SERVING THE RAILWAY INDUSTRY SINCE 1856
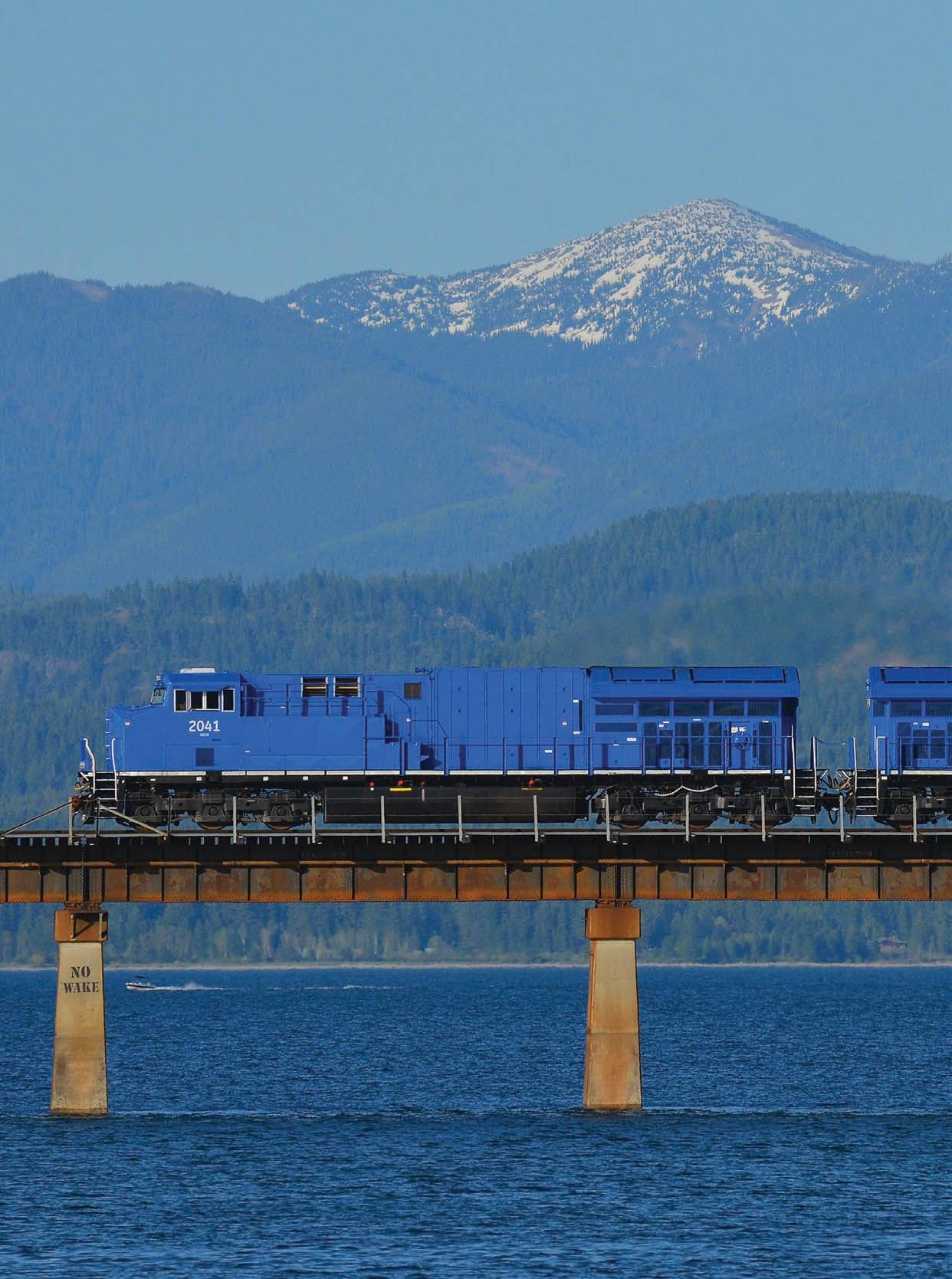
RAILINC FREIGHT CAR FLEET STATISTICS New Cars Trend Large TECH FOCUS – M/W Crosstie Developments
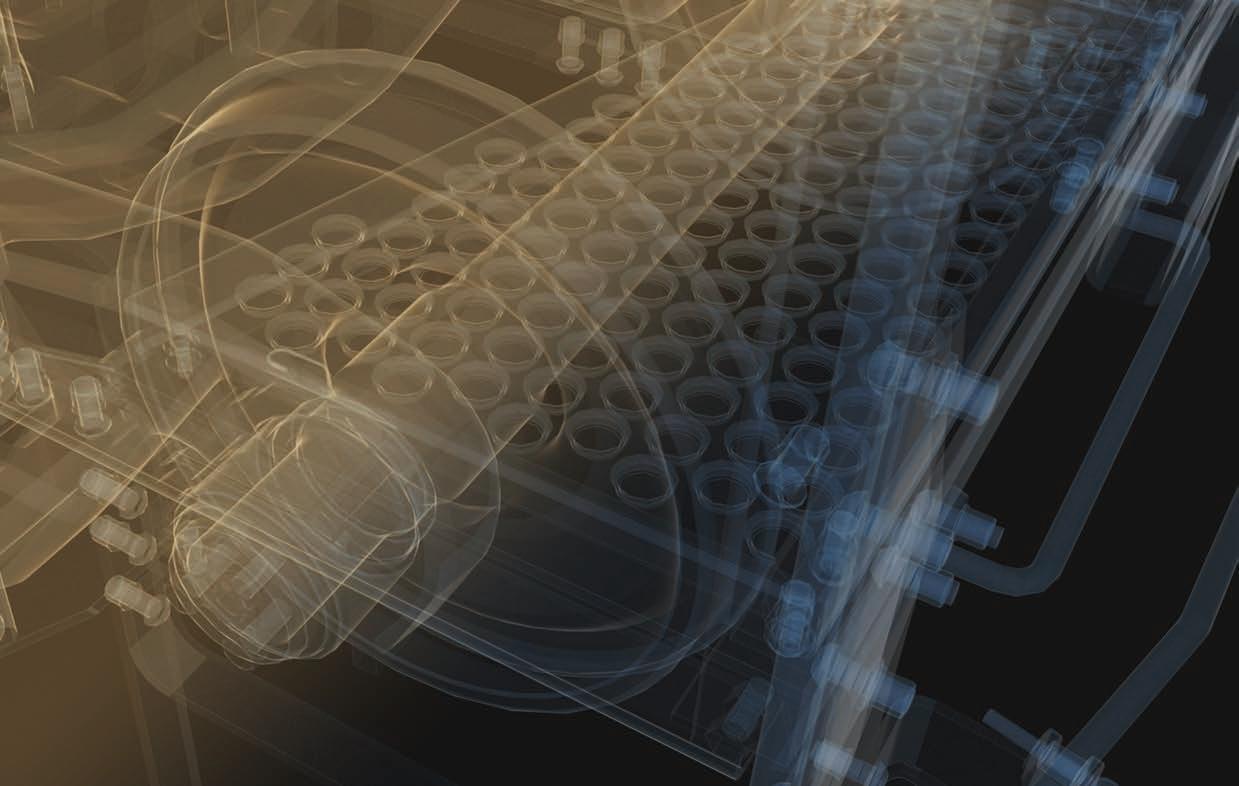
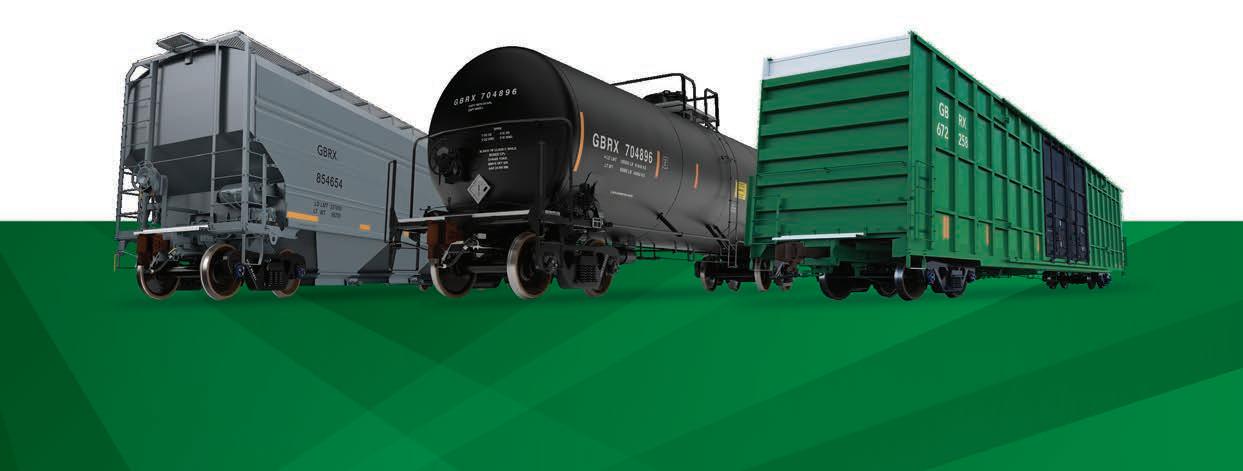
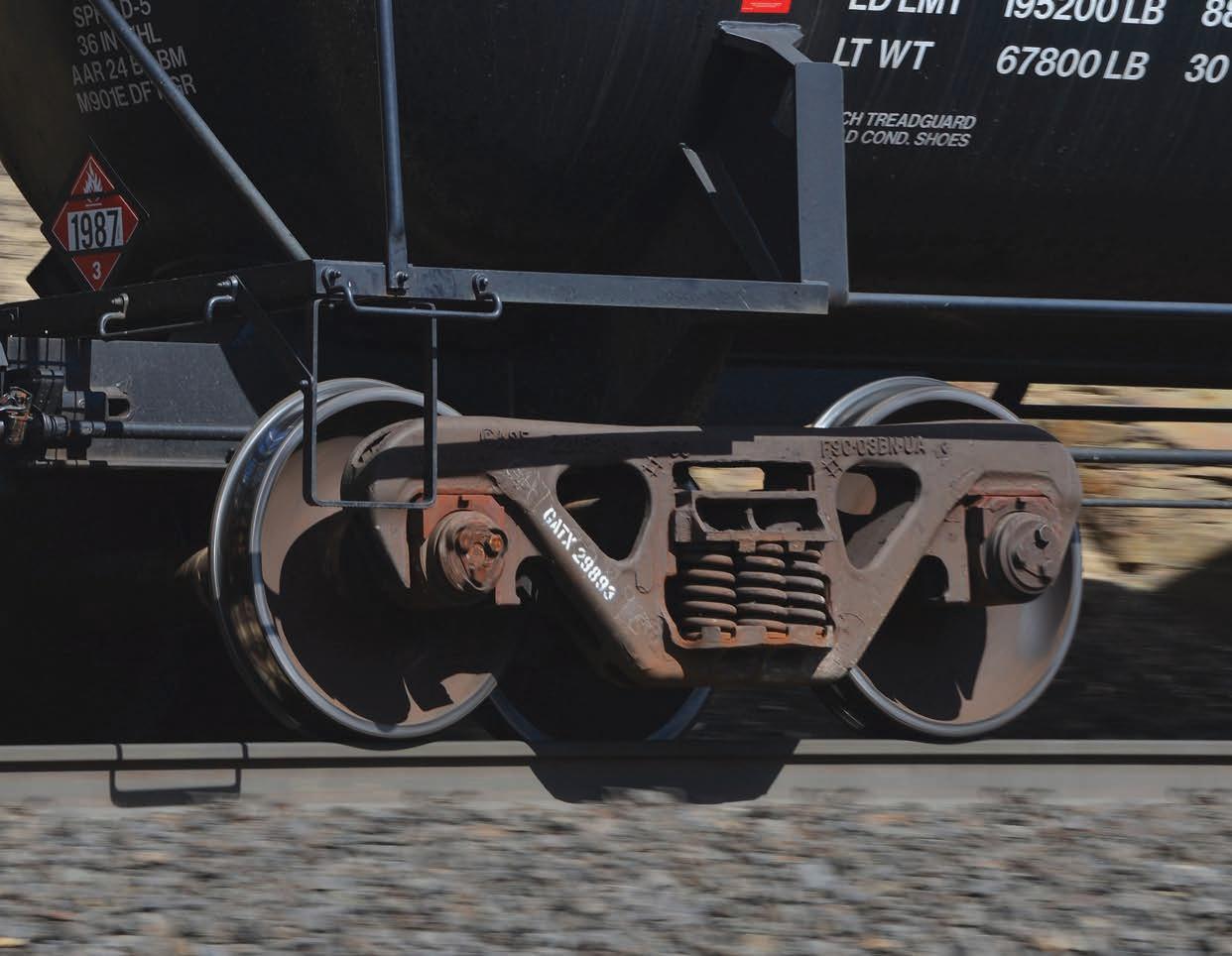
SERVING THE RAILWAY INDUSTRY SINCE 1856
RAILINC FREIGHT CAR FLEET STATISTICS New Cars Trend Large TECH FOCUS – M/W Crosstie Developments
It works in London.
It works in Stockholm. It works in Singapore. It works in Gothenburg, It works in Milan. Now, it’s working in New York City, in its first month netting more than $40 million based on revenues of nearly $52 million—right in line with projected annual figures. Ha!
“It” is congestion pricing, which the New York MTA calls “Congestion Relief Zone (CRZ) tolling.” According to the MTA, 24% of CRZ revenues comes from taxis and forhire vehicles, 66% from private passenger vehicles, 9% from trucks, and 1% from buses and motorcycles; 95% of revenue was gathered during peak tolling hours.
To understand the “dismal science” (economics) behind congestion pricing, I turned to Wikipedia: “It is a concept from market economics (double dismal!) regarding the use of pricing mechanisms to charge users of public goods for the negative externalities generated by peak demand in excess of available supply. Its economic rationale is that, at a price of zero, demand exceeds supply, causing a shortage, and that the shortage should be corrected by charging the equilibrium price rather than shifting it down by increasing the supply. Usually this means increasing prices during certain periods of time or at places where congestion occurs; or introducing a new usage tax or charge when peak demand exceeds available supply in the case of a tax-funded public good provided free at the point of usage.”
I think I get it. In any case: “According to the economic theory behind congestion pricing, the objective of this policy is use of
the price mechanism to make users more aware of the costs they impose upon one another when consuming during peak demand, and that they should pay for the additional congestion they create, thus encouraging the redistribution of the demand in space or in time, or shifting it to the consumption of a substitute public good; for example, switching from private transport to public transport.” (Emphasis mine.)
Ebbene, cosa ne sai! Doing something for the public good! What a concept!
Continuing: “Implementation of congestion pricing has reduced traffic congestion in urban areas, reduced pollution, reduced asthma and increased home values, but has also sparked criticism and public discontent. Critics maintain that congestion pricing is not equitable, places an economic burden on neighboring communities and adversely affects retail businesses and general economic activity.”
Finally: “There is a consensus among economists that congestion pricing in crowded transportation networks, and subsequent use of the proceeds to lower other taxes, makes citizens on average better off. Economists disagree over how to set tolls, how to cover common costs, what to do with any excess revenues, whether and how ‘losers’ from tolling previously free roads should be compensated, and whether to privatize highways.”
OK, listen up: You wanna drive into the Big Apple, Midtown Manhattan? You gotta pay up! Capire? As for me, I’ll take the subway, grazie mille. You gotta problem with that?
WILLIAM C. VANTUONO Editor-in-Chief
Railway Age, descended from the American Rail-Road Journal (1832) and the Western Railroad Gazette (1856) and published under its present name since 1876, is indexed by the Business Periodicals Index and the Engineering Index Service.
Name registered in U.S. Patent Office and Trade Mark Office in Canada. Now indexed in ABI/Inform.
Change of address should reach us six weeks in advance of next issue date. Send both old and new addresses with address label to Subscription Department, Railway Age, PO Box 239, Lincolnshire IL 60069-0239 USA, or call (US, Canada and International) 847-559-7372, Fax +1 (847) 291-4816, e-mail railwayage@omeda.com. Post Office will not forward copies unless you provide extra postage.
POSTMASTER: Send changes of address to: Railway Age, PO Box 239, Lincolnshire, IL 60069-0239, USA.
Photocopy rights: Where necessary, permission is granted by the copyright owner for the libraries and others registered with the Copyright Clearance Center (CCC) to photocopy articles herein for the flat fee of $2.00 per copy of each article. Payment should be sent directly to CCC. Copying for other than personal or internal reference use without the express permission of Simmons-Boardman Publishing Corp. is prohibited. Address requests for permission on bulk orders to the Circulation Director. Railway Age welcomes the submission of unsolicited manuscripts and photographs. However, the publishers will not be responsible for safekeeping or return of such material.
Member of:
SUBSCRIPTIONS: 847-559-7372
EDITORIAL AND EXECUTIVE OFFICES
Simmons-Boardman Publishing Corp. 1809 Capitol Avenue Omaha, NE 68102 (212) 620-7200 www.railwayage.com
ARTHUR J. McGINNIS, Jr. President and Chairman
JONATHAN CHALON Publisher jchalon@sbpub.com
WILLIAM C. VANTUONO Editor-in-Chief wvantuono@sbpub.com
MARYBETH LUCZAK Executive Editor mluczak@sbpub.com
CAROLINA WORRELL Senior Editor cworrell@sbpub.com
DAVID C. LESTER
Engineering Editor/Railway Track & Structures Editor-in-Chief dlester@sbpub.com
JENNIFER McLAWHORN
Managing Editor, RT&S jmclawhorn@sbpub.com
HEATHER ERVIN
Ports and Intermodal Editor/Marine Log Editor-in-Chief hervin@sbpub.com
Contributing Editors
David Peter Alan, Jim Blaze, Nick Blenkey, Sonia Bot, Bob Cantwell, Alfred E. Fazio, Justin Franz, Gary Fry, Michael Iden, Don Itzkoff, Bruce Kelly, Joanna Marsh, David Nahass, Jason Seidl, Ron Sucik, David Thomas, Frank N. Wilner
Art Director: Nicole D’Antona Graphic Designer: Hillary Coleman
Corporate Production Director: Mary Conyers
Production Director: Eduardo Castaner
Marketing Director: Erica Hayes Conference Director: Michelle Zolkos
Circulation Director: Joann Binz
INTERNATIONAL OFFICES
46 Killigrew Street, Falmouth, Cornwall TR11 3PP, United Kingdom 011-44-1326-313945
International Editors Kevin Smith
ks@railjournal.com
David Briginshaw db@railjournal.com
Robert Preston rp@railjournal.com
Mark Simmons msimmons@railjournal.com
CUSTOMER SERVICE: RAILWAYAGE@OMEDA.COM , OR CALL 847-559-7372
Reprints: PARS International Corp. 253 West 35th Street 7th Floor New York, NY 10001
212-221-9595; fax 212-221-9195 curt.ciesinski@parsintl.com
“Uncertainty shapes economic cycles—fueling booms, triggering busts, and driving debates about what comes next,” the Association of American Railroads reported last month. “Uncertainty abounds in the railroad industry, too, where evolving demand, market conditions, and economic policies constantly create both challenges and opportunities. The medium- and long-term impacts of today’s evolving economic policies—encompassing tariffs, regulations, taxes, and more—remain uncertain. What is clear, however, is that the rail industry must be able to adapt as conditions change. For now, both rail traffic and the broader economy reflect a mix of strengths and weaknesses, with some sectors proving resilient while others struggle in the face of shifting conditions.” In February, intermodal performance was again strong, with volumes rising 6.4% (66,340 units) yearover-year. Originations averaged 276,654 units per week, the most ever for a February. “This strength reflects solid consumer spending and, in part, efforts by some importers to expedite shipments in anticipation of tariffs,” AAR noted. Through the first two months of 2025, total intermodal volume rose 8.5% and container volume rose 9.5%. Year-to-date container volume was the highest ever for this period. “Continued intermodal growth will depend on sustained consumer spending, which hinges on a robust labor market and could be shaped by changes in U.S. trade policy,” AAR said. U.S. railroads originated 843,618 carloads in February, down 4.5% from last year. Carloads rose fractionally in January, their first increase in five months. In February, severe floods in the Northeast and frigid temperatures in the upper Midwest and much of the rest of the country constrained rail operations and the ability of rail customers to load and unload freight. “Without these weather issues, rail volumes likely would have been higher,” AAR said. For the first two months of 2025, total U.S. rail carloads were down 2.0%, or 37,584 carloads, from the same period in 2024, reflecting ongoing softness in key industrial sectors and the weather-related disruptions. In February 2025, six of the 20 carload categories the AAR tracks had yearover-year carload gains, led by nonmetallic minerals and paper products. Grain mill products, which include products such as soybean meal, corn syrup, and dried distillers grains, saw their 13th straight gain in February. Year-over-year carloads of chemicals rose for the 18th straight month, “reflecting the competitive advantage to U.S. chemical producers provided by low U.S. natural gas prices.” Coal, by far the highest-volume carload commodity, saw carloads fall 8.2% in February, their 14th consecutive monthly decline. Coal’s share of U.S. electricity generation fell to 15.2% in 2024—“a modern-era low.” Still, with U.S. electricity generation setting a record
in 2024 and demand expected to continue growing, some previously scheduled coal plant shutdowns have been delayed or canceled. “This won’t reverse coal’s long-term decline, but it could lead to incremental increases in rail coal shipments.” Grain carloads fell in February—their 5.8% decline was the first after a year of increases. Grain carload gains in 2024 were closely linked to grain export gains.
OMNITRAX OHIO RAIL AFFILIATE NEWBURGH & SOUTH SHORE RAILROAD (NSR) ON MARCH 21 PLACED A BATTERY-ELECTRIC LOCOMOTIVE (BEL), THE AMPS TRACTION G9, INTO REGULAR LINEHAUL REVENUE SERVICE. OmniTRAX describes its deployment as a first in the U.S.
The 125-ton AMPS Traction G9, numbered 1234, was introduced in November 2023 and recently completed testing. It is “designed to significantly reduce fuel consumption and emissions while maintaining the efficiency and reliability required for freight operations.” The locomotive is dedicated to the memory of Steve Ward, OmniTRAX’s longest-serving employee and former Division Engineer, who oversaw track safety and maintenance for 27 years until his passing in 2021.
The locomotive, one of two NSR units (the other is a conventional SW-1200 dieselelectric), was rebuilt by AMPS Traction LLC from an EMD GP-9 that had previously been converted into a “light hybrid” genset, according to AMPS Traction President and Co-owner Doug Bardwell. Its LNMC (Lithium Nickel Manganese Cobalt Oxide) batteries provide 1.2 MwH of usable power
(based on 1.4 MwH of onboard power), or 1,700 gross horsepower, allowing the locomotive to operate up to 12 hours on a single charge, depending upon tonnage hauled. This extends battery life, Bardwell explains. NSR operates a single daylight hours shift, so charging is accomplished overnight with CCS1 (Combo Charging System) DC Fast Charging equipment in just under eight hours. The batteries are liquid cooled. A patent-pending impulse absorption system with vertical and longitudinal springs protects the batteries from shocks encountered during switching/coupling and other in-train forces.
This project was made possible through a grant from the Ohio Environmental Protection Agency Diesel Mitigation Trust Fund, which supports initiatives that improve air quality by reducing diesel emissions. OmniTRAX collaborated with the Federal Railroad Administration on the deployment. NSR was selected as a grantee from the $75 million Diesel Mitigation Trust Fund, overseen by the Ohio EPA.
“This is a transformative moment for the rail industry,” said Kayden Howard, OmniTRAX Senior Vice President of Health, Safety and Environmental Programs. “For the first time, a battery-electric locomotive
is moving freight in regular, revenue-generating service. We are proving that sustainable rail operations are not just a concept for the future—they are happening right now. This milestone will help accelerate the adoption of zero-emission technologies across the industry.”
“This deployment reinforces our commitment to innovation and environmental responsibility,” said Sergio Sabatini, President and CEO of OmniTRAX. “We are proud to lead the way in bringing cuttingedge, sustainable solutions to freight rail, reducing emissions and delivering realworld benefits to the communities we serve.
OmniTRAX continues to explore and implement sustainable rail solutions, furthering its leadership in innovation and environmental stewardship.”
Based in Cuyahoga County, Ohio, NSR serves rail customers in the greater Cleveland area, hauling steel, aggregates and chemicals and offering transloading and railcar storage. Originally built and opened in 1904 as one of several railroads in Ohio to serve U.S. Steel’s Cleveland area steel mills, NSR operates five route-miles and 13 track-miles, interchanging with Norfolk Southern, CSX, Cleveland Works Railway and Wheeling & Lake Erie.
Wabtec Corp. has entered into a definitive agreement to acquire Sweden-based Dellner Couplers for $960 million in cash, financed through cash on hand and shortterm debt. The acquisition, Wabtec said, is “anticipated to provide immediate shareholder value with an accretive growth profile, accretive Adjusted EBIT margins, accretive Adjusted EPS in the first year of ownership and accretive return on invested capital (ROIC) over time.” The transaction is subject to customary closing conditions and regulatory approvals. “The purchase price reflects an estimated multiple of 12.5x projected 2025 EBITDA adjusted for transaction costs and projected run-rate cost synergies of $22 million which we expect to be realized over a three-year period,” Wabtec noted. “Dellner Couplers is expected to generate approximately $250 million of revenue in 2025 and expected growth that will exceed the company’s average growth over the next five years.” Dellner Couplers is an 84-year-old supplier of highly engineered safety-critical train connection systems and services for passenger rail rolling stock. With a global installed base of approximately 100,000 couplers and 12,500 gangways, it provides an extensive offering in train connection systems, with production, assembly and aftermarket services facilities in 13 countries serving more than 200 customers.
STADLER US will use ABB traction converters and batteries for the new trainsets it is building for METRA commuter rail in Chicago and for future CALTRANS
VALLEY RAIL passenger service between Merced and Sacramento, Calif., ABB reported last month. Metra, in 2024, awarded a contract to Stadler US for zero-emission, battery-electric (BE) single-level trainsets. The contract included a $154 million base order for eight two-car BE trainsets, including engineering, training, and spare parts, with options costing up to an additional $181.4 million for eight more trainsets and up to 32 trailer cars, which could be added to the two-car trainsets to create three- or fourcar trainsets. STV was recently selected to provide quality assurance, engineering and administrative services for the base order. The first trainsets are expected to be delivered in 2027-2028. According to ABB, each of the base order trainsets will be equipped with Pro 8C batteries and CC750 DC traction converters. ABB said its traction converters are “designed for high efficiency and reliability, working to optimize the performance of the trainsets, while the battery system will further enable Metra to reduce CO2 emissions.” Caltrans has signed
contracts with Stadler US for a total of 10 zero-emission HFC (hydrogen fuel cell) FLIRT H2 trainsets. In 2023, it awarded an $80 million base contract for four trainsets, with an option for 25 more, and in 2024, exercised an option for six additional trainsets, valued at $127 million. The first four-car trainsets are expected to enter revenue service in 2027. They are to run between Merced and Sacramento on the future Valley Rail service, an expansion of the existing ALTAMONT CORRIDOR EXPRESS (ACE) regional/ commuter rail and AMTRAK San Joaquins services that will eventually connect with the first section of California High-Speed Rail, which will stretch 171 miles between Merced and Bakersfield. ABB said it will supply Pro 8C traction batteries, CC750 DC traction converters, and CC400 DC traction converters for each of the 10 trainsets now on order for Caltrans. “The traction converter for fuel cell integration is essential in hydrogen-powered trains, enabling efficient propulsion that reduces power usage and emissions,” the supplier noted. Final assembly and testing of all ABB components will be conducted at its Traction factory in Mechanicsville, Va., which employs nearly 100 skilled production workers.
PSC GROUP (PSC), a provider of logistics and repair services to the chemical, refining, agricultural and pulp and paper industries, last month announced that it is expanding its railcar business through the acquisition of 32 RESCAR operations located across the U.S. Founded in 1969, Rescar offers repair, inspection, cleaning, switching and maintenance services for railcars and ISO containers. Following this acquisition, PSC’s second since recapitalizing with TJC and following the DELTA PETROLEUM acquisition completed in 2024, the company’s combined railcar repair, cleaning and inspection business will span 40 states and provide on-site mini-shop repair service to 35 different facilities and will operate a network of 25 mobile repair hubs with more than 100 mobile repair trucks. According to Houston, Tex.-based PSC, which also owns and operates a network of transloading and advanced recycling infrastructure to support chemical manufacturers in North America, the company’s repair offerings include tank car and service equipment qualification, lining and coating repair, railcar cleaning, railroad repair agents, inspection services, and freight car running repairs. PSC’s Railcar Repair Headquarters will be housed at its Bayport Rail Terminal, Houston.
As the dust settles following a tendentious Federal Railroad Administration (FRA) superintendency of Amit Bose, stakeholders await a successor— presumably, White House nominee David Armstrong Fink, a former president of regional Pan Am Railways (now part of CSX), who awaits Senate confirmation.
If the FRA, whose primary mission is rail safety regulation, is not to be the partisan inverse of what it allegedly was under Bose—an employment agency for rail workers at the expense of productivityenhancing innovative technology—the new Administrator must impartially follow factbased science and respect benefit-cost analysis. Quite simply, be technology-neutral and follow the rule of law.
As for FRA’s secondary role disbursing congressionally authorized grants for Amtrak, regional and short line railroads and rail safety programs, following the law may prove problematic. The President’s Cabinet members and agency heads so far appear chosen largely for unquestioned loyalty and are expected to exhibit vigor in an all-acceleration-andno-brakes legally questionable assault on funds Congress authorized.
No matter assurances the nominee may express in Senate confirmation hearings, FRA is an Executive Branch agency answerable to a President pursuing a unitary form of government with seeming unchecked power ceded to an unelected alter-ego— First Pal Elon Musk—DOGEdly overseeing a helter-skelter, chainsaw massacre of federal agencies.
Given that POTUS 47 and his First Pal have suspended federally funded domestic and international humanitarian aid and targeted funding for Social Security, Medicare and Medicaid—in contravention of congressional directives and due process— it is probable FRA headcount and funding cuts will occur.
Although as of late March the Department of Government Efficiency (DOGE) had not breached FRA’s headquarters, DOGE “whiz kids” (typically in their 20s
with masked identities) likely are delaying entry, pending arrival of the new Administrator—who will be expected by the POTUS to extend every hospitality.
At risk is some $41 billion in congressionally authorized program funding—$34 billion of which is earmarked over the next two years for Amtrak. The Supreme Court, with a record of indulging this President, eventually will rule whether the 1974 Impoundment Control Act, which prohibits such confiscation, means what it says.
Among FRA programs at risk of impoundment (dollar amounts in parenthesis) are:
• A mtrak grants for its National Network, Northeast Corridor restoration and enhancement, intercity route expansion, development of high-speed corridors and federalstate partnerships ($34 billion).
• C onsolidated Rail Infrastructure and Safety Improvement (CRISI) grants for rehabilitating or building rural-area freight rail infrastructure to improve safety, efficiency and reliability ($4 billion).
• R ailroad grade crossing elimination ($2.2 billion).
• Grants for railroad safety, research and development ($650 million).
FRA’s preeminent mission is promoting rail safety through rulemakings, accident
investigations, safety culture assessments, audits, standards settings, worker certifications and civil penalty enforcement.
It is alleged that President Biden’s FRA chief Amit Bose, in an effort to increase rail employment, diluted the agency’s safety mission by suppressing the transformative role of technology, whose positive externalities increase productivity and reduce costs—the sine qua non for railroads to meet customer expectations and compete with subsidized barges and trucks. At an event honoring Bose, two sources present say a rail union official called him “the Jesus” of rail labor.
The FRA, under Bose, mandated twoperson train crews, absent evidence the second on-board crew member increases train safety; established dispatcher and signal employee certification standards having negative benefit/cost ratios; impeded deployment of advanced train, air brake and track inspection technology; and failed to rule on carrier waiver requests to test new safety technology. Those actions are being challenged in federal courts as “arbitrary and capricious” in violation of federal law.
As for Bose’s two-person crew mandate, union officer dissidents support a carrierpreferred mutually beneficial collective bargaining approach to minimum crew size, citing opportunity to gain for members increased job security, higher wages, more predicable work schedules and greater job satisfaction. Reassigned ground-based conductors would utilize 21st century technology—drones, computers and artificial intelligence—to ensure operational safety, with FRA ensuring compliance.
If the new Administrator is sufficiently humble to seek advice, available are two highly respected fellow Republican former FRA Administrators—Allan Rutter and Ronald L. Batory. Rutter served as George W. Bush’s Administrator from 2001-2004, and Batory from 2018-2021 during the current President’s first term.
Rutter tells Railway Age that what keeps
every administrator up at night is “the black swan theory—a highly improbable event way down the bell curve of likelihood but with significant impacts.” For example, the 2005 Graniteville, S.C., misaligned switch crash resulting in release of chlorine gas killing nine and injuring hundreds; the 2002 Minot, N.Dak., derailment resulting in release of anhydrous ammonia killing one and injuring hundreds; and the February 2023 East Palestine, Ohio, derailment resulting in release of hazardous materials requiring thousands to be evacuated.
A new Administrator, says Rutter, should embrace transparency, recognizing that “security cameras, ubiquitous smart phones and drones” will provide extensive imagery on social media.
What is available to the new Administrator is artificial intelligence (AI) that Rutter only recently has been utilizing in his latest post at Texas A&M University’s Transportation Institute. AI, he says, “should help railroads and railcar owners move beyond defect detection to predictive maintenance [and assist inspectors] in completng reports with speed and accuracy. Its biggest promise could be in finding meaning amidst the flood of data being collected.”
Rutter supports granting project-specific waivers for relief from safety regulations as complementary to FRA research. “If you can find more bad-order cars through enroute technology than in the yard, there would be more work for carmen,” Rutter
says, citing an April 2019 Batory-issued waiver allowing BNSF to use wayside detectors for measuring wheel temperatures in determining brake-health effectiveness.
Between then and mid-2024, BNSF eliminated 11,215 inspection hours while providing carmen with 23,144 additional hours of repair work—“in shops rather than in yards in blistering heat and crippling cold,” Rutter says. Bose did not extend or expand the waiver as requested by BNSF.
The late Joseph Boardman, a Republican who also served as FRA Administrator (2005-2008) under Bush 43, told Railway Age in 2017 that an Administrator coming from the private sector needs a deputy “steeped in the ways of Washington’s inscrutable bureaucracy. If you don’t, you will waste too much time getting anything done.” Rutter credits his master’s degree in public administration and state government posts under four Texas governors, including Bush 43, as providing him with “professional bureaucrat training.”
Batory, a career railroader and President of two (Belt Railway of Chicago and Conrail) counsels listening to staff. “Employee opinion and expertise matter; the boss doesn’t always know best.” He also supports performance-based safety standards in place of prescriptive regulations—FRA establishing a desired outcome and carriers innovating to reach the goal. “Technology moves faster than the ink can be applied on regulations,” Batory says.
Rutter cautions the shift to performance standards “is a tough road for regulators [and] certainly a big leap for the rail industry because the consequences of rail incidents are so large.” A successful transition, he says, requires “common understanding” of data and “clearly stated standards to motivate repeatable safe behaviors.”
Into a POTUS 47-created chaotic and politically charged environment will step a new FRA Administrator whose job security depends on approval by a President who reacts menacingly to disagreement. Should much of congressionally authorized Amtrak funding and that for rail safety and rural area rail service be marched up a scaffold by DOGE, it’s going to take—to borrow a hockey term from our once-friends in Canada—an “elbows up” defense to save it.
Frank N. Wilner is author of “Railroads & Economic Regulation” and “Amtrak: Past, Present, Future,” each available from Simmons-Boardman Books at https://www. railwayeducationalbureau.com, 800-2289670.
FRANK N. WILNER
The 39th Rail Equipment Finance Conference, held March 2-5, 2025, reflected an atmosphere of cautious optimism in very uncertain (some say crazy) times, when what was thought to be the case one day makes a U-turn overnight. Here is a summary of the presentations, as well as the key takeaways.
John Orr (Norfolk Southern Chief Operating Officer), in a fireside chat with Railway Age Editor-in-Chief William C. Vantuono, discussed that increasing train velocity and decreasing loading dwell times are key NS objectives today. NS continues an ongoing pivot to service and safety and is implementing technology for customer and railroad benefit. Key notes: NS is implementing PSR 2.0— applying PSR principals while staying focused on growth.
REF’s “Railcar Guru,” Dr. David Humprey (Railinc), discussed annual changes in the national railcar fleet. Key takeaways: The fleet grew by 4,000 cars due to increases in tank railcars and covered hoppers. The boxcar fleet lost 3,000 cars in the same year. Thinking coal? Coal gondola cubic capacity has decreased 30% since 2009.
Brian Smalley (National Steel Car) addressed the railcar market from the perspective of a new railcar builder. Constrained demand for railcars continues with modest railcar storage levels and decreased loadings. Hot take: Since 2010, railcar labor and steel have increased roughly 50% and componentry has risen just over 25%.
Eric Starks (FTR) discussed the North American trade picture, why tariffs matter and how that might impact rail loads in 2025. The trade deficit between Mexico and Canada is mostly tied to commodity groups such as automotive, beverages and steel products. Key quote: (speaking of tariffs) “This is nuts! I feel like I am in a bad movie.”
Taylor Robinson (PLG Consulting) discussed the U.S. energy landscape. Loadings growth moving NGLs and resins is expected to continue through the coming years. Even with a trade war, U.S. NGLs
will find positive market traction for resale. Key takeaway: Chemicals, Propane/Butane and Renewable Diesel are markets expecting year-over-year (YOY) loadings growth.
Dan Anderson (TrinityRail) took stock of the tank car market. Commodities moved in tank railcars that generally have better rail modal share saw weakness in 2024 growth versus truck. One reason: Labor strikes forced preemptive action for rail borne high hazard commodities. Thinking growth? Over the past decade, only NGLs and refined products had a CAGR of more than 3%.
Sam Sexhus (Oliver Wyman) discussed the path for modal share growth for the railroads. Sad news? Since the pandemic and PSR, rail lost market share in all major commodity groups. Good news? There are (at least) three paths to growth: rail to truck conversion, intermodal growth and growth through short line railroads. Interesting takeaway: Without growth, transcontinental mergers may be required to boost railroad profitability.
Ron Sucik (RSE Consulting) weighed in on the intermodal market. Current intermodal issues include tariffs and goods stolen from intermodal trains. Insiders expect a pull forward of freight to avoid tariffs. Growth story? Current thinking projects a 7% YOY increase in intermodal loads; Sucik sees 4%.
Stefano Rieppi (NS) and Paddy O’Neill (Glynn Lane Consulting) talked about the steel market and trends in steel transportation equipment. Rieppi noted that NS is looking to replace older equipment with cars that use higher strength materials and asset utilization technology (such as RailPulse) and to increase car design standardization. O’Neill noted an increase in transverse vs. longitudinal coil cars since 2015 and sees value in mill gondola standardization. Scrap steel success: NS’ ultra-high-strength steel gondola car loads 231,000 pounds of product.
John Ward (National Coal Transportation Association) addressed the outlook on coal for 2025, noting that power grid disruption is causing generators to rethink closure plans on coal-fired generating
capacity. Global coal use and production increased in 2024 and is expected to increase in 2025. Burning news: Power generators believe that recent trends in railroad service have been positive with good volumes.
Doug Driscoll (Genessee & Wyoming), David Horowitz (GATX) and Anthony Petrillo (Packing Corporation of America/PCA) discussed the boxcar market. Horowitz noted that 7,800 boxcars had been scrapped in 2024. When asked how PCA could shift more freight to rail, Petrillo quickly answered, “Cost.” Driscoll described that G&W’s boxcar fleet as staying mostly level YOY, even as G&W replaced 1,000 older boxcars with newer cars.
Johanna Biggs (Biggs Appraisal), Sean Hankinson (Adaptive Rail), Pat Mazzanti (Railroad Appraisal), Greg Schmid (Residco) and Bryan Vaughn (Modern Rail) discussed the railcar equipment market. Biggs noted growth in large-cube covered hoppers and large-capacity tank railcars. In discussing valuations, the panel saw an increase in some car types but felt many values had reached valuation peaks. The panel felt that industry health was trending positively.
On Tuesday morning, Anthony “Tony” Hatch dug into whether the railroads would execute the often-promised pivot to growth in 2025. Intermodal has underperformed since 2014. An unsettled economy and a tariff ridden landscape are growth hindering concerns in 2025. Hot take: Although intermodal loads are underperforming, intermodal revenue has been larger than coal’s revenue since 2013.
Dr. Sergio Rebelo (Northwestern University), Tuesday’s Keynote speaker addressed some of the journalistic murkiness about deficits, immigration and tariffs. Trade imbalances have been and will continue to be useful tools that help to accelerate U.S. economic development. They are not things to be feared. The same is true for the value of immigrant labor to a workforce between the ages of 25-54 years old that is very close to being unable to fill all the jobs needed in today’s economy. Key takeaway: Encouraging
trade between nations has been viewed as a way to keep peace among those nations for almost 350 years.
Patrick Kurtz (AITX) dug into the covered hopper market, noting that food product loadings are following seasonal patterns and exhibiting growth while nonfood loadings are gently trending lower. There is potential enthusiasm for increased small-cube hopper demand from frac drilling. The 5,200cf and greater market maintains a 94% utilization rate. Hot take: Even with all of the growth in the covered hopper fleet, age-related retirements are outpacing new deliveries.
Paul Titterton (GATX) closed out the Tuesday program. He opined that recent (past three years or so) separation between lease rates and new car backlogs and deliveries indicates a supply-led recovery in the railcar market that is a new paradigm for the railcar industry. This thesis is backed by three primary conclusions: shorter railcar backlogs, fewer new car deliveries and more stable fleet dynamics. Key takeaway: Since 2008 to today, core carloads (except coal and intermodal) have stayed within a fairly narrow range of 1.6 million to 2.1 million car loads.
On Wednesday, Dr. David Humphrey (Railinc) again took the stage discussing the North American locomotive fleet. The national fleet grew by 100 units. Over the past eight years, an average of 290 new locomotives were brought into the fleet. Fun fact: Assuming a 25-year service life or a 15-year post rebuild life leaves roughly 1,000 locomotives at or near the end of their service life.
Don Graab (Triangle Brothers) discussed the current state of the locomotive market. The removal of the CARB locomotive regulations possibly pushes the alternative fuel shift in the U.S. back more than four years. However, in Canada the pursuit of alternative fuels will continue as a result of the Canadian Clean Air Act. Status quo alert: Graab sees neither a strong motivation for a large-scale build of today’s Tier IV locomotives nor a potential executive branch rollback of today’s EPA Tier IV emissions requirements.
Wayne Kennedy (Kennedy Consulting) got energized in discussing currently available strategies that can be expected to reduce greenhouse gas emissions for
the railroads today. Railroads, without making larger systemic changes, will struggle to meet SBTi goals they have set for the 2029-2034 timeframe. Not blowing smoke: Energy Management Systems can provide significant emissions improvements if the industry makes a commitment to the strategy.
Graciela Trillanes (HGmotive) provided an update from the leading alternative fuel tender provider in North America. The HGmotive hydrogen tender is operating successfully in revenue service on CPKC (moving coal!). Future tender designs will haul larger quantities of hydrogen (cryocompressed) or renewable natural gas. Now hear this: HGmotive is working on opportunities around the globe to deploy its technology.
Dr. Matthew Findlay (CPKC) discussed progress on the railroad’s successful alternative fuel program. CPKC sees the switch to alternative fuels as the heart of a strategy that reduces reliance on and the need for new locomotives. CPKC has partnered with CSX to put more units into service and has large-scale plans to move hundreds of fuel cell locomotives into service in the next five years. Clean getaway: CPKC’s refueling system creates a diesel-like experience, so the time refueling with hydrogen is similar to diesel.
Ryan Mueller (Progress Rail) discussed Progress’ locomotive products for battery hybrid road locomotives and battery switcher locomotives (BEL). Progress feels a battery hybrid locomotive can deliver greater tractive effort than a diesel-only locomotive. Rapid and easy to implement charging will help to increase demand for BEL lower horsepower units. Reuse redo: Progress notes that many existing locomotives can reasonably be converted to battery hybrid units.
Joseph Stack (Cummins Inc.) updated the audience on Cummins approach to engines in passenger and freight rail. The QSK95, Cummins’ flagship Tier IV compliant engine, continues to operate successfully worldwide. Cummins is continuing to develop its fuel-agnostic engine that could burn any of hydrogen, diesel, or natural gas. Hot tip: Cummins notes that there are unprecedented levels of grant money available for emissions conversion projects.
Joel McNeil (Brookville Equipment)
highlighted the pros and cons of different fueling methods at play in today’s locomotive market. In the market for fuel supremacy, legacy diesel’s ease of use and reliability will continue prominence until alternative fueling infrastructure is put in place. Hot take: Long term, battery power will be most useful for shorterhaul applications.
Jason Kuehn (Oliver Wyman) issued a call for the railroad industry to continue to address the need for locomotive fueling and technology improvements to remain competitive with trucking. Battery technology, including utilizing regenerative braking, will help to push technology improvements into standard service. BEL units need to make larger inroads in the freight market. Hot take: The last largescale technology change in locomotive power was implementation of AC traction motors more than 30 years ago.
Stuart Biggs (Biggs Appraisal) updated the new locomotive order book. There are a projected 309 units being rebuilt through 2025 mostly from the Dash 9-44CW. The largest new unit increase came from Wabtec. Key takeaway: Rebuild units outpaced new builds three to one.
In the final panel, Pat Mazzanti, Rick Ortyl (Metro East) and Greg Schmid discussed locomotive values. Older units stayed mostly firm while the valuation on newer units was split depending on manufacturer. The removal of CARB’s rules will support values on older switcher locomotives. Longevity needed? A 45-year-old GP38-2 locomotive built new for $275,000 in the 1980s has a current estimated fair market value of $295,000. Wow!
What amazing content from an amazing roster of presenters!
REF 2026—our 40th year—is March 1-4, 2026 (www.railequipmentfinance. com). See you in La Quinta!
Got questions? Set them free at dnahass@ railfin.com.
DAVID NAHASS President Railroad
orth America’s freight rail industry is sharply focused on the future as the 21st century is well into its third decade. For this annual special report, the freight rail industry’s thought leaders— the chief executives of leading North American companies—have crafted exclusive, insightful essays for Railway Age on growing and sustaining our vibrant industry, which has helped shape our society and is the backbone of transportation. Here are what they believe are their organizations’ most significant achievements.
Lorie Tekorius, The Greenbrier Companies
ABy Katie Farmer, President and CEO, BNSF
t BNSF, our Southern Transcon is the busiest route along our vast 32,500-mile network, stretching 2,200 miles from Southern California to Chicago. In fact, 70% of BNSF’s intermodal volume touches the Southern Transcon.
With intermodal business being one of our largest opportunities for growth, having the capacity to handle that growth, particularly on the Transcon, is paramount. That’s why we’ve consistently invested in our people, technology, expansion projects, services, and maintenance along this key route.
Late last year, we completed a key segment of double-tracking on the Transcon in eastern Kansas, which makes the entirety of this route 99.98% double, triple, or quadruple-tracked. We can now run multiple priority intermodal trains in and out of Southern California daily, faster between key markets to deliver consistent and reliable service to our customers. Now, just like trucks on the highway, traffic runs in both directions simultaneously with multiple
passing lanes available.
In late summer, we also completed our new main line improvement project in Becker, N.Mex., adjacent to our network’s largest fueling facility, in Belen, N.Mex. The Becker facility will minimize the time it takes for all our trains to fuel and get moving again toward their destination, improves our railroad’s total train capacity through the Southern Transcon by roughly 30%, and improves service consistency for existing customers.
As weather events have increased in both frequency and severity, we’ve made deliberate resiliency investments to harden our network along this busy corridor during extreme weather conditions, including a wind fence at Sais, N.Mex., and a satellite network to monitor intensifying weather patterns. These investments allow us to better plan in advance of weather events, ensuring quicker recovery and uninterrupted service for our customers.
BNSF’s expansion plan for this year, announced with our 2025 capital plan of $3.8 billion, builds on our investments for customer
growth by continuing to invest in facility and line expansion projects that increase network capacity. Major line expansion projects on the Transcon include continuing a multi-year project to construct approximately 20 miles of third main line track near Needles, Calif., and increasing siding capacity on our main line track near Phoenix, Ariz. On the east end of our Transcon, the multi-year expansion project at our Cicero Intermodal facility in Chicago is expected to be completed in 2026, bringing greater capacity and a better customer experience.
Our new Logistics Park in Phoenix (LPP), announced last year, will be a 4,300-acre railserved facility designed to offer streamlined supply chain solutions by responding to the dynamic needs of our customer base.
Development activities also continue at Barstow International Gateway (BIG) in California, where our state-of-the-art master planned integrated rail facility will be a steplevel evolution for the supply chain, delivering a product competitive with trucks but with the capacity, value, and emissions benefits of rail.
This approach has worked so well for intermodal, that we’re now applying it to the carload side, as well. Logistics Centers are BNSF-owned business parks that provide access to railserved origins and destinations where customers may not be able to realize the economic and efficiency benefits of rail today. We’re opening our latest Logistics Center in North Houston at Cleveland, Tex., early this summer. Construction on our next Logistics Center, in North Dallas, will also begin this summer. We continue to grow with our agricultural customers, as well, to find new markets like renewable diesel and feedstocks.
Speaking of growth, I would be remiss if I didn’t mention our breakthrough intermodal service, Quantum with JB Hunt, which has been exceeding expectations since its launch a little more than a year ago. Performance has consistently been better than the 95% on-time delivery commitment, up to a day faster than traditional intermodal service. We have a dedicated 24/7 team providing oversight of every load to consistently meet the demands of Quantum customers’ most complex freight.
We believe our ongoing focus on these key opportunities to improve resiliency across our network places our customers at the center of everything we do, and helps us remain the safest, fastest, and most efficient rail provider in North America.
At CSX, we push the boundaries of what’s possible in freight transportation. Our proven operating model and commitment to excellence fuel every decision, every mile, and every customer interaction. Because our business isn’t just about moving goods—it’s about moving industries.
ABy Tracy Robinson, President and CEO, CN
t CN, our purpose is clear: We power the economy. As railroaders, this is what we do every day. We have the privilege of serving a wide range of industries and connecting supply chains across North America. We’ve had that honor for over a century. This gives us a unique perspective on the economy, its cycles and where it’s headed.
Like the businesses we serve, we are eager to grow. We believe the best way to do that is through reliable service, by listening to our customer’s needs, and by leveraging our 20,000-mile network linking Canada’s East and West Coast ports and extending south through the Midwest to the U.S. Gulf Coast. Through these actions we can provide the resilience and flexibility that our customers and supply chain partners are looking for.
Growth remains a priority, even as geopolitical realities introduce economic uncertainty. We focus on what we can control—making strategic investments to strengthen our capacity, leveraging the strength of our unique network,
and helping our customers get their products to existing and new markets. We focus on agility, ensuring our resources are aligned to demand and that we’re well positioned to accommodate growth at low incremental cost.
Now more than ever, strong and reliable supply chains are essential for North America. Rail has the benefit of having a large comprehensive geographical reach. This allows us to offer easy and quick solutions when a customer needs to take advantage of a new market opportunity, because chances are we can get them there. We do this by working in collaboration with our customers and our supply chain partners—ports, short lines, and other Class I’s to name a few. At the end of the day, this is an effort that takes all of us, working in concert—securing markets, establishing loading terminals, expanding rail capacity and enhancing port capacity. We have a lot of experience in this, and when we all work together a lot can be achieved.
mitigate some of the uncertainties that we are experiencing. We operate in 16 states, eight Canadian provinces, and have access to major ports in the Atlantic, Pacific, and the U.S. Gulf, providing customers with key market access within North America and abroad. On top of that, we also provide interline services with other Class I railways and our short line partners, making the number of markets we can provide access to even larger.
This type of thoughtful and comprehensive market access is the vision for the Port of Prince Rupert, which CN is proud to exclusively serve. As one of North America’s most strategic gateways to global markets, the Port of Prince Rupert has traditionally focused on bulk exports and intermodal. Now, it is expanding to handle a broader range of commodities, unlocking new opportunities for North American industries.
Key growth areas for the Port of Prince Rupert include natural gas liquids (NGLs), specialty grains, lumber and wood pellets. This diversification strengthens the resource economy, making it more competitive and adaptable. CN is doing its part, as we will be completing two additional sections of double track on the Edson Subdivision west of Edmonton this year, increasing capacity by 25% through this critical link supporting our growth to the West Coast. And we’ll continue to work closely with partners at the port to invest in infrastructure that supports these expanding sectors, positioning Prince Rupert as a vital trade hub for the future.
We continue to invest in the resiliency of our network, with approximately $3.4 billion in planned capital investments this year. Consistent reinvestment in our rail infrastructure ensures that CN remains the safest and most reliable choice for customers to move their goods.
At CN, we are excited about our customerdriven opportunities that will enable sustainable growth and support the growth of the North American economy. Our investments across all regions in our network are designed to enhance resilience, reliability and efficiency across North America’s supply chains.
By investing in our network, providing reliable service and fostering strong partnerships, CN ensures that its customers remain competitive in an increasingly dynamic global marketplace. With a clear vision and a commitment to progress, we are ready to meet today’s challenges and seize tomorrow’s opportunities.
CN has a great network, and we believe that our extensive reach provides an element of flexibility that our customers can leverage to CN
We have the expertise to serve a diverse range of customers — from family-owned lumber yards and Midwest grain elevators to paper mills and global mining companies — handling any commodity — from automobiles and ag ricultural crops to wind turbine blades and construction materials.
Our footprint offers access to more than 200 rail-to-truck transloading hubs, over 600 industrial development sites and interchange connections across the entire North American freight rail network.
Our service package extends beyond rail transportation to include contracted industrial switching, port rail operations and equipment maintenance and repair.
THAT’S THE G&W WAY.
Learn more at gwrr.com or scan here
By Keith Creel, President and CEO, Canadian Pacific Kansas City
Two years ago, we created the first single-line railway connecting the United States, Canada and Mexico with what I believe is the most relevant rail network in North America. With our expanded footprint and team of 20,000 world-class railroaders, CPKC has delivered on its promise to bring new service products and customer solutions to the market to fuel growth.
CPKC has done exactly what we said we would do, creating a success story that is just getting started. As the rail industry experiences change, ranging from new political leadership to evolving trade flows to technological advancements, CPKC is positioned to capitalize on these developments. By focusing on key traffic segments, supply chain enhancements, industrial development, sustainability, and safety, we are shaping the future of the rail industry and creating value for all stakeholders. We are investing in our expanded network. Our most significant recent capital
improvement project, put into service earlier this year, is the construction of the second span of the Patrick J. Ottensmeyer International Railway Bridge over the Rio Grande from Laredo, Tex., to Nuevo Laredo, Tamaulipas, Mexico. The bridge more than doubles our capacity to move freight through the U.S.-Mexico border at the largest international trade port of entry in North America and brings new efficiency to CPKC’s secure trade corridor linking the U.S. and its largest trading partner. Additionally, targeted investments in infrastructure improvements across the U.S., Mexico, and Canada are boosting our capacity and further improving operational efficiency in this important trade corridor.
With these investments giving us room to grow, CPKC is creating unique outcomes for our customers by introducing service products that have never been possible before in our industry. In the automotive business, our unique closed-loop service model, paired with significant infrastructure investments
such as our automotive compound in Wylie, Tex., position CPKC as a leader in automotive transportation. With this service innovation on our single-line network, we are providing enhanced reliable car supply to improve service and increase the value we offer to our OEM customers.
Additionally, demand for intermodal services, particularly in the domestic market, continues to grow with the expansion of our refrigerated business and the unparalleled performance of our Mexico Midwest Express (MMX) premium intermodal service. MMX provides the fastest and most reliable singleline rail service from Chicago to Mexico in the industry, a truck-competitive option that’s never been available before in our industry.
By collaborating with customers, we are changing entire supply chains. This year, Americold will open its new cold storage facility in Kansas City, co-located at our intermodal facility and become the first location in a series being built as part of a new cold supply chain moving by rail. Future rail-served facilities in Eastern Canada, and in Mexico further reinforce these growth opportunities for produce moving north and proteins moving south in CPKC’s new fleet of temperaturecontrolled containers.
Our collaborations don’t end there. We have created a new direct Class I interchange in Alabama with the acquisition of 50 miles of the former Meridian & Bigbee Railroad. Through this direct connection with CSX, we are opening new lanes with service connecting Mexico, Texas, and the Southeastern U.S. with streamlined freight movement and reducing transit times.
We are doing all this as we keep safety at the front of everything we do.
Technology and innovation are critical to our future. Recent investments in autonomous car inspections, cold wheel technology, and predictive analytics significantly enhance safety and operational efficiency. By leveraging these advanced technologies, we are driving industry-leading improvements in maintenance and reliability.
By once again achieving the lowest Federal Railroad Administration-reportable train accident frequency ratio, we have demonstrated our commitment to operational excellence. Investments in rail inspection technologies, infrastructure enhancements, and operational best practices contribute to a safer and more resilient rail network.
By Joe Hinrichs, President and CEO, CSX
Safety in the railroad industry is a shared responsibility and a universal priority. At CSX, we firmly believe there is no competitive advantage in safety. Whether it is employees in the field, first responders on the front lines, or the communities we serve, protecting people is not a goal we pursue for ourselves alone. It is a moral obligation we hold as part of this industry. The future of rail depends on our ability to address this obligation together, and we must commit to doing so—with the help of innovation and teamwork.
Our industry has a proud legacy of service and efficiency, but we must ensure those qualities are rooted in safe practices. At CSX, safety is not just a requirement; it is a responsibility shared by all 23,000 employees across our ONE CSX team. We put this belief into action through programs like SAFE CSX, which empowers our team members to speak up, care for one another, and take ownership to make improvements. Our goal is to create a culture where every employee feels valued, included, respected, appreciated, and listened to. That is the foundation zero incidents.
To bring this vision to life, CSX has focused heavily on initiatives that enhance safety for employees and the communities along our network. Our industry-leading Responder Incident Training (RIT) program, for example, last year trained more than 1,200 first responders.
We added an innovative training locomotive to this program in 2025, enabling first responders to practice hands-on scenarios that simulate real-world rail emergencies. This practical training approach not only hones their skills but also fosters relationships with emergency personnel across the 26 states in our service territory.
Community education is another critical component. Through our Community Affairs and Incident Reduction team, CSX provides outreach and rail safety education. During “See Tracks? Think Train Week,” we collaborate with local leaders and community organizations to promote safe behaviors around trains. Efforts like these reinforce our commitment to educating the public and enhancing preparedness.
But we know there is more work to be done.
While safety depends on human responsibility, we must welcome the power of innovation. Technology is an ally we cannot afford to overlook. At CSX, we have embraced solutions like an unmanned aerial vehicle system that leverages more than 400 drones for tasks like yard mapping, facility inspections, storm response and accident investigation. Utilizing drones not only enhances safety but also significantly improves the accuracy and efficiency of our operations.
to autonomously monitor railroad crossings, tunnels and bridges, identifying obstructions in real time. At the heart of this work, we stay focused on addressing the core reasons for over-the-road derailments today, such as broken rails and wheel bearing issues. These are two of our industry’s biggest challenges that we know technology can solve. With the right investment, we can leverage tools to detect issues before they escalate and focus our skilled workforce on resolving them. Safety technology is not here to replace people; it is here to enable them. By using technology to identify issues early, we can allow our employees to do what they do best—solve problems. This approach multiplies the impact of human expertise while reducing risks for our teams and communities. We know the value of all our people. When we empower them with tools like advanced analytics and cloud-based simulations, they can make data-driven decisions that optimize our network in ways unaided human calculations simply cannot.
This blend of technology and human skill creates an exciting opportunity to build a safer, more efficient rail network. We are seeing results. Last year, CSX was the only Class I to restore pre-pandemic volume levels, and we did so while earning top ratings in customer service. This proves that safety and efficiency are not at odds. When done right, they’re complementary.
The railroad industry has a tremendous opportunity to modernize, grow and contribute to society in ways we have not seen in decades. But we can only achieve that if we change our mindset. Historically, railroads have operated in silos, with limited collaboration on safety initiatives. This approach has often hindered progress in creating safer environments for employees and customers. To build the railroads of the future, we must break down these barriers, prioritize safety as a shared responsibility, and champion collaboration and innovation. Only then can we attract the next generation of talent and earn the trust of our customers.
At CSX, we are proud to carry forward nearly 200 years of history. But we also recognize the need to change. Our mission is to inspire pride in every railroader—not just in what we do but also in how we do it. That starts with safety. It is not a checkbox or a cost of doing business. It is a commitment to our employees, our customers and our communities. With the right investments, the right mindset, and a focus on working together, we can reach a zero-incident railroad. There is no competitive advantage in achieving that goal. By prioritizing safety, we all win.
We have also partnered with our Innovation X team to prototype solutions that proactively address potential risks. One notable project the team is evaluating uses technology CSX
Rail carries one-third of our nation’s freight while reducing emissions, saving fuel and relieving highway congestion. What we transport touches individuals in all walks of life.
By Mark George, President and CEO, Norfolk Southern
2024 was a transformative year for Norfolk Southern. With a fluid network, efficient terminals, and improved service levels, we have momentum to propel our railroad and our industry forward. This momentum is the result of disciplined execution and the dedication of every Norfolk Southern employee. Now, we can enter the next phase of our transformation. Our commercial, operations, and technology teams are sharpening our focus on the customer experience and refining an operating model that drives accountability and a relentless focus on value creation to scale and grow.
Safety and operational excellence: Safety is our foundation. In 2024, we reduced our FRA-reportable main line train accident rate by more than 40%, leading the industry. We expanded safety training for both management and frontline employees, introduced new technologies, and trained more than 5,500 first responders through our Operation Awareness & Response program. Our Operations teams are demonstrating higher levels of excellence, and we are continuing to push our service to new heights. In 2024, our system speed improved by 10%, with merchandise train speed up 11%, and unit train speed up 17% in our last quarter.
And Norfolk Southern teams delivered a flawless peak season with zero controllable failures, even as we handled 7% more parcel volume per day.
Supply chain continuity through disruption: Significant weather and geopolitical events have tested our resilience, and we have proven our ability to navigate challenges. When the Port of Baltimore temporarily shut down, we worked swiftly with customers to reroute traffic to Norfolk, Va., ensuring supply chain continuity. In the wake of Hurricane Helene, our team cleared more than 15,000 trees and restored key routes within 72 hours. Our team also showed resolve and nimbleness in the face of potential work stoppages at East Coast ports, implementing contingency plans and communicating with customers well in advance to continue serving their business. These moments reinforced our ability to safely manage through difficulties and minimize customer impact.
Going above and beyond, our teams also pulled together to identify ways to help communities get back on their feet after natural disasters, delivering aid through the American Red Cross, local organizations, and our Disaster Relief and Employee Hardship Programs.
Multi-Modal solutions: In 2024, Norfolk Southern purchased a direct rail and truck-served transload and warehouse facility in Chicago to advance our strategy to convert flexible freight to rail. The Great Lakes Reload facility is exceeding expectations. Since Norfolk Southern acquired the facility, volume is up 62% year over year.
Improving ease of doing business: For customers, we’ve been focused on building more intuitive customer interfaces. For example, AccessNS serves as a single source of truth for tracking shipments and optimizing planning, while industry-leading tools like RailPulse and ModalView improve shipment visibility by providing real-time location, condition, and status updates for railcars and intermodal containers. We’re also strengthening feedback mechanisms. In 2025, we’ll look to leverage insights from our new Customer Advisory Board to ensure we continue meeting customer needs.
Industrial development and growth: Industrial development remains a key growth driver for Norfolk Southern. In 2024, we advanced more than 140 projects,
representing $4.3 billion in customer investment. Our pipeline remains strong, with opportunities in steel and metals, renewable fuels, energy, and food processing poised to drive future volume growth.
Technology-driven innovation: In 2024, Norfolk Southern doubled its autonomous train inspections and added five new Digital Train Inspection systems, bringing the network count to six sites and seven systems. This technology assisted our 24-hour wayside detector desk in identifying and addressing 85 tier-one critical defects in near real-time. This technology is augmenting the work of our railroaders, helping turn them from finders into fixers, and we have plans to bring an additional three portal sites online in 2025.
Building a Speak Up culture: Our people are at the core of our success. We are investing in leadership training, workforce development, and frontline engagement to foster a culture of excellence and accountability. We’re building a Speak Up culture where employees feel empowered to raise concerns
and share constructive ideas, and we’ve committed to our employees that when questions are asked and concerns are raised, there will be visible follow-through by our leaders.
By equipping employees with the tools and skills they need and encouraging this culture, we are ensuring a safer, higher-performing organization overall.
Looking ahead: Norfolk Southern has momentum on all fronts. With a disciplined leadership team, an engaged workforce, and a relentless focus on executing our strategy with excellence, we are building a stronger, more reliable railroad that powers the American economy and delivers lasting value for our customers.
By Jim Vena, CEO, Union Pacific
Challenges and opportunities are always a factor in our industry. Because we move products that people use every day that fuel the economy, success means being nimble, strategic, and ready to handle challenges and to win available opportunities. Others may measure success from a narrow view. I measure success by looking
at our results and asking myself: Did we deliver for our owners? Is Union Pacific in a great financial position? Is Union Pacific a company that is clear-eyed when it comes to success for our employees, our customers and the communities where we operate? And finally: Are we living up to our slogan of Building America?
Union Pacific’s foundation is strong, and our 2024 results exemplify improvements
in all key areas of our Safety, Service and Operational Excellence strategy. Financially, we delivered best-in-class in operating ratio, operating income, net income and total revenue. We achieved doubledigit improvements across most our safety metrics including injuries and derailments. And service, which is measured by what we sold our customers, improved across the board. This progress allows our customers to win in their markets and helps us succeed in growing our business.
2025 comes with its challenges and opportunities, whether it’s government action on tariffs and taxes, regulatory responsiveness or economic conditions— none of this is new for Union Pacific. Over our history, we have met similar challenges and thrived. Any mistakes we’ve made occurred when we lost sight of the fundamentals of railroading.
At Union Pacific, we work every day to improve safety with a goal to lead the industry. The vectors that make the freight rail industry the safest ground transportation solution are anchored by people and infrastructure. We continue to invest in training, workplace engagement and communication, technology, and the overall quality of our network. One example of many we have rolled out is a switching technology that cuts the number of steps a switchperson typically takes by one-sixth, making the work safer and more productive. We don’t look at the base railroad capital spend of $3.4 billion in 2025 in a yearly increment, but we use a multi-year plan to ensure our assets are maintained at an optimal level. It is this focus that allows us to operate our fastest, time-sensitive trains at 70 mph on large portions of our railroad.
In closing, our strategy is grounded on Safety, Service and Operational Excellence, which if we deliver again in 2025, will provide opportunities to grow and help our customers win. We continue to invest in our assets, we have line of sight to hundreds of business development opportunities and are clear-eyed on what success is. While I am the recognized face of Union Pacific, in fact, I am a representative for all our employees. The people of Union Pacific are proud of our company, and we look forward to delivering in 2025 and beyond.
By Peter Gilbertson, President and CEO, Anacostia Rail Holdings
Anacostia’s railroads—like most small railroads—are adding value to the global supply chain with a key focus: growth. For the rail industry, real growth is a necessity that can lead to survival. In addition, the conversion of traffic to rail has proven benefits for the environment and can support customer supply chain resilience.
Importantly, carload growth among small railroads is not primarily in revenue per unit, but in absolute volume growth. In many cases, this represents increased rail market share, which includes the Class I partners. As an example, in the seven-year period, 2017–2024, short line carloads (excluding coal and intermodal) grew nearly 5% while Class I carload volume declined nearly 4%, even with our added push.
Why? There are many reasons, but they are simple and fundamental.
Entrepreneurship: Foundationally, most small railroads have entrepreneurship in their DNA. Created during an environment challenged by declining traffic bases, decades of deferred maintenance, fleeing customers, and sometimes bankruptcy—most were inherently turnaround situations. To address these
obstacles, an action-oriented, risk-tolerant mindset has become necessary, along with a willingness to experiment. Above all, entrepreneurs need an extreme focus on customers and a persistent approach to transactions.
People: Short line railroads are small businesses where our people are always front and center. Whether the employees are represented by a union or not, culture is important. Our retention record is unparalleled, and this leads to experience and ownership of basic customer relationships. When the art and science of employee empowerment works, there will be professionalism and motivation—a powerful combination that delivers quality service safely and efficiently.
Margins: While entrepreneurs are acutely aware of financial metrics and KPIs, they don’t let them kill growth initiatives. Specifically, new rail business is often won by diverting it from truck and is price sensitive. The operating ratio (OR) of this new business can be higher than the current book of business. As a result, a railroad’s willingness to grow often means a higher OR. So be it. For small railroads, almost all business involves the challenges of the last mile: interchange, switching, spot/pull, and other aspects of direct customer interface. It is the most complex and high-cost subset of
rail operations, and the margins are naturally lower. Nevertheless, it is attention to the retail end of railroading—often handled by a short line—which permits the customer to take advantage of the reach of the highly efficient Class I main line networks.
Capital: Strategic use of capital is another important tool for attracting new customers. For example, one of our railroads worked to win the location of a major new facility for a large publicly traded company on their lines. The plant design included rail for inbound raw materials but no provision for outbound finished product. Outbound rail infrastructure was not in the budget or part of the plan. Even though we were a fraction of the size of the customer, we built the outbound dock and track and leased it back to the customer to recoup our investment. Outbound products now move consistently by rail, which was the point. Capital policy must be flexible and market-oriented.
Ancillary Services: Customers want responsiveness and simplicity. Often small railroads add ancillary services to meet this need, including transloading, brokerage services, trucking, plant switching, and industrial development. The objective is to make rail more “truck-like” and reach beyond the track footprint where our customers are often located. We often must acquire these skills for a specific opportunity—whatever it may take!
Next Steps: Small railroads represent a significant opportunity for the rail industry to finally grow market share. Industry leaders need to focus on further unlocking this opportunity. Class I’s should definitely consider creating more short lines in local, service sensitive markets. Several tactical steps can be implemented immediately: interchanges must be disciplined, measured, and reported correctly. Customer service, carload visibility, and safety technologies like RailPulse also need to be embraced and made uniform across the network. Class I’s can better leverage small railroads for market intelligence and support of coordinated marketing and sales efforts. We are the real boots on the ground.
Senior leadership at Class I’s and short lines needs to acknowledge the profound opportunities and improve channels for collaboration. While these partnerships might require some effort, they offer longer term benefits and improve the number of touchpoints with customers and potential opportunities. This may be an era where we can possibly share some of our survival skills with the large railroads.
By Michael Miller, CEO, Genesee & Wyoming
Fresh off our celebratory 125th year, G&W is intensely focused on converting opportunities from our robust commercial pipeline into tangible business and driving more freight traffic to rail.
Four pillars are critical for us to achieve that:
Safety: Seventy-six G&W railroads finished 2024 reportable injury-free, while 39 operations were zero-and-zero (no reportable injuries or human factor incidents). Moreover, 14 of our operations were recognized during our annual June Safety Month for working 20 years or more without injury. G&W’s goal of sending everyone home the way they came to work has been foundational for decades and will remain at the forefront of all we do.
In 2024, we developed an annual safety summit that gathers managers from a handful of our railroads with the biggest opportunity for safety improvement. Carving dedicated time at the beginning of the year for these roads to identify challenges, recognize underlying trends, analyze practices with our corporate safety team, and build detailed safety action plans yielded a 58% decrease in reportable injuries among this group last year. We are optimistic that we’ll see similar results for 2025.
Service: G&W relentlessly strives to be easy to do business with and responsive when customers present new or expanding opportunities. Our sales team spent many hours proactively undergoing training in 2024 to further their account management and business development skills. Our operations teams are spending more time analyzing operating plans specific to individual customer needs so we can be as flexible as possible. Our IT and commercial teams are developing tools to provide customers with real-time information about their shipments. And we have been diligently promoting our transloading and intermodal capabilities so that customers can take advantage of the safety and economic benefits of using rail as part of their supply chain.
Technology: As just one example of several technology initiatives under way, last year, railroads in our National Region piloted a new project that uses a Cordel Rugged LiDAR device to scan clearances along our rights of way. As we expand testing across our U.S. footprint in 2025, these accurate measurements will give us confidence to undertake more high-and-wide shipments, which are in high demand across the Northeast and Midwest, while simultaneously identifying
close clearances that we can address.
Our IT team continues to build applications, such as our locomotive inspection and incident notification apps, that enable frontline employees and managers to capture real-time data in standard form, making us more efficient and improving our day-to-day decision making.
Elsewhere, our participation in the RailPulse coalition to equip the North American railcar fleet with GPS and other telematics, as well as our partnership with Parallel Systems to test autonomous, battery-powered rail vehicles for shorter-haul container moves in more rural, lower-density areas along our lines, can help modernize our industry, improve the customer experience, and open new markets that have historically been dominated by truck.
People: Among G&W’s strategies for prioritizing a strong workforce are an emphasis on employee engagement and a commitment to developing leaders. Over the past two years, we have rolled out training designed to familiarize managers with leadership strategies, communicating and collaborating more effectively, and fostering a sense of belonging at their respective operations. We also increased our field HR presence and began meeting regularly with new hires throughout their certification process to support their acclimation to G&W and the rail industry, as well as gather feedback on improving the new-hire experience going forward. Moreover, G&W is leveraging technology, such as LinkedIn Learning, to personalize training for all employees, regardless of craft, level, location or schedule. We believe these efforts directly contributed to an almost 5% reduction in turnover at our company since 2022.
We’re continuously improving our talent acquisition by honing in on local recruiting strategies to expand applicant pools, reducing candidate handoffs throughout interviews, analyzing our time-to-hire and offer-to-hire ratios, and ensuring recruiters and hiring managers partner through the onboarding process to create a welcoming, informative environment for someone beginning their G&W career.
The focus of these pillars—operating safely for the benefit of employees, customers and communities; elevating our service to meet the ever-changing needs of customers; innovating at our company and with the entire rail industry to improve safety, service, and efficiency; and taking care of our people to ensure we are the employer of choice—is The G&W Way that has sustained us for 126 years and will guide us through the 21st century.
By Dan Smith, CEO, Watco
When I think about great teams, I think about great players. When I think about great businesses, I think about great people.
In business, I’m not sure there’s anything more important than developing people. Putting our team members first is fundamental at Watco. One of our core principles is Value Our People, which includes helping our team members develop their skills, broaden their experiences, and have opportunities for advancement.
One way we do that is by having a strong management development program. When it comes to the most important thing we’re doing in human resources (known at Watco as People Services), I would point to our ongoing effort to enhance our management development program.
Watco University, our training program designed to help our team members develop their leadership skills and advance throughout the organization, was established in 2010. This
program has evolved as Watco has evolved. It started as a program that simply taught our leaders core management principles and today is a program that helps our leaders be great communicators, coaches, decision makers, problem solvers, and mentors to the next generation of Watco leaders.
Watco University has been a key tool that has helped us grow the company from within by investing in the great people we have at Watco and providing them with the key resources they need to perform and grow. These courses equip managers with the tools necessary to lead effectively and ensure that they’re well-prepared to address the challenges of the transportation industry, which we all know are constant and ever-changing.
One key course offered in the Watco University program is titled Foundations of Leadership. Foundations of Leadership is designed for our team members who are new to leadership or who we’ve identified as a potential supervisor or manager, when a new opportunity arises. This course is important because no matter where we operate, our leaders hear the same
message. Watco operates with a decentralized approach across North America and Australia. We’re made up of many business units performing many different types of activities and services. Because of this, our leaders need a lot of autonomy in their decision-making — and they have that — but Foundations of Leadership gives everybody the same playbook with the fundamentals of our business, like how to onboard and manage talent and how to build and lead a team.
Foundations of Leadership also helps drive home our culture. The team at Watco has likely heard me say that I believe culture beats strategy. We’ve always talked about our culture and leadership in general, but we didn’t necessarily go into the details in a standardized way. Foundations of Leadership does just that.
Since introducing Foundations of Leadership content, we’ve noticed more promotions being filled internally and our retention has improved. I believe that one reason for that is this course. A new course, titled Coaching for Managers, launched in 2024. This was created as a direct result of Watco team member feedback. We survey every team member who goes through our courses, and overwhelmingly, everyone coming out of Foundations of Leadership requested additional training on coaching. So, our Watco University team created a two-day workshop that takes a deeper dive into the coaching skills introduced in Foundations of Leadership.
I have a deep appreciation for coaching. Having spent decades in baseball, I feel like I have a unique perspective and appreciation for how our managers can benefit from this training. The instructors dig deep into aspects of coaching and teach our managers how to strengthen their coaching approach. One way they accomplish that is by having managers do a self-assessment where they examine their own style and determine how understanding their style can change how they coach others.
I’m very proud of the work that’s been done in terms of developing our managers to lead our team members out in the field. It’s effective. Managers who have undergone these development programs are better equipped to understand and anticipate team member and customer needs. This leads to more personalized and efficient service. Our management development is helping to build stronger relationships across the company, and it’s also positioning Watco as a trusted partner in the industry.
C.
Railway Age
David C. Lester
Railway Track & Structures
Kevin Smith International Railway Journal
Railway Age, Railway Track & Structures and International Railway Journal have teamed to offer our Rail Group On Air podcast series. The podcasts, available on Apple Music, Google Play and SoundCloud, tackle the latest issues and important projects in the rail industry. Listen to the railway leaders who make the news.
By Ian Jefferies, President and CEO, Association of American Railroads
Freight rail remains the backbone of the nation’s transportation system, seamlessly linking industries, businesses and consumers. New analysis from AAR economists transforms abstract concepts
into concrete evidence, demonstrating the critical role rail plays in uniting every link of the supply chain. Amid evolving market pressures and technological advances, rail’s commitment to innovation and strategic reinvestment continues to set it apart as a powerful
force in modern logistics.
In 2023, the industry generated $233.4 billion in economic output, a figure comparable to the entire GDP of Kansas. This substantial contribution highlights the industry’s extensive reach in the supply chain and economy writ large, supporting sectors like agriculture and manufacturing and reinforcing its critical role in driving national overall growth. There is much to be said about uncertainty in the supply chain currently, fighting a bevy of headwinds, but rail and its private investments remain constant.
In 2023, Class I railroads reinvested $26.8 billion into modernizing tracks, upgrading equipment and enhancing safety. These investments ensure that rail remains a reliable, cost-effective, and high-capacity link in the supply chain, allowing businesses to plan efficiently while reducing the risk of delays and disruptions. Unlike other freight modes that rely on taxpayerfunded infrastructure, railroads own, operate, and maintain their own networks, saving billions in public spending while ensuring long-term economic resilience.
AAR’s analysis also shows that the industry directly employs 153,000 workers and supports 749,000 total jobs across the economy—nearly twice the size of Washington D.C.’s entire labor force. Ever the force multiplier, every railroad job creates about four additional jobs in sectors such as logistics, manufacturing and technology—growing fields and a key part of domestic prosperity. Nearshoring or other goals of current policymakers will—simply put— be impossible without rail serving as the ballast of the economy.
Rail companies and their employees sustain communities. These highpaying jobs drive economic stability, contributing $66 billion in household income and $14.1 billion in Railroad Retirement benefits annually, strengthening both consumer spending and regional economies.
Every $1 invested in rail drives $2.50 in total economic activity, fueling industries that depend on seamless transportation networks. Railroads also
generate $25.1 billion in annual tax revenue, helping fund infrastructure, public services and local economies.
All of which brings us back to the question at hand, which for AAR specifically, means charting a sensible, data-driven policy landscape that can sustain the prowess of rail and empower it to grow in the future.
At the heart of this is technology, which is further strengthening rail’s role in global logistics. Real-time GPS tracking, predictive analytics, and AI-driven scheduling optimize routes, reduce congestion, and improve delivery times. By integrating with trucking and port operations, rail enables supply chains to function more efficiently, ensuring goods reach their destinations on time and at a lower cost.
Yet railroads have encountered unnecessary obstacles in recent years at the U.S. Department of Transportation (USDOT) to improving safety and efficiency through technology. With change
comes opportunity, and AAR will advocate for outcome-driven rules and regulations. Whether expanding the use of automated track inspection or modernizing the waiver process, USDOT can correct past mistakes.
Looking at this Congress, which is tasked with reauthorizing the surface transportation law, AAR will also help its members add value in the supply chain by working to correct modal inequities. Trucks, while the largest customer of railroads, are also their biggest competitor and don’t fully cover their highway costs, creating an uneven playing field. The Tax Foundation notes that underpriced roads push more freight onto highways, undermining the largely unsubsidized rail network. With declining gas tax revenues, AAR will continue to push Congress to shift to a weight- and distance-based system and phase out the gas tax. Lawmakers initiated this in the last transportation bill, but USDOT
has stalled the national pilot program, which should be moved forward to support broader adoption.
The stability of the economy depends on reliable, cost-effective freight transportation, and rail is uniquely positioned to provide the long-term solutions businesses need. As global trade continues to shift, supply chains will demand greater efficiency, flexibility and investment in transportation infrastructure. A policy environment that supports rail’s ability to modernize, expand intermodal connections and drive innovation will be essential to maintaining U.S. economic leadership.
Freight rail delivers real economic value—driving trade, supporting jobs, reducing costs and strengthening global supply chain efficiency. By continuing to invest in technology, infrastructure and workforce development, rail will remain the most efficient, reliable and costeffective freight solution for a rapidly evolving global economy.
By Chuck Baker, President and CEO, American Short Line and Regional Railroad Association
Which traffic segment or segments offer top-line growth potential? Every single segment, and every single customer! There are more than 600 short lines across the country, and in total they haul almost every commodity one can think of. In particular, the agriculture, energy, industrial and manufacturing sectors are reliant upon short line service.
But the daily reality for most short lines is that it’s not about what segments are hot or where the global macro economy is heading— it’s instead about how we add one more carload from an existing customer, or secure one more customer shipping on the railroad. Each interaction with a shipper is an opportunity to help them win in their markets, to earn their trust, and to grow with them.
When we do that, every day across every short line railroad with every shipper, the industry-wide results speak for themselves. When our shippers win, we win, our railroad partners win, and the country wins.
We’re adding value to the global, multimodal supply chain. Short lines are a critical piece of the interconnected freight rail network, serving as the on and off ramps for thousands of customers. Without short line service, many communities would be effectively cut off from the economy due to a lack of competitive and cost-efficient freight transportation options to access markets.
More than one in every five carloads on the
U.S. freight rail network are handled at origin or destination by a short line. Whether customers are directly served by rail or access a short line through transloading, we are focused on helping those customers utilize the world’s premier freight rail network to move their goods between farms and factories and the broader U.S. and world markets.
While we rely on our Class I partners and ports for that full domestic and global access, short lines are the face of railroading for their customers, particularly in small town and rural America. We are focused on attracting new customers to rail, and keeping existing ones, by providing flexible, friendly, customized service. Whatever the question is, the answer is yes, and we’ll work to deliver that commitment every day.
Moving freight by rail not only meets the needs of customers for efficient access to markets, but also benefits local communities by reducing large truck traffic and thus reducing congestion, emissions, and taxpayer-funded road maintenance.
In short, without a short line, shippers would be short on options for freight transportation and communities would be short on experiencing the benefits of freight rail.
Our most significant safety improvement achievements: The top two causes of derailments on short lines are straightforward— broken rail and wide gauge, which basically means worn out track and ties. The way to address those problems is straightforward: Invest in the infrastructure.
However, given the origin story of many
short lines, starting as unprofitable branch line spinoffs with years of deferred maintenance and not much in the way of traffic density, it is a huge challenge for short lines to generate enough revenue to invest as much as they’d like and to bring their rail up to modern track standards.
Short lines hustle every day to generate the funds to make these investments—whether by earning one more carload of volume from a shipper or managing expenses by extending the life on an older locomotive by another year. Luckily, the federal government has long seen the benefit of maintaining the freight rail access that short lines provide and has been willing to invest funds alongside us into short line infrastructure.
The two main mechanisms of that support are the 45G short line railroad track maintenance tax credit and the Consolidated Rail Infrastructure and Safety Improvements (CRISI) grant program. Both programs have been remarkably successful at helping short lines invest to modernize their infrastructure, grow traffic and improve safety. In addition, the Short Line Training Center has enabled hundreds of railroaders to be trained, some remotely via an online learning management system and some with locomotive simulators and mobile classrooms delivered to the railroad.
The Short Line Safety Institute (SLSI) has entered its 10th year of operations and assists short line railroads in elevating their safety culture. Dozens and dozens of short lines have taken advantage of SLSI-conducted Safety Culture Assessments, and those that have scheduled a follow up assessment have shown measurable safety improvements.
The SLSI also offers a robust hazardous materials training program to short line railroads and training for local area first responders, and classes on Leadership Development and Structured Problem Solving.
As a result of the commitment of short lines to continuously improve safety, last year 340 short lines earned the ASLRRA’s Jake Safety Award with distinction, which recognizes short lines with zero FRA-reportable injuries for a full year period.
On May 7, 2025 the railroad industry will go to Washington for our annual Railroad Day on Capitol Hill, where we will advocate aggressively for these crucial programs. We will educate lawmakers on the benefit rail provides to communities across America, and how our elected officials can assist the industry. Join us! See: www.aslrra.org/railroadday.
By Ed Quinn, President and CEO, R. J. Corman Railroad Group
R. J. Corman is unique; we have some of the most talented people in the industry with a can-do spirit that has defined us since day one. If something can be done, the team at R. J. Corman will find a way to do it. This is the spirit we work to nurture daily throughout every level of our organization.
IKEA’s founder, Ingvar Kamprad, said: “The feeling of having finished something is an effective sleeping pill … A company that feels that it has reached its goal will quickly stagnate and lose its vitality ... We will move ahead only by constantly asking ourselves how what we are doing today can be done better tomorrow.” I like this quote. We strive for perfection each day but must settle for excellence. We know that tomorrow provides an opportunity for us to build on what we accomplished today. Beauty is in the eye of the beholder, as is the definition of success. We are focused on defining success through the eyes of our clients. The “R. J. Corman way” is listening to our clients’
wants and needs and leveraging our team members’ talents to deliver a result the client has defined. This helps us create long-term partnerships and win-win relationships. The approach we take for our external clients is the same as the approach we take with our internal clients, the R. J. Corman team members. We seek the best possible solution for their needs. Our success as a company begins with the success of each team member. This focus and level of communication are crucial for team members’ personal growth and for our companies. It is essential to listen to the voices of those in the field and for management to effectively communicate the vision and strategic plan to those team members.
We all know the railroad industry is a capital-intensive industry. It occurred to us that we have not historically celebrated our capital maintenance spend at the local level. The fact that we are spending millions of dollars on vehicles, heavy equipment, rolling stock, locomotives, ties, rail, etc. should be celebrated, and the team members that are
going to utilize the new or replacement tools should know it is a vote of confidence in them and the business. This reinvestment helps us grow, fulfill our goals, and support our clients while providing our colleagues with the right tools to get the job done.
Also, to better support our team members, we transformed our HR operations into a dedicated business partner model, which has revolutionized employee support across our network. In this streamlined system, employees from each operating company now have a single point of contact for all HR needs, ranging from conflict resolution to payroll inquiries, benefits administration, leadership development, and employee training and coaching.
This strategic shift has led to measurable improvements in response times and employee satisfaction. Instead of navigating multiple departments, employees can address their concerns through their designated HR business partner, who understands their company and the unique operational context of their division. The model’s scalability has been particularly valuable as our organization grows, allowing us to maintain consistent service quality while expanding our workforce.
This model applies also to our finance team. Our accounting business partners understand the specific needs of each organization, each division and ultimately each team member. This discovery methodology is focused on “finance” NOT using finance language. Rather, “finance” must ask about the variables in the equation that yields the financial results. These variables are really the KPIs that drive the business. Words are important but listening and understanding is critical. This strategic shift drives an entirely different conversation and has resulted in ongoing efficiency gains and improved service delivery across the company.
We continually prioritize our clients’ needs (starting with our internal customers), and that is how we grow. How do we achieve this? By saying yes. Every day our team members are empowered to think about how we can offer our clients the best solutions to their issues.
Communication is the foundation of our success. By listening to our clients, our team members pave the way for continued growth and success. Let us embrace the spirit of collaboration and innovation, constantly striving to improve each day.
By Lorie Tekorius, President and CEO, The Greenbrier Companies
At Greenbrier, we believe that supporting employee development is one of the most essential functions of human resources. Development programs are vital for uncovering hidden talent within the organization and ensuring everyone has access to opportunities.
As individuals, we often aren’t lucky enough to encounter the right person who recognizes our potential and takes the time to help us advance. Structured development programs provide opportunities for growth, education, and advancement, ensuring our companies thrive and preparing our future leaders for success.
Reflecting on my journey, I joined Greenbrier 30 years ago to manage public reporting. Given the cyclical nature of this role, I often found myself with downtime. Instead of accepting these lulls, I took them as opportunities to engage with operational departments and deepen my understanding of the rail industry. Over the years, I moved between
corporate and operational departments, which provided me with strong visibility to leadership and enhanced my knowledge of the rail industry. This experience significantly contributed to my career advancement. My curiosity and willingness to embrace new challenges allowed me to connect with others at Greenbrier, who recognized my potential and helped me progress.
our organization, from entry-level positions to upper management.
As individual contributors move into managerial and leadership positions, they require specific skills, like problem-solving and conflict resolution. We are developing comprehensive training programs that equip them with foundational managerial skills and the tools to energize their teams before they advance in the organization. This proactive approach instills confidence in our leaders and enhances team dynamics and productivity.
Training for more experienced managers is part of our continuous improvement efforts, and we offer individually tailored leadership skills courses.
I strongly advocate for early and midcareer employees to engage in stretch projects. Pairing a newer employee with a more experienced colleague to complete a project, host a presentation, or improve a process is one of the most effective ways to gain hands-on experience. This approach also helps employees gain exposure to leadership roles and develop a deeper understanding of Greenbrier’s operations.
Performance Management & Goal Setting: Our performance management tools are structured consistently across the company, so we all report on performance successes, challenges and goals similarly.
Our goal alignment workshops reinforce our development strategy. Through these sessions, employees set personal and professional goals that resonate with our broader company objectives. By aligning individual ambitions with Greenbrier’s business goals, we aim to create a sense of purpose and clarity that drives personal fulfillment and organizational success.
We also strategically focus our performance measurement on development activities rather than ratings and grades, which creates an environment that fosters growth, engagement and continuous improvement.
While the idea of “owning your development” has worked well for me and certainly carries a lot of truth—since no one is more invested in your career advancement than you—one of my missions as CEO has been to formalize training and provide clearer pathways for development across the company. At the same time, I want to ensure that individuals have the flexibility to explore different departments, take on challenging projects, and nurture their curiosity. Training & Development Programs: Through our Greenbrier University platform, we are standardizing training programs that span stages of employee development and roles across The Greenbrier Companies
Onboarding: We have formalized our onboarding program for new employees to ensure that messaging about Greenbrier, job expectations and safety topics is consistent across all locations.
We recently standardized our safety onboarding processes to ensure that both new hires and existing employees receive consistent information about our safety protocols. This unified approach protects our workforce and upholds our strict safety standards, especially since we recognize that most safety incidents occur among new employees who are adjusting to their roles and developing the physical stamina needed for heavy industrial work.
Investing in our employees is crucial not only because it’s the right thing to do but also due to the measurable benefits it brings to our business. By prioritizing employee retention, we can significantly reduce recruitment and onboarding costs while keeping a skilled workforce familiar with our safety practices. Additionally, offering clear opportunities for professional growth makes our employees feel valued and respected, which aligns with our Core Value of Respect for People.
By Jean Savage, President and CEO, Trinity Industries, Inc.
Converting freight from truck to rail in North America happens one load at a time. We cannot achieve our grand vision of volume growth and “modal conversion” unless we meet the specific needs of individual shippers, their products, and their customers with innovative tools and services. Doing so will accelerate the tipping point where rail solutions are viewed by the shipper as the first choice.
Through extensive, regular conversations with our shipper customers, the Trinity team found complexity, consistency, and cost to be the perceived barriers preventing many shippers from transitioning more freight to rail.
In terms of complexity, the industry’s seemingly endless jargon and complex system of oversight are just two examples of additional complexity relative to the over-the-road alternative. Simply put, many shippers may be hesitant because they perceive using rail to be too hard. In terms of consistency, I’ll just point out that delivery estimates in rail are provided in days when trucks typically forecast in hours. Finally in terms of cost, it is often unexpected expenses, like those around demurrage and equipment management, which can be most challenging.
To address these barriers for shippers, rail solutions providers must develop and deliver
the technological tools and professional human capital resources that are focused on optimization, planning and execution, and railcar management.
• Planning and Execution: Shippers need intuitive tools and services to execute and manage their shipments with professional support ready to step in when needed.
• Optimization: Shippers need easy access to network and industry data to benchmark their performance, monitor network performance, and maximize the value they generate from their rail-focused resources.
• Railcar Management: Shippers need solutions to maintain and improve their railcar fleets informed by experts trained in dealing with the complexity of the industry.
These capabilities can come together to support shippers with their modal transition. Rail shippers will continue to prioritize flexibility and efficiency to optimize supply chain costs and productivity. Global challenges and changing political environments, such as potential changes in tariffs and shifting markets, will continue to place importance on flexibility in planning an optimized supply chain.
In 2023, Trinity acquired RSI Logistics to augment our platform of railcar leasing enabled by manufacturing and services. With this acquisition, the Trinity solution platform expanded to include market-leading rail logistics services, transload terminal operations, and digital logistics tools. These capabilities span the customers’ need for planning and execution, optimization, and railcar management. We believe the addition of these services allows us to approach our customers looking to move more freight by rail with the tools and capabilities they need to make rail easier and identify specific opportunities to drive cost out of their supply chain. By leveraging rail-focused logistics professionals and tools, customers can keep their current workforce focused on the core business and help transition an experienced and retiring workforce.
For example, about a year ago, a small chemical producer came to RSI Logistics looking for input to make a big strategic decision in their supply chain. The chemical producer was shipping their products entirely by truck. After some internal analysis, the company determined trucking was too expensive, forcing them to miss expansion opportunities because they could not afford to extend their supply
chain. The professional team of rail logistics experts at RSI taught the shipper the basics of rail and collaborated with them to design their entire rail plan. The chemical producer also used RSI’s Rail Command® digital rail supply chain control tool to simplify the management of their new rail supply chain. This chemical shipper’s strategic shift was a big win for the company and allowed it to serve more distant
customers and grow its revenue.
This story is a good example of a small win, but that is how modal conversion will happen. It won’t be a big bang with overnight success. Modal conversion will happen through small, consistent wins with customer-centric solutions that couple the deep expertise of our industry with innovative tools that make rail easier.
An Evertrak 7000 installation on a Class I in the Southeastern United States (High Decay Zone 5).
Railway Age’s annual report on crossties offers market insights and the latest performance-boosting, sustainable products from suppliers.
BY MARYBETH LUCZAK, EXECUTIVE EDITOR
BNSF in 2025 is devoting nearly 75% of its $3.8 billion capital plan, or $2.84 billion, to maintenance, including 11,400 miles of track surfacing and/ or undercutting work and the replacement of 410 miles of rail and 2.5 million ties. For Union Pacific (UP), an estimated $1.9 billion—56% of this year’s roughly $3.4 billion capital plan— will go toward upgrading and replacing infrastructure, such as ballast, rail and ties. Such spending is critical.
Crossties have served as the foundation of
railroad infrastructure since the early 19th century, supporting the rail, as well as the safe passage of passengers and freight. While wood ties are most prevalent across the North American network, concrete, steel and composite versions are found in special applications— from high-speed rail to high-decay environments and industrial/port projects.
The following suppliers share crosstie market insights; the latest in tie technologies, including products that help boost longevity and reduce m/w costs; and updates on end-oflife disposal options.
KOPPERS INC.
“The current market condition for treated crossties is robust as the railroads’ investment in capex and maintenance is strong,” reports John P. McDonald, Vice President of Sales and Product Management for Koppers, which offers pressure-treated products (creosotetreated crossties and switch ties). “The longterm outlook from customers is uncertain due to macroeconomic events and as they interpret government policies. Tariffs do pose some supply chain risk all the way through to the end-user level.”
Koppers is “grateful for the customer partnerships that FRA’s CRISI program and similar programs have provided,” McDonald says, “even as we understand that some of that funding directed through state programs has slowed during the transition to a new Administration. Government spending, which is usually a boost for our customers and demand for our product, is facing challenges that need to be worked through, but we don’t fear important programs like CRISI will go away entirely even as infrastructure law provisions end.”
McDonald reports that Koppers is involved in many projects and is seeing growing demand along UP’s Sunset Route. “Our North Little Rock facility, which boasts a design capacity of north of four million ties per year, is perfectly situated for raw material supply and deliveries to these key heavy-haul lanes,” he notes.
Educating customers and potential customers is important to the company, according to McDonald. It recently hosted the RTA Tie Grading Seminar and has invited railroads for a tour and technical summit at the Stickney Plant in Cicero, Ill. Koppers also has an applied research facility and working laboratory that focuses on the development of new product applications, technical assistance, and comprehensive testing services. “KGTC is what advances our product formulations and helps our customers realize the value behind the investment they make in a quality product,” McDonald says. “Our door is always open.”
“We’re seeing a fundamental shift in the rail sector,” Vice President of Sales Matt Violin tells Railway Age. “Safety, sustainability and cost-effectiveness are no longer just buzzwords; they’re essential. NARSTCO is meeting these demands head-on, providing premium steel ties, turnouts, and our advanced ‘e’ clip fasteners to industrial rail yards, transit systems and Class I railroads across North America.”
The company’s ties consist of “high-quality recycled U.S. steel,” and “are free from hazardous chemicals, addressing growing environmental concerns and prioritizing the safety of rail workers,” Violin says. They offer an extended service life and reduce track maintenance and downtime, he notes. “They ensure consistent track gauge and offer exceptional durability.”
Port projects are a focus for NARSTO, including the approximately 120-acre Navy Base Intermodal Facility in Charleston, S.C., which is expected to open later this year. To
be served by Norfolk Southern and CSX, the intermodal yard will provide near-dock rail to the Port of Charleston; nearly 80,000 feet of track is slated to create a capacity of one million rail lifts in Phase 1. “We’re also supplying steel ties and turnouts to large-scale port expansions in Alabama, Georgia, Texas and North Carolina, as well as crucial projects in Quebec and Ontario, Canada,” Violin says.
The automotive industry’s increased demand for rail service is boosting business, too. “We saw significant success in 2024 with the Ford Blue Oval project in Tennessee and the Hyundai project in Georgia,” Violin says. “These projects required a large quantity of our ‘sustainable’ steel ties and turnouts.” The company expects continued sector growth.
St. Louis, Mo.-based Evertrak offers a composite crosstie made with a Glass Fiber Reinforced Polymer manufactured from recycled plastic. According to the AAR M-1003-certified company, it is “engineered to perform reliably in track for up to 50 years in high-rot regions” (see chart, top) compared with an average of 8-12 years for wood ties. It is also fully recyclable.
The company launched the Evertrak 7000 in 2017, according to Founder and CEO Tim Noonan, who tells Railway Age “7000 refers to a modulus of rupture of 7,000 psi.”
“I was talking with three Class I chief engineers, and they had seen ties rotting from the
inside out, failing in less than five years in the Southeastern U.S.,” Noonan says. “So, I believe the time is now for a new category of tie, which can stand up to the wear and tear of freight rail in the U.S. in the high-decay zones … About 3%-3.5% of the installed base [of U.S. ties] is replaced every year, except in the Southeastern U.S, where 10%-12% is replaced.”
“If you look at trends in weather, the decay zones are shifting to the Northwest,” Noonan says. “So, I think High-Decay Zone 5 and parts of High-Decay Zone 4 are great places to start. I live in Missouri. I’ve seen ties that are being replaced in 14 years. So, it’s a great place to start for what we believe is the 4 to 6 million ties a year getting replaced that are failing in less than 12 years.”
Sumitomo Corporation in January backed Evertrak with a strategic investment. The decision, it reported, “stems from a shared vision to build sustainable railroad infrastructure and the opportunity to create synergies” with Sumitomo’s existing businesses, which include the supply of rail, tie plates, wheels and axles.
Union Pacific has also partnered with Evertrak and other composite tie manufacturers, to install their products in areas where the average wood tie lifespan is 8-15 years due to decay associated with heat, humidity and subgrade, compared with other areas of the railroad where wood tie life averages 25 years. In late 2023, Evertrak ties were installed around Little Rock, Ark.; St. Louis, Mo.; Fort Worth, Tex.; and Reno, Nev., as well as on several bridges.
With a supply network of some 1,200 hardwood sawmills, Stella-Jones provides crossties and switch ties in a variety of sizes, plus creosote, borate, and copper naphthenate treatments for mixed hardwoods and oak. It also offers custom services.
Throughout 2024, the company “continued to see sustained, steady growth in demand,” due to customers’ “consistent repair and maintenance needs,” according to Vice President Global Railway Tie Sales Jim Raines. It was the 24th consecutive year of sales growth.
“We are laser-focused on being a partner of choice for our customers, and beyond our commitment to deliver quality products on time, we remain open to opportunities to collaborate with customers on projects and innovations that help them meet their goals and support healthy, resilient rail infrastructure,” Raines tells Railway Age.
Stella-Jones in 2024 continued making operational improvements to increase efficiency and workplace safety, according to Raines. “For instance, we installed a new drip pad structure at our Winslow, Ind., treating facility, a significant project that attests to our commitment to reinvest in the quality of our assets and network,” he says. “Our objective as a business is to continue to be a partner of choice for our customers through our robust operating model, as well as the quality, responsiveness and service they have come to expect from our business.”
Nortrak in January teamed with Müntschemier, Switzerland-based Sonneville AG for the sales and manufacturing of Low Vibration Track (LVT) for slab track applications.
The move was part of the company’s “continued investment in the development of fixation systems, including concrete crossties and rail fasteners, to complement its turnout offerings,” according to John Stout, Senior Vice President of Strategy and Development Fixation for Nortrak, which in 2023 acquired Spokane, Wash.-based CXT Concrete Ties from L.B. Foster Company. “Nortrak is already producing LVT blocks in its Spokane and Cheyenne plants,” he tells Railway Age. “The broader portfolio of concrete tie products helps to offset the general softness in market demand with Class I customers in the near term. The longterm demand outlook is somewhat more positive as new-build passenger projects come to fruition and freight customers begin concrete tie replacement cycles for the first generation of ties installed in the 1980s-1990s.”
Nortrak recently completed concrete tie and turnout supply for two transit projects in San Francisco, Calif., and St. Louis, Mo., and construction and commissioning is ongoing for both. “Nortrak has now shifted its focus to delivering concrete ties for West Coast industrial and port-related projects,” Stout reports.
Nortrak also sees the opportunity to grow business through “product innovation” like its Keyway Tie, according to Stout. Interspersed with wood ties, the Keyway Tie is able “to provide the same track modulus but far greater gauge holding ability compared with wood tie fastening systems,” he says. Several Class I’s and multiple passenger railroads have installed it “with excellent results, especially in curves to strengthen gauge holding, extending the service lives of the remaining wood ties and reducing maintenance intervals,” Stout reports. The addition of the Sonneville LVT system, he notes, “gives Nortrak the ability to provide
end-to-end fixation solutions for passenger rail customers including concrete main line and turnout ties for ballasted track, LVT Block and vulcanized rubber bonded direct fixation fasteners to slab track sections, all of which are now manufactured at Nortrak facilities.”
WVCO Railroad Solutions offers wood and composite tie repair and dispensing systems, as well as elastomeric coatings to protect hopper cars. “Markets remain very strong for our products, and we expect sales to continue to grow long term as we continue to prioritize service, innovation and integrity,” reports Rob Loomis, Vice President of the Transportation and Infrastructure Division at The Willamette Valley Company (WVCO). “Our SpikeFast wood and concrete tie-plugging products continue to show robust sales as a reliable, highquality solution for our customers. Interest in SpikeFast IJ-30 [for insulated joint repair] has been growing, especially in the past year.”
According to WVCO Railroad Solutions, insulated joints are typically constructed with nylon inserts that maintain insulation between adjacent rail sections. Wear and environmental exposure can lead “to failures that compromise both functionality and safety,” the company notes, which is why it developed SpikeFast® IJ-30. Described as “a rapid-setting, two-part polyurethane,” the product creates a “seamless bond that provides electrical isolation, enhances the overall stability of the joint and minimizes displacement; absorbs shocks and vibrations; resists moisture, temperature extremes and UV exposure; and helps reduce the frequency of maintenance and repair.”
WVCO Railroad Solutions also has “a dedicated in-house R&D department that collaborates with customers to develop solutions to meet their needs,” Loomis tells Railway Age
NISUS manufactures copper naphthenate (QNAP®) and Disodium Octaborate Tetrahydrate borate products (such as Cellu-Treat®) wood preservatives for railroad crossties, switch ties, bridge timbers and pilings. QNAP can be used as a stand-alone or as a dual treatment with Cellu-Treat, which can be employed as a dual treatment with QNAP or other selected preservatives.
In addition to boosting crosstie longevity, copper naphthenate facilitates crosstie disposal. At the end of their lifecycle, QNAP-treated ties
Nortrak is more than special trackwork. We offer in house design and manufacture of 100% Buy America compliant integrated railway system solutions featuring:
»
• special trackwork
• switch machines
• zentrak monitoring systems
• premium rail
• concrete ties
• direct fixation fasteners
• resilient clips, pads and insulators
• engineering design services
Are you planning to upgrade your rail infrastructure or start a new project? Get in touch with your Nortrak Sales Professional to learn how we can assist you.
voestalpine Railway Systems Nortrak ww w.v oe st alpi ne.c om/ n ort rak
can be used in residential landscaping and mulch production, for example. “But arguably more important,” reports Jeff Lloyd, Corporate Senior Vice President of Innovation and Sustainability, “they meet the EPA non-hazardous secondary materials rule and are the only treated product that’s allowed to be burned for fuel in any State-permitted boiler.”
Lloyd tells Railway Age that NISUS uses two treatment plants permitted to employ end-oflife wood for boiler fuel, plus there are peerreviewed articles on the extraction and reuse of the preservatives. NISUS also works with third parties who use waste wood from crosstie production to make synthetic oil, as well as for gasification and electricity production.
NISUS is currently working on new technologies to improve wood preservative penetration. “With a borate-creosote tie or a borate-copper naphthenate tie, you expect a 10-year performance based on the borate and then another 10-year performance based on the primary preservative in a high-hazard location,” Lloyd reports. “But the newer technologies we’re looking at now get the copper
naphthenate into those heartwood portions [of the tie that are harder to penetrate and protect] and significantly extend that life.” This is key, he says, since most wood crossties fail when the heartwood—the older, darker and denser inner wood—deteriorates. So far, results have been “fantastic,” according to Lloyd.
Omaha Track provides steel products, including new and reclaimed rail and other track material, plus railroad services, such as infrastructure reclamation, abandoned track removal, new construction, and track expansion, maintenance, inspections and repair.
“Tie repurposing is a difficult market to manage,” President Jeff Peterson tells Railway Age. “Economic shifts in the energy sector and consumer pricing coupled with uncertain political positions create some variables in our forecasts. We are always looking for new outlets or technologies for repurposed ties to find the best use for this resource. Tried and true methods of repurposing still consume most ties. The primary area of growth will likely continue to
be repurposing for landscaping, etc.”
Omaha Track has “dabbled in numerous technologies ranging from pyrolysis, biochar, mobile incineration, new energy processes, gasification and aggregate replacement,” Peterson reports. “The next magic bullet in the industry is easy to talk about but not so easy to put into practice. I am sure one day the economies will align to make a technological breakthrough in the industry. As of now, it seems the old ways are still the best ways.” The company, however, anticipates “relaxed rules in the power generation/tie fuel space,” he says, “which will increase demand and locations for repurposed ties.”
What are customers looking for most? “We are squeezed from both sides to reduce cost and pricing,” Peterson reports. “The supply side of repurposed ties is looking for value-added propositions and reduced cost, and consumers are looking for lower pricing in the final product— obviously, a tough position to be in. We are looking for efficiencies to provide some relief to our stakeholders, but rising prices on everything are making our efforts less effective.”
BY DAVID HUMPHREY, PH.D., SENIOR DATA SCIENTIST, RAILINC
Railinc’s analysis of the North American revenue-earning fleet reveals that the total fleet increased in 2024 with almost all car types accounting for the gain. One of the smallest car types— hoppers—continued to decline in 2024. The average age of cars in the revenue-earning fleet was up, and new cars continued to trend large, with the majority having gross rail loads (GRLs) of 286,000 pounds.
This report from Railinc represents the period ending Dec. 31, 2024. It provides an industry overview of the North American railcar fleet, detailing essential rail equipment statistics and overall rail equipment trends. Railinc compiled all data in the report from its Umler® system.
The Umler equipment registry contains the physical characteristics, transportation management, and pool assignments of more than two million pieces of rail equipment in North America. It is updated nearly one million times each month.
The revenue-earning fleet is a subset of the
North American rail fleet which is largely composed of freight cars that can be used in interchange service and against which an interline waybill can be placed. The North American rail equipment fleet also includes locomotives, intermodal trailers and containers, end-of-train (EOT) devices, maintenance equipment, etc., which are not included in this report. In context, the revenue-earning fleet totaled 1.64 million units, while the total count for railroad equipment of all types was 2.10 million units.
The revenue-earning fleet is made up of six subfleets: hoppers, covered hoppers, gondolas, flats, tank cars, and boxcars. Because not all intermodal trailers and containers are registered in the Umler system, Railinc does not report them as part of the revenueearning fleet.
Detailed analysis reveals the following trends:
1) The size of the revenue-earning fleet increased in 2024. The total fleet size was up 0.2% from year-end 2023 to year-end
2024, compared with a 0.7% increase the previous year.
2) Half of the car types recorded gains in the revenue-earning fleet. Covered hoppers, gondolas, and flats all saw gains, with covered hoppers—the most populous car type—up 1.7%. It was the 15th consecutive year of decline for hoppers, down 0.9%.
3) The average age of the revenue-earning fleet continued to climb in 2024. The average age rose to 20.3 years—its highest in over a decade—continuing to suggest new cars were joining the fleet at a slightly lower rate than older cars were exiting last year.
4) The trend of GRL 286K cars predominating among additions to the revenue-earning fleet continued in 2024. These cars accounted for 80% of all new additions in 2024 and about 88% in the past decade. Larger cars enable operational efficiencies that reduce costs and ease logistics challenges.
The revenue-earning fleet realized a net increase of 3,800 cars in 2024. At the end of 2024, the revenue-earning freight car fleet totaled 1.64 million units, up about 0.2% from
Figure 1: The revenue-earning fleet realized a net increase of 3,800 cars in 2024. At the end of 2024, the revenue-earning freight car fleet totaled 1.64 million units, up about 0.2% from the previous year.
the previous year (Figure 1).
Boxcars and hoppers were the two car types that decreased in the revenue-earning fleet, down 6% and 1.5%, respectively, over 2023. The revenue-earning fleet added cars in three of its subfleets—flats increased the most, up 1.8%, followed by Tanks (1%).
The average age of railcars in the revenueearning fleet in 2024 was 20.3 years, a 0.1-year increase from 2023. The average age continues to hover around 20 years as it has for the past decade (Figure 2). The slight increase in the age of the fleet in 2024 suggests that new cars are being added at a slower rate than old cars are exiting.
About 81,000 new cars have joined the revenue-earning fleet in the past two years (Figure 3). The number of new cars added in 2024 decreased 12% over 2023.
Railcars with a GRL of 286,000 pounds have made most of the new additions to the revenue-earning fleet in the past 25 years. Over that time, GRL 286K cars have accounted for 84% of all new additions to the fleet. This trend continued in 2024, as 80% of new equipment were GRL 286K cars (Figure
4). The number of GRL 263K cars added in 2024 increased by about 850 cars from 2023.
GRL 286K cars dominate among recent additions to the fleet because they enable operational efficiencies that reduce costs and ease logistics challenges. The fleet continues to add GRL 263K and GRL 268K cars, but at a much lower rate than GRL 286K cars. 2024 saw increases in GRL 220K cars added to the fleet for a third year of growth. The last year non-GRL 286K cars led among new additions to the fleet was 1992.
More than 700 equipment type codes (ETCs) appear in the Umler equipment registry. Of those, 11 ETCs accounted for 55% of the revenue-earning fleet in 2024. For the ninth time since Railinc began producing this report in 2011, nine of the top 10 car types were either tank cars or covered hoppers—the two largest car types in the revenue-earning fleet.
As the demographics of the car types change, so do the average car size and the total combined capacity of all the units in a car type. For example, with the growth in the
tank car population, the total fleet capacity has increased by 57.3% since 2009 (Figure 5). Most new tanks are large, which has pushed the average car size up by 7.8%. The total fleet capacity for covered hoppers has increased, as well, by 25.8% (Figure 6). However, the average car size has only increased slightly, with additions being nearly an equal mix of large and small covered hoppers.
In the past decade, the boxcar population has decreased, which has driven down the total fleet capacity. Large boxcars have joined the fleet, which led to an increase in average car size, but not at a fast enough rate to offset the population loss.
Several equipment types comprise the revenue-earning fleet. The following section of the report presents select car types by the kinds of commodities they carry. This provides a more nuanced view of these car types. For example, while covered hoppers carry grain, sand, plastic pellets, and other commodities, the types of covered hoppers that transport each commodity are very different in their characteristics.
This report takes a deeper look at a few of
the car types, including covered hoppers, gondolas, open hoppers, and boxcars. These car types were selected because they carry commonly shipped commodities and make up a sizable percentage of the revenue-earning fleet.
Plastics: Covered hoppers are commonly used to ship plastic pellets. This commodity subfleet added about 7,700 cars in the past two years—about 16% of what was added in the previous 10 years combined. Cars with equipment type code C214 comprise nearly the entire commodity subfleet, as defined here, and make up 9% of the revenue-earning fleet. They are the second-largest equipment type. New railcars have trended larger. Of the cars added to the commodity subfleet in the past 20 years, about 92% have had a capacity of 6,000 cubic feet or more.
Grain/Fertilizer: Railroads move grain and fertilizer in large covered hoppers. The grain and fertilizer subfleet added about 19,500 new cars in the past two years and make up about 17% of the revenue-earning fleet. Two types of covered hoppers—C114 and C113—account for about 96% of the commodity subfleet and are in the top five of the most populous equipment types in the revenue-earning fleet. Larger covered hoppers with capacities of at least 5,000 cubic feet have made up nearly 76% of the additions to the commodity subfleet in the past 20 years.
Sand & Cement: Railroads move sand and cement using small covered hoppers. There have been no significant additions of sand and cement cars in the past six years, but over the past 10 years, the revenue-earning fleet has added almost 32,000 covered hoppers with an equipment type code of C112. About 96% of the subfleet is comprised of C112s, which was the thirdlargest equipment type in 2024. Because of the density of sand and cement, the cars that carry these commodities tend to be smaller. Of the cars in the subfleet, almost all have a capacity of just over 3,000 cubic feet. Only about 3% of the sand and cement cars have capacities less than 3,000 cubic feet, and practically no cars of this size have been added to the subfleet in almost 25 years.
Coal: This commodity is shipped primarily in gondolas and open hoppers. These cars still made up a sizable portion of the revenueearning fleet—10%, or 162,000 railcars—in 2023 and 2024. About 77% of those cars were added between 1990 and 2013, and none were added in the past eight years. Nearly all the
3: About 81,000 new cars have joined the revenue-earning fleet in the past two years. The number of new cars added in 2024 decreased 12% over 2023.
4: Railcars with a GRL of 286,000 pounds have made most of the new additions to the revenue-earning fleet in the past 25 years. This trend continued in 2024.
by 57.3% since 2009.
coal-carrying railcars added in the past 30 years have been GRL 286K cars.
Aggregate: Aggregates such as limestone and crushed stone are shipped in gondolas and open hoppers. The number of these car types added to the revenue-earning fleet in 2024 and 2023 was several times greater than those added in the previous two-year period.
Find the right vendors for your business in the Railway Age Buyer's Guide. Search for products, research vendors, connect with suppliers and make confident purchasing decisions all in one place. RailwayResource.com
Nearly half the cars in the aggregate commodity subfleet have been added in the past 16 years, though they make up only 3% of the total revenue-earning fleet. About 95% of all cars added to this commodity subfleet in the past 12 years have been GRL 286K cars.
Boxcar Commodities: Boxcars are the least populous car type in the revenue-earning
fleet and are used to ship a wide variety of products—from consumer goods to automotive parts. The boxcar fleet is older than other car types. As older and smaller boxcars continue to age out of the fleet, new larger boxcars continue to be added. Boxcars with a GRL of less than 286,000 pounds make up about 25% of this car type, but most of those
were built more than 40 years ago.
The North American railcar fleet grew in 2024. The total size of the revenue-earning fleet increased 0.2% from year-end 2023 to year-end 2024.
The revenue-earning fleet added cars in
three of its subfleets—flats increased the most, up 1.8%, followed by tanks at 1%. Boxcars and hoppers contracted, decreasing by 6% and 1.5%, respectively. The average age of cars in the revenue-earning fleet increased to 20.3 years, suggesting new cars are joining the fleet at a slightly lower rate than older cars are exiting. GRL 286K cars continue
to predominate among new additions to the revenue-earning fleet. This size of car accounted for about 81% of all new additions to the fleet in 2024.
Railinc is a wholly owned subsidiary of the Association of American Railroads. For more information and to download this report and related materials, visit www.railinc.com.
By Frank N. Wilner
Railroads & Economic Regulation traces the development, failures and successes of railroad economic regulation by an insider who was a White House appointed chief of staff at the Surface Transportation Board and a senior officer at the Association of American Railroads.
“Frank Wilner has written an exhaustive history of our nation’s railroads and the complicated, intriguing and often confusing federal regulation and lawmaking.”
Nick Rahall Member of Congress (West Virginia, 1977-2015)
“As a new member of the Surface Transportation Board, the book would have been indispensable to me. It places today’s regulatory issues into context based on their history and paints a picture of the characters who have made the railroad world what it is today.”
plus S/H
Debra L. Miller Member, Surface Transportation Board, 2014-2018
BY PRZEMYSLAW RAKOCZY, SENIOR RAIL RESEARCH ENGINEER, ENSCO, INC.
Every day, trains collide with people or vehicles an average of eight times across the U.S. According to the Federal Railroad Administration (FRA), incidents at grade crossings and trespassing account for 96% of rail-related fatalities. For these reasons, improving grade crossing safety is a top priority for communities, railroads and government agencies [1].
At the Transportation Technology Center (TTC) in Pueblo, Colo., researchers are working to reduce these risks through fullscale grade crossing collision testing. TTC is one of the few places in the country where real-life crash scenarios can be safely recreated, providing valuable data to improve rail safety.
In the early 2000s, TTC conducted several fullscale crash tests to study how different vehicles and rail equipment withstand high-impact collisions at grade crossings. These tests helped engineers design safer locomotives, improve computer simulation models and better understand crash dynamics.
The first test involved a three-car consist led by an SD-45 locomotive, modified to meet Association of American Railroads (AAR) Specification S-580, impacting a stationary log truck at a grade crossing at 50.4 mph. The impact caused significant damage to the sheet steel covering the locomotive’s short hood, but the locomotive broke through the logs and continued down the track without derailing.
The anti-climber and collision posts of the locomotive remained undamaged. All the logs were broken in two, and the rear axles of the log trailer were thrown clear of both the roadway and the railway track. The locomotive’s fuel tank struck the frame extension of the tractortrailer, bending it by approximately six inches at the end. The rear axle of the tractor slid about six feet along the railway track, while the front axle remained in its original position. Despite the impact, the semi-truck remained upright throughout the collision [2].
The second full-scale impact test involved a locomotive crashing into a highway tractor and trailer loaded with two steel coils. This test was conducted at a grade crossing at the TTC on Dec. 18, 2002. The rear steel coil was aligned
with the locomotive’s right-side collision post. An anthropomorphic test device (ATD) was seated on the floor in the nose of the locomotive. The impact occurred at approximately 58 mph. Upon impact, the trucking rig was thrown clear of the track and destroyed. The chains securing the coils to the trailer broke, causing the rear coil to strike the collision post, shearing it just above the weld connecting it to the underframe. The coil then continued into the cab, destroying the windshield, control console, and cab floor. The ATD sustained severe damage, including injuries to the head, neck, left shoulder attachment and skin [3].
Similar grade crossing tests were conducted using passenger rail equipment. In two tests, a cab car traveling on tangent (straight) tracks
collided at an angle with a 41,300-pound steel coil, which was raised about four feet above the top of the rail, at a speed of approximately 14 mph. The first test featured a cab car built to pre-1999 safety standards, while the second test used a cab car designed to meet modern requirements. The goal was to compare the crashworthiness performance of the older and newer corner post designs and to validate computer models developed to simulate the structural and dynamic conditions.
One of the more spectacular tests conducted at the TTC involved a full-scale grade crossing collision between an LNG (liquefied natural gas) tender and an 80,000-pound truck at 40 mph, replicating a scenario outlined in AAR M-1004 safety guidelines. As a result of the impact, the track structure supporting the tender and locomotives experienced tie shift and rail rollover, resulting in the derailment of both tender trucks and one truck of each locomotive. However, no puncture or damage resulting in the commodity release occurred. Additionally, the safety shutoff valve successfully activated, cutting off the fuel supply of the locomotives, demonstrating that even under extreme impact conditions, the fuel tenders remained secure.
Beyond controlled research tests, TTC also conducts public safety demonstrations to highlight the risks of grade crossing collisions. In the past year, ENSCO conducted two fullscale grade crossing impact demonstrations. The first involved a locomotive colliding with a parked bus at 35 mph—simulating a real-life scenario where a stranded vehicle is struck at a crossing. The bus sustained severe damage, but the locomotive remained on track.
The second demonstration involved a locomotive hitting a highway tanker trailer, demonstrating what happens when a large truck gets stuck on a high-profile crossing. This demonstration was part of the 2nd Annual TTC Conference held in October 2024. Upon impact, the tanker was pushed off the road, rolled over in the dirt and came to rest beside the track. The locomotive did not derail, and no significant damage to the locomotive or track was observed. This demonstration also highlighted the use of in-situ high-speed video collection for video analytics and measurements [4].
Looking ahead, TTC is expanding its role in multimodal transportation safety. The
upcoming Grade Crossing (GX) Testbed will serve as a research hub where crossmodal transportation safety challenges can be addressed in a controlled environment. Unlike real-world scenarios, where regulatory and safety concerns limit testing, the GX Testbed will allow for hands-on experiments including 1) engineering solutions to prevent collisions; 2) human-factor studies to understand driver and pedestrian behavior; and 3) training programs for emergency responders.
By creating a safe and flexible space for cross-modal testing, the GX Testbed will play a key role in advancing rail and road safety nationwide.
Grade crossing safety is a major public concern, but through cutting-edge research and full-scale testing, TTC is helping reduce risks and improve safety measures for both rail passengers and roadway users. By combining past crash data, real-world testing, and new research initiatives, TTC continues to lead the way in making transportation safer for all.
To learn more about the TTC and full-scale testing, visit ttc-ensco.com
[1] www.railroads.dot.gov.
[2] Russell Walker, Barrie Brickie “Locomotive Crashworthiness Impact Test No. 3: Test Procedures, Instrumentation, and Data,” Report No. DTFR53-93-C-00001, February 2003.
[3] Russell Walker “Locomotive Crashworthiness Impact Test No. 2: Test Procedures, Instrumentation, and Data,” Report No. DTFR53-93-C-00001, February 2003.
[4] Karina Jacobsen, David Tyrell “Railcar Impact Tests with Steel Coil: Collision Dynamics,” Proceedings of ASME/IEEE Joint Railroad Conference, JRC2003-1655, April 22-24, 2003.
Union Pacific
HIGH PROFILE: Union Pacific (UP) on March 21 named Christina Conlin as Senior Vice President, Chief Legal Officer and Corporate Secretary, succeeding Craig Richardson, who retired at the end of March.
Conlin will oversee all aspects of the company’s legal affairs, including commercial transactions and litigation, labor, and employment and regulatory matters. She will also lead the company’s claims management team.
Conlin joined UP in December 2024 as Senior Vice President and Deputy General Counsel. In this role, she served as a
“steward of legal affairs, protecting the railroad’s reputation, mitigating risk and providing strategic counsel to the senior leadership team,” according to the Class I. Before joining UP, Conlin led Goodyear’s Legal Enterprise Risk group, which included legal oversight for labor and employment; regulatory affairs; environmental, health and safety; compliance and ethics; and sustainability reporting. She also served as partner at Baker McKenzie in its International Commercial group and held multiple roles at McDonald’s Corporation, including European Chief Compliance Officer. Conlin started her career as a private practice trial lawyer.
Intramotev
HIGH PROFILE: Intramotev, the technology company building battery-electric railcar retrofits, last month appointed Harry Zander as Chief Commercial Officer.
Zander brings more than 30 years of experience in the rail industry to Intramotev. Most recently, he served as Chief Revenue Officer of Patriot Rail, a short line railroad holding company with more than 30 railroads. Prior to Patriot Rail, he was Senior Vice President of New Product Development at railcar manufacturer TrinityRail. He also spent more than two decades as an executive in the rail asset leasing industry and has served on numerous industry trade association boards.
“We’re excited to have attracted a teammate like Harry,” said Tim Luchini, Intramotev CEO. “He’s a well-known and respected expert in our industry, and I’m confident his leadership will help us grow our customer base and continue delivering value to rail operators nationwide.”
Zander’s hiring came soon after Intramotev successfully deployed the world’s first independently driven battery-electric railcar in revenue service at Carmeuse Americas’ calcium mining site in Cedarville, Mich.
New York City Transit (NYCT) last month announced three appointments to senior roles: Bernard Jackson as Chief Operating Officer, William “Bill” Amarosa Jr. as Senior Vice President of Subways and Rachel Cohen as Vice President of Paratransit. With more than 38 years of experience spanning multiple transit agencies, Jackson is overseeing and driving performance and service improvements across the departments of Subways, Buses, Paratransit, and Operations Planning. This follows his service at Dallas Area Rapid Transit as Senior Executive Vice President and COO. Jackson also was COO Service Delivery at Los Angeles County Metropolitan Transportation Authority. He began his career at Chicago Transit Authority where he worked for 28 years, rising through the ranks to Vice President of Bus Operations and Director of Rail Operations. Amarosa had served as Acting Senior Vice President of Subways since the start of the year. He will continue to lead the team responsible for operating, maintaining and improving the subway system. During his time in the acting position, on-time performance grew to 83% on weekdays and 87% on weekends. Ridership also improved, with February ridership up 9% over the same time in 2024. Amarosa previously was Vice President of Operations Support, overseeing critical back-of-house functions to support subway operating divisions. Starting his career at NYCT as a high school intern, Amarosa gained 10 years of private-sector experience before returning to MTA in operations planning and budgetary roles. After being named Acting Vice President of Paratransit in May 2024, Cohen now holds the permanent role and is the first woman to do so. She oversees a team that provides 30,000 daily rides to people who are unable to use the subway or bus system due to a disability. During her tenure, Cohen has overseen Access-A-Ride ridership records, including a single-day high of 43,000 scheduled trips on March 19. Cohen will focus on more efficient scheduling for customers, fiscal responsibility and improving vendor management. She joined NYCT in 2018 after working at NYC TLC, the New York City regulatory authority for Access-A-Ride forhire vehicles, as Director of the Office of Systemwide Accessibility.
There are no new proposals or final rules to report for this issue. Be sure to check back next month to see if there are any changes to FRA regulations.
This book affects locomotive engineers, trainers and supervisors. This final rule will clarify the decertification process; clarify when certified locomotive engineers are required to operate service vehicles; and address the concern that some designated supervisors of locomotive engineers are insufficiently qualified to properly supervise, train, or test locomotive engineers. 162 pages. Spiral bound. Updated 12-30-24 BKLER Qual. and Certif. of Loco. Engineers $17.95
Order 50 or more and pay only $16.15 each
The Conductor Certification rule (49 CFR 242) outlines details for implementing a Conductor Certification Program. The FRA implemented this rule in an effort to ensure that only those persons who meet minimum Federal safety standards serve as conductors. Softcover. Spiral bound. Updated 12-30-24
Order 50 or more and pay only $14.50 each
Part 222: Use of Locomotive
49 CFR 222. This regulation provides for safety at public highwayrail grade crossings by requiring locomotive horn use at public highway-rail grade crossings except in quiet zones established and maintained in accordance with this part. Spiral bound. Updated 12-30-24
BKHORN
49 CFR 228 for records, recordkeeping, and reporting of hours of duty of a railroad employee. Also covers the construction of employee sleeping quarters and health requirements for camp cars. Softcover. Spiral bound. Updated 12-30-24.
BKHS Hours of Service of RR Employees $16.00
Order 50 or more and pay only $14.50 each