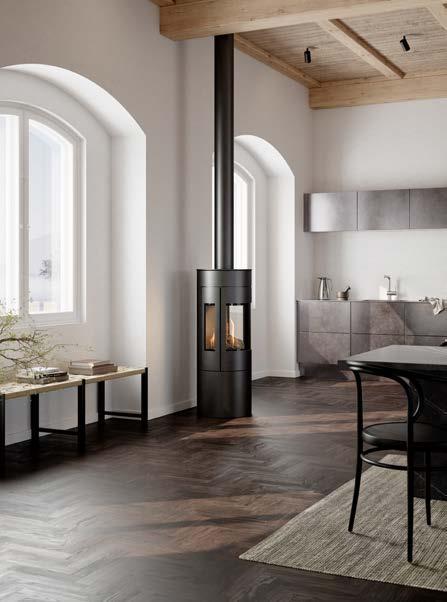
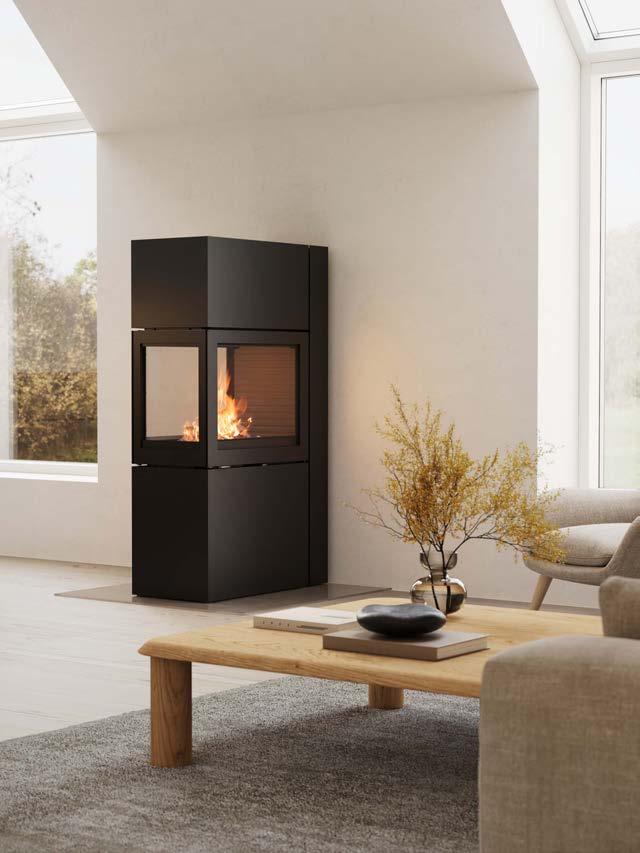
At RAIS, we are committed to playing an active and ambitious role in sustainable development. Taking responsibility is essential — not only for our future success but also for the world around us.
We also believe that documentation, transparency, and openness are fundamental principles that build trust in the market. That is why we are now publishing our first ESG report.
This ESG report marks the beginning of our journey to meet future regulatory requirements relevant to the size of our company.
In the report, we reflect on our achievements and progress since we began our strategic focus on sustainability in 2022 — sharing this year’s results, our most impactful initiatives, and future goals.
The ESG report is intended for RAIS employees, suppliers, importers, dealers, customers, and other stakeholders.
”OUR ESG REPORT POINTS TOWARD A FUTURE WITH AMBITIOUS ESG TARGETS AND A MORE SUSTAINABLE FOCUS FOR OUR SHARED COMPANY.”
Climate change, resource overconsumption, and increasingly strict regulatory requirements have made sustainable innovation, green transition, and circular economy key focus areas for any business.
At RAIS, we have in recent years intensified our focus on these areas and worked strategically with sustainability to drive more sustainable business development. This work has resulted in the ESG report you are reading now –the first of its kind at RAIS.
We report on our progress, goals, and initiatives across three focus areas defined through a materiality assessment.
Our three focus areas are Environment and Climate, People and Community, and Responsibility and Integrity – together covering the main pillars of ESG: Environmental, Social, and Governance.
At RAIS, our ESG efforts are not only about meeting increasing demands from authorities, partners, and custo-
mers – but also about making a real difference.
We believe that, as a company designing wood-burning stoves, fireplace inserts, and gas fireplaces, we carry a special responsibility.
We are committed to ensuring responsible consumption by designing and producing products with a long lifespan – products that create lasting value for our customers, both aesthetically and functionally.
And we carry an even greater responsibility to ensure that our stoves and fireplaces minimize their impact on the environment, air quality, indoor climate, and human health.
This first ESG report is an important step in the right direction and points toward a future with ambitious ESG goals and a stronger focus on sustainability across our business.
We look forward to sharing our progress and vision with the world.
Enjoy the read!!
Henrik Nørgaard CEO, RAIS A/S
At RAIS, we develop, design, and manufacture exclusive wood-burning stoves, fireplace inserts, and gas fireplaces that set new standards in design, quality, and heating. Our designs unite function and aesthetics, serving as both highly efficient heat sources and striking design objects created to complement architectural spaces.
Our design tradition stretches back more than five decades, to the early 1970s, when the first RAIS wood-burning stove came to life. Even then, unique design was at the heart of our work, and those first RAIS stoves were innovative—in function, technology, and form. With deep roots in Scandinavian design, the first RAIS stove was not just a heat source, but a design icon that added aesthetic value to the space.
Just like back then, RAIS today continues to take an architectural approach to stove and fireplace design. We believe that the spaces we live in—and how we heat them—have an impact on our quality of life. For us, design is not only about aesthetics and function, but equally about creating the best possible setting for the life we live.
At RAIS, responsible business practices are at the core of our vision and mission. As environmental, social, and governance criteria become increasingly important to both businesses and society, we are committed to integrating these principles into our operations. This commitment is also reflected in our vision and mission statements.
We aim to be perceived as an exclusive and responsible quality brand — something to be proud of owning or being part of.
We manufacture wood-burning stoves and fireplaces with a level of quality, design, and functionality that sets us apart.
We create beautiful flame views and ensure clean glass in our products, all of which meet the applicable standards in the countries where we operate.
We are committed to sustainability — it shapes our decisions and is embedded in all aspects of our work.
We take pride in our in-house production in Frederikshavn, Denmark, which gives us direct control over the entire manufacturing process and unique opportunities during the development and design phase.
At RAIS, development and production go hand in hand. Our development department and production facilities are separated by just one wall, providing us with a unique level of flexibility—allowing ideas to quickly be turned into prototypes and tested in practice.
This short distance from design to testing enables us to continuously optimize functionality, quality, and design.
This close collaboration strengthens both innovation and
our ability to deliver products of the highest quality.
Our unique combination of development, design, and production under one roof gives us full control of the entire process—from raw steel plates to finished products, ready for delivery, bringing the warmth and aesthetics of the flame into the homes of our customers.
To get there, the steel in particular goes through a series of carefully coordinated processes in our production. The production flow begins at the laser, where the steel plates are precisely cut, and ends in the warehouse and shipping area, where the finished products are ready to be sent off to our customers.
Pre-treatment for Painting Painting
and Shipping
Our responsibility goes beyond our own production. We actively engage with the entire value chain and take responsibility for environmental, climate-related, and social aspects across our suppliers, distributors, and dealers.
That’s why we work purposefully to minimize our environmental footprint, reduce CO2 emissions, and ensure responsible practices throughout the value chain. A key part of this effort is setting clear expectations for our suppliers and partners.
We carefully select our materials and prioritize sustainable
and responsibly sourced raw materials—including steel, glass, and other key components that meet high environmental and quality standards.
Through close dialogue and collaboration with our suppliers, we ensure that the production of our materials takes place under proper conditions and with respect for human rights and the environment.
We continuously work to increase transparency in our value chain and promote more sustainable alternatives wherever possible.
At RAIS, when we talk about “sustainability,” we do so thoughtfully. We recognize that sustainability is not a final goal or a fixed state, but an ongoing process—and a natural part of our mindset and company culture.
For us, sustainability means integrating environmental, social, and economic considerations into every aspect of our business activities. We incorporate responsibility into every relevant decision we make.
Our sustainability goals extends across every area of our company—from the workplace to product development, material sourcing, daily operations, and future investments.
When it comes to our products, we focus on developing and manufacturing responsible products that contribute to a more sustainable future.
We work toward sustainable development by taking responsibility for how we impact both current and future generations—their lives and their opportunities.
We evolve every day for a better tomorrow – we are On Fire for Tomorrow.
Knowledge and insight are essential to succeeding with ESG. In 2022, we conducted a materiality assessment to identify the areas with the greatest impact on our business.
The assessment provided valuable insight into the risks and opportunities associated with our activities and helped us identify strategic focus areas. From these, we prioritized the most material topics, which today form the foundation of our ESG policy and ESG strategy.
Our ESG policy reflects the principles and ambitions we have set to ensure a sustainable future and responsible growth.
The policy supports RAIS’s business objectives and contributes to our societal responsibility. To ensure this, we have
developed a core policy with eight concrete guidelines that serve as a guide for both employees and management. The core policy is outlined below.
On the following pages, we present the specific policies within each ESG area.
To turn our policy into action, we have developed an ESG strategy that ensures a targeted and structured approach in the areas where we can make a meaningful difference. The strategy is also divided into E, S, and G, with each area having an overall goal and clearly defined focus areas.
In the pages that follow, we highlight the most significant initiatives we have launched and/or completed within the E, S, and G areas.
• We will continuously reduce CO2 emissions from our factory operations.
• We will develop products that reduce CO2 and particle emissions throughout their entire lifecycle—from sourcing to disposal.
• We strive to promote the proper use of our products to ensure efficient and clean combustion.
• We will ensure a workplace that fosters well-being, joy, and personal development for our employees in their daily work.
• We will contribute to positive development in our local community.
• We take national and international responsibility for good working conditions throughout our value chain.
• We comply with national and international conventions.
• We will ensure reliable and responsible business practices that support continuous and sustainable operations.
• We aim to eliminate the use of fossil fuels at the RAIS factory.
• Our energy consumption must be continuously reduced relative to production output.
• As far as possible, we will use suppliers that operate with fossil-free processes. Secondly, we will encourage our suppliers to continuously reduce their own greenhouse gas emissions and energy consumption.
• Product design must include assessments that reduce CO2 emissions to the greatest extent possible— considering durability (lifecycle), design, and performance.
• Waste volumes must be reduced, and maximum reuse— either at RAIS or elsewhere—should be pursued.
• We strive to automate processes to reduce resource consumption—including processing time, as well as indirect time use such as storage, packaging, and internal transport.
• When our products are in use, it is essential to ensure optimal—and therefore clean—combustion.
• Products should, to the greatest extent possible, be reusable and recyclable.
• We will keep all employees regularly informed about the company’s progress, key events, ongoing activities, and other relevant updates.
• We will regularly organize shared motivational activities.
• We will ensure a good, safe, and healthy working environment.
• We support employees who need reduced working hours for various reasons, including illness, age, or disability.
• We strive for gender balance during recruitment, based on qualifications and competencies.
• We will support the local community, individuals, and associations.
• We aim to support both local and national organizations.
• We develop solutions that promote safe and proper use of our products in order to reduce environmental impact.
• RAIS and its employees act in accordance with internal guidelines for ethical conduct.
• A motivational and team-oriented leadership style must be maintained.
• All employees must have influence over their own work.
• We have procedures in place for critical processes and update them regularly.
• We follow international standards, including human rights and labor rights.
• Management prepares and annually reviews a materiality assessment to identify our own risks.
• We focus on how we handle our responsibilities in business relationships.
• Sustainability aspects must be considered in all investments and procurement activities.
At RAIS, we are committed to reducing our CO2 emissions and minimizing our overall resource consumption through sustainable choices in energy, materials, and product design.
We strive to optimize our energy usage by implementing solutions that lower our total energy consumption. We are actively working toward climate-neutral production with minimal CO2 emissions.
The choice of materials is crucial to the environmental impact of our products. We focus on responsible sourcing of raw materials and work actively with recycling, repurchasing, and proper disposal. The same applies to our packaging, where we prioritize recyclable and sustainable solutions.
We are dedicated to reducing waste and maximizing the reuse of residual materials. Our approach is based on the principles of the circular economy—minimizing resource waste and maximizing material utilization.
Through our product development, it is our ambition to integrate sustainability into the design phase. We are already working on design optimizations and have ambitions to include environmental product declarations and climate impact assessments for new products.
With our initiatives within environment and climate, we aim to take responsibility for a more sustainable future—for our company, our customers, and the society we are part of.
As part of our environmental strategy, it is our ambition to reduce our overall CO2 emissions. To achieve this goal, we focus on five key areas of action.
ENERGY CONSUMPTION
Renewable energy
Minimization of total energy consumption
Climate-neutral workplace – including CO2-neutral production
PACKAGING
WASTE AND RESOURCE OPTIMIZATION
Material selection and sourcing – with a focus on recycled and fossil-free materials
Recycling, repurchasing, and disposal
Recycling, repurchasing, and disposal
Reduction of waste volume
Maximum reuse and recycling
Construction Optimization
Sustainability assessments of new products during the design phase
Developing products with optimal combustion through testing and end-user use
An important step in our efforts to reduce our climate footprint is that, as of September 1st 2024, we have switched to an electricity agreement that supports the production of renewable energy.
This means we are actively contributing to the green transition and increasing the demand for electricity from sources such as wind power—while helping to reduce the share of electricity produced from fossil fuels.
In addition to our new electricity agreement based on renewable energy, we have also improved energy efficiency in our production by implementing a modern painting system and a heat pump. These initiatives help reduce our CO2 emissions, as we have shifted our production energy source from natural gas to electricity. Natural gas is still used for space heating but will gradually be phased out.
Through these efforts, we take responsibility for our energy consumption by improving energy efficiency and supporting a more sustainable business.
Our total CO2 emissions are
for both Scope 1 and Scope 2. This includes direct emissions from our own ope-
rations (Scope 1), such as production, and indirect emissions from purchased energy, such as electricity (Scope 2).
We have used two calculation methods to provide a more nuanced picture of our emissions. The location-based method calculates emissions using an average emissions factor for electricity in our region, while the market-based method reflects the impact of our choice to use renewable energy sources.
Since 2023, we have reduced our total CO2 emissions. Depending on the method used, the reduction is 14% and 30%, respectively.
Our products are carefully packaged to minimize the risk of damage during transport. This requires a significant amount of material—but it is necessary. That’s why we see great potential in developing and optimizing our packaging solutions to minimize resource waste as much as possible.
By reducing the width of the cross-support wooden boards—from 100 mm to 75 mm—which protect our products during shipping, we have reduced our annual wood consumption for packaging by 3,560 kg and achieved cost savings in material procurement.
In addition to wood, we also use styrofoam to protect our products during transport. In collaboration with our supplier, BEWI Denmark, we have replaced the traditional material with a more sustainable alternative—100% recycled styrofoam.
These styrofoam protective caps are specifically designed for our freestanding products. We have four different models that cover our nine product variants.
At present, three out of the four models have already been switched to the recycled version. The final model will be replaced in early 2025, once the existing stock at BEWI Denmark has been used up.
This change is an important step in our efforts to reduce resource consumption and increase the use of recycled materials in our packaging.
Overall, we have successfully increased the recycling rate of our total cardboard packaging to 85%.
Although we have achieved solid results with a higher recycling rate, we continue to work on improving our packaging solutions.
3,560 kg
106.190 L
reduction in packaging filler purchases
Instead of treating used and discarded paper from our administration and production as waste, one of our production employees came up with the idea to repurpose it as packaging filler.
Since 2023, the handles for our products have been delive-
Purchased Packaging Filler per Wood-Burning Stove
In recent years, we have intensified our efforts to reduce production waste. In 2024, the amount of residual waste per stove decreased by 5% compared to 2023.
In addition, we have improved our ability to reuse packaging from materials delivered by our suppliers—meaning a
red using shredded paper that has been given a second life as protective filler.
This initiative has allowed us to reduce waste and avoid purchasing new packing material—helping to lower our overall resource consumption and waste generation. What
was once seen as waste is now used as a valuable resource.
A total annual saving of 106,190 litres, equivalent to 24 truckloads of transport.
greater share is now classified as recycled packaging rather than waste.
This not only reduces the total amount of waste but also lowers the need to purchase new packaging materials.
Peter Sørig Owner, Peter Sørig Renovation A/S
RAIS A/S fully complies with the waste regulation passed by the Danish Parliament – and has consistently been ahead of developments.
RAIS A/S places strong emphasis on waste sorting and sets clear requirements for us as a collection company. This contributes to reducing overall waste volume and increasing the level of sorting.
At the heart of our company are our employees—their expertise, knowledge, and passion drive RAIS’s growth and innovation. The development of new technologies and products always begins with our customers in mind, which is why we place a strong emphasis on consumer health and safety.
At RAIS, we recognize that the company’s positive development is closely tied to the well-being, welfare, and sense of community among our employees.
We are therefore committed to fostering a safe, inclusive, and developmental work environment where everyone is treated with respect and dignity. We strive to promote diversity, equality, and ethical leadership at all levels of the organization.
With our initiatives under the ‘S’, we aim to create an attractive and motivating workplace that pri-
oritizes both physical and mental well-being. We work to foster a culture of openness, attentiveness, and dialogue—where everyone feels heard and respected—and we invest in ergonomic solutions to improve working conditions and reduce physical strain on employees.
In addition to our people, our customers remain central to everything we do. We focus on consumer health and safety and continuously work to improve and develop technological solutions that ensure even cleaner and more efficient combustion. We also prioritize education and guidance to support the safe and proper use of our products.
We also feel a strong sense of responsibility to contribute positively to the society and communities we are part of. Our social engagement extends beyond the workplace through financial support for local, national, and international organizations.
As part of our social strategy, it is our ambition to take active social responsibility. To achieve this goal, we focus on three key areas of action.
SOCIAL ENGAGEMENT
CONSUMER SAFETY AND SAFE USE
Mental and Physical Work Environment
Employee Diversity
Internal Communication
Financial Support for Local, National, and International Organizations
Develop solutions that support safe and proper use of our products to reduce environmental impact
In a competitive job market, attracting and retaining skilled employees is essential for RAIS’s operations and future development. That’s why, throughout 2024, we placed an increased focus on employee well-being and the working environment.
One of the new initiatives is an annual well-being survey, which we conducted for the first time in spring 2024 via the online platform Woba. The goal for the initial survey was a 70% response rate—a target we successfully met. With this high level of participation, we gained valuable insight into how our employees are doing and how they perceive RAIS as a workplace.
The overall score ended at 2.8 out of 4. Based on the survey results, we were able to identify key areas for improvement and implement targeted actions to enhance both the work environment and employee satisfaction.
Another outcome of the well-being survey was that all salaried employees were given individual Insights Discovery personality profiles.
These profiles are a valuable tool for fostering deeper self-awareness and mutual understanding among colleagues. This shared insight paves the way for stronger working relationships, clearer communication, and more effective collaboration.
In 2024, we also carried out our Workplace Assessment. For the first time, this was done digitally via the Woba platform. Participation rates were 76% for production employees and 88% for salaried employees.
The digital solution allows us to manage the assessment process more efficiently. By using Woba for both well-being surveys and workplace assessments, we have created an integrated platform that makes it easier to follow up on results and implement necessary improvements.
of employees participated in the survey
Total score
2,8 / 4
To support the development of a cohesive organization and foster a shared company culture, we have strengthened our internal communication efforts to ensure that all employees stay informed about RAIS and ongoing activities. This means we now hold three company-wide meetings annually and publish 12 monthly newsletters on our internal platform.
At the end of 2023, we launched our new internal platform: RAIS Intranet. The platform offers a more user-friendly experience and an updated, modern visual design. It has been very well received by employees and has helped raise the overall level of communication—strengthening the sense of community across the organization.
Another key initiative aimed at strengthening our internal community has been the process of articulating and clarifying RAIS’s core values.
During this process, all employees were invited to contribute their thoughts on the values that define RAIS. In the final step, they were asked to vote on the values they most associate with being part of the company.
This initiative resulted in six core values that capture the essence of RAIS: customer-oriented, quality-conscious, informal, collaborative, flexible, and loyal.
To bring these values to life and spread awareness across
the organization, several value banners were displayed throughout RAIS—and in the winter of 2023, we launched an internal video.
The video, featuring real-life footage from our daily work along with stories from our colleagues, illustrates how our values are reflected in everything we do.
This visual storytelling has not only strengthened internal understanding of our values, but also served as a tool to promote a shared identity and sense of pride among our employees.
We support selected associations and organizations—many of them local clubs and initiatives that involve our own employees. In addition, we contribute to larger national organizations that make a meaningful impact.
In 2024, we had the pleasure of supporting 15 different associations and organizations.
RESPONSIBILITY AND INTEGRITY
About the ‘G’
By upholding high standards of ethical business conduct, integrity, and accountability, we lay the foundation for the long-term success of our company.
We strive to implement best-practice principles in corporate governance, including clear and effective structures, policies, and procedures.
We are committed to acting with integrity and responsibility in all our operations and interactions with stakeholders.
We promote—and expect—responsible business behaviour from everyone involved in our value chain, from employees and management to suppliers, distributors, dealers, and other stakeholders. This includes a strong focus on ethical conduct, legal and regulatory compliance, and social and environmental responsibility at every
stage—from raw materials to production, distribution, and sales.
We have a zero-tolerance policy toward corruption, criminal activity, and regulatory grey areas, and we never compromise on our ethical responsibility, professionalism, or integrity.
Sustainable investments are also a key part of our business and its development. By prioritising sustainability in our investment decisions, we ensure that our company not only aims for economic growth but also takes responsibility for environmental and social impact.
In practice, this means striving to invest in solutions and technologies that improve the working environment, reduce our climate footprint, and contribute to a cleaner planet.
As part of our governance strategy, it is our ambition to ensure responsible and transparent management. To achieve this goal, we focus on three key areas of action.
RESPONSIBLE BUSINESS PRACTICES AND RELATIONSHIPS
Compliance with Legal Requirements Policies
Due Diligence
Code of Conduct
Whistleblower Scheme
Time Tracking
TECHNOLOGY
RESPONSIBLE COMMUNICATION
Sustainable Investments in Production
Communication Plan
Carbon Accounting
ESG Report
In recent years, we have made a number of significant investments in our production facilities, where considerations such as working environment and environmental impact have played a central role.
The largest and most comprehensive investment so far has been the replacement of our 40-year-old paint facility with a custom-designed, modern system, which was installed in the summer of 2024 following extensive research and planning.
This new production process has been optimized with a continuous flow setup, allowing products to move through painting and drying without being relocated. This improves both efficiency and ergonomics.
The investment in the new paint facility represents an important step toward a more sustainable and employee-friendly production environment. It improves working conditions for our employees while significantly reducing our environmental footprint.
Since the new paint facility runs on electricity rather than natural gas, our process-related use of natural gas ended on July 1st 2024. Although electricity consumption has increased, the shift has contributed to greater energy efficiency and a 34% reduction in total CO2 emissions.
In addition to our investment in a new paint facility, we have also acquired several energy-efficient machines for our production, including two new welding robots and upgraded welding sources for our existing robots.
These investments have significantly streamlined our welding processes by reducing the number of manual operations required.
Previously, all welds required manual post-processing, including grinding and welding spray to remove weld spatter. With the new welding sources and robots, we now achieve more precise and consistent welds with significantly lower heat input—almost completely eliminating the need for manual finishing.
This results in faster and more efficient production. An added benefit is that the new robots generate less noise, contributing to a better working environment.
We have also invested in two new fiber lasers for cutting our steel plates, a new grinding machine, and a washing unit for our production.
Our investment in a new washing machine for small components prior to painting has also had a positive environmental impact. We have replaced natural gas with electricity as the energy source and optimized both the washing and drying time. In addition, phosphate use has been eliminated, as the new machine uses only soap and recycles the water in the process.
We have also carried out several general facility upgrades, including automated LED lighting in the production area and a new roof for the building that houses, among other things, our canteen.
At RAIS, we respect our employees and want to ensure they have the best possible conditions while working with us. That’s why, at the end of 2023, we introduced our whistleblower scheme: Speak Up!
With this initiative, our goal is to provide the highest possible level of security and confidence for employees when reporting concerns. The whistleblower scheme is available via our internal platform.
We work with a number of carefully selected suppliers who provide high-quality materials and specialized expertise. When choosing new suppliers, we set clear requirements for quality, documentation, delivery reliability, and proper working conditions. In addition, we expect them to comply with environmental legislation and actively engage in sustainability efforts.
To minimize transport and reduce our environmental footprint, we prioritize suppliers located in Denmark, Scandinavia, and the rest of Europe.
All suppliers are presented with our Code of Conduct, which outlines our expectations regarding ethics, working conditions, human rights, environmental protection, and responsible business conduct. By signing the Code of Conduct, suppliers commit to meeting our standards and contributing to a sustainable value chain.
We place particular focus on ensuring that our largest suppliers accept and sign our Code of Conduct. If a supplier fails to meet the requirements, we work together to develop an improvement plan. We ensure ongoing compliance through dialogue, assessments, and documentation.
The first supplier signed our Code of Conduct at the end of 2024, and the work to obtain additional commitments will continue into 2025. It is also our ambition to develop a similar Code of Conduct for our distributors and dealers.
In recent years, we have prioritized strong collaborations with our suppliers and partners to develop more responsible and innovative solutions. We see long-term partnerships as a key factor in ensuring high quality, sustainability, and continuous improvement.
Through close dialogue and knowledge sharing, we actively work to identify and implement new materials and production methods that can reduce environmental impact and strengthen our ESG efforts. As new and more sustainable solutions become available, we reassess our requirements and standards—continuously improving our products and processes.
We believe that strong partnerships create the best solutions—not only for us, but for the entire value chain and the sustainable development of our industry.
New solutions, technology, and innovative approaches continuously open up new opportunities to take further steps toward more responsible business operations.
That’s why we continuously set new and more ambitious goals for our ESG efforts. Our focus is on identifying and prioritizing the initiatives
where we can create the most significant and long-lasting improvements. The illustrations on the following pages highlight the initiatives we have implemented since 2023, as well as our ambitions and goals for the future.
We begin by reviewing our progress within E, followed by updates on S and G.
INITIATIVES COMPLETED IN 2023/2024
Energy Consumption
• Comprehensive energy optimization plans for facilities completed (2023)
• Electricity agreement based on renewable energy – no natural gas used for production processes (2024)
• 50% reduction in natural gas consumption for space heating (2024)
Materials
• Mapping of the most sustainable material alternatives completed (2023)
Packaging
• Recycling rate of cardboard packaging at 85% (2024)
Waste and Resource Optimization
• Waste reduction plan implemented (2023)
• 100% of styrofoam waste sent for recycling (2024)
• Residual waste per standard stove: 1.71 kg (2024)
• Shredded paper reused as packaging filler for handles (2023)
• Reduction in paint and thinner (landfill) per standard stove: 0.84 kg (2024)
Design and Development
• General downcycling plan for products launched before 2024, plus packaging sorting guide (2024)
• Product-specific downcycling plans for products launched in 2024, plus packaging handling guide (2024)
Energy Consumption
FUTURE INITIATIVES AND GOALS
• 0% natural gas for space heating (2027)
• Minimization of total energy consumption (2030)
• Climate-neutral workplace – including CO2-neutral production (2050)
Materials
• Material selection and raw material procurement (ongoing target) – including recycled steel (2026)
Packaging
• 100% recycling of cardboard packaging (2035)
• 100% recycling of styrofoam (2025)
Waste and Resource Optimization
• Residual waste per standard stove: 1.25 kg (2028)
• Maximum utilization of steel plates with a minimum utilization rate of 70% (ongoing target) and a minimum steel scrap recycling rate of 99% (ongoing target)
• Reduction in paint and thinner (landfill) per standard stove: 0.6 kg (2030)
Design and Development
• Construction optimization – including sustainability assessments in the design phase regarding material selection, production, and usage, as well as opportunities for reuse and recycling of our products (2025)
INITIATIVES COMPLETED IN 2023/2024
Mental and Physical Work Environment
• First well-being survey conducted with a 70% response rate (2024)
• Launch of a new, online Workplace Assessment (2024)
Employee Diversity
• 4 apprentices (2024)
Internal Communication
• Optimization of internal communication, including status updates on company performance and upcoming activities (ongoing target)
• Conducting 3 company-wide meetings and sending 12 monthly newsletters annually (ongoing target)
• Implementation of a new and improved internal platform (2023)
Social Engagement
• Financial support provided to 15 local and national associations and organizations (ongoing target)
Consumer Safety and Safe Use
• Initiation of upgrades to installation instructions and user manuals (2024)
FUTURE INITIATIVES AND GOALS
Mental and Physical Work Environment
• Conduct annual well-being surveys with a minimum score of 3.1 out of 4 (2025)
• Conduct annual workplace assessments (APV) along with corresponding actions, aiming for zero workplace accidents (ongoing target)
• Adapt work conditions to employees’ capabilities (illness, age, disability, etc.) (ongoing target)
Employee Diversity
• Recruitment of students, apprentices, interns, working students, and flexible/ part-time positions (ongoing target)
Internal Communication
• Hold 3 all-staff meetings and distribute 12 monthly newsletters annually (ongoing target)
Social Engagement
• Provide financial support to select local and national associations and organizations (ongoing target)
Consumer Safety and Safe Use
• Develop solutions that support safe and proper use of products to reduce environmental impact (2025)
• Upgrade installation instructions and user manuals (2025)
• Implement visual support videos on the website and integrate QR codes in manuals (2026)
• Develop a concept and plan for manufacturer and dealer responsibility regarding proper firing and safe use (2026)
INITIATIVES COMPLETED IN 2023/2024
Responsible Business Practices and Relationships
• Establishment of an internal whistleblower scheme (2023)
• Development of a Code of Conduct for suppliers (2024)
Technology
• New fiber lasers (2021 and 2023)
• New grinding machine (2022)
• Integration of sustainable considerations into the decision-making process regarding investments in machinery and equipment (2023)
• New robot welding sources (2023 and 2024)
• New paint facility (2024)
• New washing machine in production (2024)
Responsible Communication
• First release of the climate account (2023)
• ESG policy developed and signed (2024)
• First release of the ESG report (2024)
FUTURE INITIATIVES AND GOALS
Responsible Business Practices and Relationships
• Procedures for critical processes are defined, developed, and continuously updated (2025)
• Avoid legal cases (ongoing target)
• Management prepares and reviews materiality assessments annually (ongoing target)
• Development of a personnel policy and employee handbook (2025)
• 20 main suppliers have signed the Code of Conduct (2025)
• Development of a Code of Conduct for distributors and dealers (2025)
• Develop a backup plan for critical suppliers and compile a list of these (2025)
• Establishment of a whistleblower scheme for external use (2026)
Technology
• Upgrading or replacing the ERP system (2027)
• Implementation of the ERP system (2027)
Responsible Communication
• ESG Communication strategy – external and internal (2025, thereafter ongoing target)
• Annual publication of the climate account (ongoing target) – including Scope 3 (2030)