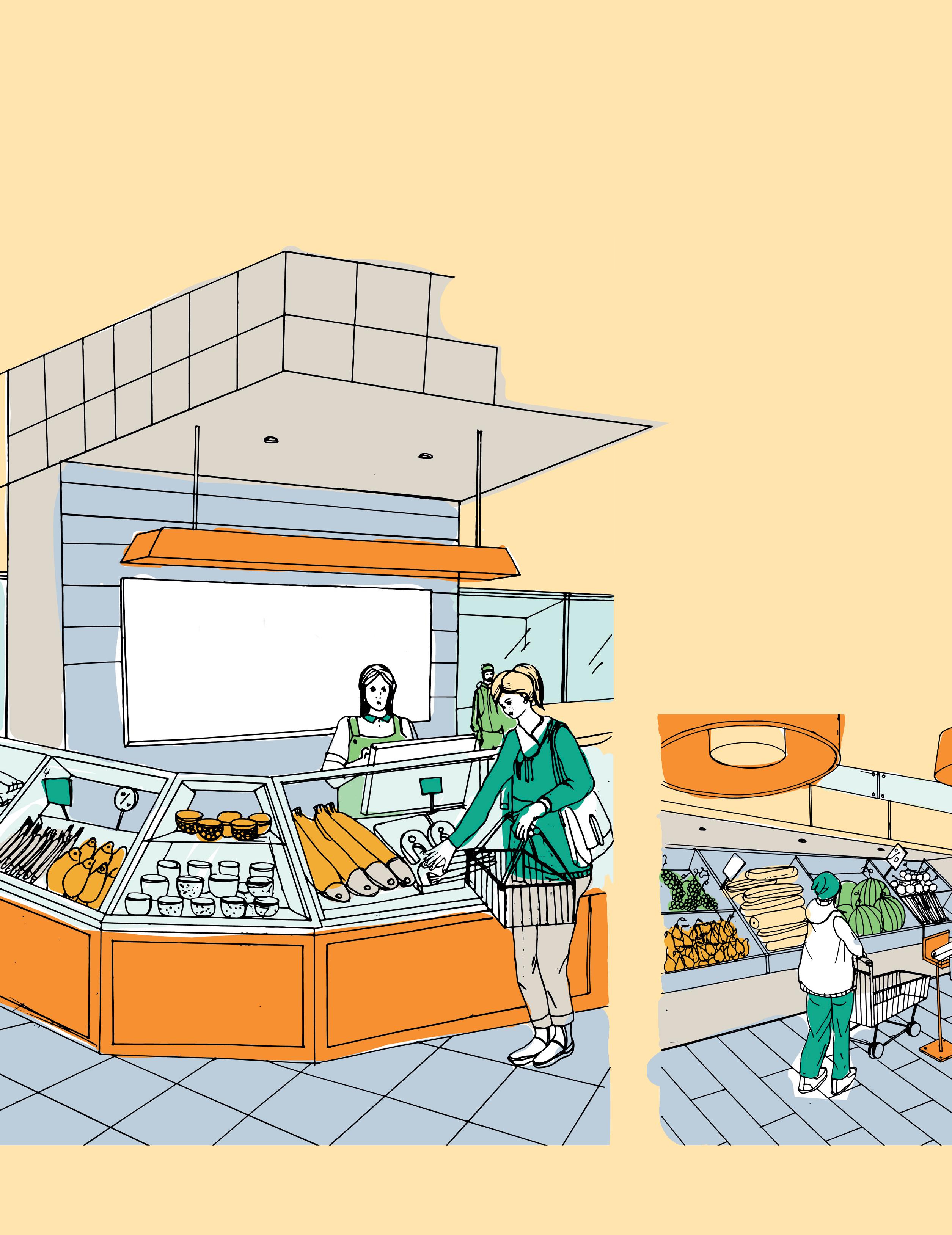
6 minute read
CARGA DE DISEÑO EN CONDICIONES
Extremas De Operaci N En Sistemas De Refrigeraci N Comercial
El diseño, instalación y mantenimiento de unidades de refrigeración destinadas a trabajar en espacios comerciales, tiene en muchos de los casos el objetivo es el almacenar, exhibir y manipular todo tipo de productos perecederos, por ello este tipo de sistemas deben estar diseñados con capacidad de refrigeración suficiente para vencer la carga de diseño (por lo general coincide con la carga máxima) teniendo en cuenta las pérdidas en la instalación particularmente en las tuberías de distribución.
En este contexto otros sistemas están diseñados para satisfacer la carga de diseño bajo unas condiciones ambientales dadas por la temperatura de bulbo seco o húmedo (usualmente la temperatura usada está cerca de la temperatura más alta experimentada en el lugar donde se encuentra el sistema).
Es importante conocer si un determinado sistema tiene la capacidad de satisfacer la carga de diseño en las condiciones extremas de operación para las que ha sido diseñado, para lograrlo se utiliza un procedimiento que debe iniciar con la fase de Planificación y Diseño.
Como primer paso se debe asegurar que el fabricante especifique lo siguiente:
• Especificaciones para la capacidad de los compresores individuales, y para la capacidad total suministrada por el fabricante de compresores
• Frecuencia y método de recogida de datos, incluyendo una descripción de cualquier software utilizado para registrar y analizar los mismos.
• Método por el cual la capacidad del sistema se puede ajustar para tener en cuenta la diferencia entre las condiciones ambientales reales y las de diseño.
Enseguida es importante comprobar que el documento de base del diseño especifica todas las condiciones de diseño, incluyendo las siguientes:
• Capacidad de diseño, incluyendo el factor de seguridad
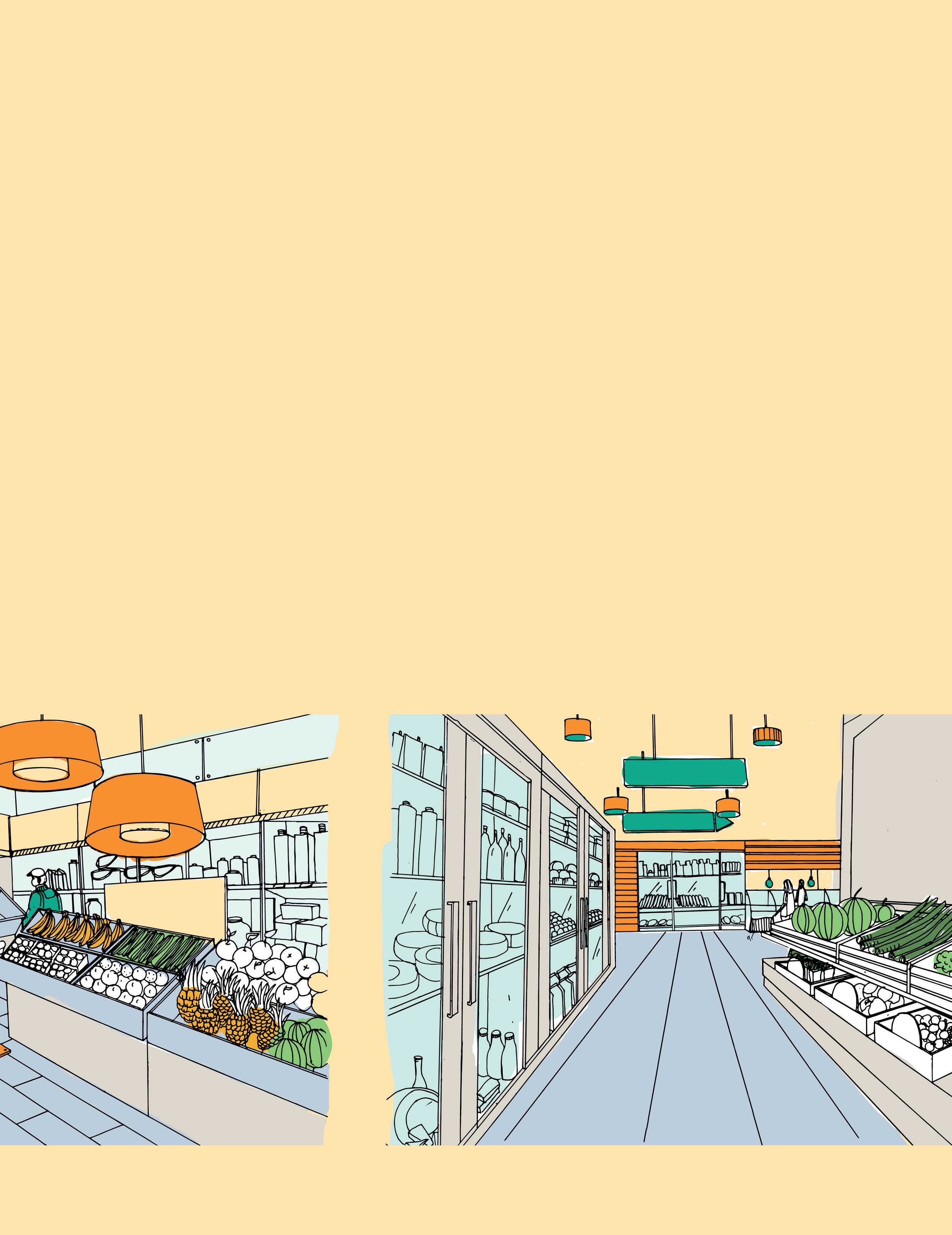
• Temperatura de diseño de bulbo seco y/o húmedo.
• Temperatura de condensación de diseño.
• Temperatura de evaporación de diseño.
En el caso de cambios en el sistema, si el sistema está siendo rediseñado de tal manera que las cargas cambian (por ejemplo, en el caso de la sustitución de muebles exhibidores abiertos por cerrados o el añadido de nuevos muebles), el diseñador debe comprobar que la capacidad del sistema es suficiente para vencer las cargas de diseño si estás están aumentando, o si el sistema reacciona de manera correcta en el caso de reducción de la carga de diseño si éstas están aumentando, o si el sistema reacciona de manera correcta en el caso de reducción de la carga de diseño. En la situación de disminución significativa de la carga respecto a la original, es necesario prestar especial atención al correcto retorno de aceite y a la parcialización del compresor con tal de asegurar la eficiencia y funcionamiento a largo plazo del sistema.
Durante la fase de construcción e instalación, se debe verificar que los sensores u otra instrumentación pertinente están instalados y configurados de acuerdo con los planes, especificaciones, requerimientos y otros documentos referentes a la construcción. Si existen cambios en el diseño original durante la fase de ejecución, se tiene que documentar y registrar los cambios de manera cuantitativa con el fin de poder utilizarlos en una evaluación futura del sistema.
Cabe mencionar que, con tal de reducir la carga de trabajo asociada al proceso de puesta en servicio del sistema, las actividades durante el arranque proporcionan únicamente un valor estimado de la capacidad del sistema. con todos los elementos del sistema operando a sus temperaturas de consigna de diseño y en las condiciones típicas de trabajo, se debe comprobar la fracción de la capacidad total del sistema que está proporcionando, y determinando si es un valor consiente con la temperatura ambiental que existe en ese momento. Si la capacidad disponible es mayor de lo esperado, el propietario puede usar el método informativo de verificación.
Durante el primer año de operación, se requiere registrar y archivar el perfil de funcionamiento del sistema en un registro de datos donde deben estar los siguientes:
• Configuración de componentes ajustables como por ejemplo las válvulas de expansión (por ejemplo, los recalentamientos que produce la válvula de expansión pueden ser verificados in situ, o la temperatura de retorno del refrigerante después del evaporador puede ser revisada).
• Condición de la presión de aspiración y descarga en los compresores.
• Las presiones de aspiración y descarga en el compresor
• Las temperaturas de descarga del compresor
• La temperatura de retorno del refrigerante en el compresor

• El compresor y los tiempos de ciclo de parada y perfiles de operación estado on/ off en cada paso de tiempo - por lo general en pasos de tiempo de 1 minuto).
• La velocidad del compresor
• El porcentaje del tiempo de funcionamiento para compresores de modulación por ancho de pulsos).
Por otra parte, en las condiciones del condensador se deberá revisar:
• Las velocidades y perfiles de operación para cada ventilador del condensador (estado on/off en cada paso de tiempo - por lo general en pasos de tiempo de 1 minuto).
• Las temperaturas de bulbo seco y húmedo ambientales.
• La temperatura del refrigerante y la presión en el condensador
• Temperatura y presión en la línea de caída.
• Temperatura de entrada del agua y temperatura de salida del agua (para condensadores enfriados por agua o evaporativos).
Respecto a las condiciones del sistema se debe verificar:
• La temperatura del colector de aspiración.
• La temperatura del líquido subenfriado.
• Presión en el distribuidor de líquido.
En cuanto a la temperatura de los expositores y arcones es importante conocer:
• Variación de temperatura durante el funcionamiento normal
• Variación de temperatura durante el desescarche
Durante el primer año de funcionamiento, es aconsejable identificar un periodo de tiempo durante el cual el sistema opere en condiciones cercanas a las ambientales, en ese caso se debe verificar que los muebles exhibidores se mantienen a las temperaturas prefijadas o por debajo de ellas. En las condiciones citadas anteriormente se debe estimar la capacidad de los compresores a lo largo del periodo establecido durante intervalos de 15 minutos o menores. Durante los intervalos en el que todos los compresores estén operando a la máxima capacidad, se ha de verificar que su capacidad es como mínimo igual a la capacidad de diseño. Si no existe ningún intervalo de tiempo donde todos los compresores operen a la máxima capacidad, se ha de realizar esta comparación con la siguiente formula:
Donde:
CMC=Capacidad máxima de los Compresores.
PCT=Porcentaje de la Capacidad Total de los Compresores en Operación.
Si el método primario descrito anteriormente no proporciona una adecuada verificación de la capacidad del sistema, el propietario de la instalación puede optar por realizar una prueba del sistema de la siguiente manera:
1. Se ponen en funcionamiento todos los muebles exhibidores a sus temperaturas determinadas de diseño.
2. Se desactivan los desescarches.
3. Si es posible se aumenta la temperatura del local comercial a 24ºC mediante el termostato del sistema de aire acondicionado.
4. Se ajusta la temperatura de condensación de tal manera que se aproxime a la temperatura de condensación esperada con la temperatura de diseño ambiental.
5. Se registran las variables citadas en el método descrito al inicio por un periodo de tiempo de al menos 4 horas.
6. Se verifica que las temperaturas de los muebles exhibidores se mantienen igual o por debajo de la temperatura de diseño.
7. Se estima la capacidad del sistema con las condiciones de los compresores para el periodo de tiempo considerando durante intervalos de 15 minutos o menos.
Durante los intervalos en el que todos los compresores operan a máxima capacidad, donde la capacidad del sistema es como mínimo la de diseño, si no existe ningún intervalo de tiempo donde todos los compresores funcionen a su máxima capacidad, se estima la capacidad del sistema de la siguiente forma:
CMC=CRC+PCT
Donde:
CMC=Capacidad máxima de los Compresores. CRC=Capacidad Real de los Compresores. PCT=Porcentaje de la Capacidad Total de los Compresores en Operación.
El funcionamiento del condensador en este método propuesto se debe de realizar de manera independiente, ya que el condensador está operando en condiciones diferentes a la operación normal. De los datos del sistema registrados durante el año, se ha de identificar un periodo de tiempo de al menos 4 horas donde el sistema este operando en condiciones cercanas a las de diseño, los más importante es que todos los ventiladores de los condensadores estén en marcha y las temperaturas ambientales sean cercanas a las de diseño. Se ha de calcular el acercamiento de temperatura para el periodo de tiempo identificado en intervalos de 15 minutos como máximo y por último se han de comparar las aproximaciones de temperaturas medidas con las de diseño. Si el acercamiento de temperaturas registrado cede la de diseño en más de un 20%, los condensadores no estarían funcionando tal como el diseño original pretendía.
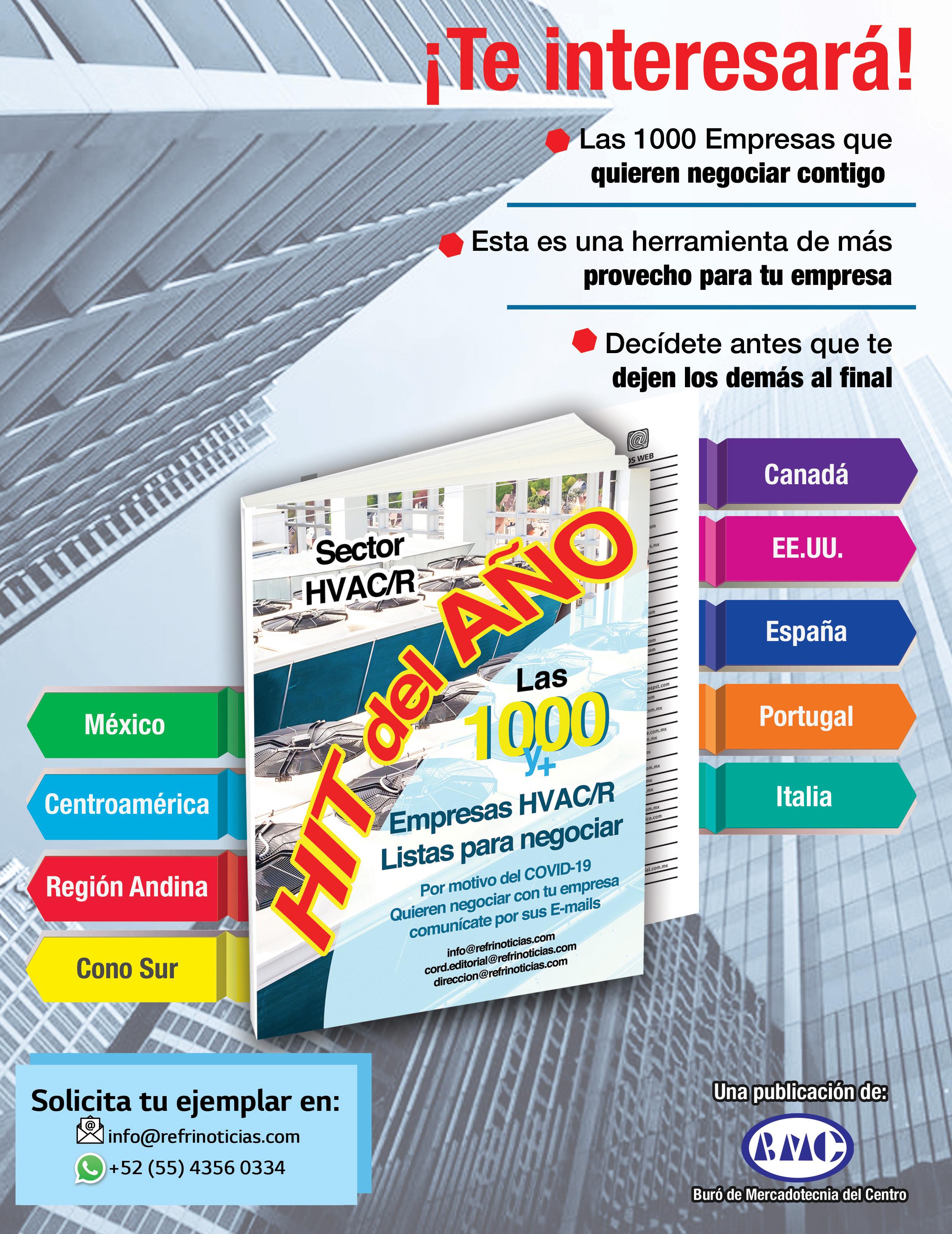