that more parts and services are readily available, reducing downtime and assisting in the movement of the 36.7 million net tonnes of goods transported by DB Cargo UK annually.
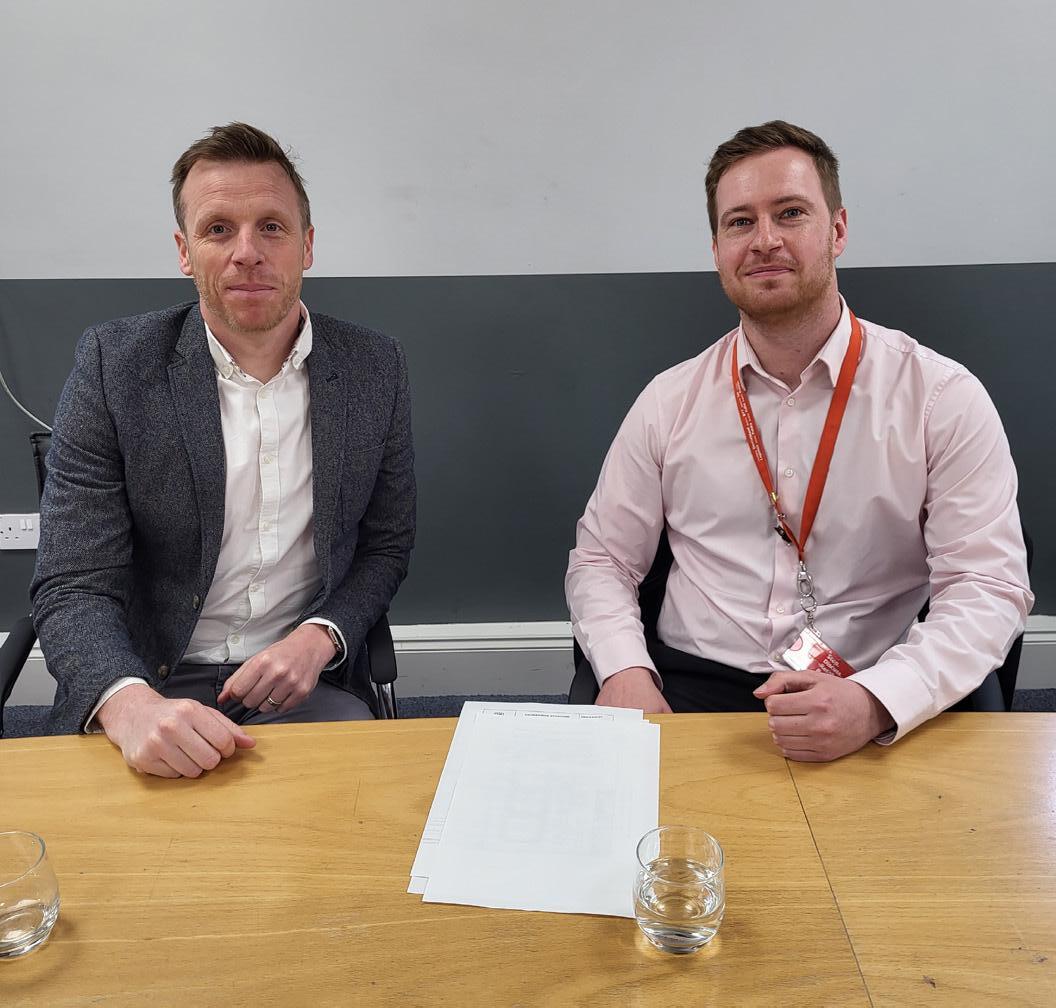
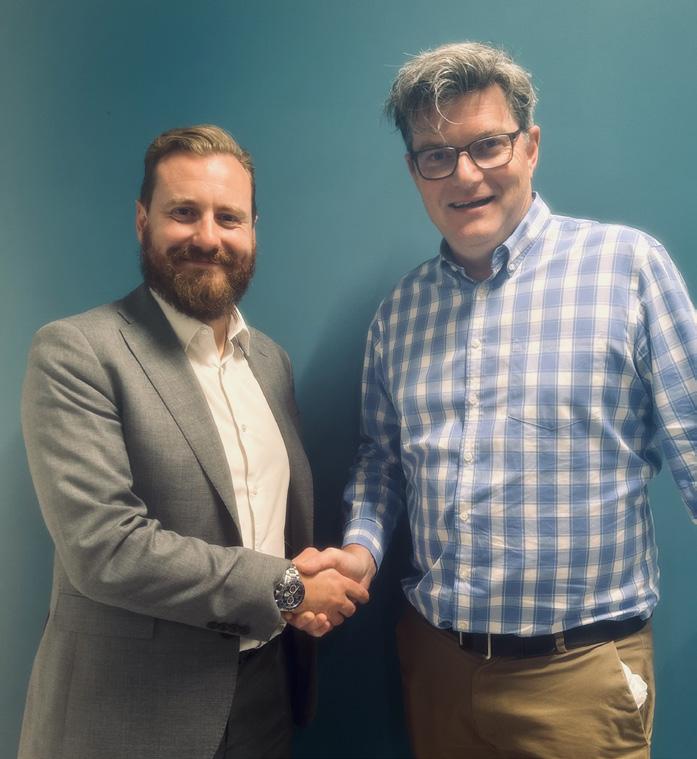
GCRE make ‘critical’ appointment
GCRE Limited has further strengthened its executive team with the appointment of Rob Forde as the company’s new Director of Strategy and Skills.
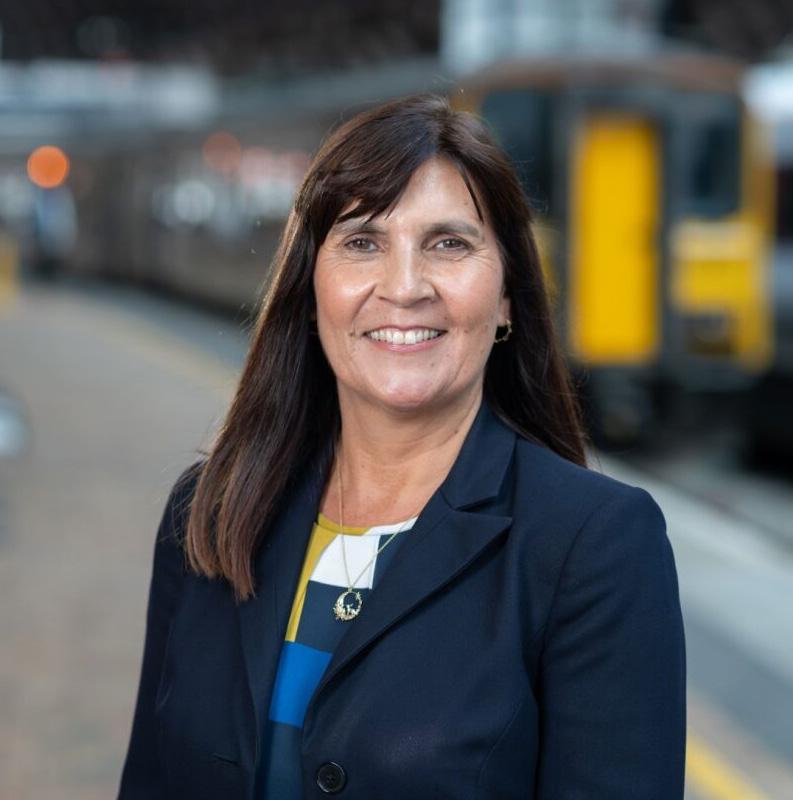
Northern appoints new Managing Director
Train operator, Northern, will be appointing Tricia Williams as its new Managing Director. Tricia, who is currently Northern’s Chief Operating Officer, will take over from Nick Donovan when he steps down from his role in spring 2024.
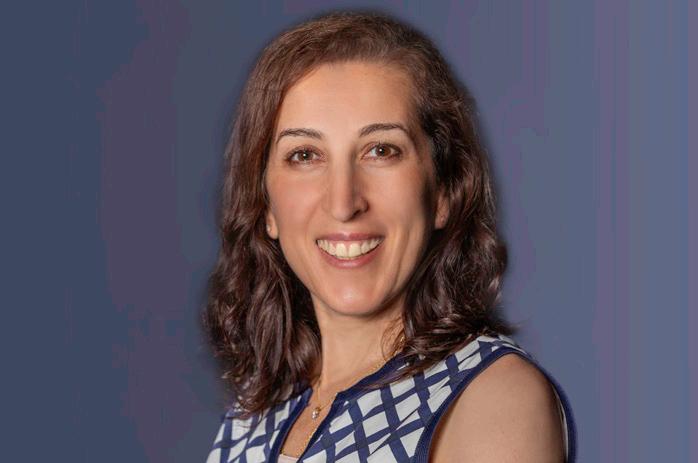
New Commercial Director appointed at rail operator c2c
Trenitalia c2c has appointed Eleni Jordan as its new Commercial Director as the rail operator continues to bolster its focus on collaboration with key businesses, partners and communities along its route.

New Merseyrail Managing Director named Neil Grabham has been named as the new Managing Director of Merseyrail.
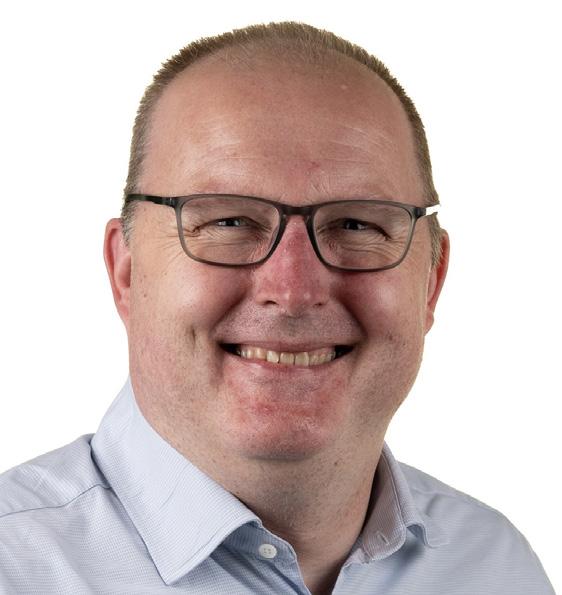
New Managing Director for Network Rail's Eastern region
Jake Kelly, currently the company’s system operator Director, has been appointed as the new Managing Director of its Eastern region, starting the role on 4 September.
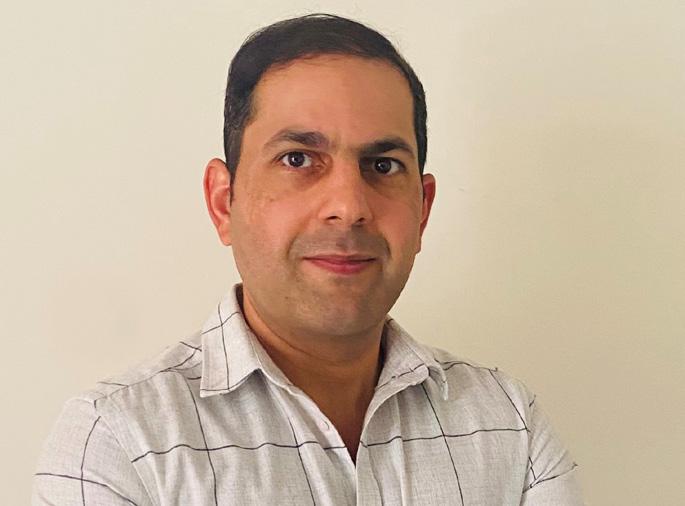
DB Cargo UK appoints new transformation and digitalisation champion
DB Cargo UK has appointed Rohan Kapoor (BEng, MBA) as new Chief Transformation and Digitalisation Officer as part of its plans to further improve the company’s operational efficiency and customer service.
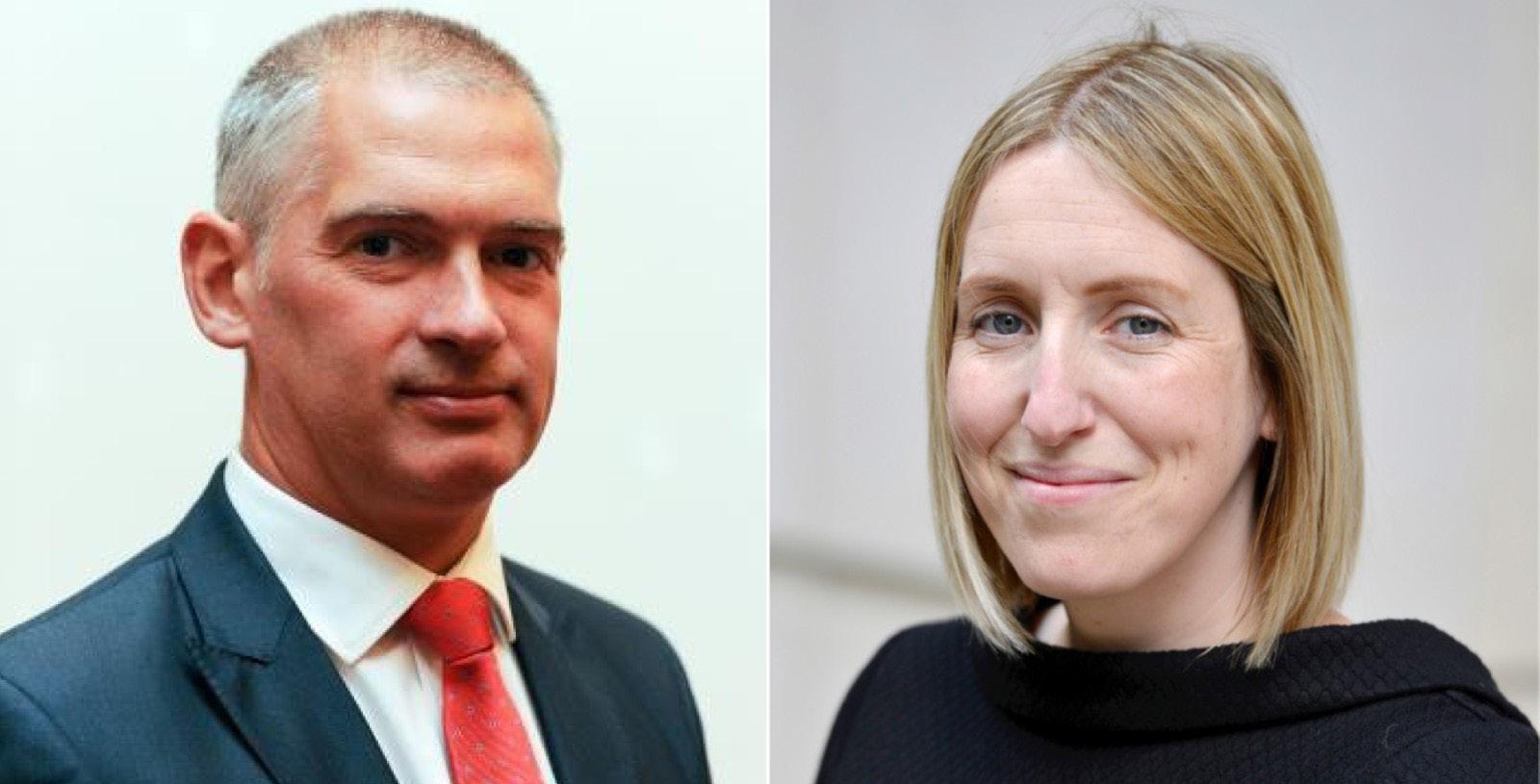
Network Rail announces new permanent senior appointments
Network Rail has appointed two regional Managing Directors to lead the Southern and North West & Central regions. Ellie Burrows has been appointed as the permanent regional Managing Director for Network Rail’s Southern region. Ellie has been in the regional Managing Director role for the Southern region on an interim basis since January this year. Rob McIntosh has been appointed as the new regional Managing Director for the North West & Central region.
A Business Built For Rail
Torrent Trackside is the only dedicated rail plant hire company in the UK Our 8 depots provide full UK coverage We have a near 100% reliability record and are one of the most compliant and safety focussed businesses in the industry We are committed to investing in the latest battery powered tools and equipment which provide outstanding levels of power and efficiency The advantages of battery power include:
l Zero emissions - better for the environment and safer for the operator
l Instant power at the flick of a switch - no tugging on pull cords
l Significant reduction in HAVs - up to 80% for some tools
l Simple recharging with long run times, no carrying heavy fuel, spillages or mixing errors
l Battery tools are smaller, lighter and easier to transport
l Quieter than petrol tools - ideal for built up residential areas and night work
For details visit our website or contact our hiredesk
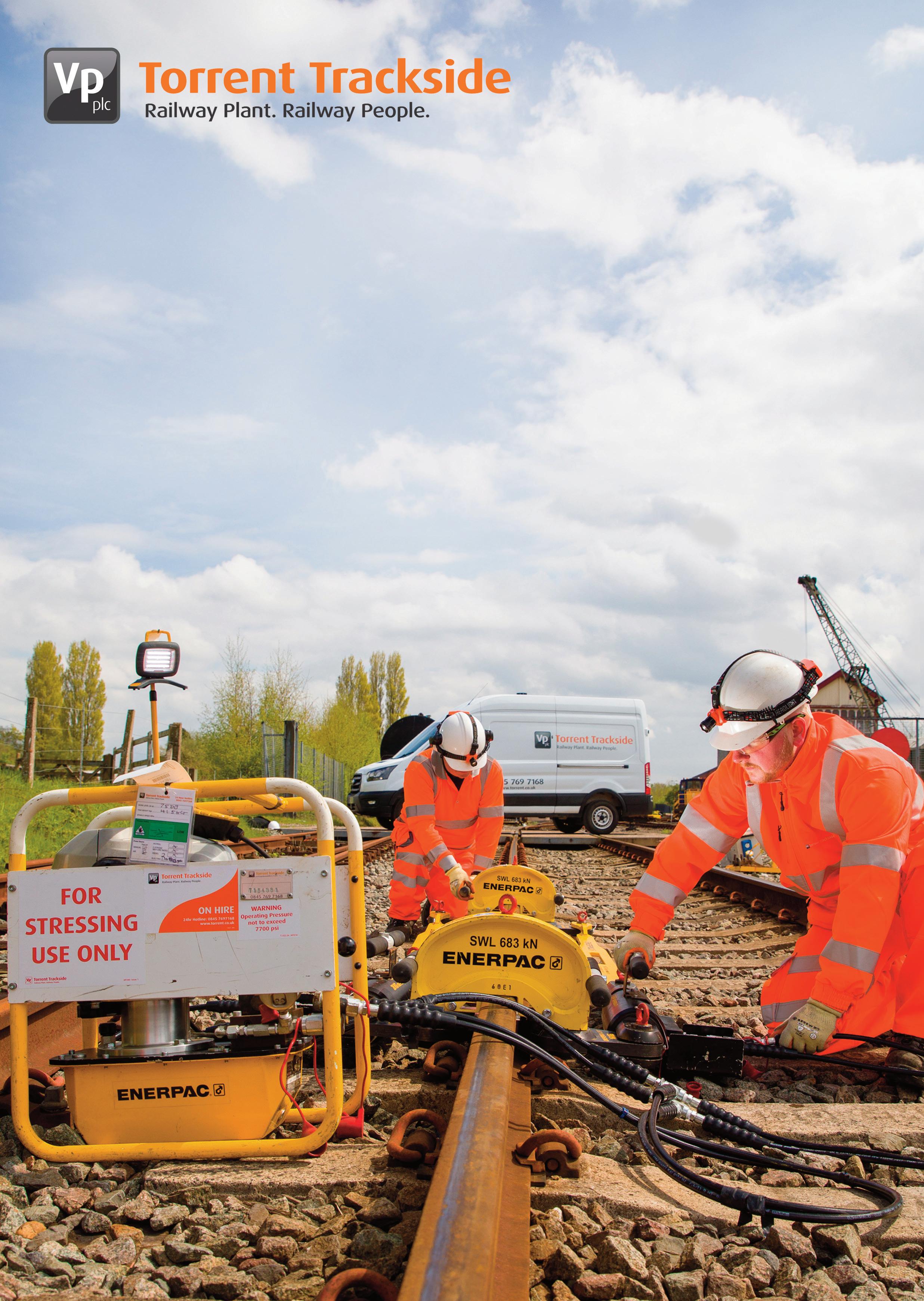



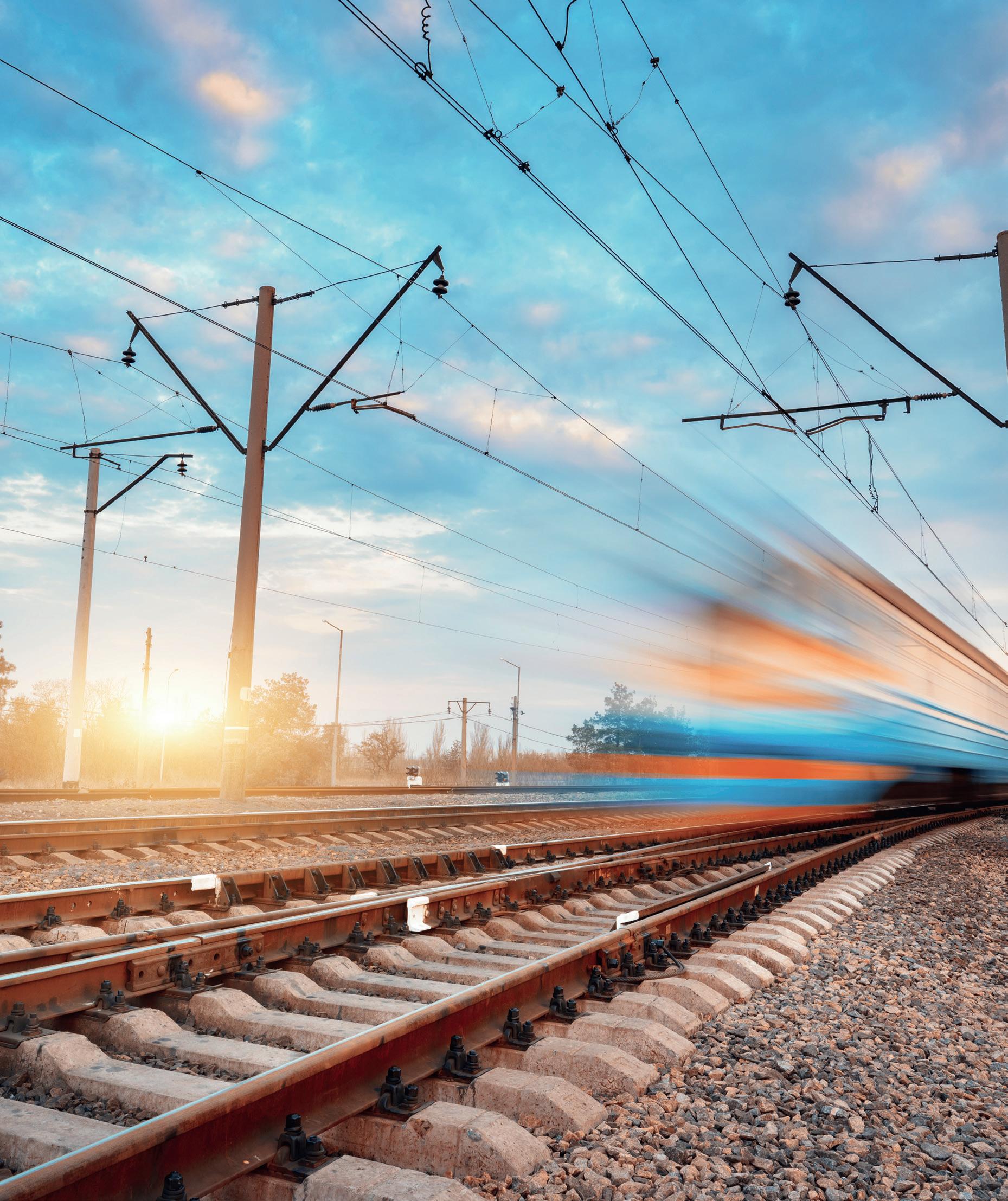
Delivering a bright energy future for high speed rail
We are experts in delivering network reliability for high speed railways through whole-life asset management. We own the total solution and its performance.
A reliable service makes travel more convenient, easier for passengers to plan journeys and gives them confidence they will arrive on time.
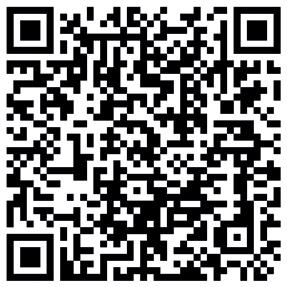
Scan here to get in touch